

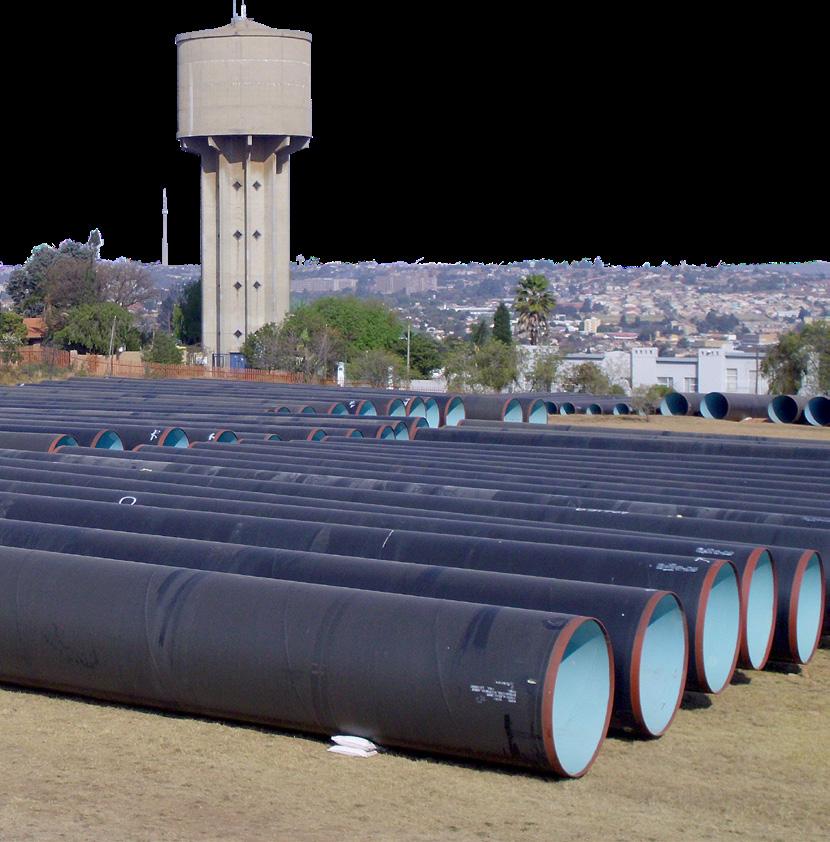
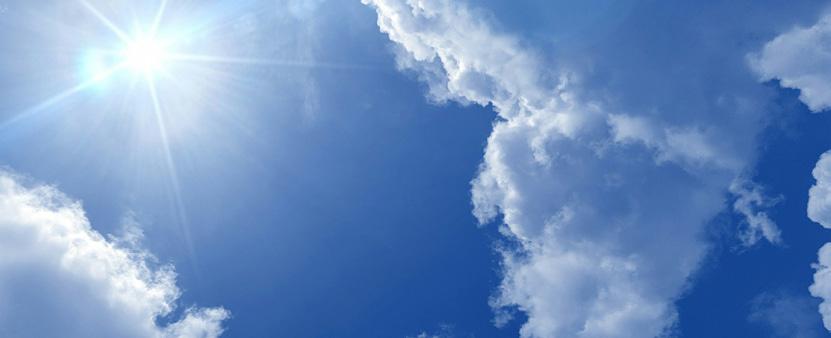
CEMENT & CONCRETE
Advances in nano technology
ENERGY
SA’s nuclear future
ROADS & BRIDGES
Canelands Bridge upgrade showcases
WATER & WASTEWATER
Addressing wastewater challenges
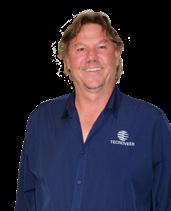
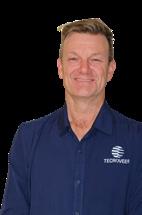
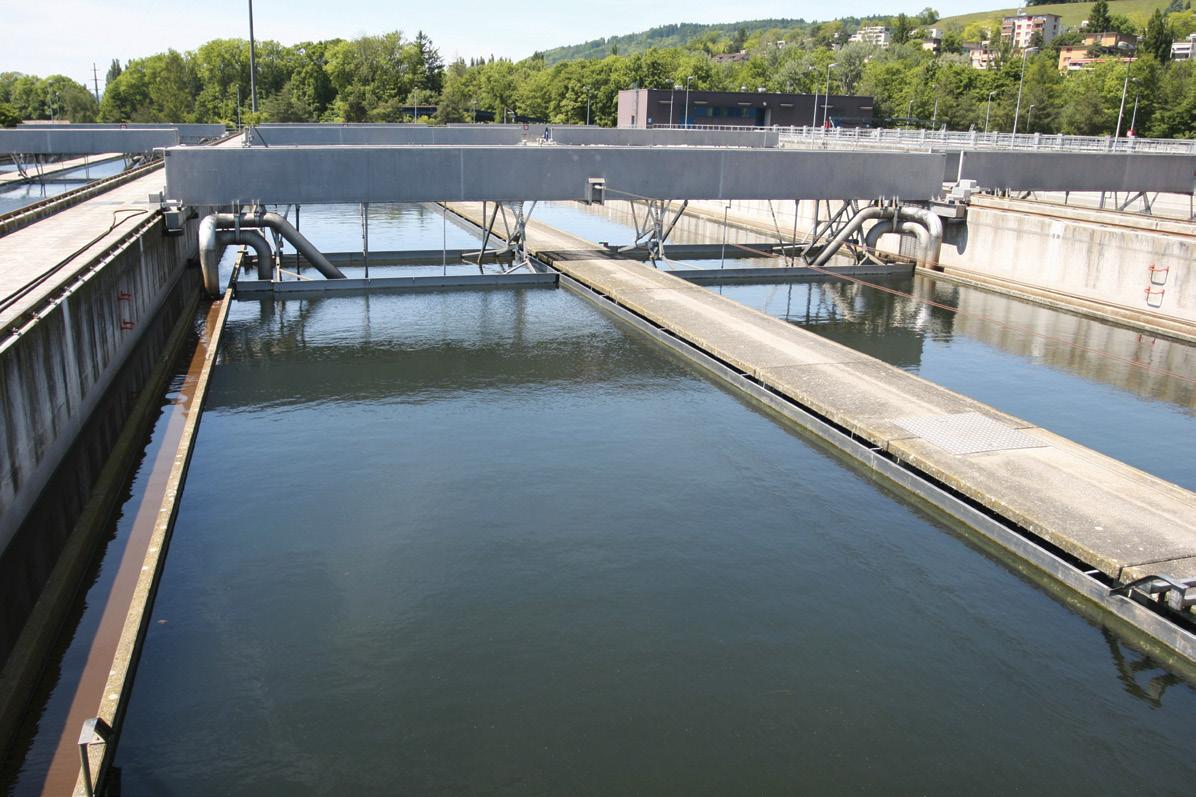
THE ULTIMATE GO-TO SOLUTION FOR
CEMENT & CONCRETE
Advances in nano technology
ENERGY
SA’s nuclear future
ROADS & BRIDGES
Canelands Bridge upgrade showcases
WATER & WASTEWATER
Addressing wastewater challenges
THE ULTIMATE GO-TO SOLUTION FOR
Sika has decades of experience in being a reliable partner with waste water treatment plant contractors, supplying products and systems on all continents. Sika has shown the industry that we are a complete solution they can trust. The products and systems are thoroughly tested in Sika laboratories before being independently checked. Sika materials are further proven by long term site testing to withstand the harsh conditions in the real environment.
ANY issues you have with your Waste Water Treatment Plant, Sika has the solution, be it: Waterproofing, Repair or Protection
Celebrating its centenary in 2024, Hall Longmore’s pioneering spirit and commitment to innovation has established the company as a local and global leader in large bore steel pipes for the bulk water, oil and gas markets. IMIESA speaks to Kenny van Rooyen, Hall Longmore’s Managing Director, about historical milestones that have helped shape South Africa’s industrial and infrastructure landscape. P6
A visionary leader in water and wastewater treatment, the Tecroveer Group has undergone a rebranding exercise that redefines its mission and purpose, building on a legacy dating back to 1976. P12
The Canelands Bridge upgrade. A novel design that links
AfriSam’s “heavy lifting” for makers of
precast beams used in hybrid
Secure your stand now and have the opportunity to:
• present your company, products and services to a target audience
• gain industry insight and meet potential partners, suppliers and clients
Sponsor a unique aspect of the conference and enjoy great
such as:
• free exhibition stands
• complimentary delegate registrations
• interact with key decision-makers and industry peers
• brand representation at the event, promotion of your company in the conference proceedings magazine and online
• free entry for guests at the social evening and much more.
t: +27 (031)266 3263
e: conference@imesa.org.za marketing@imesa.org.za www.imesa.org.za
EDITOR Alastair Currie
Email: alastair@infraprojects.co.za
DESIGNER Beren Bauermeister
CONTRIBUTORS Burgert Gildenhuys, Chetan Mistry, Ian Venter, Sibusiso Mjwara
DISTRIBUTION MANAGER Nomsa Masina
DISTRIBUTION COORDINATOR Asha Pursotham
SUBSCRIPTIONS
Email: distribution@infraprojects.co.za
ADVERTISING SALES
KEY ACCOUNT MANAGER Joanne Lawrie
Tel: +27 (0)82 346 5338
Email: joanne@infraprojects.co.za
It seemed to be touch and go for a moment, but South Africa’s fledgling Government of National Unity (GNU) has taken its first steps as it kicks off the seventh administration and the execution of the Medium-Term Development Plan 2024-2029.
A key aspect are the new ministerial appointments headed by designated GNU party representatives, reflecting a commitment to putting South Africa first, rather than competing for political position. In addition to providing more checks and balances, comparing and benchmarking performance within this evolving GNU framework will be revealing, and it will definitely shape future electoral outcomes.
In the meantime – either through necessity or innovation – the township economy forges ahead on its own and is often overlooked as one of the potential catalysts for employment, skills transfer and SMME development by public and private sector stakeholders. Examples include opportunities to invest in the township building market in transitioning shack dwellers to formal housing and addressing massive backlogs.
PUBLISHER
IMESA (Pty) Ltd
P O Box 2190, Westville, 3630
Tel: +27 (0)31 266 3263
Email: info@infraprojects.co.za
ANNUAL SUBSCRIPTION: R805.00 (INCL VAT)
ISSN 0257 1978 IMIESA, Inst.MUNIC. ENG. S. AFR.
© Copyright 2024. All rights reserved.
IMESA CONTACTS
HEAD OFFICE:
Manager: Ingrid Botton
P.O. Box 2190, Westville, 3630
Tel: +27 (0)31 266 3263
Email: admin@imesa.org.za
Website: www.imesa.org.za
BORDER
Secretary: Celeste Vosloo
Tel: +27 (0)43 705 2433
Email: celestev@buffalocity.gov.za
EASTERN CAPE
Secretary: Susan Canestra
Tel: +27 (0)41 585 4142 ext. 7
Email: imesaec@imesa.org.za
KWAZULU-NATAL
Secretary: Narisha Sogan
Tel: +27 (0)31 266 3263
Email: imesakzn@imesa.org.za
NORTHERN PROVINCES
Secretary: Zurika Louw
Tel: +27 (0)82 322 5208
Email: np@imesa.org.za
SOUTHERN CAPE KAROO
Secretary: Henrietta Oliver
Tel: +27 (0)79 390 7536
Email: imesasck@imesa.org.za
WESTERN CAPE
Secretary: Michelle Ackerman
Tel: +27 (0)21 444 7112
Email: imesawc@imesa.org.za
FREE STATE & NORTHERN CAPE
Secretary: Wilma Van Der Walt
Tel: +27 (0)83 457 4362
Email: imesafsnc@imesa.org.za
All material herein IMIESA is copyright protected and may not be reproduced without the prior written permission of the publisher. The views of the authors do not necessarily reflect those of the Institute of Municipal Engineering of Southern Africa or the publishers.
For the construction sector, important ministerial appointments include Public Works and Infrastructure, Transportation, and Water and Sanitation where implementation of vital catalytic programmes will make all the difference in countering current stagnant industry growth.
Where practical planned developments must transition to rapid approval and construction – a case in point being new builds like the R8 billion Ntabelanga Dam in the Eastern Cape, and the R26 billion uMkhomazi Dam in KwaZulu-Natal.
Jobs and investors
Job creation, however, remains the overriding priority, which can only be meaningfully executed by private sector investment within an enabling public sector environment. So, the GNU will need to focus more on listening to investor concerns if we wish to maintain and attract Direct Foreign Investment support, as well as boost trade with mega economies. Major hurdles that continue to be flagged for remediation are market over-regulation and eradicating red tape.
In parallel, the GNU now needs to play a far more proactive role in ramping up infrastructure spend in areas like roads, rail, and ports to enable macro and microeconomic goals. Directly and indirectly, this will help to close our poverty and inequality gaps in a way that cannot be achieved by approving social grant payments for a growing percentage of the population.
First and foremost, though, our youth need to be ready for the change we need to see. That will depend on ensuring that our primary and secondary education system is world class, and geared towards tertiary programmes which synch with future growth industries.
For both rural and urban start-ups, there are also key opportunities like tank fish farming and hydroponic (greenhouse) food production that should be explored by investors. They put food on the table and enable entrepreneurial expansion.
Water and energy make it happen
Ultimately though for everything to work, we need water, followed by energy. And in terms of the latter, renewable sources are key, but for sustained baseload requirements, we need to look at other green alternatives like nuclear, but not immediately on the Koeberg scale. Public resistance to nuclear megaprojects has largely been influenced by the massive cost-overruns and tender irregularities reported on other energy projects like the Medupi and Kusile power station developments. However, there are now viable and affordable nuclear alternatives that can be owned by public and/ or private entities. A prime example is the HTMR-100 reactor development by South African based entity, Stratek Global, designed to be housed in compact and scalable modular nuclear facilities that are “walkway safe”. Each HTMR-100 reactor produces around 100 MW of thermal energy, which can be extracted completely for industrial processes or converted into approximately 35 MW of emission-free electricity. Plus, there’s zero loadshedding. Going forward, considering any infrastructure investment must be a transparent process, and in the economy and the public’s best interest since no one wants a repeat of the State Capture saga. Having an appetite for risk requires a renewed focus on ethics and trust, something that the GNU is now committed to achieving.
• Members: R7 400
Register & Pay BEFORE 31 July 2024
• Non-members: R8 800
Register & Pay AFTER 1 August 2024
• Members: R8 300
• Non-members: R9 800
Register & Pay AFTER 25 October 2024
• Members: R9 500
• Non-members: R11 300
Within the built environment space, we traditionally focus mainly on physical “grey” infrastructure requirements (like dams, buildings, roads, treatment plants, and pipeline networks) since these are the essential backbone for service delivery.
However, within the context of climate change, there’s also an increasing need to factor in “green” and “blue” infrastructure interventions, which can take many forms that help combat environmental pollution, reduce the urban heat island effect, promote biodiversity, improve air quality, preserve water resources and enhance the living experience.
They both have a direct and indirect influence on current and future physical infrastructure design and execution, a case in point being Green Building construction, which – among other elements – minimises the need for HVAC and promotes rainwater harvesting.
Examples of green (living) infrastructure include vegetated roofs and facades, landscaping (using waterwise plants), city tree planting, parks, green corridors, bioretention cells, swales, and sustainable urban drainage systems (SUDS). In turn, blue examples encompass water elements like aquifers, canals, rivers and wetlands. Both green and blue infrastructure need to integrate holistically with grey infrastructure to create a functioning urban ecosystem.
waste due to littering and gaps in solid waste management. This scenario is compounded by poor wastewater treatment practices that result in the release of inadequately processed effluent and raw sewage that promote invasive plant growth.
One positive intervention in progress is the implementation of the Waste Discharge Charge System (WDCS) by the Department of Water and Sanitation following years of preparation and consultation. This came into effect for the 2023/2024 financial year. Based on an agreed tariff scale, the WDCS sets out to recover the cost of treating polluted water discharged into rivers. Essentially the formula is based on the understanding that a higher than acceptable percentage of water abstracted is already polluted. So, the final pricing for water license holders –public and private – takes this into account. Those proven polluters will then pay more as part of an equitable and transparent process, with ongoing enforcement and compliance managed by South Africa’s six Catchment Management Agencies.
Engineering (IFME). It’s an ideal platform to debate grey, green and blue issues and opportunities, as well as to showcase successful case studies.
In this respect, I’m pleased to announce that as an IFME member, IMESA has submitted an entry in each of the two competition categories (Category A: Construction Project, and Category B: Development Project – Non-Construction) for the IFME 2024 Excellence Awards competition coinciding with the event. Entries must align with up to three of the United Nations Sustainable Development Goals.
Our IMESA entries, which demonstrate South African innovation in the field, have both been submitted by eThekwini Municipality. The Category A entry is the “Construction of the pedestrian bridge over Mbokodweni River at Emansomini”, which also came first in the Community Upliftment and Job Creation category at the IMESA CESA 2023 Excellence Awards; while the Category B entry is Durban’s Transformative Riverine Management Programme, which has already received international recognition, with funding support from the C40 Cities Finance Facility.
