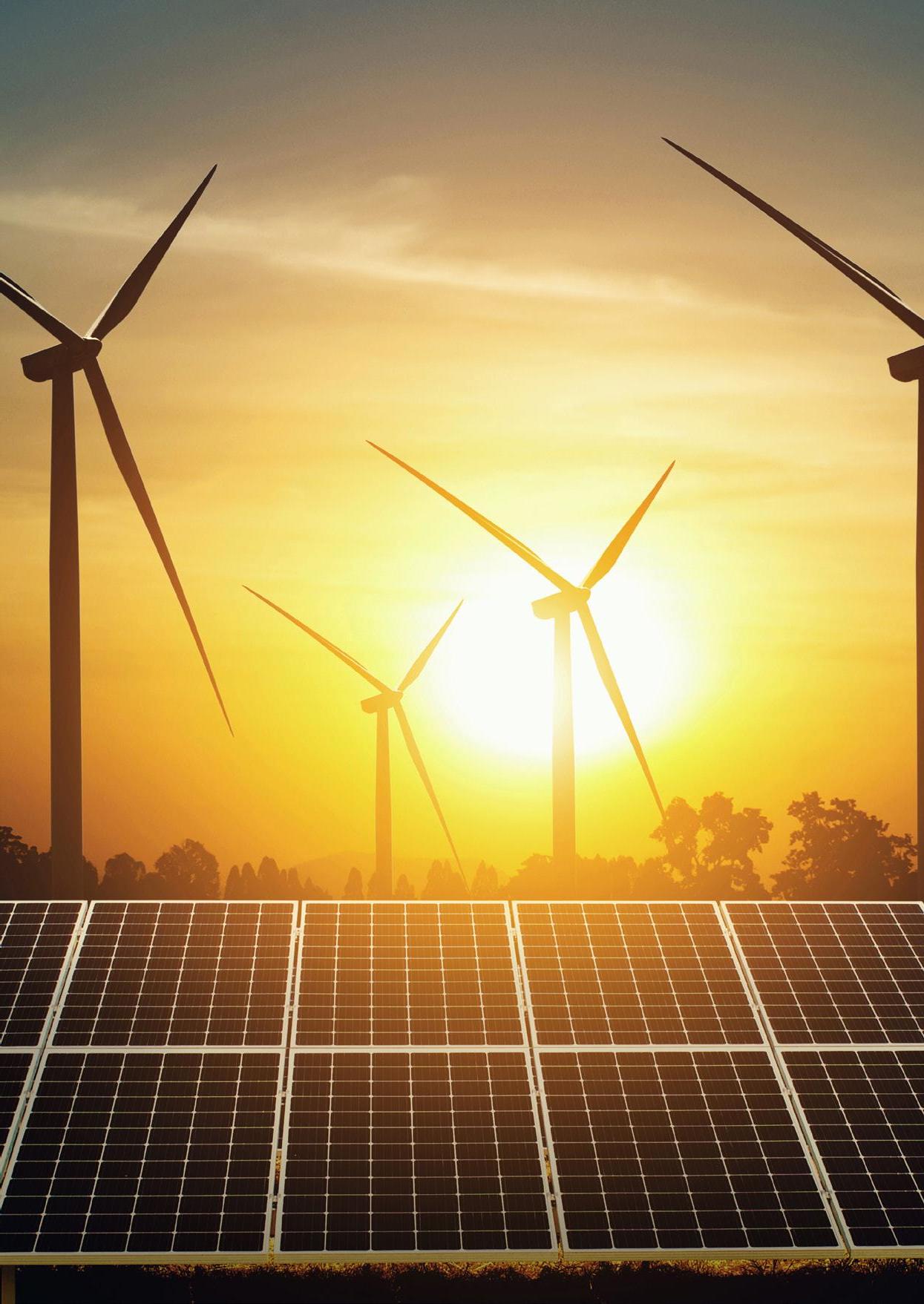
31 minute read
Materials for Energy and the Environment
Sustaining the future
In 2016-2017 Australia produced approximately 67 million tonnes of waste, but only 58 per cent of all generated waste was recovered. Not surprisingly then, the creation of new materials from waste products for increased energy demand, which are also environmentally compatible, is a growing area of interest for governments, researchers and industry bodies alike.
