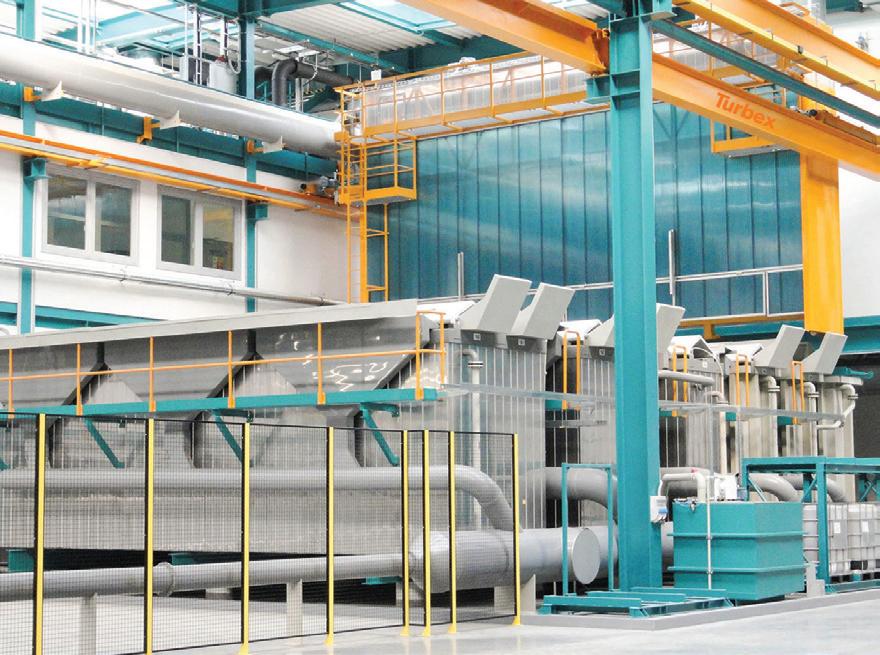
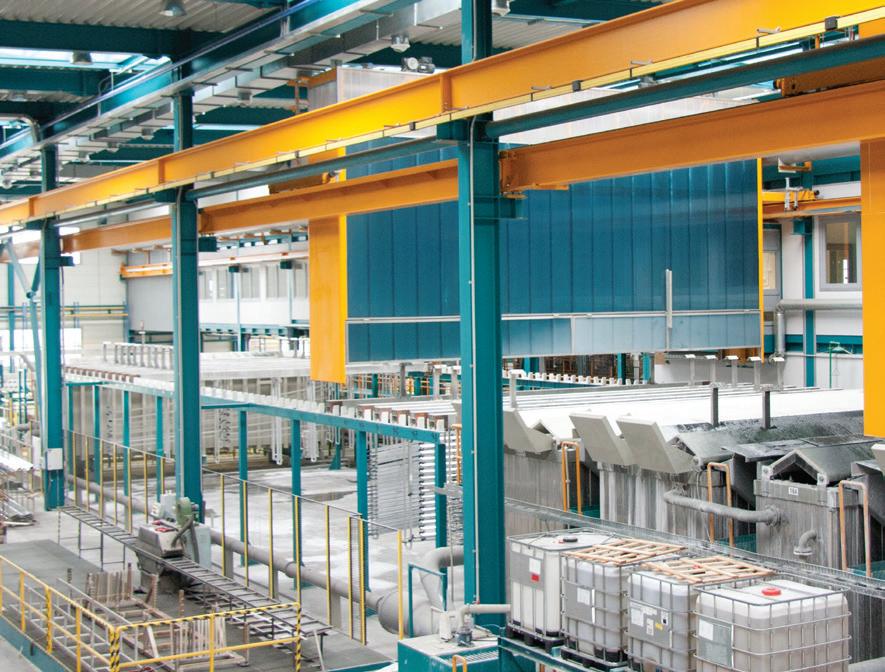
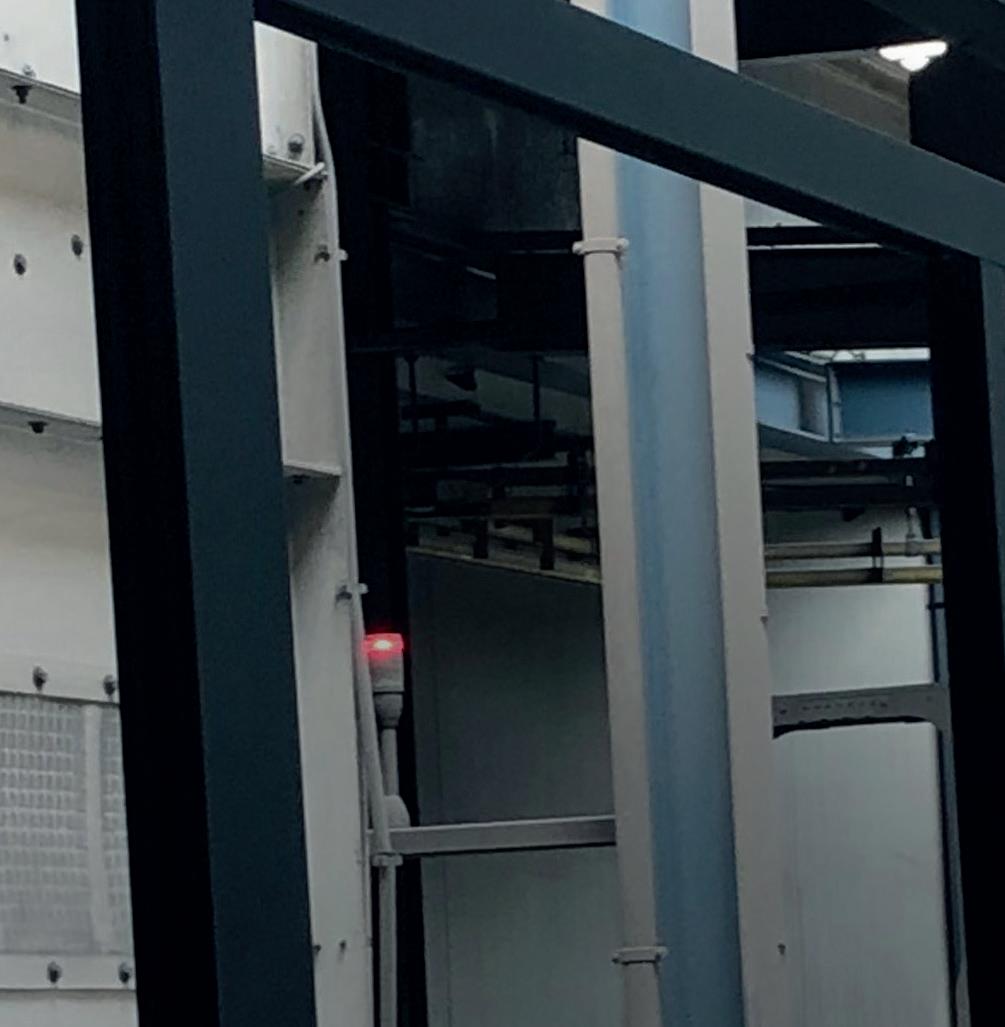
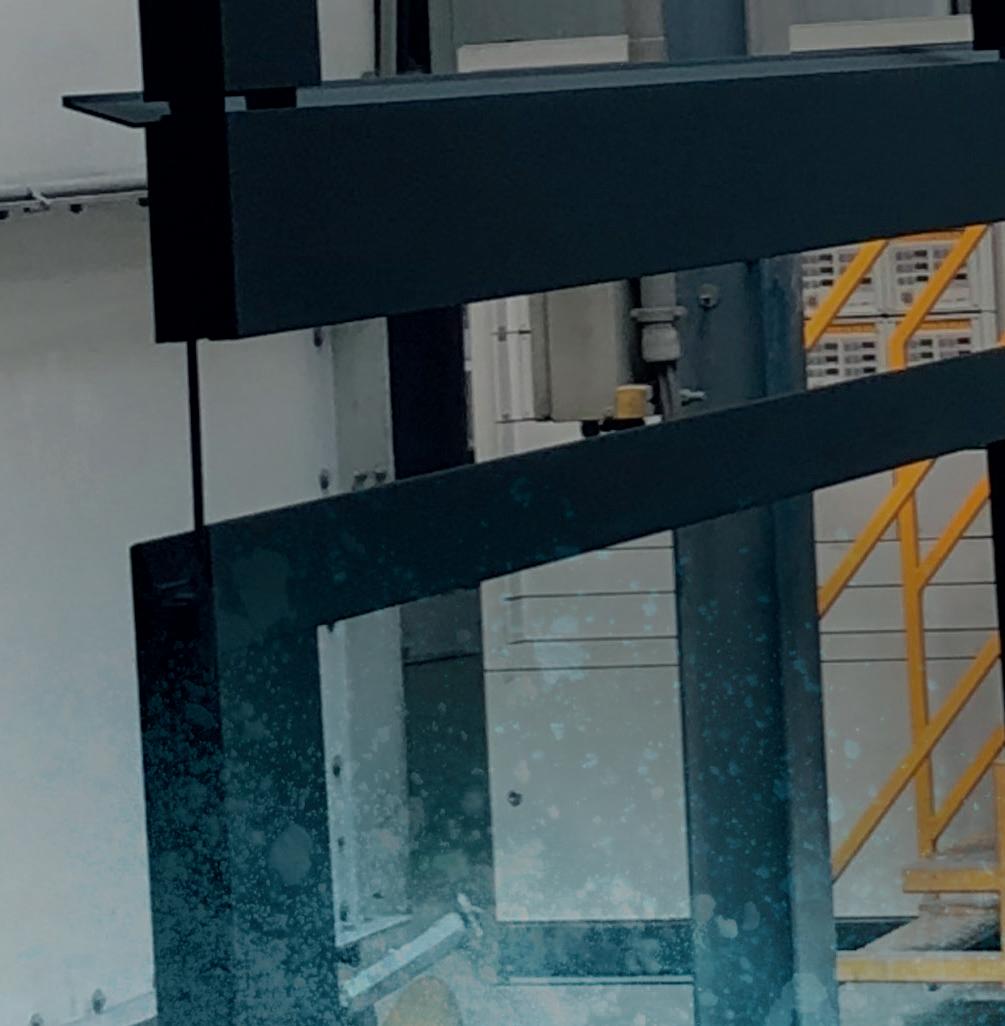
With our new Interpon D1036 Low-E powder coating, we’ve created an industry first: a powder coating that can cure as low as 150°C while still being Qualicoat class one certified. It can also cure up to 25% faster than conventional powders, reducing both energy consumption and carbon emissions, and significantly improving your coating line efficiency. Easy to apply Interpon D1036 Low-E has the same application properties as standard formulation, is backed by an Environmental Product Declaration (EPD) and has a global warranty of up to 15 years to deliver the quality performance, color and style your customers need. It is an innovation that supports our collective commitment to sustainability throughout the value chain.
MANAGING DIRECTOR & ADVERTISEMENT DIRECTOR
Nigel Bean
t: +44 (0) 1442 826826
e: nigelbean1@aol.com nigelbean@surfaceworld.com
EDITOR & GRAPHIC DESIGNER
Jane Soones
e: janesoones@aol.com janesoones@surfaceworld.com
CIRCULATION & SUBSCRIPTION DEPARTMENT
Sheena Burrus e: sheenaburrus@hillmedia.com
EXHIBITION ORGANISER
Sheena Burrus e: sheenaburrus@hillmedia.com
Hill Media Ltd, Marash House
2-5 Brook Street, Tring, Hertfordshire HP23 5ED, United Kingdom.
The Surface World magazine is published 12 times a year by Hill Media Ltd. Although every effort is made to ensure the accuracy and reliability of material published in Surface World, Hill Media Ltd and its agents accept no responsibility for the veracity of claims made by contributors, manufacturers or advertisers. Copyright for all material published in this journal remains with Hill Media Ltd and its agents.
© Hill Media Ltd – 2024 ISSN 1757-367X
We are pleased to announce an update to our quality label to recognise all powder coating that conforms to the QUALICOAT Specification.
This revision to our brand identity does not alter our fundamental principles or mission. QUALICOAT remains steadfast in its commitment to the vision, mission, and company values that have guided us for almost 40 years.
We look forward to sharing with you the future of quality Architectural Powder Coating in the next 40 years.
COMPANY SPOTLIGHT
GALVATEK SECURES MAJOR INDUSTRIAL CONTRACTS
WORTH NEARLY €20 MILLION. 4
INSTITUTE OF MATERIALS FINISHING
Become an Acknowledged Leader in Surface Engineering and Materials Finishing: INDUSTRY RECOGNISED TRAINING COURSES FROM THE IMF. 6
QUALICOAT UK & IRELAND
QUALICOAT LICENCES NEW POWDER SYSTEMS. 8
CORRODERE ACADEMY
CORRODERE ACADEMY LAUNCHES SUSTAINABILITY MODULE. 14
INDUSTRY NEWS
STRAALTECHNIEK GENERATE PROMISING ENQUIRIES AT SURFACE WORLD 2025. 18 STOWLIN LTD SHOWCASES INNOVATION AND EXPERTISE AT SURFACE WORLD 2025. 20 BASF COATINGS AND NIO AGREE ON STRATEGIC PARTNERSHIP FOR AUTOMOTIVE
AKZONOBEL EMBRACING CIRCULARITY BY REUSING INDUSTRIAL
PLASTRATUM’S NEW PURPOSE BUILT FACILITY WITH IMPROVED EQUIPMENT INCLUDING CNC MACHINING TO TAILOR INDIVIDUAL PRODUCTS ALLOWING THEM TO MEET THE CUSTOMER’S SPECIFIC REQUIREMENTS. 30
PRETREATMENT, SURFACE PREPARATION, DEGREASING & CLEANING VIXEN'S INNOVATIVE PHOSWASH SOLUTION: UPGRADING TO ENVIRONMENTALLY-FRIENDLY, NON-CHROME TECHNOLOGY.
