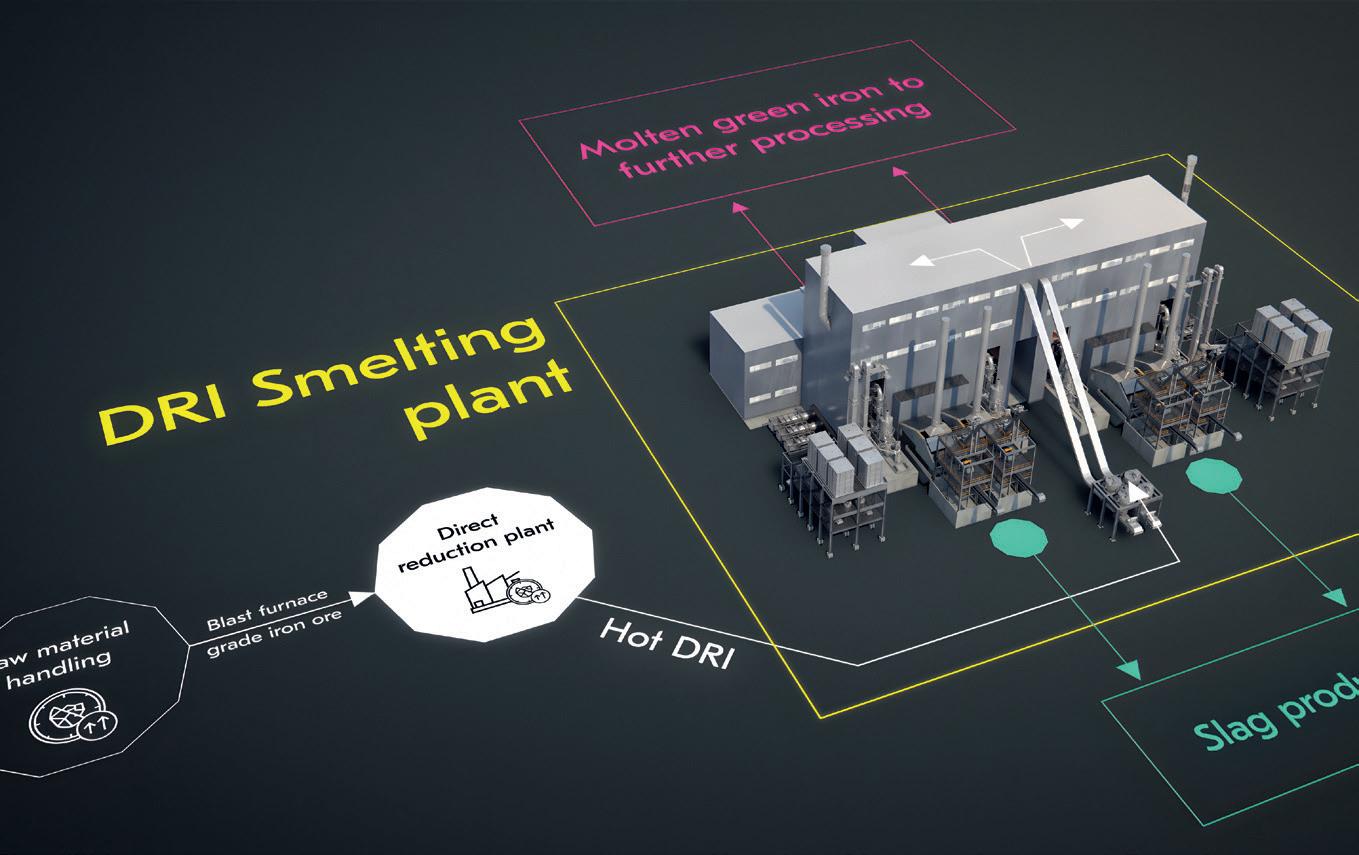
5 minute read
Mari Lindgren, Kimmo Vallo, Timo Haimi: Teknologiakehitystä terästeollisuuden hiilidioksidipäästöjen radikaaliin vähentämiseen
from Materia 2/2024
Ilmastotavoitteiden täyttäminen vaatii toimia terästeollisuudelta
Ilmastonmuutoksen vaikutukset ovat alkaneet näkyä ihmisten arjessa eri puolilla maapalloa esimerkiksi erilaisina sään ääri-ilmiöinä. Kasvanut tietoisuus kasvihuonekaasujen vaikutuksesta ilmaston lämpenemiseen luo yhteiskunnille painetta pysyä Pariisin ilmastosopimuksen tavoitteissa, mikä vaatii toimia energian tuotannossa, liikenteessä, mutta myös kaikilla teollisuuden sektoreilla. Globaalisti terästeollisuus tuottaa noin 8% hiilidioksidipäästöistä, ja siten terästeollisuuden hiilidioksidipäästöjen vähennyksellä on merkittävä rooli ilmastotavoitteiden saavuttamisessa. On selvää, että näin iso muutos ei ole mahdollista ilman murrosta, jossa uusia teknologioita otetaan käyttöön ja uusia ekosysteemejä muodostuu mahdollistamaan vähäpäästöistä ja päästötöntä tuotantoa.
