DRIVING SUSTAINABILITY IN NEW
HAMPSHIRE
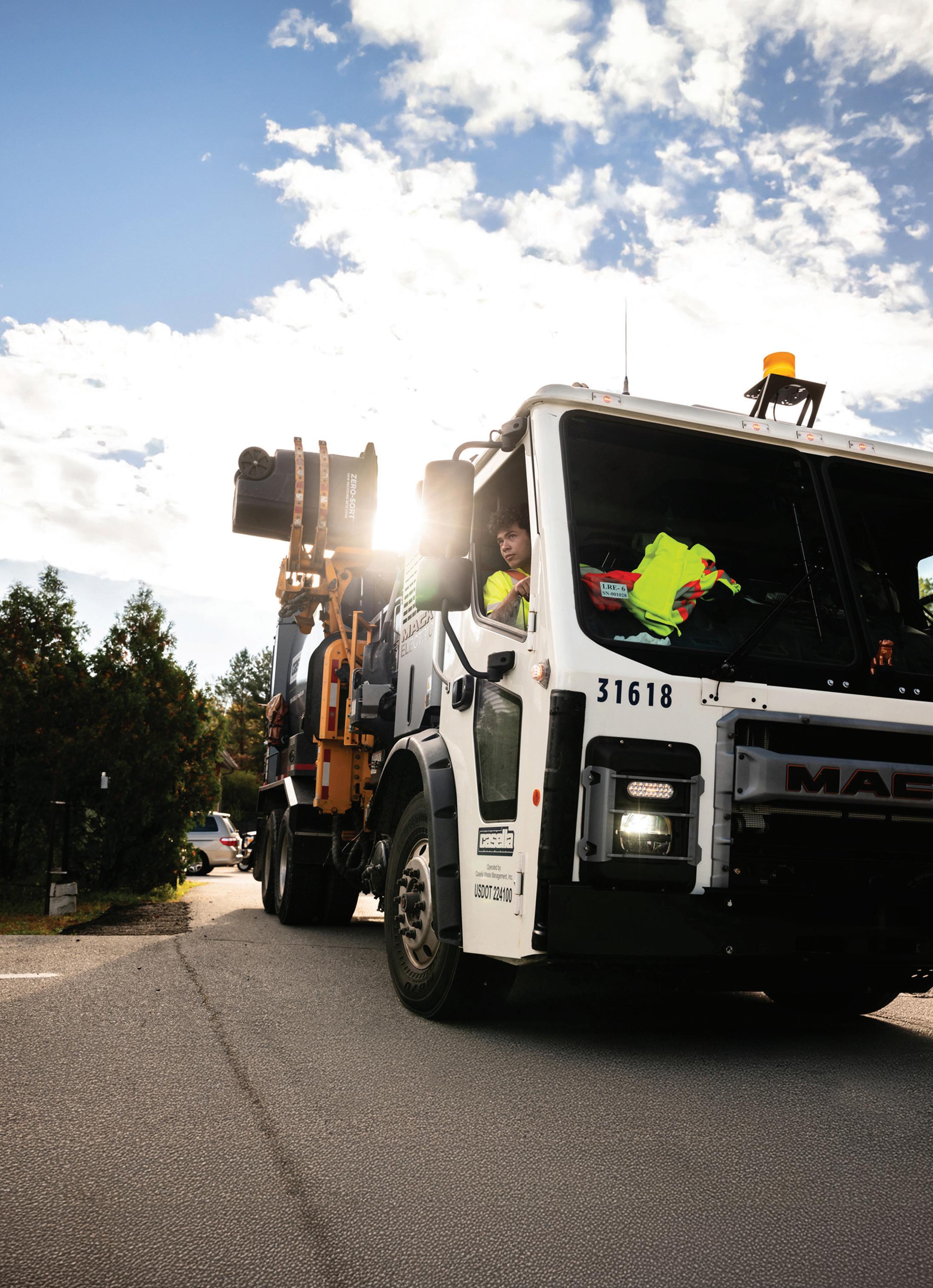
Casella celebrates 50th anniversary
Zero-sort recycling process
Drivers making a difference and more!
