Technical Manual
CLICK HERE TO DOWNLOAD THE COMPLETE MANUAL
• Thank you very much for reading the preview of the manual.
• You can download the complete manual from: www.heydownloads.com by clicking the link below
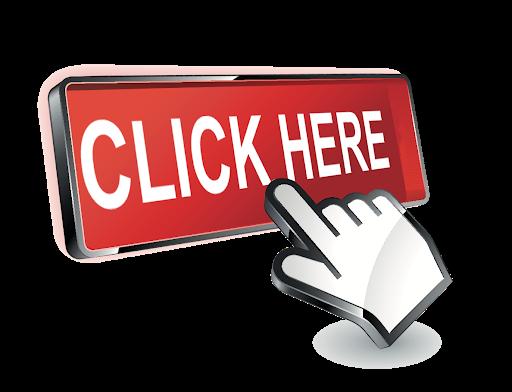
• Please note: If there is no response to CLICKING the link, please download this PDF first and then click on it.
CLICK HERE TO DOWNLOAD THE
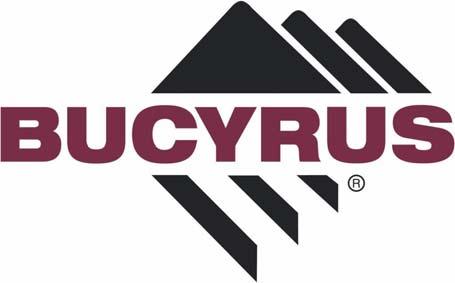
Helensburgh SWP30MB3 Miner Standard Work Procedures Folder
Index
P00428 Pull in Drum Removal & Assy 30MB3 Miner
P00429 Drive Drum Removal & Assy 30MB3 Miner
P00430 Intermediate Drum Removal & Assy RH & LH 30MB3 Miner
P00431 Centre Drum Removal & Assy 30MB3 Miner
P00432 Removal & Assy of Cutter Motor Clutches 30MB3 Miner

P00433 Removal & Installation of Cutter Head Input Gear Case 30MB3 Miner
P00434 Removal & Installation of Cutter Motor 30MB3 Miner
P00435 Removal & Installation of Cutter Head Gear Case 30MB3 Miner
P00436 Removal of the Cutter Head Support from the Main Frame 30MB3 Miner
P00437 Conveyor Chain Disassembly 30MB3 Miner
P00438 Conveyor Chain Removal & Installation 30MB3 Miner
P00439 Conveyor Raise & Lower Cylinder 30MB3 Miner
P00440 Conveyor Swing Cylinder 30MB3 Miner
P00441 Conveyor Take-up Cylinders 30MB3 Miner
P00442 Crawler Chain Removal & Installation 30MB3 Miner
P00443 Crawler Take-up Roller Removal & Installation 30MB3 Miner
P00444 Cutterhead Raise & Lower Cylinder 30MB3 Miner
P00445 Gathering Head Raise & Lower Cylinder 30MB3 Miner
P00446 Hydraulic Pump Removal & Installation 30MB3 Miner
P00447 Plow Cylinders 30MB3 Miner
P00448 Reassembly of Gathering Head Gear Case 30MB3 Miner
P00449 Removal & Installation of a Tram Drive Motor 30MB3 Miner
P00450 Removal & Installation of Discharge Conveyor 30MB3 Miner
P00451 Removal & Installation of Foot Shaft & Centrifugal Loading Arms 30MB3 Miner
P00452 Removal & Installation of the Conveyor Assy for the Miner 30MB3 Miner
P00453 Removal & Installation of the Tram Drive Gear Case Assy 30MB3 Miner
P00454 Removal & Re-fit of Tail Roller 30MB3 Miner
P00455 Removal & Replacement of Pump Drive Motor 30MB3 Miner
P00456 Removal & Replacing Gathering Head Shear Shaft 30MB3 Miner
P00457 Removal of the Drive Motor Input Gear Case & Cla Pot 30MB3 Miner
P00458 Removal & Installation of the Gathering Head from the Main Frame 30MB3 Miner
P00459 Stabilizer Shoe Removal & Installation 30MB3 Miner
P00460 Stabilizing Shoe Assy 30MB3 Miner
P00461 Trs Raise & Lower Cylinder 30MB3 Miner
P00462 Installation of Cutting Head Assy to the Main Frame 30MB3 Miner
P00463 Removal and Installation of Plow Assembly from Shovel
P00464 Hydraulic Tram Motor Installation 25M3 & 30MB3 Miners
P00465 Underground Assy of 30MB3 Miner Helensburgh Coal
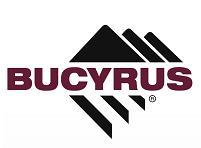
Standard Working Procedure
Title: Pull In Drum Removal and Assembly 30MB3 Miner Number P00428
Date 15/10/2008
Prepared By:
Copyright Bucyrus Underground Australia Pty Ltd
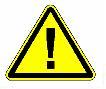
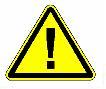
Tools and Equipment Required
Authorisation
THIS DOCUMENT ACTIVE UNTIL:15/10/2009
CONTROLLED COPIES OF THIS DOCUMENT HAVE THE COLOURED LOGO DISPLAYED.
Weight of Pull In Drum 500 Kg
Bucyrus Underground Australia Pty Ltd recommends that all Standard Working procedures should be approved and checked by Mine Officials. Bucyrus Underground Australia Pty Ltd declines all liability for direct or indirect consequences of printing errors.
Prior to starting this work, normal safety practices should be observed with regard to coal face support, Miner isolation.
This procedure does not replace the need for a local JSA to be performed by persons appointed by the mine management
Bucyrus Underground Australia Pty Ltd Standard Working Procedures only apply when fitting approved spare parts.
5/8’” A.F. Allan Key.
1 Tonne Lifting Gear (Chain block or pull lift). Sling 3 metres long x 2. General Tools, hammers, chisels, shifters, pliers, etc. 3 – Long threaded ¾” UNC bolts for Jacking off drum. Electrical Tape 1-2 rolls.
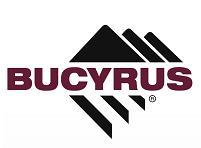
Standard Working Procedure
Procedure
Pull In Drum Removal
1) Place the miner so the front can easily be reached and there is side clearance to pull the end drums off one or both ends of the cutting head.
2) Lower the cutting head to a comfortable work height, and block it so the drums can be removed without affecting the supports.
WARNING: Inadequate or improper support while this work is performed can cause serious injury of death.
3) Remove all power from the machine and trip all circuit breakers to "OFF".
WARNING: Isolate machine as per mines isolation procedures.
CAUTION: Ensure when removing the 6 off retaining bolts (3/4” UNC x 3 ½” long – see figure 5.5) from the retaining flange. With caution, pressure may build up.
WARNING: Trapped air pressure from drums being retracted, MUST be removed before total withdrawal of mounting bolts.
WARNING: Ensure to remove any Residual Hydraulic pressure that may be behind the following retaining flange (point 4), before proceeding from this point forward.
4) Remove the six (6) ¾” UNC x 3-1/2” nyloc socket head cap screws from the centre flange of the outer pull in assembly and remove retaining flange. See Figure 5.5. (See Notes, Cautions and Warnings above)
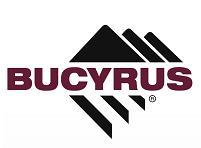
Standard Working Procedure
5) Match mark the pull in drum with the drive drum and the banjo arm section for re-assembly. This is to ensure correct pick block lacing.
6) Secure drum with lifting devices.
NOTE: Before the next step, ensure that the lifting devices have adequate tension of the drum.
7) Remove twelve (12) ¾“UNC x 3” nyloc socket head cap screws from outer pull in assembly. See Figure 5.5.
8) Remove the three (3) ¾” x 1” nyloc socket head cap screws from the three (3) jacking holes. See Figure 5.5.
9) Proceed to remove the pull in drum assembly from the cutting head via the three jacking threads.
10) Repeat steps 4 through 9 to remove the opposite side.
Pull In Drum Assembly
1) With machine in the same position as pull in drum removal and machine still isolated as per mines procedures position pull in drum for reassembly.
WARNING: Isolate machine as per mines isolation procedures.
2) Secure drum with lifting devises used for removal.
WARNING: Before next step ensure that lifting devices have adequate tension on the drum.
