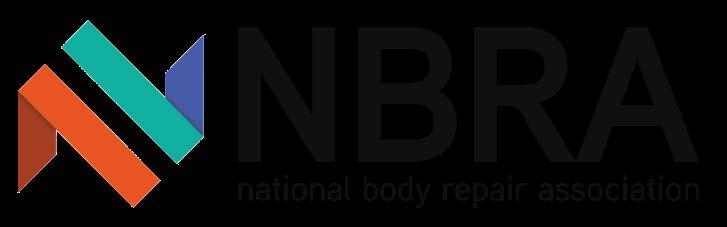
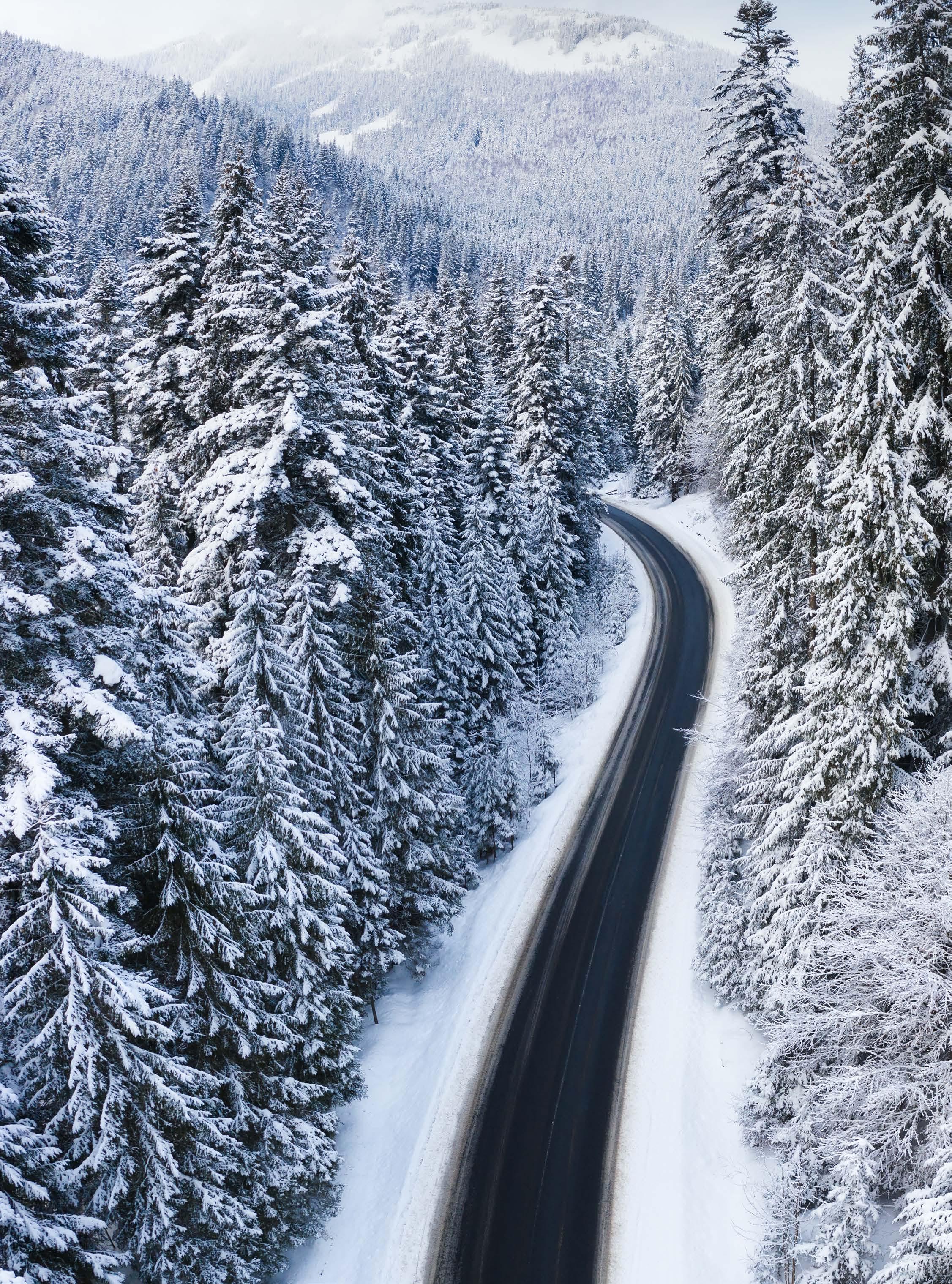
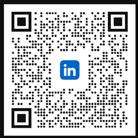

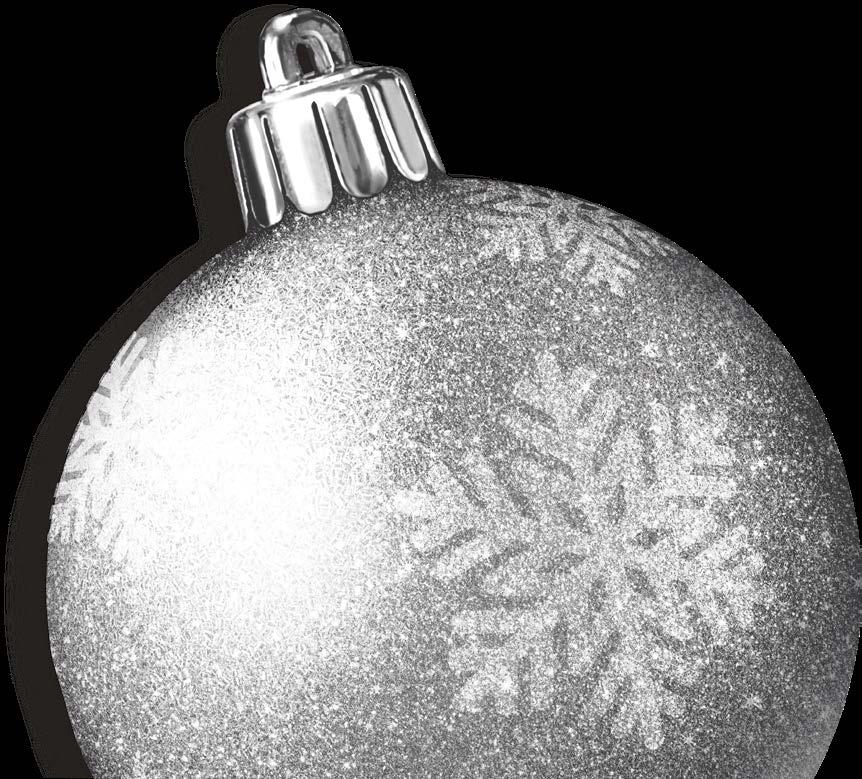
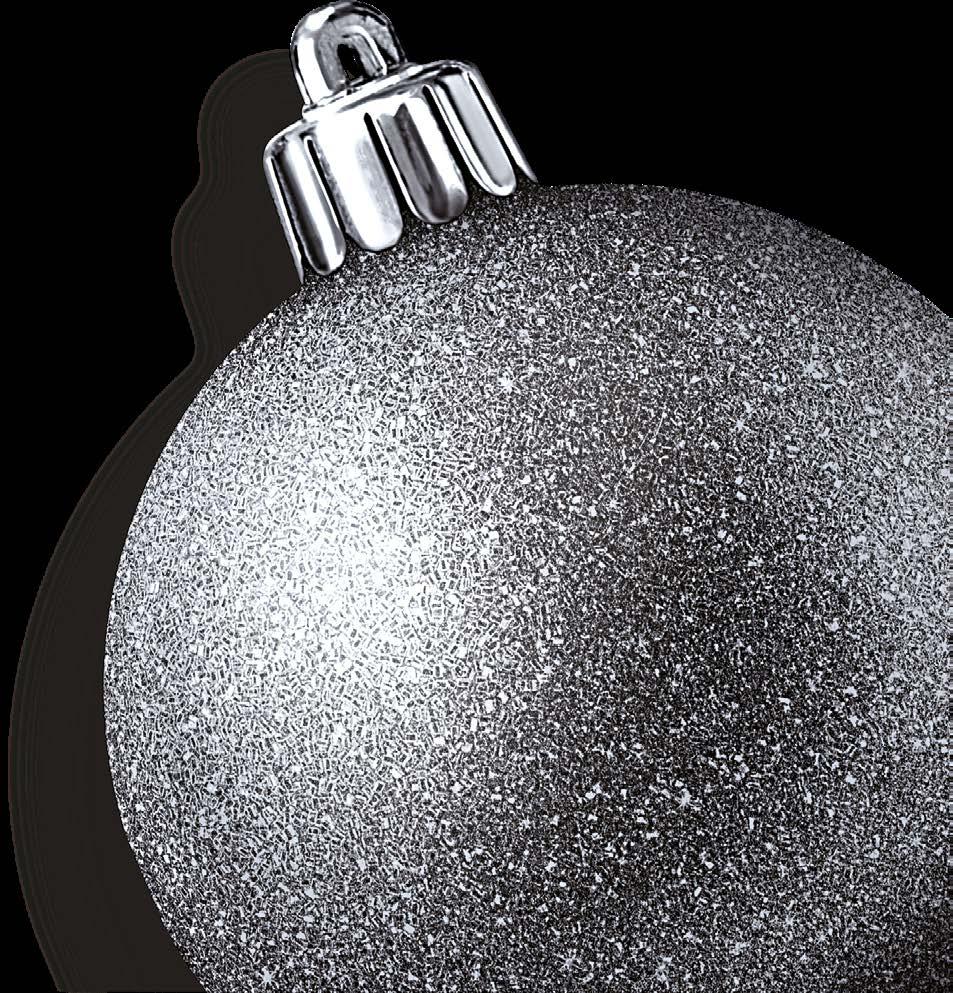
As 2024 comes to a close, it’s a wonderful opportunity to reflect on what has been an incredible year for the NBRA and to look ahead to an even brighter future.
This year, we reached a major milestone, growing our membership to over 1,000 members—a testament to the strength and unity of the body repair industry. We’ve worked hard to engage with all corners of our sector, building meaningful partnerships with insurers, networks, manufacturers, and suppliers. In June, we were thrilled to announce our partnership with Stellantis, bringing their entire accident repair network into membership—a truly significant moment for us all.
2024 also marked the launch of our regional meetings, which have been a tremendous success. The innovative “Speed Dating/Networking” format has been warmly received, creating valuable opportunities for connection and collaboration. We’re excited to expand this initiative in 2025, with at least four regional meetings already planned.
Another standout highlight of the year was the Greener Bodyshop Awards, which achieved record attendance with 364 industry professionals joining us to celebrate sustainability and innovation. The energy in the room was incredible, and we’re already counting down to next year’s event, booked for Thursday, 18th September 2025. To maintain the relaxed and intimate atmosphere that makes these awards so special, we’ve capped attendance at 370. It’s all about creating a space where every attendee can connect, celebrate, and feel part of our industry family.
This year also brought unique opportunities for personal growth and insight. In September, I was honoured to be invited by Enterprise Mobility to
visit Bronzefield Prison to witness the remarkable work the Ministry of Justice is doing to educate and train individuals in readiness for their release. The dedication and commitment to rehabilitation were truly inspiring and underscored the importance of providing opportunities for all to rebuild their lives.
We’d like to take this opportunity to extend our heartfelt thanks to every one of you—our members. Your support and dedication drive everything we do, and you play an integral role in shaping the future of the body repair industry.
To our Supplier Partners and Supplier Members, thank you for your incredible support, which enables us to provide even greater value to our repairer members.
This special Christmas edition of The Repairer is our way of celebrating your contributions and showcasing the fantastic products, services, and innovations within our industry.
On behalf of the NBRA, I wish you all a Merry Christmas and a prosperous New Year. Here’s to an exciting 2025!
Warm regards,
Martyn Rowley NBRA Executive Director
Welcome to this year’s final installment of the NBRA magazine! 2024 has, once again, seen seismic change throughout the automotive industry. In this issue we delve into the world of green parts, new technologies, championing social change, and the latest opportunities for young people in our industry. It’s been a joy to bring this year’s final issue together and we hope you enjoy! From myself and all the team, we wish you a merry festive period!
Dan Chesney, Editor
Join Us for an Industry-First Event in 2025!
Date: 19th February 2025 Venue: GTG Training Centre, Wolverhampton Time: 9:30 AM
This February, we’re teaming up with AGEAS Insurance to bring you an Equipment Expo like no other!
Click the link or scan the QR code below to register your attendance today! WHAT’S ON OFFER?
Over 40 Industry Suppliers showcasing the latest in diagnostics, distribution, green parts, paint, jigs, spray booths, and much more!
A Unique Village-Themed Experience designed to bring a fresh perspective to networking and innovation in the automotive repair industry.
Open to All — repairers, suppliers, insurers, and anyone passionate about the future of the industry!
This is your chance to explore cutting-edge equipment, connect with key industry players, and get inspired for the year ahead.
The road to sustainability and carbon neutrality is one that we, as an industry, must continue to prioritise. At the NBRA, we recognise that achieving a greener future requires commitment, collaboration, and innovation from all stakeholders. This month’s edition of The Repairer highlights an essential aspect of this journey: the use of recycled or “green” parts as an alternative approach to vehicle repair.
Green parts not only align with environmental objectives by reducing waste and the demand for new manufacturing but also contribute to a more sustainable and cost-effective repair process. These parts provide an opportunity for repairers to minimise their carbon footprint without compromising on quality or safety, helping to meet customer and industry expectations for sustainability.
The path to sustainability involves looking at every facet of our work, from energyefficient workshops to reducing emissions
in supply chains and supporting the circular economy. By incorporating recycled parts into our repairs, we are collectively taking another step forward in this journey.
In this issue, our valued green parts suppliers share insights into how their products and services are shaping the future of vehicle repair. Their work serves as a reminder that, while sustainability can feel like a daunting challenge, it is achievable through practical, incremental changes and the shared efforts of repairers, suppliers, and the wider automotive industry.
Thank you for joining us on this path toward a greener, more sustainable future. Together, we can lead the charge in creating an industry that balances innovation with environmental responsibility.
Martyn Rowley NBRA Executive Director
Finding and ordering genuine green parts has never been easier with MyGreenParts. Get fast delivery nationwide on VRA certified green parts with life-in-ownership warranties for all collision parts and reduce your bodyshop’s carbon footprint.
