COMMERCIAL VEHICLE WORKSHOP
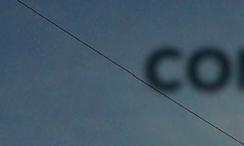
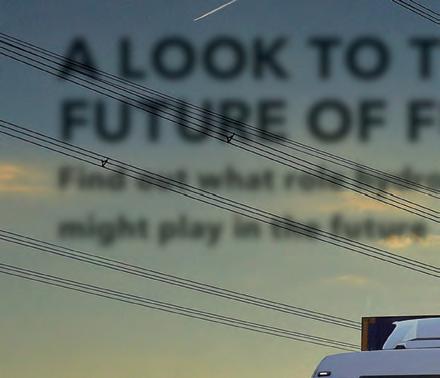


COMING IN CLUTCH
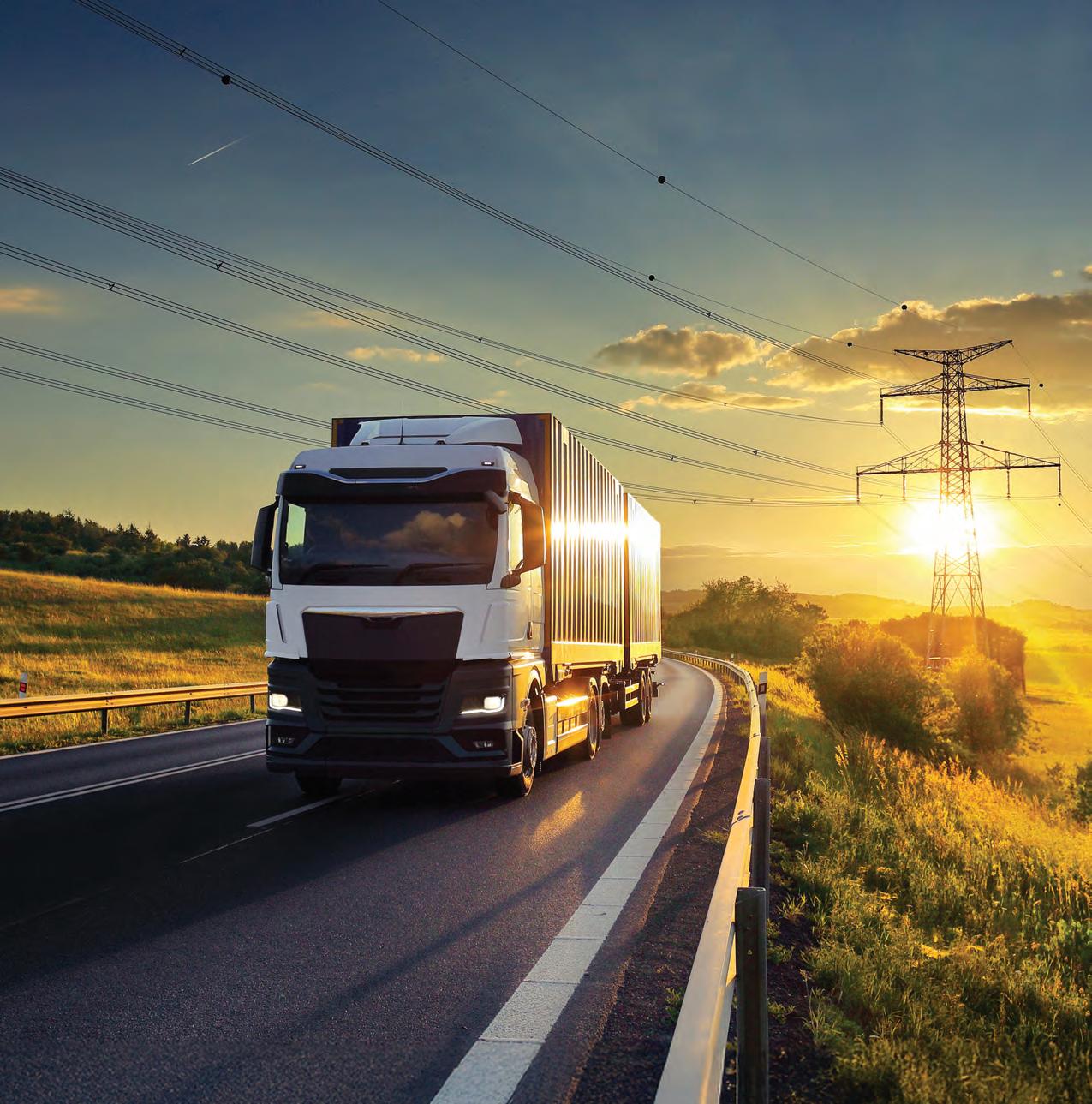
Find out what role hydrogen might play in the future
Follow along with a clutch replacement on a 2019 Peugeot Partner van
Also in this issue...
■ A helping hand in choosing the right oils, antifreezes and lubricants
■ Everything you need to know about pneumatic concentric slave cylinders
■ An exclusive look inside TIP's trailer refurbishment centre
19 Helping to address the demands of Government approved longer semi-trailers is BPW’s self-steering axle.
21 Follow along as Schaeffler’s REPXPERT Alistair Mason replaces the clutch on a 2019 Peugot Partner van fitted with a 1.6 HDI engine. 24 Top tips on servicing pneumatic concentric slave cylinders from clutch specialists febi.
26 Witham Oils on the advantages of bulk storage solutions for oil and how its transformed a couple workshops with its solutions.
28 Morris Lubricants is here to clear up any confusion you might have on oil, lubricant and antifreeze choice.
VLS’ Alan Outhwaite explores what role hydrogen might play in the UK’s race to net zero.
takes an updated look at Intangles, who keen readers might have spotted in the mag this time last year, and the work the firm are doing to reduce
Editor
FREYA COLEMAN
cvw@hamerville.co.uk
Group Editor
KIERAN NEE
Digital Manager
KELLY NEWSTEAD
Digital Assistant
LYDIA PROCTER
Advertising Sales Manager
MATTHEW BOASE
Group Manager
ROBERT GILHAM
Graphic Designer
GEMMA WATSON
Group Production Manager
CAROL PADGETT
Subscriptions
Commercial Vehicle Workshop is a business magazine for companies and individuals involved in all aspects of commercial vehicle servicing.
It is published 11 times a year and is available on free subscription to qualified readers.
Subscription rates:
UK £30 post paid
Airmail £99 post paid
Europe £70 post paid
To be removed from this magazine’s circulation, please call 01923 237799 or email circulation@hamerville.co.uk.
Printed by Stephens and George
Published by
HAMERVILLE MEDIA GROUP
Regal House, Regal Way, Watford, Herts WD24 4YF
Tel: (01923) 237799
Website: www.hamerville.co.uk
Copyright © 2025 8,249
As my editor's chair continues to warm, I find myself sitting in it less and less these days and spending more time behind the wheel of my boiling hot Mini(yes, I still haven’t sorted the A/C...). Increasingly, my work is taking me out on the road, and while that’s fantastic news for the magazine and its content, my poor back may disagree.
I’m writing this after just returning from the RTX show last week, you can read my full review and thoughts on page14 of this issue, and while I did come away with a bit of sunburn and a sore head, I also left with something much nicer: a genuine sense of warmth, and not just from the sun.
“As someone still relatively new to the commercial vehicle world, I continue to be amazed by how welcoming this sector is.”
