

INDUSTRY INSIGHT
Eddie Jansen van Vuuren Director, SprayPaveNavigating challenges and seizing opportunities
CITY OF CAPE TOWN Phase 1A at Welmoed Estate Development advances
WATER & WASTEWATER
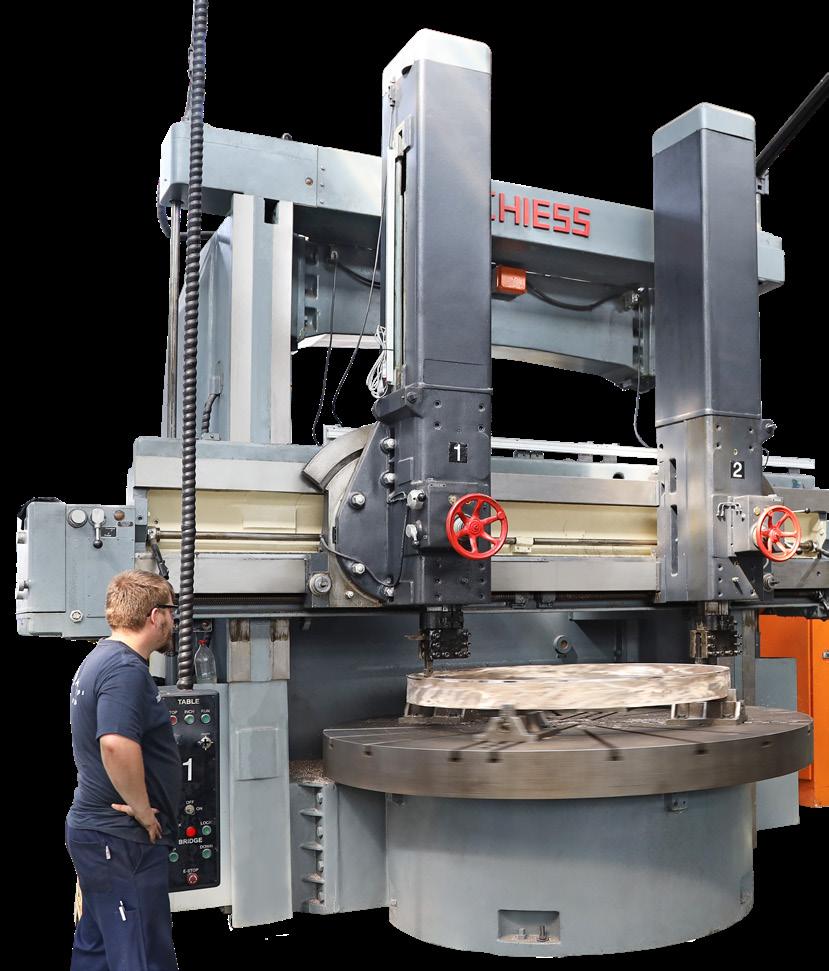

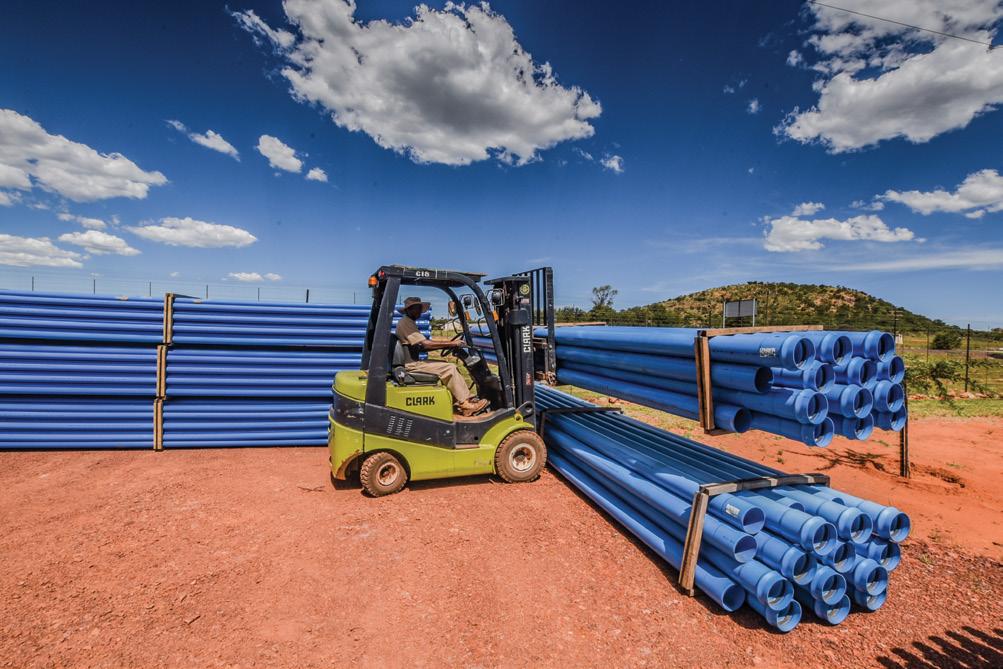
Manufacturers, suppliers and Exporters of :
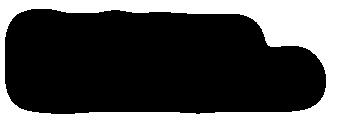
HDPE Pipes & Fittings
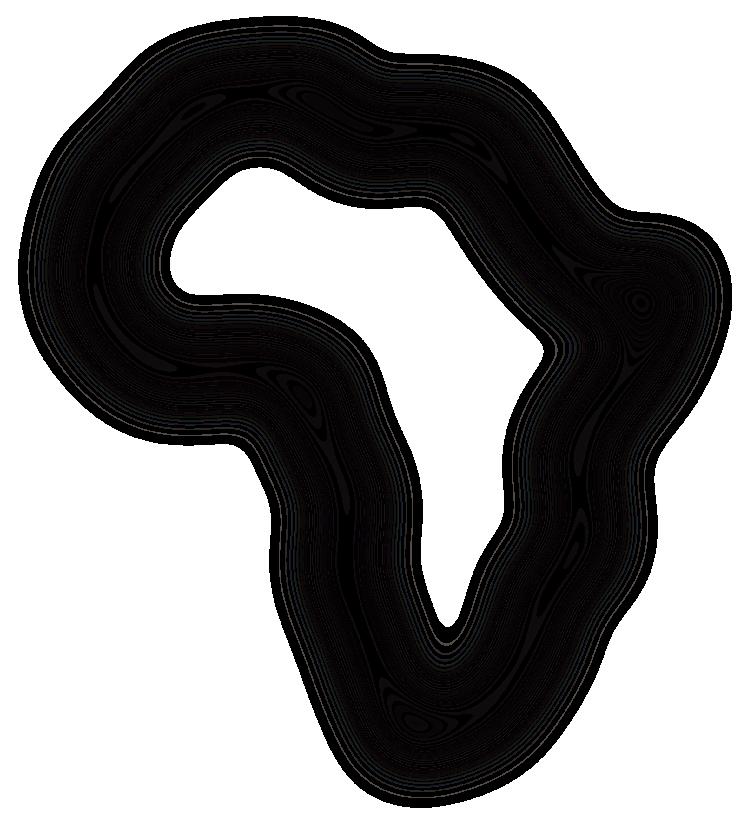
Steel Pipe & Fittings
Valves, Water Meters, & all related products
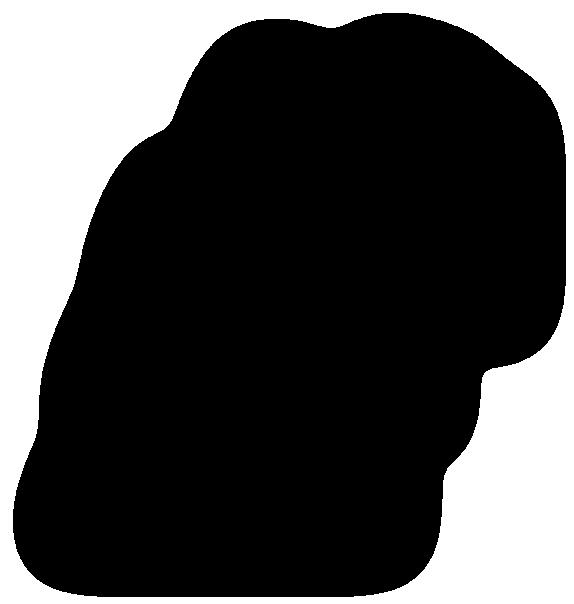
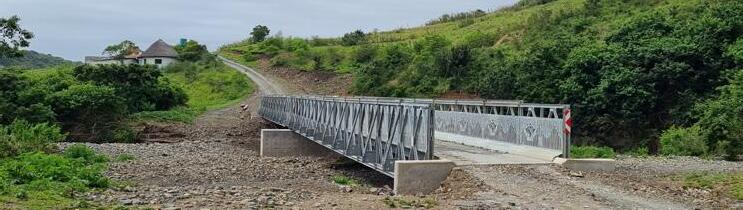
the St Helen’s Rock abstraction works for future generations
treatment plant unveiled









ON THE COVER



World class technology works in conjunction with technical expertise and applied experience, combined with continuous professional development. For original equipment manufacturers (OEMs) APE Pumps and Mather+Platt, founded in 1952, they are the essential ingredients for their success over more than seven decades. P6
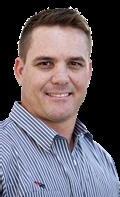
The roads construction sector in South Africa continues to face multiple challenges. However, there are signs of an encouraging turnaround and with that increased opportunities across the industry, says Eddie Jansen van Vuuren, Director at SprayPave. 12
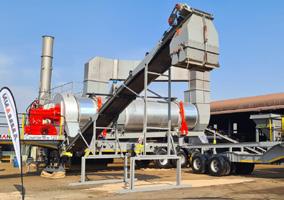
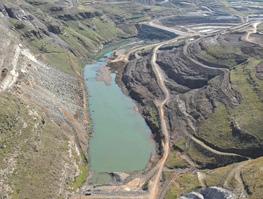
a shared responsibility
the heat with cool paint
and Selby depots to anchor Rea Vaya
trunk route
commuter rail in the spotlight
Purpose
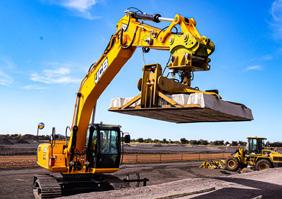



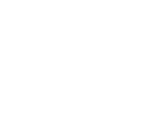
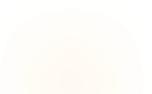
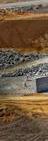
The official magazine of the Institute of Municipal Engineering of Southern Africa


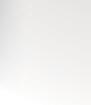




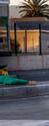

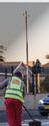

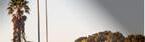

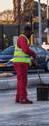


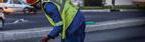







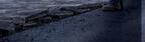




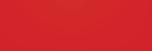


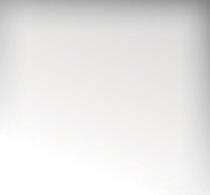
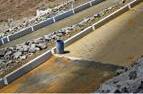
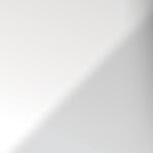





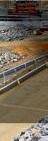

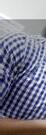

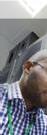




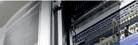

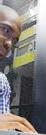


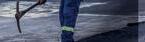
+27 (0)82 346 5338
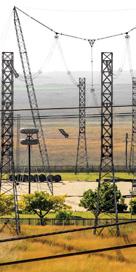
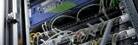
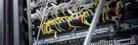

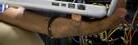












IMIESA , weekly newsletters , social media posts and www.imesa.org are the platforms used by your target audience for information on infrastructure development, maintenance and service delivery. Our readers are key decision-makers in the industry.



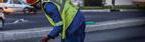
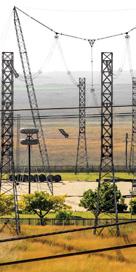
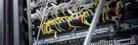





EDITOR Alastair Currie
Email: alastair@infraprojects.co.za
DESIGNER Beren Bauermeister
DISTRIBUTION MANAGER Nomsa Masina
DISTRIBUTION COORDINATOR Asha Pursotham
SUBSCRIPTIONS
Email: distribution@infraprojects.co.za
ADVERTISING SALES
KEY ACCOUNT MANAGER Joanne Lawrie
Tel: +27 (0)82 346 5338
Email: joanne@infraprojects.co.za
Mobility and road safety
Transportation infrastructure forms the backbone of any society and economy, as well as enabling freedom of movement. Within this context, public transport is a key component, both in terms of affordability, convenience, and choice.
PUBLISHER
IMESA (Pty) Ltd
P O Box 2190, Westville, 3630
Tel: +27 (0)31 266 3263
Email: info@infraprojects.co.za
ANNUAL SUBSCRIPTION: R805.00 (INCL VAT)
ISSN 0257 1978 IMIESA, Inst.MUNIC. ENG. S. AFR.
© Copyright 2024. All rights reserved.
IMESA CONTACTS
HEAD OFFICE:
Manager: Ingrid Botton
P.O. Box 2190, Westville, 3630
Tel: +27 (0)31 266 3263
Email: admin@imesa.org.za
Website: www.imesa.org.za
BORDER Secretary: Celeste Vosloo
Tel: +27 (0)43 705 2433
Email: celestev@buffalocity.gov.za
EASTERN CAPE
Secretary: Susan Canestra
Tel: +27 (0)41 585 4142 ext. 7
Email: imesaec@imesa.org.za
KWAZULU-NATAL
Secretary: Narisha Sogan
Tel: +27 (0)31 266 3263
Email: imesakzn@imesa.org.za
NORTHERN PROVINCES
Secretary: Debbie Anderson
Tel: +27 (0)83 326 3050
Email: np@imesa.org.za
SOUTHERN CAPE KAROO
Secretary: Henrietta Oliver
Tel: +27 (0)79 390 7536
Email: imesasck@imesa.org.za
WESTERN CAPE
Secretary: Michelle Ackerman
Tel: +27 (0)21 444 7112
Email: imesawc@imesa.org.za
FREE STATE & NORTHERN CAPE
Secretary: Wilma Van Der Walt
Tel: +27 (0)83 457 4362
Email: imesafsnc@imesa.org.za
All material herein IMIESA is copyright protected and may not be reproduced without the prior written permission of the publisher. The views of the authors do not necessarily reflect those of the Institute of Municipal Engineering of Southern Africa or the publishers.

It also helps to relieve urban congestion, reduce carbon emissions, and facilitate smarter mobility planning, with the Gautrain Rapid Rail Link and integrated bus feeder service, as well as BRT rollouts in metros across South Africa, being prime examples. Incorporating electric and biofuel alternatives adds greenhouse gas emission benefits.
At present, the minibus taxi industry remains the dominant player across the public transport sector in South Africa and SADC. Locally though, Passenger Rail Agency of South Africa is starting to bring more inner-city Metrorail links back online, providing important alternatives for commuters.
However, for those South Africans who can afford it, privately owned forms of transport remain the mainstay, even as petrol and diesel prices climb to record heights. Often, it’s a lifestyle choice, but lack of safe public transport options where they live is a factor.
Why aren’t bikes an option?
Within the mix, the humble bicycle gets overlooked in our market as a “last mile” transit solution, or as a standalone option for comfortable distances under 10 km. Going for an e-bike makes this even more viable because it removes most of the leg work.
In the UK and EU, e-bikes are restricted to a 250 W maximum power output – a limiter automatically capping the speed at around 25 km/h when purely battery power assisted. However, speeds will go higher with added pedal input. So, assuming an average speed of 28 km/h – e-power and pedals – that extends commuter ranges significantly, plus there are great cargo configurations now for small business.
So far, South Africa hasn’t embraced these possibilities to any great extent. And outside the leisure segment, cycling in any form is thin on the ground. This trend is in stark contrast to developed countries – particularly Europe – where bicycles are the mode of
choice for many urban dwellers, irrespective of social status or age.
The Netherlands heads the EU pack with more than 16 million bicycles owned by its citizens against a total population of 17,7 million (per 2022 estimates). Meanwhile leading developing nations like China have more than 500 million cyclists on the road.
In both cases, though, their transportation infrastructure has been designed to specifically cater for cyclists. Elements include dedicated cycle lanes, safe crossing points and traffic calming measures.
Road safety in South Africa
Apart from cultural and social influences, another reason why bicycles may not be common as a commuter choice locally is due to South Africa’s poor road safety record. Aside from blaming potentially substandard roads and potholes, a high percentage of our passenger and pedestrian fatalities are the result of driver negligence.
Worldwide it’s a problem, hence the addition of UN Sustainable Development Goal Target 3.6, which commits to halving the number of global deaths and injuries from road traffic accidents by 2030. At this stage, the World Health Organisation estimates that some 1,19 million people die annually from traffic related incidences, the highest percentage in Africa.
The ripple effect for all nations is an average annual 3% deficit in term of overall GDP (i.e. billions lost that could have been spent on social infrastructure). That’s even more impactful for developing nations working with tight fiscal budgets.
So, let’s focus on road user education that only keeps responsible drivers on the road, and gets the bulk of our urban communities to embrace intelligent public commuter transport that works. Then add bicycle modes to the equation – plus the right infrastructure – and you help promote healthy transit lifestyles that protect lives and the planet.
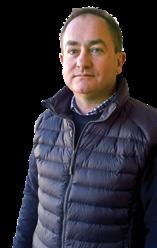

















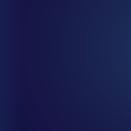



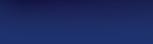

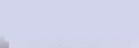
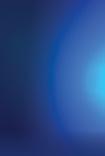
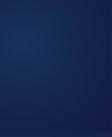
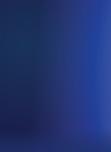








Secure your stand now and have the opportunity to:
• present your company, products and services to a target audience
• gain industry insight and meet potential partners, suppliers and clients
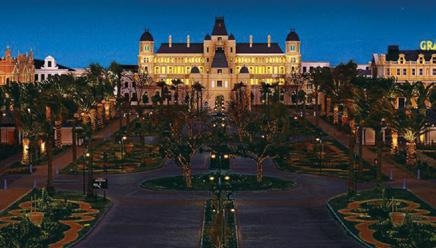
a unique aspect of the conference
enjoy great
• free exhibition stands
• complimentary delegate registrations
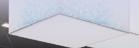



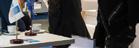
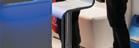
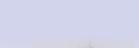
• interact with key decision-makers and industry peers
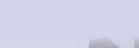
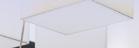

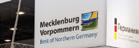
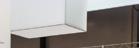

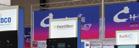

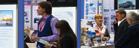
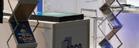
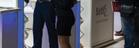
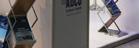
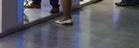
• brand representation at the event, promotion of your company in the conference proceedings magazine and online
• free entry for guests at the social evening and much more.
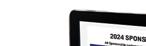
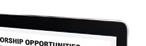
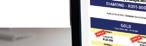


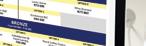
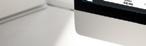
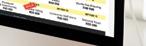
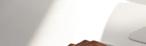
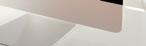

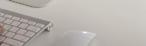
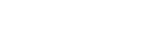
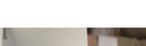
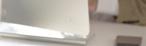
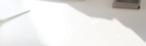
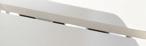
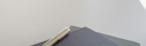
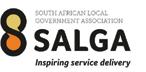
PROACTIVE ENGINEERING CAN MITIGATE FLOOD HAZARDS
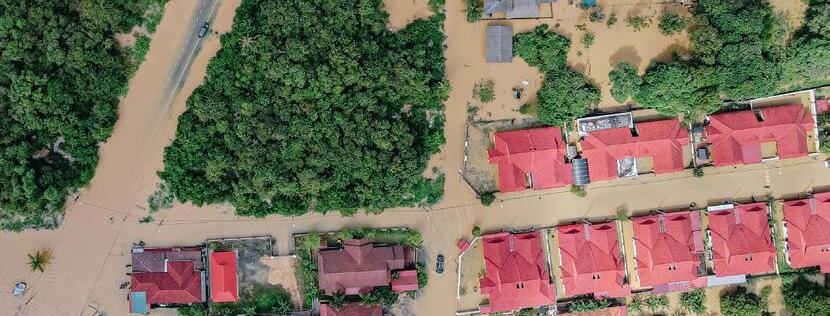
Across the world, the increasing incidence of flooding due to extreme weather events is posing a growing threat to society and economies, compounded by the spiralling cost of reinstating damaged infrastructure. For coastal zones, there’s also the longer-term flood risk posed by rising sea levels in lower lying areas due to these climate change impacts.
Locally, the KwaZulu-Natal (KZN) region remains one of the worst affected, with the April 2022 floods in eThekwini and surrounds recorded as the most catastrophic on record for the province. Unfortunately, however, there’s a high probability of more frequent events on the same scale, based on incidences in 2023, and now another devastating flood in April 2024 across eThekwini and along the KZN south coast.
There’s a clear message here. Firstly, climate change impacts are going to be with us for the foreseeable future and may be irreversible in some cases; and secondly, how we engineered infrastructure and human settlements in the past needs to be revisited and adapted to become far more resilient.
Identifying known risks
The starting point is to identify known flood plains. We must rethink how land-use policies should be planned, designed and approved going forward within legal frameworks. It’s a complex process. However, it’s a vital one because without a scientific and evidencebased approach based on modern-day hydrological data, the opportunity to mitigate flood risk is a hit or miss affair. That just perpetuates the problem and underscores the need for a standardised approach, plus universal understanding.
A practical tool kit
That was the motivation for IMESA and the Water
Research Commission to jointly lead the development of a practical tool kit in conjunction with specialist engineering practitioners, as well as academia at the University of the Free State, the University of KwaZulu-Natal, and Stellenbosch University.
Several years in the making we believe this definitive publication, entitled A Best Practice Guideline for Design Flood Estimation in Municipal Areas in South Africa, will serve as an invaluable reference and benchmark for local authorities and industry. To facilitate its rollout, IMESA is currently running a series of training workshops at six main centres nationally in April and May, with more planned in future.
Future Green City World Congress
Green interventions are a key enabler, ranging from sustainable urban drainage systems to wetland preservation, erosion control, and smart city designs that get us closer to net zero greenhouse gas emission targets. Our towns and cities need to be more circular and climate neutral.
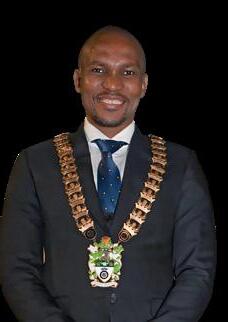
These and allied topics will be covered in-depth at the upcoming Future Green City World Congress, being held from 23rd to 26th September 2024 in Utrecht, the Netherlands. This is certain to be a highly informative event –attracting some 3 000 global
experts, and I plan to attend as IMESA’s President and IFME Board Member.
It’s a joint initiative between the Royal Association Stadswerk the Netherlands and the Royal Dutch Society for Garden Designers and Landscapers (VHG), in cooperation with World Urban Parks and the International Federation of Municipal Engineering (IFME).
In the meantime, there’s an opportunity for IMESA – as an IFME member country – to submit project entries for the upcoming IFME 2024 Excellence Awards. There are two competition categories, namely Construction Project and Development Project (Non-Construction). The ruling is one submission per category per IFME member, with nominations closing on 31st May 2024.
Presented at the Future Green City World Congress, the awards will recognise projects that deliver outstanding community outcomes, improved service standards and positive impacts for society. For South Africa and IMESA, it’s a great opportunity to showcase examples of homegrown best practice on the world stage.
Knowledge exchange is essential, and a core mandate for IFME and IMESA and between 29th and 2nd May 2024 I’ll be in Melbourne, Australia, attending the IPWEA’s International Public Works Conference. I look forward to sharing highlights in the IMIESA May 2024 edition.
In parallel, preparations are now well advanced for the hosting of IMESA’s 87 th Annual Conference, being held between 6 th and 8 th November 2024 at the GrandWest in Cape Town, with the theme “Engineering Revolutionised.” The conference will bring together the best minds from the local and international arena, serving as a vital platform for engagement across the infrastructure spectrum in implementing service delivery in South Africa.
Our training programmes are a core component of the group culture because it’s important at all our qualified technical levels to reinforce their knowledge of the physics and mechanical characteristics of what makes a pump work, specifically the correct product and process specification to recommend for the designated fluid transfer application,” explains John Montgomery, general manager for APE Pumps and Mather+Platt.
“We find that a focus on real-world case studies during these training sessions is invaluable because it enhances our understanding of client processes, highlights potential gaps in their system, and then provides us with an opportunity to put our solutions to the test,” Montgomery continues.
At times these training programmes include presentations by clients’ engineers on their plant setup and how it’s designed to operate, such as at a wastewater treatment plant, a power station or an industrial refinery, which provides core insights based on their applied experience.
“A proactive two-way information exchange is vital for long-term customer engagement and trust in support of their current and future process requirements – reinforced by our 72 years to date in the pump business across all industry sectors. That says a lot about our fabrication, aftersales and maintenance support capabilities.”
The heart of the system
Within the fluid transfer environment, pumps are at the heart of the process system, transferring fluids from point to point. However, the best efficiency point (BEP) – or “sweet spot” in terms of rated flow and head – is interdependent on how the overall network is performing. Pumps don’t operate in isolation.
The optimum BEP for pump selection is based on the system resistance. Over time, plants are frequently upgraded – pipe sizes change, and networks are extended – which must be taken

