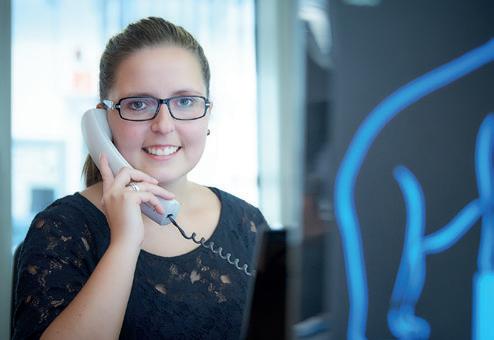
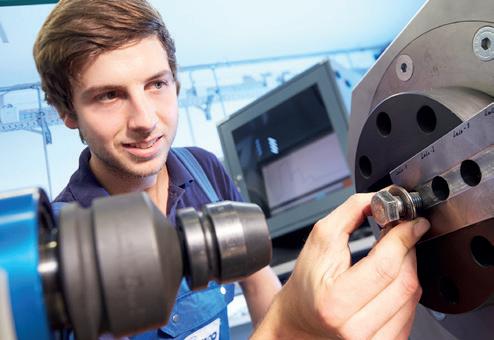
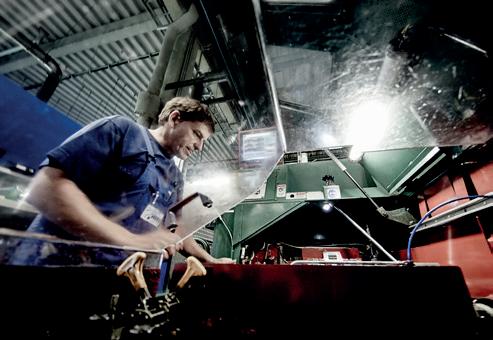

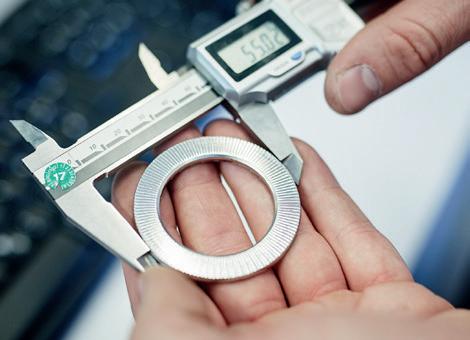
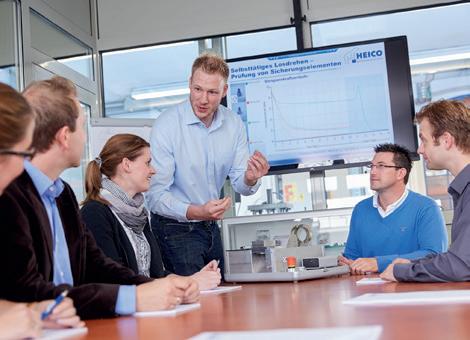
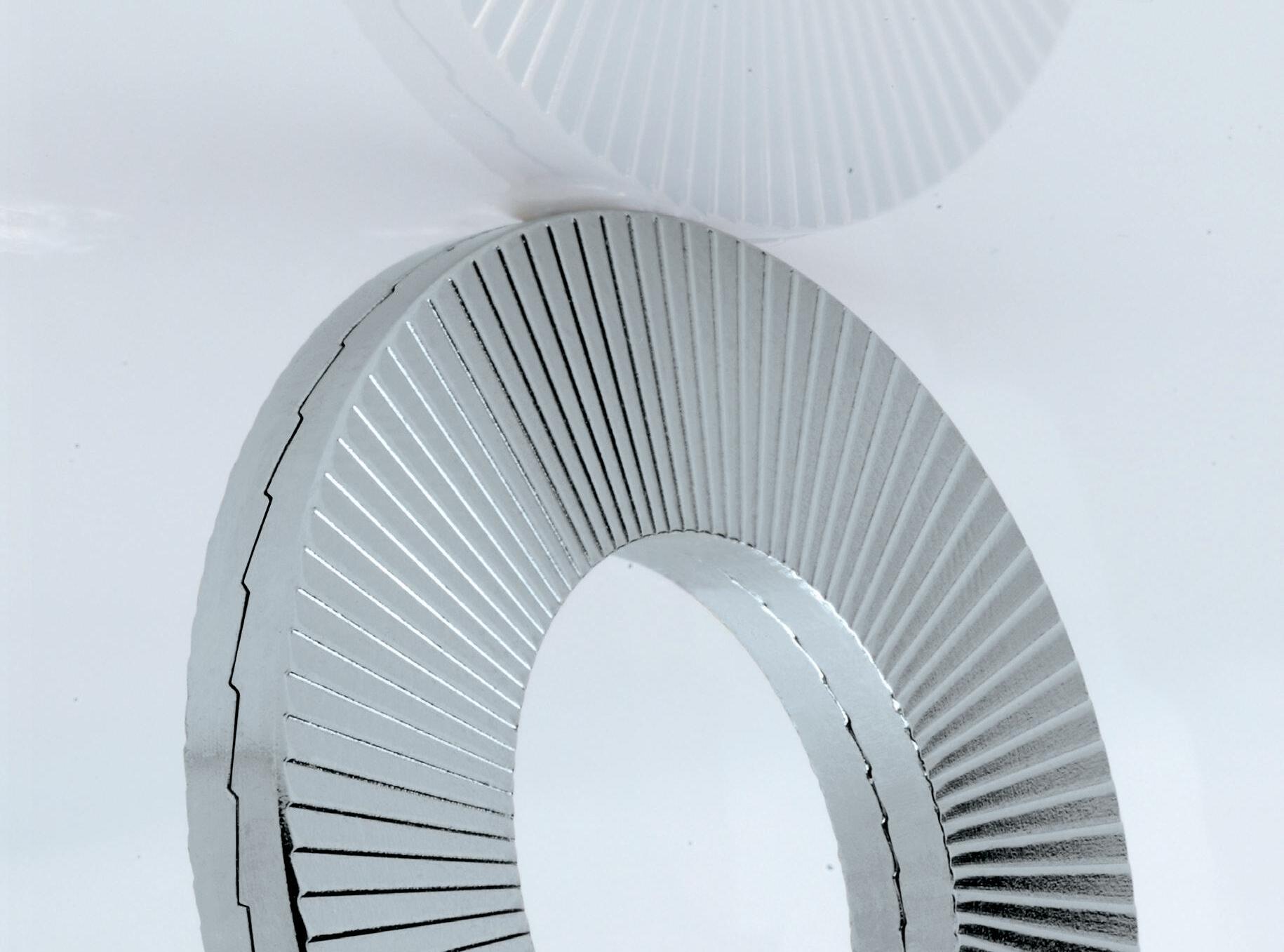
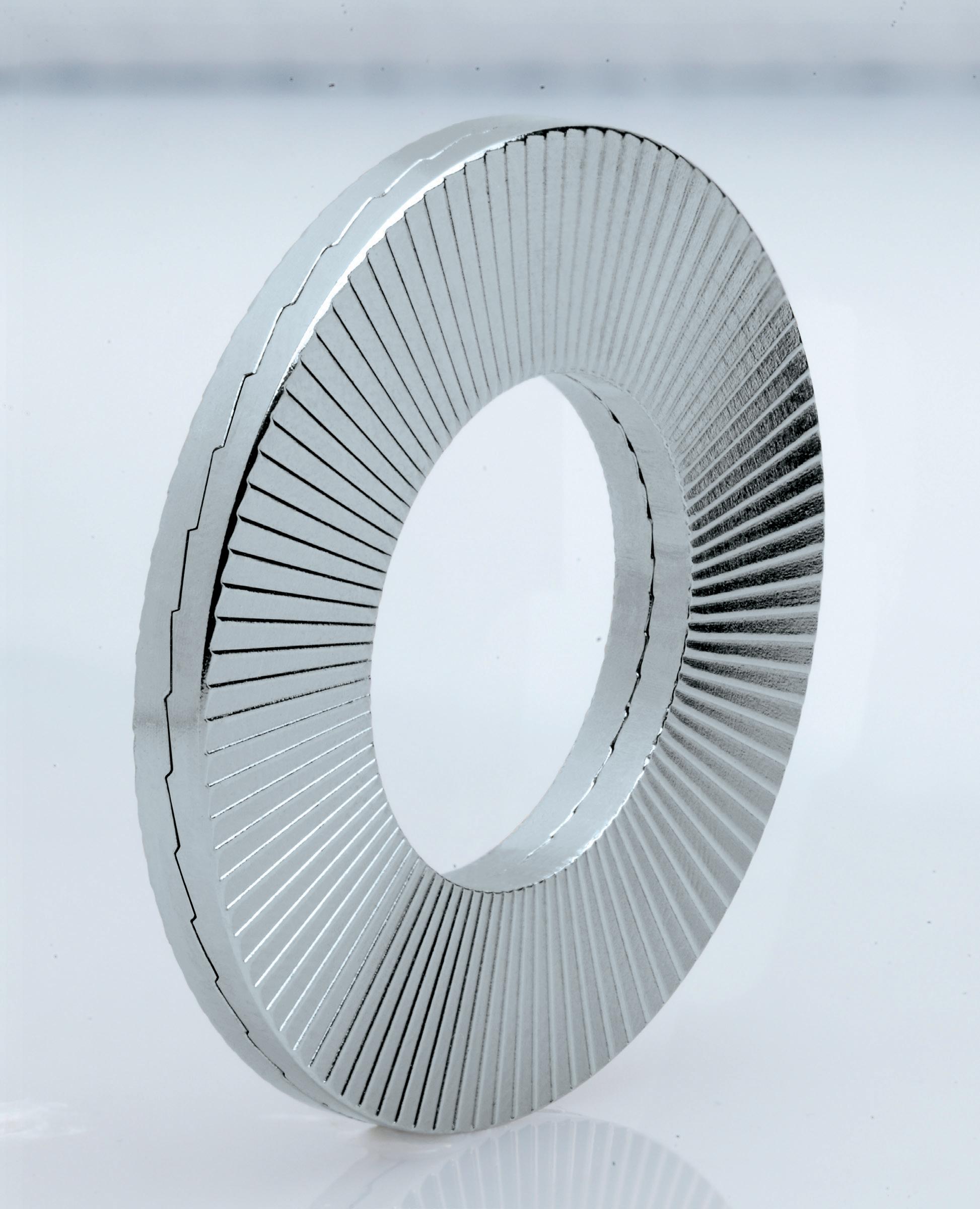



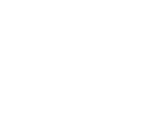
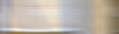
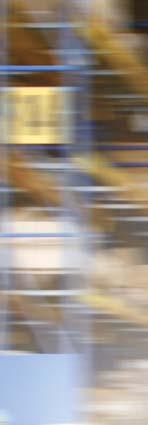
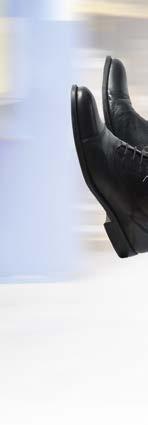

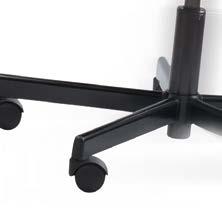



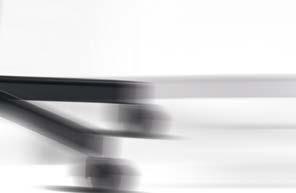

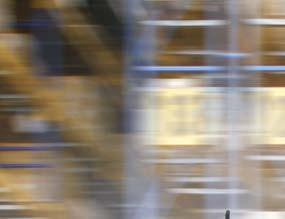
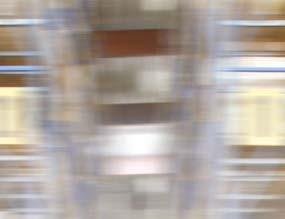
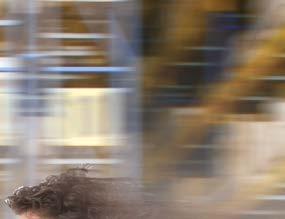
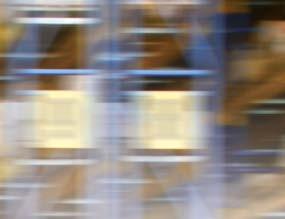
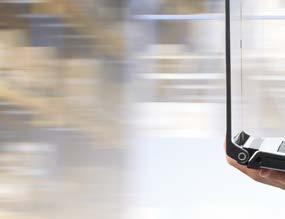
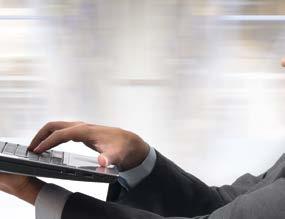
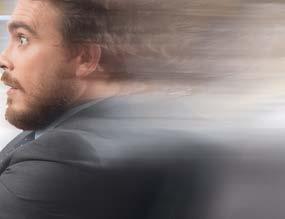
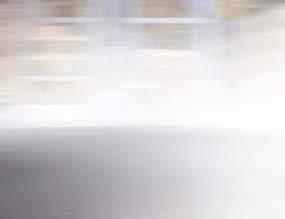
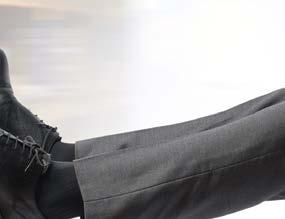

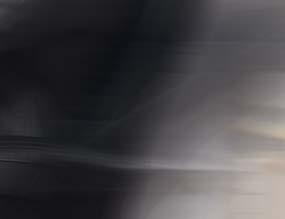
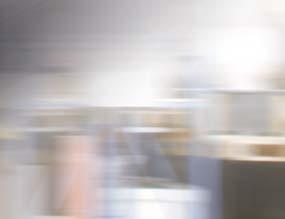



