
12 minute read
E-assisted turbo
NEW PEM FC FRONTIER FOR mtu ELECTRIC-ASSIST TURBO
Rolls-Royce's new electrically-assisted mtu turbocharger system has been successfully tested on the component test bench and on a 10-cylinder diesel engine test bench and is now ready for use in projects where increased transient response is required
The technology is suited to diesel and gas 4-stroke engines, regardless of whether traditional or new fuels are used, and is also applicable to fuel cells.
“The tests achieved significant improvements in the transient response of the engine,” says Dr. Johannes Kech, head of turbocharger development at the Rolls-Royce business unit Power Systems. “We consider electrically assisted turbocharging to be technically mature and will use this technology in projects where increased transient response is required. This applies in particular to gas engines where we need to achieve a high level of responsiveness.
“At the same time, this technology is also suitable for charging fuel cells, since in the case of fuel cells, the exhaust gas energy is not sufficient to drive the compressor via the turbine. Permanent electrical support is required.”
A simpler solution for turbo lag
Rolls-Royce Power Systems acquired the rights for the new technological approach from Germany-based G+L innotec in 2017. The system is specifically designed for engines that need a fast dynamic response, as the turbocharger can be accelerated electrically so that charge pressure can be built up earlier, thus preventing turbo lag. In the past, attempts to overcome turbo lag relied on more complex and expensive solutions involving sequential or alternating switching concepts and adjustable turbine blades. The mtu system is a return to design simplicity in comparison.
The improved dynamic response obtained is especially useful for gas engines, says Kech, as the transient behaviour of the turbocharger is essential for maintaining the dynamic response of the engine in this case. The new technology also means that emergency standby gensets will be able to deliver their full output faster than was previously the case due to the increased load response capability.
The system offers greater engine management flexibility, enabling engine operation to be optimised for reducing fuel consumption and emissions, says Kech. The use of an electric motor makes it possible to virtually decouple the operating point of the turbocharger from the speed of the engine.
Adaptability enhanced by permanent magnet technology
The electric drive uses a permanent magnet upstream of the compressor wheel, with the electrical windings integrated into the casing of the compressor. The large gap between the magnet and windings ensures that air drawn in by the compressor does not affect the aerodynamics of the charger and that existing chargers can be adapted easily to make use of the technology - the additional installation space required for the electric motor is relatively small. The system's specially designed power electronics are cooled by intake air.
