
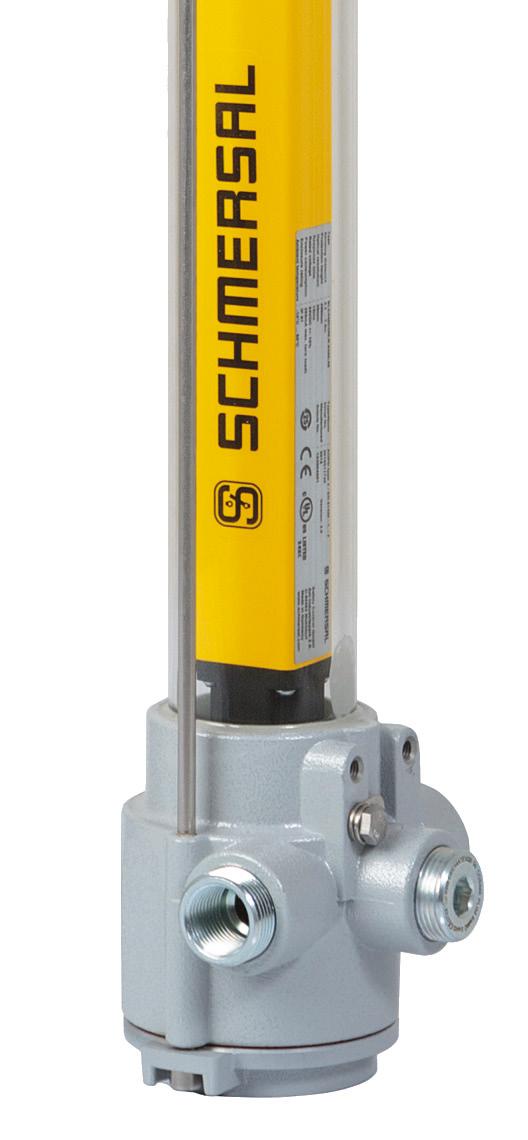

Production areas of the chemical industry, refineries, paint shops, bulk material processing, sawmills and grain processing companies have increased risk of explosion. For these applications, Schmersal has developed the ATEX certified SLC/SLG440 safety light curtains and grids.
The Ex-SLC440 for finger, hand and body detection are available in variants with a resolution of 14 and 30mm and ranges from 0.3 to 20m. The Ex-SLG440 safety light curtains are suitable for access control in hazardous areas. The waterproof and dustproof devices achieve IP66 and IP67 protection and can also be used outdoors.
The devices can be installed in potentially explosive gas and dust atmospheres, they are used to protect hazardous areas and access points for machinery. If one or more beams are interrupted, the dangerous movement is brought to a standstill.
SCHMERSAL | Enigma Business Park Malvern, Worcestershire, WR14 1GL
www.schmersal.co.uk
uksupport@schmersal.com
Chinese tech company Horizon and thin-film technology specialist Leonhard Kurz are combining their expertise to launch a joint venture: Horizon-Kurz New Material Technology GmbH.
Based in Fürth, the company brings together the strengths of both partners to develop and manufacture high-performance coating solutions for separator films in lithium-ion batteries. The partnership aims to significantly improve the safety, lifespan, and performance of lithiumion batteries—particularly for the emerging electromobility sector in Europe.
The collaboration between Horizon and Kurz brings technological expertise and automotive experience to international customers—along
with high supply security through EU-based production that meets strict quality and environmental standards. The coating is carried out using stateof-the-art processes that ensure precise and uniform layer application. Horizon-Kurz New Material Technology focuses on minimal material use and resource-efficient processes—an approach that makes both ecological and economic sense. The coated films are suitable for all standard cell formats—cylindrical and prismatic to pouch cells—enabling broad applicability, particularly in electromobility.
With resource-saving coating processes and high precision, Horizon-Kurz is a pioneer in one of the most critical technology fields of the coming decades.
Veolia, the UK’s leading resource management company, has started operations at a new 25,000 tonnes per annum Hazardous Waste Transfer Station in Newcastle-upon-Tyne. Designed to serve the chemical, agrochemical, pharmaceutical and petrochemical industries in the region, this latest facility will provide the full range of recycling and treatment options available for hazardous waste.
This latest expansion of hazardous waste management capacity will add to the company’s seven existing hazardous waste transfer stations and supporting treatment infrastructure in the UK as part of the Group’s GreenUp strategy, aimed at making Veolia the champion of decarbonisation, de-pollution and regeneration of resources.
The new secure site will serve as a central hub for complex waste streams and houses a new laboratory for analysis and identification of wastes which will segregate each item based on potential hazards, physical and chemical properties.
The facility will also be supported by Veolia’s mobile chemist service, Chempac, for segregation, labelling, packing, collection, treatment and disposal of hazardous and laboratory chemical wastes, to ensure compliance and safety for customers.
For more information visit www.veolia.co.uk
For more than 60 years, NORD has been representing reliable and innovative drive solutions
The company is characterised by longterm experience, extensive know-how in more than 100 industries, own production facilities, great production depth, and a global network. NORD can provide customers worldwide with individual drive solutions from a comprehensive range of modular products and high quality standards.
Today, NORD serves the international market with 48 of its own subsidiaries in 36 countries and further sales partners in more than 50 countries. This allows for service, advice, storing and assembly directly on site. With its sustainability strategy for 2025, NORD promises to consequently act in an ecological, economic and socially responsible manner. The manufacturer’s efficient drive solutions significantly
contribute to the reduction of energy consumption and CO₂ emissions in industry. Furthermore, the drive experts support companies with consultation services, increasing the accessibility of its services, while streamlining processes and facilitating configuration and ordering of drive technology.
Image: NORD DRIVESYSTEMS.
Titan Manufacturing, a machining and fabrication company based in Weymouth, established the partnership with the Lantern Trust in November last year. They have already donated £2000 to support the charity’s work with individuals with a range of needs in Weymouth and the surrounding area.
These much-needed funds have already directly supported four individuals secure housing with intensive private support, through the charity’s assisted rent deposit scheme.
The partnership has been strongly supported across the whole of Titan Manufacturing, with the charity already close to many team members’ hearts after one of their own colleagues experienced homelessness.
Titan Manufacturing has committed to an initial 12-month partnership, with quarterly donations each supporting a different area of the charity’s work - starting with housing and mental health support. This has included funding a range of mental health and wellbeing sessions, such as chair yoga for older, isolated individuals, creative writing workshops, wellbeing support groups, drop-in sessions with doctors, and more - typically reaching around 120 people each month. Over the next six months, Titan’s donations will support the Lantern Trust’s work in homelessness support, followed by benefits advice later in the year. Titan Manufacturing and the Lantern Trust are also exploring the possibility of offering work placement opportunities for those supported by the charity - further deepening their impact within the local community.
The Clean Energy Systems Partner Alliance (CESPA), which has been created to deliver a single source solution for innovators and developers of green tech technology, has increased its ranks to seven specialists with the arrival of Verciti.
A leader in the delivery of immersive Net Zero training, the company believes it can help bridge the widening skills gap for industry by providing access to virtual reality and augmented reality courses covering hydrogen production (plus use and storage), power electronics, machines and drives and hazardous voltage.
It joins six other experts in this field in PP Control & Automation (PP C&A), Danfoss, Emerson, Glacier Energy, Phoenix Contact and Voltserve.
Together, the members bring every discipline needed to optimise and build systems - electrical, civil and structural design, renewable energy software and automation, connection technology and electronics solutions and climate, drives and power solution products.
They now also have access to world class net zero skills
provision, machine build and control systems and energy assets and infrastructure solutions.
Manchester-based Verciti was born out of The Blair Project – a brilliant social enterprise that gets young people building and racing electric go-karts as a way into STEM. As that work grew, it noticed something bigger going on. Universities were losing their way - too slow, too expensive, too broad, whereas employers were crying out for fast, focused technical training that reflected the pace of innovation.
