AGGREGATES INDUSTRY MARKET AND PRODUCTION LINE INTELLIGENCE
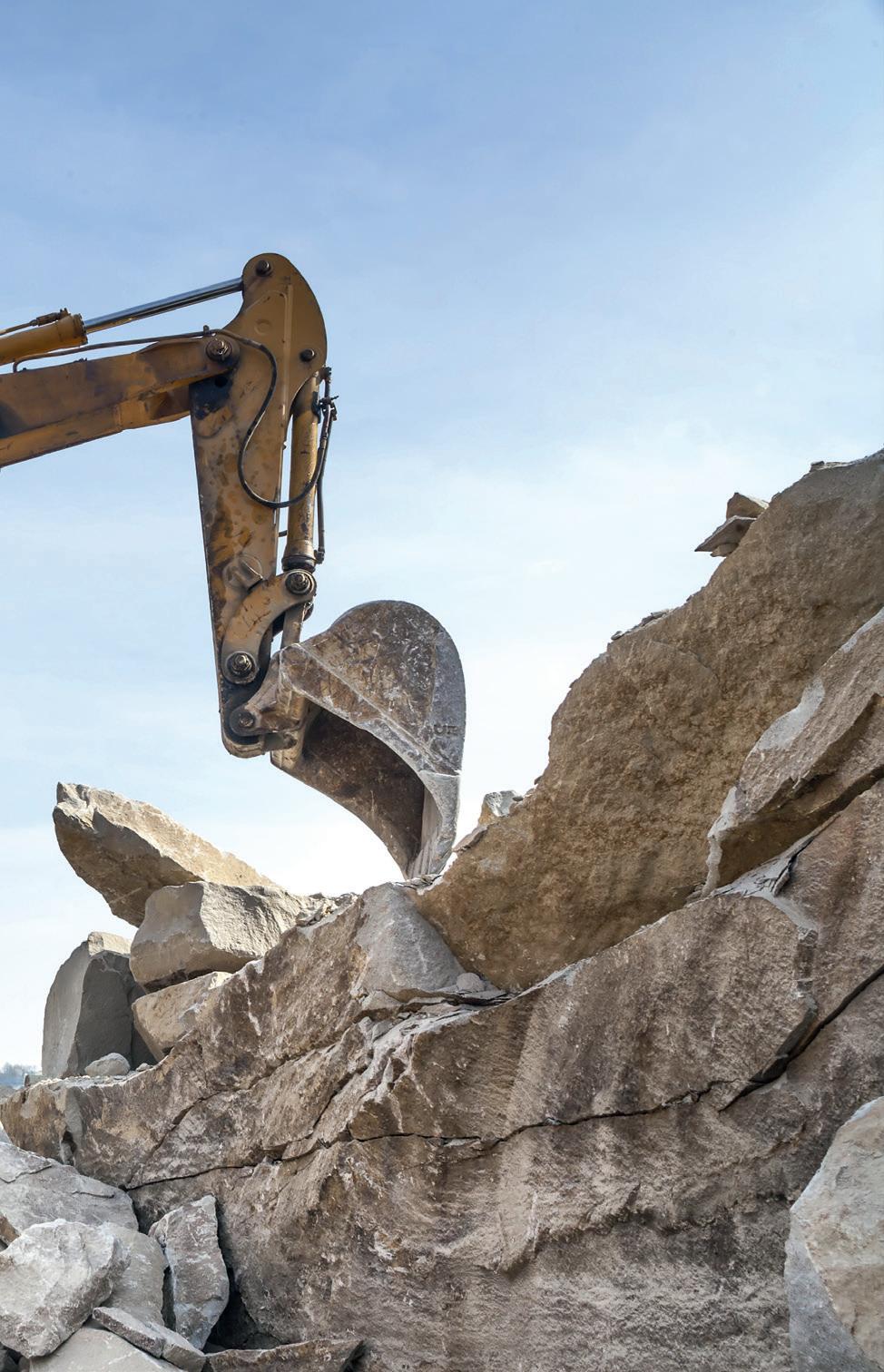
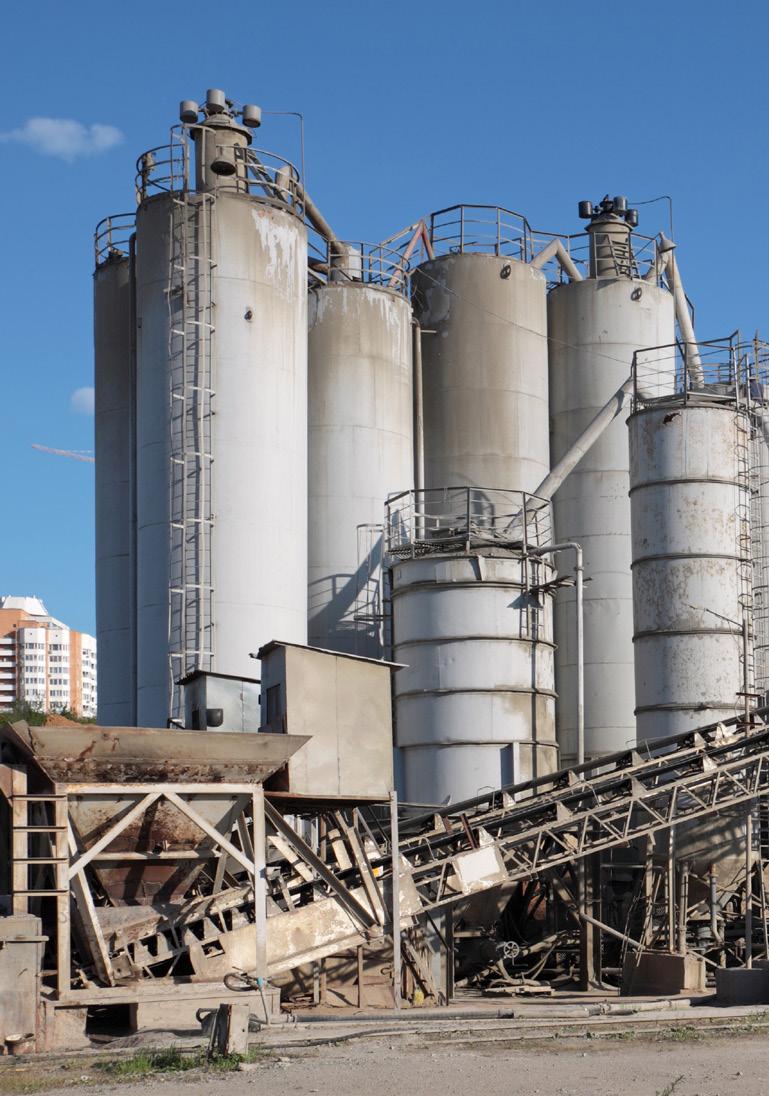
3. Use of this Document Pages 24-26
As part of the development of tools and resources for members, this document is designed to add value to their commercial understanding of specific markets and production line processes. This document, on the Aggregates industry, follows reports on the Soft Drinks industry, Confectionery, the Automotive industry, Material Handling, and most recently, Recycling in 2020.
e. Overview of challenges
EPTDA continually strives to develop relevant tools for its members, helping them stay competitive in a constantly evolving marketplace and business environment.
1. Industry Overview
2. Production Line Intelligence Pages 13-23
This section illustrates the extraction and processing of aggregates for the production of cement with a fully detailed production line schematic on sand and gravel, so as to provide an understanding of what is involved and where the opportunities lie. Key customer challenges, major product groups, typical maintenance, and improvement projects are identified throughout the line, as well as highlighting potential areas of commercial opportunity for the distributor.
EPTDA was founded as the European Power Transmission Distributors Association in 1998 on the initiative of a group of power transmission and motion control (PT/MC) industrialists who believed in bringing together PT/MC distributors and manufacturers on one unique platform. It has since become the largest organisation of PT/MC distributors and manufacturers in EMEA and is one of the most powerful and respected B2B executive platforms for the industry worldwide.
3
This first section provides an introduction and overview to the aggregates industry and gives key background information, market intelligence, and major players within the industry. It has been organised as follows:
b. Market size and coverage
Pages 4-12
OverviewPurposeof this document
d. Current and future market trends
g. Major machine & system builders
This document has been divided into three parts:
The purpose of this document is to provide distribution management and their sales forces with market and production line intelligence on the aggregates industry, primarily in crushed stone, sand, and gravel which is in turn used for cement. This document explores trends, identifies products used in the extraction of aggregates and production of cement, clarifies key challenges, and considers the opportunities and how they can be capitalised.
The opportunities within aggregates, both for MRO and OEM distribution, are significant – a minimum combined ‘scale of opportunity value’ (SOV) of 315m€ has been estimated as available for distribution of MRO Power Transmission products in the aggregates and cement aftermarkets. The final section proposes how the document could be used and provides open-ended questions that can be asked to prospective customers in order to reinforce the knowledge gained in parts one and two and to maximise the available opportunities.
a. Definition, segments within the industry, and market share
EPTDA’s mission is to strengthen its members in the industrial distribution channel to be successful, profitable, and competitive in serving customers to the highest standards. The association takes great pride in its values which focus on being a premier community for qualified members through open dialogue and mutual respect; acting with integrity, honesty, and fairness; and ensuring continuous growth and learning.
c. European sales data and evolution
f. Key producers
a variety of shades and so is often used for decorative purposes.
Aggregates are a collection of naturally occurring loose materials including sand, gravel, and crushed stone that are extracted from sources such as quarries, pits, and for some types of aggregates, taken from the sea.
Type of aggregates3 4 Source Features & application
Occasionally crushed quartzite is used in road construction.
4
Definition, segments within the industry and market share
Metamorphic rock (created by heat or pressure)
Granite
Powerful machinery and explosives are used to mine granite out of the earth.