Since the 1950s, there has been a shift from biomass, or renewable materials, to non-renewables, which include metals, fossil fuels and minerals. Today, the global population heavily relies on the goods and services delivered by these materials like shelter, communication, nourishment and education. But the impacts of extracting these materials are taking their toll on the natural world, and leading to landscape degradation, habitat loss, waste generation, decreased water quality, and ecosystem pollution. It also results in substantial energy usage. The global population is likely to rise to nine billion over the next three to four decades. By comparison, the population increased from 1.6 billion to 6.1 billion during the 20th Century alone. The need for environmental requirements to be introduced into design and development of materials has become a vital issue to meet the increased demands. In 2018, Australia adopted a National Waste Policy, which sought to shift away from the idea of ‘take, make, use and dispose’ to a circular economy. Under this new model, greater emphasis is placed on
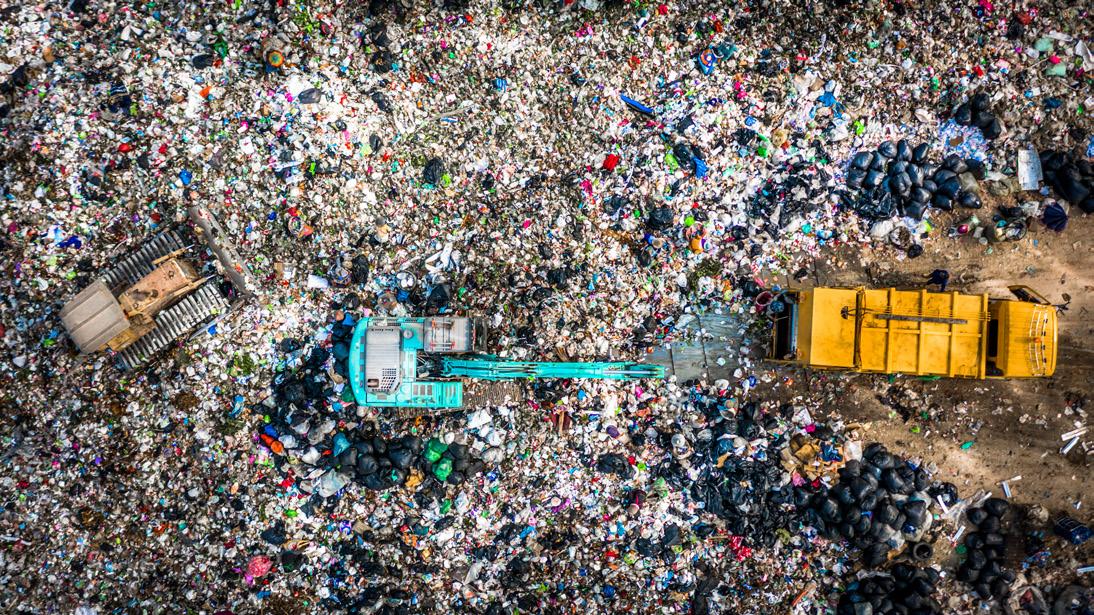
maintaining the value of resources over a prolonged period of time. The report estimated that Australia’s gross domestic product could benefit by as much as $24 billion if there was a five per cent improvement in material usage efficiency. The report also suggests waste is responsible for two per cent of Australia’s overall greenhouse gas emissions. It suggests avoiding waste altogether is the most preferable option, and highlights the role that all levels of government have to achieve that outcome. Dr Lisa Heinze from the University of Sydney said that avoiding waste and maximising the use of resources is a cultural shift. “Our landfills, landscapes and waterways are choking with plastic. Despite recent ‘plastic-free’ campaigns, global demand for plastic is on the rise, and nationally, our plastic recycling rates are below ten per cent.” “Addressing the environmental and health concerns associated with plastics will depend on all of us – individuals, institutions and governments – working together and alongside industry, toward a truly petroleum-based plastic-free future,” she said. Similarly, Professor Thomas Maschmeyer, also from the University of Sydney, said that while non-renewables, like plastic, are harmful to the environment, researchers need to focus on turning these resources into new products. “Plastic waste is a serious environmental issue, but also presents a great resource opportunity,” said Professor Maschmeyer. Australian research is leading a new era of innovation to create and maximise the benefits of a sustainable future.
Players in the Australian Market
Australia’s commitment to enhanced materials management is led by a vast coalition of research bodies and universities, who partner with industry to create real-world outcomes. The Australian Research Council (ARC), founded in 2001, is a Commonwealth entity that advises the Australian Government on research matters, administers the National Competitive Grants Program, and has responsibility for Excellence in Research for Australia. ARC is one of the Australian Government’s two central agencies for allocating research funding to academics and researchers at Australian universities.
SMaRT Green Materials
Working in partnership with business and industry, SMaRT develops green materials that are made entirely, or primarily, from the rubbish that communities throw away. The materials are cheaper and more sustainable, which result in better products for businesses, consumers, communities and the environment. Australia is responsible for almost half the global production of macadamia nuts per annum – making Australia the world’s main commercial producer. However, research undertaken by SMaRT’s Andrea Wechsler in 2013 explored the use of wasted macadamia shells, alongside pine cones and eucalyptus capsules, which were bonded with recycled polypropylene and a castor oil adhesive to be used in composite panel materials. Similarly, truck tarpaulins and advertising banners are not typically on display for a long-term. To maximise the use of these materials, SMaRT worked cohesively with an Australian manufacturer to recycle them, rather than send them to landfill. The research team finely shredded the advertising banners and used wax to hold the materials together, this created strong and waterproof flooring materials, which are resistant to chemicals and absorb no moisture. The creative method is a highly versatile material for the construction industry. Over 1.25 million mattresses are dumped in Australian landfill every year. Many mattresses are illegally disposed and not readily recycled. The average mattress consists of 12.5kg of steel, 2kg of wood, 1.5kg of foam, and produces a large amount of residual waste. However, a collaboration between SMaRT and Resource Recovery Australia, has developed and refined a range of construction panels and insulation (both thermal and acoustic). These case studies show the vast use of formerly wasted materials, and the innovative approach adopted by SMaRT. Other materials that have been sustainably recycled include tyres, glass and electronics.
The SMaRT green materials reduce demand for energy, which also helps to cut pollution and greenhouse gas emissions. All production processes are designed to minimise energy consumption, and to replace the finite natural resources, that industry relies on, with alternatives derived from waste.
The Centre describes the process as taking ‘virgin resources’ to save the energy otherwise used in mining and transport, and produce non-toxic materials that are useful.
Professor Sahajwalla is positive that her work will assist with the ongoing national commitment towards a circular economy. “The world is actually facing challenges related to waste plastics and the pollution that it causes, what we developed now is the world’s first micro-factory that is actually going to address this crisis,” Professor Sahajwalla said.