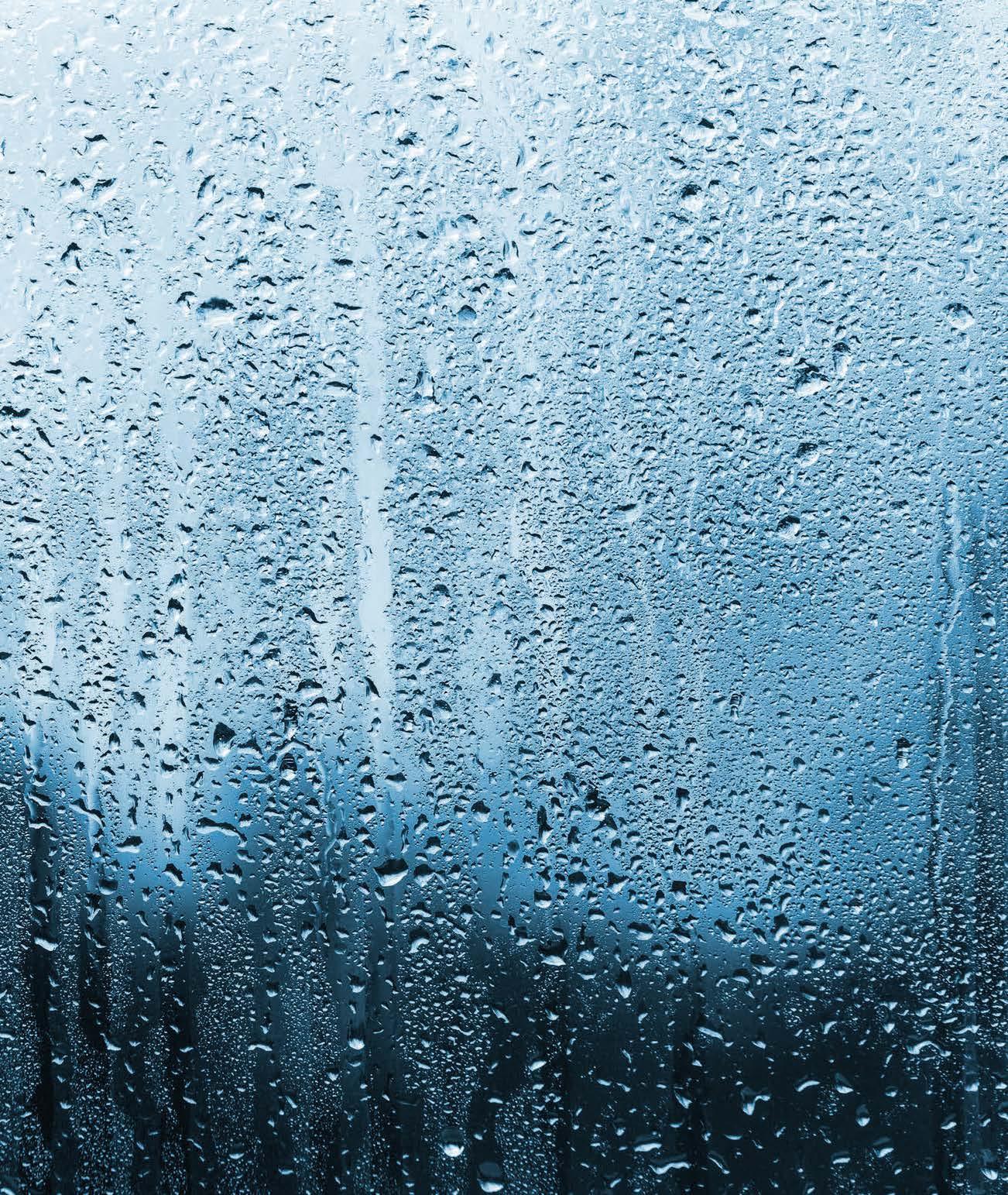
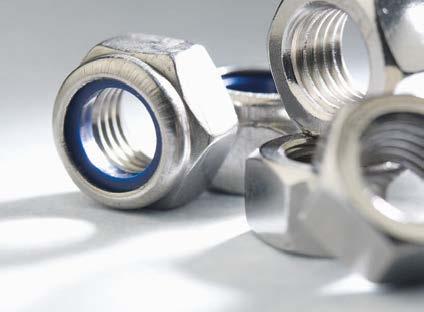

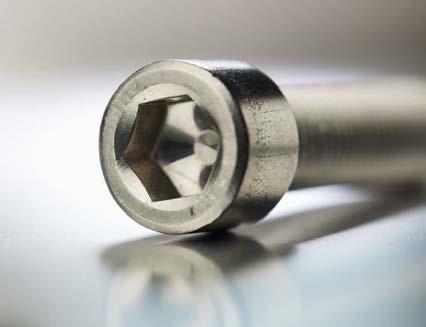
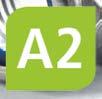
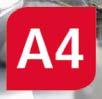
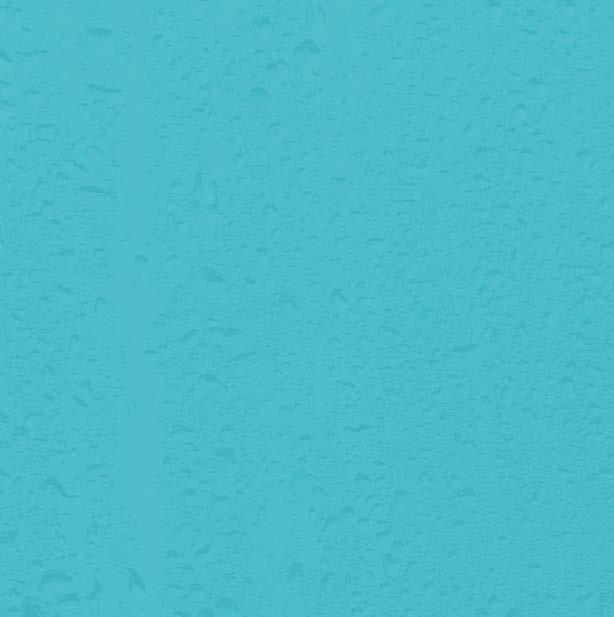


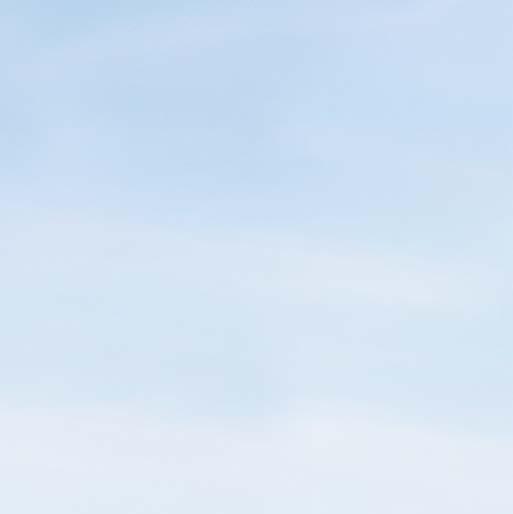



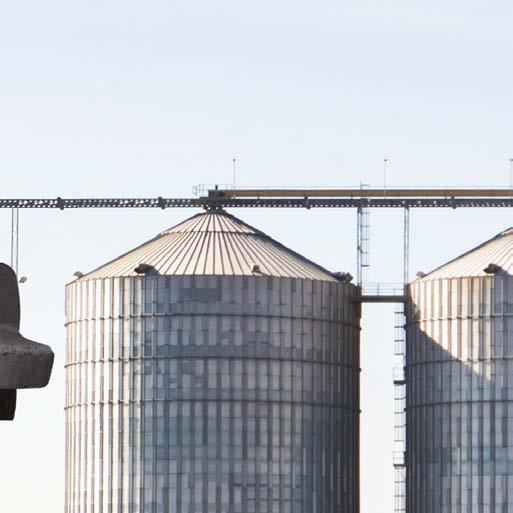
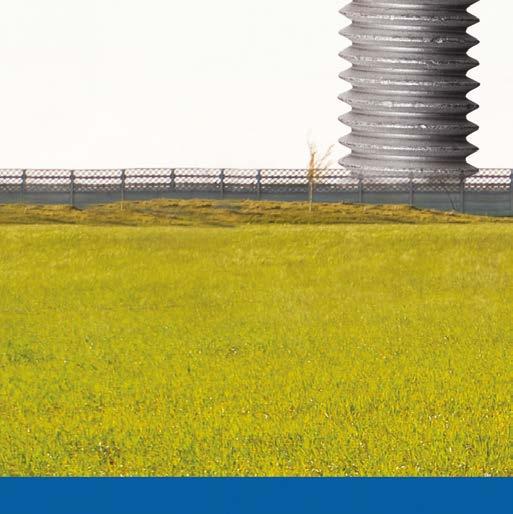
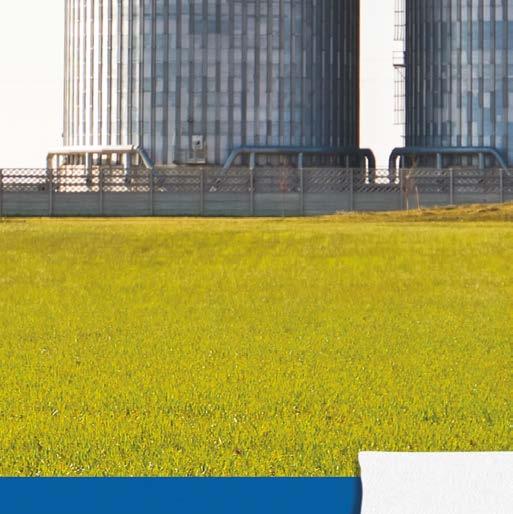
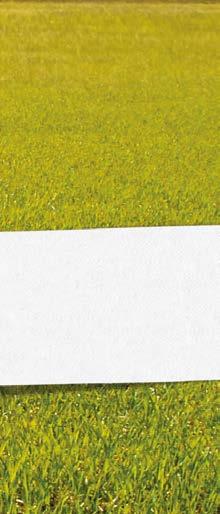
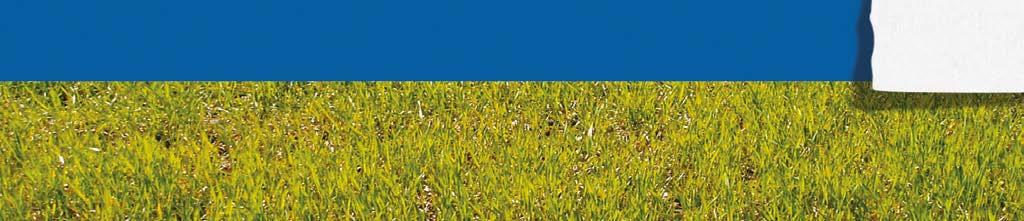
Renk Test System chose Superbolt Expansion bolts from the Nord-Lock Group to secure world’s most powerful wind-turbine test rigs, which permit simulation of any type of wind force.
Only Nord-Lock can claim more than 30 years of trusted quality in securing joints exposed to dynamic loads. Renk Test System engineers put their trust in the Superbolt technology so their customers can save millions of dollars by eliminating unwanted production stops and expensive maintanance costs.