Limestone
By volume, the consumption of aggregates is second only to the global consumption of water, with an annual production exceeding 50 billion tonnes globally. It is estimated that by 2060 this global figure will rise to 80 billion tonnes.1
One of the most popular types of dimension stone (stone quarried for the purpose of creating blocks or Comesslabs).in
One of the most commonly used types of aggregate in road construction and reinforced concrete, aside from granite and gravel.
Sedimentary rock (created by settlement of particles or organic remains in seas)
Gritstones
Used in construction as building blocks or in the groundwork, making cobblestones and for decorative statues.
Quartzites
Best aggregate for high-grade concrete.
Igneous rock (solidified molten rocks)
In addition to this, with sand and gravel being heavily in demand for the production of cement – a key binding ingredient for concrete, the focus of this latest report will be on these types of aggregates and their end use – construction material, primarily being cement.
Formed when quartzrich sandstone or chert has been exposed to high temperatures and pressures to form a dense, hard rock.
Sourced through the crushing of sedimentary rock.
rivers across the world, are used to build homes, schools, offices, foundations, and transportation infrastructure, providing stability, structural integrity, and added volume.
A decorative aggregate that is harder and more resistant to aesthetic damage than granite.
Can be used for millstones to mill flour, grind wood into pulp for paper, and used for grindstones to sharpen knives.
Basalt
PART ONE Aggregates Industry Overview
Crushed stone
Formed from the rapid cooling of magnesiumrich and iron-rich lava.
Given the wide variety of uses and applications aggregates can have, the market can be difficult to segment. However, for the purposes of this PLI report, the market is best differentiated by type, and has been broken down into crushed rock, fine aggregates (sand), gravel, and secondary and recycled aggregates.
Aggregates are the base component of construction materials, that when mixed with adhesives such as cement or gypsum, form concrete or mortar. The sheer scale of global aggregate production is a direct result of their importance to the built environment. These naturally occurring materials, taken from quarries, pits and
Gravel and ballast do not possess as much strength as their granite counterparts, but they are often cheaper to purchase.
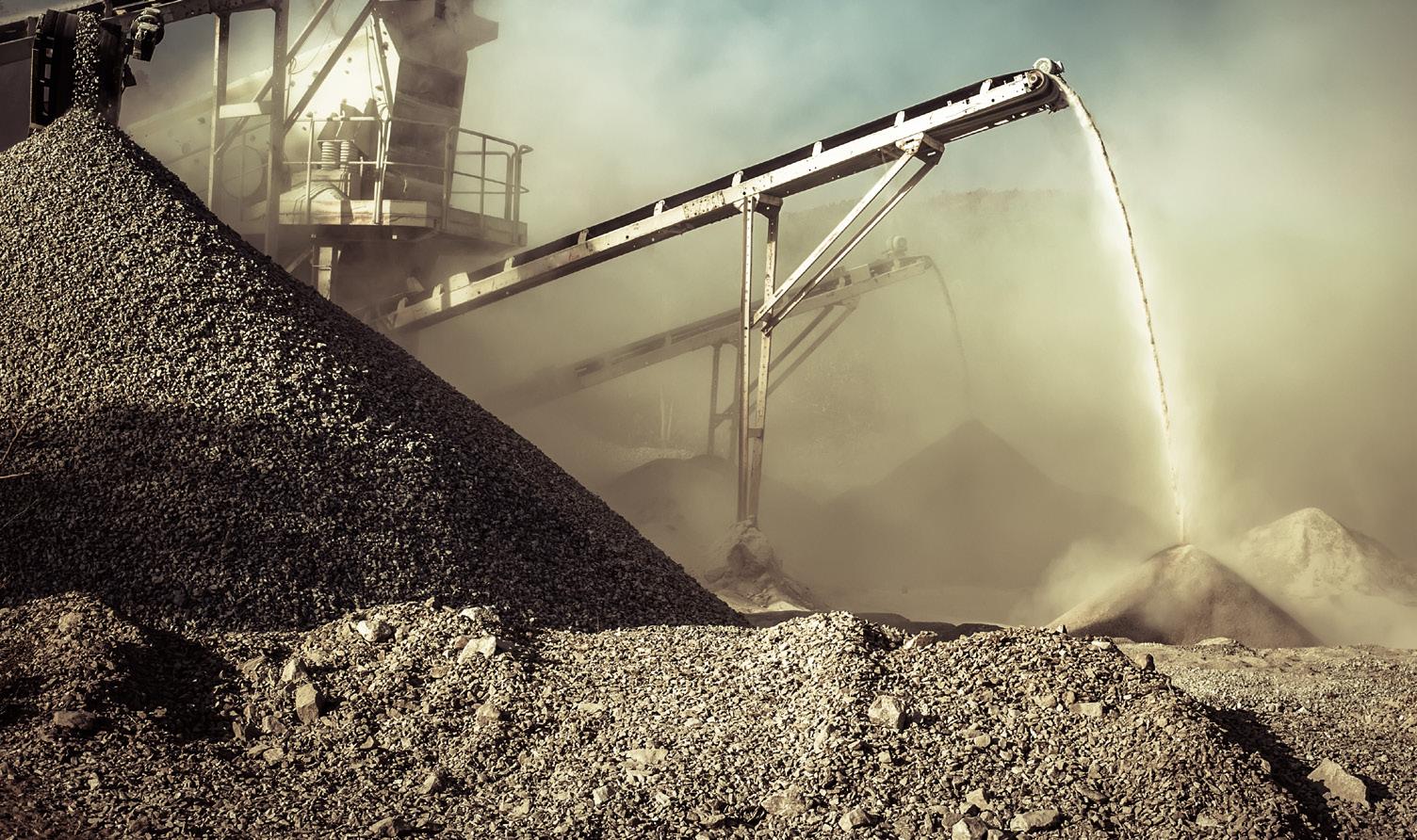
By-products of industrial processes such as blast or electric furnace slags, or china clay residues.
processing of inorganic materials
Aggregates sourced from mineral waste (generated during the extraction and beneficiation of ores and minerals).
demolition waste or engineering
Aggregates that from the previously construction and works.
Sand & Gravel Crushed Rock Recycled or Reused Marine-dredged & Manufactured Aggregates Aggregates by type, 2018 5 12% 4% 38% 46% In 2018, producedEurope 3.3 billion tonnes of aggregates. know?youDid
Low-cost and effective, they are two times less expensive than granite, but not as strong.
aggregatesSecondary
Fine Sandaggregates
Gravel also has low radioactive content.
Type of aggregates Source
are sourced
used in industries e.g.
5
/ ballast These are sourced by sifting through quarried rock and crushing natural stone.
Used for foundations and concretes as well as other products used in road construction.
It is a key part for filling in cement concrete, asphalt concrete, railway track slag, mortar, and other foundations.
Natural aggregates
60% of demolition and construction materials are recycled or secondary aggregates e.g. china clay waste used as mortar and concreting sands, or power station ash as a cement substitute with ready-mixed concrete.
aggregatesManufactured
Sand is primarily sourced from shallow water such as lakes, rivers, and occasionally sea-beds.
aggregatesRecycled
GravelGravel
Secondary or recycled aggregates
40% 15% 25% 10% 5% 3%Railway2%BallastArmour Stone ConcretePrecastConcreteArchitecturalProductsAsphaltProductsReady-mixedConcrete StructuralMaterials
Market size and coverage
6
Of all global regions in 2018, Asia took a majority shareaccounting for 65%. Much of this can be attributed to the construction of roadways necessary to develop the region’s travel infrastructure and economy. India specifically, is expected to cover nearly 50,000 kilometres by the end of 2020.7 However, it is China that leads the region and, in turn,
To fuel its rapid and continued urbanisation, in three years, China consumed more cement than the United States did throughout the entire 20th century.8 The impact on China’s demand for aggregates is accordingly immense, with China consuming more than 20 billion tonnes of general aggregates in 2019 alone.
In 2018, the global aggregates market was valued at USD 432.5 billion (EUR 366.5 billion) and is expected to grow at a CAGR of 6.5% from 2019-25.6 This growth will most likely be driven by demand for usage in concrete and cement manufacturing, road base and coverings, and railway ballast.
globally.2010 2014 2018 200025003000150010005000 China India USA Brazil Turkey FederationRussian Indonesia KoreaSouth Japan EU27 + UK Global production of cement (million tonnes)11 Distribution of global production of aggregates, 20179 Aggregate end use by construction material, 201810 Asia Oceania1%Russia + CIS Central & AmericaSouth Middle East NorthEuropeAmericaAfrica
7
close proximity of aggregates to the end user, where cement plants can even be connected via 2 – 4km long conveyor belts.
European sales data and evolution
In Europe, aggregates remains by far the largest extraction industry. Throughout the region, production amounts to just over 3 billion tonnes of aggregates per year. The result is an estimated annual turnover of 15 – 20 billion euros, with Russia, Germany, Turkey, and France taking the top four places in terms of production by country.
Given its prevalence in construction, demand for housing acts as a strong driving force for the aggregates industry throughout Europe. Yet in less densely populated countries, such as Finland or Sweden, a higher share of aggregates is used for road construction as opposed to other countries where housing is a greater priority. As such, whilst demand for aggregates is consistent, the end use is often influenced by the policies and priorities of governments across Europe e.g. better transportation, new housing, or other civil engineering services.
On the supply side, the market is extremely fractured. Dominated by Small to Medium Enterprises (SMEs), with an average of only seven employees at every extraction site, they typically produce around 115,000 tonnes each.12 This may be in part due to the necessity for
Production6005002001000300400700800 of aggregates, by country, in 2018 (million tonnes)13 Number of extraction sites, by country, in 201814 2000100050001500250030003500
to 30,000 tonnes of aggregates, roads and highways are heavily dependent on an uninterrupted supply of raw material and the availability of cement for making concrete.18
Current and future market trends
there are significantly fewer cement plants than sites sourcing, or processing aggregates. It is estimated that there are just over 300 plants producing cement clinker in Europe.20 This is due to the vast quantity of clinker that can be produced on site by these cement plants, with an annual production of 0.5 million tonnes, creating strong competition between the European market leaders.
