
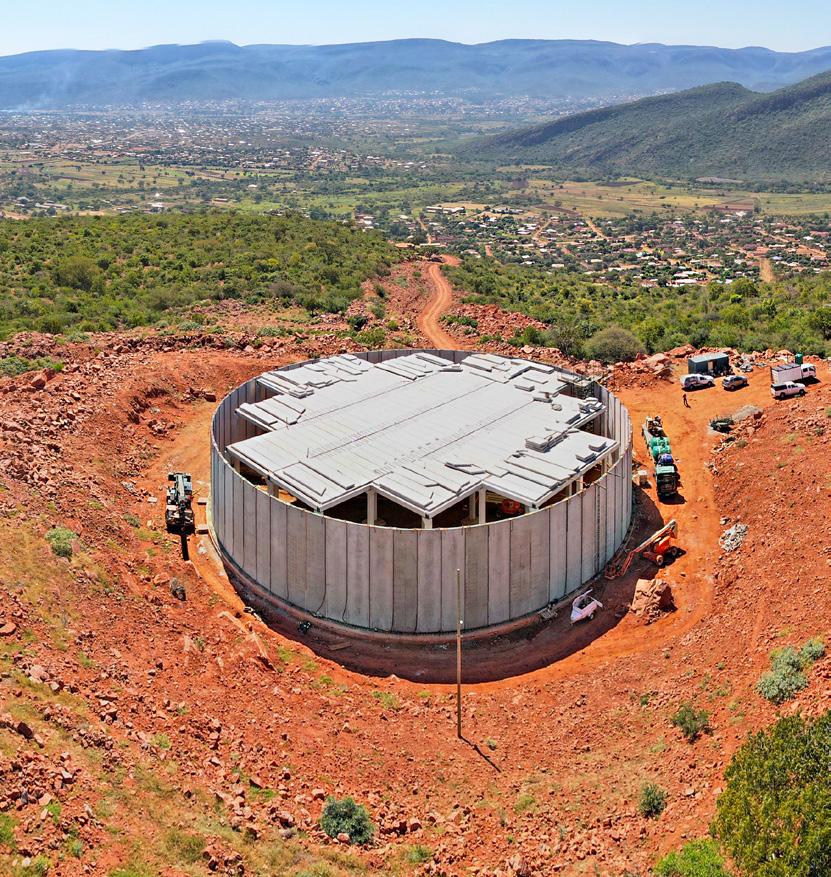
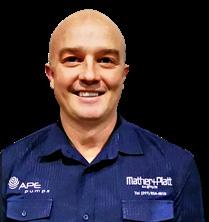
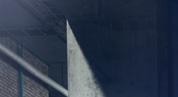
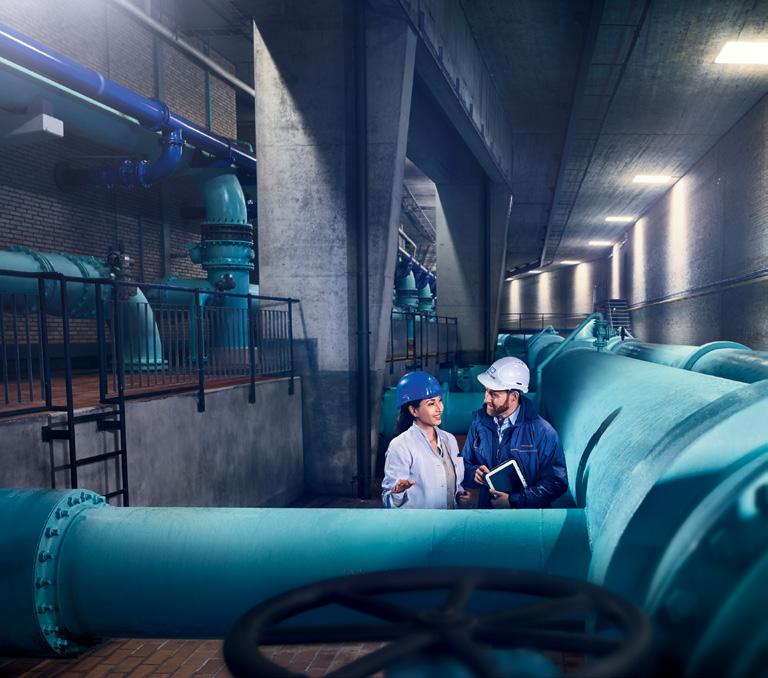




We understand the challenge of finding the right balance between plant e�ciency and compliance with industry standards and legal requirements.
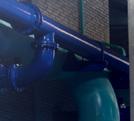

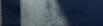


We understand the challenge of finding the right balance between plant e�ciency and compliance with industry standards and legal requirements.
You meet your e�ciency goals and reduce costs without compromising on water quality.
Improve your processes with our comprehensive portfolio of measuring instruments:
Micropilot FMR20:
Level radar with the process indicator RIA15 simplifies remote commissioning and operations.
Promag W 400: Versatile, weight-optimized electromagnetic flowmeter fits perfectly all standard applications.
Contact us to find out more
Email: info.za.sc@endress.com
Memograph M RSG45: Advanced data manager takes compliant, safe and secure operations control to a higher level.
EDITOR Alastair Currie
Email: alastair@infraprojects.co.za
DESIGNER Beren Bauermeister
CONTRIBUTORS Alaster Goyns, Chetan Mistry, Christopher Chinonge, Mike Smart, Sibusiso Mjwara
DISTRIBUTION MANAGER Nomsa Masina
DISTRIBUTION COORDINATOR Asha Pursotham
SUBSCRIPTIONS
Email: distribution@infraprojects.co.za
ADVERTISING SALES
KEY ACCOUNT MANAGER Joanne Lawrie
Tel: +27 (0)82 346 5338
Email: joanne@infraprojects.co.za
PUBLISHER
IMESA (Pty) Ltd
P O Box 2190, Westville, 3630
Tel: +27 (0)31 266 3263
Email: info@infraprojects.co.za
ANNUAL SUBSCRIPTION: R805.00 (INCL VAT)
ISSN 0257 1978 IMIESA, Inst.MUNIC. ENG. S. AFR.
© Copyright 2024. All rights reserved.
IMESA CONTACTS
HEAD OFFICE:
Manager: Ingrid Botton
P.O. Box 2190, Westville, 3630
Tel: +27 (0)31 266 3263
Email: admin@imesa.org.za
Website: www.imesa.org.za
BORDER
Secretary: Celeste Vosloo
Tel: +27 (0)43 705 2433
Email: celestev@buffalocity.gov.za
EASTERN CAPE
Secretary: Susan Canestra
Tel: +27 (0)41 585 4142 ext. 7
Email: imesaec@imesa.org.za
KWAZULU-NATAL
Secretary: Narisha Sogan
Tel: +27 (0)31 266 3263
Email: imesakzn@imesa.org.za
NORTHERN PROVINCES
Secretary: Debbie Anderson
Tel: +27 (0)83 326 3050
Email: np@imesa.org.za
SOUTHERN CAPE KAROO
Secretary: Henrietta Oliver
Tel: +27 (0)79 390 7536
Email: imesasck@imesa.org.za
WESTERN CAPE
Secretary: Michelle Ackerman
Tel: +27 (0)21 444 7112
Email: imesawc@imesa.org.za
FREE STATE & NORTHERN CAPE
Secretary: Wilma Van Der Walt
Tel: +27 (0)83 457 4362
Email: imesafsnc@imesa.org.za
All material herein IMIESA is copyright protected and may not be reproduced without the prior written permission of the publisher. The views of the authors do not necessarily reflect those of the Institute of Municipal Engineering of Southern Africa or the publishers.
The
With South Africa’s seventh National and Provincial Election now confirmed for 29 th May 2024, the countdown has begun as the country prepares for one of the most landmark events since the 1994 transition to democracy. For the first time, surveys by political analysts point to the real possibility of a coalition government at national level, rather than the existence of a single majority party in shaping future policies.
Whatever the outcome, it’s critical for the country that a common cause prevails so that major infrastructure programmes in areas like roads, rail, water, sanitation and energy maintain and increase their momentum.
South Africa has some of the most advanced legislation in the world, but one of the key challenges has been enabling implementation, compounded by compliance bottlenecks uncommon in free market economies. To work in practice, more intensive partnership with the private sector is essential to ensure that South Africa is globally competitive, with the JSE one of the main barometers of investor sentiment.
When it comes to attracting investment, South Africa continues to receive relatively strong support from the G7 block and broader G20 countries. South Africa’s BRICS membership should also provide a degree of strategic advantage given that it includes leading countries globally in terms of GDP. In the latter respect, those ranked in the top 10 by current IMF data are China, India and Brazil in 2nd, 5th and 9th place, respectively.
But every country logically has its own home ground priorities because a strong local manufacturing base is the mainstay for a healthy micro and macroeconomy. When perfected, unemployment –as reflected in G7 countries – is generally below 5%, and corporates, individuals and SMMEs flourish.
Competing against the world’s leading economies is tough and there are no consolation
prizes. Winning nations lead because they invest heavily – particularly in STEM education – in pursuit of best-in-class technological innovation, with Artificial Intelligence an increasing part of the mix.
Globally, South Africa is currently ranked 59 th out of 132 countries and 2nd for African economies (with Mauritius in 1st place regionally) according to the World Intellectual Property Organisation’s (WIPO’s) 2023 Global Innovation Index.
As the WIPO defines it, innovation scores are determined by criteria that include institutions, human capital and research, infrastructure, credit, and investment. The greater the degree of public and private alignment, the more opportunities are unlocked to grow people, businesses and the fiscus.
The ultimate enabling environment is at local government level wherever you travel in the world. Infrastructure should work optimally, maintenance should be well planned, plus future upgrades must match town and city planning projections. To achieve this, adequate budgets need to be in place, and every cent spent should be geared towards stimulating positive GDP gains.
In this respect, keeping on track in terms of capital expenditure targets is important, but South African municipalities sometimes end up not spending their full allocated funds.
Connecting the dots takes teamwork, experience, and commitment, plus it’s every citizen’s responsibility to ensure that public officials deliver on their mandate. Because South Africa needs to grow in the world by developing and nurturing its future innovators, and to achieve this infrastructure must work.
At Xylem we are 100% about water, including delivering transformative solutions across the entire water cycle. We are pioneering our approach through 360 Performance solutions, delivering source-to-tap support, products, engineering expertise, and more for real value, efficiency, and lasting performance. Let’s Solve Water is more than a slogan, it is our mission! Discover 360 Performance, the cornerstone for a sustainable water future.
Presenting the Lowara e-IXP smart pump, designed according to ISO 2858 and 5199 standards to be the 360 Performance solution for industrial and multi-storey building applications due to its ability to be energy efficient, reliable and easy to maintain. At its core lies the ability to provide real-time data, empowering users with unparalleled insights into the system and efficiency. With proactive alerts, the e-IXP takes a 360 Performance approach to maintenance, ensuring timely interventions to prevent potential issues before they escalate.
STANDARDIZATION MATCHES INNOVATION
Hosted annually on 22nd March, UN Water’s 2024 theme for its “World Water Day” campaign was “Water for Peace” drawing the international communities’ attention to the need to collectively conserve and equitably share the most vital resource on the planet. This is an urgent imperative as the climate change threat grows, while population expansion and urbanisation intensify, along with increasing food security concerns, plus energy supply shortfalls – where water for cooling and allied elements is a core component.
Within this context, water stressed economies are the most at risk. Combatting the issue hinges on two crucial elements, namely functional water infrastructure, and sound water governance. There also needs to be an intensified focus on ensuring that green and grey interventions dovetail with each other. An example of the former would be wetland preservation – a natural biofilter and absorber of CO2 – and for the latter dams, pipeline, water and wastewater infrastructure.
The World Resources Institute’s (WRI’s) Aqueduct Water Risk Atlas ranks countries in terms of their degree of water stress, defined as the ratio of water demand to renewable supply. Those countries at the top end of WRI’s severity scale are experiencing “extreme water stress,” tapping into more that 80% of their available supply. As per the 2019 data, South Africa ranked 22nd out of the top 25 in terms of WRI’s National Water Stress scale.
For other African regions, like Central Africa, there’s still a relative abundance of water, but the enabling infrastructure backbone may not be in place to support socio-economic objectives. However, as the WRI points out, demand in Africa generally is growing faster than any other region globally, stating that “By 2050, water demand in Sub-Saharan Africa is expected to skyrocket
by 163% — four times the rate of change compared to Latin America, the second-highest region, which is expected to see a 43% increase in water demand.”
However, water scarcity doesn’t have to translate into a water crisis. Classic examples include Singapore, where investments in technology within a proactive policy environment have harnessed the benefits of interventions like desalination, but especially wastewater treatment and reuse.
Worldwide, though, the uptake is slow and only around 11% of domestic and industrial wastewater produced is currently being reused, according to UNEP. South Africa has made inroads, but we need to do far more in this area in terms of industrial and potable demand, as well as for groundwater replenishment.
For IMESA, promoting sustainable water and wastewater practices is top of our agenda in terms of applied technologies, knowledge exchanges, and project execution within the municipal engineering arena.
A recent development is the signing of a letter of intent between the Water Research Commission (WRC) and IMESA to plan, coordinate and implement needs-based training, skills and development activities within municipalities using the WRC and partners’ knowledge products.
The letter of partnership intent extends the Memorandum of Understanding that we signed with the WRC for the development of A Best Practice Guideline for Design Flood Estimation in Municipal Areas in South Africa. The latter project was initiated by IMESA and co-
funded by the WRC, with a series of IMESA workshops now being rolled out nationally. (Visit www.imesa.org.za for more details.)
Arid Water Centre launched at Sol Plaatje University
Alongside training, research and development are key to finding solutions to water demand management and water security.
A landmark initiative in this respect is the WRC’s Northern Cape (NC) Provincial Partnership Support Programme. It aims to strengthening water and sanitation resilience through research and innovation in one of South Africa’s most water scarce regions.
On 12th and 13th March 2024, a follow up engagement was held at Sol Plaatje University in Kimberley and attended by representatives from the WRC, the Department of Water and Sanitation’s (DWS’s) regional office, SALGA NC, as well as stakeholders that included IMESA.
Our new letter of intent with the WRC was officially signed at this event. As IMESA President, I also gave a presentation on climate tools for preparedness and planning, as well as asset management.
Significantly, the event also saw the official launch of Sol Plaatje University’s Arid Water Centre following the signing of a five-year Memorandum of Agreement between the university and the WRC. Going forward, work carried out at the Centre will help to refine the research-based techniques needed to solve key municipal issues within the NC and broader region. These include water and wastewater treatment failures, non-compliance to drinking water quality standards, and groundwater management.
As IMESA we remain equally committed to upholding the highest professional standards because we know how crucial our pressing water issues are. Together, we’re stronger and more empowered to find the right solutions.
Precast concrete technology has a large part to play in addressing the serious water crisis with which the country currently grapples.
For years, it has been the norm to significantly fast-track the construction of large reservoirs by constructing their large roofs –time-consuming and complex components of these builds – with precast concrete elements. Combining best practice in cast-in-place construction methods and precast concrete technology, these water-retaining structures stand out as excellent examples of hybrid concrete construction.
Considering the inherent benefits of precast concrete, it was only a matter of time before entire reservoirs would be prefabricated in factories and erected on site to further accelerate service delivery infrastructure. For many municipalities, this is now the preferred method of building critical water storage infrastructure to supply constituents. Yet, this knowledge has been developed even further to significantly speed up the construction of water towers, with the first two in the country now under construction.
Corestruc has been at the forefront of this precast concrete innovation drive in South Africa’s water infrastructure market.
The company first made its mark as a precast concrete solutions provider by helping to fast-track the construction of the 50 ML
technology
Completed precast reservoir units fabricated and built using Corestruc technologies
Krugersburg reservoir to supply additional water required to host FIFA 2010 Soccer World Cup matches in Polokwane. The company’s precast concrete roof system enabled Yarena Civils to commit to an almost impossible construction deadline.
Department of Water and Sanitation Blue Drop Report for its performance thus far.
Following about five intense years of research and development, almost always a requirement for new precast concrete systems, Corestruc has taken its innovative precast concrete water towers to market, again pushing the boundaries of the possibilities of concrete prefabrication.
A few years later, Corestruc took its awardwinning complete prefabricated reservoir system to market. It is now a tried-and-tested method for the construction of reservoirs ranging in size from 10 ML to 60 ML. Notably, Bundu command reservoir, one of the first precast concrete reservoirs to be built in the country, received a 100% scoring in the latest
Already, Corestruc has helped to fast-track the construction of about 500 ML of water storage capacity, with many more projects already underway. This includes an opentop water retaining tank with a wall height of 8,5 m and total diameter of 41,71 m for one of the country’s leading miners of platinum group metals.
Certainly, it is the speed at which these precast concrete structures can be built that make them ideally suited to building both municipal and industrial water infrastructure. For example, Corestruc can complete the construction of a 10 ML reservoir and 30 ML reservoir in four and six months, respectively. Prefabrication may not always be much faster than traditional in-situ concrete construction. However, in these instances, precast concrete was selected because it facilitates a sound project start. This is considering that the various precast concrete elements that constitute the entire structure or sizeable portion thereof are already being manufactured during the
earthworks, site terracing and construction of the foundations.