Pumps need to perform at their best efficiency point
World class technology works in conjunction with technical expertise and applied experience, combined with continuous professional development. These are the definitive elements for success – they all hinge on talent management, succession planning, ongoing skills development and transfer within a proactive mentorship environment. For original equipment manufacturers (OEMs) APE Pumps and Mather+Platt, founded in 1952, these are the essential ingredients for their success over more than seven decades.
into account when determining whether existing pumps are still able to cope. Other factors to consider include water quality changes that might impact on transfer efficiencies and accelerate wear and tear on pump components.
“Some 90% of the time when we’re asked to perform a dynamic assessment, it’s a system issue rather than a pump one,” explains Thorne Zurfluh, a mechanical engineer at APE Pumps and Mather+Platt, who joined the Group some two years ago having come from an EPC background.
Standby pumps, for example, are essential in the system design, which is a standard practice. “However, we’ve experienced situations where all the pumps are running – including the standby units – to meet demand capacities,” Zurfluh continues.
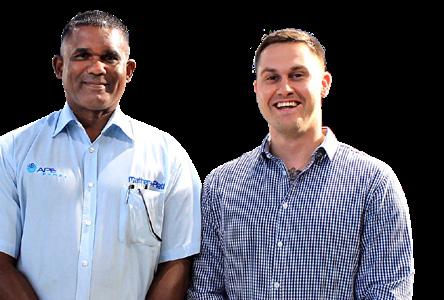
In one instance, this was in response to pipeline leakages during the transfer of raw water from the client’s river abstraction works to the potable water treatment plant. To handle these losses and balance the system, more pumps had to be added to maintain pressure and flow. That translated into increased energy costs and escalating overall process expenditure.
“Pipeline clogging will also clearly impact on
what pumps can deliver in terms of rated versus required flow. A detailed computational fluid dynamics (CFD) analysis – based on instrument diagnostic readings recorded on site, like temperature, flow, vibration, and alignment – is the only way to verify if it’s a pump or a system issue,” Zurfluh explains.
The temptation to use pirate parts to save on maintenance costs has also been an issue in industry, resulting in an increased incidence of breakdowns. In one study for a water utility, this was the case. However, they’ve now taken the decision to switch back to OEM parts. In addition, the utility was also experiencing system issues.
“In this instance, the system resistance curve was overestimated, meaning that the friction in the line was a lot less than anticipated. In this scenario, when you run the pumps at their design duty, their performance moves over to the left of the BEP curve in overload conditions. That’s problematic for pump performance. We’ve now advised them through consultations that in terms of optimisation they need to have two parallel systems running at the same time,” says Zurfluh.
Test facility
To perfect its approach, the Group is now in the process of building a test facility at its factory
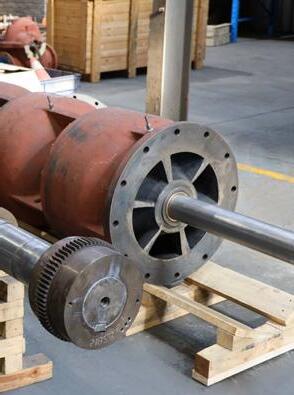
in Germiston, Gauteng, equipped with state-ofthe-art instrumentation. This forms part of APE Pumps and Mather+Platt’s turnkey strategy to bring everything in-house. Initially, this facility will test up to 75 kW for the OEM’s smaller end-suction and horizontal split case pumps.
“In terms of fluid mechanics optimisation, we’ll be able to conduct live tests, with the data fed back to the design office. This initiative forms part of our research and
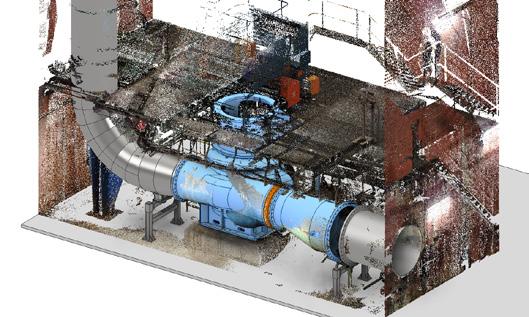
An example of a 3D plantroom scan and pump overlay forming part of a conceptual design
development programme, where we can trial new technologies, as well as finetune custom pump designs for clients,” explains Neil Richards, sales engineer for APE Pumps and Mather+Platt, adding that there are plans to expand this test facility at a later stage to handle all pump classifications.
Assembly and maintenance
Alongside pump fabrication, a key aspect of
overall quality management is the assembly phase since even the smallest part is significant to the overall build. Most components are now fabricated in-house.
“We ensure all components are manufactured to the exact design criteria, which makes the pump assembly process highly precise and efficient,” Richards continues.
From an aftersales perspective, scheduled component maintenance and changeouts are an
An example of a BEP optimisation analysis. Every pump has a design point where it should be run, and a duty point
is currently running. The degree of variance can significantly impact the life of the pump and its rated output
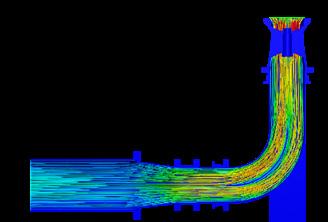
Computational fluid dynamics (CFD) simulation allows APE Pumps and Mather+Platt’s engineering teams to model hydraulic and pressure optimisation scenarios
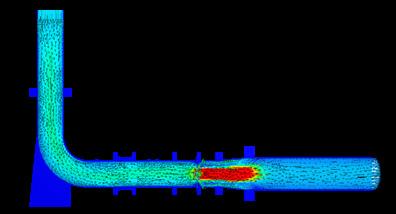
equally crucial part of pump performance optimisation during OEM specified refurbishment intervals. This typically ranges between five to eight years, depending on the application.
Routine maintenance includes oil changes in thrust assemblies and the servicing of gland packing to protect the shaft and ensure a watertight seal. The frequency
will be determined by the fluid being pumped, and whether it’s being pumped at high or low flow rates. This will further influence the wear on key components like bearings and impellers. The latter can be fabricated in cast iron, stainless steel or bronze depending on the application. Stainless steel (in various grades) tends to be the most durable, particularly for raw water transfer, while bronze impellers are common for clean and potable water transfer.
Service level agreements
“In addition to fabrication and pump commissioning, within our portfolio we also provide operations and maintenance support for clients in terms of service level agreements (SLAs),” explains Richards. “This has significant benefits for the client as we
can then ensure that our pumps and their system work in synch.”
Depending on the type of SLA, this could include the provision for Group personnel on site, working in conjunction with the client’s technical team as part of a value engineered and skills transfer approach.
Here for the future
“In all respects, as a group we are dedicated to working with our clients to achieve the best results. System analysis is crucial, especially where processes or operating conditions have changed, and where institutional knowledge may or may not exist if there are skills and personnel gaps,” adds Montgomery.
“We have pumps still in service that were installed in the 1950s across South Africa and Southern Africa. So, we know how to keep them working. That’s thanks to our investment in training and technologies, which guide customers in their quest to continuously modernise and optimise their plants at the lowest process cost. It’s a dynamic operating environment,” Montgomery concludes.
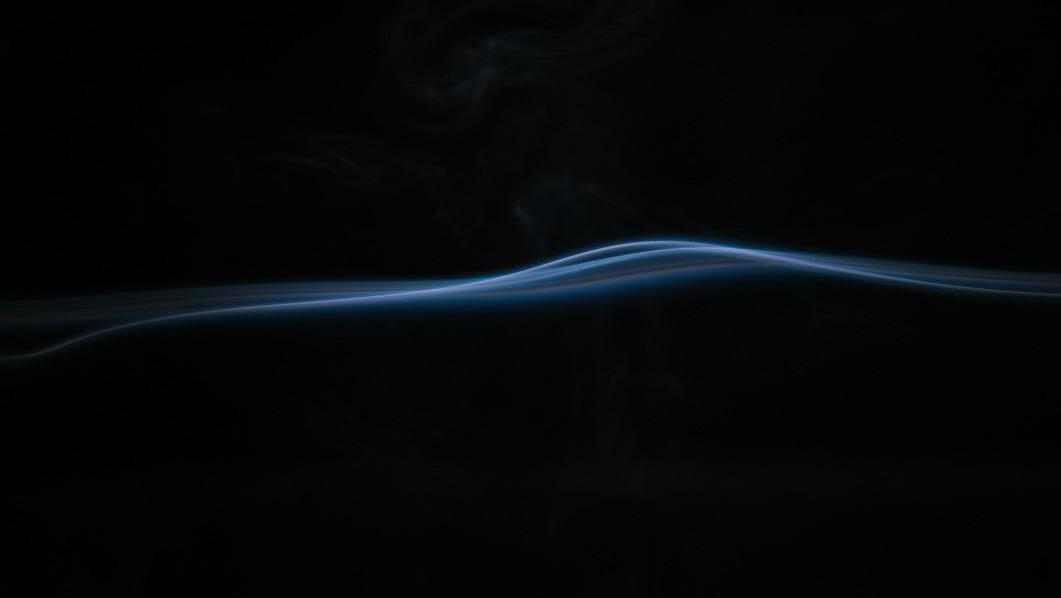

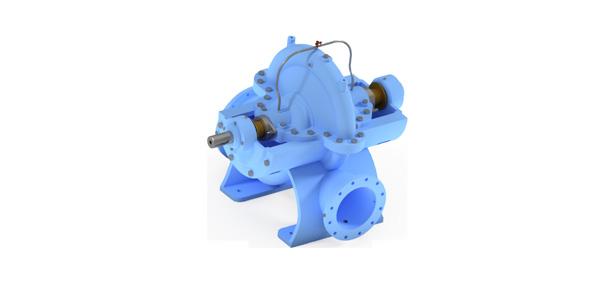
Operating Range
Flow - 10m³/hr up to 2500m³/hr
Head - 4m up to 120m
Applications
- General liquid pumping
- Power plants
- Bulk Water
- Steel mills
- Refineries
- Chemical plants
- Cooling and heating systems
WATER EFFICIENCY: BUILDING WATER FOOTPRINT MANAGEMENT FOR GREENER INFRASTRUCTURE
Water footprint awareness refers to our understanding and consciousness of the amount of freshwater used by individuals, communities, businesses, or products throughout their lifecycle.
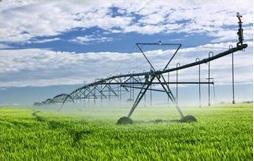
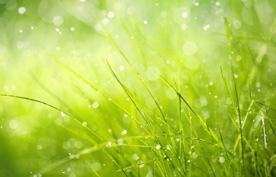
It involves recognising the impact of daily activities, consumption patterns, and production processes on water resources.
The concept of a water footprint considers not only direct water usage but also the indirect water usage embedded in the production and supply chain of goods and services.
Water footprint awareness and action is a critical component of broader environmental education and sustainability initiatives. By making individuals and organisations aware of their water footprints, it becomes possible to inspire positive changes in behaviour and encourage the adoption of water-conscious practices. This awareness contributes to a more informed and environmentally responsible approach to water management, helping to address global water challenges and promote a sustainable future.
Positive engagement
Ways to engage colleagues, and decision makers about their water footprint and the impact of everyday choices on water usage for buildings, with concrete examples:
Professional Settings
1 Employee Education Programmes
Encouragement: Implement water conservation training programmes for employees. Example: “Organise workshops to educate employees about water-efficient practices in the workplace. Empower them with knowledge on how to contribute to water conservation efforts.”
2 Smart Landscaping
Encouragement: Promote water-conscious landscaping practices around the office. Example: “Opt for native plants and implement efficient irrigation systems and practices in the office landscaping. It not only enhances the workplace environment but also conserves water.”
3 Regular Maintenance
Encouragement: Emphasise the importance of regular maintenance of water infrastructure to prevent water wastage. Example: “Incorporate regular checks for leaks and plumbing issues as part of the office maintenance routine. Quick turnaround times can prevent unnecessary water wastage.”
4 Water-Efficient Fixtures
Encouragement: Install water-efficient fixtures in workplace restrooms and kitchens.
Example: “Start by upgrading office facilities with low-flow faucets, and water-efficient toilets and then move on to consider sensor-activated taps. These changes contribute to a more sustainable and waterconscious workplace.”
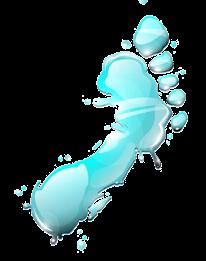
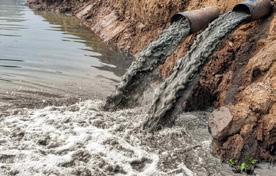
5 Sustainable Purchasing Policies
Encouragement: Advocate for sustainable purchasing practices that consider water footprints.
Example: “Consider the water footprint of products and materials when making purchasing decisions for both personal and professional settings. Choose ecofriendly options that align with water conservation goals.”
Be Water Wise
To encourage water-conscious habits, Rand Water has adopted a mixed method of education, awareness-raising, and practical activities through the Water Wise brand. By putting these examples and efforts into practice, Rand Water believes people and organisations may contribute to the promotion of a more ethical and sustainable use of water in both personal and professional situations.
Sources: https://smartwatermagazine.com https://crwater.com/whats-my-water-footprint/
www.randwater.co.za 0860 10 10 60

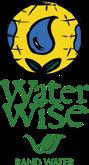
The flexibility of gabion civil and building infrastructure
Whether for civils, building or architectural applications, there are a multifaceted range of gabion solutions that provide both design appeal and durability. IMIESA speaks to Louis Cheyne, managing director at Gabion Baskets about project and product developments.
On the civils front, recent orders include the supply of gabion systems that will be used for the construction of bridge abutments forming part of South Africa’s Department of Public Works and Infrastructure’s rural bridge programme, six in the Eastern Cape and four in Limpopo. These are modular steel truss “Bailey-type” bridges that will provide vital links for remote communities. This follows a Gabion Baskets supply order for a series of bridges in KwaZulu-Natal for the same programme, which have now been completed.
Worldwide, gabion bridge abutments are a common feature on these types of structures and are especially popular in rural regions within developing countries because of their costcompetitive construction methodology. In-situ rock materials can be sourced for the gabion fill, and labour intensive techniques used for their construction, providing a welcome source of employment, skills transfer and income for the community participants involved.
FiberRock® geosynthetic sand containers provide an effective means of countering beach erosion. For optimum results, bags should be filled with a clean source of permeable sand, free from debris and other possibly damaging objects
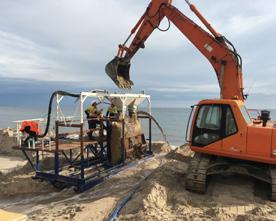
“In addition to support, these abutments –comprising gabion baskets resting on a gabion mattress foundation – also provide effective erosion protection against scouring and floods,” Cheyne explains, adding that gabions can withstand forces per m2 of 300 to 400 tonnes.
“We see huge potential for these types of
structures across South Africa, as well as in Africa where we have a growing presence.”
“Civils projects supplied to date in South Africa and Africa include extensive river erosion works and mass gravity retaining walls. Plus, we continue to supply design recommendations and products for allied structures like gabion weirs, at times combined with integrated culvert road and pedestrian crossings, plus donga counter erosion protection measures. There are also increasing enquires from mines in Africa for gabion solutions for structural and erosion applications.”
Product solutions
In addition to being a specialist manufacturer
Modular steel truss bridge abutment composed of gabion baskets founded on a gabion mattress
FiberRock ® GEOSYNTHETIC SAND CONTAINERS
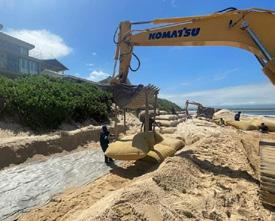
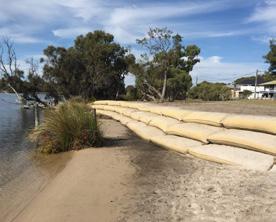
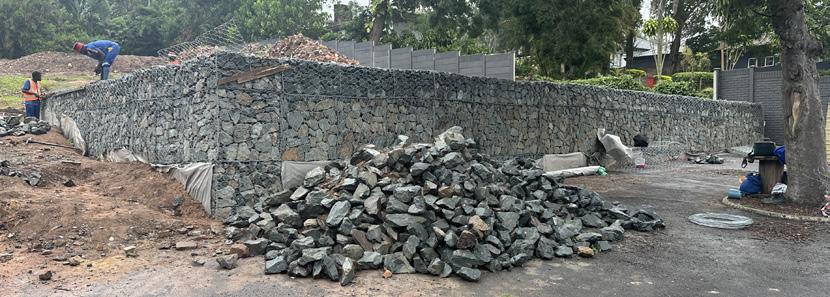
of Class A Galvanised hexagonal double-twisted woven mesh steel wire and square welded mesh systems – with the added option of more corrosion resistant Gaflan zinc-aluminium coated wire, and polyethylene coatings – Gabion Baskets supplies a range of allied products, combined with services that include training, project management supervision and installation advice.
Geosynthetic sand containers
Recent product additions include the conclusion of a distribution agreement to supply FiberRock® geosynthetic sand containers (GSCs) employed for coastal erosion and riverine protection.
Gabion Baskets also supplies its own range of gabion flood protection barrier systems, in addition to gabion barrier defence cells used for military applications. In both cases, these are built as standard using welded mesh materials to form the interconnected cells (hexagonal doubletwisted woven mesh steel wire being a secondary option), in conjunction with a heavy-duty geotextile lining to contain soil particles, using either sandy or cohesive soils.
Residential and commercial retaining wall projects
Within the civils segment, Cheyne says there’s also a growing demand for gabion systems in the
Gabion weir elevation
residential and commercial markets. Recent examples include two projects in KwaZulu-Natal where Gabion Baskets has supplied solutions.
The first was for a private residence within the Cotswold Downs residential estate in Hillcrest. This entailed the installation of a mass gravity gabion wall to retain a 4 m high embankment behind the house. For maximum aesthetic affect, square welded mesh gabion panels were used to create a flat front finish. These panels were filled with a mixture of brown and grey rock to provide a sense of depth and warmth.
The final structure measures 24 m long, with an 8 m wing wall on the left and a 4 m long wingwall on the right. The main wall measures up to 1,5 m in height, and the wingwalls 1 m respectively.
The second project in Westville entailed the installation of a 2,8 m high wall installed as the front face for a level platform to incorporate additional parking bays for a commercial client. This time, the emphasis was on function over form, with hexagonal double-twisted woven mesh wire specified for the gabion basket composition.
“Square welded mesh is the standard choice for architectural applications like building and wall cladding in land based, as opposed to submerged riverine environments. In terms of
Work at an advanced stage on the construction of a 2,8 m high wall installed as the front face for a level platform to incorporate additional parking bays for a commercial client in Westville, KwaZulu-Natal
the latter, hexagonal double-twisted wire is the mandatory choice because it caters for flex and debris impact. Square welded mesh panels are intentionally rigid to achieve precise lines and will fail in this respect. However, for those on a budget, hexagonal mesh does the job in every application,” Cheyne concludes.
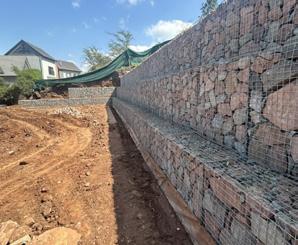
A perspective of the Cotswold Downs project in Hillcrest, KwaZulu-Natal. This entailed the installation of a gabion wall system to retain a 4 m high embankment. Square welded mesh panels were used to create a perfect flat front finish – a popular choice for landscape architecture applications and building cladding
The roads construction sector in South Africa continues to face multiple challenges. However, there are signs of an encouraging turnaround and with that increased opportunities across the industry, says Eddie Jansen van Vuuren, Director at SprayPave.
SprayPave, one of the country’s leading manufacturers and suppliers of bitumen, modified binders, and emulsions is adopting an energetic, proactive approach to ensure a sustainable future for itself and urges other players in the industry to be agile and ready for change.
Jansen van Vuuren flags what he believes to be the two most important issues currently in play. “First, our immediate future as an industry depends on us successfully navigating election dynamics. Second, we must be ready to meet the surge in demand for our products and services as roads projects eventually start to ramp up from several slow years.”
It might be argued that the South African elections on 29 May 2024 will impact the anticipated increase in roads projects, whether positively or negatively. However, Jansen van Vuuren attests that the backlog of new infrastructure and maintenance work on our roads must be a vital and pressing issue for any government in South Africa. The industry has a critical role to play in ensuring that this remains top of mind.
We must stand together
“Historic underinvestment, delays in project execution, budgetary constraints and regulatory complexities pose significant hurdles for all industry players, but we cannot simply hope for the best. If we stand together, we can remain resilient as an industry and be the change we need. It is essential to ensure we continue the upward trajectory that has been put in motion this year as SANRAL ramps up new projects.”

