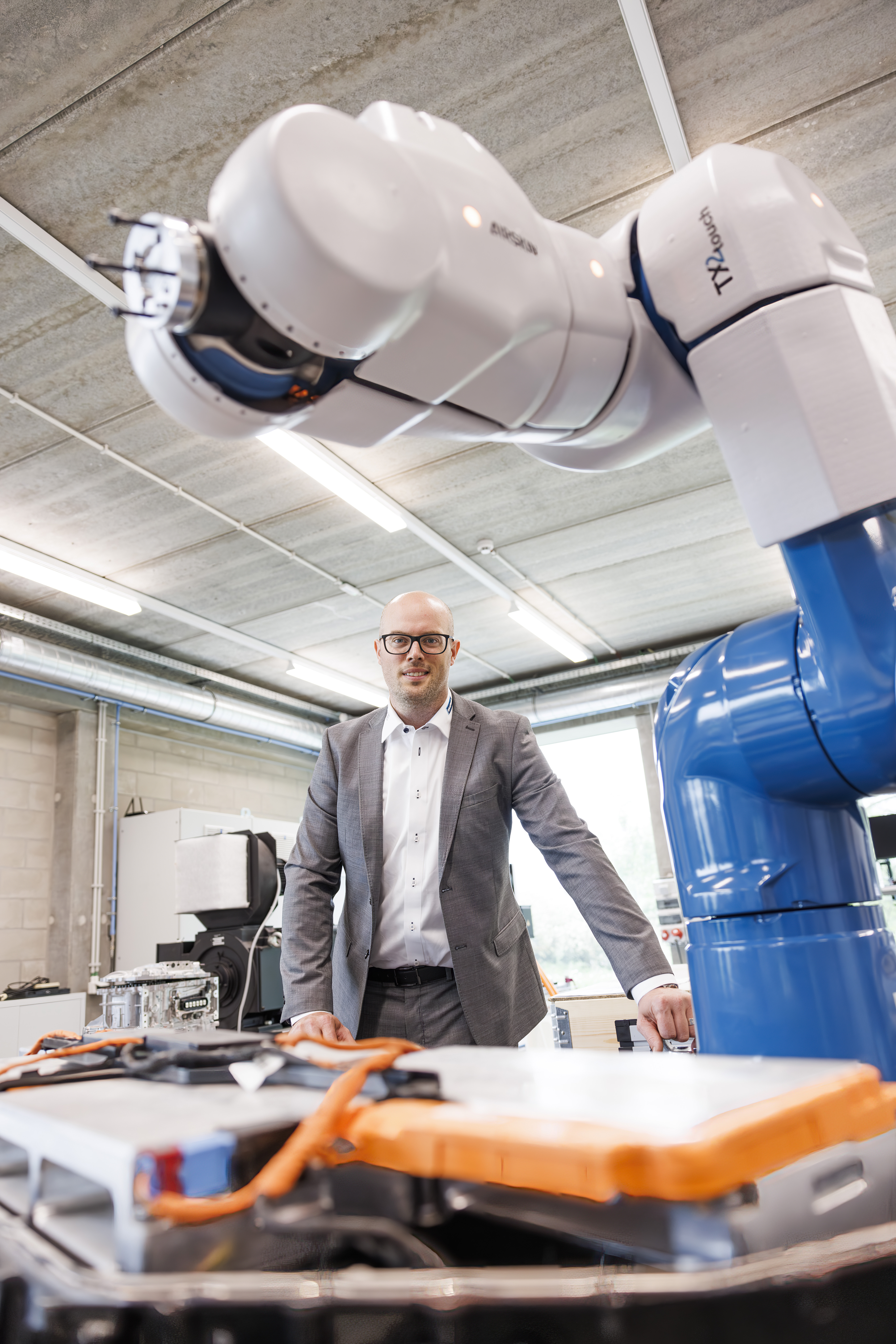
4 minute read
ECODESIGN FOR ROBOTIC DE- AND REMANUFACTURING
How can we design products that are optimally repairable, can be remanufactured when reaching their end-of-first-life, last longer and stop the accretion of waste? That is the challenge of the researchers at Professor Jef Peeters' Re- and Demanufacturing Lab. Their mission is to contribute to a circular economy in an industry 4.0. Interdisciplinarity and hands-on problem solving are indispensable prerequisites for this.
If the EU wants to meet the Green Deal targets by 2050, drastically reducing waste production is a top priority. “A significant proportion of waste consists of still of functional products and components and when recycled, actually, a lot of the materials are either lost or downcycled in the nowadays commonly used shredder-based processing”, Jef explains. “These are often products or appliances that have been discarded, only because it is today not economically viable to repair or remanufacture them.”
In these cases, robotic de- or remanufacturing are valid alternatives. Demanufacturing involves the dismantling or dissembling of a product to harvest components for reuse and to gain the maximum amount of recyclable materials. Remanufacturing goes a step further. It involves the rebuilding of a product to specifications of the original manufactured product using a combination of reused, repaired and new parts. “Automation of demanufacturing is quite different from automation in manufacturing”, Jef specifies. “In demanufacturing, you get a lot of different devices returning all together in varying conditions of which you don't necessarily have control of. To address these challenges, digital product passports with product specific information, as well as smarter process and products designs are crucial.”
Design for X
Jef is a dual master. He first studied Industrial Design at the then HOWEST university college (now University of Ghent) and then Industrial Product and Production Management at KU Leuven. In 2010, he became a PhD researcher at the Department of Mechanical Engineering at KU Leuven with professors Joost Duflou and Wim Dewulf. Jef researched demanufacturing strategies for discarded electronic devices, such as digiboxes, modems and television sets. He specialised in design for dissasembly and automated demanufacturing.
