Kuldīga is a small town in Latvia - a historical city, where great attention is paid to the study, preservation and revival of cultural and historical heritage. The Old Town of Kuldīga is included in the UNESCO World Heritage List in 2023. Its historic urban structure includes traditional local wooden architectural structures, as well as mainly foreign-influenced brick masonry and timber-frame house techniques and styles, which illustrate the ability of local craftsmen to integrate foreign influences from other Hanseatic cities and centers around the Baltic Sea, its east and west. Craftsmanship skills are noticeable in the functional and decorative details of buildings throughout the city, and craftsmen continue to make them today. The predominance of clay tiles as a roofing material contributes to the harmonious landscape of the city of Kuldīga.
We offer to explore the restoration processes of a significant wooden building –an architectural monument: the Old Town Hall, in relation to the building's heat loss prevention measures. In Kuldīga, a large number of buildings are wooden, and they need to be adapted to modern living requirements while preserving their character. Improving the energy efficiency of these buildings was a major challenge for the designers – finding and planning energy efficiency measures for a historic wooden building where seemingly nothing can be done. The surrounding preserved values include the wooden log walls to be maintained outdoors and the historic plaster and paintings on them indoors. Preserved values also include the building’s structure, framework, ceilings, wooden joinery details, individual interior elements, and details. Solutions were found by studying the existing situation and using traditional materials – historically used in the construction of the building – in the restoration, combining them with compatible modern materials. The achieved goal was to create comfortable and cozy living conditions for people in a historic building, preserving its values and reducing financial costs.
1. For reference - building data:
1.1. Public building - a building for the preservation of traditions and a tourist information center.
1.2. Year of construction 17th century, 18th century, 1806.
1.3. Suffered several fires and was renovated in the mid-19th century, partially rebuilt in the 1970s.
1.4. Granite and dolomite stone foundations, walls - wooden logs, Flooring - wood with clay filling, roofing - clay tiles, wooden joinery - doors, windows, details.
1.5. Several architects have been involved in the reconstruction of the building.
1.6. The building uses a basement, a ground floor and a built-up roof floor.
1.7. Heating type - central heating from city heating networks, installed in 1973, renovated and partially rebuilt in 2015. Heating elements - cast iron radiators have not been changed
1.8. A complex renovation project, which was implemented in 2015 by a team – a public customer, a design office and a construction company. Insulation, renovation project.
2. A brief description of the city and a description of the location of the building. Its importance in the overall development of the city.
The historical wooden sleeper building is located in the historical center of the city of Kuldīga (a cultural – urban – building – monument of national importance) and in the very heart of the city of Kuldīga, on the banks of the picturesque Alekšupīte (Fig. 1). In the 17th century, the new Town Hall Square became the central place of city life, it has retained its importance even today, because the current town hall is also located on its southern edge.

Fig. 1. The location of the historical building in the central part of the old town of Kuldīga, in the present-day market square 1
The building has acquired its current appearance as a result of several reconstructions. The building was originally built in the 17th century, and later rebuilt several times. The building stands on a high brick plinth and vaulted cellars have been built under the building, which housed the Kuldīga prison for some time. The building is characterized by a massive gable roof with partially
1 Gustovskis A., 2017. photo fixation, available in the digital archive of the Kuldīga municipality
sloping ends. The appearance of the classically symmetrical facades from the early 19th century has been preserved izskats 2 .
The building is very important to the townspeople, who actively participated in discussions about the renovation of the building and specifically asked the municipality to leave the wooden walls of the building unplastered (they had been plastered in the 1930s) and black tarred, which they believe is one of the symbols of the city.
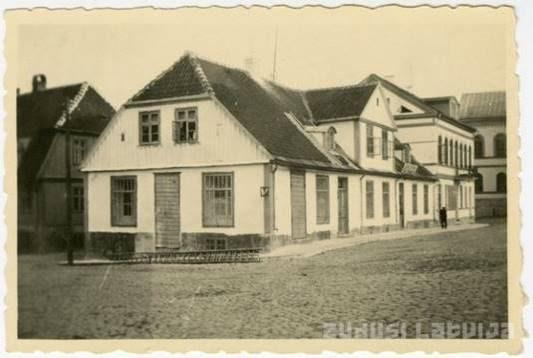
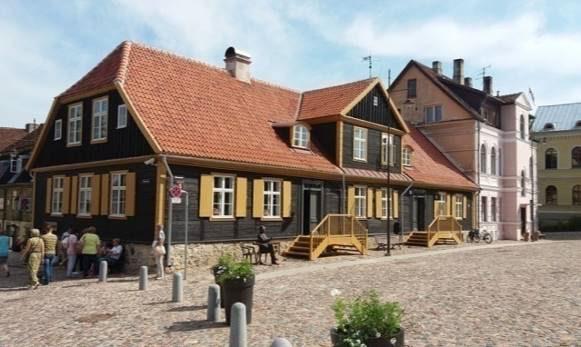
Fig. 2. and 3. Building from the beginning of the 20th century – with plaster on the walls sienām 3 of a wooden log house and the building after renovation –2016.
3. Cultural and historical significance of the building, description, cultural and historical values to be preserved. Protection status.