And, worryingly, too many people still felt like STEM ‘wasn’t for them’ - that it was for brainiacs, or people who ‘looked the part.’
The introduction to CESPA came through a networking event at the Ignite Hydrogen Labs Programme. There were immediate synergies between the alliance and Verciti, especially the organisation’s AR EdTech project that is pioneering the delivery of training and upskilling in the hydrogen industry.
For further information, visit www.cespa.org.uk.
Outsourcing is playing a key role in helping retailers and manufacturers to bridge the gap between affordability and innovation in their product development programmes.
According to the BCMPA – The Association for Contract Manufacturing, Packing, Fulfilment & Logistics, while many consumers are seeking value in the products they buy, as they continue to grapple with ongoing cost of living challenges, many are not prepared to compromise on quality. As a result, although BCMPA members are reporting a marked intensification in retailer efforts to keep prices down, this has not yet led to the deprioritising of other key shopper values such as ethical sourcing or sustainability.
While much of the growth in own label has been focused on the food sector, the BCMPA said that other categories, such as alcoholic drinks and personal care products, which in the past have been dominated by brands, are also now providing opportunities.
Altus Group, a leading distributor of capital equipment for the electronics industry in the UK and Ireland, has awarded Scienscope, a global provider of high-quality inspection equipment, with the ‘Fastest Growing and Most Dynamic Supplier’ recognition, celebrating their dynamic growth and innovative approach to electronics manufacturing solutions.
The award was presented by Richard Booth, Chairman and Founder of Altus Group and Danutek Group Companies, to Eddy Linn and Jean Wu of Scienscope.
Altus and Scienscope partnered in 2018 to introduce 2D X-ray and X-ray counter technology into the European market. At the time, Scienscope was launching its first generation AXC-800 X-ray Counter, marking the start of a partnership that has grown rapidly over the years. By 2025, Scienscope has established its European headquarters in Romania, developed a range of 2D X-ray solutions, and expanded into component management technologies, including goods-in scanning, smart storage, in batch as well and automated versions.
Today, Altus and Danutek sell nearly $2 million worth of Scienscope products annually, reflecting the strength of the partnership built on Scienscope’s focused R&D efforts and Altus Group’s robust sales and marketing support. This collaboration has played a key role in the companies’ mutual success.
Rainford Precision will be emphasising exactly why the company is widely regarded as the experts in micro-machining at the forthcoming Manufacturing Solutions Ireland exhibition.
On the 11th and 12th June at the Technological University of Shannon (TUS), Rainford will present technology like the Kern range of ultra-precise 5-axis machining centres, Finepart micro abrasive waterjet cutting technology and cutting tools from some of the world’s most prestigious brands.
Rainford Precision will also present its latest cutting tool solutions from worldrenowned brands such as Union Tool, Louis Bélet, Delmeco, Gloor, HOBE, Osawa, DTS, Iwata, 6C Tools, Swissceramill and ATOM. The respective partners are industry leaders in the manufacture of drills, end mills, reamers, boring bars, threadmills and slitting saws. Within this diverse portfolio are tools for specialist applications and material types, such as the Hufschmied brand of milling
Within this diverse portfolio are tools for specialist applications and material types, such as the Hufschmied brand of milling tools.
tools. The Graftor range of end mills from Hufschmied has been developed specifically for machining graphite, and the range can double productivity rates and tool life when compared to rival tools. With such a diverse platform of specialist cutting tools and micro tool solutions, Rainford has invested in a Keyence digital microscope to provide a complete tool investigation and consultancy service for customers in the UK and Ireland.
BG Steels Ltd was established in 2006 and has developed over the last 18 years to become the UK representation for many premier steel producers both in Europe and further afield. The products we supply, through our principals, are wide-ranging and well established.
Indeed, BG Steels with Lueling GmbH has now become the leading supplier of cold heading wire for fasteners in the UK and Ireland. Our growth over the years has been based on a thorough understanding of the
markets we serve backed up with solid management skills to ensure total supply chain solutions. The skill balance between our team is well-balanced with professional metallurgical qualifications and sound understanding of steel manufacturing and applications. Our business management skills ensure that customers needs are immediately grasped and can be matched to our principals’ product capabilities. With all our team skills, we ensure that both our customers and the companies we represent have a relationship of continuous improvement with the highest quality performances and secure source of supply.
Our product ranges are:-
• CARBON AND ALLOY COLD FORMING WIRES
• STAINLESS WIRES
• SPRING STEEL WIRES
• BRIGHT BARS
• HARDEN & TEMPERED STRIP
• FLAT & PROFILE WIRES
• LARGE DIAMETER HOT ROLLED AND FORGED BARS
• CLOSE DIE FORGINGS
www.bgsteels.co.uk
01433 631999
bj.hague@bgsteels.co.uk
Yorkshire-based leading glass manufacturer Specialist Glass Products has invested £1.2 million into new equipment to further enhance efficiency after receiving £840,000 in funding from Lombard. The company is the first in the UK to acquire this machine at a jumbo size, allowing for larger-scale production without compromising on quality and value.
At Specialist Glass Products’ glass processing factory in Huddersfield, the new Systron proHD Vertical Glass Processing machine will allow the firm to handle more jumbo glass orders up to 6000mm x 3210mm. Specialist Glass Products will also continue to process flat glass and curved glass orders to bespoke measurements.
The new machine is multifunctional and can polish, grind, cut, and shape glass into any form. It also allows for the production of 120 fully finished panels daily. This ensures that the glass manufacturer can continue to work with bespoke designs, especially those requiring identical units of the same shape and size.
Standout features of the new machine that will enhance production include consistent polishing quality with precise control over polishing pressure, guaranteed arris parallelism due to patented water-cushion guidance, vibration-free processing to prevent chipping, and protected suction cups to prevent damage during the manufacturing process.
ABB’s innovative PixelPaint technology has been deployed at the Mercedes-Benz Sindelfingen plant in Germany, where it complements the site’s conventional painting processes by enabling the precise and efficient application of intricate paint designs. The sustainable and resource-saving technology began operation in 2025 as the luxury manufacturer develops new personalized options for its most exclusive models.
PixelPaint consists of a paint head with more than 1,000 tiny, individually controlled nozzles, mounted on an ABB robot such as
In the month following the introduction of new tariffs on imported goods into America, the internationally recognised trademark, Made in Britain has seen a 20% increase in the number of companies applying to join the organisation. The introduction of 10% tariffs on all imported goods from Britain and other countries, including a 25% tariff on steel, aluminium and cars, has prompted calls for consumers to buy more British goods.
the IRB 5500 paint series. Combined with ABB’s 3D vision system and coordinated by ABB’s RobotStudio® planning and programming software, the head tracks very closely to the vehicle body to ensure that 100 percent of the paint is applied to the car with no overspray or airborne misting. This eliminates the need for labor-intensive masking and repeat trips through the paint shop, resulting in zero waste, reduced environmental treatment requirements, and lower emissions overall.
PixelPaint is just one example of how ABB’s smart technologies are transforming the paint process, completing the final piece of the puzzle in digitalizing automotive manufacturing.
PICTURED - From left: Dr. Julia Schuchardt, Head of Process Development, Coating Technology & Corrosion Protection, MercedesBenz AG; Jörg Reger, Managing Director Business Line Automotive, ABB Robotics
Last month, the Liberal Democrat Party called for a national ‘buy British’ campaign, including the use of clear ‘Made in Britain’ labelling. Made in Britain has backed this suggestion and has written to Sir Kier Starmer, Kemi Badenoch and Ed Davey to underline its established, industry-led, not-for-profit, independent and widely recognised efforts to support UK manufacturing in the UK and around the world.
As one of the largest and most experienced insurance brokers in the world, Gallagher can offer you a complimentary review of your existing insurance programme. Our team can provide detailed insights on how your business benchmarks against others in the industry, identify potential coverage gaps and recommend the appropriate values and limits for your policies. Additionally, with improving market conditions, we may be able to highlight opportunities where you could save on costs.
