Protective Coati ngs
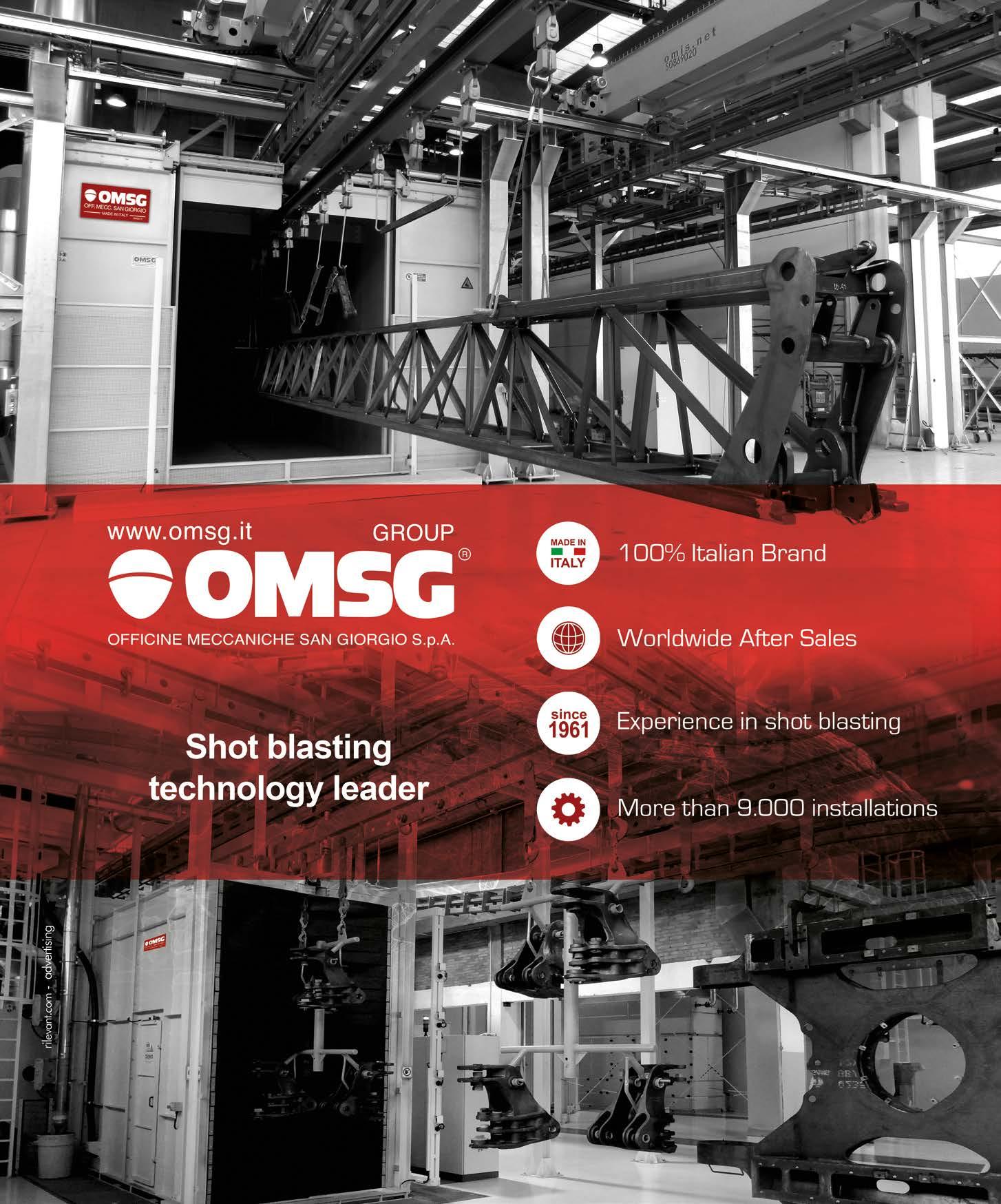
Sometimes it is what is on the outside that counts. Our zinc flake systems are suitable for all springs and hug every coil perfectly. Premium quality that protects against corrosion and at 8-20µm does not affect the mobility of the spring. However, we are not satisfied with the best and are constantly on the lookout for new solutions and innovations – for every problem, for every challenge.
Low curing temperatures
unique partner for the development
advertising is the real engine that drives the word of mouth.
Introducing a new technology into a well-defined market is an insidious process that should be thoroughly pondered. Although with the best of intentions, however, sometimes companies try to speed things up, normally with disastrous results.
It may be that the new technology is not perfectly suited to replace the existing one yet (due to development reasons, for example) or is not applicable in the same way to all sectors of the concerned market. The best option, therefore, is not abrupt replacement of the existing technology, but rather a period of coexistence, which enhances the advantages and technical aspects of the new technology without disparaging the old one aiming at its premature complete elimination.
This is what has happened with water-based paints in the world of corrosion protection. Although there exist hundreds of successful applications of water-based paints for steel corrosion protection worldwide, with proven durability in compliance with the strictest international standards such as NORSOK and ISO 12944, this coating technology is suffering from the haste with which some opinion leaders in the market tried to impose it from its very beginnings as a tout court alternative to solvent-based products, emphasising its (indisputable) advantages in terms of sustainability, health, and safety.
Today, as a consequence, in contrast to what happened in the wood sector and in that of metal for the general industry, water-based coatings are struggling to firmly establish themselves in the corrosion protection market, partly due to a lack of knowledge among users caused by a very conservative mentality and partly due to some application issues caused by that very haste. This has favoured high solid and powder products.
Precisely powder coatings could now embark on this virtuous path towards inclusion in the corrosion protection market, despite the fact that they do not appear among the technologies suggested by ISO 12944 yet and that they are still used almost exclusively indoors, rather than outdoors.
There are still steps to be taken to create products that guarantee the same protection degree as solvent-based, high solid, or very high solid liquid painting systems, and, above all, products that are maintainable over time, which is currently another major technological limitation of powders. However, virtually all powder coating manufacturers have been offering corrosion protection primers for years now, whereas numerous dual-coat systems (dry-on-dry or dry-on-fused) providing very good corrosion protection have become popular in the last five years.
In the face of a market that demands ever-increasing outdoor durability of components and structures, it is still going to take a long time to develop protective powders that are suitable for the highest ISO 12944 categories, as well as to create the industrial culture necessary to understand that surface preparation (namely, sandblasting and shot blasting) is essential to apply a high-quality and durable powder coatings.
Let us just hope that no one makes the same marketing mistake that was made twenty years ago with water-based coatings, because looking for new technologies to differentiate one’s company within the market is the most important lever for development, as shown by some of the articles in this issue of ipcm®_Protective Coatings. At the same time, as one of Southern Europe’s leading protective coating applicators said, this has to be done consciously and knowing the performance levels and limits of the new technology to be implemented.
The new solution for Flame Spray coating technology developed by Axalta ensures corrosion protection for applications in harsh environments.
Axalta has announced the launch of Abcite® 2060, a single-layer solution for Flame Spray coating technology available in a wide range of colours that provides corrosion protection without the need for a coating line and eliminates the need for primer.
The solution can be applied by depositing semi-molten polymer particles onto a heated surface, allowing particles to fuse to the surface as part of a comprehensive polymer coating and create an impermeable barrier, mitigating the degradation of materials and the associated impact of unplanned repair work. It is then suitable for use on large metal structures in a variety of harsh environments.
“We are continually developing new and innovative solutions to accommodate the ever-evolving coating requirements of projects around the world. We provide the full range of thermosetting, thermoplastic, and liquid products, which makes us more responsive to the needs of our customers, equipping them to fully rise to the challenge of ensuring outstanding surface protection, whatever the environment,” stated Pascal Nicard, the Senior Global Technology Manager at Axalta.
The new product developed by Axalta is resistant to a host of other factors which compromise surface material performance, including the presence of alkalines and acids, condensation, UV exposure and abrasions and other types of force which could otherwise cause damage.
Abcite® 2060 is compliant with the ISO 12944-6/-9 standard for galvanised and grit-blasted steel and also offers edge and corner coverage as part of a comprehensive solution that combines exceptional anti-corrosion protection with first-class aesthetics.
“Abcite® 2060 combines the exceptional anticorrosion and mechanical performance of Abcite® with the simplicity of use of Flame Spray Coating technology, resulting in major efficiency gains throughout the application process. Our compliance with numerous industry standards provides independent validation of the level of protection on offer, while our recent recognition at the R&D 100 Awards underlines the strength of our innovation credentials and expertise within the field of anticorrosion,” concluded Nicard.
The acquisition will strengthen KANSAI HELIOS’ position in the railway and ACE coatings sectors.
The KANSAI HELIOS Group has recently announced that it has completed the acquisition of Westdeutsche Farben GmbH (“wefa”), a German coatings manufacturer.
The acquisition includes all assets, business activities, brands and employees and will set up the new group company KANSAI HELIOS Wefa, based in Essen.
“This acquisition is an important step in the growth strategy of the KANSAI HELIOS Group, which will strengthen its presence in Germany. The group will serve the market as a system supplier with the combined strength of two production units, each specialized in their respective areas: KANSAI HELIOS Germany GmbH in Buchholz-Mendt and the new company in Essen,” has declared Dietmar Jost, the executive director of the KANSAI HELIOS Group.
The acquisition will allow the company to strengthen its position within
the European railway and ACE industry and other industrial coatings segments as well, thanks to wefa’s decades of experience with waterbased coatings.
Robert Scramm, the owner of wefa, will also be one of the new managing directors of KANSAI HELIOS Wefa: “This step is a milestone in wefa's almost 100-year history. Founded as a family company, the brand has now made it into the ranks of the top European coating brands.
As a new member of KANSAI HELIOS, we will benefit from additional experience and know-how within the group. This is a win for wefa and vice versa as our specialized coating formulations complete the new owner’s product range and ensure the highest product quality for a wide range of applications, especially for the railway industry.”
For further information: www.kansaihelios-wefa.de
Hempablade Edge 171 is Hempel’s new coating for leading edge protection (LEP) on wind turbine rotor blades.
Hempel, coatings supplier to the wind energy industry, announced the launch of Hempablade Edge 171, a new coating for leading edge protection (LEP) on wind turbine rotor blades.
With the highest rain erosion performance data on the market for a liquid LEP and some of the lowest dry film thicknesses, Hempablade Edge 171 provides long-term protection against rain erosion and reduces time and cost during application. “Hempablade Edge 171 is one of the simplest LEP solutions on the market to apply, yet able to withstand the toughest environmental conditions. It provides exceptional protection against rain erosion and composite damages. This extends the interval between maintenance and repairs, giving operators more uptime and lower maintenance costs”, explains Lars Rindom Jensen, Head of Solutions for Wind Blades.
Furthermore, Hempablade Edge 171 requires some of the lowest dry film thickness on the market – just 150 microns – and only needs one or two coats to ensure high protection. This increases application speeds, allowing customers to maintain more blades with the resources available.
“Hempablade Edge 171 has been developed as we listened to the industry challenges and requirements. Its low thickness reduces LEP consumption, application time and drying time, so applicators can work faster, whether they are onsite or in the blade production. It also has a wide application window – from 5-35°C – which means applicators can extend the maintenance season and working day. The result is higher productivity and less blade downtime during maintenance”, says Lars. “Hempel is recognised as the industry’s leading coatings supplier,” Lars explains.
