
11 minute read
Exothermic lime-based CCS
LIME-BASED CARBON CAPTURE SYSTEM OFFERS POWER BOOST
An Australia-based technology developer, Calix, is developing an onboard carbon capture technology that uses lime as feedstock and also captures SOx and NOx emissions
The RECAST system uses an onboard carbonator to combine engine exhaust gases with lime powder. The resulting exothermic, CO2 capture reaction generates heat to about 600oC that is recovered and used to run a steam turbine.
Phil Hodgson, Managing Director of Calix, says: “A lot of people don't realise that half the weight of a lump of limestone is actually CO2 trapped in the rock, and you need to heat that to about 950oC to drive the CO2 out to form lime. The RECAST system absorbs the CO2 back into the lime and gives off a lot of heat. That is what we're tapping in to.”
Calix has announced plans to package its RECAST technology with British firm Windship Technology's windand-solar-assisted drive train, and it will also eventually be available for other applications. In the Windship configuration, the RECAST system could supply about one sixth of a ship's propulsive power. Another third would be provided by wind power, a sixth by solar power and the remaining third by diesel gensets.
The supply of feedstock is virtually circular, as the limestone produced onboard is returned to shore and reprocessed back into lime ready to be used again. Some gypsum forms amongst the limestone as the lime reacts with SOx, and this can be replaced with a small amount of lime and recycled for use in cement production. Both powders are easily moved with blowers, says Hodgson, and apart from the carbonator, the onboard system components required are all off-the-shelf items.
The space required to store the lime is three to four times that of the bunker fuel consumed, but in the Windship Technology system, sails, solar panels and RECAST all add power to the ship, so bunker tanks can be reduced in size. In any case, says Hodgson, it is still significantly less space than will be required for some new fuels such as ammonia or hydrogen. Limestone is readily available around the world and could be made available to 80 percent of the global merchant fleet from just 12 ports.
Lime is used extensively in producing steel, aluminium, rare earths, gold and many other minerals. It's production currently emits roughly one tonne of CO2 per one tonne of lime produced and is thus a significant contributor to those industries' carbon footprints.
Calix has developed technology for CO2 mitigation in the production of lime through the European LEILAC-1 and 2 projects. Their unique kiln captures the CO2 from the raw limestone and can be powered by electricity or renewable fuels. The technology is now being demonstrated at scale at HeidelbergCement's site in Hanover, Germany, as part of the LEILAC 2 project. The demonstration plant is capable of separating 100,000 tonnes of CO2 per annum and is a critical step in demonstrating the application of the carbon capture capabilities of the kiln to the cement and lime industries.
Since then, Calix has executed a Heads of Agreement with Adbri Limited for an Australian lime production project with CO2 capture and multi-fuel options. A feasibility study is expected to be completed early in 2022. The project is framed around a five-year development and demonstration program and represents a world-first development of a commercial-scale, zeroemissions lime production facility. Funding will be sought from the Australian government. The use of low-emissions lime as both a sorbent and a fuel for the ship is a valuable new application for the company's technology portfolio, says Hodgson. Initial estimates suggest RECAST could cost less than US$50 per tonne of CO2 emissions saved by shipping, making it cost-effective as well as safe and reliable. Calix, with Windship, will be working on the conceptual design and feasibility study for marine applications over the next 12 months. A first pilot is expected to be a system of about 250kW before increasing that to an onboard demonstration of a couple of megawatts within two years.
RECAST inventor and long-term team member at Calix, Dr Brian Sweeney, said: “If RECAST technology were applied to the 25 percent of ships covering high-mileage that use 80 percent of global bunker fuel, with other technologies for the smaller emitters, our initial estimates indicate the reduction in emissions would make the total world maritime fleet carbon-zero.”
