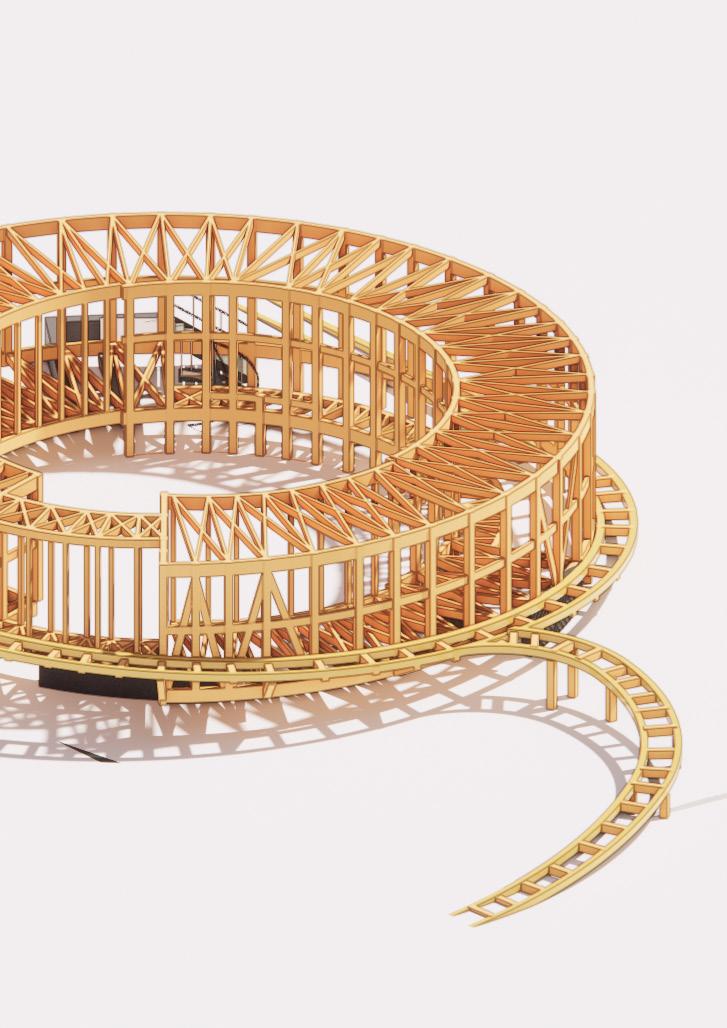
Technologies Positions 1
Architectural Design Position & Technical Detail Study Purpose
The architectural fragment chosen is a section through the ‘Silent Void’ of the building, where the pop-out window faces the courtyard. It includes a wood structure, a pop-out window, a wood suspended floor and a walkable green roof. The area will be further analysed in terms of light, climatic properties and materials to achive a better relation between user and design.
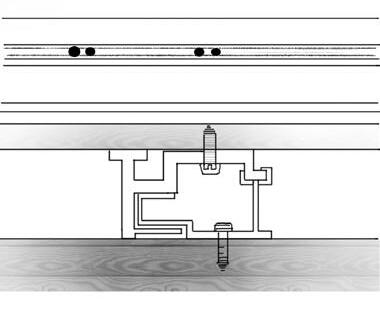
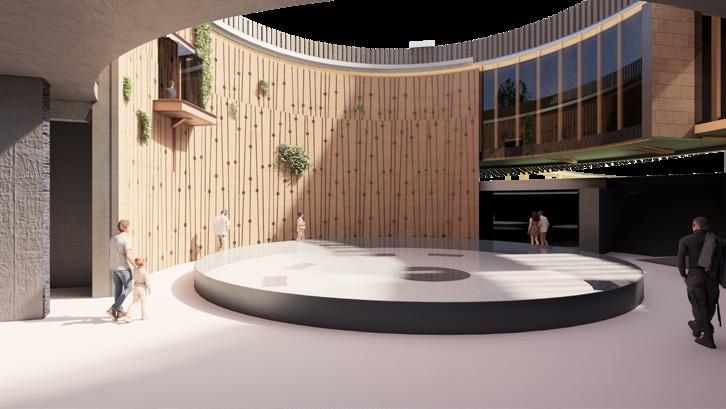
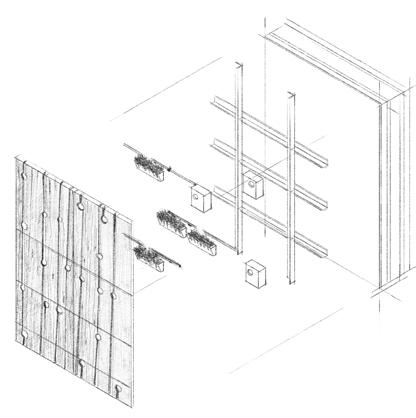
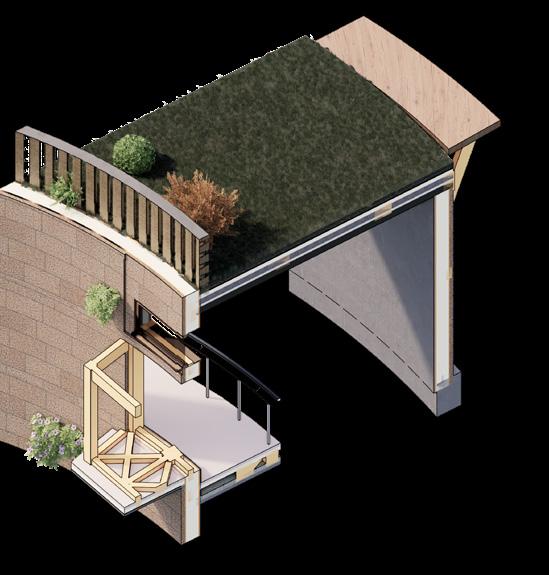
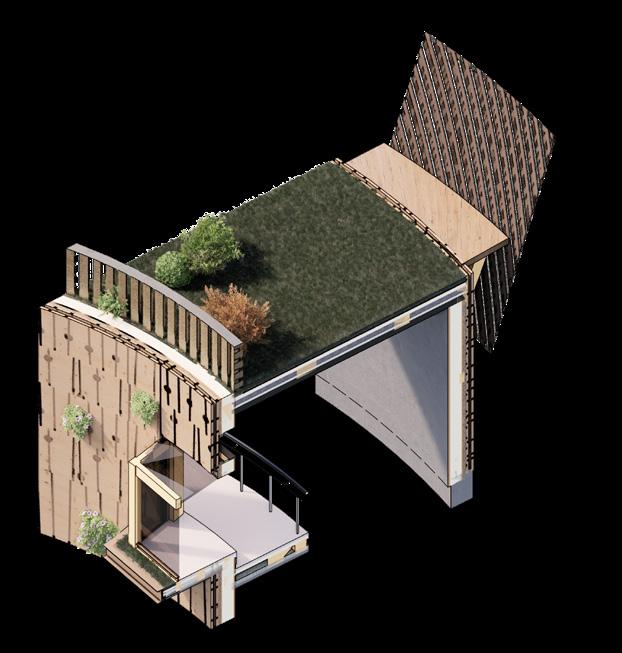
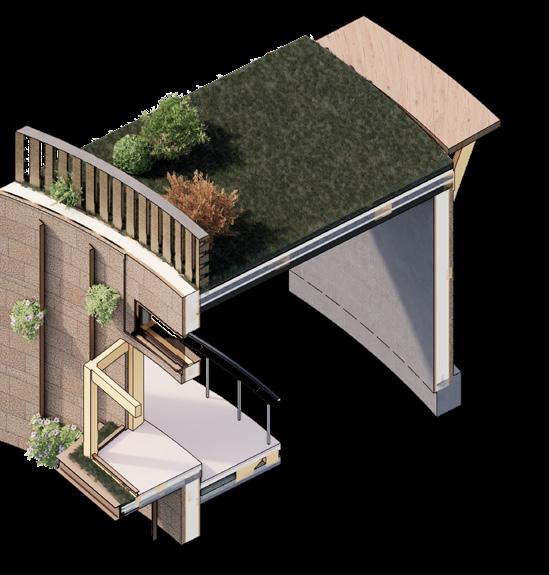
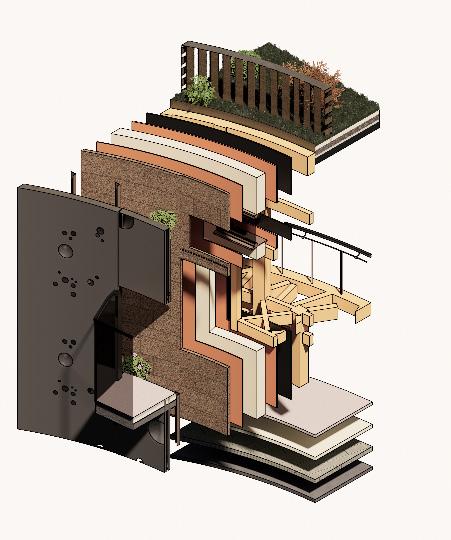
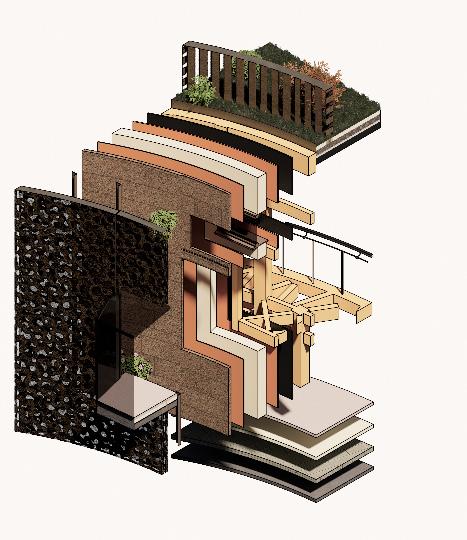
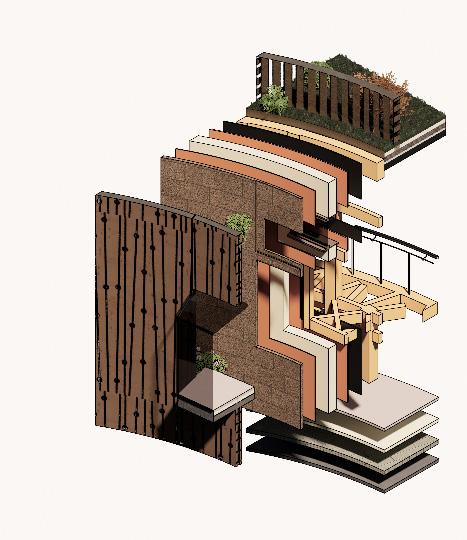
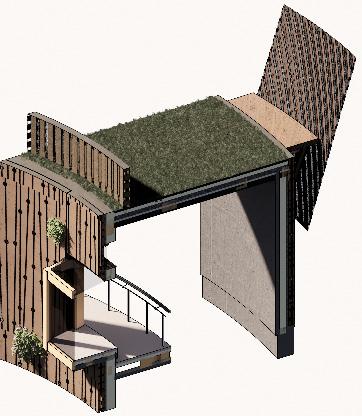
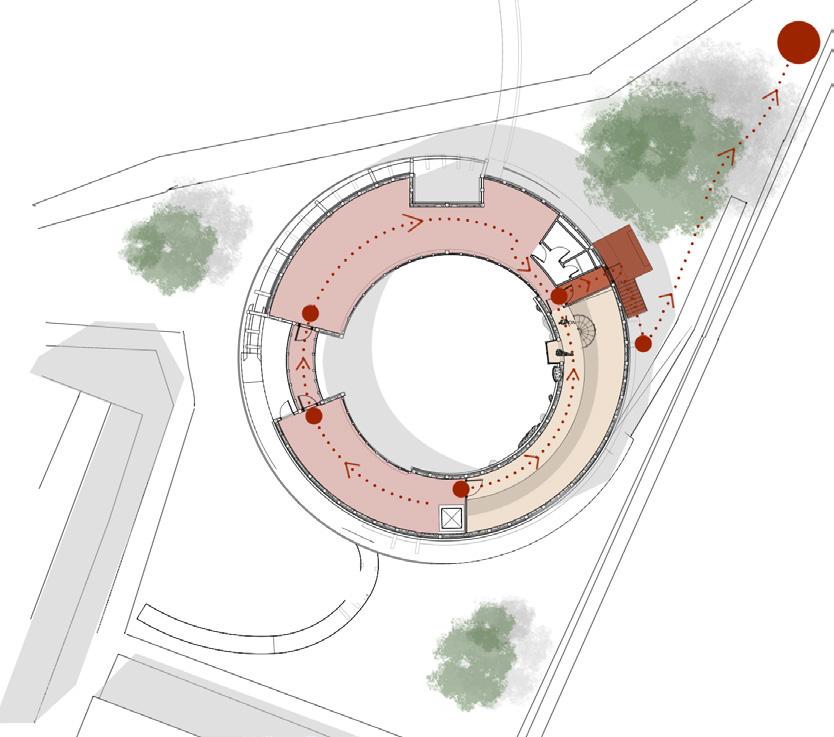
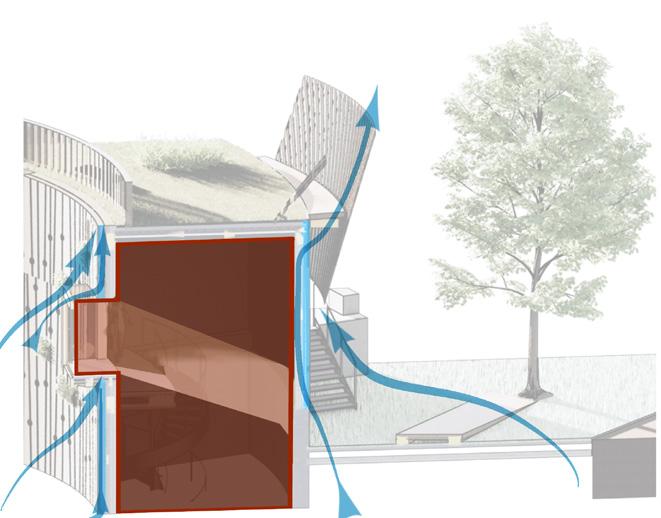
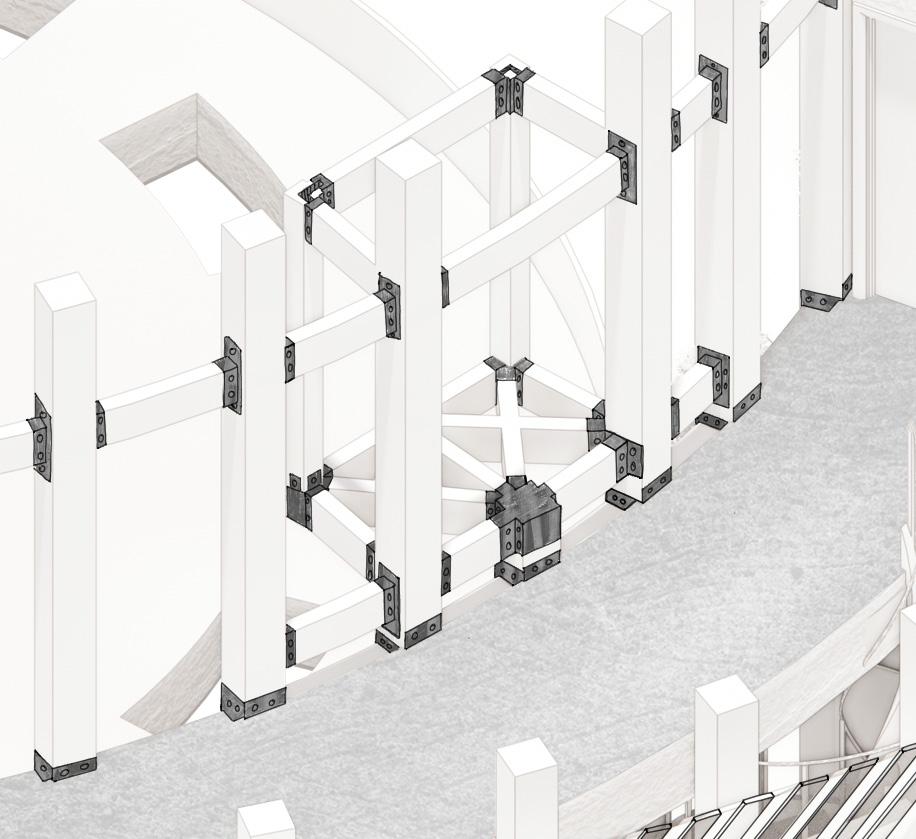