8
Furthermore, a correlation has been seen between the baby boomer population (those born between 1946 and 1964) as they have gotten older, and an increase in second homes and healthcare facilities to support the ageing demographic. The changing types of infrastructure and built environment required has therefore meant that demand for raw materials has only continued to accelerate as both new builds and updates to outdated infrastructure are needed to handle the increasing population with all of its consequences (houses, traffic, social services, trade etc.).16
Cement production (billion tonnes), 2005 201815 Did know?you The costproductionaverage
of cement is 83€.2.54.53.51.50.543210 20122005 2014 20182010 2016
Of the 26,000 sites across Europe producing aggregates, many are increasingly turning to the automation of machines used on-site. On their electric site project, Volvo CE (Construction Equipment) have been test-piloting new machines to electrify for a single tonne
Alongside the growing population, increasing wealth and expenditure has meant now more than ever, car ownership has grown, with current road and transportation infrastructure struggling to keep up.17 With nearly 1km of roadway requiring up
Taking up nearly 60% of the market, residential and nonresidential buildings are the driving force behind need for the supply of aggregates for the production of cement and concrete. This has all been propelled as Europe’s population has steadily increased year on year, contrasted with the number of people per household declining. In addition to increased need for housing, rising populations create further demand for non-residential buildings to support the societal infrastructure – from schools, offices, and shops to hospitals, for example.
Consideration of where that supply is coming from is therefore a significant factor, whereby cost of transportation is directly related to distance from supply to end destination. Bulk shipping has made transportation of aggregates more accessible, whereas land transportation beyond 250km by road is often not considered economically viable.19 This is one of the reasons why the aggregates industry is so fragmented and dominated by Comparatively,SMEs.
Covid-19
Due to the nature of aggregates and a need for close proximity, the aggregates industry benefits from short transportation distances enabling the “European Aggregates Industry [to produce] in Europe and for Europe”.
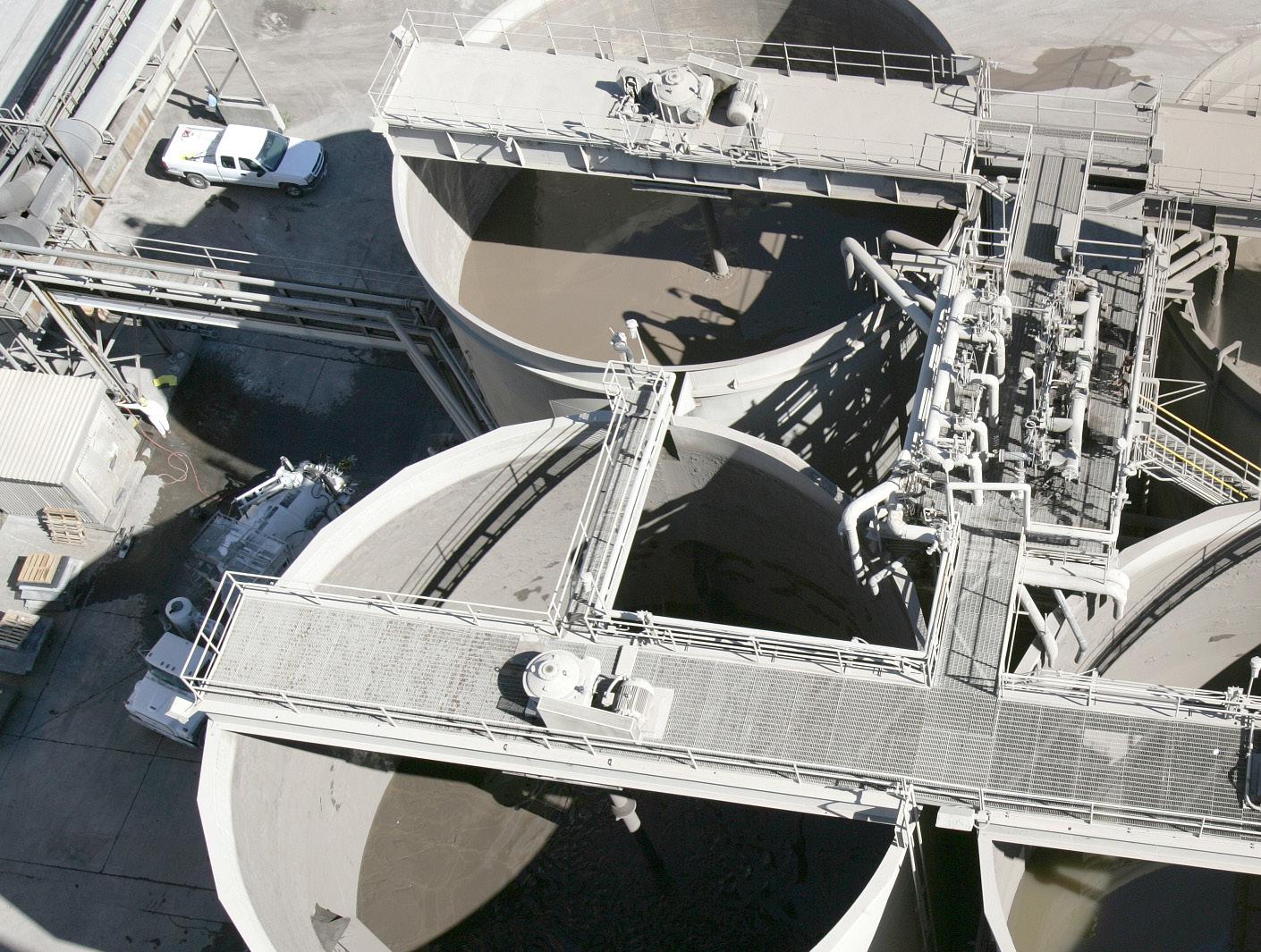
Aggregates by application, 201925
each transport stage in order to reduce on-site accidents, emissions, unplanned downtime, and ultimately improve overall efficiency.21Otherways
Challenges
Residential Buildings
WaterwaysRunways,Roads,Railways,
However, adapting to the requirements Covid-19 has brought about with every-day operations (social distancing and new safety and hygiene protocols) has impacted the demand for aggregates. As a result countries across Europe have reported varying degrees of decline in their annual production tonnages.26
of introducing automation to extraction sites have been to adopt predictive maintenance in drilling to collate data for real-time analysis of minerals available, all whilst working under extreme and harsh environments. Equipment on-site must be able to cope and withstand extreme temperature variations, high-pressure water, dust, and fluctuating shocks and vibrations.22 Predictive maintenance enables operations to react to potential alarms and incidents quickly before machine damage or injury can take place, which could then in turn be more costly than identifying potential points of weakness before that part breaks, reducing the likelihood of downtime.
Whilst in 2019 new construction for housing was a key driving force for the construction market, as the shift moves to a need for non-residential buildings such as hospitals, it has been estimated that 2020 will have seen a fall in construction output by about 10%. Therefore the uncertainty of further lockdowns and changes to systems and processes impacting construction projects will further affect how the construction market, and in turn affected industries like aggregates, will rebound.27
Another area of the aggregates industry that has been growing steadily over the last decade is demand for recycled or secondary aggregates. This is partly driven by EU directives to recycle around 70% of construction and demolition materials by 2025, increasing the availability of recycled supply.23 With increasing consumer preferences for environmentally friendly materials, and as natural resources deplete substantially, the recycled aggregates market is expected to see a CAGR market growth of 6% between 2020 and 2027.24
Schools(Hospitals,BuildingsSocialInfrastructureetc.)
Commercial Buildings
Much like steel, from the Production Line Intelligence report on Recycling, concrete is 100% recyclable after demolition. With primary raw materials so heavily in demand, recycled concrete can be re-used as a recycled aggregate in the production of new concrete, or alternatively be used unbound in applications such as road Althoughconstruction.36demandfor recycled and secondary aggregates is set to rise over the next decade, with the credibility of recycled aggregates increasing, low confidence in the strength and capability of recycled aggregates is a reason why it still only has 12% market share. Furthermore, with the lack of infrastructure in place to encourage the use or demand for recycled concrete, the cost of processing followed by transportation costs further compound this meaning that many still favour natural over recycled or secondary materials.37
The volume of aggregates extracted, particularly from land quarries, has an impact on biodiversity, land losses through erosion, change in water flows, flood regulation, water supply due to the lowering of the water table, and the climate – directly through transport emissions and indirectly through cement production.
