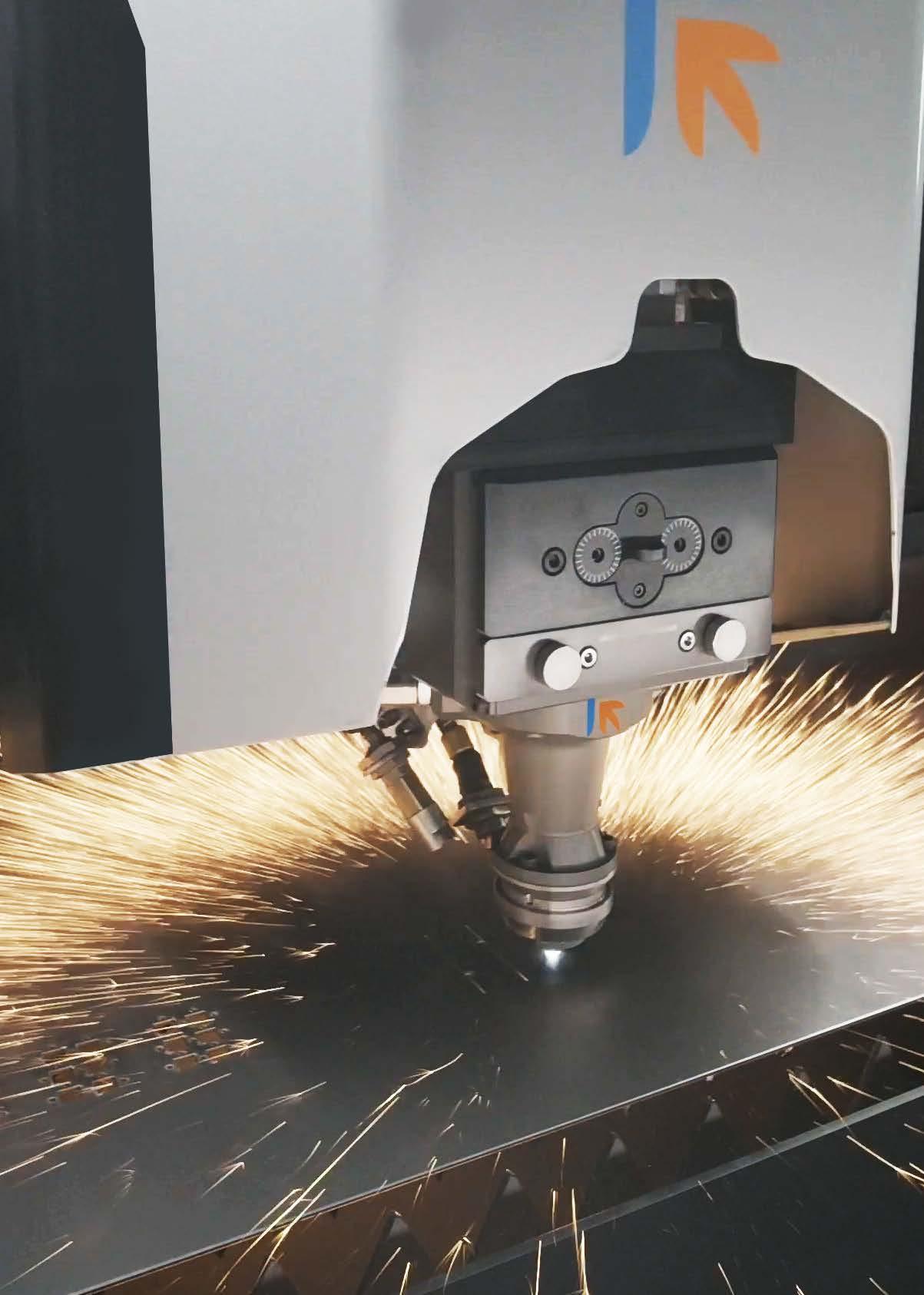
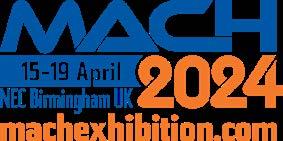
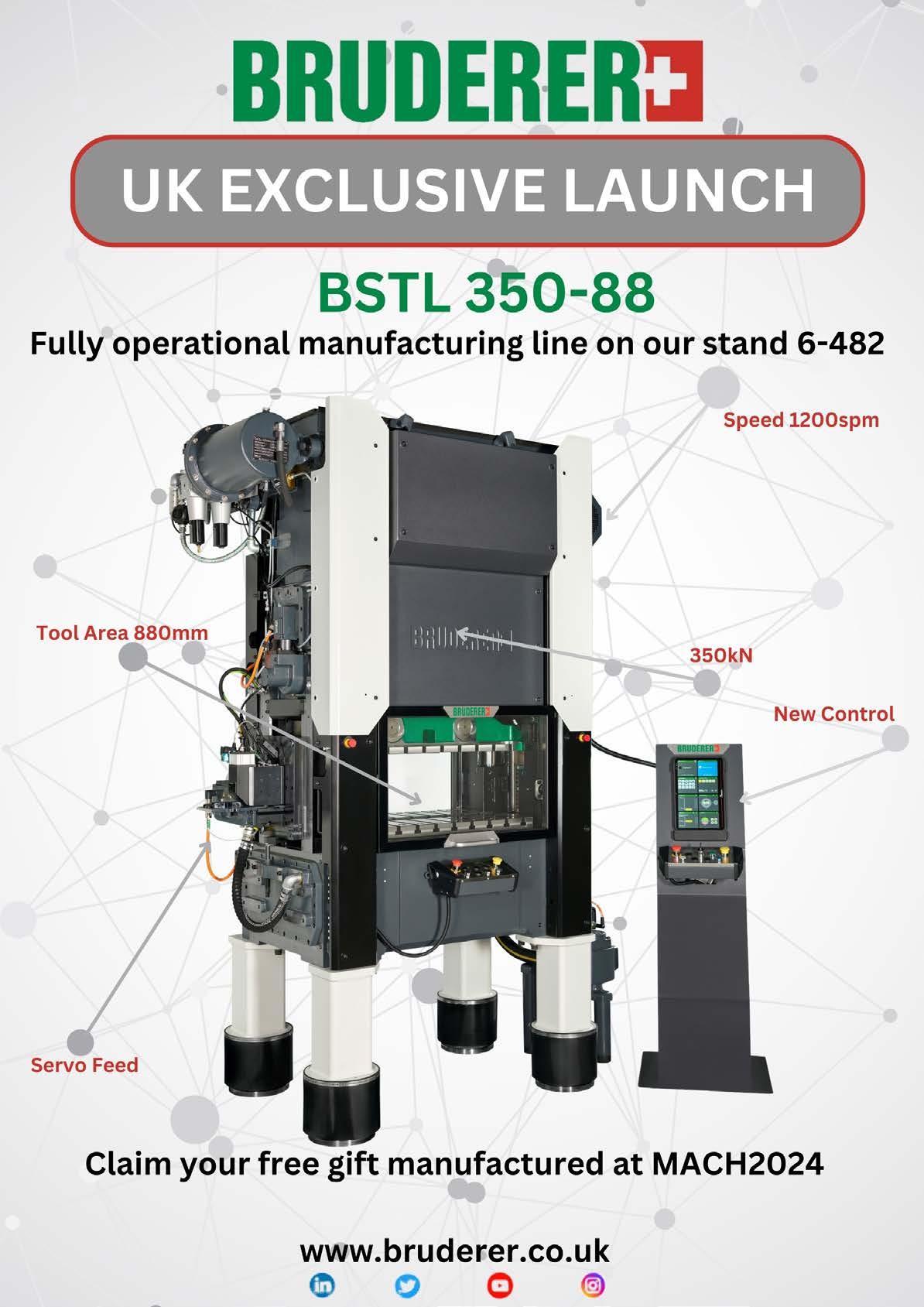
to the Sheet Metal Industries MACH 2024 Publication. This year’s MACH exhibition here in Birmingham is set to be one of the best yet. The Metalworking Village (Hall 6) is showcasing exciting innovations from all corners of the sheet metal and metal forming industries. It’s a unique opportunity for industry professionals to come together – and we’re thrilled to be sharing it with you!
Creating a sense of community and celebrating achievements within the metalworking sector is what Sheet Metal Industries – or SMI – is all about. Our digital platform, www.sheetmetalindustries.com, was born in answer to the need for a specialised voice piece for our industry. This limited-edition publication, produced in partnership with the Metalforming Machinery Makers’ Association (MMMA), is an extension of our online platform. It provides a taster of this year’s MACH highlights as well offering insights into the benefits of being a Sheet Metal Industries and MMMA member, and I hope you enjoy it.
Sheet metal forming and fabrication is a niche sector, with equipment ranging from presses, guillotines, and press brakes to various forms of sheet metal punching and shearing equipment. SMI provides an on-the-ground vehicle for sellers to describe the benefits of their equipment, and end users who buy them to demonstrate their amazing skillsets, helping companies within the sector promote and showcase their individual strengths, products, and services.
It’s also a platform for sharing up-to-date news and information that’s useful to the metalworking marketplace with a community of like-minded organisations. One such organisation is the The Metalforming Machinery Makers’ Association (MMMA) whose 2024 membership directory you’ll find inside this publication. The MMMA is intrinsic to facilitating growth and promoting the interests of the metalworking sector. Its member companies, the engineers, and their collective experiences and know-how have helped solve production manufacturing challenges since 1949. It’s an honour to be media partners with such a prestigious organisation and we look forward to sharing these benefits with our members over the coming year
Sheet Metal Industries celebrates its second anniversary this year. With an impressive 1,000+ stories published to date and over 400,000 social media interations through its website and social media channels annually, SMI showcases an unwavering determination to keep the industry discourse alive.
These stories don’t just reside on paper or screens; they encapsulate the pulse of the industry, highlighting its trends, challenges, and the triumphs of those people driving production-manufacturing change. From articles about one-man fabrication shops and international trade shows to advancements in technology and engineering practices, SMI ensures every story resonates with its readers – and benefits its ever-growing number of satisfied members.
This year, there’s lots for both members and non-members to look forward to. Our industry Golf Day on 25th September 2024 is taking place at the prestigious Warwickshire Golf Club, creating further opportunities for the market to mix and mingle. You can join on the day as a company or an individual by signing up through our website – spaces are limited. Not that anyone needs tempting but there is a chance to win a £20,000 CASH PRIZE for anyone who can hole out on its famous Hole 8!
For now, sit back and enjoy soaking up some of the latest stories and news from the world of sheet metal forming and fabrication – whether you cut, shape, form, or join, I hope to see you online very soon! sheetmetalindustries.com
HWelcome from Sheet Metal Industries founder, Jas Rai
Discover SigmaNEST, Hutchinson’s secret weapon for unprecedented efficiency
Axe & Status brings ACCURL machines to the UK market
AXYZ empowers Edmar Engineering to take control of waterjet cutting with WARDJet
Chasestead Ltd harnesses fibre laser technology with Laser Next 2141
Latest Industry News
Why BLM’s new 12 kW BLM LS7 4020 is the clear choice for ParkerSteel
How MIE Solutions’ MIETrak software has revolutionised Ludwick Precision’s processes
Meet Buck Engineering Ltd , the sheet metal machine maintenance specialists
How Bihler is meeting increased UK demand for onshore assemblies
Kerf presents ‘One-Stop-Shop’ at MACH
MD for Bruderer UK , Adrian Haller, on Britian’s next manufacturing boom
Unifabs speeds up its processes with two Haeger machines and Press Form’s expertise
Latest Industry News
Decoilers and Feeders solves outsourcing issues for Advanced Air UK with DF47 Tube Roller
Why PressCare and Ideal Heating have the perfect partnership...
PAB Coventry’s long-serving laser machine gets an ultramodern upgrade: Prima Power’s Laser Genuis 1350
White Cross Ring’s sought-after tube-bending services are taking the company to the next level
The Metalforming Machinery Makers Association - 2024 Members Directory
MACH 2024 Special Sheet Metal Indust ries Ltd
Tel: 01926 298777
Formation Media: The marketing agency for manufacturers
Unit 2, St Georges House, Cape Rd, Warwick CV34 5DJ
Email: hello@formationmedia.co.uk
In today’s dynamic manufacturing landscape, companies are constantly seeking ways to optimise their processes, boost productivity, and reduce waste. Could SigmaNEST be the single-software solution we’re all searching for?
Hutchinson is a forward-thinking designer and manufacturer of high-integrity fabrications and sub-assemblies for industries including coach building, materials handling, agriculture and defence. They have taken a significant step forward by implementing SigmaNEST, a comprehensive set of software tools crafted to elevate productivity in sheet metal fabrication.
This landmark decision and commitment to technology has not only streamlined Hutchinson’s operations but also underscores their commitment to innovation and customer-focused solutions. In this article, CEO, Mark Hutchinson, delves into the details of this tranistion.
“At Hutchinson, we’ve invested in state-of-the-art technology for many years now. We are always looking for the best solution, which ultimately gives the best solution and flexibility to our customers. For us, innovation is key. It’s important we partner with good people, who help us move the business forward. SigmaNEST, to us, is one of those partners,” states Mark.
The relationship between Hutchinson and SigmaNEST began 10 years ago when Hutchinson was looking for a way to streamline and connect its manufacturing processes.
“Our problem at the time was that we had multiple pieces of software all being meshed together,” Mark recalls.
Multiple programmers were often required to collaborate on nesting tasks for identical components. This meant Hutchinson’s programmers were managing various software packages for nesting and machine integration, as well as soliciting feedback between each step. As a result, the process often stretched beyond the timeframe expectations of Hutchinson’s customers.
“SigmaNEST has given us everything in one package, which has allowed us to consolidate our nesting processes,” explains Mark. “This has been a huge benefit to our business, and ultimately, our customers.”
The SigmaNEST fabrication software suite provides total control over business systems, CAD/CAM and the shop floor, all in one platform. Its modular structure has given Hutchinson the flexibility to select the software best suited to its operational needs, including HD SuperNEST for highly advanced nesting CAD/CAM, and SigmaBEND AP, an intuitive 3D programming system for press brake operations.
SimTrans is a transaction manager with real-time processing and feedback automation that bridges the gap between SigmaNEST and other software. It has radically improved the speed and efficiency of data processing for Hutchinson’s team, allowing them to focus on value-added tasks rather than grappling with data intricacies.
Moreover, SigmaNEST’s live sales orders and work orders integration with Hutchinson’s existing business system (ERP) has brought transparency and real-time data exchange to their operations, enhancing decision-making and reducing errors.
“Integration with ERP has been critical in this project,” says Mark. “Being able to get information quickly and accurately is very important to us.”
When it came to the implementation of the software, SigmaNEST provided full, face-to-face support. “SigmaNEST came on site and understood what our business was about and what we need from a system,” Mark explains. “Their solution has enabled us to consolidate our systems, speed up our nest times, reduce scrap, and be more competitive for our customers.”
According to the team at Hutchinson, the software has enabled them to manufacture parts faster than other software solutions by consistently nesting in the most efficient way, batching the products together, and speeding up material processing before laser cutting.
“HD SuperNEST has been a gamechanger. It’s helped us bring in multiple parts very quickly compared to other software packages. Once all parameters were set up, it’s consistently allowed us to produce the same nests at a better quality,” explains Mark.
While significant enhancements are readily apparent within the production cycle, SigmaNEST has been carefully designed and implemented to benefit the full workflow cycle.
This extends beyond just increasing manufacturing production speeds and efficiency to also encompass quoting and delivering solutions to customers, as Mark explains: “In our business, reactivity to the customer’s demand is key. SigmaNEST has transformed our quotation process and helped us to reduce the time taken for quotes by up to 30%.”
This efficiency has received positive feedback from customers, contributing
to an overall improvement in the sales process and allowing Hutchinson to optimise their lead times and profits.
Hutchinson’s achievements with SigmaNEST serve as testament to its capabilities as a unique workflow solution that accelerates production and attracts new business opportunities. SigmaNEST’s strong commitment and active engagement with its clients guarantee the seamless integration of the most efficient solutions into operations.