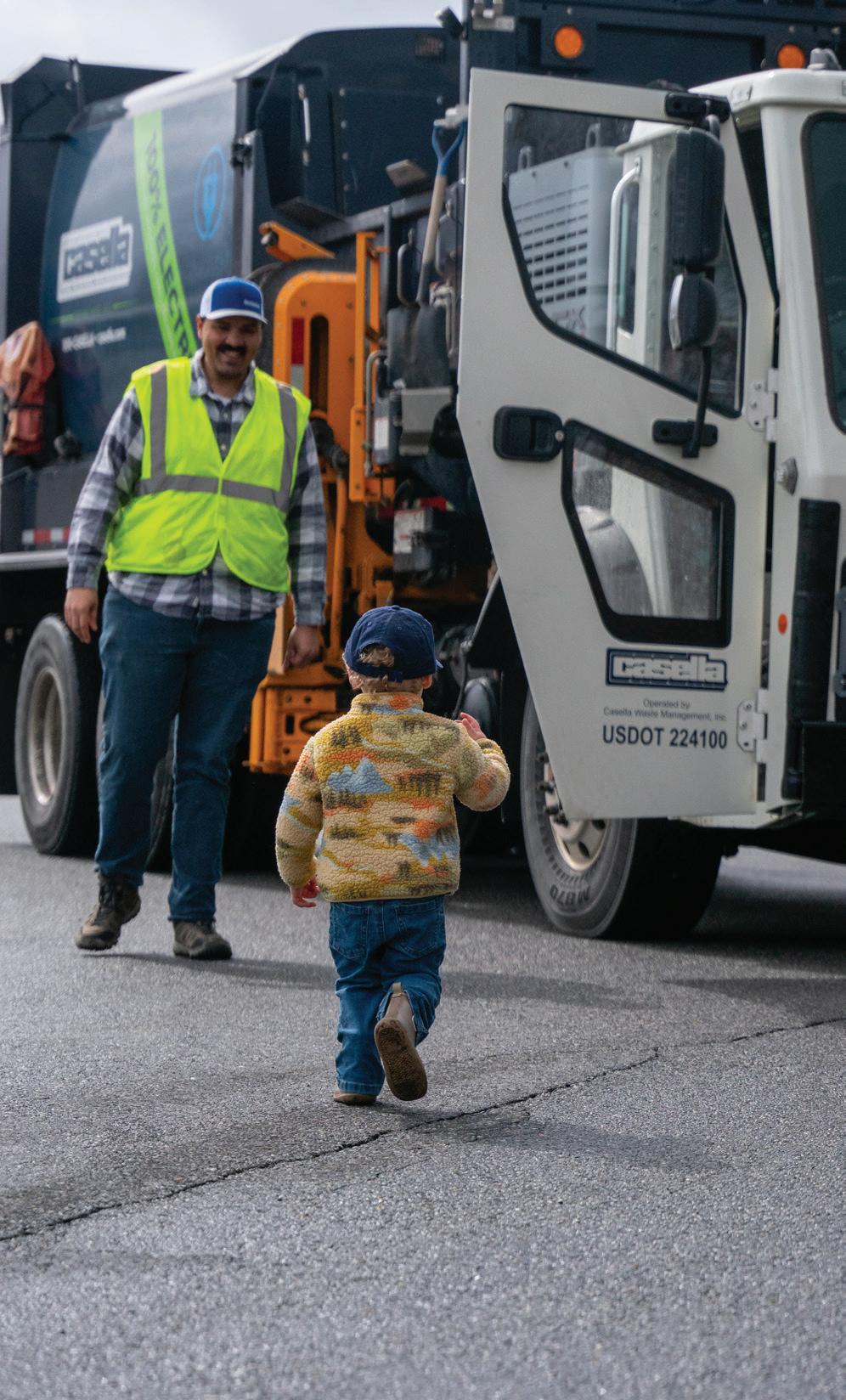
Casella celebrates 50th anniversary
Zero-sort recycling process
Drivers making a difference and more!
BY JOHN W. CASELLA CHAIRMAN & CEO
hat was true in 1976 when Ken Hier became our first employee to service Killington Mountain Resort, our first commercial customer, remains true today: Our people are our biggest differentiator and competitive advantage as a sustainable enterprise.
As our organization continues to grow, we earn the opportunity to introduce our sustainability vision and our Core Values to new customers and communities, and to new employees and their families, throughout the Northeast, Mid-Atlantic, and beyond. Guided by our Core Values, our sustainability efforts are central to all that we do. They are supported by three pillars: our people, our operations, and the value that we create and share. This year’s report details important accomplishments and milestones in all three areas.