The main focus of the void is how light enters the space. The plants on the roof and living walls regulate the interior temperature, while absorbing some of the sound from the Mancunian Way
Tools

The maintanance of the building is represented by regular check-ups on the facade panels, using a ladder
The tools needed to install the prefabricated CLT timber structure are screw drivers and steel metal connectors fixed with screws.
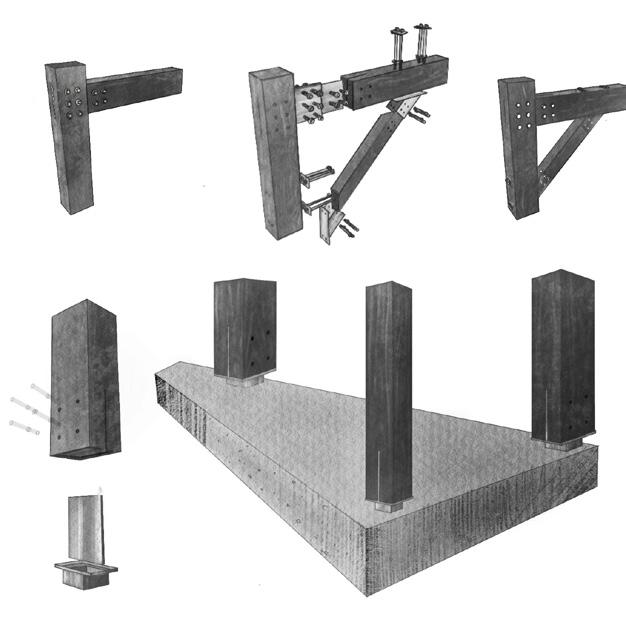
The loads supported by the wood structure are transfering to the brick-concrete walls from the underground structure and forwardly transmitted to the ground.
Building description in relation to the architectural fragment
The structure of the upper part of the building is timber, to balance the carbon affect as the underground portion is made out of concrete and brick for support and thermal qualities.
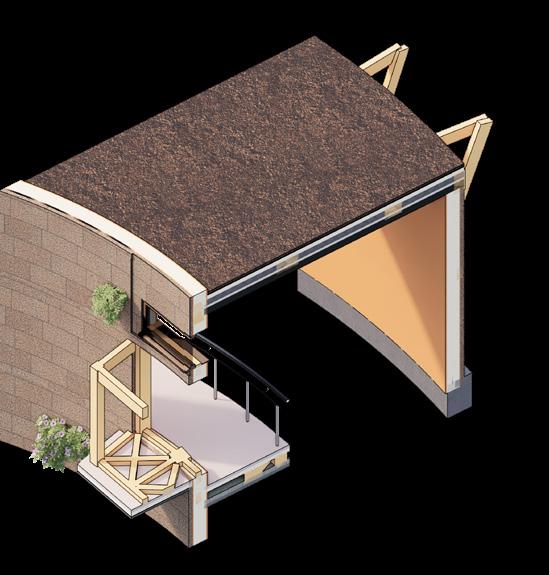
Additional testing is required on the structure and a study of material imbinations , as the timber structure may not support the exterior spiral walk path of the building, and additional steel may be added.
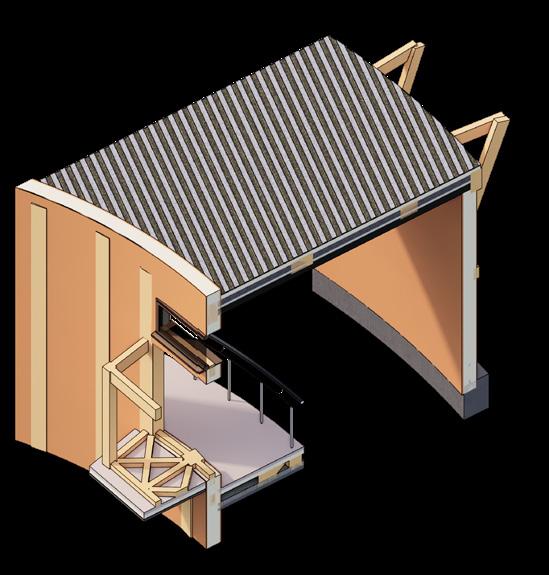