“Working with SigmaNEST and their team has been a fantastic journey for us every day. The operators and programmers enjoy working with the software. We would have no hesitation in recommending SigmaNEST to other businesses,” concludes Mark.
SigmaNEST is a singlesoftware solution that integrates your CAD/CAM, shopfloor, and business systems. It can be used to synergise your quotations, programming, production management, shipping, logistics, and inventory, providing real-time feedback to speed up processing, enhance overall efficiency, and deliver unrivalled customer service. Find out more about SigmaNEST, see sigmanest.com/en
In our business, reactivity to the customer’s demand is key. SigmaNEST has helped us to reduce the quotation process by up to 30% “
Suppliers of new production equipment, Axe & Status Machinery Ltd, have taken their provision to the next level, becoming sole UK distributors for ACCURL, one of the world’s leading manufacturers in the field of steel metalworking machinery. Here’s a first look at ACCURL’s UK offering and what Axe & Status customers can look forward to:
Being able to exclusively represent ACCURL within the UK is a great coup for us and our valued customers “
Situated in the heart of Milton Keynes, Axe & Status Machinery Ltd has demonstrated excellence in the sector for over 50 years. Born from the union of Axe Machine Tools Ltd and Status Sheet Metal Machinery Ltd in 1979, the company has evolved into a stalwart supplier of quality machine tools and sheet metal equipment.
To complement their already impressive provision of sheet metalworking machinery, which includes and CNC pressbrakes, variable rake guillotines and CNC plasma machines, as well as ranges of plate roll bending machines and fibre laser and tube laser cutting machines, Axe & Status has recently become sole UK distributor for ACCURL, a press brakes and laser cutting machine manufacturer based in China.
“The new Axe & Status partnership with ACCURL is exciting,” states Axe & Status Director, Steve Thomas. “It means we are offering the latest cutting-edge technology at a very attractive price point for our customers.”
ACCURL is widely recognised for its state-of-the-art technology and inventive solutions within laser machinery. Boasting 33 years of experience and a remarkable record of over 12,000 installed machines, ACCURL’s expert R&D team works tirelessly to research the most competitive technology for their customers. This dedicated approach aligns seamlessly with Axe & Status’s commitment to providing exceptional solutions to their clients.
“We investigated the market over a period of a year and visited the ACCURL factory in China,” reveals Steve. “We were extremely impressed with the quality, level of
technology, and the general standard of the operations; now being able to exclusively represent ACCURL within the UK is a great coup for us and our valued customers.”
ACCURL conducts exhaustive studies to offer a diverse range of fibre laser cutting technology, tailored to meet unique customer needs. This results in the production of ultralight, highprecision, and high-energy 2D fibrelaser cutters suited for a variety of industries.
The introduction of Green Hybrid Servo and Electric Servo bending technology for manipulating sheet metal gives ACCURL a substantial edge over competitors. The integration of the IPG Fiber Resonator, offering power ranging from 1kW to 30kW, further solidifies ACCURL’s position as a toptier manufacturer in the sheet metal machining industry.
Axe
Axe & Status doesn’t just sell machines; they forge lasting partnerships. Beyond importing and installation, the company offers comprehensive service support, embodying their commitment to customer satisfaction.
The company provides original ACCURL spare parts for peak performance and durability, while consultations on machine operation and maintenance empower customers with the knowledge needed for their success. This seamless experience blends cutting-edge technology with unparalleled training and support, offering a unique service that ensures businesses partnered with Axe & Status continue to thrive.
“We provide our customers with increased productivity alongside expert service and support nationwide through our team of qualified in-house engineers who have years of experience,” says Steve. “Our specialist support team is a highly important part of our business and our commitment to our customers from installation to aftercare, which includes a 3-year guarantee for customer peace of mind.”
Focused on understanding client needs, the collaboration with ACCURL delivers top-quality machinery at competitive prices, solidifying Axe & Status as UK market leaders, offering not just machines but innovation pathways.
The partnership between Axe & Status Machinery Ltd and ACCURL signifies a dynamic alliance, prepared to shape the future of the laser market in the UK. As ACCURL’s exclusive distributor, Axe & Status is not merely selling machines; they’re ushering in a new era of technological advancement and customer satisfaction.
“We chose ACCURL because of their commitment to continually updating technology and offering the most cost and power-effective machines within the international market,” says Steve. “Moving forward, we envision a long and prosperous relationship with ACCURL and for our customers in their choice of these innovative machines.” For more, see axestatus.com or visit the Axe & Status stand Hall 18, stand 330.
The founding principles set out in 1979 still guide Axe & Status today – an unwavering commitment to delivering acceptable quality and reliability at competitive prices. The company places a premium on problem-solving, inviting customers to explore their machinery offering and discuss individual production needs.
The Axe & Status showroom is testament to over four decades of industry expertise, offering customers firsthand experience of their diverse machinery range, including the latest innovations from ACCURL.
For further information on the ACCURL range, contact the team at Axe & Status Machinery (sales@axestatus.com) or call 01908 647707. New stock, including high-power lasers, is now available for demonstration in the showroom, so come and witness the future of sheet metal fabrication in action!
Outsourcing processes can be counterproductive, especially when components arrive late or are poor quality. Birmingham-based Edmar Engineering Company Ltd has taken control of its cutting capabilities, splashing out on a A-1212 waterjet from WARDJET – and the business benefits have proved manifold
Fourth generation family-run business Edmar Engineering celebrates its 80th birthday next year, but its service provision is cutting-edge as ever, thanks to its latest acquisition – a WARDJET A-1212 waterjet machine.
Edmar was founded in 1945 by former Dunlop foreman, Bill Marklew, and partner Mr Edwards. Having been commandeered by the MoD to enlist skilled, local engineers and toolmakers in the war effort, Bill decided to retain his new-found colleagues after the war and set up his own specialised precision engineering company.
The company specialises in small quantity machining, prototypes, one-offs, jigs, fixtures, and special purpose machines. From its original manufacturing base in Birmingham, Edmar offers expert support to all sectors including automotive, aerospace, utilities, food, and pharmaceuticals, working closely with customers on time-sensitive projects that require tight turnarounds.
“Our engineers love a challenge and creating things for our clients!” enthuses Co-Director Anna Hayton. “To meet their demands, you have to be reactive,” she asserts. “We don’t carry a huge order book going forward, so much of the work we do is reactive –everybody needs it now!”
for the company, as Technical Director Richard Dale explains: “When you subcontract, you lose control over quality and lead times,” he says.
“If you’re relying on parts coming in that have been produced elsewhere, they can arrive late and with a different finish than you wanted. Those parts may then need reworking, which affects everything from timescale to overall quality.”
“By bringing the waterjetting in house, our reactivity and control is much improved. If someone has an urgent requirement, we can manufacture speedily whilst maintaining our high standards. Being able to do that helps us satisfy our existing customer base and has won us new business.”
Nearly eight decades on and with Bill’s great granddaughters, Anna Hayton and Jayne Sheppard, at the helm alongside Technical Director, Richard Dale, Edmar is still true to its roots.
Prior to purchasing the A-1212, Edmar outsourced their waterjet cutting requirements, but this solution was becoming increasingly problematic Here and now!
The waterjet has also helped speed up Edmar’s milling processes by producing profiles prior to milling.
The WARDJET A-1212 has not only improved Edmar’s efficiency over the last 12 months; it’s also made the company’s use of materials more cost effective, as as Edmar’s Production Manager, Simon Danks, has observed: “We mainly use the waterjet to cut aluminium, and some plastics, which it can do very fast. Previously, we were buying material cut to order, which can incur extra time and cost; now we can buy a sheet and cut the pieces ourselves.”
“We don’t have to wait for materials to arrive on site any more or wait for them to be cut to size, which has really sped up our processes,” Richard adds.
WARDJET’s A-series waterjet is available in two sizes: the A-6012 and A-1212. “We opted for the A-1212 for its generous 1200 x 1200 operating window,” explains Richard. “It has industrial capabilities with a compact footprint and is ample for the work we do.”
Edmar’s Production Manager and machine operator, Simon Danks, also had a hand in choosing the new machine, which features dragand-drop loading and part queuing technology: “It’s a very user-friendly operating system – easy to operate and programme,” he says.
“The dropdown menu of preprogrammed parts is one of the most useful features. If I want a rectangular part, I select ‘rectangle’ from the inventory and the size I want, and the software draws it up for me. It couldn’t be simpler.”
After researching the waterjet market, Richard chose Telford-based WARDJET
Waterjets from AAG Tailored Cutting Solutions following an impressive hands-on demo experience, where he was able to bring his own CAD files to the WARDJET Demo Room and see the A-1212 go to work on his designs. “We had a good look at the operating system and were able to programme and operate the demo machine ourselves,” he recalls.
Positive endorsements from fellow industry professionals, and WARDJET’s proximity to Edmar’s headquarters, sealed the deal. “Although WARDJET machines are manufactured in the US, the UK Telford-based office is local to us, which means the support and infrastructure is local too.” Richard points out.
“All the training on the new machine was comprehensive and carried out at Edmar. And when we needed extra help with maintenance, WARDJET engineers came out to us to talk us through it. They have a good team of
people there. I’m more than happy with the products they’ve supplied and the support we’ve received – I’d recommend WARDJET to anyone.”
Anna adds: “As a small company, the waterjet was a big capital investment for us. We received some grant funding and WARDJET were helpful with the delivery and paperwork requirements of this.”
“
We don’t have to wait for materials to arrive on site any more or wait for them to be cut to size, which has really sped up our processes. Our reactivity to clients is now immediate
WARDJET is a leading manufacturer of waterjet cutting systems. Known in the waterjet industry for quality products and outstanding service/support, WARDJET thrives on designing and building custom waterjets integrated into complex processes. With a vast network of technical support teams around the world, see wardjet.com to learn more about WARDJET’s range of powerful cutting equipment.
FFrom creating and producing weapons for Star Wars film props to ultrahigh precision MOD components and assemblies, Chasestead Ltd metalwork engineers have their work cut out. To keep up with demand for manufacturing large and small metal components and assemblies, the company’s invested in a Laser Next 2141 from Prima Power – and its plus-size capabilities have meant big business for Chasestead
or nearly 60 years, Chasestead metalwork engineers have been providing world-class metalwork for prototypes and low-volume pressings, tooling, and folded and fabricated components. With its roots firmly in the automotive sector, the company boasts unmatched experience in the manufacture of prototype and pre-production automotive under-structure components and assemblies.
Its impressive 42,000-sqft Hertfordshirebased factory enables Chasestead to support even the most ambitious of projects, including automotive aluminium floors and complete chassis builds. And with the added benefit of all its activities being carried out under one roof, quality and speed of development come as standard.
In recent years Chasestead has taken its impressive engineering knowledge gained in the automotive industry and pushed into many other sectors including renewable energy, construction, defence and general fabrications.
“We pride ourselves on being a one stop shop, providing excellent customer service, with a fast response to solving customer queries and problems and the ability to supply specialist parts in very short lead times,” says Justin Sedgwick, co-MD of Chasestead.
Wednesday 25 September 2024
A relaxed, fun opportunity for those within the sheet metal, metal forming, and fabrication industry to meet up, network, and socialise over a round of golf on one of the most coveted courses in the country.
The day will include breakfast, 18 holes on the Warwickshire’s stunning Kings Course, and an awards dinner, with the option to stay in one of the many excellent local hotels.
9:00am The Warwickshire Golf Course
Join us at this unique event to cement your place in the industry and be in with a chance of winning:
• £20,000 cash prize
The Warwickshire’s Kings Course is a championship American parkland course comprising a mix of styles and challenges that are enjoyable for all levels of golfer. Pit your wits against woodland, water, and its infamous 8th Hole!
Entry Details
• A three-night stay for two at a 5* Praia D’el Rey Marriott Golf and Beach resort in Portugal, including flights, half-board accommodation, car hire, and two rounds of golf
• A Taylor Made stealth Driver
• A two-night stay for four at Marriott Forest of Arden, half-board including two rounds of golf based on two sharing each room
Book your place now!
25/09/24
Our sponsors
£300 + VAT
£80+ VAT
Team entry (4 players)
Individual entry
Entry includes:
Participants can enter in teams of up to four players; those entering as individuals are welcome and will be assigned a team on the day.
• Welcome breakfast rolls & tea/coffee
• An evening Celebratory Awards Dinner
• 18 holes of golf on the stunning Warwickshire Golf Course
As if its massive X: 4,140 mm – Y: 2,100 thermal distortion. Its topline 3D and
does a lot for staff retention. If you’ve got newer technology and your staff aren’t fighting with some 100-yearold machine, it’s always good for the business. That’s where the Prima drops in.” To find out more about Chasestead’s Next Laser 2141 fibre laser-cutting provision, see chasestead.co.uk.
From luxury automotive manufacturers to film studios, Chasestead’s varied mix of high-profile clients demands cutting-edge speed and versatility. The Laser Next 2141 delivers on both fronts, proving invaluable to Chasestead’s sustained success and agility across all
The company began taking on marine clients in 2006, shortly before the automotive industry dipped in 2008, and by embracing new technologies like the Laser Next 2141, Chasestead is continuing in this vein.
“
New machinery like the 2141 is keeping Chasestead at the forefront of the prototype and low-volume business
“Investing in new machinery like the 2141 is keeping Chasestead at the forefront of the prototype and lowvolume business,” says Justin. “It also
Chasestead specialises in prototypes and low-volume pressings, tooling, folded and fabricated components. If you have a metalworking project – big or small – get in touch today to get better results! See chasestead.co.uk or contact mail@chasestead.co.uk / 01462 480048 to find out more
HERE’S A ROUND-UP OF WHAT’S HAPPENING ONLINE. CUT THROUGH THE NOISE, SHAPE AND FORM YOUR OPINION – THEN JOIN THE DEBATE!
RECOL FIRST TO INVEST IN AUTOMATED AMADA 6kW FIBRE WELDER
Recol Ltd, a world-class provider of sheet metal fabrication, precision machined components and mechanical assemblies, has invested in a new AMADA FLW ENSISe 6kW automated fibre laser welding machine. The new machine will enhance the quality and repeatability of the company’s welding operations while eliminating several on-processes, including straightening, grinding and polishing.
Yamazaki Mazak is debuting three new machines and the new MAZATROL DX extension for its popular PC-based SmoothCAM Ai software. Customers can discuss their requirements and see machines that are entry-level, user-friendly, robot-ready, cost-effective and available with short lead times as part of Mazak’s “Building For Your Future” offering on Stand 20-330.
LANTEK BRINGS ITS FULL SUITE OF SHEET METAL SOFTWARE TO MACH 2024
Flexibility is one of the major improvements in Lantek Expert, making it easy to move nests of parts between machines in line with production requirements and without the need for manual adjustments. New is the Assembly 2 Nesting software, which allows users to import a complete 3D model assembly of parts. Visit Stand 17-319.
In a landmark year celebrating four decades of excellence, Grenville Engineering raises the bar in cutting-edge fabrication with a £250k investment in the latest RVD SmartFibre CNC tube laser cutting machine from Bison Machinery. The new machine, TF 8020.3000 model, is positioned to transform the company’s operational dynamics and market outreach.
Ficep UK, a leading supplier of cutting-edge steel processing systems, is showcasing its latest innovation, the Ficep XBLADE CNC line on Stand 20-180. Visitors will have chance to speak with Ficep UK’s expert team and gain insights into the system’s capabilities in drilling, tapping, milling, and sawing with disc blade precision.
Charles Day Steels is thrilled to introduce their latest cutting-edge machinery acquisition – the Bystronic Xpert Pro 320/4100 Press Brake. This state-of-the-art sheet metal bender is engineered to cater to a wide spectrum of requirements with unparalleled efficiency and quality; emphasising the company’s ongoing investment strategy and commitment to advancing their services.