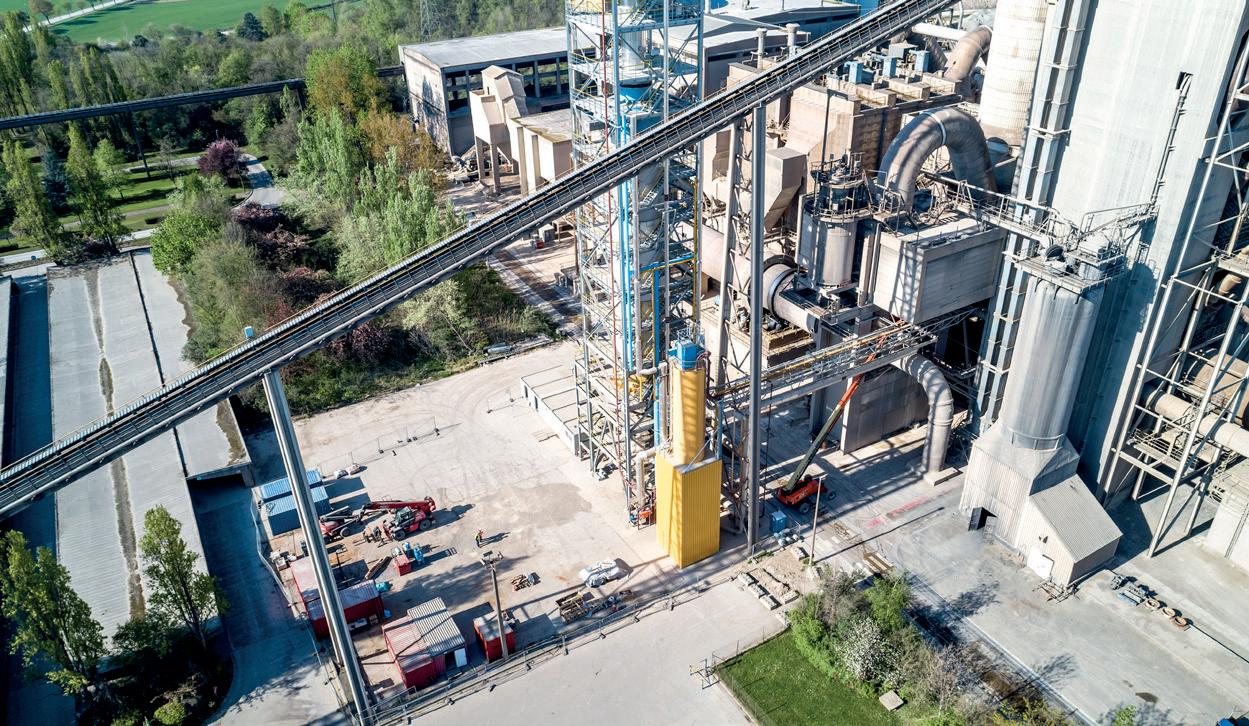
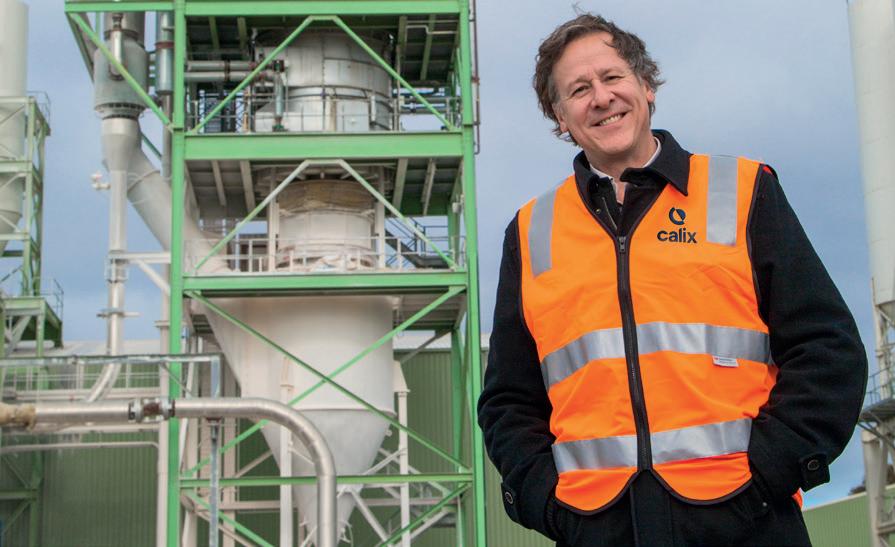
8 Calix developed
technology for CO2 mitigation in the production of lime through the European LEILAC-1 (pictured) and 2 projects. Inset: RECAST inventor and long-term team member at Calix, Dr Brian Sweeney
8 Phil Hodgson in front of the Calix Flash Calciner in Victoria, Australia
EFFICIENCIES WILL INCENTIVISE THE DIGITAL SWITCHOVER
Digitalisation solutions are increasingly penetrating engine rooms, but the industry will need to address barriers to fully benefit, writes Samantha Fisk
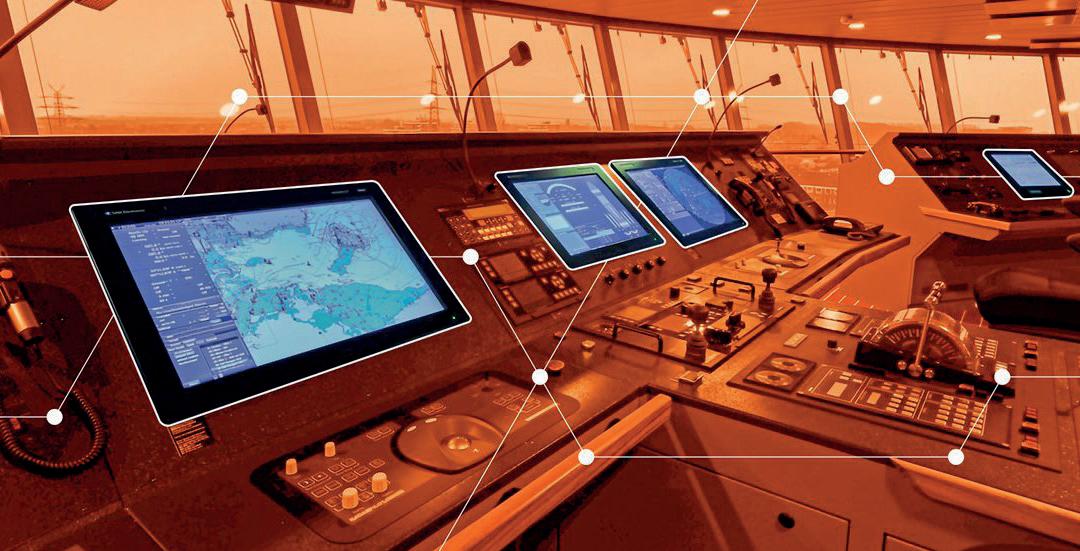
When most people consider the effects of the digital revolution on the maritime industry, digital documents or blockchain might be closer to the front of their minds than marine propulsion. Yet the potential effects of such improvements on mechanical and analogue systems are no less far reaching.
In fact, given the potential for digital solutions to improve the efficiency of engines and their fuel consumption, the potential savings for shipowners exceed those of streamlined back office operation. By extracting insights from key data from these systems, vessels will also be able to lower their emissions to meet the demands of regulators and charterers.
While the potential efficiency savings offered by such solutions have attracted interest, the adoption of digital solutions in engine rooms has been steady rather than spectacular. Not all owners have been convinced, while other owners have chosen to take a 'wait and see' approach until final product versions are released.
Engine designer and technology developer WinGD has responded by incorporating digital technology into product developments as standard. Luca Sala, Senior Manager Product Strategy at WinGD explains with the company's WinGD Integrated Digital Expert (WiDE) has now been “installed on several vessels” since its release in 2018.