Willie de Jager, Managing Director of Corestruc, notes other benefits of concrete prefabrication that makes it so suited to constructing water infrastructure, not least of which are the high quality and durability of the final precast concrete structure.
“The various precast concrete elements that are integrated on site to complete the final structure are manufactured in controlled factory environments, ensuring consistent quality and reliability. The known durability traits of concrete are further enhanced with the use of high-strength concrete mixes; reinforcing or prestressed strand cover; and pre-tensioning,” De Jager says.
Then there are the significant construction cost savings that concrete prefabrication provides client bodies, engineering teams and principal contractors. This includes significant savings in construction material costs due to the use of highstrength concrete mixes and post-tensioning. For example, a precast concrete reservoir is up to 40% lighter than one that has been built using conventional cast-in-place methods.
There is also a notable reduction in variation orders on precast concrete projects. As he explains, the success of typical concrete prefabrication projects is founded on sound upfront planning as there is very little scope for variations during the construction phase. Engineering design and all drawings, as well as the logistics behind the coordination of services needs to be finalised before manufacture of the precast concrete elements can start. This is with input from all relevant stakeholders, including the project engineer, mechanical consultant, main contractor, and precast concrete specialist.
Moreover, prefabrication ensures a very high-quality final build at competitive rates. Taking all of these factors into consideration, the reservoirs that Corestruc has built have provided, notably, between 10% and 30% savings in construction costs.
Then, there are the significant savings in operating costs that these robust water retaining structures provide municipalities over their 100-year design life.
However, clients and their engineering teams
also know that a typical Corestruc project is very well managed. This is considering the extensive upfront planning that goes into these projects, while most of the complexity of the project is also handled by the prefabricator. The company is responsible for the manufacture of the precast concrete elements; their efficient transportation to site; and integration using specialised rigging equipment. These, combined with Corestruc’s in-house design capabilities, enable the company to provide a comprehensive precast concrete solution.
This while exercising total control over each individual component of the precast value chain that plays such a critical role in ensuring a successful outcome. There cannot be a single weak link from design of the precast concrete structure to integration of precast concrete elements.
Of course, with manufacture of the elements undertaken in a controlled factory environment and then integrated by expert riggers, precast concrete projects are also safer – if undertaken by an expert according to strict health and safety protocol.
Of increasing importance to municipalities is the role that precast concrete plays in constructing infrastructure with a smaller embodied carbon footprint.
Accurate manufacture facilitates the optimal use of materials, reducing waste. Moreover, prefabrication facilitates the use of more efficient design of concrete element shapes. These would be too costly or complicated to execute with castin-place construction methods.
To remain competitive, precast concrete factories must also use energy and water efficiently. In these ways, they further reduce the carbon footprint of the concrete elements that are integrated on site. Furthermore, by building more robust structures that require minimal maintenance, less construction materials are used to upkeep the structure over its long useable life.
Despite the immense progress South Africa has played in harnessing precast concrete technology to build top-notch water, De Jager says that prefabrication is still in its infancy in the country.
“Just about everything built in other countries of the world is prefabricated because it is more efficient and cost-effective to construct quality infrastructure in this manner. As a country, we are still undergoing a very steep learning curve in terms of the design and application of the technology. As our water crisis deepens, we will have no other choice but to find more innovative ways of accelerating the construction of highquality infrastructure in a cost-effective manner,” he concludes.
www.corestruc.co.za
Given the critical state of South Africa’s water and wastewater infrastructure, and the allied need to keep power utilities at optimum performance levels, there’s never been a more crucial time for clients to engage with leading original equipment manufacturers (OEMs). IMIESA speaks to John Montgomery, general manager for group companies, APE Pumps and Mather+Platt about how their commitment to innovation and quality execution makes the difference.
What sets the group apart as an OEM leader?
JM Firstly, the fact that we’ve being in operation for 72 years in 2024 speaks volumes for our success as a business. Plus, we’re part of the global WPIL Limited (WPIL) group, headquartered in India, so we have extensive backing and leverage in terms of product solutions, where required, from our sister OEMs in regions that include Australia, Italy, Thailand, and the UK.
Foremost though, we’re a Proudly South African manufacturer and our investments, including the most recent ones to upgrade our fabrication capabilities, are geared towards ensuring that we’re self-sufficient in terms of the local and
cross border Southern African markets. WPIL is very proud of our achievements in this respect. We offer full repair, retrofit and made-toorder pumps. In addition, we are a registered 8ME (Mechanical and Electrical) contractor with the Construction Industry Development Board (CIDB), enabling us to provide a turnkey solution that includes project management of the civils component on an outsourced subcontractor basis.
To the best of our knowledge, few other South African pump OEMs have this comprehensive capacity, backed by our recruitment and training of best-in-class personnel in all related fields. These include expert design engineers and
project managers that interface with the client’s engineering team.
Our turnkey projects encompass design, commissioning, and installation of integrated systems for new and upgraded pump stations – equipped with SCADA – for leading water utilities. Past projects include work for uMngeniuThukela Water Board in KwaZulu-Natal, and Blantyre Water Board in Malawi. We also work extensively in wide ranging industrial segments, examples including the sugar industry.
What do the latest machine investments entail?
Following extensive research on our current and future manufacturing strategy, we’ve re-modelled our Germiston factory in Gauteng to accommodate four cutting-edge machine installations. These comprise a centre lathe equipped to handle jobs ranging in lengths of up to 8m and in varying diameters for components such as columns, shafts, and impellers; a key slotter; as well as a horizontal and a vertical boring mill. The horizontal boring machine is ideal for the final machining of larger impellers. In turn, the vertical boring machine is employed for the machining of split casings.
During 2024 we’ll be adding a test bay for our smaller range of split-case and end suction pumps. Once we’ve optimised this set-up, we then plan to add a larger test bay for our vertical pump range.
We’re also going green as part of our commitment to the UN Sustainable Development Goals with a major investment in rooftop solar during 2024.
Does the group have a track record in the municipal sector?
Yes, and it’s extensive given the fact that we’ve been in operation since 1952, with a footprint of installed systems across South Africa, as well as further afield in Southern Africa.
What we’re finding is that while many municipalities have retained their in-house professionally registered engineering teams, there are increasing gaps due to factors like retirement, emigration, and manpower
shortages due to vacant posts that haven’t been filled. This scenario is compounded at times by inadequate asset management procedures, plus budget constraints.
That has immediate implications for operations and maintenance (O&M) of critical infrastructure such as pipelines, pump stations, and treatment works when repair or replacement responses are due to reactive interventions, including “run to destruction” pump failures. Without a renewed focus on municipal engineering recruitment, mentorship and skills transfer, the situation will continue to deteriorate.
This issue has been underscored by the Department of Water and Sanitation’s (DWS’s) latest Blue Drop (potable water), No Drop (water conservation and demand management), and Green Drop (wastewater) assessment reports. The full Blue and No Drop assessments, and the interim Green Drop progress assessment reports were released on 5th December 2023, and the results are concerning.
There are 144 municipal Water Services Authorities (WSAs) in South Africa, but only a small percentage achieved Blue Drop and Green Drop Certification. For the DWS, the directive for WSAs is to lift their game as a matter of urgency. Proposals include skills transfers and/or O&M service provision by high-performing WSAs and Water Boards to assist them in improving their future Drop scores.
Included is a call for private sector specialists to come on board via O&M agreements. That’s excellent news for us as a Group because we already provide this service to certain Water Boards and power utilities, specifically to optimise our own OEM commissioned pump systems.
How can municipalities improve their pump performance?
For existing APE Pumps or Mather+Platt products that need refurbishment, stripping the pump is the starting point for an accurate repair cost assessment. We combine this with a full inspection and condition assessment report, which is shared with the client’s engineers. When not directly using our O&M service, our recommendation to municipalities is to start here before issuing a tender and to make sure that the third-party contractor appointed is competent in terms of pump removal, reinstallation, and commissioning. One of the classic mistakes is to incorrectly install a pump. Here even the slightest misalignment will cause excessive vibration and malfunction.
As a group we provide site, service and spares services. Parts need to be correctly installed. We’ve had experiences, for example, where the client or a third-party contractor has installed an impeller the wrong way round on a pump shaft. So, rather leave parts and service to the experts, given that larger pumps typically represent a multi-million rand investment.
Quality control is key. What are your main processes?
From our pattern shop where we make the foundry moulds for casting to our final tolerance inspections on every new, restored or repaired pump there’s a strict quality control process defined by our ISO 9001 registered systems. Measurement by hand is a traditional quality tolerance check, but our investment in 3D scanning takes this to an exact level. We can now verify the final machined tolerances with 100% accuracy against the original design. Our most recent CNC machine acquisition also comes equipped with a specialist CAM (Computer Aided Manufacturing) software programme. This downloads the approved model design to the CNC unit instead of having to manually input machining parameter settings. Our final quality inspection report further
Specifying genuine OEM parts is crucial to ensure that pumps achieve their optimum performance and longevity between rebuilds
remote monitor ongoing performance, combined with scheduled site inspections.
Are pirate parts still an issue?
Counterfeit component fabrication is an ongoing concern for most industries. Those who succumb to the temptation of perceived short-term savings due to “cheaper” prices unfortunately reap the longer-term benefits – ultimately catastrophic failure. However, before that happens there’s a progressive creep in pump inefficiency – they no longer reach the designed head or flow. That translates into escalating process engineering costs. In parallel, the pumps are exposed to the risk of cavitation, as well as imminent bearing, impeller, seal and shaft failures.
And in closing?
Pumps are at the heart of process and fluid transfer efficiencies, and they’re mission critical items that require professional attention. Our technology and qualified personnel are there for industry to use and we welcome engagement from municipalities in helping them maintain their water and wastewater systems at optimum health.
A technician uses a 3D scanner to verify that the foundry casting matches the OEM design specification and is free of flaws
2024
Secure your stand now and have the opportunity to:
• present your company, products and services to a target audience
• gain industry insight and meet potential partners, suppliers and clients
Sponsor a unique aspect of the conference and enjoy great benefits such as: SIGN UP FOR a Sponsorship NOW
• free exhibition stands
• complimentary delegate registrations
• interact with key decision-makers and industry peers
• brand representation at the event, promotion of your company in the conference proceedings magazine and online
• free entry for guests at the social evening and much more.
CONFERENCE
t: +27 (031)266 3263
e: conference@imesa.org.za marketing@imesa.org.za www.imesa.org.za
It was a sombre tone at this year’s annual AfriSam Budget Breakdown event, but sales and marketing executive Richard Tomes reminded stakeholders that the company’s 90 years in business should be an inspiration that the construction sector remains so resilient.
AfriSam’s Executive Chairman Eric Diack agreed the company had seen many ups and downs and hailed the Johannesburg event as an important forum for AfriSam and its stakeholders to gain vital insights to chart the path forward.
A regular contributor to the Budget Breakdown, Econometrix Chief Economist Dr Azar Jammine highlighted that the construction and building industries were still in the doldrums, with little sign of emerging from it soon. Dr Jammine pointed to the low economic growth rate and the poor level of gross fixed capital formation as the key culprits of the challenging milieu. While the Budget Speech contained a theoretical commitment by government to focus on infrastructure, there was not much to boost confidence.
He noted that private sector capital investment in South Africa had shown some improvement, but this was mainly in machinery and equipment. Investment in construction – including civil engineering –and building had declined 40 to 45% over the past decade. The slight recovery in residential building between 2020 and 2022, as a result of the Covid-19 pandemic, had faded.
“This is horrific, and there is little sign of it recovering,” he said. “The big loser is in the commercial space, which has fallen by 80% in terms of plans passed.”
Employment in the construction industry also continued to drop and is now 40% down from 2019 figures. The sector’s contribution to national employment is today only about 4,5%, having been over 6,5% around 2017.
“No other sector in the economy has been performing as badly,” he said. This was also reflected in the retail sales at builders’ merchants, which now ranked as the weakest segment of the retail sector.
Dr Jammine reiterated that crime was also a central factor in holding back progress in the construction industry and was encouraged
Speaking at AfriSam’s Annual Budget Breakdown event in Johannesburg, Econometrix Chief Economist Dr Azar Jammine highlighted the demanding conditions in construction, civil engineering and building
by the Business Leadership South Africa’s workstreams to work with government on energy, transport and crime.
“I don’t need to remind members of this audience of the debilitating effect that the construction mafia are having,” he said. “I only hope that government will listen to the private sector and involve them more in finding the solutions.”
With the “semigration” of many South African professionals to the Western Cape, he noted that this province had recently taken the lead over Gauteng in terms of residential building plans passed. There had been a slight rise in numbers in Gauteng recently, however, which may point to a revival.
According to Richard Tomes, AfriSam Sales and Marketing executive, the insights from Dr Jammine confirmed that the construction industry will remain under pressure for some time.
“However, what we can learn from AfriSam’s 90-year legacy is that the industry is very resilient,” he said. “Over the past 90 years we have seen good times, and we have also survived through extremely tough times.”
He said he believed the construction sector – as with AfriSam – will come through this challenging period and will continue to create concrete possibilities for South Africa.
“As AfriSam, we look forward to being the construction industry’s partner of choice through thick and thin,” he said.
Back in 1954 Bell Equipment took its first steps as an original equipment manufacturer (OEM) with the introduction of a self-loading sugarcane trailer, followed by the legendary tri-wheeler material handler in 1964 – the forerunners in a series of “yellow metal” innovations over the past 70 years. Alastair Currie speaks to Group CEO, Ashley Bell, about what makes the company a South African success story.
Seven decades in operation is a major achievement. What are some of the key milestones that have made Bell Equipment a local and international OEM leader?
AB The passion for excellence instilled by my late grandfather and founder, Irvine Bell, is alive and well to this day, and it’s a great honour to continue the family legacy as CEO from January 2024.
Research and development (R&D) have always been in our DNA and over the years our Richards Bay factory has become
Ashley Bell, CEO, Bell Equipmentrenowned locally and internationally for definitive product launches, especially in terms of our articulated dump truck (ADT) series, which today fields the widest model range of any OEM globally. Essentially, our ADTs put us on the map and they’re a core part of our business now and in the future.
The launch of the D-Series ADT line in 2001 was a major breakthrough from the perspective of our global recognition as a significant ADT OEM, with the Group gaining a foothold in the Northern Hemisphere in 2003 following the unveiling of an assembly plant in Germany to service the European markets. Then in 2012 we re-entered the USA market as Bell Equipment following an approximately 14-year supply and distribution agreement
via another OEM. Today we trade directly in this market through a distributor and dealer network across the US.
Behind the scenes, our R&D teams continued to forge ahead and in our 60th year we marked the occasion with the introduction of the B60 ADT, which at the time was the largest of its kind in the world. Competing against rigid off-highway trucks in this class, it was a gamechanger in demonstrating the possibilities for ADT evolution in niche applications.
Currently, our E-Series ADT line is the latest generation, available in ten derivatives.
Are there any other OEM products in the pipeline?
Our new motor grader series is a very exciting R&D initiative. We’ve invested significantly in this new product line, and our advanced prototype units have performed exceptionally well on field trials across South Africa.
We believe we’ve designed a class leading product that will take its place alongside our ADT line in the local and global market, founded on our reputation for manufacturing strong reliable machines, with strong reliable support.
We’ll be fielding three machine models, namely the G140, G160 and G200 with production expected to commence towards the end of 2024, with the first units delivered during Q1 2025.
In parallel, we have a series of R&D projects on the go within our forestry and agriculture line, which are being field trialed as part of the development process.
Over the past 24 months, we’ve also been working with technology partners in Europe and the USA where we’ve been testing driverless, autonomous ADTs. It’s a space that we believe is going to gain major traction – not perhaps initially in South Africa – but over time it’s an inevitable component of where the global market is going.
In March 2024 we’ll be putting the concept to the test in a commercial application at a quarry in the UK. This is believed to be a first for an above surface ADT operation and it’s a proudly Bell ADT.
Essentially, if the market wants something unique, we’re up for the challenge. A prime example is Bell Equipment’s development of a track carrier product as a utility machine for the US market. These units are designed for poor ground conditions, like marshes
and swamps. We’re now in the process of applying for a CE mark so we can explore where the potential exists within European markets.
When can we expect to see Bell electric drive earthmoving machines on the market?
Finding an alternative to diesel is high on our agenda, given the pressing need to move away from fossil fuel derived sources and lower greenhouse gas emissions. One of our proactive steps is the recent signing of a joint venture agreement with an EU company to develop a battery powered electric ADT. Whilst not a definitive solution, it’s exciting new territory for us as our R&D teams search for the most viable
solutions, benchmarked against what’s out there already within the automotive and earthmoving space. Our team is looking forward to the learnings from this project.
How does the Bell global market strategy benefit South Africa?
The in-field exposure of our trucks in every conceivable environment worldwide has obvious R&D benefits when it comes to perfecting the best performance and mechanical availability in terms of future product designs.
The fact that our Bell ADTs are a preferred choice in highly competitive markets like the UK, Europe and North America supports this viewpoint. For this
Over the past 24 months, Bell Equipment has been working with technology partners in Europe and the USA to test and develop driverless, autonomous ADTs
reason, South African customers have the assurance that our ADTs are an excellent investment. The same will hold true for the Bell grader series.
What are your future plans for the plant in Germany?