The building needed to be renovated because it was in poor technical condition. After the restoration work, it became a model of how it is possible to restore ancient wooden buildings in the Old Town area. The building is an important example of wooden architecture, which is preserved and protected as a cultural and architectural monument of national importance. The building is for public use, therefore, in order for visitors to be able to get acquainted with the traditional tradition of building wooden buildings of the early 19th century, the historical layout of the rooms and the amphilade on both floors of the building, as well as one of the two historical chimney stacks, have been restored, and the building structures, building parts and wall paintings characteristic of the era have been exposed. The original and historical structures and building parts have been preserved to the extent possible. The building was partially rebuilt in the 1970s with the understanding of the restoration of a cultural monument at that time. The last reconstruction and renovation works of the town hall were carried
2 Krastiņš J., Eniņa A., Kuldīga. Architecture and urban development. Kuldīga architecture: public buildings. Kuldīga: Kuldīga municipality. 2014. Pages 380, 381.
3 Veinberga K., Zviedrāns J., Architectural and artistic research of building. Kuldīga. 2014. Page 10.
These are the "Building Energy Efficiency Law" (in force from 2009-2013) and the Latvian construction standard "Heating technology of building envelopes" (in force in 2003). The aim of these regulations is to promote the rational use of energy resources and improve the energy efficiency of buildings. The requirements of these regulations apply to existing buildings and new buildings, but the requirements of this law do not apply to buildings that are "..cultural monuments or in which cultural monuments are located, as well as to buildings located in cultural monument territories, if the implementation of the requirements of the law threatens the preservation of these cultural monuments or reduces their cultural and historical value" 6 . In addition, “In the restoration of an architectural monument, the State Inspectorate for the Protection of Cultural Monuments may allow deviations from the requirements of this building code if the fulfillment of the relevant requirements threatens the preservation of the cultural monument or reduces its cultural and historical value.” 7 When assessing the environmental impact of historic buildings, it is recommended to evaluate existing materials, cultural, historical, social and ecological value in calculation models, not just energy value, says Kuldīga Municipality architect Dzintars Heinsbergs, who actively participated in the renovation of this building.
Each historic city also has its own local regulations – building regulations, which determine the requirements for the renovation of buildings. The Kuldīga municipality building regulations state that a historic building is "buildings built before 1940... and they are not allowed to be insulated from the outside." 8
In turn, the recommendations published by the State Inspectorate for the Protection of Cultural Monuments of the Energy Efficiency of Historic Buildings state that: "...Increasing attention is being paid throughout Europe to energy efficiency in construction, which also affects historic buildings. Approximately 3% of the total building volume is considered to be buildings of cultural and historical significance, to which cultural heritage preservation regulations apply. One of the methods of reducing the energy consumption required for the use of buildings is building insulation. The incorporation of new and effective thermal insulation materials into the enclosing structures of buildings (external walls and upper floor coverings) is associated with the physical modification of these structures. Since thermal insulation must be one of the external layers of the enclosing structures, insulation inevitably affects the architectural decoration of building facades. For many historic buildings, this is a value that must be preserved. Only in very rare cases is the insulation of facades of buildings of
6 Energy Efficiency of Buildings Law (2009-2013). Available online: https://likumi.lv/doc.php?id=253635
7 Thermal Engineering of Building Enclosure Structures. Available online: https://likumi.lv/ta/id/275015-noteikumi-par-latvijas-buvnormativu-lbn-002-15-ekunorobezojoso-konstrukciju-siltumtehnika-
8 Kuldīga Municipality Spatial Planning. Territory Use and Building Regulations 2013. Available online: http://www.kuldiga.lv/userfiles/files/Kuldigas_Novada_TIAN_2012_6_1_red.pdf
cultural and historical and architectural value permissible, because the value of a historic building is not only the shape and color of its external surface, but also the substance, constructive solution, original decor and historical patina. If it is not possible to insulate the walls of the building and change the wooden joinery products – windows and doors – in a historical building, then it is recommended to take all other possible energy efficiency measures without insulating the external walls and replacing windows and doors." 9
6. Building heat loss prevention strategy.
This building was converted from a historic building that had no energy efficiency measures in place to a historic building with increased energy efficiency. The building walls are not insulated from the outside and from the inside, as the building is a publicly accessible cultural monument and its walls are valued as a medium of information that tells the story of materials, traditions, crafts and styles from different periods.
The goals set for improving energy efficiency in this building are:
1. To maintain the existing air and moisture permeability of the building's enclosure structure materials by using appropriate traditional materials –historically used in building construction and ecological – renewable materials with minimal chemical additives.
2. To ensure maximum prevention of gaps in the enclosure structures with traditional/ecological sealing materials.
3. To insulate the building's enclosure structures in a way that does not affect the visual appearance of the building and its preserved values, using ecological materials.
