It’s becoming a 3D world. p.22
Casting call for technical talent. p.24
Wages aren’t as important as you might think. p.20
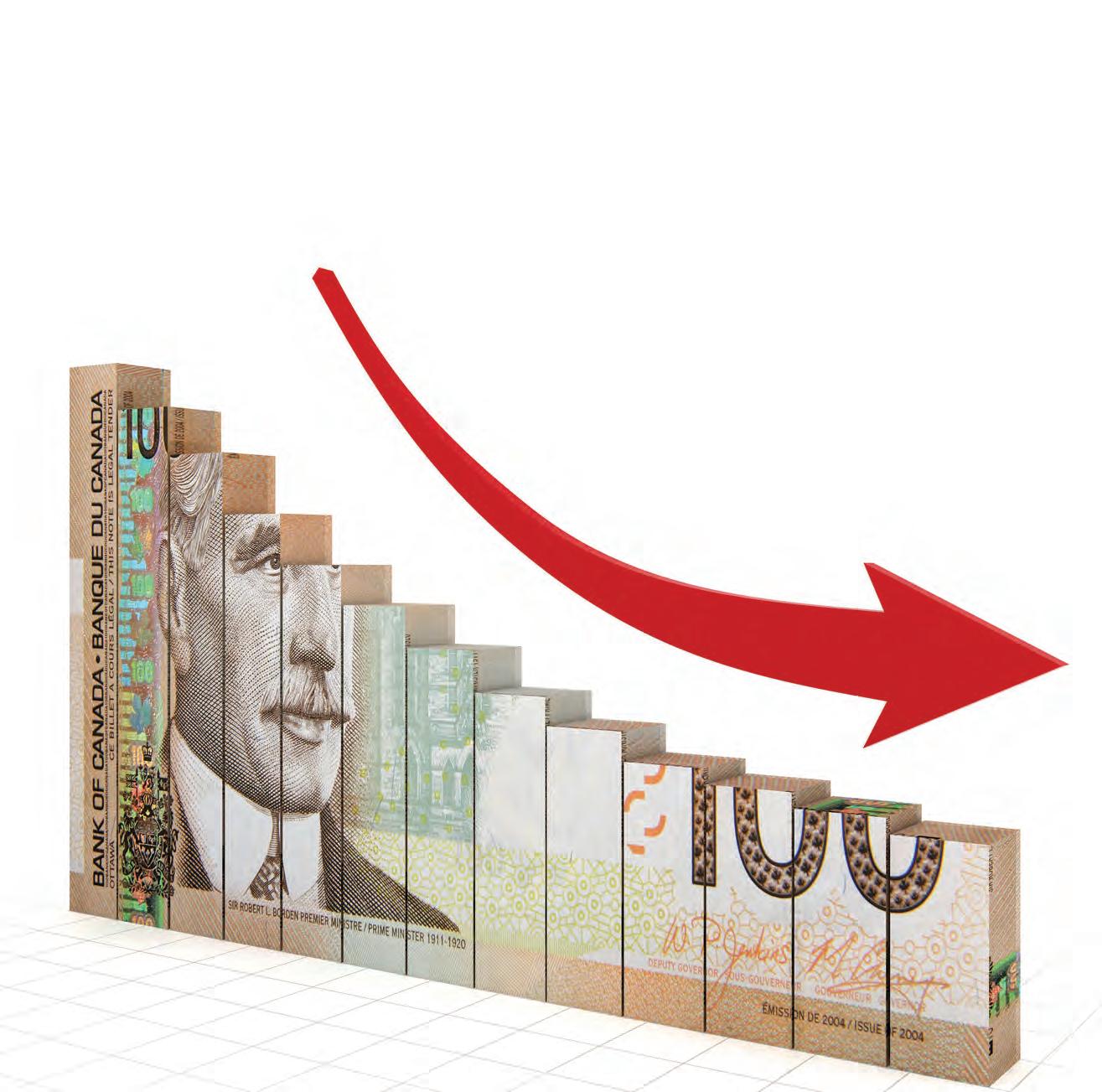
RESOURCESHUMAN
SUMMER 2022 SALARIESPLANT.CADIP
3D
DEVELOPMENTSKILLS
Executive salaries fall as pandemic impact drops.P.14
From sensor technology and data analytics to robotics and automation, you’ll see all of the latest innovations in fluid power, all in one place. Even better, you’ll have many opportunities for in-depth technical conversations with other engineers to spark new ideas, and you’ll be able to talk with suppliers about your specific challenges and the solutions they offer. Bring your question—and leave with smart new solutions to solve your most pressing technical problems.

W ITH:
SHOW
I NT ERNATIONA L FLUI D POWE R EXPO
CO-LOCATED
LAS VEGAS, NV, USA OWNERS:
LEARN MORE AT IFPE.COM
MARCH 14-18, 2023
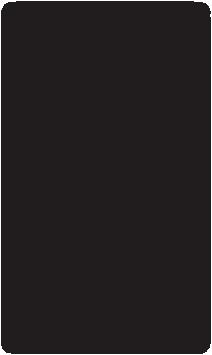
Wages aren’t as important as you might think.

Executive salaries took a dip as impact of COVID-19 falls.
SALARY SURVEY
The health of the workforce hinges on upskilling and reskilling in-demand trades.
SUMMER 2022 14 INSIDE 20242210In every issue 4 EDITORIAL 6 NEWS 28 TECH CENTRE 30 POSTSCRIPT Reflections from the Hannover Messe. Cover photo: alexsl/iStock/Getty Images Plus/Getty Images
EMC’S TAKE: SALARY SURVEY
ADVANCED TECHNOLOGY
Cover story
A foundation for a productive workplace: occupational health and safety training.
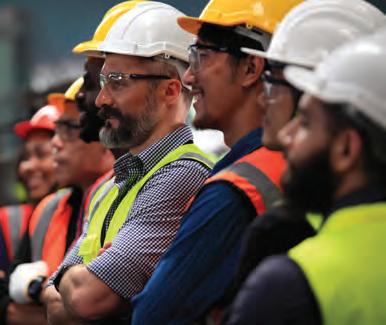
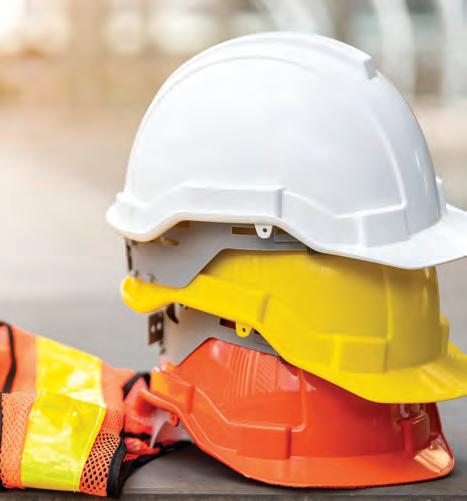
Advancing the plant industry through cloud technology.
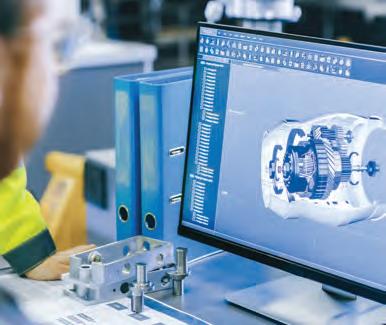
SKILLS DEVELOPMENT
Excellence in Manufacturing Consortium’s take on the salary survey results.
HEALTH AND SAFETY
HUMAN RESOURCES
A fun part of being a consultant is visiting different companies, which allows for comparison between organizations, and the ability to find organizations with innovative ideas.
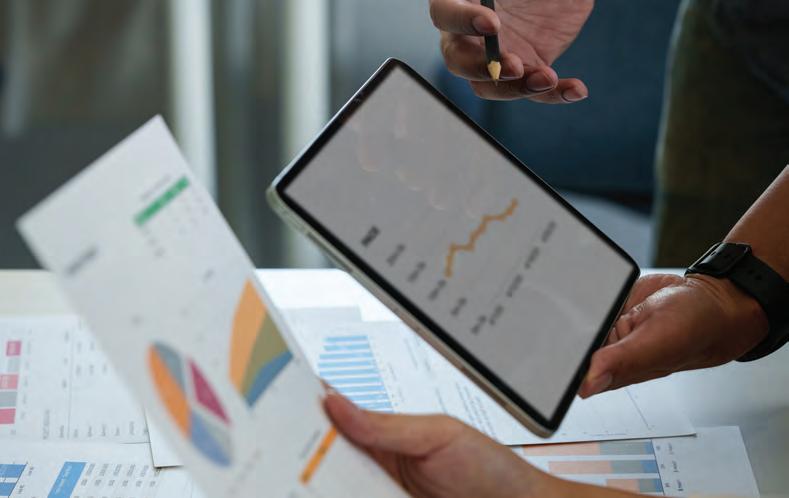
20222419141210 @PLANT_Magazine Summer 2022 / Plant 3
IT’S A 3D WORLD
PUBLICATIONS MAIL AGREEMENT NO. 40065710
2022 Salary Survey
If this trend continues, and is not simply a one year blip, this is great news for the manufacturing industry. It shows that more young workers are moving into more promi nent executive roles. In combination with the cur rent skills shortage, the number of older workers moving out of the workforce has created a shortage of workforce that is being put to the Conversely,limit.with a younger workforce, the level of experience has also seen a dip for 2022. The average years of experience in 2021 was 25.9, while this year it has dropped
BY MARIO CYWINSKI
to 22.3. While the biggest group (46 per cent) has over 25 years of experience, that is down from 57 per cent last year. With those with less than 10 years of experience seeing an increase to 19 per cent this year, up from around 10 per cent last year.
With the COVID-19 pandemic slowly moving into the rear view, it is important for those in the manufacturing industry to keep moving forward. While many positives were observed in the 2022 salary survey, issues still
Let’s start with the average salary. In last year’s survey, it was $129,685, which was a year-over-year increase. However, for 2022, it dropped to $119,726. This could be at tributed to a number of factors. For one, the respondents may not all be the same; second, we had less respondents this year, compared to last. Finally, we found this year that respondents were in younger age groups, which could mean that more are in less senior
Connect @PLANT_Magazine facebook.com/PlantMagazine/ /plant-magazine plant.ca
Women now account for one in five (20 per cent) of the manufacturing survey respondents.
NATIONAL ACCOUNT MANAGER Ilana Fawcett 416-829-1221 · ifawcett@annexbusinessmedia.com
ISSN: 1929-6606 (Print), 1929-6614 (Online).
ASSOCIATE EDITOR Monica Ferguson 416-510-5206 · mferguson@annexbusinessmedia.com
Canada – $76.00 per year USA – $201.00 (CAD) per year International – $227.00 (CAD) per year Single copy – Canada $12.00

ACCOUNT COORDINATOR Debbie Smith 416-442-5600 ext 3221 · dsmith@annexbusinessmedia.com
PRINTED IN CANADA
SENIOR PUBLISHER Scott Atkinson 416-510-5207 · satkinson@ annexbusinessmedia.com
SUMMER 2022 • Volume 80, Number 3 4 Plant / Summer 2022 PLANT.CA
Print and digital subscription inquiries or changes, please contact customer service Angelita Potal Tel: (416) 510-5113 Fax: (416) 510-6875 email: apotal@annexbusinessmedia.com Mail: 111 Gordon Baker Rd., Suite 400 Toronto, ON M2H 3R1
COO Scott sjamieson@annexbusinessmedia.comJamieson
SUBSCRIPTION RATES
Thisroles.year,
T
Return undeliverable Canadian addresses to: PLANT Circulation Department, 111 Gordon Baker Rd. Suite 400, Toronto, ON M2H 3R1
Add applicable taxes to all rates. Combined, expanded or premium issues, which count as two subscription issues.
READER SERVICE
the average age dropped to 51.1 years old, from 53.7 a year ago. The biggest shift was that the amount of respondents 56 years old and above was 39 per cent (down from 51 per cent in 2021), and those 26 to 45 was at 29 per cent (compared to 19 per cent. This middle group 46 to 55 stayed stable at 32 per cent (29 per cent in 2021).
MARIO CYWINSKI, EDITOR Comments? mcywinski@annexbusinessmedia.comE-mail

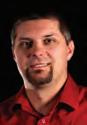
he 2022 EMC-PLANT Manufactur ing Salary Survey, was sent out into a neo-COVID-19 world. Where it is still in the back of everyone’s mind, but for many life is going back to something resembling normal. This could be the reason that we saw a few swings in the data, includ ing the average salary, average age, and level of exper ience.
Respondentsremain. found the most significant issues being: skill shortages, cost control, transportation, supplier relationship man agement, capacity utilization, technology upg rades, and many more.
EDITORIAL
with Plant magazine
111 Gordon Baker Road, Suite 400 Toronto, ON M2H 3R1
Tel (416) 442-5600 · Fax (416) 510-5134 www.annexweb.com
EDITOR Mario Cywinski 226-931-4194 · mcywinski@annexbusinessmedia.com
AUDIENCE DEVELOPMENT MANAGER Beata Olechnowicz 416-510-5182 · bolechnowicz@annexbusinessmedia.com
MEDIA DESIGNER Svetlana Avrutin
©2022 Annex Business Media. All rights reserved. Performance claims for products listed in this issue are made by contributing manufacturers and agencies. PLANT receives unsolicited materials including letters to the editor, press releases, promotional items and images from time to time. PLANT, its affiliates and assignees may use, reproduce, publish, re-publish, distribute, store and archive such unsolicited submissions in whole or in part in any form or medium whatsoever, without compensation of any sort. This statement does not apply to materials/pitches submitted by freelance writers, photographers or illustrators in accordance with known industry practices.
Age, experience, salaries dip; number of women up
GROUP PUBLISHER Paul pgrossinger@annexbusinessmedia.comGrossinger
One other aspect I’d like to focus on is the increase of women in the manufacturing workforce. Last year we did a focus piece on women in manufacturing, at that time only 13 per cent of respondents of the survey were female. For 2022, this has increased to one in five (20 per cent). While this is still the minority, a seven per cent increase year-overyear is a big increase, and hopefully is a trend goingOneforward.itemof concern is that the average male salary is $128,680, while the average female salary is $85,249. This could be a result of varying roles, and a smaller sample size; however, such a large gap is not what you want to see.
ANNEX BUSINESS MEDIA
Also, don’t miss the plethora of other informative articles within these pages. Including articles on health and safety, ad vanced technology, human resources, skills development, and the 3D world. As well as Reflections from the Hannover Messe in this month’s Postscript column.
To read all the results of the salary survey go to page 14, and to see our survey sponsor EMC’s take, go to page 19.
Stop electronic downtime with an EXAIR Cabinet Cooler System! complete line of low cost Cabinet Cooler Systems are in stock and can ship today. They mount in minutes through an ordinary electrical knockout and have no moving parts to wear out. Thermostat control to minimize compressed air use is available for all models. All Cabinet Coolers are UL Listed to US and Canadian safety standards.
High Temperature
NEMA 12 For large heat loads up to 5,600


The
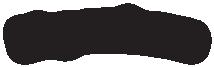
For NEMA 12, 4 and 4X applications. Available for heat loads in many capacities up to 5,600 Btu/hr. • Suitable for ambients up to 200°F (93°C) • Ideal for mounting near ovens, furnaces, and other hot locations Non-Hazardous Purge Keep a slight positive pressure on the enclosure tokeepdirtfromenteringthroughsmallholes or conduits. For use in non-hazardous locations. • Uses only 1 SCFM in purge mode • For heat loads up to 5,600 Btu/hr. • NEMA 12, 4 and 4X Benefits of Cabinet Cooler® Systems • Less expensive to purchase than refrigerant A/C units • Less expensive to operate than refrigerant A/C units • Quicker to install than heat exchangers and refrigerant A/C units • Little to no maintenance • More reliable in dirty, hot, or remote environments than alternative cooling products • Not affected by machine vibration which can cause refrigerant leaks • Ambient temperature does not affect performance like it will with alternative cooling products Don’t Blow A Fan on an Open Cabinet! It is an OSHA violation that presents a shock hazard to Thepersonnel.fanblows hot, humid, dirty air at the electronics. If you would like to discuss an application, contact: 11510 Goldcoast Drive Cincinnati, Ohio 45249-1621 (800) 903-9247/fax: (513) 671-3363 GO TO https://exair.co/18_440
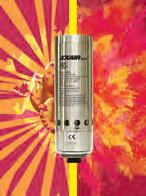
Hazardous Location
Type
For use with classified enclosure purge and pressurization systems. Available for all Class I Div 1 environments up to 5,600 Btu/hr. • Maintain NEMA 4/4X integrity • Meet UL classified requirements • CE compliant
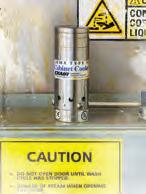
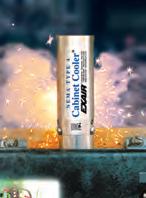
Cabinet Cooler Systems Btu/hr.
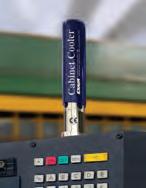
316 Stainless Steel For NEMA 4X applications available for heat loads up to 5,600 Btu/hr. • Resists harsh environments not suitable for Type 303/304SS • Ideal for food and chemical processing, pharmaceutical, foundries, heat treating and other corrosive environments

