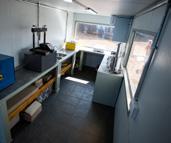
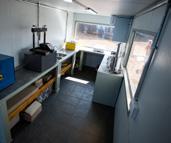
MUCH ASPHALT POLOKWANE
A small team with big ideas
GEOTECHNICAL & ENVIRONMENTAL ENGINEERING
Out of the box solutions for erosion control
LANDFILL DESIGN & CONSTRUCTION
Multicomposites in landfills
BITUMEN & ASPHALT
Sabita commits to green goals
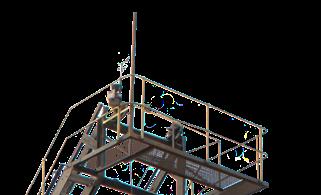
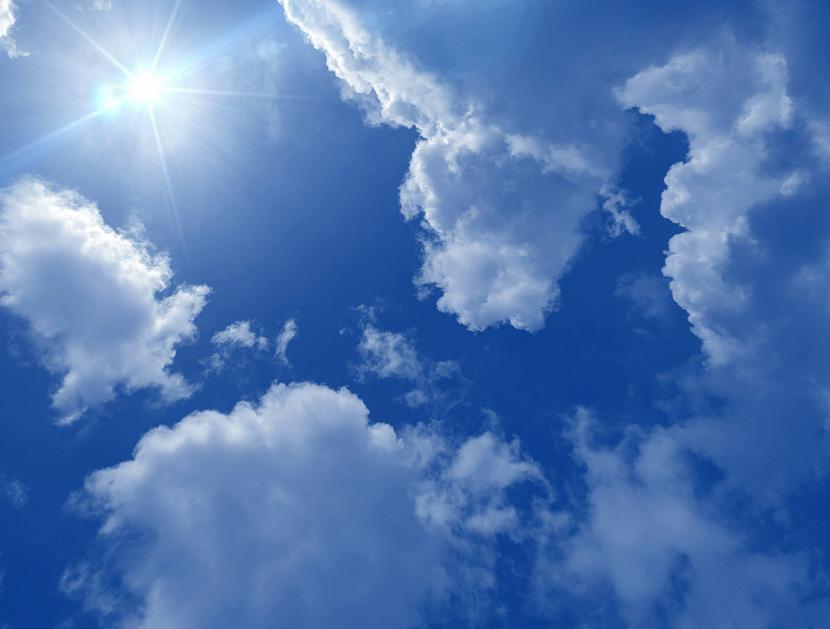
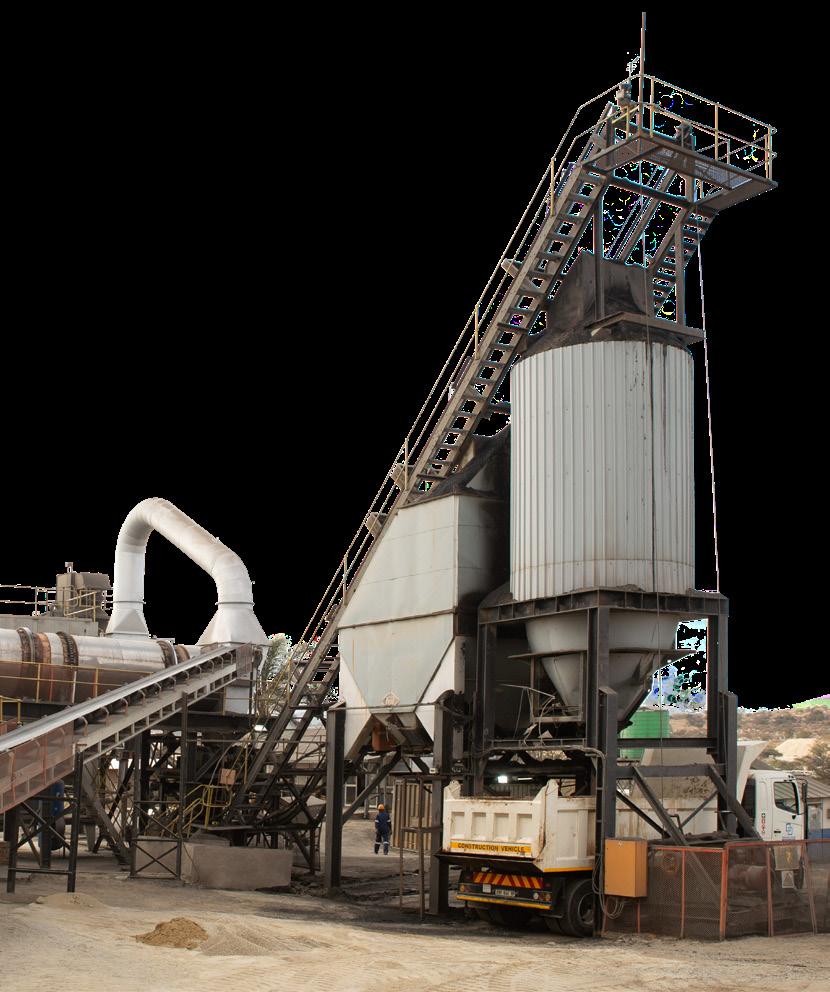
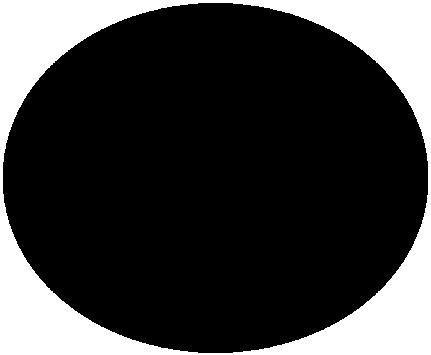
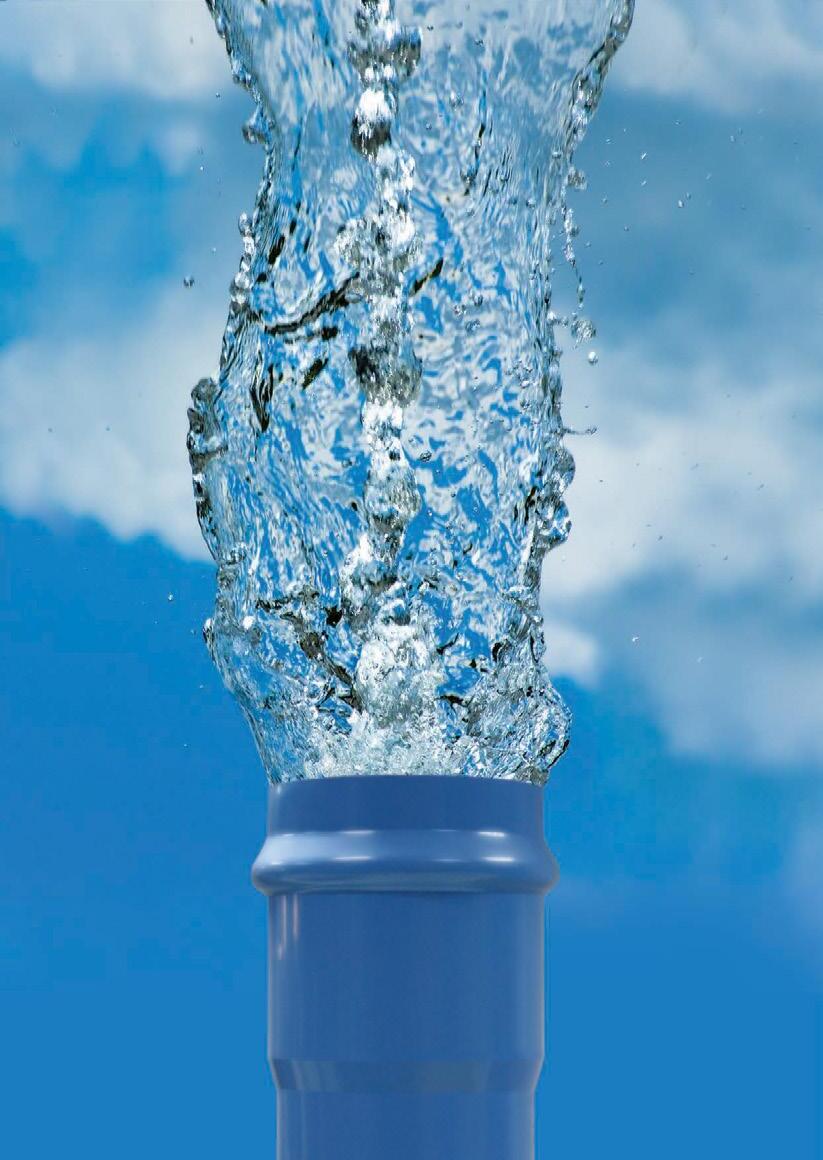

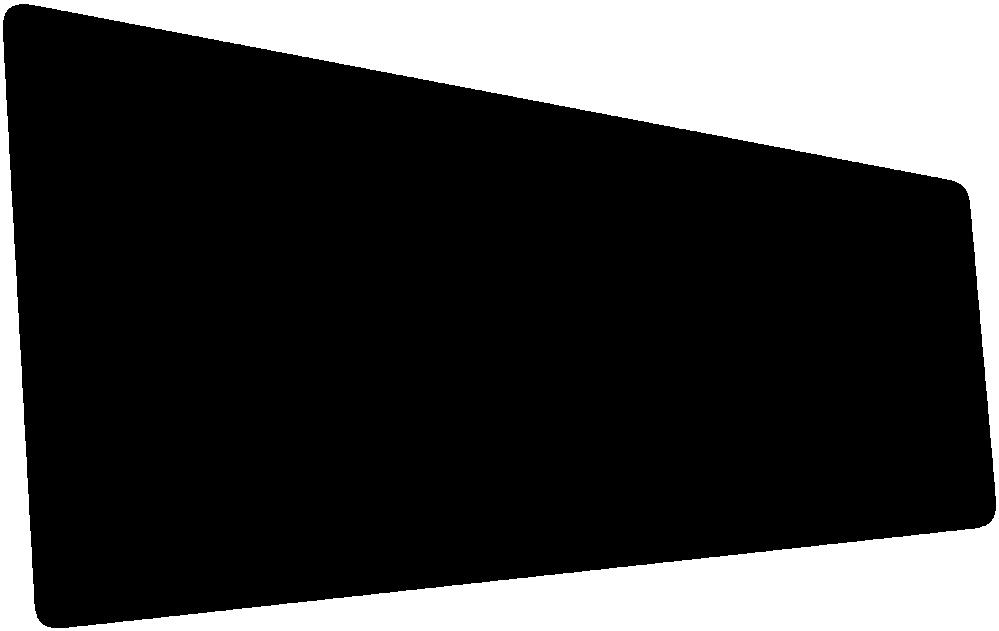
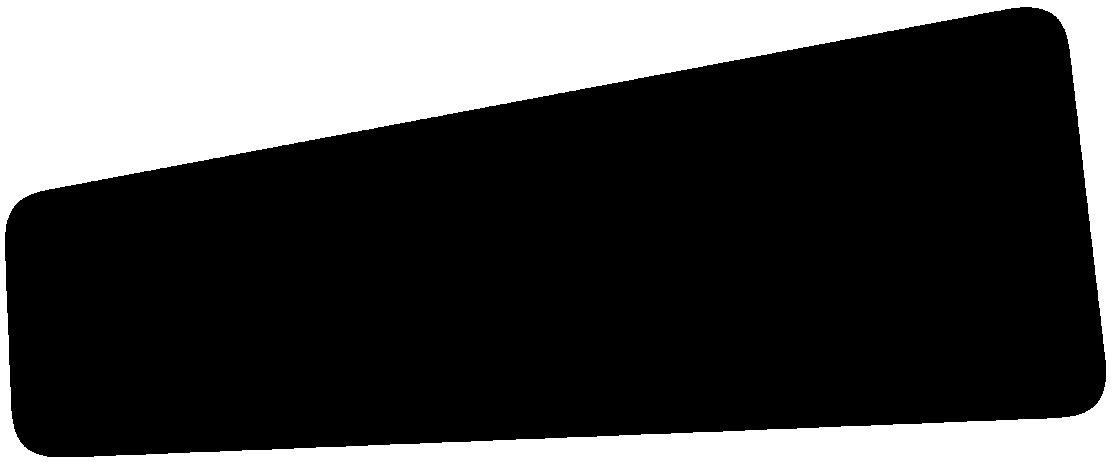













“Communication with our clients is key to ensuring the how, when and where of every load that leaves our yard.” So says Much Asphalt's Polokwane Branch Manager, Suprise Nyambi. With barely more than a year in the driver's seat, Suprise is making waves together with his small and close-knit team in Limpopo. P6

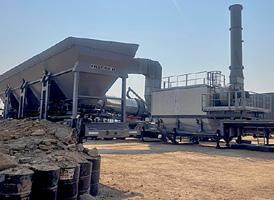
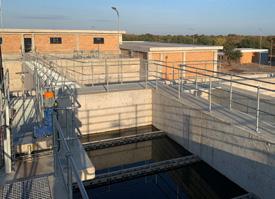
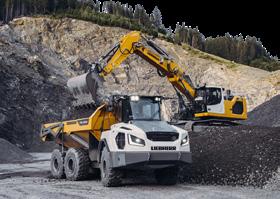









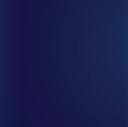



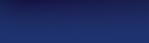

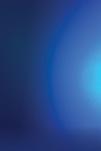
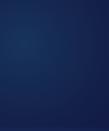
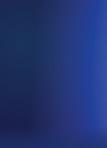





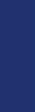























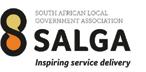
EDITOR Alastair Currie
Email: alastair@infraprojects.co.za
DESIGNER Beren Bauermeister
CONTRIBUTORS Nikhiel Budhai, Roxanne Canny, Dr Calayde Davey, Jeanine du Preez, Sibusiso Mjwara, Brandon Naidoo
DISTRIBUTION MANAGER Nomsa Masina
DISTRIBUTION COORDINATOR Asha Pursotham
SUBSCRIPTIONS
Email: distribution@infraprojects.co.za
ADVERTISING SALES
KEY ACCOUNT MANAGER Joanne Lawrie
Tel: +27 (0)82 346 5338
Email: joanne@infraprojects.co.za
Building new capacity needs enabling teamwork
The expression “Slow and steady wins the race” originates from Aesop's fable, “The Tortoise and the Hare” and remains a classic statement on why incremental planning, perseverance and phased execution works, and rushed “flash in the pan” approaches don’t.
As we gain traction on the country’s seventh political administration, this is an important observation, because past infrastructure promises have worn thin, and been fragmented. That’s not to say that gains haven’t been made, but we now need to focus on realistic goals that are implementable, and to remove bureaucratic impediments.
DPWI strategy
Working in conjunction with other departments, like Water and Sanitation, and Transportation, a vital enabler is the revitalised role played by the Department of Public Works and Infrastructure (DPWI).
PUBLISHER
IMESA (Pty) Ltd
P O Box 2190, Westville, 3630
Tel: +27 (0)31 266 3263
Email: info@infraprojects.co.za
ANNUAL SUBSCRIPTION: R805.00 (INCL VAT)
ISSN 0257 1978 IMIESA, Inst.MUNIC. ENG. S. AFR.
© Copyright 2024. All rights reserved.
IMESA CONTACTS
HEAD OFFICE:
Manager: Ingrid Botton
P.O. Box 2190, Westville, 3630
Tel: +27 (0)31 266 3263
Email: admin@imesa.org.za
Website: www.imesa.org.za
BORDER
Secretary: Celeste Vosloo
Tel: +27 (0)43 705 2433
Email: celestev@buffalocity.gov.za
EASTERN CAPE
Secretary: Susan Canestra
Tel: +27 (0)41 585 4142 ext. 7
Email: imesaec@imesa.org.za
KWAZULU-NATAL
Secretary: Narisha Sogan
Tel: +27 (0)31 266 3263
Email: imesakzn@imesa.org.za
NORTHERN PROVINCES
Secretary: Zurika Louw
Tel: +27 (0)82 322 5208
Email: np@imesa.org.za
SOUTHERN CAPE KAROO
Secretary: Henrietta Oliver
Tel: +27 (0)79 390 7536
Email: imesasck@imesa.org.za
WESTERN CAPE
Secretary: Michelle Ackerman
Tel: +27 (0)21 444 7112
Email: imesawc@imesa.org.za
FREE STATE & NORTHERN CAPE
Secretary: Wilma Van Der Walt
Tel: +27 (0)83 457 4362
Email: imesafsnc@imesa.org.za
In terms of activity, if we look at industry awards for June 2024, the values for civil projects have declined by 32% year-on-year, based on analyst estimates, with the Western Cape reflecting one of the sharpest dips. Across the country road tender values also shrank 38% during the June 2023 to June 2024 period, and those for water projects by 17%.
Reviewing performance for the first six months of 2024, the annual nominal increase in tender values was estimated at around 5%, reaching R51,5 billion in total. The upside is that there is still sustained construction activity, but building momentum is key in meeting South Africa’s delivery targets.
RPPI
As an indicator of market trends, a positive development for the housing segment is an improvement in the Residential Property Price Index (RPPI). This increased nationally by 3,5% on average in the 12 months to March 2024, according to Statistics SA. The Western Cape region was the star performer, with property values rising by 7,7% on average. When analysed over five years from March 2019, the figures are even more significant for the Western Cape, and have increased by around 35,5%. This could be indicative of a semimigration trend when compared to South Africa’s industrial hub, Gauteng, where values only increased by 16,4%.
Spurring demand for new residential construction nationally will be strongly influenced by anticipated interest rate cuts. Buying trends regionally are also an indication of where future growth in upgraded and new infrastructure will be required.
During his 2024/25 Budget Policy speech, Dean Macpherson, South Africa’s new Minister of Public Works and Infrastructure, presented the department’s strategy under the theme “Turning South Africa into a construction site – #LetsBuildSA”. One of his prime objectives is “…to work with local government and provinces to develop a more coordinated approach to infrastructure development”, which is essential for building capacity and ensuring policy alignment.
Building on previous achievements by the DPWI during the six administration is crucial both for macro and microeconomic expansion, as well as serving as a catalyst for job creation – especially youth employment –through the Expanded Public Works Programme (EPWP).
In unlocking opportunities, the DPWI’s envisaged budget allocation over the medium-term expenditure framework is R23,8 billion (2024/25: R7,6 billion; 2025/26: R7,9 billion; and 2026/27: R8,3 billion.)
Within the mix, a budget of R2,2 billion has been set aside for EPWP endeavours during the 2024/25 year. In addition, the DPWI plans to execute refurbishment, repair and capital projects for 24 departments. These include correctional centres, police stations, courts and office buildings, at an anticipated cost of around R3,5 billion in 2024/25.
As Minister Macpherson stated, “We intend to add urgency to the pace of infrastructure delivery by innovating and inviting new ideas to achieve what needs to be done.” That includes more public private partnership engagement in bankable projects via Infrastructure South Africa.
It all comes down to implementation. With the public funds South Africa has available in the current fiscal environment, we must put every taxed rand to work in achieving tangible results. I’m confident that there’s a positive resurgence in achieving this, plus renewed investor confidence to make the changes we need to see happen in practice.
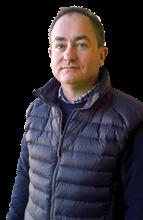







Cover opportunity
IMESA

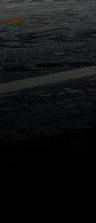



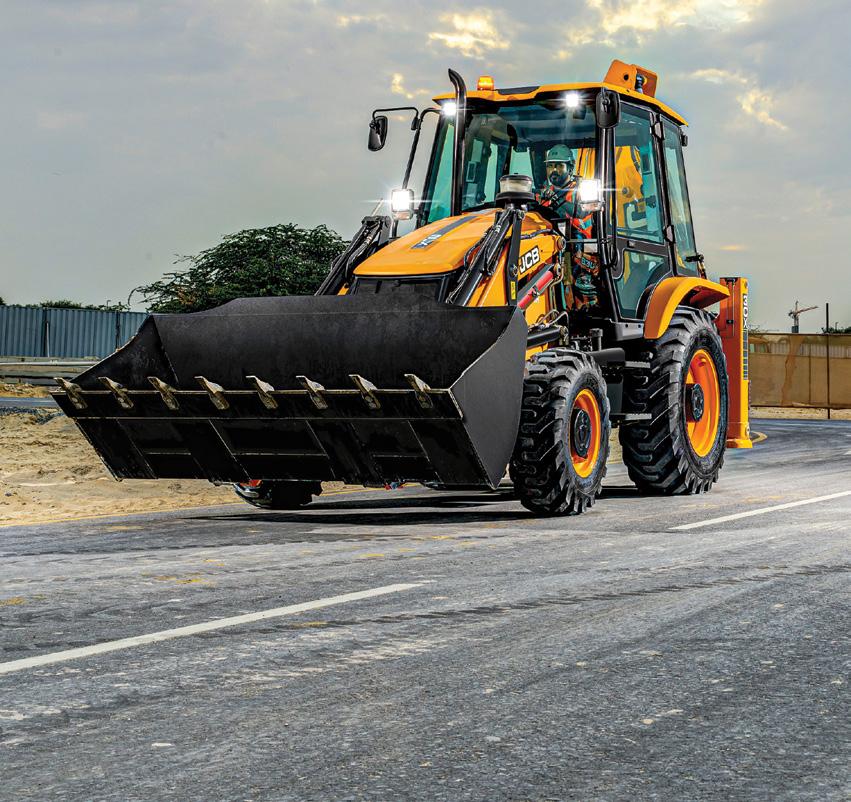






























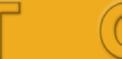





































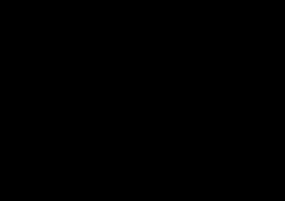


























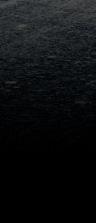
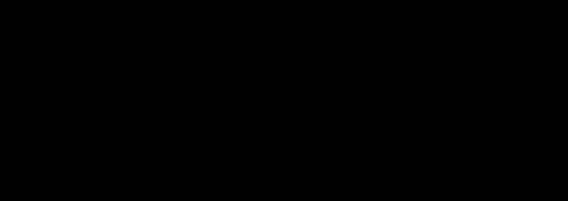
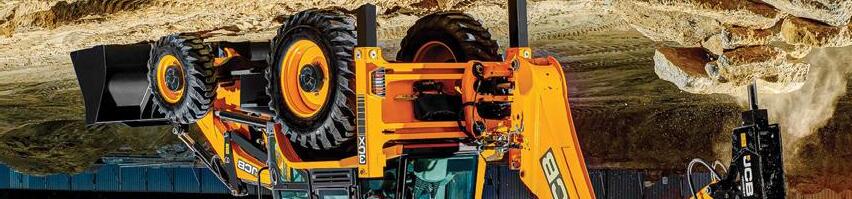
PRESIDENT’S COMMENT
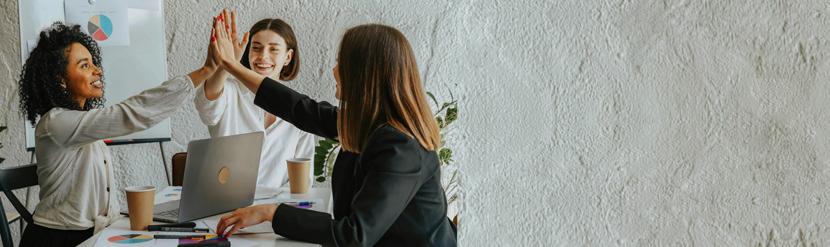
Each year in August, South Africa celebrates Women’s Month, and Women’s Day on 9 th August. The national theme for 2024 was “Celebrating 30 years of democracy towards Women’s Development”, which provided an opportunity to reflect on the progress made since the signing of the Women’s Charter in 1994.
Women’s Month highlights the need for greater inclusivity
The ultimate objective is to fasttrack reforms that enable the socioeconomic advancement of women. However, as indicated by Statistics SA’s Labour Force Participation Rates data recorded between Q2:2014 to Q2:2024 more attention is still needed as gender disparity has persisted across all education levels for women.
ECSA statistics
Within the built environment arena, we are seeing gains in terms of the number of women registered with the Engineering Council of South Africa (ECSA).
In 2012, for example, there were around 38 578 registered persons across all categories and engineering disciplines. As an indicator, some 15 168 were registered professional engineers, of which 477 were women. In turn, there were 4 066 registered professional engineering technologists, but only 133 were women.
Fast forward to March 2023 and the numbers have improved proportionally. Out of a total of approximately 48 382 registered persons, there were 18 939 registered professional engineers, and 6 479 engineering technologists of which 1 630 and 675, respectively, were women.
So, while the figures are still male dominated, the change is happening, but needs to gain impetus. Ensuring that girls entering secondary school are given every opportunity and encouragement to study maths, science, IT and related technology subjects is one of the best ways to achieve this. Where education and opportunity exist, the results speak for themselves, which is underscored by statistics sourced from Eurostat. They show that in 2022 there were close to 7.3 million female scientists and engineers working within the European Union, accounting for some 41% of total employment in these fields.
IMESA objectives
As IMESA, we are committed to the advancement of women through ongoing mentorship, training and networking events, supported by allied initiatives like the IMESA KZN YP 2 Young
Professionals Portfolio. This year, we’ve also seen an increase in IMESA bursary applications from women currently studying or planning to study engineering ahead of our 15th September 2024 deadline.
From a leadership perspective, a landmark development for IMESA was the election of Bhavna Soni as our first female President. Her 2020-2022 Presidential term was uniquely challenging at the height of the Covid-19 pandemic. However, Bhavna rose to the occasion and displayed exceptional stewardship, including the successful hosting of a Virtual Annual IMESA Conference in 2021.
As the current Deputy President, she continues to inspire the men and women serving on our EXCO and Council. Bhavna also plays a decisive role in driving IMESA’s mandate to increase our women members, as well as the percentage of women currently heading up specific Institute portfolios.
From a membership perspective, we currently have 172 women onboard: 64 are ECSA registered in candidate categories; 54 are registered in professional categories; and 54 are not presently registered. This approximately mirrors current sector representation according to ECSA stats. It’s a work in progress for IMESA and industry to create a more equitable balance.
In terms of our IMESA permanent staff complement, we are proud of the fact that it’s a 100% women team, responsible for administration, as well as planning and executing our annual conference. In the past, we used external service providers; now it’s all managed in-house.
IMESA Women’s Day events
For Women’s Day, we ran two events hosted respectively by our Western Cape and KwaZulu-Natal branches. They served as a platform
to showcase professional excellence and the integral role of women engineers.
A highlight of the KZN function was the keynote address by ECSA’s President, Refilwe Buthelezi, herself an accomplished professional engineer and a champion for the advancement of women.
Our proposal to her post the event was to assist IMESA in mobilising funding via avenues like CETA for the appointment of retired engineers to serve as mentors so we can increase the number of registered candidate engineers. Currently, many smaller municipalities don’t have existing capacity or are financially constrained.
Another positive development in August was a meeting with SAICE’s CEO, Sekadi PhayaneShakhane, coinciding with their Women’s Day events. A registered professional engineer with extensive industry experience, her vision and passion are instrumental in helping revitalise the construction industry and advancing women engineering leaders. We regard SAICE as a key stakeholder and have agreed as IMESA to collaborate on various projects going forward that enhance our municipal engineering mandate.
Olympic milestone
Equality is achievable when enabled, as demonstrated at the 2024 Summer Olympic Games during July and August. Women were first allowed to compete at the 1900 Games, but there were just 22 participants. However, for the 2024 games the split was exactly 50/50 for the first time, which is a very important milestone.
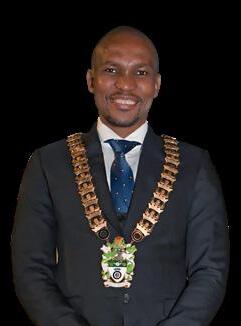
So, on that note, I’d like to congratulate all our South African Olympic champions – especially our two women medal winners. Tatjana Smith brought home gold and silver medals for the 100 m and 200 m breaststroke events, respectively, while Jo-Ane van Dyk won silver in the women’s javelin. Their courageous and competitive spirit is truly inspirational and a fitting tribute for Women’s Month.
Sibusiso Mjwara, PrTechEng, MIMESA, FSAICE, MWISA, MIPET

A small team with big ideas
Much Asphalt didn’t see a need to invest in a permanent plant in South Africa’s Limpopo Province when mobile plants could venture up north to fulfil the asphalt requirements of major projects on remote sites.
Then the announcement came in May 2004 that South Africa would be hosting the 2010 FIFA Soccer World Cup. Polokwane’s Peter Mokaba Stadium was chosen as one of 10 around the country to host World Cup games, with a capacity for about 41 500 spectators at each of its four matches. That thrust Limpopo, its capital Polokwane, and its infrastructure into the limelight, and Much Asphalt decided it was time to expand its footprint into Limpopo Province.
That was not the only reason, says Polokwane Branch Manager Suprise Nyambi. A more permanent source of supply was needed to service the Limpopo roads network, which serves as a tourist and commercial corridor to Botswana, Zimbabwe and Mozambique.
As luck would have it, Much Asphalt was able to acquire a plant previously
established by Murray & Roberts but no longer in operation. The plant needed upgrading and modernising and asphalt production started in September 2006.
The plant, with a capacity of 60 tons per hour, took its first order from Sebokoboko Construction in Senwabarwana, a town some 90 km north-west of Polokwane. “We supplied about 600 tons in total,” says Nyambi.
Product offerings
He adds that the Polokwane Branch has turned into one of the group’s most successful operations. Its capacity has been doubled to 120 tph today and the plant was upgraded from a wet scrubber system to a baghouse system, which ensures that clean air is used in the production process and improves efficiency.
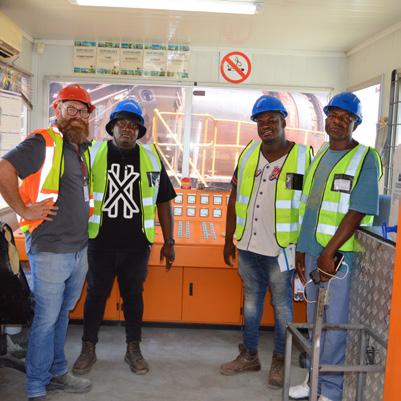
The Polokwane plant’s conventional mixes of continuous graded medium asphalt and bitumen treated base (BTB) have always been its bread and butter. “However, with the industry move to Manual 35/ Coto, we are now providing Level 3 designs for some major contracts. Our plant has the capability to service performance based, project specific multiple-mix designs.”
Much Asphalt subsidiary Spraypave manufactures, supplies and applies bituminous binders, emulsions, primes, and pre-coats, partnering with Much Asphalt Polokwane for seamless supply of these services to the Limpopo market.