“We fully understand the challenges manufacturers, operators and maintenance companies face and are the only coatings company with an in-house RET facility. During development and validation, we put Hempablade Edge 171 through more than 400 exhaustive tests to ensure it delivers extremely valuable performance and application benefits. We are very proud to offer it to our customers.”
Karl Bubenhofer AG has been developing for years energy-saving low-temperature and ultra-low-temperature powder coatings in countless applications.
The rise of energy costs and the increasing uncertainty regarding the supply of energy sources pose major challenges for the entire industry. Considering the environmental footprint of the products and processes used is becoming increasingly urgent, affecting all stakeholders in supply chains and society as a whole. Powder coatings are chemically cured at elevated temperatures and are therefore particularly affected by this issue. Coating systems that make lower oven temperatures, shorter curing times and, ideally, longer coating lifetimes possible are therefore very much in tune with the times and in the spirit of a long overdue, more sustainable orientation of this industry.
Karl Bubenhofer AG has many years of experience in the field of
energy-saving low-temperature and ultra-low-temperature powder coatings in countless applications. The amounts of energy typically used for the curing process can be reduced by 5-30% compared with conventional products. Fast-reacting powder coating systems are also suitable to increase the production speed and, due to lower heat emissions into the surrounding area of the coating line, significantly increase the workplace comfort around the system. Fast-reacting powder coatings from the POLYFLEX® series are available in a wide range of surface finishes for both interior and exterior applications in non-labelled versions - all in the spirit of a sustainable approach.
For further information: www.kabe-farben.ch
The ipcm® team is pleased to present myFAIR, a new web app to stay up-to-date with all major events happening in the surface treatment industry.
Today’s world is marked by sudden and unpredictable changes and moving at a rapid pace towards an increasingly digital ecosystem. This led us to rethink our annual Trade Show Calendar, listing the main events to be held in the surface treatment industry.
We chose to better meet the sector’s need by approaching our calendar in a new way and transforming what was previously a digital and printed brochure into a web app accessible from any device: myFAIR.
A web app is a versatile tool that can be accessed from both desktop and mobile devices, which does not require downloading from the store. Nevertheless, it is possible to create a shortcut directly in the smartphone menu, making access to the app quick and easy.
myFAIR is therefore a free, up-to-date, and highly interactive tool at the service of professionals in the surface treatment industry (and beyond) for the organisation of their trade fair agenda, both as exhibitors and visitors. Through the myFAIR web app, users can browse, filter, add to favourites, trigger alerts, and get up-to-date information on the world’s most important events happening in the industrial finishing sector.
The Exhibitions section shows all trade fairs in alphabetical order. The list can be filtered by country and category. It is also possible to type the name of an exhibition directly into the search bar for even faster access to information on a particular event.
Tapping on the name of a trade fair takes the user to the specific tab for that event, with up-to-date information on dates, location, focus,
The Exhibitions section with the (filterable) list of all trade fairs in the app and the trade fair tab with detailed and up-to-date information on each event.
The Schedule section, showing all trade fairs divided by month.
and website. From here, it is also possible to get directions to the event location directly on Google Maps and add the trade fair to favourites, in order to receive alerts in case of new updates. There is also a list of related trade fairs by sector.
The Schedule section allows filtering the trade fairs by month and year. This is an easy way to organise one’s schedule on a monthly basis and check which exhibitions are going to be held in a particular month with a few touches.
Here, too, it is possible to apply additional country and product category filters.
The Suppliers section presents a list of suppliers of various services that revolve around the world of trade fairs: from catering to stand construction, from translations to hostess and steward services, from communication to digital printing, from gadget creation to logistics. Companies can be filtered according to the services offered and a simple tap takes the user to a detailed tab with the main contact information.
myFAIR it is not only a useful tool for organising ones’ own trade fair calendar. It also offers an interesting opportunity for companies to promote themselves to a highly specialised target group, under the aegis of the prestigious ipcm® brand.
The providers of services for exhibitors have a dedicated section where they can upload their company profile and contact information. Exhibitors, visitors, and trade fair organisations can rely on three display advertising options to promote their business.
For further information: sales@ipcm.it
The Suppliers section is dedicated to all companies that offer services revolving around the world of trade fairs, such as stand construction or gadget creation.
The Cortec’s MCI® 2018, a 100% silane-based concrete sealer containing migrating corrosion inhibitors, was used to treat the concrete of the Pelješac Bridge in Croatia, one of the most strategic infrastructures of the Country.
On 26 of July, Pelješac Bridge, the largest ever EU infrastructure investment in Croatia, officially opened in grand ceremony. The bridge, providing a road link between two parts of the country is of strategic importance and is one of the most substantial EU infrastructural investments ever. It connects the region of Southern Dalmatia with the rest of the country’s mainland. The bridge will cut travel time by 37 minutes along the Adriatic coastline, improving
people’s lives and increasing economic opportunities for the region. It has 13 spans, five of which are 285 meters long, six centrally placed reinforced concrete pylons with a height of 33 meters, and two lanes together with a stop lane that will serve for bridge maintenance. Pelješac bridge is ranking among the most demanding bridges in the world—in complexity of construction and design. Bridge is 2,404-m (7,887.14-ft) long.
ln order to meet the main criteria of quality design, such as stability, durability, economy and integration into the environment, the design proposed the construction of an extra dosed bridge with an integrated hybrid structure. Structure is comprised of five central spans, each 285-m long, and six low pylons. Especially careful approach was taken to ensure durability for the extended lifespan of over 130 years. Cortec’s MCI® 2018 was specified on this project during the design phase as a silanebased impregnation with a migrating inhibitor property to protect against the harmful effects of corrosion, thus extending the service life of the bridge. MCI® 2018 is a 100% silane-based concrete sealer, containing migrating corrosion inhibitors that allow deep penetration into concrete and provides water repellence by chemically reacting with the cementitious substrate. It seals surface pores, preventing the intrusion of chlorides, reduces carbonation, and protects from the ingress of wind-driven rain. Treated concrete surfaces are fully breathable and their natural moisture-vapour transmission is not affected. After repair of surface damage and cleaning of discolorations and other surface defects, the concrete surface of the pylons needed to be protected with a colourless silane coating to improve durability and increase the resistance of the concrete surface to long-term external influences. MCI®-2018 carries CE certification that indicates conformity with health, safety and environmental protection standards for products sold within the European Economic Area (EEA).
A combination of AC coatings, cathodic protection of steel reinforcement in piles and pile heads, a concrete cover of 65–85 mm stainless steel reinforcement and impregnation of all concrete surfaces with MCI®-2018 was selected. This was chosen as the strategy to help the bridge achieve a 130-year service life. MCI®-2018 was applied on the entire substructure of the bridge. All concrete parts were coated with MCI®-2018 by a spraying technique. The work was performed in accordance with the project requirements and after surface preparation to full functionality.
Pelješac Bridge officially connected Croatia for the first time after 300 years.
MCI® 2018 was specified on this project during the design phase as a silane-based impregnation with a migrating inhibitor property to protect against the harmful effects of corrosion.
This included:
• Access to pylons
• Rehabilitation of the concrete surface of the pylons
• Cleaning the concrete surface of the pylon (washing the pillars with water)
• Impregnation of the concrete surface of the pylon with MCI®-2018.
MCI®-2018 contains time-proven Migrating Corrosion Inhibitors (MCI®). The silane component provides water repellency by chemically reacting with the cementitious substrate under proper application, decreasing the ingress of aggressive materials. The product penetrates deep into concrete, providing corrosion protection to reinforcing steel from existing water and chloride ions, or other contaminants. Continuous monitoring of the condition of the structure at one central place was done during the construction phase and will be done at the exploitation
phase to examine parameters of structural behaviour, time, seismic activity, and structural durability. The designer of the bridge specified corrosion protection for all concrete segments in order to achieve a 130-year service life.
Cortec’s CEO, Boris Miksic, Croatian-American businessman is proud that his patented technology was used on this historic project to connect two parts of his country. “Our MCI® technology is used in largest construction projects throughout the globe. Witnessing its application in my home country on this monumental bridge structure is truly a special. Pelješac bridge is huge step forward for all of us.”
A strategic investment such as this bridge, demonstrates European Commission’s commitment to bring people together and unite territories, while reinforcing the territorial cohesion of the region and helping other neighbouring countries. ‹
The designer of the bridge specified corrosion protection for all concrete segments in order to achieve a 130-year service life.
The work was performed in accordance with the project requirements and after surface preparation to full functionality.
FreiLacke supplies the Max Bögl corporate group with a polyaspartic system for concrete/hybrid towers.
The demand for wind power is booming. In order to keep up with changing market demands, the Max Bögl construction company is focusing on increasing its tower production throughput. And for that it relies on an ultra-fast-drying polyurea system from FreiLacke. Whether the trans-rapid rail line in Shanghai, metro stops in Amsterdam or Berlin’s central station – the Max Bögl Group has already succeeded in turning these, along with many other large-scale projects, from vision to reality. Nestled in Sengenthal within the Upper Palatinate region, the Max Bögl Group was founded in 1929 as a masonry company and is currently in its third generation of family ownership.
Wind power is a relatively new cornerstone of its operations: the Upper Palatinate-based company supplies modular towers consisting of threemetre-high concrete rings that are topped off by metal tips. And now the special feature: each ring is made up of three individual parts and is fully patented by the construction company. This makes transporting the components much easier – a standard truck trailer is all that is needed.
Around 30 concrete rings are stacked on top of one another and braced together before the approximately 60-tonne metal tip – a true heavyweight – is placed on top. For this reason, assorted rings are
manufactured using a special type of concrete with steel reinforcements that can permanently withstand heavy loads.
Since March 2022, the family-run company has been using a new coating system for its concrete elements. It is an ultra-fast-drying material with a polyurea base supplied by FreiLacke. “We were able to point to our broad range of experience gained from our work in the wind power industry, and not just our expertise in towers”, explains Andreas Löffler, FreiLacke’s head of international business development.
At the facility in Segenthal, the concrete components are separated after hardening and then transported directly to the paint shop.
“Special coating systems are needed because a certain quantity of residual moisture remains in the concrete. In addition, the parts may remain warm after separation due to the reaction heat of the concrete”, explains Holger Roth, Max Bögl’s production manager. The polyureabased polyaspartic coating systems from FreiLacke optimally fulfil these
requirements and enable the coating to be applied immediately.
In Max Bögl’s paint shop, the concrete rings are transported onto platforms on an automatic conveyor system. Here, the concrete surfaces are prepared and filled – and the cycle time is currently still about one hour. In addition, any pores and cavities may also be sealed in order to achieve the best possible coating adhesion. Various products may be used for this, including FreoWind’s light-grey filler.
Next comes the top coating, which is applied as standard using the Airless or mixed air procedure. At the end of the cycle, the coating will be completely dry and therefore ready for all the remaining steps.
