
10 minute read
Tried and tested training
Pekka Qvist, NAPCON, part of Neste, Finland, explains how digital training solutions can help panel operators in fault situations.
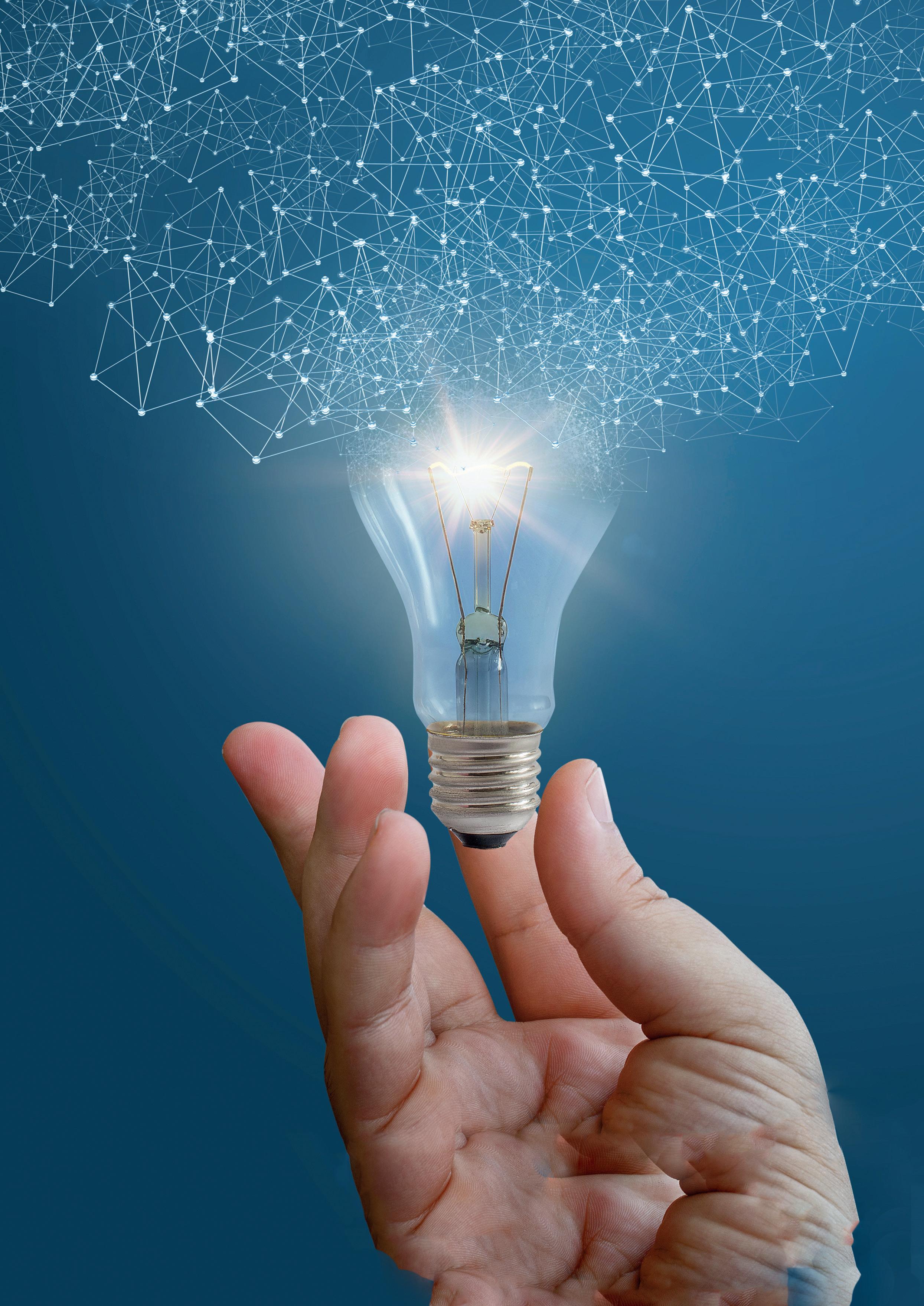
Agenerational change is taking place within many process plants all over the world, and new panel operators are taking charge. The problem is that tacit knowledge may be lost when the seasoned operators retire and younger people need to step up to the task. The same lack of experience applies to greenfield plants, where new operators do not necessarily know how the processes and systems will work in different situations, and what to do in certain fault scenarios.
It takes years for a panel operator to get to know a plant by heart, but the learning curve can be sped up substantially by using digital learning tools. An Operator Training Simulator (OTS) makes it possible to practice things that cannot be practiced in the control room; no plant wants to carry out unnecessary shutdowns and start-ups, or create disturbances for no reason.
State-of-the-art training solutions provide a digital learning environment that adapts to the users’ needs – from basic principles to safe and specific operating skills. It is also possible to support multi-user online training and remote learning by having simulators in the cloud that can be reached from anywhere.
Safe training
Operator simulator training not only helps panel operators to build up the skills required to operate a live
plant, but it also familiarises them with different situations that can arise, such as standard routine operations, start-ups, emergency shutdowns, possible upsets, and different troubleshooting scenarios. If operators had to learn all of this from a veteran operator, it would take a long time and they would have to be onsite at the exact moment when something extraordinary happened.
As such, a simulator is a great tool when it comes to learning about how to handle different scenarios. It provides a good understanding of the plant and what is happening behind the panels – in a safe environment. With simulator training, panel operators can practice and learn to operate according to safe procedures, without risking the plant’s operations.
