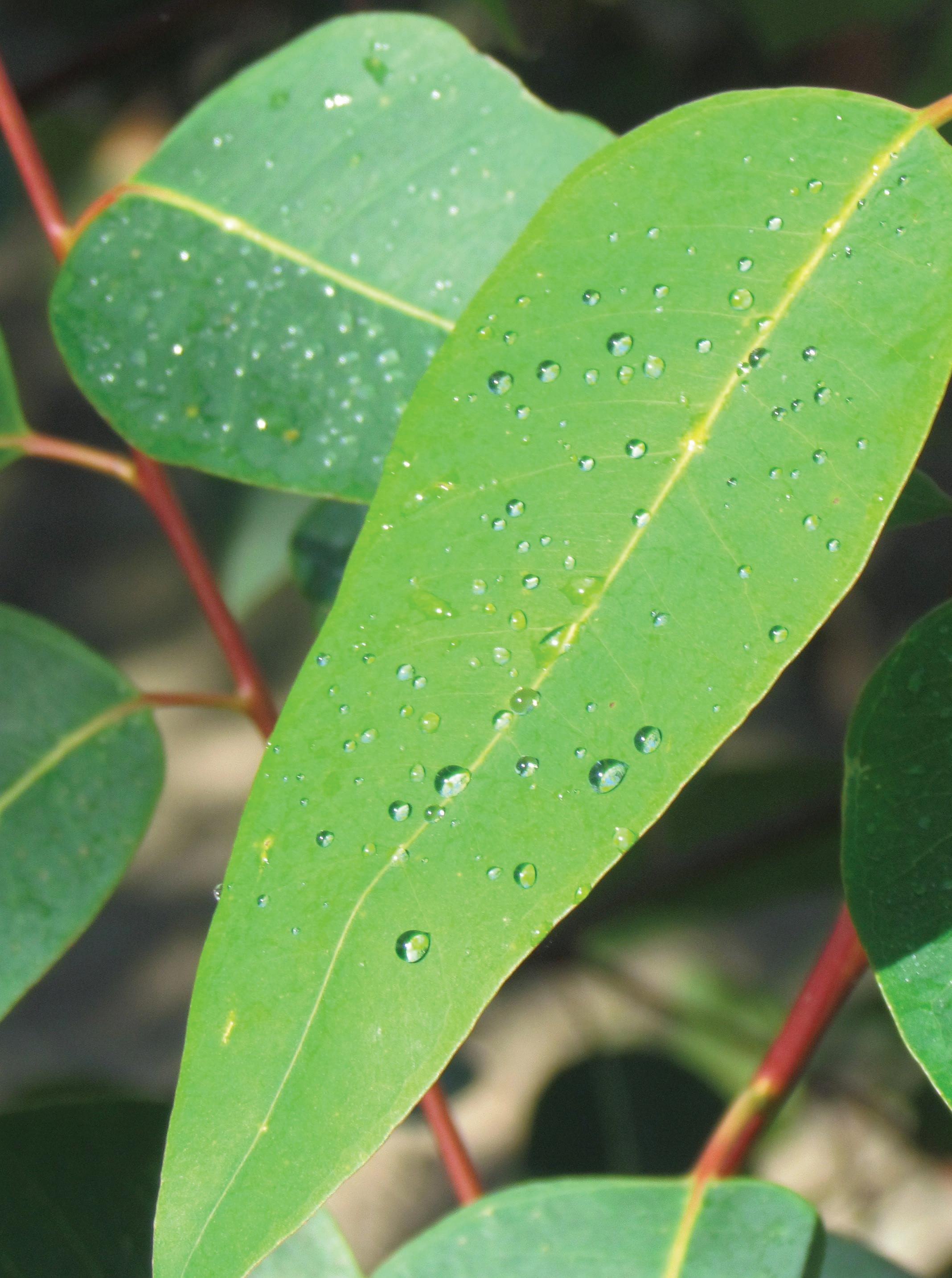
TSA TACTILE SENSATION ANALYZER
An instrument to objectively measure the overall haptic quality of nonwovens.
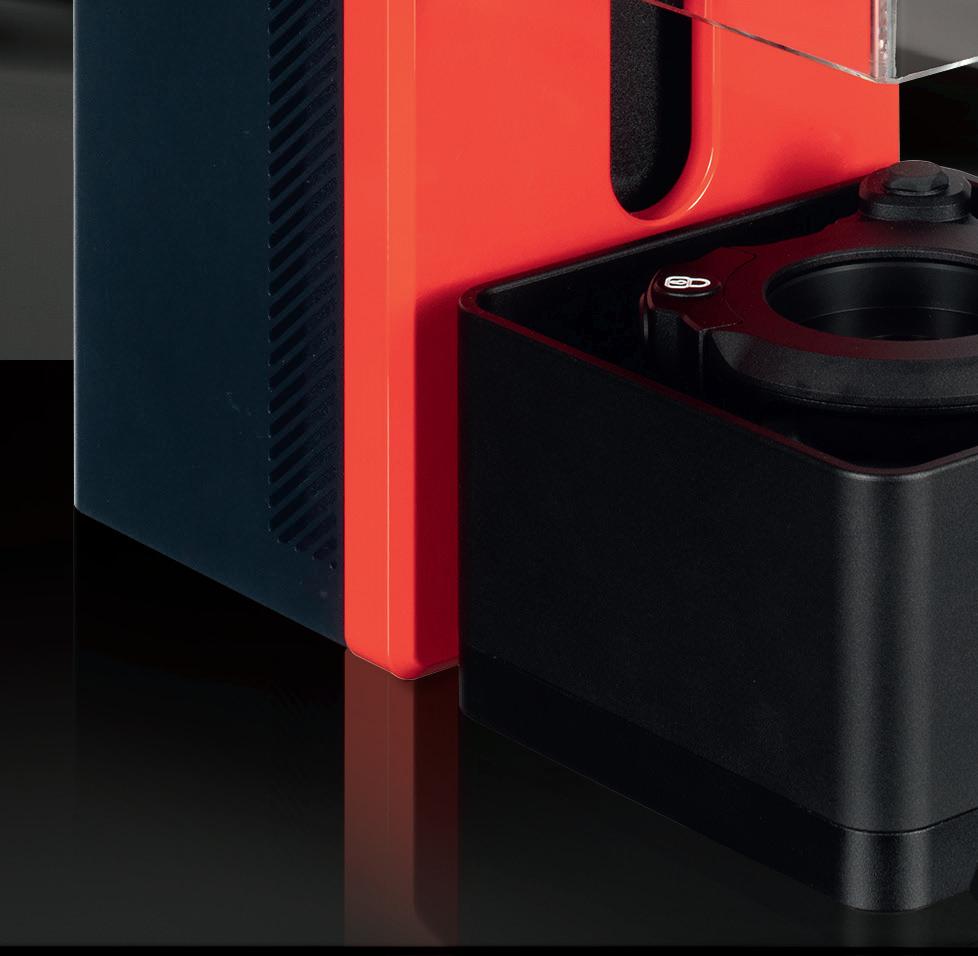

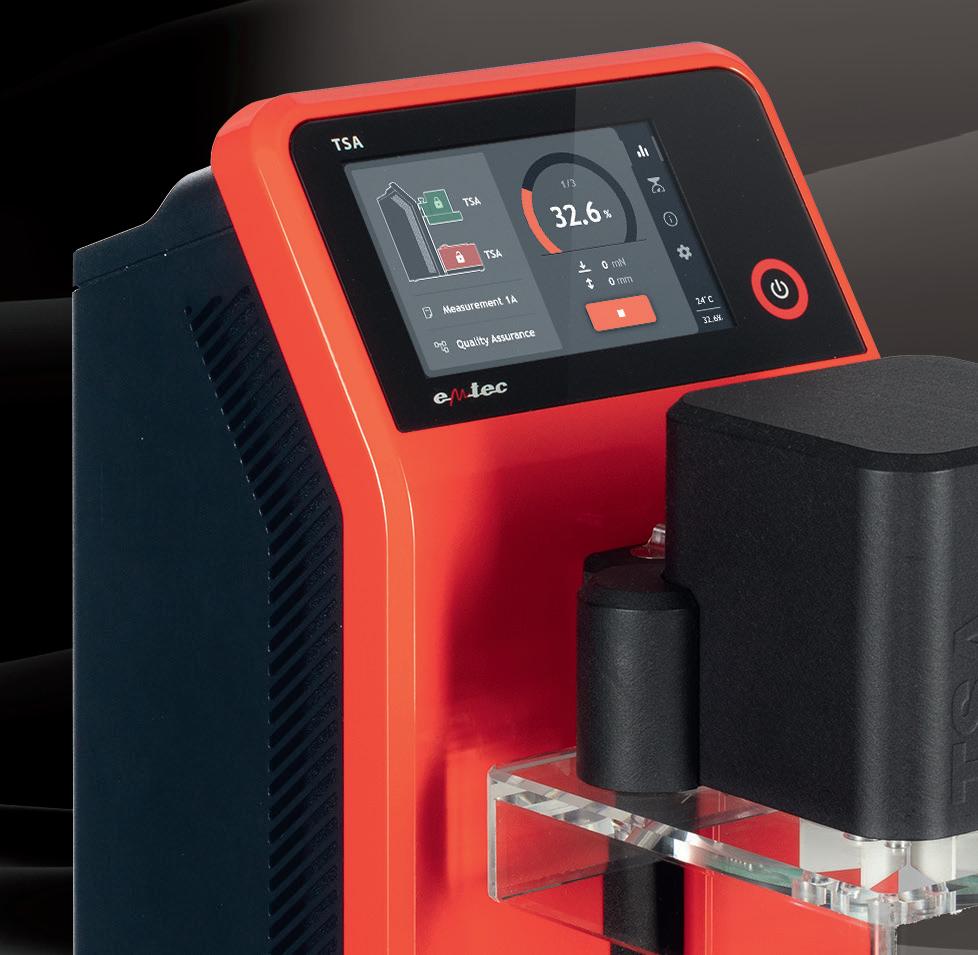



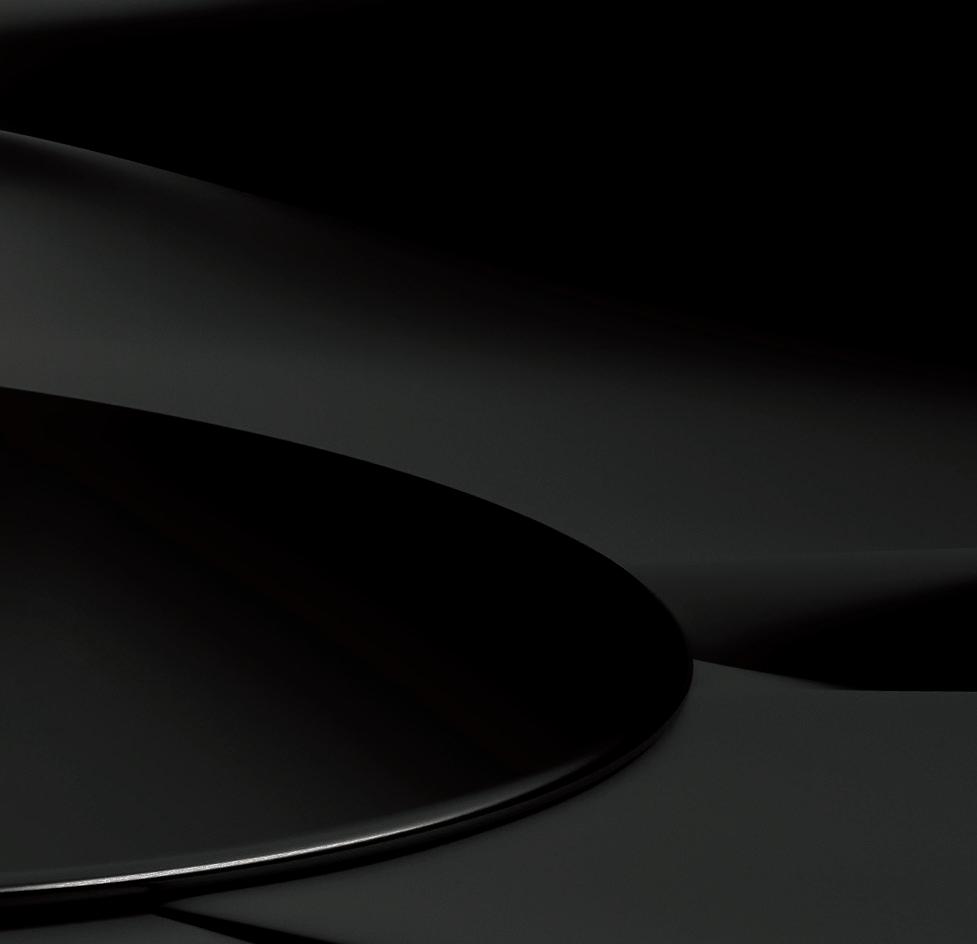


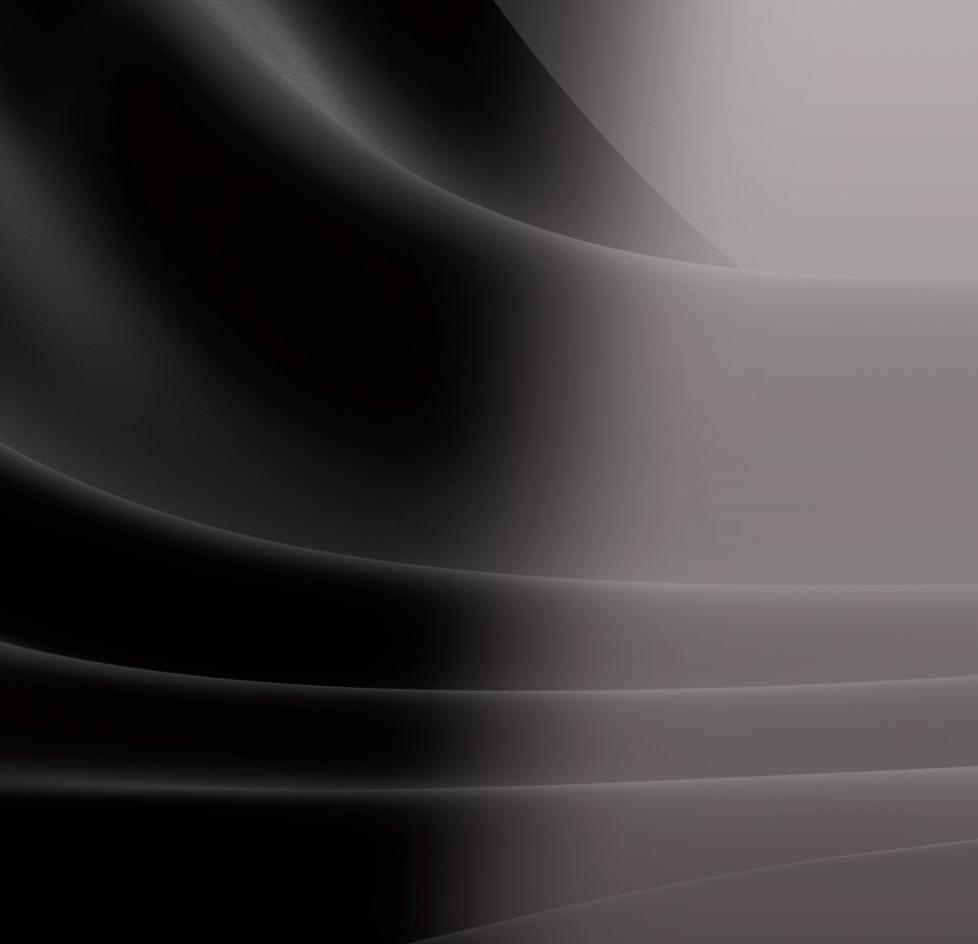
Officially unveiled
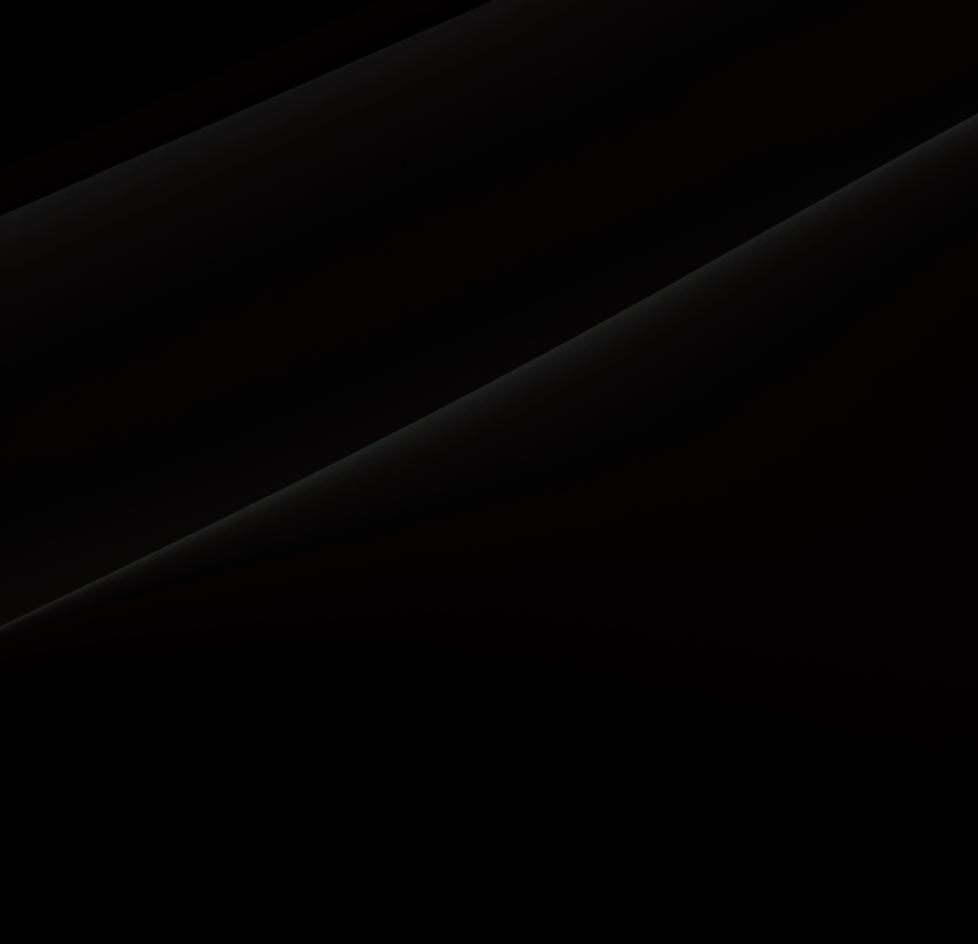
@ World of Wipes, Atlanta, USA www.emtec-electronic.de
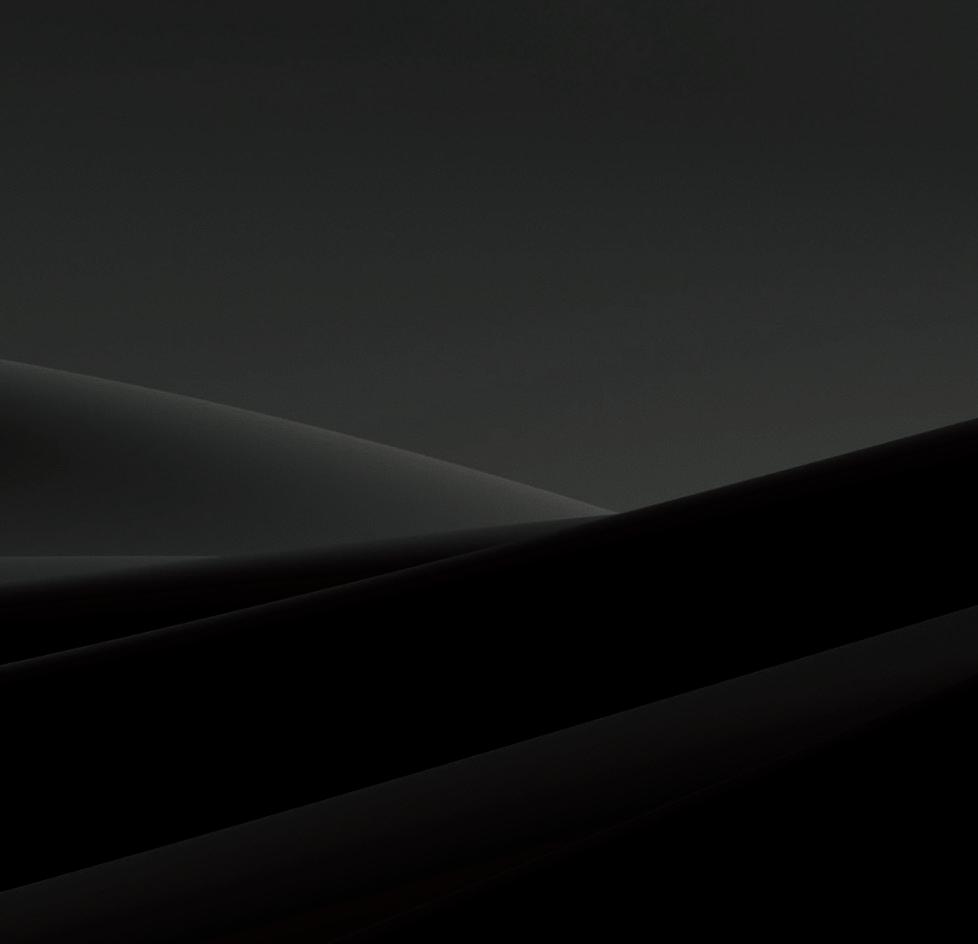
An instrument to objectively measure the overall haptic quality of nonwovens.
Officially unveiled
@ World of Wipes, Atlanta, USA www.emtec-electronic.de
Objective measurement of:
•
softness
available in 2024
with new design and new features!
•
smoothness
•
flexibility + elasticity
•
recovery behaviour
New: thermal conductivity
+ + +
(warm vs. cold handshake)
high resoluted image friction
=
hand feel calculation is possible
Some features are associated with extra costs.
2023
13 18
Solution Center: Chase Machine & Engineering –Custom Converting Equipment
Showcasing solutions for success
A Fortunate Fiber
Executive Q&A with Ananas Anam
By Caryn Smith, Chief Content Officer & Publisher, IFJ
Show Preview: World of Wipes –Seizing Opportunities for Change
Slogan or Substance –Made in America
By Marie O’Mahony
Recycling Conundrum
By Adrian Wilson, International Correspondent, IFJ
Cellulose Fibers Fill the Cotton Gap
By Geoff Fisher, European Editor, IFJ
Technically Speaking
By Chris Plotz
Emerging Frontier
By Adrian Wilson, International Correspondent, IFJ
Recognition: Collaborating on a Career of a Lifetime
6
Viewpoint Recycling … It’s Complicated
By Caryn Smith, Chief Content Officer & Publisher, IFJ
Tech Spotlight
Swedish Textile Machinery Transforming Dyeing and Finishing at ITMA 2023
Tech Notes
New Technology Briefs
Tech Talk
Functional Advanced Textiles: Way Forward Dr. Seshadri Ramkumar, Ph.D., Texas Tech University
The Fiber Year
TFY 2023 – Three-Year Loss of 19 Million Tonnes of Fibers
By Andreas Engelhardt, President, The Fiber Year, GmbH
M&A Insights
The Transfer Portal
By Len LaPorta, Managing Director, Wiley Bros.-Aintree Capital, LLC
Movers & Shakers
Industry News and Notes
We are making the best synthetic textile facilities through the power of Korea in global competition
Applications
Multi Filament Line(PA, PET, PP, Bi-Component)
- High Speed Spinning(POY, FDY, SDY)
- Micro Fiber Spinning
- Bi-Component Conjugate Spinning
Staple Fiber Line
• Industrial Yarn
• Textile Yarn
• Sewing Yarn
• Carbon Fiber
• Lyocell
• Aramid Fiber
• Acrylic Fiber
• Spandex Yarn
Chief Content Officer & Publisher, INDA Media
csmith@inda.org +1 239.225.6137
Visiting Professor, RCA, London https://www.linkedin.com/in/ dr-marie-o-mahony-94776836/
Adrian Wilson International Correspondent, IFJ adawilson@gmail.com +44 7897.913134
Geoff Fisher European Editor, IFJ gfisher@textilemedia.com +44 1603.308158
Director of Technical & Business Development, MiniFIBERS, Inc. cplotz@minifibers.com +1 423.282.4242
Seshadri Ramkumar, Ph.D.
Nonwovens and Advanced Materials Laboratory, Texas Tech University s.ramkumar@ttu.edu
Andreas Engelhardt President
The Fiber Year GmbH engelhardt@thefiberyear.com +41 7145.00682
Len
Managing Director of Investment Banking Wiley Bros.-Aintree Capital llaporta@wileybros.com +1 615.782.4107
“Often when you think you’re at the end of something, you’re at the beginning of something else.”
R– Fred Rogers, Television Personality ecycling and sustainability is my thing. In my career, I have worked with industries that focus on the three Rs – Reduce, Reuse, Recycling, in that order. The goal for recycling-minded industry is always to reduce the “footprint” first, then reuse as much as possible, before recycling (and hoping that the object is responsibly handled in second- or third-life situations).
I have tried to live up to this standard to the best of my ability.
At home, the recycling struggle is real. It took me forever to train my family to separate plastic from soiled waste in our personal trash. I still have to sort it, and I do this even though I know my local waste facilities report being overwhelmed with recycled materials, which are likely not recycled.
A 2022 article in The Guardian shared that according to a Last Beach Cleanup and Beyond Plastics report, the recycling rate for post-consumer plastic was just 5% to 6% in 2021. The Department of Energy also released a research paper, which analyzed data from 2019, and came to the same conclusion, only 5% of plastics are being recycled. Researchers reported “that landfilled plastic waste in the United States has been on the rise for many reasons, including ‘low recycling rates, population growth, consumer preference for single-use plastics, and low disposal fees in certain parts of the country.’”
Around the world it is not much different, or it’s even worse. The U.S. used to sell and ship recycling waste to China, but that ended with China’s 2017 waste import ban. Their waste issue has soared.
I also donate to local charities that sell goods to fund their mission. But the facts on this are also staggering. A whopping 84 percent of our donated clothing ends up in landfills and incinerators, according to the U.S. Environmental Protection Agency.
We all know that if the clothing is synthetic, it is not biodegradable, and eventually will release micro-plastics into the environment.
Some charities that accept home goods have gotten extremely picky, rejecting any damaged goods. So, more and more items are heading directly to landfills. It is overwhelming, don’t you think?
Early in my career, a trip overseas to visit a friend living in a very small town outside of Amsterdam was eye opening. They shopped daily at the grocery for that day’s food. They washed their dirty dishes; but didn’t run water to rinse them, instead using one pan of water. Their showers had pull cords to only release water when it was needed. Furniture and décor were modest, and “vintage.” Vehicles were mostly fixer uppers; nothing like in America.
Maybe it wasn’t a typical town; but maybe they had it right.
I feel like I personally cannot change the way things are. Maybe this is how everyone feels, ineffective to help clean the earth of harmful debris. Maybe we are waiting for others to fix it, or when it is more economical to do so.