Another way in which the aggregates industry is implementing recycling into its processes is regarding the way that it consumes water. Nearly 60% of the 26,000 aggregates sites mentioned earlier have materials washing activities held on site, with it estimated that in 2017 the industry was accountable for just over 10% of total water use in Europe.30 31
Another way some cement plants have tried to reduce their carbon footprint is through something known as ‘carbon capture and storage’. This is where the carbon generated is captured for storage or sharing with the chemicals industry, or for it to be converted into fuels. Examples of some projects include catch4climate by HeidelbergCement who in 2019 began researching ways pure oxygen can be used in clinker burning technology for heat generation.34 Cemex's FastCarb project and HeidelbergCement's catch4climate projects are just some of the ways that the European cement industry are looking to achieve the objective of carbon neutrality by 2050. In 2019, almost 8% of total EU emissions came from cement clinker production.35
The sand that is found in most deserts is predominantly unsuitable for concrete and land reclaiming, as the wind erosion process forms round grains that do not bind well. On the other hand, marine aggregates need to be thoroughly washed to remove salt. If the sodium is not removed, a structure built with it might collapse after a few decades due to corrosion of its metal structures. For concrete production, sand and gravel extracted in-stream requires less processing and produces high-quality material.28
The environment and zero emissions in aggregates
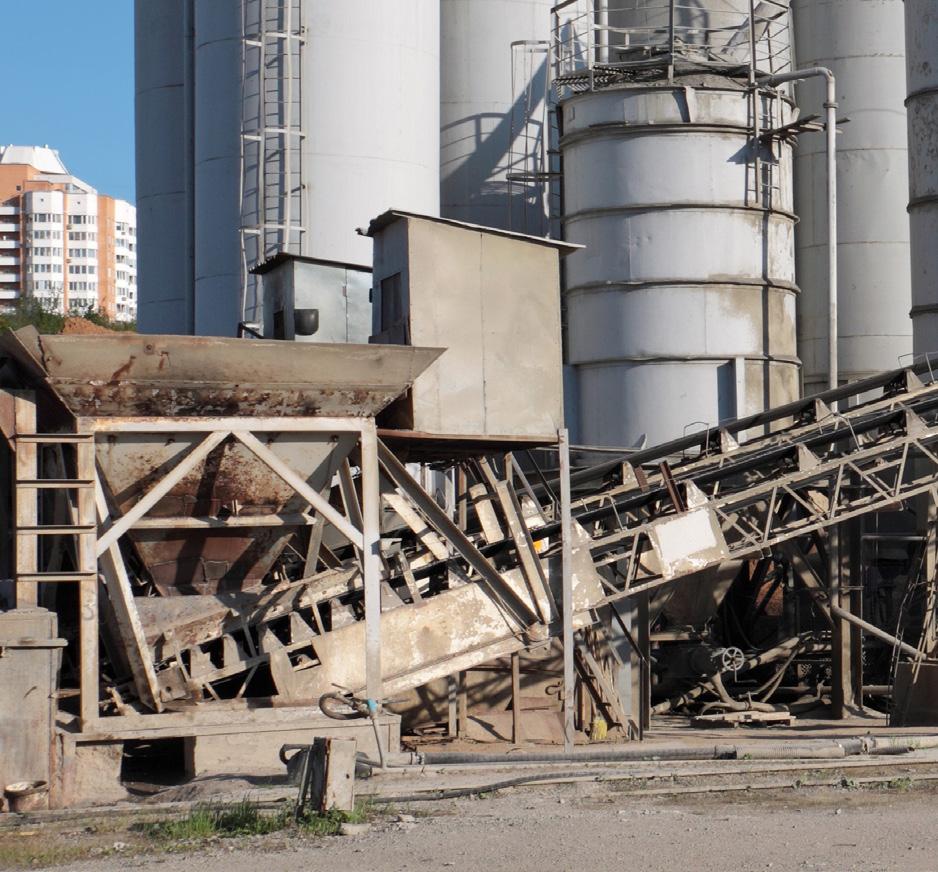
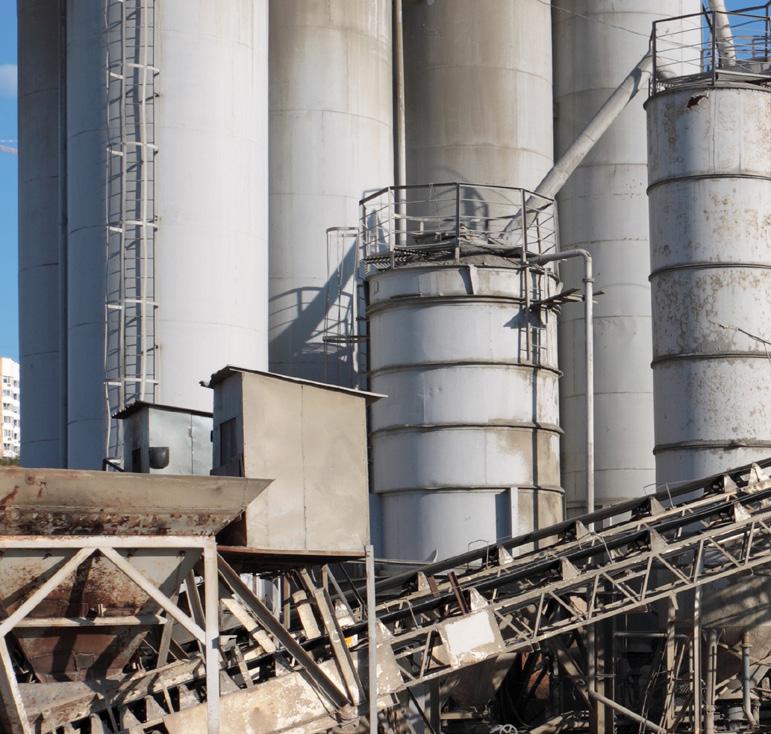
Recycled and secondary aggregates
Reducing the consumption of organic aggregates and looking at alternative sources such as recycled aggregates, has been one way that the industry is evolving and adapting to limit the effects extraction of aggregates and the production of concrete has on the environment. Consequently, demand for recycled or secondary aggregates is expected to rise. Germany, for example, recycles 87% of its waste aggregate materials.29
As a result, the industry has come under heavy criticism with how it deals with the global issue of water scarcity, water efficiency, and wastewater management, which it so greatly contributes to. One way that the industry has tried to respond is with the way it has re-purposed quarries that have been put out of action. For example in Dalarna County, in Sweden, a limestone quarry was transformed into a concert venue, whilst in Portugal, football club Sporting Clube de Braga’s stadium was carved out of a former granite quarry and is now known as ‘A Pedreira’ (The Quarry).32
Global buildings material leader, Cemex, has looked to mitigate its contribution to global emissions through their FastCarb Project with the ambition to deliver net-zero CO2 concrete (reducing the impact of the CO2 trapped inside many concrete structures) by improving the quality of the recycled aggregates that are used.33
As will be seen in the extraction and processing schematic in this report, several stages of crushing may be needed to reach the desired end aggregate size. Waste-product or aggregates that do not meet the granularity needed are collected at each stage and must be stored or sold for non-construction end users.38 This can result in high storage-facility costs, as well as take up space on-site in areas that could be potential extraction-points.

8
9
3
Key producers
1 LafargeHolcim 345.2 Switzerland 220 Anhui Conch Cement 217.2 China 32 HeidelbergCement 185.4 Germany 141 China National Building Materials (CNBM) 176.2 China 94 Cemex 91.6 Mexico 61 UltraTech Cement 91.4 India 39 China Resources Cement 79.3 China 133 Votorantim Cimentos 70.8 Brazil 59 Taiwan Cement 69.0 Taiwan 30 InterCement 53.5 Brazil 42
Global key producers of cement
Other leading cement producers include CRH (Ireland), Buzzi Unicem (Italy), Eurocement (Russia), and Dangote Cement (Nigeria).
6
Total Cement Produced (million tonnes, in 2018) BusinessPrimary Geography
The top ten global cement producers are ranked as:39
No. of Plants (globally)
2
5
Value Rank (as of 2018) Company
Waste production dependent on size of aggregates needed
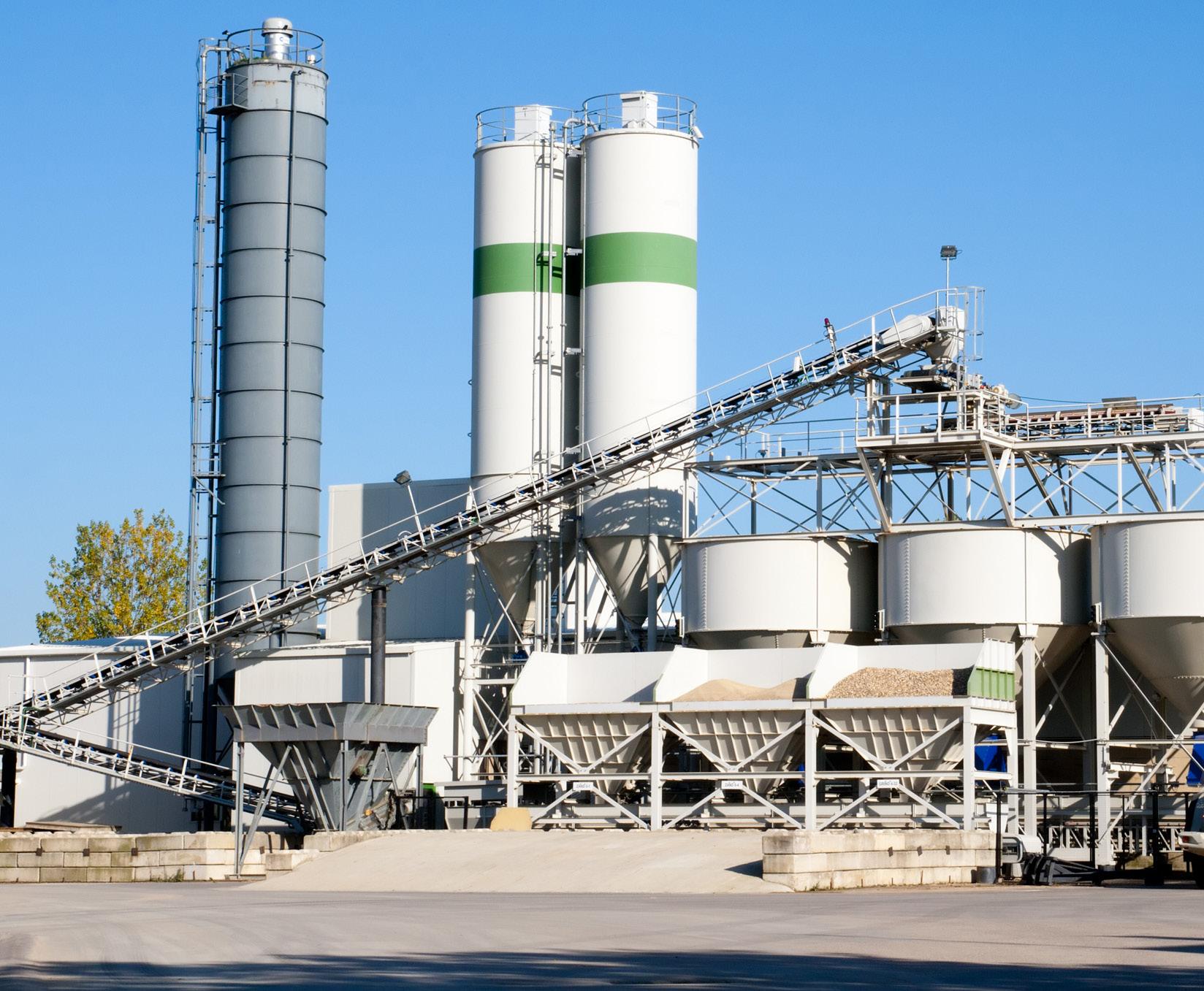

10
7
4
Promecon | www.promecon.com | Barleben, Germany
Claudius Peters | www.claudiuspeters.com | Hamburg, Germany
Operating in the cement, mining and power industries, Loesche pioneered spring-loaded air flow mills, known still today as Loesche mills. They are the global market leader for vertical and turnkey grinding mills.45
FLSmidth A/S | www.flsmidth.com | Copenhagen, Denmark
Köppern | www.koeppern-international.com | Hattingen, Germany
A global leader in conveyor and storage technology for hot and abrasive bulk materials, Aumund develop custom systems for the cement production process, including the extraction and preparation of raw materials, clinker grinding and transportation and storage.40
With over 150 years’ experience, Gebr. Pfeiffer are specialists in plant solutions for cement, coal, lime, gypsum and ceramics. As the inventors of mill drives with more than 10,000 kW, they offer a wide range of machinery for grinding, separating, drying and calcining. Their ready2grind system provides a compact modular mill system to help bring cement closer to the end user with quick and easy transportation.46
