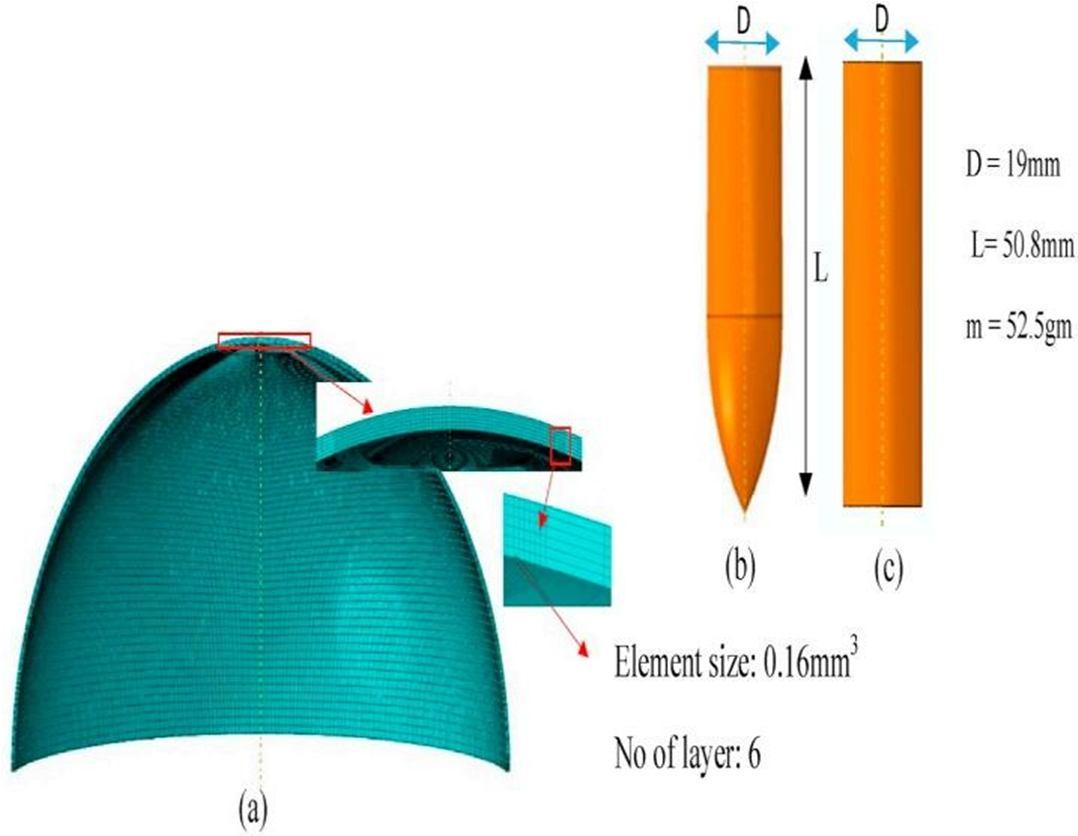
3 minute read
International Journal for Research in Applied Science & Engineering Technology (IJRASET)
from Ballistic Impact Analysis of Thin Shell and Curved Surface against Different Projectile Nose Shape
by IJRASET
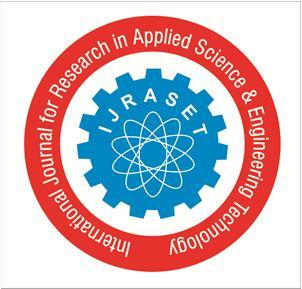
ISSN: 2321-9653; IC Value: 45.98; SJ Impact Factor: 7.538
Advertisement
Volume 11 Issue III Mar 2023- Available at www.ijraset.com
The development of lightweight structures having superior energy absorption characteristics has been drawn the majorattention of the researchers over the recent years. In this context, the sandwich struc tures have played a major role due to their very high stiffness-to-weight and bending strength-to-weight ratio. Because of these superior properties,it is widely used for civilian as well as military applications (racing cars, aerospace manufacturing, helicopters, jet aircrafts,auto mobile structures etc.). During their service life, these structures may frequently be subjected to impact load (natural or manmade), which can cause local failure and results interms of catastrophic failure of the structure subsequently. In the available literature, the impact response of the sandwich structures have been addressed with varying the material, thickness, and shape of face sheets and core against different shapes, diameters and mass of the projectile. Fiber-reinforced composite and aluminium were extensively used as face sheet material, whereas cellular and porous material was used frequentlyas core materials
Plenty of numerical and experimental studies have been carried out to explore the ballistic response of sandwich structures against projectile impact [1–8,15–19]. Yahaya et al. [3] studied the impact response of different configuration ofthe sandwich structure subjected to foam projectile at different projectile velocity. It was found that for specific impactvelocity range low (up to 175 m/s) and high (above 375 m/s)airsandwich outperformed the monolithic plate and honeycomb panel, whereas for medium-range velocity (175– 375 m/s) sandwich structure with honeycomb core showed better performance. Arslan et al. [8] carried out the ballistic performance of functionally graded face sheets withhoneycomb-core sandwich structures and found that the linear functionally graded face sheets offered the better impactresistance in terms of less deformation and high damageresistance. Kollop et al. [10] showed that the sandwich panelwith the dryfabric face sheet performed
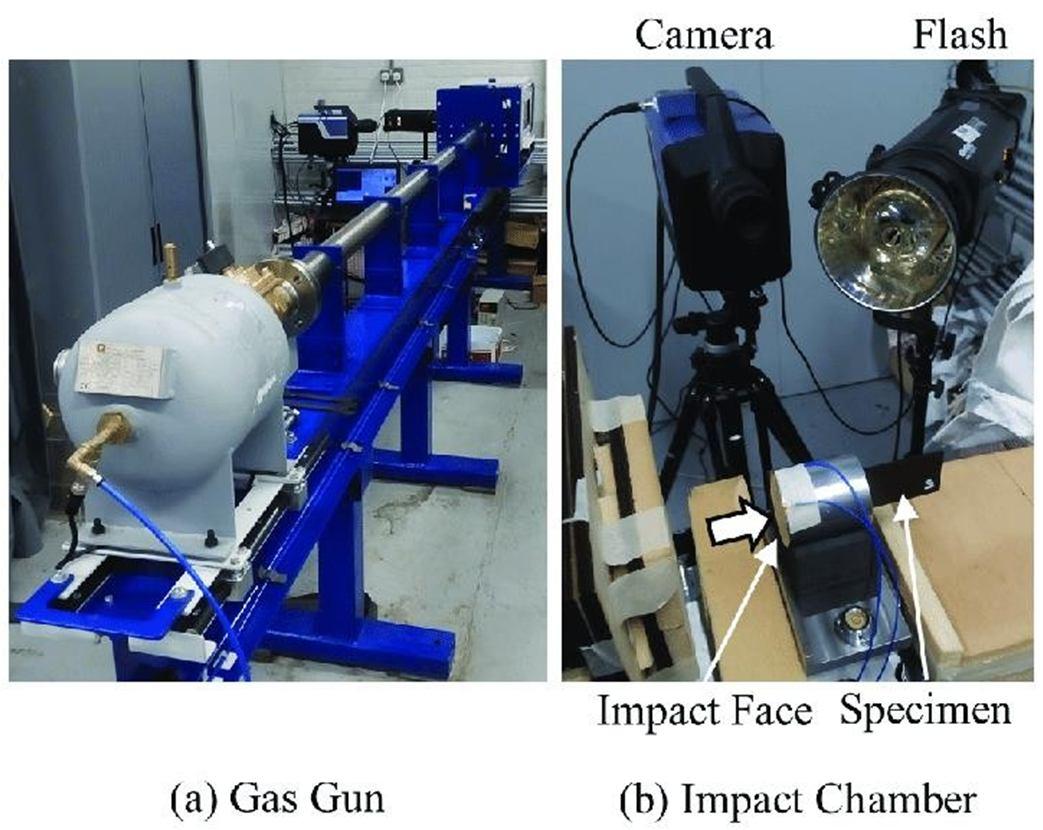
ISSN: 2321-9653; IC Value: 45.98; SJ Impact Factor: 7.538
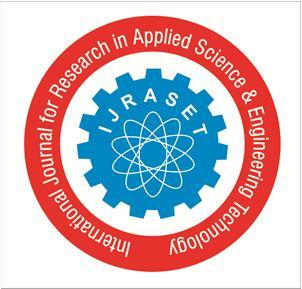
Volume 11 Issue III Mar 2023- Available at www.ijraset.com
