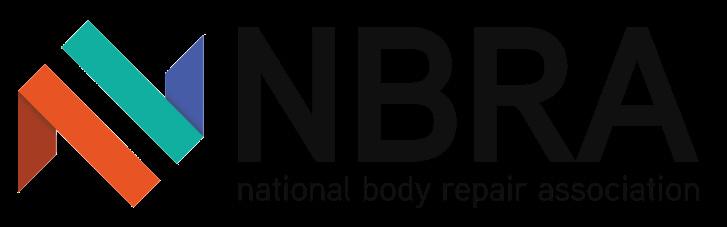
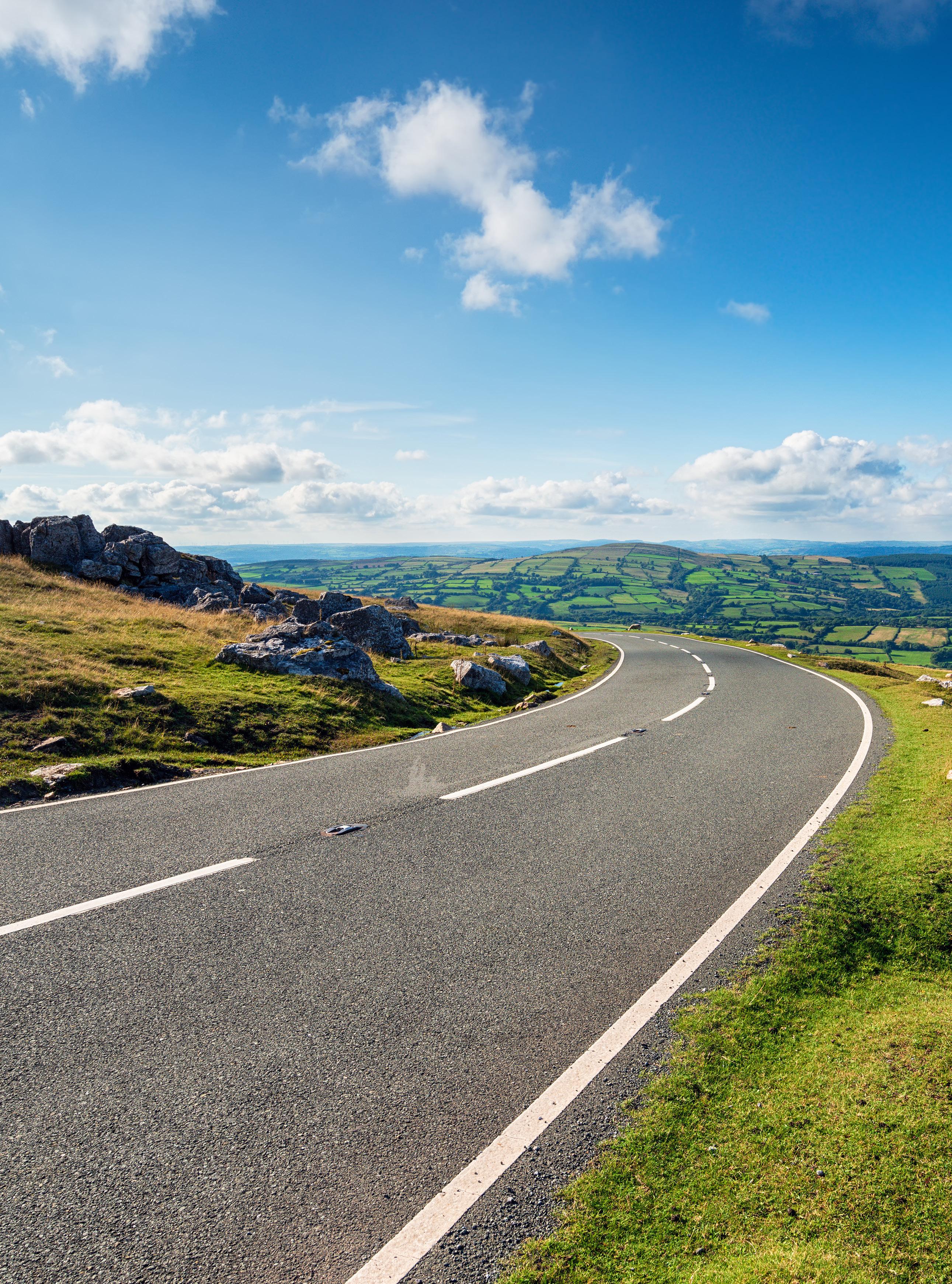
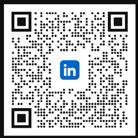
Welcome to this special edition of “The Repairer Magazine.” This issue is packed with exciting news and updates that highlight the remarkable strides our industry is making towards sustainability and excellence.
This month, we are thrilled to spotlight our esteemed emerald partners who are sponsoring the upcoming 2024 Greener Bodyshop Awards (GBA’s). The event will take place at the Coventry Building Society Arena on Tuesday, September 10th, 2024. Our sponsors have each embarked on their own inspiring journeys towards sustainability and carbon neutrality, and we are proud to share their stories. Their commitment to green practices is setting a benchmark for the industry, and we are eager to celebrate their achievements.
In addition to our focus on sustainability, we are excited to announce a major development for our community: Stellantis, one of the world’s largest manufacturers, has committed to bringing over 170 of their approved repairs into membership of the NBRA. This is a monumental step forward for both Stellantis repairers and the NBRA. The benefits of this membership will provide repairers with enhanced tools and resources, further elevating the quality and efficiency of their work.
We have also been busy with two fantastic regional meetings held in the southeast and the Midlands. These events saw nearly 160 attendees, including repairers, insurers, manufacturers, and suppliers. The feedback has been overwhelmingly
positive, and we are planning to host more regional meetings across the UK over the next 12 months. These gatherings are invaluable for networking, knowledge sharing, and fostering stronger industry relationships.
In this edition, we delve into the realm of Spray Booth Technology, featuring insights from four of our supplier members who are leading the way in this field. Their expertise and innovations are driving advancements in efficiency and environmental friendliness in repair processes.
As always, we have a range of other engaging editorials and advertisements from our supplier members that we believe you will find informative and inspiring. We hope you enjoy this edition of “The Repairer Magazine” and look forward to seeing many of you at the Greener Bodyshop Awards in September.
Warm regards,
Martyn Rowley NBRA Executive Director
It is with profound sadness that we, the members of the National Body Repair Association (NBRA), pay tribute to Gethyn Davies, who passed away on Wednesday, July 31st, 2024, at the age of 56. Gethyn was not just an exceptional professional within the repair industry; he was an extraordinary individual whose presence left an indelible mark on all who had the privilege of knowing him.
Gethyn’s career was distinguished by his remarkable contributions to every company he worked for. His successes were not merely a result of his technical expertise but were deeply rooted in his unique personality. Gethyn’s sense of humour, infectious fun, and kind,
friendly manner endeared him to colleagues and clients alike. He had a rare ability to make everyone he met feel welcome and valued, a testament to his outstanding personability.
The repair industry meant the world to Gethyn. He dedicated himself wholeheartedly to his work, always taking the time to engage with everyone he encountered. Whether it was a brief conversation or a long discussion, Gethyn made sure that people felt heard and appreciated. His approachability and genuine interest in others created a sense of community and camaraderie that will be sorely missed.
We will fondly remember the many good times shared with Gethyn— moments filled with laughter, friendship, and achievements. His legacy is one of kindness, joy, and an unwavering commitment to the industry he loved. Gethyn’s impact will continue to be felt, as those who knew him carry forward his spirit of generosity and warmth. Our heartfelt condolences go out to Gethyn’s family during this difficult time. May they find comfort in the memories of a man who brought so much light into the lives of others. Rest in peace, Gethyn. Thank you for being a colleague, a mentor, and a friend to so many. Your memory will live on in the hearts of all who knew you.
On Tuesday, 11 May 2024, the Midlands Regional Meeting was held at the picturesque Telford Golf Hotel and Spa, bringing together a diverse group of industry professionals. With 107 attendees, including representatives from 7 major insurers, 14 manufacturers, and 23 suppliers, the event promised a wealth of networking opportunities.
In a bold move, we adopted a “speed dating” format, designed to maximise interactions and ensure every supplier had the chance to connect with everyone in the room. Guests rotated tables every ten minutes, creating a dynamic and engaging atmosphere. The initial apprehension about this unorthodox approach quickly dissipated as the feedback from both attendees and suppliers has been overwhelmingly positive.
The structured format allowed for concise and focused discussions, with suppliers effectively showcasing their products and services to a wide audience. The insurers
and manufacturers appreciated the efficiency and variety of interactions, making it a win-win for all parties involved.
The success of this event underscores the importance of innovation in our industry gatherings. We are immensely grateful to all who attended and contributed to the vibrant discussions. Your participation and enthusiasm were key to the event’s triumph.
As we reflect on this successful meeting, we are already looking forward to our next regional gathering in the Northwest. We aim to continue fostering these valuable connections and exploring new ways to enhance our industry.
Thank you to everyone who made the Midlands Regional Meeting a memorable and productive experience. Here’s to many more successful meetings in the future!
The NBRA Team
WHEN:
September 10th 2024
WHERE:
Coventry Building Society Arena
Join us for an evening of recognition networking professionals in the Body Repair Industry.