3) Using lever bars turn cutter head to line up the match marks and four keys in the fixed drum with the four long keyways in the pull in drum. Electrical tape may be useful in holding the keys in place.
4) Slide pull in drum into position lining up the match marks.
NOTE: If no match marks are on drum being fitted looking across the cutter head line up the pick blocks on the other side drum. Check for welded arrow matchmarks.
5) Using new retainers start all 12-¾” x 3” long nyloc socket hex cap screws. See Figure 5.5.
6) When all 12 socket hex cap screw are started in tapped holes torque to 416 ft lbs or 564 Nm.
7) Replace centre retaining flange and start (6) ¾” x 3½” long socket hex cap screws and torque to 416 ft lbs or 564 Nm.
8) Clear area of all tools parts and debris.
9) Remove isolation tags as per mines procedures.
10) Restore power to miner as per mines to re-power procedure.
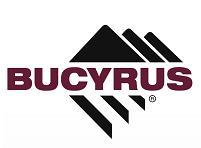
Comments / Changes required
Standard Working Procedure
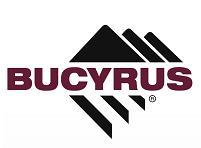
Standard Working Procedure
Title Drive Drum Removal and Assembly 30MB3 Miner : Number P00429
Date 15/10/2008
Prepared By:
Copyright Bucyrus Underground Australia Pty Ltd
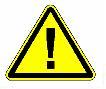
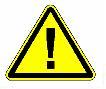
Authorisation
THIS DOCUMENT ACTIVE UNTIL:15/10/2009
CONTROLLED COPIES OF THIS DOCUMENT HAVE THE COLOURED LOGO DISPLAYED.
Tools and Equipment Required
Bucyrus Underground Australia Pty Ltd recommends that all Standard Working procedures should be approved and checked by Mine Officials. Bucyrus Underground Australia Pty Ltd declines all liability for direct or indirect consequences of printing errors.
Prior to starting this work, normal safety practices should be observed with regard to coal face support, Miner isolation.
This procedure does not replace the need for a local JSA to be performed by persons appointed by the mine management
Bucyrus Underground Australia Pty Ltd Standard Working Procedures only apply when fitting approved spare parts.
General tools hammers, chisels, shifters, pliers etc.
- ½” AF Allen Key or ½” drive in hex socket.
- 5/8” AF Allen Key or ½” drive in hex socket.
- 3/8” UNC sliding hammer.
- 2 tonne lifting block (chain block or pull lift).
- Porta Power and Jack.
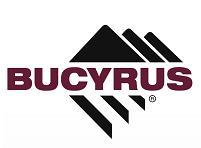
Standard Working Procedure
Procedure
Drive Drum Removal
1) Place the miner so the front can easily be reached and there is side clearance to pull the end drums off both ends of the cutting head.
2) Lower the cutting head to a comfortable work height, and block it so the drums can be removed without affecting the supports.
WARNING: Inadequate or improper support while this work is performed can cause serious injury or death.
Remove all power from the machine and isolate all circuit breakers to "OFF".
WARNING: Isolate machine as per mines isolation procedures.
3) Follow steps 4 through 9 of pull in drum removal.
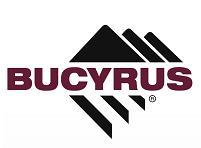
Standard Working Procedure
4) Remove pull in retainer and its six (6) 5/8” UNC x 2 ½” nyloc socket head cap screw. Ensure that the entire shim pack stay with the retainer. See Figure 5.6.
5) Remove drum pull in adaptor plate.
6) Remove eight (8) ⅝” UNC x 2½” socket head cap screws from drive drum retainer.
7) Remove drive drum lock tube and extension cylinder Figure 5.6. Ensure that the entire shim pack stay with the lock tube.
8) Remove double seal carrier using 3/8” UNC sliding hammer. It is possible to leave this retainer in place as it will not hinder the removal of the drum.
9) Secure drive drum with lifting device.
NOTE: Before the next step, Ensure that the lifting devices have adequate tension of the drum.
10) Proceed to remove drive drum. You may require a porta power and jack to start the removal of the drum initially.
11) Repeat steps 4 through 8 for opposite side.
Drive Drum Assembly
1) With the machine in the same position as the drive drum removal and the machine still isolated as per mines procedures position drive drum for reassembly.
WARNING: Isolate machine as per mines isolation procedures.
2) Secure drive drum with lifting devices used for removal.
NOTE: Before the next step, Ensure that the lifting devices have adequate tension of the drum.
3) Using lever bars turn cutter head to line up with the match marks. Match marks are a small drill hole in drums or welded arrows.
4) Looking through the splined bore of the drive drum line up the spline closest to the match marks and push drum onto spline.
5) Check the double seal carrier ‘o’ rings for damage or twisting. Replace if damaged. Install double seal carrier see Figure 5.6.
6) Using 2 chain blocks/pull lifts, secure block to the intermediate drum and attach to the drive drum 180 degree’s apart. Pull the drive drum onto the spline ensuring the drum has tightened against the large roller bearing.
7) Prepare cylinder and drum retainer for assembly.
8) Using lead wire position wire between faces of the retainer and the double seal carrier. This can be done using Silastic.
9) Fit cylinder lock tube, start 8 off ⅝” x 2½“ long SHCS and torque to 236 ft lbs or 320Nm.
10) To check lead readings remove the cylinder lock tube.
11) Using micrometers measure thickness of squashed lead wire.
12) Make up shim pack to read .005 to .007 less than the reading of the lead wire.
13) Fit shim pack to barrel and cylinder lock tube.
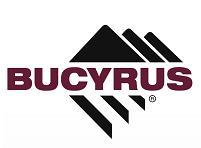
Standard Working Procedure
14) Reassemble the lock tube and extension cylinder together (ease of fitment). See Figure 5.6, using the 8 off ⅝” x 2½“long SHCS and tighten.
15) Torque retaining bolts to 236 ft lbs or 320Nm.
16) Assemble pull in drum as per pull in drum assembly.
17) Clear area of all tools parts and debris.
18) Remove isolation tags as per mines procedures.
19) Restore power to miner as per mines to re-power procedure.
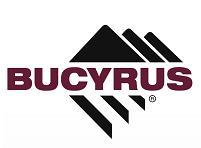
Comments / Changes required
Standard Working Procedure
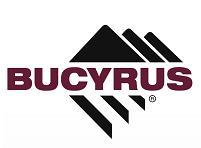
Standard Working Procedure
Title: Intermediate Drum Removal and Assembly RH and LH 30MB3
Miner Number P00430
Date 15/10/2008
Prepared By:
Copyright Bucyrus Underground Australia Pty Ltd
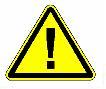
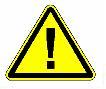
Authorisation
THIS DOCUMENT ACTIVE UNTIL:15/10/2009
CONTROLLED COPIES OF THIS DOCUMENT HAVE THE COLOURED LOGO DISPLAYED.
Tools and Equipment Required
Bucyrus Underground Australia Pty Ltd recommends that all Standard Working procedures should be approved and checked by Mine Officials. Bucyrus Underground Australia Pty Ltd declines all liability for direct or indirect consequences of printing errors.
Prior to starting this work, normal safety practices should be observed with regard to coal face support, Miner isolation.
This procedure does not replace the need for a local JSA to be performed by persons appointed by the mine management
Bucyrus Underground Australia Pty Ltd Standard Working Procedures only apply when fitting approved spare parts.
General tools - hammers, chisels, shifters, pliers etc,
- 1 – 2 tonne lifting block
- 2 – lifting chains (adjustable) 2 metres long
- 1 – 1” drive impact socket 1 7/8” AF
- 1 – 1” drive impact socket 2” AF
- 1 – torque wrench hydraulic or air driven 1” drive Torque requirement 2000 ft lbs
- 1 – Porta power pump
- 1 – small hollow ram 4” stroke for ¾” thread bar
- 1 – 3/4 “UNC thread bar 12” long with nut and washers
- 1 – Heavy soft hammer
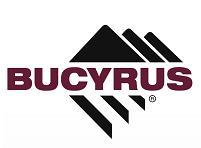
Standard Working Procedure
Procedure
Intermediate Drum Removal RH
NOTE: To carry out this procedure the complete pull in assembly is to be removed as follows.
Removal of Pull In Assembly Complete
1) Place the miner so the front can easily be reached and there is side clearance to pull the end drums off both ends of the cutting head.