The systems and enclosure structures were inspected, and it was concluded that they are not prone to freezing, and the following action plan was adopted:
1. Arrange and ensure the regulation of the gravity ventilation system,
2. Restore and seal the windows while maintaining aeration, with reflective glazing,
3. Manufacture and seal new exterior doors,
4. Seal and insulate the attic floor,
5. Seal the walls,
9 Improving the energy efficiency of historical buildings. Recommendations of the State Inspectorate for the Protection of Cultural Monuments No. 2011-3. Available online: http://mantojums.lv/media/uploads/dokumenti/vkpai_rekomendacijas/rekomendacijas_e nergoefektivitatei_29039011.doc.pdf
6. Seal the foundations.
The prevention of building heat loss has been evaluated from various aspects, and solutions have been sought in all of them that would improve the situation, while at the same time preserving the defined values of the building to be protected and preserved.
The preventable heat losses in this historic wooden building are through:
1. Gaps in the enclosure structures – by means of convection. Solution –sealing the gaps in the enclosure structures.
2. Building elements of the enclosure structures – by means of the material's thermal conductivity. Solution – reducing the thermal transmittance (W/m²K) of the building elements of the enclosure structures by using materials with lower thermal transmittance.
3. Glazing of the enclosure structures – by means of radiation. Solution –treating the glazed surfaces of the enclosure structures with heat-reflective coatings." 10
Following in the article - in the descriptions of construction processes - heat loss prevention measures are grouped and described in the following structuredescribing them in these 3 groups.
7. Construction and Implementation Process.
To prevent the heat losses mentioned in the previous section, the following actions were carried out:
1. Method for preventing heat loss – sealing the gaps in the enclosure structures. Wooden log walls.
The sealing of gaps in the wooden log walls was done from the outside using a traditional method – the gaps were carefully sealed with linen tow ropes soaked in wood tar (Figure 5).
10 Heinsbergs Dz., Prevention of heat loss in historic buildings. Presentation available in the digital archive of the Kuldīga Municipality Building Board.
This combination of tow and wood tar is flexible and durable because wood is a material that swells and dries. Larger gaps in the wood were filled with wooden parts made from reclaimed historical timber, and prosthetics were applied, considering the wood species, age, and grain direction. A good wall insulation material is lime mortar plaster applied to a lattice of wooden slats. The craftsmen aimed to preserve the plaster wherever possible (Figures 6 and 7). In other areas, a new lime mortar plaster was applied to a lattice mesh inside the building."

4.
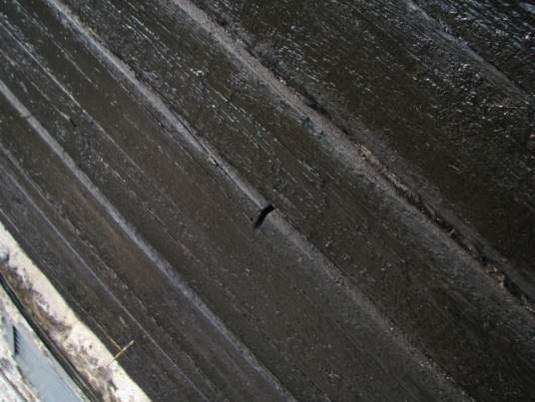
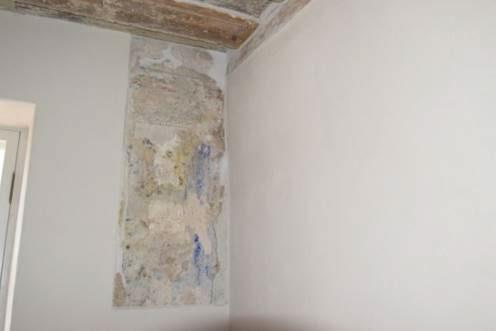

Fig. 6. and 7. Existing lime mortar plasters were preserved and new ones were created.
Wooden windows.
Windows play a significant role in the architectural image of a building:
" …Windows are an important part of the architecture of historic buildings. They are one of the most active elements of the facade, as well as a mirror of the style
and technical capabilities of the era. Every effort should be made to preserve each original window by caring for, repairing and restoring it. Window replacement should be supported only in cases where the repair of damage significantly exceeds the costs of manufacturing and installing a new, high-quality window made of the same material. As a compromise, replacement of the internal window frames is permissible. At least the original external window frames should be preserved if possible. Window replacement should be carried out only in accordance with the design of the entire building's facade solution." 11
The problems of historical, old windows, including the windows of this building, are related to the lack of regular maintenance of the windows and only in rare cases to constructive shortcomings and manufacturing quality. In order to make old wooden windows more heat-saving, two main works must be carried out: check the glass fastening and seal the windows. Until the 1960s, the windows were most often plastered, while in the second half of the 20th century, the custom of reinforcing the glass with battens was introduced, contrary to the historical tradition of plastering.
The windows in this building were made during the renovation process of the building - in the second half of the 20th century - in 1973, the glass was reinforced with battens. It was cheaper, but more uneconomical. When moisture penetrated behind the battens, the glass groove was damaged, and air flowed through these gaps. 12
First, the existing windows were evaluated, their density and a decision was made to renew the external sashes (made in 1973) with tempered glass, but to make new internal sashes, introducing an innovation – using reflective glass, which was historically impossible. This is described in more detail in Chapter 7.3. The second place through which cold air entered is the gaps between the sash and the frame, to prevent this, seals – nylon rubbers – were milled into the sashes. Residents can also purchase adhesive sealing rubbers to perform work at home, but a more sustainable solution is milling the rubbers, which is also a more complicated, more expensive process, since it must be performed by a craftsman For historic windows, rubber seals are only placed on the inner sash block.