Having taken over the agency for PEI resistance welding products from Sureweld as of the end of January 2024, Westermans International are also taking over the agency for PEI Resistance Welding Solutions in the UK and Ireland. Going forward, Westermans International will supply resistance welders directly and provide support to past and future clients.
The UK steel and aluminium specialist elevates its manufacturing capabilities with state-of-the-art laser cutting technology from BLM GROUP
In an era where steel supply chains face significant pressures, and demand from end users has been tepid, the trend among stockholders has largely been to shy away from investing in new processing machinery that could enhance the value of their offerings. ParkerSteel stands as a notable exception.
A leading steel stockholder in the UK, ParkerSteel specialises in supplying a wide range of steel and aluminium products to industries including construction, transport, agriculture and more. With a focus on innovation, quality and customer service, the company continues to invest in advanced technology to meet the evolving needs of its clients, committing over £4 million to significantly upgrade its processing capabilities in 2023.
The investment included the acquisition of two BLM tube laser cutting machines for its Dudley facility and an additional four machines for its Canterbury headquarters. The latter comprised a similar tube laser, a combined drilland-saw, a mitre saw, and notably a cutting-edge flatbed fibre laser profiling centre from the BLM GROUP, sourced through the manufacturer’s UK subsidiary based in Ampthill.
The strategic investment, spearheaded by ParkerSteel’s Managing Director Dylan Alexander, puts the company at the forefront of the sector’s resurgence. Its diverse customer base, spanning construction, transport, agriculture, manufacturing, energy, marine, utilities, highways and mining, is set to benefit from an expanded portfolio of steel and aluminium products, including precision-cut billets for machining by OEMs and subcontractors.
ParkerSteel’s journey with laser cutting technology has been progressive and forward-thinking. Starting with 10
CO2 machines in the early 2000s, the company transitioned to an automated fibre laser cutting centre equipped with twin 8 kW lasers in 2016. Despite its success, this upgrade posed new challenges, prompting Production Manager Michael Seager to seek a more flexible and reliable solution. The new 12 kW BLM LS7 4020 fibre laser cutting machine emerged as the ideal choice, offering not just operational efficiency and flexibility but also muchneeded redundancy for uninterrupted production.
The choice of the BLM LS7 4020 was influenced by its European build quality, CE marking ensuring safe operation, cost-effectiveness and the supportive approach of BLM’s UK team. Its modular design facilitated rapid on-site assembly, significantly enhancing productivity at a crucial time for ParkerSteel.
A visit to the BLM GROUP’s manufacturing facility in Levico, Northern Italy, by Mr Alexander and Mr Seager reassured them of the equipment’s reliability and the manufacturer’s support. Since its commissioning in mid-October 2023, the LS7 4020 has demonstrated exceptional productivity, attributed to its 2g table acceleration and an automatic pallet shuttle system, which together streamline operations and minimise changeover times to an impressive nine seconds.
Ease of use has been another commendable feature, with program handling and nesting and cutting cycles efficiently managed offline through SigmaNEST CAD/CAM software. The machine’s advanced features, including active piercing, nozzle centring and real-time control of cutting accuracy,
ensure precision and quality in processing a wide range of materials.
As ParkerSteel moves forward, its investment in the BLM LS7 4020 represents not just a commitment to technological advancement but also a strategic positioning for growth and innovation in the steel industry.
“The new 12 kW BLM LS7 4020 fibre laser cutting machine emerged as the ideal choice
BLM GROUP is a global leader in tube and sheet metal processing solutions. Boasting more than 70 years’ experience and thousands of applications in the development of tube and sheet metal fabrication equipment, you can now find BLM GROUP hightech solutions in nearly every sector.
The company is dedicated to designing, manufacturing, and digitising systems for processing tubes, wires, and sheet metal. Its product line includes tube bending, tube end forming, wire bending, production sawing, laser tube cutting, combined tube and sheet laser systems, and sheet laser cutting machines.
With its headquarters in Italy, BLM GROUP UK Ltd, in Ampthill, Bedfordshire, provides tube processing solutions, equipment demonstrations, service and parts support, application development, and training to the UK and Ireland. For more, see www.blmgroup.com.
Having successfully diversified their sheet metal offering, Hertfordshire-based Ludwick Precision was looking to grow the business. They enlisted the ERP expertise of MIE Solutions UK Ltd to optimise their processes and improve operational efficiency. Here, MD Ryian Ludwick outlines how MIETrak Pro software is proving an essential tool for sustainable success.
Looking at Ludwick’s range of solutions and the variety of sectors it serves, it’s hard to believe the company started out making CPU racking for the MoD. Now, it’s offerings encompass office and commercial interiors, architectural design, and even specialised benches for the medical and pharmaceutical sectors.
To make the leap, Ludwick has implemented a meticulous growth strategy, a large part of which has been integrating ERP software from Worcestershire-based providers MIE Solutions UK Ltd, as MD Ryian Ludwick explains:
“I’m a firm believer in processes. Without an operating procedure, you’re not going to grow your company,” he says. “We needed a comprehensive ERP solution to seamlessly change our production inventory and scheduling. MIE Solutions caught our attention for their proven track record in addressing these specific challenges within the manufacturing sector.”
MIETrak Pro is MIE Solution’s most comprehensive ERP system. Designed to empower manufacturing companies in overseeing all areas of their operations, it encompasses production planning, scheduling, inventory control, procurement, and quality management. By optimising these processes, MIETrak Pro helps manufacturers enhance their overall efficiency, respond more effectively to customer demands, and boost profitability.
Designed with flexibility at its core, MIETrak Pro software offers a fully customisable approach to optimising manufacturing processes. “MIE created dashboard widgets for individual departments to optimise the front end for our various users,” Ryian explains.
“Prior to MIETrak we’d use spreadsheets and emails for generating RFQs; now our estimators have standard operating procedures that are faster, smoother, and make it easy to onboard new staff.”
“We’ve also been able to set up all our own inventory categories for consumables and create our own sequential, internal codes for everything. You can change up the whole system to suit your needs and it allows you to go deep. MIE installed a number part generator for us, too, that generates the next available number on orders and avoids double entries.” .
Alongside stock control, Ludwick is benefiting from MIETrak’s scheduling module to plan and keep track of production on orders. “The backward scheduling feature allows us to enter the delivery date requested by the client and the software gives us a start date for the project,” Ryian explains.
“The scheduling module has improved our operational efficiency and led to more reliable product delivery. It’s also helped communications with
our customers on their order status, giving us more transparency, so we can be proactive in contacting them if the system flags a change to the timeframe.”
MIETrak provides real-time kiosk and shopfloor data capture, allowing manufacturers to set their own KPIs and monitor them against tangible results, something Ryian has found invaluable. “For me, one of the most important performance reports within a business is the estimated versus actual,” Ryian shares.
“No matter where I am, I can log into MIETrak and get a visual of what’s happening with the business via real-time data on my dashboard. As a business owner, you want that. The goal is to capture this data and feed it back onto our processes and training, so if we are making a loss on a job, we can implement changes to rectify it quickly.”
Providing Manufacturing And engineering companies with full business transparency
The scheduling module has improved our operational efficiency and led to more reliable product delivery. “
MIETrak’s data-driven productivity analysis has already proved its worth in helping Ludwick identify areas of the business that are primed for investment. “MIETrak monitors our capacity. It will tell you if it’s 100 hours one minute and 50 hours the next due to a lack of resource within the business because someone’s absent or that skillset just isn’t there,” Ryian says.
“The lack of skill in the UK makes it difficult to hit high-volume delivery dates. Based on MIETrak data, we’ve made the decision that, given the projects we’ve got coming in this year, we’re going to struggle unless we hire five more welders – which aren’t available - or bring in a robotic welder, which is arriving in the next month.
MIETrak’s allowed us to take a step back and work on the business rather than in it.”
A supportive partner
MIE Solution’s comprehensive training and user onboarding has helped smooth the introduction of the new software – and the MIE Solutions team are always on hand when Ludwick requires assistance, as Ryian says: “MIE have gone out of their way to help tailor the solution to our manufacturing needs. They’ve got excellent customer service and they’re competitive in terms of what other ERP systems are offering.”
“If you’re looking to achieve sustainable growth, MIETrak is a leading software in terms of its flexibility and agility. It isn’t an instant fix, but it is the answer.”
With over 25 years’ experience and a worldwide presence, MIE Solutions
UK Ltd is one of the country’s leading providers of Enterprise Resource Planning (ERP) and production control software for the professional manufacturing sector.
Discover more about MIE Solutions, see mie-solutions.co.uk
ADowntime is a death knell for productivity and efficiency. When it all goes wrong, you need a reliable repairs service that will get you back up and running – fast. Buck Engineering Ltd provides proactive servicing and repairs for sheet metalworking machinery across England and Wales. Here, founder Karl Murphy shares his expertise and insight into bestpractice maintenance and reveals how Buck Engineering can support your sheet metal business
s a time-served engineer with a strong background in the sheet metal industry, Karl Murphy was perfectly placed to spot a gap in the market when it comes to repairs and maintenance support. In answer to this, he established Buck Engineering in 2022.
“Often, facilities are dealing with lots of different suppliers and contractors for their machines; we offer a service that supports a broad spectrum of machines and manufacturers, including presses, press brakes, guillotine, bending, sawing, rollers, and formers,” Karl explains. “We cover as many sheet metal machines as we can on the shop floor to make servicing and repairs more cost effective and less time consuming for the customer.”
Buck Engineering provides a full repairs and maintenance service to the sheet metal industry across England and Wales, including breakdown support callout and repairs, and spares and parts.
With engineers stationed at various locations and access to a wide range of parts from various suppliers, Buck is able to ensure swift response times and smooth logistics. “We want the customer to feel they’re being looked after. Your emergency is our emergency,” states Karl. “We answer most enquiries within half an hour, and in most cases, we can get an engineer out to the customer within 24 hours.”
The most common issues Karl’s team sees are often caused by a lack of basic regular maintenance and inspections. “It’s surprising how many customers we come across that haven’t had their machines serviced in years, and only spend money on them when they break,” he reveals. “We see everything from gears with missing teeth, to seized rollers and oil leaks aplenty. But we also tackle far more complex issues like crowning on press brakes, pressure issues on hydraulic presses, and electrical and software issues. We can also do things like testing of oil and contaminants, load cell testing to make sure that the machine is outputting the correct load, and light screen testing.”
In addition to repairs, Buck also offers complete service packages, tailored to the individual client’s needs. “Some customers have a machine sat in the back room and they only use it every now and then, and others have a 24/7 production environment,” says Karl. “We look at how much the machine is used and tailor the service package to suit the customer. By making time for regular servicing by our specialist
engineers, we can keep machines running in better condition for longer, optimising quality product output and maximising productivity. We aim to make this process as simple and costeffective as possible for the customer.”
The team specialises in servicing and repairing machines that are 10-40 years old, which can present its own challenges and requires a certain set of expertise, as Karl explains: “A lot of machines we work on, the parts are obsolete. It involves thinking outside the box and reverse engineering! Some machines don’t have any electrical circuits and we have to use our knowledge to work through the circuit to identify the problem. And if we do need parts, we have to find suitable alternatives, which can be difficult –but that’s what we do!”
As well as preventative maintenance, Buck provides an upgrades and modifications service, to help prolong the lifespan of older machines and keep them updated with the latest technology and working at peak performance.
“We help customers improve their existing machines with package upgrades,” explains Karl. “Somebody might have a manual back gauge and we can offer a package which makes that machine CNC compatible.”
In the near future, Karl plans to offer a complete machine refurbishment and a remanufacturing service, offering customers a more affordable, sustainable alternative to purchasing a new machine. “We’re still growing. There’s a lot in the pipeline,” he says.
It’s surprising how many customers we come across that haven’t had their machines serviced in years “
Get in touch to arrange a visit to your site and see how we can help you today!
buckengineeringsolutions.com
Following Covid, the increased need for UK manufacturers to produce onshore assemblies, not just components, has led to a demand for more agile, comprehensive machining solutions. Here, Chris Sharratt, UK agent for German company Bihler, shares his insight into the growing trend for integrated processes and automation.
As Bihler enters its 71st year of designing and manufacturing bending, forming, and stamping equipment for the metal-forming industry, it’s notable how customer requiremenents have changed. Increased production speeds and automation are now essential for customers to compete in this demanding and fast-paced world. Bihler has met those requirements, providing world-leading solutions in both production speed and automation. For many years, Bihler has supported customers with full turnkey solutions, offering “plug and play” manufacturing systems that provide immediate and tangible results.
Germany-based machine manufacturer
Bihler has been a leader in the fields of innovation and automation for over 70 years. With a host of world-firsts to its name, the company developed the original automatic stamping and forming machine in 1956, and in 2000, launched its BIMERIC servo-controlled forming system, revolutionising the production of metal parts from strip and wire material.
Bihler specialises in flexible process modules and intuitive control technology, combined with costeffective automation solutions for stamping and forming parts, as well as fully integrated assembly production systems. As UK agent for the family-run business, Chris Sharratt has first-hand insight into the changing demands of the post-Covid climate.
“Although there’s still a market for the traditional cam-driven Bihler machines, the majority of customers are seeking the inclusion of additional automated processes such as welding, tapping, screw insertion, crimping, contact
Bihler’s
soldering, and even measuring and inspection to produce assemblies rather than components that require assembly,” Chris shares.
“These new servo-driven machines such as Bihler’s BIMERIC Modular, offer manufacturers huge savings on production costs, labour, and the time it takes to produce each finished assembly,” he continues.
“One automated servo machine can do what 10 skilled people did previously, not only saving on labour costs but also solving the problem of skills shortages. There’s also the time-saving benefit of building in batches without the need to store 10,000 of each component while others are being made.”
This faster turnover enables manufacturers to see a much speedier return on their investments, as Chris points out: “Producing assemblies in this way means you don’t have so much money tied up in work in progress,” he says. “Not to mention the cost of storing all those components.”
Alongside improved efficiency, Bihler’s automated integrated assembly systems give manufacturers greater control over production output. “It’s a quantum leap forward in terms of speed and quality,” Chris enthuses.
“Manual welding, especially on small components like electricals, is a dexterous task. Discrepancies are inevitable, which can be costly and cause delays. Bringing assemblies inhouse instead of offshoring them also gives manufacturers greater control over the overall quality and consistency of finished products,” he adds.
“
One automated servo machine can do what 10 skilled people did previously. It’s a quantum leap forward in terms of speed and quality
Flexible, integrated servo machine systems, such as Bihler’s new LM 2000 linear machine platform, don’t just enable in-house assemblies. They also boast mind-blowing changeover times and unrivalled efficiency, perfectly aligning production capabilities with the demands of today’s customer-driven market.
“It was Henry Ford who said: ‘you can have it in whatever colour you like as long as it’s black’,” smiles Chris. “But that mentality died out 80 years ago. Now, it’s much more usual to get 10 orders of 100,000 units in 10 different colours than one order for a million identical units. It’s a challenge; the volumes are still there but they’re not single volumes.”
To meet increased customer demand for smaller batch-produced assemblies, manufacturers are moving away from traditional cam-driven machines, which can take up to eight hours to set up, and choosing servo-driven solutions such as the the LM 2000-NC. With cycle rates of up to 250 rpm, it caters perfectly to small and medium batch sizes with a high number of variants, and thanks to its ‘plug and produce’ principle, can be set up in around 60 minutes.
“It’s a customer-driven market. To stay competitive, the new attitude has to be: ‘You’re the customer and you can have it in whatever colour you like!’” says Chris. “That’s where these faster setup times really come into their own, giving manufacturers the flexibility and agility to meet customer needs in a timely and cost-effective way.”
As Automotive OEM’s push to introduce electric vehicles (EVs), the need to produce high-volume electrical components and assemblies has increased. Bihler’s knowledge, gained
over more than 50 years of supplying manufacturing equipment to the electrical and electronics industry, means they’re perfectly positioned to cater to the demands of the emerging EV market, as Chris explains:
“Bihler has a wealth of experience incorporating assembly processes like welding, and screw cutting, tapping, and insertion into its machine platforms for producing electrical parts such as cell contact systems, busbars, switches, and shielding sleeves,” he says. “These parts are all integral to the manufacture of electric motors, of course, but these machines can also be used to produce wider automotive assemblies including seatbelt clips and seat adjustment mechanisms.”