2) Lower the cutting head to a comfortable work height, and block it so the drums can be removed without affecting the supports.
WARNING: Inadequate or improper support while this work is performed can cause serious injury or death.
3) Remove all power from the machine and trip all circuit breakers to "OFF".
WARNING: Isolate machine as per mines isolation procedures.
4) Secure RH pull in assembly with lifting devices, utilizing lifting rud links attached to the banjo arm section and wrapping sling around drum.
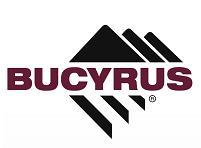
DRUM
RH INTERMEDIATE DRUM
Standard Working Procedure
RH PULL-IN ASSEMBLY
1-1/2" DOWEL (REMOVE)
1-1/4" UNC x 9" LG HEX HEAD CAP SCREWS
1-1/4" UNC x 12" LG HEX HEAD CAP SCREWS
1-1/4" UNC x 12" LG HEX HEAD CAP SCREWS
2" DOWEL (LEAVE)
1-1/2" DOWEL (REMOVE) HYDRAULIC DRUM EXTENSION INLET
1-1/4" UNC x 7" LG HEX HEAD CAP SCREWS
Figure 5.8
5) Remove eight (8) off 1-1/4” x 12” long hex head cap screws, Leaving two (2) 1-¼ x 9” long hex head cap screws supporting the assembly. See Figure 5.8.
6) Using Porta – power rams remove two (2) 1-½” dowels (see Figure 5.8) with the ¾” thread bar. Leave the 2” dowel, see Figure 5.8.
7) Remove ¾” NPT x 8” long hydraulic fitting from rear of cutter head flange.
NOTE: Before next step ensure that lifting devices have adequate tension on the assembly.
8) Remove remaining two (2) 1-1/4 “x 9” long hex head cap screws from assembly. See Figure 5.8.
9) Move assembly horizontally away from the centre of the machine approximately 12”.
NOTE: If removing the left side assembly when viewing from rear of machine a ¼ I.D pressure pipe will be connected to the extending cylinder. Unscrew pipe from left side assembly. If right side assembly is being removed pipe will not be screwed into assembly.
NOTE: When complete pull in assembly has been removed commence removal of intermediate drum.
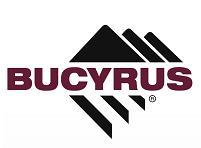
Standard Working Procedure
10) Loosen the eighteen 1" socket head cap screws that secure the wedge block assembly and the drum to the cutting head hub. Remove the cap screws and wedge. Figure 5.9.
1" UNC x 2-3/4" LG SOCKET HEAD CAP SCREWS
RH INTERMEDIATE DRUM
WEDGE ASSEMBLY
CAUTION: It is important to matchmark both the end drum and the cutting head hub to which it is attached, so that the pick block lacing is not disturbed upon reassembly.
11) Slowly pull the intermediate drum off the main assembly, and manoeuvre it away from the miner.
Intermediate Drum Removal LH
NOTE: To carry out this procedure the complete pull in assembly is to be removed as follows.
1) Place the miner so the front can easily be reached and there is side clearance to pull the end drums off both ends of the cutting head.
2) Lower the cutting head to a comfortable work height, and block it so the drums can be removed without affecting the supports.
WARNING: Inadequate or improper support while this work is performed can cause serious injury or death.
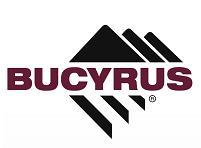
Standard Working Procedure
3) Remove all power from the machine and trip all circuit breakers to "OFF".
WARNING: Isolate machine as per mines isolation procedures.
4) Secure LH pull in assembly with lifting devices, utilizing lifting rud links attached to the banjo arm section.
LH PULL-IN ASSEMBLY
1-1/4" UNC x 9" LG HEX HEAD CAP SCREWS
1-1/4" UNC x 12" LG HEX HEAD CAP SCREWS
1-1/4" UNC x 12" LG HEX HEAD CAP SCREWS
2" DOWEL (LEAVE)
1-1/2" DOWEL (REMOVE)
1-1/4" UNC x 7" LG HEX HEAD CAP SCREWS
LH INTERMEDIATE DRUM MACHINE CENTRELINE
1-1/2" DOWEL (REMOVE)
CENTRE DRUM
5.10
5) Remove the two (2) 1 ½” dowel pins from the rear of the head structure with a slide hammer or pressing equipment. There is a ¾” UNC thread in the 1½” dowels for ease of removal. See Figure 5.10. Leave in the 2” dowels.
6) Remove six (6) 1-1/4” x 12” Hex head cap screws, as well as two (2) 1-1/4” x 9” Hex head cap screws,1-1/4” heavy hex elastic stop nuts and 1-1/4” hardened washers. These screws are torqued to 1,940 Ft-Lb. Figure 5.10.
7) Carefully move the LH pull in assembly laterally away from the inboard side of the auger gear case, stopping some 6”-8” away from the gear case bearing in mind that there is a pressure tube mounted internally of the pull in assembly. In full view should be the pressure tube, using multigrips or stilsons undo the tube from the pull in assembly and continue to remove pull-in assembly from auger head. See Figure 5.11.
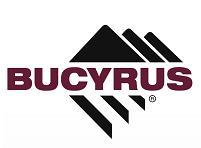
Standard Working Procedure
Figure 5.11
Proceed with intermediate barrel removal from this point (RH and LH)
8) Remove the two (2) key caps situated on the outer side of the intermediate barrel 180 degrees apart. Using a slide hammer remove key steel packer and then the barrel key. Ensure to match mark these keys with there allocated keyways see Figure 5.12.
9) Attach a lifting device to the intermediate drum being removed and apply lifting tension.
10) Loosen the eighteen 1" socket head cap screws that secure the wedge block assembly and the drum to the cutting head hub. Remove the cap screws and wedge. See Figure 5.12.
CAUTION: It is important to matchmark both the end drum and the cutting head hub to which it is attached, so that the pick block lacing is not disturbed upon reassembly.
11) Slowly pull the intermediate drum off the main assembly, and manoeuvre it away from the miner.
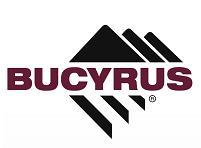
SPLINED HUB 1" UNC x 2-3/4" LG SOCKET HEAD CAP SCREWS
Standard Working Procedure
3/4" UNC SOCKET HEAD CAP SCREWS
KEY RETAINER
LH INTERMEDIATE DRUM
WEDGE BLOCK ASSEMBLY
SPACER
BARREL KEY
5.12
Intermediate Drum Assembly RH and LH
1) With the machine in the same position as intermediate drum removal left or right hand and the machine still isolated as per mines procedures. Position the intermediate drum for reassembly.
WARNING: Isolate machine as per mines isolation procedures.
2) Secure drum with lifting devices used for removal of intermediate drum.
NOTE: Before next step ensure that lifting devices have adequate tension on the drum.
3) Using lever bars turn cutter head to line up the match marks with the match marks on the centre drum or the intermediate drum on the opposite side. Match marks are a small drilled hole or welded arrows
4) By lining up the match marks two keyways 180o apart in the intermediate drum should be lined up with the keyways in the mating part.
5) Push the intermediate drum onto the mating part and force drum into position. To force drum into position use a rubber or soft hammer.
6) Using lever bars rotate the drum to line up both keyways and drive in the keys from the outside of the drum. Fit key retainers.
7) Position wedge block assembly see figure 5.12 and start the 18-1”x2 ¾” long socket head cap screws.
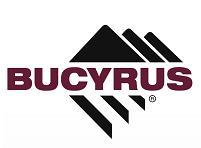
Standard Working Procedure
8) Torque the 18-1”x2 ¾” long socket head cap screws alternatively 180o apart to 550 ft lbs or 746Nm.
CAUTION:
Tightening wedge block assembly over 550 ft lbs or 746Nm will squash the splined hub preventing the pull in assembly spline entering the splined hub.
Install Complete Pull In Assembly
1) With the machine in the same position as pull in assembly removal ensure the machine is isolated as per mines procedures.
WARNING: Isolate machine as per Mine’s Isolation Procedures.
2) Position the complete pull in assembly as per removal procedure.
3) Secure pull in assembly with lifting devices utilising lifting lugs attached to the banjo arm section and wrapping sling around drum.
4) Ensure threaded pipe for cutter barrel extend is in position through the centre hole of the cutter head shaft.
