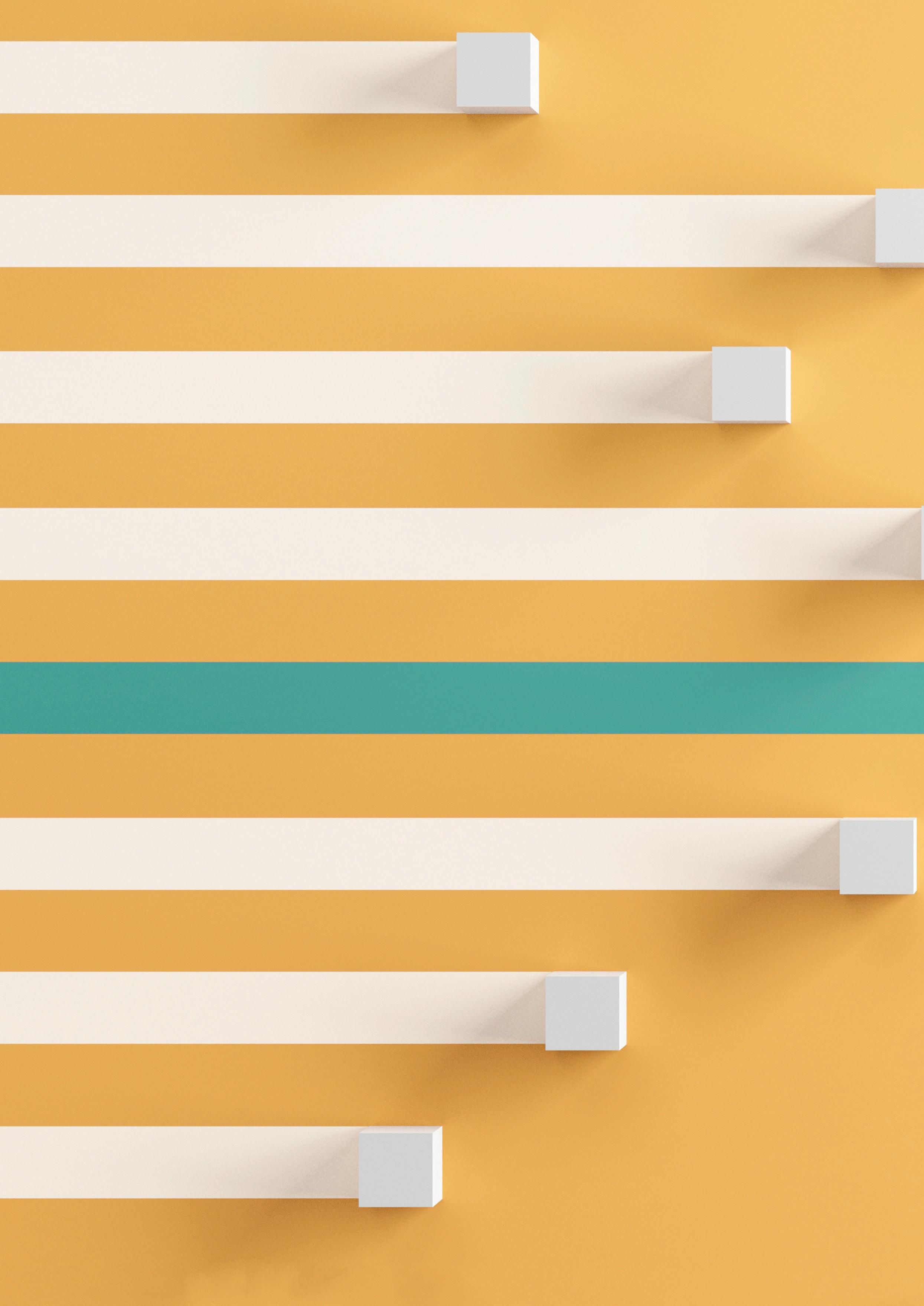
8 minute read
Enhancing steam flare efficiency
Sherri Roberts and Zach Kodesh, John Zink Hamworthy Combustion, a Koch Engineered Solutions Company, USA, consider how to improve steam flare efficiency at turndown, using staged steam injection.