A threat that cannot be ignored
A prime example is SUDS, which provides permeable pavement solutions that reduce rainfall velocities though controlled attenuation and release into groundwater sources. In addition to taking the pressure off stormwater systems – especially during floods – SUDS designs can also incorporate sub-surface rainfall harvesting tanks for greywater reuse. Reducing stormwater flows also reduces soil loss, the subsequent erosion of watercourses and sedimentation volumes.
From a blue perspective, maintaining the natural state of our water bodies within catchment zones is critical for downstream potable water treatment and future water security. At this stage, a high percentage of our rivers are contaminated by plastic and allied
Across the world, the challenges for developing and developed countries are common when it comes to climate threats, and to a greater or lesser degree interms of environmental non-compliance. All nations have a joint responsibly.
That’s why ongoing global engagement and alignment are so vital. Hence the need for industry conferences like the upcoming Future Green City World Congress, being held from 23rd to 26th September 2024 in Utrecht, the Netherlands. This is a joint initiative between the Royal Association Stadswerk the Netherlands and the Royal Dutch Society for Garden Designers and Landscapers (VHG), in cooperation with World Urban Parks and the International Federation of Municipal
There’s no doubt that the severity and frequency of extreme weather is increasing. The recent floods in Kwazulu-Natal, Eastern and Western Cape are prime examples, costing billions of rands in infrastructure damage, as well as social and economic losses – with informal settlements situated in known floodplains being among the worst affected. Paradoxically, water scarcity and droughts are also on the rise in parts of South Africa, with an associated cost for society and industry.
We know that nothing works in isolation. So, our responsibility as municipal engineers is to ensure that environmentally engineered solutions like green infrastructure increasingly dovetail with our current and future town and city planning, alongside blue initiatives. It’s the smart approach and essential for our sustainable future.
Celebrating its centenary in 2024, Hall Longmore’s pioneering spirit and commitment to innovation has established the company as a local and global leader in large bore steel pipes for the bulk water, oil and gas markets. IMIESA speaks to Kenny van Rooyen, Hall Longmore’s Managing Director, about historical milestones that have helped shape South Africa’s industrial and infrastructure landscape.
The evolution has been marked by a series technological breakthroughs, acquisitions and factory upgrades that began with the grass roots formation of CV Longmore & Co. in 1924 by Charles Victor Longmore, who served as the company’s managing director from 1924 to 1945.
He had originally arrived in South Africa in 1913 to supervise the establishment of a fabrication facility specialising in high pressure welded tubes and fittings for a UK based company. Subsequently, he went on to establish his own business via an initial venture in 1920, which culminated in the formation of CV Longmore & Co.
Then in 1936, future growth was further strengthened by the formation of a business partnership with entrepreneur, Leonard Hall, leading to the formation of Hall Longmore & Co. Hall served as chairman from 1936 to 1947, during which time the company entered the market as a major pipe producer with the establishment of a factory in Luipaardsvlei, Krugersdorp, during 1946.
The Vaal River Eastern Sub-System Augmentation Project (VRESAP): Hall Longmore fabricated and supplied a 1 930 mm diameter pipeline solution – together with a Sintakote® coating – covering some 125 km, traversing from the Vaal Dam reservoir to Knoppiesfontein near Secunda
By 1972 Hall Longmore had grown to become the largest steel pipe fabricator in South Africa, a year that also saw the acquisition of Hume Steel Pipes in Wadeville from Barlow Rand.
Ongoing diversification
“With the passing decades the company continued to grow and diversify and in 1998, with a major focus on the bulk water market, the acquisition of a large-scale and strategically located factory in Duncanville, Vereeniging, from Dorbyl, was realised. This acquisition also included Medium Density Polyethylene coating technology along with its associated Rubber Ring Joint (RRJ) system. This acquisition, however, led to a decision to sell off the Krugersdorp plant – as a ‘ non-core’ facility,” van Rooyen explains.
Following the incorporation of Hall Longmore as a wholly owned subsidiary of Murray & Roberts in 1988 ownership passed to the Barnes Group in 2014, with renewed
investments further positioning Hall Longmore for long-term expansion.
Then and now, the Wadeville and Duncanville factories continue to supply local market requirements, alongside exports, shipping to North and South America, Europe, the Far East and Africa. Combined, these plants have the potential to produce around 230 000 tonnes of steel pipe annually.
A key export market is the oil and gas sector, particularly in the USA, where Hall Longmore has a long-established presence and is licensed by the American Petroleum Institute (API) for the manufacture of line pipe to API specification 5L (PSL 1 & PSL 2) and 5CT. The API sets the highest benchmark and only a select group of manufacturers meet the stringent requirements. This underscores Hall Longmore technical expertise and dedicated focus on quality assurance, which includes International Standards Organisation (ISO 9001:2008) certification.
This attention to detail is supported by investments in advanced non-destructive testing equipment using radiographic testing (RT) to verify weld integrity as each pipe section comes off the production line.
For some time, analogue X-ray systems – the norm globally from the 1990s – have been used, successfully meeting the current sub 3% RT defect threshold required by international standards. However, while highly effective, a significant breakthrough has been the more recent development of automated digital RT technology, which has revolutionised quality control. Ten times faster inspection speeds are now possible.
“In the past, X-ray test parameters needed to be input manually within the analogue environment. However, thanks to digital RT, the process is now almost 100% automated, which makes it far more accurate in terms of defect detectability,” says van Rooyen.
Hall Longmore is believed to be the first pipe manufacturer in Africa to go the digital RT route with the installation of the technology at its Duncanville factory during 2022. The company is now in the process of switching over from analogue RT at its Wadeville facility.
From riveted to welded
“So, we’ve come a long way since 1924 driven by an innovative global steel pipe industry that has been part of the infrastructure landscape since the mid-1850s and remains the conduit of choice for water utilities. However, as would be expected, over the ensuing decades, the advances in manufacturing techniques have been considerable,” says van Rooyen.
“Back then, the standard practice was to roll steel sheets into the required shape and then rivet the seams to form the pipe. This remained a commonly applied technique up until the 1930s and there are still working examples in cities like Johannesburg. In parallel were major advances in welding technologies, which have become
Transnet’s New Multi-Product Pipeline (NMPP) development is Hall Longmore’s largest contract to date and was secured as part of the Impumelelo Pipeline Joint Venture
increasingly more sophisticated over time,” he explains.
In South Africa, Hall Longmore spearheaded the introduction of today’s cutting-edge welding technologies for pipe fabrication, namely electric resistance welding (ERW) and submerged arc welding (SAW). ERW is the preferred manufacturing process for pipes of a diameter of 24ʺ and smaller with larger diameters – up to 100ʺ – being fabricated by the helical SAW method.
In parallel are the major investments made by Hall Longmore in external and internal protective anti-corrosion coatings and linings. The former include fusion bonded epoxy, fusion bonded medium density polyethylene, and 3-Layer coatings.
“In the early days, all steel water pipes were bitumen wrapped and lined. However, internal linings were soon replaced by cement mortar/concrete coatings, and solvent free epoxies,” says van Rooyen.
“Interestingly, though, there is a modern polymer modified bitumen external wrap which
is still preferred by utilities globally and in South Africa. We cater for all requirements.”
Energy and gas
Hall Longmore built its reputation from 1924 as a preferred solutions provider for the deep-level mining sector and allied industries, especially in the Johannesburg region, which was the world’s largest gold production centre up until the 1980s. Oil and gas, as well as energy were logical integrated markets at the time, and continue to be so to this day, alongside bulk water distribution. One of the most unusual projects undertaken in its long history is Hall Longmore’s involvement in the fabrication and supply of solutions for SAFARI-1 (South Africa’s first atomic reactor installation) in Pelindaba, which was
Hall Longmore is a class leader in the application of external and internal protective anti-corrosion coatings and linings
commissioned in 1965, and subsequently the adjoining Valindaba plant, completed in 1975.
For SAFARI-1, Hall Longmore was contracted to supply the process tanks and pipework. Then for the Valindaba phase Hall Longmore secured the order to fabricate several hundred pressure vessels. These tasks required high-tech welding techniques and rigorous precision to meet stringent nuclear quality control standards and served as a springboard for Hall Longmore’s future class leadership in pipe welding technologies.
Hall Longmore was also a key supplier for Sasol I in Sasolburg – the world’s first fuel-from-coal refinery – and later for Sasol II and III in Secunda. Sasol I was completed in the 1950s, with Sasol II and III commissioned in the early 1980s.
Other energy projects in the 1990s included two major gas line projects for Gascor, the first between Olifantsfontein and Pretoria, and the second from Empangeni to Richards Bay; and the landmark Mossgas undersea pipeline near Mossel Bay, which was commissioned around 1992. 1994 also saw the completion of a 120 km gas pipeline for Columbus Steel connecting its plant with Sasol’s Secunda complex.
More recent projects include the Sastech Temane and Pande gas projects in Mozambique. The former entailed the supply of 660 mm diameter pipe to meet the API 5L X65 PSL 2 specification for a
197 km line, while the latter entailed the supply of 80 km of 660 mm diameter pipe according to the same API specification.
“More recently, we’ve also playing a key role in supplying torque tube carrying systems for concentrated solar power stations in the Northern Cape,” says van Rooyen.
A classic example of innovation and excellence in the petroleum segment are the specialist solutions provided for Transnet’s New MultiProduct Pipeline (NMPP) commissioned in 2011. Designed to replace and enlarge existing pipeline capacity, the NMPP transports petrol, diesel, and jet fuel from Durban to Johannesburg, and is a vitally important conduit.
Valued at around R2 billion, this remains Hall Longmore’s largest contract to date and was secured as part of the Impumelelo Pipeline Joint Venture. In total, some 533 km of 610 mm diameter pipe was supplied for the trunkline section from the Port of Durban to Nigel plus approximately 160 km of 406 mm diameter pipe for the distribution line from Nigel to Langlaagte, and from Waltloo to the terminus near Kendal Power Station.
To meet the project scope, Hall Longmore’s ERW line at its Wadeville factory was upgraded, with a
Radiographic testing is employed to verify weld integrity as each pipe section comes off the production line
new coating facility added to meet the API 5L X65 3LPE coating specification.
Within the water segment, a core part of the steel pipe distribution network over the past 100 years has been fabricated and supplied by Hall Longmore for South African water boards and municipalities. These range from mega projects to smaller scale greenfield and brownfield developments.
Landmark mega projects where Hall Longmore played a crucial role include the Vaal River Eastern Sub-System Augmentation Project (VRESAP) implemented by the Trans-Caledon Tunnel Authority (TCTA), following government approval in October 2004, to meet the growing demands at the time of Eskom and Sasol.
Construction began following the official sod turning ceremony in 2006, with Hall Longmore fabricating and suppling a 1 930 mm diameter pipeline solution – together with a Sintakote® coating – covering some 125 km, traversing from the Vaal Dam reservoir to Knoppiesfontein near Secunda. The full system became operational in 2009.
In the cross-border market, one of the most significant milestone projects is Botswana’s North South Carrier development – the largest
consignment of pipes
for
infrastructure investment yet undertaken by the country. Hall Longmore was part of a consortium which included Europipe of France to supply around 197 km of DN1100 to DN1400 diameter pipeline for Phase 1, which was completed in 2000.
Back in South Africa, another mega project was the Western Aqueduct development by eThekwini Water and Sanitation. Commissioned in 2019, the Western Aqueduct added some 400 Mℓ to the system supplying the Durban metro, with the water piped from the Midmar and the Spring Grove dams. Measuring some 70 km in length, pipe sizes range from 610 mm to 1,6 m diameter, with a Sintakote® coating specified.
Within the water space, the subsequent years leading up to 2024 have seen Hall Longmore supplying solutions for an ongoing series of water board and municipal upgrades. These include ongoing Rand Water expansion projects, as well as current work for Magalies Water in terms of its Pilanesberg Bulk Water Supply Scheme.
For the latter, Hall Longmore supplied 28 km of pipeline for Phase II. The pipeline extends from the Mafenya Reservoir – situated some
5 km from Sun City – through to the Mafenya pumping station for onward transfer to the 30 Mℓ Thlabane Reservoir in Rustenburg. The bulk of the order comprises DN900 pipe, apart from a 240 m section where DN1 200 was specified. Hall Longmore and its enterprise JV partner delivered the final consignment at the end of July 2023.
Other work in progress currently includes a supply order for a municipal upgrade within the town of Boshof entailing the installation of around 40 km of Hall Longmore’s Rubber Ring Joint 500 mm diameter pipe system. The project is due for completion during 2024.
The next hundred years
“Reflecting on milestone projects across our niche sectors serves to highlight just how integral Hall Longmore has been in supporting infrastructure and industrial growth, with thousands of kilometres of pipeline produced since 1924,” adds van Rooyen.
“We salute the pioneering spirt of our founders, and we’re proud to have built on their legacy, riding out the cyclical conditions in the local and global economy to become a class leader. We’ve achieved this through product excellence, technological innovation, capacity expansion, and an ongoing investment in our personnel, who rank among the best globally.
“Foremost though, our success has been founded on long-term relationships and we’d like to thank all our clients for entrusting us with their pipe requirements over the past ten decades. The journey continues to unfold, with exciting times ahead,” van Rooyen concludes.
In the first part of this series (published in the May 2024 edition of IMIESA), we showed how, in just over one and a half decades, we have moved from a tedious and laborious manual process of capturing building structures as little dots to public domain datasets available for any global location, showing the size and two-dimensional characteristics of almost every existing building.
In the second part (published in IMIESA’s June 2024 issue), we focused on data beyond building footprints, introducing building volumes and height elements. Part 2 concluded by acknowledging that our biggest challenge as urban practitioners is to make sense of the data. It is good to have all this data at our disposal, but it is incumbent on us, as data users
By Burgert Gildenhuys*
and planners, to find the value-adding components of the data. We continue to use Sandton CBD, Alexandra, and the Wynberg industrial area to illustrate the data revolution. This area includes the highly developed area of Sandton CBD, the Wynberg industrial area, Alexandra as an old established township and the higher income low residential area adjacent to them.
Unlocking the full potential
Data availability is only part of the equation; integration is the key. Skillfully integrating datasets adds value to understanding spatial development and change. We explored examples of population change assessment and de facto coverage calculations, highlighting the power of data integration.
We will use two elementary examples to show an approach to data integration and how it adds value to understanding spatial development and change.
In the first example (as shown in Figure 2), we want to assess population change at a detailed level spatially. There are two datasets available, the one showing population per enumerator area in 1996 and the second showing WorldPop (https://www.worldpop.org/ ) data for 2020 in a 100 m grid. The data is not directly comparable. At Spatial Data Services, we use MapAble®'s data partitioning function to transform both data sets to our 250 m hexagon grid. The result is that data sets are now spatially in the same format, and by subtracting the 1996 data from the 2020 data, we can show detailed population change between these periods.
In the second example (as shown in Figure 3), we took South Africa's cadastre (stands) and calculated the intersecting values of the building footprints to show the de facto coverage on each stand in South Africa. The process to generate the data for every single stand in South Africa took about an hour and a half.
The biggest challenge is keeping pace with new data and applying technology to unpack the data. There is a clear process for accelerated data releases, more detail, and refined data. Figures 4 to 6 illustrate the latest releases from the European Union with a 10 m resolution.
At an elementary level, the data (as shown in Figure 4) allows one to calculate the extent of the various vegetation surfaces. This information can be related to carbon sequestration in our built environment and the impact of vegetation on urban heat domes. The data also illustrates the impact of building density on vegetation density.
Residential building heights (as shown in Figure 5) show essential elements of urban morphology and enable the measurement of density zones. The same applies to the ability to visualise and measure the extent and height of non-residential buildings (as shown in Figure 6).
Burgert Gildenhuys is the founding Director of Spatial Data Services Africa NPC.
For further information, email burgert@sdsafrica.net and visit www.sdsafrica.net.
By combining the three datasets, a more complete picture of our urban environment emerged (see Figure 7) that was unavailable only a few months ago. As with the other datasets, one would expect releases of temporal data, which will contribute to change detection in terms of the rate and extent of change.
The exciting part of this data development is that we continuously move closer to land use data. Better commercial datasets may be available, but the gap between public domain data and commercial data is closing rapidly.
So what?
The pace of data innovation is relentless. Staying ahead of these developments is a monumental task. The critical question is, so what? What value does the data have? Pretty pictures or maps have little value unless we can find cost-effective ways in which data contribute to our understanding of our development environment and its contribution to solving our urban growth problems.
However, our commitment at Spatial Data Services Africa NPC is unwavering. As a nonprofit organisation, we aim to bridge the gap between emerging data and its practical use in municipal planning. Our mission is to empower governments to make informed decisions that promote spatial transformation and uplift the marginalised. We invite you to join us on this transformative journey.
Support us as we navigate the ever-evolving landscape of data and digital technologies, creating a brighter future for all South Africans. Together, we can turn data into actionable insights for a more prosperous nation.
