PRESSURE MANAGEMENT
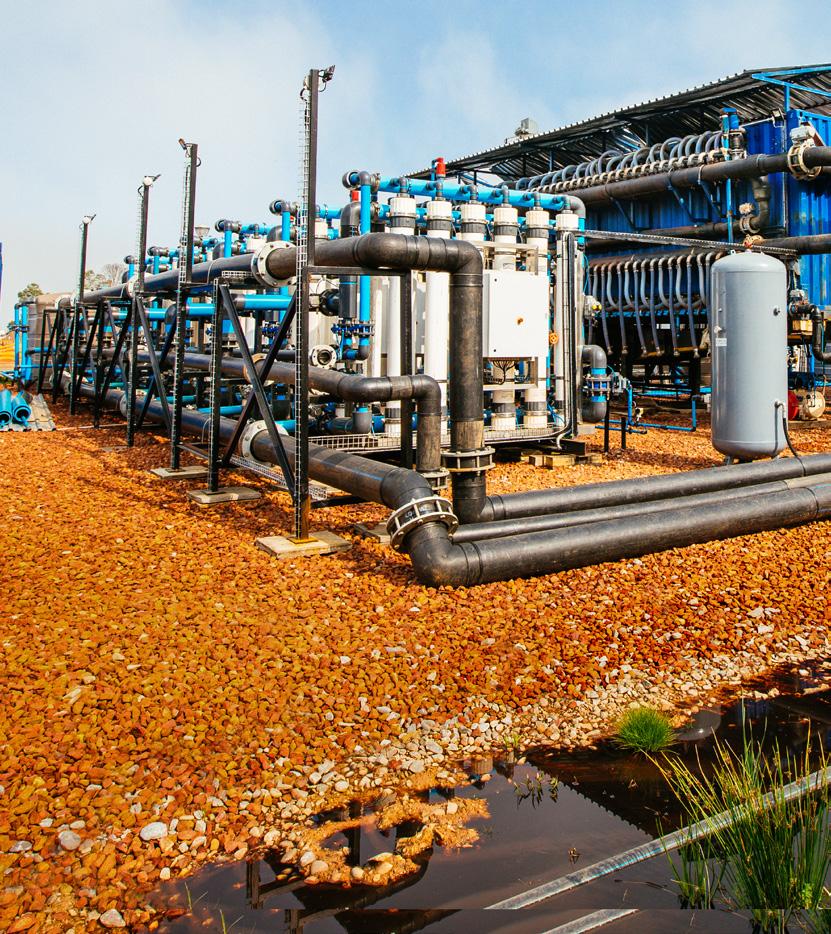

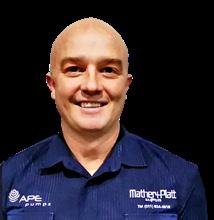
IN THE HOT SEAT
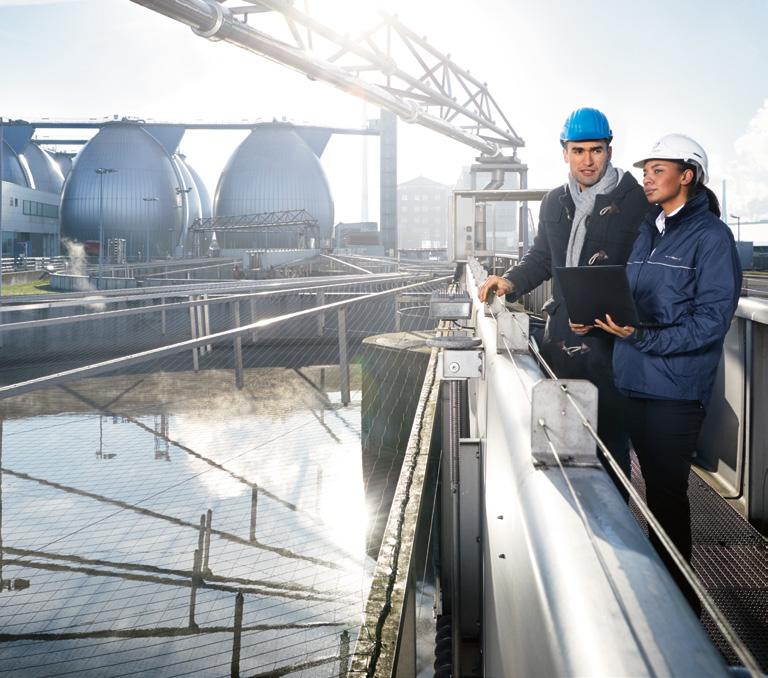
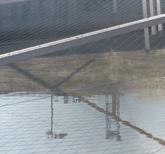

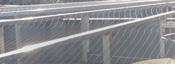
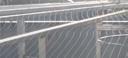



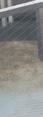
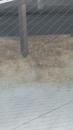
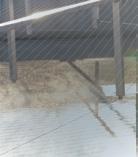















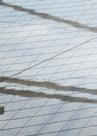



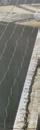



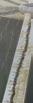



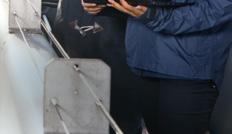
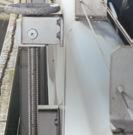

We understand the challenge of finding the right balance between plant e�ciency and compliance with industry standards and legal requirements.
We understand the challenge of finding the right balance between plant e�ciency and compliance with industry standards and legal requirements.
You meet your e�ciency goals and reduce costs without compromising on water quality.
Improve your processes with our comprehensive portfolio of measuring instruments:
Micropilot FMR20: The level radar fits even in limited spaces and reduces costs by easy Bluetooth® wireless operations.
Promag L 400: The versatile, weight-optimized electromagnetic flowmeter fits perfectly all standard applications.
Memograph M RSG45: The advanced data manager takes compliant, safe and secure operations control to a higher level.
Do you want to learn more? www.za.endress.com/water-wastewater
Water scarcity is a growing global challenge, exacerbated by climate change and increasing urbanisation. Municipalities, tasked with ensuring reliable potable water access for their citizens, are increasingly exploring innovative options to augment traditional water sources and fill process treatment gaps. Partnering with the private sector is becoming a practical and economic means for achieving this objective. P6
Fluid transfer, whether it’s for bulk water and sewage, oil and gas, or industrial cooling, is interdependent on the pumps that drive this process. IMIESA talks to John Montgomery, General Manager at APE Pumps and Mather+Platt (the Group), about their strategy and in-house solutions. P8
Boreholes and the Gauteng water crisis. “I'd
EDITOR Alastair Currie
Email: alastair@infraprojects.co.za
DESIGNER Beren Bauermeister
CONTRIBUTORS Alexander Tikhonov, Burgert Gildenhuys, Danielle van der Vaart, Geoff Tooley, Gerardt Viljoen, Kiera Bracher, Mike Smart, Peter Telle
DISTRIBUTION MANAGER Nomsa Masina
DISTRIBUTION COORDINATOR Asha Pursotham
SUBSCRIPTIONS
Email: distribution@infraprojects.co.za
ADVERTISING SALES
KEY ACCOUNT MANAGER Joanne Lawrie
Tel: +27 (0)82 346 5338
Email: joanne@infraprojects.co.za
The key takeaway from South Africa’s 2025 Budget Speech, delivered by Finance Minister Enoch Godongwana on 12th March, is the need for a balanced fiscal strategy within a currently constrained macroeconomic environment.
PUBLISHER
IMESA (Pty) Ltd
P O Box 2190, Westville, 3630
Tel: +27 (0)31 266 3263
Email: info@infraprojects.co.za
ANNUAL SUBSCRIPTION: R805.00 (INCL VAT) ISSN 0257 1978 IMIESA, Inst.MUNIC. ENG. S. AFR.
© Copyright 2025. All rights reserved.
IMESA CONTACTS
HEAD OFFICE:
Manager: Ingrid Botton
P.O. Box 2190, Westville, 3630
Tel: +27 (0)31 266 3263
Email: admin@imesa.org.za
Website: www.imesa.org.za
BORDER
Secretary: Celeste Vosloo
Tel: +27 (0)43 705 2433
Email: celestev@buffalocity.gov.za
EASTERN CAPE
Secretary: Susan Canestra
Tel: +27 (0)41 585 4142 ext. 7
Email: imesaec@imesa.org.za
KWAZULU-NATAL
Secretary: Narisha Sogan
Tel: +27 (0)31 266 3263
Email: imesakzn@imesa.org.za
NORTHERN PROVINCES
Secretary: Zurika Louw
Tel: +27 (0)82 322 5208
Email: np@imesa.org.za
SOUTHERN CAPE KAROO
Secretary: Henrietta Oliver
Tel: +27 (0)79 390 7536
Email: imesasck@imesa.org.za
WESTERN CAPE
Secretary: Michelle Ackerman
Tel: +27 (0)21 444 7112
Email: imesawc@imesa.org.za
FREE STATE & NORTHERN CAPE
Secretary: Wilma Van Der Walt
Tel: +27 (0)83 457 4362
Email: imesafsnc@imesa.org.za
All material herein IMIESA is copyright protected and may not be reproduced without the prior written permission of the publisher. The views of the authors do not necessarily reflect those of the Institute of Municipal Engineering of Southern Africa or the publishers.
Within the mix, the proposed incremental VAT increases presented (0,5% for 2025/2026 and 2026/2027, respectively) are being opposed by political parties from within and outside the Government of National Unity (GNU). What happens next will be subject to parliamentary debate and voting, with opposing financial experts arguing that a VAT increase would be counterproductive, harming consumers and the economy. The better alternative they say is to increase the tax base organically by stimulating the expansion of core industries like agriculture, manufacturing, renewable energy, and ICT, which makes business sense.
In the interim, other measures put forward include the greater capacitation of the South African Revenue Service (SARS) in collecting billions outstanding from trading entities that are not currently registered.
Either way, taxation is a reality – but it must be equitable and workable – in terms of boosting growth, combatting high unemployment, and maintaining essential social services.
To enable this, the Budget tabled places a key emphasis on accelerated infrastructure investment. Structural reforms that impede investment and service delivery are also a top priority, as is a focus on stemming fruitless and wasteful expenditure. We need to see far greater efficiencies, and a measurable return on every tax rand.
In this respect, the Auditor-General South Africa (AGSA) continues to do a sterling job in transitioning government entities towards clean audit outcomes. However, more work needs to be done to effect universal financial excellence. This is especially vital at local government level, where the mainstream economy works.
However, while the AGSA’s scope is to verify the numbers, flag non-compliance and provide recommendations, it’s clearly not there to performance manage. Within the local government arena, that’s the responsibility of the officials and respective political leaders. They need to ensure that their municipality runs as a successful trading concern, with the right skills in place. That in turn is interdependent
on efficient revenue collection for services provided, like electricity and water.
Whether it’s a defaulting consumer, or inefficient billing, it all adds up to spiralling municipal debt if not tackled correctly. When this gets to extreme levels, it has a direct impact on the municipality’s ability to run day-to-day operations, increasing its reliance on national government bailouts.
It's a proven fact that successful municipalities serve as highly effective catalysts for socioeconomic growth. Globally, London and New York compete closely for the title of best city to live, work and invest in, with the City of Cape Town ranked as a leading benchmark for South Africa and Africa. The City of Cape Town was also the only South African metropolitan municipality to achieve a clean (unqualified audit) from the AGSA for the 2022/2023 financial year. During that period, the city expended billions on infrastructure renewal. This remains a core focus in terms of its approximately R120 billion capital expenditure programme being implemented over a ten-year period from 2024. It’s serving as a magnet for major private sector investment in enterprises and property.
Across the board, other metros, district, and local municipalities are following suit; positively responding to address their infrastructure gaps and build local capacity. This will be bolstered by the GNU’s commitment to more than R1 trillion in public infrastructure spend over the next three years.
Key sectors include transport and logistics (R402 billion); energy infrastructure (R219.2 billion); water and sanitation (R156.3 billion); and transport, where SANRAL plans to spend R100 billion over the medium term. Provincial roads departments are also due to reseal over 16 000 lane kilometres.
Directly and indirectly, these and other infrastructure investments create the essential framework for a prosperous and inclusive society. That’s why it’s so important that budgets approved are realistic and achievable.
VEGA measurement technology provides precise measurement data as the basis for automatic control of the various process stages. All sensors are state of the art, certified and easy to install and commission.
The VEGA sensors in the plant: www.vega.com/watertour
Every year since the first Conference of the Parties (COP) was held in 1995, member countries (including South Africa) meet to debate and measure progress on the United Nations (UN) Framework Convention on Climate Change (UNFCCC). This multilateral treaty was adopted in 1992 and came into force in 1994.
It’s a major work in progress. The ultimate quest is to achieve Net Zero greenhouse gas emissions by 2050, with leading nations committed to assisting developing countries to close the gap. At the conclusion of COP 29, held during November 2024 in Baku, Azerbaijan, the figure pledged was a contribution of “at least US$300 billion annually” by 2035. However, this is far short of the US$1.3 trillion annually requested by developing countries to assist them in combatting climate threats. The latter includes a transition away from fossil fuels.
Positive change is happening, but at a slow place because every country first needs to focus on its homegrown socioeconomic priorities, while striving to meet the UN Sustainable Development Goals (SDGs) within tough post Covid-19 trading conditions. Essentially, it’s a case of people before planet, but everyone knows the former cannot survive without a functioning ecosystem. Therefore, any financial contribution that leading nations can make should be welcomed – including opportunities for carbon credit transactions.
Beyond that, it’s every global citizen’s responsibility to effect change at grassroots level. It’s also vital that all stakeholders understand the full ramifications of climate change.
This is why initiatives like UN Water’s World Water Day event on 22nd March each year are so important. For 2025, the theme is “Glacier Preservation”. This may seem irrelevant for South Africa and Africa, but of course it isn’t because all geographic systems are interconnected. For example, although some 90% of all glaciers exist in Antarctica, Africa does have two places on the map in
Kenya and Tanzania. Collectively, they’re all starting to melt at an accelerated pace.
Here is a chilling statistic. According to the World Glacier Monitoring Service, some 270 billion tonnes of ice is being lost annually due to global warming. In a single year, that’s the equivalent of 30 years of lost water consumption for the world’s population.
Melting ice floes are also compounding climate change issues – particularly in terms of extreme weather events, and rising sea levels.
As you can see from the 29-year plus COP timeline, none of these issues can be fixed overnight. But we all need to start somewhere. That begins with combatting pollution and preserving the immediate environment within our control. A case in point are wetlands, which are currently disappearing at an alarming rate.
While these “green lungs” only cover some 6% of the Earth’s land surface, they are home to an estimated 40% of the world’s plant and animal species. Wetlands also serve a vital role in terms of stormwater attenuation, and function as a natural wastewater biofilter. During prolonged droughts, they also serve as a short to medium term lifeline for surrounding habitats.
Locally, and according to available statistics, South Africa currently has around 300 000 wetlands left. Among the most famous is the iSimangaliso Wetland Park in KwaZulu-Natal, which covers an area of approximately 3 280 km 2, with an average depth
Tooley, Pr Eng Hon FIMESA
IMESA President: 2024-2026
less than 1 m. However, most urban areas also have wetlands, which are generally less than 30 cm deep and might even go unnoticed or ignored due to surrounding developments like housing and roads. That’s why awareness is so important, backed by legislative and municipal bylaw enforcement.
Moving forward together
Every action has a reaction. Therefore, we must ensure that everyone is on the same page. As municipal engineers, we can incorporate energy efficient systems, promote water reuse and design structures that nurture rather than damage the environment through proactive blue, green, and grey infrastructure interventions.
But these “hard” interventions cannot function in insolation. Community engagement and commitment are vital for effective resource conservation. That encompasses sustainable land-use practices that include responsible agriculture, not building in wetland and floodplain areas, minimising deforestation practices, and saying no to pollution –especially in our rivers.
Climate change threats have been decades in the making and are growing more challenging with ongoing population expansion. It’s hard to imagine, but in the early 1900s there were less than 2 billion people on the planet, compared to more than 8,2 billion today, the bulk of whom live in urban centres. The best response we have now is to do everything within our power to protect the finite resources that sustain lives and livelihoods. Working collectively, we can reach Net Zero and successfully coexist by reengineering current practices for a sustainable future.
Water scarcity is a growing global challenge, exacerbated by climate change and increasing urbanisation. Municipalities, tasked with ensuring reliable potable water access for their citizens, are increasingly exploring innovative options to augment traditional water sources and fill process treatment gaps. Partnering with the private sector is becoming a practical and economic means for achieving this objective.
Water and wastewater treatment companies like NuWater, working with a municipality, have the expertise and resources to provide reliable and sustainable solutions,” says Billy James, Executive at NuWater, a Cape Town based original equipment manufacturer and turnkey purification specialist.
A case in point is a successful partnership between NuWater and a Garden Route local municipality in South Africa’s
Southern Cape region, involving a 6 megalitres per day (Mℓ/D) water augmentation project. This is a prime example of how such collaboration can effectively address the challenges of water security.
This municipality has faced increasing pressure on its water resources due to population growth and changing weather patterns. Recognising the need for a sustainable and reliable water supply, the municipality embarked on building extra permanent capacity at its existing water treatment works. To achieve this required an interim solution to ensure continuation of supply during the construction period to mitigate water shortages.
“The objective of installing the NuWater plant was to treat and purify non-potable water sources, alleviating the municipality's overall reliance on already strained surface and groundwater resources,” James explains.
The partnership between NuWater and this municipality was built on a foundation of shared goals and mutual understanding. Both parties recognised the urgency of the situation. The municipality provided the necessary land and facilitated the rapid installation of the supporting infrastructure, while NuWater brought its technical expertise and experience in designing, constructing, and operating its purpose designed containerised plant. This division of responsibilities allowed each partner to focus on their strengths, ensuring the project's efficient execution.
A key element of the project's success was how rapidly NuWater could deploy, install, and commission its advanced water treatment plant, achieving this objective in less than four weeks.
NuWater assessed the proposed site to determine the most viable placement for the 6 Mℓ/D plant. The assessment also considered the cost-effectiveness and overall sustainability of where the plant would operate. By carefully evaluating these factors, the partnership was able to select the optimal location for the treatment technology, minimising the project's footprint and maximising its economic benefits.
The chosen treatment technology employed by NuWater for this municipality was a multibarrier approach, combining various processes to ensure the production of high-quality potable water. This approach included pre-treatment and filtration with disinfection.