There’s a strategy to shift from pure assembly to a greater level of manufacturing of our ADT at this plant driven by the growth we’ve seen in our Northern Hemisphere markets. Coupled to this we’ve seen an increase in our supplier base in that region, which has amplified the negative impact of ‘round-tripping’ materials and components to our South African plant. It makes sense to manufacture our Northern Hemisphere ADTs closer to both our suppliers and our markets.
Bell has a number of strategic OEM partners: How does this integrate with Bell Equipment’s overall solutions strategy?
Our OEM partners form part of Bell Equipment South Africa’s dealer business. We represent three exceptional OEM brands, in parallel to our Bell manufactured products, namely JCB construction and agriculture, Kobelco excavators, and Finlay mobile crushers and screeners. These partner brands are also distributed within
some of our Southern African territories via Bell Equipment branches, as well as through certain of our appointed independent dealers.
These partner products provide a logical fit within the suite of Bell OEM solutions we provide for construction, quarrying, and mining applications.
At this stage, we don’t have any plans to expand the current third-party OEM offering as we believe the present mix is optimal for now.
How has the market responded to the launch of Bell Heavy Industries (BHI)?
Our objective from the onset with BHI –launched in Q4 2023 as a standalone brand and independent division – is to employ our manufacturing skills and experience where practical to help stimulate the South African manufacturing sector via project engineering and contract manufacturing.
Our Richards Bay factory is fully equipped with cutting edge machining and fabrication technologies, together with technical experts and quality management systems, so why not assist the market in this specialised field, especially since there’s been a general contraction in local manufacturing capabilities, and an over-reliance on imports. It makes sense for BHI to manufacture products for local market
Bell Equipment’s new grader line comprises three machine models – the G140, G160 and G200. Production is expected to commence towards the end of 2024, with the first units delivered during Q1 2025
demand, using locally sourced materials where possible.
Sectors we envisage include construction, energy, mining, and transport. To date, we’ve had very positive interactions with potential clients and we’re confident BHI will grow in strength.
What does the Bell brand symbolise for customers in terms of expectations and support?
Our business has always been centred on a strong family ethos, and we see our customers as forming part of this extended family. When a customer buys a product from Bell, that translates into a lifetime relationship based on transparency and trust. We take a keen interest in the success of our customer’s business because it’s a working partnership and if our customers succeed, then so will we.
The same principles apply in terms of our human resources strategy, where we invest in training and development at all levels within the organisation on an ongoing basis. Across the world where we operate, we also place major emphasis on ensuring that all Bell and independent dealer employees understand and are universally committed to our values.
The fact that Bell Equipment has flourished for seven decades locally and globally as a South African OEM is a remarkable achievement. It boils down to inclusive teamwork between our employees, dealers, and customers. Back that with ongoing product excellence and you have a winning formula.
Diverting waste from landfill sites is a globally recognised priority, both from an environmental and downstream circular economy perspective.
Alastair Currie talks to Keith Anderson, CEO at eWASA (EPR Waste Association of South Africa) about what this means in practice in the current South African regulatory context.
In terms of the EPR regulations, how have things progressed since their introduction in 2022?
KA From a private and public perspective, the road to an optimum waste recycling solution has received intensive focus for several years now, and as CEO of eWASA I’ve been an integral part of this process, a case in point being my representation on the Department of Forestry, Fisheries and the Environment’s (DFFE’s) Ministerial Advisory Committee in 2020 in preparation for a landmark resolution.
Keith Anderson, CEO of eWASAThis followed on 5th November 2020 when the DFFE published the Extended Producer Responsibility (EPR) Regulations and notices for the Electrical and Electronic Equipment (EEE), Lighting, Paper, Packaging and Some Single-Use Product Sectors, which includes recyclate content in glass and PET packaging. The regulations came into effect on 5 th May 2021 under Section 18 of the National Environmental Management: Waste Act. These regulations require producers (defined as any people, groups, or brand owners who manufacture, convert, refurbish, or import new or used products in the defined categories) to take responsibility for their collection and recycling at the postconsumer stage. This requires them to develop comprehensive waste management strategies for every stage of the value chain.
Producers can form their own funded scheme or alternatively join a registered producer responsibility organisation (PRO) appointed to develop and implement an EPR scheme – against agreed DFFE targets – on their behalf, subject to a fee scale. The latter is the recommended route because it relieves the producer of a major administration burden in terms of interim and annual reporting to DFFE and the South African Waste Information System (SAWIS).
In terms of the legislation, each PRO is registered for the initial five-year EPR Regulations programme, extending from 2022 through to 2026.
Speaking from our perspective as one of the PROs registered, we’ve seen a very positive uptake in our membership from local and multinational producers.
However, although there was a six-month timeframe for existing producers to register either directly with the DFFE or through a PRO, there are still too many who haven’t registered or are still in the process of registering. So, there’s a lot of bedding down that needs to take place, as well as a uniform approach when it comes to penalties for non-compliance.
Are there too many PROs in the market at present?
Yes, I believe that’s part of the challenge. At present there are some 38 PROs registered with the DFFE, which can lend itself to unnecessary duplication and additional cost for industry. It can also result in a fragmented approach to implementing meaningful projects at scale. In a perfect world, the ideal would be to have a “Super” PRO responsible for all waste categories.
From the onset, we recognised the importance of this approach, becoming the
eWASA is rolling out its 40-foot e-waste recycling containers nationally in partnership with municipalities. The containers come complete with recycling tools and storage facilities
first multi-disciplinary PRO to register with DFFE. This means that instead of having to register with standalone PROs representing single segments, our EPR members can meet all their requirements under the eWASA banner. To cater for this requirement, we expanded our traditional EEE focus by bringing on board packaging experts. It’s a decision that has
worked out well. For example, we currently recycle more than 90% of the polystyrene in South Africa via our recycler network. We also exceeded our PRO targets in this area in 2022 and 2023 and will exceed them again this year. To further drive these initiatives, we’ve recently invested in imported bailing and shredder machines for the polystyrene
recycling sector for use by designated eWASA registered recyclers.
Is the EPR pricing structure viable?
Yes and no. A key issue right now is that every PRO is free to set their own pricing scale for each defined and registered waste stream. Some PROs appear to be pricing too low,
which is not sustainable for the industry as a whole: it makes it less viable for waste pickers and recyclers to make a living, with the associated risk of dumping or diversion to landfill.
However, following consultation with PROs, the DFFE recently released a draft paper for public comment on a proposed universally applied framework for the calculation of EPR fees, which is a step in the right direction. In addition to ensuring an acceptable profit margin for recyclers, we need to establish fair rates that cover the upstream costs of collection and disposal.
Within this context, it’s vital that ERPs are central to policy decisions. EEE products, for example, can function optimally for decades – especially with advances in modern-day fabrication technologies – so who knows what the actual end of life will be. The average EEE recycling rate is around 15% annually. But it can spike at any time, so reserve funding allocations for EPR compliance must be factored in by PROs.
In 2024 we plan to spend approximately R40 million on projects. That’s an increase from some R20 million in 2023, and around R5 million in 2022. So, we’ve ramped up our investment for industry initiatives exponentially.
We’re also actively engaging with municipalities across the country, helping them to evaluate the necessary
In consultation with waste picker forums, eWASA developed a purpose-designed flat-bed trolley. Locally manufactured, it’s composed of 100% recycled plastic and capable of supporting up to 250 kg
infrastructure, equipment, and resources to effect waste management and recycling projects. We are also driving initiatives to create jobs via our SMME Development Programme, as well as making provision for the training of SMMEs and waste pickers.
We’re especially proud of the successful phasing in of our 40-foot e-waste recycling containers, complete with recycling tools and storage facilities for use by SMMEs identified by respective municipalities. These SMMEs accept and process e-waste, selling the components to downstream recyclers. To date we’ve set up e-waste containers in Gauteng, KwaZulu-Natal, North West, and the Western Cape.
In consultation with waste picker forums, we’ve also developed a purpose-designed flat-bed trolley. Locally manufactured, it’s composed of 100% recycled plastic and capable of supporting up to 250 kg. So far, we’ve donated some 300 of these units across the country with more in the pipeline.
All of these initiatives adhere to the letter of the EPR regulations, which advocate for collaboration to drive waste management and recycling programmes that foster entrepreneurship, create employment, and generate opportunities that uplift the youth, women and individuals living with disabilities. We’re also reaching out to schools to inform learners about why recycling is an environmental priority.
How does the eWASA waste picker and recycler network work in practice?
Currently, our registered recyclers pay waste pickers 15c per kg as a service fee irrespective of the waste stream. The stipulation is that they need to have an ID document, contact number, and a bank account. This ensures that the money is going to the right person.
In addition, for defined waste streams like EEE the recycler will pay the waste picker the agreed rate per kg on top of the service fee. Each appointed eWASA recycler (currently numbering more than 150 nationally) submits a declaration
every month to eWASA. We then refund the amount due.
There’s a complete audit trail and to facilitate this process we funded the establishment of an independent BBBEE Level 1 environmental auditing company in 2021. The latter specialises in the auditing both of recyclers and PROs, with eWASA being their first PRO client.
This company audited around 50% of our recyclers in 2023 as well as eWASA in terms of the DFFE regulations. In 2024 we plan to get this up to 75% in terms of recyclers audited.
This year we will be sending two external audit reports to the Department: one being a financial audit, and the other an environmental audit.
How do eWASA’s consulting services assist clients in determining their legal obligations?
For our EPR fee paying members, we provide both online and on-site advisory services to ensure that clients have a full understanding of their waste declaration requirements. It’s essential to record and collate the right data.
We are also working with our recyclers to adopt technologies like barcode scanners for EEE waste to improve the credibility and accuracy of their reporting.
And in closing?
As industry pioneers in EEE since 2008 we’ve always recognised the value of recycling – a passion shared equally by our EPR members. The one key question we need to ask is what happens after the conclusion of the initial legislated five-year EPR programme, and we’ll be seeking a definitive answer from the DFFE in 2024. Either way, eWASA is certain to remain relevant and compliant.
BiobiN South Africa’s new 1 m3 mini BiobiN can process up to 800 kg of organic waste and is ideal for smaller commercial waste generators, as well as facilities with limited space.
Equipped with wheels, the mini version incorporates all the features common on its standard in-vessel composting units. These include a built-in condenser to control moisture content and a built-in biofilter to circulate air and speed up the composting process. Like its larger counterparts, no odours are generated from the mini unit – a primary concern for those considering an on-site composting solution.
With the rising cost of landfill gate fees and waste levies, taking a proactive approach to diverting as much waste as possible saves money and the environment. “If the compost from our unit is not used on-site, we often encourage our clients to donate their generated compost to local community food gardens or school planting initiatives,” says Brian Küsel from BiobiN South Africa.
Küsel says these mini units can also be placed at a centralised organic waste drop-off point for multiple users. “Our larger BiobiN’s have been utilised in this way in office parks and the new mini mobile unit has even a greater potential as it can be wheeled around making it easier to access.”
The new mini mobile BiobiN will operate according to a rental term, which includes trained operating agents conducting regular site visits, management of the unit, waste reporting and maintenance.
According to the latest available statistics, South Africans generate about 122 million tonnes of waste per year, of which only 10% is recycled or recovered for other uses. At least 90% is landfilled or dumped illegally.
However, smarter and more tech-focused solutions for the collection and transportation of solid waste are now contributing to more efficient refuse management, with reduced costs being a critical factor. For example, digital technologies in the solid waste sector now contain elements of robotics, artificial intelligence, internet of things, cloud computing, and data analysis. They all contribute to the ultimate goal of improved efficiencies and lower expenses.
“Technology allows for the accurate collection, monitoring, and analysis of data related to waste generation, collection, and disposal. This data can help waste management operators identify trends, patterns, and inefficiencies, enabling them to make more informed decisions and optimise their operations accordingly,” says
SoniaPretorius, National Sales Manager for 600SA, a division of CFAO Equipment SA.
Technology-based solutions can also facilitate the identification, separation, and recycling of specific waste streams. Furthermore, advanced sorting technologies, such as optical sensors and AI-powered algorithms, can efficiently segregate varied materials for recycling, promoting a circular economy and reducing landfill usage.
Within the mix, compactors play a key role in reducing the waste volume that is collected, and in making waste transport easier. For example, the Orakci refuse compactor, distributed locally by 600SA, integrates technologies for a cost-effective way of segregating and recycling.
“With waste being compacted and stored inside the vehicle, a refuse compactor helps maintain a cleaner and more hygienic environment compared to traditional refuse vehicles that may carry loose waste. Moreover, compacted waste is less likely to spill or leak during transportation, enhancing safety standards,” says Pretorius.
Ultimately, the key to efficient waste management is the separation and processing of recyclables at source. Here Pretorius says 600SA is investigating partnering with NPOs to encourage recyclable material collection in the informal sector.
The Orakci refuse compactor, distributed locally by 600SA, integrates technologies for a cost-effective way of segregating and recycling
South Africa is a leader in the global mining industry and produces a number of dangerous waste by-products which mining operators must ensure are safely and responsibly disposed of. As a waste industry leader, EnviroServ Waste Management offers a multitude of solutions for complex hazardous and non-hazardous mining waste.
Jason Judkins, EnviroServ Regional Sales Manager, says the company has made innovative strides in assisting mining clients in finding alternatives and minimising waste to landfill through searching the markets to see what opportunities exist. “Our focus is to ensure compliance at all times,” says Judkins.
Mines produce large quantities of primary waste such as process tailings, slimes and overburden. EnviroServ has a specialised tailings division with vast experience within the industry, capable of managing these waste streams for large clients.
Within underground operations, waste is brought to the surface by locos or conveyor belts and separated into three categories –industrial, general and hazardous waste – by EnviroServ’s well-trained on-site teams.
“Industrial waste is first checked for items that can be reused or repaired and put back into the system, such as gearboxes, jackpots and hammers, which may have accidentally been sent to the surface, but which can be
reused or repaired. High value items to be auctioned such as motors, electrical cable or steel are transported to the client’s central salvage yard, separated into ferrous and non-ferrous metals and sold to recyclers,” Judkins explains.
General waste is sorted into paper, plastic, glass, tin and any other recyclable categories, which is also sold to recyclers, minimising waste to landfill.
“Managing hazardous waste is our speciality and we have various departments specialising in hazardous waste management solutions. EnviroServ has SANAS-accredited laboratories where waste samples are analysed and classified according to the prevailing legislative requirements. Results received allows us to determine best practise should it be reuse, recycling or disposal, but remaining in line with legislation and assuring clients of best practise and peace of mind that their waste has been managed ‘cradle to grave,’” Judkins continues.
Judkins says while hazardous waste is increasingly being diverted from landfill for alternative solutions – including hydrocarbon waste, high hazardous chemical solutions to name a few – it can be costly to recycle these materials due to the limited compliant recyclers and solutions in the South African market. Searching for innovative, cheaper alternatives to divert waste from landfill is an ongoing process.
Some mining companies are starting to take on responsibility of sewage management from communities around their operations, and EnviroServ is assisting with these requirements. “Legacy waste is another issue EnviroServ helps with. Stockpiles are not healthy sitting on the land and must be rehabilitated,” adds Judkins.
“Proper management of mining waste prevents or minimises water and soil pollution arising from acid or alkaline drainage and the leaching of heavy metals, thereby protecting the environment for generations to come,” Judkins concludes.
PVC-O (Oriented Unplasticised Poly Vinyl Chloride) was developed more than 40 years ago – a revolutionary breakthrough that has gained ground ever since. By
Mike Smart, Pr Eng*The applicable South African National Standard SANS 16422
Pipes and joints made of oriented unplasticised poly(vinyl chloride) (PVC-O) for the conveyance of water under pressure – Specifications states in the introduction, “Molecular orientation of thermoplastics results in the improvement of physical and mechanical properties. Orientation is carried out at temperatures well above the glass transition temperature.” The glass transition temperature (Tg) of PVC is about 86 to 87° Celsius.
In the intervening forty years, there have been numerous improvements in PVC-O
material from Classification 315 to 500 – the nomenclature system is simply ten times the MRS (Minimum Required Strength) of the material in MPa. This classification system is common to all thermoplastics. For example, PE100 HDPE has an MRS of 10 MPa (thus its classification PE100), and PVC-U has an MRS of 25 MPa and should, more correctly, be referred to as “PVC-U 250”.
PVC pressure pipes were first used about 85 years ago and about 60 years ago they were introduced into South Africa. Now, more than 95% of domestic sewer reticulation pipes are PVC-U, an outstanding example of the correct product
being used for the correct application.
Scientists, polymer technologists and processing engineers have enabled the Allowable Design Stress ( σ ) for HDPE to be increased from 5 MPa to 8 MPa – a substantial 60% increase. The increase in PVC’s strength – created by improved technology – is even more substantial, increasing from 10 MPa to 36 MPa – an incredible 260% increase!
In the 1970s the PVC industry entered the mining services market following the development of high impact pipe PVC-HI (SANS 1283), which satisfied the mining industry’s safety requirements and enabled PVC pipes to be used for underground services. Another development, PVC-M (SANS 966-2), followed based upon PVC-HI in the mid-1990s, which was engineered by adding impact modifiers, commonly CPE (Chlorinated Polyethylene) or Rubber Toughened Acrylics, or a combination thereof, to PVC-U to increase its impact strength.