Jansen van Vuuren urges active engagement with government officials, regulatory bodies, and

A SprayPave contract between Herbertsdale and Gouritsmond for the Western Cape Department of Transport and Public Works. This was SprayPave’s first EBR (Extended Bitumen Rubber) spraying project, using bitumen produced in a 25 tonne per hour automated blending plant that incorporates waste crumbed rubber tyres in the bitumen
Navigating challenges and seizing opportunities
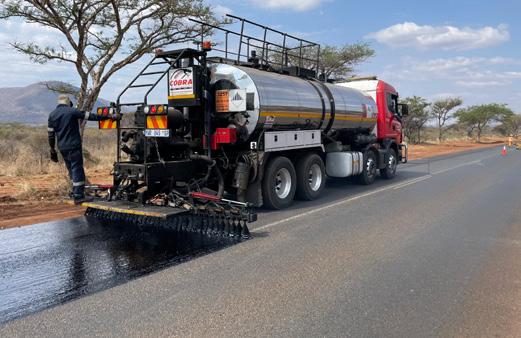
SprayPave’s fleet of bitumen distributor tankers services the whole of South Africa. This one is placing bitumen manufactured at the company’s Alrode, Johannesburg, plant on the R33 between Stofberg and Groblersdal in Limpopo in a contract for RAL
policymakers to stay informed about policy changes and advocate for continued investment in road construction projects.
Compliance with environmental regulations and sustainability goals will make businesses more attractive to government bodies and clients wishing to align with suppliers who do the right thing, he points out. “We must be compliant, we must be vigilant, and we must be adaptable to succeed and grow during what will possibly be a rocky period ahead.”
Innovate to beat the challenges
Investment in technology and innovation is key for all industry players, not only to enhance their productivity, reduce costs and improve project quality, but also to stay abreast of rapidly changing project specifications and requirements. Smart infrastructure technologies, sustainable construction practices and materials, and digital project management tools that enhance adherence to sustainable development goals will better help the industry to navigate potentially muddy waters and prepare for the future.
In an uncertain political and economic climate, the suppliers and contractors who are best
prepared to take on challenges will be the ones who win the work. Proof of sound financial planning and risk management make this pioneering spirit even more attractive to clients, Jansen van Vuuren adds.
Hand-in-glove with this, he says, is diversification. “Expansion into related sectors such as transportation infrastructure, renewable energy projects, or public private partnerships will spread the risk and give you a better chance of riding out the hard times.”
Develop and retain skills
To be properly equipped, significant multidisciplinary skills are needed. “Investment by individual companies in developing and retaining their skills at all levels is key to everything else. It also shows commitment to upskilling the industry, which is urgently required in South Africa.”
These strategies, aided by clear communication and collaboration with a view to strengthening the industry, are central to SprayPave’s vision for sustainable growth. “We are focusing on scaling our operations, upholding quality and compliance, and enhancing our project management to accommodate growth, as well as optimising our supply chain.”
Jansen van Vuuren stresses the importance of proactive engagement with not only government agencies, but also industry peers and academia, showing commitment to collective progress and addressing common challenges. “Our strategic partnerships and collaborations with suppliers, subcontractors, and other stakeholders across the value chain will help us to access additional resources, expertise, and support to scale operations seamlessly.”
A collective approach
“The roads construction sector collectively is much stronger than its components and
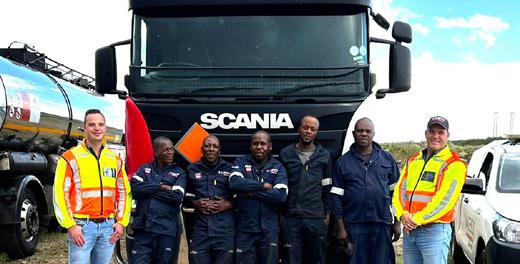
SprayPave management is involved from the start to finish of every contract. “Being visible is key and employees, customers and clients value this,” says Anton van Rooyen, Business Development and Marketing Manager. Pictured at a project start-up are SprayPave team members (from left): Anton van Rooyen; Moses Metiso, Bitumen Distributor Driver; Lucky Nhlapo, Bitumen Distributor Specialist Mechanic; Samuel Sekgobela, Bitumen Distributor Operator; Vincent Duba, Bitumen Distributor Operator; Phineas Mzizi, Bitumen Distributor Driver; and Director Eddie Jansen van Vuuren
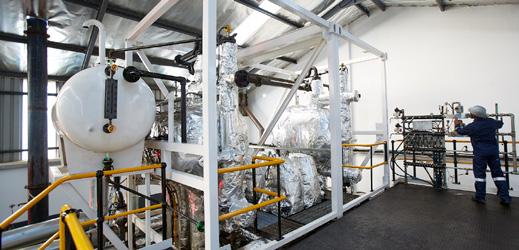
SprayPave believes that if we are all clear where we fit in and how we can add more value, that can only make us more robust
EBR application

and resilient as an industry.” Jansen van Vuuren adds that SprayPave’s commitment to industry advancement is evident in its active support of the Southern African Bitumen Association (SABITA).
“SABITA provides invaluable benefits to the sector by providing a platform for collaboration on cutting-edge technologies and practices and advocating for policy decisions to promote excellence in road infrastructure development.”
He concludes that SprayPave remains optimistic about the future of the road construction industry. “We anticipate increased post-election infrastructure spending and will leverage our expertise, innovation, and strategic partnerships to contribute meaningfully to South Africa’s development goals.”
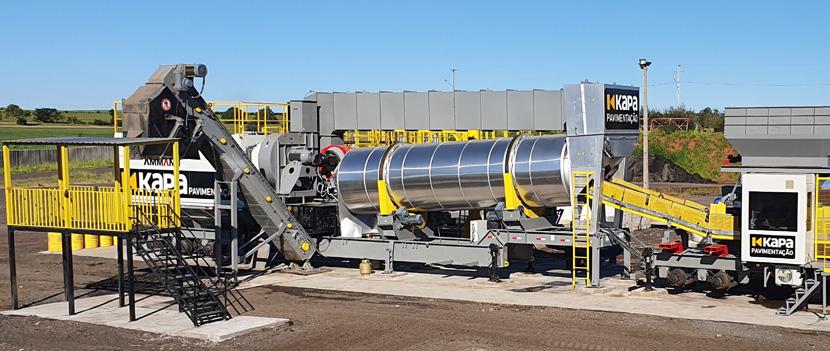
AMMANN RESPONDS TO REGIONAL DEMAND IN SA AND AFRICA
In South Africa, there’s been a notable increase in orders for retrofit plants – predominately mobile as opposed to static – as customers seek to leverage their initial investment by extending the life of their units, an area where Ammann provides specialist solutions,” explains Rocco Lehman, managing director of Ammann Kenzam.
Founded in 1869, Ammann is a class leader in the design and development of batch and continuous asphalt mixing plants, concrete plants, and construction machines. The latter comprise soil and asphalt compactors, pavers (tracked or wheeled), and light construction equipment (namely, rammers, vibratory plates, walk-behind rollers,
Within the cyclical regional roads market, Ammann Kenzam, a wholly owned subsidiary of Swiss multinational, Ammann Group Holdings AG (Ammann Group), has made concerted gains with new asphalt plants sold into the Sub-Saharan Africa region, together with a rising demand for retrofit plants, particularly in South Africa.
add-on compactors and trench rollers). These products are fabricated in specialist factories across the globe.
In Sub-Saharan Africa, Ammann Kenzam is the direct customer interface for asphalt

and concrete plants, with the construction machine range in South Africa and certain Southern African territories supplied and supported by ELB Equipment.
Asphalt mobile plant refurbishments
Ammann’s operating motto is “Productivity Partnership for a Lifetime,” which underscores the OEM’s commitment to keeping machines and plants in play for generations through progressive rebuild enhancements.
Undertaking a plant retrofit – static or mobile – may seem daunting, but Ammann’s technical support makes this a relatively straightforward process for existing customers, as well as those considering buying a used unit. These retrofits bring the plant up to the latest
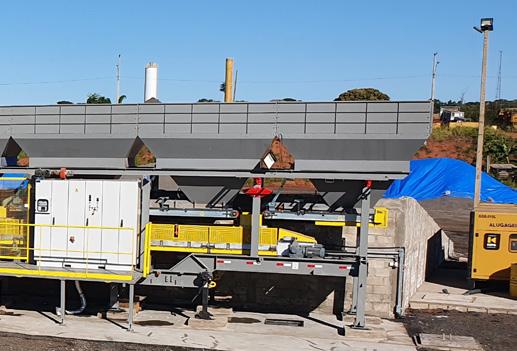
Ammann technological standards and industry production requirements (like RAP, foamed asphalt, newly designed burners for greener energy and associated additives), together with environmental compliance to an “as new” standard that can typically add another 20 years of operating life.
In South Africa, project examples include an extensive upgrade on an approximately 10-year-old ACM 140 Prime mobile continuous asphalt mixing plant, which has seen extensive local utilisation. The approximately three-month refurbishment programme took place at Ammann Kenzam’s facility in Brakpan, Gauteng. Key retrofit modifications included a new mixer to meet 25% RAP requirements, as well as an associated Ammann operating system software update.
Manufactured by Ammann in Brazil, the ACM Prime series – available in three models with outputs of 100, 140 and 210 t/h respectively – are highly mobile versions of Ammann’s static continuous asphalt mixing plants. Fitted on trailers, they come equipped with Ammann’s innovative
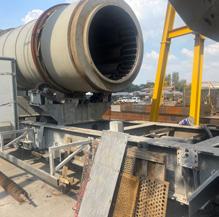
as1 Control System, as well as tried-andtested core components.
“A special benefit of these ACM Prime plants is a controllable outlet gate that enables the filling height and therefore the mixing time to be set depending on recipe and output,” Lehman explains.
Complementary products
A key competitive edge for Ammann Kenzam is its ability to locally manufacture a wide range of complementary equipment. These include bitumen drum decanting units, bunded containerised bitumen storage tanks, cylindrical storage tanks (horizontal and vertical), and bitumen drumming plants.
Within Africa, Ammann Kenzam recently secured an order for a new 10 tonne emulsion plant, which will be deployed by the client in Guinea – a new country market for Ammann.
“In addition to our more standard fabrication offering, we’re also receiving requests for more niched solutions. These include the supply of ship to shore bitumen off-loading gantries at South African and

regional ports,” Lehman continues. These gantries incorporate pump systems for bitumen transfer via installed pipe systems and greatly improve fluid transfer to awaiting tanker trucks.
New asphalt plant orders
Alongside buoyant activity within its plant refurbishment and complementary equipment portfolios, the past six months has seen a major surge in cross-border orders for new asphalt plants, driven by strong construction activity.
Within the mix, Ammann’s CounterMix 120 continuous asphalt mixing plant is a popular choice. Sales to date in 2024 include two units acquired by a customer in Zimbabwe, and a CounterMix 120 unit supplied to a DRC based client.
Available in three models with outputs ranging from 90 to 120 tonnes – with an optional equipped 50 tonne hot mix storage silo – Ammann’s CounterMix plants are manufactured by Ammann India. Key features include a high efficiency counterflow dryer drum with a fully modulating long nose burner.
“Conventional mixing plants utilise parallel flow heat transfer technology in which the material to be heated and the hot gases flow in the same direction,” Lehman explains. “In a counterflow dryer drum, however, the material to be heated and the hot gases flow in opposite directions. This process is extremely efficient, because it utilises heat from both the hot gases and the burner flame.”
In addition to fuel efficiency and enhanced environmental protection, these plants are also capable of producing mix designs that
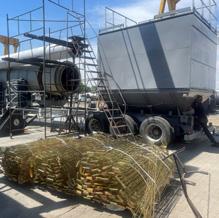

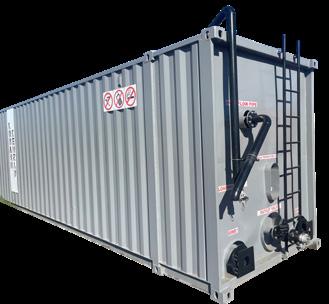

contain high percentages of RAP –meeting the increasing demand worldwide for asphalt recycling interventions.
“One of the new CounterMix 120 units being supplied to the Zimbabwean client will be trailer mounted by Ammann Kenzam to make these units road legal for on-road towing,” Lehman explains.
This will be Ammann Kenzam’s second CounterMix 120 trailer mount conversion to meet market demand, following the successful design and commissioning of its first road legal unit in 2022 for a Zimbabwe-based contractor. For the latter, the plant was set up to be transported in four trailer-mounted sections. (The number of trailer units depends on the extent
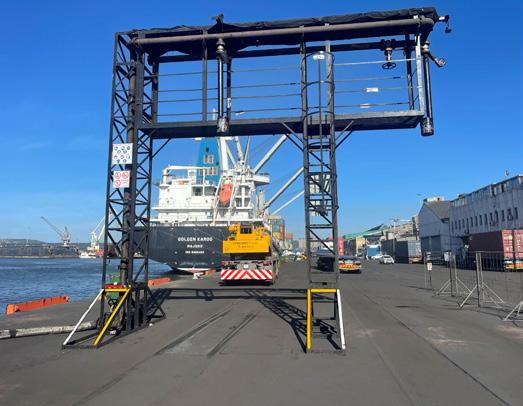
of allied elements like bitumen tanks and decanters.)
Other recent Ammann Kenzam sales include a ValueTec 140 batch plant (140 t/h output) sold to a neighbouring country during 2023, which has now also placed an order for a new CounterMix 120.
In January 2024, Ammann Kenzam also received an order for the supply of an Ammann WetMix plant for another customer in Zimbabwe.
Like the CounterMix series, all of these plants are being shipped from Ahmedabad in India. The latter facility is also responsible for the fabrication of Ammann’s value engineered compaction rollers and asphalt pavers.
Package deals and maintenance contracts
“We often receive requests for plant and machine package deals, especially in Africa, where many contractors tend to focus on providing a turnkey asphalt supply, paving and road construction solution,” Lehman explains.
To keep plants running at optimum levels, Ammann Kenzam also provides maintenance contracts with on-site and remote technical support. In terms of the latter, the Ammann Group are currently rolling out a Virtual Reality headset concept to enhance the process. The client’s technician on site wears the headset and what he or she sees is mirrored remotely on the Ammann technician’s smart device or PC.
“This is an example of how Ammann’s research and development initiatives are being applied to optimise the ownership experience so that contractors can achieve the best return on their Ammann plant and machine acquisitions. They have the added assurance of future retrofit options to keep them up to date with the latest technologies,” Lehman concludes.
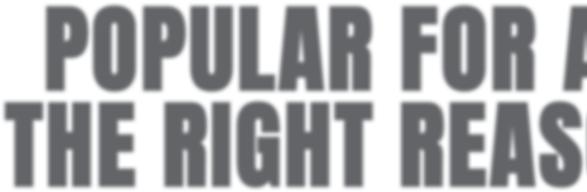
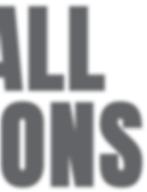
POPULAR FOR ALL THE RIGHT REASONS
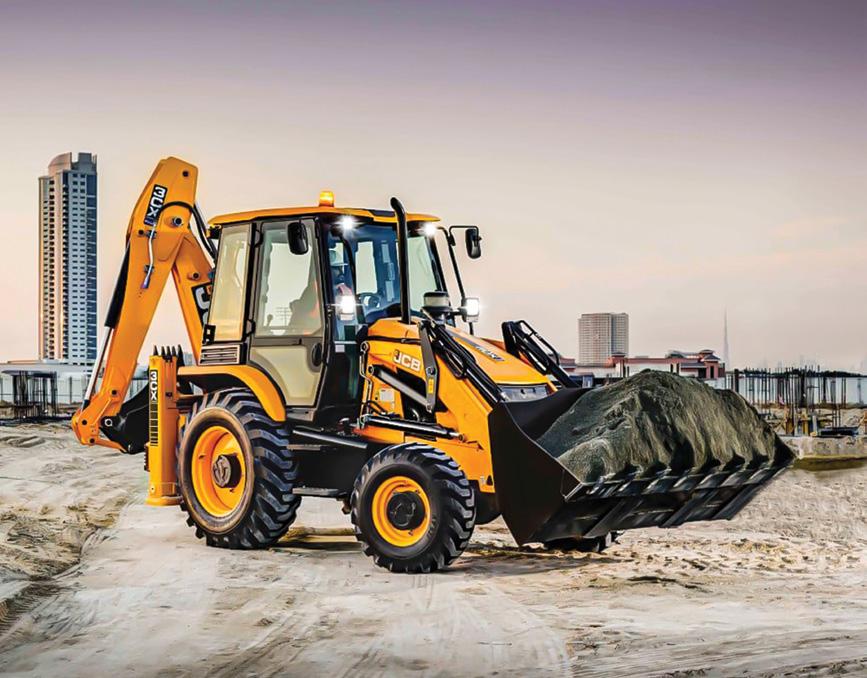
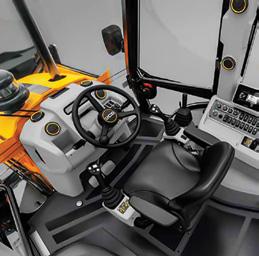
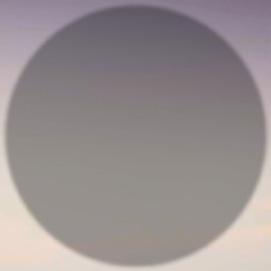
INNOVATIVE ROCK TO ROAD EQUIPMENT SET TO ADVANCE AFRICAN INFRASTRUCTURE PROGRAMMES

The World Bank describes roads as the arteries through which the economy pulses. In keeping with this analogy, Africa’s road infrastructure is in a critical condition. Astec Industries is well placed to help treat the continent’s infrastructure deficit with its expansive Rock to Road equipment portfolio.
The African Development Bank has stated that African countries need to accelerate their investments in infrastructure, but in a smarter way.
“In this respect, our smart equipment for road building in Africa is world-class, hightech and tough,” says Calvin Fennell, Regional Sales Director at Astec Johannesburg. “It is cost efficient, fuel efficient and easy to maintain.”
“Productivity, sustainability and longevity are essential. In Africa, operating conditions can be arduous, sites are often remote, and skills, resources and funding are limited. The availability of support, service and spares can make or break the project,” he stresses.
Astec’s Rock to Road range includes equipment for every phase of road building –from quarrying, crushing and processing the aggregate to concrete production and road construction. Astec supplies more than 100
products to a global customer base in the aggregates, construction, infrastructure and mining sectors, and offers worldwide training, education, service and support.
The group’s operations are divided into two primary business segments. Materials Solutions includes aggregate and other material handling and processing solutions, including crushers, screens, apron feeders and rock breakers. Infrastructure Solutions includes road building, asphalt and concrete plants, thermal and storage solutions.
Fennell notes that Astec’s Materials Solutions equipment, including robust products manufactured at the triple ISO accredited Astec Johannesburg manufacturing facility, already has a strong presence in African markets and has proved its mettle at mines, quarries and plants around the continent. “But Astec Industries never rests on its laurels. We constantly strive to improve and innovate, developing new products and technologies to drive our customers’ success and give them a competitive advantage,” he explains.
Titan cone crushers
“Examples of the latest innovations in our Materials Solutions equipment include the soon to be launched (in the Africa Middle East territory) T Series of cone crushers. Titan cone crushers are engineered to deliver uncompromising productivity, safety and easeof-maintenance for maximum uptime in tough, abrasive applications. They feature patented hybrid bearings and a more stable cone head and offer higher capacity and less friction,” says Fennell.
Milling
Astec’s asphalt milling machines, which fall into the group’s Infrastructure Solutions equipment range, are making their mark and can enhance African infrastructure projects, Fennell says. “Asphalt milling, also known as cold planing, is the removal or milling up of an asphalt surface to provide an improved surface for repaving or resurfacing. It is a costeffective and sustainable way to reconstruct an asphalt surface and it offers faster project completion times. Asphalt milling can also be used to address specific issues with small sections of roadway. When the entire surface does not need to be resurfaced, the target area can be milled without disruption to the rest of the road.”
High-performance, fuel-saving asphalt milling machines like the Astec RX-600ex are ideally suited for infrastructure programmes in Africa, he states. This is a 630-horsepower,
four tracked cold planer, capable of achieving cuts up to 330 mm deep and 2.184 m maximum width. The RX-600ex is powered by a fuel efficient Cummins engine with low exhaust emission.
“Having the optimal balance between weight and power results in excellent cutting capability. It achieves great traction while maintaining the desired depth of cut. If the machine was too light, it would be bouncing around, affecting the depth. If it was too heavy, all the weight would be in the wrong places. This machine’s balance is ideal,” Fennell explains.
Recyclers
The Astec SX-6ex recycler offers two applications in one high-performance machine, making it ideal for use on African road repair projects, he asserts.
“It can be used for both soil stabilisation and asphalt reclamation. Equipped with a 6-cylinder diesel engine that provides power to the rotor through a direct drum drive, the SX-6ex can cut up to 508 mm deep and 2,540 mm wide.”
Soil stabilisation is efficient in terms of time, money and natural resources. Rather than preparing a base with new soil trucked in from another location, the existing material is combined with binding agents and recycled.
ROAD CONSTRUCTION & MAINTENANCE

Asphalt reclamation, also known as road reclamation or full depth reclamation, is a cost-effective method of road rehabilitation. The full thickness of the asphalt surface and a portion of the underlying base is uniformly pulverised and graded to serve as the base for a new road. Additives such as cement or asphalt emulsion are often incorporated to increase strength. The result is a homogenous layer with improved structural capacity.
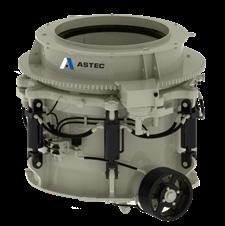
“Transporting material to a landfill then replacing it with new material is not only costly, but it is also time-consuming and wasteful. Rather than source new materials, reclamation uses the existing materials, so it is more environmentally friendly. The stronger base created during reclamation creates a solid foundation for longer-lasting, more durable roads that don’t suffer from cracks, holes or ruts,” adds Fennell.
“Just as Africa leapfrogged to mobile phones, with little time spent on landlines, and mobile banking exploded without much need for bank branches, vital infrastructure programmes in South Africa and across the continent must now leverage innovative technology and state-of-the-art equipment for their success,” Fennell concludes.