For further information, please scan the QR code.
One of Sheffield’s newest manufacturers is helping to revitalise the city’s industrial capabilities with cutting-edge materials processing technology.
Sheffield Technology is winning a growing customer base, with some key projects being attracted back to the UK from overseas. The company is eager to leverage its ability to rapidly laser-cut materials up to 60mm thick— made possible by the company’s investment in a state-of-the-art 24kW Trumpf 5060 TrueDisk laser.
With fully automated material and part handling, this machine boasts a 6-metre by 2-metre plate capacity and can cut: Stainless steel, armour, carbon, and alloy steels – up to 60mm thick, Aluminium – up to 40mm, Copper – up to 16mm and Brass – up to 12.7mm.
Beyond laser cutting, Sheffield Technology’s extensive fabrication and machining capabilities include a 400-tonne, 5.1-metre press brake and automated cobot welding, allowing the company to deliver fully integrated manufacturing solutions.
Darren Mason, Works Director at Sheffield Technology, explained: “The big advantage for us is that we have truly disruptive technology. Our high-power laser operates at a scale and precision that challenges conventional thinking. While most lasers struggle beyond 30mm, we comfortably cut up to 60mm, allowing us to compete on both quality and cost with traditional heavy-duty processes, such as plasma & profile cutting.”
The company’s rapid expansion is reflected in its workforce growth, scaling from just 10 employees last year to 58 today, including four apprentices. With a firm commitment to developing future talent, Sheffield Technology plans to expand its apprenticeship program to pass on engineering skills that have defined the city for generations.
Looking ahead, Darren commented: “We’re proud to be back in Sheffield,
helping to underpin its metal processing history, and we trust the city will continue to attract work from across the country and beyond. Our capacities and state of the art equipment really do support continued competitiveness within the UK in this important sector, underpinning jobs for our young people in the years ahead.”
Sheffield Technology’s innovation and investment in advanced manufacturing can only support the city remaining at the forefront of British materials processing & manufacturing industry.
sheffield-tech.com
Camozzi Automation and HAYLEY DEXIS | Fluid Power have joined forces to provide a fully integrated control panel for a materials processing facility, successfully completing the project in just four weeks.
The site, which produces aggregates, concrete, and recycled building materials, had experienced downtime and inefficiencies due to an ageing control panel prone to frequent breakdowns and requiring extensive maintenance. Having previously supplied a robust and reliable solution to the same customer, Camozzi and HAYLEY DEXIS were approached again to deliver a durable, high-performance upgrade.
A Camozzi representative and HAYLEY DEXIS Account Manager visited the site to assess the application and ensure a seamless replacement of the existing control panel. The goal was to quickly replace the incumbent panel while maintaining high operational efficiency and improving system durability and protection. With a clearer understanding of the customer’s operational needs, they created the custom panel solution.
The new panel replacement design featured a plug-and-play layout, offering easy installation and longterm durability for instrumentation and
electrical components in the site’s demanding environment. Custom CAD drawings were created based on the existing design to support a quick fit and reduce future maintenance requirements.
From concept to testing, the entire process was completed within four weeks of order placement. This rapid turnaround minimised plant downtime and allowed the customer to resume operations immediately. The new panel eliminated reliability issues and significantly boosted uptime, ensuring easier servicing and sustained performance.
This project highlights Camozzi and HAYLEY DEXIS’ commitment to fast delivery and engineering excellence. The customer’s decision to partner with them for a second installation is a testament to their trust in the efficiency and reliability of the previous solution. Both companies remain committed to supporting industrial customers with durable, efficient pneumatic solutions—while continuing to drive innovation and excellent service.
Camozzi Automation is the UK arm of the global Camozzi Group, a leader in the design and manufacture of components and systems for industrial automation. With a heritage
of engineering excellence and innovation, Camozzi Automation UK is headquartered in Warwickshire and serves a wide range of sectors, from packaging and food processing to life sciences, automotive, and beyond.
What truly sets Camozzi UK apart is its commitment to exceptional technical and customer support. The local team of experienced engineers works closely with customers to deliver fast, reliable advice and tailor-made solutions. Camozzi Automation UK’s is also renowned for its ability to manufacture bespoke cylinders rapidly in-house.
Camozzi Automation UK’s dedicated Automation Centre enhances its capability to deliver fully assembled pneumatic and electro-pneumatic control panels. From design to build, each project is handled in-house with a focus on quality, flexibility, and efficiency. This turnkey service allows customers to simplify installation, improve system integration, and reduce downtime – all backed by Camozzi’s trusted engineering expertise.
For tailored advice or to discuss your next automation project, contact our technical team at technical@camozzi.co.uk or call 024 7637 4114.
Businesses have been investing in warehouse automation for decades, using technology to automate routine, repetitive, and manual processes, including picking, palletising, data entry, transfer and analysis, stocktaking, quality control, and shipping.
The three most commonly cited barriers to warehouse automation are poor planning, lack of integration, and workforce readiness. Businesses need to plan and tread carefully – as unclear business value and misaligned or incompatible systems will inevitably lead to workplace confusion, data silos, a lack of communication, and the inability for data to flow seamlessly.
Fundamental steps to take are:
1. Plan and execute carefully. Understand your business case and key success metrics. Start slowly: pick off your ‘low-hanging fruit’ that will deliver early success and inspire confidence. Monitor and adapt.
2. Collaborate for success. Identify suppliers that are willing to work together to ensure that their solutions can integrate with your existing systems, particularly your WMS.
3. Align with your upstream supply chain and production partners to ensure the optimum quality of readable barcodes, 2D codes, data coming into the warehouse.
4. Align with downstream supply chain partners for complete transparency throughout the wider supply chain, particularly within a retail/consumer environment.
5. Bring your workforce along with you. Identify potential skills/digital literacy gaps and invest in training upfront. Involve your workforce in potential applications for automation where early wins can be achieved.
PTC has introduced two new offerings from its cloud-native Onshape® computer-aided design (CAD) and product data management (PDM) platform.
and compliance needs of US government agencies and defence contractors.
Listening to market demand, the digital transformation specialist has launched Onshape AI Advisor - an intelligent, generative AI-powered assistant that enables the enhancement of design productivity and expertise.
At the same time, it has also unveiled Onshape Government - a specialised solution designed to meet the International Traffic in Arms Regulations (ITAR) and Export Administration Regulations (EAR) regulatory
These offerings empower designers and engineers to work more efficiently, collaborate in real time, and bring high-quality products to market faster.
These offerings empower designers and engineers to work more efficiently, collaborate in real time, and bring high-quality products to market faster.
PTC’s Onshape AI Advisor helps users accelerate their design process with expert, AI-powered guidance on CAD workflows, PDM best practices, and platform capabilities.
Developed on Amazon Bedrock, it helps teams transition from legacy CAD, optimise designs, and improve efficiency.
Onshape Government is a purpose-built version of Onshape, designed specifically to help meet the compliance needs of US federal and state agencies, defence contractors, and organisations working on regulated projects.
Hosted on AWS GovCloud (US), it enables compliance with regulations such as ITAR and EAR while offering the same streamlined collaboration, version control and accessibility benefits that make Onshape one of the industry’s fastest-growing CAD and PDM solutions.
Three aspects of sensor technology are particularly important in image processing for industrial automation: performance, flexibility and usability. Simple Vision sensors meet these requirements. They are as easy to operate as optical sensors, plus they are as powerful as camera systems.
Vision sensors are the ‘eyes of industrial automation’. That is because these little marvels enable machines to see and interpret their surroundings. They are easier to integrate and operate than camera systems. The devices are suitable for many different tasks: They are used for presence or absence detection, parts detection, inspection, code reading, measuring or counting tasks, as well as print quality verification.