This enabled the material to exhibit “tough” characteristics that facilitated the reduction of the Design Coefficient (C) from 2 to
1.4, the fact that the MRS (25 MPa) remained the same notwithstanding, thereby increasing the Allowable Design Stress (σ) from 12.5 to 18 MPa, where σ = MRS/C.
The latest Classification 500 PVC-O materials must have an MRS of not less than 50 MPa which, together with a Design Coefficient (C) of 1.4, gives a σ-value of 36 MPa (σ = MRS/C). This is a substantial improvement of twice the Allowable Design Stress (σ) of PVC-M.
South African fabrication
Locally, Sizabantu Piping Systems’ technology partners Molecor’s TOM 500® PVC-O pipes, manufactured at their factory in the Richards Bay Industrial Development Zone (RBIDZ), exceed the required International Standards Organisation (ISO) protocol of 50 MPa at 50 years.
The 50-year MRS of TOM 500® PVC-O pipes is approximately 55 MPa and about 53.8 MPa at 100-years, thereby proving the expected working life of TOM 500® PVC-O pipes is not less than 100 years.
Innovation is one of Molecor’s core values and through technologically innovative TOM 500® branded PVC-O pipes they have increased the range of PVC-O pipes from the previous limit of 315 mm OD (outside diameter) class PN12.5 (12.5 bar) to 630 mm OD class PN25 with the M-OR-P3136 system in 2010. In 2013 they increased it to 800 mm
OD class PN20 with the M-OR-P3180 system and in 2020 they increased it to 1000 mm OD class PN16.
Currently they manufacture 1 200 mm OD class PN25 TOM®500 PVC-O pipes with the M-OR-P5012 system. PN25 pressure class pipes are now available throughout the size range of TOM®500 PVC-O pipes.
These are exciting developments for the thermoplastic pipe industry that has enabled it to compete in the large diameter high pressure pipe market throughout Africa, which was previously beyond its capability. To further support the region, an
extrusion line to produce up to and including 1 200 mm OD TOM 500® PVC-O pipes is being installed at the factory in RBIDZ and will be commissioned in 2024.
These innovations and the latest high technology polymers have enabled the service life of thermoplastic pipes to be not less than 100 years – the service life of pipelines demanded by clients and consultants. This is more than twice the ISO protocol requirement that thermoplastic pipes’ design service life shall not be less than 50 years. This illustrates the competitive nature of the market and proves an axiom of today’s world – if you are standing still, you are probably going backwards.
PVC technology has improved substantially, and is continuing to improve, thereby giving the pipeline industry proven materials to use for large diameter, high pressure, bulk supply pipelines that steel and ductile iron pipes dominated historically.
TOM 500® PVC-O pipes are lightweight, have negligible hydraulic friction increase over time, do not corrode, do not require expensive cathodic protection, give labour intensive emerging contractors equal opportunity to be competitive, have high impact strength, low creep, low celerity, and extremely low embedded energy. It may be the material to save the Earth.
*Owner of Genesis Consulting, a member of SAPPMA, and a specialist consultant for Sizabantu Piping Systems
Alongside planned and reactive maintenance interventions, intermittent supply can occur intentionally to manage peak and off-peak demand during drought conditions, or when loadshedding occurs. However, it’s not a recommended technique for reducing non-revenue water (NRW) losses in the network. The best way to achieve this is via scientifically controlled pressure management. Research has shown, for example that when pressure is lowered to the absolute minimum during low demand periods, particularly at night, substantial NRW savings can be achieved.
The ultimate goal, of course, is uninterrupted supply to all consumers. However, perfecting this pressure management approach requires the employment of the right technologies to manage flow demand and prevent water hammer. The latter is a sudden surge in water pressure that can rupture pipes and damage pumps if valves open or close too fast based on their flow characteristics. Intermittent supply also results in empty pipes, and when flow is resumed in an uncontrolled manner water hammer can have disastrous results.
“For existing system optimisation it’s essential to undertake a detailed hydraulic study since every network has its own unique requirements and typography. This way, we can accurately compare what the pressure envelope was before and after pressure reduction with the solution installed, which can
Pipeline bursts and leakages commonly occur due to ageing infrastructure and are exacerbated by intermittent supply interventions that can cause spikes in water pressure unless carefully regulated. Within this process, pressure reducing valve (PRV) systems and controllers are the key to pressure optimisation, says Peter Telle, head of specialist supplier and manufacturer, Ultra Control Valves.
either be high-tech or ‘low-tech’ depending on budget and requirements,” explains Telle. In pump stations, mechanical interventions include pump control valves and pipeline surge relief valves. End of line valves, such as reservoir level control valves, also play a major role in causing surge pressures if not operated and controlled correctly, as does check valve selection and air valves.
Essentially there are three different types of PRV, namely:
• Direct acting valves. These are very simple devices with an adjustable handle to set the pressure to the required value.
• Pilot operated pressure reducing valves (POPRVs). They are commonly used for large systems and often the only solution for housing complexes and high-rise buildings, and
•
In South Africa, Telle says there’s still a general assumption that all PRVs are pilot operated. In other words, the valve has a “pilot” module. Associated electronic fittings mounted on it to perform “smart” control in cases of pressure management (to reduce unaccounted for losses) increases the complexity.
In all instances, POPRVs require an expert technician to service and maintain them. And these skills are often not readily available within the municipal and water utility environment. The end result could be a valve
Peter Telle, head of Ultra Control Valves, with the Ultra Alpine Pressure Management solution for POPRVs. This system enables either time or flow modulated pressure management within a self-contained system with no external power required
malfunction, which for POPRVs is often in the open position when a control circuit fault occurs.
RRPVs a mainstream choice
“We believe that one of the best mainstream options for water utilities is the RRPV due to its simplicity. It consists of a piston with different inlet and outlet areas. It doesn’t even look like a valve but a simple spool piece, but it performs exceptionally well, and has been well proven in the South African mining industry for decades, with growing penetration into the local potable water market,” Telle asserts.
Key advantages of RRPVs include their tamper proof make-up; they can act in series without instability; are inherently failure proof; and not vulnerable to dirt particles. Additionally, the axial flow path enables high pressure drops (up to 5:1).
In contrast, if POPRVs act in series, they must be carefully “tuned” during commissioning. With the slightest disruption in demand or pressure, instability will occur. So, 24-hour monitoring is essential.
“For leading water utilities with in-house technical capacity and well-funded operations and maintenance programmes POPRVs are the high-tech choice, but RRPVs will do the job equally well and we supply and support both options. At times they’re even installed together as an interconnected system,” says Telle.
RRPV applications include:
• As a straight pressure reducing valve to control downstream pressure in a distribution network. The RRPV has an immediate reaction time, unlike POPRVs, which have a delayed reaction time to demand changes. This can sometimes create problems in maintaining “dead-end” control of downstream pressures when there is no flow.
• As a secondary RRPV to reduce pressure before a POPRV if the pressure drop
is too high to handle by one valve. Installed upstream, the RRPV reacts “instantaneously” to the position changes of the POPRV, with elimination of any instability issues.
• As an “energy dissipator” upstream of a level control valve when the dynamic head is in excess of 5 bar in order to overcome cavitation problems.
Ultra Control Valves supply three different types of control valves. These comprise the Ultra Alpine ACV diaphragm operated control valve; the Ultra ACV RRPV, available in sizes from 25 mm to 500 mm and pressure ratings up to 150 bar; and the Maric flow control valve, which keep the pump on its efficiency curve irrespective of pressures or demands.
either time or flow modulated pressure management within a self-contained system with no external power required: it’s either battery driven or powered by a “mini generator” fitted across the inlet and outlet ports of the control valve, which generates the required electric current.
Every control valve in industry has a particular pressure drop ratio it is able to handle without cavitation occurring. For most standard control valves this ratio is 3:1, i.e. if the incoming pressure is 9 bar the valve can comfortably handle an outlet pressure of 3 bar. However, most standard POPRVs with a maximum 3:1 capability would have to install two valves in series in the above pressure scenario.
“In contrast, our Ultra Alpine ACV valve can handle a 4:1 ratio, allowing the downstream pressure to be set at around 2.25 bar,” Telle explains, adding that the valve is based on the Cla-Val design, which has an excellent worldwide reputation, and features V Ports for cavitation prevention and low flow control.
Another important consideration for control valve selection is night-time/off-peak demand. All standard control valves have a minimum functional flow rate. If flows go below this value, the valve becomes unstable and could cause pipe breaks. To counter this scenario, a smaller valve normally needs to be installed in parallel to automatically handle low flow during night-time demand.
The upside is that the Ultra Alpine ACV has special trims available to handle low flows without the need for bypass valves.
For optimum control, the Ultra Alpine Pressure Management solution for POPRVs enables
The Ultra Alpine Pressure Management system is cloud based so its functions can be monitored and set remotely, along with near real-time performance reporting.
“Pressure management is a highly specialised discipline that needs to factor in constantly fluctuating water demand as populations grow and urbanisation intensifies,” adds Telle.
“The ultimate goal is to keep pace by constantly upgrading our pipeline and pump station network to ensure equitable service delivery. But an even more urgent priority is to stem rising NRW losses, which are well above 50% in some parts of South Africa, by focusing on fit-for-purpose interventions,” Telle concludes.
It is not enough to only measure the “blow-yield” once drilling is complete, but crucial to undertake a scientific pump test on the borehole, says SRK Consulting
As South Africa celebrates National Water Week from 20th to 26th March this year, it is important to recognise the country’s growing reliance on groundwater – and how we must improve our management of this vital resource if it is to be sustainable.
Not many people are aware that South Africa’s surface water resources – mainly rivers, dams and lakes –make up just 3% of its available fresh water. The other 97% is contained in underground aquifers which are commonly accessed by boreholes. According to Eunice Goossens, principal hydrogeologist at SRK Consulting,
these aquifer systems across the country are a vital water resource that feed many rural areas and towns.
“As our population grows and pushes up water demand, there has been a trend to drill more boreholes and pump from aquifers to increase water supply,” says Goossens. “However, this is a process that is often not carefully controlled and monitored –presenting significant risks and inefficiencies that we can ill afford.”
Complexity
She warns that the sourcing and management of groundwater is technically complex
Eunice Goossens, principal hydrogeologist at SRK Consulting
and is also subject to stringent standards and regulations – many of which are still not observed. To be good stewards of the country’s groundwater, more users will need to learn from those organisations who are currently applying best practice.
“There are growing concerns about how groundwater is being exploited without due regard for the future,” she explains. “This is a finite resource which can be compromised by poor practices and lack of expertise.”
Among the problem areas is the employment of under-qualified contractors to drill and equip boreholes, without the necessary knowledge or professional supervision.
“During my 25 years in the water sector, it is not uncommon to be requested to drill boreholes near a hilltop reservoir or close to an electricity pole – just to be closer to a storage or power point and to be more cost-efficient due to less intensive infrastructure needs,” she says. “This is not how groundwater should be approached, however, and only leads to short-lived boreholes, misspent budgets and potential damage to valuable aquifers.”
Goossens highlights that strong engineering experience needs to be applied to borehole establishment and management, including the input of qualified hydrogeologists. Each of these projects demands a business plan to be developed by a registered engineer, using a desktop study by an experienced hydrogeologist.
“By understanding where the zones of higher groundwater potential occur, engineers can develop a preliminary design for pipeline infrastructure – which can then be more accurately costed for proposal and budgeting purposes,” she explains. “The professional supervision needs to cover not just the locating of the borehole, but also the need for correct construction of a borehole, with sufficient casing and the accurate testing of its capacity. This creates the basis of managing and maintaining the borehole responsibly.”
She points out, for instance, that it is not sufficient to measure only the “blow-yield” once the drilling is complete. Rather, it is crucial to undertake a scientific pump test on the borehole – to ensure that testing is conducted to the standards demanded by the Department of Water and Sanitation (DWS).
“This process includes a calibration test, a stepped discharge test, a constant discharge test and a recovery test,” she says. “These tests allow an accurate assessment of water inflow into the borehole area, on which to base the pump’s specification and the pumping rate from the borehole.”
SRK Consulting senior hydrogeologist Lizette Goosen adds that the initial pump testing is just a snapshot of the aquifer capacity, and longer-term monitoring is still required. The data gathered over weeks, months and years is a necessary window into the aquifer’s health and performance.
“This information guides users on how they might need to adjust their usage over time to ensure the longevity of the borehole, and to protect the aquifer from permanent damage,” she says.
Goosen explains that over-pumping can dewater the fracture network where the water occurs in the aquifer; without the pressure of the water in the fractures, they can collapse permanently – leading to the loss of groundwater storage capacity.
Like all engineered installations, boreholes and their infrastructure need ongoing care and maintenance. Goosen points out that the beneficiaries of these systems – who may be communities, schools or clinics – need to be firmly engaged in the planning, installation and running of the equipment.
“Community liaison needs to be a vital part of the project business plan and its execution, or there is a risk that equipment will not last and the expenditure on the project will not achieve its goals,” says Goosen. “This is especially important where local community expectations are high, and where there may not yet be equal access to water in adjacent villages or communities.”
She also emphasises that borehole users should embrace the government’s efforts to monitor groundwater usage by registering on the National Groundwater Archive, which can be found on the DWS website.
he Minister of Water and Sanitation, Senzo Mchunu, recently initiated the construction phase for the raising of the Kempsdale Dam wall and construction of a pump station during his official visit to the Harry Gwala District Municipality on 8th March 2024.
The project forms part of the Greater Kokstad Water Supply Scheme (GKWSS) and addresses the need for a sustainable and reliable water supply for the town of Kokstad and its surrounding areas, namely Bhongweni and Shayamoya.
Zimile Consulting Engineers (ZCE) was appointed in March 2020 to provide professional engineering consulting services and will provide level 3 construction supervision and contract administration for the duration of the project. The latter will directly benefit approximately 69 146 people or 11 521 households by the year 2030.
“The processes for the environmental authorisation commenced in 2020 followed by the application for a water use license in 2021, with both only being authorised by 2022. The local municipality assisted to fast track these processes and minimise delays,” explains Deleana Naidoo, water technologist at ZCE.
“Apart from the securing of present and future water availability for the people and businesses of Kokstad and the surrounding areas, this project has provided key exposure for Zimile’s young engineers. The project included critical engineering tasks that form part of the eleven outcomes required for professional registration with the Engineering Council of South Africa,” adds Naidoo.
Minister Mchunu was accompanied by the Executive Mayor of Harry Gwala District Municipality, the Executive Mayor for Greater Kokstad Local Municipality, DWS DDG Dr Risimati Mathye, the Chairperson of uMngeniuThukela Water Board, the CE and the Executive Members of uMngeni-uThukela Water Board and many local and provincial dignitaries.
Structa Group of companies started operating in 2001 with the merger of Structacom and Dorbyl Structural Products. The current owners acquired the Dorbyl shareholding in 2003 and the Group has grown to house four principal operating divisions and a further three supporting companies. All Structa Group divisions are Level 1 BBBEE compliant.
The Group focuses on the manufacturing and supply of infrastructure related products in the fields of water storage, electrification, lighting, and communication structures, as well as industrial and building structures.
All operating divisions have active SANS certified ISO 9001 quality systems. In addition, the Group has an in-house engineering bureau, equipped with stateof-the-art analysis and measurement tools, for product design and development. This includes routine testing of structures and components to verify designs for static and fatigue loading.
Water storage solutions are designed and fabricated by the Structa Technology division in capacities ranging from 5 000 to 4,5 million litres, depending on the application requirements and the product selected. The two main lines are the flagship Prestank classical pressed
steel panel tank series, and the Circotank circular tank range.
Over the years, Structa’s 40-year-old Prestank brand has proven itself as a hygienically safe, cost effective and reliable way to store water for communities where the capacity requirements are 10 000 litres or above. Square by design, these tanks are commonly installed on elevated stands to facilitate distribution pressure. (The same approach can also be adopted for Circotank units.)
Prestanks are fully customisable, manufactured according to SANS guidelines and meet South African hot dipped galvanising standards.
One of the major advantages of their sectional tank design is that they facilitate easier handling and transportation over long distances to remote areas, regardless of the final dimensions of the
The Circotank range is manufactured from Aluzinc sheet cold rolled with a stiffening profile. The tanks utilise a PVC liner, which hugely improves the speed and quality of build, resulting in a reliable product
assembled unit. Furthermore, assembly on site is quickly achieved without the need for sophisticated tooling methods. Additionally, minimum maintenance is required because the galvanised steel panels resist weathering from the elements while maintaining the integrity of the water within from contamination of most forms.
In parallel, Structa Technology’s development of the Circotank line provides the market with a more economical, but equally robust round galvanised steel tank range, with the same quality assurances.
The range is manufactured from Aluzinc sheet cold rolled with a stiffening profile. The tanks utilise a PVC liner, which hugely improves the speed and quality of build, resulting in a reliable product. Liner replacement is possible, thus resulting in ease of maintenance and longevity.
Circotank is offered in two size ranges. These comprise the Maxi range, covering tank sizes from 100 000 to 1,5 million litres, and the Midi series covering a user-friendly
range of 5 000 to 20 000 litres. The Maxi range is aimed at medium scale water storage projects – with typical application in mass rural water supply schemes – while the Midi fills a gap not typically covered by typical moulded plastic tanks.