After four years as a postdoc in the Department of Mechanical Engineering, Jef will become an assistant professor at KU Leuven in 2020. At Group T Campus, he teaches Waste Treatment & Material Cycles, Sustainable design and Vision Systems, in the Electromechanical Engineering Technology major. He is also coordinating the Engineering Experiences in which the third undergraduate learn to design an automated system and develop a digital twin of it. As a researcher, Jef leads a group of about 20 researchers working on more than 10 parallel running research projects in the Life Cycle Engineering Research Group of which the Re- and Demanufacturing Lab is part.
Product-as-a-Service
One of the projects Jef's lab is working on with another seven European partners is 'Scandere'. That stands in full for 'Scalingup a circular economy business model by new design, leaner manufacturing and automated material recycling technologies'. “That is indeed quite a mouthful”, confirms Jef. “But we set the bar high. The technologies we develop must contribute to the worldwide transition to a circular economy, which requires a holistic approach that also includes the introduction of novel business models based on Product-as-a-Service (PaaS).”
Resource flow
“In today's consumer market of electrical and electronic appliances, manufacturers have little or no control over their products once they reach the customer”, Jef continues. “In the PaaS model, the producer does gain control over the entire resource flow in products, components and materials while committing to the availability of the product functionality. As such, a PaaS provides the producer incentives for extending the product life time and to maximise resource recovery when reaching its end-of-life.” In the project, the researchers are experimenting with commonly used devices that comprise critical metals in their batteries and electric motors, such as the Bosch robotic vacuum cleaners. This is being complemented with redesigning and rebuilding these products to facilitate human-robot cooperative flexible de- and remanufacturing.
With the new research platform for human-robot collaboration, Jef’s lab is working in this and other projects on methods to evaluate product designs for robotic de- and remanufacturing to support both designers, as well as ecolabeling and ecodesign policy developments. “In parallel, we are developing new robotic disassembling technologies to reduce the production and dismantling costs, and to enhance the process robustness, e.g. by automatic evaluation of the product state and aesthetic properties. In this way, we contribute to the transformation of the entire (critical) raw materials value chain into more competitive and resource-efficient and circular systems.”
Yves Persoons
https://scandere.nu
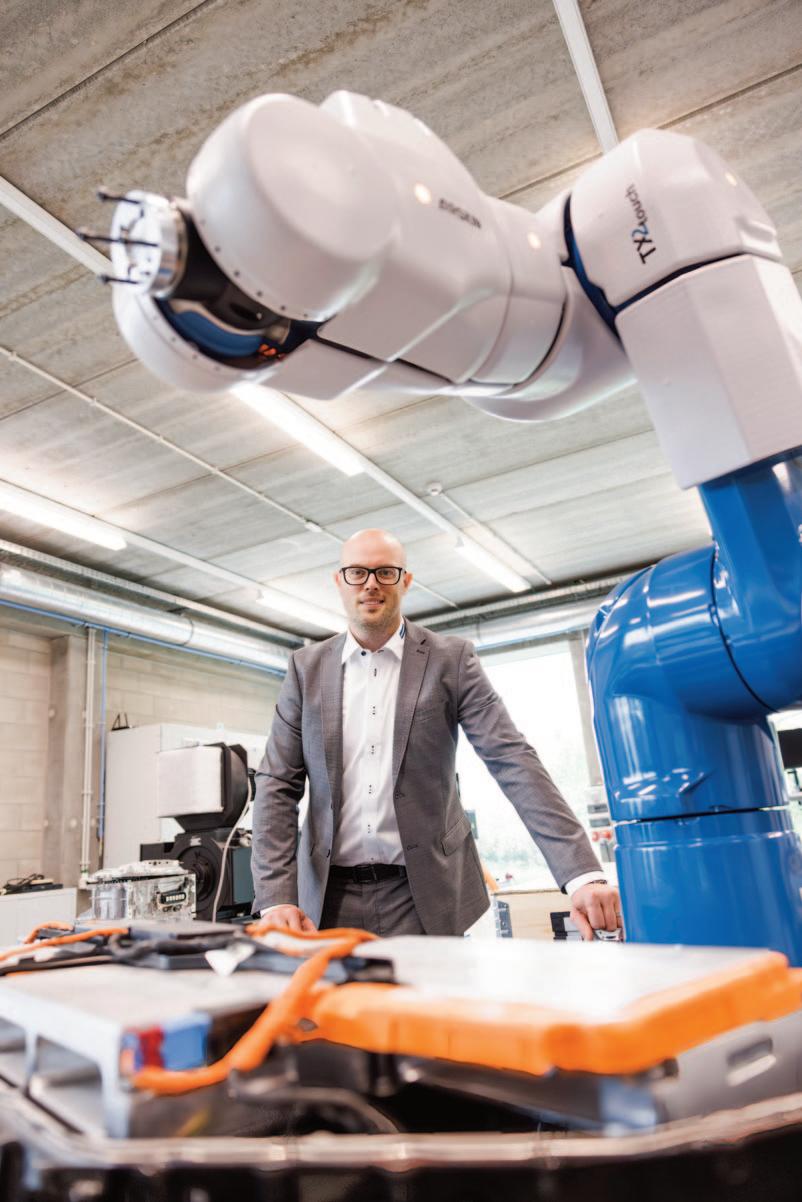