32
SECURING THE FUTURE OF YOUR SOLVENT CLEANING PROCESS. 34
DISCONTINUED 3M™ NOVEC™ ENGINEERED FLUIDS - SWITCH SEAMLESSLY TO PROSOLV® DIRECT REPLACEMENTS.
Highly automated shot blast machine for engine blocks replaces two spinner hanger blast machines: FASTER CLEANING OF ENGINE BLOCKS WITH LESS PERSONNEL.
36
40 REVOLUTIONISING COMPONENT CLEANING: THE NEXT CHAPTER IN NEAR ZERO-EMISSIONS TECHNOLOGY.
Clean medical technology products reliably and in line with requirements: CLEANING TASKS ALONG THE PRODUCTION CHAIN.
HIGH-PERFORMANCE SURFACE CLEANING SYSTEMS FOR OPTIMAL COATING RESULTS.
MECWASH ATTENDS THREE EXHIBITIONS IN A MONTH!.
44
48
52
THE ADVANTAGES OF WET BLASTING FOR PAINTING AND POWDER COATING. 56 PAINT & POWDER
BARIL COATINGS: PIONEER IN SUSTAINABLE COATING SOLUTIONS. 58 INTERPON POWDER COATINGS BRING COLOR TO THE SMART WORKSPACE
TESTING & MEASUREMENT
Reducing Dust, Waste & Disposal
4 operators can blast all day
4 operators can blast all day
Reduce abrasive consumption by up to 20%
Reduce abrasive consumption by up to 20%
Increase blasting production by up to 30%
Increase blasting production by up to 30%
EASILY SWITCH BETWEEN 4 FUNC Mist Blast Dry Blast Wash Down Blow Down TIONS
AVAILABLE IN 3 DIFFERENT PACKAGES
Single Outlet Blast Pot (6.5 cu ft) Combo Skid with Air Dryer 4-Outlet Mega MistBlaster
Does the Work of 5 manual blasters
Up to 646 ft² per hour
Use 3 (#10) nozzles simultaneously
Automate timing and speed
Blast walls, floors, even upside-down
Galvatek has recently signed two major contracts with a combined value of nearly €20 million
The company will deliver an automated cleaning line for aircraft jet engines to South Korea, for Korean Air. This line is part of a jet turbine engine maintenance facility that is currently being built in Incheon, South Korea, in the vicinity of the Seoul International Airport. Once completed, the facility will be the largest in Asia and will be capable of servicing approximately 350 passenger aircraft engines per year.
Another recently signed contract includes the delivery of a surface treatment line for the Nammo Lapua Oy artillery factory currently in construction in Jyväskylä, Finland. The system is designed with automated material handling, eliminating the need for employees to manually lift heavy components, thereby improving both efficiency and workplace safety. Both production lines will be delivered in early 2026.
“These contracts are expected to create approximately 40 full-time equivalent jobs in Finland. In addition to our own employees, we help employ a diverse network of partners both locally and internationally,” says Galvatek’s Managing Director Lasse Vilminko.
“Given that the general trend in the industrial sector has not been particularly positive recently, it is great to be able to share such news and contribute to boosting Finland’s exports. These contracts will also lead to purchases worth several million euros from our partners,” comments Jarno Virtanen, Aviation Sales Director and KAM of John Cockerill Surface Treatment.
Galvatek is a Pioneer in
Galvatek is a unique player in its field, providing customers with complete surface treatment solutions rather than requiring them to purchase different components separately.
A key feature of Galvatek’s production lines is their full automation. The company has been manufacturing automated surface treatment lines since the 1980s. Automation not only makes the production lines more efficient and precise but also safer compared to traditional systems.
“Our surface treatment plants use a control system that we have
developed and programmed in-house in Lahti,” says Vilminko.
Surface treatment lines involve various chemical processes, including the use of strong chemicals. Therefore, ensuring proper wastewater treatment is crucial for environmental protection. As a result, the company also provides water purification plants, exhaust air treatment systems, and gas scrubbers as part of its production lines.
The company employs nearly 40 professionals in Lahti, Finland, including experts in chemical engineering, mechanical engineering, software design, and process engineering.
Oy Galvatek Ab was founded in 1980. It originally operated as an internal unit of the home appliance manufacturer UPO. Over the years, the company has strengthened its position, particularly in the aerospace industry and anodizing technology. In 2019, the Belgian John Cockerill Group acquired the company. Today, Galvatek is a proud part of John Cockerill’s surface treatment division.
Turbex are the sole suppliers for Galvatek surface treatment lines in the UK and Ireland.
Telephone: +44 (0) 1420 544 909 Email: sales@turbex.co.uk Visit: www.turbex.co.uk
Are you involved with the application of coatings to enhance and protect your products? Do you need to meet client specifications to ensure the longevity of your components? Does the complex world of surface engineering and materials finishing cause you headaches?
If so, the courses offered by the Institute of Materials Finishing (IMF) could be your solution!
The IMF have been promoting knowledge in the surface finishing industries, both inorganic surface treatments including plating and the application of organic paints, lacquers and varnishes for many years. Large numbers of engineers and technicians across a multitude of industries have benefitted from the knowledge gained to enhance their careers, their standing within industry and the ability to problem solve the many challenges they face in their daily working lives!
Starting with the Foundation level course, students gain knowledge on all aspects of materials finishing, specifically aimed at their own industry requirements, but to include sections on Health & Safety, the Environment and Surface Finishing and Corrosion Protection. There is no need for a science background to be able to successfully complete a foundation course.
The Foundation Course requires study of 15 sections and requires the submission of 2 marked assignments followed by an end examination. The course, conducted by distance learning will take 16 weeks to complete. There are three specific study routes to choose from; electroplating, organic coatings and aerospace finishing. On successful completion, the student is awarded the Foundation Certificate.
To follow on, students can then elect to progress to the Technician level modules, which give more in-depth knowledge for key finishing technologies, their application and best practice methods. Again, both inorganic and organic technologies can be studied to match the industry requirements. There is a choice of eight modules, which provide study in applicable areas of surface finishing best matched to your needs.
Like the Foundation course, study is by distance learning, and the student is required to complete four marked assignments and pass an examination.
Passing two technician modules leads to the award of Technician Certificate; passing four modules leads to the award of an Advanced Technician Certificate.
If you feel your career could benefit from being a recognised specialist in your particular branch of Surface Engineering or Materials Finishing, then contact the IMF today.
Speak with our training manager Karen Yates on +44 (0)121 622 7287 or email karen@materialsfinishing.org.
Move your career to the next level and join the finishing community and all the benefits that gives through the IMF.
By Chris Mansfield - QUALICOAT Chair
Powder is the fundamental and visible component in architectural powder coating, serving as the medium that provides durability, protection, and aesthetic appeal to architectural aluminium coated surfaces. Unlike liquid paint, powder coating uses a dry, electrostatically charged powder that adheres to metal or other conductive materials before being cured under heat to form a tough, uniform finish. The quality, composition, and particle size of the powder directly impact the coating’s adhesion, coverage, and resistance to chemicals and UV exposure. Additionally, powder coatings are environmentally friendly, as they contain no solvents or volatile organic compounds (VOCs), making them a sustainable and efficient choice for specifiers in construction projects.
The latest powder coating formulations now include advanced resins, nanotechnology additives and bio-based ingredients to enhance performance, durability, and sustainability. Modern formulations incorporate superdurable, known as QUALICOAT Class 2, polyester resins for improved UV resistance, making them ideal for high-rise architectural applications. Low-temperature curing powders are now being been developed and launched to reduce energy consumption whilst maintaining strong adhesion and good mechanical properties. Additionally, antimicrobial and easy-clean coatings are gaining popularity, particularly in healthcare and food processing industries. Innovations in metallic and special-effect powders allow for a wider range of finishes, from matte textures to high-gloss and chromelike effects.
QUALICOAT membership forms a vertically integrated supply chain, not only do powder coat applicators join the Association to demonstrate their ability to supply high quality coatings, but powder manufacturers and pre-treatment systems suppliers also make up membership of the Association. Working together enables advancement in the architectural coating process which is issued in the QUALICOAT Specification that all members must adhere to and are third party inspected, then given a licence to use the coveted QUALICOAT label of conformity.
For specifiers seeking to minimise their energy consumption during their sustainability journey towards a net-zero carbon future, QUALICOAT Member Interpon have launched a new range of low-energy (Low-E) powders, to their popular Class 1, D1036 range of powders and a Low-E range of powders to their Class 2, D2525 range of powders.
Both new powder systems presents a step change in the Industry. These Low-E coating powders achieve an industry milestone by enabling curing at temperatures as low as 150°C while maintaining QUALICOAT certification.
Low-E curing powders empowers applicators and fabricators to achieve their sustainability objectives in two distinct ways: either by reducing curing temperatures by 30°C compared to conventional powder coatings or by optimising line speeds. In both scenarios, the product contributes to energy reduction, thereby lowering carbon emissions and enhancing production line efficiencies simultaneously. Notably, this innovation was conceived by AkzoNobel and is
adaptable to various applications within the built environment, including building facades and windows, railings, and doors. It can be utilised in any scenario where an architectural-certified product is typically applied.
In the current era where businesses strive to contribute to energy reduction and accelerate sustainability, Low-E powders not only support architects and applicators in reducing their own carbon footprint but also aligns with AkzoNobel’s ambitious goal of achieving a 50% carbon reduction across its entire value chain.
By optimising oven temperatures, energy reductions of up to 20% can be achieved, resulting in significantly less energy consumption and a reduced environmental impact. Conversely, setting the shortest possible curing time that the line can accommodate yields energy reductions of up to 50%. These Low-E curing powders exhibit comparable application properties to standard formulations, making it suitable for both exterior and interior applications. These new formulations are available in a diverse range of colours, including gloss, satin, matte, and fine textures.
Development continues with new formulations that offer extended sustainability with resistance to weathering. All new formulations are rigorously tested by powder system manufacturers who are members of QUALICOAT and are independently approved by the Association to conform to the QUALICOAT Specification.
Should you wish to learn more about membership of QUALICOAT please get in touch. All QUALICOAT UK & Ireland members are available to offer advice and can be found on the Association website at qualicoatuki.org
• AirBench takesdustandfumes awayfromyourbreathingzone
• AirBench drawsthemthrough theworksurface,capturingthem insidethebench
• AirBench isavailableinawide rangeofsizesandfiltertypes tosuityourapplication
• AirBench isplugandgo-only needingunwrappingandplugging intoa13ampsocket
•Yougetextractionandwork benchinonecompactunit
Contactusforanon-sitedemonstration. Doubtitcanbethatsimple?
TheVertExmodularbooth system.Dustissuessolved...
• Modular systemforfast installationandassembly.
• LowEnergy throughtheuse ofhighefficiencyfans-upto 20,000m3/hat3kw.
• FiltrationOptions fromthe standardAirBenchrange.
• WeldingandGrinding boothsalso availablewithHEPAfinalfilter.
• RapidReconfiguration -standard componentsmeanVertExbooths canbereconfiguredondemand.
Doubtitcanbethatsimple?
Innovation Oxsilan®: high-performing and suited for multi-metal applications
Technological turning point in metal pretreatment: The eco-friendly Oxsilan® technology offers long-term corrosion protection and excellent paint adhesion – and at the same time more safety, economics, flexibility and sustainability. The thin-film technology is free of heavy metals, suited for multi-metal applications and allows an unlimited throughput of common metal substrates. Expect more from Chemetall: innovative technologies, environmentally-sound processes, comprehensive technical support, a global network and dedicated people – inspired for your success.
www.chemetall.com/oxsilan · oxsilan@chemetall.com
www.chemetall.com
The world faces an urgent environmental crisis. Every year, industries in the United States generate 7.6 billion tonnes of waste, with Europe adding another 2.2 billion tonnes. This staggering amount contributes to landfill overflow, pollution, and climate change. To combat this issue, industries must adopt more sustainable practices— meeting today's needs without compromising future generations' ability to do the same.
The protective coatings industry plays a crucial role in sustainability by extending the lifespan of assets through durable coatings. However, the industry is not exempt from environmental responsibility despite this inherent sustainability benefit. In the UK alone, 80 million gallons of paint are wasted annually. Many traditional raw materials and technologies used in protective coatings significantly contribute to pollution and climate change. While innovation is ongoing, the industry must take further steps to develop a sustainable and environmentally conscious ethos. A key part of this transformation starts with education and training.
Corrodere Academy is proud to introduce its new Sustainability Module as part of its commitment to environmental responsibility. This unit is designed for professionals at all career stages, offering an accessible and engaging exploration of sustainability within the protective coatings industry.
The module covers a broad spectrum of sustainability-related topics.
It begins by examining the role of the protective coatings industry in the circular economy before addressing key challenges and innovations. Topics include raw materials, technological advancements, sustainable practices, and waste management. By the end of the course, students will have a deep understanding of both the industry's environmental impact and the measures that can be taken to mitigate it.
Following the launch of the Sustainability Module, we spoke with Brendan Fitzsimons, Technical Director at Corrodere Academy, to gain his perspective on sustainability and the inspiration behind Corrodere Academy’s latest initiative.
Q: Can you explain what sustainability means in the context of the protective coatings industry?