In addition to ease of transport, these tanks have simple foundations and can be erected without cranes. This all adds up to a very economical total cost per cubic metre of water stored.
The key to Structa Technology’s success, particularly on larger-scale projects, is early involvement between their engineers and the client is perfecting a tailored solution, both in terms of scope and lifecycle cost. The Group therefore invites municipalities and utilities seeking the optimum solutions to work in partnership to achieve successful project delivery outcomes.
A seating arrangement and fountain, placed on a bed of Terracrete permeable pavers
The wall sections feature sharp and gentle curves, integrated with three sets of Terraforce 4x4 Step Block staircases
When designed and installed correctly, mass gravity concrete retaining block (CRB) wall systems are an ideal solution for stabilising challenging slopes that often need to support integrated civil and building structures. However, their design and construction require expert and qualified experience to produce the required result.
Arecent case study underscores this, where poor construction techniques resulted in a CRB wall collapse on a housing estate in Herolds Bay, situated on the Southern Cape coast.
“Key factors included the absence of drainage pipes plus sub-standard compaction, and it was only a matter of time before the hydraulic buildup triggered the wall’s subsequent failure,” says Holger Rust, founder and head of Terraforce, a leading innovator and manufacturer of precast environmentally engineered products.
The replacement solution comprises an intricate terraced and undulating round face Terraforce retaining wall design employing L11 blocks in two stages (lower and top level), built by LFC Construction, a leading expert in CRB installation.
Providing the optimum balance between form and function, the new heavy-duty walls create space for an access road with parking bays on the lower and top level, integrating three sets of Terraforce 4x4 Step Block staircases. The latter lead up from ground level to the residential quarters situated in between the top deck and lower parking area.
Reaching up to 10 m at its highest point, the foundational wall supports a deck that incorporates a precast concrete seating arrangement and fountain, placed on a bed of Terracrete permeable pavers. The latter has proven effective for controlled stormwater infiltration.
“The Terraforce L11 was installed on the rest of the estate, so for consistency the same block size was chosen, along with the 4x4 Step block for the stairs,” explains Charl Johnsen from LFC Construction.
The walls were constructed using Y12 rebar and concrete infill, on a concrete foundation,
Engineer: Fred Laker, Icos Engineering /Terrasafe
Main Contractor: LFC Construction
Block Supplier: Mobicast (Terraforce licensed manufacturer)
while the upper rows were filled with topsoil to allow for future planting. Geofabric tiebacks were installed every 1,8 m and agricultural drains installed behind the Terraforce walls and stairs.
The very steep upper terrace wall was raised to 5,1 m – essentially creating extra space for three parking bays. Finally, lighting and irrigation, as well as balustrades and a straight edge curb for safety were installed.
Adds Johnsen: “A challenging aspect was the inaccessible nature of the project, with 470 m3 of backfill having to be compacted by hand – using 20 ℓ buckets – as no heavy machinery could get onto the site. Everything had to be done by hand, from offloading the blocks to filling them with concrete by bucket.”
Within the context of a professionally engineered and constructed solution, this further reinforces the benefits of CRB wall designs that incorporate key opportunities for labour intensive construction.
According to SANS 10400 building regulation requirements, walls can generally be constructed to a height of 1 m without consulting a professionally registered engineer. However, any walls steeper than a 70 degree inclination, and especially load-carrying walls, must be designed by a qualified engineer, even if only 1m high.
Calcamite is a specialist South African packaged wastewater treatment plant service provider that is wholly owned and operated as a subsidiary of JoJo Tanks (Pty) Ltd. With over 40 years of experience, we've consistently introduced cutting-edge and eco-friendly wastewater management solutions.
Our offerings empower you to manage, recycle, and dispose of wastewater efficiently, safely, and in an environmentally conscious manner.
Our expertise lies in decentralised packaged wastewater treatment systems, catering to a capacity range from 1 k ℓ to 250 k ℓ of average daily dry weather flow (ADDWF). Our treated wastewater meets the rigorous standards set by the National Water Act 36 of 1998, making it suitable for various non-potable uses. Additionally, we offer tertiary treatment options to upgrade the treated wastewater for potable reuse.
• Customised solutions: We provide packaged wastewater treatment plants suitable for residential, commercial and light industrial applications.
• Innovative and adaptable plants: Our smaller wastewater treatment plants are standardised and designed for swift deployment, while our larger systems can
be tailored in a variety of configurations.
• Economical and local: Manufactured and maintained locally, our solutions promise cost efficiency and longevity.
• In-house engineering expertise: We stand out as the sole wastewater treatment company with the capability to roto-mould sizable containers tailored for diverse sewage treatment applications.
• Comprehensive services: From design and production to installation facilitation and supervision, as well as routine maintenance, we’ve got you covered.
Our core solutions include:
• Wastewater treatment plants
- Process wastewater for non-potable and potable uses.
- Engineered to address diverse wastewater conditions.
- Adaptable for above ground, underground, or containerised applications.
• Septic tanks
- Africa’s sole SABS certified septic tanks.
- Features a dual chamber system for purer effluent than typical septic tanks.
- Prevents contamination of soil and groundwater.
• Conservancy tanks
- Robust roto-moulded tanks designed for subterranean conditions.
- Offers on-site, temporary wastewater storage.
- Protects soil and groundwater from contamination.
• Underground modular tanks
- Modular design allows for easy scaling and rapid installation.
- Unique inter-connecting system ensures structural robustness.
- Versatile usage, from water storage to septic tanks or wastewater treatment plants.
• Sand, oil and grease traps
- Filters out sand, oils and grease before wastewater enters drainage systems.
- Reduces water pollution and enhances wastewater quality for municipal sewers.
- Boosts the efficiency of on-site wastewater treatment systems.
• Infrastructure products
- Diverse products compatible with wastewater treatment plants and subterranean water and piping systems.
- Lightweight and resilient.
- Suitable for corrosive environments.
WEC Projects has completed the installation of a NEWgeneratorTM at Khanyisani Primary School in Lubunde, near Bizana in the Eastern Cape
WEC Projects, a local EPC water and wastewater treatment solutions provider, has completed the installation of a NEWgeneratorTM at Khanyisani Primary School in Lubunde, near Bizana in the Eastern Cape. This project marks the first commercial installation of the NEWgeneratorTM system in South Africa after extensive pilot testing at various sites around the country.
The deployment of the NEWgeneratorTM system, which connects the school’s toilet block to a water and waste treatment and recycling system, represents an important step forward for delivering proper sanitation to remote and underserved areas in the country. The region suffers
from a serious water shortage due to its remote location and, as a result, a solution was required that drastically reduced water consumption,” says Ntwanano Mandlazi, Project Manager at WEC Projects.
NEWgenerator TM was developed by the University of South Florida in the USA and built under license in South Africa by WEC Projects. It is a compact, off-grid, and modular sewage treatment solution that can be housed inside a refurbished shipping container. It incorporates an anaerobic bioreactor to treat biological matter and breakdown solids, ultrafiltration to remove solids, sequential nutrient capture tanks, and chlorine disinfection. Up to 98-99% of the water can be recycled for reuse in the system and the biogas produced can be captured and used for applications such as cooking and heating.
This project was funded through the Water Research Commission’s (WRC’s) SASTEP programme, a national system of innovation (NSI) platform that fast-tracks the adoption
of innovative and emerging sanitation technologies in South Africa through fostering local manufacturing and commercialisation.
“We customised the system to include the waste from four unisex urinals which will be redirected back to the plant to supplement the liquid content of the wastewater for treatment and recycling,” Mandlazi continues. “The treated water, which is not suitable for human consumption, is fed back to flush the toilets, resulting in a significant reduction in water consumption by the school, which relies mainly on rainwater for drinking water.”
The system is monitored and controlled both locally and remotely via an interface connected to a PLC. A school staff member has been trained to maintain and operate the system with the support of WEC. Samples of the recycled water are taken monthly for analysis by an accredited laboratory to ensure that the treated water meets DWS general discharge standards. WEC will continue to operate the system with the WRC until April 2024.
Adds Mandlazi: “NEWgeneratorTM is an effective solution for replacing dangerous pit and chemical toilets, particularly in areas where water is scarce, making it ideal for deployment across Africa in a broad range of applications, including the domestic and commercial sectors.”
It would be incorrect to say the world does not care about water. It’s our most precious resource: without water, there is no life, and water fills many different roles in our societies. By Chetan
From feeding and cooling energy systems to creating the lush greenery around us that creates oxygen, we need water. Yet, we also take water for granted, and that has consequences.
Ecosystems around the world are buckling under the pressures of overuse and pollution. The state of wetlands, rivers, and aquifers is becoming worse, and the United Nations reports that between two and three billion people today experience water shortages.
South Africa does not buck the trend: according to the Department of Water and Sanitation, 46% of the country’s water supply systems pose acute human health risks due to pollution and decaying wastewater infrastructure.
So, why are we neglecting the most crucial resource on our planet? Perhaps the issue is that we are so used to water that we cannot imagine a world without it. We think it has an endless abundance. But the reality is very different.
In 2019, the United States Geological Survey
Mistryfresh water. All the liquid fresh water comes to a mere 10 million cubic kilometres, and 99% of that is mostly inaccessible because it is deep inside the Earth’s crust (and so-called groundwater levels are also falling). If we isolate the sphere to water in rivers, dams and lakes, it’s less than 100 000 cubic kilometres. The amount of accessible drinking water is ten million times less than the planet’s size.
These numbers should shock us because that minuscule amount of water which supports every living thing on the planet is in grave peril. But there is good news: water is very resilient, and a little effort goes a long way to help it thrive.
Turning the tide
2024 is the year we can turn the trickle of water projects into a river. Modern engineering and digital technologies in the water sector deliver impressive efficiency, visibility and performance.
As governments invest more in modernising and improving water infrastructure, they will quickly see results. Businesses that take water management and recycling more seriously earn back money from savings and create long-term sustainability. And individuals who promote water saving habits around them help uplift
Our world faces many challenges, some of which still require us to develop suitable solutions. But not water. There are straightforward ways to improve water management and quality, and the sooner we act, the easier it will be
to align those actions with our current needs. We can avoid a triage where we must choose between water and profitability, or water and social cohesion. We don’t have to make hard choices, yet.
But we must start to act in unison, using the technologies and experience of the water industry. Water may be in trouble, but we can change that. It starts with making 2024 the year of water, and then the following year, and the year after.
Chetan Mistry, Xylem Africa’s Strategy and Marketing ManagerThe critical interface between well-maintained infrastructure and sustainable water provision
needs
renewed focus, with Cement & Concrete South Africa’s recent Concrete Working for Water seminar series highlighting pressing issues affecting the sector.
Held in Johannesburg, Cape Town and Durban during February 2024, the event provided an important forum to unpack the extent of the crisis and to showcase innovative solutions. In all cases, these will be driven by new build requirements for treatment plants, distribution, and storage – filling the growing gap between South African demand and supply capabilities.
“South Africa became a waterconstrained economy as early as 2002. This was when the National Water Resource Strategy indicated that the country had allocated 98% of all available water. It is no longer a looming problem,” said Dr Anthony Turton, a renowned scientist specialising in water resource management and the keynote speaker.
However, Dr Turton believes that the sanitation crisis is the single biggest challenge that South Africa currently faces. At present, only 10% of the 7 billion litres of sewage that is produced daily is treated to a standard considered safe for direct human contact.
As he pointed out, most of the country’s water and sanitation problems are due to the neglect of existing infrastructure, plus poor planning at policymaking level – at times influenced by political ideology as opposed to developing the best solutions. This is being compounded by widespread corruption.
Therefore, Dr Turton reemphasised the need for a team of apolitical technical experts to help government navigate the dire water and sanitation crisis facing the country. Greater policy certainty and good governance will also help to crowd in much-needed capital for public private partnership (PPP) type ventures that foster innovation.
“If we multiply the 38 billion m3 of water that is accessible from our dams 1.6 times, we derive at the 63 billion m 3 that we will need in about six years’ time at current consumption levels. This can only be achieved by recovery, reuse, and recycling of South Africa’s total water resources,” Dr Turton said.
As early as the 1970s, the Council for Scientific and Industrial Research had already developed the first sewage recycling technology. This technology was deployed in Windhoek as a successful solution to water scarcity in the city. South Africa also has almost 20 years of experience reclaiming and desalinating highly contaminated acid mine drainage (AMD) into the cleanest drinkable water.
A prime example of AMD innovation is the eMalahleni Water Reclamation Plant, owned by a joint venture between BHP Billiton Energy Coal South Africa and Thungela Resources. Operating since 2007, the plant consists of a collection system that pumps excess contaminated mine water from several surface and underground coal mines in the eMalahleni area for treatment. A total of 50 ML /d of AMD is currently being treated to potable standard for use by mines and the eMalahleni Local Municipality, serving as an excellent PPP example.
Another area of innovation within the mining environment is the eutectic freeze crystallisation treatment of wastewater, a technology developed by Prentec and based on research by the University of Cape Town’s Faculty of Engineering and the Built Environment.
This world-first technology – initially deployed at Glencore’s Tweefontein Colliery to treat briny wastewater into clean water and valuable salts – is a major leap towards achieving zeroeffluent discharge. In addition to recycling all components, the technology reduces the need for evaporation ponds used to treat large amounts of wastewater produced as a by-product of coal mining. The latter require large tracts of land and are costly to build, with a relatively short lifespan. Groundwater leakages can also occur.
Potential applications for the technology outside the mining sector include treating paper, pulp and textile effluent streams, as well as brines that are produced from the desalination of seawater.
Dr Turton also sees significant potential for managed aquifer recharge (MAR) on a large scale in the country. MAR provides long-term storage for drought periods, natural treatment, and is a low cost and energy saving water supply solution. It is also a way of replenishing over-exploited aquifers and safeguards water against evaporation.
A present working example is the Atlantis Water Resource Management Scheme (AWRMS) in Cape Town, which has been operating for the past 40 years. The scheme currently has a supply capacity of between 5 ML /d and 13 ML /d, which will be upgraded to 35 M L /d. This will be achieved by bringing additional water from a new wellfield situated between the Witzands and Silwerstroom wellfield. The established managed aquifer recharge component uses treated domestic wastewater and stormwater, which is diverted to recharge basins where it infiltrates the aquifer.
There are also plans to develop a state-of-the-art indirect potable reuse scheme with a capacity to deliver super-treated water in the municipal jurisdiction. Water produced by the scheme will have an extremely high reduction in viruses and bacteria, while micro-pollutants will be well below detectable levels. The final effluent will be treated at Cape Flats and Borcherds Quarry Wastewater Treatment Works to a higher than drinking water standard, and then injected into the Cape Flats Aquifer. It will be treated again after it has been extracted as part of a multiplebarrier treatment approach.
This is the first scheme of its kind in South Africa to incorporate such an advanced water treatment system. It also demonstrates the sustainable possibilities when creative thinking and funding are successfully integrated to build futureproof infrastructure.
In the arid landscape of South Africa, where water is a precious resource, the significance of reliable water infrastructure cannot be overstated, reinforced annually by the Department of Water and Sanitation’s National Water Week campaign in March.
The Southern African Plastic Pipe Manufacturers Association (SAPPMA) emerges as a key player in this narrative, with a mission to uphold the highest standards in their segment, says CEO Jan Venter.
Polyvinyl Chloride (PVC) and High Density Polyethylene (HDPE) pipes that bear the SAPPMA mark guarantee a lifespan of more than 50 years. This longevity not only safeguards water resource delivery, but also aligns with South Africa’s constitutional imperative to ensure access to water for all citizens.
Plastic pipes offer numerous advantages such as reduced friction loss, lower energy consumption, a smaller environmental footprint, and crucially, they are heavy-metal free. These factors position plastic pipes, marked by SAPPMA’s seal of approval, as a reliable and environmentally conscious choice for the country’s water infrastructure needs.
In the context of National Water Week, SAPPMA extends an earnest appeal to specifiers and end-users to prioritise the use of pipes bearing the SAPPMA mark. Furthermore, a crucial call is made to politicians and decisionmakers to urgently invest in the much-needed upgrades of South Africa’s pipe network.
As Venter points out, the intersection of National Water Week and Human Rights Day in South Africa, as well as World Water Day and Earth Hour globally in March serves as a poignant reminder of the interconnectedness of water, human rights, and environmental sustainability.
In this respect, SAPPMA’s advocacy for reliable water infrastructure, grounded in high-quality plastic pipes, is a proactive step towards securing South Africa’s water future.
For more information on SAPPMA and its members, visit www.sappma.co.za.
One of Ceenex’s flagship water projects, the Bundu water treatment works (WTW) received the secondhighest score for the performance of WTWs in Mpumalanga in the 2023 Blue Drop report, at 88%. This again reaffirms the company’s commitment to engineering excellence and leadership in the design and implementation of topnotch water infrastructure.
The Blue Drop report contains the findings of a comprehensive assessment of the state of all 958 water supply systems (WSS) in the country in every Water Service Authority (WSA). Measurables include the condition of the infrastructure and the way in which WTWs are being maintained and operated. Other important factors that are assessed include the treatment processes, monitoring and control, and the skills and qualifications of operators of the WTWs.
Bundu WTW received high scores for its general aspects, raw water handling, chemical dosing and storage, flocculation, phase separation, disinfection, high-pumpstation, sludge treatment, and process unit.
