https://doi.org/10.22214/ijraset.2023.49636
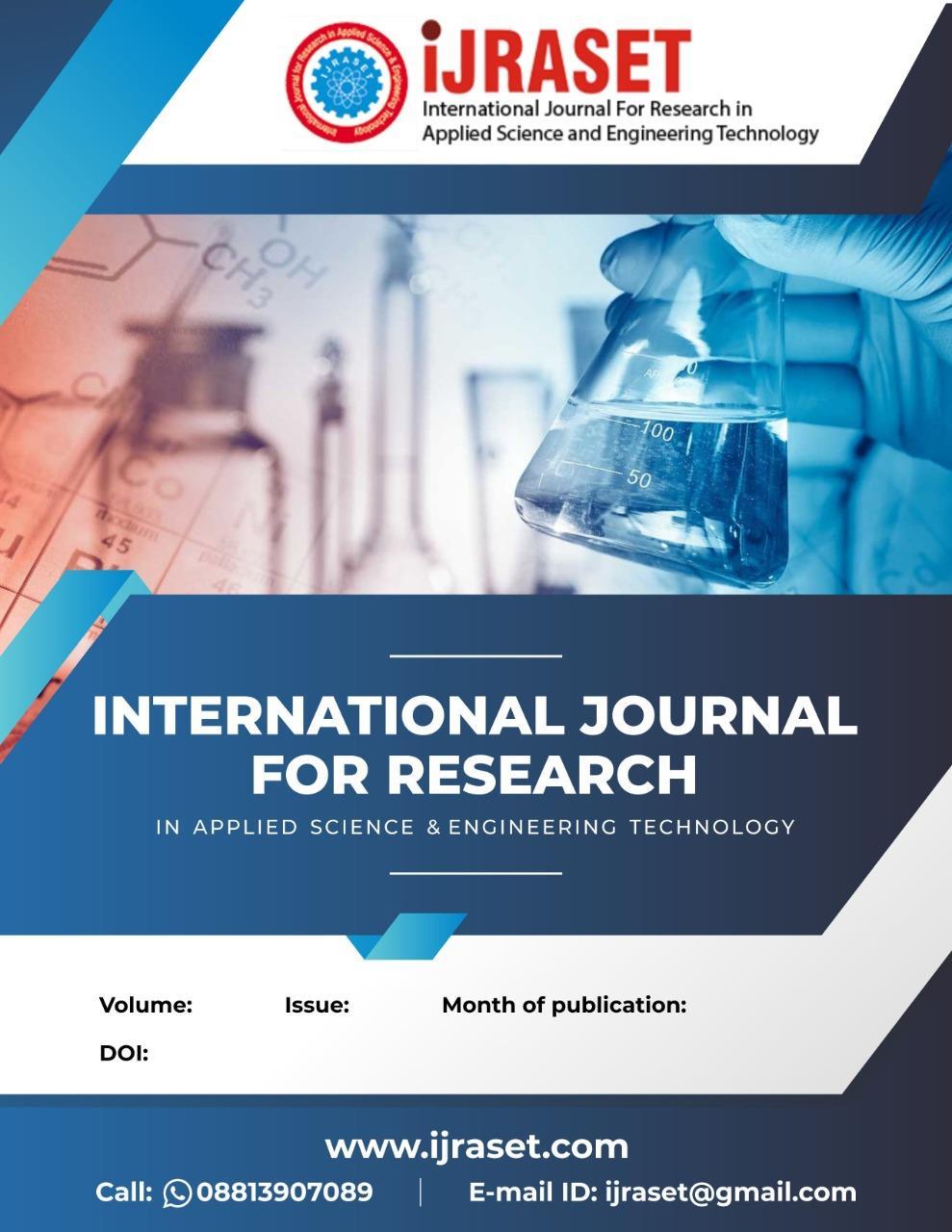
ISSN: 2321-9653; IC Value: 45.98; SJ Impact Factor: 7.538

Volume 11 Issue III Mar 2023- Available at www.ijraset.com
https://doi.org/10.22214/ijraset.2023.49636
ISSN: 2321-9653; IC Value: 45.98; SJ Impact Factor: 7.538
Volume 11 Issue III Mar 2023- Available at www.ijraset.com
1M. Tech. Student (CAD/CAM), 2Prof. , 3Principal, Shri Sai College of Engg & TechnologyBhadrawati,Chandrapur, Maharashtra, India
Abstract: Numerical simulations are increasingly becomingan important tool to obtain efficient designs of protectivestructures, and the existing literature shows that manyphenomena can be accurately described by standard methodsand models. This thesis, specifically, focuses on novelmethods of modeling and simulating ballistic impact.Experiments are needed to validate such simulations, so numerous tests were studied to investigate how projectile nose-shape, plate layering, target strength, ductility, and workhardening affect the penetration and perforation behavior ofvarious structural configurations. These tests provide new information about the behavior of materials subjected to ballistic impact, and are valuable input for the evaluation ofthe numerical simulations. As more complex materialssystems are introduced in engineering practice, the design engineer faces the of utilizing homogenization techniques or detailed numerical models. The latter offers a number of advantages, such as the ability to introduce separateconstitutive laws and failure criteria for each phase, at theexpense of computation cost. The aim of this study is to givegeneral information about the most commonly used materialsand ballistic test methods. In addition, to summarize the topicsrelated to simulation methods such as FEM and numericalmethods which are use most in ballistics.A generalizednumerical and experimental formulation is presented for theprediction of ballistic impact behavior on various surfacesagainst different projectile nose shape. The ballistic resistance,failure mechanism and the energy absorption of the structurewas investigated thoroughly through experimentation andnumerical simulations. influence of projectile shape, incidencevelocity of the projectile.
