
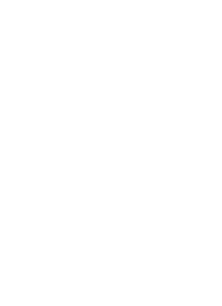
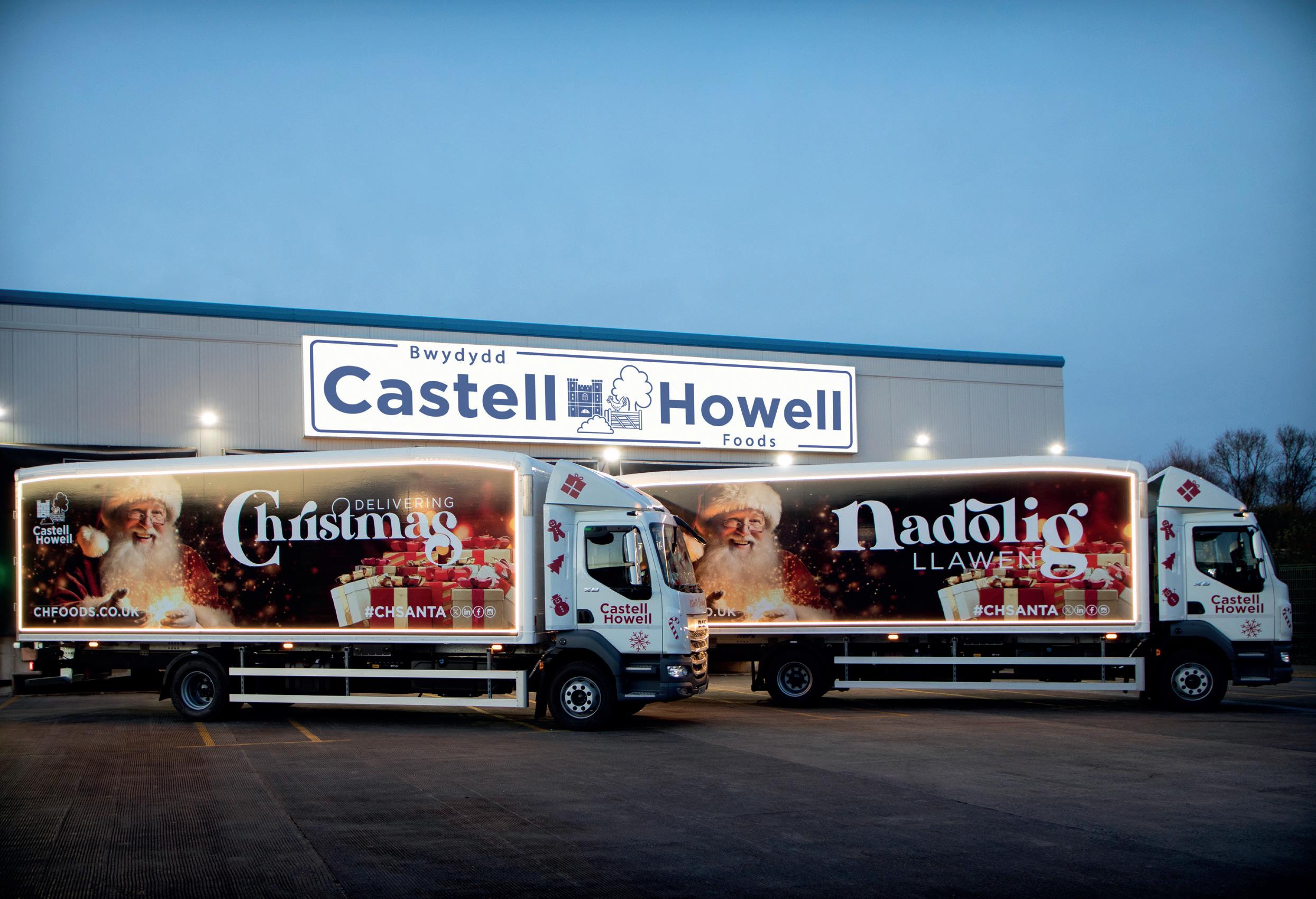


| WINTER 2024
In this issue
> An Interview with Industry Legend – John Ward
> Gray & Adams Success at TCS&D 2024
> Customer Case Study – Dale Farm
> Exceptional Quality: The Foundation of Gray & Adams’ Success And so much more
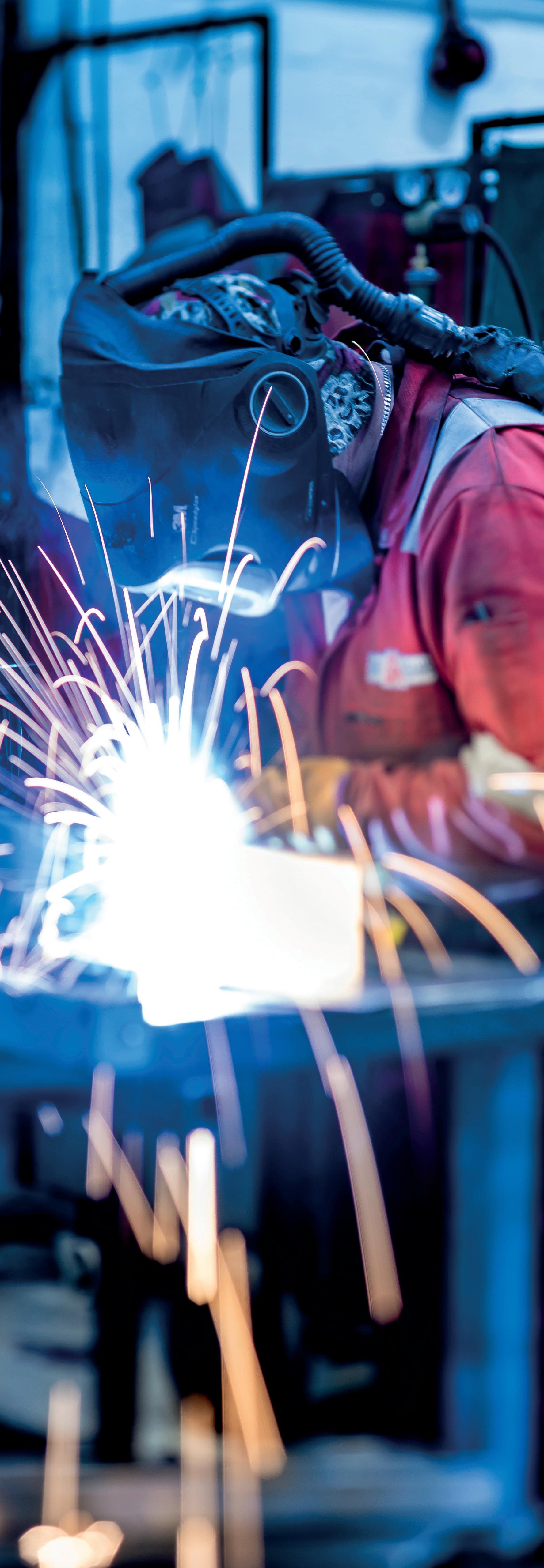

| WINTER 2024
In this issue
> An Interview with Industry Legend – John Ward
> Gray & Adams Success at TCS&D 2024
> Customer Case Study – Dale Farm
> Exceptional Quality: The Foundation of Gray & Adams’ Success And so much more
As we approach the end of 2024, we are proud to celebrate our collective effort and success for another year. We would like to take this opportunity to thank our people, customers, partners, and suppliers for their continued support this year.
Whilst we look forward to what 2025 will bring, we must reflect on the highlights and challenges of the year. 2024 has presented us with challenging legislative framework changes, creating more questions than answers, which Ian Smith, Group Engineering Manager goes into more detail on, on page 11. However, one thing we are sure of is that we will work tirelessly to minimise the impact this has on our customers. With these challenging conditions in mind, we want to thank our team across all of our depots for their unwavering commitment to our business.
In this edition, we are delighted to announce our recent investment in two new state-of-the-art machines, a 10kW Bystronic Bystar Fibre laser cutter and a twin-head Voortman V303 plasma cutting machine. This investment will improve the company’s production processes, leading to dramatic improvements in efficiency, cost-effectiveness, safety and overall operational performance (page 5).
It is, of course, the support of our customers that has allowed Gray & Adams to grow into the business it is today. Renowned for putting our customers first with quality and bespoke designs that fit our customer’s needs and drive their business forward. In this edition of the newsletter, we discuss the relationship between Gray & Adams and Dale Farm as we speak to their Group Transport & Fleet Manager (page 13). We were also delighted to feature customer, Barratlantic, where they celebrated 50 years of the company and 50 years of a key member of the team, driver Angus Macmillan (pages 14-15).
