PORTFOLIO
Nour Beydoun
Fabrication Focus
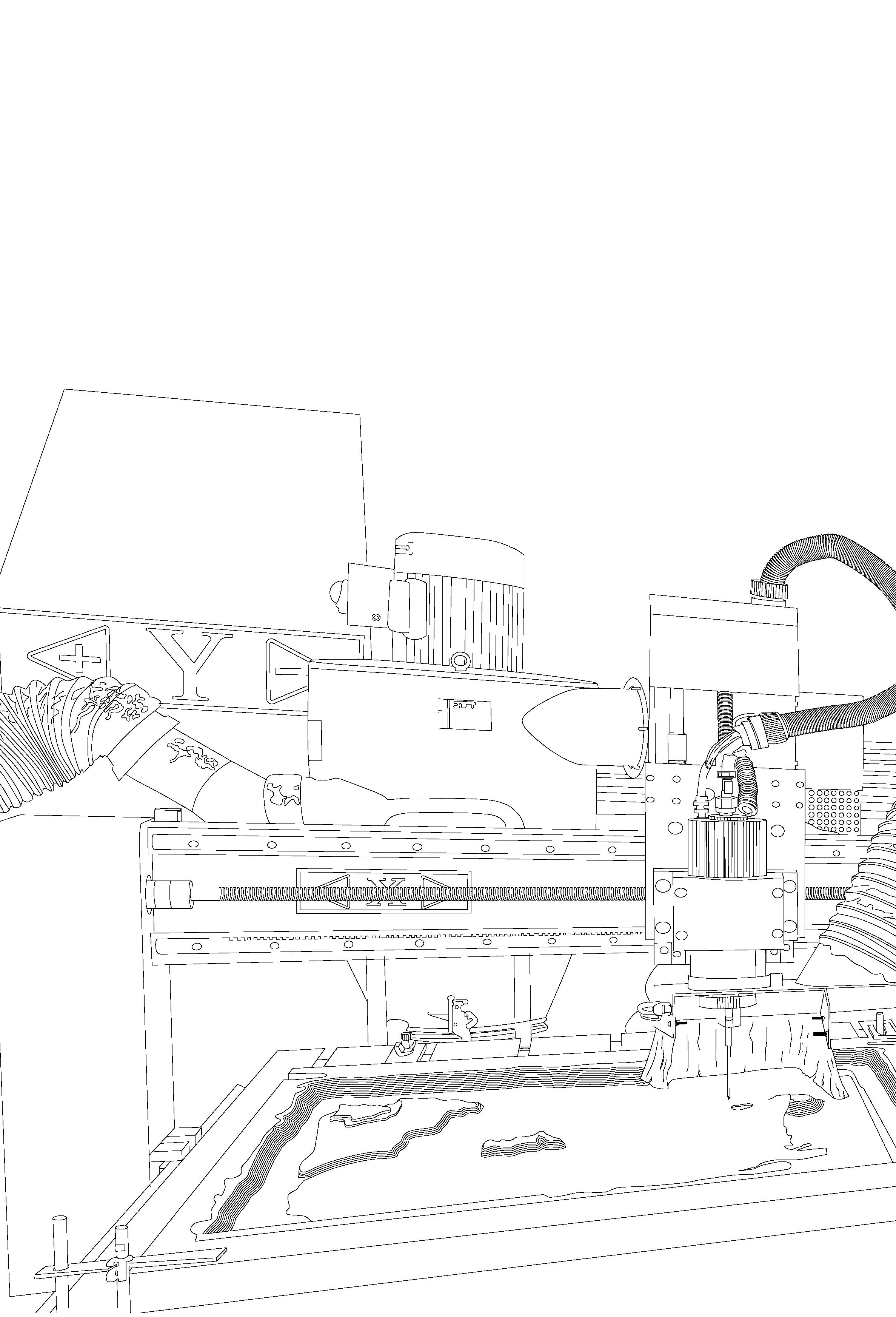
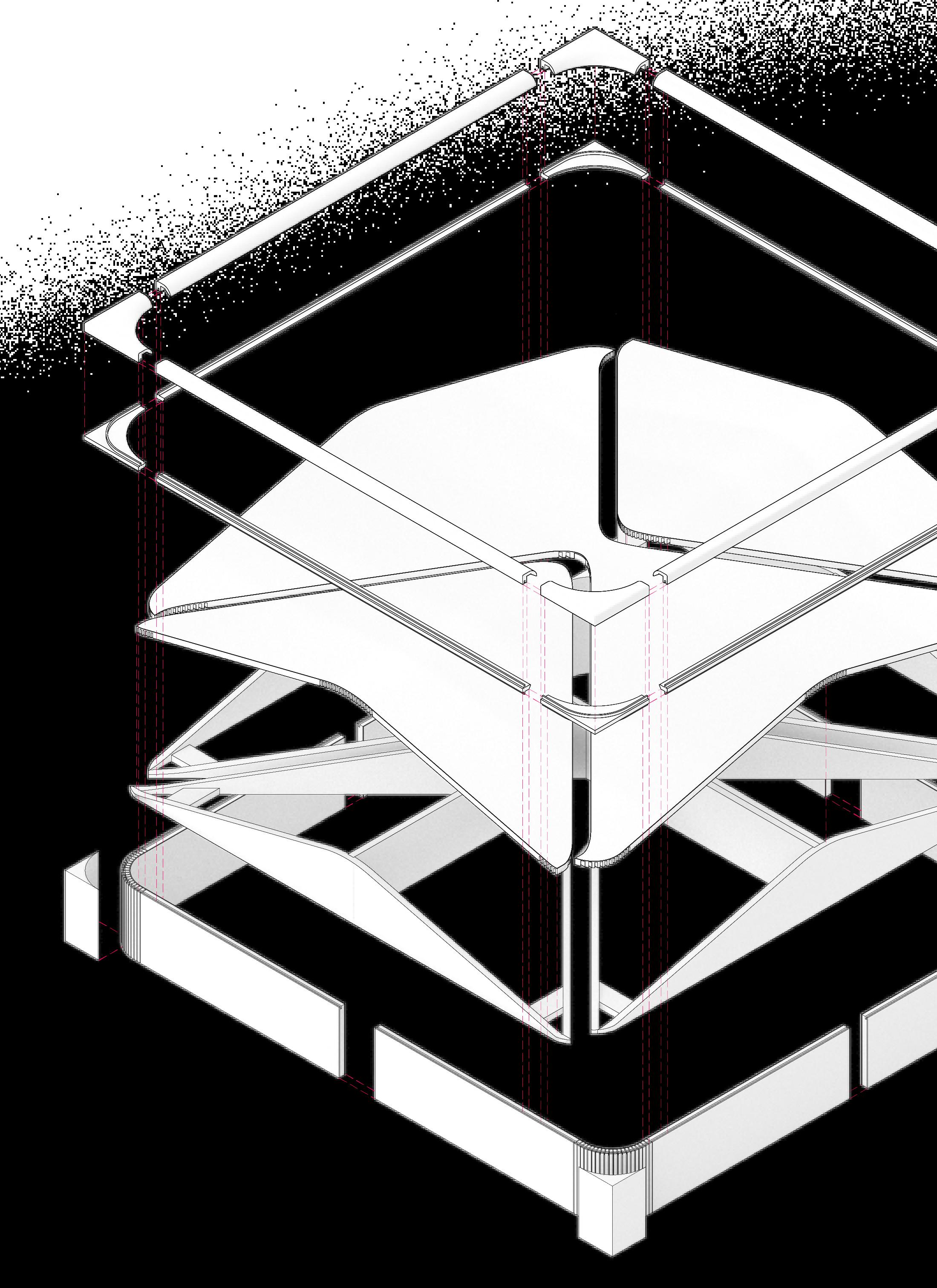
January 2023
The Cumberland ceiling consists of multiple coffers stacked next to each other to form a ceiling. These coffers are paramaterically design by Shim-Sutcliff Architects and manufactured by MC2001. My part in this project consists of managing and and preparing the production files and production flow of these modules.
A. Strips of solid wood are cut through the moulder
B. Corners fabricated using a 5-axis CNC
C. Corners fabricated using a 5-axis CNC
D. Strips of solid wood are cut through the moulder
E. Panels undergo multiple operation process on a 5-axis CNC
F. Individual pieces of the internal frame are fabricated on a 5-axis CNC
G. Strips of solid wood are cut through the moulder
H. Vertical panels are fabricated using a 3-axis CNC.
The Cumberland Ceiling consists sizes that go on the ceiling. three main parts.The first acoustical wood panels that The second is the vertical module and finally,
The microperferated panels
First, the veneer and backer MDF boards. The board is then These panels then go on the an oversized cut, and kerfing. made to mold onto the internal frame is cut on a 5-axis match the curvature of the The panels are then sandwiched and negative, and then cut shape and
Final assembly includes sliding two small panels into each by the vertical pieces and
Cumberland Ceiling Module
consists of modules of varying ceiling. These modules consists of is the microperferated, bent that intersect with one another. vertical panels that sourround the the solid wood trims.