MIX DESIGNS AND MATERIALS FOR THE BEST CONSTRUCTION APPROACH
Building safe and durable infrastructure requires a dedicated focus on quality. IMIESA talks to Nithia Pillay, Regional Product Technical Manager at AfriSam about how their solutions, focus on innovation, and technical advisory services help guide customers to achieve expert results.
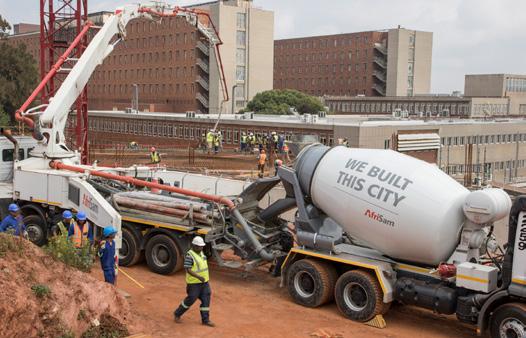
When it comes to readymix formulations, AfriSam is a class leader in custom-designed mixes. What are some of the most common, as well as unusual designs developed for clients in recent times?
NP Common mix formulations are categorised as standard (normal and pumped applications) and special (custom-designed). Standard mixes are performance based and comply with strength grades and workability as per SANS standards. Special mixes are either specified by engineers and customers or designed by AfriSam’s Product Technical team to meet specific site challenges. Examples of these are mixes with specified water:cement ratios, maximum or minimum water, cement and extender content, under water concrete, and mass concrete with maximum heat gradients. Unusual mixes we have developed include
The quality of aggregate is crucial for road performance and durability
AfriSam is a class leader in readymix custom design mixes
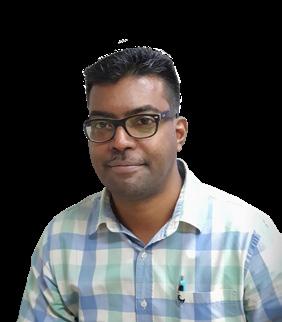
How important are good quality aggregates for road construction and what are the South African/ international standards governing these materials locally?
self-compacting concrete to improve access where this was limited or reinforcing layout was congested. Another was a mix with high doses of a strength-accelerating admixture to allow a rail crossing to be rapidly reopened for traffic. We also designed a self-compacting grout with low shrinkage properties and extended setting time to allow concrete to flow 30 metres around smaller piping within a large diameter pipe.
Aggregates form the bulk of the materials used in pavement layers, so their quality is crucial for road performance and durability. Aggregates provide structural strength and stability, distributing traffic loads to prevent deformation and rutting. High quality aggregates resist wear from traffic and weathering to enhance longevity, and properly graded aggregates enhance skid resistance to reduce accidents in wet conditions. They give roads the right porosity and gradation, for proper drainage to prevent waterlogging and erosion. Standards for aggregates including SANS 1083 (properties), SANS 3001-AG13 (quality and grading) and Committee of Transport Officials (COTO).
Should there be more focus on recycled aggregates?
Yes, for several reasons from cost and waste reduction to regulatory compliance and resource conservation. Using recycled aggregates means
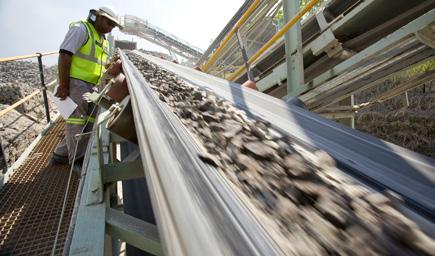
less extraction of natural resources and reduced energy consumption. Recycled aggregates can save on costs, while diverting waste from landfills, thereby extending landfill lifespan. Apart from often being a compliance requisite from government or municipal authorities, recycling preserves finite natural resources such as gravel, sand and stone – promoting sustainability.
Why is the widespread adoption of concrete roads less common in South Africa compared to other regions like North America and Europe?
The adoption of concrete roads in South Africa is influenced by our own economic, environmental, technological and policy factors. Concrete and asphalt roads each have their own advantages and disadvantages, but there are certain situations in which concrete roads may be considered better.
Durability: Concrete roads are generally more durable than asphalt roads, withstanding heavy loads with less rutting, cracking and deformation. This makes concrete roads ideal for high-traffic areas and heavy-duty applications.
Longevity: They have a longer lifespan than asphalt roads when properly constructed and maintained, and can last 30 to 50 years, whereas asphalt roads typically have a lifespan of 10 to 20 years.
Low maintenance: Concrete roads require less maintenance, and are less susceptible to damage from temperature fluctuations, moisture and chemical spills.
Environmental impact: They have a lower environmental impact, as concrete production emits less volatile organic compounds (VOCs) and hazardous air pollutants (HAPs) than asphalt production.
Reflectivity: With higher reflectivity than asphalt roads, concrete improves visibility and reduces the need for artificial lighting – enhancing safety.
Which technical committees is AfriSam currently represented on and what are some of the key standards/ specification changes in the pipeline? We contributed to the Committee of Transport Officials (COTO), to reaffirm draft specifications into working versions, as well as to South African National Standards (SANS 1083) – revising standards to include current best practice and products. AfriSam is also on the ballast working committee, providing commentary on the review of S410 and S406 specifications.
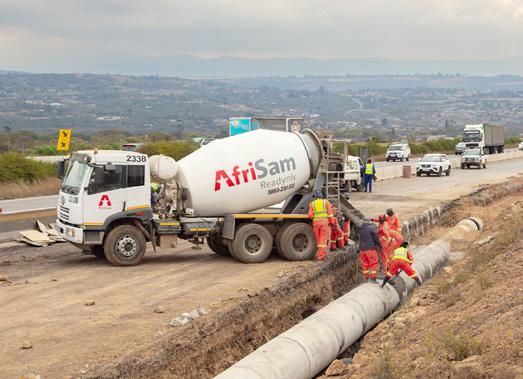
Are nano polymers the future for gravel road/low volume road subbase stabilisation or is cement still the best option?
Both nano polymers and cement have their advantages and potential applications in stabilising gravel road or low volume road subbases. Advantages of nano polymers include potentially improved soil stabilisation by enhancing soil properties such as strength, cohesion and water resistance. They can be applied easily, often requiring less equipment and labour, and may provide more flexibility and resilience to road surfaces.
However, nano polymers can be expensive, especially in large scale applications, and their longevity may vary. Some nano polymers may also have environmental impacts, such as leaching of chemicals into the soil or groundwater.
The advantage of cement stabilisation is that it has been widely used for decades and is well-understood and predictable. Cementtreated bases offer excellent strength for heavy traffic loads and durability for adverse weather conditions, and may be more cost-effective.
What material solutions does AfriSam provide for the stormwater segment (including precast manufacturers)?
AfriSam’s Rapid Hard Cement (RHC) is widely used in precast elements for stormwater management systems. Precast products demand early strength gain to enable fast turnaround of moulds, durability and cost management. We collaborate with customers to provide tailored solutions, including early
strength without the need for steam curing –leading to substantial savings.
Is there a clear understanding from consultants and contractors about which cement to specify in terms of strength?
Generally, yes. For structural concrete, the preference is for CEM I type products; however, there are now CEM II and other composite cements which offer similar strength and durability properties. Local availability of certain cement can add to transport costs.
What are some of AfriSam’s latest/ current research and development (R&D) initiatives?
AfriSam continuously undertakes R&D to remain relevant in various markets, with R&D “seeds” collected from industry stakeholders like consulting engineers, architects and contractors. We have undertaken long term durability tests with combinations of cementitious binders, manufacturing concrete specimens which are exposed to different environmental conditions around the country.
Tests include carbonation and chloride ingress, as well as shrinkage and creep testing. Collaborating with suppliers and universities, we maximise the use of supplementary cementitious materials (SCM) while still maintaining strength and durability performance for a lower carbon footprint.
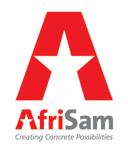
High-quality, durable modular steel bridging: A superior solution for rural South Africa
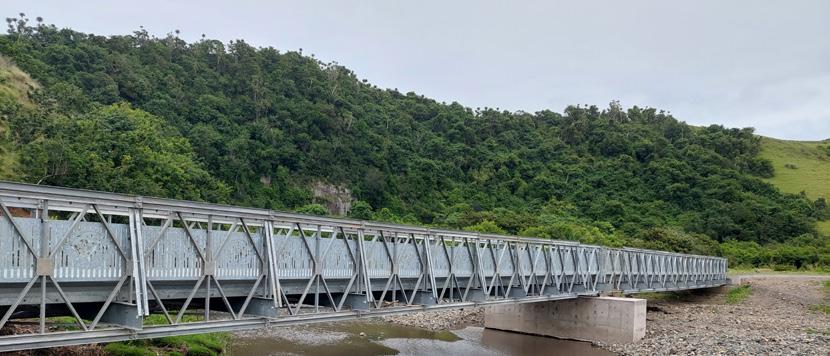
In many remote and rural areas of South Africa, access to vital services and amenities is often restricted by inadequate or non-existent road and bridge infrastructure. In these outlying communities, economic growth is constrained by the challenge of crossing difficult terrain, where rivers, prone to flooding during the rainy season, compromise access to markets, hospitals, schools, and basic amenities.
Government agencies across South Africa are mindful of the urgent need to improve these vital infrastructure links and are actively seeking solutions which will help them develop rural infrastructure quickly, safely, and efficiently.
While concrete bridges have been the most traditional option for rural bridging in South Africa, they are not the only viable solution for permanent bridging applications. With many benefits over concrete construction, cost-effective, durable modular steel bridges can help address the challenges in providing equitable, safe and sustainable access with limited resources.
Particularly for remote areas, prefabricated steel panel bridging is a better option than concrete, offering quicker project delivery with lower initial and lifecycle costs. On average, a prefabricated steel bridge can be built in less than one-quarter the time it takes to build a
comparable concrete bridge, with cost-savings of 40% or more.
This can be attributed in part to the costsavings offered through modularity and prefabrication, which eliminate the need for field welding. Furthermore, the use of a modular steel superstructure saves in material costs, as well as related expenses such as consultancy fees and reduces the contractor’s time and the amount of equipment required on site, resulting in expedited project delivery and cost-effective project efficiencies.
The lighter weight and compact size of modular bridging components make them easy to deliver to the most challenging locations. Once on site, with no falsework or concrete cure time required, assembly and installation are simply and quickly accomplished with minimal equipment, using local labour.
Versatility and long service life
Precision-engineered steel panel bridging
solutions are also extremely versatile; they can be configured to the desired length, width and strength to suit project requirements, and then, through the simple additional of standardised components, they can be lengthened, widened or strengthened to accommodate future road infrastructure development projects, or changes in highway loading requirements.
Lifecycle costs for steel panel bridges are likewise lower than those for concrete bridges, with hot-dip galvanisation providing protection against corrosion, making the structures virtually maintenance-free, depending on the environment, for a service life of up to 100 years. Furthermore, designed to accommodate high wind loads and seismic requirements, modular steel solutions are exceptionally climate-resilient and deliver superior structural robustness in climatic events.
In addition to the benefits listed above, modular steel bridge construction is a more sustainable option than concrete bridge
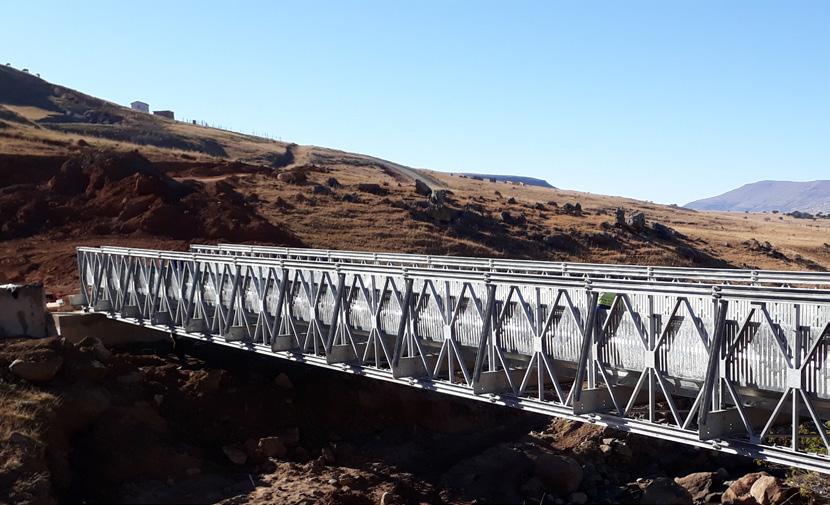
construction. Steel is the most recycled material in the world, and is endlessly recyclable without the loss of strength, performance, durability or quality. The zinc used in the hot-dip galvanisation process is similarly recyclable and has a high reclamation rate. The result of this coating is a structure that does not require repeated cleaning and painting, minimising the dangers to workers and the environment from these activities.
The lighter weight of the steel means less impact from diesel emissions during the transportation of components, as does the need for less heavy equipment during assembly and installation. Additionally, long-span solutions need no intermediate piers, which means less disruption to aquatic habitats below.
Decades of experience
The Acrow Group has decades of experience helping communities in Africa provide fast, safe, and efficient access through the use of modular steel bridging. Since the 1990s, the Group has worked with partners across Africa on the supply of more than a thousand bridges to more than 40 nations, with many installed to support the improvement of rural road networks.
In recent years we have worked on projects in Tanzania, Cameroon, Zambia, Kenya, Namibia, Mozambique, and the Democratic Republic of the Congo, among other countries, and the Group was recently selected by the Government of Ghana as the preferred supplier for a major emergency bridge programme. Brief descriptions of two successful case studies in South Africa follow.
Tsomo, Bengu and Thabane Bridges, Eastern Cape and Free State Provinces
In an effort to provide safe access to basic services and help stimulate economic growth in the area, the Eastern Cape Department of Roads and Transport together with the Maluti-aPhofung Municipality embarked on an ambitious programme aimed at installing desperately needed bridging across rivers where safe infrastructure was non-existent. Mindful of the urgent need for these vital infrastructure links,
On average, a prefabricated steel bridge can be built in less than one-quarter the time it takes to build a comparable concrete bridge, with cost-savings of 40% or more
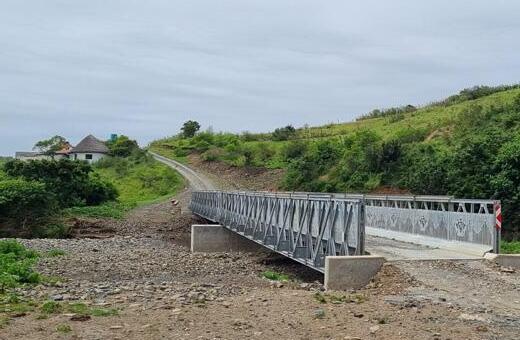
the agencies chose a rapid-build Mabey Compact 200™ (C200) bridge over more traditional concrete construction methods.
The first of the three projects was the 13-bay, 39 m Tsomo bridge, which was constructed and installed in only three days. The next project, the two-span 62 m Bengu bridge, posed complications owing to a steep-sided valley and rushing river. However, despite these challenges, the bridge was successfully built and installed in just six days.
The final two-span 52 m Thabane bridge, in the Drakensburg mountains, also required installation across a very steep valley. Although originally intended for use by pedestrians, the C200 was designed for vehicle loading; thus, when the local authority constructed an access road to the bridge to allow vehicular usage, the change in use required no modification to the structure.
The three bridges continue to serve as vital connections, providing safe and reliable yearround access for the local communities. As with the Thabane Bridge, the bridges in Tsomo and Bengu, originally intended for pedestrians, were designed for vehicular traffic, in line with plans for future road infrastructure development.
Ngqakaqheni Bridge, Eastern Cape Province
A single access road was the only route in

and out of the rural Eastern Cape village of Ngqakaqheni, which is situated at the foothill of a large mountain range and surrounded by a river. Local economic activities relied heavily on road transport, which during the rainy season could be cut off for up to two weeks at a time.
To enable safe access throughout the year, the local municipality resolved to construct a new bridge.
The remote location of the village, however, meant it would be difficult to use a concrete bridging solution. In addition to the logistical challenges of getting heavy-duty construction equipment to the site, concrete mixing and curing requirements would add additional time, so a modular steel structure would prove a better alternative for Mhlontlo Municipality.
The single-lane 40 m long C200 bridge selected for the project was safely and efficiently constructed in seven days by a local contractor, with a local work force, overseen by a Site Advisor. Now providing reliable access all year round, the bridge in Ngqakaqheni illustrates how simple, modular, off-the-shelf bridging solutions can offer significant savings to rural communities across South Africa.
Far reaching socio-economic benefits
Our work across Africa has shown us the positive societal and economic benefits of developing critical infrastructure. We know what resources are available for these projects, we understand the challenges involved, and so we are well-placed to be able to provide government agencies with the tools necessary to deliver rural infrastructure quickly, safely, and efficiently, helping them to do more with less.
For more information on how we can help with your project, please contact us at www.mabeybridge.com or contact our South African representatives, ECM Technologies, at sales@ecmtech.co.za.
ONE OF SOUTHERN AFRICA’S LARGEST NEW DAM PROJECTS TAKES SHAPE
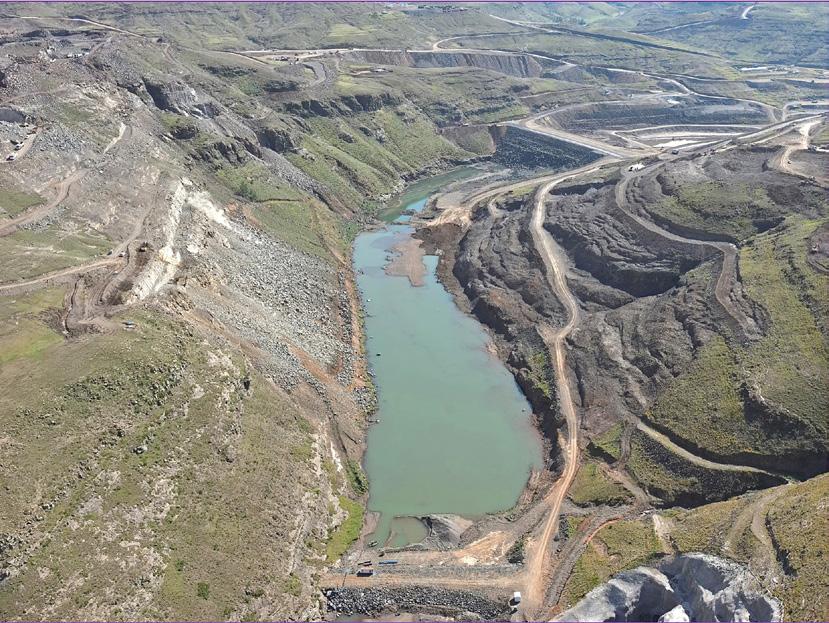
The Polihali Dam and the Polihali-to-Katse Transfer Tunnel are the main water transfer infrastructure components of Phase II of the Lesotho Highlands Water Project (LHWP), designed to increase supply to Gauteng and allied regions in South Africa to cater for current and future demand.
The current state of the main dam footprint as of March 2024. Excavation is in progress. Massive quantities of carefully selected basalt rock, in various sizes, will be the main material for the dam construction, with some 15 million m3 of rock fill specified in terms of the design
An enormous undertaking, once completed, Polihali Dam – a Concrete Face Rockfill Dam (CFRD) structure – will create a massive body of clean water that will cover more than 5 000 hectares, adding 2 325 million m3 in storage capacity to the existing scheme, comprising the Katse and Mohale Dams completed in 1997 and 2002, respectively, during Phase I. This will translate
into an increase in water volumes from 780 to 1 270 million m3 per annum, simultaneously increasing electricity generation at Lesotho’s Muela hydroelectric facility by approximately 30%.
Situated at an altitude of close to 2 000 m above sea level, the Polihali Dam site was strategically selected at the confluence of the Senqu and Khubelu Rivers, just downstream of where the main tunnel intake will feed the 5 m diameter and approximately 38 km long Polihali-to-Katse
transfer tunnel – projected for completion during 2028. Gravity fed, the latter will carry the water to the Katse reservoir, as does the present interconnecting Mohale Tunnel. Construction of the Polihali Dam began in 2023.
The tunnel boring machine (TBM) for the transfer tunnel phase is scheduled to arrive on site in the second half of 2024. (As an aside, the first blast making way for excavation works at the TBM access adit was in September 2023.)
Diversion tunnels
The diversion tunnels for the Polihali Dam were designed and excavated in advance of the construction of the Phase II main works. The role
of these tunnels is to divert water away from the natural riverbed to create a dry foundation and work area needed for the construction of the dam.
For the Polihali Dam construction, two diversion tunnels have been constructed to divert the waters of the Senqu River. Building two tunnels increases the capacity to carry floods and will provide flexibility to work in one tunnel while the river flows in the other.
These diversion tunnels – one 7 m in diameter and almost 1 km in length; and the second 9 m in diameter and also some 1 km long – run parallel to each other from the intake point to the outlet downstream of the dam. They were excavated by drill and blast methods, with the works here completed in November 2021.
The first milestone on the construction of the dam was the diversion of the Senqu River through these diversion tunnels ahead of the construction of the cofferdam upstream of the Polihali Dam wall in August 2023.
In the meantime, construction on the transfer tunnel is progressing. This includes the construction of the access adits on the Katse and Polihali sides of the tunnel; the construction of the Polihali lower and upper intake towers; and the construction of the Katse permanent access adit.
Advance infrastructure
Overall, the advance infrastructure is now

Integrated design components for the Polihali Dam. The embankment will stand 166 m high, have a crest length of 921 m and a crest width of 9 m. At its base, the embankment will be approximately 490 m wide. The Polihali dam infrastructure includes a spillway, a compensation outlet structure and a small hydropower station. The saddle dam will be 43 m high and will have a crest length of 603 m and a crest width of 9 m. Its function is to raise a low point on the reservoir margin to prevent water from by-passing the Polihali Dam
mostly complete. This includes power lines and telecommunications links, roads and bridges, offices, workshops, and residential accommodation for people working on site.
The electrical infrastructure required for the Phase II development includes the construction of new substations, upgrading of existing Lesotho Electricity Company (LEC) substations, the construction of new power
Coffer dams: first a pre-coffer dam and then the robust upstream coffer dam, protect the works from flooding. The river is diverted through diversion tunnels, which were completed in 2021
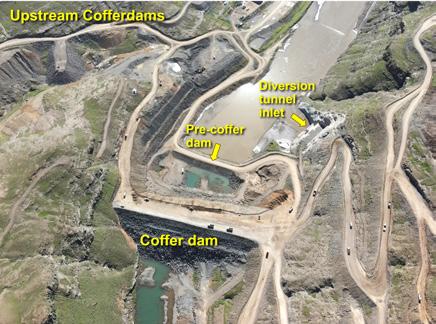
lines, and the diversion of some of the existing distribution network.
A new power substation has been constructed at the Polihali Dam site, and another has been built adjacent to the existing Matsoku diversion substation. Substations at the Katse tower intake and Ha Lejone have also been upgraded, as well as the protection and control systems of the Maputsoe, Pitseng and Matsoku diversion substations. All substations have been equipped for remote control from the LEC national control centre, located at Mabote substation near Maseru.
Additionally, a 132 kV transmission line between Matsoku substation and the new substation at Polihali has been constructed, while the existing 20 km transmission line from Ha Lejone to Matsoku has been upgraded from 66 kV to 132 kV. A 33 kV power line of 2,2 km was also constructed from Tlokoeng to Polihali to supply early power for the advance infrastructure contracts prior to the completion of the main power from Matsoku.
Road and bridge access
Road construction is one of the major components of the advance infrastructure under Phase II. In this respect, the existing Polihali Northeast Access Road (PNEAR) – a 16 km gravel route which starts in the town of Mapholaneng and runs towards the Polihali Dam site – has been upgraded to a Class A
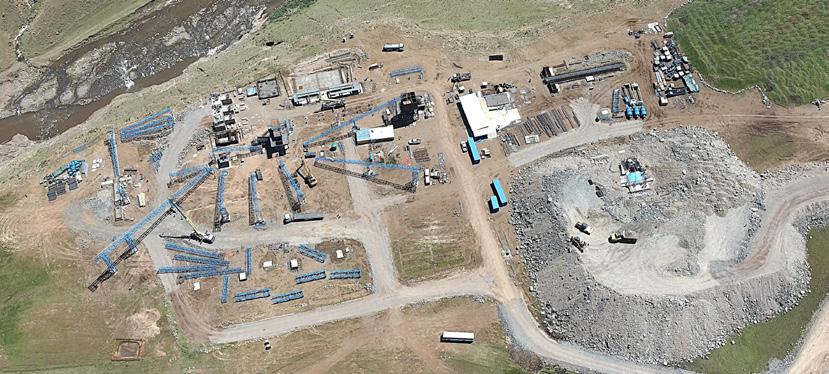
Tsilantso quarry is an area with large quantities of good rock for dam embankment fill. However, the overburden, both soft and hard, must first be removed. Millions of cubic metres of basalt in various shapes and sizes will be mined from Tsilantso to build the Polihali Dam and associated works
surfaced road. It provides access to the dam site for construction vehicles and improves ease of movement for communities in the surrounding areas.
In turn, the Polihali Western Access Road (PWAR) is a new 54,3 km paved Class A road – with construction in progress – linking Lesotho’s A8 in the vicinity of Ha Seshote in the west to Polihali in the east. It joins the PNEAR at Polihali. Three new bridges will also be built across the Matsoku, Semenanyane and Makhoaba Rivers.
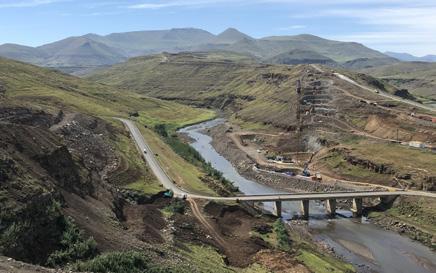