Fuel cells require a different design
On a combustion engine, electrical assistance is only needed for a short time during the acceleration phase or in case of a load step, but fuel cells need permanent electrical assistance as the exhaust energy is not high enough for the turbine to drive the compressor. The low exhaust temperature requires a completely different turbine design. As oil in the air would poison a fuel cell, Rolls-Royce has also developed oil free bearing systems.
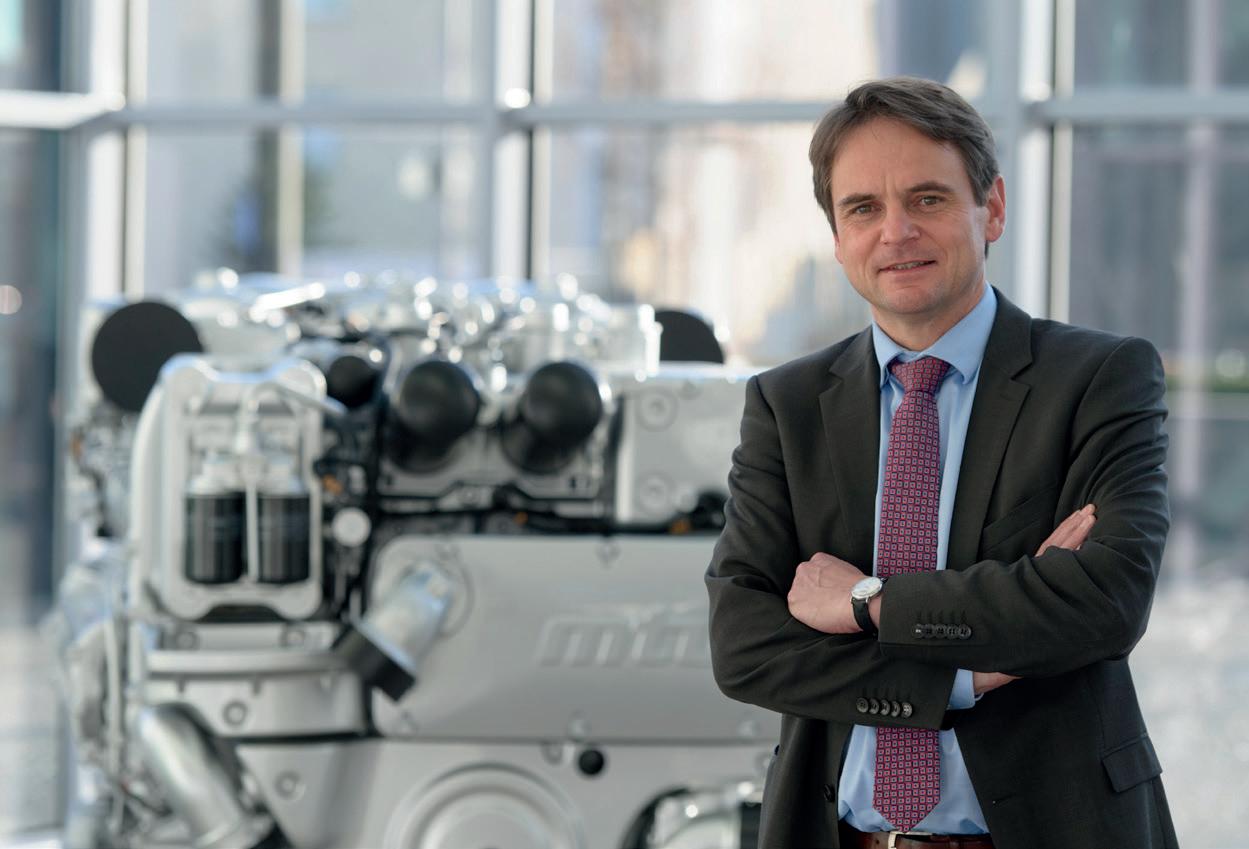
8 Dr. Johannes
Kech, head of turbocharger development at the Rolls-Royce business unit Power Systems
Deal with MAN Energy Solutions expands market potential
In June this year, Rolls-Royce Power Systems and MAN Energy Solutions established a strategic partnership that will see MAN's PBST brand distribute mtu turbochargers. The partnership aims to combine the benefits of PBST's global sales structure for turbochargers and Rolls-Royce's latest high-efficiency mtu turbocharger technology, including the electrically assisted technology. For Rolls-Royce, the partnership creates a new channel for sales in addition to Woodward L'Orange.
“MAN/PBST intends to use this cooperation to offer our turbocharger portfolio on the market, not just for itself, but to all engine manufacturers worldwide,” says Kech. “This means that the focus would be on a target market in the power range up to 10MW for high-speed diesel and gas engines.”
Kech notes that there is currently no ambition to expand the mtu portfolio or the electrically assisted technology to two-stroke engines. Rather, PBST will initially include the latest generation of the mtu turbocharger family ZR1 to ZR5 in its product portfolio and will distribute them under the series name HIRO. The mtu turbochargers are offered on the basis of a modular system for engines in the 400 to 2,500 kilowatt power range in single- and two-stage versions.
8 Dr Kech identified
gas engines and fuel cells as two areas where electrically assisted turbocharging technology offered particular advantages
Wärtsilä AND RINA PROPOSE NEW POWER GENERATION
A new ship power concept targeting tankers and bulk carriers developed by Wärtsilä and RINA relies on two 4-stroke dual-fuel LNG engines for both propulsion and electric power generation
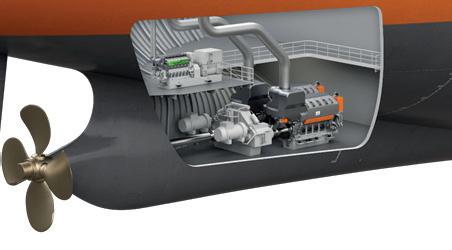
Typically, tankers and bulk carriers have a 2-stroke engine for propulsion and three 4-stroke engines for electric power generation. The Wärtsilä / RINA Smart Propulsion Machinery arrangement, however, requires just two 4-stroke dual-fuel (DF) engines, one larger than the other, with electric power back-up supplied by batteries or a small DF generator.
The design can achieve a reduction of up to half of the Energy Efficiency Design Index (EEDI) reference level value and results in immediate compliance with the IMO's 2030 targets. It also offers full redundancy, less machinery, lower capital expenditure, reduced operational complexity and optimised fuel consumption to lower costs, the designers assert.