When selecting the optimum sensor technology, it is worth considering performance in the corresponding detection, identification and inspection tasks. In addition, sensor configuration and parameterization must be as simple as possible to save time and money. It can be beneficial for system operators to focus on vision sensors that can be set up and operated without any specialist knowledge. This makes integration and ongoing operation easier, even if production process requirements change. The system sensors can thus be designed cost-effectively with minimal effort. The Sensor People at Leuze provide a product portfolio that meets these requirements with their Simple Vision concept, enabling the efficient use of image processing technology in industrial automation.
Flow control specialist Bürkert has released a new pinch valve for use in single-use biopharma applications.
The new Type 2707 Pinch Valve ensures process safety and reliability with a stainless steel locking and pinch mechanism that optimises flow while protecting the tube insertion. The versatile valve, available in modulating control and on/off versions, is compatible with a range of tube diameters, and is fast and simple to fit.
To optimise control modulation with the Element actuator version, analogue and digital positioners options are available, along with integrated pneumatic control and a position indicator LED. The actuator includes an autotune function to speed up commissioning, and enables digital connectivity via CANopen, Asi, and IO-Link, with diagnostic functions also featured.
Alternatively, the Classic actuator version of the Type 2707 Pinch Valve provides on/off control, and with compact dimensions, this design is suited for space-constrained
applications. Position feedback is also achievable for the Classic actuator version as an option.
Across both variants of the Type 2707 valve, the stainless steel construction of the locking and pinch mechanism achieves long-lasting durability and ensures reliable process control. The hygienic, corrosion-free design is also compatible with all cleaning and disinfection liquids used in the biopharma industry, and features high chemical resistance for long-lasting performance.
The efficiency of the pinch mechanism enables easy integration for tubes or single-use assemblies, with no need to bend or stretch installed tubes thanks to tube insertion at the bottom of the valve which enables easy access. Placing low mechanical load on the tube, minimising the risk of tube damage while optimising flow, the design features a sphere-shaped compressor and tube holder which partially encloses the tube. This mechanism applies only a minimal pinching action to secure the tube while ensuring an effective seal.
Anritsu Company is announcing the expansion of the analysis bandwidth along with the addition of a Tracking Generator option for the Field Master Spectrum Analysers.
The Field Master spectrum analysers provide benchtop
performance in a ruggedised handheld battery power format, indispensable for RF engineers working in a wide range of communication industries. A new software release further enhances their capability, especially for users in the aerospace and defense and security services that need to capture IQ data. A new software option expands the analysis bandwidth to 150 MHz enabling the widest capture range in any handheld instrument.
Capturing IQ data for post processing and analysis has become an essential tool for engineers who need to gain the
maximum insight into potentially illegal or unrecognised signals. Anritsu’s complimentary MX280005A IQ Signal Master Software has been updated to support the wider capture bandwidth.
An additional benefit of the enhanced analysis bandwidth is that the Real Time Spectrum Analyser (RTSA) now has an industry leading maximum span of 150 MHz. An RTSA has become the essential tool for monitoring interference in the RF spectrum as well as detecting intermittent or transient signals.
For more information visit: www.anritsu.com.
MAPAL has developed two sample parts for the aerospace sector. These socalled “generic components” represent all the demanding machining steps typically involved in producing aerospace parts such as aluminum hydraulic valve housings or titanium torsion links for landing gear.
Wherever movement is required on an aircraft – whether in flaps, rudders, landing gear, engines, or other components - there is a valve housing involved. These components are essential to hydraulic systems and come in a wide variety of designs, from small boxes to blocks measuring half a meter in size. Despite design differences, the machining requirements are similar.
The generic component created by MAPAL measures approximately 30 x 30 x 30 centimetres and involves all relevant machining processes involved in manufacturing a valve housing, from premachining to finishing. Rather than replicating an existing customer component, it was designed to reflect the machining challenges of various real-life components.
Aerospace valve housings are more complex than those used in other industries, such as hydraulics for construction machinery. In its most demanding customer project so far, MAPAL used over 130 custom tools to produce a single valve housing.
With the generic components for aerospace, MAPAL is pursuing a concept that has already proven successful in the automotive sector. There, the company developed representative components that reflect the full range of machining challenges in automotive manufacturing. Today, much of automotive production is supported by these generic reference parts. Similarly, MAPAL can now use its aerospace generic components to demonstrate the full extent of its technological capabilities in this sector.
FLIR has unveiled FLIR MIX, an advanced multispectral imaging solution designed to bring greater detail and accuracy to infrared imaging. By blending thermal and visible-light imagery with precision, FLIR MIX gives researchers and engineers a powerful new way to analyse, interpret, and share complex thermal environments with greater accuracy, delivering clearer insights to accelerate breakthroughs in defence, commercial, and academic research.
Until now, researchers have had to choose between thermal and visible imaging: one reveals heat signatures while the other provides structural detail. Recording both and trying to align them manually— or harder still, synchronizing them temporally—can be inconsistent and time consuming. The result is data that’s close but never quite complete.
FLIR MIX is a game changer in multispectral imaging, capturing and synchronising high-speed thermal and visible imagery at up to 1,004 frames per second.
FLIR MIX is a game changer in multispectral imaging, capturing and synchronising high-speed thermal and visible imagery at up to 1,004 frames per second. The camera and software work together to deliver one dataset with spatial and temporal alignment—no more missed details or second guessing, just a complete picture of fast-moving events.
By Chris Lloyd, Spelsberg UK’s Managing Director
For electrical installations, from integrating control devices through to wiring terminal connections, safety and performance depends on the quality of the protecting enclosure. Specifying the right enclosure demands a process centred on the needs of the customer for each project.
When an OEM is designing a machine or system, making considerations about the housing of electrical equipment is crucial to ensure adequate protection. Likewise for an end user or electrical installer, securing sensitive devices or electrical supplies from the elements, impacts, and intrusion, is fundamental. Yet to achieve this, the enclosure designer must think beyond just ensuring a durable, impermeable container.
Providing the right enclosure certainly demands the basis of a highly robust unit, engineered to high levels of resilience. However, the optimum enclosure for the application requires the consideration of multiple factors, and these must always be centred on the needs of the customer and those using the equipment. This means that the first essential step is a thorough analysis of the challenge before an enclosure can be specified.
First, we investigate what the equipment to be protected aims to achieve, and who will be in contact or have interaction with it. This ascertains the balance between the safety and protection of users, alongside accessibility for those who need it. Then we move to the needs of the equipment to be housed, considering the level of protection and security it requires, and how long it needs to last. The location of installation is crucial and informs decisions on IP and IK (impact) rating, and even fire protection. Again, protection must be balanced alongside points of access and potential vulnerabilities, such as cable entry points or keypads.
Linked to this, we also need to understand implications surrounding installation, such as weight or fixing points.
Considering the array of applications that industrial enclosures could be required to protect, and the variety of responses to the initial specification criteria, customisation is frequently required. Even though enclosure manufacturers have an expansive and flexible range, developed over years of engagement with customers across a multitude of uses, the capability to create a bespoke housing remains essential to many customers. Enclosures manufactured from industrial plastic may have knock-out holes to allow tool-free adaption, but a CNC service can achieve specific entry and exit points for cables, or allow other points of access, such as control interfaces. Customisation could also involve wider services such as printing, whether for branding or safety information.
The focus on providing a complete solution to the customer, partnering with them from specification through to installation and use of the enclosure in the field, means retaining accountability. While in-
house services in customisation can achieve a completed enclosure, additional services including assembly can provide a completed unit. This means that if required, all electrical components can be installed, and wiring connected, ready for installation at the host location.
The advantage of a turn-key service, where all adaptations are provided by a single supplier, makes the supply of the enclosure as a completed project much more streamlined for the customer. Along with easier management, partnering with a single supplier can also achieve a faster project completion time, and enables any issues to be rapidly resolved.