Uutta teknologiaa
Teräksen valmistuksen perinteinen masuunireitti, jossa oksidinen rautamalmi tai -rikaste pelkistetään ja sulatetaan metalliseksi raudaksi fossiilisen hiilen avulla, tuottaa noin 1,9 t CO2 tuotettua terästonnia kohti. Kun masuuniprosessi korvataan rautarikasteen suorapelkistyksellä ja sähkösulatuksella, hiilidioksidipäästöjä syntyy 0,2-0,9 tCO2/t teräs. Tässä valmistusreitissä rautarikaste pelkistetään kiinteässä tilassa joko hiilellä, vedyllä tai maakaasulla ja syntynyt suorapelkistetty rauta (DRI Direct Reduced Iron) sulatetaan sähköuunilla mieluiten uusiutuvaa energiaa käyttäen. Sähköuuni voi olla joko perinteinen romuraudan sulattamiseen tarkoitettu valokaariuuni tai uusi uppokaariuunin periaatteita hyödyntävä Metson Outotec® DRI sulatusuuni.
DRI-sulatusuunin merkittävin etu valokaariuuniin nähden on kyky käsitellä merkittäviä määriä kuonaa, jolloin nykyisin laajalti käytössä olevaa masuunilaatuista rautarikastetta voitaisiin edelleenkin prosessoida. Tällöin ei tarvitsisi siirtyä puhtaampiin ja kalliimpiin raaka-aineisiin kuten suorapelkistys ja valokaariuuni -reittiä käytettäessä. Koska nykyisin masuunilaatuisen rautarikasteen määrä on yli 90% kaikesta tuotetusta rautarikasteesta, tällaisen teknologian nopea kehitys ja käyttöönotto on terästeollisuudelle lähes välttämätöntä. DRI-sulatusuuni on myös joustava syötteen ominaisuuksille, eli syöte voi olla nykyisinkin tuotettua hiilellä tai maakaasulla suorapelkistettyä DRI:tä tai vaihtoehtoisesti vedyllä pelkistettyä DRI:tä, kunhan vetyteknologian kehittyessä sitä on saatavissa riittävissä määrissä. Tuotetun raakaraudan ominaisuudet mahdollistavat jatkokäsittelyn ja -jalostuksen nykyisillä tuotantolaitoksilla ilman merkittäviä muutoksia muissa prosessilaitteissa tai tuotelaaduissa. Kuvassa 1 esitetty suorapelkistykseen perustuva prosessiketju teräkselle mahdollistaa merkittävät, jopa 90%:n vähennykset hiilidioksidipäästöissä nykyiseen masuunireittiin verrattuna.