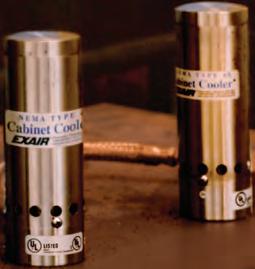
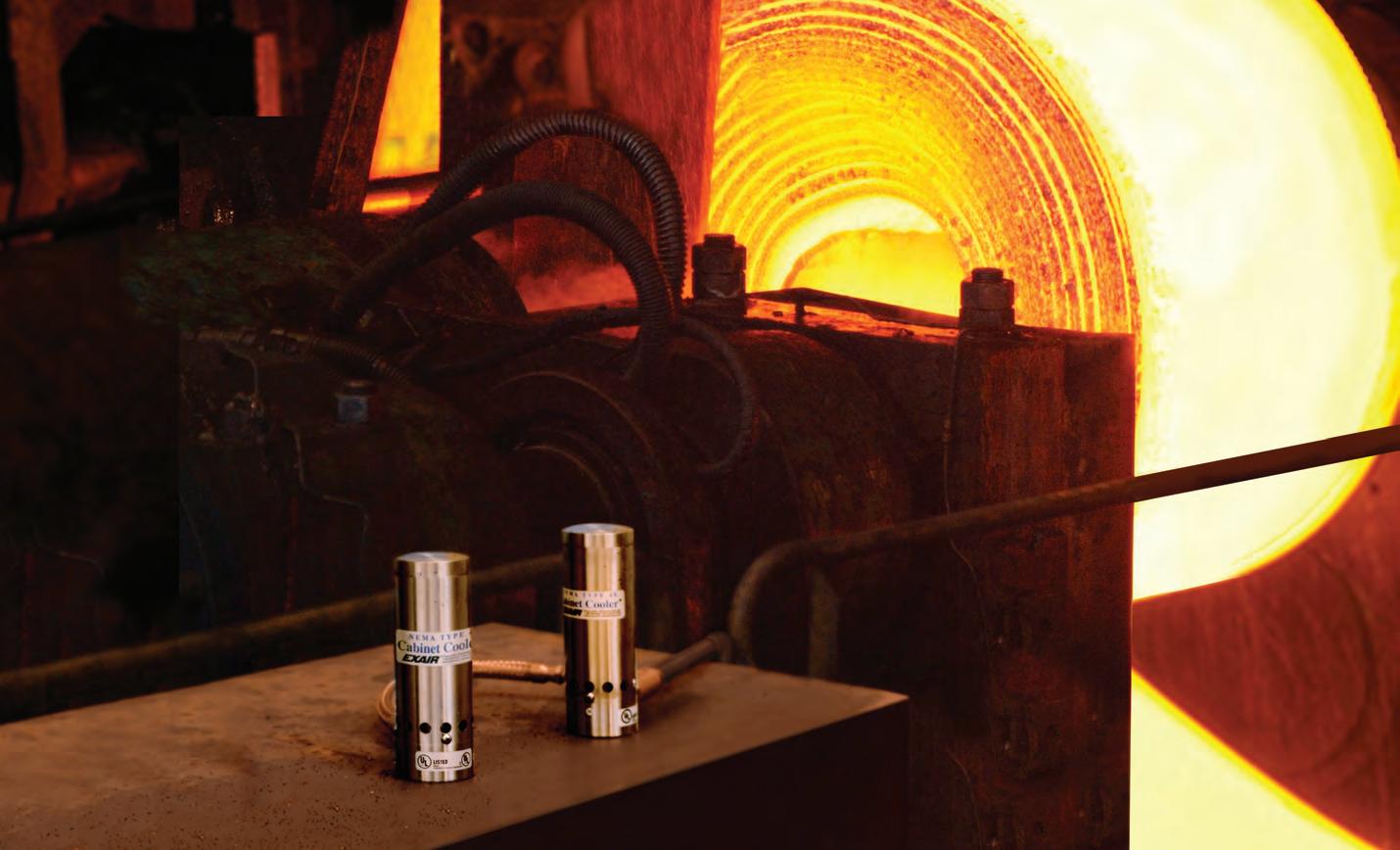
TheCoolElectronicstoSecretTheKeeping!RealSolution!
• Enclosure remains dust-tight and oil-tight • Measures 8" (203mm) high • Mounts top, side or bottom NEMA 4 and 4X For heat loads up to 5,600 Btu/hr. • Enclosure remains dust-tight, oil-tight and splash resistant • Suitable for wet locations where coolant spray or washdown can occur
Looking at the value of cloud, 91 per cent of respondents consider cloud computing to be essential for data management, while 54 per cent believe cloud transformation has had a positive impact on data governance.
6 Plant / Summer 2022 PLANT.CA
of respondents cited efficiency as the top motivator for cloud investments, increased security is the second with 48 per cent citing it as a key factor. Resilience is a primary driver of cloud computing investments for 40 per cent of companies.
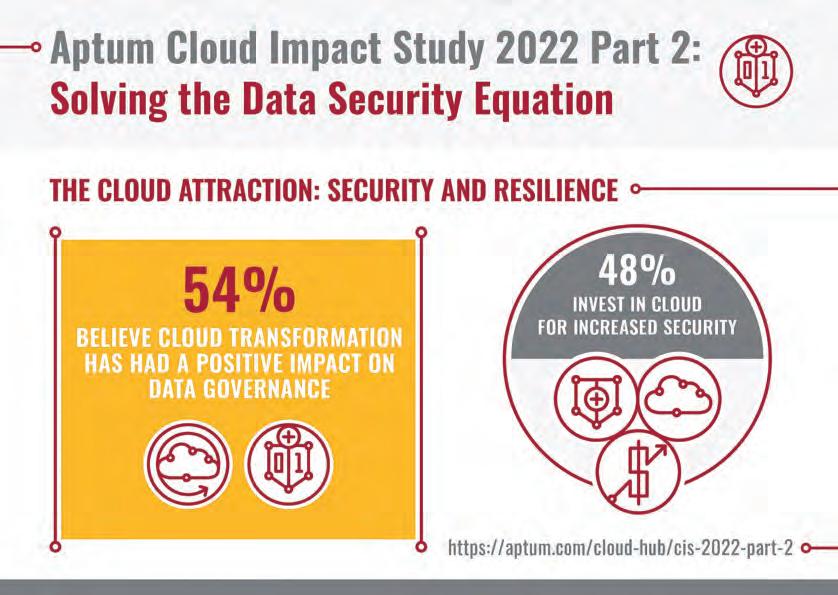
Solving the Data Security Equation. The report examines hybrid cloud environments and their implications on security, data governance, compli ance, and disaster recovery. It finds that while companies are convinced of the value of cloud computing, its drivers have evolved.
CLOUDSECURITYSTRATEGY AND DATA SECURITY: REPORT
Canada Post announced key com mitments to reduce its environmental footpr int and reach net-zero emis sions by 2050.
WINS AWARD FOR NATURAL TEXTILE DYE
CANADAELECTRIC POST TO INVEST IN REACHING NET ZERO
Financial considerations have traditionally been a common driver, the study shows a shift in focus for many organizations, especially as security concerns evolve: 50 per cent
Iris Redinger has developed an all-natural dyeing solution using microorganisms to ‘grow’ colour. Through Waterloo-based Material Futures, Redinger, was presented the Mitacs Environmental Entrepre neurRedingerAward.founded Material Futures
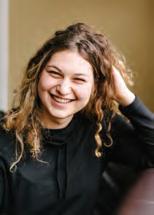
WATERLOOAWARDS INNOVATOR
in 2018, hiring researchers to help develop her method, which is patent pending. After identifying microor ganisms that naturally produce co lour, she applies genetic engineering techniques to make it their primary function. The end products are fully biodegradable colorants that can be substituted into existing manufactur ingTheprocesses.technology has gone through performance and feasibility testing to ensure the naturally dyed textiles stand up to repeated washing without fading and meet thresholds for indus try-gradeRedingerfabrics.isone of five winners of the Mitacs Entrepreneur Award who are being recognized for their efforts to turn their research into innovative businesses that impact the lives of Canadians.SheisaMitacs intern who earned her Bachelor of Architecture at Water loo University last year.
Iris Redinger Photo: Mitacs
NEWS
Photo: Canada Post AptumPhoto:
Aptum announced part two of its annual Cloud Impact Report 2022,
It has invested $1 billion to cut emissions and transform its fleet. It will change over 14,000 vehicles to non-emitting transportation, with com mitments to reach a 50 per cent EV fleet by 2030 and 100 per cent by 2040.
Additionally, opening in 2023, Can ada Post’s net-zero parcel sorting fa cility in Scarborough, Ont., will have the capacity to process over one mil lion packages a day. The $470 million f acility is the largest industrial project in Canada andevaluateandofpactwestpostalofing standardwith a zero-carbon builddesignation.CanadaPost islaunchingatrialan electric low-speedvehicleonaroutecoveringneighbourhoodsofdowntownOttawa.Thecomvehiclereachesmaximumspeeds40 kph.Itwillbeusedfordeliverycollectionactivitiesforayeartoitsperformanceinoperationsoptimalsafetyprocedures.
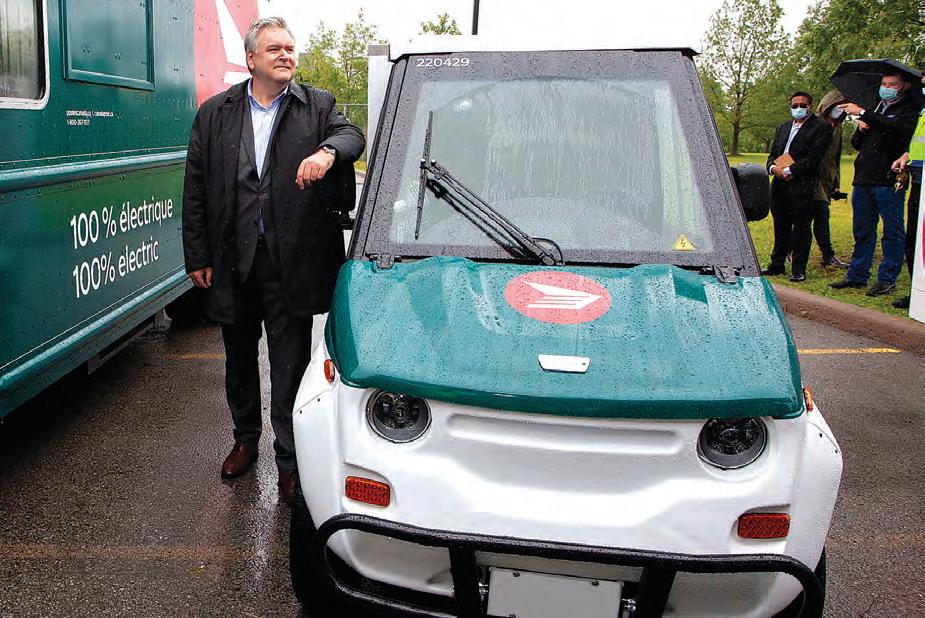
Once constructed, the solar farms will generate over one TWh of solar electricity an nually, enough to power over
Copes ser ved as COO for American EV automaker Riv ian, growing the team from a few hundred to thousands of employees globally leading up to the company’s listing on the Nasdaq. He is a graduate of the Massachusetts Institute of Technology with a Master’s in Mechanical Engineering and an MBA.
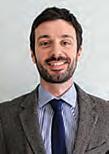
@PLANT_Magazine Summer 2022 / Plant 7
EXRO TECHNOLOGIES ADDS TO BOARD OF DIRECTORS
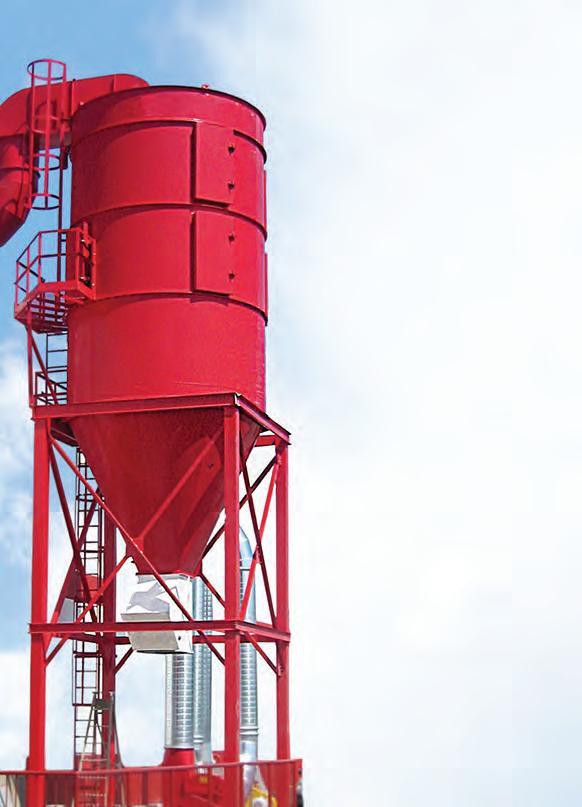
141,200 homes annually.
NAMES
• Fort Edward Solar Farm;
FIVECLEANTECHBORALEX SOLAR FARMS OF PROPOSALSAGENERATIONELECTRICUNDERREQUESTFOR
• Foothills Solar Farm; and,
over 25 years of general management, market ing, finance and operations exper ience. He joined Jeld-Wen in 2018 and has held leadership roles in North America windows and doors.
Electrovaya has appointed John Gibson as the Chief Finan cial Officer, reporting Dr. Raj DasGupta, CEO.
Boralex announced five solar farms totaling 540 megawatts (MW) of generation and 77 MW of storage have been selected by the New York State Energy Research and Development Au thority as part of its 2021 solici tation for utility-scale renewable energy cer tificates.
Gibson is a certified profes sional accountant with over 15 years of experience in public and pri vate corporations i n finance,accounting,strategic and financial planning, internal controls, and systems. He pre viously served as vice-president of finance at Adlib Software. Gibson received his undergrad uate degree in accounting from Strathclyde University and his master’s degree in information technology and business from Glasgow University.
• Newpor t Solar Farm;
NEWS MURPHY MEANS MORE More VALUE Feature for feature: Murphy packs-in more for your money. Get it done right the first time. No One Gives You More! N.R. MURPHY LTD. DUST COLLECTORS 430 Franklin Blvd., Cambridge, ON N1R 8G6 E-mail: 4nodust@nrmurphy.com (519) www.nrmurphy.com621-6210 PLT_NRMuphyr_July22.indd 1 2022-06-16 11:00 AM Credit: Boralex
Rod Copes
construction.Krausehas
Photo: Electrovaya
John T. Krause Photo: Jeld-Wen
Exro theperienceCopesoftoRodappointednologiesTechCopesitsBoardDirectors.exinelectricmobilityindustry,along

• Easton Solar Farm.
Jeld-Wen announced the promo tion of John T. Krause to Senior Vice-President and General Manager, North America. He will report to Gary S. Michel,
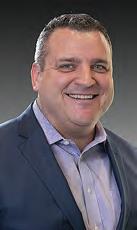
NEW CFO
John Gibson
JELD-WEN APPOINTS SVP AND GM FOR NORTH AMERICA
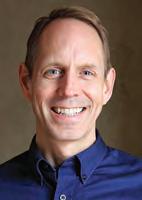
Photo: Exro Technologies
The selected photovoltaic solar electricity generation proj ects will be located across upstate New York, which include:
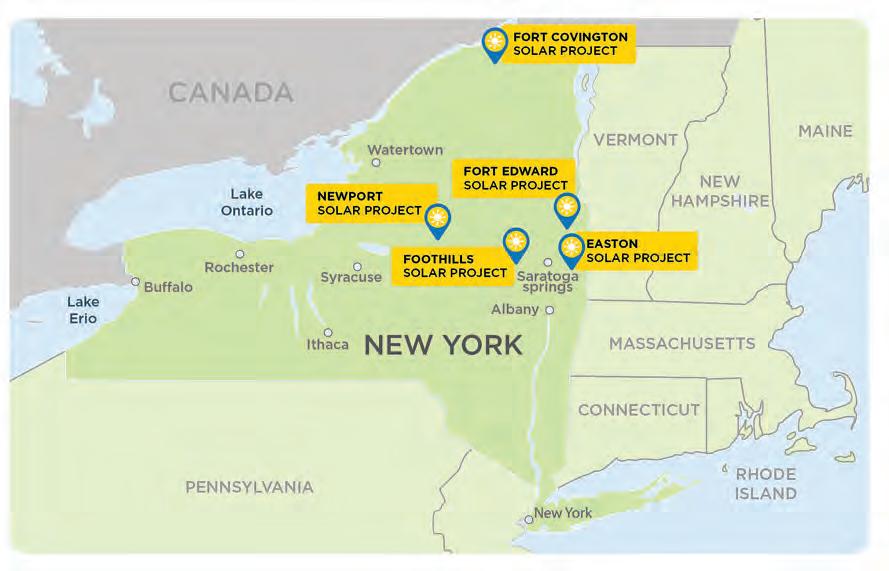
with management exper ience, will guide Exro into the com mercialization phase.
ELECTROVAYAAPPOINTMENTS
Chair and CEO. Krause, is commercialresidentialfocuseddowsAmericathemanagerandvice-presidentcurrentlygeneralforNorthwinbusiness,onand
• Fort Covington Solar Farm;
8 Plant / Summer 2022 PLANT.CA
The five-year quality, while reducingthroughput, uptime andprojects,technologyandtun will increaseingfactoriesof manufacturingdigable Jotun to implementagreement will enEmerson’sitaltechnologiesto allaspectsautomationinnewandupgradesomeof its existfactories aroundtheworld.Through the agreement,Joprocessautomationcreateastandardizeddigitalsolution for newfactorywiththegoalofincreasedproductoperatingcosts.
Industrial motor-driven systems hold potential for energy efficiency measures. Almost two-thirds of the survey respondents are upgrading their equipment to best-in-class efficiency ratings, such as high-effi ciency electric motors controlled by variable speed drives.
The global industry is accelerating investments in energy efficiency in the next five years towards Net Zero according to ABB’s energy efficiency investment survey 2022.

ABBPhoto:
The report showed half of the re spondents listed cost as the biggest bar rier to improving energy efficien cy and 37 percent felt downtime was a barrier. While 41 per cent of respondents felt they had all the in formation needed regarding energy efficiency measures.
Unde r the ESP PLUS agree ment, service life of the Dash 8-100 aircraft will be increased to 160,000 flight cycles. The aircraft previously underwent an ESP to increase their service life from the original 80,000 flight cycles to 120,000.
The survey conducted by Sapio Research targeted 2,294 companies in 13 countries, ranging in size from 500 to 5,000 employees. It outlines how industries across the world are planning to invest in energy efficiency measures to achieve Net Zero.
Photo: Emerson
DASHDOUBLESSERVICEAEROSPACEPROGRAMTHELIFEOF8-100AIRCRAFT
54%
of companies are already investing in energy efficiency.
EMERSONAUTOMATIONTO AUTOMATE JOTUN MANUFACTURINGGLOBAL PLANTS
Photo: De Havilland Canada
Emerson announced a framework agreement with paint manufacturer Jo tun to automate and digitalize its global manufacturing facilities.
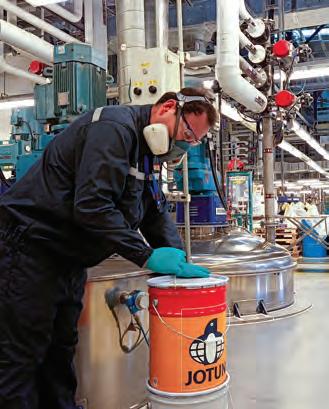
De Havilland Aircraft of Canada Limited announced Widerøe Asset AS of Norway has signed an agree ment to incorporate Canada’s Ex tended Service Program PLUS on 10 Dash 8-100 aircrafts.

GLOBALENERGY EFFICIENCY:INVESTSINDUSTRYINENERGYSURVEY
A key finding was 54 per cent of companies are already investing, while 40 per cent plan to make ener gy efficiency improvements this year. Ninety per cent will increase spend ing over the next five years while 52 per cent plan to achieve Net Zero within the same period.
Visit www.plant.ca/news for more industry news and events.
Widerøe is the largest regional airline in Scandinavia, carrying ap proximately 2.8 million passengers annually and ser ving more than 40 domestic and international destinations.InJune,the team began manufac turing ASTM medical masks to help fill another cr itical gap in Canada’s supply chain. By September, The Canadian Shield had manufactured 16 million face shields and donated nearly one million to frontline work ers across the country.
NEWS
Recently, the company announced their development of made-in-Can ada medical mask manufacturing automation lines, and machine vi sion systems equipped with artificial intelligence technology.
A
info@rolmasterconveyors.cawww.rolmasterconveyors.ca 121 AVENUE ROAD, CAMBRIDGE, ONTARIO, CANADA N1R 1C2 PLT_Rolmaster_Summer22.indd 1 2022-06-28 10:18 AM EVENT CywinskiMarioPhotos:
@PLANT_Magazine Summer 2022 / Plant 9
was a big part of the event, as many attendees have not been able to meet in-person. Over a dozen exhibitors filled the exhibit hall, which was the meeting place during networking sessions and was busy for the entire two days.
Panel discussions included CanREA’s 2050 Vision; Human fac tors presentations; Advancing operations in Canada’s renewable en ergy fleets; and Workforce development. Each had industry experts sharing their expertise to the audience. A keynote address on day two was led by Michael Levitt, founder and chief burnout officer of The Breakfast Leadership Network, who led a session on how to Burnout proof your organization. Lunchtime presentations gave exhibitors a chance to briefly speak about new products and tools.
The summit was a mix of panel discussions, networking sessions, presentations, and keynotes.
“It has been more than two years since we met in this forum and there is not enough time to unpack what we have all been through in the time since we were last together,” said Phil McKay, senior operations director, CanREA. “I want to personally thank you for keeping Canada’s wind, solar, and energy storage fleet operating during this time.”
Chain Conveyors are frequently utilized in the automotive, parts, manufacturing, warehousing, foundry, and logistics industries.

