
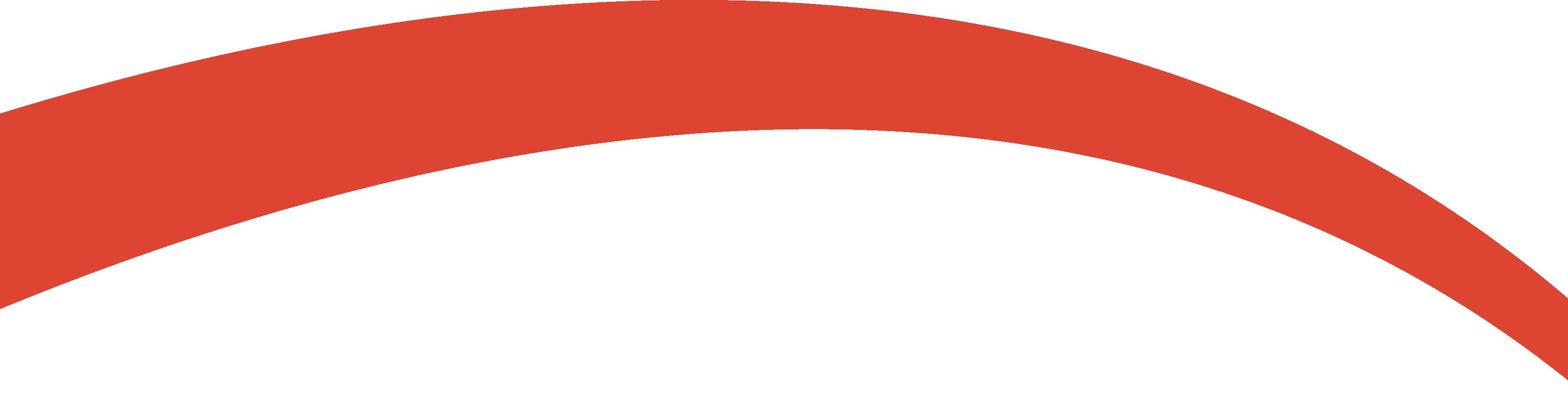
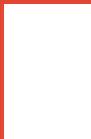
Viscosity is referred to as the thickness of a fluid. Solution viscosity in mixing can have a big effect on the best system for obtaining consistent results.
Viscosity is an interaction between different molecules in a fluid, often referred to internal friction. This internal friction will determine the energy required to make a fluid flow.
Mixing can be described as the process in fusing two or more ingredients together that are otherwide seperate and independant through an external force.
Optimum mixing results are seen as a uniform, homogeneous solution that is entirely free of agglomerates. This if easily achievable in less viscous solutions of water-like substances whereas obtaining the same results in materials of much higher viscosity can often prove a challenge. In order to achieve homogeneous, consistent results when mixing materials of high viscosity, detailed understanding of the rheologies and agitation forces involved are required.
For solutions under 5,000cP the flow that comes from mixing is considered chaotic and the action of the faces of the impeller blades in the mixer is important and can range from 2 to 10 times the diameter of the blades. Low viscosity solutions have a higher turbulence and extended flow. So in order to understand the fundamentals of high viscosity mixing, an understanding of the nature of flow, worked out by the Reynolds number, needs to be obtained.
‘The higher the viscosity, the less turbulent the flow’
Flow within mixing can vary dependant on the solution type. There are four different flow types that can be acheived in a certain volume of fluid.
• AXIAL FLOW
• RADIAL FLOW
• TANGENTIAL FLOW
• HIGH SHEAR
‘The higher the viscosity, the less turbulent the flow’
Flow is described in terms of the intensity it creates, measured by comparing the fluctuating velocity against the mean velocity. Different mixing impellers are suited to the corresponding materials in which will be mixed.
Axial Flow: Axial flow impellers are used with low viscosity media and are excellent for blending and suspension duties. The flow pattern has a strong axial suction and bundled discharge stream in the turbulent flow range. The outlet jet stream is deflected at the bottom and reaches the surface in the wall area of the vessel. The liquid is accelerated in the propellor zone.
Radial Flow: Radial flow impellers are used with a range of viscosity media and are excellent for gas liquid mixing and dispersion duties. The flow pattern is ideal for low level mixing. The liquid is accelerated via centripetal force outwards of the propellor zone until meeting the tank wall where flow is directed both upward and down to create effective mix patterns and movement. Multiple impellers required for tank geometries greater than 1:1.
Tangential: Mixquip Gate style impeller are typically used with highly viscous materials and in the laminar flow range to disrupt the boundary layer adhering the vessel walls where heat transfer is required in both heating/ cooling applications. Fingers or frames can be added to increase versatility of these impellers or combined with axial/radial blades as a countre rotating mixing system
High Shear: Mixquip’s high shear impellers are suitable for the blending and homogenization of liquid or similar or greatly varying viscosities, including the disintegration of solid and semi-solid materials. The high shear work heads are ideal for rapid size reduction of soluble and insoluble solids are the solution is dispersed through the mixer head at a great force causing consistent agglomerate free results.
Turbulence is measured using the Reynolds number. The Reynolds number helps to predict flow patterns in different fluid flow situations, and is the ratio of inertial forces to viscous forces within a fluid which is subjected to relative internal movement due to different fluid velocities.
THE REYNOLDS NUMBER
Once you have the Reynolds number measurement for a flow, you can determine the eddy currents that form.