KHD | www.khd.com | Cologne, Germany
One of thyssenkrupp’s 650 subsidiaries, Polysius manufacturers cement mills, kilns and cement factory automation systems, particularly machines for crushing, grinding and processing raw materials. 47
Schenck Process | www.schenckprocess.com | Darmstadt, Germany
Aumund12
thyssenkrupp Industrial Solutions specialises in the engineering, construction and service of all industrial plants and systems, and one of the few in the cement industry to supply a full range from crushing to storage, packing and loading.50
Polysius | www.thyssenkrupp-industrial-solutions.com | Beckum, Germany
Loesche | www.loesche.com | Düsseldorf, Germany
| www.aumund.de | Germany
Gebr. Pfeiffer | www.gebr-pfeiffer.com | Kaiserslautern, Germany
Schenck Process are leading engineers and suppliers of a variety of pneumatic and mechanical chain conveyors, industrial screens that are used in the cement, plastics and food and drink industries.49
With expertise in energy generated by hydropower, paper production, drive components and digital applications, Voith produce drive solutions for bucket elevator systems, conveyors, milling machines and combinations of fabrics, rolls and roll covers. Voith reported sales of 4.2 billion euros in 2019.51
thyssenkrupp Industrial Solutions AG www.thyssenkrupp-industrial-solutions.com| | Essen, Germany
From pneumatic conveying, grinding, clinker cooling and mixing systems to raw material storage and bagging, Claudius Peters offer a wide range of technology suitable for cement, coal, alumina and gypsum plants.41
Working towards zero emissions in mining and cement, FLSmidth is a global supplier of crushers, vibrating screens and conveying systems for bulk materials. In 2019, FLSmidth generated revenue of DKK 20.6 billion.42
With sales of 146.3 million euros in 2019, KHD are a global supplier of cement plant technology, equipment and services. They develop energy-efficient and environmentally friendly solutions for the grinding and pyro-processing stages of cement production, as well as complete new cement production lines.43
Köppern specialise in high pressure grinding and roller press technology for industries including cement, minerals and metal working.44
Voith | www.voith.com | Heidenheim an der Brenz, Germany
Promecon specialises in measurement and flow systems for the power, steel, waste and cement industries. Their technologies aim to lower emissions and energy output across the entire cement production process.48
Major machine & system builders
Thisindustry.section
The processing of aggregates such as granite that are used for decorative purposes will also have a greater emphasis on cutting (as opposed to crushing and grinding found in cement production) so to preserve and keep the raw material intact. Nonetheless, the key stages described here will be common to most types of facilities and there will be similarities that can be seen and carried across many segments of the aggregates
Introduction
This process, whilst being typical, does not represent all processing and extraction of aggregates. This is because actual plant processes may vary according to the type of raw materials and plant scale - for example large-scale blasting for limestone, and the dislodgment and removal of sand and gravel from the seabed - as well as the resulting end product.
PART TWO Cement production process – Market Intelligence
This schematic describes the typical process used for the processing of aggregates such as sand, gravel and limestone for the production of cement.
With the high demand for cement, and the highly mechanical process underpinning the production of cement for use in concrete, this production line focuses on the extraction and processing of limestone used in cement.
also highlights the key customer challenges specific to cement production. It describes the key product categories used in the process and typical projects in maintenance, repair and overhaul that are often undertaken in such a plant. Key sales opportunities are identified in relation to products and maintenance projects that are supported by distributors with real technical expertise.
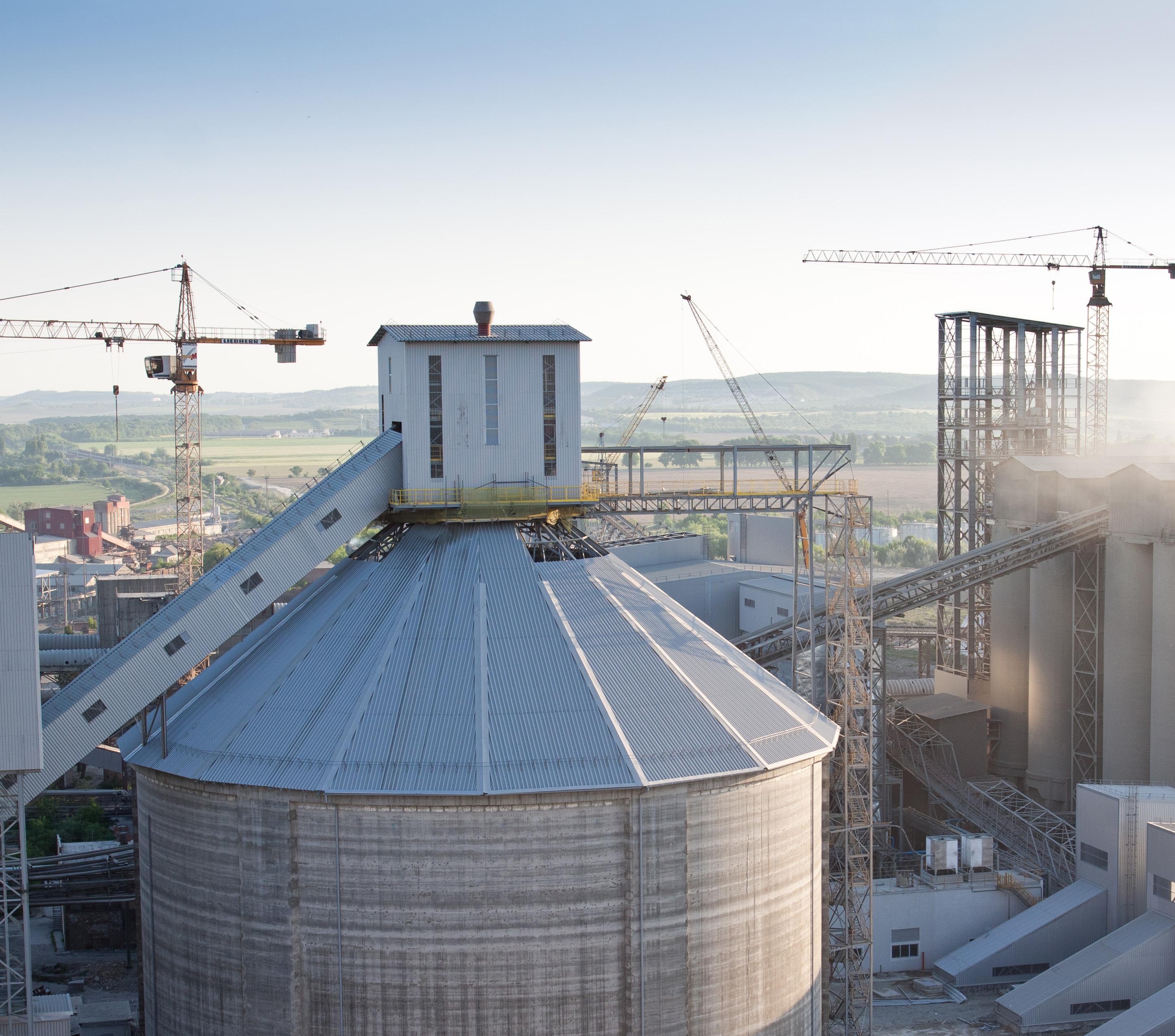
crushing & screening
14
Bulk CementContainerBoogie(BBC)Bulktankerbagtrucks
Ready-mix concrete
• OPC
The raw material is washed in a washing mill to remove any impurities before being sent to grinding mills where they are completely mixed to form a paste known as slurry before undergoing further grinding. The slurry is then fed into a collecting basin where the composition can be adjusted as required.
Excavation
Cement (10-15%), water (15-20%) and sand and gravel (60-75%) are added to a concrete mixer before being taken to a nearby site for use.
Taking place at the quarry, detonators are used to expose the limestone into smaller transportable pieces of rock. These may then be further crushed on site before being transported by road or via 2-4km of conveyor belt to the cement plant.
Raw materials preparation
Cement Production
• Bulk Boogie Container (BBC)
(JawGrindingcrusher) Silos concreteReady-mix
Transportation
TransportLimestone
material e.g. sand and clay, is proportionally added to the finely ground limestone to create a raw dry mix and crushed again.
