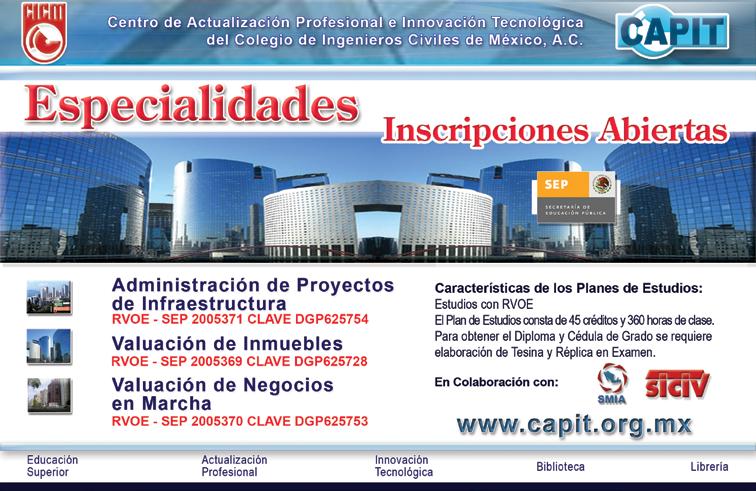
16 minute read
ALREDEDOR DEL MUNDO / IMPRESIÓN 3D, EL FUTURO DE LA CONSTRUCCIÓN
los terrenos, edificios y pertenencias en bienes raíces de la empresa pasarían a ser propiedad de la nación, sin gravamen de ningún tipo.
Los terrenos donde se establecería la Compañía Terminal estaban localizados en el extremo norte de la ciudad, donde se había instalado la primera estación. Con las diversas aportaciones de terreno, la superficie total disponible alcanzó los 620,054.97 metros cuadrados.
Advertisement
La Compañía Terminal de Veracruz desempeñaría una función esencial en las operaciones del puerto y en su enlace con el transporte ferroviario. Para ello emprendió la tarea de construir instalaciones e infraestructura: en el recinto portuario construyó dos grandes bodegas –en el muelle que originalmente llevaría el nombre de Porfirio Díaz, luego muelle número 4 y más tarde Muelle de la Compañía Terminal– con dos niveles y puentes fijos para comunicarse entre sí y puentes colgantes para el desembarco de pasajeros de los transatlánticos. Este muelle, con una capacidad de atraque que superaba los 700 metros, era la posición de desembarco más grande del puerto. Por encima de él se tenderían diversas vías para el servicio interior, a fin de que los trenes llegaran hasta las bodegas o se pudieran colocar con sus góndolas a un costado de los barcos; también se instalaron grúas hidráulicas en el costado sur y en el lado norte para hacer más expeditas las maniobras. Se construyó asimismo una casa de fuerza motriz que recibía energía para mover las grúas.
En cuanto a las instalaciones ferroviarias, se demolieron las que estaban en el área y se construyeron la Casa Redonda con su mesa giratoria y capacidad para recibir hasta 23 locomotoras de vapor, los departamentos de calderas y de herramientas, un taller de máquinas y su departamento de hierro, en cuya cimentación, estructura y techo se utilizó cemento armado. Además de los almacenes de la aduana se construyeron los almacenes generales de depósito y una casa para la Compañía Nacional Express, un almacén para aceites, cuatro básculas para carros, casa para el jefe de la estación, oficina para el maestro mecánico, etc. El edificio más importante del conjunto fue la estación de pasajeros, que se concluyó en el verano de 1911.
Estación de pasajeros
La estación es un edificio de dos plantas desarrolladas sobre una estructura arquitectónica en forma de U. La terminal se hallaba emplazada a la cabeza de la línea y los cuatro andenes; desde allí se proporcionarían todos
los servicios. La planta baja contaba con dos accesos simétricos: uno orientado al norte, hacia la calle de Montesinos, de frente a la Plaza de la República, y el principal orientado al este, hacia la bahía, adonde se extiende una pequeña plazuela. En la parte alta, a partir de un amplio corredor central, se hallaban el hotel y varias oficinas de la dirección de la Compañía Terminal. Además, había en la segunda planta distintos locales de la dirección, entre los que destacan la oficina y el salón del superintendente. El edificio se dividía en tres cuerpos con elementos de cantera, cornisas y remates. Sobre la fachada principal se aprecian, en la planta baja, siete puertas dispuestas hacia el vestíbulo. Los muros de la fachada son bloques o sillares de piedra, con acabado almohadillado de influencia renacentista. La planta alta de dicho cuerpo dispone de nueve balcones con balaustrada. Los siete baños del centro son de proporción vertical, rematados con arcos lobulados en cuya piedra clave luce una concha. La fachada muestra una amplia cornisa con gotas, decorada con azulejos y pilastras pequeñas.