CALL 1-800-461-6806 CHAIN CONVEYORS COULD BE THE SOLUTION! Talk to a Rolmaster Conveyors Technical Sales Representative TODAY! Is the movement of heavy skids weighing your operation down?
Chain Conveyors are used for transporting heavy loads, for example, pallets, industrial containers, auto parts racks, as well as a variety of other products. They can also be applied to a wide variety of configurations including side transfers, turntables and offer accurate indexing solution options.

round 150 Canadian renewable energy operations leaders took part in the Canadian Renewable Energy Association (CanREA) 2022 Operations Summit. The conference returned to in-person, after going virtual in 2021.
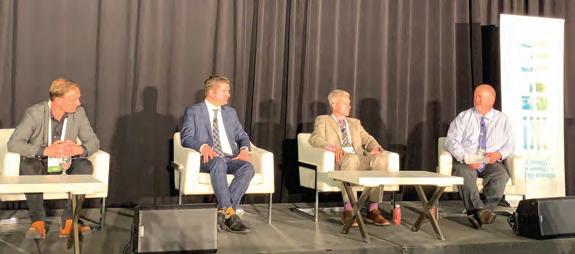
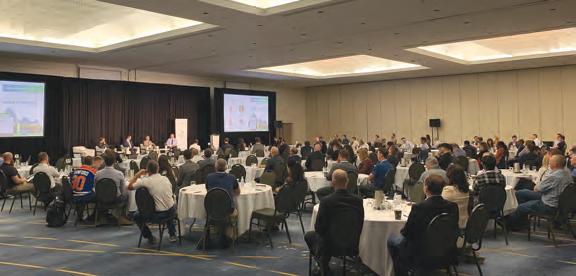
CanREA hosts first in-person Operations Summit since start of pandemic
BY MARIO CYWINSKI
“What we can do today with solar, wind, and energy-storage equipment far surpasses what our electricity system has seen in the past century, and we are limited only by our creativity to think beyond the mere replication of the status quo and to form a new system, using the experiences we have gained at the leading edge,” saidNetworkingMcKay.
Engage workers in program development
Consult health and safety leg islation to see what is required by law in your jurisdiction, some form of program is a requirement in most. Make the required ele ments your foundation and build out from there.
health and safety committee: a forum for collaborative involve ment of employees, representing both workers and the employer. These committees are legal re quirements for organizations of a specified minimum size in all Ca nadian jurisdictions. In smaller
to raise their awareness and skills.
BY CANADIAN CENTRE FOR OCCUPATIONAL HEALTH AND SAFETY (CCOHS)
Although each facility is unique and will train on procedures and proto cols accordingly, the primary purpose of any occupa tional health and safety training program is to instruct participants on protocols and procedures, and
10 Plant / Summer 2022 PLANT.CA
A foundation for a productive workplace: occupational health and safety training
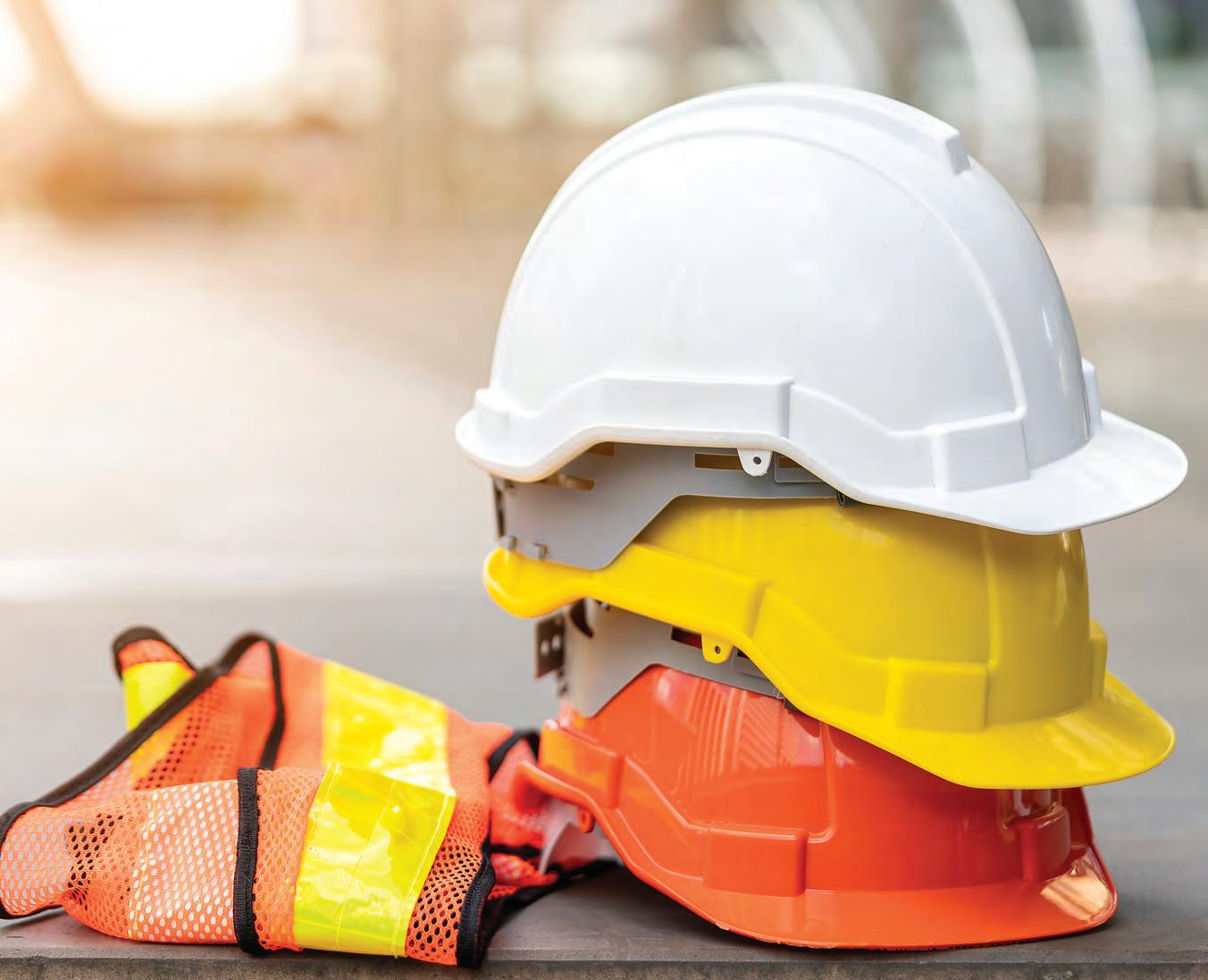
It’s crucial to get employee input and participation as you develop your training program, so that training modules accurately re flect the experiences of workers on the floor. That starts with the
HEALTH AND SAFETY FEATURE Stock©phat1978/AdobePhoto:
Maintaining a successful health and safety program in manufacturing includes training for workers that is thorough, engaging, and regularly updated.
One of the most effective ways to develop a positive safe and healthy workplace culture is to encourage a dialogue with employees as you implement procedures and work to control hazards. Knowing your health and safety program goes beyond basic requirements, is informed by workers’ experiences, and gets updated regularly can help keep workers engaged, feeling sup ported and working efficiently.
Refresh your training program regularly to ensure skills and knowledge are up to date with legal requirements, good prac tices, and current workplace procedures. Have supervisors check-in with workers to ensure
@PLANT_Magazine Summer 2022 / Plant 11
One of the most effective ways to develop a positive safe and healthy workplace culture is to encourage a dialogue with employees as you implement procedures and work to control hazards. Knowing your health and safety program goes beyond basic requirements, is informed by workers’ experiences, and gets updated regularly can help keep workers engaged, feeling supported and working efficiently.
Test, refine, and seek feedback
A health and safety committee brings together workers’ indepth, practical knowledge of specific jobs and management’s overall establishment of job in terrelationships, general compa ny policies, and procedures. As the employer, you have a duty to establish a committee that oper ates in compliance with the law, is organized and effective, has at least equal or more workers to manager participation, and has access to resources such as time, money, or meeting rooms to do its work. To function properly, the committee needs an appropriate structure, a clear statement of purpose and duties, and standard procedures for meetings.
PLT_Alps_July22.indd 1 2022-06-16 10:45 AM
The Canadian Centre for Occupational Health and Safety (CCOHS) promotes the total well-being — physical, psychosocial, and mental health — of workers in Canada by providing information, advice, education, and management systems and solutions that support the prevention of injury and illness. Visit www.ccohs.ca for more safety tips.
They should also address the hazards of the job, when safety training will occur, and any safe ty equipment required including per sonal protective equipment. In addition, the sessions should review emergency situations: what to do in case of fire or an other emergency, the locations of fire extinguisher s, first aid kits and automated external de fibrillators, first aid rooms and emergency assistance, and what to do when they have questions, are injured, or notice something off.Pace training to ensure all the information or skills are learned, avoid overloading new employ ees with too much information all at once. It’s a good idea to provide written information that outlines the points covered in the orientation sessions (this also serves as a checklist for the
carry out each step and provide feedback and positive reinforce ment where necessary.
As supervisors will often be responsible for monitoring ad herence to safety protocols and in some cases, administering the training, they should have a thorough understanding of policies and procedures and be able to explain the rationale for each. Supervisor training should cover topics such as le gal responsibilities, the internal responsibility system, audit ing, chemical safety including WHMIS, industrial hygiene, medical surveillance programs, and the duty to accommodate. Their training should also re view the procedures associated with hazard identification and control, along with conduct ing risk assessments, incident investigations, planned inspec tions and task observations. Finally, supervisors will benefit from first aid training as well as coaching to develop their com munication skills.
When conducting safety train ing for workers, plan the session beforehand, break the job down into steps, and have training aids available – documented safe work procedures are key here. With each procedure, explain what is to be done and describe the hazards and control measures. Demonstrate each step, stressing key points, and encourage and answer questions. To reinforce workers’ learning, have them
New worker orientation
workplaces where a committee may not be required, a worker representative may be appointed.
Workers require safety training at the beginning of employment, when reassigned or transferred to a new job, or when returning from an extended leave. Train ing should also occur when new equipment, processes, or proce dures are introduced or when there is a change to the legislative requirements.Healthand safety education should start with a thorough orientation when a worker joins the organization. Giving new workers a glimpse into your organization’s safety culture, ori entation sessions typically cover the functions of the work unit, organizational relationships, ad ministrative arrangements, and various policies and rules.
they’re following safe work pro cedures, if there are questions or concer ns, this could be an op portunity to review the training prog ram or retrain personnel.
person leading the orientation). All workers, but especially new, inexperienced, or transferred workers, should be encouraged to ask questions at any time.
Train your trainers
A key driver to achieve this level of competitiveness is to take advantage of new technologies. Business leaders are aware of this, as Accenture found that 77 per cent of executives know that their technology architec ture is critical or very critical for the overall success of their organization. For many, this has meant adopting a cloud computing solution to man age data and workflows, and support business processes.
Cloud computing is expected by Markets and Markets to be worth $947.3 billion USD by 2026, with a compound annual growth rate of 16.3 per cent until then. The International Data Corporation (IDC) reports that spending on compute and storage infrastructure products for cloud infrastructure increased 12.5 per cent year-over-year in the first quarter of 2021, while investments in non-cloud infrastructure increased 6.3 per cent year-over-year in the same quarter.
Stock©Tierney/AdobePhoto: 12 Plant / Summer 2022 PLANT.CA
While cloud technology may present challenges, it serves as a foundation for digital transformation in enterprises and buffers them against the competition.
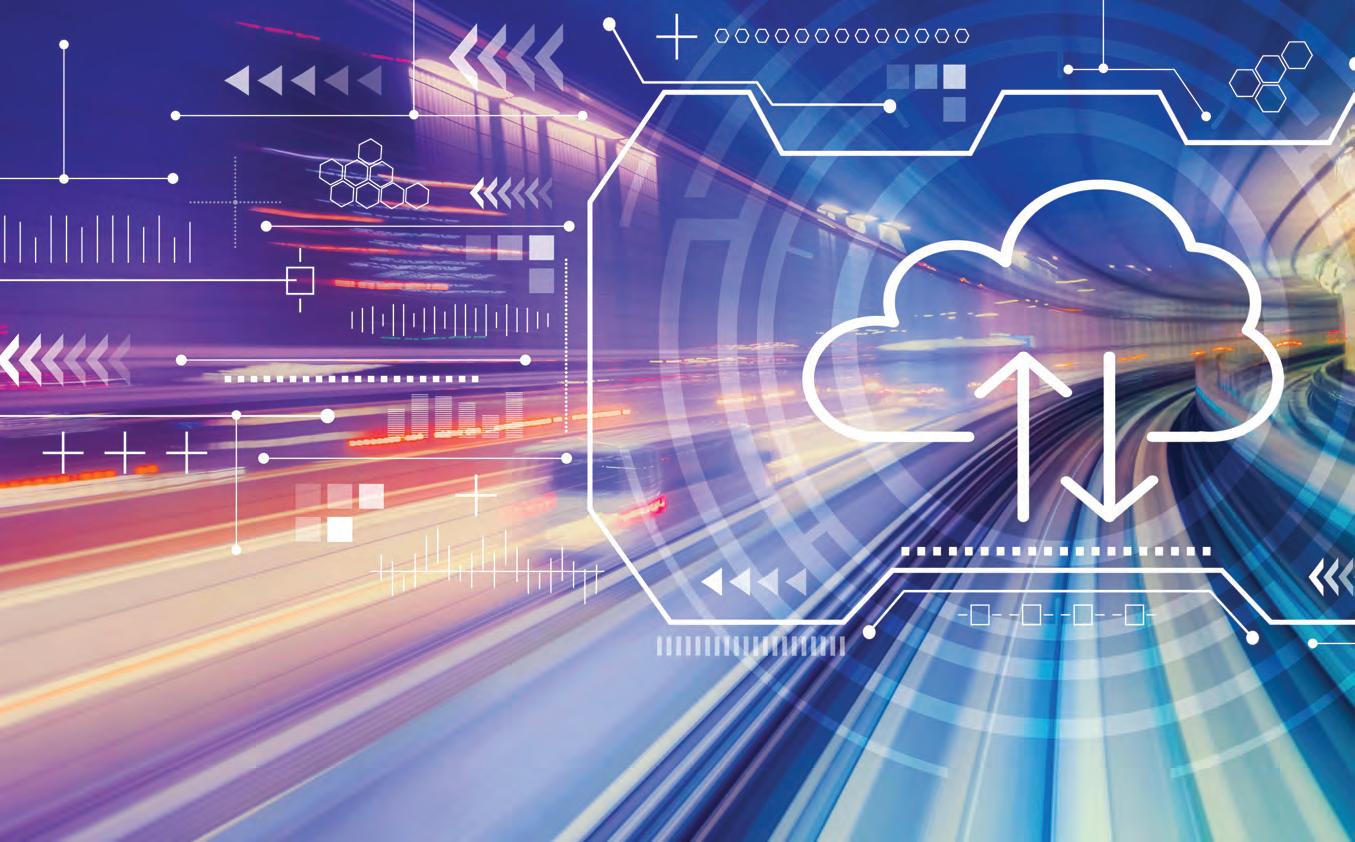
As new competitors continue to enter the plant sector, competitiveness is a key business driver for many organi zations. Manufacturing is driven by a quest for efficiency; using the least number of resources to deliver the optimal product in the shortest amount of time possible.
Advancing the manufacturing industry through cloud technology
Supply chain management
Cloud computing is useful in several ways that directly improve competitiveness in the manufacturing industry, including managing supply chains, optimizing processes, facilitating automation, and allowing remote access.
ADVANCED TECHNOLOGY FEATURE
Optimized processes
BY STEVE RICHMOND
According to IDC, by 2025 IoT devices will collect 73 zettabytes (ZB) in data. Most of the data originate from security and video surveillance industrial IoT applications. This data can be used to gain insights that will optimize processes. For instance, machine learning algorithms can work through massive data sets to find flaws in pro cesses and suggest improvements, much faster than a human could. According to an IoT survey conducted by pwc, the biggest benefits of IoT for businesses are gaining new capabilities (35 per cent) and improved efficiency.
Each entity in the supply chain - vendors, suppliers, dealers, logistics companies, wholesalers, and retailers, relies on data from others to carry out specific tasks. Cloud technology makes it possible for everyone in the supply chain to connect, which facilitates real-time information sharing and a 360-degree overview.
Process costs are directly under the control of the business. Opti mizing processes, to reduce costs and minimize waste, contributes hugely to improved competitiveness. Cloud computing achieves both these objectives by incorporating Internet of things (IoT) devices into existing business processes.
Remote access
Theerror.core strength of an intelligent manuf acturing system, such as those enabled by fourth industrial revolution technologies, is its ability to integrate various systems, orchestrate collaboration between different robots, and be interoperable with all its component systems. This requires a very high level of compute capabilities and infrastruc ture, which cloud systems offer, and display through customizable dashboards at that.
ORDER BY 6 PM FOR SAME DAY SHIPPING π COMPLETE LARGE1-800-295-5510CATALOGuline.caKEEPCOOLSELECTIONOFFANSALWAYSINSTOCK PLT_Uline_Summer22.indd 1 2022-06-21 11:27 AM
Sounds like a solution to our original quest for efficiency by us ing limited resources to deliver the optimal product in the shortest amount of time possible, doesn’t it?
There are also very practical, real-life applications of cloud comput ing solutions in the industry. For many manufacturers, it is impossible to evaluate and oversee the operations of all company facilities, it is a bad use of senior managers’ time to have them travel across the globe to do inspections. In such cases, cloud computing provides a solution, by using IoT sensors to automate manufacturing systems and remotely monitor and control operations.
Looking ahead
Modern industrial facilities are already closely integrated with cloud technologies. IoT devices, 5G connections, and affordable cloud service providers already make it easier to deploy digital solutions for plant operations. For smaller businesses, they offer a way to com pete with large organizations that have huge budgets for technology architecture and infrastr ucture.
A more advanced form of remote access is the concept of digital twinning, which Research and Markets believes will become a stan dard feature/functionality for IoT application enablement by 2028. They predict that by 2026, up to 91 per cent of all IoT platforms will contain some form of digital twinning capability.
Automation and intelligent systems
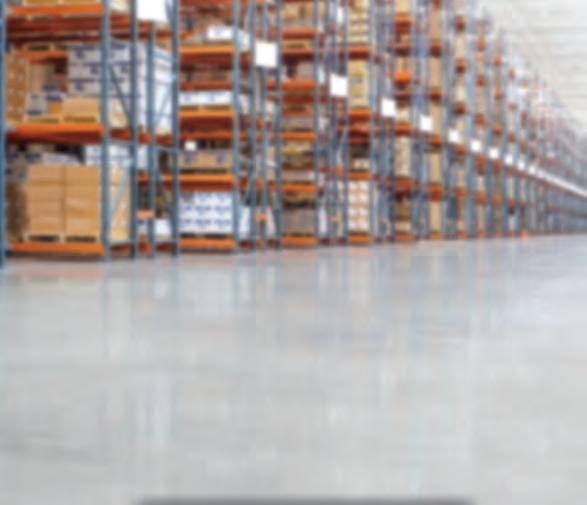
22_1412_Plant_JUL_AUG_CN Mod: May 19, 2022 2:49 PM Print: 06/16/22 3:45:18 PM page 1 v7

In these solutions, the cloud hosts virtualized representations (dig ital twins) of a plant and its machines which operate under identical conditions to those of the physical facility. This helps streamline maintenance and troubleshooting and optimizes asset performance.
While cloud technology may present some challenges, it serves as a foundation for digital transformation in enterprises and buffers them against the competition.