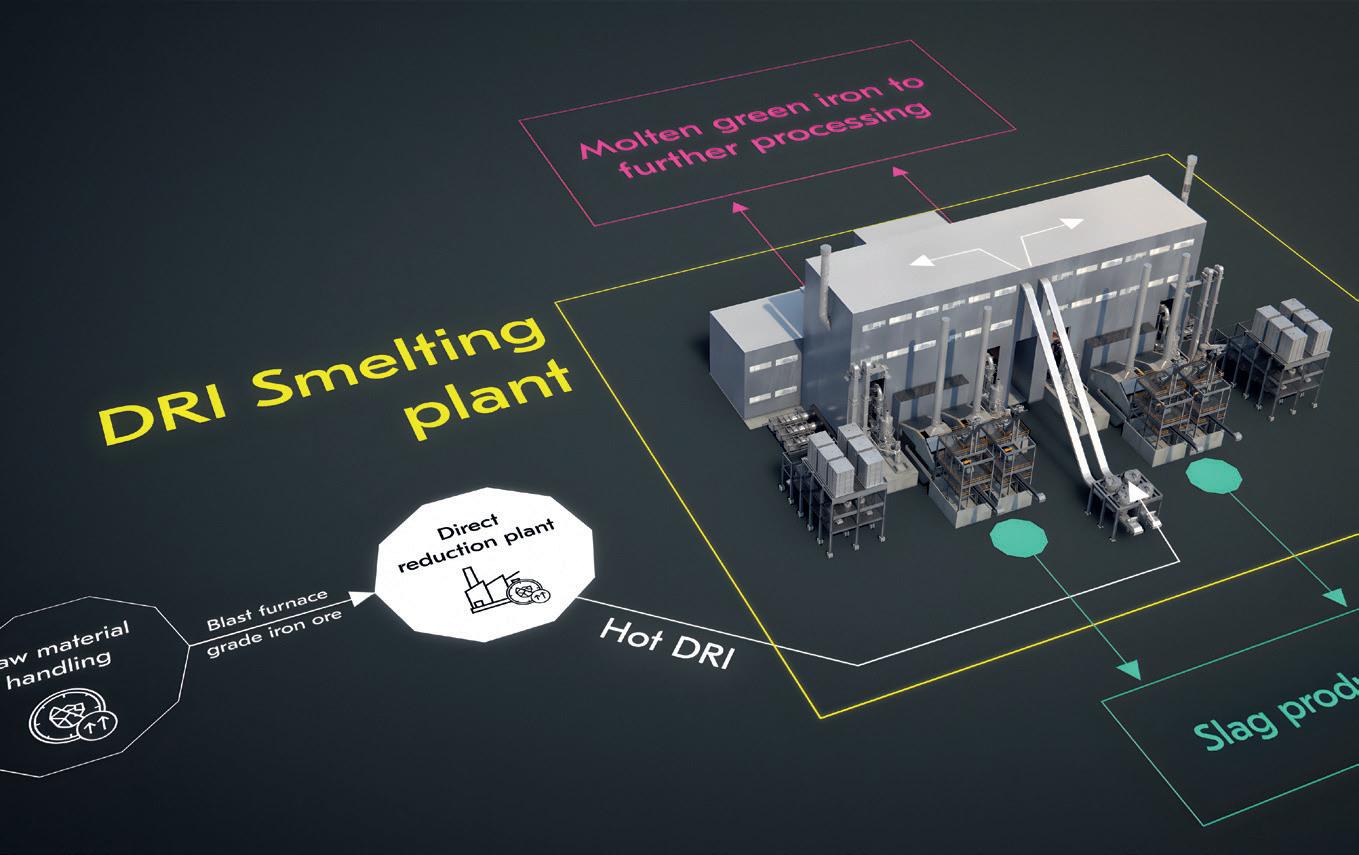
Teknologiakehityksen pitkä polku
Uraauurtavien teknologioiden kehitys on pitkä ja monivaiheinen prosessi. Kirjallisuustarkastelujen ja alustavien arvioiden jälkeen Metso on tutkinut DRI:n sulattamista laboratoriomittakaavassa (kuva 2). Kokeellisesti on selvitetty esimerkiksi raudan jakaumakertoimet metalliin ja kuonaan erilaisilla kuonakoostumuksilla sekä tutkittu eroja maakaasupelkistetyn ja vetypelkistetyn DRI:n sulatuskäyttäytymisessä. Oma mielenkiintoinen tutkimuskysymyksensä on DRI-sulatusuunilla tuotetun raakaraudan mahdollinen hiilettäminen sulatusprosessin aikana, jotta se soveltuisi suoraan käytettäväksi olemassa olevilla konverttereilla ilman suuria prosessimuutoksia. Varsinkin vetypelkistetyn DRI:n osalta tämä tulee olemaan tärkeää, koska lähtökohtaisesti sen hiilipitoisuus on hyvin matala, mikä vaikuttaa merkittävästi sulamis- ja prosessilämpötiloihin sekä käytettävän kuonan koostumukseen. Jo laboratoriokoevaiheessa on siksi myös testattu erilaisten tulenkestävien tiilien ja kuonan vuorovaikutusta, jotta skaalaus suurempaan mittakaavaan voidaan tehdä hallitusti ja turvallisesti ja samalla tuottaa alustavia tutkimustuloksia teollisen mittakaavan laitoksen tarpeisiin.