NOTE: The threaded end of the pipe should be on the left hand side of the machine when viewed from the rear of the machine. See Figure 5.13.
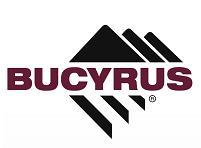
Standard Working Procedure
5) If fitting the left side pull in assembly position the assembly almost in position allowing enough room to screw the pipe into the internal tee using multigrips or vice grips and thread tape tighten pipe into tee.
If fitting right side the threaded pipe is already screwed into tee on left side. The right side is tapered to start into the hole of the cylinder in the centre of assembly. See figure 5.13. Check ‘o’ ring in cylinder where tapered pipe end fits is ok before proceeding.
6) Line up the match marks with intermediate barrel and manoeuvre the assembly into the splined hub figure 5.12.
7) Line up the face plate 1 ¼ bolt holes.
8) Start the 2-7x1 ½” long hex head cap screw and tighten enough to bring the faces together. See figure 5.10.
9) Drive in the 2-1 ½” diameter hardened steel dowel pins.
10) Install the 8-1 1/4x9” long hex head cap screw. See figure 5.10.
11) The 10-1 ¼ diameter hex head cap screw need to be tightened to 1940 ft lbs or 2630Nm. If no torque wrench is available this can be done by tightening all 1 1.4 bolts to 600 ft lbs or 814 Nm. By using a slogging spanner tighten the nut five flats.
NOTE: Reduce torque by 25% if lubricant is used on threads.
12) Replace ¾” NPT x 8” long hydraulic fitting back into the rear of the cutter head and connect hydraulic hose. Replace covers.
13) Clear area of all tools parts and debris.
14) Check oil level in cutter head gear case and top up as required.
15) Remove isolation tags as per mines procedures.
16) Restore power to machine as per mines procedure to re-power.
17) Start machine and test cutter head by rotating and extending and retracting the drums several times.
CLICK HERE TO DOWNLOAD THE COMPLETE MANUAL
• Thank you very much for reading the preview of the manual.
• You can download the complete manual from: www.heydownloads.com by clicking the link below
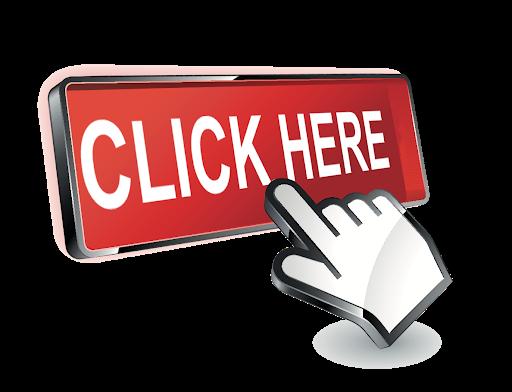
• Please note: If there is no response to CLICKING the link, please download this PDF first and then click on it.
CLICK HERE TO DOWNLOAD THE
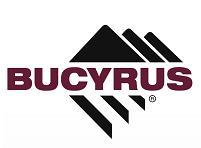
Comments / Changes required
Standard Working Procedure
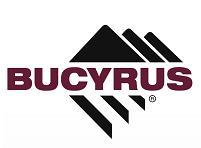
Standard Working Procedure
Title: Centre Drum Removal and Assembly 30MB3 Miner Number P00431
Date 15/10/2008
Prepared By:
Copyright Bucyrus Underground Australia Pty Ltd
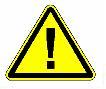
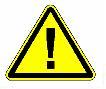
Authorisation
THIS DOCUMENT ACTIVE UNTIL:15/10/2009
CONTROLLED COPIES OF THIS DOCUMENT HAVE THE COLOURED LOGO DISPLAYED.
Tools and Equipment Required
Bucyrus Underground Australia Pty Ltd recommends that all Standard Working procedures should be approved and checked by Mine Officials. Bucyrus Underground Australia Pty Ltd declines all liability for direct or indirect consequences of printing errors.
Prior to starting this work, normal safety practices should be observed with regard to coal face support, Miner isolation.
This procedure does not replace the need for a local JSA to be performed by persons appointed by the mine management
Bucyrus Underground Australia Pty Ltd Standard Working Procedures only apply when fitting approved spare parts.
- General tools, hammers, chisels, shifters, pliers, etc
- 1 ½” AF Socket
- ¾” Drive breaker bar and ratchet
- ¾” Square extension bar 12” & 24” long
- 1 Tonne lifting
- 2 slings/chains 2 metres long
- Timber Wedges
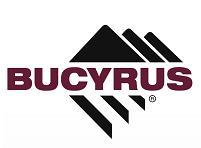
Procedure
Centre Drum Removal
WARNING: Inadequate or improper support while this work is performed can cause serious injury or death.
WARNING: Isolate machine as per Mine’s Isolation Procedures.
1) With cutter head at a comfortable working height remove the four (4) 1” UNC x 7” long hex head cap screws from the closest centre flange. Leave the eight (8) 1” UNC x 7” long hex head cap screws in the end flanges of the drum. See figure 5.14.
2) Rotate cutter head by lever bars 180o
3) Remove isolating tags and lower cutter head to floor. Ensure bottom half of centre drum is supported by the floor or otherwise lowered onto timber packing.
4) Isolate again as per mines isolation procedures.
5) Remove eight four (4) as per opposite side 1” UNC x 7” long hex head cap screws from centre flanges.
6) Remove eight (8) 1” UNC x 7” long hex head cap screws from the drum end flanges.
7) With lifting devices attached to each end of the top half of the centre drum.
NOTE: Before the next step, ensure that the lifting devices have adequate tension on both ends of the top half of centre drum.
8) Slowly raise the top half of the centre drum until it is free from the shaft
9) Lower top half of centre drum to the floor.
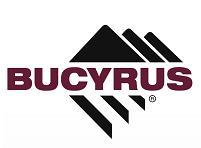
10) Remove isolating tags and re-power machine.
Standard Working Procedure
11) Raise cutter head and reverse machine away from bottom half of cutter drum.
12) There are six keys attached to the centre drum, 4 off 1” x 3/4” square and 2 off 1 ¾” x 1 ¾” square keys. Do not lose the keys if they are in good condition, they can be reused.
Centre Drum Assembly
1) With the machine in the same position as centre drum removal and the machine still isolated as per mines procedures position the bottom half and top half of the centre drum in front of the machine.
WARNING: Isolate machine as per mines isolation procedures.
2) Pack up bottom half of centre drum using match marks lined against intermediate drums.
3) Remove isolating tags and re-power machine as per mines procedures.
4) Tram machine with cutter head raised enough to clear bottom half of centre drum. Tram into position that allows cutter head to be lowered into the bore of the drum.
5) Check keys are in position and lower cutter head onto bottom half of centre drum.
6) Isolate machine as per mines procedures.
WARNING: Failure to isolate machine as per mines procedures may cause injury or death.
7) Using lifting gear as per disassembly procedure position top half of drum over cutter head.
WARNING: Ensure that lifting devices have adequate tension on both ends of the top half of centre drum.
8) Position the 4 keys into keyways of the cutter head shaft.
9) Lower the top half of the drum into position resting the top half against the bottom half.
10) Start all bolts and tighten the nuts finger tight.
11) Tighten all retainers using ¾” square drive and socket.
12) Remove isolating tags and re-power machine as per mines procedures.
13) Raise cutter head to a comfortable working position to allow torquing of the fasteners.
14) Isolate machine as per mines isolation procedure.
WARNING: Failure to isolate machine as per mines procedures may cause injury or death.
15) Torque the 8-1” hex head cap screw within easy reach to 970 ft lbs or 1315Nm.
NOTE: Reduce torque by 25% if lubricant is used on threads.
16) Using lever bars rotate head 180o and torque the remaining 8-1” hex head cap screws to 970 ft lbs or 1315Nm.
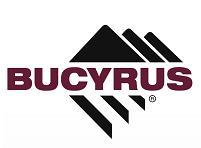
Standard Working Procedure
NOTE: Reduce torque by 25% if lubricant is used on threads.
17) Clear all tools, parts and debris around work area.
18) Remove isolation tags as per mines procedures and re-power machine as per mines procedure.
19) Start machine and check centre drum by rotating and stopping cutter head several times.
