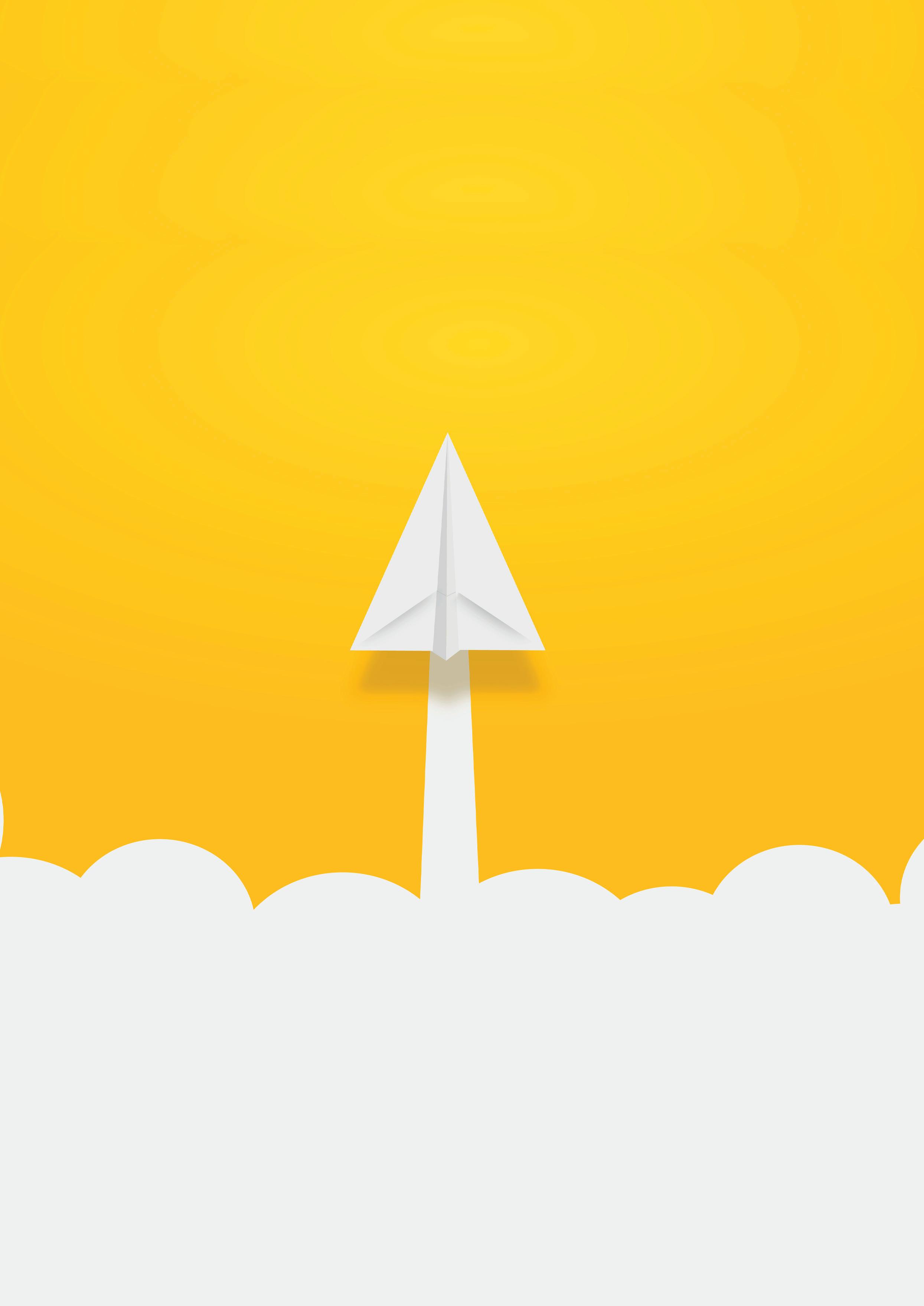
9 minute read
Boosting performance
Alexandra Markle, Blasch Precision Ceramics, USA, lists the performance benefits of discrete temperature zones in a Claus reaction furnace.
