
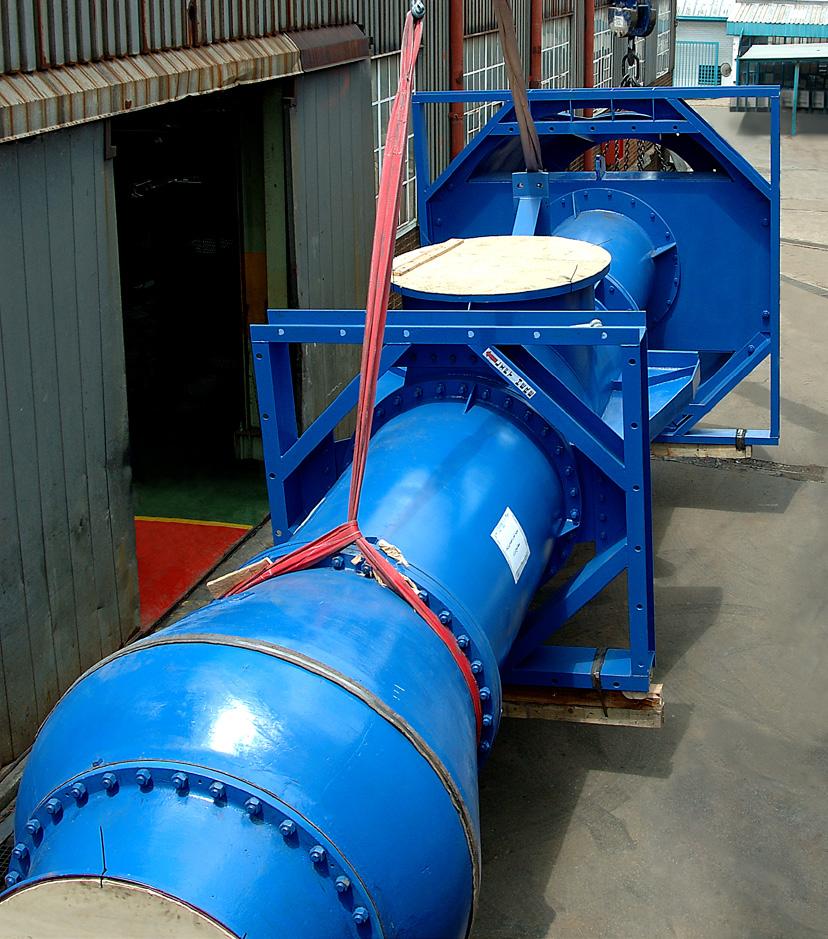
This revolutionary system delivers optimal performance while reducing your total cost of ownership. It also offers unparalleled flexibility and simplicity on a whole new level. You might even say it thinks for itself. We invite you to enter a new era in wastewater pumping with Flygt Concertor.
One powerful solution. Unlimited possibilities .
Delivering potable water to every household is one of the primary objectives in South Africa and worldwide. That requires sustainable and engineered responses that are interdependent on public and private sector collaboration.
IMIESA speaks to NJ Bouwer, executive at NuWater, about their workable solutions based on selecting the right choices. P14
7 - 9 June 2022 CTICC, Cape Town, South Africa
Gain FREE access to three days packed with strateic conference sessions and technical workshops.
Join facilitated matchmaking to help connect you with the right contacts as well as dedicated networking areas, meet and greets and social events.
Connect with the world’s leading products and services providers, from across the power, energy and water value chain, all under one roof.
MANAGING EDITOR Alastair Currie
SENIOR JOURNALIST Kirsten Kelly
JOURNALIST Nombulelo Manyana
FEATURES WRITER Ziyanda Majodina
HEAD OF DESIGN Beren Bauermeister
DESIGNER Lizette Jonker
CHIEF SUB-EDITOR Tristan Snijders
CONTRIBUTORS Solomon Kganyago, Isak Malherbe, Chetan Mistry, Gert Nel, Jonathan Schroder, Jacques Smith, Bhavna Soni, Altus Strydom, Jan Venter
PRODUCTION & CLIENT LIAISON MANAGER
Antois-Leigh Nepgen
PRODUCTION COORDINATOR Jacqueline Modise
GROUP SALES MANAGER Chilomia Van Wijk
BOOKKEEPER Tonya Hebenton
DISTRIBUTION MANAGER Nomsa Masina
DISTRIBUTION COORDINATOR Asha Pursotham
SUBSCRIPTIONS subs@3smedia.co.za
PRINTERS Novus Print Montague Gardens
ADVERTISING SALES
KEY ACCOUNT MANAGER Joanne Lawrie
Tel: +27 (0)11 233 2600 / +27 (0)82 346 5338
Email: joanne@3smedia.co.za
PUBLISHER Jacques Breytenbach
3S Media
Production Park, 83 Heidelberg Road, City Deep Johannesburg South, 2136
PO Box 92026, Norwood 2117
Tel: +27 (0)11 233 2600
www.3smedia.co.za
ANNUAL SUBSCRIPTION: R600.00 (INCL VAT)
ISSN 0257 1978 IMIESA, Inst.MUNIC. ENG. S. AFR.
© Copyright 2022. All rights reserved.
IMESA CONTACTS
HEAD OFFICE:
Manager: Ingrid Botton
P.O. Box 2190, Westville, 3630
Tel: +27 (0)31 266 3263
Email: admin@imesa.org.za
Website: www.imesa.org.za
BORDER
Secretary: Celeste Vosloo
Tel: +27 (0)43 705 2433
Email: celestev@buffalocity.gov.za
EASTERN CAPE
Secretary: Susan Canestra
Tel: +27 (0)41 585 4142 ext. 7
Email: imesaec@imesa.org.za
KWAZULU-NATAL
Secretary: Narisha Sogan
Tel: +27 (0)31 266 3263
Email: imesakzn@imesa.org.za
NORTHERN PROVINCES
Secretary: Ollah Mthembu
Tel: +27 (0)82 823 7104
Email: np@imesa.org.za
SOUTHERN CAPE KAROO
Secretary: Henrietta Olivier
Tel: +27 (0)79 390 7536
Email: imesasck@imesa.org.za
WESTERN CAPE
Secretary: Michelle Ackerman
Tel: +27 (0)21 444 7114
Email: imesawc@imesa.org.za
FREE STATE & NORTHERN CAPE
Secretary: Wilma Van Der Walt
Tel: +27 (0)83 457 4362
Email: imesafsnc@imesa.org.za
South Africa is widely recognised as a country admired for its Constitution and its strategic role within Africa and the world. Staying the course, however, depends on vibrant and ethical leadership, which – from an investor’s perspective – is especially important.
In this respect, the appointment of Raymond Zondo as South Africa’s new Chief Justice, effective 1 April 2022, sends a clear and positive message to the market. Zondo previously headed the Judicial Commission of Inquiry into Allegations of State Capture, Corruption and Fraud in the Public Sector including Organs of State. His appointment by President Cyril Ramaphosa signals a fresh approach to ironing out issues that have hampered development. Together with a strong and independent Reserve Bank and backed by an emerging alliance between the public and private sector, renewed attention on legal and policy frameworks is great news in terms of repositioning South Africa for sustained growth.
Blessed with a wide array of metals and minerals, South Africa’s mining sector remains one of our most important economic sectors, alongside agriculture and manufacturing. The same is equally true for construction, which, despite its continued negative ranking in terms of GDP, is our most significant enabler in support of all industry segments. Roads, transportation, water and sanitation are among the critical driving forces for macro- and microeconomic initiatives and, going forward, need special-purpose vehicles to prioritise their investment.
A prime example is government’s proposal to establish a National Water Resource Infrastructure Agency (NWRIA), which is the right step. Without a concerted focus on water, meaningful progress cannot be achieved.
According to a media statement, “The entity is envisaged to undertake the building, operation, financing and maintenance of national water resources assets, while the department retains responsibility for planning, regulation, policy and price setting.”
A key mandate of the NWRIA is to work with private
sector investors to ensure South Africa’s current and future water security. Given the generally poor state of the country’s water and wastewater plants, this provides opportunities for outsourced operations and maintenance – a practice common in both the developed and developing world.
The world remains invested in our economy, underscored by the 4th South Africa Investment Conference. Some 80 investment pledges were made, totalling some R332 billion.
Adding up the tally from all four conferences, the total amount of investment pledges now stands at approximately R1.14 trillion. Sectors include automotive, renewable energy, telecommunications, steel, and mining.
From an enabling and implementation perspective, South Africa’s municipalities have a crucial role to play, spurred on by programmes that include CoGTA’s District Development Model (DDM). The DDM is one of the key mechanisms geared towards unlocking capacity and crowding in investment within municipalities and the towns and cities they represent. In parallel are allied initiatives that include the Western Cape Provincial Government’s R10 million Municipal Ease of Doing Business Fund. According to a press statement, “Knysna, Hessequa, George and Drakenstein have already benefitted from the 2021/22 iteration of the fund, which focused on improving government-facing services in the construction and planning sector.”
Across the board, infrastructure investment is the basis for real growth, and the sooner this starts in earnest the better – for all stakeholders – so that South Africa can forge ahead with its Economic Reconstruction and Recovery Plan.
•
•
•
• brand representation at the event, promotion of your company in the conference proceedings magazine and online
• free entry for guests at the social evening and much more.
Sadly, Russia’s invasion of Ukraine shows how fragile our world can become in an instant, displacing communities, causing death and devastation to homes and infrastructure, and harming regional and global economies. This is already evident in South Africa and abroad as a major spike in oil prices results in escalating fuel and food inflation.
Within the global context, IMESA is a member of the International Federation of Municipal Engineers (IFME), which in turn forms part of the World Federation of Engineering Organisations (WFEO). Through its members, the WFEO represents engineers in some 100 countries.
On 6 March 2022, WFEO’s executive board approved a resolution at a meeting in San José, Costa Rica, in response to the Ukraine conflict, which IFME supports. Extracts from the resolution state:
• WFEO, as an associate NGO to Unesco and an NGO in consultative status to the UN Economic and Social Council, with the constitutional mission “to foster peace throughout the world”, values multilateral cooperation and dialogue, and supports all efforts, especially within the scientific and technological global community, which would facilitate a peaceful resolution of the armed conflict.
Achieving the UN’s Sustainable Development Goals is imperative for the preservation of our planet and the socio-economic well-being of its citizens. This is interdependent, however, on a unified front from every nation worldwide, which doesn’t factor in conflict – especially wars.
• WFEO calls for UN institutions and national governments to take every possible measure to protect human lives and to preserve civil infrastructure, schools, hospitals, transports, communications, food, and energy supply.
• WFEO has member institutions in both Ukraine and Russia, as well as in most neighbouring countries in Eastern Europe. We encourage them to maintain an open dialogue that will be in the best interest of their communities, and to support any initiative to provide assistance in the context of the humanitarian crisis, within and beyond the borders of Ukraine.
Within the context of a post-Covid-19 recovery, WFEO stressed the need for more integrated approaches to address climate change and build global resilience. “In such a context, the military confrontation is not only something that we all reject, from the engineers’ standpoint, it is something that no country and community in the world can afford,” WFEO stated.
Back at home, the role of engineers has never been more important in terms of supporting government’s reconstruction and development programme, with IMESA spearheading enabling initiatives in the municipal space.
One of our most important forums for public and private sector debate in this area is the annual IMESA Conference, which takes place between 2 and 4 November this year at the Birchwood Hotel and OR Tambo Conference Centre in Gauteng.
The 2022 theme is ‘Adapting to our changing world’, and delegate registration opens on 3 May. Since this is again a physical conference, we’re looking forward to a great turnout, with an excellent group of speakers, and vibrant indoor and outdoor exhibitions.
Let’s use the opportunity to help engineer a strong and prosperous South Africa as our contribution to building a better world. And for Ukraine, we pray for a speedy resolution.
In a world of change, excellence remains constant. In the case of APE Pumps and sister entity Mather+Platt, that translates into decades of quality, innovation and product leadership, with the Group celebrating 70 years in business in 2022.
As a Group, we’ve always invested in our people first and foremost, and this has paid major dividends for us over the years, resulting in the formation of long-term customer relationships and enabling us to progressively expand our footprint across South Africa, as well as further afield in Africa,” says John Montgomery, GM, APE Pumps and Mather+Platt.
A key factor that defines the Group’s commitment to the industries it serves is that a blueprint exists for every pump model it has manufactured. “That includes legacy products we inherited as a Group prior to our formation in 1952. A classic example is an approximately 100-year-old pump – imported from the UK – that we remanufactured for Rand Water based on the original drawings,” Montgomery explains, adding that Mather+Platt’s original lineage can be traced back to Great Britain’s First
Industrial Revolution in the late 18th century.
Today, of course, APE Pumps and Mather+Platt have embraced the Fourth Industrial Revolution with cutting-edge technologies that include telematics for the remote monitoring and control of pump health and performance. Advancements in metallurgical research have also resulted in improved casting techniques, as well as the strength and durability of key components like bearings and impellers. “However, the principles of pump technology remain the same,” Montgomery continues.
Dovetailing tried and tested techniques with modern technologies is a hallmark of APE Pumps and Mather+Platt’s success. Today, for example, the Group is one of the few OEMs that still has a pattern-making shop, headed by a master artisan.
While the Group has embraced 3D printing as part of its research and development initiatives, Montgomery says that nothing replaces the age-old art of handcrafted wooden moulds painstakingly perfected to meet the exact design tolerances of the final casting elements.
“Harnessing this capability, we can also replicate any pump where the original OEM is no longer trading, even where the drawings no longer exist,” he points out.
Going global, staying local APE Pumps and Mather+Platt were acquired by Indian multinational Worthington Pumps in
2012 and now form part of a group of leading pump OEMs. These include Sterling Pumps in Australia, Mathers Foundry in the UK, and Gruppo Aturia in Italy.
In 2017, the APE Pumps and Mather+Platt production facilities were expanded by around 8 000 m2 to keep pace with market demand and the Group continues to modernise its machinery in line with evolving technologies.
“A Proudly South African company, we are committed to and invested in South Africa, and APE Pumps and Mather+Platt products are 100% locally cast by South African foundries using local materials,” Montgomery explains. “That has major advantages for the market because we are not reliant on imports and can design and fabricate pump systems within remarkably short turnaround periods.”
APE Pumps and Mather+Platt’s processes are ISO 9001 accredited to ensure strict adherence to quality assurance standards. Material certificates are issued as a guarantee.
“High-pressure environments like bulk water transfer depend on exact tolerances and there’s no margin for error, which is why our Group has been a market leader since 1952,” Montgomery continues.
As part of its commitment to inclusivity and transformation, the Group recently concluded a BBBEE equity deal with a 100% black-owned company, which has now acquired a minority stake in the business.
“We’re very excited about this development and it marks a major milestone for our 70th anniversary celebrations,” says Montgomery.
for water utilities. At times, these are mission-critical projects where an emergency repair is required.
A recent example is a project for Umgeni Water at the Durban Heights Water Treatment Works (WTW) following a critical shaft pump failure on 11 November 2021. Housed at the base of an approximately 190 m deep purpose-built shaft, this pump conveys raw water from the aqueduct 200 m below ground level to the WTW for potable
services. In some cases, customers are also concluding sole-source servicelevel agreements. This essentially means that APE Pumps and Mather+Platt are contracted to service and support their installed systems.
“O&M has definitely been a growing area in the past decade, and we see this trend continuing. From our perspective, we see opportunities to expand into the municipal market, providing a fully outsourced
Mather+Platt is renowned for its high-head multistage and single-stage split-casing pumps. In turn, APE Pumps specialises in end-suction pumps, multistage high-pressure pumps, split-casing pumps, vertical industrial turbine pumps, and vertical suction pumps.
Major growth in recent years has been supported by the Group’s Projects Division, which provides turnkey design, engineering, installation and commissioning services for pumps, valves, motors and electrical switchgear.
Ranked as an 8 ME (Mechanical and Electrical) contractor in terms of the Construction Industry Development Board grading system, APE Pumps and Mather+Platt have completed numerous landmark projects over the years. Outside South Africa, these include work for leading utilities that include the Blantyre Water Board in Malawi, and Lusaka Water Supply & Sanitation in Zambia.
Durban Heights
Locally, the bulk water segment is a key market for the Group, providing solutions
treatment and subsequent distribution to eThekwini Water and Sanitation.
The sudden failure of the shaft pump resulted in severe water shortages within eThekwini’s Central, Southern and Northern systems.
In response, Umgeni Water appointed APE Pumps and Mather+Platt as the mechanical and electrical contractor on 12 November 2021 to remove and repair the multistage shaft pump, which has a designed output of around 610 ℓ /s at a 180 m head.