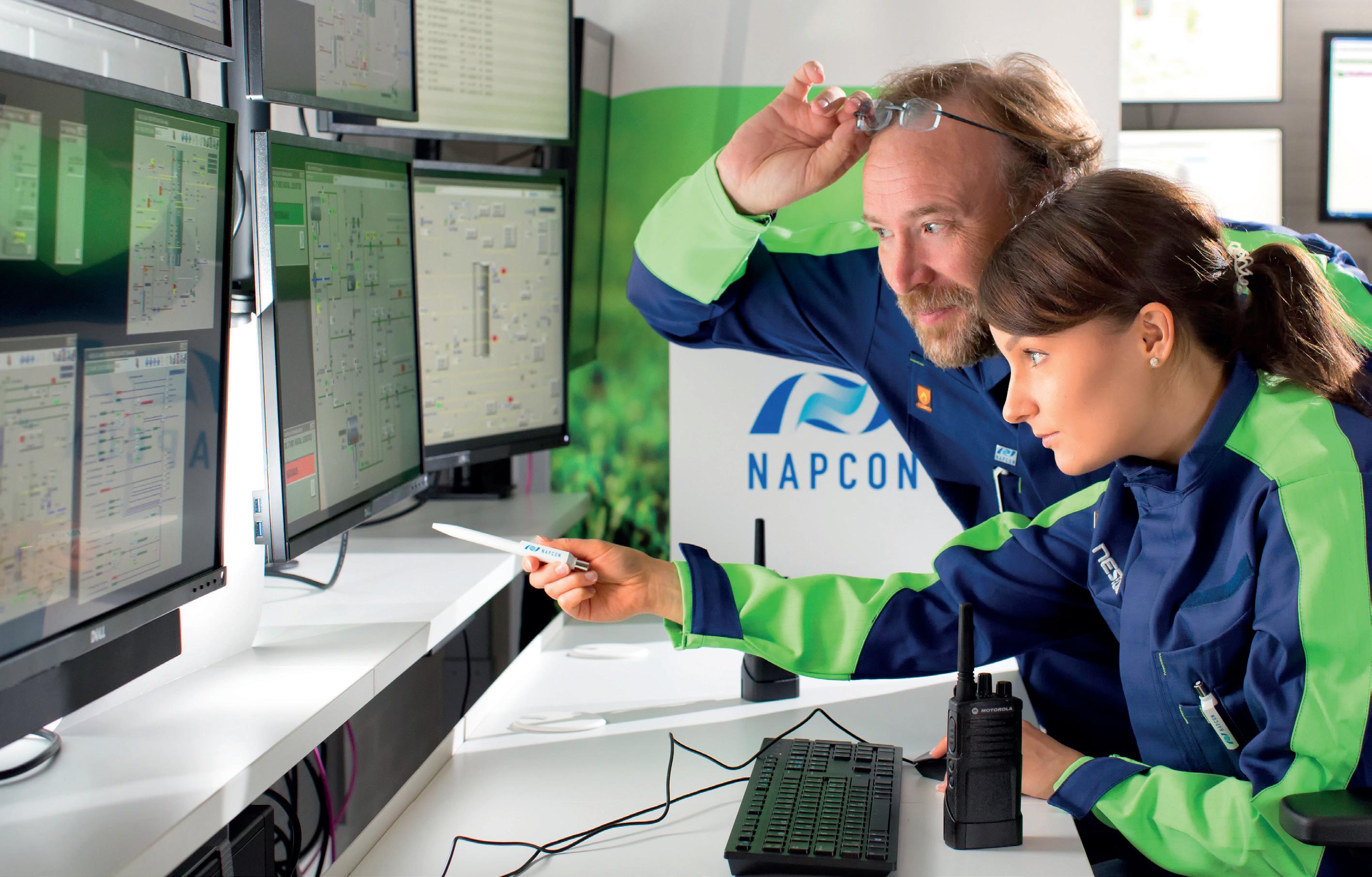
Figure 1. Simulation training brings a real-life plant into the virtual world, making training and testing safe and exciting.
Figure 2. NAPCON cloud OTS provides full operator simulator training capabilities anywhere and anytime, over a cyber-secure internet connection.
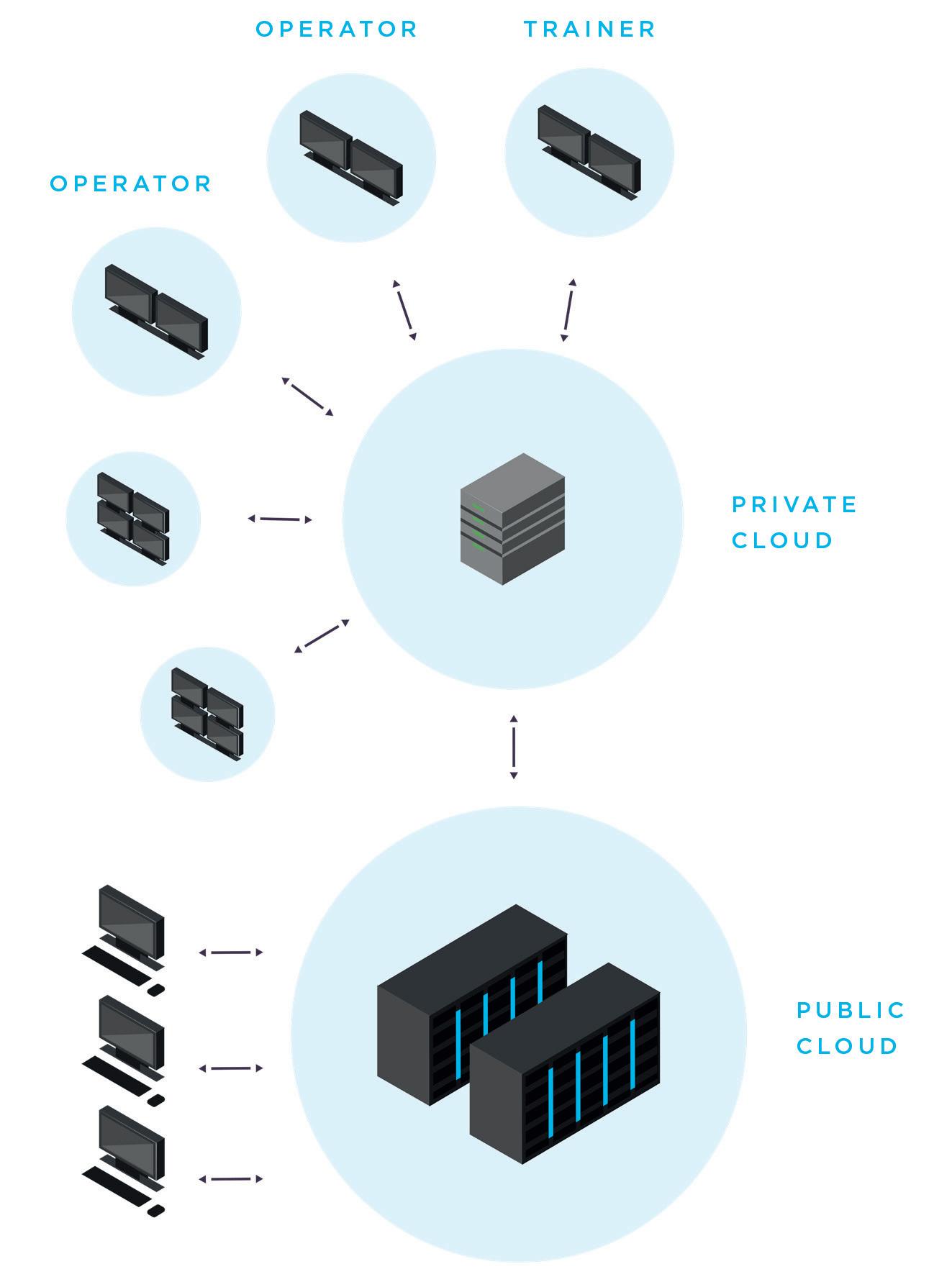
Simulator in the cloud
An OTS arms trainers and panel operators in a process plant with the efficient tools not only for training, but also for testing the operation of the plant safely, as it simulates a real-life plant and brings it to the virtual world in form of a digital twin. Cloud OTS is an even more modern way to handle basic training, as the simulators are based in the cloud. This novel approach offers features that change the way that process plant operators are trained. Above all, it is a tool that can be quickly deployed in a ready-to-use format, without the need for onsite hardware installations and configurations.
One of the driving forces behind the development of the cloud-driven OTS was the COVID-19 pandemic, which made remote work the new standard in many companies, and resulted in an understanding that staff training also required new approaches.
One of the most beneficial approaches is the cloud-based training solution, through which the competence of the process plant operators can be developed independently of location. The cloud simulator can be accessed from anywhere in the world through the internet with secure connectivity, and it provides a multi-user, classroom-like experience without the need for a physical classroom. This way, portions of an actual process plant or a generic plant can be accessed by personnel outside of the site.
Flexible environment
A cloud-based solution shown on one or maybe a couple of monitors cannot be compared to a full-blown simulator, but it is a much lighter solution than a simulator in a classroom, i.e. it is a learning solution that is reachable from anywhere in the world, and can be delivered to the customer in a couple of weeks instead of months, which is the timeframe required when delivering a tailored operator training simulator.
The cloud simulator provides the possibility to offer training that is equivalent to classroom-based training, via multi-user sessions. This is powered by public cloud computing capabilities, and is cyber-secured by nature.