Process
Jaw or cone crushers use compression and impact to break the rocks. These are then separated based on their size and may be crushed several times until they reach the desired size. The stones are then washed to remove any remaining clay particle.
bulk tanker
1011123 3
• Cement
bag trucks
Other raw materials proportionally added: Wet process
Other raw materials proportionally added: Dry Additionalprocessraw
Excavation of raw material e.g. limestone
Process
Clinker treatment
The cooled clinker is ground finely in a ball or tube mill –using pressure and shearing forces – with powdered gypsum added as a retarding agent (to regulate the setting time).
The ground cement is conveyed, often using bucket elevation conveying systems, for storage in silos before being distributed in bulk or in bags to the sites where it will be used.
Cement storage in silos
The fine powder (known as raw meal) is preheated through various chambers before being sent to the kiln.
Air is admitted at the base of the rotary kiln where the clinker is collected, before moving along a grate cooler so that the clinker can be cooled from 1200°C down to 100°C.
The kiln is supported by concrete columns and roller bearings in a slightly inclined position. The pre-heated raw meal from the dry process – or the slurry from the wet process – is injected into the kiln from the upper end.
Cooling
Grinding (Ball mill)
Screening
Wet-processing mix Ball mill Cement roller press elevationBucket Dry-processingmix Pre-heatingtowerRotary kiln cooolerGrate ** Please note that all figures represent the estimated Scale of Opportunity value (SOV). rawVerticalmill 4 6 987 5
The lower part (clinkering zone) has a very high temperature causing the raw material to react and fuse together to form small and hard stones known as clinkers (varying between 5-10mm in size).
Rotary kiln
Pre-heating tower
The mixed clinker undergoes another round of grinding through a cement roller press where two rollers rotate in opposite directions, further grinding the cement powder through pressure force.
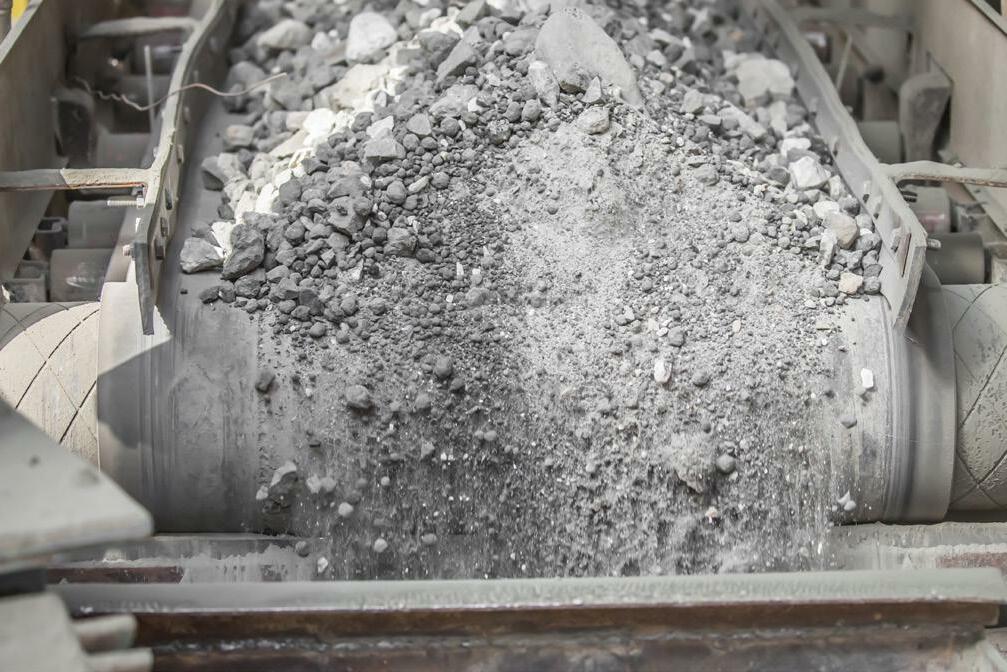
15
Pyro processing
Finish (Cementgrindingrollerpress)
Excavation & grinding - key product groups
• Replacement hoses for one backhoe truck. SOV: 5k - 10k€.
• Hydraulics - brakes and pumps
Excavation & grinding - critical projects
Raw materials preparation
• Double-layer jackets
Key critical projects within the preparation stages of aggregates or in the case of cement, primarily limestone from the quarry and the initial steps at the cement plant, have been highlighted along the schematic to help make it easy to identify which areas of the process have the most opportunity. This includes the excavation and grinding, crushing and screening, and the creation of a dry or wet mix.
• Fans
16
(JawGrindingcrusher)
• Seals
• Due to the dusty environment, double layering of jacket wrapping helps the belt become more resistant to wear and degradation, allowing for a margin of slip in case of damage from jamming.
Excavation
• Lubricants
• Trommel
• Replacement of bearings: SOV: 1.5k€.
• Where connected, there may be between 2 - 4km of conveyor belts between the quarry site and cement plant.
• Belts - powerband belts, synchronous belts, toothed belts, v-belts
• Bearings - axial roller bearings, pillow blocks, shaker screen bearings, spherical roller bearings
Explaining the opportunities and projects
• Hydrostatic drive
Cement Production
• Tensioners
• Bi-annual replacement for a large section of 1" v-belt (there may be up to 8 - 10 multi-banded belts per machine). SOV: 8k - 10k€.
• Pillow blocks used on conveyors. SOV: 400k - 500k€.
• Hose - hose assemblies and adapters
Wet-processing mix
• Bearings for vibration screens must be shock and vibration resistant.
Screening
• Typically screen bearings are changed every 1 - 2 years depending on the age of equipment and how regularly lubricated they are. Annual replacement for a simple quarry. SOV: 5k - 10k€.
• Seals
• Fans
• Hydraulics - motors and pumps
Dry-processing
Opportunity
Dry & wet processing mix - key product groups
• Bearings - ball bearings, cylindrical bearings, spherical roller bearings, tapered roller bearings
• Hose assemblies and adapters
• Lubricants
• Belts
• Conveyors can be powered by a mixture of chain and rubber belts.
• Bearings - axial roller bearings, ball bearings, cylindrical roller bearings, pillow blocks, spherical roller bearings, tapered roller bearings
rawVerticalmixmill**
• Replacement of two bearings per wheel, where there may be up to 6 wheels. SOV: 20k - 40k€.
Crushing & screening - critical projects
Dry & wet processing mix - critical projects
Crushing & screening - key product groups
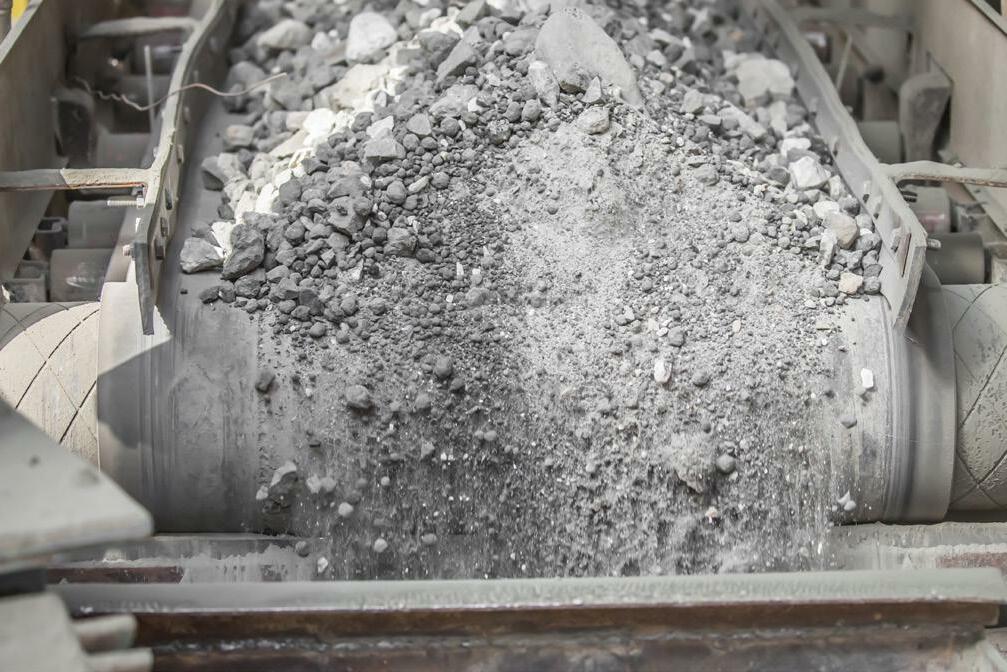
• Belts - synchronous belts, v-belts
• Couplings
• Trommel
• Fans and fan drives
Please note that all figures represent the estimated Scale of value (SOV).
• Hose and hose fittings
Raw materials preparation
17
• Motor gear
• Bearings - axial roller bearings, plain bearings, spherical roller bearings
• Gearbox
• Pneumatics
• Replacement of rotary chain, sprockets and motor gear. SOV: 22k€.
• Sprockets
Silos
Pyro processing & clinker treatment
• Chain
• Replacement of conveyor chain, sprocket segments and hubs, and bearings. SOV: 45k€.
• Due to the slow speed and high torque, a high capacity and large, heavy-duty belt is required. SOV: 2k - 3k€.
18
Clinker treatment - key product groups
• Bearings - cylindrical roller bearings, spherical roller bearings, tapered roller bearings
• Belts - synchronous belts, v-belts
• Conveying - bucket elevation
• Replacement of bearings often needs a production stop of 2 - 3 days.
• Electric motor
Cement storage (silos)
• Belts - synchronous belts, v-belts
Grinding in a ball mill or cement roller press
• Bearings - pillow blocks and spherical roller bearings
Key critical projects within the pyro processing and clinker treatment stages have been highlighted along the schematic to help make it easy to identify which areas of the process have the most opportunity.
• Ball mills are more commonly found in smaller plants than vertical roller mills.
