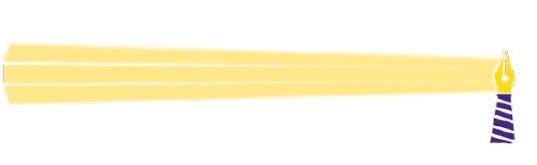
7 minute read
Can Humans Effectively Collaborate with Robots in the Workplace?
Dawn Smith
Two crucial aspects of manufacturing are wanting products to be better than a competitor’s and producing those products as fast as possible. A company must always search for ways to improve the quality of the product they’re producing and keep their workforce trained on the latest innovations in order to
Advertisement
reach and stay at the top of a certain industry. There is a new generation of robots emerging in industry: collaborative robots. Any type of improvement made to either a process or the addition of machinery will cost the company money. Collaborative robots are designed to work alongside a human counterpart. The prices for these types of robots are generally thought to be high, but the collaborative robot has a listing price averaging less than $30,000 per unit, with prices expected to drop to less than $18,000 by the year 2020 (Satyavolu, 2017). With emerging technology, especially in the manufacturing sector, utilizing robots may be the answer to achieving both productivity and the highest possible quality with limited cost to the company.
The idea behind pairing a robot with a human counterpart is to increase productivity, as well as perform precise and/or repetitive tasks. Repetitive tasks to a human worker can become cumbersome and, over an extended time, prove to be nonchallenging. Boredom could have a negative effect on the employee’s job performance and could end up costing the company money in poor production. While some people may be fine performing the same tasks day after day, other workers want to be a part of making improvements in the workplace. If your place of employment makes reliable products in a timely manner, it’s only helping the workforce keep their jobs.
While robots can track production numbers and provide alerts for lower productivity, it takes a human to take this data and use
it to apply changes to processes that need improvement. The thought process behind this is, “Workers with analytical skills will bring premium assets to manufacturers in multiple ways, such as supply-chain optimization, product quality, and asset optimization” (Satyavolu, 2017, p. 3).
Pairing robots with humans can prove to be a win-win for a company, as what one lacks in skill or knowledge, the other can provide. Artificial intelligence (AI) can be given the ability to learn, but a machine doesn’t understand human emotion or
reasoning. Humans have an ingrained need
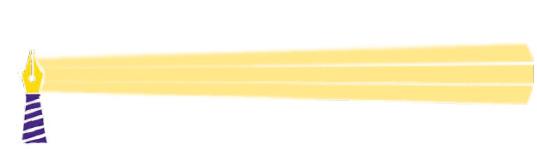
for acknowledgement and recognition for a job well done. This need, at times, may play into decisions made in the workplace that are more geared to an individual’s ego rather than what is truly best for the company. On the other hand, a robot would have no such reasoning and can only do the tasks without any emotion influencing it.
In order to take a position of this coordinated effort, organizations must see how people can successfully enhance machines, how machines can improve what people excel at, and how to update business procedures to help the association. Rules need to be created in order to enable organizations to thrive in their businesses through exploration and work in the field. One company that is working towards robot/human integration is Siemens, an industry leader in the areas of electrification, automation, and digitalization. They are embracing the emerging technology of robotics by finding new and innovative ways for robots and humans to work towards a common goal.
Robots are relentless laborers, yet they don’t ad-lib well. This is when human intuition and
creativity can make a difference. Changes on the sequential construction system require meticulous reconstruction by people, making it difficult to switch up what a manufacturing plant produces. Presently, scientists at German mechanical goliath Siemens say they have an answer: an industrial facility that utilizes AI to arrange the manufacturing of things to come, by both programming robots and passing out assignments to the people working near them. The responsibilities of each can be targeted easily by recognizing the capabilities that a robot and its human counterpart possess, Siemen’s research scientist Juan Aparicio states, “Increasing the intelligence of machines doesn’t mean that fewer people will be working in tomorrow’s factories,” and insists that “humans and machines can amplify each other” (“Automating Automation,” 2018).
Accentuating robotic and human capabilities creates a partnership between the robot and its human counterpart. Florrian Michahelles, who currently heads Siemens’ “Web of Things” research group in Berkeley, CA and his group are developing an AI program called a “reasoner.” The hope is, once completed, this program will be able to govern the steps required to manufacture a product, then determine how the product will be assembled, taking into consideration the robots’ abilities.
Dr. Wang Zi Jian, an expert research scientist for Siemens in Beijing China, is in the process of performing research and testing the latest technologies as a major aspect of a project called “Autonomous Systems Revolution” (“Working with robots: the future of collaboration,” 2018). For a little more
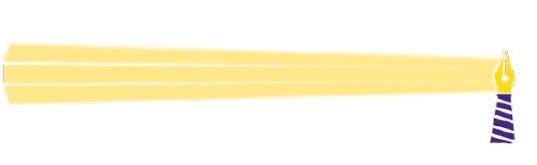
than a year, Zi Jian and his research team have been working on what is called a data glove. The glove is a device that enables a person to control and direct a mechanical arm. Utilizing distinctive sensors, the glove interprets and translates movements and gestures of the human hand. The expectation is the robot will work with the human counterpart in the assembly of a product (“Working with robots,” 2018). It is believed that using this will allow a human to direct a robot to assemble a car, which will alleviate the physical impact felt by the human counterpart of lifting substantial or bulky materials. This is an excellent example of robots and humans working side by side in the workplace. The human dictates to the robot the tasks that are to be performed; in this instance, one cannot perform the job without the other.