Unlike training sessions in a classroom, the cloud-based OTS offers a highly-scalable and flexible environment, allowing for the dynamic adding or removing of seats. This also makes it very cost effective, as the resources are only used when needed. For internationally-operating companies, one of the key points is that the training is easy to scale out globally. It is also hardware-independent, because all of the calculations are made in the cloud. This means that all modern computers can be used to access the simulator.
No time wasted
As cloud OTS can be deployed very quickly, it is a great way of handling the initial trainings of, for example, a
greenfield process plant that will start up in a couple of years. The teaching can then become more specific as the plant’s specifications become clearer.
After receiving the theoretical basic knowledge of the plant that is being built, the cloud OTS can be finished in a relatively short time. After this, training can start immediately. The principle is to first learn on a more general level, and then gradually dive deeper into the subject alongside the design and construction phases of the greenfield plant. This way, no potential training time is wasted, and when the commissioning of the plant is approaching, the training can be moved to a fixed simulator that has been developed in the meantime, and that is an exact match of the plant.
Digital model
The cloud simulator is enabled by today’s technology that makes it possible to digitally model a whole plant, with all process and automation systems in place. It is an example of how an agile development of digital systems permits the swift creation of new solutions that really meet the training and competence development needs.
A large classroom with an array of monitors can be overkill if there is only a need for training some smaller parts of a big process. With the cloud solution, however, it is possible to create a detailed copy of a single process that can then be run on just a couple of monitors, or in some cases even on a single laptop.
Additionally, there is no requirement to attend a physical training class, but rather to become familiar with the actual process from anywhere where there is an internet connection. This means that the cloud simulator could also be an effective learning tool in technical universities and schools, complementing specific theoretical lectures, for example.