Meanwhile, the existing Northern Access Road (NAR) has been repaired and resealed, including existing bridges. Slope remediation has been done at critical places, as well as minor road safety upgrades. This rehabilitated section stretches for 96,38 Km from the Pitseng village up to Katse village. It provides access to the Katse Dam basin, and ties into the PWAR at Ha Seshote to provide a further link to the Polihali basin.
Major bridges programme
Once the Polihali Dam reservoir is impounded, some communities will need to be reconnected via three major bridges along the Maseru to Mokhotlong A1 Road at the Mabunyane, Khubelu and Senqu Rivers. These will provide access to Mokhotlong town across the reservoir even at full supply and retain connectivity to the national road network along the A1, the main road between the Mokhotlong district in the mountainous north-east of the country and Maseru.
The major bridges programme is complemented by associated works. These include the construction of four pedestrian bridges and six vehicle bridges under the feeder roads and bridges programme to maintain connectivity and ensure mobility for communities in the reservoir area.
On the critical path is the 825 m long and over 90 m high Senqu Bridge, the largest of the three major bridges. The other two key new structures are the Khubelu Bridge, which will be approximately 270 m long with nine 30 m
An artist’s impression of the new Senqu Bridge following the impoundment of the Polihali Dam reservoir. (Image credit: Zutari)

spans and two abutments; and the Mabunyaneng Bridge, measuring 120 m in length with four 30 m spans and two abutments.
Africa’s first “extradosed” bridge
The flagship Senqu Bridge is believed to be the first “extradosed” bridge in Africa. This extradosed design, which combines a prestressed box girder bridge and a cable-stayed bridge, was chosen to eliminate the need for a central pier that would
have caused major construction challenges standing mid-stream in the Senqu River.
The 3,5 m deep bridge deck (including the cable stay towers and cable supported deck sections) will be incrementally launched out over the valley along the top of the piers in 25 m increments until the two deck halves meet in the middle.
Using cable stays to support the 100 m main span during the incremental launch of the deck substantially reduces the reliance on a temporary
The new Senqu Bridge deck will be constructed using the incremental launch technique.
(Image credit: Zutari)
nose gantry in front of the deck to help span across the 50 m gaps between the piers.
Once the Polihali Dam is complete and the reservoir fills up, almost the entire Senqu Bridge supporting structure will be under water, making it one of the deepest bridges in the world. This will subject the tall bridge piers and massive foundations to loading factors not often encountered in bridge design. These include the effect of water currents pushing against almost the entire height of the tall slender piers, combined with the intense water pressure at 80 m depths.
For those travelling across the Senqu Bridge, and allied bridge structures – once all associated dam construction phases are completed – it will be a milestone experience in the celebration of one of Africa’s modern-day responses to water demand management and security.

THE IMPORTANCE OF A WATER AUDIT IN AN EL NIÑO SEASON
Water, a resource that has been readily available for use by us, and long misunderstood to be plentiful, has in recent times outlined just how scarce of a resource it is, particularly in our day-to-day activities, under climate change.

Water utilities face mounting pressure due to factors like the ongoing El Niño season and other diverse climatic conditions such as droughts, and flooding events. Added to this, the No Drop report also requires various compliance factors which need to be achieved and delivered on. This underscores the vital importance of water audits to encourage the efficiency of a business’s water management practices.
Why conduct an audit?
incorporating these changes and the potential savings thereof, from the reduced usage.
Key outcomes of a water audit are:
Leaks detection
Water audits help in detecting leaks that are otherwise non-visible to the eye, daily. Consequently, these allow for a timely repair of leaks, preventing unnecessary water loss and subsequent costs associated with high water use.
Reduced water bills
Monetising each litre of water saved can go a long way in outlining the importance of a water audit. Identifying and addressing inefficient water use and implementing water-saving strategies to address these can result in reduced water bills in a building, keeping more money in one’s pocket.
• For example: If each kilolitre of water = R30, using a total of 30 Kℓ of water each month would cost R720, i.e. R30 × 30 Kℓ - 6 Kℓ for free basic water and wastewater services.
Water use audits, like their energy counterparts, are an important first step toward understanding both a building’s water use and what can be done to reduce it. These trace the water footprint – from its point of entry into the building right through to its discharge, into the sewer channels. They identify each point of water use within and around the building and estimate the quantity of water used at each of these points, outlining high use hotspots in the building. Further, water audits help identify and quantify unaccountable water losses and possible leaks – providing building owners with a “road map” of the implementation costs of
• A leaky tap that drips at the rate of one drip per second can waste more than 11 Kℓ (11 000 litres) per year.
• To put this into perspective, that equates to 73 bathtubs, full to the brim.
Water efficiency
A water audit identifies areas of inefficient water use, allowing for the implementation of strategies to minimise wastage and promote conservation.
• Reducing water usage by a certain percentage can result in water bill savings each month; and that money can be used to further incentivise other revenues incurred by the organisation.
The Water Wise brand exhorts all businesses to initiate water auditing as a prudent business approach to minimise water use and maximise energy efficiency.
#BeWaterWise Sources:
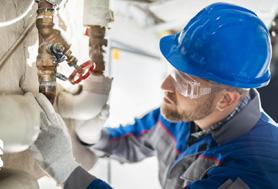
• Efficient hardware changes include the installation of aerators in kitchen and bathroom taps, which in turn reduces the amount of water you use by up to 60% or roughly just over 1 Kℓ (1 000 litres) each month.
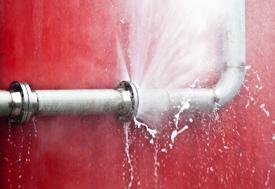

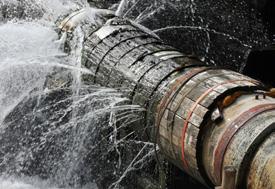
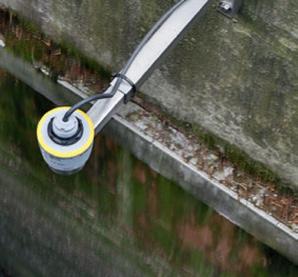
ITAKING THE PRESSURE OUT OF WATER PRESSURE MEASUREMENT
Water treatment systems demand careful monitoring and management processes across sprawling networks, making the use of pressure transmitters an essential aid for the personnel in charge of ensuring the optimum operation of the many moving parts involved.
n theory, these instruments allow facilities managers to easily automate their processes. However, not all instrumentation is created equal, and having a range of different OEM products installed can be challenging as each has its own configuration and calibration setup, which may not synch as a whole in terms of overall process monitoring and management.
From VEGA’s perspective as a leading OEM in this field, the best approach is to go the standardisation route to ensure a single source of truth across the network in terms of pressure readings. The benefits include universal understanding and consistent accuracy of the recorded data – so crucial in avoiding potential equipment damage, process delays and added treatment costs.
In this respect, VEGA offers invaluable support to their clients, touring facilities and finding custom solutions for their unique challenges and needs. And it’s not just the time invested: VEGA sensors offer unparalleled ease of configuration, precision, and reliability.
For ease of use, VEGA has introduced sensors equipped with Bluetooth connectivity, which allows operators to wirelessly monitor, set up and adjust them through the VEGA Tools app, which is available for download in the Google Play store, as well as the Apple App Store.
Sensors for specific roles
Each VEGA sensor has its purpose-designed role. For example, VEGADIF 85 universal pressure transmitters handle influent
and effluent flow metering in locations throughout systems. Here the VEGADIF 85 functions as a multivariable sensor through integrated measurement of absolute reliable pressure.
In turn, the VEGABAR 38 pressure sensor can be utilised to measure levels on tanks and chemical feed and fill systems, making it easier for system operators to view the pressure status thanks to the sensor’s configurable colour LED light ring, in addition to on-site operation with its VDMA menu structure. As a further plus, this sensor offers easy integration into control systems through IO-Link communication.
The VEGABAR 82 pressure transmitter measures at the inlets and outlets on vaults. This unique sensor offers an abrasionresistant ceramic measuring cell, ensuring reliable operation in the toughest process conditions. It provides reliable measurement down to the last drop through the smallest measuring ranges with high accuracy. This in turn can enable massive savings on maintenance costs.
Continuous level measurement
Allied to the water treatment space, VEGAWELL 51 is suitable for continuous level measurement in deep wells, reservoirs, and rivers, with a maximum cable length of 1 000 m. This robust ceramic measuring cell offers maximum overload and vacuum resistance, making it a highly reliable addition to any water treatment and distribution facility’s process automation arsenal.
Whether it’s water or wastewater, VEGA offers the true benefits of process
automation to public and private utilities. A proven mix of precise, reliable instruments and commitment to customer support means that plant operators are empowered instead of struggling with usability or maintenance, freeing them to focus on their other responsibilities. By doing that, VEGA takes the pressure out of pressure measurement.
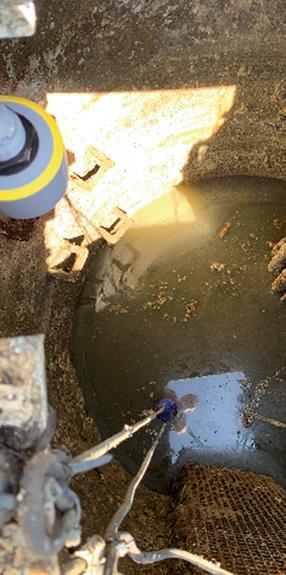
REMODELLING THE ST HELEN’S ROCK ABSTRACTION WORKS FOR FUTURE GENERATIONS
Situated some 9 km inland from the Indian Ocean on the shores of the Mzimkhulu River, raw water is abstracted and piped to the Bhobhoyi water treatment works (WTW) from the St Helen’s Rock high lift pump station built in the 1970s – via a balancing dam constructed in the mid2000s – providing the vital potable supply needs of Port Shepstone and its neighbouring KwaZulu-Natal coastal communities.
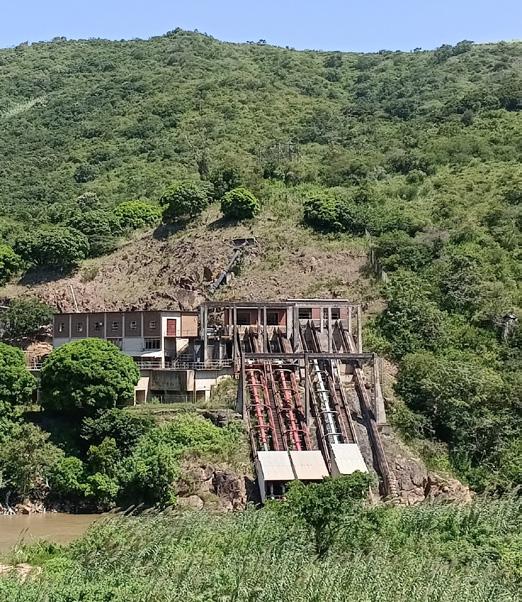
PROJECT TEAM
Client: Ugu District Municipality
Lead engineer: ENsync Engineers
Electrical Engineer: WillpowerWorx
Environmental: Nemai Consulting Specialist hydraulic modelling: Stellenbosch University
Geotechnical investigations: Drennan Maud
The region has a major tourism driven economy, alongside agricultural and industrial endeavours, with an approximate population of some 250 000. As with any community, water security and its quality are an overriding priority, a concern that local authority, Ugu District Municipality, continues to address through sustained infrastructure improvements.
St Helen’s Rock’s current pumped capacity is 81 Mℓ/d and in synch with the same inflow to the Bhobhoyi WTW plant. However, consumption demand is climbing, compounded by climate change impacts (increasing drought and flood events) which has necessitated a planned upgrade in the overall system capacity to treat 108 Mℓ/d in the immediate future.
That should meet future regional requirements for the next 30 years or so, says Benjamin Fredlund PrEng, Principal Engineer: Water at ENsync Engineers, which was appointed by Ugu District Municipality in 2021 to undertake a modern-day upgrade of the St Helen’s Rock abstraction works and allied infrastructure. Coordination of all the design elements is in 3D using the latest Autodesk suite.
During flood conditions, the existing abstraction pumps and their housing can be mechanically winched above the rising water levels. However, during drought conditions, the current set-up means that the pumps struggle to reach the water when river levels drop – the motivation for an innovative design alterative
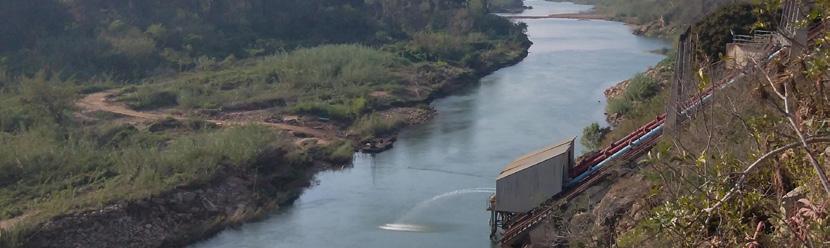
Two key phases
There are two implementation components. In the first phase, which is planned to go out for tender in mid-2024, a 450ND steel pipeline interconnecting the existing pump station, raw water balancing dam and Bhobhoyi WTW will be replaced by a 3,4 km long 700ND steel equivalent. This will increase total raw water supply pipeline capacity to 1.25m3/s in line with the 108 Mℓ/d process improvement. Some of the associated infrastructure was already upgraded to meet this future capacity in 2009.
The second phase – the most critical and planned to go out to tender in early 2025 – entails the construction of a new low lift 1,4 m3/s abstraction works that will incorporate four immersible pumps (two on duty and the balance on standby), and a 145 m long weir. The latter will feature a weir low notch level of 4,3 m asl and a 1 in 100year flood level of 21 m asl. Overall, this will be a major construction project spanning 24 to 36 months.
Extended reach
As Fredlund explains, the need for a weir is essential going forward to ensure water supply. “Historically during more severe drought conditions, the river level drops to a
point where it cannot be reached effectively by the current abstraction pumps.”
In terms of the 1970s set-up, the abstraction pumps are installed on rails to enable them to slide into and out of the river via a mechanical winch system. This design also makes provision for flood conditions, where the pumps can be safely retracted.
“Droughts also have another downside because low river volumes result in seawater inflows up the estuary and can result in higher than acceptable salt content. This makes the raw water abstracted undrinkable,” Fredlund continues.
“This presented the business case for the weir to counter the cyclical problem of saltwater intrusion. We also needed to revisit the current abstraction works layout with an emphasis on integrating as many of the existing mechanical and electrical elements as possible. However, the days of the pump abstraction slide system are numbered.”
Hydraulic model simulation
To perfect the ultimate design, in 2021 ENsync Engineers appointed Stellenbosch University’s (SU’s) Hydraulics Laboratory to carry out detailed physical modelling of a concept weir
arrangement. A key consideration was the best way to manage and control sediment build-up behind the planned weir to prevent blockages to the abstraction pump intakes.
With these and other tasks in mind, SU’s Hydraulics Laboratory built a 1 in 40 scale model of ENsync Engineers’ new abstraction works and weir proposal, factoring in a 1 in 100-year flood scenario, which is standard practice. Detailed lidar information of the topography was incorporated, in addition to bathometric survey data of the river channel.
The allied use of computational fluid dynamic modelling all subsequently helped to create the final hydrodynamically shaped design.
“They put various high and low flow scenarios through the scale model and monitored how the sediment shifts in the river. This included the assumption that the river level would be even higher during a 1 in 100-year event once the new weir was installed,” Fredlund explains.
“That was a key consideration because there’s an existing railway bridge crossing the river upstream of the pump station which obviously couldn’t be impacted.”
A gravel trap, intake screens to remove coarse material, a hopper shaped sand trap flushed by a dredge jet pump, plus a radial
Upstream and downstream perspectives of the revamped abstraction works building and 145 m long weir design created by ENsync Engineers
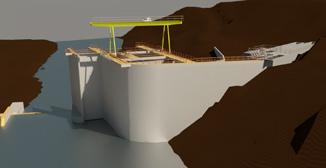

gate are included in the final sediment containment design elements.
Diaphragm walling
A geological study was also an essential component to verify the riverbed composition, which revealed that bedrock is some 20 m below the overlying sedimentation layers. This subsequently led to the decision to use diaphragm walling techniques for the weir’s construction, as well as for parts of the new abstraction works building foundation.
EIA
Throughout the design process, protecting the ecosystem has been of paramount importance, with the environmental impact assessment (EIA) study nearing finalisation. Interventions that have already been incorporated include fish ladders and eel ways for migrating species.
Integrated water demand management
The upcoming St Helen’s Rock developments are not happening in isolation, but form part of a broader strategy being overseen by the Department of Water and Sanitation. For example, upstream of St Helen’s Rock on the
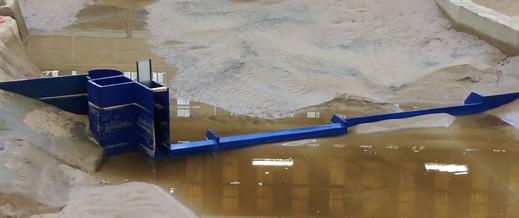
Mzimkhulu River, uMngeni-uThukela Water Board plans to build the Cwabeni off-channel storage dam and weir.
“From our standpoint as design engineers, we’ve conducted extensive due diligence with
Scan the QR codes to experience a virtual perspective of the design details on the future St Helen’s Rock pump station upgrade and new weir abstraction works.
industry stakeholders on the upgrading of the St Helen’s Rock pump station and associated works. Now we have a real-world applied model that we’re confident will work exceptionally well in practice,” Fredlund concludes.



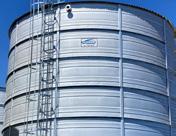

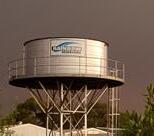

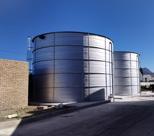


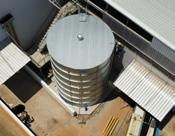
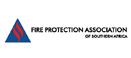
GROUNDBREAKING TREATMENT PLANT UNVEILED
In April 2024, Interwaste, a Séché Environnement Group company, marked a new milestone for sustainable wastewater management with the unveiling of its R100 million, state-of-the-art leachate and effluent treatment plant – a first of its kind in South Africa.
Situated in Delmas, Mpumalanga, the plant represents a paradigm shift in the treatment and processing of various liquid waste streams. It’s designed to accept and treat various effluent waste across two categories, including leachate produced by Interwaste’s own or other waste disposal facilities, and liquid waste streams from various industries such as manufacturing, mining, oil and gas.
Engineered to the highest standards, the plant boasts advanced technologies that not only effectively treat these waste streams (43 million litres of effluent a year) but also recover an impressive 80-90% as clean, reusable water. The clean water produced by the plant exceeds the Department of Water and Sanitation’s safe discharge limits and
yield approximately 36 million litres of clean water per annum.
“Our new treatment plant is not just a testament to our commitment to environmental sustainability but also a testament to the power of collaboration between local expertise and global knowledge – a project that has created jobs and ensures skills transfer and upliftment through the development and operation of the facility,” says Jason McNeil, CEO at Interwaste.
Multi-stage process
The Interwaste plant employs a multi-stage treatment process that ensures the efficient removal of contaminants while maximising water recovery. Key features include:
• Flexibility to treat and process a range of liquid waste types including leachate.
• Bespoke pretreatment processes, which balance pH levels and remove elements such as suspended solids, pollutants, and oils to ensure the optimal blend is created.
• Refined concentration methods that separate salts from water.
• Advanced filtration systems to remove remaining constituents from the water.
• Continuous monitoring and control systems to ensure optimal performance and compliance with regulatory standards. In addition to its technological prowess, the Interwaste treatment plant is also designed with sustainability in mind. Minimal waste generation, and responsible chemical usage are integral aspects of its operation, further underscoring Interwaste's commitment to environmental stewardship.
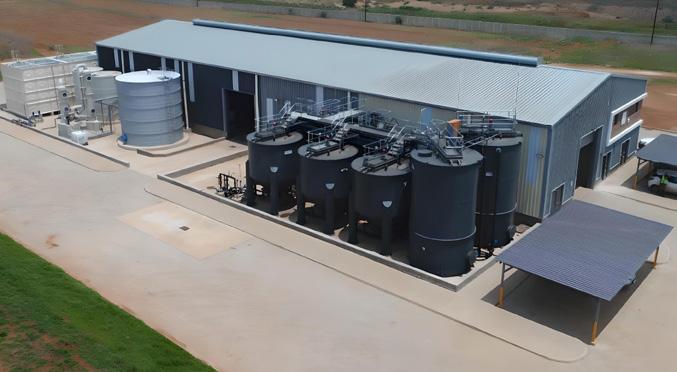
Interwaste’s leachate and effluent treatment plant in Delmas employs a multi-stage process that ensures the efficient removal of contaminants while maximising water recovery