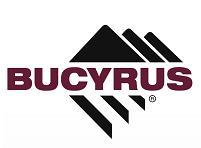
Comments / Changes required
Standard Working Procedure
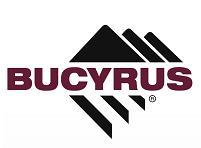
Standard Working Procedure
Title: Removal and Assembly of Cutting Motor Clutches 30 MB3 Miner Number P00432
Date 15/10/2008
Prepared By:
Copyright Bucyrus Underground Australia Pty Ltd
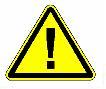
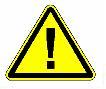
Authorisation
THIS DOCUMENT ACTIVE UNTIL:15/10/2009
CONTROLLED COPIES OF THIS DOCUMENT HAVE THE COLOURED LOGO DISPLAYED.
Tools and Equipment Required
Bucyrus Underground Australia Pty Ltd recommends that all Standard Working procedures should be approved and checked by Mine Officials. Bucyrus Underground Australia Pty Ltd declines all liability for direct or indirect consequences of printing errors.
Prior to starting this work, normal safety practices should be observed with regard to coal face support, Miner isolation.
This procedure does not replace the need for a local JSA to be performed by persons appointed by the mine management
Bucyrus Underground Australia Pty Ltd Standard Working Procedures only apply when fitting approved spare parts.
General tools – hammer, chisel, shifting spanner, pliers etc, - Medium size long screw driver
- 15/16 AF socket ¾” square drive
- ¾” drive ratchet
- ¾” square drive extension
- 10 mm AF Allan Key
- Special tool part number 482287
Procedure
The cutting head top cover must first be removed to gain access to remove the clutch.
WARNING: Isolate machine as per Mine’s Isolation Procedures.
1) Remove all power from the machine, and isolate all circuit breakers to "OFF".
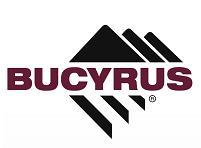
CUTTER MOTOR
CLUTCH COVER
CUTTING HEAD FRAME
Standard Working Procedure
CUTTING HEAD GEARCASE
5/8" UNC x 1-3/4" LG HEX HEAD CAP SCREWS
5.15
2) Place clean rags or cardboard on this area and keep dirt off these parts by keeping them covered until needed.
3) Remove the cutting motor cover on top of the auger head structure.
4) Remove eight (8) 5/8”UNC x 1-½” hex head cap screws from clutch cover. See Figure 5.15.
5) Remove clutch cover by sliding to the rear of the machine and position to allow long shaft to be removed.
6) Remove six (6) 5/16” UNC x 1 ¼ long hex head cap screws from seal cap and remove seal cap and internal retaining ring including shims. See Figure 5.16.
RH INPUT GEARCASE
CUTTER MOTOR
INPUT SHAFT
RETAINING RING SEAL CAP
5/16" UNC x 1-1/4" LG HEX HEAD CAP SCREWS
SHIMS
MACHINE CENTRELINE
DRIVE SHAFT
5.16
NOTE: Do not misplace the drive shaft shim, as they will be required when a new or the existing clutch is refitted.
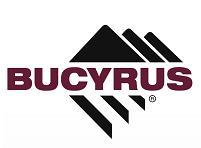
Standard Working Procedure
7) Using 5/8 UNC hex head cap screws remove the input motor shaft from the clutch-motor.
8) Remove six (6) socket head cap screws 12 mm x 40 mm long from clutch assembly. This allows the pressure plate to be removed. Figure 5.17.
9) Remove the output hub and friction plates from the clutch. The spring cup assemblies will also come with the output hub.
10) Using screwdriver remove spiral retaining ring and remove the lock-screw securing the locknut.
11) Remove multipoint locknut using special tool or chisel. Special tool part number 482287.
12) Remove input hub from motor.
SPIRAL CIRCLIP
LOCKING SCREW
OUTPUT HUB
SOCKET HEAD CAP SCREWS (12mm x 40mm LG)
MULTI-POINT
LOCKNUT
(TORQUE TO 150 Ft lbs)
Clutch Assembly
1) With the machine in the same position as for clutch removal and machine still isolated as per mines procedures get clutch ready for mounting.
WARNING: Isolate as per Mine’s Isolation Procedures.
2) Dismantle clutch to be fitted by removing six socket head cap screws from clutch assembly see Figure 5.17
3) Remove the output hub, friction plates and spring assemblies from clutch.
4) Fit input hub onto the spline of the electric motor.
5) Fit and tighten multipoint locknut to retain clutch see figure 5.17 using clutch retaining tool part number 482287 torque to 150 ft lbs or 203Nm.
CLICK HERE TO DOWNLOAD THE COMPLETE MANUAL
• Thank you very much for reading the preview of the manual.
• You can download the complete manual from: www.heydownloads.com by clicking the link below
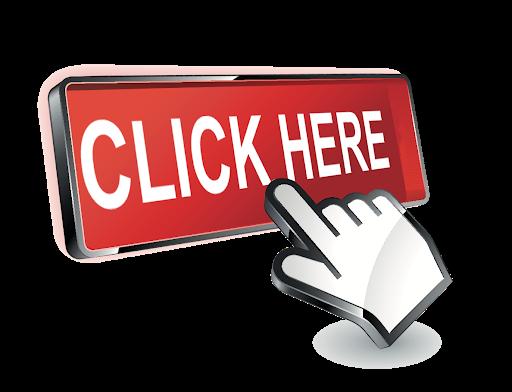
• Please note: If there is no response to CLICKING the link, please download this PDF first and then click on it. CLICK HERE TO DOWNLOAD THE
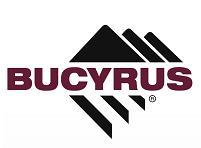
Standard Working Procedure
6) Line up slot of multipoint locknut with the ¼” UNC tapped hole in the input hub and fit locking screw see figure 5.17.
7) Fit spiral circlip.
8) Reassemble springs, friction discs and output hub to the input hub.
9) Fit six 12 mm x 40 mm long socket head cap screws to output hub and pressure plate and torque to 102 ft lbs 138Nm.
10) Check ‘O’ ring in seal cap and replace if necessary 3/32 x 2 7/8” od.
11) Fit seal cap and tighten 5/16” retaining bolts.
12) Fit clutch cover and tighten bolts to 226 ft lbs or 306Nm.
13) Refit top covers.
14) Re-power machine as per mines re-power procedure and test for correct operation.
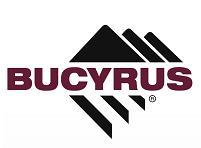
Comments / Changes required
Standard Working Procedure
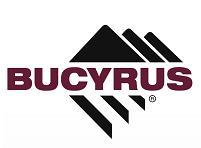
Title: Removal and Installation of the Cutter Head Input Gear Case
Standard Working Procedure
30MB3 Miner Number P00433
Date 15/10/2008
Prepared By:
Copyright Bucyrus Underground Australia Pty Ltd
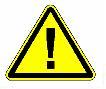
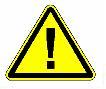
Authorisation
THIS DOCUMENT ACTIVE UNTIL:15/10/2009
CONTROLLED COPIES OF THIS DOCUMENT HAVE THE COLOURED LOGO DISPLAYED.
Tools and Equipment Required
Bucyrus Underground Australia Pty Ltd recommends that all Standard Working procedures should be approved and checked by Mine Officials. Bucyrus Underground Australia Pty Ltd declines all liability for direct or indirect consequences of printing errors.
Prior to starting this work, normal safety practices should be observed with regard to coal face support, Miner isolation.
This procedure does not replace the need for a local JSA to be performed by persons appointed by the mine management
Bucyrus Underground Australia Pty Ltd Standard Working Procedures only apply when fitting approved spare parts.
- General tools – hammer, chisels, shifters, pliers etc, - Internal circlip, pliers medium size
Procedure
NOTE: The complete cutter head gear case needs to be removed from the machine to carry out this procedure.
WARNING: Inadequate or improper support while this work is performed can cause serious injury or death.
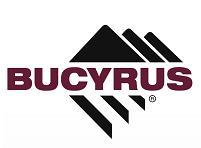
SHIMS
RETAINING RINGS O'RING
2 THREADS EXPOSED WHEN TIGHTENED
DRIVE SHAFT
ACCESS PLUG
Figure 5.21
1) Remove the access plug at the rear of the input gear case (see Figure 5.21)
2) Remove the first of two retaining rings and a plug and its captive O-ring. Figure 5.21.
