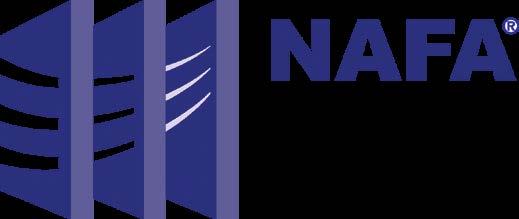
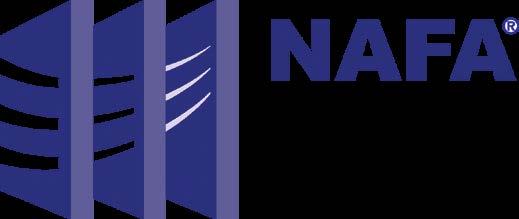
AIRMEDIA
nafahq.org ■ The Global Source for Expertise, Education and Best Practices in Air Filtration.
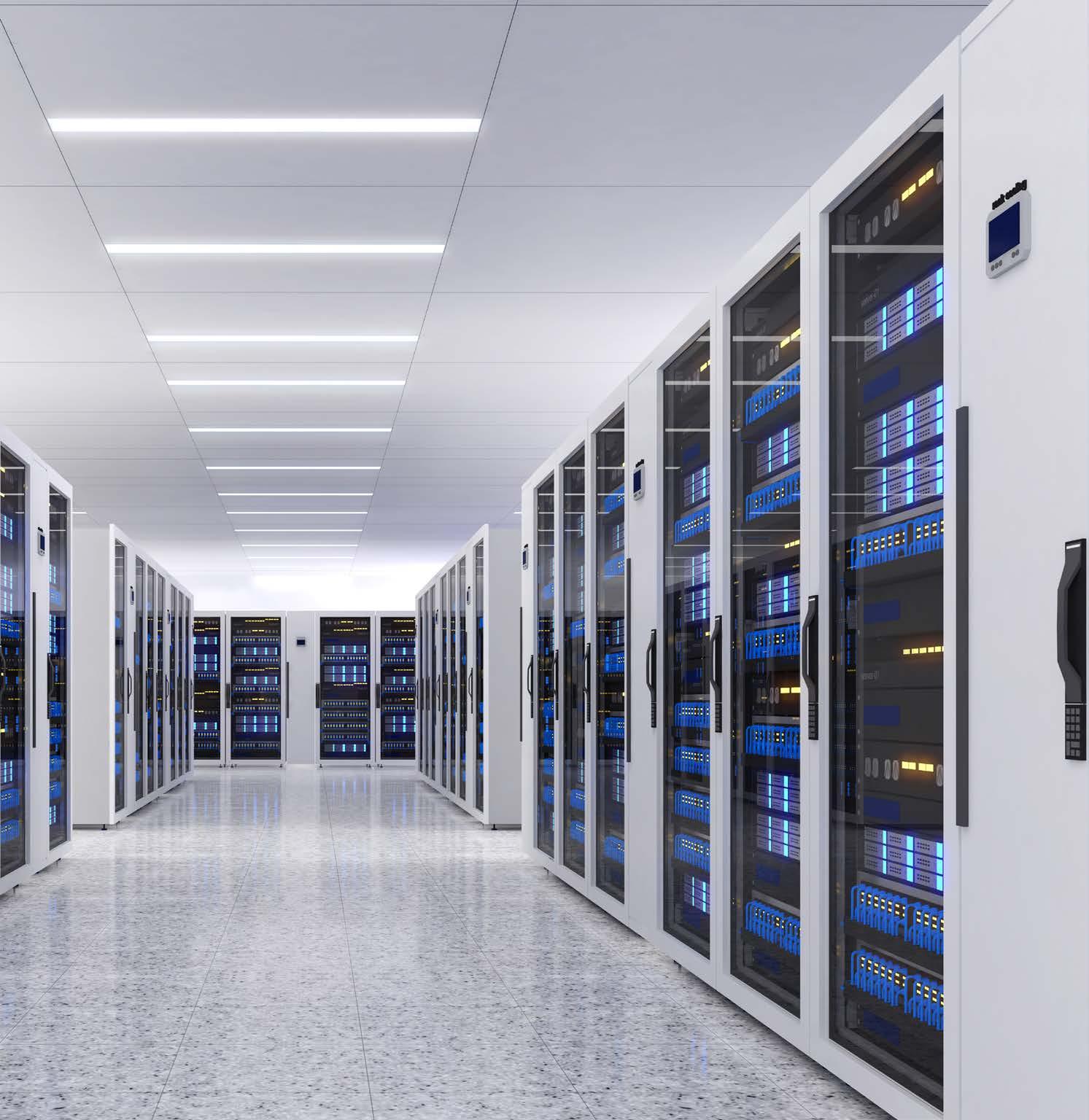
MITIGATING CORROSION-INDUCED HARDWARE FAILURES IN DATA CENTERS using
Air Filtration Technology
The Gears of Grategy®
Innovating Air Filtration Workplace Culture
How do I Best Filter My Recycled Dust Collector Exhaust?
A Glimpse into the Standard Setting Process of the New NFPA 660 Consolidated Standard for Combustible Dusts
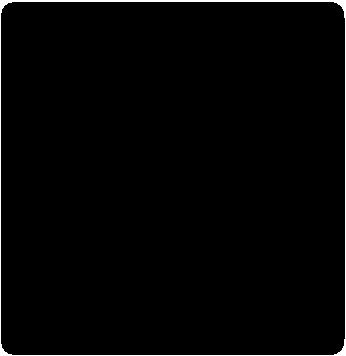
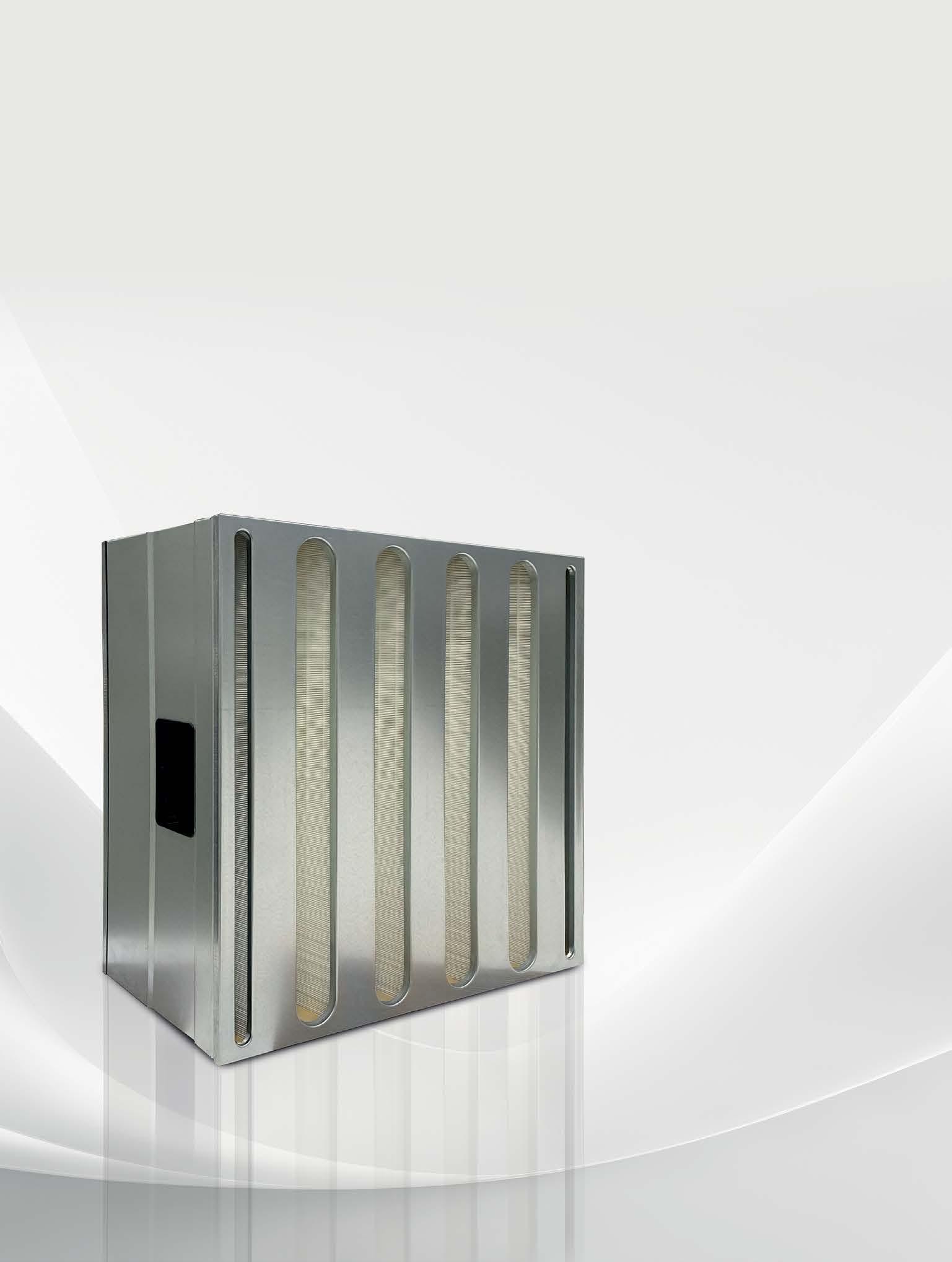


AIRMEDIA
PUBLISHER
National Air Filtration Association
EDITOR
Emily Bardach, CAE
NAFA Executive Director
CONTENT EDITOR
Terry Driscoll
NAFA Association Manager
PUBLISHER’S NOTE
Air Media magazine is published three times per year by the National Air Filtration Association. Annual dues are $520 for Distributor Membership and $945 for Manufacturer Membership; dues include a paid subscription to Air Media
Air Media provides a forum for the free exchange of opinions and information. The views expressed herein do not necessarily represent those of NAFA, its officers, directors, membership or staff. Your contributions help make this magazine an interesting and informative forum for exchanging ideas and recognizing the advancements in our industry.
Neither NAFA nor Air Media is responsible for claims made in advertisements.
Editorial and advertising closing dates are the first of the month prior to issue. Front Cover: Getty Images
1818 Parmenter St, Ste 300 Middleton, WI 53562
Phone: 608-310-7542
Email: nafa@nafahq.org
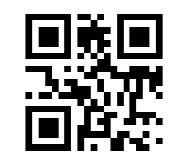
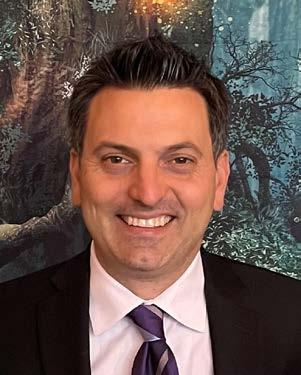
PRESIDENT’S MESSAGE
PATRICK ROSENTHAL, CAFS, NCT
NAFA President
DEAR FELLOW NAFA MEMBERS,
As NAFA's President for 2024, I am excited to collaborate with our members and sponsors to advance our sector, foster collaboration, and drive innovation.
Our recent 2024 NAFA Technical Conference in Dallas saw all time record attendance, with an outstanding turnout of 281 air filtration professionals.
Additionally we have not only met, but exceeded our 2024 sponsorship goal! This achievement is particularly significant as it marks the successful launch of our new sponsorship program. Moving away from traditional à la carte sponsorships, our transition to annual sponsorship packages - Platinum, Gold, Silver, and Bronze - not only establishes a more sustainable financial structure for NAFA but also provides our sponsors with maximum value for their investment.
Moreover, we are delighted to share the release of the muchanticipated 2024 5th edition of the "Installation, Operation, and Maintenance (IOM) of Air Filtration Systems" guide. This invaluable resource not only showcases our industry expertise but also underscores our commitment to the NAFA Certified Technician (NCT) program.
But our journey does not stop there. Looking ahead, we are excited to announce that the NAFA Foundation board is launching a Request for Proposals (RFP) to identify our next association research project. This initiative underscores our unwavering commitment to advancing the field of air filtration through cutting-edge research and innovation.
Additionally, we are pleased to share that we will be launching a stream of new podcasts this spring, offering our members yet another avenue for staying informed and connected with the latest industry trends, insights, and best practices.
As we celebrate these achievements and look ahead to the opportunities that lie on the horizon, we are filled with gratitude for each and every one of you who contributes to the success of our association. Together, we have achieved remarkable milestones, but our journey is far from over. With your continued support and collaboration, we are confident that we will continue to push the boundaries of what is possible, shaping the future of our industry for generations to come.
Sincerely,
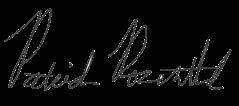
Patrick Rosenthal, CAFS, NCT
2024 BOARD OF DIRECTORS
President
Patrick Rosenthal, CAFS, NCT
TEX-AIR Filters
Austin, Texas www.texairfilters.com
President-Elect
Matt Solis, CAFS
Rensa Filtration Moline, Illinois www.smithfilter.com
Treasurer
Steve Griffiths, CAFS
Independent Filter Service P/L Heidelberg West, Victoria Australia www.independentfilter.com.au
Secretary
Randy Brannen, CAFS, NCT II
Kleen-Air Filters Groesbeck, Texas www.kleenairfilters.com
Immediate Past President
Michael Corbat, CAFS
Rensa Filtration Aurora, Illinois www.rensafiltration.com
Directors
Branden Deilgat, CAFS, NCT
American Metal Filter Company Nashville, Tennessee www.amfco.com
Will Denton, CAFS, NCT II
Joe W. Fly Co., Inc. Dallas, Texas www.joeflyco.com
Keith Jordan, CAFS, NCT
Colorado Air Filter LLC Denver, Colorado coloradoairfilter.com
Dave Miller
Complete Filter Media Lancaster, Ohio www.cfm.global
Sharon Needham, CAFS, NCT
BGE Indoor Air Quality Solutions Calgary, Alberta Canada www.bgecleanair.com
Bobby Singer, CAFS
Blue Heaven Technologies Louisville, Kentucky www.blueheaventech.com
Timmy Timbs, CAFS
Wallner Expac Olive Branch, Mississippi www.expac.com
WELCOME TO NAFA
Distributor
3T Corp Clean Air Div
Scott Otto Evansville, Indiana
ATL Filtration (Abatement Technologies)
Greg Parlee, CAFS Fort Erie, Ontario Canada
Filtration Technology Inc.
Scott Matthews Greensboro, North Carolina
Florite Filters
Mindy McKee Pocatello, Idaho
FreshAir LLC
James Vanoy Hurricane, West Virginia
Kleen-Air Filters
Randy Brannen, CAFS, NCT II Groesbeck, Texas
Ohio Industrial Filter Products
Mitch Carr Newark, Ohio
OTC Industrial Technologies
Kate Brown Gallatin, Tennessee
Tech Valley Filtration, LLC
Justin Fiederlein Wilmington, Delaware
Manufacturer
Auhlyours
Brandon Elston Lancaster, Texas
ECOAIR Air Conditioning Manufacturing L.L.C
Nitin Sebastian Umm Al Quawain United Arab Emirates
GuangZhou CleanLink Filtration Technology Co.,Ltd
Jing Zhou Guangzhou, Guangdong China
MGT Filtre Sanayi Ve Ticaret Anonim Sirketi
Onur Tongut İstanbul Turkey
Nanomeld, Inc
Ashley Scott Clover, South Carolina
Reviveaire LLC
Nick Agopian Kenilworth, New Jersey
The Filter Factory, Inc.
L. Robert Baker Lompoc, California
Ulpatek Air Filters
Ferhat Gurer İstanbul Turkey
WPT Nonwovens Corp.
Travis Robbins Beaver Dam, Kentucky
ZFT Group
Andrew Sharp Warwick, Warwickshire UK
Professional Individual
John Chavez
hvacMENSCH Austin, Texas
Robert Williams, CAFS
Far East Connection LLC Chester Springs, Pennsylvania
Lifetime Individual
Julie Engelstad, CAFS
Louisville, Kentucky
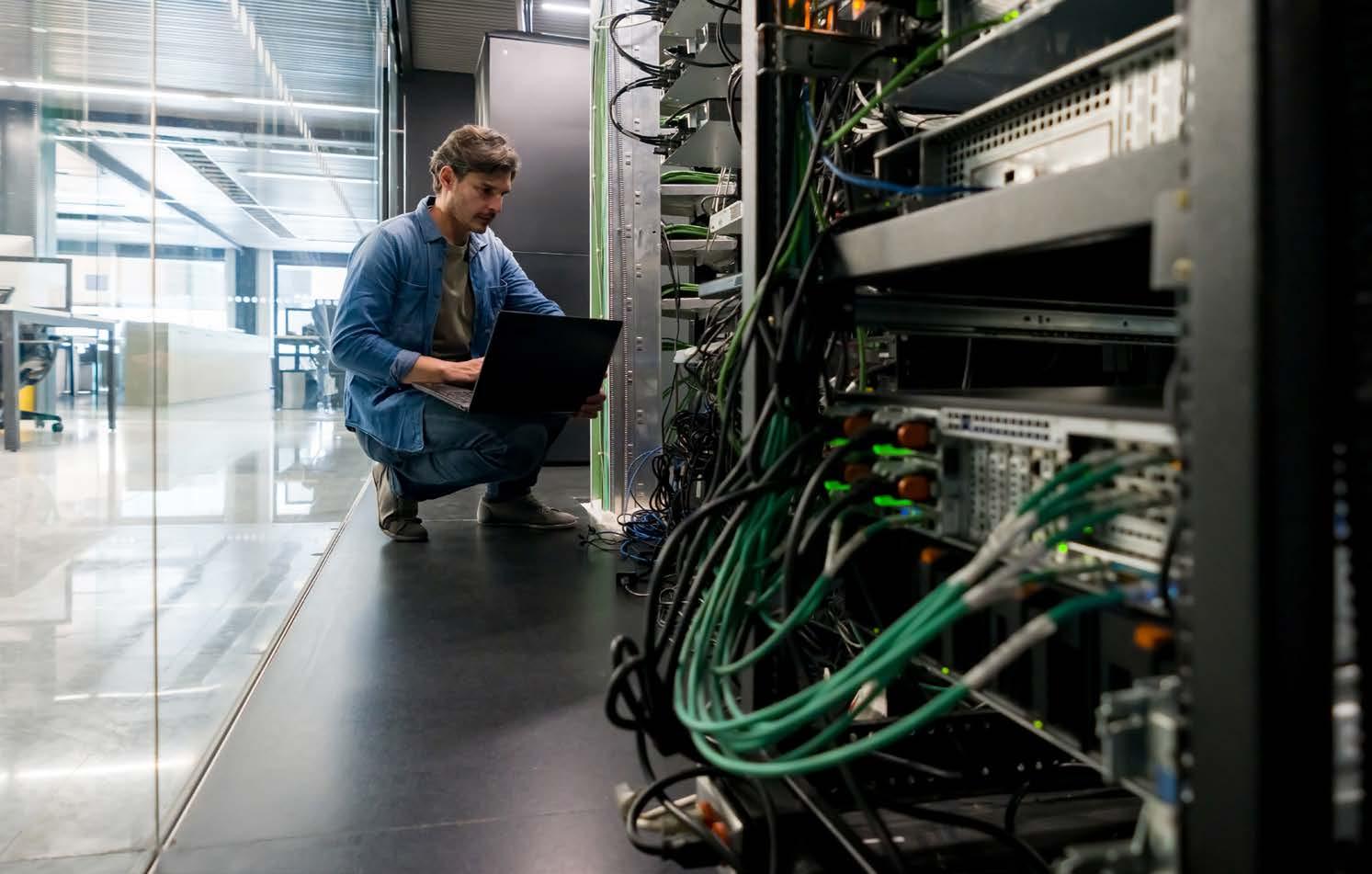
MITIGATING CORROSION-INDUCED HARDWARE
FAILURES
IN DATA
CENTERS
using Air Filtration Technology Retaining Top Talent in Air Filtration