As someone still relatively new to the commercial vehicle world, I continue to be amazed by how welcoming this sector is. From engineers on the tools, to marketing teams, salespeople, and PR companies. Every person I spoke to at the show was friendly, insightful, and completely engaged with the work they do and was excited about the industry and the work that we can do together. There’s an infectious energy in this industry and it's clear that people care deeply not just about the vehicles, but about each other, and about getting things right for the end user and, more importantly, reducing downtime for customers.
It’s a world full of collaboration, mutual respect, and stories that deserve to be told and it’s a privilege to help tell them. The commercial vehicle sector isn’t just driven by diesel (or hydrogen!) and data; it’s driven by people, and the passion they bring to every conversation, every product, every innovation.
So yes, this month’s viewpoint might read a little on the sentimental side, but can you blame me? A heatwave and a few days surrounded by some truly brilliant folks will do that to a person. Here's to the road ahead, to more great conversations, and to one of the most down-to-earth, engaging industries I’ve ever had the pleasure to be part of.
Have a brilliant summer and don’t forget your suncream.
Freya Coleman
Editor
■ Fleet operators brace for fuel shortage. This is following the collapse of major fuel supplier Prax Group into administration last month. As the group owns approximately 200 petrol stations under the Breeze and Harvest energy brands, this threatens to disrupt operations and increase costs for the transport industry.
■ Speed of charging tops EV choice factor for fleets. According to the Arval Mobility Observatory Barometer, 69 per cent name this consideration compared to efficiency at 66 per cent and range at 60 per cent.
■ Fleet financial and the AA join forces. Central to the partnership, The AA has crafted an accident management solution that meets the needs of Fleet Financials’ customer base, including large and medium-sized corporate customers, in addition to a dedicated SME provision.
■ Emissions tracking scheme launched by Zemo Partnership. Called RFAS Fleet, it enables fleet operators to provide its customers with independently verified evidence of greenhouse gas emissions savings resulting from its use of renewable fuels.
The IRTE has introduced the inaugural HGV skills challenge; a national competition aimed at spotlighting the UK’s top HGV engineers.
Hosted in partnership with DAF Trucks, the event will take place 30th of September to the 1st of October 2025 at the DAF Apprentice Academy Nottingham, a £3.5 million training facility. The challenge is said to build on the 13 years of success enjoyed by the PSV Skills Challenge, bringing the competition’s approach to celebrating excellence within the HGV sector for the first time. Participants will engage in a range of both theorical, and practical assessments designed to test and
refine their technical knowledge, problemsolving, and teamwork. Competitors will also gain networking opportunities with their peers and industry experts, alongside the opportunity to work on the latest technology.
NAPA Auto Parts has announced the opening of its first commercial site. This expands the NAPA network, bringing commercial vehicle parts and service solutions directly to customers throughout Leicester and surrounding areas.
The new NAPA Auto Parts –Commercial site joins a network of over 290 stores across the UK and Ireland, alongside the global network of more than 6,000 NAPA Auto Parts locations.
Robin Hill, general manager of NAPA Auto Parts – Commercial, said: “This opening marks a significant step in the
growth of our commercial vehicle network. We understand the demanding nature of commercial automotive operations and we are excited to provide commercial vehicle professionals access to same marketleading service current NAPA Auto Parts customers have been accustomed to.
“Our NAPA Truck product offering continues to grow, so to be able to offer this alongside market leading brands such as Bosch, Valvoline, Haldex, Knorr Bremse and Wabco among others, really puts us in a position to be a one-stop-shop for all commercial vehicle needs.”
77 %
of UK fleets either have an electric charging strategy in place or are planning to adopt one according to the 2025 Arval Mobility Observatory Fleet and Mobility Barometer.
£
759,000
the amount a milk distribution company has been hit with for repeated overloading offences. This is the largest ever levied in a DVSA prosecution.
1 %
the amount UK road death rose by yearon-year in 2024 according to provisional data from the Department for Transport. This equates to at least four people every day.
125,000
the vehicle sales milestone Isuzu celebrated in the UK back in June. This is after arriving in the UK almost four decades ago in 1987.
FOR UP-TO-DATE NEWS, SIGN UP FOR OUR WEEKLY E-NEWSLETTER. SIMPLY SCAN THE QR CODE
Logistics UK has said the London Congestion Charge for electric vehicles will penalise operators, who currently operate in the capital without facing a charge.
The organisation has said that TfL’s consultation on the congestion charge recognises the importance of commercial vehicles to the economy by creating a clear distinction between commercial vehicles and domestic road users, however the new proposals will still present a significant increase in costs for electric vehicle operators.
Logistics UK’s senior policy manager –Road Freight Regulation, Chris Yarsley, said: “It is vital TfL incentivise operators to decarbonise fleets and we continue to press for the continued exemption from the charge for electric vans and HGVs. Any increase in charges is a disincentive for operators to serve the capital and congestion charges should be used to encourage road users to use alternative modes of transport – an option that is not available to logistics operators.
“Operators have made significant
investments moving to electric vehicles and they simply cannot afford to soak up additional costs so it is likely that any increase in charges will have to be passed on which will ultimately lead to increased prices for the end user.
“London depends on logistics businesses to keep the capital stocked with everything its businesses and consumers rely on every day, and the transition to alternatively fuelled vehicles should be incentivised, not penalised in this way.”
Environmental Waste Management, a liquid waste management specialist based in Essex, has recently purchased a set of Stertil-Koni mobile column lifts to support the in-house maintenance of its vehicle fleet.
The investment gives the company greater control over servicing, reduces downtime, and cuts long-term costs.
To enable safe outdoor maintenance of its trailer tankers, the company selected StertilKoni’s mobile column lifts, supplied with an A-Frame trailer beam adaptor. This allows the team to lift trailers via the kingpin connection –without the need to invest in a specialised trailer lift.
The set of six ST1075 mobile columns each has a lifting capacity of 7.5 tonnes, providing a combined capacity of 45 tonnes. The trailer beam itself offers a lifting capacity of 7.2 tonnes - ideal for the heavy vehicles in Environmental Waste Management’s fleet.
Febi investigates a common fault that can be found in air tanks and a common fault in oil separators.
Function
Many important and safety-relevant systems in commercial vehicles are operated with compressed air, such as the air suspension, the transmission control, or the brake system. To make sure the necessary operating pressure is always available, the compressed air must be stored. The air storage in the air tank makes it possible to use more air than the air compressor produces for a short period of time.
Cause of failure
Seams that have not been properly welded can suffer from air leaks or can even experience bursting. The material used also plays an important role: only the use of high-quality steel with a certain yield strength ensures safe operation.
The surface coating plays an important role in preventing corrosion on both the inside and outside of the air tank. If the protective paint layer is too thin or damaged, rust can easily take effect. The service life of the tank is then reduced and the risk of leaks increases –even with the possibility of bursting.
In piston engines, the combustion process in the cylinder unintentionally creates excess pressure in the crankcase. To reduce this pressure, a venting process must take place somewhere in the engine. This is done by a crankcase ventilation with oil separation. So-called centrifugal oil separators, such as febi 171457, are often used.
They separate the oil - which is part of the gases in the crankcase in the form of oil mist or droplets - by means of a rapidly rotating conical disc stack. The separated oil then flows back into the oil sump and the remaining gases are fed into the intake area of the engine.
Cause of failure
Centrifugal oil separators operate at speeds of 7000-9000 rpm. The tapered disk pack is mounted on a shaft which is supported by two ball bearings. If these ball bearings are worn out, the after-running of the centrifugal oil separator can be noticed by humming noises of the defective ball bearings after switching off the motor. If the oil separator is not replaced; the intake area can be heavily contaminated with oil by unfiltered crankcase gases.