Up to 75% cheaper than the new OEM RRP equivalent
High-quality and fully traceable for maximum compliance
Over 340,000 genuine parts in stock
SYNETIQ an IAA company, one of the UK’s largest integrated vehicle salvage, dismantling, and recycling companies, is leading the automotive industry’s transition to sustainability.
As a vehicle recycler we have key role in what will be an electric dominant future. Every day we seek to maximise both the financial and environmental value of every vehicle we receive.
The number of electric vehicles coming our way for salvage is indicative that the cost to repair EVs continues to be a challenge and is driving the increase in total loss vehicles. We have seen an increase of 55% EVs compared to the previous year.
As electric vehicles (EVs) continue to grow in popularity, we’re providing a sustainable solution for electric vehicle repair through our green parts initiative.
This not only supports the circular economy but also helps reduce the environmental footprint associated with EV production, repair, and maintenance.
We’re proud of our expertise in dismantling electric vehicles is particularly valuable as the industry grapples with the complex logistics of battery recycling and hazardous material handling.
Our colleagues have recently completed the HEVRA (Hybrid and Electric Vehicle Repair Alliance) training. Demonstrating exceptional dedication and expertise, each technician achieved a completion rate of 97% or above.
We’re a market leader in the vehicle recycling and salvage industry. We operate with a
commitment to innovation and sustainability, providing services that extend across salvage and auction, green parts and mechanical solutions.
With over an inventory of 340,000 green parts, each on is carefully tested, cleaned, and recertified for resale. These green parts are used in the repair and maintenance of all types of vehicles, including conventional internal combustion engine (ICE) vehicles and now, electric vehicles.
A green part is a non-safety critical part, such as doors, tailgates, lights, bumpers and major mechanical items such as engines and gearboxes — safety components are strictly excluded.
Our green parts are sourced from end-oflife electric vehicles, meticulously tested are certified in line with VRA standards.
The supply of green parts directly addresses to the growing number of electric vehicles on the road and the environmental concerns that come with their production and disposal.
Electric vehicles are a greener alternative to traditional cars, but they still require maintenance, repair, and replacement parts. Sourcing brand-new components for EVs, however, can involve significant energy consumption and resource extraction, both of which add to the environmental impact of EV ownership.
• Batteries: Reclaimed batteries from damaged or end-of-life EVs are tested and assessed for reuse.
• Body panels and interior components: exterior and interior parts from salvaged vehicles are refurbished and recertified for use in other vehicles.
• Electronic components: electronic components are tested and repurposed.
What are the benefits of SYNETIQ’s green parts
• Environmental impact reduction: by reusing components, we’re helping reduce the demand for new parts, which in turn minimises raw material extraction and energy-intensive manufacturing processes. This supports the automotive industry’s drive towards carbon neutrality.
• Cost savings: green parts cost up to 75% less than new. By using these components, vehicle repair costs can be significantly reduced, benefiting consumers and businesses alike.
• Increased circular economy: By extending the lifecycle of vehicles, we’re reducing waste and promoting resource efficiency.
• Availability: As the demand for parts increases, we’re providing a reliable source of highquality, sustainable parts that are immediately available, reducing wait times for repairs and helping drivers get back on the road faster.
Our green parts offer an innovative and sustainable solution for the growing electric vehicle market and to those repairs aiming to get electric vehicles back on the road.
By reclaiming and recycling parts from endof-life electric vehicles, we’re helping reduce waste, lower repair costs, and promote a more environmentally friendly automotive industry.
We’re not only addressing the environmental impact of EVs but also demonstrating that the future of automotive repair and maintenance can be as green as the vehicles themselves.
For more information about SYNETIQ green parts, visit www.synetiq.co.uk.
With Vin Queries included as standard, parts prices seamlessly updated daily and vehicle models updated every 2 weeks, estimates completed in GT Motive are right first time, every time.
Auto Plas Bumper Recycling specialise in the recycling of car bumpers and other automotive materials >
We offer a free-of-charge collection service, and our central location enables us to easily service bodyshops nationwide, with the capacity to collect over 2000 bumpers a day.
Automotive plastic bumper recycling is an essential process in the automotive industry, driven by the need for sustainability and the reduction of waste. As vehicles have evolved, so too have the materials used in their construction, with plastic bumpers being particularly suitable due to their lightweight properties and ability to absorb impacts. However, the disposal and recycling of these plastic components present significant challenges.
Automotive bumpers are primarily made from a variety of thermoplastic and thermoset polymers, with materials such as polypropylene (PP), polyurethane (PU), and acrylonitrile butadiene styrene (ABS) being predominant. These materials provide flexibility, durability, and resistance to impacts, which are crucial for vehicle safety. The specific type of plastic used can vary based on the manufacturer and model, making standardization in recycling processes more complex.
The recycling of automotive bumpers involves several key steps:
1. Collection and Sorting: The first step in recycling is the collection of damaged bumpers from repair shops. Bumpers are sorted based on material type, which is critical for efficient recycling.
2. Processing: After sorting, the bumpers undergo processing where they are cleaned to remove contaminants such as paint, metal reinforcements, and other residues. This cleaning is vital to ensure the quality of the recycled material.
3. Shredding and Granulation: The cleaned bumpers are then shredded into smaller pieces
and granulated into plastic pellets. This size reduction facilitates easier handling and improves the efficiency of subsequent recycling steps.
4. Reprocessing: The resulting plastic pellets can be reprocessed to create new products. Depending on the quality of the material, these pellets may be used to manufacture new bumpers or other automotive components, as well as non-automotive items like containers and consumer goods.
Despite the clear benefits, there are significant challenges associated with bumper recycling. The process can be costly, and fluctuating prices of virgin plastics can deter manufacturers from opting for recycled materials. Additionally, the market demand for recycled plastic products can be inconsistent, affecting investment in recycling infrastructure. However under new EU Directives, which the UK will adopt, by 2030 all vehicle manufacturers must use a minimum 25% of recycled plastic in new vehicle construction.
Recycling automotive bumpers significantly contributes to environmental sustainability. It helps reduce landfill waste, conserves natural resources, and lowers greenhouse gas emissions associated with the production of new plastics. By recycling bumpers, the automotive industry can minimize its environmental footprint, contributing to a circular economy.
The future of automotive bumper recycling looks promising, driven by advancements in technology and increasing regulatory pressures
for sustainable practices. Innovative methods, such as chemical recycling and enhanced sorting technologies, may improve the efficiency and efficacy of the recycling process. Furthermore, the development of biodegradable and recyclable composite materials could pave the way for more sustainable bumper designs.
Industry collaborations and initiatives aimed at increasing awareness and investment in recycling technologies are also crucial. As consumers demand more eco-friendly products, manufacturers are likely to prioritize recycling
efforts, leading to improved systems and greater use of recycled materials in production.
In conclusion, automotive plastic bumper recycling is a vital component of sustainable practices in the automotive industry. While challenges remain, ongoing advancements and a commitment to environmental responsibility offer a pathway toward more effective recycling and a reduction in the industry’s overall ecological impact.
The automotive repair industry stands at a critical crossroads in the journey toward environmental sustainability. With increasing emphasis on reducing carbon emissions and adopting ecofriendly practices, the role of Green Parts in vehicle repairs has become more significant than ever. Charles Trent Limited (Trents), a leader in the Green Parts and automotive recycling sector, has positioned itself as a pioneer in offering high-quality, sustainable solutions for bodyshops and repair networks. Vehicle repairers can contribute to environmental conservation without compromising reliability or efficiency by integrating Green Parts into the repair process.
At the heart of Trents’ operations lies a commitment to sustainable practices. The company’s advanced Green Parts production
facility is powered by solar energy, underscoring a dedication to reducing environmental impact and ensuring that green parts are produced in a green manner. By leveraging electric-powered forklifts, electric baler and powering this entire operation from renewable energy, Trents minimises its carbon footprint, creating a ripple effect that extends throughout the supply chain.
Repairers that partner with Trents directly contribute to a greener future. By choosing Green Parts, they reduce the demand for manufacturing new components, which require significant energy and raw materials. This circular economy approach ensures that valuable resources are reused, cutting down on waste and emissions associated with new parts. Trents continuously strives to pair the environmental benefits of Green Parts with a fast, quality-driven service to ensure Green Parts are the optimum alternative in vehicle repairs.
A common misconception about recycled parts is they may not meet the same standards as new components. Trents has debunked this myth through rigorous quality assurance processes. Every part undergoes meticulous inspection throughout the entire operation to ensure only the best quality parts are delivered to valued partners. From precise dismantling with its state-of-the-art technology to secure recycled packaging, Trents ensures every Green Part arrives in optimal condition, ready to be used in vehicle repairs.
This focus on quality makes Green Parts a viable and trustworthy alternative for repair professionals. Repairers can confidently incorporate these components into their workflows, knowing they are picking an environmentally friendly option, delivered the next day and driving their operations towards net zero.
The environmental benefits of Green Parts are clear, but their advantages extend beyond sustainability. By choosing recycled components, repairers can significantly reduce costs without sacrificing quality. This makes Green Parts an attractive option in an industry where cost efficiency is key. Using recycled parts also appeals to a growing segment of environmentally conscious consumers, demonstrating a commitment to reducing environmental impact.
As an industry leader, Trents offers more than just parts; it delivers comprehensive solutions for partners aiming to adopt greener practices. Trents newest Parts Portal offers a one-stopshop solution for repairers to easily integrate an instant ordering of Green Parts into their operations. Each part comes with a carbon saving certificate and a monthly statement is provided to showcase how much carbon has been saved on all parts purchased. Showcasing a platform that allows users to easily search for parts from an inventory of over 90,000 parts, Trents is dedicated to innovation and processes that help repair networks easily adopt a greener method of vehicle repairs.
The adoption of Green Parts is more than a trend; it is a necessary step toward a sustainable future for the automotive repair industry. By integrating these components into their operations, repairers can play a pivotal role in reducing carbon emissions, conserving resources, and promoting a circular economy.
Charles Trent Limited is proud to partner with repair professionals seeking reliable, ecofriendly solutions. For those ready to embrace the benefits of Green Parts, Trents offers a seamless pathway to sustainability. Together, we can drive positive change — one repair at a time.
Since 1926, Charles Trent Limited has led the automotive industry to offer innovative solutions for vehicle recycling and green parts.
Trent’s newest parts portal offers a one-stop shop solution for vehicle repairers and repair networks to easily integrate an instant ordering of green parts into their operations.
This innovative portal provides a seamless process to search next day availability from our growing 90,000 inventory.
Utilising high-quality green parts has never been easier so that your operation can work towards a circular economy.
With
over 90,000 green parts ready for next day delivery
Trents partner with insurers and repairers to offer tailored solutions for green parts. Our state-of-the-art parts production facility is the future of green parts and offers vehicle repair solutions that reduce your carbon footprint.
As the automotive industry increasingly prioritizes sustainability to support cost efficiency, the role of the “Green Parts Specialist” has never been more important. A UK-based leader in green parts supply, operating for over 50 years, evolving to meet the changing demands of the industry and setting standards for quality, sustainability, and service innovation. With a commitment to customer satisfaction, The Green parts Specialists has earned awardwinning partnerships with leading insurance providers. These collaborations have secured the trust of repair industry to increase the use of green parts in vehicle repairs, making them both more accessible and reliable for insurance claims, reducing average repair costs whilst meeting the commitments of ESG goals.
One of the major advantages of using this Green Parts Specialist are the associated cost savings. Customers can save, on average, 50% on parts compared to the recommended retail price (RRP). This substantial saving, paired with the environmental benefits of using recycled parts makes the green parts option an attractive choice for both car owners and repair shops. It’s a powerful example of how embracing sustainability can also lead to significant financial savings.
The company’s operations are spread across four strategic locations, with plans for expansion to eight sites. This growth ensures the business can meet the increasing demand for green
parts while maintaining exceptional service levels across the UK. Operating a fleet of 32 vans, which is set to grow to over 50, this fleet expansion will allow the company to increase its reach and maintaining its promise of nextday delivery, and reducing its carbon footprint through efficient logistical solutions.
The Green Parts Specialists innovative technological solutions is a key differentiator against the rest of the dismantling industry. The company has developed a self-contained, userfriendly GPS platform that tracks a wealth of key management information (MI). This platform provides valuable insights into inventory levels, delivery times, real time tracking, and carbon savings generated from the use of recycled parts.
For vehicle repairers, the integration of the GPS platform with estimating platforms and Business Management Systems (BMS) is another significant development. This seamless connection empowers technicians to quickly and accurately source the necessary green parts in real time without the requirement to default from their normal estimating process . The integration streamlines operations, reduces administrative burdens, and ensures that the repair process runs smoothly from initial assessment to parts delivery and installation.
In addition to its green parts offerings, the company has recently expanded its service portfolio by introducing a new mechanical
solution service. This full end-to-end service addresses mechanical downtime by providing a supply-and-fit solution for major mechanical items like engines, gearboxes, and differentials. With the added benefit of vehicle collection and return delivery, the company offers a comprehensive solution which reduces downtime for customers, putting the vehicle back to work and offered with a 12-month warranty. It is no wonder that the company now holds a reputation as a one-stop shop for sustainable, high-quality automotive repair solutions.
The company’s dedication to part provenance, VIN matching and quality plays a crucial role in ensuring the reliability and safety of the parts used in repairs, with industry leading fulfilment each part is fully traceable and delivered
on time in the condition that was promised. Industry confidence is key to the highly regarded reputation of The Green Parts Specialists.
In conclusion, the Green Parts Specialist is leading the way to provide a range of eco-friendly parts and innovative solutions that benefit both customers and the environment. With awardwinning insurance partnerships, a self-developed parts procurement platform and the introduction of a comprehensive mechanical solutions service, the company is setting a new standard for the industry. Customers can rely on The Green Parts specialists for quality, cost-effective, and sustainable solutions that reduce both repair costs and environmental impact, supporting a greener future for the automotive repair industry.
The right part, first time, and on time, every time.
The Green Parts Specialists offer a wide range of high quality, used Original Equipment Manufacturer (OEM) green parts.
