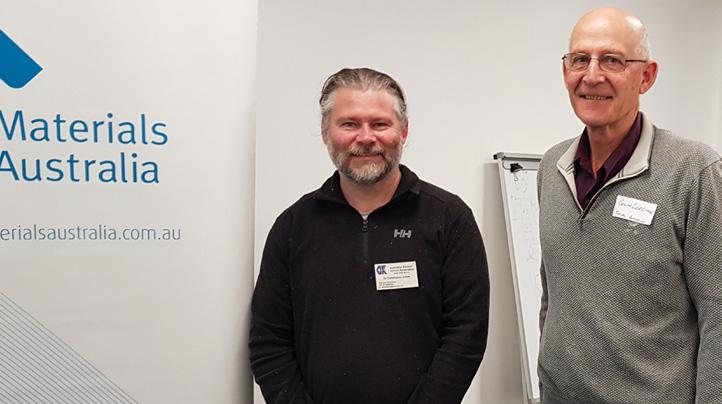
4 minute read
WA Branch Technical Meeting - 10 August 2020
WA Branch Technical Meeting - 10 August 2020 It’s Not Magic – The Chemistry And Physics Of The Lithium-Ion Battery
Source: Dr Chris Jones, National Secretary, Australian Electric Vehicle Association
Dr Chris Jones describes himself as a passionate advocate for reducing mankind’s impact on the planet which sustains us, and sees electric vehicles (EV) as the ‘least worst’ option for transport in the 21st century. As a long-time EV enthusiast, he recently had the opportunity to undertake a major desktop review of lithiumion battery technology, as used in EVs, as a first stage in a potential commercial development project. The review redirected his activities from his home base in plant genetics and biochemistry, into the field of electrochemistry.
Characterising the periodic table as ‘a fundamental of the universe’, Dr Jones explained why lithium is the ideal choice for EV batteries. It is the lightest metal, and with its high electrode potential, allows higher energy storage capacity, both per unit mass and unit volume, as compared to potential alternatives. At the same time, it is relatively more abundant, and hence cheaper, though, as it turns out, lithium is not the major cost component in lithiumion batteries. Dr Jones described the three aspects of EV batteries as the cell (a single anodecathode unit), the battery (or module) which is a collection of cells connected in series or parallel to produce the required voltage or storage capacity, and the pack. The battery pack is the ‘bolt-in unit’ containing the module, fuses, contactors, and battery management system, which commonly includes a cooling system. The challenge in EV development is the design and production of high-energy battery packs. The electrochemical basis for lithium ion batteries is the oxidation of lithium metal to lithium ions, with the corresponding release of electrons. This occurs at the anode during discharge. However, the anode material is not solid lithium metal. Instead, the anode is made of conductive graphite, in which metallic lithium atoms are weakly bound (intercalated) between two-dimensional graphite sheets. Oxidation takes place in situ, with
L to R: Dr Chris Jones with fellow EV enthusiast Colin Lorrimar.
lithium ions diffusing out of anode into the adjacent electrolyte. There are many options for the corresponding reduction reaction at the cathode, but the most common choice, at present, being reduction of tetravalent cobalt ions to the trivalent state. The necessary chemical linkage between the lithium and the cobalt is made by using a cobalt dioxide cathode, which has a crystal structure that allows two-dimensional diffusion of unbonded lithium ions within the solid. When cobalt is reduced to the trivalent state, the charge on the oxygen anions is balanced by chemical (ionic) bonding of lithium ions into the structure. Thus, as the cell is discharged, lithium ions are drawn from the adjacent electrolyte into the cathode, converting it from CoO 2 (tetravalent cobalt) to LiCoO 2 (trivalent cobalt). The electrolyte is replenished at the anode side with the lithium ions from the oxidation of the metallic lithium atoms. The usual non-aqueous organic carbonate electrolyte is highly flammable, and side reactions generating carbon dioxide and ethylene must also be minimised. Both the anodic and the cathodic reactions are reversible during charging, and stability of all materials determines the maximum number of charge-discharge cycles the battery can withstand. The cobalt cathode is the most expensive component of such cells; there are alternatives, but these have disadvantages in achieving the desired combination of power density and current density. The current practical limit is about 265Wh/ kg (700Wh/litre). Whilst his is orders of magnitude less than the energy density of liquid hydrocarbon fuels, Chris’ view is that if capacity could be improved to 500Wh/ kg, EVs would effectively be better overall than diesel vehicles. Dr Jones described the pros and cons of various techniques used for packing cells into batteries, and then into packs; this must balance size, allowable current, heating, and cost. Thermal management strategy is the key to battery longevity, and high temperatures combined with high states of charge are especially damaging. Even though the battery management system built into the pack is essentially there to make it ‘idiot-proof’, the strong advice is ‘do NOT keep your EV fully charged during summer in Perth!’ In answering questions from the audience about differences between lithium-ion cells and other types of lithium-based batteries, Dr Jones referred to the promise offered by the lithium sulfur cell, which has potential for use in powering aircraft. Questions also dealt with the future of car ownership and of the car industry, and Dr Jones’ experiences with electric motorcycle road racing. He also reflected on the commercial factors involved in the forty-year development of lithium-ion batteries (forty years being the period since the operating principles, of lithium-ion batteries, were first established.).