Within a five-week turnaround period, APE Pumps and Mather+Platt completed a full overhaul of the pump (including bearings and bushes), and reinstalled and recommissioned it on-site.
Operations and maintenance (O&M) Currently, around 30% of the Group’s business is in the provision of O&M
O&M service for water and wastewater treatment plants. Many of these are in a poor state across South Africa and need expert attention, which is where we come in,” Montgomery continues.
“Over the past 70 years, our expertise and institutional knowledge have defined us. This will continue in the coming decades, as we prepare upcoming generations of leaders and specialists to take APE Pumps and Mather+Platt to new heights,” Montgomery concludes.
www.apepumps.co.za
Since its inception 12 years ago, the Consulting Engineers South Africa (CESA) Business of Consulting Engineering (BCE) Development Programme has helped shape entrepreneurial skills and business success.
Ziyanda Majodina speaks to Chris Campbell, CEO, CESA, and Brenda Lacey-Smith, head: School of Consulting Engineering (SCE), CESA, about the key benefits.
Speaking on what was the driving factor for the conception of the BCE, Campbell says, “There was a realisation that many students are opting to enrol for MBA qualifications, which are often not specific to the industry and do not offer the requisite leadership skills needed to apply for management positions within the consulting engineering field.
“More often, engineers come into the industry with only the technical body of knowledge and for them to be well prepared – or rather prepared for roles in middle to senior management of companies – they have to be knowledgeable in managerial aspects as well,” he continues, adding that challenging trading conditions, particularly in the construction section, make it even more important to have sound commercial skills.
“The remote way of working imposed by Covid-19 has also made it difficult for young professionals to gain invaluable, on-the-job skills in preparing them for a
future role as business leaders,” LaceySmith explains. “This is where the BCE and allied SCE courses are designed to bridges these gaps.”
The programme focuses on developing non-technical skills – from project inception to project completion. Key modules include project delivery, business and project finance, legal and contractual matters, plus interpersonal skills.
“Especially beneficial for young professionals, they obtain a broadbased comprehension of the consulting engineering framework and the entrepreneurial business side, which helps them accelerate into management roles,” Lacey-Smith continues.
The BCE development programme runs over nine months, comprising 120 hours of online contact sessions. Over 50 topics are covered by some 15 subject matter experts. Access to individual student facilitator support is provided, as well
as extensive training material, including textbooks and detailed study notes.
A BCE graduate from the class of 2018, Xolani Mandindi, senior engineer at AECOM, says the programme has positively impacted his career. “Our company registered four engineers in the programme, which underscored their confidence in the outcome.
For me, it was a positive and life-changing experience.”
To be eligible for the programme, BCE candidates need to hold a BSc or BTech degree and have a minimum of two years’ postgraduate experience in a consulting engineering firm, or a technical diploma with a minimum of five years’ postgraduate experience. Otherwise, a relevant non-engineering qualification (business management, finance, HR, legal) with a minimum of three years’ experience in a consulting engineering firm is acceptable.
JG Afrika, a proudly South African consulting engineering firm, is celebrating 100 years of engineering and environmental excellence.
This significant milestone bears testament to the skills, experience, dedication and passion of a strong team of people who are committed to JG Afrika’s core values: Experience, Quality and Integrity.
The company was first founded in Johannesburg in 1922.
Formerly known as Jeffares & Green, it has since grown into a leading multidisciplinary engineering and environmental consultancy operating locally and internationally.
“I am exceptionally proud of this accomplishment as it demonstrates the sustainability of our business. There are only a few South African companies – and now only two local engineering firms – to have reached this milestone. Over the years, we have survived a world war, many far-reaching changes in government and its ideologies and, more recently, a pandemic that has wreaked havoc on the global economy. We have always been quick to
adapt to change and emerge stronger than before,” says Paul Olivier, managing director of JG Afrika.
The company’s proud legacy was started by John LS Jeffares, when he established JLS Jeffares Consulting Practice in Johannesburg. Soon thereafter, Jeffares was awarded an OBE to pioneer a railway route from Victoria Falls to Walvis Bay. Five years later, he was joined by Harold H Green and, together, they undertook work throughout sub-Saharan Africa, including the hydrological study and access roads for Kariba Dam. In 1947, they formed a partnership, and the name Jeffares & Green was used for the first time.
Throughout the years, the firm continued to progress and evolve and, in 2016, Jeffares & Green rebranded to JG Afrika to better reflect its African roots and commitment to uplifting the continent. The firm has continued to build on the reputation for quality engineering services that was established many years ago.
Multidisciplinary expertise
Apart from the main operating company focusing on the provision of consulting services in all fields of civil and structural engineering, the firm has since grown its professional service offering to include as many as 23 different disciplines and fields of expertise. These are in high demand and the company’s extensive skills and experiences are being deployed in everything from large infrastructure through to smaller, community-based projects.
Olivier remains proud of all of JG Afrika’s projects, especially those improving the lives of the most vulnerable. “Our communitybased projects are designed to have a significant positive socio-economic impact right from the early implementation phases. This is by providing ample opportunity for the training and development of members of poor communities located within the project footprint,” he explains.
“It helps to create jobs in areas where there is high unemployment, while also ensuring the long-term sustainability of infrastructure, because community members have been adequately trained in monitoring and maintenance. Extensive public participation and stakeholder engagement processes also ensure project buy-in and unite different factions so
The South32 Desalination Plant at the Hillside Aluminium Smelter, commissioned in September 2016. As principal agent, JG Afrika was responsible for the overall conceptual solution development, as well as all the detailed civil engineering works, raw water pipeline, pump selection and brine pipeline designs
that we can all work together efficiently towards achieving a common goal,” Olivier continues.
Innovation has remained at the heart of the firm for all these years. This is evidenced by, among others, the many awards JG Afrika has received for its projects from leading professional bodies, such as the South African Institution of Civil Engineering and Consulting Engineers South Africa. However, innovation will play a considerably larger role for the company as it harnesses new technologies and enters other markets that provide more opportunities for growth.
This is in line with the company’s drive to expand its footprint in Africa and other continents, increasing its client base and, in so doing, ensuring business sustainability for many more years to come.
Olivier is convinced that he has the best team to help him drive this heightened focus on innovation. An environment has been created that encourages people to be innovative and find unique solutions to challenges. The company has preserved its strong family values and culture over the years. For most employees, JG Afrika is a ‘home away from home’ and they have remained
loyal to the firm for many years. This culture and working environment also attract the best young talent to the company to ensure continuity.
Certainly, this milestone would also not have been possible without the support that the company continues to receive from its clients. Many have nurtured a longstanding professional relationship with JG Afrika. They value the firm’s ability to keep pace with their changing requirements and the demands of industry, especially over the past 10 to 15 years. This has been a period of significant change in the engineering and environmental sciences
An environment has been created that encourages people to be innovative and find unique solutions to challenges
market. It is a trend that is expected to carry on unabated. Olivier is confident that the firm will continue to adapt to this disruption and respond to the immense opportunities it brings.
“JG Afrika is only 100 years young, so there is still a lot of potential to learn and grow to ensure that we remain the best at what we do. We are looking forward to many more years of providing leading technical services, as well as innovative and sustainable solutions to our growing client base,” Olivier concludes.
Construction completed on an additional carriageway along a section of the Bakwena N1N4 Toll route. Construction supervision was carried out by JG Afrika, with the works executed by a joint venture between Raubex and Enza Construction
Using building information modelling (BIM) software as a design platform, Naidu Consulting has value-engineered a sustainable solution for the upcoming Canelands Pipe and Pedestrian Bridge project. The client is eThekwini Water and Sanitation’s Design and NRW Branch.
Completed some 100 years ago for South African Railways & Harbours, the existing Canelands pipe bridge crosses the Mdloti River in Verulam and features five 33 m spans of 5.5 m deep structural steel trusses. These are simply supported on reinforced concrete piers and abutments.
The original bridge was built to support a 400 mm diameter ductile iron sewer pipe, and 350 mm diameter and 400 mm diameter steel water pipes, together with an open cable tray accommodating electrical cables. The bridge further serves as a pedestrian crossing for the surrounding community.
shows no signs of distress. Based on a costbenefit analysis, it was therefore proposed that only the current steel superstructure be replaced.
“The final design recommendation accepted by the client will see the construction of a 165 m long precast concrete bridge deck that will accommodate water and sewer line infrastructure, as well as improved and safer access for pedestrians,” explains Josh Padayachee, director: Bridges & Buildings at Naidu Consulting.
The design solution passes on the following key benefits for the client:
The use of the existing steel trusses to launch the new bridge deck means that no cranes are required in the river to place the prestressed beams between the supports.”
A condition assessment investigation of the entire bridge confirmed that the structural steel trusses were at an advanced stage of corrosion and required immediate replacement. However, the existing substructure is still in good condition and
• Since substructure demolition and replacement with new abutments, piers and piles is not necessary, this reduces the environmental impact and results in substantial cost savings.
• An environmental authorisation and wateruse licence is not required.
• The use of the existing steel trusses to launch the new bridge deck means that no
The new Canelands Pipe and Pedestrian Bridge modelled utilising BIM software
cranes are required in the river to place the prestressed beams between the supports.
• An intrusive geotechnical investigation was not needed, which would in general have had negative environmental impacts.
• There will be no construction in the river channel, thereby avoiding negative environmental impacts and the risk of project delays due to inclement weather and flooding.
• The engineer’s estimated construction period duration was reduced by approximately seven months.
Utilising industry-recognised software programmes, the existing and new portions of the bridge were modelled in 3D incorporating BIM principles. This provided a key visual aid to the design team so they could make informed decisions regarding the new design, sequencing of construction, risks, and limitations.
Although the new bridge superstructure is comparatively simple in form, the correct sequencing of the demolition and new construction works is integral to the success of the project. Therefore, an intricate demolishing and construction sequence process was developed and will include the following:
- construction of temporary pipe and pedestrian walkway structures attached to the sides of the existing bridge
- diversion of the existing sewer, water and cable infrastructure services to the temporary structures
- extension of the height of the existing substructure
- construction of a temporary launching system comprising two steel A-frame structures that slide on a steel rail track
- launching of the new precast beams in a sequential manner to their respective positions
- laying of new 400 mm diameter HDPE water
and sewerage pipes on the new bridge deck and encasing them in concrete
- jacking of a new 600 mm diameter steel water pipe through the void of the new bridge deck
- transfer of the water and sewer services from the existing lines to the newly constructed lines
- demolishing of the existing bridge steel truss superstructure, temporary structures and existing services in a sequential manner by utilising the A-frames to transport the various steel elements off the bridge.
“The utilisation of BIM is often marketed for the long-term benefits it offers a project. However, it can also be utilised as a powerful tool at the initial stages of a project,” adds Padayachee.
“The Canelands Pipe and Pedestrian Bridge project demonstrates that thinking out the box and embracing technology can provide innovative solutions in an everchanging world to ensure that the service delivery of infrastructure is prioritised,” Padayachee concludes.
Final deck cross section subsequent to demolitionOUF is the pressurised separation of water and colloidal solids using membrane technology. NuWater employs a low-pressure, 0.03 micron barrier to remove solids, bacteria and viruses. It provides consistent water quality (<0.1 NTU) irrespective of variation in feedwater quality
Delivering potable water to every household is one of the primary objectives in South Africa and worldwide. That requires sustainable and engineered responses that are interdependent on public and private sector collaboration. IMIESA speaks to Bouwer, executive at NuWater, about their workable solutions based on selecting the right choices.
ne of the key drivers for success in any sector of society is the ability to understand and embrace technological evolution. Within the water sector, for example, advances in treatment processes like ultrafiltration (UF), reverse osmosis (RO) and a variety of oxidation technologies are delivering revolutionary benefits. They form the core of NuWater’s technology suite, specialising in scalable modular automated package plant solutions for the water, wastewater and desalination markets.
The advantages of RO and UF include reduced process costs, since both systems use membrane technology, substantially negating chemical dosing requirements. Compared to conventional treatment plants, UF processes and oxidation technologies are also far better suited to dealing with the higher degree of raw water variability induced by climate change and downstream pollution.
NuWater’s solutions are benchmarked against international best practice technologies with
proven applications for private and public water users. “Within the municipal space, our objective is to ensure that their engineering departments are kept informed on the best choices from both environmental and lifecycle costing perspectives,” Bouwer explains. “Conventional process technologies that are decades old cannot compete with modernday alternatives and the advancements in membrane technologies in terms of final treated water quality.”
While conventional water and wastewater plants cost millions to build, NuWater’s compact modularised ‘plug and play’ type solutions are far more affordable and relatively quick to build, deploy and commission.
An operating life of up to 40 years is achievable, and NuWater plants are available on a rental basis, as an outright sale, or supplied in terms of build-own-operate (BOO) and buildown-operate-transfer (BOOT) agreements. Many options exist to solve current problems.
“A conventional concrete treatment works might last 100 years or more, but that’s not
what South Africa’s looking for right now as they take too long to establish and incur great costs. We need more immediate, affordable solutions that address the growing potable water supply gap,” says Bouwer.
Rising water demand, ageing infrastructure and PPPs
Population growth and urbanisation are placing increasing strain on ageing treatment plants, now frequently overloaded well beyond their design capacity, and not always process compliant. Increased water demand also puts available water allocation capacity at risk, without factoring in non-revenue water (NRW) losses.
NRW estimates indicate that between 25% and 50% of treated potable water doesn’t reach the consumer, primarily due to leaking pipes. This places further financial strain on municipalities in terms of lost billings, plus it’s a terrible waste of water.
“Our ageing infrastructure places South Africa’s socio-economic future at risk if we
NuWater’s compact trailer-mounted plants are designed to provide communities anywhere with safe clean water
don’t implement quick wins. In my view, government’s primary focus should be on repairing, replacing and upgrading South Africa’s national water transmission network. In turn, government and municipalities should embrace the advantages of oursourcing water and wastewater treatment to private sector specialists – a trend where NuWater sees a positive mindset shift,” states Bouwer.
This view is supported by the publicprivate partnership (PPP) model envisaged in the South African Infrastructure Fund and the allied Economic Reconstruction and Development Programme.
Local municipal partnerships
A prime example of a PPP in practice is NuWater’s agreement with various local municipalities to operate several UF package plants. These are being run as either BOO or BOOT plants.
One such municipality’s total potable water output is around 120 Mℓ/day, with NuWater contracted to deliver a significant portion, with raw water sourced via the local dam. This water is characterised by high concentrations of heavy metals (typically iron and manganese), as well as sulfates.
“Our analysis of this municipality’s conventional plants showed that there was plenty of opportunity for optimisation and improvements in efficiency. Essentially, the existing process could not bring the water into specification at the best cost, plus the existing process configuration and dosing strategies posed a risk of forming harmful by-products, which are potentially carcinogenic,” Bouwer explains.
The UF process, by comparison, eliminates suspended solids and rejects viruses, and bacteria. Pre- and post-oxidation processes reduce the threat of forming harmful by-products and ensure the water is sanitised for distribution.
A key advantage of BOOTs is that municipal personnel involved receive ongoing training, plus the municipality retains the asset at the end of the agreement. During the concession period, the contractor must also deliver according to
predetermined performance guarantees and are accountable for any cost overruns. That provides great peace of mind for the client.
NuWater’s unique operational approach
In terms of NuWater’s BOO and BOOT business model, all upfront costs for installation and commissioning are carried by the company. Only once NuWater starts producing are they compensated in terms of the agreement. Bouwer says this underscores NuWater’s absolute confidence in their systems.
“When you need us, we respond,” Bouwer asserts, citing a solution in a coastal town as an example. Situated in a drought-prone region, this town experiences severe water shortages that threaten the sustainability of its predominantly tourist-based economy.
“We offered and installed a desalination system, with the municipality meeting us halfway with the power connection,” he explains. “Problem solved.”
Working with government agencies and social investors, NuWater also has solutions for remote rural communities without formal network supply. These come in the form of compact trailer-mounted units that municipalities can use to provide outlying communities with safe clean water, when and wherever needed.
Cross border, NuWater recently supplied a far more sophisticated solution for a remote settlement in Mozambique, whose only source of drinking water came from contaminated wells, with further plants being built. NuWater’s solution comprised four completely autonomous solar-driven desalination plants.
Back in South Africa, NuWater is also responding to off-grid requests in the private sector – a recent example being for a luxury guest farm in the Karoo. The borehole water available contains high salt and iron concentrations. The treatment strategy developed incorporates media and membrane technologies with energy sourced from a solar panel installation.
Alongside the municipal segment, NuWater is expanding its base across segments that include agriculture, industry, mining and residential. Many of these interventions take further pressure off the municipal and national water and wastewater network.