Request a part through our streamlined online portal or app
In-house VIN matching so you always find the exact part you need
We source parts & provide you with a quote in under 30 minutes
PartsXchange is a B2B marketplace that has been tailor-made for the Bodyshop industry. Bodyshop’s can list their parts for free to sell back into the industry and buy parts from certified sellers, this includes accredited Bodyshop’s, main dealers and VRA accredited recyclers. We aim to make purchasing of parts easy and by streamlining all parts into one platform, to prevent Bodyshop’s receiving 100’s of leads spamming their inbox from multiple sellers, all parts in one place. PartsXchange streamline the buying process by having an automated parts lead integration, this works when an estimate is merged into a BSM. We provide a basket of parts directly to your PartsXchange account relating to the registration of the vehicle and send an email lead with all parts included.
We have heavily invested our time and resources into green parts over the last year, trying to bridge the gap between Bodyshop’s and recyclers. We have seen the many benefits they provide to Bodyshop’s and the industry as a whole. The benefits from using recycled parts for is improving sustainability and reducing sites carbon footprint. These two factors alone make a huge difference, not only to the collision repair industry and the world we live in but also profitability (the part we love to champion!).
Living in a world with overheads rising due to higher wage demands and growing running costs, green parts are a great way to make profit back on the bottom line. Majority of work providers / insurers are accepting the use of green parts as well as suggesting that Bodyshop’s start using green parts and some even pay full retail value. Not long ago, one of our PXC members reported that they have focused on the use of green parts more recently and in one month they added additional 16% to their parts profit, which has the potential to be thousands more revenue each month.
The use of green parts can be very effective when a vehicle is close to being a total loss. By acquiring green parts (which can be up to 70% cheaper than the brand-new OEM equivalent) we can keep cars on the road benefiting the owner and the Bodyshop, as they earn labour on the repair. No one wants multiple vehicles taking up valuable space on site you can’t repair.
Another great way Bodyshop’s can use green parts is to help cut down on repair time. Due to the ongoing issues in the world, brand-new OEM parts have become harder and harder to source, some with no expected delivery date. Green parts can be a great alternative, by getting the vehicle back on the road quicker to help speed up repair time, also being more sustainable, lowering carbon emissions and lowering the repair cost for the work provider.
As well as this, Green parts fit better than other well known alternative ‘aftermarket’ parts. This will save the Bodyshop valuable time and effort when it comes to fitting the recycled part to the vehicle. On some occasions like a door, it may come already built up and it may even be the same colour to the vehicle being repaired, which saves even more time. Green parts are also handy for spare parts just in case the strip fitter unfortunately breaks something.
Our goal is to help expose green parts into the collision repair industry even further, making sites more sustainable, reducing their carbon footprint, helping to reduce repair times and help make Bodyshop’s more profitable.
Bodyshops that incorporate reclaimed parts into their workflow unlock a wide range of economic and environmental benefits; reducing costs and increasing profitability, improving workshop productivity and key-to-key times, supporting sustainability through the circular economy and cutting carbon emissions by reducing the need for newly manufactured parts.
From a practical perspective, speed of service gains from the use of readily available reclaimed parts improve efficiency and the customer experience, whilst carbon savings appeal to motoring consumers and work providers alike, enhancing reputation and compliance with environmental targets and regulations. A bodyshop can differentiate its brand from the competition through its environmentally responsible practices, promoting its re-use of parts which may otherwise go to landfill; reducing waste, conserving resources and helping to reduce the carbon footprint of the repair industry.
Demand for reclaimed parts continues to increase, but the market is still young and bodyshops, whilst recognising the benefits, require confidence that they provide a reliable alternative within the repair process. Areas of concern can include cost; parts provenance; parts quality; parts recall checks; parts number accuracy; availability and back orders; and professional packaging and delivery. At Silverlake we invest in people, technology and data analytics to give bodyshops confidence in our product and a positive customer experience.
Our parts offer savings of up to 70% of RRP subject to external factors such as scarcity, demand and cost to acquire donor vehicle. Our pricing
is dynamic and we analyse internal and market data to offer the most competitive price. We are certified to the VRA UK Standard for Reclaimed Parts, providing provenance reports on all parts and supplying them quality graded and warranty assured. We guarantee that all our donor vehicles are checked through the manufacturers’ AutoRecall system, preventing the sale of recalled parts. We have built relationships with the leading motor manufacturer brands and use technology to cross reference parts numbers to help give our customers better clarity. We use data analytics to ensure we are dismantling the parts our bodyshop customers need. Removing the labour intensive requirement to check multiple online platforms, we have a dedicated premium bodyshop service with a highly responsive team on hand to deal directly with customer orders and have designed a bespoke back-order system which proactively notifies them when any missing parts are in stock. Boosting parts availability further, we have recently invested in our parts storage facilities increasing our capacity to store over 10,000 panels and doors. Silverlake parts arrive in the expected condition and promised timescale, professionally packed and delivered by our in-house delivery fleet. Our service is nationwide and bulk deliveries to our Midlands hub are used to reduce carbon emissions generated by transportation, for orders received from the north of the country. We still believe we can do more. We are committed to building a partnership with our bodyshop customers to create a future that is better for their business and ours, and one that is far greater than either of us could achieve individually.
Our partnership approach to our reclaimed parts service is the foundation of our ongoing success. In the last year, bodyshop demand for our parts has grown by over 200% reflecting confidence in our product and service. We were proud and humbled to win the Green Parts Supplier Award at this year’s ABP Club Night of Knights, a Repairer’s Choice Award voted for by bodyshops throughout the industry.
We organise in-depth tours of our automotive recycling site for bodyshops to see our entire reclaimed parts process first-hand. The insight gained combines our knowledge and
skills with those of our bodyshop customers and informs the way we deliver our service. In 2025 we will be rolling out our new parts portal designed for bodyshops by bodyshops!
If you would like a tour of our Southampton facility, please contact tharvey@silverlake.co.uk
For further information please contact: Silverlake Press Office
Anne.staunton@peak-marketing. co.uk / 07813 339840
Founded by Dan and Lauren Chesney, OnyxPDA is a perfect synergy of marketing expertise and industry understanding.
Drawing on experience from across the motor, insurance, medical and legal industries, we are dedicated to helping businesses stand out from the competition.
We understand the importance of clarity and trust, in our industry, when communicating with your customers or partners. Whether you’re seeking to refine your brand’s presence, launch a new product, or engage your audience through compelling marketing campaigns, we have the knowledge to deliver results. With a global perspective and local expertise, we’re equipped to help businesses across various industries. We’ve had the privilege of working with a diverse range of businesses and products, from FNOL solutions and ATE insurance to cutting-edge AI technologies.
Our data-driven approach means we develop tailored strategies that are both effective and impactful. We pride ourselves on making marketing fun and engaging, injecting a bit of humour and personality into every campaign.
Proposition, Definition, and Articulation— three core pillars that define how we approach every project. Proposition asks, “Who are you?” – the foundation of your brand’s identity. Definition answers, “What do you do?” – the services or products that you offer. And Articulation is how we communicate your message to the world.
By focusing on these three elements, we ensure that every business we work with has a clear, compelling presence.
Supported by a talented in-house team of graphic designers and marketing professionals, we have the tools to elevate any brand and introduce fresh, innovative ideas to any industry.
We offer a full suite of services, from logo and website design to comprehensive marketing strategies and campaigns. Whatever your needs, we’re here to help you achieve your goals.
As the NBRA’s tried and trusted marketing partners, we’re ready to help turn your business from bland to brand in 2025, ensuring that you stand out in a crowded market.
We’re committed to setting trends rather than following them. We’ve been creating innovative strategies since 2020, and we’re just getting started...
1. Clarify your brand message – Make sure your business’ identity is clear and consistent across all marketing materials. Define who you are, what you do, and why customers should choose you.
2. Utilise local SEO – Optimising your website for local search terms is essential in this industry. Make sure your business appears in local directories, maps, and Google My Business so that potential customers know exactly where to find you.
3. Engage on social media – Staying active on social platforms such as Facebook and LinkedIn is key to attracting and retaining your audience. Share valuable content, industry insights and engage your followers with thought-provoking discussion.
4. Offer exclusive promotions –Run limited-time offers or discounts to attract new customers and encourage repeat business. Make these promotional activities easily accessible through your website and social media.
5. Encourage feedback – positive reviews and testimonials are arguably the most valuable marketing tool in this industry. Ask satisfied customers to leave reviews on Google or Trust Pilot to build credibility and trust.
6. Invest in paid ads – use targeted advertising on platforms like Google Ads or Facebook to reach potential clients who are actively searching for the services you offer.
7. Leverage email marketing – Build an email list of current and potential clients and send regular updates, tips, or exclusive offers to keep your audience engaged and informed.
8. Network within the industry –attend industry events (such as the NBRA regional meetings) to build relationships with other professionals and gain valuable contacts.
9. Create educational content – positioning yourself as an expert through publishing blogs, videos or infographics that educate your audience about your services or industry trends builds reputability and respect.
10. Partner with OnyxPDA for expert marketing – oops... how did this get in here?! Collaborate with us in the new year to elevate your business’ image with data-driven, engaging marketing strategies.
“It’s been a great experience helping NBRA/ VBRA define and execute comprehensive marketing strategies throughout 2024. We’ve really enjoyed playing a part of the growth in their members, suppliers, and partners. Brand presence is crucial in our industry, and our role in supporting the NBRA’s development keeps pushing us to innovate and evolve”
Get in touch today to discuss how we can revolutionise your business’ image in the new year!
Email: dan@onyxpda.co.uk
Phone: 07470086911
Website: www.onyxpda.co.uk
Dan Chesney, Managing Director
As Executive Director of the NBRA, I often focus on issues directly affecting our industry: market trends, legislative changes, sustainability, training initiatives, etc. However, this month, I want to shift the spotlight to a topic that impacts many individuals in ways often misunderstood or overlooked - menopause.
Having been married to my wife for 35 years, I witnessed firsthand the profound effects menopause can have on a woman’s life. My wife began experiencing symptoms in her late 30s, earlier than many might expect. Her journey opened my eyes to the physical, emotional, and mental challenges women face during this natural phase of life. It also made me realise how important it is for men, both as partners and colleagues, to be educated and empathetic about this subject.
What Is Menopause?
Menopause marks the end of a woman’s reproductive years, typically occurring between the ages of 45 and 55. However, some women experience early menopause in their 30s or 40s due to genetics, medical conditions, or treatments like chemotherapy. The menopause transition can span several years, often starting with perimenopause, where hormone levels begin to fluctuate, leading to a variety of physical and emotional symptoms.
While menopause is a natural biological process, its effects can be challenging and, for some women, even debilitating. It is crucial to understand these challenges not just for those experiencing them but also for the men in their lives – this could be in the form of partners, colleagues, and employers.
Common Symptoms
Menopause symptoms vary greatly among women, but some of the most common include:
• Hot flushes: Sudden feelings of heat that can be uncomfortable and disruptive.
• Night sweats: Severe sweating during sleep, often leading to disturbed rest.
• Mood swings: Feelings of irritability, anxiety, or depression due to hormonal fluctuations.
• Fatigue: Persistent tiredness that can impact productivity and concentration.
• Memory issues and “brain fog”: Difficulty focusing or remembering tasks.
• Physical discomfort: Joint pain, headaches, or changes in weight and skin.
These symptoms can affect a woman’s daily life, including her work performance and overall well-being. Why Should the Body Repair Industry Care?
In an industry traditionally dominated by men, menopause may seem like a distant or irrelevant topic. As leaders, you should be setting an example by championing menopause awareness and consider this:
• Many of your colleagues, employees, and even customers are women who may be navigating this challenging phase.
• Understanding the impact of menopause can help create a more inclusive and supportive workplace culture.
• Menopause symptoms don’t just affect individuals; they can influence team dynamics, productivity, and morale if not addressed empathetically.
Employers and colleagues can play a crucial role in supporting women during menopause. Here are some signs to watch for:
• Increased absenteeism: Healthrelated absences may spike.
• Decline in performance: Difficulty concentrating or meeting deadlines may stem from fatigue or brain fog, not lack of effort.
• Emotional changes: Irritability or withdrawal may be a response to hormonal shifts, not personal grievances.
Creating a menopause-friendly workplace doesn’t require large investments but does demand awareness and empathy.
At the NBRA our initiatives, have included the implementation of a menopause policy in which we can provide a template for other organisations to adopt.
Here’s how you can support your staff too:
1. Start the Conversation
Openly acknowledge menopause as a natural part of life. Host awareness sessions or include it in health and well-being documents. Normalise discussions about it to reduce stigma.
2. Offer Flexibility
Some symptoms, like fatigue or hot flushes, may be better managed with flexible working hours or remote work options.
3. Adjust the Environment
Simple changes like providing fans, ensuring access to water, or creating quiet spaces can help women feel more comfortable.
4. Educate Managers
Train line managers to recognise symptoms and provide support without judgment. A sensitive, informed manager can make a huge difference.
5. Provide Access to Resources
Share information about menopause and encourage women to seek medical advice if needed. Offering health support through workplace benefits can also be invaluable.
Additional Resources available to all include:
• The NHS website for information on menopause symptoms
• The British Menopause Society For Partners and Colleagues
Men, whether as colleagues or partners, play a vital role in supporting the women in their lives. Here’s how:
• Listen: Sometimes, just being a sounding board can help.
• Be Patient: Understand that mood swings or forgetfulness are not intentional.
• Educate Yourself: Learn about menopause to better empathise with what she’s going through. Menopause and the Law
On 22 February 2024, the Equality and Human Rights Commission (EHRC) published new guidance on menopause in the workplace. This guidance helps employers understand their legal obligations when supporting workers experiencing menopausal symptoms. It explains how these symptoms may be
protected under the Equality Act 2010 and outlines the responsibilities employers have under the Act. Research from the Chartered Institute of Personnel and Development found that two-thirds (67%) of working women aged 40-60 reported that menopause symptoms had a significant negative impact on their work.
It’s important to note that while menopause is not a specifically protected characteristic under the Equality Act 2010, employees may still be protected under related characteristics, such as age, disability, gender reassignment and sex.
Employers must consider how to support employees experiencing menopause symptoms and ensure that no one is treated less favourably as a result.
The body repair industry is built on teamwork, precision, and resilience - qualities that thrive in a supportive and understanding environment. Addressing issues like menopause reinforces our commitment to not only professional excellence but also personal well-being.
As men, whether as partners or colleagues, your understanding and empathy can have a transformative effect on the women around you. Recognising and supporting women through menopause is not just a kind gesture; it’s a necessary step toward building stronger relationships and more inclusive workplaces.