Brendan Fitzsimons: "Protective coatings are essential for safeguarding industry assets, especially structures like oil platforms, wind turbines, bridges, and jetties. While coatings
remain the best option for corrosion protection, we must be mindful of their environmental implications. Most coatings come in tins, and their application involves various materials that can contribute to waste and pollution. However, advancements in coating technology can allow for thinner layers, reduced maintenance, and more user-friendly formulations. By using fewer abrasives, fuel, and liquid coatings over a structure’s lifecycle, we can promote sustainability within the industry. Surface treatment and coating applications can be complex, and some traditional methods are not environmentally friendly. Education is crucial in identifying and addressing these challenges. Sustainability means placing environmental concerns at the forefront of innovation and development."
Q: What motivated Corrodere Academy to develop the new Sustainability Module?
"We developed this module in direct response to industry needs. More companies now recognise the importance of operating sustainably and want their employees to be trained accordingly.
Measures and records oven temperature profiles
6 K-type thermocouple ports
High temperature stainless steel barrier box for long run times
Download, view, and analyze data using PosiSoft Desktop Software or export to .CSV
Over the years, we've seen a growing emphasis on sustainable practices—not just in protective coatings but across the entire industrial sector.
Sustainability is no longer just a regulatory requirement or a consumer demand; it has become a core component of corporate responsibility. As a company dedicated to education and training, we understand that our actions influence the industry. By introducing a dedicated sustainability module, we aim to lead by example and set a new benchmark for environmental consciousness. Sustainability is deeply embedded in our ethos, and this initiative represents our commitment to making a positive impact on the environment, our communities, and the industry's future."
Q: How do traditional protective coatings impact the environment?
"Despite the industry’s inherent sustainability benefits, protective coatings can have significant environmental consequences. As outlined in our module, challenges exist in the sourcing of raw materials, application technologies, and waste management. Many coatings contain toxic chemicals that emit greenhouse gases and have the potential to contaminate air, soil, and water. Addressing these concerns requires a shift in how coatings are formulated, applied, and disposed of."
Q: What are the biggest sustainability challenges facing the protective coatings industry today?
"One of the primary challenges is reducing the use of harmful chemicals and volatile organic compounds (VOCs) without compromising coating performance and durability. Finding solutions that balance effectiveness with environmental responsibility remains a top priority. Another major challenge is waste management. The protective coatings industry generates a significant amount of waste, much of which is classified as hazardous. Proper disposal is complex, and reducing waste at the source
through efficient application methods is essential. Training plays a crucial role in minimising paint waste and ensuring responsible material use."
Q: What are some recent innovations in protective coatings that promote sustainability?
"The industry has made significant strides in sustainability, with companies prioritising environmental concerns in their operations. One notable advancement is the use of overspraylimiting technologies, such as electrostatic spray systems. Unlike traditional airless sprayers, which generate excessive overspray and airborne particles, electrostatic systems attract coating particles to the substrate, significantly reducing waste. Additionally, advancements in product formulations have led to coatings with lower VOC emissions and improved environmental performance. These innovations are helping to shape a more sustainable industry."
Q: In your opinion, what is the most exciting development in sustainable protective coatings today?
"The most exciting development is the growing collaboration between material technologists, equipment manufacturers, and industry professionals. By working together, we can drive sustainability forward through innovative materials, advanced application techniques, and comprehensive education. Strength in numbers will be the game-changer for the industry."
Q: How will the Sustainability Module help professionals carry out their work in a more sustainable manner?
"The training is designed for all personnel in the protective coatings industry. It raises awareness, enhances understanding, and encourages professionals to consider environmental impact when undertaking surface treatment and coating applications. Even if we make a small difference by increasing awareness, we have achieved our goal."
Q: What are the expected outcomes for students who complete this training?
"Many professionals perceive sustainability as a gimmick or an obstacle to profit and growth. This perception is misguided. Sustainability offers tangible benefits beyond environmental protection, including cost savings, regulatory compliance, and enhanced industry reputation. Our training aims to shift this mindset and demonstrate that sustainability and success can go hand in hand."
Q: What future trends do you foresee in sustainability for the protective coatings industry?
"Government policies promoting green energy and sustainability will inevitably impact our industry. For instance, increased investment in wind farms presents new opportunities for advancements in protective coatings. The industry must stay ahead of these trends and adapt accordingly."
Q: What final message would you like to share with industry professionals about sustainability? "Sustainability is not just a passing trend—it is a necessity. Every industry professional is responsible for contributing to a more sustainable future."
The Sustainability Module is now available as an optional component with all Corrodere Academy courses, including Train the painter, Coating Inspection, and Specialist. Students who complete the module will receive a Certificate of Completion, signifying their commitment to a more sustainable industry.
For more information about the Sustainability Unit please contact Corrodere Academy:
info@corrodere.com
+44 (0)1252 732 236
Programming-free coating of any shape! Gema
The second generation of Dynamic Contour Detection detects the object contour fully automatic and positions the guns individually even for thin objects and at high conveyor speeds. Due to the programming-free adaption of all relevant line settings the application range is significantly extended.
Email: uk.sales@gema.eu.com
Straaltechniek had a great couple of days at the Surface World exhibition this year and want to thank everyone who visited them and expressed interest in their products and services.
James Lees, UK Sales Manager at Straaltechniek said “The show gave us a great platform to showcase our energy efficient high-performance long-life blast wheel technology, in this case being used on our new design versatile table shot blast machine which includes fixtures for blasting steel wheels as well as a basket for tumbling smaller components, so basically a 3 in 1 shot blast machine.
The versatility of this table allows us to engage with potential customers from various industries which proved to be the case throughout the show over the 2 days having received great feedback and promising enquiries generating current and new prospects.”
From a marketing point of view, the advertising opportunities that relate to the Surface World Show has also proven beneficial to Straaltechniek UK allowing them to reach out to not only customers within the UK but customers further afield.
Rebecca Beever, Key Accounts Manager & Marketing, said, "Attending Surface World this year was a valuable experience, and I’m thrilled to have had the opportunity to organise our stand. The show provided us with great exposure, allowing us to demonstrate the full range of services and solutions we offer. We are excited to build on the connections made and explore new opportunities in the future."
Straaltechniek UK Ltd offer many services into the surface preparation industry including manufacture and supply of equipment, new or 2nd hand refurbished, aftermarket spares, and equipment modernisation (including the High-Performance Long Life GN Blast Wheel) as well as maintenance support through service contracts and breakdown cover. With their office, workshop and showroom based in the Steel City of Sheffield, Straaltechniek UK Ltd are proud to be a member of Made in Sheffield, one of the Worlds great brands.
Telephone: 0114 2571077
Email: info@straaltechniek.co.uk
Visit: www.straaltechniek.co.uk
Surface World is the UK’s premier exhibition for surface treatment, product finishing, and coatings technology. The 2025 event, held on 26th - 27th February at the NEC, Birmingham, provided a fantastic opportunity for Stowlin Ltd to connect with industry leaders and demonstrate how our solutions can support businesses in achieving their goals.
As part of the 2M Group of Companies, Stowlin Ltd has a long-standing reputation for delivering highperformance cleaning solutions, surface treatment chemicals, and bespoke formulations. With over 75 years of combined expertise, our team was proud to showcase our technical capabilities, sustainable innovations, and customer-focused approach at Surface World. The event reinforced our dedication to continuous improvement and forward-thinking solutions that address the evolving needs of the industry.
Throughout the exhibition, we engaged with customers and industry professionals, highlighting our latest
developments in cleaning and surface treatment technologies. Our specialists provided insights into how Stowlin’s tailored solutions can enhance efficiency, reduce environmental impact, and drive long-term value for businesses.
Rhys Davies, Account Manager at Stowlin, reflected on the event’s success: “After a busy and productive few days at Surface World, we’d like to extend a huge thank you to everyone who visited our stand. It was fantastic to meet so many customers, industry professionals, and potential new partners. The event was a great opportunity to share our expertise and discuss the future of surface treatment.
We now look forward to supporting our existing customers and exploring the exciting new opportunities uncovered during the show.”
As part of the 2M Group of Companies, Stowlin Ltd benefits from a global network of industry-leading brands, including 2M Manufacturing, 2M Equest, 2M Services (MP Storage and Blending, SampleRite UK, SampleRite China), the Banner Chemicals Group (2M Water Treatment, 2M CASEPL, Stowlin), CE-O2 Trockeneis, Laboratorios Prady Normapiel, and the Surfachem Group (2M Laurichem USA, Bregaglio Italy, Chemir Spain, Ingretech France, Surfachem Germany, Surfachem Nordics, Surfachem Poland, Surfachem UK).
Our presence at Surface World 2025 reaffirmed our commitment to innovation, sustainability, and delivering high-quality solutions that meet the challenges of today’s industries. We look forward to building on the momentum of this event and continuing to support businesses with cutting-edge technologies and exceptional service.
Telephone: +44 (0)116 278 5373
Email: info@stowlin.com Visit: www.stowlin.com
BASF Coatings, a leading global supplier of innovative coatings solutions, and NIO, a pioneer in the global smart electric vehicle market, have announced the signing of a Letter of Intent (LoI) aimed at establishing a strategic partnership to enhance cooperation in the automotive coatings sector. This collaboration marks a significant step towards achieving a long-term and mutually beneficial relationship, focusing on automotive exterior coatings for NIO’s electric vehicles.
tailored to meet specific technical requirements and will offer valueadded services including color design, color development, digital solutions, sustainability initiatives, workshops, and industry-leading technical support.
The agreement lays out the framework for ongoing discussions between the two companies, facilitating annual strategic dialogues to negotiate the implementation of this partnership. Both parties are committed to fostering platforms for cooperation that encompass market and customer development, project management, and information exchange.
As part of the strategic cooperation, BASF Coatings intends to provide NIO with an extensive range of products
”The signing of today’s strategic partnership agreement builds on ten years of successful collaboration. NIO has established a leading position for electric vehicles through advanced technology and a clear brand identity. Together, we will keep on exploring innovative technologies and we will support NIO in reaching its sustainability targets and future goals,” said Uta Holzenkamp, President of BASF Coatings.
NIO recognizes BASF Coatings as its strategic partner for automotive exterior coatings, emphasizing the importance of this collaboration in achieving shared goals. Both companies will work jointly on the development and application of new coating materials and technologies on a global level, aiming for sustainable development and carbon neutrality. The partnership represents a significant milestone in the automotive industry, as BASF Coatings and NIO aim to enhance their cooperation through innovation and strategic alignment. Both companies are excited about the opportunities that lie ahead in shaping the future of electric vehicle coatings together.
NIO is a global smart electric vehicle company founded in November 2014. Dedicated to shaping a sustainable and brighter future together by providing high-performance smart electric vehicles and exceptional user experiences, NIO is the first car company listed on the NYSE, HKEX and SGX. NIO currently has three major brands under its umbrella: NIO, ONVO and firefly.
Ten years into establishment, NIO is now one of the leading companies in the global premium smart electric vehicle market, committed to fostering its own research and development capabilities for core technologies. As of the end of December 2024, the company had filed for and obtained over 9,800 patents. Additionally, NIO has developed NIO Full Stack, a collection of 12 technology domains.
NIO has R&D and manufacturing facilities in Shanghai, Hefei, Beijing, Nanjing, Shenzhen, Hangzhou, Wuhan, San Jose, Munich, Oxford, Berlin, Budapest, Singapore and Abu Dhabi. The company has also established sales and service networks in China, Norway, Germany, the Netherlands, Sweden, Denmark, the UAE, Israel and Azerbaijan.
NIO Inc. currently offers nine premium smart electric vehicle models under the NIO brand and one smart electric vehicle under the ONVO brand. firefly has started its pre-orders in China. As of January 31, 2025, NIO Inc. had delivered a total of 685,427 vehicles, leading the premium BEV segment priced above RMB 300,000.
The Coatings division of BASF is a global expert in the development, production and marketing of innovative and sustainable automotive OEM and refinish coatings, decorative paints as well as applied surface treatments for metal, plastic and glass substrates in a wide range of industries. We create advanced performance solutions and drive performance, design and new applications to meet our partners’ needs all over the world. BASF shares skills, knowledge and resources of interdisciplinary and global teams for the benefit of customers by operating a collaborative network of sites in Europe, North America, South America and Asia Pacific. In 2024, the Coatings division achieved global sales of about €4.3 billion.
Solutions beyond your imagination – Coatings by BASF.
For more information about BASF Coatings and its products, visit www.basf-coatings.com.
Following two strong years of growth, PSI Global Training is looking to expand upon it’s offering of courses for prospective and current professionals in the Industrial Services sector, adding to the already successful Industrial Painting courses currently offered.
PSI Global Training began following PSI Global Recruitment becoming the first agency affiliate member of Train the Painter in 2022. This was a great opportunity to help close the skills gap in the industry and get more people in the communities PSI Global operates in back to work. Following a successful start, the dedicated training centre in the North West was opened in late 2023.
Much of the training initially done was on site for various clients of PSI Global. A skills gap within the on-site workforce would be identified by the employer who would then contact PSI Global Training Director Rebecca Law to discuss a bespoke training session on-site.
“We set up the training school as a way of addressing the skills shortage in our industry, while also wanting to encourage young people to consider this as a career option,” explained Rebecca. “Running these courses on-site, whether upskilling or teaching a new skill, was a way of helping our clients while also seeing the potential for growth in this division.”
PSI Global’s team of experienced trainers and consultants continue to work closely with clients to identify their unique needs, and design customised training programs that help them meet their Corporate Social Responsibility (CSR) and community engagement goals.