To ensure the best seal, it is necessary to individually assess the required gasket size for each window so that the seal is sufficient and not standardized for all the building’s windows. Careful installation of gaskets with the appropriate thickness and length is needed, with special attention to corner joints to minimize heat loss as much as possible. The third area where significant (invisible) losses occur is
11 Improving the energy efficiency of historical buildings. Recommendations of the State Inspectorate for the Protection of Cultural Monuments No. 2011-3. Available online: http://mantojums.lv/media/uploads/dokumenti/vkpai_rekomendacijas/rekomendacijas_e nergoefektivitatei_29039011.doc.pdf
12 Jākobsone J., Veinberga K., Zariņa I. Guide for renovators of historical buildings. Building insulation. Kuldīga. 2013. Page 32. Available online: http://kuldiga.lv/images/Sadalas/Vecpilseta/CELVEDIS.pdf
the fastening of the window casing to the wall, as only tow was used, which was superficially sealed. Traditionally, tow was also soaked in gypsum, making it denser. This method would conduct moisture but also accumulate it. In the wooden log building, it was not possible to apply plaster externally as done with masonry buildings; it was applied only indoors, where it is not sufficiently flexible, leading to heat losses in this area. It may have been necessary to pack the tow more tightly or choose modern installation materials that could be visually covered by the decorative wooden trim of the window while fulfilling their function more effectively
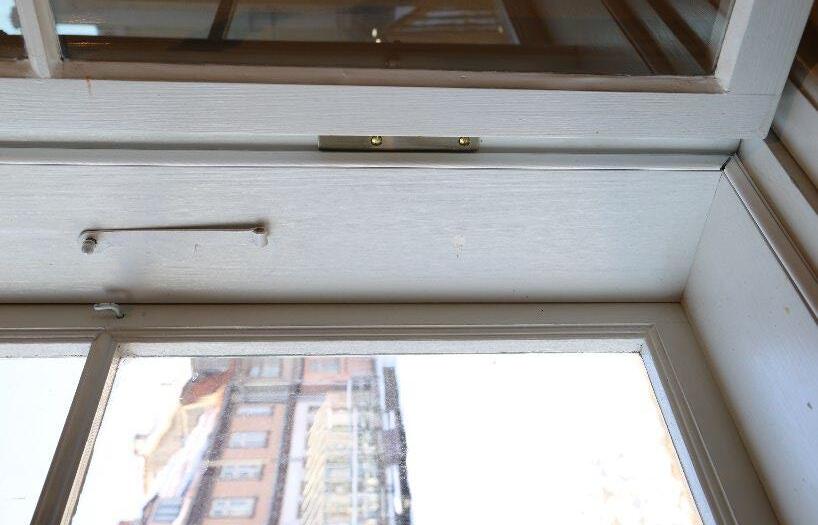
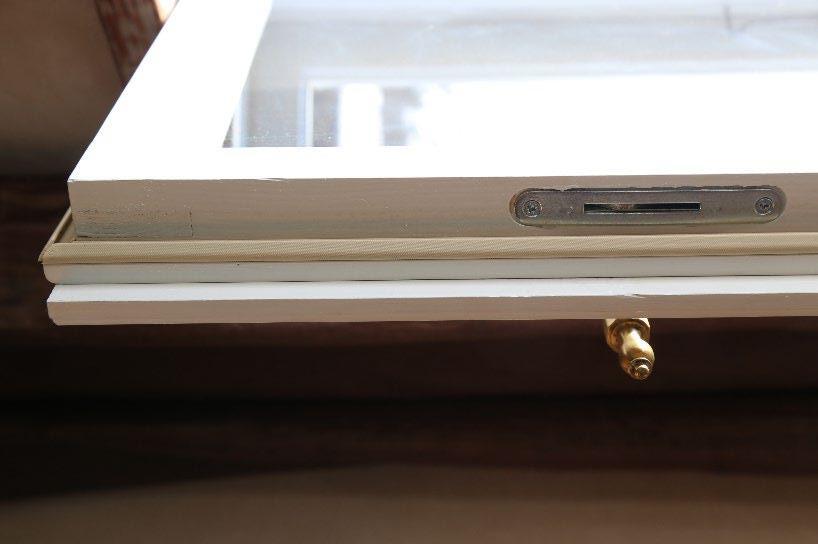
Fig. 8 and 9. A renewable window with built-in sealing solutions – rubber seals and tempered glass in the outer sashes. 13
13 Technical project documentation. Kuldīga. 2015. Available in the archives of the Kuldīga Municipality Construction Board.