Stay tuned for more details on ticket and table bookings in the coming weeks – you won’t want to miss this.
For any remaining sponsor opportunities,
Nominations are
Tickets are available to BUY NOW
OnyxPDA is a full-service strategic design and marketing agency, we exist to make you stronger than your competition.
Brand creation & development
Website design & build
Social media management & digital marketing
Creative marketing campaigns
Detailed understanding.
.co.uk
We are thrilled to announce that Ellie Soden has joined the National Body Repair Association (NBRA) as our new Central Business Development Manager, effective June 3, 2024. With a rich background in business development and a passion for the automotive industry, Ellie brings a wealth of experience and a fresh perspective to our team. Ellie’s role will focus on driving growth and fostering strong relationships within the body repair industry. Her extensive experience and strategic approach will be instrumental in advancing NBRA’s mission to support and advocate for our members.
“I am excited to join NBRA and look forward to working closely with our members to enhance the services we offer and address the challenges facing the industry,” Ellie said. “Together, we can continue to drive innovation and excellence in body repair.”
Please join us in welcoming Ellie Soden to the NBRA family. We look forward to her contributions and the positive impact she will undoubtedly make.
1. Can you tell us a bit about your professional background and what led you to join NBRA?
I have extensive experience in automotive business development, being involved with and working with Accident Management, OEM’s, Dealer Groups, Car Ownership/Fleet Management, Compliance and recruitment. My passion for improving operational efficiency and driving business growth led me to join NBRA.
2. What attracted you to the role of Central Business Development Manager at NBRA?
The opportunity to leverage my skills in a dynamic environment and contribute to the growth and success of body shops /suppliers nationwide was very appealing. Being the only female on the team, I also saw a chance to bring a fresh perspective and drive diversity initiatives.
3. What are your immediate priorities for the first six months in this position?
In my first six months, I will focus on:
• Member Engagement: Connect with current members to understand their needs and enhance our support.
• New Member Acquisition: Expand our membership base by showcasing NBRA benefits.
• Strategic Partnerships: Build partnerships with industry stakeholders to offer more resources.
• Digital Marketing: Boost NBRA awareness through targeted digital campaigns.
• Internal Processes: Streamline processes for improved member support and operational efficiency.
In a nutshell. In my first six months, I will focus on engaging with current members to understand their needs and enhance our support, expanding our membership base by showcasing NBRA benefits, building partnerships with industry stakeholders to offer more resources, boosting NBRA awareness through targeted digital campaigns, and streamlining internal processes for improved member support and operational efficiency.
4. Can you share your long-term vision for NBRA’s business development?
My long-term vision for NBRA’s business development includes establishing NBRA as a leading authority in automotive body repair, significantly growing our membership base and retaining, by enhancing value, promoting eco-friendly practices, integrating advanced technologies for better member services, developing educational programs to keep members updated on industry trends, and strengthening our advocacy to influence policies benefiting the industry. By focusing on these areas, we can drive growth and success for NBRA and our members.
5. What trends do you see currently shaping the body repair industry?
The current tends shaping the body repair industry are technological advancements, sustainability, skills shortage, digitalisation, and higher customer expectations are the key trends shaping the industry.
6. How do you think NBRA can best support its members in navigating these trends?
NBRA can support its members by offering training and education, advocating for industry policies, providing resources and best practices, facilitating networking opportunities, and helping with technological integration.
7. What do you enjoy most about working in the business development field?
I enjoy the dynamic nature of business development, particularly the challenge of forging new partnerships and especially in identifying market trends and creating innovative solutions to drive growth.
8. Outside of work, what are some of your hobbies or interests?
Outside of work, I find fulfilment in fitness, which keeps both my mind and soul healthy, and I indulge in spicy food, especially Thai cuisine, alongside interests in cars, interior design and fashion.
9. Is there a message you would like to convey to the NBRA members and the wider body repair community?
I want to emphasise the importance of collaboration and knowledge-sharing within our industry. By working together and staying informed about the latest technologies and best practices, we can elevate our standards of service and ensure we meet the evolving needs of our customers. To continue to innovate, support each other, and strive for excellence in everything we do.
We are your supportive partner in a
Helping your business to thrive with our end to end solutions
Academy
Largest in-house technical team Sustainability training course
LKQ is by your side in this changing world, and we are here to support you in moving towards a more sustainable future.
Sustainability does not necessarily mean additional cost for your business, but it does require change. This course focuses on 3 core pillars to help your bodyshop thrive in both the short and the long term.
Drawing from real life examples, key trends and industry problems relating to sustainability, this course will give you the knowledge you need to make informed choices in terms of investments, costs, and savings potential. Our 3 core pillars: Product Process Equipment
Areas covered:
• Masking
• Priming
• Paint Cups
• Plastic Repair
• Paint Platforms
• Spraybooths
• Can Crushers
• Dust Extraction
Course attendees will:
• Understand current and future sustainability trends and their impact on the industry
• Understand the principles of the 3 core pillars of change
• Appreciate the significance of adopting the right products, processes, and equipment for the size of operation
• Understand CO2, VOC, and wastage costs within the bodyshop environment
• Leave with practical tools to make data-driven decisions and positive changes
• Be inspired to act now and make practical changes
From £250 per candidate (EX VAT)
Optional extras available: Personalised sustainability report, On-site support.
Scan the QR code to take you to the LKQ Academy bodyshop prospectus to see our full eLearning and practical course offering, including 12 new courses!
Are you looking for a partner to help measure, monitor and improve your CO2 emissions?
If so, the Sustainable Repair Network from AkzoNobel is for you. It delivers the tools and experience to make a tangible, meaningful and measurable difference to a bodyshop’s drive to reduce its carbon footprint. We’ll help you assess the current level of sustainable performance, convert the energy you consume into the CO2 you create, and show you how you can reduce both to build an even more sustainable and efficient business.
Find out more about the Sustainable Repair Network by scanning the QR code.
Body shops & repairers pride themselves on providing exceptional customer experiences. The range of methods & channels clients can use to contact your business is ever increasing, making providing that exceptional communication experience harder than ever.
AllThingsCX can provide a replacement for your existing telephony solution. We provide a feature rich, robust platform to make communicating over the phone easy Whether you choose handsets for your workshop & desks, or decide on desktop & mobile driven applications, you can work from anywhere, answering calls easily.
If you’ve moved on from just offering a phone number, AllThingsCX is here to assist you in making interacting with customers easy, no matter what the channel. No need to worry about managing your phone system, handing the phone with WhatsApp around the team, fighting over emails in a shared inbox & remembering what the Instagram password is.
By supporting over 20 different channels, such as Voice, Email, Chat, Facebook, SMS, WhatsApp, YouTube, Instagram, LinkedIn & more, RingCX gives you every customer contact within a single view for your team
With escalate to video you can turn any conversation into an opportunity to really see what your customer needs assistance with, reducing the back & forth & moving the repair journey along at a greater pace.
Add further insight into your journeys through the application of easy AI, insights on how your team are handling customer queries & alerting you to any opportunities for improvement. By applying intelligence across your customer conversations & combining with your garage management systems, the AllThingsCX team works with NBRA members to identify key contact reasons, introduce automation to simple updates, reducing effort for both your business & your customers
£9,950.00
EQUIPMENT
• Lifting table capacity 3T.
• Max. lifting height 1300 mm.
• Min. table height 120 mm.
• Lifting with hydro-electric pump and remote control included.
• Can be installed inground or above ground.
www.blackhawkcollision.com/en-gb/
Over the years, the automotive repair industry has witnessed significant advancements in spray booth technology. What was once a rudimentary setup for applying paint has transformed into a sophisticated system designed with precision, efficiency, and sustainability at its core. This evolution is not only a testament to technological innovation but also a response to the growing need for environmental responsibility.
Spray booths have traditionally been one of the biggest energy users in body shops. From the initial stages of the painting process to the final curing phase, these booths consume considerable amounts of power to maintain optimal temperatures and ventilation. However, as the world becomes more conscious of its carbon footprint, the spray booth industry has not lagged in adopting greener practices.
The journey towards sustainability in spray booth technology involves several pivotal changes. Modern booths are equipped with energyefficient systems that reduce power consumption without compromising on performance. Advanced filtration systems now minimise the release of harmful VOCs (volatile organic compounds), ensuring a safer environment for both technicians and the planet. Furthermore, the integration of smart technologies allows for better control and monitoring, leading to optimised energy use and reduced waste.
This editorial brings together insights from four leading spray booth manufacturers who are at the forefront of this sustainability
journey. Each manufacturer has contributed an editorial explaining their unique approaches and innovations in making their spray booths more sustainable. These companies are not just adapting to the current demands for eco-friendly practices; they are leading the charge, setting new standards for the industry, and helping repairers cut their carbon emissions significantly.
The following editorials from these manufacturers will delve into the specific technologies and strategies they have implemented to create more sustainable spray booths. From energy-efficient designs to advanced environmental controls, their contributions highlight the strides being made to ensure that spray booths are as eco-friendly as possible. These advancements not only benefit the environment but also enhance operational efficiency and cost-effectiveness for body shops.