M.S.GIRI NANDAGOPAL
PhD, Product Development Engineer, Excelair Filters, Century Mechanical Systems Factory LLC
DATA AND ENERGY
In the realm of web and social media, as well as cryptocurrency mining and online commerce, there is a growing need for data centers to store the vast amount of data supporting these online activities. Data centers operate continuously, 24 hours a day, 7 days a week, 365 days a year. The average person at rest is estimated to emit 400 to 450 Btu/hour, while a single rack of IT equipment can generate between 17,060 Btu/hour (5 kW) and 102,360 Btu/ hour (30 kW). This, in turn, contributes to the overall increase in electricity consumption. Projections indicate a 12% annual growth in electricity usage in data centers.1
A significant portion of the energy used in data centers is attributed to the compressor-based cooling. With the rising cost of electric power and a focus on reducing operational expenses, there is a growing trend among data center designers to
employ direct outside air for cooling IT equipment. This approach is increasingly seen as a viable alternative to traditional chilled-water cooling, particularly in various environments. Some studies propose that utilizing outside air for cooling can result in energy savings ranging from 20 to 30% compared to a closed data center that relies less on outside air.2
CORROSION IN DATA CENTERS
The growing adoption of outside air for data center cooling raises concerns about potential damage to metallic components. Issues such as copper creep corrosion or silver termination corrosion on circuit boards, caused by gaseous pollutants, are known risks. The 2009 ASHRAE particulate and gaseous contamination white paper recommended that copper and silver corrosion rates should be less than 300 Å/month to minimize the impact of corrosion on IT equipment reliability.3
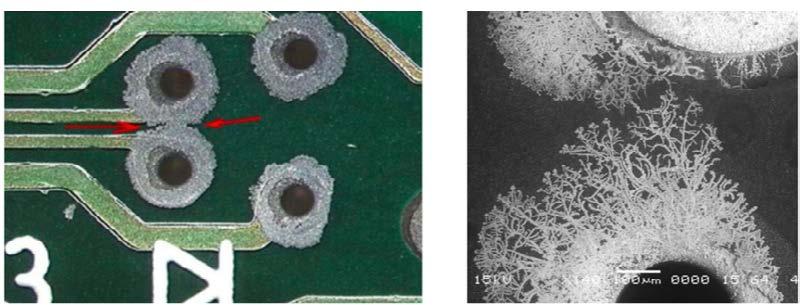
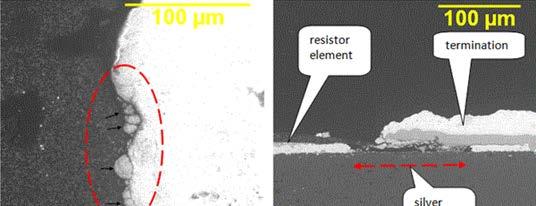
AIR HANDLING IN DATA CENTER
FIGURE 1: A visual representation illustrating,
a) Copper Creep Corrosion- Photographic and electron microscopic images depicting the degradation of copper plating on printed circuit boards as it transforms into copper sulfide. This progression extends across the boards, resulting in electrical shorts between nearby features and ultimately culminating in system failures.4,6
b) Silver Termination Corrosion- Electron microscopic depicting the silver terminations in surface-mounted components resulting in the degradation of silver metallization and the eventual occurrence of open circuits in components such as resistors.5,6
Data centers utilize air filtration systems that differ from conventional setups. They incorporate specialized units like the Computer Room Air Conditioner (CRAC) / Computer Room Air Handler (CRAH), housing filters along with fans, and cooling coils to ensure consistent room filtering. They are specifically designed to cool and regulate the temperature and humidity in the data center. Additionally, a standard Air Handling Unit manages incoming air from outside. Figure 2 illustrates the air handling system within a data center.
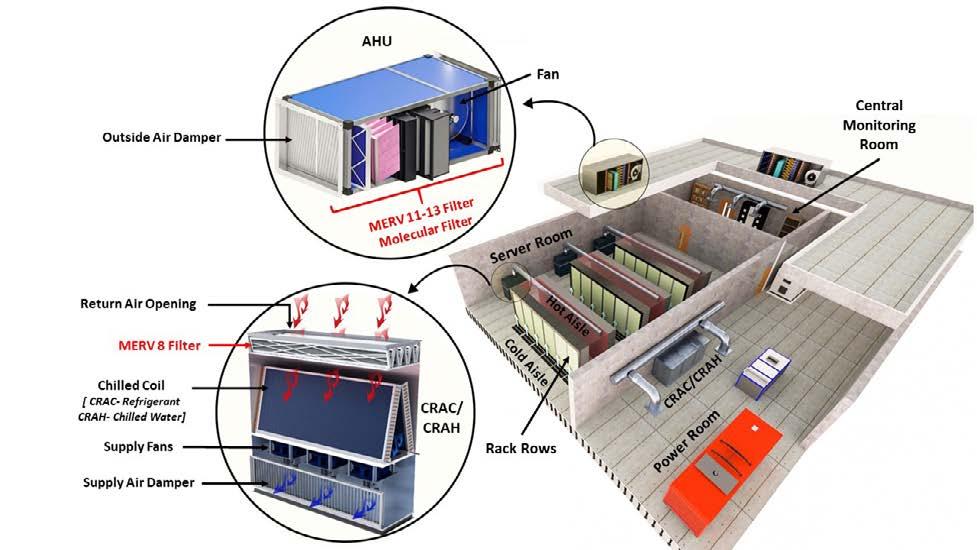
a)
b)
FIGURE 2: Illustration depicting the air handling system within a data center
MITIGATION OF PARTICULATE CONTAMINATION
Effective particulate contamination control can be achieved with commonly available filters. ASHRAE recommends continuous room air filtering using MERV 8 filters, and suggests higher filtration levels like MERV 11 or MERV 13 for incoming air. Due to the energy-intensive nature of data centers, filters with low pressure drop and high dust holding capacity are preferred. Recently, Nanofiber filters, featuring thin layers on supportive substrates, have gained attention for their surface loading, which allows for effective dust accumulation. While in contrast, traditional filters experience depth loading over time, leading to blockages and increased pressure drops.3
MITIGATION OF GASEOUS CONTAMINATION
To manage gaseous contamination, specialized filters called molecular filters are used. In data centers situated in areas with high gaseous contamination, it is recommended to deploy molecular filtration systems for both incoming and internal air. Table 1 outlines gaseous elements present in the environment, highlighting potential threats to data center components if they exceed specified control limits.
GASEOUS COMPONENTS
Active Sulfur Compounds: Hydrogen sulfide (H 2 S), Elemental sulfur (S), Mercaptans (R-SH).
Sulfur Oxides (SO 2 , SO 3)
Nitrogen Oxides (NO, NO2, N2O4)
Inorganic Chlorine Compounds (Cl 2 , ClO 2 , HCl)
Ammonia and Derivatives
(NH 3, NH 4 +)
Ozone (O 3)
< 3 ppb
<10 ppb
<50 ppb
<1 ppb
<500 ppb
<2 ppb
COMPONENTS
Low ppb levels can rapidly attack copper, silver, aluminum, and iron alloys.
Reaction with metals normally occurs when these gases dissolve in water to form sulfurous and sulfuric acid (H2SO3 and H2SO4).
These gases are thought to exhibit a catalytic effect on the corrosion of base metals by chlorides and sulfides. Additionally, in the presence of moisture, some of these gases can form nitric acid (HNO3), which subsequently corrodes a wide range of metals.
When exposed to moisture, these gases produce chloride ions, which s ubsequently corrode a variety of alloys , including copper, tin, silver, and iron. These reactions remain notable even when the gases are present in low parts per billion (ppb) levels. In elevated concentrations, chlorinated gases oxidize numerous materials upon exposure.
Notable risk of corrosion, especially for copper and copper alloys.
Powerful oxidizing agents.
TABLE 1: Gaseous elements present in the environment and their impact on data center components when surpassing specified control limits.6
Molecular filters utilize adsorbent or chemisorbent media designed to capture gaseous contaminants. Depending on system design and contaminant characteristics, the media can be in the form of pellets, granules, or modules. Adsorbents, attracting molecules through forces like van der Waals forces, effectively capture low concentrations of non-reactive gases such as volatile organic compounds (VOCs), odors, and hydrocarbons. Activated carbon, with its extensive surface area, is a commonly used adsorbent capable of adsorbing a wide range of gases.
Chemisorbents chemically react with contaminants to form stable compounds, suitable for removing high concentrations of reactive gases like acids, bases, oxidants, and corrosives. Impregnated activated carbon, treated to enhance reactivity, is a frequently used chemisorbent in molecular filtration.7 Some molecular filtration systems optimize performance by combining adsorbents and chemisorbents. For example, a system may use an adsorbent layer followed by a chemisorbent layer to eliminate both VOCs and acids from the air stream.
Table 2 outlines various adsorbents widely used to address specific gaseous pollutants. Numerous ongoing studies are being reported aimed at developing new adsorbent materials with significant adsorption capacity.
MEDIA
Virgin Activated Carbon
Activated carbon substrate impregnated with potassium hydroxide (KOH)
Activated alumina substrate impregnated with 8% potassium permanganate (KMnO4)
50% Activated alumina substrate impregnated with 8% KMnO4 and 50% virgin activated carbon
Activated carbon cellulose filter
Micro-granulate adsorbent Particles (50 / 50 Blend of Carbon & KMno4) embedded in dual layer synthetic media
TARGET GASEOUS CONTAMINATES
Volatile organics, hydrocarbons, chlorine, and ozone
Hydrogen sulfide, sulfur dioxide, methyl mercaptan, hydrogen chloride, chlorine, and acid gases
Hydrogen sulfide, sulfur dioxide, methyl mercaptan, other acid gases, ethylene and formaldehyde
VOCs, HCs, chlorine, ozone, sulfur compounds, methyl mercaptan, ethylene and formaldehyde
VOCs, Benzene, Toluene, Ethylbenzene, m-xylene, 1-butanol
VOC’s, vehicle exhaust, Sulphur compounds, NOx, ammonia, Ozone and other gases
TABLE 2: List of commonly used adsorbents employed to target particular gaseous contaminants
When selecting a molecular filtration system for a specific application, several factors come into play, including the type and concentration of gaseous contaminants, the required airflow rate and pressure drop across the system, the desired removal efficiency and outlet concentration of contaminants, the operating temperature and humidity conditions, as well as the available space and budget for system installation and maintenance.
References:
1 Steve Greenberg, Evan Mills, and Bill Tschudi, Peter Rumsey, Bruce Myatt, Best Practices for Data Centers: Lessons Learned from Benchmarking 22 Data Centers, 2006, ACEEE Summer Study on Energy Efficiency in Buildings, 3, 76-87.
2 Henry C. Coles, Taewon Han, Phillip N. Price, Ashok J. Gadgil and William F. Tschudi, Air Corrosivity in U.S. Outdoor-Air-Cooled Data Centers is Similar to That in Conventional Data Centers, 2011, Lawrence Berkeley National Laboratory, 1-29.
3 ASHRAE, Gaseous and Particulate Contamination Guidelines For Data Centers, 2011
4 What is Creep Corrosion and How to Avoid or Mitigate It? (URL: https://knowledge.ni.com/KnowledgeArticleDetails?id=kA00Z000000kIpsSAE)
5 Craig Hillman, Joelle Arnold, Seth Binfield, Jeremy Seppi, Silver And Sulfur: Case Studies, Physics, And Possible Solutions,2007, DfR Solutions, 1-13.
6 Chris Muller, What’s Creeping Around in Your Data Center?, 2010, ASHRAE Transactions, 1-15.
7 Jones, G., Rohrbach, R., Unger, P., Bause, D. et al., Wicking Fiber Chemisorption for Air Quality Improvement, 1997, SAE Technical Paper 970555,1-7.
NAFA NEWS
Glasfloss Industries
Promotes New Director of Engineering
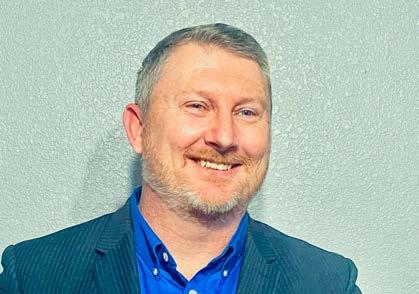
Desoto, TX – Scott Lange, President, today announced the promotion of Todd McGrath to the new position of Director of Engineering.
“Glasfloss Industries is proud to announce the promotion of Todd McGrath to Director of Engineering.Over the past 24 years Todd has progressed through several engineering positions within the company. In his newly expanded role Todd will spearhead and align engineering efforts across the entire organization. In addition, Todd is currently serving his third year as Chair of ASHRAE Standard 52.2 committee,“ said Scott Lange, President.
Glasfloss Industries Promotes New Director of Inventory, Logistics and Distribution
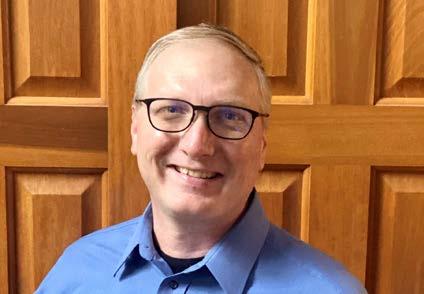
Desoto, TX – Scott Lange, President, today announced the promotion of Greg Gardner to the new position of Director of Inventory, Logistics and Distribution.
“Glasfloss Industries is pleased to announce the promotion of Greg Gardner to Director of Inventory, Logistics, and Distribution. Greg has distinguished himself in several positions during his 29 years at the company. His new role will lead and coordinate efforts to optimize inventories and logistics across operations nationally,“ said Scott Lange, President.
Rensa Filtration Announces Multiple Acquisitions
Glasfloss Industries
Promotes New VP of Manufacturing

Desoto, TX – DJ Heffline, COO, today announced the promotion of Brian McGarity to the position of VP of Manufacturing.
“Glasfloss Industries is pleased to announce the promotion of Brian McGarity to VP of Manufacturing. During his 23-year tenure Brian has climbed the ladder from the production floor to Director of MFG. In 2005 he became the plant manager of our Jacksonville FL location and has been a key member of our manufacturing group ever since. Brian’s new role will be to guide and direct manufacturing teams at all facilities,“ said DJ Heffline, COO.
AURORA, IL – January 18, 2024 – Rensa Filtration, a manufacturer and distributor of consumable, mission-critical air filtration products, announced today that it has acquired several businesses that provide distribution, sales and service of air filters to commercial and industrial customers and end-users in California, Illinois, New York and Arizona.The four companies joining Rensa are Air Filter Supply, Air Filter Engineers, R.P. Fedder, and Dave Downing & Associates. Terms of the transactions are not disclosed.
“I am pleased to announce this new chapter of growth as we continue our journey to become a leading provider of air filtration products and services,” said Brandon Ost, Rensa’s founder and CEO. “The addition of sales, service and distribution operations and their world class sales and service teams in these key regions enables Rensa to provide our air filters and filter change services to contractors and end-users in demanding education, healthcare, high-tech manufacturing and data center applications.”
Rensa Filtration will be exhibiting at the AHR Expo in Chicago January 22-24, 2024 at Booth N1134. For more information on Rensa Filtration and its products, please visit: rensafiltration.com
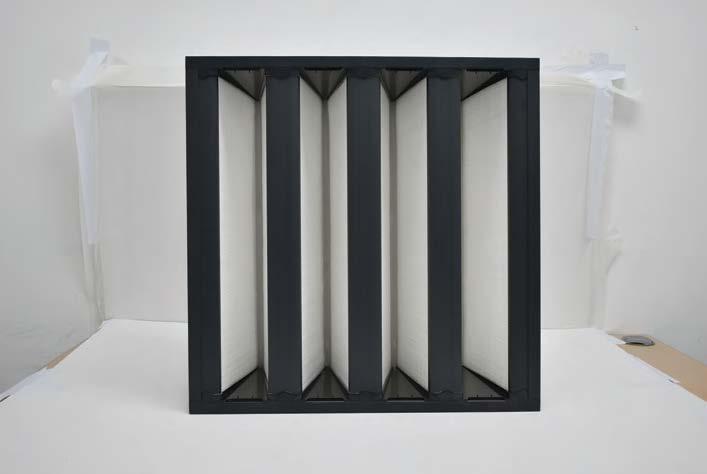
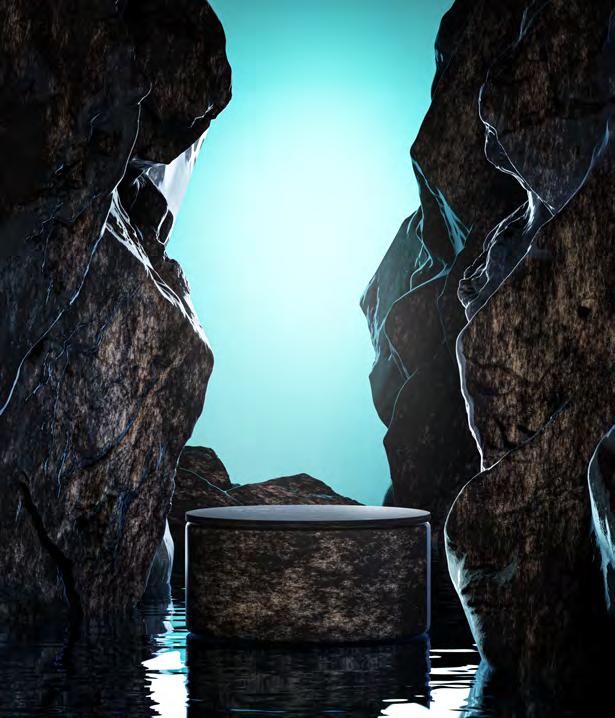


