
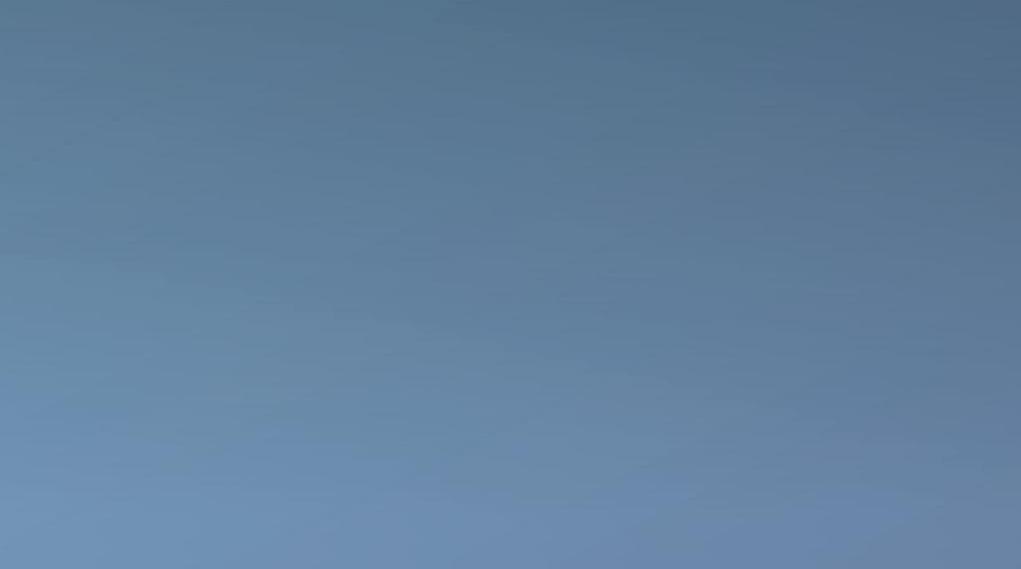

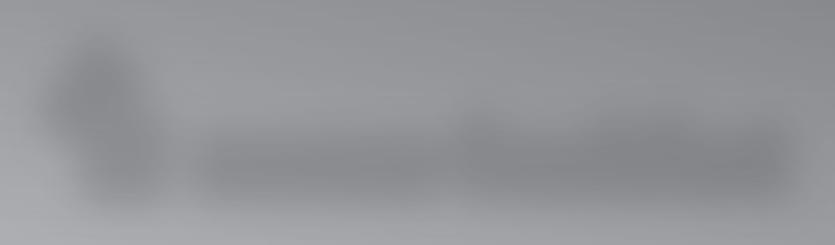

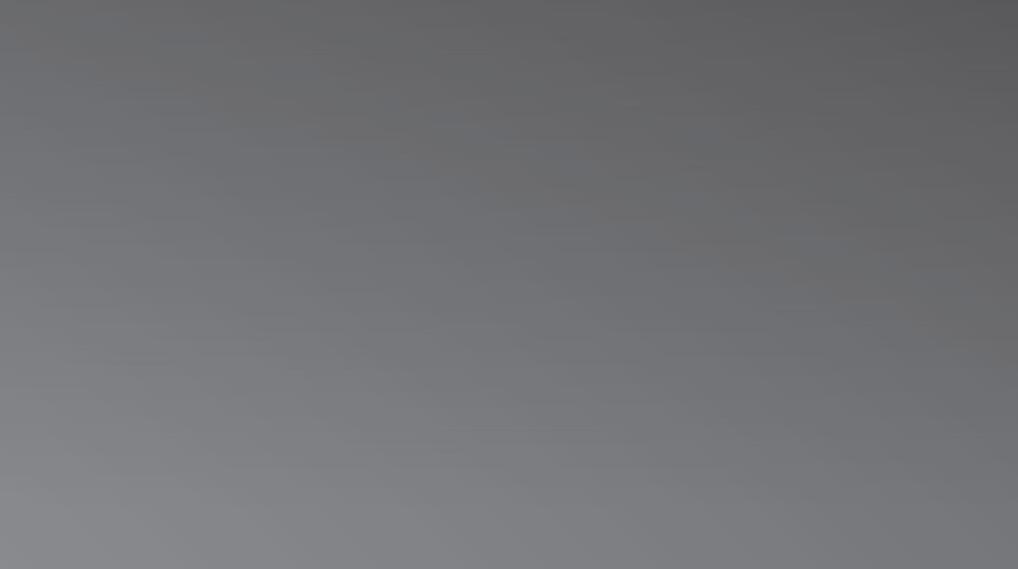



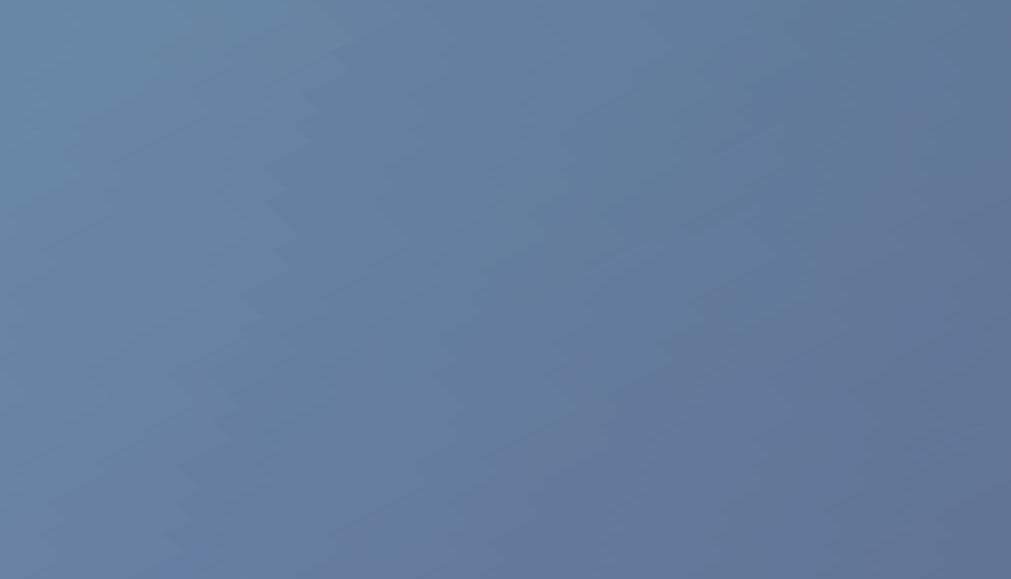

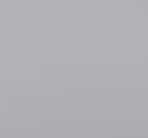

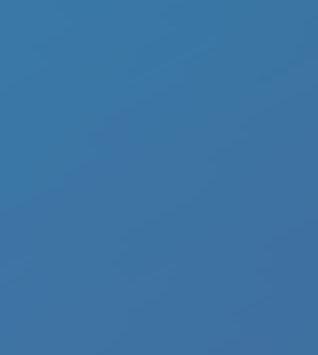
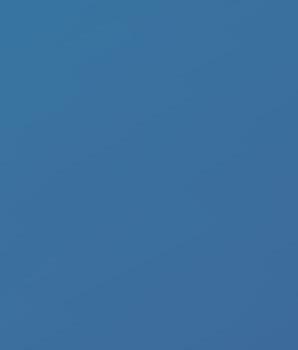
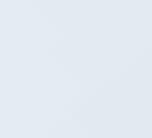
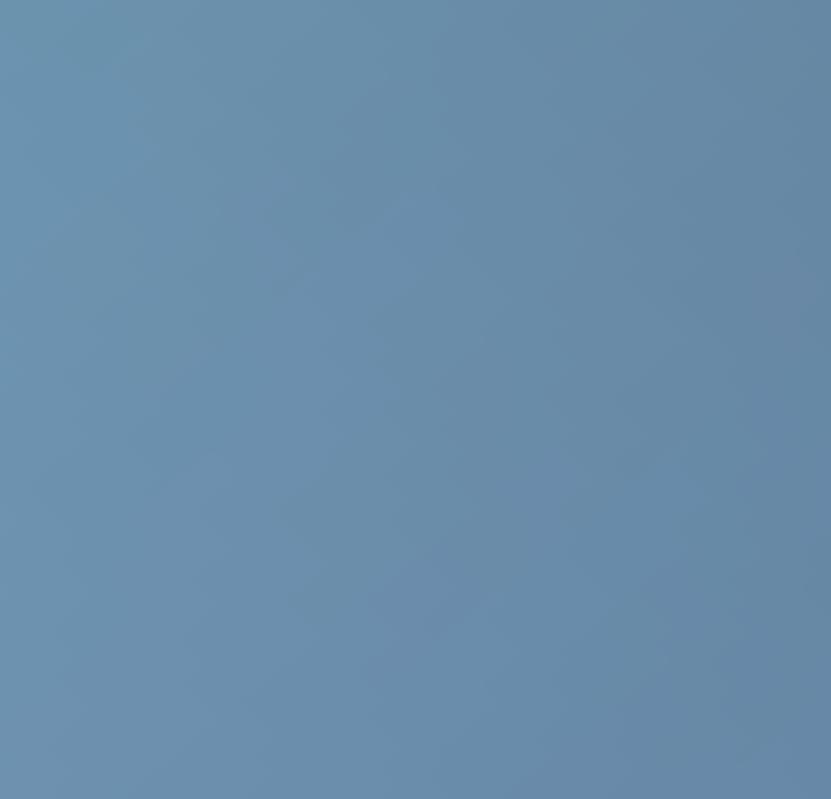
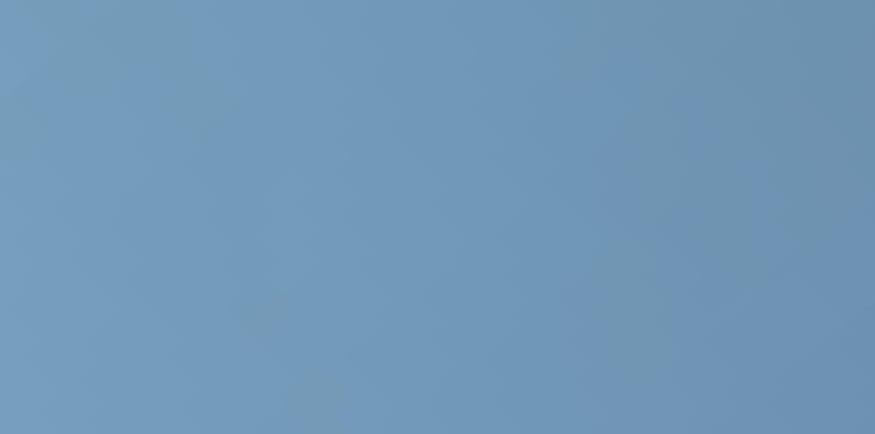
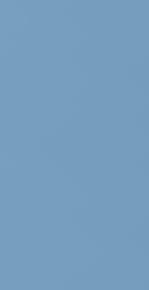
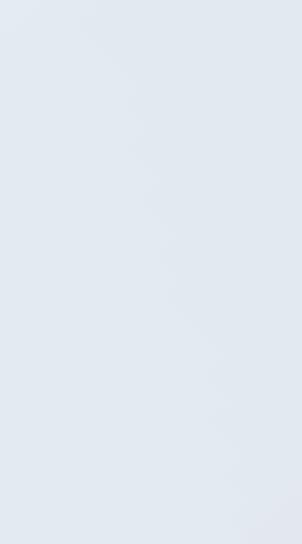
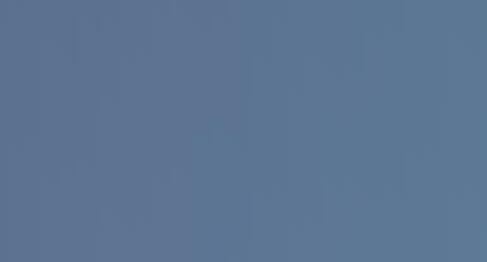

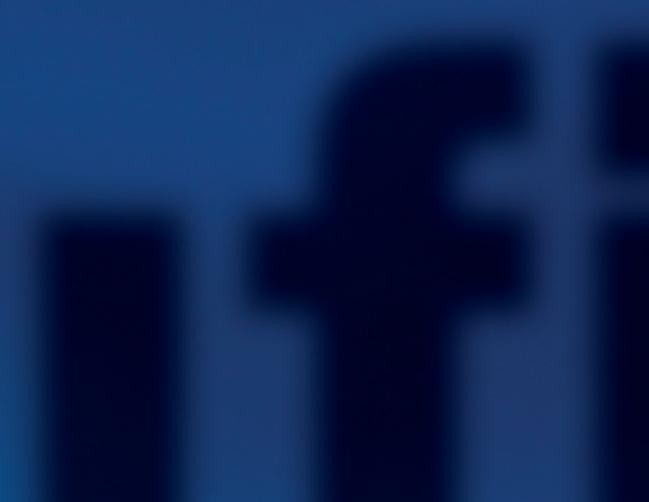

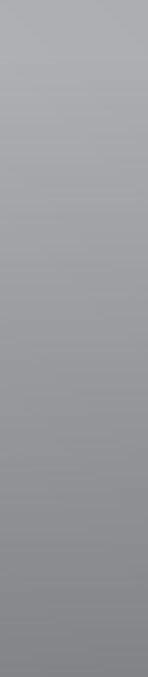
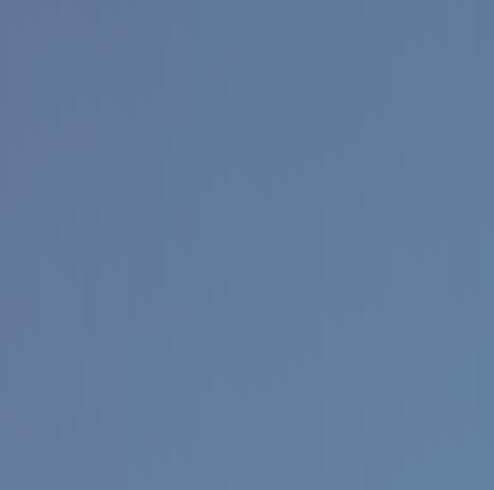
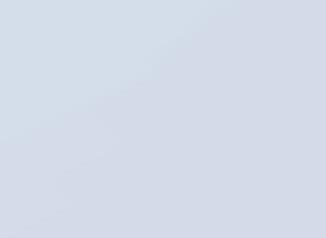
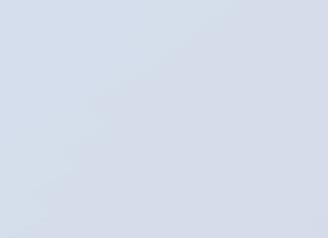
CIRCULARITY Gather


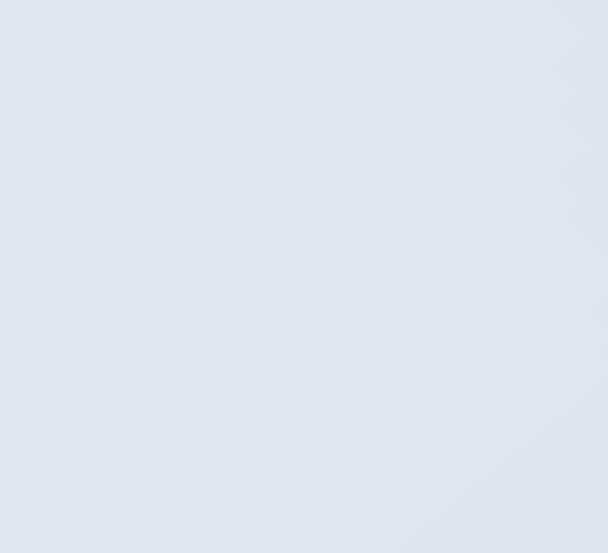

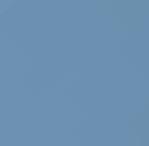
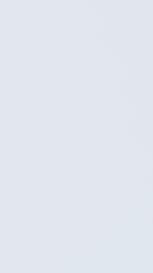


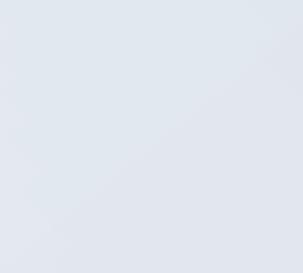
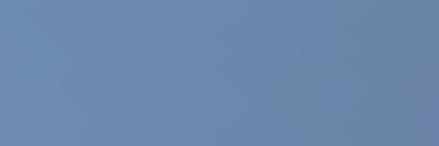
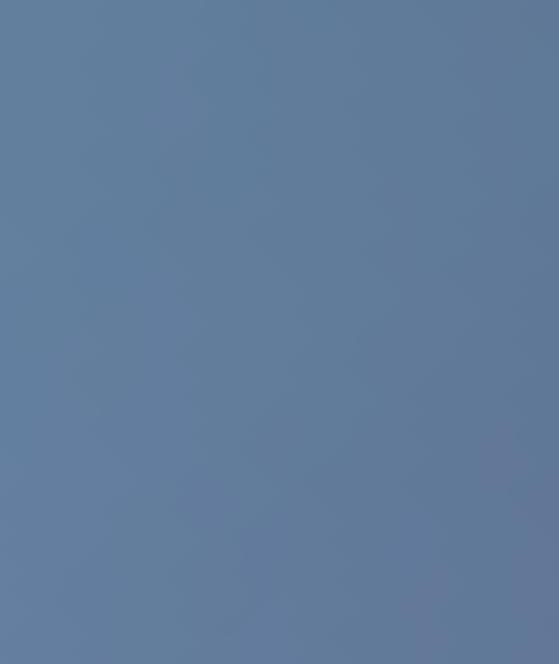
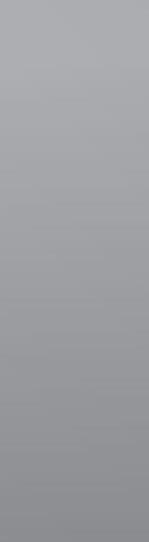
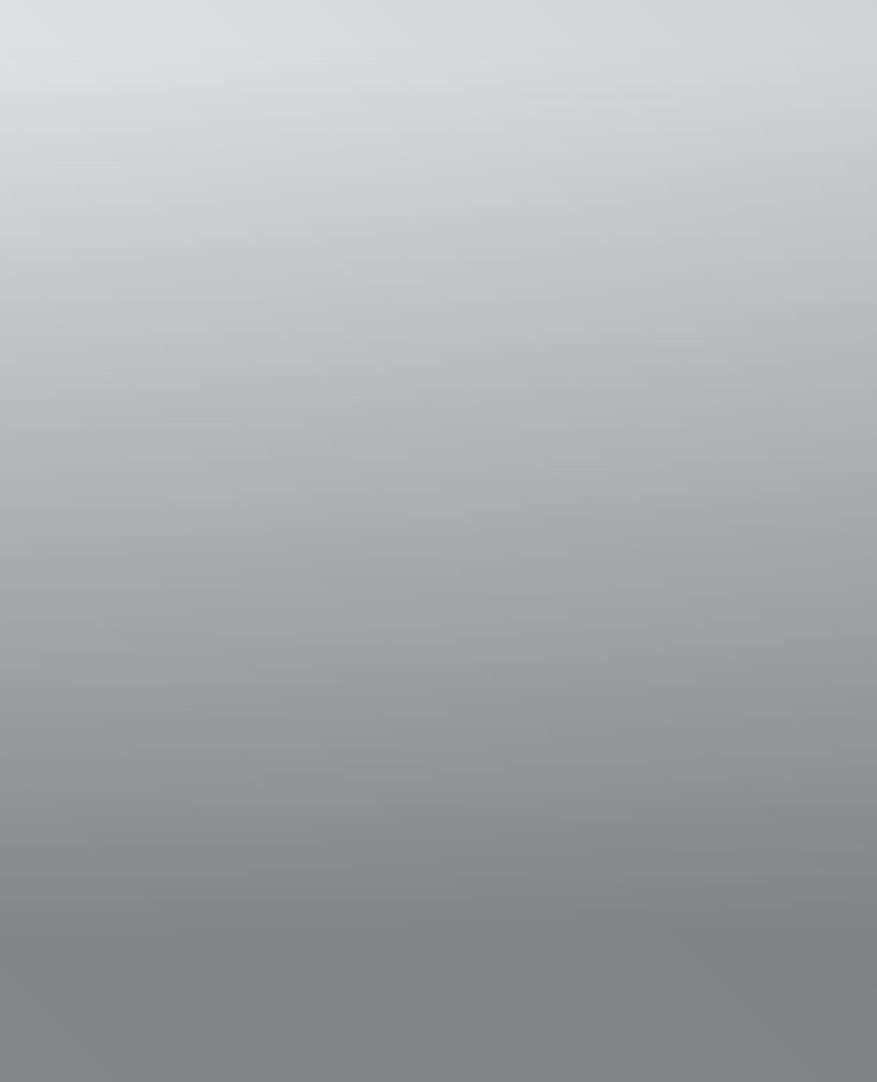
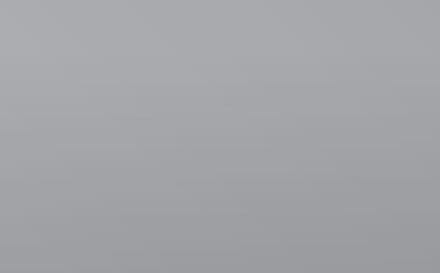
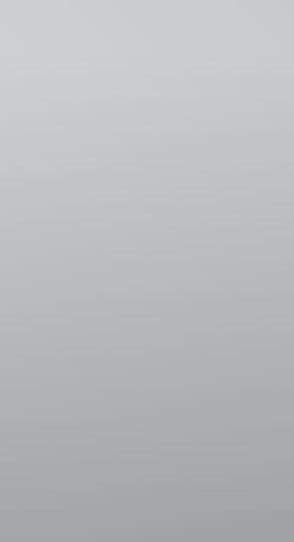
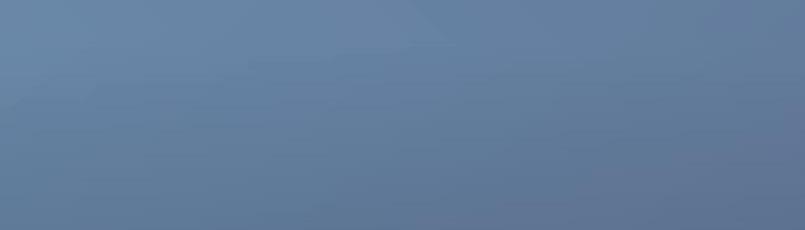