*Pr. Pln, MIAM (London), ILGM, B(TRP), BAdmin (Municipal Administration)
What are the origins of the name Tecroveer?
A visionary leader in water and wastewater treatment, the Tecroveer Group has undergone a rebranding exercise that redefines its mission and purpose, building on a legacy dating back to 1976. IMIESA speaks to Izak Cronje (IC), CEO: Tecroveer Group, and Rob Holmes (RH), Head of Business Development, about the significance for the market and the Group’s future business philosophy.
IC The name Tecroveer was formed via an amalgamation of the words “Technology”, “Rotor” (referencing the horizontal aeration mechanisms employed for activated sludge treatment), and “Pasveer Ditch” technology. The latter was a biological process developed in The Netherlands. Tecroveer adopted and adapted it for local applications, subsequently spearheading revolutionary advances in biological treatment processes for the South African market.
This was during an era in the 1970s and 1980s when South African wastewater engineers were renowned internationally for innovative developments that became benchmark references globally. Within the mix, Tecroveer was part of that knowledge base.
How has the business developed since 1976?
RH From inception we applied an Engineering, Procurement and Construction turnkey methodology, supported by our own inhouse fabrication facility for proprietary mechanical components, which we retain to this day. We also branched out into the Design Build and Operate (DBO) market, which has been a major success, backed by our registration with the Construction Industry Development Board for civil, electrical and mechanical works.
The business started out with a primary focus on domestic sewage treatment serving the requirements of small to medium municipalities. From there a solid foundation in this field logically formed the platform for an expansion into mining and industrial effluent treatment.
Landmark examples include our involvement on the Eastern Basin Acid Mine Drainage Project in Springs, Gauteng – a first of its size in South Africa to neutralise highly contaminated water and make it safe for release. It remains one of the largest projects of its kind in the world and was constructed between 2014 and 2016.
We were responsible for the mechanical and electrical phases, as well as being appointed to operate the plant following its commissioning for a period of three years. This provided invaluable experience for future largescale projects of increasing sophistication.
From there we expanded into the broader industrial market for key segments that include FMCG on a DBO basis. The organic waste streams that need to be processed are similar in nature to domestic sewage and we’ve refined our offering by partnering with international technology partners.
Meeting rising potable water demand is an urgent priority. How is Tecroveer responding?
IC As water engineers and scientists, we’ve always had a passion and commitment for adding value, both for industry and communities. We see this as our core social responsibility and the rationale for Tecoveer’s existence. This motivated us to explore integrated solutions, a prime one being the DBO project we developed for Lonmin’s operations in North West province, with ownership subsequently transferring to Sibanye-Stillwater. We designed and built three wastewater treatment plants within the mine’s
footprint to serve two purposes for the client and communities. The first was to ensure that surrounding municipalities and their constituents would have a sustainable way to treat and manage domestic wastewater; and the second was to supply the mine with reuse water treated to a suitable standard for mining requirements. These plants were constructed some 15 years ago and are still run by Tecroveer under an operations and maintenance (O&M) agreement.
In terms of market developments within the public arena, the South African government has placed increasing emphasis in recent years on prioritising the implementation of water and distribution infrastructure. This applies both to new facilities and services, as well as the modernisation and upgrading of older treatment plants. So, we embraced this as a major growth opportunity going forward.
What is the inspiration for Tecroveer’s recent rebranding?
RH In the past 48 years we’ve grown and diversified significantly, and the water landscape has changed dramatically in terms of supply and demand constraints, so we decided the timing was right to revisit our core values and align them with current and future market requirements.
Essentially, we asked ourselves, why do we do what we do, and what’s our purpose?
Fundamentally, We Clean Water, so we chose this as our new brand message because its straightforward and to the point. With technological advances, there’s been a quantum shift in process engineering capabilities, but the essence hasn’t changed. However, the environmental priorities and threats have escalated exponentially.
Our rebranding exercise therefore reflects our vision to reshape the world of water, blending
innovation with purpose. And we wanted to reflect this strategy in a fresh and modern way, that’s inspirational for our company culture.
Our logo change illustrates this – maintaining a link with the past – but in a dynamic new way that’s holistic and encompasses our highly diversified solutions, plus technological advances. It’s spherical in shape to represent the earth, with a flow through design that illustrates positive process transformation.
What does Tecroveer’s new vision statement set out to achieve?
IC At Tecroveer, we envision a world where clean water isn’t just a necessity, but a fundamental right. We’re committed to turning this vision into reality, one community at a time. We want to ensure a future pollution-free world where children can play – thanks to engineered outcomes – in pristine rivers and oceans, and drink safe and pure water from the tap.
Our core values are all geared towards achieving this through responsible and efficient use of natural resources by employing eco-friendly practices and technologies.
Is this vision being realised on your current Hammanskraal project?
RH This project perfectly aligns with our dedication for innovation and excellence and making a meaningful difference for clean water solutions.
For Magalies Water, we were awarded a contract in March 2024 for the supply of a 50 Mℓ potable water treatment package plant solution for Hammanskraal as an emergency intervention. This 12-month project will see the progressive implementation of four interconnected 12,5 Mℓ modular steel units on an existing water treatment plant site that will tie in with the current process system.
Each of these measures 15 m in diameter with a height of 7 m, so the scale of the project is unprecedented in South Africa, as well as their speed of execution, and really put our design
capabilities to the test. These units are being manufactured at Tecroveer’s fabrication facility, which was expanded for the project, with the first module required to be operational by October 2024. The following three will be installed progressively.
The client requested a modular solution so that the design enables the potential for units to be unbundled, transferred and reconnected to other municipalities that might need a similar, immediate requirement in future.
Where does your diversification into waste-to-energy fit in?
RH Clearly, this is an environmental imperative and one that supports a zero organic waste to landfill strategy, while helping to eliminate pollution and water resource contamination.
We’ve harnessed existing anaerobic biological technologies used to treat high-strength industrial effluent to take this a step further to produce biogas. We’ve done this for some time for industrial clients to generate electricity via their wastewater treatment streams. However, we’ve now taken this another step further by treating organic solid waste.
A current Tecroveer project is a solution being implemented for Pepsico’s Simba plant in Isando, Gauteng. Some 50 tonnes of organic solid waste will now be processed daily on site to produce biogas and electricity to run some plant operations.
Another development is Tecroveer’s present involvement in a consortium that is restarting and repositioning a previously stalled waste-to-energy project in Cape Town. The entity will trade as Cape Town Biogas, with the carbon neutral biomethane products produced sold into the market as a fuel, as well as liquid CO2
And in closing?
IC Prioritising biodiversity preservation for future generations is key for society and the planet’s well-being. And none of that is achievable without clean water. It all interconnects with the UN Sustainable Development Goals to which South Africa is aligned and committed.
Climate threat changes are real and growing, so environmental stewardship is non-negotiable. In this respect, Tecroveer remains dedicated to building on our class leadership over the past 48 years to close the gaps and leapfrog positive change.
This can only be achieved via technology and innovation by optimising and retrofitting existing water and wastewater treatment infrastructure, fast-tracking new builds with modular plant applications, and preventing waste streams from entering and polluting our fragile ecosystem.
Adherence to standards, skills development, and adopting proven technologies are crucial for ensuring quality infrastructure execution within South Africa's thermoplastic piping industry. In all respects, the role of industry practitioners is paramount, with knowledge sharing as a core component in shaping innovative practices. By Ian Venter
One of the critical advancements in the thermoplastic pipe context is the application of trenchless technologies, particularly horizontal directional drilling (HDD). This method allows for the efficient installation of services without the need for disruptive open-cut trenching. Trenchless applications are used globally but still have reasonably limited adoption locally. However, the Southern African Society for Trenchless Technology (SASTT) is spearheading a renewed focus in this area, and I had the opportunity to present at a recent SASTT webinar on 18th June 2024, which delved into the benefits of HDD and micro tunnelling for long crossings.
In trenchless techniques, industry practitioners play a critical role in evaluating and selecting the most suitable technologies and materials, such as high-density polyethylene (HDPE). Their expertise allows them to confidently specify the optimum products in their designs, ensuring proper installation techniques are followed. (See Table 1 for the benefits of PE 100+ and PE 100 RC pipe in trenchless applications.)
Adhering to industry standards is a vital part of the process, particularly in the case of HDPE pipe. Standards such as SANS ISO 4427: 2023 for polyethylene (PE) ensure the quality and safety of water supply and drainage systems.
A former technical manager at the Southern African Plastic Pipe Manufacturers Association (SAPPMA), Ian Venter launched Polymers and Piping Systems in June 2024. The company will specialise in producing high-quality thermoplastic products and providing comprehensive solutions for piping systems. Ian holds a National Higher Diploma in Polymer Technology and has significantly contributed to advancing industry standards in his field.
An example of a failed asbestos cement pipeline section. Reinstating with an HDPE line using HDD techniques is a recommended approach
It's not a “one size fits all” approach. In this respect, SASTT and the South African industry have been instrumental in ensuring that international standards suit local conditions, making them more accessible and applicable to the region's needs.
The introduction of oriented unplasticised PVC (PVC-O) has revolutionised our industry. The ISO 16422-Parts 1, 2, 3, 5, replacing the current SANS ISO 16422:2016 standards, have set new benchmarks for PVC-O pipes and fittings, pushing the boundaries of performance, reliability, and safety.
By introducing more stringent minimum values, refining tolerances, and specifying cutting-edge test methods, we're not just keeping pace with global trends but setting them. For South African engineers, embracing these changes means staying at the forefront of innovation and ensuring our projects stand the test of time.
While SANS standards form the cornerstone of our industry, it's crucial to cast our net wider. The ISO standards, particularly SANS ISO 17050-1 & 2:2010, offer complementary frameworks for conformity assessment. Understanding and incorporating these standards enhances our global competitiveness and broadens our expertise.
The Standard CEN TS 17176-7 elevates conformity assessment of PVC-O to new heights. Its emphasis on testing methods and frequencies, how to incorporate them into
SANS ISO 9001, and long-term record-keeping provides a more comprehensive approach to ensuring the ongoing quality of PVC-O pipes.
The flexibility of self-declaration and conformity statements (SANS ISO 17050-1 & 2) is another powerful tool. It allows companies to demonstrate compliance efficiently, fostering a culture of responsibility and transparency.
Implementing a robust Quality Management System (QMS) aligned with ISO 9001 principles is not a one-time task but a continuous process. It offers numerous benefits across industries, including enhanced customer satisfaction, improved organisational efficiency, and better process control.
The Plan-Do-Check-Act (PDCA) approach emphasises continuous improvement based on systematic audits and review processes.
While implementing a QMS is often a prerequisite for conformity assessment of products, South Africa takes a different approach. Unlike the global trend of integrating standards, South Africa maintains a separation between product standards, assessment of conformance standards, and QMS standards.
A recent case study highlights the importance of QMS practices. In this instance an investigation of the piping supplied to a contractor for a municipal project revealed that the product lacked the required certification to the applicable SANS ISO standard, with no production data available for comparison. On request, the manufacturer failed to provide adequate compliance evidence and subsequently went out of business, preventing further inquiry.
A review of the independent lab tests should have raised an immediate red flag for product tests. The construction inspection pointed out that about 10% of the pipes were excessively deformed, and 20% of constructed pipes exceeded construction tolerances. Additionally, 25% of pipeline welds required repair.
Weld integrity is vital during the pipeline installation phase—whether trenchless or open-cut—and needs more attention regarding training, equipment utilisation, and application. When purchasing welding machines for PE 100+ and PE 100 RC Compounds, it's
crucial to consider a range of factors to ensure compliance with SANS ISO 4427, ISO 4437, and related normative standards.
These machines fall into the following categories:
1. Electrofusion welding machines: Electrofusion couplers are suitable for joining PE pipes and fittings.
2. Butt fusion welding machines: Used for joining PE pipes end-to-end.
3. Socket fusion welding machines: Ideal for smaller-diameter pipes and fittings.
SANS ISO 4427:2023 now references several jointing-related standards, including ISO 11414 for butt fusion, ISO 17885 for mechanical joints, ISO 9624 for flanges, and ISO 7-1 and ISO 228-1 for threaded connections. The standard outlines various jointing requirements, covering electrofusion, spigot end, mechanical, and socket fusion joints.
Specific preparations are detailed for different joint types, emphasising proper assembly according to manufacturer instructions and consideration of tolerances and operating conditions.
Testing and performance criteria are specified, including conditioning temperatures and conformance to mechanical characteristics outlined in Table 6 of the standard. The standard applies to systems with a maximum allowable operating pressure of up to 25 bar at a reference temperature of 20°C. Additional considerations include angular deflection limits for larger diameters and proper handling of adhesive layers in pipes with peelable layers.
It's important to note that this summary may not encompass all requirements from the complete SANS ISO 4427:2023 standard, and reference to the entire document is recommended for comprehensive specifications.
As the South African piping industry continues to evolve and face new challenges, professionals in their field play an enabling role, and their input is crucial in building more resilient and sustainable infrastructure for the nation.
TABLE 1: Benefits of HDPE for trenchless applications
Properties
Crack Propagation Resistance
SCG Resistance
Accelerated Conditions Performance
Specialised Testing Compliance
Stress Crack Resistance
Ductile Failure Mode
100+
High resistance, enhancing durability in trenchless applications
Increased side branches for improved slow crack growth resistance
Better resilience in high temperatures and surfactant exposure
The Full-Notched Creep Test (FNCT) and Strain Hardening Test are aligned with ISO standards
More side branches on tie molecules for a tenfold increase in time to failure
Ductile mode exhibited in tensile creep tests for reliable pipeline integrity Advantages of Trenchless Projects
Ease of Installation
Longevity and Low Maintenance
Environmental Friendliness
Jointing Flexibility
Comparative Advantages in Trenchless Projects
Crack Propagation Resistance
Tensile Strength
Chemical Resistance
Flexible and lightweight, reducing labour costs
Extended service life with minimal required maintenance
Recyclable, with a lower carbon footprint and minimal production impact
Seamless connections that reduce leak risks
100+ and PE 100 RC Pipes
Superior to other materials' performance
High tensile strength, resisting pulling forces and external pressures
Reliable in various chemical exposures due to corrosion resistance
As the dedicated wastewater treatment service provider for the City of Ekurhuleni, ERWAT plays a crucial role in directly and indirectly maintaining a core portion of Gauteng’s water balance. IMIESA speaks to Managing Director, Kennedy Chihota, about the business plan and operational approach.
Currently, ERWAT serves a population of some 4 million people, and supports around 8 000 industries via 19 Water Care Works (WCW) that treat and release some 1 000 M ℓ daily back into the ecosystem via four demarcated drainage districts.
ERWAT’s ongoing plan is to reduce this WCW footprint (ranging in plant capacity from 1 M ℓ to 170 M ℓ per day) to ten by decommissioning older plants – some dating back to the 1950s. The remaining 10 will then be progressively upgraded with the addition of enhanced technologies to improve running costs and efficiencies. In parallel will be a need to reconfigure and upgrade the sewer line distribution network, including pump stations.
“Before the formation of Ekurhuleni metro, the 19 WCWs in our system were all originally
set up to serve individual towns. Our ongoing goal has been to shift from a decentralised to a centralised network managed in real-time via SCADA so we can monitor all processes – a key one being aeration performance – to opimise running costs,” Chihota explains.
Key plant upgrades due for implementation, following the finalisation of design approvals, include Waterval – ERWAT’s flagship WCW – and Olifantsfontein, its second largest, which are both currently over-capacitated at around 240% and 200%, respectively. The interim plan is to tackle the problem by incrementally constructing 50 Mℓ integrated concrete containment tanks at both plants.
overload
“When a plant is overloaded hydraulically, it’s not possible to immediately contain the incoming effluent volumes. That challenges the standard detention time (or resident time) typically required to complete the first of up to five treatment stages that all depend on a biological purification process,” Chihota continues.
“In other words, there are naturally occurring time factors involved. In the first stage, the raw effluent would typically need to be detained for, say, approximately an hour, but when overloading occurs, this requires a mitigation solution.
“We solve the problem at Waterval WCW, for example, by diverting incoming effluent to temporary attenuation ponds during peak flows. Then during the offpeak period, we reintroduce this raw effluent back for first stage treatment. It’s a demanding logistical exercise, but an essential one for compliance. But we know it’s not sustainable longer-term and we remain affected by external factors, like escalating pollution.”
As Chihota points out, water and wastewater are a collective responsibility, with the Department of Water and Sanitation’s (DWS’s) announcement in June 2024 of four new Catchment Management Agencies (CMAs), namely Limpopo-Olifants, Vaal-Orange, PongolaUmzimkulu, and Mzimvubu-Tsitsikamma, forming a vital part of this process, working alongside the existing BreedeOlifants and Inkomati-Usuthu CMAs.
“Across the board, it’s imperative to ensure that untreated effluent doesn’t enter our ecosystems because that has obvious universal environmental threats. Plus, the ongoing abstraction of contaminated river sources downstream by other municipal water treatment works places an added burden in terms of process costs that put allocated budgets under strain,” he continues.