In fact, owing to the machine’s flexibility, there are few industries Bihler doesn’t serve. “We cross so many fields from fountain pens and shavers to washing machines and wind turbines!” Chris says.
No matter the industry or product, the importance of proactive machine maintenance is critical to time-and cost-effective manufacturing. Bihler’s digital app gives operators live, indepth insight into the health and efficiency of each machine. “It will tell
you how the machine is running, if there’s a problem and what common errors you’re seeing, improving efficiency and reducing potential downtime.” explains Chris.
Bihler has taken its commitment to customer support one step further with its Augmented Reality (AR) Remote Service. Machine operators use headsets with integrated cameras that transmit a live feed of the operator’s viewpoint of the machine to a Bihler technician. The technician then uses AR to illustrate on screen the areas of the machine that require attention and talk the operator through how to fix it.
“It’s real-time fault analysis and troubleshooting that empowers operators to make their own adjustments and minor repairs while learning more about their machine,” says Chris.
As we enter 2024 and the global exhibition season begins, we look forward to welcoming visitors to the Bihler stands at all the exhibitions and discussing your manufacturing challenges. Find us at MACH 2024 in Hall 6 stand 579.
Chris Sharratt is Director of MI Automation Ltd, exclusive representatives of Bihler equipment in the UK and Ireland. To learn more about Bihler and what its solutions can do for your business, see miautomation.co.uk
or visit Bihler’s main website: bihler.de/en
As well as giving UK exhibition premieres to new product lines, the Kerf Developments stand at MACH 2024 has a more diverse and expansive range of products on show than ever before
The new Ultra marks the arrival of the next generation of profile cutting technology “
Rochdale manufacturer, Kerf Developments, is well known for supplying industry leading oxy/ fuel, plasma, waterjet, and fiber-laser cutting machines. This year at MACH, attendees have the chance to see two new machines in Kerf’s offering: the Kerf Ultra and the LINC-CUT FIBER 1530A Fiber Laser system. These latest premieres, showcasing on Stand 330 in Hall 6, are also complemented with automated cutting and welding solutions from technical partner Lincoln Electric. To c
The first new machine showcasing at MACH 2024 is the Kerf Ultra. This new arrival provides both oxy/fuel and plasma cutting in a single machine solution. This combination machine drastically expands the cutting
capabilities, flexibility, and processing speed for end users while reducing setup time and material changeovers.
For customers of the longstanding industry-leading Kerf models, the new Ultra is a technological leap forward that marks the arrival of the next generation of profile cutting technology. This innovation brings the performance, speed, and precision of laser cutting to a plasma cutting platform for the first time.
With significantly improved speed, precision, repeatability and cut quality than previous models, the new Ultra achieves these elevated parameters by introducing a brand-new motion system and new linear slide technology that sits upon a brand-new machine frame design.
This combination of factors provides vibration-free cutting under the most
challenging conditions, subsequently delivering a remarkably smooth cutting motion and an unparalleled cut quality that eliminates secondary hand finishing.
The Ultra is designed around a solid fabricated portal frame utilising independent rails that are available in cutting table sizes from 3m x 1.5m right the way through to 40m x 4m.
The machine is controlled by the industry leading Burny 10 LCD PLUS CNC control system and has a new heat shielding system that extends the performance and longevity of the machine.
The Ultra can be configured with UltraSharp plasma technology, as a single or multi-head oxy-fuel cutting machine, or as a combination machine with both technologies supported on the same machine. It is available in a range of widths and lengths to suit customers’ requirements. There is also a wide range of Lincoln Electric Fineline plasma units to choose from.
A unique feature of the new Ultra machine is the oxy/fuel Automatic Gas Console (AGC) available from Kerf. Designed to address the current skills shortage within the manufacturing industry, the AGC replicates the skill and knowledge of an experienced machine operator using pre-programmed technology databases. Through digital proportional valves, this technology sets variables such as cut heights for piercing, low and high preheat gas pressures, and the pierce curve, reducing spatter and blow back.
The new AGC on the Kerf Ultra also reduces gas consumption, increases consumable life, improves cut quality, and helps to de-skill the process for the machine operator.
The second machine premiering at MACH 2024 is the LINC-CUT FIBER
1530A Fiber Laser system, which is brand-new to the UK. For more details on this exciting new addition, visit the Kerf stand (Stand 330 in Hall 6) where Kerf are proudly showcasing the machine and sharing news of their partnership with Lincoln Electric, the world’s largest manufacturer of cutting and welding equipment.
As an outright industry leader, the reputation of Lincoln Electric is unsurpassed in its field. On the Kerf MACH stand, you’ll find Lincoln representatives presenting the latest Linc-Cobot system for collaborative robotic welding as well as demonstrating the Python X automated cutting technology alongside the Zeman automated beam welding technology.
With the new product arrivals complementing their already impressive portfolio, Kerf is now the UK’s leading partner for all your profiling requirements. The diversity of highquality cutting solutions, combined with the welding and automation technology from Lincoln Electric displaying on Stand 330 in Hall 6, make it a ‘one-stopshop’ for all your cutting and welding requirements.
Founded in 2002 as a service centre for profile cutting machines, Kerf Developments is built on its inside knowledge of the most reliable and robust cutting machines on the market. Now, Kerf is the UK’s leading supplier of quality oxy/ fuel, plasma, waterjet, and fiber-laser cutting machines, delivering turnkey solutions backed by the highest levels of post-sales support and service. For more information, visit kerfdevelopments.com or call 01706 757670.
Managing
Bruderer UK, Adrian Haller, tells us about the potential of a manufacturing boom taking place in the country and the reasons behind it
Bruderer manufactures and builds high-speed, precision stamping machines for all kinds of industries. Its machines are used to create products for all industries, from the medical to the automotive sectors, from electronics to the food industry. The odds are that at some point today you touched a product whose components have been in a Bruderer machine.
“It leads us to lots of different projects and with that come all sorts of different enquiries where we have to bring customers solutions for components new and old,” says Adrian Haller, Managing Director at Bruderer UK. “What we find in our industry is that due to the lack of skills and the more intense relationships businesses seek out with their suppliers, what we offer now is a full turnkey solution, from the ground up. It empowers us to build the machine itself, the tooling, the guarding, ensure it is conforming to all relevant standards and deliver it to the customer who will press the button and make the parts they need.”
The company sells itself with a multipronged attack. It offers high-speed production coupled with high levels of precision. It has been validated to provide products to industries that demand the highest standards, and with good reason.
“To serve industries such as the medical industry, validation can take up to two years,” Haller points out. “We can go through these processes and meet all customer and regulatory requirements. We pride ourselves on being professional within the manufacturing sector, for metal components, plastic components and more, applying that knowledge to any part of the manufacturing sector.”
In Haller’s view, the manufacturing sector in the UK is the most exciting place to be right now.
“Nobody has a crystal ball, but you can see a manufacturing boom is happening,” he insists. “There are a lot of factors around that, but one of them is that Covid demonstrated very acutely that the UK has no supply chain close to home. It shone a very bright light on what the UK can and cannot do for itself.”
Haller argues that more companies are starting to invest in the UK, both the companies already here and the international companies that have seen the potential of the nation’s manufacturing economy. It is a good news story, although one that has not received as much widespread media coverage as it might have. “People say Britain doesn’t make things anymore, but we make a lot of stuff,” Haller says. “Not the cheap stuff, but where there needs to be a lot of thought and a lot of technical ability, British manufacturing has the know-how and technology to bring it to fruition. We have gone from strength to strength”
Haller points to Bruderer’s own project portfolio as powerful evidence of just that.
“The roots of these projects are embedded in the UK economy. We cannot but make them in the UK, so those products are staying here,” he says. “The onset of EV technology has helped with the boom for battery manufacturing, while the boom in housing construction is encouraging manufacturing there. The electronics sector, as we all know, has had semiconductor supply chain issues, but now that sector is racing to meet demand.”
It is an industrial boom that Haller wants to put at the heart of the country – literally. Bruderer has moved its head office from Luton to Shropshire, close to the heart of manufacturing and engineering in the UK.
“86% of Bruderer is Midlands based. So, we are doing this from an efficiency perspective, and a sustainability perspective, so we do not keep running cars up and down the motorway,” he says. “The future needs to be in the Midlands. It is the heart of the industrial revolution; it is the middle of the country.”
Bruderer’s own heavy investment in the UK as a Swiss company is a vote of confidence in the industry. Bruderer has been present here for 55 years, and that is because of the British manufacturing sector.
“If the business was not there in the UK we would not be investing,” Haller says. “We have stood on our own two feet in the UK for 55 years. The owner would not have us here if we did not make money. It makes us
proud that the UK manufacturing sector is doing as well as it is. We are seeing work come back from China, driven by the push for sustainability. What is the sense of sending aeroplanes back and forth across the world when it can be made here on our own soil?”
But for the country to truly make the most of that boom, it needs skills, and that is Bruderer’s next priority.
While industries are growing, that very growth is putting pressure on what is currently the UK’s very finite skill pool.
“There are not many skills around at the moment and the training schools are working very hard to develop our future through schemes such as apprenticeships, but there is a massive hole in the middle from the period when this country did not invest in training,” Haller says. “The big conglomerates are now paying excellent money to get engineers on site. We get around the problem by making sure our staff are paid well, and that the environment they work in is comfortable, so work is more pleasure than chore.”
The company’s move to Telford is part of creating that environment, including its brand-new plant and showroom, complete with a new rebuilding area, boardrooms, and canteen facilities.
“It has everything to help our people be more comfortable in the working environment while bringing in new people via apprenticeship schemes and working closely with companies to breed our own skilled people,” Haller says. “We will take on several apprentices a year through our training programme, not just for Bruderer but to build a wealth of knowledge that will grow the UK industry’s pool of skilled engineers.”
This forward-looking, industry-wide approach will continue to be at the heart of Bruderer’s strategy in the UK.
“We are going to be working with more partners to provide machine tools and full turnkey solution lines,” Haller says. “Our
five-year plan is to take on at least six more people within Bruderer UK in the electronics and mechanical engineering fields. We want to build to a point where we can increase the lines we put out to market, providing a greater range of machine tools supported by even higher levels of service.”
“
It makes us proud that the UK manufacturing sector is doing as well as it is
Formed in 1968, Bruderer UK has established a reputation of unrivalled excellence in the sphere of high-speed precision stamping. From their central location, Bruderer UK supplies its many customers with authentic Bruderer-made spare parts plus service support from a UK-based team of factory trained service personnel.
Over the years Bruderer UK has developed a policy of providing not only high-speed presses but a comprehensive range of other products and services to its customers, including tooling, coil handling, and feeding equipment, to complete turnkey packages.
Today, the company’s slogan is: “One name, a multitude of possibilities”; For more reasons to choose Bruderer UK as your one-stop-shop show for all press shop machinery and ancillary equipment, see Bruderer.co.uk and visit the Bruderer stand, UK Hall 6 Stand 482.
HERE’S A ROUND-UP OF WHAT’S HAPPENING ONLINE. CUT THROUGH THE NOISE, SHAPE AND FORM YOUR OPINION – THEN JOIN THE DEBATE!
GROUP RHODES TO SHOWCASE ITS BESPOKE METALFORMING MACHINERY AT MACH 2024
Group Rhodes, a leading manufacturer of metal and composite forming machinery, is demonstrating one of its innovative metalforming presses on Stand 6-599. The machine consists of two Rhodes Interform multi-axis presses, a complete robotic handling line and an integrated conveying system, capable of processing components at a rate of 1 part per 70 seconds.
YOUR POTENTIAL: THE APPRENTICESHIP PROGRAMME AT JC METALWORKS
Ready to embark on a transformative journey in metal fabrication? From operating CNC cutting and forming machines to learning TIG, MIG, and spot-welding techniques, the JC Metalworks apprenticeship programme offers hands-on exposure, allowing apprentices to choose a specialisation that aligns with their capabilities and interest for a fulfilling career in the industry.
AP&T’S PRESS-HARDENING CONCEPT LIVES UP TO CAR MAKERS’ INTEREST IN LARGE BODY COMPONENTS
Economical, lightweight, and more eco-friendly, press-hardened body components are simpler to produce. Made using large blanks consisting of many smaller welded parts, processes such as ArcelorMittal’s multi-part IntegrationTM (MPI) are wellsuited to AP&T’s press-hardening concept, which is enjoying unprecedented success thanks to the industry’s growing interest.
Several of these beams reached impressive sizes: 914 x 305 x 201 and 610 x 305 x 238. Barrett Steel then processed these huge sections including shotblasting, primer painting, cut and drill, in-house, at Barrett Steel Shoreham and Barrett Central Processing depots. Barrett’s state-of-the-art facilities set them apart, providing a distinctive advantage in precision and quality control.
Compass Business Finance is promising a lot of ‘buzz’ on its stand (6-44), where visitors can learn more about growing their business profitably and the best possible financial solutions to pursue and develop the latest innovations. There will also be some fun competitions and prizes up for grabs.
This state-of-the-art machine will now allow JW Laser to efficiently offer metalbending services which will vastly improve the quality products manufactured. With the Amada HRB1003’s 8-axis control system, the company can now achieve the most intricate bends with absolute accuracy. This expanded level of control allows JW laser to handle a broader range of applications.
From automotive to aerospace, the significance of tube-bending machines cannot be overstated. At the forefront of this technology stands AMOB, a global leader in manufacturing top-quality tube bending machinery. Originating in Portugal, the company’s commitment to innovation, quality, and customer satisfaction has driven its expansion across the globe over the last six decades.
Unifabs’ growing workload was putting increasing demand on its single Haeger 824MSPe press. Luckily, their partners at Press-Form Machinery Ltd had the answer: two Haeger 824OT Lites, which have more than doubled the company’s capacity for insertion overnight
Unifabs Ltd has experienced unprecedented growth since it first launched 16 years ago. Starting with a single machine and two employees, the Midlands-based manufacturer, which produces precision sheet-metal parts and products, now offers a full design-to-delivery service to a broad customer base of UK brands and global manufacturing companies across a range of market sectors.
Its Nuneaton facility, which offers CNC punching and laser cutting, press braking and panel bending, inserting, welding, powder coating, and assembly has expanded to incorporate an impressive 54,900-sqft. The Unifabs’ team now totals 150 dedicated staff with a flourishing apprenticeship programme that nurtures newcomers to the sector. It’s the kind of industry success story that puts British manufacturing on the map.
Along with fast growth and increased demand comes the need for improved productivity – and Unifabs has embraced this wholeheartedly through automation.
The company’s invested £3.25 M in new equipment and its facilities over the last three years, including partnering with metalworking machinery suppliers Press-Form Machinery Ltd to develop its fastening capabilities using their Haeger presses.
“Continual investment in state-ofthe-art manufacturing technologies such as the Haegers has helped us
achieve this sustained growth,” says Jenny Millington, Unifabs’ Marketing Executive. “By staying at the forefront of technology and adopting automation where possible, we can maintain our position as a leading manufacturing partner to our customers.”
After trialling a single Haeger 824MSPe press in place of their existing PEMSERTER, Unifabs was pleased with the service they received from Press-Form and impressed with the Haeger’s performance. The company decided to expand their capabilities further, exchanging the 824MSPe for two brand-new Haeger 824OT Lites, a switch Press-Form was happy to make as part of their ongoing contract.
“With our expanding workload, we were often coming across panels with multiple different fasteners in one part,” explains Unifabs’ Technical Director, Matt Grealy. “One of the main selling points for the 824OTLs was the ability to automatically insert multiple kinds of fasteners in one handling. It also allows us to fit all the fasteners and sizes we currently use as well as offering further scope for future needs and solutions.”