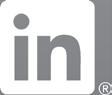

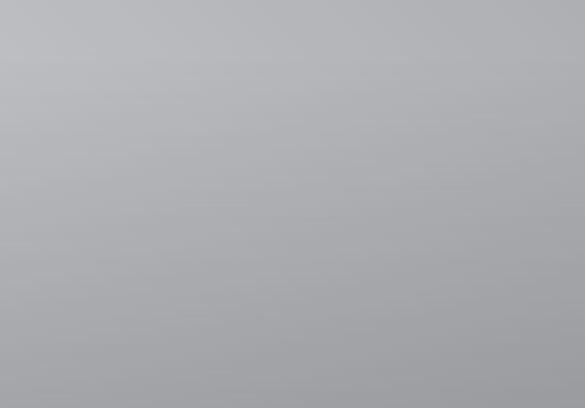

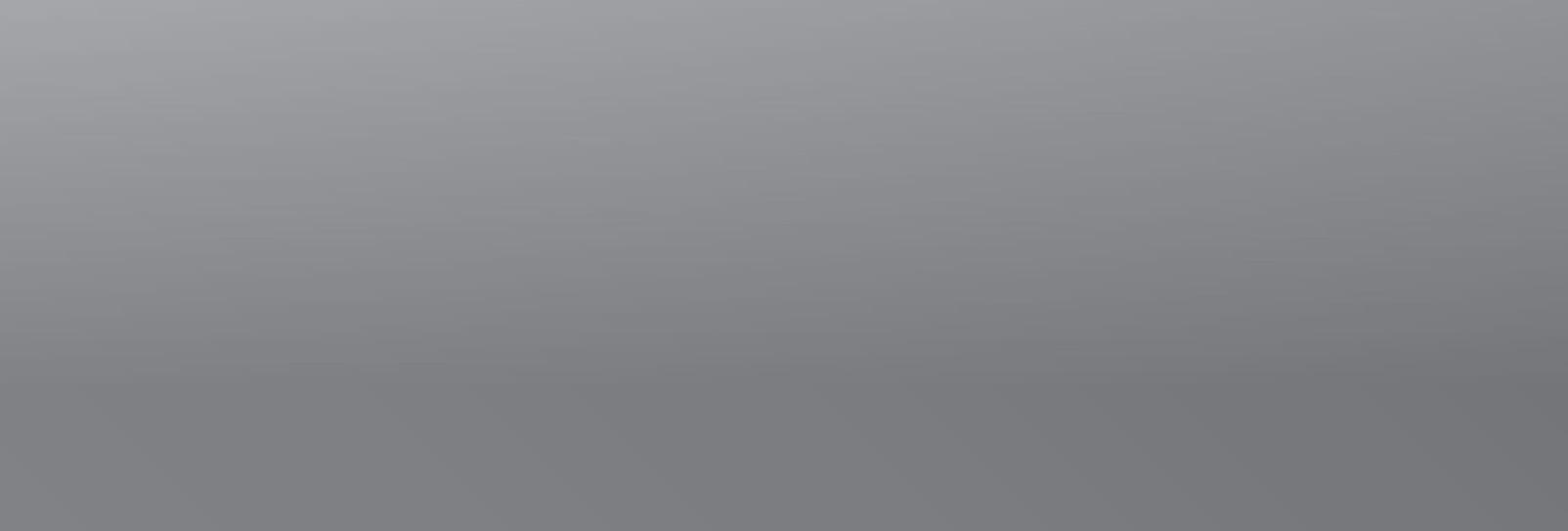

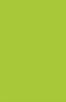









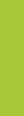
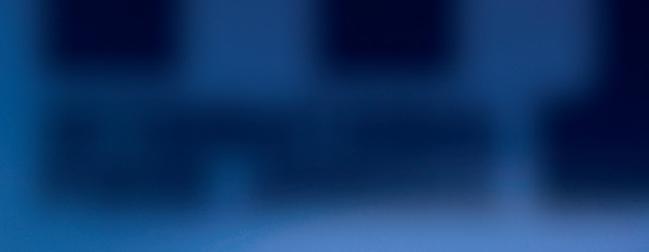
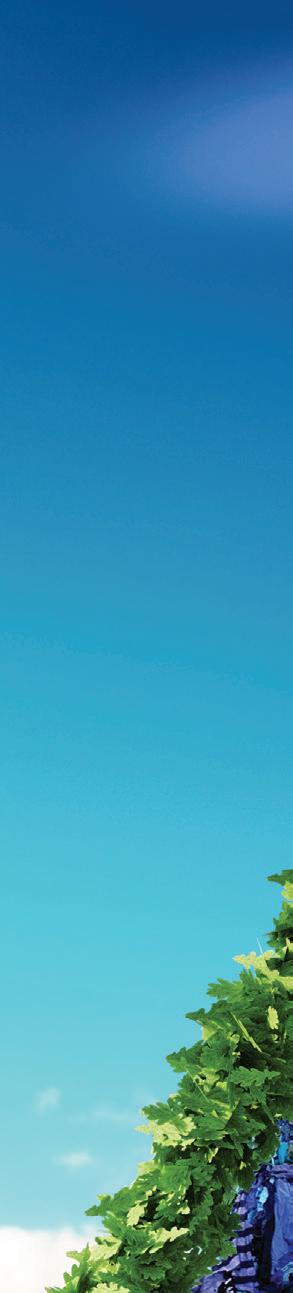