Working with key suppliers, where we have developed strong, long-term relationships is one of the strategies we use to continuously deliver quality to our customers. Gray & Adams has worked with BAKO since 1995, delivering solutions within their multi-temperature vehicle fleet. In this edition of the newsletter, we discuss the new fleet BAKO, Durham, received from Gray & Adams earlier this year (page 17).
On pages 8 & 9 we had the pleasure to speak with industry legend John Ward. John tells us of his career journey from working in a family business to heading up the Vehicle Maintenance Unit at Morrisons, one of the UK’s leading supermarket chains.
As we approach Christmas, a time for celebration and giving, Gray & Adams is proud to have supplied long-term customer Castell Howell, with Christmas light-up trucks that bring community cheer to the festive period (page 4).
At Gray & Adams, we value our people; they are what keeps the business moving forward and have been an important part of our story for over 65 Years. In this edition, we celebrate the long service of Ian Strachan who has been with the company for 25 years (page 19) and Derek Byron who celebrates 40 years with Gray & Adams (page 20). On page 16 we proudly supported Doncaster employee, Jonny Wallace, through the sponsorship of his sons local kickboxing team as they attended the World Kickboxing Championships earlier this year.
In this edition we also celebrate some success from the second half of the year, including our TCS&D success, achieving Refrigerated Trailer of the Year 2024 (page 12), and Bidcorp UK’s Supplier of the Year 2024 award (page 6). On page 10, we also celebrate the success of 12 employees at our Dunfermline depot completing a Root Cause Analysis Training Course.