Press-Form carried out case studies to help Unifabs select the best machine for their needs. “Press-Form helped us identify a bottleneck in the department and suggested the right machine to alleviate it,” Matt explains. “They conducted case studies on our regular parts and gave us time-saving data based on using the new machines as well as a demonstration of the 824OTL’s features.”
The 824OT Lite is Press-Form’s most versatile and compact Haeger solution for fastener insertion. It boasts 3-second tool changes and a new feed bowl design that allows for a feed rate of two different fasteners every three seconds.
This increased efficiency has seen Unifabs’ insertion capacity more than
double overnight. “It’s also allowing us to streamline and improve the process with no detriment to quality,” Matt asserts. “We can now offer many more inserting options to our customers thanks to the tonnage and versatility of tooling on the 824OTL. The compact design of the machines has allowed us to fit them into our production area without taking up too much valuable production space.”
The Haeger’s combined upper tool changer and 3D part display make it easy for operators to see where the next fastener is positioned without the need to manually load it, while the fastener and length detection features guarantee the inserts are placed correctly every time. “This has helped increase productivity and improved the quality of the parts,” says Matt.
“The step-by-step wizard and easy-tomanage tool changeover have made daily life easier for the operators. We now have the ability to quick change up to four different tool set ups,” he shares. “Removing the need to manually load the inserts and double handling of parts has made the department massively more efficient without increasing labour. It’s also helped reduce scrap and issues caused by human error.”
Press-Form’s comprehensive service has provided Unifabs with ongoing support to develop its insertion capabilities. From recommending the right machine to installing the 824OTLs and onboarding operators, Press-Form has partnered the Unifabs team – and continues to do so with advice, training, and servicing.
“Any issues have been quickly responded to and resolved. We’ve also found Press-Form helpful when looking for bespoke tooling solutions, and we’ve received further training in recent weeks to help develop the department,” says Matt.
“After our experience with our previous Haeger press, Press-Form was our first choice when looking to expand our inserting capacity. We are very happy with the 824OTLs and the service from Press-Form. We would definitely recommend them to anyone looking to streamline their fastening needs.”
“
It’s also allowing us to streamline and improve the process with no detriment to quality
We can now offer many more inserting options to our customers
With over 30 years’ experience in the supply and servicing of sheet metal working machinery, Press-Form Machinery is firmly positioned as one of the UK’s leading providers of metal process equipment.
The Yorkshire-based company represents many high-profile equipment and system manufacturers from Europe, USA and Canada, and has an extensive range of productionenhancing machinery for sale.
Its extensive expertise within the industry provides a firstclass service to clients. For more information, see Press-form.co.uk or visit the Press-Form stand, Hall 6 Stand 580
After suffering supply chain issues and serious production delays, Advanced Air UK Ltd turned to coil processing experts Decoilers & Feeders Ltd for a bespoke solution to bring their tube rolling provision in house.
Delays are an inevitable part of manufacturing; at some point in the process, things are going to go wrong. Whether it’s a machine or a supply chain breakdown, there are some days when projects just aren’t moving forward. But when those days turn into weeks – or even months, that’s the time to reassess whether current processes are in fact working at all.
This was the case for Advanced Air UK Ltd, an established supplier of air distribution products to the UK building industry. They approached Decoilers & Feeders Ltd in 2022 to address their tube rolling issues following months of supply headaches and delays caused by sourcing components from overseas.
“Our previous component supplies were sourced from the EU,” explains Dave Burrows, Senior Manufacturing Engineer for Advanced Air UK. “We found there were various factors that meant we weren’t in control of the supply chain. These issues were exacerbated by the need to forecast demand six months prior to delivery.”
Advanced Air, a Norfolk-based company, celebrated its 50th birthday last year. Its growth has come from innovative product development, in particular its energy efficient fan coil that boasts the lowest energy consumption of any in the marketplace.
A leading supplier of quality air distribution products to Mechanical and Electrical (M&E) contractors, Advanced Air specialises in supplying high-profile projects throughout the UK in areas such as Canary Wharf and the City of London. These projects include government, commercial, residential, industrial, and hospital buildings.
“The products we supply are often specified by the building design specialists or selected by the M&E
contractors with applications related to fire safety, smoke control, and managing comfort conditions such as applied heating, or cooling and ventilation,” Dave explains. “This means that as well as being on time, it’s vital our products are made to meet exceptionally high industry standards.”
Advanced Air was one of the first companies in this sector to be registered to BS ISO 9001. Its factory test facilities allow for real room mock-up, with test cells to demonstrate product performance on heating or cooling.
“Our products are independently tested to the highest standards for fire safety performance, smoke control, both cooling or heating output, and noise levels to ensure that data issued to customers is precise and accurate,” Dave continues.
These strict tolerances, coupled with the pressure of meeting major project deadlines and the need to expand their product line, were key factors in Advanced Air’s decision to invest in a bespoke DF47 Tube Roller from Decoilers & Feeders.
“We could foresee that as our planned product range expanded, our existing supply issues would become even more significant and problematic,” Dave shares. “This drove the decision to bring our tube rolling in house, giving us more control over our supplies, processes, and overall quality of the components, helping to reduce waste and improve efficiency at the same time.”
With a very specific need to produce smaller than average tube diameters, Advanced Air sought the coil processing expertise of Decoilers & Feeders to come up with a bespoke tube rolling solution.
“We looked at general purpose tube rolling machines but couldn’t identify a suitable system for manufacturing smaller tubes,” recalls Dave. “Once we realised we couldn’t source an off-the-shelf solution for our needs, we approached Decoilers & Feeders to discuss the project.”
“We came up with a detailed specification for a bespoke tube rolling machine, outlining the process method, operating parameters, and key features and attributes that needed to be achieved by the new process. We then worked closely with D&F to develop a machine concept and design brief, fully defining the fundamentals of the operation method, its goals, and inbuilt safety features, including light guards controlling the work environment and a specially developed control panel.”
Despite being outside their usual remit and a first for the company, Decoilers & Feeders drew on the information provided by Advanced Air to great success, working through the various design and process challenges to develop a machine that nailed the client’s detailed and demanding brief.
“The DF47 was designed with ease of use as an integral function enabling rapid set up from a predetermined list of individual component programs,” Dave explains. “Once the diameter is set up in the machine and the program is saved, it’s ready for bulk production of quantities on demand.”
The DF47 produces accurate rolled tubes of various lengths and diameters from flat profiled sheet metal blanks of thin gauge galvanised steel. The resultant butt joint is then TIG welded on a purpose-bought, dedicated tube welding machine, producing an excellent quality butt welded joint.
The new machine has been satisfying production demand for two years, proving a reliable addition to Advanced Air’s processes and a more than worthwhile investment.
“We now have full control of our supply chain, quality, and productivity,” enthuses Dave. “We’re no longer required to order bulk quantities of individually sized tubes at excessive lead times, consuming valuable storage space and the logistics associated with this – and we’re no longer at ransom to shipping delays. With the DF47, we can produce and dispatch finished products within days of lead-time instead of planning for months upfront.”
In conjunction with resolving their supply issues, Advanced Air has also been able to introduce two further product ranges that utilise components manufactured on the DF47.
Key to the DF47’s success and the resulting improvements to Advanced Air’s processes, is the working relationship Decoilers & Feeders has with
their clients. The company’s ability to listen to customer needs and collaborate on projects from start to finish sets them apart from the competition.
“We have a long-standing relationship with Decoilers & Feeders and have various pieces of equipment and processes supplied and supported by them,” says Dave. “Although they specialise in sheet metal processing equipment, they’ve also applied their skills and expertise in resolving, presenting, and delivering manufacturing solutions that are not perhaps considered to be their normal speciality – that really speaks for their capabilities.”
In addition to designing the DF47, Decoilers & Feeders fully installed and commissioned the equipment on site; their support included minor adjustments to aid manufacturing, and full operator and maintenance training for Advanced Air’s production personnel.
“Their support has been much appreciated. To date, the DF47 has performed well and proved totally reliable, and we know Decoilers & Feeders are always on the end of a phone should we need them.” Dave concludes.
We now have full control of our supply chain, quality, and productivity.
Incorporated in 2014, Decoilers & Feeders Ltd offers over three decades of coil processing machinery experience to the automotive, electrical, furniture, retail, and white goods industries to name but a few.
The company provides UKwide servicing to upgrade, refurbish, and maintain metal coil feeding equipment, as well as supplying and installing new and refurbished machines and parts.
Decoilers & Feeders also design and supply electrical control panels, specialising in creating, troubleshooting, and developing software on metal coil feeding equipment and in other industries.
The company’s experience, customers, and supplier base continue to strengthen every day. For more, see decoilersandfreeders.com
Ideal Heating has been manufacturing top-quality boilers for over 100 years. When the company needed to update its presses, they turned to expert suppliers PressCare UK Ltd for a modern, automated solution – the SEYI SLG2-400-S5
With over a century of boilerbuilding experience under their belts, Ideal Heating is more than just a household name: it’s a British institution. Founded in 1906, the company was among the first to bring central heating to lower-cost British homes. Its pioneering Cookanheat, a revolutionary 1920’s design, combined an open fire, central heating boiler, cooking oven, and hot cupboard in one freestanding unit, making heating and hot water more affordable to the masses.
Now, over 100 years on, Ideal Heating is continuing to lead the way with award-winning boiler designs that marry technology and innovation with efficiency in the home. Its Hullbased facility produces and supplies over 500,000 boilers a year. To do this, the company needs to ensure its manufacturing processes are as modern and effective as its heating systems.
“Up until a few years ago, we were using manual presses to produce the domestic steel boiler chassis, with operators swapping the parts over by hand,” says Head of Engineering Services for Ideal Heating, Paul Jasper. “This manual process was causing a bottleneck and affecting our output; our domestic range of products needed a faster, automated process to keep up with demand and allow us to maintain supply and improve our efficiency.”
In their quest for the perfect supply partner, Ideal Heating struggled to find the right combination of Power Press machine and automation to meet their needs. “A lot of the companies we approached wanted to do a full turnkey solution using their equipment and automation, which didn’t provide us with what we wanted,” Paul explains.
After considering six potential suppliers, Ideal Heating began working with PressCare in 2014. They chose the company based on the strength of their SEYI machines and their flexible approach to working with a third-party automation provider.
“PressCare had the optimum solution for us and were willing to work with an outsourced automation company of our choosing – AP&T – to perfectly tailor the system to our needs,” says Paul. “We knew what we needed to achieve, and PressCare were quick to understand our requirements. They made suggestions around what could work without us having to compromise.”
PressCare is a West Midlands-based engineering company specialising in power presses, coil handling equipment, and automation systems. Alongside its sheet metal working services, they are the UK agent for the SEYI press manufacturing group, based in Taiwan.
SEYI presses are designed and built to the highest standards to meet the demands of the modern stamping room floor. Over the last 60 years, the company has gained a global reputation for excellence, continually evolving its press designs to implement the latest technological advances and manufacturing techniques.
these machines also gave us some additional versatility being crank linked presses was key in helping us make our selection,” says Paul.
With 400 ton of force available, the SEYI SLG2-400-S5 has the headroom to produce any part Ideal might expect to manufacture within their industry.
“The largest component we can make on the SEYI is around 1200mm x 800mm, which is well above our current requirements, but does leave us with options in the future if needed,” shares Paul.
The machines facilitate multiple precision stages in blanking, piercing, bending, and forming for single or progressive application. The moving bolster system allows for super-quick tooling changeovers and its ability to prepare for the next setup whilst the machine is still running significantly reduces downtime.
“Where you’d normally take an hour or so to change this type of press over, we can do it on the SEYI in 10-15 minutes,” says Paul. “We can now produce in excess of 700 components an hour.” The parts are then stacked using tailored automation.
SEYI SLG2-400-S5
PressCare spent several years working with Ideal Heating to find a solution that best fit the company’s specific requirements. They decided on two SEYI SLG2-400-S5 straight sided, twin crank, link drive mechanical presses with a bespoke integrated moving bolster system to reduce tool changeover times.
“The main factors we were looking for were bed size and tonnage; the fact
“
The volume of boilers we’re able to produce has increased massively since 2012; we’re now producing around 3,000 boilers a day – that’s over 50,000 a year!
The presses were installed at Ideal’s plant in Hull in May 2018 and integrated with automation systems supplied by AP&T to give a highly flexible, automated production line.
“The main win for us is faster process times and the ability to now react quickly to any changes in demand, even on a daily basis if needs be,” reveals Paul. “The volume of boilers we’re able to produce has increased massively since 2012; we’re now producing around 3,000 boilers a day – that’s over 50,000 a year! It’s also given us more flexibility to change the variant of boiler we produce.”
Ideal’s setup uses two SEYI presses working side by side. “The parts go through one press directly into the other press. The two machines are synced to constantly adjust their speed to work in time together and give us the best strokes per minute,” explains Paul.
The simplicity and speed of the machines’ tooling changeovers, coupled with their easy-to-use controls, have made them a welcome addition to the shopfloor.
“At first the operators were a little overwhelmed by the size and complexity of the equipment compared to the manual presses we had previously,” says Paul. “But having received training support from PressCare and AP&T, the team is now very comfortable running the SEYIs. Feedback has been that setting the machines and the press side of things are lot simpler.”
Six years on and the twin SEYIs are still going strong, proving reliable and trouble-free assets to the Ideal shopfloor. “I can’t fault the machines,” says Paul. “We’ve seen a great improvement in our workflow, and
with our process being a lot faster and more efficient it’s created a cost-saving benefit to our customers. We’ve also been able to significantly reduce our lead times for purchasing a boiler.”
PressCare continues to work with Ideal Heating to service the SEYIs and provide ongoing support and advice to further develop their manufacturing techniques. “We’ve had discussions with them regarding improvements with the process in and around the machine cell,” reveals Paul. “The working relationship we have with PressCare has proved to be very successful. I would think anyone would benefit from using PressCare for any Power Press projects they have in mind,” he concludes
PressCare UK Limited was established in 2002 and offers a range of services to the sheet metal working industry including
servicing, safety inspections, electrical and mechanical repairs and modifications, preventative maintenance programmes, machine moving, installation and commissioning, guarding solutions, CE marking, turnkey project management, and general consultancy.
They are also the UK Agent for the SEYI press manufacturing group, providing a comprehensive service from initial advice on machine selection through to installation, after sales technical support, breakdown callout, and ongoing preventative maintenance schedules. For more information, see presscare.co.uk or call 0845 226 7617. Visit the PressCare stand in Hall 6, Stand 33
Mechanical / Hydraulic / Servo Presses
Coil Handling Equipment
Press Automation Systems
Press Ancillaries
Tool Protection Systems
Guarding Solutions
Full Machine Rewires
Safety Surveys & Upgrades
Installations & Inspections
Preventative Maintenance
Servicing & Spare Parts
Twenty years and nine machines later, the relationship between PAB Coventry Ltd and Prima Power is still going strong. So, when the time came for the Midlands-based manufacturer to invest in the latest fibre laser technology, Prima Power’s 8kW Laser Genius+ 1530 was naturally top of the list. Here, MD Danny Wheldon tells us why PAB bleeds blue and orange.
With 17 years of dependable service under its belt, the old Prima Power 4kW CO2 laser at PAB’s Coventry facility was still fit for purpose when PAB sought a more modern alternative.
Thanks to Prima Power’s regular servicing and maintenance, and the machine’s inherent reliability, the old Co2 has delivered over 100,000 hours of use since 2007. But advancements in technology and new customer requirements necessitated an upgrade to keep PAB at the cutting edge of the sheet metal sector, as MD Danny Wheldon explains:
“A new sector we’ve started to work with requires thicker steels than our standard product. The previous Co2 struggled with the speeds and quality of cut at the new heavy gauges, so we decided to upgrade for improved efficiency, quality and reliability –
17 years is very old for a laser!” he says.