These specific technologies were tailored to the characteristics of the source water – as verified by NuWater’s in-house laboratory –ensuring the removal of contaminants and the production of water that meets or exceeds all relevant quality standards. This meticulous approach to water treatment guaranteed the safety and reliability of the augmented water supply.
“For this project, in consultation with the client, we specified an ultrafiltration (UF) system for the plant. Another option would have been media filtration, which although highly effective, is an older technology, and less energy efficient,” James explains.
Installed on site for more than two years during the treatment works upgrade programme, NuWater’s 6 M ℓ /D plant has significantly contributed to the municipality's resilience to drought and other waterrelated challenges. This has benefitted residents by ensuring a reliable water supply and supported local businesses and economic development.
With its mission completed, this plant will subsequently
be redeployed to perform a similar role at a municipality in Mpumalanga, where NuWater already has various modular plants installed to supplement existing water treatment process capacity.
As James points out, the success of its partnership approach serves as a model for other municipalities facing similar water challenges. However, to achieve optimum results, there are key factors to consider, namely:
• Early engagement and collaboration: open communication and collaboration between the municipality and the private sector partner are crucial from the initial stages of project development. This ensures that the project aligns with the municipality's needs and priorities and that all stakeholders are informed and engaged.
• Clear contractual agreements: a welldefined contract that clearly outlines the roles and responsibilities of each partner is essential for the success of the project. The contract should address project timelines, performance metrics, and risk sharing.
• Community engagement: engaging with the local community is crucial to ensure public support for the project. This can be achieved through public meetings, information campaigns and other outreach activities.
A 55 M ℓ /D reverse osmosis desalination facility designed and developed using NuWater’s proprietary technology for a client
• Sustainability: the project should be designed and operated with sustainability in mind. This includes considering the environmental impacts of the project, as well as the financial sustainability of the operation. Being modular, NuWater’s plants are scalable, enabling ongoing extensions, where required, to meet the need for
increasing process demands. Where water body characteristics change over time, NuWater also has a range of technologies that can be added. So, the solutions offered are highly flexible, adaptable, and cost-efficient.
“Ultimately, it’s about tailoring fit-for-purpose solutions, where we have extensive experience locally and internationally in serving both public and private sector clients. Our plant capacities typically range from 50 000 litres per day up to 20 Mℓ/D. However, we have designed plants up to 60 Mℓ/D,” James continues.
In addition to local plant sales and rentals, NuWater is also progressively expanding into international markets. Standout examples include a 55 Mℓ/D reverse osmosis desalination facility designed and developed using NuWater’s proprietary technology for a client in Singapore, and a 15 M ℓ/D leachate treatment plant supplied to a mining client in Ghana. NuWater also recently shipped its first plant to Mexico for an industrial application.
“Water scarcity continues to be a pressing issue locally and globally, increasing the need to safeguard access to clean and reliable water for all. That requires the right technologies and partnerships,” adds James.
“In this respect, the Garden Route project exemplifies the power of collaborative problemsolving, combining the strengths of the public and private sector to address critical infrastructure challenges with sustainable solutions,” James concludes.
www.nuwater.com
Fluid transfer, whether it’s for bulk water and sewage, oil and gas, or industrial cooling, is interdependent on the pumps that drive this process. IMIESA talks to John Montgomery, General Manager at APE Pumps and Mather+Platt (the Group), about their strategy and in-house solutions.
What are the Group’s key objectives for 2025?
For the past 73 years, APE Pumps and Mather+Platt have built a class leading reputation for innovation and excellence in the design, fabrication and installation of specialised pump systems that meet all industry requirements. Our two mainstay markets are water and energy – predominately for largescale bulk handling pumps – where in the past seven decades we’ve provided solutions to most of South Africa’s coal-fired power stations, leading Water Boards, major industrial clients, as well as a range of municipal Water Service Authorities.
We now plan to ramp up our pump penetration into existing and new markets that include the endsuction segment for applications such as HVAC, and systems for the municipal process engineering sector, namely water and wastewater. Another potential growth area is desalination.
Allied to this is the planned expansion of our contracting division, which presently has an 8 ME grading in terms of the Construction Industry Development Board scale. We intend to transition to a 9 ME over time so we can take on projects of unlimited value.
This year, we will also continue to extend our manufacturing lines at our Wadeville plant to support increasing local and cross-border demand. Within South Africa, we’re particularly excited about government’s multi-billion rand commitment to expanded water and wastewater infrastructure, as well as the visionary role being played by leading metros that include the City of Cape Town.
The latter’s approximately R120 billion capital expenditure programme, being implemented over
John Montgomery, General Manager, APE Pumps and Mather+Platt
a ten-year period from 2024, will be primarily focused on infrastructure development. A core component are water and sanitation upgrades amounting to some R82,28 billion.
We are anticipating that this renewed infrastructure drive will be replicated across other metros, where there’s a pressing demand for new water and wastewater pipelines, as well as associated pump stations. Upgrades, as well as the construction of new treatment plants is also a top priority.
In response, we’ve expanded our in-house group capabilities through the ongoing recruitment and training of engineering personnel, backed by cutting-edge technologies. Except for foundry pump castings, everything else is handled in-house.
From a quality control perspective, our smaller pump test bay – now installed – is undergoing the certification process in terms of SANAS accreditation. In the meantime, we’re constructing a test bay for our large vertical pumps, which is expected to be completed by our financial yearend in March 2026.
As part of WPIL Limited, how will their recent acquisitions shape the Group’s turnkey solutions?
Headquartered in India, WPIL Limited is a growing force internationally, originally focusing on OEM pump products, but now also expanding into the Engineering, Procurement and Construction (EPC) market.
Recent examples include the acquisition of Eigenbau in South Africa. A leading civil and mechanical engineering contractor, Eigenbau has a well-established track record for the construction of water and wastewater infrastructure, as well as hydropower stations. This makes it a logical fit in terms of potential joint venture opportunities in conjunction with APE Pumps and Mather+Platt.
WPIL also continues to acquire leading pump OEMs globally. A recent development is the acquisition of a 100% shareholding in MISA, based in Italy. With a rich heritage dating back to 1901, MISA specialises in large pump station projects, as well as the fabrication and supply of pumps and hydro turbines, working across Europe, the Middle East and North Africa.
Locally, APE Pumps and Mather+Platt are actively researching pump OEM acquisition opportunities to complement our extensive range and enter new segments.
Is the take-up for Service Level Agreements (SLAs) on the increase?
Definitely, and they’re not unique to South Africa. SLAs have quantifiable benefits as we are solely responsible for the operations and maintenance on our installed OEM systems. These agreements are typically concluded for a five-year period, with the option to renew. Depending on the scale, containerised offices and workshop facilities are established on the client site, together with all the necessary specialised tooling.
SLAs pass on major efficiency gains for the client, while capping OPEX costs in terms of an agreed fee scale. Being a transparent process, SLAs further help to reduce wasteful expenditure and potential tender award irregularities.
Popular in both the public and private sector, SLAs also alleviate client skills gaps and eliminate the potential for a costly “run to destruction” approach where maintenance is not adequately handled in-house. In terms of our SLAs, we constantly collect and analyse pump performance metrics – both through remote monitoring and on-site instrumentation data collection. Working with the client’s engineering team, we can then
APE Pumps and Mather+Platt’s engineers make extensive use of 3D virtual models to interrogate and perfect their installation designs
collectively optimise process systems, respond to output changes, and provide recommendations on the best timing for a component replacement, pump refurbishment or replacement.
Refurbishment is the preferred route for clients and here we can repair or rebuild any pump manufactured by the Group since its formation in 1952. However, warranties are only valid where APE Pumps and Mather+Platt do the installation.
Ensuring best-in-class performance can significantly contribute towards meeting compliance with international standards, as well as local audits in terms of the Department of Water and Sanitation’s No Drop, Blue and Green Drop criteria.
In your opinion, will AI and Machine Learning play a greater role in future?
There’s no doubt that Artificial Intelligence (AI), Machine Learning and related IoT technologies will play an increasingly important role. It’s already inherent in most of the CAD packages our design engineers are using within the realm of 3D digital twinning.
There are exciting opportunities to harness AI for real-time monitoring and control, as well as
Originally installed in the 1980s, this 650 Mℓ/D Mather+Platt pump at Rand Water’s Lethabo raw water abstraction pump station recently underwent a major overhaul
the efficient interrogation of big data to improve design and maintenance planning workflows. It’s a new and rapidly evolving frontier that we are keenly exploring to enhance our service offering.
What are some of your recent key projects?
Last year, we completed the refurbishment of the first of four 650 Mℓ/D Mather+Platt units at Rand Water’s Lethabo raw water abstraction pump station – all originally installed in the 1980s. They are probably the largest bulk water pumps ever installed in South Africa.
Commissioned and again operational in Q1 2025, our test curve results confirm that this pump is performing better than when it was originally new. This is thanks to advancements in component technology. Working within the client’s schedule, we will now continue with the progressive refurbishment of the remaining three.
Meanwhile, in the Western Cape, the Group’s vertical dewatering pump replacement project at the Palmiet Pumped Storage Scheme has been successfully completed. APE Pumps and Mather+Platt’s scope entailed the installation and commissioning of four new pumps – replacing an older competitor OEM pump set-up that had reached its end of life. Two of the Group’s new pumps serve a standby role.
Other recent orders include four new pumps installed at Foskor’s production facility in Richards Bay. The turnkey scope included the installation of the valves, pipework and baseplates.
Another contract was recently completed for the Namibia Water Corporation (NamWater). This entailed the refurbishment of a strategic bulk water river abstraction pump (model: 3636 ALEY) within the Caprivi Strip designed for a capacity of 10 800 m3 per hour at 26,8 m head, with the pump rotating at around 595 rpm. Installed by the Group in 1996, this pump has consistently delivered but now needed a refurbishment. It was shipped to APE Pumps and Mather+Platt’s factory. From there it was rebuilt and recommissioned on-site within three months.
And in closing?
Without pumps, no fluid transfer is possible and optimising their performance is an exact engineering process. At APE Pumps and Mather+Platt we have the proven expertise and commitment to ensure that every system we design and install is fit-for-purpose. That’s based on an in-depth cost-benefit analysis.
www.apepumps.co.za
Industry representation and collaboration are vital for a sustainable construction industry. IMIESA speaks to Andile Zondi, Acting CEO at the South African Forum of Civil Engineering Contractors (SAFCEC), a voluntary employer body organisation that celebrates its 86th anniversary in 2025, about their repurposed vision.
The South African civil engineering sector has faced tough trading conditions pre and post Covid-19. How has this affected SAFCEC?
As an industry, adaptation is key and SAFCEC is an integral part of this process in assisting contracting members to weather tough business cycles – given a sharp decline in public infrastructure spending for key works that include road and rail, port services, and human settlements. That has also meant that SAFCEC as an organisation has also had to reposition itself to remain relevant and add value.
As an indication of the cost pressures in the period between 2020 and 2024, our membership fell by around 54%. There are several reasons for this. Chief among them is that our membership revenues were significantly impacted by the demise of some of the longstanding JSE-listed and leading privately owned construction groups. With few exceptions, they were predominately graded 9 – the highest rating in terms of the Construction Industry Development Board (CIDB) rankings. These top tier contractors historically contributed a major portion of our organisational funding, alongside a relatively smaller contribution from our growing SMME contracting component, including specialist subcontractors.
The upside is that we are now experiencing a positive upturn – with universal civil industry support – through a more competitive fee structure. In parallel are ongoing internal organisational changes to ensure that all our past services, such as SHERQ, contractual affairs consultation, training, and engagement with key entities that include the Bargaining Council for the Civil Engineering Industry (in terms of the Labour Relations Act 66 of 1995) remain in place and are enhanced.
What is the current state of the civil engineering industry?
According to economic advisory specialists, Industry Insight – who compile our quarterly State
of the Industry reports – statistics indicate that our sector in terms of Q4 2024 data has shrunk to half its size in the past decade. Investment in infrastructure is also at its lowest level in 14 years.
Since civil engineering is the mainstay for public works infrastructure, it’s clear that government entities – whether at SOE, national or local government level – need to urgently revisit the proactive implementation of available budget spend to meet set development targets that both sustain the construction sector and unlock socioeconomic development.
Clearly, it’s vital that we have a healthy and vibrant construction industry across the CIDB spectrum – from Grade 1 to 9. That’s especially important from a mentorship standpoint, since large contractors (Grades 8 and 9) play a crucial role in nurturing upcoming SMME contractors.
As the Acting CEO, what are your key mandates in terms of the turnaround strategy?
I’ve invested around 20 years in the civils sector and have a keen understanding of the challenges
contractors are facing, plus the instrumental role that SAFCEC has historically played.
Covid-19 was a major reset for most industries, and the South African, regional and global economy has been slow to recover. The knockon effect has been a sharp decline in bottom line performance for many companies, and the need to cut costs. In response, as Acting CEO one of my key tasks is also to ensure that our organisation is right sized and cost-efficient. While change is never easy, our current challenges represent an opportunity for SAFCEC to revisit what has worked well in the past, and to realign the organisation to address what our members’ needs are right now.
To do this, we need to leverage the benefits of information and communications technology (ICT) so that SAFCEC can be more efficient and responsive in terms of our interactions and the services we provide. Our members have stressed that near real-time access to information and advice is a top priority in providing them with a competitive edge, and we’re aligning our systems and personnel accordingly. Harnessing ICT will in turn aid in streamlining our operating costs.
Andile Zondi, Acting CEO at the South African Forum of Civil Engineering Contractors (SAFCEC)
Membership fees currently represent around 80% of our income. Therefore, going forward we recognise the need for business diversification to better weather the cyclical nature of the construction industry. Examples include expanding our training division, as well as lobbying for funding and sponsorships for contractor development. One possibility is support from the Construction Education & Training Authority (CETA), which we’re in the process of proactively engaging.
First and foremost, we must ensure SAFCEC’s financial stability. That requires embarking on a concerted membership drive to regain older members and add new ones. We’re aiming for a membership base increase of 50 to 60%, which will be bolstered by diversification into allied spaces like the mining sector.
Does SAFCEC still have the resources in place to provide a full suite of services to members?
Absolutely, although our personnel complement will be leaner than it was in the past. The upside is that we’ll be more targeted and responsive in providing facilitation roles.
SAFCEC’s past and current model is based on outcomes generated through technical committees composed of industry experts equipped to address complex issues, like legal and contractual affairs. Many of these committees include recently retired professionals who are committed to giving back to the industry by sharing their invaluable knowledge and experience. For our growing SMME contractor base tapping into this knowledge pool is a core benefit of being a SAFCEC member, along with the dedicated training workshops that we provide nationally.
Has meaningful transformation in the SA construction industry been achieved?
The progress is there, but we definitely need to see more traction as an industry. In this respect, SAFCEC plays an essential facilitation role in interconnecting the main contracting and the sub-contracting segments, as well as in meeting the CIDB’s transformation mandate. Currently a major portion of those registered and working in our sector are in the 1CE to 3CE band and need to advance further up the grades to play a more impactful role within the South African construction industry.
Main contractors are predominately reliant on skilled sub-contractors, so if there’s a lack of skills and capacity in terms of the latter it’s obviously an impediment both to industry growth and meaningful BBBEE development in fulfilling government’s 30% tender allocation for emerging SMMEs.
So, at SAFCEC we are committed to building two-way partnerships. A case in point is our encouragement for SMME companies to join
SAFCEC committees and grow their business network within the context of enabling legislation. In terms of our own networking drive, SAFCEC recently joined Construction Alliance South Africa (CASA), which collectively represents the leading built environment associations. Combined they are a powerful lobbying group in addressing public sector investment bottlenecks that are causing an insufficient volume of work that impedes SMME development. Another key concern is delayed payments for work completed on projects, which when it occurs has a negative ripple effect from the main contractor through to its subcontractors that can and does cause company closures. No one in industry can afford to work in silos: we need to be unified and focused.
One of our most successful empowerment training programmes for emerging contractors is our Diamond Academy initiative. This highlevel learning programme is designed to equip business managers and owners of developing companies with the essential management skills (such as tendering, pricing, contract documentation, claims, programme management and SHEQ compliance) to become a successful contractor.
We’re proud to state that a number of our past Diamond Academy graduates have today grown from 1 or 2CE CIDB contractors – when they attended the programme – to 5 or 6CE contractors today.
So, it’s about building the right foundation. From there, the plan is for SAFCEC to work at all levels within our membership base to help ensure that all South African civil engineering contractors are world class and futureproof.
Despite ongoing challenges in the construction sector, South Africa’s economic outlook is showing encouraging signs of improvement. This was one of the key messages at AfriSam’s Annual Budget Breakdown event held in Johannesburg in February 2025, where Dr Azar Jammine, Econometrix Director and Chief Economist, highlighted a renewed sense of business confidence.
As a leading supplier of construction materials, AfriSam has long been at the forefront of industry developments, supporting infrastructure growth and economic progress. Speaking at the event, Dr Jammine noted that indicators such as the Bureau for Economic Research’s Business Confidence Index and Absa’s Purchasing Managers’ Index reflected a marked improvement in sentiment over the past six months.
“The latest data shows increased optimism with businesses expecting better conditions ahead,” he said. “Key factors include reduced load shedding and a government more open to private sector collaboration.”
Jammine attributed part of this shift to Eskom’s recent leadership changes, which have prioritised skills and expertise, as well as the formation of the Government of National Unity (GNU), which is fostering greater oversight and reducing corruption. He also pointed to stronger cooperation between government and business as an essential step in revitalising economic growth.
However, significant challenges remain, particularly in the construction sector. Structural constraints, such as inefficiencies in logistics and the continued decline in investment, continue to weigh on economic growth. Gross fixed capital formation – a key driver of demand for cement and other construction materials – remains well below international benchmarks. This has had a direct impact on infrastructure projects and commercial developments.
Despite these concerns, AfriSam remains committed to supporting the industry. AfriSam Executive Chairman Eric Diack said that AfriSam has strategically positioned itself to weather industry fluctuations while safeguarding its expertise and operational capacity.
“We understand that maintaining a strong foundation of skills, experience and technical proficiency is critical to ensuring long term sustainability,” he said. “By continuing to invest in our people, processes and infrastructure, AfriSam has remained resilient, ready to support the industry’s growth as market conditions improve.”
This steadfast approach has allowed AfriSam to reinforce its role as a trusted partner in the construction sector, ensuring customers continue to receive high quality materials and reliable service. Diack added that AfriSam’s commitment extends beyond its own operational stability, as the company also plays a proactive role in driving industrywide progress.