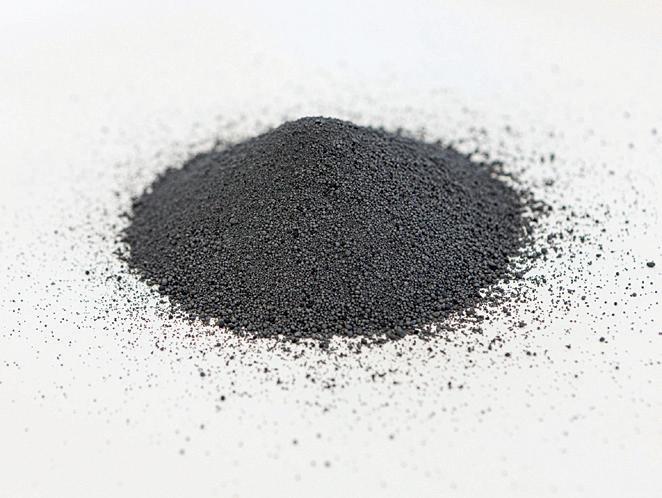

Laboratoriomittakaavan koetulokset ovat antaneet tärkeää lähtötietoa teollisen mittakaavan laitoksen suunnitteluun. DRI-sulatusuunille on laskettu investointi- ja käyttökustannuksia ja hiilijalanjälkeä erilaisissa kapasiteetti- ja raaka-ainetilanteissa. Lisäksi on suunniteltu CircoSmelt-kokonaisuus, eli Metson Circored® -leijupetipohjaisen pelkistysteknologian integrointi Metson DRI-sulatusuuniin. DRI-sulatusuunin integrointi myös muihin suorapelkistysprosesseihin etenee asiakasprojektien kautta.
Kuvassa 3 on havainnollistettu kuonan määrän ja energiantarpeen vaihtelua erilaisilla DRI-syötteillä. Laitoksen toimintaa erilaisissa toimintaympäristöissä on mietitty sekä arvioitu, millainen on optimiratkaisu terästehtaan yhteyteen ja millainen taas tarvitaan tuottamaan granuloitua raakarautaa ulkopuoliseen myyntiin. Tuotetun kuonan kiertotalousratkaisut ovat myös erittäin tärkeä tutkimuksen kohde, sillä esimerkiksi valokaariuunireitillä tuotettu kuona ei sovellu korvaamaan masuunikuonaa sementinvalmistuksessa. Sitä vastoin DRI-sulatusuunilla voidaan tuottaa sementtiä korvaavia kuonia, mikä merkittävästi vähentäisi sementtiteollisuuden hiilidioksidipäästöjä.