Nord-Lock is number one in bolt securing systems for all kinds of great reasons. Discover them all at www.nord-lock.com
Part of the Mack Brooks Group Romeland House, Romeland Hill, St Albans, Herts, AL3 4ET, UK
Tel: +44 (0) 1727 814 400 Fax: +44 (0) 1727 831 033
www.fastenerandfixing.com
Publishing Director Jamie Mitchell jamie.mitchell@fastenerandfixing.com
Executive Editor
Phil Matten phil.matten@ fastenerandfixing.com
Editor
Will Lowry will.lowry@ fastenerandfixing.com
Deputy Editor Claire Edwards claire.edwards@ fastenerandfixing.com
Senior Advertising Executive
Harry Whyte harry.whyte@ fastenerandfixing.com
Advertising Executive
Emiliano Pagliaroli emiliano.pagliaroli@ fastenerandfixing.com
Advertising Executive
Ilana Bernstein ilana.bernstein@fastenerandfixing.com
Production Manager
Andy Clow andy.clow@fastenerandfixing.com
Production Assistant Jo Lightfoot jo.lightfoot@fastenerandfixing.com
Fastener + Fixing Magazine is a dedicated, trade-only publication which is circulated freely throughout the European trade.
Disclaimer
The Publisher cannot be held responsible or, in any way, liable for errors or omissions, during input or printing of any material supplied or contained herein although the utmost care is taken to ensure that information contained is accurate and up to date. The Publisher also cannot be held liable for any claims made by advertisers or in contributions from individuals or companies submitted for inclusion within this publication. The opinions expressed are not necessarily those of the Editor or Fastener Fairs Ltd.
Copyright
Entire contents copyright © Fastener Fairs Limited 2015. No part of this publication may be reproduced, stored in a retrieval system, or transmitted in any form or by any means without the prior permission of the publisher.
Annual subscription (6 issues) to non-trade and outside EU is €160.00
®
• Lockbolts and structural blind fasteners for heavy-duty industrial applications
• The stem is mechanically locked into the body
• High hole-fill capabilities
• New Blind Lockbolts in diameter 10 mm
• Strong vibration resistance
For further information: www.rivelit.com service@rivelit.com
• Exceptional shear and tensile strength
• Secure joints
• Multi-grip capabilities
• In Aluminum, Steel or Stainless Steel
• In diameters up to 10.0 mm
• RoHS compliant
by
For the November issue of Fastener + Fixing Magazine the editorial team has racked up the miles – including visits to Germany, Italy, Taiwan and the National Motorcycle Museum in Birmingham, UK – to ensure that we are always bringing you unique insight into the latest news and developments in the fastener industry.
Ihad the pleasure of visiting several German companies for our special ‘Made in Germany’ feature in November. My visits included our Cover Story company – HEICO Group – to discover how the Group has expanded over its 115 year history and focused on new capabilities and markets, including the development of its HEICO-LOCK® division. Other trips involved: Adolf Menschel Verbindungstechnik GmbH, to find out more about its production capabilities and in particular its ME-RIPP self-locking screw; R+FK Schulte KG showcased its production capabilities and its commitment to become a ‘one stop shop’ for both standard and special washers;
and Bäcker GmbH highlighted how it has become a specialist for plastic control elements, screws, nuts and washers similar to DIN, as well as customised plastic parts.
Whilst I was in Germany, Executive Editor Phil Matten visited Taiwan to find out more about the plans and prospects for next year’s Fastener Taiwan 2016 show, which promises to be bigger, longer and better than previous editions – underlining its importance to the fastener industry.
We also have a first-hand report from the FASTENERS MEETALY conference, which organisers described as the ‘first world convention focused on fasteners’ and included thought-provoking
presentations and discussions from leading fastener professionals.
Closer to home, Deputy Editor Claire Edwards visited GripIt® Fixings to find out more about the UK manufacturer and its meteoric rise; and we have reports from the Construction Fixings Association conference at the National Motorcycle Museum in Birmingham, as well as the Torque-Expo exhibition held in Silverstone.
To add to all this, we give an in-depth look at the backstory to the recent strategic acquisition of Barton Cold Form Ltd by Optimas OE Solutions LLC, and what it means for both companies; as well as a focus on bolting failure analysis, with an insightful article from Nord-Lock Group.
The European Union has given notice of appeal to the WTO in response to the compliance panel ruling issued, following China’s complaint that the EU’s anti-dumping measures on fasteners had not properly complied with WTO rules.
On 9th September the EU notified the WTO Dispute Settlement Body of its decision to appeal to the Appellate Body in relation to issues of law and legal interpretations in the Compliance Panel Report relating to Dispute DS397. On 14th September China notified the DSB of its decision to cross-appeal.
Three members of the WTO’s seven-strong appellate body will hear the appeal. A decision is normally issued within three months of the appeal being lodged. The appeal must be based on point(s) of law and cannot reopen factual findings made by the panel.
The dispute originated in July 2009 when China requested consultations regarding EU regulation 91/2009, which imposed definitive anti-dumping duties on imports of certain iron and steel fasteners originating in China. Following a Panel Report
in December 2010, and a subsequent Appellate Body Report issued in July 2011, the EU did make some amendments to the anti-dumping measures including a reduction in the non-company specific tariff level to 74.1%.
In October 2013 China began proceedings, resulting in the request for a Compliance Panel to address a number of alleged failures by the EU to meet its obligations under WTO rules. The Compliance Panel report was issued in August 2015. According to trade defence specialists, a key ruling was that the EU was found not to have correctly defined the domestic industry in its investigation. This, the Compliance Panel ruled, rendered the resulting injury determination inconsistent with the obligations of Article 3.1 of the WTO anti-dumping agreement. A summary of the case to date and the Compliance Panel’s findings can be read at:
https://www.wto.org/english/tratop_e/dispu_e/cases_e/ds397_e.htm
Following an expiry review the EU determined the continuation of anti-dumping measures applied to imports of certain wire rod from the People’s Republic of China.
With the exception of one group accorded a lower duty the extended measure applies duty at 24%. The review determined that China currently has some 50 million tonnes spare capacity (50% more than actual output) in wire rod production and according to the Chinese export database shipped some 9 million tonnes worldwide in the year to 30th June 2014. Depending on the geographic market the average cost per tonne of exported wire rod fell by between 14% and 19% from 2012 to 2014.
Full details of the Commission’s decision are to be found in Council Implementing Regulation EU 2015/1846.
Bufab Group reported third Quarter sales up 8% to SEK 577 million (61.5 million euros) but said after adjustment for currency and acquisitions like for like sales remained unchanged against the same Quarter 2014. Nine month sales rose 11% to SEK 1,847 million.
Operating profit for Quarter Three was SEK 52 million (2014 Q3: SEK 48 million) equating to an adjusted operating margin of 9%. Net sales for the nine months to date rose 11% to SEK 1,847 million (197 million euros) with an underlying sales growth of 3%. Operating profit was SEK 159 million (2014 9 months: SEK 141 million). The adjusted nine months operating profit was SEK 159 million, unchanged from 2014 same period with an adjusted operating margin of 8.6%, which was down from 9.5% in 2014.
President and CEO Jörgen Rosengren estimated underlying demand for Q3 to be weaker than in Q2 and in the corresponding Quarter in 2014. He noted that the change was tangible amongst many customers, particularly in Norway and Sweden.
Flos B.V, which Bufab acquired at the beginning of the year, was reported to have developed well and contributed good sales and profitability in Q3. International sales grew but at a lower rate than earlier in the year with growth coming from acquisitions and increased market shares. Swedish net sales declined but this remained due to a major customer that switched to own production in Q4 2014.
Jörgen Rosengren said that the favourable margin trend seen in Q3 was attributable to previously announced measures to implement price increases, achieve purchasing advances and effect cost savings.
Manufacturing and distribution of rivets, insert nuts and riveting tools
COMMERCIAL BRANCHES:
GERMANY bralo.de@bralo.com - UNITED KINGDOM bralo.uk@bralo.co.uk - FRANCE bralo.fr@bralo.com
PORTUGAL bralo.pt@bralo.com - SPAIN bralo@bralo.com - CZECH REPUBLIC bralocz@bralo.com
- ITALY bralo.it@bralo.com
- CHINA bralo.cn@bralo.com
- TURKEY bralo.tr@bralo.com
- MEXICO bralo.mx@bralo.com
www.bralo.com
Gruppo Fontana has signed a definitive agreement to enter a strategic partnership with Bagla Group of India.
Based in Aurangabad, Bagla Group has annual sales of around INR5 billion (68 million euros) servicing the automotive, engineering and domestic appliance sectors with aluminium die castings, wheels, electrical components, and fasteners. Customers include VW, Maruti Suzuki, Tata Motors, Piaggio, Bajaj Auto, Delphi, Bosch, Behr and Magna.
In a statement Bagla said: “The partnership with Gruppo Fontana would enable the fasteners business of Bagla Group to acquire necessary technological expertise, size and scale to become the largest fastener manufacturer in India.”
Bagla started making fasteners in 2006. Its fastener plant is ISO/TS 16949 accredited producing M4 – M14 male threaded parts and nuts to M18. Formers range up to 6 die, and it has in-house continuous heat treatment line and electroplating and zinc flake lines.
Giuseppe Fontana, Fontana vice-chairman, said: “India is the most promising economy in the world at this stage and we are committed to serve our global customers that have a presence in India. Additionally, the Fontana Gruppo proposes to use the local manufacturing capabilities and engineering expertise in India to serve its customers in various countries.”
Bossard Group sales for the first nine months were CHF 498.4 million – up 5.9% year-on-year. Quarter 3 performance was slightly stronger than the first two Quarters.
Reporting on its third Quarter
Bossard Group said it had further consolidated its market position as a result of acquisitions. Thanks to the investment policy sales for the first nine months increased 5.9% to CHF 498.4 million (approximately 458 million euros). Growth through acquisition offset the impact of the Swiss franc appreciation earlier in the year. Excluding acquisitions, sales were down 1.2% in local currency, translating to a 4.5% reduction in Swiss francs.
For the first nine months Bossard’s European business grew 4.8% in local
currency, translating to CHF 294.7 million and a 3.1% year-on-year decline. Bossard said the figures reflected the difficult and inconsistent demand situation in some European markets, especially Switzerland where customers had been hit by the currency depreciation.
As a result of the acquisition of Aero-Space Southwest Inc, at the beginning of the year, American sales grew 36.4% to CHF 126.4 million. Underlying sales fell 3.2% in local currency but grew 2.6% in Swiss francs. In the third Quarter Bossard benefited from increased volume from the largest US electric vehicle manufacturer but continued
to be confronted with lower demand from its second major customer, operating in the agricultural technology sector.
Bossard saw ‘pleasing growth’ from most Asian markets but this was dampened by business conditions in China. Although in China generally weak demand from existing customers was compensated for by new business.
Bossard projects its full year sales at around CHF 660 million, with an operating margin on par with the first half of the year. It expects business in Europe to continue to be uneven, with Swiss demand down on the previous year.
Bulten reported Quarter 3 sales of SEK 618 million (65.5 million euros) up 4.1% on the same period 2014. EBIT operating earnings were SEK 36 million (Q3 2014: SEK 25 million). Earnings after tax were SEK 22 million (2014: SEK 17 million).
Year to date sales were SEK 2,027 million (214.8 million euros) up 13% on the same period 2014. EBIT was SEK 118 million (2014: SEK 95 million) corresponding to an operating margin of 5.8% (2014: 5.3%). Earnings after tax were SEK 87 million (2014: SEK 66 million).
Bulten confirmed it had won a new full service provision contract worth 20 million euros during the Quarter. Order bookings for the 9 months were up 8% to SEK 2,000 million.
The report noted that growth in the third Quarter had been affected by the slowdown in China and by two FSP contacts reaching full volume around the same time last year. Profitability had strengthened thanks to higher volumes and more favourable exchange rates together with the benefit from an “ongoing optimisation programme”.
Bulten reported it would indirectly acquire the property of its Swedish production unit in Halstahammar at which it was already the head tenant. Bulten will pay SEK 113 million for the property company Söderport Hallstaham Hall AB and will see an annual operating profit improvement of around SEK 8 million as a result.
All our products are available on the digital catalog
Behind a great Product there is always a great Company and a great Job
Ambrovit S.p.A.