Testimony to ERWAT’s quality assurance commitment to date is their performance in the DWS’s 2022 Green Drop Certification Programme. The latter audits all public and private wastewater facilities in South Africa and for 2022 the results were concerning. This is underscored by the fact that out of close to 1 000 registered WWTW plants, only 22 were Green Drop certified.
The threshold for Green Drop certification is a 90% score. If a specific plant doesn’t have sufficient capacity, then 15% is immediately subtracted, irrespective of how efficient the other stages are run, which in ERWAT’s case is exemplary. However, despite the massive volumes it needs to treat, seven out of ERWAT’s 19 plants were Green Drop complaint and obtained certification for the 2022 programme, which is a major achievement. Addressing capacity constraints will subsequently result in total Green Drop compliance.
“Across South Africa, there are numerous factors for non-compliance, but a key one is that many municipal Water Service Authorities don’t currently have the necessary specialist in-house technical skills to run and manage wastewater plants effectively. Often, they also don’t have an accurate asset management register that speaks to realistic maintenance and expansion funding requirements. In response, our business plan includes offering an operations and maintenance (O&M) service to those municipalities in need to help them get on top of the situation,” Chihota explains.
As a leader in its field, ERWAT has a highly competent team of engineers, technicians and plant operators who are well placed to transfer their knowledge and experience.
by ERWAT’s
SANAS 17025 accredited laboratory service, as well as the provision of sludge beneficiation and water reclamation reuse solutions.
The latter is geared towards providing treated water to near potable standard for industrial and irrigation purposes – a service ERWAT currently provides to customers, which passes on major water use savings as an alternative to potable supply – while the former strategy explores the commercial opportunities of packaging beneficiated sludge for product applications that include agricultural fertilisers. Long-term, ERWAT also plans to build a dedicated plant for treating industrial effluent as part of its vertical integration strategy. As Chihota points out, industrial effluent dumping remains an issue and must be countered.
“So far, we’ve concluded an O&M agreement with a Gauteng municipality and are currently treating one of their plants, with the potential to increase this to cover other plants within their footprint. We are also in discussions with one of the largest district municipalities in the province to provide a similar comprehensive O&M solution. In future, our goal is to offer this service across the South African municipal landscape, where
In the meantime, ERWAT continues to explore the best fit-for-purpose technologies, some as medium-term fixes while it expands its plant capacities longer-term. These include the modular HYBACS® solution supplied by OEM, Bluewater Bio, through its local partner Headstream Water. To date, a HYBACS system has been installed at ERWAT’s Tsakane WCW, which enabled an immediate upgrade in capacity from 10 Mℓ/day to 20 Mℓ/day.
The key benefit of the HYBACS “plug and play” system is that it’s quick to install on a tight footprint, while enabling an existing activated sludge plant to treat double the flow and load. Power consumption associated with aeration can also be reduced by up to 30%.
“Finding the right return on investment solutions is an urgent priority to meet our capacity challenges that unless addressed will impede socioeconomic development. And for those municipal plants that are failing I believe the DWS needs to apply blanket emergency funding interventions to reverse the current trend since the situation is reaching crisis proportions,” adds Chihota.
“At ERWAT we are strategically positioned as an expert partner to help bring municipal wastewater plants back to compliance, counter the growing pollution threat and help sustain South Africa’s water security. We are also engaging far more with the private sector, in collaboration with public entities, to co-develop wastewater treatment plants for future residential, commercial and industrial developments,” Chihota concludes.
Leaks amongst others are the main factors that exacerbate water scarcity. Key causes include network failures due to incorrect installation, lack of maintenance, aging infrastructure, and too high water pressure. The environmental impact is significant. For example, left unattended, a constantly dripping tap or a leaking toilet can result in an average daily water wastage of 30 to 60 litres. Therefore, effective water leak detection, fixing, and maintenance is crucial, plus these interventions will help prevent potential damage to residential and commercial buildings.
Early detection:
The first line of defense
Modern technology offers innovative solutions:
1 Smart leak detectors: These devices can be installed throughout your property, alerting you to potential leaks via your smartphone. They are particularly useful in bathrooms and kitchens where leaks are most common.
During winter, property owners must be prepared for the additional challenges that cold weather brings, like potential pipe bursts due to sub-zero temperatures, along with the all-year round challenge of water leaks that can lead to significant damage if not addressed promptly, especially during freezing conditions. www.randwater.co.za
2 Regular inspections: Schedule professional inspections at the start of winter. Professionals use advanced tools like thermal imaging cameras to spot hidden leaks behind walls and under floors.
3 Water meter monitoring: Reading your water meter at the beginning and at the end of each week or at least monthly can help you gauge your household/property’s water consumption, while allowing you to quickly detect any unusual spikes in usage, which can indicate a hidden leak.
Tackling leaks head-on
Once a leak is detected, timely repairs are crucial to prevent further damage and water loss. Here are some steps to take:
1 Immediate action: Turn off the water supply to the affected area to prevent further leakage, which in turn also can cause damage to carpets, fixtures and fittings, and even walls.
2 Professional repair services: Hire certified plumbers who can accurately diagnose and fix the leak. Avoid DIY fixes, as they may only provide temporary relief and could lead to more significant issues. Again, insurance may not cover leaks that are repaired using the DIY process.
3 Quality materials: Ensure that any repair work uses high-quality materials designed to withstand seasonal temperatures. Insulated pipes and frostresistant materials are essential for winter repairs.
Preventive maintenance is key to avoiding leaks, especially during the cold months. Here are some tips:
1 Pipe insulation: Insulate all exposed pipes to prevent them from freezing and bursting. Foam pipe insulation is affordable and easy to install.
2 Regular maintenance checks: Schedule regular maintenance checks, especially for older properties. Focus on areas prone to leaks, such as roofs, bathrooms, and exterior walls.
3 Gutter and drain maintenance: Keep gutters and drains clear of debris to ensure proper water flow and prevent ice dams, which can cause leaks in roofs and walls.
conclusion
Effectively managing water leaks in the built environment requires a combination of proactive detection, timely repairs, and regular maintenance. By utilising modern technology, such as smart sensors and thermal imaging, property owners and facilities managers can significantly enhance leak detection capabilities. By putting these examples and efforts into practice, Rand Water believes people and organisations may contribute to the promotion of a more ethical and sustainable use of water in both personal and professional situations.
10 10 60
Think about opening a tap only to see a tepid stream of water flow from it. How does that make you feel? Frustrated? Concerned? Even fearful? The connection we make with water is primal. There are few experiences that so readily stoke feelings of insecurity, panic and dread like not having access to water.
Today, protests over water shortages are becoming more common across South Africa, even in major metros such as Johannesburg and eThekwini. Yet, those communities are still in a relatively positive position, considering that 19% of rural SA doesn't have access to reliable clean water.
The recent WISA 2024 Conference, hosted by the Water Institute of Southern Africa at the Inkosi Albert Luthuli International Convention Centre from 12-14 th June, provided an excellent platform to tackle these problems. The best minds and most passionate changemakers gathered to see what we can do about South Africa's critical water issues.
Foremost, several speakers said that we need to change attitudes around water. It's not someone else's problem – water concerns everyone. South Africa needs a culture shift towards protecting water, similarly to how the nation reacted to the electricity crisis.
Encouraging water knowledge and community ownership improves water conservation, pollution reporting, rainfall capture and greywater recycling. Smaller and rural communities can control their water through solar borehole pumps and low-maintenance infrastructure, and community farms save considerably when they use techniques such as drip irrigation and water recycling.
Delegates discussed the problems at local government water facilities, notably crumbling infrastructure and budget shortfalls. Non-revenue water losses such
By Chetan Mistry
as leaks and water theft are harming service delivery, sustainability and funding. But there are effective ways to tackle these issues.
Through smart metering and billing solutions, for example, municipalities can better predict water consumption and appropriately bill large water consumers. Modern technologies can detect leaks and water theft, recouping lost earnings without halting operations. Industries including mines, farms, and manufacturers, can also leverage smart water technologies to save money and reduce risks and losses around water rationing and quotas.
The topic of water pollution surfaced often during WISA 2024 discussions. Several experts lamented the dire state of local rivers and wetlands. They urged much greater urgency and collaboration to act on water issues, with an emphasis on stopping pollution at the source and rehabilitating heavily polluted waterways. Many of these changes can happen through private and municipal treatment operations.
Process efficiency gains
Modular water treatment solutions integrate new technologies into established treatment sites. Resilient
Chetan Mistry, Strategy and Marketing Manager at Xylem Africa
and variable-frequency pumps require less maintenance while handling a wider range of solid objects and fibres that normally damage traditional pump systems. UV and ozone systems complement chlorine disinfection while reducing reliance on and storage of corrosive chemicals. Selfcontained modern bioreactors remove harmful bacteria without requiring regular maintenance or costly manual interventions. These examples apply to public and private use cases: industrial, food processing, and agricultural sites can deploy modular waste treatment systems that increase water efficiency and lower costs. And we can widen the scope to include aggressive enforcement of pollution laws, rehabilitating wetlands and rivers, and recharging aquifers.
The WISA 2024 Conference produced many more ideas to help turn the tide on water shortages. It's crucial that we do so. The anguish caused by strained water resources is very evident in our society. People are concerned and angry. We are in the midst of a growing water crisis. Yet, we have the expertise and technology to change the tide and keep water flowing. It's not too late to change the picture and
According to the UN Convention to Combat Desertification, up to 40% of the Earth’s land is degraded, directly affecting some 50% of the world’s population. The number and duration of droughts has also increased by 29% since 2000 and without urgent interventions this may affect over three-quarters of the global population by 2050.
This formed a core part of the theme “Our Land, Our Future. We are #GenerationRestoration” for this year’s World Environment Day, marked annually in June and led by the United Nations Environment Programme. For 2024, the focus was on land restoration, desertification, and drought resilience. And while it’s a once off event, the call to action is ongoing.
In acknowledgement of its importance, Elisabeth Nortje, Associate Director: Environment, Africa, and Jonathan Schroder, Technical Director - Water Resources, at trusted infrastructure consulting firm AECOM, discuss the significance of the 2024 theme of drought resilience for South Africa.
A good example of the importance of such awareness raising and the stakes involved is the current situation in Johannesburg and Tshwane, highlights Nortje. “We have an
almost perfect storm of not the best planning, combined with infrastructure that is ageing rapidly and not being maintained properly.”
Schroder notes that the metros in KwaZuluNatal are over-abstracting their resources by about 20% as a result. “Our water losses are increasing, and we have more and more water being extracted from the resource that is not necessarily reaching the end users.”
Despite this, key dams are going into the dry season all full due to an over-overage wet
period. “Again, people do not realise the risk. They do not perceive that we are actually in a deficit. Decision makers and authorities are very reluctant to try and communicate the status quo because it is complex to articulate, and they do not want it to reflect on them as a potential failure,” says Schroder.
General awareness of South Africa’s challenging water situation is sorely lacking. “Unfortunately, it takes everyone to be part of the solution because you cannot just shut the taps off at the top end; consumers must willingly reduce their consumption. They do not know there is a looming problem, so they do not do so. On top of that, the lack of service delivery over the years has also made people more reluctant, or unable, to reduce their overall consumption,” adds Schroder.
AECOM participates in consortia and partnerships with other consultants to support the Department of Water and Sanitation (DWS) in developing and implementing drought operating rules. This includes work in the
KwaZulu-Natal metropolitan area and the Crocodile Catchment Area over the past three years.
It has also been assisting the DWS and key stakeholders with the development and implementation of reconciliation strategies. These reconciliation strategies are designed for short, medium, and longterm planning to ensure sustainable water supply to growing water needs and mitigate the risks associated with drought.
Nortje adds from an environmental perspective: “Our focus is complementary. We incorporate measures in our permitting and planning activities to protect habitats and manage catchments effectively. This holistic approach helps build resilience against desertification and climate change impacts, including drought.”
Schroder warns that South Africa is stressing its catchment areas by adding more and more water users. “Our development of associated water resources is lagging. In many instances, we are actually overabstracting our systems a bit. That makes us more vulnerable to smaller droughts. The one good thing is that although climate change is an issue, many parts of the country are projected to actually be getting slightly wetter on average. Although this comes with potentially more extreme weather events.”
South Africa has inherent climate variability. Over the past 40 years it has developed world-leading approaches to quantify and manage the risks associated with this variability. AECOM, through its legacy companies, has been part of the development. As a result, a lot of AECOM’s planning and support for the custodians and operators of water resources is geared towards quantifying the risks and managing droughts and drier periods.
AECOM has a proven track record in implementing drought resilience projects. From 2013 to 2016, it supported the development and implementation of drought operating rules in KwaZulu-Natal and Mpumalanga. Using well-established models and risk-based approaches, AECOM helped the responsible authorities to allocate water resources efficiently and in a robust, defendable manner during droughts. The end goal is protecting essential human needs and economic activities.
Nortje stresses the importance of local expertise in projects and effective stakeholder engagement. “Engaging with local stakeholders and consulting experts with regional knowledge ensures that our projects are practical and well-received,” she says. While innovative technology is valuable, sometimes traditional methods prove most effective.
Schroder adds that data collection and stakeholder communication are vital for successful drought and water scarcity management. “We rely on historical drought data for accurate planning. Effective communication with operators, authorities and communities is essential to ensure their buy-in and cooperation,” he explains.
Both Nortje and Schroder agree that a major help in managing water scarcity would be for more community awareness and participation in taking on the challenges, which are growing worldwide. By leveraging global expertise and fostering collaboration within their teams, AECOM continues to address South Africa’s environmental challenges effectively. “Our global strategy and learning approach allow us to draw from a wealth of knowledge and apply best practices tailored to local conditions,” Nortje concludes.
The VEGAMET 842 controller feeds the connected 4 ... 20 mA sensors, processes the measured values and displays them for continuous level measurement of liquids and bulk solids
In an African city on a scorching afternoon, an engineer is assessing instrumentation at a water reservoir. The management team have long grappled with the daunting task of accurately gauging levels, a critical aspect for ensuring a dependable water supply, particularly during heatwaves or maintenance.
In this scenario, the ageing equipment has been prone to errors and frequent breakdowns, making the situation seem impossible. However, a new wave of smart technologies has emerged from VEGA Instruments, holding the promise of revolutionary enhancements in efficiency and dependability.
Precisely measuring and monitoring water resources is vital to prevent waste and ensure equitable distribution. In this respect, traditional methods often fall short due to inaccuracies and the inability to provide real-time data of high quality.
This is where the VEGAPULS cutting-edge radar level sensor provides a sustainable solution. Specially designed for accurate and fail-safe bulk liquid measurement, its innovative technology offers unparalleled precision regardless of environmental conditions and the medium.
Reporting and analysis
By offering real-time data, the VEGAPULS helps municipalities manage water resources with unprecedented control. From an asset management perspective, this also minimises maintenance needs, saving municipalities both time and money, by enabling prompt responses to any issues, averting potential risk escalation.
Within the municipal water utility arena, the overriding priority is that reservoirs don’t run dry. Thanks to the VEGAPULS, engineers have the tools to help ensure that communities and industries receive uninterrupted supply.
Work with nature during the cold months. Accept your kikuyu lawn's winter dormancy – and drastically reduce watering dormant lawns. Water conservation is essential in South Africa and wasting water by irrigating a dormant lawn in mid-winter is not an environmentally responsible choice for gardeners.
Kikuyu in nature always goes dormant during winter, where the grass will turn brown
Adopt an intelligent approach to lawns during the cold months. As your grass enters a state of graceful dormancy in late autumn, honour its natural cycles and recognise that you can drastically reduce watering.
Follow these tips from the Water Wise Team on how to maintain your kikuyu lawn during the cold months by using much less water, building resilience, and making sure it returns to life and vigorous growth in the spring season.
Kikuyu
Pennisetum clandestinum, commonly known as kikuyu, is the most widely used lawn grass in South Africa. It is native to east Africa and has an aggressive growth form. In South Africa, kikuyu is only listed as an invasive plant (Category 1b) in protected areas (nature reserves) and wetlands – where it has to be removed by law.
Kikuyu is drought tolerant, inexpensive, and easy to maintain because it is a tough grass. It is mostly planted as an instant lawn for sports fields, golf course construction, and rehabilitation. It has a mat root and herbaceous growth habit. It however doesn’t grow well in shaded areas.
This notwithstanding, most suburban kikuyu lawns are grossly overwatered – particularly in the cold winter months. Which is why research is currently underway to work out the minimum water requirements for kikuyu lawn and indigenous Cynodon varieties.
Acknowledgement
This article was co-authored by Rand Water - Water Wise and Evergreen Turf, aiming to raise awareness among the public and customers about sustainable practices for watering and maintaining kikuyu lawns.
Dormancy refers to a period where growth of the grass temporarily slows down, and grass goes into a resting state for one season. Kikuyu in nature always goes dormant during winter, where the grass will turn brown.
However, brown kikuyu grass does not mean it is dead; it has simply gone dormant. Lawn in a state of dormancy is simply “resting” and conserving energy for the new growing season.