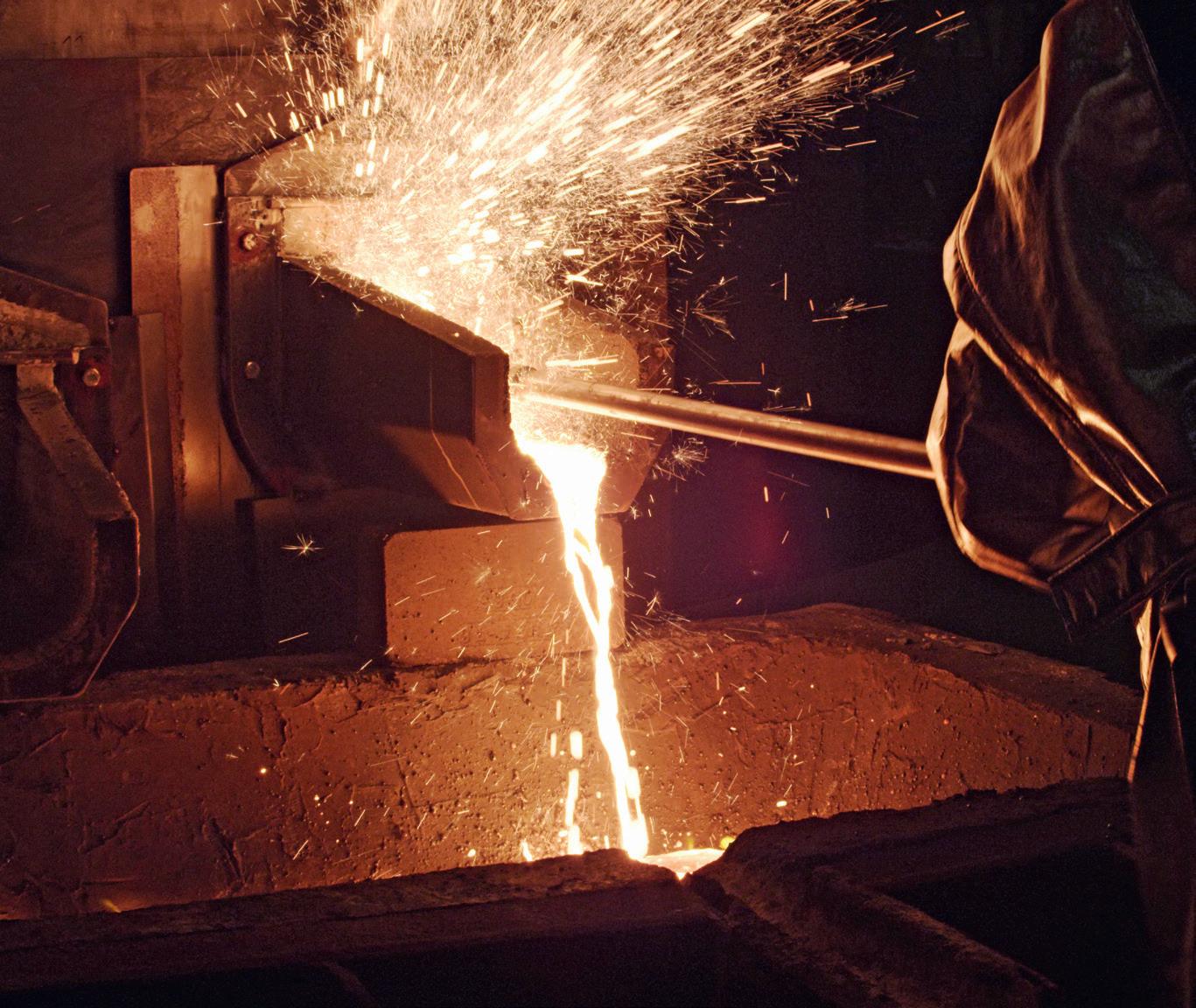
Kokeellisen toiminnan puolella Metson tutkimuskeskuksessa Porissa on pilotoitu modifioidulla, pyöreällä AC-uunilla maakaasupelkistetyn DRI:n hiilettämistä ns. syötekasan kautta (kuva 4). Kampanjassa pystyttiin nostamaan raakaraudan hiilipitoisuus yli 3%:n, mikä vastasi kokeelle asetettuja tavoitteita. Kampanjan toteuttamisaikaan maaliskuussa 2023 ei ollut saatavilla vetypelkistettyä DRI-rautaa koetoiminnan vaatimassa määrin. Koeajon aikana pystyttiin selvittämään prosessin metallurgista käyttäytymistä, mutta uunin erilaisesta muodosta ja pienehköstä koosta johtuen Metso investoi pilot-mittakaavan suorakaiteen muotoiseen ”3-in-line” -uuniin Porin koetehtaalle, (kuva 5). Uusi ”3-in-line” -uuni on pienennetty versio teollisen mittakaavan ”6-in-line” -uunista. Sen nimitys tulee rakenteesta, jossa sulatustyön suorittavat kuusi elektrodia on asennettu jonoon. Koeuunin mitat ovat noin 3x2 m ja syöttö noin 1000 