The company works with a diverse range of clients, including large corporations, small businesses, non-profits, and government agencies. Each client
approaches PSI Global with the aim of helping to make a positive impact on their communities, and they trust the team to help them achieve their goals.
As the business continued to grow, so did the need for a dedicated training centre to run regular courses from. Leveraging the latest technology and teaching methods, PSI Global Training created a program of courses to ensure engaging, interactive, and effective training took place during each session.
With this plan and program in place, the Training Centre began to take form and officially opened its doors in November 2023. Located in the North West, the state-of-the-art facility has given a number of people the opportunity to not only upskill, but to kickstart their career in Industrial Painting. Many have come with the help of a grant from the local Job Centre, and through this programme PSI Global Training has put a number of people back to work.
“Opening this facility marks an exciting step forward in our commitment to building careers in the industrial coatings sector," said Rebecca. "Through initiatives like our partnership with the Job Centre, we're not only filling crucial skills gaps but also creating pathways for new talent to gain meaningful, hands-on experience. This facility is designed to be more than just a training centre – it’s a launchpad for careers that support essential industries and skills.”
The courses are led by experienced instructor Jonathan Hewitt, who maintains consistency in providing high quality training to help individuals develop the knowledge and skills necessary to succeed in their career. Helping students achieve their goals is an important step in bridging the skills gap and addressing an issue that’s become all too common in the industry.
“I’ve been privileged and honoured to work with some of the best in the industry, which today has given me the opportunity to be able to give back to the next generation of Painters, Blasters, and Sprayers,” Jonathan shared.
PSI Global Training is dedicated to building a workforce for the future. The team is committed to helping organisations develop and implement effective strategies to get more people back to work and are committed to helping workers succeed and progress in their career.
With that in mind, the company is looking ahead to offer not only Train the Painter courses, but a wide range of courses for professionals across a number of sectors, including Construction, Rail, Civils, and more. The additional courses available from late 2024 will include GWO (Basic Safety Training, Advanced Rescue), IRATA (Rope Access Level 1-3), Offshore Medicals, CITB (CSCS Card Test, SSSTS, SMSTS, etc.), and City & Guilds Confined Space.
In addition to these courses, the training division also became accredited to ECITB in October 2024, which means expanding the course offering further. This will include CCNSG (safety passports and renewal), and short courses covering Working at Height, Manual Handling, Abrasive Wheels, and Confined Space.
PSI Global Training will also be able to provide Technical Testing for a wide range of skills including Industrial Coatings Brush Application, Airless Spray Application, and Abrasive Blast Cleaning. Beyond this, the Training division are also approved to deliver further tests that include Welding, Pipefitting, and Thermal Insulation.
If you would like to learn more about PSI Global Training or to discuss creating a bespoke training courses on your site, contact Training Director Rebecca Law at Bookings@psiglobaltraining.com.
Working Across Aluminium Industries to Improve Your Processes
Specialist in the Supply of Anodising & Metal Finishing Technologies
QUALICOAT Approved Chrome & Phosphate Free Technologies
Low-Temperature Degreasing & Sealing Solutions
PUMPS & FILTERS
L SERIES | Medium flow rate filter
P SERIES | Ultra-high flow rate filter
Supplied with Excellent Technical Suppor t CONVERSION COATING PRETREATMENT ANODISING
FILTER MEDIA
L-TECH | Pleated cartridge
| Filtration bag
| Extruded cartridge
| Wound cartridge
| Anode bag
ACIDPURE | Acid recycling
EASYPURE | Fluid recycling IONPURE | Ionic filtration
Industrial residue is being used by
Nearly a third of the total residue generated during industrial effluent treatment at the Mauá plant in São Paulo goes into the manufacture of Coral Pinta Piso floor paint.
As well as helping to eliminate landfill disposal, it’s also contributing to the preservation of natural resources.
“This is a fantastic initiative which will play an important role in helping us achieve our ambition of 100% circular use of materials in our own operations by 2030,” says Wijnand Bruinsma, AkzoNobel’s Director of Sustainability.
“In 2024 alone, the initiative contributed to the reduction of around 272 tons of CO2 emissions – equivalent to the amount produced by nearly 400 cars over the course of a year*.”
Industrial residue is the waste formed
after the treatment of industrial wastewater. Currently, around 30% of the total treated residue in Mauá (which is free from sanitary or biological sewage) is used to formulate the Coral Pinta Piso line of paint. Following the quality control process, any residue not suitable for use in the product is transformed into briquettes for energy recovery.
Although legislation allows the site’s liquid effluent to be treated and disposed of in a watercourse, AkzoNobel has invested in the treatment plant in recent years, which allows 100% of the treated water to be reused in processes and products.
Coral Pinta Piso is suitable for areas with a high flow of people, both indoors and outdoors. It’s part of a segment that saw an 8.5% increase in its share of the paint market in 2024, according to recent data from ABRAFATI (the Brazilian Paint Manufacturers Association).
In addition to Brazil, the product is sold in several other countries, including Bolivia, Paraguay and Suriname.
The Mauá site uniquely sits within a large area of Brazilian rainforest known as the Tangará Reserve.
Since 2007, the company has been restoring 70 hectares of the reserve to native woodland in an effort to safeguard the fragile ecosystem.
*Assuming the cars drive an average of 20km a day. Source: Brazilian Vehicle Labeling Program, published by Inmetro (National Institute of Metrology, Quality and Technology).
Since 1792, we’ve been supplying the innovative paints and coatings that help to color people’s lives and protect what matters most. Our world class portfolio of brands – including Dulux, International, Sikkens and Interpon – is trusted by customers around the globe. We’re active in more than 150 countries and use our expertise to sustain and enhance everyday life. Because we believe every surface is an opportunity. It’s what you’d expect from a pioneering and long-established paints company that’s dedicated to providing more sustainable solutions and preserving the best of what we have today – while creating an even better tomorrow. Let’s paint the future together
Visit: www.akzonobel.com
Threadlocking and sealing specialist Inlex Locking has welcomed two new experts into its team as the Wolverhampton business continues to grow.
Chris Hines has joined the business as Quality Manager, while Simon Elwell has been given the position of Sales and New Business Manager.
Chris has joined having being transferred to Inlex from another business within the Anochrome Group, where he held the position of Quality Manager.
The 55-year-old from Wolverhampton had previously worked in a similar role in the make to print industry before
securing a position within the Anochrome Group two years ago.
He said: “Being part of the Anochrome Group has been very interesting. There is lots of variety and areas to get involved in.
“This move within the Group represents a new and exciting challenge for me. I have already begun reviewing all the systems within Inlex involving products, suppliers and customer service and working with the team to achieve best practice.”
Simon, meanwhile, has joined Inlex from The Electrolytic Plating Company Limited (EPC) after the Walsall business fell into administration following more than 120 years of trading.
Wolverhampton Electro Plating (WEP), part of The Anochrome Group, was able to salvage sections of EPC, saving 12 jobs in the process.
Simon, also 55-years-old, started in the coatings industry with Prelok Ltd in 1987. Prelok was acquired by Inlex in 2014.
Simon said: “I started in the lab on coatings and moved up to production manager before switching to patching in 1997.
“The industry has progressed over the last 38 years in terms of new technology and automation and I enjoy continually learning and progressing.
“It’s fantastic to be part of the Inlex team. There is more support here than I have had previously working with experienced staff who all strive to help us deliver the best services for our customers.”
As well as supporting existing customers and seeking new ones, Simon is involved in planning jobs for production to ensure a streamlined service.
Kev Walton, Group Thread locking, Sealing & Purchasing Director at Inlex, said: “We are delighted to strengthen our team with the addition of Chris and Simon, who each have decades of experience in their areas of expertise.
“Inlex continues to excel and grow and Chris and Simon can help us to offer industry-leading customer service.”
Inlex provides a comprehensive range of threadlocking and sealant products for today’s high-tech fastening applications, serving a variety of sectors including automotive, off-highway and construction.
For more information, visit www.anochrome.com
SurTec 717 - Modular, Alkaline Zinc/Nickel Process for all Applications
Modular process for rack, barrel and special applications
Tolerates higher process temperature up to 35°C
Easy to control, automatically limits the nickel content below 16%
SurTec 680 - Cr(VI)-free Thick Layer Passivation for Zinc & Zinc Alloys
For highest quality requirements (heat resistance & corrosion protection)
Usage without waste water is possible
Highest cost-effectiveness when using the SurTec regeneration process
precote Product Range - Thread Locking and Sealing
Specially developed pre-coating products for locking, sealing & clamping
Based on unique microencapsulation technology
Excellent service and high-quality products made in Germany
Owing to a significant increase in demand for manually operated and fully automatic metal finishing chemical engineering plant and equipment together with fume extraction and fume scrubbing systems,effluent treatment plant and equipment and D.I water generation, all of which is designed, manufactured, installed and commissioned by our skilled engineers from our newly established factory at Minworth, Birmingham.
We are the only company in our industry that are able to provide the entire chemical engineering scope of supply giving our customers the confidence of uninterrupted continuous production and back-up from one source.
Plastratum is an integral part of the Safety Critical Plastic Solutions Group involving a further four complimentary companies throughout the UK enabling enhanced production and productivity from which our customers are already benefitting.
We have introduced a training scheme and attracted a number of young and capable employees who are progressing well and we are confident that this will ensure a continued, progressive and enhanced company future.
We serve the general metal finishing industry and aerospace with our speciality products, along with the automotive industry as well as developing bespoke products and services with consultation.
Please allow us the opportunity of serving your company.
Telephone: 0121 314 1191 Visit: www.plastratum.com
Vixen provides bespoke phoswash solutions to customers all over the world. Recently, a customer needed to upgrade their previous Vixen machine due to legislation changes. This machine had lasted for over 10 years; they chose to come back to us for the upgrade due to the exemplary results and quality. We were able to quickly and efficiently provide this customer with a brand new solution catering to their needs. This new machine upgraded their process to be non-chrome and much more environmentally friendly.
This customer’s existing Vixen Phoswash has provided excellent service for excess of 10 years. However, changes in legislation in the UK in relation to the use of yellow and green chromates (which have been the technology of choice for many industries such as Aerospace and architectural) meant they needed to update their equipment. The customer came back to Vixen and have elected to invest in a new 7 Stage NONChromate Phoswash machine. The new process consumes much less water and subsequently less energy to heat the double skin insulated tanks and to further reduce their carbon footprint. The customer has elected to include our Duel fuel Electric and Gas Heating system complete with 7 day programmable heating that will allow the machine to be programmed to heat up more economically overnight ready for a shift to start. His machine is overall more environmentally friendly and complies with new legislations. This machine was designed and fitted in a pit to account for larger components. This customer processes aluminium windows, so the large size was an important requirement.
Vixen will continue to support this customer and give them comfort with our Careplan which includes scheduled
engineers service visit to keep the machine in optimum condition. With this, along with our service and support and their expertise, they have been able to offer their existing customer base and potential new customers in-house powder coating that is capable of achieving BS EN 12206 to Qualicoat standard.
Vixen has a full inhouse design team so following a consultation we can provide you with a Turnkey solution to fulfil your Phosphating requirements for all current standards. Whether you are positioning a solution in a PIT to eliminate double handling on require a pass-through system for track we can provide you with a full and detailed drawing so you can plan your floorspace our machines are much more compact and require much less energy than multiple dip tank systems and in most cases more cost effective than inline track systems.
Here you can see some of our smaller Phosphwash machines we have designed and manufactured for other customers.
Please visit our website or get in touch directly for more information.
Telephone: 01642 929976
Email: info@vixen.co.uk Visit: www.vixen.co.uk
process of choice for many companies.
For many years, solvent cleaning has been widely accepted as a fast, effective way of removing oils, greases etc. from metal components. In its early days, the process, known as ‘vapour degreasing’ involved placing contaminated, metal components in hot solvent vapour, which would condense on the cooler metal and the generated liquid would dissolve any oil and grease present. When components were removed from the process, the residual solvent would evaporate, leaving parts clean and dry.
The term vapour degreasing is still widely used today, although most modern solvent cleaning processes employ complete immersion of components in the cleaning fluid, often assisted by ultrasonic agitation. This change is due, in no small part, to solvent cleaning having to adapt and evolve as manufacturing processes have changed, newer processing fluids have been developed, polymeric materials and composites have seen wider application and ever more stringent cleanliness standards have been demanded. Added to these changes in manufacturing practice there has also been the ongoing tightening of health and safety and environmental legislation. Despite these demands however, ongoing development of fluid formulations and more efficient cleaning machines have helped solvent cleaning remain the
D&S Ultra-Clean Ltd is the UK distributor for TergoTM precision cleaning fluids manufactured by MicrocareTM LLC, a company with over 40 years’ experience of providing cost effective solutions to critical cleaning problems. Because MicrocareTM is absolutely committed to research and development, we are well placed to provide sustainable, long term solutions to today’s component cleaning challenges.
The TergoTM family of precision cleaning fluids includes products that have been specially formulated to provide the highest standards of cleanliness across a wide range of applications in industries such as: oxygen approved applications, aerospace, automotive, medical devices, electronics, telecommunications and precision engineering. All are highly effective, provide low cost-per-clean and reduce environmental impact. We have readily available alternatives to NovecTM fluids for anyone currently looking to find replacements ahead of their impending withdrawal from the market.
We are also now have the TergoTM XCF range, the latest additions to the family that are formulated to be completely PFAS free, thus underlining our longterm commitment to the supply of precision cleaning fluids to the UK market.
TergoTM precision cleaning fluids have been designed to operate safely and
efficiently in modern vapour degreasing equipment such as our ‘Cleanseal’ ultrasonic cleaning machines. Our customers tell us that the combination of TergoTM and ‘Cleanseal’ combines excellent cleaning performance with low running costs, many enjoying significant cost savings since switching from competitive fluids.