Yet, I can’t help but feel responsible for the world I am leaving for my children.
Recently, I attended INDEX 23. One presenter, Pontus Lindstedt from Molnlyke, a Swedish healthcare solutions provider, said something that struck home. He said, “Another way must be possible.” His company is working toward viable options to reduce medical waste.
Maybe more of us just need to adopt that mindset, and ask ourselves, “WHAT other way is possible?”
If you have thoughts on this, I would love to hear them. Email me at csmith@inda.org.
CORRESPONDENT, EUROPE Adrian Wilson
ADVERTISING | SALES
PUBLISHER Driven By Design LLC advertising@inda.media
+1 239.225.6137
BUYER’S GUIDE Joan Oakley
CHINA Zhang Xiaohua
EUROPE & INDIA Sabine Dussey
ITALY Ferruccio & Filippo Silvera UNITED STATES Frank Strazzulla
ADVERTISING COORDINATOR Vickie Smead vsmead@inda.org
+1 919 459 3700 x 3720
AUDIENCE | CIRCULATION
CIRCULATION
FILAMENT
Two members of the Textile Machinery Association of Sweden (TMAS) – are at the forefront of a brand-backed revolution in replacing water and energyintensive technologies for the dyeing and finishing processes that will take center stage at this year’s ITMA exhibition in Milan from June 8-14, 2023.
“There are currently an estimated 90,000 jet dyeing machines in operation worldwide and between 60-70% of them are outdated to a factor of two-to-three in terms of the savings in energy, water and dyes and finishes that can be made – even with the latest conventional systems,” says TMAS secretary general Therese Premler-Andersson. “That productivity gap is considerably higher when considering the latest highly digitized and precise non-contact spray systems for these processes that have been introduced to the market by TMAS companies Baldwin and imogo in the past few years.”
Baldwin’s TexCoat G4, a non-contact spray technology for textile finishing and remoistening engineered and manufactured in Sweden, not only reduces water, chemicals and energy consumption, but also provides the flexibility to adapt to a customer’s requirements in terms of single and doublesided finishing applications.
It is designed to allow a controlled and optimal coverage of the exact amount of finish chemistry for reaching specific characteristics of the fabric through a combination of precision valve technology coupled with optimized software algorithms
to ensure accurate and even finishing coverage with virtually no waste.
TexCoat G4 can reduce water consumption by as much as 50% compared to traditional padding application processes. In today’s world of volatile energy prices, imagine cutting gas and electricity costs by 35-50%. Productivity is also increased by 50% because of the lower wet pick up which allows for higher line speeds. Putting it simply, for replacing every 2-3 pads with a TexCoat G4 is equal to adding the productivity of an additional finishing line at a fraction of the cost, with no additional floor space and no added labor.
“Traditional textile finishing by padding is a wasteful, antiquated process,” says Rick Stanford, Baldwin’s VP of global business development. “High pick-ups drive high energy consumption and frequent bath changes generate a lot of avoidable chemical waste. Brands and mills are thankfully now starting to see environmental and economic benefits with the help of our non-contact precision spray systems. These systems increase product quality, improve mill profitability and deliver quantifiable sustainability benefits.”
Similar impressive savings can also now be made in textile dyeing with imogo’s Dye-Max spray dyeing technology.
It can slash the use of fresh water, wastewater, energy and chemicals by as much as 90% compared to conventional jet dyeing systems as a result of an extremely low liquor ratio of 0.6-0.8 liters per kilo of fabric. At the same time, considerably fewer auxiliary chemicals are required to start with.
The application unit of the Dye-Max consists of a closed chamber containing a series of high speed digitally controlled valves with precision nozzles for accurate and consistent coverage.
Fast changeovers with virtually no waste together with a high production speed enable a high productivity and unmatched production flexibility.
At ITMA 2023, the proven Mini-Max laboratory unit – used alongside Dye-Max installations for pre-determining application volumes and color matching for Right First Time dyeing – will demonstrate the principles of imogo’s technology.
The huge potential of Dye-Max has been quickly recognized by brands seeking solutions to their sustainability targets and an industrial-scale installation is currently being commissioned. Further details will be announced prior to ITMA 2023.
www.tmas.se
For details on how to submit your company’s technology for consideration as a “Technology Spotlight” in IFJ, contact Ken Norberg at ken@ifj.com or +1 202.682.2022.
Kelheim Fibres has teamed up with Italian seamless knitting machine builder Santoni on the manufacture of energy-efficient and zero waste production menstrual underwear.
Under the terms of the project, the specialty viscose fiber manufacturer and Santoni Spa have jointly developed an innovative and sustainable menstrual underwear garment based on advanced machine technology and high-quality performance viscose fibers. The product consists of a soft outer layer and an inlay made from special wood-based fibers from Kelheim. The result is a sustainable and high-performance product that combines comfort and functionality.
The soft outer layer is produced either on the Santoni SM8-TOP2V circular knitting machine or on the SM4-TL2 machine. One of the major advantages of these circular knitting machines is that they significantly reduce the amount of cutting waste or even allow production with zero-waste.
The Santoni XT-Machine, originally developed for the footwear market, is used for the functional inlay of the period panty. The unique XTMachine allows for different layers to be produced with different yarns and knitting structures. This enables all three functions of the inlay – the absorption and distribu tion layer ADL, the absorbent core, and the back layer – to be knitted in a single tube. This reduces production time and costs and enables zero-waste production.
