
5 minute read
Miscibility Gap Alloys: Commercialising A ‘Missing Link’ For Renewable Energy
Source: MGA Thermal Industry
Large scale (>200 MWh) gridconnected energy storage is arguably the greatest challenge standing in the way of a complete transition to renewable energy. Lack of adequate storage is preventing full penetration of renewables into the market, and the continued burning of fossil fuels is adding to the problem. There are very long lead times for the implementation of new gridscale storage technologies such as photosynthetic production of hydrogen, efficient ammonia production, Na ion batteries, flow batteries, as well as for older large-scale technologies such as pumped hydro. What is missing is a transitional technology that builds off existing infrastructure to the maximum extent. New macroscopically solid Thermal Energy Storage (TES) materials, known as Miscibility Gap Alloys (MGA), may pave the way for this transition.
What is an MGA?
Miscibility Gap Alloys (MGA) are a class of thermal energy storage materials comprising a high thermal conductivity matrix enhanced by an internal Phase Change Material (PCM) dispersed as fine particles. The particles, which are typically present at 50% by volume, are completely encapsulated and separated by the matrix phase into a non-percolating microstructure. The PCM embedded within the MGA melts and stores energy as latent heat, while the material remains macroscopically solid and stores sensible heat. MGA were originally devised from pairs of essentially immiscible metals. However, traditional methods of production, such and melting and casting, lead to the unsuitable ‘natural microstructure’, in which the lower melting point metal forms the matrix around the particulate high melting point metal. Processing adaptations and design are required to produce the desired ‘inverse microstructure’, in which the metal acting as a PCM is trapped within the conducting matrix.
Natural microstructure (Sn white, Al dark).
Competing TES materials
Thermal energy storage can be accomplished by simply raising the temperature of a solid or liquid (sensible heat), accessing the enthalpy associated with a phase change (latent heat) or moving a compound through a dissociation and re-combination cycle (thermochemical storage). Each has its strengths and weaknesses. Thermochemical storage promises very high energy density, however in order to separate and then recombine reactants. generally requires a particulate system. Particulate systems have extremely poor thermal transport properties and so large scale implementation has proven elusive. Latent heat storage also has the allure of high energy density, however containment, erosion, thermal expansion and thermal contact problems have made it similarly elusive. Sensible heat storage often relies on large quantities of very low cost materials (concrete, rocks, sand and various salts) which also generally have very poor thermal transport properties. This can be overcome with liquid sensible heat storage, by vigorous circulation of hot liquids using pumps, and extensive heat exchange infrastructure leading to the state-ofthe-art TES technology, two-tank molten (nitrate) salt storage. Graphite overcomes the thermal transport problem in a solid material, but at increased material cost.
Enter MGA
By accessing the latent heat of fusion of the included metal particles, MGA offer a number of advantages over other TES media. Latent heat is accepted and delivered at near constant temperature,
Inverse microstructure (Sn white, Al dark).
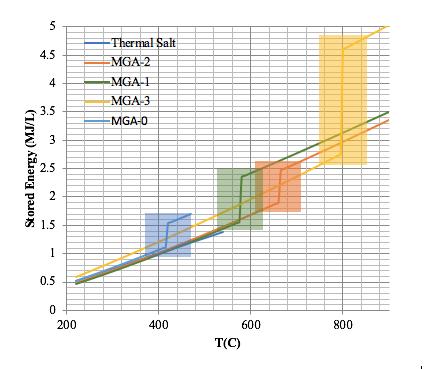
and so by choosing a different PCM component, an MGA material can be made to match a particular end use such as a steam Rankine cycle operating around 600 C. This gives a consistent quality heat such as is required by many thermodynamic systems. Latent heat also means that the energy density is high. If we include 100 C of sensible heat around the phase change, MGA systems store and deliver between 0.65 and 2.2 MJ/L. High thermal conductivity means that thermal energy is accepted and delivered, from storage, by conduction. This allows the materials to be agnostic to the source of heat, adapting equally well to heating via a heat transfer fluid, electrical resistance or direct absorption of concentrated sunlight. An additional benefit is derived because the materials are macroscopically solid with no secondary heat transfer fluids. Compared with two-tank molten salt storage, there is greater system simplicity for thermal energy storage systems, and no parasitic energy consumption for trace heating, which can be as high as 24% in those
systems. The final advantages are that by choosing a suitable PCM, higher operating temperatures are accessible and the constituents are recyclable. Stored thermal energy for some MGA systems as a function of temperature
MGA Thermal Pty Ltd
The commercialisation of MGA materials has been taken up by MGA Thermal Pty Ltd. Several technical advances have been made which allow the manufacture of larger storage modules. Current manufacturing capacity produces 6.4 litre modules with a thermal storage capacity of 5.8kWh. The company has partnered with E2S Power AG, based in Switzerland, which is developing a TES product to repurpose retired power stations. Valuable infrastructure, from the more than 6,000 power stations worldwide that currently run on coal combustion, can be converted into large scale energy storage facilities, by accepting surplus (otherwise curtailed) renewable energy via the grid, storing it as heat, and re-dispatching as electricity. The repurpose process commences by fitting modular storage units, containing MGA materials, to augment the boiler. MGA used in this application operates in the temperature band of 500 – 700 C, to ensure a good fit with power station infrastructure such as the turbines, generators, and grid connection. This allows plants to run on stored renewable energy charged from the grid at times of excess availability, which is growing exponentially. As the transition to renewable energy progresses, additional storage units will be added, until the heat source for the plant is completely supplied by stored renewable energy.