“We recognise the importance of collaboration in revitalising the sector and we continue to engage with stakeholders across the value chain to find solutions that benefit everyone,” he said.
Political and economic analyst and strategist, Dr Frans Cronje also addressed the event, reinforcing the theme of resilience and collaboration. He highlighted strong public support for pragmatic governance, noting that the GNU aligns with the economic aspirations of South Africans across demographics.
“The majority of South Africans want policies that foster stability, growth and job creation,” said Dr Cronje. “This reflects a positive longterm trajectory for the country.”
AfriSam’s Annual Budget Breakdown remains a key platform for industry insights, reinforcing the company’s role as a leader in South Africa’s construction sector. With renewed optimism in the economic environment and a commitment to sustainable growth, AfriSam continues to support the development of vital infrastructure, helping to shape the country’s future.
Gauteng, South Africa's economic heartland, is facing an escalating water crisis. Despite being one of the most urbanised regions in the country, it has failed to adequately plan for and manage the increasing demand for water and sanitation services. The situation did not emerge overnight; it resulted from decades of neglect, political inertia, and a systematic underestimation or a lack of understanding of the extent of urban growth. By Burgert Gildenhuys*
For at least 15 years, the signs of an impending crisis were evident, yet no meaningful corrective action was taken. Cities like Tshwane, Johannesburg, and Ekurhuleni have been operating on outdated growth and infrastructure capacity assumptions. Decision-makers repeatedly ignored data-driven warnings about the unsustainability of their approach. Today, Gauteng's residents are paying the price for this failure, facing intermittent supply, deteriorating infrastructure, and a rising threat to public health and economic stability. Within this context, we will focus on Tshwane for no other reason than the fact that our experience with these issues in the city goes back more than 20 years.
One of the most glaring issues underpinning the water crisis is the sheer scale of urban growth. Gauteng's cities have expanded far beyond initial projections. The City of Tshwane, for instance, has seen its population more than double from approximately 1.8 million in 1996 to over 4 million by 2022. The current growth rate estimates are more than 34 000 households annually. To put this into perspective, 120 out of the 213 municipalities in SA (56%) have fewer total households than Tshwane's annual growth. Municipal planning frameworks consistently failed to account for the true extent of this growth. Data from the Tshwane Infrastructure Investment Framework (2007) and the Strategic Asset Management Plan (2018) show that the Council's system systematically understated household demand, land use, and water consumption estimates. This misalignment between understanding population expansion and infrastructure delivery policies has created severe service backlogs, particularly in water and sanitation.
The inability to deliver has been aggravated by a complete disconnect between service delivery policies, land use management and the ability to understand the operating consequences of a capital investment-driven policy approach. South Africa has a blind preoccupation with capital expenditure.
Capital expenditure and unconstrained visions of a long-term utopia drive the measures of success in government – we must spend our budget or treasury will take back the money! The question is whether we are spending capital on the right projects, or more importantly, do we know the longterm operating consequences of capital projects? It is not annual capital budgets that leads to recurrent expenditure problems or our inability to meet our operating obligations but rather the cumulative impact of politically driven capital expenditure and service delivery approaches.
Beyond sheer numbers, the form and nature of urban growth also contribute to the crisis. Highdensity, low-income settlements have proliferated,
Burgert Gildenhuys, Director: BC Gildenhuys & Associates, and Founding Director: Spatial Data Services Africa NPC
often without proper service connections. Backyard dwellings, informal settlements, and rapid suburban expansion have significantly increased water demand without a corresponding increase in investment in bulk infrastructure.
Escalating non-revenue water concerns
One of the most critical issues exacerbating the crisis is the level of non-revenue water (NRW) –water that is lost due to leaks, theft, or unbilled consumption. In Tshwane alone, NRW accounts for over 32% of the total water supply, translating into massive losses daily. The extent of current unaccounted water covers the demand for at least the next 5 years. This implies that the water that the city will need is already in the system. Tshwane supplies an average of 1 013 Mℓ/day, with NRW amounting to 32.6% (330 Mℓ/d). The per capita use (total population) is approximately 326 ℓ/c/d, but based on the people with access to water, as reported in the Council's Annual Report, it is 458 ℓ/c/d. The design norm for higher-income households is 230 ℓ/c/d. It is not a sustainable situation.
In the last two decades, successive administrations prioritised increasing service coverage rather than ensuring long-term sustainability. While politically popular, this fixation on capital expenditure, the decline in institutional capacity and inappropriate policy regimes have led to an unmanageable system where consumption will eventually exceed supply. Waterborne sanitation, for example, was expanded without considering the principles behind basic service delivery, proper investment in wastewater treatment, increasing daily demand, and creating treatment backlogs. As far back as 2007, it was projected that Tshwane would, by 2016, need an additional 383 million litres of
water per day, nearly 50% of the yield of Phase 1 of the Lesotho Highlands Water Project. Despite these alarming figures, no strategic mitigation plans were implemented.
It is well documented that both municipal administrators and political leadership have been aware of these challenges for at least 15 years, yet no meaningful policy interventions have been implemented. Reports prepared in 2007 and 2018 warned about critical infrastructure capacity shortfalls, yet planning documents continue to use doubtful population estimates and service models.
This inaction is symptomatic of broader governance failures:
• Successive city administrations have paid lip service to long-term infrastructure planning in favour of short-term political gains.
• Despite the availability of comprehensive spatial and service demand data, municipalities, and Tshwane in particular, failed to integrate this into decision-making processes.
• Different municipal departments operate in silos, leading to contradictory policies and inefficiencies. The city still operates without an integrated data policy and has a built-in
bureaucratic resistance to sharing information between internal departments.
• Budget misallocation: large amounts of capital expenditure were directed toward service expansion at inappropriate levels rather than maintenance and renewal of critical infrastructure.
If the current trajectory continues, the water crisis will deepen in the coming years. Without intervention, one risks reaching a point where water rationing becomes permanent, undermining economic growth, public health, and urban resilience.
The Gauteng water crisis is not merely an infrastructural failure but a governance failure. The crisis was predicted, well-documented, and entirely avoidable. The key challenges – urban growth, infrastructure underinvestment, and NRW – were flagged years ago. Yet, systematic neglect of these issues linked to low economic growth has created structural impediments and an emergency with no easy solution. A fundamental shift in governance and planning is required:
• Data-driven decision-making: accurate, real-time data must guide investment and infrastructure planning.
• A reassessment of the level of service and service delivery policies.
• Reconsidering the municipality's free basic services or indigent policies, specifically the financial and water consumption implications.
• Prioritisation of maintenance and renewals: the NRW crisis must be tackled urgently to reduce water losses.
• Political accountability: leaders must be held responsible for failures in service delivery.
• Sustainable water governance: the province needs long-term investment strategies prioritising resilience over expansion.
If municipalities continue on their current path – ignoring facts, resisting expert advice, and prioritising political expediency over long-term sustainability – the water crisis will not just persist; it will become permanent.
For further information and engagement, please contact me at burgert@bcga.co.za, or via phone at +27 (0) 83 450 0077 and visit www.bcga.co.za.
*Pr. Pln, MIAM (London), ILGM, B(TRP), BAdmin (Municipal Administration)
and why we may soon not have the choice
On 15th February 2025, Gautrain services between Rosebank and Park Station were halted due to an illegal borehole that caused water and soil seepage into an underground tunnel. This article explores the unintended consequences of the growing water crisis in Gauteng and the interplay between public and private infrastructure across sectors.
By Danielle van der Vaart and Kiera Bracher
Recently, Gauteng residents have faced interrupted water provision due to intermittent supply, excessive use, and ageing infrastructure. This is the latest instalment in a series of water supply issues for the City of Johannesburg. In fact, the situation is so dire that Rand Water has warned of a total system collapse and has urged consumers in Tshwane, Johannesburg, and Ekurhuleni to reduce consumption as storage levels reportedly drop at an alarming rate.
According to a system status report released by Johannesburg Water, 28 out of 61 reservoirs and towers are either critically low or completely empty, and 350 areas have been affected by outages. In October 2024, Rand Water issued a statement warning of “a real risk of supply depletion” unless municipalities implement recommendations, including the reduction of water losses, repairing of leaks, and addressing illegal activity. Large portions of the limited supply available are being wasted, with Rand Water already extracting at maximum levels. Improperly maintained ageing infrastructure and delays in key projects are also contributing to the crisis.
As a result, boreholes have become to the water crisis what private rooftop solar panels are
to loadshedding. Consumers with purchasing power are choosing to spend additional money to access basic services and help to relieve demands on public infrastructure. In 2016, Johannesburg Water partnered with the Borehole Water Association to encourage residents to switch to boreholes to save water. The City of Johannesburg has also encouraged those living in more affluent areas to install boreholes to increase the availability of municipal water for other consumers.
According to the City of Johannesburg's Land Use Scheme, 2018, written consent from the municipality is required to install a borehole under section 14(1), and the application form is available on the city's website. Furthermore, municipal engineers and the Environmental Infrastructure Service Department must provide comments on whether the proposed borehole would impact existing infrastructure. Section 46 of the Gauteng Transport Infrastructure Act, 2001, provides that no person may make a structural alteration below the surface of a provincial road without the permission of the Member of the Executive Council of the Province.
With illegal boreholes reportedly increasing amidst Gauteng's water crisis, compliance with local bylaws before drilling is crucial, as these restrictions are designed to prevent interference with existing infrastructure. However, with long wait times for municipal consent and poor enforcement of bylaws against the backdrop of intermittent water supply, it is concerning but not surprising that illegal boreholes are becoming more commonplace.
The future of water infrastructure in South Africa
Water is becoming an increasingly pressing issue for the government. On 27th August 2024, President Cyril Ramaphosa approved the South African National Water Resources Infrastructure Agency SOC Limited Bill (Bill), aimed at establishing the South African National Water Resources Infrastructure Agency (Agency). The Agency’s purpose is to manage and secure funding for national resources infrastructure more efficiently. During his 2025 State of the Nation Address, President Ramaphosa acknowledged the growing water crisis and confirmed that investment in expanding water resources is a top government priority. He further mentioned that the Infrastructure Fund has secured R23 billion for seven large water infrastructure projects and that delays in Phase II of the Lesotho Highlands Water Project and the uMkhomozi Dam have ended. Furthermore, the National Water Resources Infrastructure Agency is due to be established within the year to increase investment in water projects, and the Water Services Amendment Bill will introduce a licensing system for water service providers and remove licenses where providers fail to meet standards for quality drinking water.
Public infrastructure and private intervention
According to Gautrain Management Agency CEO Tshepo Kgobe, the disruption caused to the Gautrain by an illegally drilled borehole has caused major inconvenience to commuters and is expected to cost over R1 million in short-term temporary repairs. There is also the additional loss of revenue for Gautrain as a result of the illegal drilling activity. However, the incident is a stark reminder of a much bigger issue: infrastructure does not exist in a vacuum, and when one sector starts to fail, there are knock-on effects on other parts of society.
For the last decade, public and private attention has been largely focused on solving the country's electricity crisis. The Renewable Energy Independent Power Producer Procurement Programme (REIPPPP) is one of the most compelling examples of the change that can occur when government and private actors work together towards a common goal. However, given finite resources, the country must now turn its collective attention to improving water infrastructure, which could follow a similar model. The United Arab Emirates has successfully implemented an independent water producer programme where the private sector is contracted to develop, operate, and maintain reverse osmosis plants and enter into water purchase agreements with the relevant state-owned entity.
The Department of Water and Sanitation (DWS) manages South Africa's water resources through policy, regulation, and bulk water management, while Water Service Authorities (municipalities) deliver water services to their respective communities. Any water equivalent of the REIPPPP would likely rely on these two bodies to improve water-related services and infrastructure.
In January 2023, the DWS publicly committed to fostering more public-private partnerships (PPPs) to develop mega-infrastructure projects. However, there has been limited appetite for large-scale PPPs in the sector. If a focused programme similar to the REIPPPP were introduced, it would not only address growing concerns about water security but also attract investment and stimulate economic growth.
The World Bank noted that Build-OperateTransfer and Design-Build-Operate PPPs for desalination and wastewater treatment plants have become increasingly common in developing countries such as Mexico and Brazil. In these cases, private funding is raised, often with the help of guarantees to mitigate risk. These projects do not present the challenge of a private party managing an existing public workforce because they are often new builds or substantially new builds. However, the country still benefits from private investment, expertise, technology, and sustainable operations.
Another growing trend internationally in the water and sanitation space is the use of
performance-based contracts to address issues such as leak management and increased connectivity. The focus of PPPs of this nature is on knowledge and skills transfer, meaning that the public sector runs day-to-day operations of a utility but benefits from private sector expertise. Based on its track record of successfully implemented PPPs and independent procurement programmes, South Africa is theoretically well placed to address the looming water crisis. However, the Constitution states that water supply is a municipal function and therefore poses a challenge to implementing large-scale PPPs that have proven so successful internationally. There is the possibility of individual municipalities running programmes akin to the REIPPPP within their jurisdiction. However, the potential for municipal mismanagement and the lack of requisite resources and knowledge would make it a challenging solution to implement. What is clear, however, is that proper water management should be at the top of both government and the private sector's agenda for the foreseeable future.
2025 Bloemfontein - 24 March 2025 Mbombela - 12 May 2025
2025
2025 Durban - 05 March 2025
- 02 June 2025
Bloemfontein - 25 March 2025
Mbombela - 13 May 2025
JUNE 2025 Mafikeng - 03 June 2025
South Africa’s Extended Producer Responsibility (EPR) regulations came into effect in May 2021, with the initial implementation timeline now being managed by respective and registered Producer Responsibility Organisations (PROs) from 2022 through to 2026. IMIESA speaks to Keith Anderson, CEO of eWASA, and one of South Africa’s foremost waste recycling pioneers, about how their PRO is making a difference.
What are the implications of the regulations?
In the pipeline for many years, the EPR regulations introduced by the Department of Forestry, Fisheries and the Environment (DFFE) under Section 18 of the National Environmental Management: Waste Act have major implications for all producers. These are defined as any people, groups, or brand owners who manufacture, convert, refurbish, or import new or used products in specified categories, who must now take responsibility
for their collection and recycling/safe disposal at the post-consumer stage. This requires them to develop comprehensive waste management strategies for every stage of the value chain, which is an onerous task that requires expert PRO facilitation.
How is eWASA responding?
From eWASA’s perspective, we are currently extending our reach in terms of engagement with existing and new producers within our defined waste categories, namely electrical and electronic equipment (EEE), lighting, portable batteries, paper and packaging, and lubricant oils.
More focus and emphasis will be spent on cross-pollination in the true spirit of a one stop shop experience for these producers to simplify their EPR obligations and subsequent reporting. This cross-pollination further aims to drive down EPR fee costs by leveraging off existing collection and recycler networks within the eWASA stable. This strategy will also allow for more rapid deployment and implementation of initiatives that include new waste stream collection protocols, assessments, and treatments into the existing infrastructure.
Keith Anderson, CEO of eWASA
The core objective of the EPR regulations is to promote a circular economy that minimises landfill footprints, protects the environment and aids the world in reaching Net Zero greenhouse gas emission targets. At the same time, the regulations recognise the opportunity and need to leverage the ensuing growth in the waste recycling sector to create sustainable employment, skills transfer and SMME opportunities that help eradicate endemic poverty and unemployment. eWASA is fully committed to this process.
Are the EPR regulations now universally enforced?
EPR enforcement is gaining traction, but there’s still a lot of work to be done to achieve universal compliance. A positive development in this respect is increased capacitation within the DFFE’s Environmental Management Inspectorate, also known as the Green Scorpions. Their inspectors work nationally at provincial and local government level and have received specific training on EPR regulation enforcement.
Over the past 12 to 18 months, the DFFE has issued a plethora of pre-compliance and compliance notices to producers who are deemed to be free riders, i.e., currently not registered with a PRO and not paying EPR levies. The latter are required to run each PRO as well as to fund their various mandated obligations in terms of the regulations.
Currently more than twenty-six customised EEE dismantling containers designed for the receipt, sorting and assessment of electronic waste have been deployed by eWASA nationally to municipalities
In response, there’s been a flurry of producers applying to join our PRO or shopping around to join another PRO of choice. However, there are still too many free riders out there adopting a wait and see strategy, but the gap is closing, and producers need to understand how noncompliance can have negative consequences for their businesses.
What are the implications of South Africa’s pending Climate Change Act?
The Climate Change Act will introduce stricter carbon reduction obligations, directly impacting the waste management value chain and placing increased pressure on recyclers, waste processors, and landfill operators.
Key regulatory shifts, such as stricter landfill emissions controls, mandatory carbon reporting, and incentives for waste-to-energy projects will require businesses to rethink operational strategies.
However, tighter landfill emissions regulations will create higher demand for recycling and material recovery solutions, benefitting recyclers who can provide alternative waste treatment options.
In future, businesses in the waste sector, including recyclers, buy-back centres, and material recovery facilities, will likely need to track and report their carbon footprint, particularly related to transportation emissions,
processing activities, and energy consumption. Recyclers with low-carbon processing methods, such as decentralised collection systems and solar-powered sorting facilities will have a competitive advantage in attracting investment and partnerships.
Going forward, eWASA’s Projects Department is strategically placed to facilitate the introduction of sustainable solutions, including chemical recycling and advanced waste management technologies. Via eWASA’s Environmental Audit and Compliance Department, we are also equipped to develop carbon impact assessment tools to help recyclers comply with current and future reporting requirements and identify opportunities for carbon credit participation.
Is eWASA’s municipal penetration gaining traction?
eWASA has projects in most of the larger metropolitan municipalities and is expanding its footprint across the local government arena. A key focus during 2025 is on rural municipalities and districts to boost their waste and recycling adoption. In collaboration with ward councillors and waste management officers, the plan is to establish buy-back centres there run by locally based SMMEs tasked with handling specific waste streams.
The establishment of these centres will also have downstream benefits for existing collectors and processors, with eWASA project funding in place to assist them in expanding the types of waste they now handle.
For example, an existing buy-back centre might currently only process packaging material but could be assisted with the necessary equipment
and training to incorporate the sorting and dismantling of electronic waste. That in turn provides a new opportunity for community-based waste picker initiatives.
Currently more than twenty-six customised EEE dismantling containers designed for the receipt, sorting and assessment of electronic waste have been deployed by eWASA nationally to municipalities. Run by SMMEs nominated by their local municipality, eWASA has provided specific training in e-waste dismantling, as well as supplying PPE, tools and equipment. In some cases, eWASA is also covering some of the OPEX costs for a period ranging from 6 to 12 months.