Excelair. The Air You Breathe.
Excelair is a leading manufacturer of HVAC air filters specially in medium & High Purity range , dedicated to providing high-quality air filtration solutions. With our Office & Warehouse spanning approx. 80,000 square feet in Houston, Texas, we are committed to meeting the needs of our customers with efficiency and excellence. Our extensive warehouse space allows us to maintain a vast inventory, ensuring prompt delivery and exceptional service. Partner with us for superior air filtration solutions that enhance indoor air quality and promote a healthier environment.
What matters is the air you breathe... EXCELAIR
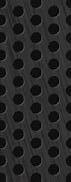
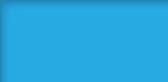
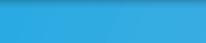

































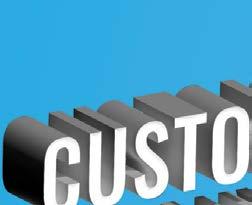



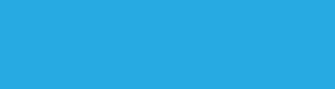

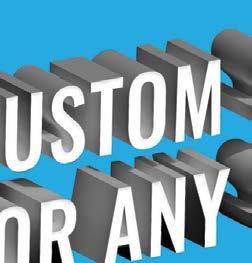









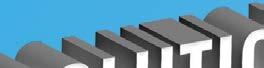
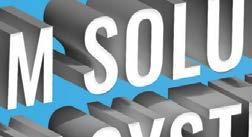
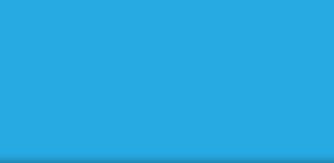
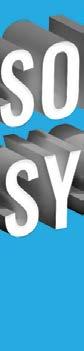
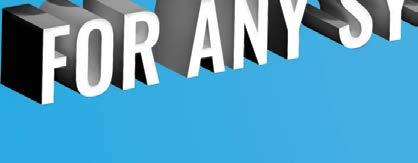
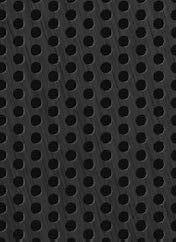


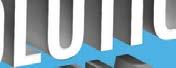

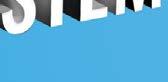












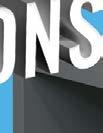
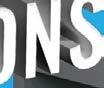
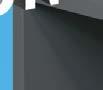

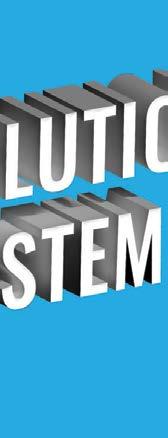
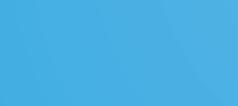
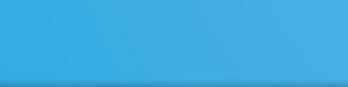
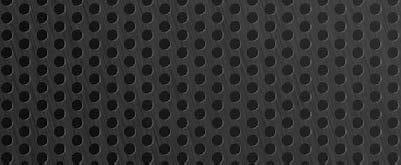






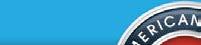
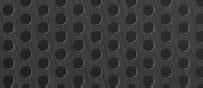
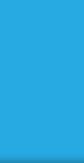
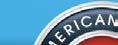
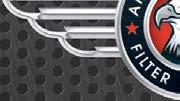



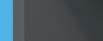

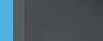
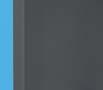




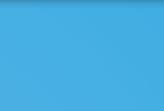

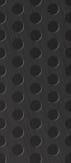
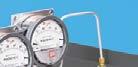
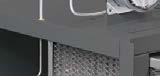

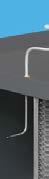


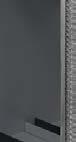

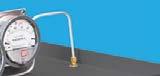
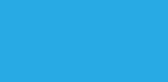
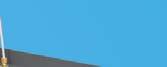
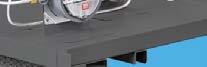
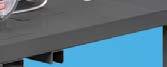
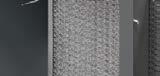
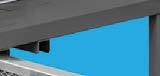
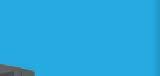






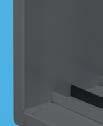
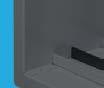

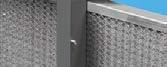
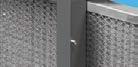
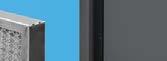





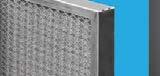
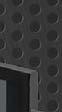
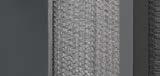



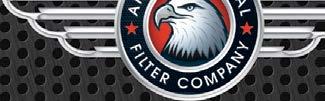
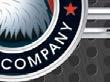



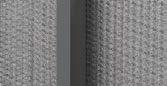

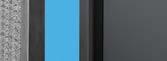


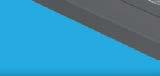





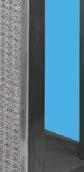
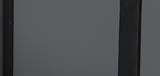

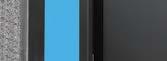
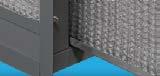
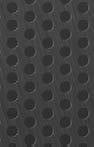

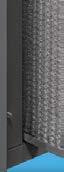
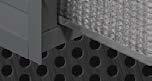

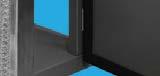

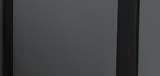
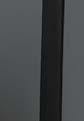

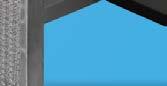

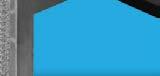
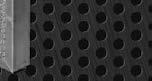
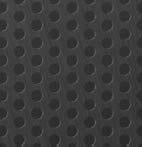
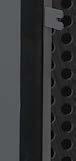
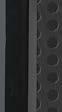





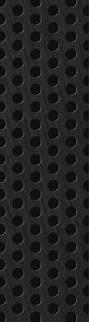
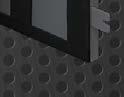
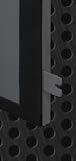
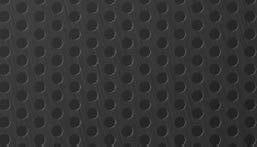
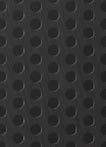

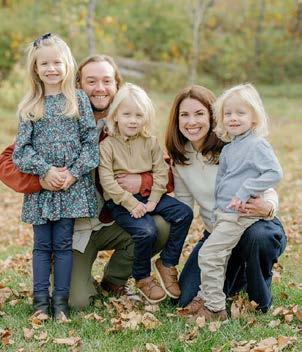
EXECUTIVE PROFILE
CRAWFORD HOUSTON Director of Commercial Operations GRAPHIC PACKAGING
Crawford Houston, Director of Commercial Operations of Graphic Packaging grew up in Crestwood, KY and attended Georgetown College. Crawford now resides in Pewee Valley, KY with his wife Margaret, daughter Sylvie and twin boys Sammy and Whitt. Having been in air filtration for 15 years, Crawford enjoys the people aspect of his everyday life as a business leader.
COMPANY HISTORY
Graphic Packaging (NYSE:GPK) is a worldwide company focused on fiber-based packaging. Our purpose is to package life’s everyday moments for a renewable future. We serve hundreds of the world’s most recognizable brands and are always looking ahead to help our customers meet changing consumer demands and their business goals.
How did you get your start in the filter industry?
After college I worked as a laborer for an electrician while I interviewed for my career. After a couple of months, I interviewed at Lithocraft, a small family-owned business specializing in paperboard packaging and air filter frames. I started at minimum wage as a trial period for both me and the owners. 8 years later the owners sold to Graphic Packaging and the rest is history. I am forever grateful they hired me 15 years ago and blessed to be working for a company now that share the same values.
How do you motivate your employees?
We hire the right people. It sounds cliché but if you empower capable self-starters to make calculated decisions for your business the numbers take care of themselves. I’m a believer that if you need to count calls for salespeople or have daily check ins with ops leaders you’ve hired the wrong person. Instead, I let them run their business and come to me for any obstacles that get in the way.
Did you have a business mentor and if so, who is/was it?
I have 3 influential individuals that mapped my career. I started under what was eventually our director of sales and operations planning. I learned the math behind the business, and the decision making to estimate and produce efficiently under Tim Daniel’s supervision. Ray Rieber was our lead salesman at the time and we collectively sold together for almost a decade. Perseverance, humility, and the art of selling without being a “pest” are traits he had in spades. That workmanship and craft rubbed off on me during my early twenties and I carry those lessons today. Finally, Dan Keefe the VP/GM for the specialty division of Graphic Packaging was my superior for the last 5 years. He’s a thoughtful, big picture leader that allowed me to look above the clouds to make the best decisions for our business. He taught me corporate America and was instrumental helping to grow our small business into the world leader of filter frame manufacturing.
What's the best piece of advice anyone ever gave you?
There’s a lot over the years, my father owns a consulting firm and mentors CEOs through the Vistage organization. Growing up our nightly dinners revolved around business, budgets, and workrelated stories. In fact, they still do weekly at our family’s Sunday Supper. Two that come to mind when dealing with challenges throughout my career I gleaned from him. The first is that pressure is a privilege, never lose sight of that when you’re in the
thick of it. The second is a quote from Mike Tyson before he fought Holyfield but rings true in business “everyone has a plan until they get punched in the mouth.” It happens to all of us, how we respond determines our success.
What is the most challenging aspect of running a filter company?
I’m lucky that both companies I’ve worked for understand the value of relationships. I am deeply close to this industry and the customers and friends I’ve made along the way. Filters are a unique niche and a tight knit family. Having that mindset and focus on relationships has paid dividends for us and we cascade that respect and value on people to our employees.
What do you think is the biggest challenge the air filtration industry currently faces?
It’s a solid business with high probability of sustaining for decades. The challenge is we don’t know our end users demand the way other industries do. Every virus, natural disaster, or even strange weather patterns are variables our customers face that impacts ordering
patterns. As an industry we have to recognize that and be prepared for the ebbs and flows of filtration in both equipment and personnel.
Do you have any words of wisdom for up and coming filter professionals?
Think like a small business owner. Maintaining the mindset of “would I do that if I owned the company?” has mapped a lot of my decisions and steered me in the right direction. Secondly, challenge yourself for the next role before you think you’re ready. Most successful people I know were pushed past their comfort level at one point in their career. Be open minded about something uncomfortable, it can change your life for the better.
How has your company benefitted from NAFA membership?
I can honestly say it’s been the best investment we’ve made. The fellowship and networking NAFA provides has been instrumental in the growth of our business over the last 15 years. I am a huge advocate for organizations that gather decision makers in an educational, professional, and fun manner. I’ll continue to support NAFA and cascade the importance of it for my entire career.

THE GEARS OF GRATEGY ®
Innovating Air Filtration Workplace Culture

In the wake of the pandemic, the air filtration industry faces a unique set of challenges and opportunities within an increasingly employee-driven and competitive market. The adage, "Times are changing," rings truer than ever, marking a definitive shift from the “good ole days” of 2019. This article will give air filtration professionals the strategies needed to keep their top talent from becoming someone else’s.
Leveraging my extensive experience of over a decade in industrial sales, including a seven-year stint in the welding industry, I've observed the distinctive practices that catapult organizations to best-in-class status. A key component of these company’s success has been the power of blending Gratitude with Strategy—what I've coined as Grategy®. Implementing Grategy cultivates a work environment where excellence is not just pursued but flourished, and loyalty is deeply rooted.
To demystify this approach and revolutionize our understanding of workplace culture, I've developed the "Gears of Grategy." Far from being a mere set of tools, this innovative framework is designed to attract and retain top talent by nurturing a workplace culture anchored in positivity, recognition, and personal growth – and it all starts with YOU.
Integrating these gears into your air filtration business signifies a profound commitment to cultivating a culture that doesn't just
attract good people but fosters their development and contribution towards your shared success. I'd like to hear how these gears have transformed your organizational culture and propelled your company forward. Without further ado, here they are.
THE SIX GEARS OF GRATEGY®
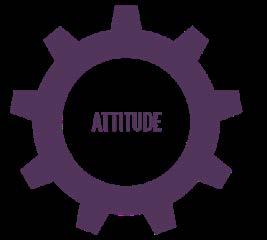
1. #Attitude: The Foundation: Above all else, your attitude matters. Beyond simple optimism, it's about embracing change as an opportunity, viewing innovation as essential, and committing to continuous improvement. Your perception and response to shifts in this dynamic sector greatly influences your professional growth and leadership potential.
The air filtration field's rapid evolution, marked by new technologies and regulations, demands an adaptable mindset. Seeing these changes as chances for growth, rather than obstacles, sets you apart and fuels your drive for innovative solutions. Resilience, fostered by a positive outlook, is key. It allows you to bounce back from setbacks and face challenges with confidence. Such an attitude is critical in a sector impacting public and environmental well-being. Embracing every situation as a learning opportunity prepares you to tackle both current and unforeseen challenges creatively.
Ultimately, adopting the right mindset is indispensable. Change, while intimidating, opens doors to growth and innovation. Your choice of attitude is totally up to you. Choose wisely.

2. #Appreciation: The Personal Touch of Gratitude: The second gear in the Grategy® model is appreciation, where you embrace gratitude on a personal level. My venture into gratitude began in 2009, a pivotal shift that has steered me through challenging times, including the recent pandemic. This journey has revealed that gratitude is more than positivity; it's a mindset that prompts you to find the good in every situation, backed by research showing its power to rewire your brain towards focusing on the positives, enhancing mental and physical health.
Making gratitude a daily practice helps you consistently recognizing the positives, even in adversity. This habit not only
benefits you but also those around you, encouraging a deeper appreciation for the contributions of each member within your professional circle. Genuine acknowledgment of others' efforts enriches interactions, strengthening your leadership by demonstrating the importance of everyone’s role. This attitude of gratitude is not just beneficial—it's transformative, paving the way for a fulfilling professional and personal life.
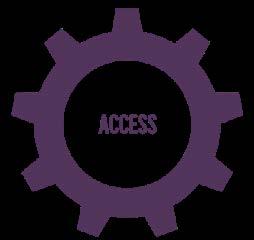
3. #Access: Open Doors, Open Minds: This gear revolves around cultivating leadership that is not just approachable but genuinely accessible, fostering an environment where every member feels valued and their voice heard. It's about dismantling the traditional barriers between management and employees, thereby not merely opening doors, but also broadening minds.
Access transcends mere physical availability; it encompasses creating avenues for both personal and professional advancement. This involves implementing comprehensive training programs and providing resources that enable individuals to thrive, both within and beyond the confines of the workplace. When members feel supported in their growth, they are inspired to contribute their best.
The era of the one-size-fits-all approach to company culture is behind us. The contemporary workplace demands flexibility to accommodate the diverse needs and aspirations of its members. Leaders are encouraged to be not just physically present but actively engaged, seeking out feedback, and staying attuned to the workforce's evolving needs through proactive engagement methods like "stay" interviews. These discussions are gold mines of insight into the ambitions and concerns of employees, offering a proactive means to address potential issues and mitigate turnover risks.
By championing open communication and ensuring accessibility, you lay the foundations for trust and loyalty, which are crucial for retention. The Access gear guarantees that dialogue moves fluidly in both directions, cultivating a transparent and supportive culture that boosts engagement and propels the organization towards success.
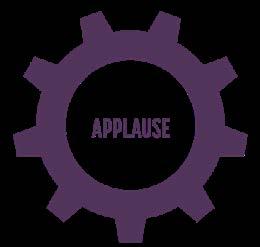
4. #Applause: Recognizing and Celebrating Success: In the air filtration industry, recognizing achievements, both big and small, plays a pivotal role in driving progress and innovation. This is where the concept of #Applause becomes vital. Expressing gratitude, whether through verbal praise or a thoughtful handwritten note, not only creates memorable moments but also cements a culture of appreciation within your organization. Celebrating the milestones in the development of air purification technologies or acknowledging the dedication behind meeting stringent environmental standards fuels motivation and uplifts team spirit.
Personalization in recognition is key. Understanding what resonates with each member of your team, perhaps through preferences noted on an "All About Me" sheet, enhances the impact of your appreciation. Remember, there is no one-size-fits-all approach when it comes to recognizing the efforts of your people. Moreover, recognition doesn't need to be extravagant. Simple gestures, such as a sincere "thank you," a personalized note, or a highlight in the internal newsletter, can significantly brighten someone's day. Encouraging peer recognition further strengthens team bonds, fostering a sense of unity and shared purpose.
In essence, the act of acknowledging and celebrating success is not just about boosting morale; it's about reinforcing the behaviors and innovations that lead to cleaner air and healthier environments. By integrating #Applause into your organizational culture, you highlight the importance of every achievement and contribution, big or small, in advancing the industry’s collective mission.
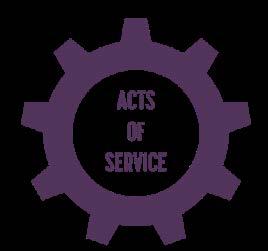
5. #ActsOfService: This fifth gear means extending the impact of your expertise in air filtration beyond the confines of daily tasks. It involves embedding corporate social responsibility and volunteerism into your core operations, significantly contributing to the health and well-being of communities and the environment. This initiative aligns perfectly with the deep-seated motivations that drew you to the air filtration industry: the desire to improve public health and protect the planet.
By participating in projects that enhance air quality, promote environmental sustainability, or educate the public about the
benefits of clean air, you live out the values that attracted you to this field. Demonstrating to your team how their work transcends ordinary responsibilities to contribute to a grander mission fosters a profound sense of purpose and belonging.
This dedication to service transcends basic job functions and financial rewards. It's about showing the world the significant impact your industry can have. Through acts of service, you not only bolster team unity and attract like-minded professionals but also develop a brand that stands for meaningful change. For you, as part of NAFA, integrating acts of service into your ethos is crucial for inspiring continued innovation and leadership in air filtration, making every effort count towards a healthier, sustainable future.
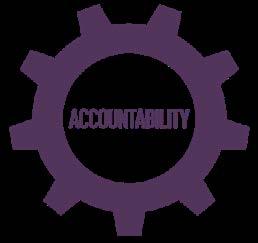
6. #Accountability: Ensuring Alignment and Continuous Improvement:
In the air filtration industry, #Accountability is crucial, serving as the cornerstone that ensures every effort contributes to your overarching goal: cleaner air and environmental protection. It's about more than just meeting benchmarks; it's a commitment to continuous improvement and adaptation. By implementing Key Performance Indicators (KPIs) specific to air quality enhancements and operational efficiencies, you measure the tangible impact of your work. However, accountability in this field goes beyond numbers; it's about being ready to evolve your strategies and technologies in response to new research and regulations.
This dedication to progress ensures that the pursuit of excellence is a never-ending journey. What may be effective today could be improved tomorrow, highlighting the necessity for ongoing adaptation and refinement. In the dynamic world of air filtration, accountability means embracing change and seeking ways to advance industry methods and outcomes continually.
By fostering a culture that values persistent growth, you encourage both leadership and team members to take ownership of their contributions to the mission. This approach doesn't signal an endpoint but rather propels the industry forward, ensuring that it remains at the forefront of environmental health and safety. Accountability, therefore, is not just a principle but a practice that reinvigorates your collective efforts, driving you towards innovation and excellence in every aspect of your work.
WHY THE GEARS OF GRATEGY® MATTER
In the air filtration industry, the Gears of Grategy® are foundational to building a culture that not only attracts but also retains the brightest minds. At a time when professionals seek fulfillment beyond financial rewards, these gears offer a structured approach to fostering an environment that values, respects, and nurtures its talent. For NAFA members, embracing the Gears of Grategy® equips you to empower your teams, elevate performance levels, and forge a legacy of a positive workplace culture.
These gears are a testament to a commitment towards excellence. They envision a workplace where every individual feels valued, heard, and integral to the collective mission of improving air quality and environmental health. In the intricate and ever-evolving landscape of air filtration, adhering to the Gears of Grategy® shines a light on the path for leaders aspiring to steer their teams with compassion, integrity, and relentless dedication to excellence.
As we chart our course through the complexities of today's business environment, the Gears of Grategy® emerge as beacons for those determined to redefine standards of workplace