At the NBRA, we believe in championing not just industry-related challenges but broader issues affecting our members and their teams. By raising awareness of menopause, we aim to raise understanding and inclusivity within the body repair sector.
Let’s ensure the women in our lives and workplaces feel supported, valued, and understood during every stage of their journey. After all, a strong industry is one that cares for its people - not just as workers but as individuals.
Gaining even a little knowledge about menopause and understanding someone else’s experience is far more powerful than remaining unaware. Together, we can create meaningful change - starting today.
Can we be honest
Mediocre marketing just won’t cut it in 2025!
As the NBRA’s tried and trusted marketing experts, we’re here to turn your business from bland to brand. If you’re looking to stand out in the new year, get in touch today.
Vehicle diagnostics and Advanced Driver Assistance Systems (ADAS) have revolutionised the automotive repair industry, becoming integral to ensuring vehicles are safe, efficient, and road-ready. With continuous advancements in vehicle technology, repairers now face complex challenges, from recalibrating ADAS sensors to diagnosing intricate system faults. In this feature, we delve into how diagnostics and ADAS have transformed the industry and spotlight six leading diagnostic suppliers shaping the way forward.
Storm Auto Services was established, as a “one stop shop” for the body shop sector to address the challenges repairers face when repairing ADAS systems. We consulted with repairers and insurers alike to understand where they needed help with the repair processes around ADAS, coding, and programming. The answer that surprised us most, was that being cheap is not what they wanted, but a reliable and dependable service. We also asked what they expected from us regarding documentation and compliance processes, and again adapted our systems and processes to support this. Our portfolio includes a network of mobile technicians, covering all vehicles from small cars to HGV’s. We also have an officebased team of remote technicians, a secure tablet solution and an IMI accredited training centre with highly qualified technical trainers covering all body shop disciplines.
We are in a competitive industry with most of our competitors using the same technology as us. We believe it is how you work with a repairer, to make their job easier and deliver the service efficiently and effectively whist offering the support and advice they need, when they need it. A major issue for every business is employing the right skilled staff, which is essential when carrying out complex tasks around ADAS systems, module coding, programming and general fault finding, so our team are able to successfully complete a job. When setting up our remote service, we evaluated several remote devices to connect to a car, but quickly realised that what really matters to a repairer is not the technology, but quality of the technician at the end of the phone, or online portal chat, who can make sure the vehicle is actually repaired.
It is key that vehicle safety systems are returned to their pre accident condition (as well as identifying non-accident-related faults) and essential that we use the right tool for the job. The increased use of secure gateways and manufacturer tokens needed to access systems for diagnostics, updates and programming is reducing the effectiveness of older tools being. As a result we are now seeing a significant increase in the amount of pre and post scans our teams are generating. We are constantly investing back into our business to maintain the high level of technology we need to complete the job. With a clear eye on the future, we are continuing to expand our fleet and remote teams, we are already working with HGV and commercial repairers, investing in specialist repair areas such as EV battery diagnostics and repair, developing an approved partner network and VDA support systems to name just a few, to keep us relevant to our customers in this fast-moving industry.
We have noticed that “ADAS” has now become a generic phrase or “buzzword” to cover a wide range of additional services post repair. For example, front camera calibration, new radar programming and radar calibration are three different operations on one car but are typically referred to as “ADAS” in an estimate, which causes problems with authorities or lost revenue for the repairer not knowing what systems needs attention. It is also concerning to see how some companies can do the job properly, observing compliance and safety at the low rates seen.
In the collision repair industry, there is always someone who will “do it cheaper” but we are proud that we are often called upon where competitors or even main dealers have been unable to diagnose and repair a fault. Which seems to prove the old saying of buy cheap buy twice!
A1 ADAS Solutions and A1 Remote Diagnostics, part of the A1 Group, are fast becoming the collision repair industry’s trusted partners for ADAS and diagnostic work.
The A1 Group, which operates a nationwide mobile ADAS service, says its success is largely down to its expertise in being able to offer bodyshops a choice in the way they handle ADAS work.
Managing director, Iain Molloy, says the group is unique in that it helps to take the ‘pain’ out of ADAS by helping bodyshops with a choice of two routes. Both massively reduce keyto-key times and increase overall profits.
He said: “There’s no right or wrong; it’s what’s best for your bodyshop. Some want to invest in ADAS, become specialists, and generate a whole new revenue stream. Others don’t want to take on the liability. What’s important, is deciding how you’re going to do ADAS calibrations following collision repair work.”
For bodyshops who want to keep ADAS work in-house, A1 is a product distributor of ADAS and diagnostic equipment via its ‘set up for you’ service. As an independent distributor, it advises on the best equipment for each individual workshop, taking in considerations such as available floor space and lighting. After delivering and setting up the equipment, A1’s team also provides training and ongoing support.
Molloy continued: “Most ADAS distributors have experienced salespeople, but no ‘hands on’ experience. That’s where we’re different. We do ADAS calibrations day in day out, we live and breathe ADAS. It puts us in the best position to offer unbiased and specialist advice.
“This element of trust is important for our customers. ADAS equipment isn’t a plug and go purchase. Any technician carrying out ADAS calibrations needs to hold the IMI’s AOM230 qualification and have access to ongoing technical support. With all this in place, our ‘set up for you’ service helps to create a whole new revenue stream for the business. We see bodyshops maximising their return on investment in as little as two to three months.”
For bodyshops who don’t want to invest or have the liability of carrying out ADAS work themselves, the A1 Group also provides a ‘done for you’ ADAS and diagnostic service. This is where the bodyshop outsources the work –and liability – to A1’s technicians. Crucially, the vehicle never leaves the bodyshop.
Workshops can request A1’s ‘done for you’ service by either booking one of its mobile dealer-trainer technicians which operate from A1’s national mobile ADAS fleet, or by remotely dialling into A1’s HQ via an interface. Jobs dialled in via the interface are typically answered by one of A1 Remote Diagnostic’s technicians in just two minutes.
The A1 Group says the difference it’s making to bodyshops is game-changing. Previously, following body work, the vehicle would be sent to the main dealer to calibrate the ADAS system. In many cases, this could take up to 15 days. Now, A1 is turning around those same jobs in just 15 minutes – and the vehicle never leaves the bodyshop.
“Both routes will take the ‘pain’ out of ADAS for bodyshops,” concludes Molloy. “And whilst they’ll both reduce key-to-key times, make bodyshops more profitable, and reduce workflow stress, the most important thing is that ADAS calibrations are being done correctly.
“Our message is simple; do ADAS right, or don’t touch it at all. We make no bones about it.
“These are safety systems and bodyshops have a duty of care to ensure vehicles leave their premises with ADAS systems working exactly as the manufacturers intended.
“It’s one of the reasons A1 ADAS Solutions and A1 Remote Diagnostics are growing at pace. Bodyshops, fleet companies, and garages tell us we’re their trusted partners for anything to do with ADAS and diagnostics.
“It’s a reputation we’ve earned through our trademark honest advice and being true to our values, and one which I’m proud to put my name to.”
For further information contact www. a1adassolutions.co.uk or call 0333 772 9211.
The automotive industry is undergoing a transformation, with advancements in vehicle technology demanding higher standards in diagnostics, repair, and calibration. All Clear Diagnostics and Calibration, established in the USA in 2019, has emerged as a pioneer in this evolving landscape, delivering top-tier diagnostic and ADAS (Advanced Driver Assistance Systems) services. Their mission is simple yet impactful: “fix it once and fix it right.” With their expertise and commitment to OEM (Original Equipment Manufacturer) standards, All Clear is quickly becoming a trusted name in vehicle diagnostics and repair.
Revolutionising Diagnostics and Calibration in the USA
All Clear has built a robust reputation for addressing critical industry gaps. From advanced diagnostic programming to OEM-grade ADAS calibrations and EV repair capabilities, the company’s services cater to the growing complexities of modern vehicles. Emphasis on precision and quality has resonated across the USA, enabling the company to expand rapidly, in just five years, All Clear has established a presence in 17 states, supported by over 130 highly trained technicians.
The unique business model is a key driver of success; employing highly skilled, ex-dealer technicians and providing end-to-end solutions to meet OEM standards, All Clear has streamlined repair processes for body shops, garages, fleets, and windscreen replacement businesses. Their model allows flexibility of insource services, whether hourly, temporary support, or permanent on-site resources, this adaptability has made All Clear an indispensable partner.
Addressing Vehicle Technology Challenges
Modern vehicles have increasingly sophisticated systems, from ADAS to electric drivetrains, making repairs and calibrations more complex. ADAS technology, in particular, requires precise calibration to ensure safety and functionality, especially in crash repair. Failure to adhere to OEM guidelines can compromise vehicle performance and safety, a risk that All Clear is committed to eliminating. All Clear’s services are designed with these challenges
in mind. By leveraging OEM-approved tools, equipment, and processes, they guarantee that every vehicle they touch meets the highest safety standards. This commitment not only builds trust with customers but also aligns with the broader industry’s push for regulatory consistency in ADAS calibration and repair.
Recognising similar gaps in the UK and Europe, All Clear recently launched its European Division on November 1, 2024. The timing couldn’t be more critical, as the region’s repair industry grapples with balancing speed, cost and quality in the face of rapidly advancing vehicle technology.
In the UK, All Clear Europe will elevate repair standards by introducing their proven business model. By focusing on skilled technicians, OEM compliance, and safety-first protocols, All Clear will make a significant impact. Their services will cater to a range of clients, including body shops, garages, fleets and ADAS calibration providers. Additionally, their emphasis on collaboration with existing remote and mobile service providers reflects a commitment to enhancing industry-wide quality and efficiency.
As the automotive repair industry evolves, All Clear is leading the charge toward a safer and more reliable future. Through OEM standards and their innovative service model address pain points for businesses and consumers alike. By raising the bar for diagnostics, repair, and calibration, All Clear is setting a new benchmark for quality in the UK, and beyond.
By demonstrating the importance of adherence to OEM guidelines, All Clear is not only protecting vehicle safety but also paving the way for a more accountable and professional repair industry.
The Road Ahead
As All Clear continues to grow, one thing remains certain: their commitment to “fix it once and fix it right” will drive them to new heights, shaping the future of automotive diagnostics and calibration across the globe.
Providing cutting edge solutions to everyday problems, efficiently, using the correct tooling and methodology with the necessary qualifications.
AutoCure are leading the way with our innovative solutions. Covering all areas of diagnostic, ADAS and electronic repair, we offer our services remotely (over the air), via our mobile van network or our workshop solution. We specialise in taking care of the deeper level electrical and diagnostic work that is easier, more efficient and more profitable to outsource.
All of our remote service customers have been outfitted with our Autocure Remote tool station. This includes our remote access device, a tablet with 5G data sim to connect to the internet wherever you are and utilise our interface, a GYS battery support unit and trolley to store and move the setup with ease.
We take away the need to think about access to the right tools, methods and time needed for complex repairs. With one call, we are either attending remotely, on-site or recovering the vehicle to our workshop and taking care of the job for you. Utilising our services will increase technician efficiency and improve return on every job.
With years of combined experience, qualifications, training and access to the right equipment and software, Autocure are specifically positioned to assist with all complex repairs, software or hardware issues and are able to provide the right answer, every time.
Our combined knowledge and skill-set allow us to carry out the following tasks and much more to the most professional of standards;
• ADAS Calibrations (all types)
• ADAS Diagnostics
• ADAS Repairs
• Module programming/coding
• Fault code scanning, analysis and clearance
• Advanced Diagnostics
• Auto Electrical issues
• Coaxial cable repair
• Loom repair
• Plug replacement
• EV Specialist Safety Functions
• EV Battery Removal
• EV Battery Diagnosis
• EV Battery Repair
• Key/Immobiliser replacement, recoding and repair
• Vehicle software updates
• Module diagnosis & repair (where possible)
With a ZERO CANCELLATION policy, we do not see any job loss rate whatsoever. This is due to our extensive access to methodology, technical documentation and our constant training of staff that allows us to successfully keep up with the
constant, changing demands of new technology within the car parc. The last thing we ever want to tell our customers is that a vehicle needs to go to a dealer. Utilising our mobile van network and workshop solution, we are able to either have a colleague on site or recover a vehicle to our site in order to further diagnose and solve issues. Our team will remain in constant communication with our clients to ensure they are up to date on vehicle completion times, developments within diagnosis or further parts required so they can remain adaptive and update their customers where necessary. This allows us to have a seamless repair process where we take the worry and stress off our customers shoulders.
Autocure prides itself on the ability to adapt to the necessary needs of our customers. We
always take our time to talk to our client base to gain insightful feedback into how we can improve our service and provide a better, more comprehensive service. Based on some feedback from outside of our customer network, we have put together our trade in offer to see our 2024. The offer will be running until the end of January and will allow new customers to trade in any active remote diagnostic tool against their purchase of our Technical Support Pack which entitles them to their first FIVE jobs for free.
As new NBRA suppliers, we are really excited and looking forward to engaging with members over the coming months and exploring how we can better assist you.
Complete Diagnostics, born out of a need to streamline processes in the tow bar industry, has become a game-changer for Bodyshop’s. Offering remote diagnostic and ADAS calibration solutions, the company delivers timesaving, cost-effective services while increasing productivity for independents across the sector. Managing Director Andy Bolton shares insights into how this technology is addressing critical challenges in the repair industry.
Complete Diagnostics evolved from its sister company, Right Connections, a leader in wiring harness design and development for cars. As vehicle technology advanced, aftermarket retrofitting became more complex, often requiring main dealer programming. To address this, Complete Diagnostics was established, providing a remote service that keeps vehicles on-site while complying with manufacturer specifications. “We realised our customers were struggling to install our products due to manufacturer coding,” says Bolton. “Our service reduces keyto-key times and eliminates the need for costly main dealer visits. Technicians can begin work within 30 seconds of a request, performing tasks like recalibrating ADAS systems or programming components remotely.”
The connection device costs just £899, with no subscription fees. Services are billed on a pay-per-use basis, avoiding the expenses of training, equipment, and software updates. “Our trained technicians handle diagnostics remotely, saving businesses from high costs and skill shortages,” Bolton explains.
Bodyshop’s benefit from reduced work-in-progress (WIP) and faster turnaround times, avoiding delays caused by transporting vehicles to dealerships. Additionally, technicians can focus on other tasks while apprentices manage device connections.