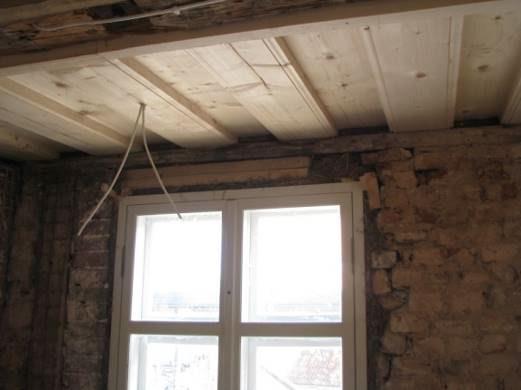


Wooden doors.
Door sealing - their installation in the openings, the installation of rubbers in the frames is done similarly, but the profile of the milled rubbers is different. Sealing is a big challenge for traditionally made wooden solid doors, because historically the windbreaks and stairwells were not heated and therefore there was no need to worry about heat loss. Heat loss does not occur from unheated rooms. But in order to use the building as efficiently as possible, the solution introduced in 1973 was maintained, that the windbreaks are heated and the doors are made new traditional ones, in which the sealing rubbers are milled. This type of door is a place of heat loss.
Mantel chimney.
A mantel chimney or chimney stack, also called a great chimney, is a large chimney that rises to the entire height of the building and narrows in a funnellike shape at the top.
14 Kuldīga Municipality electronic photo archive.
This was a characteristic principle of the planning of historical public buildings in Kuldīga, which was often the same as for residential buildings. Work and living spaces were arranged around a chimney stack, which was located in the center of the building. The plan scheme with a kitchen in the center was preserved in the construction of residential and public houses until the end of the 19th century. In the Town Hall, the chimney stack located in the center of the building adjoined the hallway, from which one could get to two rooms at both ends of the building.
In general, this planning principle with a mantel chimney in the center of the building and the mantel chimney itself have survived to this day in several residential houses in Kuldīga. In turn, in buildings accessible to visitors, until the renovation of this building, it was not possible to see the characteristic mantel chimney of Kuldīga. Therefore, it was especially important to restore it, while ensuring that there would be no heat loss through it.
The mantel chimney was built by craftsmen, in accordance with traditions, while ensuring that the space created in it would be used for the functions of the building – exhibitions, etc. It was necessary to provide a seal for the chimney – a hatch that could be lifted if a fire was lit in it and food was cooked, for which the chimney was used historically. A dense lifting hatch solution was created, which ensures heat saving.
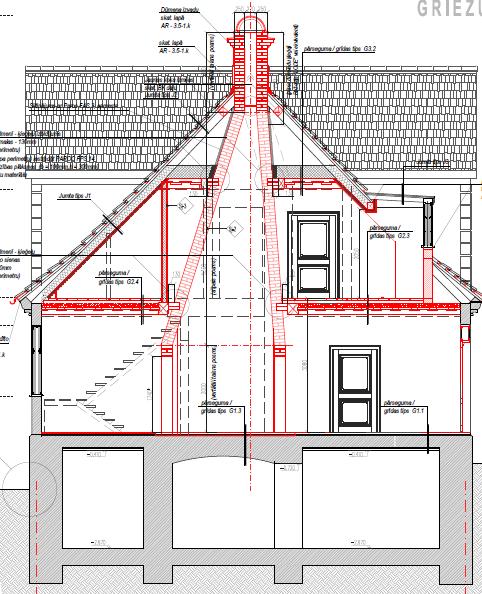
Fig 13. Restorable mantel chimney in the building section (marked in red).

Fig. 14. The mantel chimney outlet and its intended sealing – insulated roof hatch, sealed roof covering joints at the chimney. 15
15 Technical project documentation. Kuldīga. 2015. Available in the archives of the Kuldīga Municipality Construction Board.
Basement and foundations.
The building has a heated basement - cafe premises. The municipality renovated only the premises at its disposal, but the premises rented to private businesses were not affected, as the available funds were limited. When solving the renovation of the building, solutions were developed only up to the level of the basement floor.
2. Method of preventing heat loss – reducing the thermal conductivity (W/m²K) of the building's enclosing structural elements by using insulation materials.
In a historic building, insulation materials should only be used based on the recommendations of a specialist – an architect – as all solutions must be considered comprehensively, including the addition of new materials and the restoration of existing ones
Ceilings.
In the attic, clay was used for ceiling insulation. It was removed during the reinforcement of the structures and then reinstalled. The clay filling in the ceilings serves not only as insulation but is also dense and heavy, providing tension to the structure as it originally did when the building was constructed. If it were removed, gaps in the structure could increase due to changes in load.
When insulating the ceilings, special attention was given to roof ventilation. The project initially included a sand-ceramsite material for the ceiling, but all construction participants agreed to restore the clay filling instead.