What are the key factors for SMME success in the buy-back segment?
Aside from access to finance and markets, expert mentorship – an eWASA specialty – is the key for any successful startup. SMMEs need to know how to navigate the complexities of what is generally a high volume, low margin type of business. Each waste stream requires specific waste management technologies and processes, with plant requirements ranging from something as small as a baler to a fullblown plant.
Another key factor of sustainable operation is managing the cost of logistics in shipping the processed waste to saleable markets. Buyback centres also need to be close to the waste source, and there needs to be sufficient volume.
Can more waste be used in construction materials?
Definitely. However, this does come with the need for rigorous product testing and adherence to industry standards, plus any initiative must have full industry support.
A prime example is the potential widespread use of unmarked plastic aggregates. This is already a practice internationally, with some niche pilot-type applications in South Africa for asphalt production and masonry blocks.
Mainstream adoption comes down to available material volumes. At present the
An eWASA branded MellowVans electric delivery vehicle forming part of a municipal waste recycling partnership initiative
tonnages received and processed by South African waste recyclers are not at sufficient scale. From eWASA’s perspective, we believe it would require a lot of education and awareness raising to get recyclers to take on more plastics of this nature to reach the volumes required.
Additionally, the logistics and associated costs for this approach at present are not viable unless recyclers invest in small shredders that can shred the plastics and make them cheaper and more cost effective to transport to producers. To ensure longer-term viability, the pricing also needs to be right to make this proposition attractive for both recyclers and product manufacturers.
What are some of the key trends in waste recycling?
In our opinion the move away from very large and costly recycling technologies to more bespoke and modular solutions make for more efficient and cost-effective solutions within all spheres of waste recycling, but more especially in e-waste recycling.
Artificial Intelligence (AI) and automated sorting technologies will also become more commonplace, particularly in buy-back centres and material recovery facilities. By integrating AI-driven material identification, recyclers can significantly improve sorting accuracy and streamline operations.
We have a local example where an AI material identification pilot at an eWASA member recycler has demonstrated promising results in accurately classifying waste streams, enhancing efficiency, and reducing contamination rates. This technology is particularly beneficial in handling complex waste materials such as e-waste, plastics, and multi-layer packaging, where precision sorting is critical for downstream processing.
Chemical recycling is also gaining traction as an advanced solution for transforming plastics into high-value materials, complementing traditional mechanical recycling. Additionally, the chemical processing of batteries is improving, supporting the safe recovery of valuable metals like lithium and cobalt, essential for the growing renewable energy and electric vehicle markets. Locally, eWASA has now implemented a bespoke solution for lithium-ion battery recycling and metals recovery.
E-waste valorisation is another critical area of advancement, with new methods emerging to extract rare earth metals from discarded electronics.
Furthermore, the advent of carbon credits in the waste sector is creating financial incentives for sustainable waste management practices. Various eWASA member recyclers are increasingly exploring carbon credit programmes, where verified reductions in emissions from waste diversion and material recovery can generate tradable credits. These credits not only support corporate sustainability goals but also provide additional revenue streams for recycling initiatives.
How are things progressing regarding the formalisation of the waste picking industry?
Despite ongoing industry challenges in integrating and formalising waste pickers, eWASA is making significant strides through its African Waste Entrepreneur Programme. This initiative is structuring the inclusion of waste pickers, buy-back centres, and other stakeholders in the waste value chain through a combination of training, infrastructure support, and fair compensation.
Financially, eWASA has so far allocated R2 336 318,55 to direct waste picker support and disbursed R1 006 832,43 in waste picker service fees to ensure equitable compensation. As a result, 3 097 waste pickers are now engaged in formalised operations, demonstrating growing participation in structured recycling efforts.
Aligned to this initiative, some 838 waste pickers have received structured training on waste sorting, material handling, and workplace safety to enhance professionalism and efficiency within the sector.
Furthermore, in 2024 a total of 237 trolleys – purpose-designed and manufactured for eWASA – were distributed to assist waste pickers with efficient collection. We also supplied 840 Conti suits, 972 heavy-duty gloves, and 690 pairs of gumboots to enhance safety and hygiene. Additionally, 2 300 bulk bags have been distributed to improve material handling and logistics.
However, while progress is evident, several structural challenges remain. Waste pickers in the industry continue to struggle with inconsistent earnings, highlighting the need for standardised pay models and improved financial security. Additionally, many lack access to essential social benefits, such as health insurance and retirement plans, requiring engagement with policymakers to introduce safety nets.
Should some waste streams be banned to combat pollution?
We feel at eWASA that more bespoke solutions are sought utilising EPR fees combined with collaboration between producers, PROs and recyclers to find alternative solutions that will address the problem and, in that way, eliminate any banning of products. However, the producers do need to play their part in cleaner production measures, design for recycling and include more recycled material content into their products. In this respect, eWASA hosts quarterly working group meetings where our producer and recycler members discuss relevant challenges and suitable solutions.
ERWAT (Ekurhuleni Water Care Company) has received a clean audit for the 2023/2024 financial year from the AuditorGeneral South Africa – it’s first since 2010.
Responsible for domestic and industrial wastewater treatment and water reuse in the Ekurhuleni region, ERWAT has been working diligently to address past challenges and implement robust governance practices. The clean audit reflects the positive impact of these efforts, demonstrating that ERWAT is
now on a path of financial sustainability and accountability.
Kennedy Chihota, Managing Director of ERWAT, says the clean audit is not just a symbolic achievement; it has practical implications for ERWAT's operations and stakeholder confidence.
Kennedy Chihota, Managing Director of ERWAT
With improved financial health, ERWAT can now focus on applying for funding to expand its infrastructure and services to meet the growing demands of the region.
Urgent challenges that ERWAT faces include the upgrading of water care works, enhancing water reuse initiatives, and ensuring that the company can continue to provide essential services to the community.
The clean audit also opens opportunities for ERWAT to attract more investment and partnerships, further strengthening its ability to deliver on its mandate. ERWAT’s commercial business wing is continuously marketing its ability to treat industrial wastewater in both the private and public services sector.
ERWAT's success story highlights the importance of strong leadership, transparency, and a commitment to continuous improvement. By setting a precedent for good governance and fiscal responsibility, the organisation is paving the way for other municipal entities to follow.
An undeniable reality of living in the 21st century is that we are increasingly being confronted with changing weather patterns. In densely populated communities, which are common in developing nations as people look for economic opportunities, unforeseen natural phenomena such as flooding can be massively destructive.
By Alexander Tikhonov
From extreme heat and severe thunderstorms to the reality of rising sea levels and torrential rain (with the flooding it causes), it is becoming more important than ever to be able to deal with the destructive power of nature.
For example, the floods in KwaZulu-Natal over the past few years are a stark reminder that the phenomenon of flooding is becoming more frequent. The province was hit by flooding in July 2016, twice in 2017, three times in 2019, again in 2020 and 2022, twice again in 2023, with more occurrences in January and June 2024.
The devastation caused by flooding has been significant, leaving deaths, displacement and immense property damage in its wake. The flood in April 2022 alone caused the deaths of at least 459 people, and displaced more than 40 000 people.
The problem with floods isn't just that they are increasing in frequency, it is also that traditionally they have been unpredictable. Having little to no visibility into factors such as rising river levels or water speed makes it impossible to respond to an impending flood, leaving residents at the mercy of the elements. That is where analytics and artificial intelligence (AI) can greatly aid us in closing this gap.
While analytics enables us to derive value from a variety of sources of clean data, AI can help us sift through large volumes of this data at a fraction of the speed possible by human beings. It can also use the data to suggest actions that we may not have arrived at on our own, far more quickly.
Using advanced analytics, we can process data and generate flood forecasts, as well as perform risk assessments. Combining this with real-time monitoring, we can leverage AI to continuously monitor flood-prone areas and calculate the possibilities of potential floods.
Much like data, AI and analytics are being used to forecast earthquakes and provide residents with advance warning, so that they respond accordingly, and these technologies can similarly help provide advance warning to those in a flood's path.
Already we have the capability to bring together data from several sources, including weather forecasts, river levels, and historical data. This allows for accurate flood forecasting and early warning services.
Alexander Tikhonov, regional director, SAS Middle East, Türkiye and Africa
Along with IoT enabled sensors, it is now possible to garner a complete picture of fastchanging flood conditions, such as rainfall, rain rates, soil saturation, topography and elevation – any of which can rapidly change the dynamics of a flood. With the relevant insights at hand, organisations, governments and cities can not only respond to a flood that is in progress, but they can also do proactive planning – implementing mitigation strategies well in advance of a possible natural disaster. We are already seeing these capabilities in action from the likes of the SAS D[n]A Factory initiative. A key part of the initiative is enhancing community preparedness by offering insights into how communities can leverage SAS tools to improve their preparedness and better response to flood emergencies.
If there is a silver lining to global climate change, it is that regions like KwaZulu-Natal are not alone in their vulnerability to floods. How other nations are leveraging AI and analytics can serve as successful examples of how the risk of floods can be offset by the right use of technology and offer hope.
For example, the capital of Indonesia, Jakarta, is highly vulnerable to flooding due to its location – a delta in a lowland area. It must also contend with monsoons and rising sea levels. The city is already protecting itself by using a flood control system that combines sensor data and weather forecasts, and which is integrated into its super-app, JAKI. This has significantly strengthened Jakarta’s flood response, while enabling it to reduce the adverse effects.
While the reality is that floods, and other climatological events, are a near certainty in today's world, the silver lining is that we do have technology at hand to help better prepare for these events. Climate change is undeniable, but with the right tools, we can save lives.
Water scarcity is a growing global concern, driven by urbanisation, population growth, and climate change.
Urban water consumption is expected to rise by 62% from 1995 to 2025, with potential shortages by 2050.
To address this, preserving existing water resources and reducing potable water demand is crucial.
In construction, rising water costs and sustainability concerns are pushing developers to adopt alternative water sources like greywater reuse and rainwater harvesting. Integrating these systems into residential, commercial, and industrial projects helps cut costs while promoting environmental responsibility.
Why alternative water sources?
Alternative water sources were long underutilised in industry but are now gaining popularity in urban water management. Greywater alone can cut potable water use by up to 30% in homes and 60% in commercial buildings, while reusing it for irrigation can boost household savings by 40%. In construction, alternative water sources reduce reliance on potable water for dust suppression, concrete mixing, equipment washing, and site irrigation.
underground
Some alternative water sources to choose from:
1 Rainwater Harvesting
Maximise seasonal rainfall by installing rainwater tanks and guttering systems to capture and store runoff. This water can be used for non-potable site activities and even potable use with proper filtration that meets the SANS 241 drinking water quality standard. Benefits: Reduces municipal water use, especially in the dry season.
Greywater Systems
Water from baths, showers, and sinks (excluding kitchens) can be reused for non-potable construction activities such as equipment washing, landscape irrigation or flushing the toilets. Greywater systems filter and direct this water to lawns, ornamental plants or where it can be collected for use.
Borehole Water
Accessing underground aquifers through boreholes ensures a reliable water supply, particularly in areas with scarce surface water. Although installation can be expensive, borehole water can support all construction activities requiring water and, with proper treatment, can also be used for domestic purposes.
How alternative water sources cut costs
1 Lower Water Bills: Using greywater can cut water costs by up to 50%, especially on largescale projects that require significant water usage. Further savings can be realised with the incorporation of other alternative water sources.
2 Reduced Sewer Discharge Fees: Reusing greywater means less wastewater enters the sewer system, lowering municipal disposal charges.
3 Operational Efficiency: On-site alternative water source systems reduce dependency on municipal supply, preventing costly delays during droughts or water restrictions.
4 Enhanced Project Valuation: Sustainable practices improve a project's marketability and can elevate the overall EDGE score for green building accreditation.
Utilising alternative water sources is not just cost-effective, it is a step toward sustainable building, positioning companies as leaders in efficiency and environmental responsibility.
can cut potable water use by up to 30% in homes and 60% in commercial buildings
Water is the lifeblood of any major city. It fuels industries, sustains households, and is integral to sanitation and public health. However, in South Africa’s large metropolitan areas –such as Johannesburg, Durban, East London, and Cape Town – ensuring a stable and secure water supply has become increasingly complex.
Infrastructure is aging, population growth is outpacing supply, and climate change is exacerbating periods of drought and heavy rainfall, straining already fragile systems.
Since it’s not built around a major river, Johannesburg relies on an extensive network of reservoirs, pump stations, and pipelines to meet its water needs. Unfortunately, in recent years, supply disruptions have occurred due to crumbling infrastructure and power failures affecting pump stations. Durban, a coastal city with high rainfall variability, faces challenges from both droughts and floods. Severe storms overwhelm wastewater treatment plants, while dry spells reduce dam levels, forcing water restrictions. In East London, ageing pipelines lead to frequent leaks and bursts, resulting in significant water losses before the supply even reaches consumers. Meanwhile, Cape Town, which narrowly avoided “Day Zero” in 2018, continues to walk a tightrope between supply and demand, with desalination, aquifer extraction, and water reuse initiatives helping to supplement the strained system.
In each of these cities, the need for real-time monitoring and precise control over water
Water towers perform an essential role in maintaining steady supply, particularly during peak usage periods. To help manage demand, technologies like the VEGADIS 81, a remote display unit, enable operators to monitor tower levels from a centralised control room, ensuring a rapid response to fluctuations
distribution has never been more critical. Here VEGA’s range of pressure sensors and level instruments play an important role in ensuring that water systems operate efficiently, reducing losses and maintaining
stable pressure levels to prevent service interruptions.
In the pumprooms that regulate drinking water supply, maintaining optimal pressure is essential. Too little pressure and entire suburbs may go without water; too much, and pipes can burst, leading to expensive repairs and further disruptions. In response, the VEGABAR 38 is a durable pressure sensor that ensures that pump stations operate at the correct pressure levels by providing continuous monitoring and early warning of any anomalies.
Alongside it, the VEGAPOINT 23 acts as a reliable point-level sensor, detecting whether pumps are running dry, which can lead to damage and unplanned outages. By integrating these instruments, municipalities can ensure that water is delivered at consistent pressure, preventing outages, shortages and infrastructure failures.
Water towers, a familiar sight, especially in Johannesburg, serve as vital buffer storage to maintain steady supply, particularly during peak usage times. These towers must be carefully managed to prevent overflow and ensure that sufficient reserves are always available. Here, the VEGABAR 82, a high-precision pressure sensor, provides real-time measurement of water levels within the tower, allowing for automatic adjustments to maintain an optimal balance between supply and demand.
Allied to this, the VEGADIS 81, a remote display unit, enables operators to monitor tower levels from a centralised control room, reducing the need for manual inspections and allowing for rapid response to fluctuations. This level of automation is particularly beneficial in cities like Cape Town, where water conservation remains a priority, and in Johannesburg, where high consumption rates require careful management to prevent shortages.
Pipeline performance
In the extensive network of pipelines that transport drinking water across cities, pressure fluctuations can lead to significant losses and structural damage. Old pipes, particularly in cities like East London and Johannesburg, are prone to bursting under excessive pressure, leading to costly repairs and supply disruptions.
In this respect, the VEGABAR 30 pressure sensor provides continuous monitoring along key pipeline sections, detecting pressure variations before they escalate
into full-blown failures. The VEGAPOINT 21 complements this by serving as an overflow detection system, preventing excessive pressure buildup and ensuring that water distribution remains smooth and efficient. By leveraging this technology, municipalities can reduce water losses, extend the lifespan of infrastructure, and ensure a reliable supply to residents and businesses.
Conclusion
The importance of a secure water and sanitation system cannot be overstated.
T: +27 (0)16 362 9100 | Meyerton
Sales: Godfrey Mpotu contracts@structatech.co.za | 079 035 6997
Estimator: Judy van der Walt watertanks1@structatech.co.za
Director: Rodney Cory rodney@structatech.co.za | C: 082 575 2275
Structa Technology is a Level 1 BBBEE Contributor , and is part of the
A range of VEGA level measurement sensors designed to communicate with the VEGAMET 842 controller and display instrument
Without a stable supply, economic activity slows, public health is jeopardised, and service delivery protests become more frequent. South Africa’s metros are standing at a junction where investment in smart monitoring and automation is no longer optional – it is a necessity. By implementing advanced measurement and control solutions such as those provided by VEGA, cities can take proactive steps toward water security, ensuring that millions of residents have access to clean, safe water, both now and in the future.
Structa Technology’s Prestanks are hygienically safe, cost effective and a reliable way to store water for commercial sectors, private sectors and even for personalized storage. Temporary or permanent erection at mines, powerstations, building sites, hospitals, water affairs, municipalities, rural communities and agriculture.
South Africa is classified as a water-stressed country, receiving an average annual rainfall of 497 mm – nearly half of the global average of 860 mm. This challenge is further exacerbated by a growing population, intensifying concerns about water security and emphasising the need for effective water management and conservation strategies.
In recent years, non-revenue water has emerged as a significant threat to water availability, with an estimated 47.5% of water lost due to leaks, inaccurate metering, and theft. As a result, there has been increasing interest in smart water metering as an innovative solution to monitor and reduce water wastage. Smart water meters provide real-time insights into water consumption, enabling early detection of inefficiencies, minimising costs, and supporting water conservation efforts.
Although smart water metering systems are still in their early stages of implementation in South Africa, municipalities such as George and Saldanha Bay are actively exploring their rollout. These systems enable accurate and continuous
monitoring of water usage, enhancing revenue collection and reducing water losses due to leaks.
For property owners, smart water meters offer an effortless way to track consumption patterns and reduce water bills. Unlike traditional meters, they provide real-time data, eliminating the uncertainty of estimated billing. This precision ensures fair and accurate charges while helping to detect leaks or irregular usage before they develop into costly issues.
Cost Savings and Efficiency
Smart water metering allows municipalities and property managers to dramatically reduce water expenses in the long term. Early detection of leaks and excessive usage allows for prompt corrective action, avoiding wasteful costs and ensuring more efficient water management in the immediate term.
Manual readings and unexpectedly large water bills are a thing of the past. Smart water meters provide remote monitoring via userfriendly apps and web portals that may be downloaded to your phone. These apps provide users (municipalities, property owners, and building occupants) with real-time, detailed water use reports. This level of control increases accountability and promotes prudent water use on both residential and business buildings.
Global water shortage is becoming a bigger issue, and smart water meters help manage water resources sustainably. Municipalities, property owners, and building occupants may all play a critical role in protecting this essential resource by encouraging conscientious consumption and minimising waste.