The Much Asphalt Polokwane team (from left): Lesley Mathloko, Mathews Molele, Suprise Nyambi, Percy Nematwerani, David Mogale, Patrick Mashabela, David Phetla, Jim Ngobeni, Noxolo Hlatshwayo, Nelly Ramahoyo, Prince Tanzwani, and Louis Mehlaphe. (Bruce Mboweni was on leave)
Chesney Glossop, Much Asphalt Regional Manager (left), explains the workings of the plant to contractor employees
Products are produced and delivered by tanker direct from Spraypave’s Alrode plant in Gauteng or produced on site via mobile modified emulsion and modified bitumen plants. Spraypave offers chip and spray application from bitumen distributors or drummed delivery.
Teamwork and communication
Nyambi believes the high demand for asphalt mixes from the Polokwane plant is down to product quality, good rates, and reliable service from its team of just 13 people. “We also reach out regularly to our current and potential clients to understand their needs and how we can improve to satisfy them.”
Part of great service is being willing and able to adapt to changing markets, he adds. “We closely monitor future work in the area and do what we have to do when the need arises. This may mean upgrading our plant capacity and doubling up on shifts to meet our clients’ supply needs.”
The Polokwane operation is currently upgrading its hot storage capacity from 80 to 200 tons. “We see this plant as critical to the group’s success due to its strategic location to service a relatively large area and will continue to improve the operation through new technologies and greater customer-centricity,” explains Chesney
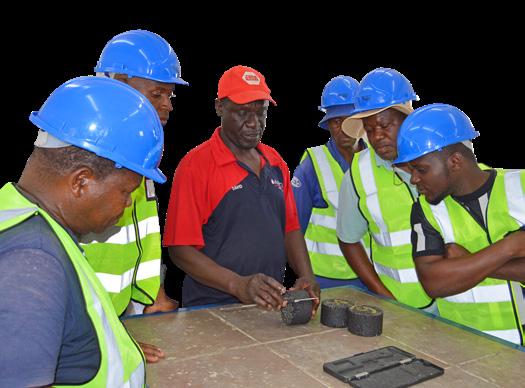
Glossop, Much Asphalt Regional Manager for non-coastal branches outside Gauteng.
Planning
“Detailed daily production planning around tonnages requested for the following day helps us to reduce haulage costs and get the mixes to sites at the right temperature,” Nyambi continues. “Communication with our clients is key to ensuring the how, when and where of every load that leaves our yard.”
Planning and implementing includes everyone on the team from weighbridge to maintenance to the laboratory to
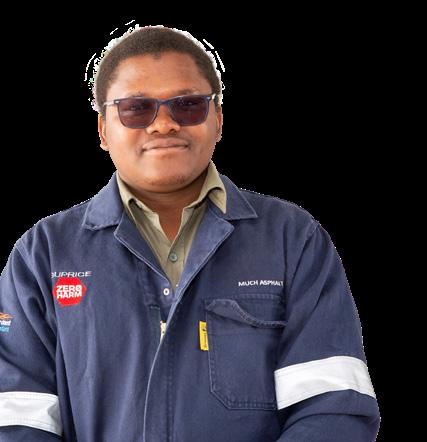
Communication with our clients is key to ensuring the how, when and where of every load that leaves our yard.”
administration. “It comes down to a joint team effort, plus good support from our regional offices.”
Lilithalethu Trading 41 in Polokwane is a long-time client that has used Much Asphalt products on more than 20 projects and collected well over 50 000 tons of asphalt from the Polokwane plant. Lilithalethu’s contracts manager, Mutize Kudzanai, says the companies share a good business relationship due to the quality of product, reliability of supply, and good service provided by the Much Asphalt Polokwane team.
Customer training
Joint efforts extend from the asphalt plant
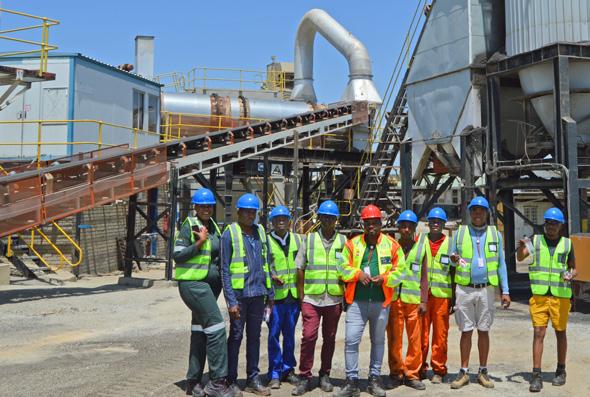
A lesson in quality control from David Mogale, Quality Assurance Supervisor on site
Workshop delegates at the Polokwane plant
Polokwane Branch Manager Suprise Nyambi
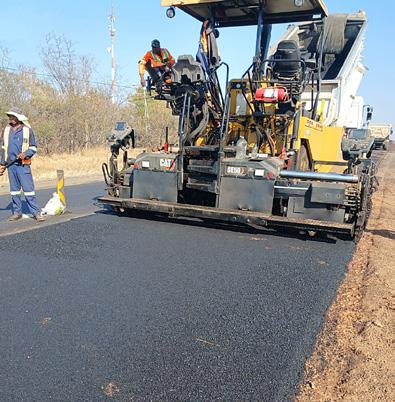
Emergency repairs currently under way by Razzmatazz and BCB Solutions using asphalt supplied by Much Asphalt on the N1 between Makhado and Musina
to the project site. Much Asphalt includes clients in its efforts to improve and sustain asphalt surfaced road networks through a training programme that strives to ensure all involved are on the same page.
In November last year the Polokwane branch hosted its first Best Practice Workshop on Hand-Laid Asphalt . Five construction companies, BCB Solutions, Shonisani Rambau Construction, Chauke Business Enterprise, Manengena Construction & Maintenance, and Botlhabatsatsi Group, sent a total of 40 employees for training.
The workshop included a presentation using Much Asphalt’s in-house written and designed publication, Best Practice HandLaid Asphalt Guide, a tour of the plant, and practical site demonstrations of pothole patching and repairs using both hot and cold mix applications.
“It is in everybody’s interests to ensure that our products are used correctly,” says Glossop. “Client training may well become a regular fixture at the Polokwane plant.”
Projects
With maintenance projects ramping up in the dry winter months, Much Asphalt Polokwane has a lot going on at present.
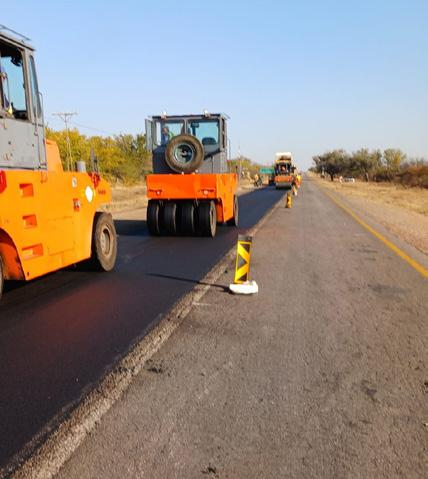

“We are currently supplying an Emergency Pavement Repair Works contract on the N1/29X (Makhado to Musina) for SANRAL, as well as RAL (Roads Agency Limpopo) projects in Makhado, Sebasa, Lebowakgomo, Jane Furse, and Burgersfort. We also have quite a few municipal and Routine Road Maintenance projects on the go.”
SANRAL’s 50km resurfacing project between Mokopane and Duvenhageskraal on the N1 is in the pipeline.
Glossop clarifies that most work is prioritised out of the static plant, but

mobile options are available. “When quoting, we weigh up the risk of haulage and the size of the tender and make a call from there.”
While Suprise Nyambi has only been in the hot seat as Much Asphalt Polokwane Branch Manager since May 2023, his strong work ethic, love for the product, and team-focused leadership are helping to keep this operation on a strong growth trajectory.


Speed up Projects. Enhance Productivity.
Discover the ultimate blend of affordability and convenience with the Lintec ECP ECO concrete batching plant. Its modular design ensures seamless transportation, rapid installation and effortless dismantling, saving valuable hours. Simplify your project with minimal foundation and loading ramps required. With quadrant or linear aggregate bin options, there is always a perfect choice for your project needs.
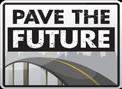
Available Models
ECP60 ❘ 60m3/hr
ECP90 ❘ 90m3/hr

www.lintec-linnhoff.com
Women engineers are building a better world
Recognising the role and importance of women in engineering, the IMESA KwaZulu-Natal (KZN) and Western Cape branches celebrated Women’s Day in style this August, with respective events attended by members, industry practitioners and key stakeholders. These were led respectively by Roxanne Canny, the IMESA KZN Vice-Chairperson and Women’s Day Committee Chair for the province, and Jeanine du Preez, the IMESA Western Cape Chairperson. They report on the event highlights.
IMESA KwaZulu-Natal:
By Roxanne Canny
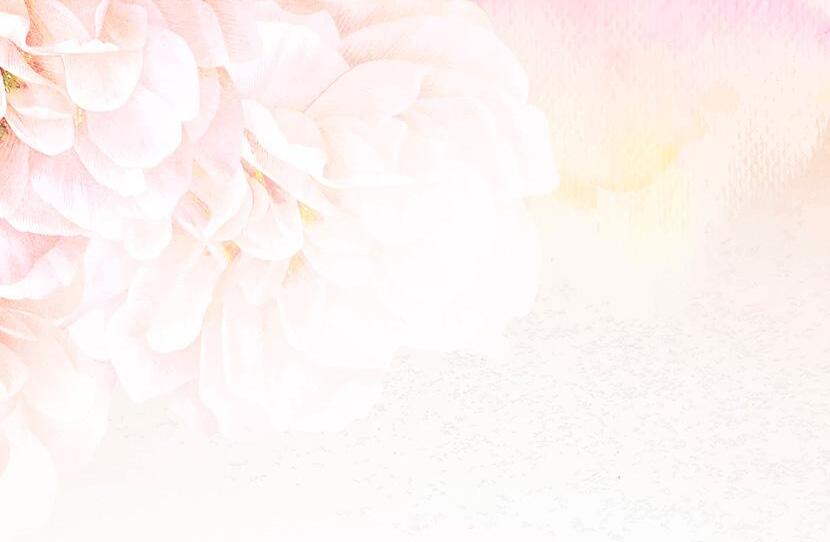
“Engineering Her Revolution: Bold Women, Bright Futures!”
This year’s IMESA KZN Branch Women’s Day event was an outstanding success, held on August 8 th 2024 at the prestigious Oyster Box on the stunning Umhlanga Promenade. The event embraced the theme “Engineering Her Revolution: Bold Women, Bright Futures!” and brought together a vibrant community of women in engineering to celebrate, inspire, and empower.
The event was graced by an impressive lineup of distinguished speakers, each offering unique insights and experiences that resonated deeply with the audience.
Keynote address
One of the standout moments was the keynote address delivered by ECSA President, Refilwe Buthelezi, whose words left a lasting impact on all in attendance. She delivered an inspiring message on the transformative power of volunteerism, reminding us that taking the initiative to give back can open unexpected doors and lead to unforeseen opportunities.
She emphasised the importance of recognising and embracing our own value, encouraging everyone to confidently say “I can” and trust in their ability to navigate
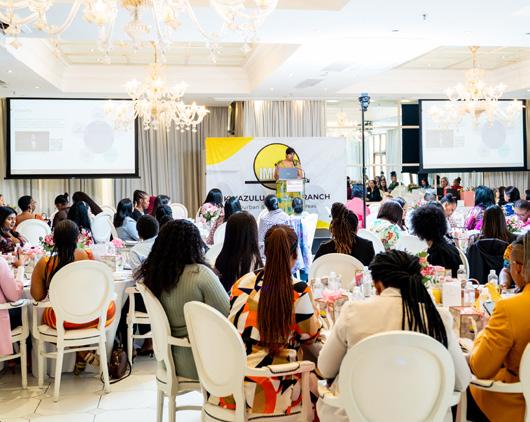
challenges as they arise. Her words served as a powerful reminder that growth often comes from stepping out of our comfort zones and believing in our potential to learn and adapt along the way.
Importance of mental health
Dr Keshika Singh, a psychiatrist, emphasised the critical need to prioritise mental health, advocating for a shift in how women approach their daily lives.

Her message challenged the widespread belief that women need to juggle multiple responsibilities simultaneously to succeed, advocating instead for a more balanced and mindful approach to life and work.
EQ
Samista Jugwanth, Technical Director at Zutari, shed light on the profound impact of emotional intelligence and introspection in shaping a successful engineering

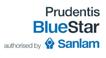
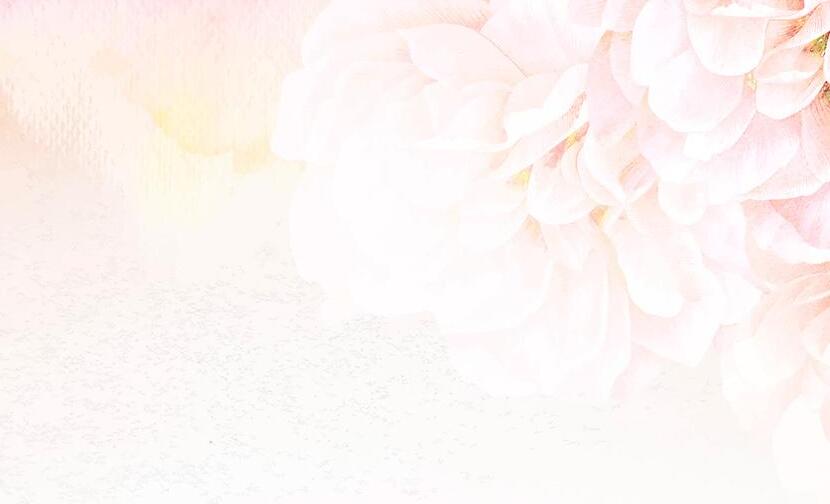
1 2 3 4 5

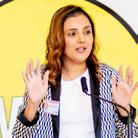
career. She articulated the importance of deeply understanding one’s personal boundaries and core values, which are crucial for making informed decisions and maintaining resilience in a demanding field. By fostering self-awareness and emotional insight, professionals can better navigate career challenges, build meaningful relationships, and stay true to their personal and professional goals. Her insights emphasised that a strong grasp of emotional intelligence not only enhances individual performance but also contributes to a more fulfilling and balanced career trajectory.
Dignified sanitation
Preyan Arumugam, PhD, Senior Research Scientist at the WASH R&D Centre, UKZN, presented groundbreaking technologies designed to enhance the quality of life for underprivileged communities. Her presentation underscored the profound impact of these innovations on addressing essential needs and highlighted how fundamental conveniences, such as having access to a functioning toilet, are often taken for granted.
Dr Arumugam’s remarks served as a poignant reminder of the disparity in basic amenities and the importance of leveraging technology to improve living conditions and promote dignity for all. Her work exemplifies how engineering solutions can make a significant difference in addressing global challenges and improving everyday life.
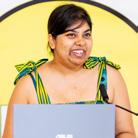
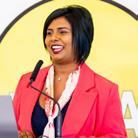
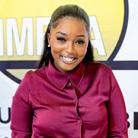
1 ECSA President, Refilwe Buthelezi, was the keynote speaker at the KZN Women’s Day event
2 During her presentation, Dr Keshika Singh, a psychiatrist, emphasised the critical need to prioritise mental health, advocating for a shift in how women approach their daily lives
3 Samista Jugwanth, Technical Director at Zutari
4 Preyan Arumugam, PhD, Senior Research Scientist at the WASH R&D Centre
5 The panel discussion was led by Philile Mphemba from Maswazi Marketing and Distribution
Panel discussion
Another highlight of the day was the dynamic panel discussion, led by Philile Mphemba from Maswazi Marketing and Distribution, which featured trailblazing women from
panellists engaged in a thought-provoking conversation on overcoming challenges, leveraging opportunities, and shaping the future of engineering. Their collective wisdom offered actionable insights and encouraged attendees to approach their careers with greater intentionality.
The success of the event was not only reflected in the powerful speeches and discussions but also in the sense of community and inspiration that permeated the room. The energy was palpable, and attendees left feeling motivated and rejuvenated, ready to make their mark in the engineering world.
Thanks to our sponsors, speakers and delegates
We owe this success to the unwavering support of our sponsors, the dedication of our speakers, and the enthusiastic participation of all attendees. Your contributions made this event a truly memorable celebration of women in engineering. We eagerly look forward to next year’s event, where we will continue to champion the cause of women in this vital industry.
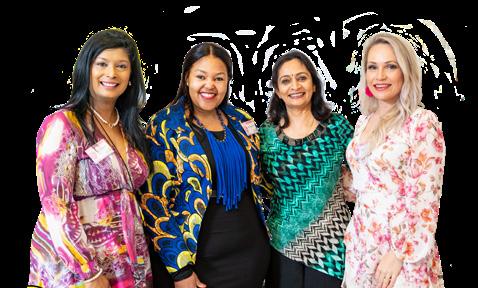
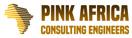

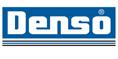


From left: Vanessa Govender, Governance Lead, Standard Bank Group; ECSA President, Refilwe Buthelezi; Bhavna Soni, IMESA Deputy President; and Roxanne Canny, IMESA KZN Vice-Chairperson
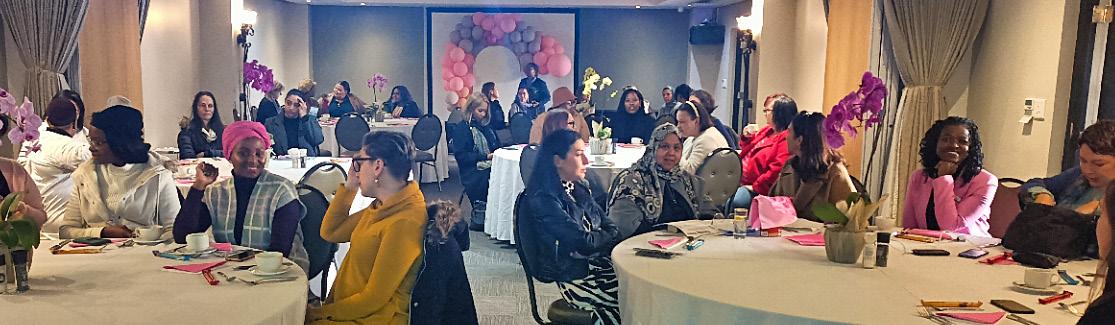
“Visionary Women Shaping Our World” IMESA Western Cape:
IMESA Western Cape celebrated Woman’s Day on 8 August 2024 at the Protea Hotel in Durbanville. Fifty ladies joined this special day where woman’s achievements, without regard to divisions –whether national, ethnic, linguistic, cultural, economic or political – was celebrated.
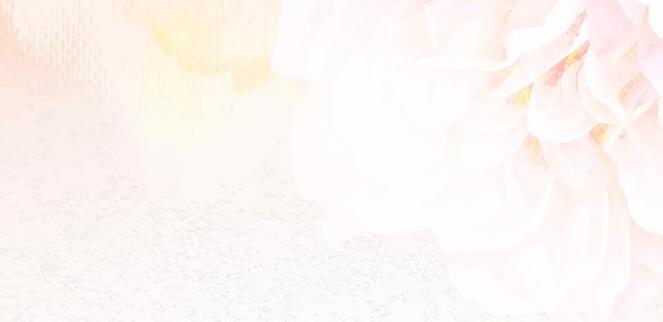
with the Wind. Among her many talents, Hedy devised a method of encrypting signals to prevent enemy spies from listening to sensitive information, which was used during WWII. Without her, there would have been no wireless communication in our modern world.

Setting the trend for the day, my opening presentation commemorated “Four Powerful Women in Engineering” starting with Edith Clarke, the very first female engineer. Born in 1883, Edith created the Clarke calculator for graphing electrical properties, setting the then benchmark for industry.
Another influential pioneer was Dr Ellen Ochoa, former director of NASA’s Johnson Space Centre, who was the first Hispanic woman to venture into space. She amassed a remarkable career marked by four space flights and nearly 1 000 hours spent in the cosmos.
A big surprise was Hedy Lamarr, an incredible actress and brilliant female inventor, known for playing alongside Clark Gable in Gone
PATHFINDERS
1 Edith Clarke created the Clarke calculator for graphing electrical properties, setting the benchmark for industry at the time, with the invention patented in 1925
2 Dr Ellen Ochoa, former director of NASA’s Johnson Space Centre, who was the first Hispanic woman to venture into space
3 Hedy Lamarr, who played alongside Clark Gable in the landmark Gone with the Wind movie epic, devised a method of encrypting signals to prevent enemy spies from listening to sensitive information during WWII
4 Dr Patricia Bath was the first African American woman doctor to receive a medical patent. She developed cutting-edge technology for treating and removing cataracts through her Laserphaco Probe
Last, but not least, Dr Patricia Bath was the first African American woman doctor to receive a medical patent. She developed cutting-edge technology for treating and removing cataracts through her Laserphaco Probe.
Speakers
The first speaker for the day, Shenaaz Moos, a registered counsellor from Happy Confident Me Counselling Workshops, reminded us of the many roles woman play in society and at home, through her “Discarding Roles to find Authentic Freedom and Joy” presentation. Her informal manner in addressing these roles hit the spot and gave direction to inner exploration of our own roles, identifying “the good, the bad and the ugly” in our own lives.
Roles discussed included “Mother”, “Victim”, “Martyr”, “Invalid”, “Warrior Princess”, “Bitch” and “Girl-Woman”. A clear message of “Facing the fear of change and acting in spite of it creates freedom” resonates still in my mind.
After an extravagant buffet breakfast –where opportunity was given to networking, building new industry connections and lasting friendships – Monique Albertyn, National Technical Marketing Engineer from Kaytech presented a technical paper on “Sustainable Solutions at Coastal Park Landfill: A Case Study”.
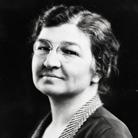

By Jeanine du Preez
Her insightful presentation provided a process flow in achieving innovative and environmentally friendly methods to manage waste sustainably. This included discussion on various geotextiles that were used in the design and construction of a new landfill cell and the capping of an existing one. One of the biggest challenges was the threat of differential settlements and the long-term mechanical breakdown of the organic content in the waste body. This posed significant settlement risks to any infrastructure built within or upon the completed cell.
Once completed, the Integrated Waste Management Facility (IWMF) at Coastal Park landfill site provided numerous advantages to the City of Cape Town. The existing waste collection and disposal routes could remain unchanged, ensuring that all waste continues to be delivered to Coastal Park, even after the landfill's closure. This not only guarantees uninterrupted public refuse collections, but also provides cost certainty for future operations. Additionally, the facility's proximity to the local informal waste sector, already established due to the landfill's presence, is beneficial.
The use of existing City of Cape Town-owned land, previously designated as unusable for other developments, frees up other areas for critical infrastructure projects. Furthermore, the site already has established solid waste management operations, including operations staff, weighbridges and administration offices, enhancing its functionality and efficiency.
Our last speaker for the day, Jacqui Gooch, Lead: Transport Planning from Zutari,
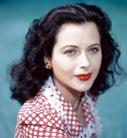
1 2 3 4
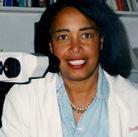

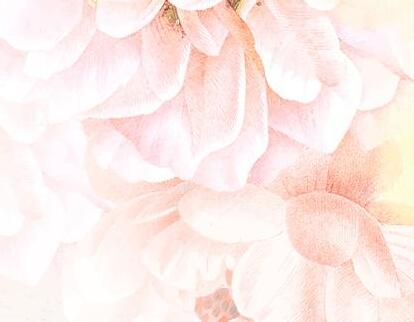
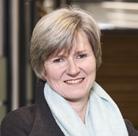
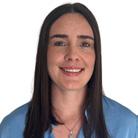
enlightened us with “The Do’s and Don’ts from a Woman’s Perspective”.
As past Head of Department at the Western Cape Government: Transport and Public Works, later known as Department of Infrastructure, Jacqui walked the walk. As she stated, “There is something special about a woman who dominates in a man’s world. It takes a certain grace, strength, intelligence, fearlessness and the nerve to never give up.”
As Jacqui stressed, one of the most important “Do’s” to remember is to understand and focus on your “Why”. Why am I here? Why do I do the work that I do? Why will my team follow me? Another important requirement to success is to build a strong team where you encourage active dissent, as it adds value to your team and organisation.
Different opinions create thought provocation, leading to better solutions. However, as Jacqui highlights, be aware of the “Don’ts”. You need to be able to identify your blind spot; this can be your own behaviour or a person, which can hold you back or destroy your goals.
So, in summary, focus on resilience, building partnerships and being compassionate while staying decisive. Mobilise your team, inspire, connect and activate them, but remain the final decision maker and last resort.
In closing, I’d like to extend my thanks to all the ladies that joined us on this special day. Let us recognise the significance of woman in our lives and in society and inspire all for a great future of achievements.
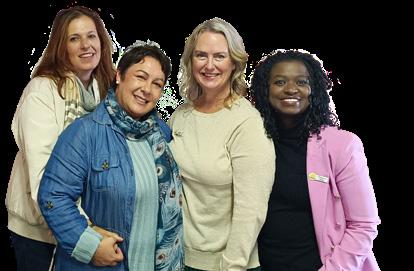
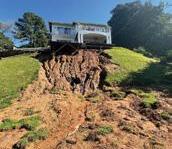
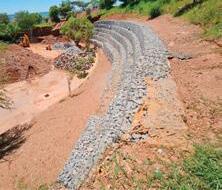