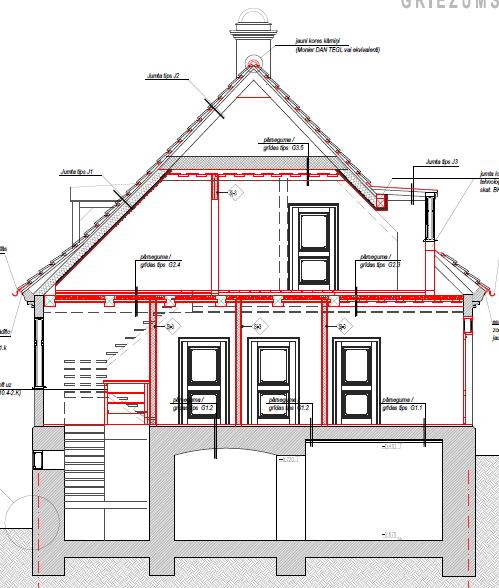

Fig. 15. and 16. Building reconstruction drawing - section - replacement coverings between existing load-bearing structures, and insulated roof planes. Materials and structures to be replaced and used additionally are indicated in red 16 On the right side, the removed and put back - the restored interfloor clay filling.
Roof.
The method of roof insulation and usage has been changed. The previously cold attic spaces are now adapted for the building’s functions, with the entire roof level utilized across its full area. Historically, the heated spaces were located at the center of the roof level, enclosed by half-timbered walls (wood and brick) or wooden plank walls. During Soviet-era renovations, these walls were insulated with wood wool panels; some of these walls have been partially dismantled or openings created in them, with the roof plane behind them now insulated. At the same time, roof ventilation has been ensured, as this function is no longer carried out by the cold attic spaces and roof area as it was previously.
16 Tehniskā projekta dokumentācija. Kuldīga. 2015. Pieejams Kuldīgas novada pašvaldības būvvaldes arhīvā.
During the restoration process, a ventilated and insulated roof structure was created. Moisture removal beneath the tiles has been ensured. The solutions were implemented using modern, compatible materials, including wood fiber boards, wood wool panels, cellulose insulation (loose fill, 300 mm thick), and a vapor diffusion membrane.
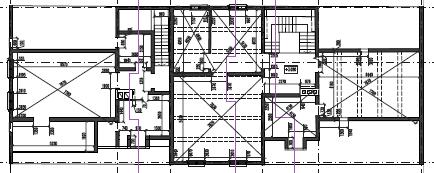
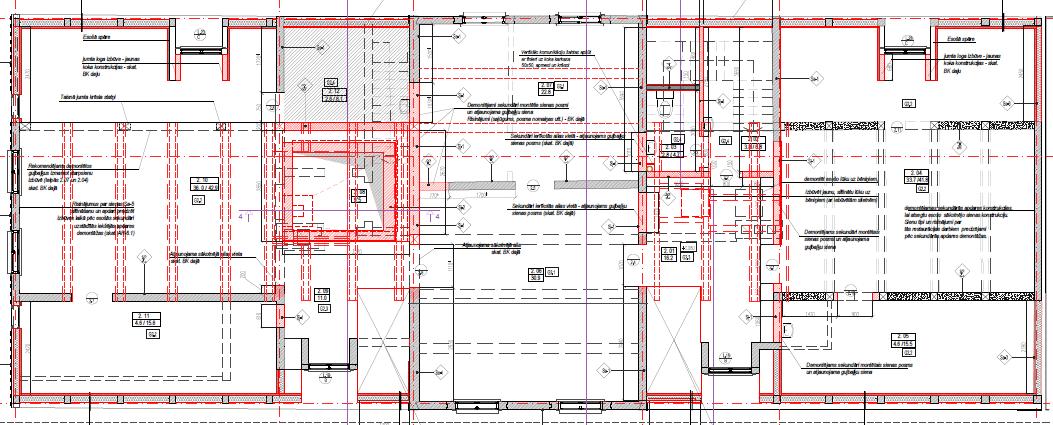
Fig. 17. and 18. Plan of the utilized spaces in the roof level (up to the cold attic spaces), with the left side showing the layout before reconstruction and the right side after reconstruction (with the built and insulated attic spaces of the building – existing structures and materials shown in black, and new ones in red). 17
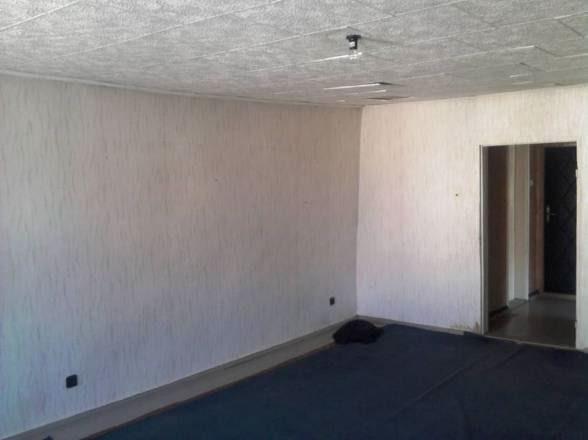
Fig. 19. Before reconstruction. The premises built in 1973 were renovated at the end of the 20th century. 18
17 Technical project documentation. Kuldīga. 2015. Available in the archives of the Kuldīga Municipality Construction Board.Tehniskā projekta dokumentācija.