Making the switch to TergoTM is simple and straightforward and we can manage the whole process. First step is that a member of our technical team will make an initial evaluation of the current cleaning process and fluid to allow us to recommend the most appropriate TergoTM alternative. Step two involves carrying out free, no obligation, cleaning trials on sample components to confirm that we achieve at least an equivalent standard of cleanliness. Thus far, many customers making the switch have told us that they have seen an improvement in cleaning performance. Finally, our service team will carry out the conversion of the cleaning machine, optimising process conditions etc. to provide maximum benefit from running with TergoTM.
If you would like more information on making the switch to TergoTM and securing the long-term future of your component cleaning process.
Contact us on sales@ds-ultra.com or visit our website at www.ds-ultra.com
Microcare and Tergo are trademarks or registered trademarks of Microcare LLC
In December 2022, 3M™ announced their plans to discontinue their Novec™ range of PFAS substances (per- and polyfluoroalkyl) in its product line. Final order dates were on March 31st 2025 and the supply of these products will end on December 31st 2025.
This affects the following 3M™ product lines:
3M™ Novec™ Engineered Fluids
3M™ Fluorinert™ Electronic Liquids
The phase-out has left many industries, including electronics, aerospace, medical, and precision engineering, scrambling for viable replacements
that match the performance characteristics of Novec™ products, and businesses around the world who rely on these solvents for vapour degreasing applications are now seeking reliable alternatives.
EnviroTech Europe offers a range of direct replacements for the discontinued 3M™ Novec™ products, providing companies with a seamless transition without compromising performance, safety, cost, or compliance. Our ProSolv® Direct Replacements have been specifically developed to be exact chemical replacements for all Novec™ fluids. These high-performance solvents are designed to match all the properties and specification of the relevant Novec solvent, ensuring an easy transition with minimal process modifications.
Seamless integration: Compatible with existing vapour degreasing and precision cleaning systems. Superior cleaning performance which effectively removes oils, greases, and particulate contaminants.
Environmentally responsible: Low GWP, non-ozone depleting, REACH-compliant, safe and sustainable, non-flammable and designed for long-term availability.
Support: Our technical staff provide free-of-charge consultation visits and product trials to help guide your transition away from 3M™ Novec™ engineered fluids.
Businesses must act fast to maintain operational efficiency. EnviroTech Europe can provide a full assessment of your current cleaning process to put in a plan to help ensure a seamless transition. We have already successfully transitioned many Novec™ users globally to our ProSolv® Direct Replacements range, ensuring
reliability and compliance for years to come.
EnviroTech Europe also supplies ProSolv®5408e, a PFAS-Free high performance vapour degreasing solvent - offering next-generation, multi-purpose solvent cleaning with zero ODP (Ozone Depletion Potential) and near zero GWP (Global Warming Potential). ProSolv®5408e is tested to a number of industry standards including ASTM D3828, ASTM E918, Stock Loss ARP1755B and ASTM F945-1.
For expert guidance on transitioning to ProSolv® solvents, contact EnviroTech Europe today and make the switch with confidence.
Please visit our website www.envirotech-europe.com/ replacements-for-3M-Novecengineered-fluids for more information about replacing 3M™ Novec™ solvents.
Visit www.envirotech-europe.com/ prosolv5408e for information about our next-generation PFAS-free vapour degreasing solvent cleaners. For more advice, please telephone us on +44 (0) 20 8281 6370 or use our website contact form.
All products are supplied and supported by EnviroTech Europe Ltd. Manufactured in the United Kingdom and available on short delivery times through our dedicated team of distributors worldwide.
Hot dip galvanizing provides you with long-term protection against rust and corrosion of steel products. With 14 plants across the UK, Wedge Group
Galvanizing is the UK’s largest hot dip galvanizing organisation offering a national service, collection and delivery and 24hr turnaround on request. The group can process anything from small components to 29m structural beams.
With an innovative shot blast machine, one of the largest foundries in Turkey has expanded its capacity for de-sanding and cleaning of engine blocks. A significant factor in the decision for the RMBS 1-6-400-30 shot blast system from Rösler was the high degree of automation of the work piece handling and the shot blast process. Compared to spinner hanger machines the RMBS system offers not only drastically shorter cycle times but also requires less personnel. In addition, by replacing the two existing blast machines the new system helped provide valuable additional manufacturing space.
Among other products the renowned Turkish foundry supplies grey and nodular cast iron engine blocks, which are used in commercial vehicles and ships. The raw castings have dimensions of max. 900 x 330 x 140
The engine block blast machine RMBS allows the fully automatic de-sanding and cleaning of one large or several smaller engine blocks in very short cycle times.
mm and weigh up to 237 kg. To date, for de-sanding and cleaning the work pieces, the customer, as well as many other foundries, used spinner hanger blast machines. In this particular case the customer used two – one for de-sanding and the other for general cleaning. However, because of a steadily growing production volume the shot blasting operation became increasingly a bottle neck. For this reason, the company decided to purchase an additional, respectively, alternative shot blast system. The customer project team
talked with four different equipment manufacturers, one of which was the Rösler Oberflächentechnik GmbH.
Contrary to the other equipment suppliers, Rösler offered a unique, highly innovative and efficient equipment concept, namely the RMBS 1-6-400-30 engine block blast machine. This blast system, specially adapted to the customer requirements, allows the fully automatic simultaneous blast-cleaning of one large or several smaller engine blocks within short cycle times. Towards this purpose the machine is equipped with a specially engineered gripper-manipulator. After a robot has precisely positioned an engine block in the blast chamber, the gripper picks up and firmly holds this engine block. Once the blast chamber door has been closed, the blast program, tailored to specific work pieces, starts. The gripper precisely rotates the work piece through the blast media stream. To increase the exposure of certain surface areas of the engine block to the blast media, the rotation can be slowed down or interrupted for a pre-defined time period. For simultaneously processing of several smaller engine blocks, these are mounted to a special work piece fixture. The entire fixture is then picked up by the gripper and rotated through the blast media stream.
With the old spinner hanger blast solution, the work pieces had to be manually loaded onto a special “hanger” before they could be blasted. The new system achieves the required blast results by the targeted movement of the engine blocks
through the blast stream. The resulting cycle time savings are such that the de-sanding and surface cleaning operation can now be combined into one single process. This resulted in a significant increase in the overall shot blasting capacity so that the two spinner hanger blast machines used in the past were no longer needed. Moreover, the risk that certain work piece areas are shielded from the blast stream by other work pieces could be completely eliminated. Besides the higher productivity and process reliability, the customer decision for the Rösler system was also influenced by the fact that the new system needs considerably less personnel. In foundries it becomes increasingly
difficult to find people for the physically demanding and exhausting work.
The desired shot blast results are quickly achieved by the six blast turbines, type Gamma 400G-8 HD, each with an installed drive power of 30 kW. These turbines, specially developed for shot blasting in foundries, are equipped with eight throwing blades in the typical “Y-design as compared to the standard Gamma turbines with six blades. Another major feature of the HD turbine version is that its housing is lined with extremely wear-resistant tool steel. Through this special design the throwing blades achieve an up to three times longer uptime than their standard equivalent. This minimizes work for maintenance and ensures significantly higher productivity and cost-efficiency. The special throwing blade design generates an up to 20 percent higher blast intensity with, at the same time, lower energy consumption. This guarantees a highly effective shot blast operation. Another feature of the Gamma turbines is that both sides of the throwing blades can be used resulting in significant cost savings for spare parts. Blade changes are facilitated by a quick- change system that requires no removal of the turbine from its housing.
The blast chamber was also designed for high wear resistance. It consists of sturdy manganese steel and is additionally lined with easily replaceable plates made from wearresistant steel. Areas directly exposed to the blast stream are lined with special cast wear plates.
Contact: Rösler UK, Mr. Colin Spellacy Telephone: 0151 482 0444 Email: c.spellacy@rosler.com Visit: www.rosler.com
The industrial cleaning sector is experiencing a remarkable transformation with the advent of new fully sealed vapour degreasing technology. This state-of-the-art solution, utilising vacuum vapour degreasing with Modified Alcohol, Hydrocarbon, or Perchloroethylene, is set to redefine component cleaning by combining environmental responsibility with exceptional operational performance. Engineered to meet the demands of modern manufacturing, this breakthrough system offers a robust, sustainable, and cost-effective alternative to traditional cleaning methods.
“It isn’t just about meeting today’s standards; it’s about setting tomorrow’s benchmark for excellence in industrial cleaning,” says Graham Fraser, MD.
At the heart of this vapour degreasing technology is its fully enclosed design that effectively contains solvent vapours, resulting in *near-zero emissions. By preventing the escape of chemicals into the workplace, the system ensures compliance with the strictest environmental and safety standards. This containment not only contributes to a cleaner environment but also eliminates the need for bulky abatement equipment, thereby simplifying maintenance and overall system architecture.
* PCE – 28 g/hr fugitive emissions
Designed for continuous operation, the system supports uninterrupted production cycles through its dual stills and integrated filtration. This enables in-process cleaning and routine maintenance without significant operational interruptions, a critical feature for high-volume applications where even minor downtimes can lead to considerable losses in productivity.
Cost efficiency is another cornerstone of this innovative cleaning solution. Reduced chemical consumption, minimal waste production, and lower operational costs combine to deliver a strong return on investment. The system’s design prioritises longterm reliability and performance, ensuring that the investment remains viable even as regulatory and operational requirements evolve over time.
Industry sectors including aerospace, automotive, and precision engineering have expressed strong interest in this technology. Early adopters of the technology have reported encouraging results regarding its performance and environmental benefits.
Such as one clients trial who have high-volume, dirty components, where the high solvency of the modified alcohol paired with the vacuum drying allowed us to reduce the cycle time by 50%.
These initial indicators underscore the potential of this system to become an indispensable asset for companies committed to excellence in component cleaning.
Fraser Technologies excels in support and service, tailoring solutions to each client’s unique cleaning challenges.
Their comprehensive assistance, from evaluation and cleanliness testing to process audits, ensures optimal performance and cost efficiency. By identifying improvement areas and recommending adjustments, they maintain high cleaning standards, enhance operational reliability, and reduce costs. In-house trials empower informed decisions, enabling a confident transition to this nextgeneration cleaning solution.
Contact us today to start your journey towards nearzero cleaning emissions.
Visit: www.frasertech.co.uk
Product Overview
Manual Monorail Systems
Unit loads up to 3000kg
Monorail Chain Conveyors
Unit loads up to 300kg
Power & Free Conveyors
Unit loads up to 7000kg
Floor Conveyors
Unit loads up to 500kg
Stewart Gill Conveyors Ltd have been supplying overhead conveyors into all sectors of industry for over 70 years.
As a long time member of the Railtechniek van Herwijnen BV Group based in the Netherlands, Stewart Gill Conveyors can offer a comprehensive range of overhead conveyor products which are capable of handling unit loads up to 7000kg.
Stewart Gill Conveyors Ltd offer complete manufacture, installation and commissioning, coupled with fully documented instruction, operation and maintenance manuals.
We do:
In-House 3D CAD engineering
In-House manufactoring in the UK and EU
In-House design of PLC/PC control systems
Industry 4.0
Worldwide installation and commissioning
Remote support, service & inspection Stewart
Part of the
The range of medical technology products is extremely diverse and places specific demands on parts cleaning and packaging. For example, particulate and filmic contamination must be reliably removed from manufacturing processes. In addition, there is compliance with the regulatory requirements from the MDR and FDA with regard to product identification and the qualification of systems, documentation and traceability of components and processes. These stringent requirements can only be met with cleaning processes and systems that are optimally adapted to the task at hand along the entire production chain in a reliable and cost-effective manner.
The high technical and regulatory requirements in the manufacture of medical technology parts can only be met with cleaning processes and systems that are optimally adapted to the application.
The manufacture of medical technology products such as instruments, implants for human medicine and dentistry, disposable items (e.g. syringes, cannulas, tubes and valves) and devices for diagnostics and therapy is carried out using different technologies and usually in several production steps. Manufacturing processes such as machining or additive manufacturing inevitably leave material residues (particles) as well as operating and auxiliary materials, such as cooling lubricants, drawing and forming oils and release agents, on the surface.
These impurities can hinder the feasibility and quality of subsequent processes, pose a risk to patients or impair the proper functioning of devices. One example is the manufacture of a knee implant, which must be free of production media, particles and germs before packaging. The blank produced using a casting process or additive manufacturing is machined, polished, possibly coated, finally cleaned and packaged. Each of these processing steps places individual requirements on the surface. This results in different tasks for parts cleaning.
Thanks to their modular design, ultrasonic multi-bath immersion systems such as the UCMPerformanceLine can be optimally adapted to tasks such as cleaning before coating or final cleaning before packaging.
The following questions play a role in the selection of the technically and economically suitable solution for the respective cleaning step: Which part needs to be cleaned and in what quantity? What cleanliness specifications must be achieved? Which cleaning process and chemicals are suitable? Which environmental regulations, standards and laws need to be taken into account? What steps must be taken to fulfill all criteria? Are there any intermediate steps that need to be included? Does the logistical
NO PRICE INCREASES FOR 2025
with
combining wet
process fit? What role do employees play in the cleaning process? What budget is available for the purchase? How high are the ongoing operating costs, e.g. for new media, disposal, energy and maintenance? On this basis, it is possible to determine how many and which cleaning steps are required with which process, which medium is most suitable and which drying technology should be used.