The system is simple: connect the device to the vehicle’s OBD port and WiFi. Using a secure portal, repairers select the required service while technicians verify vehicle details and perform necessary tasks. Bolton highlights that technicians often advise on additional procedures, such as calibrating RADAR after bumper removal.
“Our trained staff ensure the process is seamless,” Bolton says. “Customers can trust us to deliver manufacturer-specific expertise efficiently.”
Training is straightforward, and even nontechnical staff can quickly learn to use the system. Complete Diagnostics’ team offers live demonstrations to potential clients, who often adopt the system after seeing its simplicity.
The company’s reputation extends beyond independent Bodyshop’s. It has collaborated with a multi-brand vehicle manufacturer to provide ADAS calibration services for its approved network and is the first remote coding company to achieve BS 10125 certification.
• “Great response times and nothing is too much trouble.” – Touchups Glasgow
• “Your service helps us be the best we can be!” – Phil Taylor Towbars
Key Benefits at a Glance
• Easy to Use: Simple setup and operation.
• No Dealer Delays: Immediate technician availability.
• Flexible Pricing: Pay-per-use with no subscriptions.
• Automatic Updates: No upgrade costs.
• Fast Response: Technicians start work within 30 seconds.
• Comprehensive Coverage: Covers
95% of the car parc, often supporting vehicles before launch.
Bolton sums up the appeal: “Whether you use us 10% or 100% of the time, the investment is minimal, and the benefits are significant.”
Complete Diagnostics is revolutionizing how Bodyshop’s manage diagnostics and coding, delivering efficiency and expertise when it’s needed most.
As the largest global supplier of Remote Diagnostics Services, Repairify is pioneering the research and development of innovative technology which provides bodyshops and repair centres with access to over 100 tools, supported by over 30 IMI-trained and certified technicians to ensure the correct and safe diagnosis and repair of automotive electronic systems. By accessing these services, repairers can retain diagnostics and calibrations in-house rather than moving the work to a main dealer. The result is incremental revenue streams are generated, and a significant reduction in key-to-key times of jobs is achieved.
Repairify’s continuous investment in technology development and data acquisition ensures repairers can be confident they are employing the safest, most reliable, and upto-date ADAS repair solutions available. Recently, the European Patent Office awarded Repairify Inc with patent EP 2 656 200 B for our Remote Services. This latest award aligns with Repairify’s global patents which we hold in the US and Australia as well as other markets, strengthening our position in Europe, and recognising our considerable efforts in research and development.
Our innovative solution helps workshops repair vehicles effectively and safely by enabling the VCI tool side to interface with a VCI in Repairify’s own data centre, connecting the vehicle to an OEM tool and undertaking scanning, programming and calibrations successfully over the air.
The speed of the connection ensures thousands of jobs are completed quickly every day, with an average wait time for a technician of just 1.8 minutes. This means jobs are significantly speeded up through our unrivalled Remote Services and technical support.
For that added layer of protection, our Remote Services are fully underwritten by a worldwide insurance policy, and our technicians employ OEM tools and methods to guide repairers through ADAS repairs, providing users with total peace of mind. Throughout the process, there is a chat function that is accessible via the Repairify app, which is fully translatable to cope with the global footprint and would fully support any claim that is made. Alongside this, the online application is accessed by the technician on his/her tablet whilst at the vehicle and is wholly interactive, supported by our technicians through the end-to-end process.
Our ‘pay as you calibrate’ initiative supports bodyshops by removing upfront costs involved in purchasing ADAS equipment. Instead, repairers can pay as they use the equipment based on a small number of calibrations per week.
As more vehicles roll off the production line packed full of ADAS systems, which use radar, cameras, sensors and other technology to perceive their surroundings, process data, and make decisions in real-time, bodyshops and repair centres can be confident that Repairify is supporting them every step of the way.
Our fully *warranted Remote Diagnostics Services solution utilising trained certified technicians and our comprehensive tools data centre will ensure that vehicles are returned to the road safely once calibrated, programmed or scanned keeping customers safe and sound this holiday season.
*Repairify guarantees, warranties and indemnifies against claims arising from errors in Repairify scans and services.
School of Thought will be opening our special portal to nearly 3 million young people in 2025 making it easy to find companies in their area offering Work Experience, Apprenticeships or a job and it’s ‘FREE’ for the company and the applicant.
Step One: www.schoolofthoughtautomotive.co.uk Step Two: Register for AWE24 as an Employer.
For more information contact Dave Reece or Julie Eley at dave@ready4work.uk or julie@ready4work.uk or contact us through the website. www.schoolofthoughtautomotive.co.uk
On September 24th a number of senior managers from commercial organisations spent time in prison! One of them was Martyn Rowley the Executive Director of NBRA & VBRA Commercial and you’ll be pleased to read he was released at the end of the day to continue his work and life outside custody!
Martyn was one of many delegates invited by Enterprise Mobility (vehicle hire) and New Futures Network to an “open day” at HMP Bronzefield to explore recruiting prison leavers from what might be considered an unusual talent pool. HMP Bronzefield is a closed women’s prison near Heathrow which holds and cares for around 530 mid to long term female offenders. Some are coming up for release and others will transfer to open conditions to continue the remainder of their sentence.
The reason for the event? To showcase the work the Prison Service does to the people in our care around making serving prisoners more work-ready and to leave prison with more enhanced opportunities to gain employment and lead law abiding lives in our communities.
The event was held in the large Visits Room – a stark, symbolic reminder that the representatives of those companies were experiencing what the inside of a prison looks like. The programme also included a tour of the workshops, education facility and
vocational training programmes to see prisoners at work, gaining new skills and qualifications to enhance their CV’s and ability to secure a job on release.
Highlight of the day was a serving prisoner, due for release in twelve months, who spoke to the attendees about her experience before ending up in prison, the skills and work experience she already acquired (she held a senior role in marketing) and her plans. Two organisations were so impressed, they asked her to make contact on release and explore recruiting her!
The buffet lunch was prepared and served by prisoners on the Catering & Hospitality course – it was superb and presented and served beautifully. Returning for seconds was order of the day for most people!
Our woman and delegates spoke freely and openly during the tour and lunch, which formed an important part of persuading the attendees to consider employing prisoners in a range of sectors, such as manufacturing, construction, hospitality, I.T, retail, and logistics. In each prison, New Futures Network (part of HMPPS) have driven the campaign to have specialist colleagues in place to support companies who want to recruit from us. Our Prison Employment Leads, I.D & Banking Administrators and Work Coaches work with your recruitment teams to help fill vacancies that you might have challenges to fill. Other benefits outlined on the day were our manufacturing facilities (we put 11,000 prisoners to work each in our prison industries manufacturing goods for our own internal needs and commercial companies).
The Prison Service will forever have its challenges, but the drive to support prison leavers into work and accommodation has never been in such sharper focus. James Timpson has pioneered this work since 2010, opening workshops and training academies in prisons and these have a become a hotbed for successful recruitment into the Timpson Group of companies, where a sizeable percentage of his colleagues work in a broad range of roles. Lord Timpson as he recently became, is now the Minister for Prisons and Probation.
To counter the cycle of reoffending, resources have been put in place to link with external business who might have their own recruitment issues and might not have thought their next superstar colleague could come from a prison environment.
13 million people in the UK have a criminal conviction more serious than a speeding violation. It is therefore safe to say we all know a family member of someone in our friendship groups who would have spent time in custody. Giving people a second chance is not only morally the right thing to do and is good for business too.
New Futures Network is the bridge between your Job Description and the right prisoners to fill that vacancy.
There are toward 80,000 people in 115 prisons across England & Wales, the “churn” is around 130,000 per year – newly convicted offenders coming to us from the courts and those we release at the other end of their sentence. We, HMPPS, cannot be the total solution for reducing reoffending and that’s where organisations like Enterprise Mobility and NBRA/ VBRA membership companies are key to helping us make our prisoners return to law-abiding members of our communities, glue their families back together and be part of the solution to your recruitment needs. We need more and more companies to join the growing number of companies who we work with already. Yours could be one more that helps change the life of a prison leaver and be beneficial to your organisation as Martyn has discovered.
On 4th December a virtual event on Teams is being held (0930 – 1100) and we would welcome members to attend – Martyn is living proof of life after time inside prison!
For more information of our work and how you can become involved, contact Lance.harris1@justice.gov.uk
Who is New Futures Network?
New Futures Network is the specialist employment team in HM Prison and Probation Service (HMPPS) that partners businesses and prisons and supports prisoners to be job ready. These partnerships support businesses to fill skills gaps and increase employment outcomes for prisoners and prison leavers.
How do they support businesses?
The four types of partnership New Futures Network support businesses with include:
1. Prison industries and academies: when businesses set up commercial workspaces in prisons, staffed by serving prisoners.
2. Release on Temporary Licence (ROTL): when risk-assessed prisoners leave prison each day to work for employers in the community.
3. Apprenticeships – when businesses offer serving prisoners access to industry-
standard qualifications, whilst gaining valuable employees on release.
4. Employment on release: when employers offer opportunities to individuals, following their release from prison.
How do they support prisons?
New Futures Network support prisons to create the systems and infrastructure that will result in more prison leavers securing employment. They have worked with ninety-three prisons across England and Wales to establish:
Prison Employment Leads (PELs) who are responsible for job-matching suitable candidates and managing the Employment Hubs in prisons.
ID and Banking Administrator (IDBA) who are responsible for processing prisoners’ ID and bank account applications.
Employment Hubs which are equivalent of job centres in prisons, providing a single place for prisoners to access support on employment.
Employment Advisory Boards (EABs) to connect employers, business leaders and third sector organisations with prisons. The Boards advise prisons on their employment strategy, in the context of local labour market needs.
What are the benefits of hiring prison leavers for employers?
Many employers recognise that lots of people in prison will have valuable skills that were gained before or during their time in prison. And if someone can give a prison leaver a second chance, they will show a great deal of commitment in the job.
How many prison leavers are going into employment on release?
The proportion of prison leavers in jobs six months post-release has more than doubled over the past three performance years, from 14% in 2020/21 to 31% in 2023/24.
For 15 years, Autotech Group has been a steadfast partner to the automotive industry, consistently providing tailored solutions to overcome challenges faced by the aftermarket. Now, the group is deepening its focus on supporting the body repair sector, addressing its unique needs and the hurdles it must clear to stay competitive.
The body repair sector is facing an uphill battle. Vehicles increasingly resemble complex digital systems, requiring advanced technical know-how to handle intricate software updates and calibrations when carrying even the most basic repairs. Alongside this is the stark reality of a skills shortage across the industry—a situation exacerbated by an aging workforce, a decline in new talent entering the sector, and a lingering misconception that automotive repair is a career of the past.
At the heart of Autotech Group’s approach to meet the nuanced needs of the aftermarket lies an emphasis on skills. From covering skills gaps through its network of temporary vehicle technicians to upskilling, attracting a new generation of skills, and bridging the skills gap with technology.
One of the key challenges bodyshops face today is the ability to adapt to complex, softwaredriven vehicles. While this evolution creates opportunities, it also heightens demand for a workforce with cutting-edge expertise and adaptability. Autotech Group has shown a deep understanding of these needs, investing heavily
in training programmes which are delivered through its Autotech Training brand. From technical courses including EV and ADAS, which can also be delivered on the premises of any workshop across the UK to reduce costs and downtime, to CPD which ensures technicians remain compliant, such as with the requirements of BS1015 and the IMI TechSafe™ register.
Technology itself is transforming how the industry works, and body repair shops are under pressure to integrate these advancements swiftly. Autotech Connect has addressed this with tools like Assisted Reality (AR) headsets, which allow technicians to connect with OEMs and experts remotely, enabling real-time collaboration and diagnostics. The result? Faster repair times, streamlined processes, and reduced costs.
Equipping existing workforces with training and technology is, however, only part of the solution. To truly thrive, the sector must attract fresh talent, but this remains a constant hurdle. The Apprenticeship Levy has failed to meet the needs of many in the body repair sector, so it is time for fresh approaches. Practical solutions, like internships and tailored fast-track programmes, are crucial for building a pipeline of skilled workers who meet industry demands. These methods not only address immediate talent needs but also reshape perceptions around a career in automotive repair—one now defined by innovative technology. Leveraging Autotech Academy’s unique internship
model, businesses can change this narrative, showcasing the opportunities available while nurturing talent at an early stage. Autotech Academy effectively bridges the gap between education and employment by pre-vetting and equipping newly qualified technicians with tools and a uniform before placing them with an employer on a 6-12 month paid internship. This enables body repair businesses to grow their own talent and assess the interns capabilities before offering them permanent employment.
This all-encompassing, strategic approach will help bodyshops foster a culture of continuous improvement and empower them to take a proactive stance in preparing for
future challenges, resulting in a more unified, agile workforce capable of weathering the demands of a rapidly changing landscape.
With the festive season upon us, Autotech Group extends its best wishes to all within the body repair industry. This is a time of reflection and renewal—a chance to celebrate achievements and set ambitious goals for the year ahead where together, we can transform obstacles into opportunities and pave the way for a thriving, sustainable future for the body repair sector.
Mark Armitage, Chief Revenue Officer, Autotech Group
After a short break, Apprenticeship Central is proud to be returning to serve the industry as your outsourced apprentice solutions provider. Many of you will already know and use our services, having experienced our expertise in RECRUITING and RETAINING the best apprentices for your business.
Our dear friend Bob Linwood, together with his wife Morag, set up Apprenticeship Central to support and encourage young people on their journey into the industry. Sadly, Bob passed away earlier this year, after which we assisted Morag with business support for a short time. However, after a great deal of thought, Morag decide she did not want to continue heading up the business.
Today, Eleanor Baker Barnes heads the business as a major shareholder and Commercial Director. Morag will remain with Apprenticeship Central in the critical role of Head of Safeguarding and we are pleased that previous senior team members, Mandy and Jake, remain on board.
Eleanor joins Apprenticeship Central from within the bodyshop industry, having a proven track record of success. Eleanor is surrounded by an experienced team which includes Chris Oliver who, along with his business partners, have been pioneers. Among a number of innovative initiatives, they were the first Fix Auto body shop in the UK and the very first to be awarded BSi PAS 125 status.
Back in 2012, Chris modernised apprentice training and standards through new Apprentice Trailblazers. Only a handful of Trailblazers gained government approval; the bodyshop multi-skilled programme was one of the most successful. It remains the programme of choice for bodyshops over a decade later.