With the advent of 5G, factories will likely be built entirely of highly interconnected, powerful, and continually updated devices. These devices will be capable of processing data throughout the manufac turing process with the same level of speed, reliability, and security that we currently anticipate from our smartphones.
Cloud infrastructure is behind many of the latest technologies de ployed in manufacturing. Components such as logic controllers, pneumatic and hydraulic systems, robots and cobots have become commonplace as they supplement human work and counteract hu man
In addition, Industry 4.0 requires advanced analytics and deci sion-making based on machine learning techniques, a major part of AI, all of which are facilitated by cloud computing.
The number of sensor systems used, and the diversity of their applications are ever increasing. These sensors can even “talk” to one another and collaborate or call on a human to intervene from anywhere in the world. Maintenance personnel can do visual inspec tions remotely using drones, robotics, augmented reality, and virtual reality, all made possible by cloud technology.
@PLANT_Magazine Summer 2022 / Plant 13
Steve Richmond is the CEO and founder of Projetech Inc
SALARY SURVEY SPONSORED BY

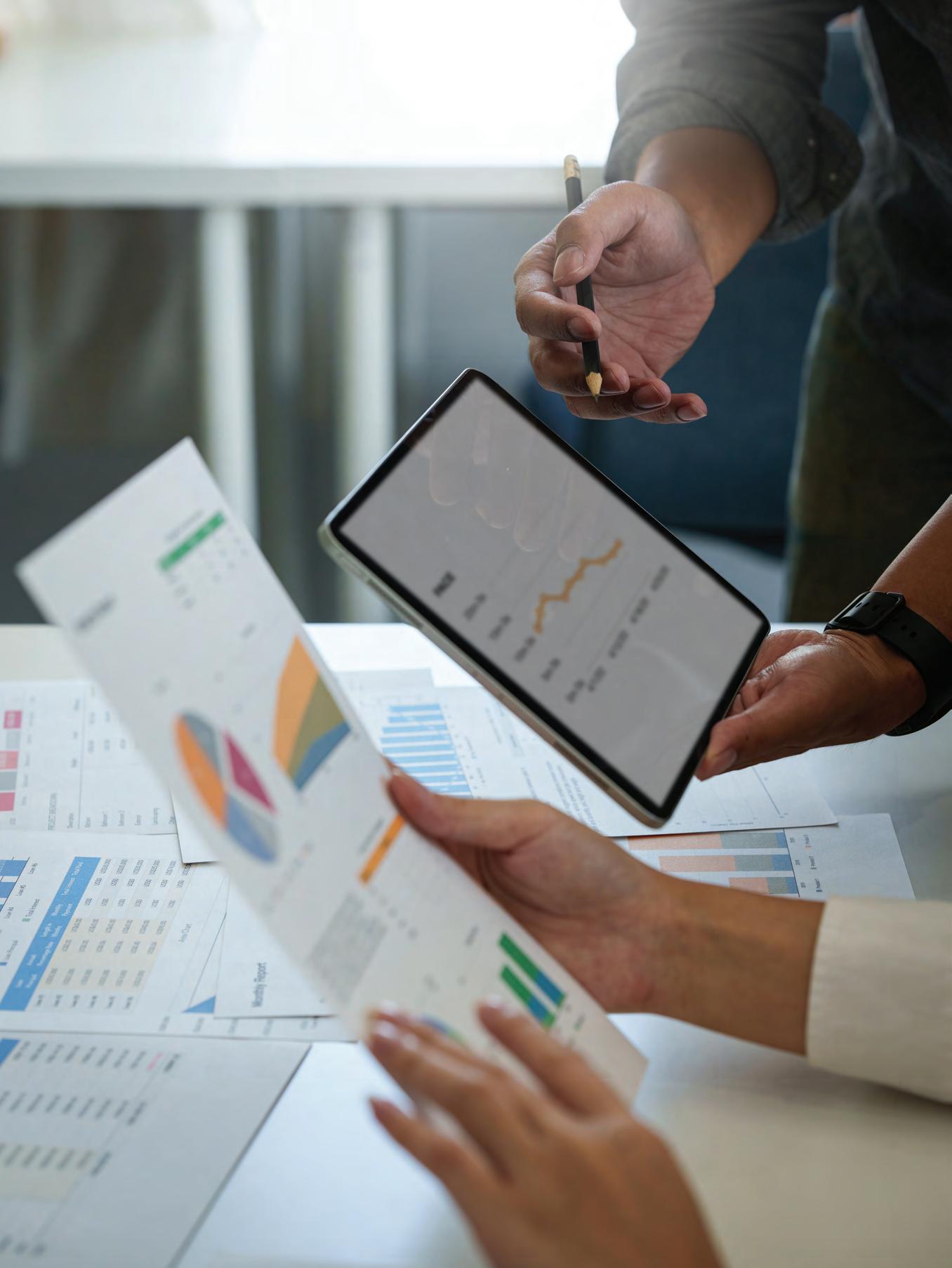
PLANT.CA14 Plant / Summer 2022
ImagesPlus/GettyImagesMeepian/iStock/GettyWoraweePhoto:
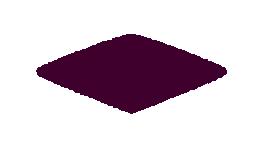
Average $178.3M
change was not a result of COVID-19, and five per cent were not sure. When asked if COVID-19 affected their compensation, 15 per cent said it had a negative impact, with 10 per cent said it had a positive impact, and 75 per cent said it had no impact.
REVENUES
COMPENSATIONEFFECTCOVID-19ONXYes,positively10%Yes,negatively15%No75%
When we sent out the 2022 EMC-PLANT Manufacturing Salary Survey, from March to June, the landscape around the pandem ic had shifted. We have entered a neo-COVID period, where it is still considered, but life is going back to (almost) normal.
While executive salaries fell, the average age of respondents moved younger. BY MARIO CYWINSKI
In 2021, Plant magazine ran its salary survey as COVID-19 restrictions were in place around many parts of the country, with COVID-19 protocols (which were introduced in 2020) being the norm across the manufacturing industry.
9%$30M-<$50M6% DEMOGRAPHICSSALARIES DIP
Once again, the survey was jointly conducted by Excellence in Man ufacturing Consortium (EMC), a national not-for-profit organization based in Ontario, and Plant mag azine , a part of Annex Business Media. In all, 308 company execu tives, and senior management level personnel completed the survey, with an additional 11 answering at least
Starting in 2020 and into 2021, many companies had to cut shifts, lay off employees, and temporarily or permanently close their doors due to COVID-19. In 2022, a larger portion of respondents moved to a new orga nization (eight per cent), while one per cent of respondents said they were laid off from the organization they worked for. The largest groups were: same job and salary but more respon sibility due to reduced staff (26 per cent), and no change (46 per cent). Positively, 11 per cent of respondents wereOnlypromoted.11per cent of respondents believe their employment status change was a result of COVID-19 in 2022, while 43 per cent said they had no change in employment status, 40 per cent said their employment status
“Our view is that it has caused manufacturers to look more carefully at ways to ensure production is sus tained when one or more elements of people, plant and/or process are impacted by external factors,” said Scott McNeil-Smith, Vice-President, Manufacturing Sector Performance, EMC.“Whether
JOB MOVEMENT AND COVID-19 IMPACT
@PLANT_Magazine Summer 2022 / Plant 15
COVID-19 or other human illness, scarcity of supply/ disruptions/costs, technology and other impacts such as cyberattacks, manufacturers better understand that having clear strategies for securing people, plant and process is vital to their immediate and long-term fu ture, regardless of the opportunities, challenges or threats to success.”
part of the survey. For a total of 319 useable submissions.
WHAT IS YOUR HIGHEST LEVEL OF EDUCATION?
WHAT IS YOUR ROLE IN YOUR COMPANY?
EMPLOYEES Average 478 40%<5050-24934%250-49912% 6%500-999 7%1,000-4,9995,000>2% Two per cent or less represents a small sample and should be considered with caution. <2526-35 36-45 46-55>6556-65 <1% 8% 21% 32%10%29% AGE Average age 51.1 Management role only 69% Controlling ownership and management role 12% Minority ownership and management role 7% Equal partnership stake and management role 2% Other 11%
3%CEGEPHigh school or 9%less 55%degreeUniversity 16%diplomatechnicalTrade/ 17%diplomaCollege
21%$1M-<$5M 15%$5M-<$10M 20%$10M-<$30M 10%$50M-<$100M 9%$100M-<$250M 7%$250M-<$500M 5%$500M-<$1B
$1B plus
Forecasting 20%
Outsourcing 12%
CHANGES NEXT FIVE YEARS
Capacity utilization 25%
51%
Environment/Corporate Social Responsibility 10%
MANAGEMENT ISSUES
23%
Investing in new production equipment/processes
68%
30%
Acquiring other companies or lines of business
Downsizing lines of business
3%
Technology upgrade 23%
Closing of company
Cybersecurity 10%
3%
Overseas sourcing 16%
IT issues 8%
Financing for working 8%

Moving on to skills, the survey found that the top skills that respondents feel they need
SALARY SURVEY SPONSORED BY 16 Plant / Summer 2022 PLANT.CA
MOST IMPORTANT SKILLS 56%SupervisoryManagement/ 45%ProblemInterpersonal/36%AnalysisSolvingNegotiationskills25% 39%(leanimprovementContinuousProductivity/etc.) Sales skills 45%Communication25% 31%demand)(forecasting,PlanningIndustry 37%technicalspecificskillsFinancial(budgeting,accounting)28% 36%managementProject Technical 24%programming)(software,skills
Expanding plant size
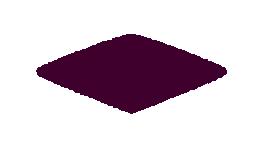
From 2019 to 2021, the average years of experience in the industry went from 25.4 to 25.9 years. However, in 2022, that number dropped to 22.3 years. A majority (46 per cent) of respondents have been in the indus try for over 25 years, while 36 per cent at 10 to 25 years, and 19 per cent with less than 10 years’ experience. What has changed yearover-year is that the over 25 years group is shrinking, and those with less experience is increasing, especially those with under 10 years’Lookingexperience.athow long respondents have been in their current jobs, the average time has dropped to nine years (from 12.9 years in 2021), 12.6 in 2020, and 12 in 2019). In all, 66 per cent have been in their current jobs for less than 10 years, with 25 per cent 10 to 25 years, and nine per cent over 25 years. In what has become the norm, years with the current company continues to decrease, down to 12.1 years, down from 16.4 in 2021. Years with the current company breaks down to 50 per cent (less than 10), 35 per cent (10 to 25), and 15 per cent (over 25).
MOST ISSUES
Other 8%
8%
Transportation 30%
Downsizing plant size
6%
capital
Enter new geographic markets
WHAT COMPANIES PAY FOR 454759%%27%% MembershipcoursesEducational in programscertificationProfessionalNoneassociationsprofessionalofthese 38%bonusorPerformanceother 24%expensesTravel25%allowanceCar/gas 15%vehicleCompany 7%optionsStock 39%contributionsRSP 20%sharingProfit Access to 11%healthcareprivate 21%hoursFlex21%Pension 6%membershipsClub19%developmentexecutiveTraining, 3%Other13%programWellness 12%salarybenefitsadditionalNoto PAY PERKS X
19%
3%
EXPERIENCE/SKILLS
22%
SIGNIFICANT
Cost control 49%
Global market expansion 5%
Supplier relationship management 27%
Resource/asset management (ie. HR, capacity, financing) 23%
37%
Skills shortage 62%
Risk management 20%
Downsizing employees
The pandemic 16%
Reorganization 15%
Enter new lines of business
Merging with another company
Hiring new employees
Added/entering new lines of business
$1M to just less than $5M $109,162$88,017$87,153 21%
SALARIES DROP
$50M to just less than $100M $102,321$164,443$166,54910%
$1B plus $146,075$151,326$142,221 6%
Eight percent or less represents a small sample and should be considered with caution.
JOB
Maintenance Manager $127,273$127,645$121,680 5%
Production Operations Manager $109,604$106,107$98,913 15%
Looking at the COVID-19 period as an abnormal time, the drop in annual salary of nearly $10,000: $119,726 from $129,685, isn’t much of a shock. Comparing it to 2020, which shows a smaller drop from $125,452, and when comparing it to 2019, the last non-COVID year, it has only dropped by just under $3,500, from $123,204.
Director $140,287$153,769$149,27810%
Much like in 2021, this year most respon dents (77 per cent) believe that over the next three years their salary will increase, with 32 per cent seeing a one to three per cent increase, 23 per cent a three to five per cent increase, 14 per cent a five to 10 per cent in crease, and eight per cent seeing an increase over 10 per cent. On the flip side, 20 per cent don’t see any change to their salary in the next three years, and three per cent think their salary will decrease.
When asked how satisfied respondents were with different aspects of their job, we found that while the numbers are in the 69 to 88 per cent range, satisfaction could still be higher. Overall, satisfaction with job security was the highest at 88 per cent, the job overall at 87 per cent, vacation time (81 per cent), compensation (81 per cent), healthy work
Materials Manager $95,000$82,000$84,0002%
$5M to just less than $10M $102,084$132,325$126,392 15%
Plant Manager $115,829$147,064$141,5878%
SALARY COMPARISONS
Vice-President
Much like in previous years, survey re spondents rated a healthy work life balance as an impor tant aspect of job satisfaction
$100M to just less than $250M $135,900$186,327$178,6559%
again in 2022 (at 98 per cent); how ever, this years’ competitive salary (99 per cent) took the top spot, followed by comprehensive benefits package (94 per cent), vacation time (93 per cent), job security (89 per cent), and support for career and professional development (87 per cent).
$30M to just less than $50M $137,625$135,820$131,2409%
Safety manager
Looking at salaries by province (only in cluding those which had at least five per cent of total respondents), we see that Quebec has the highest salary at $127,064, Ontario is next at $122,391, British Columbia at $112,270, and Alberta at $109,631. Other provinces had higher (Manitoba, PEI) or lower (all others); however, as these had only a few respondents, they cannot be considered accurate.
JOB TITLE 202220212020%
$500M to just less than $1B $133,050$173,892$163,738 5%
$182,100$191,617$194,1278%
$10M to just less than $30M $128,038$130,014$126,34620%
CEO/President $172,474$166,824$159,586 6%
$71,886$93,286$94,1432%
Logistics Manager $82,367$117,500$110,5002%
Design Engineering $126,436$108,392$105,492 5%
Administrative Management $83,051$107,823$105,94712%
Quality Assurance Manager
more training, include: financial budgeting and accounting (27 per cent), industry spe cific technical skills (26 per cent), people; inter personal, relationship, management (25 per cent), productivity and continuous improvement (24 per cent), project manage ment (24 per cent), and technical; software and prog ramming (21 per cent).
With the average age dropping to 51.1 years old in 2022 (from 53.7 in 2021), and as more peo ple are leaving the industry (namely retirement), new talent has a plethora of options for a career in manufacturing.
GENDER
$73,200$93,165$91,363 3%
REVENUETITLE
Plant Engineering $93,072$118,326$121,789 6%
Technician/Technologist $104,931$89,330$87,380 4%
The manuf acturing sector is very diverse and has many different organizations. We amalgamated the list of sectors for 2022, to have a smaller number of categories. The most common include: electrical equipment, appliance, and component (17 per cent), plastics and rubber products (14 per cent), motor vehicle products and parts (13 per cent), chemical and petroleum manufactur ing (11 per cent), and food manufacturing (11 per cent).
Compared to the skills respondents feel are most needed in a job today: management supervisory at 56 per cent, communication at 45 per cent, interpersonal problem solving at 45 per cent, Productivity and continuous improvement at 39 per cent, and Industry specific technical skills at 37 per cent. It is clear that the skills workers need improve ment in, are not all in demand.
Owner/partner $154,833$141,435$131,0959%
@PLANT_Magazine Summer 2022 / Plant 17
REVENUE 202220212020%
Purchasing/Supply Manager $85,525$96,527$95,832 4%
$250M to just less than $500M $152,000$127,906$125,352 7%
(20$85,249Female%)
Average $119,726$129,685$125,452
(80$128,680Male%)
life balance (78 per cent), benefits (74 per cent), and support received for career and professional development (69 per cent).
Aerospace product and parts
$116,885$118,075$106,575 5%
Motor vehicle products and parts $125,845 N/AN/A 13%