Via Giulio Natta, 29 - 27026 Garlasco (PV) Italy
Tel. +39.0382.810280 - Fax +39.0382.1760014
email sales@ambrovit.it - web www.ambrovit.it
Hex lag screws | Chipboard screws | Carpentry screws
Drywall screws | Dome screws and Euro screws
Machine screws | Nuts, Washers, Bolts, Threaded rods
Self Tapping screws | Concrete screws
Self Drilling screws | PVC screws | S.S. A2 screws
Optimas OE Solutions LLC has announced the acquisition of UK fastener and parts manufacturer Barton Cold Form Ltd, in a move that enhances supply chain security and fl exibility of support for key OEM customers.
With an eighty year manufacturing history, Barton now operates from a custom-built 5,100m2 facility in Droitwich Spa, to which it moved in 2006.
Barton’s current machine park includes 19 heading, 9 rolling and 35 secondary operation machines. The plant is ISO/TS 16949 accredited and supplies leading automotive OEMs and tier suppliers, including through Optimas. Annual revenue is around GB£8 million and Barton employs 70 people, including those in a sales office in Katowice, Poland.
Optimas was established in July 2015 when senior management took Anixter’s OEM Fasteners segment private, supported by American Industrial Partners – a New York-based, operationally oriented, middle market private equity investor.
Barton becomes Optimas’ second manufacturing site, joining the Wood Dale facility in Chicago, USA. Anixter acquired Wood Dale in 2008 but the plant gained strategic significance following a major investment programme started in 2012, which included installing new National FORMAX headers.
Commenting on the Barton acquisition, Optimas president and CEO, Ian Clarke, said: “Considering the growing need of our customers around the globe, increased manufacturing capacity and expertise enables Optimas to better keep pace with demand, protect supply chain pipelines, and continue to offer custom solutions that are otherwise unavailable elsewhere.”
The UK plant will retain the Barton name and continue to be led by Andrew Nuttall, as operating director, and his current management team. Nuttall said he firmly believed the partnership with Optimas would “lead to positive benefits for our suppliers and customers”. He added: “Our partnership with Optimas solidifies the long-term stability of our business, accelerating our ability to act on growth opportunities with the industry.”
Barton employees were informed of the new ownership on 2nd November. For the presentation Andrew Nuttall was accompanied by Dan Jack, Optimas SVP EMEA; Mike Tuffy, SVP global procurement; and Tim Taylor, newly appointed as Optimas vice-president for global manufacturing.
Following a video welcome from Ian Clarke to the entire Barton team, Tim Taylor quickly established his manufacturing credentials. A 30 year career in manufacturing started at
Ford Motor Company. Advancing through Huck International he moved on to fulfill senior roles with McLean-Fogg Company for eleven years, which included heading its global vehicle systems business with plants and offices in North America, Europe and Asia. Taylor served three years as president and COO of Tempel Steel Company, Chicago, until 2007, since then he has been managing partner of a manufacturing consultancy.
Referencing recent events in UK fastener manufacturing, Taylor’s primary emphasis was on how Optimas could now invest to grow Barton’s size and capability, providing enhanced employment security for its employees.
The Barton and Wood Dale manufacturing operations now report to Taylor, who, says Ian Clarke, “will split his time between Wood Dale and travelling globally as he leads our effort to expand our manufacturing strategy and footprint around the world”.
Dan Jack underlined the significance of the Barton acquisition to major OEM customers, particularly in supporting rapid growth from key automotive accounts. “This is all about a growth strategy for Optimas,” he stressed. “We’re successful, we want to be more successful and key to that is an integrated supply chain.”
Mike Tuffy reminded the audience he had known Barton Cold Form since the 1990s. “I always admired what you were doing –the passion to make parts in the UK and to sell in the UK, before broadening to develop sales overseas.” He outlined how Barton’s manufacturing capability would dovetail to an overall procurement strategy that carefully identifies which parts to manufacture within Optimas and which to source from the company’s global portfolio of strategic vendors. After the presentation, Tuffy reiterated to this magazine that the investment would not represent a major shift in supplier relationships. “Having our own manufacturing is fundamentally a growth strategy, underpinning the critical supply chain security our customers now demand. It also provides a solution-oriented engineering capability, which we have already demonstrated at Wood Dale enables a tighter, more effective relationship with our customers’ own engineering and design teams. That all contributes to the growth and profitability of Optimas, which is what ultimately matters to all our stakeholders.”
For the full backstory on Optimas’ strategic acqusition of Barton Cold Form read pages 60-62.
The latest report from the World Steel Association shows the world steel capacity utilisation ratio fell to 68% in August, compared with 71.6% at the same time last year.
While there is a seasonable dip in output in late summer the average ratio in 2015 is running at least two points lower than in 2014. Over capacity is impacting the steel industry throughout the world. This was starkly illustrated in the UK during September when SSI announced the closure of its Redcar blast furnace and Tata Steel confirmed the closure of two Scottish operations and the mothballing of its plate mill in Scunthorpe, with a consequent loss of 1,200 jobs. Tata Steel’s wire rod mill, which produces cold heading wire, was not directly affected by the cuts.
A Reuters survey of steel analysts forecasts that iron ore prices will remain below US$50 per tonne for the coming two years as supply of the raw material continues to outstrip demand, particularly in China. Analysts that had previously forecast Chinese steel production would continue to rise until 2020 now suggest the peak was reached in 2014. Credit Suisse projects Chinese steel production to fall from 823 million metric tonnes in 2014 to 812mmt this year. By 2018 it believes the figure could be down to 745mmt. At this level, though, China will continue to have massive over capacity, expected to continue depressing world steel prices. Despite many Chinese steel companies
reported to be making substantial losses there remains little evidence of significant reductions in output, with many focusing on overseas sales to compensate for weak domestic demand.
The China Iron & Steel Association has announced that medium and large-scale steel mills in the country lost the equivalent of US$4.4 billion in the first nine months of 2015. It also, though, confirmed that reduction in output was still at a lower pace than the fall in domestic demand.
Steel analysts MEPS (www.meps.co.uk) recently raised other concerns relating to the growth in exports of Chinese steel products. China incentivises steel companies to export but restricts tax rebates to alloy grades. However, the threshold of alloying element content to achieve eligibility for export rebate is low. This, MEPS says, brings into question the degree to which the mechanical properties of the material are improved and may create performance risks, particularly in relation to weldability. MEPS also highlights massive discrepancies between official Chinese data for exports of certain types of steel when compared with the receipts from Chinese suppliers recorded in other countries. The analyst’s conclusion is that the Chinese reporting mechanisms are not fit for purpose.
Trifast Plc has announced that it has acquired Kuhlmann Befestigungselemente GmbH & Co KG for a total consideration of 8.5 million euros, of which 6.76 million euros was paid on completion in cash, with 0.04 million euros in Trifast shares. 1.7 million euros will be deferred for 12 months as a retention against potential warranty and indemnity claims.
Kuhlmann is based in Verl, close to Bielefeld and distributes fasteners to the German domestic market. It employs 18 people and reported 2014 revenue of 6.7 million euros and pretax profit of 1.74 million euros. Previous owners Frank Niggebrügge, Eric Hütter, and Peter Henning, will continue as the management team.
Trifast will be investing into Kuhlmann to further develop the opportunities in the German market and expects the acquisition of Kuhlmann to be earnings enhancing in the first full year of ownership.
Commenting on the acquisition, Malcolm Diamond MBE, executive chairman of Trifast, said: “As investors know, we have a strong philosophy when it comes to acquiring profitable businesses – in our key sectors – backed up by respected and experienced management. Kuhlmann provides just this and the base from which to grow our presence and sales into the largest manufacturing country in the EU region. Everyone at TR looks forward to working with the Kuhlmann team to achieve this objective.”
Trifast’s chief executive, Mark Belton, added: “This is a very positive step for both TR and Kuhlmann and we welcome everyone into the Trifast family. Having already built a close trading relationship between our two businesses and respective management teams, we are now establishing a strong local presence and a base for what we see as an exciting opportunity for both TR and Kuhlmann. We are confident that combining local knowledge and culture with increased technical expertise, in what is the largest industrial market in Europe, will enable us to leverage the Group’s existing business and open up additional opportunities for further growth, both locally and internationally.”
Frank Niggebrügge at Kuhlmann commented: “We have known the TR team for a number of years and we have mutual respect for each other’s business. The opportunity for Kuhlmann to become part of an international business opens up new markets and opportunities, as well as us being able to benefit from the international manufacturing, sourcing and purchasing resources, and worldwide marketing capabilities that the Trifast Group has to offer. We look forward to working with the Trifast team and exchanging ideas and initiatives.”
The ABA Original clamp in stainless steel –for the most extreme environments
The new ABA Original SMO is developed for use in harsh environments where low-grade or acid-proof stainless steel proves insufficient. The new clamp is made entirely of SMO 254 – an austenitic stainless steel designed for maximum resistance to pitting and crevice corrosion. It also has a very good resistance to various types of stress corrosion, making it the ideal material for clamps used in high chloride environments, such as seawater or high chloride process streams.
On 19 th October PwC was appointed as administrator for sixteen Caparo Industries Group companies including Darlaston-based Caparo Atlas Fastenings Ltd. At the end of October the closure of the historic UK fastener manufacturer was announced.
Caparo Industries Group is part of global network of businesses operating under the Caparo name, formed by Lord Paul in the 1960s when he moved to Britain from India.
The announcement that sixteen UK mainly steel related Caparo companies would enter administration came as Chinese President Xi Jinping visited the UK. The decision was strongly linked to the impact of low cost steel imports from China, also cited as a major factor in the closure the previous week of a UK blast furnace and the subsequent announcement of 1,200 job losses at Tata Steel’s UK operations.
Realistically this does not explain PwC’s assessment that Caparo Atlas Fastenings (‘Atlas’) was unviable, which became clear on 30th October when the announcement was made that the Darlaston business had been closed with immediate effect, making 122 employees redundant. Caparo Forging Europe, which has two UK sites, and two other Caparo companies also closed. PwC said: “It is with regret that we have made these decisions today, but the commercial prospects of the affected businesses render them unviable.” 1,200 people continue to be employed in the rest of the Caparo companies in administration.
Situated in the UK’s so-called Black Country, the 19th century
heart of England’s industrial revolution, ‘Atlas’ traded on the same site for close to 130 years. In 1887 FW Cotterell Ltd began manufacturing at Atlas Works in Darlaston – the eponymous founder having been recorded as making coach bolts as early as 1800. The company introduced the famous trade emblem of Atlas standing on a nut and bolt supporting the world on his shoulders, representing the role the company came to play in global fastener supply. From 1919 the site manufactured nuts, bolts and studs, as part of Guest, Keen & Nettlefolds. By the end of the Second World War, Atlas Works covered more than twenty acres (8 hectares) and employed 3,000 people. In 1982 the business was acquired by Armstrong and, incorporating the other acquisitions of GSF and Charles Richards, became Armstrong Fastenings Ltd. Caparo acquired Armstrong in 1989. In 2006, unable to reach a negotiated settlement with trustees over a GB£36 million pension fund liability, it placed Armstrong into administration. The Darlaston plant was reacquired from the administrators as Caparo Atlas Fastenings Ltd.
‘Atlas’ has been a major supplier to the UK automotive sector for many decades, from before the original Mini through to Jaguar Land Rover and JCB. It supplied a wide range of other sectors including construction, oil and gas, and defence, with fasteners from M4 to M24 diameter.
Trifast Plc has issued a half year interim report showing pre-tax profit increased by 43.9% to GB£ 7.1 million (10 million euros) for the six months to 30 th September.
Group revenue increased 5.6% to GB£78.1 million. At constant currency, revenue grew 8.7% with acquisitions representing 5.4%. The report also shows organic growth at constant currency of GB£4.6 million from TR’s top fifty multinational OEMs.
Trifast has completed an expansion program at SFE, its production facility in Taiwan, increasing capacity by 15%. Additional investment in computer controlled ‘lean-lift’ stock storage technology in the UK has halved pick times and allowed the consolidation of TR’s Poole warehouse into Uckfield, delivering operational efficiencies while maintaining customer service.
Chairman Malcolm Diamond commented: “We are pleased to report a solid first half performance, which has delivered an underlying pre-tax profit increase of 24.8% to GB£8.3 million and a 23.2% increase in underlying EPS. Our order pipeline across our key locations remains encouragingly healthy. We continue to focus on cost control and supply chain management, particularly from ongoing investment into efficiency drivers. The positive impact this is having on our margins is expected to continue.”
He added: “Overall, taking into account the current business climate we are operating within, the board remains optimistic about the Group’s prospects and continues to expect its trading for the financial year as a whole to be in-line with its expectations.”