Products
Gabions and River Mattresses
Hexagon Wovenmesh
Square Weldmesh
Gabion Tool Sets
Biodegradable Soil Blankets
Soil Bioengineering
Gabion Rocks
Geotextiles
Sandbags
Gabion Barriers
Gabion Barrows Ser vices


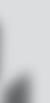
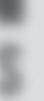
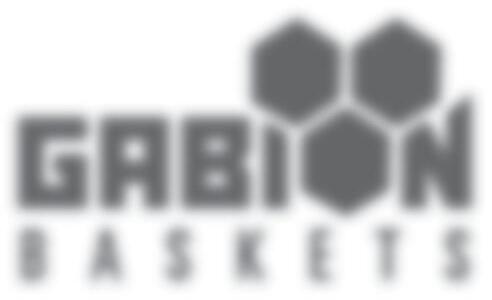

From left are Michelle Ackerman, who runs the branch’s Membership/Secretary portfolio; Emmarentia Stipp, who forms part of the branch’s ad-hoc seminar/event team; Jeanine du Preez, IMESA Western Cape Branch Chairperson; and Princess Muke, from the IMESA ad-hoc seminar/event team.
Shenaaz Moos, a registered counsellor from Happy Confident Me Counselling Workshops
Monique Albertyn, National Technical Marketing Engineer at Kaytech
Jacqui Gooch, Lead: Transport Planning from Zutari
AMMANN DEMONSTRATES CLASS LEADERSHIP IN ASPHALT
PRODUCTION
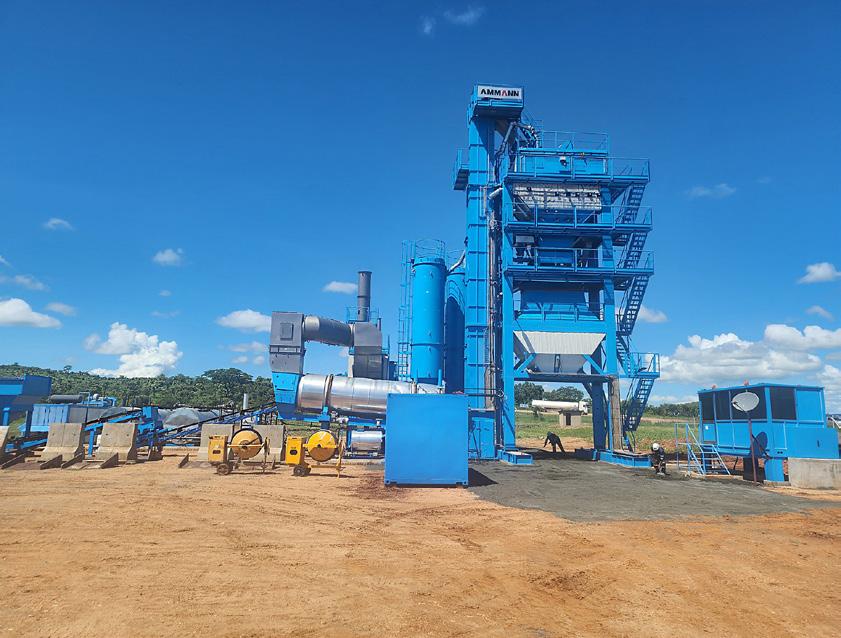
Strong demand for Ammann batch and continuous mix asphalt plants during 2024 has further strengthened the Swiss original equipment manufacturer’s (OEM’s) penetration into the local and Southern African market. IMIESA speaks to Rocco Lehman, Managing Director of Ammann Kenzam South Africa, about market developments that include allied growth for its complementary product range.
Akey trend in the market at present is the increase in requests for mobile solutions so that contractors can relocate their plants to new job sites in the shortest timeframe possible, in turn reducing associated costs. And while we do have standard trailer-mounted models, like the ACM Prime Series produced by Ammann in Brazil, these are not road legal in South Africa and Southern Africa, so we needed to find a solution,” Lehman explains.
Ammann Kenzam’s research and development (R&D) team has responded with the design of trailer-mounted configurations for Ammann’s ACC 120 CounterMix plant produced in India, the latter being a top seller in the Southern African region.
Environmentally friendly, the ACC 120 combines the simplicity of existing continuous drum-mix plants with the added efficiency achieved through counterflow technology. Additionally, the plants produce mix at a lower cost than traditional parallelflow drum-mix plants and require less
Perspectives of an Ammann ValueTec 140 (140 tonnes per hour) batch plant. Cold-mix recycling options cater for up to 25% RAP. The plant can also be upgraded for hot-mix recycling to process 40 to 45% RAP materials
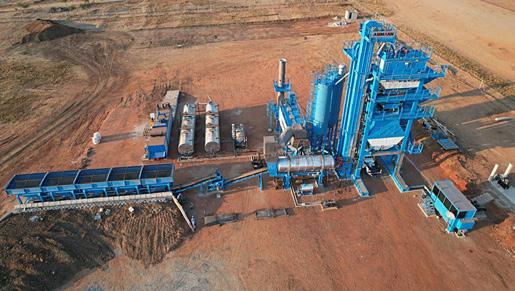
energy to heat materials, contributing to reduced emissions. An added benefit is the option of incorporating a recycled asphalt (RAP) component.
To date, Ammann Kenzam’s in-house engineering team have successfully modified two ACC 120 CounterMix plants, both for contractors based in Zimbabwe. The first unit was commissioned in 2022 for Exodus & Company, and the second
for Road Trackers Construction during July 2024. Exodus & Company's order included a purpose-designed containerised laboratory, which is skid-mounted.
“The first conversion was a great success and was also the first 120 CounterMix plant in the world to be trailer-mounted for legal on-road towing. Feedback from Exodus & Company has been very positive and during July we had an opportunity to put
our design to the test when our technical field service team worked with the client to relocate their plant for a new project. It took approximately two weeks to breakdown the plant and recommissioning it at its new site – ready for full production output – which is an exceptional timeframe in industry,” Lehman continues.
He adds that a key advantage of the trailer-mounted design is that no cranage is required, which is especially beneficial when working in more remote locations.
Ammann Kenzam is currently busy with its third ACC 120 CounterMix mobile plant conversion for a South African client.
Local fabrication
Ammann South Africa first established a presence in South Africa some 14 years ago, with a direct interface with the market for its asphalt plant range. The one element that was missing was a local fabrication arm, which led to the subsequent acquisition of Kenzam Equipment by Ammann Group Holdings AG (Ammann Group) during 2022 to form Ammann Kenzam as a wholly owned subsidiary. This development followed Kenzam Equipment’s appointment as Ammann South Africa’s asphalt plant dealer in May 2020.
As a specialist OEM, Kenzam has a longestablished track record for the design and manufacturing of products for the asphalt and bitumen markets in South Africa and Africa. Key examples include containerised emulsion plants, bitumen drum decanters and bulk bitumen storage solutions, all of which are best-in-class and comparable with the highest standards globally.
“This acquisition is significant for two reasons. Firstly, it represents the establishment of the Ammann Group’s first fabrication facility in Africa. And secondly, we are now able to extend out market offering via Kenzam’s existing product line (which we refer to as our complementary line), and in parallel harness their mechanical engineering capabilities to provide locally sourced custom builds and plant retrofits

as part of our turnkey solutions strategy. Our trailer-mounted designs are a prime example,” Lehman explains.
Following the acquisition, the Ammann Group has made further investments at the Ammann Kenzam fabrication facility, based in Brakpan, Gauteng. This includes extra cranage, new working platform areas, machinery and stores warehousing.
Recent complementary line orders include Ammann Kenzam’s design, fabrication and delivery of a 10-tonne constant output emulsion plant for a client in Guinea, together with a 55-tonne containerised bitumen storage tank facility.
Plant
sales
Ammann Kenzam continues to grow its asphalt plant footprint, with seven new units sold over the last twelve months within Southern Africa. Included in the mix is the sale of a ValueTec 140 (140 tonnes per hour) batch plant for a client based in Rustenburg, North West province, with an allied enquiry for an emulsion plant.
“This is a very positive sign for the local market, which has experienced a dip in activity over the past three years. However, we are optimistic that the new wave of SANRAL project awards in regions like the Eastern Cape and KwaZulu-Natal, plus an anticipated resurgence in provincial and
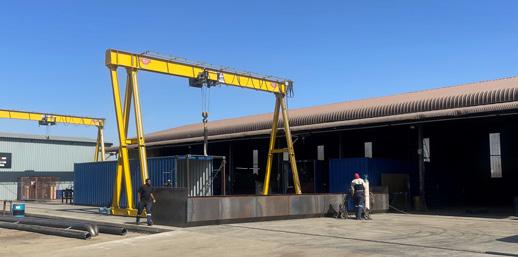
A trailer-mounted ACC 120 CounterMix plant configured for legal on-road towing, set-up for production on a project site in Zimbabwe. This is Ammann Kenzam’s second ACC 120 CounterMix plant conversion to date
municipal road infrastructure investments, will act as a catalyst for renewed expansion. This view is supported by an increase in enquires for new plants,” says Lehman.
Ammann India: manufacturing
Like the ACC CounterMix series (available in two models with outputs of 90 and 120 tonnes per hour, respectively), the ValueTec range is manufactured at Ammann India’s facility in Ahmedabad. The latter comprises four models with respective output capacities of 80, 140, 180 and 260 tonnes per hour.
The ValueTec range claims to offer the lowest product life cycle cost of all plants in this segment. They feature a fully modulating burner with a simple and easy to adjust mechanism to set the air to fuel ratio for efficient combustion and pollution control. Customised options include the utilisation of RAP, a foam mix option for the production of energy-saving warm mix, and capabilities for liquid and solid additives that enable the customer to adjust mixes to a specific design. Cold-mix recycling options cater for up to 25% RAP. The plant can also be upgraded for hot-mix recycling to process 40 to 45% RAP materials.
Machine line
In parallel, the Ahmedabad factory is also responsible for the fabrication of Ammann’s value engineered compaction rollers and asphalt pavers, which are supplied and supported in South Africa via Ammann’s official dealer, ELB Equipment. These machines are often sold as part of a packaged solution alongside Ammann plants for those contractors who specialise in both asphalt supply and pavement construction. An important development in this respect is the Ammann Group’s recent acquisition
Ammann Group has invested in upgraded facilities at the Ammann Kenzam fabrication facility, based in Brakpan, Gauteng. This includes extra cranage, new working platform areas, machinery and stores warehousing
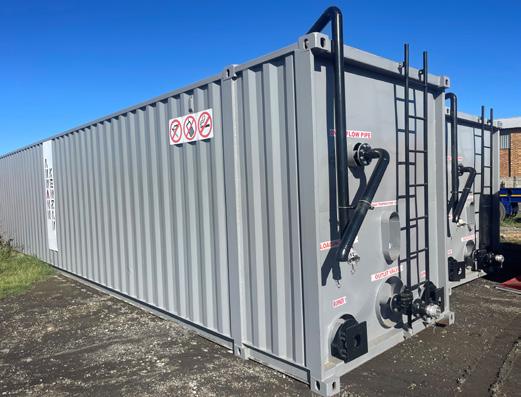
of the ABG paving product line from Volvo Construction Equipment (CE) to further refine its holistic roadbuilding offering.
The acquisition includes the transfer of Volvo CE’s paving businesses in Linyi (China) and Bangalore (India) as well as Volvo CE´s ABG facility in Hamelin (Germany). ABG pavers and screeds will continue to be produced at the facility in Hamelin, while Ammann production facilities in Ahmedabad, and Suzhou, China will also be a source in the near future. The Ammann ABG line is scheduled for release in South Africa from Q1 2025.
Training
As a major manufacturing hub, the Ahmedabad facility also incorporates a training centre that caters for global Ammann subsidiaries and dealers, as well as customer personnel. A key programme is the training provided for plant operators.
“Whether for our technicians responsible for maintaining and commissioning plants, or for customer personnel, this training is crucial for best-in-class plant performance and lifecycle cost optimisation,” Lehman explains, “A number of our staff have recently returned from Ahmedabad and we’ve seen the benefits.”
Ongoing training and human resource development is a top priority for Ammann Kenzam to ensure the OEM meets customer expectations in terms of field service and
technical advice. Collectively, Ammann Kenzam’s key personnel currently have in excess of 200 years of applied experience in the asphalt industry, which is progressively being transferring via various mentorship programmes.
Plant selection, retrofits and RAP “When it comes to technical advice and plant selection, it’s important to emphasise that each model has its purposed-designed production parameters, with the option of upgrading with the latest Ammann retrofit technologies,” says Lehman.
“Our role as an OEM is to work with the customer to devise a solution that meets their current and future downstream requirements. A case in point is the increasing specification of RAP materials as a sustainability measure by local and global roads authorities,” he continues.
Bitumen storage tanks designed and manufactured by Ammann Kenzam
“RAP capabilities can range from 15 up to 95% depending on the specific Ammann plant. For the European Union region where there’s current demand, 95% RAP plants are common since there’s a readily available supply of recycled material. However, the South African and African market are not there yet, so our plants sold locally are generally designed for a 15% RAP capability, an example being the ACC CounterMix 120,” says Lehman.
As Lehman points out, as the RAP percentage increases, so too does the virgin material temperature, for example 277 degrees Celsius for a 30% RAP as opposed to around 180 degrees Celsius for 25% RAP. To upgrade an existing 25% RAP plant to meet a 30% RAP requirement, one of the recommended retrofit options would be the addition of a new mixing drum capable of meeting up to 300 degrees Celsius virgin material temperatures.
“An alternative is to investigate other options like foamed bitumen in-placed recycling, where you can compact your layers at around 80 degrees Celsius and mix at approximately 120 degrees Celsius,” adds Lehman.
“Within the Ammann Group we have the solution for all asphalt paving designs. The key is to ensure that the plant specification matches the contract requirements. Here we’re well placed as industry leaders to tailor-make solutions that deliver the best results,” Lehman concludes.
55-tonne containerised bitumen storage tank facility
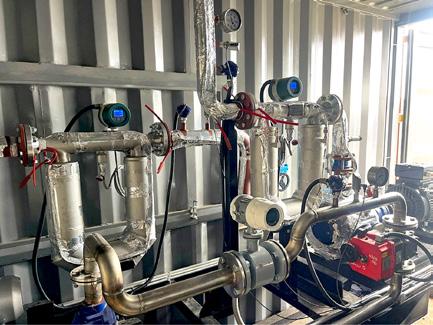
Ammann Kenzam recently secured an order for the design, fabrication and delivery of a 10-tonne constant output emulsion plant for a client in Guinea, together with a

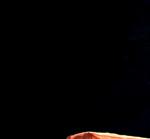
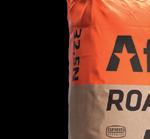

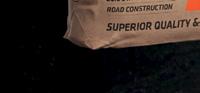


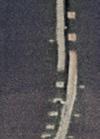

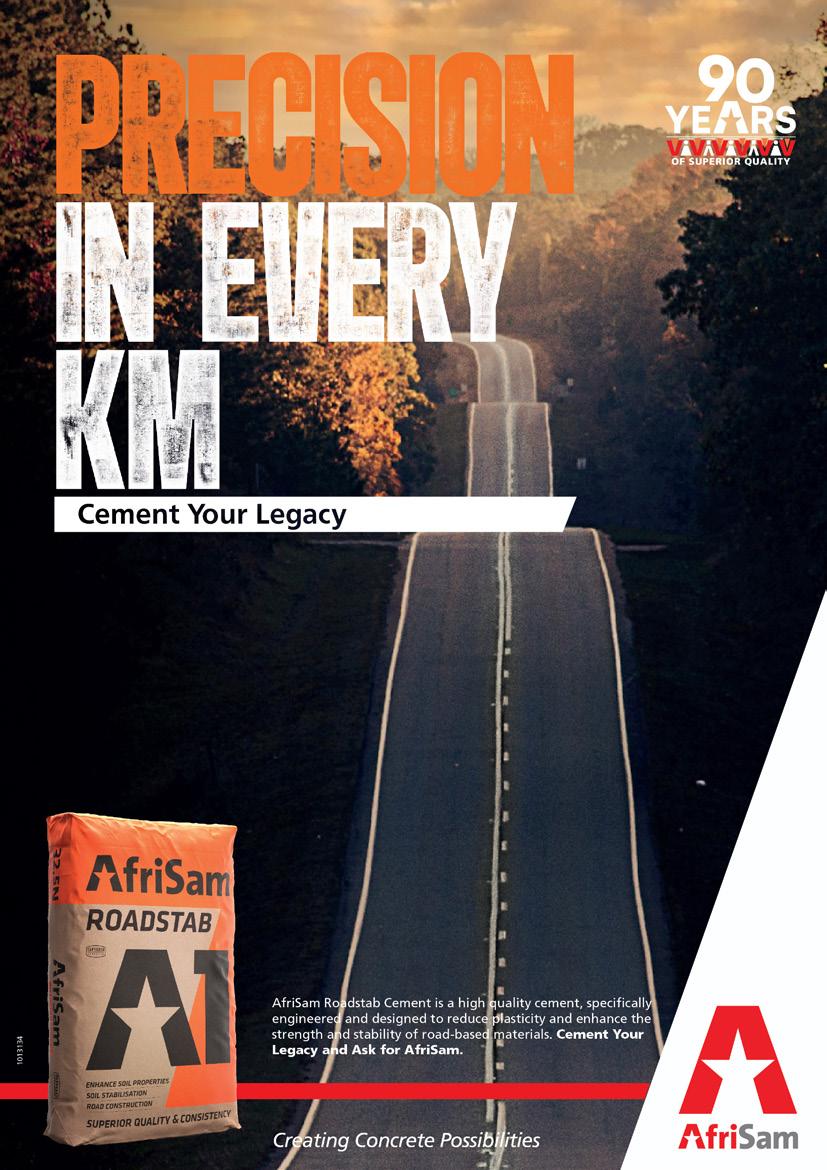
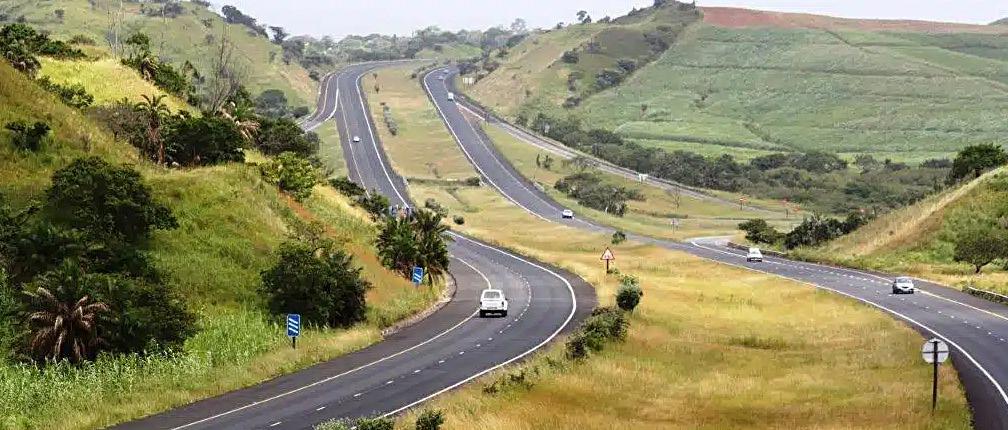
Sabita commits to green goals and industry excellence
As a world leader, South Africa continues to showcase innovation and fit-for-purpose solutions for the flexible pavement industry. IMIESA speaks to Phil Hendricks, CEO of the Southern African Bitumen Association (Sabita) about key trends and initiatives, including the launch of their Sustainability Charter.
Has 2024 been a positive turning point for the SA roads industry?
When we look back at the 2023 budget announcement, some R903 billion was allocated over the next three financial years for infrastructure expenditure. Of this, approximately R351 billion was allocated to transport and logistics.
The bulk of the roads work currently in progress is being driven by contracts awarded by the South African National Roads Agency (SANRAL) for strategic projects such as the N3 Pietermaritzburg to Durban upgrade, and the N2 Wild Coast development, as well as SANRAL network maintenance.
The latest 2024 budget confirms that over the forthcoming period i.e. the next 5 to 10 years, SANRAL intends to implement the N2 and N3 flagship projects with more
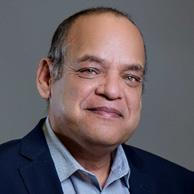
than R24.5 billion in road infrastructure investment. The implementation of backlog projects also sees the payments to service providers for road maintenance increasing from R26.3 billion in 2023/24 to R27.7 billion in 2026/27.
The budget indicated that SANRAL would increase contract awards across its network from 1 500 km during 2024, to around 3 000 km in 2025/26, an increase of around 34% over the medium-term expenditure framework. However, the full value of the proposed spend flowing through to industry remains to be seen.
Has South Africa shifted to an almost 100% reliance on bitumen imports?
The statistics show that up until around 2021, South Africa’s global ranking as a bitumen importer was placed somewhere between 95 th to 125 th position. In other words, our import volumes were traditionally very low. Historically, South Africa was also a strong bitumen exporter, however current annual bitumen shipping is only approximately 35 000 tonnes. This has reduced from 130 000 tonnes in the heydays, due to the closure of key South African refineries.
If we look at the latest figures, during 2023
South Africa climbed to around 15th position as an importer, with some 275 000 tonnes of bitumen entering the country. The reality is that this trend is set to continue for the foreseeable future. The upside is that supply is not an issue. The downside is consistency of product quality and price volatility. Sabita has established importation guidelines, and it is essential that all importers adhere to these protocols, ensuring safe and consistent delivery of product to their clients.
Aside from the logistical challenges, another related development is that our testing regimes have intensified to ensure that these imported products are compliant in terms of our Performance Grade (PG) specification. We also need to ensure that as an industry we’re consistent in terms of testing. In 2023 we partnered with the Asphalt Institute in the USA to provide training for South African laboratories on PG binder testing. A similar initiative for asphalt PG testing during 2024 is needed.
Are new guidelines being developed for the local industry?
We’re in the process of transitioning the PG Technical Guideline to a SANS specification. In response to the 2023