PAB Coventry Ltd.’s partnership with global manufacturer Prima Power spans two decades. The companies first joined forces in 2004 when PAB’s then-MD Mark Brazier was looking to grow the business and broaden its offering. They chose Prima Power for the impressive performance of its machines and the steadfast reliability of its cradle-to-grave customer support.
“We’re one of the biggest users of Prima Power products in the UK and have an excellent relationship with them,” shares Danny. “Over the years, Prima Power has become a valued partner due to the levels of service provided from installation right through the life of the machine and the reliability of its products.”
Twenty years on, the same attributes put Prima Power at the top of PAB’s shortlist for its brand-new acquisition: a 8kW Laser Genius+ 1530, representing the very latest in fibre laser technology with an automated tower storage and load/unload system. For the new machine, PAB had some specific requirements for production, including the ability to process thicker materials and to boost productivity.
“We knew we needed automation, and the tower was our option of choice.
During a visit to Prima Power’s HQ in Italy, they were able to demonstrate this automation process efficiently and effectively. We were impressed with the technical ability of the Laser Genius+ – its speed and the quality of its cuts – and also the improved data feedback compared to previous models,” Danny says.
The new machine has been in use at PAB for several months now. Beyond meeting the company’s cutting requirements, its overall performance has exceeded expectations in more ways than one. “The Genius+ is considerably quicker than our old machine. With the higher power and newer technology, we’ve seen large gains in cutting speed and quality of cut on thick materials - up to 25mm plus on steel,” says Danny.
“We knew this would be the case, but there’s also the added value we didn’t expect, like the small diameter holes it has the power to produce in thick gauges. We’ve cut holes down as low as 3-4mm in the 20 mil, which is brilliant! Previously, this would have been completed as a secondary process on a CNC machine, but doing this now on the Laser Genius+ has allowed us to cut down on costs and production times.”
These increased capabilities have allowed PAB to create a new product range that’s enabled them to broaden their client base and made the company more competitive. Danny explains:
“Our longstanding customers are the likes of Aston Martin, Lotus, and McLaren. The medium-to-low-volume niche vehicle market doesn’t need 20mm-thick parts. With the new, thicker product we’re supplying, it’s allowed us to look at other sectors including a large defense supplier, which has given PAB a USP against some of our competitors in the local market. It’s also taken the risk away of being reliant on the automotive market.”
Operators at PAB have been impressed with the intuitive design of the new interface on the Laser Genius+, which has been developed and manufactured by Prima Power. “The new interface is very user-friendly, and the programming software and smart tools
are easy to use,” reports Danny. “The excellent operator and programmer training provided by Prima Power has made for very smooth installation and onboarding process with the new machine.”
Lights-out production is now more reliable, thanks to its increased precision and automated processes. “Features like the auto nozzle change and auto centering, and the ability to skip parts or sheets when working lights-out has reduced the need for manual intervention to increase our unmanned output,” says Danny.
PAB’s highly demanding customers are at the forefront of their industry, with a wide range of product requirements that call for high-speed, precision output. The benefits of the Laser Genius+ have been clear.
“Many customers, old and new, have been impressed with the look of the machine and the range of materials it will cut,” Danny shares. “Its faster cutting speed and tight tolerances means reduced costs and a betterquality product for our customers, which has opened up new opportunities for the business.”
It’s not just the quality and precision of the parts produced on the new Prima Power machine that gives PAB its customer appeal, however. Their committed partnership with Prima Power has seen the company acquire a total of nine Prima Power machines –eight currently under its roof – including 2D and 3D lasers, press brakes, and a CNC punch. It’s an impressive sight to behold.
“This is our ninth installation with Prima Power over the years. If Prima Power is looking to sell a product to another manufacturer, we often invite their potential clients to look around our factory,” Danny says. “When we walk our own customers around, seeing
the Prima Power colours and branding across the whole facility makes a real statement. It shows we’re a modern, forward-thinking company that’s embracing the very latest technology and manufacturing techniques. And it shows we’re serious about investing in the best for PAB as a business, and our customers.”
“
It’s allowed us to look at other sectors and given PAB a USP against our competitors
Global supplier Prima Power provides businesses of all sizes with targeted dynamic technologies that enhance profitability in sheet metal working.
With one of the widest product ranges in the industry, the company covers all stages of sheet metal working including 2D and 3D laser machines, punching and combined punch/laser and punch/shear machines, press brakes, panel benders, Flexible Manufacturing Systems, and automation.
Offering a full range of modular solutions, Prima Power’s customer-centered approach provides unrivalled cradle-to-grave support. For more information, see primapower.com
MOVE IT, CUT IT, SELL IT LEVEL UP YOUR PRODUCTIVITY WITH THE SPEED OF OUR MODULAR SOLUTIONS
Our 2D laser machines are made to suit your real needs, simple as that. Run your big or small batches in highly competitive lead times and always deliver the best-in-class cutting quality.
Best-in-class performance with up to 20% faster cycle times, thanks to 28 m/s² acceleration and 180 m/min trajectory speed.
Optimal cost-effectiveness with gas savings up to 40% and a remarkable 96% sheet utilization
Seamless integration with modular and scalable automation solutions, from stand-alone setups to fully automated production cells, integrable at any time.
Partner with the knowledge and dynamism of Prima Power. Evolve by integration
With its sought-after tube-bending services and expertise, Bradford-based White Cross Ring Co Ltd has embraced the latest technology to keep up with customer demand
White Cross Ring has been manipulating metal for over 50 years. The company was founded in the 1960s when two partners set up a business manufacturing angle rings, washers, and flanges.
Soon, their quality products and entrepreneurial mindset saw White Cross Ring expand its offering into tube bending and fabrication. Five decades on, White Cross Ring’s services are still evolving to meet the ever-changing needs of its customers.
“Our willingness to explore innovative fabrication processes and techniques has always been one of our major strengths,” says MD Tom Horner. It’s led to White Cross Ring supporting some exciting and unusual bespoke projects over the years including the restoration of York Minister’s famous Rose Window after the devastating fire of 1984.
Years of experience catering to a diverse range of clients has given White Cross Ring the edge when it comes to economical solutions for tube and metal section bending. With demand in this sector steadily increasing, White Cross is continuing to forge the way as a leading bespoke supplier by investing in new equipment and staff training.
To support the company’s continued growth and the escalating need for its tube-bending services, White Cross’s most recent investment is an ELECT 52 Multi-Stack All-Electric CNC Tube Bending Machine from BLM GROUP.
“We’ve had a few good years recently and I want to ensure we continue to invest in the latest equipment,” says Tom. “We’ve seen a lot of growth in the section-bending and tube-manipulation areas of the business. This kind of machinery and technology will keep us on the cutting edge of the industry and
make it easier for us to pass those skills on to the younger workforce.”
With two BLM NC842 tube benders already pulling their weight on the shopfloor, BLM was a natural choice for White Cross Ring’s investment. “The BLMs have been really good machines,” says Tom. “And knowing we’d get the right level of support through BLM UK was like a comfort blanket; nothing was a problem.”
BLM’s ELECT range boasts machines capable of manipulating tubes up to 150mm in diameter. White Cross Ring opted for the ELECT 52, a mid-range machine capable of handling tubes of up to 50mm despite its relatively compact footprint.
Its features include left or right-hand multi-radius bending, simultaneous multi-tool capabilities, automatic seam and hole detection, and a pneumatic split bend die for bending square and rectangular tubes.
The machine is now well embedded at White Cross’ Bradford-based facility. Its multi-tool functionality has proved invaluable in producing ladders for the commercial industry, as well as
machining other steel, stainless steel, and aluminium parts, including safety collision barriers, bicycle parking, and furniture components.
“The ladders get bent and then rolled, which is a long, lengthy process,” Tom says. “Normally, we’d have to put them on two different machines, but with the ELECT, we can bend the material and roll it in one sequence. We can now do higher cycle jobs to compete with higher volume customers, because the cycle time’s a lot quicker.”
White Cross Ring’s eagerness to embrace the latest technology has given the company a vision of the future – quite literally – using BLM’s Visual Graphic Programming (VGP) software. It gives operators a computer-generated 3D rendering of the workpiece being machined prior to production, highlighting any problems, such as collisions, before work commences.
“Unless you’ve got vast years of experience, you can spend hours trying to work these things out on an older machine.” Tom points out.
“Having a visual of what you’re going to bend beforehand is really helpful. It cuts down on wasted time and materials and prevents collisions, which helps speed things up.”
VGP also allows for clients’ STEP or IGES files to be directly imported, a convenience that really appeals to White Cross’ customers. From these, the software generates a simulation for bending the part and works out the necessary settings. “Some small tweaks may be required, but it takes a lot of the legwork out of the job,” Tom says. “You can’t buy the experience we have on the shopfloor – some of these lads have been working here 30 years. But on new jobs, it’s probably up to 50% quicker to set up.”
This smart programming, which stores corrections and data from each new job, means the ELECT 52 is constantly learning, improving its accuracy and repertoire to make for faster, more efficient working.
“Once we’ve stored a job, then all those pressure settings and intricate bits you do by hand on an older machine are all in the computer. The more you use it, the more it learns,” says Tom. “It makes the changeover and running of the machine is a lot simpler and allows for a super-fast turnaround on repeat jobs, which is a real plus for our regular customers.”
White Cross Ring’s customer tooling options are now limitless thanks to BLM’s Tool Designer, an online digital platform that automatically creates and supplies bespoke electronic tooling drawings on demand. These can then be used to generate accurate customer quotes for the cost of the tooling prior to manufacture, and then launch production of the required tools once a customer has confirmed the job.
“There’s a constant investment in tooling,” says Tom. “It can be
expensive, but with the BLM online Tool Designer software, we can get all the bespoke tooling we need for our customers and provide accurate quotes for the job. It’s allowed us to expand our offering and take on more challenging work.”
One of the many advantages of running several BLM machines is fully interchangeable tooling, something White Cross takes full advantage of with their vast BLM bend tooling library.
A true family business, White Cross Ring is now in its third generation, with Tom’s vison firmly fixed on the future.
“The hope for this machine is it continues to get high quantity work out the door and we get the level of skill on the shopfloor to use it across the board,” he says. “The ELECT 52 is long-term investment. We want to invest in our infrastructure but, equally, the lads, to make sure they’ve got job security and to secure the future [of the business] for the next 20-40 years.”
Tom confirms that White Cross Ring’s next investment will be a ring rolling machine, to replace their 1978 model that’s finally begun to struggle. “I was gobsmacked when we got the serial number off it!” he laughs.
“But it just shows that if machinery is well maintained it should last a long time. And that’s something we’re trying to push now, year on year, is looking for that next investment. History is important but what we do today matters most, and we recognise that.”
White Cross Ring Co Ltd is a Bradford-based manufacturer specialising in the manufacture of bespoke bent, rolled, and fabricated components from steel sections and tubes. The company offers a comprehensive range of services and skills that cater to customer’s specific requirements, always finding the most efficient and economical solution to ISO 9001 standards.
With over 50 years’ experience serving a vast range of sectors and the very latest tube-bending technology at their disposal, White Cross Ring welcomes challenging projects! For more information, visit whitecrossring.co.uk or call 01274 669933
It’s allowed us to expand our offering and take on more challenging work “
Promoting companies involved in the manufacture and sale of sheet metal, metal forming, fabrication machinery, and ancillary technologies
Managing Director, Bruderer UK Ltd
Chairman, Metalforming Machinery Makers Association (MMMA)
As Chairman of the MMMA, I would like to welcome you to the 2024 Members’ Directory. I trust that this will provide a useful tool in us all achieving our collective goals.
At the heart of the MMMA’s activities is the highly anticipated MACH Exhibition. This event holds special significance for us, particularly due to the Metalworking Village that we proudly host bi-annually. This village epitomises the essence of the MMMA, providing a unique platform for customers, as well as professionals in training and sales, to immerse themselves in the latest advancements in the world of metalforming.
New developments are always a thrill to show. I am particularly excited about this year’s showcase of cutting-edge technologies, where Bruderer UK is set to unveil its groundbreaking press, the BSTL 350-88 in an exclusive UK launch. Within the Metalworking Village, visitors will have the opportunity to witness a comprehensive demonstration of the BSTL 350-88, and receive full details of our new-to-the-UK BSTA 710-220B press, alongside a plethora of stateof-the-art technologies presented by our esteemed MMMA members.
In addition to unveiling new innovations, we are eager to welcome new members into our community, offering them insights into the MMMA and encouraging their participation. This year’s Metalworking Village in Birmingham promises to attract industry professionals from across the globe, making it an exceptional event for both the sectors we operate in and the MMMA. I invite you to join us and be part of this remarkable experience.
I must also highlight the MMMA Gala Dinner, an annual event where we celebrate the outstanding talent within our industry through prestigious awards. This year, we are expanding our awards ceremony to further honour the remarkable contributions of individuals and businesses in the metalworking industry.
As Chairman of the MMMA, it is a privilege to lead an organisation that not only recognises the significance of our sector but also actively advocates for the diverse needs of our members, whether it pertains to technology, workforce development, human resources, or financial support.
Our mission at the MMMA is to elevate our members’ businesses and products within the manufacturing sector through various channels, including extensive social media presence and collaborative initiatives with leading financial institutions such as Lloyds, Compass Finance, and Finance for Industry, leading specialists in finance for engineering, print, plastics and machinery.
Moreover, the MMMA serves as a unified voice for our industry, providing a platform for open dialogue and constructive discussions on pertinent issues affecting our members, ranging from financial challenges to regulatory compliance.
Reflecting on our journey, I am immensely proud of the MMMA’s growth over the past 12 years, evolving from a modest membership to a robust community of 52 members. This growth underscores the resilience and vitality of the manufacturing industry in the UK, which remains integral to the UK economy and the global manufacturing landscape.
Looking ahead, we are optimistic about the government’s proposed investment in our sector and remain committed to driving innovation and excellence within UK manufacturing. Despite external challenges such as geopolitical tensions impacting trade routes, we are steadfast in our dedication to promoting domestic manufacturing and nurturing the next generation of skilled professionals.
As we navigate the opportunities and challenges that lie ahead, let us remember that manufacturing is deeply ingrained in the fabric of our nation’s history and identity. The MMMA stands as a steadfast supporter of UK manufacturing, and together, with the enthusiasm and dedication of our members, we are poised to shape a vibrant and prosperous future for our industry, one that is not only economically significant but also socially impactful.
I invite you to immerse yourself in the excitement of this year’s MACH exhibition and join us in the MMMA Metalworking Village, where innovation meets collaboration. Your participation is key to realising the collective vision of a thriving manufacturing industry.
Warm regards,
Adrian Haller Managing Director, Bruderer UK Ltd Chairman, Metalforming Machinery Makers Association (MMMA)The MMMA’s 75th Anniversary is an opportunity to celebrate its rich heritage and achievements while anticipating a promising future, forging new paths in the metalforming machinery industry
This year marks a significant milestone for the Metalforming Machinery Makers Association (MMMA), an institution that has been at the forefront of the UK’s sheet metal industry for 75 years.
The MMMA’s journey is one of growth and adaptation. Established in 1949 to form a central national organisation for manufacturers in the Power Press making and allied Industries, what began as the British Power Press Manufacturers Association has evolved into a cornerstone entity, dedicated to representing the multifaceted needs of the sheet metal and forming industry.
In 1971 it became the MMMA, to encompass manufacturing companies outside the UK. The MMMA is the only association to represent the needs of the sheet metal industry and, more recently, its associated technologies, demonstrating its commitment to supporting an industry defined by technological innovation and service diversity.
The MMMA maintains a steadfast dedication to driving innovation in UK manufacturing. Its approach is one of collaborative strength, establishing partnerships with niche companies to provide its members
with comprehensive support that spans a range of vital business sectors including insurance, finance, health and safety, human resources, and legal counsel.
These efforts have been crucial in boosting productivity and setting the standard for industry practices.
As the MMMA approaches its 75th Anniversary in 2024, the occasion is not just a look back at its history, but also a moment to cast an eye forward to the promising future of its members and the manufacturing sector at large.