Installing smart water meters is a proactive investment rather than a temporary fix. Smart technology-enabled properties are more appealing to tenants and buyers that respect sustainability and efficiency. With the current economic challenges, everyone is searching for methods to lower their living expenditures.
Proactively educating consumers about appropriate technologies is a key component of sustainable water conservation. Acceptance and adoption will be strongly influenced by the measurable benefits of built-in features like water consumption monitoring and control on smart water metering – driving down costs and helping to conserve our most precious resource.
www.randwater.co.za 0860 10 10 60
Imagine you are pitching a business proposal to investors: you have a product with a limited supply and a never-ending demand. Everyone needs it to survive, and no one can live without it for the next 100 years. Sounds like a solid investment, right? By Gerardt Viljoen*
Now, let’s look at the business model: for every 1 000 units produced, 4% must be given away free of charge. All units must be delivered directly to the consumer. However, due to logistical challenges, nearly half – 47% – of all units shipped are lost and never paid for. This means that production, distribution, storage, and all associated costs must be covered by revenue from just 49% of the units produced. And, if you ever run out, there is no way to manufacture more. It’s a finite resource –when it’s gone, it’s gone.
Would you still consider this a good investment? More importantly, is this model sustainable?
The reality of water as a finite resource
Water is a finite resource, with approximately 1 400 million cubic kilometres circulating through the Earth’s hydrological cycle. However, the vast majority of this is salt water, while most of the remaining fresh water is locked away in glaciers or deep underground. In fact, only 0.01% of the world’s water is readily available for human consumption.
In South Africa, water losses are a growing crisis. The 2023 No Drop Report revealed that non-revenue water (NRW) had reached 47%,
up from 41% in 2018 and 37% in 2012. This means that nearly half of all water produced is lost before it generates any revenue. Of this, 38% – or approximately 18% of total water losses – is due to apparent losses, including ageing meters, illegal connections, and poor data transfer (such as incorrect meter readings). Clearly, the business case for sustainable water management is becoming increasingly dire.
role of quality precision measurement and data accuracy
To create a sustainable water management model, investment must start with precision measurement and reliable data. This means using approved and compliant water meters and improving data capturing systems. By doing so, NRW can be reduced to around 30% – a significant improvement that would help generate the revenue necessary to maintain and upgrade South Africa’s ageing water infrastructure. Without these investments, municipalities will continue to struggle with water losses that ultimately threaten the sustainability of the entire system.
Measuring to manage Water sustainability begins with knowing where water is going and ensuring that every drop delivered is accounted for. As the saying goes, “If you cannot measure it, you cannot manage it.” Similarly, IT professionals remind us of the adage “garbage in, garbage out.” Senseless measurement and unreliable data lead to poor management decisions and financial shortfalls in the water sector. Quality precision measurement devices and reliable data capturing are not optional – they are essential. To build a sustainable water supply for all South Africans, municipalities and utilities must prioritise NRCS-approved water metering products that comply with our Legal Metrology Act. By doing so, we can take a crucial step toward ensuring the longevity and viability of our most precious resource: water.
For any questions or assistance in your water metering journey, please do not hesitate to visit a Precision Meters office near you.
*Non-Executive Chairman at Precision Meters
Environmentally Friendly and Sustainably Manufactured South African Activated Carbons
Environmentally Friendly and Sustainably Manufactured South African Activated Carbons
Since the completion of its multi-billion rand upgrade in October 2024, the City of Cape Town’s Zandvliet Wastewater Treatment Works (WWTW) has been producing significantly improved treated effluent, benefitting both the environment and future water reuse initiatives.
The city invested R2 billion in upgrading and refurbishing the facility, enhancing its conventional activated sludge treatment module and introducing a state-of-the-art membrane treatment module. This advanced technology enables the plant to treat wastewater to the highest standards, while increasing its capacity from 72 to 90 million litres per day (Mℓ/day).
Zandvliet WWTW treats incoming waste from the sewer network in Khayelitsha, Delft, Kuils River, Blue Downs, Blackheath and Eerste River. These upgrades have been instrumental in ensuring that infrastructure development provides for rapid population growth.
“Prior to the upgrade, the plant struggled with ageing infrastructure and capacity overload, resulting in a compliance rate of approximately 50% with its licence conditions. Following the enhancements, compliance has surged to 90%, meeting the stringent standards set by the National Department of Water and Sanitation,” says Councillor Zahid Badroodien, Mayoral Committee Member for Water and Sanitation.
Between July 2022 and June 2023, Zandvliet WWTW’s annual effluent compliance stood at 63%.
Following the upgrades, average compliance leaped to 86% between July 2023 and June 2024.
Key drivers of the improved effluent quality include the addition of primary sedimentation, refurbishment of ageing infrastructure, and the
expansion of the membrane bioreactor system. This innovative treatment process ensures cleaner, safer water for further treatment for reuse and responsible discharge into the environment.
Faure New Water Scheme
Zandvliet WWTW is strategically linked to the City’s New Water Programme, particularly its role in future potable water reuse. The high-quality treated effluent from Zandvliet will be transferred to the Faure New Water Scheme, planned to be built on the same grounds as the existing Faure Water Treatment Plant (WTP). There, an advanced multi-barrier purification process will further treat the water to drinking water standards before blending it with dam water. Thereafter it will undergo additional treatment at the existing Faure WTP, then be blended into the water supply system for distribution.
“Introducing potable water reuse is essential for Cape Town’s long-term water security. Through this initiative, we will be able to augment the city’s drinking water supply by 70 to 100 Mℓ/day, protecting us from unpredictable climate change and drought,” Badroodien continues.
“To further bolster treatment capacity, a future expansion project is in the pipeline at Zandvliet WWTW. The next upgrade will add another estimated 60 Mℓ/day of capacity with improved sludge treatment processes, including energy recovery. Planning is already under way, with construction anticipated to begin in the 2034/2035 financial year. This investment
ensures that Cape Town remains ahead of future challenges by continuously improving wastewater treatment capacity and efficiency.”
During this financial year (2024/25) R2 billion is earmarked to be spent on extensions and upgrades at WWTWs. These extensions will expand the capacity of key facilities that include:
• Potsdam: upgrade from 47 Mℓ/d to 100 Mℓ/d (construction stage)
• Athlone: refurbishment and treatment process upgrade Phase 1 (construction stage)
• Bellville: final phase of refurbishment and treatment process upgrade (construction stage)
• Macassar: upgrade from 34 Mℓ/d to 80 Mℓ/d (design stage)
• Wesfleur: aeration system replacement/ refurbishment (currently at awarding tender stage)
• Wildevoëlvlei: refurbishment and upgrade of the mechanical sludge dewatering facility (tender evaluation stage)
“Of the approximately R120 billion committed to the city’s 10-year infrastructure pipeline, the Water and Sanitation investment represents 42% of the city’s commitment to infrastructure upgrades and rehabilitation,” adds Badroodien.
“This financial commitment will not only fund our New Water Programme, but also our investments into much-needed upgrades at our wastewater treatment works. This will allow the city to cope with future population growth and to protect our environment by producing improved treated effluent quality,” Badroodien concludes.
With over 50 years of combined experience nationally and internationally, Mainline Civil Engineering ensures professional project delivery every time.
Mainline Civil Engineering is a specialist civil engineering contractor in the field of pipeline construction, trenchless installation of underground pipelines and utilities, and trenchless pipeline rehabilitation and tunnelling in both the public and private sectors.
We are at the cutting edge of pipeline construction, rehabilitation, and tunnelling in South Africa and throughout Southern Africa. At Mainline, we use the latest techniques and equipment to ensure minimal environmental impact and offer comprehensive infrastructure technology to all service providers and utilities. With Mainline contracting team’s vast range of experience in the field at home and across our borders, our attitude is “nothing is impossible”. We offer the best solutions from our comprehensive trenchless toolbox, using our experience, knowledge, and equipment to ensure professional project delivery for all stakeholders.
Hidden from view, the underground water, sewer and stormwater infrastructure that run for thousands of kilometres in any major town or city serve a crucial function, with the need for strict asset management.
This is a field where Mainline Civil Engineering Contractors is an industry leader in installing and rehabilitating these essential utilities as a No Dig specialist.
Employing state-of-the-art equipment, Mainline Civil Engineering Contractor’s four key solutions comprise micro-tunnelling; guided auger boring; pipe jacking; and pipe lining. In terms of the latter, the techniques utilised are spirally wound pipe (SWP) and cured-in-place pipe (CIPP) lining systems for rehabilitation works – effectively creating a new “pipe within a pipe”.
Globally, No Dig solutions are a proven technique for high density urban environments. Unlike open trench methods, it enables construction with minimal disruption to traffic, communities and businesses, while also greatly reducing any environmental impact.
“It is also the only practical one for pipe lining, as well as installations below structures that include roads, rail, rivers, residential and commercial buildings,” explains Justin Spreckley, Mainline Civil Engineering Contractor’s General Manager.
“In fact, there’s never been a greater need for No Dig techniques in fixing South Africa’s growing pipe maintenance backlog, as well as in meeting the country’s water and sanitation new build targets to keep pace with urbanisation trends,” says Spreckley.
“At present, our non-revenue water (NRW) losses are far too high, primarily due to failing pipeline infrastructure, making rehabilitation – either via replacement or lining – a top priority.”
This viewpoint is underscored by the Department of Water and Sanitation’s 2023 “No Drop Report”, which found that national NRW had risen to approximately 47%, with some 40.8% directly due to potable water pipe leakages.
A current flagship contract for Mainline Civil Engineering Contractors is the Cape Flats (CF) Bulk Sewer Rehabilitation Project in Cape Town. Divided into various framework projects, this is the city’s first pipeline rehabilitation project using SWP to restore sections of the two 14 km parallel lines (CF 1 and 2) forming part of the system (ranging in diameter from 1 000 mm to 1 800 mm). Originally constructed in the 1960s/70s, both lines start in Athlone and end at the Cape Flats wastewater treatment works in Zeekoevlei.
Works commenced first on CF 1 in 2020, which like CF 2, is severely degraded in terms of corrosion and sediment build-up at up to 80% of its capacity. The latter required a dedicated and skilled Mainline Civil Engineering Contractors manentry team to safely clear the debris and clean the pipe before lining operations could commence.
To date, Mainline Civil Engineering Contractors has lined approximately 9.54 km, with installations taking place under live conditions using purposedesigned SWP equipment. The watertight PVC liner improves the pipe’s existing velocity without reducing its capacity.
“SWP was selected because it provided a fast installation timeframe to restore these critical, large diameter installations,” says Spreckley.
Mainline Civil Engineering Contractors is also currently working on other pipeline rehabilitation
projects within the City of Cape Town using the CIPP method at upwards of 4 km per month. These resin-impregnated polyester liners are primarily inverted and then cured using steam. Diameters typically start from around 150 mm.
“To enhance CIPP efficiencies, our investment in areas like robotic cutters, CCTV pipeline inspection cameras, and steam generators have greatly enhanced our capacity to meet our client’s needs,” Spreckley expands.
In terms of new construction, recently completed works include micro-tunnelling projects in Vredendal and Paarl. The former entailed the installation of a 1 417 mm diameter pipeline under a railway line tying in with an upgrade at the Vredendal water treatment works. Meanwhile in Paarl, four bulk water pipelines were installed under the N1, with diameters of 1 200 mm and 1 350 mm, respectively.
“Twenty years ago, No Dig systems might have been seen as an ‘exotic’ option for South Africa. However, today it’s an absolute necessity if we’re going to avoid serious underground infrastructure failure scenarios. All major centres are at risk. However, regions like Gauteng – where South Africa’s population is the greatest – are arguably among the worst affected,” adds Spreckley.
“Across the board, the City of Cape Town leads in terms of No Dig implementation. It’s time for other municipalities to follow suit. At Mainline Civil Engineering Contractors, we’re committed to being part of that process,” Spreckley concludes.
One of the biggest challenges that contractors face when constructing a reservoir is ensuring that it is watertight. In addition to being able to withstand leaks, the waterproofing system of a typical above-ground reservoir must also have sufficient elasticity. This is in addition to being able to resist the effects of wall and floor expansion and contraction.
Taking these factors into account, industry leading practices were recently deployed to waterproof the new 5 ML Oliphantskop reservoir in Langebaan, Western Cape. Built by Rawucon, this 39 m diameter and 2,5 m deep structure was constructed alongside an existing 2 ML reservoir, with matching top levels. Furthermore, the new pipework installed makes provision for an additional 5,7 ML reservoir to meet future demand, as well as acting as a storage buffer during drought periods.
A key challenge when constructing watertight structures is that most concrete eventually cracks due to curing, shrinkage, settling and seismic activity. This can result in leakage and contamination unless effectively countered.
“The best way to reduce the likelihood of these problems occurring in the future
is to select the best waterproofing system for concrete reservoirs,” explains Andre Vermeulen, Managing Director of Citi-Con.
“Research and plan ahead to avoid future problems or simply deal with an expert right from the outset. There is no reason why a well-designed and built reservoir that is also appropriately maintained should not continue functioning as intended.”
The state-of-the-art waterproofing system applied – for which Citi-Con is an approved applicator – is among the best on the market.
This enables the company to guarantee its workmanship for the maximum term available.
Based on plasticised polyvinylchloride and manufactured in specific profiles, quality waterstops were used to seal joints. These particular waterstops were selected because they provide long durability when installed by a skilled and experienced contractor.
As Vermeulen notes, joints between pours are some of the most vulnerable areas of reservoirs. If these systems have not been installed correctly, water retaining structures will leak.
A competent waterproofing contractor will avoid common mistakes such as installing waterstops too close to steel reinforcement; misalignment; and roll ends overlapping but not welded or spliced together. Issues also arise when waterstops have been installed adjacent to poorly consolidated concrete and when it extends on flanges that have not been removed before the second concrete pour. Curing to form a durable rubber like seal – a two-component sealing compound based on a polysulphide polymer blended with fillers and chemical curing agents – was used as a joint sealant. Citi-Con selected a sealant that
is resistant to ultra-violet light and ozone, making it particularly well suited for sealing drinking water reservoir joints.
Joint design and surface preparation Vermeulen explains that joint design is critical. For water retaining structures and where shear movement is anticipated, a 2:1 width to depth ratio should be maintained. This ratio provides the optimum geometry to allow movement to occur within joints without placing excessive force on their faces. These should be parallel and their width at least four times the maximum anticipated movement. When placing the sealant, Citi-Con made sure that joint openings were central to their maximum compression/expansion cycles.
the sealant. (Repriming is undertaken where primer has lost tack after three hours.) The primed surface is protected from dust and dirt, which can interfere with sealant adhesion.
To complete the process, the company then installed a high quality Hypalon bandage system over the sealed joints to reinforce the waterproofing. “For this application, we selected a high-performance joint and crack sealing system. It allows variable and high levels of movement in one or more directions, while maintaining a high-quality watertight seal. The product consists of a modified flexible Polyolefin waterproofing tape with advanced adhesion properties,” Vermeulen says.
Various quality waterproofing systems were also used to further waterproof the reservoir’s internal wall and floor slab. This included a high two-component cementitious mortar that seals hairline cracks already present on substrates. Also approved for use in potable water systems, a flexible slurry based on a special synthetic resin dispersion and a blend of selected cement mixed with carefully graded aggregate was then deployed.
Surface preparation and priming must also be undertaken correctly. All surfaces need to be clean, sound and dry, as well as free of all laitance before being primed. Citi-Con also pays particular attention to voids and hollows and allows for at least 30 minutes for the solvent to evaporate before applying Adaptable, scalable water infrastructure solutions.
Our multidisciplinary teams address the water cycle holistically, ensuring solutions are sustainable, efficient and adaptable to future needs. Our local and global network provides our clients access to international best practice and specialised expertise across the entire water cycle.
Engineering positive change. smec.com
In addition, an additive was used to waterproof the cement mixes, improving the bond of subsequent treatments. The various waterproofing layers were also reinforced with alkali-resistant glass fibre mesh and associated textiles.
A high-quality bituminous membrane was applied to the concrete floor slab to complete the process. Again, Citi-Con followed the recommended techniques for bitumen waterproofing. This included the use of the appropriate tools to ensure an even and consistent coverage. The company also applied the membrane according to the recommended thickness and overlapping requirements to achieve optimal waterproofing results.
“Bitumen is highly valued for its excellent waterproofing capabilities by forming a durable and impermeable barrier. The material’s inherent durability makes it an ideal choice for this and other waterproofing applications. It can withstand extreme weather conditions, temperature variations, and heavy loads, providing long-lasting protection,” Vermeulen concludes.
A perspective of the georeferenced BIM model for the Northern Wastewater Treatment Works
In April 2022, KwaZulu-Natal, particularly Durban and its surrounding areas within eThekwini Municipality, experienced catastrophic flooding due to prolonged heavy rainfall. The disaster resulted in loss of life and significant infrastructure damage, including the destruction of homes, roads and bridges.
Among the hardest-hit infrastructure was the Northern Wastewater Treatment Works (NWWTW), where the entire 70 Mℓ/d plant was submerged, rendering it completely inoperable. This vital facility, which processes both domestic and industrial effluent from the northern suburbs of Durban, is part of a broader network of wastewater treatment facilities in the region, contributing to the overall sanitation infrastructure that serves the greater Durban area.
Following the floods, eThekwini Water and Sanitation responded swiftly by initiating
emergency repairs to partially restore the NWWTW’s operations, followed by a comprehensive refurbishment to repair damaged components of the older 20 Mℓ/d and newer 50 Mℓ/d plants to enable the facility to achieve its full capacity efficiently.
eThekwini Water and Sanitation engaged SMEC South Africa's Integrated Solutions team in November 2023 to lead the extensive refurbishment of the facility. This decision reflected confidence in the team's proven capabilities, earned during their involvement in the emergency repair efforts in 2022.
At the heart of the team’s current work is the finalisation of a 3D twin model, a highly versatile tool that creates a digital representation of a physical asset, process or system. The twin model of the NWWTW integrates advanced instrumentation and monitoring systems, offering real-time access for engineers and the client. This enables precise execution of maintenance and refurbishment activities, thereby optimising operational efficiency and reducing downtime.
The twin model not only facilitates the current restoration but also provides a foundation for long-term infrastructure management. With virtual access to every component of the plant, future interventions can be executed efficiently, ensuring that the facility remains resilient and functional for years to come.