Keywords: Ballistic impact loading, Analysis Projectile,Cylindrical ,Structures(key words)
Investigation pertaining impact response of the shell has secured its own place in different engineering disciplines likedesigning of helmet, boilers, compressors, aero plane, navalindustry (boat hull) and outer-body shells of automobiles andnow in the field of lithium ion batteries. The development oflightweight structures having superior energy absorptioncharacteristics has been drawn the major attention of theresearchers over the recent years. In this context, the sandwichstructures have played a major role due to their very highstiffness-to weight and bending strength-to-weight ratio.Because of these superior properties, it is widely used for civilian as well as military applications (racing cars, aerospacemanufacturing, helicopters, jet aircraft, automobile structuresetc.). During their service life, these structures may frequentlybe subjected to impact load (natural or man made), which cancause local failure and results in terms of catastrophic failureof the structure subsequently. Fiber-reinforced composite andaluminium were extensively used as face sheet material,whereas cellular and porous material was used frequently ascore materials.
ISSN: 2321-9653; IC Value: 45.98; SJ Impact Factor: 7.538
Volume 11 Issue III Mar 2023- Available at www.ijraset.com
The development of lightweight structures having superior energy absorption characteristics has been drawn the majorattention of the researchers over the recent years. In this context, the sandwich struc tures have played a major role due to their very high stiffness-to-weight and bending strength-to-weight ratio. Because of these superior properties,it is widely used for civilian as well as military applications (racing cars, aerospace manufacturing, helicopters, jet aircrafts,auto mobile structures etc.). During their service life, these structures may frequently be subjected to impact load (natural or manmade), which can cause local failure and results interms of catastrophic failure of the structure subsequently. In the available literature, the impact response of the sandwich structures have been addressed with varying the material, thickness, and shape of face sheets and core against different shapes, diameters and mass of the projectile. Fiber-reinforced composite and aluminium were extensively used as face sheet material, whereas cellular and porous material was used frequentlyas core materials
Plenty of numerical and experimental studies have been carried out to explore the ballistic response of sandwich structures against projectile impact [1–8,15–19]. Yahaya et al. [3] studied the impact response of different configuration ofthe sandwich structure subjected to foam projectile at different projectile velocity. It was found that for specific impactvelocity range low (up to 175 m/s) and high (above 375 m/s)airsandwich outperformed the monolithic plate and honeycomb panel, whereas for medium-range velocity (175– 375 m/s) sandwich structure with honeycomb core showed better performance. Arslan et al. [8] carried out the ballistic performance of functionally graded face sheets withhoneycomb-core sandwich structures and found that the linear functionally graded face sheets offered the better impactresistance in terms of less deformation and high damageresistance. Kollop et al. [10] showed that the sandwich panelwith the dryfabric face sheet performed
ISSN: 2321-9653; IC Value: 45.98; SJ Impact Factor: 7.538
Volume 11 Issue III Mar 2023- Available at www.ijraset.com
The projectile nose shape strongly influenced the performance of sandwich structures under a distinct range of impact velocity and sandwich parameters such as core density (cell wall size, cell wall thickness, and core height) and face sheet thickness [1–5,16–19]. Flat-ended projectile offered the highest ballistic limit and higher energy dissipation than the conical and hemispherical nosed projectile, whereas the conical nosed projectile required the least energy for perforation [1, 15,17]. Keplar et al. [6] compared the ballistic performance of three different projectile nose shapes (small conical, large conical, and hemispherical) against the sandwich panel and found that both the pointers nosed projectile penetrated the panel easily compared to the hemispherical nosed projectile. Furthermore some researcher found that the ballistic limit of sandwich panel was increased linearly with the increase in the face sheet thickness [1,2,15]. Honeycomb core geometry had a dominant influence on the dynamic response of the sandwich structure. The ballistic limitof the panel increased with the increase in cell wall thickness and decreased with the increase in cell size [2]. Thehoneycomb structure having thinner cell wall, larger cell size and shorter core height provided higher specific energy absorption [2]. However, the influence of the core height was barely perceptible on the ballistic limit an energy absorption ofthe structure [1,4,7].