As a steadfast advocate for progress, sustainability, and global competitiveness the association is poised to continue its legacy of fostering industry excellence and shaping the future through apprenticeships and training initiatives.
The highlight of the year will be the MMMA Gala Dinner in November 2024. This event promises to be a splendid opportunity for industry professionals to come together and honour the strides made in the sector. The introduction of awards at the gala is poised to become a new tradition, celebrating the achievements
and setting a precedent for future excellence.
As the association embarks on this historic 75th year, it invites members, partners, and the broader community to join in the festivities.
MACH 2026 promises exciting things for the industry with the addition of an all-new Sheet Metal, Metalforming and Fabrication Zone
The Manufacturing Technologies Association (MTA) have added a new zone to the floorplan for their flagship event, MACH 2026. Working in collaboration with the Metalforming Machinery Makers Association (MMMA), the new zone will be the home for all companies involved in supplying sheet metal, metalforming, and fabrication technology. Located in Hall 6, the new zone will sit alongside the existing MMMA Metalworking Village, creating a bigger area and focal destination for exhibitors specialising in this type of equipment.
Commenting on the new zone, James Selka, CEO at the Manufacturing Technologies Association (MTA) who owns and organises the event, said: “We have seen a steady growth in exhibitors showcasing flexible sheet metal, tube forming, metalforming, and fabrication technologies as well as an increase in visitors looking for these products for their applications. The zone provides a showcase for suppliers of this technology while making it easy for visitors to see everything in one area of the show. We are delighted to be working with the MMMA to develop and grow this new zone.”
The MMMA Metalworking Village, located in Hall 6 at MACH, is a popular destination for visitors to the event. The additional space allocated for the new zone will complement the existing village, giving visitors even more reason to attend the event.
Adrian Haller, Chairman of the MMMAcommented: “This enlarged area presents a wonderful opportunity to come together in strength and display a vast array of production equipment, designed to help improve productivity for UK manufacturing. The MMMA are delighted to be partnering the MTA on developing this area, showcasing our sectors specialisms.”
MACH has seen significant growth trends from diverse manufacturing areas using machine processes such as metal bending, folding, coil processing, cold forming, cutting systems including laser and water jet, fastening, high speed stamping, presses, sheet handling, shearing, welding, punching, plate rolling – to name but a few. The MTA and MMMA both predict this sector will continue to grow, driven by the use of these technologies in modern manufacturing processes.
As the UK’s national event for
inspiring, innovating and connecting manufacturing, MACH is the UK’s only event showcasing sustainable, innovative technologies used across the manufacturing spectrum in a live, working environment.
MACH attracts an audience of over 26,000 to meet and network with around 500 exhibitors with business attributed to the most recent event in excess of £180M.
We are delighted to be working with the MMMA to develop and grow this new zone
MACH 2026 will see the addition of an all-new Sheet Metal, Metalforming and Fabrication Zone in Hall 6
64-66 Somers Road, Rugby, CV22 7DH
Tel: 01788 542271
Email: sales@awprecision.co.uk
Website: www.awprecision.co.uk
Our manufacture of the best quality Punch and Die products on the market, that suit to a large range of universal machines, is the reason that we are the leading manufacturer of these components in Europe and the USA. Specifically selected, the high quality materials we use withhold many attributes that can extend Punch life; high wear resistance, reduced tension, and good stability are just a few qualities we can guarantee.
City Road, Derby, Derbyshire, DE1 3RP
Tel: 01332 648200 / 07968 694609
Email: info@aida-europe.com
Website: http://www.aida-global.com
AIDA is a global press manufacturer that offers a diversified product line, total turnkey packages and automation. AIDA’s UK facility provides crucial after service support that includes maintenance, stock delivery on spare parts for AIDA, Bliss, Manzoni and Rovetta presses. Aida S.R.I UK Branch is the authorised provider for service, parts and support of all AIDA, Manzoni, Rosetta and Bliss press models.
Hougoumont Farm, Collinbourne Ducis, Wiltshire, SN8 3ET
Tel: +44 (0) 1264 850490 / 07799887699
Email: sales@antonsaws.co.uk
Website: antonsaws.co.uk
At Anton Saws and Machinery, we have been supplying industrial saw machines across the UK for over 30 years. Our extensive range of band, circular and wood saws come from top quality, well established suppliers and manufacturers from all over the world. We also provide tooling, servicing and supply of all metal forming machines.
AP&T UK Branch, 1 Bordesley Chambers, Albert Street, Redditch, Worcestershire, B97 4DA
Tel: 07811 266577
Email: christian.wright@aptgroup.com
Website: aptgroup.com
AP&T develops, manufactures and markets complete production systems, automation, presses, tools and related aftermarket services for manufacturers of formed metal parts. We constantly aim to achieve the highest possible level of customer satisfaction and security by offering a high degree of availability and complete solutions for which we are fully responsible – a concept we call One Responsible Partner®.
Building 56, Second Avenue, The Pensnett Estate, Kingswinford, West Midlands, DY6 7XN
Tel: 01384 280400
Email: paul.day@asc-uk.net
Website: asc-uk.net
ASC UK Ltd. was founded in 1995 and designs, manufactures, and services roll forming equipment for customers worldwide at its Kingswinford, West Midlands facility. Our ASC engineering team has over 100 years of experience in roll forming design and manufacturing and can provide a custom solution to enable your business to succeed. ASC UK designs and manufactures roll forming equipment for a wide variety of applications and industries.
School Lane, Gentleshaw, Staffordshire, WS15 4LX
Tel: +447885292197
Email: sharrattcm@miautomation.co.uk
Website: www.bihler.de/en
Automation solutions in stamping, forming, welding and assembly technology. Your one-stop-shop in metal-forming, welding and assembly processes. Electrical and electronic parts and assemblies, including connector technology. Automotive applications including e-mobility (busbars, hairpins, connectors, shielding sleeves, etc.). Domestic, food, medical and household appliances. Plug & Produce –tool compatibility.
Unit H, Cradock Road, Luton, Bedfordshire, LU4 0JF
Tel: 01582 560300 / 07798 903621
Email: mail@bruderer.com
Website: www.Bruderer.co.uk
Bruderer UK, the leading supplier of engineering excellence in the stamping & metal forming sector. We supply Precision High speed Power presses & the best of the rest: tooling components, press ancillaries, servo feed systems, coil handling systems, complementing our portfolio, alongside our full turnkey services for full manufacturing production line processes. One point of contact for complete assurance for efficiency & reliability. Accredited SN EN ISO 9001:2008
Sweden House, 5 Upper Montagu Street, London, Greater London, W1H 2AG
Tel: +44 7869 025 134
Email: info@cidanmachinery.com
Website: cidanmachinery.com
CIDAN Machinery Group offers solutions for sheet metal, construction, and manufacturing. Originating as Göteneds Mekaniska Verkstad AB in 1907, it’s now known for power folders and mechanical shears under brands Göteneds and CIDAN in 30+ countries. Coil processing products, under Forstner brand, are made in Austria since 2018. Targeted customers include industrial and architectural applications.
Compass House, Medway Wharf Road, Tonbridge, Kent, TN9 1GH
Tel: 01732 833477
Email: sarah@compassbusinessfinance.co.uk
Website: compassbusinessfinance.co.uk
Compass Business Finance specialises in financing for the metalforming machinery sector. We understand market intricacies and offer optimal, tax-efficient funding solutions. Whether you’re investing in machinery, needing cash flow support, or restructuring debt, we ensure your success with straightforward finance. Our dedicated finance experts work closely with you to tailor solutions to your needs.
Via Venezia 144, Schio (VI), Italy, 36015
Tel: +39 0445 675000
Fax: +39 0445 675110
Email: AGrendene@costalev.com
Website: costalev.com
Costa Levigatrici S.p.A. is a world-leading manufacturer of automatic sanding equipment for the treatment of Wood, Metal and Composite materials. For over 50 years, Costa has been offering high quality sanders with unchallenged level of reliability, a commitment that continues through investments in innovation, manufacturing and after sales services.
22 Neptune Business Park, Tewkesbury Road, Cheltenham, Glos., GL51 9FX
Tel: 01242 221204
Email: sales@cotswold-machinery-sales.co.uk
Website: cotswold-machinery-sales.co.uk
Sole Importers of Metal Fabrication Machines for Punching, Bending, Press Brakes, Notching, Ring Rolling, Bus Bar, Tube Forming and Tapping/Support Arms, Sales, Service, Repair, Tooling & Spares. Euromac,CNC punching Horizontal Bending, Press brake Machines. Ehrt punching , bending fabrication machines. Roscamet tapping machines.
Crossgate Drive, Queens Drive Ind Est, Nottingham, NG2 1LW
Tel: 0115 824 4855
Email: alex@daltonswadkin.com
Website: www.daltonswadkin.com
Daltons Wadkin are leading suppliers and manufacturers of industrial machinery for processing various materials including, composites, plastics, metals, solid wood, wood based panels and more. Operating from purpose built premises in Nottingham with extensive showroom facilities Daltons offer specialist advice and expert guidance. Products include Kimla Fiber Lasers, CNC Routers, Milling Machining Centers, and Houfek Wide Belt Sanders.
Unit 3, Octagon Business Centre, Miller Street, Birmingham, B6 4NF
Tel: 0121 359 3978
Email: info@decade.co.uk
Website: www.decade.co.uk
DECADE, a UK-owned company, serves the manufacturing industry with off-the-shelf and bespoke products. Specialising in automation, load monitoring for power presses, process monitoring in assembly machines, and production recording. With 25+ years in load measurement, we offer OEM modules, PC software, calibration, testwork, breakdown support, consultation, and training, prioritising swift service.
Unit 1, Keystone Enterprise Factory, 39 Brunel Way, Norfolk, IP24 1HP
Tel: 01842 821467
Email: info@decoilersandfeeders.com
Website: decoilersandfeeders.com
Decoilers and Feeders Ltd, est. May 2014, started with service & spares for metal coil feeding machinery. Now, with vast experience, they design and manufacture Decoilers, Levellers, Servo Roll Feeds, & more. They offer servicing, upgrades, new machinery installation, refurbishment, relocation, spare parts, software assistance, and electrical control panels, prioritising client needs.
Plackett Mill, Church Drive, Sandiacre, Nottingham, NG10 5EE
Tel: 0115 939 1888
Email: info@espritautomation.com
Website: www.espritautomation.com
Our distinctive blend of innovation and experience has enabled Esprit Automation to become the leading British manufacturer of CNC plasma cutting machines. Built to last with exceptional quality, first-class service support and the flexibility to meet your needs, Esprit machines are 100% British-made and installed in over 30 countries worldwide. CNC Plasma Cutting Machines CAD/CAM Software Hypertherm Plasma Cutters.
Unit D Telford Court, Chester Gates Dunkirk, North Chester, CH1 6LT
Tel: 01244 257216
Website: www.financeforindustry.co.uk
Finance for Industry specialises in financing solutions for engineering, print, plastics, and machinery sectors, offering bespoke options. With a nationwide team of experienced finance professionals, they prioritise strong relationships and rapid service. Their Machinery Protection covers mechanical and electrical breakdown, accidental and malicious damage, repair or replacement costs, and transfer of cover, providing peace of mind.
Unit 3, City Estate, Corngreaves Road, West Midlands, B64 7EP
Tel: 01384 895150 / 07967 098838
Email: sales@formit.co.uk
Website: www.formit.co.uk
Formit excels in roll form tooling and equipment, offering comprehensive solutions from section design to production line setup. Design is streamlined with the German CAD system COPRA. Specialising in ‘Duplex,’ cladding lines, and quick-change ‘C’ and ‘Z’ purlin rollformers, Formit caters to diverse needs like steel framing, plasterers’ angle bead, and more. Contact for detailed data sheets on tailored rollforming lines.
Fronius
Maidstone Road, Milton Keynes, Buckinghamshire, MK10 0BD
Tel: 01908 512 300
Email: info-uk@fronius.com
Website: www.fronius.co.uk
We aspire to produce more than just welding systems; hence we are the innovation leader for arc welding and are constantly developing welding processes further. Alongside welding technology for robot applications, we offer solutions for manual gas shielded arc welding for MIG/MAG, TIG and MMA welding processes. We also implement automated, complete welding solutions tailored to customer requirements in the field of welding automation.
Unit C2, Platinum Jubilee Business Park, Hopclover Way, Ringwood, Hampshire BH24 3FW
Tel: 0333 242 0424
Email: sales@gemachinery.co.uk
Website: www.gemachinery.co.uk
GE Machinery, the top supplier of Deburring, Polishing and Finishing machines in the UK & Eire, brings years of expertise to all industries. We offer machinery, ancillary equipment and unparalleled service, ensuring optimal performance and client satisfaction. From product selection to installation and training, we guide you every step of the way. We guarantee top machinery conditions with in-house demonstrations and expert technicians.
The Red House Glass Cone, High St, Wordsley, Stourbridge, West Midlands, DY8 4AZ
Tel: 01384 485 274
Email: jobs@glencallum.co.uk
We’re a seasoned recruitment firm specialising in automotive, engineering, and industrial sectors across UK, Europe, and globally. With 19 years of experience, we provide discreet and credible services, ensuring a positive experience for clients and candidates alike. Our team handles a wide array of placements, from engineers to directors, offering professionalism and confidentiality throughout.
Unit 21, Calder Vale Road, Wakefield, West Yorkshire, WF1 5PE
Tel: 01924 371161 / 07775 586870
Email: information@grouprhodes.co.uk
Website: www.grouprhodes.co.uk
Rhodes Interform Ltd is a leading European manufacturer of CNC and PLC controlled metalforming machinery, specialising in bespoke mechanical and hydraulic presses. Part of Group Rhodes, they are world leaders in superplastic forming and diffusion bonding (SPF/DB). Exporting to over 30 countries, they maintain quality with patented designs and international awards, supported by a UK-based export manager and global network of distributors.
361 West Dussel Drive, Maumee, Ohio, USA, 43537
Tel: 0014198954356
Email: sales@helminstrument.com
Website: www.helminstrument.com
Established in 1962, Helm Instrument Company is a premier provider of process control systems, force transducers, and software for metalforming industries. Pioneering press load monitoring in 1968 and in-die force sensing in 1972, we hold multiple patents. Based in the industrial Midwest, we offer global support through our extensive representative network.
Unit 11, Bingswood Industrial Estate, Whaley Bridge, High Peak, SK23 7LY
Tel: 01663 734627 / 07711 186454
Email: mike@industrialclutch.com
Website: http://www.industrialclutch.com
ICP is the UK distributor of Goizper pneumatic and hydraulic clutch brake systems. Goizper is a respected Spanish manufacturer of clutch brakes for mechanical power presses, with many customer references for their clutch brakes installed in power presses used in automotive and can making applications. The ICP/Goizper partnership offers application assistance and a high quality, cost effective solution for your press clutch brake needs.
Unit 4 Grosvenor Business Centre, Vale Park, Evesham, Worcestershire, WR11 1GS
Tel: 01386 443366 / 07712406629
Email: Sales.uk@kaller.com
Website: www.kaller.com
KALLER, a world-leading brand for gas springs and hydraulic systems, serves stamping dies, counterbalance, and heavy-duty off-road vehicle suspension. Operated by Strömsholmen in Tranås, Sweden, it’s a part of Barnes Group Inc. (NYSE:B) in the U.S. Pioneering gas spring technology since 1983, with roots tracing back to 1876, it boasts a 95% export share, solidifying its global leadership.
Lloyds Bank Commercial Finance, 6th Floor, 110 St Vincent Street, Glasgow, G2 5ER
Tel: 07551 134151
Email: Oliver.Batley@lloydsbankcf.co.uk
Website: www.lloydsbank.com/business/industry-focus/manufacturing.asp
Committed to supporting Britain’s manufacturing sector, our relationship managers, trained by Warwick Manufacturing Group at the University of Warwick, offer specialised manufacturing awareness to assist your business ambitions with tailored finance solutions. Lloyds Banking Group, our parent company, reinforces its dedication to UK manufacturing through a £1m annual sponsorship of the Lloyds Bank Advanced Manufacturing Training Centre.