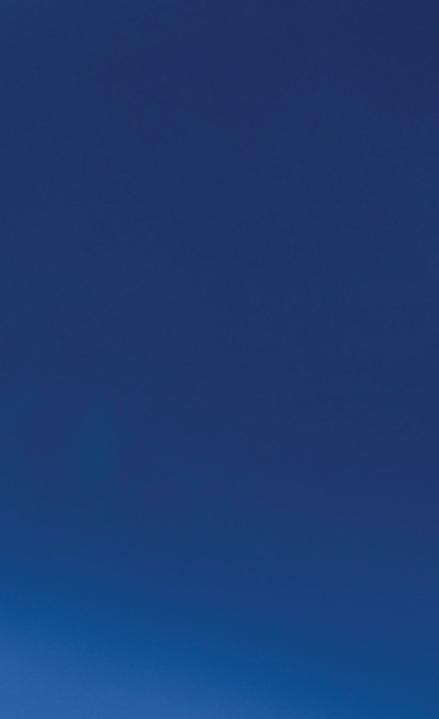
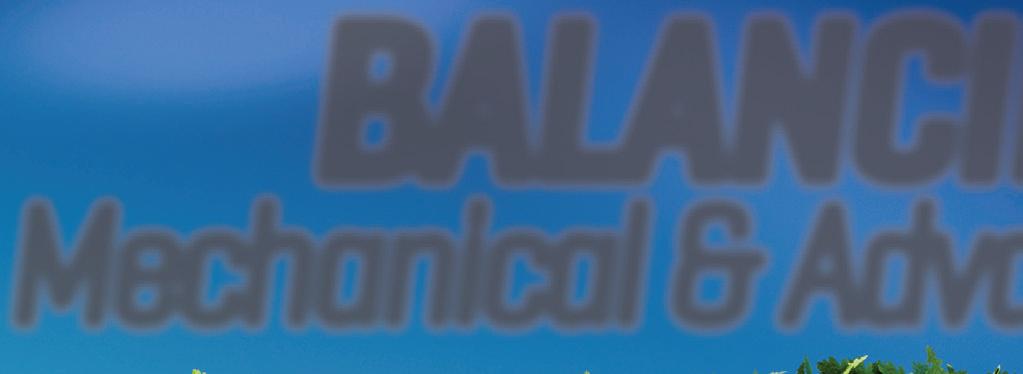
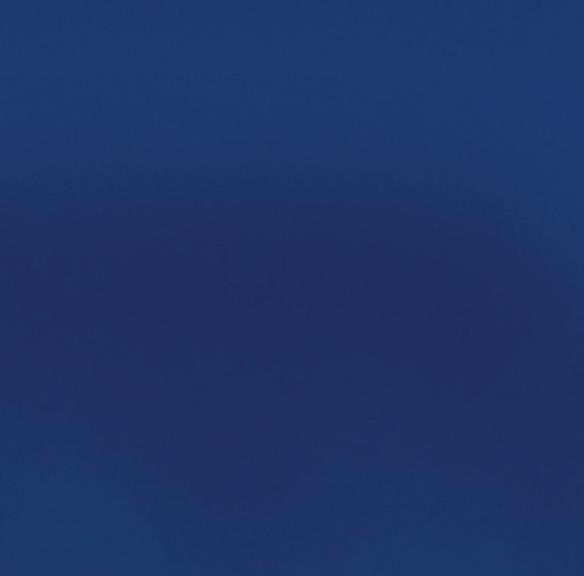
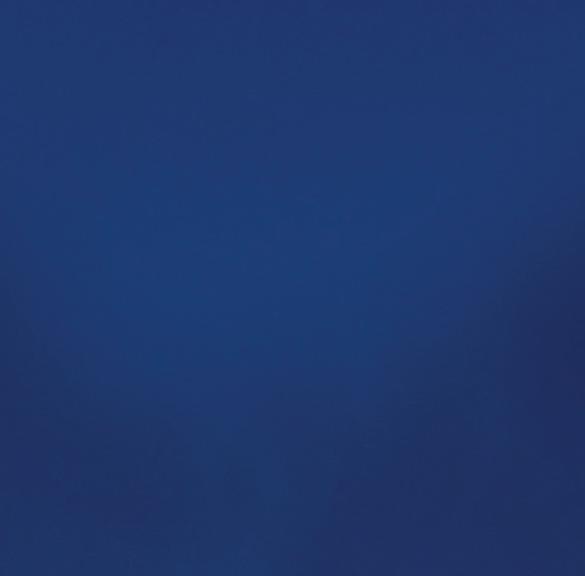
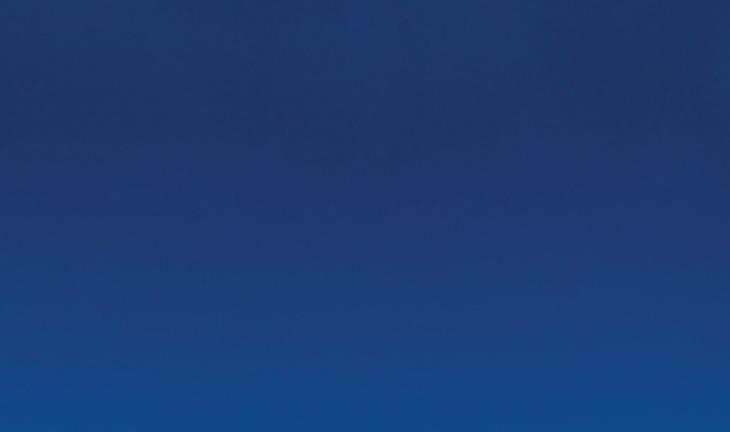
CIRCULARITY Gather
Executive Q&A: Asia Pacific Rayon By Arun Rao
CEO Q&A: Fiberpartner By Caryn Smith, Chief Content Officer & Publisher, IFJ
Showcasing solutions for success Solution Center: Andritz
Showfloor Showcase: Fi-Tech, Zund
The Recycling Loop By Adrian Wilson
Textile Waste Recycling: Weaving a Sustainable Future By Mireia Fernández
“It Is Not Easy, Being Green” How Advanced Recycling Helps By Svenja Fromm
Recycling Garments with Stretch Fibers By Geoff Fisher, European Editor, IFJ
Transformation of Textiles and Fashion Industry by Circular Design Process By Daniel Aeschbacher
FOCUS ON NONWOVENS
Leveraging Cellulose in Nonwovens Sustainability By Gregorich Katharina
Tailor-Made Calcium Carbonate By Barbara Bonavoglia, Martin Brunner, Christophe Roux
Show Reviews: Techtextil Frankfurt LOPEC
Cellulose Fibre Conference
Show Previews: Techtextil North America CAMX
Viewpoint Sizing Up Textile Waste Handling By Caryn Smith, Chief Content Officer & Publisher, IFJ
Tech Spotlight Coatings: Biopolymers from Bacteria Protect Technical Textiles
Tech Notes
Technology Briefs Movers & Shakers
Caryn Smith
Chief Content Officer & Publisher, INDA Media csmith@inda.org +1 239.225.6137
Geoff Fisher
European Editor, IFJ gfisher@textilemedia.com +44 1603.308158
Svenja Fromm
Marketing and Communications Director, Indorama LifeStyle Europe Indorama Ventures Fibers Germany svenja.fromm@de.indorama.net
Adrian Wilson
International Correspondent, IFJ adawilson@gmail.com +44 7897.913134
Daniel Aeschbacher Design Management, Industrial Design, Research, Societal Transition epeaswitzerland gmbh aeschbacher@epeaswitzerland.com
Mireia Fernández Leader, Chemical Recycling Department, AIMPLAS www.aimplas.es
Marie O’Mahony Feature Writer, IFJ Visiting Professor, RCA, London marie.consultant@gmail.com
If you have an interest to be more involved in International Fiber Journal as an IFJ Editorial Advisory Board Member, we are accepting applications for the opportunity to work with subject matter development, industry experts and professionals in an enhanced capacity. Please contact Caryn Smith at CSmith@inda.org to receive IFJ Guidelines and Expectations of Service. This is a unique opportunity to help inform, educate and inspire the global textile fiber industry.
International Fiber Journal is actively seeking contributed technical and thought leadership articles from qualified industry professionals and those allied to the fiber industry. If you would like to pitch an article for publication in IFJ, please contact Caryn Smith at CSmith@inda.org or +1 239.225.6137. Inquire to receive a listing of this year’s issue topics.
International Fiber Journal reaches a vast network of qualified professionals who employ fibers, nonwovens, technologies, equipment and more to optimize operations. With unique readers in markets that have strong crossover, IFJ offers print and digital opportunities to maximize marketing investments with a range of solutions based on true thought-leadership platforms. IFJ subscribers are in 67 countries. There are 17 countries with signficant readership (print and digital) that include USA, Hong Kong, Germany, China, India, Italy, United Kingdom, France, Spain, Belgium, Japan, Canada, Australia, Mexico, Switzerland, Brazil, and Taiwan. Email to receive a Media Kit to Advertising@inda.media today!
“Waste is a design flaw, the ability to create circularity of all materials eliminates waste and builds a sustainable world.” – Kate Krebs, Director, External Affairs at Closed Loop Partners
ore and more internal and external demands are being made on the textile industry supply chain, calling for change to end waste. It is a topic of every textile conference that I have attended over the last few years, as experts explore viable ideas and applications to tackle problems. In this issue, we asked a variety of experts to weigh in on the subject, and we believe we’ve gathered an interesting collection of perspectives. There is no end to opinion on this topic, but our thought leaders reveal headway being made.
In “The Recycling Loop” on page 22, Adrian Wilson looks at the implications of the introduction of a new Extended Producer Responsibility (EPR) scheme, where “no longer allowed to be either land filled or incinerated, over seven million tons of waste textiles will have to be separately collected each year within the EU and will be paid for by the brands.” Whether mechanical or chemical, recycling is the new buzz to bring second-use applications to as many waste materials as possible. Is it achieveable? It is too early to tell, but major companies are giving it a go.
Continuing a look at options on page 26, Mireia Fernández, Leader of the Chemical Recycling Department at AIMPLAS, reviews options in mechanical and chemical recycling. Recycling technologies are highly complex, and she believes their ultimate effectiveness will take a collaboration of research and development, more in-depth understanding of the specific challenges of industry, and defining actions by the European Union in order to promote feasible and sustainable business models.
On page 32, in “It Is Not Easy Being Green,” Svenja Fromm, of Indorama Ventures Fibers Germany, believes “advanced recycling has a very big advantage over mechanical recycling as it allows modi-
fications, like a flame retardant one, at polycondensation level. This type of modification is the most sturdy and sustainable one, i.e., modifications do not leach out or off gas into the environment.” She says, “Circularity and the advanced recycling of products wherever possible will allow for the reduction of virgin material usage, no matter which raw material base.”
On page 34, Geoff Fisher explains the complications of elastane in recycling. He says, “Many of the yarns and fabrics used to manufacture clothing are easily recyclable when in 100% form, such as pure cotton, polyester or polyamide, but the introduction of elastane in materials, even if only in small quantities, makes recycling using conventional methods difficult, if not impossible.”
On page 37, Daniel Aeschbacher, of the epeaswitzerland team, advocate for companies to define circular and sustainable pathways into the design process. ‘Transformation by Circular Design Process’ is a tool and methodology positioned at the very beginning of any business design strategy. Its purpose is to define and build a long-term future vision through education and knowledge building and creative networking by sharing pluralistic perspectives. This exercise will reveal systems dependencies and missing links in the product system.
Ultimately, even with the overwhelming number of options and varying opinions, the good news is that each industry development will bring us one step closer to achieve what most of us really desire, a better planet for our children, without needless textile waste.
Textiles for technical applications often derive their special function via the application of coatings. This way, textiles become, for example, wind and water proof or more resistant to abrasion. Usually, petroleumbased substances such as polyacrylates or polyurethanes are used. However, these consume exhaustible resources, and the materials can end up in the environment if handled improperly.
The German Institutes of Textile and Fiber Research Denkendorf (DITF) are researching materials from renewable sources that are recyclable and do not pollute the environment after use. Polymers that can be produced from bacteria are of particular interest.
These biopolymers have the advantage that they can be produced in anything from small laboratory reactors to large production plants. The most promising biopolymers include polysaccharides, polyamides from amino acids and polyesters such as polylactic acid or polyhydroxyalkanoates (PHAs), all of which are derived from renewable raw materials. PHAs is an umbrella term for a group of biotechnologically produced polyesters. The main difference between these polyesters is the number of carbon atoms in the repeat unit. To date, they have mainly been investigated for medical applications. As PHAs products are increasingly available on the market, coatings made from PHAs may also be increasingly used in technical applications in the future.
The bacteria from which the PHAs are obtained grow with the help of carbohydrates, fats and an increased CO2 concentration and light with suitable wavelength.
The properties of PHA can be adapted by varying the structure of the repeat unit. This makes polyhydroxyalkanoates a particularly interesting class of compounds for technical textile coatings, which has hardly been investigated to date. Due to their water-repellent properties, which stem from their molecular structure, and their stable structure, polyhydroxyalkanoates have great potential for the production of water-repellent, mechanically resilient textiles, such as those in demand in the automotive sector and for outdoor clothing.
DITF has already carried out successful research work in this area. Coatings on cotton yarns and fabrics made of cotton, polyamide and polyester showed smooth and quite good adhesion. The PHA types for the coating were both procured on the open market and produced by the research partner Fraunhofer IGB. It was shown that molten polymer can be applied to cotton yarns by extrusion through a coating nozzle.
The molten polymer was successfully coated onto fabric using a doctor blade. The length of the molecular side chain of the PHA plays an important role in the properties of the coated textile. Although PHAs with medium-length side chains are better suited to achieving low stiffness and a good textile handle, their wash resistance is low. PHAs with short side chains are suitable for
achieving high wash and abrasion resistance, but the textile handle is somewhat stiffer.
The team is currently investigating how the properties of PHAs can be changed in order to achieve the desired resistance and textile properties in equal measure. There are also plans to formulate aqueous formulations for yarn and textile finishing. This will allow much thinner coatings to be applied to textiles than is possible with molten PHAs.
Other DITF research teams are investigating whether PHAs are also suitable for the production of fibers and nonwovens.
www.ditf.de
For more information, contact PD Dr.-Ing. Thomas Stegmaier, Deputy Member of Executive Board, Deputy Head of Competence Center Textile Chemistry, Environment & Energy. Email: thomas.stegmaier@ditf.de or Tel: +49 (0)711 93 40-219.
For details on how to submit your company’s technology for consideration as a “Technology Spotlight” in IFJ, contact Ken Norberg at ken@ifj.com or +1 202.682.2022.
Eastman, a specialty materials company and producer of Naia™ cellulosic fibers, has formed a strategic collaboration with Debrand, a prominent, nextlife logistics company specializing in finding sustainable solutions to apparel waste for some of the world’s top apparel and footwear brands.
Teaming up with Debrand for collection of the waste, Eastman is using its cutting-edge molecular recycling technology to recycle 5,000 pounds of preand post-consumer apparel waste. The process breaks down apparel waste to its molecular building blocks and uses the certified recycled material to create Naia™ Renew fibers – circular fibers made from 60% sustainably sourced wood pulp and 40% recycled waste material via Global Recycled Standard-certified mass balance.
Eastman and Debrand are showcasing the transformative potential of molecular recycling technology to address the textile waste crisis. By providing more circular solutions for apparel waste, this partnership sets a new standard for sustainable practices in the fashion industry. Prior to its collaboration with Eastman, Debrand secured a strategic investment from Waste Management, the leading provider of comprehensive waste management in North America, to deliver circular solutions across the U.S. and Canada. www.eastman.com
U.S.-based textile treatment specialist Green Theme Technologies (GTT) is broadening its water and PFAS-free finishing platform into the South Korean market through a partnership with functional textile manufacturer, Hwasung International. Hwasung International will become the inaugural Korean mill to offer GTT’s advanced Empel brand of dry-finishing formulations.
These formulations have undergone rigorous testing and certification to ensure they are entirely free of PFOA and PFOS chemicals, commonly
Cone Denim® launched COLOURizd sustainable alternative technology for denim at the Kingpins Show Amsterdam, in April. This technology, developed by COLOURizd LLC, allows for a wide range of colors and textures while minimizing processing steps, resulting in a more sustainable and efficient approach to textile coloration.
“Cone Denim is excited to launch this unique innovative color technology,” said Cone Denim Director of Innovation Caitlyn Holt. “Not only is this a first for Cone, but it is new to the industry. This technology will allow us to have a quantifiable impact with unprecedented natural resource savings per yard produced.”
COLOURizd’s revolutionary QuantumCOLOURTM technology transforms textile coloration by directly infusing pigments and a binder into the yarn fibers. This advanced process enhances the yarn with vibrant colors, can create visual texture, and also eliminates the need for traditional dye baths and lengthy wet processing. By doing so, it significantly reduces environmental impact, paving the way for a new era in sustainable fashion. It is bleach-safe and provides excellent shade matching and color consistency. www.conedenim.com
known as PFASs, by Bureau Veritas.
The collaboration between Green Theme Technologies and Hwasung International is a milestone in promoting environmentally friendly textile treatments in South Korea. By introducing PFAS-free finishing solutions, both companies are contributing to the industry’s shift towards sustainable and safer manufacturing practices.
www.greenthemetech.com
Asahi Kasei, a diversified Japanese multinational company, has developed a new technology for recycling carbon fiber plastic compounds together with the National Institute of Technology, Kitakyushu College and Tokyo University of Science.
Carbon fiber reinforced plastics (CFRP) are highly attractive for various industries in demanding application fields due to their unique balance of rigidity, mechanical strength and light weight – also compared with conventional glass fiber reinforced plastics. However, CFRPs are expensive and challenging from a recycling perspective, as it is difficult to extract the carbon fibers from the resin after usage.
Together with its project partners at the National Institute of Technology at Kitakyushu College and the Tokyo University of Science, Asahi Kasei developed a recycling method that allows carbon fibers to be extracted from CFRP or carbon fiber reinforced thermoplastics (CFRTP) used in automobiles. This results in high-quality, inexpensive continuous carbon fiber that can be recycled perpetually, contributing to circular economy. Unlike carbon fiber that is chopped up during the recycling process, Asahi Kasei’s method allows carbon fiber to be extracted from a plastic compound seamlessly, resulting in continuous strands of carbon fiber that can be reapplied in exactly the same manner while retaining properties identical to the original substance.
The conventional technologies for recycling carbon fibers by chopping and re-applying them results in a product with lower quality and less durability, insufficient for high-performance applications. To address this issue, Asahi Kasei has developed an “electrolyzed sulfuric acid solution method” that allows the carbon fiber to retain its original strength and continuous nature while fully decomposing the resin the carbon fiber is embedded in. This allows for its continued use in high-performance applications and presents an inexpensive, circular solution to the end-of-life dilemma of carbon fiber plastic compounds. www.asahi-kasei.com
CARBIOS, a pioneer in the development and industrialization of biological technologies to reinvent the life cycle of plastic and textiles, and Hündgen Entsorgungs GmbH & Co. KG, a waste management expert in logistics, sorting services and the recycling of recyclable materials from waste mixtures, announced a signing of a non-binding Memorandum of Understanding relating to the sourcing, preparation and recycling of 15kt/year of post-consumer PET waste using CARBIOS’ biorecycling technology at its first commercial plant in Longlaville, France, starting late 2026.
The partnership will leverage Hündgen’s expertise and network in the sourcing and preparation of light packaging waste collected from German households. This PET waste will be prepared into flakes ready
Fuze
Fuze Technology recently announced the Environmental Protection Agency’s (EPA) registration and approval for its products used in textiles and surfaces for antimicrobial effects, as well as lifetime durability of its application.
“This is huge news for Fuze and for the textiles industry,” said Andrew Peterson, Fuze CTO. “The EPA has reviewed our product and verified that it is an antimicrobial that is retained by the fabric for more than 100 washes. That is a first in the industry.”
The EPA’s approvals uniquely position Fuze in the market, making Fuze the only antimicrobial that can last the life of the textile it is applied to. Fuze uses its patented process to create its products that are applied to fabrics using various application methods.
In addition to its antimicrobial features, Fuze’s technology leads with its chemical-free, anti-odor capabilities which also promote moisture wicking and significantly faster drying times, while not disrupting the fabrics look or feel.
www.fuze47.com
for biorecycling using CARBIOS’ enzymatic depolymerization technology, which produces food-grade PTA and MEG, further re-polymerized into PET.
The supply partnership with Hündgen contributes to securing the majority of CARBIOS’ feedstock needs for its first commercial plant in Longlaville, France. This plant will have a 50kt/year capacity when fully operational and is currently under construction. This latest sourcing announcement comes in addition to previously announced agreements, such as with Landbell Group for food trays from Germany, and the winning CITEO tender for trays in France. The location of the Longlaville plant is strategically close to nearby waste supplies in Belgium, Germany and Luxembourg. www.carbios.com
Asia Pacific Rayon (APR) is a leading integrated viscose rayon producer in Asia, with manufacturing operations in Riau province, in Sumatra, Indonesia. In November 2021, the company launched its APR2030 sustainability agenda, covering four main pillars, aiming for 20% recycled textile content, net zero land emissions, and halving product carbon intensity per ton of VSF production by 2030.
APR’s operations not only meet but surpass EU and industry standards like EU BAT, Polymer BREF, and RaoZero Discharge of Hazardous Chemicals ManMade Cellulosic Fibres guidelines. It also undergoes yearly evaluations by groups like the Sustainable Apparel Coalition and other ESG reviews.
The company has adopted clean manufacturing processes as a key pillar of its APR2030 strategy. Efforts include capturing and re-using chemicals and chemical by-products, reducing and eventually
eliminating the use of hazardous substances in production processes, treating and recycling wastewater, practicing proper waste management, and implementing air pollution control methods.
International Fiber Journal: Since we are doing an interview for the first time, please provide a history about your company, such as when it was started and about your facilities.
Tapan Kumar Sannigrahi: Asia Pacific Rayon (APR) was established in 2018 as a producer of viscose staple fiber (VSF) and is part of the RGE group of companies. Our manufacturing facility is located in Riau Province in Sumatra, Indonesia and our operations are vertically integrated from plantations to fiber, which is a unique differentiator for us. Our manufacturing plant, our VSF R&D department and our textile R&D facilities for spinning, knitting, weaving, dyeing and printing units are located in the same complex.
“We are a relatively young company and we started out with sustainability at our core. In practice, this means we’re embedding sustainability in our policies, procedures, and in our approaches to everything we do.”
Sourcing from certified suppliers is critical to our activities and we are guided by APR’s Pulp Sourcing Policy commitments. We only source materials from suppliers with the necessary certification from the PEFC (Programme for the Endorsement of Forest Certification).
IFJ: Please share details about manufacturing infrastructure and annual capacity?
TKS: APR has two production lines and an annual cellulose fiber production capacity of 300,000 tons. We supply these fibers in 1.2 and 1.5 denier and in cut lengths of 32 mm, 38 mm, 44 mm and 51 mm. The first line was started in 2018 and had a manufacturing capacity of 200,000 tons per annum and then it was ramped up to 300,000 per year. With more than 50 percent market share, we are now the leading VSF player in Indonesia.
IFJ: What are the core company products and solutions you offer for the market?
TKS: Open End yarn manufacturers prefer 32 mm cut length but some customers prefer 38 mm as well, while Ring and Vortex spinning mills opt for 38 mm.
When cellulose fiber is blended with polyester fiber, the mills prefer 44 mm or 51 mm cut length, because it offers more productivity.
Our fiber is used in both knits and wovens. Knits are mainly used for womenswear and wovens are used in trousers, shirts, blouses and skirts. About 60 percent of cellulose fiber goes in to manufacturing 100 percent cellulose fiber fabrics or garments, while 40 percent is used in blending them with cotton, polyester, nylon or linen fibers.
IFJ: What is the role of R&D in developing products offered by your company?
TKS: Our R&D capabilities extend across the whole textile value chain beginning from plantations to fabrics. The R&D department has an automated pilot cellulose fiber production plant which replicates the process of the main manufacturing plant. The R&D department also develops fibers based on customer demand. One example could be high tenacity fibers which help our customers attain higher productivity. The department also develops new strains of fibers for testing ahead of commercial production.
We also have a small spinning and fabric unit where the R&D department tests the various fibers that they develop by converting fibers first into yarns and then fabrics. These fabrics are further dyed or printed in the R&D department.
The department also develops various yarn types, like those which reduce yarn imperfections. The path adopted by our R&D department in developing a new yarn or fabric helps our customers develop their yarns and fabrics similarly. The R&D team also helps our fiber customers in improving quality and productivity and reducing costs, in line with our QPC – Quality, Productivity & Cost commitments.
IFJ: Have you launched any new products recently or are planning to launch in the near future?
TKS: We are now coming out with Lyocell fibers which are third generation manmade fibers which have a manufacturing process different from other cellulose fibers. Lyocell is a stronger fiber and is closer to cotton, in properties. We also have plans to introduce recycled cellulose fibers as well.
IFJ: What were the main challenges faced by the cellulose fiber industry since the start of the pandemic and what more challenges do you foresee in the next few years?
TKS: COVID-19 created havoc across the whole value chain. There were significant supply chain disruptions, which
affected our engagement with customers. However, our plant ran continuously during the two years of the pandemic and we were very pro-active during the period in reaching out to customers to address their needs. So there was relatively little impact on our operations during the two years.
In terms of looking after our people, we created isolation wards for our infected employees within our complex and they received the best treatment. Testing was also done frequently and if anyone was infected, the people surrounding that person were tested. We had stan dard operating procedures in place to manage the wellbeing of our employees and stake holders, overseen by a COV ID-19 monitoring committee.
IFJ: Where do you see the cellulose fiber market share heading in the next few years in comparison with cotton and polyester fibers?
TKS: The market share of cellulose fibers is around 6.5-7.0 percent of over all fiber consumption which is around 110 million tons. The growth of overall fiber consumption in the last few years
is around 3 percent, but that of cellulose fibers is around 6 percent. One reason for this higher rate of growth of cellulose fibers is because consumers now want comfortable, sustainable products and we are seeing this growth in our key global markets.
IFJ: What efforts is APR putting to increase per capita cellulose fiber consumption?
TKS: We have a very strong domestic cellulosic fiber textile and garment market in Indonesia and the Indonesian government is promoting “Made in Indonesia” products. We also have a Jakarta Fashion Hub, where the whole value chain is represented along with fashion designers and traders. We give a lot of support to the fashion hub in terms of sourcing, marketing, designing and new product development. For export markets, we take part in various international exhibitions as well as conduct customer meets to provide information and education on cellulose fibers.
In Indonesia, we have collaborated with a fashion retail chain called Matahari, where we have trained their sales persons to talk about the benefits of buying cellulose fiber garments to consumers. We also release fashion trend collections every year to help our customers to visualize the upcoming trends of the
On a side note, our group manages a hotel in the same complex where
our plant is located. All the textiles used in the hotel, like towels, bed sheets, table covers and napkins, are manufactured from our fibers.
IFJ: APR has invested in circularity of its operations. Please share details of this project?
TKS: We have adopted a collaborative approach for circular textiles. We have partnered with spinning mills, weaving mills and garment factories to ensure that the pre-consumer waste is collected. We also have partners who segregate and sort the cotton or manmade and cellulose fibers pre-consumer waste. Once the cellulose fibers are sorted, they are recycled either through a manual or chemical process. In this too, we have partnered with Matahari, which collects used clothing, which is then sent to our sorters.
IFJ: How important is sustainability for your company? What sustainable products or solutions do you offer to your customers?
TKS: We are a relatively young company and we started out with sustainability at our core. In practice, this means we’re embedding sustainability in our policies, procedures, and in our approaches to everything we do.
In November 2021, we launched our APR2030 sustainability agenda, covering four main pillars and the corresponding targets for the next decade. Key targets include achieving 20 percent recycled textile content in our VSF production; net zero emissions from land use and halving our product carbon intensity per ton of VSF production.
We want to be seen as a world-class VSF facility. We continue to meet and exceed many requirements of the European Union Best Available Techniques (EU
At Fiberpartner we provide fiber in many forms and shapes. We support a broad variety of industries, and we are happy to help whether you are looking for traditional polyester, the newest plant-based technology, or something in between.
Fiberpartner is a Danish advisor and supplier of textiles including PrimaLoft®Bio™. We understand the urgent need to transform polyester production and consumption for a more sustainable future.
We recently added PolyPlant® – a new innovative fiber that looks, feels, and acts like polyester, while not sharing its impact on the environment.
Feel free to contact us or our dedicated partners.
BAT) Polymer BREF and ZDHC MMCF guidelines, above and beyond local regulations. We have also submitted to annual assessments by the Sustainable Apparel Coalition and other ESG reviews.
We also look for independent, thirdparty certifications to confirm our sustainable production and approaches satisfy international requirements. For example, we look to improve the quality of our VSF and in turn the yarns, by adhering to standards that include OEKO-TEX®, FKT, and OK biodegradability labels.
Adopting clean manufacturing processes is a key pillar of our APR2030 strategy. Our efforts include capturing and re-using chemicals and chemical by-products, reducing and eventually eliminating the use of hazardous substances in our production processes, treating and recycling wastewater, practicing proper waste management, and implementing air pollution control methods.
Tel. +45 79 44 77 22
cation is the sarong, a traditional men's lower body dress which is made from cellulose fibers.
IFJ: What are the key trends in consumer demand and the growth trajectory of the Indonesian as well as global apparels market in context of cellulose fiber usage?
The growth of overall fiber consumption in the last few years is around 3 percent, but that of cellulose fibers is around 6 percent. One reason for this higher rate of growth of cellulose fibers is because consumers now want comfortable, sustainable products and we are seeing this growth in our key global markets.
Our efforts and processes comply with local regulations. They also align with international and industry standards, guidelines, and best practices, including World Health Organization guidelines, the Zero Discharge of Hazardous Chemicals Man-made Cellulosic Fibres (MMCF) guidelines. In 2022, we contracted an independent third party to assure our chemical recovery data ahead of new requirements coming into effect.
IFJ: Please share details on APR’s CSR activities?
TKS: In alliance with our main supplier, our sister company APRIL, we are also looking to eradicate extreme poverty within a 50-km radius of our operations. We are also looking to promote inclusive prosperity and gender equality, through livelihood initiatives aimed at women
and young people, and better access to maternal health, integrated childhood development and nutrition programmes.
IFJ: What are the benefits of wearing a cellulose fiber garment vis-à-vis clothing made from either cotton or polyester fiber?
TKS: When buying clothing, everyone thinks of look, feel and comfort. The biggest advantage of cellulosic fiber clothing is that it drapes and looks well. The feel is also good and, when considering comfort, it has very good moisture management properties. It is also bio-degradable. All these attributes make cellulosic fiber a very reasonable choice for consumers. Cellulose fiber consumption in Indonesia is very high at around 20-25 percent of all fibers because Indonesia does not produce cotton. For example, one appli-
TKS: Consumers have now more disposable incomes and their lifestyles too have changed. Consumers now aspire for better quality apparels and also prefer more comfortable clothing. This is driving growth of cellulose fiber apparels. The growth projections of our group are matching the actual growth of demand for cellulose fibers worldwide. As of now, we expect cellulose fibers to grow at 6-7 percent annually.
IFJ: Please share details of your presence in the Indonesian domestic and export markets?
TKS: About 45 percent of our fiber production is sold in the domestic Indonesian market and the rest is earmarked for exports. We are now exporting to more than 16 countries with our main export markets being Turkey, Pakistan, Bangladesh, Vietnam etc.
Arun Rao started his career in the textile industry and has worked across the segments of spinning and weaving production. He forayed into the sales function, beginning with selling branded innerwear and graduated to selling clothing of wellknown brands. He then joined Fibre2fashion, a B2B textile website, as News Editor for seven years. Recently, he launched Taurus Communications, a PR & advertising agency focused on the textile industry value chain. With a love for journalism, he freelances for renowned textile magazines, along with managing the agency. He is the India foreign correspondent to the IFJ
