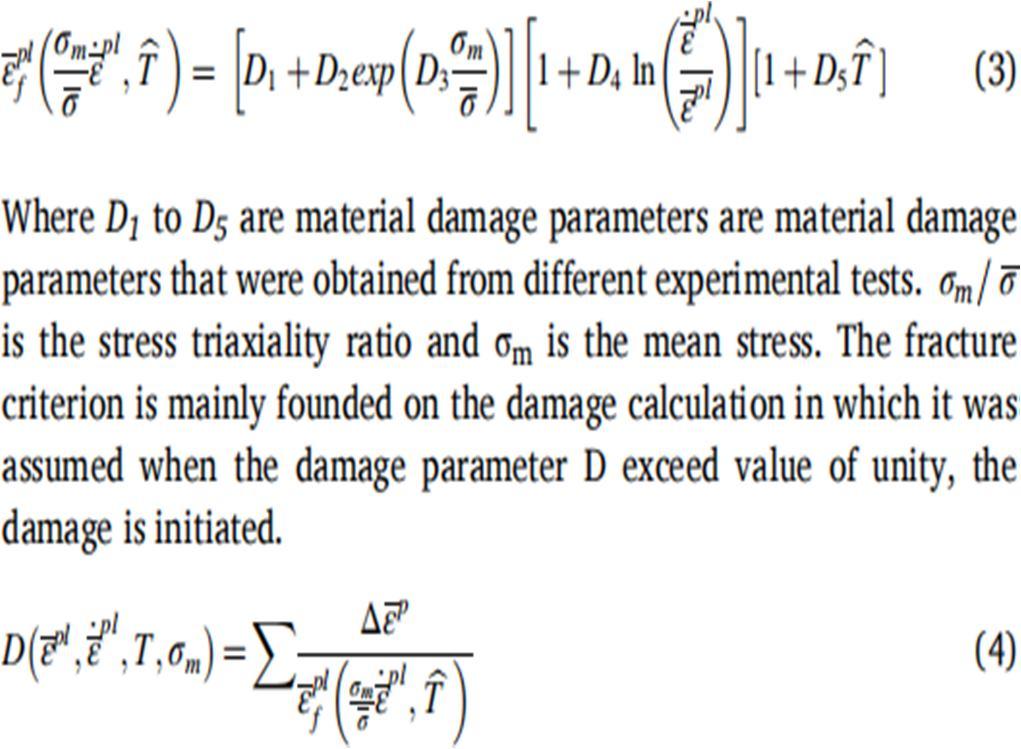
1 minute read
International Journal for Research in Applied Science & Engineering Technology (IJRASET)
from Ballistic Impact Analysis of Thin Shell and Curved Surface against Different Projectile Nose Shape
by IJRASET
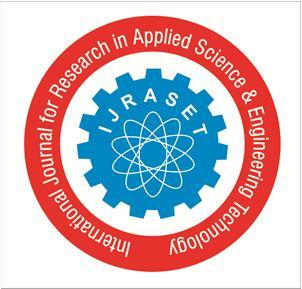
ISSN: 2321-9653; IC Value: 45.98; SJ Impact Factor: 7.538
Advertisement
Volume 11 Issue III Mar 2023- Available at www.ijraset.com
III. PROBLEMSTATEMENT
A major impact phenomena studying is to identify those important parameters of both target and projectile that influence penetration. The most important physical andmaterial parameters that affect ballistic penetration are: impactvelocity, hardness and shape of the projectile, hardness,density and toughness of the target facing plate, as well as therigidity and strength of the backing plate, thickness ratio of aplates, etc. Earlier research was carried out based on a largenumber of assumptions for simplifying the analysis procedure.These methods provided approximate estimations ofmechanical properties, but they cannot be used to analyzevariations of mechanical properties with some importantarchitecture parameters due to introduced oversimplified assumptions. On the other hand, due to the immense variety ofavailable composite materials and possible fabric architecture,it is impractical and very time-consuming to obtain materialcharacterizations of various composites by an experimentalapproach. As a result, there still is a need for comprehensivedesign modeling tool capable to bridge the gap between composite processing parameters and their structural responseon variety of loading conditions, addressing in the same time both geometry and material characteristics.
Where ε, σ, ν, τ denote Strain, Principal stress, Poisson’s ratio,Shear stress and subscripts denote the principal directions. Thethird equation defines the nonlinear shear stress parameter α The fiber matrix shearing term augments each damagemode:

A. Numerical Modelling
Numerical simulation was carried out through commercially avail able finite element code Abaqus explicit solver. Hemispherical sandwich shell structure consists of two face sheets, the adhesive layer, honey comb core and projectile which has been shown in . Also the different configuration of cell size used in numerical simulation shown The adhesive layer of 0.2 mm was employed between the face sheets and the core. Honeycomb core was discrete using 4 noded shell elements, whereas the face sheets and the adhesive layer were discrete using the 8 nodded solid elements. To capture the accurate result and proper failure mechanism mesh size at projectile - sandwich struc ture contact region was kept finer (aspect ratio 1), however at the non contact region, it was kept coarser (up to aspect ratio 8). For the face sheet and adhesive layer at the contact region, mesh size was kept 0.16 mm3 The number of the element through the thickness for 0.7 mm, 1 mm, 1.5mm and 2mm face sheet was kept.