At a detailed level the report notes that the production cost gap between Italy and Taiwan is “narrowing enticingly”. Trifast is currently reviewing the potential to increase manufacturing at VIC, the Italian manufacturer it acquired in 2014, which it also reported had continued to yield strong results in the half year.
Malcolm Diamond said: “Organic growth remains only part of our strategy and we will continue to look for our next strategic acquisition to complement the Group’s existing global, product and sector footprint.” Trifast says it is exploring a number of geographic areas, including Spain and Mexico, for new business opportunities.
On 1st October Mark Belton, handed over his role as chief financial officer to Clare Foster and took on the position of CEO, following the planned retirement of Jim Barker.
The Bossard Group will invest 14 million euros to build a modern warehouse at its German location in Illerrieden.
Bossard Group and subsidiary KVT-Fastening will use the new 6,100m² warehouse as a logistics hub for all product deliveries within Germany, and the central and eastern Europe region. The investment will increase capacity at the site fourfold.
“Illerrieden was specially selected for its central location in Europe. From here, we can reach all export countries in the EU relevant for our Group. This is beneficial for domestic as well as international Bossard and KVT-Fastening customers. Shorter routes, translates to shorter lead-time in product deliveries,” explains Frank Hilgers, member of the executive committee of Bossard Group.
The groundbreaking ceremony for the new building (visualisation pictured) took place in September with commissioning planned for early 2017.
In a submitted editorial on pages 114 – 116 of Fastener + Fixing Magazine, Issue 95 September 2015, it was stated that the source of the Figure 2 graph –on the efficiency of popular locking wedge washers according to Junker, EDYZ and NAS tests – was sourced from Hard Lock technical reports. 2007, Vol 2.
Following our investigation of a complaint registered by the author Mr Jozef Dominik it was demonstrated that the Hard Lock Company was only the source of the first row (NAS 3354) in the graph. The remaining results for the EDYS and Junker tests were carried out by Jozef Dominik’s company – Ferodom s.r.o. We are, as always, pleased to set the record straight in this way.
Fastener + Fixing Magazine takes all reasonable care to ensure the accuracy of submitted editorial, but its publication policy is explicit that it cannot be held responsible or, in any way, liable for errors or omissions, during input or printing of any material supplied.
To read the corrected version of the article please visit: www.fastenerandfixing.com/news/testing-bolting-resistance-to-vibration
Since October 2015 Norm Group company Uysal Makina has been able to apply GEOMET® coating under a NOF licence.
Uysal Makina explains that GEOMET® coating is suitable for all kinds of fixings and metal parts and provides high corrosion resistance and controlled friction. It is preferred by the automotive and heavy construction industries because it is water-based and, therefore, more environmentally friendly. It is non-electrolytic, being applied by dipping, rotating or spraying methods. The coating, which can be applied as a thin layer, is hexavalent chromium and other heavy metals free but still takes full advantage of the anti-corrosion properties of zinc. The coating process does not introduce the risk of hydrogen embrittlement making it particularly suitable for high-tensile products. The coating makes repeated fastening and disassembling easy.
Uysal Makina will apply the coating for Norm Group companies, using a brand new modern and automatic facility with a capacity of 400 tonnes per month.
www.normcivata.com
At a prestigious Top 100 awards ceremony held in Essen, Germany, HEICO Befestigungstechnik GmbH received an award as one of the most innovative medium-sized companies in Germany.
The Top 100 award is based upon a two stage scientific analysis developed by Prof Dr Nikolaus Franke and his team from the Vienna University of Economics and Business. A company‘s innovation management and success is evaluated by more than 100 parameters in five different categories. The final decision is then made by the academic leadership.
implementation of good ideas is also a key competitive factor. That is why HEICO has put a lot of effort into its innovation management effort, which has now been recognised with this prestigious award.
This year, Dr Franke and his team had to consider an unprecedented number of applications. From an initial 302 companies who entered, 234 made it into the final of this year’s competition with these companies then divided into three equal sized groups. 178 companies were finally awarded with the Top 100 seal (a maximum of 100 companies in each group).
“The secret of our success is that we never shy away from being innovative,” declares Jan Bernd Heimann, general manager at HEICO Befestigungstechnik GmbH. “At peak times more than 30 HEICO employees are responsible for the research and development of new products.” According to Mr Heimann the fast
Among the Top 100 award winners were 71 national leaders and even 31 world leaders – with two-thirds of the Top 100 companies being family owned businesses. The Top 100 companies registered 3,405 patents within the last three years with approximately 41% of their revenues being realised by improved products and technology new to the market (the German average is 6%). This success was not just a matter of chance, on average these companies reinvest 10.5% of their revenues in research and development of new products whereas the German average is 1.5%.
In accepting the award Mr Heimann offered his thanks and appreciation to his employees, whose ideas and commitment made winning the Top 100 accolade possible.
www.heico-lock.com
RCF Bolt & Nut Co (Tipton) Limited has recently invested in a new forging machine to keep up with ever increasing customer demand to supply ‘Made in the UK’ quality products.
Based in the West Midlands, RCF Bolt & Nut manufactures and distributes an extensive range of fasteners to suit almost any application. The company has gone from strength to strength over the last few years and says its stockholding is now at the highest value ever.
“Our customers are asking more of us month-on-month. We were hitting higher production runs and needed more capacity to keep up with our ever increasing order book. Our decision was not easy, nor cheap, but our newly installed
Normed and standardized parts
Norm- und Standardteile
DIN, ISO, EN and others / und andere
Special parts and special materials
Sonderteile / Sonderwerkstoffe
machine not only ups our production, it also gives us the flexibility to offer new items, longer lengths, flexibility, quicker lead times and new jobs,” explains Shaun Collinson, sales and development manager at RCF.
Shaun continues: “We are fully in control of every part of the manufacturing process. From the steel bar, to when the finished item is bagged, labelled, and fully certified. From standard to bespoke items, RCF can offer full mill certifications with any classification of testing required.”
Using the HARDLOCK Nut provides its users with a solution to resist loosening in threaded joints that is proven to out-perform every other fastener available.
The HARDLOCK Nut has met the testing requirements of multiple vibration and impact tests including the NAS3350 and 3354 National Aerospace Standard. Its proven reliability enables its users to benefit from a significant reduction in their maintenance costs.
The HARDLOCK solution utilises the wedge principle. Firstly the lower convex fastening nut generates axial torque in the same way as a normal nut. Then, as the upper concave lock nut is tightened, the wedge effect generates stress perpendicular to the axis, which pushes the lower convex nut against the screw thread. When the upper concave nut is completely tightened, the HARDLOCK Nut produces a stable self-locking force with the result that it remains unaffected by external vibration or impact.
HARDLOCK can be used with any standard bolt or thread
The HARDLOCK Nut is used extensively in safety critical applications to provide the most robust solution to prevent failure in threaded joints. HARDLOCK also has versatile applications beyond its use in infrastructure projects and the rail industry. The HARDLOCK Nut and its variants the HARDLOCK Bearing Nut and the HARDLOCK Set Screw excel at working in extreme vibration and temperature environments in many types of application including: Electronic Switchgear and Connectors, Electric Pylons and Radio Masts, Automotive Assembly, Off-Road Vehicles, Marine Craft, Theme Park Rides, Wind Turbines, High Rise Buildings to name but a few.
For more information about HARDLOCK please call Staytite: 01494 462322 or email: fasteners@staytite.com | www.hard-lock.co.uk
The plight of the steel industry keeps on hitting UK headlines. First the closure of the SSI steel works at Redcar, closely followed by the announcement TATA Steel would shut plate mills in Scotland and Scunthorpe. The direct impact is 2,700 job losses; the wider pain in these steel communities will be far, far greater.
For its Quarter ending September, TATA announced European steel operations incurred a loss of some 33 million euros. It further wrote down its UK business bringing in a total charge of some 1.2 billion euros. TATA said it faced “a structurally challenging environment of weak domestic manufacturing demand, surging imports, a strong pound, and steep regulatory and business costs”. Some of these issues are UK specific but low cost imports from China and the CIS are impacting severely across Europe. Europe’s largest steel maker ArcelorMittal recorded a Quarter Three operating loss of 23 million euros. European CEO, Aditya Mittal, said: “Record, and still rising, levels of imports are materially impacting steel prices. Certain EU anti-dumping investigations are underway, but the process is slow and needs to be more efficient in order to effectively and fairly protect European steel producers from unfair trade.”
The plight of the steel industry seemingly also resulted in the closure of one of the UK’s oldest fastener manufacturers. Caparo Atlas Fastenings was one of sixteen group companies placed in insolvency in October; an action linked by the administrator PwC directly to the steel crisis: “The recent impact that low commodity prices, exchange rates, and China’s steel production has had on the UK steel industry, extended to certain companies within Caparo Industries Plc, impacting results and the funding requirements of the business.” At the end of October PwC
announced the complete closure of the Darlaston fastener plant, with the immediate loss of 122 jobs.
In this case there is real difficultly in reconciling the linkage with the steel crisis. ‘Atlas’ primarily produced high added value parts for the currently burgeoning UK automotive sector. Sources close to ‘Atlas’ say the decline and ultimate failure of the fastener maker was far deeper rooted, and far more to do with sustained under investment.
Changing tack to forward-looking fastener manufacturers, I found the FASTENERS MEETALY conference, excellent and thought provoking. One gripe. Some speakers simply cannot recognise that there is far more value to their organisation in delivering an authoritative and engaging presentation than indulging in a sales pitch. Fortunately, in Milan they were the exception.
The afternoon forum of key fastener figures worked hard to relate some of the morning’s visions to the current position of the fastener industry. Inevitably, two topics dominated: The impact of China and the dominant influence of the automotive sector on fastener demand. Four days later the revelation of the Volkswagen emissions scandal underscored the difficulties of forecasting as it surely heralded radical changes in vehicle powertrains. Far from negating the value of the conference, though, it reinforced Sergio Pirovano’s, president of UPIVEB, hope that it could become the first of a regular series of similar events.
Phil Matten reflects on some of the key topics currently involving the fastener industry
Alcoa Fastening Systems and Rings (AFS&R) signed an approximately US$1 billion contract with Airbus for high-tech, multi-material aerospace fastening systems. The deal is Alcoa’s largest fastener contract ever with the aircraft manufacturer. Alcoa’s fasteners fly on every Airbus platform.
As part of this agreement, AFS&R will supply advanced fastening systems, such as those that enhance the assembly of aircraft panels and engine pylons on newer airplanes, with sophisticated design features. Alcoa fasteners are made using a variety of materials including stainless steel, titanium and nickel-based super alloys, which improve fatigue life, enable lightning strike protection, and improve wear and reusability on conventional and composite aircraft. Alcoa will produce these fastening systems at fourteen of its global manufacturing facilities.
Alcoa fasteners will be used to assemble some of Airbus’ latest high growth airplanes, including the A350 XWB, Airbus’ newest commercial airplane, and the A320neo. Airbus will also use Alcoa’s fastening systems for longer-running platforms including the A330.
“Our growing aerospace capabilities, technology strength, and global, first-rate customer service continue to strengthen Alcoa’s decades long partnership with Airbus,” said Alcoa CEO Klaus Kleinfeld. “Alcoa is proud to partner with Airbus to provide breakthrough technologies for some of the most advanced aircraft in the world.”
For the third consecutive month, the seasonally adjusted September Fastener Distribution Index fell below 50 (47.5), consistent with the tough current environment for many distributors.
Added contraction was driven by the lowest seasonally adjusted sales figure (32.4) yet recorded for the FDI. In addition, employment contracted for the first time since April 2013.
Pricing and supplier deliveries were largely unchanged, and the long-term outlook for industry sentiment declined.
“Overall, we believe that fastener distributors continue to face material demand pressure from lower commodity prices, forex, and weaker industrial production. We maintain our cautious outlook on the industry.”
85% of total respondents reported sequentially flat or lower sales for September, consistent with sluggish recent
growth from Fastenal (+1.6% year-on-year in August versus a five year average of +13.2%), Grainger (-2% in August versus FY’15 guide of 0% – 2%), and MSC (company estimated +2.2% in June versus +7.6% last year).
The September employment index (48.7) showed a contraction in overall headcount for select distribution respondents for the first time in 30 months.
“We believe these results are consistent with recent contraction from Fastenal, which reduced total headcount on an absolute basis in August for the first time in seven months.”
Point-of-sale pricing for September was unchanged versus August for 74% of survey participants. “We believe the
overall environment for price increases remains notably soft given material demand pressure (declining commodity prices, forex, weaker industrial production) and minimal inflation.”
What does this mean for public distributors? “In our view, the data reflects overall weakness within the domestic economy, and 2015 has proven difficult thus far for many industrial distributors. We believe lower energy spending is at the root of weaker sales, with currency woes further compounding the slowdown.”