The coating primarily serves to boost the visual appearance of the components, but the finishing layer also provides them with an outstanding mechanical strength and dirt-repellent properties. Two additional workstations in the hall are used for carrying out finishing work on the heavyweights. When this work is complete, the
components are stored outdoors in their fully coated state. They are now permanently exposed to the wind and weather – with the best possible protection.
The construction company switched to the FreiLacke system with the primary goal of increasing its concrete component production throughput due to the high demand for new wind power systems – the war in the Ukraine has acted as a catalyst for this, explains Andreas Löffler. As a result, the company is planning for a significant boost to its production figures from this summer and onward.
As Andreas Löffler has already explained, the switch to the new coating system was a straightforward procedure, and an application technician had also joined him on site in Sengenthal. Only the coating supply for each ring main required a small amount of pre-planning. “Employees have actually thoroughly enjoyed working with the system”, says
Löffler, “as the primer filler is especially easy to handle and is also very well-suited to the current application technology – our colleagues at FreiLacke’s head office in Bräunlingen-Döggingen/Black Forest have worked meticulously on the rheological adjustment.”
Furthermore, Max Bögl has also been actively involved in wind power itself: Bavaria’s most powerful wind turbine, which features a tower supplied by Bögl, was commissioned in the Winnberg area of the Neumarkt district in 2011. With a total height of 180 metres and a power input of 3.4 megawatts, the turbine produces more than one third of the overall power that the community uses.
And what’s more, the specifically established Max Bögl Wind AG and system suppliers GE Wind Energy have held the record for the highest wind turbine in the world since 2017.
The company in Upper Palatinate supplied the towers for four wind turbines in Gaildorf/Baden-Württemberg at a hub height of 178 metres and an overall height of 246.5 metres. ‹
FreiLacke has stood for innovative paints and coatings since 1926. The family-owned company has already entered its third generation and develops customised solutions for clients from the wheel and vehicle manufacturing industries, as well as those in the fields of mechanical and apparatus engineering, job coating, rail vehicles, wind power, functional furniture, storage technology, construction and sanitation, directly through its 600 employees at its Döggingen base in the Black Forest. As a modern family-run company now in its third generation, the safeguarding of the head office is just as important as our worldwide sales and our international subsidiaries and partners.
The product range of Europe’s leading system coating provider covers the entire spectrum from industrial coatings, powder coatings and electrodeposition coatings to composite solutions.
International sales are handled by a global network of subsidiaries and partners around the world.
Environmental protection has always been a key priority for FreiLacke.
Therefore, the company makes every effort to develop environmentally friendly products, reduce emissions, packaging materials and waste and use resources sparingly.
In 2019, FreiLacke was honoured as one of the top 100 employers in Germany in the “Great Place to Work” competition and attaches great importance to training with a quota of 10%.
From 5,5
The Contractor King protective coatings family of sprayers come in 45:1, 60:1 and 70:1 pressure ratios.
Graco provides users with the latest heavy-duty and compact size solutions to maximize productivity and portability.
Founded in the USA in 1926, Graco is a world leader in systems and components for fluid handling, and have been offering products that move, measure, control, dispense and apply a wide range of fluids and viscous materials. It owes its success to its unwavering commitment to technical excellence, the high quality of its manufacturing and its customer service. The company works exclusively with qualified distributors to provide equipment for spray finishing, protective coating, paint circulation, lubrication, and dispensing sealants and adhesives, along with power application equipment. In order to make easier the protective coatings’ applications even when the operating conditions are
severe, Graco developed the latest innovative solutions: the Contractor King™ and the Silver Plus HP Spray Gun.
The new Contractor King air-powered protective coatings sprayer is designed around single-person mobility and high performance. This affordable line of air-powered sprayers is the perfect addition to every contractor’s fleet: it delivers full King power and performance, but is lighter and on a more compact footprint. It’s ideal for contractors looking to maximize productivity and portability.
• Field-proven design virtually eliminates icing to keep you spraying
• Durable aluminium, steel and composite construction for years of service
• Delivers superior finish with limited pulsation, even with multiple guns
• A simple design for easy serviceability
• Oversized porting for maximum air flow.
• QuickChange™ Endurance pump for quick and easy on-the-job pump removal and maintenance
• Chromex Rod and stainless steel cylinder for maximum life and performance
• Fleet-friendly design uses same wear parts as other King sprayers.
• Nearly 38 kg lighter than comparable models for easy, one personhandling
• Integrated lifting points for easy positioning on any job site
• Flat proof tires resist job site debris for maximum convenience.
The Contractor King protective coatings family of sprayers come in 45:1, 60:1 and 70:1 pressure ratios, and are available in a variety of packages.
This includes the new “Big 45” ready-to-spray package configured with pressure-rated accessories such as 45 m of Xtreme Duty™ high-pressure fluid hose, Silver Plus spray gun, fittings and XHD spray tips.
The Silver Plus HP™ spray gun is pressure rated up to 500 bar and is designed to handle today’s protective coatings, including high-solid coatings. Featuring a compact and durable structure and external fluid passages, this legendary design keeps hands cool, while providing allday spraying comfort.
Thanks to this innovative design, it also is up to 35% lighter than other guns in its class, and requires less trigger pull force for an easier application.
The Silver Plus HP Spray Gun’s key-features at a glance
• Durable steel and aluminium design features oversized fluid passages for less pressure loss
• Durable forged aluminium withstands harsh work environments
• Lighter weight than competitive guns Polished body is easy to clean
• The convenience of a single gun that works with all units in every fleet
• Fluid flows directly to the tip through the gun fluid tube
• Provides the ability to spray heavier materials
• Including high solid coatings and mastics. ‹
According to Donelli Alexo, the future of corrosion protection lies in the use of FBE powder coatings for the interior of structures intended for critical environments and in the ecological and digital transition of companies in the sector. With this forward-looking vision, the Lombardy-based group has already started to rethink its organisation and integrated its production equipment with a new 4.0 plant for the powder and liquid coating of the internal and external surfaces of valves and actuators.
The Donelli group is one of the longeststanding corrosion protection specialists in Italy. Founded in 1911, it has always evolved at the same pace as the history and development of metal corrosion prevention and protection. “When I joined the company about twenty-five years ago,” states Alessio Trisolino, now the CEO of Donelli Alexo, “we still employed an inorganic zinc coating, which at that time was very difficult to apply, to protect components intended for very harsh conditions of use. Today, the corrosion protection coatings market has made giant strides. The challenge for firms like ours, specialising in protective treatments for various substrates (metal, concrete, wood, etc.) intended in particular for the petrochemical, energy, industrial, and construction sectors, is to be able to pick up on the most innovative trends and anticipate any developments. Currently, in particular, the ecological transition that is affecting the entire manufacturing industry globally is underway in the corrosion protection field, too. Donelli is coping with this by applying powder coatings, including FBE (Fusion Bonded Epoxy), for protecting not only internal surfaces, which is already an established technology, but also of the external surfaces of structures.”
One of the companies in this century-old group, Donelli Alexo Srl (Cuggiono, Milan, Italy), focuses on the FBE coating of valves for contact with drinking water, in compliance with the main KIWA, AWWA, and WRAS standards, and with hydrocarbons up to 95 °C, in compliance with the most stringent end-user specifications such as, for example, SAUDI ARAMCO (APCS-102A, APCS-102B, APCS-102C). It also coats the external surfaces of fittings with both one-layer and dual-layer FBE systems (2LFBE, DLFBE), with the possibility of adding a finish featuring high abrasion resistance (Abrasion Resistant Overcoating, ARO).
The powder and liquid coating plant installed by Eurotherm and the overhead conveyor with an automatic transfer system.
“With the aim of quickly becoming a centre of excellence for corrosion protection in Central and Southern Europe,” says Luca Donelli, the Market Development Manager of the Donelli, “we have been investing for years in the latest technologies to implement our production capacity and respond more and more flexibly to customer requirements. The latest investment concerned our fourth powder and liquid coating plant, installed in June this year, which complemented the three systems already in operation at our Cuggiono, Ravenna and Voghera (Pavia, Italy) sites and which was supplied to us by Eurotherm (Volpiano, Turin, Italy). We chose the name “CX” for this plant because it has a dual meaning: if read as Roman numerals, it refers to our group’s 110-year history, whereas in letters it stands for the most extreme corrosion category that was included in the 2018 updated ISO 12944 standard for offshore and industrial environments with high humidity.”
“Our customers,” emphasises Trisolino, “require higher and higher asset durability. This is why our surface treatments are always conceived
based on the combination of two concepts, reliability and durability, which at first glance might seem synonymous, but are in fact very different. Standards such as ISO 12944 indicate the steps needed in order for a coating to be more durable, but it is through the optimal management of surface preparation and coating processes that we can reliably guarantee a high-quality product. This in turn can be achieved with a corporate organisation based on skill differentiation: whereas until 2010 our group’s plants were able to perform all kinds of treatment to serve customers from different sectors within a radius of 75 km, we have now chosen to have each site specialise in one process. At present, the Voghera plant performs thermosetting liquid coating operations; in the Cuggiono CX facility, we powder and liquid coat products up to 2 tonnes; and the plant of the Cuggiono facility –our headquarters that is located 700 metres away - treats components up to 100 tonnes.”
From Alessio Trisolino’s words, it is clear that the future of the company also includes increasingly environmentally friendly technologies: “Our vision (and forecast) for the ecological transition takes the form of the further development of powder coatings, which
presumably will replace solvent-based products in various instances. This is not going to happen in short term, because we are convinced of the need to first create an industrial culture that fully embraces this technology and the associated surface preparation processes. Once the ground has been prepared, the relevant bodies will finally be able to integrate the ISO 12944 standard with specifications for the application of powder coatings on exterior surfaces as well, an item that is still missing precisely because this technology is still in the development phase.”
In its Cuggiono CX facility's plant, Donelli Alexo handles smaller asset components. The parts treated in the new coating system have a maximum size of 6x2x3 metres. “This plant is designed for manual
painting,” explains Eurotherm CEO Paolo Ghiazza, “and it is equipped with an automatic transfer system and two lifting stations with a maximum load capacity of 4 tonnes each. Donelli Alexo required two powder coating booths, a special curing oven capable of reaching a temperature of 350 °C, two pressurised liquid coating booths with oblique flow and a drying unit reaching 80 °C, and a manual shot blasting cabinet with an automatic shot recovery system. All stations are aligned at the front and fed via an overhead conveyor equipped with sliding guides and mechanical switches, so that the workpieceholding bars are automatically moved along the path and stopped at the various workstations through manual insertion, with the additional possibility of storing them in a buffer area. The rail is made of pressfolded galvanised sheet metal and it accommodates the trolleys onto which the workpieces are hooked.”
The special feature of the plant is certainly its curing oven. “In order to achieve the required temperature,” indicates Ghiazza, “we used interlocked modular panels made of galvanised sheet metal on the outside and of stainless steel in the outside. To optimise insulation and create an effective barrier to heat loss, several layers of highdensity rockwool (100 kg/m3) were inserted inside the panels for a total thickness of 250 mm (350 mm for the access door) instead of the standard 150 mm. In addition, the oven’s internal structure is specifically designed to enable the inner walls to adapt to the expansion caused by the high working temperatures. Based on this specific requirement, we also designed special load bars and a large trolley that can withstand the highest temperatures. For the largest valves, there are also additional trolleys in the oven and the shot blasting cabin, which run on rails on the floor, designed to support higher loads. The entire plant is linked to a production management system 4.0 integrated with the company’s whole workflow.”