In the inlay, wood based Kelheim specialty fibers such as trilobal Galaxy or the hollow Bramante fiber replace synthetic materials. www.kelheim-fibres.com
British textile testing solutions provider James Heal has developed a solution to improve sustainability of water repellency testing in textiles. The company developed TruRain, the next generation Bundesmann tester with a water recirculation unit. Compared to the traditional options on the market, this new system uses 99% less water during testing based on a weekly program of conducting 150 tests, reducing consumption from 2,100 liters to just 23 liters for the week.
In addition, TruRain makes significant energy cost savings per workday, leading to 83% total cost reduction. Productivity is also increased through greater ease of use than traditional Bundesmann tests and can be run continuously for a week without the need to change the water. An innovative automated shower guard that protects the operator from getting wet during testing is an improvement welcomed by lab technicians using the instrument. www.jamesheal.com
Fong’s Europe has constantly evolved its dyeing systems based on the Airflow principle for achieving excellent dye penetration and uniformity while minimizing color differences between different areas of a fabric.
At ITMA 2023 in Milan, the company will introduce its latest THEN Synergy Airflow and THEN Airjetwin machines which exploit the principle to provide high-quality, efficient and eco-friendly dyeing processes for a variety of fabrics.
The THEN Airflow dyeing machines have several innovative features, including several parallel functions for reducing process time. The VPR system shortens the rinsing time and water usage and the well-proven robust and homogeneous spraying device in the nozzle ensures a uniform dyeing in the shortest process time. The very short liquor ratio also reduces the use of salt and chemicals.
THEN Airflow systems also have a unique dyeing process control system that allows for precise control over dyeing parameters such as temperature, pressure, and chemical dosing, ensuring consistent and high-quality results. www.fongs.eu
The Textile Machinery Association of Sweden (TMAS) will focus on automation at ITMA 2023 in Milan in June. “Technologies such as artificial intelligence (AI), machine learning and automation are becoming increasingly important in the textile industry and Swedish companies will showcase new machines and software that can help streamline production and improve efficiency,” says TMAS secretary general Therese Premler-Andersson.
Among exhibitors are ACG Kinna and its refined robotic pillow filling system, which drew considerable crowds back in 2019. The system has been further developed to include new features such as QR codes with production details. Eton Systems which specialize is
automated handling and thereby minimizing waste by efficient transportation within production will launch its new software platform, ETONingenious™ which is a real-time system used to manage, control and follow up on production in the Eton system. ETONingenious™ continuously gathers, processes and presents powerful, value-adding product information to operators, supervisors, quality control personnel and management. www.tmas.se
An extensive range of technologies and services related to textiles from the UK will be on display at ITMA 2023 Milan, with over 30 members of the British Textile Machinery Association (BTMA) in attendance. “Sustainability, circularity and Industry 4.0 have been the primary themes coming from the market for some time now and our members have responded with innovations spanning the entire supply chain – from fibers to finishing – and with a specific emphasis in many cases on improved software and digitized control solutions,” said BTMA Jason Kent.
Fibre Extrusion Technology (FET), which recently opened the new Fibre Development Centre will showcase its ability to accelerate new fiber trials and product R&D.
Tatham, known for its established machinery for the processing of natural staple fibers – and most notably, its technologies for the decortication, fiber opening and fabric forming of hemp, will showcase its ability to help companies that are entering the field of natural fibers, such as hemp production.
Optima 3D will show its further development of 3D weaving machines, and digital control systems.
FedEx has selected First Line Technology (FLT) of Virginia as one of its Top 100 Small Business entries in the Small Business Grant Competition. FLT was selected for its development of Synthetic Opioid Safety (SOS) kit, which consists of Dahlgren decon formulation and FiberTect decontamination nonwoven wipe. First Line Technology designs and manufactures disaster preparedness and emergency response equipment taking ideas from the lab to lifesaving products. www.firstlinetech.com
Cygnet Texkimp will showcase its extensive portfolio for handling fibers like carbon and glass.
Roaches International, which supplies a range of autoclave and thermosetting technologies, will showcase its well-known textile performance testing instruments, and its innovative machines that can be integrated with existing manufacturing plants.
Alchemie Technology will display its Endeavour, waterless, low energy dyeing and Novara, low energy textile finishing technologies, that seek to disrupt manufacturing processes that are responsible for over 3% of global CO2 emissions and 20% of global water pollution. “Our solutions both dramatically reduce the environmental impact and the cost of dyeing and finishing, which has proven to be a compelling combination,” said Alchemie founder and CEO Dr. Alan Hudd. www.btma.org.uk
or over 68 years Chase Machine and Engineering has been designing and building a variety of standard and custom converting machinery for WovenNonwoven fabrics, Films and Foils. From integrating independent modules to supplying Full-Scale Production Lines, we offer a comprehensive range of machinery that play an essential role in the success of wellknown brands and products worldwide.
As one of the premier design and manufacturing companies for custom web handling machinery, Chase serves a wide range of customers in the Textile, Medical, Nonwoven, Converting, Geotextile, Extrusion, Filtration, and Packaging Industries. We partner with leading manufacturers to produce application-specific equipment ranging from Festooners, Accumulators, Inspection Machines, Unwinds/Rewinds and Traverse Winders, to Ultrasonic Slitters, Laminators, and CutTo-Length Machines.
Chase specializes in the integration of technologies such as Ultrasonics, Impulse Welding, RF Welding, Band Sealing, Hot Air Welding, Glue Dispensing, Hot Knives and Conventional Blade Slitters as well as Vision and Marking Systems.
Chase is a vertically integrated company, utilizing State-Of-The-Art 3D Solid Modeling Software for our machine designs. Within our 28,000 sq. foot facility, located in West Warwick RI, we program our PLC’s and HMI’s, build our Electrical Control Panels and Machine, Weld/Fabricate, Paint and Assembly our Equipment while maintaining tight control of quality and delivery.
We place a high priority on customer and product confidentiality, and constant-
ly seek to improve our quality and process controls as we help our customers improve their products and processes. Working together with our customers, Chase will deliver equipment that is Newer, Faster, more Efficient, and more Reliable for a timely return on your investment.
For those interested in product development, the Chase Materials Application Lab exists to help your team take their ideas to the next level. Whether creating new products or improving existing ones, Chase can determine the optimum method for manufacturing.
Lab capabilities include web handling systems with ultrasonic technology for laminating, embossing, welding, slitting as well as impulse welding machines.
When you think of a pineapple, what comes to mind is hospitality, luxury, status, and good fortune. Sustainable plant-based textiles do not readily come to mind, but that is exactly what Ananas Anam, the makers of Piñatex®, want you to consider. In fact, the luxury plantbased nonwoven materials developed by company founder Dr. Carmen Hijosa utilizing pineapple bio-waste brings all that the fruit represents into any end use application, and more. The material provides an array of benefits to product developers, offering a unique commercially produced textile that has positive social and economic impacts, while also maintaining a low environmental footprint throughout its life cycle.
The company has achieved B-Corporation certification since 2020, which means they maintain high standards of verified performance, accountability, and transparency on factors from employee benefits and charitable giving to supply chain practices and input materials.
The story of Ananas Anam began while Dr. Hijosa, a leathergoods expert, was consulting on the Philippines leather export industry in the 1990’s. Disturbed by the environmental impact of mass leather production and chemical tanning, she realized this should not continue but knew that PVC alternatives were not the solution. She was driven to research a sustainable alternative.
Inspired by the abundance of natural resources, including the use of plant fibers in traditional weaving such as the delicate Barong Tagalog garments, she sought out to create Piñatex®, and now, utilizing the same raw material, pineapple leaf fiber,
the company has expanded into offering a second product, Piñayarn.
Piñatex ® is used across fashion, accessories, upholstery and automotive industries, and has been used by over 1000 brands worldwide including Hugo Boss, H&M and the Hilton Hotel Bankside. With the new product complimentary to Piñatex, Piñayarn can help create a wider positive impact, serving more industries for new and different products.
Here is the inspiring story told by company executives Josep Taylor, Managing Director of Fibre Processing Plant and Melissa Braithwaite, Piñayarn Product Development Manager.
International Fiber Journal: Tell us about Ananas Anam founder Dr. Carmen Hijosa and her work.
Josep Taylor: As as expert in the leather business, Carmen was consulting for the World Bank. She visited the Philippines and was distressed by the conditions she witnessed. She started visioning a more sustainable way of production, for both the people and the planet. There is not much change you can make with real leather; so, she began researching natural fibers in the Philippines on creating a sustainable replacement.
As a result of her extensive research Hijosa began development of Piñatex® in 2011, filing a patent for the process of transforming fiber into an alternative leather and other textiles.
Melissa Braithwaite: Piñatex® officially launched in 2014 and was first commercialized in 2016. Dr. Carmen saw the opportunity to utilize pineapple harvest
IN THIS ISSUE: JOSEP TAYLOR
Managing Director of Fibre Processing Plant
Piñayarn Product Development Manager
waste – instead of them being burned, which speeds up the preparations to plant again for the next pineapple fruit harvest. Utilizing this waste also provides an opportunity for a second stream of income for communities of farmers. Pineapple fibers had traditionally been used for textiles generations prior for hundreds of years, mainly in raw form. With the Philippines as a global pineapple producer, Dr. Carmen concentrated on the knowledge of the people to help develop these plant-based textile solutions.
IFJ: Share about the company’s facilities.
Taylor: The corporate headquarters is in the UK. Our primary production facility was established in the Philippines to be near the pineapple plantations. Mid-2021, we began development of the factory in Spain as a growth strategy. We are positioned to serve our customers and nearby our suppliers. Plant production began in July 2022.
We have since divided the company into different production units. For instance, in the Philippines they work on developing the nonwoven. In Spain, we prepare the fiber to get carded and to become the newest product line, Piñayarn.
IFJ: How do you work with the farmers on the fiber extraction?
Braithwaite: First, let’s look at the lifecycle of the pineapple. It’s important to know that we partner with farming cooperatives, where their first business priority is the fruit harvest. So, we are never competitive with fruit production. We collaborate with chosen farming cooperatives to extract the fiber from the leaf waste after fruit harvest.
Quite often, the pineapple leaves get burnt to remove field waste and prepare for a second fruit harvest. Utilizing the field waste helps to reduce CO2 emissions. We work with them to extract fiber, using a decorticating machine as part of their farming practices. After extraction, the fibers get washed in water and then are dried naturally in the sun. At this
point, Ananas Anam buys the fibers. The fibers get sent to our facilities in the Philippines or Spain to be mechanically processed to textile grade standard, before being processed into either Piñatex® or Piñayarn.
We work with the farming cooperatives through the whole process for social and quality reasons. We help them with their training, and sometimes provide the machinery. We ensure that the work sites are safe, and that they know all the correct ways in which to extract fibers.
While the process is labor intensive, we’ve already had quite a lot of progress in automating our farming machinery. For us, the most beneficial positive impact we make is to provide an abundance of jobs in these rural communities.
It is important to note that in every step in our process, we utilize waste. For example, any waste from the extraction process is then repurposed as bio content for soil nutrition. It is beneficial for the plants to get the positive nutrients back into the soil, so it’s a closed loop system.
Taylor: We partner with several farming co-operatives and farms and provide over 550 jobs. The company is growing, and our sources are growing, including farmers now in Bangladesh and Africa. It is most important to our company to have a positive social impact. The entire family – except children – can work on fiber extraction which is beneficial for their livelihood. Conditions of the workers is our priority, so we conduct audits to check compliance with the agreed upon rules.
IFJ: Tell us about your purification process?
Taylor: Once we have fibers, we treat the fluff-like pineapple leaf fiber (PALF) with natural enzymes to remove any impurities. We don’t use any chemicals or bleach, so this sets us apart from others who do. I would say that to my knowledge we are the only ones that are doing this enzymatic process. Then, we cut them to the length dependent on the end use.
For the drying process, while we have industrial dryers in Spain, in the Philippines we are lucky to have the sunlight or drying ovens. We rely on natural sunlight in our facilities which is more sustainable in terms of energy. With sunlight it might take longer, but we’re not using any resources except the sun and the air.
IFJ: How much do you produce and how many brands are using the fiber?
Taylor: We are producing, last year, about 260 tonnes.
We have clients in over 90 countries and many brands we work with, whom we co-brand with marketing. For instance, most notably Nike® launched the Happy Pineapple shoe brand. Hugo Boss,
H&M and the Hilton Hotel Bankside are some other large brand partners. Also, it’s a plus especially for smaller brands to distinguish themselves, and associate with the name of Piñatex®, because it provides the certainty that we are vegan, chemical free, we are traceable, and totally sustainable.
IFJ: What are GOTS certified pigments that you utilize?
Braithwaite: That means we use water and energy-efficient pigments and have achieved Zero Discharge of Hazardous Chemicals (ZDHC) compliance. To make the Original, Pluma and Mineral collections, the Piñafelt is colored using GOTS certified pigments. Then a resin top coating is applied to give additional strength, durability and water resistance. A foil is heat pressed on to create the Metallic collection and a high solid PU transfer coating is used to create Piñatex® Performance and Light.
IFJ: What are Ananas Anam collections?
Taylor: Piñatex ® has five collections. Original, Mineral, Metallic and Performance all have a non-woven felt backing, but slightly differ with the top coating and finished look. Piñatex® Light has a knitted backing and is the thinnest collection to date. End use and applications include footwear, accessories, apparel and interiors.
IFJ: What is the Piñayarn and how did it come about?
Braithwaite: Piñayarn came about in 2020 when the company won a grant from the UK government through UKFT to produce sustainable PPE alternative (facemasks) made from the same pineapple leaf fibers as Piñatex®.
To create these facemasks, we had to create yarn to an industrial standard and therefore we needed to create a new supply chain for the company, and on-board suppliers and producers for this yarn and facemasks.
There had been some questions on how Piñatex® can be used in a wider variety of products to offer more flexibility and lighter weight. So, essentially Piñayarn grew to be the second product offering to compliment Piñatex® and to supply our customers with the potential of creating more products using this yarn that Piñatex® wouldn't have been able to supply at that time.
It’s also an alternative to the yarns that are already on the market for a higher environmental impact. The same clients that use that use Piñatex® are interested and use Piñayarn.
IFJ: How do you help companies with their sustainability stories?
Taylor: We have a great opportunity to help grow a sustainable mindset. Many companies are not going to change overnight, but there is lots of interest to have lower-impact materials. It takes time.
Our business model helps to unlock the potential of natural fibers and bring socio-economic stability to rural areas of the Philippines and Bangladesh. We are always looking for brand partners and companies to align with our vision both socially and ecologically.
Braithwaite: We make it quite easy for brands because they all have various ways of how they view sustainability, and how they want to market their products. We have a full Life Cycle Analysis for both of our products – Piñatex® and Piñayarn. Our LCA measures the full impact of the product, from the carbon footprint, water usage, to toxicity, and transport emissions. We work closely with our customers sharing data on our products to help them calculate the impact of their end products.
IFJ: How do you view the sustainability adoption rate of the industry?
Taylor: It is pure economics. It is a change of model. It takes time. Everybody is aware the world needs to change. A company like ours, we see the future. We only have one planet, and we must take care of it. Corporations understand that they must change, but they still have the economic part to factor in. It is the future.
The consumer is the one who chooses which way to go, this is the reality. The consumer still does not know all information that we know in this industry. Carmen says, we must teach school children the importance of sustainability and to respect the planet, as well as to be more conscious on new ways of producing things.
Braithwaite: On product development, it is easiest sometimes to work with small brands and companies because they can react to change much quicker and easier. I also think adopters of nonwoven and plant-based non-woven materials need to appreciate the excellent qualities Piñatex® offers, and not compare it to leather. These materials are not going to react the same as protein-based leather goods.
I agree, education is key. Also what is essential, is the need for the textile industry to be more closed loop from the start. We know that microfibers and waste streams are a huge problem for any sort of textiles. Fully closed loop systems would help, as well as the ability to compost materials –that’s the future of sustainable fabrics.
IFJ: What are the plans for the company?
Taylor: Our edge is that we can trace producers and partners in our supply chain, this is so important. Others don’t have this kind of engagement with the landowners or fiber producers.
This is a business. We want to show our customers that when they choose us as a supplier, this is a good business decision.
Braithwaite: We listen to the customers and what they need. We ultimately make raw materials for our customers to make their products. But, along the way, if we can somehow make a sustainable difference for our customers by using our material, that’s our future.