18 Kuldīga Municipality electronic photo archive.

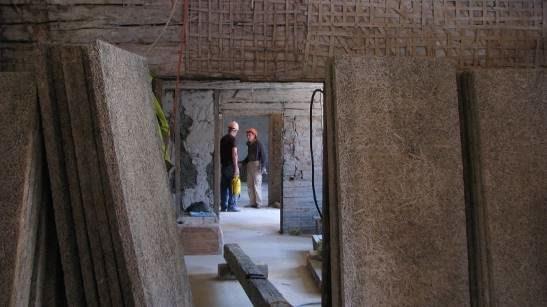
Fig. 20. and 21. During the reconstruction: Exposed cold attic spaces and their structure, as well as the dismantled materials used in the 1973 renovation, including wood wool panels (fibrolite sheets).
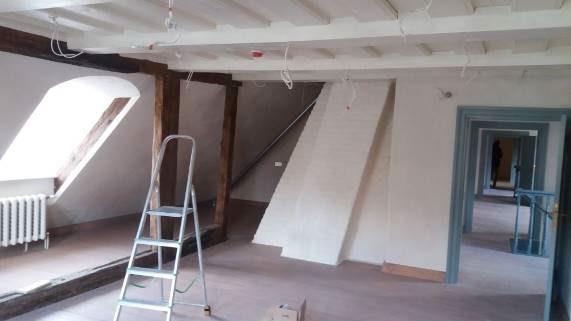
Fig. 22. att. After the renovation. Exposed cold attic spaces and their structure have been added to the heated and used space.


Fig. 23. and 24. After reconstruction: Cold attic spaces were partially integrated into the heated area, with openings in the half-timbered walls to allow lighting from the newly built roof extentions.
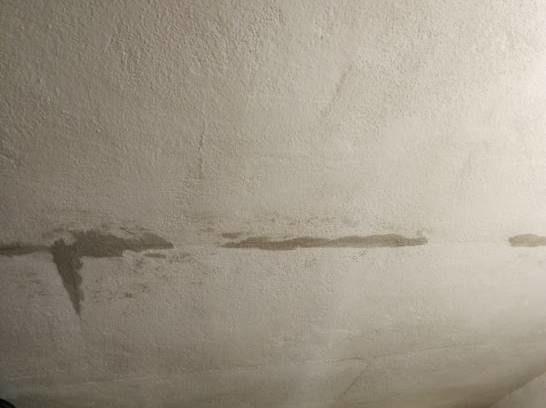
Fig. 25. After reconstruction. Plaster applied to fibrolite boards is a solution for reconsidering, especially in a historic wooden building, where it still settles after renovation and cracks appear between the boards and therefore in the plaster 19. It is recommended to finish this type of board with wooden planks, in which cracks would not be visible.
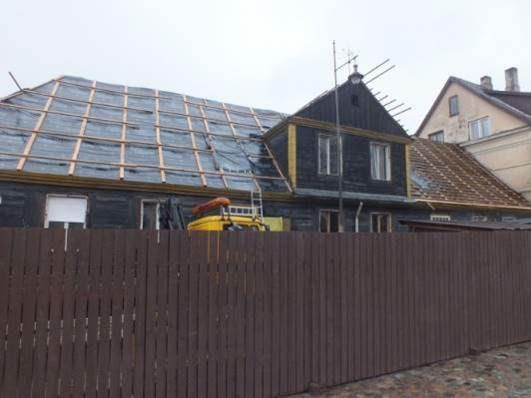
19
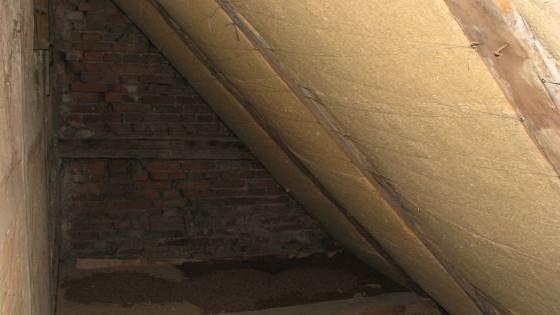
27. Roof plane insulation with wood fiber plates.
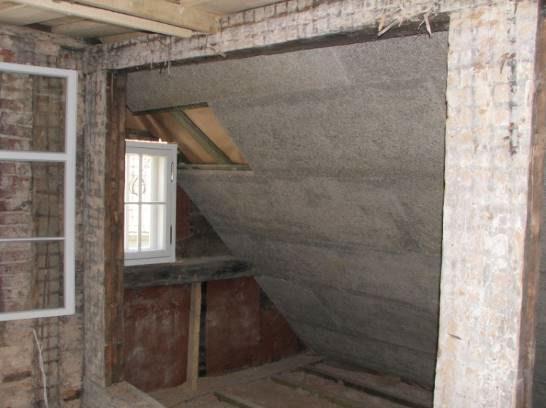

Fig. 28. and 29. A vapor barrier, lath and a layer of fibrolite are installed over the fiber plates, then a layer of lime mortar plaster is created.
3. Method of preventing heat loss – Finishing the glazed surfaces of enclosing structures with heat-reflective coatings.
Heat-reflective glass (commonly referred to as selective or insulating glass) with a thickness of 4 mm was incorporated into the inner sashes. This type of glass can be easily installed into existing wooden window frames and is particularly significant for inner sashes as it reflects heat.