WANT TO FIND OUT MORE? Make sure to scan the QR code!
CVW was recently given an exclusive guided tour of TIP Group’s Trailer Refurbishment Centre.
After navigating a few wrong turns off the A500, I arrived at TIP’s expansive 12.75-acre facility in Stoke-on-Trent. I was immediately struck by the sheer scale and organisation of the site. This isn’t just a workshop –this is a full-scale trailer hospital. Before having a look round and waiting for the rain to calm down a bit, I sat down with Mark Jones, TIP’s strategic account manager and Ian Edmundson, marketing manager UK & Ireland.
“We acquired this facility back in October 2024,” explained Mark “It’s now the largest trailer refurbishment centre of its kind in the UK.” Every question asked was met with a brief answer followed by a collective ‘I think it would be better to just show you!’, so that’s exactly what we did.
So, we donned our striking orange high vis jackets, and it was time to get to it, just as the sun was coming out. Walking through the site, I could see a hive of activity despite the slightly bleak weather. Over 100 skilled technicians are busy at work across 41 individual bays. There’s a mix of trailers in various stages of transformation –curtainsiders, box vans, reefers, chassis and flatbeds –all undergoing anything from cosmetic refreshes to full mechanical overhauls.
The process, Mark told me, starts with a full wash and steam clean. From there, trailers are moved to a repair bay where they’re stripped down and carefully assessed. “We’ve got a dedicated team of inspectors here who scope out each job and provide a detailed estimate before we get started.” he explained.
Parts that need replacing are sourced by the on-site parts team, and then it’s on to the more intensive work. I was led past bays where shot blasting is taking place, trailers stripped to bare metal, preparing for a fresh coat of paint. Once blasted, they’re moved into prep bays to be masked and prepped before being spray-painted in one of several professional booths. It was
explained that blasting was the best and quickest way of getting any trailers brought in back to zero. Furthermore, any paint stripped from the trailers in this process gets reused, which is always a bonus.
From there, trailers move into finishing bays. New curtains are fitted, and crisp vinyl branding is applied using precision vinyl-cutting machines. I found this to be one of the most satisfying parts of the process, the vinyl really making the trailers look brand spanking new. Finally, trailers reach the ‘final fit’ area, where any previously removed parts are reinstalled.
The journey ends with a comprehensive quality check. “Every trailer gets a walkaround inspection, a rewash, a team clean, and a full-service check,” says Mark. “We even have two drive-through lanes authorised for MOT testing, which helps local operators stay compliant.”
One thing I personally found really impressive was the sustainability behind it all. “By refurbishing trailers instead of replacing them, we’re significantly reducing waste and emissions,” Mark explained. “And we’re embracing circular economy principles too as any parts we can’t reuse get recycled rather than scrapped.” Essentially, nothing is wasted and only the parts that need replacing are replaced.
I was told on the tour that operators typically gain another five years of life from a refurbished trailer. It’s a win-win: better for the environment, and a more cost-effective solution than investing in brand-new units.
By refurbishing trailers instead of replacing them, we’re significantly reducing waste and emissions.
The centre also supports two commercial models: TIP can refurbish trailers already on hire, or purchase trailers from fleet owners, refurbish them, and lease them back, freeing up capital and reducing the burden of asset ownership.
Before we head off, and after a rather delicious lunch, Mark pointed out that TIP includes an environmental benefit illustration in every refurbishment proposal.
“It’s all about helping our customers align with their ESG goals while getting the most out of their fleets,” he added.
“By refurbishing rather than replacing trailers, we are not only cutting down on emissions but also delivering a cost-effect alternative that meets the highest quality standards. We now have the largest trailer refurbishment facility of its kind in the UK and will continue to set new industry standards in this field in order to support our sustainability ambitions.”
Beyond the environmental gains, refurbishment also means less downtime. New trailers can be expensive and slow to deliver, but planned refurbishments, typically taking up to 10 days, allow fleet managers to stay ahead, avoid disruptions, and control costs. TIP also provides support for scheduling, helping operators plan their refurbishment cycles around peak usage periods.
Even in typical British weather (yes, it was damp during our visit), the 41 indoor bays mean the team can keep work moving, rain or shine. There’s a sense of preparedness here that mirrors the whole ethos of the centre –proactive, precise, and built for the long term.
TIP’s Stoke-on-Trent facility isn’t just a refurbishment centre, it’s a vision of the future. A strategic hub built to support a smarter, greener, and more efficient transport industry, and it was a pleasure to see the centre first hand!
Read all about the three days the CVW team recently spent at RTX at the NAEC, Stoneleigh Park.
My first visit to the Road Transport Expo certainly didn’t disappoint, though my feet may never recover.
Make sure to scan the QR code!
Clocking up well over 10,000 steps a day, I quickly realised just how expansive the show has become. If you didn’t plan your time carefully (as I warned in my last viewpoint!), you’d easily miss half of what was on offer. Between navigating the halls, grabbing interviews, and catching up with familiar faces, there wasn’t much time to sit down –Matt and I were flat-out over the three days chatting to visitors, shaking hands, and spreading the good word of CVW
This year’s show was bigger than ever, attracting over 14,000 visitors –a remarkable 34 per cent increase on last year’s attendance –and featuring more than 330 exhibitors from across the road transport and logistics sector. The industry clearly showed up in force, with all eight major truck OEMs represented: DAF, Iveco, Isuzu Truck, MAN, Mercedes-Benz, Renault Trucks, Scania, and Volvo.
There was also plenty of electric innovation on show, including a sleek allelectric model from Volta Trucks and the UK debut of a 7.5-tonne electric truck from
Chinese manufacturer Yutong, displayed by Pelican Engineering –a sign of how international the UK market is becoming. Another highlight was the Knowledge Zone, a packed seminar programme tackled everything from decarbonisation and fleet safety to regulatory updates and future challenges.
As for us, the CVW stand was located in the GR Hall, which turned out to be more marquee. Our group manager Rob Gillham looked close to melting in the heat –but being British, of course, we can't complain when we see the sun!
All told, RTX 2025 was a huge success and a clear sign of the strength and
resilience of the road transport industry. It’s a must-attend event if you want to keep pace with the latest trends, connect with suppliers, and see where the sector is heading next. Just don’t forget your walking shoes and maybe a portable fan. Although, you might not need the latter for the inaugural RTX Scotland in November!
With a vast background of visual planning, both manual and online, CVW hears about the history of T Cards Direct.
When it comes to visual planning not many companies can say they have the experience of T Cards Direct. The company first started manufacturing T Cards back in the 60’s when systems where they were most common in the MOD and the National Health Service.
Since then, the company has gone through many changes, but the personnel have mainly stayed the same. Set up by Fred Heine and his wife Margaret, a large part of the business was supporting trade clients. Then in the early 90’s when Fred’s daughter Sarah joined, the firm started to grow direct business, mainly to better support the end user. Mainly focusing on the Motor Trade and Engineering companies the business were approved suppliers to many big brands like Mercedes Benz, Landrover, Coke-Cola, Trebor Basset, to name but a few.
Sarah’s background of business improvement helped T Cards clients get a grip with improving efficiency through continuous improvement programs like Kaizen and Lean Manufacturing. T Cards is a perfect tool for those applications as well as for simple workflow processes like workshop control. T Cards provide a “Go to Board” whenever anyone needs an update to the status of work, or information, compared to being inaccessible or just in people’s heads.