The FDI is a monthly survey of North American fastener distributors, conducted with the FCH Sourcing Network and the National Fastener Distributors Association.
TriMas Corporation reported Aerospace segment sales – which consists of Allfast Fastening Systems, Monogram Aerospace Fasteners, Mac Fasteners, and Martinic Engineering – increased 65.6% to US$45.4 million (41.8 million euros).
The improvement was primarily due to the results of Allfast, which was acquired in October 2014, and higher demand from OEM customers, partially offset by lower sales to large distribution customers. Q3 aerospace segment profit jumped 83% to US$7.1 million due to higher sales levels and related operating leverage, continued productivity initiatives and a more favorable product mix. Aerospace segment sales during the first nine months of 2015 grew 55% to US$134.3 million, with segment profit gaining 55.7% to US$22.4 million.
Applied Industrial Technologies Inc has acquired its first fastener company – the 100% employee owned, Massachusetts-based commercial and aerospace hardware distributor Atlantic Fasteners.
The company name becomes Atlantic Fasteners – an Applied MSS Company. Employee owners of Atlantic Fasteners “made off very well” with the acquisition, Tony Peterson, president of Atlantic, told GlobalFastenerNews.com. In addition, there is a “great opportunity for younger people here for advancement within Applied”. Peterson said he expects most of Atlantic’s 48 employees will stay with the new company. Peterson plans to stay with the new firm as vice-president/general manager. Peterson said the new consolidated office/warehouse in Agawam, where Atlantic moved earlier this year, has double the space and may take on more usage by Applied.
“Atlantic Fasteners provides the market presence, products and capabilities to further enhance our Applied Maintenance Supplies & Solutions offering to a broad array of industrial customers,” said Applied CEO Neil Scheimaher. “It has an ideal fit with our business strategy and growth plans.”
Applied Industrial is an industrial distributor of five million parts to MRO and OEM customers. Founded in 1923 by Joseph Burning as the Ohio Ball Bearing Co the name changed to Bearings Inc in 1953. In 1995 sales topped US$1 billion and in 1997 the company became Applied Industrial Technologies. By 2007 sales topped US$2 billion and in 2014 reached US$2.5 billion. By contrast, during its 30th anniversary in 2011, Atlantic announced sales of US$13 million. Today Applied has 570 facilities in the US, Puerto Rico, Mexico, Canada, Australia and New Zealand, and is headquartered in Ohio.
Atlantic Fasteners was founded in 1981 by Patrick O’Toole and Carol Peters. O’Toole created a new Atlantic Fasteners out of the remnants of a twice-bankrupt distributorship. Atlantic at that point had “a bad reputation with suppliers,” and it was Peters who jumped in to convince SPS, Unbrako and other suppliers to work with the new distributorship. In 2005 O’Toole and Peters sold the company to employees. Atlantic Fasteners is an ISO 9001:2008 and AS9120 certified distributor that stocks 15,080 varieties of inch and metric fasteners.
Stanley Black & Decker Inc reported industrial sales decreased 7% to US$479.3 million (440.9 million euros) in the third quarter of 2015, as price (+1%) was more than offset by lower volumes (-1%) and currency (-7%).
Engineered Fastening achieved 3% organic growth as strong global automotive and electronics revenues more than offset weaker industrial volumes. Overall industrial segment profit rate was 17.8%, up from the Q3 2014 rate of 17.7%, as favorable volume leverage from Engineered Fastening, productivity gains, and cost control, more than offset the impacts of currency and lower infrastructure volumes.
Industrial sales during the first nine months of 2015 declined 4.6% to US$1.46 billion, with segment profit falling 5.7% to US$254.4 million.
Overall Stanley Black & Decker Q3 sales declined 2% to US$2.8 billion, as positive volume (+5%) and price (+1%) were more than offset by currency (-8%). Net earnings dropped 5.2% to US$233.4 million.
Illinois Tool Works Inc reported Q3 revenue declined 9% to US$3.35 billion. Organic revenue fell 1.7%. Continued solid organic growth performance in automotive OEM, food equipment, and construction products, was offset by deteriorating end market trends in welding, test and measurement, and electronics.
Quarter 3 operating income dipped 1.4% to US$761 million (700 million euros) , while net income dropped 3.8% to US$511 million. EPS gained 9% to US$1.39. Operating margin increased 180 basis points to a record of 22.7%.
Automotive OEM revenue, including fasteners, fell 3% to US$612 million, which included 5.2% organic revenue growth –outpacing flat worldwide auto builds. Automotive OEM organic revenue increased 12% in Europe, 5% in North America and declined 5% in China. Operating income was US$156 million, and operating margin of 25.4% was up 200 basis points.
Q3 construction products revenue, including fasteners, declined 8.1% to US$409 million, which included organic revenue gains of 4% driven by 7% growth in North America and 5% growth in Asia Pacific. Operating income totaled US$94 million, and operating margin was up 420 basis points to a record 23.1%. Automotive OEM revenue in the first nine months of 2015 declined 2.8% to US$1.91 billion, which included organic revenue growth of 6%. Operating income reached US$478 million, with an operating margin of 25%.
Nine month construction products revenue fell 7.4% to US$1.21 billion, with operating income totaling US$241 million and operating margin of 19.9%.
www.fastinfo.ru
On 9 th September the offi cial opening of Bervel factory for high strength fasteners took place in Rybnovsky District of the Ryazan Region, Russia.
Bervel’s factory was built from the ground up, the total investment amounting to more than three billion rubles (approximately 44 million euros), and after the launch of the second stage it will exceed five billion rubles. The planned production volume with the launch of the first phase is 71,000 tonnes of products per year, rising to 108,000 tonnes per year when the second phase is launched. Products from the plant will be used in the construction of bridges, cell phone towers, transmission towers, production shops and other areas of construction. Also among the large consumers of the fastening products will be such industries as machine building and railway facilities. Currently there are already requests for the supply of products from potential consumers: For high strength fasteners it is about 50,000 tonnes per year, for sized rolled rod – about 97,000 tonnes per year. It is planned that 300 people will work at the plant.
On 16th – 17 th September the All-Russian Conference Wire Fasteners 2015 was held in Yekaterinburg. The two day conference programme included plenary sessions with the leading players of the hardware market in Russia and the CIS countries as speakers.
The head of Prommetiz Association, the directors of NLMK-Metiz and NLMK-Sort, Beloretsk Metallurgical Plant, and Severstal-Metiz, analysed the overall questions of the market function. Also discussed at the conference were the issues and technical problems of hardware production, the interaction of manufacturers and suppliers, and the problem of distribution.
Participants of the conference visited some modern hardware production sites – the workshop for application of zinc lamella coatings of Durer Engineering and the NLMK-Metiz site in Berezovsky.
Oleg Kovalev, the governor of Ryazan Region, said that it is hard to overemphasise the importance of Russia’s first plant for the production of high strength fasteners and sized rolled rod. “The volume of production will allow the Russian Federation to replace about 20% of imports of similar products.”
“When we were looking for a site for the plant, we considered a lot of regions in Russia. It was not by chance we chose this place. I think, in terms of logistics it is the perfect place,” said Yuri Medvedev, the director of Bervel high strength fasteners plant. Adding that main consumers of the plant products will not only be in Russia, but also Europe and the Middle East.
Yuri Medvedev commented on the opening day: “This opening is confirmation that the construction of the plant is completed. Now we have no less difficult work – the launch of the whole complex of equipment and reaching the planned targets.”
On 17 th – 18 th November 2015 the fourth specialised conference – ‘Fasteners. Quality and Responsibility’ was held in St. Petersburg, Russia.
The annual event was organised for standards developers, manufacturers, distributors, consumers of fasteners and hardware, as well as for representatives of laboratories, technology services, and companies involved in the training of employees at enterprises. The organisers of the conference are: VO RESTEC, Prommetiz Association, and Fasteners, Adhesives, Tools and...Magazine.
The conference addressed the general problems of the industry, the progress of work on new standards for fasteners and issues in mastering their manufacturing. The requirements for fasteners from leading consumers of different industries and construction was also considered.
Vyacheslav Tarasov, head of the fasteners department of the CFI Group of companies, considered the hardware product market through the eyes of a trading company.
ALLTHREADS, MACHINE SCREWS, HEX HEADS AND CUP SQUARES
• M3-M12 OR 5/32”-1/2” L10mm-180mm
• METRIC, UNC, UNF, BA, BSW, BSF THREADS
• BRASS, BRONZE, ALU, STEEL AND STAINLESS
• CUSTOMER SPECIALS ON REQUEST
ASK FOR A COPY OF OUR EXTENSIVE STOCK LIST
Park Lane, Halesowen, West Midlands B63 2QY, UK T: +44 (0)1384 569 832 E: sales@londonscrew.co.uk www.londonscrew.co.uk
ESTABLISHED 1870
Manufacturer of Quality Industrial Fasteners
REYHER is one of Europe's leading distributors of fasteners and fixing technology supplying customers worldwide.
The Federal law on ‘Standardisation in the Russian Federation’ came into force on 29 th September 2015.
The Federal law defines the objectives and tasks of standardisation; the principles of standardisation; the state policy of the Russian Federation in the field of standardisation; as well as members of the work on standardisation and documentation.
The Federal law also regulates the planning of work on standardisation; development and approval of documents of the national standardisation system; international and regional cooperation in the field of standardisation; information support of standardisation and funding in the area of standardisation.
According to Alexey Abramov, head of Rosstandard, the new law makes it possible to properly meet the challenges Russia is now facing. “The task now is to master the production of new products in the territory of the Russian Federation in the context of import substitution. This is impossible without new standards,” Abramov concluded in his speech at the panel discussion: ‘Standardisation and import substitution: Synergy for the new economy,’ held at MIA ‘Russia Today’ in July.
The production of a new generation of professional power tools will be created in the Special Economic Zone (SEZ) Alabuga.
Supported by a loan from the Industry Development Fund production of a new generation of professional power tools –24 various items, including heavy drills, building mixers, screwdrivers, milling cutters and trimming saws –will be set up in the SEZ Alabuga in Tatarstan. The project will create 142 high performance jobs and the total project will cost 962 million rubles (approximately 14 million euros).
Sergey Nazarov, chairman of the board of directors of Interskol, said: “Last year we decided to significantly increase the share of Russian production and launched the first phase of the plant for the production of power tools Interskol-Alabuga in Tatarstan. Our new production facility will provide up to 40% of import substitution in the most popular groups of power tools. In today’s situation, the development of the industry is the main engine of economic development.”
Mariya Valiakhmetova, editor in chief, Metiz Magazine, UkraineOn 25th September the Belarus Steel Work (BSW) opened its new No: 2 long product rolling mill. Alexander Lukashenko, president of the Republic of Belarus, participated in a grand opening, meeting the collective at the plant and personally starting a wire drawing line.
Belarus Steel Work’s new section rolling mill has an initial capacity of 700,000 tonnes a year with the prospect of increasing to 1 million tonnes. It facilitates full treatment of casting and blooms, and also the manufacture of higher added value products. The new line addresses a deficiency in wire rod, which the BSW factory has faced for the last few years as demand for steel cord and other hardware products has grown. It will completely fulfill the requirements of Rechitska metyzni zavod, which is part of BMK holding. The mill is planned to increase industrial output volume by 2.8% annually equating to a gain of 86 million euros a year.
The new mill will produce steel wire rod in 5.5mm to 22mm diameters. About 75% of output is expected to be exported, substituting imports of wire rod to the Russian Federation market and fulfilling more than 90% of domestic factories’ requirements for bar products.
The contract to develop the mill was signed in 2011. Italian company Danieli – a long-standing partner of the factory and a
world leader in this area – supplied the equipment. The Eurasian bank of development and Belarusbank provided credit lines.
The new long product mill was included in the list of the major projects of the Belarus industry that have essential influence on the country’s development. It is the key project in the BSW modernisation programme for the current five year period, and one of the biggest in the history of the factory.
A special advantage of the Danieli equipment is the universality of the furnace, which can work with both blanks and blooms, providing high uniformity of temperature range, and low parameters of scale loss and fuel usage. In general world practice separate lines are used for blooms and blanks. The furnace also has a special hot water boiler fueled by waste gas heat, which produces steam as a source of secondary energy to heat buildings. The new line will produce a wide range of products with small adjustments at high-speeds to provide high-levels of efficiency.
Tel: 01942 520250 Fax: 01942 520251 sales@smithbullough.com www.smithbullough.com
SCHNORR® is an international leader in engineering and producing safety washers and disc springs for automotive, aerospace and mechanical applications.
