Advanced Manufacturing Training Facilities: Where Education Meets Innovation
The design of an advanced manufacturing training facility should reflect the exciting, high-tech nature of the activities it houses. Most importantly, design professionals should endeavor to engage the users of the facilities who truly understand the needs of these spaces.
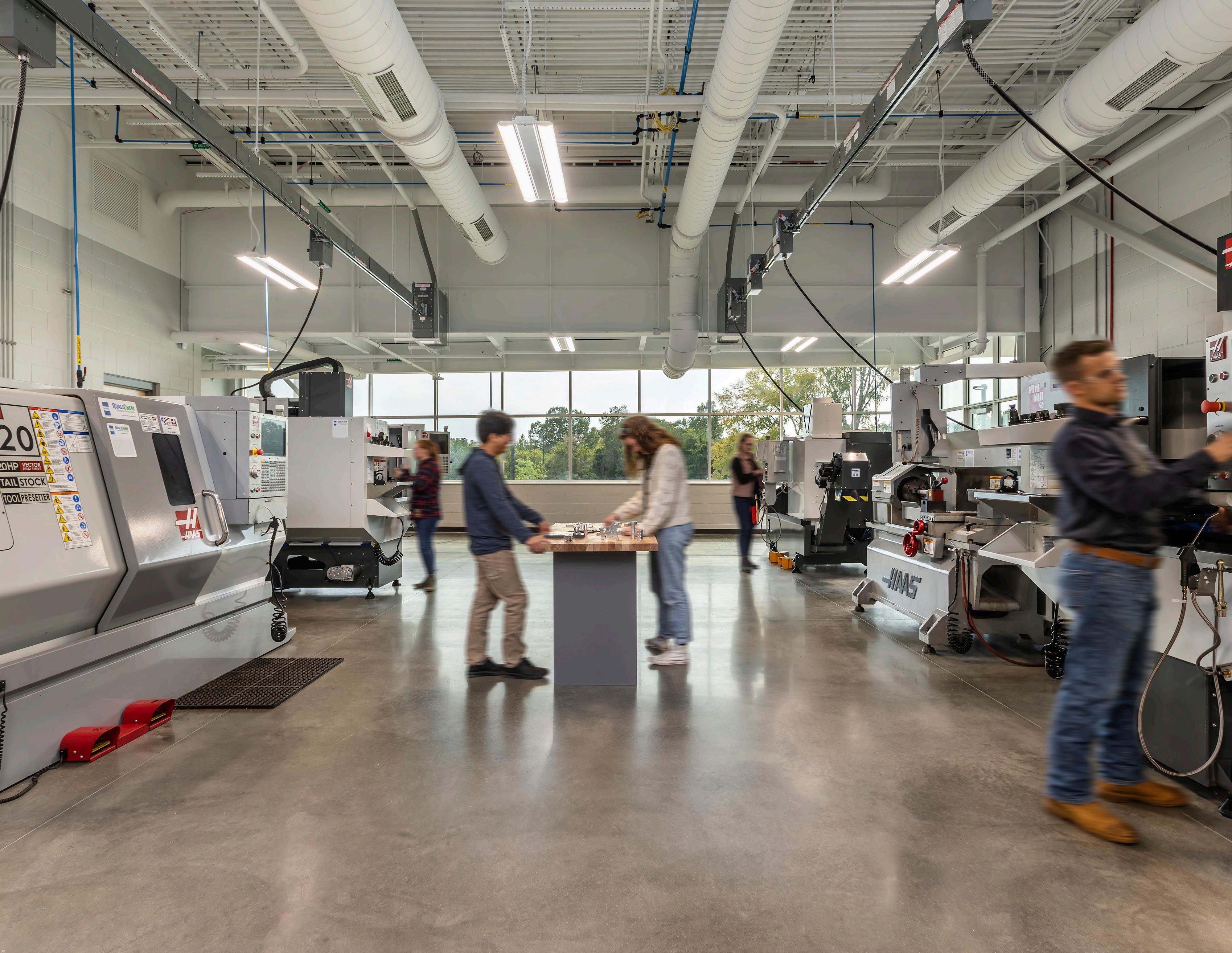
Hinkley ASSOC. AIA, NCARB // Senior Practice Professional
In the past, manufacturing could be a dirty business - literally. Welding, machine milling, and metal fabrication took place in metal shops that required manual labor and expertise on one or two tools that a worker would use over the duration of a career. Old-school manufacturing facilities were designed for the heavy, gritty work of machining, milling, lathing, and welding.
While the old-school techniques are still alive and well, today’s advanced technology has re-shaped manufacturing spaces and processes. As manufacturing processes become more automated, technicians need to be trained (or re-trained) to operate and maintain new technology which performs the same type of work with greater speed, consistency, and precision.
Educating the Workforce of the Future
The transition to advanced manufacturing hasn’t just transformed how we fabricate; it has also transformed how we teach people to fabricate. As manufacturers retool and re-skill employees for modern ways of working, community and technical colleges are critical to filling the skills gap. New advanced manufacturing training programs (sometimes referred to as industrial
tech programs) are training the next generation of workers in skills such as robotics, mechatronics, CNC, metrology, and other cutting-edge digital manufacturing and automation technologies.
These programs teach students how to program, operate, and maintain the modern manufacturing software and equipment that helps execute the craft of manufacturing in a different way. However, it’s not enough to train students on the tools they’ll use today. Students also need to build the transferable knowledge they’ll need to adapt to evolving industry needs and a rapidly changing manufacturing landscape. Training facilities face a similar challenge: rebuilding their curricula to focus on today’s automated design and manufacturing processes while teaching students how to adapt to the impacts of tomorrow’s evolving technologies.