The face sheets were more effective than honeycomb core onthe energy absorption capability of the sandwich structure and increase in FML skin thickness can result in a more significantincrease in the energy absorption. The absorbed energy of the“2/220” panel is over 60% greater than that of the “1/1-20”panel [14]. Increasing of impact velocity and decreasing offace sheet thickness, core relative density and curvature radiuscan enhance the energy absorption capability of sandwichshells. The increase of energy absorption becomes slow for theimpact velocity below 125 m/s but rapid for the velocity above150 m/s. This is because the deformation of sandwich shells isdominated by bending of the front face-sheet for the low velocity impact while it is dominated by the global large inelastic deformation with severe local compression of core [18]. The energy dissipation in all the deformation modesincreased with increase in span diameter and thickness of shellagainst both projectiles. The increase was gradual for spandiameter and sharp for shell thickness. For a given spandiameter and thickness, the energy dissipation was maximumin shear stretching while it was minimum in polar stretching.The energy dissipation in radial and elevation stretching wasalmost equal for a given span diameter and thickness, and itwere found in-between the other two extremes (shear andpolar stretching) [29]. Due to their excellent crash worthinessperformance and energy absorption ability [43, 44], sandwichstructures have become attractive candidates in many engineering applications, including automotive industry [45], aeronautics [46], transportation engineering [47] and personalprotective equipment [48]. During the period of their serves,sandwich structures are susceptible to low-energy/low-velocity impacts, such as runway debris, hailstones, toolsdropped during maintenance and so on [49-51]. Unlike high-velocity impact, damages caused by low velocity impact are often internal and invisible but can significantly reduce stiffness and strength of the structures, which will result in shortening service life of the structures.
ISSN: 2321-9653; IC Value: 45.98; SJ Impact Factor: 7.538
Volume 11 Issue III Mar 2023- Available at www.ijraset.com
Most of the impact energy would be absorbed and dissipated during the process while the rest is retained in the impactor as rebound kinetic energy [52]. Afterimpact, an undetectable or barely detectable by visual inspection residual plastic indentation may be left ontop face-sheet of the sandwich panel. Indentation characteristics and energy absorption property are basically determined by crashworthiness of the structure, which is extremely sensitive to the mechanical property of matrix material [53]
ISSN: 2321-9653; IC Value: 45.98; SJ Impact Factor: 7.538
Volume 11 Issue III Mar 2023- Available at www.ijraset.com
The impact behaviour of the target was also examined by investigating the energy absorption characteristics of the targetplate subjected to projectile impact. Iqbal et al. [19] and Tiwarietal. [20] reported the experimental and numerical studyon the energy dissipation character of the thin plates and shellsof Al 1100-H12 aluminium and concluded that the maximum energy of the projectile dissipated in tangential stretching of the target.
This research aims to optimize the construction of structure byhybridization in order to achieve the improvement of ballistic performance and reduction in weight. To achieve this aim, the research objectives are organized as follows.
1) Understanding the ballistic response of structures under impact. This includes different ballistic characteristics, energy absorption, as well as failure modes under ballistic impact.
a) Different ballistic characteristics of each layer will be analyses experimentally and numerically, such as ballistic resistance fracture time, transverse deflection, stress distribution, energy absorption and ballistic limit. This investigation will reflect the different ballistic resistant efficiency of each layer in the panel, through which the mechanisms of energy absorption can be identified.
b) Failure modes are important aspects to reflect ballisticresponse under impact. It will be systematically investigatedthrough the photographic observations of post-impact panelslayer by layer. This work will provide a wealth of physical evidences to reflect different ballistic characteristics of eachlayer.