In order to extract pipeline-quality natural gas fuels from acid gas reserves, a processing plant must start with gas sweetening – separating the sweet gas from the acid gas. Byproducts of gas sweetening, or amine treating, are the gaseous forms of hydrogen sulfide (H2S) and carbon dioxide (CO2) – atmosphere pollutants that will negatively impact the quality of local and global environments should they be released directly. A refinery can minimise its environmental impact while meeting governmental standards through the optimal application of the Claus process. Unlike other gas purification processes, the primary goal of the Claus process is the recovery of elemental sulfur from acid gas streams containing high concentrations of H2S rather than yielding grades of fuel. The downstream benefits of an effective sulfur recovery unit (SRU) cannot be overstated in both protecting and extending the longevity of heat exchangers, ducting, and other valuable equipment prone to acid attack, as well as mitigating the environmental impact of energy production. Modifications to the Claus process, such as a
split medium and low-pressure flow, as well as configurations in the number of catalyst beds, are made with the goal of achieving a more complete conversion of sulfur and other species into more desirable compounds.
Due to the multitude of possible species and potential reactions that occur through a Claus furnace (upwards of 300), it cannot be simulated completely using computational fluid dynamics (CFD). Researchers must make several simplifying assumptions and are unable to assume equilibrium because many reactions will continue to occur through the waste heat boiler (WHB) and out of the furnace. The 1993 study by Monnery and Moore demonstrated that equilibrium calculations were inadequate in predicting the product distributions exiting the thermal reactor.1 Because of the limitations with equilibrium models, the bulk of this article’s discussion of the kinetics will centre around the benefits experienced as a result of using the Blasch Vector Wall, relying on simulation data only as a secondary means of validation. The primary scope is observations and testimonials of SRU operators, and the proposed fundamentals of thermodynamics and chemistry that support observed results.
The Claus process
Over 8 million t of elemental sulfur was produced in 2011, the majority of which was as a byproduct of petroleum refining, natural gas processing, and coking plants.2 Historically, the price per ton has been low. However, sulfur has been experiencing massive fluctuations recently, from as low as US$84/t in February 2020, to the value of US$720/t in June 2022.3
There are several processing steps in the recovery of sulfur from gasification processes, the first of them being acid gas removal (AGR). This sulfur-rich gas, containing a mixture of primarily H2S and CO2, serves as the feed gas in an SRU, where it will first undergo sub-stoichiometric combustion, followed by secondary and tertiary reactions with conversion rates determined by temperature and contact time between particles. As mentioned, hundreds of species of reactions occur through a Claus unit, however the 14 most relevant are compiled to the left. After thermal cracking, which removes approximately 60% of the available sulfur, the process gas is then cooled through a WHB, before being routed through catalytic reactors to precipitate the remaining 39.9%. The final step of the process gas is the tail gas unit (TGU), where a thermal reactor combusts what little remaining contaminant is left, and exhausts below the maximum ppm.
SRU operators understood that efficiency could be increased with additional mixing, and hoped to achieve this through incorporating choke rings and checker walls into their thermal reactors. These technologies, while providing some additional back mixing, result in a broad residence time distribution with some particles back mixing, while others travel straight through. To achieve more desirable results, Blasch developed a system that provides both superior mixing, as well as radiant shielding of equipment downstream.
First-generation vector tile
The first generation of vector tiles by Blasch were designed to provide additional fluid mixture through a thermal reactor unit. By placing a matrix of independently-positioned channels through the cross-section of the furnace, flow bias and the resultant residence time distribution can be controlled. The process benefits experienced by more conformity in particle path lengths are more complete reactions and higher percentage yield of desired precipitants. Field results indicate that the furnace experiences two discrete temperature zones: the hotter zone upstream of the vector wall, closest to the burner; and the cooler zone closest to the WHB.
Because the flame is prevented from directly impinging on the refractory-lined front of the WHB, both the service life of the WHB and the lifetime of the ferrules are extended.
The first chamber promotes back mixing and combustion, as radiative heat is concentrated to the front of the furnace rather than against the WHB. This results in the first chamber being substantially hotter than the rest of the reactor, and the temperature required for ignition is achieved with increased efficiency.
After the vector wall, the most common tile arrangement results in a flow that spirals along the length of the furnace. This spiral has two notable effects on the quality of the reaction: it allows for a more precise residence time distribution, and introduces a longer path length for any length of thermal reactor. In sub-stoichiometric reactions, slow-to-react species require a minimum time in contact in order to achieve complete conversion. With an increased path length and added variability, the probability of a more complete conversion increases as well.
Through the first generation of vector tiles, it was observed that the vector wall was unintentionally acting as a heat shield for the tube face of the WHB. This effect was further improved through the third generation of vector tiles, with a geometry that produced a tighter turn, as well as completely shielding the WHB from the radiative effects of the burner.
