ELEVATING EXCELLENCE
WITH EVEN BETTER MANAGEMENT
Discover how the CowScout™ monitoring system became a top investment for Kayharts.

AUTOMATED BATCH-STYLE MILKING
HIGH-TECH MILK MONITORING
MYTHBUSTING TEAT DIPS
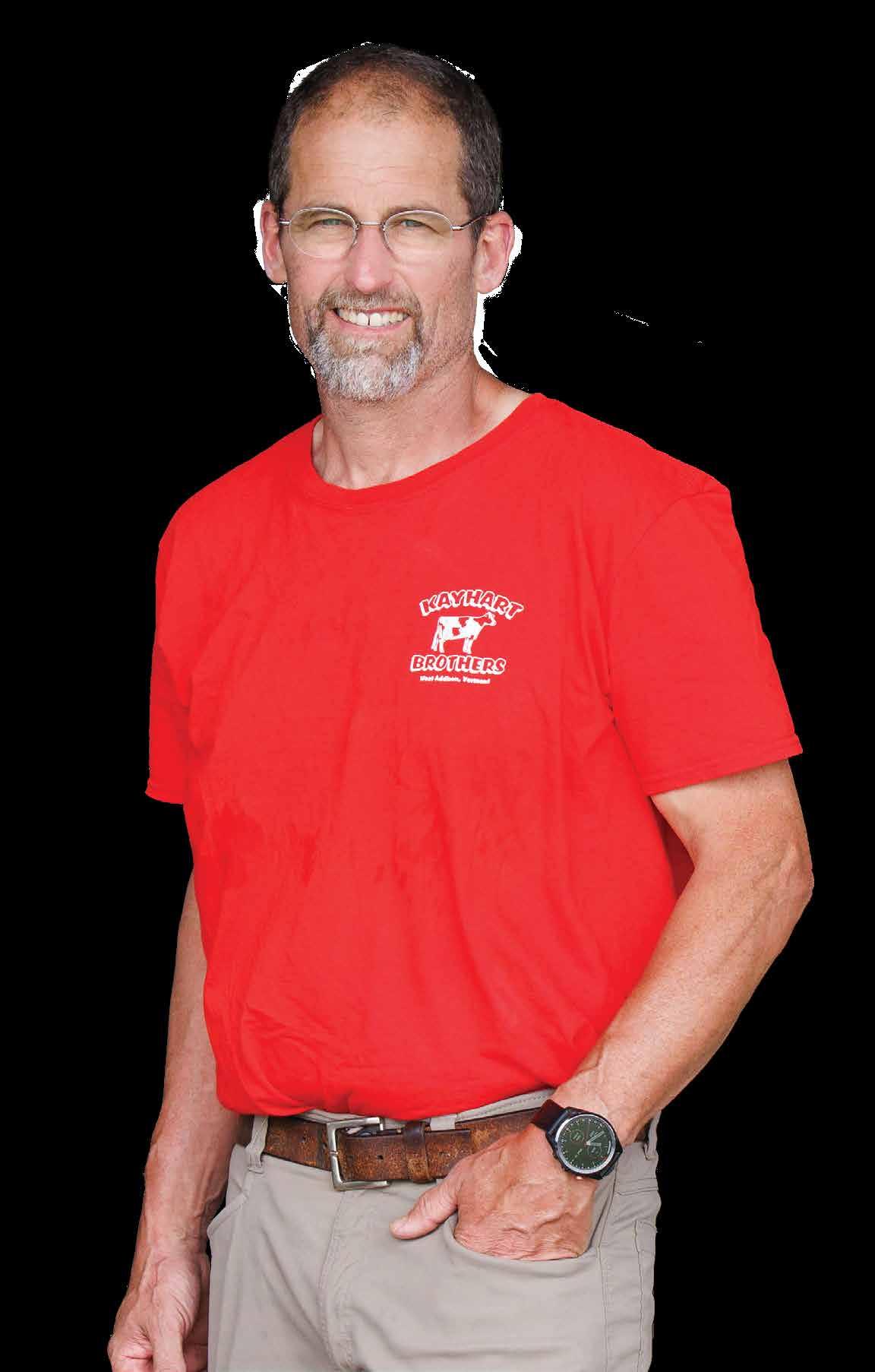
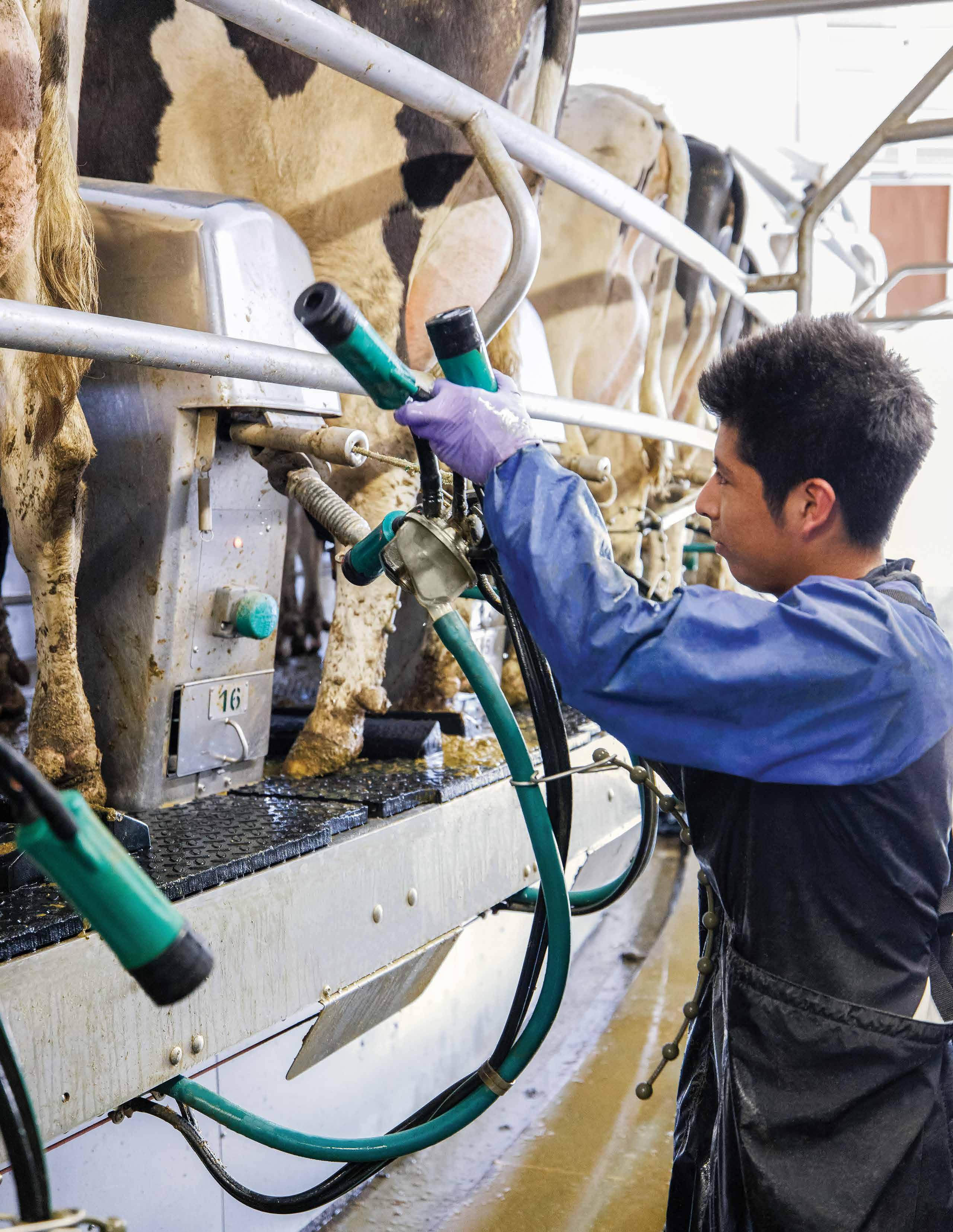
Discover how the CowScout™ monitoring system became a top investment for Kayharts.
AUTOMATED BATCH-STYLE MILKING
HIGH-TECH MILK MONITORING
MYTHBUSTING TEAT DIPS
GEA understands that the farm of the future is efficient in labor and management, strengthened by technology and sustained by cow comfort. Our team brings solutions for attaining the greatest operational efficiencies, consistent milk quality and enhancements to herd performance.
Our producer-proven technologies and continual advancements in automation help you achieve success. By collaborating with you and your staff, we can help your dairy perform at its best, so your cows can perform at their best.
Dairy Illustrated was a premier dairy publication in the 1970s and 1980s, with the second highest circulation among dairy magazines in the U.S.
If your family was dairying during this time, chances are they received a copy in their mailbox. GEA is excited to bring this publication back and carry on the tradition of sharing customer stories, management tips and new technology with today’s dairy farmers.
it up a notch at Kayhart Brothers Dairy
brings nextgeneration home
Why the CowScout™ monitoring system is one of the top investments they’ve made.