Chemical/ Petroleum manufacturing $123,386 N/AN/A 11%
Plastics and rubber products $108,975$138,809$144,791 14%
SALARY SURVEY SPONSORED BY
$104,376$117,577$114,93717%
Research Methodology
EXPERIENCE 2022 % < 10 $96,044 19% 10 to 24 $118,472 36% 25+ $131,607 46% Average Years of Experience 22.3 AGE 20222021 2020% Under 25 $56,000$66,000$66,000
202220212020 % replies
Paper, Printing and related support activities $106,850 N/AN/A 8%
In 2022, when we asked respondents what the most significant issues their com pany will face in the coming year, skill short age came out on top again at 62 per cent (up seven per cent from 2021), cost control (49 per cent), transportation (30 per cent), supplier relationship management (27 per cent), capacity utilization (25 per cent), technology update (23 per cent), resource and asset management (23 per cent), risk management (20 per cent), forecasting (20 per cent). The pandemic was only cited by 16 per cent (down from 68 per cent in One2020).thing
Food manufacturing $114,476$165,617$167,344 11%
$132,129$148,000$143,813 55%
CEGEP $109,444$108,500$103,000 3%
Leather and allied product $127,000 N/AN/A 1%
COMPANY PERSPECTIVE
Textile Product & Clothing manufacturing $90,160 N/AN/A 2% Wood product $133,210$134,653$122,8278%
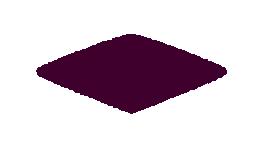
Most pressing, is hiring new employees (68 per cent), followed by investing in new production equipment and processes (51 per cent), expanding plant size (37 per cent), add new lines of business, (30 per cent), enter new geographic markets (23 per cent), enter new lines of business (22 per cent), and acquire companies or lines of business (19 per cent).
Mario Cywinski is the editor of Plant magazine, Machinery and Equipment MRO magazine, Food and Beverage magazine, and a member of the Automobile Journalists Association of Canada. He has over 15 years of editorial experience; over four years of maintenance, reliability, and operations experience; nearly 20 years of automobile industry experience, and small business industry experience.
EDUCATION 202220212020%
College diploma
that is constant, is change. Our final question asked respondents, “Thinking about the next five years, what changes do you anticipate occurring with in your company?”
Electrical equipment, appliance and component $123,140$133,396$128,54817%
University degree
The average age dropped,has and is now at 51.1, down from 53.7 in 2021, and 53 in 2020.
As we continue to look at a neo-COVID world, more companies are saw an in crease in their revenues in 2021 (com pared to 2020 or 2019). When asked “Thinking about 2021, would you say your company’s revenues have increased, decreased, or remained the same com pared to 2020?”, 58 per cent said they have increased. Asking the same question but comparing to 2019, 56 per cent said they have increased.
46 - 55 $132,846$130,056$125,99832% 56 - 65 $122,768$138,314$136,51729% Over 65 $115,782$129,737$125,65110% AGEYEARSEDUCATIONINDUSTRYOFEXPERIENCE Some industries were grouped together this year; past numbers were therefore not used. Eight per cent or less represents a small sample and should be considered with caution.
SALARY COMPARISONS
Beverage and tobacco product $91,167 N/AN/A 2%
18 Plant / Summer 2022 PLANT.CA
Research was conducted online between March and June 2022 among 319 Canadian Manufacturing leaders in partnership with Excellence in Manufacturing Consortium. Results were prepared by the Canadian research firm Bramm Research Inc. www.brammresearch.com
Trade/technical diploma $110,593$122,726$115,882 16% High school or less $96,296$104,710$105,762 9 % <1% 21%
26 - 35 $75,274 $92,277$86,1508% 36 - 45 $117,566$125,344$118,826
INDUSTRY
Computer and electronic product $125,316$141,889$129,333 7%
BY MARIO CYWINSKI
SALARY SURVEY – EMC’s TAKE
PLANT: The average years of experience dropped for 2022. Do you attribute this to younger working joining the work force or older working leaving?
• Turnover in the occupations re porting, with the ‘new’ person earlier in their career (hence a lower salary) but in the same pay range.
EMC: The overarching way we do this is by connecting the manufacturers with the best and brightest experts to help them solve the problems directly.
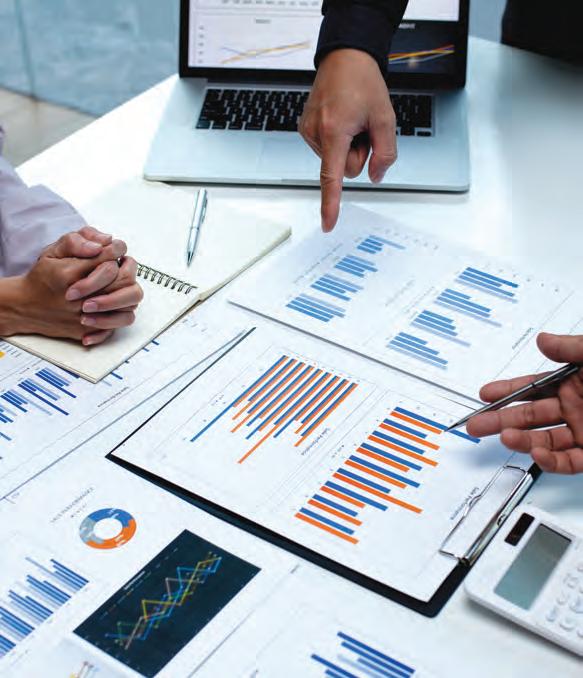
Mario Cywinski is the editor of Plant magazine, Machinery and Equipment MRO magazine, Food and Beverage magazine, and a member of the Automobile Journalists Association of Canada. He has over 15 years of editorial experience; over four years of maintenance, reliability, and operations experience; nearly 20 years of automobile industry experience, and small business industry experience.
PLANT: The percentage of females in the industry continues to increase (up to 20 per cent for 2022). Do you see this trend continuing in the years ahead?
Engaging women (along with youth and other underrepresented
@PLANT_Magazine Summer 2022 / Plant 19
including demographic shift and people retiring).
• Cost of manuf acturing through adoption of best practices, efficiencies, technol ogy, advanced manufacturing processes. EMC is supporting directly with group model pro grams designed to reduce the cost of cer tain elements, such as energy, health and safety, training, materials and more.
Fur ther, $10,000 is not a significant shift in the aggregate salary average and is likely due to the following:
EMC: Absolutely. It is encourag ing that more women are pursu ing careers in manufacturing, as this is a key strategy EMC and the sector is employing, to grow the future workforce supply.
EMC: Yes. We currently see 20 per cent of the workforce eligible to retire over the next 10 years. The current supply entering the workforce is not sufficient to ad dress this expected retirement, let alone the current vacancies and demands for talent.
PLANT: Skill shortage and cost control are the most significant issues facing companies. How can compa nies tackle these problems?
EMC: A younger workforce would speak to future viability; however, the workforce age is still quite high. With approximately 20 per cent of the workforce eligible to retire in the next 10 years, compounded by the current gaps, vacancies and shortages, the demand for replacing this aging workforce will require a 20 to 30 percent growth (through 2030) in workforce supply just to sustain. Like sala ries, this is also a statistic that is affected by different respondents answering the question, and turn over in the occupations reporting, with the ‘new’ person earlier in their career, for same occupation.
EMC: Our understanding / expe rience is the salaries themselves have remained consistent; how ever, bonuses and other benefits may have changed due to eco nomic impacts.
Plant Magazine sat down with Jean-Pierre Giroux, President, and Scott McNeil-Smith, Vice-President, Manufacturing Sector Performance, from survey partner Excellence in Manufacturing Consortium (EMC), to get their take on the manufacturing industry and the salary survey results.
EMC also connects them with each other, to leverage the con sortium for advantage.
groups) represents a significant opportunity for manufacturing employers to address current skills gaps and labour shortages. It is a long-term strategy that is looking to immediate needs, but also five-, 10- and 20-years out.
• Address capacity issues related to staffing (skills and labour), supply chain relation ships and sources, logistics for getting finished goods into customer hands.
PLANT: The average age of survey respondents for 2022 dropped by over two and half years from 2021 (51.1 from 53.7). A younger work force is a great sign, isn’t it?
Stock©David/AdobePhoto:
PLANT: The average salary has dropped nearly $10K between 2021 and 2022, to $119,726. What do you attribute this to? And do you see this as a trend, or a short-term drop?
• Labour/vacancies can be addressed through work in tegrated learning, on-the-job placements, pre-appren ticeships, recruiting foreign trained workers, and other experiential, path-to-employ ment opportunities.
• Skills shor tages strategies.equityingmicro-credentials,upskilling/reskilling, throughtraining,onboardtoolsforemployers,and,diversityandinclusion
• Different respondents answer ing the question. (Conversely, the only way to assume is if the identical group of peo ple answered for both years;
Early in my career, 20 years ago, a bad boss would have been commonly defined as someone who yelled at their employees or slammed doors and pound ed their fist. Today, a bad boss might be polite and helpful but not provide enough feedback, encouragement, or support to their
Remote work opportunities:
Wages aren’t as important as you might think
Not all that long ago, a “compet itive” wage, coupled with benefits,
is how the definition of a “bad boss” has broadened in its scope.
Theemployees.mainreason we aren’t attracting and retaining talent today is because our view of what is appealing is outdated. Is wage important? Sure it is, and it’s often the fastest way to sift through dozens of job openings to identify opportunities.
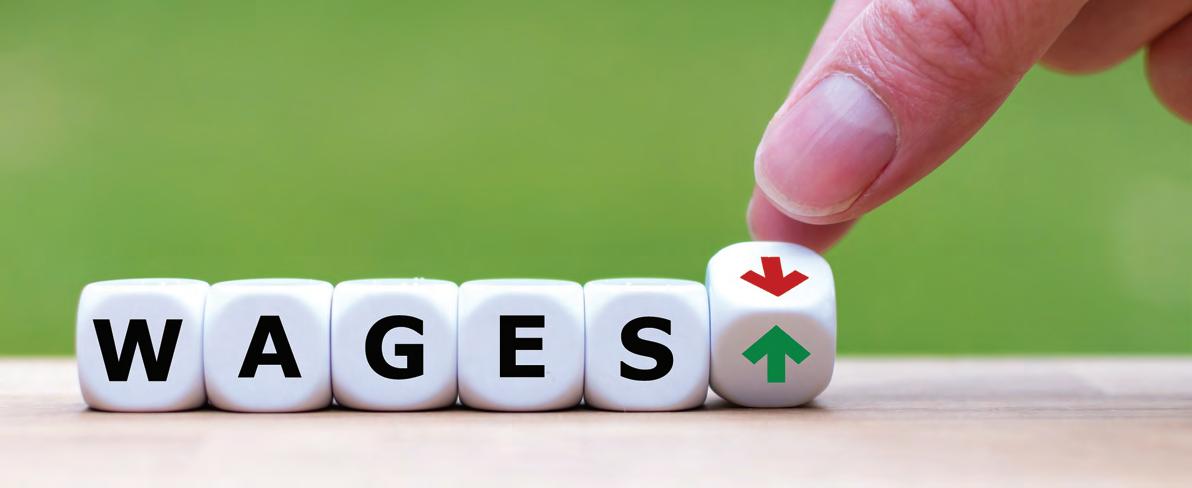
According to a study by Great Place to Work - post pandemic, a great percentage of millennials no longer feel the need to return to an office. For many, having proven working from home can be successful is enough to chal lenge the idea of having to spend their days commuting to and from an office, just to see col leagues who they could connect with in other ways.
It seemed like an odd response, considering my first job came with a starting wage of $4.35 per hour. On the other hand, he had a point. After all, what can you get for $16 these days? If you’re lucky, it’ll buy you lunch, but that’s about it.
20 Plant / Summer 2022 PLANT.CA
Last week I stopped by the adrive-thru,McDonald’spickinguphotfudgeSundae for my two boys following their very warm, but successful base ballAsgame.Ipulled up to the order kiosk, I noticed a faded piece of paper taped to the board an nouncing that McDonald’s was hiring. Starting wage was $16 per hour and increased to $19 per hour for a shift leader. My oldest son, who mows a neighbour’s lawn, commented that he made almost three times that wage in one hour of mowing the lawn.
I’m not suggesting that these wages are too low, but rather an ‘hourly rate that is competitive’ is no longer enough to incentivize today’s younger employee to give up their time.
couldn’t commit to regular working hours. The president de cided to create a “work what you can” shift, appealing to younger students to work any days or hours they could. The last we spoke, they now have nearly a dozen students employed parttime, with many others seeking the opportunity.
It’s not until we dive deep into what younger generations are seeking in a job that we uncover new offerings and benefits that will attract and retain top talent in a tight job market.
Flexible work: I was recently speaking with the president of a wood pallet manufacturing com pany. He mentioned that for years he struggled to hire stu dents. When he asked his neph ew why he never asked for a job, his nephew responded that he
BY SHAWN CASEMORE
was enough to lure employees. Today, with most of the working population between the ages of 25 and 40 years of age, benefits aren’t all that appealing, at least not yet. Therefore, what else can an employer offer to attract the millennial generation given that wages and benefits don’t seem to cut Hereit?are a few areas to consider:
Accelerated career progression opportunities: A study conducted by Gallup found that 87 per cent of millennials are at tracted to companies that offer rapid career progression opportu nities. The days of expecting an employee to stay for years in a role, or even a single department like sales or accounting, are gone. Demonstrating career path op tions early on, and then support ing employees in pursuing these oppor tunities are a key attraction and retention tool.
Shawn Casemore is keynote speaker, consultant, and author of three books, including his latest book, The Unstoppable Sales Machine. To learn more about Shawn and his work, visit www.shawncasemore.com.
Despite introducing benefits such as these, the main reason most employees decide to stay or leave, is their boss. A fact discussed by Leigh Branham, author of The 7 Hidden Reasons Employees Leave. Although this isn’t new, what’s not so obvious
HUMAN RESOURCES FEATURE
Stock©Fokussiert/AdobePhoto:
APPLICATIONSUBMIT STUDENTSHIRE GETSUBSIDYWAGE Get Talent Get Money Get Started todayapply Today’s students will become part of your workforce. You can help shorten the distance. 1 2 3 to*up ,000 Per Placement Contact Wendy Gray , Senior Pr oject Co ordinator: wgray @emccanada.org WORK INTEGRATED LEARNING