The business was again boosted when Fred’s son Philip joined the company in the mid 90’s and with the growth of the internet, T Cards were able to spread the word of how to keep track, allocate and improve efficiency by implementing simple tools like T Cards. The website shop help cast the “net” internationally and since then, orders are regularly sent as far away as New Zealand and Australia. Indeed, the export business has continued to steadily grow and is today an important part of the business. Back in the UK the business has been building with the client base in different markets such as construction and accounting, but the simplicity of the system means it can be adapted to almost any application. Health and safety is an obvious example where visual communication is essential. An excellent example is Weetabix. It needed to improve its near miss reporting system. To them T Cards seemed an obvious tool. A clear simple process, not relying on
staff opening emails for awareness of potential hazards. It proved to be a costefficient solution. Since then, hundreds of companies have implemented the system, which can cost less than £100.
In the mid 2000’s Sarah and Philip decided to use their experience and create a digital version of T Cards. Right from the word go it was all about what clients wanted – low cost, adaptable, easy to customise and accessible for users and the management. With the internet being more accessible and the technology available, it was clear that a web-based T Card system was the way to go. Having a “Go to Board” that was accessible from anywhere was going to be huge benefit for clients. T Cards then reached out and asked clients what features were most important. Since then, the system has continued to evolve off the back of client feedback.
In essence, T Cards Online was designed to replicate the simplicity of the manual system, where you can easily customise the structure with column titles and T Card designs to suit individual planning needs. Having come from a visual planning rather than a software background the system has the advantage of being built for the desired purpose of making processes visible whilst being simple to setup and most importantly, easy to use.
One key advantage for T Cards is its people. Having that experience to help people setup their systems and run through requirements with a client would sometimes incur a cost but not at T Cards.
Gareth Down at Marshall Mercedes Commercials in Hampshire is a proud advocate of the system and has used the system for many years now: “We have been on a journey with T Cards Online, the system has been a real help in developing our business. They have regular updates where features are always being improved, some of which has really benefited us. The free APP has helped our engineers whilst out on the road. And the API functionality has been fantastic with integrating with Sage. What separates the team at T Cards from others is their personal support. Whenever there has been a problem, they have been right on top of it.”
T Cards Online has been a huge success in helping hundreds of companies, large and small over the last 12 years. Updates are planned in over the next two years which will include some exciting features.
With the internet being more accessible and the technology available, it was clear that a web-based T Card system was the way to go.
Nevertheless, you might be surprised to hear that the manual system is still proving a hit. Even Philip is surprised with more than three a day being sent out!
Philip commented, “It’s a real testament to the simplicity of the manual systems that they are still proving so popular, if you need something quick, simple and easy to use then the boards offer something tangible for companies”. He continued. “The T Cards online system has just added
Make sure to scan the QR code!
another string to our bow, and it now allows us to support clients who wouldn’t even have considered something like this, that is so cost effective. What really drives us though as a company is realising our clients’ needs especially when they bring ideas and suggestions.”
“Unfortunately, Fred passed away several years ago without seeing the real success of T Cards Online and seeing how his ideas have developed. However, he would have been delighted with the next generation now contributing. Sarah’s son Joe has joined the firm and has been hard at work making efficiencies and improvements in the software and managing the whole team that supports the platform. With the code and support being managed internally, here in the UK, allows us to be nibble and agile with regards to helping clients.”
CVW hears about how BPW’s self-steering axle is addressing the demands of Government approved longer semi-trailers.
As delivery routes tighten, fleet operators face increasing pressure to improve manoeuvrability, reduce environmental impact, and comply with evolving regulations. The BPW LL self-steering axle aims to offer fleet operators a proven and practical solution for longer semi-trailers (LSTs), helping operators enhance vehicle handling, extend tyre life, reduce fuel consumption, and simplify compliance with the latest regulatory demands.
In 2023, the Department of Transport (DfT) approved the use of even longer LSTs, adding a further 2.05 metres to increase the length of a UK semi-trailer from 13.6 to 15.65 metres. Since then, there has been a renewed focus on the need for efficient and compliant axle technology. LSTs support the government’s priority to drive further economic growth, cut emissions and strengthen supply chains. However, these benefits come with added operational responsibilities, including detailed route planning, enhanced driver training, and compliance with specific trailer configurations.
The BPW LL self-steering axle addresses these demands with a passive design that operates entirely without the need for external power or complex steering stabilisers. Unlike conventional active or control steering systems, the axle uses a simple yet effective mechanism where the
axle beam and axle stub are connected through a kingpin system, with thrust washers. This offers trailers improved manoeuvrability in tight or narrow spaces and small delivery yards.
When driving straight (zero position), the crowns in the thrust washers keep the wheels in the correct and stable straightahead position. As a result, it has been highlighted that the life of the tyres on the front axle can increase by up to 50 per cent, while those on the rear axle can increase by as much as 70 per cent.
Engineered with real-world practicality in mind, the BPW LL self-steering axle also features an automatic self-locking facility that engages when reversing. To engage the mechanism, the trailer should be straightahead, allowing greater stability and ease of operation. Forces acting on the tyres when cornering are then distributed more evenly.
The BPW LL self-steering axle is available with steering angles of between 12 and 27 degrees, with the latter being suited for LSTs. Based on the proven beneficial principles of its existing self-steer, this increased steer angle enables a standard trailer license holder to consider a 27-degree steer axle.
Where the LL self-steering axle proves its real value is in the demands of day-today operations. Its improved manoeuvrability and reduced turning radius offer more straightforward vehicle handling, less tyre wear and lower fuel consumption. Over 100,000 kilometres, fleet operators can save as much as 1,000 litres of fuel and more than four tyres per vehicle –just work that out for your entire fleet!
The BPW LL self-steering axle says to continue to provide a robust and costeffective answer to the modern transport challenges posed by LSTs. With its intelligent design and long-standing reliability, it remains a key asset for fleet operators focused on smarter, greener and more compliant logistics.
Shaeffler’s REPXPERT Alistair Mason is replacing the clutch on a 2019 Peugeot Partner van fitted with a 1.6 HDI engine.
This Peugeot Partner came into the workshop with over 110,000 miles on the clock. The driver is reporting that the clutch seems to be “slipping” and a short road test confirmed this. Clutch replacement was advised, the repair priced and authorisation given to carry out the work. With a book time of 5.4 hours and no specialist equipment required, this makes a great repair for any independent garage.
Prior to starting the repair, it is good practice to scan the QR code on the LuK clutch box ( Fig.1 ) using the REPEXPERT app. Firstly, this will highlight if there is any service information relating to this product and it will also give you the repair instructions including torque settings – not forgetting the bonus points that can be exchanged for goods in the bonus shop.
Vehicle Information
With the vehicle placed on the lift, open the bonnet, disconnect and remove the battery (Fig.2). You will have to unclip some wiring to aid battery removal. Remove the plastic tray that the battery sits on and then unbolt the battery carrier and remove from the vehicle. This now gives good access to the top of the gearbox area.