11 – 13 September Dornbirn, Austria
16 – 30 September Online on demand
The 63rd Dornbirn Global Fiber Congress (GFC) and the 4th Innovation Days will take place from September 11 to 13 at the Kulturhaus Dornbirn.
In addition to groundbreaking advances in the topics of ber innovations, circular economy and sustainability, the focus in 2024 will be on ad-vanced technologies in the energy sector.
Event highlights:
125 expert presentations: Get insight from leading experts from industry, academia and research institutes.
4th Innovation Days: Meet 25 innovators presenting their latest products and technologies.
Fiber Innovation Platform: Discover new concepts and technologies that will revolutionize the industry.
Networking Platform: Network with colleagues and industry leaders during the 3-day congress.
Energy Solutions Session: Innovative solutions in the eld of sustainable energy conversion.
Young Scientist Award: Lenzing Young Scientist Award for Bachelor and Master students.
Important dates of the Dornbirn GFC
Early Bird Ticket available until June 15, 2024
Combi ticket available for:
Dornbirn GFC, live in person in Dornbirn, from September 11 - 13, 2024
Dornbirn GFC online on demand from September 16 - 30, 2024 (Presentations as videos and the presentations for download as PDF les.)
What is the connection between bers and energy?
Bernhard Schmenk, Head of the Corporate Development Department at RWTH Aachen University, explains a planned block of lectures on the topic:
“Experts from industry and research will focus on pioneering approaches ranging from more energyef cient melt spinning processes to innovative ber-based products for energy harvesting and novel shading systems for buildings.”
Visit our website at www.dornbirn-gfc.com for more details and to register. Stay connected via our channels on LinkedIn and YouTube for updates and previews of what’s coming up.
iber and textiles companies are investing significantly in sustainable efforts to extend the life of goods, make them more degradable over time, and lessen the role of toxic chemicals in their manufacturing. One textile, polyester, is a significant area of focus because of its problematic environmental qualities. It is however not a fiber that is going away any time soon. Instead, it is being reimagined with solutions to maintain its versatile use, but amplify its bio-factor.
Making a splash at the Index® show in April 2023 as an exhibitor, Fiberpartner caught our attention with their clever branding, “Polyester is No Longer Immortal.” The company is all about “fixing” polyester. Fiberpartner is an advisor and supplier of textile fibers with a clear mission to lead the transition to non-petroleum-based fibers. Acting as a trusted advisor, they connect fiber producers with global clients in the non-woven and filling sectors.
Their mission is to minimize the environmental impact of fiber products through continuous testing and investment in innovative, responsible solutions. In 2020, they became the global licensee of PrimaLoft® Bio™, a groundbreaking technology that makes synthetic insulation and fabric fibers biodegradable.
Their mission is to minimize the environmental impact of fiber products through continuous testing and investment in innovative, responsible solutions. In 2020, they became the global licensee
of PrimaLoft® Bio™, a groundbreaking technology that makes synthetic insulation and fabric fibers biodegradable.
The company won the 2023 Index® Innovation Award for another product, BicoBio® – a bico stable fiber comprised of biobased PE mix with recycled PET, combined with PrimaLoft® Bio™ inside, and designed to biodegrade in various environments, including ocean water, wastewater, landfills, and soil.
The 160-year-old Danish company with the energy of a start-up is on a mission to fix polyester; they supply polyester, polypropylene, and bi-component stable
fibers, divided in three categories: virgin, recycle and bio to meet the technical and logistical needs of its growing clientele. The segments they serve include hygiene, automotive, home & apparel, fiberfill, nonwovens and spinning.
International Fiber Journal caught up with the CEO Thomas Wittrup at the recent Techtextil in Frankfurt, Germany, to discuss their strong momentum in what almost seems to be a personal mission effort to change the fiber industry.
International Fiber Journal: Your company has a long history, yet you have reinvented your mission. Tell us about how you ended up here today.
Thomas Wittrup: Fiberpartner is a family business based in Denmark that goes back about 160 years, established in 1860 by Theodor Wittrup; I am generation number five. We used to produce woolen products like blankets, yarn, and carpets. That segment of the company was sold in 1976 to a major Danish carpet manufacturer by my father, Ole Wittrup. Then, my father started importing similar yarns, machinery, and technology.
I joined the company in 1999, bringing my background in the nonwovens industry to it. Expanding into synthetics, I founded Fiberpartner when this was really emerging. In 2001, China became a part of the World Trade Organization. So, I went to China, locating different manufacturing partners, and throughout the years, we've since opened locations
We all need partnerships. We need to take a common responsibility and at the same time, keep our businesses running healthy. We needed each other.
in different places, like Mexico and South Africa. We have now had an office in Sofia, Bulgaria, for five years handling the eastern European corridor.
Our headquarters are located in Denmark, and we currently have 17 employees, making our organization relatively small.
IFJ: Explain the product development and growth of the company in recent years.
Wittrup: In terms of volume, we are growing, serving small and large customers globally. Recently, we made an agreement with Stein Fibers to handle distribution of our responsible products in the U.S., such PrimaLoft® Bio™ – an additive technology specifically developed to return to materials found in nature to reduce the environmental impact of microfibers and garments throughout their life. The additive attracts microbes, which then eat and digest the fiber in about three years rather than 1,000. With this, you have the beauty and properties of polyester, yet they are biodegradable. It can be done on virgin or recycled fibers.
Also, we are about more than providing fiber solutions to increase sustainability. We also help the customer to communicate and declare the environmental benefits. Especially in Europe, it's quite strict on what you can and cannot say. We have teamed up with a leading commercial consultancy in Copenhagen to help us communicate appropriately with our customers, but most importantly, our customers’ customer. So, what can they say? What can they claim? The wording is important in all that.
So that's a differentiating part of our company; not only the technology, but
Fiberpartner bases their expertise on 25 years in the polyester business and over 150 years in textiles. Fiberpartner
also the communication – how can we help our customers to avoid greenwashing accusations.
Our latest addition is a fully biobased fiber named PolyPlant®. The idea is a Standard PLA, with a percentage of an additive technology made from sugarcane. It enhances the standard properties of PLA in terms of soft touch, elongation, tenacity, and biodegradation. We take some of the cons of standard PLA, and adding our technology, we're changing them so it's easy for the customers to process. The end product is very close to the polyester. It is certified biobased and certified biodegradable, so that's fairly new for Fiberpartner. We've been working on this for the last eight months.
At this exhibition, we are launching a PLA microfiber core sheath, which is very softly cannot feel the difference. It is a fiber for spun lace, and a short cut for wet laid. We expect to have a composability certificate soon.
IFJ: What kind of customers are you attracting right now?
Wittrup: Right now, we see massive interest in any sustainable solution. Our approach is a one-stop shopping, meaning whatever is the aspiration of the client in terms of, responsible fiber production is, we have a solution. Meaning, whether they are looking for a recycled polyester fiber, a recycled biodegradable fiber, a virgin biodegradable fiber or a bio-based biodegradable fiber, we have those options.
The idea is to create solutions at different levels of a sustainable approach. Of course, there is a premium to biobased, but we work with them on the kind of
products they are you going to make, and the idea is to give the customer all the options. Part of our 10-year strategy is also to develop a carbon neutral or even carbon negative fiber over the next couple of years. We are already in the process and hope to have something to share in the next 20 months.
IFJ: When you started Fiberparter, basically reinventing it from your original family business, did you intend to go in this direction?
Wittrup: I think this has increased in importance and impact over the last five years or so. Today, more than 70% of our total volume is either 100% or mixed recycled content. And we are trying to increase that volume as much as we can. We see that being a Danish company helps us in terms of credibility as Denmark is known as a front-runner on the sustainability agenda.
Our Danish roots have shaped us profoundly. In Denmark, we hold the nature in high regard, and our commitment to innovation is ingrained in our DNA. This definitely sets us apart.
IFJ: Will we see the pricing of biomaterials come down soon or over time?
Wittrup: Of course, right now there is a premium, and that is an entry barrier because who is going to pay? In Europe, there are upcoming regulations that will push the transformation forward but we also need partners who are eager and willing to jump on this and see the long-term perspectives, so we can increase the volume and then reduce the cost.
Luckily, we have lots of partners, but we're always looking for others to make that kind of difference. Of course, we also need to make a business.
Our core business of recycled polyester fiber is helping us to develop new responsible solutions. I think in all business –not only for fibers – the coming transition is a difficult balance of keeping the core business healthy and operating, and also generating resources for development. Consumers may still be hesitating – asking themselves if they want to pay more for biodegradable products.
However, in Europe, with Scope 3, large companies with more than 500 employees must report on carbon footprint improvements, and that is generating a lot of demand. So, the regulations will be driving the development. I'm not particularly fond of regulations, but I must admit in this case, it helps. And maybe if we are going to see the necessary change, this is the way forward.
IFJ: How did the arrangement with Stein Fibers come about? And why them?
Wittrup: We met at Index® by coincidence and started talking. We are a little ahead on the sustainable agenda. They are very strong in their U.S. distribution. We have found that in the U.S., you really need a strong distribution channel. We have seen quite a lot of interest in the solutions, but
were not able to supply according to what is required from the U.S. Ultimately, Stein was looking for solutions like ours, and we were looking for someone like Stein. They are very nice and skilled people with good distribution, and a long-term strategy. So we decided, to work exclusively together on this for North America and Mexico.
Especially in Europe, it's quite strict on what you can and cannot say. So, what can they say? What can they claim? The wording is important in all that.
IFJ: What does the future look like to you and how long do you think it will take to achieve a more sustainable industry?
Wittrup: What we see is a lot of promising technologies popping up in lots of places. People are trying to find sustainable solutions. In my opinion, there will not be one solution. There will be many and it will be much more fragmented than it is today. Also, if we only address polyester, the current capacity has been built up over the last 50 years. It will take a while before enough capacity is simply available, in terms of processing. So again, if we talk polyester fiber, you need enough raw material of something that can be divided into many.
I think the nonwovens industry will be a challenged by of many types of sustainable solutions – different technologies for different applications. Investments should be considered long term, and, with that,
PolyPlant® is a biobased fiber made from sugarcanes. It is biodegradable* in landfill and ocean water, it can be composted, and it is fully recyclable. This results in a significant improvement in circularity compared to traditional oil based polyester.
it will be much more complex. Regulatory compliance also requires much more transparency for the whole supply chain. How do we keep those investments coming and, simultaneously, reduce the cost so the consumers will adapt?
IFJ: What do you what do you do about high-production textile countries that focus on low cost goods? How can they change and still maintain their marketplace?
Wittrup: They're producing what their customers want. Yet, even Chinese and other manufacturers are now seeking more responsible solutions because customers are asking for them. I think it will be a mix of a push and a pull between manufacturers, retailers, and consumers. Export/import laws may even come into play or consumers in America will determine what is bought and sold. It’s a long road to get there.
We’re starting in Europe. To some degree it is about being conscious to the quality. Maybe there is a shift to higher quality that lasts longer. I think the younger generations, whether it's Europe or U.S., are seeing this increasingly as a more serious issue.
We have quite a few exciting things in the pipeline, and we are trying to shift ourselves to becoming an integrator of different technologies – innovative, responsible ideas – bringing those options to our customers and partnership discussions.
Nobody, not even the largest companies, can do this alone. We all need partnerships. We need to take a common responsibility and at the same time, keep our businesses running healthy. No company is an island. We needed each other.
NDRITZ has always been a pioneer in providing industrially and economically viable solutions that bring the circular economy to the world of textile fibers. Thus, ANDRITZ is not only a reliable supplier but also a knowledge provider. The company offers everything from automated textile sorting and textile fiber preparation to mechanical and chemical recycling and combined processes.
The latest development in the textile recycling area is the automated textile sorting process. This process is the result of an ambitious partnership between textile recycling company Nouvelles Fibres Textiles, waste sorting specialist Pellenc ST, and international technology group ANDRITZ, a specialist in textile recycling machinery and processes. Capable of automatically sorting garments by composition and color, the line meets the needs of both post-consumer and post-industrial waste markets. The line also removes hard parts such as buttons and zippers to prepare the material
for further processing in an ANDRITZ tearing machine. The automated textile sorting line can process textile waste to produce recycled fibers for the spinning, nonwovens, and composites industries.
ANDRITZ has huge experience in the recycling of textiles, with both mechanical and chemical solutions. The mechanical tearing process has been developed by ANDRITZ Laroche for over a century. Thanks to this expertise and more than 2,000 reference projects worldwide, customers can process almost all types of pre-/post-consumer textile waste. Today,
ANDRITZ offers a complete range of tearing equipment, from 50 to 3,000 kg/h, suitable for a large variety of textile materials, natural, animal, synthetic, artificial, and mineral fibers. This technology aims to preserve the original character of the fibers, e.g. cotton, by maximizing fiber length and strength.
In the area of chemical textile recycling, ANDRITZ is a key player in this evolving industry. Not only because of the expertise in chemical process technology, but also because the recycling processes can utilize the same equipment that ANDRITZ successfully uses in pulp and paper production. Chemical and mechanical processes
are fully complementary in the drive to achieve the desired result, but the addition of chemical treatment is a game changer for textile-to-textile recycling.
ANDRITZ has huge experience in the recycling of textiles, with both mechanical and chemical solutions. Now with its expertise in sorting, complete lines from collected textiles to full recycling is possible, representing a revolution in circularity for the industry.
www.andritz.com/textile-recycling
In today’s rapidly evolving world, innovation is the heartbeat of every industry.
To stay competitive, producers of fibers, nonwovens and technical textiles need leading edge solutions. At the forefront of this transformative landscape in N. America is Fi-Tech, Inc, a successful manufacturer’s representative, and distribution company headquartered in Richmond, VA. Fi-Tech is dedicated to
Our principals include:
providing these industries access to cutting-edge solutions from our well-known base of suppliers. For over 50 years, FiTech, Inc. has connected the fiber, nonwoven and technical textile industries to the leading suppliers of machinery and technical components.
Fi-Tech is pleased to exhibit at Techtextil North America in Raleigh, NC August 20-22. Our Team will be on hand at the Fi-Tech stand #1200 to meet you
and to update you on all the latest innovations from our principals.
From our bases in Richmond, VA and San Luis Potosi, Mexico, the Fi-Tech Team is dedicated to providing excellent service and to your success. Contact us to see why we are Your Global Connection.
fi-tech.com
und America with headquarters in Oak Creek, Wisconsin, is the sister company of Zünd Systemtechnik AG, the family-owned Swiss manufacturer of multifunctional digital cutting systems. Zünd has been developing and manufacturing digital cutters for four decades – in fact, 2024 marks the 40th anniversary of Zünd Switzerland, while Zund America is proud to be celebrating its 20th!
Zünd has gained a worldwide reputation for being the leading manufacturer of high-quality cutting solutions uniquely geared towards meeting the needs of each customer and industry. While Zünd systems are widely used in textile/technical textile, and composites, they can also be found in countless leather, graphics, packaging, and many other industrial applications. Built for 24/7 operation and powered by application-specific control software, Zünd cutters offer an extensive selection of modular, specialized tool options and workflow automation. Zünd makes digital cutting of textiles – and many other types of flexible or rigid materials – simple, productive, and profitable.
Zünd has created production workflows for state-of-the-art, digital textile cutting that begin well before any actual cutting takes place and don’t end as soon as cutting is over. Innovative solutions are available for every phase of the process, including the latest version of the powerful MindCUT Studio Production software with a range of exciting new features.
Among these is Feature Recognition, a digital workflow that enables the software to detect motifs and different parts of a garment using AI. In the blink of an eye, it selects the model, aligns the motif and reference points, and attributes individual parts for perfectly precise subsequent cutting. This automates a previously very time-consuming, manual process. MindCUT now also offers a Printed Cut func-
tion that automatically captures printed designs in addition to Pattern Matching, which recognizes repeating patterns, compensates for material distortions, and automatically matches the markers to the pattern.
The new Roll Handling System – RHS is the latest Zünd material-handling solution for textile applications. The system can hold up to ten rolls of fabric, which can be identical or of different types. The large, fully automated RHS enables extended,
uninterrupted production cutting by autonomously feeding material onto the cutter. The only remaining operator intervention consists of scanning barcodes of individual rolls while loading them onto the RHS. The material assignment and the RHS itself are controlled directly through the MindCUT software.
Key Features
• Zünd modular, multifunctional digital cutting systems can be tailored to individual production needs with a wide range of specialized tool options for maximum versatility, cut quality, and efficiency.
• All Zünd cutters can be expanded and upgraded any time with additional tooling and workflow
automation to meet increases or changes in demand.
• Zünd’s open architecture makes these cutting systems easy to integrate in existing production environments.
• Modularity, versatility, productivity, and low cost of ownership: Your First choice in digital cutting—for 40 years.
www.zund.com
Also exhibiting at Foam Expo 2024, Booth 2518, Novi, MI; Advanced Textiles Expo, Booth E1838, Anaheim, CA.
Adetailed study of the available recycling options for textiles – either mechanical, thermal or biochemical – and their varying levels of industrial readiness, was prepared for the European Commission by the Belgian research institute Centexbel back in 2020.
It came ahead of the Commission’s Strategy for Textiles, which is calling for all textile products on the EU market to be durable, repairable or recyclable – and largely made of recycled fibers – by 2030.
Beginning in January 2025, the problem of garment waste will be proportionately thrown back at the brands putting their products on the EU market.
No longer allowed to be either landfilled or incinerated, over seven million
tons of waste textiles will have to be separately collected each year within the EU and will be paid for by the brands via the introduction of a new Extended Producer Responsibility (EPR) scheme.
The Centexbel study stresses that while businesses pursue the ‘Holy Grail’ of closed-loop recycling, established openloop systems already successfully re-process textile waste into usable products and a combination of reuse and closed and open-loop solutions will be required to comply with the new strategy.
Many nonwovens are already based on long-established open-loop mechanical recycling processes, currently largely from industrial waste by-products, but with the
potential to be made from post-consumer waste too.
For the automotive industry for example, recycled fibers are employed to make insulating webs for sound and heat insulation, hard-pressed parts for floors, doors and seat linings, luggage compartment and boot linings and some filter media.
In the furniture industry, recycled fiber applications include mattress covers and webs, seating padding, wallcoverings and wiping cloths, in addition to carpet backing and underlay.
There are also extensive applications in building and construction for recycled fibers, in a range of insulation products and as filling materials.
Many of these products are often considered ‘second life’ materials and their
manufacture has been somewhat demeaned by being termed ‘downgrading’, by champions of a fully circular economy.
In reality, effectively doubling the life of any product that can’t enter a fully circular system will be extremely useful in attempting to meet the near-term goals of the EU’s Textiles Strategy.
Things have now moved on considerably since Centexbel’s 2020 report and the Gold Standard for mechanical recycling is without doubt Nouvelles Fibres Textiles, based in Amplepuis, France, which has been established in partnership with machine builder Andritz Laroche and sensors specialist Pellenc and was inaugurated in November 2023.
Sorting has been identified as a major bottleneck in the recycling industry, and during a web talk organized by the textile machinery branch of Germany’s VDMA on March 26th this year, Charles Junker, head of sales at Andritz Laroche, observed that the challenge is to be able to automatically classify garments in order to maximize the value of the fibers they contain.
The Nouvelles Fibres Textiles system employs a sequence of processes to consistently refine the textile waste, starting with a sorting line for full garments, a second for cutting and secondary sorting, and then on to a cleaning and tearing line.
Junker provided an example of how the system handles a bale of cotton and cotton polyester denim waste clothing.
In the first step – after garment spreading to avoid overlapping – the system can be set to separate all cotton items that are more than 90% blue in color from the rest, removing all non-cotton and other colored items and producing a second bale.
This is then cut into clips and fed through the second line to remove everything remaining that is not cotton or blue, such as pocket linings, and then baled again.
The cleaning and tearing line then removes all other remaining impurities such as buttons and zipers, to result in a bale of 98-99% pure fiber.
Junker said the Nouvelles line will soon be at the stage of handling three tons of material an hour, and by the end of this year is targeting six tons an hour.
“Mechanical recycling is an immediate response but won’t be the only solution,”
he said, adding that Andritz is now working with Rieter on the development of a refined system for the production of recycled yarns and also on chemical recycling treatments.
“Nonwovens companies are early movers in looking at the potential of postconsumer waste, realizing that there’s going to be a big demand for the relatively pure waste from mill operations,” Junker said. “The nonwovens industry should be proud of the applications for recycled fibers it has already developed. Even with the latest fiber-to-fiber chemical recycling methods being commercialized, only 3040% content can be incorporated into yarns for conventional spinning and we are already achieving 100% in many highvalue nonwoven products.”
Chemical recycling routes meanwhile promise to achieve the conversion of synthetic fibers back to their component polymers or monomers at an unprecedented scale and a frontrunner here, has been Eastman Chemical, headquartered in Kingsport, Tennessee.
In March this year Eastman announced that it had already achieved on-spec initial production at its new molecular recycling
facility in Kingsport and is now generating revenue from the operation.
The company, which has also just signed a deal with leading outdoor brand Patagonia, expects to ramp up production of the new facility over the coming months and to achieve approximately $75 million in earnings from it this year. Once fully operational, it will have an annual capacity of 110,000 tons.
A second plant in Port-Jérôme-surSeine in Normandy, France, is planned for start-up in 2026 and will also have an initial capacity of 110,000 tons in its first phase, rising to 200,000 tons in the second phase of development. The company plans to have a third plant at a location yet to be decided in the USA also operational by 2026, which will bring its total polyester recycling capacity to 330,000 tons by that time.
Via a chemical process it calls methanolysis, Eastman’s polyester renewal technology enables waste to be broken down into its molecular building blocks and then reassembled to become virgin-quality material without compromising performance. Eastman is enabling the potentially infinite use of materials by keeping these molecules in production, in a material-tomaterial high-yield loop. The waste plastic can be converted into virgin quality food contact polyesters with lower greenhouse gas emissions than traditional methods.
“By demonstrating molecular recycling at this scale, we have solidified our position as a leader in the creation of a circular
Even with the latest fiber-to-fiber chemical recycling methods being commercialized, only 30-40% content can be incorporated into yarns for conventional spinning, and we are already achieving 100% in many high-value nonwoven products.
economy,” said Eastman CEO Mark Costa. “Demand for recycled materials at virginquality levels from our new plant is strong and we are excited to announce this significant milestone in our journey.”
Paris-headquartered water solutions leader Suez his also partnering with SK Geo Centric (SKGC), a subsidiary of the South Korean chemicals giant SK Group, to establish a €450 million PET plastic and fiber recycling plant in Saint-Avold, France, based on the technology of Loop Industries.
With commissioning planned for 2025, the new recycling facility will manufacture 100% recycled and infinitely recyclable virgin-quality PET resins with a planned capacity of 70,000 tons per year.
Loop Industries, headquartered in Montreal, Canada, owns patented and proprietary technology that can depolymerize PET plastic and polyester fiber waste currently of little or no value, including plastic bottles and packaging, carpets and textiles of any color, transparency or condition, and even ocean plastics that have been degraded by the sun and salt. The resulting monomers are filtered, purified and polymerized to create virgin-quality Infinite Loop-branded PET resin suitable for use in both food-grade packaging and fibers. The monomers can be recycled infinitely without degradation of quality, the company claims.
The French project will follow on from the first Infinite Loop manufacturing facility which is being built in Ulsan,
South Korea, and will also have an annual capacity of 70,000 tons.
In January 2024, UK-headquartered investment firm Reed Management announced it will provide financing of $66 million to Loop Industries, with the aim of further rapidly accelerating the production of 100% recycled polyester fibers and PET plastics in Europe.
The Eastman and Suez/SK projects alone will establish the chemical recycling of an annual 400,000 tons of polyester and as such serve to illustrate the key advantage of chemical fiber recycling routes in scaling up, especially for synthetic fibers.
It would take many, many mechanical recycling operations to equal the capacities that these projects will bring to market. At the same time, there is not the same level of sorting required, since in many chemical recycling methods proposed, the materials are being taken back to their original constituent monomers.
Mechanical recycling, on the other hand, is well proven and demonstrably cost-effective for new players who may be considering entering what will be a rapidly expanding market in the next few years.
Centexbel’s White Paper on Textile Fiber Recycling Technologies can be downloaded at www.centexbel.be
Adrian Wilson is an international correspondent for International Fiber Journal . He is a leading journalist covering fiber, filtration, nonwovens and technical textiles. He can be reached at adawilson@gmail.com.
YOUR PARTNER FOR TEXTILE RECYCLING PROCESSES ANDRITZ is the right partner when it comes to textile sorting, textile fiber preparation, mechanical and chemical recycling or combined recycling solutions for pre- and post-consumer or industrial textile waste. We accompany you throughout the product life cycle and beyond.
Take advantage of our profound experience and skills to leverage your production, create new products, and make the right investment decisions. To complete our scope, we also provide engineering, project and site management, manufacturing and assembly, logistics, service and improvement processes, automation, and digital solutions so that you can recycle your textiles into success.
Known for its rapid production and consumption cycle, the textile industry currently generates between seven and 7.5 million tonnes of textile waste per year in the European Union (EU-27 and Switzerland). This is equivalent to more than 15 kg of textile waste per person per year. As recently indicated in the McKinsey report, approximately 85% of this waste comes from clothes and home textiles discarded by end consumers while the remaining 15% originates from textile industries and textile retailers in the form of industrial offcuts and production surpluses.[1]