With respect to laminar and turbulent flow regimes:
• Laminar flow occurs at low Reynolds numbers, where viscous forces are dominant, and is characterized by smooth, constant fluid motion; this is a figure of around 2,000.
• Turbulent flow occurs at high Reynolds numbers and is dominated by inertial forces, which tend to produce chaotic eddies, vortices and other flow instabilities. Turbulent flow is represented at a figure of around 20,000.
Turbulent flow is the relationship between the fluid velocity and a point in a related eddy, a sizing that can fluctuate according to the turbulence type. These flows will eventually move into each other and form new eddies; causing chaotic turbulence. This results in a better mix and a more uniform structure, however the challenge of high viscosity mixing is creating this chaotic turbulence by relying on the pushing structures of impellers rather than then left over momentum from the last push of the impeller.
When mixing viscous solutions, the end goal is to bring the same uniformity and homogeneity found in a turbulent systems to the laminar system. Below is a list of points to help enable you to select the correct high viscosity mixer depending on your process.
High viscosity mixing requires a mixer that moves the solution with high intensity with a high degree of interlacing. Interlacing creates angles and pushing movement of the impeller to force two streams of laminar motion to collide into one another. If using a viscous system, the radial or tangential impeller is a better choice when compared to the axial impeller type, as these impellers increase the surface area. Eddy currents are less likely to form when substances are being mixed in the viscous range, and the mix moves in a streamlined way and actually stops flowing before it reaches the blade.
Mixes here are not promoted through any turbulent flow. The energy from the blade itself also tends to dissipate, leading to heat buildup around the blade and within the substance mix, but no exchange of heat. This kind of reaction leads to a low Reynolds number and differential of velocities between streamlines.
Mixing is conducted to blend two or more solutions together in a unform way. The outcome in uniformity of the end product affects many parameters in the resulting mix. Consideration of the characteristics of the mix that you are trying to prioritize is first, this could range from durability to reaction rate. Consideration of actors that you will need to achieve your mark, including mix, load and cleaning technique along with hardware downtime, mixer design and power consumption is also important, as well as temperature and pressure controls and vacuum on the mixer itself.
Shear is usually created within processes of a low Reynolds number. The stress that occurs between the differences leaves a byproduct of heat, a stress that tears apart the particles. This condition is formed within the viscous flow range. If you are looking to maintain the size of the particles during the mixing phase, you may not want shear, although it is helpful in the process of deagglomeration.
Any mixture above 500cP means that it is a non-Newtonian fluid. If the mixture is below this figure, this mean that it is a Newtonian fluid and the viscosity will be low and constant. Read about the three different types of non-Newtonian fluids:
1. Thixotropic mixes have a lower viscosity compared to that of rheopectic products where viscosity will rise in a time dependent system with a consistent shear rate.
2. Time independent systems with increasing shear will cause pseudoplastic products to decrease in viscosity whilst dilatant mixes increase.
3. Viscoelastic fluids will be able to recover elastically if it is deformed by the mixer blade flow. The most common type of fluid sub-class in this profile are polymeric fluids. Polymeric fluids also exhibit the Weissenberg effect, and effect that causes the mix to move up the shaft.
Extra equipment may be required if a process must be kept between a certain range of temperatures, for cooling or heating purposes. If the case is especially demanding, you may need an automated, command control system for heat exchange. Every device that you add here will require a higher investment of time and capital, including operation and maintenance costs.
As you consider your process and mixer required to obtain best results, there is a list of points to take into account.
Speak to our team on 1300 20 70 20 or mixquip@teralba.com if you have any questions relating to viscosity or flow types.
• Shear is directly related to the speed in the Newtonian system.
• Shear increases viscosity in dilatant substances and decreases viscosity in psuedoplastics in non-Newtonian systems. As shear is held constant in a non-Newtonian system, the viscosity of rheopectic and thixotropic materials is directly related to time.
• As the space between the blade mixers and the shell of the tank increases, shear and power demand increase alongside viscosity.
• You can produce shear through themotion of the blade through the mix. The shear that you produce is afected by a number of factors: blade width, speed, design, number, product viscosity and the proximity of the blades to the wall and to each other.
• Rotational type high viscosity mixerswork at low blade tip speeds with a range between 200 to 800 ft/min.
• Horizontal mixers can be especially good if the geometry of the blades are in order alongside having the correct viscosity and rheology of the product. If you get no tumble from the product, you can compensate by using Z type blades with dual arms that force extrusion action. These blades cost substantially more, however.
• If you need to improve the axial batch movements in a vertical mixer, use an auger. They should be operated alongside a tubular shell in order to maintain their vertical efficiency. Budget extra time for cleaning.
• You can obtain both vertical and horizontal mixers with a saw tooth or high speed chopper blade type; you do not have to use the high torque, slow speed blades that most mass production efforts use. High speed blades with a tip speed between 2,000 and 5,000 ft/min generate more shear. However, high-speed blades will only generate flow within a short distance when it comes to viscous materials. In most cases, a lowspeed blade is used as a feeder into the highspeed blade to improve homogeneity andheat transfer. This is especially important if the overall batch viscosity at the beginning of the process is low.
• If you are looking to maximize the performance of your open helical blades, use them alongside supplementary agitation. You may also lower or raise the blade. This extra energy will reduce the incidence of stationary toroidal vortices.