As an experienced full-service provider of future-oriented and globally available solutions for industrial component cleaning, surface treatment and automation, Ecoclean and UCM cover the entire spectrum of cleaning processes used in medical technology. The portfolio also includes turnkey solutions including cleanroom and packaging systems.
Pre-cleaning is required both for additively manufactured components and after machining. The aim is to prepare the workpieces for the subsequent process by removing adhering powder (depowdering) or particles and processing medium. This step is usually carried out in singlechamber systems which, depending on the processing medium used, are operated with solvents, e.g.
hydrocarbons or modified alcohol, or a coordinated water-based cleaner.
Intermediate cleaning steps are used to remove polishing pastes and residues from grinding processes, for example after mass finishing. Depending on the cleanliness requirements, they are carried out in a single-chamber cleaning system such as the EcoCwave or a multi-stage ultrasonic multi-bath immersion system such as the modular UCMSmartLine with an aqueous cleaning medium.
The state of the art for cleaning before coating as well as final cleaning and passivation are multi-stage ultrasonic multi-bath immersion systems with corresponding water treatment. For example, the UCMPerformanceLine can be easily adapted to the respective task using modules with integrated electrical and control technology for the cleaning and rinsing process steps with variable ultrasonic equipment for mono-, twin- and multi-frequency, drying with vacuum, hot air and infrared drying, loading and unloading as well as a flexible transport system. In addition, various systems are available for these tasks, such as the UCMIndexLine rotary indexing solution for small precision parts or the UCMSprayLine GMP, which meets high cGMP quality requirements.
The effect of the cleaning medium is enhanced by various applicationspecific process technologies, for example for spray, high-pressure, immersion, ultrasonic and plasma cleaning, steam degreasing, injection flood washing, pulsed pressure cleaning (PPC) or ultrasonic plus, thereby reducing the cleaning time by up to 50 %.
By integrating a low-pressure plasma process as the final step in a solvent or aqueous batch cleaning process, the component surface can be effectively and efficiently prepared for subsequent coating, among other things. The PPC pressure change process is used in particular for intermediate and final cleaning processes of components with narrow cavities, fine capillaries and porous surfaces. It enables contaminants to be removed reliably and quickly even from these hard-to-reach areas.
Whether in a chamber or ultrasonic multi-bath immersion system, the cleaning of medical technology products is often based on validated process parameters, compliance with which must be monitored and documented. These include the ultrasonic frequency and power. The Acoustic Performance
Measurement (APM) systems from Ecoclean make this possible inline and reproducibly up to an ultrasonic frequency of 2,000 kHz. Monitoring is carried out using a condenser or laser acoustic microphone, which is aligned with the surfaces of the ultrasonically equipped cleaning and rinsing tanks of a multi-bath immersion system. The measurements are thus carried out without movement or contact, ensuring the reproducibility of the results. In addition, APM technology makes it possible to detect ultrasonic frequency and sound pressure through "walls". It can therefore also be used in closed cleaning and rinsing tanks as well as chamber cleaning systems. Analysis, evaluation and storage of the recorded data are carried out by the measuring system software.
In addition to final cleaning, the packaging of various medical technology products has also been
a critical component of the product since the introduction of the MDR. The Group's turnkey solutions include appropriate cleanroom, packaging and sterilization solutions.
Pre-validated packaging is already available for certain products.
APM technology enables the reproducible, movement-free and contact-free monitoring of ultrasonic frequency and power. The recorded values are automatically evaluated and saved.
Software solutions and RFID technologies specially developed for medical technology applications and audit trails in accordance with CFR 21 also ensure that all regulatory requirements are met and that seamless automatic production data acquisition and traceability are guaranteed. The experts also offer
support with qualification (IQ;QQ;PQ) and risk analysis.
Contact: Ecoclean GmbH, Fabio Cordaro, Global Business Development Manager CLP, 52156 Monschau, Germany, fabio.cordaro@ecoclean-group.net, www.ecoclean-group.net
CLEANING AND DEBURRING SYSTEMS FOR VARIOUS INDUSTRIAL PARTS AND COMPONENTS
Surface Cleaning Systems play a critical role in the success of coating operations.
Correct surface preparation significantly affects the adherence and protective properties of the coating. These systems effectively perform the degreasing, etching and phosphating processes required to prepare the parts for painting processes.
COATING SYSTEMS
Minimum Chemical and Water Consumption:
Environmentally friendly operations and reducing operating costs.
Maximum Energy Saving and High Efficiency: Energy efficiency with advanced technology heating and insulation systems.
Modern Security Applications: Safe working environment in compliance with CE standards.
Tailored Solutions: Customizable design and functionality to suit each customer's specific needs.
Our surface cleaning systems offer high-performance and reliable solutions, where every detail is carefully designed by the technical team. Each project is developed specifically taking into account the customer's production conditions and needs, thus ensuring optimal results.
Telephone: +90 (212) 222 23 45
Email: info@electron.com.tr
Visit: www.electron.com.tr
MecWash Systems has launched into 2025 at full speed, with a successful presence exhibiting at Southern Manufacturing & Electronics 2025, before taking the stand at Mazak Europe for the Manufacturing Solutions UK & Make Measurement Matter with GTMA, and finally Surface World Live at the NEC.
Paul Jarratt, sales manager, reflected on the fast-paced start to the year:
“It has certainly been a busy month for MecWash! Southern Manufacturing is always a terrific event with a fantastic range of toolmakers and machinery specialists in attendance and key note speakers sharing valuable insights into their applications. With an increase in the footfall this year, it shows a promising sign for British industry. It is always a pleasure to catch up with our connections.
“Our calendar has been enormously busy throughout February, and we headed to Mazak Europe for the GTMA event. A highlight was speaking with Quentin Wilson, of Fifth Gear fame, who was very engaged with the intricate processes of the systems created by MecWash.
“We also attended Surface World Live, which focuses on surface treatment and coatings. The finishing expertise on show at the NEC is second-to-none and it was invaluable to hear about the advancements of the industry. I am certain we can carry this momentum throughout 2025!” said Paul.
John Pattison, managing director, is pleased with the frenetic start to 2025: “Three exhibitions in one month was certainly a dynamic start to the year. It was useful to discover and discuss the latest technologies across manufacturing. We had many new visitors to the MecWash stand at Southern Manufacturing & Electronics
this year and we also enjoyed catching up with our existing blue-chip customers from across automotive, medical and precision engineering.
“Visiting Mazak Europe in Worcester for the GTMA event gave the MecWash team a fascinating look into the innovation going on within UK manufacturing. It was a very productive event and gave the opportunity to speak with key companies from precision engineering, rapid product development, toolmaking, tooling technologies, and metrology sectors. These are key areas of manufacturing and the latest technology available.
“Surface World Live was an opportunity to talk with some of the biggest names in the surface finishing industry. The finish quality provided by MecWash systems is a critical part of the process, so this event is a chance to keep up to date with the latest practices and advancements in surface treatment. The recent work that we did with Materials Solutions, the innovative additive manufacturers, exemplifies the detail of the MecWash’ approach regarding chemical compounds and overcoming the complexities of different applications.
“These exhibitions have allowed us to connect with key sectors of our customer base and provided a terrific launchpad for the year. The MecWash team has lots of experience communicating with other enthusiastic manufacturers about optimising processes and the connections we made throughout February will serve us well moving forward,” said John.
Telephone: +44 (0) 1684 271600
Email: enquire@MecWash.co.uk
Visit: www.mecwash.co.uk
Machined castings. Turned parts. Complex pressings and extrusions. Customers expect parts to be pristine. PRECISION AQUEOUS CLEANING demands MecWash. MecWash s aqueous wash systems
Achieving a durable and high-quality finish when painting or powder coating starts with thorough surface preparation. Wet blasting is a well-established and advanced method for cleaning and finishing metal and composite surfaces, ensuring superior coating adhesion and durability.
Wet blasting uses water mixed with an abrasive to clean surfaces removing oils, grease, rust, burrs, old coatings, and other contaminants whilst simultaneously creating a uniform surface to a specific Ra surface roughness that is perfect for the adhesion of paints and other coatings. It’s an ideal cleaning and finishing process for industries that require high-performance coatings, the aerospace, military, tooling and medical industries for example
Wet blasting does not damage underlying substrates like the fibres of composites, and it does not alter the geometries of components manufactured to high tolerances. The cushioning effect of the water in the process reduces abrasive impact, minimising the risk of warping or micro-cracking on delicate materials.
Another advantage of the water in the process is the containment of dust, which can be an issue when dry blasting, along with the risk of warping and micro-cracking mentioned above. Dust can not only compromise the successful application of coatings but can be an explosion hazard too. Wet blasting doesn’t use harmful chemicals either and thanks to the recycling of water and abrasive it is a comparatively environmentally friendly process too.
There are two main wet blasting machine options for coating preparation, manual or automatic. Manual machines are ideal for infrequent or low volume use and
where a variety of different components need preparing, they also have the advantage of lower initial cost. Automatic machines on the other hand suit frequent or mid to high volume use and where batches of similar components require processing. Whilst initial outlay costs might be higher, longer terms costs are lower thanks to increased productivity. Another advantage of automation is repeatability – every component is cleaned and finished to the same uniform high standard.
Based in the UK, the original innovators of the wet blasting machine are Vapormatt, and thanks to continued R&D investment they remain world leaders in wet blasting technology with a comprehensive range of manual and automatic wet blasting machines suited to a broad range of different industries from tooling and aerospace to medical and defence. The company has accumulated many decades’ experience when it comes to preparing component surfaces for coatings and especially applications where the coating has to perform to a very high standard, cutting tool insert PVD or CVD coatings for example.
Vapormatt is the original innovator and global leader in wet blasting technology, providing innovative surface preparation solutions across a range of industries, including aerospace, automotive, and wire manufacturing. With a strong commitment to research and development, Vapormatt continues to set new standards in efficiency, sustainability, and performance.
Telephone: +44 (0) 1823 257976
Email: sales@vapormatt.com
Visit: vapormatt.com
In an industry where durability and sustainability often seem to be at odds, Baril Coatings proves that high-performance coatings can go hand in hand with environmental responsibility. As a frontrunner in the development of innovative coating solutions, they specialize in high-quality, sustainable coatings for industrial and architectural applications. They provide coatings that not only protect and enhance materials but also minimize ecological impact. By combining cutting-edge technology with a commitment to sustainability, they empower customers to make responsible choices without compromising on quality.
One of the key differentiators of Baril Coatings is the dedication to reducing CO2 emissions and extending the lifespan of coated materials. The portfolio includes a broad range of products, from anti-corrosion coatings for steel structures to decorative finishes for wood and other substrates. What sets them apart the ability to merge sustainability with performance, ensuring that the coatings not only meet but exceed industry standards.
A prime example of the commitment to innovation is the groundbreaking DualCure technology. It’s superior sustainability combined with extremely quick curing time.
The patented DualCure coatings form a new generation of cold-cure coatings without the addition of extra energy or warmth. Because of the reaction with moisture from the air a very dense molecular mesh forms. This mesh makes the coating very strong and flexible. With this technology, they prove that it is possible to combine outstanding quality, processability and sustainability in one product.
The benefits of DualCure technology are manifold. First and foremost, it significantly reduces energy consumption compared to conventional curing methods, making it an ideal solution for companies looking to lower their carbon footprint. Additionally, the superior adhesion and mechanical properties of DualCure coatings extend the lifespan of coated surfaces, reducing maintenance costs and material waste over time. And foremost, the thin layer technology also makes it, that less paint is needed. DualCure offers optimal protection witup to 60% thinner layers.
The use of DualCure directly leads to a strong reduction of CO2 and VOC emissions. Even with a total layer thickness of 100 µm DualCure provides 25 years of protection (in a C3-environment).
Sustainability should never come at the expense of performance. DualCure coatings provide a future-proof solution that meets the demands of modern businesses and the planet alike
A greener future through coatings—that’s what #paintingarenewablefuture is all about. Discover more about these win-win solutions for your industry by visiting Baril’s website or sending an email for more information.
Email: info@barilcoatings.nl Visit: www.barilcoatings.com
•
•
•
•
•
•
•
The Interpon powder coatings team from AkzoNobel is supporting Telebooth, a Chinese manufacturer of innovative office pods, video rooms and cabins, with premium powder coating products and new color inspiration to claim its leading position in the European market.
Telebooth has been collaborating closely with Interpon’s technical experts to develop new color solutions and a diverse range of customized finishes. This collaboration ensures that Telebooth’s products not only maintain their exceptional durability and longevity, but also stay ahead of design trends. By using the Interpon team’s expertise, Telebooth can also
offer clients unique, high-quality products that elevate modern workspaces.
Qinhua Hou, General Manager at Telebooth, is excited to work with a partner with a shared commitment to quality and innovation: “At the heart of our collaboration is the ability to create vibrant, colorful designs that define the Telebooth experience,” he explains.
“By blending functionality with visual appeal, Telebooth’s color selections transform smart workspaces into inspiring environments that promote productivity and creativity. Working with AkzoNobel gives us a competitive edge with features like enhanced gloss retention, environmental protection, and durability.”
Telebooth’s business has grown by 50% year-on-year by offering phone booths in a selection of bold, eyecatching colors for the Chinese market. The company is now expanding into new markets in Europe and North America to sustain its rapid growth. Different markets have different needs, especially in terms of aesthetics, and the Interpon Technical Services team has played a key role in advising Telebooth on the enhanced color
palette and metallic effects required to meet a wider customer demand for innovative styling.