WiDE allows the collection and analysis of ship and machinery data in order to proactively predict component anomalies to offer support through live troubleshooting and diagnostic advice to the crew.
Sala explains that WiDE gives better visibility to how the engine is functioning. “It enables crew to be more effective at their job and gives proactive advisory to the crew.” The advantage of having such as solution is that you can “learn from the fleet” and update how vessels operate quickly.
WinGD has received positive feedback from customers that have installed WiDE with one highlighting that it has seen improved performance monitoring, reduced time for trouble shooting, improved maintenance planning and has empowered crew onboard in the way they work.
The steady pace of technology adoption onboard vessels may be slower than some would like but its advantages mean it is likely to continue in a phased way over the coming years. However, shipping's conservative nature may have been a strength when it comes to adopting these new technologies.
Sala notes that the industry will see more hybridisation integration in the transition period as digital technology starts to be adopted. A key element of having all these technologies onboard will be how they communicate with each other. “You can reduce up to 25% on the overall operating costs by integrating efficiently different technologies by using a digital master system to ensure every component is working properly and at the same time operate them as one solution.”
Jarle Blomhoff, Team Leader Systems Engineering, DNV comments about the rollout of technology, that it first needs: “Enablers to have things in place so that things can be digital, such as sensors, infrastructure and central data. These will also need to be standardised and secure.”