University of New South Wales
Twelve years ago, ARC Laureate Fellow Scientia Professor Veena Sahajwalla founded the Centre for Sustainable Materials Research and Technology (SMaRT) at the University of New South Wales (UNSW). SMaRT works with industry, global research partners, not-for-profits, local, state and federal governments, on the development of innovative environmental solutions for the world’s biggest waste challenges. The centre boasts 30 personnel, state-ofthe-art furnaces and laboratories, and sophisticated analytical and processing equipment. SMaRT’s key intentions include: • Leading scientific and engineering research advances in the sustainability of materials and manufacturing processes • Developing novel and innovative technologies and products that reduce environmental impact and enhance community benefits • Activating sustainability research through the innovation-researchdevelopment-translation value chain in partnership with industry. Underlying these aims, SMaRT also engages the wider community with sustainability research to address global waste issues. Professor Sahajwalla is an internationally recognised materials scientist, with expertise in revolutionising recycling. She said her work at SMaRT is about producing a new generation of green materials and products. “It’s really all about taking different products and materials that typically might have ended up in landfill, recycling it, reforming it. This is what’s going to ultimately be good for our economy and good for our environment,” she said.
University of South Australia
The Future Industries Institute (FII) at the University of South Australia (UniSA) is primarily focused on transforming current industries to more sustainable practices in the future. The multi-million dollar institute specialises on four key topic areas: 1. Minerals and resources engineering strives to improve rates of discovery, optimise process performance, reduce energy and water usage, and assist in the assessment and introduction of technological innovations across the resources value chain
2. Energy and advanced manufacturing involves scientists and engineers who specialise in polymer chemistry, materials science and surface engineering technologies working closely with industry partners to develop new products and innovative ideas in the automotive, defence, health care and renewable energy sectors
3. Environmental science and engineering draws on expertise in biogeochemical processes to develop innovative solutions to the challenges facing agriculture and the environment 4. Biomaterials engineering and nanomedicine supports the development of precision medicine by leveraging long standing expertise in nanomedicine.
‘Living within limits’ is a key element of UniSA’s approach to materials management, as researchers seek to develop management systems to create sustainable living under a changing environment and population. The research theme of ‘scarce resources’ brings researchers together to create and implement those strategies that restore, protect and optimise social, cultural, economic and environmental resources.
Professor Christopher Saint is the Dean of Research and Innovation in the Division of Information Technology, Engineering and the Environment at UniSA.
“The scarce resources theme at the University of South Australia is looking to answer one big question: how do we eliminate waste in this state?” Professor Saint asked.
Researchers have used ground concrete, and old tiles to produce a new, more environmentally sustainable concrete. Similarly, toxics and plastics, which can be quite dangerous, have also been transformed into new materials that are safe for industry-wide use. “It’s about building a circular economy from waste, creating more jobs and new industry. There are so many ways that we can restore, protect and optimise our resources,” Professor Saint added.
CSIRO
CSIRO’s Materials for Energy and the Environment (MEE) Group is responsible for solution-focused outcomes for industrial challenges, and reducing the impact that many materials and processes create on the environment. At the height of Australia’s recyclable waste crisis in 2017, where over 80 per cent of all recycled waste was exported to countries in Asia, CSIRO published The Recycled Plastics Market: Global Analysis and Trends Report. The report focused on developing a comprehensive and authoritative analysis on the plastics recycling industry. Through this, the report assists with the future identification of research and development opportunities to overcome market challenges and support growth. The recommendations in the report included: • The research suggests that there is a strong case for the development of innovative technologies that overcome identified challenges and support continued growth • There are opportunities across the recycling industry, including: - increasing the cost effectiveness of waste collection - providing more efficient sorting and reducing rates of contamination - using low value or underutilised feedstocks - delivering higher quality resins that can compete with virgin materials on price and quality. The report also undertook a macroeconomic analysis of the political, economic, social, technological, legal and environmental factors that may influence the implementation of a successful waste management scheme in Australia. Ten stakeholder interviews were conducted as part of the report, in addition to independent intellectual property landscape studies, CSIRO-authored and independent market analysis reports into the plastic recycling industry. The results from the interviews showed that there is an increasing consumer focus on environmental issues and sustainability, which has helped to drive the market. This has translated into both a shift in preference towards global brand owners with sustainable processes, and increased political action from governments to introduce legislation and policies that support plastic recycling measures.
Monash University
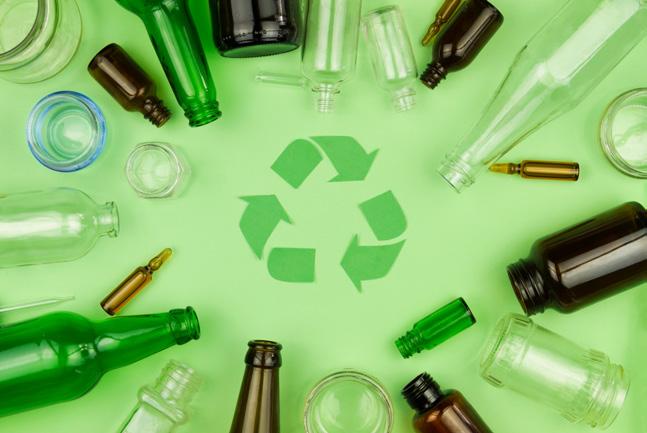
Researchers at Monash University’s Materials Science and Engineering Department are interested in maximising a wide range of materials for a suite of applications. The materials range from nanostructured to electronics, energy storage and also magnetic materials, which can be used in healthcare. Professor Yuri Estrin, an Honorary Professorial Fellow, has led a project that could revolutionise the construction industry, assist areas affected by natural hazards, and even become used in space exploration. The project has developed archimats, which is an emerging area of ‘architectured’ materials that have an organised intertwined or interlocked inner architecture. Professor Estrin explains that archimats can expand the design space that conventional composite materials cannot process. They also provide an ease of assembly and disassembly and nearly full recyclability of the elements used. “Archimats therefore offer smarter, safer and more sustainable materials for use in manufacturing and industrial design, with the building industry being arguably the greatest potential beneficiary of this design concept,” Professor Estrin said. They can be engineered to possess superior strength, undergo significant plastic deformation, tolerate damage, good thermal insulation and sound absorption. While the European Space Agency is already considering archimats for the construction of a lunar base, Professor Estrin said the material could also be used for everyday items in the home.