3) Remove the second retaining ring and any shims installed behind the retaining ring. This will expose the drive shaft. Keep shim pack for reassembly.
4) Using the threaded 5/8 UNC puller, hold in the end of the drive shaft, extract the shaft completely.
5) Remove the eight (8) ¾” UNC nyloc socket head cap screws. The case is also secured by a ½“dowel as shown in Figure 5.21. This may require the removal of a couple of the ½” UNC cap screws securing bearing retainers on either side of the case, and using a sliding hammer with a ½” threaded end to ease the case away from the main gear case structure.
Installation of Cutter Head Input Gear Case
1) Clean down mating faces and apply light smear of grease to stop corrosion.
2) Position gear case and line up mounting bolt holes.
3) Start and lightly tighten 8 ¾ socket head cap screws. See figure 5.21.
4) Fit ½ x 2 ½ long hardened steel dowel.
5) Torque ¾” socket head cap screws to 118 ft lbs or 160Nm.
6) Remove access plug at rear of input gear case. See figure 5.21.
7) Install driveshaft the end with the spline that has a circular undercut at the rear of the spline is the end that goes into the cutter head.
8) Install shims see figure 5.21 and fit retaining ring.
9) Measure clearance between end of shaft with the shims and the cir-clip. Clearance should be .020” to .044”. Add or remove shims as required.
10) Refit ‘o’ ring plug and second retaining ring.
11) Screw in access plug and tighten. Make sure 2 threads are exposed to ensure access plug does not contact inside sleeve.
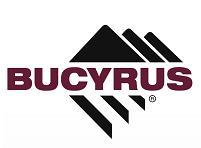
Comments / Changes required
Standard Working Procedure
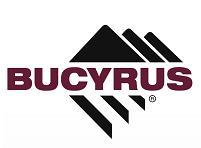
Standard Working Procedure
Title: Removal and Installation of Cutter Motor 30MB3 Miner Number P00434
Date 15/10/2008
Prepared By:
Copyright Bucyrus Underground Australia Pty Ltd
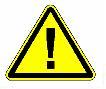
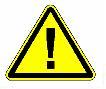
Authorisation
THIS DOCUMENT ACTIVE UNTIL:15/10/2009
CONTROLLED COPIES OF THIS DOCUMENT HAVE THE COLOURED LOGO DISPLAYED.
Tools and Equipment Required
Bucyrus Underground Australia Pty Ltd recommends that all Standard Working procedures should be approved and checked by Mine Officials. Bucyrus Underground Australia Pty Ltd declines all liability for direct or indirect consequences of printing errors.
Prior to starting this work, normal safety practices should be observed with regard to coal face support, Miner isolation.
This procedure does not replace the need for a local JSA to be performed by persons appointed by the mine management
Bucyrus Underground Australia Pty Ltd Standard Working Procedures only apply when fitting approved spare parts.
General tools – hammer, chisel, shifting spanner, pliers etc
- Medium size long screw driver
- 15/16 AF socket ¾” square drive
- ¾ drive ratchet
- ¾ square drive extension
- ½ AF Allan key
- 1 ⅞” AF Slogging spanner
- 2 off 1 tonne lifting blocks
- 2 off 1 tonne slings 2 metres long
- 2 off crow bars
Weight of Cutter Head Motor 1250 kg
Procedure
WARNING: Inadequate or improper support while this work is performed can cause serious injury or death.
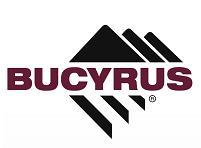
NOTE: Access to area under cutter head boom is required. Lower gathering head and fit safety support pins to cutter boom.
1) Raise cutter head and fit safety support pins.
2) Isolate as per mines isolation procedures.
3) Remove bottom cover item. Figure 5.20.
4) Using 1-7/8” A/F slogging spanner remove bottom two (2) 1-¼” UNC extended head cap screws on motor. See figure 5.19.
5) Remove isolation tags and lower cutter head using mines re-power procedures for continuous miners for mechanical maintenance.
6) Isolate machine as per isolation of continuous miner for electrical and mechanical maintenance.
7) Follow procedure for removal of cutter motor clutch 1 to 12.
8) Using 1-7/8” A/F slogging spanner remove top two (2) 1-¼” UNC extended head cap screws from motor.
9) Remove water hoses from electric motor and mark so reconnection will be correct.
10) Electrician is to disconnect and insulate left of right hand cutter head contactor in the main flameproof enclosure depending which motor is being removed. Disconnect the load side cables and the Thermistor leads. Then disconnect cable from motor.
11) The motor is now ready to be lifted from the cutter head frame.
12) Using lifting devices lift cutter motor from cutter head frame.
13) Remove isolation tags from traction circuit breaker.
WARNING: Cutter head and conveyor circuit breaker must be isolated and locked in the off position.
14) Tram machine away from cutter motor.
Installation of Cutter Motor
1) Using the same lifting gear and setup as cutter motor removal lift the motor high enough to tram the miner under the motor.
2) When miner is in position to allow the motor to be lowered into the cutter head isolate machine as per mines procedures.
WARNING: Failure to isolate machine as per mines isolation procedures may cause serious injury or death.
3) Before lowering the motor into position smear a light coating of Silastic on the face of the motor and use o-ring that is supplied.
4) Lower the motor into position and lever the motor forward using crowbars until motor spigot enters the bore in the cutter head frame.
5) Start and tighten the 2 top motor mounting bolts and pull the faces together. No need to torque at this point.
CLICK HERE TO DOWNLOAD THE COMPLETE MANUAL
• Thank you very much for reading the preview of the manual.
• You can download the complete manual from: www.heydownloads.com by clicking the link below
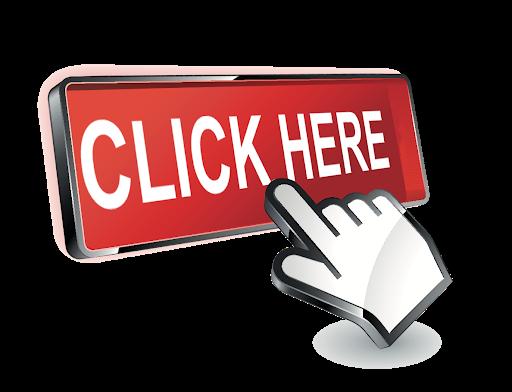
• Please note: If there is no response to CLICKING the link, please download this PDF first and then click on it.
CLICK HERE TO DOWNLOAD THE
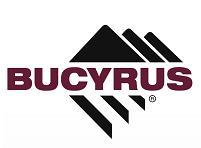
Standard Working Procedure
6) Remove isolation tags as per mines procedures and re-power machine as per mines procedures.
7) Raise cutter head and place cutter head safety support pins in position.
8) Isolate machine as per mines procedures.
WARNING: Failure to isolate machine as per mines procedures may cause serious injury or death.
9) Start 2 bottom motor mounting bolts and torque to 1940 ft lbs or 2630Nm.
NOTE: Access to area under cutter head boom is required. Lower gathering head and fit head safety support pins to cutter boom.
10) Replace bottom cover and torque 5/8 unc mounting bolts to 226 ft lbs or 306Nm.
11) Remove isolation tags as per mines procedures and reapply power as per mines procedures.
12) Remove cutter head safety support pins and lower cutter head to floor.
13) Isolate machine as per mines procedures.
WARNING: Failure to isolate machine as per mines procedures may cause serious injury or death.
14) Electrician to rewire electric motor and reconnect the contactor in the main flameproof enclosure.
15) Remove isolation tags as per mines procedures reapply power to machine as per mines procedures.
16) Start machine and check direction of motor.
NOTE: RHS MOTOR – Rotates clockwise when looking at clutch end.
NOTE: LHS MOTOR – Rotates anti clockwise when looking at the clutch end.
17) Isolate machine as per mines procedures.
WARNING: Failure to isolate machine as per mines procedures may cause serious injury or death.
18) Torque top motor bolts as per above instructions on torque of bottom motor bolts.
19) Replace splined shaft, clutch and clutch cover as per clutch replacement procedure at start of this section 5.
20) Replace water fittings and connect water hoses.
21) Replace top cutter head covers.
22) Clean up all tools, parts and debris around work area.
23) Remove isolation tags as per mines procedures and re-power machine as per miner repower procedure.
24) Start machine and check cutter head for rotation.