1. Timber frame structure -colum (240x220) -beam (100x220)
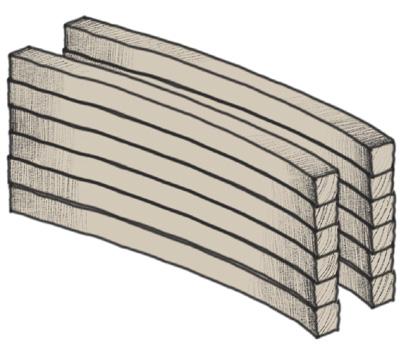

2. Interior finishing: deorative bioconcrete 20mm
3. Vapour Control Layer 15 mm
4. 120mm Sheep wool insulation 100mm Sound insulation
5. Damp proof membrane 15 mm
6. Plywood panels 55mm
7. ‘L’ Steel facade support 60x60mm
8. Perforated Plywood panels 60mm with plants
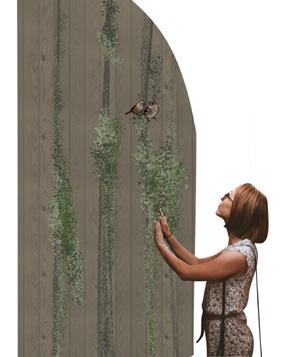
Environmental Section of fragment
Section of fragment Facade iterations of materials
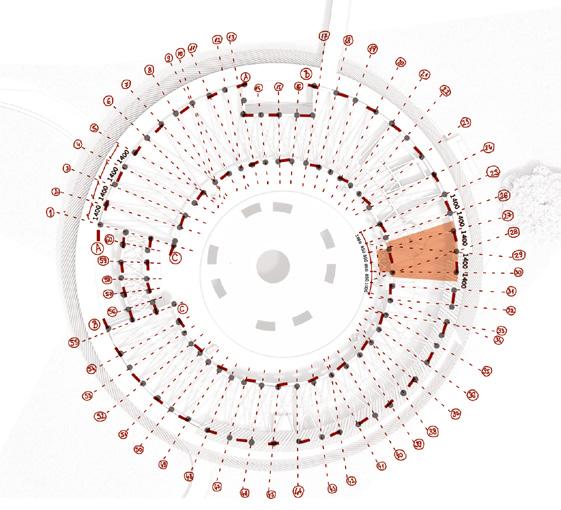
Cork + Sustainable, easy to perforate, good sound insulator -Expensive, high maintanace, vulnerable to damage
Metal + Reflects light in the courtyard low maintanance -Unsustainable, heavy, expensive
Plywood Panels + Sustainable, light, local, easy to perforate, low maintanance
The main feature of the facade is the perforations of the exterior cladding. Through the testing of materials the environmental performance of the building changes, with that its carbon impact as well. As the facade is formed out of two layers (double facade system), where one serves as the support for the plants and bird houses, the perforations of envelope are contributing to the tactile feel of the facade.
9. Interior ceiling finishing- decorative cement 40mm
10. Vapour Control Layer 15mm
11. 100mm Rigid insulation 40mm Sound Insulation
12. Damp Proof Membrane 17mm
Retention Tee 12mm
Aeration Layer 10mm
13. Drainage Layer 50mm
14. Root Barrier 15mm
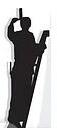
Engineered soil 100mm
15. Vegetation 100mm
Building & Life Safety
The upper floor of the void is accesed via a spiral staircase located near the pop-out window.
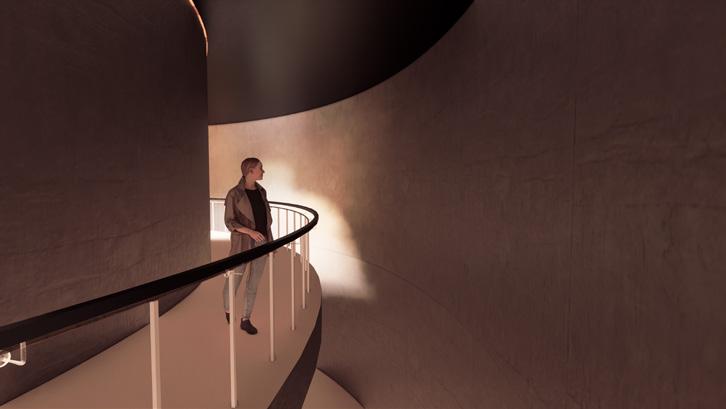
The red rectangle represents the fire exit, and the dotted lines the routes in case of fire emergency. The meeting point is located near the mancunian Way after the trees.
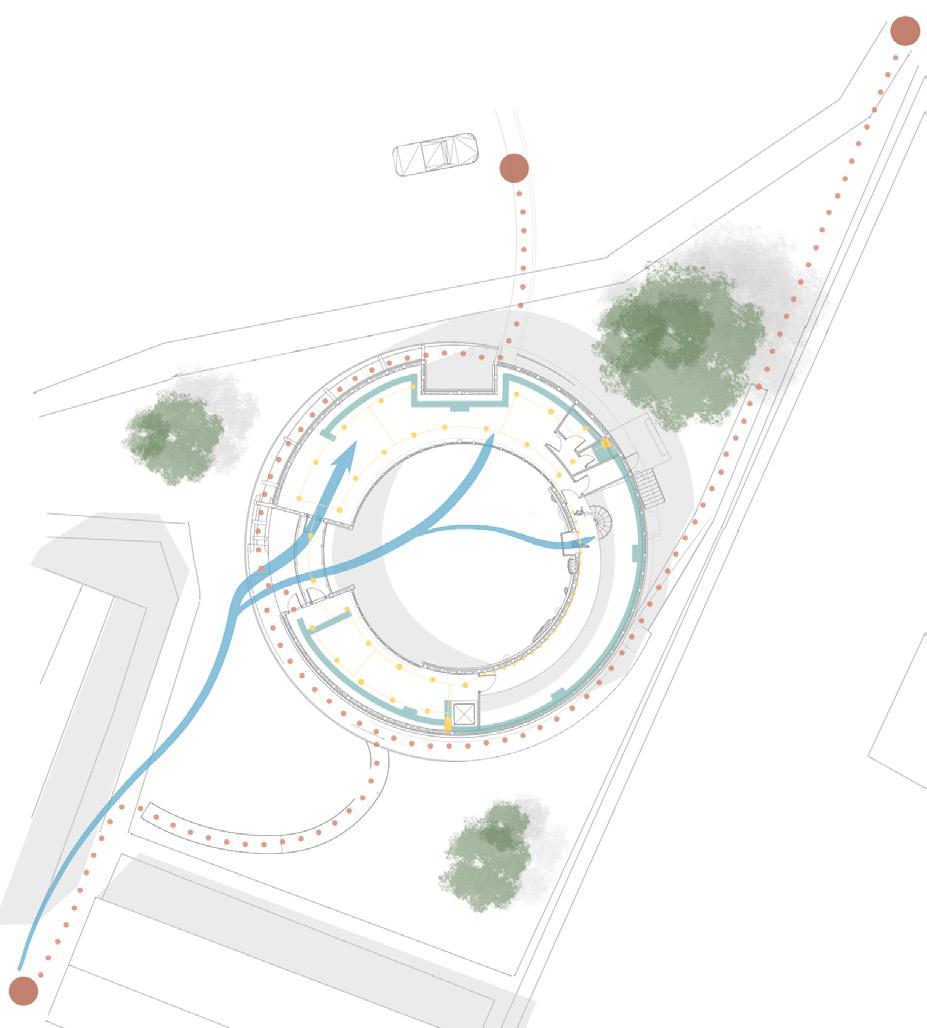
As the spiral staircase is situated so close to the fire exit, it should be moved to cover a different route of escape, plus is not in accordance with fire regulations as it doesn’t present a landing.
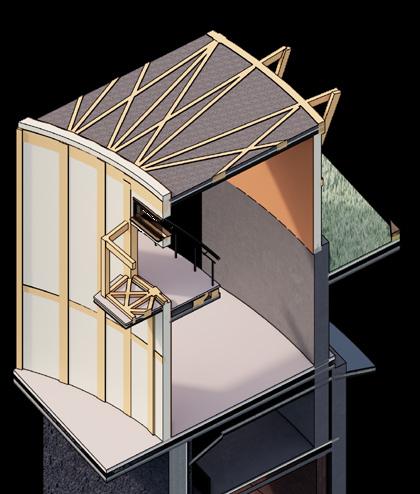
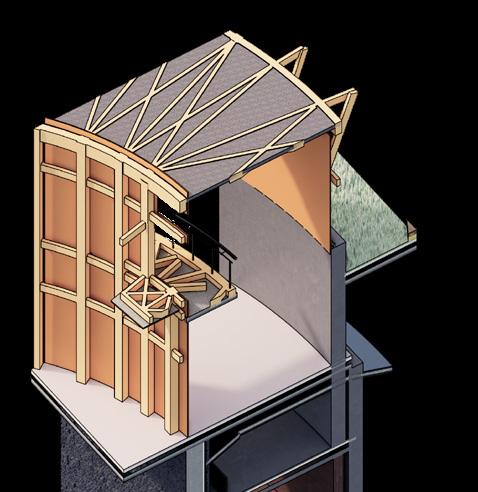
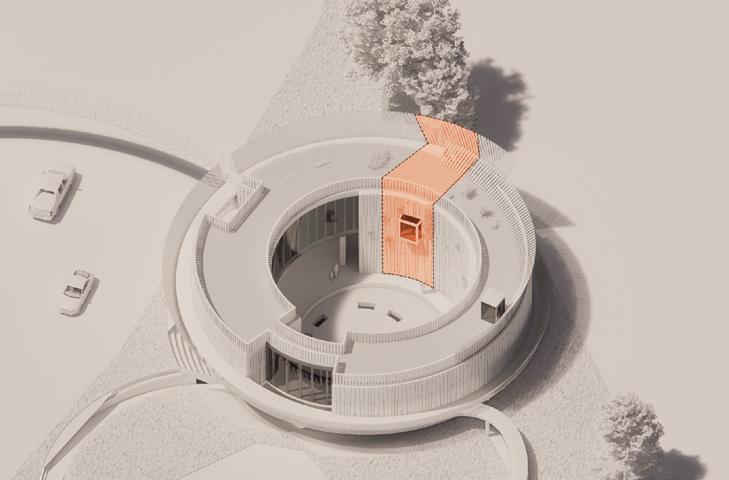

The facade shelters plants and birds, helping with the spread of fire, as it is formed out of 2 layers.

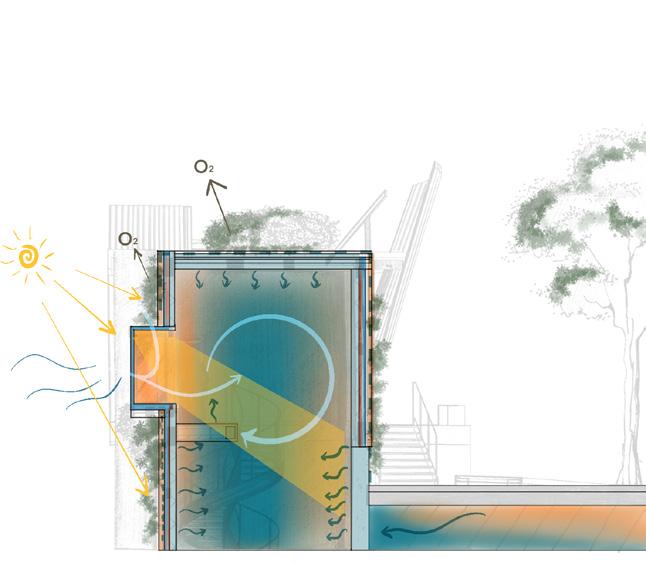
Accesibilitty is made via the spiral footpath and the bridge over the Mancunian way. The ramp has an inclination of 13.7 decrees, reaching the top terrace, so it is suitable for disabled people.
The building is well ventilated naturally and presents additional mechanical systems of ventilation. The plant rooms are situated next to the elevator and fire exit, where cable boxes are located.
The natural ventilation could be increased in the void by adding another window on the opposite wall, to drive the air across the room.
Constructability
The CLT structure (1.) panels (8.) and timber spiral system (19.) is pre-fabricated and transported to the site with trucks. The structure is fixed to the sandconcrete.
15. Floor finish- concrete screed 60mm
16. Sheep wool insulation 150mm
17. Wood Panel 100 mm
18. Ceiling Finish- decorative cement 40mm
Processes
The life cycle of timber in the building is represented in the diagram on the right. After being used in the construction of the structure, the wood is recycled into new furniture or recycled wood panels, that can be forwardly used onto the facade.