Pilot Manufacturing Plant
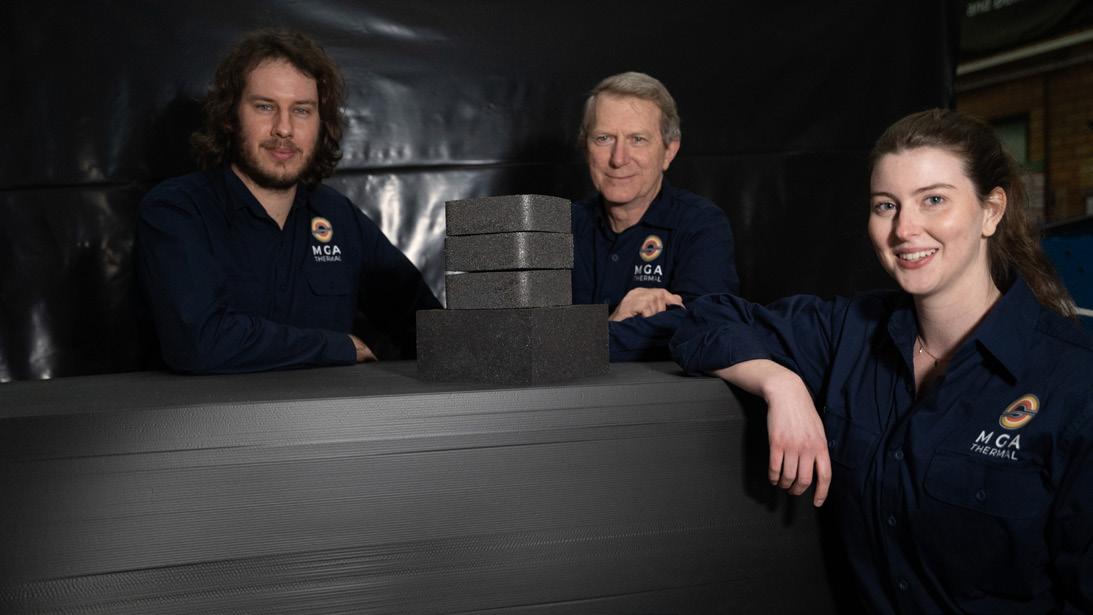
MGA Thermal has recently taken seed investment from Capital Pitch Ventures, and been awarded an Accelerating Commercialisation Grant from the Australian Government Department of Industry, Science, Energy and
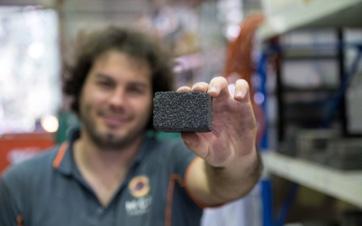
Founder and CRO Dr Dylan Cuskelly holding an MGA block. Photo by Jedidiah Cranfield.
Resources. Together, the investment and grant will fund the development of a Pilot Manufacturing Plant to demonstrate scale up and semi-automation of MGA module production. Heat is ubiquitous in energy systems as a source, intermediate or final form, and 52% of energy worldwide is consumed as heat. MGA materials possess properties which make them amenable to use in a wide array of applications where thermal storage can assist in power generation, and the distribution and regulation of energy. In addition to the conversion of existing power stations, this includes concentrated solar thermal power, waste heat recovery, process heat, domestic and commercial building heating, grid stabilisation and electric vehicle heating.