Microperferated Panels
panels undergo multiple steps. backer are pressed to full sized then cut into smaller panels. the CNC for microperferation, kerfing. The panels are then internal frame. The internal 5-axis CNC to have their top the final shape of the panel. sandwiched between a positiove on the CNC to their final and size.
sliding the big panel and the each other, surrounding them finally gluing on the trims.
The Desert Pavilion is a lounge area located in Egypt. The roof structure is parametrically designed using grasshopper with three layers of the same repetitve pattern. Each layer doubles the ratio of the previous layer. The three layers come together to form one complex module, which was later 3D printed. My main focus on this project was the fabrication of different modules, material testing and assembly.
The curvature of the layers was achieved by laser cutting two layers of thick cardboard. The boards were then placed between two CNC milled foam blocks, which act as a cast. The boards were drenched with water and made to perfectly mold to the curves of the foam blocks. When dry, the curvature of the boards resembled the curvature of the structure.
Resin 3D printed Colum at a scale of 1:100
Testing the limits of a resin printer in comparison to PLA plastic. Resin required little structural support while printing in comparison to the PLA printer.
Lasercut Screen at a scale of 1:100
Testing the limits of the lasercutters at the Daniels Faculty, Dertiming how thin the material could be cut withount it breaking down.
The top most layer was done at the Daniels faculty shop in which strips of wood were cut using the table saw and then angled to come together. However, the second and third layer were laser cut. These seperate layers were then pressed and glued together whithout the use of a jig.
A detailed 3D model of the module was made and sent to the 3D starch printer. This module came out very detailed in comparioson to the wooden one. However, it was more fragile. Starch 3D printing required no support for the module, in compariosn to a PLA 3D print.
Transcendence is a memorial design for the victims of the Beirut port exoplosion of August fourth. The hand is a symbol of hope for those who survived the explosion and the 200 LED lights along the exterior of the cedar wood honors the victims. The three glass walls of varrying opacity obscure the direct sight of the wooden hand, representing the the uncertainty which Beirut lived through in this period of time. Moreover, lightly etched along the two exterior rings of the memorial are the masked citizens of Lebnanon who came together after the explosion to clear the rubble off the streets. The path into the structure is not direct as opposed to its exit which present a perspective view of the Mediterranean Sea.
This module was printed from PLA plastic using the Creality Ender 3D printer. This was made to be a high quality print. Therefore a dense lattice infill was used to make the model more durable and portray the design’s details. It is important to note the print’s imperfections at areas of a steep slope due to a lack of bottom supports while printing.
Cerebrum is an isolation pod located in Queen’s Park, Toronto. It’s inspired by COVID-19, allowing individuals to be ‘isolated’ in nature yet still find a place to work, study and remain connected. Cerebrum explores three complex parametric patterns designed using grasshopper that are overlayed to present its inhabitants with unique shading patterns. The curves along the interior seating area of the pod also provides a multiuse space. An environmental study for this pod was also conducted to determine the optimal orientation and positioning for its location.
A portion of deconstructed extrior shell was broken into pieces which perfectly fit into each other to be assembled on site. These pieces were later 3D printed at a scale of 1:2 using PLA plastic, assembled and glued together to increase rigidity.
Queen’s Park radiation analysis. This determines the direction which recieves the most radiation throughout the year.
Queen’s Park wind analysis. This determines the direction which recieves the strongest wind throughout the year.
Toronto’s weather conditions were downloaded and programmed into grasshopper for an enviromental study. The structure was then placed and depending on the radiation and wind conditions, its orientation was determined in a way to allow the most sunlight, in order to highlight the shading on the interior, and to limit wind.
The Diamond Pavilion presents a kinetic roof which folds and flattens based on the position of the sun. Its glass walls allow the sunlight to access the structure, therefore making the roof the only shading system that this pavilion has. The kinetic model shows the way the roof operates. The gear and handle were 3D printed with PLA plastic, and finally the strings were attached at the ends of the folds to emitate the automated movement of the structure.
The gears used for the kinetic model were 3D printed out of PLA plastic, They were initially printed at a smaller scale. However, they needed to be scaled up due to the limitations of the printer and its ability to produce detailed small scale prints. Supports were added to the outward folds to increase rigitdity, and facilitate the movement of the folds.