“With this machine,” says Trisolino, “we mainly coat valves and actuators for the energy and water sectors. These are the smallest components of large assets, but they still require timeliness, superior quality, and
quick responses to customers. The high oven temperature is actually necessary to cure FBE coatings and all other thermosetting coatings, such as PTFE. Finally, we requested two liquid painting booths because we also are coating aeronautical components in this plant, for which we are currently awaiting certification.”
The standard system for components intended for the energy sector includes the manual shot blasting of those parts that, due to their conformation or masking needs, cannot be processed automatically, the application of the primer, a pre-heating phase, the application of the FBE coating, and curing. It is also possible to carry out combined systems involving the application of powder + liquid paint or the application of powder in one or two coats, particularly in the case of aesthetic finishes with epoxy or polyester powders applied through dry-on-dry or dry-onfused techniques.
“In this sector,” adds Trisolino, “tolerances are kept to a minimum, and the Industry 4.0-oriented features of the line that we have designed with Eurotherm help us maintain full control of the process thanks to
the recording of data characterising the different processes. These powder coatings call for higher thicknesses than conventional powder paints and, therefore, for a greater use of product, which needs to be monitored to optimise consumption. Moreover, we aim at collecting CO2 emission data as well. Our plants in Voghera and Cuggiono are already able to formulate an energy balance for each process. However, we would like to be able to tell each customer what was the environmental impact of the processing of its specific order. For us, this will be an additional element of differentiation on the market.”
By November, the company will have completed the interconnection of all devices. “It is not enough to buy an industry 4.0 ready equipment to become a 4.0 factory: the actual transformation does not only take place at the logistical level, but also, and above all, at the mental level,” states Donelli. One has to learn to approach the work in a completely new way – and changing one’s own mentality is the most difficult aspect. A relevant effort was required by our administrative department, whose accounting and order management data had to be connected with those related to quality control and energy consumption: we opened up the production department to them and brought their administrative
management system into the factory. These two worlds sometimes seem to proceed on separate tracks but, thanks to our digital transition project, they are now becoming truly interconnected. This is made possible by the ongoing support of all partners involved in the Cuggiono CX investment including not only Eurotherm and OMSG, but also OMNICON (SCADA), Intech (medium to low voltage systems), Omis (overhead cranes), Clavenna (low voltage systems), Idroimpianti (gas and water systems), Oikia (civil works), Studio Croci (project management), Tecnohabitat (permitting), BCOM (IT, network) and Monti&Russo (administrative software).”
From left to right:
The liquid coating booth.
The curing oven can reach a temperature of 350 °C.
The OMSG automatic shot blasting machine.
The Donelli group has chosen the path of differentiating its sites’ specialisations, but each division is able to support the other ones whenever necessary, since their equipment is complementary and interchangeable. “When we have to deal with a large batch that has to be delivered quickly or is characterised by parts with special shapes or weights,” states Donelli, “we choose the most suitable system based on our experience. Over the years, we have integrated, learnt about, and optimised all the technologies available on the market. This expertise level gives us the flexibility to meet any coating requirement that comes our way. For example, if we have to process small parts whose external surface can be sandblasted automatically, we use the OMSG shot blasting machine that we acquired together with the coating plant with one of our latest investments.”
“One of the most important aspects to achieve a high-quality coating
results is surface preparation. In the general industry sector, around 60% of powder applicators do not carry out any pre-treatment before coating. Shot blasting, however, is crucial for the removal of contaminants and for guaranteeing proper paint adhesion,” confirms Trisolino. The shot blasting machine installed in February is a hanger type from the CAPRI 20/25 H22 series, equipped with two 2000-kg hoists and four direct-drive 7.5-Kw turbines and capable of integrating into the company’s main management system 4.0. The two hoists allow carrying out workpiece loading/unloading and shot blasting operations simultaneously.
“Donelli was also a pioneer in the adoption of the most advanced liquid coating equipment,” notes Trisolino. “We were among the first companies in Italy to implement a number of Graco product lines, but also to use both traditional powder application technologies where required, namely the Venturi system and the Smart Inline technology,
supplied by Gema Europe. This should offer a glimpse into the variety of requests we receive and into the flexibility level that must characterise a company like ours: it is the type of component to be treated that dictates the choice of the right coating system and, consequently, of the most suitable equipment to apply it.”
“We operate in a niche market,” points out Donelli, “and we cannot afford to choose partners that are not up to the mark: our customers demand a certain level of technical expertise from us and we do the same with our suppliers.”
“The journey into the world of corrosion protection that Donelli undertook more than a century ago still continues, with the aim of achieving new goals,” concludes Donelli. “First of all, the ecological transition towards the use of solvent-free paint products such as powders, for the use of which, however, as mentioned before, there is still fertile ground to work on, particularly in terms of improving their effectiveness on exterior coatings. The second objective is to transform ourselves into a centre of excellence and a benchmark supplier, expanding our market and reaching other Central and Southern European countries in addition to those we already serve, from Portugal to Slovenia. The success of Donelli and of these projects can only be achieved with the support of the passionate people who are part of our team, always attentive to the latest innovations, and through our partnerships with suppliers boasting high technical know-how, starting with Eurotherm.” ‹
As professionals working within the coatings industry, we are all acutely aware of the issues that corrosion poses and want to provide our customers and end-users with the best quality products to tackle this $2.2trillion global issue [NACE 2016]. Anti-corrosion coatings have become a necessity for industries to safeguard the huge investments they make in terms of money, property and safety of workers. Whether coating to protect pipelines, aeroplanes or computer gadgets – customers are united in their battle against corrosion. Historically, some of the most effective corrosion inhibitors have been based on chromium. However, these chemistries are currently being phased out globally – leaving a gap in the market for a highly effective inhibitor that is non-toxic and noncarcinogenic. Following strong R&D efforts and lengthy extended testing, many coatings companies have turned to phosphate-based systems. This article highlights a step-change alternative that can save 10-30% on the cost of anti-corrosives as well as offering customers more sustainable coatings that require no hazard warning label.
Currently, 45% of the corrosion inhibitor market is currently dominated by phosphates. Industry testing and academic research show that adding zinc phosphate can inhibit the anode process of metal corrosion and
consequently prevent the horizontal diffusion of the corrosive medium into the coating/metal interface and slow down the disbonding of the coating [Hongxia Wan, 2017]. Additionally, phosphates don’t pose the same health and environmental hazards as chromates, however, they do still present environmental issues through leaching. In its form as an inhibitor – it is classed as a Category 1 Environmental Hazard. Within the coatings system, at loadings of 2.5% and above, the paint will be classed as a Category 2 Environmental Hazard so will still require hazard labelling [United Nations, 2021].
Innovative and trusted technology working together
Zinc phosphate salts on their own are not initially very effective due mainly to their low solubility. As a result, in a corrosive environment, significant amounts of time must pass before there are sufficient concentrations of phosphate anions to react with the metal surface cations to form an anticorrosive precipitative layer. This leads to a time delay where corrosion can proceed unimpeded [M.Cohen, 2022].
Intelli-ion® uses ‘smart release’ technology which senses and reacts to corrosive ions very quickly – buffering the time delay seen with phosphate inhibitors. It sequesters corrosive ions which triggers the release of the
‘active ingredient’ to form a very fast inhibitive layer at the site of corrosion. Phosphate inhibitors then fill the gaps to form a strong polymeric layer with the metal ions and metal surface. Intelli-ion® provides the initial protection backed up by the zinc phosphate precipitate layer to provide an optimised co-blend anti-corrosion solution (Figs. 1, 2 and 3). Additionally, like highly effective chromates, Intelli-ion® is both an anodic and cathodic inhibitor. This ensures that the technology can reduce the rate of metal dissolution at the anode and simultaneously decreases the rate of reduction reaction (both oxygen reduction and water reduction), via blocking the interfacial transfer of electrons.
Sustainability is a key market driver within the coatings industry. In the past, mandatory regulation was the most important factor, but now, we are seeing a fundamental shift in the societal demand with respect to sustainability and responsible business behaviour [Cynthia Challener, 2018]. In short, customers are looking for products that are environmentally sound.
Co-blending existing phosphate-based anticorrosion systems with Intelli-ion® at loadings less than 2.5% by weight in a paint moves a coating from Environmental Hazard Classification 2 (H411) to Classification Category 3 (H412). Category 3 presents a lower risk to aquatic life so no warning label is required on the paint packaging. In turn, this has storage, transportation, and disposal benefits – not to mention the environmental advantages.
Due to the high efficacy and lower loadings – ‘smart’ coblend formulas with other phosphate containing metal salts can deliver anticorrosive cost savings of 10-30% per litre of paint. In addition, Intelli-ion® also has a significantly lower Specific Gravity than ZnP reducing the need for reformulation changes when lower weights of anticorrosives are incorporated.
Independent academic research at Swansea University, Wales
The independent research conducted by Dr Phil Ansell of SPECIFIC Innovation & Knowledge Centre, Swansea University (Wales) aimed to understand the relationship and optimal loadings between Intelli-ion® and zinc phosphate (ZnP) corrosion inhibitor co-blends.
Various volume combinations (PVF – pigment volume fractions) of Intelli-ion® and ZnP were applied to a steel substrate, and timelapse photography was used to measure the combined inhibitor effect on the rate of cathodic disbondment (Kdel) over 24 hours.
In Figure 4, the blue line represents the rate of coating delamination when Intelli-ion® is held at a low PVF (0.025) and the PVF of zinc phosphate is increased from 0.025 to 0.075. Coating delamination increased with higher concentrations of ZnP. Conversely, the orange line shows that when the PVF Intelli-ion® is kept high and constant (0.75 PVF) and the amount of ZnP varies from low (0.025) to high (0.075)–disbondment dramatically decreases. This demonstrates the synergistic effect of the co-blend is optimised when there is a higher loading of Intelli-ion® within the coating system.
Figure 5 shows the best performing co-blend combination where Intelli-ion® and ZnP are both at higher levels.
Industry standard accelerated weathering tests with on-the-market phosphate-based coatings vs. Intelli-ion®- containing primers also demonstrate comparable or better performance. The above mild steel samples were coated with an alkyd primer (+/- topcoat) and then scribed using an Elcometer 1638 DIN scratching tool fitted with a 1 mm cutter. The samples were then placed in a salt spray chamber (at 45° angle) and run-in accordance with ASTM B117 continuous salt spray fog testing. Following 500 hours, the samples were rinsed using distilled water and dried using lint free cloth before being analysed (Figs. 6 and 7).
The inhibitor loading level was optimised for cost and environmental benefits - at a 3:2 ratio – to lower the phosphate content to below 2.5%. This co-blend approach removes the environmental warning labels from packaging, however, the imagery clearly demonstrates that Intelli-ion® offers has a synergistic relationship in performance with both zinc phosphate and polyphosphates too.
In 2021, the top 15 paints and coatings companies accounted for a total market share of approximately 58.52% (AKI Research, 2022).