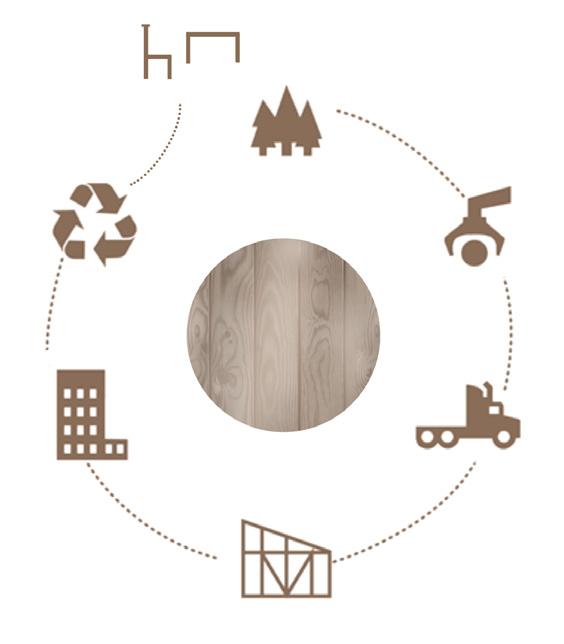
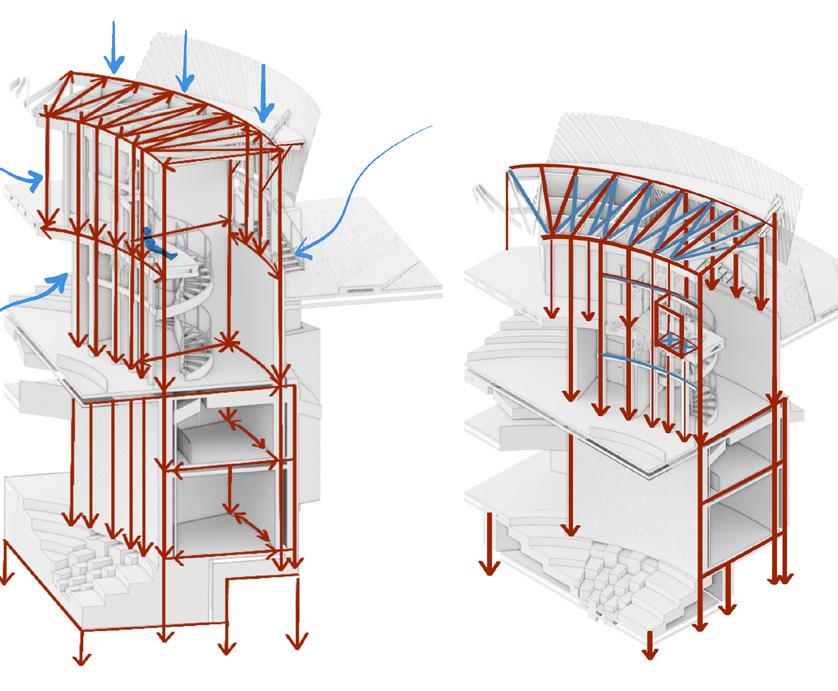
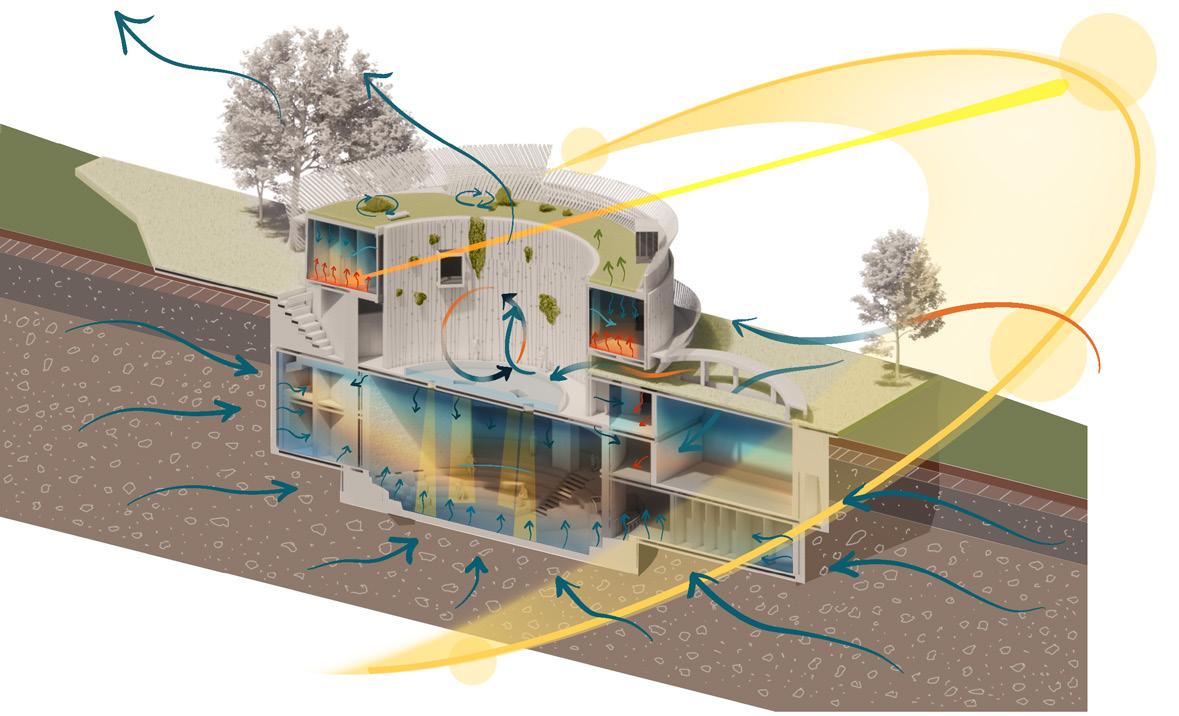
Connecting the structure Vapour control layer Sheep wool insulation fixing instalation
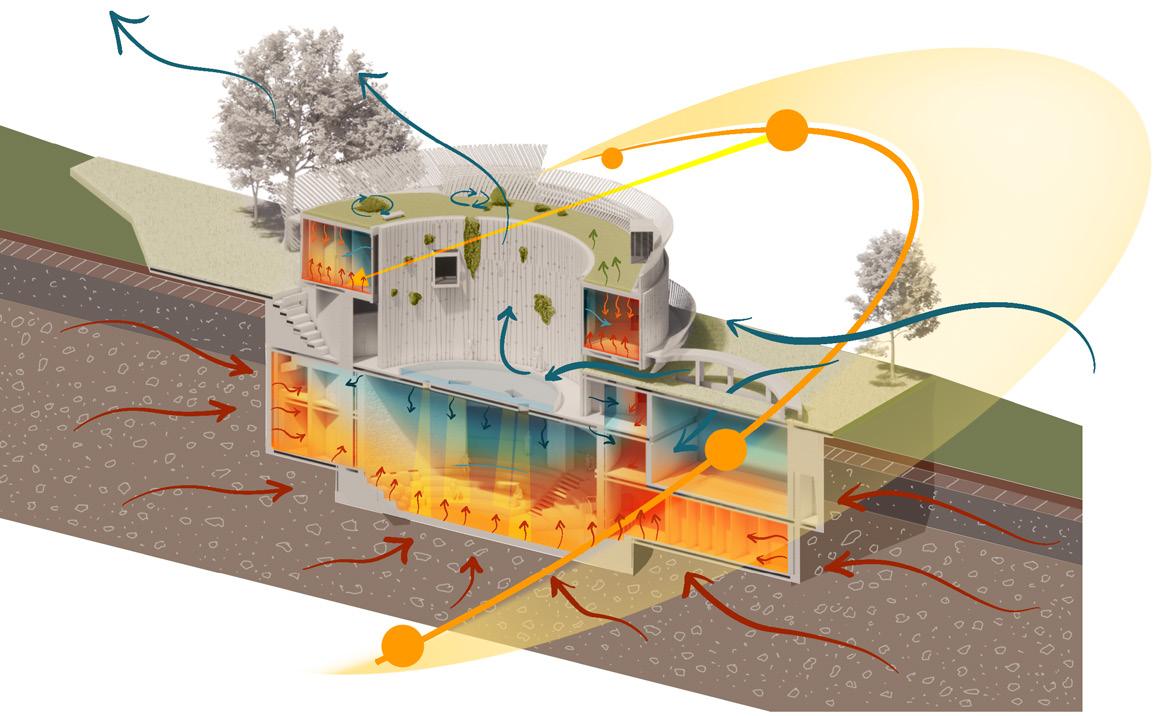
Prototyping 2 Iterative Testing & Record of Process
Physical model- structural resistance
Test 1: Interaction with the facade- Pop-out window iterations
The void is a space dedicated to silence and nature cognition. The iterations of the pop out window signify diferent forms of interaction with the facade where birds and plants are sheltered. The different textures and perforations of the materials contribute to how a new ecosystem of Mayfield is experienced.
Initially: the window space where people can sit and observe the constantly changing facade was formed out of a timber structure, that was limiting the design aesthetically characteristics, and the experience of the user, as the timber interrupted the view and experience of the sitting space. Moreover, water was accumulating in the top window (fig. 3)
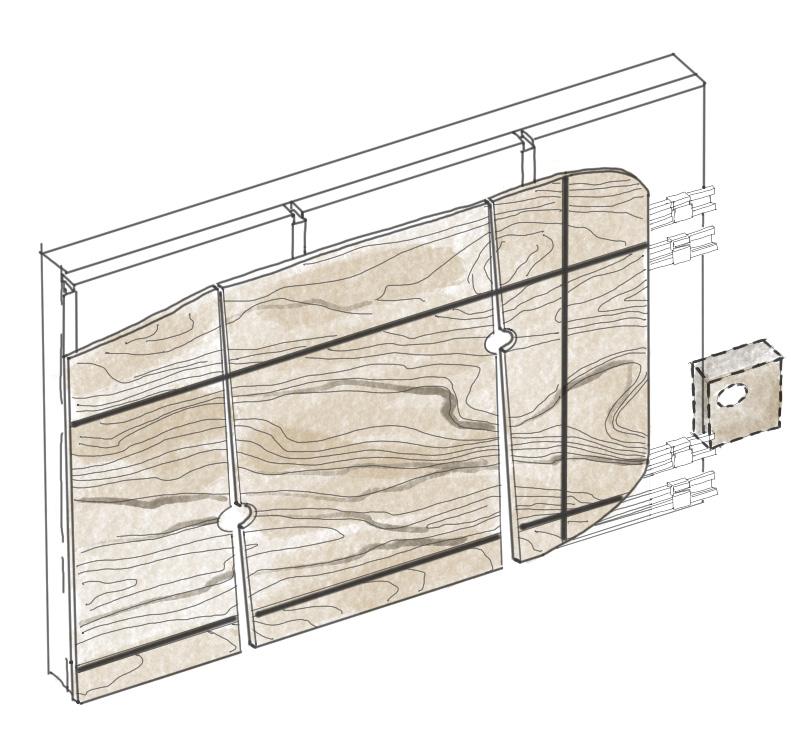
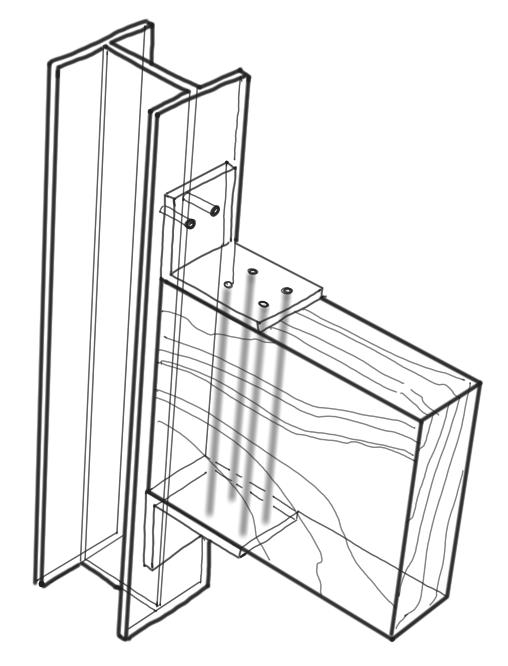