Chris founded the charity AutoRaise, creating the apprenticeship framework that transformed our industry. Working alongside Bob, their collaborative efforts at AutoRaise created a lasting foundation that continues to shape apprenticeship training today. Chris comments, “I am very pleased to be supporting Eleanor and working again in the apprenticeship area of the industry. The landscape has changed enormously since that very first Trailblazer apprentice scheme. Everyone now accepts the value of having apprentices in their teams. That job now is supporting apprentices, their mentors and bodyshops to accelerate growth”
Partnering with the National Body Repair Association is the natural thing to do for Apprenticeship
Central as, collectively, we believe together we can deliver solutions to tackle the skills shortage.
Whilst the landscape may have changed, bodyshops continue to face significant challenges, with daily workloads placing even greater demands on their limited time.
Bodyshops continue to tell us the two biggest hurdles to employing apprentices are firstly, in finding them, and secondly, in keeping them. We have solutions to address both of those challenges.
Our Apprenticeship Central ‘RECRUIT’ product addresses the problem of finding oven-ready apprentices.
• Our first step is to have a twenty-minute discovery call with bodyshop owners to understand requirements. We do not do onesize-fits-all; every bodyshop is different and we tailor our approach to your individual needs.
• Following that consultation, our team devise a personalised and detailed recruitment campaign across multiple channels which gives us the largest recruitment pool for your needs.
• We will receive, manage and record all applications taking the time and pain away from you.
• Our unique pre-employment programme (PEP) helps select only the best candidates from that pool. Candidates are given aptitude tests,
and we give you the tools and techniques to choose the candidate that is right for you.
This is how one customer describes the value of the programmes:
Once you have recruited the right candidate for your business how do you hang on to them?
We have a ready-made solution for that too; our ‘RETAIN’ product.
In an ever-changing, challenging world, entering the workplace can be a daunting prospect. We will provide you and your apprentice with ongoing support that ensures the transition from education to the workplace is smooth and successful.
RETAIN manages and motivates your apprentices, so they stay engaged throughout their apprenticeship, and acts as the well needed glue between the apprentice, the bodyshop and training providers.
What is RETAIN?
• Our first step is to effectively onboard and integrate your apprentice into the workplace to ensure that they get the best possible start on their apprenticeship journey.
• Education co-ordination forms a vital part of the full “learning journey management” and, from day one, we take responsibility for the organisation and distribution of:
- Course content
- Assessment schedules
- Term dates
- Training schedules
- Curriculum reporting
• Off the job training is also considered and our regular, scheduled meetings help support the
apprentice to stay on track. This includes:
- Reporting
- Two-way feedback
- Engagement tracking
• The final piece of the puzzle is the responsibility of safeguarding and pastoral care. We create all of the necessary handbooks, polices and guidance documents for your business to adapt and we take responsibility for updating them whenever legislation or government guidance changes.
• We maintain a direct relationship with your apprentices through regular, scheduled communication, undertake bi-weekly proactive contact to check on their wellbeing and, when necessary, we fully engage and support any team members through any issues they are having to deal with.
If you’re thinking ‘this looks like hard work’ you would be correct, but that’s where Apprentice Central come in! With our RETAIN product, our qualified team do it all for you to ensure that after the end of their qualification period, you have a valuable and skilled member of staff.
There are lot of myths and half-truths about apprentices. Here are some independently sourced hard facts.
Why hire an apprentice? Well, the simple answer is; if you don’t, someone else will.
With the reported average age for skilled technicians being 47 years old and rising, it is clear to see that an aging workforce is not sustainable in the long term and bodyshops need to future proof their businesses.
Added to that, technicians’ salaries are rising and this is against the backdrop of a market where profits are under increasing downward pressure.
The simple solution to rising labour costs and lower profits is a younger, dynamic workforce. Finding the time, resource and experience to focus on that is hard but as your outsourced apprentice service provider here at Apprenticeship Central, we will do all that for you – making your business fit for the future.
If you’d like to know how we can help you, reach out to us at Apprenticeship Central and we can discuss the solutions to future proof your business.
Eleanor Baker Barnes
enquiries@apprenticeship-central.co.uk
07496 571590
Two of the greatest challenges facing the Vehicle Refinish market in years to come centre around people and products.
Attracting new talent into the industry and equipping them with the appropriate skills to manage a broad range of tasks across an equally diverse range of vehicles will be vital to keeping up with demand.
Concurrently, the development of new and more sustainable coatings products, with different application characteristics, requires current and future painters to develop the appropriate skillsets to maximise the new opportunities being created through innovation.
Alongside new painting systems are new digital technologies to assist bodyshop managers in optimising efficiency, maximising productivity, and managing their environmental performance. All of which requires training.
It was with these issues in mind that AkzoNobel has committed to a multimillion-euro global program to expand and upgrade its network of Automotive Training Centres (ATCs). Its mission is simple: to further upskill painters, bodyshop managers and OEM engineers on a new generation of coatings and technologies to support the industry in delivering a more sustainable future.
For the initial phase, the business is investing €3 million to create new or upgrade existing sites across Europe, and Asia, Australia and Thailand. The programme is underway and will continue to be rolled out throughout 2025.
As well as supporting bodyshops and the wider automotive industry in rethinking their approach to sustainability, AkzoNobel is also addressing a worldwide shortage of future talent. As many as 300 or more trainees will be accommodated at each site in a typical year.
Each of the sites will be equipped with the latest spray booth technologies and various digital tools created for bodyshops to manage and monitor the high-tech process of vehicle repairs. These include Carbeat, a production workflow tool, PaintPerformAir (PPA), which helps bring even greater consistency and efficiency in the painting process, and Colormatchic, a digitally led color matching and mixing system.
The Automotive Training Centres are being created, upgraded and equipped to accommodate local business, environmental and regulatory needs.
AkzoNobel’s ATC in Belgium, for example, is the first to have undergone a major upgrade by moving to a new state-ofthe-art facility. It was officially opened in September, and it is the first training centre to feature a hydrogen-powered spray booth to help bodyshops significantly reduce their carbon emissions.
AkzoNobel’s existing training centre in France is being expanded and developed to include a fully electric-powered spraybooth, while an upgrade to an existing site in Spain includes two spray booths, developed in collaboration with USI Italia.
AkzoNobel has ATC’s in more than 40 locations, across every major region where its customers are located, including Europe, North America, China, and the United Arab Emirates.
Through these centres, including its dedicated Automotive Training Centre in Didcot, Oxfordshire, it is offering a wide range of training programmes including application training, product and system training, and training in new digital color processes. There is also an emphasis on quality improvement, process improvement, and repairs to RADAR capable vehicles as well as the next generation of Electric Vehicles.
By Paul James
Strategic Accounts Manager
Vehicle Refinishes UK & Ireland
Virtual Reality (VR) technology is being incorporated to support spray paint training with a simulator that mimics a fully customised paint application environment. Each of the centres will also provide environments for testing and developing new products including waterborne basecoats, topcoats and associated paint systems.
The automotive industry of the future requires painters of the future who are fully conversant with the latest technologies and techniques. It also needs management and technicians who understand what’s possible, and how different paints, application processes and digital technologies are transforming the vehicle repair industry of the future.
AkzoNobel understands how important collaboration is to success and by investing in its global Automotive Training Centre network, it is supporting bodyshops and the wider industry on their journey to become even more sustainable and ensuring there is the future talent to overcome a worldwide skills shortage.
Learn more at Sikkensvr.com
‘Switch on’ to a more consistent, sustainable application
In the spraybooth and the paint process two factors play an essential role: humidity and ambient room temperature. PaintPerformAir, AkzoNobel’s innovative high-technology application enhancing device optimizes air flow temperature and humidity to create standardized working conditions for a reliable First Time Right result and a more sustainable and profitable bodyshop operation.
Ready to ‘switch on’ to standardized working conditions? Check out the video to find out more.
A heartfelt thank you to all our partners, customers, and staff for an incredible 2024. Wishing you all a joyful Christmas and every success for a prosperous 2025!
From
Tailored solutions for your courtesy vehicle needs.
Find out more at enterprise.co.uk/courtesy-car-solutions
Twenty-four-year-old Lauryn Palmer, a third-year paint apprentice with FMG Repair Services in Milton Keynes, was the judges’ choice in the Farécla Apprentice & Student Bonnet Painting Competition. Held for the 3rd time, the competition designed to highlight and reward the amazing skills of the current crop of young painters in Automotive Refinishing and Aftermarket returned for the first time since 2019 after being paused due to COVID and its subsequent impact on apprenticeships.
Lauryn’s bonnet features sunrays/angel wings airbrushed elements, fine lining, and utilised custom paints such as shimmer silver that she uses outside of work on custom jobs demonstrated clearer mastery of airbrushing which ultimately led to her victory in the Farécla Bonnet Painting Competition.
Lauryn was announced as the winner by guest judges Mick Finch (AkzoNobel’s Senior Technical Service Specialist in Vehicle Finishes EMEA and Chairman of the Judges for the 2024 Competition) and Richard Hutchins (IMI’s Skills Competition Manager) in a special livestream presentation that was broadcast simultaneously across YouTube, LinkedIn, Facebook and Instagram
Lauryn won £1000 cash, the complete Farécla G360 Super Fast Polishing System, and the NEW G Plus Cordless Rotary Polishing Machine – in addition to a GoPro awarded for her video showcasing the creation of her bonnet as the Best Multimedia Submission
Lauryn was also in attendance at the ABP Club Annual Convention (which also played host to the NBRA
National Meeting) where her bonnet was on display and to receive her plaque from guest judge Daryl Head (Group Talent Facilitator at ZIGUP & 2017 World Skills Abu Dhabi Silver Medalist) at the Farécla stand.
Looking to the future, Lauryn commented: “I’d like to focus on airbrushing and custom pieces, but it would also be great to do more work with the next generation of apprentices to spread the message that the motor trade is for anyone and everyone and can lead to a really rewarding career.”
Lauryn finished ahead of second-placed Kayleigh Meadows from Motofix Northampton and a trio of other Grand Finalists including her FMG RS colleague, Jackson Bailey, who works in the group’s Stockport branch, Rylee Gale (Barnfield College, Luton), and Aaron Marshall (Motofix Swindon) – each earning a cash prize and Farécla product bundle.
David-John Cousins, Farecla’s Sales & Marketing Content Coordinator and organizer
for the contest, was delighted with industry response and the standard of entries:
“As a showcase for excellence but also a practical learning opportunity for young painters; it was an absolute pleasure to bring back to the contest and have the opportunity to witness the talent of these amazing young painters first-hand, and the interest and positivity the competition generates.”
Speaking on Lauryn’s entry: “It came down to fine margins with the Final Five – but Lauryn’s bonnet not only stood out for its genuine sparkle but also its crisp execution, finish and attention to detail.”
“We’d like to thank everyone who took part and congratulate all of our Grand Finalists. Our contest was only viable with their support.”
For a full recap of the contest – including interviews with each of the finalists and an on-demand version of the Grand Final livestream - visit www.farecla.com/bpc
At LKQ we’re not just here to provide paint, sell collision parts or speak to insurance providers. We want our customers and partners to grow and thrive, profitably and sustainably.
A major way they can do this is by becoming more sustainable – it’s good for their bottom line AND good for the planet. We spoke to Lee Berridge, Head of Technical and Training at LKQ Academy, who told us more.
“Let’s take energy costs, called out by bodyshop professionals as the single biggest threat to their business. At LKQ Academy we’ve been looking at sustainability since 2019 and have been running a course on the subject for almost four years, with the latest being our Introduction to Sustainability, our best and most in-depth one yet which launched in 2024. The course provides bodyshops with tailored sustainability plans that don’t have to cost the earth and that are suited to their individual operations and investment capabilities.
Reducing operating costs, cutting emissions and waste, and freeing up capital for investment in training will help bodyshops of all sizes to stay relevant and profitable while taking steps to address the skills gap. Time and time again customers have told us this has made a real impact, direct cost savings by being smarter with things like cost per bake cycle, solvent recycling, can and aerosol crushing, and many other practical initiatives. In fact, it’s proven to help bodyshops save up to 95% on carbon emissions and costs, across products, processes and equipment.
The course also focuses on reducing plastics and VOCs and, following their attendance at the course, we’ve had customers who have now removed plastics from their bodyshop. They’ve done this whilst keeping their processes efficient and maintaining throughput at the same time as becoming more sustainable.
BUT we haven’t stopped there – we’ve launched further sustainability support for bodyshops, using new technologies to have even more of a positive impact on their costs, creating greater efficiencies as well as doing the right thing for the environment.”
After the huge success, and selling out completely in 2024, our Introduction to Sustainability course is back for 2025 with courses running every month throughout the year. You can expect a mixture of theory and practical with a minimum of two and a half hours of practical sessions and demonstrations. Book early to avoid missing out!
The LKQ Academy offer courses for all levels of skills, from beginners and Apprentices to advanced. We’ve got something for everyone.
Intelligent Repair – A very popular new course helping our bodyshop customers to guarantee quality, low-cost repairs, as well as offering traditional replacement parts, is key. And intelligent repair brings sustainability benefits, minimising the carbon emissions associated with the manufacturing and delivery of new parts as well as reducing the number of used parts sent to landfill.
Introduction to Preparation – This course will offer fundamental knowledge and skills necessary for panel preparation.
Advanced Panel Preparation – Customers attending this course will possess enhanced knowledge and greater awareness of different preparation processes, their impact on achieving “Right First Time” results, and the environmental considerations associated with each process.
Introduction to Refinish Application – This course is geared towards technicians without previous application training, apprentices, and industry newcomers wanting to transition to paint.
Advanced Refinish – Three separate courses covering advanced panel preparation, advance refinish application and special effect colours.
Alloy Wheel Cosmetic Repair – Acquire the foundational knowledge and practical skills necessary to confidently undertake cosmetic alloy wheel repairs.
To book any of our courses visit www.lkqacademy. co.uk or speak to your Account Manager.
Unmatched performance.
The Mirka® DEROS II and Mirka® DEOS II are not just power tools; they are game changers. It’s precision and power like never seen before, featuring new brushless electric motors with as much as a 20% increase in power, providing better efficiency in performing tasks.
For further information or to arrange a demonstration, please contact Customer Services on 01908 866100.
Where craftsmanship
Spectrum Vehicle Repairers Bodyshop Group,
The Commercial Vehicle Accident Damage & Refinishing Company with sites in Thurrock, Essex & Sidcup, Kent covering London & the Southeast have now completed the redevelopment of their site in Thurrock, Essex.