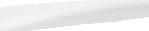

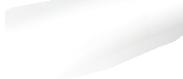



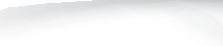
excellence. They are a call to action for setting a new benchmark in the air filtration sector, emphasizing the importance of a workplace where innovation thrives, and every team member's contribution is recognized. If you're inspired to elevate your workplace using these principles, it's time to connect and embark on a transformative journey together.
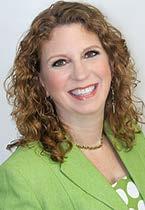
LISA RYAN, Chief Appreciation Strategist and Founder,
Grategy where she is pioneering workplace culture transformation through the power of gratitude and strategy.
To learn more, please visit: LisaRyanSpeaks.com
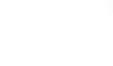
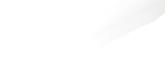
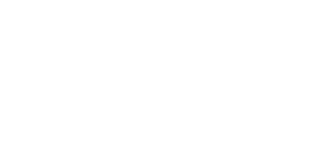

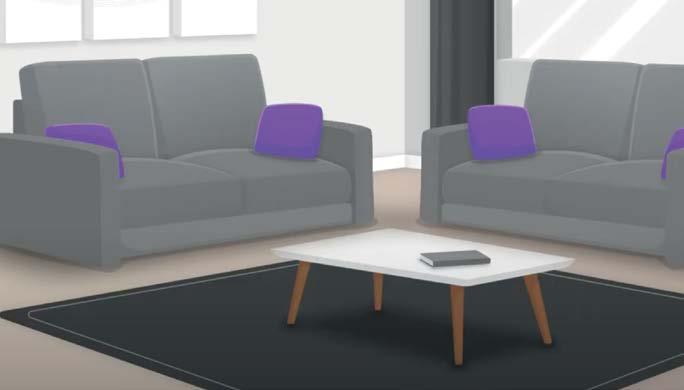
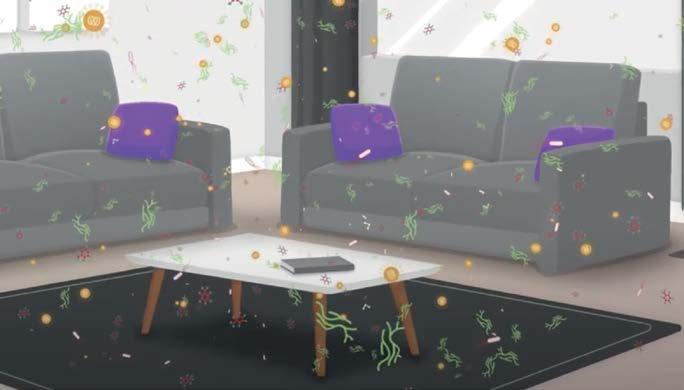
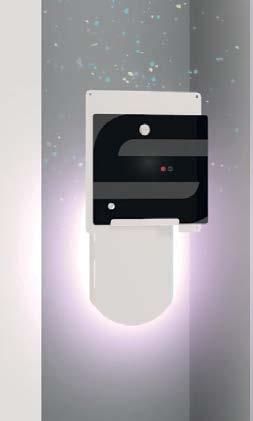

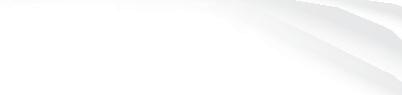


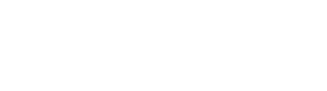
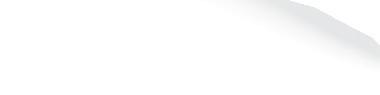
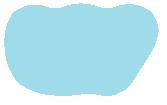

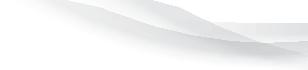



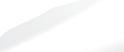
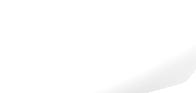
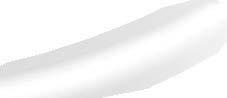


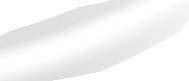

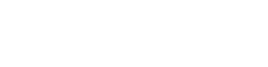
KATHLEEN OWEN
ASHRAE Fellow
LINDA LEE
Dr.PH, Member ASHRAE
AIR CLEANING IN ASHRAE STANDARD 241
REPRINTED FROM ASHRAE JOURNAL, FEBRUARY 2024
©ASHRAE, www.ashrae.org. ASHRAE Journal, February 2024.
Everything helps in Standard 241, because ASHRAE’s standard Control of Infectious Aerosols allows a building owner or facilities manager to choose from multiple options to meet the air needs required to provide the specific amounts of clean or cleaned air per person in occupied spaces. Once the air needed by your building or space and where it is needed are determined, you decide which solutions to use. You can bring in outdoor air (assumed clean of human pathogens); reduce occupancy; or use air filters, ultraviolet light (UV), reactive air cleaners (RAC) or other air cleaners to make your building safer. Or you can use some combination of the above to get clean air. In some cases, using air cleaners may be the most cost-effective and easiest way to meet the clean air levels recommended by ASHRAE Standard 241 requirements and to reduce infectious aerosol exposure in the occupied space.
This standard is intended to be implemented when there are high levels of community spread of communicable respiratory pathogens and a reason to reduce the risk of continued spread of these airborne pathogens. This status is called infection risk management mode (IRMM) and is recommended by an authority having jurisdiction (AHJ) to take measures to safeguard human health.
The AHJ will vary across locations. The most likely decision makers include the local, state or federal health authorities or the Centers for Disease Control and Prevention (CDC) and World Health Organization (WHO), but it could be the facility infection preventionist or industrial hygienist working with the local health department. The AHJ could be anyone in a position of authority over building operations or public health acting on community spread of disease.
It is also possible to use the guidance in Standard 241 when IRMM is not in place, if desired. Building readiness plans, including the information needed to put Standard 241 into place, should be prepared well in advance of the next public health emergency. Thatway, you are prepared to implement IRMM. These plans could be as simple as modifications to your current emergency management plans, including response to information on infectious aerosols.
Energy use optimization, air cleaner purchases and simple instructions for implementation can be produced before IRMM is declared and save you money, energy and even lives.
EQUIVALENT CLEAN AIRFLOW
Standard 241 works on the principle of equivalent clean air per person (ECAi) that leads directly to the needed total airflow for a given space (VEACi), which equals the number of people times the ECA. Table 5-1 in the standard provides values of ECAi for many types of use, including offices, medical space and residential space. Your building may have multiple uses (also called types of spaces) such that different rooms or zones have different air needs. When determining your total clean air needs, you must also determine where it needs to be provided. This consideration of different uses and locations also helps in preparing for implementation, as you can choose options to increase clean air to one section without needing to provide the highest level of ECA for all spaces.
UNDERSTANDING “CLEAN AIR”
For Standard 241, “clean air” includes clean and cleaned air. The term is used to mean the portion of the air that is free of pathogens. This can be confusing as a concept, so it helps to think of simple situations. The simplest example of clean air is outdoor air. Assuming that the air in a building is not pulled directly from somewhere sick people congregate, it is free of human pathogens. This does not mean it is clean for other purposes, as it may include, for example, noninfectious particles or ozone.
A second example of cleaned air is contaminated air passed through an air filter. If, for example, 100 cfm (47 L/s) of contaminated air flows through a 50% efficient air filter, you get 50 cfm (24 L/s) of clean air. Of course, the filter does not actually

separate the air into a perfectly clean and totally contaminated flow; this is a construct to help us understand the air.
Remember, too, that, in the math, clean air being cleaned again does not increase the amount of cleaned air. This means that an outdoor airstream combined with returned air from within an occupied space that goes through an air filter yields a total amount of clean air equal to the amount of outdoor air added to the amount of returned air multiplied by the filter efficiency. The clean air produced in this scenario is not equal to the combined airflow times the filter efficiency.
Thus, for outdoor air, the contribution is simple as the airflow of outdoor air is the same as the VACS (air cleaning system equivalent clean airflow rate) for the outdoor air. Outdoor air may be brought into a building by the HVAC, or it can come through windows, doors, cracks, etc. For planning purposes, you will need to be able to measure the amount of air. You must also be able to provide the amount of air expected. Consider whether the HVAC can run nonstop whenever the building is occupied. Also, note whether windows are likely to be open year-round (in North Dakota, you may need to assume they will be shut in winter. In North Carolina, assume they need to be shut during summer). We do not know when IRMM will be required, so you should plan for different seasons and even for bad outdoor air, such as during wildfires.
To meet the need for clean air, in addition to outdoor air, you may use cleaned air produced by devices in HVAC systems or air cleaners that work by cleaning the air in the rooms. Standard 241 allows you to use both types of air cleaners. However, you must have good- quality efficacy data for any air cleaner. For some of these devices, there are recognized test standards. For some,
there are not. The rest of this column addresses how to determine how much air cleaning you may use in your calculations for different types of devices. Standard 241 has also set safety standards for most of these devices.
AIR CLEANING METHODS, DEVICES AND TESTING
Air Filter Testing
The simplest device to include, due to having long- established and used air cleaner test methods and no new safety testing requirements, are air filters. Any filter with an efficiency of MERV-A 11-A or higher may be included. Until Jan 1, 2025, a regular MERV is acceptable. MERV-A is the efficiency level based on an ASHRAE Standard 52.2 test using its optional Appendix J conditioning step that allows the test to look for efficiency drop as particles are collected. The comparable rating from an ISO 16890 test may also be used. For HVAC-mounted filters, you determine the clean air contribution by multiplying the airflow through the filter by the efficiency value in Table 7-1 of Standard 241 based on the MERV level.
Nonfilter Testing
For nonfilters, you must use one of the accepted tests, as shown in Table 1, and meet the safety requirements. These tests include bioaerosol challenge tests for all devices that are mounted in an HVAC duct and work within the duct. In addition to HVAC-mounted devices, residential in-room air cleaners (IRAC) may be tested with Association of Home Appliance Manufacturer (AHAM) tests, as shown. Note that all air cleaners except media filters have safety requirements spelled out in Standard 241 Appendix A as discussed in the next section.
TABLE 1
CURRENT AIR CLEANER EFFICACY
ASHRAE 52.2 (both the Regular Test and the Bioaerosol Test for Non-UV Devices [App L])
ISO 16890
HVAC Duct Mounted
HVAC Duct Mounted
ASHRAE Standard 185.1 HVAC Duct Mounted
AHAM AC-1
AHAM AC-5
Residential IRAC
Residential IRAC
FIGURE 1: Air filters and UV lamps installed in HVAC system
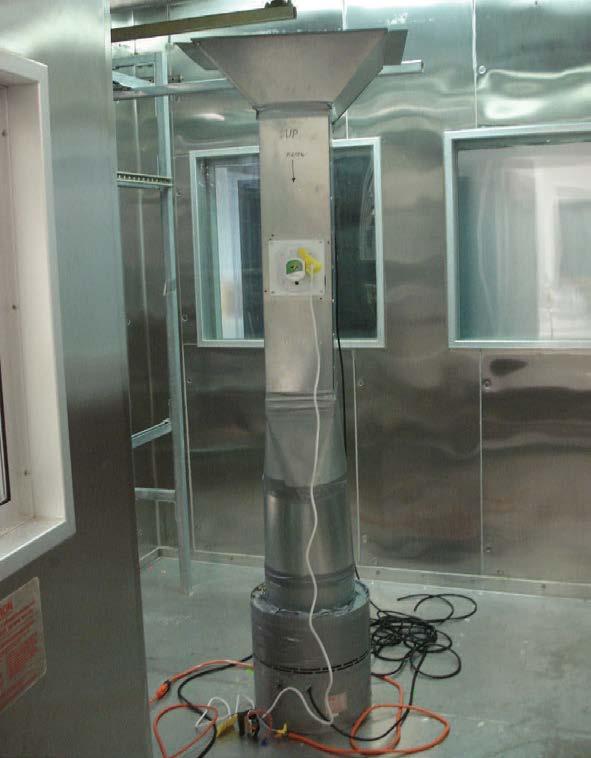
Available Testing for Other Devices
For devices that do not currently fall under a standard test, guidance exists for what should be included in a good test as described below. Note that ASHRAE, and others, are currently developing a variety of new test standards that may be added to Standard 241 in the near future. The desired cfm per person, as required by Standard 241, may not be achieved based only on outdoor air and the main HVAC unit, or it may be too costly. Or there may be no HVAC system. For these cases, and when simply desired for control near sources, IRAC may be used. These IRACs must be tested and challenged to ensure the product performs as required by the standard.
Challenges in Testing for MS2 Bacteriophage
The Standard 241 recommendations include more than the details shown in Table 2. The most important detail is that the challenge for any bioaerosol test must be MS2. MS2 bacteriophage is considered a good surrogate for COVID and other respiratory viruses but is harder to kill. MS2 offers a relatively safe and cost-effective surrogate to challenge room air cleaners. The use of the same
organism also makes the data across devices comparable to help in the selection of the more appropriate device for each application. These test requirements are discussed in Appendix A and mirror those used in the accepted chamber tests but allow testing of devices that are currently not covered.
TABLE 2
RECOMMENDATIONS FOR NON-STANDARD AIR CLEANER TESTS FOR IN-ROOM AIR CLEANERS
Parity: Same Conditions for Effectiveness and Safety Tests
Construction: Surfaces Shall Be Smooth, Nonporous, Produce Minimal Emissions, React Minimally with Air Cleaners, and Be Electrically Grounded
Chamber Shall Have Low Leakage and Be Easy to Flush Between Tests
Control: Temperature ~73°F, Relative Humidity ~50%
Testing Laboratory: Compliant with Requirements of ISO/IEC 17025 25 or Equivalent
Test Chamber: Chamber Volume of at Least 800 ft3 (22.7 m3)
Test Duct: For In-Duct Air Cleaning Systems That Clean Air in the Occupied Zone, Use a Test Duct That is a Recirculating Duct Connected to or Within the Test Chamber
Test Microorganism: MS2
UV Devices
The safety requirements in Table 3 are based on research showing that some devices may be dangerous or may make the air less acceptable when operating. The first, and long understood, safety issue is for ultraviolet (UV) devices. UV devices must be tested for electromagnetic radiation between 100 nm and 400 nm and must not exceed the permissible exposure limits or other published threshold limit values (TLVs). For devices that are not covered by the standard tests, the safety requirements include those in Table 3.
Formaldehyde and Limonene Testing
These requirements investigate whether a device is likely to produce formaldehyde. Standard 241 is a response standard to infectious aerosols, but the indoor air will include gaseous contaminants whether there is a respiratory pathogen present or not. Thus, the limonene test is reasonable even if it appears to not be directly related to bioaerosol control. Limonene is a common air pollutant and has been shown to lead to formaldehyde and to
FIGURE 2: Air cleaner with added duct and fan under test in a chamber.
3
SAFETY REQUIREMENTS
Limonene Challenge Test Showing Formaldehyde Produced
Emission rate < 50 µg/h
Ozone Per UL 2998 or Equivalent < 5 ppb
Particle Counts (> 0.3 µm) per ISO 14644-14
One Cleanliness Class > Empty Chamber
ultrafine particles when some types of air cleaners are used. While these safety tests do not represent all possible issues, they are a big step in the right direction to allowing facilities managers to choose the proper air cleaners for their intended use. Knowledge of the safety and efficacy of the specific air cleaner helps ensure better outcomes for building occupants.
CALCULATIONS
Once you know the efficiency, ε (expressed in %), of devices that work in the duct and the likely duct airflow through the device, Q, you calculate:
VACS = Q × ε in cfm or other airflow units
For multiple devices operating in sequence in an HVAC duct, you either need to use test results for all the devices together or calculate a combined efficiency based (not additive) as shown.
Combined ε = 100 – 100 × (1- εdevice 1/100) (1- εdevice2/100) etc.
For in-room devices, the clean air delivery rate (CADR) is the VACS For devices that are mounted in the HVAC but work in the room air, the VACS is also the CADR.
VACS = CADR in cfm or other airflow units
For devices using AHAM AC-1 particle test results, the VACS is a weighted average of the three different particle challenges to approximate the likely size of particles emitted by people. This reflects the same weightingas HVAC media filters, which uses the efficiencies determined for the three size ranges used to determine the MERV in ASHRAE Standard 52.2.
Provided airflow to a space also depends on how much of the air from a source goes to that room, so outdoor air intake may supply more than one room. The total VACS to an occupied space is calculated using the amount of air that goes to that space. Multiple air cleaners may be used for the same space. The
simplest option would involve adding an IRAC to a space served by an HVAC with a filter located in it.
VECAi = VACS outdoor + VACS HVAC working devices + VACS in-room working devices
CONCLUSION
Thus, it is quite simple to work with any of the clean air options. Air cleaners can offer a safe, simple and cost-effective alternative to the main HVAC renovation or modification. This builds in flexibility and empowers the building manager to cost effectively and safely manage building operation, reducing the risk of community spread of respiratory viruses. It is even simple to have more than one option prepared to use depending on the season when the next pandemic hits. Please review Standard 241 for more information.
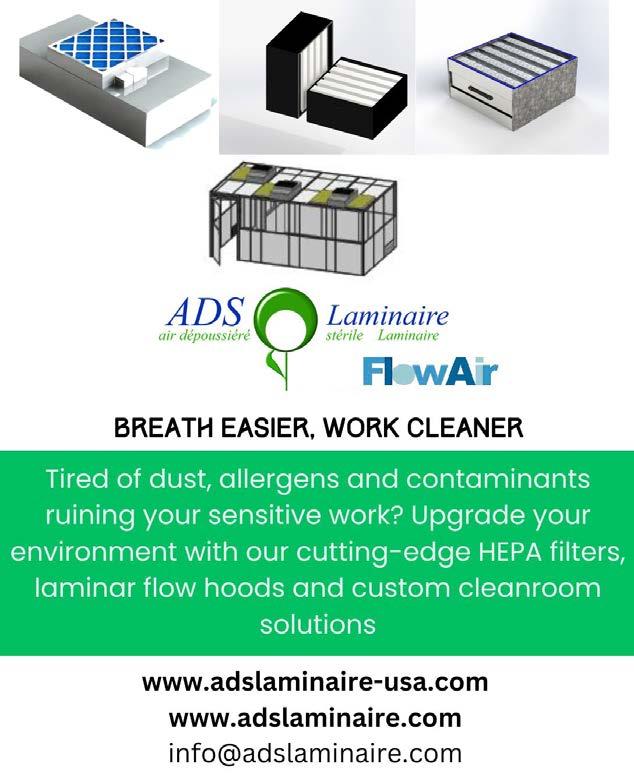
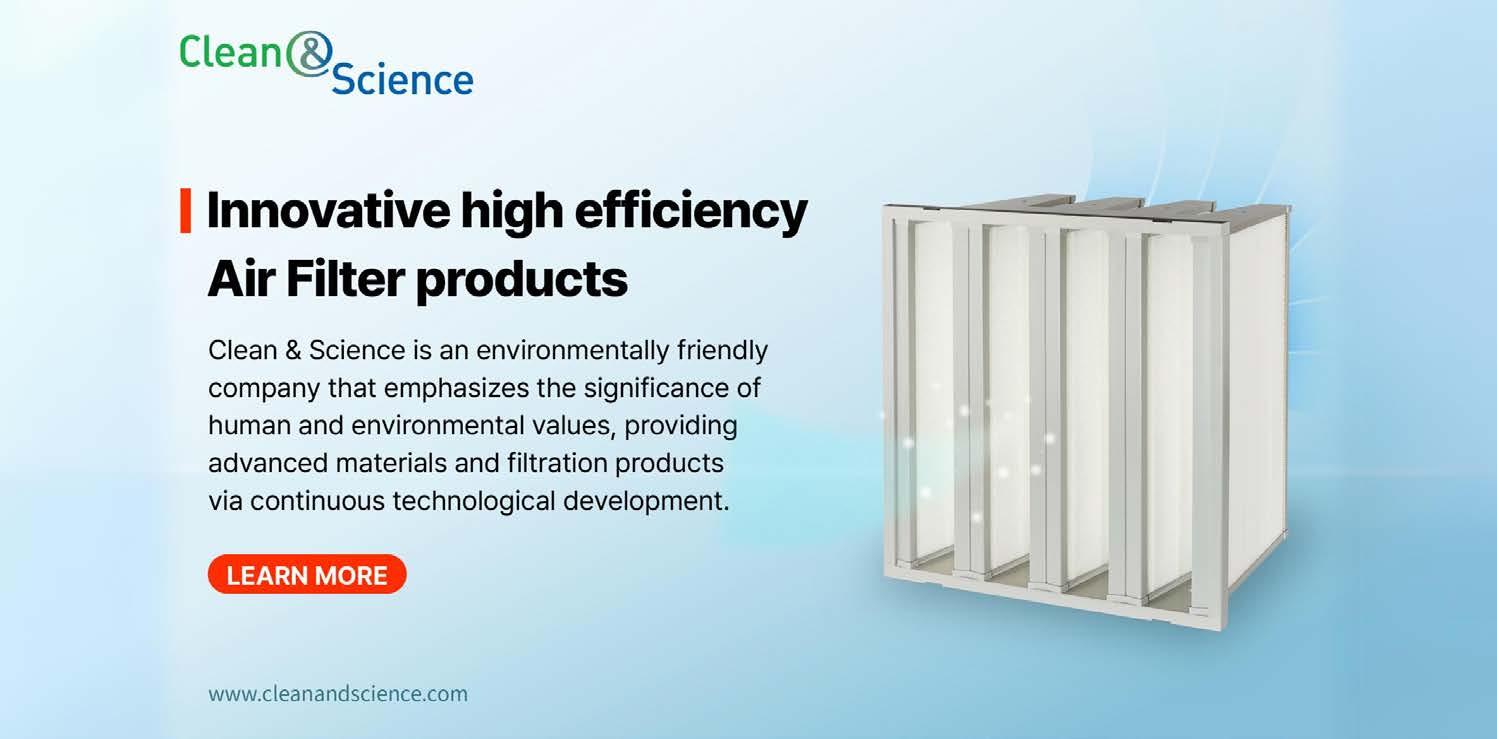