For repeat orders, procuring an industrial enclosure from an online search or catalogue could be a fast and practical approach. However, for new projects or specific installations, it’s often faster in the long-run to engage the input of an enclosure engineering service.
With a customer-centric philosophy, and a relationship for each project that focusses on the demands of the application throughout, the right enclosure can be realised.
Titan Enterprises shares key insights to help engineers and operators navigate challenges of precision batching to ensure accurate measurements and smooth process operations.
Metering batches of liquids may seem straightforward at first glance - install a flowmeter in the product line, connect it to an instrument, control the measurement with on-board software, wire in a valve, enter your required volume, press a button and the right amount of liquid is dispensed into your vessel. However, real-world applications reveal a host of complexities that must be addressed to achieve precise and repeatable results.
Today’s advanced process and liquid handling systems demand highly precise flow measurement. From adding water to food production mixers, dispensing flavourings to beer or cider at point of sale, to handling aggressive chemicals, even slight inconsistencies in system design can lead to inaccuracies, wasted product, or disrupted processes.
For batching systems, the critical factor is repeatability – ensuring the required volume is delivered consistently every time. To achieve this, ideally the system should maintain consistent process conditions; however, this is not always feasible. For instance, temperature fluctuations throughout the day can
alter fluid viscosity and volumetric flow measurements. Similarly, a decrease in the feed liquid tank level supplying the process pump can reduce the dispensing rate, impacting the accuracy of the flow meter and the flow control valve. Therefore, as a starting point, batching system designs should aim to minimise as many variables as possible within a reasonable cost. Once this foundation is established, equipment such as flow meters, pumps, and valves can be selected to effectively compensate for any parameter variations.
Titan’s NSF-Approved Beverage Flowmeter is designed specifically as a flow measurement solution for the drink dispensing market. With its exceptional repeatability, this low-cost device is installed around the world enabling industries to unlock higher yields.
1. System Repeatability:
Hydraulic stability is essential. Air pockets in the line can lead to dynamic flow situations, causing volumetric errors in delivery. Ensuring a hydraulically locked system eliminates such variability and enhances repeatability.
2. Stable Process Conditions:
Changes in pressure, temperature, or flow rate can push flowmeters into unpredictable operational zones, affecting calibration and accuracy. Maintaining consistent conditions is vital for reliable performance.
3. Pulsating Flow Management:
Selection of the pump type is important to avoid pulsating flow. Pulsation from certain pumps can disrupt flow rates, especially
in aggressive chemical applications. Pressure regulators and pulsation dampers should be incorporated into flow systems to achieve a smooth and constant flow.
4. Strategic Placement of Flowmeters:
Positioning the flowmeter just before the dispense valve minimises fluid inertia and improves measurement accuracy.
5. Understanding Flowmeter Resolution:
Low-resolution meters, such as those with one pulse per litre, may lack precision in small batch applications. However, going too high in resolution is an unnecessary expense when choosing equipment. Selecting the appropriate resolution for the task is critical for reliable performance.
6. Valve Selection and Calibration:
The type of shut-off valve used can impact delivery accuracy. Fastacting solenoids are ideal for smaller pipelines, while larger setups benefit from solutions like multi-stage shut-off systems or “batch overrun compensation” programming to finetune results.
7. Optimising Electronic Flowmeters:
High-performance batching meters (such as Titan’s ultrasonic Atrato® flowmeter) can predict stop signals in advance, ensuring consistent delivery even at high speeds.
By accounting for these factors during system design and commissioning, engineers can eliminate common pitfalls in liquid metering and achieve extremely good accuracy. And investing in the appropriate flow measurement technology that suits the application requirements will ensure that the batching system performs with precision and consistency.
Radiometry Enables Pixel-Level Temperature Data from Compact, Highly Sensitive Uncooled Thermal Infrared Camera Modules.
Teledyne FLIR OEM, part of Teledyne Technologies Incorporated, announced the availability of radiometric models of its highperformance Boson®+ thermal and Hadron™ 640R+ dual thermal-
visible camera modules. Built for defense and industrial applications with size, weight, and power (SWaP) optimization, the NDAA compliant and ITAR-free radiometric Boson+ and Hadron models provide real-time temperature measurement of every pixel within a scene.
The eight new radiometric Boson+ models include 640 x 512 and 320 x 256 longwave infrared (LWIR) resolution options, multiple lens options, and shared mechanical and electrical interfaces with the existing non-radiometric Boson+. Automatic gain control (AGC) and direct data entry plus (DDE+) deliver dramatically enhanced scene contrast
and sharpness, including lower video latency that enhances tracking, seeker performance, and decision support, day or night. The Boson+ also features multiple video output interfaces, including USB, CMOS, and MIPI for maximum integration flexibility.
In addition to an integrated radiometric 640x512 resolution Boson+, the new Hadron 640R+ is also equipped with a 64MP visible camera, featuring dual 60 Hz video output via USP or MIPI. At 56 grams and with an IP54-rating for dust and water protection in the elements, the dual-sensor payload offers longer flight time and extended battery life for unmanned aerial applications.
All Boson+ and Hadron 640+ models are compatible with Teledyne FLIR OEM’s Prism AI detection, tracking, and classification models along with Prism ISP libraries for super-resolution, turbulence mitigation, contrast enhancement, and more.
To learn more or to purchase, visit www.flir.com/oem.
Devices designed for capturing rapidly changing analog signals must respond quickly while consuming minimal power, especially in battery-operated applications. To address these demands, Microchip Technology has released the PIC16F17576 microcontroller (MCU) product family with integrated low-power peripherals and the ability to precisely measure volatile analog signals.
PIC16F17576 MCUs feature a new low-power comparator and voltage reference combination that can operate while the MCU core is in sleep mode, allowing for continuous analog measurement while consuming less than 3.0 µA of current. The Analog Peripheral
Manager (APM) controls which peripherals are active to minimize total energy consumption and enable battery-operated applications to monitor signals effectively without excessive power drain.
Engineered for applications that measure volatile analog signals, PIC16F17576 MCUs include operational amplifiers (op amps) with software-controlled gain ladders. This feature enables a single op amp to switch between multiple gain options, helping mitigate noise while maintaining
precision and power efficiency. Equipped with up to four op amps and a 12-bit differential ADC with automated averaging, the MCUs enable precise signal measurement over a wide range of inputs.
PIC16F17576 MCUs are well suited for measuring analog signals in a number of industries, including environmental and industrial monitoring, smart home and building automation. Key applications include vibration and strain measurement, flow metering, gas detection, cold asset tracking and motion sensing.
A new report into the 2025 skills and recruitment outlook of small and medium-sized enterprises (SMEs) in England reveals just over nine in 10 in manufacturing are anticipating some kind of skills gap within their business, with a third at entry level.
Now in its third year, the Skills Horizon Barometer, launched by the Skills for Life campaign and featuring commentary from manufacturers Southbourne Rubber, also found that nearly four in 10 SMEs in the industry have noticed a skills gap in specialist areas.
More widely across England, when it comes to specialist skills, opportunities with AI are firmly on the radar for the year ahead, as nearly a
quarter are poised to train their staff in AI related skills or recruit those with knowledge in the field. The research found one in five are regularly using AI in day-to-day operations, and one in five also say experience in AI is an asset on a CV for potential new recruits.
While AI knowledge is high on the recruitment agenda for SMEs, they are also looking beyond the skillset to find human characteristics or transferable skills that are the right fit for their organisation too.
Exploring the type of candidates manufacturing SMEs are looking for reveals employers looking to offer opportunities to those early on in their career, but crucially candidates who have some experience. While one fifth
of businesses still look to hire those from traditional academic routes, such as university, just over a fifth of firms would hire straight from school or college, supporting young people with relevant training to build up their skills, and 25% would look to hire candidates with experience from a different field.