The Kenneth A. Hier Sr. Training Center has trained more than 300 new drivers and technicians with a focus on safety, service, and commitment to excellence. Our total investment in training newly minted Commercial Driver’s License (CDL) drivers is nearly $1.5 million to date. Company-wide, we continue to invest in our people: mechanics, technicians, front-line leaders, and all our other vital personnel. We are committed to serving each other, our customers, and our communities so that our organization will continue to flourish. In 2023, as part of our efforts to reinforce this commitment to touch all facets of the company, we restructured our annual incentive compensation plans. Now, all bonus plans include a goal to improve safety and employee turnover performance year over year. Both targets were exceeded in their first year.
The investments we’ve made in engagement, safety, training, recruitment, and retention are passed on exponentially to the
customers and communities we serve. And as more of our customers demand sustainable solutions to their most complex waste challenges, we remain uniquely positioned to deliver.
The integrated waste and recycling services we provide are essential to protecting the environment and public health. We continue to make thoughtful investments in our capacity to recover value from the waste stream while reducing greenhouse gas emissions. In 2023, we completed a full retrofit of our Boston, Massachusetts, material recovery facility with stateof-theart equipment and technology—all designed to increase capacity, enhance safety, improve product quality, and provide best-in-class operations for our customers. This investment provides infrastructure that is essential to meeting the service and sustainability needs of customers throughout the region.
We also reached an important climate leadership milestone in 2023: We estimate that for every ton of greenhouse gas we emitted through our operations, we helped prevent more than five tons of greenhouse gas emissions elsewhere in the economy through our recycling, renewable energy, and carbon sequestration services. This accomplishment reflects our focus on simultaneously reducing our emissions and growing
our emission-reducing services. We expect progress will continue as we work to advance renewable natural gas infrastructure and make further upgrades to recycling infrastructure.
Sustainable communities are built through service and cultivated through investment in the people who are called to serve. We could not be prouder of the work that we have completed in recent years. In 2023, we successfully achieved our goal of contributing $2 million annually to our local communities through in-kind services, sponsorships, and cash contributions. The threeyear process to get to this point has included bringing strategic focus to our giving initiatives, along with improved reporting, and reflects the culture of service we embrace at all levels of the organization. This year, we launched the Casella Foundation, which will help us to sustain our giving initiatives throughout our operations. Having achieved our giving target, we are now turning our focus to employee volunteering, with a goal to attain 21,000 hours of annual community volunteering by 2030. As society continues to evolve, people expect that their products, goods, and services will become more sustainably produced and delivered. Our customers and communities can attest: Our people are driven to get them there. n
Great people, sustainable resource management and a commitment to innovation have fueled the growth of Casella Waste Systems for 50 years.
In 1975, Doug Casella used his high school savings to buy a truck he used to collect trash from around the Killington area. His brother, John Casella, who had been working in the hospitality industry like their parents, assisted with administrative work.
After about a year, John Casella officially became his brother’s business partner full time. Today, he is the company’s Chairman CEO.
“One of the things that we saw early on was, whenever we go into the landfill, there was a tremendous amount of corrugated cardboard,” says Casella. "Even back then, cardboard had value as a recycling commodity, and it was also very difficult to manage in the landfill."
By 1977, the brothers had built Vermont’s first recycling facility. Then, they went to Maine to buy an upstroke baler from a defunct woolen mill to compact cardboard into something that could be sold.
“We did the research for all the paper mills in New England, started building relationships with them and started selling all of the cardboard coming out of the waste stream,” Casella says.
“We ended up going into the landfill with a load of waste and coming out of the landfill with a load of cardboard back to the recycling facility.”
Vermont’s bottle bill had taken effect just a few years earlier, so Casella’s recycling facility also processed glass, PET plastics, aluminum and steel.
Ned Coletta had been working at med-tech companies in the early 2000s, and after leaving a company he cofounded, he was looking to get more business experience working with senior leadership.
“The first day I met John Casella, he said, ‘Ned, I'm going to interview you at 8 a.m., but show up at the Walmart parking lot at 4 a.m. Have boots on, jeans, work gloves, and I’ll have one of my drivers pick you up,’” Coletta says. “I worked my butt off all morning.”
Casella and the driver met in between the collection and the interview to assess Coletta’s efforts. It must have been a satisfactory report; Coletta was hired as vice president of finance and investor relations in December 2004. Since 2023, he’s been president.
“I appreciate the fact that the CEO of this company cared about his employees so much and wanted to know that people who were joining his team had empathy for how the work gets done,” Coletta says.