The arrangement features Wärtsilä 31DF engines operating with LNG fuel. The engine has the flexibility to use future zero-carbon fuels without major conversion effort, thereby facilitating the pathway to decarbonisation, and has already been tested and verified for hydrogen, bio-LNG and synthetic LNG. Tests for LNG fuel combined with up to 30% ammonia are underway . “To stay compliant with future legislation, you need to have a very modern engine and one with the flexibility to use future fuels,” says Johnny Kackur, General Manager, Merchant and Gas Carrier Segment, at Wärtsilä.
The diesel version of the Wärtsilä 31 engine type has been recognised as the world's most efficient 4-stroke diesel engine. The platform has a second-generation common rail fuel injection system, quick load response, low smoke formation and accurate, twin needle technology. It also features variable valve timing with stepless inlet valve timing, on/off exhaust gas valve timing and extreme miller timing. While high-pressure 2-strokes are thought to offer the best GHG emissions performance, Kackur says that when total energy consumption at actual ship speed is considered, this is not necessarily correct, and the Smart Propulsion Machinery concept with Wärtsilä 31 series engines becomes very competitive.
Optimised for realistic ship speeds Optimised for realistic ship speeds
The propulsion machinery is optimized for actual ship The propulsion machinery is optimized for actual ship speeds, not maximum speeds, and at normal ship speeds, speeds, not maximum speeds, and at normal ship speeds, one engine is enough to cover all propulsion and electric power generation on board. With only one main engine in operation most of the time, the vessel can operate at high engine load and high efficiency levels.
The concept includes compact shaft generators and a controllable-pitch propeller enabling propulsion efficiency to be optimised over a wide range of speeds, rather than just design speed, says Kackur. Although a reduction gearbox is required, the configuration gives absolute freedom to vary propeller rpm. The ability of the shaft generator to operate in heavy seas without overloading the engines reduces installed and auxiliary power requirements and lowers operating costs. The Smart Propulsion Machinery concept also includes a two-stage turbocharger as standard, and this improves efficiency, particularly at part load. As the design also eliminates the use of HSFO on board, the design removes the need for purifiers and the boiler and steam systems on bulkers.
At current ship speeds, the system performance of the new arrangement provides at least the same, or better, efficiency than an equivalent 2-stroke design, Kackur says. At even slower speeds, the new 4-stroke configuration has the
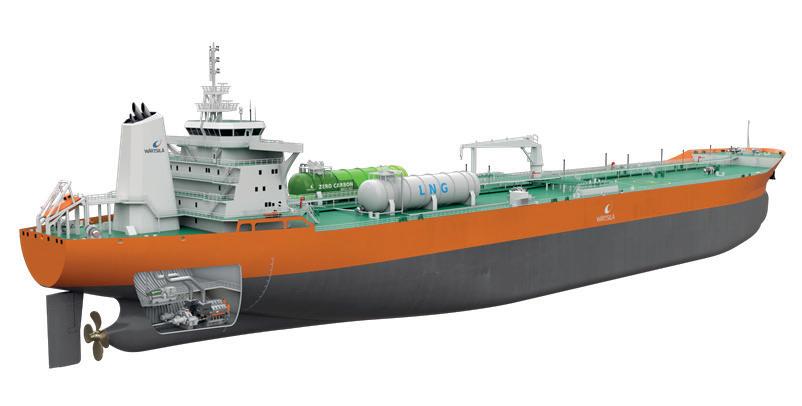
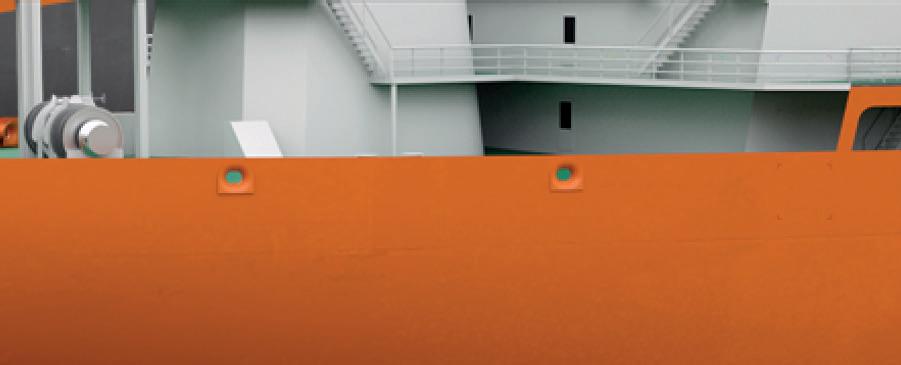
8 The Wärtsilä/
RINA Smart Propulsion Machinery arrangement features two 4-stroke dual-fuel (DF) engines and a small DF genset
8 The concept
includes compact shaft generators, a controllablepitch propeller and a two-stage turbocharger as standard
potential to reduce fuel consumption and emission levels further still. He notes that current engines operate far below their optimum. Sailing speeds are around 20% below the typical design speed specified around a decade ago resulting in a 50% decrease in engine power requirements.