Piñatex® is used across fashion, accessories, upholstery and automotive industries, and has been used by over 1000 brands worldwide including Hugo Boss, H&M and the Hilton Hotel Bankside. Ananas Anam fiber processing plant in Canet de Mar, Spain. Ananas Anam q PALF pineapple leaf fiber. Ananas Anam
Innovation across industry niches often overlaps in methodology, technology and manufacturing. The best and brightest of the wipes niche are invited to join at the World of Wipes® International Conference, known as WOW, in Atlanta from July 17-20, 2023. When looking for sustainability solutions for filtration and textiles, there is much to learn from producers of wipes, still in high consumer demand and still in the hotseat of sustainability. The event presented by INDA, Association of the Nonwoven Fabrics Industry, spotlights current insights and future trends driving this surging $11 billion industry forward. The event attracts more than 400 professionals and a host of tabletop exhibiting companies.
“I’m very excited to see the program evolve to meet the changing dynamics of the industry,” says WOW Committee Chair Jonathan M. Layer, Director of Commercial Business Development and Marketing, Fibertex Nonwovens. “I’m especially confident that adding new sessions, such as the CEO Panel and Energy Inputs, will provide unique added value and perspective to the event. The committee focused on ensuring that we’re putting forth the best content addressing the most critical topics in the industry.”
This year, WOW introduces new elements for attendees, including pre-conference webinars. The pre-show webinars are a new place to connect, converse and to gain content. Details on the offerings can be found at www.worldofwipes.org/ preconference-webinars.html.
Among the regular networking opportunities, another new aspect are the WOW LIGHTNING TALKS – “supersized elevator speeches” from industry suppliers. This is a limited-space, firstcome opportunity for tabletop exhibitors to present their latest innovations just
ahead of the networking reception to get attendees excited about their innovations.
WOW’s featured WIPES ACADEMY provides an educational deep dive into operational excellence, presented by Instructor Heidi Beatty, CEO, and Paul Davies, Ph.D., Senior Consultant, Crown Abbey, LLC. It is directed at raw material and packaging suppliers, brand and private label wipe converters, retail buyers, research and development professionals, marketing and product managers, and rising entrepreneurs.
Each year, WOW shines a light on excellence in innovation. The World of Wipes Innovation Award® recognizes companies from within the value chain that utilize nonwoven fabric/ technology in a way that expands the usage of nonwovens, in categories such as raw materials, roll goods, converting, packaging, active ingredients, binders, additives and end-use products.
Gaining market intelligence is a priority to WOW attendees. Over 30 speakers
are expected to share their expertise and insight over the two and a half days of the main event. Attendees are encouraged to lean in and learn from their peers who are moving the needle towards a sustainable future and supporting cross-industry collaboration.
The new CEO Panel promises a look at priorities and predictions, moderated by Chris Astley, Consultant. Inflation, supply chain and capacity/demand balance remain top concerns for wipe producers in 2023. Discussion topics will touch on inflationary impacts across an organization, surging wages, re-shoring, as well as domestic and international drivers to supply/demand balance. The panelists are Steve Gallo, CEO, Diamond Wipes; Markus Müller, Sales Director, Reifenhäuser Reicofil GmbH & Co. KG; R.J. Rudolph, Group Director – CMS-RT, Rockline Industries; Jodi Russell, Vice President R&D, Cleaning Innovation, Packaging & Sustainability, The Clorox Company; and, Robert Weilminster, EVP & General Manager, U.S. & Canada –Health, Hygiene, and Specialties Division, Berry Global.
There are pressing issues that the wipes industry must address in coming
years to remain strong. “We as machine supplier must find solutions to deal with supply chain issues, high energy costs, inflation and the general political situation especially in Europe,” notes panel participant Markus Müller. “The industry must deal with the general ‘plastic shaming,’ i.e., sustainability requirements, such as how to produce wipes energy and resource-efficient, as well as how to avoid ‘green-washing’ in this context.” The hope is that attendees will hear about challenges in this industry and understand possible solutions.
“I want attendees get a better understanding of the evolving landscape of the entire wipes sector post-pandemic,” Jodi Russell comments. “What has changed? What has stayed the same?”
Russell believes the industry must address technology and business issues. On technology she cites: “Asset utilization –how does the industry cope with unpredictable demand cycles?; Transitioning from plastic to non-plastic materials in a cost-effective manner without compromising on attributes consumer expects; and, AI – how will it integrate and be adopted into the nonwovens industry?”
On business, issues include to: “Reverse trend on commoditization across all wipes categories – what type of messaging can the trade create to upgrade the perception of wipes products as a premium experience?; and, to gain a better understanding of changing regulatory landscape and its impact on various vectors, specifically the tightening legislative/regulatory landscape around plastic waste,” she says.
A series of power-sessions weave together one urgent industry issue – “Plastic Policy: Closing the ‘Intentional’ Gap.” Moderated by Olivia Reiber, Key Accounts Manager, Wipes & Specialties, Berry Global, she leads the analytical presentations from Matt Seaholm, CEO, Plastics Industry Association, Murat Dogru, General Manager, EDANA, as well as a representative from Kimberly-Clark Corporation.
“The Nonwoven Wipes Supply Chain Response to ‘Plastics Free’” with presenter Phil Mango, President, Philip Mango Consulting, considers the European Union’s Single Use Plastics Directive and
its explicit inclusion of disposable wipes in 2019, which calls for an accelerated response from the industry. Much of the response has been product related, but he suggests that the better answer is a broader, total supply chain response from raw material providers, production equipment suppliers, nonwoven producers and wipes converters who all play important roles.
Rounding out the day’s discussion are three discussions on sustainability manufacturing practices, reducing CO2 footprint while targeting CO2 neutrality by 2035 and utilizing technologies for sustainable products.
WOW’s second full day presents consumer-centric sessions: “Give the People What They Want! A Road Trip Through the Consumer Mindset on Plastics, Packaging, Recycling, and What They Expect from the Brands They Buy From” with Suzanne Shelton, President & CEO, Shelton Group; “Closeness to the Consumer – Goodwipes to Uranus: To Boldly Go Where No Toilet Paper Company Has Gone Before” presented by Sam Nebel, Co-Founder, Goodwipes; “A Holistic Approach Towards Wet Wipes
Preservation,” with Paul Salama, Ph.D., CTO & Head of Innovation, Sharon Laboratories; and “Transparency in the Supply Chain,” with moderator Jonathan Layer, Director of Commercial Business Development and Marketing, Fibertex Nonwovens.
The final half-day on day three explores the flushability factor, a topic INDA is tackling head on. Five industry experts will present aspects of the issue from fiber innovation, legislative issues, and standards development.
“It’s my hope that the attendees will walk away with a clearer picture of the industry dynamics in a way that allows them to make informed decisions to guide their businesses,” says Layer. “I also want to encourage innovation in the way we operate – not only in product development but also in supply chain, strategy, and operational sustainability. WOW is the must-attend event of the industry and this year’s program will set the bar in enabling success for each attendee or exhibitor.”
www.worldofwipes.org
Gaining market intelligence is a priority to WOW attendees. Over 30 speakers are expected to share their expertise and insight over the two and a half days of the main event.
Politicians like nothing better than a catchy slogan: “Made in America” and “Buy American” certainly fit those criteria, but are these phrases beguilingly simple? The origins can be traced back to the Buy American Act of 1933, when legislation required the federal government to purchase American-made iron, steel and manufactured goods where possible. Under the guidance provided, a product could be described as made in America if it met the requisite minimum 50% of its materials or constituent parts having originated in the United States. More recently, one of the very few things that the Trump and Biden administrations have agreed on is the desirability to move manufacturing back, near-shoring or re-shoring, in addition to encouraging American consumers to purchase American-made products more consciously.
While the U.S. textile industry is in favor of these policies, the counter and temperance arguments ought not be ignored. “Buy American policies actually cost jobs” is an argument made by Adam Posen, President of the Peterson Institute for International Economics (PIIE), writing in the Spring 2023 issue of Foreign Policy magazine. The National Council of Textile Organisations (NCTO) meanwhile point to a U.S. textile industry supply chain that employed 538,067 workers in 2022, as well as government estimates that each textile manufacturing job itself supports three further jobs.
The purpose of this article is not to express an opinion on the U.S. policy, but instead to look at some of the proposals emerging from the debate that have the potential to make the textile industry stronger, while generating positive societal impacts that stretch beyond U.S. borders.
The U.S. is the third largest exporter of textile-related products in the world with textile and apparel shipments worth $65.8 billion in 2022 according to the National Council of Textile Organizations (NCTO). An impressive figure but might it be higher?
In Posen’s claim that “Buy American policies actually cost jobs,” he points to “rules of origin” as increasing product costs thereby making U.S. business less competitive on the international marketplace. Under the North American Free Trade Agreement (NAFTA), the “yarn-forward” agreement demanded that the majority of textiles and apparel from the yarn stage forward had to be made within the region in order to qualify for duty-free status.
There were some exceptions, which the United States-Mexico-Canada Agreement (USMCA) looks to close through the introduction of “chapter rules,” thereby extending the application of rules to sewing threads, narrow elastic bands, pocketing, and coated fabric.
Bill Jackson, interviewed last year in his position as Assistant U.S. Trade Representative for Textiles, described the measures as having “strengthened the regional supply chain for textiles and provide new market opportunities for the U.S. textile and apparel sector.” Jackson pointed to the Dominican Republic Central America FTA (CAFTA-DR) trade agreement that under the yarn-forward rules gives apparel made in Central America duty-free access to the U.S. market, providing what he believed to be a “foundation upon which the industry can grow, while at the same time supporting jobs in the U.S. industry, which supplies much of the fibers, yarn and fabric used in apparel production in CAFTA-DR countries.” The U.S. government has been encouraging new investment with CAFTA-DR partners to strengthen the regional supply chain.
Reflecting industry views, Steve Schiffman, president of the Advanced Textiles Association (ATA) comments: “The stance of [United States Industrial and Narrow Fabrics Institute] USINFI is that it needs to continue to be Yarn Forward, and the rules of origin should not be weakened to offer other countries the chance at an
end run around the current requirements. USINFI opposes any attempt to weaken the Yarn Forward rule of origin under the CAFTA-DR or any free trade agreement.”
Trade lawyer Lori Wallach, directs the Rethink Trade program at the American Economic Liberties Project, and cautions that “this [Biden] administration has articulated goals like creating good jobs for workers with and without college degrees and strengthening economic resilience, and our trade policy and deals must deliver not damage that.”
One of President Biden’s first actions when he was appointed to office in 2021 was the signing of two Executive Orders aimed at reducing vulnerabilities in the supply chain. One outcome was the National Strategy for a Resilient Public Health Supply Chain (2021), a roadmap for building and sustaining resilient supply chains for PPE and other essential medical products. The risk of obsolescence makes it too
risky for the government to store a high level of inventory in the Strategic National Stockpile (SNS). “I think the roadmap for building and sustaining resilient supply chains for PPE and other essential medical products is a good start and we’ll have to see how it plays out in the future,” believes Steve Schiffman. “USINFI supports legislation such as the [Homeland Procurement Reform] HOPR act which includes medical PPE, uniforms, etc. This is to help government contracts go to small businesses. This is an example of legislation that is part of the building blocks to help strengthen the supply chain.”
The demand for PPE is not consistent and this has already impacted U.S. mask producers with the American Mask Association estimating by September 2021 that as many as ten out of twenty-nine domestic manufacturers had ceased production, with some being forced to file for bankruptcy. There is the potential to put safeguards in place particularly for smaller producers. One possibility would be reservation contracts, whereby the government could exercise an option with suppliers for increased production should the need arise.
“Detailed research has repeatedly shown that policies aimed at maximizing domestic manufacturing employment rather than the development and adoption of new technologies are not only doomed to fail but crowd out the very industrial and trade policies that contribute the most to innovation, national security, and decarbonization,” warns Posen. He argues for the prioritization of technology adoption over technology production. This is an important differentiation, with so much focus on the protection of intellectual property (IP) the risk is of technology obsolescence before an innovation has been properly taken up. The outcome is to starve the next level of innovation that is served by the iterative process of lessons learned and improvements needed that can only be properly seen when a technology is used at scale.
The move to a more digitally connected manufacturing environment, such as
In Posen’s claim that “Buy American policies actually cost jobs,” he points to “rules of origin” as increasing product costs thereby making U.S. business less competitive on the international marketplace.The Advanced Functional Fabrics of America (AFFOA) is spearheading the push for advanced and smart manufacturing as essential to the timely commercialisation of innovation in textiles and apparel, particularly smart textiles and wearables.
Marie O’Mahony
industry were lost in the period between 1979-2019 as the industry looked overseas for low-cost manufacturing.
The United States Fashion Industry Association undertakes an annual USFIA Benchmarking Study, with most recent being for 2022. It points to respondents concerns about attracting and retaining employees, moving the issue from one of medium ranking to one of the top five business challenges they face. Companies have indicated an average of six different positions they are looking to hire: supply chain specialists; sourcing specialists; environmental sustainability-related specialists; market analysts; and, trade and custom compliance specialists.
Industry 4.0, further exacerbates this negative impact. Technology adoption provides the opportunity for a more highly skilled and engaged textile workforce, essential for good employee retention. However, education and training is not the only issue, as experience in Europe shows. Germany has an abundance of training centers from the Textilakademie NRW to the Texoversum at Reutlingen University, yet in 2021 there were 63,000 apprenticeship and training positions that remained unfilled. The pandemic would partly account for this, however one third of these remained unfilled at the end of 2022 in the region of Saxony and Thuringia alone, according to Dr. Uwe Mazura, Director General, Confederation of the German Textile and Fashion Industry. Demographic changes are one reason, according to Dr. Mazura, with more people retiring from the industry than there are young people entering.
While Germany is looking at ways to attract and retain a young workforce, the UK launched a campaign in Spring 2023 to entice recent retirees back to the workforce. An estimated 630,000 people retired in UK between 2019 and 2022 and the British government wants them back at work. In the U.A. Jerome Powell, the Fed Chairman, bemoans 3.5 million
people absent from the workplace since the pandemic, with many over 50 years old and, like the UK, often newly retired. In the UK, around 42% of the workforce is aged over 50 with the figure set to rise to 47% by 2030 – the figure in U.S. is thought to be one third of that.
To attract recent retirees, “work will need to offer different incentives – flexibility, purpose and community, for example,” according to Aviva Wittenberg-Cox writing in Forbes magazine earlier this year, pointing to an additional expectation that an employer should offer “a conscious rejection of ageist systems and policies, the continued investment and development of careers for people 50+.”
In 2022, most of the apparel sold in America was manufactured in other countries, with the Sourcing Journal putting the figure as high as 97%. The U.S. Bureau of Statistics estimates that 81% of jobs in the
In contrast, the report also found no sign that fashion companies planned to near or re-shore manufacturing, with positions in sewing machine operators and general management their least likely positions to increase. Asia remains the strongest supply source for U.S. fashion, with over 37.5% planning to source for a greater number of suppliers and countries over the next two years. CAFTA-DR is growing in importance for the apparel industry with 60% of respondents planning to increase their sourcing from the region as part of a sourcing diversification strategy.
“Made in America” and “Buy American” are prompts for deeper questioning around benefits and impacts, from economic to social and environmental.
Dr. Marie O’Mahony is an industry consultant, author and academic. She the author of several books on advanced and smart textiles published by Thames and Hudson.
Switzerland ranked top in the list of the world’s most innovative countries for the 12th year running in 2022, keeping the USA in second place, according to Vancouver, British Columbia-based media company Visual Capitalist, using data from the United Nations’ WIPO Global Innovation Index.
This ranking may come as a surprise to many since globally, four of the five biggest R&D spending companies – Amazon, Alphabet, Microsoft and Apple – are all in the USA.
Switzerland’s intellectual property rules, however, are considered worldclass and they are complemented by strong collaboration between universities and industry. In addition, the country attracts top talent thanks to its high quality of living.
Innovation was very much to the fore at a press event held in Bern from March 16-18, 2023 by industry association Swiss Textile Machinery, ahead of this year’s ITMA exhibition in Milan from June 8-14. A key focus, not surprisingly, was on sustainable production and specifically new processing options for textile waste.
“The separate collection of this waste will become mandatory for all EU member states on January 1, 2025, when its landfilling or incineration will be banned,” explained association president Ernesto Maurer. “A major aim is to greatly increase the use of fiber-to-fiber recycling from the current pitifully low level of just one per cent.”
Switzerland is the base for two of the leading manufacturers of conventional textile spinning technology – Saurer and
Rieter – and both outlined the challenges of accommodating recycled fibers in their production lines.