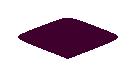
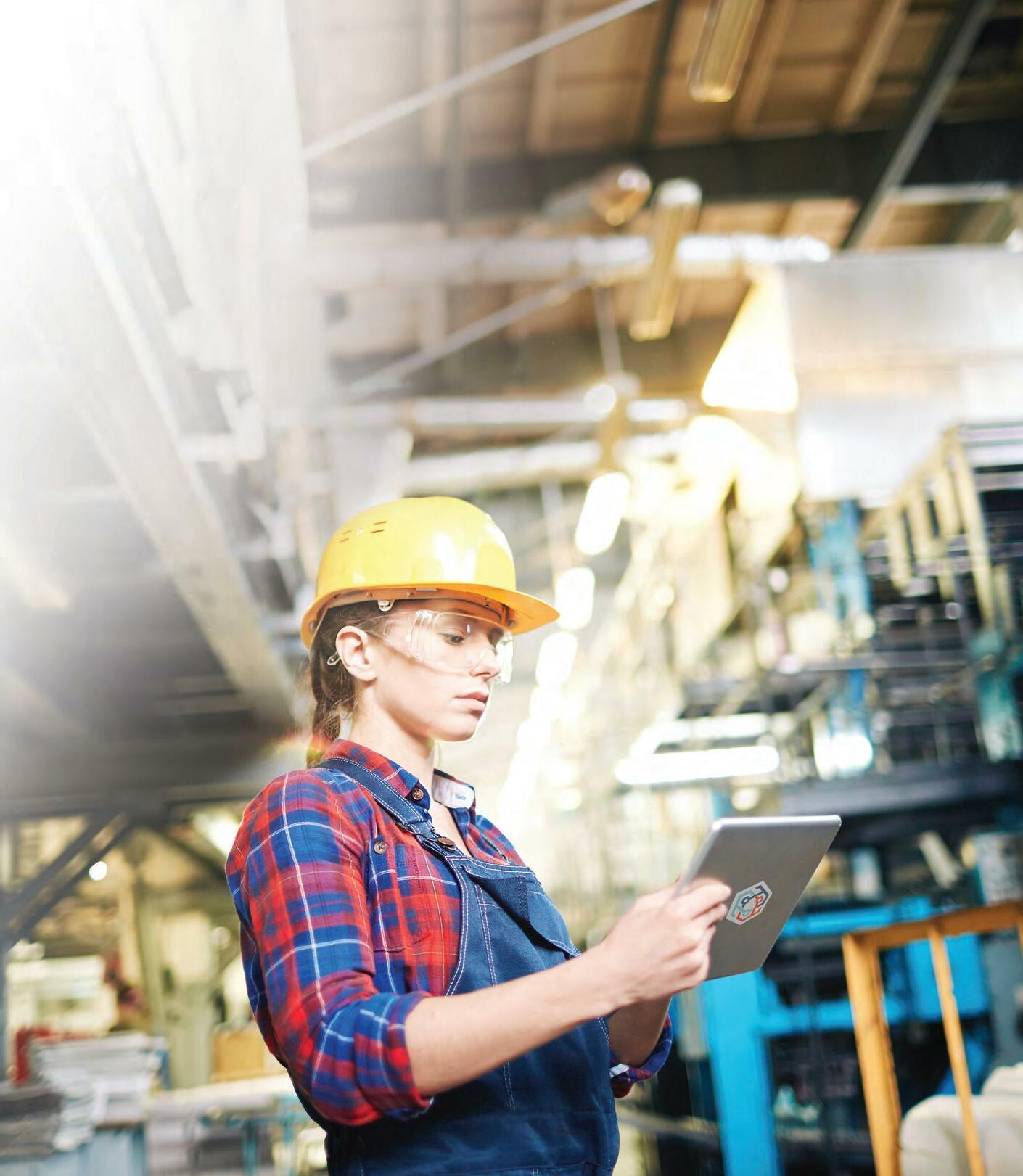
Figure Assembly2 validation
Stock©Gorodenkoff/AdobePhoto:
Moving to 3D
Beyond the original benefit of being able to model full assemblies to check for interference and fit, there is a cor nucopia of tools able to import a 3D model for a variety of analyses.
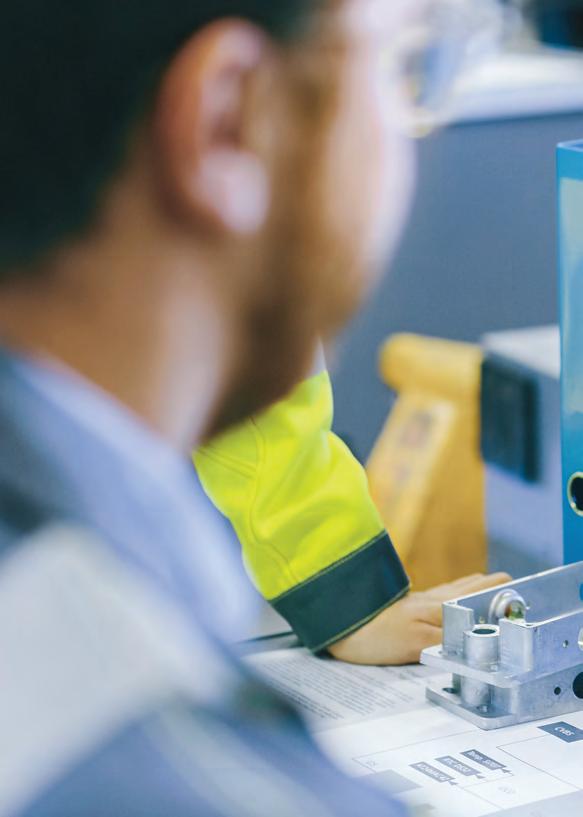
22 Plant / Summer 2022 PLANT.CA
Although 3D design does seem to be ex pensive still, hardware costs have come down. For the same cost as a 1980s word processor, you can get a good workstation today. Gone are the days of high-end reduced instruction set com puter (RISC) workstations from various companies. Now regular PC hardware, properly specified, can get the job done. Cost is not a real obstacle from a hardware perspective. Software, and its accompanying maintenance, or an nual licences fees, can still be a concern for small to medium sized enterprises, although there are lower cost products available that are affordable.
Back in those days, 2D was expen sive and 3D design tools cost fortunes. I remember at various subsequent employers we had two designs teams –one with drafting tables and one with a 3D CAD (Computer Aided Design/ Drafting) tools. As 3D was emerging technology at the time, the hardware and software was so expensive firms could not afford to convert all at once.
For parts involving castings, the abil ity to simulate metal flow and cooling for the parts after pouring is a great feature. High end software tools can all contribute to improving the designs of castings, improving product quality and yield. Such analysis could detect part shrinkage, and directional solid ification, resulting in the potential to add a riser(s) at critical locations in the mold. It is better to find problems, and
Eventually, the cost of both hardware and software came out of the strato sphere. Instead of paper and electronic design/drafting teams, we had a com bination of 2D and 3D teams. Paper was slowly being phased out. With 2D, there was some improvement in overall drafting time. Derivative parts were easier to create. Electronic information sharing got simpler both internally and externally. Then, and still today, com panies print a hard copy for signature. This prolongs the concept of paper as the master data source.
It’s a 3D World
Photo: Velan Inc.
If the fixtures have been designed in 3D, then the process team can often also check for machine, or tool, interference with the fixture. Not only is there a decrease in the cycle time to prepare for production, there is a decrease in tool-part-fixture collisions potentially causing serious damage, injury or delay.
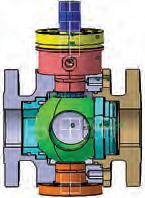
2D was the rage
BY STEPHEN CHERLET AND MANOJ KUMAR
But what about the benefits?
Figure 1 Part re-creation Photo: IDS Infotech Ltd (India)
Surprisingly, a lot of paper drawings are still in use today. Though I seldom encounter companies generating new paper-based drawings, the legacy data still remains intact as hard copy. Typ ically the vellum and old prints have been scanned making the drawing available in an electronics format, usu ally through PDF, these are typically old items that are not in production but needed for spare parts. They can be part of really old designs. When the need for change arises, these compa nies may take the opportunity to redraw the part using a CAD tool. This slowly brings everything into a digital world. Depending on the item, firms
FEA guides designers as to whether a product will break, and at what point, or work the way it was designed.
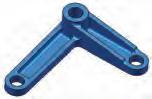
From the design side, having a 3D model lends itself to design valida tion through finite element analysis (FEA). FEA can be used to predict how a product will reacts to real-world forces, vibration, heat, and fluid flow.
Back when studying engi neering, everything was pencils, t-squares, set squares, ovals and perhaps a flex-curve. My first job at the aircraft factory, the design team had massive tables and full-sized drawings of the “master lines” of the aircraft. The print room worked with aperture cards and printed massive amounts of paper. Working as a support engineer, we had to ask for a fresh print (hard copy) to check even a few dimensions. Back then, there was no such thing as looking at information on a screen except for standard items like for fasteners, wash ers, and rivets, all of which could only be viewed on microfiche, microfilm, or in a parts catalogue.
MOVING TO 3D FEATURE
Also, we cannot forget about industrial engineering. Computer aided manufac turing (CAM) software facilitates the creation of numerical control programs for the production of machined parts, laser and water jet cutting, electrical dis charge machining (EDM) and robotic welding. In addition to generating tool paths, the software can often check for interference between part and machine.
may only re-create the part in 2D. This is especially true if the part is not used in a higher assembly, eliminating the value of creating the item in 3D to check for fit.
A fun part of being a consultant is visiting different companies, which allows for comparison between organizations, and the ability to find organizations with innovative ideas. However, you also get to where their is still opportunities for improvement or progress.
Some firms are scanning plants and piping to generate models of the “asbuilt” configuration. This provides the foundation for documenting the state of the building and can be integrated with EAM and CMMS.
Therefore, it is becoming a fully digital world and the time has come to embrace it. From concept to produc tion, all the processes in between are accomplished easier dig itally. Digital supports both customer and supplier collaboration. Mock-ups and models can be produced for visualization to aid in the design process. At the other end of the supply chain, suppliers can get ready for production, and produce faster, with a full 3D model. Take full advantage.
process are permitting the use of advanced materials. Direct metal laser sintering (DMLS) is an indus trial metal 3D printing process that “pr ints” fully functional metal parts in days from start to finish. A range of metals produce final parts that can be used for end-use applications. Those materials now include cobalt chrome, titanium, Inconel, tantalum, tungsten, stainless steels, and custom alloys.
Figure Holding4 fixture for machining
Simulations can be produced as instructional videos. They can guide machine operators with respect to fixture installation on a machine, part placement in the fixture, and provide a preview for the tool path. In the as sembly department, videos can be used as general training aids or for specific tasks. Still images from any of the sim ulation can also be used. If you have customer ser viceable products, the inhouse assembly videos can be turned into instruction aids for customers or authorized repair centres. Ultimately, all of this can be done in a completely immersive virtual reality environment.
The availability of the digital ob ject is a key to supporting supplier collaboration for any process. Some foundries will offer to run the casting simulation for you if the 3D model is provided. Machine shops, and many suppliers with robotic processes (like welding or painting), will also appreci ate being supplied with a model.
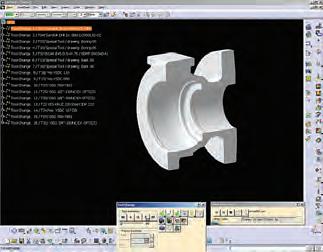
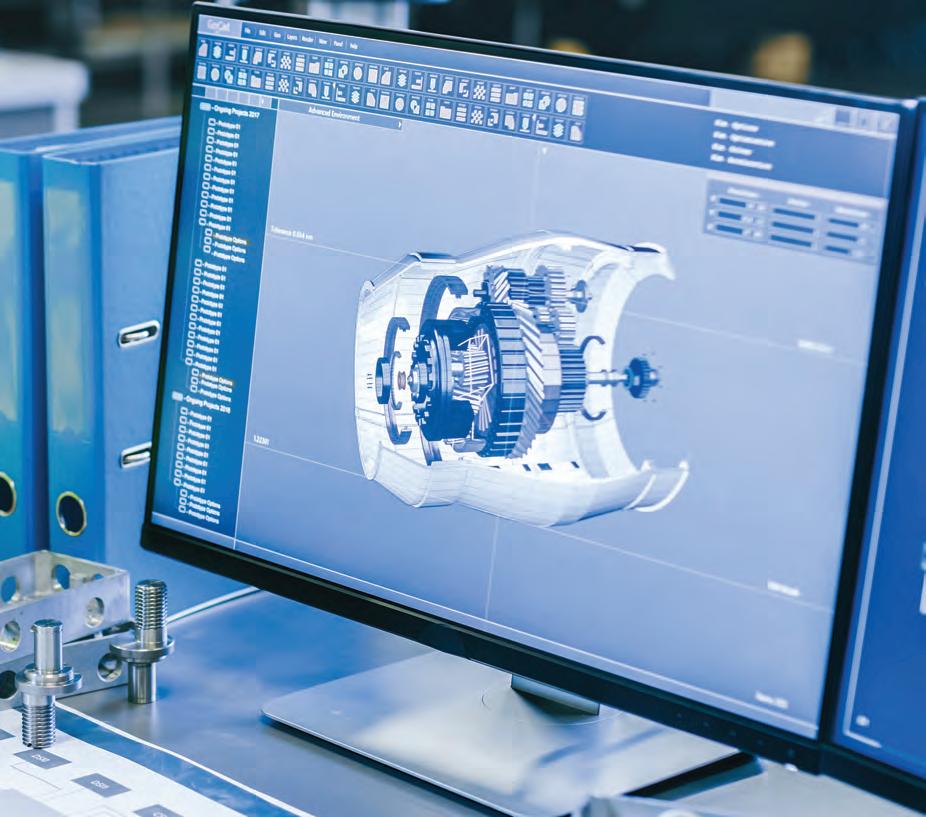
For those who still have hard copy documents, there are a variety of services to digitize your information. Scanning services to produce 2D vec tor drawings have been around for a long time, and the quality of the output has improved. Some services will offer
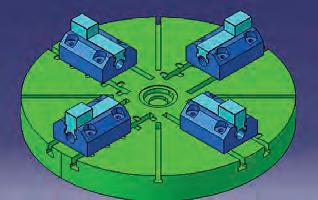
The glue that binds all this digital information together is the product lifecycle management (PLM) system. PLM provides the relationship of all the data to each other, manages chang es and allows you to execute at speed.
human expertise to review and clean up the newly vectorized results.
Where to next?
@PLANT_Magazine Summer 2022 / Plant 23
resolve them in advance, instead of on the foundry floor.
The real issue is getting from paper, or 2D CAD, to 3D. This still takes a human being, so, if you are not doing this in-house, you will need to contract a services company. Choosing a business partner with the correct experience is paramount to a successful conversion project. A critical success factor is to have an agreement on the key pa rameters of the model, dimensioning standards, defined use of layers, and tolerances on precision. This is needed to ensure the quality of the result and to avoid over specifying needs, which can result in massive file sizes.
Stephen Cherlet is a senior management professional with 35+ years of experience. Stephen is the owner/founder of FarStar S.A.C. Consulting. He is also the Chair of the National Board of Directors at Supply Chain Canada. He can be contacted at stephen@farstarconsulting.com Manoj Kumar is a senior management professional with 22+ years of experience. He is working as a Business Head at Inde Dutch Engineering & Aerospace Services Limited (IDEAS). Manoj can be contacted at manoj.k@ideasengg.com
How do I get there from here?
Another option is to use 3D scan ners and create the basic model from an actual part. Scanners have come down in price but are still expensive. Depending on the part, some holding fixtures could be needed, but it is still a faster way to get started on your digitization project. The downside is the model will reflect the as-is dimen sion of the actual part, not nominal dimensions with tolerances. That will have to be applied afterwards.
With the advent of 3D printing or additive manufacturing, companies can send the digital model to a sup plier and receive a physical part back. Also, the option to invest in the print ing equipment and bring the process in-house, is available. New printing
Figure 3 NC programming Photo: Velan Inc.
Photo: Velan Inc.
SKILLS DEVELOPMENT FEATURE
BY REHANA BEGG
The intended theme of the FABTECH Canada 2022 leadership exchange panel, was that advanced manu facturing introduces new technology to enhance, rather than replace, tradi tionalHowever,manufacturing.thatcentral idea would inexorably alter focus, as no Canadian conference agenda can be complete without a nod to the reality that about 700,000 skilled trades workers are ex pected to retire between 2019 and 2028.
Manufacturers ought to look to technology to help manage Canada’s workforce, Cloake said, because we can no longer expect people to stay on the job for 30 years. “That’s just not what young folks coming into the workforce today are looking for. That’s not necessarily a good or bad thing, we just need to adapt.”
designed his business process in a manner that allowed the plant to train an employee to run machines within two“Hemonths.ishiring 19 or 20-year-olds at a machine shop and is basically expecting them to produce within a few months and stick around for two years,” said the CEO of Raven, a manufacturing tech nology firm that develops automated contextualization and OEE software.
Casting call for technical talent
The research to support the changing landscape due to the uptake of digi tization has been floating around for some time. According to the Canadian
700,000
# of skilled trades workers expected to retire between 2019 and 2028.
24 Plant / Summer 2022 PLANT.CA
Holistic approach
Rather than a hindrance, data gen erated by the manufacturing process ought to be viewed as a collaborative tool for an incoming generation of tech-native employees, Cloake said. Much like a vehicle’s GPS system, technology can enhance efficien cy, particularly when it runs in the backg round and serves to provide operators with actionable insights, so they can complete tasks efficiently, he explained. Over the long haul, advanced manufacturing technology could be used to solve the reskilling problem by using it to eliminate in efficient processes on the shop floor.
Stocksittinan/Adobe©Photo:
The health of the workforce hinges on upskilling and reskilling in-demand trades.
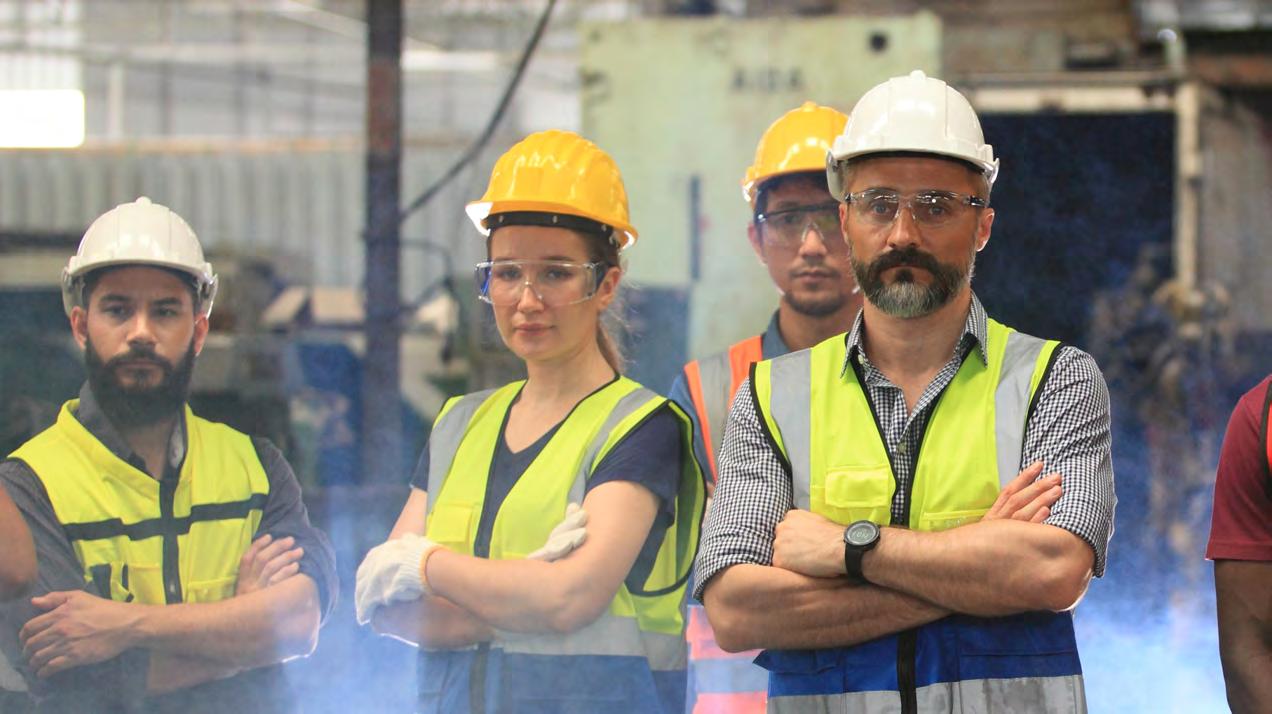
Talent and technology
For panelist Martin Cloake, ad vanced manufacturing is an idea whose time has come, and the logical progression is for the industry to harness the promise and potential of new technology to address labour shortages. To drive home his point, Cloake relayed a story of a machine shop owner, presumably a client, who
“Some people invest in technology without determining what are they trying to cure,” said Howcroft. “What are they trying to address? Is it the right technology for them? I think engage ment of your staff is crucial. But I also think it’s important to engage with your customers. How can we provide success to the customer base? What are you doing to make sure that what you’re providing them is meeting their needs now and into the future? I think you must take all that into account.”
smartphones most commonly used in the construction sector. Included in this mix is the trend to incorporate electronic sensors/controllers into equipment, and diagnostics and
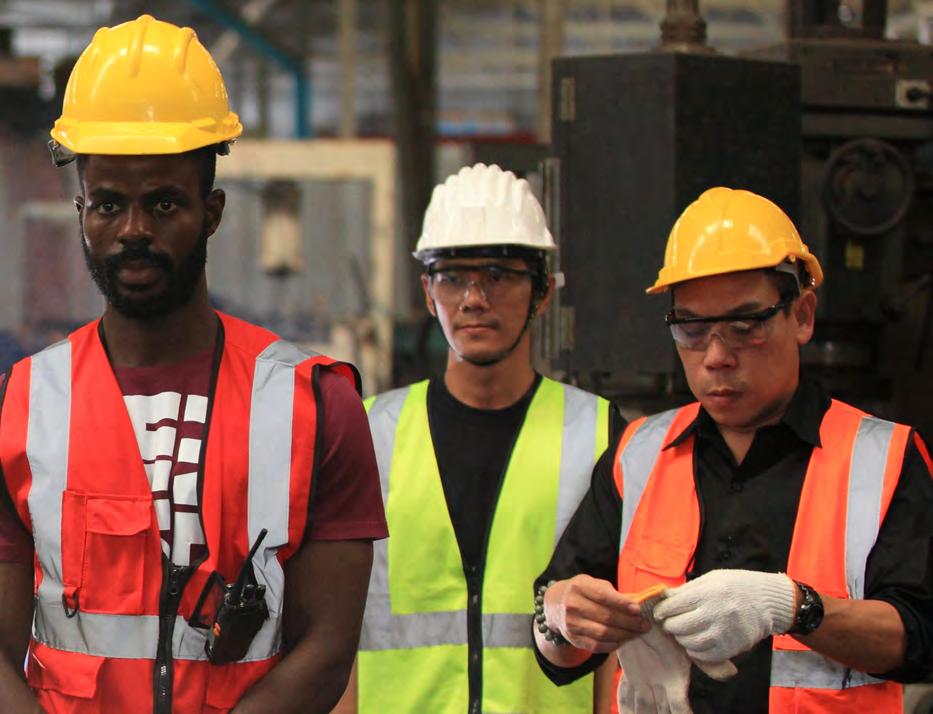
WorkatSucceeding/CanadaSkillsProcessingFoodCredit:Photo
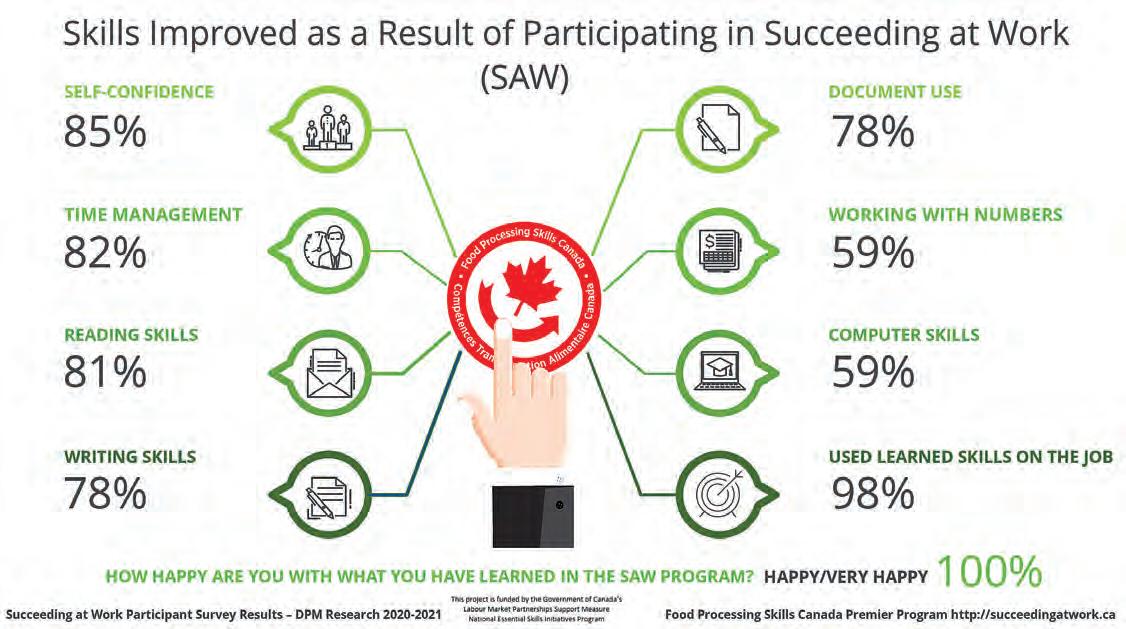
electronics-based testing equipment and the programming of machinery andIanequipment.Howcroft, CEO, Skills Canada, and a fellow panelist, agreed that tech nology has given operators and com panies far greater control than they’ve ever had “in terms of understanding and prediction,” but was less inclined to declare it an industry-wide magic bullet, particularly for manufacturers who have grappled with addressing per ception and skills shortages for decades.
Apprenticeship Forum’s Apprenticeship Analysis, 90 per cent of businesses use digital technology at the workplace with computers most commonly used in the service and manufacturing sectors and
The average age for starting an appren ticeship is 28, which indicates a missed oppor tunity, said Howcroft. “What we need to do is get into the schools, get in front of kids at a younger age and let them see what manufacturing is about, what technology is about and give them exponential opportunities to get hands-on experience.”
Recalibrate skillsets
@PLANT_Magazine Summer 2022 / Plant 25
The program offers basic computer literacy, as well as soft skills, such as critical thinking, adaptability, and troubleshooting. A defining charac teristic, however, is that the Job Seek er program attracts non-traditional sources to the labour pool. Initially set up at Trent University, the program in vites a diverse cohort of students and targets not only individuals who have faced barriers to employment. Deanna Zenger, regional coordinator and national project manager, Food Processing Skills Canada, explained that program addresses these barriers through workplace essential skills and social-emotional learning, or emo tionalTheintelligence. SAWLanguage Stream proj ect is a subset of the program, which offer s instruction in six languages in addition to English and includes e-courses in digital technology, good manufacturing practices, workplace industrial safety, lock out tag out, and oral communication. A lack of com prehension places immigrant workers at risk of being furloughed due to the
“I was leading a class that was very geopolitically at odds with one another,” said Zenger. “We have many different cultures from many different countries. When we first started, there were people who would not sit next to each other, which was surprising to me. But one must respect those differences. Within several weeks, not only having the tech nical courses, but working through the emotional intelligence programming, we began to see changes in people. It was as though they gave themselves per mission to be able to do and say things that they were afraid to do or say. In many cases, especially with women, the growth of the individuals was incredi ble, as were the literacy gains.”
Set priorities straight
Stock©sittinan/AdobePhoto: 26 Plant / Summer 2022 PLANT.CA
“But when you have an online learn ing system that is narrated, and you also see the written word, the literacy gains are outstanding.”
Rehana Begg is a freelance writer. Reach her at rehanabegg@rogers.com.
The program includes 23 courses designed to validate benchmarks of learning along the way. Since employ ees can take the courses in their own time, there is no loss of production or operations time.
Zenger has found that learning from home is often preferred. “Many employees are not digitally literate,” she said. “In our industry, we have a generational gap in the knowledge of technology. We have many people who have never finished grade eight. It’s just the way it is. And we have many new Canadians and many women who have never finished high school. To have a certificate nationally recognizing you in your own name [means a lot].”
One of Skills Ontario’s mandates is to meet prospective students across the province to help motivate them to pursue skilled careers. Skills On tario’s latest initiative, Trades and Tech Truck, is designed to inspire youth to explore skilled trades and technologies. Fix Network, the auto motive aftermarket franchise network for collision, glass and mechanical repair services is a major partner and has helped to kit out the mobile learning unit with activities and sim ulators, such as modules simulating auto-painting , welding, electrical systems, and heavy machinery. Other partners are the Government of On tario, Black & McDonald, Carpenters’ Distr ict Council of Ontario, Collège Boréal, CWB Welding Foundation, IHSA, LiUNA, Milwaukee, Mohawk College, Sheridan College, St. Clair College, and Workplace Safety & Pre ventionHomingServices.inon the food and bever age industry, where nearly 8,000 food and beverage manufacturing entities employ about 300,000 workers, Food Processing Skills Canada (FPSC) is another organization proving its commitment to helping employers build skilled and motivated employee teams. For example, Succeeding at Work (SAW) is FPSC’s two-stream (job seeker and employer), fully fund ed training program with an industry specific cur riculum and the facility to match participants with employers.
With no immediate signs of the skills gap going away, Howcroft and Zenger will attest that demand for innovative, practical solutions that address the changing needs to suc ceed in the workplace is high priority. Cloake might add that advanced manufacturing technology is integral to the equation.
Retention and productivity
extra effort required to keep them in formed, stated the SAW web site. To this end, Ontario, home to the largest number of sector businesses (2,530 or 35 per cent), is especially vulnerable.
Food and beverage manufacturers are short an average of 25 per cent of their workforce, according to Public Safety Canada. That makes labour a key issue preventing the sector from realizing its growth potential, noted Food and Beverage Canada.
All would agree that the future health of manufacturing is tied to the evolution of the hiring pool. “We need to take a look to see what the employ ers need,” said Zenger. “Because we have less than one generation to res cale and upskill the entire industry.”
SKILLS DEVELOPMENT FEATURE
“What we need to do is get into the schools, get in front of kids at a younger age and let them see what manufacturing is about, what technology is about and give them exponential opportunities to get hands-on experience.”
SAW offers benefits for people who have established roles in the industry. The program’s employer stream was created from a need to address not only retention issues but also produc tion issues. “We have a labour force shortage, so it’s very difficult to take people away from operations and production,” said Zenger.