The driver he worked with that morning was Ken Hier, Casella’s first employee in 1976 with a 40-year tenure.
In 2020, Casella created a driver training school that now bears his name: the Kenneth A. Hier Sr. CDL Training Center. More than 300 employees have completed the program.
“He enjoyed getting up at 1 a.m. to start his route every day, always ending the day to clean his truck to make sure it upheld those expectations that Casella set forward,” Hier’s daughter said at the training center dedication. “He rarely took a vacation to hunt or fish, but when he did, he always checked in on his customers, making sure everything was OK.”
Ned Coletta President
In 1997, Casella Waste Systems became a publicly traded company on the NASDAQ.
“One of the reasons for the public offering was we had significant opportunities to grow, similar to what we've done in the last 20 years, so we took advantage of that,” Casella said.
A strong couple of decades at its launch and strong recent growth bookend a period of uncertainty for the company. Acquisitions and a massive landfill development initiative at the start of the millennium stressed Casella’s debt burden.
“When I became CFO, in 2013, we were levered, which means how much debt we had to how much cash we produced in a year was close to six times, which is very, very high,” Coletta says. “We were having a really hard time investing back into the business.”
A new strategic plan was implemented to change up the company’s capital allocation, maximize capacity at the landfills and work with customers on recycling prices.
“In 2017, we put forward a new strategic plan that said ‘let’s start working on development projects again,’” Coletta says. “We created a new adjacent market for us to vertically integrate our landfills and recycling facilities. Since that point, we’ve acquired 70 companies across the Northeast and really accelerated growth.”
In the eight years since that plan launched, they’ve tripled revenues.
Today, Casella has facilities in 10 New England and midAtlantic states, more than 5,000 employees and a market capitalization of $7 billion.
From the first purchase of a second-hand baler, Casella has supported its growth through improvements and expansions to recycling.
“I was here when we first started rolling out Zero-Sort® recycling to customers, and that was really revolutionary,” Coletta says.
Continued investments in technology have made it so that the company can process even more recyclables, faster, and have a cleaner product to sell at the end.
Casella recently completed renovations to their Charlestown, Mass., and Willimantic, Conn., recycling centers. As a result, the throughput of Zero-Sort® recycling has increased nearly 40%, and the quality of the material being shipped to market has increased about 35%.
The company also worked to create a formula to help reduce the volatility of selling recycled material.
“One of the biggest innovations we've had as a company in the last decade is something called the Sustainability Recycling Adjustment Fee,” Coletta says. “Almost 10 years ago, we created a floating fee on our customers’ bills that, if commodity prices are low, we charge a slight fee to our residents or commercial businesses. If commodity prices go higher, we reduce that fee. And all of a sudden, we created a model that took a lot of recycling commodity risk and gave a very small piece to millions of different customers.”
Casella also has clients in 47 states that they work with on waste reduction measures.
“The sustainability piece was always in our blood right from ’77, but the level of sophistication has changed,” Casella says. “We're now providing circular services to industrial companies like Becton Dickinson, which is a large medical device company, helping them with hard-to-recycle plastics that are coming off of their manufacturing process.”
Overall, these programs are helping to shift more waste away from landfills and put them back into circulation.
“We want to be a partner, and we want to help to understand what our customers’ needs are, especially from a sustainability standpoint, and how to help them achieve those goals,” Coletta says.
“The future is very bright,” Casella says. He expects improvements in artificial intelligence and robotics will continue to make recycling more efficient and thus more accessible to all. Landfill technologies have improved the environmental safety of facilities and more efforts are going into leachate treatment and methane capture.
“We're going to be the first to cannibalize ourselves in the landfill business,” Casella says. “If we can find a higher and better use and put material through the recycling processing facility, we'll generate more free cash flow by doing that. It's very consistent with the financial implications of the business. Not many people understand that. They think that waste companies make all of their money on the disposal side, in the landfill, and it's not the case anymore.”
In partnering with customers, Casella improves the circular economy and finds solutions to benefit communities.
“Our business enables our customers to be more sustainable and have more of a positive impact on the world around them,” Coletta says. “For each ton of carbon Casella emits — running our trucks, our recycling facilities, our landfills — every day, we reduce close to five tons through our actions of how we run our business: through recycling, organics management, carbon sequestration, clean energy. It's kind of an amazing story that each day we run our business, the world gets five times better.” n
OUR NEW HAMPSHIRE OPERATIONS RECOVER NEARLY 20,000 TONS OF RECYCLABLES, AND OVER 7,000 TONS OF ORGANICS, CONSERVING DISPOSAL CAPACITY AND RETURNING VALUABLE RESOURCES TO THE ECONOMY.