Kayhart Brothers Dairy, established in 1979, is a thriving dairy business run by brothers Steve and Tim Kayhart.
Originally started by their parents, the farm has grown significantly over the decades. In 2010, Steve and Tim took over the operation, continuing the family legacy with a focus on innovation and sustainability. Steve manages the cattle and bookkeeping, while Tim oversees cropping and machinery.
The farm features a new dairy facility that started up in 2017 and is now milking 750 cows. The introduction of the GEA CowScout™ monitoring system has revolutionized their operation, enhancing reproductive and health monitoring, improving labor efficiency and contributing to the farm’s economic success.
“Hands down, CowScout is one of the better investments we’ve made over the last couple of years,” says Steve. “It has been an excellent tool for improving the labor efficiency on our dairy and the health and reproduction of our cattle.”
The CowScout system has streamlined their daily tasks and provided valuable insights into herd health, ensuring quicker interventions and better outcomes.
Hands down, CowScout is one of the better investments we’ve made over the last couple of years.
Can you give an overview of your facilities?
Today, we operate two milking parlors — a double-10 herringbone from the 1970s and a new double-16 GEA parallel parlor we built in 2017, expandable to a double-24. Next year, we plan to build another barn and move all animals to our newer facilities.
What drew you to animal monitoring systems?
Labor challenges in recent years led us to monitoring systems to help supplement labor and better allocate resources.
Why did you choose GEA CowScout?
After evaluating various systems, we chose the GEA CowScout system, powered by Nedap, for its reliable information and local dealer support. Our local dealer has been a great partner for many years.
How has the system changed your chore routines?
Checking the attention-list cows is part of our daily tasks every morning. It may be nothing more than visually putting our eyes on a cow, but it’s a new job we have. I’m happy to allocate resources to it because it’s paid itself back many times.
Also, we used to tail-chalk cows. Locking them up at least once daily to refresh their paint was common. That no longer happens. Now, we utilize the CowScout information to determine who to breed and when.
How has your reproduction management evolved?
We use CowScout on the lactating herd and youngstock, totaling over 1,300 collars. Our goal is to put a collar on breeding-age heifers a month before we want to breed them so we can start seeing their natural heats. Once a heifer is 60 days pregnant, we use her collar for another animal.
We still use timed AI, but have altered our protocol when diagnosing pregnancy. Our hormone use has decreased since the system was put in place.
Did it impact your reproduction performance?
Our reproduction performance, which was good before, has improved. Since we installed the system, our pregnancy rate has increased about five percentage points year over year.
Has it changed other management practices?
Before CowScout, we locked up fresh cows daily, walked the pen, reviewed milk weights, and looked for health problems. Today, we do none of that. We stay out of the fresh cow pens and let the system tell us when a cow doesn’t feel well. The system has also helped us find cows with mastitis or lameness.
Watch this video to hear Kayhart’s story
What surprised you about the system?
Initially, we bought the system for its reproduction benefits but quickly found that the health information was just as important — if not more. I can count numerous examples of when we’ve been alerted to an animal needing attention, and almost always, there was a reason to intervene. By intervening quicker, the outcome is better.
What’s the most impressive feature?
The alerts tell us if a cow is not eating or ruminating like normal. We deal with some diseases, such as systemic mastitis, that make cows very sick. The alerts help us channel our energy into fixing the right cows and doing the right things to help them at the right time.
How does CowScout animal monitoring help you when you’re away from the farm?
With the mobile app, I can check what’s going on from a hotel room in Chicago or my in-laws’ house in Maryland. Having that information wherever we are also motivates our staff to do a better job
Initially, we bought the system for its reproduction benefits but quickly found that the health information was just as important — if not more.
What impact has it had on your bottom line?
Today, we have more pregnant cows in our herd on a percentage basis, and our herd has grown more naturally. We have fewer “do not breed” cows because we failed to get them pregnant. Those things all trickle down to driving the economic success of our business.
How did the system make you an even better manager?
It’s helped elevate our game. I’m a perfectionist, and it gives us information that we can use to identify lost opportunities and try to find the cows that were invariably slipping through the cracks. It’s an opportunity to make a difference.
Some monitoring systems are standalone systems. Others are all-in-one solutions that integrate with animal identification components — such as a parlor, milking robot, sort gate or cow location. In one tag, CowScout offers the best in behavior monitoring and can be used as the ID tag, simplifying management.
Find out:
• Can the system integrate with your existing identification components?
• What capabilities does it have for the future?