With regard to the management of post-consumer textile waste, a study carried out in 2022 by EURATEX, the European Apparel and Textile Confederation, reveals that only 33% of post-consumer textile waste is collected separately in Europe, whereas the remaining 67% is incinerated or ends up in landfills around the world. Of the post-consumer textile waste collected, 60% is sorted and separated for sale in second-hand shops while the remaining 40% is sent to recycling streams. [2] In addition, according to the European Environment Agency, more than 1.4 million tonnes of textile waste exported outside the European Union in 2020.[3]
All these data on the generation of textile waste and its poor management are aggravated by what is known as fast
fashion. Industries design and manufacture fast-paced, low-cost clothing collections in order to follow the latest fashion trends. The industry therefore offers consumers access to newly designed garments at affordable prices on a continuous basis, thus incentivizing the generation of textile waste. When combined with the lack of solid collection systems, this leads to an increase in global incineration and landfill rates.
Moreover, the wide variety of composition of today’s textiles (ranging from synthetic polymers such as polyester, polyamide and elastane to natural materials that include cotton, wool and linen) is another factor that hinders their circularity. All this implies the need to develop new separation and sorting technologies to determine the most appropriate destination. Artificial intelligence is now playing a key role in automating this process by making more efficient and accurate sorting possible.
However, uncontrolled production and consumption and the need for separate
collection and sorting technologies are not the only critical points in the textile industry. Recycling processes are also in need of innovation and improvement to cope with the amount of textile waste generated worldwide. The complementarity of existing recycling technologies (described below) will play a key role in increasing sustainability in the industry.
The above mentioned data, together with the challenges of the industry, have led the public authorities to launch actions aimed at redirecting the industry towards a more sustainable business model, such as the amendments to the EU Waste Framework Directive. The revision of May 2018, specifically in Article 11, paragraph 1, requires EU Member States to set up separate collection systems for textile waste by January 1, 2025.[4]
In July 2023, the Commission presented new common rules with the aim of making manufacturers responsible for the entire life cycle of textile products
Recycling processes are also in need of innovation and improvement to cope with the amount of textile waste generated worldwide.
and supporting sustainable waste management in the European Union. In other words, the Commission has suggested the implementation of mandatory Extended Producer Responsibility (EPR) systems for textile products in all EU Member States. The aim of this initiative is to accelerate progress in separate collection, sorting, reuse and recycling in line with the EU Strategy for Sustainable and Circular Textiles, adopted in March 2022.[5]
EPR systems have been shown to improve waste management for a variety of products such as packaging, batteries and electrical and electronic devices, where producers bear the costs associated with waste management. Applied to the textile sector, this approach will provide an incentive for producers to reduce waste generation and encourage the circularity of textile products by promoting the design of more sustainable products at source.
But the European Commission is not only focusing on collection systems, but also takes into account the efficiency of sorting, repair, reuse and recycling processes, as set out in Article 9(1) of the revised Framework Directive. This paragraph was amended to encourage the reuse of textile products by promoting repair activities.[4] Furthermore, Article 11, paragraph six now states that the European Commission must consider and establish targets by 31 December 2024 for “preparing for reuse and recycling of separately collected textiles.”
Therefore, the effectiveness and efficiency of sorting and recycling processes are also critical points to be addressed by the industry in order to try to increase recyclability rates of textile waste.
Let’s discuss the textile recycling processes that currently exist and the most promising emerging technologies that technology centres such as AIMPLAS are studying, developing and implementing in the market as innovative solutions for the industry.
In the textile industry, there are different recycling technologies that can be applied depending on the type of textile waste stream to be treated. Upstream sorting and separation processes are therefore crucial to ensure good recycling methods. The different technologies include:
• Mechanical Recycling. This technology uses physical forces such as cutting and shredding to convert textiles into usable fibres. After the fibers are obtained, they undergo a spinning process, which involves cleaning, disentangling and arranging the recycled fibers in parallel, then refining and twisting them together to obtain recycled yarn. This is a widespread process in the textile industry characterized by low-energy consumption and high cost-effectiveness. It can be used for all kinds of textile waste depending on the type of material (natural, synthetic or blends), the type of product (e.g. yarns, fabrics, used garments, carpets) and the structure (knitted, woven or nonwoven). However, during tearing, cutting and shredding processes, there is a reduction in fiber length of up to approximately
30-40%, which reduces to some extent the quality of the final yarn and limits its use in new textile products. This is a major challenge for these recycling technologies and the industry has addressed them by blending shorter recycled fibres with longer virgin fibres.
• Thermo-Mechanical Recycling. This recycling technology uses extrusion processes that combine specific pressure and temperature conditions to melt synthetic textiles such as polyester and polyamide and recover them in pellet form. This process is not suitable for natural fibers such as cotton and wool, or for cellulose-based synthetics such as viscose. Thermo-mechanical recycling is a mature technology that has been implemented on an industrial scale in other sectors such as plastics. However, it is less developed for the textile industry. Energy consumption is relatively low, and these technologies produce higher quality materials than those obtained using the mechanical processes described above. Nonetheless, for textile waste to be recycled and processed using these technologies, input waste requirements are very strict. The composition must be at least 99% monomaterial or ensure 99% compatibility between polymers when processing a multi-material textile.
For example, in the OCEANETS project[6] (coordinated by AIMPLAS in collaboration with the Universidad de Vigo, the Port of Vigo Fishing Shipowners’ Cooperative (ARVI), ECOALF, SINTEX and Asociación Vertidos Cero and financed by the European Commission’s Executive Agency for Small and Medium-Sized Enterprises and the European Maritime and Fisheries Funds, EASME), these recycling techniques were used to obtain high added value products in the textile industry from fishing nets. The picture shows one of the extruders at the AIMPLAS pilot plants where this kind of operation is carried out.
With controlled amounts of oxygen, gasification is used to produce synthesis gas (syngas) through the partial oxidation of polymers. Recovered virginquality syngas is mainly used to obtain substances of industrial interest such as methanol, ammonia, synthetic fuels, oxo alcohols for plasticizers, and adhesives. Thermochemical recycling is a basic
polymer chains and use solvents to recover the initial monomers. These techniques are known as solvolysis. Depending on the type of solvent used, they are referred to as glycolysis, hydrolysis and methanolysis, etc. Chemical recycling processes require more energy than mechanical recycling but have the basic advantage of
• Thermochemical recycling. Thermochemical recycling includes different recycling technologies depending on the amount of oxygen used in the process. Pyrolysis takes place in the absence of oxygen and is used mainly to obtain pyrolysis oil, which can be used as a fuel and also refined to obtain new raw materials with high added value. Pyrolysis it is more consolidated at industrial level in other industries such as plastic waste. Waste that contains oxygen in its chemical structure decreases the quality of pyrolysis oil, which is why these technologies are not so widespread in the textile industry due to the abundant presence of polyester, polyamides and elastanes.
technology used on a commercial scale. However, this technology must be adapted or developed for treating textile waste the way it is done in pyrolysis processes. In this case, the input stream can be even more varied, as there are fewer restrictions on the amount of oxygen present in the chemical structure of the waste. The picture shows the pyrolysis and gasification equipment at the AIMPLAS pilot plant, where research is being carried out to bring these technologies more in line with the textile sector and other industries.
• Chemical Recycling. Chemical recycling involves a wide variety of technologies and its main purpose is to break
producing higher quality fibers with properties nearly identical to those of virgin fibers. To obtain chemically recycled fibers, the monomers obtained during the process must first be repolymerized. These technologies are selective for synthetic condensation polymers (e.g., polyester, polyamides and polyurethanes), so they can be applied to multimaterial fabrics for depolymerization and to separate the other components not susceptible to these techniques.
AIMPLAS is developing different projects in this line, such as the Textended Project,[7] where it is responsible for research into the recycling of textile waste using solvolysis processes, including industrial textile products and polymer blends such as polyester/polyurethane. In fact, it is also working on activities to ensure that recycled products obtained from the textile industry are used. Textended is an EU-funded project coordinated by the VTT Technical Research Centre of Finland. The picture shows AIMPLAS pilot plant reactors, where chemical recycling processes involving solvolysis are carried out.
Hyatt Regency Minneapolis | Minneapolis, Minnesota | June 17-18, 2024
Go behind the scenes to discover the essentials of bringing a new wet wipe to life, from wipe professionals who’ve run hundreds of projects across multiple categories and geographies.
Gain insights into the nonwovens, lotions, and packaging aspects of a successful wipe. Acquire an understanding of key test methods and when approvals are needed from the FDA or the EPA for your wet wipes.
Know wet wipes from a nonwoven, formulator, and a packaging perspective…and how to bring it all together to launch your next product.
• Raw material & packaging suppliers
• Brand & private label wipe converters
• Retail buyers
Course Instructors:
This course is essential for everyone in the wipes industry, including:
• R&D
• Marketing & product managers
• Entrepreneurs
• Physical or dissolution recycling. Although solvents are also used in these recycling techniques, unlike the case of chemical recycling technologies, the polymer chain is not broken to recover the initial monomers. In this case, dissolution processes are applied for the recovery of textile components in polymer form (in polymeric materials) or in pulp form (in cellulose materials). The latter is known as the pulping process and allows cotton to be recovered in the form of cellulose so it can be recycled as viscose. These dissolution technologies can also be applied to dissolve the polymers that make up fabrics and to extract the adhesives that hold the different layers of multilayer technical textiles together. This produces delamination and separation of the layers (which are usually of different composition to offer specific technical properties to the final fabric), thus allowing them to be recycled individually and increasing process efficiency and effectiveness. This type of operation is carried out in the reactors shown in the above picture.
Dissolution processes can also be used to remove contaminants and dyes from textile waste. Along these lines, AIMPLAS is developing dye-removal methods within the CISUTAC Project.[8] This European project is coordinated by the CENTEXBEL VKC, Research Institute in Belgium, which aims to remove current bottlenecks to increase textile circularity in Europe. The aim is to minimize the industry’s total environmental impact by developing large-scale, sustainable, innovative, and inclusive European value chains. This will be achieved through the development of three pilots focusing on: digital repair and dismantling, new recycling processes, and changes in industry and customer behaviors.
Research and development of new recycling technologies is necessary to treat more waste, regardless of its complexity. It is therefore urgent to address textile waste management and specific challenges of the industry. Actions must also be taken by the European Union, such as those outlined in this article, to promote a more sustainable business model.
1 https://www.mckinsey.com/industries/retail/ our-insights/scaling-textile-recycling-in-europeturning-waste-into-value
2 https://euratex.eu/wp-content/uploads/EURATEX_ FactsKey_Figures_2022rev-1.pdf
3 https://www.eea.europa.eu/publications/eu-exportsof-used-textiles
4 https://eur-lex.europa.eu/legal-content/EN/TXT/ PDF/?uri=CELEX:32008L0098
5 https://eur-lex.europa.eu/legal-content/EN/ TXT/?uri=CELEX:52022DC0141
6 https://oceanets.eu/
7 https://textended.eu/about/
8 https://www.cisutac.eu/
Mireia Fernández is the leader of the AIMPLAS Chemical Recycling department, working as a researcher there since 2020. She studied Chemistry at the Universitat de València and has a master’s degree in Sustainable Chemistry from the Universitat Politècnica de Valencia (UPV). She has experience in the synthesis of polymers through low environmental impact routes as well as in the organic synthesis of high-value-added additives from biomass. Her research is focused on the valorization of plastic waste through physical recycling such as dissolution and extraction processes and chemical recycling techniques.
AUGUST 20 – 22, 2024
RALEIGH, NORTH CAROLINA
SMART TEXTILES
Network with the creators shaping the industry
AUTOMATION ADVANCEMENTS
View and engage with the latest technology CIRCULARITY
Gather insight and stay up-to-date on future trends
Scan the QR code for registration information.
Our little friend Kermit from The Muppets were part of my childhood in Australia and that melancholy song of the little green friend lingers. And now, many years later, “green” is still the color. Or again? In view of all mankind and green friends we must act. But how?
Sustainability is a driving force of doing business today yet is also very complex. Speaking of the textile industry, what does “sustainability” mean? In many cases, the mere source of the raw material is considered. Though this is an important indicator, it is not that simple. What are we considering? How was that raw material produced? Obtained? What was needed for production? How much energy? Water? And what about the chemicals involved, even “simple” ones like fertilizers, bleach, or dyestuffs? Are secondary production steps needed? And so forth.
But is there not enough “raw material” available already today? Would it not be sustainable to reduce consumption, use products longer where possible, reuse those, and recycle them? The solution is advanced (molecular) recycling. This means not to go back to the very first “harvesting” steps, but smartly reusing what we already have. Still, that is easier said than done.
The task is huge, so best start with a speciality product that has an active community and multiple pillars in place already: branded high performance flameretardant polyester known in the textile contract business for more than 40 years and used by a community eager for sustainable solutions. As a man-made product, the ingredients of polyester can be selected. By working together with industry
partners, knowledge is being actively developed. PET can be advanced recycled and broken into its single base materials. But would it be possible to produce highend FR modified polyester and extrude filament yarns that pass the important
FR textile fire standards, matching the performance levels of virgin material?
Advanced recycling has a very big advantage over mechanical recycling as it allows modifications, like a flame retardant one, at polycondensation level.
The solution is advanced (molecular) recycling. This means not to go back to the very first “harvesting” steps, but smartly reusing what we already have.
This type of modification is the most sturdy and sustainable one, i.e. modifications do not leach out or off gas into the environment. This further adds to the sustainable footprint of such a product.
The first 150kg trial made at our production facility in Guben, Germany, from 100% advanced recycling resin obtained from post-consumer recycled PET packaging material (like PET bottles) was done back in autumn 2022. The filament yarns were extruded in a lab and then woven into a fabric by a partner for performance tests. The results were good, very promising and learnings from it allowed for a second, slightly more challenging trial.
For the second trial, 100% advanced recycled resins originated from mechanical recycled packaging material, which was no longer suitable further production of PET goods, was used. This not only added to the complexity but addressed yet another sustainability issue – reduce the waste from the food packaging industry. Though mechanical recycling allows one to reuse material, this can only be done for a certain number of times before the raw material “wears out”. Furthermore, for this trial lot, the production readiness on commercial batch lines was tested. This second 1,5mT trial lot showed improved results in the final FR fabric.
With the success of both trials in hand, Q4 2023 allows the planning of a third trial lot. Not only will staple fibers be made available for the first time, but also larger volumes will be ready for conversion.
Though the usage of advanced recycled material of “common” packaging material is a fantastic first step to obtain knowhow for using such materials, it cannot
stop here. The ultimate answer can only be circularity – the usage of textiles as raw material. Now textiles will have, let us call them “impurities.” They can be blended with different raw materials, have laminations (for example upholstery fabrics), back coatings (for example black out curtains) or simply have dye stuffs. They also need to be collected and sorted and made readily available for reusage. Discarded years ago, and piling up in the most unusual places like the Atacama desert, textiles need to be a resource, raw material. And we have to learn how to reuse them.
For the high-end FR modified polyester and the trademark tested fabrics made thereof, a Take-Back system for the entire textile value added chain in Europe has been set up years ago. Suitable for mechanical upcycling today, these textiles are collected at an industry partner and are the raw material for new high performance FR polyester material tomorrow. Thanks to the trademark testing scheme and a marker which has been added to the filaments and staple fibers during production, these used FR textiles – this raw material – can be identified and sorted. By learning more and more
on advanced recycling, gearing up our skills and machines, circularity can be achieved. And must. Because circularity and the advanced recycling of products wherever possible will allow for the reduction of virgin material usage, no matter which raw material base.
Being “green” means to be holistically in our activities. And we, the entire textiles industry, must team up with and take all our consumers on this journey too. After a long use of the products wherever possible, these need to be returned to collection points, sorted, and made available for reuse. There is a price to pay, yet we earn much. The planet, the smiles of the next generation, the respect.
As a community we can work together to make it easier “being green,” dear Kermit.
Svenja Fromm is the marketing and communications director at Indorama LifeStyle Europe, part of Indorama Ventures Fibers Germany GmbH, in Hattersheim, Germany. She received her Technical Diploma in Textiles and Apparel Techniques (Fachabitur in Textilund Bekleidungstechnik) at Luise Schröder Schule, Wiesbaden, Germany.
Each person in Europe generates on average around 15 kg of textile waste each year, mostly used clothing and home textiles, which creates disposal problems, either by incineration or landfill, both inside and outside Europe.
At the same time the textile industry has recycling challenges: less than 1% of apparel worldwide is currently being recycled back into garments (fiber-to-fiber recycling), although more than 14% is made into other materials.
Europe currently has a garment collection rate of 30-35%, with much of the unsorted waste exported outside Europe, particularly to Africa, according to a 2022 study by McKinsey. In addition, most fiber-to-fiber recycling technologies have strict input requirements, with some demanding mono-fiber apparel only.
Under the European Union’s Waste Framework Directive, used textiles must be collected and recycled throughout the EU from January 1, 2025. However, the recycling of mixed textiles can be challenging – especially if they contain elastane (also known as spandex).
Many of the yarns and fabrics used to manufacture clothing are easily recyclable when in 100% form, such as pure cotton, polyester or polyamide, but the introduction of elastane in materials, even if only in small quantities, makes recycling using conventional methods difficult, if not impossible.
According to Emanuel Boschmeier, a researcher at the Institute of Chemical, Environmental and Bioscience Engi-
neering, Vienna University of Technology (TU Wien), Austria, elastane is so elastic (as the name suggests) that shredders used to shred textiles before recycling cannot cope with it: elastane leads to soiling, blockages and clumping in the machines.
Speaking at last September’s Dornbirn Global Fiber Congress, Jean Hegedus, director of sustainability at the Lycra Company, USA, asserted that some garments with an elastane content of 2-5% can be mechanically recycled, while garments with 5-10%
elastane content are typically being recycled into such items as insulation for buildings and the interiors of automotive seating – the main issue is clothing with more than 10% elastane content.
There are several challenges for recycling garments that contain elastane:
• Accurate, computerized fiber sorting and pre-processing are not yet available at scale, making fiber identification difficult;
• Fabrics with elastane can sometimes clog filters, forcing shut-downs and system clean-outs;
• Depending on the specific recycling technology and what chemicals are being used for purification, elastane can sometimes affect the viability of companion fibers.
Scaling the circular economy for textiles will require updated scanning and sorting technologies, recycling systems that can handle fiber blends that include elastane and scalable systems that can help reduce costs and increase output, said Hegedus. If these barriers can be overcome, McKinsey estimates that by 2030 fiber-to-fiber recycling could handle 18-26% of gross textile waste worldwide.
To address the elastane recycling issue, the Lycra Company is developing a Lycra fiber that can be easily extracted from clothing, collected and re-spun into new garments, and is working with selected recyclers on several technologies for recycling various Lycra fiber blends, such as with cotton, polyamide and polyester. Eventually, this could be combined with the company’s bio-derived technology so that bio-derived Lycra fiber could be recycled from garments. However, when using recycled elastane, Hegedus noted that maintaining optimum molecular weight is critical to both fiber spinnability and performance.
Also presented at Dornbirn was Lycra T400 – a stretch fiber although not an elastane. It is an elasterell-p bicomponent yarn (an elastomultiester polyester
comprising polyethylene terephthalate and polytrimethylene terephthalate) that adds elastane-free stretch to fabrics. Around 15-18% of the fiber content of Lycra T400 EcoMade is sourced from plantbased materials, such as corn.
The Lycra Company has started trials with a recycler using glycolysis, a wellknown chemical recycling method, to evaluate blends with polyester, which showed that Lycra T400 does not disrupt standard polyester recycling streams.
Further, the fabric performance of the recycled fiber was found to be acceptable and, with slight adjustments during chip production, could achieve aesthetics comparable to a control fabric.
Another trial is looking at depolymerizing dyed fabrics of standard polyester and Lycra T400 back into its monomers for separation and reuse to make new fibers.
Meanwhile, Teijin Frontier, the Japanbased Teijin Group’s fibers and products converting company, has developed a technology to eliminate polyurethane (PU) elastane fibers from discarded polyester apparel.
The technology features a new processing agent used during the pretreatment phase of the chemical recycling process, which helps improve the quality of the recycled polyester fiber. In addition to removing the elastane fiber, the new technology eliminates foreign materials such as dyes.
The company has been conducting tests of this technology since October 2022 and is working with the supply chain to establish a comprehensive ecosystem including used clothing collection, sorting and recycling, with the aim of expanding the scope of fiber-to-fiber recycling.
The new technology swells the PU elastane fibers, breaks their chemical bonds and dissolves them. For system cost control and environmental load reduction, the processing agent can be collected and reused. Recycled polyester materials generated by this method can be used in the existing chemical recycling process, said Teijin Frontier.
With the EU’s forthcoming directive on used textiles, improved recycling processes are urgently needed to deal with the huge volume of used textiles in an efficient and environmentally friendly way.
A novel elastane quantification tool has now been developed, based on midinfrared spectroscopy, which measures how much elastane is actually present in a garment.
The next step was to find a method to separate elastane from other fibers. The TU Wien researchers experimented with different solvents and carried out theoretical studies, finally coming across a harmless solvent that selectively removes the elastane, leaving the reusable fibers intact.
A patent application has been filed for the method in which materials such as polyester or polyamide can be virtually completely recovered – even the solvent itself can be recovered and reused.
Further, when wool is combined with polyester and elastane, the individual components can be reused. The wool is broken down with enzymes under mild, harmless conditions, producing an amino acid cocktail that can be utilized in the cosmetics industry or in fertilizer production. In the next step, elastane is separated, and recyclable polyester remains.
TU Wien has developed methods that not only better detect elastane and in a more environmentally friendly way than previously, but can also separate elastane gently, allowing the recovery of other fibers undamaged. The key is determining the right solvent.
The first step was to find a reliable and fast method to accurately detect elastane contents in textiles. “During our research, we discovered that no such method existed until now,” said Boschmeier. “The usual test method uses a solvent that is classified as harmful to health and is also extremely time-consuming.”
Since the late 1960s, the textile industry has predominantly relied on elastane to impart elasticity to fabrics. However, a relatively recently introduced polyolefin-based elastomer – XLance (pronounced “excellence”) – differentiates itself from the polyurethane-based structure of traditional elastane.
“This ensures that garments made with XLance maintain their stretch and performance for a longer period, underscoring the importance of durability in sustainability, especially in a world where more than 90% of textile waste finish up in landfills,” explained Costantino Colnaghi, chief executive officer of XLance, Novara, Italy, in a recent interview.
Additionally, XLance uses a melt spin production system, in contrast to the dry spin method for elastane. The company has also invested heavily in research and develop-
Italy-based XLance offers an alternative to traditional PU-based
ment to enhance the recyclability of garments made with XLance, said Colnaghi.
At present, used textiles are sorted almost exclusively by hand. For fiber-to-fiber recycling, currently the most sustainable textile recycling option, the key is to sort textiles by fiber composition. However, this cannot be reliably done manually – by feel – especially with fiber blends.
Annika Datko, a bachelor’s graduate at the Institut für Textiltechnik, RWTH Aachen University, Germany, has demonstrated how used textiles can be sorted by fiber composition using near-infrared (NIR) sensor technology. This is already state of the art for recycling plastic waste but is still in its infancy when it comes to sorting used textiles.
The process works by irradiating a textile sample with NIR light. Based on the wavelengths of the reflected light picked up by the detector, a material-specific spectrum can be created that resembles a fingerprint.
Datko compared the spectra of textiles with different fiber components. She was able to prove that it is possible to differentiate between different fiber compositions using NIR and that the method has an average mean error of just 4% on a laboratory scale.
Geoff Fisher is the European editor of International Fiber Journal and editorial director of UKbased Textile Media Services, a B2B publisher of news and market reports on transport textiles, medical textiles, smart materials and emerging markets. He has more than 35 years of experience covering fibers and technical textiles. He can be contacted at gfisher@textilemedia.com or +44 7803 718443.
One in eight workers of the total global workforce of 3.5 milliards is involved in the textiles and fashion business. The three billion mostly very small enterprises generate between $ 1.7 to $2.5 trillion in revenue (depending on the source of the data). From 2023 to 2030 the business is projected to grow by 7.6% annually.
The textiles and fashion industry faces problems like overproduction; massive waste (92 million tons end up in landfills) fueled additionally by fast fashion; is responsible for 10% of global CO2 emissions (global warming); with use of 60% synthetic fibers (like polyester) it relies heavily on fossil sources; and the emission of microplastics into the biosphere and uptake into living organisms.
Since the 1990s, more products and materials are being “down-recycled,” resulting in inferior quality of post-consumer recyclates with diminished functionality and often accumulated toxic and hazardous
substances transferred into new products, which will eventually harm the biosphere, human beings, and other organisms. In turn, more virgin materials must be mined and negative ecological and social impacts continue.
In the same period, pioneering companies began to optimize sustainability employing “ecodesign” methods in conjunction with Life Cycle Assessment (LCA). Although, this efficiency-driven approach allowed for slow incremental improvements, it perpetuated linear thinking in the industrial systems, producing ever more waste and irreparable damage to the environment and societies.