2) Optimization of the ballistic structure design. Theconstruction of the structures will be optimized by combining different components of ballistic materials in the most effective positions. To design the hybrid structure, the mechanisms of hybridization will be analyzed and identified before the design principleis put forward.
a) Selection of components for hybridization will be studied. In this research, Metallic materials, composites as well as fibers are studied and will be used as components for hybridization. Ballistic performance of these structures will be investigated on their advantages and disadvantages for ballistic protection.
b) The hybridization effect will be investigated by analyzing the ballistic performance of hybrid structures and hybrid materials. Layering sequences of different components will be explored to determine the better combination manner of materials
3) This study will be carried out using two research approaches, namely the experimental method and the Finite Element (FE) analysis. The experimental studies will be centered on ballistic tests andphotographic observations of post impact panels. FE numerical simulation will be used to explore the ballistic response of the structure. These data then helps to find out ballistic resistance, ballistic limit, failure modes and the energy absorption characteristic of structures against different projectile nose shape.
4) Effect of cell wall thickness. Cell wall thickness plays a significant role in enhancing the impact resistance of the sandwich structure. Cell wall thickness 0.03 mm, 0.05 mm, 0.07 mm and 0.09 mm were used to find out its effect on the ballistic performance of the hemispherical sandwich shell structure. Similar to the face sheet thickness, the velocity drop increased with increase in the cell wall thickness, see it was found that with the increase in the cell wall thickness, the ballistic limit of the panel increased.
ISSN: 2321-9653; IC Value: 45.98; SJ Impact Factor: 7.538
Volume 11 Issue III Mar 2023- Available at www.ijraset.com
A major impact phenomena studying is to identify those important parameters of both target and projectile that influence penetration. The most important physical andmaterial parameters that affect ballistic penetration are: impactvelocity, hardness and shape of the projectile, hardness,density and toughness of the target facing plate, as well as therigidity and strength of the backing plate, thickness ratio of aplates, etc. Earlier research was carried out based on a largenumber of assumptions for simplifying the analysis procedure.These methods provided approximate estimations ofmechanical properties, but they cannot be used to analyzevariations of mechanical properties with some importantarchitecture parameters due to introduced oversimplified assumptions. On the other hand, due to the immense variety ofavailable composite materials and possible fabric architecture,it is impractical and very time-consuming to obtain materialcharacterizations of various composites by an experimentalapproach. As a result, there still is a need for comprehensivedesign modeling tool capable to bridge the gap between composite processing parameters and their structural responseon variety of loading conditions, addressing in the same time both geometry and material characteristics.
Where ε, σ, ν, τ denote Strain, Principal stress, Poisson’s ratio,Shear stress and subscripts denote the principal directions. Thethird equation defines the nonlinear shear stress parameter α The fiber matrix shearing term augments each damagemode:
Numerical simulation was carried out through commercially avail able finite element code Abaqus explicit solver. Hemispherical sandwich shell structure consists of two face sheets, the adhesive layer, honey comb core and projectile which has been shown in . Also the different configuration of cell size used in numerical simulation shown The adhesive layer of 0.2 mm was employed between the face sheets and the core. Honeycomb core was discrete using 4 noded shell elements, whereas the face sheets and the adhesive layer were discrete using the 8 nodded solid elements. To capture the accurate result and proper failure mechanism mesh size at projectile - sandwich struc ture contact region was kept finer (aspect ratio 1), however at the non contact region, it was kept coarser (up to aspect ratio 8). For the face sheet and adhesive layer at the contact region, mesh size was kept 0.16 mm3 The number of the element through the thickness for 0.7 mm, 1 mm, 1.5mm and 2mm face sheet was kept.
ISSN: 2321-9653; IC Value: 45.98; SJ Impact Factor: 7.538
Volume 11 Issue III Mar 2023- Available at www.ijraset.com
ISSN: 2321-9653; IC Value: 45.98; SJ Impact Factor: 7.538
Volume 11 Issue III Mar 2023- Available at www.ijraset.com
The numerical results corresponding to residual velocities of different configurations (0.5/0.5, 0.67/0.33, 0.33/0.67) and span diameters (68, 100, 150 and 200 mm) of the shells have been presented in Table 2 against ogive nosed projectileimpact. The predicted residual velocity for 1 mm thick monolithichemispherical shell was quite close to actual residual velocity. Further, the graphical representation of similar results has been shown in Fig. 3 for direct comparison of the monolithic target with different layered configurations of 68, 100, 150 and 200 mm span diameter. All double-layered hemisphericalshell configuration offered larger drop in the residual velocitythan the monolithic hemispherical shell. Moreover, the double layered configu ration with equal thickness 0.5/0.5 showed highest decrease in the re sidual velocity followed by the0.67/0.33, 0.33/0.67 and the single layered target, respectively.The maximum deviation in between the experimental and thenumerical results was found to be 10.43 m/s for 200 mmdiameter. The influence of target configurations was muchsignificant close to ballistic limit which subsequentlydecreased with increase in the incidence velocity of theprojectile, see Fig. 3. Similar trend was found for plastic deformation of the shell with incidence velocity of the projectile. The deviation of numerically predicted results fromactual experimental results was quite small.