The third generation of vector tile is defined by the complete ‘hood’ geometry. It can be used in conjunction with, as an alternative to, or to replace existing first-generation tiles. This allows for each SRU to be designed to its specific process conditions, with desirable levels of mixing and temperature shielding achievable through the modularity of a mixture of tiles, tile arrangement, and ability to direct the flow through the thermal reactor.
As the temperature of a flame increases, so does the spectral energy density, i.e. the effects of radiative heat increase dramatically. The WHB face is protected from direct flame impingement by refractory material, but this material’s life is greatly reduced with increasing extremity of its environment. Decreased life results in increased cost and shorter campaign lengths. An SRU can be run more productively in a two-zone configuration because of the less extreme temperature experienced in the second
stage, while still achieving the temperatures needed for the initial combustion.
CFD demonstrates this phenomenon with two simple temperature plots: one prior to the Blasch Vector Wall, and one directly after.
Benefits of discrete temperature zones
The reactions that occur through the thermal reactor can be divided into three parts: oxidation, pyrolysis, and the competing reactions. Oxidation occurs when H2S and ammonia (NH3) combust in an oxygen-rich environment. This is followed by pyrolysis, where the H2S and NH3 are thermally cracked under anoxic conditions. The final and slowest species of reactions occur the deepest into the reactor, with the conversion rate determined by the quality of mixing.
Temperature, or thermal energy, is only part of the necessary conditions for complete conversion; the reaction will only occur should local concentrations of all constituents exist as well. Therefore, it can be inferred that an increased number of particle collisions directly increases the probability that a specific concentration will exist at a time in the reaction furnace. In other words, turbulent mixing inside of the thermal reactor is crucial to ensuring efficiency in a system.
By creating a furnace with an initial zone that isolates the burner from the WHB, an environment exists that promotes both oxidation and pyrolysis. This allows for the back end of the furnace to be dedicated to promoting more complete reactions through additional mixing and contact between available species. This, paired with the tighter residence time distribution, allows for greater control and efficiency in SRU operation.
Conclusion
The furnace directly accounts for only 50 – 60% of the sulfur recovered through the Claus process; however, the furnace performance drives efficiency of the catalytic reactions downstream.4 Incorporating a Blasch Vector Wall into a thermal reactor creates an environment that is beneficial to the kinetics involved in the Claus process. The two stages aid oxidation and pyrolysis in the front, and the slower competing reactions through the back. The radiant shielding provides another benefit of extending the life of the WHB and refractory material that lines its front face.
References
1. PIERUCCI, S., RANZI, E., and MOLINARI, L., ‘Modeling a Claus Process Reaction Furnace Via a Radical Kinetic Scheme’,
Computer Aided Chemical Engineering, Vol. 18, (2004), pp. 463 – 468. 2. ‘Sulfur Recovery’, EPA, https://www.epa.gov/sites/default/ files/2020-09/documents/8.13_sulfur_recovery.pdf 3. Sulfur Price, https://sulfur-price.com/ 4. NABIKANDI, N. J., and FATEMI, S., ‘Kinetic Modeling of a Commercial Sulfur Recovery Unit Based on Claus Straight Through Process: Comparison with Equilibrium Model’, Journal of Industrial and
Engineering Chemistry, Vol. 30, (25 October 2015), pp. 50 – 63.