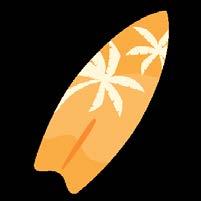

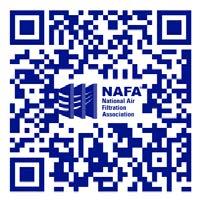
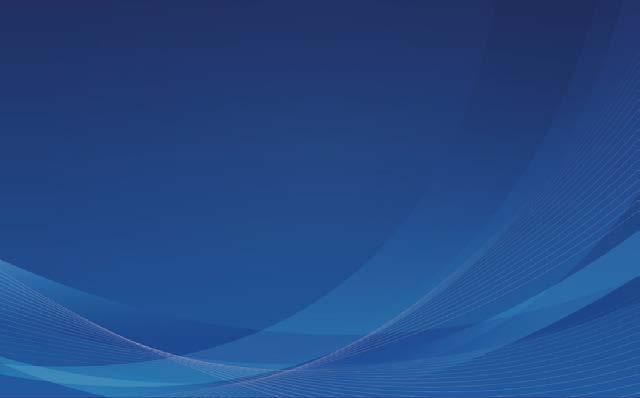
PASSING THE TORCH
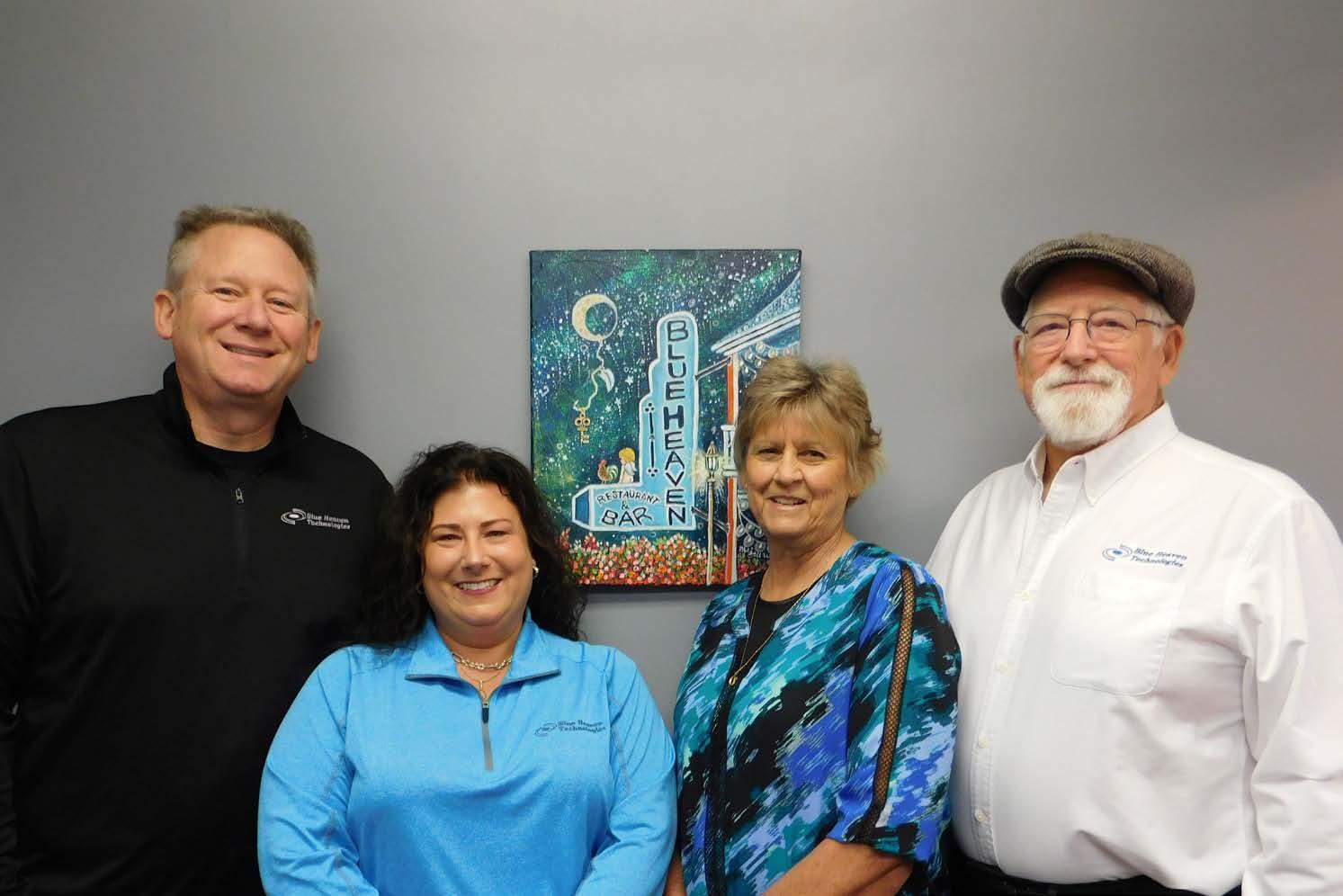
When operating a highly successful testing laboratory, one grows accustomed to answering technical questions. The question one doesn’t expect to hear so often is, “how in the world did you come up with that name?”
Bob and Connie Burkhead, like many couples, had “their song”. This song happened to be “Blue Heaven Rendezvous”, by Jimmy Buffet. The love for the song inspired them to visit Key West, where they frequented the inspiration for the song, Blue Heaven Restaurant and Bar. Considering also their shared love for all things Kentucky, it’s apparent that Blue Heaven became a predominant theme on many levels.
Bob Burkhead began his career in filtration at AAF in Louisville, KY in 1977. After 15 years in several engineering positions there, he was offered a position as engineering manager at Freudenberg in Hopkinsville, KY. Bob spent 10 years there before he and Connie decided it was time for a new adventure. The opportunity to start his own filtration testing laboratory presented itself back home in Louisville. Blue Heaven Technologies was born!
After a year of moderate growth, Bob found himself in need of a lab manager to conduct and oversee the day to day activities. Bobby Singer had 15 years of experience doing just that at Air Filter Testing Laboratories and had worked with Bob many times. After a chance encounter between the two at a Kohl’s department store, well, the rest is history.
Blue Heaven Technologies experienced exponential growth from 2005 to 2024, growing from about a 6000 square foot area to the current footprint which spans about 20,000 square feet. New capabilities were added along with a staff that grew from just Bob and Bobby to over a dozen technicians, engineers and a shining star ISO 17025 quality certification.
Having built such a successful business, the next step for the Burkhead’s was obvious. Retirement. A succession plan between them and Bobby and his wife, Jacqueline (JJ), was reached in the early 2020’s. The transition became official on February 10, 2023. Bob and Connie now spend their time either boating in Vero Beach, Florida or spending time with kids, grandkids and great grandkids at their home in Louisville. The Singer’s now look to continue and build upon the foundation and culture of what can best be described with two simple words. Blue Heaven.
(l-r) Bobby Singer, CAFS, JJ Singer, Connie Burkhead, Bob Burkhead
DAN