“Archimats are also suitable for micro manufacturing. They can be produced using desktop or benchtop manufacturing processes, without the need for heavy equipment and large amounts of material.”
“This opens up new possibilities for industry to explore the use of archimats for application in smart manufacturing, in particular the development of gear for microelectromechanical systems, micro devices and miniaturised drones, as well as superior structural materials for the automotive and aerospace industries,” Professor Estrin said.
University of Queensland
In Australia’s sunshine state – where there is an abundance of natural resources – there is a range of impactful research being undertaken, led by the University of Queensland. Solar Technology A milestone was achieved earlier this year as researchers from the university set a world record for the conversion of solar energy to electricity. The process used tiny nanoparticles called ‘quantum dotes’, which pass electrons between one another to generate electrical current when exposed to solar energy. The breakthrough was led by Professor Lianzhou Wang. “This opens up a huge range of potential applications, including the possibility to use it as a transparent skin to power cars, planes, homes and wearable technology,” he said. The researcher also discussed the extent of the discovery at a global level. “Eventually it could play a major part in meeting the United Nations’ goal to increase the share of renewable energy in the global energy mix,” Professor Wang said. Low Carbon Future Professor Andrew Garnett proposed a scheme that could reduce carbon emissions by 13 million tonnes, or the equivalent of taking 2.8 million cars off the road each year. The research investigated benefits of a carbon capture and storage scheme, which transports carbon from power stations through a pipeline and stores it more than 2.3km underground. “Carbon capture and storage may be essential to buy us the significant amount of time required to develop reliable, affordable, low-carbon, baseload power, and other decarbonisation technologies,” Professor Garnett said. The International Energy Agency and the Intergovernmental Panel on Climate Change believe that this technology is a critical tool to ensure global emission reductions are met over the next several decades. Professor Garnett said three to four years may be required to confirm the option as feasible, then a further timeframe to commercialise and finalise engineering processes. “The next steps would be to gather more field data, consult with communities, carry out regulatory investigations and conduct a full feasibility study.” Waste Glass Liquid silicate from waste glass can be used in thousands of products such as concrete sealers, fertilisers, detergents and toothpaste, according to research from PhD candidate Rhys Pirie and Professor Damien Batstone. The liquid can be extracted and turned into marketable products, leaving minimal waste behind. The researchers also say it is environmentally sustainable and cost effective. “We estimate the process is more than 50 per cent cheaper than conventional ways of producing silicate,” Pirie said. “It requires less energy, raw materials and capital, and that’s before you consider the reduced social and economic costs compared to landfilling material.” The two researchers said the motivation for their innovation came from the ABC’s War on Waste series, which challenged the way that Australians dispose of their waste. The investigation is researching methods by which waste glass could be used to create a low-cost silicon-based additive to increase fertiliser efficiency.
Australian National University
Multidisciplinary research at the Australian National University (ANU) is providing sustainable and scalable solutions for industries and the broader community. The research focuses on discovering new materials to meet the needs of future applications in the electronic, mechanical, energy, biological, manufacturing and public health sectors. ANU’s School of Electrical, Energy and Materials Engineering has four major research areas: 1. Composite Materials research develops new and improved recyclable and sustainable materials with an ease of manufacturing 2. Nanomaterials research explores how tiny structures can be applied to reduce environmental risks and address challenges in health and global energy 3. Biomaterials research explores bionanotechnology to create new materials and imaging sensor technologies with a focus on improving health 4. Computational Mechanics research investigates prototyping and testing materials for automotive, aerospace and biomedical applications. Victoria University is another important player in Australian materials research. The Institute for Sustainable Industries and Liveable Cities investigates Australia’s ageing infrastructure, particularly those that are susceptible to further damage, such as bridges and buildings. It then develops and considers alternative aspects of designing and assessing structures. The Institute utilises dynamic analysis techniques, simulated blasting techniques and fire modelling to base its research on the National Research Priorities of the Australian Research Council (ARC) under an environmentally sustainable Australia and safeguarding Australia priorities. Victoria University researchers consider how to mitigate damage and build resilient infrastructure through the usability of recycled materials to create sustainable buildings and enhance their structural properties. They also examine Specifically, the composite materials research identifies, creates and modifies existing and future materials for practical applications. It addresses the fundamental question – will it fail? – through collaborative partnerships within ANU and with industry partners, like the Ford Motor Company. An example of the work undertaken at ANU includes the reduction in weight of automobiles in order to ensure the use of less fuel and to reduce emissions. the carbon footprints and embodied energy of new projects to guarantee that they are environmentally efficient. The Australian Government identified nine scientific research priorities in consultation with industry leaders, government and The research is a direct response to the increasing industry reliance on new light-weight, strong, durable and environmentally sustainable materials for the future. While there are some complex, multi-year projects, others are conducted over a shorter period. The University uses Australia’s fasted supercomputer facility and state-of-the-art testing equipment to
Victoria University
conduct their research. research bodies to position support on the most important challenges facing Australia. The priorities include energy; resources; advanced manufacturing; environmental change; transport; food; soil and water; cybersecurity and health.