• Chain
• Hose assemblies & adapters
• Gearbox
• Sprockets
Explaining the opportunities and projects
Cement Production
Rotary kiln - key product groups
• Replacement of spherical roller bearings for at least two large rollers in the hydraulic roll press. SOV: 10k - 30k€.
• Replacement of 2 pillow blocks for 1 shaft. SOV: 1k€.
• Screw compressor
Clinker treatment - critical projects
• Fan drives
Rotary kiln - critical projects
elevationBucket
Pre-heatingtowerRotary
Cement roller press
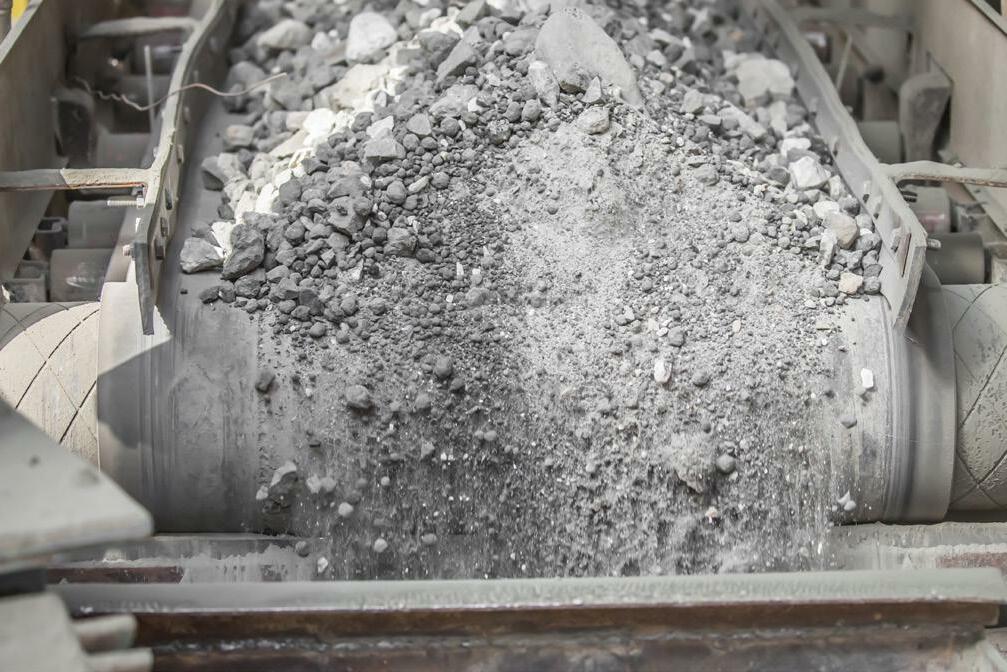
19
kiln cooolerGrate ** Please note that all figures represent the estimated Scale of Opportunity value (SOV).
Pyro processing & clinker treatment mill
Ball
• Pumps
concreteReady-mix Bulk CementContainerBoogie(BBC)Bulktankerbagtrucks
Key critical projects within the transportation stages have been highlighted along the schematic to help make it easy to identify which areas of the process have the most opportunity.
• Chain
Cement Production
• Hydraulic drum
Transportation
• Bearings - spherical roller bearings for conveyors, tapered roller bearings for vehicles
• Conveying - bucket elevation
• Electric motors
• Screens
• Screw compressor
• Agitator / mixers
Transportation - key product groups
Explaining the opportunities and projects
20
• Belts - synchronous belts, v-belts
• Gearbox
** Please note that all figures
General - key product groups
General - key critical projects
• Drive chain, motor and gearbox replacement every 18 - 20,000 hours of operation. 1k - 2.4k €.
• Air conditioning control
• Belts - synchronous belts, v-belts
General
• Replacement of bucket elevator chain following 812,000 hours of operation. SOV: 80k - 100k €.
• Replacement of rotary or off-set chain following 1820,000 hours of operation. SOV: 10k - 15k €.
• Operating in highly contaminated environments requires regular greasing and maintenance.
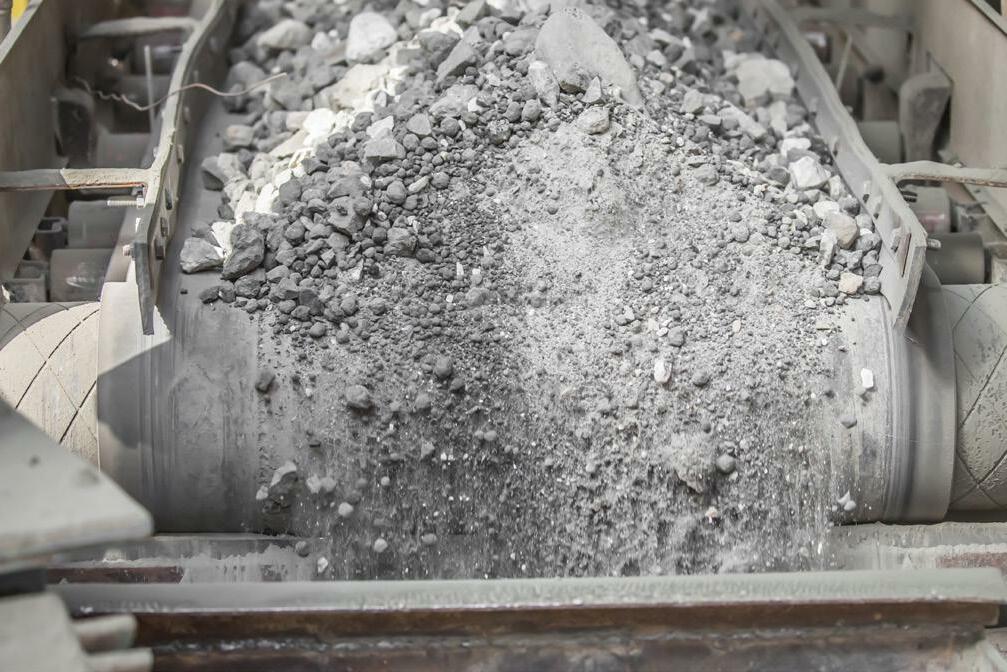
• Chain
• Some sites have control rooms for labs or testing on-site.
• Replacement of reclaim chain. SOV: 20k - 40k €.
• Often plants are not just looking for the parts, but also for the servicing and maintenance - typically a special safety license is needed in these cases.
• Scraper chain, which can be between 30 - 60m in length replacement. SOV: 80k - 150k €, including scrapes and sprockets.
21
• Long-term contracts for MRO needs are often favoured as when issues arise the problem needs to be fixed fast and within a few hours to reduce downtime. represent the estimated Scale of Opportunity
value (SOV).
production process – ‘Putting it all together’
of PT aftermarket sales across the aggregatesEuropeanindustry200m€115m€
The approximate value
The approximate value
22
of PT aftermarket sales in the European cement production industry
Cement
Cement Production
Estimated cement production costs, 201654 Energy Labour and fuel costs MaintenanceRawmaterials Bearings Chain Fluid (Hydraulicspowerandpneumatics)Drive-motorsandgearboxesBelt Seals Couplings aftermarketvalueApproximateofbearingssales40m€ ** Please note that all figures represent the estimated Scale of Opportunity value (SOV).
Production costs vs average selling price of cement
Of the 309 cement production sites across Europe53, each site produces an average of just over 0.5 million tonnes of cement annually. This means that of the 22% spent on maintenance, the production cost for this can be anywhere between 3.8 – 14.3 million euros per site.
23
Proportion of replacement products in the cement production line
With a big demand for aggregates in the production process of cement, in 2017 it was found that the average selling price of cement in Europe was around 60€ per tonne, compared with its production cost ranging from 35€ to 130€ per tonne.52 This was highly dependent on the individual plant and whether carbon capture technology e.g. post-combustion or oxy-combustion techniques were used.
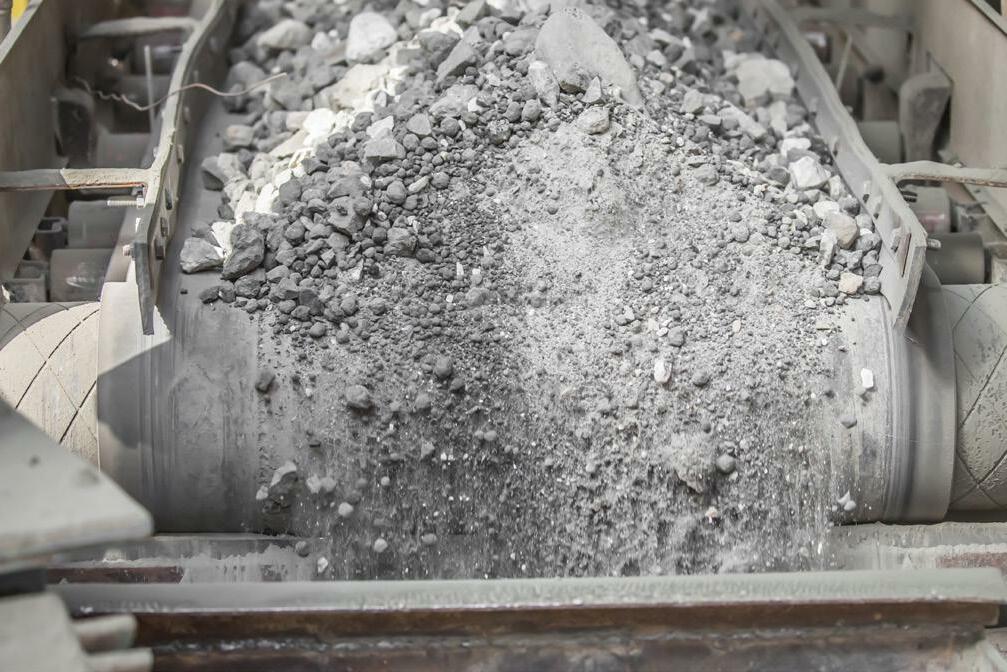
• What kind of questions will you ask (in relation specifically to who will be seen)?