“Today only between 30-35% of textiles are collected separately, but by 2030 the aim in Europe is that up to 80% will be recycled in some way and that the share of fiber-to-fiber recycling will grow to 18-26%,” said Saurer’s managing director Marcus Rennekamp. “A high degree of contamination, lower production speeds and a lot of personnel intervention are all common consequences of using recycled short-staple fibers in a rotor spinning mill.
“Extreme recycling is the new challenge for yarn producers, with ultra-short fibers bringing conventional spinning machines to their limits. We have developed a patented performance kit for dealing with these ultra-short fibers and
the first trials using it have shown an increase in production of more than 30%.”
Fully automatic rotor spinning essentially consists of four key processes – spinning, winding, automatic piecing (splicing) and the automatic doffing (removal and replacement) of yarn packages, or bobbins.
On the Saurer Autocoro spinning machine, the first three processes have been integrated into each individual spinning position through individual drive technology and the new doffing cleaning units (DCUs) on the Autocoro 10 system have been designed to help spinners to achieve both higher yarn quality and personnel efficiency.
When doffing a package, rotor cleaning is carried out simultaneously by the DCUs which travel from spinning position to spinning position. Up to eight DCUs can
be configured differently on Autocoro machines depending on the machine length, package size, yarn count and raw material.
Each DCU can be precisely adjusted to the quality requirements of its lots and work areas and the most important task in the context of yarn quality assurance is to clean the rotors, both pneumatically and mechanically. On the Autocoro 10, this is now even more efficient, with cleaning processes digitally controlled using the latest linear motor technology. A new movement mode for the cleaning scraper has been integrated, and its positioning in the rotor groove is more precise and significantly more efficient thanks to an additional circuit.
This new cleaning technology loosens and removes even the most stubborn dirt and sticky residue in the rotor to leave them impeccably clean and leading to a more reproducible yarn quality, regardless of fiber type.
systems over the past decade and we are now responding to the latest challenge of the five million tons of recycled fibers that will need to be accommodated by spinners in the next five years,” Rennekamp concluded.
Saurer sold more than a million spindles on deliveries of its Autocoro spinning units in 2022.
Franziska Häfeli, head of marketing and systems for spinning machine specialist Rieter, outlined the options for recycling via either mechanical tearing, which is already established, or by emerging chemical recycling processes for both cotton waste and blends which break down fibers into their chemical building blocks. This can involve, for example, spinning new fibers from pulp in processes being largely developed in Scandinavia, or the melt spinning of recycled PET pellets to make new polyester yarns.
Virgin cotton, she said, has an average short-fiber content of 24.6%, but short-
fiber content in recycled pre-consumer yarn waste has an average short fiber content of 46.9%, which makes turning it into new yarns challenging.
Many Rieter customers, however, have been processing such yarn waste for decades, with the preferred option being on the company’s R37 or R70 rotor machines.
“Many of these spinners have not even claimed to be using this recycled material and have included it purely for making raw material costs,” Häfli said. “Rotor spinning is best suited for processing yarns with a high short-fiber content but there is also now an increasing demand for recycled ring yarns which need a higher tenacity to go into weaving, but fiber counts for soft touch fabrics are the goal. This, however, is very difficult due to the neps and high short fiber content.”
This problem is considerably greater when it comes to post-consumer waste, even if it is comparatively pure, she added.
A batch of fibers from recycled white 100% cotton t-shirts, for example, will have an average short-fiber content of 71.3%, with an average fiber length of just 9.8mm.
Rieter has been involved in the two-year Texcircle project with partners Coop, Lucerne University, Rieter, Rohner, Ruckstuhl, Texaid and Workfashion, to explore the potential of integrating different types of recycled waste into textile supply chains.
During market launch tests, the cleaning technology proved effective for all fibers that are difficult to spin, including recycled and regenerated types.
A patent on the DCU has now been granted and the new rotor cleaning system will be integrated into all newly delivered Autocoro 10 systems from Summer 2023, as well as being made available for retrofitting to older machines.
“We have achieved an energy consumption reduction of 38% on Autocoro
Funded by the Swiss Innovation agency Innosuisse, other project partners include the Federal Office of Civilian Service (ZIVI), Nikin and Tiger Liz Textiles, with additional support through collaborations with nonwovens producer Jakob Härdi and yarn spinner Marchi & Fildi.
At the Bern conference, six prototypes at various stages of the production process were displayed from the project, the result of joint developments spanning design, collection and sorting trials through to tearing and spinning production trials.
The project was able to recycle 2.5 tons of pre- and post-consumer textile waste into product prototypes, with Swiss sock maker Rohner already commercializing sports socks made from 50% ring spun yarns made from a consignment of surplus ZIVI t-shirts and unworn pants from Coop bakeries, along, with 50% Lenzing Refibra, which also consists of recycled post-consumer waste and regular virgin cellulose.
Other prototypes included a sweater knitted from recycled denim jeans with Rieter rotor yarns, with the percentage of recycled fibers between 70 and 90%, and carpet made from old winter coats with a wool content of at least 70%. Prototype bags and fleeces were also developed from raw materials including shredded old black t-shirts and polyester padding collected by Texaid and processed by Jakob Härdi.
Building on its findings, Rieter plans to unveil a number of new developments related to recycling and system integration through digitization at ITMA 2023, with a focus on cost per kg of yarn, raw material, energy consumption and automation. It will also extend its Com4 branding program to include certain recycled yarn content ranges.
A third Swiss company, Uster Technologies, also plays a crucial role in the conventional fiber spinning world.
The Uster Statistics have become the industry benchmark for achieving and guaranteeing quality in yarn spinning. First introduced as a three-page document back in 1957, the reference manual now includes some 4,500 graphs and
process parameter guidelines and the 2023 edition will include a section on the processing of recycled fibers for the first time. Now available as an app, the 2022 edition has been downloaded more than 23,000 times.
Uster’s executive vice-president of marketing and business development Sivakumar Narayanan said that a major bottleneck in spinning with recycled yarns is achieving the necessary quality.
“Spinning yarn blends of virgin and recycled fibers is a much bigger challenge than any other commonly used blend, but the results can still be acceptable with comprehensive quality testing, knowhow and experience,” he said. “The use of mechanically recycled fibers in spinning has specific quality considerations – such fibers have a higher short fiber and nep content and may often be colored, particularly if post-consumer material is used. It’s also true that recycled yarns have limitations in terms of fineness.”
Officially, a yarn can be branded “recycled” when spun with more than 20% recycled fibers, according to the Global Recycled Standard (GRS), a voluntary product specification for tracking and verifying the recycled content of materials in a final product.
“Blending virgin and recycled cotton together is well known as a challenge for spinners,” Narayanan said. “The smartest spinners and world-class processes simply can’t overcome the fact that some important quality parameters will be adversely affected and even the most sophisticated spinning machinery won’t fix the problem. Awareness of the risk of yarn quality deterioration with recycled fiber blends means that quality control is the only way to assure customer satisfaction and even then, the task is far from simple. When spinning new materials, Uster strongly recommends taking both numeric test results and graphic evaluations into account, to eliminate the risk of problems in further processing.”
“The experience of spinners around the world combined with the latest technology in quality control and analysis systems, represent a promising basis for the future,” concluded Ernesto Maurer. “The new reality of the need for closer communication and cooperation will include all players from fiber to fabric. It’s an essential debate for everyone – and the member companies of Swiss Textile Machinery are ready to assist in accelerating this transformation.”
Further new developments were presented at the Bern conference by the companies Autefa, Benninger, Bluesign, Crealet, Heberlein, Itema, Jakob Müller, Loepfe, Luwa, Retech, Santex Rimar, Stäubli, Steiger and Swinsol.
Adrian Wilson is an international correspondent for International Fiber Journal. He is a leading journalist covering fiber, filtration, nonwovens and technical textiles. He can be reached at adawilson@gmail.com.
Awareness of the risk of yarn quality deterioration with recycled fiber blends means that quality control is the only way to assure customer satisfaction and even then, the task is far from simple.Rieter’s Franziska Häfeli explains the processes explored in the two-year Texcircle project. A.Wilson
Cellulose fibers are steadily making their way into a wide range of applications, including textiles, hygiene products and packaging. These fibers have a low ecological footprint, produce no microparticles and consist of 100% renewable carbon.
Cellulose is the main component of plant cell walls and a natural polymer. It is bio-based and biodegradable, even in marine environments, where its degradation does not cause any microplastic particles.
Moreover, cellulose fibers when washed do not produce microplastics –unlike the laundering of synthetic fiber clothing, which is estimated to be the cause of 35% of the marine microplastics already in the world’s oceans.
In addition, various production technologies for extracting cellulose from plants can be used for the recycling of cellulose, which offers the possibility of circularity of the material.
With a compound annual growth rate of 5 to 10% in recent years, the use of cellulose fibers within the global textile market is increasing, with major investments being made in the circular bio-economy.
Similar growth rates are expected in the future, which makes cellulosic fibers among the fastest growing fiber group in the textile sector.
The textile industry has identified two ways of reducing its pollution: fiber-tofiber recycling and upcycling of textile waste. At the same time, the packaging industry is looking into alternative materials, including the use of recycled textile fibers. However, the recycling of cellulose does present some hurdles.
The fourth Cellulose Fibres Conference (CFC) held in March in Cologne, Germany, and online, organized by Nova-Institut, examined how technology can overcome these obstacles, how markets can achieve circularity of the material, and how the cellulose fibers industry can contribute to the sustainability and circularity of the textile sector.
This unique two-day event, first held in 2020, focused on the increasing use of cellulose fibers in the fields of textiles, hygiene products and packaging. It attracted more than 225 participants from 30 countries, with 42 speakers and special panelists – of whom more than 40% were female, coinciding with International Women’s Day on March 8 – around
20 exhibitors and almost 20 poster presentations, both onsite and online.
The conference presented several case studies that introduced novel solutions that attempt to solve the dilemma of textile waste recycling. Other new application fields included cellulosic materials as a precursor for carbon fibers and the use of post-consumer clothing as a raw material to produce protective packaging.
Wood pulp is forecast to account for around 7% of global textile fiber production in 2025. However, cellulose fiber producers are now looking for alternatives to wood as a raw material – the fibers can be made from residues, by-products and side-streams of various industrial processes, explained Dr. Asta Partanen, senior expert, Nova-Institut.
But with global cotton production stagnant, the cellulose gap has been filled in recent years by the growth in synthetic fibers. Manuel Steiner, business development director of LIST Technology, Switzerland, highlighted the need to find new sources of cellulose. Recycled cotton-rich textiles as a raw material for the lyocell dissolving technology could be a solution, he said.
Dr. Alexander Deutsche, R&D director at Metsä Tissue, pointed out that raw materials from renewable resources are essential for an effective circular economy. Ensuring recyclability and efficient fiber reuse while reducing and replacing plastic as part of the shift from fossil-based raw materials to renewable biomaterials is the ultimate goal, added Anna-Stiina Jääskeläinen of Kemira, Finland.
According to the Ellen MacArthur Foundation, used and unused textile materials valued at US$100 billion are wasted each year. Meanwhile, Textile Exchange estimates that less than 1% of textile fibers are made from textile waste owing to the lack of textile-to-textile recycling systems, adding that global textile fiber production, which has doubled in 20 years to 109 million tonnes in 2020, is expected to grow 34% to 146 million tonnes in 2030.
During a panel discussion at CFC, participants agreed that an effective textile collection system is far from reality and that this will take time to implement. It will also require close cooperation –and trust – between the whole textile value chain. In addition, designing for circularity and end-of-life solutions will be key requirements.
The EU-funded New Cotton Project comprises a consortium of 12 participants across the textile industry production value chain to demonstrate that creating new clothing from regenerated cotton textile waste can be commercially viable.
The project has demonstrated a cellulose carbamate technology that allows the transformation of textile waste into cost-efficient, cotton-like Infinna fibers with superior qualities, said Paula Sarsa-
ma of Finland’s Infinited Fiber Company, one of the project’s participants and the lead innovator.
She explained that overcoming potential bottlenecks to scaling up circular textile production will require:
• finding steady and suitable postconsumer textile streams;
• developing suitable machinery for the separation and fiber identification processes;
• defining suitable textile streams from sorters to recyclers;
• ensuring financial viability of recycling post-consumer garments into new fibers; and
• understanding the post-consumer market and comparing these results to market data on feedstock availability, production flows and current disposal alternatives, such as landfill or incineration.
In collaboration with major global brands Adidas and H&M, biodegradable activewear and denim apparel were made from 100% post-consumer textile waste clothing as part of the New Cotton Project and launched to consumers in autumn 2022.
TexChain 3 is a project led by The Loop Factory and Wargön Innovation, together with 32 textile producers and stakeholders in Sweden. The project explores the possibility of generating a more circular flow of textile residuals that mainly originates from worn-out workwear and production-related waste streams.
Trials have been made within eight different prototypes with industrial waste as the raw material, with the goal of creating five products ready for commercialization. Maria Ström and Roos Mulder of The Loop Factory outlined some of the pilot projects, which include upcycling and recycling workwear, and developing a material mixture from old train seats for further processing into new products.
With the market for reusable diapers currently valued at US$53 billion a year with an annual growth rate of 5%, products currently on the market often lack reliability. Due to the high volumes of fluids involved, a highly absorbent construction with fast acquisition and optimized fluid distribution is required to deliver no leakage and low rewet to the skin.
At this year’s CFC, Germany-based start-up Sumo and German specialty viscose fiber manufacturer Kelheim Fibres presented their high-performance absorbent pads for a reusable diaper, which
According to Natalie Wunder, project manager at Kelheim Fibres, and Luisa Kahlfeldt, founder and designer of Sumo, the washable, fitted cloth diaper consists of a waterproof cover and absorbent inserts.
Kelheim’s functionalized viscose fibers with adjusted cross-sections have been integrated, together with polylactic acid bicomponent fibers, into a needlepunched/thermally bonded nonwoven construction to produce a high-performance absorbent pad that uses no fossilbased materials.
Birgit Kosan, of the Thüringisches Institut für Textil- und Kunststoff-Forschung (TITK), Germany, explained that the lyocell process is a particularly environmentally friendly process with almost complete solvent recycling.
Although wood-based dissolving pulps for lyocell applications are well
blend of locally sourced unbleached summer hemp and Lyohemp, a regenerated fiber made from hemp straw. This underwent a rotor spinning process followed by knitting on flat-bed knitting machines.
ments made from 100% wheat straw, and the first prototypes have shown the technical feasibility of bio-based garments with good properties of the wheat straw cellulose-based textiles.
For more than 50 years, Fi-Tech has successfully worked with manufacturers of machines and key techical components used in the production of:
Our customers trust us to provide the best quality and rely on our commitment to their needs when exploring new opportunities to grow and to improve their manufacturing businesses.
Equally, our suppliers highly value the service, dedication, and access to the markets we provide.
Rita Valério of CeNTI – Centre for Nanotechnology and Smart Materials, Portugal, outlined the Fiber4Fiber project, which aims to develop optimized dissolving pulp from Portuguese Eucalyptus globulus trees to produce man-made cellulosic fibers, such as lyocell and viscose, which can be traced along the value chain.
As part of the project, modified lyocell fibers are being developed with properties that are appealing to the end user and meet more demanding technical and performance requirements in the market, such as antimicrobial and flame-retardant properties.
Much of the second day of the Cellulose Fibres Conference was devoted to the results from the EU-funded GRETE project, which aims to overcome the bottlenecks in the wood-to-textile value chain, explained Joan Colon of the BETA Tech Center, University of Vic–Central University of Catalonia, Spain.
The initiative aims to improve the existing textile value chain by using a new raw material based on standard paper-grade pulps, implementing novel green technologies based on ionic liquid chemicals and a recovery process for cellulose dissolution with a novel post-modification process to obtain regenerated man-made cellulosic fibers with improved technical properties.
For the third time, Nova-Institut organized the Cellulose Fibre Innovation of the Year award, sponsored by GIG Karasek, Austria, as part of the Cologne event. The conference advisory board selected six products from 20 nominations, which were put to an audience vote on the first day of the event, with the awards ceremony taking place in the evening.
In a close-run competition, the overall winner was Nullarbor high-tenacity lyocell fibers made from bacterial cellulose. Developed by Nanollose of Australia and Birla Cellulose of India, Nullarbor is significantly stronger than lyocell made from woodbased pulp – even adding small amounts of bacterial cellulose to wood pulp increases the fiber toughness, said Nanollose executive chairman Wayne Best.