Topics such as food safety contain critical information that cannot be watered down or shortened, and Ze nger said she has rewritten some the prog ramming to clarify the language.
Another “aha” moment stemmed from developing a hybrid curriculum (including in-person and online com ponents) for English as a second lan guage (ESL) learners. “We know from exper ience that knowledge of spoken English is better than written [knowl edge] when you have programming instruction with an instructor who speaks slowly, clearly, to make them understand concepts,” said Zenger.
Utilizing exper ience and spreadsheets, they went about their planning. After devel opment of a complex matrix including all the capabilities, capacity limits and inter connected variables, the solution provided was a software package that automates the entire order scheduling process. The solution also ties into the existing ERP, allowing for quick inventory checks, and reordering of raw materials to satisfy the schedule.
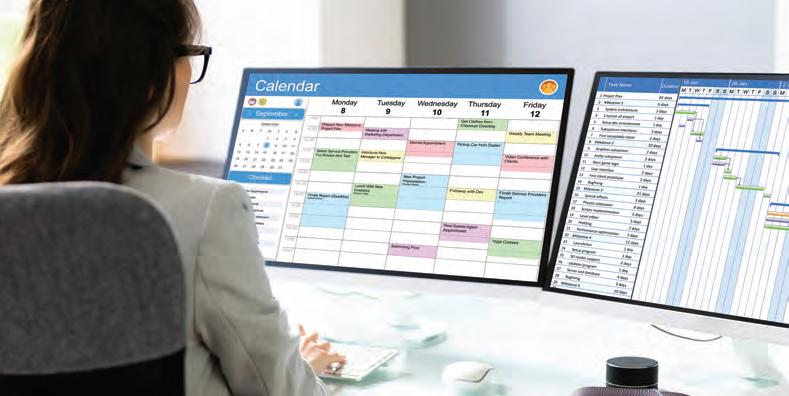
Manufacturing execution systems (MES) innovations are enabling manufacturers to better assign skills and tasks, and to manage contingencies. They provide precise, re al-time data to help with decision-making. While keeping the plant on track of the prog ress made on each product order and update the production schedule in real-time. A sig nificant aspect of more resilient plant opera tions is the attention paid to production monitor ing, quality, traceability and mainte nance, and MES scheduling software helps in this regard.
The scheduling interface can be accessed locally or remotely. It runs through a set of queries such as: what makes the most sense to produce; what would be the most produc tive; and what would get the company closest to its customer s’ lead times?
activities consider that it requires a measured and forward-thinking approach. Upfront consultancy between the supplier and the cus tomer is crucial to the success of the project. This in conjunction with current and future manufacturing requirements, will drive the selection of the appropriate MES solution.
Identifying the ideal partnership and end-to-end solutions
Addressing the issues
When looking to automate scheduling
Anything related to supply chain is relevant to a company’s well-being. Although efficient scheduling does help in the manufacturing phase, we can’t ignore the logistics side, where warehousing facilities need solutions to track their finished goods more effectively. Access to all this real time data is essential, and advances in cyber security ensure that cloud-based applications will have a part to play. With this data, operations staff have the tools to make decisions that result in produc tion targets being met, maximized capacities, and satisfied stakeholder s.
problem. They had hundreds of product SKUs running on multiple production lines, each line having slightly different capabilities and capacities. Couple that with competing customers looking for immediate fulfillment and the task becomes even more challenging. All while only one experienced person han dled the scheduling tasks for the entire plant.
SCHEDULING FEATURE
@PLANT_Magazine Summer 2022 / Plant 27
The project doesn’t end with the initial implementation. It is important to work with a partner who offers full support throughout the project lifecycle and with a solution that is easy to integrate, while being scalable and measurable. Most importantly customers want to find a supplier who understands their business, their needs and expectations and has the wherewithal to deliver on those elements.
Scheduling in the manufacturing business can be quite complicated. Looking at an ex ample in the packaging materials industry, a company who needed help with increasing overall production capacity, but found that it was production scheduling that was the
Nigel Flynn is the client manager with Actemium Toronto.
It starts by looking at the data and devel oping an understanding of how the current processes are working for a manufacturing facility. This may involve having an industrial processes consultancy on site working with a company’s IT group and implementing a solution to gather the information on how plant production lines are performing. This is always the first step in a facility knowing where they are at and what problems they may be Whenfacing.itcomes to production scheduling, all internal roles need to come together. Meaning full customer engagement and communications on all fronts. The engineer ing department must ensure the system is properly specified and all equipment is fit for pur pose. The maintenance department must ensure that the systems are properly main tained and fully available for production. The IT g roup must ensure the network and connectivity to the shop floor automation is robust and able to transfer data. Operations and human resources must be ready with properly trained staff capable of carrying out their daily tasks. With alignment of all stakeholders and systems, only then can the scheduling system push forward and deliver on the production requirements.
Scheduling optimization helps manufactures with supply chain woes
The outcome is an effective production schedule that maximizes productivity and finds the most efficient production route possible. The company can even set rules in the scheduler system for ‘priority’ customers.
Addressing future requirements
StockPopov/Adobe©AndreyPhoto:
An effective production schedule maximizes productivity and finds the most efficient production route possible. BY NIGEL FLYNN
NEW PRODUCTSTECH CENTRE
The joints can be equipped with nitrile boot covers for abrasion and oil resistance. They are manufac tured from alloy steel for high torque ability or stainless steel. https://www.ruland.com
FANDISAUTOMATIONDIRECTFILTERFANS
nal of an encl
Virdis series are available in NEMA 12 and 3R models. NEMA 12 rated models are for indoor use, and NEMA 3R versions are designed to preserve components housed within an electrical enclosure located outdoors.
The discharger frame is mounted on casters for mobility, while a hinged subframe supporting a surge hopper, flexible screw conveyor and support mast can pivot down for maneuvering through doorways and low-headroom areas.
FLEXICON MOBILE SANITARY UNLOADINGIBCCONVEYOR
APPLICATIONBLOCKCHAIN TO AUTHORIZE CAD DATA
Photo: Ruland
The IBC frame is forklifted onto receiving cups, which position the IBC outlet onto the surge hopper inlet. Material flowing from the IBC into the charging adapter of a flexible screw conveyor is pro pelled at an incline and discharged into elevated process equipment and storage vessels.
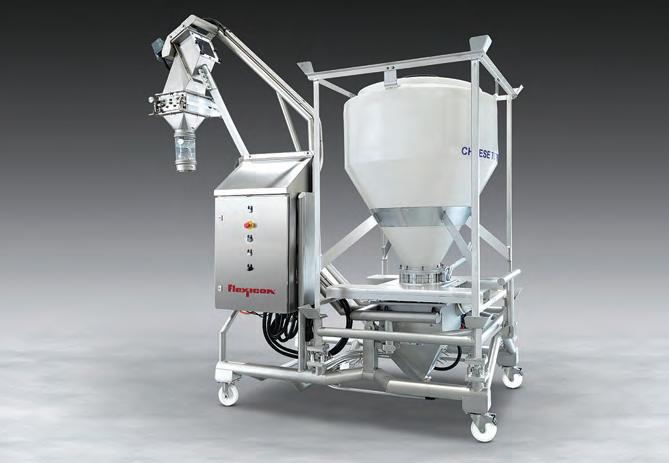
It combines high strength resins with ultraviolet light stabilizers and vapor phase corrosion inhibitor technology. This film construction provides multi-metal protection for parts, equipment, and vehicles for up to three years in aggressive outdoor
https://www.automationdirect. com/enclosure-fans
VpCI-126 HP UV shrink film may be supplemented with other VpCI ma terials such as VpCI oil additives, VpCI emitters, and VpCI fogging fluid for flexibility and protection.
Rite-Hite added to its lineup of rubber doors with Raptor Max, designed for a variety of openings (interior, exterior, and high-wind applications).Coveringopenings up to 20 feet tall by 20 feet wide, Raptor Max doors are made from quarter inch styrene-butadiene rubber.
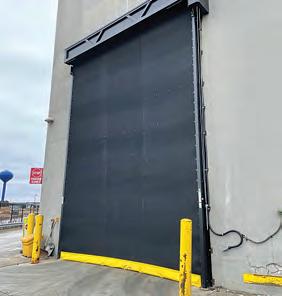
AutomationDirect added a line of enclosure filter fans to their inventory of thermal manage ment devices. Fandis Virdis series filter fans have a thermal manage ment solution for applications where the surrounding cooler air can be used to reduce inter-
Ruland friction bearing universal joints are available in various sizes, styles, and materials. Components are manufactured to tight tolerances for accuracy, torque capabilities and d urability.Components are selectively heat-treated and ground for higher strength, giving them a precise and prolonged life. Single universal joints are suited for space-constrained applications with angular misalign ment up to 45 degrees. Double universal joints are designed for applications with a wide distance between shafts or those in need of extreme angular misalignment accommodation up to 90 degrees.
Photo: Rite-Hite
Prostep showed how technology can be used to prove the authorship of CAD models at a blockchain committee set up by the German Association for Mechanical and
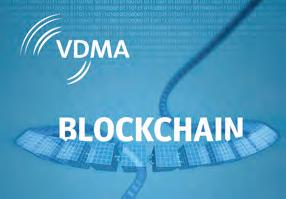
Photo: Prostep.
The screw is the only moving part contacting material and is driven by an electric motor positioned beyond the discharge point. The system is available in carbon steel with industrial coating, with stainless steel material contact surfaces, or in all-stainless steel. www.flexicon.com
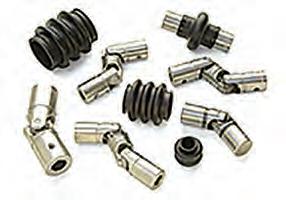
RITE-HITE RAPTOR MAX DOORS
www.cortecpackaging.com
Fandis filter fans are available in various voltages and dimensions, with roof mount units offered for limited space applications.
Photo:AutomationDirect.
Dr. Martin Holland, head of strategy and business development at Prostep, presented a block chain-based solution for the forgery-proof exchange of 3D printing and process data and the identification of the printed components. It was originally developed as part of the collabora tive SAMPL project.
Photo: Cortec Cortec VpCI-126 HP UV shrink film allows for expanding storage outdoors with corrosion protection.
The film can be shrink wrapped with a variety of shrink tools to create a streamlined unit that provides a secure environment for protecting idle assets from the elements.
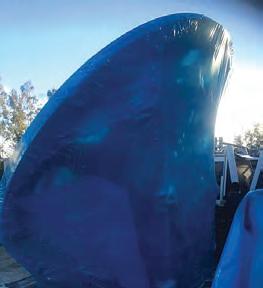
Based on wind load requirements in the American Society of Civil Engineers criteria, Raptor Max doors—depending on exact size— can take on static wind loads of up to 20 psf, which is the equivalent to a 115-mph wind.
The solution can store history de scribing the creation of CAD models in the blockchain and provide proof of the authorship of the data. https://www.prostep.com
FRICTION UNIVERSALBEARINGJOINTS
CORTEC STORAGEOUTDOORSHRINKFILM
Flexicon mobile sanitary IBC unloading and conveying sys tem transfers contamination-sensi tive bulk solid materials from intermediate bulk containers to downstream processes, dust-free.
Plant Engineering.
Photo: Flexicon.
The series includes vents and grilles that draw filtered cooler ambient air into the enclosure.
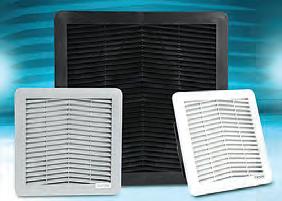
https://www.ritehite.com
Corrosionconditions.inhibitors in the film vaporize and condense on metal surfaces within the enclosed space to protect metals in direct contact with the film and those in recessed areas.
28 Plant / Summer 2022 PLANT.CA
Photo: Yaskawa Motoman
Walter’s profile milling cutter, Xtra·tec XT M5460, offers precision, tool life, and surface quality in machining of freeform surfaces and deep cavities. It has an internal coolant channel, enabling chip evacuation using
BPS does the upfront engineering and sizing of control components based on the mechanical design and
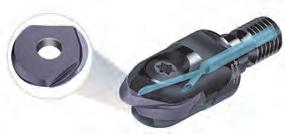
INTEGRATESWORKCELLSARCWORLD ROBOTICS INTO WELD PROCESSES
Photo: Fluke Networks
@PLANT_Magazine Summer 2022 / Plant 29
Samotics launched Sam4 Energy, a product that offers energy savings of 10 to 15 per cent and cuts CO2 emissions.Sam4Energy provides industrial companies access to a 24/7 energy audit, generates advice on how to reduce electrical inefficiencies and, once advice is implemented, Sam4 Energy tracks subsequent energy savings and carbon offsets. The energy efficiency platform provides a reporting tool enabling real-time insight into the performance of assets across a variety of performance metrics.
compressed air or MQL.
BPS CONTROL SYSTEMS FOR BULK PROCESS
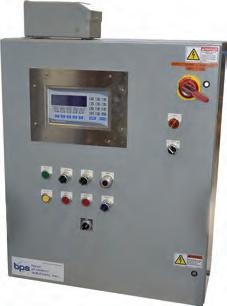
FLUKE CONNECTIVITYEXPANDSNETWORKSNETWORKTESTING
ArcWorld expanded its family of pre-engineered robotic arc welding workcells. They include the ArcWorld RS and ArcWorld HS, which are flexible and compact options for integrating robotics into current weld processes.
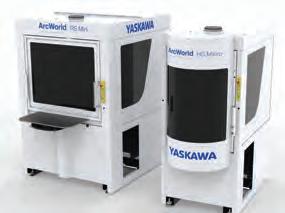
WAGO’s new Edge Computer is ideal for Linux users who want an industrial grade computer running their applications such as Node Red, Grafana, AI and digital twins.
Requiring 25 square feet of floorspace, the ArcWorld RS utilizes a rotating station design, manually indexed by the operator with two fixture tables and a 100-kilogram payload capacity per side. This facilitates quick changeover, allowing parts to be safely loaded and unloaded while the opposite station part is welded. Parts up to 425 x 700 x 990 millimetre can be processed.
Samotics’ has launched Sam4 Energy to market, following successful industrial trials. One trial deployment identified a foul pump at a sewage pump station that was operating at a very low efficiency caused by low flow operation.
WAGO EDGE COMPUTER
Thisinformation.industrialcomputer offers low latency control and simplified north/south connection with cloud-based services.
Xtra·tec XT M5460 has been designed for difficult materials, particularly for hard machining of steels up to 63 HRC. In field tests, the M5460 with this latest grade WHH15X, achieved increases in tool life of up to 500 per cent.
specification of the equipment and bulk processing control needs.
Photo: Wago.
Following automatically generated advice to open a partially closed discharge valve, yearly electricity savings of 40 to 55 per cent were achieved.
This profile milling cutter can be used in steels, cast irons, stainless steels, and hard materials. www.walter-tools.com/us
WALTER PROFILE MILLING CUTTER
BPS handles the startup and commissioning of the system, instal lation oversight of mechanical equipment and electrical paneling. www.bpsvibes.com
SAMOTICS EFFICIENCYENERGYSOLUTION
ArcWorld HS needs 15 square feet of floorspace and offers a hinged station design, allowing access for loading and unloading of parts. The workcell has a single fixture table with a 100 kg payload capacity and can process parts up to 550 x 500 x 1,050 mm in size.
Photo: Samotics
Each solution is designed for optimizing small- to medium-size part production for medium volume fabrication. Offering a single high-speed, six-axis AR900 arc welding robot with YRC1000 control ler and a digital weld interface for all power source brands.
LinkIQ can now be configured to perform IPv4 or v6 ping tests and will display the response time for four pings to a target device of the user’s choosing. The test results display the DNS and DHCP servers and the gateway router. LinkIQdisplays the IP address of the nearest switch. The new version of LinkWare PC includes this information in its test reporting. www.flukenetworks.com/LinkIQ
BPS systems utilize networking technologies available from control manufacturers. Using these networking and control technologies allows BPS control systems to be installed and implemented in shorter periods.
BPS controls systems are done from start to finish, and can design and fabricate control systems for an existing operation.
With a dual-core i7 Intel proces sor, 16GB RAM and 256GB flash, this device has the capacity to store large amounts of information, and the flexibility to align to industrial hardware specifications. www.wago.com
Fluke Networks upgrade its LinkIQ Cable+Network Tester that expands the tester’s ability to test and troubleshoot IP networks, test industrial Ethernet cabling, and support users in 12 languages.