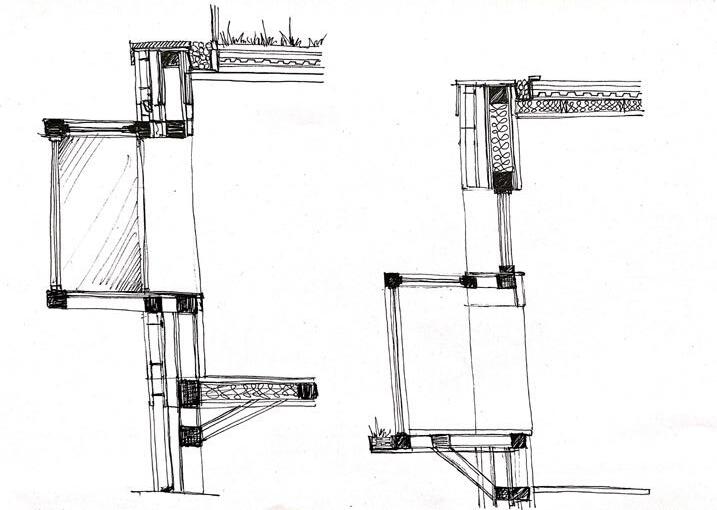

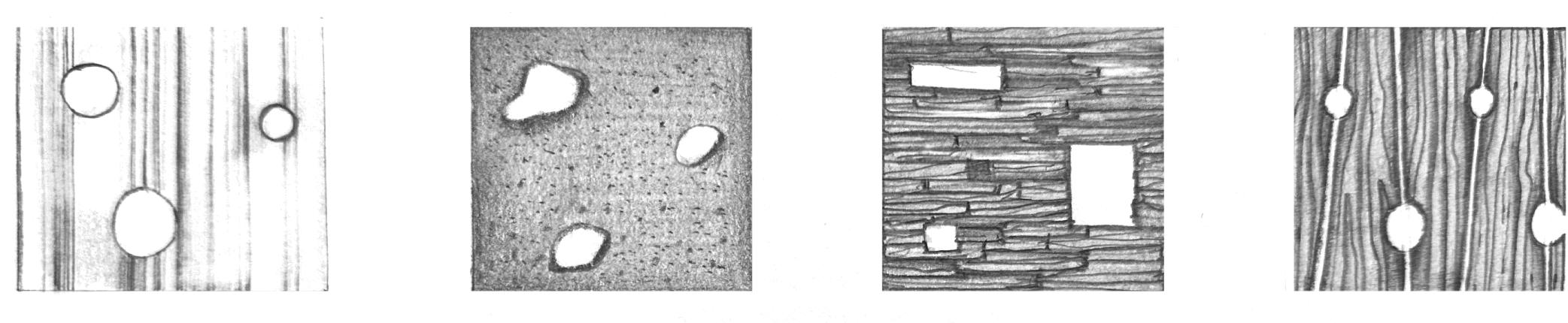
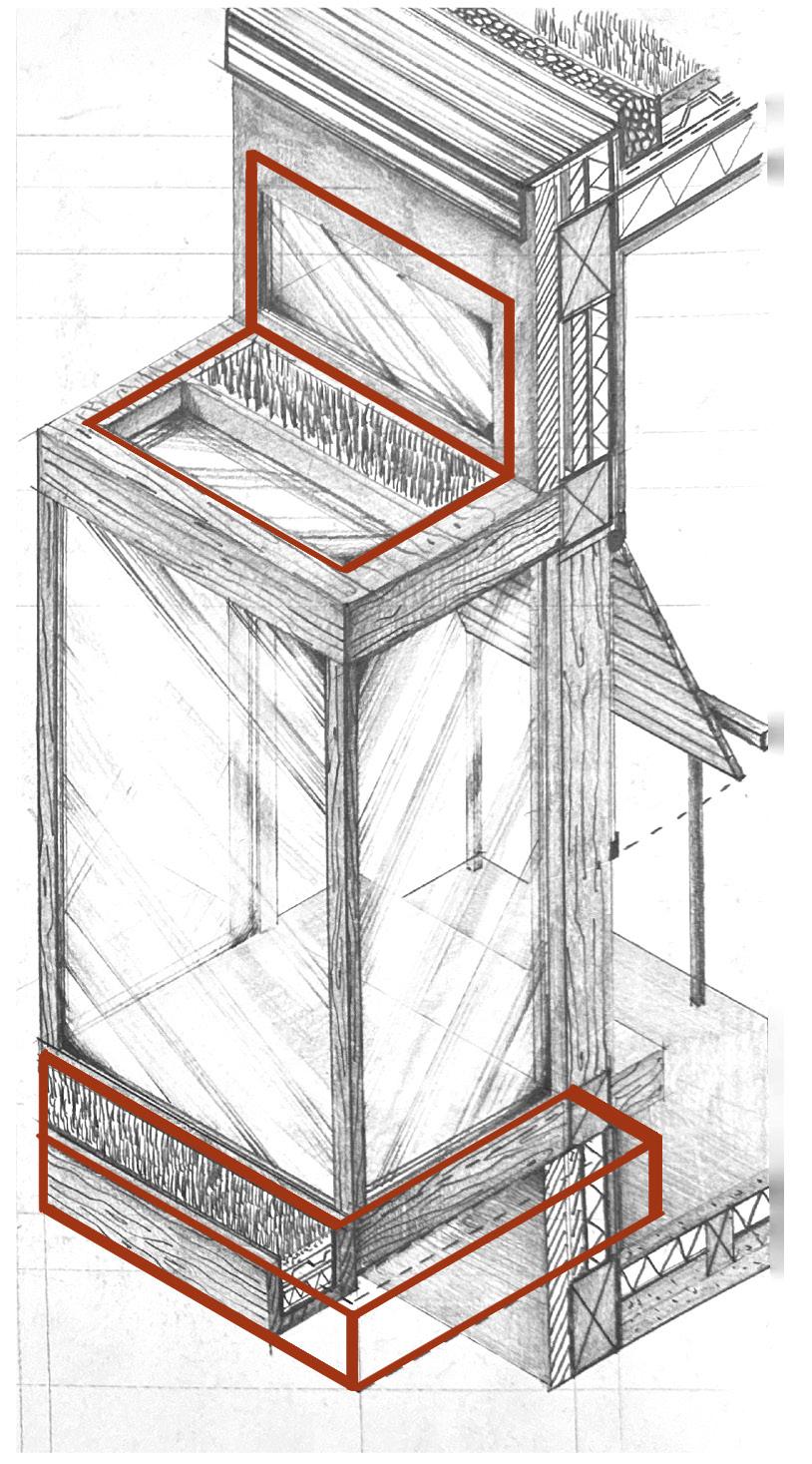
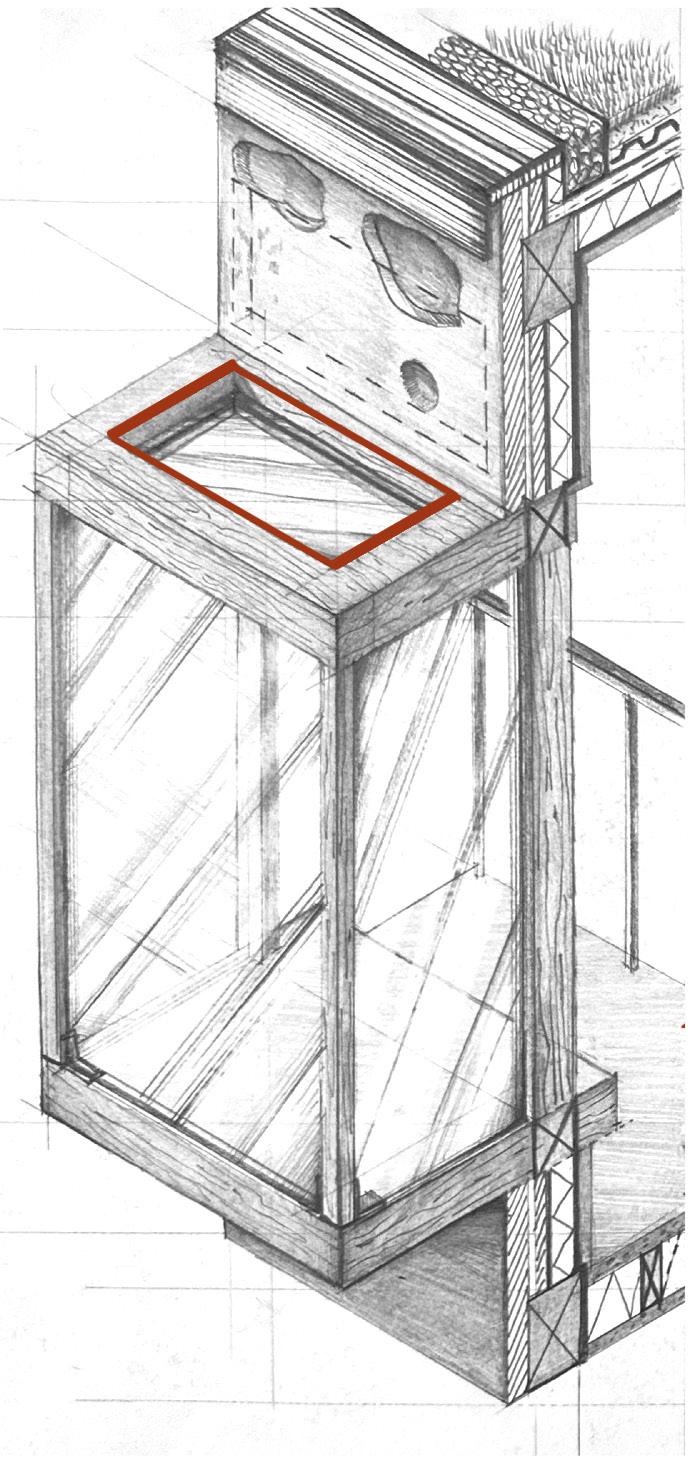
Changes: the wood structure was eliminated and replaced with silicon connections, for the expirience to not be disturbed. By adding a sill with vegetation, the view from the interior is continuous, in ambience with the facade, the windows are a tinted and reflective, for the birds to not be scared by the people sitting in the space. By inclining the window, water is no longer accumulated.
2000mm

After testing the timber structure with a physical model, the results determined that the timber is not strong enough to maintain the structure stability of the window, thus steel will be implemented in this part of the structure.
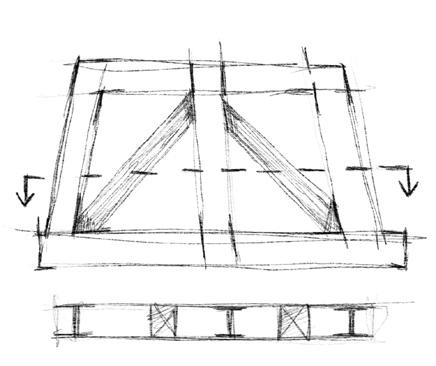
Test 2: Light analysis and analysis of atmosphere
As the window is the only source of light during the day, testing was crucial to determine the final atmosphere wanted.
The void is dark, with a oppressive feeling that is brought by the sun path.
The experience is changed by the sun, that is interacting with the facade and interior.
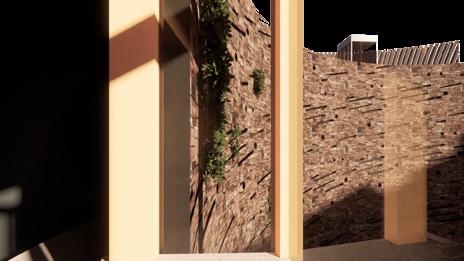
Test 3: Material impact on atmosphere and facade assembly systems
The different textures of the exterior had a direct impact on the ecosystem of the facade. As birds are supposed to be curious of the pattern of the facade, where there will discover sheltered bird houses, a metal and cold facade will not suit these needs, and will disturb the natural outside feel of the design. Natural materials were the best alternative. Birds are familiar with materials like cork and wood, but cork would be an expensive and high maintenance cladding, thus, plywood panels were implemented on the facade.
The panels are fixed to the wall with ‘L’ shaped steel lintels, where the bird houses, plants and the irrigation systems are fixed. The panels are cut at the margins to be fixed to the steel connectors on the lintels.
900mm
700mm
The experiments started with iteration A, where the light would be disrupted by the wood structure, and the space was looking like a parasite in the facade. Moving to iteration B, the light enters through 2 different windows, increasing the level of light, that forwardly would be implemented and developed in the other iterations. By still maintaining the exposed columns, the atmosphere was not continuous. The laast iteration, (C) represented the most continuous way of experiencing the space, without disruptions and where light could have its own uninterupted path. As the void needed a second source of natural light, 2 small windows were added in the opposite part, where the sun of the morning could enter the space.
Test 4: Structural changes to the pop-out window
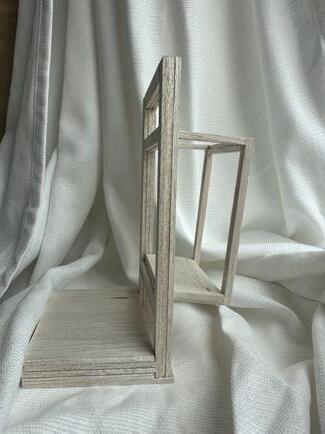
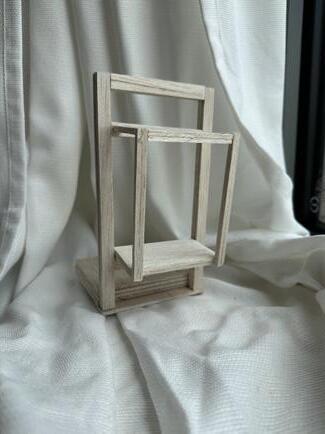