El sistema constructivo de la estación terminal es a base de marcos rígidos de concreto armado, apoyados en columnas aisladas. Su cimentación se basa en zapatas aisladas y corridas de concreto armado con varillas cuadradas de acero de 3/8 y 1/2 pulgada de espesor. Los entrepisos y techos de losa fueron realizados con concreto armado, en una época en que este material era de escaso uso en el país. Este sistema constructivo fue en esa época de los precursores en la utilización de concreto armado. Por lo que se refiere a su estilo, debe señalarse que es un ejemplo de la arquitectura ecléctica del periodo, que asimila influencias semiclásicas y neobarrocas.
Se utilizaron materiales de magnífica calidad; los aplanados compuestos –como los del tercer cuerpo de la fachada, constituidos por pasta de cemento y polvo de mármol– han permanecido en buenas condiciones desde hace diez décadas de cara al oriente, soportando la humedad y la lluvia, así como los constantes nortes que se abaten sobre la región. En los interiores se usó madera de cedro para puertas y ventanas. El mármol fue utilizado en diferentes secciones de la planta baja y en la escalera de acceso a la parte superior.
El edificio fue concluido en el verano de 1911. En una época en que las carreteras no se extendían aún a lo largo del territorio, y un gran número de gente llegaba por vía marítima a través del océano Atlántico, Veracruz afianzó su vocación de puerta de acceso principal.
En las décadas posteriores a los años veinte, el ritmo de actividad de la compañía terminal se sostuvo y creció en forma notable en los años cincuenta, cuando amplió el radio de sus actividades por haber obtenido la concesión del muelle de altura número 6, que tenía una longitud total de atraque de 724 m y era hasta ese momento el más grande de los existentes. Fue inaugurado en 1952 como parte de un conjunto de obras portuarias que puso en marcha el presidente Miguel Alemán. Al mismo tiempo, se efectuaron diversas innovaciones tanto de la Casa Redonda, que se modernizó parcialmente, como en los muelles y patios, con la adquisición de dos grúas de portal de 20 t, tres grúas de 5 t y dos grúas locomotoras de 40 t. También de este periodo data la conversión de la vía angosta a vía ancha del Ferrocarril Interoceánico y creció el número de vías del patio de maniobras, de 44 a 48.
Desde los años treinta se hablaba en la prensa de la incosteabilidad de las operaciones de la Compañía Terminal, pero ya en 1962, concretamente el 9 de febrero, se expidió un decreto en cuyo primer artículo se advierte que el patrimonio de la Compañía Terminal de Veracruz, al concluir legalmente sus funciones, se incorporaría a los bienes de dominio público de la federación, por estar destinado a la prestación de servicios públicos.
Se establece que la zona marítima sería administrada por la Secretaría de Marina, mientras que la ferroviaria se incorporaría al patrimonio del organismo público descentralizado Ferrocarriles Nacionales de México, que tomaría a su cargo el mejoramiento, la conservación, la administración y la explotación de los servicios que allí se desempeñaban.
Aunque este decreto dio fin a la vida de la compañía, no concluyó con las actividades ferroviarias y marítimas que hasta entonces se habían llevado a cabo. La estación de ferrocarril siguió tan activa como siempre, e incluso adquiriría una mayor relevancia administrativa cuando en ella se instalaran las oficinas de la Dirección del Ferrocarril del Sureste. Actualmente, la planta alta del edificio está ocupada por la dirección de este ferrocarril, que administra y dirige las operaciones ferroviarias en toda esa zona del país. En la planta baja se continúan desarrollando hoy los servicios que desde 1911 brinda la estación
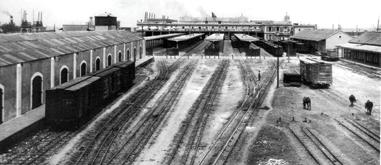
Andenes de la estación terminal. A la izquierda se observan las bodegas originales del Mexicano, que más tarde serían derribadas. A la derecha está el edificio circundado por un andador cubierto, que era la parte posterior de la estación.