As we explore the individual approaches of these manufacturers, it becomes clear that the future of spray booth technology is green. The commitment to reducing environmental impact while maintaining high standards of performance is a shared goal that drives innovation and progress in the industry. This collective effort is paving the way for a more sustainable future in automotive repair, one where cutting-edge technology and environmental stewardship go hand in hand.
We invite you to read on and discover how these trailblazing companies are shaping the future of spray booth technology with sustainability at the heart of their mission.
by Junair
In the evolving landscape of industrial manufacturing, sustainability has emerged as a critical priority. For companies specialising in spray booth manufacture, perceived as significant contributors to environmental pollution, the transition towards sustainable practices marks a transformative journey. This shift is not merely about regulatory adherence or corporate social responsibility but a commitment to environmental stewardship, economic viability, and social equity. This editorial explores the sustainability journey of Junair Spraybooths Limited, a mid-sized company that has become a leading example of innovation and responsibility in the spray booth industry.
Junair began its sustainability journey over two decades ago, recognising the need to mitigate the environmental impact of its equipment. Initially, the company’s efforts focused on meeting environmental regulations and reducing waste. However, as the global conversation on sustainability intensified, Junair realised that more profound changes were necessary to create a meaningful impact.
The cornerstone of Junair’s sustainability strategy was the development and implementation of ecofriendly spray booths and paint finishing systems. Traditional spray booths often rely on high levels of volatile organic compounds (VOCs) and substantial energy consumption. Junair addressed these issues by designing booths that utilise water-based paints and coatings, significantly reducing VOC emissions. Furthermore, the company integrated advanced filtration systems that capture overspray materials, minimising waste and environmental contamination.
Energy efficiency became another pivotal aspect of Junair’s sustainability agenda. The company
invested heavily in research and development to create the most energy-efficient spray booth on the market; it’s innovative range of solutions, including Heat Recovery, Variable Speed Drives, QADS and LED Lighting, collectively branded as ‘EcoPlus by Junair’ reduces energy consumption by up to 90%.
Junair’s commitment to sustainability extended beyond technological innovations to encompass the entire value chain. The company established rigorous sustainability criteria for its suppliers, ensuring they adhered to environmentally friendly practices. By fostering close collaborations with suppliers, Junair was able to source sustainable materials and improve overall supply chain efficiency. This collaborative approach also spurred innovations in raw materials and processes, further enhancing the company’s sustainability credentials. Another key factor in Junair’s sustainability journey was cultivating a culture of environmental responsibility among its workforce. Comprehensive training programs were launched to educate employees about sustainable practices and their critical role in achieving the company’s goals. Initiatives such as green teams and
Transparency and accountability were integral to the success of Junair’s sustainability efforts. Junair adopted stringent reporting standards,
openly sharing its progress and challenges through annual sustainability reports. This transparency not only built trust with stakeholders but also provided a framework for continuous improvement and innovation. Junair achieved Carbon Neutrality in 2021. In conclusion, the sustainability journey of Junair Spraybooths exemplifies the transformative potential of integrating environmental, economic, and social objectives into a cohesive strategy. As the company continues to innovate and lead by example, it underscores the notion that sustainable manufacturing is not just an aspirational goal but an achievable reality. Junair’s journey serves as a model for other spray booth manufacturers, illustrating that prioritising sustainability can mitigate environmental impact while driving economic growth, fostering innovation, and building a resilient future.
STL’s ethos to energy efficiency and Sustainability starts at the design stage where intelligent design decisions are taken over all aspects of the Spraybooth. We choose our supply chain partners to ensure that the quality of supplied parts improves the longevity of our products. We also have a strong ethos of buying from UK manufacturers to reduce the “airmiles” of our supplied parts.
Utilising UK manufactured, insulated panels designed with a unique castellated and symmetrical tongue and groove joint that gives excellent “air tightness”. This along with the thermal transmittance values (U-value) of 0.25 W/m²K means that the STL booth is designed to keep energy within the spraybooth and not wastefully heat the outside space.
UK manufactured high efficiency gas burners, which are direct fired, and as such are virtually 100% fuel efficient. Automatically modulating heat output to match operator requirements for accurate temperature control and maximum efficiency. Close control of temperature stops the spraybooths fluctuating widely and going over temperature thus preventing the use of greater amounts of energy.
Designed and manufactured in house, our LED
lighting system, has an elongated lifespan tide to the fact that the fittings are constantly “washed” with clean temperate air that moderates the temperature the lights experience through all the spraybooth modes. This negates costly ongoing maintenance but also reduces lifetime costs to the user and the environment of replacing worn out parts. STL can also include for motion sensors that will turn off lights when no movement is detected within the cabin.
Over recent years, there has been more emphases on energy efficiency to reduce the spraybooth carbon footprint and costs. Through an extensive R&D programme STL developed the first range of fully electric booths our patented TEMPO in 2012. Over the ensuing years we have further developed a comprehensive range of electric solutions for any Spraybooth requirement. Being a pioneer of sustainability in the industry has enabled STL systems to operate at reduced energy consumption.
STL’s R&D initiatives alongside paint manufacturers who have developed products with reduced cure temperatures, ensures STL technology works harmoniously with each product, whilst minimising energy use.
STL recognises each individual sites constraints whether it be Electrical load or Gas provision, STL being a solution provider has developed a new range of HYBRID Spraybooths tailored to each individual sites available service provision. This reduces the reliance on fossil fuels whilst utilising an electrical load from a standard distribution board without the requirement for expensive upgrades to existing Gas or electric infrastructure to the building.
Combining on site power generation, such as solar panels, with an STL Spraybooth system enables customers to run on 100% green energy when available, the ultimate sustainable solution.
STL have designed a new “Heat Recovery Unit” to overcome the use of standard air to air heat exchangers used in HVAC but incompatible with use in Spraybooths. The fully integrated design is space efficient and easily serviced. The unit relies on a high transfer efficiency copper panel that doesn’t add resistance to the system like traditional air to air heat exchange units. Thus, no additional fan energy is required. It has a long life expectancy with low cost replaceable internal heat transfer panels. It has no expensive additional filters to protect the exchanger. It also has a builtin bypass system to prevent heat gain during warm external ambient weather conditions, which is a shortcoming of the typical heat exchanger.
Our control system uses a powerful Siemens PLC system that provides accurate temperature and airflow control ,allied to an automatic energy saving system. This along with the Variable Speed Drives on the fans allows the STL spraybooth to automatically recirculate air on standby and flash off modes. The use of airflow switches in the “tool air” supplied to the spraybooth allows the STL booth to automatically control airflow within the spraybooth if a sustained period of inactivity is detected. Once again, the control system will move the air handling system from its most expensive running mode to a lower cost running mode and then shuts off completely. This is also available as an upgrade to any spraybooth already in service.
Our range of Energy Efficient Spraybooths:
Cyclone HB & Spraymate HB (Hybrid), Cyclone HR & Spraymate HR (Heat Recovery)
Cyclone E, Spraymate E, TEMPO & Smart Repair Bay (Fully Electric)
At Rowley, a fusion of tradition and innovation drives our operations. With over 40 years of experience, we pride ourselves on adapting to the evolving needs of the industry while consistently delivering exceptional results for our customers.
Recognising the need for change, we committed ourselves to doing what is right for both our customers and the environment. Gone are the days of dimly lit spray booths with long cycle times and poor filtration systems, which were once a common headache for body shops. Older spray booths suffered from high energy consumption, inadequate ventilation, and poor heat retention, leading to increased operational costs and significant environmental and health risks due to high emissions and substandard air quality. LED lighting was the first staple in our spray booths, not only providing better lighting for higher quality finishing, our LED lights last around 10-20 years reducing replacement and maintenance costs as well as an energy cost saving of around 60-90% depending on usage.
Next, we shifted our attention to heat retention, by capturing and reusing heat from the exhaust air we have been able to significantly reduce the energy needed to maintain optimal booth temperature. Improved insulation and sealing techniques have further enhanced this leading to more energy-efficient spray booths.
To further minimise our carbon footprint, we have also begun partnering with carbon-neutral and green suppliers. By sourcing materials and services from suppliers who prioritise sustainability and eco-friendly practices, we ensure that our production processes contribute to a lower overall environmental impact. This strategic approach aligns with our dedication to sustainability also helping us provide higher-quality, energy-efficient solutions to our customers while supporting the global transition to a greener economy.
At Rowley, we are poised to lead the industry into a sustainable future. Why? Because we believe in doing the right thing and have implemented several technologies to help us achieve our goals.
One such technology is Solar Panel technology on our external booths and POD’s giving us a renewable energy source and improving operational costs. By harnessing Solar Energy we can make a step forward into a greener future.
In addition to Solar Panels, we have implemented Far Infrared heating systems or FIR. FIR heating provides a more efficient heating solution compared to traditional methods. Not only improving the drying or ‘bake’ process by ensuring higher quality finishes but also enhancing the
overall efficiency of our spray booths, making them more eco-friendly and cost-effective for our customers. FIR has proven to reduce cycle costs with huge annual energy savings being reported. We have successfully developed and trialled all-electric and hybrid systems, positioning us to make a significant impact on greener solutions in the marketplace. Technological
advancements in FIR and green technologies have driven our substantial successes in this area. By integrating electricity and gas, we ensure that our carbon footprint is minimised while maintaining the high operational efficiency for which Rowley Spray Booths are renowned.