Within the residential segment, NuWater is currently contracted to deliver water and wastewater solutions for a new property development under way on the north coast of KwaZulu-Natal.
NuWater is responsible for inbound and outbound water treatment. Potable water will be sourced from seawater intake and wells, while the treated effluent will be reused via a secondary network for applications like irrigation.
Industrial wastewater and reuse are further core markets for NuWater, with PPP potential. “Similar to discussions on wheeling tariffs for privately owned solar installations, we see the potential for something similar in the industrial wastewater treatment space, separate or in collaboration with municipal infrastructure. As municipal treatment works become overloaded, it’s imperative that industry has a safe and sustained disposal solution for its effluent,” Bouwer explains.
“In the end, conservation and management should be priority number one for all water users, whether public or private. And as a strategic partner, NuWater remains fully committed to investing in the best technologies so that municipalities are equipped to deliver world-class services,” Bouwer concludes.
www.nuwater.com
A NuWater modular water treatment plant being commissioned for a local municipalityClimate change, population growth and urbanisation are placing increasing pressure on South Africa’s water and wastewater infrastructure. Finding sustainable solutions requires a value-engineered approach that looks beyond conventional design, says Dr Michele Kruger, functional general manager: Water Infrastructure, SMEC South Africa.
By Alastair CurrieThe introduction of the UN Sustainable Development Goals (SDGs) marked a turning point for the world by placing the emphasis on people and the environment first, rather than pure economic gain. Participating SDG countries, which include South Africa, as well as member firms, are required to effect meaningful change.
“In many respects, the SDGs are a race against time and, from SMEC’s perspective, our responsibility is to design and execute positive outcomes, based on engineered solutions,” says Kruger, who prior to joining SMEC was an advisor to South Africa’s Minister of Water and Sanitation.
Kruger’s passion for this field has been recognised both at home and abroad. In 2007, she won the Young Engineer of the Year Award at the SAACE Glenrand MIB Engineering Excellence Awards. Internationally, her doctoral research in water treatment was honoured by the UK’s Federation for Water Research as the best paper by a young South African in the field of water science and technology.
“My key mandate is to make practical and implementable connections between water
Dr Michele Kruger, functional general manager: Water Infrastructure, SMEC South Africa
security and life-cycle costing,” Kruger explains. “That’s because our problems and challenges are heavily weighted towards treatment, or the lack thereof, where there’s minimal room for error.”
Asset registers, operations and maintenance, cost-reflective tariffs From previous experience and working as a Green Drop auditor in 2021, Kruger has a clear understanding of the current performance status of South Africa’s water and wastewater treatment plants. As defined by the Department of Water and Sanitation, “The Green Drop process measures and compares the results of the performance of water services authorities and their providers, and subsequently rewards (as incentive-based regulation) the municipality upon evidence of their excellence (or failures) according to the criteria that have been defined.”
One of the key Green Drop audit criteria is an up-to-date asset register with evidence of how effectively this speaks to the municipality’s operations and maintenance (O&M) programme. The asset register – as a status report – forms the basis for a lifecycle costing model, based on a detailed risk analysis that identifies the critical gaps.
“The fact that a higher-than-acceptable percentage of water and wastewater treatment plants are dysfunctional points to poor O&M, which can be improved together with the active management of asset registers,” says
Kruger. “Municipalities need to increase their inspection periods and response times, as well as develop realistic maintenance budgets and an action plan that works. Being able to collect cost-reflective tariffs is of course also essential to be able to afford such plans.”
On a positive note, Kruger points out that there are treatment works that have passed their end of life but are still performing optimally. In these instances, this shows that the maintenance plan has worked exceptionally well. This presents opportunities to share success stories with struggling municipalities so they can improve their O&M capabilities.
Before building or upgrading a treatment plant, Kruger says the first step is scenario planning and risk analysis. The foremost consideration from a potable water perspective is establishing current and future security of supply. From a wastewater perspective, changing raw water quality and the effluent quality discharged to rivers or how the limits for these might change in future becomes a factor.
From there, a risk register can be developed that ranks the likelihood of something happening, like a drought, and its impact, with a recommended contingency response.
“Wastewater plants are designed for a specified treatment strength. In an extreme drought, however, like the situation experienced in Cape Town during the ‘Day Zero’ threat, you can end up receiving half the flow, but twice the contamination,” Kruger explains. “That makes it very challenging to treat to the required quality; however, in Cape Town’s case, they rose and overcame these challenges, thanks to contingency planning and process optimisation.”
When conducting an upfront design, one of the key challenges facing consulting engineers in general is pressure from the client to discount their fees as a perceived saving on the final project. However, these are relatively small upfront costs compared to the longer-term life-cycle costs of a plant.
“Every plant design should be fit for purpose, with sustainability in mind, and that’s the starting point. As consulting engineers, our responsibility is to give the client the best solution based on the capital and operational budget available to them. In a metro, full plant automation with remote monitoring and control may be a requirement, while our recommendation to a rural municipality might be to stick with a manual plant operation model from maintenance cost and practicality perspectives,” says Kruger.
The advent of the Fourth Industrial Revolution (4IR) has introduced a host of exciting new internet of things possibilities when it comes to life-cycle costing. For clients going the automated route, for example, this includes near real-time diagnostics on influent per second, as well as chemical and electricity use. These days, automated plants can also be controlled remotely via smart devices.
“Running in parallel with 4IR is 5IR, which balances the equation by emphasising that technology exists to benefit humanity. In this respect, 4IR uses machine intelligence to perfect life-cycle costing models in response to SDGs,” says Kruger.
Energy savings
backwash operations so that they occur during off-peak electricity consumption periods. Then there are technology interventions like variablespeed drive motors on equipment that further reduce energy use during lower demand.
SMEC’s designs also include renewable energy options. “While the upfront cost may be high, the longer-term financial and environmental benefits on a large-scale plant are significant,” she explains. As an aside, Kruger mentions visiting a 400 Mℓ/day water treatment plant in Abuja, Nigeria, which runs entirely on solar power.
Another area where plant owners can save costs is on chemical dosing, like the use of disinfectants, precipitation chemicals and polymers, as part of the water and wastewater treatment processes. The objective is not to compromise the system, but again to refine efficiencies.
As one of the first treatment stages, raw water is traditionally dosed with polymer to facilitate the separation of solids during flocculation; however, it’s not uncommon for plants to cut costs by using low-cost polymer, with a subsequent reduction in efficacy. Similarly, the use of polymers in belt presses affects the life-cycle costing if the maximum dosing requirements are not well specified and adhered to during the procurement process.
Going forward and in line with the SDGs, plants need to be designed, constructed or retrofitted to reduce waste and keep
from the sustainability of construction materials selected right through to the sludge beneficiation techniques applied. Plants also need to be designed up front for sustainable closure.
“Conducting an in-depth risk and life-cycle cost analysis, combined with scenario planning, provides a coherent roadmap for project and service delivery sustainability,” says Kruger. “As consulting engineers, we have so much value to add walking the road together with our clients.”
In parallel, among the interesting developments are the opportunities presented by South Africa’s Infrastructure Fund, with a weighting towards publicprivate partnerships (PPPs) and concession agreements like build-own-operate-transfer models. Water and wastewater plants are already part of the PPP mix, hopefully ramping up speedily; however, getting to financial bankability relies heavily on life-cycle costing and sustainable offtake agreements.
“Public clients stand a far better chance of attracting private investors and making projects bankable if all the feasibility, cost and risk data is in place,” she adds.
“Either way, as the pressure on South Africa’s water and wastewater systems mount, the best route is a collaborative one that brings together public and private stakeholders in a common quest to meet the SDGs and support a resurging economy,” Kruger concludes.
The average amount of water available per person in South Africa is estimated at about 2 000 m3 , compared to 15 000 m3 in the USA. This extreme highlights the fact that South Africa is a water-scarce country, which increasingly relies on groundwater to supplement available supply. By Jan Venter
Despite the decline in water availability, and rising pollution, it is mind-boggling that South Africa’s leaders and citizens seem to have a complete lack of urgency and motivation to rectify the situation. Hundreds of faulty municipal water and sewage plants can be found all over the country, while thousands of litres of water continue to be lost daily due to poorly maintained pipelines.
Within this context, plastic pipe is dominant in secondary water distribution and has a key role to play in combating non-revenue water losses and ensuring safe drinking water supply. Spearheading this drive is the Southern African Plastic Pipe Manufacturers
Association (SAPPMA), which represents more than 80% of all certified plastic pipe produced in the country.
Our two main areas of focus are product standards and quality – both of which are indispensable in the bigger picture. And while we’ve made great strides in these areas from a materials, design and manufacturing perspective, the overarching responsibility for water conservation and management rests with government in the form of the Department of Water and Sanitation.
SAPPMA is therefore again making the following urgent appeals to government: • to seriously address the widespread pollution of rivers, dams, and wetlands • to intervene in the mismanagement
Below is an extract from a UN report comparing the proportion of good-quality raw water available in South Africa against snapshots of other African counties.
Source: UN Water (www.sdg6data.org)
of municipal water and sewage treatment plants
• to depoliticise the management of water in the country and fully utilise all locally available engineering skills.
Plastic pipe is a sustainable solution Corroding pipes and poor jointing are two of the major causes of water loss. For this reason, old steel or asbestos pipes around the world are being replaced with plastic pipes that do not rust and have leak-proof joints (if done correctly).
A great deal of municipal pipe networks are beyond their useful life and should have already been replaced. The consequence of failing to do so is the substantial loss of precious, treated water in most municipal areas. This is clearly something the country cannot afford. The benefits of using plastic pipe as opposed to other materials have been well documented and tested. Apart from having a lifetime that is more than double that of other materials, plastic pipes are also quicker and easier to install, have lower failure rates, less corrosion, fewer joint leaks and are lower in price compared to the other pipes.
Without delay, municipalities should spend the money allocated in their budgets to upgrade and replace old and failing water infrastructure. This will place us in the position to save enough purified water to significantly reduce the impact and long-term effects of below-average rainfall, an overreliance on groundwater, and the potential threat of ‘water-shedding’ in the years to come.
The Southern African Plastic Pipe Manufacturers Association
(SAPPMA) has announced a call for papers ahead of its much-anticipated PIPES XIII conference, taking place on 6 and 7 September 2022 at Emperors Palace, Gauteng. It will be hosted in collaboration with the Plastic Pipe Conference Association (PPCA).
“The PPCA hosts the biggest international pipe conference every second year, which takes place either in Europe or the USA. A spinoff conference is organised every alternate year and this year it is coming to South Africa,” explains Jan Venter, CEO of SAPPMA.
The theme of SAPPMA’s PIPES XIII conference is ‘The Versatility of Plastic Pipe’ and the speaker line-up will include at least 10 of the best papers presented at PPCA’s PIPES XX conference in Amsterdam
last year. Local speakers interested in sharing the stage with international experts in plastic pipes are invited to submit a proposed topic, short abstract, and their contact details to SAPPMA by no later than Wednesday, 20 April 2022. Presentations must be 25 minutes long and allow five minutes for questions and answers. Content must be strictly noncommercial, relevant to the plastic pipe industry and in accordance with one of the following session themes:
• Pipeline design
• Installation
• Standards, testing and certification
• Extrusion technology
• Water problems in Southern Africa
• Infrastructure
• Raw materials
• Rehabilitation of old pipelines.
Delegates attending PIPES XI at Emperors Palace in 2018
SAPPMA will publish the final programme by the end of April 2022 and speakers will receive notice of acceptance or rejection of their abstract shortly after the deadline. Venter concludes: “We are very excited and honoured to be able to stage this truly international event in South Africa. As with all our PIPES conferences, CPD points will apply. We encourage the industry to make the most of this fantastic opportunity to be exposed to world leaders in the field by participating in this year’s PIPES XIII conference as a speaker, sponsor or delegate.”
For more information or to register for PIPES XIII, visit the Events Page on www.sappma.co.za or contact the conference organiser, Enrike Albasini, at admin@sappma.co.za
Proudly brought to you by the Southern African Plastic Pipe Manufacturers Association, in collaboration with the Plastic Pipe Conference Association (PPCA).
This year’s international speaker line-up will include at least ten of the best papers that were presented at the PPCA’s PIPES XX conference in Amsterdam last year, along with local experts in all aspects relating to plastic pipe, including:
• Pipeline design
• Installation
• Standards, testing and certification
• Extrusion technology
• Water problems in Southern Africa
• Infrastructure
• Raw materials
• Rehabilitation of old pipelines
“A high quality conference with excellent networking opportunities” - Chemsystems
“A great platform for learning and interacting with my South African and international peers” - Safripol
“I will definitely attend SAPPMA’s PIPES conferences in
future. I highly recommend it to anyone! I really enjoyed the last two days and learned a lot” - Alprene Plastic Products
South Africa is becoming more reliant on groundwater every day but is not adequately measuring or controlling how much is abstracted. To avoid squandering this vital but limited resource, the country will need to raise more awareness among our younger generation.
By Gert Nel*The country’s smaller towns have long been reliant on groundwater for their survival, and ongoing urbanisation is placing growing pressure on aquifers. Clearly, access to water is a basic human right and water is an essential service that municipalities are mandated to provide – so expectations from residents are high. Many municipalities are spending considerable resources to get access to additional land where boreholes can be drilled.
The problem with this scenario is simply that it is unsustainable. Groundwater sources are limited and cannot generally be pumped without consequence. Each aquifer will have a scientifically discernible recharge rate, and the extraction rates must be commensurate if the well is not to run dry. Many aquifers are shallow and are largely dependent on frequent recharge from rain. However, the national need for groundwater is currently being pursued without sufficient regard for both the supply and demand sides of the equation.
There are certainly moves afoot to better monitor the volumes of water being extracted from our aquifers, through regulations to register water users and track their usage. So far, though, the trend is for more water to be extracted without giving due consideration to sustainability. In many cases, there is a need to re-emphasise the vital importance of water demand management.
The challenge is really for communities to participate actively in ensuring sustainability in their water supply. The matter of access to water is by no means simple; there are local issues regarding inequality, affordability and wasted water from unmaintained infrastructure, and global issues such as climate change that make it increasingly difficult to predict water supply levels and recharge rates in certain aquifers.
The fact remains, though, that residents of any community need to be part of the balancing act – ensuring that the water demand does not outstrip what their area can sustainably supply. It is also clear that not much progress is being made on this front, with the institutional focus almost entirely on exploiting new groundwater sources.
It needs to start with proactive awareness raising, knowledge sharing and collaboration. As far back as 2012 – and probably earlier – it was being acknowledged that waterrelated information was not really reaching communities in a way that had any impact on behaviour. In 2012, a report from the Water Research Commission noted that the way knowledge was being disseminated, particularly by government, was not encouraging individuals to question their water use practice or consider how to adapt it.
All participants in the study agreed that presenting ‘factual’ packaged information was not enough; rather, learning resources were more effective when they engaged learners with water issues as they experienced them. “There is no shortage of water research knowledge in South Africa,” says the report. “But this knowledge is not presented in a way that is understandable to non-specialists.”
The authors recommend that more thought and funding be put into the dissemination of resources, with a focus on how they were
Not only is water an interesting subject for learners in primary and secondary schools, but it also governs so much of what goes on around them
shared and by whom. In my experience, among the most receptive institutions to this kind of learning are schools – where teachers are imparting a scientific approach to learners, and water is a topical and relevant everyday concern.
Not only is water an interesting subject for learners in primary and secondary schools, but it also governs so much of what goes on around them – from personal health and hygiene to food, farming and other economic activities. Schools could provide sciencebased input on water resources, perhaps focused on groundwater, that children could take home and share with their families. This could be a powerful channel to initiate and advance our national discussion about water. There are many water professionals and academics who would be happy to contribute to school efforts like this and could bring their own insights and experience to share with learners. Such collaboration would help to raise awareness while also initiating valuable discussions that could lead to longer-term solutions.
At the local level, this kind of initiative could feed into broader efforts to publicise South Africa’s increasingly fragile position as a
Water knowledge practice happens locally, not at a national level. Any knowledge generated from practice on the ground should first be fed back into local practice, because that is where it belongs.”
water-scarce country. Most importantly, it could create platforms for engagement and action – so that communities could participate in finding answers to waterrelated challenges.
There is another benefit that could come out of this kind of engagement: inspiring young learners to consider a career in the groundwater sector. In my experience, there are very few hydrogeologists at local or district municipality level. Water-related decisions are at best taken mainly by civil engineers, or by others with little training or experience in the water science field. If local communities could begin to nurture an interest in this vital discipline, that would certainly help to fill a serious skills gap.