Phil Hendricks, CEO of the Southern African Bitumen Association (Sabita)
CAPSA conference resolutions, we have also started to update our Manual 35 Asphalt Hot-Mix Design Guideline for South Africa to address design gaps. We’re also currently updating Manual 19 on Bitumen Rubber Asphalt Wearing Courses, based on the latest industry research. At a later stage, other planned updates include Manual 36 on Reclaimed Asphalt, and Manual 17 on Porous Asphalt Mixes. The Technical Guideline 1 on the Use of Modified Bituminous Binders in Road Construction is currently being updated to reflect current practice and including aspects related to in mix and recycled plastic modifications.
In parallel, our work on cold-mix asphalt product certification has been an important development on behalf of our members and industry, with buy-in from South African roads authorities.
Is road maintenance receiving adequate funding and support?
At national level, SANRAL is leading the charge. At the provincial level, with the latest transfers of R51.8 billion over the Medium-Term Expenditure Framework to the provincial road maintenance grant, the latter has declined by R2.7 billion on the maintenance component.
An additional R14,6 billion has been allocated to the grant for capital expenditures.
A key supporting endeavour in this area is the Road Maintenance Forum (RMF), a joint initiative led by CESA, the CSIR, IMESA, SAT, SAFCEC, SANRAL, SARF and Sabita, which
is intended to share best practices and technologies. The establishment of task groups with specific national objectives is another core priority, along with training support for emerging contractors.
We recently held our 5 th RMF on 17th July 2024 where key topics included initiatives by the Department of Transport (DoT) to promote the adoption and use of the Asset (SANS/ISO55001) and the Construction Management Systems (SANS1393). There was also an update on the Vale Zonke initiative – a labour-intensive programme to fix potholes across South Africa. The latter is being implemented by the DoT and led by SANRAL in supporting local authority implementation. The CSIR also presented on Smart Mobility Pavement Asset Management, and there were technical presentations on crack sealing techniques.
The Vale Zonke initiative is gaining ground, but at present available provincial and municipal maintenance budgets are not being fully utilised. As an aside, an interesting development is an indication by provinces of their intention to develop in-house maintenance capabilities.
As in South Africa, road maintenance is a top global priority. To highlight its importance, for example, the European Asphalt Pavement Association (EAPA) hosts International Road Maintenance Day in April each year and launched its own RMF along similar lines to South Africa in 2024.
The resolutions for the 5th RMF are pivotal. They include running a dedicated workshop that deals with training related issues currently hampering industry performance.
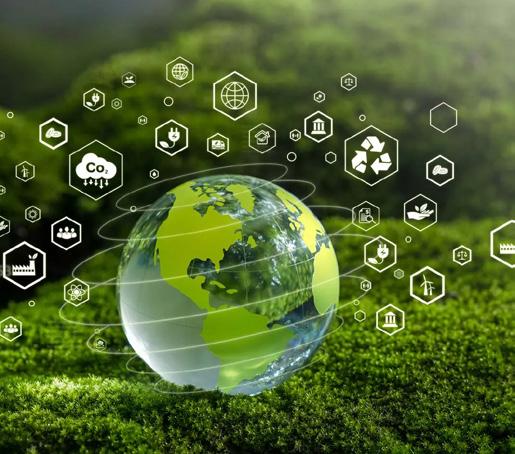
Sabita unveiled its Sustainability Charter earlier this year, which commits to achieving carbon neutrality in the manufacture of road construction materials by 2050. The Charter has identified various potential actions across the pavement life cycle, as shown in the above diagram
What are the key drivers of Sabita’s Sustainability Charter?
In line with the Department of Transport’s Green Transport Strategy, Sabita is committed to promoting practices that enable a netzero emissions future. This was the prime motivation for the adoption of our Sustainability Charter earlier this year. Our charter commits to achieving carbon neutrality in the manufacture of road construction materials by 2050. Ways to achieve net-zero emissions entail promoting the specification of environmentally friendly products that include cold laid and warm-mix asphalts, bitumen rubber and high modulus asphalts, and nano modified emulsions. A greenhouse gas calculator will also be introduced for manufacturing plants to assist with regulatory compliance and carbon offset initiatives.
Within the mix, the use of PG specifications for binders is key to ensuring durability and ease of maintenance, as is encouraging designs that mitigate climate change effects and facilitate adaptation to new environmental norms. The latter includes greater emphasis on the reuse and recycling of materials, such as using crumbed rubber and modified binders in asphalt production.
As we gain traction, Sabita will release Sustainability Progress Reports to our
Maintenance & preservation
Use stage Construction
Strategic actions across the pavement life cycle
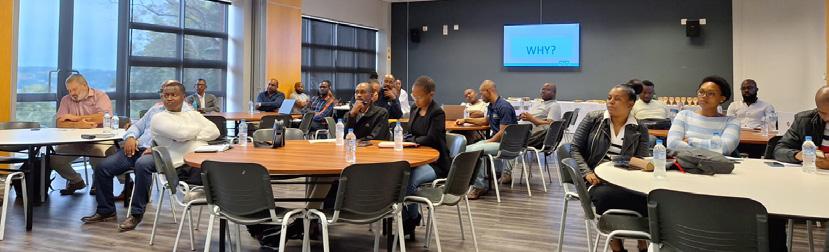
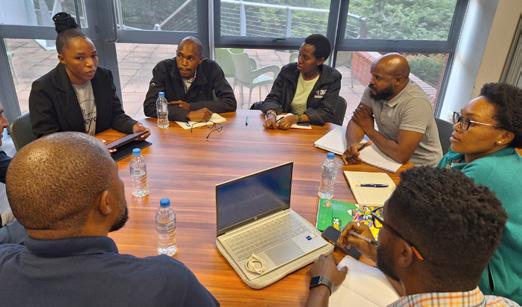
members and industry, showing actual outcomes versus objectives.
What’s an example of an international asphalt trend?
Sabita’s Technical Committees have worked extensively over the years to develop Guidelines for industry to suit specific applications. These include warm-mix asphalt production and paving techniques as a green alternative. Sabita’s Manual 32 drills down into the details.
During a recent trip to Europe, it was therefore revealing to see that there is also a major push in this region to increase the utilisation of warmmix asphalt to reduce emissions in response to government policies and commitments to COP Paris Agreement targets.
The benefits of warm-mix asphalt include reduced fuel consumption, lower mixing temperatures during manufacturing, with an ensuing reduction in emissions. It’s also a much safer product in terms of health and safety for workers. Therefore, I believe warm-mix asphalt adoption is going to become far more widespread in future and will support the South African government’s sustainability strategy, alongside other asphalt products.
Is there scope to increase labour-based construction (LBC) techniques?
A regional initiative to establish a forum for industry and academia to work together by enabling students’ participation and providing quality research has been set in motion and is gaining traction. Two workshops have already taken place, one in the Western Cape and the second as a combined KwaZulu-Natal/Eastern Cape session. Shown here are delegates at the KwaZulu-Natal/Eastern Cape workshop
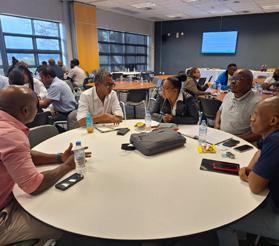
For LBC to work effectively requires specialist design and project management capabilities. Sabita has a dedicated suite of videos and reference materials on LBC, and there are certainly opportunities. However, the emphasis should be on empowering emerging SMME contractors. Early work on LBC tended to focus on temporary job creation rather than skills transfer. We now need to focus on the latter.
How can the industry improve gravel road standards?
Upgrading to a flexible pavement standard comes at a cost, especially for low-volume roads, so that’s not a viable option. However, quarrying commercial aggregates does deplete an increasingly scarce resource. So, in this respect, there is an opportunity to “weather” proof unpaved roads using nano technologies. That will help to reduce the effects of rain on these sensitive pavements and lower overall gravel maintenance costs.
And in closing?
Technology, as well as safety, health and the environment are among Sabita’s critical pillars in ensuring that South Africa is benchmarked against the best practices globally. In addition to our Technical Committees, Sabita continues to achieve this by working extensively with
research institutes and universities – in consultation with our members – to develop and implement appropriate bituminous products.
A case in point is the introduction of an Industry and University Forum, following requests by Sabita members at CAPSA 2023. Members said they needed to keep abreast of current university research and development (R&D) programmes and to leverage this knowledge base. This also creates opportunities for members to provide R&D funding support. To date we’ve hosted two forums, one in the Western Cape, and the other as a combined forum for the Eastern Cape and KwaZulu-Natal regions. We now plan to host a Gauteng based forum as we expand the industry and regional university network.
Having an inclusive and well-informed industry is crucial, which is why Sabita is on a membership drive. This includes a new and affordable SMME membership category. Bitumen importers have also joined us as new members, which is an important development in the total value chain. Collectively, we can make a meaningful difference, with the skills and capacities in place to deliver on South Africa’s road transportation objectives.
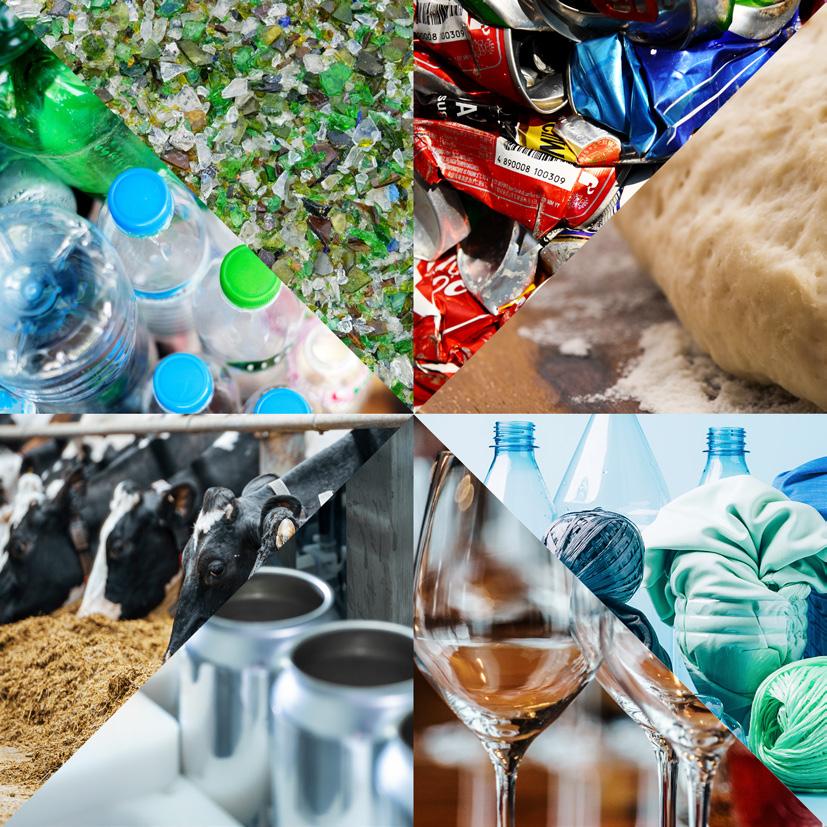
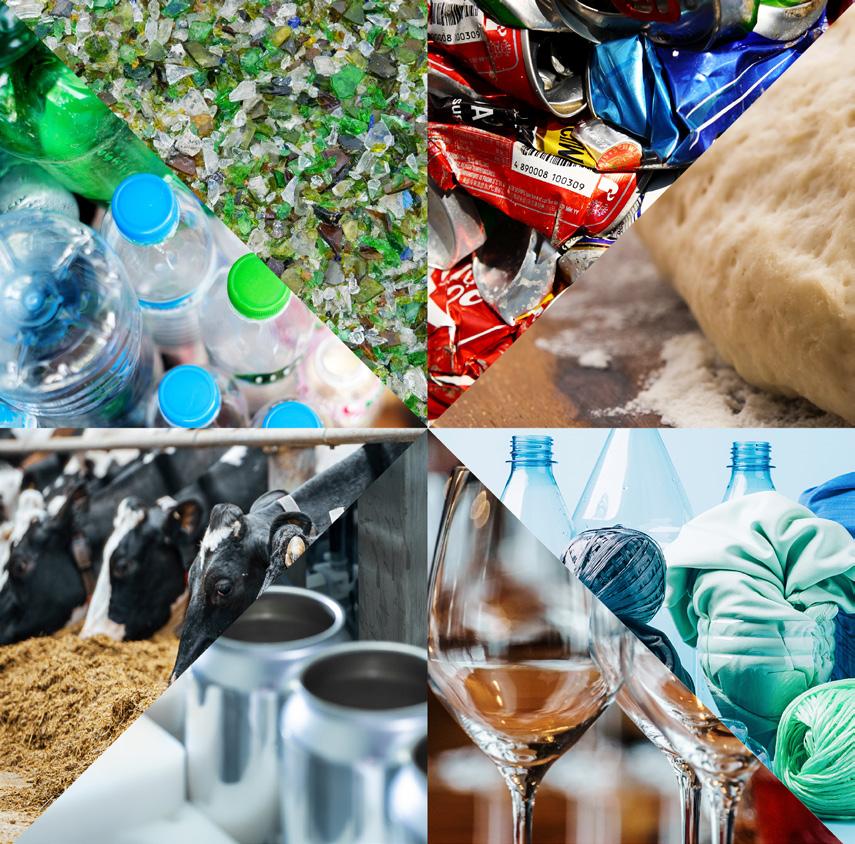
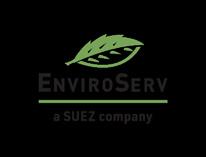
PEOPLE AND PLANET

ENVIROSERV’S SUSTAINABLE DEVELOPMENT TARGETS CREATE A SAFER ENVIRONMENT
With a renewed commitment to sustainable development and generating
shared value for customers, EnviroServ, a leader in waste, water and wastewater management, is focused on reaching significant milestones in three key areas.
EnviroServ, a SUEZ company, is in alignment with the global group's sustainable development priorities, focusing on the pillars of climate, nature, and social responsibility.
“Ambitious targets were set based on analysis of the industrial realities of EnviroServ’s activities, using global external benchmarks to identify best practices,” explains EnviroServ CEO Dean Thompson.
The company’s stated goals include reducing its greenhouse gas emissions at its six waste management facilities by 60% by 2028; doubling the amount of renatured and restored capped landfill areas by 2027 using 100% indigenous species; reducing the frequency and severity rate of accidents; and growing the number of people trained in the workforce to 76% by 2028.
Climate pillar
The Intergovernmental Panel on Climate Change has reported that methane, a potent greenhouse gas, is at least 28 times more effective than carbon dioxide at trapping heat in the atmosphere over 100 years. According to the United Nations Environment Programme, cutting methane emissions by 45 percent by 2030 could help meet the Paris Agreement's goal of limiting global warming to 1.5°C.
EnviroServ is actively contributing to energy decarbonisation by enhancing the sustainability of its waste management facilities. By capping the working face of a landfill as soon as possible, the smallest amount of surface area is exposed
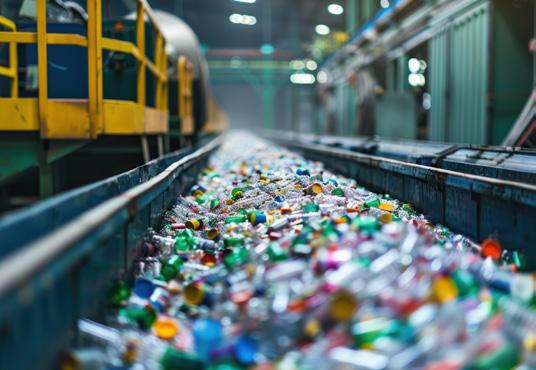
to the environment, minimising the risk of odours and methane that is released, while reducing the amount of contaminated stormwater and leachate.
“Adapting our sites using international best practice has resulted in a 19% decrease in greenhouse gas emissions since 2022, so we have already made a significant stride towards our 60% goal for 2028,” says Thompson.
Biogas feasibility studies have been done at EnviroServ’s waste management facilities situated at Shongweni in Hillcrest, Chloorkop in Johannesburg and Vissershok in Cape Town looking at carbon credit reductions where EnviroServ can carbon trade. “We also hope to double the volume of landfill gas which is currently being flared at Chloorkop and Shongweni to reduce emissions.”
Nature pillar
Almost 26 hectares of land will be renatured across EnviroServ’s operating sites as the company plans to double the amount of land restored by 2027. Within the same timeline, no phytosanitary products will be used in any of the company’s green spaces or facilities.
“Through improved training and reporting we are targeting a 5% improvement in waste sorting efficiency, which is essential in the
recovery of recycled waste. Proper separation and categorisation of waste at source minimises the amount sent to landfill, conserving resources and reducing environmental impacts,” Thompson continues.
Social pillar
EnviroServ is tracking well against health and safety benchmarks, with frequency and severity of accident rates already substantially below the targets the company sets for itself. “We will continue to contribute to the sustainable development of the communities in which we operate, maintaining 50% spend among local small business suppliers and growing development of employees through training programmes from 63% to 76% by 2027.”
“As a business operating in the environmental space, we are taking our share of responsibility for the preservation of resources and people, and are working to position ourselves as best-inclass," adds Thompson.
“We have kicked off this journey by disclosing baseline figures and will share updates on how the business is tracking towards our stated targets. These commitments are a powerful driver for our employees and we are proud that we have already seen tangible results,” Thompson concludes.
SAVING ENERGY AND REDUCING WASTE
During the 2020 renovation of Pick n Pay On Nicol, the retailer discovered the significant environmental benefit of refurbishing Air Handling Units (AHUs) instead of replacing them. To date, 14 stores have had their AHU refurbished, with another 17 in the pipeline. This includes converting masonry plants and refurbishing water-cooled packaged units to air-cooled ones, focusing on the waste hierarchy of reducing and reusing to improve sustainability. Each refurbishment keeps two tonnes of polystyrene – which isn’t recyclable –from landfill.
“Existing equipment, which often relies on technology over 40 years old, was designed and installed using energy-inefficient technology. By using new technology such as computer-aided design and sophisticated computer programs, we can optimise a supermarket’s air-conditioning
requirements and reduce the size of equipment required,” says mechanical consultant Nigel Pengelly from VMG Consultants.
This initiative is part of the retailer's broader sustainability strategy focused on enhancing energy efficiency and reducing carbon emissions, with key emphasis on refrigeration, lighting, and air conditioning. Pick n Pay has set a target to be net zero carbon by 2050 and is in the process of setting credible emission reductions targets through the Science Based Targets Initiative.
It also aims to divert 75% of general waste produced at Pick n Pay-owned operations by 2025, and, throughout its business, is looking for opportunities to reduce all waste streams. Pick n Pay Clothing stores, for example, repurpose materials during renovations and new store builds – 150 stores are Green Star Level 4 certified, while the flagship Sandton store is Level 5. Additionally, almost half of the retailer’s product
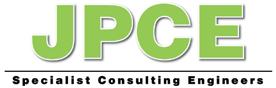

Steffen Burrows, Head of Sustainability at Pick n Pay, in front of a refurbished Air Handling Unit. Each refurbishment keeps two tonnes of polystyrene – which isn’t recyclable – from landfill
range is sustainably sourced, and since 2021 Pick n Pay Clothing has planted more than 5 000 trees at Platbos Nature Reserve for every store opening.
“By focusing on refurbishing rather than replacing it with new materials and resources, Pick n Pay not only cuts costs but also reinforces its role as a leader in sustainable retail practices, paving the way for a greener future,” adds Steffen Burrows, Head of Sustainability at Pick n Pay.
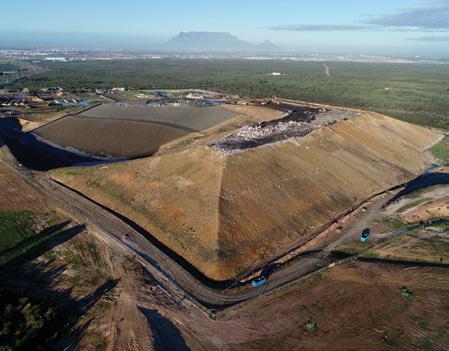
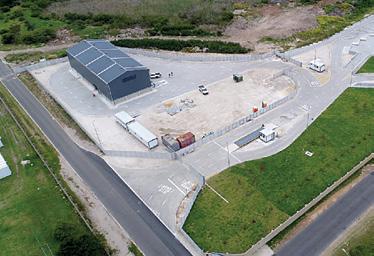


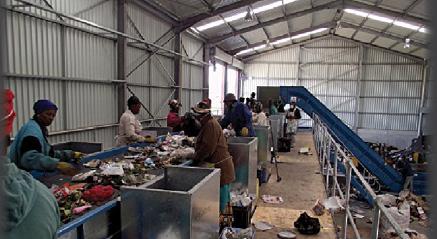


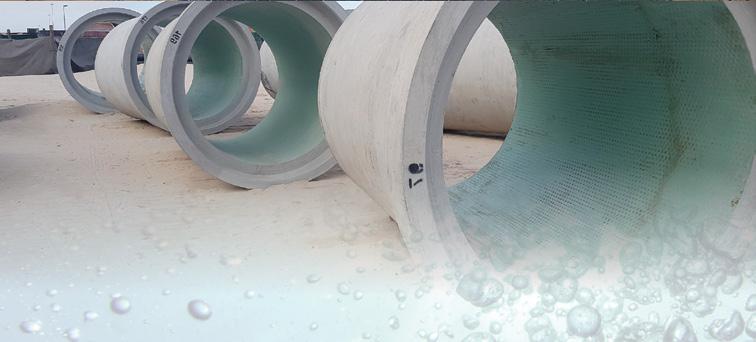
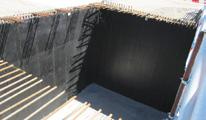
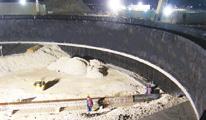
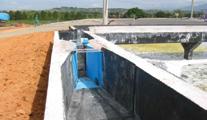
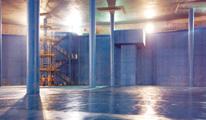
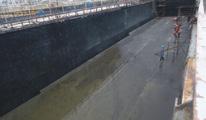

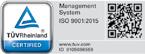
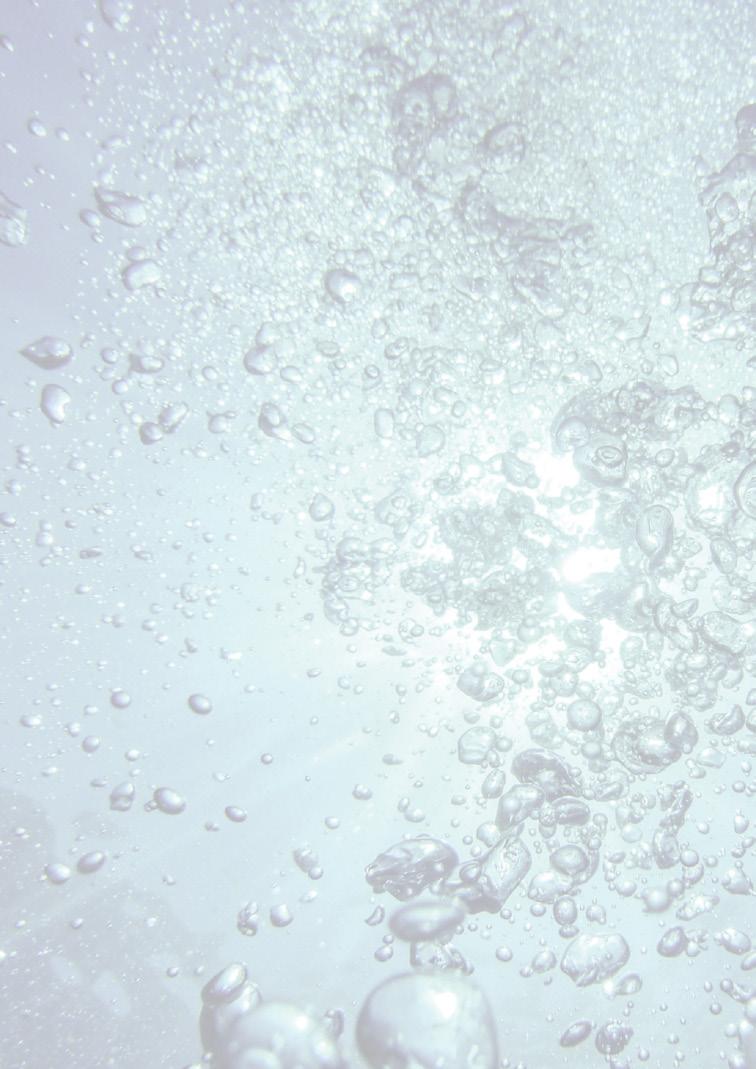
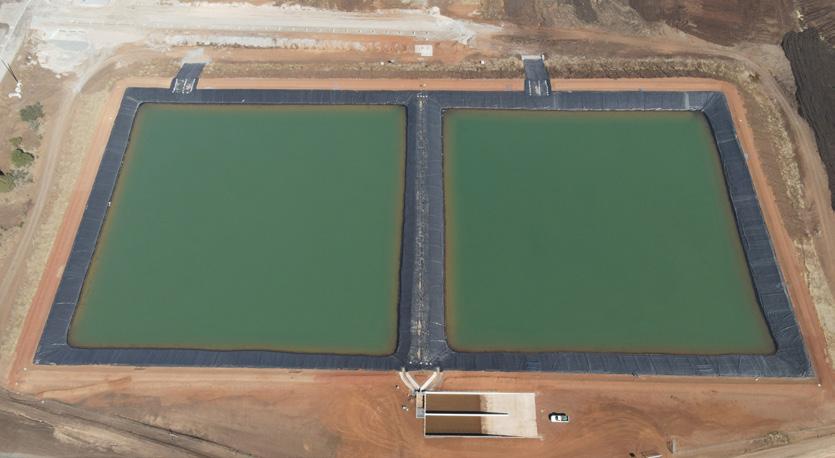
The leaders in containment liners
Geoliner™ is used in the construction of environmentally critical facilities like landfill sites, tailings facilities and ash storage facilities, ensuring that contaminated effluent does not seep into the groundwater
Designed specifically for use in chemically aggressive environments, AKS Lining Systems supplies a range of lining solutions utilised extensively in infrastructure containment projects.
AKS Lining Systems is a manufacturer of thermoplastic liners, specialising in geomembrane and corrosion protective liners. The company has grown to become a competitive global producer and its products are exported to more than 30 countries worldwide, where they are used in diverse applications such as mining, environmental conservation, water treatment and general infrastructure.
With its plant situated in Cape Town, AKS Lining Systems naturally also offers strong support to the local South African and SADC regions.
Various containment and corrosion resistant solutions
According to Peter Hardie, Technical & International Sales Manager of AKS Lining
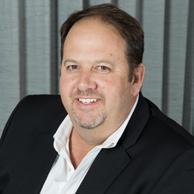
Systems, the company’s geomembrane range of products, Geoliner™, are manufactured from HDPE or LLDPE resins which are considered chemically inert.
Designed specifically for use in chemically aggressive environments, Geoliner ™ is manufactured using the “flat-die” process and is supplied in 7 m wide rolls in long lengths up to 220 m on a roll, with various surface finishes, such as smooth, textured or mega textured. These finishes can be supplied in combinations of either single- or double-sided. Our state-of-the art laboratory ensures that all liners produced meet or exceed international standards such as GRI-GM13, GRI-GM17 and the local standard SANS1526.
Geoliner™ is used in the construction of environmentally critical facilities like landfill sites, tailings facilities and ash storage facilities, ensuring that contaminated effluent does not seep into the groundwater. Crucial conservation of water makes Geoliner™ the high-performance barrier of choice.
In addition to the Geoliner™ range, AKS Lining Systems have their flagship product, AKS ™ Corrosion Protection Liner. AKS™ (Anchor Knob Sheet) is a liner extruded with a matrix of anchors. It is used extensively in acid proofing concrete structures by being cast into the concrete. The
mechanical bond into the concrete means the product can be used in a vast range of applications, from mining to sewerage treatment and large outfall sewers. Due to the extremely high wear resistance and abrasion resistance, the AKS™ internal lining in sewer systems is ideally suited for trenchless installation of large diameter pipes.
Being ISO 9001:2015 certified ensures that management systems and quality procedures are maintained and reviewed at the highest possible levels. These systems and procedures follow through right from resin suppliers, shipping and logistics, to finished product, testing and delivery.
Quality and traceability
For identification, tracking and traceability, all AKS™ and Geoliner™ rolls are individually labelled and numbered. The in-house Manufacturing Quality Control system ensures traceability of each roll and its components right through from incoming resin, in-line production testing, QC testing and final MQC Certification.
With a wealth of experience and knowledge, our sales engineers will provide you with technical assistance and custom solutions for your project. Our competent logistical team ensures expert handling and loading of trucks and containers, along with paperwork and all other commercial requirements.
We have an open-door policy, inviting customers to inspect and review their product during manufacturing and testing, giving them peace of mind when materials start arriving on their sites. Contact us at +27 (0)21 983 2700, visit our website www.aks.co.za or send an email to aksmarketing@aks.co.za.
Peter Hardie, Technical & International Sales Manager at AKS Lining Systems
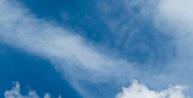
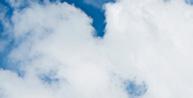

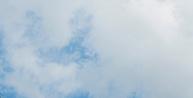
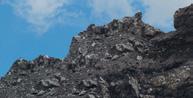
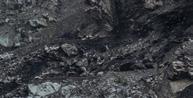
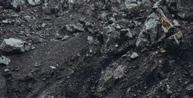

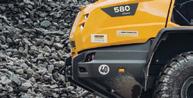
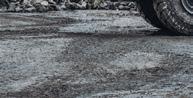
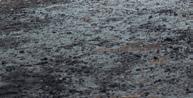
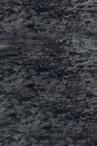
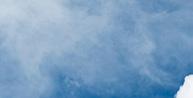


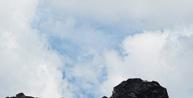
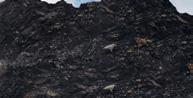
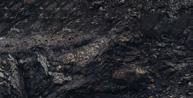
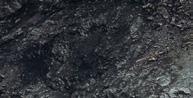
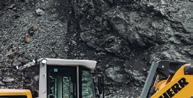
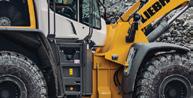
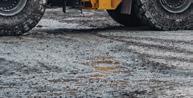
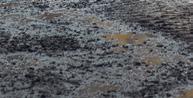
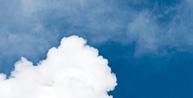

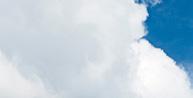
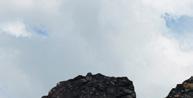
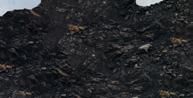
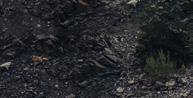
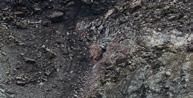
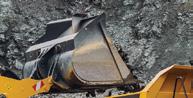

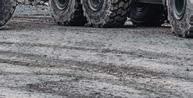

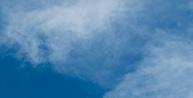

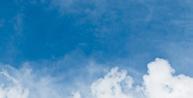
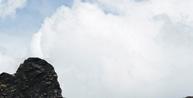
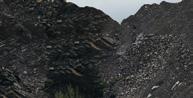
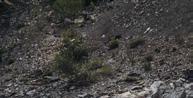


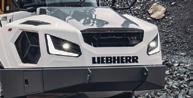

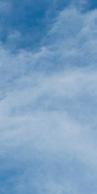
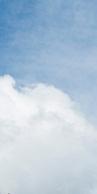
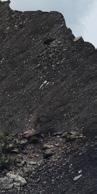
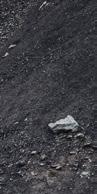

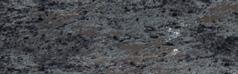
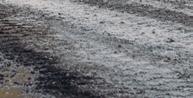


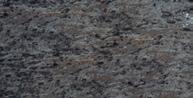

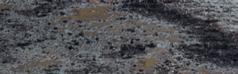

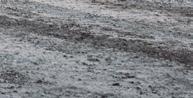

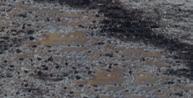
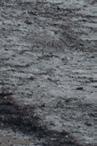