The highlighted findings from the latest Skills Horizon Barometer look to help SMEs understand all the technical education training and employment schemes available to them, including Apprenticeships, T Levels, Skills Bootcamps, HTQs, as well as numeracy and digital skills courses.
To find out more, visit: find-employer-schemes. education.gov.uk.
Rowan Crozier, CEO of Brandauer, has steered the company to invest more than £400,000 into vocational learning since 2016 and this has seen the firm create toolmakers, engineers, quality specialists and experts in logistics, reducing the average age of his workforce to just 44.
He believes the influx of youth and energy has been fundamental in helping the business evolve into its position as a world class supplier of precision stamped components and tooling to customers in more than 26 different countries.
Many of the youngsters have continued to be sponsored to complete degree courses and
HNCs, with Adam Burgoyne now holding the position of Operations Lead, responsible for several critical business functions, including facilities, management systems and quality.
Tom Madge is the latest apprentice to join Brandauer, starting last week as the company’s new Sales and Marketing Coordinator.
The 22-year-old will work directly with Rowan and Technical Sales Manager Graham Allison to help digitise the firm’s lead generation system, as well as supporting social media, comms, SEO optimisation work and content on the company’s website.
He will also work with PR company Cucumber PR on the business’ external relationship and communications, using his photography skills to tell the inside workings of Brandauer’s operations and product development.
For further information, visit www.brandauer.co.uk.
At Queen’s University Belfast, researchers leveraged FLIR’s A8583 cooled mid-wave infrared (MWIR) camera and 5x microscope bayonet lens, and FLIR Research Studio software to investigate the electrocaloric effect—temperature changes in dielectric materials under an electric field.
Understanding this effect is crucial for developing energy-efficient, solid-state cooling systems that could revolutionise electronics cooling and sustainable refrigeration. However, capturing these rapid thermal changes required a high-speed, highly sensitive thermal imaging solution capable of detecting minute temperature variations in real time.
To address this challenge, Butler Technologies provided Queen’s University Belfast with a FLIR A8583 MWIR cooled camera and 5x microscopic optic and FLIR Research Studio software for advanced data analysis.
Researchers successfully identified thermal fluctuations at the same frequency as the electrical stimulus, confirming the electrocaloric effect in real-time.
This precise ability to capture transient thermal changes enabled a more detailed examination of how electrocaloric materials respond under different conditions, offering insights into their feasibility for solid-state cooling technologies.
These findings contribute to the ongoing exploration of electrocaloric materials for nextgeneration cooling solutions, with potential applications in electronics thermal management, sustainable refrigeration, and materials science.
A groundbreaking humancentered approach to change management has played a pivotal role in accelerating digital transformation within RollsRoyce’s manufacturing supply chain.
The method, developed by Aston University academics, was part of an innovative study funded by InterAct, the Made Smarter Innovation programme.
It applied the ProcessOriented Holonic (PrOH) Modelling Methodology to 100 companies in Rolls-Royce’s digital supply chain system, known as Connected Tempest, which supports the development of the next-generation Tempest aircraft.
By integrating soft systems principles and focussing on human factors to address challenges in strategy, culture, technology, and operations, the project helped manufacturing partners enhance their digital maturity.
The collaboration provided an opportunity to explore the broader potential of PrOH and create tools, training materials, and a website to further engage the wider industry and academia.
Professor Ben Clegg, Professor of Operations Management at Aston University, has spent the last decade developing PrOH Modelling as a way of improving the human aspect of change management to enable the manufacturing industry to accelerate its rapid digital transformation and adopt advanced technologies such as AI, automation, and IoT.
The project worked with 100 companies in Rolls-Royce’s supply chain, including suppliers of materials, metals, and machinery,
to use the PrOH Modelling Methodology to identify key factors for improving digital maturity. It also involved workshops with industry professionals and academics to develop strategies for digitalisation, culture, process, strategy, data, and training. A workshop at AMRC Sheffield brought together these groups to further develop and deliver outcomes focused on these key areas.
Looking ahead, the project team - which also included Dr Krishna Balthu, lecturer in Operations Management and Systems Thinking at Aston Business School, and Dr Ehsan Eslamian, Developer and Business Intelligence Manager at Williams F1 - plans to offer short courses on PrOH Modelling and systems thinking for supply chain improvement, in collaboration with industry bodies such as the Operational Research Society (ORS) and the Institute of Engineering and Technology (IET).
InterAct was a £4.4 million Made Smarter Innovation-funded, Economic and Social Research Council-led network that brought together economic and social scientists, UK manufacturers, policymakers, and digital technology providers to address the human issues resulting from the diffusion of new technologies in industry.
To learn more about PrOH Modelling visit the InterActfunded website http://prohmodeller.org. For more impact stories about the work of InterAct visit https://interact-hub.org/
LEFT: Professor Janet Godsell, InterAct co-director from Loughborough University
BELOW: Ben Clegg in a PrOH modelling workshop
West Yorkshire’s manufacturing and engineering businesses are being encouraged to put forward their brightest young talent for the 2025 Leeds Manufacturing Festival Awards as nominations officially
open for this year’s celebration of the industry’s future leaders and most forward-thinking employers.
Now in their fourth year, next month’s awards are a key event in the Leeds Manufacturing Festival
calendar, designed to shine a light on the achievements of young people in the sector and help businesses to bridge the skills gap and secure the future of the industry by attracting a new generation of talent.
Nominations are open until Monday 2 June, with the awards ceremony taking place at Leeds Beckett University on 12 June. This year’s award categories include Apprentice of the Year, Rising Star, Future Manufacturing Leader, and Employer of the Year. A special Manufacturing Ambassador award will also be presented to an individual who has gone above and beyond in championing the sector and inspiring the next generation.
Entry details and nomination forms are available via the Leeds Manufacturing Festival website leedsmanufacturingfestival.co.uk.
£100,000
The Way Youth Zone has announced NIS Group as its first ever Cornerstone Patron, following a transformative £100,000 investment into supporting young people across Wolverhampton and the surrounding areas.
Part of the donation will launch a new employability programme:
Way2Work - Building Futures Together, a long-term partnership between the two organisations that will empower local young people with the skills, confidence, and opportunities they need to shape their own futures and gain meaningful employment.
This commitment will deliver accessible support to individuals and families, with activities including confidence-building and teamwork sessions for children, employability skills development and career exploration for teenagers.
There will also be dedicated family and SEND guidance through joint workshops and mentoring opportunities, whilst the programme is aiming to extend its reach into the wider community through outreach youth work and targeted employability activities.
By combining the organisation’s industry and training insight with the Way’s youth work expertise, the new partnership will inspire young people to unlock their potential, educate through first-class training, empower them to take control of their futures, and transform prospects for generations to come.
People in engineering work to make businesses and everyone’s future prosperous and safe
• EEMUA’s guidance publications and other resources help people in engineering to get their work done, using proven and practical how to guidance
• Developed ‘by industry, for industry’ incorporating the collective experience of EEMUA’s Members and other stakeholders with reference to appropriate national and international standards, e.g. ISO and API
• Practical resources used by engineers in their work wherever they are, whatever time they have
• Available to all in industry all publications and many other resources are ready for immediate download from EEMUA, where you can also register to take part in EEMUA events and training
• All resources free or discounted for Members and Associates. New corporate Members are always welcome to share EEMUA resources and influence.
Functional Safety Seminar
22 May 2025 – Manchester, UK
159 TankAssessor course
9-12 June 2025 – Live online – GMT+3 to suit Middle East & Africa time zones
Communications Workshop
13 June 2025 – Manchester, UK
Inspection Seminar
25 September 2025 – London, UK
Storage Tanks Seminar
27 November 2025 –
ABB has turned to its own technology to understand and optimise energy consumption at its Stonehouse manufacturing and calibration centre in the UK. The result has been a 20% reduction in electricity usage plus wider sustainability benefits.