The Integrated Solutions team is undertaking a multi-faceted approach to restore the facility’s full 70 Mℓ/d capacity by December 2025, with the plant currently operating at 36 Mℓ/d. Key deliverables include:
• Ensuring effluent released from the plant into the Umgeni River complies with stringent water and environmental quality standards and does not contaminate the surrounding water bodies.
• Installing new components and refurbishing existing infrastructure, including:
- Combined inlet works with screening, degritting and flow measurement.
- Rehabilitation of the older 20 M ℓ/d and newer 50 Mℓ/d plants, including a vortex degritter and biological nutrient removal (BNR) reactor, as well as primary settling tanks and secondary sedimentation tanks.
- Five maturation plants.
- New chlorination infrastructure and system.
- Sludge handling systems, including dissolved air flotation (DAF) units, primary sludge gravity thickeners, anaerobic and secondary digesters, gas holder and belt presses for dewatering.
1 A virtual rendition showing sections of the works
2 Refurbishment of settlement tanks
3 Dredging of maturation ponds
4 Civil works on primary and secondary digestors
5 50 Mℓ/d aeration basin
Under the leadership of Ahmad Hoosen (Senior Project Manager), the multidisciplinary team brings exceptional expertise to the project, combining sustainable practices with innovative solutions to ensure long-term value and measurable impact. The team’s collaborative approach and technical excellence are integral to delivering resilient, community-focused infrastructure. The team includes Dr Michele Kruger (Process Engineer), a specialist in
wastewater process optimisation; Dr Faria Mhlanga (Chemical Engineer), an expert in environmental and chemical sustainability; Telez Augustyn (Mechanical Engineer), focused on rehabilitating critical mechanical systems; and JJ van Tonder (Electrical Engineer), who ensures reliable and sustainable power solutions. Together, their expertise drives the success of this transformative initiative.
Setting the benchmark for resilient infrastructure
This project highlights SMEC's integrated approach, combining multidisciplinary expertise to deliver comprehensive solutions. Its success is driven by internal collaboration, a focus on client and community needs for long-term value, and the integration of sustainable practices to mitigate climate risks and protect natural resources.
The restoration of the NWWTW is not only a response to immediate challenges but also a blueprint for sustainable development. By combining cutting-edge technology with a community-centric approach, the Integrated Solutions team has set a benchmark for future projects across South Africa and beyond.
6 Southern half of the Northern Wastewater Treatment Works 1 2 3 4 5 6
The 2022 floods were a stark reminder of the increasing frequency and severity of extreme weather events that are driven by climate change. By building resilience into critical infrastructure, projects like this play a pivotal role in protecting communities and ensuring sustainable growth. Through innovation, collaboration and an unwavering commitment to excellence, SMEC and the wider SJ Group continue to lead the way in transforming challenges into opportunities for progress.
Reliable access to clean water remains a critical challenge for many rural communities in South Africa, an area where Makhaotse, Narasimulu and Associates (MNA) has extensive experience in designing and delivering lasting solutions.
Aprime example is the roll-out of the Nkubungwini Water Supply Project, where MNA was appointed by the uMzinyathi District Municipality (UMDM), in its capacity as the Water Services Authority (WSA) and Water Services Provider (WSP), to oversee the design and construction monitoring of Phases I, II and III.
Building on the foundations laid by Phases I and II – which have now been completed – Phase III, which is currently in progress, targets villages and surrounding areas within the Msinga Local Municipality (MLM), which is located approximately 40,5 km northwest of Greytown. With no existing bulk water infrastructure, residents here have historically relied on boreholes equipped with hand pumps, and inconsistent water tanker deliveries.
The villages affected in Phase III include:
- Thulini Lwezulu (Wards 8 and 12)
- Chunu B (Wards 8 and 10)
- KwaNtabadini (Wards 8 and 10)
- Ekuvukeni (Wards 8 and 10)
- Embangweni (Wards 8, 5, and 6)
- KwaMathonsi (Wards 8 and 6)
- Nxamalala (Ward 8)
To ensure an accurate understanding of the region’s needs within the Phase III footprint, a site investigation was conducted in October 2022, in conjunction with representatives from UMDM and local community leaders. This comprehensive assessment of the project area revealed that 160 households, home to approximately 800 people, currently lack access to a dependable water source.
Based on population growth trends from Statistics South Africa’s 2016 Community Survey, this figure is expected to rise to 1 254 residents across 251 households by 2043. Therefore, meeting this increasing demand is crucial not only for basic human
dignity, but also for driving economic and social development within these villages. This shaped the scope of work required to make Phase III a sustainable success.
Given the greenlight, Phase III was divided into two sub-stages, namely Phase IIIA (a geohydrology study) and Phase IIIB (construction). The former focused on identifying and securing reliable water sources from borehole supply. The drilling investigation confirmed an adequate yield, but at low quality.
With the study approved, MNA –responsible for Phase IIIB implementation – then progressed with the implementation of its design for the construction of rising main pipelines to a designated reservoir. From there, gravity mains and reticulation pipelines will distribute potable water to some 42 communal standpipes, ensuring accessibility for all.
In terms of the design, abstracted water will be treated at a modular plant according to SANS 241:2015 standards and then pumped to the newly installed 305 KL steel tank via a 5,1 km rising main pipeline. The initial high-pressure rising main component comprises a steel section, culminating in a PVC final delivery line.
Socioeconomic gains
The Nkubungwini Water Supply Project, Phase IIIB is more than just an infrastructure initiative – it is a lifeline for MLM rural communities.
Beyond providing clean water, this project also has positive ripple effects. By creating job opportunities during implementation, the initiative is upskilling community members, fostering local economic development.
A community member draws potable water from a standpipe connection during the official handover ceremony of Phases I and II of the Nkubungwini Water Supply Project
“As March unfolds, marking UN World Water Day and South Africa’s National Water Week, I find myself reflecting on the vital role water plays in our everyday lives,” says Zamekile Fakude, MNA’s project engineer for Phase IIIB.
Additionally, improved water access is expected to enhance public health, hygiene, and overall quality of life. Families will no longer have to rely on inconsistent water deliveries or travel long distances to fetch water. Instead, they will have access to safe, treated water from a dedicated source.
“Leading this project fills me with a sense of purpose and responsibility, and an overwhelming sense of urgency, knowing that what we do here will directly impact the lives of many,” she continues.
“Ultimately as an engineer, leading the Nkubungwini Water Supply Phase IIIB project
goes beyond making decisions; it’s about collaboration, building relationships, and uniting a diverse group of professionals towards a common goal.
“Through this process, I’ve learnt the importance of empathy, adaptability, and strategic thinking. Like any other project, there have been challenges – both technical, social and even emotional – but with each obstacle we’ve overcome, the reward grows clearer: the future of a community with consistent, sustainable access to clean water,” Fakude concludes. Potable
• Highly economical cost to volume ratio
• Easily transportable, especially for multiple tanks
• Easy assembly, even at elevated heights
• NO CRANES REQUIRED
• Robust steel tank with high life expectancy
• Replaceable liner allows for extended life
Work is surging ahead on the new Mabunyaneng and Khubelu river bridges forming part of the Lesotho Highlands Water Project Phase II Polihali Dam programme.
Driving this progress is the Concor-Nthane Brothers M&K Bridges Joint Venture, which began work in January 2024 on the two structures. The bridges will provide crucial access to the town of Mokhotlong once the existing roads and tracks are inundated by the Polihali reservoir. The current road network is being realigned to accommodate the expected full supply water level of this dam.
The Khubelu Bridge will comprise nine spans of 30 m each
In terms of dimensions, the Khubelu Bridge will comprise nine spans of 30 m each, while the bridge across the Mabunyaneng River will have four 30 m spans. Both bridges will have two abutments and will be 13,5 m wide.
“The basic design includes standard pillar type piers, with a pier head to receive the precast beams; completed by a reinforced concrete deck,” explains Concor Contracts Manager, Jaco Verreynne.
At the Khubelu Bridge, piers are dowelled into competent rock while the abutments each receive 12 piles. However, while the one abutment on the Mabunyaneng Bridge is on competent rock and can be dowelled, the other will be piled – as will the piers. The pile depth is between 8 m and 12 m.
“Another component of the project is a reinforced earth wall at the eastern abutment of the Mabunyaneng Bridge, where a vertical wall is being built next to the new road to accommodate traffic during bridge construction,” Verreynne continues. This retaining wall is about 8 m high and 180 m in length.
The Concor-Nthane Brothers M&K Bridges Joint Venture has also been tasked with several road cuttings involving blasting and earthworks.
Bypasses are also being constructed at the outer abutments to allow traffic to continue as some of the bridge abutments are in the existing road.
Precast beams are being manufactured on site close to the project’s concrete batching plant, allowing the beams to be transported just 1 to 2 km to the bridges. There will be a total of 91 beams cast – 28 for the Mabunyaneng Bridge and the balance for the Khubelu Bridge.
“We will manufacture and stress the beams on site, using two 275 tonne cranes to move these onto bogey-type trucks with self-steering dollies,” Verreynne explains. “This will allow us to navigate the turns in the road as we transport the beams to the bridge areas.”
Cement and fly ash for the concrete is ferried by road to site, with aggregate coming from a source near the Senqu Bridge as well as from local suppliers.
“By the end of the project, we will have used about 11 000 m3 of concrete for the two bridges, with another 2 000 m3 for the temporary works that we executed in establishing infrastructure such as the batch plant and gantry crane,” adds Verreynne.
The bridges are scheduled for completion in October 2025.
Precast beams are being manufactured on site close to the project’s concrete batching plant, allowing the beams to be transported just 1 to 2 km to the bridges
Designed and installed to prevent back-flow, check valves play an essential role in pressure management optimisation on bulk water transfer networks. However, where they fail to perform as intended, this can cause severe water hammer, resulting in pipeline damage. Here multiple stage air release and vacuum break valves provide an effective solution. The extent of this, however, will depend on the pipeline dynamics and the check valve derivatives installed. By Peter Telle
Water hammer typically occurs when there’s a sudden closure of one or more check valves, resulting in unintended water column reversal. Due to reverse flow, the valve will move into the closed position in a very short space of time – a phenomenon known as slamming.
To avoid this hydraulic shock, a check valve should reach the closed position as soon as the flow stops and before the column reverses. Where water hammer does occur, there are a series of ripple effects. There’s an immediate pressure rise at the initial downstream side of the check valve. Simultaneously, a pressure drop occurs at the initial upstream side of the valve.
This pressure drop can be so large that a vapour bubble will grow at the initial upstream
side of the valve. The disappearance of such a vapour bubble then causes a further and sudden pressure spike, which may lead to a reopening of the valve. The second closure of the valve may again reach excessive vapour pressure levels, thus leading to a repeat of the slamming effect.
The solution is to install anti-shock air release and vacuum break valves before and after the check valves. This will have the following effect:
This valve will allow the intake of a relatively large volume of air into the pipeline downstream of the check valve due to possible column separation. The intake of air will cease as soon as the column loses momentum and
stops. This will have the effect of breaking any negative pressure that may occur on the downstream side of the valve or for that matter across the valve.
On reversal of the column – and assuming that the check valve is in the closed position – the air will be released in a controlled manner due to the cushioning effect of the non-slam function.
This valve will prevent the formation of any possible negative pressures that occur on the upstream side of the valve (like a vapour bubble). This valve will also assist with the initial controlled release of air when filling the pipeline; the check valve will initially be in the closed position due to the pressure exerted by the column downstream.
There are numerous check valve types on the market and careful selection will result in fewer problems. The rule of thumb is that the further the valve closing member needs to travel from fully open to fully closed the greater the potential for water hammer. (The greater the return velocity, the greater the water hammer potential.)
For convenience we start with the worst offenders and finish with the most effective. The scoring used is from 10 (the worst) to 1 (the best) on our “Water Hammer Potential Scale”.
Ball check valves require less velocity to “float” the ball out of the flow path. However, they will react extremely slowly to reverse flow and are therefore the worst offender, scoring a 9. These valves do not suffer from turbulent flow and have a relatively low head loss, but they are seldom used in critical applications.
Conventional swing check valves require at least 3m/sec. velocity to be in the fully open position. The “door” has a top mounted hinge assembly and therefore the greatest distance to travel from open to closed – increasing the potential for flow reversal and the sudden stopping of the column.
An Alpine nozzle check valve. Nozzle check valves are among the best options for optimum water hammer reduction and low head loss
The use of lever and weight and/or lever and weight with hydraulic damper has minimal effect on alleviating the water hammer potential. Additionally, these valves must not be fitted directly after a pump or bend. Overall, this valve scores a 9.
disc check valves
Tilting disc check valves with lever and weight also require at least 3m/sec. velocity to be in the fully open position. The “disc” has a centre pivoted disc and therefore has a relatively long distance to travel from open to closed. The fitting of a lever and weight assists with the closing cycle but has minimal influence on the speed of closure. These valves should also ideally not be fitted directly after a pump or a bend. This valve scores a 7.
seat check valves
Slanted seat check valves require at least 2.5m/sec. velocity to be in the fully open position. The valve has an off the centre line pivoted disc and therefore has a shorter distance to travel than the types mentioned above from open to closed.
The fitting of a hydraulic damper decelerates the disc before it reaches the fully closed position, allowing a small amount of reverse flow but still helping to alleviate water hammer. This valve should also ideally not be fitted directly after a pump or a bend. On the scale, this one scores a 5.
Double door check valves
Double door check valves require approximately 1.5m/sec. velocity to be in the fully open position. The discs are hinged in the centre and therefore have a relatively short distance to travel from open to closed; thus, the potential
for flow reversal and the sudden stopping of the column is reduced. These valves are also not suitable for fitting after pumps or bends and should be at least 10 X ‘D’ from any source of turbulence.
As an aside, this type of valve has been extensively copied following its first introduction by a leading USA manufacturer in the 1950s. The valve remains available to this day as a trade marked product. There are subtleties in the design of the hinges and springs that most copies simply do not appreciate. Performance wise, this one scores a 4.
Silent check valves require approximately 1.5m/sec. velocity to be in the fully open position. The discs move axially (like a piston) and therefore have a relatively short distance to travel from open to closed, so the potential for flow reversal and the sudden stopping of the column is substantially reduced.
Furthermore, these valves are suitable for fitting after pumps or bends and need not be 10 X ‘D’ from any source of turbulence. Additionally, these valves have a relatively low head loss, which saves on pumping costs. This is a great valve option and scores 2 on the scale.
Diaphragm check valves
In terms of this valve design, the diaphragm retracts from a centreplate that has machined
An Ultra diaphragm check valve. The inherent elasticity in the rubber diaphragm ensures a quick closure and with dampening due to the stretch of rubber into the holes
holes in it and a centre torpedo around which the diaphragm seals. The inherent elasticity in the rubber diaphragm ensures a quick closure and with dampening due to the stretch of rubber into the holes. This valve is another excellent option and scores a 2.
Nozzle check valves require approximately 2m/sec. velocity to be in the fully open position. The discs move axially (ring type disc) and therefore have a relatively short distance to travel from open to closed. They are suitable for fitting after pumps or bends and need not be 10 X ‘D’ from any source of turbulence. The valves have a relatively low head loss which saves on pumping costs and tops our scale with a score of 1.5.
Water pipelines are designed to perform under pressure, and the optimum goal is to avoid intermittent “stop-start” scenarios, aside from the need for routine maintenance interventions and emergency repairs when pump systems go down.
In all instances, check valves are there to ensure that utility operators have ultimate control. In this respect, multiple stage air release and vacuum break valves add an extra layer of protection. That is especially important for ageing pipeline infrastructure, which is far more vulnerable to the causes and effects of water hammer. Ultimately, the same principle applies to new construction works in achieving the best return on asset investments.
As a technology partner, Dynamic Fluid Control’s (DFC’s) RGXII air valve solution forms an integral component of Siza Water’s process optimisation. Kimolin Venkatasen, Maintenance Manager at Siza Water, expands on the wastewater efficiency gains.
How has Siza Water's adoption of RGXII technology helped improve sewage management?
At Siza Water, we are committed to delivering high-quality services by investing in innovative solutions that enhance efficiency and reliability. The implementation of RGXII air valves has significantly improved sewage management by optimising air regulation within our pipeline network.
By preventing air entrapment, these valves reduce the risk of blockages and pressure surges, ensuring a stable and efficient system. Their advanced design contributes to energy conservation and improved pump performance, which aligns with our goal of delivering innovative solutions while maintaining highquality infrastructure. The result is enhanced operational efficiency, reduced maintenance demands, and uninterrupted service to the communities we serve.
What were the main challenges that you faced before partnering with DFC, and how were they addressed? Before partnering with DFC, we encountered
challenges related to air accumulation in pipelines, leading to inefficiencies, pressure fluctuations, and increased strain on critical infrastructure. Traditional air valves required frequent maintenance and were prone to premature failure, causing operational disruptions. The RGXII air valves addressed these issues through cutting-edge design, incorporating a self-cleaning mechanism, corrosion-resistant materials, and superior sealing capabilities. These enhancements have significantly reduced maintenance interventions, ensuring a more reliable and high-performing water and wastewater system that consistently serves our customers and stakeholders.
Can you describe the impact of the RGXII air valves on pipeline reliability and maintenance schedules?
Reliability is a key focus at Siza Water, and the RGXII air valves have played a critical role in improving system resilience. By ensuring optimal air release and preventing vacuum formation, these valves protect our pipelines from structural damage and reduce the risk of leaks. The RGXII boasts low pressure sealing capabilities of 7Kpa (1Psi), with a patented design that ensures reliable sealing. This helps us extend infrastructure lifespan by lowering maintenance costs and minimise disruptions. The durability and efficiency of these valves have optimised our maintenance schedules, allowing our teams to focus on proactive improvements rather than frequent reactive repairs, ultimately benefitting the communities we serve.
How has the partnership with DFC influenced Siza Water's ability to serve the community effectively?
At Siza Water, we prioritise people-centric solutions by working with trusted partners who share our commitment to operational excellence. Our collaboration with DFC has enabled us to implement high-quality, innovative products that enhance system performance and reliability. Their technical expertise and responsive support have strengthened our ability to reduce operational challenges, allowing us to allocate more resources toward infrastructure expansion and service reliability. This has resulted in a more sustainable and efficient water and sewage system for our community.
What roles do innovative technologies like the RGXII air valves play in Siza Water's long-term strategic goals?
Innovation is at the heart of Siza Water’s strategy, and we continuously seek advanced solutions that enhance system efficiency and reliability. Technologies such as the RGXII air valves align with our commitment to delivering high-quality water infrastructure by reducing energy consumption, minimising maintenance costs, and ensuring the long-term sustainability of our operations. As we modernise our network, these innovations play a crucial role in enhancing service delivery, reducing water losses, and maintaining a resilient infrastructure that meets the needs of our growing communities.