PHASE 1A AT WELMOED ESTATE DEVELOPMENT ADVANCES
The rapid pace of migration, population expansion and urbanisation within the City of Cape Town has placed an unprecedented demand for social and affordable housing, with the Western Cape Department of Infrastructure (which now incorporates the province’s former Department of Human Settlements) forging ahead on a range of projects.
Aprime example is the Welmoed Estate Development project, which is situated in Blue Downs to the east of the City of Cape Town municipal area, surrounded by the Blackheath, Eersteriver suburb, and the Stellenbosch farmlands.
The development, which makes provision for approximately 8 000 Breaking New Ground (BNG) housing units within an approximately
200 ha land track, is divided into two phases, with Phase 1 further divided into three subphases (Phase 1A, 1B, and 1C). Currently, only Phase 1A is under way, entailing the construction of 1 348 BNG units, together with supporting civil and electrical engineering services, as well as bulk services.
For Phase 1A, valued at around R763 m, the professional team comprises iX engineers as the project managers, with SMEC South Africa
Standing at a height of 12 m with a 40.8 m internal diameter, the Welmoed Estate Development’s reservoir is a post-tension concrete structure featuring walls with a thickness of 425 mm. Its construction involved a combination of cast in-situ elements and precast elements
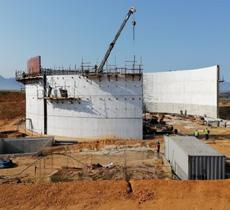

Once all phases have been completed, the Penhill Farm site (as it is commonly known) will be transformed into a high-density residential and mixed-use development incorporating various tenure options and housing typologies, along with community facilities, and commercial opportunities. The long-term objective is to cater for both low and middle-income earners in a township that is well-integrated with employment opportunities and conveniently located near public transport and municipal services.
Phase 1A commenced in August 2019, with the estimated completion date scheduled for September 2024. As Johan Basson, Function Manager: Urban Development at SMEC South Africa explains, the design intention from the onset was to create employment opportunities
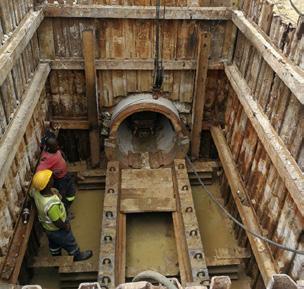
The installation of the bulk sewer pipeline required pipe jacking to cross under road and rail sections
via the Expanded Public Works Programme, utilising labour-intensive construction methods wherever technically feasible and economically viable. An allied focus has been the development of emerging contractors registered with the Construction Industry Development Board (CIDB), further contributing towards black economic empowerment initiatives within the local communities.
Present status
To date, significant headway has been achieved during Phase 1A, with successful completion of the following notable milestones:
• The construction of two access bridges (Amatola Culvert Bridge and Bannerman Bridge)
• The installation of a 7,3 km bulk sewer pipeline
• The construction of the sandtrap facility along the bulk sewer pipeline, and
• The installation of both the bulk water supply to a new 15 Mℓ reservoir and the distribution pipeline to the development.
SMEC South Africa’s scope of works
SMEC South Africa has been responsible for various key project phases in terms of bulk water and sewer infrastructure design and construction monitoring. A central one was the establishment of a 15 ML reservoir, which was identified as a priority.
“This decision was based on the Annual Average Daily Demand (AADD) for the ultimate development, confirmed by the City of Cape Town at 6 560 KL per day,” explains Basson.
“The AADD encompasses water demand from 8 000 housing units and backyard dwellers (two per Integrated Residential Development Programme house).”
The reservoir, standing at a height of 12 m with a 40.8 m internal diameter, is a
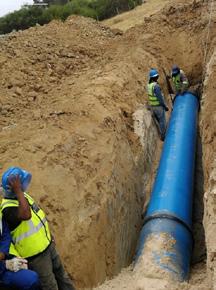
The Bannerman Bridge serves as one of two access points for the estate
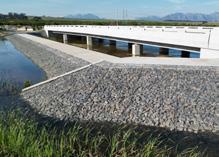
post-tension concrete structure featuring walls with a thickness of 425 mm. Its construction involved a combination of cast in-situ and precast methodologies. Elements such as footings, walls, and the floor slab were cast in-situ, while beams, columns, and hollow core roof slabs were all precast.
The reservoir is supplied by a 500 mm diameter PVC-O pipe from an existing City of Cape Town bulk water network, with the supply pipeline measuring 1.2 km in length.
The distribution pipeline from the reservoir to the development comprises three different pipe sizes: a 710 mm diameter PVC-O pipe from the reservoir to the Jacobsdal and surrounding future development’s connection points (approximately 960 m in length); a 500 mm diameter PVC-O pipe from this point to the first distribution point within the development (approximately 415 m in length); and thereafter a 400 mm diameter PVC-O pipe to the last distribution point within the development (approximately 450 m in length).
Bulk sewer infrastructure
The bulk sewer route spans approximately 7.3 km, and it operates entirely as a gravity main, with one designated sand trap incorporated as the pipeline departs from the Welmoed Estate Development.
Bulk water installations in progress
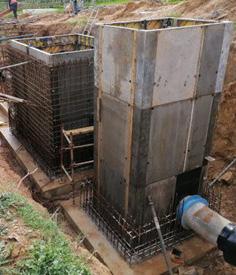


The pipeline commences with a 350 mm diameter structured walled high-density polyethylene drainage pipe (SWHDPE) and transitions into a 500 mm diameter SWHDPE after covering 372 m. Just before exiting the development boundaries, it further increases in diameter to a 700 mm diameter SWHDPE.
The 700 mm diameter SWHDPE then continues along Van Riebeeck Road (R102) until the intersection of R102 and Stratford Avenue. At this junction, it turns west and traverses the centre of one lane in Stratford Avenue, eventually connecting to the Black Mac pipeline (700 mm diameter asbestos pipe) adjacent to a stormwater canal.
A parallel line (800 mm diameter SWHDPE) was installed from this point to redirect the Black Mac flow. This new 800 mm diameter SWHDPE line runs parallel to the Black Mac pipeline until it links with the Blue Downs pipeline (900 mm diameter pipe) just before Old Faure Road.
“Conveying the sewers from Welmoed to the connection point also involved pipe jacking to cross existing roads and railways. The installation of the bulk sewer pipeline also included the restoration of existing roads where affected,” adds Basson.
“Now that the network is in place, the imminent construction of the top structures in Phase 1A will add the finishing touches, bringing the first BNG recipients a step closer to calling the Welmoed Estate Development home,” Basson concludes.
MANAGING FLOOD RISKS IS A SHARED RESPONSIBILITY
The introduction of A Best Practice Guideline for Design Flood Estimation in Municipal Areas in South Africa provides an essential tool kit for local authorities and is a multi-stakeholder initiative led jointly by IMESA and the Water Research Commission (WRC).
Key input has been provided by specialist engineering practitioners, as well as the University of the Free State, the University of KwaZulu-Natal, and Stellenbosch University to address the increased incidence of infrastructure flood damage, plus the need for applied approaches to mitigate risk to society and the economy. Research in the latter area is being driven by the National Flood Study Programme (NFSP) Task Team, among other entities.
“It is well known that climate change poses a real threat in terms of extreme weather impacts. However, we cannot keep blaming climate change for poor planning,
implementation, and management,” points out Professor Kobus Du Plessis, one of the authors of the Guideline and a specialist in the field of hydrology and environmental engineering at Stellenbosch University.
Capacity building workshops
He also serves on a voluntary basis as IMESA’s Technical Director for Training and Skills Development and forms part of a group of presenters rolling out one day capacity building workshops on the Guideline during April and May 2024. These are being held in six centres (Cape Town, George, Gqeberha, Durban, Bloemfontein and Johannesburg/Pretoria), with further workshops planned at a later stage. (For more details visit https:// www.imesa.org.za/courses.)

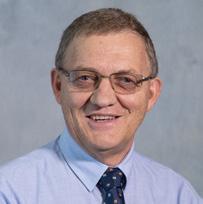
Legal framework and bylaws
The Bill of Rights enshrined in South Africa’s Constitution has an Environment section which states that:
“Everyone has the right to an environment that is not harmful to their health or well-being; and to have the environment protected, for the benefit of present and future generations through reasonable and other measures that prevent pollution and ecological degradation; promote conservation; and secure ecologically sustainable development and use of natural resources while promoting justifiable economic and social development.”
“One of the key messages is that political decision-makers, officials, and engineers within municipalities have a legal and moral obligation to ensure best practice. It’s also essential that municipal engineers are equipped and empowered to implement effective flood mitigation practices and that there’s a common understanding and appreciation of the issues involved. The Guideline serves as a platform for a standardised approach,” Professor Du Plessis explains.
“It’s also important to emphasise that the risk of inadequate urban and town planning, infrastructure design or construction cannot be contracted out or transferred to an external consultant. There’s a shared responsibility – with the Department of Water and Sanitation having a key role to play.”
The workshop unpacks key legislation that includes the Water Services Act, National Water Act, the Disaster Management Act, as well as the requirement for the approval of plans in terms of the National Building Regulations and Standards Act.
Specific bylaws also need to be in place and approved by the Council. That includes the type of information that must be supplied to and by developers and consultants for design and planning purposes. The larger metros have extensive bylaws in place, but Professor Kobus Du Plessis says this is less the case for smaller municipalities, so that’s a work in progress.
In the Guideline, typical bylaws are referred to as examples for application or modification by all local authorities. An example could be a bylaw stipulation that human settlements cannot be built below a 1:20 year flood line.
Expertise and skills gaps
The purpose of the workshops is to inform all decision-makers, but the ultimate application of the Guideline requires an expert approach, with qualified and experienced personnel in place. This is especially crucial, because the design flood estimation process must factor
in a myriad of variables using commercially available software simulation packages on the market.
“Within the municipal environment, technical skills gaps are a growing concern, particularly within smaller and rural local authorities where engineers are often required to manage and respond to a diverse range of infrastructure disciplines, compared to the larger metros where higher levels of departmental specialisation exist. The Guideline takes this into account so that practitioners with limited experience in flood design are still equipped to ask the right questions and reach out to recognised experts before approving internal or external land-use development and infrastructure proposals in line with Integrated Development Plans,” explains Professor Du Plessis.
“Only a true expert can analyse and model scenarios based on available and accurate data for flood risk and/or flood level assessment. A number of the leading metros do have excellent data sets based on their own hydrological monitoring systems or sourced from South African and international bureaus, but less so across the board.”
Catchments are dynamic
As the Guideline illustrates, weather patterns – influenced by climate change – continue to evolve. For this reason, catchments must be viewed as dynamic systems that are constantly being influenced by infrastructure and related commercial, industrial and residential development. That means that the mandatory 1:100-year flood line (as stipulated by the National Water Act) is not cast in stone – it needs to be revisited on a regular basis and recalibrated accordingly to predict current and future water levels, as well as their anticipated velocity.
“What we’ve set out to achieve with the Guideline is a landmark initiative. It’s a practical tool for compliance, and an essential one for avoiding known flood risks, and minimising the damage from unpredictable extreme weather events,” Professor Du Plessis concludes.
INPUT
The implementation and management process outlined in the Guideline for Design Flood Estimation
OUTPUT Design Flood Estimation
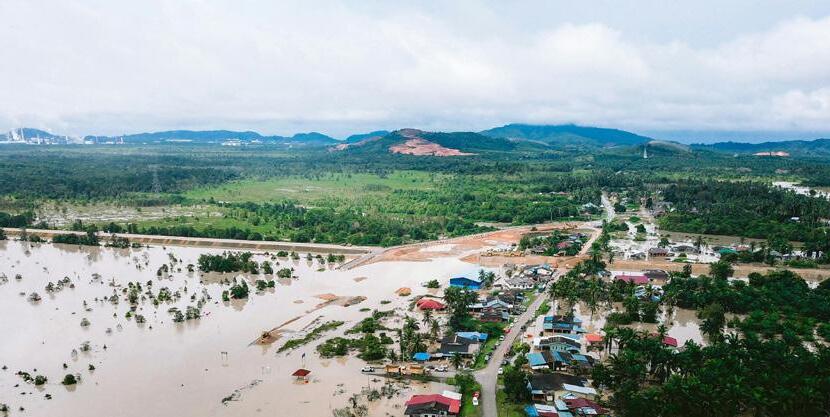









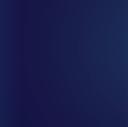



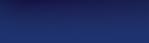

2024 CONFERENCE IMES A
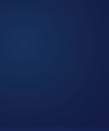

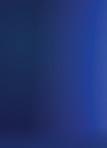





EARLY BIRD REGISTRATION
Register & Pay BEFORE 31 July 2024
• Members: R7 400
• Non-members: R8 800
t: +27 (031)266 3263
e: conference@imesa.org.za marketing@imesa.org.za www.imesa.org.za











STANDARD REGISTRATION
Register & Pay AFTER 1 August 2024
• Members: R8 300
• Non-members: R9 800
ANNUAL GOLF DAY
R650/person excl. Golf Cart & Caddy Light Lunch
Prize Giving & Awards 5 November 2024
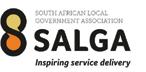













LAST MINUTE REGISTRATION
Register & Pay AFTER 25 October 2024
• Members: R9 500
• Non-members: R11 300
COMPANION PROGRAMME
6 November 2024
R600/person excl. Social Evening Refreshments & Lunch Entry to Opening Function
Reflecting the heat with cool paint
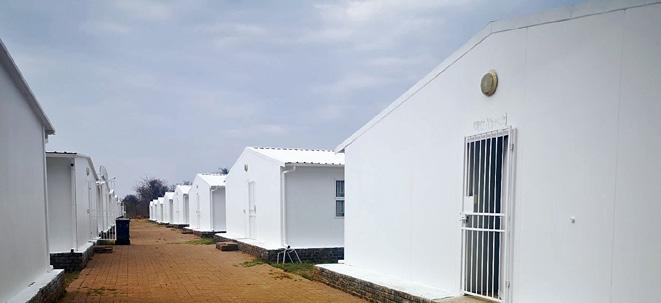
Paint that cools down buildings and saves electricity sounds either too good to be true or like science fiction. It is, in fact, neither. The science has been proven, as has practical application.
The largest single cool surface project ever in Sub-Saharan Africa is currently being rolled out on military bases in South Africa’s Limpopo province. The data that is being gathered will be used to advise policy in the country. And the scale of this project is impressive: the first phase involves 470 800 m 2 and the second 900 000 m 2 of cool surface paint by the end of 2025 when the five-year project is scheduled to be completed.
Cool surface paint is known as a passive building/structural energy efficiency measure. In cooler buildings, air-conditioning units don’t have to work as hard, which saves electricity.
While about 30% more expensive than ordinary paint, cool surface coatings have a minimum lifespan of 10 years, which cuts down on routine maintenance expenses. As an added benefit, the paint waterproofs the surface area it encapsulates to a large extent (if applied properly) and acts as a
fire retardant, giving people up to two extra hours to vacate a burning building.
By the end of 2023, 366 000 m2 of building envelope, i.e., walls and roofs, had already been painted, turning personnel housing, schools, creches, clinics and mega military structures into far more comfortable working and living spaces.
“The paint contains a compound similar to what is found in sunblock and works in much the same way in that it pushes heat and light away from the building,” explains Dr Karen Surridge who leads this collaborative project on behalf of the South African National Energy Development Institute (SANEDI).
Cool bubble effect
As a scientist, Surridge is particularly interested in the data that is being gathered as the project rolls out. She explains that the scale of the initiative enables SANEDI to study
the so-called “cool bubble” effect for the first time in South Africa.
International research has already proven that in high-density built-up areas, a bubble of cooler temperature forms over and between buildings as the paint pushes away heat. “The large bases we are painting are like towns themselves, making them ideal to measure the cool bubble effect under local conditions,” says Surridge.
“The project with our military partners is not even halfway yet and already we are seeing great results. The data shows a marked difference between coated and uncoated buildings, and the energy savings are considerable.”
Cool surface paint is available in a spectrum of colours. While white delivers the best cooling effect, all light colours will deliver a good result. Even black cool surface paint has an impact.
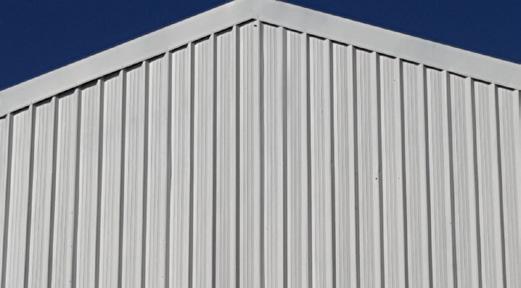
Cool surface paint is known as a passive building/structural energy efficiency measure. In cooler buildings, air-conditioning units don’t have to work as hard, which saves electricity
The Johannesburg Development Agency’s (JDA’s) implementation of the Rea Vaya Phase 1C along Louis Botha Avenue to Sandton is progressing well, with much of the work already being completed.
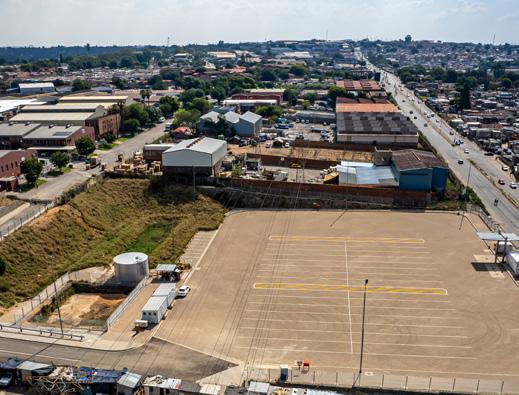
ALEX AND SELBY DEPOTS TO ANCHOR
REA VAYA PHASE 1C TRUNK ROUTE
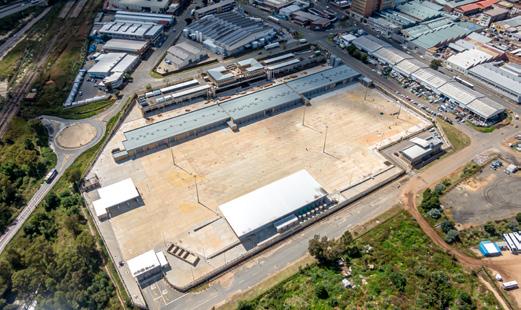
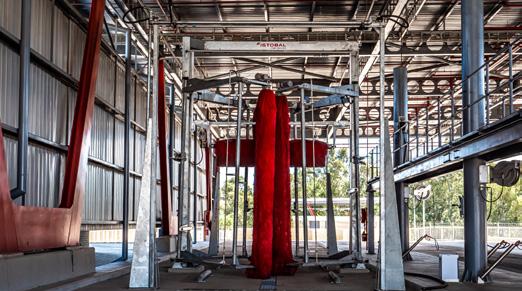
The trunk route will comprise 13 lowflow stations, five interchanges, improved bridges, cycle routes, and pedestrian walkways. And the introduction of Rea Vaya Phase 1C will bring safe, affordable, and reliable public transport to Joburg CBD, Hillbrow, Bellevue, Yeoville, Orange Grove, Cheltondale, Highlands North, Balfour Park, Griswold, Bramley, Wynberg, Alexandra, Marlboro, Athol, Sandton, Sandown, Longmeadow, and Greenstone.
The route will have 141 low-entry buses, as well as an interchange via Pan Africa connecting Rea Vaya with other modes of public transport.
Two depots will be key to enabling the Rea Vaya BRT System Phase 1C trunk route, playing pivotal roles in its operation. One in Alexandra, where buses will be parked and maintained, and another in Selby, which will be used by the Alexandra Bus Operating Company (ABC).
Serving as key hubs along the route, these depots will serve as vital nerve centres for the maintenance, storage, and dispatch of buses, ensuring the smooth and efficient operation of the BRT system.
As the backbone of the Phase 1C trunk route, the depots will not only facilitate the seamless flow of buses, but also serve as dynamic hubs for commuters, providing essential services and connections to various parts of the city.
Alexandra depot complete
The Alexandra depot houses 30 buses and will serve as a transportation hub for the community and enhance the public transport infrastructure in the Louis Botha Corridor.
The depot, now complete, will be an additional component for Phase 1C operations from Sandton to Alexandra, along Rivonia Road and Katherine Drive, and the trunk route from Parktown to Alexandra, along Louis Botha Avenue.
The scope of work for the construction of the Alexandra depot included, but was not limited to, earthworks, retaining walls, subsoil drainage, stormwater drainage and an attenuation pond, paving, security fencing, provision of water/electricity services, landscaping and road lane markings.
In quarter four of 2023, the JDA completed the access road to the depot. Stormwaterassociated infrastructure was also extended and tied in with the existing system and the existing drainage inlet structures.
The Alexandra depot includes a bus parking platform, diesel and AdBlue refuelling storage tanks and dispensers, admin staff prefabricated office structures and ablutions, as well as a refuelling canopy and oil separator pit.
Selby BRT depot being finalised
The new Selby BRT depot is anticipated to further enhance the efficiency and reliability of the city’s BRT system. The depot will service two Rea Vaya BRT operating companies for major and minor maintenance by maintaining in-service and out-of-service buses.
The depot’s central location in the inner city will minimise dead mileage and the time lost by buses in traffic congestion between depots and route starting points. The Selby BRT depot will be able to accommodate up to 270 buses.
The administration building of the Selby BRT depot will function as the working space of the facility and is currently being refurbished and renovated to feature modern amenities. The scope of works will see the refurbishment of workshop areas, the construction of a new canteen and gymnasium.
The modern administration building will also feature new offices, administration rooms, boardrooms, and storerooms, a new main foyer and reception areas, plus the refurbishment of courtyard spaces. It will provide a central hub for managing the operations.
The construction of additional toilet blocks, new lifts to aid accessibility, service ducts, pedestrian and vehicular access with security offices, and external works will also form part of the scope of work.
The completed works on the Selby depot include the construction of the bus depot workshops, a new double-volume wash bay building, two new refuse buildings, refuelling garages, and the construction of the administration building, which houses the Intelligent Transport System (ITS) control centre, and a new gatehouse.
The new Selby BRT depot will also allow Rea Vaya operators to maintain their fleet with newly installed specialised equipment. The equipment includes brake testing facilities, spray booths, automatic and manual bus washing facilities, and a refuelling facility with AdBlue dispensers.
“The JDA is excited about the progress of the Rea Vaya Phase 1C projects, particularly the completion of the Alexandra depot and the finalisation of the Selby BRT depot. These depots are not just buildings; they are the beating heart of the city’s BRT system, ensuring the smooth operation and maintenance of the fleet,” says Siyabonga Genu, JDA’s Executive Manager for Project Implementation.

“With their strategic locations and state-ofthe-art facilities, they will play a crucial role in providing safe, reliable, and efficient public transportation to the people of Johannesburg,” he adds.
The Rea Vaya Phase 1C trunk route is the third BRT trunk route to be implemented since 2009.
Rea Vaya’s Phase 1A started running in 2009, with a trunk route operating between Ellis Park in Doornfontein and Thokoza Park in Soweto, linking with several feeder routes in Soweto.
The Phase 1B services were rolled out on 14th October 2013, with routes from Thokoza Park through Noordgesig Extension, Westbury, Auckland Park, Milpark, Parktown, and to Library Gardens in the Joburg CBD.