As it has been since our inception in 1957, we are a family business, first and foremost. Despite materials shortages impacting the global supply chain, our people remain of utmost importance. Page 18 focuses on how Gray & Adams builds a lifetime of value, through a focus on quality and how it is the foundation of Gray & Adams’ success. Highlighting the importance of attracting and retaining specialists and talented individuals we have featured a spotlight on the UK Careers Fair attendance where we have the opportunity to inspire the next generation (page 7).
With Christmas and 2025 on the horizon, we would like to thank each and every one of our team for their unwavering commitment and we hope you enjoy the festive period with your loved ones.
James Gray OBE and Peter Gray OBE Joint Managing Directors
Castell Howell, Wales’ leading independent food service wholesaler, is spreading holiday cheer across the country with their dazzling Christmas-themed light-up trucks. This annual festive initiative, which started in 2017, combines creativity, community engagement, and a touch of holiday magic.
Decked out with eye-catching livery and sparkling lights, these trucks are hitting the roads of Wales and beyond, delivering not only goods but also smiles and holiday joy. To make the season even brighter, Castell Howell has organised a series of special events and giveaways, including surprise visits to schools where Santa will distribute gifts and a luxurious food hamper competition.
Fans of Castell Howell’s iconic #CHSANTA trucks are invited to join in the festive fun by snapping photos of the illuminated vehicles. Participants can share their pictures across social media platforms, offering hampers to the winners.
Over the years, Castell Howell has introduced numerous initiatives to engage with local communities. From school art competitions where children design truck livery, to fundraising campaigns for charitable causes, the company has consistently demonstrated its commitment to giving back.
Martin Jones, Director of Transport Operations, Castell Howell, says of the light-up trucks,
“It’s all about spreading a little bit of cheer and putting smiles on people’s faces. The light-up trucks are a creative way to connect with the community and make the season memorable.”
Gray & Adams, Castell Howell’s trusted supplier, plays a key role in bringing these festive trucks to life, by contributing to the trucks’ vibrant lighting displays, making them a standout feature on the roads. This year, Castell Howell also unveiled an electric vehicle in their fleet, reinforcing their commitment to sustainability while celebrating the season.
The brightly lit vehicles are travelling routes across Wales, from rural areas to major depots in North Wales, South Wales, and even the South West of England. Customers, including schools and local businesses, can request special deliveries to bring the festive spirit directly to their doorstep.
Castell Howell’s light-up trucks are a testament to their dedication to both the holiday season and the communities they serve. Gray & Adams is delighted to play a part in this heartwarming mission to deliver fun and spread joy to local communities.
Gray & Adams Ltd is proud to announce a significant investment by purchasing a state-of-the-art 10kW Bystronic Bystar Fibre laser cutter and a twin head Voortman V303 plasma cutting machine. This investment will improve the company’s production processes, leading to dramatic improvements in efficiency, cost-effectiveness, safety and overall operational performance.
Laser Cutting: A Quantum Leap in Speed The upgraded laser cutting machine has dramatically reduced cutting times, for example, one process used to take 1 hour and 14 minutes and with the new machine the time has been slashed to a mere 23 minutes. This represents an 80% reduction in processing time. This efficiency increase will translate to numerous benefits for the organisation, including:
• Increased production capacity
• Shorter lead times
• Reduced operational costs
Plasma Cutting: Precision and Sustainability The new plasma cutting machine offers a range of advantages, including:
• Enhanced Consumable Life: Real-time monitoring of consumable wear provides operators with valuable insights, allowing for timely replacements and reducing unnecessary downtime.
• Optimized Energy Efficiency: Advanced power management systems minimize energy consumption, contributing to lower operational costs and a reduced environmental footprint.
• Superior Cutting Quality: The machine’s precision cutting capabilities deliver high-quality parts with minimal material wastage.
By leveraging these advanced technologies, Gray & Adams Ltd is committed to delivering exceptional products and services while minimizing its environmental impact. This investment underscores the company’s dedication to innovation and its position as a leader in the industry.
Gray & Adams is delighted to have been recognised as Bidcorp UK’s Supplier of the Year at their annual awards ceremony.
Bidcorp UK, which includes Bidfood UK, has been a valued customer of Gray & Adams for over 30 years and is one of the UK’s leading foodservice providers, working behind the scenes delivering food to over 40,000 customers, 365 days a year, including hospitality, education, workplace, travel and leisure. It is positioned as a one-stop-shop for caterers of all sizes from the smallest independent operator to the largest high street brands, contract caterers, hoteliers and the public sector.
Bidcorp suppliers were recognised in a number of categories including the coveted Supplier of the Year Award. Each year, the Supplier of the Year award recognises a partner who has demonstrated exceptional commitment, reliability, and quality in collaboration with Bidcorp UK. This accolade highlights the vital role that suppliers play in supporting the operations of the business and contributing to success. The Bidcorp team put considerable thought into their nominations, and after a thorough evaluation, Gray & Adams was honoured to be recognised for outstanding performance and unwavering dedication to Bidfood.
Announcing the Award, Dave Wilson, Head of Fleet at Bidcorp UK, said,
“This year’s supplier of the year provides a high-quality product in considerable capital-intensive volumes, exactly to timetable, exactly to specification. Their communications are exemplary, they are often on call at unsociable times with us, any problems that do arise as part of their production are dealt with in a proactive way and in a very common-sense approach that enables the seamless transfer of their product into our business. I am delighted to say that the winner of the Supplier of the Year award for 2024 is Gray & Adams. Congratulations to them, well done to Geoff & Chris and the team and thank you for all your help over the last 12 months.”