Steam-assisted flares are a proven technology that can effectively combust waste hydrocarbons in refineries, petrochemical plants, and other applications. Over the past 15 years, new technology has enabled flare emissions measurements that were previously impossible. These measurements have shown that at high turndown, steam-assisted flares can be operated in such a way that the destruction efficiency is significantly lower than the expected 98%.
This data was the basis for new regulations addressing flare operations. To compound this issue, plant operators have steadily decreased the amount of vent gas sent to flares, increasing the level of turndown at which the flares normally operate. The reduction of vent gas flows is an overall positive outcome, reducing waste and carbon dioxide (CO2) emissions, but this challenges the flare to operate effectively at even smaller flow rates.
This article will describe the technology that facilitates the high turndown operation of a steam-assisted flare, while maintaining high destruction efficiency.
New regulations addressing flare operations have been implemented for the refinery (40 CFR 63.670) and ethylene (40 CFR 63.1103) sectors. These new regulations have increased operational restrictions, which can have a significant impact during high turndown operations, where most flares operate the majority of the time. Flares subject to these regulations must meet the Net Heating Value of Flare Combustion Zone (NHVcz) value of 270 Btu/ft3 any time that regulated material is sent to the flare. The equation for the NHVcz value requires the calculation to include all assist steam that is sent to the flare, as well as the vent gas. This means that at very low vent gas flow rates, the flare can approach and/or drop below the minimum allowed NHVcz.
While the solution for this seems to be simple – reducing the steam flow until the NHVcz is above the minimum – the actual operation of the flare is more complicated. For proper operation of steam-assisted flares, most flare vendors recommend a minimum amount of steam be sent to the flare to protect the tip during low flow conditions. This minimum steam, often called cooling steam, helps to prevent flame pulldown that can damage a tip over time. The cooling steam also keeps the steam injectors cool, as the steam temperature is cooler than flame. In addition to this, the cooling steam keeps the steam lines warm so that when a flaring event requires a rapid increase in steam flow there is not a large amount of condensation in the line that could form a slug of water,