In an industry dominated by so few – its increasingly important to differentiate your coatings and offer customers quality at a cost they can afford. Co-blending Intelli-ion® anti-corrosives with phosphate-based systems offers a step-change alternative that enhances current coating systems without changes to the manufacturing process. At an optimised 3:2 ratio, coatings manufacturers can remove hazard warning labels from their packaging, reduce their anticorrosion costs – all whilst benefiting from comparable or better performance. ‹
• AKI Research. (2022, April 9th). Global Paints & Coatings Market
Competition: Top 15 Players in 2021. Retrieved from AKI Research: https:// www.akiresearch.com/post/paints-coatings-market-share-2021
• Cynthia Challener. (2018, April). An Update on Sustainability in the Coatings Industry. Retrieved from Coatings Tech: https://www.paint.org/coatingstechmagazine/articles/an-update-on-sustainability-in-the-coatings-industry/
• Hongxia Wan, D. S. (2017, June). Effect of Zinc Phosphate on the Corrosion Behavior of Waterborne Acrylic Coating/Metal Interface. Retrieved from Materials: https://www.ncbi.nlm.nih.gov/pmc/articles/ PMC5554035/#:~:text=Results%20showed%20that%20adding%20 zinc,the%20disbonding%20of%20the%20coating
• M.Cohen, M. (2022). The Inhibition of the Corrosion of Iron by Some Anodic Inhibitors. Journal of The Electrochemical Society, Vol 100, Number 5.
• NACE. (2016, March 1st). Economic Impact. Retrieved from NACE International: http://impact.nace.org/economic-impact.aspx
• United Nations. (2021). Globally Harmonized System of Classification and Labelling of Chemicals (GHS). Retrieved from UNECE: https://unece.org/sites/ default/files/2021-09/GHS_Rev9E_0.pdf
Belzona supplied a customer with its 5871 and 3211 (Lagseal)
series products to insulate and protect oil dispersant vessel’s surfaces.
Aclient who deals with environmental spills was faced with a unique problem when insulating its underslung oil dispersant vessel. The vessel would need to be carried underneath a helicopter over sub-zero temperature conditions to decontaminate the water after potential oil spills. Due to the vessel’s requirements, the insulation material needed to fit very particular specifications.
The job specifications required the insulation material to withstand -25°C temperatures without allowing the dispersant within the vessel to freeze, as well as protecting the vessel against corrosion and damage.
When the client considered insulation methods, conventional means proved to be technically not suitable for the operating conditions due to weight restrictions and the potential effects of salt water ingress through standard insulation cladding joints and seams. Also, the proximity of the vessel to salt water in cold temperatures would expose the seams to sea water spray which could cause the insulation to become damp, resulting in CUI problems; a vessel not being adequately sealed leaves the system vulnerable to corrosion. Belzona and its licensed Contractor, Grade2, jointly recommended the use of corrosion protection system, Belzona 5871, applied in three layers for maximum insulation and corrosion protection, of a total of 9mm dry film thickness (DFT). This would provide an effective, solvent-free, thermal barrier, while also eliminating condensation, contact damage, anti-icing issues, waterlogging and corrosion. Belzona 5871 is a uniquely placed thermal barrier coating able to also provide long term corrosion protection having been thoroughly tested to ASTM B117 (Salt Spray) for 4500 hours, among other corrosion resistance tests.
The client chose to overcoat the insulation with acrylic emulsion membrane, Belzona 3211 (Lagseal), for additional waterproofing, UV and fire protection. They also mixed in orange pigment at a ratio of ≤ 5% for high visibility in its working environment, as Belzona was able to adapt to the Customer’s needs.
The products were applied in a controlled factory environment in the North of England, after careful surface preparation to ensure good adhesion to the stainless-steel vessel. The substrate was grit blasted to achieve the standard minimum specification of ≥ 75μm, Sa 2.5
cleanliness vacuumed and clean degreased. Once the surface preparation was finished, Belzona 5871 was decanted into Belzonaissued cartridges and used in conjunction with a pneumatic cartridge spray gun. This sped up the application, keeping within the working life at ambient temperature. The product was spray applied at approximately 1mm wet film thickness (WFT), which expanded to 3mm DFT once cured. Within the overcoat window, a further two coats were applied, giving a final DFT ≥ 9mm. This was necessary due to the extreme conditions in which the vessel needed to operate.
Belzona 5871 was able to adhere very well to the vessel shell, giving a uniform DFT across all geometries, ensuring an effective corrosion barrier at the recommended ≥ 9mm total DFT. The Belzona 3211 (Lagseal), mixed with safety orange pigment, was applied by roller, as a final topcoat.
The application of the products added just ≤ 10mm thickness onto the vessel dimensions, ensuring that the client’s weight and protection specifications were met far more effectively than would have been possible using traditional cladding.
Successful application represents future insulation potential Belzona’s solution has performed extremely well in tests over its first year in service, which shows the effectiveness of the products. The polymer technology enabled the client to protect the vessel against the extreme conditions in which it operates, while also meeting specifications such as weight and thickness. Belzona proved more effective than traditional cladding, and the successful application demonstrates the potential for its use across multiple industries.
at University of
research,
active—de-icing
smart, hybrid—meaning
collaborating with researchers from the University of
This coating integrates the sensors into the material while enabling heat to dislodge ice without the need for a person or machine to physically
explains
of us have had the misfortune of sitting on a plane waiting for
about missing a connecting flight,” says
report co-author. “Our new technology takes a hybrid approach by adding sensors within an ice repellent coating that can easily be added to aviation or wind turbine blades.”
Dr. Zarifi explains that undesired ice accumulation is problematic with many renewable energy technologies such as wind turbines and hydroelectric dams, aviation and power transmission. Ice mitigation strategies can be divided into either active or passive methods. Active de-icing involves an external energy input used to remove the ice, typically through thermal, chemical or mechanical methods. In contrast, passive de-icing either reduces the accretion rate of ice, lowers the adhesion strength between ice and the surface or both.
“Neither route towards an ice-free surface is seen as a cure-all today, as active de-icing methods utilize substantial energy but passive de-icing coatings cannot keep a surface ice-free indefinitely,” he adds. “A hybrid system that combines passive and active de-icing technologies may be an attractive solution to the ice-accretion problems.”
This is why the sensor—which lives beneath the coating that will be applied to a turbine or aircraft—could be a game-changer. The sensor acts as an ice detector and prompts the embedded heaters to melt the ice automatically.
This creates a substantial improvement in energy efficiency and is what sets this latest innovation apart from existing approaches, says Zahra Azimi Dijvejin, doctoral student and lead author of the study.
“The hybrid approach allows the operator to quickly and accurately monitor the equipment sustainably,” she says. “The equipment won’t need to be de-iced unnecessarily—avoiding wear-and-tear and wasteful energy usage—because the sensors can determine the need.”
The sensors, which are integrated into innovative materials, could keep surfaces ice-free without the need for further chemicals or energyintensive methods.
“We are moving from our experimentation phase into real-life usage, and have seen the technology hold up to harsh conditions,” explains Dr. Zarifi. “We’re currently working with Canadian turbine manufacturers to incorporate the technology for the upcoming winter.”
The research, partially funded by the Department of National Defence Canada, Tekmar, Mitacs, and the Canada Foundation for Innovation, was also selected as one of the Top 50 best recently published papers in this area by “Nature communications”. ‹
UBCO engineering Professor Dr. Mohammad Zarifi examines a prototype test blade with doctoral student Zahra Azim and lab manager Mandeep Jain. The blade has been equipped with a microwave sensor, heaters and a low interfacial toughness coating, so ice will melt automatically when detected by the sensor.
Mohammad Hossein Zarifi is an associate professor at the Okanagan campus of the University of British Columbia. He received his PhD from the University of Tabriz in Iran for his research in high-speed and low-power analog circuit design, analog-to-digital converters for biomedical and communication applications. Following completion of his PhD, Dr. Zarifi undertook a post-doctoral fellowship at the University of Alberta investigating microwave planar structures for sensing applications. He is the 2015 recipient of the CMC-NRC first place award, on industrial collaboration, for the innovative microwave sensors. Dr. Zarifi is a senior member of the IEEE Solid-State Circuits Society, and the IEEE Circuits and Systems Society and serves as a reviewer for several journals and conferences.
The riblet structures of BASF Novaflex BladeUp film provide a 3% increase in power output.
Energiekontor AG has announced a partnership with the international maintenance company Omega-Tools GmbH to gradually equip its wind turbines with the functional film Novaflex BladeUp, developed by the Coatings division of BASF.
The microscopic line structures of the film generate an increase in the yield of wind turbines, making them more efficient. The riblets reduce the formation of unfavourable air turbulence on the surface of the blades, allowing to use a larger proportion of the wind for generating electricity.
“An integration into the manufacturing processes of the blade manufacturers would also be possible, so that new wind turbines can directly generate a higher electricity yield,” has explained Jörg Lenz, head of the Beyond Paint Solutions division at BASF.
BASF Novaflex BladeUp was installed on a 1.3-megawatt SWT 1,300 turbine in Ilsede (Germany). The subsequent measurement campaign led by the involved companies – that has lasted over a year – has reported a 3% increase in power output.
“We are impressed with the significant increase in power yield with Novaflex BladeUp. This makes it all the more important that we implement this option for our plants in a timely manner and thus contribute to the energy transition,” has stated Carsten Schwarz, a member of the Management Board of Energiekontor AG.
Omega-Tools GmbH will be in charge of equipping other wind turbines of the tested type with Novaflex BladeUp. In the long term, Energiekontor aims to equip all available turbines (their own and those managed by their company) with the film developed by BASF.
“The subsequent application of the functional film to existing wind turbines is feasible without long idle times of the plant and can be performed for every model,” has declared Olaf Dostalek, the managing director of Omega-Tools GmbH.
The new supreme high gloss metallic topcoat system of Jotun will complete the MegaGloss family of products.
Jotun has recently launched MegaGloss Metallic Topcoat, its new supreme high gloss metallic topcoat system for the Superyacht market segment. The new solution will complete the MegaGloss family of products, which also includes MegaGloss AC and MegaGloss HG. The company has been active in the superyacht niche for over twentyfive years and – thanks to its 90 years of experience in the marine environment – it is then now able to provide a full system of marine coatings consisting of corrosion protection, advanced antifouling properties, primers, fillers and topcoat. In addition, it also offers technical support at every stage of the coating project via the JotunCare lifecycle service.
“The company has built an in depth understanding of the needs and challenges of the customers within this demanding market. Superyachts demand the very best solutions. If the owner would like their yacht to
match their supercar, we can provide tailor made colours to help them stand out from the crowd. High DOI combined with excellent abrasion resistance helps to protect the yacht from scratches and ensure long lasting beauty,” has stated Tracey Warner, the Yachting Category Manager of Jotun.
“Metallic topcoats have always been the most difficult to apply, so it was a vital feature that we could offer a system designed to give applicators the opportunity to achieve the best possible result. By offering excellent levelling properties combined with specialist technical support at every stage, you can rest assured that the final finish will exceed expectations,” has commented Roelof Barelds, the sales director of the Yachting division at Jotun.