Just a few years ago, I listened to a mayor of an important Eastern Cape city address a conference of water engineers and scientists. She appealed to us all to help find solutions to the region’s water needs. Among those solutions, there needs to be a more active engagement and collaboration with civil society about how water is consumed and conserved. It should start at our schools.
*Partner and principal hydrogeologist, SRK Consulting
t: +27 (031)266 3263 e: conference@imesa.org.za marketing@imesa.org.za www.imesa.org.za
Since the democratisation of the country in 1994, groundwater’s role in South Africa has undergone a major change. Previously an undervalued resource generally for private use, groundwater has gained national recognition as a major life-giving source for domestic supply, agriculture and industry.
Groundwater supports more than 50% of towns and communities in the country, and is the sole supply to many mines, hundreds of towns and villages, and thousands of farms.
The importance of groundwater can no longer be underestimated. It is a critical resource that can help address growing water demand due to a booming population, food insecurity, environmental degradation and climate change.
In 2016, the updated National Groundwater Strategy (NGS) was developed, whereby the proper valuing of this previously neglected resource was highlighted. This was done to direct investment into its protection, conservation and sustainable use. The NGS, available on the Department of Water and Sanitation’s website, with its Implementation
Guidelines did not come at a better time, as there are serious warning signals that groundwater use is on an unsustainable path. Based on national monitoring networks, it is clear that not only our major aquifers, the karst and coastal aquifers, but also our hardrock aquifers, are under pressure in many locations. This is due to a combination of overabstraction causing declining water levels, and pollution causing poor water quality.
Since 1978, the GWD has taken up the banner as a neutral player, aiming to bring different stakeholders together to solve and prevent problems. One of its recent additions is the establishment of a database of professional (SACNASP registered) groundwater specialists that are active in the country and subscribe
• Established in 1978
• 5 April: Webinar – What geohydrologists need to know about borehole construction, pumps, VSDs and borehole operation
• 20 April: Webinar: Decision support groundwater modelling - in spirit or in fact? (GWD Gauteng)
• 29 April: Online course –Groundwater Resources
Management New Online Course –2022 (RWSN)
to a code of ethics. These specialists offer the knowledge and skills needed to manage groundwater sustainably, and are rooted in a scientific approach. In addition, the published abstracts database that offers an overview of all scientific papers and posters presented at the last five Groundwater Conferences, is a rich source citing research topics and work done across the country.
Through its ongoing initiatives (conferences, seminars, courses and outreach), the GWD strives to build awareness and create a platform to address all the issues around groundwater, its use, appreciation and preservation.
• Essentially a non-profit association, it is committed to upholding and promoting professionalism in the field of groundwater among its membership
• The GWD is a community of professionals and other vested stakeholders who help South Africans understand and manage groundwater
• In 2023, South Africa is hosting the 50th Congress of the International Association of Hydrogeologists in Cape Town as a joint partnership between its South African National Chapter and the GWD of the Geological Society of South Africa. This is a great opportunity to showcase our country’s competence in groundwater science
• The GWD focuses on networking, knowledge transfer, as well as capacity and awareness building through initiatives such as conferences, seminars and courses, talks and media relations, publications and sponsorships
• It has a large database of registered professional hydrogeologists
• For more information, visit the GWD website: gwd.org.za
South Africa’s National Water Quantity Monitoring System (NWQS) provides the first ever fully automated, accurate and detailed monthly report of the country’s volumetric surface storage, as well as water quality, captured by near real-time satellite imagery.
The process used to analyse and capture the data on the NWQS has been developed by GeoTerraImage in collaboration with EkoSource Insights, with their service provided under a licensing agreement to the South African National Space Agency (SANSA), the NWQS’s current funder.
“SANSA’s involvement followed a direct request from the Department of Water and Sanitation (DWS) to investigate the possibility of a satellite-based service to measure the quantity of water – to assist water management – in South African dams,” explains Imraan Saloojee, chief sector and business developer at SANSA. “As the value of data lies in its use, we see tremendous value in providing the resulting information to as many users as possible in terms of knowledge transfer.”
While the primary data user is the DWS, the NWQS is freely available to all national, provincial or local government entities, as well as appointed companies working for these public entities for the purpose of aspects like water resource use allocation and modelling, operational dam management, national water planning and strategy support. (To view the site, visit www.water-southafrica.co.za.)
“State-of-the-art, cloud-based software –combined with the latest satellite imaging technology – provides an unprecedented level of information. Essentially, you know where the water is and how much you have left,” explains Mark Thompson, Professional GISc Practitioner and director at GeoTerraImage, adding that the NWQS service is built around ‘free-to-access imagery’ sourced from the European Space Agency.
Water practitioners now have a cost-effective and comprehensive picture of all natural and man-made water resources – including small farm dams, major impoundments, pans and wetlands, plus large rivers – from space. Additionally, every one of South Africa’s catchments is monitored and measured.
Tested against the best
During a Global Water Round Robin hosted by the European Space Agency, GeoTerraImage and EkoSource had the opportunity to test their system against those from other similar organisations around the world in terms of surface water detection capabilities. They were provided with various globally located test sites in regions that include Mexico, Europe and Central Africa – way outside their normal operating sphere – and ranked in the top third out of 15 competitors.
“A key distinction of our service is the ability to provide individual water feature volumetric information, which actually went beyond the scope of the Round Robin evaluations,” says Thompson.
GeoTerraImage and EkoSource’s system has been operational for the past five years, and they have been working with SANSA for close to three years in terms of the NWQS national service to South Africa. “However, we pushed the data back to 2016 because of the availability of the satellite imagery that we work with,” says Thompson.
The DWS uses the in situ measurements to monitor its approximately 254 strategic dams nationally. These major dams have been used to verify the accuracy of the NWQS. They represent more than 60% of the overall water supply. But smaller dams also have
a massive impact, and they number in the thousands. This makes overall strategic monitoring a critical requirement in terms of potential supply constraints for both rural and urban communities. Where necessary, the data enables informed decisions on where and when to impose water restrictions.
“In South Africa and across the continent, there’s a lack of adequate water resource information available. Over the years, our service has improved dramatically, both in term of its ability to find water and then to delineate the outer extent of the water body itself,” says Jason Hallowes, hydrologist, director and technical specialist at EkoSource.
“The key advantage of using satellites is that we can start to bridge the data gaps relatively quickly and effectively.”
Another key benefit of the data is that it generates reports on dams that potentially breach safety regulations and guidelines; as well as identifies dams that – due to their size – should be registered but aren’t captured. In some cases, dams (including mine tailings dams) can become too full, posing a potential risk to downstream users unless the necessary interventions are taken.
Where dam levels have dropped to low levels during extreme droughts, the system further allows for the generation of sedimentation profiles. The latter are crucial in determining their current storage capacity and the impact on their reduced life due to upstream soil erosion.
“The NWQS enables improved drought and flood reporting, which has both environmental and socio-economic implications. If dam levels are low, the area is clearly under stress, which has a knock-on effect for agriculture
and industry. When catchment dams are full, heavy rainfall can pose a flooding hazard and dams can fail, causing extensive downstream damage to structures,” Hallowes explains.
“The NWQS measures the overall stress on the national water network.”
Alien vegetation is another factor that needs to be monitored, measured and countered by the DWS in terms of water quality. A prime example is the profusion of water hyacinths and the presence of cyanobacteria (blue-green algae) on some dams, fed by abnormal nutrient loads due to high levels of pollution.
“We have the capability to measure water quality and are currently refining the process for reporting purposes,” says Hallowes. “From
an imaging perspective, floating vegetation does result in area discrepancies in terms of volume measurement; however, we’re working on solving this. For example, hyacinths are blown around by the wind, so we’re experimenting with observation techniques that can map out the true water surface area over time,” Hallowes continues.
“However, the same challenge, when seen from the opposite perspective, can also assist in providing detailed knowledge of where and how many dams are impacted by vegetation infestation.”
Recent breakthroughs by GeoTerraImage and EkoSource include the use of a combination of synthetic aperture radar and optical data
to provide an all-weather reporting capability. This means that cloudy weather is no longer an issue, with the technology enabling monthly cloud-free water surface data set composites to be generated – from which the water volume intelligence is modelled.
Another key technological enhancement is the overall speed of data processing, which has improved from weeks to mere hours through the use of cloud platforms, big data volume processing and artificial intelligence.
Outside South Africa, GeoTerraImage has worked with the Permanent Okavango River Basin Water Commission, as well as the Zambezi Watercourse Commission, on projects that involve the participation of affected countries within the SADC region.
“Based on the success and interest of these projects, our goal, subject to support from funders, is to make our service freely available throughout SADC, so that there’s a detailed monthly report on all regional hydrological catchments,” adds Thompson.
“We believe in the democratisation of data, because without a clear picture, we cannot realistically manage climate change impacts, or plan for future water demand and security,” Thompson concludes.
According to the Stockholm International Water Institute (SIWI), groundwater provides half of all drinking water, over 40% of irrigation water, and a third of the industrial sector’s global need for water. Worldwide, about 2.5 billion people depend solely on groundwater to satisfy their daily drinking and other domestic water needs.By Isak Malherbe & Jonathan Schroder, AECOM
Demand for groundwater is increasing due to population growth and changing global consumption patterns. In this regard, groundwater depletion is largely driven by irrigated agriculture to satisfy needs for basic global food security and luxury crop outputs. Ever-deeper boreholes and tube wells, as well as more powerful pumps, put a strain on groundwater reserves that are not rejuvenated in a lifetime. Shared groundwater resources are also threatened due to climate variability and change, as well as quality deterioration, reports the SIWI.
There is a growing need for society to understand what role it plays in water solutions. Governments, while providing
frameworks and legislation, essentially respond to the way society, as the end-users, behaves around water use and pollution. As the general public, we need to be more concerned with water, and how we impact and use it to be able to achieve true, longterm sustainability. Securing a safe water supply was once a primary focus of people. We need to, once again, become more conscious every time we open our taps and use this water.
Traditionally, rural areas in Africa have used groundwater as their main resource, with surface water developed mainly for urban areas. As a result, there has been a stigma attached to groundwater over the
years as a potentially less-desirable source of water. However, the recent devastating droughts across the continent have proven the resilience of groundwater, with an attendant shift towards tapping into this resource. An important part of this shift has been the realisation that implementing and operating large-scale surface water schemes can be prohibitively expensive to diffuse communities in our beautiful but hilly terrain. This has resulted in a renewed appreciation of the sustainability of groundwater resources, as well as more local surface water resources.
For example, we have a specialist team focusing on groundwater development planning and associated remedial work such as pollution monitoring and mitigation. In
most instances, we pull in specialists, but we consider the conjunctive use of groundwater. We have also provided our expert support to various environmental studies to classify and protect water resources, which involves a holistic consideration of both groundwater and surface water resources.
End-to-end African solutions
A particular focus for us has been water resource projects in Africa and the Middle East, where we are conducting water-yield studies for a range of dam and irrigation projects. A close interface with the civil infrastructure side of the business gives the water resources team the capability to run with projects from inception to implementation, and even long-term monitoring. Essentially, we provide seamless, end-to-end solutions for our clients.
Surface water looks more closely at rainfall run-off and modelling to best manage river systems and catchment areas. We look at where it is required to build new infrastructure to meet growing water requirements and how to optimise existing infrastructure. This is important to allow us to navigate droughts and manage overuse of our water resources. The primary goal is sustainable, long-term water resources security.
Looking at the entire catchment system, the interaction between surface water and groundwater needs to be taken into consideration. In some systems, these are quite separate, with long-term processes impacting on the groundwater resources. In other specific catchment areas like Tshwane, Gauteng, the prevalence of dolomitic structures allows for a much more dynamic interaction between the two.
Prestank tank capacities range from 1 500 litres to 4.2 million litres designed to SANS 10329:2004 guidelines and SANS structural codes. Our Hot Dipped Galvanising units are easily transported and assembled on even the most remote sites.
As a broad rubric, water management also encompasses scarcity issues and sustainable use, in addition to stormwater management and flooding. Here, the trending concepts are sustainable urban drainage systems (SUDS) and watersensitive urban design. Historically, this simply involved discharging such run-off into a distant river.
However, sustainable solutions now include recharging aquifers by promoting natural drainage. The ‘greening’ effect associated with managing water resources optimally has also been shown to have a major influence on the well-being and quality of life of local communities, which is particularly important given the toll that the coronavirus pandemic has taken on the global population.
A thriving manufacturing industry creates jobs and business opportunities, enables skills development and improves our competitiveness in global markets. A first step is procuring locally manufactured goods, this has obvious benefits for national competitiveness and economic growth.
SABS’ mandate is to provide standardisation, voluntary conformity assessment, and local content verification services to enable the achievement of the country's industrial, economic, and developmental objectives. Start your Local Content Verification by scanning our QR Code below or Contact us!
Certify your Municipality for SANS 18091:2020 Quality Management Systems (QMS) Guidelines for the application of ISO 9001 in local government
SANS/ISO 18091 is applicable to all local government processes at all levels (i.e. strategical, tactical-managerial and operational) in order to constitute a comprehensive quality management system that focuses on the local government achieving its objectives. The comprehensive character of this system is essential to ensure that all the areas of the local government have a specified level of reliability (i.e. effectiveness of the processes). Improve Delivery to Municipalities through Quality Management.
SABS provides services to assist the implementation of best practice solutions
• Manage and develop South African National Standards
• Laboratory Testing Services for a diverse range of Products. Supporting of Municipal delivery through: Testing of water quality, Testing/Certifying Water Meters, Smart Meters, and other products/systems
• Certification of Companies to Management System Standards
• Certification of Products and the Application of the SABS Mark Scheme
• Training of Management and Employees on Implementations of SANS
• Local Content Verification for South African manufacturing industry
SABS a Trusted Partner in Delivering Quality Assurance. Contact SABS to establish support for your Standardisation, Testing, Local Content Verification, Training and Certification Aspirations.
As many of South Africa's major dams fill to capacity, we can breathe a sigh of relief. But we cannot become complacent. We must invest in South Africa’s future by managing these dams and their sources, and supporting the infrastructure that connects that water with communities.By Chetan Mistry
According to the Water Research Commission, South Africa has over 500 government dams, holding a combined quantity of 37 000 million m3 of water (or 15 million Olympic swimming pools), and around 4 000 privately owned dams.
Dams are investment accounts for water. Most of South Africa’s rainfall would end up in the oceans, yet dams capture approximately 70% of the mean annual run-off from the land surface.
The Massachusetts Institute of Technology (MIT) estimates that the world has spent US$2 trillion (R30 trillion) on large dams and reservoirs. This is because dams have many different uses:
• Irrigation: 40% of farmlands irrigate using water from dams (Source: MIT).
• Energy: Hydroelectric power generates 5% of South Africa’s electricity – a figure that will grow with renewables (Source: Journal of Energy in Southern Africa).
• Water supplies: Most of the water used by local communities comes from surface water (Source: UN Water).
The Hazelmere Dam was established in 1977 and its primary purpose is to serve for irrigation and domestic use
• Flood control: Major dams, such as the Vaal Dam, help control water flow after major downpours.
Managing dams
Unless well managed, dams can run dry or become contaminated. As cities such as Cape Town and Chennai, India, have experienced recently, it is an enormous concern when dam levels get very low.
There are several actions South Africa can focus on to improve and maintain water availability:
• Support infrastructure maintenance: Improving infrastructure maintenance and monitoring can improve water delivery. Modern equipment and digital management solutions make maintenance more predictable and affordable.
• Invest in modern treatment: Treatments to make water consumable can damage the environment, including dam ecosystems. Investing in new treatment technologies such as ozone and ultraviolet (UV) significantly reduces water contamination without raising prices.
• Reduce non-revenue water: Roughly 40% of our water does not generate revenue due to leaks or inadequate metering data. Municipalities can raise significantly more revenue if they use new methods such as acoustic leak detection and wireless meter readings.
• Promote water savviness: Growing towns and cities consume more water, but nearby dams can’t increase overall volumes to match. Promoting savvy water use will reduce the pressure on water supplies.
• Recharge water sources: Most of South Africa’s water comes from the surface – dams, reservoirs and rivers. But a substantial amount emerges from groundwater. We can maintain and improve those resources through strategic water planning, reducing water pollution, and recharging aquifers.
Xylem, a leading water solutions company, provides technology that improves maintenance, management and costs –including power-saving variable-speed pumps, UV and ozone water treatment, and big data water management solutions.
Phase II of the Lesotho Highlands Water Project (LHWP) comprises the construction of the Polihali Dam and reservoir, water transfer tunnel and the associated access roads, bridges, accommodation, electrical transmission lines and telecommunications infrastructure.