OUT OF THE BOX SOLUTIONS FOR EROSION CONTROL

Recent storm events across the Western Cape and within eThekwini highlight the importance of erosion protection measures. IMIESA speaks to Louis Cheyne, managing director of Gabion Baskets about key project interventions, as well as product developments.
The flood risks are intensifying in nature, putting major pressure on riverine environments, as well as natural slopes and engineered embankments, emphasising the need for effective retention control solutions. Marine environments are also being hit hard by stormrelated wave action,” explains Cheyne.
One of the best responses traditionally are gabion system interventions. In mass gravity, land-based retaining wall applications they provide both a natural interface and controlled permeability in cohesive and noncohesive soil conditions. They are also the best option for river embankment stabilisation due to their controlled permeability in submerged scenarios.
“From experience, however, we’ve found that in beach stabilisation situations gabions work
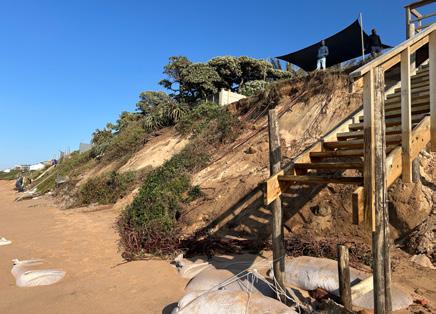
best in conjunction with sandbag systems, an area where we’ve recently expanded our offering in order to meet demand for beachfront infrastructure and property protection,” Cheyne continues.
A prime example is a current project at Salt Rock on the KwaZulu-Natal coastline, where Gabion Baskets is supplying a solution. In this case, sections of the beach in front of various seafront properties have become progressively undermined by wave action. The bordering embankment has also been subjected to slippages and become unstable.
“Due to the sucking and side-swell effect of tidal surges – compounded by extreme storms – gabions are not ideally suited for direct wave
contact because it will result in stone fill losses overtime and eventual structural failure,” he expands.
“The best approach, therefore, is to install a gabion mass gravity wall, founded on a gabion mattress to stabilise the embankment, and then to install purpose-designed sandbags as the front face to dissipate wave impact, as well as on the flanks to prevent lateral drift. A non-woven geotextile liner is also required below and behind the gabion wall to prevent sand migration.”
In addition to FiberRock® beach bags, as well as traditional sandbags, Gabion Baskets supplies Gabion Barrier Defence Cells. The latter are designed for applications that include emergency flood situations and military
Evidence of severe erosion along a beachfront section at Salt Rock in KwaZulu-Natal
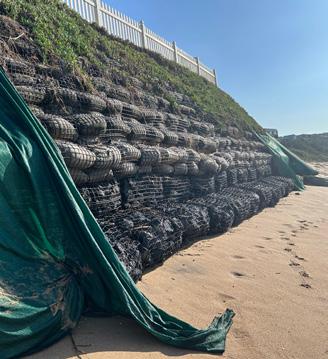
defence measures. Their composition comprises a welded-mesh interconnected concertina frame for rapid deployment, lined with a heavy-duty geotextile that can be filled with any readily available soil materials.
Slope protection on steep terrain Across the board, gabions remain one of the best
for
stabilisation options for countering erosion on steep slopes – an area where Gabion Baskets has extensive experience in providing design recommendations and project management services, alongside the fabrication and supply of gabion systems. These installations frequently combine a landscaping and engineered approach. Three recent examples comprise mass gravity
for a
solutions for two property owners in Cape Town at the prestigious Constantia Nek Estate in Hout Bay, and a solution for a residential estate in Umdloti, KwaZulu-Natal.
For the first project, a 40 m long gabion structure was installed during Phase 1, which also served to create a lawn area above the wall. A 4 m buttress was also added at the end of the wall.
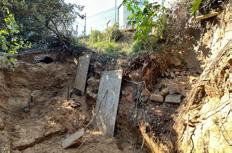
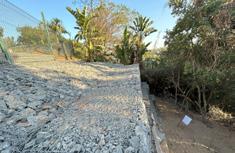
A gabion mattress was installed at the top of the embankment to prevent washaway around the gabion walling system as a further protective measure
Completed retaining wall sections in a stepped back configuration
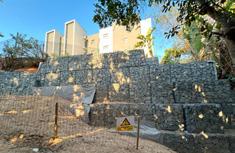
Gabion mass gravity wall designs
embankment stabilisation
residential complex in Umdloti, Kwazulu-Natal
An example of an existing erosion protection measure on another section of the Salt Rock site
A design concept example for a mass gravity gabion retaining wall with front face FiberRock® beach bags
A failed embankment section at the Umdloti site, which threatened to undermine the parking area
Phase 2 involved constructing a 10 m long gabion wall, 1 m in height, curving at the driveway entrance. For this section, Table Mountain sandstone was specified, which complements the natural surroundings.
The second project entailed a 16 m long wall designed with a step-down of 250 mm every 4 m, creating a terraced effect that enhances both stability and aesthetic appeal.
Meanwhile, for the Umdloti project, an intervention was required to remediate washaways in the aftermath of the 2022 eThekwini floods, as well as ensuing heavy storms thereafter. The environmental damage had undermined the estate’s parking area, and an urgent reinstatement was required.
The accepted design recommendation led to the construction of a series of mass gravity gabion walls in heights ranging from 3 to 5 m.
A gabion mattress was also installed at the top of the embankment to prevent washaway around the gabion walling system as a further protective measure. Additional wall extensions are now in progress.
Designing
and building safe structures
“A key consideration for all construction projects is safety, so it’s crucial to emphasise that all gabion systems designed for a mass gravity retention role above 1,5 m in height must have the final design approved by a registered professional engineer specialising in this area,” Cheyne stresses.
“The fact that these systems are also intended to remediate an often already unstable embankment must be factored in upfront during the project health and safety methodology statement.”
Another key issue is the need to ensure that suitably trained and experienced contractors are employed. As Cheyne points out, while the wireframed composition of gabions is well-suited to labour-based practices, and may appear simple to construct, these are engineered structures intended to support site specific loads in accordance with known hydrological conditions and the underlying geology. Left in untrained hands, poor construction practices could result in the retaining wall sliding away from the embankment and overturning, with potentially catastrophic results.
For the installation phase, Gabion Baskets conducts CETA accredited NQF practical site training for contractors, with certification via Tjeka Training Matters, a registered FET college.
The right materials
Along with design is the need to ensure that gabion wire materials meet industry specification, both from installation longevity and structural integrity perspectives.
“Our baskets are made from Class A galvanised mild tensile steel wire in accordance with the SANS 675 specification. Additionally, the baskets and mattresses are manufactured in strict accordance with SANS 1580,” says Cheyne, adding that site installations must also be in accordance with the latest SANS 1200 specification.
To promote ease of gabion panel assembly in the factory, Gabion Baskets has now switched to using hog ring clips installed with pneumatic guns. In the past this was a manual wire lacing process. Specialist manual and pneumatic tools are also available for on-site basket connections. Both are faster and more efficient, further enhancing worker ergonomics and safety.
CONSTANTIA NEK ESTATE, HOUT BAY
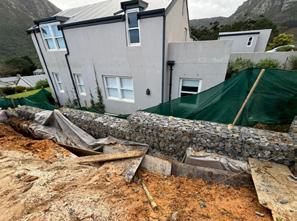
Retaining wall construction in progress at the Constantia
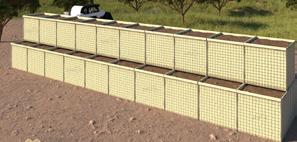
An artist’s impression of a
“The key advantage of gabions is their design flexibility, ease and speed of construction. However, aside from the structural benefits, one of their most notable features is the rockfill. In expert hands, they can be transformed into aesthetic masterpieces that both protect and enhance the built environment,” Cheyne concludes.

Nek Estate in Hout Bay, Cape Town
gabion barrier system design
MULTICOMPOSITES IN LANDFILLS
Multicomposites combine the characteristics of several geosynthetics into one product, i.e., geotextiles, geogrids, geosynthetic liners, and drainage layers. A multicomposite is useful for complex projects that require multiple geosynthetic layers in one application, which eliminates the need for supply and installation of several products on-site.
By Nikhiel Budhai* and Brandon Naidoo**
In addition to the reduced installation time, the technical characteristics of multicomposites can be custom designed and manufactured depending on the design requirements of the geosynthetic layers.
How can multicomposites benefit a project?
A major aspect of the design of geosynthetic layers is ensuring that interface frictions, such as internal sliding and instability between geosynthetic layers have an acceptable safety factor, depending on the function of the geosynthetic material, i.e., filtration, separation, protection, barrier, erosion control, reinforcement, and drainage. Multicomposites enhance the overall performance of designs by eliminating various interface frictions.
Multicomposites promote sustainability by reducing the natural resources required, reducing bulk earthwork requirements, and thus the overall environmental footprint of
the project. Transportation of geosynthetic materials can become quite costly and is dependent on a project’s location. Eliminating the need for the transportation of several products reduces the overall transportation costs, whilst limiting carbon emissions, thus promoting sustainability on the project.
Incorporating multicomposites into landfill designs
Soil veneer refers to a thin layer of soil covering a surface such as a slope. Natural slopes are subject to various stresses including gravitational forces and environmental factors like rainfall and wind, and the presence of soil cover adds additional stress to these slopes.
Historically a capping system includes a drainage layer, geogrid, erosion control mat, and a High-Density Polyethylene liner or a geosynthetic clay liner, all individual components (Figure 1). The multicomposite combines the drainage layer, geogrid, and erosion control mat into a singular product, which streamlines the installation
FIGURE 1: The multicomposite consists of a drainage core in polypropylene extruded monofilaments encased by two nonwoven geotextiles, with one side of the multicomposite mechanically bonded with a reinforced geomat.
process and offers a variety of benefits. The 3D monofilament geomat extruded onto a polyester geogrid provides soil veneer reinforcement.
The combined structure of the polyester geogrid and 3D monofilament geomat helps to distribute the stresses more uniformly by reinforcing the soil veneer, thus lowering the risk of erosion or slope failure. The drainage core of the geocomposite has a “W” configuration with longitudinal parallel channels that provide a high in-plane capacity to drain water from the surface and prevent any intrusion into the waste area.
Case History:
Cava de’ Tirreni landfill, Italy
A multicomposite design was proposed for a capping system of the landfill near Cava de’ Tirreni, close to the Amalfi Coast (Figure 2). Abandoned in the early 90s, the landfill became a health and safety concern for the local community. The landfill remained exposed for a lengthy period and began to produce leachate from the mixture of rainwater and waste. The nearby Bonea stream was polluted, resulting in the landfill being placed under sequestration.
The capping system was developed utilising multiple geosynthetics: a drainage layer using a geocomposite comprising of a W-shaped core coupled with two geotextiles, an impermeable layer using a geosynthetic clay liner with one side laminated by a polyethylene film that does not allow permeation; in combination with the other geosynthetics, a multicomposite comprised of thermobonding a non-woven geotextile, a W-shaped geomat, another non-woven geotextile and a geomat reinforced with geogrids (Comparative analysis of CSA CAVA de TIRRENI materials –Maccaferri materials 2020).
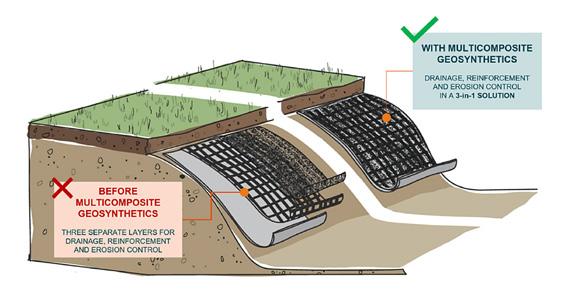
The multicomposite product used in this case history was created by heat-welding a drainage geocomposite to a high-resistance geomat, ensuring a strong bond between two materials. This manufacturing technique creates an intimate connection between the two materials, enhancing the junction point strength beyond what each material could achieve individually.
FIGURE 2: A visual representation of the multicomposite utilised in the Cava de’ Tirreni project, which consists of a drainage core thermal bonded to a non-woven geotextile with the addition of a 3D monofilament geomat extruded onto a polyester geogrid.
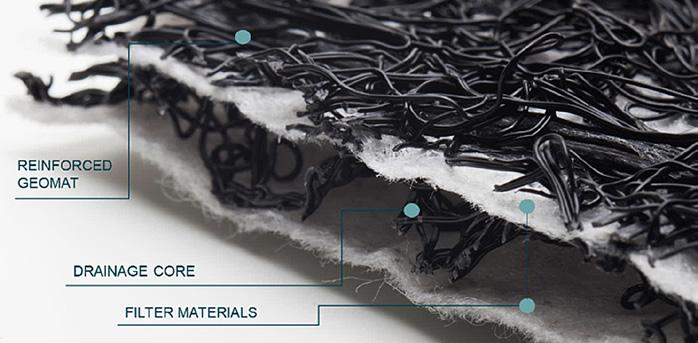
As a result, the capping system offers superior performance and durability, providing effective containment and management of the landfill site.
The proposal of the multicomposite over the traditional method resulted in a shorter construction time as the rollout of a single product vs multiple individual components was less time-consuming. A cost saving on the transport, installation, and overall performance was observed. Table 1 shows a comparison between the main characteristics required by the special tender specifications (referred to as CSA) for the geocomposite in question and the respective results for the proposed solutions.
Tests were carried out in accredited laboratories, which met the requirements of the CE 2+ certification. As can be seen from the comparisons made in Table 1, the materials proposed, concerning the technical standards currently available, are at least equivalent or, for specific aspects, superior to those required by the CSA for the creation of the capping of the former landfill in the Cannetiello area of Cava de’ Tirreni.
Conclusion
The proposed geocomposite reflects the performance of the specifications, proving, in terms of drainage capacity, superior to the requests. Among various applications, the material can be used as drainage behind reinforced concrete or earth walls.
The product flow rates, for this application, are reported at gradient i=1. The geomat component is a 3D mat structure embedded into reinforcement that is a synthetic geogrid. The
puncture resistance
mm 18 mm (*) (*) This is a product equipped with a double filter, each with a resistance of 36 mm; one can therefore consider an overall value equal to half of the single filter.
reinforced geomat optimises the performance of the multicomposite by reinforcing it with requisite strength to maintain equilibrium conditions. The equilibrium conditions refer to the stability and balance of the forces within the capping system. Various forces act upon the materials due to factors such as waste settlement, water infiltration, and external loads. The reinforced geomat helps distribute and resist these forces, ensuring that the system remains stable and balanced over time.
The geomat effectively mitigates the direct impact of external loads on the geocomposite.
In addition, the geomat serves to shield the geocomposite, safeguarding it from puncture damage during soil placement. Additionally, it facilitates vegetation growth, thereby enhancing its environmental sustainability. The geomat is plant-friendly and easily accepts hydroseeding and shrub planting where more rapid colonisation is required.
*Nikhiel Budhai, Commercial Civil Engineer, Maccaferri SA. Email: n.budhai@maccaferri.com
**Brandon Naidoo, Commercial Civil Engineer Maccaferri SA. Email: b.naidoo@maccaferri.com
REFERENCES
Chen, Y. Z. (2010). Geosynthetic Fundamentals in Landfill Design. Springer, Berlin, Heidelberg. R. M. Koerner, T.-Y. S. (2005). Analysis and design of veneer cover soils. Rowe, R. K. (2000). Geosynthetics: Innovative Materials and Rational Design. Melbourne: ISRM International Symposium.
TABLE 1: Project requirements for the geocomposite drain vs the multicomposite performance
The La Almudena Cemetery retaining wall system at an advanced stage of completion. In total 10 500 Terraforce L12 blocks were installed to create a visually striking rock face finish
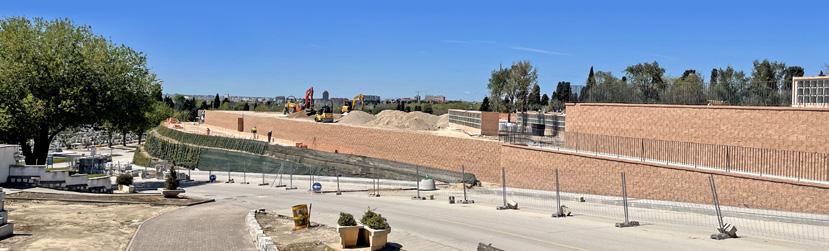
SPANISH CEMETERY EXPANSION WITH SEGMENTAL RETAINING WALLS I
In the reclamation of a plot previously filled with waste, retaining walls were necessary to create new horizontal platforms and garden areas for the La Almudena Cemetery in Madrid, Spain.
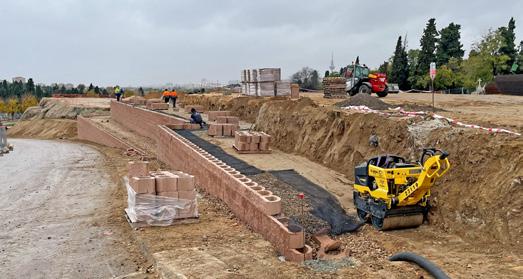
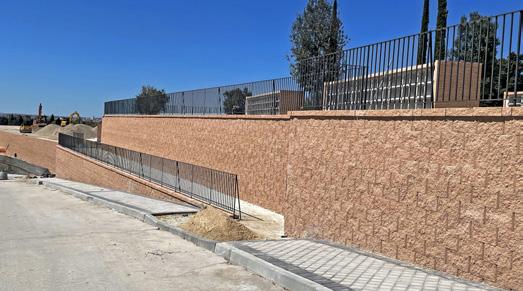
nitially, the plan involved the construction of poured concrete walls. However, the presence of extremely soft soils led the project team to seek alternatives, as the foundations required for the concrete walls would have been prohibitively expensive.
Geotechnical surveys and investigations
Says Miguel Seller, civil engineer, ORBE Técnicas y Medioambiente: “Following the initial engineering study conducted by ORBE, we recommended the installation of green reinforced soil walls (Green Walls) in certain areas of the plot to be reclaimed, and segmental walls in other sections of the project. The segmental walls, designed by ORBE, feature Terraforce L12 rock face blocks, which are manufactured by Prensagra Prefabricados near Madrid as prefabricated elements for the visible surface.”
Seller explains how in-depth geotechnical testing helped formulate the best design for the site: “The project is not particularly notable
Celebrating its 45th anniversary in 2024, Terraforce, headquartered in Cape Town, is a locally and internationally renowned pioneer in the development of environmentally engineered precast concrete systems. Their licensed systems are now manufactured exclusively by specialist concrete precast companies in Canada, Australia, Spain, India, Morocco, Nigeria, Eswatini, Lesotho, Ghana, the United Kingdom, Namibia, the United Arab Emirates, Egypt and South Africa. All products adhere to SANS 207, BS 8006 and ASTM-D6916-18 standards.
Due to soft soil, ORBE proposed reinforcing the foundation beneath the segmented wall with geogrids and improved soil
Ramps and rails

in terms of wall height, with the walls being only 3 m maximum height, whereas ORBE has previously constructed walls up to 10 m with Terraforce blocks. However, it is especially significant that the supporting soil was very soft to great depths, as confirmed by our penetration tests.”
“Internal stability was analysed as usual using Terraforce’s Maxiwall Pro software; this
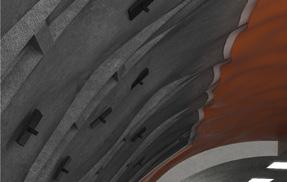


analysis was subsequently compared with other software owned by ORBE, along with a global stability assessment. Based on these studies, we proposed reinforcing the foundation beneath the segmented wall with geogrids and improved soil,” adds Seller.
In total 10 500 Terraforce L12 blocks were installed at the cemetery, resulting in visually striking rock face finish walls. Reinforced
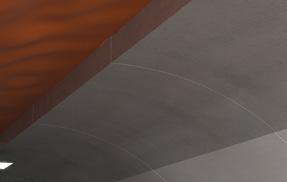
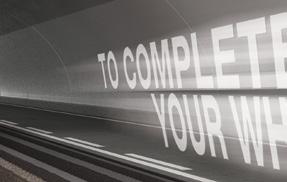
with geogrids every second row and stepped outwards at intervals with precise 90 degree corners, the walls also accommodate gently sloping access ramps and rectangular garden features.
To finish off the overall linear look, straightlined steel rails were set into blocks – filled with concrete for that purpose – and sharp-edged concrete caps set along the top rows of blocks.

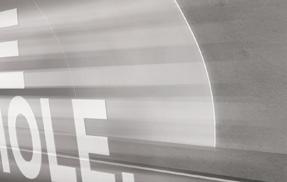
TECHNOLOGY FOR UNDERGROUND CONSTRUCTION
• Alkali-free set accelerators for shotcrete
• Products for mechanized tunneling: foaming agents for soil conditioning, polymers, sealants, lubrificants
• Products for grouting and consolidating
Learn more on www.utt-mapei.com, info@mapei.co.za
• Products for concrete repairing, protection and coating
• Products for waterproofing: synthetic waterproofing membranes, waterproofing accessories
Steps, corners and garden features constructed with Terraforce blocks
Three very neat corners installed by ORBE
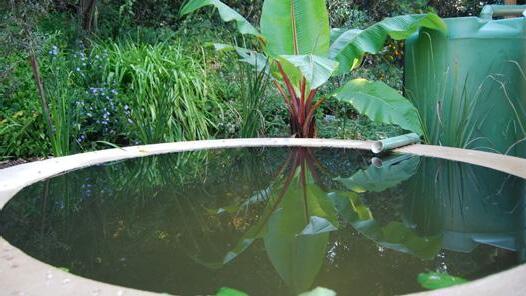
CLEARING THE AIR
Greywater is wastewater that can be reused for other purposes. Greywater makes for as much as 70% of all residential buildings water use.
THE TRUTH ABOUT GREYWATER AND ITS BENEFITS
WHAT IS GREYWATER?
Although greywater and blackwater are typically combined, separating the two, greywater on its own provides several reuse opportunities such as toilet flushing, and garden irrigation. This can additionally assist in lowering potable water use in arid areas by up to 30% for households and up to 60% for corporate buildings. Furthermore, saving money on garden irrigation through reuse can boost household savings by 40%.
Greywater can be collected from the source by installing a plumbing system from an outlet of a bathroom/kitchen to a garden or for toilet flushing. To this, a greywater treatment system such as wetlands can be installed to help filter large particles, nutrients and pump treated water through irrigation pipes.
Blackwater, on the other hand, is toilet water that contains faecal matter and urine. Faecal matter is a breeding ground for harmful bacteria and pathogens that can cause diseases.
Through this publication, Rand Water tries to simplify the myths associated with greywater.
Myth 1: Greywater is unsanitary
One of the most pervasive myths is that greywater is unsanitary and poses a health risk. When properly treated and managed, greywater is perfectly safe for non-potable uses. It
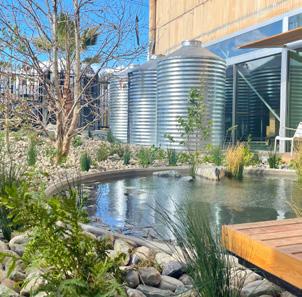
Myth 3: Greywater can't be used for plants
is essential that the correct source of greywater is selected; in this way the health risk is equally reduced.
For an example, greywater containing potentially infectious pathogens should not be used for overhead irrigation or any non-potable activities. This includes water used to wash nappies or soiled sheets. Furthermore, to reduce odour and bacteria, greywater should be used within 24 hours of collection.
Myth 2: Greywater systems are complex and expensive
Another common misconception is that greywater systems are too complicated and costly for the average household. Rand Water - Water Wise has developed a simple and cost-effective solution to treat domestic greywater for use in the landscape.
This low-cost sub-surface horizontal constructed wetland system is designed to be implemented in garden and urban landscapes and can be adapted to suit the volume of greywater produced. The design of this system ensures that there is no pooling of greywater on the surface and no smell or waterborne pests such as mosquitoes.

The guide can be accessed and downloaded for free by going to the Rand Water website, clicking on the Water Wise logo and looking under the Green Industry tab.
Some believe that greywater is harmful to plants due to soap residues and other chemicals. On the contrary, greywater is often rich in nutrients that benefit plant growth. Greywater provides essential nutrients such as total nitrogen (2.75 to 21.00 mg/ ℓ) and total phosphorus (0.062 to 57.00 mg/ℓ) that mainly originate from the kitchen (kitchen residues/waste) and hand basins (soap), respectively. These nutrients nourish our soil and plants, promoting healthier growth and vibrant blooms.
By using biodegradable and plant-friendly soaps, greywater can be a valuable alternative resource for irrigation and reducing the need for chemical fertilisers.
Myth 4: Greywater harms the environment
Concerns about greywater harming the environment stem from misunderstandings about its treatment and reuse. The use of greywater provides us with an opportunity to use an average of approximately 35 - 234 litres (per person per day, depending on lifestyles) of greywater, which can be repurposed for garden irrigation or toilet flushing where little human contact is achieved. This in turn reduces the demand for fresh water and decreases the volume of wastewater entering our sewage systems, ultimately benefiting the environment.
Always be #WaterWise!
www.randwater.co.za 0860 10 10 60

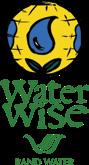
This state-of-the-art infrastructure is supplying water to about 57 000 people residing within Kwaggafontein
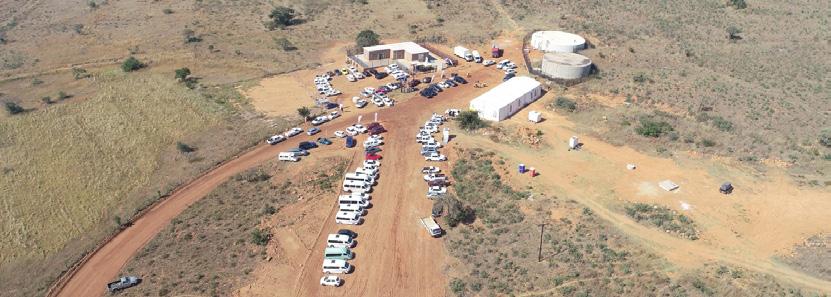
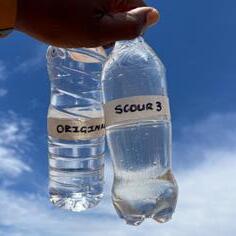
This state-of-the-art infrastructure is supplying water to about 57 000 people residing within Kwaggafontein by extending supplies from the Bundu water supply system.
Water is pumped from the Bundu water treatment works via a rising main into the two Boekenhouthoek B reservoirs. They are connected to the existing pipeline and the new Boekenhouthoek B pipeline that feeds the two Boekenhouthoek A reservoirs. From there, the pipeline feeds the new 10 M ℓ command reservoir and two water retaining structures in Mathyzensloop.
“Considering our longstanding professional relationship with THLM, which started when we were initially engaged to determine available surface water sources in the jurisdiction, we were again consulted to extend supply to Kwaggafontein. This would be done by constructing a booster pump station in Mathyzensloop where the Bundu water supply scheme terminated,” explains Kabelo Ringane, a Ceenex project manager.
The new booster pump station has a capacity of 7,5 Mℓ/day. It delivers water from Bundu reservoir to a new water retaining structure in Kwaggafontein via a 250 mm diameter PVC-O pipeline measuring approximately 3,5 km in length.
Pump station layout
The pump station water infrastructure comprises three booster pumps. Provision was made for a fourth unit to bolster capacity should demand increase at a later stage. Two pumps operate
DELIVERING WATER TO KWAGGAFONTEIN
Ceenex, a leading provider of quality water engineering solutions, recently handed over the new Mathyzensloop to Kwaggafontein Booster pump station to Thembisile Hani Local Municipality (THLM), and its constituents.
simultaneously, interchanging with the third unit to reduce strain on the system. A generator was also installed to supply back-up power during loadshedding and unforeseen interruptions in grid electricity supply.
Working with two very competent contractors, Ceenex achieved practical completion of the infrastructure within 16 months. Notably, this was two months ahead of the initial contractual completion date.
The mechanical scope of work for the booster pump station was successfully completed by Mbako Group, while Tshwele Logistics was tasked with constructing the new pipeline to Kwaggafontein.
Ceenex had worked with both contractors on the Bundu Water Augmentation Scheme. Therefore, excellent team dynamics were already established between the engineering and contracting teams when they mobilised to site.
Fit-for-purpose components
As is the case with all Ceenex projects, an optimised lifecycle centred philosophy was
adopted in the design of the water infrastructure. This included the use of fit-for-purpose materials to construct the booster pump station.
For example, top-of-the-range KSB Pumps were specified. Locally based, KSB can provide fast and efficient technical support to THLM to mitigate downtime. Moreover, high quality imported valves that are supplied by a local company were deployed. This is considering that they comply with the ISO Valve International Standard, namely ISO – 5209 – 77.
As far as possible, materials were sourced locally. When they were unavailable in Mathyzensloop and Kwaggafontein, the construction teams still sourced materials in the province.
The hand over of the infrastructure was undertaken at a prestigious event hosted on the 24th May 2024. Zeph Nkosi, THLM’s hands-on project manager, best describes the importance of the occasion, stating, “‘Water is life, but access to water and sanitation is dignity’, a motto well echoed by The Department of Water and Sanitation. With Ceenex’s help, we delivered exactly that!”
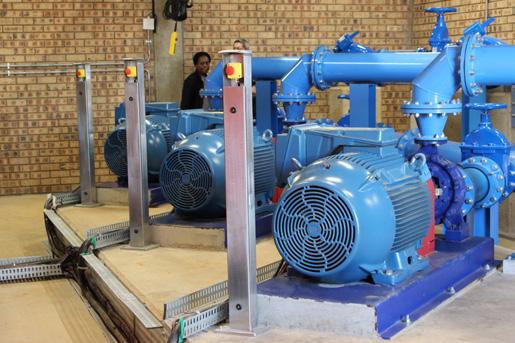
The pump station layout comprises three booster pumps, with provision made for a fourth unit should demand increase at a later stage