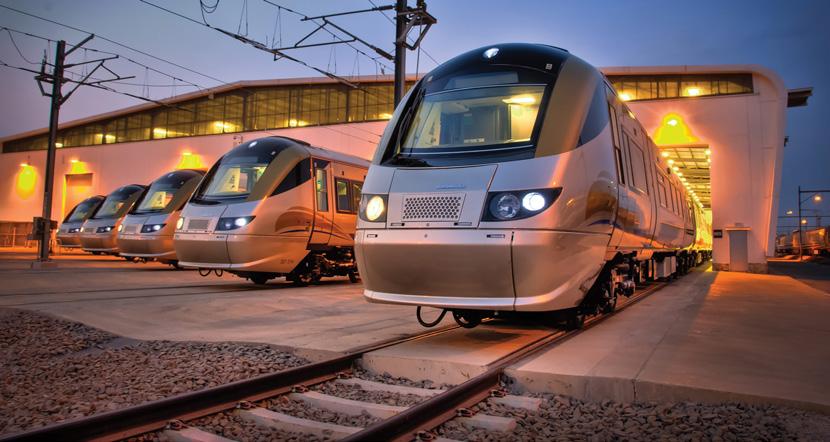
South Africa’s commuter rail in the spotlight
Commuter rail is a key aspect of any strategic public transport network, “And we cannot afford for commuter rail in South Africa to fail,” says James Anafi, Market Sector Lead: Rail, Africa at AECOM.
He reveals that statistics from the 2019 National Household Travel Survey (NHHTS) for Gauteng, the country’s largest economic hub, showed a huge decline in commuter rail market share compared to 2014, as indicated in Table 1.
Even before 2014, the commuter rail modal share had already declined from previous years due to a drop in service quality and related aspects, such as reliability, punctuality and passenger security. The Covid-19 pandemic further severely impacted commuter rail services after 2020 to the point of them almost being non-operational.
Commuter rail generally is a very efficient mode to transport passengers in dense and high-volume commuting corridors. Due to its efficiency, commuter rail in most instances is also more affordable to both government and passengers, despite it being reliant on subsidies. But when not managed optimally in terms of affordability and availability, there are ripple effects.
This is reflected by consecutive travel surveys, which report that increasing portions of household disposable income are being spent. But affordability is declining, with many commuters even being forced to walk unacceptably long distances to work, due to them not being able to afford any motorised transport modes.
Reference projects
Globally AECOM has significant experience and expertise in the rail sector in Africa, as well as internationally. Worldwide, it is currently ranked as a leader in terms of transit rail, with major projects such as Neom in Saudi Arabia and the California High-Speed Rail programme in the USA.
AECOM has also worked on the feasibility of the Ethiopia-Sudan Railway, a proposed 1 522 km standard gauge railway that will connect Addis Ababa in Ethiopia to Port Sudan on the Sudan Red Sea coast.
AECOM became involved after the sponsors, African Development Bank and the Ethiopian
TABLE 1 Statistics from the 2019 National Household Travel Survey (NHHTS) for Gauteng
government, approved funding for the feasibility study, which was completed in December 2022.
“We have done quite a bit of work around sustainable transport. The revitalisation and role of rail is quite a prevalent issue in South Africa at the moment,” says Chris Britz, Director: Transportation and Leader of the Transportation Business Line in Africa at AECOM. Here there are two aspects, namely commuter rail and its diminishing role, and freight rail and its impact on economic growth.
“The planning and strategic notion that a rail network needs to form the backbone of your public transport system is commendable, but currently this is definitely not the case in South Africa,” adds Britz.
Population expansion and equitable access
As Anafi points out, South African cities are still growing quite rapidly. Transporting this expanding population within an urban context in a sustainable manner therefore requires a high capacity, high efficiency transportation mode, namely a strong, capable commuter rail system.
Omitting commuter rail from the transport equation results in an unbalanced sector, says William Makwela, a railway designer at AECOM. It has resulted in the predominance of the minibus taxi industry, which transports 80% of public transport passengers in the country at present. Its lack of regulation has seen a range of social issues, whereas if it had been allowed to develop in conjunction with commuter rail, it would have been much more integrated and controlled than it is now.
“Transport is part of our everyday lives, but not a lot of people are really aware of the significance of it, especially rail. Commuter rail ticks all the boxes in terms of the environment, society and the economy in many First World countries. For South Africa to achieve a similar level, we must place more emphasis on our commuter rail system,” says Salita Wudraj, a railway designer at AECOM.
Policy environment
Government is committed to making commuter rail the backbone of urban public transport in South Africa and to improve efficiency and sustainability. In light of the 2021 National White Paper on Transport Policy and the National Rail Policy, rail is envisioned as an affordable, competitive, integrated, reliable, safe and sustainable transport mode that, by 2050, will be the backbone of South Africa’s freight logistics and passenger mobility systems.
“Whether or not government’s goal of 2050 is feasible depends on what is required to get there,” cautions Britz.
National rail policy aims to transform passenger rail through new investments in infrastructure and separating infrastructure ownership and operations: the National Department of Transport (NDoT) is currently preparing a National Rail Plan to guide new investment.
The White Paper calls for the commuter rail function to be devolved to either provinces or transport authorities at a provincial level in Gauteng’s case or at a local level in Cape Town. Britz points to commuter rail’s dominance in the past, compared to the present 5% of the public transport market share held by the Passenger Rail Agency of South Africa (PRASA), as an indication of its true potential.
NDoT is also currently compiling a National Devolution Strategy to guide devolution of rail functions, which should be completed by mid2024. In turn, PRASA is currently busy with a rebuild-and-recovery programme of its existing commuter lines, restoring services in addition to its ongoing train replacement programme for 600 new EMUs.
Sustainable Legacies
AECOM remains highly supportive of the development of an efficient commuter rail system in South Africa, especially the mooted expansion of the Gautrain network. “It also aligns well with our Environmental, Social and Governance (ESG) strategy called Sustainable Legacies,” says Anafi.
This strategy ensures AECOM embeds ESG principles into everything it does, from the way it runs its business to the work it carries out in partnership with its clients. It includes limiting the company’s carbon footprint and that of its projects.
“The development and active use of a lowemission transport mode like commuter rail goes a long way to reduce transportation’s carbon footprint,” says Anafi.
He calls for a renewed focus on expanding and improving commuter rail and thereby enhancing the quality of life for all. “More efficient and reliable transportation cuts across all sectors. If you have a better transportation system, everybody in South Africa benefits.”
Adds Britz: “We have had huge investments in rail infrastructure and services over the years. The low-hanging fruit is to revitalise and reinstate and improve on what one has. It will then give us a basis for a properly integrated and functional public transport system in future.”
A key enabler is private participation, says Anafi. This needs to be encouraged to revitalise commuter rail, as government alone cannot come up with all the necessary funding and necessary expertise.
“Any restoration programme must focus on high demand corridors to provide a good, reliable and competitive service that then begins to bring high impact and confidence into the sector, so that people start seeing it as a viable option to use,” he explains.
Get the community involved
An additional bonus are the socioeconomic and local community development benefits associated with commuter rail expansion and operation. “A major problem is vandalism and theft. If we uplift communities as part of the commuter rail network, they will have a sense of ownership of this vital infrastructure and the need to preserve it for future generations,” Anafi continues.
Going forward
However, the institutional model around passenger rail service provision must be addressed. “A proper concessionary structure is necessary to oversee quality and efficiency,” says Britz.
“Therefore, we need to look at the institutional arrangements in place in terms of roles and responsibilities. That is a fundamental basis for more effective and efficient provision of commuter rail services,” Britz concludes.

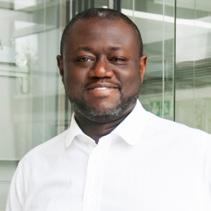
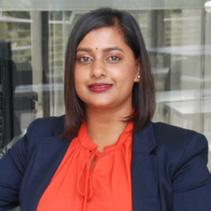

FOR RAIL MARKET INNOVATIVE EXCAVATOR ADAPTATION
Earthmoving equipment suppliers are generally not keen to entertain requests from customers to fit specialised equipment to standard machines that may require some “out of the box” thinking and adaptation – all except one supplier, Bell Equipment.
This is the opinion of Gary Ollewagen, the youngest of three brothers who, together with their financial director, own and manage W.O. Trackworks (WOT), a specialist company that will get involved at the inception stage of projects with prospective clients and, where applicable, manage the designs and undertake construction of new railway trackwork/networks. Furthermore, WOT undertakes the maintenance of existing rail networks, and offers the design and manufacture of custom concrete products related to railway infrastructure.
“W.O. Trackworks was started by our father, Winston Ollewagen, in 1982 and currently me, my older brothers, Winston and Ian, and the Financial Director, Raynard Weyers, manage the company,” says Gary.
“Our father is a platelayer by trade, which to the layman is a
person who regularly inspects the section of railway track that he is responsible for from an operational safety perspective, checking for geometrical deviations, wear on the rails, sleepers and fastenings, and the general safety of the surrounding area as well.”
Local and international track record Gary and Winston draw on their extensive experience in civil engineering and mechanised on track plant, with Ian in support and focusing on construction and concrete
products and the installation thereof. WOT has an impressive resume with projects undertaken successfully on four continents, including large parts of Africa (including South Africa), the Middle East, and even as far as Vietnam and Mexico.
“Approximately 12 years ago we decided to investigate the opportunity to introduce a more mechanised system in our industry by using standard earthmoving equipment that we would then adapt to better suit our purposes. We subsequently grew our skills set tremendously, which enabled us to tender and be awarded higher value, and more complex contracts,” Gary adds.
Earthmoving machine acquisitions
“We bought our first JCB JS140 excavator in 2017 and the adaptability of the machine with our special attachments, coupled with its reliability, prompted us to expand our fleet of JCB equipment in 2022 by purchasing additional units, i.e. JCB 3DX backhoe loaders and a JCB JS205 excavator. These transactions were concluded with the advice and assistance of Bell Equipment’s Sales Representative, André Jordaan,” Gary continues.
“An interesting fact is that not all suppliers of such equipment are keen to take on the additional work of adapting a standard machine to our needs. Bell Equipment, as
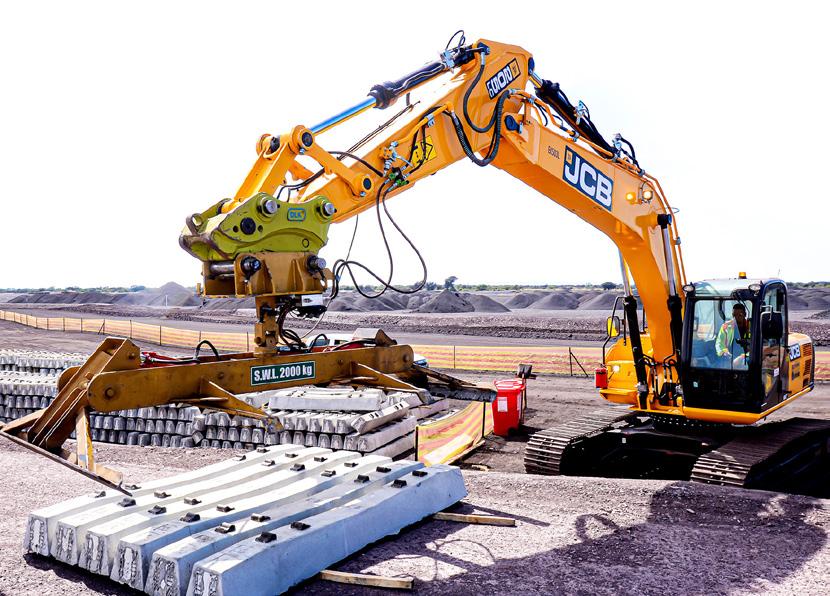
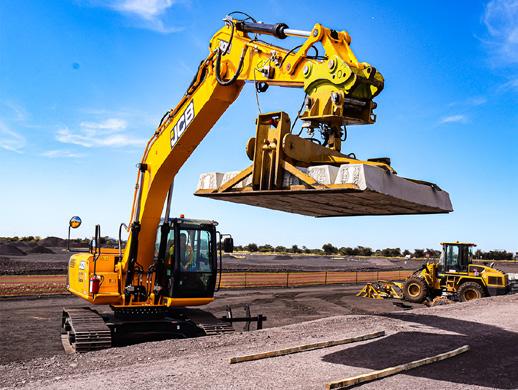
the South African supplier of JCB, however, agreed to partner with us, which in turn led W.O. Trackworks to become a loyal customer going forward.”
Custom built WOT attachments
Gary explains that although the attachments may be readily available in the Northern Hemisphere, the foreign exchange and importation costs make this option very prohibitive. WOT supplies their own design of bespoke attachments and then request Bell Equipment to fit these attachments to standard 20 t JCB JS205 excavators.
“We require Bell Equipment to remove the bucket and decrease the hydraulic flows on the JCB JS205 excavator. They then mount a switching panel in the cab that will control the increased three auxiliary functions that

we need for our specific tasks namely to grab five sleepers and place them, grab five sleepers and place them to exact spacing of predetermined widths, and finally grab and place two sections of rail of 18-metre lengths weighing more than two tons and place them accurately.”
The fact that Bell Equipment, as the supplier of the equipment, does the post-market conversion, ensures that the warranty on the JCB JS205 excavator is not affected, which is a huge advantage for WOT.
Gary has designed a cam-lock system which, when attached to the boom of the JCB JS205 excavator, allows for two 18-metre lengths of rail to be safely lifted simultaneously and placed in position on the concrete sleepers. By using these attachments efficiently, a team of only three people can place 940 metres of
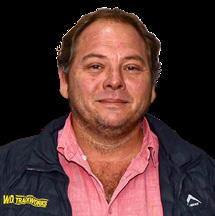
concrete track sleepers in a seven-hour shift while another team, also consisting of only three people, can lay 40 pairs of 18-metre rail track in the same timeframe. This makes for reduced labour, faster turnaround times and improved safety on a site, the latter being a huge plus factor for clients that consider safety and risk paramount.
“These attachments have worked so well for us and the reduced hydraulic flows on the JCB JS205 excavator makes it the ideal machine for our purposes,” Gary says. “Proof of this is the two more similar machines we bought in March and June 2023 which we believe will be with us for a long time to come. Furthermore, with our specialised and to a certain extent, limited usage, the JCB excavators won’t run up large hours at all.”
“This is also the reason we don’t take extended warranties as we believe the JCB JS205 excavators are solidly designed and built,” he says. “Fuel consumption is not that important to us due to the short periods for which the machines are used, but our experience has taught us that, once again, the reduced hydraulic flows do cut down on fuel consumption as the engines do not run hard.”
WOT’s JCB 3DX backhoe loaders are used for their projects on internal hires to fulfill housekeeping duties and keep the sites tidy.
“To say that we are pleased with our purchases of the JCB JS205 excavators would almost be an understatement as the machines fulfill a very important role in our company by decreasing labour input, whilst still completing the job efficiently, safely and to the client’s satisfaction,” Gary says.
He adds that pivotal to their satisfaction is the fact that, “Bell Equipment was prepared to listen to our needs, think innovatively, and is true to our company’s own nature. This makes it a market leader as much as we, W.O. Trackworks, would like to think we are too.”

TERRAFORCE CELEBRATES 45 YEARS OF RETAINING
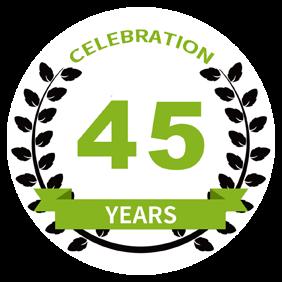
Carving out their own path, while honouring a family legacy that spans over four decades, Elgin Rust and Karin Johns (née Rust) are taking over the reins of the retaining wall business conceived 45 years ago by their father, Holger Rust.
The dynamic duo is not only driving forward the company’s success, but also redefining the role of women in the construction and retaining wall industry.
Rooted in innovation
The story of Terraforce is rooted in the vision and entrepreneurial spirit of Holger Rust. In 1979, he began importing gabions – a conventional method of retaining walls. However, he soon pivoted towards developing innovative and proprietary precast earthretaining solutions to meet the demands of
This led to the design and development of a unique interlocking concrete retaining wall system that is now manufactured exclusively by local and international specialist concrete precast companies in Canada, Australia, Spain, India, Morocco, Nigeria, Eswatini, Lesotho, Ghana, the United Kingdom, Namibia, the United Arab Emirates, Egypt and South Africa.
Growing up surrounded by the construction business, Elgin Rust and Karin found their calling, inheriting their father’s passion for innovation and excellence. As women in a (still) predominantly male-dominated industry, they faced numerous challenges along the way. Yet, their resilience and unwavering commitment to quality allowed them to overcome barriers and earn respect within the construction community.
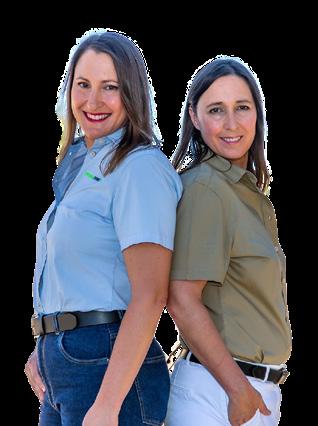
Quality-driven
In a market where cheaper, less durable replicas are finding their way onto sites, Rust and Johns caution the market to ensure that the product specified, and the one used on site, is indeed a genuine Terraforce product. Terraforce stackable, no-mortar retaining wall blocks adhere to local and international standards, having undergone extensive laboratory
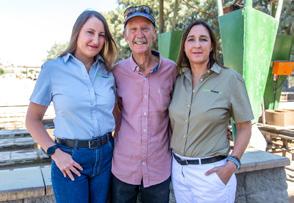
testing – based on SANS 207, BS 8006 and ASTM-D6916-18 – by professional accreditation agencies. In addition, licensed manufacturers must adhere to strict minimum specification and regular compressive strength tests as set out by Terraforce, ensuring that the end user is supplied a quality product.
The way forward
Rust and Johns are dedicated to honouring their father’s legacy, while charting a new course for the company’s future. Their story serves as an inspiration to aspiring female entrepreneurs and professionals, proving that with vision, discipline, determination and a willingness to challenge the status quo, women can and do thrive in the construction business.
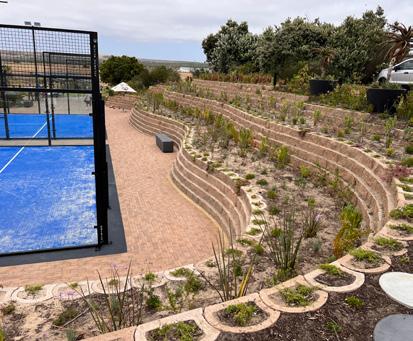
CURVACEOUS RETAINING WALLS FOR ATLANTIC BEACH PADEL COURTS
In August 2023, Decorton Retaining Systems – a Western Cape based Terraforce recommended contractor – commenced construction on several terraced and undulating rock face finish retaining walls for the padel courts at Atlantic Beach Estate in Cape Town. Also incorporated in the works were Terraforce 4x4 Step Block access stairs and wide staircases wrapping parts of the courts.
The walls were required to lower the padel courts to the same level as the clubhouse to help reduce wind damage and to beautify the whole area. The client was looking for a rustic effect and ultimately chose the Terraforce® L12 rock face finish.
Comments SP van Blerk at Decorton Retaining Systems: “Our installation of Terraforce earth retaining walls and 4x4 Step Block steps for the padel courts at Atlantic Beach Estate shows the true versatility and functionality of Terraforce products. The blocks are incredibly adept at creating the most stunning undulating retaining walls, able to follow almost any site contour.”
The blocks are designed to simply stack using a distinctive horizontal interlock, a shape that allows for unrestricted wall gradients and curves to suit each project – unhampered by nibs and slots – to provide a cost-effective, and versatile earth retaining system.
Even though the blocks are lightweight for easy delivery and installation, they are heavy in mass when filled with soil, gravel or concrete, providing additional vertical interlock for added structural integrity and durability.
PROJECT TEAM
Architect: Harry Greenberg
Main Contractor: Plastotop Barrett’s Sports Courts
Sub-Contractor: Decorton Retaining Systems
AfriSam All Purpose cement
still a cornerstone for diverse construction applications
AfriSam All Purpose Cement is recognised as a fundamental component in various construction applications, embodying versatility, reliability, quality and affordability. This premium product is designed to meet the needs of a wide range of construction projects from largescale commercial and infrastructure developments to smaller residential and DIY projects.