CONTRIBUTED BY NEW HAMPSHIRE EMPLOYEES
EMPLOYEES IN NH OVER 970
ESTIMATED VOLUNTEER HOURS IN NH PAYROLL AND TAXES
124,000 $24M+ 290
HOUSEHOLDS SERVED IN NH
BUSINESSES
11,000+ AND ORGANIZATIONS SERVED THROUGHOUT NH
Through investments in infrastructure, innovation and education, Casella aims to be recycling two million tons per year by 2030. Since 2019, Casella has increased the tonnage we recycle annually by nearly 400,000 tons.
Modern recycling facilities use advanced technology to separate mixed recyclables into clean recycled commodities that can be manufactured into new products.
Processing technology continues to advance. Recent innovations deploy optical sensors, robotics and machine learning to simultaneously optimize efficiency, productivity and commodity quality. Many of these technological advancements can be seen in our facilities.
Sensors visually scan and identify target materials then separate them using compressed air and/or robotics.
DISC SCREEN
Rotating shafts with rubber discs are calibrated to capture cardboard and paper while allowing other items to fall through.
GLASS BREAKER
A specialized disc screen separates glass fragments, which are then cleaned and sized using ballistic separators and blowers.
MAGNET
Magnetic separators — often in the form of large rotating magnetic drums — pull metals from other recyclables.
EDDY CURRENT
Rotating magnets induce a charge in nonferrous metals such as aluminum and repel them from the other materials.
ROBOTICS
Robotics are increasingly used to both identify and capture target materials at high rates of speed and accuracy.
AI TECHNOLOGY
Advancements in artificial intelligence and machine learning can support productivity, product quality and material data.
YES You can recycle dry, unwaxed cardboard; paper; plastic bottles, jugs, tubs and lids; metal cans; and glass jars and bottles.
NO Please don’t include plastic bags or bagged recyclables; clothing or fabric; tanglers like wires, ropes or hoses; scrap metal; batteries; anything smaller than 2x2 inches like plastic cutlery and straws; food waste or liquids (compost this!); electronics.
MATERIALS RECYCLING FACILITY
Recyclables must be empty and clean. So, take that last sip, enjoy that last bite and rinse your container well.
Remember to keep it loose! Bags are a drag! Bagged recyclables cannot be sorted, so if you collect your recyclables in a bag, be sure to dump them out when you get to your bin.
CONTAMINATED MATERIALS
CONTAMINATED & REJECTED MATERIALS
WHEN IN DOUBT,
IT
Americans toss far too many non-recyclable items in their recycling bins. These sorting mistakes add up and hurt recycling programs. We all need to understand what’s acceptable in our local recycling program and remember: When in doubt, throw it out.
DON’T FORGET TO REDUCE AND REUSE! Recycling is great, but waste reduction and reuse can be even better. Don’t forget to reduce and reuse whenever you can. 1 2 4 5 3
When recycling, remember shape matters! Small and narrow items slip through the cracks in our sorting equipment and cannot be recovered. They should go in the trash. Caps are OK if you twist them back onto the container.
CASELLA EXPECTS IT WILL RECYCLE
250,000 MATTRESSES IN 2025, a testament not only to its commitment to waste management but of its pursuit of innovative solutions to find ways to reuse products and materials regarded as throwaway only.
We're constantly looking to innovate solutions around needs out there,” says Trevor Mance, senior business development manager with Casella. Using a hub-and-spoke network, Casella has more than 30 tractor trailers strategically placed throughout the Northeast to accept old mattresses. Most mattresses come from residences, hotels, hospitals, or colleges and universities.
Once full, the trailer is trucked to one of Casella’s processing facilities located in Buffalo, N.Y. and Willimantic, Conn.. There, 75% of the materials that make up a unit (a unit is the mattress or box spring) are processed for reuse.
When Mike Crowell arrived in Willimantic a few years ago as market area manager, he says he was only slightly aware of the extent of a mattress's recyclability.
Crowell, who has been in the recycling industry for almost 30 years, was excited by the prospect of entering a new market with Casella's recent acquisition. "I was vaguely aware of mattress recycling, but my entire background was in commercial, industrial, and household recycling, so to me mattress recycling was a whole new opportunity."