The LHWP Phase II builds on the successful completion of Phase I in 2003. It delivers water to the Gauteng region of South Africa and uses the water delivery system to generate electricity for Lesotho.
Polihali diversion tunnels
The two diversion tunnels were constructed in preparation for the Polihali Dam construction and ahead of the appointment of the dam contractor. The Lesotho Highlands Development Authority (LHDA) celebrated the double breakthrough of the tunnels in August 2021, marking the completion of 1 870 m of excavation. Excavation inside the two Polihali diversion tunnels commenced in June 2020 and mostly advanced from the outlets. Construction was completed in November 2021. The contractor and consultant have demobilised from site.
Bulk power
The electrical infrastructure required for the Phase II development includes the construction of new substations, upgrading of existing Lesotho Electricity Company (LEC) substations, the construction of new power lines, and the diversion of the existing LEC 33 kV distribution network between Let š eng and Mokhotlong, which is below the Polihali Dam full supply level. A 33 kV power line of 2.2 km from Tlokoeng to Polihali to supply early power for the advance infrastructure contracts and the Polihali village prior to the completion of the main power from Matsoku was completed in June 2021. The construction of a 38 km 132 kV transmission line between Matsoku substation and the new substation at Polihali have been completed and both were energised in mid-January 2022.
Polihali and Katse infrastructure works
The works at Polihali and Katse – including the potable water supply system and sewer reticulation to permanent and temporary residential areas, water treatment facilities, access roads and street lighting –are complete.
Environmental and social impact assessments and environmental management plans for the Polihali Western Access Road (PWAC) and associated infrastructure are completed.
Records of decision (RoDs) authorising the construction of the Polihali Dam, Polihali Transfer Tunnel, PWAC and its associated components have been granted by Lesotho’s Ministry of Tourism, Environment and Culture.
Furthermore, the environmental management plans have been approved, while the RoDs for the Polihali North East Access Road (PNEAR), the construction of the diversion tunnels and for the quarries and borrow pits associated with the major components like the Polihali Dam and Polihali Transfer Tunnel and the major bridges have been granted.
Main works milestones include the procurement of the contractors for the Polihali Dam, Polihali Transfer Tunnel and major bridges. The award of the contracts is expected in 2022.
The completion of additional hydropower feasibility studies and the Lesotho government’s approval to proceed with
the procuring of a service provider for the detailed design and supervision of the oxbow hydropower scheme are further main works milestones.
Recent advance infrastructure construction tenders awarded include those for the Katse Lodge and Katse Village upgrades, and the construction of the Polihali Village. Construction work has commenced on these two components.
Changes in the overall design/construction programme
Projected milestones as per the current master programme are as follows:
• Impoundment of the dam: June 2025.
• Water delivery (tunnel): December 2027. Several factors have contributed to the programme changes. These include the complex decision-making processes, the cancellation and repeat of some procurements, and Covid-19 – which brought the LHWP to a halt for a period. Activities then resumed with restrictions to protect LHDA employees, consultants, contractor teams and communities in the construction area. Adverse weather and community unrest also caused delays.
Construction under way
• Access roads: Construction of the PWAR East and West, PNEAR and the Northern Access Road is progressing but is behind schedule.
• Housing: In recent months, construction has begun on the Katse Lodge and Katse Village upgrades, and the construction of the Polihali Village. These are two
of the four Phase II housing contracts packaged to enhance local participation, especially of small- and medium-sized contractors. Procurement is advanced for the construction of the Polihali Operations Centre and the Polihali Commercial Centre.
• Bulk power: Upgrades to the substations at the Katse intake tower and Ha Lejone – and to the protection and control systems of the Maputsoe, Pitseng and Matsoku diversion substations – are under way.
Polihali Dam will add another 2 325 million m3 to the LHWP storage capacity. The current annual royalty revenue will increase when Polihali is commissioned, as the volume of water transferred to South Africa will increase incrementally from the current supply rate of 780 million m3 per annum to more than 1 270 million m3 per annum.
Royalty revenues on the transfer of water to South Africa will vary from year to year, depending on the volume of water transferred and inflation. At the end of 2021, the cumulative water transfer royalty revenue was M12.545 billion (at a 1:1 ratio to the South African rand).
The water conveyance system also generates electricity for Lesotho, which has reduced the country’s dependence on imported electricity, saving on import costs and contributing to the country’s GDP by stimulating local industry and economic growth. At the end of December 2021, the cumulative electricity sales revenue from the time the ‘Muela Hydropower Plant
that was commissioned in 1998 amounted to M1.276 billion.
Community upliftment and skills transfer
Community upliftment and skills transfer are fundamental to the LHWP. Besides compensation for lost assets and the resettlement of affected households, livelihood restoration and social development programmes are being implemented.
The construction of the first replacement houses for households affected by the access roads and bulk power developments has started. There are also financial literacy education programmes to help communities affected by the implementation of Phase II to make informed choices about the use of their compensation funds, especially largesum compensation payments.
There is also a public health programme to sensitise communities, including high school students in the project area, to the potential impacts of an influx of people. This focuses on sexually transmitted diseases, pregnancy, sexual exploitation and abuse, as well as human trafficking.
Demonstration projects in the four community councils of Menoaneng, Mokhotlong Urban, Mphokojoane and Seate are being implemented to enhance capacity building and to illustrate viable projects than could be replicated by individual households and communities. These are already familiar activities such as the rearing of village chickens, vegetable production in protective tunnels and beekeeping.
A social development master plan (SDMP) is in preparation. It involves intensive consultation with local communities to identify needs, priority projects for implementation, and the roles and responsibilities of stakeholders, among others. Projects within the SDMP could include water and sanitation, rural electrification, public health, agriculture, tourism, social protection, as well as educational enhancement such as skills and enterprise training and development. All consultants and contractors are required to implement skills development and technology transfer programmes for their staff and to provide opportunities for young professionals to be mentored and trained. The young professionals are recruited through the LHDA’s Young Professionals Programme (YPP).
The YPP is the LHDA’s skills transfer initiative that provides learning opportunities within Phase II of the LHWP for young professionals from Lesotho and South Africa. The programme targets young graduates from tertiary institutions with no work experience and aims to address the problem of an inadequate skills market.
The YPP builds on the rich legacy of a similar on-the-job-training programme that jump-started the engineering careers of young professionals under the first phase of the LHWP. Several of the former Phase I young professionals (interns) now hold executive positions at the LHDA or are project managers and resident engineers on Phase II consultancy and construction contracts. By February 2022, approximately 33 young professionals had been placed.
The consultants and contractors are also required to include enterprise development in their work plans. This includes a training, development and mentoring plan for the small to medium enterprises.
On a construction level, unskilled labour is reserved for Lesotho nationals and may be sourced from across the country. Skilled and semi-skilled opportunities are made available to Lesotho nationals and then extended to South African nationals should the skills not be available within Lesotho. For professional and technical opportunities, preference is given to Lesotho nationals followed by South Africans and people from South African Development Community member states, and then international workers, in that order, provided the required skills and experience levels are met.
A
local water and wastewater treatment contractor, WEC Projects, is installing a compact, portable and modular sewage treatment solution for Khanyisani Primary School in Lubunde, near Bizana in the Eastern Cape.
The sewage system, based on the NEWgenerator 100 model designed by a team of engineers at the University of South Florida (USF) in the US, is built under licence in South Africa by WEC Projects.
“Khanyisani Primary School is located in a rural area that lacks a consistent water supply. The NEWgenerator system will treat the sewage produced by the school’s toilet block. The treated water produced by the sanitation process will be recycled back to the toilet block for reuse, ensuring a consistent water supply. While the recycled water will not be treated to human consumption standards, it will be suitable for reuse in the toilets. In addition, the biogas produced by the sewage treatment process will potentially be utilised by the school for cooking and heating purposes, resulting in a reduction in its power consumption,” explains Tim Fisher, manager: Process Engineering, WEC Projects.
“This is a particularly exciting project for us, as it is the first commercial installation of the NEWgenerator system in South Africa. Up to now, it has been deployed on a pilot project
basis in the country, first in eThekwini, in conjunction with the University of KwaZuluNatal, and then on a larger scale in Soweto. These projects are overseen by the Water Research Commission (WRC) under the auspices of its South African Sanitation Technology Enterprise Programme (Sastep).
“WEC Projects was chosen by the WRC as its commercialisation partner to manufacture NEWgenerator units in South Africa under licence from USF. By manufacturing the units locally and, where possible, utilising local components, we will be able to build units more rapidly while reducing the overall cost. Local production also means that the cost of shipping will be reduced considerably, making them ideal for market conditions throughout the SADC region,” he adds.
Funded by the WRC’s Sastep programme, WEC Projects is using the contract as an opportunity to optimise the design of the NEWgenerator unit for local conditions. For example, the company will build the unit into a larger shipping container to allow more space for equipment and operational staff. WEC Projects will incorporate the NEWgenerator unit into the school’s existing toilet block and will also provide the infrastructure for reticulating the biogas.
• Incorporates an anaerobic digestor utilising appropriate microorganisms to treat the sewage and produce biogas
• Clean water is filtered – with bacteria, viruses and any remaining solid particles removed – and then disinfected through a chlorination system
• Up to 99% of the water can be recycled for reuse in the system
• The nutrient-rich treated waste is an ideal crop fertiliser for use by local smallscale and informal farmers
• Offers employment and franchisable economic opportunities for local small businesses and entrepreneurs who can provide not only sales, installation and maintenance of the units to the surrounding communities but also training and upskilling for the youth
• Flexibility in design and installation also makes it ideal for use in various industries – from tourism to mining
Responding to growth in the renewable energy sector, Actom continues to reposition its offering in the electromechanical field to meet current and future technological demand.
When looking at the traditional coal requirements from a coal power station and engineering perspective, it was clear that Actom had to make a distinct shift by enhancing existing designs, looking towards new technologies, and designing new product lines,” says Mervyn Naidoo, CEO, Actom.
As a result, Actom has been positioning itself to align with Eskom’s ‘Just Energy Transition’ (JET) plan, which is to decommission 10 coal-fired power stations by 2040 and an additional three by 2050. The JET plan presents an opportunity to repurpose these sites into agrivoltaics, photovoltaics and gas generation, and migrate towards a cleaner and greener energy future while creating new job opportunities for those displaced by the replacement of coal technologies.
A 2.7 MVA 690 V to 33 kV step-up pad-mounted transformer installed at Kangnas Wind Farm in the Northern Cape
“Traditionally, Actom supplied switchgear, protection technologies, control schemes and electric motors. What is transpiring now with renewable energy projects is that engineering procurement contractors (EPCs) are requiring an integrated offering,” Naidoo explains.
This dynamic shift into the renewable energy space has triggered a whole new migration in Actom towards evolution engineering in new design technologies and embracing a new approach in the Fourth Industrial Revolution. Examples include Actom’s development of new software, systems and technologies to enable the remote monitoring of wind and solar plants scattered across the country from an operations and maintenance perspective.
Wind power currently tops the list as the most promising renewable energy source in South Africa. According to Christian Barret, divisional CEO: Actom Energy, “When Round 7 of the Renewable Energy Independent Power Producer Procurement Programme is fully implemented, we are estimating that we could have approximately 70 wind farms operational, which will host 2 500 turbines.”
“By integrating Actom’s locally manufactured electrical equipment, repairs and services – together with its energy solution, frontend engineering and project management capabilities – we can provide customised solutions for most of our clients’ wind farm requirements,” Barret continues. Each wind farm presents two distinct areas of Actom High Voltage Equipment assembly staff doing final checks on highvoltage transformers to be installed in solar and wind farm substations
The Groeipunt Substation between Springbok and Aggenys in the Northern Cape connects Kangnas Wind Farm to the grid via Actom’s 250 MVA 220/132/22 kV transformer and related substation equipment
opportunity for Actom. The first is the supply and maintenance of the electrical components and turbines, which convert the aerodynamic force from the rotor blades into electricity through a gearbox-generator subassembly. The second is the balance of plant (BoP), which collects the power generated by each turbine, steps up the voltage and transmits it into the national grid.
“To this end, we have completed two turnkey contracts for the latter: the first was the Nordex Kouga Wind Farm in the Eastern Cape, and the second for Vestas at the Tsitsikamma Community Wind Farm. We have also submitted additional bids for Bid Window 5 and are busy working on aligning with the recently announced successful bids,” says John McClure, operations manager: Actom Power Systems.
Biomass
In addition to wind power generation, Actom is actively involved in other large-scale green energy projects. These include a biomass power plant installation, established under South Africa’s Independent Power Producer Programme, which has been completed as a joint venture between John
Thompson’s Industrial Watertube Boilers (IWTB) – an Actom division – and Lesedi Nuclear Services. The 25 MW power plant is adjacent to the Sappi Ngodwana pulp mill in Mpumalanga. According to Russel Warren, GM: IWTB, the installation took 20 months.
The JV company will operate and maintain the entire plant, comprising the boiler, turbine and balance of plant, over a five-year contract period.
Another growth market for Actom is hydropower, which currently accounts for 17% of electricity generation in Africa on average. In some countries – such as the DRC, Ethiopia, Malawi, Mozambique, Uganda and Zambia – hydropower exceeds 80% of electricity generation.
Marthinusen & Coutts, a division of Actom, is the largest aftermarket service provider of electrical and mechanical rotating machines in Africa. The division works extensively on hydropower plants and has recently been contracted to refurbish a synchronous condenser at the Inga River hydro project in the DRC.
Within the energy mix, South Africa is also well placed to take advantage of a worldwide market for green hydrogen that could be worth US$2.5 trillion (R31 trillion) by 2050. This will be bolstered by South Africa’s plans to link its massive platinum reserves to the green hydrogen market.
“In our perspective, we are looking to see how we can participate in hydrogen, but we see it as a key part of the energy mix and will actively get involved,” says Naidoo.
African penetration
Running in parallel is Actom’s expansion strategy within the African Continental Free Trade Area. “The way I look at it is that Africa as a continent generates 170 GW of power for about 1.4 billion people. Whereas China also has a population of 1.4 billion people, but they generate 2 200 GW of power,” adds Naidoo.
“So, you can see there is a radical gap, and it is a no-brainer that Africa must gear up when you look at an analogy of what is happening with mobile phones in Africa. Like in Nigeria, they went from 7 000 landlines to the point of 150 million mobile phone contracts in under 10 years,” Naidoo concludes.
Within any construction project, there are budgets and penalties for cost overruns. Alastair Currie speaks to Andrew Skudder, CEO of RIB CCS, about his company’s BuildSmart construction cost management and ERP software, which provides an unmatched level of real-time control.
How does BuildSmart differ from other programmes out there?
AS BuildSmart was developed by software developer and founder Peter Cheney, more than 30 years ago, in the old DOS (HB87) environment. The major transition from there occurred in the early 2000s with the advent of the Windows platform and the offering of a web-based solution.
From inception, Peter’s objective was to build a fit-for-purpose construction financial management solution, based on his extensive experience in the construction industry. His objective has evolved with next-generation updates. Today, this ensures that construction companies, led by key players like quantity surveyors and project managers, can track all their costs, after estimates
have been done, through the life cycle of a project. The core BuildSmart areas covered are labour costs, materials, plant and equipment, and subcontractors.
Most similar financial systems treat a supplier as a supplier. BuildSmart defines this into two distinctive categories: 1) materials, plant and equipment suppliers, and 2) subcontractors. This distinction allows for the subcontractors to be managed on a certification basis, tracking all advances and retentions, rather than on a simple order and invoice process as is used for normal suppliers.
In what way does it provide a competitive advantage for contractors?
BuildSmart provides a major competitive advantage due to its ability to link directly
with a project’s initial estimate and ongoing valuations. This allows contract procurement to be linked directly to the estimate’s materials at both a quantity and unit price level, ensuring budget controls are built into the process from the start.
BuildSmart also makes use of live accruals, meaning any cost that may not have been fully processed by finance can still be reflected as an accrual to the contract. This approach means that accurate actual versus allowable reporting can be done, without having to wait for the completion of the financial process.
Cutting down on this reporting cycle empowers project teams to identify and act on any deviations in a timely manner.
BuildSmart works seamlessly with Candy, RIB CCS’s estimating and project cost control solution
Does BuildSmart provide a coherent/secure platform for PPP projects?
From a project programme perspective, BuildSmart on its own is not a standalone solution. However, as part of RIB CCS’s overarching MTWO 5D BIM enterprise construction cloud software, there are tangible benefits where BuildSmart can integrate from a financial perspective in terms of real-time costing. As a cloud-based platform, MTWO provides a collaborative and coherent environment where public and private stakeholders can operate. However, the primary user of BuildSmart and MTWO is the contractor employed to deliver the project. Then from an owner perspective, MTWO enables an accurate report on progress against budget and programme status.
in terms of accounting practices, the contractor is still able to provide the subcontractor with a full tax invoice for the contra charges.