Approximately 10 years ago, the buzzword “circular economy” emerged. It had long been part of the method Cradle to Cradle, christened by the two inventors Michal Braungart and William McDonough in end of the 1980s. What is today commonly hailed and practiced as “circular economy” is driven largely by the very same linear mind-set. No fundamental change.
On February 10, 2021 the EU Parliament approved with a large majority the European New Green Deal which sets a legally binding target of net zero greenhouse gas emissions by 2050. The European Commission installed a system of operational policy initiatives to implement the European Climate Law in all 27 member states by 2030 for the textile and fashion industry. With the decoupling of economic growth from continuous virgin material mining, while reintegrating postconsumer “waste” streams into the industrial process, the availability of sufficient material for production shall be secured and a new Industry shall be built.
These policies establish common standards and definitions and include the European Climate Pact, the New Circular Economy Action Plan, the Green Deal Investment Plan, the Sustainable Chemical Strategy, the Farm to Fork Strategy, the Sustainable and Smart Mobility Strategy to mention the most challenging. Within the New Circular Economy Action Plan is the Corporate Sustainability Reporting
Directive (since January 23), which will be replaced in 2024 by the more severe and far-reaching European Sustainability Reporting Standard. The Green Deal Investment Plan together with the integrated Taxonomy, the Non-Financial Reporting Directive and the Corporate Sustainability Due Diligence define and control that investments are in support of reaching the net-zero 2050, while companies will be liable to uphold Human Rights and environmental protection laws along their entire (global) product supply chains. The Chemical Strategy for Sustainability, based in parts on REACH, will require total transparency to prevent harmful toxic emissions into the biosphere, besides reducing greenhouse emissions. Observations show, that the European commission is adopting much of the very stringent Cradle to Cradle™ standards.
These regulatory instruments shall transform the European industry and societies and will affect, directly and indirectly, the world economy. An effective educational preparation, knowledge and capacity building for a regenerative culture and industry is urgent to move away from linear thinking. Small and mid-sized companies often are strategically and operationally overwhelmed to tackle the task. Although offers of educational programs are mushrooming, they continue reinforcing mostly linear thinking and cause more confusion. Transformations and, with itm innovations are inevitable at all levels (material sourcing, production technologies, product design, business strategy, marketing communication, industrial reintegration of end-of-life products).
What then is the right educational approach and what should be the core focus? The European regulatory requirements certainly have triggered the pertinence of a new and different train of thoughts. Long before, I understood that the only viable system and method was Cradle to Cradle. Together with my personal professional observations, experiences, and experiments as an industrial designer, responsible for curriculum development of sustainability and design at BA Design
Approximately 10
years ago, the
buzzword “circular economy” emerged. It had long been part of the method Cradle to Cradle, ™ christened by the two inventors Michal Braungart and William McDonough in end of the 1980s.
Management, International at Lucerne University, it became evident that professional support from a field expert was needed to prepare students effectively for their professional challenge. Together with Albin Kälin, the CEO of epeaswitzerland, over the last eight years we experimented successfully, equipping, and enabling students with tools of Cradle to Cradle,™ and The Reference Model Cradle to Cradle, applied over years successfully in professional workshops.
Currently, epeaswitzerland has an educational mandate with several state governments in Switzerland to teach Cradle to Cradle™ for professionals.
The experience in the past years made clear that the single most important necessity to invest in change of mindset, regardless of the branch of industry. Without such fundamental change, linear thinking, and linear economics with all its consequences as we are fully aware by now, will prevail which means business as usual.
The 62nd Global Fiber Congress in Dornbirn 2023, provided the opportunity to present ‘Transformation by Circular Design Process’ in the context of the Fashion & Fiber Industry. As I outlined before, this industry is facing serious challenges for some time, but now the regulatory requirements of the European Green Deal are indisputable game changers to implement circular transformation, not merely recycling as upcycling – part of linear business. The tool Transformation by Circular Design Process is designed to be applied to any industries, not only for the Textiles and fashion business.
How does ‘Transformation by Circular Design Process’ work?
‘Transformation by Circular Design Process’ is a front-end tool, designed to break out of this vicious cycle of linear thinking through a radical change of mindset. The tool can be applied as a preparational stand-alone module, or in conjunction with the Reference Model Cradle to Cradle , in which case mindset-change thinking merges into innovation thinking of applied Cradle to Cradle® objectives.
‘Transformation by Circular Design Process’ is a journey in 8 stages, based on edu-
cation, transdisciplinary and co-creational workshops. The focus in the first stage is setting parameters like objectives, the participants functioning, and skills- and capacity building. In the following three stages participants converge on a collective, desirable long-term vision. Next in stages 5 to 7 teams identify and converge collectively on specific product systems opportunities. Stage 8 concludes with the preparation for the next module ‘product system implementation’. Recommended is the Reference Model Cradle to Cradle™
An effective transformation requires a radical departure from current practice, engaging in a process of confronting, learning, and building a future vision by practicing interdisciplinarity and transdisciplinarity. Collective educational learning about how to build resilience instead of hanging on to sustainability, and understanding systemic circular thinking instead relying on analytical incrementalism will be discussed. The multi-disciplinary group of participants reflects diversified interest and provides the societal pluralism needed in this co-creative process. A positive-minded, creative thinking business outsider leads systems insiders as experts and a core team of business
Process ‘Transformation by Circular Design Process’ by Daniel Aeschbacher, epeaswitzerland (2023).
members and close partners. As much as realistic business parameters are required, such is the disruptive, radical, and imaginative permeability emerging in the process through iterative co-creation.
In stages 2 through 4 a desirable future scenario of life, set purposely for a longrange date, for example 2060, is worked out and visualized in collaboration with specialized designers.
Previous learnings about regenerative principles, Cradle to Cradle circularity and methods, Sustainability Development Goals etc. are being reflected with the help of various models. In iterative sessions of co-creation and creative frictions, validity of a collective acceptable future scenario is defined and agreed on in a final imaging which sets the direction and context for the next stages.
In stages 5 to 7 participants, once they agree on industry and branch, dive into the future vision. Through iterative circular workshops series of contextualized situations and stories, are being generated and documented with the assistance of artists and designers. These will be reflected and examined by various group constellations to seek extended scope of values and possible product systems
long-term product systems strategy, the gatekeeping for resilience of biosphere through positive products, it’s continuous infinite upcycling as resources, the use of renewable energy, building transformational skills and competence, while securing the ongoing transformation across all ecosystems.
‘Transformation by Circular Design Process’ is a tool and methodology positioned at the very beginning of any business design strategy. Its purpose is to define and build a long-term future vision through education and knowledge building and creative networking through sharing pluralistic perspectives. This mindsetchanging process establishes the navigational pathway towards the development of product systems based on truthful circularity, regenerating the lifeline ecosystems by abandoning the waste bin.
Companies, which have adopted a business strategy to be fit for the coming years by following a longer-term vision, defining product systems based on positive products (suitable for grandchildren), geared towards a growing sustainability conscientious consumer community recognize the need for important changes, that go beyond incrementalism. Experience shows over and over that willingness to foster changes is spurred by the top management, then companywide communication, before products and communication to the public follows.
in conjunction with business strategic thoughts. Further, systems dependencies and missing links in the product system identified. As this is key to this process, not problems but opportunities shall be listed, before examining impacts and further required actions.
The final stage of ‘Transformation by Circular Design Process’ ends with consolidating the results and preparing for the follow-up module ‘Product system implementation’ by prioritizing the action plan. Consolidation and prioritization include the positivity of its
The mind change is needed to reinnovate business at all levels based on healthy, suitable for “grandchildren products.” At epeaswitzerland we have been building a Network of Trust by epeaswitzerland™ with thousands of small and midsize companies globally, implementing such products. Over the past 3 years epeaswitzerland was appointed by MIGROS as expert for material health and product circularity to pre-evaluate the M-check for non-food products. MIGROS is the largest retailer in Switzerland with sales of CHF 29.9 billion (2020) to foster this change of mind followed with innovation in thousands of products and suppliers.
Being designed as front-end co-education and co-creative iterative tool,
‘Transformation by Circular Design Process’ is applicable to every industry branch and any company size. Conceived to trigger the process of mind-changing it opens towards innovation at all levels including business strategies. Typically, executives responsible for business strategy, purchase and supply chain, production, product design and marketing would be the first to participate in this workshop. This workshop based on educational input raises knowledge and broadens solution-oriented discussions.
It shall assist decision makers. It might show that more time is needed for further internal talks, or to move directly to the next round, the innovative track with the recommended follow up tool Cradle to Cradle™ Projects Reference Model.
References
• Guinée, J.B., Heijungs, R., Huppes, G., Zamagni, A., Masoni, P., Buonamici, R., Ekvall, T., Rydberg, T. (2011). Life cycle assessment: past, present and future. Environ. Sci. Technol. 45 (1) (2011) 90-96.
• Nebel, B. (2020). Cradle to Cradle, LCA and Circular Economy: a love triangle. Published NZ Manufacturer magazine. Retrieved from: https://www.thinkstep-anz.com/resrc/ blogs/cradle-to-cradle-life-cycle-assessment-and-circulareconomy-a-love-triangle/
• Guldmann, E., Bocken, N. M. P., and Brezet, H. (2019), A Design Thinking Framework for Circular Business Model Innovation, Vol. 7, No. 1, pp. 39-70
• Kirchherra, J. Piscicellia, L., Boura, R., Kostense-Smith, E., Muller, J., Huibrechtse-Truijens, A., Hekkert, M. (2017). Barriers to the Circular Economy: Evidence From the European Union (EU). online 30 April 2018, 0921-8009/ © 2018 Elsevier B.V. All rights reserved.
• Korhonen, J., Honkasalo, A., Seppälä, J. (2016). Circular Economy: The Concept and its Limitations. www.elsevier. com/locate/ecolecon (29.04.2020)
• Kopnina, H. (2018). Circular economy and Cradle to Cradle in educational practice. Journal of integrative Environmental Sciences, 15 (1), 119-134. https://doi.org/10.1080/1943 815X.2018.1471724
• William McDonough & Partners (1992). The Hannover Principles. Design for Sustainability. Prepared for EXPO 2000 The World’s Fair Hannover Germany. Published by William McDonough Architects.
• Daniel Christian Wahl (2016). Designing Regenerative Cultures. Axminster England. Published by Triarchy Press. epeaswitzerland....
• Fritjof Capra, Pier Luigi Luisi (2014). The Systems View of Life. A Unifying Vision. Cambridge UK, Published by Cambridge University Press.
• Latour, B. (2019). Down to Earth. Politics in the New Climatic Regime. Paris. First published by Éditions La Découverte; Reprinted Cambridge UK by Polity Press.
• Orr, D.W. (2004). Earth in Mind. On Education, Environment and the Human Prospect. Washington, DC, published by First Island Press.
• Princen, T. (2010). Treading Softly. Paths to Ecological Order. Cambridge Massachusetts, published by Massachu-
Daniel Aeschbacher is Swiss. He studied architecture, holds a Bachelor Degree of Science in Industrial Design from San Jose State University California (SJSU), a Master in Environmental Technology and Management, post graduate degrees in University Teaching and Societal Transition from DRIFT Transition Academy, Amsterdam. Between 1978-1980 he worked as architect with Max Bill, from 1980-1989 he studied Industrial Design at SJSU and worked with Hartmus Esslinger at Frogdesign in California. 1989, Ettore Sottsass, Milano Italy, invited Aeschbacher to work with him on numerous avantgarde projects as architect and designer. From 1990 to 1995, he was invited as guest lecturer at Europe Art Center College of Design in Switzerland. In 1991 he opened his design consultancy in Switzerland, practiced Product Design and Design Management, founded with partners Eurodesign in France, collaborated with partners in Zurich Switzerland and in the Silicon Valley. In 1995 he took on the mandate as design Manager at Plantronics Santa Cruz California and later at HewlettPackard, Grenoble. For his design works he received several international awards. From 2001 till 2022, Daniel Aeschbacher held teaching mandates at the Schule für Gestaltung Bern (SfGB), joined Design Management International (DMI) at Lucerne University of Applied Sciences and Arts (HSLU) in 2004. Until 2022 he was core team member and co-managed the curriculum development. As professor at DMI he has been in charge of all modules and courses about design, sustainability and circularity. In April 2022 Daniel Aeschbacher became a member of the epeaswitzerland team and network, in charge of professional educational modules.
setts Institute of Technology.
• Michaels, F.S. (2011). Monoculture. How One Story is Changing Everything. Canada. Published by Red Clover Press.
• McDonough, W., Braungart, M. (2002). Cradle to Cradle. Remaking the Way we Make Things. New York, published by North Point Press.
• McDonough, W., Braungart, M. (2013). The Upcycle: Beyond Sustainability - Designing in Abundance. New York, published by North Point Press.
• Cox, K. D., Covernton, G. A., Davies, H. L., Dower, J. F., Juanes, F., Dudas, S. E. (2019). Human Consumption of Microplastics. Published in: Environ. Sci. Technol. 2019, 53, 7068−7074.
• Fleischmann, K. (2013). Social Entrepreneurs and Social Designers: Change Makers with a New Mindset? James Cook University School of Creative Arts, Townsville, QLD 4811, Australia. Published in: International Journal of Business and Social Science.
• Loetscher, S.,Starmanns, M., Petrie. L. (2017). Changing fashion. The clothi9ng and textile industry at the brink of radical transformation. Environmental rating and innovation report 2017. Switzerland, published by WWF Switzerland.
• D’Itria, E.; Colombi, C. (2022). Biobased Innovation as a Fashion and Textile Design Must: A European Perspective. Sustainability 2022, 14, 570. https://doi.org/10.3390/ su14010570
• Williams, N., Collet, C., (2021) Biodesign and the Allure of “Grow-made” Textiles: An Interview with Carole Collet. Published by GeoHumanities, 7:1, 345-357, https://doi.or g/10.1080/2373566X.2020.1816141
• Fuad-Luke, A., Hirscher, A-L., Moebus, K., (2015). Agents of Alternatives and the Individual Contributors. Berlin, published by Agents of Alternatives.
• Eurotex, (2022). Facts and Key Figures of the European Textile and Clothing Industry. Brussels, published by Eurotex Economics and Statistics, The European Apparel and Textile Confederation.
• Heim, H., Hopper, C., (2022). Dress code: the digital transformation of the circular fashion supply chain, International Journal of Fashion Design, Technology and Education, 15:2, 233-244, DOI: 10.1080/17543266.2021.2013956. Link: https://doi.org/10.1080/17543266.2021.2013956
• Kouloumpi, I., Cunningham, G., Saliba, M., Papú Carrone, N., Cruz, R., (2022). Creating Circular Fashion Ecosystems. A Roadmap for Systemic Change. London, published by Circle Economy (commissioned by the British Fashion Council’s Institute of Positive Fashion (IPF).
• Montagna, G., (2015). Multi-Dimensional Consumers: Fashion and Human Factors. Published by Elsevier B.V. This is an open access article under the CC BY-NC-ND license (http://creativecommons.org/licenses/by-nc-nd/4.0/). Peer-review under responsibility of AHFE Conference doi: 10.1016/j.promfg.2015.07.954
• Plan Miljo. (2022). Synopsis Report on the consultation on The EU Strategy for Sustainable and Circular Textiles. Danemark. Retrieved from: www. planmiljoe.dk.
• Williams, D., Forst, L., Vladimirovab, D.,Evans, S. (2021). Building our worlds: Co-Developing Future Scenarios as a Methodology for Fashion Researchers and DesignerInnovators. Lancaster, published 14th EAD Conference.
• Chattopadhyay, S. (2019). Holding Space for Generative Conversations. Learning into Emergence. Published in Age of Emergence. Retrieved from: fhttps://medium.com/ age-of-emergence/holding-space-for-generative-conversations-78bcf9d9bf84 (15.07.2023)
• Warden, J. (2021). Regenerative Futures. From sustaining to thriving together. London, published by Royal Society for Arts, Manufacturing and Commerce.
• Design Council & The Point People. (2021). System-shifting design. An emerging practice explored. London, published by British Design Council.
• Schipper, M. (2019). Six designer changing the future of fashion. Retrieved from: https://nextnature.net/story/2019/bio-textiles (05.05.2023).
• Health Environment Justice. Sustainable Fashion. Retrieved from: https://sustainfashion.info/circularity/recycling/ (06.05.2023).
• Driesenaar, D., (2020). How to scale a regenerative business model. Retrieved from: https://medium.com/ swlh/how-to-scale-a-regenerative-business-model601a4d972cc8 (10.05.2023).
• Fullerton, J. (2015). Regenerative capitalism. How universal principles and patterns will shape our new economy. Stonington CT, retrieved from: https://capitalinstitute.org/ about-us/ (11.06.2023).
It is well understood in today’s society, that single use plastics can lead to dramatic global waste problems when ending up into the environment where they pollute oceans and land.
The responsibility on preserving the environment for next and future generations is close to the heart of Lenzing AG. Lenzing sees itself therefore in a pioneering task to bring forward LENZING™ Nonwoven technology (formerly known as LENZINGTM Web technology), a unique emerging spinning technology consolidating the full supply chain on Lyocell-based cellulosic nonwoven roll good production.
This technology platform can directly produce 100% cellulosic, certified biodegradable and binder free nonwoven materials using the sustainably sourced wood. This unique processing spins endless cellulosic filaments, which are laid down in a wet process directly into a web formation. The combination of the natural bonding of the filaments and further hydroentanglement allows to produce materials without the use of any finishes or binders.
The technology controls to control fabric properties like liquid management and fabric haptics by setting the filament diameter distribution and the amount of
filament binding (merging). LENZING™
Nonwoven Technology materials are characterized by their homogeneous filament distribution and high dimensional stability. It is currently scaled to a pilot scale which is capable to seed small markets in the basis weight areas of 15 to 100 gsm in roll widths up to 70 cm.
Due to the versatility of fabric properties which can be achieved with this cellulosic materials, a wide range of application fields can be covered, from cosmetic sheet masks, over durable nonwovens like filtration, the hygiene sector and wipes sector. For the wipes sector, this patented manufacturing process allows for adjusting the abrasiveness of the material in dry and wet state according to the required cleaning tasks. The inherent properties of cellulosic filaments naturally regulate liquid absorption and release. This leads to a fast uniform distribution of the liquid within the material, whether during converting or in use as a wipe. Especially in the wipes sector, Lenzing has come a long way by prototyping the final wipe in flow pack and canister application, being able to showcase unique fabric properties like the increased dimensional stability of the low elongating wet wipes.
The filtration sector can benefit from an adjustable air permeability within the
materials and the hygiene sector, like diapers or feminine pads, from an adjustable liquid distribution with this new technology’s material. Furthermore the fact, that the materials are binder and finish free, make them an ideal choice for personal care products.
The technology platform will be further enhanced through a wetlaid pulp technology integration to further broaden offered fabric properties such as softness and scale technology output. The pulp is thereby integrated solely over spunlacing into the Lyocell based carriers, creating binder free pulp composite fabrics. The produced fabrics can serve a broad application field as well, for example in wipes, absorbent hygiene products, durable nonwovens and filtration sector. They have, especially for the wipes sector, an increased soft touch versus the pulp free materials and show increased liquid spreading properties.
Lenzing is interested in co-developing material and optimizing the technology platform together with a partner. Currently, Lenzing is seeding small markets with commercial versions of these innovative materials. This will enable converters and brands to produce next generation sustainable nonwoven materials and test consumer preference.
Katharina Gregorich studied biotechnical engineering at the University of Applied Sciences, lower Austria and finished her master studies in 2010. Additionally, she graduated with a MBA in Innovation Management and Entrepreneurship in 2023. She started her career in Lenzing Fibers GmbH, Heiligenkreuz, Austria beginning of 2011 as a process engineer for Lyocell process and joined then an international program working on various Lenzing sites. In 2013 she joined Lenzing’s Global R&D department as project manager in the area of product development. Since a few years she is a member of the LENZING™ Nonwoven Technology team, leading the product development activities and is also responsible for market related activities. She is happy to be recently announced as part of the global fiber congress program committee.
• Advanced digital cutting technology
• Reliable cutting & kitting automation
• Superior workflow integration, productivity
• Maximum material yield
• Modular, versatile, adaptable
www.zund.com
Calcium carbonate is widely used for decades in rigid and flexible polymer applications and is, for example, a functional mineral modifier in sensitive products like hygiene breathable films. The use of calcium carbonate with a tailored particle size and particle size distribution is already known in polypropylene (PP) nonwoven applications1 and this article will highlight the advantages of using calcium carbonate in polylactic acid (PLA) and polyester (PES) fiber and nonwoven applications.
Given the sensitivity of the fiber spinning processes, partly linked to the denier of the fibers themselves, it is clear that a finely ground and highly pure calcium carbonate needs to be selected, in order to secure stable production. A strict control on larger residues and contamination is also required to meet the high-quality standards and durable performance requirements of the final articles.
Since calcium carbonate for polymer applications is typically commercially available in powder form and direct addition of powders during the fiber spinning extrusion process is not possible on commercial scale, first the development of suitable masterbatches is needed. The masterbatch can then be fed to the spinning extrusion line to achieve the desired target concentration of calcium carbonate in the fiber.
During the production of the masterbatch particular attention is needed
in securing the right dispersion of the mineral modifier in the polymer matrix. From a calcium carbonate perspective, the particle size distribution and surface treatment play critical roles for achieving excellent dispersion as they influence powder flowability and compatibility to the polymer matrix. Another important factor to consider is the temperature stability of the surface treated calcium
carbonate to avoid the formation of die build-up and deposits which directly lead to spinning disruptions and quality issues.
Polymers of the polyester family, like polyethylene terephthalate and polylactic acid, are also often sensitive to degradation by hydrolysis. The choice of surface treatment for calcium carbonate is therefore very important to minimize the natural hygroscopicity of the mineral. Various chemistries are available for coating calcium carbonate, a wise choice of functionality, as developed by Omya, can reduce humidity pick up and protect the polymer from degradation.
To validate the performance of the above mentioned surface treated calcium carbonate, extensive technical evaluations in PES and PLA nonwoven systems were done at well-known research institutes, e.g. the European Centre of Innovative Textiles (CETI, Tourcoing) in France and the Saechsisches Textilforschungsinstitut (STFI, Chemnitz) in Germany. For all the trials the surface treated calcium carbonate Omyafiber® 800 from Omya International AG, Switzerland, was used.
During the first trial, bobbins of 2 denier PES filaments were produced on the Hills melt spinning line at CETI adding calcium carbonate via a 50% concentrated masterbatch (Figure 1). As base resin for the fibers, the Invista grade RT 5140 was used and addition levels of 5% and 10% of calcium carbonate in the fi-
nal fiber were achieved. The fibers were stretched on 110˚C heated godets at a stretch ratio of 1:3 and the line was running at a final speed of 1490 m/min. No processing issues were highlighted during the trial which lasted for several hours.
Similar to what is seen in PP nonwovens1, the addition of calcium carbonate to PES fibers and nonwovens is significantly improving the whiteness, increasing the opacity and reducing the gloss, giving a more natural appearance and cotton like haptics to the fibers.
On top of reduced gloss, the effect of adding the treated calcium carbonate in a PES nonwoven is that of improved visual homogeneity and better coverage, as can be seen in Figure 2, where 50 GSM spunbond thermal bonded nonwovens with (right) and without (left) calcium carbonate can be compared.
Other solutions currently exist in the market to increase whiteness and opacity of fibers and nonwovens, the main one being titanium dioxide (TiO2). The carbon footprint of TiO2 is however quite high2 with a Greenhouse Gas (GHG) emission value of 4900 kg CO2eq/1000kg, compared to only 300 kg CO2eq/1000kg for surface treated calcium carbonate3. Considering a typical dull fiber formulation based on polyester an increase of +1.3% in GHG emissions over the value of the pure polymer4 would be expected by add-
On top of reduced gloss, the effect of adding the treated calcium carbonate in a PES nonwoven is that of improved visual homogeneity and better coverage.
bonate via 50% concentrated polyester masterbatch.
The data presented in Figure 4 show a typical bonding curve measured on a 50 GSM nonwoven. The darker colors represent the machine direction (MD) values and the lighter colours the cross direction (CD) values. The bonding temperature is reported on the x-axis.
ing 2% TiO2. If, instead, the same lustre is achieved by adding calcium carbonate, a reduction in GHG emissions is obtained, as shown in Figure 3.
Another advantage of adding calcium carbonate is expected when fibers and nonwoven are consolidated by means of heat, e.g. via thermal calendering or airthrough bonding process. Given the difference in thermal conductivity between polymers and calcium carbonate (Table 1), heat is indeed expected to transfer faster upon addition of calcium carbonate, enabling bonding at lower calender or oven temperatures.
To confirm these assumptions, trials were performed at CETI on their Hills spunbond and thermal calender system using Invista RT 5140 as base polyester resin and adding the treated calcium car-
In grey the tenacity of the nonwoven system without calcium carbonate at different calender temperature is reported, with its optimum achieved at 222.5˚C. On the right hand side of the graph, the bonding curve upon addition of 5% calcium carbonate can be seen (blue bars). Already at 205˚C excellent MD and CD values can be achieved, that can only be slightly improved by increasing the calender temperature up to 218˚C. The positive effect of calcium carbonate on reducing energy costs by reducing the bonding temperature without compromising on performance was confirmed in this pilot scale trial.
The second polymer system tested in combination with the surface treated calcium carbonate was polylactic acid (PLA). Before starting with nonwoven production, it was however important to validate that the masterbatch containing calcium carbonate received the certification of industrial compostability, since PLA is often the polymer of choice when
Amount extracted in water (mg/sqinch) < LoQ < LoQ
Amount extracted in heptane (mg/sqinch) < LoQ < LoQ
Organoleptic defect deriving from packaging –Olfactory test (odor assessment)
Organoleptic defect deriving from packaging in contact with food – Gustatory test (taste assessment)
it comes to industrially compostable applications. For this purpose, a sample of the masterbatch MB 165-CBN based on PLA and 65% surface treated calcium carbonate was sent to TÜV in Austria for validation and it indeed received the certificate approving the use of the “OK Compost Industrial” conformity mark.
We therefore proceeded with tests on PLA nonwovens systems, which were performed at STFI on their Reicofil 4 spunbond and thermal calender line. The PLA used were the 6100D and 6202D grades from NatureWorks Ingeo Biopolymer and the surface treated calcium carbonate was added via the TÜV approved, 65% concentrated masterbatch based on PLA. During the trial, 30 and 50 GSM nonwovens were produced with the addition of 5% and 10% calcium carbonate and results for the 50 GSM nonwoven based on PLA 6100D are reported in Figure 5. Like in previous graphs, the light colour represent the values in cross direction and the darker colors the values in machine direction. The nonwoven was bonded with a calender temperature of 150˚C.
As can be seen, a further advantage was confirmed when adding calcium carbonate with the appropriate surface treatment to PLA. Given the sensitivity of PLA to degradation and hydrolysis, the addition of an untreated calcium carbonate or of a calcium carbonate with an unsuitable surface treatment would have led to loss of mechanical performance, e.g. of tensile strength. Adding, instead, calcium carbonate with the appropriate surface treatment leads, as seen in Figure 5, to an improvement of tensile proper-