The following items can be removed: air ducting from front panel to air box assembly, gearbox earth strap and reverse light switch multiplug. Unclip the loom, ease the wiring loom off the top bellhousing bolts and then remove the top bellhousing bolts and upper starter motor bolts. Disconnect the gear change cables (Fig.3) and remove the accessible linkage bolts. Raise the vehicle lift to waist height and remove both front wheels, the N/S hub nut and the N/S wheel arch liner. Raise the vehicle lift to gain access to the underside, as we now need to remove the front subframe by disconnecting both bottom ball joints and anti-roll bar links. Unbolt the exhaust mounting and DPF sensor at the rear of the subframe (Fig.4), then remove the lower gearbox pendulum mounting and steering rack retaining nuts. Secure the steering rack to the vehicle to keep it in place when the subframe is removed. Supporting the subframe with the transmission jack, remove all subframe mountings and remove the subframe from the vehicle. Drain the gearbox oil and, whilst draining, disconnect the exhaust front pipe at the flexible joint. Refit the oil drain plug and torque to the manufacture’s specification. At the rear of the engine, remove the heat shield to gain access to the starter motor, remove the lower starter motor retaining bolts, support bracket and then remove the lower bell housing bolts. Remove the three retaining bolts from the O/S driveshaft support (Fig.5). This will allow us to leave the driveshaft in position and ease the support housing out of the gearbox. Remove the N/S driveshaft and then, moving to the front of the engine, remove the two slave cylinder retaining bolts and ease away from the gearbox, leaving the hydraulics connected.
In this instance, wear was evident on the ball pivot and the release arm so both were replaced with the customer’s authorisation.
Now remove the nut and stud (Fig.6) that secures the catalytic converter bracket to the engine block with the use of a female Torx socket. This needs to be removed to gain access to a bell housing bolt, once removed, remove the bell housing bolt. Supporting the engine with a suitable support, access the engine bay and remove the top gearbox mounting. Lower the engine and gearbox slightly to aid gearbox removal. Support the gearbox with a transmission jack and remove the final bell housing bolts. Ease the gearbox away from the engine. Once the gearbox input shaft is clear of the clutch assembly, lower the gearbox on the transmission jack and remove from the vehicle.
Remove the six clutch retaining bolts and remove the clutch assembly. At this point the clutch problem was evident. The clutch had reached the end of its service life as the lining had worn down to the rivets (Fig.7). Clean the face of the flywheel using emery cloth. This will also remove the glaze and then wash off with clutch and brake dust cleaner.
Now inspect and replace the release system in the gearbox bell housing, remove the release bearing and release arm. Inspect the ball pivot, release arm and bearing guide tube for any wear. In this instance, wear was evident on the ball pivot and the release arm so both were replaced with the customer’s authorisation. Clean the bell housing area, removing old clutch dust. Apply a light smear of high melting point grease to the guide tube and gearbox input shaft and install the release system.
Finally, mount the new clutch plate onto the input shaft. This will confirm it is the right fitment and also evenly distribute the grease. Remove the clutch plate and wipe off any excess grease. Ensure the flywheel
and clutch pressure plate are clean and degreased using clutch and brake dust cleaner. Using a clutch alignment tool (Fig.8), mount the clutch plate onto the flywheel ensuring “gearbox side” is facing outwards. Mount the clutch pressure plate onto the dowels, insert the six bolts, tighten in an even and sequential sequence and torque to the manufacturer’s specification. Before installing the gearbox, ensure both alignment dowels are fitted correctly and are in good condition. Replace, if required, and ensure cables and looms are clear for gearbox installation.
It is also highly advisable to replace the driveshaft oil seal in the O/S driveshaft support housing as this has been removed.
Place the gearbox onto the transmission jack. Bring the gearbox close to the clutch assembly and spend a little time aligning the gearbox with the clutch assembly. Align the N/S driveshaft, then ease the gearbox into position, ensuring the gearbox locates onto the alignment dowels correctly. Insert two bell housing bolts and tighten. Using the transmission jack, raise the engine and gearbox, mount the top gearbox mounting and secure in position. Installation is in reverse order of removal. Remember to replenish the gearbox oil with the correct quality and quantity of oil, reset all electrical consumers after battery installation and always carry out a full road test to ensure a quality repair.
Make sure to scan the QR code!
Clutch specialist febi shares everything you need to know about pneumatic concentric slave cylinders and some top tips on servicing them.
In commercial vehicles, the clutch system is an essential component that ensures smooth power transfer between the engine and the transmission. The traditional mechanical clutch actuation systems have evolved to meet the demands for better fuel efficiency, improved driving experience, and reduced driver effort. One of the significant advancements in clutch technology for commercial vehicles is the development of electronically controlled pneumatic clutch actuation. This system offers numerous benefits, including improved efficiency, reliability, and automation.
The concentric slave cylinder is crucial for transferring the necessary force to the pressure plate to disengage the clutch. It is a wear item since it overtakes the function of the release bearing and the clutch actuation mechanism from mechanical clutch actuation systems.
With electronically controlled pneumatic clutch actuation, the clutch is actuated via a pneumatic concentric slave cylinder, which is precisely controlled in its release travel by a control unit via a special valve. The system automatically records the data transmitted via the CAN bus, such as engine and transmission speed as well as the accelerator pedal position and uses this to determine the optimum release position. This supports the driver in demanding driving situations, such as manoeuvring, starting uphill with a heavy load or on slippery roads.
After replacing clutch parts or the concentric slave cylinder, recalibration must be carried out using a suitable diagnostic device. The vehicle manufacturer’s specifications must be observed. Calibration is necessary for the following reasons, among others:
● Recalibration of the travel sensor.
● Detection of component wear by the control unit.
● Compensation for free travel.
● Faster response behaviour.
● Comfortable starting.
● Comfortable manoeuvring.
If the concentric slave cylinders are not calibrated after the repair, an error message may appear in the vehicle display. The clutch may slip when starting off and the vehicle may be difficult to manoeuvre under load.
● Recalibration of the biting-point (describes the moment at which the clutch slowly engages, and the force is transferred to the transmission input shaft).
WANT TO KNOW MORE? Make sure to scan the QR code!
Calibration problems can arise if the vehicle’s compressed air supply is insufficient or the air pressure is too low due to a blockage in the coarse or fine air filter. Besides the parts for pneumatic clutch actuation like concentric slave cylinders, febi offers a wide range of clutch components including clutch discs, pressure plates, release bearings and release forks.
Unfortunately, oils and lubricants are one of the most common reports of pollution, contributing to over 15 per cent of pollution incidents each year in theUK. It can harm people, plants and marine life, damage rivers, soil, destroy natural habitats and drinking water supplies, as well as ruining workshop and garage environments.
Oil storage regulations are governed by the control of pollution (oil storage) (England) Regulations 2001. This requires anyone in England who stores more than 200 litres of oil to provide secure containment facilities for tanks, drums, intermediate bulk containers (IBCs) and mobile bowsers. There are different regulations for England Scotland and Northern Ireland, so let’s take a closer look at oil storage for the workshop.
The basic principles
There are two main principals in storing lubricants, product integrity and environmental requirements. The basis is always to create an area which is safe, clean and appropriate. Basic rules include:
Oil must be stored at least 10 metres away from inland or coastal waters, flood areas and 50 metres clear of a spring.
Tanks should be on flood level or below ground level and must never be stored above roof level and kept away from areas that risk damage via impact, machinery and weather. The full legal requirements are outlined in detail in the oil storage regulations for businesses –
The Witham Group explains the advantages of its bulk storage solutions for oil, sharing a couple examples of some workshops it has helped transform.
GOV.UK website which covers storage of quantities of 201 litres and above. There are however different regulations that apply, depending on where you store your oil, how much you store and what you are using the oil for. If you choose not to comply with these regulations, you can be served an anti-pollution works notice and face prosecutions.
Lubricants are supplied in many ways, bulk, barrel, and various drums and small packs to meet the needs of a wide customer base. Bulk and barrels are generally supplied to commercial workshops and the other sizes to both the commercial and retail market. With the exception of bulk, the remaining sizes can all come in either
“Oil not only needs to be stored safely and properly because it’s the law, but it should also be stored to help with the environment.”
plastic or metal containers depending on the supplier and also the type of product. Lubricants stored in a factory fresh sealed container will not normally degrade. Obviously, metal containers can be subject to corrosion over extended periods. In essence, the largest single container must be contained within 110 per cent of its volume.