Customers buy Telebooth products both for their functionality and because of their ability to blend into their office environment, reflecting the colors and aesthetic of a company’s brand: "We receive many requests for different colors,” Hou explains. “AkzoNobel’s technical team has been extremely helpful in this regard, supporting on color inspirations. This way, we can give our clients what they want and at a price that is competitive."
Sustainability has been a core part of Telebooth's long-term strategy, especially as it looks toward entering the European market. “In the future, we aim to leverage AkzoNobel's sustainable powder coating solutions to enhance the environmental performance of our products,” adds Hou.
James Bao, Commercial Director North Asia of AkzoNobel Powder Coatings says that the collaboration between the two organizations represents an exciting opportunity to showcase the versatility and durability of Interpon powder coatings in a rapidly growing sector: “At AkzoNobel, we are committed to color innovation to give our customers the competitive edge, and working with Telebooth also aligns perfectly with our goal to deliver innovative, sustainable solutions that reduce environmental impact.”
For more information, visit: https://www.interpon.com/insights/ telebooth-testimonial
Pre-Treatment Solutions Group Ltd supply unique chemistries for an array of metal processes.
Our Phos-Prep® range of chemicals are chrome free, eco-friendly and cost effective all while maintaining quality and performance.
With over 50 years experience within the industry we pride ourselves on finding the right solution for your metal treatment. Whether that be degreasing, etching, phosphating, paint stripping and more!
“We have been a customer of PTS for over 20 years and during our time we have relocated our business, changed our pretreatment process with the full support and expert advice to implement changes from the PTS team. A great company who always go the extra mile to support their customers.”
P.Allen, West Midlands.
“We have been fortunate to have partnered with PTS for over ten years now. They are consummate professionals and always exceed expectations in terms of delivery of service, knowledge and customer care.”
E.Smith, Hampshire.
, ten a
“We have had the great pleasure in working with PTS for over 5 years. No matter how big or small our queries are, PTS always come up trumps and in rapid time. The team are always willing to visit our site to help out with any issues we have or just for a general catch up with our staff. We have a very good relationship with the whole team at PTS and long may this continue.”
R.Glasbey, West Yorkshire.
As a new member of the Sprint 2 product family, the Sprint 2 Expert manual powder coating system offers unique additional functions for special requirements. Clever assistance functions such as the WAGNER Wizard and DSO (Digital Surface Optimizer) as well as process documentation options make every user an expert in manual coating in no time at all.
The perfect recipe as if by magic
All relevant parameters for the coating job are set via the WACON Sprint 2 Expert control unit with 7-inch touchscreen. The intuitive menu navigation also offers recipe management, error history, operating hours and maintenance counters as well as user management. The highlight of the control system is the WAGNER Wizard: With the intelligent coating assistant, even inexperienced users can find the right recipe for every coating job. In 5 simple steps, you select the workpiece geometry, size, coating structure, desired coating thickness and type of powder, and the Wizard uses these parameters to determine the ideal recipe. So that you can get started straight away, it also provides recommendations for suitable accessories (e.g. nozzle type, nozzle extension) and the required gun distance.
With the DSO (Digital Surface Optimizer) assistance function, overcharge effects such as orange peel or edge build-up can be reduced at the touch of a button. This advantage is particularly relevant for decorative coatings on complex components or with demanding powder coatings.
New injector offers numerous advantages
Just like the Sprint 2, the Sprint 2 Expert also features the new Quick-Link injector. Optimized nozzle geometries reduce the air requirement and hose diameter needed, resulting in a significantly softer powder cloud at a lower speed. This results in a wide range of applications - from fine, decorative coatings on small parts to corrosion protection for large components. The injector also speeds up the cleaning and color change process: all powder and air hoses can be detached in one easy step using the Quick-Link coupling. The integrated scraper ring in the swivel arm scrapes the powder off the outside of the lance. For even faster color changes - in less than 30 seconds - a special cleaning set with automated internal cleaning of the suction lance is available as an option for the Sprint 2 Expert.
Sprint 2 Expert manual system is available in two versions - for feeding powder directly from the original box (top picture) or alternatively from a 60-liter container (bottom picture).
• Ideal for frequent & fast color changes
• High degree of automation for optimum efficiency
• Double-designed fresh powder station for increased productivity
A powder scale under the base plate is used for precise monitoring of the powder consumption. This scale shows the weight in the powder box and automatically sets measuring points, which are documented in a logbook with the active user, selected recipe and coating period. This allows relevant coating data to be bundled and evaluated. The user can download all process data from the control unit via USB for further processing. Additional interfaces are optionally available for the control unit to enable connection to higher-level systems, robot technology or a cloud solution - such as the COATIFY information and management platform.
The multifunctional head module of the Sprint 2 Expert with the standardized perforated plate structure offers dust-protected storage areas and hanging options for tools and accessories. This keeps everything tidy and within easy reach. The manual system can also be quickly upgraded to a double system with two guns. The head module offers space for the installation of a second control unit.
Both the Sprint 2 and the Sprint 2 Expert are available in two versionsfor powder feeding directly from the original box or a 60-liter container.
The mobile cup gun case set is suitable
for individual parts and small quantities as well as for laboratory and development purposes. It is easy to set up anywhere and can be operated directly from the case. The 3-liter table set includes a compact vibrating table with a 3-liter fluid container attachment, a Hi-Coat injector and 9 mm hose in addition to the control unit and manual gun. This setup is used to achieve extremely fine coatings - e.g. in laboratory environments, for special applications such as the non-destructive testing of cast parts or for small parts with very high surface quality requirements.
Find more information on: go.wagner-group.com/sprint-2
Telephone: 01327 368410
Email: enquiries@wagner-group.com
Visit: www.wagner-group.com
New and used vibratory finishing machines and systems from 2 litres to 4000 litres
Finishing media; Ceramic, Plastic, Wood, Steel and Maizorb
Liquid / powdered / paste compounds
Abrasive finishing wheels
Vibratory separators / sieving machines and re-meshing service
Repairs and relines
Effluent water treatment systems
Redundant machines purchased
Consultancy
Subcontracted finishing and industrial sieving services
Experienced Engineers After sales technical support Nationwide deliveries
Sharmic Engineering Ltd
Tel: +44 (0)1299 822135 / 878123/4/5
Email: info@sharmic.co.uk www.sharmic.co.uk
“Don’t get stuck finding a thru-process monitoring solution”
Designed for PTFE / Teflon® coating applications, the PhoenixTM high temperature Finishing System travels through the oven with your product to measure the exact temperature profile of the substrate and the atmosphere within the product vicinity.
Compared with conventional paint or powder coating cure applications the challenge of PTFE cure monitoring is the significantly higher cure temperatures employed. Obviously different formulations of PTFE will vary in exact cure requirements but typically curing will require 30 to 60 mins @ 350 to 450 °C.
To protect a data logger passing through the oven at temperature up to 450 °C it is unlikely that standard paint or powder coating thermal barriers, offered on the market,
will be up to the task. To address the thermal challenges of the PTFE cure application PhoenixTM can offer a variety of thermal barrier options to suit.
The stainless-steel thermal barriers protect the data logger safely at oven temperatures up to 450 °C maintain the data logger operating temperature at less than 80 °C. This protection obviously prevents thermal damage but also maintains the measurement accuracy via the thermocouple using the data logger’s accurate cold junction compensation feature. Even with changing temperature of the data logger thru-process, which is a given, the accuracy of the data logger will remain ±0.3 °C.
A typical thermal barrier offering is the TS01-120-1 which is 120 x 196 x 350 mm (HxWxL) and 6.4 kg. Dual phase thermal protection is achieved through combining high performance microporous insulation with a phase change heat sink. The thermal barrier provides an impressive thermal protection of 1.5 hours @ 300 °C or 30 mins @450 °C.
Affordably measures uncured powder coatings using
Dedicated stand-alone unit is ready to measure right out of the box
Fast measurement speed—ideal for moving lines and swinging parts
Scan Mode continuously takes measurements—ideal for analyzing large areas
Storage of 999 readings with onscreen averaging. Stored readings can be downloaded to PosiSoft Desktop Software
Powder Inspection Kits
Complete solutions for measuring powder coating before and after cure are available
NO PRICE INCREASES FOR 2025
16A Long Drive, Meadway, Berkhamsted, Herts HP4 2PN t: 01442 879494 www.dftinstruments.co.uk e: sales@dftinstruments.co.uk
Lanemark gas burner systems offer users reliable, high effi ciency, process heating solutions.
FD Series Packaged Oven/Dryer Burners
•Speci cally designed for process air heating applications in convection ovens and dryers
•High turndown/short ame lengths providing accurate process temperature control
•High ef ciency gas + air modulation, gas only modulation and simple high/low control options
•Heat Input Range: 9 kW – 1550 kW
TX Series Gas Fired Process Tank Heating Systems
•High ef ciency (80%+) heating of all types of spray and dip process tanks
•Compact high ef ciency small diameter immersion tube heat exchangers occupying minimum tank space
•Accurate performance modelling using Lanemark TxCalc design software
•Heat Input Range: 15 kW (1½") – 1150 kW (8")
Midco HMA Series Air Replacement or “Make-Up” Air Heating Burners
•Direct red, high ef ciency burner systems, for high volume air heating applications such as paint spray booths, ovens and dryers.
•Supplied either as Midco burner heads for OEM system integration or as Lanemark DB or FDB complete packaged systems including modulating gas valve trains and controls
•Wide range of ring rates to suit alternative temperature rise and air velocity system requirements
•DbCalc system design software
The thermal barrier is compatible with the PTM1210 allowing monitoring from 10 Type K Thermocouples with the option of RF telemetry allowing real time live monitoring of product temperature direct from the oven as the PhoenixTM system passes through on the monitoring run.
For even more thermally demanding applications especially for large substrates PhoenixTM can offer even more protection from its extensive thermal barrier range used in coating and heat treatment industrial sectors.
Operating above 300 °C unfortunately conventional PTFE / PFA coated thermocouple cable cannot be used having an upper temperature threshold of 265 °C. To address the higher temperatures, it is necessary to employ type K thermocouples constructed with either glass fibre (<500 °C) or mineral insulated cables (<1200 °C). At above 300 °C conventional magnetic attachments will not work efficiently; hence it is recommended that the exposed junction thermocouple is physically attached to a test substrate with a screw & washer or other mechanical fixing. A mineral insulated thermocouple option fitted with a washer allows easy fixing in this manner.
Complementing the physical measurement system PhoenixTM offers a choice of Thermal View Software packages (Thermal View or Thermal View Finishing Software) to set-up the data logger, review, analyse and report the temperature profile obtained.
Using a variety of analysis tools including Time @ Temperature and Phoenix Factor (Cure Index Calculation) the cure performance of the PTFE product can be assessed against the manufactures cure schedule recommendations. With such information the quality of the cure can be determined to prevent problems such as:
Under Cure of PTFE Brittle coating with adhesion problems
Over curing of PTFE Black PTFE coatings have unwanted chalky residue
Reduced Gloss Levels
>500 °C Toxic gaseous by-products released
If problems are experienced the profile data is invaluable in any oven optimisation / fault finding investigations to allow corrective action to be taken. Use the PhoenixTM Thruprocess Temperature Monitoring system to Find, Fix and Forget your Finishing problems!
*Teflon® is a registered trademark of DuPont.
For more information: Contact Dr Steve Offley - Product Marketing Manager
Telephone: +44(0)1353223100
Email: Steve.Offley@phoenixtm.com
Visit: www.phoenixtm.com
In industries ranging from machine building and metalworking to the extraction of ores, coal, petroleum, and gas, cutting tools play a crucial role. These tools, typically made from sintered hard alloys, are engineered for durability, to withstand the wear associated with heavy industrial applications. Materials such as tungsten (W) and cobalt (Co) alloys offer exceptional hardness, ensuring long-term performance. However, as the demand for precision and efficiency grows, so does the need for coatings with enhanced cutting. The next generation of cutting tools is embracing thinner, sharper coatings to push the boundaries of performance, and precision XRF analysis is emerging as a game changer for the industry.
A key advancement in cutting tool technology is the use of coatings like titanium carbonitride (TiCN), titanium carbide (TiC), and titanium nitride (TiN) on the cutting edges. These coatings are applied in thin layers (5 to 15 µm) and significantly improve cutting durability. This is particularly important for automated production lines, such as those in the automotive sector, where precision machining of parts is critical. These coatings increase the life expectancy of tools and improve the quality and consistency of the final product.
Accurate coating thickness measurement is essential for quality control. One of the most effective ways to do this is through X-Ray Fluorescence (XRF) technology. XRF has long been used to measure the
thickness of plated deposits and is well-suited for measuring coatings like TiCN. The process works by directing an X-ray beam onto the sample, causing the elements in the coating and base material to emit fluorescent X-rays. These X-rays are detected by a sensor, and the data is analysed to determine the coating’s composition and thickness.
In the past, XRF technology was hindered by older detectors (i.e., gas-filled proportional detectors) that limited sensitivity and resolution, often leading to noisy or unreliable measurements, especially with large or irregularly shaped samples.
The latest generation of Bowman XRF instruments offers major improvements, overcoming the limitations of older XRF systems. The introduction of modern solid-state silicon drift detectors (SDD) provides
energy resolutions that are five times better than those of traditional detectors, allowing for much more precise measurements.
The Bowman L Series XRF is particularly engineered to optimise testing for large, varied samples. The sample chamber is the largest available meaning industry professionals are no longer limited to palm-sized components and can extend the capability of this innovative technology onto whole parts up to 550 x 550 mm x 280 mm in size.
One of the standout capabilities of Bowman XRF systems is the ability to measure TiCN coating thickness to as low as a few nanometres. This level of sensitivity meets the future needs of hard alloy
technologies, ensuring that manufacturers can meet the increasingly stringent requirements for coating precision.