The first pilot batch of 260 kg of Nullarbor (from the Latin Nulla arbor, meaning “no trees”) was produced in 2022 with a 20% bacterial pulp share, and several fabrics and garments have been produced with this fiber. The collaboration between Nanollose and Birla Cellulose is now focusing on increasing the production scale and amount of bacterial pulp in the fiber.
Second place in the innovation award went to Renewcell of Sweden for Circulose, a branded dissolving pulp made from 100% textile waste, such as used clothing and production scraps, which provides a material for fashion that is fully recycled, recyclable, biodegradable and of virgin-equivalent quality. Circulose can be used by fiber producers to make staple fibers or filaments such as viscose, lyocell, modal, acetate or other types of man-made cellulosic fibers.
Third place was awarded to Vybrana, a new-generation banana fiber upcycled from agricultural waste from Gencrest Bio Products, India. Raw fibers are extracted from the banana pseudo-stem
at the end of the plant’s lifecycle and the biomass waste is treated by Gencrest’s Fiberzyme technology, which removes the high lignin content and other impurities and helps fiber fibrillation. The company’s proprietary cottonization process provides fine, spinnable cellulose staple fibers suitable for blending with other staple fibers and can be spun on any conventional spinning systems, explained Sandesh Saxena, head of marketing.
The other innovation award nominees were HeiQ AeoniQ, a climate-positive continuous cellulose filament yarn that reproduces the properties of polyester and polyamide yarns in a cellulosic, biodegradable and endlessly recyclable
fiber; Lenzing’s Tencel Luxe lyocell yarn that offers an alternative to silk, long-staple cotton and petroleum-based synthetic filament yarns; and sustainable, plasticfree, biodegradable and compostable sanitary pads from Sparkle Innovations, USA.
Next year’s Cellulose Fibres Conference will be held from March 13-14, 2024, again in Cologne. For further information, visit www.cellulose-fibres.eu
Geoff Fisher is the European editor of International Fiber Journal, editor of MobileTex and a director of UK-based Textile Media Services, a B2B publisher of news and market reports on transport textiles, medical textiles, smart materials and emerging markets. He has more than 35 years of experience covering fibers and technical textiles. He can be contacted at gfisher@textilemedia.com or +44 1603 308158.
Agricultural and seaweed residues were investigated as feedstock for the HighPerCell process, which uses ionic liquids as the direct solvent in the spinning of cellulose filaments.
The hot topic of fiber recycling is not without significant challenges for textile fiber applications, like apparel and home goods. Yet, technical fibers introduce their own set of properties that will need higher consideration in the circular economy, due to the demand from specific industries for strength and high performance derived from synthetic properties.
Here, we will consider the formulation of technical fibers and what makes them a challenge to recycle, key processes and benefits in recycling industrial fibers, regulatory issues surrounding recycled industrial fibers, as well as how industrial fibers are creating both challenges and new opportunities.
Technical fibers are synthetic or natural fibers that have been engineered to have specific physical, chemical, or mechanical properties that make them suitable for specialized applications in a variety
of industries. Unlike traditional textile fibers, technical fibers are designed to provide specific functionalities beyond basic comfort and aesthetics.
Specifically designed to meet the requirements of exacting applications, such as aerospace, automotive, construction, and medical industries, technical fibers are typically synthetic. These fibers are known for their superior strength, durability, and resistance to harsh environments, making them essential to produce high-performance materials. However, the production of technical fibers can have a significant environmental impact due to the high consumption of energy, water, and other resources, as well as the generation of waste and emissions. Recycling technical fibers is an effective way to reduce this environmental impact and create a more sustainable life cycle for these materials.
The production and use of technical fibers also raises environmental and health concerns, particularly related to the use of synthetic polymers and chemi-
cals. Efforts are underway to develop sustainable and eco-friendly technical fibers, as well as to improve recycling and disposal practices for end-of-life products.
Technical fiber recycling, also known as closed-loop recycling, is a process of recycling industrial and commercial waste fibers into new usable fibers, without any degradation in quality, which is a significant challenge. Technical fibers are typically made from materials such as polyester, nylon, and polypropylene, which are commonly used in the manufacturing of clothing, carpets, automotive parts, and other industrial products.
Recycling technical fibers involves the process of collecting and processing post-industrial waste, end-of-life products, and surplus materials to recover the raw materials and convert them into new products. The recycling process typically involves several stages, including sorting, shredding, cleaning, and reprocessing. During the sorting stage, the
materials are separated based on their composition, color, and other characteristics. Then, the materials are shredded into small pieces and cleaned to remove impurities and contaminants. Finally, the clean fibers are reprocessed into new products, such as yarns, fabrics, and composites.
One of the key benefits of recycling technical fibers is that it conserves natural resources and reduces waste. Technical fibers are made from non-renewable resources, such as petroleum-based plastics, which have a limited supply and contribute to climate change. Recycling these fibers reduces the demand for virgin materials and decreases the amount of waste that ends up in landfills or oceans. Recycling also reduces energy consumption and greenhouse gas emissions associated with the production of new materials, as recycled fibers require less energy and resources to manufacture.
In addition to the environmental benefits, recycling technical fibers also enables regulatory compliance. Many countries have regulations and policies in place to encourage or require the use of recycled materials in industry. By recycling industrial fibers, companies can comply with these regulations and demonstrate their commitment to sustainability.
As an example, the European Union (EU) Waste Framework Directive (WFD) is a comprehensive piece of legislation that sets out a framework for waste management in the EU. The WFD was first adopted in 2008 and was recently updated in 2018 to further improve waste management practices and increase recycling rates. The WFD sets targets for the reuse and recycling of waste materials, including textiles.
The European Commission is currently working on a new Circular Economy Action Plan, which was adopted in March 2020. This action plan sets out a range of new initiatives and legislative proposals aimed at further promoting a circular economy in the EU. As part of the Circular Economy Action Plan, the European Commission has proposed several legislative initiatives, including a new Sustain-
able Products Initiative and a new EU strategy for textiles.
The Circular Economy Action Plan includes measures to address key sustainability challenges such as resource depletion, waste generation, and greenhouse gas emissions. It also includes proposals to support the implementation of the WFD and to further promote the use of recycled materials in industry.
While the U.S. may not have a comprehensive circular economy framework at the federal level, there are several laws and initiatives aimed at promoting sustainable waste management practices and encouraging the use of recycled materials, as well as growing interest in the circular economy model among businesses and other stakeholders.
There are obvious and indirect challenges associated with recycling technical fibers.
The recycling process can be complex and require specialized equipment and expertise, which can make it more expensive than producing new materials. The quality of the recycled fibers may also be lower than that of virgin materials, which can limit their use in certain applications. Additionally, not all technical fibers are currently recyclable, which limits the potential for recycling in some industries.
To overcome these challenges, it is important to invest in research and development to improve the efficiency and quality of the recycling process. This includes developing new technologies for sorting, cleaning, and reprocessing fibers, as well as improving the design of products to facilitate their recyclability.
The process of technical fiber recycling involves several steps, including:
1. Collection and sorting: The waste fibers are collected and sorted based on their type, color, and quality.
2. Cleaning: The fibers are cleaned to remove any contaminants, such as dirt, oil, and other impurities.
3. Shredding: The fibers are shredded into small pieces to facilitate the recycling process.
4. Melt extrusion: The shredded fibers are melted down and extruded through small holes to form new fibers.
5. Spinning: The new fibers are spun into yarn or fabric, which can then be used in the manufacturing of new products.
Recycling technical fibers presents several hurdles that are not encountered when recycling more conventional materials such as paper, glass, or metal. Some of the key challenges to recycling technical fibers include:
• Complex composition: Technical fibers are often composed of multiple layers of different materials, such as polymers, metals, and other additives. This makes these fibers difficult to separate and recycle effectively.
• Contamination: Technical fibers may be contaminated with dirt, oil, or other substances that can make them unsuitable for recycling.
• Difficult to process: Some technical fibers may require specialized processing methods, such as high temperatures or chemical treatments, which can be expensive and energy intensive.
• Limited demand: The market for recycled technical fibers is often limited, as they may only be suitable for specific applications. This can make it difficult to achieve economies of scale and make recycling economically viable.
• Lack of infrastructure: Recycling technical fibers may require specialized equipment and facilities that may not be widely available or accessible.
Despite these challenges, there are ongoing efforts to develop new technologies and processes that can enable the recycling of technical fibers more effectively. For example, some companies are exploring the use of chemical recycling methods that can break down complex materials into their component parts, while others are developing new applications for recycled technical fibers, such as in building materials or automotive parts.
There are many new commercial industrial fibers commercialized globally but few match the properties and end-of-life challenges as carbon. Carbon fiber is difficult to recycle because it is a highly durable and lightweight material made up of long, thin strands of carbon atoms that are tightly woven together. The properties that make carbon fiber so desirable in many applications – its strength, stiffness, and lightness – also make it difficult to break down and recycle.
Carbon fiber recycling involves recovering the carbon fibers from end-of-life carbon fiber reinforced polymer (CFRP) composites and repurposing them for new applications. Recycling of carbon fibers is gaining increasing attention as the use of CFRP composites continues to grow in various industries, including aerospace, automotive, and sporting goods.
There are two main methods of recycling carbon fibers: mechanical recycling and chemical recycling. Mechanical recycling involves the physical separation of carbon fibers from the polymer matrix using techniques such as milling, grinding, and pyrolysis. The recovered carbon fibers can then be used to produce new CFRP composites or other products that require high-strength and lightweight materials. The disadvantage of mechanical recycling is that the resulting fibers are typically shorter and may have lower performance properties than virgin carbon fibers.
Chemical recycling, on the other hand, involves breaking down the polymer matrix using chemical processes to release the carbon fibers. The resulting fibers are often longer and have similar properties to virgin carbon fibers. Chemical recycling methods include solvolysis, hydrolysis, and pyrolysis. The disadvantage of chemical recycling is that it requires significant energy and resources to carry out the chemical processes.
In addition to the recycling of carbon fibers, there is also research into the development of biodegradable CFRP composites that can be broken down by natural processes, reducing the need for recycling. However, these materials are still in the early stages of development and may not yet be suitable for many applications.
Predicting specific technologies that will be available in 10 years for recycling technical fibers is difficult, as the field of recycling and sustainability is constantly evolving and advancing. Recycling technical fibers is an essential step towards creating a more sustainable future. It conserves natural resources, reduces waste, creates economic opportunities, and promotes sustainable development. While there are some challenges associated with recycling technical fibers, these can be overcome through investment in research and development, education, and policy support.
MiniFIBERS is leading the way in industrial fibers from the creation, converting and recycling. We continue to innovate and solve problems that are sustainable, efficient, and impactful.
Chris Plotz is the Director of Technical and Business Development at MiniFIBERS, Inc. in Johnson City, TN. Plotz is a business leader with 25 years of technical product and business development in a number of industries. He is responsible for leading and supporting all segments of growth of MiniFIBERS markets including C.A.S.E., nonwovens, composites and textiles of both synthetic and natural fibers. He can be reached at cplotz@minifibers.com or +1 423 616 2171.
There are many new commercial industrial fibers commercialized globally but few match the properties and end-of-life challenges as carbon.
n April this year, India overtook China as the world’s most populous country according to the United Nation’s population estimates – the most significant shift in global demographics since records began.
According to the UN’s projections, which are calculated through a variety of factors, including census data and birth and death rates, India now has a population of 1,425,775,850 people. That’s a big market.
The production of nonwovens and the consumption of products made from them – especially absorbent hygiene products (AHPs) and disposable wipes – has always grown alongside population growth and the rising prosperity of a country and now it looks like it may be India’s turn.
Nonwovens production in India has already grown by over 50% in the past five years, according to Business Consulting House (BCH), the New Delhi-based consultancy and industry advisor, from 410,000 tons in 2017 to 874,000 tons in 2022. Most notably, this new capacity is going to the AHPs market, for which non-
wovens production has rocketed from 16,600 tons to 84,395 tons over the same period.
“India’s nonwovens and AHP industries are currently seeing great momentum,” said Samir Gupta, BCH managing director. “New players are entering the market and existing participants are in expansion mode. Raw material supply is gradually becoming localized and import substitution is on the rise. As India gears up for the next hygiene revolution, it is witnessing new market trends coupled with a change in production dynamics. A neverseen-before user awareness is making the business very exciting.”
At this year’s INDEX 2023 show in Geneva there was a notable presence of major new Indian nonwovens manufacturers, including Global Nonwovens, based in Nasik, Maharashtra, and Spunweb, in Rajkot, Gujarat, both of whom were only founded in 2015.
Global Nonwovens was the first nonwovens company in India to set up two state-of-the-art Reifenhäuser Reicofil R4 five-beam spunmelt lines and has since become the first company in the country to install a Reicofil R5 line – the most
advanced spunmelt system for the production of AHP nonwoven components introduced at INDEX 2017.
“Every sector of the consumer lifestyle in the Indian market is growing in sophistication all the time, but the market penetration of AHPs in India is still low, primarily due to affordability,” according to Global Nonwovens CEO Anubhav Poddar. “The only way to increase market penetration is to keep the product cost low by the use of low basis weight nonwovens without compromising quality. The latest generation Reicofil RF 5 can
produce ultra-thin nonwovens with good mechanical properties, softness, uniformity and finer denier filaments.”
Meanwhile, Spunweb, based in Rajkot, Gujarat has consistently invested in technology for spunmelt nonwovens and now has five lines with an annual capacity of 33,000 tons, with a similar focus on growing the domestic market.
There was also good news for the country at the Geneva exhibition with Indian company Sparkle Innovations being first nominated for no less than three separate categories in this year’s INDEX Innovation Awards and then going on to claim the Sustainable Product category award for its SugaFluff absorbent cores for AHPs.
Sparkle is operating a state-of-the art converting plant in Kamrej, Gujarat, with the capacity to manufacture over one million sanitary pads per day and has established a sustainable and, in part, fully closed loop system for its products by working with local partners in India.
Sparkle sanitary pads are made from renewable resources designed to biodegrade in warm and humid conditions, with their top sheets, absorbent cores, release papers, pad wrapping papers and outer packaging all made of cellulosebased fibers.
SugaFluff absorbent cores are made from sugarcane bagasse – one of the world’s most abundantly available lignocellulose agricultural residues. In India alone, over 100 million tons of it is produced each year. Unlike planting softwood or hardwood trees, no extra land is required for bagasse as a widely available by-product of the sugar industry.
(Read our CEO interview with Sparkle’s CEO and co-founder, Chirag Virani in March-April 2023 issue of IFJ.)
In considering the entire life cycle of its products, Sparkle is going further and also piloting its GreenCycle project in Surat, Gujarat, as a first step for making the large-scale composting of absorbent hygiene products a reality.
Consumers signing up to the program are supplied with leak and odor-proof compostable bags for their used products, with a waste-management partner carrying out monthly doorstep collections.
“Many of our customers want to do their part to protect our planet by composting their used period products,” says Sparkle co-founder Hetal Virani. “However, for someone living on the 20th floor of an apartment building in an urban area without access to a backyard for composting, this is difficult. With the GreenCycle program, we aim to make it easy for our cus-
tomers to live a sustainable life by offering them a service to pick up their used products every month and turning them into compost.”
Just how quickly India’s market could grow was illustrated in one of a series of Continental Briefings held during INDEX 23, presented by Kazuaki Baba, secretary general of ANFA, the Asia Nonwoven Fabrics Association.
Baba supplied detailed production figures for the five leading nonwovens producing countries in Asia – China, India, South Korea, Taiwan and Indonesia.
With the addition of 301,000 tons of product made outside these Asian countries, the region’s total output was said to be just over seven million tons in 2022.
India is already the second biggest
nonwovens manufacturer behind China in volume terms, but there is a vast difference between the two nations, with China producing some 5.3 million tons of nonwovens compared to the 874,000 tons made in India in 2022.
China’s rise over a 25-year-period, however, has been phenomenal – back in 1997 it produced just 228,000 tons and its domestic market has been on an upward curve ever since.
There is no reason to suggest the same can’t now happen in India.
Adrian Wilson is an international correspondent for International Fiber Journal. He is a leading journalist covering fiber, filtration, nonwovens and technical textiles. He can be reached at adawilson@gmail.com.