Most monitoring systems claim a battery life of five to eight years. Tags that use the battery for parlor ID (three times a day on most farms) and animal monitoring in the barn will drain the battery faster, impacting longevity. CowScout utilizes a passive ID system for parlor ID, which helps preserve battery life. It’s why CowScout has the best tag life on the market and a <1% failure rate on farms worldwide. Plus, with passive ID, even if the tag’s battery fails, the cow will still be identified in the parlor as usual.
Does the system require battery life for parlor ID?
What is the average tag life?
Why it matters: Animal monitors are an investment. You want them to last throughout the lifetime of the cow to minimize changing tags, missing data or issues with parlor activities.
Most monitoring systems interface with herd management software, such as DairyComp and PCDART, but capabilities vary. CowScout can integrate with these popular herd management programs. Many farmers set up automated tasks with their software to make breeding and health chores easier.
How do the animal monitors interface with the herd management software preferred on your farm?
What is the partnership between the herd management software and animal monitoring solution companies?
Can you automate tasks on individual cow behavior? Or, is it solely an interface that displays inputs?
Why it matters: These capabilities increase ROI by ensuring the right cows get attention. Automating the process also reduces dependence on skilled labor.
CowScout™ has the best tag life on the market and a <1% failure rate on farms worldwide.
If the internet is a challenge on your farm, find out if it’s required to access the monitoring system. CowScout only requires internet access if you want to use CowScout mobile or GEA’s multi-site platform (CowScout Cloud). Other systems are solely cloud-based, which can impact your user experience if you have a poor internet connection.
Find out:
• Does the system require internet for certain features?
• How can your breeding technician and other consultants access the system?
Why it matters: Spotty internet or outages can hold up your daily tasks. Be sure your system can function reliably when you need it.
Only some monitoring system companies have a local technical support team or a 24/7 hotline you can call. CowScout has a North American-based staff of specialists that proudly carry the name “Herd Nerds.” They help farms transition to animal monitoring and can help optimize herd management protocols over time to get the most out of your system.
Find out:
• Where is the technical support team based?
• How can they be accessed?
• What hours are they available?
Why it matters: If you have trouble with your system, you need locally based experts to call for immediate support.
Robotic milking system and new monitoring tools maintain family interest in farm business.
In the heart of Vermont, B & T Black Creek Farm is taking their dairy into the future, thanks to the adoption of robotic milking technology. Liam Howrigan didn’t picture himself coming back to the farm, but the incorporation of technology fueled his passion for managing cows.
The Howrigans installed six GEA DairyRobot R9500 robotic milking systems into their existing six-row freestall barn. The robots feature M6850 SCC sensors for fast, effective mastitis detection. They also incorporated the CowScout™ animal monitoring system and sort gates to streamline daily tasks, improve animal welfare and boost overall efficiency.
“The technology behind the robots is impressive. The system can detect health issues like mastitis more accurately and a lot easier than our parlor,” says Liam.
A critical component of this technology is the DairyNet app, which enables remote monitoring and management of the herd.
The app offers a comprehensive overview of cow health, milk yield, and other essential metrics, making management more efficient and less labor-intensive.
“Even when I’m down the road at home, I can go into the app and check out how the cows are doing and almost manage it from home,” Liam shares.
We’ve had several cows hit over 200 pounds a day and that’s been remarkable to see.
Kerri, Liam’s mom, has enjoyed incorporating more technology on the farm and watching her family and cows thrive.
“Liam didn’t grow up working on the farm, so he wasn’t a veteran at caring for cows. Even my husband, Matthew, wasn’t always the cowman or herdsman — his focus has always been on feeding,” says Kerri. “But I believe the technology between the CowScout collars and the R9500 robot has allowed Matthew and Liam to take care of the cows better than ever before — maybe even better than someone who’s been a herdsman for 20 years.”
Howrigans downsized their herd to accommodate the robots, but have made up for it in production gains.
“We’ve had several cows hit over 200 pounds a day and that’s been remarkable to see,” she says.
The Howrigan family’s adoption of robotic milking technology illustrates the profound impact innovation can have on a dairy. By integrating technology into existing facilities, they improved efficiency, enhanced animal welfare and paved the way for the next generation to create a sustainable future.
The DairyMilk M6850 SCC sensor is an option for GEA robotic milking systems.
The industry’s first SCC monitor that continuously analyzes milk flow from each individual quarter throughout the entire milking process.
REAL-TIME ANALYSIS
Watch this video to hear Howrigan’s story
INDIVIDUAL QUARTER ANALYSIS
HIGHLY RELIABLE DATA NO CHEMICAL REAGENTS
Gain all the benefits of milking robots with minimal management changes.