Since robots can work anywhere and perform in basically any environmental condition, they can be used in a chemical industry setting, such as a nuclear power plant dealing with spills that would otherwise pose a major health concern for humans. In order to sustain these newer technologies and keep people safe, a company must employ personnel whose primary responsibility is to ensure the robots and systems put in place continue to perform as designed with humans in the workplace. These personnel are called safety engineers, and they uphold robot safety requirements and standards.
Robotics in the workplace continue to improve but still has limitations. A robot currently can’t think for itself or perform outside its programming. Humans are still far more efficient than robots when it comes to
making decisions, handling difficult situations, brainstorming, and making quick decisions if something goes wrong on the production line. As robots become more of a staple in manufacturing and their responsibilities are more developed, we as humans will become more dependent upon them. Companies will want to maintain and increase the revenue
this new technology can generate for them. Statistics show the use of manufacturing robots is increasing rapidly. Figures from the International Federation of Robots (IFR) show a 15% increase in robot sales in 2015
in relation to 2014, with a projection of approximately 2.5 million industrial robots in the workplace in 2019 (The Impact of Robots on Productivity, Employment and Jobs, 2017).
With this emerging technology are some fears regarding robots replacing humans in the workforce. While this concern is
understandable, robots will not fully replace all jobs performed by humans. According to the IFR, less than 10% of jobs can be made fully automated (The Impact of Robots, 2017). Research indicates that robots will only supplement human labor in factories rather than substitute, which will in turn increase
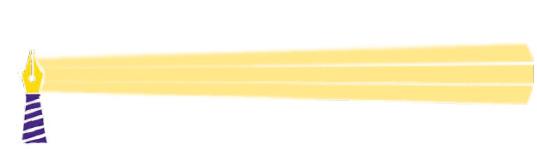
the quality of the work and cause a rise in demand for a higher skilled worker, resulting in higher wages. While not all workers will benefit from increased job security or attain a higher skilled position, those that are willing and able to attain the needed skills to work in
a collaborative environment with robots will
create opportunity for advancement. ■
Dawn Smith is currently a Senior enrolled at East Carolina University studying Industrial Engineering Technology with a concentration in manufacturing. She received her Associates degree in Business Administration from Maryland Community College in 2004. Dawn has over 25 years experience working in manufacturing, spending the last 13 years with the same company as a Quality Technician handling internal issues for the fabrication department in addition to supplier quality issues for the entire facility. Upon graduation, Dawn would like to become a Quality Engineer in the healthcare industry. Works Cited
Automating Automation. (2018). Retrieved from https://www.siemens.com/innovation/ en/home/pictures-of-the-future/digitalization-and-software/artificial-intelligencerobotic-research.html
How Humans and AI Are Working Together in 1,500 Companies. (2018). Retrieved from https://hbr.org/2018/07/collaborative-intelligence-humans-and-ai-are-joining-forces
nternational Federation of Robotics. (2017). The Impact of Robots on Productivity,
Employment and Jobs [Ebook] (pp. 2-10). Retrieved from https://ifr.org/img/office/
IFR_The_Impact_of_Robots_on_Employment.pdf
Satyavolu, P. (2017). A human, a bot, and a manufacturing shop: Welcome to the future workplace. Machine Design, 89(8), 55. Retrieved from http://search.proquest.com. jproxy.lib.ecu.edu/docview/1953989767?accountid=10639
This AI Factory Boss Tells Robots And Humans How To Work Together. (2018).
Retrieved from https://www.fastcompany.com/3067414/robo-foremen-could-directhuman-and-robot-factory-workers-alike
Working with robots: the future of collaboration. (2018). Retrieved from https://www. siemens.com/global/en/home/company/jobs/what-we-do/working-with-robots.html
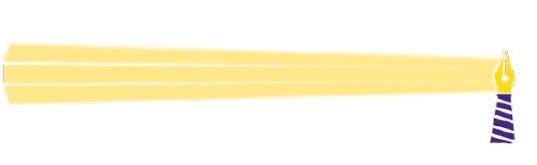
Creative Works
Kenly Cora
Jarod Jordan
Miranda Cox
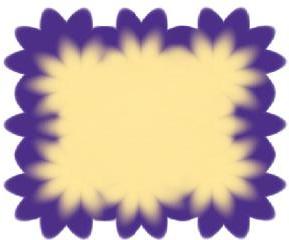
Kathryn Poulsen
Ashley Costa