AfriSam All Purpose
Manufactured in AfriSam’s state-of-theart facilities, where quality management systems of the highest standard are a priority, the cement complies fully with the SANS 50197 specification for common cements. Its constant monitoring and maintenance of composition ensure it delivers high quality performance within the 42,5N MPa strength class.
Important additives
The addition of fly ash and slag, where indicated, to this specially developed cement improves the overall workability of concrete as fly ash introduces microscopic spheres that effectively reduce the water demand of mortars and plasters. This makes the mix not only more cohesive, but also enhances its ease of application. The improvement in texture and consistency ensures a superior bond in plaster applications, attributed to the increased stickiness of the mix. Consequently, this leads to a more efficient application process and results in smoother, more durable finishes in construction projects.
Heat hydration and alkali-aggregate reactions
The unique composition of AfriSam All Purpose Cement addresses the industry’s need for a cement that reduces heat hydration in mass concrete works and enhances concrete’s resistance to chemical attacks, including sulphate, chloride, and exposure to soft water.
The use of AfriSam All Purpose Cement in projects also significantly improves resistance to alkali-aggregate reactions and decreases the permeability of concrete in water retaining structures, contributing to the sustainability and longevity of these projects.
AfriSam All Purpose Cement is suitable for a wide range of applications, from structural concrete and residential projects to brick and block making, as well as plaster mortar and shotcrete.
AfriSam All Purpose Cement is a
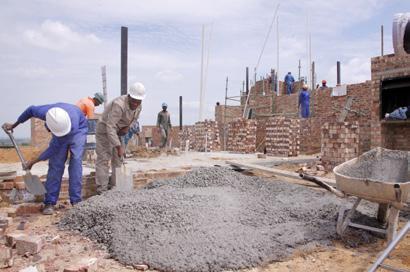
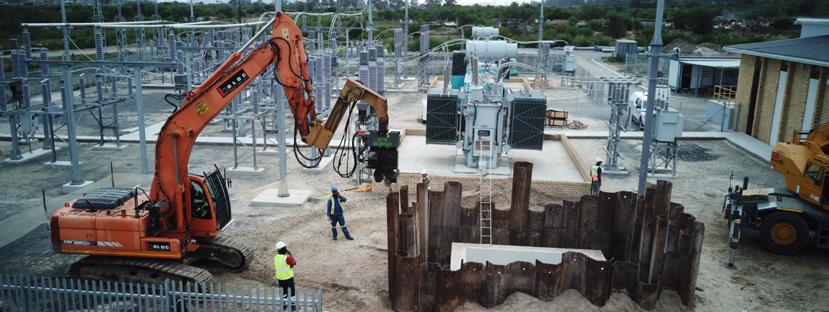
MULTIDISCIPLINARY APPROACH SPURS BUSINESS EXPANSION
BLOC Contractors (BLOC) celebrates its 20th anniversary in 2024, a major milestone that marks a series of evolutionary changes in the business in terms of ownership, market penetration and diversification strategies. IMIESA speaks to Byron Field, BLOC’s managing director, about project and group developments.
As a civil engineering contractor, the backbone of our operations are in the geotechnical and trenchless technology fields. Allied to this is the progressive growth of our structural concrete business, and entry into new markets that include construction services for the rapidly growing renewable energy market – especially rooftop solar,” Field explains.
Headquartered in Durban, with a branch in Johannesburg, BLOC operates across South Africa, as well as within the Southern African region, where it has a registered company in Zambia.
Major geotechnical works being undertaken by BLOC as a specialist subcontractor include SANRAL projects on the N3 between Pietermaritzburg and Durban (up to Town Hill) to accommodate the addition of new north
and south bound lanes, as well as similar upgrades on the N2 route between King Shaka International Airport and the city of Durban.
The provision for new lanes on some of these sections requires a series of cuttings and/or the creation of embankments. From a geotechnical perspective, these works then need to be reinforced with lateral support interventions, and mechanically stabilised walls.
Permanent lateral support elements being carried out by BLOC include rock anchors, soil nails, and shotcreting, along with temporary lateral support in the form of sheet piling. The geotechnical scope also includes pipe jacking for stormwater culverts.
“There are major production demands because the permanent lateral support phases need to be completed within strict timelines to enable the main contractors to access and
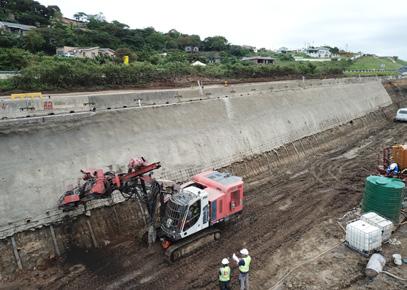
execute their road upgrade programmes,” says Field, adding that these embankments range from 50 m to 1 km or more in length and up to 12 m in height, which requires creative solutions from an equipment perspective.
In this respect, and in conjunction with its ongoing OEM equipment acquisitions, BLOC has its own in-house mechanical design and fabrication capability for custom builds to tackle specific projects. These include purposedesigned booms and attachments for varying lateral support heights.
“Each geotechnical project is unique, so we respond accordingly. Classic examples are culvert and pipe jacking where we design and build our own shields and thrust blocks, among other elements, to ensure we execute a perfectly aligned installation within tight tolerances,” Field continues. “The pursuit of
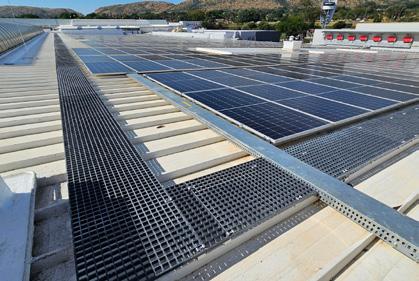
innovation in these and other areas is the key to winning new work.”
This is underscored by BLOC’s first entry into the mining sector following the securing of a subcontract order on a South African colliery. BLOC’s scope entails the installation of lateral support for a 20 m deep box cut in preparation for the construction of a new incline shaft. To meet the project timeline, BLOC’s teams are working 24-hours a day, six days a week.
BLOC Concrete Solutions
Within the business mix, concrete products – like shotcrete employed for lateral support – is a mainstay of geotechnical engineering. However, BLOC’s expertise in this area goes a lot further via its specialist division, BLOC Concrete Solutions, which focuses on a range of services such as concrete rehabilitation, cutting, coring and joint sealing.
Historically, this includes concrete road construction for SANRAL on N2 and N3 sections within KwaZulu-Natal, as well as other projects.
“Concrete pavements are highly technical structures – particularly in terms of joint sealing – with contractor guarantees typically required for around 12 years, so getting the job done right is crucial,” explains Field.
BLOC Composite Structures
Allied to these activities – when it comes to construction or infrastructure upgrades – is the BLOC Composite Structures division, which designs, fabricates, supplies, and installs fibreglass reinforced plastic (FRP) products. These include gratings, hand railing, ladders,
structural profiles, channels, I-beams, walkways, and stairways, mainly for marine, mining, industrial and acid environments where corrosion is a factor. The latter include water and wastewater treatment works.
A recent project in Eswatini entailed the manufacture and supply of structural profiles for two 56 m diameter tanks for a biogas plant, which will generate electricity from agricultural byproducts. These are believed to be the largest composite tanks in Africa to date. The sides and roofs of the tanks are composed of HDPE sheeting, which are attached and supported by the structural profiles supplied by BLOC, such as I-beams, channels and tubing.
The key advantage of BLOC’s fibreglass solutions is their design flexibility and adaptability.
A prime example is the rooftop solar panel market where BLOC is carving out a niche for lightweight service walkways. These include installations for warehouses and factories with steel sheet roofs that are not designed for the weight of direct foot traffic. In response, installing fibreglass walkways safely spreads the load and allows maintenance teams to access the solar panels when required.
Building the team
“The securing of largescale projects within the geotechnical field, as well as within our sister divisions, has had the added benefit of enabling us to upscale the company as a whole. We’ve strengthened our middle management and site operations teams by recruiting the best talent from industry. Backed by succession planning at all levels to support our growth, we see exciting times ahead,” Field concludes.
www.bloc.co.za | www.compositestructures.co.za | www.concrete-solutions.co.za
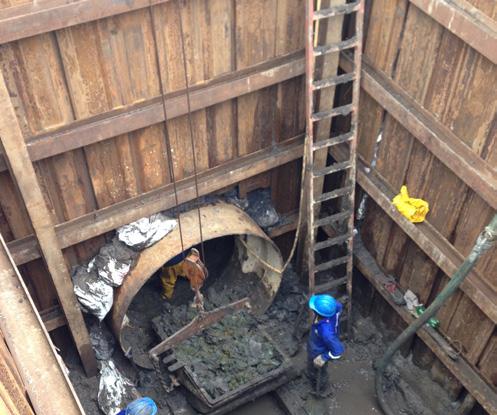
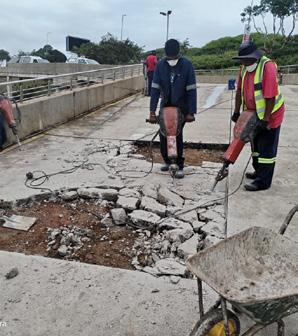
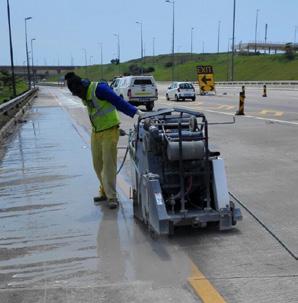
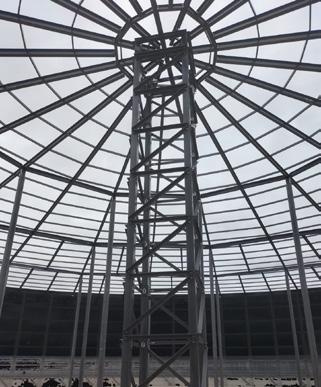











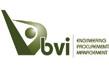



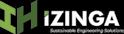
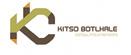







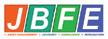
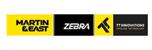
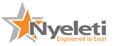
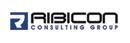












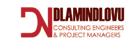
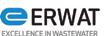
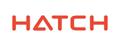

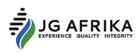




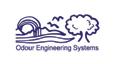



















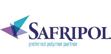


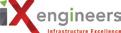







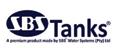
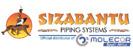








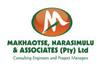










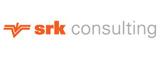
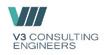


siphokuhle.dlamini@aecom.com
AFI Consult banie@afri-infra.com
ARRB Systems info@arrbsystemssa.com
Asla Construction (Pty) Ltd johanv@asla.co.za
BMK Group brian@bmkgroup.co.za
Bosch Projects (Pty) Ltd mail@boschprojects.co.za
BVI Consulting Engineers marketing@bviho.co.za
CCG puhumudzo@ccgsytems.co.za / info@ccgsystems.co.za
Corrosion Institute of Southern Africa secretary@corrosioninstitute.org.za
Dlamindlovu Consulting Engineers & Project Managers info@dlami-ndlovu.co.za
EFG Engineers info@efgeng.co.za
Elster Kent Metering Mark.Shamley@Honeywell.com
EMS Solutions paul@emssolutions.co.za
ENsync Engineers info@ensync.africa
ERWAT mail@erwat.co.za
Gabion Baskets mail@gabionbaskets.co.za
GIBB marketing@gibb.co.za
GIGSA secretary@gigsa.org
GLS Consulting info@gls.co.za
Gorman Rupp Cordeiro@gormanrupp.co.za
Gudunkomo Investments & Consulting info@gudunkomo.co.za
Hatch Africa (Pty) Ltd info@hatch.co.za
HB Glass Filter Media info@hardybulkinglass.com
Herrenknecht schiewe.helene@herrenknecht.de
Huber Technology cs@hubersa.com
Hydro-comp Enterprises info@edams.co.za
Infrachamps Consulting info@infrachamps.co.za
INFRATEC info@infratec.co.za
Institute of Waste Management of Southern Africa iwmsa@iwmsa.co.za
IQHINA Consulting Engineers & Project Managers info@iqhina.co.za
iX engineers (Pty) Ltd hans.k@ixengineers.co.za
Izinga Holdings info@izingalabezi.co.za
JBFE Consulting (Pty) Ltd issie@jbfe.co.za
JG Afrika DennyC@jgafrika.com
KABE Consulting Engineers info@kabe.co.za
Kago Consulting Engineers kagocon@kago.co.za
Kantey & Templer (K&T) Consulting Engineers ccherry@ct.kanteys.co.za
Kitso Botlhale Consulting Engineers info@kitsobce.co.za
KSB Pumps and Valves (Pty) Ltd salesza@ksb.com
KUREMA Engineering (Pty) Ltd info@kurema.co.za
Lektratek Water general@lwt.co.za
Loshini Projects muzi@loshini.co.za
Makhaotse Narasimulu & Associates mmakhaotse@mna-sa.co.za
Mariswe (Pty) Ltd neshniec@mariswe.com
Martin & East gbyron@martin-east.co.za
M & C Consulting Engineers (Pty) Ltd info@mcconsulting.co.za
Mhiduve adminpotch@mhiduve.co.za
MPAMOT (PTY) LTD mpumem@mpamot.com
Mvubu Consulting & Project Managers miranda@mvubu.net
Nyeleti Consulting naidoot@nyeleti.co.za
Odour Engineering Systems mathewc@oes.co.za
Prociv Consulting & Projects Management amarunga@prociv.co.za
Rainbow Reservoirs quin@rainbowres.com
Re-Solve Consulting (Pty) Ltd maura@re-solve.co.za
Ribicon Consulting Group (Pty) Ltd info@ribicon.co.za
Royal HaskoningDHV francisg@rhdv.com
SABITA info@sabita.co.za
SAFRIPOL mberry@safripol.com
SAGI annette@sagi.co.za
SALGA info@salga.org.za
SAPPMA admin@sappma.co.za / willem@sappma.co.za SARF administrator@sarf.org.za.co.za
SBS Water Systems marketing@sbstanks.co.za
Silulumanzi Antoinette.Diphoko@silulumanzi.com
Siroccon International (Pty) Ltd admin@siroccon.co.za
SiVEST SA info@sivest.co.za
Sizabantu Piping Systems (Pty) Ltd proudly@sizabantu.com
Siza Water (RF) Pty Ltd PA@sizawater.com
Sky High Consulting Engineers (Pty) Ltd info@shconsultong.co.za
SKYV Consulting Engineers (Pty) Ltd kamesh@skyv.co.za
Smartlock jp.alkema@smartlock.net
SMEC capetown@smec.com
SOUTH AFRICAN VALUE EDUCATION Sabiha@savegroup.co.za
Southern African Society for Trenchless Technology director@sasst.org.za
SRK Consulting jomar@srk.co.za
Star Of Life Emergency Trading CC admin@staroflife.co.za
Structa Group info@structatech.co.za
TPA Consulting roger@tpa.co.za
Ultra Control Valves peter@ultravalves.co.za
V3 Consulting Engineers (Pty) Ltd info@v3consulting.co.za
VIP Consulting Engineers esme@vipconsulting.co.za
VNA info@vnac.co.za
Water Institute of Southern Africa wisa@wisa.org.za
Wam Technology CC support@wamsys.co.za
Wilo South Africa marketingsa@wilo.co.za
WRCON ben@wrcon.co.za
Zutari Rashree.Maharaj@Zutari.com
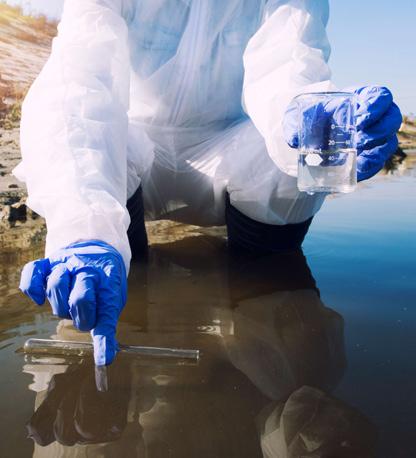
An enzyme that can help oil spills disappear
The Oil Spill Eater II (OSE II) was developed in 1989 in the USA and has been used to clean up more than 44 000 spills.
Approved by the US Environmental Protection Agency (and featured on the National Contingency Plan List), and the UK Marine Management Organisation, it is an environmentally safe and cost-effective bioremediation process for mitigating hazardous waste, spills and contamination.
Gavin Ford, national marketing manager for Lubrication Engineers (LE) South Africa, explains that OSE II uses a biological enzyme to convert spill waste into a natural food source for bacteria found in aquatic environments. The product has nutrients in it that appeal to indigenous bacteria, which then rapidly multiply and break down the oil. He says it is an excellent solution for managing oil spills because it doesn’t introduce any alien bacteria and the final byproducts from the process are just carbon dioxide and water.
The application of the product is relatively simple. It is mixed using a ratio of one part OSE II with 50 parts non-chlorinated water and is then applied using a surface sprayer. (Nonchlorinated water will contain bacteria, which is important to activate the process for cleaning up an oil spill.) A higher concentration of OSE II can be used for older or heavier spills.
In addition to oil spills on oceans and lakes, OSE II can be used to help clean underground spills, airport tarmacs, ship decks, asphalt and concrete spills, fuel tanks, ballast water tanks, bilge tanks, and clean-ups of all kinds of oil leakages.
The refuse compactor has unique polygonal disc wheels for optimum crushing and BOMAG’s proven compaction concept with scrapers and toothed wheels for versatility and efficiency
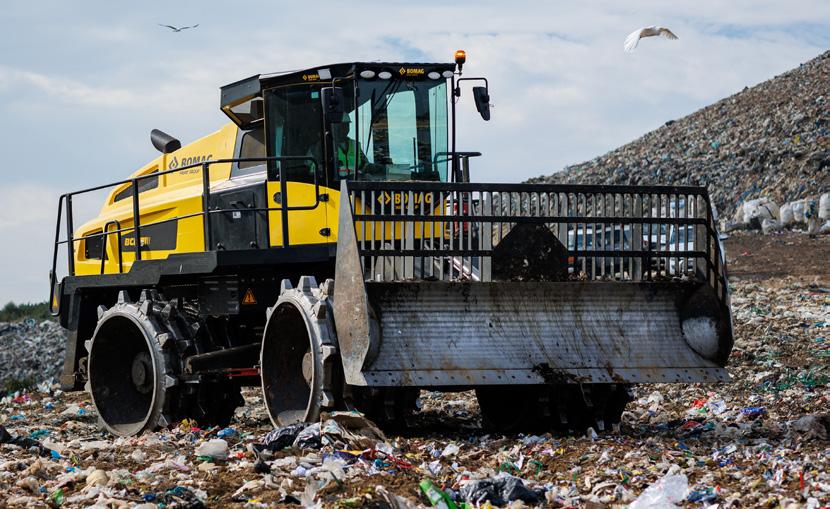
ENVIROSERV TRIALS “AFRICA TOUGH” WASTE COMPACTOR
A newly imported demo waste compactor model, designed especially for developing countries by German equipment manufacturer BOMAG is being trialled in South African conditions by EnviroServ Waste Management.
The 37,5 t compactor, with a Cummins engine, is designed for countries such as those in Africa and South America and offers better compaction of waste. New smart features such as a hydraulically operated engine hood and high air intake make work easier and more efficient.
The machine will spend two months at EnviroServ’s Chloorkop general waste management facility, followed by two months at the Holfontein hazardous waste management facility, to ensure it is trialled under a variety of conditions.
The basis for a landfill’s success is the optimal compaction of various waste
materials. BOMAG Area Manager for Southern Africa, Randhir Haripersad, describes the new blade version RB and shovel version RS as “a true multitool among compactors, enabling allin-one compaction, loading and transporting, saving time and costs.”
“The decision to ask EnviroServ to test the new model is because it can be tested across general and hazardous waste conditions, and we know the machine will really be put to test, working eight to 20 hours a day in high temperatures,” says Haripersad.
Trained for the trial
Comments EnviroServ’s Senior General Manager of Operations, Rhyno Gouws: “We
are ecstatic to have been selected by BOMAG for this trial as it shows that we are recognised as an African leader in waste management. Being associated with a premium brand like BOMAG means quality and reliability, and we have supported the company for many years,”
“Our operators have been trained on the new waste compactors; the functions are the same, just modernised with touch button functioning. There is improved durability, operator comfort and dashboard information, all designed to suit the harsh African operating environment found on landfills,” Gouws explains.
If it passes the trial, it will be available for purchase in South Africa through BOMAG’s local supplier, Kanu Equipment, who supply mining earthmoving and mining equipment. Adds Twan Bell, MD of Kanu Equipment South Africa: “This is an ‘Africa tough’ machine and Kanu will support its servicing and maintenance requirements.”
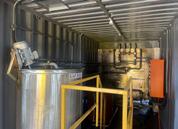
UNLOCKING EXCELLENCE IN ASPHALT TECHNOLOGY
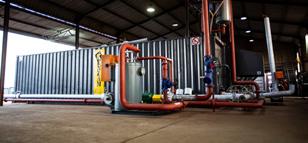
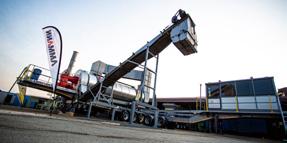
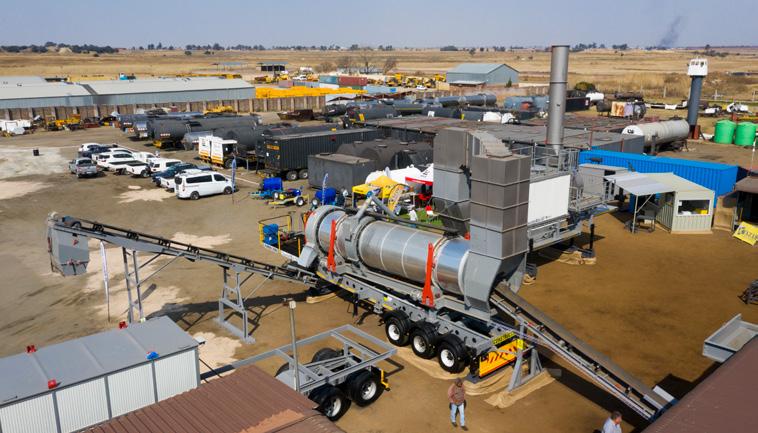
Looking to elevate your asphalt production capabilities? Discover Ammann Kenzam – your premier partner in the import, export, and servicing of asphalt plants and bitumen-related equipment.
WHAT CAN AMMANN KENZAM OFFER YOU?
• Asphalt Plants: Explore our range of high-performance asphalt plants tailored to meet your production needs efficiently and sustainably.
• Bitumen Equipment: Access top-quality bitumen-related equipment designed for durability and optimal performance.
• Retrofit Services: Enhance your existing asphalt plant with our expert retrofit solutions, integrating the latest innovations seamlessly.
• Comprehensive Services: From pipework installations to complete plant de-establishment and re-establishment, our skilled team delivers turnkey solutions..
CONTACT US
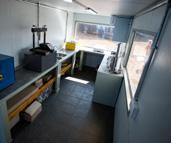
WHY CHOOSE AMMANN KENZAM?
• Industry Expertise: With years of experience, we understand the intricacies of asphalt production and offer solutions that drive results.
• Global Reach: As import-export specialists, we source and deliver cutting-edge equipment from leading manufacturers worldwide.
• Service Excellence: Our commitment doesn’t end with equipment sales – we provide comprehensive support and maintenance to keep your operations running smoothly.
Travis Freel | Regional Sales Manager
Mobile: +27 820 52 1921
Rocco Lehman | Managing Director SA
Mobile: +27 784 88 2945
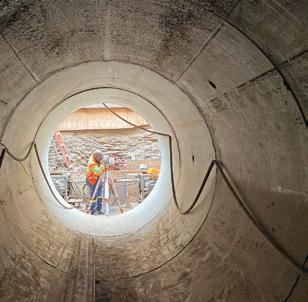
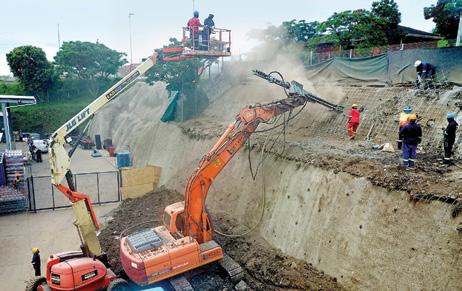
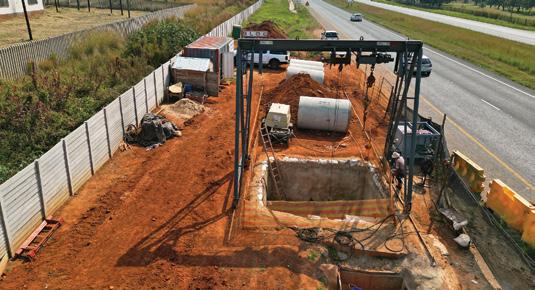
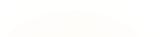
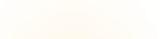
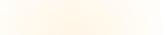

www.bloc.co.za
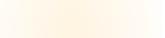

+27 (0)31 833 5330
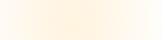

info@bloc.co.za


@bloccontractors

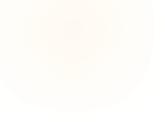
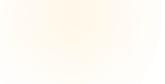
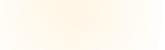
bloc-geotechnical-contractors
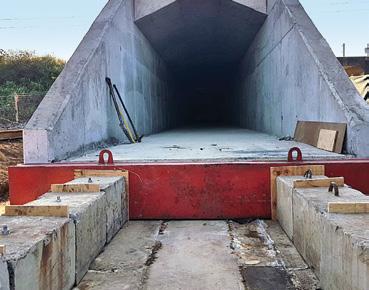
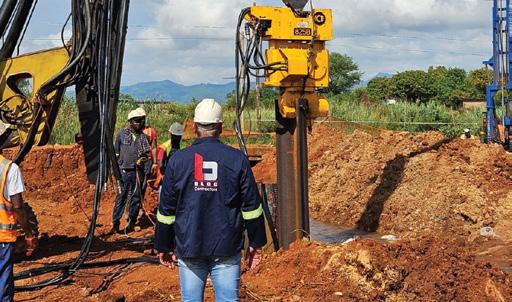