It was important to us that we not only made our spray booths more environmentally friendly but also that we made significant strides towards what we do internally, within our own business. Rowley Spray Booths is dedicated to a sustainable future, aiming for carbon neutrality and achieving ISO accreditation. With the launch of our new Greener spray booth range, we set a new standard in eco-friendly industrial solutions. These advancements underscore our commitment to reducing environmental impact while maintaining high-quality performance and efficiency. Join us in embracing a greener future with Rowley’s innovative and sustainable spray booth technologies.
Working towards a sustainable future
Sustainability
At Todd Engineering this is a core principle guiding our mission and operations. Our commitment to reducing the carbon footprint of our spray booths while maintaining exceptional performance and efficiency is central to our journey towards sustainability.
A Commitment to Green Innovation
Our journey began with a clear vision: to create cutting-edge spray booth solutions that are environmentally friendly and highly effective. This vision has driven every step we’ve taken and every product we’ve developed. At the heart of our efforts is the integration of advanced technologies that minimize energy consumption and emissions.
Flagship Achievement
The Zeus all-electric spray booth. Unlike traditional spray booths that rely on fossil fuels, the Zeus operates entirely on electricity, significantly reducing greenhouse gas emissions. By utilizing far infrared (FIR) technology, the Zeus ensures efficient and precise paint finishes, curing the paint at a molecular level. This method not only speeds up the drying process but also reduces energy usage, resulting in a substantially lower carbon footprint.
The Development Journey of Zeus
The development of the Zeus spray booth was an extensive journey, spearheaded by our dedicated R&D department. From the outset, sustainability was at the heart of our
research and development efforts. We meticulously analysed every aspect of the spray booth’s design and functionality to identify opportunities for reducing energy consumption and emissions.
PAS 2060 certification for carbon neutrality milestone.
This certification reaffirms our commitment to reducing the environmental impact of our operations and products. The Zeus all-electric spray booth can also operate on renewable energy sources, further enhancing its sustainability credentials and aligning with global efforts to reduce dependence on fossil fuels.
Comprehensive Sustainability Measures
Our commitment to sustainability extends beyond technology to the entire lifecycle of our products, from design and manufacturing to installation and maintenance.
Design and Manufacturing: We use high-quality, recyclable materials in our spray booths. Our manufacturing processes are optimized for minimal waste.
Energy Efficiency: All our spray booths are equipped with energy-saving features such as Eco+ energy savers and advanced air handling systems.
Reduced Maintenance: One of the highest maintenance factors in traditional spray booths is the heating plant. By eliminating fossil fuel-based heating systems, the Zeus spray booth requires little to no maintenance apart from general housekeeping. This not only extends the life of the spray booth but also minimizes downtime and further reduces the carbon footprint.
Customer Support: We work closely with our clients to ensure that their spray booths operate at peak efficiency. Our service department provide regular maintenance and support.
Join Us on Our Journey
Whether you are looking for a new spray booth or seeking ways to make your existing operations more eco-friendly, Todd Engineering has the solutions you need. Together, we can make a significant impact and drive the industry towards a more sustainable future.
Let’s build a greener future, one spray booth at a time.
As the world faces the urgent challenge of climate change, Avant Consult Ltd, along with its subsidiaries Bodynet and Avant Repair Network, is committed to leading by example with a comprehensive sustainability strategy.
At Avant, we are not just meeting sustainability goals—we are setting new standards. We have transitioned to 100% renewable energy by partnering with certified green energy providers, dramatically reducing our carbon footprint. Our commitment to a paperless workplace has reduced waste, streamlined operations, and we have eliminated single-use plastics from our offices.
Our eco-friendly commuting initiatives, including carpooling programs, subsidised public transport passes, and incentives for cycling, have not only cut greenhouse gas emissions but also boosted employee health and well-being.
Looking ahead, Avant is committed to achieving carbon neutrality by December 2024 and net zero emissions by 2030. We will join the Science Based Targets initiative (SBTi) for science-based carbon reduction targets. Implementing a circular economy involves recycling, reusing programmes, and creating long-lasting, recyclable products. Achieving LEED or BREEAM certifications and retrofitting buildings for energy efficiency are also key steps in our journey.
Avant’s long-term vision focuses on continuously expanding our use of renewable energy and investing in emerging technologies to maintain energy independence. Our aim is to achieve zero waste by implementing comprehensive waste reduction practices and fostering a culture of sustainability. Integrating sustainability across our supply chain, into all business decisions and cultivating a corporate culture that prioritises environmental responsibility will ensure our long-term success.
Since 2004, Avant has been at the forefront of the collision repair sector, consistently pushing the boundaries and setting industry standards.
Avant, award-winning market leading provider of automotive services, with over 20 years of excellent service delivery and innovation.
Bodynet, connecting the industry with cutting-edge vehicle repair estimating and management software solutions.
Avant Repair Network, the multi award-winning vehicle collision repair network.
Recruit, working to future-proof recruitment and training solutions for the automotive industry.
"Your Trusted Partner in Automotive and IT Excellence."
1. Can you tell us a bit about your background and how you got started in the automotive repair industry? I left school at 16 and started a Youth Training Scheme (YTS) as a Trainee Panel Beater at a Morris Minor Restoration centre in Kent. I then went on to complete a Panel Beating apprenticeship at a Renault dealership. During my working career I’ve worked at a couple of Accident Repair Centre’s and Main dealer bodyshops. I also ran my own bodyshop in Kent for a few years prior to starting with the VBRA in October 2014 as Southern Area Manager.
2. What drew you to the NBRA, and what has your journey with the organization been like so far? Having experienced some of the industries challenges as a bodyshop owner myself, I decided to apply for the role with VBRA when I saw the vacancy. I liked the idea of helping bodyshop owners and being part of a collective to strive improvements for our sector.
3. What are some of the key responsibilities and challenges you face as a Business Development Manager at the NBRA? As a Regional Business Development, my key objectives are to bring as many bodyshops into membership as possible, get in front of existing members when requested and at every given opportunity to remind them of the NBRA benefits and keep them up to date with the NBRA Supplier Member solutions available. The biggest challenge is finding ways to ensure our members remember the benefits they have access to, to ensure they fully utilise their membership.
4. Can you share a particularly memorable success story or achievement during your time with us? About a year ago I was informed that a member whom I had recruited a few year previous had expressed that he wished to cancel his membership. It was the day before I was due to go on holiday so I thought I I’d give the bodyshop owner a call to see whether he was experiencing financial issues and whether there was a way I/NBRA could assist. He informed me that a work provider owed him circa £30k plus he had a few other well overdue outstanding invoices. As a result he was struggling to cover wages etc and to say he was stressed is an understatement! I asked he why he hadn’t used our Debt Recovery service to assist him. He explained that owing to the stresses he was experiencing, it slipped his mind that this was one of our available benefits (hence my answer to question 4 above!). Before going on leave that day, I set the wheels in motion with my colleague Antony to attempt to recover the outstanding money. By the time I returned to work almost three weeks later, the person concerned had received the outstanding monies. Those moments make my job so worthwhile!
5. What initiatives or projects are you currently working on that you’re excited about?
NBRA Greener Bodyshop initiative, which I founded in 2015, holds a special place for me as it was developed from my initial idea. I find it tremendously rewarding to see the event continue to grow each year and I’m delighted to see that Martyn embraced the concept from the moment he joined us here at the NBRA. He has brought further great ideas into the initiative and with his wealth of experience of planning events etc, I’m excited to see what this year’s event will bring!
6. In your opinion, what is the most valuable benefit NBRA provides to its members? The Debt Recovery service has to be the best insurance policy that any bodyshop owner can have in their back pocket!
7. When you’re not working, how do you like to spend your free time? When we’re not spending time with family or friends, I enjoy going to the gym, cycling and going to music concerts/festivals (mostly 80’s bands!).
8. Do you have any hobbies or interests that might surprise your colleagues? I’ve practised various martial arts since the age of ten including Judo, Karate and Kickboxing. I was proud to be awarded Black Belt 1st Dan in Shotokan Karate in 1995. I’m obsessed with 80’s music and can often be found ripping up a dance floor or at 80’s festivals and concerts!!!!
9. What personal values or principles do you hold that influence your approach to work? I always treat people as I would like to be treated myself and I believe honesty always has to be the best policy. If I say I’m going to do something, I make it a priority to get it done.
Since the last magazine both Jerry Braddock and Tom Hudd had been remarkably busy by visiting commercial repairs new and existing supporting them and enabling them to achieve the elite truck and van standard.
So first up we have two existing members that have achieved the Elite Truck & Van Standard (Structural) congratulations to Spectrum VR Essex & Kent, David Philps (Edinburgh) & Spectra Vehicle Commercial Repair all of whom hold vehicle manufacturer approval except for Spectra.
I am pleased to announce an exciting new partnership within the Commercial Repair sector between Akzo Nobel and the VBRA. Paul Ryley - National Sales Manager CV UK. We are excited to work with the VBRA and see the Elite Truck & Van Standard as an important turning point in the sector and as such will be inviting all Acoat members to join the VBRA and achieve the standard.
We held the VBRA Exec meeting on the 30th of May in Liverpool at Core Diagnostics HQ covering lots of current issues and listing to specific suppliers that could benefit Commercial repairers and Bodybuilders Core Diagnostics presented on programming components and re calibrating ADAS on site with their tooling which enables VM passthrough making sure that the software is the current updates required.