Odor intensity of sample significantly equal to the reference
Organoleptic defect intensity of sample significantly equal to the reference
From a regulatory perspective, the suitable surface treated calcium carbonate used in above studies is food contact approved according to U.S. Food and Drug Administration (FDA) and European Union regulations.
ties that is proportional to the mineral modifier concentration.
Similar results were seen on 30 GSM nonwovens as well as when using the Luminy L130 from TotalEnergies Corbion.
Last but not least, another interesting aspect of using the suitable surface
Odor intensity of sample significantly equal to the reference
Organoleptic defect intensity of sample significantly equal to the reference
treated calcium carbonate in polyester and PLA nonwovens is the significant improvement in process stability and the reduction of static charges leading to a safer material handling and production process.
From a regulatory perspective, the suitable surface treated calcium carbonate used in above studies is food contact approved according to U.S. Food and Drug Administration (FDA) and European Union regulations. When fibers and nonwovens are used as packaging components in contact with food, it is however also important that no undesired substances migrate into the food and that the organoleptics of the aliments are not negatively impacted. For this reason tests at Merieux Nutrisciences laboratory were performed with PLA nonwovens. For the taste and odor evaluation and the migration tests in water and heptane respectively the ISO 13302:2003 method and the FDA 21 CFR 176.170 were followed. The exposure of the PLA nonwoven to water and heptane was of 30 min at respectively 100˚C and 49˚C and the limit of quantification (LoQ) was 0.4 mg/sqinch for both. Results are summarized in Table 2.
The nonwovens had been produced on the Hills spunbond line at CETI and the surface treated calcium carbonate had been added to PLA (NatureWorks Ingeo Biopolymer 6100D) via a 65% concentrated masterbatch.
As can be seen, the addition of this specific calcium carbonate in PLA does not change the taste and odor performance of the packaged aliments, nor does it increase the level of migrated substances in food simulants like water and heptane. It
can therefore be recommended for use in food packaging applications like for example tea bags (Figure 6).
Next to food packaging applications, hygiene, personal care and textile applications also have stringent requirements when it comes to product safety. Samples of the surface treated calcium carbonate as well as breathable film samples containing up to 50% calcium carbonate were therefore shared with the Merieux Nutrisciences and the Senzagen Laboratory respectively for skin irritation patch testing according to the MP 1299 rev 4 2019 procedure and skin sensitization testing according to GARDskin assay methodology. Both tests gave the response of “no skin irritation” and “no skin sensitization”.
Considering that the final concentration of the treated calcium carbonate in PES and PLA fibers and nonwovens is lower than 50%, it can be concluded that the addition of the treated calcium carbonate is safe in use.
To conclude, the results of several fiber trials confirmed that the addition of calcium carbonate can have beneficial effects on the process and performance of polyester and PLA fiber and nonwovens.
References
1. M. Brunner, M. Knerr, L. Clapp, “Calcium carbonate enables sustainability in polymer fiber applications,” International Fiber Journal, Issue 1, 2021
2. TDMA (Titanium Dioxide Manufacturers Association) August 2021
3. Industrial Minerals Association North America, Fact Sheet, Life Cycle Analysis Calcium Carbonate
4. Eionet Report – ETC/WMGE 2021/3 “Greenhouse gas emissions and natural capital implications of plastics (including biobased plastics)”
5. https://matweb.com
The selection of the right surface treatment and the tailored particle size and particle size distribution enabled running several trials without issues like rise in pressure or formation of die build-up. A reduction of static charges as well as the opportunity to reduce calender temperature, without compromising on nonwoven performance, were demonstrated.
Especially in the case of PLA the mechanical performance of the nonwoven was even improved, thanks to the protective effect of the surface treated calcium carbonate on the polymer.
In polyester nonwovens, the improvements in natural appearance, brightness and haptics can pave the way to a more sustainable nonwoven solution for example in personal care or textile applications.
Last but not least, calcium carbonate has a very low carbon footprint and can be considered as a renewable raw material8 hence enabling production of more sustainable solutions. The specific surface treated calcium carbonate tested in this study is also food contact compliant and was proven to be non skin irritant and non skin sensitizing, making it a perfect solution for sensitive applications like for example hygiene, food and personal care.
NOTE: This development was done by Omya. Omya is a global producer of calcium carbonate for industrial applications. It is a privately owned Swiss company with more than 175 plants and own mineral deposits around the world. Omya implements sustainable business principles throughout the entire organization. More detailed technical results are available from Omya for further discussion.
6. O. Zmeskal, L. Marackova, T. Lapcikova, P. Mencik, R. Prikryl, “Thermal properties of samples prepared from polylactic acid by 3D printing”, AIP Conference Proceedings, 2305 020022 (2020)
7. M.D. Roussel, A.R. Guy, L.G. Shaw, J.E. Cara, “The use of calcium carbonate in polyolefins offers significant improvement in productivity”, 2005 PLACE conference proceedings
8. Calcium Carbonate Association – Europe, ”Calcium Carbonate is a Renewable Raw Material,” 2016, https://www.ima-europe.eu/sites/ima-europe.eu/files/ publications/Renewability%20Statement.pdf
Barbara Bonavoglia, Ph.D., earned a master degree in Chemical Engineering from Politecnico di Milano, Italy, and a doctorate in Polymer Chemistry from the ETH Zurich, Switzerland. Prior to joining Omya she worked for 16 years in Application Development for the Polyethylene Business of Dow Chemical, where she was responsible for the development of solutions for the hygiene, packaging and fiber markets. After 1 year as Marketing Director for the Hygiene Business at Berry Global, she joined Omya in May 2022 in the Innovation Department of the Polymer Business. She holds numerous patents and scientific publications in a variety of polymer applications. She can be reached at +41 62 789 2929 or barbara.bonavoglia@omya.com.
Martin Brunner is a Technical Service manager for polymer applications with Omya AG. He has a degree in Chemical Engineering. Prior to joining Omya, Brunner was employed by Ciba-Geigy and Ciba Specialty Chemicals in Switzerland where he focused on R&D for the company Plastic Additives Segment. He developed several successful commercial products for Ciba and Omya, and he has authored and co-authored several scientific publications and holds 30 patents and patent applications. He can be reached at +41 62 789 2411 or martin.brunner@omya.com.
Christophe Roux earned a Master in Physics and Chemistry of Materials with a specialty in Polymers completed by a MBA in Business Management from Grenoble University (France). In Omya since 20 years, he acted in various Sales positions before joining the group Sales and Marketing as Head of Market Development and Innovation Europe for Polymers applications in 2016. Prior to joining Omya he worked for 11 years for Multibase Company, a French compounder, in various positions as Pilot plant manager, Technical Service for Packaging applications, Sales and Purchasing. He can be reached at +33 6 80 41 44 75 or christophe. roux@omya.com.
The textile industry is seeing signs of growth as established and start-up players jockey for position in an instable world full of unknowns. Companies are up and down, focused on managing current offerings – and holding onto market share earnings – while carefully balancing rising costs to do business. Plus, some are investing heavily in farreaching research and development on “sustainable” growth initiatives.
What is painfully consistent industrywide, however, is the inconsistent use of the words sustainable, circular, biobased, and green – varying with interpretations and swayed by the light of unfolding perspectives on the future expectations on the industry. This, however, is not stopping the fast-moving sustainability train, engineered currently by the European Union’s Digital Product Passport initiative, among other EU initiatives.
Techtextil and Texprocess 2024 in Frankfurt, Germany is a leading trade fair for the apparel and textile processing industry hosted by Messe Frankfurt. What stood out was how technology will play a key role in future manufacturing, the growth of sustainability measures, and the rise in the number of suppliers of downright beautiful bio-based textiles that rival any natural or synthetic high-end material.
Detlef Braun, member of the executive board of Messe Frankfurt, noted that 53 countries and 1,700 exhibitors were in attendance. “We are stronger than ever. Today, we are celebrating the 20th Jubilee of Techtextil. It is larger than ever, with an increase of about 29% on Techtextil in comparison to the last edition, and a 27% increase on Texprocess.”
He also announced a new Vietnam International Trade Fair for Apparel, Textiles and Textile Technologies (VIATT) show in 2025, the Cinte Techtextil China
in Shanghai, September 19-21, 2024, and other niche shows, noting, “It’s about connecting people with ideas and people with opportunities.”
In the next 10 years, artificial intelligence (AI) has the potential to revolutionize sustainability and industrialization, according to the opening panel talk, “From textile recycling to garment processing –the role of AI.” Panelists were Chloé Salmon Legagneur, Director, CETIA; Prof. Dr. Ingo Rollwagen, AMD Akademie Mode & Design/Hochschule Fresenius, Senior Advisor IMP Consulting; Elgar Straub, Managing Director, VDMA Textile Care, Fabrics and Leather Technologies; and Olaf Schmidt, Vice President Textiles &
Textile Technologies, Messe Frankfurt (pictured above).
They highlighted four key dynamics: acceleration, amplification, emulation, and sustainable industrialization. AI will enable faster, better, and more innovative solutions, leading to a significant reduction in waste and an increase in the reuse of materials. There was optimism about AI’s potential to contribute to the sustainable development goals and sustainable industrialization, and potential applications such as tailored textile solutions, aerospace technologies, and medical segment.
Development will not stop with the amplification and reusing materials much more than today. Sustainability is also about resilience, and we will see industry not only do things faster and better, but we will do completely different things. We will be seeing textile solutions, which are much more oriented in different qualities, as well as different pricing.
Data is AI currency. Companies will need to have theirs in order, especially when it comes to workflow, which is easier said than done. Building a successful AI environment takes time. But once you have your data and the principal product passport established, companies will also be more competitive and profitable with smarter use of resources.
Collaboration across the supply chain will become more critical as data, automation and transparency become keys to doing business, as will talent development within organizations.
The panel agreed that the high expense of technology is a worthy investment to improve quality, eliminate waste, elevate competence, and boost overall competitiveness.
Interestingly, one Texprocess Innovation Award given in the “Digitization and AI” category is to Valvan, a company focused on improving textile recycling with AI. Less than 1 percent of used garments are reprocessed into new clothing. Recycling is complicated because garments often contain parts such as zips, buttons, labels, or elastic bands. Removing them requires a thorough sorting process, often still carried out by hand today. The Belgian company has developed a machine that automatically recognizes and removes non-textile parts from old garments.
How the idea for Trimclean came about is quite curious: the inspiration apparently came from quality control in the production of Belgian fries. “We asked ourselves whether a technology that sorts out faulty fries would not also be able to recognize non-textile parts in textiles,” says Jean-François Gryspeert, Sales & Business Developer at Valvan. “We use AI in combination with a special camera to better separate fabric parts from nontextile parts,” and can even remove patches, seams, and prints. “The AI technology making Trimclean possible did not even exist a few years ago,” says Gryspeert.
VDMA held an interesting “product passport – impact on the industry” panel, and included Andreas Schneider of Global Textile Scheme; Markus Reichwein of
The integration of digitalization and sustainability in the textile industry was discussed, with a focus on the importance of differentiating between standardized communication and information sharing. The need for trustworthy data sources was emphasized, as well as the potential impact of the European Union’s proposed Digital Product Passport (DPP) system on the value chain, which aims to streamline data exchange and processing for AI development. The importance of standardization, data sharing, and cooperation between companies to prepare for industrial automation is essential to the DPP success.
“The elephant in the room is how much of the supply line is effected,” says Andreas Schneider, noting that there is no joint data language. “We would need to change that,” and it is quite an undertaking.
Overall, data sharing from the customer level seems to be a potential obstacle, too, as companies do not want to share proprietary information. Customers are hesitant to provide data for the DPP due to concerns about competition and data
privacy, but may be willing to share data if it provides additional business value. Data requirements for sustainability are complex and time-consuming, but automating data exchange can ultimately save costs. Trust, as well as data quality and privacy, are essential for successful implementation.
Requirements are still unclear, but resources like the SURPASS Project[1] can provide guidance. Digitalization, data collection, and AI/machine learning can increase efficiency and sustainability in the textile industry if different stakeholders collaborate. Organizational structure within companies needs to support crossfunctional cooperation between departments like IT, sustainability, and supply chain management. And, the DPP represents both a regulatory challenge and opportunity – companies that can demonstrate sustainability leadership through data transparency may gain competitive advantages.
The panel agreed that DPP offers more opportunity not only for the supply chain, but for machinery manufacturers to provide new business models supporting systems designed for the digital product passport and to provide new services to make this system efficient.
There was much innovation to be seen at Techtextil. These companies caught the eye for their advancements.
SENSIL® – The nylon fabric company NILIT® launched a new Nylon 6.6 stretch fabric yarn to their line. The new “Flow” yarn offers comfort without elastane or spandex, and can loop back into the beginning of the textile production process, unlike apparel made with these blended fibers. In performance tests, it is shown to have very similar results as its blended counterparts. The hand feel of Flow is soft, strong, and beautiful for next-tobody garments.
Recycled apparel made with SENSIL® Flow reduces consumption of virgin raw materials, natural resource consumption, and the buildup of apparel waste in Earth’s ecosystems. “According to industry experts, more than 90 million tons of apparel end up in landfills each year,” says Michelle Lea, NILIT’s Chief Marketing and Sustainability Officer. “Only about a fifth of discarded clothing is reused or recycled. The SENSIL® Flow approach eliminates waste throughout the
production chain and enables brands to design apparel that lasts longer and, at the end of an extensive life, can be more easily recycled.”
Additionally, NILIT partners with recycling experts to facilitate the efficient recovery and recycling of fabric waste and post-consumer fabrics and clothing that would otherwise end up in a landfill or incinerator. These partners are expected to create high-quality recycled nylon chips that can be reintroduced into NILIT’s Nylon fiber spinning process, resulting in high-quality outputs, as well as other engineering plastics. Certificates will validate circularity and provide transparency and accountability for partners committed to building a circular textile economy.
Sensoptic – The newest technology, Sensoptic Vision, is the first system that allows you real-time detection and visualization of micrometric faults of round and flat targets with outstanding image quality. Its Profile Sensors PXL are mostly used in production machines of magnet wires, bare wires, fine cables, and extrusion lines of mono- and multifilament. Companies focused in delicate yarns,
such as medical sutures, can benefit from this technology to pinpoint defects and act accordingly.
Archroma – With the launch of Cartaseal® OGB F10, those seeking a coating with superior oil resistance will also benefit from a bio-based chemistry, and the ability to take advantage of the recyclability and repulping processes. “We are excited to introduce our latest barrier solution that addresses key challenges in the packaging industry while upholding our commitment to sustainability,” said Sameer Singla, CEO PP&C at Archroma. “With its unmatched oil and grease resistance, exceptional foldability, and sustainability features, Cartaseal® OGB F10 represents a significant advancement in packaging technology, empowering businesses to meet evolving consumer demands while reducing their environmental footprint.”
Andritz and Teknomelt – In 2021, the Andritz project was started to install a nonwovens production line supplied to Teknomelt Teknik Mensucat San. ve Tic. A.S., Kahramanmaras/Türkiye. The new state-of-the-art neXline wetlace CCP (carded-carded-pulp) line combines the benefits of two technologies – spunlace and wetlaid – and produces nonwoven roll goods for biodegradable, plastic-free wet wipes.
Production stalled due to a 7.8 magnitude earthquake in Türkiye on Feb. 6, 2023, at the center of the company’s production site. Tobias Schäfer, Vice President Sales, Nonwovens Division, Andritz, spoke about the respect he gained for the company’s resilient leadership as they continued the project in record time, all the while helping devastated employees find housing, food, supplies, and more in relief efforts.
Topp Textile – Believing hemp is the future, Topp set out to develop a hemp fiber knitting yarn suitable for automotive, garment, luxury and home goods. They found it difficult to purchase good quality hemp in China, and decided to cultivate their own raw materials.
Elvan Sentürk, Head of Application Projects, shared how Topp is co-founder and shareholder of Kender Cucc Kft, in Hungary, founded in 2022 to cultivate, grow and process small commercial scale hemp, in hopes to grow production for larger scale production. In 2022, 30 tonnes of hemp straw were spun into high-tenacity yarns. It is also investing to grow hemp in Germany to find the right business model.
The hemp yarn is strikingly whiter, unusual for the earthy hemp plant, and Topp’s hemp materials can also supply automotive interior composites, (seen in inset above), mattress toppers, and other goods to replace cotton, and provide the environmental benefits of hemp in manufacturing. Sentürk says, “We are confident it’s the right way for innovations,” as an alternative to cotton. The company is still far from commercialization, but is getting closer as it looks for new applications, with an eye on filtration at the moment.
says Scheizer, naNea is novel synthetic textile material designed to replace conventional polyester. naNea performs like conventional PET, but its novel polymer structure renders biodegradability in the open environment. It is flame retardant, hydrophilic, and boasts amazing hand feel. naNea is currently used in outdoor fashion with G-LOFT®, and has broad applications in sportswear, functional apparel, home textiles, technical and automotive applications.
SAFAK – Located in Istanbul since 1958, SAFAK is a family-owned third generation manufacturer of technical textiles. While they have strong textile roots, they are innovators at heart. The newest offering is Corium™ that rivals any true luxury leather for a plethora of applications, from shoe uppers to book covering to upholstery to jewelry. The materials are made
up of recycled man-made fibers combined with water-based PU. It is a never-beforeseen textile with material qualities similar to both technical fabrics and synthetic leather – yet entirely unlike anything currently on the market.
OceanSafe – Manual Scheizer, founder and CEO, shared about his high-grade recycled feedstock for polyester. As a Cradle to Cradle Certified® Gold yarn, “The first and only one in the world,”
Produced using a unique process developed by SAFAK, Corium™ is a family of single-layer homogenous textiles that serves as an entirely new fabric and developed as a sustainable textile requiring significantly less water in production and avoiding the use of chemicals currently under regulatory scrutiny. Products made with Corium™ are water repellent, hydrophilic, and flame retardant.
Simon Papo, the company’s president, was the mastermind behind its development, and says, “As a synthetic leather, you cannot tell the difference. We designed and built a new production manufacturing line to produce it, which is waterless, and very unique in itself.”
[1] https://www.surpass-project.eu. The EUfunded SURPASS project will lead the transition towards more safe, sustainable, and recyclable by design (SSRbD) polymeric materials for Small and Middle Enterprises in building, transport and packaging sector.
New developments in Printed Electronics (PE) and Flexible Hybrid Electronics (FHE) were shown at this year’s LOPEC held in Munich on March 5-7, 2024. This is a field of growing market significance for e-textiles, and smart composites with market applications across health and medical, transport, energy and industrial – essentially anywhere that electronics are conventionally being used. This review concentrates on transport, and the automotive in particular, from dynamic smart surface pattern to road safety to weight-saving and smart batteries. In some instances, fibers and textiles are already being used, while in
other examples there is strong potential for textiles to replace other flexible materials so that opportunities and barriers are discussed.
“The technology is already an integral part of vehicle construction today and is indispensable for the mobility of the next generation,” according to Wolfgang Mildner, General Chair of LOPEC and CEO of the consulting and technology company MSWtech. There are a number of attributes that appeal to the automotive sector such as the thinness and flexibility that brings a reduction in weight and allows them to be integrated more seamlessly coming closer to, or even onto the surface of the vehicle
interior. Design, color material finish (CMF), haptics, integration with textile and lighting are all combining to raise consumer and brand interest. There are now well established examples of PE and FHE in transport, from seat heating and occupancy sensors, to airbag control and surfaces with button controls giving way to a more streamline interface with touch functions.
Indicative of the strength of innovation in the automotive sector were two LOPEC awards given to the sector this year. The Public Choice Award at LOPEC went to EURECAT for their 3D HMI Automotive development that showcased an HMI just 3 millimeters thick. This al-
lows users to interact and communicate with a machine, software or intuitive system with integrated LEDs and capacitive sensors designed to be embedded into the central electronic control system of vehicles. The Best Publicly Funded Project went to Joanneum Research, Arkema Piezotech Innovation Lab and Rise, for their smart wheel energy autonomous sensor system for smart tires amongst other applications. The development
harvests mechanical motion and vibration from the environment, converting it into electrical energy using piezoelectric elements to power sensors and transmit data. These self-powered sensors are especially useful where they are needed in places that are difficult to access and where the use of batteries requires a high level of maintenance. The growth in rental e-bikes has led to a need to monitor bike conditions remotely. The smart tyre is particularly aimed at this market, as it can be used for the automatic remote monitoring of the pressure of bike
tubes helping to reduce maintenance costs and decrease energy consumption. The bicycle tube uses a thermoplastic polyurethane (TPU) found to be more robust and resistant in needle penetration tests than conventional butyl rubber. The pressure of the bicycle tyre affects ride comfort, puncture resistance, grip and rolling resistance. The latter impacting on the battery life. In the automotive sector tyre pressure monitoring is required by law. E-bikes are generally not classed in the same way as yet, however Alaska has classified e-bikes as “motor-driven cycles” requiring a license to operate one but not registration or insurance. In North America e-bikes are subject to the Energy Labelling Rule (16 CFR Part 305), that applies to electrical products
and appliances. This points to one of the challenges in compliance and standards for new products, showing that in addition to product area specific regulations, developers may also need to take account of additional directives directed at the product as a whole, a subset component or function.
There are 1.19 million fatalities on the road each year according to IEE, with 94% of these due to human error. According to the National Highway Traffic Safety Administration (NHTSA), 42,514 people lost their lives in car crashes in North America in 2022. In addition to the human cost, the financial burden is put at a staggering 3% of GDP for most countries worldwide. Regulations are driving the process of implementing both active and passive safety systems. The growth of autonomous or self-driving vehicles (SDVs) is expected to likely to increase safety according to NHTSA, however a recent British Government Transport Committee report on SDVs echoes wider public concern about their safety. SDVs allow for the driver to take their hands off the steering wheel. However, with Hands off Driving (HOD) functionality there has to be a clear distinction between when the vehicle and when the driver is in charge as there are instances when the driver is asked to take back control. The Automated Lane Keeping Systems (ALKS) is regulated by UN R157, and this includes
Arkema-Piezotech have developed piezoelectric polymer sensors for use in the structural health monitoring of composite hydrogen tanks. The French company specialize in a unique range of electroactive polymers.
IEE are using a flexible sensor mat integrated into the driver’s steering wheel to detect human contact with the wheel within half a second. Messe München
a “hands on” detection system to be in place as a key condition for the transition from automated to manual driving mode. IEE have used flexible and stretchable electronics integrated into the steering wheel of the vehicle to create a capacitive sensing system. This is used to monitor the presence of the driver’s hands on the steering wheel and control of the driving. It can be integrated into any steering wheel and is not impacted by additional technologies such as wheel heating systems. The technology has already been used in over a million vehicles.
Structural health monitoring is growing in importance for transport, and for aerospace in particular. Smart composites that can integrate sensors for continuous detection of impacts and cracks. Advances in manufacturing allow for sensors and actuators to be embedded reducing the number of assembly steps, materials and cost. There is an additional positive from an environmental point of view as the repair and maintenance extends the use phase of the aircraft.
The EU-funded Morpho is concerned with embedded life-cycle management for smart multimaterial structures. It is focused on developing a new generation of aeronautical structures around the three pillars of innovative industrial processes, foreign object damage and
environmentally friendly manufacturing. Fraunhofer IFAM with ten partners from six European Union countries, are undertaking research and development in engine components, with the program started in 2021 and scheduled for completion in September 2024. Their ambition is to endow engine fan blades with cognitive capabilities and to optimize their manufacture and lifecycle management. Embedded printed sensors, datadriven hybrid twin and machine learning technologies are all being employed.
Printed thermocouples are being used for temperature measurement and printed piezoelectric sensors for impact detection, both printed on carbon fiber reinforced plastic (CFRP) composites in lightweight components. There are three layers to the printed piezoelectric sensors. The top and bottom layers both with electrodes and the middle carrying a piezoelectric layer. Thermocouples type T (Cu-CuCuNi) are applied to the CFRP using an aerosol jet printing process. These are seen as particularly useful in monitoring temperature change in components that are difficult to reach such as aircraft parts and the engines.
Arkema-Piezotech have developed piezoelectric polymer sensors for use in the structural health monitoring of composite hydrogen tanks. The French compa-
ny specialize in a unique range of electroactive polymers. “Electroactive polymers are fine, lightweight and flexible, and can be integrated using simple procedures” according to Fabrice Domingues dos Santos, Head of Development for the Piezotech range, “They cost very little in terms of energy and offer infinite opportunities.” Looking to growth predictions of six million hydrogen tanks likely to be produced globally by 2030 (The Hydrogen Council), Arkema is developing a number of solutions that are aimed at improving the performance and the carbon footprint of hydrogen vehicles.
Their Elium liquid thermoplastic resin is being used with carbon fibers for the high-pressure storage of on-board hydrogen. This allows the polymerization to be carried out during the winding process avoiding the additional curing time required by traditional epoxy resins. This saves both time and energy with good recycling potential at the end of life. Keeping the tanks in use for as long as possible and guarding safety, the company have developed fluorinated electroactive polymers in their Piezotech range of materials. These are used as sensors embedded in the composite to provide continuous monitoring of the hydrogen tanks for shock, acoustic vibration and composite deformation.
Illumination in many forms was a focus at LOPEC for the automotive market in particular. Function and aesthetics were brought together as never before. “Light is the new chrome” one speaker quoted Klaus Bischoff, Chief Designer at VW that seemed to sum up the mood. However, it was the BMWi5 Flow Nostokana, a tribute to the 1991 Esther Mahlangu Art Car that gained attention at LOPEC. Challenging how the driver and spectator sees and considers surface pattern and color, the dynamic surface pattern is a collaboration with E-ink, using their latest E Ink Prism 3 color e-paper technology to demonstrate its capability as fully pro-
EU-funded Morpho project focused on embedded life-cycle management for smart multimaterial structures, shown here is the Aerosol Jet Printing of temperature sensors (Cu/ CuNi-thermocouples) on carbon fiber reinforced plastic (CFRP) being developed by Fraunhofer IFAM and partners from six EU countries.