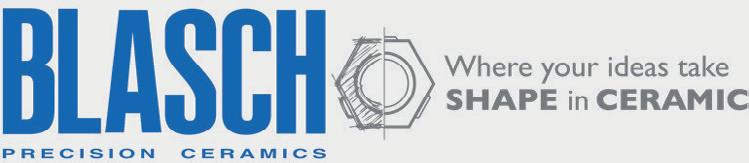
Bulk of radiant Bulk of radiant trapped in front zonetrapped in front zone
Hotter here Hotter here
Tight residence Tight residence time distributiontime distribution Cooler here Cooler here Spiral creates much longer Spiral creates much longer “contact pathway”, or overall “contact pathway”, or overall distance in close contact to distance in close contact to react, even with lower react, even with lower temperatures heretemperatures here Solid perimeter for backmixing Solid perimeter for backmixing - same as choke ring- same as choke ring
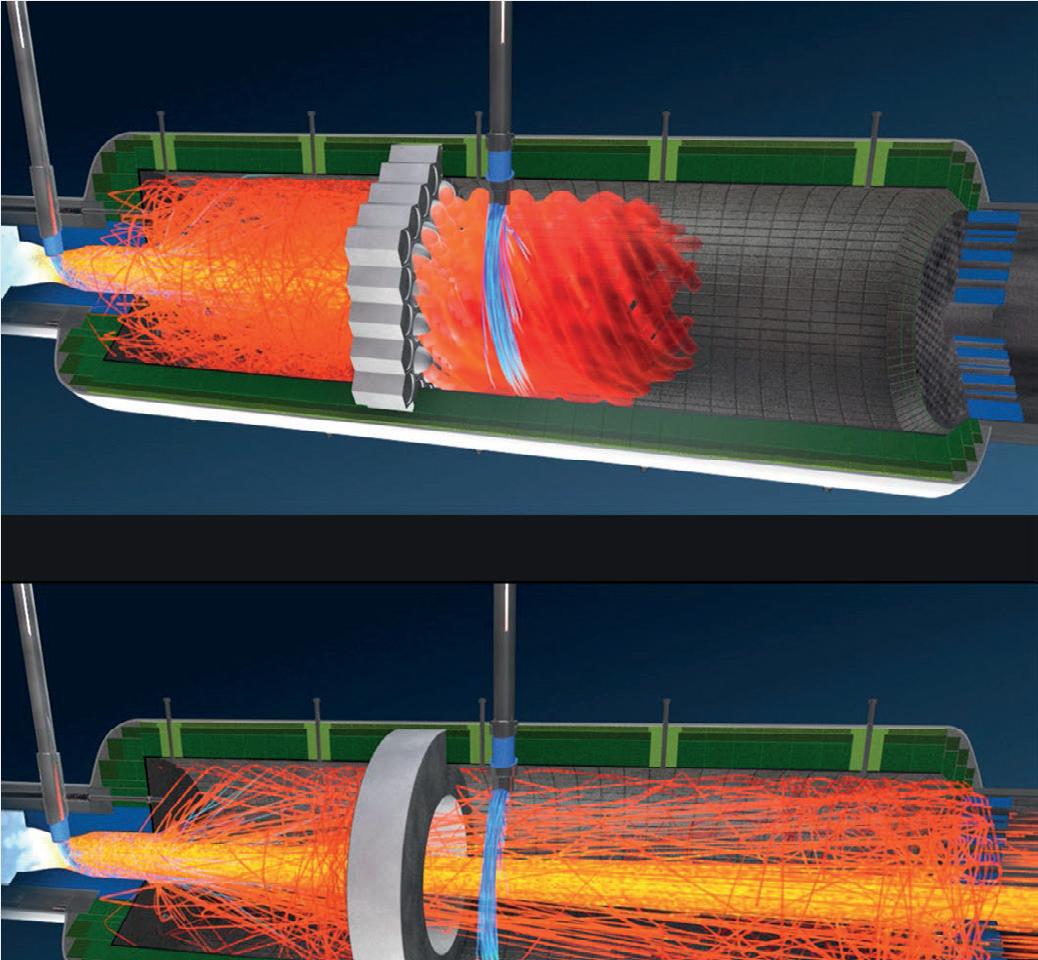
Increased velocity and Increased velocity and temperature carried to temperature carried to tubesheet tubesheet
Broad residence time Broad residence time distribution means insufficient distribution means insufficient RT for some of the reactionsRT for some of the reactions

What does this mean for SRU Operators?What does this mean for SRU Operators?
More complete Ammonia Destruction/increasedMore complete Ammonia Destruction/increased capacity to process NH3 if desiredcapacity to process NH3 if desired Better BTEX DestructionBetter BTEX Destruction Better protection for tubesheet refractory/coolerBetter protection for tubesheet refractory/cooler temperatures going into WHBtemperatures going into WHB More efficient use of furnace volume meansMore efficient use of furnace volume means increased capacityincreased capacity Better mixing and longer distance together meanBetter mixing and longer distance together mean more complete reactionsmore complete reactions Lower energy costs when co-firing or in tail gasLower energy costs when co-firing or in tail gas incineratorsincinerators
What does this mean for sulfur burning acid What does this mean for sulfur burning acid plants? plants?
No more fireflies at furnace exitNo more fireflies at furnace exit Increased capacityIncreased capacity Lower Pressure drop compared to bafflesLower Pressure drop compared to baffles