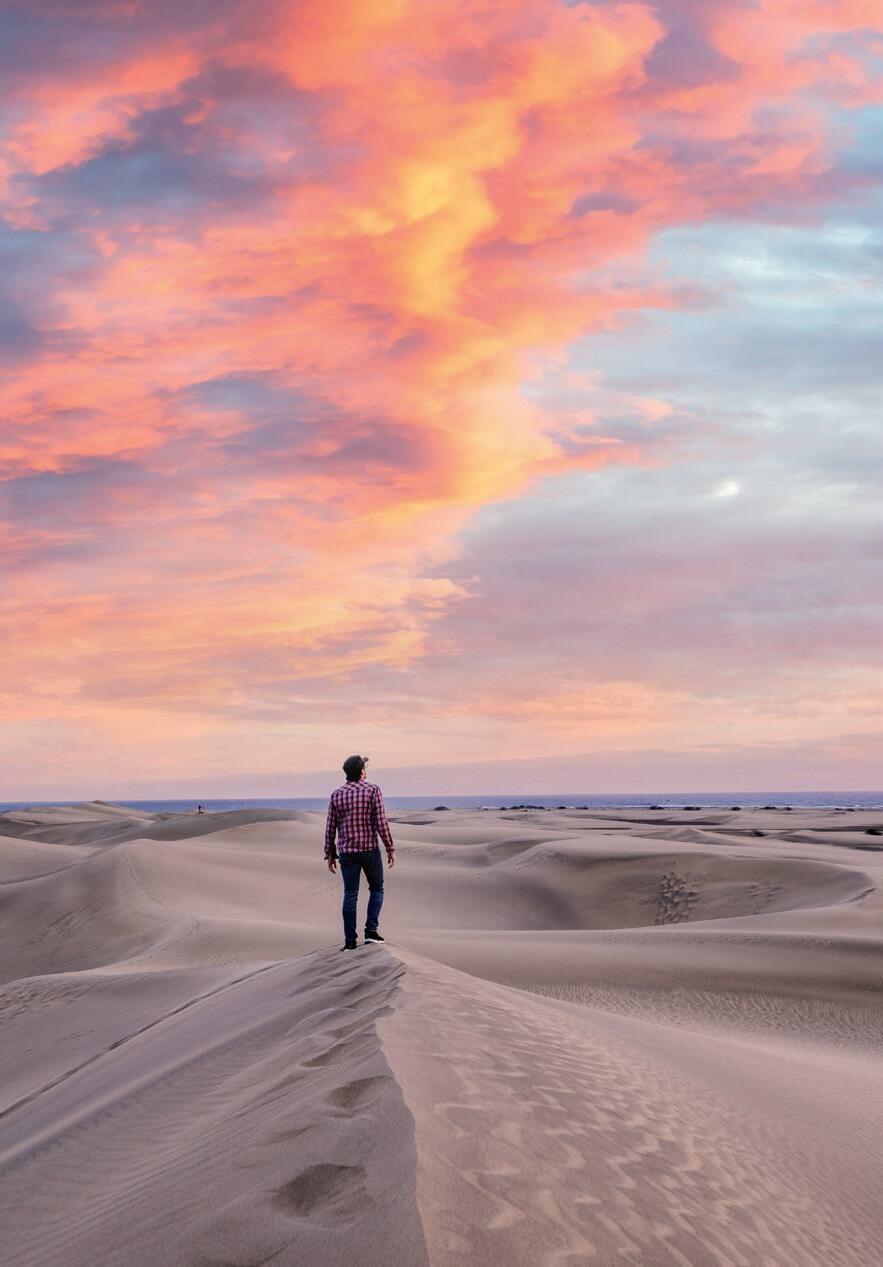
Simulating it all
When a large process plant is up and running, or when the start-up of a new plant is approaching, it can be wise to have a dedicated classroom with an in-house training simulator that allows for the possibility of replicating and assessing the operational readiness of all of the plant assets.
One such example of this is a full-scale OTS that simulates all of the possible production states, such as start-ups, shutdowns, or special breakdown situations. It is also possible to cover process phenomena, plant equipment and process automation within the training.
In the classroom, the training can be made very realistic, including the use of alarm signals that sound when the operator’s attention is required for a specific issue. It also includes all of the reporting that must be done to ensure that every step of the protocol for dealing with a specific topic has been taken. A comprehensive digital trail of training sessions and reporting capabilities allows for the monitoring of staff competence development, and training progress when needed.
Graphical interface
The emulated user interface in both the classroom simulator and the cloud simulator creates high-fidelity training simulations regardless of which DCS is used in the plant that the training is intended for. As part of the ongoing training programme within a plant, the operators can also focus on specific process phenomena to gain a deeper understanding of different process models through the detailed graphical user interface. This way, even a relatively novel operator can learn how to handle different problems in advance, and be able to make the right decisions when the scenario is for real.
The emulated DCS also provides the operators with a very similar user interface and user experience to the real DCS. As a result, both training and learning happens in an environment that matches the actual operator panels – in the form of a digital twin.