For further information: www.jotun.com
Trends change very quickly, as do user behaviours and social dynamics. To keep up with the times and not be perceived as obsolete by consumers, brands may decide to make changes to their corporate image.
When it comes to the visual identity of a company, the first element that comes to mind is the logo as it represents the graphic element that makes a brand most recognizable to consumers. The shapes, style, colours chosen by a company for its logo give the brand an identity and allow users to more easily associate products with a specific company.
For this reason, the logo is one of the first elements that are questioned when a company feels the need to update, revamp or brush up its visual identity based on what are the trends and dynamics within its target market. This process goes by the name of redesign.
Carrying out a logo redesign is anything but simple. In this article we will learn more about what a logo redesign is, what aspects to take into consideration, the main logo design trends and some examples, more and less successful.
The term redesign refers to the process of revamping a logo and, consequently, the entire visual identity of a company. When redesigning a logo, it is possible to either do a simple touch up or completely change it. Obviously, the two processes require different communication strategies: if the logo is completely modified, it is advisable to create a transition strategy that allows users to become acquainted with the new graphic design and to get used to recognizing the new logo.
When a redesign is carried out, only the visual and “superficial” aspect of a brand is changed, while values, mission and vision that distinguish the company remain the same.
In the event that these elements are also modified, we speak of rebranding.
The reasons why a company decides to change its logo are generally related to concrete needs and to the business. We don’t change a logo that works only because we no longer like it on an aesthetic level; this choice must be justified by real strategic reasons, including for example:
• Relaunch: renewing our logo is a way to show consumers our ability to keep up with
the trends of the time, respond to market developments, and to convey the image of a lively brand, linked to its values but capable to communicate them on a graphic level in a more contemporary way.
• Product portfolio change: over time, companies may decide to diversify their catalogues by introducing new products, or to open a new business unit. Changing the logo can respond to the need to effectively
embrace and communicate all the most important news related to the brand and its business.
• Leadership change: when in a company there are ownership changes, acquisitions and/or mergers, these changes can also be communicated through a new logo.
• Reaching new targets: when we need to reach targets of different generations, rethinking the logo could be a way to embrace different targets. The tastes of Generation Z, for example, do not always coincide with those of their parents. Creating a logo that is fresher and in line with current trends is certainly a great way to be perceived and positioned in the correct way.
Furthermore, technological changes also affect a company’s logo. In the past, logos were only paginated on paper such as brochures, catalogues, letterheads, business cards, etc. However, today, logos have to adapt digitally too - from social media to the website. Consequently, if our logo is no longer compatible and cannot be easily viewed on every technological device, then a redesign should be evaluated, opting for a more practical logo.
What aspects to keep in mind when redesigning a logo?
During the redesign process of a logo, it is necessary to evaluate both the internal elements that make up a logo and the external ones. As for the former, we need to study which are the characteristics of our logo (colours, shapes, fonts, etc.) that work and those that don’t; then we should focus on the latter, carrying out market research, studying the current trends and analysing the tastes and needs of our target audience. After having considered these aspects, we can move on to the creative part. When creating a new logo, we have to keep in mind that, even after the redesign, the brand must continue to be clearly recognisable in the eyes of consumers. We cannot launch a logo that is completely detached from the previous corporate image; the risk is that users are no longer able to recognise our brand and that the efforts
made in previous decades to grow and market our business will be for nothing. Maintaining a reference to the old logo (be it a colour, a font or a graphic shape) is essential to create continuity between the old and the new logo. Let’s see some examples.
3 logo redesigns that actually work: Nike, Apple and Pepsi
Renowned international companies such as Nike, Apple and Pepsi have changed their logo several times over the course of their history, without ever losing their identity and remaining easily recognisable in the eyes of consumers.
The Nike logo has undergone four redesign processes since 1971, the year of its foundation. As you can see from the following image, the four logos have a common element: the iconic Swoosh, which has always been the protagonist of the brand image of Nike, is what actually makes the company recognisable all over the world.
The same thing happens with the giant from Cupertino, which from 1977 to today has only ever changed the colours of its logo. The rainbow apple has been replaced by single-colour logos - first black, then blue, then white and then black again. A logo which is effective, practical and easy to use on any support.
Finally, the Pepsi logo has undergone numerous redesign operations. If we consider the first logo from 1898 and the current one, it almost feels like they are of two completely different companies (and in contrast to what has been explained so far). However, the strength of Pepsi was to bring about a gradual transformation through minimal changes: the red cursive font has acquired greater thickness over the years, up to being integrated into the 1950 logo, which introduced for the first time the bottle cap marked with the colours of the US flag. Then, the company opted for an uppercase font, probably more readable and impactful, which developed into the current logo, in which the brand name is abandoned and only its iconic colours - red, white and blue - are retained.
Therefore, maintaining consistency between the identity of the initial logo and the current one allows brands to keep being recognisable by both old and new customers.
Another interesting thing to note is that all the brands considered so far have been able to communicate so effectively on the market that it is unnecessary to include the company name in the logo: we all know that the Swoosh refers to Nike and the eaten apple refers to Apple.
Although there are brands that over time have been able to brush up their logo successfully, without losing their identity, there are also some companies that have lost their bearings during the logo redesign process. An example is the American clothing brand GAP.
The historical logo of the company consisted of a blue square and the brand name written in Spire Regular font.
In October 2010 the company, due to the collapse of sales following the financial crisis of 2008, decided to redesign its logo with the aim of
giving new impetus to sales and reaching new consumers. The new logo, however, did not have any element in common with the logo with which the brand was known up to that moment: the square, in addition to having been reduced in size, also underwent some changes - the bright blue was transformed into a nuanced light blue. The brand name also changed from uppercase to lowercase. A different font was used too. As soon as it was released, the logo was harshly criticised by users and labelled as a logo created with “poor creativity”. The criticism was so heavy that the company was forced to withdraw the new logo a week after its launch. This episode is still remembered today as Gapgate and testifies that what we said above is fundamental during the creation of a new logo.
The redesign of a logo needs to go hand in hand with a marketing strategy to effectively communicate the reasons that led to the change. In fact, changes often confuse the public and it is advisable to involve and accompany customers along the process that led to the development of the new image.
Graphic design trends change very quickly and it is always good to be up-to-date with new trends when we decide to redesign our logo. However, in recent years the key seems to be minimalism. Alongside it, other trends are also very popular. Let’s see them.
For several years now, architects and designers have loved the “less is more” concept. It is an explicit reference to aesthetics, simplicity, functionality and essentiality: principles that find their way in minimalism – a trend that is also embraced in the digital world by graphic designers and web developers.
Regular shapes, soft colours and essential lines are the main elements taken into consideration when creating a website or a logo. But, in order to be successful, a logo can’t just be aesthetically pleasing or elegant. It is essential that it adapts to the ethics, mission and values of our company. The risk is that it may be modern but also inadequate for our brand.
In addition to an aesthetic issue, minimal logos are also more practical than others, as they are more suitable to be displayed on screens of different sizes and on any type of support. Given these reasons, there are many brands that in recent years have decided to redesign their logo, heading towards a simpler and more minimalist style. Apple, Nike and Pepsi –mentioned previously – are an example of this: abandoning fonts that are difficult to read, strange shapes and the overabundance of colours, these three logos are characterised by simplicity and essentiality.
An even more recent example is that of Barilla, an Italian multinational in the food sector. In January 2022, on the occasion of its 145th anniversary, it unveiled its new logo. The logo used by the company for over 65 years was designed by Erberto Carboni,
a designer and architect from Parma and member of the post-Cubism culture. It presented a red and white flattened oval shape and the name of the brand in the centre of it. Over the years, the logo has been modified several times, but never completely changed.
There have been small interventions on the logo, but they never changed the typical oval shape resembling a hard-boiled egg cut in half. A few months, however, the logo adopted by the brand has embraced a more minimalistic look: a single and simple shape, an even sharper contrast between the two colours and a clearly legible font.
Finally, it is worth mentioning the world of fashion and automotive, sectors in which the trend towards minimalism is very popular, perhaps to the point of flattening way too much the image of the brand.
The Covid-19 pandemic has contributed to radically change our daily habits and routines. In this difficult time, when creating new memories was almost impossible, people sought solace in the past and nostalgia became a shared theme among users. TV series, films, music, fashion and obviously graphic design offer us a way to go back to the “good ol’ times”.
A brand that has embraced this trend in 2021, having great success internationally, is Burger King.
The famous fast food restaurant franchise has decided to return to the historic 1994 logo. The reason is soon explained by the company’s top management: going back to one’s roots allows to create an emotional, familiar and reassuring connection with customers, making them feel at ease.
Furthermore, the company’s growth in terms of sales was achieved precisely from 1969 to 1994. Consequently, returning to the iconic original logo also represents a way to remember the times when the fastfood achieved tremendous results from a commercial point of view.
Burger King is not the only brand that has recently decided to adopt a vintage-style logo. Kodak also took a step back in time, adopting a revised version of its 1971 logo in 2016.
In recent times, animated logos are also becoming popular. Understanding why this is happening is not difficult if we consider how our brain is stimulated more by dynamic images than static ones. Just as videos and animations on websites and social media are on the rise, so are animated logos.
To create an animated logo that works, it’s best to create a rather simple, linear animation, lasting only a few seconds. Here are two exams of two giants of the web which created an animated version of their logo: Google and Meta.
This trend is not new but it continues to grow and be embraced by many brands. The most emblematic example is Instagram. The logo of Zuckerberg’s social network was almost completely changed in 2016, when the company decided to replace the vintagecoloured logo with one with brighter colours.
In recent weeks, after 6 years, Instagram released the new logo created with an innovative 3D modelling process.
The differences between the 2016 and 2022 logos are minimal: now the colours are even
brighter. The choice comes from the fact that colour gradient gives more dynamism to images and the brighter the colours, the more visible they are on all digital devices. Adobe has also revolutionized its brand identity by unveiling the new icon of its Creative Cloud.
The logo, which previously boasted a combination of red and white colours, now sports a rainbow gradient - from red to green, from fuchsia to blue. This variety of shades “brings the colours of our product brands and our new corporate red together into one beautiful gradient that represents the importance of creativity”, the company explained.
Summing up Redesigning your logo can bring many benefits. First of all, it allows to communicate the brand identity in an effective and coherent, lining up with the internal and external changes of the company. It also allows to be perceived as a brand attentive to the dynamics and values of the company, as well as to graphic design trends1 However, in order to redesign the logo in an effective way, it is good to take into consideration the aspects we have addressed in this article. ‹
Concrete may account for the largest total surface area among all construction materials. While major emphasis has been placed on the use of steel as a substrate for corrosion resistant coatings, it is believed that the total area of concrete surfaces is even greater, although there is a substantial portion of them that do not require coatings. Concrete itself is considered a corrosion-resistant cladding and it is often applied over steel to prevent it from corroding. Indeed, where concrete is well placed and dense, it is one of the best corrosion protection coatings available for steel. It provides a thick, dense, waterresistant barrier, as well as creating an inhibitive atmosphere that retards steel corrosion.
In this article, we will deal with the systems available for the inspection of concrete surface preparation.