How does Siza Water support the country's broader goals for sustainable water infrastructure?
Siza Water is dedicated to sustainability and responsible water management. We contribute to national sustainability goals by investing in modern, high-performance infrastructure that optimises water conservation, reduces environmental impact, and improves operational efficiency. By incorporating cutting-edge technologies like the RGXII air valves, we reduce energy consumption and extend the lifespan of our infrastructure. Additionally, our peoplefocused approach ensures that communities
have access to reliable and sustainable water services, aligning with the broader goal of securing South Africa’s water future.
What feedback has Siza Water received from the community or stakeholders regarding the improvements in water and sewage services?
The response from the community and stakeholders has been positive. Residents have noticed fewer service disruptions, and enhanced wastewater management. Additionally, the reduction in emergency maintenance incidents has strengthened stakeholder confidence in Siza Water’s ability to deliver consistent and high-quality services.
Could you share an example of a specific project or system upgrade where RGXII valves were instrumental?
One of our key projects involved upgrading a major sewage pump station that was experiencing frequent air entrapment issues, leading to inefficiencies and increased maintenance costs. By integrating RGXII air valves into the system, we successfully
RGXII air valves feature a cutting-edge design, incorporating a self-cleaning mechanism, corrosion-resistant materials, and superior sealing capabilities
eliminated pressure surges, improved pump efficiency and reduced downtime. This upgrade has resulted in a more reliable and cost-effective sewage management process, improving service delivery to thousands of customers.
What lessons have you learnt from this partnership with DFC, and how might it influence future collaborations or innovations?
Our collaboration with DFC has reinforced the importance of choosing the right partners who share our commitment to quality and innovation. We have learnt that investing in advanced technologies not only improves efficiency but also reduces long-term operational costs. This experience will guide our future
collaborations, ensuring we continue to prioritise durable, high-performance solutions that enhance infrastructure resilience. Additionally, the ongoing support and expertise from DFC have highlighted the value of strategic partnerships in driving long-term success.
What advice would you give to other utility providers considering advanced pipeline solutions like RGXII air valves for their operations?
For utility providers looking to improve pipeline efficiency and reliability, we strongly recommend investing in advanced air valve solutions like the RGXII series. These valves provide exceptional performance, lower maintenance costs, and ensure long-term system stability. It is crucial to align technology investments with sustainability goals and infrastructure longevity. Furthermore, selecting a trusted partner like DFC ensures that implementation is seamless, and ongoing support is readily available, maximising the benefits of these advanced solutions.
As South Africa marks National Water Week (20 th to 26 th March 2025) and World Water Day (22 nd March 2025), citizens are urged to use water sparingly and support initiatives aimed at conserving the country’s most precious resource.
With the theme of this year’s campaign focused on educating the public about water conservation, urgent attention is also being drawn to the deteriorating state of municipal water infrastructure and the pressing need for investment in high-quality piping solutions to ensure water security for future generations.
Water crisis in South Africa:
A looming threat
Towns and cities throughout South Africa have been experiencing frequent and widespread water outages, particularly in early summer when demand rises with higher temperatures. According to the National Department of Water and Sanitation’s (DWS’s) Water Security Dashboard (www.dws.gov.za) the balance between supply and demand is expected to persist until the completion of Phase II of the Lesotho Highlands Water Project, the Polihali Dam, scheduled for 2028. Additionally, years of underinvestment in municipal infrastructure have led to
declining service levels, with theft, vandalism, and loadshedding further exacerbating the crisis.
A significant concern is the high level of municipal water losses, which includes both non-revenue water (NRW) – water that is pumped but not paid for – and real or physical losses, which refer to water lost through leaks and system failures. In Johannesburg, for example, NRW currently stands at a staggering 46%, while the figures for Ekurhuleni and Tshwane are 30% and 36%, respectively. Real losses, which should be below 15%, are currently at 35% in Johannesburg, 28% in Ekurhuleni, and 33% in Tshwane. With approximately 500 leaks reported in Gauteng metros daily, urgent infrastructure maintenance and upgrades are needed to stem these losses.
The role of high quality pipes in water security
Jan Venter, CEO of the Southern African Plastic Pipe Manufacturers Association (SAPPMA), highlights the critical role of reliable water infrastructure and the importance of using high quality pipes that meet international standards.
“Our country is facing a water crisis that is worsening every year due to infrastructure failures and excessive water wastage. The only way to ensure a sustainable water future is through urgent investment in durable, high quality water infrastructure,” Venter explains.
“It is crucial that municipalities specify the use of only pipes bearing the SAPPMA logo in all water repairs, upgrades, and installations. This guarantees that the pipes meet international quality standards and will not fail prematurely, leading to further water losses.”
To enforce these standards, SAPPMA continues its Operation Superior Quality, which includes ongoing unannounced audits and strict compliance checks to ensure that only the best quality pipes are used in South Africa’s water infrastructure projects.
Collaborative efforts to strengthen water security
The DWS, in collaboration with Rand Water and Gauteng municipalities, has been working on a coordinated response to address water supply challenges since 2022. In June 2024, the Platform for a Water Secure Gauteng (PWSG) was established to bring together public sector entities, private sector stakeholders, and civil society to tackle the crisis collectively.
In his 2025 State of the Nation Address, President Cyril Ramaphosa acknowledged the dire state of municipal services, including disruptions to water and electricity supply, neglected roads, and failing sanitation systems. He announced that national government would begin working with municipalities to establish professionally managed, ring-fenced utilities to ensure sustained investment and maintenance of water and electricity infrastructure.
Ramaphosa further outlined plans to review the municipal funding model, as many local governments lack a sustainable revenue base. The government is engaging financial institutions and investors to unlock R100 billion in infrastructure financing, with revised regulations for public-private partnerships (PPPs) aimed at mobilising private sector expertise and funding.
Over the next three years, government has pledged to allocate over R940 billion to infrastructure development, with R375 billion earmarked for spending by state-owned enterprises (SOEs). This funding is intended to revitalise roads, bridges, dams, and waterways, modernise ports and airports, and support economic growth. The Infrastructure Fund has already approved 12 blended finance projects worth nearly R38 billion over the past year.
However, SAPPMA remains cautiously optimistic about these promises. “We sincerely hope that these commitments do not become yet another set of empty promises and failing pipe dreams. South Africa desperately needs substantial investment in its water infrastructure, and we need to see genuine political will to see these projects through,” says Venter.
A call to action for water conservation
While systemic changes and infrastructure investments are necessary, individual and collective action remains crucial in addressing the current water crisis. Citizens, households, and businesses must actively participate in water conservation by reducing consumption, fixing leaks, and using water-efficient technologies.
As South Africa observes National Water Week, the message is clear: every drop counts, and every pipe matters. “Through proper infrastructure investment, improved municipal management, and responsible water usage, we can safeguard South Africa’s water future for generations to come,” Venter concludes.
For more information visit www.sappma.co.za.
SAPPMA is an Association of leading companies in the plastics piping business, with the purpose of facilitating high standards of ethics, product quality and technical information. It is an open association, registered as a non-profit Section 21 Company and is well regulated by strong Articles of Association and Code of Conduct.
01
SAPPMA represents more than 80% of the plastic pipe market in Southern Africa and is the only representative plastic pipe forum in the country. Members have a collective voice at engineering associations, consulting engineering firms, municipalities, water authorities and contractors and are also afforded valuable networking opportunities, social interaction and enjoy a sense of community.
SAPPMA members have access to objective, expert information on technical matters by way of personal consultations, technical publications, industry conferences and webinars and market survey results/reports.
02
03
Members have free access to the latest product and SANS standards, quality systems and test procedures, test facilities, monitoring and quality control and have representation at SANS Technical committees and other certification authorities.
Members who are pipe producers and installers are set apart from other players in the market by passing the SAPPMA factory audits and adherence to the SAPPMA Code of Conduct.
05
04
& COMMUNICATION
The SAPPMA mark on a product has become a soughtafter quality guarantee that gives customers and end-users the peace of mind that their product meets local and international quality standards. Members are therefore supported by an established brand that is solely aimed at protecting the customer and the infrastructure of the country, as communicated through our marketing and advertising campaigns.
THE FOLLOWING BUSINESSES AND INDUSTRIES CAN QUALIFY FOR A SAPPMA MEMBERSHIP:
• Pipe & fittings manufacturers
• Raw material suppliers
• Consultants
• Construction companies
• Municipalities
• Water Boards
• Contractors & Installers
• Individuals
In 1858 the first comprehensive investigation into fatigue failure in materials was conducted by German engineer August Wöhler and became known as the Wöhler Curve or S–N Curve. This measures the relationship between the applied cyclic stress S and the number of cycles to failure N. It is usually plotted as S vs. N, S vs. log N, or log S vs. log N.
By Mike Smart Pr Eng*
For thermoplastic pipe materials, there’s a distinctive S–N Curve in each instance that determines its ultimate structural performance. Let’s use the example of a polyethylene (PE) polymer test sample (as shown in Graph 1) – plotted in S vs. log N format – to illustrate the point.
Here the Alternating Flexural Stress at 10⁷ load cycles is the Flexural Fatigue Strength of 18.5 N/mm²: the Fatigue Limit or Endurance Limit of a PE polymer. The Fatigue Strength of most thermoplastics is about 20-30% of the Ultimate Tensile Strength (UTS) in short-term tensile tests.
GRAPH 1
The stress cycle frequency is limited to 10-30 Hz (DIN 50014) to prevent increase in temperature caused by internal friction.
With the Fatigue Strength from alternating bending stress, the Fatigue Strength from Pulsating Bending Stress and the Flexural Creep Strength recorded, the Smith Fatigue Strength Diagram is constructed as the next step. As shown in Graph 2, this illustrates that the sample failed at +23 N/mm² after 10⁷ cycles.
At the 45° line, at a Mean Stress of 15 N/mm², the stress amplitude is +15 N/mm²; excluding the stress amplitude 26.5 N/mm² is the
Rupture Strength. This is the Creep Strength at 278 hours (10⁷ cycles at 10 Hz) because the stress is no longer cyclic at this point. A higher frequency will move the point towards the origin and represent the Creep Strength for a shorter time at a temperature higher than 20°C caused by internal friction.
Therefore, the Fatigue Limit for a PE thermoplastic may be taken as 10⁷ cycles; an occurrence every six minutes throughout the 50-year design life of a PE pipe gives 4.38 x 10⁶, less than half this value. Thus, the strength at 10⁷ cycles may be taken as 25% of the polymer’s UTS.
Pressurisation and PVC
Thermoplastics respond to high rates of loading by exhibiting greater strength and stiffness, because the entangled molecular structure resists deformation. At higher rates of pressurisation pipes resist the higher surge stress levels better because the material’s strength increases with higher rates of loading.
GRAPH 3
At typical surge pressure increase rates of 0.1 to 10 bar per second, all thermoplastic pipes have strength significantly greater than their static stress ratings. Therefore, rapid pressure increase associated with surge is not a problem.
Many random high-pressure surges do not cause fatigue problems, and the allowable maximum pressure peak must be specified (EN 805). With high rates of pressure rise (surge) thermoplastic pipes generally withstand >2 x PN. Stress ranges (R ratios) of 0.1 to 0.5 make a negligible difference to the lifetime of the pipeline. Stress range, not peak stress, is the primary influence on the time/cycle failure. Therefore, stress ranges (R ratios) are used to compare fatigue data at 1 Hz for PVC-U, PVC-M and PVC-O samples of similar thickness.
There is limited evidence of brittle growth on the fracture surface that exhibits the stress whitening associated with ductility. Graph 3, plotted as log N vs. log S for different PVC types shows an excellent consistency, and all, except PVC-O have identical fatigue characteristics and exhibit a
“knee” in the graph. PVC-O has greater fatigue resistance and hence a higher Fatigue Re-rating Factor.
Design
The number of fatigue cycles relevant to water supply systems is generally less than 25 000, one every 17.52 hours, for the 50-year design life. The number of fatigue cycles being >25 000 is rare in water supply systems (ISO/TR 4191). However, if this figure is considered too low, Table 1 contains Fatigue Re-rating Factors for daily occurrences from 4 to 1 200. The latter is an event every 72 seconds.
Therefore, knowing the Stress Range (R ratio) of the system and the expected frequency of events, the Required Pipe Class (PN) can be obtained as follows:
Required Pipe Class (PN) = Stress Range (R ratio) x Re-rating Factor (FR)
TOM®500 PVC-O
The design of all thermoplastic pipes is based upon the Creep Rupture Regression Curves (CRRC) for the polymer. The Minimum Required Strength (MRS) at 50 years (438 000 hours) is divided by C (Design Coefficient) to obtain σ (Allowable Design Stress), that is σ = MRS/C.
In Graph 4 the blue curve is TOM®500 PVC-O, which must have a minimum MRS of 50 MPa at 50 years (438 000 hours) to be
Classification 500 material; it is approximately 55 MPa. Furthermore, it is approximately 53.8 MPa at 100 years (876 000 hours) thereby proving it has a service life greater than 100 years.
A proprietary innovation of the multinational Molecor group, headquartered in Spain, TOM®500 PVC-O is manufactured in South Africa by technology partners Sizabantu Pipe Systems at the latter’s factory within the Richards Bay Industrial Development Zone. Recent factory upgrades will now enable the production of TOM®500 PVC-O pipes from DN 110 to DN 1 200 mm OD in all pressure classes from PN12.5 up to PN25 in accordance with the new ISO 16422 standard.
Conclusion
PVC-O is superior to other thermoplastic pipe material for use in fatigue applications. TOM®500 PVC-O takes this a step further as the best performer compared to other Classification 500 PVC-O pipe. That translates into outstanding durability.
*Head of Genesis Consulting
For further information, contact the author at +27-82-555-2065 or email mike@genesislabour.co.za
Hall Longmore is recognised as one of the leading steel pipe manufacturers across the globe with our products being installed across most of Sub-Saharan Africa, Nigeria and beyond to locations such as Australia and the oil fields of Texas. In 2024 we celebrated our first 100 years of supplying to South African industry and infrastructure and, while we are rightly proud of this achievement, it is to the future and the next 100 years that we are focused on.
With factories in Duncanville, Vereeniging and Wadeville, Germiston Hall Longmore has the widest manufacturing range (8″ – 100″) of all the Southern African producers, married to which is the most comprehensive range of corrosion protection solutions.
To enhance our pipe making capabilities we offer a wide range of “value add” processes over and above the more recognised coatings and linings, including the aforementioned VeP and epoxy systems, such as Reinforced Cement Mortar weight coating, Polymer Modified Bitumen (PMB) Fusion Bonded Epoxy and others. With
Hall Longmore has always been at the forefront of steel pipe technology with a number of South African firsts in the fields of pipe making technology and pipe corrosion protection. These include the introduction in the 1970s of the ERW manufacturing process for pipes in the range of 8 ″ to 18 ″ - subsequently upgraded to accommodate 24 ″ - and internationally accepted corrosion protection systems such as Three Layer Polyethylene (3LPE) and Medium Density Polyethylene (MDPE).
More recently we have introduced digital real-time X-ray inspection on SAW-H manufactured pipe and a number of innovative corrosion protection solutions such as Visco-elastic Polyisobutane (VeP) and various wet coat epoxy systems favoured by the mining industry.
regard to pipe end details, over and above the standard bevel and Bell end joints which require welding on site (and the required skill set which that entails) we also offer flanged, coupled, Rubber Ring Joint systems (RRJ) and, our most recent innovation, a Spherical Slip-in Joint with heat sink. The latter allows the welding of epoxy lined pipes without the need for internal lining rehabilitation at field joints.
While our project legacy boasts some of the most important infrastructure supplies of the past 100 years – some of the more recent include:
In the short to medium term we can expect movement on major projects in the following regions:
• Mpumalanga
• Limpopo
• KwaZulu-Natal
• Gauteng
• Eastern Cape
And in the medium to long term:
• Eswatini
• Northern Cape
• Namibia
• New Multi Product Pipeline (NMPP) for Transnet
• North South Carrier 1 for Botswana Water Utilities
• Gauteng Network Pipeline (GNP) for Sasol
• Western and Northern Aqueducts for eThekwini Water & Sanitation
• Multiple installations for DWS, uMngeniuThukela Water, Rand Water and Magalies Water.
It is to the future that we look for continued growth and innovation and more than a little optimism for the company in particular and the industry as a whole.
Production of the highly anticipated Bell motor grader range will begin in Q3 2025 for Stage 3 developing markets. Designed to meet the evolving needs of the industry, the new machines promise to deliver high productivity and precision accurate control with superior operator station ergonomics and visibility.
According to Bell Equipment
Product Manager, Jeremiah Mokhomo, the company has drawn upon its 70 years of design and manufacturing experience and spent years of expensive research and development to ensure that Bell graders are able to demonstrate their capabilities in a variety of demanding applications.
Highlighting the grader’s robust design and reliability, he says: “Grading applications demand a powerful and dependable machine that can consistently deliver precision and efficiency. Our new Bell motor graders have been rigorously tested to ensure they meet the highest industry expectations. We are confident that they will compare favourably with established industry leaders.”
A versatile product for international markets
The Bell motor grader range consists of three base models, each available in either a 4WD or 6WD configuration. The G140, which will be on display at bauma 2025 in April, is well suited to all maintenance and light to medium construction tasks. The G160, with its increased power and performance, is designed to handle heavy construction applications, while the G200 is designed for bulk earthworks and the mining industry.
Jeremiah explains: “From the outset, we factored in the requirements of a six-wheel drive configuration. This early integration, as opposed to trying to add it to the platform later, has resulted in a better-performing, more controllable, and robust machine that is easier to maintain. The significant improvement in performance achieved by adding front-wheel drive is only useful if it is reliable for the life of the grader, so we have invested time to make sure this is the case.”
Bell motor graders are powered by Cummins engines paired with ZF transmissions. The Bell G140 is fitted with a 6.7ℓ Cummins engine and ZF ERGOPOWER transmission, while the larger G160 and G200 are driven by a 9ℓ Cummins engine with the ZF cPOWER transmission.
Jeremiah says: “The Cummins engines are known for their quiet operation, fuel efficiency, low maintenance, and reliability, and they met
our expectations during testing. Additionally, these engines are Stage 3A certified, do not require exhaust gas recirculation (EGR), and are compatible with both hydrotreated vegetable oil (HVO) and B20 biodiesel. Stage 5 graders will be launched in time and will meet the EU and USA emission regulations.