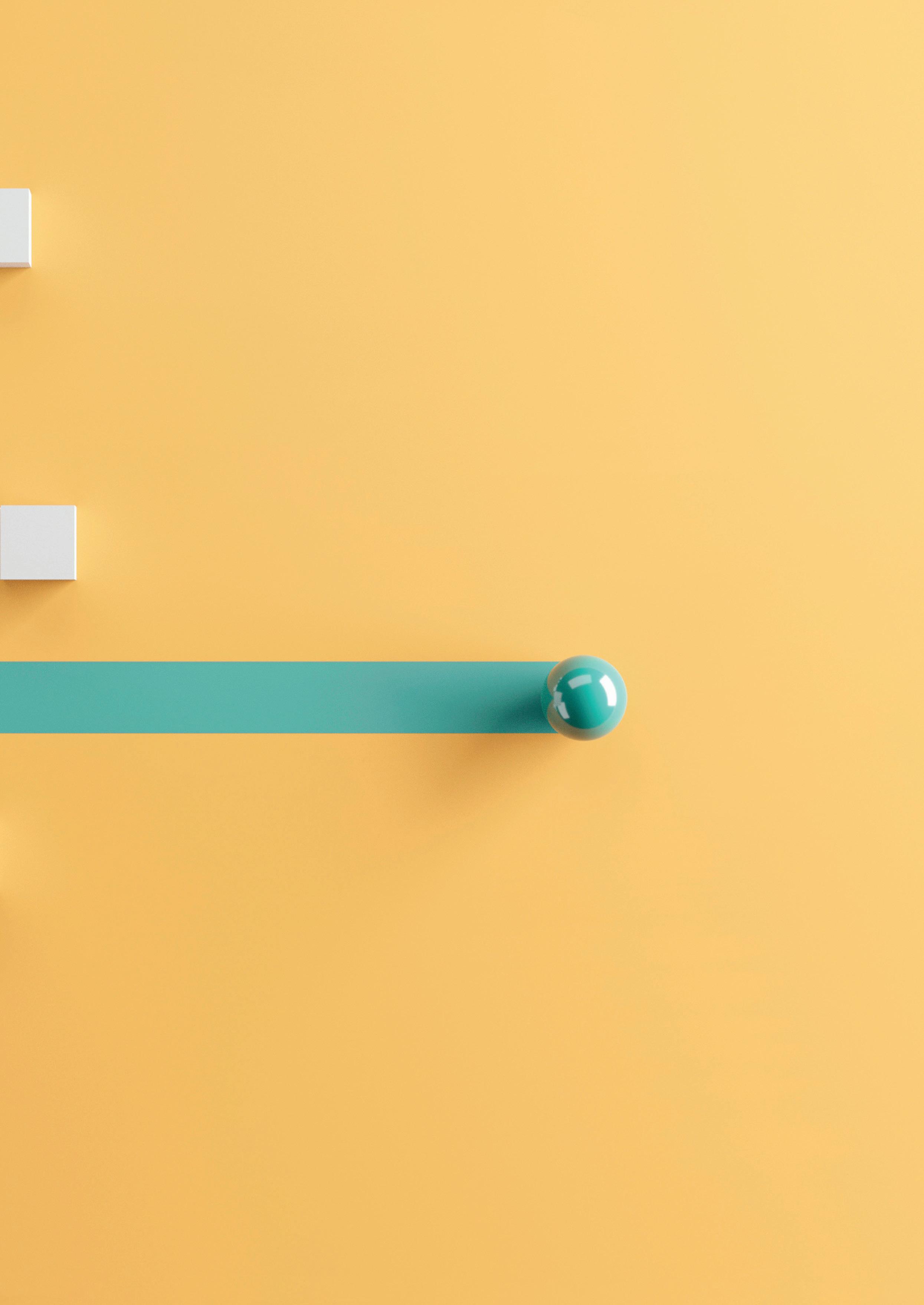
producing water hammer that can damage equipment. Given that the minimum steam rates cannot simply be decreased without having adverse effects on equipment life, many flare operators will be forced to add supplemental gas to their vent gas to meet the NHVcz limitation of 270 Btu/ft3. The addition of supplemental gas can be a significant operating expense, and can also increase greenhouse gas (GHG) emissions.
The Steamizer XP flare tip (see Figure 1) is the latest steam flare technology from John Zink Hamworthy Combustion (JZHC), a Koch Engineered Solutions company. In recent years, it has been installed as a solution for many flare users in order to meet demanding flare regulations. It can offer improved smokeless capacity and lower steam usage during all operation points. Additionally, to improve ease of operation, it has only one steam injection location vs the multiple locations that older style designs employ. Control of the steam injection in older designs must be carefully coordinated to ensure proper operation of the tip, and to avoid damaging it.
The flare tip also has a much longer tip life than older designs. One recent example is when several tips endured steam outages during the unprecedented freezing conditions along the US Gulf Coast in 2021. None of the tips in the area had to be replaced, while other steam flare technologies required replacement immediately after the freezing event.
Additionally, the Steamizer XP offers very stable combustion in olefin applications. Older designs can have unstable combustion, particularly in ethylene service, which can result in severe noise and vibration. There are still minimum steam requirements with the Steamizer XP tip that may require additional fuel gas to meet the NHVcz limit.
Aware of the developing regulations and their potential impact, the need for lower steam rates at turndown conditions became a focus of JZHC’s flare technology development. From that effort, a patented Staged Steam technology was developed, which was then applied to the Steamizer XP design. The Staged Steam XP has very low steam consumption at turndown. This low steam requirement is a significant benefit to meeting the stricter US Environmental Protection Agency (EPA) rules at turndown, and minimises or eliminates the need for supplemental fuel gas.