The drive towards greater operational efficiency and sustainability is a boardroom conversation in every industrial organisation. Reducing energy consumption and emissions, however, is difficult to achieve without a granular picture of resource utilisation and effective strategies for realising tangible benefits. A recent exercise by ABB to enhance the efficiency of its own operations demonstrates that knowledge is indeed power when it comes to identifying areas for optimisation.
ABB’s Stonehouse facility in Gloucestershire in the UK manufactures flowmeters and other devices for the analysis of gas and
ABB’s Stonehouse facility in Gloucestershire in the UK manufactures flowmeters and other devices for the analysis of gas and water treatment.
water treatment. The site features a dedicated calibration capability, where flowmeters measuring up to 2,800 litres per second are tested and certified before delivery to customers in the water treatment and process industries.
ABB has pledged to the EP100 global corporate energy efficiency initiative, led by Climate Group, with the goal of significantly improving energy management throughout its worldwide facilities by 2030. In 2024, Stonehouse set precise targets to monitor, analyse, optimise and control energy efficiency, including adoption of the ISO 500011 standard.
An initial obstacle to achieving these objectives was a lack of accurate data about the performance and energy efficiency of electrical systems at the roughly 40-year-old facility. This affected facilities managers’ ability to identify areas on site offering the greatest promise for achieving quantifiable reductions in energy consumption.
Key to the solution implemented at Stonehouse is ABB Ability™ Building Analyser, that’s been implemented as part of a broader energy management strategy. ABB’s buildings and utilities data analysis platform offers comprehensive tracking of energy consumption that encompasses various points of electricity, gas, and water usage throughout the facility. This enables comprehensive tracking of energy consumption, enabling personnel to monitor and analyse electricity and utility consumption in real time.
At Stonehouse data from multiple connected devices and systems across the site – including electricity, gas, and water flow meters – is displayed via Building Analyser’s
intuitive interface. Meters are connected to a programmable logic controller (PLC), with the Building Edge gateway also connecting to the PLC over Modbus TCP. This solution allows personnel to monitor and understand utility consumption in real time, revealing insights to enable cost savings while improving energy efficiency, sustainability, and occupant awareness.
Data collected and assessed with the aid of Building Analyser, quickly revealed valuable insights for the Stonehouse team. Five critical areas were identified as major contributors to overall energy consumption, accounting for 47 percent of the facility’s total energy usage. By focusing on these high-impact areas, the team has been able to drive substantial energy savings and contribute to sustainability efforts.
As a consequence of exercise, the Stonehouse team has been able to successfully identify several opportunities for improvement, including some surprising findings that have been put to good use.
Exploration of energy usage by the test facility’s large calibration pumps revealed higher consumption in the afternoon than in the mornings. This highlighted a lack of formal operating procedures for running the pumps, with two operating personnel handling the pumps differently. One operator adjusted the pump speed to vary the flow, while the other ran the pumps at full capacity and controlled the flow using the bypass valve. Initial results from standardisation of pump operations indicate a reduction of 500 kilowatt-hours (kWh) per day while maintaining optimal performance, amounting to substantial savings over the course of a year.
Analysis of energy consumed by the building’s heating system indicated higher usage on Sundays than on Saturdays. This was traced to hot water timer settings on Sunday being identical to those on weekdays, leading to an adjustment of timer settings that’s achieved significant costs savings over the course of the week.
Another anomaly was uncovered in gas heating settings in the canteen area. Despite the canteen being unoccupied after lunch the heating
Analysis of electricity usage also revealed that an air compressor system was needlessly running on Sunday outside production hours, leading to an adjustment of compressor timer settings.
timer remained on until 3pm, resulting in unnecessary energy consumption. Timer settings were adjusted to align with actual occupancy hours, leading to a saving of approximately 10 hours’ worth of gas heating per week.
Analysis of electricity usage also revealed that an air compressor system was needlessly running on Sunday outside production hours, leading to an adjustment of compressor timer settings.
Recognising the opportunity to reduce energy consumption during the Christmas holiday season, a planned 10.5-day shutdown was implemented. Many devices in the facility operate on seven-day timers. Despite the holiday shutdown, these devices would still activate during this period. To address this, facilities managers manually turned off equipment including ovens, HVAC, water heaters, gas heating, air compressors, computers,
demineralisation plants, conveyors, and vending machines. This strategic management of equipment usage during the holiday shutdown has achieved substantial cost savings and more sustainable operations.
More opportunities for energy savings and greater sustainability
In addition to these primary energysaving measures, managers at ABB’s Stonehouse facility have implemented several supplementary initiatives to further reduce energy consumption and costs.
All non-LED light fixtures have been replaced with energy-efficient LED fittings, improving lighting quality and significantly reducing electricity usage. What’s more, the installation of PIR (Passive Infrared) sensors in the warehouse and flat roof areas ensure that illumination is only active when needed, minimising unnecessary energy expenditure.
The cumulative effect of all these energy-saving initiatives is enabling a remarkable 20 percent improvement in annual electricity consumption, equivalent to the energy needed to power 91 households in the United Kingdom for a year. The project at Stonehouse is just one example of how organisations can manage their decarbonisation journey with the help of data-driven insights that translate into tangible reductions in energy consumption and carbon emissions.
Cloud and On-Premise install options
Recombinant alternative to the conventional LAL assay
Non-animal derived
High sensitivity testing with less lot-to-lot variation
Recombinant cascade reagent (rCR) assay
Colorimetric (KCA) assay
Lot matched to a specific Control Standard Endotoxin for optimal performance
Help minimise your impact on
Industrial process heating equipment and solutions specialist Babcock Wanson UK is pleased to be a founding member of Electrify Industry, a new body representing businesses seeking to decarbonise the UK’s industrial base through electrification.
Electrify Industry is working with innovators to create a voice to ensure that the right
A leading light in developing decarbonised products...
policy is developed for electrification, which is the most efficient option to decarbonise the UK industrial sector.
A leading light in developing decarbonised products – including a range of electric powered industrial process heating systems - and services for boiler houses, Babcock Wanson is well placed to contribute to Electrify Industry’s campaigning work.
babcock-wanson.com
Leading heat pump manufacturer, STIEBEL ELTRON, has announced the appointment of John Felgate as its new Managing Director (MD) for the UK and Ireland.
John takes over from the departing Mark McManus, who leaves the organisation this week, having spent 17 years with the company, with John beginning on 1st May 2025.
With over 25 years of experience in building services manufacturing, John has an impressive reputation as a commercial and technical expert in the industry, and has been instrumental in growing STIEBEL ELTRON UK’s presence in the county’s renewable heating market.
John, who previously served as Head of Technical, worked closely with Mark to see STIEBEL ELTRON UK experience significant growth, expand its product portfolio, and become a driver of the UK’s transition to lowcarbon heating solutions.
Most recently, under their guidance, STIEBEL ELTRON UK expanded its training capabilities with the launch of a new state-ofthe-art training centre at its Wirral headquarters.
In addition to his role at STIEBEL ELTRON, John has served as Chairman of the Domestic Heat Pump Association and is currently Chairman of the Electric Space and Water Heating group at BEAMA.
Well versed in product development, customer service, sales and marketing, John was awarded the Contribution to Energy Efficiency Award in 2013 by the Energy Efficiency and Renewables Awards and was recognised with the Richard St. Clair Award from BEAMA for his role in developing heat pumps, electric heating and hot water in 2022.
For more information visit: www.stiebel-eltron.co.uk
Has been instrumental in growing STIEBEL ELTRON UK’s presence in the county’s renewable heating market.
Effective immediately, Judson Smythe is announced as the new Managing Director of MGS Technical Plastics, one of the nation’s fastest growing injection moulding firms serving all industries and markets.
Forming a critical part of the company’s wider growth strategy, incumbent Managing Director Neil Garrity will continue to serve as Chair. At the same time, Mark Preston is named as the new Commercial Director. Following a management buy-in by all three leaders in mid-2024, the transition to Managing Director will be seamless assures Judson.