Elaborado por Helios Comunicación con base en las siguientes fuentes: Bernardo García Díaz, La terminal ferroviaria de Veracruz, México, SCT, 1996. Carlos García Dávila, El ferrocarril mexicano, una ruta vital para el país.
México en el tiempo, septiembre-octubre de 1998.
¿Desea opinar o cuenta con mayor información sobre este tema? Escríbanos a ic@heliosmx.org
Impresión 3D, el futuro de la construcción
Después de más de 25 años de investigación, desarrollo y uso, la impresión tridimensional (3D) en varios dominios industriales, como el aeroespacial, el automovilístico y el médico, continúa creciendo con la adición de nuevas tecnologías, métodos y aplicaciones. Uno de los métodos que se están explorando actualmente, tanto en la academia como en la práctica de la construcción, es la impresión 3D de concreto.
La impresión 3D es una fabricación aditiva, que consiste en la suma de material por capas. Surgió en 1983 con el uso de estereolitografía, un proceso que involucra disparar un rayo láser ultravioleta en una masa de fotopolímero, que luego se convierte en plástico sólido.
En 2004, el profesor Behrokh Khoshnevis, de la Universidad de Carolina del Sur, intentó la primera pared impresa en 3D. Desde entonces, esta innovación ha explotado y ahora es posible construir una casa en sólo 20 horas. Khoshnevis desarrolló una impresora 3D con el método de deposición fundida (FDM), montada en un brazo robótico, que extrude capas de concreto en lugar de plástico para crear un modelo 3D. Su descubrimiento marcó el comienzo de la impresión 3D en la construcción.
Las más recientes investigaciones en el ámbito de la ingeniería y la construcción han llevado a combinar la impresión 3D con el modelado de información para la construcción (BIM) para el seguimiento y monitoreo de nuevas variables orientadas a crear un entorno de trabajo dinámico en un sitio de construcción.
La combinación de BIM con impresión tridimensional facilitaría la creación de componentes de construcción altamente personalizados y abriría paso a los diseños
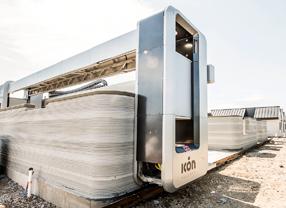
METROPOLISMAG.COM
El principio básico de la impresión 3D en construcción es añadir capas de material una sobre otra. complejos y sofisticados. Sin embargo, todavía hay numerosos desafíos relacionados con la escala, los materiales, el sistema de entrega y la adecuación a entornos adversos.
Aunque el trabajo de los investigadores en el campo aeroespacial y manufacturero ha demostrado que la impresión 3D podría ser la solución para reducir costos, no hay ninguna investigación que apoye que los mismos ahorros se aplicarían a la industria de la construcción. Sin embargo, se puede aceptar que el uso de la impresión 3D podría minimizar el costo de construcción de aplicaciones utilizadas en el sector, con base en el análisis de costos realizado por investigadores en otros campos.
Teniendo en cuenta la demanda mundial de reducir las emisiones de CO2, es necesario contar con tecnologías de construcción innovadoras que no sólo allanen el camino hacia una construcción sostenible, sino que también reduzcan los costos de construcción y gestión de las instalaciones, al tiempo que proporcionen una ventaja competitiva.
Con la tecnología de impresión 3D, el diseño de estructuras no se limitará a una colección de elementos prefabricados. En la punta de estas investigaciones se encuentra el Centro de Impresión 3D de Singapur (SC3DP), que desarrolla una investigación con posibles optimizaciones topológicas destacando la importancia de incorporar BIM.
Tecnologías de vanguardia
El rápido desarrollo de la tecnología de impresión de concreto 3D a gran escala en la mayor parte de la bibliografía se clasifica en dos técnicas: inyección de aglutinantes y método de deposición de materiales (MDM).
El principio básico de ambas técnicas es construir cualquier estructura compleja añadiendo pequeñas capas de material una sobre otra. Comienza con la creación de un modelo CAD 3D, que se divide en varias capas 2D, y luego se imprime con un material asignado de una manera incremental para obtener el prototipo como se describe en el modelo CAD.
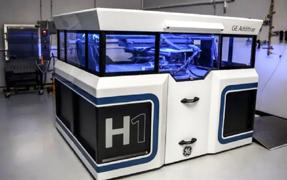
3DPRINTINGMEDIA.NETWORK
El método binder jetting pega gradualmente secciones 2D del componente previsto a cada capa de material pulverizado.