Traditional steam injection systems use fixed discharge nozzles, and are designed to operate at specific design steam flow rate. Typically, the design steam flow rate is achieved with a steam pressure of around 100 psig (6.7 barg), which achieves steam discharge velocities of greater than 1500 ft/sec. When operating at design conditions, the tip achieves near maximum efficiency (lowest steam to hydrocarbon ratio for smokeless combustion) due to the momentum of the steam being at its maximum (steam momentum is what entrains air and mixes it with the vent gas).
When operating at high turndown, the steam flow can be around 1 – 3% of the design rate. These low flow conditions result in steam pressures in the range of 0.15 – 0.015 psig (0.01 – 0.001 barg), which result in steam discharge velocities of around 50 – 150 ft/sec. The ability of the steam to entrain air and mix it with the vent gas is very poor at these low-momentum conditions, resulting in the need to increase the steam rate to achieve smokeless combustion. Increased steam flow at turndown can force an operator to add supplemental fuel gas to meet the NHVcz limitation, and ensure good combustion efficiency from the flare. It is ironic that the best operators – those who minimise vent gas flow to their flares – can be punished for responsible operation by being forced to dump supplemental fuel gas into their flare header.
The patented Staged Steam XP flare tip uses multiple steam nozzle designs to significantly improve efficiency at turndown. In addition to the traditional steam manifold described above, additional steam manifolds are added to the tip. These additional manifolds are designed to flow low volumes of steam at high pressure. This allows the tip to operate at higher efficiency during turndown conditions. As these manifolds are specifically constructed to operate at the lower flows, much less steam is required to provide the momentum for keeping flame off the flare tip and achieving
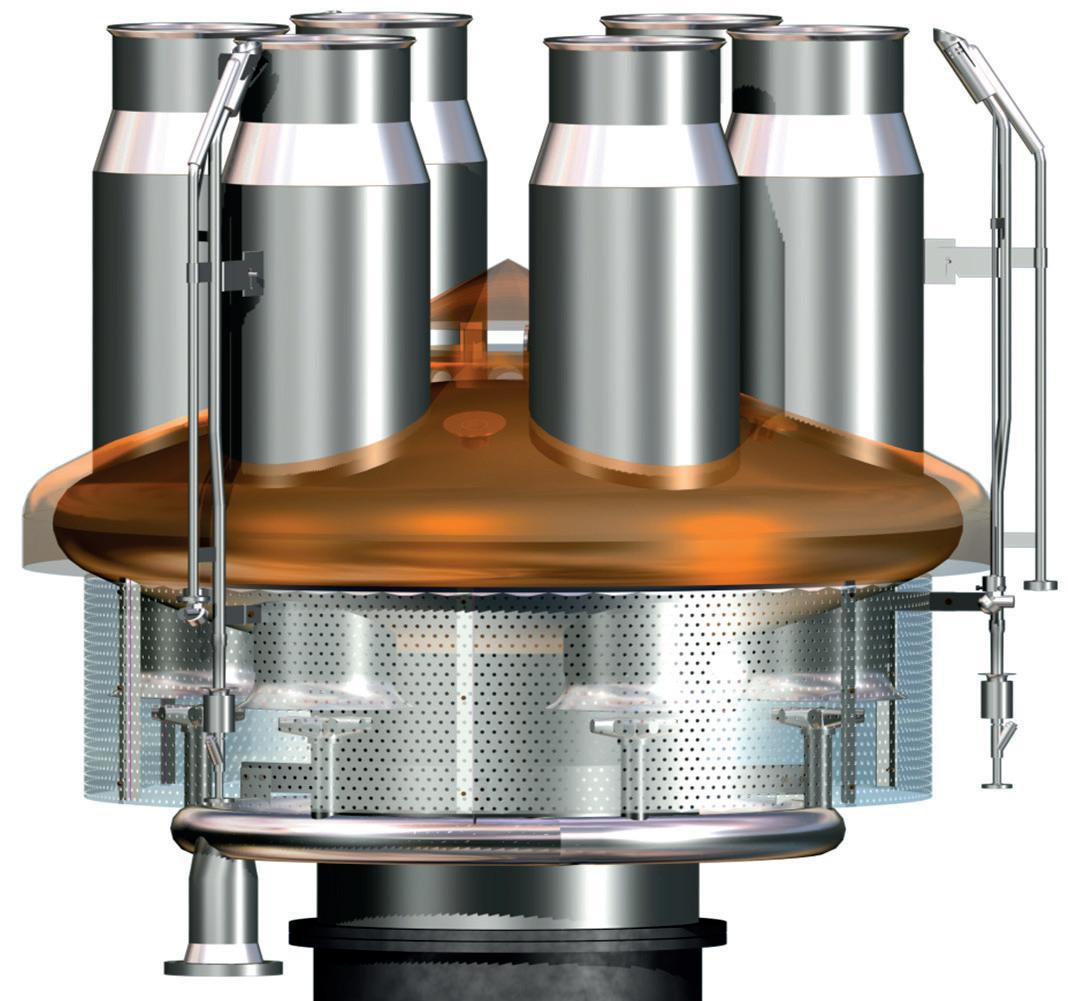
Figure 1. The Steamizer XP.