Storage and movement of containers is guided by lifting at work regulations, so heavy containers are to be lifted correctly and with suitable and appropriate machinery.
The temperature of the surrounding environment can affect the lubricant, for example heat is a huge risk to oil, not only from a fire point of view, but also from a volumetric point of view. Oil volume will increase as the temperature rises so contained vessels need to be vented.
Once a container is opened it will come into contact with the environment and whilst lubricants often contain antioxidants they will start to oxidise when in contact with the atmosphere. If for example you were to leave a sample of hydraulic fluid in a glass jar open to the atmosphere for a period, you would see it darken in colour as this happens. Elevated temperature will, as will almost all reactions, increase the speed.
Is there a way to manage lubricant storage sustainably?
“Yes” explains Nigel Bottom of Witham Group. “Oil not only needs to be stored safely and properly because it’s the law, but it should also be stored to help with the environment and health and safety. Bulk Storage tanks are an ideal solution of metal tanks in your garage that removes the need for all plastic packaging. The simple colour coded tanks have sight gauges, taps or pumps and come labelled with each lubricant name and its application and are filled in bulk deliveries, saving the need for plastic drums and waste. This system is easy to use for all the workshop team, helps keep working spaces ship shape, avoids spills from containers and helps avoid important oil contamination, whilst helping the environment by using no packaging. With annual maintenance the longevity of bulk tanks will last over 50 years. This is a very sustainable process indeed as the defunct metal tank can then be simply recycled and the metal used again.”
This method of storage and use also helps tick all the regulation requirements for oil storage and keeps users and the workshop environment as safe as possible.
What's the number one thing to consider when storing lubricants?
Nigel explains, “The best piece of advice we can give is to treat lubricants as if you
were storing drinking water. Always avoid storing any products outside where water could penetrate the lid or seal. Many people assume the seals on barrels are watertight, they are generally not and are simply used as an anti-tamper method. If no other option but external storage is available always store barrels on their side. Moisture and dirt ingress are the two main factors. Moisture can be overcome by always keeping the bulk storage at as close to the same temperature as possible.
In addition to this, using air operated or electric transfer pumps and guns stops the contamination of oil in dirty transfer jugs. If jugs are used, they need to be kept in a clean environment also, upside down and empty when not in use. Bulk storage tanks should be fitted with return flaps to stop wastage of unused clean oil which can be returned to the bulk tank.
There are many storage solutions on the market, bulk tanks are excellent for larger volume products and bulk tanks can simply be raised off the workshop floor and downpipes fitted to both fill and empty. A simple process which will not impact the workshop floor space at all.
Bunded racks and trays are also available for smaller sizes. Try and avoid storing products for extended periods and just buy as much as your immediate needs require.
Benefits of bulk storage tanks:
● Keeps workshops clean and tidy.
● Helps the environment by using less container packaging.
● Creates more space in workshops and garages.
● Easy to distinguish different lubricants for various uses.
● Helps avoid oil spills and contamination.
● Long lasting storage solution – with good maintenance these will last up to 50 years.
We are pleased to announce the successful installation of two new bulk storage tanks at Spitfire Engineering in Northamptonshire.
A long-standing customer of our paint products, Spitfire Engineering sought to streamline their oil supply process by switching to bulk deliveries. After careful consideration of their specific requirements, we determined the ideal tank size and oil type to meet their needs. Our swift delivery from our Soham facility ensured a seamless transition. To aid inventory management, our lorry driver marked the tanks at the halfway point (200 litres), providing a clear visual indicator for reorder timing. The positive feedback from Spitfire Engineering underscores our commitment to providing exceptional customer service and tailored solutions. We look forward to continuing our strong partnership and supporting their future needs.
Witham Group is proud also to have supplied our oil to Sanders Coaches in Norfolk. For over three decades, it has been a reliable supplier of essential products and services to this wellrespected coach company. Our recent delivery of a quantity of 100 gallon, singleskinned storage tanks to Sanders Coaches’ workshop further strengthens our commitment to supporting their operations. These tanks will provide a safe and efficient storage solution for their workshop needs.
What oil, lubricant and antifreeze coolant should you use? Confused? Morris Lubricants is here to help!
In the commercial vehicle sector, the landscape of emissions, engine designs, driveline configurations, hybrid technologies and increasing performance requirements to cope with environmental and legislative impacts, is ever changing.
The original equipment manufacturers (OEMs) are continually developing new engine and transmission designs. The formulations for engine oils, antifreeze coolants, differential oils, gear and transmission oils are therefore constantly changing to comply to these new requirements. It is so important for lubricant manufacturers like Morris Lubricants to keep abreast of the latest specification and approval changes.
The number of different formulated engine oils, transmission oils, antifreeze coolants and other lubricants will continue to increase as the technology and commercial vehicle hardware changes. This is a neverending process. Legislation continues to drive innovation, and the truck, HGV and other commercial vehicle OEMs are adopting their own strategies to remain compliant.
Euro 7 is just around the corner and the OEMs are not only moving at different speeds but are introducing new oil, lubricant
and antifreeze coolant specifications that may or may not be compatible across different brands or makes. This has led to the development of very tailored oils, lubricants and antifreeze coolants and these newer formulations are not always suitable for older commercial vehicles.
In the world of commercial vehicles, it is important that a vehicle is kept on the road and out of the workshop. A commercial vehicle in a workshop being fixed, is not contributing to the bottom line. This means that the correct selection and use of engine and transmission oils, antifreeze coolants and lubricants has become more critical.
Of course, we shouldn't overlook the equally important selection of oils, lubricants and antifreeze coolants for older commercial vehicles. These vehicles are often still being used and will need to be kept on the road. Using the incorrect products can lead to engine breakdown, blocked aftertreatment devices or even catastrophic mechanical failure. Therefore, following the correct OEM guidelines and specifications for oil, lubricant and antifreeze coolant use in all ages of vehicle will help to ensure optimum performance and reliability.
All these changes to vehicle requirements and the wide variety of product choices available can be confusing, even daunting especially considering the damage that can be caused if the wrong oil, lubricant or antifreeze coolant is used. The good news is that Morris Lubricants is here to help. The company have provided technical support since the 1980s and in today's environment this has become even more crucial, as downtime and loss of business is not an acceptable option.
Providing information, advice and support for buyers and users of oils, greases, lubricants and other maintenance products has been part of the Morris Lubricants’ service offering for many, many years. It has always been the underlying philosophy at Morris Lubricants that selling a quality product should be backed up with technical support when required.
The technical services department at Morris Lubricants is available to provide buyers and users with a point of contact, should help and advice be needed. It is headed up by Adrian Hill, technology manager, who has accumulated over 40 years of oil and lubricant industry experience. Adrian leads a team of advisors
who have chemistry backgrounds, hands on mechanical experience and various lubricant industry qualifications. This combination of skills and deep practical knowledge helps to provide accurate guidance and assistance.
Rapid correspondence via telephone calls, e-mails, social media DMs and website contact forms, are actioned by all the team, including Ian Haslum, technical advisor. The team also make visits to customers’ premises to assess their commercial vehicles, equipment and machinery to check what oil and lubricant solutions are required. These visits are often managed by Morris Lubricants’ technical support engineer, Ryan Woolley, who can provide hands on help where face-to-face is a preferred form of contact.