Dormancy is a natural way for lawn to conserve moisture and nutrients in cold and dry seasons. It is therefore completely unnecessary to apply a lot of water to your kikuyu during winter.
Water Wise watering of kikuyu:
• Drastically reduce watering kikuyu lawns when they slip into dormancy in late autumn.
• It is completely acceptable to reduce or stop watering kikuyu lawns during the cold Highveld winter months of June and July.
• When the lawn appears to be dry, apply deep watering once or twice a month and only water in the morning (between 6 am – 10 am) until optimal moisture is reached.
• Avoid watering in the evening to prevent prolonged moisture on the grass, which can lead to fungal diseases.
• Newly installed kikuyu will only require more water during its settling or establishment period. Gradually decrease the frequency of watering after this phase.
• During summer, water in the early morning or late afternoon as this reduces water lost to evaporation.
• Overwatering kikuyu lawns is a waste of precious water.
• Most kikuyu lawns will thrive with as little as 8 mm of irrigation a week during dry weeks in summer.
• Turf professionals maintain that kikuyu lawns should never be watered more than 20 mm during dry weeks (with no rainfall) in summer.
• Use a trigger nozzle if watering kikuyu with a hose.
Smart maintenance of kikuyu:
• Stop mowing your lawn: with reduced grass growth in winter, longer blades insulate roots and soil from cold temperatures while roots remain active.
• Only apply organic fertiliser as part of your spring treatment towards the growing season and when night temperatures rise.
• As spring approaches, prepare for weed emergence on your lawn by hand-picking or spot-treating weeds with organic herbicides.
Always be #WaterWise!
www.randwater.co.za
0860 10 10 60
The City of Cape Town’s Catchment Stormwater and River Management Branch of the Water and Sanitation Directorate is working to commence procurement for the rehabilitation of the Sand and Langevlei Canal confluence area in Coniston Park, Retreat, by September 2024.
The initiative, which forms part of the city’s Liveable Urban Waterway (LUW) programme, is currently in its design phase, with work scheduled to commence in the fourth quarter of 2025 for scheduled completion by March 2026.
Cape Town’s LUW programme was developed in response to increasingly unpredictable climate conditions and serves as an implementation mechanism for waterway rehabilitation projects. It promotes the use of water-sensitive design, naturebased solutions, and green infrastructure approaches.
LUW projects are developed through a collaborative approach where catchment stakeholders work together to identify project briefs and co-design the projects using a bottom-up approach that leverages the knowledge and skills of local communities.
Consistent with a whole-of-society approach, LUW projects include active community participation not only in the design and development phases, but also in the management and activation phases.
Three public participation (i.e. co-design) workshops were held at two locations within the catchment in July, September, and November 2022. These workshops engaged the community on the historical use of the site and proposed design concepts for the rehabilitation of the wetland space.
The Sand Canal spans over a 5,4 km distance, flowing from Little Princessvlei in Heathfield, while the Langevlei Canal spans over a distance of approximately 3,6 km from immediately downstream of Main Road, Bergvliet. After converging at the project site, the canal flows into the upper reaches of Zandvlei in Muizenberg.
The vision of this project is to:
• Develop a river corridor plan and landscape masterplan through a collaborative process to inform rehabilitation interventions.
• Use nature-based solutions and green infrastructure to enhance existing ecosystem services and introduce new ones.
• Rehabilitate the Sand Canal and Langevlei Canal, the existing wetland, and the canal downstream of the wetland towards a more natural form and function.
This major rehabilitation project offers multifaceted benefits, including reducing the silt and litter load entering Zandvlei, creating a renewed wetland space for improved water quality and aquatic biodiversity habitat, reducing flood risk within the catchment, and providing residents with a safe, green open space to enjoy.
The structure comprises three sections or “rotations” consisting of columns that are connected to that portion of the spiral beam
The City of Ekurhuleni’s Water & Sanitation Department is at the cutting-edge of precast concrete technology. This water services provider has already successfully completed the construction of four prefabricated reservoirs. With another precast concrete water retaining structure nearing completion, it was just a matter of time before the Water & Sanitation Department would take its concept even further.
Anew water tower is being constructed alongside one of these precast concrete reservoirs. It too, when completed later this year, will have been almost entirely prefabricated in a state-of-the-art
The superstructure consists of 12 tapered beams connected to the columns of the last rotation
factory and skilfully integrated on site. The only in-situ components include the tank floor slab and the foundation. When finalised, this will be the first precast concrete water tower in Africa. It will have a final height of 36 m and a capacity of 2,5 Mℓ
The municipality opted for a precast concrete water tower because it was faster and more cost-effective to build. This while also providing a final structure of an exceptionally high quality which, in turn, will provide operating cost savings through reduced maintenance requirements.
The efficacy of prefabrication had proven itself time and again on each of the projects the Water & Sanitation Department completed.
Meanwhile, its professional team had also become more proficient in executing the works, refining and honing the sophisticated method from one project to the next.
The water services provider is again being supported by Tangos Consulting Engineers, the design engineer and project manager, and Infinite Consulting Engineers, a structural engineering firm with an extensive pedigree in the design and supervision of precast concrete structures. This is in addition to RSMM Construction, the principal contractor, and Corestruc, a precast concrete turnkey contractor.
Partnering Corestruc with its extensive precast concrete know-how, which includes manufacture, transport and rigging, RSMM Construction has earned a reputation for the exceptionally high quality of its water retaining structures. This while building them in a fraction of the time that it would have taken using conventional cast-in-place methods.
The construction of the precast concrete water tower will be completed in only 14 months compared to between the two and three years
that it would take using traditional methods.
Considering that this is the first precast concrete water tower to be built by the team, it is taking slightly longer to construct. The other water retaining structures will be completed in only nine months, bearing in mind that the tower constructed above the footing took only six months to build. It will also have a design life of 100 years if maintained appropriately, considering the high-performance concrete used to manufacture each individual component.
Corestruc’s quality control technicians precisely calculate the moisture content of aggregates and factor in water from admixtures to make the necessary modifications to maintain the optimum water-to-cement ratio. The company is also judicious in its selection of aggregates to ensure that they are as impermeable as possible. Furthermore, admixtures are used to modify fresh or hardened concrete. All of these produce an almost impermeable concrete element that can withstand damaging chloride and sulphate ions, as well as aggressive chemicals. The water tower design is the outcome of years of research and development by Corestruc and Infinite Consulting Engineers, followed by a sizeable investment into the new formwork required to manufacture the various concrete elements that make up the structure. These are already being used to fabricate the precast concrete elements for another precast concrete water tower that is also being built in the municipal jurisdiction. Further structures are also being planned by other municipalities as they explore more efficient and costeffective ways of augmenting water supply, a critical challenge in the country.
They include the forms used to manufacture the 12 columns and spiral beam elements
Using a robotic total station, 15 mm tolerances have been achieved throughout the various rotations
for each of the three sections or “rotations” that comprise the outer portion of the tower. These 30 interconnected semi-circular prefabricated elements wrap around the structure providing the necessary support, while also offering a striking aesthetic effect. The two columns are fixed via the protruding dowels that pass through the underside and topside of the spiral beam, which is then filled with in-situ concrete. This process was repeated until the columns reached their final height.
Then there are the 15 prefabricated elements that make up the 3,6 m diameter shaft, which is constructed at the same time as the outer portion of the structure. Equipped with precast concrete stairwells with balustrades, it leads to the underside of the prefabricated tank. Thereafter, the shaft connects with stacked precast concrete pipes equipped with a cat ladder. Cast into the reservoir floor slab, this top portion of the shaft will traverse through the water retaining structure to a manhole on the roof.
The superstructure consists of 12 tapered beams connected to the columns of the last
rotation. Resting on bearing pads, they will carry and distribute the load of the precast concrete tank and its contents.
Installed in the triangular shaped junctions between the tapered beams, cut-to-size and shape hollow-core slabs serve as the shutter for the in-situ foundation for the water retaining structure. Coping panels have been installed along the perimeter, providing an aesthetically pleasing finish.
To ensure the very high levels of accuracy required for this precast concrete structure, Corestruc has also invested in a robotic total station. It is also fast and highly efficient, which is precast concrete’s ultimate value proposition. This technology is making the company even more efficient at what it does so well.
Meyer van Rooyen, a seasoned Corestruc Project Manager who has supervised all precast concrete work thus far, says that there is very little scope for error on this project.
“We have achieved tight 15 mm tolerances throughout the construction of the three rotations of the substructure, starting with the placement of the firstrotation columns on the in-situ foundation,” he explains.
Resting on bearing pads, the 12 tapered beams will carry and distribute the load of the precast concrete tank and its contents
“Among other factors, this is also facilitated by our precise manufacturing processes. Each element undergoes extensive quality assurance before it is dispatched and again once it has arrived on site. Once the elements have been safely transported to site and as the last component in Corestruc’s precast concrete value chain, the responsibility rests
with my team of riggers to maintain the highest levels of productivity, efficiency and accuracy.”
His team is supported by a state-of-the-art 150 t mobile crane, which has the capacity to lift the heavy precast concrete elements and reach to efficiently place them. The 12 tapered beams, for example, each weigh a staggering 18,5 t and the columns for the second and third rotations slightly less.
While the tank is significantly smaller than the reservoirs that Van Rooyen and his team have already built, constructing it many metres above ground poses unique challenges.
Safety of employees is top of mind for RSMM Construction and Corestruc. Therefore, the companies have contracted the services of a specialist work at height safety consultant to assist with occupational health and safety protocol. It will also provide specialist training to the team.
Four sub-contractors who have been sourced from communities located within the
construction footprint will work alongside Corestruc’s team to construct the floor slab.
A total of 104 m3 of concrete will be placed to construct the 350 mm thick floor slab.
One of the challenges is the heavy reinforcement in the beam junctions. Therefore, the placement of concrete will have to be carefully managed to ensure that the correct compaction is achieved. This while also ensuring that the top portion of the cast-in-place shaft is watertight.
An articulated boom lift has already been placed on top of the superstructure to assist with the installation, as well as the grouting of the 34 tank wall panels. This is in addition to the two buttress panels for post-tensioning, which will be undertaken in the same way as all of Corestruc’s other reservoirs. All of the wall panels will be propped during their installation, considering the wind speeds at this height. Conventionally, only the first wall panel is propped to free up space.
Meanwhile, the roof structure consists of four columns and beams, as well as 150
hollow-core slabs. The centre portion or “core” will be constructed first, and the outer section completed as part of the final aspects of the programme.
While the structure, itself, demonstrates excellence in precast concrete design and implementation, Van Rooyen says that RSMM Construction and Corestruc have also had an opportunity to show off their extensive expertise in cast-in place concrete methods.
“Supporting this water tower is a 1 m thick and 25 m diameter foundation consisting of 500 m2 of 30 MPa cast-in-place reinforced concrete. It is underpinned by 200 m2 of mass concrete blinding. This took 10 hours to place, starting at 05h00 and using two concrete pumps, while also isolating an entire readymix concrete plant just for this purpose,” he adds.
Van Rooyen has all the reason to be proud, considering how well the project is progressing. He will soon be able to boast that he has again played his part in yet another project that has demonstrated the efficacy of precast concrete.
EVLink is part of Schneider Electric’s EcoStruxure eMobility offering, which is an overarching architecture that sees the integration of EV charging solutions with building energy distribution and management systems. EVLink is an end-to-end connected solution that is easy to install, maintains building power reliability and provides a convenient experience for EV drivers.
Karim Yasser, Home and Distribution Business Unit Leader for Anglophone Africa at Schneider Electric, says the launch of the EVLink solution was prompted by the accelerated adoption of EVs in various African countries, particularly South Africa, Kenya, Ethiopia, Ghana, Nigeria and Egypt.
“These countries are currently at the forefront of EV adoption in Africa, having implemented various governmental policies and laws aimed at pushing the switch from internal combustion engines to electric-powered vehicles,” Yasser explains.
Addressing pain points
EVLink has been launched in the region to address one of the major pain points for EV owners, which is the lack of supporting infrastructure.
In this respect, EVLink Home caters for individual EV owners who are looking for a smart charging solution that can be installed at their residential premises. These chargers are designed for slow charging, with an alternating current (AC) range of up to 11 kW. Typically, a full charge can be completed overnight (six to eight hours), and the charger is available in two variants – traditional and
Schneider Electric, the leader in the digital transformation of energy management and automation, has launched its electric vehicle (EV) charging solution in Africa. Known as EVLink, the solution addresses the requirements of both private and fleet owners.
smart. The smart version can be monitored and controlled with a smartphone.
In turn, EVLink Pro AC is designed for commercial use and can be installed at sites such as office buildings, public parking facilities and shopping malls. This is a faster charging solution with higher capacity (AC range of up to 22 kW) to ensure that a full charge can be completed in three to four hours. With an RFID card, building or facilities managers can authenticate and provide or deny access to users while tracking their energy consumption.
Schneider Electric will also launch the EVLink Pro DC solution later this year, which is a fast charger with a direct current (DC) range of up to 180 kW. This offering will be suitable for use in transit, such as at charging stations, and will be able to provide a full charge in a short time (30 minutes to an hour). EVLink Pro DC is also suited to electric mass transit buses that require higher power demand for charging.
“As a global leader in energy management, we offer comprehensive e-Mobility solutions that go beyond simply providing EV charging infrastructure. We connect the entire electric mobility ecosystem to create a seamless and convenient charging experience for homes, buildings, and fleets,” adds Yasser.
“Beyond the chargers, our solution includes energy sourcing that use microgrid solutions, software, and electrical protection with smart low voltage and medium voltage. Our goal is to minimise downtime and prioritise the use of renewable energy to move towards a net-zero future. We are here to support you on your transition to eMobility,” Yasser concludes.
South Africa joined the nuclear energy segment back in July 1985 with the full commissioning of Cape Town’s 2 000 MW Koeberg Power Station, which has since provided the main source of electricity for the city and the Western Cape. It remains Africa’s sole nuclear power station and features a pressurised water reactor design that has enjoyed a perfect safety record. By Alastair Currie
Since then, there’s been a long hiatus with no further South African plants developed, partly influenced by public perceptions of higher payback costs compared to coal-fired and renewable options, as well as perceived safety and environmental risks.
However, Dr Kelvin Kemm – a globally renowned South African nuclear physicist and chairman of Stratek Global – feels the time is ripe to revisit misconceptions and dispel the myths once and for all. This is thanks to cutting-edge research and development (R&D) undertaken by his company that makes nuclear power in a modular form commercially viable, scalable, and sustainable, following the breakthrough design of their HTMR100 reactor.
These installations are so compact that the power plant set-up can fit on a football field, and because they are meant to integrate with urban footprints, special attention has been
given to developing architectural designs that are aesthetically appealing. In other words, the plant exterior can take any shape or form structurally to blend in, instead of portraying a hard industrial profile.
“South Africa is the world’s third oldest nuclear country after the USA and the UK and our entry started with the SAFARI-1 reactor development in the 1960s, transitioning to the Koeberg development. To this day, we still have an exceptional pool of talent standing by for the next wave,” says Dr Kemm.
A case in point is the large number of South African specialists who have been involved on the soon to be commissioned 5 600 MW Barakah Nuclear Energy Plant. Once all four APR1400 nuclear reactors are online, they will supply up to 25% of the UAE’s electricity needs.
The scale of the UAE plant is groundbreaking, and a substantial investment undertaking that would be challenging to replicate at this stage
in South Africa’s current fiscally constrained environment. However, the advent of modular plants provides a medium-term solution that is within reach.
A great deal of work has already gone into the development of compact power stations locally, thanks to the pioneering development of the Pebble Bed Modular Reactor (PBMR) initiative. A 2 000 strong R&D team was extensively involved for around a decade and were ready to launch their prototype in 2008. However, local government funding and international investor support dried up in the ensuing 2008 global financial crisis, and the PBMR initiative was shelved.
Back to the drawing board, some members of the PBMR group subsequently went on to pursue alternatives, which led to the formation of Stratek Global. After some 11 years of R&D, the ultimate result is the HTMR-100, a Generation IV reactor. The latter features the latest fail-safe systems incorporated following the lessons learnt by
Japan’s Fukushima nuclear accident – the result of an unprecedented earthquake and tsunami event.
“As an aside, Koeberg was built on a firstof-its kind anti-earthquake raft to cater for events ranging between 7 to 7.5 on the Richter scale – just in case. This shows how advanced South Africa’s thinking was back then,” Dr Kemm observes, adding that Stratek Global’s HTMR-100 reactor is “walkaway safe” with passive interventions that prevent any risk of a meltdown.
There are crucial differences between the PBMR and the HTMR-100 in terms of build requirements and cost-efficiencies.
For starters, the former has a gas outlet temperature of around 940 degrees Celsius, which is high by international standards. The technology was also configured to feed the helium gas heated during the process from the reactor directly into the turbines to produce electricity. That requires a highly complex turbine design.
“The rationale for the HTMR-100 was to make it faster, easier, and cheaper to construct. The temperature has been reduced to 750 degrees Celsius, and the design incorporates a water-heat exchanger that produces stream to run conventional turbines,” Dr Kemm explains.