For more information, or to arrange a demonstration of the Bowman XRF systems, email enquiries@scimed. co.uk or call 0161 442 9963.
Total Filtration is a Division of The Westbury Group of Filtration Companies, is your one stop shop for the manufacture and supply of liquid and dust filter cartridges and associated components.
Our Industrial Dust Extraction Collectors are fitted our own UK manufactured filter bags and cartridges
The industries we serve are: Automotive Chemical Construction Engineering Food & Beverage HVAC/Ventilation Paper, Pulp & Woodwork Pharmaceutical Plastics Powder Coating Shotblast & Beadblast
We carry a vast selection of filter media, including Cellulose blends, Polyester, Anti-Static Polyester, PTFE coated and Membrane, Nano, Flame Retardant coated, to name a few.
Our bespoke range covers most major OEM and retrofit manufacturers, below are a few examples.
Our Airmaster Dust Filter equivalent is a pleated cartridge made in two lengths, 450mm
(type 1) and 920mm (type 2). The end caps can be Galvanised Steel or Stainless Steel, there are three types of filters available with spun polyester standard, Anti-Static, PTFE media and Anti-Static PTFE.
The Altair dust filter equivalent range are cartridge filters made in several lengths: 600mm, 660mm, 1000mm and 1200mm (Other lengths available). These are available in a range of medias as detailed below.
We manufacture our own range of Goldcone style filters, without the cone, available in the length of 1000mml. These are available in a range of medias which include:Cellulose blend 80/20FR, STD Polyester, A/Stat Polyester.
Retrofit
We manufacture a range of square top filters in both 325mm and 225mm (closed end cap sizes). These are also known as Camfill Farr Tenkay Mark
1, 2, 3 and 4 alternatives. They are available in a choice of lengths and medias (All lengths are also available in the round end cap version).
Dantherm Cartridge Filter
Retrofit
Our ABS Dantherm Cartridge Filter Alternative (also known as an Airmaster, Nederman or Disa Dust Filter Cartridge.) is made of lightweight strong plastic version of the Type 66,44,40,22 and 20. (Also available in carbon impregnated for Anti-static requirements).
Donaldson Siloair Filter
Retrofit
Our DCE Torit Siloair Filter equivalents are perfect for silo vending machines. These filter cartridges are made in three lengths: 565mm, 800mm and 1000mm. They are available in a range of medias including Standard, Anti-Static, PTFE Standard and Anti-Static PTFE.
Donaldson TDS Equivalent
Retrofit
The Donaldson TDS Equivalent single or double
ended filter cartridges are available in three basic diameters (202mm, 325mm and 350mm) with six different lengths. They are available in different medias. (Depending on the application), these include Nano Fibre, Spun Bonded Polyester, PTFE, and anti-static.
ECB/
Our Donaldson TORIT Cartridge Filter retrofits come in two basic diameters (325mm and 350mm) with six different lengths. There are several medias to choose from. (Depending on the application), these include Nano Fibre, Spun Bonded Polyester, PTFE and anti-static.
Retrofits
We also manufacture a complete range of Unicell type cartridge filters which include the two size 70mm x 475mm x 1004mm with 5.00M2 or 70mm x 475mm x 800mm with 4.00M2. These two sizes of cell filter can be made using any of the following filter media: 260g Spunbonded Polyester, AntiStatic finish / Oleophobic coat / PTFE Coat or Membrane.
Retrofit
We manufacture Mahle Catchplate
Alterative / Dustcheck twist lock cartridge filter alternative in 328mm O/D x 600mml, available in single open end or double opened ended,
using a choice of high-quality medias including: - Cellulose blend 80/20 FR, Nano fibre, STD Polyester, Antistatic Polyester and both STD and Antistatic PTFE membrane.
Screw thread
RD72/62/100 Retrofits
Total Filtration can manufacture a parallel version of the RD60/RD72/ RD100 screw thread filter. This dust filter is available in both Galvanised and Stainless-Steel finish. Available in several lengths from 200mml to 1200mml. Media Options include STD Polyester/ A/Static Polyester. STD PTFE Membrane/ Antistatic PTFE Membrane.
We manufacture 3 lug filters in a range of sizes:145mm O/D, 150mm O/D, 225mm O/D. 370mm O/D and 397mm O/D. In a range of materials available including Aluminium, ABS Plastic and Resin. All Lengths available up to 1400mml. Medias include: - Cellulose blend 80/20 FR, STD Polyester, Antistatic Polyester.
Total Filtration carries out LEV and COSHH Testing all over the UK on all types of extraction systems. Our Engineers will work advise and repair any remedial work that is required to ensure you
work in a safe environment.
Total Filtration manufacture a range of Dust Collectors, Metal Recycling Plants and Metal Grinding Booths. Our engineers have over 30 years’ experience in supplying, servicing and maintaining dust extraction systems.
Our latest range of TOTALFLO Dust Collectors are suitable for cartridges and bag filters. Here’s just a few of the many benefits of our new range.
All our machinery is manufactured in the UK with a full range of sizes to suit all airflow requirements.
All our dust collectors can be offered to ATEX standard to ST1 & ST2 and can be provided with full certification. Our Range of Dust Collectors and Extractors include:
Reverse Jet Dust Collectors. Technical Advice, Evaluation and Sizing for all customers. Downflow and Crossflow dust Collectors, to suit specific processes. Unicell style Dust Collector. Full turnkey installations, Large & Small.
For more information on our Dust range contact Mark Longworth on 01282 459744 or email sales@totalfiltration.com
Dyne Testing, an Intertronics brand, presents the Sigma 702 Force Tensiometer from Biolin Scientific, a standalone instrument for precise surface tension and interfacial tension measurement. The Sigma 702 Force Tensiometer features a precision balance, motorised sample stage and an intuitive user interface, meaning minimal training is required for operation. The instrument is used across multiple industries including chemicals, coatings, food and beverage, pharmaceuticals, energy, and the environmental sector.
A force tensiometer measures surface tension by determining the force required to detach a probe or ring from the liquid’s surface, that force being directly related to the liquid’s surface tension. Sigma 702 Force Tensiometer has a motorised sample stage, and an ultra-sensitive balance. The integral control screen allows you to simply set parameters and press start to conduct the measurement. The results are shown on the screen immediately after a measurement is completed.
“The Sigma 702 Force Tensiometer does a lot of the work for you and is easy to get to grips with. Once you’ve placed your beaker of sample liquid on the stage, you can push a few buttons and the measurement is complete,” said Alison Fox, Dyne Sales Manager at Intertronics. “As well as surface tension and interfacial tension measurement, it can measure for critical micelle concentration (CMC) and density.”
Accuracy and precision come from the simple automated process, the positioning resolution of the motorised sample stage (to 0.26µm), and the ultra-sensitive electromagnetic balance capable of measuring forces with a resolution of 0.01 mg. The Sigma 702 has a measuring range of 1-1000
mN/m with a displayed resolution 0.01 mN/m.
The Sigma 702 is a self-contained, standalone instrument, which does not require a separate computer. It comes with data collection software and, if needed, can be connected to an external computer for additional data storage and simple reporting. Alternatively, an optional printer can be attached for instant hard copy reports.
The instrument comes with both du Noüy ring and Wilhelmy plate measurement capabilities. Surface tension and interfacial tension results with the du Noüy ring are available with both Huh-Mason and Zuidema-Waters correction. In Wilhelmy plate mode, both dry taring and wet taring can be selected. Parameters for stabilisation time and surface detection limits are also adjustable according to the user’s needs and preferences.
The Sigma 702 force tensiometer is a robust, versatile instrument, offering precision and sensitivity. Measurements are automated and repeatable, reducing the human error which comes from a manual tensiometer. It enables batch testing with minimal operator input, useful for quality control applications. It is easy to use with a simple interface, and the results are shown on the screen immediately after measurement is completed.
To discuss ways of introducing reliable testing that brings about consistent, repeatable results for measuring surface tension and surface energy, contact Dyne Testing at info@intertronics.com or sales@dynetesting.com.
Measure the adhesion of coatings to metal, wood, concrete and more
n Impact and scratch resistant color Touch Screen display with keypad
n Wirelessly connect the PosiTest AT-A to your smart device using our free app
n Record the results as pass/fail and the nature of fracture cohesive, adhesive and glue failures
A Glasgow-based galvanizing company has supported a local craftsman in future-proofing a bespoke garden feature.
Kevin Hope, Founder of WKD Burners, was commissioned to fabricate a unique woodland-themed garden centre piece for a customer. In order to protect it from the harsh weather conditions, he worked with long-term partners, Scottish Galvanizers Ltd, to prevent rust and corrosion.
He said: “With over 25 years’ experience in the fabrication industry, I’m incredibly passionate about creating longlasting and carefully crafted pieces for customers to enjoy for many years. At WKD Burners, we produce quality handcrafted log burners, fire pits and garden sculptures that are set to become the talking point of any environment.
“Recently, a customer wanted two woodland-themed steel spheres. We fabricated one inspired by a Highland cow and the other a stag, in keeping with this desired style and aesthetic. In total, they took around three days to complete – from the initial design stage through to welding the 600mm sphere onto the base.
“As these were garden sculptures, it was paramount that they were galvanized to protect them for decades against the harsh Scottish weather conditions.”
Kevin worked with the team at Scottish Galvanizers, where the spheres were dipped into a bath of molten zinc at temperatures around 450C to allow for a metallurgicallybonded coating to be formed.
Paul Tait, Commercial Manager at Scottish Galvanizers, added: “Having worked with Kevin now for a number of years, we’re always fascinated to see his stunning handcrafted sculptures arrive at the plant. It’s such a pleasure to support Kevin and his team in ensuring they’re protected against rust and corrosion, allowing them to be admired for more than 70 years.”
Scottish Galvanizers Ltd is part of Wedge Group Galvanizing Ltd, the largest hot-dip galvanizing organisation in the UK with a history dating back over 150 years. With 14 plants strategically placed across the country, the firm offers a truly galvanizing service.
For further information, please contact Wedge Group Galvanizing on 01902 601944 or visit www.wedge-galv.co.uk
Steel Shot (High & Low Carbon)
Steel Grit
Stainless Steel Shot and Stainless Steel Grit (Cr & Cr/Ni)
Chilled Iron Grit
Glass Bead
Ceramic Bead
Fused Alumina Cut Wire
www.ampereabrasives.com sales.uk@ampereabrasives.com
Tel : 0121 244 1809
17 School road, Hall Green Birmingham B28 8JG
High Carbon Steel shot and Grit.
Low Carbon Steel Shot and metal Bead
Stainless Steel Cr and Cr/Ni.
No 5, Queensway Link Industrial Estate
Stafford Park 17, Telford, Shropshire TF3 3DN
Tel: 01952 299777
Fax: 01952 299008
Scangrit
We
E-mail: sales@pometon.co.uk Eastfield Road, South Killingholme, N.E. Lincolnshire, UK
Tel: +44(0)1469 574715
Fax: +44(0)1469 571644
• PLANT CONTROL SYSTEMS
• DATA MANAGEMENT SYSTEMS
• BARRELS - PROGALVANO ROTOR
• BARREL AUTO LOADING SYSTEMS
• PROGALVANO FILTERS
• SEMI/AUTOMATIC FILTER SYSTEMS
• CENTRIFUGAL DRYERS L g R g )
• AUTOMATIC DRYING SYSTEMS
• ROTARY PAINTING/LAQUERING
• TOP COATING/SEALING SYSTEMS
• VIBRATORY POLISHING EQUIPMENT
• LUBRICATION EQUIPMENT
• RECTIFIERS Conventional & Pulse
e-mail: sales@scangrit.co.uk www.scangrit.co.uk
• A/HOUR METERS & DOSING PUMPS
•
Hot dip galvanizing provides you with long-term protection against rust and corrosion of steel products.
✔ 14 plants across the UK
✔ 1.5mm washer to a 29m beam
✔ 24hr turnaround on request
Scan to find your nearest plant
info@wggltd.co.uk 01902 601944
telephone: 0044(0)1509 237415 fax: 0044(0)1509 264455
•
•
•
•
•
•
RDM Industrial Services Ltd
Parkfield Industrial Estate
Kemp Street Middleton Manchester M24 4AA Tel: 0161 643 9333 Fax: 0161 655 3467 www.rdm.u-net.com.
Contact: Robert Horwich or Geoff Ball Spraybooths, rooms, ovens, conveyors, pretreatment, powder plant and air replacement units.
Unrivaled probe interchangeability for all of your inspection needs.
Coating Thickness Probes
n Ferrous n Non-Ferrous n Combination n Ultrasonic
Surface Profile Probes
n Depth Micrometer n Replica Tape Reader
Environmental Conditions Probes
n Integral n Cabled Magnetic Probe n Anemometer Probe
n 1/2” NPT n Infrared
Hardness Probes
n Shore n Barcol
Salt Contamination Probe
n Bresle Method
Ultrasonic Wall Thickness Probes
n Corrosion n Multiple Echo Thru-Paint n Precision
n Low Frequency n Xtreme
Customized Inspection Kits...
Build your own kit from a selection of gauge bodies and probes to suit your needs.
Backwards Compatibility! The redesigned PosiTector gauge body accepts ALL coating thickness (6000/200), environmental (DPM), surface profile (SPG/RTR), salt contamination (SST), hardness (SHD/BHI), and ultrasonic wall thickness (UTG) probes manufactured since 2012.
01442 879494 f: 01442 879595
www.dftinstruments.co.uk e: sales@dftinstruments.co.uk