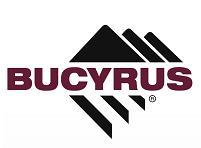
Comments / Changes required
Standard Working Procedure
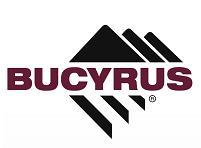
Standard Working Procedure
Title Removal and Installation of Cutter Head Gear Case 30MB3 Miner : Number P00435
Date 15/10/2008
Prepared By:
Copyright Bucyrus Underground Australia Pty Ltd
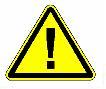
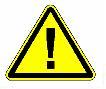
Authorisation
THIS DOCUMENT ACTIVE UNTIL:15/10/2009
CONTROLLED COPIES OF THIS DOCUMENT HAVE THE COLOURED LOGO DISPLAYED.
Tools and Equipment Required
Bucyrus Underground Australia Pty Ltd recommends that all Standard Working procedures should be approved and checked by Mine Officials. Bucyrus Underground Australia Pty Ltd declines all liability for direct or indirect consequences of printing errors.
Prior to starting this work, normal safety practices should be observed with regard to coal face support, Miner isolation.
This procedure does not replace the need for a local JSA to be performed by persons appointed by the mine management
Bucyrus Underground Australia Pty Ltd Standard Working Procedures only apply when fitting approved spare parts.
- General tools – hammer, chisels, shifters, pliers etc,
- Hydraulic or pneumatic operated torque wrench torque requirement
2000 ft lbs
- ½” x 400 long steel round bar
- 7 lb hammer
- 1 7/8” AF slogging spanner
- 1 7/8” AF impact socket 1” drive and ¾” drive
- ¾ drive ratchet
- ¾ drive extension short and long
- 2 lifting devices 10 tonne each
- 4 lifting chains adjustable 5 tonne each
- 2 crow bars
- 1” x 12” long round bar
(Complete with pull in assemblies)
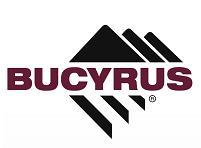
Standard Working Procedure
Procedure
The cutting head gear case must sometimes be removed from the miner by itself for replacement of internal components such as the input gear cases. The cutting head gear case assembly may be removed with the cutting drums installed.
1) Lower the gathering head to the mine floor.
2) Support the auger head frame by using manufactured safety support pins in the locations provided on either side of gathering head.
3) Remove all power from the machine and isolate all circuit breakers to “OFF”.
WARNING: Isolate as per Mine’s Isolation Procedures.
WARNING: Inadequate or improper support while this work is performed can cause serious injury or death.
WARNING: Access to area under cutter head boom is required. Improper setting of safety supports while this work is performed can cause serious injury or death.
4) Remove eighteen (18) 1-¼” UNC x 11” long hex head cap screws from the bottom of the mounting flange. Leave the 2 (one each side) 1 ¼” x 9” long hex head cap screws securely tightened as they will support the cutter head extensions. Figure 5.19.
WARNING: Isolate machine as per mine’s Isolation Procedures.
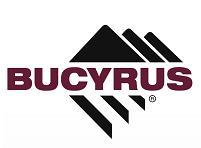
Standard Working Procedure
LH PULL-IN ASSEMBLY CENTRE DRUM LH INTERMEDIATE DRUM
(4-0FF) 1-1/4" UNC x 9"LG HEX HEAD CAP SCREWS DO NOT REMOVE
(16-OFF)1-1/4" UNC x 12" LG HEX HEAD CAP SCREWS
Ø2" DOWEL PIN
(4-OFF) Ø1-1/2" DOWEL PIN
(20-OFF) 1-1/4" UNC x 11"LG HEX HEAD CAP SCREW
CUTTER MOTOR CLUTCH COVER
1-1/4" UNC EXTENDED HEAD HEX HEAD CAP SCREW
5.19
5) Remove bottom cover. Figure 5.20.
5/8" UNC x 1-1/2"LG HEX HEAD CAP SCREWS
5.20
BOTTOM COVER
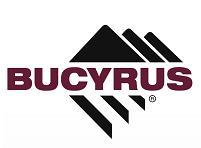
Standard Working Procedure
6) Using 1-7/8” A/F flogging spanner remove four (4) 1 ¼” UNC extended head cap screws from bottom of motors. Note: 2 each motor.
7) Remove isolation as per mines re-power procedures.
8) Apply power to miner.
9) Raise cutter head and remove safety support pins.
10) Lower cutter head to floor.
NOTE: Do not force cutter head into floor.
11) Re-isolate and tag as per mines procedures.
12) Remove covers from top of auger head allowing access to the auger motor and clutch mounts.
13) Remove the cutting motor clutch cover from the RH and LH side motors hex. As per clutch removal procedure.
14) Remove the seal cap and internal retaining ring which restrains the motor input shaft.
15) Remove internal retaining ring including shims.
16) Disengage the motor (input) shaft from the inside of the RH and LH cutting motors going into the input gear case assemblies using 5/8” UNC bolt to pull out.
17) Using 1-7/8” A/F slogging spanner remove top four (4) extended head hex head cap screw from motors. 2 each motor.
CAUTION: In this configuration, each cutting head motor is held in place by the motor spigot and bore in the support frame at the front. Raising the cutter head to an excessive height might cause the motor to dislodge. Do not raise cutter head motors to a position above horizontal.
18) Remove the top row of 1-¼” x 11” long socket head cap screws 18 off holding the cutting head gear case to the cutting head support frame. Do not remove the 4 (two each side) 1 ¼” x 9” as they support the cutter head extensions. Figure 5.19.
19) Disconnect hydraulic extend and retract hoses and extended fittings. One each side of cutter head. There is no need to disconnect water hoses.
20) There are two (2) of 2 inch dowel pins which are press fitted into the support frame. See figure 5.19. Upon separation, they should remain in the support frame and care must be taken to prevent damage to these points.
21) Using lifting gear and crow bars lever cutter head complete assembly away from support frame flange.
22) Isolate the cutting head circuit breaker located on the display box. This will lock out power to the cutting head while power is applied to the miner for tramming.
23) Remove isolation as per mines procedures from the main circuit breaker.
24) Apply power to the miner.
WARNING: Ensure that the cutting head circuit breaker is isolated and do not attempt to start the head.
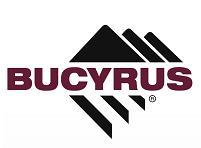
Standard Working Procedure
25) Slowly tram the miner away from the cutting head gear case.
CAUTION: In this configuration, each cutting head motor is held in place by a support spigot and the motor bore hole in the support frame at the front. Excessive bumping might cause the motor to dislodge.
Reinstall Cutter Head Gear Case
(Complete with pull in assemblies)
1) With the machine in the same position as removal procedure and isolated as per mines isolation procedure, position the cutter head in front of machine.
2) Using the same lifting gear as gear case removal lift cutter head into a position that the 2 faces to be bolted are parallel.
3) Re-power machine as per mines re-power procedure.
4) Ensure cutter head circuit breaker is isolated.
5) Tram miner onto the cutter head gear case until faces are as close together as possible.
6) Remove all power from machine and isolate as per mines procedures.
WARNING: Failure to isolate machine as per mines procedure may cause serious injury or death.
7) Using lever bars (crow bars) manoeuvre gear case to allow top row of bolts to be started use 1 ¼ bolt. Lengths as shown in figure 5.18.
8) Position all top row of bolts and pull faces together until slightly touching.
9) Enter and drive home 2 (one each side) 2” hardened steel dowels.
10) Tighten top row of bolts (do not torque to requirement).
11) Start 4 motor bolts, the top 2 of each motor and torque to 1940 ft lbs or 2630Nm.
NOTE: To achieve this, torque the 1 ¼ bolts to 600 ft lbs or 814Nm. By using a slogging spanner tighten the nut. Five flats.
NOTE: Reduce torque by 25% if lubricant is used on threads.
12) Re-power machine as per mines re-power procedures.
13) Start machine in mining mode.
14) Raise cutter head and set cutter head safety support pins. One each side.
15) Reisolate machine as per mines isolation procedures.
WARNING: Failure to isolate machine as per mines procedure may cause serious injury or death.
16) Fit bottom row of 1 ¼ bolts and torque to 1940 ft lbs or 2630Nm. This can be achieved by torquing bolts to 600 ft lbs and using a slogging spanner tighten nut. Five flats.