With the addition of cloud OTS, all of the training does not have to take place on the premises, as the cloud set-up permits flexible training rooms, resulting in the capacity to train multiple units and trainees simultaneously. The OTS offers the
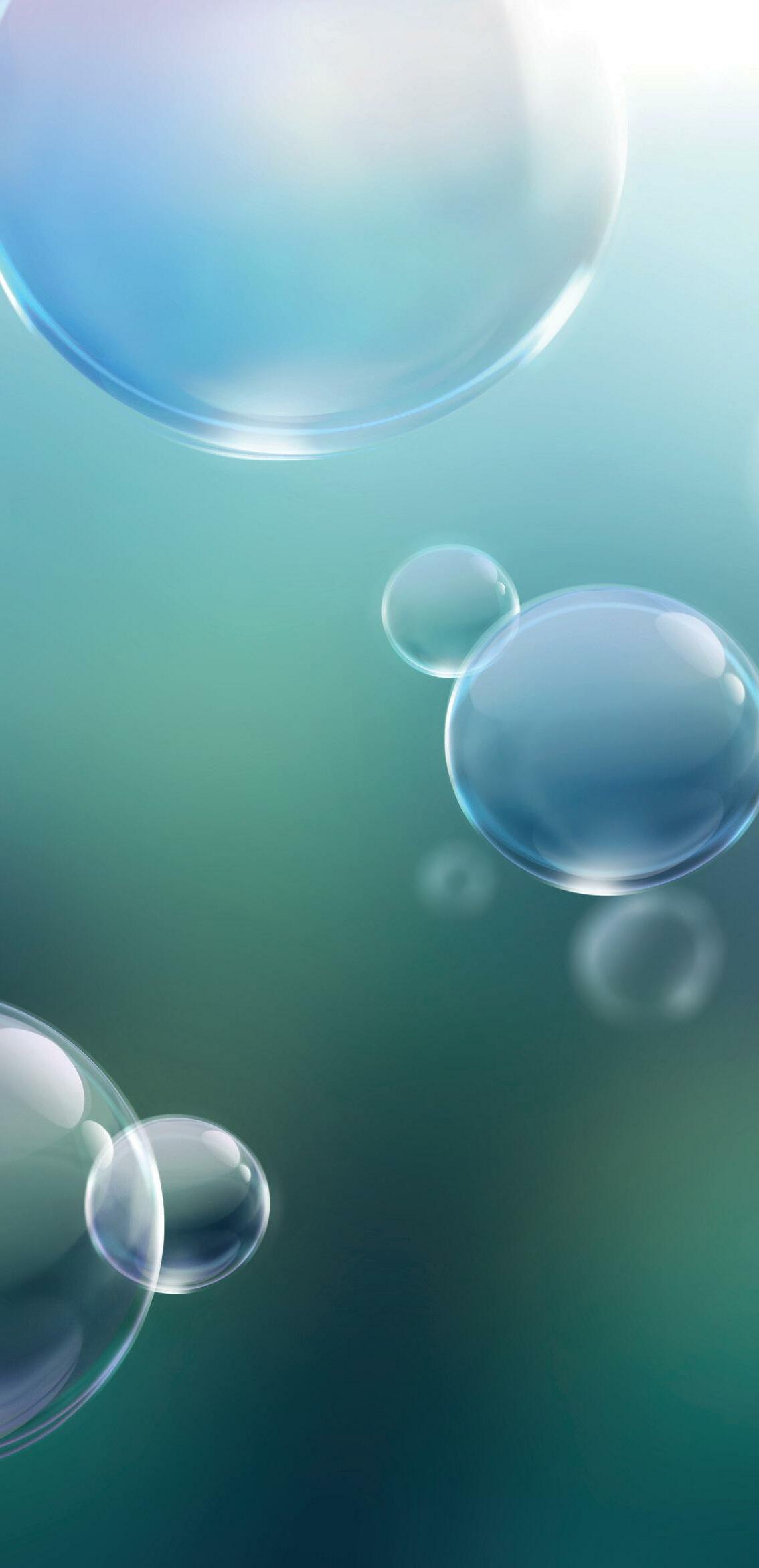
The future is now with our technologies for tomorrow.
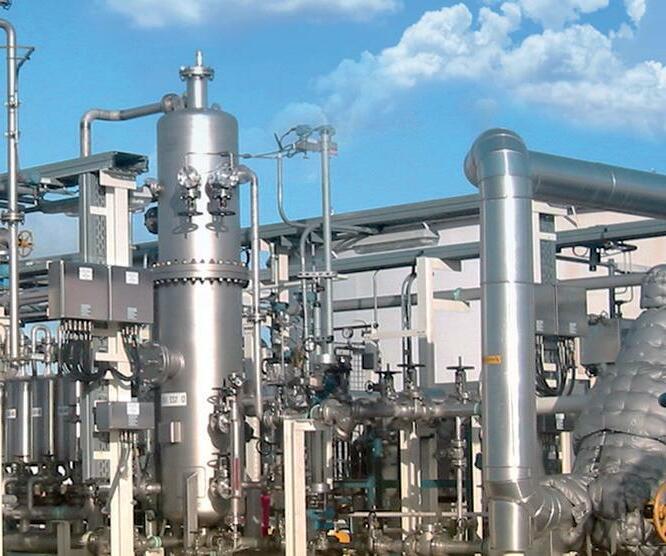
Think. Create. Change.
Discover our innovative process technologies and other solution concepts that make you fit for the future. We look forward to welcoming you at ADIPEC 2022, stand 8718.
Let’s discover together where our ideas will take you.
ADIPEC 2022
31.10. – 03.11.2022 in Abu Dhabi, United Arab Emirates.
instructor an easy-to-use graphical interface for introducing various faults and disturbances not only to the process, but also to automation and instrumentation systems. Learning to solve unexpected issues safely, according to the proper procedures, is an important part of the OTS training scenarios.
Learning the fun way
Aside from training simulators, a gamified training tool is a modern way to boost plant operating skills in refineries. The simulation-based educational games are not only aimed at the plant operators, but all plant personnel, in order to improve their competencies.
Training through simulation games is a flexible way to practice operating skills and level-up the competencies through solving fault problems in a fun way. Gamified training is also a way to engage the younger generation of operators to practice different situations that they do not face in everyday work.
Games coupled with theoretical eLearning modules can provide a comprehensive, basic-level training package focused on specific topic areas that are required for refining or process industries, such as distillation, furnace operation, heat exchangers, boiling or condensation.