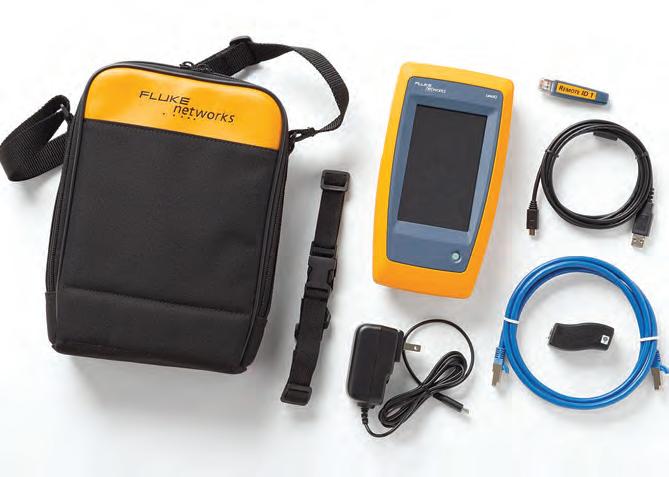
https://www.samotics.com
Photo: Best Processing Solutions.
Photot: Walter USA, LLC.
Wago has introduced 752-9800 Edge Computer, which can help increase plant floor performance by leverag ing applications operating in docker containers fed with harvested plant floor
For more products, visit: plant.ca/technology-centrewww.
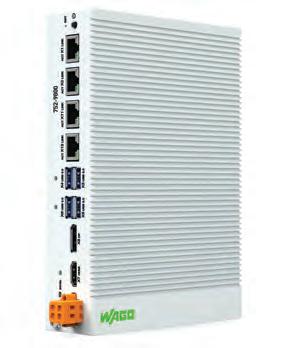
being there in person and situated in the Digital Ecosystem exhibit hall. I’m sure next year will be bigger and will once again draw the international audience that previous shows have.
Labour and talent shortages are not only a concern for manu facturers in Canada, but around the world.Yet, I couldn’t help but think advanced manufacturing will be in pretty good hands in the future and how great it would be to invite a cohort of Canadian students to attend the fair. I’m sure it would be equally as excit ing for them. Like me, I’m sure Hannover Messe would leave a lasting impression.
Jayson Myers, the CEO of Next Generation Manufacturing Canada, is an award-winning business economist and advisor to private and public sector leaders. E-mail jayson.myers@ngen. ca. Visit www.ngen.ca.
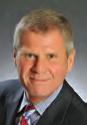
POSTSCRIPT
BY JAYSON MYERS
When these two perspectives come together, magic happens. When they don’t, tech providers don’t get much business at the fair. Manufacturers who pursue the tech for tech’s sake usually end up disappointed because they don’t improve their business, often because they don’t have the expertise, IT capacity, or skill sets to implement in a profitable way.
Reflections from the Hannover Messe
Stock©Wirestock/AdobePhoto: 30 Plant / Summer 2022 PLANT.CA
fter two years of pan demic lock downs the Hannover Messe fair reconvened in person earlier this year. Hannover Messe is the largest advanced manufac turing trade show in the world.The fair usually takes up 43 mega-size exhibition halls and attracts over a million visitors a year – most of them engineers, technicians, and high-level decision makers – from around the world. It is the place to go to see the latest in advanced manufacturing technologies, equipment, and industrial energy solutions and to exhibit innova tion and production capabilities to a global audience. Ultimately, it’s a great place to meet people and do NGenbusiness.brought several of its members to the fair. We partnered with the Canadian, Ontario, Quebec, and Alberta governments to host an exhibit highlighting Canada’s advanced manufacturing capabilities in digital technologies and AI, au tomation, and electric vehicles. We were joined by several other Canadian exhibitors who were also participating in the show, in cluding a delegation of hydrogen technology companies. All parts of Canada were represented. Our reception on the Tuesday evening drew a huge crowd.
it’s smart products, process es, and materials, with digital solutions everywhere.
The last day of the show is usu ally open to students from across Ger many, and as usual this year they flooded into the fair. Noise levels kicked up a notch that day. You could feel their excitement and see their interest and the engaged discussions they were having with exhibitors.
A
Most of the solution provid ers I spoke to talked about the impor tance of helping their cus tomers identify opportunities for implementation to improve pro cesses, demonstrate applications in actual use cases, manage data, and develop the skill sets required to manage their technologies productively. As impressed as they were with the technologies on display, most manufacturers were simply looking for solutions to the business challenges they face in delivering higher value to customers or cutting costs. It’s difficult to look beyond the tech in Hannover Messe, but that’s exactly what manufacturers need to do to figure out where in their business, production, or
Gor ve, the young employee from Siemens Canada who took our delegation on a tour of the Siemens exhibit.
supply chain processes new solu tions could be implemented to improve performance and meet business objectives.
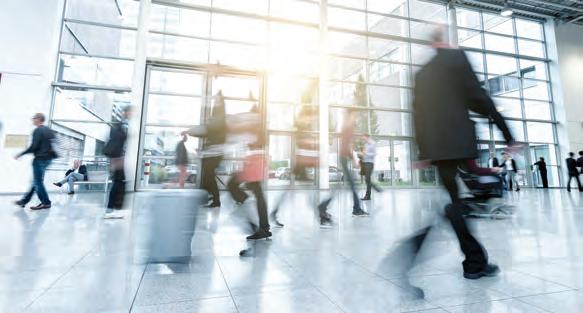
Ten years ago, advanced manu facturing exhibits were contained in one hall. This year most of the industry exhibits were about digital manufacturing and auto mation systems. It was only four years ago that the fair highlighted AI applications. The year before that it was additive. In 2019, it was cloud computing and 5G networks. Now connectivity is taken for granted. Additive, AI, and advanced computing capa bilities were not only highlighted throughout the show but part of the automation and control systems on display. We are past the dawn of Industry 4.0. Now
After four days of intense net working, we came away tired but also with some lasting impres sions. First and foremost, how g reat it was to travel and meet people again. There was a real buzz at the fair this year and a lot of good discussions. Partic ipants seemed to want to meet each other more than ever and to have fun, and our delegation made great However,connections.therewere some notable gaps this year. A lack of many Chinese companies and very few American exhibitors; making it a primarily European show. Uncertainty and limited prep time played a role. We found it difficult to recruit as many com pany reps in person as we would have liked to, but made up for that by running a virtual showcase and
You can’t attend Hannover Messe without having a sense of how fast advanced manu facturing is changing. With the exception of EVs and hydrogen systems, there weren’t as many new manufacturing technologies on display this year, there wasn’t a particular technology theme like the fair has had in previous years. However, what became clear from walking the floor, was in every field of application – from product design and development, automation systems, energy, mo tors and drives, robotics, additive, to dig ital systems – how much connectivity, high power cloud and edge computing capabilities, and AI have become embedded in the latest technology solutions available to manufacturers.
Which leads me to perhaps my biggest takeaway of all. I was highly impressed by the enthusi asm and expertise of the young people exhibiting adv anced manufacturing solutions at the fair. Leon, a graduate from Pad erborn University, who is setting up an open-source AI platform for systems optimization. Sylvie, whose start-up company is work ing with nanomaterial coatings for EV batter y casings. Mark, the 20-something CEO of a lean con sulting company that specializes in automation and AI installa tions for auto parts suppliers.
In my discussion with exhib itors, I was impressed by how similar their views are of the chal lenges and opportunities they see when it comes to adopting their technologies. The show is always a good place for engineers and technicians to meet, see what their competitors are up to, and find potential business partners. Yet, when you ask how business is going, the response is pretty much the same, and much differ ent from what I hear in Canada. Tech providers are finding it dif ficult to make the business case to manuf acturers. It’s not just about the features or potential benefits of their technology; it’s about how it can be integrated into operations, successfully managed, and sustained.
PLEASE TAKE A FEW MINUTES TO COMPLETE THE SURVEY.
Everyone who completes the survey will have the opportunity to enter into a draw for a $500 Best Buy Card.
The Advanced Manufacturing Report, will be released this fall with the survey findings and additional commentary from industry experts on the challenges and solutions to effectively implementing Advanced Manufacturing Technology.
CANADA’S LARGEST ANNUAL SURVEY MANUFACTURERSOF

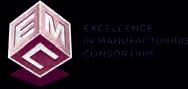
Plant magazine and CanadianManufacturing.com are undertaking an annual survey focusing on Advanced Manufacturing and the Canadian manufacturing sector that will be the foundation of a blueprint report for Canadian companies to use on their next-generation manufacturing journey.
This in depth survey takes under 10 minutes to complete and will provide analysis of the overall awareness and the current status of Canada’s manufacturing sector and the level of understanding of the future benefits of the “connected factory”.
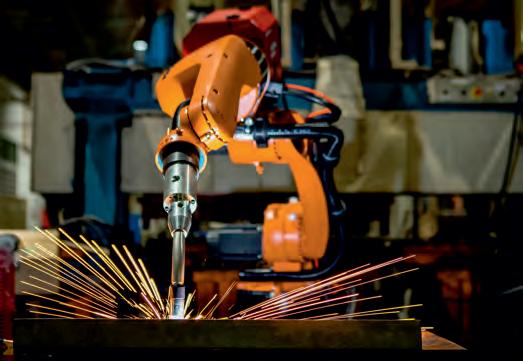
Available • AC variable frequency drives
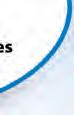
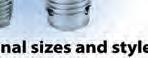
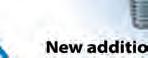

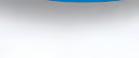
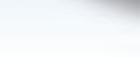

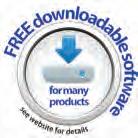
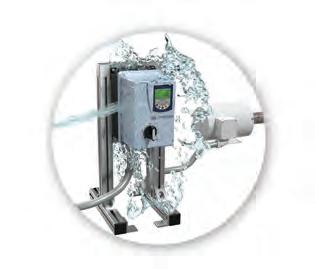


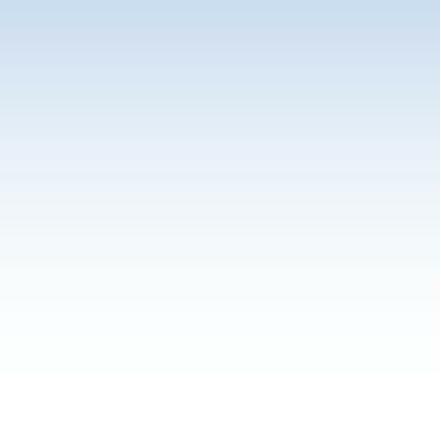
Also (VFDs) and electrical connection everything need to complete

solutions • Just about
SureFrame

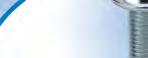
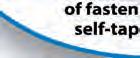
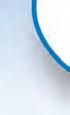
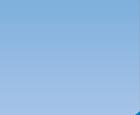




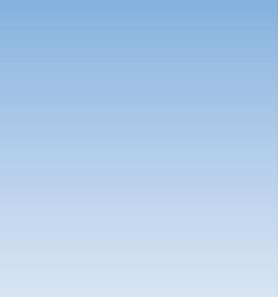

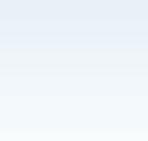
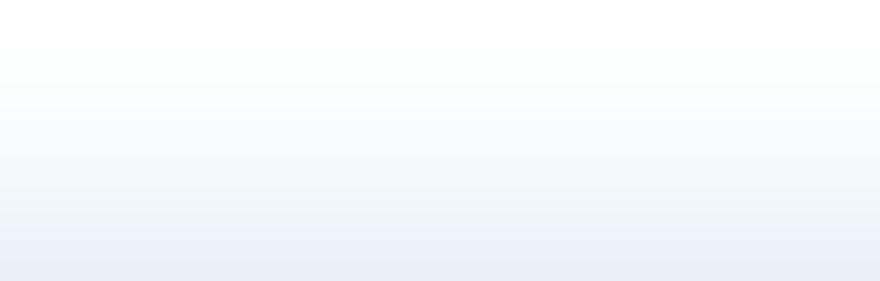

We also offer a full selection of assembly hardware for T-slotted rail systems, which includes T-nuts, fasteners, connecting components, joining plates and brackets, as well as floor, door and panel elements. SureFrame T-slotted rails, along with the assembly hardware components offered, are compatible with many other brands.
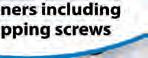
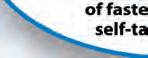
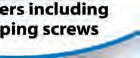
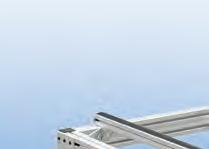
T-Slotted Aluminum Rails NO CUT FEES, EVER! CUT TO YOUR SPECIFICATION AND DELIVERED TO YOU IN 2-DAYS! Sureframe AutomationDirect McMaster-Carr80/20 Framing Tech 34.5” (4) 1.5” x 3” light weight 77” 1.5”(4)x3” light weight 27” 1.5”(4)x3” light weight $277.20 1530CL $415.80 47065T809 $348.36 1530-LS $349.08 1.5X3.0/240INCH $124.20 1530CL $186.30 47065T809 $163.06 1530-LS $161.36 1.5X3.0/240INCH $97.20 1530CL $145.80 47065T809 $130.36 1530-LS $128.24 1.5X3.0/240INCH Unknown upfront, added during billing. 3-4 day only available Hidden in pricing $3.16/cut $2.25/cut $498.60 $747.90$641.78$638.68 $0.00$0.00 $747.90$942.16$1,027.72$300.38$389.04 Cut TotalChargeExtrusion Cost 2 Day Delivery Total Cost All prices are U.S. published prices. AutomationDirect prices as of 04/06/2022. Prices and specifications may vary by dealer. McMaster-Carr prices are from https://www.mcmaster.com 2/10/2022. 80/20 prices are from https://8020.net 2/10/2022. Framing Tech prices are from https://www.framingtech.com 2/10/2022. Prices subject to change without notice. Prices for aluminum do fluctuate. Check vendors websites for latest current pricing. TM Orders over $49 get FAST FREE SHIPPING Our shipping policies make it easier than ever to order direct from the U.S.! Fast free standard shipping* is available for most orders over $49 U.S., and that includes the brokerage fees (when using an AutomationDirect nominated broker). Using our choice of carrier, we can reach most Canadian destinations within 2 to 3 days. *Free shipping does not apply to items requiring LTL transport, but those shipments can take advantage of our negotiated super-low at rates (based on weight) that include brokerage fees. See Web site for details and restrictions at: www.automationdirect.com/canada To see all products and prices, visit www.automationdirect.com All prices shown are U.S. Dollars
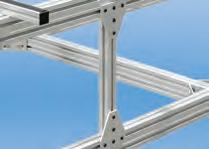

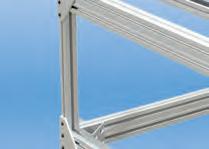
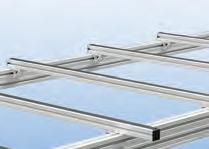
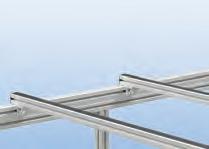
you
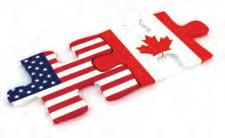
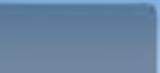



Slotted Aluminum Rails Cut how you need it and shipped fast Research, price, buy at: www.automationdirect.com/t-slotted-rails the #1 value in automation Order Today, Ships Fast! * See our Web site for details and restrictions. © Copyright 2022 AutomationDirect, Cumming, GA USA. All rights reserved. 1-800-633-0405 • You specify length and cut angles for each piece • No cut fees • Free 2-day delivery on all orders over $49* • Available in 1 inch, 1.5 inch, 30mm, 40mm and 45mm profiles • Complete selection of Fath installation hardware available Features
your automation projects!

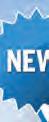
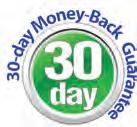


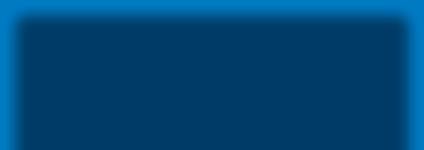
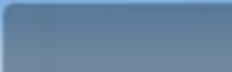
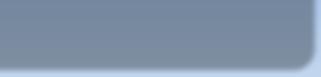

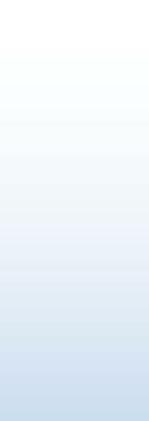
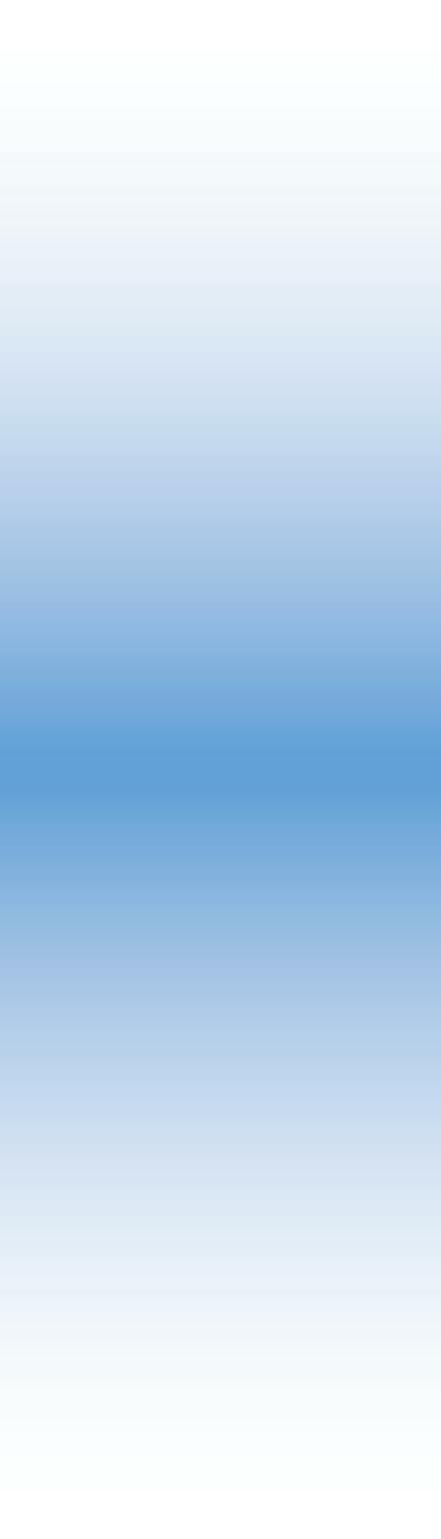
SureFrame T-slotted aluminum rails are available in the most popular profiles and dimensions. T-slotted rails are ordered in your custom cut-to-length sections for maximum flexibility and minimum waste.
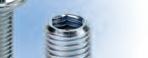
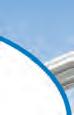
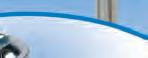

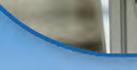

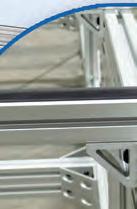
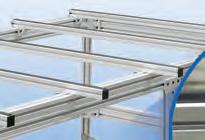


• Motors • Wiring
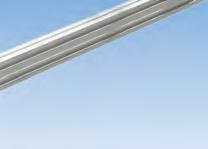