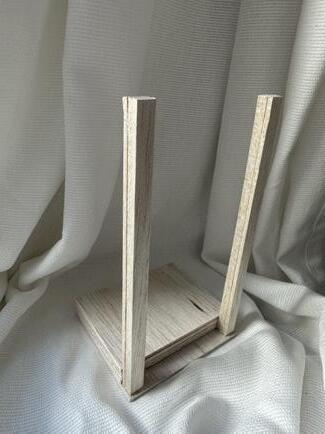
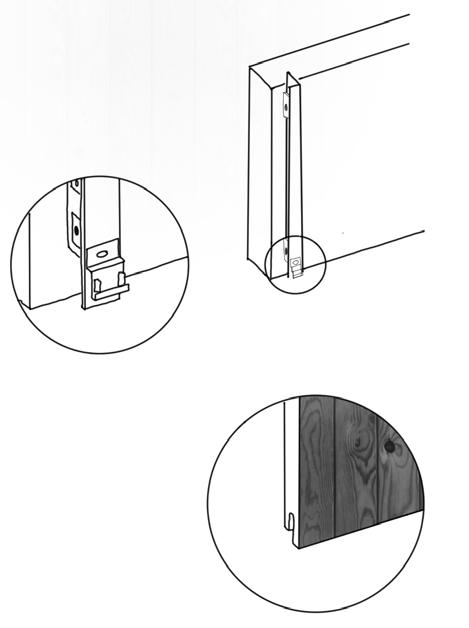
As the exterior span of the window is 500mm and the sill is 300mm, the timber structure will no support the loads of the window, wind, vegetation of the sill and a person sitting in the space. Thus, the structure was adapted to a hybrid timber and steel one.
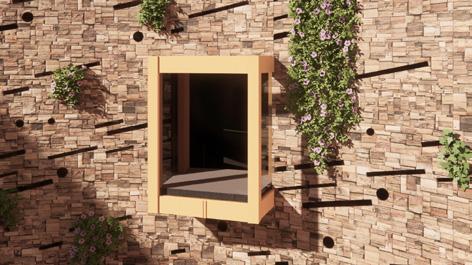
The columns of the walls are still made out of timber, while the structure of the window was replaced by steel ‘I’ columns and beams. The grid of the woodfloor slab is a hybrid, and the main steel beams are connecting to the timber columns as well.
Test 5: Building & Life safety- ventilation and fire safety
The space had flaws in terms of fire safety routes and access points, as well as natural ventilation. The materials are fire resistant, and the timber structure is fire treated, in order to maintain a safe environment in case of emergencies. The ballustrade of the building has a hight of 1100mm in relation to Building regulations. Moreover, the building doesn’t present high risk areas from which a fire can start. The walls of the plant room are made out of concrete, to eliminate any risk of fire spreading from short circuits. Staircase change
Previously, the void was accesed on the first floor by a spiral staircase.
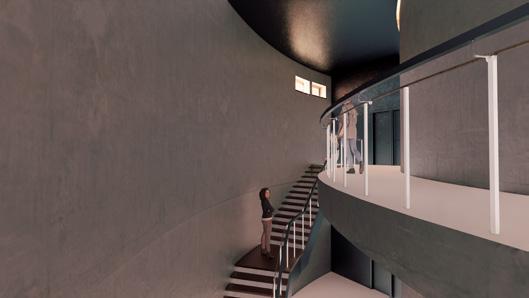
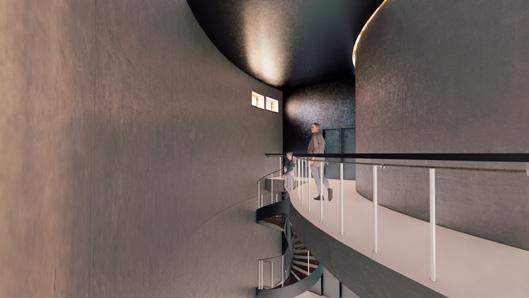
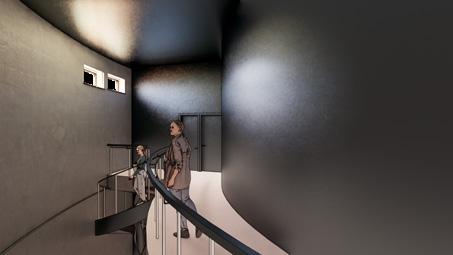
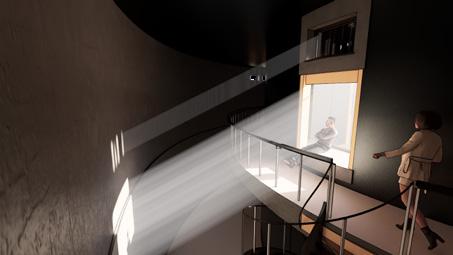
The form of the stairs was not accesible for everyone, as it did not had a landing. Moreover it was not in accordance with building regulations for fire.
The staircase was changed to one that has two landings, one after 8 stairs and the other after 10. It was moved to the oposite part of the void, in order to have 2 different ways of evacuation in two directions.
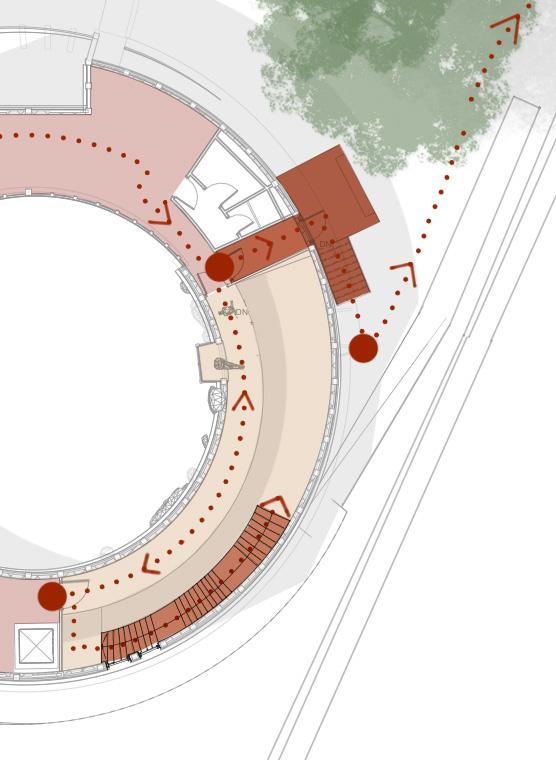
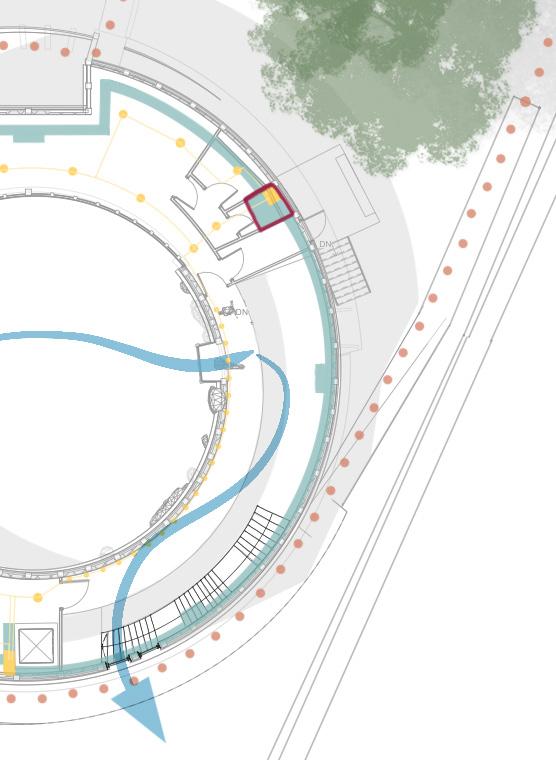
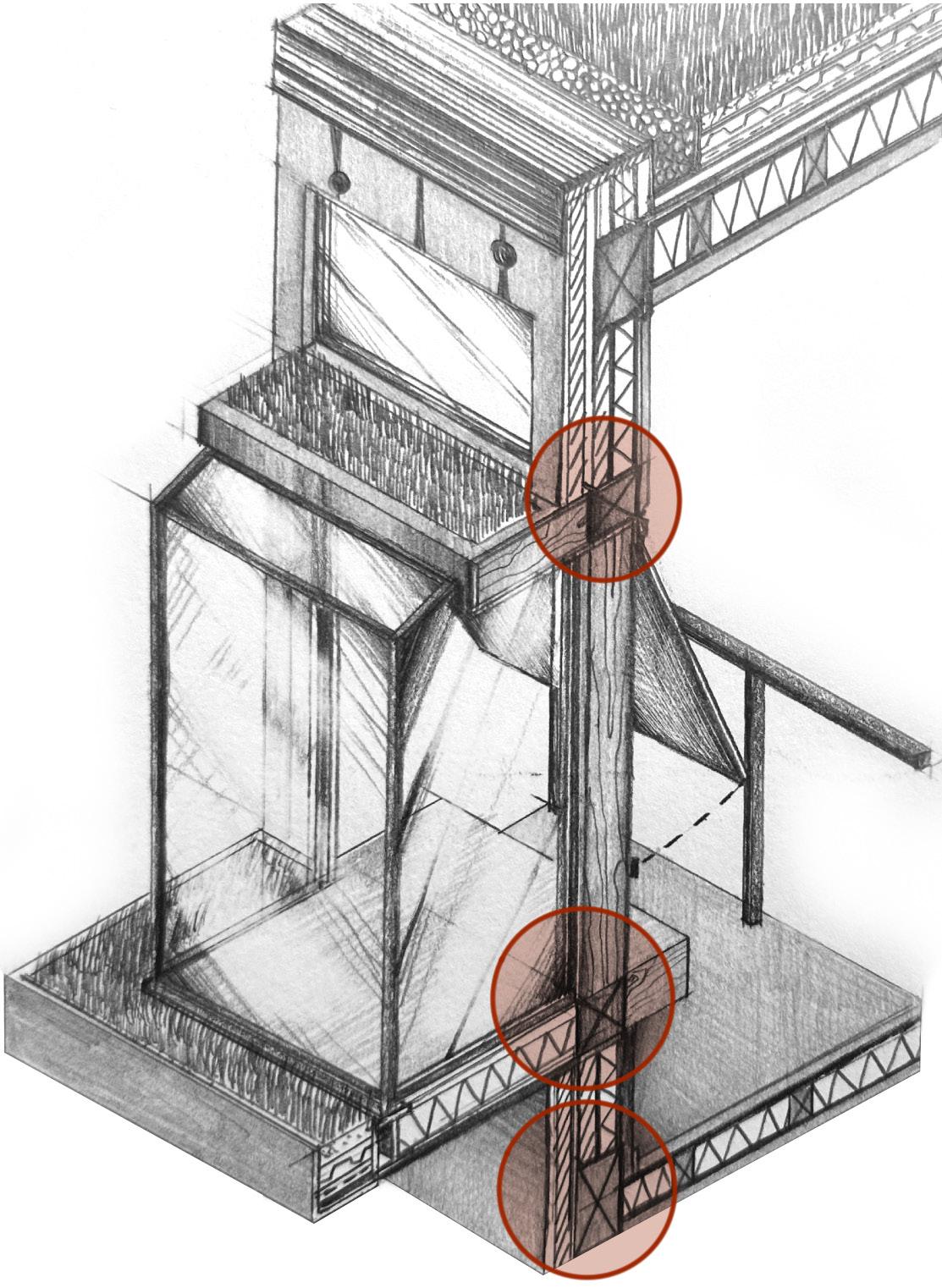
Test 6: Thermal bridge analysis of the void

Ventilation Updated fire escape routes
Before, the void did not have any natural ventilation, the natural air could enter the space only from the opening above the pop-out window.
Thus, by implementing another set of 2 windows in the oposite part of the void, air is crossing the entire space, naturally ventilating it and providing fresh air to the visitors.
By analysing the wall structure using rockwool.com, an exact U-value calculation was made for the exterior walls. With an increase of 80mm in the thickness of the thermal insulation and reducing the sound insulation by 20mm, the U-value decresed from 0.30 W/m2K to 0.18 W/m2k, being below the limit of the Part L Building Regulations of 0.26 W/m2K.
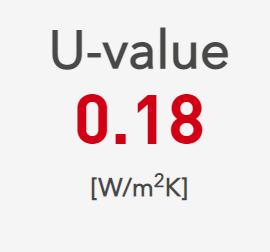
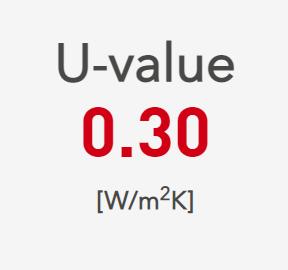
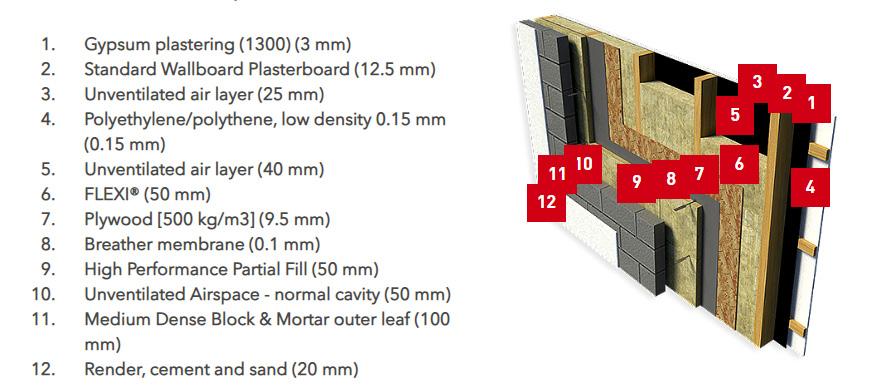
By testing the thermal bridge of the space, gaps where the air could get in were observed. The building is tight, and its thermal bridge is not affected by any exterior weather conditions.