Advice can also be sought from the company’s online oil and lubricant lookup tool Whatoil, which can be found on the Morris Lubricants’ website and can therefore be accessed 24 hours a day 7 days a week. The correct product can be found on this lookup tool by entering a truck registration number or you can select from a wide variety of different commercial vehicles,
equipment and machinery by using a series of simple dropdown menus. Once the vehicle or piece of equipment is selected, the recommended oils, antifreeze coolants and maintenance fluids are presented.
Apart from helping with immediate needs, especially if a commercial vehicle is sat in a workshop, more extensive and detailed reporting can be employed, especially if equipment lists and multiple vehicle fleet surveys are required. The technical services department can provide advice on how to rationalise product stock holdings across different brands whilst maintaining conformity to OEM specifications and best practices.
The technical services department also offer used oil analysis from an independent specialist laboratory. This is important to help diagnose vehicle conditions, especially where customers are seeking advice on commercial vehicles in service. With enough
Make sure to scan the QR code!
data it is also possible to use these tests and analysis as a preventative measure to reduce downtime or predict failure, enabling corrective action to be implemented, saving money and lost productivity.
There are also many different informative videos on the Morris Lubricants’ YouTube channel. Featuring the company’s brand ambassadors Guy Martin and truck racer Dave Jenkins, who ask Adrian some real tricky questions about commercial vehicle oils, antifreeze coolants and lubricants.
As highlighted by Adrian, “Whatever the future brings, Morris Lubricants will be well placed to supply what is needed. We are committed to providing high-quality products, all backed up with information, advice and support so that buyers and users are making the correct informed choice and not relying on guesswork.”
CVW spoke to Alan Outhwaite, head of the Verification of Lubricant Specifications (VLS) technical review panel, about the role of hydrogen in the net zero transition.
The race to net zero has been on for some time. Electric vehicles were seen as the answer, with OEMs developing hybrid and full electric vehicles to meet emissions targets. Hydrogen was also being explored as a potential solution – both in fuel cell operation and in combustion engines.
How do hydrogen vehicles work?
There are two main types of hydrogenpropelled vehicles: a hydrogen fuel cell and a hydrogen-fuelled vehicle, and they both work in different ways.
A hydrogen-fuelled vehicle replaces conventional road fuel with compressed hydrogen gas or liquid gas. In these vehicles, the pressurised gas or liquid is injected directly into an engine’s pistons, and combustion takes place like a normal internal combustion engine vehicle. The primary emission from hydrogen combustion is water, a property that makes it an environmentally attractive fuel.
Most modern ICEs wouldn’t require much modification to run on hydrogen gas or liquid, but durability has not been proven in these systems, and appropriate lubricants are needed. These need to be formulated to minimise the potential for pre-ignition events, as well as manage increased levels of water in the crankcase
to prevent corrosion, sludge formation and reduce wear. Service stations could be converted to dispense hydrogen gas or liquid with extensive changes required, and refuelling will take as much time as conventional fuels.
Specific engine management and filters can remove airborne contaminants such as NOx and SOx present due to the air intake for combustion to unmeasurable levels of emissions. The hydrogen gas is less dense than petrol or diesel, and the by-product of the combustion process is water vapour. Like conventional ICEs, hydrogen-fuelled vehicles still require specialist engine lubricants.
In a hydrogen fuel cell, instead of burning hydrogen gas, as is the case with hydrogen ICE-fuelled vehicles, the vehicle produces electricity through a chemical reaction between hydrogen from the storage tank and oxygen from the air in something called a fuel cell stack.
The stack powers the heart of the vehicle and generates electricity in the form of direct current (DC) from electrochemical reactions that take place in the fuel cell. Unlike a conventional battery, which stores electrical energy made elsewhere and releases it, hydrogen is an energy source in itself and releases some of its energy in an electrochemical reaction in the fuel cell. Electricity is then produced on demand.
The main advantage for vehicle owners is that, unlike pure electric vehicles, refuelling a tank for a hydrogen fuel cell from a pump takes less than five minutes. In contrast to ICEs, hydrogen fuel cell vehicles require no engine lubricants, though specialist fluids are required for transmission, braking and cooling systems.
Are hydrogen vehicles a viable solution?
According to some OEMs, the answer is yes. In 2023, engineers at JCB Power Systems in the UK unveiled a hydrogen combustion engine, developed using and adapting established engine technology
“Hydrogen combustion engines are well-suited to heavy-duty, long-distance applications that are hard to electrify.” Jonathan Hall, Mahle Powertrain.
with readily available components. Their prototype backhoe loader, fitted with the new hydrogen motor, could do everything its diesel-powered equivalent could do.
The company described hydrogen as a “better way”, saying, “On a practical level, a hydrogen motor uses similar technology to existing propulsion systems. It’s also robust, cost-effective and it could be integrated into all forms of powertrain. Most importantly, a familiar technology and lack of complexity make hydrogen an ideal zero-carbon solution for our customers, with demand being met by our existing, high quality manufacturing supply chain.”
JCB installed one of its super-efficient hydrogen engines into a 7.5 tonne Mercedes-Benz Sprinter van to demonstrate the potential of hydrogen ICE vehicles. The white van retrofit was completed in just two weeks.
More recently, the testing phase of Project Cavendish, a £9.8m governmentfunded programme facilitated by the Advanced Propulsion Centre UK (APC), began. The project is designed to drive hydrogen fuel use in existing heavy-duty truck engines with a clear path to enable hydrogen combustion using current platforms and infrastructure, accelerating the decarbonisation of the haulage sector.
Jonathan Hall, Mahle Powertrain’s head of research and advanced engineering, said: “Hydrogen combustion engines are well-suited to heavy-duty, long-distance applications that are hard to electrify. Its use allows industry to take advantage of years of
development and investment as a means to accelerate the transition towards net zero.”
Toyota launched its third-generation fuel cell system (3rd Gen FC System) as part of its continued efforts toward “the realisation of a hydrogen society”. In 2024, Hyundai outlined its approach to hydrogen in their “Hydrogen Vision 2040: A roadmap toward a hydrogen society”, saying that hydrogen fuel cells are “pivotal in assessing the technological prowess of FCEVs”. The company hailed the progress of its XCIENT fuel cell electric heavy-duty trucks, which surpassed a cumulative driving distance of 10 million km in Swiss fleet usage, described as “a testament to the world-class hydrogen fuel cell technology’s long-term reliability.”
H2 generation is attracting a lot of investment in different methods. Green hydrogen is a ‘clean energy’ made using electricity from renewable energy sources, such as solar or wind power, to electrolyse water. Green hydrogen currently only makes up a small percentage of overall hydrogen production, but increased investment will help reduce costs over time, just as energy from wind power has reduced in price.
In the meantime, many fleet operators will hang onto their current ICE vehicles for as long as possible, as shown by the already ageing vehicle parc. According to the Automobile Manufacturers Association (ACEA) 2025 ‘Vehicles on European Roads’ report, the average age of vans is now 9.8 years, up from 7.8 in 2021. Trucks are now, on average, 11.6 years old, up from 7.3 years in 2021, and buses are now 16 years old, compared to 9.9 years in 2021.
For lubricant and specialist fluid manufacturers, motor factors and workshops, this means dealing with a more extensive and complex product range for the near future, catering to the needs of older vehicles as well as the latest models and a variety of powertrains.
CVW takes an updated look at Intangles’ AI product and how its helping fleets predict breakdowns and reduce downtime.
New to the UK industry, Intangles provides predictive maintenance alerts for fleet operators – basically flagging vehicle issues before a vehicle fault code is triggered. This aims to create substantial savings in operating costs through improving fuel efficiency and reducing downtime. It also decreases maintenance costs by improving turnaround time with lower costs of repairs.