Teams at the processing facilities disassemble each unit to extract and repurpose certain material. For instance, the different kinds of foam padding that come from a mattress are used by one of the world's largest rug manufacturers for carpet padding. Fabrics, wood and
“We are centered on the separating, processing and getting recyclable material back into the market.”
—TREVOR MANCE, SR. BUSINESS DEVELOPMENT MANAGER
metal from the coils are also extracted and reused.
“Yes, you can recycle a mattress,” says Crowell. “It’s not a theory; it's reality.”
Beyond the benefit of providing material for new products, the mattress recycling program benefits the trash haulers, the landfill operators, the landfill itself, and, ultimately, the environment.
“You have constrained landfill capacity. You have operators that can't reach the load weight in transfer stations. You've got equipment operators at landfills with springs wrapped around the axles and driveshafts and stability issues if they're not properly managed in the open face of a landfill,” says Crowell. “And New Hampshire is well aware of the landfill space capacity restraint. So we're excited, because by pulling out each one of these mattresses, we're saving a cubic yard of airspace.”
Casella is working with partners in the bedding industry to identify ways and materials that might lead to greater than 75% of material recyclability.
“We have a conference every year, and everybody gets
together — from the manufacturers to the wholesalers to the recyclers — and we talk about how we can get to that zero-waste mark,” says Crowell. “If I had to guess, between all our efforts, I'd say within the next 10 years it's totally doable and likely that every mattress will be able to be recycled 100%.”
As Casella looks for ways to completely recycle mattresses and box springs, it is also looking at other products once thought to be throwaway only.
Unwanted ski boots are just one example of a product they might be able to recycle, according to Mance.
Casella kept a million tons a year of waste out of landfills last year through its recycling efforts, and what is reused as a result can be significant.
“It’s part of that forest that doesn't need to be cut down for paper. It's oil that doesn't need to be pumped into plastic. It's metal that doesn't need to be mined toward metal,” says Mance. “We at Casella are very centered on the separating, processing and getting recyclable material back into the market.” n
Marc Morgan realized early on he wanted a career in waste management.
“My motivation has always been caring for creation and taking care of the natural world. And when I was in college, I can remember being asked: What do you want to do? What's your career path? And I was uncertain and ended up doing a work study job assisting the management of the college recycling program,” he says.
That has led to a nearly 30-year career in waste management.
“My whole life has been garbage,” he says.
Most recently, Morgan is a division manager overseeing the North Country Environmental Services landfill in Bethlehem. Before that, he was Casella’s strategic account manager in eastern Connecticut where the company operates several facilities. He is one of nearly 300 Casella employees in New Hampshire who manage 537,300 tons of solid waste, recyclables and organics.
When it came time to work in the private sector, he says Casella Waste Systems “was the only company I was looking at. Casella reflected a lot of my own personal philosophies. It runs through the company — our recycling group, the solutions group. To have that as part of the corporate philosophy just made a lot of sense to me.”
Recycling and reuse have been the focus of Morgan’s work since the beginning.
Before graduating from Keene State College in 1997 with a degree in environmental policy, he did an internship with the City of Keene. His senior thesis devised contract language focused on waste diversion, addressing a wide-scale demolition project underway in Keene. He also worked part time at the town of Chesterfield’s transfer station.
After college, he worked in the public sector — for Westchester County in New York, Lebanon, N.H., and the state of New Hampshire — in waste management and recycling planning.
“Solid waste and recycling represented a very tangible way to have an impact on the natural world. It was something that you could see — managing waste
at a landfill and doing that properly, having that as a backdrop to taking care of the environment,” he says.
For a while, he was one of the State of New Hampshire's solid waste planners.
“My position was the recycling coordinator for the state, and I did technical assistance across the state with municipalities and businesses on how to divert more material from the waste stream and how to do it properly,” he says.
Returning to New Hampshire to work with Casella in 2024 was like coming home for Morgan.
“Connecticut was fantastic. I worked with some amazing people there. I met some great people doing good work there,” he says. “But I'm really, really glad to be home here in New Hampshire.”
Much of his current work is waste diversion — identifying those waste streams that would otherwise take up precious space in the landfill.
When it comes to the needs for disposal versus the needs of protecting the environment, Morgan says, “Casella provides that kind of pathway.”
“As a company, early on, we were really focused on waste diversion, recognizing that, if we pull this out, the hole lasts longer,” he adds. “For me, it's an obvious balance of waste diversion and the need for disposal.”