Excellence is something to celebrate, especially for those who have used their career achievements for the benefit of the others. The nonwovens industry is known for its collaborative and innovative professional community who persistently push the envelope on materials, technology, education, and applications for nonwoven solutions. Each year, INDA, the Association of the Nonwoven Fabrics Industry, honors individuals who have accomplished all of this, and more. IFJ caught up with this year’s honorees to discuss their careers. Each one cites their peers as the defining factor to their successful work life.
Service to others is the highest form of career dedication. Throughout her career, Jan O’Regan could always be depended upon to volunteer her time and talents for the advancement of nonwoven applications.
As Director, Strategic Initiatives and Nonwovens Marketing, for Cotton Incorporated, she uncovered new opportunities for cotton to bring value into the nonwovens industry. Her work included leading efforts in strategic planning, technical and market project management, and sharing new ideas and results with the global supply chain.
She started her trek by earning a BS in Textiles and Business, summa cum laude, from Penn State University and an MBA from New York University’s Stern School of Business.
Serving and volunteering with INDA, the Association of the Nonwoven Fabrics Industry, for decades, O’Regan most recently chaired the World of Wipes® committee, which she efficiently organized to produce innovative conferences for the wipes industry. She was a frequent speaker at INDA, INSIGHT, EDANA, and other events, and for nearly two decades was a “go to” source of information for cotton fibers in nonwovens and hygiene.
Of her recent award, she said, “INDA’s Lifetime Service Award is an honor that belongs to a very, large group of industry professionals who over years have volunteered time, effort, and intelligence, with a sense of humor, for the benefit of the nonwovens industry. To be a team member with everyone has been a highlight of my career. Receiving this honor is something I never imagined.”
O’Regan spent over four decades in the nonwovens industry in various roles, including sales, marketing, strategic planning and business management. She notes
her proudest accomplishment to be, “Opening doors for natural fibers in an industry engineered for compatibility with synthetic raw materials of defined specifications was a challenge. The opportunity to be a part of this evolution was extremely gratifying.”
Her market responsibilities included consumer and industrial markets on regional, national, and global teams. In recent years, she applied these broad experiences to new markets for cotton in nontraditional applications. Marketing is an important part of corporate strategy and her work directly contributed to the growth of cotton in nonwovens. “My first assignment with Cotton Incorporated involved research to determine if there was a place for cotton in the nonwovens industry. I must admit to lucky timing. This happened when the baby wipes market was growing very quickly. Marketing strategic ideas about cotton through consumer, technical, sustainability and economic research was crucial to stimulating interest in the potential for business success and motivating organizations to overcome the technical challenges.”
Along the way as the notion of sustainability grew, she witnessed the industry’s adoption of new mindsets. “Fifteen years ago seems like a lifetime ago! In the nonwovens industry, then, products and materials were promoted as sustainable when the particles were small enough to be ‘unrecognizable in the environment.’ That was a beginning,” she notes. “Over time, our global industry has evolved to embrace the complexities of sustainability throughout the supply chain. Today, there is a wealth of information to consider from how raw materials are produced through to end of life and/or next life for end products.”
She offers this advice to those blazing their own career path: “No one can do it all alone. Success is built upon a community. Make friends. Provide thought-provoking ideas. Listen. Share. Be willing to work hard at what you believe in. And ... enjoy the ride!”
“Over time, our global industry has evolved immensely to embrace the tremendous complexities of sustainability throughout the supply chain.”
Dr. Seshadri Ramkumar, Ph.D., has led a distinguished career built upon a strong foundation in academics and research with nonwovens in the United States and India. Recognized with the 2023 INDA Lifetime Technical Achievement Award, the association points to Ramkumar’s over twenty-five years of experience within the technical nonwovens space. As Professor, Nonwovens & Advanced Materials Laboratory conducting industry leading research and educating nonwovens professionals at Texas Tech University (TTU), in Lubbock, Texas, he is known for establishing the university’s Nonwovens Laboratory. Many of Ramkumar’s students have gone on to become technical leaders within their organizations and the nonwovens industry.
“The recognition by INDA shows that our industry values academic research and the collaboration between academia and industry,” says Ramkumar. “More importantly, as many of the students from academia are gainfully employed in the nonwovens and advanced textiles sector, the recognition is for all the students who have worked with me and enabled to advance the field. The award is for all the students from our laboratory, who are the pillars of the industry.” He continues, “We learn from students – which is an important aspect of my work on a daily basis. Many new ideas evolve based on student interactions. Interacting with energetic and enthusiastic students serves as motivation for me and academics in general.”
Ramkumar led his team in groundbreaking research leading to innovations that he says are his proudest career highlight to date. “Translation of research from our laboratory that finds use in the fields of human health, environmental safety, and personnel protection are of what I am most proud,” he says. “More importantly, our work such as FiberTect® and cotton-based nonwovens for toxic chemical decontamination and oil absorption have become very useful, which is humbling for us.”
FiberTect® is a three-layer, inert, flexible, drapable, nonwoven composite substrate for absorbing and adsorbing chemical warfare agents, toxic industrial chemicals, toxic industrial materials, and pesticides. It is com-
monly used as the fabric of a handworn mitt or packaged wipes used primarily in emergency response. It has also been recognized by the American Chemical Society as a notable success of federally supported innovation, endorsed by Lawrence Livermore National Laboratory, and adopted by multiple branches of the government.
Providing insight into global nonwoven industry growth, he says, “The COVID-19 timeframe has clearly highlighted the usefulness and the need for advanced textiles such as nonwovens. With the help of INDA, we created awareness of the nonwovens sector in India way back in 2007. Today, this sector is receiving patronage from the Government of India and the advanced textiles sector is recognized as a growth engine in India.”
Ramkumar advocates that professionals surround themselves with peers as much as possible. “A career is always filled with ups and downs. Interaction with industry professional and fellow academics is very important in progressing. Associations like INDA enables people to progress, so it important that we engage in professional associations. Not only professional associations, but outreach and engagement with community is also important. These have helped me, and I would certainly encourage active participation with professional societies and the community.”
In addition to many peer-reviewed publications, articles, and columns (collectively over 500), including one on nanofibers that has been cited over 2,100 times, Ramkumar has contributed his expertise on the editorial boards of multiple fiber, nonwoven, and textile journals. He holds three patents and several invention disclosures.
Ramkumar has also organized conferences for nonwovens and textiles and actively promoted INDA and its technical training offerings for over 15 years. His work in India, organizing conferences and workshops, has helped to elevate India’s nonwoven textiles on the world stage.
He is a longtime member of the INDA Technical Advisory Board, been recognized by TAPPI, Society of Dyers and Colorists (UK), the Textile Institute (UK), and the Textile Association (INDIA), and received numerous awards from TTU.
Ramkumar holds a Bachelors of Technology (Textiles), Graduated with Distinction, and a Masters of Technology (Textiles), University First Rank in the Discipline, Anna University, India and a Ph.D. (Textile Materials) from the University of Leeds, UK.
“Many new ideas evolve based on student interactions. Interacting with energetic and enthusiastic students serves as motivation for me and academics in general.”
The contributions to industry made by Ed Thomas take on many forms, which is being recognized by INDA in the form of its 2023 Lifetime Technical Achievement Award. “Being recognized by my peers is perhaps the most rewarding part of this,” he says. “I can get great satisfaction from accomplishing a task, especially if the solution is novel, but to be recognized by my peers for years of effort in the industry is, to me, quite remarkable and humbling. It has been a true pleasure to participate in and contribute to the technical advances that make nonwovens such an exciting industry.”
Thomas retired after 39 years, with 32 years in the nonwovens industry, and has remained active teaching the Intermediate Nonwovens Training Course for INDA and The Nonwovens Institute at North Carolina State University, as well as providing consulting services to the industry.
As an educator, the excitement of learning something new is a driving force. “Without exception, everyone in the courses is there to learn something new and their appetite is obvious. I enjoy watching them absorb the information, answering their questions, sharing personal insights and relative experiences, and very often watching them experience an ‘ah ha’ moment. This is when the light comes on and they now have something they can take back and use to advance their own or their company’s future.”
Thomas’ corporate experience includes Process Engineering Manager and Plant Management, DuPont; Technical Director, Reemay; VP of Research and Operations, VP of Operations and Technology, and Global VP of Research and Development for Fiberweb/BBA Nonwovens; and Head of Research and Product Development, First Quality Nonwovens.
He holds 10 U.S. nonwoven patents and he and his teams have been awarded more than 250 patents for numerous and diverse innovations that have played significant roles in the success of the nonwovens industry. These include applications for the global hygiene market, industrial nonwovens, and filtration media.
During his career, he led multiple teams to create textile solutions for various customers. “Most of my personal patents involved meltspun nonwovens, although my diverse teams were engaged in most of the nonwoven technologies,” he notes. “As a nonwoven producer, we constantly examined the industry trends looking for unmet needs whether they were articulated by a
particular customer. In some cases, we would analyze competitive offerings and develop alternative options. Obviously intellectual property issues were forefront. In some cases, the customer’s goal or objective was either not well defined or only partially disclosed.”
In an industry where information is held tightly to remain competitive, he reflects on his team collaborations, “This ‘over the transom’ development as we called it was challenging. A particularly memorable experience was a discussion with a customer about a new material they were looking for; not a competitive replacement or something they had already prototyped themselves. We started with the basic physical and performance characteristics they were looking for and in a collaborative effort, came up with viable solutions by integrating our prior developments. In many cases, a novel idea is generated by an individual and, in some cases, by a small group of collaborators. But once the idea is reduced to practice, scaleup and commercialization, it requires different sets of skills, so that’s how we formed our teams. Activity would be transferred between team members as the work progressed.”
Thomas also has presented several keynote addresses and papers to industry conferences, participated in North Carolina State University’s Nonwovens Cooperative Research Center (NCRC) prior to it becoming The Nonwovens Institute (NWI), INDA’s Technical Advisory Board, INDA’s Sustainability Committee, and was Vice Chair of NWI’s Industrial Advisory Board prior to retirement and remains an Emeritus member. He is also a Vietnam veteran and received his mechanical engineering degree from SUNY Buffalo.
A highlight of his career is difficult to single out. “Perhaps it is this award,” he notes. “All our careers are filled with highs and lows but having the ability and responsibility to play from the initial conception to the ultimate manufacturing of novel and valuable materials is exhilarating. But leading an international group of scientists and engineers that collaborated closely with each other to deliver impressive results and being referred to as a wizard by a chief executive is high on the list.”
In the end, it is people he credits for his success, and he encourages others to put people first. “Manage by a set of principles and consistency rather than rules. Focus on each individual’s strengths, which builds powerful teams that can do more than any single person. Not all new ideas will be broadly accepted, so be passionate about yours and get creative about ways to convince others how your organization will excel with them.”
“Manage by a set of principles and consistency rather than rules. Focus on each individual’s strengths, which builds powerful teams that can do more than any single person.”
pportunity” is a key word that Jim Robinson uses to describe his career, as he reflects on being a 2023 recipient of INDA’s Lifetime Technical Achievement Award. “Over my entire career I found the industry to be filled with opportunities to help people solve problems and to mutually share with them the technical understanding of our engineered products. I had fun many more days than not and, along the way, got to meet so many fine people and develop lasting, rewarding relationships.”
“Receiving this is especially gratifying,” he continues. “It means that what you have spent a career doing and enjoying has made a difference that others appreciate.”
With a long and full career comes many highlights. Choosing one that stands out is difficult, says Robinson. “When you reflect on over 35 years of technical work, it is hard to select one thing. Further, no accomplishment is achieved alone, and I have been fortunate enough to be able to collaborate with many talented people. I think what I am most proud of in general is having the opportunity and good fortune to help a lot of really great people solve problems.”
Jim Robinson has 33 years in the absorbent hygiene industry, including 28 years as a Technical Service Manager at BASF. He led technical teams that focused on the application of superabsorbent polymers (SAP) in hygiene products. Robinson has extensive knowledge of SAP applications, absorbent core formation, and hygiene article design, performance and testing. While with BASF, Robinson led efforts with multiple external companies to provide co-supplier solutions to hygiene converters. Robinson has a BS in Chemistry from HampdenSydney College and an MS in Chemistry from Duke University.
“My work was always lab based, customer interactive support for a wide group of diaper producers,” he says. “Since I started in the 90’s, the industry underwent heavy consolidation which has continued to this day. However, we are also witnessing a new growth in boutique or specialty producers that is beginning to stratify the market again.
The one change that I feel has stifled the pace and opportunity for innovation is that diaper producers used to let you on the production floor and to be part of trial work. It was very collaborative and helped suppliers quickly solve issues. Now, floors are off limits and collaboration is not as strong.”
Robinson’s extensive understanding of test methods and test method development led to his coordinating the establishment of fitness for use standards of adult incontinent products with the National Association for Continence and involvement in development and review of absorbent product test methods with INDA/EDANA.
He is also an active contributor to INDA’s Technical Advisory Board and Hygienix organizing committee and was a contributing developer in establishing the INDA Absorbent Hygiene Training Course. Robinson has provided numerous presentations at INSIGHT, Hygienix, and RISE on performance and interactions of absorbent system components.
Recently, Robinson has been consulting and contributing to the success of multiple start-ups including those having been nominated for INDA product awards.
As an instructor in hygiene training, potential comes to mind. “The folks that participate in my class always impress me with having a thirst to learn. There is an element of surprise at times when the complexity of a diaper or other hygiene product is revealed. Then, as we peel back the layers and explore the topics that drive product performance, you can see the understanding that happens in a visible way. That’s fun. Some of the participants will surely drive the future of the industry, while others may just be passing through. They all have the common interest of gaining and applying knowledge.”
His advice for a fullfilling career is simple. “Hang out with people who a smarter than you. Hang out with people who are very different than you. Give credit to others. Don’t talk a lot; rather, listen and listen with empathy.”
“Hang out with people who a smarter than you. Hang out with people who are very different than you. Give credit to others. Don’t talk a lot; rather, listen and listen with empathy.”
Seshadri Ramkumar, Ph.D., is professor of nonwovens and advanced materials at Texas Tech University. He is a member of Technical Advisory Board at INDA, Association of the Nonwoven Fabrics Industry. He was the immediate past chair of the Nonwovens Engineers & Technologists (NET) Division of TAPPI, and he publishes a column called TexSnips. He can be reached at s.ramkumar@ttu.edu.
What is the next phase for the advanced textiles sector? Functional textiles that provide added applications and at the same time support sustainability is the way forward for the sector.
Functional characteristics must be part of the textile chain right from the fiber level. The industry has gained recognition at the “common man” level since COVID-19, which is predominantly due to performance characteristics such as the filtration of high surface area substrates like nonwovens, nanofibers and activated carbon. This global recognition provides opportunities for the sector to build on the momentum to diversify and grow beyond current markets, receive major government support, and enable many new start-ups.
As a table stands on four legs, advanced textiles sector should stand on four legs 1) Performance; 2) Comfort; 3) Sustainability; and 4) Cost.
First and foremost, enhancement of performance characteristics beyond the current level is an important task for the industry. In addition to active performance capabilities, another important aspect is comfort, including breathability, next-to-skin friendliness, fit, and light weight, to name a few.
While performance and comfort are two major performance attributes that will drive the industry
forward, immediate efforts must be dedicated by the industry to two additional aspects, namely sustainability and cost.
The industry should focus on having nextgeneration fibers with improved functionality. The textile industry has advanced in this area, with regard to synthetic fibers and regenerated fibers. Dedicated attention should focus on the natural fiber industry. As the natural fiber sector is dependent on weather, it is subjected to volatility regarding quality, quantity, and cost. There needs to be a better handle on these aspects as judiciously and efficiently as possible by this sector.
The United States’ cotton sector has been at the forefront in enhancing the yield per acre, using supplemental irrigation and practice conservation approaches such as no till farming. Currently efforts are focused on avoiding plastic contamination and enhancing better flow of commodities. The global cotton sector in regions such as Asia and Africa should enhance this sector as this industry provides lifelines to many small farmers who own less than one hectare of land.
The nonwoven and advanced textiles sector, which has been heavily dominated by synthetic fibers such as polypropylene and polyester, is now looking into cotton and other alternate
fibers. In this regard, it is worthy to highlight international collaborative activity between U.S.-based Texas Tech University and South India-based Jayalakshmi Textiles. Natural cotton-based nonwoven substrates evolved out of this partnership, which resulted in environmentally friendly oil absorbents. These are some real-world examples of sustainable nonwovens, which find applications in environmental protection and healthcare markets.