Originally planned in 2018 but delayed due to Covid, work started in July 2023 and has now been completed with an opening scheduled for 2nd of December 2024.
The 19,000 Sq. Ft facility which includes new workshops and offices has been built to the very latest environmental standards with sustainability very much in mind
Solar (PV) panels provide the majority of energy required along with the latest in building insulation cladding and water recycling systems which has enabled the new building to achieve an impressive BREEAM Environmental Certificate.
Several ‘Considerate Constructors’ awards and various other accreditations were won during the 14-month construction.
The office development includes several large meeting rooms equipped with the latest video technology to facilitate training and can be used for regional conference meetings and events.
The Spectrum VR Group are approved by most
major insurers and accident management companies and have recently joined the VBRA Elite Truck Standard Scheme to further improve the services offered and demonstrate our commitment to safety and quality in the CV sector.
Managing Director Marc Watts said ‘We are hugely proud of our new facility and the opportunities it brings us, as well as the room to grow our business further. It provides a fantastic working environment for our staff and the latest Bodyshop technology, to repair our customers vehicles to the highest standards. In addition to the continual investment in facilities, I believe that joining schemes such as the Elite Truck Standard shows commitment to the long term and the desire to continually offer amongst the best services in the industry’.
Get in Touch With Us
2-3 Allerton Road, Rugby, Warwickshire
CV23 0PA
Tel: 0207 291 9750 ex 3447
Email: bodyshops@rmif.co.uk
Contact the team:
Martyn Rowley Executive Director
Tel: 07741 908448
Email: Martyn.Rowley@rmif.co.uk
LinkedIn: www.linkedin.com/in/martyn-rowley-ab350824/
Thomas Hudd National NBRA/VBRA Technical & Southwest Business Development Manager
Tel: 07487 604046
Email: Thomas.Hudd@rmif.co.uk
LinkedIn: www.linkedin.com/in/thomas-hudd-bb5b5a67/
Michael Wicks Southeast Business Development Manager
Tel: 07776 294746
Email: Micahel.Wicks@rmif.co.uk
LinkedIn: www.linkedin.com/in/michael-wicks-81760ab9/
Antony Barnes Northern Business Development Manager & Member Support
Tel: 07824 876215
Email: Antony.Barnes@rmif.co.uk
LinkedIn: www.linkedin.com/in/antony-barnes-6115b583/
Gerry Braddock VBRA National Manager, Elite Standard Manager
Tel: 07776 294744
Email: Gerry.Braddock@rmif.co.uk
LinkedIn: www.linkedin.com/in/gerald-gerry-braddock-744443127/
Ellie Soden Central Region Business Development Manager
Tel: 07774 107764
Email: Ellie.Soden@rmif.co.uk
LinkedIn: www.linkedin.com/in/ellie-s-0a5b5725/
As the festive season is upon us, BDQ extends warm wishes to our members, partners, and the repair community. We know how important it is to stay efficient, even during busy times, which is why BDQ and BDQ Lite are designed to support your workflow and improve your customer’s experience.
With BDQ and BDQ Lite, you get:
• A Seamless Online Experience: No installations or downloads—a cloud-based tool at a fixed monthly subscription.
• Transparent Pricing: Configurable, accurate quotes for both you and your customers.
• BDQ Lite Benefits: Offer free instant quotes on your website and social media, plus custom flyers with QR codes to drive customer engagement.
NBRA members enjoy a waived setup fee on BDQ and BDQ Lite!
Book Your Free Online Demo
For more info, or to schedule a demo, please contact Sheila Bradley at: sheila. bradley@ridgewaytechnologies.co.uk
Let’s kick off 2025 with the tools to drive efficiency and success!
CPD has launched a new service, VanDemand, aimed at simplifying how businesses manage their commercial vehicles. As part of CPD, VanDemand combines trusted expertise with a fresh focus on offering a one-stop shop for buying, customising, and financing light commercial vehicles (LCVs). With VanDemand, businesses can take care of everything in one place— whether it’s purchasing a new vehicle, arranging bespoke conversions, or sorting flexible finance options.
To make things even easier, VanDemand has launched a new website, which showcases the products which are in stock and available to buy, the conversion packages available, and finance options. The new site is easy to navigate and its quick to send an enquiry through to one of their experts.
As part of CPD, VanDemand benefits from decades of industry experience and a reputation for delivering highquality service. The new brand ensures businesses can manage their fleets with confidence, whether they need a single van or a full fleet solution.
Tom Pearson, CPD’s Commercial Director, highlighted the benefits of VanDemand: “With VanDemand, we’ve created a service that takes the stress out of managing commercial vehicles. Whether it’s buying, converting, or financing, we’re making it as simple as possible for businesses to get exactly what they need, when they need it, all in one place.”
Visit the new VanDemand website today to find out how they can help you with your fleet needs. For more information, contact www.vandemand.com
We are delighted to be NBRA’s latest gold partner, helping us to introduce JDK’s cloud-based platform which offers mobile optimised solutions for seamless vehicle tracking, from customer images to collection and return, integrating directly with estimates.
Our products enable repairers to capture all images throughout the lifetime of a customer claim and send them directly onto the estimate, whichever system you are using.
Snap-IT walks the customer through the process of taking images of their vehicle and we store and present the images in a resolution that enables you to genuinely estimate remotely. If you don’t get all the images you need, no problem, simply re-open the customer link and stipulate what is missing in the JDK portal and we’ll guide the customer through the process!
Once a vehicle is onsite you can use the JDK Technology Workshop App to capture images of Driver Collection, Courtesy Car issued, Estimator, Workshop, Quality Check, Handover & Courtesy
Car returned. You can download the App onto any phone or tablet.
All the images are stored against the individual case within the secure JDK Technology portal and can be exported, downloaded, or securely shared. We will keep your jobs archived securely for 7 years so if the need arises you can access them whenever you wish.
One of our most popular innovations is RepairChat™ which gives you the ability to communicate with your customer via WhatsApp – Request further images, send images & updates to the customer from the JDK Portal or utilise the platform for general communication. Customers expect more & we are creating the tools to give real choice.
We have more innovations arriving in the new year including AI face blurring & more AI filters to ensure GDPR compliance. Our Workshop App will include many new features in 2025 including a full check in process & a courtesy car check in/out process with digital signatures and the ability to send documentation directly to
NBRA members can take advantage of a special offer exclusive to members only. Any member that signs up to use the system will not pay anything for the first month.
https://www.jdk.technology/
With combined industry knowledge spanning 25 years, JDK Technology is a software as a Service provider for the repairer community within the automotive industry. With the Bodyshop at the forefront of its values JDK designs products in partnership to streamline the imaging process for insurance work, retail work & smart repairs.
the customer through WhatsApp, email or SMS with full transcripts that can be added to your management system.
Come & join JDK Technology who think differently through the eyes of the repairer. 300 Bodyshops trust JDK and now it’s your turn!
Simply go to https://jdk.Technology/ and sign up to use the system.
If you would prefer to speak to JDK first, you can contact their team at info@ jdk.technology for further assistance.
JDK will run 45-minute online training sessions for new customers.
https://nbra.org.uk/
The National Body Repair Association was launched in March 2017 and brought together the National Association of Bodyshops and the repairer members of the Vehicle Builders and Repairers Association. NBRA members displaying the CTSI Approved Code Logo operate to a strict Code of Practice approved by the Chartered Trading Standards Institute. The NBRA is the only trade association for car body repairers in the UK.
TAKING COLOUR CAPABILITY TO THE NEXT LEVEL
® EXTRA
› EXTRA Tinters
› 8x EXTRA Formulations
› PPG LINQ™ now available
› MOONWALK ® now available
On the first day of coaching, my Exec Coach gave to me…. The environment to speak my mind freely
On the second day of coaching, my Exec Coach gave to me … Tools to improve processes
On the third day of coaching, my Exec Coach gave to me … Key business stratagems
On the fourth day of coaching, my Exec Coach gave to me … Best practice frameworks
On the fifth day of coaching, my Exec Coach gave to me … Tools to effectively prioritise things
On the sixth day of coaching, my Exec Coach said to me ... Six more sessions need purchasing. (Thank you very much)
On the seventh day of coaching, my Exec Coach gave to me … Successful active listening
On the eighth day of coaching, my Exec Coach gave to me … Kate's key to high performance thinking
On the ninth day of coaching, my Exec Coach gave to me … Plans for team enhancing
On the tenth day of coaching, my Exec Coach gave to me … Confidence in leading
On the eleventh day of coaching, my Exec Coach gave to me … Lean ways of working
On the twelfth day of coaching, my Exec Coach gave to me … Self-doubt expung-ed, leadership on a solid footing. My work here is done.
I'm a better Coach than I am Poet. If you'd like to discover what 6, or 12, sessions of coaching could do for you please get in touch.
30-minute discovery sessions are free.
❄ AS THE COLD MONTHS ARE UPON US, NOW MORE THAN EVER WE NEED TO BE AWARE OF THE ACCIDENTS THAT CAN HAPPEN ❄
The road to recovery shouldn't be a bumpy one! ��
�� **WHY CHOOSE US?** ��
�� Our team of experienced assessors utilizes cutting-edge technology to provide precise vehicle damage assessments, ensuring no detail is overlooked.
⏱ We understand the importance of swift action. Our assessments are delivered promptly, helping expedite your claims process and enhancing customer satisfaction.
�� No matter where your clients are located, our network of assessors can reach them. We provide comprehensive coverage across the country
�� We offer competitive pricing without compromising quality Efficient processes mean cost savings for your company.
�� We believe in partnership. Work closely with our team to customize our services to fit your unique needs and objectives
DON'T MISS THE CHANCE TO ELEVATE YOUR GAME! LET'S WORK TOGETHER FOR A SAFER AND SMOOTHER ROAD TO RECOVERY.
�� Contact Charles H G Griffin at [0777 617 3333]
�� Email us at [charles griffin@tecreports co uk]
a
s
your EV charging journey starts here... All EV Charging Solutions
C o m p e t i t i v e P r i c e s : W e p r o v i d e c o s t - e f f e c t i v e s o l u t i o n s t h a t d e l i v e r t h e b e s t
v a l u e f o r y o u r E V c h a r g i n g n e e d s .
N a t i o n w i d e D e l i v e r y : R e c e i v e f a s t a n
We provide tailored solutions to drive sustainable success.
With a commitment to transforming businesses, we specialise in providing strategic solutions that drive growth, efficiency, and sustainability.
We optimiSe processes, streamline workflows to maximiSe your performance.
We reduce your wip, reduce cycle times, increase production throughput and increase profit
Video is projected to make up 82% of all internet traffic in 2025.
Make your New Year's Resolution to invest in professional video production!
We work with businesses to create impactful videos that engage customers, build trust, and elevate brands. Whether it’s showcasing your services, capturing client testimonials, or covering key events, our videos are designed to:
✅ Attract more Customers: Turn views in to leads that puts your business in the spotlight
✅ Elevate Your Brand: Stand out from competitors with polished visuals that reflect your expertise.
✅ Deliver Results: Create memorable content that speaks directly to your audience’s needs GET IN TOUCH
Emtec, part of Nottingham College, is looking to collaborate with local businesses this FESTIVE PERIOD.
It’s the perfect time to learn more about our body repair provision.
OUR BODY REPAIR PROVISION INCLUDES:
LEVEL 3
Vehicle Damage Paint Technician
Vehicle Damage Panel Technician
Vehicle Damage Mechanical, Electrical and Trim (MET) Technician
LEVEL 4
Vehicle Damage Assessor
To enquire about joining our team of industry leading employers, visit: nottm.co/enquireapps
We’ve been keeping vehicles on the road for over 135 years. Trust us for reliable, innovative solutions to keep your fleet moving, no matter the weather, this holiday season. From hinges to latches, we’ve got you covered – so you can focus on delivering holiday cheer!
MERRY CHRISTMAS AND A HAPPY NEW YEAR!
We’re extremely grateful for a year of growth and additional new partnerships benefiting our dedicated repairers. We extend our warmest thanks to every repairer, claims management company, and supply chain partner for your invaluable support and collaboration.
Working together with our truly great independent repairers has been a pleasure, and we look forward to more shared success in the New Year.
Wishing you a joyful Christmas and a prosperous 2025!
Email: enquiries@orbitalrepairsolutions.com www.orbitalrepairsolutions.com
As we close out 2024, we ' re proud to celebrate a year filled with milestones This year, we saw the successful launch of Rowley Projects a venture that opens new possibilities for our customers and our brand We've welcomed new team members who bring fresh ideas and expertise, with even more talented professionals joining us to elevate Rowley Spray Booths to new heights in the new year.
We’re grateful for the trusted partnerships we ' ve built, creating a foundation that fuels our shared vision for the future Together, we’re committed to advancing innovative and sustainable solutions that set new industry standards.
Our journey towards sustainability is just beginning, and 2025 promises to bring exciting steps forward as we work to deliver a greener, more efficient range of spray booths while embedding sustainable practices across our own business.
This Christmas, we extend our heartfelt thanks to everyone who has been part of our journey. Here’s to another year of growth, innovation, and lasting impact.
George Rowley - MD
Todd Engineering is proud to announce an early Christmas gift—winning the Repairers Choice Award for Spray Booth Manufacturer of the Year 2024!
This incredible recognition is the perfect way to wrap up the year, celebrating the dedication, innovation, and teamwork that define Todd Engineering.
Winning this award is more than just a trophy for the mantelpiece—it’s a glowing acknowledgment of the journey we’ve embarked on as a company. This milestone reflects our unwavering commitment to providing sustainable, high-performance solutions for the automotive refinishing industry. At the heart of this success is our revolutionary Zeus all-electric spray booth, designed to bring both innovation and environmental responsibility to the forefront.
The Zeus spray booth is a true game-changer. Powered entirely by electricity, it eliminates the need for fossil fuels and features far infrared curing technology to deliver faster drying times and exceptional efficiency. This technology doesn’t just boost productivity—it also helps bodyshops reduce their carbon footprint, supporting their
journey toward carbon neutrality. It’s the perfect solution for businesses looking to embrace a greener future without compromising on quality.
This recognition highlights the strides Todd Engineering has made in leading the way toward a more sustainable and efficient automotive refinishing industry. The Zeus spray booth exemplifies how innovation and environmental responsibility can work hand in hand to create smarter, greener solutions for bodyshops everywhere.