Fuel optimisation is a key area of development for digital solutions as the cost savings offer shipowners clarity about the potential value of solutions. Dr Marlies Koch, Customer Experience Leader. Group Digital, MAN Energy Solutions SE adds that: “Fuel savings are an important part and are realised today, but the actual savings depend on the used fuel type/price, the operating mode, etc.”
However, Dr Koch also explains that it is important to also
8 A common
connectivity standard remains high on the wish list of solutions providers
consider other factors when looking at cost saving such as engine type, age and operating condition of the engine, as these can affect the type of cost savings that can be achieved. Another advantage of tools for vessel optimisation is that they aid in the “prevention of unplanned outages (leading to off-hire, drydocking, etc), by replacing low-cost spare parts early on, preventing major repairs later, which is also a big lever,” Dr Koch adds.
Bringing it all together
However, one of the challenges that has been particularly highlighted over the recent year is the lack of connectivity onboard vessels and steps to how the industry will overcome this is still unclear. “Practically there is no existing connectivity standard - we see frameworks for standard-setting (i.e. ISO 19848 or 19847), it still remains open, how these translate and are adopted into practical solutions”, comments Dr Koch.
Currently we are seeing more solutions that are coming on to the market that will need connectivity to be able to maximise their full potential. “The need to connect is present, may it be OEMs, owners, managers, licensees, etc. - as each party has only a share of the data, that they ideally need to share to get the most insights”, Dr Koch says. “Mid-term some Cloud2Cloud solutions will gain a critical mass to organically force new partners to its standards, so we will see a consolidation”, Dr Koch adds.
Overcoming the challenges
Technical challenges still lay ahead mainly with connectivity. As Dr Koch explains that: “Establishing the connectivity cabling/hardware/firewall and satellite configuration itself is a challenge with vessels that ad-hoc change routes and where time in port is short.”
Sala also highlights that there is also a need to create trust in the solutions and that by working with customers and other industries bodies will help to create that trust in the industry.
However, Norwegian-based ScanReach are also looking at this with the solutions that they are providing to the industry. ScanReach has seen substantial growth from entering the market as a start-up to now becoming a full-grown business with its technology implemented on 40 vessels.
Its main service is as a wireless IoT company which has seen that there is a need in the maritime industry for better connectivity onboard vessels. Initially ScanReach introduced to the market its life saving solution Personnel Onboard (POB) Control that allowed crew to traced onboard in an emergency such as a fire.
This solution was developed by using wireless technology. Jacob Greg Eide comments about the development of the technology that: “the cost factor of re-cabling a ship is too high. So we looked to wireless.” From this ScanReach has now moved from being a technology provider to a solution provider with its wireless platform. It offers three solutions to the market which are its ConnectPOB, ConnectFleet and ConnectFuel.
With its ConnectFuel product Eide explains that owners can monitor fuel consumption at any time. “Vessels can see a 5% saving just by imposing certain thresholds”, he comments. From systems becoming more connected, more data will be harvested that will also allow shipowners to get a better view of how systems are operating and to make more critical decisions or how systems are operated.
Dr Koch also adds that: “Data will be the basis to develop new insights and today we do not know, which data will be of importance tomorrow, connectivity and storage are becoming ever cheaper and these help to enable retention of as large a pool of historic data as possible.”
There is lots of value in data, if the right data is extracted and will give shipowners further insights into operations. “Data will be the basis to generate insights both for serving the customers today with optimizing their OPEX, but also going forward in improving engine design to be even more reliable, flexible, efficient and with an ever-lower environment footprint”, Dr Koch explains.
Data sharing also needs to be done in the proper way, Sala comments. How to manage data and support digital solutions is a discussion that is happening in the maritime industry.