This edition site visit was to conduct a renewal accreditation of the Elite Truck & Van Standard at Vehicle Bodycare Centre
Ltd in Leeds Prestige Vehicle Accident Car Commercial Repair Leeds, West Yorkshire | Vehicle Bodycare Centre Ltd (vehicle-bodycare.co.uk)! Now then I ask you who travels on a Friday to Leeds from Bristol and back in a day and to be honest I was asking myself the same question….. However, I have never visited a site so well equipped to deal with so many vehicles of shapes and sizes holding JLR, Tesla, VAG & Lamborghini Approval to name a few and then we have the commercial vehicle aspect which is very impressive.
I was introduced to George the owner and Lady, George’s security! both Tom McGrath & George gave me a tour of the business.
The first Commercial bodyshop to have dedicated commercial ADAS equipment and calibration target boards.
from Left to right – Sam Blom (Structural Panel Technician) –Tom McGrath (VDA) – George Boyes (Owner) – Gerry Braddock (VBRA)
One of the Jobs that they have straightened after the Trailer hit a low bridge and twisted the chassis frame, king pin and base plate all repaired to a high standard using the correct equipment and vast experience.
The VBRA have been working with Bremco for the last 18 months and Brett Maycock MD of Bremco is the leading authority in Chassis alignment and straightening in the UK.
Brett has a keen interest in the Elite Truck and Van Standard created by the VBRA and has dedicated a significant amount of energy to developing an IMI certified training course in commercial vehicle chassis alignment and straightening. This pioneering course, the first of its kind, is attracting considerable positive attention from both repairers and engineers.
Why is it important to create a certified training course in this area? The answer is straightforward: it is crucial to know which repairers are competent in repairing the chassis of a commercial vehicle. A 44ton vehicle that is not repaired correctly could lead to catastrophic consequences. Commercial repairers who already possess the necessary knowledge can undertake this course to provide evidence to work providers that they are competent. This certification can save both the repairer and the vehicle owner time and money. If the chassis is overheated and shrinks to the point of rendering it scrap, the costs can be exorbitant and the key-to-key time can extend by weeks, if not months.
I recently caught up with Brett from Bremco and James Hannaford, a Structural Panel Technician at Spectra Commercial Repairer. I asked if I could assist in (or at least view) repairing the front chassis legs on a Volvo FM flatbed/Hi AB eightwheeler. They were correcting a vertical
bend and performing local chassis leg repairs. It had been a while since I got my hands dirty with commercial vehicles, I thoroughly enjoyed it. The science behind Brett’s logic on how to correct a bend or a twist in the chassis leg was fascinating. Witnessing the process firsthand is crucial to understanding it fully.
The equipment used to support the vehicle for chassis repair and to correct the damage is impressive. Advances over the past 10 years have made rams lighter, more powerful, and much smaller, enabling easier access to areas that were previously extremely hard to reach without extensive stripping.
Auto Plas Bumper Recycling specialise in the recycling of car bumpers and other automotive materials
We offer a free-of-charge collection service, and our central location enables us to easily service bodyshops nationwide, with the capacity to collect over 2000 bumpers a day.
PC-based camera radio system. The „Technical Revolution“ in mobile, electronic wheel alignment for almost all types of commercial vehicles!
Readings recorded by radio transmission
AXIS4000 Computer-based wheel alignment system for commercial vehicles
The AXIS4000 wheel alignment system is a new and innovative development from HAWEKA. This top-of-the-range product is the culmination of many years of experience in the field of portable wheel alignment.
This high-quality wheel alignment system enables realtime, highly accurate and fast measurements to be made.
place in an „as driven position“ — there is no need to lift up the vehicle.
• Different designs of magnetic feet ensure fast fitting to steel rims.
A PC or Notebook is needed to record the readings. USB connection to receiver unit.
The key factors that led to HAWEKA’s decision to continue with the development of this measuring process were the high global demand for vehicle wheel alignment — combined with flexibility and accuracy of the measuring technology.
The result is AXIS4000 , a wheel alignment system that meets the standards of car wheel alignment systems, in terms of ease of handling and measuring accuracy.
Fast fixing of the magnetic scales for setting up the AXIS4000 wheel alignment system.
The measurement can begin once the cameras with alignment clamps have been fitted to the vehicle and the scales have been aligned to the vehicle using the software.
• The patented ProClamp clamping device with grapplers is ideal for aluminium rims.
• 360°rotating camera measuring heads guarantee instantaneous recording of actual data.
• The adjustment is immediately displayed on the monitor.
• The printout shows the „before“ and „after“ readings and setting values.
• The readings are recorded by radio transmission directly onto the printout.
Simply moving the camera records all of the actual data and transmits it directly to the program.
The use of camera technology significantly simplifies wheel alignment and adjustments to these vehicles can be carried out speedily.
With additional adapters, toe, caster, offset and out of squareness can be quickly and accurately aligned.
Specially cushioned „softline“ feet mean that transporter wheels can also be simply and easily aligned using this system.
For vehicles with multiple steering axles
Even vehicles with double steering axles can be aligned quickly simply with two additional turn plates.
Following the simple selection of the vehicle to be aligned, all of the relevant vehicle data can be quickly and conveniently selected — the dimensions of the rim can, for example, be entered individually.
The AXIS4000 can thus be used to align almost all types of commercial vehicle right up to small transporters.
The preparation needed to align the wheels of a vehicle is clearly explained to the user by means of a simple and clear graphic display.
The information obtained is avail–able to the user while making the adjustments, either in digital or analog format, in a large and easily understood display.
The operator is led through the individual stages thanks to the well laidout menu structure and clear instructions. The readings are displayed instantaneously for each step.
The possible measurement processes for each vehicle axle are displayed on selection buttons.
The readings are listed separately for each vehicle axle. This axlespecific display of the readings enables the user to make fast adjustments.
Well laid-out overview of the readings for all vehicle axles in one display.
The overview shows the individual readings for each axle. This provides a clear comparison between starting and finishing readings. The readings can then be printed in a printout.
Number of channels 10
Transmission power 10 mW
Charger
Operating time with fully charged batteries > 10 h
System requirements for AXIS4000
Required operating system: Windows Vista, 7, 8.1, 10
Minimum hardware requirements:
Processor: Pentium IV– AMD Athlon 1 GHz, RAM: 512 MB (Windows XP) / 1024 MB (Windows Vista, Windows 7), available hard disk space: 100 MB, graphics: resolution 1024 x 768 pixel / high colour, sound card, port: USB 1.1, CD-ROM drive
Recommended:
Processor: Pentium or AMD with 1,6 GHz or larger, RAM: 1024 MB, graphics card with AMD (ATI) or NVIDIA chipset greater than 16 MB, resolution 1280 x 1024 pixel / true colour, WLAN (option for portable handheld model), printer Measuring
A stable trolley ensures that all components of the AXIS4000 can be kept conveniently and securely and provides space for a printer, which can be positioned in a cupboard.
Tailored solutions for your courtesy vehicle needs.
Find out more at enterprise.co.uk/courtesy-car-solutions
NOPE, not a return to remembering the cuddly toy on the conveyor belt - I am showing my age there (and the fact that I’m Gen X) … but an intro into the world of leading multi-generational teams
What’s the difference between a Gen Z’er and a Millennial apart from their age? What’s Generation I?! Who’s a Boomer?
It can seem confusing. But it’s also critical knowledge for someone who is managing a team of people of different ages.
Why? Because the differences between the generations run deeper than how old someone is.
For most people, your generation impacts your core values, what is important to you, how you think, how you process information, and therefore, how you flourish in lifeand in your work environment.
It’s worth educating yourself about what the core characteristics of each generation are, and what the age ranges are, to support your management skills and create strategies to help you interact with members of your team who are not the same generation as you.
In an industry with a skills crisis, this kind of knowledge and understanding is transformational for your management style and can be the difference between successful recruitment and retention of your staff, or unnecessary churn and loss of future talent.
A 90-minute coaching session could be all that stands between you and transforming your interview, recruitment and management strategies.
If you’d like to know more email me at kate@ampliocoaching.co.uk
Coaching is not just a conversation.
It’s a tangible way to upskill you and your team to be more productive, improve communication skills and boost employee performance. www.ampliocoaching.co.uk
The value all-makes range of parts with over 12,000 products SUSTAINERA REMANUFACTURED ORIGINAL EQUIPMENT PARTS As good as new, for less GENUINE PARTS
The brands your customers know and love
WELCOME TO DISTRIGO - GENUINE AND ALL-MAKES PARTS TO THE TRADE
Parts for all makes and all models and at competitive prices, Distrigo Parts Distribution guarantees the right parts at the right time, delivered to your door. We look after your every need with our extensive local stock from our nationwide distribution network of 85
Choose from our four fantastic
As a bodyshop owner, managing your daily operations and staying competitive is a constant challenge. Amidst the pressures of repair jobs, customer service, and supplier relations, social media management often falls by the wayside. However, in today’s digital age, a strong social media presence is essential. This is where Small Torque comes in – offering a hassle-free, done-for-you social media service, tailored specifically for bodyshops.
Why Choose Small Torque?