Mark, Judson and Neil’s stories are indicative of the opportunities that the sector continues to offer
professionals with the drive to make a difference. All three began their careers as apprentice toolmakers, Judson in South Africa and Mark as one of the first to complete a UK technician engineer’s apprenticeship. Having all worked their way up within the Lancashire business makes the MGS leadership team uniquely positioned to appreciate the diverse career pathways and progression opportunities, relays Judson.
Offering additional holiday leave for long serving team members is just one perk that Judson announced when sharing the leadership changes.
PICTURED LEFT: The new leadership team at MGS Technical Plastics, Mark Preston (L), Judson Smythe (C) and Neil Garrity (R)
Pentagon, pro-actively supporting you from the early stages of design assistance right through to mould tool manufacture and repeat production of your injection moulding project. Your new or existing plastic injection moulding project will benefit from years of technical moulding experience!
Laura Hedley, Head of Consultancy and Talent Services at the OPC, explores why some employees struggle with fundamental safety practices.
In many organisations, safety performance fluctuates, with periods of high accident frequency which can prompt renewed vigour or new safety initiatives. These efforts often lead to temporary improvements, but longterm safety gains can sometimes remain elusive, leading to cycles of fluctuating safety performance.
Laura Hedley from the OPC said, “While equipment or insufficient training can contribute to poor safety performance, human factors are often the primary cause. Even though most employees adhere to safety protocols, everyone makes mistakes. In many cases, incidents occur simply because we just don’t get the basics right.”
“When we talk about the basics, these can include ensuring the availability and proper condition of PPE; thorough equipment checks and maintenance; conducting safety briefings before any work; strict adherence to industry regulations; and prioritising safety over operational or commercial pressures.”
Laura also points out, “The NonTechnical Skills (NTS) of vigilance and conscientiousness also play a crucial role in the basics of safety, e.g., tools left on site or untidiness could lead to an incident. Risk and situational awareness are also vital in identifying and mitigating potential hazards.”
So, what prevents employees from mastering the basics of safety?
Through research and having undertaken hundreds of Post-Incident Assessments (PIA), OPC psychologists have found several common obstacles to mastering the basics of safety:
• Effor t vs. Payback: Skipping the safety basics, preferring convenience over compliance.
• Balancing the job vs. the basics: Prioritising job completion over safety.
• Over-reliance on experience: In the absence of an incident or ‘near-miss’, we might believe there’s no need to focus on the safety fundamentals.
• Why Bother! A lack of positive senior leadership action to safety concerns can lead to employee disengagement.
• False sense of security: Overconfidence and a failure to recognise potential risks can hinder sticking to the basics.
• Not my responsibility! This pervasive attitude can mean a culture of disengagement and neglect, ultimately leading to failure in getting the basics right.
Laura emphasised, “Recognising human fallibility and promoting a culture where safety is everyone’s responsibility is essential. Employees must also feel empowered to report unsafe behaviours without fear. Regardless of role or seniority.”
The OPC identified some key factors why employees find challenging unsafe behaviour in others hard, such as:
• Fear of reprisal, rejection or ridicule.
• A lack of confidence in their own safety knowledge inhibits them challenging others.
• Social dynamics, such as not wanting to upset colleagues – ‘You don’t rat on your mates.’
• An organisational culture that may prioritise productivity over safety.
To overcome these barriers, creating a supportive environment where safety issues can be openly discussed without fear or negative consequences is crucial. A recent OPC client survey of over 600 workers revealed that more than 90% prefer having their safety mistakes pointed out.
“Making the workplace safe isn’t just down to one person—it’s about all of us looking out for each other,” said a Maintenance Delivery Manager. “We need to speak up and hold each other accountable, even if it means having difficult conversations.”
The OPC offers various training initiatives to improve safety performance, including:
• Non-Technical Skills training
• Back-to-Basics workshop
• Accelerate Your Safety Leadership (AYSL) workshop.
Contact the friendly OPC team if you think your operations need some help getting back to the basics of safety.
E: admin@theopc.co.uk
T: +44 (0)1923 234646
W: www.theopc.co.uk
With over three decades of safety-critical expertise, the OPC delivers bespoke solutions that strive to improve people performance, identify talent and nurture a safer culture.
Our expert psychologists help to:
Discover top talent through specialised recruitment support and role profiling.
Improve performance using Non-Technical Skills and safety initiatives.
Develop best practices, stand-out safety leaders, and deliver post-incident support for a safer culture.
Partnering with the OPC means collaborating with a dedicated team focused on safety and people performance. Trust us for tailor-made solutions from pre-selection to employment. We prioritise safety and strive to enhance your processes to go beyond industry standards.
SQUIRREL CAGE MOTORS | SLIP RING MOTORS | DC MOTORS
Motors up to 25 MW and 13.8 kV
• Low voltage slip-ring and squirrel cage motors up to 3,000 kW
• Medium voltage slip-ring and squirrel cage motors up to 15,000 kW
• Direct current motors up to 2,000 kW
• Frequency converter-proof drives
• In-house load test facility up to 13.800 V, 2.300 kVA, 120 Hz
Customized special designs
• Custom designs for special applications and operating conditions
• Optimized motor design for higher efficiency
• Mechanically and electrically interchangeable motors
• Commissioning worldwide
MENZEL Great Britain Ltd. | UK Branch Office
Martin Rooney | Tel.: +44 1664 500 844
martin.rooney@menzelgb.co.uk
menzel-motors.com
Finding themselves with an influx of work, Lyndhurst Engineering was keen to bring some fresh talent on board to help.
Recruiting the right people has typically proven a challenge for Technical Manager Andy Wilding, as he explains. “You get the CVs through, but you don’t always get the right person matching the CV. Working with T Level students gives us a much better chance to find out whether they’re the right fit.”
Connecting with their local college led Lyndhurst Engineering to hosting a group of T Level students for an Open Day, which included a tour of the facility and an opportunity to chat. Andy was pleasantly surprised by the number of students interested in
joining them for a work placement and how engaged and interested they were about a career in the sector. “First and foremost, we want to encourage more young people into engineering,” Andy says. “Working with T Level students gives you a really good insight into whether they’re right for the job, and what direction they want to go in –whether that’s apprenticeships or something else.”
The company is also keen to encourage more gender diversity in a typically male-dominated industry. “I’ve been really heartened by how many young women have been applying for a placement here, I’d say it’s been an even split,” Andy says. “Two out of our three current students are female, and they’ve been working closely with our apprentice, Katie – she’s a brilliant inspiration. We’d love to encourage more women into engineering and support them to thrive.”
Lyndhurst Engineering has worked with several T Level students over the last few years, and they’ve made a significant impact on the business.
“Once they’ve been given a bit of induction and training, they’re able to do jobs that really need doing. We don’t make up tasks just to keep them busy; they get stuck in and add real value.”
The students have applied technical knowledge learned from their course and are particularly skilled at using CAD systems. They’ve also been helping with maintenance work, fixing electrical components, milling, turning, fabrication and fitting. Andy continues: “You get a feel for what the students are good at. Our current student, Lucy, was great on the semi conversational programming for our long bed CNC machines with Heidenhain controls. Dan, one of our experienced machinists showed her how to use it and she picked it up straight away, we were really impressed.”
The students are completing their 45-day industry placement in chunks throughout the year. Andy says: “If I could’ve had them all back this week, I’d have leapt at the chance! We really could use the extra hands to get us through a busy spell.” He’s lost count of the number of positive comments he’s had from other members of the team and is talking to the students about returning as apprentices, on completion of their course. “We would love to see them back here to carry out their 4-year apprenticeship and grow with our business.”
Andy would encourage other businesses to try T Levels as a route to recruitment. “If each company in the industry took on just one student, we could all benefit; it’d be a better picture all round. I’d recommend taking on T Level students to any business, small or large – you can’t go wrong.”
For more about hosting a T Level student, click HERE.