• Do they have in-house maintenance engineers?
The 'Excavation Site' or 'Processing Plant'
Do the system suppliers provide aftermarket warranty service?
• What do you know about them already? (hint: search LinkedIn)
Its scale in terms of capacity, output etc?
• What is your proposed agenda?
An excavation site of raw materials with crushing and grinding capabilities?
• What are you visiting?
• Who decides on purchasing?
For many of these questions you may already know the answers. Others might be used on a regular basis when you visit customers and prospects in other industry sectors. It is meant as a resource to act as a prompt and reminder allowing your business to fully capitalise on this market intelligence and production information.
• What kind of support material do you need to take with you?
BreadthPresentationExploratoryofservice
Preparing – before the visit
The size and throughput?
The people to meet
Is this then conveyed directly or transported by road or rail for processing?
• How old is the facility?
• Who are you going to see?
• What is your initial summary as to the main challenges they face in relation to purchasing the types of products you can supply?
There are three parts that deal with:
b. The people to be seen and which department
• What is their role or speciality (facility manager/ maintenance manager/technical manager and do they cover maintenance, repair and purchasing)?
• What are your primary objectives for the meeting – what do you want to achieve?
Using this document to develop business
24
The stages of the cement process it has (raw materials preparation, pyro processing, clinker treatment, storage and transportation)?
1. Preparing (before any visit takes place) – this provides questions to think about and address before attending the company’s site. This further breaks down into two sections being:
• How many people do they employ?
The following provides the reader of this document, either General Management or Sales Team, with some template questions to help generate revenue from this Production Line Intelligence overview and so develop business in the aggregates and cement industries.
• Does this company have other facilities in your region/ territory?
General
• What are the fall-back objectives if the primary objectives are unachievable?
• What is your plan for follow ups to this meeting (further meeting/proposal/meeting with other people)?
2. The meeting – questions to ask during the meeting to understand the needs, requirements, and potential sales opportunities in the prospective customer
PART THREE
• What do you already know about:
3. The follow up – questions to ask or to reflect on, at the end of the meeting or afterwards
A cement processing plant - from crushing, screening, to cooling, storage, bagging and distribution?
a. Detail of the company itself
• What are the problems in the process that affect continuity?Whatare the main issues in relation to maintenance?
• Who in your business do you need to share this information with?
• What are the processes used from receipt to dispatch?
What have been the success stories? How can these be replicated?
The actual meeting 'Excavation Site' or 'Cement Processing Plant'
• What sort of plant or facility is this e.g. excavation of aggregates or processing of raw materials?
The follow up
25
• What were the main points you learned from the visit?
• How are the main machines maintained and repaired?
• What are the next steps?
• What are the main issues in relation to maintenance?
• What kind of support do you look for from your service providers in relation to on-going or emergency maintenance?
The most utilised products
• Do they have existing projects carried out in relation to maintenance or energy management etc? Are existing partners – suppliers or distributors – assisting?
• What is your biggest current problem with your parts suppliers?Howdo you like your supplier partners to assist?
DryGrindingorwet-processing mix
Maintenance, planning and issues
• What is the estimated annual spend on maintenance?
• How are you going to use this information?
The facility
Pyro Clinkerprocessingtreatment - grinding and storage
• Where is the process most prone to failure or maintenance problems?
Internal team, external team, machine builder service engineers?
Are there on-going projects to deal with this?
• What are the main concerns in relation to type of production parts that are needed to maintain and improve the line (e.g. bearings, mechanical power transmission, pneumatics, etc.)?
• What other types of follow up will you undertake and why?
• What are the key maintenance/industrial supplies objectives for the facility?
(If not already known, any of the preparation questions can be asked during the meeting to establish site type, size, capacity, age, as noted).
• What parts are used most on an annual basis? What are the issues/challenges faced getting those parts?
Suppliers
• How are you going to store this information?
• What are the next steps you need to take and when?
• How will you ensure that these follow ups are completed?
Transportation - distribution and ready-mix concrete
• What do you value most in relation to a supplier/ distributor like us?
Can we come back with a proposal to help you with some of this?
• What sort of regular maintenance does the plant undergo?
What are they caused by?
Regular shut-down periods or other?
• How will you complete these?
Are they using partners – suppliers or distributors –to assist you in this process?
Also to a number of technical experts from distributor members of EPTDA operating in this sector, who have provided the concrete examples included in the text and without whose contribution the document would lack its operational and commercial relevance and power for distributors.
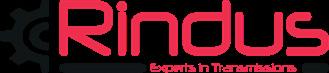
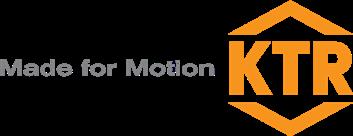
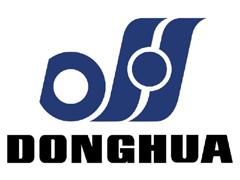
Acknowledgements
26Sources: 1. Science Mag, ‘The World Needs to get Serious About Managing Sand says UN’ 2. Marble, ‘How is Granite Mined’ 3. Mineral Products Association, ‘Aggregates’ 4. Grand View Research, ‘Aggregates Market Size, Share and Trends Analysis Report by Type’ 5. UEPG, ‘Annual Review 2018-2019’ 6. Grand View Research, ‘Aggregates Market Size, Share & Trends Analysis Report by Type’ 7. Ibid. 8. Forbes, ‘China Used More Concrete in 3 Years than the Entire 20th Century’ 9. Aggregates Business, ‘Global Aggregates Growth Examined by GAIN Convener Jim O’Brien’ 10. UEPG, 'Annual Review 2018-2019' 11. CEMBUREAU, ‘Main World Producer – The G20 Group Cement Production’ 12. UEPG, ‘Annual Review 2018-2019’ 13. UEPG, ‘Annual Review 2019-2020’ 14. Ibid. 15. Statista, 'Cement Production Worldwide from 1995 to 2019' 16. Vulcan Materials Company, ‘The Future of the Construction Industry: Impact on Aggregates Demand & Supply’ 17. Grand View Research, ‘Aggregates Market Size, Share & Trends Analysis Report by Type’ 18. Research Gate, ‘Aggregates and Construction Markets in Europe: Towards a Sectoral Action Plan on Sustainable Resource Management’ 19. Volvo CE, ‘Carbon Emissions Reduced by 98% at Volvo Construction Equipment and Skanska’s Electric Site’ 20. Cemnet, ‘Gobal Cement Report’ 21. Volvo CE, ‘Carbon Emissions Reduced by 98% at Volvo Construction Equipment and Skanska’s Electric Site’ 22. Quarry Magazine, ‘Delivering Predictive Maintenance for Exploratory Drilling’ 23. Quarry Magazine, ‘Global Market Still Cold on Recycled Aggregates’ 24. Business Wire, ‘Recycled Construction Aggregates Market to Surpass 6.2 Million Tons by End of 2027’ 25. UEPG, ‘Annual Review 2018-2019’ 26. UEPG, ‘Annual Review 2019-2020’ 27. Property Forum, ‘Europe’s Construction Industry will be Hard Hit by Covid-19’ 28. Green Facts, ‘The Mining of Sand, a Non-Renewable Resource’ 29. Science Mag, ‘The World Needs to get Serious About Managing Sand says UN’ 30. Quarry Magazine, ‘Water Management in the Extractive Industries’ 31. UEPG, ‘Water Management in Aggregates Quarries and Sand and Gravel Sites’ 32. Volvo CE, ‘Four Things You Should Know About the Quarry and Aggregates Industry’ 33. Aggregate Research, ‘Aggregates Group CEMEX Moves Towards Net-Zero CO2 Concrete’ 34. HeidelbergCement, ‘Cement Producers Have Founded an Oxyfuel Research Corporation’ 35. Argus Media, ‘European Cement Sector Eyes Net Zero by 2050’ 36. CEMBUREAU, ‘Construction & Demolition Waste’ 37. Mineral Products Associates, ‘Aggregates: Recycled Aggregates’ 38. Vulcan Materials Company, ‘The Future of the Construction Industry: Impact on Aggregates, Demand & Supply’ 39. Global Cement, ‘Global Cement Top 100 Report 2017-2018’ 40. Aumund, ‘Cement’ 41. Claudius Peters, ‘About Claudius Peters’ 42. FLSmidth A/S, ‘About Us’ 43. KHD, ‘Company Profile’ 44. Köppern, ‘Home’ 45. Loesche, ‘Cement Industry’ 46. Gebr. Pfeiffer, ‘Company Profile’ 47. Wikipedia, ‘Polysius’ 48. Promecon, ‘Cement’ 49. Schenck Process, ‘Company’ 50. thyssenkrupp Industrial Solutions, ‘Cement’ 51. Voith, ‘Cement’ 52. Europa, ‘Competitiveness of the European Cement and Lime Sectors’ 53. Cemnet, ‘Global Cement Report’ 54. Europa, ‘Competitiveness of the European Cement and Lime Sectors’
Authored by:
Finally to the individual members of the EPTDA Know Your Market Committee and particularly to its Task Group, who have freely given their advice, guidance and inputs throughout the process of producing this document.
Disclaimer: costed examples contained in this document are illustrations taken from real practice. They are, however, not predictions of future value achievable from various projects that can be undertaken in this sector. The authors, contributors and EPTDA do not accept any liability for any commercial decisions that may be taken as a result of these examples.
The
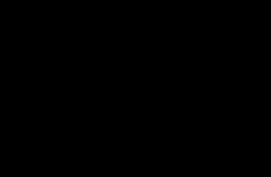
Acknowledgements and a sincere thank you to the following manufacturer members of EPTDA for the generosity of the technical and commercial information and advice that they have supplied and which has given real authority to the document.
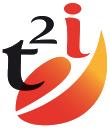
27
28 WWW.EPTDA.ORG Copyright © 2021 EPTDA. All rights reserved. This work is registered with the IP Rights Office Copyright Registration Service Ref: 284738692