Finding reliable, well-trained labor to milk cows is becoming increasingly difficult. With new or inexperienced staff doing the milking, there’s also a greater need for operator safety and simplicity.
GEA’s DairyRobot R9600 automated batch milking system offers a new way for farms to address labor concerns while improving cow comfort and herd management.
Automated batch-style milking combines the labor savings and technology benefits of a robot with the management style of a parlor. With automated batch-style milking, cows are milked in groups at fixed milking times using a row of box robots, simulating a conventional parlor setup.
This milking style gives dairy farmers another option to milk their cows with more data and consistency. It also gives dairies the flexibility to upgrade their milking facilities while using existing barns, holding pens and sorting areas.
Here’s more benefits you can realize with batch-style robotic milking:
Automated batch-style milking significantly reduces the need for several well-trained people to perform cow prep procedures and handle milking tasks during every milking shift.
Unlike a parlor, this system does not require anyone to be present in the milking area, reducing labor costs and the challenge of finding reliable workers. Employees can thrive with streamlined, flexible job tasks, while the robots handle the standardized processes.
When accessing the cow is required to complete tasks like mastitis treatment or dry-off, GEA’s box robot allows for easy rear access to the udder to safely treat cows, much like a parallel parlor.
maintenance and milk flow
With automated batch-style milking, the boxes and milkhouse are in closer proximity compared to some traditional box-robot farms. This centralized system reduces milking and chore interruptions and makes maintenance easier.
If a robot requires service during milking, GEA’s “plug-and-play” service module makes it easy to swap out the system’s mechanics with a spare module, allowing the boxes to continue milking.
efficient cow flow
Automated batch-style milking can save time handling cows, minimize disruption and make it easier to complete tasks. Cow flow and management resemble conventional parlor milking systems.
There are no cows to fetch since you’re bringing the cows up to the boxes to be milked. With all cows exiting the boxes at a fixed milking time, it’s easy to sort out cows that need attention instead of looking at a fetch list and finding them hours later.
Other tasks, such as running a foot bath and hoof trimming, can be completed just like they are with a traditional parlor.
Another advantage of automated batch-style milking is the opportunity to address individual cow nutrition.
You can top-dress the bunk ration by feeding more energy and protein in the robot. This helps you push individual cows while controlling costs at the bunk.
Automated batch-style milking is also a great way to bring more consistency and efficiency to the milking process.
GEA’s In-Liner-Everything™ technology performs every step of the milking process in a single attachment — all within the teat cup.
This streamlined process maximizes the milk letdown effect from the cow for faster milking times, which leads to better box times and more cows milked per hour.
Automated batch-style milking can deliver an efficient, stressfree process for your employees and cows — and you can keep many of your barn management practices the same.
New GEA DigiFlow flow-through milk meter delivers precise monitoring for optimal milking control.
Today’s dairy cows produce more milk than ever before. To support increased production, higher capacity and more precise monitoring are essential during milking.
The new GEA DigiFlow milk meter is part of GEA’s smart digital milking control package designed to take your parlor into the future.
GEA DigiFlow optimizes the milking process for every cow, boosting overall efficiency. What makes this new meter better?
• No milk flow bottlenecks — fill and dump measuring is gone. Milk flows continuously through large inlets and outlets without any slowdowns.
• Precise real-time milk measurement — engineered to measure milk accurately, even during the highest and lowest periods of flow throughout milking.
• Stable vacuum levels — provides the right balance between air and milk volumes, nearly eliminating vacuum fluctuations for the gentlest milking.
• Accurate detaching — more precise unit detach from cow to cow thanks to better measurement capabilities throughout the milking process.
• Conductivity and temperature monitoring — during the milking and wash processes for even more cow and parlor insights.
With GEA DigiFlow, farms can achieve greater efficiency, smarter animal health management and enhanced milk quality.
The step-by-step process at GEA’s Wisconsin manufacturing plant.
A growing number of dairies are using rotary milking parlors to enhance milking speed and efficiency. They allow farms to milk more cows per hour using less labor.
In 2023, GEA moved the manufacturing of rotary parlor platforms destined for the North American market to its milking equipment plant in Wisconsin. Here are the key steps to manufacturing a GEA rotary parlor:
1. All new products or new features to an existing product start as an idea. A team of engineers comes together to discuss options and identify the products or upgrades that will be most suitable for the market. Potential projects are further evaluated on the business side and then tested and proven in the laboratory setting. Innovative projects go through the patenting processes.
2. Next, engineers work closely with the manufacturing team to move the product into full production. In the case of rotary parlors, many pieces are custom-made for the farm upon order, based on the parlor’s size and desired features.