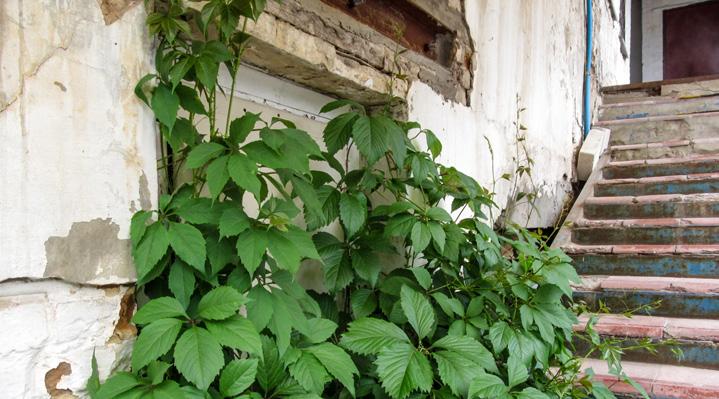
New Research Hub to Tackle Global Waste Crisis
Source: Sally Wood
Minister for Education, the Honourable Dan Tehan recently announced an $18 million collaboration, which will focus on reducing Australia’s landfill waste and transforming reclaimed waste into new materials for use in construction and other manufacturing sectors.
The Australian Research Council Industrial Transformation Research Hub for Transformation of Reclaimed Waste Resources to Engineered Materials and Solutions (TREMS) for a Circular Economy, will bring together leading scientists, researchers and industrial experts from nine Australian universities and 36 state, industry and international partners. It will be led by RMIT University. Australia’s landfill space is expected to reach capacity by 2025, with roughly 67 million tonnes of waste generated every year, and 30 per cent of that waste going to landfill. The hub will draw from expertise across multiple disciplines including civil, chemical, materials and construction engineering, artificial intelligence, behavioural sciences, environmental procurements and policies and standards. Minister Tehan said the research hub will undertake research with applications in the real world. “Our Government is investing in research that will foster strategic partnerships between university-based researchers and industry organisations, to find practical solutions to challenges facing Australian industry,” Tehan said. RMIT Professor Sujeeva Setunge, who will lead the research hub, said the multisector collaboration will focus on holistic solutions to address the waste crisis, codesigned in partnership with stakeholders. “Our investigations will include changing behaviours, smart designs to minimise waste, optimum processing of waste and converting waste to energy, developing novel materials using recycling and upcycling technologies, and metrics and tools to encourage uptake of new materials and solutions,” she said. Partnering closely with Deputy Director of the TREMS Hub, University of Melbourne Professor Priyan Mendis, Professor Setunge also said she is looking forward to working with local, national and international partners and acknowledged existing long-term collaborations with several Victorian municipalities including the Cities of Brimbank, Kingston and Hobsons Bay, as well as the Municipal Association of Victoria. “There is currently a material shortage for Australia’s $14 billion heavy construction industry, so this research to reclaim waste and transform it into new materials will deliver benefits both economically and environmentally,” Professor Setunge said. Deputy Vice-Chancellor for Research and Innovation and Vice-President Professor at RMIT, Calum Drummond said the hub would deliver novel solutions for reclaiming Australia’s waste resources and position Australia as a leader in research contributing to a circular economy. “At RMIT we work closely with industry and other partners to tackle complex environmental, economic and social issues,” he said. “We are proud to be leading such a globally significant research hub that will help transformation towards a circular economy and contribute to the United Nation’s Sustainable Development Goals.” The new hub will focus on 10 challenging waste streams: textile waste; biomass; tyres; glass; paper and cardboard; construction and demolition waste; fly ash; plastics; biochar and timber.
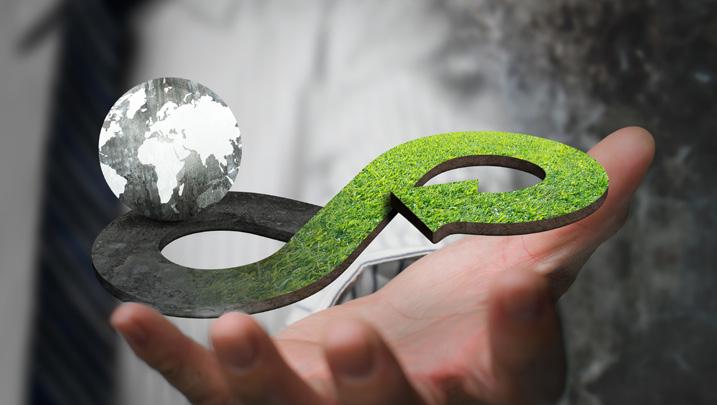
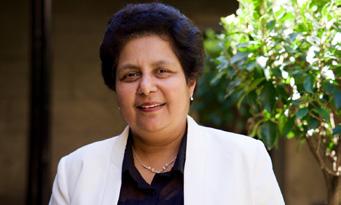
RMIT’s Professor Sujeeva Setunge will lead the TREMS research hub.
It will feature eight Australian universities who will partner with state and industry bodies. The industry-based stakeholders come from a large suite of sectors including energy networks, engineering, urban
After the demise of Victoria’s premium recycling service, SKM Recycling, over 30 local governments began shifting recycled waste into landfill in 2019.