Notably, drinking water from Bundu WTW achieved a 99,58% chemical compliance status according to the SANS 241:2015 drinking water specification. For drinking water to be considered safe for human consumption, it must achieve at least a 95% chemical compliance.
Engineers from Ceenex’s Infrastructure Discipline are proud to be associated with the design and construction supervision of a WTW that has been described as being “in secure and excellent condition” in the 2023 Blue Drop report. However, there is also a sense of achievement in the fact that the plant is being well-operated by municipal staff. According to the report, municipal staff are motivated and very proud of their WTW.
To simplify the operation of the WTW, Ceenex designed a conventional treatment process. It uses a high-pressure pumping system that comprises top-of-the-range variable speed pumps that have been sourced locally. Designed to provide central access to the control system, the human-machine interface system is easy to operate. In addition, a novel mechanical rapid gravity sand filter is used to remove fine suspended solids from the water. This limits operator intervention to periodic maintenance inspections. Powdered Activated Carbon was also incorporated into the treatment process to remove colouring from the water, which is being extracted from the Moses River.
With a capacity of 3 ML/d, this is Thembisile Hani Local Municipality’s first WTW. The municipality previously relied upon other WSAs for the supply of bulk water. This hindered uninterrupted supply of drinking water to constituents.
The WTW is part of a water augmentation scheme that Ceenex recently completed to bolster water supplies to Boekenhouthoek, Mathysenloop, Machipe and Bundu in Mpumalanga. Funded by the Municipal Infrastructure Grant, this is the largest service delivery infrastructure project to have ever been undertaken by the municipality.
As part of the project, Ceenex also designed and supervised the construction of a new 5 ML weir and abstraction point on the Moses River, a new 10 ML command reservoir in Bundu, and sections of the 8 km bulk pipeline associated with the scheme.
Notably, the command reservoir is one of the first to be built in the country using precast, prestressed concrete. The use of prefabricated concrete technology saved in construction time and ensured a robust structure that will continue to add value for many years. The Blue Drop report notes that the water-retaining structure is leak free and in good condition, featuring telemetry with a sensor to measure water levels remotely.
“We are committed to our vision of being a centre of engineering excellence or ‘Ceenex’ in short. This guides everything that we do. While a proud moment for our Infrastructure Engineering Division, it remains a serious concern that as many as 958 WSSs in the country in 62 Water Service Authorities were identified as being in a dire state in the latest Blue Drop report. This is compared to the 174 WSSs that needed urgent intervention in the 2014 report. Thus, there has been a significant decline in our WSSs over the past nine years,” explains Kgomotso Sekgobela, executive director of Ceenex
“To avoid a serious crisis, we can no longer delay upgrading existing and building new water infrastructure. We need to act now,” Sekgobela concludes.
Precast concrete beams and hollow-core slabs supplied by Concrete Manufacturers Association member, Cape Concrete Works, have been used to roof a new reservoir in Piketberg, 80 km east of Saldanha Bay. Commissioned by the Bergrivier Municipality, the structure will add 4 ML to the town’s existing 3 ML storage capacity.
Erected on the site of a disused open reservoir built in the early part of the 20th Century, a site which entailed the lowest environmental impact, the new unit is situated next to a 2 ML reservoir, and both are fed by a third reservoir that in turn draws its supply from the Piketberg water purification plant.
With a roof area of just under 1 400 m² and shaped as a quadrilateral, the new reservoir was constructed by main contractor, Hiload
Inyanga and was designed by iX engineers, the project’s consulting engineers.
The original intention had been to build a 2 ML circular reservoir on the site of the old reservoir, but a subsequent geotechnical investigation revealed an existing 200 mm thick solid concrete floor which could be deployed as sub-base material for the new structure.
Three options
“That left us with three options,”explains the
reservoir’s design engineer, Alwyn Le Roux. “We could stick with the original plan and build a 2 ML reservoir inside the old structure, or we could opt for a 4 ML reservoir by relining a section of the old structure and adding a roof to it. The third option entailed revamping the old structure as a 5 ML storage unit, but it was never given serious consideration.”
“This was because the Bergrivier Municipality wanted to allocate some of the old unit’s floor space for vehicle access and the construction of an above ground valve control chamber adjacent to the new reservoir,” Le Roux continues.
“Although we went to tender on the first two options, it was soon apparent that the second offered the best solution because a circular reservoir would have entailed additional excavation, work which was unnecessary in the construction of the 4 ML option. What’s more, on a cost per-cubicmetre storage basis the 4 ML unit proved the better proposition and that was the clincher.”
“We proceeded on the basis of retaining the old structure as a liner for the new floor and the three embankment walls. Although its concrete strength was more than adequate, over the years lateral movement
between panels had taken place, which meant it could only be used as a sub-base layer,” Le Roux expands.
Construction began with the erection of a 5,6 m cantilevered wall, which formed one of the four reservoir walls and divided the old reservoir into two sections: two thirds for the reservoir itself, and one third for the control chamber and vehicle access. With a tapered outer face, the wall is 600 mm wide at its base and 300 mm at the top.
The wall footing was anchored to the old floor with Y20 shear studs, and 25 tonnes of rebar were required to build the footing and the wall. Both are 37 m across, and to accommodate the slope of the old floor, footing height varies from 1,2 m to 700 mm. The bulk of its 3,5 m width falls within the reservoir to create the cantilever effect, and it was cast in two lifts with protruding rebar and vertical sides to buttress the wall.
An 80 mm no-fines drainage layer, also used as a concrete correction layer, was the first of three new concrete strata cast on the original concrete surface. However, some of the old embankment walling consisted of a stone-pitched concrete conglomerate, which required remedial work in preparation for the no-fines layer in those sections.
A 10 mm plastered layer was trowelled to seal off the no-fines concrete layer, and a reinforced concrete lining – varying between 150 mm and 200 mm – formed the third layer.
Perforated pipes are imbedded in the nofines floor sections for sub-surface drainage, leak detection and pressure relief, whereas embankment drainage is channelled through the no-fines layers into the flooring’s perforated pipes.
“We used the same rebar for the embankments and the floor and we opted for a dry mix to minimise cracking and to make the embankment casting process easier. The steep embankment slopes in some areas required shuttering at the floorend and the casting was done in stages to prevent the concrete from sliding down. Both the floor and the embankments were cast with protruding rebar for the construction of the column bases,” Le Roux explains.
The columns were cast at varying heights to ensure that the hollow-core slab roof fell 1° to either side of the central beam structure for drainage. Five rows of parallel beams support the hollow-core slab roof covering and each of the two rows on either side of the central row are slightly lower than the preceding row to
The
accommodate the roof slope. Cape Concrete sub-contractor, CPI, took only five days to install the 38 beams and 240 slabs using a 100 tonne mobile crane.
All the hollow-core slabs are 150 mm thick and most are 5,7 m long. However, some are only 1 m while others are as long as 6,8 m. Moreover, some of the slabs ends are splayed to accommodate the structure’s quadrangular shape and prior to delivery, Cape Concrete cut them to fit. The control chamber, which provides easy access to the inlet and outlet valves, was also roofed with hollow-core slabs.
Cape Concrete inserted polystyrene void formers into the hollow cores of the roof slabs to limit the amount of concrete which could enter the cores during the screeding process. A layer of clean-washed aggregate forms a third and final roof layer and precast coping, cast on site by Hiload Inyanga. This was installed on the roof edges to create a barrier for the aggregate and to improve the overall appearance of the reservoir.
In 2023, the City of Cape Town embarked on a project to upgrade the existing Montague Drive Bulk Sewer – a 4 km long section that functions as a major collector sewer with an internal diameter varying between 700 mm and 975 mm. Servicing a 3 320 ha catchment area, it forms a vital part of the city’s sanitation provision now and in the future.
The existing bulk sewer starts at the intersection of Montague Drive and Railway Road, intercepting the Sanddrift, Century City and Edgemead sewers, and follows Montague Drive to the Koeberg Road Pump Station. The existing bulk sewer was installed between 50 and 60 years ago and comprises asbestos cement and reinforced concrete pipe materials.
Phase 1 commenced on 1st March 2023 for scheduled completion by Q1 2025 and
entails the parallel reinforcement of the existing bulk sewer through the construction of the new Montague Gardens Bulk Sewer using microtunnelling techniques. Included in the scope is the construction of a new sandtrap and screening facility at the Koeberg Road Pump Station, as well as ancillary works.
Phase 2 will entail the rehabilitation of the existing Montague Drive Bulk Sewer using trenchless rehabilitation methods. This will commence once the new line is installed and flows can be diverted from the older system.
Route
The preferred route for the new Montague Gardens Bulk Sewer was identified to start in Bosmansdam Road at Station Road. It follows an alignment along Railway Road, Platinum Street, Esso Road, and Stella Cove across Koeberg Road to end at the Koeberg Road Pump Station. This route was considered the most favourable due to undeveloped land along the majority of the route.
A flow assessment was conducted to verify the required capacity of the bulk sewer system. The current peak daily dry weather flow (PDDWF) of the Koeberg Road Pump Station catchment area was estimated to be 30 626 kℓ/day while the current theoretical instantaneous peak dry weather flow (IPDWF) was estimated to be 723.1 ℓ/s.
The process followed to determine the future PDDWF of the Koeberg Road Pump Station catchment area included calculating the anticipated growth rates for the various
land use categories in each sub-catchment area from the information provided by the city. The calculated growth rates were applied over a maximum densification period of 20 years. The future PDDWF was estimated to be 34 508 k ℓ /day while the future theoretical IPDWF was estimated to be 814.9 ℓ/s.
Groundwater infiltration and stormwater ingress
The infiltration of groundwater into the sewer reticulation system servicing the catchment area can occur through joints and cracks, and through defects in sewer manhole walls. The quantum of groundwater infiltration is a function of topography, geology and the condition of the sewer infrastructure, and will vary from site to site. Following a review of the various design standards and guidelines, a suitable groundwater infiltration rate was applied in the hydraulic model.
Stormwater ingress into the sewer system occurs during rain events and can result in considerable peak flows in the sewer system. Common points of stormwater ingress include open sewer manholes where manhole covers were not closed properly or were broken or stolen, and illegal
connections of building rainwater downpipes into the sewer system.
The required pipe diameter for the new bulk sewer was verified during the design stage of the project using a hydraulic analysis of the
upgraded conveyance system (flowing to the Koeberg Road Pump Station) for the current and future flow scenarios.
The Montague Drive Sewer System was modelled and analysed using the PCSWMM computer software, which uses sewer unit hydrographs to simulate sewage flows in
the sewer system in time steps to determine the peak flows in each section of the system. The software also simulates the sewer pump stations in the system to account for the associated attenuation effect.
The hydraulic model was populated with sewer flows by assessing the type and counting the number of land use categories present at each node of the sewer system and assigning the corresponding quantities of the associated sewer unit hydrographs to the representative node in the hydraulic model.
The 37 pump stations in the Koeberg Road Pump Station catchment area were added to the hydraulic model to simulate the associated attenuation effect, as well as the relatively high flow peaks occurring when several pump stations discharge sewage directly into the Montague Drive Bulk Sewer at the same time. The sump sizes of the respective pump stations were included in the hydraulic model to accurately simulate the frequency and duration of pumping cycles.
Based on the hydraulic analyses, it was determined that the design of the new Montague Gardens Bulk Sewer has to be based on 970 mm ID concrete sewer installed at a minimum gradient of 1:500 from the start at Station Road up to the Montague Drive Bulk Sewer connection just after the Koeberg Road crossing (i.e. approximately 3 790 m in length). From there a 1 350 mm ID concrete sewer will be required at a minimum gradient of 1:1 250 up to the Koeberg Road Pump Station (i.e. approximately 260 m in length).
Sandtrap and screening facility
A new sandtrap and screening facility will be provided for the Koeberg Road Pump
Station to prevent sediment build-up in the wet well and to circumvent pump failures due to blockages.
The new sandtrap and screening facility to be constructed upstream of the Koeberg Road Pump Station was designed with a duty and standby configuration with two complete separate flow paths to allow continued operation during maintenance or routine cleaning of one flow path.
A flow transition zone was provided for at the inlet of the sandtrap where the incoming sewage flow stabilises to the laminar flow conditions required for sediment settlement. A trash rack and an automated multi-rake bar screen will be installed in each flow path of the screening facility to prevent debris entering the Koeberg Road Pump Station and blocking the pumps.
The new sandtrap and screening facility to be constructed at the Koeberg Road Pump Station is illustrated in Figure 1.
Rehabilitation of the existing Montague Drive Bulk Sewer
Phase 2 of the project comprises the rehabilitation of the existing Montague Drive Bulk Sewer by means of trenchless rehabilitation methods. The trenchless rehabilitation methods most commonly applied in the industry for the rehabilitation of bulk sewers are sliplining, cured-in-place-pipe (CIPP) and spiral wound pipe (SWP). Following a comparison of the various trenchless rehabilitation methods, CIPP was selected as the preferred rehabilitation method for rehabilitating the existing Montague Drive Bulk Sewer.
The two methods generally employed to install the liner during the CIPP process are the pull in method and the inversion method. The pull-in method is not preferred for the rehabilitation of the Montague Drive Bulk Sewer due to the high groundwater table at Montague Gardens, even during the summer months, and the inversion method is therefore preferred.
ASTM F1216-09 was selected as the preferred design standard to calculate the liner wall thickness for the rehabilitation of the existing Montague Drive Bulk Sewer as it is well accepted internationally and is the most commonly used standard in the South African industry.
The liner thickness is a function of the condition of the host pipe and its ability to support imposed loads throughout the life of the rehabilitated pipe. Due to the numerous sewer failures that have occurred along the existing Montague Drive Bulk Sewer, the sewer was classified as a fully deteriorated pipe.
Based on the calculations, an unreinforced felt liner with a thickness of 19 mm will be required for the rehabilitation of the existing 900 mm internal diameter Montague Drive Bulk Sewer.
Since manholes are the only point of access into sewer systems, it is essential that those constructed along the existing Montague Drive Bulk Sewer are also rehabilitated so they have the same design life as the CIPP liner, providing the city with a durable infrastructure investment.
A significant occasion to recognise the pivotal role of engineering in shaping our world, this year’s theme for World Engineering Day on 4 th March was “Engineering Solutions for a Sustainable World.” It showcases how engineers develop innovative solutions to address global challenges such as climate change, poverty and inequality in support of the UN Sustainable Development Goals (SDGs). Celebrating engineers raises awareness about their contributions and inspires young minds to pursue careers in engineering, ensuring a talent pipeline for future generations. Leading consulting engineering and infrastructure advisory firm Zutari showcases four exceptional women engineers from its ranks.
Hirna is the lead design engineer for civil infrastructure projects associated with residential and mixed-use developments, from concept to closeout. Her responsibilities involve designing, collaborating with professionals across various disciplines and ensuring deliverables align with Zutari’s standards.
“I enjoy a challenge and find immense joy in overcoming obstacles,” says Hirna. Her passion for sustainability drives her to get involved in projects with sustainability components. As a woman in civil engineering, she relishes bringing a unique and diverse perspective to the profession, fostering a dynamic and inclusive environment.
Hirna proudly shares that she was part of a womendominated consulting team for the Nine Palms and
On-Park development, adding that collaborating with women leads in architecture, landscaping, mechanical, and structures was a career highlight. Lastly, witnessing the tangible impact of her work in projects like Ratanga Park in Century City was an incredibly fulfilling moment.
“I envision creating safe spaces in both society and the workplace, where women feel empowered and secure. This includes fostering a culture of respect, support and equal opportunities for women to thrive and contribute fully,” says Hirna.
Her advice to young women is to find a mentor for guidance, to be confident in their unique contributions and take initiative in shaping their career path. “Embrace your authenticity; you do not have to change who you are to make a powerful and lasting impact,” stresses Hirna.
This is the third year that Meaghan has been a part of a team consisting of both process and mechanical engineers in the Tshwane office. She works mainly on projects in the industrial, oil and gas and petrochemical sectors.
“The fact that I constantly get to work on new and exciting projects keeps me passionate about what I do. I love being challenged and solving new problems. Doing this every day is very fulfilling,” says Meaghan.
Working with Zutari’s industryrecognised professionals has been a highlight to date. “The knowledge I am gaining from their guidance is setting me up for success,” says Meaghan.
Having already worked on several projects with different teams and people, she has been in meetings and on-site as the only woman present. “I have learnt to recognise my own skills and talents. I strive to ask questions and absorb knowledge, no matter who is in the room, so that one day I may be the best engineer I can be.”
Vera is a professional civil engineer specialising in traffic engineering and transport planning, forming part of a team of senior and young engineers and transport economists from different backgrounds. She is currently an Associate in the transport planning team at the Tshwane office. Apart from being a line manager responsible for the day-to-day technical operations of the team, her critical role entails creating an enabling environment for holistic career growth for individual team members, which fundamentally has inclusivity as one of its pillars.
Just like the human circulatory system carries blood to the various organs to keep it functional and alive, so do transport systems and services improve the welfare of communities and economies by linking people to opportunities and desired places to enhance their quality of life.
“My passion for making a difference is reignited when I see transport projects I worked on being implemented and making a difference, even in the smallest way, like recommending a walkway in a school vicinity,” says Vera.