HOW DO I BEST FILTER MY RECYCLED DUST COLLECTOR EXHAUST?
A Glimpse into the Standard Setting Process of the New NFPA 660 Consolidated Standard for Combustible Dusts
The National Fire Protection Agency (NFPA) standard on the appropriate media to use when recycling indoor air from dust collectors is a topic that just begins to scratch the surface on some of the challenges the standards development agency has faced during its current process of merging six separate NFPA combustible dust standards into one comprehensive standard, NFPA 660 Standard for Combustible Dusts, which is set to be released in early to mid 2025. This article will share some insight on this standard setting process through a close up look on the specific standard of the recycling air indoors from dust collectors. The six standards set to be consolidated are the following:
NPFA 61 Standard for the Prevention of Fires and Dust Explosions in Agricultural & Food Processing Facilities
NFPA 484 Standard for Combustible Metals
NFPA 652 Standard on the Fundamentals of Combustible Dust
NFPA 654 Standard for the Prevention of Fire and Dust Explosions from the Manufacturing, Processing, and Handling of Combustible Particulate Solids
NFPA 655 Standard on the Prevention of Sulfur Fires and Explosions
NFPA 664 Standard on the Prevention of Fires and Explosions in Wood Processing and Wood Working Facilities
NFPA was founded in Quincy, MA in 1896 and for more than 125 years has been writing safety standards with the primary mission to help save lives and reduce loss. This has been accomplished
through the development of safety code by the expertise of its more than 250 committees and over10,000 global volunteer committee members. These members include architects, analysts, engineers, government officials, manufacturers, first responders, and many others. The national electric code (NEC) is one of many standards that NFPA authors and maintains.1
Six separate combustible dust standards have been independently published for many years, with the first NFPA standard on combustible dust dating back to the early 1920’s in response to a series of fatal combustible dust accidents in the agricultural and food processing industries. Through the years, these independent standards became harder and harder for users to navigate and apply consistently. Approximately 5 years ago, a decision was made to begin a merge process with the objective to make easier the application of the standards to reduce risk of often fatal accidents involving combustible dust explosions.2
Consolidating these standards has been a herculean task, consuming its many volunteer committee members now for years. This effort has included analyzing, combining, and debating hundreds of pages of guidance across the six standards on combustible dust safety. The distillation process of many years of effort and hard-fought advances in combustible dust safety has been challenging to say the least.
An example of one topic in particular that demonstrates the challenge of creating shared language around a single standard has been the guidance involving the indoor recycling of exhaust air from dust collectors.
PRATHER President of DualDraw,
The benefits of recycling filtered air from a dust collector are clear:
1. No reconditioning of air required. This amounts to a significant amount of cost savings through saving energy to heat or cool replacement air, particularly in more variable climates.
2. No burdensome permitting required. Exhausting outdoors in most if not all municipalities requires facilities to go through an air permitting process. Depending on the local, state, and national regulations where the facility is located this can be quite onerous, expensive, and time consuming for organizations to endure.
3. No pressure re-balancing required. Exhausting large amounts of air creates unwanted negative pressure inside facilities that needs to be balanced with additional air. If the amount of air being exhausted outside a facility varies over the course of operations, this becomes an ongoing operational challenge. The hazards of recycling exhaust air from a dust collector are also clear — when filtering combustible dust in a dust collector, there is considerable risk of creating an explosive environment if the dust collector equipment and its respective integral filtration is not properly managed and consistently monitored by operators. A few of those risks include:
1. Fugitive dust accumulation. An over-accumulation of combustible dust inside a collector due to not properly managing filter changes can quickly result in an abundance of fuel that, when dispersed, could easily result in an explosive dust cloud.
2. Filter breach. If filters are not properly installed or managed, a filter breach can occur. This could cause combustible dust to bypass the filter and then be widely exhausted back into a facility. This dust cloud dispersion is a key ingredient in the recipe for a deflagration or explosion event.
3. Miscalculation of particle size. If the application being addressed is producing particles smaller than the efficiency of the filter, this could result in small explosive particles making their way through the filter media and being exhausted back into the facility, with similar potential results as the bypass event cited in #2.
When it comes to the most effective way to specify the level of cleanliness of filtered air prior to recycling back into a facility from a dust collection system, the existing six standards offer conflicting guidance. The question is clear – what should the
commonly accepted level of filtration become for the new consolidated NFPA 660 to best ensure the safety of recycled air from from dust collectors?
A task group was created and the scope defined. Our objective was to determine the best common language across the six standards that would guide users of the standard to understand how to approach handling this important facility management decision when selecting and managing dust collection systems.
The most compelling idea put forth by a task group member was to use widely accepted MERV values 3. as a way to guide users towards the most efficient and safe approach to appropriately size filtration prior to recycling air. MERV relates to filter efficiency and could be matched to the related particle size of the material being processed to allow for maximum capture of the particular combustible dust being generated. Using common language that incorporated MERV makes a lot of sense – but unfortunately we could not gain consensus on its use within our task group.
Ultimately, we decided to use more general language that leads users to refer to the “applicable industrial hygiene exposure limits” – based on the particular application in question and materials being processed. This approach felt like a compromise. While the applicable industrial hygiene exposure limits often are very stringent, my belief is that the universally known MERV ratings are much more accessible, easier to digest, and straightforward to apply. Task group members felt like the use of MERV more applied to HVAC and not dust collection, and that the potential to overlook combustibility concerns was present if we used MERV.
At the end of the day, we achieved what we set out to do — establishing common language in the new NFPA 660 that provides guidance on how to approach filtration of recycled exhaust air from a dust collector. What was also learned was that consensus and common decision-making when developing standards is often challenging, slow process. The goal, however, of keeping facilities safe and giving users a guide to do so has been maintained. If you encounter combustible dust in your environment, keep an eye out for the release of 660 coming soon to your local code enforcement officials.
Footnotes:
1. National Fire Protection Agency, https://www.nfpa.org/About-NFPA
2. Dust Safety Science, https://dustsafetyscience.com/nfpa-660-standard-for-combustible-dust/
3. United States Environmental Protection Agency, https://www.epa.gov/ indoor-air-quality-iaq/what-merv-rating
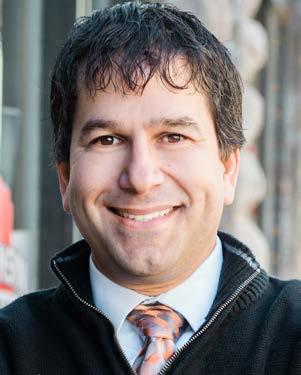
FROM THE ASSOCIATE DIRECTOR
TONY VEROEVEN, CAE, CNAP
NAFA Associate Director
CLEAN AIR AWARDS: INTRODUCING A COMPREHENSIVE TOOLKIT FOR YOUR BUSINESS AND YOUR CLIENTS
As guardians of indoor air quality (IAQ), we understand the critical importance of providing our clients with solutions that meet and exceed their expectations. Today, we are excited to introduce you to a powerful initiative that enhances IAQ and strengthens client relationships: the Clean Air Award program.
PROMOTING EXCELLENCE IN IAQ:
At NAFA, we are committed to promoting excellence in IAQ management, and the Clean Air Award program stands as a beacon of our dedication. This program recognizes buildings and facilities demonstrating exceptional commitment to IAQ, showcasing their efforts to prioritize occupant health and well-being.
EMPOWERING NAFA MEMBERS:
The Clean Air Award program is more than just a recognition; it's a tool that empowers NAFA members to become strategic partners in their clients' success. By guiding clients through the nomination process and helping them achieve Clean Air Award recognition, members can position themselves as trusted advisors committed to delivering top-tier IAQ solutions.
OUR CURRENT STATUS AND GOAL:
While our initial participation in the Clean Air Award program is commendable, we recognize significant room for growth. In 2023, only 22 out of our 156 distributor members participated, resulting in 88 recognitions. Our goal for the upcoming year is
ambitious yet achievable: significantly increasing participation by 20% and solidifying NAFA members as leaders in promoting clean indoor air. That’s only 4 or 5 more distributors. We think we can exceed that for certain.
A COMPREHENSIVE TOOLKIT:
To support our members in promoting the Clean Air Award program to their clients, we have developed a comprehensive toolkit that includes:
• Clean Air Awards Website: A user-friendly website providing comprehensive information about the program, including award categories, nomination process, and resources for building owners and facility managers. (www.cleanairaward.org)
• Client Brochure: An engaging brochure empowering building owners and facility managers to pursue Clean Air Award recognition. This brochure outlines the urgency of clean air, the business case for IAQ improvements, and a roadmap to achieving earning the Clean Air Award.
• Member Brochure: This informative brochure, aimed at NAFA members, details the benefits of helping clients earn Clean Air Awards and provides a step-by-step guide to nominating clients for the program.
• Client-focused PowerPoint Presentation: NAFA members can use a customizable presentation to educate their clients about the Clean Air Award program and its benefits.
HIGHLIGHTING THE IMPACT:
Achieving Clean Air Award recognition can profoundly impact buildings and facilities. It can lead to increased occupancy rates, improved tenant satisfaction, and higher per-square-foot rental rates. By prioritizing IAQ and earning this prestigious recognition, buildings and facilities are committed to providing occupants with a healthy and safe environment.
BUILDING TRUST AND LOYALTY:
By leveraging the Clean Air Award program, NAFA members can enhance IAQ and build trust and loyalty with their clients. Clients working with an NAFA member to win and renew their Clean Air Award will experience higher trust and loyalty, knowing they are partnering with an industry leader committed to their well-being.
TAKE ACTION TODAY:
We urge all NAFA members to seize this opportunity and leverage the Clean Air Award program to strengthen client relationships and enhance IAQ. Take the first step by visiting the
Clean Air Awards website (www.cleanairaward.org), downloading the marketing collateral from the nafahq.org Member Hub (under Resources), and exploring how to become a leader in promoting clean indoor air.
DOWNLOAD THE RESOURCES AND GET STARTED TODAY!
Together, let's strive towards increasing participation and championing clean indoor air for all.
For more information and details about the Clean Air Award program, please get in touch with NAFA at nafa@nafahq.org or visit our website at nafahq.org.
If you have questions about the program, strategy, or leveraging the award in your marketing and business development efforts, please get in touch with Tony Veroeven, CAE, CNAP, NAFA Associate Director, at tveroeven@nafahq.org.
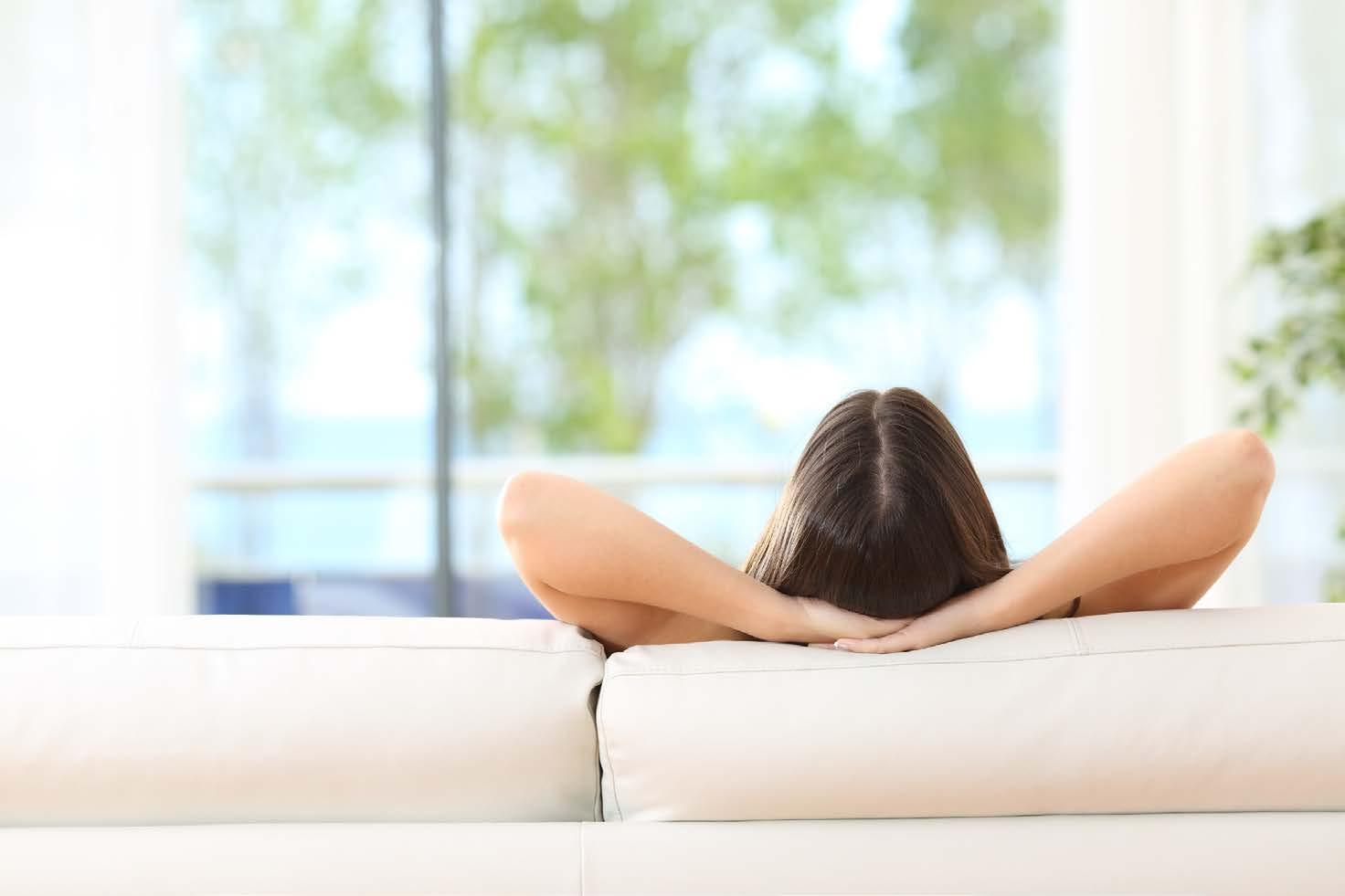
Your Partner for Healthier IAQ
North America’s largest manufacturer of HVAC expanded metal for Retail, Commercial, and Industrial Applications. Employee-owned and manufactured in California, Georgia, Texas. Developers of X-Mesh®, engineered for filter media backing. U.S. Patent 8,696,781
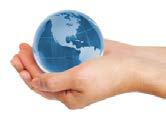
INDUSTRY CALENDAR
2024
2024 ASHRAE Annual Conference
June 22 - 26
Indianapolis, Indiana
Dominating The Digital Domain: Social Selling Strategies
June 27
NAFA Webinar 4:00 PM - 5:00 PM (EDT)
BOMA Convention
July 13 – 16
Philadelphia, Pennsylvania
NAFA NCT II Training & Testing
July 31
Des Plaines, Illinois
NAFA Virtual CAFS Q&A/Tutorial
September 18
2:00 PM - 4:00 PM (EDT)
2024 Annual Convention
October 1 - 3
Maui, Hawaii
PHCCCONNECT2024
October 7 – 10
Birmingham, Alabama
NAFA NCT II Training & Testing
November 13
Washington, North Carolina
2024 NADCA Fall Technical Conference
September 6 – 8
Cary, North Carolina
AHR Expo
February 10 – 12
Orlando, Florida
NADCA 36th Annual Meeting & Exposition
March 17 – 19
Savannah, Georgia
ACCA 2025
March 24-27
Austin, Texas
2025 Technical Seminar
April 2 – 3
Tempe, Arizona
2025 FiltXpo
April 29 - May 1 Miami, Florida
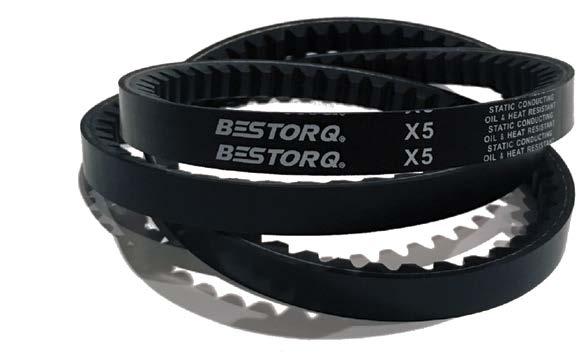


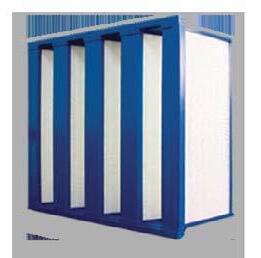
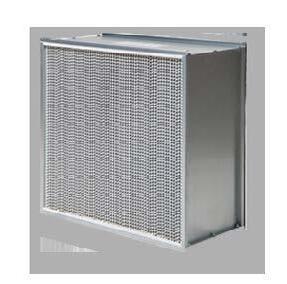


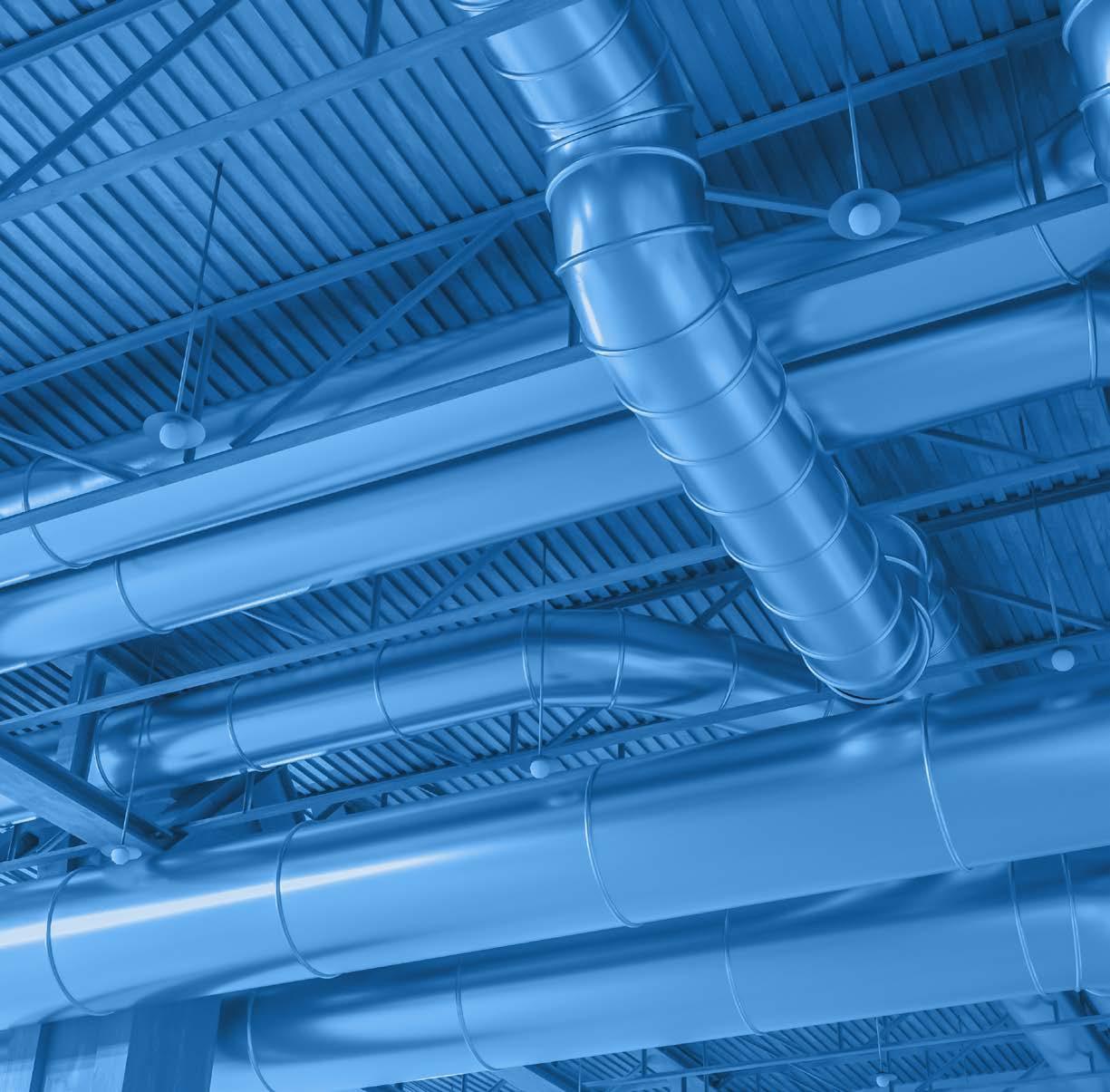
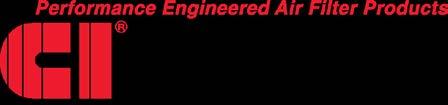
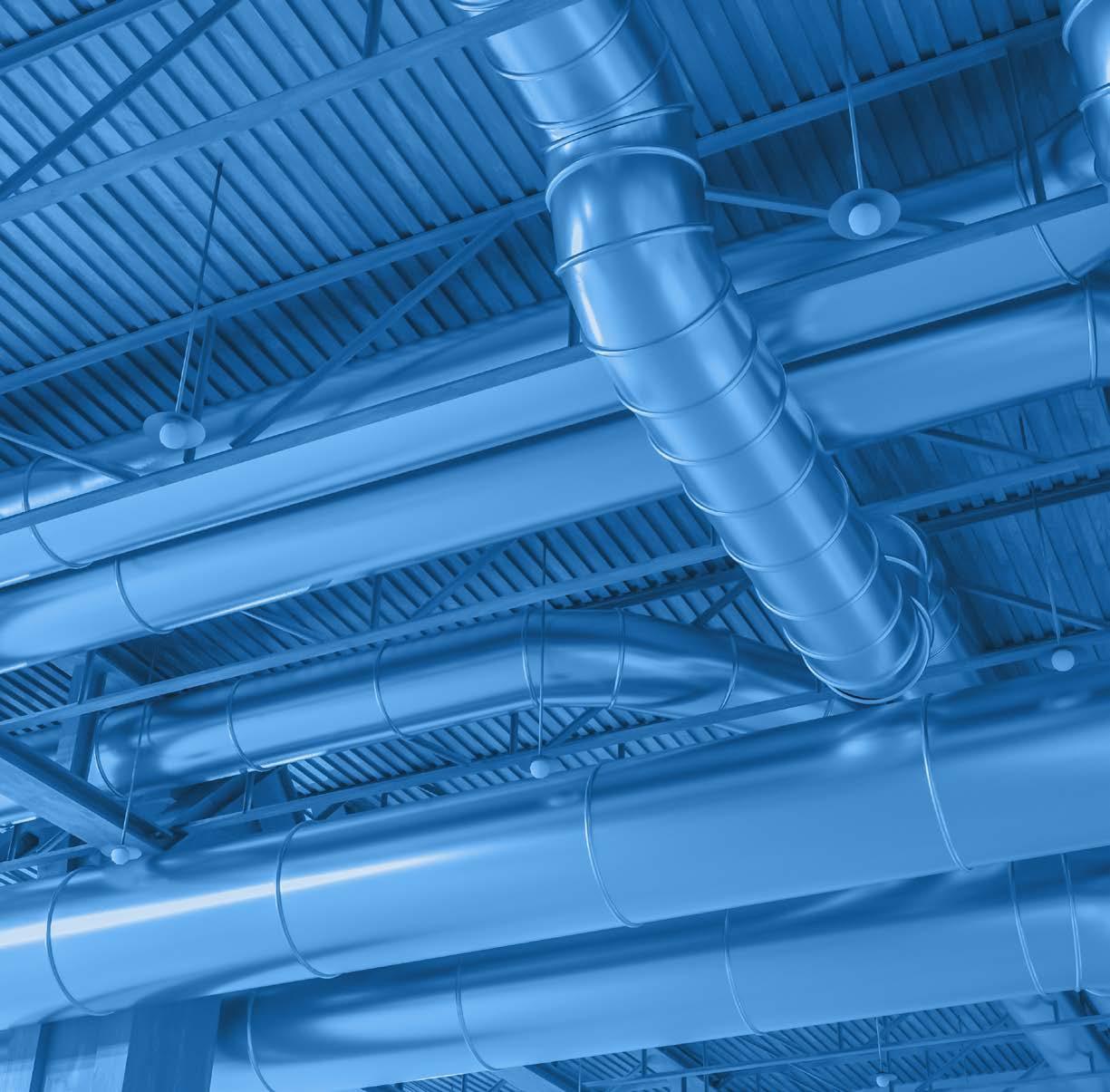
Installation, Operation and Maintenance of AIR FILTRATION SYSTEMS MANUAL 5 TH EDITION
In reviewing, updating, and making corrections to any document, you have to realize that you’re only as good as the sources you confer with. In this case, I would be remiss if I didn’t start off by thanking all the named and unnamed sources that I received input from, assistance with and discussions that were held to check or confirm the correctness of materials contained in this, the 5th Edition of the IOM. Additionally, having the guidance of Hunter Most as Committee Chairperson was invaluable. Of course, we must also recognize all of the contributors to the 1st through 4th Editions of the IOM, who developed and wrote the original content, which is still timely.
Overall, we made almost 1400 changes to the 4th Edition including replacement of content with updated information or corrections, many insertions of new data or wording to clarify content and of course, many deletions of items that were outdated or incorrect based on new knowledge.
Some of the key changes and additions are: Greater background on the new types of filters with ways to select and install/maintain based on updated recommendations from industry and manufacturers. How to properly manage multiple filter systems (2 and 3 filters) and updated criteria on how and when to change these filters based on utilizing available pressure drop data. Information on the importance of proper gasketing or sealing filters in both side-load and front-load filter systems to help prevent bypass and improper pressure data readings. Reference to updated ASHRAE 52.2 and ISO16890 standards. Inclusion of new worker safety
recommendations based on local, state and federal guidelines.
We tried our best to correlate any references in the IOM to the recently updated NAFA Guide To Air Filtration 6th Edition. Emphasis was on making sure that standards were consistently referenced, and any guidelines or recommendations were correct with current practices. As always, the science of Air Filtration is a dynamic one, and I’m sure that you’ll find instances where we will need to keep ahead of new technology, knowledge, and practices. If you do, please make a note of these items and forward them to NAFA Staff for inclusion in the next edition.