Aging water infrastructure and poor maintenance in KZN have led to ongoing water supply disruptions, which have been further exacerbated by recent extreme weather events and the 2022 riots
WATER CHALLENGES IN KZN DEMAND MORE RESILIENCE THROUGH COLLABORATION
Acting alone, industrial companies in KwaZuluNatal (KZN) are finding it harder to mitigate water risks related to supply and quality; what is now required is a collaborative approach to build the necessary resilience.
According to Tamaryn Hale, principal environmental scientist at SRK Consulting’s Durban practice, the recent extreme weather events and the 2022 riots have only aggravated the water supply interruptions being experienced as a result of aging water infrastructure and poor maintenance.
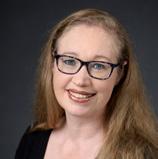
“We have seen more clients struggling with the reliability of their water supply and adequate water quality – factors that pose considerable risk to their businesses,” says Hale. “These companies are responding individually as best they can, but many of these challenges are outside of their control. It now needs a shift towards a more collaborative approach, which can build not
With SRK Consulting for 14 years, principal environmental scientist Tamaryn Hale has specialised in water stewardship, environmental management, and environmental auditing and compliance.
This work has seen her providing clients with gap assessments in terms of Alliance for Water Stewardship standards, and environmental impact assessments in mining, energy and industry.
Tamaryn also undertakes construction and operational environmental compliance audits for industrial sites and in-situ housing upgrades, and compliance audits for water use licenses required by wastewater treatment works and industries.
With experience in South Africa and the Democratic Republic of Congo, she has conducted stakeholder engagement processes with communities, and has managed water license implementation planning and monitoring. Tamaryn has a BSc (Hons) degree in environmental sciences and is registered with the South African Council for Natural Scientific Professions and the Environmental Assessment Practitioners Association of South Africa.
only their corporate resilience but that of other stakeholders in their catchments.”
Poor state of water systems
The Department of Water and Sanitation’s Blue Drop report published last year showed that, while most of KZN’s water systems achieved “average performance” of 50-80%, the next largest category was “poor performance” of 31-50%. Twenty-one of the province’s water systems were in a “critical state”, scoring less than 31% on the Blue Drop measure.
Among the avenues pursued by companies to address their water risks, she explains, are borehole drilling, river abstraction and rainwater harvesting. While these are constructive, they often involve complex and time-consuming regulatory processes –sometimes with uncertain outcomes.
“These options might seem like an easy and quick solution to companies’ water woes, but the legal processes required to obtain approval – for boreholes as an example – is complex and often not a viable alternative,” says Hale. “Moreover, the quality of groundwater is often not at the specification required, so costly purification processes are needed to treat the water before it can be used.”
She points out that reducing water use certainly presents some opportunities in terms of better maintenance and staff education, but achieving real savings in water consumption usually means process enhancements, which demand equipment retrofitting and other capital investments.
LOWER SCORES ON BLUE DROP RATING
The results of the Department of Water and Sanitation’s (DWS’s) Blue Drop national incentive-based regulatory programme are a useful indication of the water challenges that are being faced by industrial companies and other stakeholders in KwaZulu-Natal.
In its 2023 Blue Drop report, the DWS noted that only three of the province’s 172 water supply systems qualified for this certification – by scoring more than 95% against the standards. This was down from the eight systems certified in 2014.
Of the 172 water systems audited for the 2023 report, 21 were in a “critical state”, 34 were in a “poor state”, and 95 were in an “average state”. Just 22 systems were regarded to be in a “good” or “excellent” state.
The technical site assessments to rate the water systems did see the lowest score increase from 28% in 2014 to 50% in 2023, but the overall performance trend regressed between 2014 and 2023. While the highest score for a water system in 2014 was 99%, this dropped to 90% in 2023.
“The more sustainable answer to today’s water challenges can be found in the water stewardship approach, which considers not just a company’s on-site conditions but the broader catchment,” she explains. “Industries within a catchment will face similar challenges, so they need to see the bigger picture and strive for closer collaboration in the ways that they develop solutions.”
She acknowledges that this level of cooperation sometimes seems like a daunting
task, but the water sector has in fact developed the expertise and tools to pursue this route. For instance, the Alliance for Water Stewardship (AWS) – a global membership collaboration comprising businesses, NGOs and the public sector – has developed the AWS International Water Stewardship Standard.
“The AWS framework is a valuable and proven resource and credible framework for collaboration that organisations can use to identify the water risks they face, not only
for their site but for the catchment in which their site is located. From this foundation, they can set up a plan to address and mitigate the risks.”
The first step in the AWS certification process involves gathering data to understand shared water challenges and water risks, impacts and opportunities, she explains. This includes understanding relevant stakeholders and their water-related challenges, as well as each site’s ability to create influence beyond its boundaries.
“The next step is for the partners in such an initiative to commit to action and begin the necessary planning – through the compilation of a Water Stewardship Plan. Using the information gathered, they will establish the desired outcomes to address shared water challenges and set out the practical actions to achieve the outcomes,” Hale continues. Hale, who is a credentialled AWS specialist, highlights that KZN businesses should draw inspiration from the country’s recent Rugby World Cup slogan – Stronger Together – as they find ways to build water resilience through closer cooperation.
MINING | INDUSTRY | MUNICIPAL | AGRICULTURE | FOOD AND BEVERAGE | FIRE FIGHTING

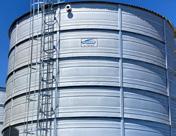

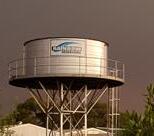

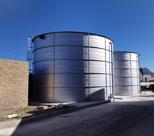


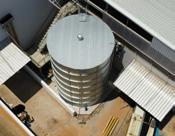
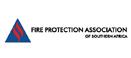
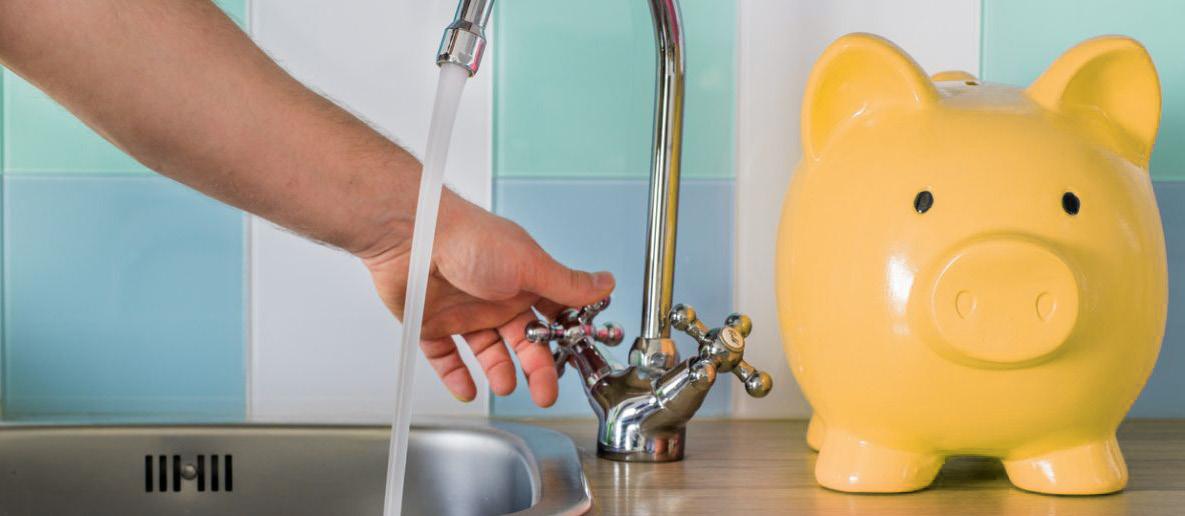
This environmental brand was established in Rand Water in 1997 and encourages the wise use of water. The main objective of the brand is to provide information, awareness and education to promote the sustainable use of water and other environmental resources.
T1
here are six water wise action pillars that provide the basis for all of Water Wise’s principles and values. These are:
Respect water, respect life: By respecting and protecting water, you are respecting
the life on Earth. Action: Always consider the effect of what you do on our water and environment.
2 Don’t waste water: By misusing water, unnecessary amounts of potable water are put back into the wastewater treatment
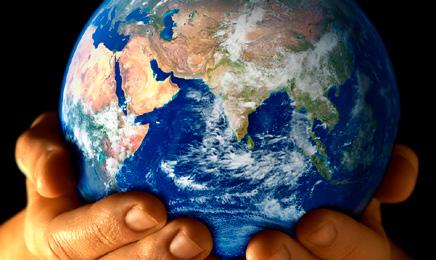
TIPS AND TOOLS
A vast selection of educational and exciting information is available in the form of pamphlets, brochures, posters, lesson notes, booklets, and downloads. The most efficient way of accessing this information is by visiting Rand Water’s website, www.randwater.co.za, and clicking on the Water Wise logo. This action will reroute you to the Water Wise website, where you will find all you need to know about water in the environment.
To stay updated on our activities, kindly visit our social media platforms using the following handles: Facebook: Water Wise; YouTube channel: Water Wise; Instagram: waterwiseza and on X: @water_wise
system, where it requires cleaning, which costs money. Action: Record how much water you use monthly and actively try to reduce it.
3 Don’t pollute water: Very highly polluted water may be too polluted to be effectively cleaned for consumption. Action: Reduce, reuse and recycle your waste so that it does not threaten our environment or water ecosystems.
4 Pay for your water services: This allows for sustainable provision of this service. The purification and pumping process of raw water requires machinery, chemicals and labour. Action: Pay your water bill every month.
5 Take environmental action: Every South African has a responsibility to care for our water and environment. Action: Become aware of your water and carbon footprints and take steps to reduce them.
6 Conserve water and conserve the environment: By conserving water, we are conserving our environment and ensuring the survival of all life on Earth. Action: Support local parks, wetlands, rivers and nature reserves. This encourages their continued conservation.
www.randwater.co.za
10 10 60
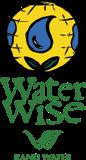
New 16 MLD water treatment plant for Kasane

Amulti-stage water treatment plant project undertaken by WEC Water, a leading South African engineering, procurement and construction (EPC) company specialising in water and wastewater treatment, has been completed and commissioned at Kasane in the northern region of Botswana.
The water treatment plant produces 16 MLD of potable water for a local population of 90 000 people, as well as for businesses in the region. It replaces an older facility that was no longer capable of treating water to meet the increased demand of a local economy undergoing rapid growth.
WEC was appointed as the mechanical and electrical sub-contractor and was responsible for the design, manufacturing, delivery, installation and commissioning of the water treatment works.
Abstraction and treatment
Raw water is drawn from the Chobe River and is treated by clarification, followed by gravity sand and activated carbon filtration and final disinfection by dosing chlorine dioxide.
Comments Ruan Kellerman, Senior Project Manager at WEC Water: “The recent economic growth of Kasane, particularly in the tourism sector and associated businesses, has spurred the Botswana government to upgrade

its municipal services in the area. This upgrade aims to accommodate not only the influx of tourists and tourism facilities, but also the resultant increase in the number of associated businesses and workers that are flocking to the area.”
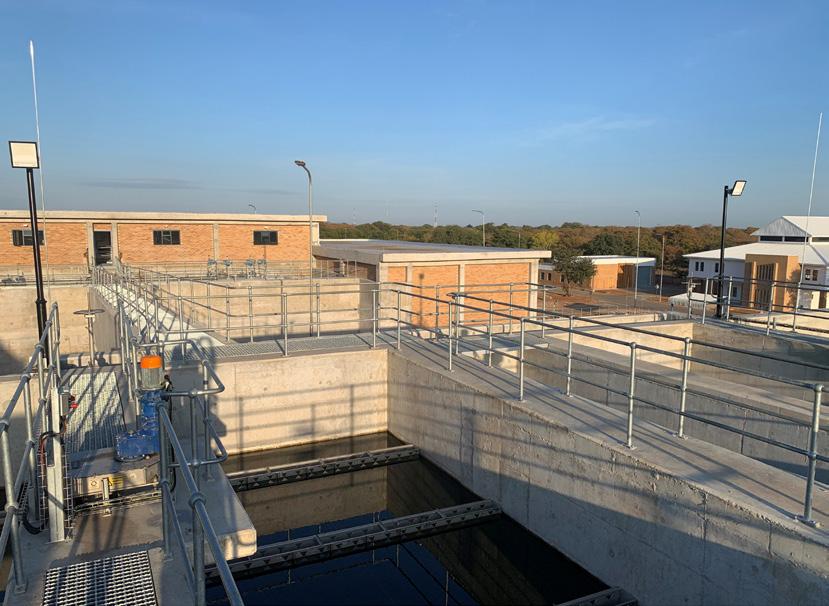
The primary objective of the project was to guarantee that the treated water adhered to the BOS 32:2015 drinking water standards. The plant is also designed to accommodate future scalability.
Lamella clarification section of the new Kasane water treatment plant in northern Botswana
Abstraction from Chobe River
Sludge thickener
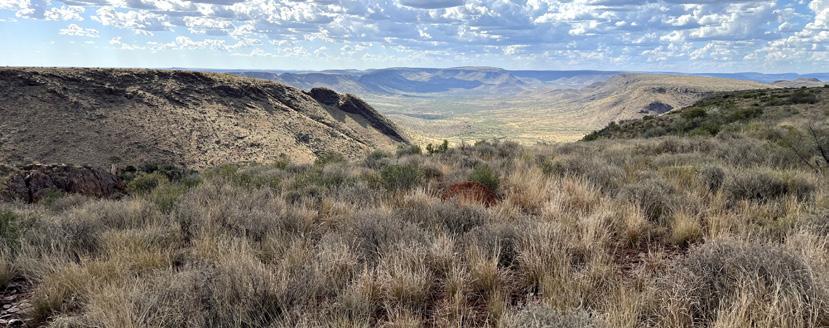
The windfarm comprises twenty-one 6,6 MW turbines concentrated on a mountain range to the south of the chemical plant and associated structures that include the adjacent battery storage building
PLANNING ADVANCES ON SA’S UNIQUE GREEN AMMONIA PROJECT
Currently at an advanced preparation stage, the Prieska Power Reserve (PPR) project in the Northern Cape will be the first of its kind in South Africa to implement a hybrid renewable energy system to produce green ammonia and green hydrogen – initially for the local market, and longerterm for export as well.
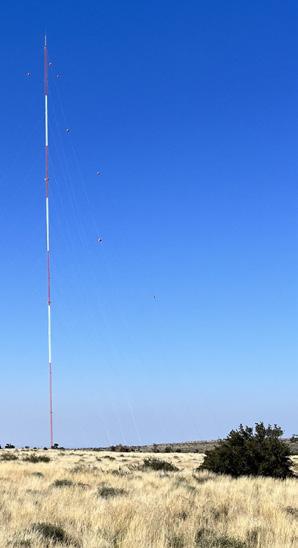
Studies over the past 24-months have shown that the wind is significantly better at night, with an average of 8,6 m/s compared to just over 7 m/s during the day
ammonia production, along with the region’s ideal climatic conditions for solar PV and wind turbine systems, all of which have contributed to making the project commercially viable. The term “green” is applied because this colourless gas is created using renewable energy in a zero CO2 emissions process.
The first phase of the PPR project will target the production of 80 000 tonnes of green ammonia per annum with a green hydrogen content of 14 000 tonnes, beginning in 2028. And the site is well-placed to deliver to local and future global markets, given its location on the outskirts of the town of Prieska, with direct railway access through to South African ports, as well as a connection to National Route 10 via the R357 for on-road delivery. From an investor perspective, Memorandums of Understanding have already been signed with local off-takers for the total production allocation in Phase I.
“Currently, South Africa is a net importer of ammonia, so there’s an excellent business case for the PPR in creating local capacity and reducing exposure to import price volatilities,” explains Martin Walzer, technical director at CENEC and a director of the PPR venture.
Representing a capital investment of some R70 million to date, this groundbreaking initiative has been gazetted as a Strategic Infrastructure Project and is being led by Central Energy Corporation (CENEC) in collaboration with the Industrial Development Corporation (IDC) and Mahlako a Phala as its investment partners.
The project’s location within close proximity to the Orange River was strategically selected as the piped water source needed for green
“Plus, we believe this catalytic project will help accelerate the drive towards the inevitable adoption of green ammonia as a more sustainable, price competitive alternative to brown and grey ammonia – the latter made using fossil fuels as the feedstock, and now under increasing pressure as a redundant technology as the world recalibrates for a net-zero greenhouse gas emissions future,” Walzer continues.
Markets for green ammonia include agricultural fertilisers (representing some 70% of demand), explosives for the mining sector, textile manufacturing to create synthetic fibres, plastics, and the pharmaceuticals sector.
In turn, green hydrogen applications include the fuel cell electric vehicle segment, industrial process applications, as well as for renewable energy storage.
Perfecting the plant design
In contrast to brown or grey ammonia (the former requiring coal gasification, and the latter natural gas), the raw materials for green ammonia are hydrogen (obtained through the electrolysis of water), and nitrogen (sourced from the air using an air separation unit).
Green ammonia is then synthesised from nitrogen and hydrogen using the Haber Bosch process – the standard method adopted globally for commercial ammonia manufacturing. Historically, the foundational process was developed in 1909 by German chemists Fritz Haber and Carl Bosch, both of whom subsequently received the Nobel Prize in Chemistry for their work.
“One of the key challenges to date has been finalising the chemical plant design for the PPR project,” says Walzer. “Based on our prefeasibility study, the first specialist manufacturer we engaged with – based in Europe – presented a package design proposal that was almost double our planned plant capex allocation, citing factors that included price escalations due to Covid-19 supply chain constraints.”
“That meant we had to go back to the drawing board. However, this has turned out to be a plus, as we’ve been able to source a solution locally, working with a leading South African chemical engineering consultancy with extensive experience in this field. Thanks to their input, our revised plant design is now even more energy efficient,” Walzer continues.
Preparing the groundwork
In November 2021, engineering and infrastructure consultancy firm, SMEC South Africa, was appointed to provide project management services to the PPR to establish the framework for implementation.
In addition to providing programme development, scheduling, risk mitigation and scope development services, the SMEC team has also been overseeing progress monitoring
and reporting; cost, quality and communication management; procurement management; and project control.
The SMEC team, made up of a group of bestin-class project managers, engineers and technologists, has also been instrumental in the PPR project reaching numerous key milestones, including the completion of the technical and prefeasibility studies for the chemical plant; the wind, solar, and battery energy storage system configuration, plus micro-grid control optimisation; attaining environmental approvals; as well as preliminary civils designs and cost estimations for future construction.
Power configuration
The solution for Phase I is a power generation set-up designed to deliver 180 MW via solar PV, and 138.6 MW via wind generation, together with 106.16 MWh of battery storage.
Each of the two 90 MW solar PV installations in Phase I is spread over an approximately 150 ha footprint, while the windfarm comprises twenty-one 6,6 MW turbines concentrated on a mountain range to the south of the chemical plant and associated structures that include the adjacent battery storage building. Connecting all three power generation sites is an extensive 132 kV powerline network.
“From the onset, our renewable energy power studies were based on a hybrid model because
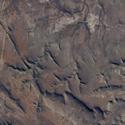



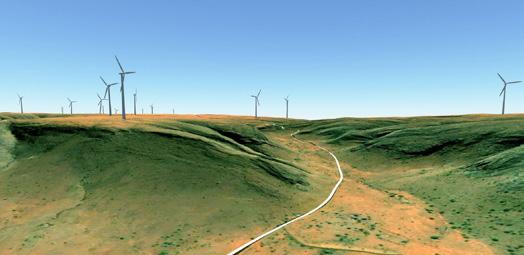
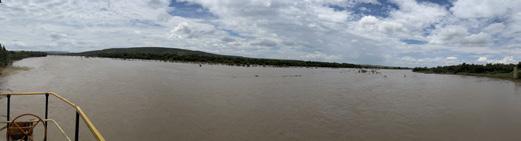
the chemical plant needs to run constantly, irrespective of whether the sun shines or not,” explains Phillip Heine, project manager for the PPR at SMEC South Africa. “Our studies over the past 24-months have shown that the wind is significantly better at night, with an average of 8,6 m/s compared to just over 7 m/s during the day.”
“Within the mix, the role of the battery storage facility is to balance and float the operation in conjunction with a synchronous condenser. The latter automatically responds to any short fluctuations caused by wind gusts or lulls, so the
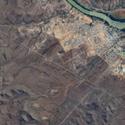
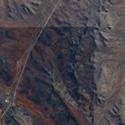
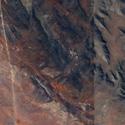
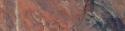
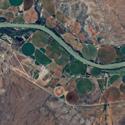
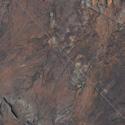

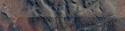
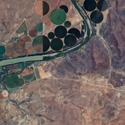
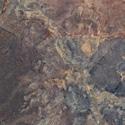
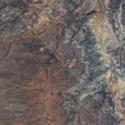


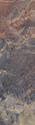
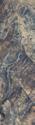

power remains constant, which is an essential requirement. Some 90% of the total energy will be used to run the plant’s electrolysers, and the balance for the synthesis and airseparation units.”
The next stages
With the alternative chemical plant design now completed, SMEC will be working with Prieska Power Reserve to bring the project to financial close in preparation for the construction programme. The preferred approach for the construction of the chemical plant and related infrastructure is an Engineering Procurement and Construction (EPC) contractor model.
According to the project timeline, Walzer says the goal is to finalise investment decisions by the second half of 2025; thereafter transitioning to procurement and contracting.
“We are also currently engaging with the market to bring on board additional strategic equity partners, with a number of fruitful discussions having taken place,” Walzer explains.
Building a funding pipeline is key to a successful ramp-up and gaining early traction in the South African market. Thereafter, the PPR plans to increase green ammonia production to over 500 000 tonnes per annum by 2032, powered by an evolving renewable energy footprint to serve broader international markets.
“Based on available statistics, ammonia produced from green hydrogen is on the increase and is expected to account for around 5% of total production by 2030 as industries focus on decarbonising their operations. From there, however, it is forecasted to climb exponentially to 80% by 2050, so the PPR is well placed to serve this burgeoning market, harnessing local resources,” Walzer concludes.
A map overview of the overall layout for Phase I of the PPR
The water abstraction point on the Orange River
Cape Town nets R36 m in carbon credit sales

The City of Cape Town has announced the successful auction of R36 m in carbon credits generated by reducing gas emissions at its landfill sites via waste-to-energy initiatives. These funds will be ring-fenced for Urban Waste Management projects to reduce pollution and improve environmental health.
The City Council recently resolved to auction the carbon credits to take advantage of attractive rates due to demand for credits on the South African market currently exceeding supply by around 3,4 times. Carbon credits are earned for each tonne of greenhouse gas (GHG) that is destroyed through city projects that have been registered with the UN-approved Clean Development Mechanism (CDM).
Landfill gas infrastructure has been installed at the Bellville, Coastal Park and Vissershok sites to reduce methane emissions, known to have a global warming potential approximately 25 times greater than carbon dioxide.
“We are just getting started in scaling up our waste-to-energy initiatives at our landfill sites. These are win-win projects which reduce emissions, generate electricity, and bring in revenue from carbon credit sales for more infrastructure investment,” explains Cape Town Mayor Geordin Hill-Lewis.
Climate resilience
Around 40% of Cape Town's record R120 bn 10-year infrastructure pipeline is aimed at upping the City's climate change resilience. This includes major water and sanitation investments and waste management improvements.
“We expect our landfill waste-to-energy initiatives to pay for themselves in time between the sale of carbon credits and a reduction in bulk electricity purchases from Eskom,” says Alderman Grant Twigg, Mayoral Committee Member for Urban Waste Management.
“To convert this gas into electricity, perforated pipes or ‘wells’ have been dug into landfill sites to extract methane gas. The gas is then channelled as fuel to produce electricity to power our operations at landfills,” adds Twigg.
Infrastructure finance agreement
In June 2024, the City of Cape Town also secured a further R3,5 bn in financing towards its plans for a South African record infrastructure investment over three years following the conclusion of an agreement with Nedbank.
Cape Town plans to spend R39,5bn on infrastructure from July 2024 to June 2027, as approved in its “Building for Jobs” budget. This is South Africa's largest ever three-year infrastructure investment by a metropolitan municipality.
The city accounted for a full 60% of the R100 billion in overall government infrastructure projects announced nationally in 2023, according to Nedbank's updated
Capital Expenditure Project Listing for 2023, published in February 2024.
“We are pleased to secure further finance towards our ambitious infrastructure investment agenda, which we estimate will create 130 000 construction-related jobs alone over three years. Lower-income households will also directly benefit from 75% - or R9bn - of Cape Town's R12 bn infrastructure spend in 2024/25,” says Mayor Hill-Lewis.
“Cape Town will soon be SA's most populous city, and we are preparing for this by targeting our fastest growing, and poorest areas, with infrastructure projects that will, over time, unstitch the unjust legacy of our country's past.”
In October 2023, the City published a request for funding proposals (RFP) regarding financial years 2023/24 and 2024/25, which was followed by extensive engagements with local and international lenders.
Alongside the Nedbank finance approval in June 2024, the City Council further approved US$150 m in finance from the International Finance Corporation (IFC), and in April 2023 greenlit €100 million developmental financing from the Agence Française de Développement (AFD).
The city is following a blended finance model, which includes funding from its own healthy balance sheet, as well as finance from the local and international markets. Further financing agreements are set to be served before Council during the 2024/25 financial year regarding the balance of the funding requirements for the City's infrastructure plans.
As the infrastructure arm of the City of Johannesburg, the Johannesburg Development Agency (JDA) has been spearheading the implementation of multidisciplinary turnkey projects in the Greater Orange Farm region valued at around R625 million.
Key spatial interventions include infrastructure development, basic services and social facilities, plus improved mobility by investing in new linkages, internal roads and public transport.
In Lakeside, Orange Farm, the JDA’s catalytic interventions will see 2,5 km of roads being upgraded from gravel to tar in Wards 1,2,3,4,5 and 131. The overall scope of works includes the re-gravelling of access roads, installation of stormwater infrastructure, public environment upgrades and streetlights.
The JDA has also commenced with other projects within Ward 3, namely on the 16th and Moyane Drive public environment upgrades, as well as the continuation of stormwater upgrades on Ingonyama Street.
Orange Farm Public Transport Facility on track
In the meantime, the Orange Farm Public Transport Facility is currently 88% complete.
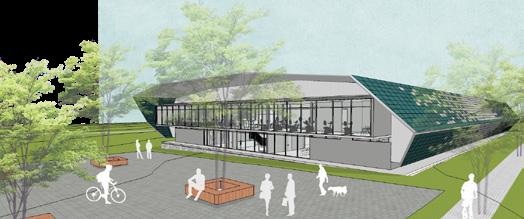
Orange Farm region revitalisation advances
Constructed at a cost of around R55 million, the facility will include covered trading areas, ablution facilities, bicycle racks, and a refuse yard. Streetlighting and perimeter lights will ensure safety within a suitable radius of the facility.
Chris Hani Sports Complex
Another landmark development for the region is JDA’s implementation of the Chris Hani Sports Complex project on behalf of the city's Community Development Department.
The project includes the construction of a multipurpose hall, an athletics and soccer stadium, a gatehouse, an aquatics centre, and a high-performance centre.
Drieziek Recreation Park
Community wellness and social cohesion are also core elements in the construction of the Drieziek Recreation Park in Drieziek Extension 3. The park has been designed as a dedicated space for families, social groups, and individuals to gather, engage in recreational activities, and promote healthier lifestyles.
“The JDA is committed to transforming Orange Farm into a thriving community with enhanced infrastructure and opportunities for all residents,” comments Siyabonga Genu, JDA’s Executive Manager for Project Implementation. “The Orange Farm Turnkey Programme projects are pivotal steps towards realising this vision.”