Working within the Transmission and Distribution (T&D) team, Majd mostly specialises in earthing and lightning protection studies for various energy facilities such as photovoltaic plants, battery energy storage facilities and substations. In addition, she is involved in the design and construction management of electrical distribution projects. “We are committed to fostering the growth of younger staff, empowering them to evolve into skilled and independent engineers. The continuous learning opportunities make each day at work both rewarding and exciting, transforming what could be routine into a dynamic experience,” says Majd.
She initially came from a different academic background, but once she delved into the T&D industry, she found it so fulfilling she could not imagine going back to her initial
career aspirations. “It was a bit harder to fill the gap; it required a lot of self-studying and bothering my seniors for guidance,” she adds.
“Though we have made significant strides, I believe there is still room for improvement within the construction environment. Shifting our focus towards one’s capabilities and experience, rather than factors like gender, religion, race, etc., will naturally foster an inclusive space for everyone.
“You are the main character of your story; you (and you alone) dictate the timeline and narrative. There may be plot twists and supporting characters, but they are there to enhance the story. Just keep on writing it,” concludes Majd.
Municipal audit outcomes tend to receive extensive media attention, with ongoing commentary on the need for financial audit compliance – the lack thereof generally viewed as a major contributor to poor service delivery. Why non-compliance remains widespread is due to numerous factors, including how municipalities approach the essential discipline of maintaining accurate asset registers in terms of Generally Recognised Accounting Practice (GRAP) requirements. By Christopher
ChinongeMere compliance with GRAP does not necessarily result in improved infrastructure planning and service delivery. In other words, it is possible for a municipality to achieve financial compliance and emerge with a “clean” audit with regards to its asset accounting and yet have a register that does not enable it to practice good asset management.
One of the key pillars of asset management relates to the gathering of relevant and accurate information. Here engineers have a key role to play since they are responsible within the infrastructure space for design, development, and maintenance. So, the exercise is not exclusively an accounting function.
Developing a sound asset register
Currently, many asset registers are presented in Microsoft Excel and maintained that way although some municipalities have software that stores the asset data in SQL based databases. Either way, in order to develop a good asset register, practitioners need to consider certain minimum requirements, with the following steps recommended as a good practice approach:
1 Determine the level of component detail: The most important feature that makes an asset register worth the effort is componentisation. The latter refers to the breaking down of infrastructure assets into their smaller constitutive parts. The component detail should be guided by the level at which assets can be maintained or refurbished. For an accountant, almost any level of component detail would suffice, but for an engineer the question of component level carries far more significance.
2 Decide on the condition and asset performance grades to be used: Condition data is used to determine an organisation’s infrastructure capital and maintenance requirements. Condition data can be very useful in timing and optimising infrastructure expenditure.
There are numerous condition grading scales that can be used for infrastructure projects. The choice of condition grading is determined by the level of complexity desired and that would perhaps bring more value for money in terms of the municipality’s available resources. The choice of grading scale is a technical decision that
would require the knowledge of the deterioration mechanisms and the most important failure modes of the assets under consideration.
For asset management purposes, the condition grading should be augmented by other criteria such as performance, utilisation and criticality. Each of these measures should have a grading scale. Surely this exercise is a purely engineering one?
3 Establish estimated useful life of the components: The useful life of an asset is an estimate that is often based on the manufacuturer’s specification or industry norms. Various assets, such as pumps and motors, have useful lives that can be based on make, model and capacity. Other assets such as civil infrastructure would be based on the construction materials used and their exposure or loading conditions. Concrete deterioration presents a good example.
Alexander and Beushausen (2019) and others have demonstrated that the service life of concrete structures should be adjusted based on local conditions. There are equations governing the service life of concrete based on carbonation depth and other deterioration mechanisms. These equations can be adapted to local conditions in order to predict estimated useful life and to adjust it yearly based on the deterioration curves derived.
Accounting standards require that the useful lives should be re-evaluated annually and a remaining useful life should be established. It is vital that the remaining useful life is based on expert engineering opinion and has a rational basis.
4
Determine the unit rates for each component: The unit rates of various assets will be based on their replacement costs. The rates need to take into account the nature of the material being used, the design and construction methods required to install or construct components, and the overhead costs involved, as well as the municipality’s internal costs.
Such information requires a knowledge of construction methods, equipment, materials and rates build-up. Accurate unit rates lead to more efficient municipal budgeting and to financially viable projects.
Many municipalities use historical costs to account for their assets. This goes against government requirements and international best practice. Best practice advises the use of current replacement cost. This is a technical exercise that requires a knowledge of construction, as well as mechanical and electrical equipment.
Therefore, since a high percentage of what goes into an asset register will have a direct bearing on scheduled maintenance, it should be identified as engineering work. In fact, key activities involved in establishing and maintaining an asset register do form part of the outcomes for registration as a professional engineer with the Engineering Council of South Africa (ECSA).
According to ECSA, engineering work is defined as, “The process of applying engineering and scientific principles, concepts, contextual and engineering knowledge to the research, planning, design, implementation and management of work in both the natural and the built environments.” (ECSA, 2022)
Group A outcomes for ECSA registration deals with engineering problem solving. The engineer is required to identify, analyse, and solve complex engineering problems using a mathematical formulation “where necessary.”
In this respect, the development and maintenance of asset registers – meeting the requirements of outcome 2 of the ECSA registration stipulations – can be defined as a complex engineering problem. According to the ECSA competency standards, a complex engineering problem can be one that is ill-posed, under or over specified and requires identification and refinement.
As a first step, the engineer needs to determine which level of componentisation best represents each asset’s essential features. The “essentiality” of a component is based on its value, size, and criticality to the operation of the parent asset, to which it is a component. Making this determination requires an understanding of the factors that influence the performance and operation of the component.
In developing an asset register, the engineer needs to address the following criteria:
• What level of component detail is appropriate for a particular asset?
• To which asset category should the asset be allocated? This can be influenced by the spatial segmentation of a service.
• What is the expected useful life of the asset?
• What depreciation method should be recommended that more favourably aligns with the deterioration mechanisms of the asset?
• Which unit rates are most appropriate for the construction methods involved in creating the asset?
• What criteria will be used to determine the performance measures and grading of particular assets?
The answers to the questions above will require the solving of sub-problems such as deterioration mechanisms, construction methodology, material characterisation and may also require
the utilisation or development of geographical information systems.
In addition to the requirements above, a complex engineering problem can also be defined as involving wide ranging and or conflicting issues. These include technical and engineering issues and interested and affected parties.
A problem is wide ranging when it has impact beyond the local scenario. An example of wide ranging impact can be seen in how projects are funded. The budgets that are received come from National Treasury, and perhaps other funding agencies whose budgets are influenced by the financial needs of municipalities. The service delivery challenges, though local, may often impact bulk infrastructure provided by a provincial or national agency.
Therefore, the development of an asset register, with its associated data model and hierarchy, involves wide ranging and or conflicting issues. The engineer has to balance the requirements of accounting practice, the budgetary and operational restrictions of municipalities and the capacity of the municipality to maintain the asset register and data at a specific level of detail.
The question as to whether the accountant or the engineer should be the custodian of the asset register is not a trivial one. Based on the factors presented in this article, it is safe to assume that even if one takes the position that the custodian of the register should be an accountant, the engineer should have a major role to play in its development and maintenance.
- National Treasury South Africa and i @ Consulting (Pty) Ltd, Cities Infrastructure Delivery Management System Toolkit Edition 1(CIDMS), 2018, Accessed on 01 June 2023, https://cidms.co.za/cidms-toolkit/
- Accounting Standards Board, Generally Recognised Accounting Practice 17 Property Plant and Equipment, 2010, Accessed on 01 June 2023, https://www.asb.co.za/wp-content/uploads/2021/03/GRAP-17-Property-PlantEquipment-1-April-2021.pdf
- Engineering Council of South Africa (ECSA), 2022, Standard for the identification of engineering work, Accessed on 12 May 2023, https://www.ecsa.co.za/ ECSADocuments/Shared%20Documents/IDoEW-01-STD%20Standard%20for%20 the%20Identification%20of%20Engineering%20Work.pdf
- Alexander, Mark & Beushausen, Hans., 2019, Durability, service life prediction, and modelling for reinforced concrete structures – review and critique. Cement and Concrete Research. 122. 17-29. 10.1016/j.cemconres.2019.04.018.
There are significant benefits to installing services below ground level rather than at or above ground. This is especially so in congested inner city and residential areas where people, vehicles and services compete for space. Burying services does not disrupt surface activities. What’s more, the services do not have to be supported, which then adds to the surface obstructions.
By Alaster Goyns Pr Eng*Pipelines have been used for more than 5 000 years to transport water from one location to another, with the first being those used by the Egyptian and Babylonian civilisations.
Traditionally, pipelines have been installed by digging trenches, which require surface space and depth. In effect, these pipelines use the three-dimensional space below the surface. As there are surface obstructions and depth limitations to digging trenches, this makes pipeline installation complex, especially gravity systems such as sewers and stormwater drains. As water is heavy, it needs energy to move it, whether it is being conveyed in a gravity or pressure system.
The upside is that the development of trenchless techniques for rehabilitating
existing pipelines or installing new pipelines since the 1960s and 1970s has reduced construction costs, as well as significantly reducing surface disruption in high density urban areas, plus environmental impact during the installation period.
The concept of trenchless techniques as understood today falls into two broad categories, namely the installation of new pipelines and the rehabilitation of existing pipelines. The installation of new pipes by jacking and directional drilling has been around for some time. In South Africa it started in the early 1960s.
In turn, pipe lining was developed by an agricultural engineer, Eric Wood, in 1970 to
reline the ducts on his mushroom farm as this was less disruptive. The technique was subsequently referred to as cured-in-place piping or CIPP. Several related techniques have subsequently been developed.
Irrespective of whether a lining is being installed in an existing pipe or a new pipeline is being constructed, there are four technical factors that need consideration, namely the primary one of hydraulic performance, as well as strength, water tightness, and durability.
However, a clear distinction needs to be made between rehabilitation and new installation techniques and how to handle these technical factors. In both cases, the pipes are buried, but the external loading conditions differ. With rehabilitation, the lining is placed within a host, which still carries the surrounding soil pressures. The lining is generally thin and smoother than the host pipe, so it does not negatively impact the capacity. Furthermore, it must be able to handle any water pressure that develops between the lining and the host pipe due to leaks, and protect the host pipe from corrosion.
With a new installation, the pipe is placed within the hole that is made and must support the external loads, as well as meeting the other requirements of capacity, water tightness and durability.
Online replacement techniques
Subsequent to developing lining and new installation techniques, online replacement techniques were introduced. These were hybrids of the rehabilitation and new installation techniques. In their case, a hole already exists through the soil, but this may have to be increased in size due to inadequate capacity of the existing pipeline or because it is on the point of collapse. The
existing pipe is then broken into pieces by specialised equipment and a new pipe is simultaneously pulled into place. As a result, the new pipe must be able to handle all four technical factors.
Due diligence
As with all pipeline construction, it is essential that there should be a careful study of both the surface and subsurface conditions before any
trenchless work is started. In addition, with pipeline rehabilitation or online replacement, the performance and condition of the existing pipeline must be determined first so that any problems are identified, underlying causes established, and the necessary remedial measures taken before rehabilitation or replacement commences.
Sharing details of these developments via webinars
With the rapid development and densification of urban areas in South Africa, resulting in limited available space, it is more difficult to install buried services using traditional trenching techniques. The benefits of trenchless techniques, including improvement of the service provided, has not been fully appreciated by many service providers. With this in mind, the Southern African Society for Trenchless Technology (SASTT) has arranged a series of mini webinars covering various aspects of trenchless technology.
During 2023 these events covered:
• An overview of trenchless technology
• Performance and condition assessment
• Pipelining techniques
• Online replacement techniques
For 2024 the planned events and dates are:
• New installations over short distances: pipe ramming and jacking (16th April)
• New installations over long distances: directional drilling and microtunnelling (18th June)
• Supporting services: pipe cleaning, over pumping and point repairs (20th August)
• Market developments: international, local and attendance at No-Dig 2023 (15th October)
These webinars are based on a simplified version of the International Society of
complex loading will be handled will depend upon the technique and material used. The first two webinars this year covering new installations will briefly consider the handling of these loading conditions and the materials used, followed by the practicalities of these techniques presented by contractors who specialise in these activities.
The simplest of these techniques is pipe moling. This is used for small diameter service installation over short distances. Moling requires a pit at the entry and exit points and is generally not steerable. The driving force is a percussion hammer that pushes the torpedo shaped mole through the soil by displacing the material and simultaneously pulling in a new pipe. Apart from the entry and exit pits, no material is removed. However, it is essential that the soil conditions be assessed as an impact mole can only pass through soils that can be compressed or displaced.
As already stated, there is a significant difference between the impact of the factors to be considered with renovation of existing versus installation of new pipelines. With an existing pipeline that needs renovation, its condition is assessed before relining and the required structural properties of the liner are designed to meet the groundwater pressure.
However, when a new pipeline is being installed, it is essential to establish the soil conditions, including the groundwater level, as it needs to carry both the water and soil pressures and must have the lateral support of the surrounding material. In addition, the
of any other services
needs to be established before construction starts.
With a new pipeline, a new hole is created through the soil. The way in which the more
Pipe ramming consists of driving an openended steel casing through the soil by using a percussion hammer from a drive pit. The soil is then removed from the casing by an auger or water jetting. Much less material is removed than there would be if a trench was dug. Ramming is usually used as a sleeve for a new pipeline or services passing under a transportation route. The operation requires the construction of guide rails cast into a solid base in the launch pit. Similar soil conditions are required to those applicable to pipe moling.
Pipe jacking is done by pushing pipes through a tunnel that can be excavated through a range of subsurface conditions. In South Africa this is done only with man entry sized pipelines. The lead pipe has a shield attached to it to maintain direction, protect the labour doing the excavation, and prevent material from falling into the pipes. As the pipes are pushed, they are subjected to high compressive forces, requiring reinforced concrete pipes. Concrete pipes are jointed and these are susceptible to damage if the gradient and alignment are not controlled.
Microtunnelling is a more advanced technique than pipe jacking. It can be used for smaller diameters through many different soil
conditions, varying from waterlogged sands and gravels to solid rock using specialised equipment for greater distances. Reinforced concrete pipes are generally used as they have high compressive strength to handle the pushing forces and, with correctly designed joints, can tolerate gradual curves.
Lubricating the gap between the pipes and the tunnel with a bentonite mud or a combination of bentonite and polymer reduces the frictional forces that develop between the pipes and surrounding material as they are pushed through.
Directional drilling is probably the most flexible of the trenchless techniques as it can follow a straight or curved alignment to avoid obstructions. A whole range of drilling equipment is available covering various pipe diameters and lengths of crossings under rivers, canals, and transportation routes.
The technique has been used mainly for pressure pipelines where gradients are not critical. Recent developments offer better control of gradients and internationally there has been a greater use for gravity pipelines. A distinct feature of directional drilling is that a pilot hole is drilled initially and then enlarged by reaming until it is large enough to accommodate the required size of pipeline. However, keeping the hole open and preventing the soil from collapsing onto the new pipeline presents a challenge. This is addressed by paying special attention to the lubricant placed between the drilled hole and the new pipeline.
An essential part of the preinstallation investigation for new installations below urban areas, especially with major projects involving microtunnelling and directional drilling, is to establish the location of other buried services to be avoided along the route. This is done by using ground penetrating radar.
Once site investigation and asset condition – where necessary – have been assessed, the most appropriate technique for rehabilitation or installation of a new pipeline can be selected for below a congested urban area to minimise surface disruption. Our 2024 SASTT webinars will drill down into the details.
*Board member, Southern African Society for Trenchless Technology
Enterprising built environment professionals are using the Cement & Concrete SA (CCSA) concrete CO2 model to design concrete mixes with reduced carbon footprints.
Among the many users of the CCSA’s concrete CO2 model are cement manufacturers, readymix producers, consulting engineers and architects.
“Climate change due to the warming effect of greenhouse gas (GHG) emissions is of everincreasing importance to the built environment profession. Considering the size of the concrete industry, it can play a significant role in reducing GHGs,” explains Gary Theodosiou, a Technical Consultant to CCSA.
“Our model enables built environment professionals to measure the carbon footprint of concrete mixes so that they can make informed choices regarding the use of the construction material. It is also raising awareness of ‘green’ concrete, as well as facilitating and recognising environmental leadership.”
The concrete CO2 model, which is based on a comprehensive study completed in 2010, determines the carbon dioxide equivalent (CO2e) associated with the production of a
cubic metre (m3) of concrete according to a user-defined mix design. Users of the CO2 concrete model can select the type of cement deployed in the mix and the end application for concrete, such as roof tiles, bricks, precast concrete elements or cast-in-place construction methods.
It considers the embodied carbon of the various actions of concrete production, namely transportation and mixing. This is in addition to the various concrete components, including admixture, aggregates, CEM I cement, fly ash, ground-granulated blast-furnace slag (GGBS) (both fly ash and GGBS are often referred to as extenders), water and steel reinforcing.
CCSA defines these emissions according to the internationally recognised GHG Protocol,
which is also used by the World Business Council for Sustainable Development’s approved cement emission model. CCSA also developed and refined the latter to make it more relevant to concrete as part of the development of its concrete CO2 model.