Inyección de aglutinantes
La inyección de aglutinantes (binder jetting) es un proceso de impresión 3D que crea objetos depositando capa por capa sobre un lecho o base de polvo. El aglutinante se expulsa en forma de gotas sobre una capa delgada de material en polvo extendida sobre la bandeja de construcción. Este método pega gradualmente secciones 2D del componente previsto a cada capa de material pulverizado. El ciclo se repite hasta que todo el objeto 3D esté completo. Cualquier materia prima que no esté pegada por el aglutinante permanece dentro del contenedor, constreñido, y se utiliza para soportar capas posteriores. Este método permite que los diseños tengan vacíos y características salientes para la impresión de geometrías complejas. Tiene una resolución relativamente alta, que resulta en un buen acabado superficial, debido a la distancia mínima entre las capas. Este valor de espesor de capa está determinado por la penetración del aglutinante.
Actualmente, una empresa de Gran Bretaña trabaja con esta tecnología para imprimir componentes de gran escala para las industrias de la arquitectura y la construcción.
Método de deposición de materiales Similar a la modelización de deposición fundida (MDF), el método MDM es un proceso de impresión 3D que sucesivamente coloca el material según el modelo CAD. El material extrudido debe ser capaz de soportar su propio peso y el peso de cada capa posterior para alcanzar el diseño final sin ninguna deformación. Hay varios sistemas automatizados que utilizan MDM como su proceso de fabricación del núcleo:
Elaboración de contornos (contour manufacturing). Sistema basado en una suerte de lanzadora que extrude el material capa por capa. Su característica clave es el uso de paletas unidas a la boquilla; la paleta guía el material impreso para crear superficies excepcionalmente suaves y precisas.
Dosificador. El stick dispenser es un dispositivo de impresión manual que consiste en una amalgama de palillos que, recubiertos con pegamento para madera, caen al azar y forman una estructura porosa agregada que luego se evalúa a través de análisis basados en volumen. El dosificador es guiado por una cámara de profundidad y un proyector en tiempo real.
Plataforma digital de construcción. Sistema utilizado para la detección, análisis y fabricación in situ. Está diseñado a base de un manipulador telescópico y un pequeño brazo robótico; el uso de sensores de referencia en tierra y un acelerómetro permiten que el sistema de bucle cerrado posicione con precisión el cabezal del brazo.
Impresión de concreto. Similar a la elaboración de contornos, es un sistema que extrude concreto capa por capa siguiendo un modelo digital.
La mayoría de los métodos de deposición de materiales se clasifica como impresión de capas planas; en ésta se extrude el material en un plano bidimensional capa por capa hasta que alcanza el volumen deseado. Este método de impresión crea debilidades mecánicas como propiedades anisotrópicas y problemas visuales, como el efecto de escalera en la superficie de impresión. Recientemente, se introdujo otro método de impresión de capas curvas, que mejora las propiedades estéticas y mecánicas de una pieza impresa.
Fabricación basada en flujo. Investigadores del MIT diseñaron un sistema para extrudir geles de polisacáridos a base de agua y compuestos naturales con un único sistema de extrusión neumática unido al cabezal de un brazo robótico de seis ejes. El diseño y la fabricación avanzada de materiales heterogéneos y estructuras anisotrópicas dará lugar a una alta rigidez, menor peso y mayor resistencia. Las nuevas aplicaciones para este trabajo van desde la construcción automatizada de fachadas arquitectónicas con diferente translucidez hasta estructuras temporales de sombreado ligero.
Miniconstructores. Un sistema coordinado de tres robots individuales se diseñó para la fabricación en sitios de construcción; los robots son ligeros, compactos y tienen movilidad autónoma; cada uno tiene una función diferente durante el proceso de impresión.
Molde de malla. Esta técnica utiliza un gran robot de seis ejes para extrudir polímero de termoplásticos para imprimir estructuras in situ libremente en el espacio 3D. El enfriamiento preciso mediante aire a presión en la boquilla durante la impresión permite un alto nivel de control,
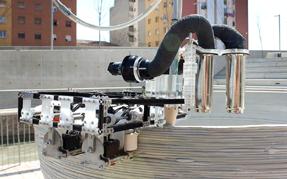
IAAC.NET
Minibuilders: ligeros y compactos.
facilitando así el tejido de estructuras de armazón. En esta aplicación, las estructuras actúan como refuerzo para el concreto; éste se vierte sobre el encofrado y luego se compacta manualmente para alisar la superficie.