Original SCHNORR® safety washers:
• Highly vibration-resistant
• Patented technology
• Extensive range
Original SCHNORR® disc springs: As a result of our merger with HUGO BAUER Nachf. GmbH, we now offer both turned and fine-blanked disc springs:
• Various applications
• Best price-performance ratio
• Customized solutions
Please contact us. Together we will find your tailor-made solution.
Taiwanese automotive fastener maker Boltun Corporation has invested 3.5 million euros to acquire Frank Sieber GmbH, a 50 year old family business located south-west of Hamburg, Germany.
Sieber specialises in the design and production of tooling for cold forming and hot forging and employs around 60 people. The key benefit of the acquisition for Boltun is access to tooling for complex net shape parts, which further enhances the Taiwanese manufacturer’s capability to produce special components.
In August 2014 Boltun acquired an 85% stake in ESKA Automotive GmbH for 45 million euros. ESKA is a 70 million euros annual turnover fastener and parts
manufacturer – servicing the automotive sector, particularly with high precision, high strength power train parts.
Boltun was founded in 1988 and is headquartered in Tainan. Majority owned by the Wu family, it now has annual Group turnover of US$500 million and employs some 3,400 personnel in 21 facilities in five countries, including manufacturing plants in Taiwan, China, Germany and Thailand. It also has logistics operations in the US and Mexico.
While its core range is dedicated to
Despite continued low price levels from mainland China, Taiwan’s China Steel Corporation (CSC) has announced it will keeps prices for December deliveries to the domestic market unchanged.
The decision ends eight months of price cuts by China Steel, which had been reacting to the decline in prices from two of its biggest Chinese competitors –Baosteel Group and Wuhan Iron & Steel Corporation.
CSC told Taiwan business media global steel demand continued to be in the doldrums because of the flagging global economy. The company’s statement noted: “The fourth Quarter is usually a high season for the steel industry, but demand has not materialised this year.”
It went on to say that it expected China to launch new economic stimulus measures to boost domestic demand, which could help stabilise the steel market.
automotive it has diversified strongly into hot forged fasteners for the wind energy sector, holding supplier approval from all the major wind turbine makers. It is currently testing robotic transfer of blanks from induction heater to press to more accurately control temperature at the point of forging.
Around half of Group output, which is roughly divided into thirds of bolts and screws, nuts, and specials, is supplied to distribution, 22% direct to OEMs including Ford, VW and Siemens, and 28% to tier suppliers.
Gem-Year Industrial Co Ltd released half-year financial results showing the company lost CNY 20.77 million (approximately 3 million euros).
In the corresponding period last year Gem-Year reported a net profit of CNY 94.85 million. In the first half 2015 operating income fell 30% to CNY 1.16 billion, attributed to decreased income from the rail fastener market.
Gem-Year said the drop in steel prices in the first half of 2015 and the consequent drop in average price led to weak profit growth in fasteners despite the fact that the sales volume expanded. Additionally, delayed delivery for high-speed rail orders resulted in a 70% fall in sales of high-speed rail fasteners, which impacted profitability.
Report from: Fastener World Magazine
Zhejiang Xizi Aerospace Fasteners Co Ltd, located in Hangzhou, China, has spent three years undergoing a technological upgrade and investment programme to successfully develop blind fasteners, now approved by the Chinese aerospace sector.
Xizi is now an approved supplier to the Aviation Industry Corporation of China (AVIC) and the Commercial Aircraft Corporation of China (COMAC). The latter has just rolled out its C919 narrow body commercial jet, for which the company says it has already received more than five hundred orders. In 2013, Xizi Aerospace became a Tier 1 supplier to Bombardier Inc receiving orders from Bombardier from 2014 for more than 2,000 components. Xizi Aerospace has also supplied Cessna.
Fastener World Magazine says the agreement signed between Airbus and Xizi means that the company has won “a ticket” to enter the global market, which could provide a solid base for Xizi to win orders from Boeing and Bombardier and also develop in the Russian aerospace market.
T: +44 (0)1686 621 300
Fastener World Magazine reports that Jau Yeou Industry Co Ltd, one of the top 10 fastener makers in Taiwan, is actively making inroads into the aerospace industry.
Subsidiaries JYR (aerospace logistics) and Rising Fast Technology (aerospace component manufacturing), have made Jau Yeou Industry the second Taiwanese fastener company to enter the aerospace supply chain.
Jau Yeou Industry has been operating for thirty-five years.
It established Rising Fast Technology and JYR in 2011. Rising Fast Technology has obtained the AS9100 certificate from SAI, and seven Nadcap certificates for aerospace grade special manufacturing process. Among these is an X-ray certificate for which there are only two holders in Taiwan. In addition,
Jinn Her Enterprise Co Ltd, the largest bolt maker in Taiwan, has been in active business transition and upgrade towards the development of high-level detective screws, reports Fastener World.
President Tsai says the company has gone through five years of R&D and developed a new high-level detective screw with impending patents from the US, Europe, Taiwan and Japan. The product, which will be a ‘secret weapon’ for the company’s future growth, will go into mass production as soon as the patents have been acquired.
President Tsai says the detective screw is scheduled for mass production next year with an initial planned monthly capacity of 100 tonnes. The unit price is expected to be as high as TW$10,000 (approximately 280 euros), equivalent to the total value of 2,000 pieces of common screws. The detective screw will be mainly used on disaster warning systems for gas explosion, earthquakes, and fire. With the detective screw the operator will know whether the structures of bridges, roads, or buildings have displaced or loosened, and whether there is any abnormal temperature change in the structures.
JYR is the only AS9120 (aerospace logistics and distributorship) certified company in Taiwan.
Jau Yeou Industry has now successfully entered the global aerospace supply chain, becoming a supplier of engine fuel pipe parts and machined parts to global aero-engine makers. Since February 2013 it has received TW$550 million (15.6 million euros) worth of purchase orders and expects order growth –having maintained zero defect performance for more than seven continuous months. JYR acts as a logistics centre for Asia Pacific aerospace components.
Sundram Fasteners Limited posted a net profit of 517 million rupees (approximately 7.14 million euros) for the Quarter ending 30 th September 2015, compared with 510 million rupees for the same Quarter of the previous fiscal year.
Total revenue for the Quarter was 6.6 billion rupees (approximately 91.2 million euros) up 6.7% on the same Quarter the previous year. Export sales for the Quarter were 2.31 billion rupees up from 2.27 billion.
Sundram also reported it had cut its stake in the German company Windbolt GmbH. Windbolt was established as a joint venture to manufacture fasteners for the wind energy sector but due to the uncertain outlook and lack of improvement in the German market it filed for insolvency in August. Sundram originally took a 24.99% equity stake of total capitalisation of 133,332 euros. Windbolt contributed the equivalent of around 300,000 euros to Sundram turnover in 2014, and around 450,000 euros to profit before tax at the end of March 2015. Sundram says it has filed claims according to German insolvency law but is not yet able to determine the probable loss, although it is not expected to be material. Windbolt is no longer an associate member of Sundram Fasteners.
The Gang Shan Life Temple, situated in the heart of Taiwan’s major fastener production cluster, has erected a five hundred kilogram, two metre high statue of Matsu constructed entirely from fasteners.
Matsu or the Buddha is one of Taiwan’s most significant religious deities but is generally portrayed in statues carved from wood or stone. The fastener Matsu is a hollow design, with the outer shell constructed from screws and nuts welded together. Construction took more than one month. Inside the statue, LED lights have been installed to emit an eye-catching radiant light.
Source: TAITRA
During July a series of business meetings were held in São Paulo between groups of Turkish fastener and tool manufacturers and Brazilian entrepreneurs.
The mission, called ‘Turkish Hardware Cluster’, is part of work carried out by the Istanbul Minerals and Metals Exporters (IMMIB) and sponsored by the Republic of Turkey Ministry of Economy.
Revista do Parafuso Magazine interviewed Ms Havva Deniz (pictured), a specialist in the organisation and management of overseas trade events and a member of the delegation. Ms Deniz told us that this mission to Brazil – which would also include a visit to Chile – involved 17 Turkish companies seeking to expand their export business by increasing their visibility in far away markets, which they find hard to reach individually.
The project started in December 2012 with the selection of the companies, which were trained according to their particular needs. Ms Deniz said: “The mission already visited Iran, France, and Saudi Arabia. In November we will visit in Dubai ‘The Big 5’ exhibition – the largest construction event in the Middle East.”
Three years after an acquisition by US company Lamons, a Brazilian manufacturer specialising in the oil and gas sector appears to have ceased operations.
In 2011 the Companhia Industrial de Fixadores & Afins (Cifal), a Brazilian manufacturer specialising in fasteners to the oil and gas sector, celebrated the tenth year since its foundation. In 2012 Cifal was sold to Lamons, a US company that is a holding of the TriMas Corporation. Headquartered in Houston, Texas, Lamons is an important player in the supply chain of products such as nuts, bolts and gaskets. It was taking an interesting venture in developing business in South America, including with Cifal customers such as Odebrecht, Braskem and Petrobras.
However, after three years the industrial plant in São Paulo and the sales office in Rio de Janeiro are disabled, without any information being issued about what has happened. The website continues to give the impression of normal activities.
Recently, the GASKET Vedações Ténicas Ltda unit, which manufactures gaskets, was an exhibitor in Brazil offshore, a main trade fair for the Brazilian oil and gas market. Revista do Parafusos Magazine tried to make contact with the company, including with its president Mr Kurt Allen, but so far without answer.
Since the beginning of 2015 the Real – the Brazilian currency – has depreciated dramatically, affecting the national economy. However, there are some positive effects for domestic manufacturers caused by this situation.
According to Ricardo Marques Castelhano (pictured), CEO of Jomarca Fasteners – one of the largest Brazilian companies in this sector, some fasteners, such as chipboard screws made in China, were coming into Brazil 40% cheaper than local industrial plants. Now this kind of domestically produced screw, as an example, is priced 10% – 15% cheaper than imports.
Throughout its 115 year history, HEICO Group has consistently shown its commitment to innovation –both in the products it supplies and the unique production processes and tooling it uses. However, its most notable innovation has been the development of new divisions within the Group that have enabled it to continue to expand its capabilities and focus on new growth markets.
Originally the family company focused on processing steel wire, sheet steel and sheet brass to manufacture upholstery nails, decorative nails and security nails –with two production plants in Ense, at the heart of the Ruhrgebiet.
In the 1990s the company introduced HEICO Umformtechnik GmbH, which concentrated on cold forming technology and gained a reputation for specific cold forming parts and mouldings. Due to the commitment to innovation and the experience within the company, its cold forming business was very successful within the automotive industry.
“Our cold forming capabilities are quite special as we do not produce any standards – all articles are based on the specifications of customers’ drawings and requirements,” mentions Jan Bernd Heimann, general manager at HEICO Group and 4th generation of the family business. “Our long-standing customers include leading car manufacturers and other well known companies from various branches of industry – which we serve nationally and internationally.”
At the end of 2010, HEICO was ready for the next step in its development and looked at how it could move forward using the capabilities that it already had within the company. “After careful consideration we decided that the best option was to develop a new division focusing on a new range,” explains Jan Bernd Heimann.
Through a combination of know-how, machinery, and its own tool building department –as well as the commitment to innovation and quality management –HEICO developed its HEICO-LOCK® business and introduced the HEICO-LOCK® Wedge Lock Washers.
The HEICO-LOCK wedge locking system consists of a pre-assembled pair of washers that have key faces on the inside and radial teeth/ridges on the opposite side. Tightening of the bolt and/or nut leads to a gripping action of the teeth thus seating the mating surfaces. The range is available in a standard range of M3 – M76 and in steel, stainless steel, SMO and Inconel materials.
“Due to the low friction between the single washers, movement is only possible across the face of the cams on the inner side,” explains Tobias Grobe, head of sales at HEICO Group. “As the wedge angle of the inner key faces is greater than the angle of the thread pitch, any movement of the bolt between the washer leads to elongation of the bolt – as the cams move across each other. When the bolt rotates in a loosening direction this cam movement increases the preload force and blocks the self-loosening action.”
Meeting the requirements of DIN 65151 and DIN 25201-4, the HEICO-LOCK Wedge Lock Washers proved such a success for the company that within only four years HEICO had expanded its product range to meet customer demand.
“We can now supply most of the product sizes globally within a few days,” says Jan Bernd Heimann proudly. “We are also able to supply non-standard sizes depending on customers’ demands.”