With the understanding that a large number of NAFA members are both CAFS and/or NCT I / NCT II Certified and own both a Guide to Air Filtration as well as the IOM, we made sure to align any references in both manuals, as well as spent quite a bit of effort to ensure that the Glossary of both manuals have the same definitions to terminology, something that I was surprised to see was lacking in the previous edition of the IOM. Any omissions or incorrect definitions are strictly my responsibility and not those of NAFA staff.
The overall intent of the IOM is to provide a useful tool to technicians who must have knowledge of Air Filtration Systems, how they operate and the correct manner in which to provide the best service possible to our/their customers. It is not a technical guide to the science of air filtration as the NAFA Guide provides that knowledge. With that in mind, we did not go into standards or technology except for providing a basic understanding required to perform duties related to technicians’ needs. As stated in the Chapter 1 Introduction, “This book is not a substitute for the IOM Instructions which Air Filter System
Manufacturers supply with their equipment”. It is impossible to consider every nuance of a manufacturer’s equipment and summarize those in one manual. In summary, this IOM highlights the important details involved in the IOM of most air filtration systems.
Thank you as always for the opportunity to help contribute to the education of our Air Filtration Professionals. I look forward to hearing how you successfully implement the ideas and techniques contained in the updated Installation, Operation and Maintenance of Air Filtration Systems Manual, 5th Edition.

JAY REESE, CAFS, J & BR Associates, LLC

• Standard & Special Size Mini-Pleats Available.
• Fiberglass & Synthetic Media Options.
• 2-V, 4V & 5V Models Available.
• Performance Ranges from MERV 11 thru 99.99%
• Quick, Reliable Lead Times.
• 5 U.S. Plants to Serve You.
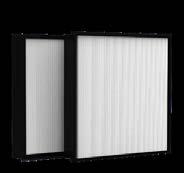


Desoto, TX Jacksonville, FL Juneau, WI Lancaster, OH Reno, NV
For more information, please contact us: (214) 741-7056 or inquiry@glasfloss.com
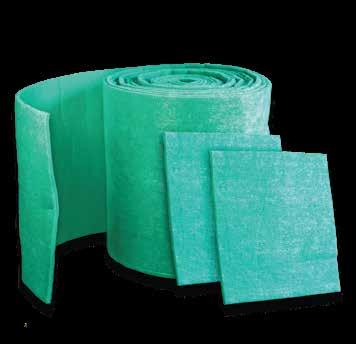
Puracell® VP & VPX
Puracell® II-S & II P-S
Puracell® II P & PH
APRIL 17-19, 2024
IRVING, TEXAS
NAFA TECHNICAL SEMINAR
RECORD-BREAKING ATTENDANCE FUELS LEARNING AND CONNECTION
The 2024 NAFA Technical Seminar in Irving, Texas, shattered attendance records, welcoming a recordbreaking 281 air filtration industry professionals. This two-day powerhouse event fostered an environment of learning, connection, and collaboration, leaving attendees empowered and equipped with actionable strategies for success. Speaker presentations can be found in the Member Hub online.
INSPIRING KEYNOTES:
• Traci Brown, CSP: Ignited the event with her engaging keynote, "Liar, Liar Pants on Fire," equipping attendees with valuable deception detection and fraud-spotting techniques. Now we know!
• Elizabeth McCormick, CSP, CW2: She motivated attendees with her "Soar Your Sales" keynote and equipped them with actionable strategies for achieving sales goals. And…everyone in the room learned to fly a helicopter! You had to be there.
INFORMATIVE EDUCATIONAL SESSIONS:
• "Leveraging NAFA Guidelines for Enhanced Sales and Customer Service" by Keith Jordan, CAFS, NCT: This session explored how to leverage NAFA guidelines to boost sales and elevate customer service.
• "Using Air Cleaning Devices with ASHRAE Standard 241": Michael Corbat, CAFS, and Kathleen Owen, ASHRAE Fellow, co-presented this session, which highlighted the critical role of air quality standards and filtration technologies.
• "The Future of Indoor Air Quality Post-Pandemic": Kyle Megna explored emerging market trends and legislative updates shaping the future of indoor air quality.
• "Assessing the Real Benefits of Filtration": Dr. Jeffrey Siegel provided practical methods for evaluating air cleaning performance across diverse environments.
ENGAGING PANEL DISCUSSION:
The final day culminated in a dynamic panel discussion titled "Selling Solutions: Insights from Filtration Industry Leaders." Moderated by Jeff Thibodeau, the panel featured industry stalwarts Phil Dugan, NCT II, Edward Gainsborough, CAFS, NCT, and Jon Holmes, CAFS, who shared their expertise on strategic sales approaches across various product segments and markets.
NETWORKING AND KNOWLEDGE SHARING:
Beyond the informative sessions, the seminar provided invaluable networking opportunities. Participants connected with peers exchanged ideas and gained valuable knowledge from renowned experts. NAFA members also enjoyed the NAFA Foundation Golf Outing , a premier networking activity that raises funds for critical research initiatives. Donations and revenue generated from the outing will support the NAFA Foundation's primary research in air filtration in 2025. This research will contribute significantly to advancing air filtration technology and benefit the entire industry.
The event concluded on a high note, leaving attendees energized and equipped with actionable strategies to navigate the everevolving air filtration landscape.
Many thanks to your 2024 sponsors for making this event possible. Special thanks to Rensa Filtration for sponsoring our opening reception and Graphic Packaging International for sponsoring our golf tournament!
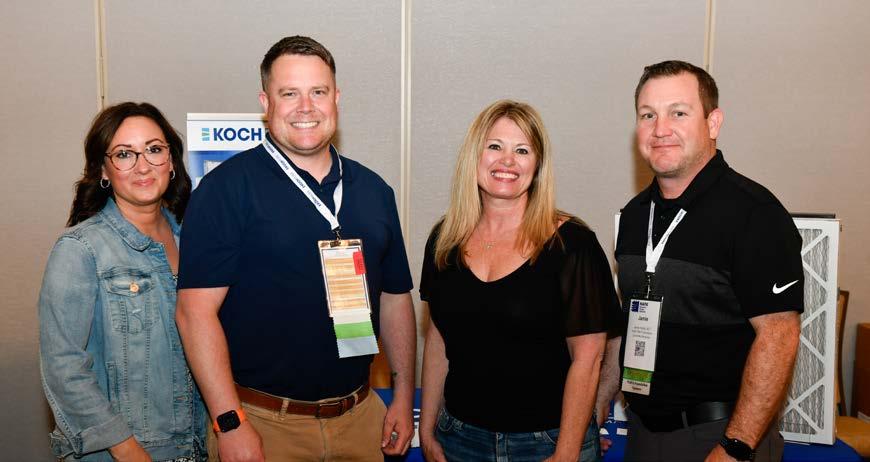
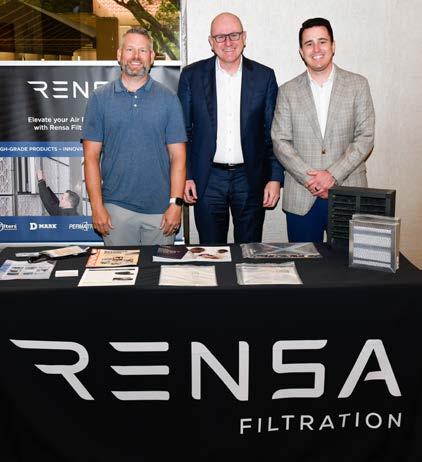

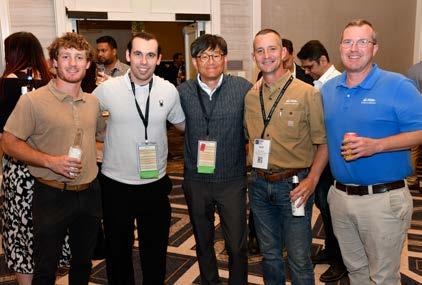


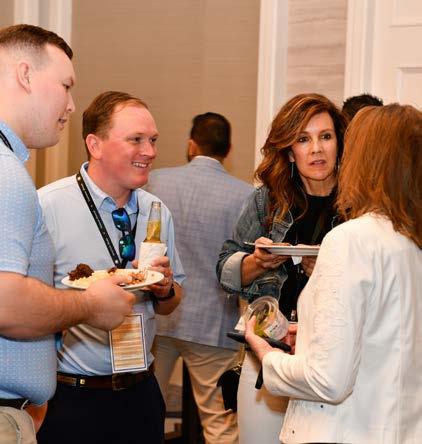
We hope you can join us next year in Tempe, AZ, April 1-3, 2025
SAVE THE DATE!
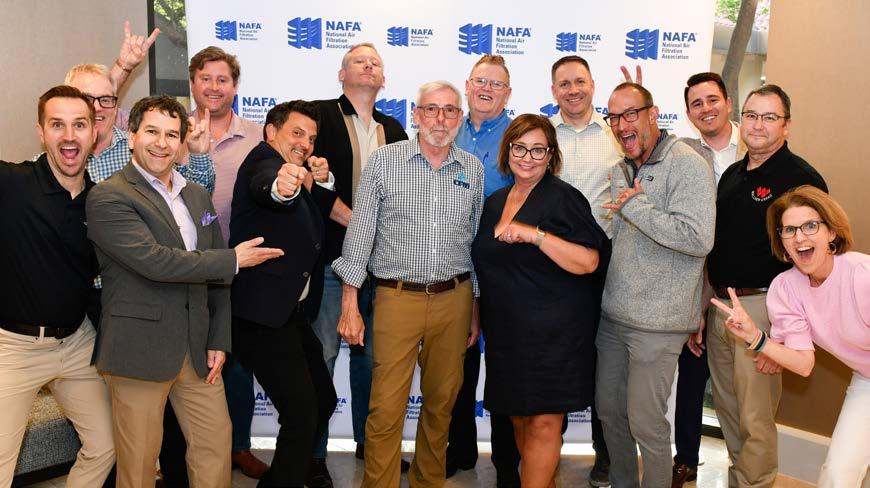
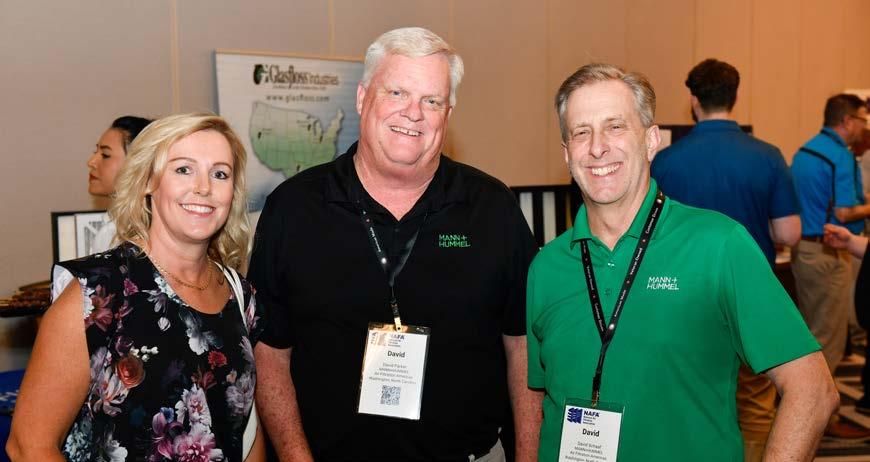
“ Connecting with like-minded professionals, experts, and organizations in the air filtration industry has been invaluable to Mikropor. We have formed lasting partnerships and friendships that have enriched our business journey.”
Jeff Thibodeau, Vice President – Atmospheric Air Filtration Mikropor America, Inc.
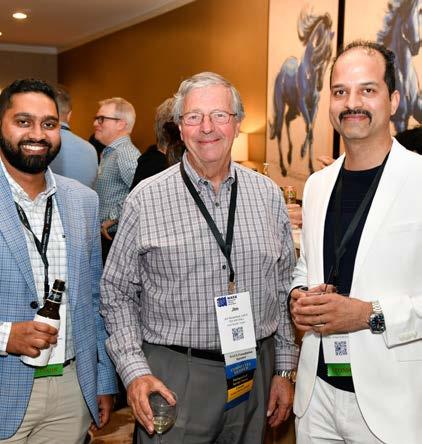


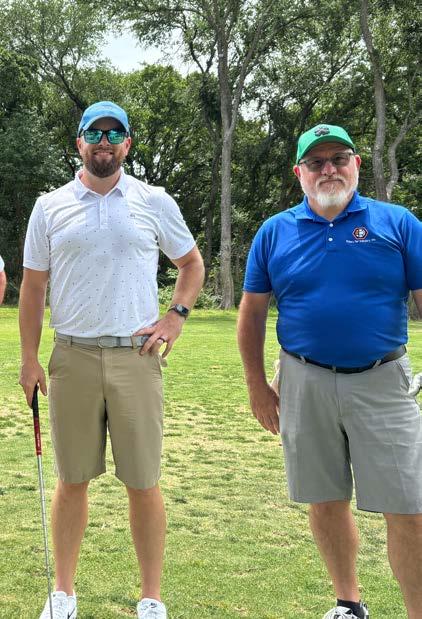
PLATINUM
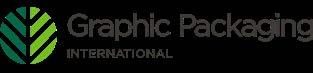

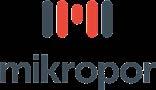
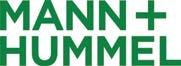
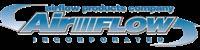

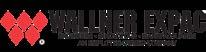

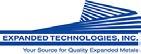
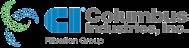
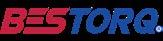
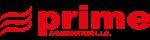

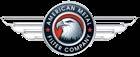


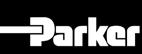
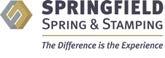

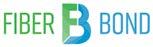
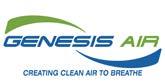

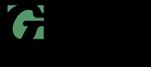

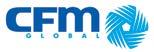
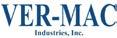
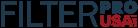