He credits the state for its emphasis on recycling.
“I've been in New Hampshire for a long time, and I think New Hampshire does a pretty good job. Is there room for improvement? Absolutely, there's always room for improvement,” he says. “There are programs that we've set up that are either no additional cost or a savings. There's a lot of opportunity available for communities and businesses to divert more material.
He lauds the Granite State's cooperative nature among the various entities that a waste management system encompasses: the state, the municipalities, the policymakers and the consumers.
“Everything New Hampshire has accomplished has been through collaboration,” he says. “For New Hampshire to reach its stated goals it will take continued collaboration of industry professionals, policy makers, and consumers moving in the same direction.” n
“When it comes to the needs for disposal versus the needs of protecting the environment, Casella provides that kind of pathway.”
–MARC MORGAN BETHLEHEM LANDFILL DIVISION MANAGER
For Casella driver Marc Lamkin, service is more than just a job; it’s a way to build lasting connections with the community he serves. With more than a decade of experience driving his collection route in Derry, Marc has turned everyday interactions into meaningful relationships, earning the trust and appreciation of his customers.
“My favorite thing about my job is my customers,” Marc says. “Meeting people and helping people is why I do what I do.”
To Marc, service means going above and beyond without expecting recognition. Whether it’s moving collection bins down for an elderly customer, or ensuring each stop receives the highest quality care, he takes great pride in making a difference. His dedication doesn’t go unnoticed; thank-you notes, birthday cards and kind words from longtime customers serve as reminders of the impact he makes daily.
“This is a customer-focused business, and I strive to care for people’s needs,” he says. “I would want the same if I were in their position.”
For Marc, every route is an opportunity to serve, connect and give back to the community that means so much to him.
With more than 35 years of dedicated service, Donnie Dunn has set the standard for excellence in landfill operations at Casella’s North Country Environmental Services site in Bethlehem. A master of heavy equipment operation, Donnie’s expertise in landfill compaction has earned his site recognition as one of the best in efficiency and environmental stewardship.
Donnie’s leadership extends beyond his technical skills; he is a mentor, a problem-solver, and a trusted resource for colleagues and customers. Whether training new operators, ensuring compliance with environmental regulations, or helping drivers navigate the site safely, Donnie’s commitment to excellence never wavers.
“Donnie is respectful not only to his fellow workers but also customers of the landfill, from the biggest transfer station hauler to the smallest pick-up,” writes Al Sabino, vice president of acquisitions and transportation for Casella. “He works with them to get them in and out safely with a sense of pride.”
His ability to navigate the toughest weather conditions of the White Mountains while maintaining top-tier performance speaks to his resilience and dedication.
For Donnie, every day is about more than just operating machinery. He creates a safer, more efficient and customerfocused work environment. His contributions have earned him numerous accolades, including Casella’s Circle of Excellence Award, solidifying his reputation as one of the best in the industry.
For many children, their local Casella driver provides a weekly dose of excitement and serves as a shining example of hard work and dedication. Since its inception in 2021, the Casella Super Fan Box initiative has taken on a life of its own, spreading joy to over 500 kids throughout our communities.
“I love getting little kids involved with the trucks and seeing their smiling faces,” says driver Paul Riopelle of Salem. “I get to have fun and drive a trash truck every day while serving and engaging with my local community.”
This vibrant care package is bursting with Casella-branded fun. Inside, you'll find a soft, stress-reliever toy waste truck that's ready for play. Children can also dive into creativity with an activity book featuring the Recycling Raccoon. It's the perfect opportunity for them to color and learn with Casella. Plus, we include crayons to get them started right away!
And, of course, every young fan needs the proper gear. A Casella hat and reflective safety vest allow them to immerse themselves in imaginative playtime.
Casella drivers often go the extra mile to brighten their customers' days, including their furry family members. Inspired by daily driver interactions, our Casella dog treat tins have become a cherished token of appreciation along our collection routes.