The tests in HTFlux show that the building is not loosing the interior heat. The most interesting aspect of the analysis was the temperature distribution along the materials, and how the heat travels in the walls.
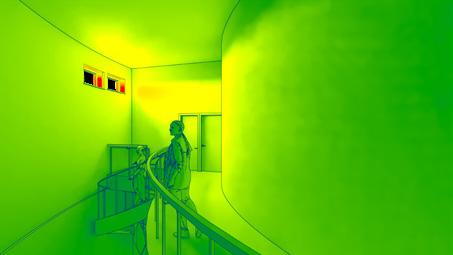

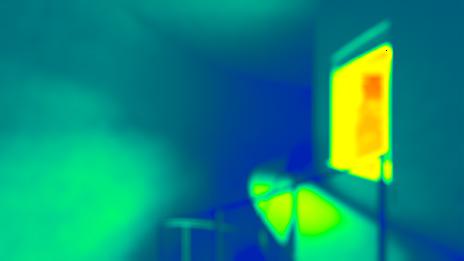
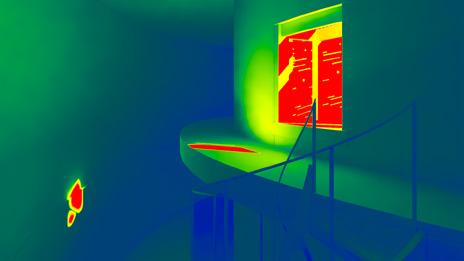
Also, by adding the living wall between the two envelopes of the facade, the thermal anaysis will increase in value.
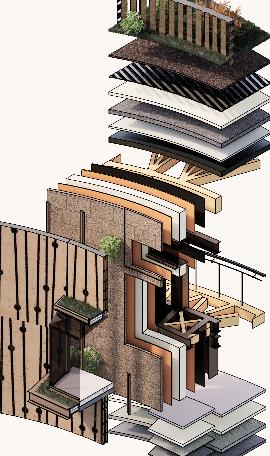
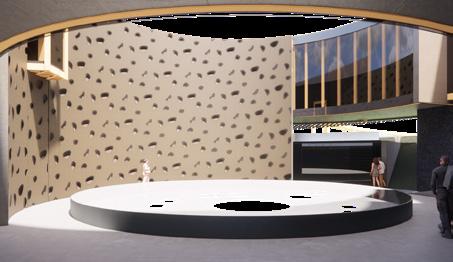
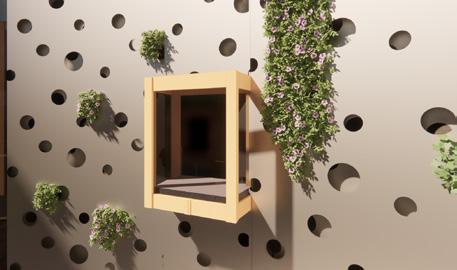
A. Detail section using HTFlux with the thermal bridge, and exterior temperature (blue) between -10 and 0 degrees, and interior temperature set at 20 degrees (red)
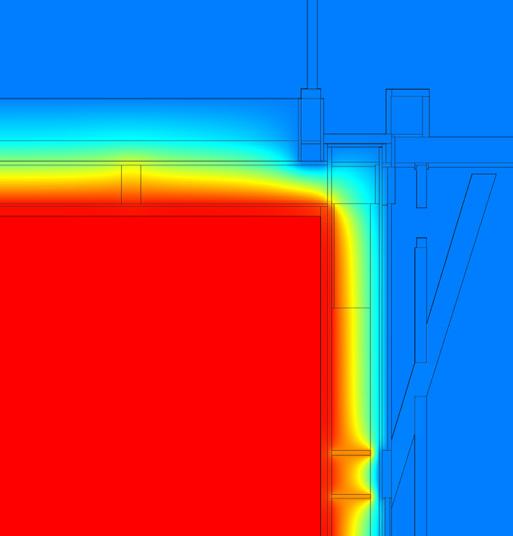
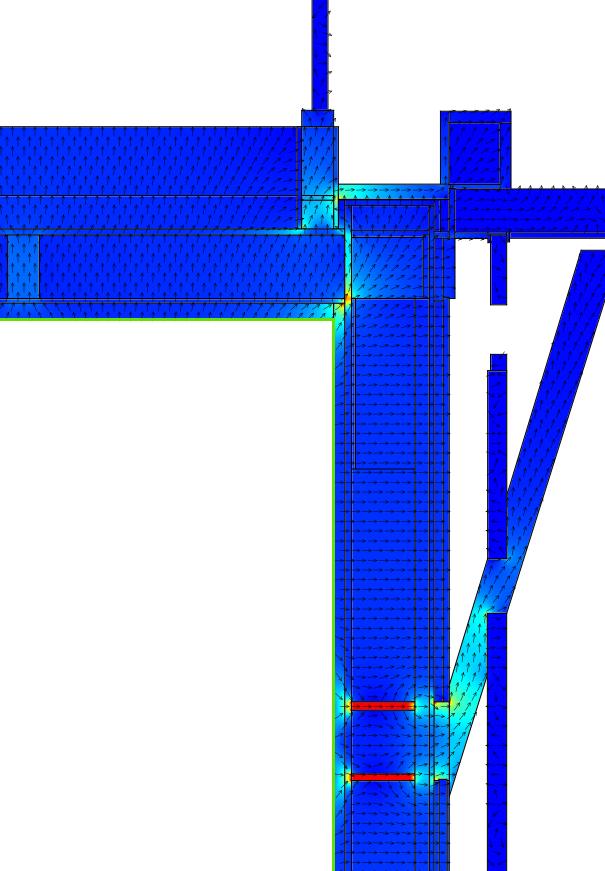
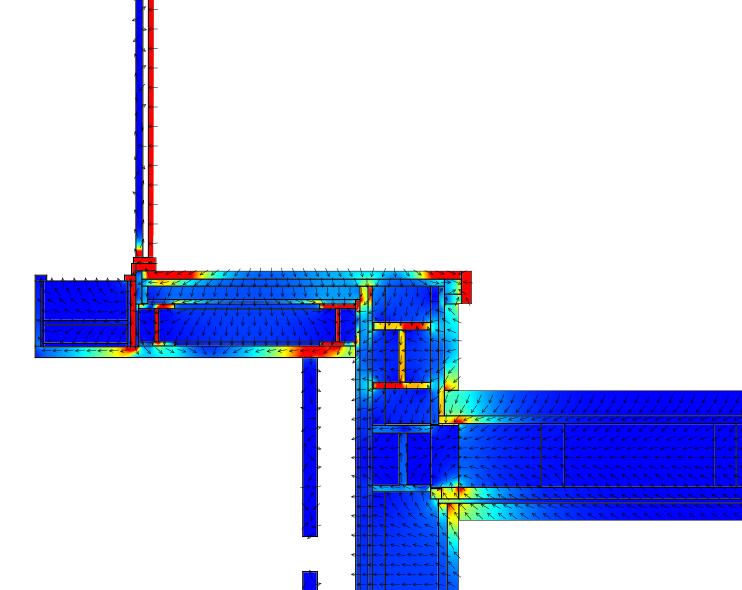
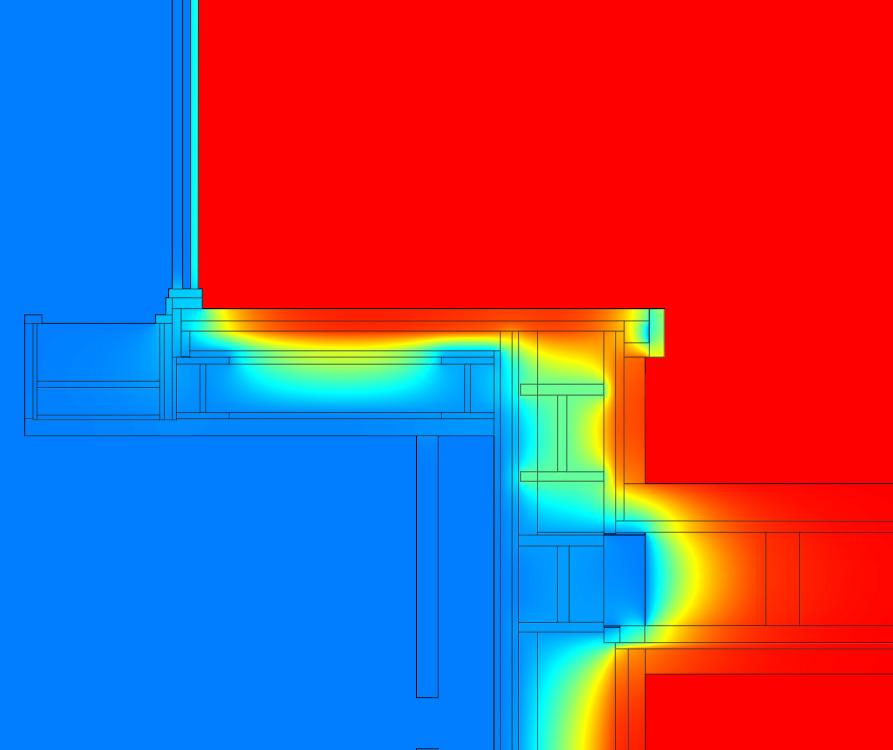
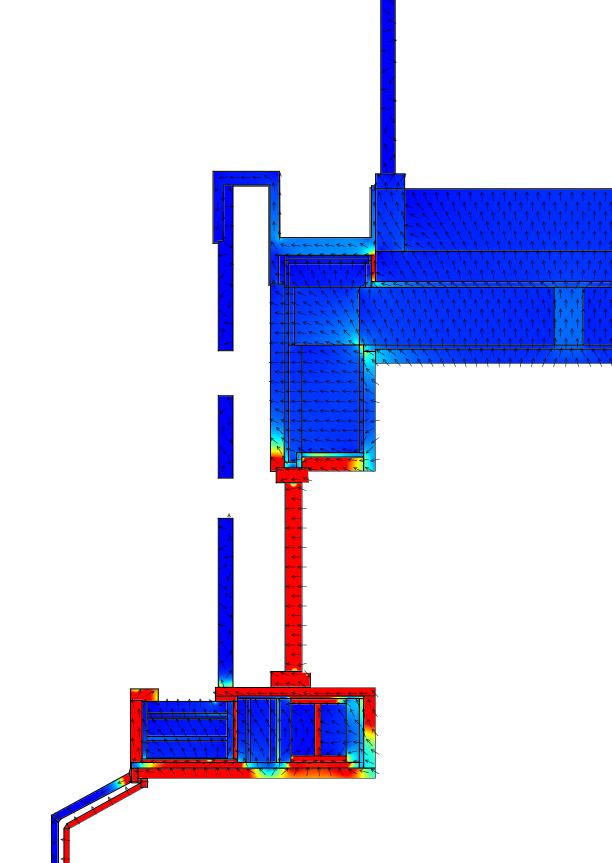