kg/t. Tekniset ratkaisut tulevat olemaan vastaavat kuin teollisen kokoluokan laitteessa. Uunilla on tarkoitus tehdä omaa tutkimus- ja kehitystyötä ja myös testata erilaisia raaka-aineita asiakkaiden tarpeisiin. ▲
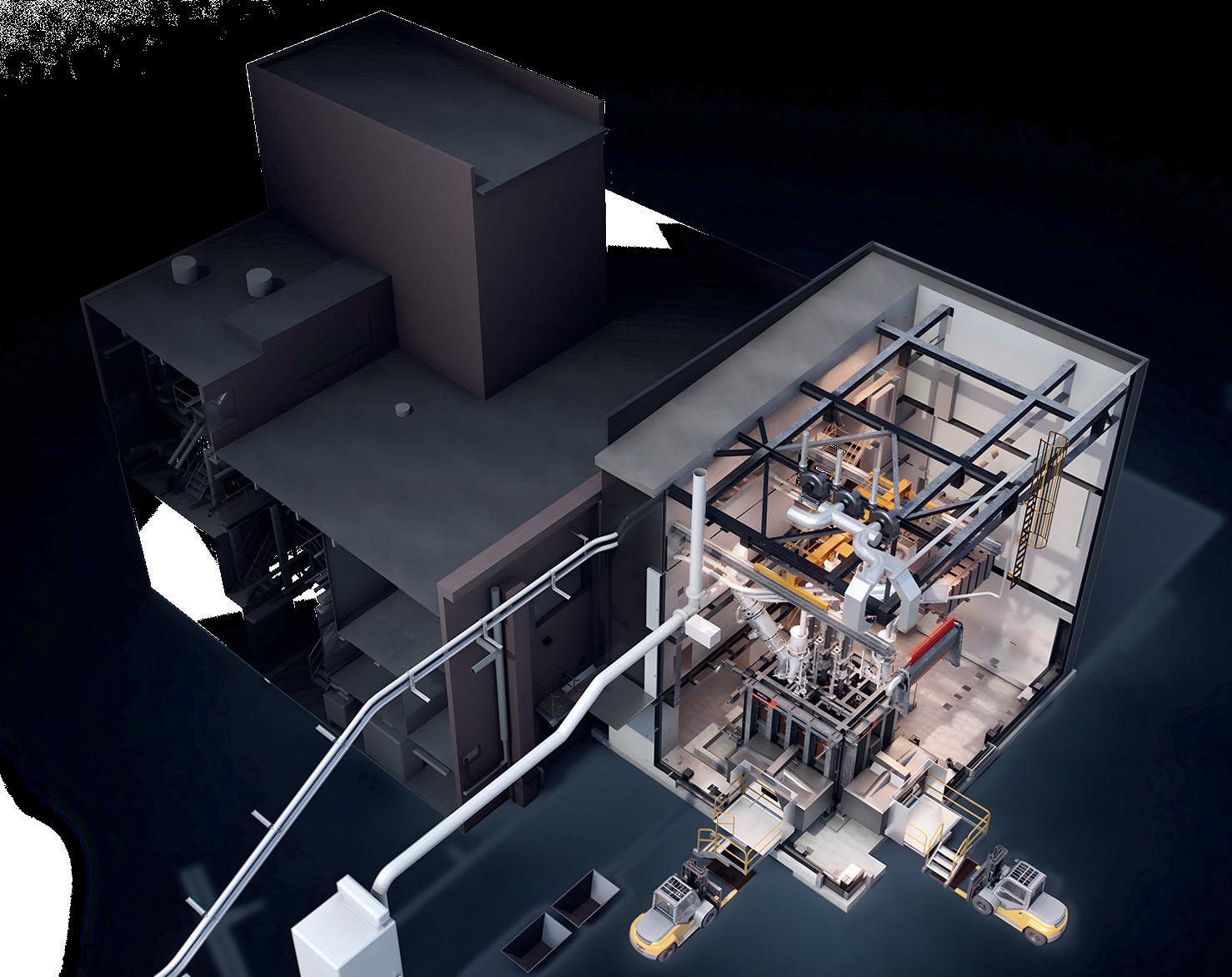
Muutosten äärellä
Uusien vihreiden teräksen valmistustekniikoiden kehitys on nopeaa, ja useat teknologiatoimittajat pyrkivät saattamaan omia teknologioitaan markkinoille. Metso on kehittänyt Outotecin -teknologiaan perustuvan DRI-sulatusuunin, joka yhdistettynä rautarikasteen suorapelkistyslaitokseen mahdollistaa masuuniprosessien korvaamisen teräksen valmistuksessa ja siten merkittävät vähennykset hiilidioksidipäästöissä. Teknologian kehitys on vaativa monivaiheinen ketju, jossa seuraava lenkki on ”3-in-line” -pilottiuunin rakentaminen ja teknologian varmentaminen askel kerrallaan kohti teollisen mittakaavan laitteita ja laitoksia. Talven taituttua pilottiuunin rakentaminen on päässyt kunnolla käyntiin ja laitoksen käynnistäminen on ajankohtaista loppuvuodesta 2024.
TEKSTI: MARI LINDGREN, KIMMO VALLO JA TIMO HAIMI, METSO