Inspection requirements for surface preparation of concrete are basically drawn up to determine whether specification requirements are met concerning as follows:
• The removal of contaminants that inhibit coating adhesion or induce early coating deterioration
• The roughening of smooth surfaces to improve coating adhesion
• The removal of any weak surface layer to establish a strong base required for many coating systems.
There are many methods that may be used to prepare a concrete surface for coating. They include broom, vacuum, and air blast cleaning; water, detergent and steam cleaning; mechanical abrasion and with hand or power tools; water blast cleaning; abrasive blast cleaning and acid etching. The standard SSPC-SP 13/NACE No. 6 “Surface Preparation of Concrete” covers the preparation of concrete surfaces prior to the application of protective coating or lining systems. This should be used by specifiers, applicators, inspectors, and others who are responsible for defining standard characteristics of cleanliness, strength, profile, and dryness for prepared concrete surfaces.
Prior to surface preparation of new concrete, the Inspector may be required to verify that the concrete is fully cured. The proper curing time, with sufficient moisture and temperatures, before coating is normally stated in the specification.
Prior to surface preparation of new and older concrete, the Inspector may be required to verify that the concrete is sound. The soundness of a concrete surface can be determined by measuring the surface tensile strength with an adhesion tester (ASTM D 4541).
On the new concrete, protrusion and concrete spatter should be removed by power grinding or stoning (scouring of surfaces with a carborundum or other abrasive bricks). Tie-rod holes, bug holes, and other surface indentations should be filled prior to surface preparation. In a chemical environment, it is particularly important that bug holes are filled and fins ground flush to allow a good film integrity. It should be noted that the above repairs are normally the responsibility of a concrete personnel. However, the Inspector should verify that the manufacturer’s recommendations are followed when repairs are made. Otherwise, problems may arise due to low tensile strength or bond of the cement repair materials.
• The Inspector should verify that surfaces are not contaminated by grease, oil, or form release agents. These contaminants must be removed, to permit very good adhesion of coatings to concrete. There are three common sources of grease/oil contamination:
• Oil on the hands of the applicator or Inspector
• Oils used to lubricate compressors and power tools
• Diesel exhaust.
Grease and oil can sometimes be detected when not visually apparent by spraying the concrete surface with a fine mist of water. If the concrete surface is clean, the water will wet and darken the surface and spread well. If the surface is contaminated by grease, oil, or form release agents, it will resist wetting, i.e. it will not darken and/or the water will form beads or droplets on the surface.
If grease, oil, or form release agents are detected on a prepared surface, the Inspector should verify that they are removed by the specified procedure, e.g. solvent cleaning, before coating application is allowed to proceed.
If surface cleaning is specified, the inspector should verify it is done according to the job specification and referenced standards. ASTM D 4258 and ASTM D 4262 describe basic procedures for cleaning concrete and concrete unit masonry surfaces, respectively, to remove dust, oil, grease, dirt, and loose material prior to coating. These cleaning procedures include: broom cleaning, vacuum cleaning, air blast cleaning, water cleaning, detergent water cleaning, steam cleaning, and mechanical tool cleaning. They are not intended to alter the surface profile. While visual standards are not available for cleaned concrete, surfaces a “filed standard” may be prepared as described for steel.
• Broom, vacuum and air blast cleaning – Surface dirt, dust, and other loose solid material can be removed by broom, vacuum cleaning, or a stream of clean compressed air (ASTM D 4285). These methods will not remove grease, oil, or laitance (a weak brittle layer that results when concrete is overly wet or overworked).
• Wire brushing – Efflorescence is a fluffy deposit formed by reaction of soluble alkaline products that migrate to the surface with carbon dioxide. It should be removed from cementitious surfaces by dry wire brushing before any washing occurs. Water washing will merely drive it into the concrete. Efflorescence does not normally occur on new concrete.
• Water, detergent, and steam cleaning – Grease and oil are best removed from concrete by alkaline cleaning solutions or by steam cleaning with added detergent. Heavy deposits of grease or oil should first be removed by scraping. Solvent cleaning tends to drive these contaminants into the concrete. These methods do not remove laitance effectively. For plaster, stucco, dry wall, plaster board, and other cementitious surfaces with limited structural strength, washing with a mild detergent solution is normally sufficient to remove dirt and other loosely-held contaminants. Power washing with a detergent solution up to 14 MPa may be necessary on surfaces that are strong enough to withstand these pressures.
ABRADING – ASTM D 4259 describes surface preparation of concrete prior to coating. This practice is intended to roughen the surface profile of the concrete and remove foreign materials including existing coatings and weak surface concrete, such as laitance. These procedures include mechanical abrasion, water blast cleaning, and abrasive blast cleaning. Power tools can be used to remove loose or otherwise defective concrete. A scarifying machine can be uses effectively on large areas of concrete floors. Care should be taken no to damage the floors with this machine. Water blasting (with or without injected abrasive) may also be effective for surface cleaning of concrete, although it introduces water into the concrete and thus requires drying time before coating operations can begin. Abrasive blasting of sound concrete is often the most effective method of cleaning. If abrasive blasting is specified, the inspector should verify that it is done according to the job specifications and referenced standards. Blasting pressures and nozzle-to-concrete distances must usually be controlled carefully to prevent excessive removal of concrete.
ACID ETCHING – ASTM D 4260 describes the use of the acid to prepare concrete surfaces for coating. The practice is intended to roughen the surface profile of the concrete and remove foreign materials and weak concrete laitance. Acid etching should only be used where other method are not possible. This is because:
• There are concerns regarding the disposal of the residue as hazardous waste.
• It wets the surface at a stage late in the application process.
• It may not be a reliable surface preparation method, depending of the type of contamination (e.g. organics or oily contaminants).
Acid etching, frequently with a 10% solution of muriatic acid, can be used to roughen smooth surfaces to produce better coating adhesion. It should be noted that standard safety and environmental procedures must be followed when using acids or other chemicals. Specially designated procedures must be followed when disposing of chemical wastes. Chemical spills should be cleaned up according to procedures specifically prepared for it.
Acid used in etching should be neutralised with bicarbonate solution and the clean surfaces rinsed with water. Care should be exercised to scrub the concrete surface to ensure that the salt deposited from the acid etching process are removed. The process of acid etching followed by neutralisation with bicarbonate may produce insoluble salt compounds that are not removed by water rinsing. It may therefore be necessary to further clean the rinsed surface by a method such as vacuuming (ASTM D 4285). The concrete should be allowed to dry sufficiently prior to applying the coating. In the next article, we will deal with tests for surface contamination after surface preparation. ‹
The European Corrosion Congress – EUROCORR, the EFC’s annual conference, is the flagship event of the international corrosion calendar. Attracting upwards of a thousand delegates, it is held every year after summer in a different European country. EUROCORR is famous for its high technical standard and its popular social programme EUROCORR 2022 was organised by DECHEMA (Society for Chemical Engineering & Biotechnology) and GfKORR (Society for Corrosion Protection) in Berlin.
Under the motto “Corrosion in a Changing World – Energy, Mobility, Digitalization” the event took place from 28 August to 1 September 2022 in the heart of Berlin, at the Berlin Central District Hotel (managed by Marriott).
The EUROCORR attracts over one thousand corrosion experts from all over the world every year. More than 1.200 international delegates from industry and academia attended the conference in August 2022. The high level of scientific expertise of the participants has made EUROCORR as the global leading scientific conference on corrosion research and is a permanent item on the agenda of experts from universities and industry. For young colleagues the Young EFC provides a platform to exchange ideas with expert colleagues and to become part of a unique network.
The conference programme included plenary meetings, keynote lectures, oral and poster presentations, supported by the various EFC Working Parties along with specific workshops.
Sponsoring & exhibition is an integral part of EUROCORR 2022 and offers a unique opportunity to promote technologies, products and services and a unique networking opportunity with personal contact to leading scientists, representatives of research institutions, university and industry and graduate students.
Among the sponsors of Eurocorr 2023 there were:
• 3X ENGINEERING (3X), one of the world leading companies specialized in pipeline maintenance using composite technology. Mainly operating in Oil & Gas industry, 3X expertise also extends to Power and Construction sectors.
• Cortec Corporation®, the world leader in innovative corrosion protection solutions and biotechnology. With 6 facilities in the US and Canada, and 4 production, logistics and office locations in Croatia, Cortec delivers environmentally responsible VpCI®and MCI® corrosion control technologies, for corrosion problems in packaging, metalworking, construction, electronics, oil and gas, and many other industries.
• ELANTAS Europe belongs to the ALTANA group and is leading manufacturer of insulating materials and specialty chemicals.
• Monti Group, with MontiPower® and Corronation®, is leader in the innovation for surface preparation in the broadest sense from cleaning, preparation, coatings, testing/ inspection and education. Monti group MBX® and Bristle Blaster® Technologies to remove, clean and profile a substrate are truly unique.
• Q-Lab Corporation, a global provider of material durability testing products since 1956. Q-Lab designs and manufactures standard test substrates and corrosion coupons as well as corrosion, weathering & light stability, and corrosion testers.
• ReCorrTech, the Zagreb based company provides customized testing, inspection and monitoring systems for coated infrastructure and products. Its Quantitative Coating Quality (QCQ) measurement technology captures the temporal patterns of barrier coating behaviour that are a key to coatings ability to uphold as the first line of defence against coating defects and coating failure.
Eurocorr 2023 will take place in Brussel, Belgium, from 27 to 31 August 2023. The main topic will be: “Driving corrosion prediction and protection towards a circular economy.”
further information:
The 30th SMM, the leading global maritime trade fair, took place on exhibition campus in Hamburg (Germany) from 6 to 9 September 2022.
The enthusiasm was palpable. After a four-year wait, the international maritime community was finally able to meet for a physical SMM in Hamburg again: for four days, 2,000 exhibiting companies and over 30,000 industry visitors from more than 100 countries formed the “United Nations of Shipbuilding”. “There was an enormous sense of anticipation, and expectations were high. The more enthusiastic I am to see that we have been able to confirm our status as the leading global maritime trade fair once again,” said Bernd Aufderheide, President and CEO, Hamburg Messe und Congress. The maritime energy transition and the technologies and expertise it requires, along with a clear commitment to making the necessary changes, were at the top of the agenda throughout the fully occupied exhibition campus and the accompanying conference programme of SMM. Retrofitting ships was one of the key topics of this fair. The industry is facing the enormous challenge to retrofit its fleet of roughly 60,000 merchant ships progressively to make them more ecoand climate-friendly. The presence of political leaders attested to the special importance of the shipping industry in the efforts to achieve the climate goals.