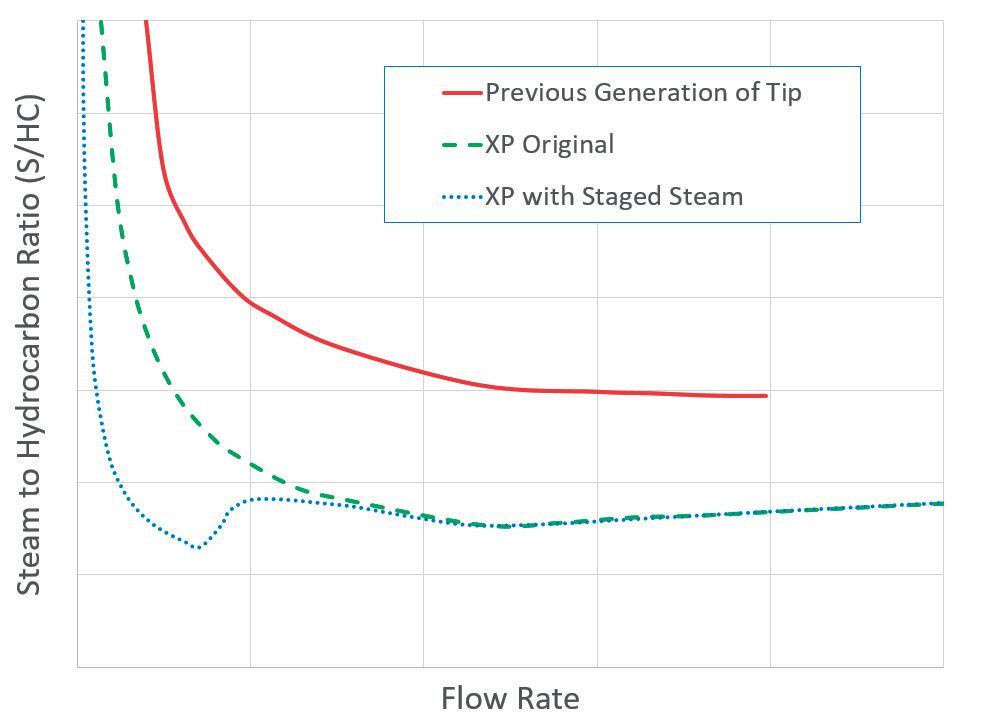
Figure 2. Steam comparison olefin service.
smokeless combustion. It is also important to note that even with the additional steam manifolds, steam operation with the patented Staged Steam XP is still very simple. All steam is injected into the same location of the flare tip, which eliminates the possibility of misoperation of the flare tip, creating internal burning and unstable combustion.
Figure 2 shows the lower S/HC ratios that are possible using the patented Staged Steam XP flare tip (Advanced XP-SS Flare). The graph also shows a comparison with a standard steam flare tip that uses upper and lower steam injection.