How effective is BuildSmart in managing/minimising cost overruns?
and Transnet in South Africa. They both employ legacy solutions called iTWO and its successor, MTWO, with which BuildSmart can be integrated. These SOEs use RIB’s software suites to determine their budgets, manage their contractors and subcontractors, and monitor progress and costs within their portfolio of projects.
How are subcontractors managed?
Within BuildSmart, subcontractors are managed via the dedicated subcontractor certification process. The certification process makes allowance for the work completed to date as well as for claims for other contractual obligations such as escalations, materials on-site, advances and retentions. In addition, contra charges are also handled correctly to ensure the correct output VAT is calculated. An example would be the supply of materials by the contractor to the subcontractor, such as the provision of electrical cabling. The contra cost plus output VAT is deducted from the final payment due to the subcontractor. And although no actual money is exchanged,
Due to the fact that approvers have full visibility of their allowable quantities and costs during the entire procurement process, BuildSmart is able to flag and prevent cost overruns prior to any commitment being made to a supplier. In the event that the allowables do need to be exceeded, users who have this authority will need to be involved in the approval process.
A dispute process is also built into the subcontractor certification process to track any discrepancies between the subcontractor’s claim and what has been certified, potentially due to poor workmanship or other reasons.
Are public sector infrastructure clients using RIB solutions?
Worldwide, the RIB Group’s suite is used extensively by government departments and SOEs responsible for infrastructure implementation. For example, in Germany, which is the home of the RIB Group – RIB CCS’s holding company – prime SOE examples include Die Autobahn and Deutsche Bahn, the equivalent of Sanral
There’s a definite business case for integrated platforms like MTWO, together with financial tools like BuildSmart, for employment within the South African public space.
Is it one of the solutions for combating corruption/wasteful expenditure?
RIB’s software solutions ensure that all information encapsulated is freely available to all designated users, so there’s a high degree of transparency and traceability. This results in better governance and tighter control of procurement management. In BuildSmart, for example, when purchasing against a resource list, linked to the original estimate, controls can be set to ensure quantities, rates and the total allowable for the items are not exceeded.
And in closing?
The overwhelming feedback from contractors is that BuildSmart provides them with a high degree of financial control. It’s also revealing to note that virtually all of our clients who came on board more than 20 years ago are still BuildSmart users and are commercially successful.
Speaking at AfriSam’s recent National Budget Breakdown function, an annual event now in its fifth year, Dr Azar Jammine of Econometrix gave a thumbs up to the 2022 budget, describing it as “highly satisfactory with no harm”.
He cautioned, however, that servicing the national debt was becoming increasingly onerous and now accounted for 14% of government expenditure. He also expressed the view that there was nothing in the budget “to make one believe sustainable growth will improve forthwith”.
Jammine congratulated the Minister of Finance, Enoch Godongwana, for making a commitment to increased spending on capital assets while, at the same time, attempting to curb the growth in the public sector wage bill. “We’re now seeing an attempt to slow down the compensation of employees as a percentage of the overall tax bill and to increase the amount of investment in capital assets,” he said.
Jammine was the main speaker at the event and reviewed both the global and local economy. Sharing the stage with him was Trevor Manuel, who served as South Africa’s Minister of Finance from 1996 to 2009, making him the longest serving finance minister in South Africa’s history. Manuel provided valuable and insightful commentary, based on his intimate knowledge and experience. He also fielded many questions from the floor and enlightened the audience
with his unique insights into the South African economy.
Manuel referred to the “ravages of state capture”, saying it was not just about corruption but also the destruction of institutional capacity. As an example, he noted that the South African Police Service (SAPS) would be underspending its budget in the 2021/22 fiscal year by around R20 billion, challenging the often-heard claims that the SAPS was underfunded.
He added that the situation was even more chaotic at a provincial and municipal level.
On the challenge of water supply, he asked how it was possible that one of the major metros in the country – Gqeberha – had failed to maintain its water infrastructure.
He also referred to “this horrible phenomenon called the construction mafia”, saying that it basically meant that the pricing of contracts could not be realistic and that projects could sometimes not commence, never mind be completed.
Reviewing the global economy, Jammine said it had grown by 5.9 % in 2021, with the International Monetary Fund (IMF) predicting that this figure would fall to 4% in 2022 and
3.8% in 2023. By contrast, South Africa had shown 4.6% growth in 2021, well below the global average, with the IMF forecasting that this would drop to 1.9 % in 2022 and a paltry 1.4% – the lowest of any major economy – in 2023.
“Since 2009, South Africa’s growth trajectory has lagged that of the world economy,” he said. He added that while activity in the world economy was back to the levels seen before the onset of the Covid-19 pandemic, this was not the case with South Africa, mainly due to structural factors that inhibited growth.
These structural impediments included skills shortages, state capture and corruption, cadre deployment, the deterioration of SOEs, lack of infrastructural investment, over-regulation and non-payment for work, and labour market restrictions.
On the subject of debt, Jammine told his audience that government debt-to-GDP ratios worldwide were “quite terrifying”, with US debt, for example,
now amounting to 120-130% of GDP. He also noted that since 2020, the US Federal Reserve had injected a massive stimulus recovery package of around US$5 trillion (R75.7 trillion) into the economy – to counter the economic effects of Covid-19 – and that other countries had followed suit. The result was sharp upward pressure on prices.
“The genie is now out of the bottle in the form of a massive surge in inflation the likes of which we have not seen in 40 years in the world economy,” he observed. He added that South Africa’s inflation rate was below that of the US for the first time in 30 years.
Referring specifically to South Africa’s budget, Jammine said SARS had collected R182 billion more in taxes than anticipated, with this economic windfall giving Minister Godongwana considerable leeway in formulating the budget. He pointed out that the windfall was largely due to increased payments by
the mining industry, which have benefitted from the current surge in commodity prices. Turning to some of the specifics of the South African economy, Jammine said construction – AfriSam’s primary market –had been the weakest sector of the economy over the past decade and now accounted for just 2.5% of GDP. This was due to gross capital formation in South Africa having declined, as a percentage of GDP, from 19% around 2014 to the current 13%.
Concluding his presentation on a positive note, Jammine said the construction industry
could receive a big boost from an increase in infrastructural spending. He noted that 51 well-defined projects worth R340 billion had been identified in the 2020 Economic Recovery and Construction Plan, and that the project pipeline has since been expanded to include an additional 55 projects worth R595 billion.
This amounted to a grand total of R935 billion, representing 126% of total annual fixed investment. He said that if all or even just some of these projects were implemented, it would be a game changer for the industry and a major boost to the economy, with growth increasing by as much as 2% a year.
Desalination set to take off in a big way
According to Global Water Intelligence (GWI), the UK-based market intelligence provider for the water industry, Egypt is planning to place new orders for desalination projects using seawater, amounting to 2.8 million tonnes of daily water production by 2025. It eventually aims to supply 6.4 million tonnes of water per day through desalination plants drawing on seawater by 2050.
Doosan Heavy Industries & Construction recently signed a memorandum of understanding (MoU) on a project in Egypt, signalling the company’s entry into the North African desalination market. The South Korean corporation announced it had signed an MoU with Hassan Allam, a large-sized construction/ developer firm in Egypt, and Almar Water Solutions, a company formed through a Saudi Arabia-Spain joint venture, agreeing to cooperate on a reverse osmosis desalination project.
The companies agreed to enter a comprehensive partnership regarding the delivery of the project. Through this project, they aim to produce a daily supply of 1 million tonnes of water for Ismailia, a seaport city in the middle of the Suez Canal.
“Over the past 40 years, Doosan Heavy Industries & Construction has built around 30 seawater desalination plants in the Middle East region, which has led to widespread recognition by clients for our technical expertise,” says Inwon Park, CEO: EPC at Doosan Heavy Industries & Construction.
Converting solid waste into electricity
VR Holding AB has been appointed by the Kenyan government to carry out a solid waste-to-energy project in Kakamega County. Costing US$53 million (R802 million), the construction of the Kakamega Solid Waste-to-Energy plant will provide employment opportunities for residents, simultaneously contributing to the socio-economic growth of the county.
According to Kakamega Governor Wycliffe Oparanya, VR Holding has nine months to deliver the facility. In addition to diversifying the electricity mix and decentralising power generation, the Kakamega authorities want to provide a sustainable solution to the problem of solid waste pollution.
This project is being launched less than a year after the commissioning of a medical waste treatment plant in the same county. The unit built in Kakamega has a capacity of 60 tonnes per day. The new facility uses biodigestion or anaerobic digestion technology to treat medical waste.
Grindrod flags plans to expand Port of Maputo
The Maputo Port Development Company (MPDC) has announced plans to triple capacity at its Maputo terminal (GML) and Matola Drybulk terminal (TCM) in Mozambique in response to rising demand for coal exports from South Africa. Grindrod and the government of Mozambique are the MPDC’s major shareholders.
This extension is projected to boost South Africa’s mining exports on a yearon-year basis, increase volume exports by existing port users, and promote port access to new users.
GML’s throughput capacity will treble – from 1.5 million tonnes per annum to 4.5 million tonnes annually – by the first half of this year. The expansion at TCM will increase from 7.3 million tonnes per annum to 12 million tonnes per annum in the short to medium term, and 20 million tonnes per annum in the long term.
Diversifying energy mix through nuclear
The US and Ghana are partnering under the Foundational Infrastructure for Responsible use of Small Modular Reactor Technology (First) programme to support Ghana’s adoption of nuclear technology. Japan has been a valuable partner with the US on the First initiative and will build on its existing partnership with Ghana. This includes support for stakeholder engagement, advanced technical collaboration, and project evaluation and planning.
According to Ghana’s Minister of Energy, Dr Matthew Opoku Prempeh, the decision to include nuclear power in the nation’s energy mix has led to establishing Nuclear Power Ghana Limited as an owner-operator and project developer. The First programme will help Ghana develop the competencies of Nuclear Power Ghana to build and operate Ghana’s first nuclear power plant safely.
“Clean, reliable and safe nuclear energy could provide significant benefits to the people of Ghana, including clean energy, agricultural improvements, clean water and advanced medical treatment,” says Stephanie Sullivan, US ambassador.
Drawing on 60 years of US experience working with nuclear energy, the First programme provides capacity-building support to partner countries as they develop their nuclear energy programmes. To date, the US has announced US$7.3 million (R110 million) to support First projects around the world.
Initial training in Ghana during 2022 will focus on stakeholder engagement, licensing and regulatory development, financing, workforce development and nuclear security, safety and non-proliferation.
Rehabilitated road in Mhondoro-Ngezi district
Close to 200 km of road has been repaired using the Zimbabwean government’s allocation of devolution funds and the Emergency Road Rehabilitation Programme (ERRP2).
The ERRP2’s focus is road resealing, road rehabilitation and construction, gravelling, spot regravelling, drainage structure construction and repair, wash-away and gully reclamation, erosion works and drainage, vegetation clearing, and pothole patching.
Apart from regravelling most roads, the Mhondoro-Ngezi Rural District Council is finalising tarring a 4.6 km stretch of Binya Road that connects Selous-Ngezi highway and Turf township, which was impassable during the rainy season.
Council engineer Miriam Jima says the Binya Road works are now 74% complete. “With ERRP2, we are
planning to do 198 km in MhondoroNgezi and Muzvezve constituencies. Five of the roads are 100% complete while the other remaining roads are 70% complete, with works now left to be done on culverts.”
Electricity generation from Nile dam begins Ethiopia is now producing electricity from its Grand Ethiopian Renaissance Dam (GERD) – a massive hydropower plant on the Nile River that neighbours Sudan and Egypt.
In February, Prime Minister Abiy Ahmed officially inaugurated electricity production from the mega dam. While Sudan and Egypt maintain that the dam will cause severe water shortages downstream, the prime minister sought to assure neighbouring nations his country did not wish to harm their interests.
“Ethiopia’s main interest is to bring light to 60% of the population who is suffering in darkness, to save the labour of our mothers who are carrying wood on their backs in order to get energy. As you can see, this water will generate energy while flowing as it previously flowed to Sudan and Egypt, unlike the rumours that say the Ethiopian people and government are damming the water to starve Egypt and Sudan,” he said.
GERD is set to be the largest hydro-electric scheme in Africa but has been at the centre of a regional dispute ever since Ethiopia broke ground there in 2011. The US$4.2 billion (R63.5 billion) project is ultimately expected to produce more than 5 000 MW of electricity, more than doubling Ethiopia’s electricity output.
Ethiopia, the second most populous country on the continent, has the second biggest electricity deficit in Africa according to the World Bank, with about twothirds of the population of about 110 million lacking a connection to the grid.
It is often said that roads are the ‘arteries through which the economy pulses’. For this reason, it’s important to collectively debate future road funding models, and especially the role of public-private partnerships (PPPs) in bridging infrastructure gaps.
By Solomon KganyagoAcross the world, there is broad recognition that road funding models are moving beyond the traditional solutions of direct budget allocations, fuel levies that will be impacted by green energy, and one-sizefits-all toll networks.
Private sector companies such as the Bakwena Platinum Corridor Concessionaire – with a strong track record in road expansion and management – are able and available to contribute to the discourse on other models and to promote the value of partnerships between the private and public sectors.
We should, however, recognise that whatever funding model is decided upon, the citizens will continue to pay, whether through taxes, tolling, rising prices for goods and services resulting from higher fuel levies, or additional transport costs associated with a poorly maintained road network.
It is, thus, of the utmost importance that existing road networks – especially primary roads such as the Bakwena Platinum N1N4 highway – be maintained according to the highest standards. Wellplanned and well-maintained roads are catalysts for balanced and accelerated growth, and this contributes to the
fundamental transformation of society. At present, more than 85% of the national road network is funded directly from the national fiscus. A further 7% is managed by Sanral as toll roads through toll levies and the borrowing of funds for construction on commercial markets, while the remaining 6% is run as PPPs with concessionaires.
Hard choices on priorities
Government has to make hard decisions on its spending priorities. Immediate socio-economic needs in the fields of education, healthcare, social welfare and security make legitimate demands on the annual budgets. Road projects have to compete with other strategic infrastructure projects such as water, power and sanitation. However, a sustained lack of investment in roads has clear negative impacts on long-term development and sustainability. If the required resources cannot be found within a constrained national budget, alternative funding options should be considered. In this respect, PPPs present a proven model that has been implemented with great success across the world and in South Africa.
Bakwena’s example
A concession contract to finance, construct, manage, upgrade and maintain a reliable road infrastructure along the N1 and N4 arteries was signed between
Sanral and Bakwena in 2000. For more than two decades now, Bakwena manages a world-class road network on the N1 between Pretoria and Bela-Bela (95 km) and 290 km of the N4 connecting Gauteng through Rustenburg and Zeerust to the Botswana border – 385 km in total. In addition to the obvious benefits the road brings to communities in Limpopo, Gauteng and the North West, it is also a primary link for the transportation of goods, services and people into the Southern African Development Community region. The traffic growth on this network and the rising value of goods transported underscore the importance of this road for the regional economy.
Infrastructure Fund approach
Across the board, the country is faced with the vexing question of how best to fund its vital road infrastructure. Public infrastructure spending has been on a steady decline in recent
years, and it currently amounts to only 13% of total expenditure. It will have to accelerate rapidly in the remainder of the decade if it wants to achieve the 30% by 2030 envisaged in the National Development Plan.
President Ramaphosa has repeatedly committed the government to the promotion of ‘aggressive infrastructure investment’ and supporting its delivery.
At the Infrastructure Development Conference in 2020, he indicated that the country hopes to unlock some R1 trillion in infrastructure.
This will be administered through the Infrastructure Fund, which is a blended financing instrument jointly governed by the public and private sectors and multilateral development banks. With this approach, projects are derisked to make them more attractive for private sector participation.
The Infrastructure Investment Plan subsequently released by government was a major step in the right direction. It offers a framework for future investments and provides details of credible and bankable projects that are in the pipeline.
Importantly, it recognises the central role played by PPPs – especially in the transport and construction sectors –and commits government “to remove policy bottlenecks in engaging with the private sector”.
Investment in road infrastructure has to be at the core of the economic
transformation strategy. On the list of infrastructure projects announced by government are several shovelready construction and maintenance projects. These will be implemented in all nine provinces and improve the quality of life of all citizens.
A sustained lack of investment in roads has clear negative impacts on long-term development and sustainability.”