The projectile nose shape strongly influenced the performance of sandwich structures under a distinct range of impact velocity and sandwich parameters such as core density (cell wall size, cell wall thickness, and core height) and face sheet thickness [1–5,16–19]. Flat-ended projectile offered the highest ballistic limit and higher energy dissipation than the conical and hemispherical nosed projectile, whereas the conical nosed projectile required the least energy for perforation [1, 15,17]. Keplar et al. [6] compared the ballistic performance of three different projectile nose shapes (small conical, large conical, and hemispherical) against the sandwich panel and found that both the pointers nosed projectile penetrated the panel easily compared to the hemispherical nosed projectile. Furthermore some researcher found that the ballistic limit of sandwich panel was increased linearly with the increase in the face sheet thickness [1,2,15]. Honeycomb core geometry had a dominant influence on the dynamic response of the sandwich structure. The ballistic limitof the panel increased with the increase in cell wall thickness and decreased with the increase in cell size [2]. Thehoneycomb structure having thinner cell wall, larger cell size and shorter core height provided higher specific energy absorption [2]. However, the influence of the core height was barely perceptible on the ballistic limit an energy absorption ofthe structure [1,4,7].

A. Energy Absorption
The face sheets were more effective than honeycomb core onthe energy absorption capability of the sandwich structure and increase in FML skin thickness can result in a more significantincrease in the energy absorption. The absorbed energy of the“2/220” panel is over 60% greater than that of the “1/1-20”panel [14]. Increasing of impact velocity and decreasing offace sheet thickness, core relative density and curvature radiuscan enhance the energy absorption capability of sandwichshells. The increase of energy absorption becomes slow for theimpact velocity below 125 m/s but rapid for the velocity above150 m/s. This is because the deformation of sandwich shells isdominated by bending of the front face-sheet for the low velocity impact while it is dominated by the global large inelastic deformation with severe local compression of core [18]. The energy dissipation in all the deformation modesincreased with increase in span diameter and thickness of shellagainst both projectiles. The increase was gradual for spandiameter and sharp for shell thickness. For a given spandiameter and thickness, the energy dissipation was maximumin shear stretching while it was minimum in polar stretching.The energy dissipation in radial and elevation stretching wasalmost equal for a given span diameter and thickness, and itwere found in-between the other two extremes (shear andpolar stretching) [29]. Due to their excellent crash worthinessperformance and energy absorption ability [43, 44], sandwichstructures have become attractive candidates in many engineering applications, including automotive industry [45], aeronautics [46], transportation engineering [47] and personalprotective equipment [48]. During the period of their serves,sandwich structures are susceptible to low-energy/low-velocity impacts, such as runway debris, hailstones, toolsdropped during maintenance and so on [49-51]. Unlike high-velocity impact, damages caused by low velocity impact are often internal and invisible but can significantly reduce stiffness and strength of the structures, which will result in shortening service life of the structures.