While the obvious improvements from the patented Staged Steam XP are steam savings and enhanced performance at turndown conditions, this also allows flare users to meet the NHVcz while minimising or eliminating supplemental gas. Meeting the NHVcz allows the flare to operate within regulations, the purpose of which is to promote good flare destruction efficiency. Operating costs are reduced by lower steam consumption and decreased supplemental gas consumption. Additional benefits from this solution are the carbon emissions reductions from the lower supplemental gas requirements, and reduced fuel burned by the boiler.
Using the EPA’s Greenhouse Gases Equivalencies Calculator, the following is an example comparing steam savings and CO2 emission savings from an SA-style (older internal tube design) flare with upper and lower steam rings vs the patented Staged Steam XP. The SA-style flare tip would require 1200 lb/hr for the cooling steam rate, while the Staged Steam XP flare tip would only require around 600 lb/hr for the cooling steam rate. This is easily seen as a more than 50% saving on steam alone, while the CO2 emissions savings on producing the steam would equate to around 320 tpy. There would also be additional CO2 emission savings if the lower steam rate resulted in a reduction in supplemental assist gas to meet the NHVcz requirement.
In response to today’s increasing demands for minimising flaring and lowering CO2 emissions, innovative solutions are available to help steam flare users meet these goals. This is especially critical with updated flare regulations that can require supplemental gas at turndown conditions, which is counter-intuitive for lowering CO2 emissions. When those requirements were implemented, steam flare users had to pick between possibly limiting the life of their flare tip by going below the recommended cooling steam rates, or spending additional money and increasing emissions by adding supplemental fuel gas. The Steamizer XP technology combined with Staged Steam technology provides high performance with lower operating costs and emissions than traditional steam flare designs.
Bibliography
• ALLEN, D. A., and TORRES, V. M., ‘TCEQ 2010 Flare Study Final Report’, (2011). • ‘Greenhouse Gases Equivalencies Calculator - Calculations and References’, Environmental Protection Agency, https://www.epa.gov/energy/greenhouse-gases-equivalenciescalculator-calculations-and-references
Need a reprint?

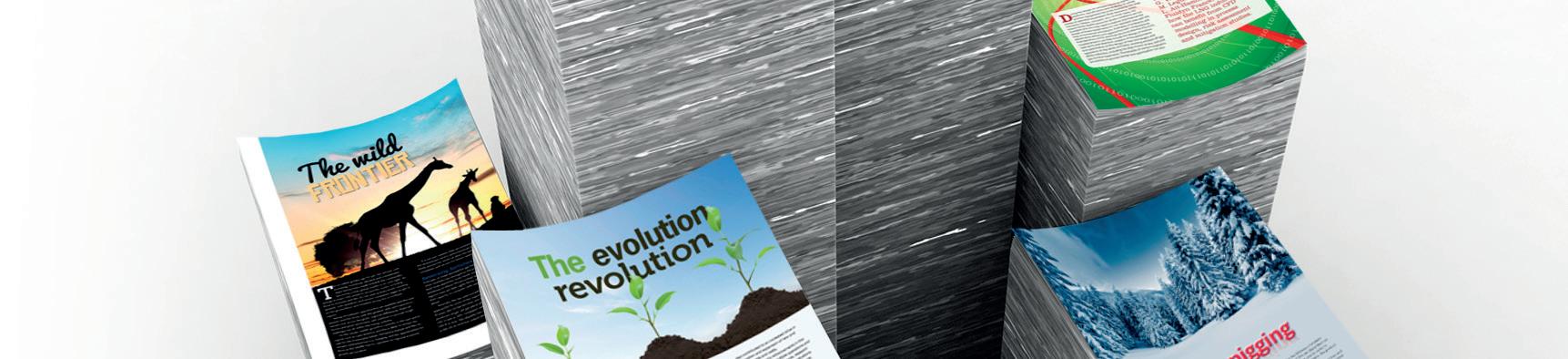