3. The foundation of the rotary parlor starts with industrial beams. Straight I-beams are bent using a roller system to achieve the proper radius of the parlor, which depends on the size of the rotary. If the radius is off, the parlor won’t fit together when assembled on farm.
4. Heavy-duty nylon rollers (shown already installed) help the rotary turn on the beams. These rollers have a special profile in the frame for minimum wear and safe alignment.
5. Pieces for the parlor platform are cut out of sheets of stainless steel with an automated laser machine and holes are cut for wires and other parlor mechanics. These sheets go through a bending machine to form the shape of the plates that will be the primary structure of the deck the cows will ride on. The deck is later covered in concrete on the farm. Stall dividers are also made and assembled in the plant.
6. The center swivel of the rotary parlor is a critical component. It must go back and forth between the machining and assembling processes to ensure that the many individual pieces come together in an extremely precise way.
The Galesville, Wisconsin plant began making SURGE milking equipment more than 50 years ago. Today, it produces some of the world’s most advanced parlor technology. More than 100 dedicated employees work at this facility with an average tenure of 15 years. These specialized tradesmen and milking system engineers, many of whom have farming backgrounds, take great pride in delivering the highestquality milking equipment to today’s dairy producers.
7. The pipeline is made from straight pieces of stainless steel that are cut and sent through a roller, which slowly forms the correct curve to match the parlor’s radius. It might take two to three passes through the roller to accomplish this. Holes are drilled where the milking hose for each stall will be connected, and the nipples are welded into place. It can take approximately 20 pipeline sections to form a complete circle in a 120-stall rotary parlor.
8. The pipeline surrounding the deck connects to receiver jars. Special welding and grinding skills are required to combine three separate pieces of stainless steel into a jar that meets sanitation requirements. The jars are sanded completely smooth because they are for food-grade use. Outlets and nipples are added when the jar is complete.
9. Once all pieces of the parlor are finished, they are boxed and labeled with a color-coded system for easy assembly. The final product is complete when all the system components are installed on the farm to create the rotary.
GEA is proud to be the only milking equipment manufacturer making rotary milking structures in the U.S.A. We’re able to respond faster to our customers’ growing demands.
I really like the arms — they have a more natural movement to attach.
And there are no buttons to push — which doesn’t seem like a lot until you start doing it eight to 10 times a minute for an hour at a time. The ergonomics make it almost effortless for the milkers to milk.”
AJ Leonard Double P Dairy Wisconsin
I really love the rotary parlor.
I think cows are calmer. When you’re standing in the center of the deck and see 110 cows looking at you chewing their cud happy as can be, that’s a really good feeling.”
Reese Burnett Burnett Dairy Wyoming
GEA has spent decades building the best rotaries on the market. The latest model can be seen at a farm near you!
What excites me most about the rotary is the calmness of the cows. They load magnificently on and off the platform and we’re getting wicked milk letdowns. Our cows are happy and so is our team.”
Vincent Bilow Bilow Farms LLC New York
Cow flow and cow comfort in the rotary is awesome.
Cows are milked 3 times a day at a rate of 550 cows per hour, with a cow getting on the platform every 5.3 seconds.”
Steve Abel Abel Dairy Farms Wisconsin
number of stalls:
CatteEye detects and predicts lameness in cows quickly using an artificial intelligence system. It also provides critical data to assess body condition scores (BCS), which helps analyze cow health after calving, determine ration adjustments and monitor the cow’s general physical condition.
This information allows you to take immediate action to improve the welfare or productivity of your herd. The data can be accessed anytime via a dedicated app on your smartphone. CattleEye can be integrated into new or existing farms, regardless of the type or brand of milking system.
The GEA DCPro dairy control will be your new best friend in the parlor. Have complete CIP wash control of your milking and cooling systems, temperature recordings, tank fill levels and accompanying alarms. The integrated cloud-based analytics are designed to give you peace of mind when preserving your high-quality milk. Top features include:
• Summary for all wash stages — with peak and drain conductivity and temperatures
• Full tank silo wash, agitate and cooling control (up to four vessels)
• Manual or automatic loadout controls
• Milk vat control (milk pump controlled off level or flow)
3.
4.
5.
The new GEA XT Suspension system for GEA liquid manure tankers delivers uniform weight distribution, superior traction and stability even in the roughest terrain. Wider axles, three independent hydraulic circuits and extended drawbar travel all improve drivability. It’s the latest in smart engineering and design for optimal manure transportation and spreading.
6. See it in action!
You can have it all with Kommand™ Lux, a non-iodine low-drip barrier teat dip. Its ready-to-use formula forms a viscous barrier on teats to protect against mastitis-causing pathogens between milkings.