The ballistic limit velocity(V50) was obtained toquantify the per formance of the target against the ogivenosed projectile. It was obtained through the average of themaximum projectile velocity, at which target couldn’t getperforation and the minimum projectile velocity and thevelocity at which the target completely perforated. Theballistic limit velocities of different span diameter withvarying configurations have been shown in Table 3 which wasfurther represented in Result showed that the ballistic limit ofthetarget was increased with increasein the span diameter ofthehemispherical shell. Moreover layering of the hemispherical shell enhanced the ballistic resistance of theshell. How ever, the double layered target (0.5/0.5) showedthe highest ballistic limit followed by the (0.67/0.33),(0.33/0.67), and 1 mm monolithic target.
The ballistic limit of the layered hemispherical shell 0.5/0.5, 0.67/ 0.33, 0.33/0.67 for 68 mm diameter was 16.8%, 9.54% and 6.55% higher than the monolithic hemispherical shell, for 100 mm span.
The following is the standard test procedure with proper safety
1) Configure/Set up test fixture
2) Turn on helium pressure in trailer
3) Turn on power to electromagnetic coils and data acquisitionsystem
4) Ifnecessary, set up high speed video
5) Close trigger ball valve
6) Insert projectile into gun barrel
7) Ifnecessary, set up gun barrel wire trigger
8) Set regulator on nitrogen bottle
9) Ifnecessary, turn on lights for high speed video
10) Close and lock all test area doors
11) Chargehelium bottle to desired test pressure
12) Turn weapon keylock to “weapon ready”
13) Press “system ready” button
14) Arm data acquisition system
15) Press “test” button
16) Press “arm” button
17) Activate siren
18) After 5 second audible count down, press “fire” button
19) Press “endtest” button
20) Turn weapon keylock to safe position andremove
21) Ifnecessary, turn off lights for high speed video
22) Ifnecessary, save high speed video recordings
23) Record projectile velocities from data acquisitionName:
24) Close valves on nitrogen cylinder andhelium trailer
25) Remove specimen from test fixture
ISSN: 2321-9653; IC Value: 45.98; SJ Impact Factor: 7.538
Volume 11 Issue III Mar 2023- Available at www.ijraset.com
Its wide applications such as in aircraft leadingedges and flaps, boat hulls, car, and caravan body panels. Moreover, the influence of configuration and core structure against projectile impact has also not been reported in the available literature. Therefore in depth study is required to investigate the response of curved sandwich panel against projectile impact. it is widely used for civilian as well as military applications (racing cars, aerospace manufacturing, helicopters, jet aircrafts, auto mobile structures etc.). During their service life, these structures may frequently be subjected to impact load (natural or manmade), which can cause local failure and results in terms of catastrophic failure of the structure subsequently. In the available literature, the impact response of the sandwich structures have been addressed with varying the material, thickness, and shape of face sheets and core against different shapes, diameters and mass of the projectile. Fiber- reinforced composite and aluminium were extensively used as face sheet material, whereas cellular and porous material was used frequentlyas core materials.
1) Automobile Industries and E- Vehicle for BatteryblastProtection.
2) For Aeroplane Framework and Casing.
ISSN: 2321-9653; IC Value: 45.98; SJ Impact Factor: 7.538
Volume 11 Issue III Mar 2023- Available at www.ijraset.com
3) For Electrical Transformer.
4) For Bullet Proof Jacket And MilitaryAppliences
5) For Marine Vehicles.
6) In Defence Industries.