Gray & Adams is delighted to be named Bidcorp’s Supplier of the Year. This award is a testament to the hard work, dedication, and innovative spirit of the entire team. Gray & Adams prides itself on delivering exceptional quality and value to our customers, and it is an honour to be recognised by a partner like Bidcorp, who shares the company’s commitment to excellence.
As a leading manufacturer in the temperaturecontrolled industry, Gray & Adams made an impactful appearance at the UK Careers Fair in October. This was an excellent opportunity to showcase the company’s strengths, highlight available career pathways, and attract young talent.
Gray & Adams was delighted to meet with prospective employees and present a variety of career opportunities. The company’s exhibit at the fair highlighted a wide range of roles across the company. This year, Gray & Adams placed special emphasis on skilled trades and technical roles, such as Manufacturing Operatives, Commercial Painters, Welders and many more.
Through engaging in discussions with students, recent graduates, and professionals from various disciplines, the team provided insight into the work culture, growth opportunities, and career progression that Gray & Adams offers. With a history of more than 65 years in the industry, the company underscored its commitment to building long-term careers and fostering an environment where innovation and teamwork thrive.
Gray & Adams also emphasised its well-regarded apprenticeship and training programmes which are designed to provide hands-on experience, mentorship, and a robust foundation to begin your career. With a commitment to skill development, many apprenticeships lead to permanent positions for many participants. Gray & Adams has a history of retaining skilled workers, with many apprentices moving into senior roles within the company, making it an appealing choice for those looking for a stable and rewarding career path.
Attending the UK Careers Fair demonstrates Gray & Adams’ commitment to building a talented, skilled, and sustainable workforce. The careers fair was more than just a recruiting opportunity, it was a chance to inspire the next generation of professionals and reinforce the company’s reputation as a leader in the temperature-controlled industry.
As the company moves forward, those who join Gray & Adams will become part of an organisation that not only leads in industry standards but also fosters meaningful careers and a culture of innovation and excellence.
“Looking back over my career, I feel proud of the journey I’ve taken—from working in a family haulage business in Leeds to heading vehicle maintenance for one of the UK’s largest supermarket chains. It’s been a path shaped by challenges, partnerships, and innovation, and I’m grateful for the experiences along the way.
I started in the family business, George Wards Haulage, which, as far as I know, was the oldest haulage company in Yorkshire. For many years, we provided critical services to industries like steel. But when the steel strike of 1981/82 hit, it caused serious disruptions. We couldn’t recover, and in 1982, at the age of 28, we had to close the business.
I didn’t stand still for long and shortly after, I started working for Charthire Services, a contract hire company, as a Workshop Manager.
From there, I moved on to Leaseway Services in a similar role. Then, in 1994, I joined Morrisons, and that’s when things really started to take shape. At first, I worked as a Workshop Manager, but within a few years, I stepped into a much bigger role, heading up the Vehicle Maintenance Unit.
It was an exciting time to be at Morrisons. In 2004, when Morrisons took over Safeway, we were seen as the smaller company taking on a much larger operation. Integrating the two businesses was a massive challenge, especially from an engineering and logistics perspective, but it was one I embraced. It also marked the beginning of a long and rewarding partnership with Gray & Adams, the leading specialists in refrigerated vehicles.”
John continues,
“Gray & Adams’ engineering expertise and willingness to collaborate helped us innovate in ways that truly transformed Morrisons’ logistics. When Gray & Adams introduced double-deck refrigerated trailers, this significantly reduced distribution costs by maximising load capacity. We also participated in the national trial for 15.6m trailers, which added four additional pallets per delivery. These solutions weren’t just cost-effective— they were groundbreaking.
During the trial, Morrisons had the largest fleet of 15.6m trailers in the UK. The collaboration with Gray & Adams stood out because they didn’t just sell us trailers; they worked with us to design and refine them to our exact specifications. Their commitment to quality and customer service was second to none, and we built a relationship that lasted for years.
This relationship continued beyond my retirement and was showcased from my invite to Prince Charles’ Royal Visit to Gray & Adams headquarters for a factory tour. It was an honour to be part of that day and to see how the partnerships I had built continued to be celebrated.
I was delighted to retire in 2015, at 62 and in good health. I’ve spent the past nine years enjoying life—looking after my grandchildren, travelling, playing golf, and simply appreciating the time I now have.
Looking back, my career taught me the importance of resilience and collaboration. From the early days in the family business to leading logistics innovation at Morrisons, I’ve always valued the people and partnerships that made success possible. For me, it’s not just about the milestones— it’s about the journey and the relationships built along the way.”
— John Ward
A group of twelve dedicated employees from Gray & Adams’ Dunfermline branch are celebrating a milestone after successfully completing Root Cause Analysis (RCA) Training, earning their pass certificates and bringing enhanced problem-solving skills to the company.
Gray & Adams, a prominent name in manufacturing temperature-controlled vehicles, provided the RCA training as part of its commitment to quality improvement and continuous development for its team members. RCA is a vital process in quality management, equipping employees to identify, analyse, and address the underlying causes of issues to prevent future occurrences and boost overall operational efficiency.