At a national level, waste management has also been impacted. China restricted the importation of foreign wastage in 2017, which impacted 30 per cent of Australia’s recyclables. It also placed increased pressure on other countries in the region like Malaysia, Thailand and Indonesia who could not cope with the increased demand.
At the height of the waste crisis, Australia was exporting 80 to 87 per cent of all recycled plastics to South-East Asia.
Engineers Use Electricity to Clean Up Toxic Water
Source: Sally Wood
Engineers at the University of Sydney have used electricity to clean up heavily polluted industrial wastewater.
The School of Chemical and Biomolecular Engineering developed an electrochemical oxidation process with the aim of cleaning up complex wastewater that contained a toxic mix of chemical pollutants. They hope the findings will help wineries, pharmaceutical manufacturers and other industries that must comply with strict wastewater regulations. The study was completed by Julia Ciarlini Junger Soares, who is completing a PhD in Chemical and Biomolecular Engineering under the supervision of Dr Alejandro Montoya. “Our study, published in Algal Research, involved industrial wastewater that had been heavily contaminated with a cocktail of organic and inorganic species during a biofuel production process,” said Junger Soares. The wastewater, which contained carbon, nitrogen and phosphorus, was generated in a pilot plant, designed by the team for the production of biofuels using naturally abundant microalgae. The process involved treating wastewater with electricity using specialised electrodes. They discharged electricity, then drove oxidation reactions near the electrode surfaces, transforming the organic contaminants into harmless gasses, ions or minerals. The research team employed a powerful process to eliminate even the most persistent non-biodegradable pollutants, like pharmaceuticals and pesticides, and other various classes of organic compounds, which are typically found in many industrial effluents. “The process is relatively simple, does not require the addition of chemicals or severe operation conditions, and does not produce additional waste streams,” said Junger Soares. “Wastewater is a significant issue for our environment, as well as for many industries who use substantial volumes of water in their processes, such as in reactions, transport, and washing and cooling. “The electrochemical method that we used can be readily applied to industries that must comply with strict regulations for wastewater disposal, such as pulp and paper processing, wineries, as well as pharmaceutical production facilities,” she added. Junger Soares says that globally researchers are investigating other methods for the development of biofuels from algae. “Developing alternatives for the treatment and reuse of this industrial effluent is a hot research topic and can bring opportunities for energy and resource recovery within a circular bio-economy framework,” she said. The team will soon carry out research focused on specific contaminants to better understand the chemical transformations that take place during electrochemical

Julia Ciarlini Junger Soares showcasing her work at the University of Sydney. The researchers used an advanced oxidation process that eliminated stubborn organic aqueous pollutants. Credit: Julia Ciarlini Junger Soares, University of Sydney oxidation and will upscale the process. In 2017, a UNESCO report discovered that the opportunities from exploiting wastewater as a resource were vast, and that safely managed wastewater is an affordable and sustainable source of water, energy, nutrients and other recoverable materials. The World Water Development Programme (WWAP), devised by UNESCO, encourages countries to adopt sustainable water management practices in line with the 2030 Agenda for Sustainable Development and its 17 Sustainable Development Goals (SDGs). The Agenda calls for united action to improve the lives of people, therefore achieving a large number of SDGs can partly be measured by assessing a particular country’s water management. The School of Chemical and Biomolecular Engineering focuses on five research themes that cover: biomolecular and cellular engineering; carbon and neutral futures; chemical and process innovation; food industry transformation; and water, resources and the environment. It offered Australia’s first university-level chemical engineering program. Since then, researchers have been committed to both teaching and research in chemical engineering; biochemical engineering and biotechnology; energy and environment; green product and process design; minerals processing; process systems engineering and sustainability. Junger Soares is two and a half years into her PhD, which is dedicated to the advancement of electrochemical processes applied to industrial wastewater treatment and resource recovery.
Next-Generation Solar Cells Pass Strict International Tests
Source: Sally Wood
For the first time, Australian scientists have produced a new generation of experimental solar energy cells that pass strict International Electrotechnical Commission testing standards for heat and humidity.
The light-weight, cheap and ultra-thin, perovskite crystals have promised to shake-up renewable energy for some time and research undertaken by Professor Anita Ho-Baillie at the University of Sydney means they are ready to take the next steps towards commercialisation. The research, which was recently published in Science journal, is an important step towards commercial viability of perovskite solar cells. “Perovskites are a really promising prospect for solar energy systems,” said Professor Ho-Baillie. “They are a very inexpensive, 500 times thinner than silicon and are therefore flexible and ultralightweight. They also have tremendous energy enabling properties and high solar conversion rates.” Solar energy systems are now widespread in both industry and domestic housing. Most current systems rely on silicon to convert sunlight into useful energy. However, the energy conversion rate of silicon in solar panels is close to reaching its natural limits. Scientists have been exploring new materials that can be stacked on top of silicon in order to improve energy conversion rates. One of the most promising materials to date is a metal halide perovskite, which may even outperform silicon on its own. The past ten years has seen the performance of perovskite cells improve from low levels to being able to convert 25.2 per cent of energy from the Sun into electricity. It took around 40 years for scientists to develop silicon-cell conversion rates of 26.7 per cent. However, unprotected perovskite cells do not have the durability of silicon-based cells, which means they are not yet commercially viable.
ABOVE LEFT: Professor Anita Ho-Baillie in the lab. Photo courtesy of UNSW. ABOVE: A sample of some of the perovskite cells used in the experiment. Photo courtesy of UNSW.