In this study, the ballistic performance of aluminium hemispherical sandwich thin shell structure was studied experimentally and numerically against ogive nosed projectile impact within sub ordnance velocity regime. Moreover, the effect of face sheet thickness, cell wall thickness and cell size on the sandwich shell performance also examined through numerical simulation. Bullet Impact with Aluminium PlateWith Different Angle Orientation using # ABAQUS
The work in this thesis was mainly on the study of experimental and numerical approach for the prediction of ballistic impact behavior on various surfaces against differentprojectile nose shape. Little emphasis was put on empirical and analytical modeling. Experiments were designed to serveas a basis of comparison to numerical simulations while still providing useful data to advance the field. The numerical contribution was to use and evaluate rather novel methods to Solve the penetration problem.
[1] Z. Wang, H. Tian, Z. Lu, W. Zhou, High-speed axial impact of aluminumhoneycomb–Experimentsand simulations, Compos. B Eng. 56 (2014) 1–8.
[2] B.L. Buitrago, C. Santiuste, S. Sanchez-Saez,
[3] E. Barbero, C. Navarro, Modelling of composite sandwich structures withhoneycomb core subjected to high-velocity
[4] impact, Compos. Struct. 92 (9) (2010) 2090–2096.
[5] J. Kepler, Impact penetration of sandwich panels at different velocities-Anexperimental parameter study: part I-Parameters and results, J. Sandw. Struct. Mater. 6 (4) (2004) 357–374.
[6] I. Iva~nez, S. Sanchez-Saez, Numerical modelling of the low-velocity impact response of composite sandwich beams with honeycomb core, Compos. Struct. 106 (2013) 716–723.
[7] K. Arslan, R. Gunes, M.K. Apalak, J. Reddy, Experimental tests and numerical
[8] modeling of ballisticimpact on honeycomb sandwich structures reinforced byfunctionally graded plates, J. Compos. Mater. 51 (29) (2017) 4009–4028.
[9] C. Menna, A. Zinno, D. Asprone, A. Prota, Numerical assessment of the impact
[10] behavior of honeycomb sandwich structures, Compos. Struct. 106 (2013)326–339.
[11] A. Kolopp, S. Rivallant, C. Bouvet, Experimental study of sandwich structures as armour against medium-velocity impacts, Int. J. Impact Eng. 61 (2013) 24–35.
[12] D. Zhang, Q. Fei, P. Zhang, Drop-weight impact behavior of honeycomb sandwich panels under a spherical impactor, Compos. Struct. 168 (2017) 633–645.
[13] Y. Chen, S. Hou, K. Fu, X. Han, L. Ye, Low-velocity impact response of composite sandwich structures: modelling and experiment, Compos. Struct. 168 (2017)
[14] 322–334.
[15] I. Elnasri, H. Zhao, Impact perforation of sandwich panels with aluminum foam core: a numerical and analytical study, Int. J. Impact Eng. 96 (2016) 50–60.
[16] C. Liu, Y. Zhang, J. Li, Impact responses of sandwich panels with fibre metal laminate skins and aluminium foam core, Compos. Struct. 182 (2017) 183–190.
[17] W. Hou, F. Zhu, G. Lu, D.-N. Fang, Ballistic impact experiments of metallic sandwich panels with aluminium foam core, Int. J. Impact Eng. 37 (10) (2010) 1045–1055.
[18] I. Iva~nez, C. Santiuste, E. Barbero, S. Sanchez-Saez, Numerical modelling of foam cored sandwich plates under high-velocity impact, Compos. Struct. 93 (9) (2011) 2392–2399.
[19] C. Liu, Y. Zhang, L. Ye, High velocity impact responses of sandwich panels with metal fibre laminate skins and aluminium foam core, Int. J. Impact Eng. 100 (2017) 139–153.
[20] L. Jing, C. Xi, Z. Wang, L. Zhao, Energy absorption and failure mechanism of metallic cylindrical sandwich shells under impact loading, Mater. Des. 52 (2013) 470–480 (1980-2015).
[21] L. Jing, Z. Wang, L. Zhao, Response of metallic cylindrical sandwich shells subjected to projectile impact experimental investigations, Compos. Struct. 107 (2014) 36–47.
[22] R. Mohmmed, F. Zhang, B. Sun, B. Gu, Finite element analyses of low- velocity impact damage of foam sandwiched composites with different ply angles face sheets, Mater. Des. 47 (2013) 189–199.
[23] S. Long, X. Yao, H. Wang, X. Zhang, Failure analysis and modeling offoam sandwich laminatesunder impact loading, Compos. Struct. 197 (2018)
[24] Eason, B. Noble, and I.N. Sneddon, “On certain integrals of Lipschitz- Hankel type involving products of Bessel functions,” Phil. Trans. Roy. Soc. London, vol. A247, pp. 529-551, April 1955. (references)