BIM
Un flujo de proceso basado en BIM para la impresión 3D puede reducir significativamente el tiempo total de entrega del proceso al integrar cada paso y hacerlo ejecutable a través de una única interfaz o software. Esto podría hacer frente a la cuestión de los cambios constantes en el diseño, que es relativamente común en la industria de la construcción. Se puede cambiar el diseño o hacer una gestión de cambio más rápida sin incurrir en grandes pérdidas, en comparación con otros procesos convencionales. BIM también puede ayudar a automatizar todo el proceso de impresión, ya que puede almacenar y sintetizar equipos e información de fabricación, como datos de control de la impresora, sistema de entrega de materiales y operación posterior al acabado. Los gigantes de la construcción se están dando cuenta rápidamente del potencial de las tecnologías 3D y su impacto en el futuro de la construcción. Se pronosticó que el mercado de la impresión 3D de concreto alcanzaría los 56.4 millones de dólares en 2021, y cada vez más empresas del sector están creando proyectos innovadores.
Algunas obras impresas
El 26 de diciembre de 2016, se inauguró en Madrid el primer puente peatonal impreso en 3D, en el parque urbano Castilla-La Mancha en Alcobendas. Mide 12 metros de largo por 1.75 de ancho. La construcción de este puente se llevó a cabo por fases. El diseño arquitectónico se realizó separadamente, y la impresora 3D la fabricó otra empresa para colocar materiales únicamente donde fuera necesario, lo que permitió la construcción del puente con total libertad de forma.
Una empresa holandesa desarrolló un método de construcción único llamado WAAM (wire arc additive manufacturing), que le permite imprimir estructuras metálicas en 3D con un robot de seis ejes que deja caer 2 kilos de material por hora. El robot está equipado con un soldador y una boquilla, con el que suelda capa por capa varillas de metal.
Luego de seis meses de impresión y años de desarrollo, en 2018 creó un puente de acero inoxidable, una hermosa masa de 12.5 metros de acero inoxidable ondulante. Debido a las restricciones ambientales y de permisos, la empresa construyó el puente dentro de su laboratorio. De allí, podría en algún momento transportarse mediante una embarcación de carga hasta su emplazamiento permanente, un famoso canal del centro urbano histórico de Ámsterdam.
Se necesitaron cuatro robots, casi 4,500 kilogramos de acero inoxidable, cerca de 1,100 kilómetros de cable y seis meses de impresión para construir la estructura sinuosa y ondulada de superficie rugosa.
La fase final incluye la instalación de una serie de sensores inteligentes que monitorearán la salud del puente y tomarán una gran cantidad de mediciones en tiempo real, incluyendo la calidad del aire y la dispersión del peso. Los datos del sensor también se implementarán en una maqueta del puente, un gemelo digital, que ayudará a los ingenieros a comprender cómo trabaja el puente a lo largo del tiempo, para mejorar y ajustar los futuros diseños.
En el centro industrial del distrito de Baoshan de Shangái, los peatones ahora pueden caminar sobre un puente de concreto impreso en 3D. Con 26.3 metros de longitud y 3.6 metros de ancho, es una de las impresiones en 3D más grandes de su tipo jamás creada en la industria de la construcción. Compuesto de 68 bloques laterales y 64 bloques para la puerta de enlace, incluye sensores que ayudarán a reunir información sobre viajes para mejorar los diseños futuros.
En tan sólo unos días, China introdujo dos plataformas impresas en 3D, una de plástico y otra de concreto, uniéndose a las pocas iniciativas que ya se han visto en el mercado, como el puente de acero en Ámsterdam o el puente en Madrid.
El proyecto fue dirigido por el profesor Xu Weiguo de la Escuela de Arquitectura de Tsinghua, requirió sólo 450 horas de impresión –aproximadamente 18 días–, dos brazos robóticos y 10 trabajadores; su costo representaría dos tercios de los costos del puente original, en el cual se inspiró, cuya construcción tomó 11 años.
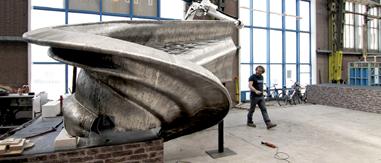
Una de las piezas del puente holandés de acero inoxidable.

HATSNEW.COM
El muro impreso en 3D más grande del mundo.