It contains GEA’s exclusive LactiFusion™ technology, bonding dodecyl benzene sulfonic acid (DDBSA) and lactic acid for dynamic killing power. It stacks up against the best 1% iodine teat dips at an incredibly economical price to meet the cost pressures dairy farms face today.
The new GEA Super Pump for a trailer or 3-point hitch was designed for convenience and efficiency. This pump has remote controls, centralized hydraulics, gate valves around the unit and an inline cooling pump — with no belt. The PTO stays connected to the trailer and it can reach a 4-foot pit depth. Other features include:
• Reinforced pump head
• Twin short agitation nozzle (fits opening size 36’’ x 42’’)
• Stainless steel ball joint nozzle
• New oil cooling reservoir bolted on the housing
It is becoming increasingly important for parlor operators to quickly recognize key information and operate controls intuitively. The new DigiTron milking parlor control prioritizes operator comfort with ergonomic positioning and easy-to-use buttons that can be customized for your farm.
The LED lights provide clear, color-coded messages that are easily visible from a distance at any angle in the parlor. DigiTron seamlessly integrates with GEA’s DairyNet management software, streamlining diagnostics and system updates.
Know what to look for when selecting a teat dip to get the best results.
Not all teat dips are created equally. The right dip can help ensure you harvest high-quality milk and minimize mastitis incidence with proper practices. Knowing what to look for can help you find an effective teat dip for your farm’s most common mastitis-causing pathogens.
If you haven’t reviewed your teat dip program in a while, now is a great time to do so. Many new developments in teat dip technology give you more choices that meet today’s market needs.
As you evaluate, here are four common myths to watch out for:
Myth 1: Iodine is the gold standard teat dip germicide.
Times have changed and prices have adjusted. Iodine costs have increased by more than 80% in the last few years. Glycerin costs have risen fourfold and propylene glycol threefold. Because of this, new formulas using different germicides have been developed to bring more economical choices to the market.
When testing the killing power of these new germicide options against iodine, many have proved to be as effective or more against the most common mastitis-causing pathogens.
A farmer in Pennsylvania, using shavings and robots on their 340-cow dairy, switched three of their five robots from an iodine-based teat dip to a non-iodine dual germicide. Even after a 50-degree temperature drop and an inch of rain, there were no new mastitis cases and teat condition was unchanged. They have since switched entirely to this non-iodine choice, aiding in farm profitability.
Just because a teat dip contains a germicide known to be effective doesn’t mean the teat dip is effective. The parts per million (ppm) of germicide does not solely determine efficacy. Surfactants, secondary germicides, skin conditioners and other ingredients all play a part in the performance.
Efficacy testing, teat scoring, field testing and performance on-farm are all ways to measure a teat dip’s effectiveness. Always ask for the testing results of your farm’s teat dip selection and be sure the results are specific to your dip (or the one you are considering), not a generic study based on a similar formula.
When deciding which teat dip is best for your farm, consider the mastitis-causing organisms challenging your herd and the level of skin conditioning you need based on the environment. Matching your farm’s needs to the right teat dip will help prevent mastitis, save money, maintain a low somatic cell count (SCC) and yield more quality premiums.
Your local GEA hygiene and milk quality specialist can help prescribe a teat dip for your farm. The following questions can guide your discussion:
• What are your recent bulk tank culture results?
• Do you track your clinical mastitis? If so, have you cultured your clinical cases?
• What type of bedding do you use? Have you ever cultured it?
• Have you cultured your udder towels?
• How often do you groom and bed your stalls or lots?
When your hygiene specialist shares their teat dip recommendations, ask if they have efficacy data. Also, ask if other farmers can share their experience using the dip they recommend.
If you experience an increase in clinical mastitis or SCC, it can be tempting to change your teat dip as a quick fix. However, you should first consider other factors like environmental and herd changes, and then adjust your teat dip program accordingly. For example, you will likely face more environmental challenges during prolonged rainfall. You may need to adjust your bedding program and switch to a barrier teat dip to keep your milk quality in check.
When you make a teat dip change, plan for at least three to four weeks to start seeing a difference — if all other variables stay constant. Remember, teat dip helps prevent mastitis, not cure it.
The right teat dip can help you achieve your milk quality goals. Look for an efficacious teat dip backed by research and real results.
Save labor, fuel and wear and tear on your equipment.
How does your dairy push feed and manure? Do you rely on a skid loader and an employee?
Shifting these responsibilities to automation frees up your labor pool and reduces demand on your everyday farm equipment. It also helps you realize benefits, like higher dry matter intake (DMI) and milk production, as well as greater cow comfort and cleanliness.