Expertise in the Automotive Industry Small Torque’s services are designed by bodyshop people for bodyshop people. This unique understanding of the automotive industry ensures that the content created and managed by Small Torque resonates with your target audience, creating a robust online presence that reflects your brand’s expertise and values.
Comprehensive Social Media Management
Small Torque takes social media off your “to-do” list, allowing you to focus on what you do best – repairing vehicles. Their comprehensive services include:
• Content Provision: Regularly posting specialist content tailored to your bodyshop, from local news and events to industry-specific content that educate, advise, and inform your audience.
• Growth Marketing: Running targeted local advertising campaigns to build your followers and expand your reach.
• Professional Media: Capturing professional photos and videos of your bodyshop for use across social media and your website.
Benefits of Partnering with Small Torque
Increase Retail Opportunities Proactively promoting your services across multiple social media channels taps into huge retail opportunities, driving more business to your bodyshop.
Promote Manufacturer Approvals Small Torque ensures compliance with manufacturer approval guidelines by automatically posting mandatory manufacturer content, helping you maintain and promote these much valued accreditations.
Build Your Brand Online Consistent and strategic communication establishes your bodyshop as a thought leader in the industry, increasing brand awareness and customer trust.
Reach New Audiences With over 3.9 billion users on social media, there’s a vast audience waiting to discover your services. Small Torque helps you reach these potential customers through targeted strategies.
Engage with Customers Regular interaction with your audience humanises your brand, builds trust, and fosters a deeper connection with your customers.
Through consistent communication, Small Torque strengthens relationships with your audience, improving both conversion rates and customer retention.
Enhance Customer Satisfaction By monitoring business performance through customer satisfaction surveys and online reviews, Small Torque helps you refine your strategies for better results.
Boost Website Traffic Social media posts from Small Torque drive traffic directly to your website, increasing enquiries and potential business.
Small Torque offers a range of bolton solutions to further enhance your social media strategy including:
• Instagram Management: Regular imageled updates and strategic hashtags to keep your Instagram page active and engaging.
• Professional Photoshoot: On-site visits to capture high-quality photos and videos of your facilities.
• Online Review Management: Monitoring and responding to reviews, ensuring swift handling of any negative feedback.
• Targeted Facebook Adverts: Setting up and managing ads to reach local audiences and grow your following.
• Social Media Page Setup: Assistance in setting up new pages with custom graphics and headers in line with your branding.
• SEO Website Blog: Monthly optimised blog posts to keep your website on the first page of Google search results.
Customers rave about Small Torque’s seamless and effective service:
• Martin Robson from Brian Robson Coachworks appreciates the hassle-free management of their social media platforms, maintaining a consistent presence that communicates effectively with their followers.
• The FCW Group highlights the peace of mind Small Torque provides by taking control of their social media, while still allowing input for specific posts.
• Peggs ARC has seen a significant positive impact on their online presence, thanks to Small Torque’s engaging and informative content.
It’s never been easier to enhance your bodyshop’s social media presence. Visit Small Torque’s website and choose a plan that suits your needs. With no contracts and the flexibility to upgrade or cancel anytime, you can start transforming your online presence today.
For more information email hello@ small-torque.co.uk.
Transform your bodyshop’s social media presence with Small Torque and focus on what you do best while they handle the rest!
ECA Business Energy invites your bodyshop to become Carbon Neutral in accordance with PAS2060.
Their energy specialists have helped over 500 bodyshops:
• Save an average of 60kg emissions per Scope 1 job
• Save an average of 11.6kg emissions per Scope 2 job
• Reduce Scope 1 & 2 emissions year on year by 15%
• Save over 1,000 tonnes of carbon
• Save 1.3kg of carbon per job
• Offset over 60,000 tonnes of carbon
• Support UK and worldwide projects
ECA Business Energy can implement more sustainable practices and carbon reporting to future proof your bodyshop from environmental regulations, such as:
• Streamlined Energy and Carbon Reporting (SECR)
• Energy Saving Opportunities Scheme (ESOS)
• Science Based Target Initiative (SBTi)
• Net Zero
The auto repair energy experts can also help you:
• Purchase greener energy
• Implement energy reduction strategies
• Access and install energy efficient LED lighting
• Access and install EV charging points
• Conduct regular site surveys
• Conduct desktop surveys
• Generate power on-site
The vehicle body repair industry is evolving with innovative technologies that enhance efficiency and cost-effectiveness. One such advancement is the Plastic Fusion Pro Advanced Station from Eco Repair Systems, which offers significant benefits for plastic repairs on vehicles.
Repairing plastic components using is far more economical compared to replacing entire parts. The station allows technicians to fix damaged bumpers, wheel arch liners, headlamps, and wing mirror housings, reducing the need for expensive replacements.
The Plastic Fusion Pro Advanced Station ensures strong, durable repairs by using nitrogen to increase the integrity and strength of the welds. This method guarantees a high-quality finish that meets or exceeds the original manufacturer standards.
Better value utilities, independent energy and carbon management, from people who care about the body repair industry. Reduce costs, attract more business and help the environment.
One of the standout features of the station is its built-in nitrogen generator. Traditional plastic welding methods just using heat can cause plastic to burn, leading to toxic fumes and compromised weld integrity. The nitrogen generator plays a crucial role in eliminating impurities from the weld and ensuring a purer, stronger weld.
The station is engineered for both common types of plastic welding in the bodyshop environment. The comprehensive kit includes universal welding rods designed to work alongside nitrogen, and three different staples to facilitate diverse repairs, and a scraper. The system features sensors that remember temperature settings and an automatic cool-down when not in use.
For more information on the Plastic Fusion Pro Advanced Station, visit ecorepairsystems.co.uk or 0203 649 9371 to arrange a demonstration.
By David Catanho
Sustainability Transformation
Manager for
AkzoNobel’s vehicle refinishes business
The Sustainable Repair Network is a program that delivers the products, services and digital tools to make a measurable difference to a bodyshop’s goal to reduce its carbon footprint. By visiting bodyshops and carefully evaluating various aspects of their operations, we can identify opportunities to help them start their journey or enhance and accelerate their existing strategies.
While most businesses focus their attention toward addressing Scope 1 and Scope 2 emissions, and direct and indirect emissions, AkzoNobel deliberately targets Scope 3 which considers those emissions that extend
Sustainability has transitioned from being a buzzword to a core component of business strategy. As the world struggles with shrinking resources, a fast-growing population, and the serious effects of climate change, sustainable business practices have become a decisive element in a company’s future success.
As a business, AkzoNobel has ambitious targets for reducing carbon emissions by 50% across the value chain by 2030, and as a supplier to the bodyshop and repair shop industry, it is committed to supporting its clients’ ambitions in making their business more sustainable. One of the ways it is helping with these ambitions is through the Sustainable Repair Network.
beyond a company’s own operations. The Sustainable Repair Network program specifically targets emissions that occur downstream – arguably the data that is the most difficult to measure, influence and manage.
By leveraging its market leading product assortment, long-standing experience and innovative digital tools, the program aims to significantly reduce an organization’s carbon footprint in line with industry goals.
Within the Sustainable Repair Network are three main ‘Services’ that enable AkzoNobel to create journeys that are bespoke to each customer and that provide them with the actionable insights to drive sustainable change.
The first tool is the ‘Carbon Pulse’, which is designed to comprehensively assess and quantify the carbon footprint created by a bodyshop’s operation. By collecting energy consumption and production data, including vehicle throughput and repair statistics, AkzoNobel can deliver key performance indicators (KPIs) to
help businesses evaluate their current emissions status and develop targeted strategies for future improvement.
Helping the bodyshop to achieve its emissions target is the second service. ‘Energy Pulse’ is effectively an audit that covers all areas of energy consumption in a bodyshop from the spray booth, and illumination to HVAC. Every aspect of operations can have a significant impact on energy consumption over the course of a year, so even a seemingly small change can be crucial for helping clients reduce their carbon footprint and increase its energy savings.
Element three is the ‘4 R Pulse’ - repair, reduce, reuse and recycle – and which of the ‘Rs’ are best used at a particular time. Replacing a bumper with a new part may be more economical than repairing what’s there. But when all factors are taken into consideration – the manufacture, shipping, and transport of the new part and the disposal of the old – it may not in fact be the most cost-effective option, neither is it the most sustainable, and ‘repair’ may be the better option.
Rather than solely focusing on the financials, the key lies in shifting the mindset toward durability and sustainability. So how we can change our perspective and prioritise long-term sustainability over short-term financial gain?
When it comes to sustainability, fostering open dialogue is crucial. At AkzoNobel, we actively drive change in the market by identifying and recognising that collaboration with competitors is essential, and learning from our peers can have a positive impact on other businesses who are also committed to building a sustainable future.
Understandably, however, appetite and demands can differ depending
on where you are in Europe. Some regions are more advanced than others in their thinking and their actions, and in the progress being made. With the Sustainable Repair Network, we are following the pyramid principle, seeking to initiate a change from the ground up, and from the broadest base.
Our ambition is to have the whole repair industry joining our initiative. It is open to all players within the value chain so that we can collectively create a positive impact throughout the industry as a whole. Success will be measured not only in the number of bodyshops we help, but also how that support is having a tangible impact on meeting our own 50%1 reduction target, pinpointing the precise contribution, with real data and no longer estimations, made by those within the network.