Cost benefits
Kachur says that while some believe that maintenance costs for medium-speed 4-strokes are higher than 2-strokes, this is no longer the case. Wärtsilä's 31 engine series achieves maintenance intervals that are the same as or longer than 2-stroke engines. “The total maintenance costs for our Smart Propulsion Machinery concept are typically lower than for conventional machinery, partly because of lower installed power.” Additionally, remote monitoring and control means that Wärtsilä is able to support ships' crews in optimising performance and minimising downtime. With only one engine running at sea, there is less risks for failure, and sharing running hours between the two engines means the larger engine can be overhauled every five years, and the smaller, less-used engine every 10 years. The two-engine redundancy also allows for the overhaul of a main engine at sea if ever required.
“The combination of fewer running components and 100 percent redundancy, with a single engine capable of handling both propulsion and electric power, even in port, promotes both safety and reliability,” says Antonios Trakakis, Greece Marine Technical Director at RINA. Additionally, he says, early indications from shipyards are that initial investment is the same or less than a corresponding 2-stroke design. Finding space to fit an LNG bunker tank is unlikely to be an issue, as the 4-stroke engines are much shorter in stature than the 2-stroke engine they would replace. This means there is room to fit an LNG bunker tank on deck above the engine room.
LNG into the future
Natural gas is the cleanest burning and fastest growing fossil fuel, accounting for almost one third of total energy demand growth through the last decade - more than any other fuel, and Trakakis says the strong future for LNG globally is something that the shipping industry shouldn't ignore. Demand for natural gas is projected to grow by over 1,200 BCM in the next 20 years, and production is expanding. For example, Qatar Petroleum signed a contract for its North Field LNG project expansion, aiming to boost the country's LNG output by 40% a year by 2026. More than half of expected future LNG demand is expected to come from countries with net zero emissions targets, and 65% of gas demand growth in the next 20 years is expected to come from non-power sectors as emissions are reduced from industry and transport.
There are now over 120 ports with LNG bunkering facilities, and this is anticipated to increase to 170 by 2022. The LNG bunkering fleet is also anticipated to double in size over the next two years.
Trakakis predicts that fossil LNG will still account for a significant percentage of shipping's fuel mix in 2050. However, before then, it provides a clear path to carbonneutral methane. Carbon capture technology is particularly promising because it can be used, together with green hydrogen, to catalytically convert recycled carbon molecules into carbon-neutral fuels.
New fuels pose challenges
On an energy basis, the cost of synthetic methane equals that of methanol, he says, and a recent study from Delft University of Technology suggests that for same energy content, green ammonia might be twice the price of carbon neutral methane. Other studies attribute the synthesis cost of green ammonia to be three times that of methane. These new fuels will definitely come at a premium, Trakakis says, and it is questionable whether the shipping industry will accept and pay this premium, although other sectors, with fewer options, might. LNG has always shown less price volatility than liquid bunker fuel, and the increase in supply and rapid expansion of markets will result in even lower and more stable prices.
Aside from price, new fuels pose technical challenges. Ammonia has a very slow sped of combustion which results in less engine efficiency and higher consumption, says Trakakis. It has narrow flammability limits and requires an unrealistic compression ratio of 35 or a large percentage of pilot fuel. Bunker tanks would need to be twice the volume of LNG tanks, difficult to achieve, particularly on bulk carriers, and ensuring there were no ammonia leaks or ammonia slip would be a costly, but necessary, component of any ship design.