Fraunhofer Institute for Manufacturing T echnology and Advanced Materials IFAM
grammable, low energy and durable. The 240 segments on the BMW I Vision Dee could display up to thirty-two different colors, with the potential for tens of thousands of pattern combinations. The latest BMWi5 Flow Nostokana has been outfitted with 1,349 segments each can be individually controlled to allow for even more color and pattern designs to be created.
Sustainability ran throughout as speakers and exhibitors addressed the question when discussing new developments. Use of raw material, design for disassemble, recyclability and energy were just some of the topics raised around this. There was much creativity and innovation, with E-ink a good example. The company is a member of The Climate Pledge and the Science Based Targets Initiative (SBTi), committed to achieving zero carbon by 2040. A mark of this progress is that they are the first display technology to receive the Dark Sky Certification from the International Dark Sky Association and in this way helping to combat and raise awareness of light pollution.
Dr. Marie O’Mahony is an industry consultant, author and academic, the author of several books on advanced and smart textiles published by Thames and Hudson. She can be contacted at marie.consultant@ gmail.com. https://www.linkedin.com/in/drmarie-o-mahony-94776836/
The Cellulose Fibres Conference 2024 was held in March at the Maternushaus, Cologne, Germany. Nova-Institute
an-made cellulosic fibers (MMCFs), which are most commonly derived from wood, account for a growing share – forecast at 8% in 2030 – of global fiber production, behind synthetic fibers, such as polyester, and cotton. With environmental awareness among consumers increasing, these bio-based materials are being used in a wide range of applications.
However, the European cellulosic fibers industry has been overshadowed in recent months by Swedish company Renewcell’s filing for bankruptcy in February after failing to secure sufficient long-term funding from its existing lenders and investors, including its biggest shareholder, H&M, to continue operations. Several bids have been received for the business and its assets.
Founded by innovators from Stockholm’s KTH Royal Institute of Technology
in 2012, Renewcell has developed patented chemical technology to recycle used cotton textiles and post-industrial waste into a premium-priced feedstock – a dissolving pulp called Circulose – for producing yarns such as viscose and lyocell, usually in blends with other fibers.
The company went public in November 2020, opening the world’s first industrial-scale chemical textile-to-textile recycling facility in November 2022, in Sundsvall, Sweden, with an investment of US$91 million.
Renewcell launched a strategic review in November 2023, after it emerged that demand for its recycled raw material was much weaker than expected. The company then managed to raise US$10 million in short-term funding.
Although it had major customers, including H&M, Inditex, Levi’s, PVH and Bestseller, to which it supplied Circulose from the items the brands sent in, Re-
newcell reduced its production capacity and slashed its workforce by 25%.
According to analysts, Renewcell’s bankruptcy has dealt a blow to efforts to introduce new, more sustainable materials to the market at scale. With overall demand for circular fashion still growing and new extended producer responsibility regulations coming into force, particularly in the European Union (EU), the rest of the textile-to-textile recycling industry is watching the situation carefully and hoping to learn lessons.
Meanwhile, Finnish fiber supplier Spinnova has launched a cost-cutting review and restructured its management team following disappointing financial results for 2023, which saw revenues tumble and losses mounting.
The company’s results show that revenue fell to €10.6 million last year, com-
With environmental awareness among consumers increasing, bio-based materials are being used in a wide range of applications.
pared with €24.3 million in 2022, while operating losses increased from €13.1 million to €20.9 million, and investment dropped to €9 million from €17 million.
Spinnova’s mechanical technology produces textile fibers from multiple raw materials from wood to leather, textile, agricultural, food industry and beverage waste, without using harmful chemicals. The Spinnova fibers are biodegradable and circular, and the company is committed to using only sustainable raw materials such as FSC-certified wood and waste.
Earlier, Spinnova signed a letter of intent with Brazilian pulp and paper
ing wood-based Spinnova fiber opened in 2023 in Jyväskylä, Finland. The Woodspin factory acts as an industrial demonstration of Spinnova’s technology and Suzano’s textile microfibrillated cellulose technology and is used for qualifying the process and fiber output to support the investment decision for the new facility.
Amidst this disheartening financial environment, the fifth Cellulose Fibres Conference held in March in Cologne, had its own challenges, including industrial action in the form of airline, airport and public transport strikes in Germany, and a short power cut on the second morning
manufacturer Suzano for a potential new production facility for wood-based Spinnova fiber. Spinnova and its partners will deliver the fiber production technology to Suzano, which will be the owner and operator of the facility.
The preliminary annual target capacity of the new facility is 20,000 tonnes of fiber, and it is likely to be located near an existing Suzano pulp mill. The pre-engineering phase is expected to commence in the second half of 2024.
Spinnova and Suzano have been joint venture partners since 2020 in Woodspin, whose first production facility produc-
of the event followed by a fire alarm test.
Nevertheless, the conference, organized by Germany’s Nova-Institute, attracted 214 participants and 23 exhibitors from 27 countries. Around 40 presentations demonstrated the growth and potential of the cellulose fibers industry, supported by the policy framework to reduce single-use plastic products, such as the Single Use Plastics Directive (SUPD) in Europe.
Leading international experts introduced new technologies for the recycling of cellulose-rich raw materials and gave insights into circular economy practices
in the fields of textiles, hygiene, construction and packaging.
Nova-Institute’s Asta Partanen, who was responsible for the content of the conference, said: “We received very positive feedback from the participants for the focus on cellulose fibers, the in-depth content and the good atmosphere as well as the many new contacts along the entire value chain.”
While fashion brands may not yet be quite ready to make the leap to adopting circular textiles, Łucja Wanicka of AFRY Management Consulting, Finland, explained that the MMCF industry has undergone rapid transformation in response to the growing demand for more sustainable fibers.
Since the early 2000s, and particularly over the past decade, there have been several new players entering the MMCF market, especially in China and South America, with existing players defending their positions by expanding capacities and integrating vertically into the largest manufacturing cost component for their fibers: dissolving wood pulp (DWP).
DWP has now been transformed from a specialty to a commodity product, she said, with wood costs and scale becom-
ing major drivers of competitiveness. And with DWP typically accounting for around 40% of the manufacturing costs of viscose, backward integration has been key for controlling costs. “There is increasing interest in using textile waste and agricultural residues as feedstocks for MMCFs; however, a technology gap still exists,” said Wanicka.
With the global population set to rise from eight billion to more than 10 billion by 2059, per capita fiber demand will grow. However, there are environmental concerns associated with increased consumption of synthetic fibers and cotton, noted Dr Sascha Schriver of the Institut für Textiltechnik of RWTH Aachen University, Germany.
MMCFs offer the potential to fill the cellulose gap, but with growing demand for renewable and sustainable bio-based fibers, alternative feedstocks and new technologies for their production are needed.
The biodegradability of cellulosic fibers offers the potential to avoid polluting the soil, river, lake and ocean environments with microplastics, although biodegradation of MMCFs is a “controversial” issue, admitted Jo-Ann Innerlohinger of Lenzing.
Discussing the biodegradability of cellulosic fibers through environmental and laboratory testing, Dr. Miriam Weber, a marine biologist and director of Hydra Marine Sciences, Germany, noted that a geotextile, which has to last for around three years to stabilize the ground, needs to be made from a slowly biodegrading material, whereas a wet wipe, in use for some 10 seconds, should be made from fast or very fast biodegrading materials.
Addressing the “cellulose enigma,” in which cellulose fibers have been seen to accumulate in the environment, she pointed out the influence of processing and treatments, such as cross-linking, bleaching, dyeing or antimicrobials, which could reduce the biodegradation rate or even hinder or “mask” the biodegradability of these fibers.
While consumer studies continue to demonstrate the need for wipes, based largely on convenience and transportability, the high level of plastics – typically 70-80% polyester with 20-30% viscose – has put these singleuse products under regulatory pressure, such as the EU’s SUPD.
Outlining biodegradable and compostable wipes and absorbent hygiene products, Rahul Bansal, head of the global nonwovens business of Birla Cellulose, India, explained that a number of plastic-free options have been developed, using various blends of viscose, lyocell,
Cellulosic fibers, especially cotton but also MMCFs, can be turned into a dissolving pulp-like feedstock for the production of new cellulosic fibers.
cotton and wood pulp, and modifications to wetlaid, airlaid and hydroentanglement technologies.
Plastic-free products that are both biodegradable and compostable are already available, but major brands have been slow to adopt these. “Regulators are pushing for the shift to plastic-free singleuse products,” he said. “Change is inevitable; either we as an industry drive this change or we will be pushed to change –or perish.”
According to the Ellen MacArthur Foundation, only 13% of all clothing is currently recycled and just 1% is recycled in a closed-loop system in which materials are recycled in similar or higher-value applications, noted Heli Kangas of Valmet Technologies, Finland. The recycling of post-consumer textiles, and therefore less reliance on virgin materials, represents a major challenge to the existing disposal methods of landfill and incineration.
While the overconsumption of textiles during the past three decades – largely due to the fast fashion industry that relies on cheap, disposable clothing that is produced quickly in low-wage countries and sold at low prices, then discarded after use – has led to growing amounts of waste, used textiles have been recognized as an important and plentiful material resource, although the proliferation of blends presents its own challenges.
Cellulosic fibers, especially cotton but also MMCFs, can be turned into a dissolving pulp-like feedstock for the pro-
duction of new cellulosic fibers, which offers an opportunity to introduce circularity into a currently mostly linear textile economy.
Michael Hummel of Finland’s Aalto University said textile waste is a multimaterial mix of different fibers and additives such as dyes and finishes. Pretreatment procedures such as bleaching are needed to separate the fibers and remove these undesired components. He presented strategies to recycle dyed cellulose waste to produce spun-dyed fibers that can be recycled without any loss in the dye intensity.
The production of cellulosic fabrics from agricultural waste and industrial by-products was again a feature of the Cologne conference, with presentations on the use of banana plant pseudostem, jute from imported coffee sacks, residual industrial hemp and other bast fibers, biomass waste streams, such as lignocellulosic waste from the food industry, and even used banknotes.
For the fourth time, Nova-Institute presented the Cellulose Fibre Innovation of the Year award at the conference. Sponsored by GIG Karasek, Austria, the award recognizes applications and innovations
that lead the way in the transition of the industry toward sustainable fibers.
The winning entry, voted on by conference delegates, was the Straw FlexiDress by DITF and Vretena, both from Germany – a knitted garment using HighPerCell filaments based on unbleached straw pulp.
Second place was the Honext FR-B board from Honext Material, Spain, a flame-retardant board made from 100% upcycled waste fibers from the paper industry, while TreeToTextile, Sweden was third with its “new generation of biobased and resource-efficient fiber.”
Next year’s Cellulose Fibres Conference will be held from March 12-13, 2025, again in Cologne and online. For further information, visit www.cellulose-fibres.eu
Geoff Fisher is the European editor of International Fiber Journal and editorial director of UK-based Textile Media Services, a B2B publisher of news and market reports on transport textiles, medical textiles, smart materials and emerging markets. He has more than 35 years of experience covering fibers and technical textiles. He can be contacted at gfisher@textilemedia.com or +44 7803 718443.
The future of technical textiles and nonwovens will be on display at Techtextil North America 2024, where textile professionals from across the nation unite for business networking and industry development. The event takes place August 20-22 in Raleigh, North Carolina, a city and state steeped in historical significance and one of the prime hubs for the textile industry.
More than 190 exhibitors are expected at the event, held at the Raleigh Convention Center, covering everything from Agrotech, Buildtech, Clothtech, Geotech, Hometech, Indutech, Medtech, Mobiltech, Oekotech, Packtech, Protech and, Sporttech. These segments will be broken down into categories, from research and planning to yarn, coatings, adhesives, technology and machinery, to name a few.
In addition to the exhibitors, there will be other venues where participants can learn and take the pulse on the industry.
Symposium: The highly acclaimed Symposium gives attendees the opportunity to listen and learn from industry leaders and subject matter experts as they discuss some of the most pivotal advancements in research and technology and shed light on the current global economic state and its effects across industries. Topics covered include Supply chain and risk management; High Performance Textiles and Sustainability
in a time where the industry is turning away from PFAS; Sustainability in textiles, Medical textiles, Military textiles, and student research projects, to name a few.
Student Posters: The Student Research Poster Program has become a must-see show floor attraction at Techtextil North America. Featuring the latest scientific developments in technical textiles, nonwovens, and sewn products design and manufacturing, the program attracts students from across the globe who are involved in both undergraduate and graduate-level research and textile innovation. Participating students will have a platform to share their research findings with peers and potential employers/sponsors on the show floor and could even be selected to present their research in front of a captive audience in the Innovation and Research Zone.
Tech Talks: There will be show floor tech talks on a series of educational discussions covering highly charged, solution-oriented sessions focusing on new technologies, and more. This is an opportunity to enjoy a unique blend of networking and knowledge-sharing, promising to elevate your industry engagement.
Innovation Awards: The Techtextil Innovation Award will be presented to honor exceptional performance in the fields of research, new materials, products and technologies as well as applications The awards have been designed to make cutting-edge developments visible, promote unconventional thinking and intensify dialogue between researchers, manufacturers and users.
Social Events: As usual there will be receptions after the show, popular for social networking. For those who want to learn more about the industry before and now, there is the The Museum, where visitors can view the history of textiles, presented by North Carolina State University. This is a great opportunity to see how it all began, from early pieces of machinery to cutting-edge technologies and the new phases of automation.
techtextil-north-america.us.messefrankfurt.com
CAMX – The Composites and Advanced Materials Expo to be held in San Diego, September 9-11, announced that Maurice Conti will be the keynote speaker for the CAMX 2024 General Session. Conti, a globally recognized futurist, innovator, and technology strategist, will bring his unparalleled insights and vision to the premier event for the composites and advanced materials industry. He is among the architects of the emerging technologies that are evolving humanity and the world around us: Artificial Intelligence, immersive reality (AR/VR/XR), advanced robotics and manufacturing, and technology for sustainability. He is a rare blend of hands–on practitioner and big thinker.
CAMX 2024 Steering Committee Chair Fletcher Lindberg said, “We are delighted to welcome Maurice Conti as our keynote speaker for CAMX 2024. I anticipate his message will provide inspiration and invaluable insights into the future of materials innovation and its impact on industries worldwide.”
Conti is a sought-after and trusted advisor to the leadership teams of global companies, including Amazon Web Services, Lululemon, Mercedes AMG, NielsenIQ, Ralph Lauren, and Blackline Systems, on how to think about and deploy AI for the benefit of people and business.
“I am honored to join CAMX 2024 as keynote speaker,” said Maurice Conti. “The composites and advanced materials industry plays a pivotal role in shaping our future, and I look forward to exploring the intersection of technology, innovation, and sustainability with industry leaders and innovators.”
Working at the intersection of disruptive innovation, emerging technologies, and the future of work, cities, mobility, and climate, Conti is a vocal champion for the creation of technologies whose foundations are rooted in positive, hu-
man-centered purpose. More than 12 million people have watched his popular TED talks, and his engaging speaking style, deep subject-matter expertise, and relatable insights are based on decades of work “in the trenches” with leading brands, including Nike, Tesla, Disney, Amazon, Airbus, and Ford.
CAMX 2024 will take place from September 9 – 12, in San Diego, bringing together professionals from across the composites and advanced materials ecosystem to network, learn, and collaborate on the latest advancements and trends shaping the industry.
CAMX is the largest, most comprehensive composites and advanced materials event in North America. With a robust education program and an expansive exhibit hall with hundreds of manufacturers, distributors, and suppliers. A panel of industry leaders will be there to discuss current projects within the industry that are pushing boundaries and leading the way with new processes and technologies. Visitors can hear how the latest innovations are changing the market and what that means for businesses.
There will also be a presentation of Technical Papers, Education Sessions and Poster Sessions. The latter is a competition that attracts the next generation of researchers, engineers and industry professionals from universities and organizations around the globe. Posters are presented during CAMX and are judged on overall presentation, significance to the future of composites and advanced materials, and their commercial application. Deadline for the Poster Session is June 1.
CAMX 2023 hosted a total of 5,700 attendees from 61 countries, with 125 technical presentations, and 42 posters.
www.thecamx.org
The world’s largest fiber innovation congress – Dornbirn-GFC –will dedicate this year’s event to Fiber Innovations, Circularity, Energy and Emerging Tech. The European show, held in Dornbirn, Austria, kicks off September 11-13, and this marks the 63rd event, dedicated to the fiber industry.
The fiber conference is poised to be a groundbreaking event that will bring together experts, innovators, and stakeholders from the global fiber industry. As the premier conference in the field, it aims to foster collaboration, share insights, and explore the latest advancements shaping the future of fibers and textiles.
One of the key highlights of the conference will be the lineup of esteemed speakers and panelists who will delve into a wide range of topics. From sustainable fiber production to cuttingedge textile technologies, attendees can expect thought-provoking discussions and deep dives into industry trends that are driving innovation and sustainability. More than 125 international speakers from industry and research will present their latest papers.
In addition, Dornbirn-GFC will offer young companies a stage for the fourth time as part of the 4th Innovation Days. In the exhibition area, visitors will find 25 important companies from the fiber industry. The presentation of the Young Scientist Award by Lenzing AG and the Paul Schlack Award in cooperation with CIRFS are planned and will provide insights into the research topics of the next generation.
Fiber innovations is the core focus, including all applications like apparel, home, automotive, technical textiles etc. Nonwoven applications alone show very high innovative potential and will be part of this group. Natural fibers like cotton,
wool and others will enrich the wholistic approach in the fibers space. Raw materials for the manmade fiber production like Pulp and upstream materials for synthetic fibers will extend this core pillar.
Circular Solutions & Recycling & Sustainability. Due to rising awareness of the climate change and the implementation of the “Green Deal”, “Sustainable Development Goals,” “ESG” and others, this pillar became enormously relevant over the years including:
• Sustainability in general for textiles and nonwovens
• New and upcoming sorting- and separation technologies
• Mechanical recycling and chemical recycling
Energy Solutions: As energy is becoming significantly important for the whole value chain in terms of costs and sustainability, there will be a strong focus on energy innovations at the next congress.
Emerging Tech: Topics around Digitalization, AI, Transparency and Traceability will get high influence in the value chain and thus open up new approaches in innovation. www.dornbirn-gfc.com
Loop Industries, Inc., a clean technology company whose mission is to accelerate a circular plastics/fiber economy by manufacturing 100% recycled polyethylene terephthalate (“PET”) plastic and polyester fiber, has concluded an agreement with Ester Industries Ltd., one of India’s leading manufacturers of Polyester Films and Specialty Polymers, to form a 50/50 India joint venture. The purpose of the India JV is to build and operate an Infinite Loop™ India manufacturing facility which will produce a unique product offering of lower carbon footprint recycled dimethyl terephthalate (“rDMT”), recycled monoethylene glycol (“rMEG”) and specialty polymers in India, using the Infinite Loop™ technology which offers significant advantages over traditional mechanical PET recycling. www.loopindustries.com
Suominen will strengthen its capabilities in sustainable products by enhancing and upgrading one of its production lines in Bethune, South Carolina, USA. The investment is made in line with Suominen’s strategy and supports company’s vision to be the frontrunner in nonwovens innovation and sustainability.
“With this investment we strengthen our position as the leader in sustainable nonwovens in Americas market and respond to the increased demand of environmentally friendly products. This investment also enhances our operational performance in terms of safety, quality and productivity,” said Tommi Björnman, President and CEO of Suominen.
The total value of the investment is approximately EUR 10 million and the investment project will be completed in the first half of 2025. www.suominen.fi
Australia-based Ansell announced it has entered into a binding agreement to acquire 100% of the assets that constitute Kimberly-Clark’s Personal Protective Equipment business {(KCPPE) for US$640 million.
The Acquisition is expected to complete by September 2024, subject to satisfaction of antitrust approval and other customary closing conditions.
Commenting on the Acquisition, Managing Director and CEO Neil Salmon said:
“For many years, we have assessed a combination with KCPPE as one of our most attractive acquisition opportunities and I’m delighted that we have now reached agreement with Kimberly-Clark that the optimal path forward for this business is under Ansell ownership.
The KimtechTM and KleenGuardTM brands we are acquiring and the experienced KCPPE business team behind them have strong reputations for quality and innovation built over many years of industry leadership. These are similar qualities to Ansell, however KCPPE has particular areas of strength across product portfolio, geographic position and sustainability differentiation that will meaningfully enhance Ansell’s overall position in the marketplace and customer differentiation.
Our existing footprint, in addition to our global organization and supply chain, creates the opportunity to generate significant synergy value from the acquisition while also enhancing our combined organic growth potential and we are excited about the benefits this will create for Ansell’s customers and shareholders.” www.ansell.com
NDA, the Association of the Nonwoven Fabrics Industry, announced three worthy recipients for the INDA Lifetime Service Award and Lifetime Technical Achievement Awards.
David Powling, Paul Latten and Arnold Wilkie are being recognized for their key contributions to the advancement of the nonwovens industry and INDA.
“It is our pleasure to recognize David, Paul, and Arnold with these well-deserved awards. INDA appreciates their contributions in advancing the nonwovens industry and being advocates for INDA,” said Tony Fragnito, INDA president and CEO. “These Awards honor individuals with long-established records of service and technical achievement. All three have given their best both personally and professionally to the nonwovens industry and INDA.”
Powling and Latten will receive their awards at the World of Wipes® (WOW) International Conference, June 18 beginning at 4:30 p.m. Wilkie will receive his award at the RISE® Conference, October 1 at 4:30 p.m. www.inda.org
MAS, the Swedish Textile Machinery Association, has become the latest Associate Member of the ITMF (International Textile Manufacturers Federation), which continues to expand as the international forum for the global textile manufacturing value chain. ITMF members include companies responsible for approximately 90% of global textile and apparel production. The Federation’s reach continues to be extended through ventures such as this year’s Annual Conference, which will take place in Samarkand, Uzbekistan, from September 8-10, alongside the International Apparel Federation’s 2024 Fashion Convention. This follows on from the highly successful 2023 ITMF Annual Conference which took place in Keqiao, China. TMAS members have a similar global perspective as the leading Swedish companies providing textile technology. www.itmf.org
TADVERTISING | SALES PUBLISHER Driven By Design LLC advertising@inda.media • +1 239.225.6137
Frank Strazzulla UNITED STATES franks@tmsmedia.net • +1 949.459.1767
Sabine Dussey GERMANY, FRANCE, AUSTRIA, SWITZERLAND, SCANDANAVIA, BENELUX sabine.dussey@dussey.de • +49 2129.348390
Joan Oakley BUYER’S GUIDE & CLASSIFIED ADS joakley@inda.media
Silvera & Filippo Silvera
Zhang Xiaohua CHINA ifj_china@126.com
INDA, the Association of the Nonwoven Fabrics Industry, announced the three finalists for the World of Wipes Innovation Award®, to be presented at the World of Wipes® (WOW) International Conference, June 17-20, at the Hyatt Regency Minneapolis in Minneapolis, Minnesota.
The three products vying for this Award are multi-purpose cleaning wipes from Kimberly-Clark Professional, a bio-binder technology from OrganoClick, and facial care wipes from Rockline Industries. The winner will be announced on Thursday morning, June 20th.
The three companies competing for the Award are:
Scott® Xtreme Multi-Purpose Cleaning Wipes by Kimberly-Clark Professional: Scott® Xtreme Multi-Purpose Cleaning Wipes are great for tackling extreme cleaning tasks, like removing oil, grease, grime, paint, adhesives, caulk, and more, yet are gentle enough to clean hands. Featuring a patented citrus cleaning solution, the dual-action cleaning fabric incorporates a textured side to increase scrubbing action for cleaning tough soils and a smooth side for wiping surfaces clean. Scott® Xtreme Multi-Purpose Cleaning Wipes are truly a must-have for any DIY job and cleaning on-the-go.
OC-Biobinder® Lily1450 by OrganoClick: OC-Biobinder® represents a series of bio-based and biodegradable binders
intended for the nonwoven and paper industry. They are produced from renewable raw materials and residual streams from the food industry and replace traditional fossil-based plastic binders. OCBiobinder® is available with many different properties adapted to the production of home compostable nonwoven materials such as premium napkins, table cloths and wet wipes.
Facial Care Wipe with Glycine Amino Acid Complex by Rockline Industries: Rockline has innovated a new Skin Care Wipe containing a unique multifunctional complex of two medium chain glycine, a phospholipid and a blend of special glycol ingredients that provides for a multitude of skin care benefits as well as providing a unique preservation system for nonwovens. The Skin Care Wipe provides substantiated improved skin smoothness, elasticity, and hydration alongside an anti-ageing claim. This innovation is amongst the first to use these unique glycine ingredients in a Skin Care Wipe formulation.
INDA’s Technical Advisory Board selected the finalists based on the creativity, uniqueness, and technical sophistication employed in finding novel ways to expand the utilization of nonwovens. Categories considered for the award were wipes-related raw materials, roll goods, converting, packaging, active ingredients, binders, additives, and end-use products. For more information or to register for WOW 2024, visit: www.worldofwipes.org
PET/PBT/PBAT/PBS/PTT/PLA/PETG/PC/PA6/PA66..
POLYMER: Physics / Chemistry
BDO/EG/MeOH/Heat recovery and comprehensive u�liza�on
HP
Hydrogen Peroxide, H2O2
Own R&D Center and pilot plant R&D
Project EPC Contrac�ng (Turn-key)
POLYTEX is a professional chemical engineering company and technology supplier integra�ng R&D, engineering, equipment manufacturing, procurement and EPC management services. From technology licensing, project planning, equipment manufacturing and engineering design, procurement and construc�on management, as well as start-up and opera�on services, Polytex provides diversified services and one-stop solu�ons to customers all over the world.
POLYTEX ENGINEERING GROUP
Corp: 5th Floor, No.20 Wenchang Mid Rd. Yangzhou, Jiangsu, PRC.
Head: No.1, Private Industrial Park, Yuetang, Yizheng, Jiangsu, PRC.
Tel: +86-514-85553618; +86-514-87859276
Mail: market@polytex.cc; polytex@vip.sohu.com
Website: www.polytex.cc
Bo�le grade, Tex�le grade, Film grade PET chips will be launched soon. Our own factory capacity in phase-1st will reach up to 1260 tons per day.
China Sales:
Mr Sun Mob: +86-133 1990 0139; Email: sg_sun@e-plastmer.com
Mr Cao Mob: +86-181 5290 1436; Email: cao@e-plastmer.com
Ms Pu Mob: +86-185 0992 5214; Email: pu@e-plastmer.com
Russia and Central Asia Sales:
Mr Li Mob: +86-189 5105 3772; Email: �ger@e-plastmer.com
Mr Gao Mob: +86-138 5159 0251; Email: gaocx@e-plastmer.com
Mr Dos Mob: +86-135 1991 0418; Email: dos@e-plastmer.com
Other markets:
Ms Emma Mob: +86-158 9939 1075; Email: emma@e-plastmer.com