From the shop floor to the executive suite, the focus lies in fostering collaboration between key stakeholders and suppliers, with sustainability as the driving force. This shift is driven by a growing awareness of sustainability
issues and the desire to drive positive change.
In today’s constantly evolving business landscape, AkzoNobel’s vehicle refinishes business is not only exploring how it works just with the bodyshops. For the future of the Sustainable Repair Network, AkzoNobel is currently actively exploring partnerships with third parties in order to elevate our positioning as leaders in the sustainable and Net-Zero landscape.
There is still a long way to go, and the journey is only just beginning, there are many unknowns and as an industry we are all mindful of greenwashing, which means we have to establish trust. And what we do know is that access to real data can bring real, meaningful change.
From its creation to where we all find ourselves today, BS10125 has often been frowned upon and seen just as a necessity to gain work provision. What we should never forget in all of this is that the standard was created to assure the quality and safety of repairs after vehicles have sustained accident damage. If implemented in isolation of other business processes (such as health & safety, understanding work provision requirements) as a standalone product, we can see why businesses often adopt a negative view of it. We like to look at BS10125 as a tool to support business development, improvement, growth and if implemented in the right way, will achieve that. There are many different interpretations of requirements out there and methods that businesses adopt to demonstrate compliance.
You can overpay for training, equipment checks, support systems, purchase equipment you may not need, implement processes that don’t provide value or take an excessive amount of time to complete.
Why have 4 pieces of paper, when one may suffice? By providing a service that covers aspects of all areas either directly or indirectly affected by BS10125, H&S or work provider requirements,
we ensure that you are implementing what is needed for the business in the most effective manner and tailored to suit what works for you.
Whether you are at the start of your BS10125/H&S journey, considering them or indeed have these, we can provide an insight into getting you started, reviewing your compliance or enhancing your journey.
We Care – your business, your people, your goals, matter to us.
Results Driven – your goal is our goal and we know the best way to get you there.
Innovative – using our expertise to provide the right solutions for you.
Geography – we cover the whole of the UK including Northern Ireland.
Highly Regarded – recognised as a leader in the services that we provide.
Transparency – No hidden agendas or costs. We cut out the BS.
Skills & Experience – 30+ years of working within BSI and implementing management systems.
WQSS Digital Compliance Portal
(servicing all your BS10125/H&S/ work provider needs)
ARE YOU FED UP OF:
• Wiping dust of folders
• Printing off records to update folders
• Not knowing where to find records you need
• Compiling/updating spreadsheets
• Forgetting what needs to be done when
• Spending your day with auditors
• Undertaking tasks that don’t bring value
• Not knowing if sites within your group are maintaining systems
• Policies, procedures, forms (with change history)
• Equipment
• Training
• Annual people reviews
• Subcontractors
• Materials
• Audits
• Risk assessments
• COSHH
• Weekly email alerts for updates needed
• Head Office management facility
• Remote logon functionality for 3rd party auditors – reducing time on site
• Records all in one place
• Pre-populated training / equipment / subcontractors / frequencies
• Real time support on queries/records
“I am a compliance auditor and during a visit to Belfast came across the WQSS Portal for the first time. When covid hit I had to carry out a lot of audits remotely. Repairers would let me have a unique login to access their portal which saved time and effort. This also reduced the amount of intrusion into the repairer’s working day by two thirds. Hence, we have carried on using remote audit for repairers with the portal. I’d recommend the system to any repairer looking to reduce the burden of audits by work providers and other stake holders.”
Kulwant Soor
Web: www.wrightsqss.co.uk
Email: info@wrightsqss.co.uk
Tracy: 07450313728
Sustainability is a hot topic in the ART sector but what does it mean for the industry and what are repairers doing about it?
At Mirka, sustainability is at the forefront of the business because it aligns neatly with its clean commitments. These are a set of four global principles that embrace Performance, Partner, Production and Proactivity, and reinforce the business’ journey towards becoming a more sustainable company. Mirka is proactive when it comes to sustainability, and this is highlighted by what is being led by the head office. The company has a focused investment when it comes to sustainable technology such as hydropower, which has enabled the business to produce fossil-free electricity at all its production facilities in Finland. This has also led to a 56 per cent reduction in carbon dioxide emissions within scope 1 and 2. In addition in Jakobstad, Finland, there has been a focus on geo-energy from geothermal holes, which has allowed the site to reduce its annual carbon dioxide emissions by around 900 tonnes. There was also investment in a purification and heat recovery system for the Oravais plant in Western Finland. This has led to a transition from oil heating to recycled energy using the extra heat and since it was implemented the site has not gone back to oil heating.
Alongside what is going on in Finland, Mirka is putting sustainability first at production facilities in sunnier climes such as Fino Mornasco in Lombardy, Italy. At this site, the business has installed solar panels which has led to the operation harnessing the sun’s energy and enabling it to be entirely powered by solar.
The other way Mirka looks at sustainability is from a financial perspective. Being a financially sustainable business is important, especially in the ART sector where margins are so tight. This is where Mirka and its expanding product portfolio come into play. For Mirka, it is all about providing a high-quality abrasive at a price point that makes sense for the business but also the customer purchasing the product. By doing this, Mirka is seeing a concerted switch to more premium products. This move is taking users away from the slippery slope that is ‘buy cheap buy twice’. The reason for this is simple. It is because cheaper options might provide a slight monetary saving in the beginning however, it is quickly wiped out when the user has to purchase the same product very quickly down the line. In comparison, premium products are built to last longer, and will provide the same end product or service, whether it is being used for the first or hundredth time.
In addition, Mirka helps businesses become sustainable by conducting regular physical audits of their processes to help streamline them. The way this is achieved is pretty simple. Its team of experienced technical experts works with the repairer to see if it is getting the most out of the products being used. The audits and the documentation that are produced then enable the technical team to show where savings can be made, which, in turn, leads to an action plan being agreed upon and implemented. This plan covers best practices, which include specific processes for jobs or the recommendation of certain products for the business based on the surfaces being sanded. As a result, Mirka has seen how the plan has helped businesses streamline their processes, increase the overall efficiency of the jobs that are
being completed and enable financial savings to be made that can be invested back into the business.
Another way Mirka helps with financial sustainability is through its training programmes, which can either take place onsite or at the training centre in Milton Keynes. These programmes are not a one-size-fits-all offering but are customisable based on the business’ needs and requirements and ensure it is maximising the efficiencies of the products and abrasives it uses. This usually results in subtle cost savings that add up over time, while also increasing productivity and the overall quality of the finish.
Training also ensures that when attendees go back to their business, they have the necessary knowledge and skills to make the most of the tools they are using and can efficiently complete the processes that require the use of Mirka’s products. Overall, sustainability in its many forms is here to stay and as a business Mirka understands the importance of researching and investing in sustainable technology that will benefit the industry, while also ensuring there are sustainable high-quality products and processes end users can access.
Navigating the complexities of BS10125 compliance has never been easier, thanks to the innovative Ezi Compliance System (ECS). This cloud-based platform is designed to streamline your compliance processes, reducing the administrative burden and increasing efficiency across your bodyshop.
One of the standout features of ECS is its user-friendly interface, which is designed to be intuitive and easy to navigate for all users.
Cloud-based central storage conveniently manages all your paperwork and procedures online, in one central location.
Realtime, fully diarised system that sends push notifications to alert you and your suppliers when any service, calibration, assessment, or internal audit is due.
The Ezi Compliance team of experts are always on hand to provide ongoing support for complete peace of mind.
Online paperless system improves security and productivity with remote access via any device.
Easily and conveniently manage staff training and assessment, equipment calibration and maintenance, internal audits and subcontractors with just a few clicks.
Book a free demo today and find out how the Ezi-Compliance System can revolutionise your compliance management.
ECS has already earned rave reviews from Bodyshops in the sector. Fix Auto Dagenham applauds ECS for revolutionising their compliance management, making the process centralised and paperless. Autocraft Telford highlights the time and effort saved, thanks to ECS’s user-friendly interface and live notifications.
Call Phil on: 07415 302313 Or Ben on: 07923 563260 hello@ezicompliancesystem.uk
award provides learners with an introduction to the skills required to work on heavy electric and hybrid vehicles, including buses and coaches. Our 2-day IMI Level 2/3 Award in Preparing Heavy Electric/Hybrid Vehicles for Service/ Repair course will introduce learners to the knowledge, understanding and practical skills required to work safely when preparing for service/repairs on heavy electric/hybrid vehicles’ high energy systems. Specially designed for technical staff encountering heavy electric/hybrid vehicles within an operational environment, this course contains the knowledge and skills required to work safely around a vehicle that may require a service or have incurred damage to its high energy/electrical system.
Women’s Aid is the national charity working to end domestic abuse against women and children. For 50 years now, Women’s Aid has been at the forefront of shaping and coordinating responses to domestic abuse through practice, research and policy. Women’s Aid exists for all women who have survived domestic abuse and our members who support them with live-saving services. Throughout the article we refer to ‘survivors’ rather than ‘victims’ as we aim to empower those we support.
What is domestic abuse?