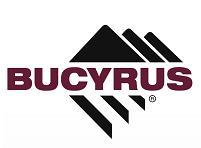
Standard
Working Procedure
NOTE: Reduce torque by 25% if lubricant is used on threads.
17) Start and torque 4 bottom motor bolts as above.
18) Replace bottom cover and torque 5/8 retaining bolts to 226 ft lbs or 306Nm.
19) Re-power machine as per mines re-power procedures.
20) Apply power to machine.
21) Raise cutter head and remove safety support pins and lower cutter head so drums are almost touching floor.
22) Torque the top row of 1 ¼ bolts as described above.
23) Replace motor input shaft.
24) Replace internal retaining ring including shims.
25) Replace seal cap and retaining bolts.
26) Replace clutch cover and torque 5/8 hex head cap screws to 226 ft lbs or 306Nm.
27) Replace top cutter head covers.
28) Refill gear cases with mine supplied gear oil. Refer to section 11 for details.
29) Refit hydraulic extend and retract fittings and hoses.
30) Clean up all tools, parts and debris around work area.
31) Remove isolation tags as per mines procedures and re-power machine as per mines repower procedure.
32) Start machine and check cutter head rotation and extend and retract functions.
33) Extend and retract cutter extending drums several times to bleed air out of cylinders.
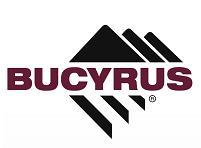
Comments / Changes required
Standard Working Procedure
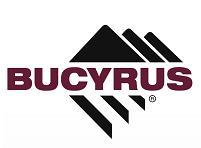
Standard Working Procedure
Title: Removal of the Cutting Head Support from the Main Frame 30MB3
Miner Number P00436
Prepared By:
Copyright Bucyrus Underground Australia Pty Ltd
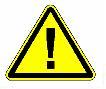
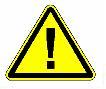
Authorisation
THIS DOCUMENT ACTIVE UNTIL:15/10/2009
Date 15/10/2008
CONTROLLED COPIES OF THIS DOCUMENT HAVE THE COLOURED LOGO DISPLAYED.
Tools and Equipment Required
Bucyrus Underground Australia Pty Ltd recommends that all Standard Working procedures should be approved and checked by Mine Officials. Bucyrus Underground Australia Pty Ltd declines all liability for direct or indirect consequences of printing errors.
Prior to starting this work, normal safety practices should be observed with regard to coal face support, Miner isolation.
This procedure does not replace the need for a local JSA to be performed by persons appointed by the mine management
Bucyrus Underground Australia Pty Ltd Standard Working Procedures only apply when fitting approved spare parts.
- General Tools – hammers, spanners, chisels, shifters, pliers etc
- 2 lifting blocks/devices 10 tonne
- 2 lifting blocks/devices 5 tonne
- 2 lifting chains adjustable 10 tonne each 2.5 metres long
- 2 lifting chains adjustable 5 tonne each 2.5 metres long
- Sliding hammer 1” UNC
Weight 9000 kg – without the cutter head gear case attached to the faceplate.
Procedure
NOTE: The support frame can be removed with or without the cutter head gear case attached or removed.
1) Place the machine to a location where both sides are accessible in front of the crawlers and can be reached easily.
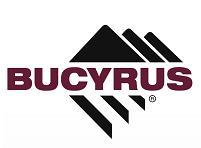
Standard Working Procedure
2) Lower the gathering head until the shovel blade rests on the mine floor.
3) Lower the cutting head until its frame rests on the floor or gathering head frame if the cutter head gear cases have been removed.
4) Remove all power from the machine, and trip all circuit breakers to "OFF".
WARNING: Isolate machine as per Mine’s isolation procedures.
5) Clean off an area of the machine where parts can be set. Place clean rags or cardboard on this area and keep dirt off the parts by keeping them covered until needed.
6) Remove any necessary access covers and isolate machine as per mines procedures.
NOTE: A competent Electrician is needed from this point.
7) Electrician to disconnect and insulate left and right hand cutter head contactors, horizon control unit and headlights in the main flameproof enclosure. Disconnect and insulate the load side wiring of each component.
WARNING: Failure to isolate machine as per mines procedures may cause serious injury or death.
NOTE: Ensure to remove mine water supply from the machine.
8) Disconnect electrical leads from the RH and LH cutting head drive motors, horizon control unit and headlights and flow switches. Tag these leads for identification in re-assembly. Pull them rearward off the support frame and lay them on the machine chassis.
9) Disconnect water lines going to the cutting head. Tag them and lay them on the chassis.
10) Disconnect lubrication and hydraulic lines going to the cutting head, and all lubrication lines to the main pivot pins and hydraulic cylinder pins. Tag them and set on the machine chassis.
NOTE: Cables, water and hydraulic lines to the gathering head do not need to be disconnected or removed.
11) Position 10 tonne lifting blocks one each side above lifting lugs at front of cutter head position 5 tonne lifting blocks above rear lifting lugs.
12) Relieve pressure in each cutting head raise circuit.
13) Remove the two (2) 3/4" UNC flat head cap screws and keeper plates from the upper cylinder pins on each side (see Figure 5.22 & 5.23).
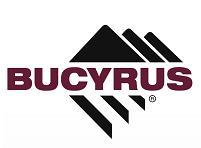
PIVOT PIN RETAINING KEY
CUTTING HEAD PIVOT PIN
PLATE
CUTTING HEAD SUPPORT FRAME A
MAINFRAME OUTER PIVOT BUSHING
5/8" UNC x 2-1/2"LG SOCKET HEAD CAP SCREW
PIVOT RETAINING KEY
CYLINDER PIN BUSHING
KEEPER PLATE
5/8" UNC x 1-3/4"LG HEX HEAD CAP SCREWS
Standard Working Procedure
KEEPER PLATE
UPPER CYLINDER PIN
CUTTING HEAD RASIE CYLINDER
LOWER CYLINDER PIN
5.22
CUTTING HEAD PIVOT BUSHING
MAINFRAME INNER PIVOT BUSHING
CUTTING HEAD PIVOT PIN
CUTTING HEAD SUPPORT FRAME
LOWER CY PIN LINDER
CYLINDER PIN BUSHING
LOWER CYLINDER CLEVIS
5.23
WARNING: Place timber blocking under the forward end of both raise cylinders before removing the upper cylinder pins.
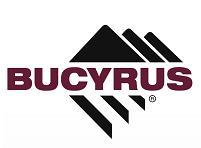
Standard Working Procedure
14) Using 1” UNC thread bar use a slide hammer to remove the upper cutting head cylinder pin from both sides of the cutting head frame.
15) When pin is removed cylinder should fall onto timber blocking.
16) Remove the two (2) 5/8” x 2 ½” long socket head cap screws from the retaining keys on the RH and LH main pivot pins (see Figures 5.22 and 5.23)
17) Remove the retainer keys.
WARNING: Ensure that the cutting head support frame is well supported at both main pivot pins.
18) On either side of the miner, force the main pivot pin inward from the outboard side, using a long 2” diameter bar or 1” sliding hammer from the inside of the machine.
NOTE: Should the pivot pin be difficult to remove, recheck to see that the support frame is properly blocked and weight is removed from the pivot.
19) Repeat Step #17 for the other side of the machine.
20) The cutting head assembly can now be lifted using the lifting gear from the machine.
21) Ensure cutter head and conveying systems are isolated and locked out as per isolation procedures.
22) Remove isolating tags and re-power machine tram machine away from cutter head.
CLICK HERE TO DOWNLOAD THE COMPLETE MANUAL
• Thank you very much for reading the preview of the manual.
• You can download the complete manual from: www.heydownloads.com by clicking the link below
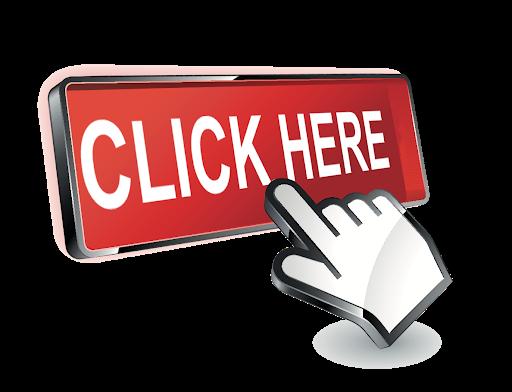
• Please note: If there is no response to CLICKING the link, please download this PDF first and then click on it.
CLICK HERE TO DOWNLOAD THE