The training program involved a mix of interactive workshops, real-life problem-solving exercises, and practical assessments. By the end of the course, participants had honed their skills in analysing complex problems, identifying root causes, and implementing effective solutions — skills that are invaluable in the high-stakes field of manufacturing. With their new RCA certification, the twelve employees are well-positioned to contribute to Gray & Adams’ reputation for quality and reliability.
Derek Murray, General Manager at Gray & Adams, Dunfermline, praised the achievement:
“Our team’s commitment to professional development and continuous improvement is outstanding. The RCA certification not only highlights their individual dedication but also strengthens our company’s capacity to deliver topnotch, error-free products to our clients. We are immensely proud of each of them.”
One of the newly certified team members, said,
“The training was intense but incredibly rewarding. We’ve learned techniques that will not only improve our own work but also positively impact the entire team. It’s great to work for a company that invests in our growth and values our contributions.”
The RCA training aligns with Gray & Adams’ ongoing efforts to foster a culture of accountability and quality in every aspect of its work. By investing in such programs, the company ensures that its employees are equipped with industry-leading skills that contribute to sustained success and customer satisfaction.
With the RCA certification under their belts, the newly trained employees are excited to put their knowledge into practice, enhancing operational processes and contributing to the continued success of Gray & Adams.
With a constantly changing legislative framework, these changes are creating more questions than providing answers to the post Brexit world of Type Approval, carbon reduction targets and indeed our operating licence compliance requirements.
Whilst we look forward to what 2025 will bring, we must reflect on the highlights and challenges of the year. 2024 has presented us with challenging legislative framework changes, creating more questions than answers, which Ian Smith, Group Engineering Manager goes into more detail on, on page 11. However, one thing we are sure of is that we will work tirelessly to minimise the impact this has on our customers. With these challenging conditions in mind, we want to thank our team across all of our depots for their unwavering commitment to our business.
As a manufacturer, operator and representative of the industry in several forums, it is noticeable that the burden of change is ever increasing.
In this juggling act, the hot potatoes are the European Commission’s introduction of the Vehicle Energy Consumption Tool (you may have heard the term “VECTO” being brandished about), General Safety Regulation 2 (known as GSR2),– what should be included in the GB Type Approval framework and closer to home, the additional text which appears in the 2024 Guide to Maintaining Roadworthiness in regard to periodic preventative maintenance brake performance assessments –we won’t mention railroading the introduction of Smart Tachograph 2, despite the “system” being not even close to satisfactory for roll out, but hey lets just load the expense and burden onto operators in any case with an “interim” fix.
So, lets jump into the 2024 Guide to Maintaining Roadworthiness, and particularly the requirements around brake performance monitoring at every mandatory periodic safety inspection.
This in itself is not a new requirement, so there is not an increased frequency of brake performance monitoring, as some may have interpreted, what is new and effective from April 2025, is the focus around brake performance assessments in particular the use of Electronic Brake Performance Systems and where that sits in regard to the alternative methods of assessment that have been in use such as Roller Brake Test (RBT) and decelerometers.
The guide is written in such a way that, in my opinion, leads the reader along the path that EBPMS is the preferred method of monitoring brake performance, even though, in the case of an articulated combination, the “system” cannot distinguish between a tractor or trailer fault. When a deterioration of the parameters is
noted, further investigation is required and inevitably, again in my opinion, that will lead to a foundation brake assessment including assessing brake force effort using a RBT.
However, it is the very fact, that a deterioration of performance data is noted in service, rather than waiting until a safety inspection draws the attention to a defective brake, that makes the system a winner.
EBPMS allows for continuously monitoring brake performance, why would you not want to do that (I ask myself with a fleet engineering head on?).
Where EBPMS is not used, the guide goes on to say that the expectation (read as must do), is that a minimum of 4 laden brake tests spread evenly across the year are carried out (including the RBT check at MoT).
Now, if your inspection frequency based on mileage, age, nature of operation (to name but a few considerations), dictates that this is undertaken at 12-week intervals, each inspection requires a laden brake test. If your inspection frequencies are 6 weeks, you’ll undertake 8 safety inspections, 8 brake tests, 4 of which must be laden. (Every second inspection to maintain an even spread throughout the year). The thing here is that to have a meaningful assessment of brake performance, in my opinion, every safety inspection should wherever possible be conducted with the vehicle or trailer in a laden condition.
I hear the groans, about the impact on service delivery additional cost and that sometimes this is just impracticable, that’s why the guide also gives a little breathing space, vehicles can have their laden RBT brake test up to 14 days before the scheduled mandatory safety inspection.
With the last paragraph in mind, it is therefore, again in my opinion, no change to what I believe should be happening, regarding planned safety inspections and in particular brake condition monitoring.
I’m sure you’ll agree that we all want to ensure the highest of standards when it comes to the safe operation of our fleets, this is another step in the right direction.
Check out the details by reading the 2024 Guide to Maintaining Roadworthiness for full details, available on the gov.uk website (it’s always worth a refresher).
Gray & Adams attended the annual TCS&D show on the 9th & 10th of October at the NEC in Birmingham. With a newly built stand, we were delighted to have partnered with Gist and Castell Howell to feature two vehicle displays.