“This means that aside from our reactor, all the other components to build the power
station are commercially available and don’t require unique fabrication. A further plus is that compared to Generation III technology, Generation IV units require minimal water input – thanks to helium gas cooling –which is highly beneficial in water scarce regions like South Africa.”
Each HTMR-100 reactor produces around 100 MW of thermal energy. This can be extracted completely for industrial processes or converted into approximately 35 MW of emission-free electricity at a cost approximately the same as coal-fired generation.
Stratek Global has so far developed four options in response to specific client enquiries. These comprise the Kudu “All Africa” model for towns and cities; the Impala for manufacturing and mining; the Oryx for desert conditions; and the Sable for seasonal snow bound environments.
Depending on downstream demand, clients would typically start their HTMR100 journey with one, but ideally two modules to ensure a standby solution for routine maintenance interventions. The bulk of the upfront cost is in the enabling infrastructure, with further reactors then added over time. The control room and associated infrastructure of a single site can take up to ten
reactors individually added if and when the owner wishes.
The fuel required consists of cricket ball-sized “pebbles” that can be safely handled in their inert state. They are easy to transport and once the fuel is expended it is safely disposed of in purpose-designed concrete containment cells according to strict global standards.
The business case and interest in modern-day modular nuclear plants is growing worldwide because of its relative affordability, bolstered by the European Union’s classification of nuclear as a green technology in 2022.
As Dr Kemm points out, it’s certainly no longer an exotic option, but predictably will become far more mainstream internationally. In South Africa’s case, these plants are a viable clean power alternative in replacing outdated coal-fired plants, offering similar 24/7 baseload capabilities to meet city and industrial electrification demand.
“Renewables like solar and wind are important additions, but they can’t realistically provide the constant power needed to drive an electric train from Johannesburg to Cape Town, enable a functioning city
key metros with 100% of their conventional power, along with all the other towns and cities making up South Africa outside the Western Cape. The total area is vast, equating to the size of Western Europe.
ongoing discussions locally with interested parties that include the Limpopo Provincial Government. The latter is exploring the possibility of an eight-reactor installation, in two clusters of four, to power Special Economic Zones. Positive enquires have also come from the South African agricultural industry to install reactors to run full supply chain production and manufacturing processes.
“The entry of the HTMR-100 into the international arena is no longer an academic debate. This is underscored by the fact that China fully commissioned their own similar concept last year for commercial application,” Dr Kemm continues.
Globally, electricity demand has doubled in the past 25 years, and all nations now need to find answers that support population and macroeconomic expansion. As and when coal-fired plants are decommissioned, in line with the UN Framework Convention on Climate change, alternatives must be found, and nuclear is one of them.
commuter rail network, or drive heavy industry and manufacturing,” points out Dr Kemm.
As with the current coal-fired electricity setup, all other energy alternatives are dependent on transmission networks. In Koeberg’s case, this network needs to light up the Western Cape, while for the larger-scale solar farms in the Northern Cape to be viable –given their remote location – a significant investment in power line infrastructure is required to reach consumers in major centres that include Gauteng.
The same has always held true for conventional coal-fired power stations, based at source in Limpopo and Mpumalanga. Although far removed from main centres, they currently supply
“The advantage of the HTMR-100 approach is that these plants can be built anywhere, serving dedicated town and city electrification at the point of use within an independent or interconnected national grid,” says Dr Kemm.
First SA demonstration unit
Plans are now in place for the construction of Stratek Global’s first HTMR-100 demonstration plant, which will be housed at the birthplace of SAFARI-1, namely the Pelindaba nuclear research facility some 32 km outside Pretoria.
This follows accumulated funding support from global investment agencies based in regions that include Australasia, Africa, North America, Europe, and the Middle East to cover the envisaged five-year period needed to construct and commission the demo plant.
However, buy-in from South African public and private sector investors is also crucially important, with Stratek Global currently in discussions with potential stakeholders. In the meantime, Stratek Global is in
“Our world will increasingly be smart and driven by major advances in information and communications technology that are dependent on the rollout of power-hungry datacentres,” Dr Kemm continues. “Plus, the power deficits in developing regions are enormous, and for this reason many African countries have now recognised nuclear as a priority to bridge the gaps and enable meaningful socioeconomic development.”
“So, we need a mindset change in South Africa, acknowledging that green nuclear power is not just an option, but a welcome necessity, with the added advantage that the fuel sources are homegrown,” Dr Kemm concludes.
The fuel balls employed to power the HTMR-100 reactor are safe to handle in their inert state. Just six of these balls would supply electricity for a family of four for a decade
The detrimental impact of sediment loads in rivers on the functionality of pumping systems is often overlooked and leads to the premature failure of many abstraction projects for irrigation and other purposes.
Pumping specialist Darren Ward, area manager for KSB Pumps and Valves, says
Damage to both sides of a pump’s impeller as well as internal damage occurred within just months due to incorrect specification of pumps and other irrigation components
sediments, comprising sand, silt, clay and gravel pose a significant challenge to the efficiency and reliability of water abstraction processes and should be carefully studied before undertaking projects.
“The presence of sediments in rivers poses multifaceted challenges for pumping systems, with abrasive particles such as sand and gravel causing wear and tear on critical pump components, notably the impeller and casing. This wear not only compromises pump efficiency, but also escalates maintenance requirements and operational costs,” Ward explains.
“Fine sediments like silt and clay are identified as stealthy culprits, capable of
clogging pump intake screens and filters, thereby obstructing water flow and impeding pump performance. This phenomenon often leads to a cascade of inefficiencies and frequent breakdowns within poorly specified pumping systems.”
The importance of proactive measures, including the use of abrasion-resistant materials for pumps, installation of sediment filters and adherence to stringent maintenance schedules is paramount. However, the threat of sediment load extends beyond pumps, with pipes and valves within water systems also vulnerable to wear, reduced flow capacity, valve malfunction, corrosion and maintenance nightmares.
“It is always a safe option to make use of an accredited SABI engineer with the skills and credentials to evaluate the requirements and specify a system based on the average and seasonal sediment loads in our waterways,” Ward concludes.
Spanning the Mdloti River in Verulam, the steeltruss Canelands Bridge acquired by eThekwini Water and Sanitation (EWS) has stood the test of time for more than 100 years, serving as a pedestrian and pipe bridge carrying trunk water and sewer lines, as well as medium voltage cables.
Due to the age of the bridge most of the steel members were at an advanced stage of corrosion, making it unsafe for pedestrians, and an extensive refurbishment was needed. The bridge connects Ward 58 and Ward 60.
“This bridge certainly has an interesting history. The starting point was transferring it to our asset register, with that process dating back to around 2008. At the time, owners included Spoornet (which became Transnet), a previous municipality, and a private enterprise that had subsequently dissolved, including Saambou Bank,” explains Leisel Bowes, Pr Tech Eng, EWS Water Design and NRW Department.
Studies at the time looked at the best approach to rehabilitate the bridge due to its deteriorated condition. These included coatings and specialist welding options, with a construction tender released. Upon tender clarification, the client was advised that rehabilitation was possible. However, the lifespan guarantee was only 15 years and would not be economically feasible. This then led to EWS going out to tender on a new bridge design proposal in 2018, with Naidu Consulting subsequently appointed.
“A detailed investigation was undertaken and found that the existing substructure, which included the five existing reinforced concrete piers – which span the river at 33 m intervals – as well as the abutments, were structurally sound. This meant that only the steel superstructure (or deck) needed to be replaced, passing on substantial costing savings in executing the final design,” explains Santosh Soobryan Pr Eng, at Naidu Consulting.
“In addition, the reuse of the existing substructure allowed for an innovative design solution for the superstructure, which mitigated against the requirement for construction within the watercourse. This in turn meant that additional water use licence approval was not required.”
Switching from precast to in-situ deck beams
Naidu Consulting’s design team first considered the employment of individual
Forming the U-beam for the new deck.
To avoid the establishment of formwork and falsework extending down into the river, the contractor strengthened the steel base of the existing superstructure to temporarily support the castings
Demolition in progress to remove the old steel truss superstructure
33 m pre-tensioned precast concrete beams jacked across and supported on the existing piers to form the new superstructure.
However, when the appointed contractor, Afrostructures, established on site their alternate proposal was that it would be more feasible to cast the beams in-situ – one of the chief reasons being space constraints; the other being the alternative necessity of casting off site and then transporting the beams to the bridge location.
The contractor was required to strengthen the steel base of the existing superstructure to temporarily support the cast in-situ beams in order to maintain the original design intent of negating the need for temporary falsework extending down to the river channel. “This was approved by us and the client in the alternate design,” says Soobryan, adding that once completed, the cast-in situ deck was then post-tensioned and all of the 100-year plus steel work was dismantled and removed.
The added benefit to the project was that the alternate design created additional employment and skills transfer opportunities for community-based participants and SMMEs in line with Contractor Participation Goal requirements.
It’s significant to note that the groundwork for the bridge’s execution between the client, consultant and tenderers all had to take place
An internal perspective of a cast U-beam section capped by a slab that supports the installation of new 400 mm diameter HDPE water and sewerage pipes above. The U-beam void was designed to incorporate a new 600 mm diameter steel water pipe forming part of the connection between the Hazelmere Water Treatment Works and Grange Reservoir
The Canelands Bridge upgrade at an advanced stage of completion. The balustrading is reminiscent of the profile created by the intermittent gaps between the 5,5 m deep structural steel trusses at each pier location on the old bridge, providing an important aesthetic link with the past. The 10 m high gabion wall installed was built following flood damage to the northern abutment to ensure its future integrity
virtually within the Covid-19 environment. Full restrictions locally by the South African government were only repealed in June 2022. In response, Naidu Consulting applied an innovative solution and used its investments in 3D design software technologies – including BIM modelling – to provide a virtual briefing and visualisation of the construction methodology.
“From our perspective as the client, it’s a major achievement that the consultant and the contractor jointly arrived and implemented a solution to essentially build a ‘bridge within a bridge’ while ensuring that the existing services continued to function during construction,” says Bowes.
During construction, the existing sewer, water, and cable infrastructure services and pedestrian walkways remained in operation and were only decommissioned and removed at completion when final tie-ins took place.
Built with pedestrians in mind
“Although probably not part of the original plan when it was first built, the growth of residential and industrial nodes in the
passing years has led to Canelands serving as a key pedestrian access route. In the old bridge design those pedestrians –numbering in the hundreds daily – needed to navigate a narrow passage, which was far from ideal in terms of health, safety, and comfort,” comments Adrian Pillay Pr Tech Eng, Naidu Consulting.
“For this reason, enhancing the pedestrian component in our design was a top priority for the client, being an essential facility for the community within the two Wards to reach required destinations. Reconfiguring the pedestrian walkway now means that communities can save on public transport costs, especially for those who chose not to tackle the old bridge to reach places of work and residences,” Pillay continues.
Photo-luminescent polymer concrete coating
“Our design went a step further by incorporating photo-luminescent polymer concrete coating elements into the distinctive architectural balustrading
that form the new bridge. The latter are reminiscent of the profile created by the intermittent gaps between the 5,5 m deep structural steel trusses at each pier location on the old bridge, providing an important aesthetic link with the past,” adds Pillay.
Naidu Consulting’s first adoption of photo-luminescent technology was on the eZimbokodweni Pedestrian Pipe Bridge in Umlazi. Key advantages include its ability to sustain light for up to 10 hours, improving safety for pedestrians, while minimising the need for electric lighting.
“This strategic upgrade underscores EWS’s commitment to improving public utilities for the community and showcases the innovative teamwork by the consultant and the contractor. The fact that the project was executed with no environmental impacts is also highly commendable, and the ultimate result is something we can all be proud of, with thousands of pedestrians now crossing safely every day,” Bowes concludes.
AfriSam celebrates a longstanding relationship with CPMs
CPMs often have demanding requirements for specialised mix designs and final product quality
Manufacturing concrete products is an industry segment that faces its own special demands, and AfriSam’s 90 years of experience allows it to take some of the weight of these challenges off its customers.
Some of the country’s leading concrete product manufacturers (CPMs) have been our customers for over 40 years,” says Adele Wentzel, Sales Manager Cement Manufacturing Gauteng at AfriSam. “Relationships like these give us real insight into their daily concerns, and how we can add value to their operations.”
With its need for efficient production lines and quick cycle times, the CPM segment relies extensively on AfriSam’s Rapid Hard (52,5R) cement and its High Strength (42,5R) cement. Concrete products need to be removed from moulds as quickly as possible, and in most cases there are stringent demands on quality, finish and strength.
“While many customers have applications that need our ‘Rolls Royce’ product – the Rapid Hard cement – there are also segments where their concrete products are better suited to other classes of cement,” explains Wentzel. “Whatever the application, though, customers rely on the AfriSam service team to ensure they receive the right cement and the optimal mix to achieve the best results.”
Centre for Product Excellence
Among current priorities in the CPM segment is to reduce energy consumption – as steam curing is generally energy intensive. A key
AfriSam’s Rapid Hard Cement allows for quicker setting and mould stripping times
resource for AfriSam customers is its Centre for Product Excellence (CPE), which helps find innovative and cost-effective solutions.
“The CPE’s depth of expertise – backed up by sophisticated testing and laboratory infrastructure – means there are specialists available in the field of concrete products,” she says. “One of our initiatives has been a collaboration with a leading admixture provider, combining our skills and products with theirs to find ways to reduce costs for customers.”
These initiatives include focused interventions for customers to achieve strategic improvements in their operational efficiency, she notes.
“Our ability to provide these value-adds stems from the trust we've built over many years within the CPM segment through sustained relationships,” she emphasises. “Throughout the years, we have practically demonstrated our contribution to customers’ businesses, providing a tangible contribution cementing the necessary trust.”
This trust is a vital foundation for a segment faced with varying levels of loadshedding, as
CPMs rely heavily on electricity supply for curing concrete products.
“With our flexibility, responsiveness and qualified specialist advice, we help customers to manage operational uncertainties, while still ensuring the highest quality of product,” Wentzel concludes.
AfriSam plans
cement deliveries around customer requirements
What is reputedly South Africa largest privately owned bridge spans the Berg River at Val de Vie, a luxurious lifestyle housing estate near Paarl in the Western Cape. Measuring some 70 m in length, the bridge links the Val de Vie Estate with the R45 provincial road and has reduced the travel time to towns such as Stellenbosch and Somerset West.
Aworking monument to the practical and aesthetic attributes of hybrid precast and in-situ concrete bridge construction, it was designed by Daneel Strydom of Bigen Africa with sub-consultant assistance on the precast beam design by Pieter Louw and Associates.
Built by the main contractor Empa Structures, a subsidiary of the Raubex Group, the structure differs from traditional utilitarian bridge construction in that considerable emphasis was placed on its aesthetic attributes, and as such it is referred to as an “architectural” bridge.
The original concept was based on a stone bridge with multiple spans reminiscent of medieval bridges over streams. However, the Department of Water and Sanitation (DWS) would at first not allow any construction activity within the full width of the riverbed. At this point there was little choice other than a more modern steel-and-concrete composite arch bridge.
Sixteen of the eighteen beams are in place between the abutments and the central pier
Permission was eventually granted by the DWS to construct a midspan single pier in the riverbed with the proviso that formwork or any form of staging would not be allowed within the primary river course (under the western span) and stringent guidelines regarding spillage into the river were imposed. Water quality up and downstream had to be monitored weekly to ensure that construction activity did not result in any contamination.
“Given the restricted access, we had no other option but to use as much precast concrete
as was feasible,” said Strydom. “However, we were permitted to use in-situ construction for the central support pier, the two abutments and several other elements such as the reinforced deck and the concrete balustrades. The area under the eastern span forms part of the flood plain and construction access to the pier was originally only possible from the east.”
In order to facilitate easy access for workers and supervisory staff from the main site camp to the pier construction area, Empa Structures prefabricated and installed a temporary steel pedestrian bridge over the main channel.
Supplied by Concrete Manufacturers Association member, Cape Concrete Works, the precast concrete elements included huge prestressed beams, large facing panels, coping and culverts. Permanent shutters were precast on site by Empa Structures.
The revised design had a heavy but shallow arch appearance with the stone elements being used where possible. However, the community was not entirely happy with this revised proposal once renders had been circulated and an alternative design submitted by the estate’s architect, Boogertman and Partners, was implemented.
In harmony with the architecture in other parts of the estate, the bridge has a single shallow arch rising to the central pier between the abutments and was built with a combination of steel and concrete balustrades to afford visibility of the river and surrounding countryside. One of the architectural requirements was the use of smooth precast facing panels, which were mounted on the sides of the bridge to accentuate the shallow arch.
The abutments were generously proportioned and were fringed with arched and embellished walling to create a prominent entrance to the estate. They also provide viewing platforms for people on foot and for the tethering of horses. Additional viewing coves were constructed on cantilevered platforms situated over the central pier.
Purpose-designed pretensioned beams
The initial precast design was based on the use of post-tensioned beams that could be cast on site. However, the contractor opted for pretensioned beams constructed off-site for commercial reasons.