Reflective glass was installed in the inner sashes due to its advantageous properties reflecting indoor heat and other considerations, such as its reflectivity and glass surface texture, which do not align with the architectural solutions of a 19th-century wooden log building. For the outer sashes, a decision was made to glaze them with the existing 2 mm wavy glass as used during the
original window construction. Where this was not possible, new identical glass was installed.
8. Specialists involved in the process of preventing heat loss in this building: research, design, restoration process, operation, and its supervision.
Since this building, the Old Town Hall of Kuldīga, is both a significant wooden building for Kuldīga and a public-use building, a large team of specialists was involved in its restoration to create a model of traditional building restoration and provide the best possible solutions. In everyday situations, such as the restoration and heat loss prevention of residential buildings, it is recommended to start addressing these issues with a practicing architect, who will involve the necessary specialists if required, due to calculations, detailing, or regulatory requirements.
In the restoration process of a specific building – the Old Town Hall of Kuldīga –a large team of specialists worked overall, each performing their assigned tasks within their area of expertise. This included research, design, project management, and construction. Unified solutions, teamwork of specialists, evaluation of various aspects, and balancing of interests during the design stage were ensured by the project manager and the client.
Before the project, technical research was carried out by a construction engineer, and the architectural and artistic inventory was conducted by an architect. During the project stage, an independent expert in the relevant field developed the temporary energy certificate for the building, while the designers, including engineers and architects, developed the construction project. The compliance of the project solutions with regulations and the client's requirements was reviewed by other designers. The involved state and municipal institutions, the building authority, and the client coordinated the project. Local government specialists, including architects, restorers, and project managers, were actively involved. The work was led by a professional builder and restorer. The author team, client representatives, and the construction supervisor – a construction engineer –oversaw the work.
9.
Users' and building owners' opinions on the process
and results.
Since the building is a public-use facility, it is constantly accessible to users, and no special usage regime can be maintained. According to user feedback, before the restoration, the building's energy efficiency was marked by very uneven room
temperatures – excessively hot office spaces and comparably cold common areas. After the restoration, the temperature difference between the office spaces and the common areas has been balanced – it is now uniform, and heating bills have decreased, even though all rooms are equally warm, meaning more square meters are now heated (including the newly built cold attic spaces on the second floor).
Users also mentioned that there are no longer any drafts or issues with the building's structure or details that would disturb the working conditions, as was the case previously when it was impossible to place a desk by the window for work. However, the user pointed out that the building's air has become dry after the restoration, and additional air humidifiers are needed during the heating season.
10. Conclusions, benefits, lessons for the future.
Ideologically:
• By using only traditional materials – those historically used in building construction – and changing the traditional use of building spaces (such as creating cold attic spaces, heating cold vestibules, and adding heated areas), it is not possible to ensure the improvement of the building’s energy efficiency. It is possible to use modern but compatible materials to prevent heat loss (sealing, reflection). For example, when preventing heat loss in windows, it is not effective enough to rely only on traditional materials – the use of modern seals and reflective glass is desirable.
• Restorers of historic buildings need to be familiar not only with traditional restoration solutions but also with the usability of modern materials in historical buildings. Today, buildings undergo transformations that change their usage and function, so compatible, modern improvements with appropriate materials are necessary. This may require involving specialists, especially in the field of energy efficiency, with the right knowledge and qualifications.
• A clearly defined concept for the restoration of a heated building is required, not only for the restoration of the building but also for the prevention of heat loss.
In Design:
• Any type of project requires detailing and material selection not only in the restoration and construction sections but also in the section related to heat loss prevention and energy efficiency.
• Great attention must be paid to the choice and analysis of possible engineering system solutions. The number of nodes already developed in the project stage should be sufficient in scale and detail to enable precise thermal calculations, the selection of engineering systems, and subsequent construction work.
• For the successful implementation of a complex project, competent professionals should be involved in specific energy efficiency issues –analyzing thermal bridges, developing sealing solutions for enclosing structures, specifying technical parameters of insulation materials, and having experience in conducting comprehensive building energy consumption analysis.
• Clearly defined construction quality control principles and achievable indicators.
• An example of the required detail: a justified and effective choice of the percentage of the reflective coating and the type of coating for the window glass to be installed. It is necessary to evaluate the actions to be performed during glass installation, whether applying putty and cleaning it mechanically (with a razor blade) could affect the properties of the selective coating. The putty is applied and then the remaining putty and paint are cleaned mechanically, which may damage the glass. The putty can also be cleaned using dry chalk before it dries. It needs to be verified whether the soft selective coating is resistant to mechanical action (this is crucial to clarify, as these same actions are common in window restoration processes). It is necessary to inquire with selective glass manufacturers about how it reacts (or does not react) to linseed oil and what coatings are recommended for such conditions, as well as their technical parameters. What needs to be known about selective glass: installation, mechanical durability, coating type and thickness, and technical specifications.
In Construction:
• Changes to the project should be evaluated from various aspects, including energy efficiency, and should be coordinated with specialists who assess materials not in isolation but in relation to the other planned solutions.
• During the building construction stage, regular quality control checks are carried out, such as conducting an air tightness test (BlowerDoor), to identify and address any existing shortcomings early on.