Exhibit one was Castell Howell’s first all-electric rigid vehicle, which is based on a Volvo chassis, with a Carrier TRS electric refrigeration unit. This distinctive all-electric vehicle is fully wrapped and consists of many exciting features such as triple rear doors, safe step access and a newly designed moving bulkhead with an integrated crew access door.
Exhibit two was a 44-pallet lifting deck trailer complete with a Thermoking Advancer 500 refrigeration unit. The trailer was in the new Gist livery designed to reflect its new owners, M&S, and also fitted with the new, part-galvanized, chassis-less frame.
Gray & Adams sales team were on hand to answer questions from existing and potential new customers. The show attracted a good number of high-profile customers over the two days and the team thoroughly enjoyed the show.
Gray & Adams were also delighted to attend the TCS&D Awards evening, which is a celebration of the outstanding companies, services, and individuals who positively impact the temperature-controlled industry. Gray & Adams proudly accepted the award for ‘Trailer of the Year 2024’ at this year’s gala dinner, making it the eighth win since 2016.
We would like to extend our warmest congratulations to all the award winners and issue a huge thank you to all who have supported Gray & Adams, including our customers, supply chain, employees and the organisers and judges of TCS&D.
Dale Farm is Northern Ireland’s largest Farmerowned Co-op, and the 1,300 farmers that Dale Farm collect milk from, own the company.
Employing over 1,200 people across the UK and Ireland, Dale Farm is one of the most expansive dairy companies in the UK. The business spans the food chain, from animal feed to collecting milk from farms, from processing products to store delivery. Dale Farm dairy is supplied to retail, food service and ingredients markets in more than 45 countries.
Gray & Adams spoke with Adrian Currie, Group Transport & Fleet Manager at Dale Farm,
“The relationship with Gray Adams spans more than 40 years and long before my time with the company. We use Gray & Adams solely for our fleet of twenty refrigerated trailers and sixty refrigerated rigids ranging from 7.2 tonnes to 26 tonnes.
When we first started working with Gray & Adams, Dale Farm milk was stored in glass bottles and transported in plastic crates. They supplied us with unique custombuilt sliding-side door trailers to transport the crates to the various depots. We have now moved from glass to plastic bottles, which are placed on wheeled trolleys and transported in conventional fridge trailers or rigid bodies with a tail lift. It is imperative that the vehicle transporting our milk must be robust to take the day-to-day loading/ unloading of the heavy-wheeled trolleys and Gray & Adams provides us with a vehicle that does just that.”
Adrian continues,
“We typically keep our rigid body vehicles for seven years and our trailers for ten, and even after this time in service we still have a high-quality vehicle to sell. Gray & Adams quality is second to none.
When working on a new project with Gray & Adams, we always receive a first-class service, from drafting the technical specifications through to production and aftersales care. We recently approached them to design a body for a new 12tonne vehicle for school deliveries that would match our requirements, from listening to what we needed, the design, production and delivery service was seamless, resulting in a vehicle that suits our needs perfectly.
We entrust Gray & Adams to maintain, service and repair all Dale Farm tail lifts, rigid bodies and refrigerated trailers at their Gray & Adams Newtownabbey site and this helps us meet our operational and compliance requirements.”
In celebration of Barratlantic’s 50th anniversary, we sat down with one of their longest-serving employees, Angus Macmillan, a dedicated driver who has been with the company for almost its entire existence. His journey reflects the evolution of both the company and the fishing industry in the area, marking a story of growth, adaptation, and commitment.
The story begins in the early 1970s. Fresh out of school, he worked initially on building sites, constructing houses, before trying his hand at the local fish factory, which had just opened its doors in April 1974. With a stroke of luck, he left the building site on a Friday and, after a quick phone call, was offered a position at the factory by Sunday evening. By Monday morning, he had begun what would become a lifelong career at Barratlantic.
Starting as a fish filleter, he learned the ropes, working handson with freshly caught seafood. This period was one of change and growth for the company; initially handling only crabs, Barratlantic soon expanded to process various types of fish as the business grew.
The company’s journey wasn’t always smooth. Just five years in, Barratlantic faced a period of downturn, followed by a shift in ownership that brought renewed energy. John King acquired the business, and under his leadership, the company rebounded and set off on a path of steady growth.
One of the major changes he observed was in the transportation side of the business. In the early days, flat lorries without refrigeration were the standard, with the fish being refrigerated only within the factory itself. As refrigerated lorries became the industry norm, Barratlantic adapted to ensure the freshness of their seafood, particularly for transport across the UK. By the early 1980s, he had transitioned fully into driving, moving from flat lorries to modern refrigerated trucks, a change that made a significant difference in product quality and logistics.
A career in driving has come with many memorable moments. A highlight was his role in the scallop shell trade, transporting shells from Barra to a business in Weymouth that used them for food presentation.
“It’s been a great adventure,”
he reflects, recounting the numerous trips, and the regular ferry rides back to Barra.
John King’s legacy lives on in the company, now managed by his daughter and spearheaded by Donald, a key figure who has almost matched the driver’s own tenure at Barratlantic. Donald’s unwavering commitment has greatly contributed to the company’s lasting success. With a short stint at Calmac before returning to Barratlantic, Donald embodies the spirit of the company and has been instrumental in steering it through the years.