Numbering 18, the Val de Vie precast beams are 35,62 m long and 2 m high. Weighing 64 tonnes apiece, their manufacture required the construction of a dedicated stress-bed and
All the beams are in place and in situ construction is underway
an 80 tonne gantry crane at Cape Concrete’s production yard.
“We entered unchartered territory with this project and were obliged to operate to extremely tight deadlines,” said Cape Concrete managing director, Darty Louw.
“Everything happened simultaneously; the construction of the laying bed, the erection of the gantry crane, the manufacture of the moulds and the preparation of the beams’ reinforcing frame assemblies. The latter comprised a combination of rebar as well as 38 pretensioned 15,7 mm diameter strands at the bottom of each beam. An additional six fivemetre long Y40 reinforcing bars at both ends of each beam were also required.”
The pretensioned strands in the bottom of the beams neutralise the mid-span bending moment, whereas the Y40s restrain the tension forces in the top due to moments at each beam end. In addition, the Y40s protrude asymmetrically from one end of each beam. When laid end-toend as the beams were, the Y40 extension bars overlapped with the bars of the facing beams, thus creating a knitting effect.
“In order for the trouble-free execution of this Y40 link-up, tolerances had to be extremely tight
and the Y40s had to be positioned with great accuracy prior to casting,” said Louw. Concrete pouring commenced once all the beam strands were evenly stressed. A combination of external and poker vibration was used to compact the concrete. This provided a very good surface finish with minimal blow holes.
Steam cured
As soon as the pouring was completed, a tarpaulin was placed over the mould and steam was injected under the cover to accelerate the hydration process. This meant that a strength of 40 MPa could be achieved in 20 hours and enabled Cape Concrete to produce one beam a day. The final strength required was 60 MPa which was achieved within 28 days.
The de-tensioning of the prestressed strands took place once the concrete had reached 40 MPa using four 250 tonne hydraulic jacks. Retarder paste was applied at the end of each beam after casting and was washed off
The central diaphragm’s reinforcing prior to the pouring of concrete. The Y40s can be seen protruding from the ends of the beams in a knitting formation
A precast facing panel is lowered into position
with water the next day to create a rough exposed aggregate finish. This provided a good bonding surface for the assembly of the bridge.
The facing panels were also steam cured, the largest units measuring 4 m x 3 m. These panels were cast with a glass-smooth finish and attached with cleverly designed fingers that eliminated the use of visual fixing on the front face. Some of the panels were curved, for example those which were used for cladding of the central viewing coves.
A juggernaut was required to deliver the
The paving of the road and pavements was done by Highland Paving using clay pavers
beams to site by road, one at a time. And a mobile crane company, Teemane Cranes, was contracted to offload and place the beams. Due to the drought conditions being experienced at that time in the Cape, a dry area suitable for the mounting of two of the three mobile cranes used for off-loading and placing the beams was put to use.
The Western Cape’s largest mobile crane, a 460 tonne behemoth, was the only mobile crane sufficiently large enough to hoist the beams off the delivery vehicle unaided. The first nine beams were placed on the ground close to the river’s west bank. They were then lifted from each end by the 460 tonne
crane and a 220 tonne crane positioned on the other side of the river and placed into position between the western abutment and the central pier.
The operation for the positioning of the second nine beams on the eastern side of the bridge was somewhat different and entailed the use of the third mobile crane, also positioned on the eastern side of the river.
Once all 18 precast beams were in position, five diaphragm transverse beams were cast in-situ between the precast beams. They comprised a central beam which binds all 18 precast beams together, two mid-span beams and two beams above each abutment. The central beam was the largest, being 1,5 m wide and 2 m high. Empa Structures’ construction team had to create working platforms on either side of the diaphragm sections by fixing anchors into the pier and abutments. This gave them working space to erect the vertical shuttering.
In addition to normal reinforcing, the central diaphragm beam was further reinforced with the installation of four post-tensioned cables, two at the bottom and two at the top.
Permanent deck shutters were cast in Empa Structures’ site yard and were used to close the remaining gaps between the precast beams. Measuring 1,2 m x 300 x 50 mm they rested on recesses which had been cast into the beams for that purpose. Concrete was then poured onto the shutters to create the deck.
The deck comprises a 250 mm thick road section and a 335 mm pavement section. Heavily reinforced, it included a substantial quantity of Y32s. The casting of the pavements was especially challenging because provision had to be made for the attachment of the precast cladding on each side of the bridge.
This involved the use of box-outs to create holes into which the panels’ concrete fingers could be inserted. Once the fingers of a panel were inserted and tied temporarily to the deck, final lining adjustments were made using jacks before final grouting took place.
Empa Structures contracts manager, Gareth Stander said that time saving was another benefit of using precast concrete.
“The beams were cast in parallel with the construction of the sub-structure and were completed more or less at the same time and this saved at least nine weeks in construction time.”
Before construction began a hydraulic assessment of the river course and the flood plain was undertaken.
“Top water levels for a one-hundredyear flood was calculated, as well as the approximate scour depths around the pier and abutments during a one-hundred-year flood. The bridge was constructed above the onehundred-year flood line and the panels on the
side of the bridge are all positioned above it. So even in a worst case scenario, the bridge should stand clear and proud of the water,” Strydom explained.
Moreover, the piles on which the entire structure is supported were carefully designed to ensure stability of the bridge even during deep scouring.
“Not being a national thoroughfare, the bridge is unlikely to bear unusually heavy
traffic. Therefore, our design incorporated the standard NA loading and an NB24 loading, the latter being the lighter loading for abnormal loads,” added Strydom.
“However, although it was not specified, the bridge can actually take the NC loading (described as a super load in the design code). Because of the bridge’s span lengths, the NA loading resulted in the largest design moments,” concluded Strydom.
Colloidal silica P3 can be applied as an admixture to concrete as it is being produced. However, many contractors still prefer to treat concrete slabs with colloidal silica P3 after they have been cast
Ultra-high durability levels are being imparted to conventional concrete mixes with a simple addition of nano-sized materials. This is helping to construct more durable infrastructure and significantly prolong the service life of existing structural assets.
Colloidal silica post-placement pozzolan (P3), “colloidal nano silica” or “nano silica” is a cutting-edge nano technology. It has been used for more than two decades throughout the world, including in South Africa, to make the oldest commodity-based material more durable and, therefore, longer lasting. This includes municipal service delivery infrastructure, such as wastewater treatment plants and sewers.
More recently, colloidal silica P3 is being specified for manhole repairs. The technology is used to neutralise and remove contaminants from existing concrete before the manholes are repaired. When applied to the entire manhole area, corrosion potential can be substantially reduced. This, in turn, potentially increases the service life of the infrastructure by 20 years or more.
A chemical-resistant coating is generally applied over colloidal silica P3-treated concrete in wastewater treatment plants, as well as sewers and manholes.
These amorphous silicon dioxide particles are less than 100 nano metres in size and suspended in water. They are sprayapplied to horizontal, vertical or overhead concrete slabs after they have been cast. This single-spray application is permanent.
Colloidal silica P3’s small size provides a tremendous amount of reactivity and pozzolanic potential – even greater than that of un-densified silica fume. This reaction takes place in the capillary voids and pore space that are created in concrete as bleed water exits the construction material. In this way, they are filled with more calcium-silicate hydrate (C-S-H). C-S-H is the same reaction product that provides concrete with its strength and durability traits. Even under hydrostatic pressure, the movement of water through concrete is restricted. This waterproofing action considerably reduces waterborne contaminant ingress, including the transport of chlorides, through concrete.
Chlorides damage the protective hydroxide layer on reinforcing bar. Also referred to as “passivation”, this layer is formed by the high alkalinity of concrete. Once it has been compromised, wet or dry cycles accelerate the continuous corrosion process. This is the lead cause of premature concrete failure. By extending the period it takes for chlorides to reach reinforcing bar, years can be added to the lifecycle of concrete structures.
Three laboratories have tested colloidal silica P3 technology’s ability to significantly deaccelerate the rate of chloride through concrete. Using chloride diffusion testing, chloride concentrations at various depths were ascertained. These informed the calculation of an average diffusion coefficient that predicts the length of time it will take chlorides to reach reinforcing steel and penetrate the passive layer around it. This modelling was undertaken with sophisticated software, including Life 365. The simple and transparent model is used by many design consultants to estimate the service life and lifecycle costs of alternative protection systems in the design of reinforced concrete structures that are exposed to chlorides.
Notably, colloidal silica P3 achieved a 69% reduction in chloride diffusion coefficient for concrete with a water-to-cement (W/C) ratio of 0,57 and 0,45. For concrete with a W/C ratio of 0,40, a 75% reduction in chloride diffusion coefficient was achieved. Certainly, colloidal silica can also be applied as an admixture to concrete as it is being produced.
However, many contractors still prefer to treat concrete slabs after they have been cast with colloidal silica P3. This allows the particles to penetrate the concrete deeply after the voids have been formed and close them in the interaction zone.
Permeability, durability and curing
According to Carl White, Managing Director of Spraylock Africa, 99% of the world’s concrete is placed with excess water because it is needed to achieve the initial chemical reaction, despite the use of effective chemical admixtures.
“The permanent bleed-water channels created in the concrete as a portion of this excess water exits increases the permeability of the construction material. Concrete permeability and durability are intrinsically linked. Concrete that is less permeable is going to be more durable and will, therefore, last longer and fulfil its service life capabilities at a low maintenance cost,” he says.
In addition to serving as a very effective base waterproofing system and densifying concrete, there is another important way that colloidal silica P3 raises the durability of concrete. This is by facilitating optimal curing.
Curing is an essential component of quality assurance and control during construction. This is considering the significant role that it plays in ensuring high-strength gain; minimising thermal, plastic and dryingshrinkage cracks and making concrete more watertight; and improving abrasion resistance. Moreover, proper curing advances the microstructure of concrete by assisting the cement-hydration reaction to progress steadily. The calcium-silicate hydrate gel that is created during this process binds aggregates to form a rock-solid mass. This makes concrete denser; decreases porosity; and enhances the physical and mechanical properties of concrete.
Colloidal silica P3 retains water that would normally evaporate. The technology’s ability to facilitate continued hydration is the improved compressive strength and significant dryingshrinkage reduction of concrete treated with the technology. Colloidal silica P3-treated concrete even outperforms moist-cured concrete. Moist curing is considered the “gold standard” of curing practices.
Notably, more than 100 research papers authored by over 15 research teams have demonstrated the improved properties of concrete containing colloidal silica that has either been applied as an admixture during mixing or after slabs have been cast. Moreover, two ASTM working groups have been assigned to just work on colloidal silica specifications.
Formerly known as the American Society for Testing and Materials, ASTM develops and publishes voluntary consensus technical
international standards for a wide range of materials, products, systems and services.
Notably, a representative of United Statesbased SprayLock Concrete Protection (SCP) serves on one of these working groups. SCP is the foremost manufacturer and supplier of colloidal silica P3, which conforms to the EN1504-2 durability standard. The company’s spray-applied products have earned a solid reputation the world over for their ability to protect concrete from contaminants.
The United States has been at the cuttingedge of colloidal silica research, not least of which are the significant efforts made by the US Army Corps in the field since the early 2000s. This stimulated worldwide interest in the technology.
Even in a highly developed country such as the United States, concrete structures have not been performing as they should. The leading cause of the premature failure of concrete structures in the country is as a result of alkali–silica reaction. This can be attributed to higher alkali cements, more reactive aggregates and ineffective pozzolans.
About US$48 billion is invested in new concrete structures in the United States every year. Yet, US$8,3 billion is spent annually maintaining them as a result of physical and chemical attack.
According to the American Society of Civil Engineers’ Infrastructure Report Card of 2012, one in six of the more than 600 000 concrete bridges in the country were in severe need of replacement or repair at the time. Meanwhile, the findings of a study undertaken by the American Society of Military Engineers in 2015 revealed that the mix designs for 40% of the country’s concrete
bridges had a life expectancy of less than 30 years.
At the same time, the International Concrete Research Institute expects building repair costs in the United States to be about US$20 billion a year, with most structures only expected to last between 50 to 60 years. In areas of the country where de-icing salts are used on sidewalks and pavements, this infrastructure only lasts for five years. Where the salt melts, snow build-up creates saltwater slush that enters concrete. Once inside the concrete, it refreezes. This additional pressure starts breaking up concrete. In addition, salt water itself contains magnesium chloride, as well as sulphate and hydrogen carbonation ions. This corrodes the concrete and rebar. SCP technology has been very effective in
safeguarding new and existing concrete that is exposed to fresh and salt water. This includes bridges, dams, piers and other concrete structures that are located within 0,8 km or more of a body of water. The company’s top-of-shelf formulation improves concrete durability of structures exposed to harsh marine conditions by 90% or more. This is according to the EN 12390-8 testing standard. It specifies the method for determining the rebound number of an area of hardened concrete using a spring-driven hammer.
SCP also improves chloride diffusion by 50% and reduces forced chloride ingress by 25% or greater, according to the ASTM C1556 and NT Build 492 testing standards, respectively. ASTM C1556 is the standard
test method for determining the apparent chloride diffusion coefficient of cementitious mixtures by bulk diffusion. An alternative to ASTM C1202, the NT Build 492 laboratory test is used to determine the chloride migration coefficient in concrete and mortar.
Conclusion
“South Africa is also grappling with a growing infrastructure backlog, while existing service delivery assets are deteriorating because of insufficient maintenance. Therefore, the focus is increasingly on extending the life of existing and developing new infrastructure that continues to add value over its entire lifecycle while reducing maintenance costs. SCP products enable this,” White concludes.
Sika South Africa prides itself on having a range of LiquidApplied Roofing (LAR) systems designed to meet the diverse needs of the South African construction industry. These cutting-edge solutions offer superior performance, durability, and ease of application, setting new standards in the roofing sector.
Our LAR solutions provide seamless, flexible, and fully bonded waterproofing membranes that adapt to any roof shape and size. They are ideal for both new builds and refurbishment projects, ensuring long-term protection and low maintenance requirements.
Sikalastic ®-560 was specified as the waterproofing membrane for Bosjes Chapel’s distinctive roof structure
• Durability and flexibility: Sika's LAR systems are resistant to UV radiation, temperature fluctuations, and mechanical stress, ensuring long-lasting performance in South Africa's varied climate conditions.
• Seamless application: The liquid-applied nature of these systems allows for easy application around complex roof details and penetrations, creating a continuous and watertight seal.
• Environmentally friendly: Sika's LAR products are solvent-free and low in volatile organic compounds (VOCs), making them an eco-friendly choice for sustainable construction practices.
• Versatility: Suitable for a wide range of substrates including concrete, metal, and bituminous roofing, these systems offer unparalleled versatility in roofing applications.
• Sikalastic® range: This series of polyurethanebased waterproofing membranes is designed for a wide range of roofing applications, providing high elasticity and excellent crackbridging properties.
• SikaRoof® MTC systems: Featuring Moisture Triggered Chemistry (MTC), these systems cure upon contact with moisture, allowing for rapid and reliable application even in uncertain weather conditions.
Sika's LAR systems have been successfully implemented in numerous high-profile projects across South Africa, showcasing their reliability and performance in real-world scenarios. From commercial buildings to residential complexes, Sika's roofing solutions have proven to deliver outstanding results.
For more information on Sika’s LAR solutions, visit Sika South Africa's LAR Page.
Leading consulting engineering and infrastructure advisory practice, Zutari, is continuing its involvement with the worldleading MeerKAT radio telescope array situated in South Africa’s Northern Cape province, where it has played a leading role since the project first broke ground.
Zutari has been involved with this initiative for about 15 years. It is one of our flagship projects and very close to our heart. We are very proud and privileged to be a part of such an exciting global venture,” says Jana Jooste, Major Projects Director.
“What makes our ongoing involvement unique is that, whereas we previously only designed the infrastructure for MeerKAT, our current appointment is as a professional services consultant for the client. It means we are embedded in the client’s team, a testament to the incredible collaboration we have had as part of a global professional team on this flagship international project.”
With the main client, the Square Kilometre Array Observatory (SKAO), based in the United Kingdom, Zutari’s current role is to guide the infrastructure construction contractors through the designs and subsequent construction work.
“The local design and construction activities need to be closely aligned with other work packages being developed, specifically the telescopes being developed in China. Where this becomes interesting and challenging is coordinating all of these global efforts and to find ways, tools, and mechanisms to make sure that ultimately there is a single integrated telescope array,” explains Jooste.
“We regularly sit in on meetings with the other design teams, based all over the world,” she adds.
Zutari is also developing power solutions for the site. “Hence, there is an international flavour to what ultimately will be a South African solution on the ground here in the Northern Cape.”
Zutari’s longstanding involvement with the project extends to assisting the National Research Foundation (NRF) with the necessary technical support to ensure South Africa could demonstrate that it had the capability to host the telescope. The telescope is operated by
Jana Jooste, Major Projects Director, Zutari
Dr Gabi Wojtowitz, Associate Design Director, Zutari
the South African Radio Astronomy Observatory (SARAO), a NRF facility.