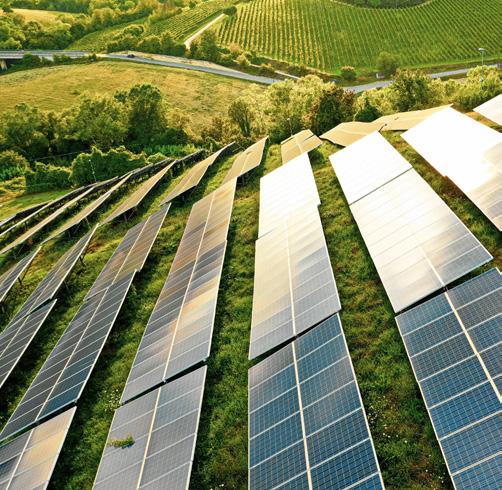
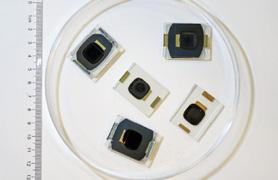
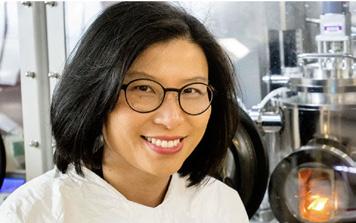
“Perovskite cells will need to stack up against the current commercial standards. That’s what is so exciting about our research. We have shown that we can drastically improve their thermal stability,” Professor Ho-Baillie said. The scientists achieved this by suppressing the decomposition of the perovskite cells using a simple, low-cost polymer-glass blanket. Professor Ho-Baillie remains an adjunct professor at the University of New South Wales, where the research work was completed by lead author Dr Lei Shi at the School of Photovoltaic and Renewable Energy Engineering. Under continual exposure to the Sun and other elements, solar panels experience extremes of heat and humidity. Experiments have shown that under such stress, unprotected perovskite cells become unstable, releasing gas from within their structures. “Understanding this process, called ‘outgassing’, is a central part of our work to develop this technology and to improve its durability,” Professor Ho-Baillie said. “I have always been interested in exploring how perovskite solar cells could be incorporated into thermal insulated windows, such as vacuum glazing. So, we need to know the outgassing properties of these materials,” she added. For the first time, the research team used gas chromatography–mass spectrometry (GC-MS) to identify the signature volatile products and decomposition pathways of the thermally stressed hybrid perovskites commonly used in high-performance cells. Using this method, they found that a lowcost polymer-glass stack with a pressuretight seal was effective in suppressing the perovskite ‘outgassing’, the process that leads to its decomposition. When put to strict international testing standards, the cells the team was working on outperformed expectations. “Another exciting outcome of our research is that we are able to stabilise perovskite cells under the harsh International Electrotechnical Commission standard environmental testing conditions. “Not only did the cells pass the thermal cycling tests, they exceeded the demanding requirements of damp-heat and humidity-freeze tests as well,” Professor Ho-Baillie said.
Professor Ho-Baillie joined the University of Sydney’s Nano Institute earlier this year where she is a recipient of the inaugural John Hooke Chair of Nanoscience. In this role, she hopes to harness the enabling properties of new and emerging materials for lost-cost, high-performance clean energy devices at the nanoscale.
Your Commuter Coffee Made Sustainable Thanks to South Australia Industry Partnership
Source: Sally Wood
In an innovative local collaboration, design and manufacturing packaging company, Detpak, has teamed up with the University of South Australia’s (UniSA) Future Industries Institute (FII) to ensure it stays at the forefront of innovation in the production of resilient but recyclable takeaway coffee cups.
Associate Professor Drew Evans, who is the lead collaborating researcher from UniSA, says the design problem for disposable coffee cups has always been about delivering a product that offers recycling opportunities and does not leak. “Being able to work with Detpak on a sustainability challenge is very rewarding,” Associate Professor Evans said. “Our expertise in thin film coatings is helping Detpak to further test innovative sustainable products.” It is estimated that Australians use one billion throw away coffee cups each year, around the world that figure skyrockets to 16 billion. “Regular takeaway cups have relied on a plastic lining, making them difficult or impossible to recycle.” “We have been working with Detpak to test coffee cups and understand the full benefits of their next generation lining, that is readily removable. With Detpak cups no changes to the recycling process have been required, so the cups can live again as recycled paper products,” Associate Professor Evans explained. Through the Future Industries Accelerator program supported by the South Australian Government, Detpak teamed up with South Australia’s Coatings Group at UniSA’s FII to conduct an analysis on coatings applied to takeaway coffee cups in the market today. Detpak Innovation and Marketing General Manager Tom Lunn says the research collaboration with UniSA will continue to improve sustainability. “At Detpak, we are constantly assessing new technologies to improve the sustainability of our products and working with UniSA gives us the opportunity to validate coating technology and continue to bring the best solutions to the market such as the new Detpak RecycleMe™ cups.” “Previously recognised with the Excellence in Sustainable Packaging Award from the Australian Packaging Covenant Organisation, Detpak is proud to be working at the forefront of packaging innovations that promote recycling and


recovery of materials because we want to be part of recycling solutions,” Lunn said. Lunn said the partnership with UniSA is beneficial to Detpak’s line of work in building a sustainable future that focuses on the environment and corporate social responsibility. “Their scientific analysis, expertise in research and development, and understanding of the chemistry of coatings technologies has been invaluable and we are excited carry on that relationship as we continue to explore how we can employ innovative coatings in the manufacture of other packaging products to encourage easy recycling,” he said. As a member of the Detmold Group, Detpak is a specialist paper and board packaging manufacturer dedicated to the foodservice industry. They have been recognised by the Australian Packaging Covenant with Excellence in Sustainability. Detpak’s range of packaging solutions are primarily focused on the grocery and food service sector, including cups, napkins, trays, wraps, and paper. However they also provide custom print packaging solutions and have been assisting Australians with their production of face masks during the COVID-19 crisis. The company is based in Adelaide but operates ten manufacturing sites across seven countries including: the Philippines, South Africa, Vietnam, Indonesia, India and China. It has also partnered with brands of every size, led by a sales teams in 23 global offices. Detpak combines global reach with local expertise and offers a large range of ready-to-go packaging items as well as custom-print, tailored packaging solutions.