A Changing Educational Landscape
If the shift from manual machining to advanced manufacturing drove the first wave of growth in training programs, the pandemic drove a second wave. While COVID-19 necessitated an immediate shift to online teaching and learning and created uncertainty about career
paths and university programs, the pandemic had a similar impact on the manufacturing industry. Workforce management and supply chain issues became apparent, requiring manufacturers and training programs to adopt new digital technologies such as automation and the Internet of Things (IoT).
These changes led to new opportunities. For many students and their families, advanced manufacturing training programs are an efficient pathway to a desirable career. A twoor three-year advanced manufacturing program is less expensive than a traditional four-year degree from a university, and students enter the workforce as well-qualified, highly sought-after technical specialists.
Furthermore, advanced manufacturing training programs are working with industry partners to better understand industry standards and identify the skills local industries need, creating a win/win/win situation: the schools get a partner in delivering programs that directly impact their students, the students are getting trained for what is actually going on in the industry, and the manufacturers get a robust talent pipeline tailored to their process.
These partnerships also benefit communities through boosted economic development, which can lead to further industry growth and investment. Training programs and their associated coursework are often driven by location and the needs of prospective nearby employers. The curriculum in one county may be tailored towards automotive manufacturing and diesel technology, and towards automation and digital manufacturing in another.
Design Considerations
Designing advanced manufacturing training facilities requires a slightly different approach from more traditional educational spaces. The aesthetics are often a direct response to the cutting-edge technological and fabrication-based curricula which they support. Paired with a highly-functional layout and finishes, these facilities lend themselves to a refined, machined aesthetic with clean lines, durable materials, and exposed building systems. Training labs, efficient and intriguing, are the heartbeat of these facilities and are generally on display from within the building. Classrooms, whether lecture, computer, or training-specific, typically supplement the training labs, with adjacencies varying according to client preferences.
Structural and MEP systems are often left exposed and are celebrated as part of the architecture, so careful consideration must be given to their appearance in addition to serving their respective purposes. Having an experienced MEP team who understands the intricacies of advanced manufacturing processes (and has a willingness to be creative) is critical to project success. It is normal for a training facility to have a variety of lab types, each with different MEP requirements including ventilation, particulate extraction, and humidity control, all operating concurrently. These systems require next-level controls sequencing, commissioning, testing, and balancing to perform as expected.
The design of the building should reflect the exciting, high-tech nature of the activities it houses. Most importantly, design professionals should endeavor to engage the users of the facilities who truly understand the needs of these spaces. Facilities teams, instructors, staff, and students are experts in how their buildings should operate and can provide valuable information which helps guide the design: architecture designed with the users, for the users.
Advanced manufacturing programs are a big draw for the schools that offer them. Design professionals must provide an environment that accommodates the functional and educational needs of the curriculum while also providing an experience that aids in the attraction and retention of students and staff. The facility, as an extension of the programs and processes within, is a significant recruiting tool for schools who want to showcase the curriculum and entice students to explore advanced manufacturing as a career option.
Meet Will
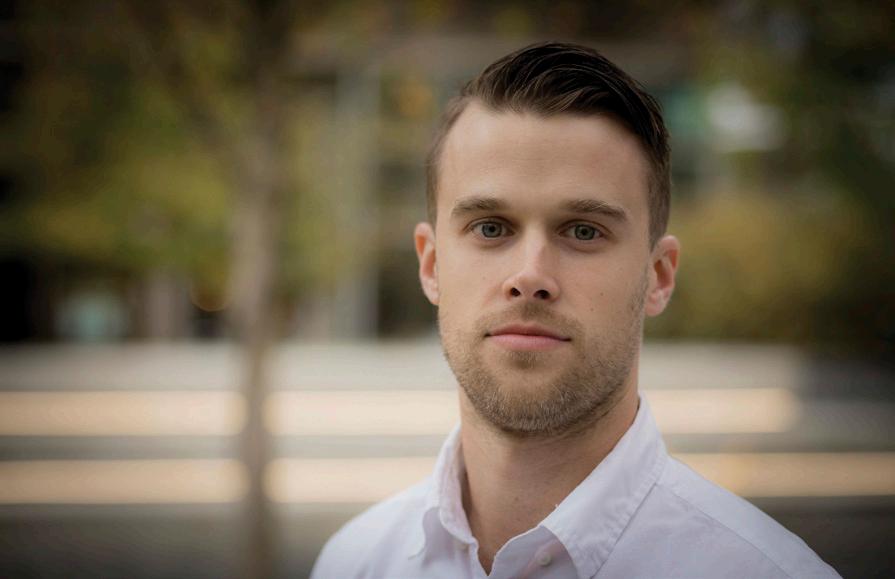
Senior Practice Professional Will Hinkley brings a passion for design and innovation to every project, along with advanced technology skills that streamline and enhance the design process. Since first joining LS3P as a student intern in 2014, Will has worked on a diverse portfolio of designs for higher education, industrial manufacturing, and commercial clients. Notable recent project work includes Piedmont Technical College Upstate Center for Manufacturing Excellence, Ogeechee Technical College Industrial Systems and Robotics Training Center, Johnston County Advanced Manufacturing Training Facility, Southern Regional Technical College Industrial Technology Building, Master Plan and Market Study for Bon Secours Wellness Arena, and renovations for Clemson University’s Littlejohn Coliseum and Memorial Stadium. In the advanced manufacturing sector, Will’s experience includes spaces for welding, metal fabrication, carpentry, auto body & collision, automotive technology, diesel technology, electrical technology, HVAC technology, gunsmithing, CNC, robotics, mechatronics, Internet of Things (IoT), Programmable Logic Controls (PLC), metrology, and others.