Midlands Power Press Services Ltd
Unit 2 High Street, Princes End, Tipton, West Midlands, DY4 9JA
Tel: 0121 520 4320 / 07734 490912
Email: admin@mpps.co.uk
Website: www.mpps.co.uk
Midland Power Press Services Ltd offers top-level, comprehensive support to the Power Press, Metalworking, and allied industries. With a skilled team of engineers, we’ve served for 35 years, delivering prompt and cost-effective engineering solutions. Our clientele includes bluechip companies in automotive, aerospace, white goods, forging, and food & beverage sectors. Proudly, we’re now the UK Agency for Sales and Service of OMERA.
Unit 9, Moons Park, Burnt Meadow Road, Moons Moat North Industrial Estate Nr., Redditch, Worcestershire, B98 9PA
Email: sam@mie-solutions.co.uk
Website: www.mie-solutions.co.uk
Based in Worcestershire, MIE Solutions is one of the country’s leading providers of Enterprise Resource Planning (ERP) and production control software for the entire manufacturing sector including in the sheetmetal, metal forming and fabrication industries. With over 25 years of experience and a worldwide presence, MIE Solutions has developed capacity planning software made by manufacturing professionals for manufacturing professionals.
Unit A3 Firs Industrial Estate, Ricketts Close, Kidderminster, Worcestershire, DY11 7QN
Tel: 01562 744 873
Email: info@mtlengineering.co.uk
Website: www.mtlengineering.co.uk
MTL Engineering limited are experienced engineers for all kinds of CNC sheet metal machines and have been established in the market for over 21 years. Carrying out Sheetmetal repairs fault finding using electrical and hydraulic schematics drawings. Retrofitting of new cnc controllers, HMI and safety PLCs to Pressbrakes and metal cutting machines. Offering UK Sales, support and service for Dener and HSG products.
Tel: +41 58 360 96 96
Email: alan.akers@oerlikon.com
Website: www.oerlikon.com/balzers/uk/en
Oerlikon, a leading global technology Group, offers market-leading technologies and services. Organised into Surface Solutions, Manmade Fibers, and Drive Systems segments, each with its own brands and strategies, Oerlikon has a strong presence in Asia, particularly in China and India. With significant investments in R&D, it filed 91 patents worldwide in 2017, continuing its innovation legacy.
19 Sugarbrook Road, Aston Fields Industrial Estate, Bromsgrove, Worcester, B60 3DN
Tel: 01527 579123
Email: michael.burton@ortlinghaus.co.uk
Website: www.ortlinghaus.co.uk
Ortlinghaus has worked in metal forming technology for over 75 years, with a reputation for quality and superior engineering globally. We offer products across the entire spectrum of mechanical and servo presses, from clutch/brake units, slide locking devices, brakes to mechatronic control systems. Ortlinghaus UK have stock parts for many lines, along with the knowledge and capability to optimise and service your Ortlinghaus products.
H6 New Yatt Business Park, New Yatt, Witney, OX29 6TJ
Tel: 01993 220263
Email info@osa.systems
Website: www.osa.systems
Created in 2019 as a sister company to One Stop Automation, OSA Systems Ltd purchased the intellectual property and assets of PJ Hare Ltd’s servicing arm, and now provides servicing and maintenance for Hare Presses. Our engineers are experienced with a wide range of press types including servo-hydraulic and hydro-pneumatic presses. Combined with One Stop Automation, we provide solutions above and beyond usual servicing and maintenance.
1 Shenstone Drive, Northgate, Aldridge, Walsall, West Midlands, WS9 8TP
Tel: 01922 743414
Fax: 01922 454951
Email: sales@phoenixtooling.co.uk
Website: www.phoenixtooling.co.uk
Phoenix Tooling and Development Ltd, est. 1990, has a well-established reputation for high quality precision press tooling and an industry recognised standard for customer satisfaction and service. Phoenix Tooling continues to lead the way in tool design and manufacture thanks to continual investment in the latest tool room equipment, cutting edge design and development technology, and its long standing apprenticeship program.
Unit 7, Greens industrial estate, Caldervale Road, Wakefield, WF1 5PE
Tel: 01924 291463 / 07809 163800
Email: alan@press-techniques.com
Website: www.presstechniques.co/
UK Manufacturers of Low profile hydraulic and bespoke presses, and automated assembly equipment. Supplier of “Turn Key” projects from concept to commissioning service of single to full line sheet metalworking equipment. Press Techniques do competitive rates on all Press Service Requirements. Our mechanical & electrical engineers deal with all your Press Service Requirements whatever make or age of your Press or Ancillary Equipment.
162 Netherton Lane, Netherton, Wakefield, WF4 4HH
Tel: 01924 271540
Email: info@press-form.co.uk / sales@press-form.co.uk
Website: www.press-form.co.uk
With over 30 years of experience in the supply and servicing of sheet metal working machinery, Press-Form is firmly positioned as one of the UK’s leading providers of metal process equipment. Our extensive expertise within the industry ensures we provide a first class service to our clients. We are the official UK agent for ACF Corner Former, Dimeco, Haeger, Sangiacomo, Galdabini, Zani, Vicla, EHRT, Technology Italiana, and Virtek.
Unit 6 Wall End Close, Leamore Industrial Estate, Walsall, WS2 7PH
Tel: 0845 226 7617
Email: sales@presscare.co.uk
Website: www.presscare.co.uk
PRESSCARE UK LIMITED, based in the West Midlands, specializes in power presses, coil handling equipment, and automation systems. We design and integrate machine control and safety systems, ensuring alignment with UK and EU safety standards. Whether modern multi-press transfer lines or older machines, we optimise equipment for peak performance.
Unit 1, Phoenix Park, Bayton Road Industrial Estate Nr. Coventry, Coventry, West Midlands, CV7 9QN
Email: barry.rooney@primapower.com
Website: www.primapower.com/en
Prima Power UK Ltd specialises in sheet metal working and additive manufacturing machinery. Our product range covers 2D/3D laser processing, punching, bending & automation; we also offer additive manufacturing technologies. We serve the UK and Ireland for sales and service, using advanced servo-electric technologies for high performance. We deliver cutting-edge solutions for laser cutting, sheet metal machinery & automation systems.
Unit 314, Elm Drive, Hartlebury Trading Estate, Kidderminster, West Midlands, DY10 4JB
Tel: 01905 621882
Website: qm-systems.com
QM Systems specialises in bespoke automation solutions, serving various sectors including manufacturing, robotics integration and press handling. We boast a track record of delivering high-quality automation systems to major industries such as automotive, rail, and aerospace. With ISO accreditations and a commitment to excellence, we partner with world-class clients to achieve success efficiently and effectively.
2A High Street , Dronfield, S18 1PY
Tel: 0114 2495400
Email: info@qualimach.co.uk
Website: qualimach.co.uk
UK Agent for FACCIN leading manufacturers of Plate Bending Rolls, Section Bending Rolls, Dishing & Flanging Lines. Stock New and Used Metalworking Machinery. EAMTM Members, European Association of Machine Tool Merchants.
Macarthur Road, Cradley Heath, West Midlands, B64 7RP
Tel: 01384 565997
Email: slr@raybould.com
Website: www.raybould.com
Raybould Machine Tools Ltd, a top UK supplier, offers new & used mechanical and hydraulic power presses, press feeding, and coil handling equipment. Representing brands like Boxin, Pressix, and HongEr, we provide quality machinery. With over 47 years of expertise, we specialize in supplying, purchasing, and disposing of manufacturing equipment, offering Asset Disposal Solutions for various industrial needs.
7th Floor, Forum House, 15-18 Lime St, London , EC3M 7AN
Tel: 07380861518
Email: jdavenport@rck.partners
Website: www.rck.partners
RCK Partners, a leading Financial Consultancy, prioritises your security. We specialise in tax incentives and innovation funding, with expert advice in R&D Tax Credit Relief and Patent Box. With a commitment to exceptional service, we provide tailored solutions, partnering with various stakeholders to maximise value. Led by a dedicated Senior Consultant, we ensure efficient and timely delivery, maintaining a personal touch throughout.
Unit 9 B village, Endeavour Park, Baker Road, Nelson Park West, Cramlington, Northumberland, NE23 1XA
Tel: 01670 281400
Email: sales@roemheld.co.uk
Website: www.roemheld.co.uk
Roemheld (UK), leading in hydraulic workholding, enhances efficiency with press die clamping solutions. Quick change products cut downtime, boosting productivity. Range includes swing sink, sliding clamps, and new magnetic options for diverse industries, even at high temps. Optimize with Roemheld for peak productivity.
Brineton Street, Quayside Drive, Walsall, West Midlands, WS2 9LA
Tel: 01922 619113 / 07766 136952
Email: PhilipLeath-Dawson@schulergroup.com
Website: www.schulergroup.com
Schuler Presses UK is the largest company servicing the pressing industry in the UK and offers comprehensive services for mechanical and hydraulic presses made by Schuler and many others. The brands: Schuler, Mueller-Weingarten, Clearing International, Verson Wilkins, Wilkins & Mitchell, Bronx, Clearing, Bliss, Niagara, Spiertz, Beche, SMG, GMG, Hydrap, Schaefer, Schleicher, Erfurt, Eitel and Beutle.
Unit 2, St Georges House, Cape Road, Warwick, Warwickshire, CV34 5DJ
Tel: 01926 298 292
Email: editorial@sheetmetalindustries.com
Website: www.sheetmetalindustries.com
All the latest industry news for sheet metal, metal forming and fabrications industries. Sheet Metal Industries launched in 2022 and brought to market through a dedicated team of media and industry experts dedicated to the field of content generation and media publishing. SMI is dedicated to the niche field of sheet metal, metal forming and fabrication and aims to serve and highlight key innovations and strengths attached to the sector.
Unit 10-11, Amber Business Village, Amington, Tamworth, Staffordshire, B77 4RP
Tel: +44 (0)2476 982299
Email: chris.cooper@cambrio.com
Website: www.sigmanest.com/en-GB
SigmaNEST: Industry’s best nesting software. Developed by expert mathematicians and engineers, it ensures optimal material use and nesting efficiency. Versatile, scalable, and customisable, SigmaNEST streamlines your workflow from import to report. Compatible with all cutting machines, it offers fast, high-yield nesting with minimal waste, providing a comprehensive solution for all machine types.
95-111 Tyburn Road, Erdington, Birmingham, B24 8NQ
Tel: 0121 328 1908 / 07768 666834
Email: Tim@tmaeng.co.uk
Website: www.TMAeng.co.uk
TMA: the largest independent power press specialists is the UK. With a team of mechanical and electrical service engineers. Full ‘in house’ machining, assembly, electrical, spare parts and CAD departments for all your power press requirements. At our manufacturing facility we make all our spares and carry out modifications and repairs. We supply all types of press guarding to your specifications.
Unit B2B, Holly Farm Business Park, Honiley, Kenilworth, Warwickshire, CV8 1NP
Tel: 0800 999 1090
Email: Info@workshoppress.co.uk
Website: www.workshoppress.co.uk
The Workshop Press Company UK is a leading supplier of hydraulic press machinery in the UK. We offer a wide range of hydraulic presses, plus expert advice and support on all aspects of hydraulic press machinery. We understand that every business has different needs so we offer a customised approach to hydraulic press sales and support. We work to understand your specific requirements and recommend the right hydraulic press for you.
Mayflower Close, Chandlers Ford Industrial Estate, Eastleigh, Hampshire, SO53 4AR
Tel: 023 8026 0266
Email: info@towermachinetools.co.uk
Website: www.towermachinetools.co.uk
Tower Machine Tools Ltd remains the only authorised dealer for Muratec Wiedemann CNC Turret Punch Presses for the UK, Eire and France. Tower is also the UK Distributor for Farina and Italtec CNC Press Brakes, Shears and Plasma machines. Tower is the only approved supplier of Wiedemann’s cost effective turret tooling which is manufactured at our 2,300 sq.m.
6 Beddington Farm Road, Croydon, Surrey, CR0 4XB
Tel: 020 8667 0333 / 07773 780343
Email: nick.moody@voith.com
Website: www.voith.com
Voith offers innovative hydraulic systems and components as well as self-contained servo drives for a wide variety of applications. Among others, hydraulic press solutions from Voith are used in mechanical engineering, the automotive sector and in the energy sector.
As an international partner with high system competence, we develop modern fluid technology - customized and tailor-made to your requirements.
Holly Farm Business Park, Honily, Kenilworth, Warwickshire, CV8 1NP
Tel: 01392 833991
Email: info@whittit.co.uk
Website: www.whittit.co.uk
Bill Whittit founded “MK1” specifically to meet the insurance needs of the precision engineers and toolmakers in the Midlands. The business ethics and foundations he laid over fifty years ago remain in place today. The Whittit Mk1 Group is now represented thorough out the UK. Like the precision engineering and toolmaking industry, we have evolved with modern technologies to enable us to remain at the forefront of our business.
Unit 4, Crescent Industrial Park, Peartree Lane, Dudley, West Midlands, DY2 0QQ
Tel: 01384 392266
Email: Sales@worcesterpresses.co.uk
Website: www.worcesterpresses.co.uk
Worcester Presses offers a combination of mechanical Chin Fong presses, Hydraulic presses, Tomac coil handling equipment and press transfer. Offering complete turnkey solutions which can incorporate guarding, load monitoring, QDC and additional ancillary equipment to increase productivity. Worcester Presses offer countrywide sales and service coverage, emphasis on quick response.
68 Glover Street, Birmingham, West Midlands, B9 4EL
Tel: 0845 230 7040
Email: sales@zebramachinery.com
Website: www.zebramachinery.com
Zebra has the experience and a wide selection of new and used machinery in stock to suit your requirements. Whether laser cutting, CNC bending, press braking, rolling, shearing, punching, machining, pressing or non CNC plug and play machines, they have the engineers to install and service the machines onsite and help you with training and tooling. They will consider buying anything from single machines to complete factory contents.
Holding the position of Honorary President at the Metal Forming Machinery Makers Association (MMMA), it’s with a profound sense of pride that I serve an organisation instrumental in the advancement of the UK’s sheet metal industry over the past 75 years.
The MMMA has come a long way since its establishment in 1949. Originating as the British Power Press Manufacturers Association, it has grown to be the primary trade association representing the sheet metal and forming industry’s diverse needs.
In 1971, we expanded our reach to encompass the myriad forms of sheet metal machinery, in line with our commitment to nurturing an industry rich in technological diversity and service offerings.
Our dedication to the sector remains steadfast. We take great pride in delivering substantial value and driving innovation in UK manufacturing.
Through our partnerships with niche companies, we provide our members with comprehensive support in vital business sectors, including insurance,
finance, health and safety, HR, legal counsel, training, and recruitment — essential elements of our endeavour to boost productivity and foster exemplary industry practices.
As the MMMA nears its 75th year in 2024, I am filled with pride reflecting on our history and the bright future ahead for our members and the broader manufacturing sector.
This year, the MMMA Gala Dinner, taking place in November 2024, represents a splendid opportunity to honour our industry’s achievements alongside peers, colleagues, and clients. The introduction of awards at the gala is a new step, affirming our belief in celebrating success. I eagerly anticipate the gala on the 1st of November and look forward to many of you joining us for what promises to be a memorable evening.
The MMMA remains a staunch proponent for progress, sustainability, and global competitiveness. As we move into our landmark 75th year,
I am thrilled to be associated with an organisation that is not only steeped in heritage but also geared up for the promising challenges and opportunities both from an industry and next generation apprenticeship and training level.
FRI 01 NOV ‘24
The Copthorne Hotel
The Waterfront, Level St
• Apprentice of the Year
• Subcontractor of the Year
• Net Zero Contributor of the Year Introducing... 3 industry Awards
Brierley Hill DY5 1UR mmma-gala-awards.co.uk BOOK Your Tickets Today
Scan the QR code to submit your entry for the awards or to book tickets today