As we deck the halls and look ahead to a bright new year, we extend our heartfelt thanks to everyone who has supported us—our customers, partners, and the wider bodyshop community. Together, we’re building a greener future for automotive refinishing.
From all of us at Todd Engineering, we wish you a joyful holiday season and a successful year ahead!
Ready to join the journey?
Discover the power of the Zeus spray booth and our sustainable solutions. Visit our website or contact us today to learn more.
Fixico enables you to find the repair jobs that best fit your business and offer a seamless customer experience.
Minimise manual tasks with digital workflows. Receive damage details and schedule repairs digitally for improved efficiency and control.
Get a constant flow of repair requests tailored to your preferences, as each damage is matched with the best repairer based on criteria such as availability, location and certifications.
Fixico’s repairer dashboard provides full visibility into your repairs, cycle times, customer reviews, and business performance, ensuring complete control.
Personalised support with service agents and account managers ready to assist with operational, specialisation, certification, and equipment needs.
Become part of our network of over 3000 repairers across Europe and beyond
"Fixico's platform is an efficient digital tool for accepting and quoting repairs, aligning booking dates with customer needs and workshop schedules, and managing workflows. It simplifies reporting delays and streamlines processes. Having used it for years, I’ve always appreciated the great support from the team. With its preloaded data and user-friendly interface, Fixico is an invaluable tool for repair management."
Tania Davis – Owner of UK AutoLinks
"Partnering with Fixico has been a game-changer for UK Carbody. Their digital platform has helped us better manage our repairs, offering smoother workflows and more efficiency. We’ve been able to reduce administrative work, focus on what we do best, and deliver an improved customer experience. The team at Fixico understands the needs of repair shops like ours. Their transparency and support have helped us grow our business."
Devin Cavanagh – Managing Director of UK Carbody
This festive season, meet the Three Wise Products — bringing the gifts of precision, efficiency, and durability to workshops everywhere. These stars of the repair shop will guide your business to success!
This state of the art tower is designed to make pulling damage easier, faster and more efficient than ever before!
Mobile floor suction dent pulling tower.
Pulls upto 250kg with a maximum 8 bar pressure.
Can be used to pull glue, steel and aluminium.
Slimliner is a complete working station for panel repair that’s compact and ideal for small workshops.
Touchscreen Spotwelder.
Sliding hammers, pulling bars and Dentliner.
Speedpuller for precise and efficient dent removal.
Our Plastic Fusion Pro Advanced System ensures robust repairs, using nitrogen to increase the weld integrity and strength.
Better control over pressure and temperature.
Nitrogen generator means no gas bottle required.
Integrated hot staple tacking system.
Gold Supplier Member
From the team at ACG
We wish a Merry Christmas to everyone at the NBRA, its members, and supply partners.
Thank you for all your support throughout this year, and here's to a prosperous 2025.
Here for your invoice funding needs
Authorised Funding is a straightforward method for bodyshops to sell invoices for insurer and network-approved repairs –receiving payment within 24 hours.
Quick decision making
Rapid funding
No pressure or minimum volumes
Professional support & guidance
Unlock your exclusive ACG x NBRA member offer! T&Cs apply.
Log in to the member area now.
info@acg.co.uk 01925 591566 www.acg.co.uk
Tel: 01562 543581
Email: luke@atticusinsurance.co.uk
As many of you may have observed during your insurance renewals this year, the UK insurance market is steadily increasing rates for both Personal and Business policies, including Motor Trade Insurance. On average, most insurers are implementing a rate increase of around 10% for businesses that have maintained a clean claims record over the past year.
With a collective experience exceeding 35 years, our team is dedicated to supporting Bodyshops and Commercial Body Builders
We have established strong partnerships with top Motor Trade Insurers and are recognised as brokers who comprehend the unique risks within this sector
Our comprehensive evaluation will review your existing insurance coverage and recommend improvements to enhance your overall policy
A RECENT MEMBER SAVED MORE THAN £5,000 ON THEIR ANNUAL PREMIUM.
We were approached to present an alternative solution for a member who had received incorrect advice from their current broker Collaborating closely with the client, we ensured that we could meet the necessary levels of coverage for their business, often enhancing the coverage to support their growth.
Through our efforts, we successfully negotiated a proposal with Aviva Insurance that met all expectations, resulting in a premium savings of over £5,000 for the client!
A RECENT MEMBER SAVED MORE THAN £5,000 ON THEIR ANNUAL PREMIUM.
Enhanced Coverage Collaborated with Aviva Insurance
Professional Guidance to help the member understand their policy details
U K E J O N E S
Insurance premiums are consistently increasing across all categories of insurance products It is crucial to partner with an insurance broker who offers tailored advice and ensures that the renewal options presented align with your business needs.
As an independent broker, we are committed to providing exceptional service to all our clients while consistently protecting their interests
With best wishes for the season & year ahead, thank you from all of us.
Better value utilities, independent energy and carbon management, from people who care about the body repair industry.
Reduce costs, attract more business and help the environment.
We wish all our customers and partners all the best for the festive season.
The auto repair energy experts can help you:
• Purchase greener energy
• Implement energy reduction strategies
• Access and install energy efficient LED lighting
• Access and install EV charging points
• Conduct regular site surveys
• Conduct desktop surveys
• Generate power on-site
Empower your team with a digital workflow that streamlines processes and boosts productivity. Bodyshop 360 mobile provides a paperless customer experience from check-in and lets you easily manage your shop from the palm of your hand.
Engage in an entirely paperless experience from vehicle check-in to customer checkout.
Capture and send before and after photos to the bodyshop management system.
Personalise your business documents by adding your logo and terms and conditions.
Conveniently arrange a courtesy vehicle at check-in.
For more information, contact us at B360support@entegral.com
Complete
Gecko Risk is the UK’s most powerful New Energy Vehicle Data Platform. Gecko provides in depth data with a specific focus on Accident Frequency and Severity, Repair Costs and Times, Make and Model Differentiation and Driver Behaviour.
There are now more than 1.3 million Electric Vehicles on the road in the UK and this is rapidly growing. Companies in the automotive industry do not have access to data to understand the associated risks and pricing. Gecko’s easyto -use dashboards make it simple for anyone in the company to access and use valuable accident and repair data. With Gecko's unparalleled expertise in electric vehicle data across the UK, they empower companies to navigate and manage risks effectively as the market accelerates.
Gecko Risk – Electric Vehicle monthly updates
£3,434.90 Average cost to repair a BEV in 2024
£2,885.00 Average cost to repair a Petrol Hybrid in 2024
Gecko currently has four data dashboards:
o Repair costs
o Repair times
o UK charging data
o Vehicles on the road
£1,180 .00 Average labour cost to repair a BEV in 2024
£1,358.00 Average parts cost to repair a BEV in 2024
If you would be interested in a demo of our data dashboards, please get in touch.
www.geckorisk.com
support@geckorisk.com
As holiday season approaches, repairers brace for an uptick in repair volumes. Winter weather often leads to hazardous driving conditions, resulting in an increase in accidents and a surge in demand for bodyshop services. This festive season not only presents an opportunity for increased business but also necessitates optimised operations like never before. Enter Onyx, a game-changer BMS designed to transform the way repairers manage workflows and drive profitability.
Traditionally, a BMS has served a singular purpose: facilitating job allocations through platforms like CAPS. While this remains vital, a robust BMS can offer much more. In today’s competitive landscape—marked by electric vehicles and advanced driver assistance systems (ADAS)—repairers must rethink their strategies and fully leverage their BMS capabilities to thrive.
As repair volumes fluctuate and competition intensifies, many bodyshops increasingly rely on insurers and accident management companies. However, securing and maintaining these partnerships can be challenging without a comprehensive understanding of operational metrics. Without real-time insights into repair volumes, site performance, and financial health, repairers risk jeopardising their profitability during this critical winter period.
Data-driven decision-making
To navigate the complexities of the automotive repair industry, repairers must embrace a data-driven approach to management. Key performance indicators such as average repair costs, Net Promoter Scores (NPS), cycle times, and key-to-key times are essential for assessing efficiency and customer satisfaction. Unfortunately, many existing BMS solutions fall short in easily delivering these insights in realtime, forcing repairers to rely on cumbersome manual data extraction processes. This reactive can leave teams feeling overwhelmed and unprepared to tackle the winter influx of repairs. Onyx addresses these challenges head-on. Designed with a focus on proactive management, Onyx empowers bodyshops with actionable insights that streamline day-to-day operations. Its rworkflow and task management system automatically generates live ‘to-do’ lists for every team member, eliminating the need for manual reports and ensuring that everyone knows their tasks and deadlines.
The winter season is a critical time for bodyshops, and Onyx offers several features to help repairers stay ahead:
1. Stay ahead of deadlines: Onyx’s task management system helps teams maintain SLAs without the constant need to sift through reports, ensuring timely repairs.
2. Drive profitability: Repairers gain realtime visibility into average repair costs, enabling informed pricing strategies that ensure competitiveness while maintaining healthy margins.
3. Strategic decision-making: Onyx facilitates easy access to historical data for trend forecasting and resource planning.
For repair groups managing multiple locations, a centralised, real-time view of repair data is vital. Onyx allows these groups to consolidate data across sites, enabling better resource allocation and performance benchmarking. By breaking down silos, repairers can identify best practices and enhance operational effectiveness— essential during the bustling winter months.
Conclusion:
As we enter the festive season, it is essential for bodyshop repairers to embrace a new mindset towards their Bodyshop Management
Systems. Onyx offers not just a tool for job acquisition, but a strategic asset that empowers repairers to optimize operations, enhance customer satisfaction, and drive profitability.
This winter, as the demand for repairs surges, let Onyx help you harness the power of data and task management to not only meet the challenges of the season but thrive in an increasingly competitive landscape. It’s time to rethink, retool, and revolutionize the way we manage bodyshops— ensuring that this holiday season is not just merry and bright, but also profitable and efficient.
Visit www.onyx-bms.com today to book your free demo.
Introducing the new ‘eBooth 63A’ from Junair, the perfect blend of technology and sustainability.
Experience precision and efficiency with the new eBooth 63A. Powered entirely by just 63amps of electricity without compromising on the latest technology and features you’d expect from Junair. eBooth 63A offers clean, consistent spraying with zero direct fossil fuel emissions. Perfect for eco-conscious professionals seeking high-quality finishes and sustainable solutions.
• No LPG or mains gas supply required
• No excessive electric demands
• Less mechanical parts equals lower maintenance
• Cheaper to run than a conventional mains gas spray booth oven
As environmental concerns grow, the automotive repair industry is seeking methods to reduce energy consumption, minimise waste and maintain vehicle integrity Keco Body Repair
Products addresses these concerns with their Glue Pull Repair (GPR) technology, providing a greener alternative to traditional methods.
One of the significant advantages of Keco's GPR system is the elimination of energy-consuming grinding before dent pulling Unlike traditional dent repair techniques, Keco's GPR system adheres directly to the paint, preserving the factory finish and reducing the environmental footprint of the repair process This method not only conserves energy but also maintains the aesthetic and protective qualities of the original paint, also removing the need to re-apply ecoat to the backside of panels to restore corrosion protection This is crucial for the longevity of the vehicle and reduces the need for additional protective coatings, which can be both costly and environmentally taxing Keco’s GPR system also eliminates the need for high energyconsuming welding By using adhesive tabs and a cold repair process, Keco ensures that the repair is strong and durable without the high energy costs associated with welding This process is not only more sustainable but also safer for the vehicle and technician
Keco's commitment to sustainability extends to the recyclability of their GPR consumables The adhesive tabs and other materials used in the GPR process are designed to be recyclable, reducing waste and supporting a circular economy By choosing GPR, repair shops can contribute to environmental conservation while maintaining high standards of repair quality The large surface area tabs and double-action tools used in Keco’s system allow for smooth dent removal This efficiency reduces the amount of filler used during a repair, resulting in a quicker and more environmentally friendly repair process
With the rise of electric vehicles (EV’s), there is a need for repair methods that do not interfere with the vehicle's electrical systems Keco’s cold repair process is safe to use on powered EVs, providing a crucial advantage in the growing EV market
Keco Body Repair Products provide a revolutionary approach to auto repair, emphasising sustainability and efficiency By eliminating energy-consuming grinding and welding, reducing hazardous dust, and maintaining the integrity of e-coat, Keco sets a new standard in eco-friendly vehicle repair Their recyclable GPR consumables and applicability to aluminium and electric vehicles further highlight their commitment to a greener future For repair shops and technicians looking to reduce their environmental impact while delivering high-quality repairs, Keco’s GPR system is the clear choice
EFFICIENCY
PRODUCTIVITY
PROFITABILITY
WISHING ALL THE MEMBERS A MERRY CHRISTMAS
L E A D I N G T H E W A Y I N T H E A U T O M O T I V E R E F I N I S H I N G I N D U S T R Y
Get in Touch With Us
2-3 Allerton Road, Rugby, Warwickshire
CV23 0PA
Tel: 0207 291 9750 ex 3447
Email: bodyshops@rmif.co.uk
Contact the team:
Martyn Rowley Executive Director
Tel: 07741 908448
Email: Martyn.Rowley@rmif.co.uk
LinkedIn: www.linkedin.com/in/martyn-rowley-ab350824/
Thomas Hudd National NBRA/VBRA Technical & Southwest Business Development Manager
Tel: 07487 604046
Email: Thomas.Hudd@rmif.co.uk
LinkedIn: www.linkedin.com/in/thomas-hudd-bb5b5a67/
Michael Wicks Southeast Business Development Manager
Tel: 07776 294746
Email: Micahel.Wicks@rmif.co.uk
LinkedIn: www.linkedin.com/in/michael-wicks-81760ab9/
Antony Barnes Northern Business Development Manager & Member Support
Tel: 07824 876215
Email: Antony.Barnes@rmif.co.uk
LinkedIn: www.linkedin.com/in/antony-barnes-6115b583/
Gerry Braddock VBRA National Manager, Elite Standard Manager
Tel: 07776 294744
Email: Gerry.Braddock@rmif.co.uk
LinkedIn: www.linkedin.com/in/gerald-gerry-braddock-744443127/
Ellie Soden Central Region Business Development Manager
Tel: 07774 107764
Email: Ellie.Soden@rmif.co.uk
LinkedIn: www.linkedin.com/in/ellie-s-0a5b5725/