We welcome President Ramaphosa’s commitment to a more coordinated engagement between government, the private sector and other players in the infrastructure financing space. This will, no doubt, lead to greater private sector participation in both the planning and implementation of critical road projects. Moreover, National Treasury is preparing legislative changes to enable retirement funds to invest more readily in infrastructure projects – a move that will further release critical funding.
The use of tolling to fund road projects is a workable and cost-effective approach. It ensures that the money received from toll
fees is ploughed back into road assets for construction and maintenance purposes.
Compared to traditional tax-based funding, PPPs also accelerate the availability of initial resources for delivering road infrastructure earlier, while providing opportunities for the private sector to invest in a new class of assets.
In its most recent report, the National Planning Commission notes the concern that the state does not have the institutional or financial capability to finance infrastructure to the required scale. It then concludes: “Given the government’s limited finances, private sector funding will need to be sourced for some of these investments.”
PPPs such as Bakwena transfer the risk from the public sector to the private sector. The concessionaire assumes full responsibilities and risks for the condition of the road pavement, the management of traffic volumes, the collection of toll revenue, as well as the costs associated with maintenance, rehabilitation and expansions for the duration of the concession.
The toll revenues collected are used to recover costs for debt servicing, capital expenditure, maintenance and a return on equity to the investors with a defined cap. This offers a winwin option for the companies, the government and citizens, and ensures that vital infrastructure – such as the N1 and N4 routes Bakwena manages –continues to flourish.
Fuel costs are estimated to be the second largest expense in a fleet’s budget. Thus, the priority to reduce fuel spend is not new but, with unprecedented price hikes on the horizon, it’s time to refocus on efficiencies.
Collecting and analysing data, involving drivers and using analytics are the go-to ways to spur change, says Eugene Herbert, CEO of MasterDrive.
“In a world vastly different to the one that existed when fuel-saving strategies first started, an updated approach is needed. Not only are corporate objectives important, but so are environmental and societal considerations,” Herbert explains.
He runs through a list of important fuelsaving strategies:
• Avoid idling: idling for more than 10 seconds uses more fuel and emits more emissions than switching the vehicle off. Educate drivers on when to switch off and when idling is acceptable.
• Get a fuel card: this provides data to keep track of whether fuel spend equals kilometres travelled.
• Empty vehicles: require drivers to remove any unnecessary weight from their vehicles weekly. Every 50 kg removed from a vehicle improves fuel efficiency by 1% to 2%.
• Correct tyre pressure: it is estimated one
out of four drivers travels with underinflated tyres. Underinflation can increase fuel consumption by 10% on long hauls and cause a 15% reduction in tyre life. Implement policies to monitor tyre pressure regularly, particularly in cold months.
• Cruise control: this can smooth acceleration on highways and flatter terrain. With inclines and curves, however, cruise control will not be as effective as drivers in reducing fuel consumption.
• 93 vs 95: higher-octane fuels do not always increase fuel efficiency as commonly believed. Instead, know when to use each type of fuel – e.g. naturally aspirated vs turbocharged engines and inland vs coastal driving.
• Reduce speed: reducing speed by 20 km/h can help reduce your fuel consumption by as much as 15-20%. Online tools can calculate additional fuel spend over certain speeds and give drivers more insight on how speeding affects consumption.
• Preventative maintenance: put fleets on regular maintenance schedules to spot issues before they become problems.
• Air-con policies: while an air conditioner can be more fuel efficient in certain circumstances, unnecessary use can increase consumption by >5%. While it is unrealistic to ban air-con use, train drivers on how and when to use it. For example, the optimal temperature is around 22˚C, park in the shade or use sunshades to keep vehicles cooler, and avoid using the air con while stationary.
• Aerodynamics: conversely, wide-open windows on highways increase aerodynamic drag, resulting in a 10% decrease in economy. Anything that affects the original aerodynamics of a vehicle must be correctly fixed as soon as possible to reduce drag. Avoid moving cargo on a roof, for example.
Now, more than ever, Herbert says fleet managers need to do whatever necessary to keep costs as low as possible.
“Training initiatives like the Eco-Driving programme for fleet owners – available from MasterDrive – are a necessity, unlike previously where they were perceived as a bit of a luxury,” Herbert concludes.
AThanks to the vision of Deborah Terhune, founder of Growing Up Africa, the development of the Devland Soweto Education Campus went from concept to completion over a period of seven years and is set to make a lasting difference.
non-profit organisation,
Growing Up Africa’s mission is to build resilient education structures and related infrastructure for a future of ecological, social and economic sustainability.
Every potential project begins with extensive research. In South Africa’s case, this revealed that access to technology was not keeping up with the educational needs of underserved communities. When presented with the Devland Soweto site as an opportunity to build an education campus, Growing Up Africa set on a path to design and build a facility to anticipate innovation and the technological needs of the future.
Growing Up Africa’s research was aligned with the findings of Professor Tshilidzi Marwala, vice chancellor of the University of Johannesburg (UJ). In a paper co-written with fellow UJ faculty member Dr Bo Xing, entitled ‘Implications of the Fourth Industrial Age on Higher Education’ (The Thinker, Vol. 73, 2017), he states, “The fourth industrial revolution (4IR) is powered
by artificial intelligence, and it will transform the workplace from task-based characteristics to human-centred characteristics. Because of the convergence of man and machine, it will reduce the subject distance between humanities and social science as well as science and technology. This will necessarily require much more interdisciplinary teaching, research and innovation.”
The Devland Soweto Education Campus is located on a site that was home to a former industrial park, and the region is currently undergoing transformation. “Devland Soweto is a place where the innovation of 4IR is needed and a place where it will happen,” says Terhune.
Growing Up Africa’s development model is based on designing state-of-the-art projects and infrastructure with minimal direct cash funding. The world-class design of its projects serves as an incentive for companies and corporations to become involved by contributing professional
expertise, materials, transport and time.
“People want to be part of a successful project that has a tangible and positive impact on the community, and we led the way. This type of development does not happen overnight. We did not wait for funding. We started with the idea,” Terhune explains.
Over the years, the Devland Soweto project has involved over 225 companies and individuals from South Africa and around the world. Critical team members include: Boogertman + Partners as architect of record, William Reue Architecture NYC as the design architect, Mark Laburn Architects, SDP, SMEC Engineering, Spoormaker & Partners, WACO International, ENSAfrica, and Tiber Construction. These companies and many more were essential to the project’s success.
The construction of the building provided jobs and training for members of the local community, and the building itself is an important node for future community development. All professionals and contractors provided their services pro bono, and most
of the building materials for the project were donated by local and international sponsors.
Terhune believes that without CSI or tax credits, this level of involvement by companies and individuals would not have happened. “The incentives are absolutely critical. This is a case study in impact investing,” she explains.
When it all comes together
The campus comprises a 2 000 m2 building and support infrastructure situated on a 7 000 m2 landscaped site. The building itself comprises a series of multipurpose teaching spaces, open-plan work areas, a lecture hall, and administrative offices anchored by a large auditorium.
The site’s outdoor spaces have been developed to accommodate tree-shaded seating, an amphitheatre, an expansive double-height porch, a guardhouse and a refuse building. Another distinctive feature is an extraordinary biophilic sculpture designed by industrial design students from UJ.
A personal vision achieved
“It’s incredibly heartwarming to see Devland Soweto become a reality, and I feel it was a project that was destined to be,” says Terhune, who some 10 years ago packed up her apartment in New York City and set off on a journey to change the lives of those most in need.
“At the time, I was nearing retirement, and wanted to leverage my 30 years of real estate and development experience to make the greatest impact. By happenstance, a doorman suggested that I read The Billionaire That Wasn’t, a book about Chuck Feeney’s life of philanthropy. So, it all started with a New York City doorman, a book, and a country – South Africa,” she explains.
After 10 years of steadfast work toward a laser-focused mission, Terhune’s unique approach to humanitarian development has caught the attention of leaders in the non-profit industry. And now that the Devland Soweto Education Campus is complete, those who have come to know Deborah wonder what’s next for Growing Up Africa.
What is certain is that the world will always need a tireless champion willing to move mountains in service of worthy goals and Growing Up Africa has shown the way.
In the meantime, and thanks to Terhune’s sterling efforts, the Devland Soweto Education Campus is now operational and ready to grow with its community. Ownership of the facility has been donated to UJ, who will take the campus on the next leg of its journey.
Over the years, the project has involved more than 225 companies and individuals from South Africa and around the world
On 1 February 2022, the Property Practitioners Act (No. 22 of 2019; PPA) came into operation, bringing with it a series of new requirements. For property owners, it’s important to understand how the new Act influences and forces them into compliance with other property-related Acts and the role that the land surveyor plays in the compliance process.
By Altus Strydom, GPr LS*The PPA replaces the Estate Agency Affairs Act of 1976. Its main purpose is to establish the Property Practitioners Regulatory Authority, which will supersede the Estate Agency Affairs Board. The purpose of this new authority is to regulate the affairs of all property practitioners, to allow for transformation in the property sector, and to provide consumer protection.
Few people realise the significance of certain clauses and how it will affect the sale of their property, because this Act places the responsibility on the seller/landlord and indemnifies the agent if negative information regarding the property is not disclosed.
Parts of the PPA that affect property owners are there to protect the consumer and here there are two major and significant sections.
Section 67: Completed and signed disclosure form
The agent must not accept a mandate unless the seller or lessor of the property has provided them with a fully completed and signed mandatory disclosure in the prescribed form; and must provide a copy of the completed mandatory disclosure form to a prospective purchaser or lessee who
intends to make an offer for the purchase or lease of a property.
The completed form must be signed by all parties and attached to the agreement of lease or sale. If such a form was not completed and attached, it is understood as if no defects or deficiencies of the property were disclosed to the purchaser.
Section 58: Limitation on relationships with other property market service providers
The PPA prohibits the practice in which a practitioner provides a consumer with an incentive to use a particular conveyancer or service provider.
Property practitioners who contravene this section of the PPA are not entitled to remuneration and must repay it to the consumer and may even be fined. The purpose of this section is to prohibit agents asking for, or service providers offering, payment for services rendered.
Most of the questions on the form relate to parts of the property that are quite obvious or where certificates need to be issued in any case. These include but are not exclusive to items such as the roof, structures, sewerage system, electrical and so forth.
There are, however, questions where compliance is more complex. Here, a professional land surveyor (GPr LS) is the only professional qualified to answer. The relevant questions in this respect are:
- I am aware of a boundary line dispute, encroachments, or encumbrances in connection with the property
Geomatics Profession Act (No. 19 of 2013; GPA) and Land Survey Act (No. 8 of 1997; LSA)
A proper understanding of the words ‘encroachments’ and ‘encumbrances’ is required and extends beyond only encroachments in respect of property boundaries. It includes encroachment upon encumbrances where encumbrances include servitudes, title deed restrictions, building lines, land use rights, height of building, coverage, and floor area ratio.
Only a registered professional land surveyor is qualified to answer not only the question regarding boundary disputes and encroachments, but also encroachments on encumbrances such as the height of building, position of building line, the extent of the building, position of servitudes, coverage, floor area ratio, and positional restrictive conditions in the title deed which affects the property.
National Building Regulations (NBR) and Building Standards Act (No. 103 of 1997; BSA)
Section 11A specifies clearly that if in doubt the municipality will request the owner to appoint a GPr LS to verify the boundary of a property and confirm that the above does not affect the property.
From a zoning certificate and the LUMS, the GPr LS can also confirm adherences or address contraventions of encumbrances. These can include land use, coverage, floor area ratio, number of storeys, etc.
- I am aware that any additions or improvements made to or any erections made on the property have been done or were made only after the required consents, permissions and permits to do so were properly obtained
The Sectional Tiles Act (No. 95 of 1986; STA) and Sectional Titles Management Act (No. 8 of 2011; STMA)
This question is very relevant, especially where sectional titles are concerned and illegal additions to buildings can contravene some or all of the above.
Once more, the land surveyor is the only person that may sign the certificates that these were adhered to when lodging an extension of a sectional plan.
- I am prepared to provide approved building plans of all the structures on the property to the purchaser.
Under normal circumstances, the local municipality will have copies of the approved building plans but, during the past 20 years, many plans were lost and misplaced when municipalities merged or moved offices.
Most land surveyors deal with the municipalities in their area of operation and know where to find these plans if they still exist.
What are the effects if the consumer withholds vital information?
There are numerous negative effects but the most significant are that the seller (not the agent) will be liable if the purchaser lays claims for non-disclosure at a later date.
Some of the things that can go wrong are:
- The owner (and agent) might lose a sale if the bond holder finds out that there are no approved plans, encroachments, or any of the matters mentioned above.
- In the situation of rental property, the landlord can be held liable if somebody is injured where there is an illegal structure. Examples would include where a child drowns in a pool that is not fenced in; or a fire demolishes a building where a thatch lapa catches fire and no fire certificate was issued.
- If at a later date a buyer finds out about matters mentioned above, the seller can land up in expensive court actions and be held liable for rezoning, building line relaxation and other costs.
- Insurance claims will not be successful if there are no approved building plans. It is therefore in the interest of the buyer to ask for copies of approved plans.
- The municipality can instruct you to demolish the illegal extension or encroachment (see
Section A 25 of the NBR).
- If a building encroaches over a property boundary, it can lead to expensive subdivision applications and rezoning applications.
What the land surveyor can do to help the seller comply
The land surveyor can issue a land audit certificate to certify in respect of encroachments, encumbrances, rights, and restrictions relating to the property. Such a certificate will include reference to property boundaries, encroachments, encumbrances, encroachments on encumbrances, building alterations erected contrary to building plans, title conditions, land use and zoning stipulations.
It would be prudent if owners and landlords obtain such a certificate prior to selling or letting a property to minimise subsequent complications. It would also be prudent if buyers and tenants are more aware and ask for a land audit report issued by a professional land surveyor for assurances prior to entering contracts.
The key point to reinforce is that the PPA places the responsibility on the seller and landlord to comply with the Acts mentioned above. Clarification and compliance should therefore take place prior to the sale or lease of a property.
*Chairperson: Northern Provinces, South African Geomatics Institute
All the raw materials used to produce concrete are variable. And the readymix supplier must absorb these variances in his production process to produce concrete that meets the specification. This is inherently the risk that readymix suppliers will carry, making testing a vital part of the quality validation process.
By Jacques Smith, Pr Eng*The first party that needs to know whether the readymix supplier is producing concrete within the strength requirement is the supplier himself. To that end, he will take samples normally at the plant from the back of the truck to have them tested as process control samples. It is up to the client to take samples for cube-making and testing for acceptance control for quality assurance purposes.
These two types of testing are very similar, yet there are fundamental differences between the two. The main difference in testing is the sampling that is done from the back of the truck at the plant for process control testing, whereas on-site sampling is done from a moving stream after the first 15% and before the last 15% of concrete has been offloaded for acceptance control for quality assurance testing (SANS 5878 para. 12.2).
The criteria for assessing these results are then also different. Normally, process control cubes are not (but may be in certain circumstances) accepted as acceptance control testing for quality assurance.
The following things can go wrong with the testing (of perfectly good concrete):
1. Process control cubes are too high.
2. Process control cubes are too low.
3. Acceptance control cubes are too high.
4. Acceptance control cubes are too low.
In number 1 above, this would give a false sense of security and, even unknowingly, substandard concrete may be produced that could result in a failure and huge claim.
In number 2 above, the readymix supplier will increase cement contents because he is scared of a claim. The customer will be very happy with this concrete, which will give higher strengths and even earlier strengths, but this comes at the readymix supplier’s expense.
In number 3 above, it is great for everyone, until something goes wrong and cores are requested. This could then result in huge failures.
In number 4 above, the specification rules that the engineer may call for the process control test results and will then call for cores to be drilled, if the situation cannot be resolved. Ultimately, the concrete will be accepted but with mistrust and unhappiness due to delays and penalties – and the additional cost of the drilling and testing of cores. The readymix supplier will probably increase cement contents to prevent possible failures.
laboratory testing
Due to our involvement in disputes and court cases, Go Consult has been asked on a
number of occasions to investigate the state of testing at a laboratory. On one occasion, eight of the eleven laboratories visited in a sample run were doing testing commercially at the time.
Not one of the laboratories included in this article was accredited by Sanas (the South African National Accreditation Systems) for concrete testing. Sanas accreditation would imply that they have a management system in place to ensure the proper documentation of everything they do, plus systems in place to ensure a repeatable test that will reproduce a similar test result every time.
At every laboratory, there were signs of incorrect crushing of cubes with tensile cracks and the cubes only being crushed on one side, with the other side failing in tension. This error will definitely give a lower result and create the impression that the concrete is of substandard quality.