After decades on the road, he is now contemplating retirement, potentially at the end of this year. Despite the idea of retirement, there’s a sense of pride in the journey he’s had with Barratlantic, a journey marked by hard work, resilience, and loyalty.
Barratlantic’s trucks and trailers, manufactured by Gray & Adams, have always been high-quality—a point of pride for the company. With four trailers currently in their fleet, they have relied on Gray & Adams for years, cementing a relationship that underscores the commitment to excellence shared by both Barratlantic and their longest-serving driver.
Reflecting on his time with Barratlantic, he says with pride,
“I’ve played a big part in it.”
Angus’ story is a testament to the dedication that has helped Barratlantic thrive. Through the ups and downs, he has been a vital part of the company’s journey.
As Barratlantic celebrates this milestone, Angus’ story serves as a reminder of the importance of loyalty, adaptability, and community in building a legacy that spans generations.
Gray & Adams is proud to work with Barratlantic, a company that shares our values, recognising that the success of the company comes from the commitment and high-quality work from our employees.
As part of our CSR strategy, Gray & Adams offers support to the local communities that we work within as part of our commitment to our heritage as a family business and our colleagues who live and work in the areas. It is important to us that we support causes and events that are close to our employees’ hearts and that we do what we can to make a difference in the community.
Jonny Wallace has worked with Gray & Adams Doncaster for almost eight years, primarily working in the yard and completing a range of duties for the business such as forklift operation. Jonny’s 16-year-old son, Joe, has a passion for kickboxing and is a member of the ACMAC Martial Arts School which has various gym locations near our Doncaster depot.
In 2022, Gray & Adams sponsored the team as they competed in the World Championships in Ireland, where they brought home a total of 27 medals. Gray & Adams was once again delighted to support the young athletes by sponsoring the team this year, in the 2024 World Championships in Portugal.
Team ACMAC proudly took home 31 medals in this year’s World Championships, with Jonny’s son Joe contributing to the total with a bronze medal. This was the biggest England squad that has ever taken part in the World Championships with 300 English competitors, 20 of which came from ACMAC.
Joe is currently working for Gray & Adams on a Saturday in the repairs department, as a part-time job alongside school. In his free time, Joe teaches martial arts classes at Rossington School on Tuesdays and at another club on Fridays, he is also currently undertaking his instructor’s course. He is aiming to be at college in the new year, to complete a BTEC in sports to become a teacher or a physio.
In 2025 the World Championships will take place in Niagara Falls, Canada, with the national qualifications in springtime, which Joe hopes to be successful in.
Jonny shares his pride in his son’s achievement,
“Joe has been training in martial arts for twelve years and has shown a real passion and talent for it, as a father I want to do all I can to support him to achieve his goals. Gray & Adams as an employer is a fantastic support as they have not only contributed financially which allowed the ACMAC team to compete, but they have shown a real interest in what is important to me and my family. The whole ACMAC team is grateful for the support of Gray & Adams.”
Gray & Adams would like to wish Joe & the remainder of his ACMAC team all the best in their future endeavours.
Quality: A Partnership Built for Success
BAKO, a leading supplier of bakery products and ingredients, has recently taken delivery of a new fleet of vehicles from Gray & Adams, marking a continuation of their long-standing partnership. Known for servicing bakers across the United Kingdom, BAKO prides itself on providing an extensive product range with exceptional service. Their relationship with Gray & Adams, which began in 1995, has been pivotal in ensuring the company’s transport solutions match the needs of its demanding delivery schedule.
In 2024, BAKO introduced 13 new 26-tonne rigid vehicles, fitted with dual-compartment bodies specially designed by Gray & Adams. These vehicles replace ageing fleet assets and have been tailored to meet the challenges of regular, temperature-controlled deliveries across the north of England and all of Scotland.
Gemma Webster, Group Marketing Manager at BAKO, shared insights into the company’s decision:
“We needed to modernise our fleet to ensure consistent performance and reliability for our customers. Gray & Adams delivered a specification that exceeded our expectations. We are particularly impressed with the innovative technology featured in this fleet, such as underslung fridge motors powered electrically via an engine-driven PTO. This helps us deliver bakery products in perfect condition while being mindful of energy efficiency.”
Gray & Adams worked closely with BAKO and its suppliers to design a solution that aligns with the company’s operational demands. These vehicles are engineered for durability, with a robust design capable of serving for 10–12 years. The bespoke dual-compartment bodies allow seamless temperature control, ensuring both frozen and chilled goods arrive in top condition.
Gray & Adams commented:
“We are proud to have supported BAKO for nearly three decades, providing innovative and high-quality transport solutions that enhance their delivery operations. This latest fleet reflects our commitment to meeting their needs now and into the future.”
The new fleet is already making a difference in BAKO’s operations, enhancing delivery efficiency and reliability. Gemma Webster emphasised the impact:
“We’re extremely happy with the performance and quality of the new fleet. These vehicles allow us to continue delivering temperature-controlled products to our customers on schedule, and the Gray & Adams team has been excellent throughout the process. Andrew Brown and Ryan Davies have been fantastic partners, ensuring our fleet replacement went smoothly.”
Looking ahead, BAKO’s confidence in Gray & Adams is evident. The company has already placed an order for six additional vehicles of the same specification, scheduled to arrive in March 2025.