Simulation-based educational games offer an efficient way to complement other training methods. It is an independent learning method that also makes it possible to utilise standby time during work shifts. All simulation games utilise the same platform, which makes extending the training easy. Additionally, the games are available anytime and anywhere. As they use the same process simulation engine as the OTS, the simulation of the processes is just as accurate as with the OTS, but permits learning in a fun way.
Conclusion
Digital training solutions are an important part of the toolset for organisation-wide competence development. Highly-trained staff are essential to ensuring that an industrial plant is operated in a safe way but under optimal process conditions, maximising the value of the refined products. Bridging the gap between theory and practice is simple, with different digital training tools tailored specifically to the different phases of the learning curve. Hybrid availability both onsite and remotely is not only a benefit but a standard for the post-pandemic world.
NAPCON provides a comprehensive digital toolset to fit different phases of an operator learning path. The OTS will turn a process plant into a safe training environment. This can be tailored to most process industries, and for greenfield plants. The Cloud OTS enables the global use of the simulator through the public cloud, offering features that are changing the way that process plant operators are trained. Lastly, simulation-based educational games offer gamified training that sits well with the younger generation’s ways of approaching life.
IMPROVE COMPETENCE DEVELOPMENT WITH DIGITAL LEARNING SOLUTIONS
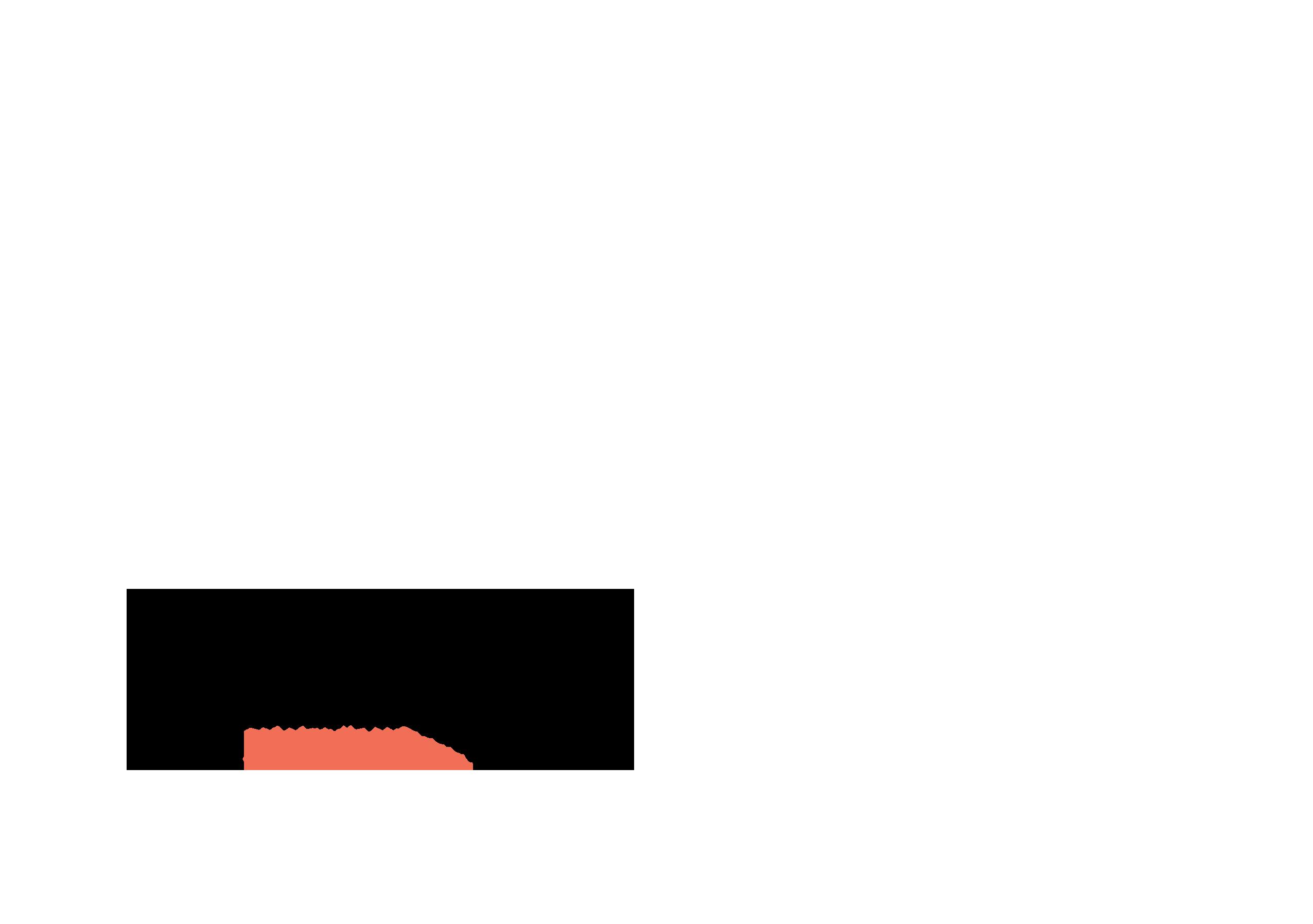
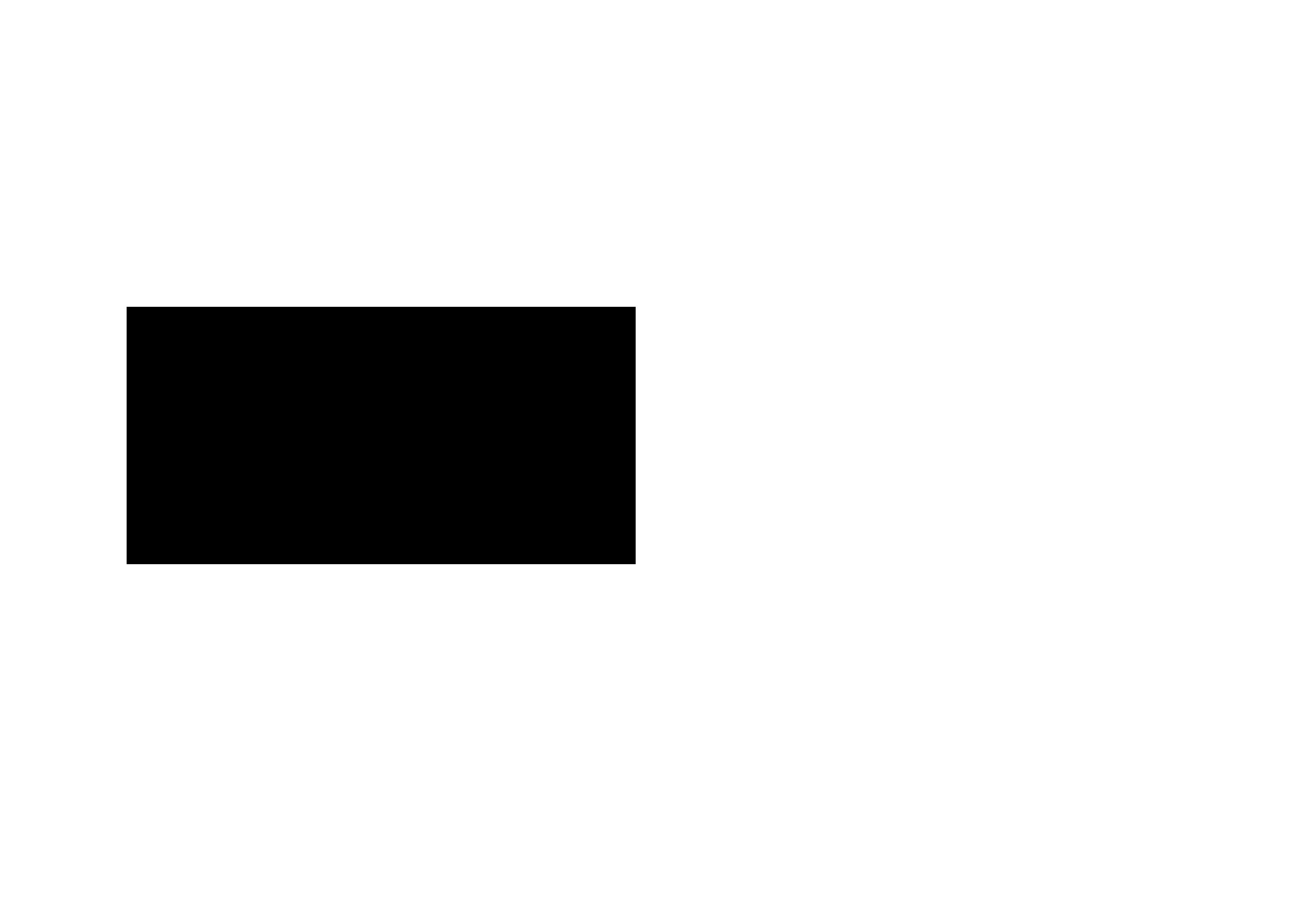
NAPCON BRINGS YOUR REAL LIFE PLANT INTO THE VIRTUAL WORLD TAKING OPERATOR TRAINING TO A WHOLE NEW LEVEL.
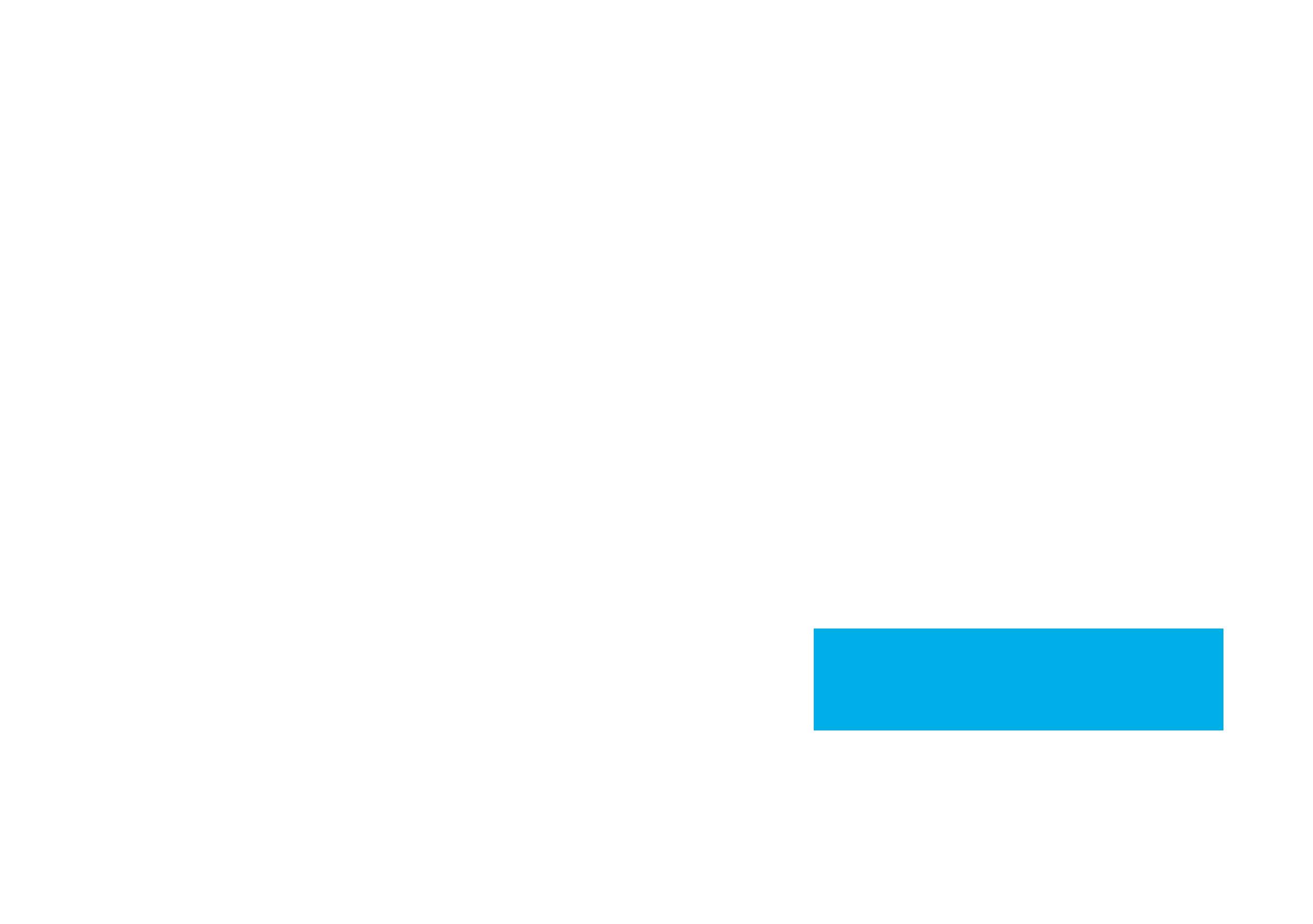
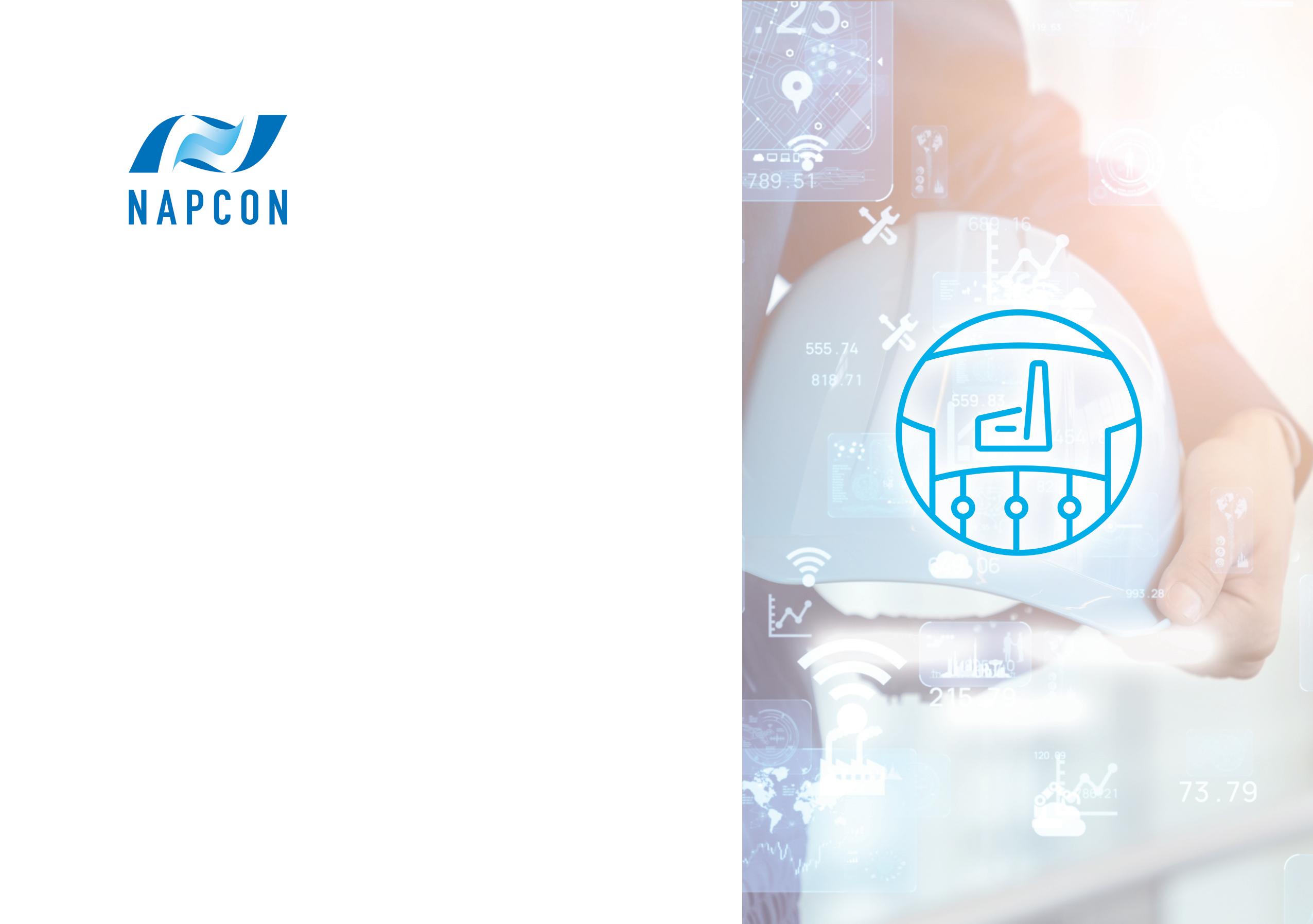
C Crerea atete a a r ri is sk-fk-freree e a an nd d m mo od de er rn n d di ig gitita al l e envnvi iroron nm me en nt t for training your staff to ensure that plant operations are safe and effective under any conditions due to improved operator skills.
Contact us: napconsuite.com