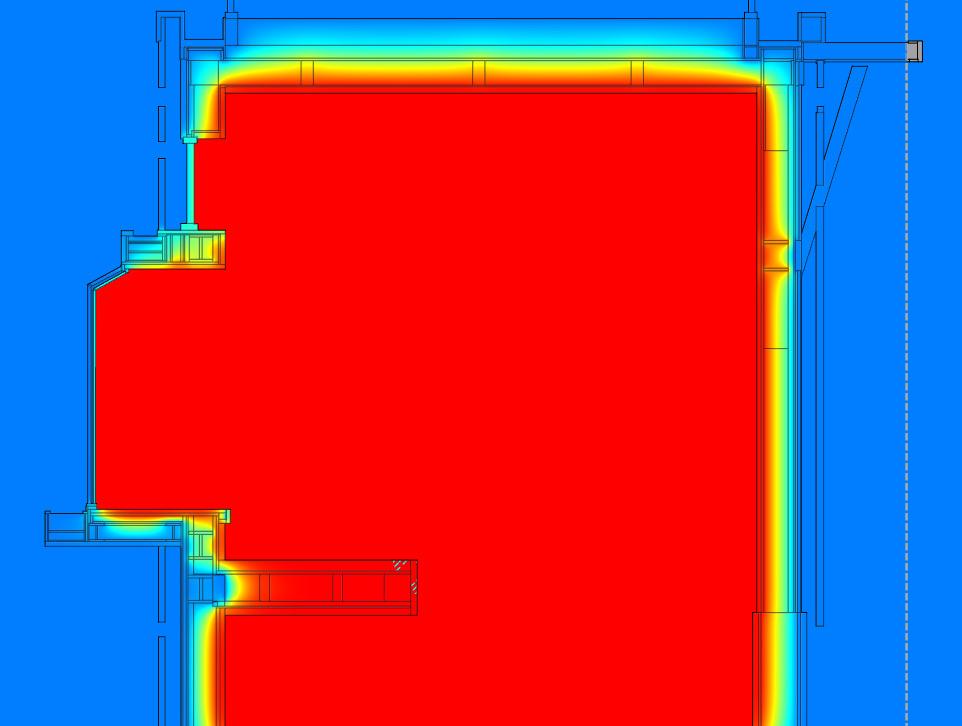
B. Material distribution in HTFlux
C. Heat transmition through envelope materials in the connection with the roof
D. Heat transmition through envelope materials in the connection with the floor slab
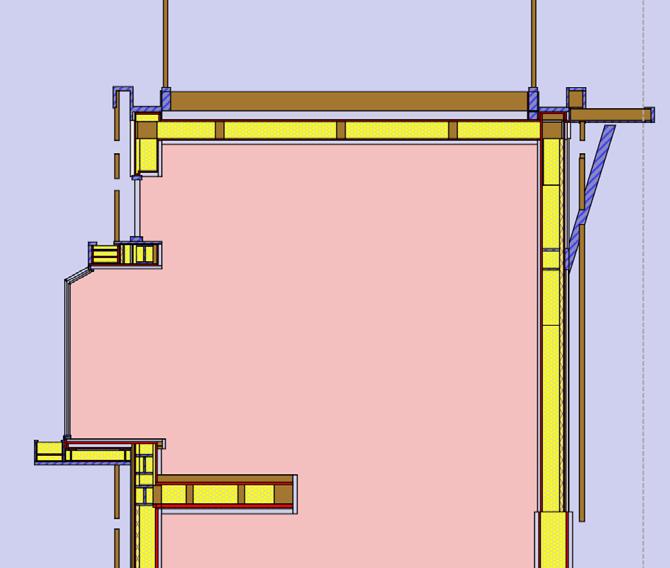
E. Heat transmition through envelope materials in the connection with the spiral ramp
F. Heat flux through the connections of materials www.rockwool.com/uk/u-value-calculator
Design conclusions
Challenges: the structure of the pop-out window represented the main aspect that had to be changed in order to achive structural stability.
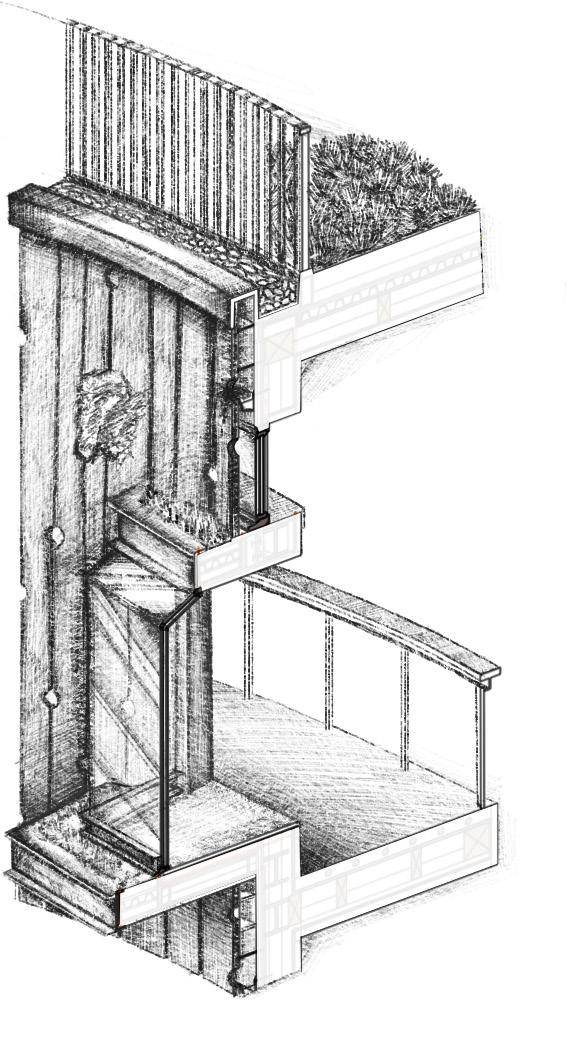
The facade system is simple and created from perforated panels, so the circularity of the design is not afecting the production of the facade system.
The structure needs to be prefabricated in order to achive the circular angles, so this aspect may increase its carbon operational processes, as the factories will need to create custom components for the assembly of the building.
Reflections: Circular buildings are hard to be designed, in terms of spatial arrangement and structure, a lot of spaces need to be thought through and the structure needs to be prefabricated. Thus, this kind of buildings may have a higher level of embodied carbon.
By using natural materials and a hybrid timber and steel structure, the carbon emissions are minimised in term of materials. Concrete is a good conductor for heat, and the use of this material brings high quality termal conductivity, passively heating the building in winter. It is as well a very durable material, low maintanence and good sound insulator.
RIBA Sustainable Outcomes
Net Zero Embodied Carbon
-The concrete used in the building is formed out of the sandstone extracted from the escavated soil. The sandstone is mixed with cement on site, offering a lower embodied carbon by the use of materials from the site’s soil
-The materials are all sourced from the UK, and the brick in the underground is recycled from many demolished warehouses along Mayfield.
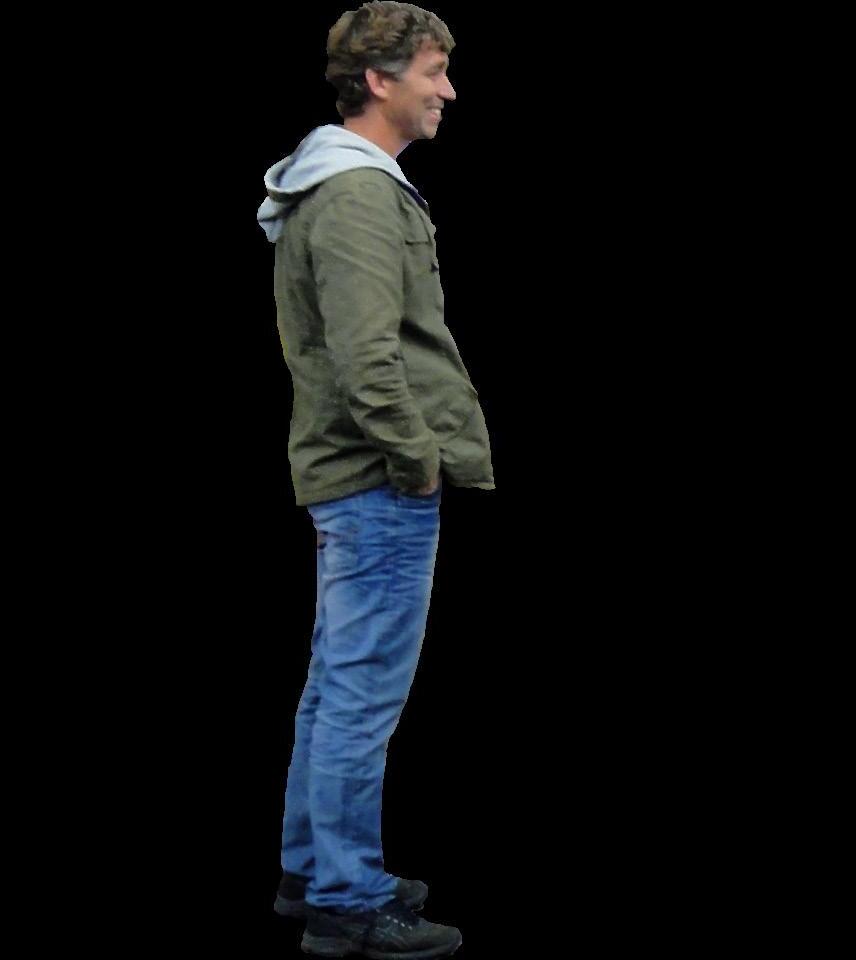
-The building presents smart electrical systems and passive strategies for heating and cooling
Sustainable Land Use & Ecology
-The entire facade of the building is a living eco-system, where birds and various types of vegetation are sheltered, contributing to one of the aims of the project: interracting with the nature of Mayfield creating a habitat that enhances bio-diversity
-The existing trees were all maintainted on site and a range of green spaces were created on the roof and courtyard
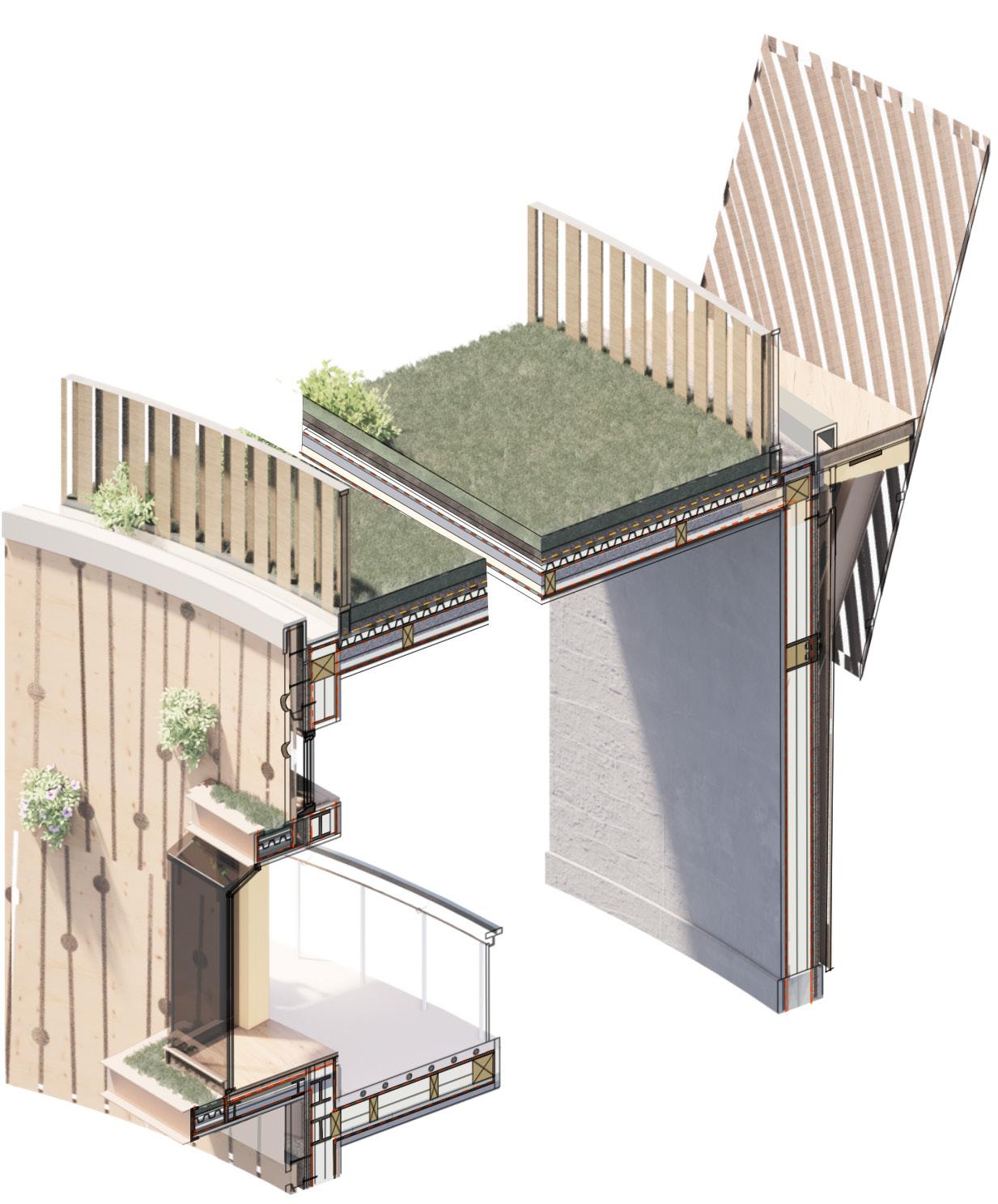
Good Health & Wellbeing
-The entire design is based on the connection with nature and the outside, natural air gets into the building and naturally ventilates the interior

1. Steel Lintel 25mm
2. Gravel 180mm
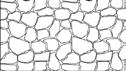
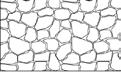
3. Plywood perforated panel 40mm
mm thick
34. Wood flooring 22mm
35. Silicone adhesive 5mm
36. Concrete screed 30mm
37. Vapour barrier 10mm
38. I Steel beam 140mm
39. Wood margin 22mm
40. Steel connector 15mm
41. Air gap 12mm
42. Sheep wool insulation 80mm
43. Sound insulation 50mm
44. Damp proof membrane 12mm
45. Wood exterior finishing 30mm
46. Vegetation plastic pot 6mm
47. Concrete screed 80mm
48. Service cables void 40mm diametre
49. Aluminium ballustrade rail 50x20mm
50. Aluminium ballustrade batten 30x30mm
Primary prefabricated timber beam 260x260mm 52. Prefabricated steel connecting system for exterior wood spiral 45mm 53. Wood exterior flooring 120mm 54. Prefabricated steel connecting system for exterior spiral system 50mm 55. Circular steel beam connector 70mm 56. I steel column support for exterior spiral 57. Timber joist facade system 100x100 mm
58. Timber joist connector 130x130mm
59. Steel circular beam prefabricated connection for exterior spiral 300x300mm 60. Steel beams connectors 75x75mm