The enduring partnership between BAKO and Gray & Adams highlights the power of collaboration and innovation in addressing industry-specific challenges. By combining BAKO’s expertise in bakery distribution with Gray & Adams’ advanced vehicle solutions, the companies continue to raise the bar for quality and reliability in food service logistics.
2024 has been a remarkable year for Gray & Adams, characterised by outstanding achievements and an unwavering commitment to excellence. This success is built on the extraordinary dedication and craftsmanship of the individuals who meticulously oversee our products, from inception to completion.
Our focus on quality and customer satisfaction has once again been validated through glowing customer testimonials and a consistent stream of repeat business. These endorsements underline the trust our clients place in us. Notably, Gray & Adams was honoured to receive the prestigious Refrigerated Trailer of the Year award at the TCS&D Awards in October—for the eighth time since 2016. This unprecedented achievement is a testament to the superior quality and innovation we bring to the industry, and we take immense pride in this milestone.
The cornerstone of our success is our dedicated team of Quality Inspectors, who ensure that every product is manufactured to exact customer specifications and completed to the highest possible standard. The Gray & Adams attention to detail underpins our promise of quality in every product delivered to our customers.
Our commitment extends beyond internal excellence. Over the past 12 months, external audits have consistently delivered highly positive results, reinforcing our adherence to the standards and certifications that define our reputation. This commitment to compliance with regulations and quality benchmarks remains steadfast as we strive to exceed expectations.
Looking ahead, Gray & Adams is committed to elevating standards even further. In 2025, we will introduce new initiatives, cutting-edge improvement programs, and advanced technologies across all facets of our operations. These enhancements aim to streamline our processes, optimise production efficiency, and uphold our unparalleled quality standards.
A key aspect of our forward-looking strategy is investing in our people. By providing comprehensive education, skill development, and the necessary resources, we empower our team to excel in their roles, prioritise health and safety, and champion sustainable thinking. This proactive approach ensures we remain at the forefront of our industry.
With an exciting year of progress and innovation on the horizon, Gray & Adams is ready to set new benchmarks in quality and service. We look forward to sharing more updates as we continue to lead the way in delivering exceptional solutions to our valued customers.
– Davy Smith, Group Quality Manager
At Gray & Adams, we are proud of our people, and we work hard to attract and retain talented individuals. As a result, we have a number of valued team members who have worked for the business for many years.
In this edition, we speak to Dunfermline’s Assembly Manager, Ian Strachan who celebrated his 25th anniversary with Gray & Adams this year.
What is your role at Gray & Adam’s and what are your day-to-day responsibilities?
My current role is Assembly Nightshift Manager, responsible for assembly, safety, staff performance, training and mentoring.
What brought you to Gray & Adams, and what has kept you there for so long?
Being originally from Fraserburgh, Gray & Adams were and still are the largest employers in the town. So, it made sense when an opportunity came through word of mouth to work here, I jumped at the chance and started in the assembly department. The reason for my length of service is down to how Gray & Adams put its employees first, this was shown to me first-hand when my request to work from the Dunfermline depot was swiftly granted due to moving to Edinburgh back in 2007.
Also, during the Covid-19 pandemic, the extraordinary measures that were put in place to put staff safety and welfare front and centre have cemented my opinion of Gray & Adams and kept me here.
What has been your biggest achievement while working for Gray & Adams?
My biggest achievements are training and mentoring younger members of staff, seeing them take up senior positions throughout the company and having an input into the huge increase in production over the past 17 years.
If you could do someone else’s job (at Gray & Adams) for the day, whose would it be and why?
I’d like to do a salesperson’s job for the day as this side of the business would interest me, I think my product knowledge would lend itself well to this role.
What is the best thing about working for Gray & Adams?
The best thing about working here apart from the above mentioned is simply the people.
At Gray & Adams, we are proud of our people, and we work hard to attract and retain talented individuals. As a result, we have a number of valued team members who have worked for the business for many years.
In this edition, we speak to Dunfermline’s Quality Inspector, Derek Byron who recently celebrated his 40th anniversary with Gray & Adams this year.
What is your role at Gray & Adam’s and what are your day-to-day responsibilities?
My current role is and has been for over 30 years, a Quality Inspector. I make sure each vehicle is inspected to a high standard and any faults are rectified before being forwarded to the customer.
What brought you to Gray & Adams, and what has kept you there for so long?
I was 16 when I started at Gray & Adams through a friend who was a customer of Gray & Adams’. I suppose I have been there so long because I enjoy what I do, plus Gray & Adams have always treated me fair. Also, there’s always been plenty of work through new and existing customers.
What has been your biggest achievement while working for Gray & Adams?
Probably lasting over 40 years and being a Quality Inspector for so long.
If you could do someone else’s job (at Gray & Adams) for the day, whose would it be and why?
To be honest, I just enjoy what I do, and I must be ok at it to last this long. I respect everyone in what they do and a lot of the jobs are more challenging, so I’ll stick to what I know.
What is the best thing about working for Gray & Adams?
I would say, everyone respects one another so it makes things a lot easier for everyone involved, regardless of what position they do, also you are always learning, even after 40 years in the job. Work has always been plentiful and it’s good to see great-quality vehicles being built to the highest standard.