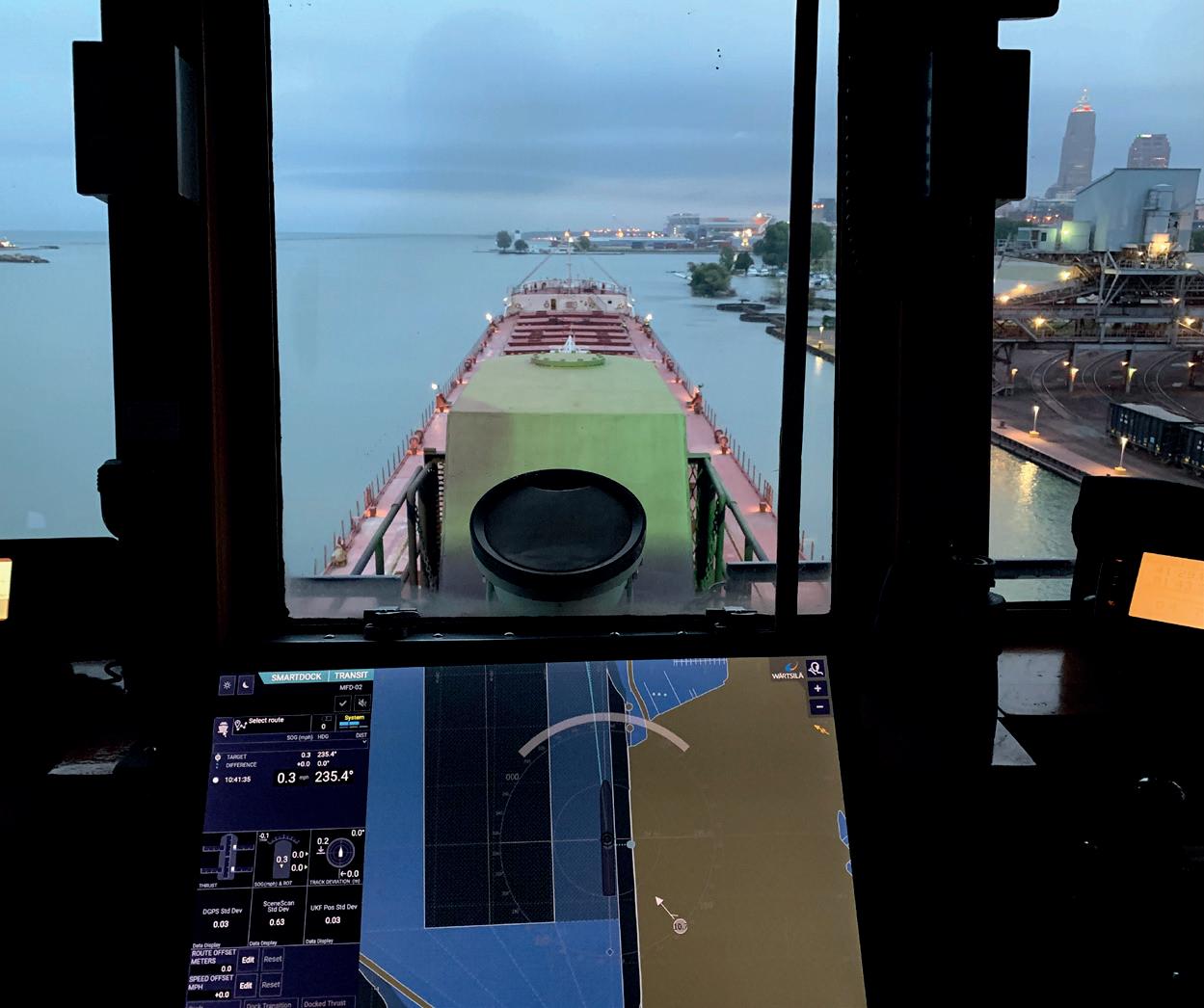
8 Safety concerns remain paramount in the introduction of digital solutions
It's all about safety
While digitalisation is a highly topical subject, and encompasses a wide range of solutions, it also offers safety benefits for ship owners and operators. Through the adoption of digital technologies, safety is expected to increase due to better monitoring and processes that it will bring. Safety concerns remain paramount in the introduction of digital solutions.
An area that is also getting more interest is that of cyber security, with the implementation of digital products and also the recent pandemic, shipowners are now becoming more aware of the need to protect their digital assets from hackers. Blomhoff highlights that the industry is now thinking about cyber security and currently there is “little cyber security around the engine room” and notes that as more digital solutions get installed onboard there is a “higher probability of attack”.
IMO launched its IMO2021 cyber security resolution that aims to help shipowners tackle this new threat. The rules have been based on the IEC International 62443 code with maritime amendments. Blomhoff notes further work needs to be done in educating the industry. DNV is currently working alongside an engine manufacturer that is looking to address this. WinGD has also been looking at its own cyber resilience when it comes to it digital solutions and take a three-stage approach to its cyber security. The first is in the infrastructure of the business, the second is in the operating systems. WinGD is looking at having the first embedded system approved. The third stage is at company level, to make sure that people, processes and procedures are all compliant.