This, of course, would raise the following logical questions (as the advocate would certainly ask in court): How many of the cubes were tested like that? Which ones were they and what would the effect of that be? This should result in a rejection of all test results, as we know that some results are lower, but we do not know which and we do not know by how much, so we cannot use any of these results. We, therefore, might have to drill cores to determine the
- Is there a paper label on each cube with at least some reference number on it?
strength of the concrete. These are often incorrectly done and interpreted, which has led to instructions to break out perfectly fine concrete on numerous occasions.
So, what can readymix suppliers/ contractors do?
The first step is to visit the laboratory that is testing for you and check the following items. The fact that you are checking should encourage the lab to ensure their methods and systems are up to standard –or so one hopes.
- Is every cube properly marked on the side (paper labels tend to come loose in the water)?
- Are the edges sharp?
- Are the cube moulds square?
- Are they oiled?
- Is each cube tamped enough? (25 times for two layers on 100 mm cubes and at least
- Do the two halves of each cube mould correspond (see the stamped marks on each cube)?
- Do they have a slump rod or vibrating table to compact the cubes with?
- Do they understand that no vibration is allowed after the cubes have been made?
- The curing temperature in the curing tank is often not correct. It should be between 22-24˚C.
- Is the curing tank heating system always on and plugged in (not only in the day when the generator is working)? The specification states that site cubes that have to stay on-site for an extended period should be covered and then placed in water (at the above temperature).
- Is there a pump stirring the water constantly to prevent hot spots due to heat of hydration of the cement? (This is not a requirement of the test method.)
- Are all of the cubes constantly submerged
- Is there a calibration certificate and is it less than 18 months old? And was it done by a Sanas-accredited organisation for press calibrations?
- Are there locating pins on the platens to ensure that the cube is placed right in the centre between the platens? (Just marks –circles or lines – on the platens alone too often leave it to the operator to locate cubes and they do not do it correctly.)
- Did they ensure that two faces formed by the cube mould were against the platens while crushing?
- Is the top platen loose to swivel?
- Is the machine clean?
- Has the operator been trained to operate the machine?
- Has the loading rate (N/s) been adjusted for the type of test? (It should be different for different sizes of cubes and even cores.)
Should a dispute arise, Go Consult can assist to settle this and put it in perspective. Go Consult is also available to do an audit at the laboratory to ensure proper test results.
Concrete is the most vital building material to create the infrastructure to sustain South African urban and rural settlements and the road networks that link them. Concrete provides the essential material properties to economically build vital buildings, dams, bridges, warehouses, roads, airports, as well as water and sewage treatment plants, to name just a few important facilities,” Perrie states.
Buildings and homes constructed with concrete, for example, offer exceptional energy efficiency, with the material’s thermal mass guarding against temperature fluctuations and helping reduce heating and air-conditioning expenditures. Concrete’s high thermal mass means that when it is warm, it absorbs unwanted heat, slowing the rise in temperature in indoor rooms. When temperatures fall in the evening, concrete releases the heat absorbed during the day, keeping indoor rooms at a comfortable temperature.
Because concrete is designed for each specific project, there is usually very little waste, and the material enjoys unlimited flexibility in applications ranging from high-rise structures to parking lots, bridges and stadiums. And when a concrete structure has served its purpose, the material can be crushed and recycled. Designed properly, concrete infrastructure is resistant to fire, impact, wind, floods, storms and earthquakes. With climate change increasingly producing devastating weather conditions, the ability of concrete
Concrete will play an essential role in the government’s plans to implement long-awaited infrastructural projects this year, says Bryan Perrie, CEO of Cement & Concrete South Africa (CCSA).
structures to survive major disasters should also not be overlooked. Concrete structures can last for decades – even centuries. The Channel Tunnel, linking Britain and France, for example, is contractually guaranteed to last at least 120 years.
“Concrete may be our oldest building material, but modern innovations in technology and technique keep it at the forefront of sustainable design and construction. Today, it can be cast into virtually any shape or form, which allows for exciting design freedom and an almost infinite variety of applications,” Perrie explains.
Perrie says concrete construction drives economic growth, innovation and jobs. “A recent study by La Bipe (Euroconstruct) management consultants documented that for every job created in cement and concrete in the construction industry in Europe, nearly three jobs were created in the wider economy. Similar – if not greater – benefits would apply to South Africa where unemployment is such a challenging factor,” he continues.
Another infrastructural benefit offered by concrete is the provision of roads. Concrete pavements offer substantial benefits over the long term and, in economic terms, are often the most favourable solution based on lifecycle costs. This is even more so when user costs are considered, as concrete pavements require minimal maintenance.
“Concrete pavements have a crucial role to play in the provision of new infrastructure, as well as for the upgrading of existing pavement infrastructure,” says Perrie.
Concrete overlays and inlays provide an ideal solution for the upgrading of existing asphalt and unsurfaced pavements for all categories of traffic. The development of ultra-thin concrete pavements has added to the various types of concrete available to the road design engineer. The reflectivity of light-coloured concrete paving and sidewalks also helps reduce the urban heat island effect.
Perrie adds that the resources of CCSA are readily available to assist in infrastructural developments in all parts of South Africa. Some of these services cover:
• Education and Training: With the skills challenges facing the industry, this is an essential requirement for the future of a qualified and suitably skilled construction industry. CCSA’s School of Concrete Technology offers a wide range of internationally recognised courses, ranging from the basic ‘Introduction to Concrete’ to the highly acclaimed ‘Advanced Concrete Technology’ course.
• Information Centre: This is one of the largest and most respected sources of information on concrete in the southern hemisphere. It is widely used by the construction industry and students.
• Consulting: CCSA offers invaluable advice on concrete-related issues including onsite visits by technical staff.
CCSA members have access to all the association’s services, either free or at special discounted rates. A range of membership options is available at different fee levels, with associated benefits. For further information visit www.cemcon-sa.org.za.
The School of Concrete Technology offers important training courses for RMC truck drivers and concrete batchers
Cement & Concrete South Africa’s School of Concrete Technology (SCT) offers two training courses particularly important for the readymix concrete (RMC) industry, says Matthews Magwaza, lecturer at SCT, who presents both courses.
“The courses have proved extremely popular in the construction industry, as they provide delegates with a fundamental understanding of concrete and the core requirements of concrete in the RMC industry. Importantly, customer relations also form part of the training,” Magwaza explains.
The two courses are:
Concrete for RMC truck drivers (SCT 14)
This course introduces RMC truck drivers to concrete and tests that may be carried out in their presence. The course imparts basic concrete technology and will help drivers understand their importance as front-line staff members, interfacing with the client.
The syllabus includes factors that affect the strength of concrete; bleeding, workability, cohesion, and segregation of concrete; and the significance of slump and cube tests. Also covered are the effects of hot or cold weather on the transport of concrete; delays, contamination, or spillage during transport; movement of the concrete around the site after discharge; and the effect of the addition of water to RMC.
Concrete for batchers and batch plant staff (SCT 15)
This course covers important topics that will provide batchers and staff at a batch plant with essential concrete education and theory to competently do their jobs and produce quality RMC.
The syllabus includes batchers’ responsibilities; constituent materials and their effect on concrete; fresh properties of concrete and ancillary tests; and the basics of mix design. Testing for the hardened properties of concrete, as well as the basic management of a batch plant are also included.
“This course has been developed specifically for batchers, but would also greatly benefit persons working as supervisors, laboratory and sales staff, and general labourers in the RMC supply sector,” adds Magwaza.
For more information about the courses and the scheduled dates for 2022, phone +27 (0)11 315 0300 or email rennisha.sewnarain@cemcon-sa.org.za.
ROCLA is South Africa’s leading manufacturer of pre-cast concrete products.
Surpassing 100 years of product excellence.
• Pipes
• Culverts
• Manholes
for our nationwide branches
AECOM
siphokuhle.dlamini@aecom.com
AFI Consult banie@afri-infra.com
Alake Consulting Engineers lunga@alakeconsulting.com
ARRB Systems info@arrbsystemssa.com
Asla Construction (Pty) Ltd johanv@asla.co.za
BMK Group brian@bmkgroup.co.za
Bosch Projects (Pty) Ltd mail@boschprojects.co.za
BVI Consulting Engineers marketing@bviho.co.za
CCG puhumudzo@ccgsytems.co.za / info@ccgsystems.co.za
Corrosion Institute of Southern Africa secretary@corrosioninstitute.org.za
Dlamindlovu Consulting Engineers & Project Managers info@dlami-ndlovu.co.za
EFG Engineers eric@efgeng.co.za
Elster Kent Metering Mark.Shamley@Honeywell.com
EMS Solutions paul@emssolutions.co.za
ERWAT mail@erwat.co.za
GIBB marketing@gibb.co.za
GIGSA secretary@gigsa.org
GLS Consulting nicky@gls.co.za
Gorman Rupp Cordeiro@gormanrupp.co.za
Gudunkomo Investments & Consulting info@gudunkomo.co.za
Hatch Africa (Pty) Ltd info@hatch.co.za
Herrenknecht schiewe.helene@herrenknecht.de
Huber Technology cs@hubersa.com
Hydro-comp Enterprises info@edams.co.za
Infrachamps Consulting info@infrachamps.co.za
INFRATEC info@infratec.co.za
IQHINA Consulting Engineers & Project Managers info@iqhina.co.za iX engineers (Pty) Ltd hans.k@ixengineers.co.za
JBFE Consulting (Pty) Ltd issie@jbfe.co.za
JG Afrika DennyC@jgafrika.com
KABE Consulting Engineers info@kabe.co.za
Kago Consulting Engineers kagocon@kago.co.za
Kantey & Templer (K&T) Consulting Engineers ccherry@ct.kanteys.co.za
Kitso Botlhale Consulting Engineers info@kitsobce.co.za
KSB Pumps and Valves (Pty) Ltd salesza@ksb.com
KUREMA Engineering (Pty) Ltd info@kurema.co.za
Lektratek Water general@lwt.co.za
Makhaotse Narasimulu & Associates mmakhaotse@mna-sa.co.za
Malani Padayachee & Associates (Pty) Ltd admin@mpa.co.za
Maragela Consulting Engineers admin@maragelaconsulting.co.za
Mariswe (Pty) Ltd neshniec@mariswe.com
Martin & East gbyron@martin-east.co.za
M & C Consulting Engineers (Pty) Ltd info@mcconsulting.co.za
Mhiduve adminpotch@mhiduve.co.za
Much Asphalt bennie.greyling@muchasphalt.com
Mvubu Consulting & Project Managers miranda@mvubu.net
NAKO ILISO lyn.adams@nakogroup.com
Nyeleti Consulting naidoot@nyeleti.co.za
Odour Engineering Systems mathewc@oes.co.za
Prociv Consulting & Projects Management amarunga@prociv.co.za
Rainbow Reservoirs quin@rainbowres.com
Re-Solve Consulting (Pty) Ltd maura@re-solve.co.za
Ribicon Consulting Group (Pty) Ltd info@ribicon.co.za
Royal HaskoningDHV francisg@rhdv.com
SABITA info@sabita.co.za
SAFRIPOL mberry@safripol.com
SAGI annette@sagi.co.za
SALGA info@salga.org.za
SAPPMA admin@sappma.co.za / willem@sappma.co.za
SARF administrator@sarf.org.za.co.za
SBS Water Systems marketing@sbstanks.co.za
Sembcorp Siza Water info-sizawater@sembcorp.com
SiVEST SA info@sivest.co.za
Sizabantu Piping Systems (Pty) Ltd gregl@sizabantupipingsystems.com
Sky High Consulting Engineers (Pty) Ltd info@shconsultong.co.za
SKYV Consulting Engineers (Pty) Ltd kamesh@skyv.co.za
Smartlock jp.alkema@smartlock.net
SMEC capetown@smec.com
Southern African Society for Trenchless Technology director@sasst.org.za
SRK Consulting jomar@srk.co.za
Star Of Life Emergency Trading CC admin@staroflife.co.za
Syntell julia@syntell.co.za
TECROVEER (Pty) Ltd info@tecroveer.co.za
TPA Consulting roger@tpa.co.za
V3 Consulting Engineers (Pty) Ltd info@v3consulting.co.za
VIP Consulting Engineers esme@vipconsulting.co.za
VNA info@vnac.co.za
Water Institute of Southern Africa wisa@wisa.org.za
Wam Technology CC support@wamsys.co.za
Wilo South Africa marketingsa@wilo.co.za
WRCON ben@wrcon.co.za
WRP ronniem@wrp.co.za
WSP Group Africa ansia.meyer@wsp.com
Zutari Rashree.Maharaj@Zutari.com
Rocla rectangular portal culverts were used to rehabilitate a section of the R61 in the Eastern Cape
Recent heavy rains led to the collapse of a bridge forming part of the R61 at Tsomo Junction between Ngcobo and Cofimvaba in the Eastern Cape and required urgent rehabilitation. As part of the emergency response, Rocla was contracted to supply 30 rectangular portal culverts.
“The team at Rocla double-stripped a RP2100 gang mould so that we could increase our manufacturing output to six culverts per day and get the culverts on the road as quickly as possible,” explains Graham Howell, sales consultant for Rocla in Gqeberha.
Measuring 2 100 mm x 2 100 mm, Rocla rectangular portal culverts consist of a deck and two legs placed on a concrete base that can be cast in situ or prefabricated. The standard strength classes are 75S, 100S and 125S. Special intermediate strengths or heavier loading requirements can be designed and manufactured. Additionally, skew culverts can be manufactured for angled road crossings.
“The only alternative roads for motorists who used the R61 regularly after the road collapsed were the R409 between the junction and the N2 at Ndabakazi, and the R408 between the N2 at Idutywa and R61 at Ncgobo,” comments Mike Coetzee, regional manager for Rainbow Civils. “The rehabilitation of this section of road therefore required immediate action. We worked with Rocla before and knew the quality of their product. We also knew their manufacturing capability would enable them to respond quickly.”
The order was placed in late January 2022 and the first culverts arrived on-site on 4 February, with the last delivered on 15 February. “The culverts were on schedule and were as per our required specifications. Rocla’s service is renowned throughout the industry, and this R61 project was a perfect example of how they respond to a critical situation,” Coetzee concludes.
One of the distinctive features of the new 77 m long Nancefield Bridge is a prominent pair of 13 m high hands, which are essentially extensions of the centre piers. This ‘welcoming’ bridge forms part of Sanral’s approximately R640 million Musina Ring Road Project in Limpopo, scheduled for completion during Q2 2022.
For the bridge phase, Chryso Plast Omega 174 – an advanced, new-generation, waterreducing plasticiser – was selected for the concrete mixes on the decks, balustrades
and piers with hands. Just over 3 000 m3 of the admixture was required to form the various sections.
A key challenge was presented by ambient temperatures of up to 45˚C, which is typical of Musina in summer. However, the concrete temperature needed to be kept under 30˚C to prevent thermal cracking. This was achieved by a combination of measures, which included keeping the concrete under shade and cooling it with sprayers.
“Chryso Plast Omega 174 is a multidose admixture, which allows concrete to exhibit extended workability characteristics,” explains
Ben Myburg, technical consultant, Chryso Southern Africa.
“It improves the cohesion and lowers the viscosity of a concrete mix, which results in an improved homogeneity and compaction, allowing for superior off-shutter finishes, thereby eliminating the risk of repairs. By reducing the need for extra water, it increases the durability of concrete by reducing permeability,” he adds.
Chryso Plast Omega 174 forms part of the wider Plast Omega range, designed for applications such as underwater concrete, pumped concrete, large pours and flowing concrete.
87% of marketing professionals use video as a successful marketing tool.
3S Media provides the interface to host, manage and broadcast live as well as on-demand webinars.
Our pla�orm ensures the highest quality video and audio technology. This ensures flawless digital broadcas�ng by using enterprise-grade streaming solu�ons.
Book your webinar today and participate in robust thought-leadership panel discussions and anchor desk interviews with captains of industry.
Novus Print (Pty) Ltd t/a 3S Media is a proud Level 2 BBBEE Contributor.
Marketers making use of video get 66% more qualified leads per year.
Video engages users for longer on a website. The average user spends 88% more time on a website with video content.
3S Media offers robust thought-leadership panel discussions and anchor desk interviews with captains of industry.
Webinars are ideal marke�ng pla�orms for product launches, training events and industry announcements. Our pla�orm ensures the highest quality video and audio technology.
Novus Print (Pty) Ltd t/a 3S Media is a registered member of National Treasury’s Central Supplier Database for Government.
Supplier Number: MAAA0016423
Unique Registration Ref Number: FFA60BC9-37E6-4596-89D9-A00025D4C50F