“The ERGOPOWER transmission is well respected in the grading application for entrylevel units and we’re particularly excited about the hydro-mechanical transmissions in the larger models, which are new for the industry and are performing exceptionally well for us in heavier duty applications.
“The Bell grader is a truly global product, engineered to meet different international emission standards and operator control preferences. The staged global rollout will commence in Africa, South America and Southeast Asia followed by North America and Europe later.”
Built for the toughest challenges
Drawing on over two decades of experience in the supply, maintenance, and repair of motor graders, along with insights from industry experts, Bell Equipment has developed a clear view of what is important to make this product work. While retaining familiar controls and layouts, the Bell motor grader incorporates a range of advanced components and features that will help operators to improve productivity, accuracy, maintain costs, and deliver work efficiently.
As Bell has achieved success with its ability to intelligently automate specific functions within the ADT industry, automation also played a key role in the motor grader design process. This automation allows the operator to focus on precision grading while benefitting from improved fuel efficiency and extended component life.
Recognising the diverse range of applications and often remote uses of motor graders, Bell has standardised on high-quality, low-maintenance components, such as a fully sealed circle bearing. This allows extended service intervals and consistent grading performance without the need to make regular adjustments. To further simplify operations, advanced diagnostics are incorporated into the machine to reduce the complexity of daily checks and servicing. Utilising industry-leading components for all systems has been instrumental in achieving an efficient and robust machine. “Getting
established components to work well together is what our system engineers do well, and in a highly operator-sensitive product like a motor grader, we knew that we had to get the overall feel 100% right,” Jeremiah explains.
Importantly, Bell Equipment’s focus on durability across all structures ensures that the Bell grader’s gooseneck main frame –engineered as a single piece construction to eliminate fatigue on fabricated joints – will give maximum confidence in hard applications.
In addition, the tandem axle, with enhanced bearing life and interaxle cooling, provides reliable performance in long-haul applications.
Proven performance in real-world applications
Bell Equipment’s test and pre-production demo graders have been operating with great success in a wide variety of applications, from landscaping, heavy ripping, and final levels to overall road construction.
Bell has standardised on high quality, low maintenance components, such as a precision sealed circle bearing, which is standard across the range
Automation played a key role in the Bell motor grader design process and allows the operator to focus on precision grading while benefitting from improved fuel efficiency and extended component life
“It has been really pleasing to see the improvements in efficiency and performance identified during the design stage being confirmed on real-world job sites,” adds Jeremiah.
“We’ve been encouraged by the positive feedback we’ve received from expert advisers and operators who have experienced our preproduction machines. We’re excited to introduce the Bell motor grader and illustrate some of the advances we’ve made to a complicated piece of equipment,” Jeremiah concludes.
• Alkali-free set accelerators for shotcrete
• Products for mechanized tunneling: foaming agents for soil conditioning, polymers, sealants, lubrificants
• Products for grouting and consolidating
Learn more on www.utt-mapei.com, info@mapei.co.za
• Products for concrete repairing, protection and coating
• Products for waterproofing: synthetic waterproofing membranes, waterproofing accessories
Completed in April 2022, the 100 ML reservoir built at Contermanskloof, Cape Town, serves as an iconic example of the innovative application of precast construction to form the structure’s 14 500 m² roof. These precast elements, comprising I beams and hollow-core slabs, were purpose designed and fabricated by Concrete Manufacturers Association (CMA) member, Cape Concrete, with the works executed by CSV Construction.
The water storage unit is 160.5 m long and 90.9 m wide and its maximum water depth is 8.5 m. The structure comprises an in-situ 200 mm concrete floor flanked by 5.5 m high 1:2.5 sloping concrete embankments topped with 4.6 m high vertical retaining walls. The roof’s precast beam and hollow-core slab assembly is supported by 99 x 9 m (height) x 700 mm (diameter) in-situ concrete columns on elastomeric bearing pads.
The roof has an apex on the longitudinal centre line and slopes at 1:150 to the perimeter walling on either side for drainage. The first roof section was completed in August 2021 and the second was finalised in November 2021.
The hollow-core slabs are supported by 108 I beams and the perimeter walling.
The I beams measure 13,5 m (length) x 1.2 m (height) x 500 mm (base width) and the hollow-core slabs span 8.8 m (length) x 1.2 m (width) x 200 mm (thickness).
The roof comprises 48 panel sections. These consist of two or three hollow-core bays with 11 hollow-core slabs in each.
The panel sections are interlinked with transverse in-situ beams which run the full width of the structure; this creates larger panels and a more robust structure. Cast with a joint former between them, these beams also act as expansion joints.
In addition, the design includes three longitudinal expansion joints, which run the full length of the structure. They too are filled with a joint former inserted in the gap between the opposing panel sections located above the precast beams. All the expansion joints are waterproofed with a flexible bandage.
The roof includes a 70 mm mesh-reinforced structural topping cast over the panel sections to ensure proper shear transfer between individual slabs. The topping’s reinforcing was tied to the exposed reinforcing in the precast beams, which added continuity to opposing hollow-core bays in the panel sections and increased the overall continuity of the roof structure.
The reservoir structure was designed by Peter Loubser and the structural team of GIBB Engineering in 2016, acting as specialist structural sub-consultants to WSP, which was responsible for the overall contract. Initial site work was begun by a joint venture comprising NMC and Botes & Kennedy in 2017 but came to a halt in 2018 when both parties went into liquidation. Construction resumed early in 2021 when CSV Construction was appointed as the main contractor.
“We looked at the comparative costing of precast versus in-situ for the roof construction during the design stage, and precasting proved to be a significantly better option both in terms of cost as well as total programme time. In addition, it avoided the disruption that extensive support scaffolding would have caused,” said Loubser.
The roof includes several galvanised steel manholes to provide light during maintenance work inside the reservoir. Additional manholes are situated above the reservoir discharge and scour outlets for maintenance work.
Slab and beam production
Cape Concrete was awarded the contract to manufacture the beams and 1 358 pretensioned slabs in 2017. “We had already cast 98 beams at the time of the shutdown in 2018,” said Cape Concrete director, Walter Botes. “So, we decided to cast the remainder and store them in our yard until the project was resumed.”
“The beams were prestressed and were cast on a single 75 m soffit between the stressing heads. This enabled us to cast five beams on one soffit at a rate of one-a-day from Monday to Friday,” Botes continued.
“We used five sets of end plates and one set of side moulds – the latter being reused for each beam casting. The beams were steam cured so that the side shutters could be removed the day after casting. The beam cast on Friday reached 35 MPa on Saturday, which meant that all five beams were ready for de-tensioning.”
The roofing required 12 083 m of prestressed hollow-core slabs and Cape Concrete used four 150 m casting beds for their production in a strictly controlled quality protocol. They were cast with 12.7 m prestressed strands to yield a strength rating well above the required 50 MPa. Hot water was circulated under the casting beds to accelerate the curing process.
“The beams, which weighed 12,5 tonnes each, were installed with a 440 tonne crane with a 65 m reach operating from outside the reservoir. We also used a 220 tonne crane and a 180 tonne crane for the installation of the hollow-core slabs. During the installation of the first roof section the cranes were positioned 17 m away from the perimeter wall, which complicated the installation process,” Botes explained.
The reservoir was built with a sub-surface drainage system to disperse ground water. It comprises a layer of no-fines concrete under the slab together with a combination of perforated pipes that follow the grid lines and drain into a concrete gallery, which runs under the reservoir. All the pipes are clearly marked so that the source of any possible leakage can be identified.
The concrete columns were cast after the main floor slab had been completed, and the column reinforcing was tied in with the
slab reinforcing to transfer the load through the column base to the slab. The sloping concrete embankment slabs were cast in sections using a back shutter system to prevent the concrete from slumping towards the bottom of the slope.
Rubber water bars, which allow for movement and prevent leakage, were installed on all the joints in the flooring and walling, and prior to completion the joints were covered with a final waterproof bandaging system.
Furthermore, the embankments beneath the perimeter walling were cement-stabilised to improve bearing and shear capacity, and the outer walling was backfilled to a metre below the top of the wall. A service road was then subsequently built on top of the embankment.
Supplied by the Voëlvlei Dam and associated water treatment works via an existing delivery pipeline, the Contermanskloof reservoir now stands as an enduring structure ready to deliver for current and future generations.
AECOM
siphokuhle.dlamini@aecom.com
AFI Consult banie@afri-infra.com
ARRB Systems info@arrbsystemssa.com
Asla Construction (Pty) Ltd johanv@asla.co.za
BMK Group brian@bmkgroup.co.za
Bosch Projects (Pty) Ltd mail@boschprojects.co.za
BVI Consulting Engineers marketing@bviho.co.za
Camjet info.jhb@camjet.co.za
CCG puhumudzo@ccgsytems.co.za / info@ccgsystems.co.za
Civtech Engineers (Pty) Ltd admin@civtech.biz
Corrosion Institute of Southern Africa secretary@corrosioninstitute.org.za
Dlamindlovu Consulting Engineers & Project Managers info@dlami-ndlovu.co.za
EFG Engineers info@efgeng.co.za
Elster Kent Metering Mark.Shamley@Honeywell.com
EMS Solutions paul@emssolutions.co.za
ENsync Engineers info@ensync.africa
ERWAT mail@erwat.co.za
Gabion Baskets mail@gabionbaskets.co.za
GIBB marketing@gibb.co.za
GIGSA secretary@gigsa.org
GLS Consulting info@gls.co.za
Gorman Rupp Cordeiro@gormanrupp.co.za
Gudunkomo Investments & Consulting info@gudunkomo.co.za
Hatch Africa (Pty) Ltd info@hatch.co.za
HB Glass Filter Media info@hardybulkinglass.com
Herrenknecht schiewe.helene@herrenknecht.de
HSA Technology (Pty) Ltd cs@hubersa.com
Hydro-comp Enterprises info@edams.co.za
IMQS Software (Pty) Ltd shemine.adams@imqs.co.za
Infrachamps Consulting info@infrachamps.co.za
INFRATEC info@infratec.co.za
Institute of Waste Management of Southern Africa iwmsa@iwmsa.co.za
IQHINA Consulting Engineers & Project Managers info@iqhina.co.za iX engineers (Pty) Ltd hans.k@ixengineers.co.za
Izinga Holdings info@izingalabezi.co.za
JG Afrika DennyC@jgafrika.com
KABE Consulting Engineers info@kabe.co.za
Kago Consulting Engineers kagocon@kago.co.za
Kantey & Templer (K&T) Consulting Engineers ccherry@ct.kanteys.co.za
Kitso Botlhale Consulting Engineers info@kitsobce.co.za
KSB Pumps and Valves (Pty) Ltd salesza@ksb.com
KUREMA Engineering (Pty) Ltd info@kurema.co.za
Lektratek Water general@lwt.co.za
Loshini Projects muzi@loshini.co.za
m4a fagan@m4a.co.za
Makhaotse Narasimulu & Associates mmakhaotse@mna-sa.co.za
Mariswe (Pty) Ltd neshniec@mariswe.com
Martin & East gbyron@martin-east.co.za
M & C Consulting Engineers (Pty) Ltd info@mcconsulting.co.za
Mhiduve adminpotch@mhiduve.co.za
MPAMOT (Pty) Ltd mpumem@mpamot.com
Mvubu Consulting & Project Managers miranda@mvubu.net
Nyeleti Consulting naidoot@nyeleti.co.za
Prociv Consulting & Projects Management amarunga@prociv.co.za
Rainbow Reservoirs quin@rainbowres.com
Re-Solve Consulting (Pty) Ltd maura@re-solve.co.za
Ribicon Consulting Group (Pty) Ltd info@ribicon.co.za
Royal HaskoningDHV francisg@rhdv.com
SABITA info@sabita.co.za
SAFRIPOL mberry@safripol.com
SAGI annette@sagi.co.za
SALGA info@salga.org.za
SAPPMA admin@sappma.co.za / willem@sappma.co.za
SARF administrator@sarf.org.za.co.za
SBS Water Systems marketing@sbstanks.co.za
Silulumanzi Antoinette.Diphoko@silulumanzi.com
Siroccon International (Pty) Ltd admin@siroccon.co.za
SiVEST SA info@sivest.co.za
Sizabantu Piping Systems (Pty) Ltd proudly@sizabantu.com
Siza Water (RF) Pty Ltd PA@sizawater.com
Sky High Consulting Engineers (Pty) Ltd info@shconsultong.co.za
SKYV Consulting Engineers (Pty) Ltd kamesh@skyv.co.za
Smartlock jp.alkema@smartlock.net
SMEC capetown@smec.com
SOUTH AFRICAN VALUE EDUCATION Sabiha@savegroup.co.za
Southern African Society for Trenchless Technology director@sasst.org.za
SRK Consulting jomar@srk.co.za
Structa Group info@structatech.co.za
Superior Filtration (Pty) Ltd info@superior-filtration.com
TPA Consulting roger@tpa.co.za
Ultra Control Valves peter@ultravalves.co.za
V3 Consulting Engineers (Pty) Ltd info@v3consulting.co.za
Videx Storage Tanks sales@vidextanks.co.za
VIP Consulting Engineers esme@vipconsulting.co.za
VNA info@vnac.co.za
Water Institute of Southern Africa wisa@wisa.org.za
Wam Technology CC support@wamsys.co.za
Wilo South Africa marketingsa@wilo.co.za
WRCON ben@wrcon.co.za
Zutari charmaine.achour@zutari.com
Werner Pumps’ Impi 12 500ℓ combination vacuum and jetting truck is 100% locally manufactured at the company’s headquarters in Springs
Mogalakwena Municipality is putting its new Werner Impi 12 500 ℓ combination highpressure jetting and vacuum truck to good use to clear sewer lines and eradicate spillages.
Manufactured by Werner Pumps, this jetting unit forms part of a larger “yellow fleet” provided to the municipality by Mogalakwena Anglo Platinum Mine in terms of its social and labour plan.
Speaking at the unit’s handover, Mayor Ngoako Taueatsoala said the Werner Pumps unit will be invaluable for optimum sewer system maintenance. He said the municipality would work with ward councillors to ensure that sewage spills were an issue of the past. He also called on the people of Mogalakwena to report spillages timeously and to cooperate with the municipality in addressing them.
George Jolly, National Sales Manager at Werner Pumps, says the Impi unit is a popular choice for municipalities. It simultaneously allows sewers to be cleaned using a high-pressure water hose with a specialist jetting nozzle that dislodges waste and flushes it down the gully hole. From there, the waste is vacuumed up and deposited into a sludge tank via a suction hose.
“The cleaning of sewers with simultaneous jetting and vacuuming increases the efficiency of the line clearing process,” Jolly explains.
The Werner Impi unit has a capacity of 295 litres per minute and a maximum pressure of 135 bar. It also features a hydraulic slewing suction boom, two hydraulic-driven hose reels and multiple toolboxes.
Jolly says it’s gratifying to hear that Mogalakwena Municipality is able to improve service delivery, as well as sanitation, through the Impi truck. “We love seeing government officials excited about being able to serve their communities better, and being a part of that,” he adds. “We hope the truck serves the people of Mogalakwena Municipality well for many years to come.”
Through collaboration with Hearts in Hands Food Bank, the need for an upgrade at Lusana creche – a vital early childhood development (ECD) centre in rural KwaNgcolosi – is being realised.
This ambitious project will require the collective support of multiple stakeholders, sponsors, and donors to bring it to fruition. Makhaotse, Narasimulu and Associates (MNA) is proud to stand alongside Hearts in Hands Food Bank as one of the title sponsors, contributing towards the realisation of this vision.
Sthandiwe Mdlalose, a resolute young entrepreneur, leveraged her Business Administration Learnership and ECD certification to establish the creche in 2023, which now provides a nurturing environment for some 50 children aged 0-5 years. However, the existing facilities – while functional – are rudimentary and require a capital injection to modernise and enhance the learning experience.
This is where Hearts in Hands Food Bank has taken up the challenge, spearheading a campaign to attract donations and sponsorships from stakeholders within the surrounding community.
The upgrade project is split into two phases. Phase I focuses on the main building, which requires extensive internal and external refurbishment, including electrical wiring and lighting. In parallel, Phase II will entail allied building upgrades and extensions. These include a kitchen
and storage room; dedicated office space for administration; ablution facilities for children and staff; installation of water storage tanks; and a formal playground area.
Implementation of the various phases commenced in March 2025 for scheduled completion in October 2025, subject to available financial support.
For MNA, the project aligns with their operational philosophy as consulting engineers and project managers of designing and delivering solutions that uplift communities.
“We are honoured to stand alongside Hearts in Hands Food Bank as one of the title sponsors, supporting the realisation of this vision – one that aligns with MNA’s legacy of engineering excellence with purpose. It is a privilege to contribute to a project that transforms the lives of young learners, with the hope that it will inspire
and shape the next generation of engineers,” says Sagren Narasimulu, managing director and co-founding director of MNA, which celebrates its 25th anniversary in 2025.
Adds fellow co-founding MNA director, Martin Makhaotse: “At MNA we recognise that civil engineering is not just about constructing physical structures, but also about creating liveable spaces that empower future generations. As one of the leaders in the civil industry, we are committed to giving back in the regions where we work to address critical needs in underserved communities. A solid foundation in education shapes a brighter tomorrow.”
A testament to the power of collaboration, the Lusana creche upgrade continues to gain traction as more sponsors come on board, with the project team working towards completion and official handover in November 2025.
For further information visit www.facebook.com/heartsinhandsfoodbank
The RGXII boasts low pressure sealing capabilities of 7Kpa (1Psi), the patented design ensures reliable sealing in demanding sewage and wastewater applications
NSF/ANSI/CAN 61 certified
The float cage ensures easy cleaning
Valve Rated Pressure: PN16 (16 Bar)
Valve Test Pressure: 24 Bar (1.5 x PN Rating)
Valve Inlet/Outlet Sizes: DN50, DN80, DN100, DN150, DN200
We manufacture quality water meters and offer cutting-edge solutions to government, businesses and individuals.
Equipped for postpaid, prepaid, and AMI (Automatic Meter Infrastructure).
Pre-plumbed & pressure tested to ensure zero leaks.
Various NRCS approved water meters DN15 & DN20.
An internal 3-way (open/close/ trickle) SABS approved municipal ball valve is fitted upstream of the meter.
UV-stabilised lid for extra strength.
Keyed fittings to prevent rotation. Upgrade your postpaid meter to prepaid or smart without removing the entire unit.