Engineers Find Neat Way to Turn Waste Carbon Dioxide into Useful Material
Source: Sally Wood
Previous technology to convert waste carbon dioxide into useful industrial products has been expensive and complicated.
But chemical engineers from the University of New South Wales (UNSW) have developed new technology that helps convert harmful carbon dioxide emissions into chemical building blocks to make useful industrial products like fuel and plastics. The new process could give the world breathing space as it transitions towards a green economy. The research, published in the Advanced Energy Materials journal by Dr Rahman Daiyan and Dr Emma Lovell from UNSW’s School of Chemical Engineering, details a way of creating nanoparticles that promote conversion of waste carbon dioxide into useful industrial components. The researchers show that by making zinc oxide at very high temperatures using a technique called flame spray pyrolysis (FSP), they can create nanoparticles that act as the catalyst for turning carbon dioxide into ‘syngas’ – a mix of hydrogen and carbon monoxide used in the manufacture of industrial products. The researchers describe this method as cheaper and more scalable to the requirements of heavy industry than what is available today. “We used an open flame, which burns
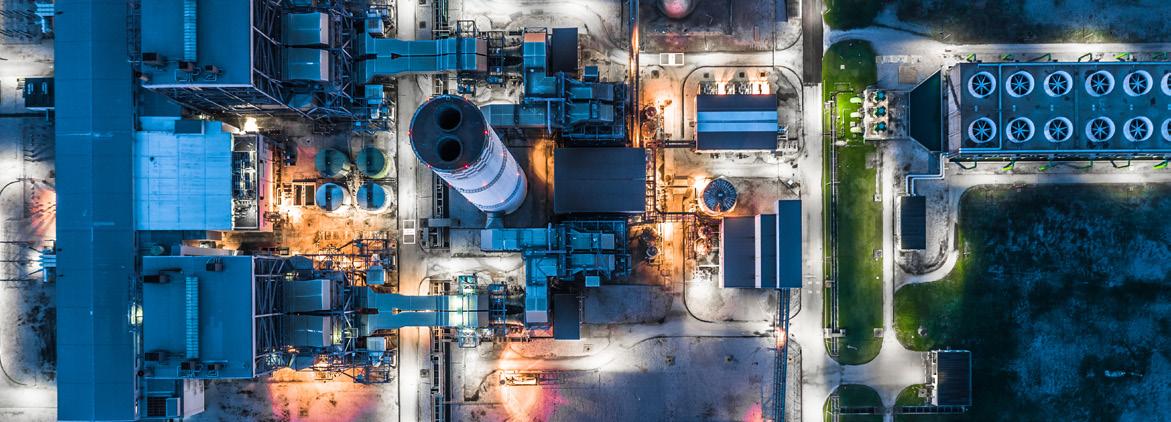
at 2000 degrees, to create nanoparticles of zinc oxide that can then be used to convert CO 2 , using electricity, into syngas,” said Dr Lovell. “Syngas is often considered the chemical equivalent of Lego because the two building blocks – hydrogen and carbon monoxide – can be used in different ratios to make things like synthetic diesel, methanol, alcohol or plastics, which are very important industrial precursors. “So essentially what we’re doing is converting CO 2 into these precursors that can be used to make all these vital industrial chemicals,” Dr Lovell explained. Closing the Loop In an industrial setting, an electrolyser containing the FSP-produced zinc oxide particles could be used to convert the waste CO 2 into useful permutations of syngas, said Dr Daiyan. “Waste CO 2 from say, a power plant or cement factory, can be passed through this electrolyser, and inside we have our flame-sprayed zinc oxide material in the form of an electrode. When we pass the waste CO 2 in, it is processed using electricity and is released from an outlet as syngas in a mix of CO and hydrogen,” he said. The researchers close the carbon loop in other industrial processes that create harmful greenhouse gases, by making small adjustments to the way the nanoparticles are burned by the FSP technique, they can determine the eventual mix of the syngas building blocks produced by the carbon dioxide conversion. “At the moment you generate syngas by using natural gas – so from fossil fuels,” Dr Daiyan said. “But we’re using waste carbon dioxide and then converting it to syngas in a ratio depending on which industry you want to use it in.” Cheap and Accessible In choosing zinc oxide as their catalyst, the researchers ensured that their solution has remained a cheaper alternative to what has been previously attempted in this space. “Past attempts have used expensive materials such as palladium, but this is the first instance where a very cheap and abundant material, mined locally in Australia, has been successfully applied to the problem of waste carbon dioxide conversion,” Dr Daiyan said. Dr Lovell adds that FSP flame system to create and control these valuable materials also makes this method more appealing. The group’s next project will be to test their nanomaterials in a flue gas setting to ensure they are tolerant to the harsh conditions and other chemicals found in industrial waste gas.