Calculating your return on investment (ROI) is integral to your decision-making. Use your farm’s specific labor and financial data for the most accurate information. Consider how much time you spend scraping manure or pushing feed per day. Then, consider how much you pay employees.
For example, scraping manure takes 30 minutes each morning and 30 minutes each night. Your employee is paid $15 an hour. Then, you factor in $20 per hour for skid loader fuel consumption plus wear and tear. In this scenario, your labor, fuel and wear and tear costs would be about $13,000 annually.
If you are scraping one hour daily, you can typically install a manure scraper (on one side of an average-size freestall barn) for about $25,000 to $30,000. At that rate, the manure scraper pays for itself quickly in two years.*
Installing a feed pusher in the same barn can cost approximately $30,000. Depending on how frequently you program it to push feed and the dynamics of your previous feed management program, you could realize a payback in about two to three years.*
there are several other factors to consider when looking to purchase a new piece of technology for your barn:
• Ease of installation. What does the installation process look like? How easy is it to install in existing facilities?
• Service and maintenance. What are the service needs? How often does maintenance need to be performed? Can you train a team member to do it? When will you need to rely on your dealer?
• Programming. How does the programming work? Does it run via a mobile app? How can you control the system if the app goes down? How many routes can the system be programmed to run in a day?
Automated feed pushers keep feed in front of cows, typically increasing DMI and improving milk production.
Gramer Farms LLC, in Michigan milks 250 cows and previously spent two and a half hours per day pushing feed. With the GEA RoboRebel automated feed pusher, they were able to save this time and focus on other tasks while increasing milk production by 2 to 3 pounds per cow. They also maintained production in the hot summer months they had typically lost.
Not every feed pusher works the same. Do your homework and visit farms that already have them installed to see what they like and don’t like. Feed pushers that follow a magnetic strip maintain a stronger connection to the robot and are more likely to stay on track. Feed pushers that run on a pin system can get offtrack more easily. Be sure there will be no RFID interference before installation to keep the pusher running smoothly.
Also, consider how the pusher moves the feed. Some robots only move the feed pile closer to the bunk, following a straight path, which can deliver different results depending on the time of day and how much feed is present. Others, like the GEA RoboRebel, can adjust for the remaining feed volume by moving closer or further from the bunk during its route to push the feed more optimally for easy cow access.
Automated alley scrapers continuously scrape manure from the barn’s main walkways, keeping cows cleaner and preventing manure from splashing onto their udder. They also don’t disturb cows while eating, drinking or resting.
You can install manure scrapers on almost any size of operation, including heifer facilities.
Alley scrapers are generally low maintenance but require some upkeep. Greasing corner wheels every week, checking cables and taking the time to thoroughly review the system each month are recommended.
There are many options of alley scrapers available to fit different farm situations. GEA specialists will evaluate your barn, take measurements and provide an ideal solution.
Keeping feed in front of cows and the manure behind them to a minimum helps ensure they can focus on comfortable resting and eating to produce high-quality milk.
*Scenarios demonstrate common ROI figures for standard installations. Figures may vary depending on farm needs and specifications. Cost estimates are as of May 2024.
In 2004, GEA (then known as WestfaliaSurge) began sponsoring the World Dairy Expo ice cream stand to help raise money for local FFA programs. That year, they served over 17,000 cups of delicious, locally sourced ice cream straight from a bulk tank, creating a lasting impression on expo-goers.
Fast forward 20 years, and the tradition is stronger than ever! You can’t visit World Dairy Expo without a stop for ice cream. Hundreds of FFA members continue volunteering to scoop ice cream, which has contributed to more than $212,000 raised in support of their chapters and educational programs.
Thanks to the GEA manufacturing team at the Wisconsin plant, a real 3,000-gallon bulk tank was modified to include a serving counter just weeks before the first ice
We are excited to celebrate the 100th anniversary of the landmark launch of the SURGE bucket milker. In 1922, many companies dismissed Herbert McCornack’s milking invention as impractical — but the Babson brothers saw its potential. After two years of meticulous refinement, they introduced it as the SURGE bucket milker in 1924, revolutionizing the industry as the first effective, hygienic milking machine. In its prime, the SURGE bucket milker had a 76% market share and set a milking standard for decades.
At GEA, we’ve been dedicated to supporting your farm’s legacy for over a century. From our Herd Nerds™, who thrive on herd management data, to our network of over 100 North American dealers, we’re committed to helping your farm prosper.
Whether you’re optimizing current equipment, exploring new technologies, or planning to expand your operation, you can rely on our team for unwavering support.