If you ask most people what AI is they will point you towards large language models like ChatGPT or Gemini, however the reality is that AI is already firmly embedded in the road haulage industry, be it through driver behaviour monitoring, geolocation and smart route mapping. However, no system to date has come close to predicting when a vehicle is going to fail, until now.
Intangles has developed an AI product that can do just this. Intangles systems operate at a 95 per cent accuracy rate. Customer fleets in the US are reporting a reduction in fuel use of up to 10 per cent due to greater efficiency, reduction in maintenance costs of
up to 10 per cent, and a reduction in breakdowns of up to 75 per cent, figures that represent enormous savings.
The system intelligently monitors all the data that is processed in a vehicle’s CAN bus in real time. This equates to millions of data points every day. Its algorithms then use physics-based modelling to produce a digital twin of each individual vehicle’s systems. This is then used in conjunction with the information from the live vehicle to create an accurate model of current vehicle health and then raise alerts to the fleet manager where there are causes for concern, along with the ordered recommendations to address them. This means that a vehicle could be on a run, and a minor predictive alert could be raised informing the maintenance staff of work that can be scheduled upon the vehicle’s return, or in the case of a critical alert, the vehicle could be diverted to a safe location along its route to avoid breakdown and costly recovery.
The Intangles system has been installed on over 300,000 vehicles worldwide and as a result the dataset is incredibly rich – it holds over 60 TB of curated data – a figure that increases daily. When new engine platforms are introduced to the AI, accurate and tailored new models are created within just a few days of vehicle operation.
WANT TO KNOW MORE? Make sure to scan the QR code!
The Intangles solution is OEM and powertrain agnostic and currently supports over 3,000 different engine specifications across multiple vehicle classes and fuel sources (diesel and petrol ICE, alternative fuels, and electric). The Intangles InRoute platform also contains a full suite of telematics and driver behaviour monitoring features allowing fleets to maintain a broad perspective of all aspects of their operations from within a single view. The user interface has been carefully designed to make it easy to use and simple to learn. The platform comes with a convenient iOS and Android mobile app which can keep you informed on critical alerts while on the go. Device installation can be done in just a few minutes and is guaranteed to not interfere with any other existing systems in the vehicle.
Overall, the Intangles solution offers fleets value through multiple areas of benefit. Fleets will experience lower maintenance and fuel costs along with increased availability thanks to the accuracy of the insights that the system provides.
CVW takes a closer look at Liftmaster’s
BP 65-215 King Pin Press.
Liftmaster have spent decades supplying the very best in workshop equipment. From quality lifts, brake testers and even specialist tools, to help you get the job done efficiently and safely.
The BP 65-215 S3 King Pin Press is one of those rare tools – a solution built to meet the rigorous demands of commercial vehicle workshops. Purpose-built for the safe and controlled removal and installation of king pins, bushings, and wheel bearings, it’s a press that makes heavy-duty work feel effortless.
Robust, adaptable, and engineered to the highest standards, the BP 65-215 S3 isn’t just a tool – it’s an investment in speed, safety, and workshop innovation.
What is it – and what does it do?
The BP 65-215 S3 is a 65-tonne mobile king pin press, built for use in truck and bus maintenance workshops. Thanks to its electro-hydraulic system, this press delivers massive force, making light work of tasks that once required brute strength and an uncomfortable level of risk. It
The BP 65-215 S3 removes the need for all that. It takes the guesswork out of pressing, providing a safe, repeatable, and efficient solution your team can rely on.
Why choose the BP 65-215 S3?
Workshops across the UK rely on this unit for one simple reason: it delivers. Here’s why:
● Unrivalled mobility – the unit can be wheeled directly to the vehicle, avoiding the need for disassembly or unnecessary lifting.
● 65 tonnes of pressing power, making it suitable for even the toughest applications.
● A modular design, allowing it to adapt to a wide variety of axle and bushing types.
operates with a double-acting cylinder, giving users complete control during both pressing and retraction. This makes it ideal for working on commercial vehicles where access is limited, tolerances are tight, and downtime is costly.
The problem with traditional methods
Let’s be honest – manually removing king pins isn’t just frustrating. It’s dangerous. Technicians are often left battling with sledgehammers, heating tools, and improvised setups. Not only is this timeconsuming, but it’s also inconsistent, unsafe, and often damaging to surrounding components.
● Easy operation, with an intuitive control panel and consistent pressing speed.
● But beyond that, it’s the peace of mind that sets it apart. Your team can focus on the job, not the tools – knowing the BP 65-215 S3 has the muscle to get it done.
The BP 65-215 S3 King Pin Press represents the kind of innovation we champion: engineered strength, backed by thoughtful design. If you’re looking to reduce vehicle downtime, protect your technicians, and bring your workshop operations in line with the demands of modern fleet servicing, the BP 65-215 S3 is a press that earns its place on your floor.
Ivor Searle has added the PSA 2.2 litre BlueHDi engine for Citroën Relay, Peugeot Boxer and Vauxhall Movano van applications to its all-makes range. Covering over 90 per cent of the UK’s vehicle parc, the leading remanufacturer is constantly adding to its extensive programme of engines, gearboxes and turbochargers for cars and LCVs.
Delivering a power output of 140bhp, the four-cylinder Euro 6 diesel engine covers vehicles produced from 2019 onwards. Ivor Searle engines cost up to 40 per cent less than OE and are remanufactured to exceed the BS AU257:2002 code of practice for engine remanufacturing.
WANT TO KNOW MORE?
WWW.RDR.LINK/VBW013 GOTO
Imexpart (IMEX) has launched a new range of NOx Sensors, with hundreds of references now catering for a vast array of vehicles. The IMEX-branded EM Sensorsync NOx Sensors are designed to meet the needs of a wide range of popular truck makes, employing the latest software for enhanced performance, and all backed up with a three-year warranty across the board. A standard feature on commercial vehicles since Euro 5, NOx sensors determine nitrogen oxides in the flow of exhaust gas, making up part of the urea-based selective catalytic reduction (SCR) treatment process. Thanks to NOx sensors, correct levels of AdBlue can be applied, ultimately reducing nitrogen oxides in exhaust gases.
WANT TO KNOW MORE?
WWW.RDR.LINK/VBW014 GOTO
Here is a useful summary of all the adverts that appear in this issue of Commercial Vehicle Workshop. Each is listed with its page number and a direct URL that will get you straight to the relevant online information.
Borg Warner ............................................................(page 18)
www.rdr.link/VBW100
Febi ..........................................................................(page 4)
www.rdr.link/VBW101
ISN Europe Ltd ......................................................(page 23)
www.rdr.link/VBW102
Liftmaster Ltd ..........................................................(page 6)
www.rdr.link/VBW103
MAHA UK ..............................................................(page 10)
www.rdr.link/VBW104
Mann+Hummel (UK) Ltd ........................................(page 20)
www.rdr.link/VBW105
Mechanex ..............................................................(page 25)
www.rdr.link/VBW106
Merridale Ltd ..........................................................(page 29)
www.rdr.link/VBW107
Premier Pits ............................................................(page 17) www.rdr.link/VBW108
Robert Bosch Ltd ....................................................(page 9)
www.rdr.link/VBW109
SIP Industrial Products ..........................................(page 34) www.rdr.link/VBW110
Stertil UK Ltd ..............................(page 2, Inside front cover) www.rdr.link/VBW111
Totalkare ................................(page 36, outside back cover) www.rdr.link/VBW112
UFI Filters ..............................................................(page 29)
www.rdr.link/VBW113