These initiatives are more than just a fun package — it's a way to build connections, foster community spirit and bring smiles to faces young and old. Whether it's through engaging with enthusiastic kids or delighting our four-legged friends, Casella drivers are making a positive impact every day. So next time you see your local driver, know they're not just collecting waste, they're spreading joy and building community bonds, one Casella Super Fan at a time. n
TRUST RESPONSIBILITY INTEGRITY CONTINUOUS IMPROVEMENT TEAMWORK SERVICE
RESPONSIBILITY INTEGRITY CONTINUOUS IMPROVEMENT TEAMWORK SERVICE TRUST
INTEGRITY CONTINUOUS IMPROVEMENT TEAMWORK SERVICE TRUST RESPONSIBILITY
CONTINUOUS IMPROVEMENT TEAMWORK SERVICE TRUST RESPONSIBILITY INTEGRITY
TEAMWORK SERVICE TRUST RESPONSIBILITY INTEGRITY CONTINUOUS IMPROVEMENT
SERVICE TRUST RESPONSIBILITY INTEGRITY CONTINUOUS IMPROVEMENT TEAMWORK
TRUST RESPONSIBILITY INTEGRITY CONTINUOUS IMPROVEMENT TEAMWORK SERVICE
RESPONSIBILITY INTEGRITY CONTINUOUS IMPROVEMENT TEAMWORK SERVICE TRUST
INTEGRITY CONTINUOUS IMPROVEMENT TEAMWORK SERVICE TRUST RESPONSIBILITY
CONTINUOUS IMPROVEMENT TEAMWORK SERVICE TRUST RESPONSIBILITY INTEGRITY
TEAMWORK SERVICE TRUST RESPONSIBILITY INTEGRITY CONTINUOUS IMPROVEMENT
SERVICE TRUST RESPONSIBILITY INTEGRITY CONTINUOUS IMPROVEMENT TEAMWORK
TRUST RESPONSIBILITY INTEGRITY CONTINUOUS IMPROVEMENT TEAMWORK SERVICE
RESPONSIBILITY INTEGRITY CONTINUOUS IMPROVEMENT TEAMWORK SERVICE TRUST
INTEGRITY CONTINUOUS IMPROVEMENT TEAMWORK SERVICE TRUST RESPONSIBILITY
CONTINUOUS IMPROVEMENT TEAMWORK SERVICE TRUST RESPONSIBILITY INTEGRITY
TEAMWORK SERVICE TRUST RESPONSIBILITY INTEGRITY CONTINUOUS IMPROVEMENT
SERVICE TRUST RESPONSIBILITY INTEGRITY CONTINUOUS IMPROVEMENT TEAMWORK
TRUST RESPONSIBILITY INTEGRITY CONTINUOUS IMPROVEMENT TEAMWORK SERVICE
RESPONSIBILITY INTEGRITY CONTINUOUS IMPROVEMENT TEAMWORK SERVICE TRUST
INTEGRITY CONTINUOUS IMPROVEMENT TEAMWORK SERVICE TRUST RESPONSIBILITY
CONTINUOUS IMPROVEMENT TEAMWORK SERVICE TRUST RESPONSIBILITY INTEGRITY
TEAMWORK SERVICE TRUST RESPONSIBILITY INTEGRITY CONTINUOUS IMPROVEMENT
SERVICE TRUST RESPONSIBILITY INTEGRITY CONTINUOUS IMPROVEMENT TEAMWORK TRUST RESPONSIBILITY INTEGRITY CONTINUOUS IMPROVEMENT TEAMWORK SERVICE
RESPONSIBILITY INTEGRITY CONTINUOUS IMPROVEMENT TEAMWORK SERVICE TRUST
INTEGRITY CONTINUOUS IMPROVEMENT TEAMWORK SERVICE TRUST RESPONSIBILITY
CONTINUOUS IMPROVEMENT TEAMWORK SERVICE TRUST RESPONSIBILITY INTEGRITY
TEAMWORK SERVICE TRUST RESPONSIBILITY INTEGRITY CONTINUOUS IMPROVEMENT
SERVICE TRUST RESPONSIBILITY INTEGRITY CONTINUOUS IMPROVEMENT TEAMWORK
TRUST RESPONSIBILITY INTEGRITY CONTINUOUS IMPROVEMENT TEAMWORK SERVICE
RESPONSIBILITY INTEGRITY CONTINUOUS IMPROVEMENT TEAMWORK SERVICE TRUST INTEGRITY CONTINUOUS IMPROVEMENT TEAMWORK SERVICE TRUST RESPONSIBILITY
CONTINUOUS IMPROVEMENT TEAMWORK SERVICE TRUST RESPONSIBILITY INTEGRITY
TEAMWORK SERVICE TRUST RESPONSIBILITY INTEGRITY CONTINUOUS IMPROVEMENT
SERVICE TRUST RESPONSIBILITY INTEGRITY CONTINUOUS IMPROVEMENT TEAMWORK Learn more at casella.com