The advanced textiles sector is now looking into developing products using hemp, ramie, coarse wool, and jute. Much attention is also being paid to industrial applications for hemp and ramie. Opportunities are there for nonwoven machinery makers and the specialty chemical industry to develop products that will enable cost-effective applications for these natural fibers.
“Natural fibers, such as hemp, are an exciting part of the growing global bioeconomy because they provide a sustainable alternative to petroleum-based synthetic fibers. Natural fibers are
also exciting because they each have their own properties when woven into textiles or made into advanced textiles using a myriad of technologies and can provide consumers with a wide range of sustainable and advanced textiles,” stated Professor Brendan Kelly, fiber expert in the Department of Plant and Soil Science at Texas Tech University.
New medical applications can emerge if collaborations exist between the biomedical, functional chemicals, fibers, and nonwovens sector. Vector repellant and viral barrier fabrics, which are cost effective, provide new opportunities for the nonwovens and advanced textiles industry.
Nonwoven and advanced textiles sectors have opportunities in developing cost-effective, sustainable and health-friendly products. Single-use applications involving green products will be accepted in markets such as enhancing human life, environmental safety, and protection. Such efforts will lead to positive symbiotic relationships with academia, regulatory bodies, and research organizations.
Annual textile yearbook covering natural and manmade fibers, feedstocks, nonwovens, trade data, 20 country profiles and a wealth of further information helping to conduct business.
In addition, major associations and industry experts provide their views on the markets.
Publication: May 2023
https://thefiberyear.com/
info@thefiberyear.com
Andreas Engelhardt, a former senior manager at Oerlikon Textile International Business, is the founder and president of The Fiber Year GmbH. The company’s mission is to provide international expertise, analyses, strategy consulting, and customized solutions to the international textile industry. Andreas can be reached at +41 71 450 06 82 or engelhardt@thefiberyear.com.
The Fiber Year 2023 is nearing completion and is ready for publication as of May. Some final confirmations for manmade fiber manufacturing are still pending but the former appraisal proved true. Development of both natural and manmade fiber segments was similar to 2020. The cumulative three-year loss in fiber supply accounted for 19 million tonnes. Polymer-based nonwovens continued their decline unsurprisingly. This year’s outlook remains uncertain and rather cautious as IMF in its April World Economic Outlook slightly lowered projections for 2023 and next year. First quarter export data from 10 major Asian industries underline skeptic prospects.
pposing dynamics remained in the fourth consecutive year with natural fibers increasing and manmade fibers shrinking for the third time in the century. Improvements in natural fiber segments were visible across the board and, in particular, in the three largest sectors of cotton, jute and wool with a cumulative share of 94%.
The manmade fiber business saw losses in both wood-based cellulosic and synthetic fibers. All mainstream subsectors suffered from negative growth. Identification of segments with expanded manufacturing volume required to dig deep into
small-scale fiber types such as aramid, carbon and lyocell fibers.
Aramid benefited from high demand in optical fiber cable markets, an improvement in automotive applications after almost a 6% growth in world vehicle production and an uptick in protective clothing.
Carbon fibers experienced surging demand from wind energy and robust recovery in the commercial aerospace market as consequence of an improvement in air traffic, fleet replenishment and the launch of composite-rich freighters and business jets.
Lyocell fibers were again the best performing fiber sector to achieve a double-digit growth rate following the successful ramp-up of new projects. Superior fiber properties, growing awareness of plastic waste and of consumers for environmentally safe clothing are to deliver bright prospects for future growth.
The main reason for opposing dynamics of both fiber categories is that manmade fibers quickly can be controlled to match demand unlike natural fibers that have a time lag between planting decision and harvesting for subsequent processing.
Using both sector’s average annual growth rate between 2000 and 2019 and extrapolate their pre-pandemic volumes accordingly leads to a theoretical threeyear loss of 5 million tonnes of natural fibers and even 14 million tonnes of manmade fibers.
The precise rate of change for all fiber types will be available in The Fiber Year 2023.
The spunlaid business witnessed its second straight annual decrease after 33% boost in 2020. Contrary to fiber industries, spunlaids achieved a three-year gain of more than one million tonnes as result of outsized demand for face masks and hygiene articles despite falling short half a million tonnes last year.
Nevertheless, the pandemic has also caused a significant deceleration of growth momentum from more than 8% between 2000 and 2019 to a three-year growth rate during pandemic at about 6%.
The World Health Organization (WHO) revealed in March that it expects to declare an end to the COVID-19 pandemic later this year. This will further normalize the consumption of such hygiene products but leads to the question about future applications for machinery and equipment installed for face mask production.
Surrounding conditions for a sustained recovery are not yet in place with the ongoing war in Ukraine, geopolitical tensions, elevated inflation, high cost of living and food prices, uncertainties in semiconductor supply, increasing interest rates, shortage of workers and still weak demand in many applications.
Strong labor markets with U.S. unemployment rate at 3.5% in March and in the European Union at century’s record low of 6.0% in February and wages that have been rising at a historically rapid pace might justify a rebound of consumer spending. It seems to be noticeable already for holidays and airline tickets, entertainment and restaurants while consumers rather cut spending on non-essentials like apparel with wardrobes mostly overfull. Demand for clothing has seen some improvement in segments
like formal and corporate wear as an increasing number of people have returned to office. Casual wear and fast fashion seem to underperform reflected by an increasing number of store closures of major retailers and brands. Demand for outdoor and sportswear reportedly has not yet picked up as such recreational activities were in great demand during the time of the home office.
Home textile end-uses are expected to remain extremely weak as home improvement projects were brought forward at the beginning of pandemic when people all of a sudden spent much more time at home.
Automotive and aircraft manufacturing recorded gradual expansions with volumes still below pre-pandemic levels. Crisisproof hygiene demand is not anticipated to experience noticeable growth due to lower disposable incomes; it may rather see some material shifts in an attempt to reduce production costs.
The lifting of pandemic restrictions has caused higher spending on services which is expected to remain with positive effects for the refurbishment of hotels, restaurants and cruise ships. In addition, social events, fairs and conferences returning to normal will stimulate event textiles and the necessity of more frequently using formal wear.
A more detailed analysis will provide further information and will shine a light on specific country risks, for example arising from international reserves in Pakistan shrinking to a nine-year low in February 2023 and standing at two-week import coverage, or the impact of massive polyester feedstock investments on supplying industries. The full picture of the latest market developments will be available in The Fiber Year 2023 in May, including a wealth of information from feedstocks to fibers, yarns, nonwovens and trade data including Q1 2023 update.
The main reason for opposing dynamics of both fiber categories is that manmade fibers quickly can be controlled to match demand unlike natural fibers that have a time lag between planting decision and harvesting for subsequent processing.
Len LaPorta is a managing director of Investment Banking at Wiley Bros.-Aintree Capital, LLC – a 75-year-old firm, located in Nashville, TN, focused on investment brokerage and underwriting municipal bonds for utility districts in the state of Tennessee. Len brings to the Firm experience in crossborder M&A transactions between USA and Europe, advises business owners on sell-side and buy-side transactions, capital advisory, and valuations. Len is a graduate of the U.S. Naval Academy with MBA from Boston College and a veteran of the U.S. Navy. He is also a member of INDA’s non-woven Technical Advisory Board. llaporta@wileybros.com or (615) 782-4107.
We are in a unique time, when smalland medium-sized companies are in the trenches competing to win talent, as we have never seen before. During the past 24 months, we have witnessed a multiplier expansion in the number of third-party groups providing all types of support to business owners.
In many cases, these third-party providers are convincing the owner to work with them for two to four years to “prepare” the business for sale.
What happens if the owner needs to sell the business now? Enter your investment banker and team from the transfer portal.
The management team at most firms will work very well with the M&A team once they begin their due diligence. In most cases, the M&A team will make one visit to the firm’s facility and then complete most of their work remotely during the next nine to 12 months. Maintaining a low profile is ideal for the M&A team and reduces stress among the business owner’s employees.
If a firm has engaged a third-party group to help them prepare, then tension may exist when the M&A team walks in the door and their client attempts to move into the next phase of their multiyear plan – selling the business. How would your third-party team feel when your nearly two years of work is but a futile effort?
The M&A Team has their standard due diligence lists and the management team should easily produce materials to satisfy the specific section. Let’s use sales and marketing as an example.
Due diligence request for sales and marketing:
1. Marketing and sales literature and forms, including price lists, catalogs, purchase orders, technical manuals and user manuals.
2. Marketing agreements and material agency and advertising contracts.
3. All agreements or proposed agreements with distributors, dealers and sales representatives.
4. List of any warranty claims, and reserves and expenses related thereto.
5. Listing and description of all co-branding, private label, alliance, joint venture, partnerships, co-marketing, distribution, licensing, or similar agreements with other entities use by the companies.
6. Copies of all side letters and oral agreements.
7. List and general description of commission or other compensation arrangements with sales personnel.
8. E-commerce statistics and SEO results.
9. Client’s five- or 10-year transaction history and profit analysis.
In some instances, the third-party provider is filling a role that the owner has had trouble hiring for within the management team. My previous example focused on the sales and marketing due diligence efforts – maybe the third-party individual is temporarily fulfilling that role for the management team. Once the M&A team is in place, perhaps the next logical step would be for the owner to offer a full-time job to the third-party provider. In essence, that third-party individual or team has just moved into their own transfer portal.
The M&A team should embrace and collaborate with all members of the management team regardless as to whether they are full time staff or a third-party service provider.
Firms with a solid management team generally receive higher marks during the M&A process which can ultimately result in creating more value for the owner.
Federal Reserve Bank of Philadelphia, Third District Coincident indexes, March 2023 (See table page 46):
In the three months to March, the coincident index for Pennsylvania rose 1.1 percent. The level of payroll employment increased over the past three months. The unemployment rate decreased during the three-month period. In addition, average hours worked in manufacturing increased. Overall, Pennsylvania’s economic activity as measured by the coincident index has risen 3.4 percent over the past 12 months.
In the three months to March, the coincident index for New Jersey increased
0.1 percent. The level of payroll employment increased over the past three months, and average hours worked in manufacturing increased. However, the unemployment rate increased during the three-month period. Overall, New Jersey’s economic activity as measured by the coincident index has risen 3.2 percent over the past 12 months.
In the three months to March, the coincident index for Delaware rose 1.4 percent. The level of payroll employment rose over the past three months. The unemployment rate decreased during the threemonth period but generally remained higher than its pre-pandemic level. Additionally, average hours worked in manufacturing increased. Overall, Delaware’s economic activity as measured by the co-
incident index has risen 2.6 percent over the past 12 months.
Good luck closing your transaction!
This article has been prepared solely for informational purpose. This article does not constitute an offer, or the solicitation of an offer, to buy or sell any securities or other financial product, to participate in any transaction or to provide any investment banking or other services, and should not be deemed to be a commitment or undertaking of any kind on the part of Wiley Bros. –Aintree Capital, LLC (“WBAC”) or any of its affiliates to underwrite, place or purchase securities or to provide any debt or equity financing or to participate in any transaction, or a recommendation to buy or sell any securities, to make any investment or to participate in any transaction or trading strategy. Any views presented in this article are solely those of the author and do not necessarily represent those of WBAC. While the information contained in this commentary is believed to be reliable, no representation or warranty, whether expressed or implied, is made by WBAC, and no liability or responsibility is accepted by WBAC or its affiliates as to the accuracy of the article. Prior to making any investment or participating in any transaction, you should consult, to the extent necessary, your own independent legal, tax, accounting, and other professional advisors to ensure that any transaction or investment is suitable for you in the light of your financial capacity and objectives. This article has not been prepared with a view toward public disclosure under applicable securities laws or otherwise.
Ocean State Innovations, a leading textile provider, announced the acquisition of Cloud9 Fabrics of Cranford, New Jersey. Cloud9 Fabrics predominately offers organic fabrics to the quilting trade. Ocean State Innovations was formerly known as Brand and Oppenheimer and acquired another quilting fabric company, General Fabrics, in 2018. Cloud9 has been in business for over 14 years and also offers a selection of apparel fabrics for home sewing. They use only 100% certified organic cotton in the manufacturing of their cotton base cloths and eco-responsible low impact dyes for printing and dying.
www.osinnovate.com
ADVERTISING | SALES
PUBLISHER Driven By Design LLC advertising@inda.media • +1 239.225.6137
Sabine Dussey
GERMANY, FRANCE, AUSTRIA, SWITZERLAND, SCANDANAVIA, BENELUX sabine.dussey@dussey.de • +49 2129.348390
Joan Oakley BUYER’S GUIDE & CLASSIFIED ADS joakley@inda.media • +1 248.347.3486
Ferruccio Silvera & Filippo Silvera ITALY & SPAIN info@silvera.it • +39 02.284.6716
Frank Strazzulla UNITED STATES +1 949.459.1767 • franks@tmsmedia.net
Zhang Xiaohua CHINA ifj_china@126.com • +86 13522898423
ADVERTISING COORDINATOR VICKIE SMEAD vsmead@inda.org • +1 919 459 3700 x 3720
he Lenzing Group, a world-leading provider of specialty fibers for the textile and nonwoven industries, has successfully completed the conversion of a production line from generic viscose to TENCEL™ branded modal fibers for textiles and clothing at its facility in Nanjing, China. Lenzing is therefore in a position to offer its Chinese customers locally produced TENCEL™ fibers for the first time and meet the structural growth in demand more quickly. Thanks to the conversion of the production line with a nameplate capacity of 35,000 tonnes per year, the fiber portfolio of the Chinese production site now solely consists of eco-friendly specialty fibers. In addition,
Lenzing also offers LENZING™ ECOVERO™ branded fibers for textile applications and viscose eco fibers for nonwoven applications in China.
Celebrations for the launch of the new production line took place in April 2023, as part of a customer event.
www.lenzing.com
pex Mills, a fully integrated domestic supplier and manufacturer of custom technical and specialty textiles and fabrics, has named Joan Izzo as new Senior Marketing Manager. She will build greater awareness of the company brand as an innovative supplier and fabricator as well as promote newly expanded capabilities. She brings 25 years of experience with global manufacturers of fibers, fabrics, elastomeric films, and engineered materials across a wide variety of industries.
Most recently, she was Marketing Director at INDA, the Association of the Nonwovens Industry.
Izzo has strong expertise in the For -
tune 500 B2B arena, marketing to diverse sectors including apparel, automotive, consumer products, healthcare, filtration and furnishings.
Apex Mills’ recent acquisition of the former Hanesbrands Inc. facility in Woolwine, VA offers new opportunities for its customers, “With her excellent experience, Joan will increase awareness of Apex Mills by marketing our innovative solutions for customers seeking high quality, made in USA products,” said Jonathan Kurz, Apex Mills President and Chief Executive Officer. “She will play a critical role in developing and supporting growth strategies.”
www.apexmills.com
Discover everything happening in the nonwovens and engineered fabrics industry. Visit inda.org and join the momentum.
World of Wipes® (WOW)
FiltXPO™ | International Filtration/Separation
International Conference Exhibition & Technical Conference
July 17-20, 2023
Marriott Marquis - Atlanta, GA
October 10-12, 2023
Navy Pier - Chicago, IL
HYGIENIX™ | The Premier Event for Absorbent Science for Engineered Fabrics) Hygiene & Personal Care Markets
RISE® (Research, Innovation &
September 26-27, 2023
NC State University - Raleigh, NC
November 13-16, 2023
The Roosevelt - New Orleans, LA
Nonwoven Product Development & Innovation
June 20-23, 2023
Fiber & Filament Extrusion Fundamentals
September 12-14, 2023
The Nonwovens Institute, NC State University - Raleigh, NC
The Nonwovens Institute,
WIPES Academy
July 17-18, 2023
Marriott Marquis - Atlanta, GA
Intermediate Nonwovens Training Course
August 1-4, 2023
NC State University - Raleigh, NC
Filter Media Training Course
October 9-10, 2023
Navy Pier - Chicago, IL
Intermediate Nonwovens Training Course
October 24-27, 2023
INDA Headquarters, Cary, NC & The Nonwovens Institute, & The Nonwovens Institute, NC State University - Raleigh, NC NC State University - Raleigh, NC
INDA Headquarters, Cary, NC
Absorbent Hygiene Training Course
August 8-10, 2023
INDA Headquarters - Cary, NC
Elementary Nonwovens Training Course
August 22-23, 2023
INDA Headquarters - Cary, NC
Fabric Property Development & Characterization
December 5-8, 2023
The Nonwovens Institute, NC State University - Raleigh, NC
For more information visit inda.org