The GHG Protocol defines three categories of emission sources, namely Scope 1 (direct), Scope 2 (indirect), and Scope 3 (other indirect). Direct GHG emissions are derived from sources that are owned or controlled by the reporting entity. In turn, indirect GHG emissions are a consequence of various activities of the reporting entity. However, they occur at sources owned or controlled by another entity and include GHG emissions from the consumption of purchased
Gary Theodosiou, a Technical Consultant to CCSAelectricity, heat and steam. Business travel, final transportation of product by a third party, and outsourced activities are a few examples of other indirect emissions.
Once the emission sources for concrete were identified, a questionnaire requesting specific activity data was sent to providers of services and components for concrete production. A primary focus of this aspect of the study entailed quantifying the energy consumption involved in each activity and component associated with concrete production. This is considering the large contribution that this function, alone, makes to the carbon footprint of the various actions and components linked to concrete production.
The only exception is the cement industry where as much as 50% of its emissions are generated from the calcination/decomposition of limestone in kilns. Electricity and fuel consumption make up the balance of the cement industry’s carbon footprint.
Based on data received from three major producers, CCSA determined the embodied carbon of CEM I cement to be 985,4 kg
CO2e/t. 83% of this is made up of Stage 1 emissions. Stage 2 and Stage 3 emissions contribute 15% and 2%, respectively.
The carbon footprint of aggregate production is 5,36 kg CO 2 e/t. Diesel consumption accounts for most of the industry’s Scope 1 emissions, which make up 64% of the embodied carbon of aggregates. The bulk of Scope 2 emissions are derived from electricity consumption.
Blasting accounts for a small portion of quarrying-related emissions. This is considering that although explosives have a large carbon footprint, they are used in small amounts in these operations compared to the formal mining industry.
The carbon footprint of fly ash is 1,51 kg CO2e/t. Considering that it is a by-product of the electricity industry, fly ash is produced regardless of demand from the concrete and cement industries. Therefore, only those emissions produced after primary production were measured by the CCSA in developing the concrete CO2 model. The vast majority of emissions associated with fly ash preparation is generated from the consumption of electricity.
The carbon footprint of GGBS was determined to be 128,6 kg CO2e/t. GGBS is a by-product of the steel industry. Therefore, similar to fly ash, it is produced irrespective of demand from the concrete and cement industries. For this reason, CCSA again only regarded the specific emissions of post-primary production. The majority of emissions associated with GGBS preparation are produced by burning fuels for drying and electricity consumption for grinding.
Reinforcing
Reinforcing bars produced from virgin steel has the largest carbon footprint of 2 735 kg CO2e/t. This is considering that the steel industry is very energy intensive with the primary source of its emissions derived from the coking process. The majority of reinforcing bars are produced from recycled steel with a carbon footprint of about 1 700 kg CO2e/t.
As part of the study, the embodied carbon of eight concrete mixes with a 30 MPa strength were compared. All of these mixes incorporated CEM I as a base cement and were designed with and without admixtures for comparative purposes. Moreover, to evaluate the effects of fly ash, GGBS, admixtures, aggregates and water demand on CO 2 emissions, raw material amounts were varied in each concrete mix design.
CCSA found that the carbon footprint, including Scope 1, 2 and 3 emissions, of an average 30 MPa in-situ concrete containing a CEM I 42.5 cement with varying quantities of extenders and admixtures ranged between 195 kg of CO2e/m3 and 483 kg of CO2e/m3 Meanwhile, an un-extended concrete mix has a 295 kg of CO2e/m3 carbon footprint.
Notably, only 234 kg CO 2e/m 3 Scope 1 emissions are associated with an average South African concrete mix using a CEM I cement with an admixture. This is compared to a Scope 1 emissions range of 251 kg CO2e/m 3 to 273 kg CO 2e/m 3 for a similar concrete mix that is produced in Australia. In the UK, 266kg CO2e/m3 of Stage 1 emissions are associated with a similar concrete mix. Scope 1 emissions were used for comparative purposes because they are readily available as it is a minimum international requirement to report these. Meanwhile, 169 kg CO2e/m3 of Scope 1 emissions are associated with a South African extended cement consisting of a 70/30 fly ash blend.
Scope 1 emissions contribute as much as 75% to the embodied carbon of an average
South African concrete mix using a CEM 1 and admixture. Scope 2 and Scope 3 emissions account for 18% and 8% of the carbon footprint, respectively.
Theodosiou says that CSSA’s concrete CO2 model demonstrates that the carbon footprint of concrete can be reduced in three ways. This is by using a cement extended with fly ash or GGBS, an admixture, or a good quality aggregate and sand with a low water demand.
When plasticiser admixtures are added to a CEM I mix design, water demand is reduced by 10%, resulting in a 17,6% decline in cement requirement. Overall, the use of admixtures lowered CO2 emissions by 16%.
Fly ash can lower associated emissions by 23%. When used with an admixture, emissions can be reduced by a further 15%, resulting in a 38% decrease in the carbon footprint.
The inclusion of GGBS in the concrete mix can reduce CO2 emissions by 36% and 45% when used with an admixture. This is considering that it can replace up to 50% of cement in the concrete mix.
The final test involved using decomposed granite sand as an aggregate input. This was to demonstrate that the type of aggregate used in the concrete mix can also reduce CO2 emissions. A decomposed granite sand mix has a high-water requirement (240 l/m3) of 76% or more. In turn, this leads to an increased cement requirement of 53%, raising the carbon footprint of the decomposed granite sand mix by 36%.
“Due to its flexibility and many other inherent benefits, concrete is the most widely used construction material. About one tonne a year of concrete is consumed a year for every human being. Therefore, its responsible and innovative use can make a substantial contribution to the sustainability of the built environment. Our concrete CO 2 model facilitates this,” Theodosiou concludes.
A concrete mix would first be proportioned according to the proposed application of the concrete, before/together with carbon footprint considerations. This is as mentioned above that the carbon footprint of concrete can be reduced by using extended cement with fly ash or GGBS. The more extender used, the less CEM I cement is required. CEM I cement has the high carbon footprint.
There are certain applications where high extender contents are required, especially where durability is a requirement. Such instances include reinforced concrete in marine zones, the use of alkali reactive aggregates, sulphate attack, and large placing of concrete. There are other applications where high extender contents are not recommended, for example, high-strength concrete and floors on the ground with sawn joints.
The value of the worldwide lithium-ion battery market is projected to top US$193 billion by 2028, reflecting a 23,3% compound annual growth rate from 2021. This has proven to be the catalyst for the construction of sustainable and efficient battery giga factories, with the potential for building retrofits.
According to research, investments in battery giga factories hit US$131 billion in 2022, a 24% increase over the previous year. These were predominantly led by China. However, North America is catching up, with its manufacturing capacity expanded by 49% in 2022, compared strongly to China’s 65% year-on-year increase.
“From new builds to refurbing and converting previously used manufacturing facilities, or expanding existing traditional battery manufacturing facilities, to giga factories, securing these investments requires a holistic approach that encompasses construction, optimisation, power supply, site selection, feedstock sourcing, sales strategy, regulatory compliance and a sustainability lens,” says Peter Hodgkinson, director for Strategic Growth and Major Projects: Property & Buildings at WSP in Africa.
“Battery design, and therefore the design of battery giga factories, is a rapidly evolving industry. To truly drive industry growth, it’s essential to embrace innovation, future-readiness and prepare for the changing landscape. Ultimately, the emergence of battery giga factories will help the world embrace a more sustainable future,” Hodgkinson concludes.
Peter Hodgkinson, director for Strategic Growth and Major Projects: Property & Buildings at WSP in Africa
AECOM siphokuhle.dlamini@aecom.com
AFI Consult banie@afri-infra.com
ARRB Systems info@arrbsystemssa.com
Asla Construction (Pty) Ltd johanv@asla.co.za
BMK Group brian@bmkgroup.co.za
Bosch Projects (Pty) Ltd mail@boschprojects.co.za
BVI Consulting Engineers marketing@bviho.co.za
CCG puhumudzo@ccgsytems.co.za / info@ccgsystems.co.za
Corrosion Institute of Southern Africa secretary@corrosioninstitute.org.za
Dlamindlovu Consulting Engineers & Project Managers info@dlami-ndlovu.co.za
EFG Engineers eric@efgeng.co.za
Elster Kent Metering Mark.Shamley@Honeywell.com
EMS Solutions paul@emssolutions.co.za
ENsync Engineers info@ensync.africa
ERWAT mail@erwat.co.za
Gabion Baskets mail@gabionbaskets.co.za
GIBB marketing@gibb.co.za
GIGSA secretary@gigsa.org
GLS Consulting info@gls.co.za
Gorman Rupp Cordeiro@gormanrupp.co.za
Gudunkomo Investments & Consulting info@gudunkomo.co.za
Hatch Africa (Pty) Ltd info@hatch.co.za
HB Glass Filter Media info@hardybulkinglass.com
Herrenknecht schiewe.helene@herrenknecht.de
Huber Technology cs@hubersa.com
Hydro-comp Enterprises info@edams.co.za
Infrachamps Consulting info@infrachamps.co.za
INFRATEC info@infratec.co.za
Institute of Waste Management of Southern Africa iwmsa@iwmsa.co.za
IQHINA Consulting Engineers & Project Managers info@iqhina.co.za
iX engineers (Pty) Ltd hans.k@ixengineers.co.za
Izinga Holdings info@izingalabezi.co.za
JBFE Consulting (Pty) Ltd issie@jbfe.co.za
JG Afrika DennyC@jgafrika.com
KABE Consulting Engineers info@kabe.co.za
Kago Consulting Engineers kagocon@kago.co.za
Kantey & Templer (K&T) Consulting Engineers ccherry@ct.kanteys.co.za
Kitso Botlhale Consulting Engineers info@kitsobce.co.za
KSB Pumps and Valves (Pty) Ltd salesza@ksb.com
KUREMA Engineering (Pty) Ltd info@kurema.co.za
Lektratek Water general@lwt.co.za
Loshini Projects muzi@loshini.co.za
Makhaotse Narasimulu & Associates mmakhaotse@mna-sa.co.za
Mariswe (Pty) Ltd neshniec@mariswe.com
Martin & East gbyron@martin-east.co.za
M & C Consulting Engineers (Pty) Ltd info@mcconsulting.co.za
Mhiduve adminpotch@mhiduve.co.za
MPAMOT (PTY) LTD mpumem@mpamot.com
Mvubu Consulting & Project Managers miranda@mvubu.net
Nyeleti Consulting naidoot@nyeleti.co.za
Odour Engineering Systems mathewc@oes.co.za
Prociv Consulting & Projects Management amarunga@prociv.co.za
Rainbow Reservoirs quin@rainbowres.com
Re-Solve Consulting (Pty) Ltd maura@re-solve.co.za
Ribicon Consulting Group (Pty) Ltd info@ribicon.co.za
Royal HaskoningDHV francisg@rhdv.com
SABITA info@sabita.co.za
SAFRIPOL mberry@safripol.com
SAGI annette@sagi.co.za
SALGA info@salga.org.za
SAPPMA admin@sappma.co.za / willem@sappma.co.za
SARF administrator@sarf.org.za.co.za
SBS Water Systems marketing@sbstanks.co.za
Silulumanzi Antoinette.Diphoko@silulumanzi.com
Siroccon International (Pty) Ltd admin@siroccon.co.za
SiVEST SA info@sivest.co.za
Sizabantu Piping Systems (Pty) Ltd proudly@sizabantu.com
Siza Water (RF) Pty Ltd PA@sizawater.com
Sky High Consulting Engineers (Pty) Ltd info@shconsultong.co.za
SKYV Consulting Engineers (Pty) Ltd kamesh@skyv.co.za
Smartlock jp.alkema@smartlock.net
SMEC capetown@smec.com
SOUTH AFRICAN VALUE EDUCATION Sabiha@savegroup.co.za
Southern African Society for Trenchless Technology director@sasst.org.za
SRK Consulting jomar@srk.co.za
Star Of Life Emergency Trading CC admin@staroflife.co.za
Structa Group info@structatech.co.za
TPA Consulting roger@tpa.co.za
Ultra Control Valves peter@ultravalves.co.za
V3 Consulting Engineers (Pty) Ltd info@v3consulting.co.za
VIP Consulting Engineers esme@vipconsulting.co.za
VNA info@vnac.co.za
Water Institute of Southern Africa wisa@wisa.org.za
Wam Technology CC support@wamsys.co.za
Wilo South Africa marketingsa@wilo.co.za
WRCON ben@wrcon.co.za
Zutari Rashree.Maharaj@Zutari.com
In a pioneering step towards energy independence and environmental sustainability, Wilson Bayly Holmes-Ovcon (WBHO) has installed largescale solar panel arrays on the three buildings of its headquarters in Wynberg, Johannesburg. Costing around R20 million, all systems are due to be fully activated by May 2024.
What is ground-breaking about the project is the unique model WBHO has developed of the daily, weekly and seasonal load cycles of the premises to address the challenge of balancing the buildings’ unique fluctuations in energy demand and fluctuating solar supply supported by battery storage. This model enables the company to ensure safe, stable access to energy throughout the day, and can be refined and customised for wider application as part of a future-orientated construction offering.
The project involved structural changes to the buildings with concrete blocks placed on the roofs to secure maximum solar panel metreage. 140 t of ballast were placed on the roofs and 50 t of steel mountings were installed.
The solar system installed has a total capacity of 560 kWp, along with battery storage of 1 576 kWh. The energy supply mix also includes 750 kW of inverter capacity.
As a consequence of the solar installation, the buildings can now mitigate up to prolonged Stage 5 loadshedding. Prior to this, the company spent more than R100,000 per month on diesel to mitigate Stage 6 loadshedding at its head office.
The project, which is the culmination of years of planning, continues WBHO’s longstanding commitment to energy efficiency. It was preceded in 2016 by an energy audit, replacing all electrical equipment in the buildings with energyefficient alternatives. In 2022, the company’s large plant and services yard in Chloorkop, Midrand, began to shift its energy mix towards greater reliance on large-scale photovoltaic arrays by installing a 336 kW system there as well.
Solar power has also been a priority in some of WBHO’s Corporate Social Investment projects. In 2021, for example, the company supplied Maserunyane High School in Mapela, Limpopo with the energy delivered by a solar system of 19,2 kWp, 15 kW inverter and 19,4 kWh battery storage capacity installed on their premises.
WBHO’s “Going Green” project has also provided an opportunity to upskill younger employees at the company. And the experience and expertise gained in the modelling and construction of energy infrastructure are now being used on other much larger projects.
Comments Russell Adams, Director at the Projects Division of WBHO: “Our teams now use these cutting-edge learnings in bids for other clients. We can translate this relatively small-scale endeavour into big projects.”
WBHO is currently constructing solar projects totalling 325 MW.
Work is progressing well on the Wolf Wind Farm in South Africa’s Eastern Cape province, with Concor carrying out the civils balance of plant – including an innovative design for a steeply inclined concrete road to the site.
The contract, which is being tackled in a consortium with Murray & Roberts company OptiPower for developer Red Rocket, will see Concor building 17 foundation bases for wind turbine generators on a ridge in the Klein Winterhoek mountain range.
Concor contracts manager and lead project manager for the consortium, Stephan Nel, explains that the bases are for two sizes of turbine: there will be five 6,2 MW Vestas V162 turbines – the largest in South Africa – and twelve 4,5 MW V163 models.
“The foundation bases for V162 turbines measure 22,5 m in diameter, while the V163 foundations are 21,2 m,” says Nel. “The larger bases will consume over 650 m3 of concrete each, with the slightly smaller bases taking almost 600 m3.”
Concor is conducting over 180 000 m3 of bulk earthworks for the base excavations and roadways on site, which includes 15 km of access road to reach the 17 wind turbines. A total of 100 000 m3 of rock will be blasted during the construction of the project. After cleaning, a concrete lining is applied and specially designed anchor cages of steel reinforcing bar – weighing either 64 t or 70 t, dependent on the base size – are installed.
Construction of the first half of the concrete access road up the 18% incline towards the top of the mountain to ensure safe access for the turbine components
Concrete from the batch plant at the foot of the ridge will – like all other wind turbine components and related equipment – have to traverse a steep 18% incline gradient to reach the top of the ridge where the turbines will be located. He highlights that this challenge required an innovative solution that could be rapidly executed.
“In collaboration with the client, consultants and specialist service providers, we designed a concrete roadway that could be constructed using the slipform method,” he says. “The 1 100 m roadway, measuring 7 m wide, was completed in January this year, paving the way for the on-schedule execution of the project.”
Among the challenges in the road construction was designing a concrete mix with a 35 slump – to prevent the poured concrete from moving on the slope – that would still be workable for the required window period. Nel notes that high daytime temperatures of 36 degrees Celsius and above aggravated this issue further.
The road was continuously poured at an advance rate of about 200 m a day, consuming some 1 600 m3 of concrete reinforced with anchor beams and intermittent steel bars.
“After considerable planning, investigation and trialling, a solution was developed to allow the slipform paver and the cement trucks to operate on the steep incline, and to lay down the concrete road as planned,” Nel concludes.
Construction and installation of the earth mat on the IPP substation for the Wolf Wind Farm project
Ultra
Ultra
Ring