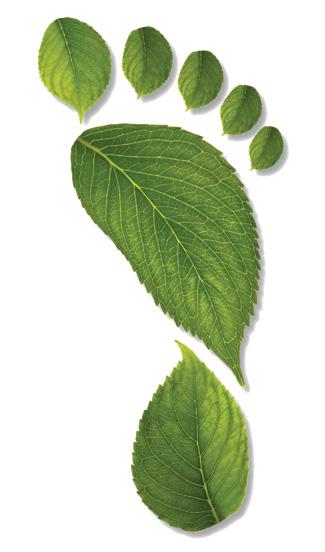
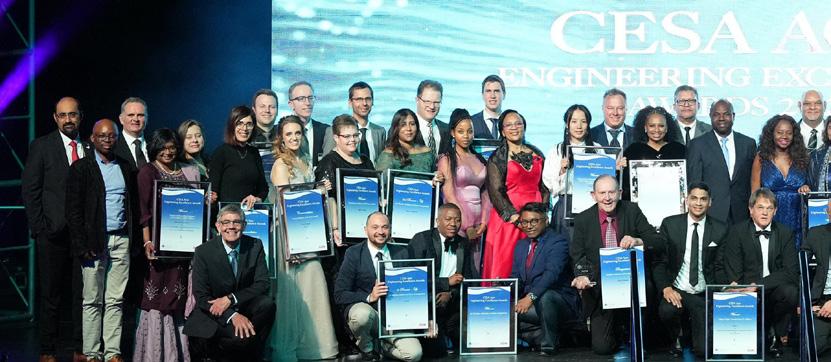
CELEBRATING COLLABORATION AND EXCELLENCE
The 2024 CESA Aon Engineering Excellence Awards
The 2024 CESA Aon Engineering Excellence Awards, held in Midrand, north of Johannesburg, on 14th August, celebrated and honoured the outstanding contributions of South Africa’s consulting engineering sector towards infrastructure development locally and internationally.
Celebrating its 52 nd year, this event, supported in more recent times by platinum title sponsor Aon South Africa, highlighted the crucial partnerships and collaborative efforts driving the industry forward.
Reflecting on the evening’s significance, CESA CEO, Chris Campbell, remarked: “The CESA Aon Engineering Excellence Awards celebrates not just the achievements of our industry, but also the spirit of collaboration, innovation and partnership that defines our profession.”
He drew a parallel to the Olympic Games, emphasising the importance of teamwork and the relentless pursuit of excellence.
“Just as our athletes push their limits to achieve gold, we too must aim for excellence in our projects and endeavours.”
Campbell noted that the awards recognised more than just successful projects; it represented a commitment to contributing to enhancing the quality of life for all citizens.
Aon South Africa CEO, Dr Nolwandle Mgoqi, added that the awards honoured and
celebrated the exceptional achievements, hard work and unwavering determination in the various infrastructure projects that are fundamental to shaping the world and livelihoods for the better. “Aon has had the privilege of witnessing and supporting the critical role that infrastructure plays in the sustainable development and delivery of basic services to society.”
As the industry continues to evolve, the 2024 CESA Aon Engineering Excellence Awards serve as a reminder of the impact that collective efforts have in building a sustainable future for all South Africans.
Category Winners and Commendations
In the Young Engineer of the Year category, Dr Andries Nel from Spoormaker & Partners was the winner, with Erika Braune from AECOM and Istiaan Lubbe from Zutari both receiving a commendation in this category.
SCIP Engineering Group was the winner in the category of Projects with a value less than R50 million for the Monaghan Farm Road Bridge Remedial for the Clewer Development
Trust. A commendation was awarded to Naidu Consulting for the SANRAL N.002-270-2022/1: For Repairs to B999A Mhlali River Bridge on National Route 2, Section 27, km 15.42.
The Lifetime Industry Achievement award recognised Alan Chemaly’s lifelong dedication and substantial contributions to dam engineering and safety, spanning over 50 years.
Bigen Group was the winner of the Mentoring Company of the Year Award, while Isak Frederik Malherbe from AECOM was the winner in the Mentor of the Year Award category.
This year’s winner in the Business Excellence Award category is the BVi Group, while Bigen Group received a commendation in this category. The winner of the Small/Medium Company of the Year was AvenirHoldings.
SMEC South Africa was the winner in the category for Projects ranging from R50 million to less than R250 million for the N4 Montrose Interchange Upgrade project for Trans African Concessions. WSP Group Africa received a commendation in this category for RejemLinton JV’s MediMix Ancillary Building.
In the Engineering Technology and Innovation category, Knight Piésold won the Renewable Energy Systems Design Excellence Award for the Kikagati Hydropower Plant for Kikagati Power. Zutari received a commendation for the Water Sanitation and Hygiene Design Excellence Award for the Coegakop Water Treatment Works project for the Mandela Bay Municipality.
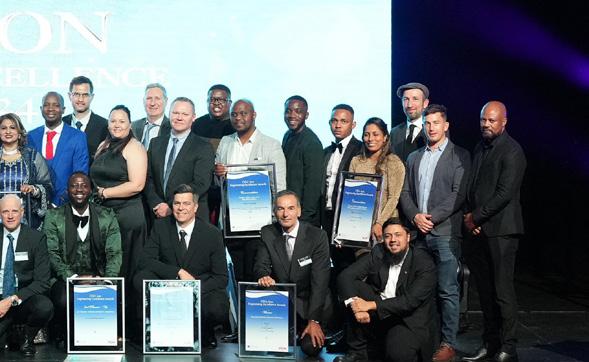
In the Smart Building Systems Design Excellence Award category, a commendation was awarded to Spoormaker & Partners for the NuMeRI Main Centre.
MPAMOT & WSP JV were the winners in the category for Projects with a value ranging from R250 million to less than R1 billion for the Southern Corridor Phase 1 – Farm 694 Kosovo Housing Development for the Western Cape Department of Infrastructure.
The Publisher of the Year – Trade was awarded to Creamer Media, while Independent Online received the Publisher of the Year – Daily News award.
The winner of the Job Shadow Initiative & Poster Competition was Mariswe, with Zutari as the first runner up, followed by BVi Consulting Engineers and Ensync Engineers, both as second runners-up.
In the Best International Projects category, Zutari was the winner for the PAIX DKR1 Senegal
21 project in Senegal for PAIX. The company also won in the category for Mega Projects greater than R1 billion for the Upgrading of the Zandvliet Wastewater Treatment Works project for the City of Cape Town.
“On behalf of Aon, I congratulate all of the winners and entrants for the tremendous accomplishments they have achieved. Stay committed to excellence, raise your business resilience, invest in building a better society through your deliberate actions,” said Dr Mgoqi.
Campbell concluded: “Congratulations to the finalists and the winners of the 2024 CESA Aon Engineering Excellence Awards! Each award reflects your success in delivering projects that make a difference in enhancing the quality of life and the value of infrastructure development in driving economic growth in South Africa and beyond. We celebrate your achievements and the standard you have set for engineering in this country.”

ASTEC’S SX-6EX SOIL STABILISER AND RECLAIMER IS A WINNER
The ideal machine for South African road builders
Weight balance and power allocation are critical in all stabilisation and reclamation applications. In this respect, the weight of the SX-6ex is perfectly distributed between the two axles, allowing the machine’s engine to work as efficiently as possible with maximum tractive effort
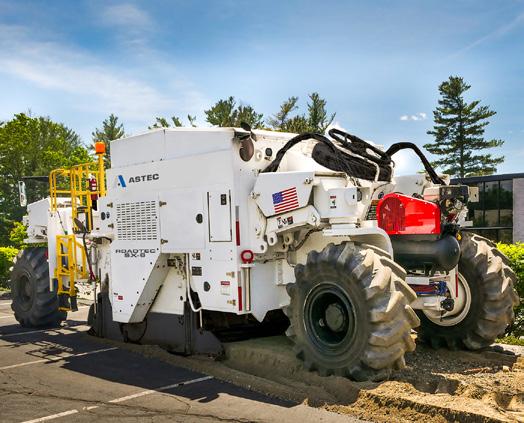
The devastating floods in KwaZulu-Natal and more recently in the Western Cape underscore the importance of ensuring that South Africa’s roads are built, maintained and rehabilitated to the highest standards, to ensure that they are safe, reliable and climate resilient.
The Private Markets for Climate Resilience (PMCR) report produced by the Inter-American Development Bank (IDB) and the Nordic Development Fund (NDF) estimates that the potential impact of climate change on South Africa’s national road network may be as high as US$96 million in 2030 if no adaptation measures are taken. These measures include pre-emptive upgrades of roads, the report notes, adding that the high cost of road construction and maintenance is an obstacle.
High-performance, multi-function, time saving machines like the Astec SX-6ex soil
stabiliser/reclaimer offer an ideal solution for South African roadbuilders, according to Philip Saunders, product sales manager at Astec Industries Africa Middle East. Offering two applications in one high-performance machine, the Astec SX-6ex was introduced into the Southern African market two years ago. It is supplied locally by Astec Industries South Africa, based in Johannesburg.
Soil stabilisation and asphalt reclamation
Saunders says that the SX-6ex is ideal for use on African road projects. “It can be used for both soil stabilisation and asphalt
reclamation. It is built to work with strength and precision in the toughest environments.
With a 447 kW (600hp) Cummins QSX15 engine and a weight of 33 112 kg, the midsize SX-6ex offers a rare combination of power and mobility, allowing it to excel in a variety of applications,” he states.
“The SX-6ex’s high performance 6-cylinder diesel engine provides power to the rotor through a direct drum drive. The machine is equipped for cutting up to 508 mm deep and 2.44 m wide. Whether performing road rehabilitation, cold recycling or soil stabilisation, the SX-6ex will exceed expectations.”
Frame durability and leg assemblies
The SX-6ex is manufactured with a durable frame built at Astec from extremely strong A656 grade 80 steel. Saunders explains that this steel has twice the yield strength as the mild steel used in other machines on the market. The custom-made frame is designed to perform in all terrains by providing substantial ground clearance.
The wheels are suspended by four independently controlled, hydraulically adjustable leg assemblies that are bolted to the mainframe. “This feature allows the depth of cut to be selected using a push button. The cutter housing is also securely fastened to the mainframe, providing strength and precision while the machine is working,” he notes.
Cooling and dust reduction
The SX-6ex cooling system introduces air from the top of the machine at the cleanest possible area, before it is exhausted away from the machine and engine through the rear radiator package. By pulling air from the top of the machine, the amount of dust travelling through the cooling system is limited. Furthermore, clean-out panels provide convenient access for radiator maintenance. A variable speed fan also provides efficient cooling based on engine demand.
Visibility and ergonomics
When it comes to operator comfort and productivity, the Astec SX-6ex offers excellent visibility and ergonomic controls.
The operator station’s seat slides laterally and swings 90 degrees to help create the perfect vantage point from which to work. The operator platform also slides 457 mm past the right of the machine for additional visibility. A full view cab gives the operator an excellent view of the cutting edge and any obstacles that may be in the way. Mirrors on both sides provide the operator with additional viewpoints of the machine’s surroundings.
On the move, a backup camera system provides additional visibility while the machine is operated in reverse. Plus, a screen inside the cab conveniently displays the area directly behind the stabiliser as soon as reverse is selected. The backup camera adds a level of comfort and convenience when navigating the SX-6ex around other machines and obstacles.
This machine’s controls and display screen are conveniently arranged and move with the seat to allow for safe and ergonomic machine operation. Joystick controls and four different steering modes increase the machine’s manoeuvrability and ease of operation. Furthermore, an air conditioning and heating system, along with a cab pressuriser, give the operator a comfortable and dust-free environment in which to work. The cabin is also built with soundproofing and is rubber isolated to keep noise levels down.
Power to weight ratio where it counts Weight balance and power allocation are critical in all stabilisation and reclamation applications. The weight of the SX-6ex is
When it comes to operator comfort and productivity, the Astec SX-6ex offers excellent visibility and ergonomic controls
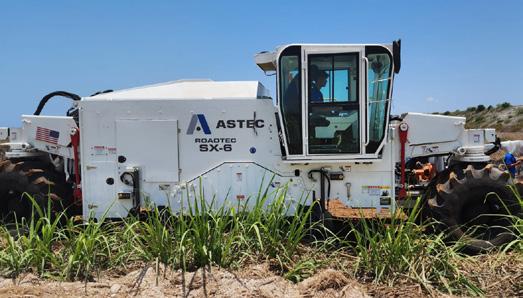
perfectly distributed between the two axles, allowing the machine’s engine to work as efficiently as possible with maximum tractive effort.
“With ideal weight placement and balanced four-wheel drive, the machine is better equipped to consistently perform in the most difficult project environments,” Saunders explains.
A variable geometry cutter housing enables the SX-6ex to achieve superior cutting, sizing and mixing. With additional room behind the drum and heavy-duty hydraulically adjustable front and rear doors, the SX-6ex provides unmatched mixing and sizing, he notes. The machine’s cutter housing is fixed to the mainframe, allowing it to easily handle the forces of bidirectional cutting with no weak points.
The SX-6ex has a cut width of 2,44 m with a variety of drum options to achieve a cut
With a 447 kW (600hp) Cummins QSX15 engine and a weight of 33 112 kg, the mid-size SX-6ex offers a rare combination of power and mobility, allowing it to excel in a variety of applications
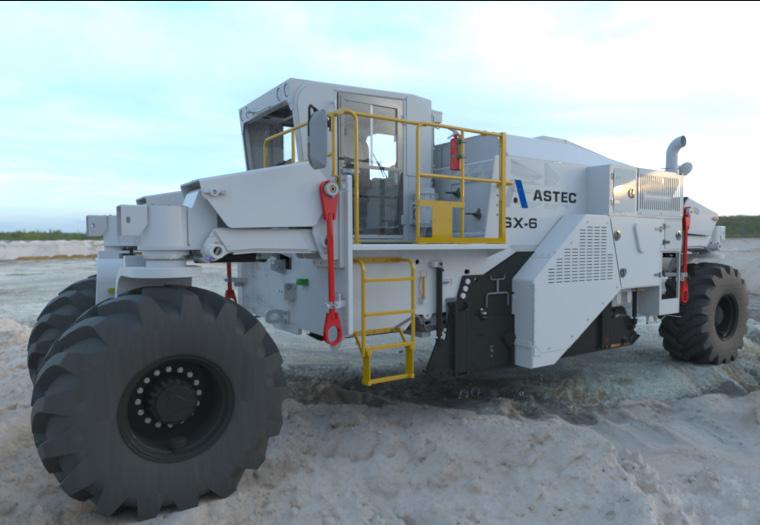
depth of up to 508 mm. The heavy-duty, Quick Change Tooling System with welded bases are available along with different tooth spacing to fit the demands of the project environments. The SX-6ex cutter is driven by a mechanical, multi-groove V-belt drive. These drives are hydraulically tensioned, delivering consistent and efficient power to the cutter drum. Boltless entry to the cutter drive also provides quick and easy access.
“Accessibility, performance and durability are the exemplary features of the Quick Change Tooling System,” Saunders expands. “This unique tooling design increases wear life and drastically reduces the amount of time to change worn cutter components.”
Diagnostics and maintenance
The SX-6ex has a standard, 24-volt electrical system with a 105-amp alternator. CAN-based electronics with on-board and remote diagnostics allow for simple troubleshooting throughout the machine. Grease maintenance points are also clearly labelled with recommended amounts and are conveniently placed around the machine to make preventative maintenance as simple as possible.
Easy access is another of the SX-6ex’s important features. “Hydraulically adjustable doors allow for better access to the engine compartment, while ground level, slide-out racks provide easier access to the machine’s battery compartment. There’s also quick and easy belt maintenance access on the side of the machine,” Saunders concludes.
Following the official local launch of the Liebherr TA 230 Litronic articulated dump truck (ADT) in June 2022, which marked Liebherr-Africa’s debut in the highly contested ADT market in southern Africa, several units are now hard at work in South Africa and Zimbabwe, where the ADT has proven its mettle in some of the toughest mining applications.
Having made its local debut some two years ago, the Liebherr TA 230 has proven itself in some of the toughest operating environments in southern Africa. With several units already operating in the field, clocking about 35 000 – 45 000 market hours in the process, Tendayi Kudumba, GM: Earthmoving, at Liebherr-Africa, expects the
sales of the Liebherr TA 230 to pick up steam on the back of increased enquiries in the region.
“The ADT market in southern Africa is very competitive, but we are very happy with the sales performance and enquiries of the TA 230 to date. Several customers have shown immense interest in the machine, and we expect to put more units into the market soon,” says Kudumba.
Biggest customer
With five units in its fleet, Orca Group, a prominent mining contractor operating in Zimbabwe, runs the biggest fleet of Liebherr TA 230 machines in southern Africa to date. In fact, the company was the recipient of the first ever TA 230 in the region, which was handed over during the official launch at the Liebherr-Africa headquarters in Springs, Gauteng, South Africa, in June 2022. The company initially took delivery of three units, before expanding the fleet with two more machines.
The five machines have been deployed in a taxing application at Bindura-based Freda Rebecca Gold Mine, hauling ore from the underground tunnels to the overland
Liebherr TA 230 Litronic gains
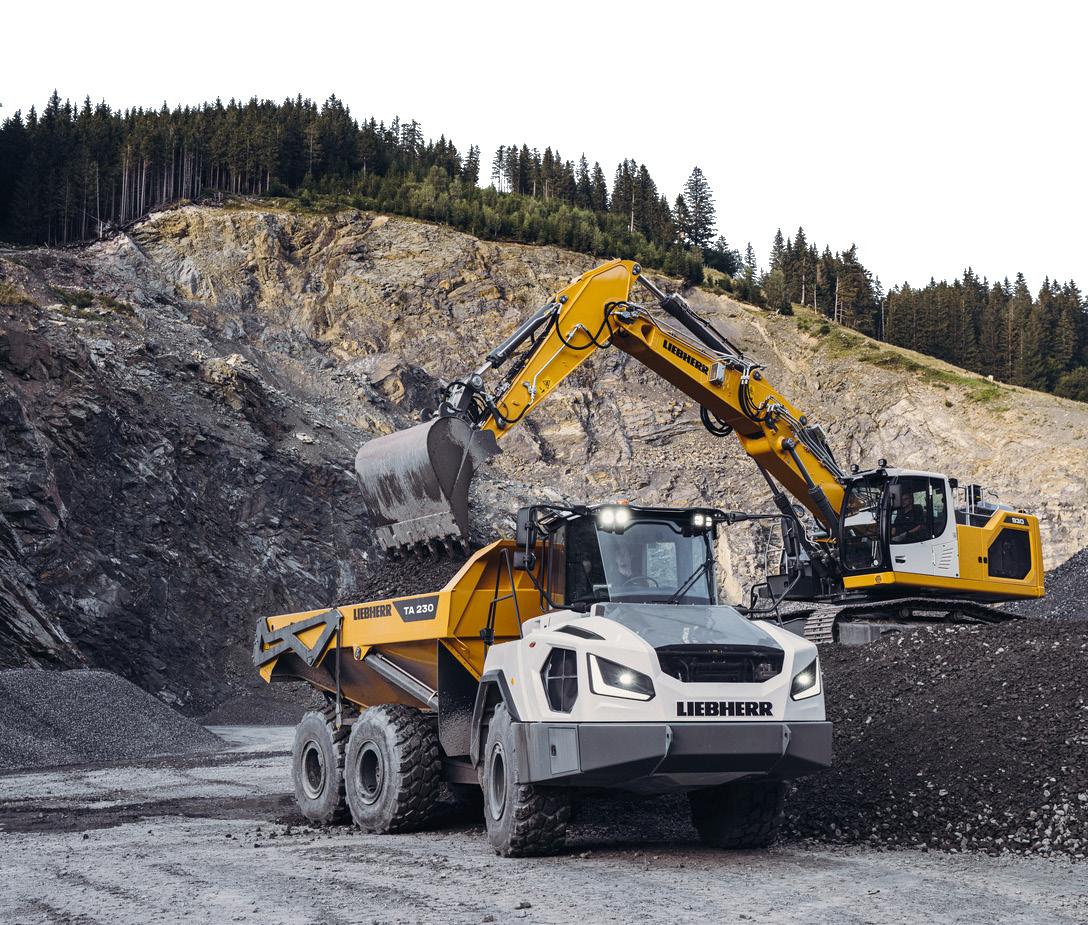
crushers. Lavell Ruthman, Head of Sales, Earthmoving Technology at Liebherr-Africa, says the machines have already clocked between 6 000 and 7 000 hours in this challenging application, travelling 15 km out of the pit fully loaded in extremely hot conditions.
More units
Two of the first batch of five units to be delivered in southern Africa are hard at work in the Palaborwa area in South Africa. Running at this particular site for over a year now, the two Liebherr TA 230 units have already passed the 6 000-hour mark.
“Despite the heavy and abrasive nature of magnetite, the two machines have proven
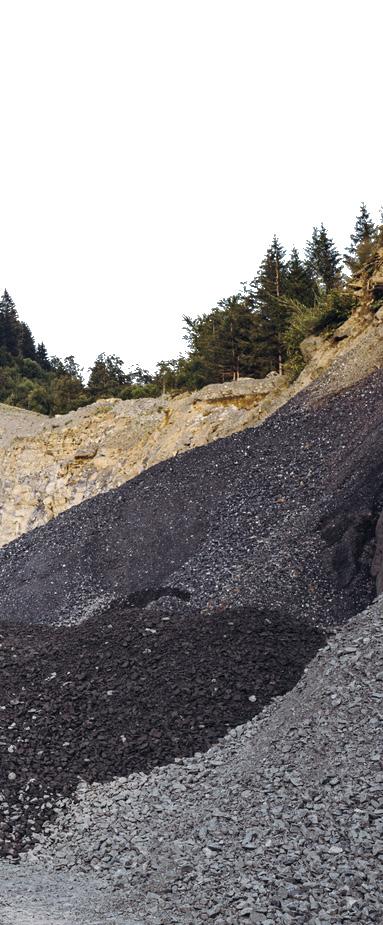
their mettle in this tough application, meeting the requirements of the customer in terms of uptime, efficiency and productivity,” says Ruthman.
“The machine’s 28 000 kg payload with a dump body capacity of 18,1 m³ also fits the bill for the customer’s production requirements. The 6-cylinder Liebherr engine with a 12-litre displacement, producing 265 kW of power, has been praised on site for delivering enough power when needed.”
Another TA 230 operating in South Africa has been deployed in a chrome application in Limpopo. Delivered in late 2023, the machine has so far performed beyond expectations in what is known to be an abrasive application. The feedback from the customer, confirms Ruthman, has been very positive, with prospects of delivering more units in the near future.
Why TA 230?
Powered by a 265-kW 6-cylinder Liebherr engine with a 12-litre displacement, the TA 230 Litronic is driven by an automatic 8-speed powershift transmission which ensures optimal force distribution
Several customers who have purchased the TA 230 to date have expressed satisfaction with Liebherr’s new machine concept, which has been developed especially for challenging off-road applications. Modern designs in the front-end area create maximum ground clearance for greater off-road performance.
The newly designed articulated swivel joint creates sound off-road capability; it allows independent movement of the front and rear ends, thus ensuring maximum manoeuvrability. The positive-locking swivel joint with tapered roller bearing is perfect for the shear stresses associated with tough underfoot conditions, while it also withstands maximum loads and provides optimal force distribution.
The front and rear axles of the machine are secured using sturdy A-rods at the articulated swivel joint and at the rear end. On front, the truck uses hydropneumatic suspension for maximum comfort, which is key to the smooth driving. The shock absorbers at the articulated swivel joint and the position of the separate and oscillating A-rods of the rear axles at the rear end, provide maximum ground clearance.
Powered by a 265-kW 6-cylinder Liebherr engine with a 12-litre displacement, the TA 230 Litronic is driven by an automatic 8-speed powershift transmission which ensures optimal force distribution. The machine impresses with great driving performance and massive pulling force,
even in the most difficult ground conditions and on challenging gradients.
“A combination of balanced weight distribution, permanent 6 x 6 all-wheel drive, solid, flexible mounting and large bank angle as well as the machine’s high ground clearance, enable the TA 230 Litronic to deliver unparalleled performance on uneven terrain,” says Kudumba.
The actively controlled inter-axle differential locks mean that the Liebherr TA 230 has automatic traction control. As soon as one axle experiences wheelspin, it is decelerated, and the traction is intelligently redistributed to the other axles. In addition to maximum forward drive, this reduces the power requirement and therefore translates into lower fuel consumption.
Efficiency is further enhanced by the smart gear selection, which enables the machine to adjust automatically to its current speed and load to ensure optimum torque and fuel consumption at all times. The machine therefore automatically reduces its fuel consumption per tonne of transported material.
With productivity in mind, the optimised trough ensures that more material can be moved in a short time. The front of the trough – designed for the effective transport of a 28-t payload – is straight and the sills are low so that loading with a wheel loader, for example, is easily possible across the entire length of the truck.
A standard Liebherr weighing system shows the current payload during loading on the display in the operator’s cab, helping eliminate guesswork in loadout processes. An optional loading light on both sides at the back of the operator’s cab shows the loading level outdoors.
In order to accelerate the release of the material during unloading, the inner edges of the new trough are tapered. The two tipping cylinders at the side give the TA 230 Litronic high tipping pressure. The load can be tipped against the slope easily and quickly.
“During transportation, the long chute at the end of the trough ensures minimal material loss. The trough volume can be increased with the optional tailgate. Thanks to the large opening width, tipping of large and bulky transported material is easily possible. Even with the tailgate the overall width of the TA 230 Litronic is still below three metres, which allows the machine to be easily and quickly transported on a lowbed truck,” Ruthman concludes.









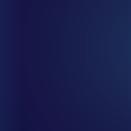



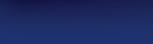
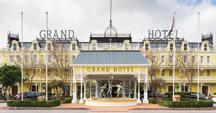

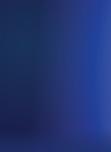










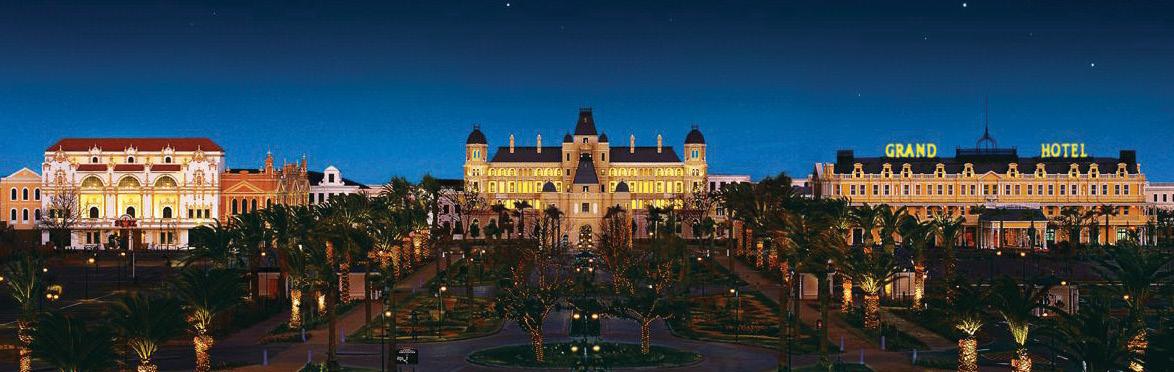
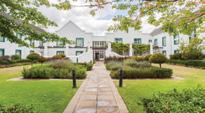
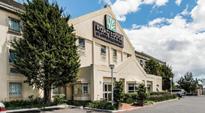
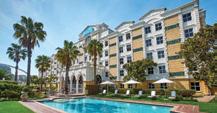
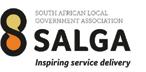
KSB’s MagnoChem range of magnetic drive pumps are essential in industries where handling hazardous and valuable liquids without leakage is paramount. Traditionally, these pumps use mechanical seals, often requiring double mechanical seals for extra protection against leaks.
However, these double seals demand an additional sealing system using buffer or barrier fluids to prevent the pumped liquid from escaping into the atmosphere. This method, while effective, has significant drawbacks, including the potential contamination of the pumped fluid, with pressurised systems, and the added complexity and cost of maintaining the sealing system.
Fridah Magoro, KSB’s Market Area Manager for Petro-/Chemicals and Energy in SubSaharan Africa, explains that the contamination of valuable fluids due to seal leaks can result in additional costs. Recognising these challenges, KSB has developed the MagnoProtect system, which enhances the reliability and safety of magnetic drive pumps by eliminating the need for traditional mechanical seals and their associated drawbacks.