The 64-dish MeerKAT is the largest radio telescope in the Southern Hemisphere and one of two SKA precursor instruments based in South Africa. It was expanded with an additional 24 dishes under the MeerKAT+ project. This was jointly funded in 2019 by SARAO and the MaxPlanck-Gesellschaft (MPG) of Germany and since 2020 with the Istituto Nazionale di Astrofisica (INAF). The telescope will later be gradually integrated into the Square Kilometre Array Midfrequency telescope (SKA-Mid).
The SKAO has a global footprint, consisting of its global headquarters in the UK, the two telescopes at radio-quiet sites in South Africa and Australia, and associated facilities to support the operation of the telescopes. Once fully operational, the SKAO will be a single global observatory operating two telescopes across three continents on behalf of its member states and partners.
Local community engagement is a high priority for the SKAO. “The telescope will be operating for an extended period of time, and therefore the buy-in and benefits to the local community is a major focus area,” says Jooste, adding that the area where the telescope is being constructed has a high level of poverty and unemployment.
As a result, a range of initiatives have been implemented to benefit and upskill local companies and entrepreneurs, from providing physical labour, local contractors and suppliers to related soft services. “We are looking at the entire region both during construction and postconstruction when the telescope is operational,” confirms Jooste.
Another benefit for the South African economy is the anticipated construction of a data centre and operations centre based in Cape Town, which will attract international researchers and boost local tourism.
“We are proud to have provided the critical base infrastructure needed for these SKA dishes to operate effectively,” says Dr Gabi Wojtowitz, Associate Design Director at Zutari, who oversaw the foundation and geotechnical work.
Zutari conducted preliminary and detailed design, verification and construction monitoring for the 24 dish foundations for MeerKAT+, as well as the power and fibre needed to collect and relay data over vast distances. The project included the complete design verification and design of the access and foundation elements for the remaining 109 dish positions for the SKA-Mid array.
Under the bonnet, the JCB 3CX range benefits from improved hydraulic efficiency thanks to new variable displacement piston pumps that are standard across all models
The highly anticipated range of updated JCB 3CX backhoe loaders arrives on South African shores in July 2024 – replacing the existing JCB 3CX Eco, 3DX and 3CX Global product lineup – and comes equipped with new features designed to provide improved comfort, versatility, and productivity.
The new cab makeover is the most noticeable change and is bound to impress,” says Massyn Jansen Van Vuuren, Bell Equipment Sales Product Manager for JCB products, adding that the striking new design uses high quality moulded plastics, and the pillars and roof are light grey in colour to give a lighter and more spacious feel.
“Most importantly, the new cab places a huge focus on operator safety, comfort, and ease of operation. For example, the loader lever has been simplified to operate like a wheel loader,” he continues.
The 3CX range now has a single lever loader control incorporating an F-N-R directional switch so an operator can control the loader and transmission with one hand. In addition, there is a proportional switch on the side of the lever to operate the 6-in-1 bucket, which further reduces the effort needed to operate the machine.
The new EasyShift transmission with “kick down” is standard across the range and simplifies gear changing, which is done by
rotating the F-N-R directional lever next to the steering wheel. The kick down switch is located on the floor and allows the operator to drop from second to first gear when extra push power is needed for loading or site stripping.
“All cabs are ROPS/FOPS certified and the seat rotation area is larger to give the operator more room, which together with improved cab sealing to keep out water and dust, creates a cleaner and more pleasant workspace. There is also improved visibility to the working area behind the machine,” explains Jansen Van Vuuren.
In addition, the 3CX Plus and 3CX Pro models feature a new high-performance HVAC system with 21 adjustable air vents strategically positioned around the front console, B pillar and rear of the machine to direct air flow to maximise comfort and demisting performance. The 3CX has a fan mounted on the B pillar as standard.
Under the bonnet, the JCB 3CX range benefits from improved hydraulic efficiency thanks to new variable displacement piston pumps that are standard across all models. The larger pump provides 150 lpm, a 39% increase over the previous model. This
The Plus and Pro models have a Smooth Ride System for improved roading as standard and can be provided with a 6-in-1 shovel, with the option of flip over forks for added versatility
3CX
55kW naturally aspirated engine
Manual controls
Front general purpose (GP) bucket
Optional: flip over forks
Fixed dipper
Rear 600 mm bucket with optional trenching bucket
Fan only
3CX Plus
68.6kW turbo engine
Manual controls
Front general purpose (GP) bucket
Optional: 6-in-1 bucket
Optional: flip over forks
Fixed dipper
Optional: “extradig” dipper
Rear 600 mm bucket with optional trenching bucket
Optional: Rear auxiliary hammer pipework
Standard HVAC
Various other attachments available on request
allows the engine speed to be reduced while maintaining productivity, effectively reducing fuel consumption. Furthermore, the variable flow pump only provides flow on demand and backs-off the flow when not required to reduce load on the engine and improve fuel consumption.
The Plus and Pro models have a Smooth Ride System for improved roading as standard and can be provided with a 6-in-1 shovel, with the option of flip over forks for added versatility.
“The 6-in-1 shovel can be used for dozing, loading, digging, grabbing, spreading, and grading, while the optional flip over forks are ideal for machines that will double up as a forklift for pick and place activities
around the work site and to unload vehicles,”
Jansen Van Vuuren continues.
Lighting has been improved with six LED work lights instead of halogen lights. Two adjustable LEDs are fitted on the front and four on the rear, of which two can be adjusted. During nighttime operations, the operator will be able to safely exit both the machine and worksite by aid of a “guide me home” light system that keeps the work lights illuminated for 30 seconds after the ignition has been turned off.
Other useful standard features include an in-cab boom lock, front and rear wash/ wiper functions, Return to Dig function, electronic throttle control, Bluetooth radio
3CX Pro
68.6kW turbo engine
Seat mounted servo controls
Front 6-in-1 bucket
Optional: general purpose (GP) bucket
Optional: flip over forks
Fixed dipper
Optional: “extradig” dipper
Rear 600 mm bucket with optional trenching bucket
Rear auxiliary bi-directional circuit
Standard HVAC
Various other attachments available on request
and USB ports, front and side LCD display, an adjustable steering column, and a battery isolator key, which allows the operator to isolate the machine’s electrics while carrying out machine maintenance.
“All in all, the new 3CX range has a machine to suit all requirements and we expect these new machines to add real value and strengthen JCB’s position as the world’s leading brand of backhoe loaders,” adds Jansen Van Vuuren.
“We have a fleet of units that will be used across the country to familiarise customers with the new range and the improvements, so we encourage customers to contact their nearest Bell dealer and experience the machines for themselves,” Jansen Van Vuuren concludes.
The 3CX range now has a single lever loader control incorporating an F-N-R directional switch so an operator can control the loader and transmission with one hand
AECOM siphokuhle.dlamini@aecom.com
AFI Consult banie@afri-infra.com
ARRB Systems info@arrbsystemssa.com
Asla Construction (Pty) Ltd johanv@asla.co.za
BMK Group brian@bmkgroup.co.za
Bosch Projects (Pty) Ltd mail@boschprojects.co.za
BVI Consulting Engineers marketing@bviho.co.za
CCG puhumudzo@ccgsytems.co.za / info@ccgsystems.co.za
Civtech Engineers (Pty) Ltd admin@civtech.biz
Corrosion Institute of Southern Africa secretary@corrosioninstitute.org.za
Dlamindlovu Consulting Engineers & Project Managers info@dlami-ndlovu.co.za
EFG Engineers info@efgeng.co.za
Elster Kent Metering Mark.Shamley@Honeywell.com
EMS Solutions paul@emssolutions.co.za
ENsync Engineers info@ensync.africa
ERWAT mail@erwat.co.za
Gabion Baskets mail@gabionbaskets.co.za
GIBB marketing@gibb.co.za
GIGSA secretary@gigsa.org
GLS Consulting info@gls.co.za
Gorman Rupp Cordeiro@gormanrupp.co.za
Gudunkomo Investments & Consulting info@gudunkomo.co.za
Hatch Africa (Pty) Ltd info@hatch.co.za
HB Glass Filter Media info@hardybulkinglass.com
Herrenknecht schiewe.helene@herrenknecht.de
HSA Technology (Pty) Ltd cs@hubersa.com
Hydro-comp Enterprises info@edams.co.za
IMQS Software (Pty) Ltd shemine.adams@imqs.co.za
Infrachamps Consulting info@infrachamps.co.za
INFRATEC info@infratec.co.za
Institute of Waste Management of Southern Africa iwmsa@iwmsa.co.za
IQHINA Consulting Engineers & Project Managers info@iqhina.co.za
iX engineers (Pty) Ltd hans.k@ixengineers.co.za
Izinga Holdings info@izingalabezi.co.za
JG Afrika DennyC@jgafrika.com
KABE Consulting Engineers info@kabe.co.za
Kago Consulting Engineers kagocon@kago.co.za
Kantey & Templer (K&T) Consulting Engineers ccherry@ct.kanteys.co.za
Kitso Botlhale Consulting Engineers info@kitsobce.co.za
KSB Pumps and Valves (Pty) Ltd salesza@ksb.com
KUREMA Engineering (Pty) Ltd info@kurema.co.za
Lektratek Water general@lwt.co.za
Loshini Projects muzi@loshini.co.za
Makhaotse Narasimulu & Associates mmakhaotse@mna-sa.co.za
Mariswe (Pty) Ltd neshniec@mariswe.com
Martin & East gbyron@martin-east.co.za
M & C Consulting Engineers (Pty) Ltd info@mcconsulting.co.za
Mhiduve adminpotch@mhiduve.co.za
MPAMOT (Pty) Ltd mpumem@mpamot.com
Mvubu Consulting & Project Managers miranda@mvubu.net
Nyeleti Consulting naidoot@nyeleti.co.za
Prociv Consulting & Projects Management amarunga@prociv.co.za
Rainbow Reservoirs quin@rainbowres.com
Re-Solve Consulting (Pty) Ltd maura@re-solve.co.za
Ribicon Consulting Group (Pty) Ltd info@ribicon.co.za
Royal HaskoningDHV francisg@rhdv.com
SABITA info@sabita.co.za
SAFRIPOL mberry@safripol.com
SAGI annette@sagi.co.za
SALGA info@salga.org.za
SAPPMA admin@sappma.co.za / willem@sappma.co.za
SARF administrator@sarf.org.za.co.za
SBS Water Systems marketing@sbstanks.co.za
Silulumanzi Antoinette.Diphoko@silulumanzi.com
Siroccon International (Pty) Ltd admin@siroccon.co.za
SiVEST SA info@sivest.co.za
Sizabantu Piping Systems (Pty) Ltd proudly@sizabantu.com
Siza Water (RF) Pty Ltd PA@sizawater.com
Sky High Consulting Engineers (Pty) Ltd info@shconsultong.co.za
SKYV Consulting Engineers (Pty) Ltd kamesh@skyv.co.za
Smartlock jp.alkema@smartlock.net
SMEC capetown@smec.com
SOUTH AFRICAN VALUE EDUCATION Sabiha@savegroup.co.za
Southern African Society for Trenchless Technology director@sasst.org.za
SRK Consulting jomar@srk.co.za
Structa Group info@structatech.co.za
TPA Consulting roger@tpa.co.za
Ultra Control Valves peter@ultravalves.co.za
V3 Consulting Engineers (Pty) Ltd info@v3consulting.co.za
VIP Consulting Engineers esme@vipconsulting.co.za
VNA info@vnac.co.za
Water Institute of Southern Africa wisa@wisa.org.za
Wam Technology CC support@wamsys.co.za
Wilo South Africa marketingsa@wilo.co.za
WRCON ben@wrcon.co.za
Zutari Rashree.Maharaj@Zutari.com
The Johannesburg Development Agency (JDA), the infrastructure arm of the City of Johannesburg, has commenced the construction of the Drieziek Recreation Park as part of the Orange Farm Turnkey programme.
Working in conjunction with Johannesburg City Parks and Zoo (JCPZ) – the entity responsible for greening initiatives in the city – this development marks a significant milestone in enhancing the quality of life for residents of Drieziek Extension 3. The park's design has been refined to reflect the unique preferences and aspirations of its future users, following extensive stakeholder engagement.
“The Drieziek Recreation Park stands as a testament to the JDA's dedication to holistic urban development, where infrastructure projects not only meet the needs of residents, but also contribute to the social, economic, and environmental well-being of the community,” says Siyabonga Genu, JDA’s Executive Manager for Project Implementation.
The park is designed to encourage physical activity and wellness, providing amenities such as play and exercise equipment, multipurpose courts, and a futsal court. The incorporation of an agricultural component further seeks to promote community resilience through urban farming.
Thirty percent of the contract value will be allocated to SMMEs, demonstrating JDA’s commitment to inclusive growth and economic empowerment. Jobs created via the Expanded Public Works Programme will also focus on empowering women and youth in the construction sector, enabling them to participate in and realise the vision of this landmark development.
In the ever-evolving world of maritime logistics, optimising the efficiency and productivity of port operations is
essential for staying competitive.
Lenny Naidoo, acting National Operations Manager at Heavy Lift, a division of CFAO Equipment SA, says the solution to meeting these requirements lies in harnessing the potential of innovative and advanced technologies from reputable global manufacturers.
“At Heavy Lift, we specialise in the sale of heavy-duty forklifts tailored for container handling in port operations. As an industry leader in material handling and industrial equipment, we know all too well the challenges facing our customers, and that is why we remain committed to providing them with optimal technological solutions to streamline their operations and ensure maximum efficiency and productivity,” Naidoo explains.
While fully autonomous machinery may still be on the horizon, current technological advancements, such as those offered by Konecranes and Terberg, are revolutionising port operations.
To this end, predictive maintenance has become indispensable in reducing downtime
and enhancing operational efficiency. Here, advanced monitoring systems track machinery usage in real-time and predict when maintenance is required based on operating hours. This allows for precise planning and ensures that machinery is serviced before issues arise – maintaining peak performance and minimising disruptions.
“Transparency and accountability are also key to driving productivity,” adds Naidoo. “Features such as Konecranes’ CheckApp system and Terberg Connect platform enable drivers to perform daily checks on their equipment via smartphones or tablets, where they can log issues, and upload pictures or videos.”
“This real-time information is accessible to supervisors and managers, streamlining maintenance processes and ensuring swift responses. By eliminating delays associated with paper documentation, the system keeps everyone informed and responsible.”
Data analytics and real-time insights are becoming indispensable in various operational metrics. The MD4 display in the cabins of Konecranes equipment offers drivers critical information on performance, including the number of boxes lifted, fuel consumed, idling
times, and speed. This data empowers operators to make informed decisions.
Safety is a core component of Heavy Lift’s mandate, and its equipment solutions have an array of features to meet this commitment. This includes electronic scales to prevent overloading by displaying cargo weight, as well as geofencing technology that sets speed limits in specific areas and cautions drivers to slow down. Additionally, tyre monitoring systems ensure optimal tyre pressure, which greatly reduces wear and tear.
“The real-time data provided can also help in identifying port congestion and bottlenecks, allowing for greater planning and resource allocation,” explains Naidoo.
Konecranes provides online training modules for both technical staff and equipment operators. These modules ensure employees are up to date with the latest practices and technologies, creating a well-informed workforce.
“By embracing predictive maintenance, transparency, continuous training, and data analytics, ports are setting new standards in their operations. These innovations ensure that port operations are more efficient, productive and safe – meeting the ever-evolving demands of the global supply chain,” Naidoo concludes.
SAPPMA is an Association of leading companies in the plastics piping business, with the purpose of facilitating high standards of ethics, product quality and technical information. It is an open association, well regulated by strong Articles of Association and Code of Conduct and is registered as a Section 21 Company incorporated not for gain.
Members have a collective voice at engineering associations, consulting engineering firms, municipalities, water authorities and contractors.
Access to expert technical information: advice, consultations, technical manual, conferences, webinars, technical publications and ongoing training.
Access to the market survey results/reports, product standards, quality systems, test procedures.
Free access to the latest SANS standards, with representation at certification authorities and test facilities in terms of standards, testing, monitoring and quality control.
Members are set apart from other players in the market by passing the SAPPMA factory audits and adherence to the SAPPMA Code of Conduct.
As a member of SAPPMA, you will be participating in the only representative plastic pipe forum in the country. Members are afforded valuable networking opportunities, social interaction and enjoy a sense of community. 01 03 05 02 04 06
NEED MORE REASONS TO JOIN? CONSIDER THIS...
• SAPPMA represents more than 80 % of the plastic pipe market in Southern Africa. Members are supported by an established brand that is solely aimed at protecting the customer and the infrastructure of the country.
• Our members represent manufacturers, polymer manufacturers, suppliers, individual members and certification bodies.
• The SAPPMA mark on a product has become a sought-after quality guarantee and give customers and end-users the peace of mind that their product meets local and international quality standards.
THE FOLLOWING BUSINESSES AND INDUSTRIES CAN QUALIFY FOR A SAPPMA MEMBERSHIP:
• Pipe & fittings manufacturers
• Raw material suppliers
• Consultants
• Construction companies
• Municipalities
• Water Boards
• Contractors
• Installers
• Individuals