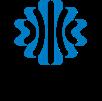
TO THE NATIONAL AIR FILTRATION ASSOCIATION
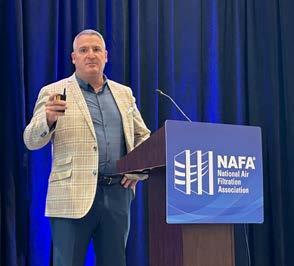
I am writing to express my sincere appreciation for the invaluable support and opportunities the National Air Filtration Association (NAFA) has provided Mikropor over the past several years. As a member and sponsor of NAFA, our journey has been remarkable, and we owe a significant portion of our growth and success to NAFA and everything the organization offers.
Since Mikropor's affiliation with NAFA began, we have witnessed tremendous growth. The wealth of knowledge, networking, and industry insights that NAFA offers has been instrumental in our progress. The resources provided by NAFA have allowed us to match our products and service, keeping us at the forefront of the air filtration industry.
One key aspect that makes NAFA stand out is the sense of community it fosters. There is no better networking organization in our industry! Connecting with like-minded

professionals, experts, and organizations in the air filtration industry has been invaluable to Mikropor. We have formed lasting partnerships and friendships that have enriched our business journey.
Furthermore, the support and exposure we've received as a sponsor of NAFA have been remarkable. This partnership has enhanced our brand recognition and positioned us as a trusted industry leader. The increased visibility has undoubtedly played a significant role in our company's growth and brand recognition.
I am grateful to NAFA for being a beacon of knowledge, collaboration, and opportunity. Mikropor's journey as a member and sponsor of NAFA has been a remarkable one, and we look forward to continuing our partnership and experiencing even greater success in the future.
Thank you, NAFA, for your unwavering commitment to the air filtration industry and for driving your members’ growth. We genuinely appreciate all you do and are excited about the future of air filtration and NAFA’s guidance.
Sincerely,
Jeff Thibodeau Vice President – Atmospheric Air Filtration Mikropor America, Inc.
To learn more about sponsorship visit https://www.nafahq.org/sponsor-program/
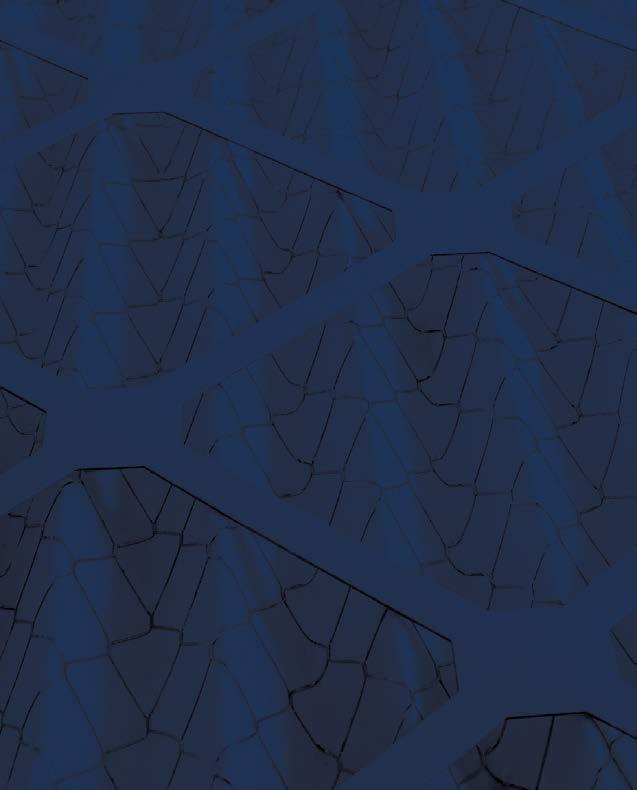
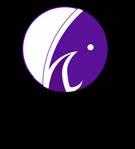
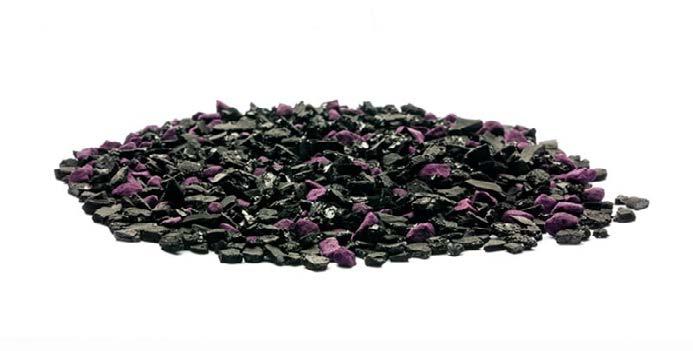
NEW CERTIFIED PERSONNEL
CAFS
Rob Castor, CAFS
ATL Filtration (Abatement Technologies)
Jason McGhee, CAFS
Colorado Air Filter LLC
Ramnethesh Manivannan, CAFS Century Mechanical Systems Factory, LLC
Joe Randolph, CAFS Camfil USA, Inc.
Dale Campbell, CAFS Filter Sales & Service, Inc.
Carry Somboune, CAFS Filter Sales & Service, Inc.
Lisa Greenfield, CAFS FilterPro USA LLC
Leo Lake, CAFS Filter Sales & Service, Inc.
Robert Shepard, CAFS
BGE Indoor Air Quality Solutions Ltd.
Hamilton Armstrong, NCT II, CAFS
Capital Air Filters, Inc
John Davidson, CAFS Camfil USA, Inc.
Jason Stringer, CAFS Camfil USA, Inc.
Sachin Bapu Bharati, CAFS Century Mechanical Systems Factory, LLC
Ashok Kumar Koneti, CAFS
Century Mechanical Systems Factory, LLC
Nick Royalty, CAFS
Capital Air Filters, Inc
Scott Meyer, CAFS Columbus Industries, Inc.
Maddox Henry, CAFS
Air Filter Sales & Service (MS)
Ryan Oddo, CAFS Clean & Science Co., Ltd.
Justin Hughes, CAFS Filtech, Inc.
Shannon Allmer, NCT, CAFS The Filter Man, LLC
Robert Snyder, CAFS Filter Services, Inc.
Maura Malartsik, CAFS Filter Services, Inc.
David Harney, CAFS Filter Services, Inc.
Michael Wigstrom, CAFS Filter Services, Inc.
Spencer Jezegou, CAFS
ATL Filtration (Abatement Technologies)
Katherine Foster, CAFS
ATL Filtration (Abatement Technologies)
Jonathan Baldin, CAFS
ATL Filtration (Abatement Technologies)
NCT
Brandon Deilgat, CAFS, NCT American Metal Filter Company
Cesar Valdes, NCT Air Quality de Mexico
Dylan Burrows, NCT BGE Indoor Air Quality Solutions Ltd.
Kevin Monty, NCT BFC Solutions/Pure Air Sales
Connor Croak, CAFS, NCT Genesis Air
Rebecca Garcia, NCT TEX-AIR Filters
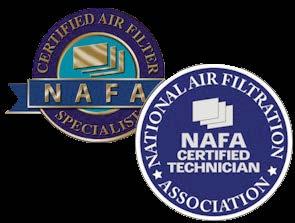
Samuel Mena, NCT Advanced Filtration Concepts, Inc.
Hector Rivera Santa Cruz, NCT VECO, SA de CV
Pat Borg, NCT The Filter Shop
Jebb Lakey, NCT POA
Marcus Prettyman, NCT POA
Dean Schmitz, NCT Air Filter Plus, Inc.
Stephen Taylor, NCT Air Filter Plus, Inc.
Moses Newton, NCT Goodwill Industries of San AntonioBusiness Services
Shannon Allmer, NCT, CAFS The Filter Man, LLC
Jack Edwards, NCT The Filter Man, LLC
Hector Trevino, NCT The Filter Man, LLC
Charles Washington, NCT The Filter Man, LLC
Kevin Benitez, NCT Advanced Filtration Concepts, Inc.
Raheel Rabbani, NCT
BGE Indoor Air Quality Solutions Ltd.
Mike Kostuik, NCT
BGE Indoor Air Quality Solutions Ltd.
Ronnie Malibiran, NCT
BGE Indoor Air Quality Solutions Ltd.

When clean air is critical. Introducing our NanoWave 16/16A.
World’s only synthetic 100% mechanical bag filtration.
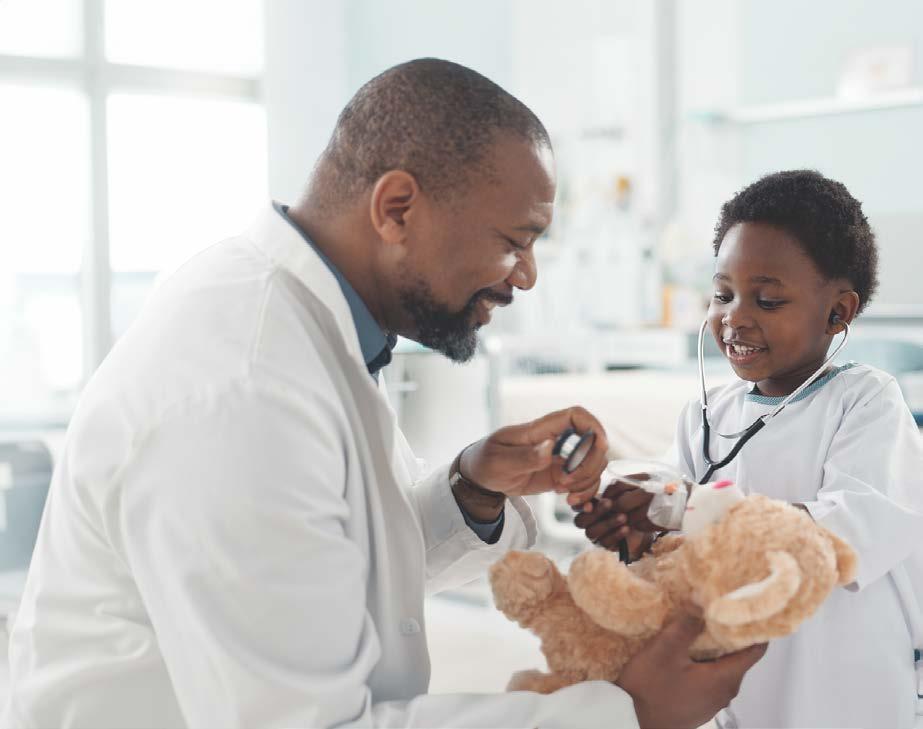
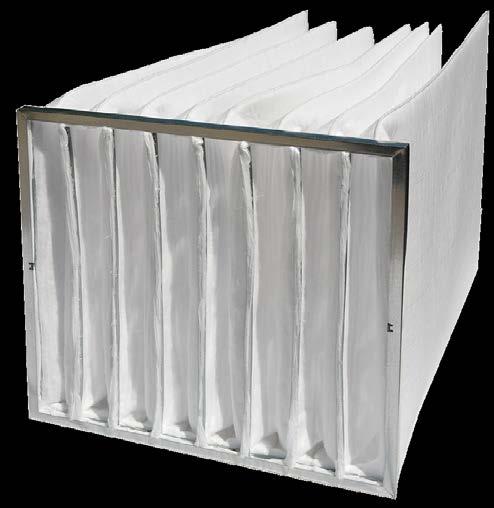

NanoWave Media
Synthetic media is moisture resistant and uses internal “waves” to increase surface area.

Pocket Filters
Its gradient density, multi-layer 3D design achieves MERV 16-A Appendix J at a lower pressure drop than competitive materials at a MERV 13 Appendix J.
Testper52.2AppendixJ
2.5x more effective media area for a 15-30% lower pressure drop

High DHC (790 gms) with Low IR (0.34”) for a 8 pocket 22” depth filter

40% estimated energy savings after 1 year of usage


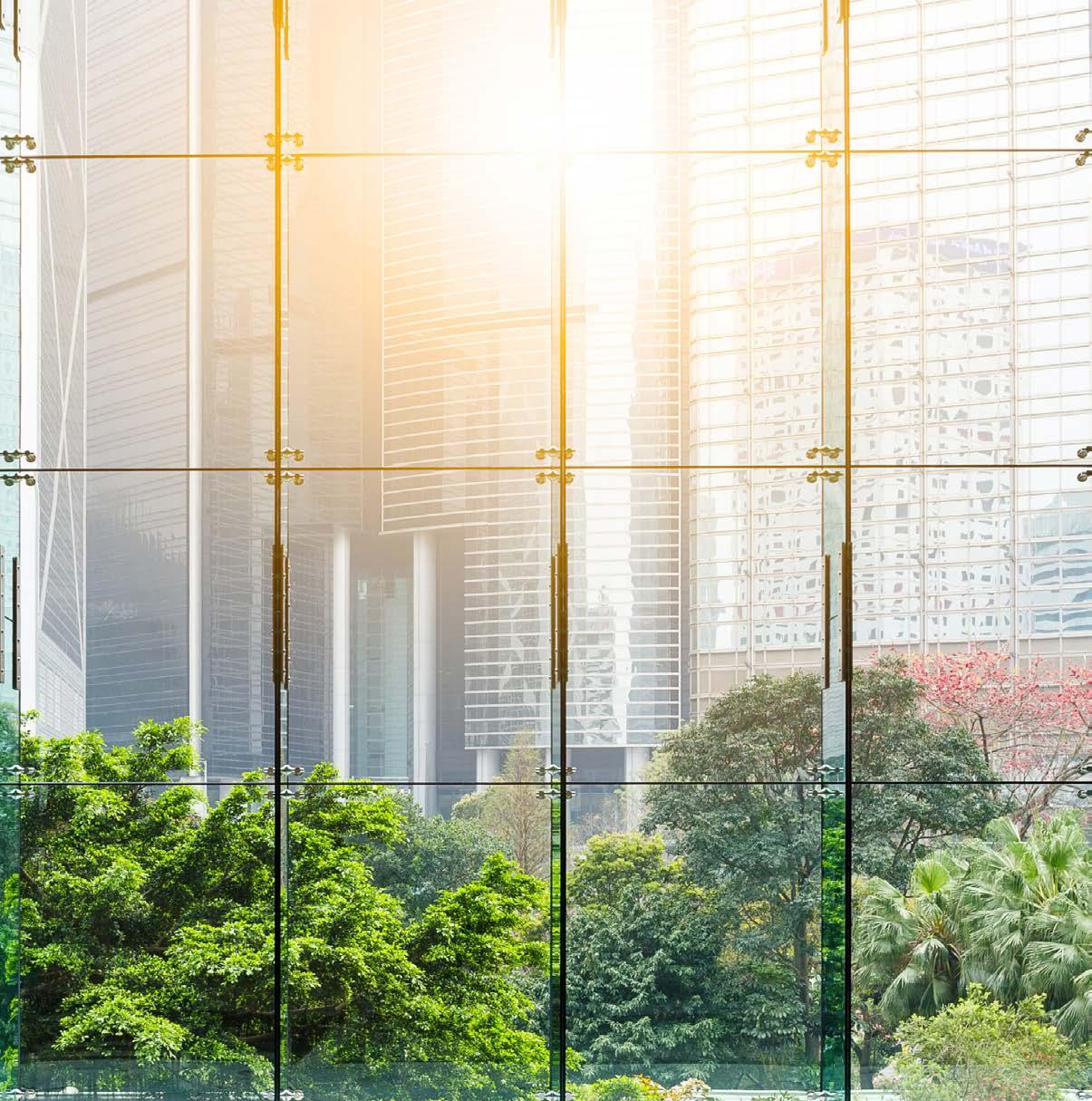
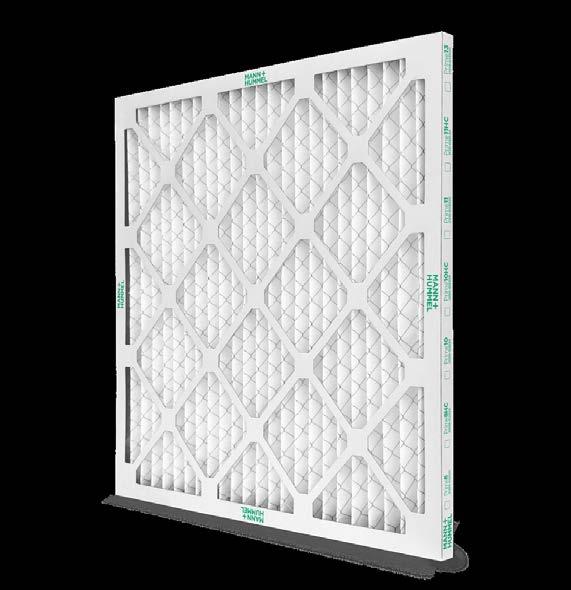
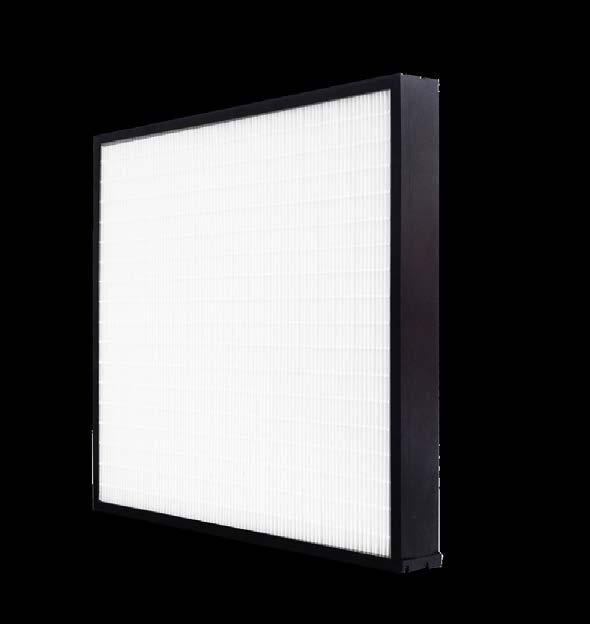
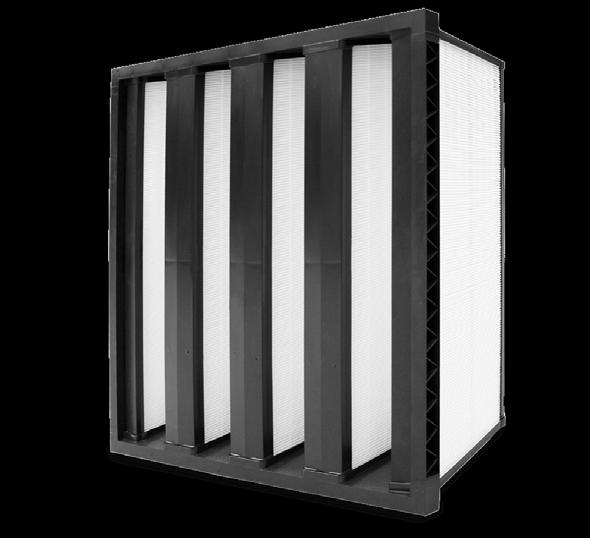
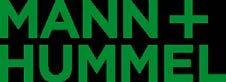