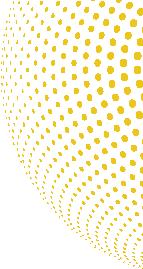


New system improves performance of magnetic drive pumps
KSB
Pumps and Valves has introduced its groundbreaking MagnoProtect system for the local petrochemical, chemical and general industry markets
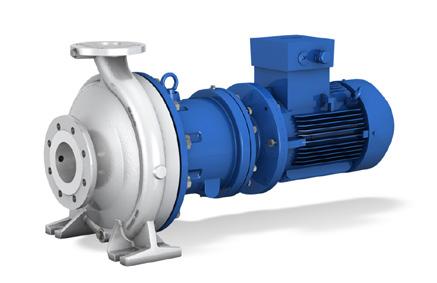
“Compliance with stringent industry standards and regulations is non-negotiable in chemical and petrochemical operations, and our MagnoProtect system ensures that our MagnoChem pumps meet the relevant international standards, including API 685 and ISO 5199. This compliance guarantees that the pumps are suitable for use in highly regulated environments, providing peace of mind to operators and plant managers,” she explains.
Dual shell design
“Our MagnoProtect system is essentially an
The MagnoProtect system enhances the reliability and safety of magnetic
to enhance the safety and performance of its magnetic drive pumps.
upgrade to the existing MagnoChem pumps, which are designed with magnetic drive to inherently avoid the leakage issues associated with mechanical seals. The new MagnoProtect system incorporates a dual shell or ‘candesign’, which is an evolutionary to provide yet another layer of security against leaks,” Magoro continues.
“To do this it features an inner and outer shell, with the space between these shells filled with a monitoring liquid and maintained at a vacuum. This design ensures that any breach in the inner shell results in a detectable change in pressure in the space, providing early leak
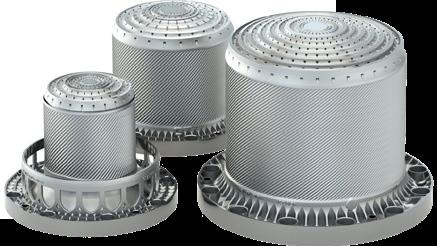
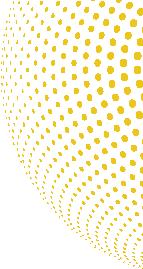

detection. The vacuum between the dual shells is continuously monitored. Atmospheric pressure within this space indicates an outer shell breach, while an increase in pressure signals an inner shell breach. This dual monitoring system allows for early detection and preventive maintenance, minimising the risk of hazardous leaks.”
She continues that the new design also features grooves that help reduce eddy current losses by up to 20% compared to previous models. This improvement not only enhances pump efficiency, but also reduces operational costs as a result of energy savings. This efficiency also extends to maintenance. The modular assembly can be quickly replaced, which further minimises downtime and ensures that the pump can return to operation swiftly. Existing MagnoChem pumps can be upgraded with the MagnoProtect system, providing users with the latest safety and efficiency enhancements without the need for a complete pump replacement.
“Our new MagnoProtect system represents a significant advancement in the field of magnetic drive pumps and offers improved safety, efficiency and ease of maintenance. By addressing the limitations of traditional mechanical seal systems and providing a better solution for handling hazardous and valuable liquids, users can continue to prioritise safety and efficiency with either new or retrofit systems,” Magoro concludes.


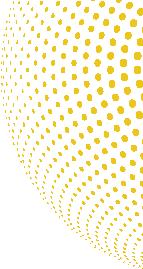

A KSB MagnoChem pump
drive pumps
COMING TOGETHER FOR
A GREATER PURPOSE
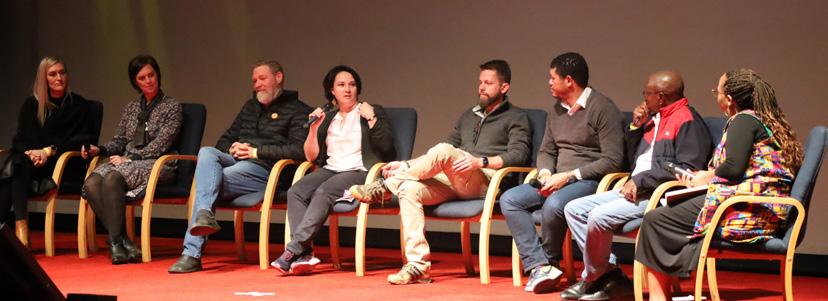
The role of BIMHarambee in preparing the built environment for BIM
As we stand on the brink of a demographic wave that will see Sub-Saharan Africa’s population double in the next 25 years, the need for smarter, faster, and more sustainable building practices has never been more pressing. By Dr Calayde Davey
Africa will see the biggest growth in urbanisation and built environment trends by 2050, with Sub-Saharan Africa’s built environment expected to double, and over 70% of construction yet to occur (Deloitte, 2020; Intergovernmental Panel on Climate Change, 2022; UN-Habitat, 2020). This rapid growth offers both obstacles and prospects for sustainable progress in the face of climate change, long-term socio-economic sustainability, and many other related challenges.
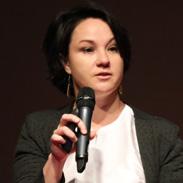
Building smarter for an African future
African buildings alone contribute to 61% of Africa’s final energy consumption and 32% of CO2 emissions (UNEP et al., 2020). Therefore, the expected doubling of urban stock and infrastructure by 2050 calls for innovative development, construction, and design tailored to Africa’s current and future needs. To meet this demand will require a transformative change in the 21st century African built environment industry.
Additionally, the African digital economy is projected to hit US$712 billion by 2050 (International Finance Corporation, 2020). In Sub-Saharan Africa alone, over 230 million jobs will require digital skills by 2030, resulting in almost 650 million training opportunities (World Bank, 2021). The burgeoning African digital economy will also have major impacts in the African built environment sector.
This sector, encompassing construction, urban planning, and infrastructure development, is increasingly reliant on digital technology for design, simulation, and management. As such, professionals in this field will need to be proficient in digital tools, methodologies, and skills to drive innovation and efficiency.
The African Union’s Digital Transformation Strategy is poised to significantly influence the built environment sector by fostering an integrated and inclusive digital society (African Union, 2020). It emphasises the creation of a
Dr Amanda Filtane, Lecturer, Department of Construction Economics and Management, University of Cape Town. Dr Filtane was the facilitator for the Panel Sessions at BIMHarambee 2024
Dr Calayde Davey, Senior Lecturer and Postdoctoral Research Associate, Department of Architecture at the University of Pretoria, and BIMcommunityAfrica board member. Dr Davey chaired the BIMHarambee 2024 event
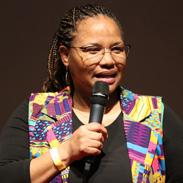
Presenters and panellists at BIMHarambee 2024
harmonised regulatory framework to facilitate investment and financing, aiming to close the digital infrastructure gap. This strategy is expected to catalyse innovative growth, ensuring that digital advancements benefit the entire continent, from urban planning to construction, and beyond.
Birthing digital skills for the challenge
The current supply of digital skills in Africa is insufficient to meet the socio-economic and infrastructure demands of 2050 (World Bank, 2021). This is particularly true for the African built environment sector (Deloitte, 2020; UNEP et al., 2020). Therefore, equipping Africa’s workforce with relevant digital competencies is crucial for fostering innovation and economic expansion across the continent.
Moreover, the integration of digital skills across various industries is vital for enhancing productivity and addressing issues such as climate change and urban growth. As the African digital economy advances, professionals in the built environment equipped with digital expertise will be instrumental in developing future-fit African cities.
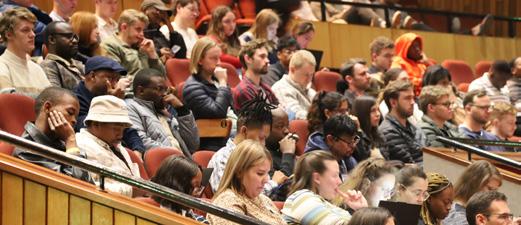
Our youth, representing an ever-growing portion of the global workforce, are the future citymakers and the guardians of our environment.
BIMHarambee 2024 – preparing people and companies for a BIM future
A key driver is BIMHarambee, an annual event organised by BIMcommUNITY.Africa and this year hosted by the Faculty of Engineering, Built Environment and IT at the University of Pretoria in July 2024.
However, BIMHarambee is not just an event, it’s a movement towards embracing innovative technologies and methodologies that will lead us to build for tomorrow, today. We are committed to fostering education and skills development to ensure that our workforce is equipped to meet the challenges and opportunities that lie ahead.
Join us in our journey to reshape the landscape of African cities and infrastructure, to create a legacy that we can be proud of – and to Raise the BIM Tide.
BIMHARAMBEE 2024 DELEGATE COMMENTARY
“I had the incredible privilege of being a panel speaker at the recent hashtag BIMHarambee conference, themed ‘Fit for BIM’, held at the University of Pretoria. The conference focused on BIM from two key perspectives: People (roles, responsibilities, skills development, career paths) and Business (organisational imperatives), exploring how to craft ‘BIM Fit’ people and organisations.
Students and professionals across the AEC environment came together to connect, collaborate, and learn about the transformative potential of BIM across various sectors.
Over the two days, I participated in three engaging panel discussions:
1. The BIM Team Organogram: We delved into the essential roles, responsibilities, and skillsets needed for an effective BIM team.
2. Getting Your People BIM Fit: This discussion focused on the culture, mindset, and strategies for training and upskilling to make your team BIM Fit.
3. How to build a BIM Fit Organisation: We discussed the digital transformation journeys for both small and large organisations to become BIM Fit, emphasising the crucial balance between People, Processes, and Technology.
A key takeaway from these discussions is that achieving BIM fitness hinges on the seamless integration of these three elements. All must be in equal balance for true success.
One memorable question from the audience was: How do I convince a client to pay for BIM? Beyond getting client and
Recordings of all the presentations have been uploaded on the event page at www.bimcommunity.africa/bimharambee where the 2024 BIM Book is also available for download.
If you would like to be a part of BIMHarambee 2025, please get in touch. E-mail: angela@bimcommunity.africa.
stakeholder buy-in, this led us to explore the importance of not only convincing clients but also ourselves and understanding the immense value BIM can bring to your organisation. Investing in BIM isn’t just about meeting client demands—it’s about realising the significant returns it offers you and your business.”
Fabio Companie, Head, Construction Management, City of Cape Town
“I appreciate the opportunity to connect with like-minded professionals. Your event was insightful and engaging, providing valuable knowledge that I’ll apply for digital change and evolution in the future daily work. The People (BIM roles, responsibilities and skills development) and Business (organisational imperatives) of BIM was well established from sessions. Also, thanks to Dr Amanda Filtane for unlocking my old school mind – seems it’s becoming a BIM-ing year. The event was a wonderful experience, and I’m excited exploring new ideas and strategies discussed during the sessions.
Melvern Govender’s presentation showcased that the City of Cape Town is one of the public sector leaders in the implementation of BIM adoption, demonstrating alignment and moving side by side with the South African Council for the Built Environment and the Construction Industry Development Board.
Also, a special shoutout and salute to Dr Calayde Davey for chairing and the presenters, facilitators and sponsors for their innovativeness, insights and hard work.”
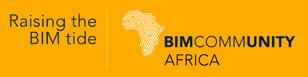
BIMHarambee 2024 delegates
Anien Nauta, BIM Manager, AECOM

PROFESSIONAL AFFILIATES

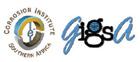
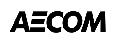
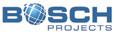
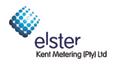













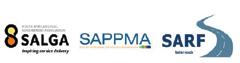
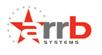








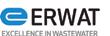


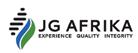

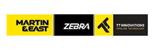
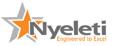
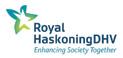













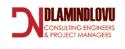

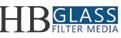







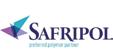
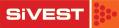
















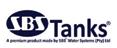
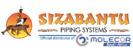
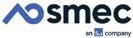






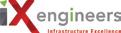

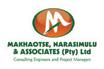






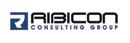





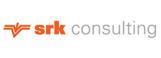
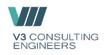
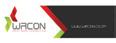
AECOM siphokuhle.dlamini@aecom.com
AFI Consult banie@afri-infra.com
ARRB Systems info@arrbsystemssa.com
Asla Construction (Pty) Ltd johanv@asla.co.za
BMK Group brian@bmkgroup.co.za
Bosch Projects (Pty) Ltd mail@boschprojects.co.za
BVI Consulting Engineers marketing@bviho.co.za
CCG puhumudzo@ccgsytems.co.za / info@ccgsystems.co.za
Civtech Engineers (Pty) Ltd admin@civtech.biz
Corrosion Institute of Southern Africa secretary@corrosioninstitute.org.za
Dlamindlovu Consulting Engineers & Project Managers info@dlami-ndlovu.co.za
EFG Engineers info@efgeng.co.za
Elster Kent Metering Mark.Shamley@Honeywell.com
EMS Solutions paul@emssolutions.co.za
ENsync Engineers info@ensync.africa
ERWAT mail@erwat.co.za
Gabion Baskets mail@gabionbaskets.co.za
GIBB marketing@gibb.co.za
GIGSA secretary@gigsa.org
GLS Consulting info@gls.co.za
Gorman Rupp Cordeiro@gormanrupp.co.za
Gudunkomo Investments & Consulting info@gudunkomo.co.za
Hatch Africa (Pty) Ltd info@hatch.co.za
HB Glass Filter Media info@hardybulkinglass.com
Herrenknecht schiewe.helene@herrenknecht.de HSA Technology (Pty) Ltd cs@hubersa.com
Hydro-comp Enterprises info@edams.co.za
IMQS Software (Pty) Ltd shemine.adams@imqs.co.za
Infrachamps Consulting info@infrachamps.co.za
INFRATEC info@infratec.co.za
Institute of Waste Management of Southern Africa iwmsa@iwmsa.co.za
IQHINA Consulting Engineers & Project Managers info@iqhina.co.za iX engineers (Pty) Ltd hans.k@ixengineers.co.za
Izinga Holdings info@izingalabezi.co.za
JG Afrika DennyC@jgafrika.com
KABE Consulting Engineers info@kabe.co.za
Kago Consulting Engineers kagocon@kago.co.za
Kantey & Templer (K&T) Consulting Engineers ccherry@ct.kanteys.co.za
Kitso Botlhale Consulting Engineers info@kitsobce.co.za
KSB Pumps and Valves (Pty) Ltd salesza@ksb.com
KUREMA Engineering (Pty) Ltd info@kurema.co.za
Lektratek Water general@lwt.co.za
Loshini Projects muzi@loshini.co.za
Makhaotse Narasimulu & Associates mmakhaotse@mna-sa.co.za
Mariswe (Pty) Ltd neshniec@mariswe.com
Martin & East gbyron@martin-east.co.za
M & C Consulting Engineers (Pty) Ltd info@mcconsulting.co.za
Mhiduve adminpotch@mhiduve.co.za
MPAMOT (Pty) Ltd mpumem@mpamot.com
Mvubu Consulting & Project Managers miranda@mvubu.net
Nyeleti Consulting naidoot@nyeleti.co.za
Prociv Consulting & Projects Management amarunga@prociv.co.za
Rainbow Reservoirs quin@rainbowres.com
Re-Solve Consulting (Pty) Ltd maura@re-solve.co.za
Ribicon Consulting Group (Pty) Ltd info@ribicon.co.za
Royal HaskoningDHV francisg@rhdv.com
SABITA info@sabita.co.za
SAFRIPOL mberry@safripol.com
SAGI annette@sagi.co.za
SALGA info@salga.org.za
SAPPMA admin@sappma.co.za / willem@sappma.co.za
SARF administrator@sarf.org.za.co.za
SBS Water Systems marketing@sbstanks.co.za
Silulumanzi Antoinette.Diphoko@silulumanzi.com
Siroccon International (Pty) Ltd admin@siroccon.co.za
SiVEST SA info@sivest.co.za
Sizabantu Piping Systems (Pty) Ltd proudly@sizabantu.com
Siza Water (RF) Pty Ltd PA@sizawater.com
Sky High Consulting Engineers (Pty) Ltd info@shconsultong.co.za
SKYV Consulting Engineers (Pty) Ltd kamesh@skyv.co.za
Smartlock jp.alkema@smartlock.net
SMEC capetown@smec.com
SOUTH AFRICAN VALUE EDUCATION Sabiha@savegroup.co.za
Southern African Society for Trenchless Technology director@sasst.org.za
SRK Consulting jomar@srk.co.za
Structa Group info@structatech.co.za
TPA Consulting roger@tpa.co.za
Ultra Control Valves peter@ultravalves.co.za
V3 Consulting Engineers (Pty) Ltd info@v3consulting.co.za
VIP Consulting Engineers esme@vipconsulting.co.za
VNA info@vnac.co.za
Water Institute of Southern Africa wisa@wisa.org.za
Wam Technology CC support@wamsys.co.za
Wilo South Africa marketingsa@wilo.co.za
WRCON ben@wrcon.co.za
Zutari charmaine.achour@zutari.com
The hall's surroundings have been enhanced with the installation of paving, and a dedicated parking area has been provided to accommodate visitors

Verulam hall built for the community
AfriSam, a leading construction materials company, has reaffirmed its dedication to the sustainable development of the communities surrounding its operations with the completion of the Verulam Community Hall.
This initiative not only showcases AfriSam's commitment to social responsibility, but also highlights its support for local small, medium, and micro enterprises (SMMEs) and the creation of employment opportunities for community members.
The Verulam Community Hall, constructed by a local SMME, has been thoughtfully designed and features a fully equipped kitchen, as well as modern ablution facilities. In line with AfriSam's commitment to environmental sustainability, the building also incorporates eco-friendly features that include a water tank installed to collect rainwater, promoting water conservation and reducing reliance on municipal resources.
Additionally, the hall's surroundings have been enhanced with the installation of paving, providing a safe and accessible area for community members, plus a dedicated parking area has been provided to accommodate visitors.
Comments AfriSam's Community Development Professional, Senzi Mabaso: "We are proud to have partnered with a local SMME for this project, as it aligns with our commitment to supporting local businesses and uplifting the communities in which we operate."
The completion of the Verulam Community Hall is a testament to AfriSam's commitment to creating concrete possibilities for all.
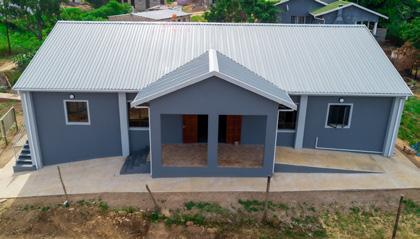
The Verulam Community Hall will serve to foster social cohesion and provide a space for personal and collective growth
There were many smiling faces and great anticipation at the Forte Secondary School in Dobsonville, Soweto on 7th August 2024 when a newly refurbished science laboratory sponsored by Bell Equipment under the auspices of the South African Medical and Education Foundation (SAME Foundation) was officially taken into use.
Bell Equipment, South Africa’s worldrenowned manufacturer of mining, construction, and agricultural equipment had, through its SocioEconomic Development (SED) initiative, committed to getting involved in the project when it was approached by the SAME Foundation during a Mandela Day event, painting a school in Gauteng in 2023.
SAME Foundation is a non-profit organisation which raises funds and manages socio-economic development allocations to improve the health and education environment in South Africa. The Foundation boasts a track record of completing well over 150 high-impact projects in the last 20 years, investing hundreds of millions of rands and positively influencing millions of South Africans. Its sole aim is to improve healthcare and educational facilities in poverty-stricken communities.
“We as a foundation were heartened when Bell Equipment showed its eagerness to become involved in this very worthwhile project at the Forte
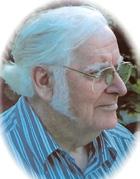
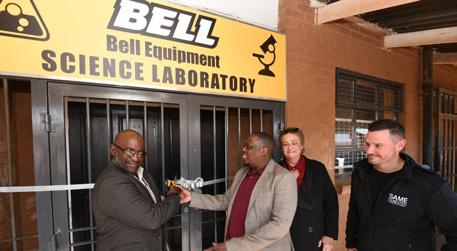
Bell Equipment’s Bruce Ndlela and Forte Secondary’s Headmaster Mokgosi Mudavhi cut the ribbon while the SAME Foundation’s Dianne Pols (founding member) and Tyrone Pols look on
Bell Equipment and SAME Foundation launch refurbished science laboratory
Secondary School,” says Tyrone Pols, spokesperson for the SAME Foundation. “The science laboratory at this school was in a dilapidated state and with Bell Equipment’s generous funding, we could oversee the replacement of the floor, ceiling, windows, doors and security gate as well as several coats of durable paint.”
“We could then order new laboratory benches, stools and cupboards before new laboratory equipment applicable to the curriculum was acquired. Advanced technology has been added with a touchscreen white board and digital projector.”
Speaking during the function to mark the unveiling of the refurbished laboratory, Bruce Ndlela, Bell Equipment’s Director: Business and Public Sector Development, urged the learners to set their
personal education goals high and reminded them that no goal was too high to attain.
“We as Bell Equipment employ around 4 000 people worldwide and, as we’ve assisted in the refurbishment and equipping of many similar laboratories and centres of learning in South Africa, it shows that we believe in our youth and the potential that they show,” says Ndlela.
All the work to refurbish the laboratory was completed during an eight-week period spanning April and May 2024. Bell Equipment’s donation covered the entire construction, fixtures and equipment expenses.
The Forte Secondary School fulfils a vitally important role of educating 2 400 learners from Grade 8 to 12.
In Memoriam
Remembering Graham Keppie
Graham Keppie passed away peacefully at his old age home in East London, aged 95 years, on 19th August 2024.
Prior to his retirement, Graham’s last leadership role was a key one, serving as the Chief City Engineer for East London, which is now known as the Buffalo City Metropolitan Municipality.
Graham joined IMESA as an aspiring municipal engineer and registered as a professional engineer in 1972. He subsequently spearheaded the establishment of IMESA’s Border Branch as the formative Chairman. Graham was also the Bulletin Editor for IMESA’s evolving national communications platform at the time.
His commitment to IMESA was ultimately recognised by his election as President for the May 1988 to May 1989 term and he remained a member of the IMESA EXCO until 1993. A highlight in his post-retirement years was his attendance at the IMESA 2011 Annual Conference, alongside other past Presidents.
In his personal life, Graham was also a longstanding member of the East London Rotary Club and former President, dedicated to enabling positive socioeconomic outcomes for localised communities.
As IMESA, we honour him for his tireless commitment to excellence and support of all our Institute endeavours. Our sincere condolences go out to his wife Patricia, extended family and friends.
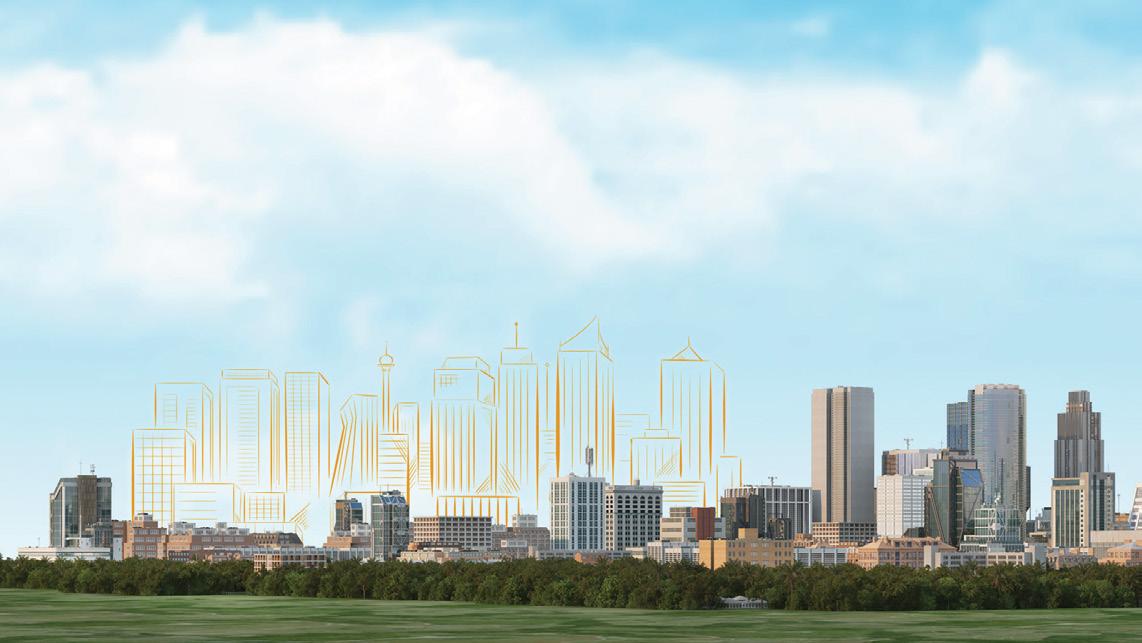
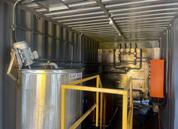
UNLOCKING EXCELLENCE IN ASPHALT TECHNOLOGY
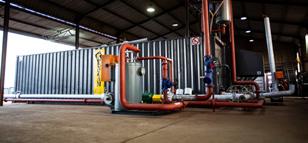
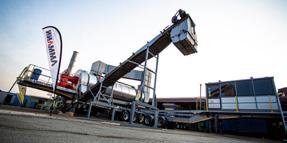
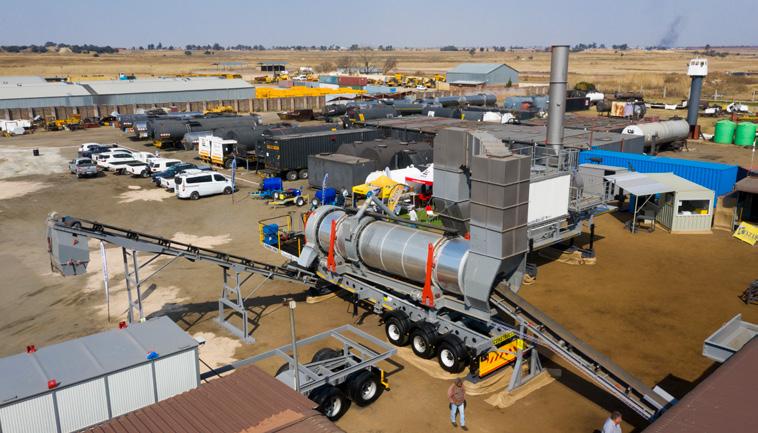
Looking to elevate your asphalt production capabilities? Discover Ammann Kenzam – your premier partner in the import, export, and servicing of asphalt plants and bitumen-related equipment.
WHAT CAN AMMANN KENZAM OFFER YOU?
• Asphalt Plants: Explore our range of high-performance asphalt plants tailored to meet your production needs efficiently and sustainably.
• Bitumen Equipment: Access top-quality bitumen-related equipment designed for durability and optimal performance.
• Retrofit Services: Enhance your existing asphalt plant with our expert retrofit solutions, integrating the latest innovations seamlessly.
• Comprehensive Services: From pipework installations to complete plant de-establishment and re-establishment, our skilled team delivers turnkey solutions..
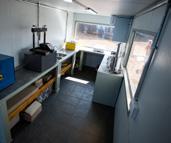
WHY CHOOSE AMMANN KENZAM?
• Industry Expertise: With years of experience, we understand the intricacies of asphalt production and offer solutions that drive results.
• Global Reach: As import-export specialists, we source and deliver cutting-edge equipment from leading manufacturers worldwide.
• Service Excellence: Our commitment doesn’t end with equipment sales – we provide comprehensive support and maintenance to keep your operations running smoothly.
Travis Freel | Regional Sales Manager Mobile: +27 820 52 1921 Rocco Lehman | Managing Director SA Mobile: +27 784 88 2945