“The risks of handling hydrogen are well known to people, but it's different to apply them onboard ships than to apply them ashore,” he says. Using liquid hydrogen onboard is difficult due to excessive boil off or the need for 700 bar storage pressure. Bunker tanks would need to be around three times that of LNG, so even more difficult to accommodate than ammonia tanks.
The use of bio-diesel raises food or fuel issues around the feedstock used, and methanol, per unit energy output, only achieves an 8% reduction in CO2 emissions compared to current liquid fuels. LNG achieves a 26% reduction. Further, consumption of bio-methane serves as a sink for greenhouse gases and has the same supply and distribution network as LNG.
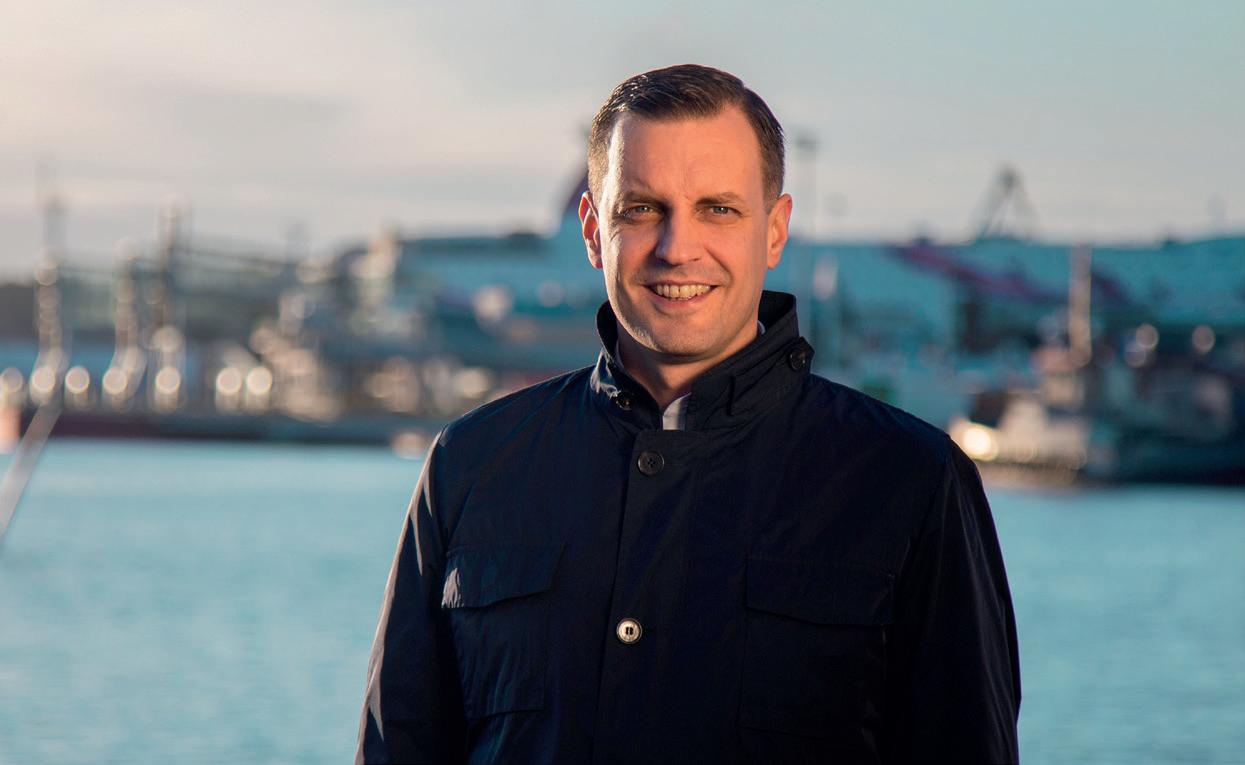
8 Johnny Kackur,
General Manager, Merchant and Gas Carrier Segment, at Wärtsilä
No time to wait
Trakakis says that while many believe new fuels will be available over the next decade, indications are that this will not really be the case. He believes that new, green fuels won't be available in large quantity until beyond 2040, so shipowners should rethink any plans to waiting and just relying on slower sailing speeds until then. This risks competitiveness. He says the facts clearly demonstrate that the wider energy generation markets are embracing LNG, and shipping cannot justify taking a separate pathway or waiting for new fuels. When zero carbon fuels do start to become available, shipowners that have waited will have to either make a big investment for an older age vessel or decommission that ship before the end of its useful service life.