Domestic abuse is a pattern of incidents of controlling, coercive or threatening behaviour within an intimate or family relationship. Research shows that domestic abuse is most commonly experienced by women. It is rarely a one-off incident. Every woman’s experience of domestic abuse is of course unique, however, there are common factors that are very often involved. Abusive behaviours could include physical assault such as grabbing, hitting or strangulation, but they also include emotionally abusive behaviours such as belittling, threats, manipulation tactics, isolating the other person and gaslighting. It can also include sexual abuse, financial abuse, and stalking and harassment, including online stalking, digital abuse, monitoring and tracking the other person’s movements.
What is tech abuse?
Tech abuse is a tool for coercive control. The behaviour is designed to increase the survivor’s isolation. Technology can be used to extend someone’s reach so even when they are not with a survivor, they can keep tabs on where they are and what they’re doing.
They may do this openly (e.g. constantly texting when their partner is out with friends, checking their emails) or they may hide their behaviour (e.g. using covert spyware). Perpetrators are increasingly hiding GPS trackers in cars and other possessions to monitor a survivor and where they’re going. This happens not only within the relationship, but afterwards too, so they can continue to stalk a survivor even without physical access.
In the Women’s Aid survey of survivor’s experiences during the Covid 19 pandemic, we found a fifth (21%) of domestic abuse survivors had experienced their abuser turning up unexpectedly or knowing their whereabouts. This is becoming increasingly easy to do, with the rise in AirTags and connected car apps. More than one in ten (13%) survivors had experienced location tracking apps being used on their device. They told us:
• “He has to know where I am all the time and is constantly checking to see what time I’ve been on my phone.”
• “Made me turn my location on so he can see where I am constantly.”
• “I had to account for what I was doing to stop him from doing things. If I told him I was out he would drive to family members’ houses to see if my story added up and who I was with assessing if their vehicles were at home or not.”
Unfortunately, we are hearing more and more from women being found by their perpetrators using vehicle trackers. We were recently contacted by a survivor through our Live Chat who had fled to a family member’s house and was found by a
vehicle tracker her abusive partner had hidden in her car. Another woman had seen an app for a car tracker on her husband’s phone. She had been concerned that her husband had been tracking her for months but was unsure how. When asking him about how he was doing this he had told her she was ‘delusional’ and ‘crazy’.
What you can do if you find a tracker in someone’s car:
The key thing to keep in mind is safety. Is the customer/ woman by themselves? Or are they accompanied by their partner/ husband/ family member?
If they are accompanied by someone this will be a lot more difficult to address. It may be the case that you are unable to safely let someone know about the tracker, in which case there’s not much you can do. There may be an opportunity to say, ‘I had to remove the tracker to access the X, Y and Z’, but please do this with caution and if it doesn’t feel safe to do so then best to avoid this. If you notice any visible injuries or if you have some serious concerns that someone is in danger, we would always encourage you to call the police rather than attempt to handle the situation yourself.
If the customer is by themselves then it will be easier and safer to let this person know that you have found a tracker in their car, and you can ask them if they knew it was there. If they were unaware of the tracker and there are concerns that someone has placed it in their vehicle, then you might want to let them know that this is a form of stalking and abuse, and there is help available. You can suggest that they reach out to Women’s Aid for confidential help and support.
Domestic abuse can be a difficult subject to talk about but remember you don’t have to have all the answers. The key thing to keep in mind is to respond sensitively to any concerns, let that person know that they are not to blame for the abuse and there is help available. Try to avoid telling that person what to do; keep in mind that perpetrators of abuse will often be telling the other person what to do, what to say and how to think, so it’s important to try and give that control back to the survivor.
How
We run an online Live Chat which is available MonFri 8am-6pm and over the weekends 10am-6pm. Fully trained female support workers will be on hand to talk through the situation in more detail. Support workers will not tell
a service user what to do but they can give support, practical information, and discuss any options that are available based on their specific circumstances. Friends or Family members can also come through to Live Chat if they are worried about someone else.
You can also email for help and support around any issues relating to domestic abuse, and will receive a response within 5 working days, as long as it is safe to respond: helpline@womensaid.org.uk.
The Survivor’s Forum is an online community of women who have experienced domestic abuse or who are still in abusive situations. The Forum is for survivors only.
The Survivor’s Handbook includes information about the help and support available to survivors, including information about refuges, injunctions, child contact and safety planning. There is a specific section on how to support someone you know experiencing domestic abuse.
Love Respect is a website specifically designed for young women who are experiencing domestic abuse. The website includes a relationship health check, survivor stories and practical advice.
Cover Your Tracks Online provides information and guidance around digital safety.
You can find the contact details of local domestic abuse services in your area via our online directory by typing in your City/ Town
Workplace fundraising is a fantastic way to bring colleagues together, boost comradery and do something for a good cause! Whether you’re hosting a bake sale or taking on an inspiring challenge, we’ll be hand on to provide dedicated support, fundraising materials, and ideas to get your staff involved. Contact the team by emailing partnerships@womens.aid.ord.uk.
Revitalise Your Bodyshop with ExpertServicesConsultancy from NBRA Supplier Member Bodyshop Consulting.
Our consultancy services are designed to address the unique challenges faced by bodyshops today. From streamlining workflow processes and enhancing customer service to implementing cutting-edge technology and ensuring compliance with industry standards, we provide comprehensive solutions that drive real results. HAVE YOU A PROJECT
In the fast-paced repair industry, staying with the competition, let alone ahead, requires more than just technical know-how; it demands strategic insight and operational excellence. At Bodyshop Consulting, we specialise in transforming bodyshops into high-performance businesses through tailored consultancy services. With over fifty plus years of industry experience, our team of experts are dedicated to helping you optimise your operations, boost productivity, and increase profitability.
As environmental concerns grow, the automotive repair industry is seeking methods to reduce energy consumption, minimise waste and maintain vehicle integrity Keco Body Repair
Products addresses these concerns with their Glue Pull Repair (GPR) technology, providing a greener alternative to traditional methods
One of the significant advantages of Keco's GPR system is the elimination of energy-consuming grinding before dent pulling Unlike traditional dent repair techniques, Keco's GPR system adheres directly to the paint, preserving the factory finish and reducing the environmental footprint of the repair process This method not only conserves energy but also maintains the aesthetic and protective qualities of the original paint, also removing the need to re-apply ecoat to the backside of panels to restore corrosion protection This is crucial for the longevity of the vehicle and reduces the need for additional protective coatings, which can be both costly and environmentally taxing Keco’s GPR system also eliminates the need for high energyconsuming welding By using adhesive tabs and a cold repair process, Keco ensures that the repair is strong and durable without the high energy costs associated with welding This process is not only more sustainable but also safer for the vehicle and technician
Keco's commitment to sustainability extends to the recyclability of their GPR consumables The adhesive tabs and other materials used in the GPR process are designed to be recyclable, reducing waste and supporting a circular economy By choosing GPR, repair shops can contribute to environmental conservation while maintaining high standards of repair quality The large surface area tabs and double-action tools used in Keco’s system allow for smooth dent removal This efficiency reduces the amount of filler used during a repair, resulting in a quicker and more environmentally friendly repair process
With the rise of electric vehicles (EV’s), there is a need for repair methods that do not interfere with the vehicle's electrical systems Keco’s cold repair process is safe to use on powered EVs, providing a crucial advantage in the growing EV market
Keco Body Repair Products provide a revolutionary approach to auto repair, emphasising sustainability and efficiency By eliminating energy-consuming grinding and welding, reducing hazardous dust, and maintaining the integrity of e-coat, Keco sets a new standard in eco-friendly vehicle repair Their recyclable GPR consumables and applicability to aluminium and electric vehicles further highlight their commitment to a greener future For repair shops and technicians looking to reduce their environmental impact while delivering high-quality repairs, Keco’s GPR system is the clear choice
Prasco
We’re expanding our already unbeatable range with brand new parts for Landrover, Jaguar, MG and BYD.
Get in Touch With Us
2-3 Allerton Road, Rugby, Warwickshire
CV23 0PA
T: 0207 291 9750 ex 3447
E: bodyshops@rmif.co.uk
Contact the team:
Martyn Rowley Executive Director
Tel: +44 (0) 7741 908448
Email: martyn.rowley@rmif.co.uk
LinkedIn: www.linkedin.com/in/martyn-rowley-ab350824/
Thomas Hudd National NBRA/VBRA Technical & Southwest Business Development Manager
Mob: 07487 604046
Email: Thomas.Hudd@rmif.co.uk
LinkedIn: www.linkedin.com/in/thomas-hudd-bb5b5a67/
Michael Wicks Southeast Business Development Manager
Mob: 07776 294746 (Direct to me)
Email: Micahel.Wicks@rmif.co.uk
LinkedIn: www.linkedin.com/in/michael-wicks-81760ab9/
Antony Barnes Northern Business Development Manager & Member Support
Mob: 07824 876215
Email: antony.barnes@rmif.co.uk
LinkedIn: www.linkedin.com/in/antony-barnes-6115b583/
Gerry Braddock VBRA National Manager, Elite Standard Manager
Mob: 07776-294744
Email: gerry.braddock@rmif.co.uk
LinkedIn: www.linkedin.com/in/gerald-gerry-braddock-744443127/
Ellie Soden Central Region Business Development Manager
Mob: +44 (0) 7774 107764
Website: nbra.org.uk
LinkedIn: www.linkedin.com/in/ellie-s-0a5b5725/
Thank you to all our supplier members and partners