SMM delivers important stimuli to achieve this goal, said Knut ØrbeckNilssen, CEO of DNV Maritime, the main sponsor of the flagship fair: “SMM is one of the best events in the maritime calendar. It is truly global, and with its focus on innovation, it gives people an impression
what the future of shipping will look like.” The industry has set its goal: achieving climate-neutral shipping by 2050. This calls for practicable solutions from engineering firms, shipyards and suppliers, but also from fuel manufacturers. “As a marketplace for innovations, SMM is an important basis for investment decisions of German shipowners. The focus is on the climate-neutral transformation of the maritime sector,” said Dr Martin Kröger, Managing Director of the German Shipowners Association (VDR). “We are communicating about this with shipbuilders and suppliers as well as experts around the world, many of whom we can meet at SMM in Hamburg.” Technologies for the energy transition It is not by coincidence that SMM is the international platform of the maritime industry, from small start-ups through to global market leaders. For example, propulsion system specialists Wärtsilä Voyage showcased their new Fleet Optimisation System (FOS). “This holistic platform for data analytics, voyage planning and fleet performance optimisation can help shipping companies operate their ships and fleets with optimum safety, efficiency and sustainability,” explained Sean Fernback, President of Wärtsilä Voyage. Engine manufacturer Rolls-Royce presented fuel cell concepts, hybrid systems and engines designed to operate on e-methanol. “For the future, we are firmly committed to this ship fuel which we want to pioneer,” said Denise Kurtulus, Vice President Global Marine at Rolls-Royce. Mecklenburgische Metallguss (MMG) offer a portfolio of optimised-flow ship propellers which are used by shipowners such as Hapag-Lloyd to retrofit a major portion of their fleet in operation,
enabling fuel and CO2 savings of more than 10per cent. As a symbol for the entire fair, a highefficiency MMG propeller was displayed at the entrance to SMM to greet the industry visitors. The technology company ABB exhibited a new semiconductor power switch for safe, energyefficient next-generation direct-current systems. Thorsten Strassel, Global Product Manager at ABB, said: “SMM is an ideal platform to present this innovative technology in support of the energy transition in the shipping sector.” Renewable energies, battery storage and smart grids are key factors in making shipping more sustainable, he added. RWO, a leading supplier of smart water management solutions, featured their latest oil-water separator system (OWS) at the flagship fair. RWO CEO Stratos Papamichalis explained: “We are pleased to offer owners of larger ships an efficient, flexible and cost-effective OWS solution that is suitable for both, newbuilds and retrofitting projects.” Retrofitting ships was one of the key topics of this fair. One of the challenges the industry faces is retrofitting its 60,000 merchant ships step-by-step to make them more eco- and climate-friendly. An enormous market for Europe’s supply industry is opening up here, was the forecast given by Stephen Gordon, Managing Director of Clarksons Research. Inventions such as the Mewis Duct, which earned the two shipbuilding engineers Friedrich Mewis and Dirk Lehmann the German National Environmental Award during SMM week, are significant contributions to climate protection. The flow optimisation device, which is sold by Becker Marine Systems, has already saved more than 12 million tonnes of CO2 worldwide. Managing Director Henning Kuhlmann was more than pleased that SMM was able to take place in the customary form again: “There is no other place where so many customers, suppliers and other market stakeholders can meet within such a short time span. We have not only seen familiar faces but also introduced ourselves to many new people; we followed up on ongoing projects and signed several major new contracts,” he reported. Kuhlmann’s conclusion: “For Becker, SMM is and will always be the world’s most important shipbuilding trade fair.”
SMM was again accompanied by high-profile conferences covering specific topics such as digitalisation (Maritime Future Summit), ocean research (Offshore Dialogue), as well as security and defence (International Conference on Maritime Security & Defence). A conference which received special attention this year was the global maritime environmental congress, gmec: for the first time, one of the panel discussions was open to the general public. Environmental campaigners and industry decision-makers discussed the responsibility of the shipping industry for climate protection. Apart from providing opportunities for knowledge-sharing, the organisers of SMM placed major emphasis on networking formats, providing the new Transition Stages as a new, dedicated platform for exhibitors to highlight their favourite
topics. Additional highlights included the Start-up Award as well as the Maritime Career Market where young talents were able to make contact with interested potential employers. “There is no better opportunity to familiarise the general public, including young talents who are so important for our future, and political decision-makers with the breadth and depth of our industry,” recapitulated Dr Reinhard Lüken, General Manager of the German Shipbuilding and Ocean Industries Association (VSM). An assessment confirmed by surveys among trade fair visitors, 97 per cent of whom said that SMM is the most important trade fair of the maritime industry, with 86 per cent being determined to return for the next SMM. 97per cent of visitors confirmed that SMM provides an excellent opportunity to make contact with international stakeholders. The next SMM will take place in Hamburg from 3 to 6 September 2024.
For further
InnoTrans 2022 (Berlin, 20-23 September) closed successfully with 137,394 international visitors from 131 countries.
Sustainable mobility is the dominant theme in the industry –
InnoTrans 2022 clearly confirmed that. From 20 to 23 September 2022 all the leading manufacturers and actors gathered at the international trade fair for transport technology and mobility in Berlin. Exhibitors and visitors drew a positive conclusion after the four-day event. 2,834 exhibitors from 56 countries presented the mobility sector’s entire range of products and services on the Berlin Exhibition Grounds, which were fully booked. Among the exhibits were 250 world innovations, 128 vehicles and 14 buses. Alternative drive systems, battery-electric and fuel cell-powered buses and trains were the main topics at the trade fair.
137,394 international visitors from 131 countries came to the German capital to find out about this uniquely wide-ranging overview of the industry’s products and services.
This year’s InnoTrans once again lived up to its reputation as an international forum and driving force of the industry.
At InnoTrans, Dr. Richard Lutz, CEO of Deutsche Bahn, and Oleksander Kamyshin, CEO of Ukrsalisnyzja (UZ), the state-run Ukrainian rail network, signed a memorandum of understanding. The agreement guarantees UZ support for reconstruction after the war, and includes collaboration on expanding goods supply corridors and terminal capacity as well as wide-ranging consultation services for introducing European rail operation and management standards.
At InnoTrans, Poland’s rail vehicle manufacturer Pesa and the mineral oil company and fuel station operator PKN Orlen reached an agreement to collaborate on hydrogen-powered rail vehicles. As a group, the two companies will put together an offer for rail transport
companies that will include supplying rolling stock as well as hydrogen and refuelling solutions.
At InnoTrans, Saudi Arabia was able to move forward with ambitious plans for expanding its rail network. The country had already signed agreements with Deutsche Bahn and Siemens, said Dr. Bashar Khalid Al Malik, CEO of the Saudi Arabian Railway Company, at the trade fair. With Deutsche Bahn, the project included a knowledge transfer, while with Siemens the topic was also ticketing, he said.
According to a representative survey, exhibitors and trade visitors gave a positive assessment of their attendance at the trade fair. 90 per cent of trade visitors were highly satisfied with their visit. 94 per cent of exhibitors had a positive overall impression of the trade fair. At 91 per cent respectively, both groups said they would readily recommend InnoTrans to others. A high percentage of trade visitors attended in a decision-making capacity, with almost 50 per cent occupying a senior position in their company. 57.3 per cent of trade visitors came from abroad. Trade visitors from Europe showed particularly keen interest in the trade fair. Almost two-thirds came from the EU. A high proportion of exhibitors (around 18 per cent) reported successful business deals. Nine out of ten exhibitors expected good follow-up business.
Numerous exhibitors made use of the rail track and outdoor display area at InnoTrans to draw maximum attention to their world innovations. Among manufacturers, sustainable mobility was the dominant theme. On the rail track and outdoor display area, Siemens
Mobility presented the Mireo Plus H, the next generation of hydrogenpowered trains, as well as the Mireo Plus B, which features a modular high-performance battery system. For the first time Stadler displayed its hydrogen-powered FLIRT H2 multiple-unit train for the American passenger rail market. Visitors could even witness Alstom’s Coradia iLint hydrogen-powered passenger train live, which was operating twice daily from Berlin-Spandau to Berlin-Ostbahnhof. Hitachi presented its Blues Train, which combines diesel, electric and batteryelectric drive systems. Vossloh exhibited its DM 20 hybrid locomotive, which can also rapidly switch operating modes and energy systems. Deutsche Bahn was represented with several innovative trains (Ideenzug). The City version was incorporated in the middle carriage of Hamburg’s digital S-Bahn. That particular innovative train is still a future concept. However, the one operated by Südostbayernbahn, a double-decker carriage, is real and was exhibited by DB Regio on the outdoor display area.
Once again, one of this year’s highlights was the Bus Display, featuring 14 buses being driven on the 500-metre long demonstration course in the Summer Garden. For the first time Solaris presented its Solaris Urbino 18 hydrogen, an 18-metre long bus with hydrogen as its main energy source. The ŠKODA H’CITY also uses hydrogen as a sustainable drive system. Van Hool was represented with its A12 electric bus. Ebusco presented its all-electric city bus 3.0 on the Bus Display. Also being shown was the Modell 2.2, the new electric bus for Berliner Verkehrsbetriebe (BVG).
An outstanding supporting programme featuring wide-ranging discussion rounds, lectures and events gave visitors an opportunity to find out about all the latest topics and trends in the mobility sector, including driverless rail vehicles, tunnel construction, smart public transport and innovative passenger experiences. New: recordings of the livestreamed events are available after the trade fair on the InnoTrans Plus online portal.
InnoTrans is the world’s leading trade fair for transport technology and takes place every two years in Berlin. The five segments at InnoTrans are Railway Technology, Railway Infrastructure, Public Transport, Interiors and Tunnel Construction. InnoTrans is organised by Messe Berlin. The 14th edition of InnoTrans will take place in Berlin from 24 to 27 September 2024.
EDITOR IN CHIEF
ALESSIA VENTURI venturi@ipcm.it
EDITORIAL DIRECTOR M.d.L. PAOLO RAMI paolorami@hotmail.it
EDITORIAL OFFICE
PAOLA GIRALDO giraldo@ipcm.it
MONICA FUMAGALLI fumagalli@ipcm.it
MATTEO SOTTI sotti@ipcm.it
BARBARA PENNATI pennati@ipcm.it
ILARIA PAOLOMELO paolomelo@ipcm.it
GABRIELE LAZZARI redazione@ipcm.it
MEDIA SALES
FRANCESCO STUCCHI stucchi@ipcm.it
BARBARA PENNATI pennati@ipcm.it NICOLE KRAUS kraus@ipcm.it
SVEN KRAUS sven.kraus@ipcm.it
CLAUS GÖRLICH goerlich@ipcm.it
GRAPHICS
ELISABETTA VENTURI grafico@ipcm.it
Eos Mktg&Communication srl www.eosmarketing.it - info@eosmarketing.it www.myipcm.com - info@ipcm.it
Redazione - Sede Legale: Via Pietro Mascagni, 8 - 20811 Cesano Maderno (MB) - Italy Tel. +39.0362.503215 - Fax. +39.0362.1794768
Prof. Massimiliano Bestetti Department of Chemistry, Material and Chemical Engineering, Politecnico of Milan - Section of Applied Chemistry and Physics
Prof. Paolo Gronchi Department of Chemistry, Material and Chemical Engineering, Politecnico of Milan – Chemical Engineering Section
Massimo Cornago Oil & Gas Specialist
Edoardo Tevere Indipendent Nace inspector lev. 3 QC/QA
Ing. Luca Valentinelli Materials Engineer, PhD, Nace inspector lev.3
Rates
Single
LAYOUT
myFAIR is a free web app that can be accessed from both desktop and mobile devices, which allows you to stay up-to-date with the leading events of the surface treatment sector.