A key part of HEICO’s ability to launch the HEICO-LOCK Wedge Lock Washers into the market were the warehouses and offices it had already established in key markets across the world. In addition to its headquarters in Germany, HEICO has sales offices in France, Italy, Poland, Russia, the Czech Republic, Spain, Switzerland, the UK, the USA and China.
“With our 13 company owned sales subsidiaries and numerous sales partners all over the world, we are well positioned in the market,” points out Jan Bernd Heimann. “Our customers benefit from this closeness to the market by receiving excellent and professional technical support and short delivery times. Moreover, due to many years of experience and know-how in the field of fastening technology, we are always able to respond to our customers’ special requirements.”
“Having our branches across the world has definitely been a key advantage in supplying customers with a first-rate service,” adds Tobias Grobe. “It is important that you have a direct presence in the market, so that you can have a strong relationship with customers.”
Based on the success of the HEICO-LOCK Wedge Lock Washers, the company decided to introduce its next innovation – the HEICO-LOCK® Ring Lock Washers. Supplied as a pre-assembled system, the HEICO-LOCK Ring Lock Washers consist of a polyamide ring and the HEICO-LOCK Wedge Lock Washers.
“The HEICO-LOCK Ring Lock Washers include a plastic ring that offers a big advantage to users as it ensures that the washers are kept together and in the same position they need to be used,” mentions Tobias Grobe. “This helps provide solutions to processes as it makes it very easy to reinstall and remove the washers.”
In 2014 HEICO expanded its HEICO-LOCK portfolio even further by adding the HEICO-LOCK® Wedge Lock Nut and Wheel Nut. By combining a nut with its HEICO-LOCK Wedge Lock Washers –in a captive and rotary way – HEICO guarantees that they are fixed permanently in the correct position with the wedge lock washers securing the bolted joint using the HEICO-LOCK principle – without loss of quality or function. This results in a locking system that makes securing bolted joints more efficient, effective and easier under the most extreme vibrations and dynamic loads.
“The introduction of the HEICO-LOCK Wedge Lock Nut underlined that we are always focusing on the demands of our customers,” points out Jan Bernd Heimann. “Thanks to our manufacturing capabilities we are able to produce all of the HEICO-LOCK products at competitive prices, but more importantly on a continuously stable and high-quality level.”
A key factor in HEICO-LOCK’s high-quality standards was the experience of process stability and quality management the company has gained from its cold forming division. “When we set up the HEICO-LOCK division, we decided to use all the quality standards and processes that we had developed for the automotive market through our cold forming division,” explains Tobias Grobe.
“We realised that we could not differentiate between automotive production and washer production,” adds Jan Bernd Heimann. “You can only have one philosophy within a company and with our cold forming division we already had a philosophy that enabled us to meet the high demands and needs of the automotive industry, which helped us achieve the ISO/TS 16949 standard. That is why we adopted the same quality systems and lean production process methods for the production of the HEICO-LOCK range.”
HEICO’s commitment to quality was further underlined when in 2012 it increased its capabilities for testing bolt securing systems in its testing laboratory. Laboratory services that are now available include vibration testing according to E DIN 25201-4 Appendix B; torque/clamp force testing according
to ISO 16047; dimensioning and calculation of bolted joints –e.g. according to VDI 2230; as well as a variety of customised tests according to individual customer applications.
“The development of the testing laboratory is a really important step for us,” says Jan Bernd Heimann. “We now have the capability to carry out various tests up to M33 and are working with independent institutes across Europe.” In addition to the certifications from TÜV, DNV and other external laboratories – such as Institute IMA in Dresden, University of Cologne, CETIM in Paris – HEICO’s wedge locking system is also approved by customers, including Deutsche Bahn AG, Siemens and Alstom.
Jan Bernd Heimann continues: “Customers are also welcome to carry out their own testing in our laboratory and we can produce an in-depth test report, which they can use for their individual requirements or specifications. We also offer seminars – either in-house or at customers’ facilities – as well as regularly present speeches at different events and seminars that focus on our vast capabilities and solutions.”
Finding the best solution is a mantra that runs through the heart of the Group and its 450 employees. From speaking to Jan Bernd Heimann and Tobias Grobe there is a clear drive and dedication to continuously optimise processes. This is supported by an investment programme that has seen new machinery and systems constantly being added – helping to improve efficiency and guarantee optimum production.
“Our commitment to innovation and continually evolving is still as strong today as it has ever been,” concludes Jan Bernd Heimann. “We look forward to continuing to develop new products in the future and reliably provide customers with the very best solutions – ‘Made in Germany’.”
www.heico-lock.com
Since its market launch in 1967, SPAX – a chipboard screw with cross recess – has set benchmarks in the field of joining technology, becoming synonymous with innovation and quality in the manufacturing of screws.
Today, SPAX International GmbH & Co KG is the European market leader in the field of chipboard screws and produces up to 50 million screws per day with approximately 500 employees at its headquarters and production facility in Ennepetal, Germany. Even though SPAX products are sold worldwide, manufacturing still takes place in Germany – with the company proud to represent ‘Made in Germany’ quality.
The company’s success story actually began back in 1823 when ALTENLOH, BRINCK & CO was the first company in Germany to start with industrial screw production. From the very beginning SPAX was consistently developed as a quality brand and exclusively sold under the brand name in its typical green packaging. Through its commitment to tradition and innovation, the brand SPAX is the epitome of the modern universal screw for handymen on all continents.
Today SPAX International is an autonomous corporate division of the ALTENLOH, BRINCK & CO Group. The company operates globally and has sales subsidiaries all over the world. However, it still remains loyal to its home country
and the quality seal ‘Made in Germany’ and will continue to do so in the future.
“In times of globalisation, the ‘Made in Germany’ product label is gaining importance amongst consumers as a vital buying criterion,” comments Stephan Alberts, international compliance manager at SPAX International. “After all, Germany stands for quality, innovation and the safeguarding of local jobs and apprenticeships. Many German customers therefore consciously opt for local products because they trust the quality and wish to support the German economy. Customers in Europe and the rest of the world also trust the ‘Made in Germany’ label because it still stands for quality and reliability.”
SPAX customers not only have the SPAX promise, but also an official verification that the products are ‘Made in Germany’. TÜV (the German Technical Inspection Association) has a ‘Made in Germany’ certificate of origin, which it awards to companies that have a special commitment towards Germany as a production location. Certified companies have to actively show their social responsibility and make a traceable effort to create and sustain jobs and
apprenticeships. The certificate of origin is therefore in the interests of product clarity and consumer protection.
SPAX International chose to voluntarily undergo this extensive testing procedure so that its joining elements could be certified by TÜV with the ‘Made in Germany’ seal. This guarantees customers of the SPAX brand a high-level of safety, quality and continuity.
“SPAX International is consciously making an important contribution to safeguarding Germany as a production location for the future, and also to offering customers and partners the utmost transparency,” says Stephan Alberts. “After all, the company’s goal is still to produce high-grade, quality controlled products, without ever losing sight of its social responsibility and the interests of its customers.”
Stephan Alberts adds: “SPAX International stands for state of the art joining technology in the fields of DIY, craft, industry and planning. Ongoing developments, product innovations, and optimised production methods, are ensuring that this will also remain the case in the future.”
Our SPAX branded products can be purchased around the globe, in the familiar green packaging that specifies their origin in the address field: Ennepetal –company head office and production location. And this is exactly where the certification “Made in Germany” was carried out for SPAX screws by the German Technical Inspection Agency (TÜV) during a sophisticated test procedure.
SPAX International is and will remain based in Germany. This, in particular, guarantees its customers the high degree of safety, quality and continuity associated with the name SPAX.
For more than 100 years Adolf Menschel Verbindungstechnik GmbH & Co KG –a business unit of Würth Group – has produced high-quality fasteners on state of the art machinery at its site in Plettenberg, Germany.
The Menschel product range comprises of more than 50,000 different kinds of fasteners – the majority special parts made to drawings. “We specialise in self-cutting and self-tapping screws but we can produce a wide variety of products,” explains Stephan Wennrich, sales management at Adolf Menschel. “Even products with a complicated geometry are no problem for us, and we can produce smaller quantities starting from 20,000 pieces.”
Menschel’s production range includes self-tapping screws, grooved screws, screw and washer assemblies, self-locking screws, as well as cap screws. All these screws can be purchased with different finishes – galvanised, organically coated and, if required, with microencapsulated locking compounds. Head styles include pan head, countersunk head, raised countersunk head, cheese head or mushroom head, as well as hexagon, also with a collar. Customers can choose between hexagon recess or cross recess Phillips, POZIDRIV® or MESTERN. Furthermore, Menschel can also supply special and cold formed parts made of steel and stainless steel according to standards, drawings or samples.
A leading product for Menschel is the ME-RIPP – a self-locking screw that is available from M5 – M20 and has received Deutsch Bahn approval under DIN 25201/BN 205 03i-01. During installation there is no chip formation and special ribs under the head of the ME-RIPP ensure that there is no damage to the surface of the mating material – which Menschel says helps reduce losses in pre-tensioning force and enables the ME-RIPP to offer a perfect response when tightened.
“The ME-RIPP screw can be used in a wide variety of industries including commercial vehicles and agricultural machinery,” explains Stephan. “Thanks to the know-how of our staff, and 100 years’ experience, we are able to reliably provide the ME-RIPP to customers – guaranteeing them a high-quality product that provides a high-level of safety.”
Menschel’s ability to consistently produce high-quality products is thanks to its state of the art production department, which includes the latest technology in multi-stage presses. The company recently added two new five stage cold form presses that enable it to produce all current head shapes and drive systems up to 12mm diameter and 90mm length. Menschel also has another five stage press, which is equally state of the art and enables it to produce all current heads and drive systems up to 22mm diameter, 120mm long.
“A key part of our success is our vast manufacturing capabilities, as well as the close relationships we have with our customers,” points out Stephan. “We build strong partnerships with our customers and look to work with them to put their ideas into practice. We offer a complete service package where we visit customers’ facilities and identify their fastening requirements. We can then advise, consult and design the perfect fastener solution that will meet the customers’ needs.”
Menschel’s high-quality special products are required by the automotive industry – where it is an approved OEM supplier, the optical and electrical engineering industry, electrical industry, as well as plant and machine engineering sectors. The company is accredited to ISO/TS 16949, ISO 9001 and ISO 14001.
“We are very proud of our capabilities and the high-quality of our products we can supply customers around the world,” says Stephan. “For us ‘Made in Germany’ is not just a statement of where the product was produced. It is a seal of approval for our consumers and business customers and stands for sustained good quality, safety and a high technical standard.”
The achievements of ME-RIPP and ME-ZAHN are remarkable indeed, the reasons in favour are unsurpassed: More cost-effective than securing systems with adhesives or cramping. Both can be tightened several times. During installation there is no chip formation and special ribs under the head of the ME-RIPP ensure that there is no damage to the surface of the mating material, which helps reduce losses in pre-tensioning force and enables the ME-RIPP to offer a perfect response when tightened.
On customer request, both ME-RIPP and ME-ZAHN can be supplied with a partial thread on a reduced shaft. The screws are also available in a large number of variants ex-warehouse and have received Deutsch Bahn approval under DIN 25201/BN 205 03i-01.
Safe, high quality and low cost
DIMENSIONS
M5 – M20
Length final product up to 80mm
MATERIAL
Steels for tempering and hardening, non-corroding materials
CUSTOMER BENEFITS
Safe, low cost, easy on the surface, available ex-warehouse. DB-approval under DIN 25201/BN 205 03i-01.
Amongst the picturesque hills and valleys on the edge of the Sauerland, in the south eastern part of North Rhine-Westphalia, Germany, you will fi nd the modern facility of Bäcker GmbH & Co KG –a specialist in producing plastic control elements, screws, nuts and washers similar to DIN, as well as customised plastic parts for customers globally.
Based in the Jägersgrund industrial estate in Erndtebrück-Schameder, Bäcker’s premises have gone through a series of expansions since the company was established in 1977. Most recently the production and storage areas were extended and doubled in 2000, and a new administration and distribution centre was built in 2013.
“As the demand for our products has grown, it was necessary to expand,” explains Gerhard Bäcker, founder and general manager at Bäcker GmbH & Co KG. “We have always grown the business organically and ensured that our production hall includes the latest machining technology to meet demand as it increases.”
Bäcker has over twenty-four of the latest generation modern and fully automatic ARBURG injection moulding machines. Machine sizes ranging from 250kN to 2,750kN enable the company to supply a wide range of injection moulded products, weighing between 1g and 600g.
“The aim of our production department is to be precise and modern,” explains Gerhard. “Thanks to the experience and professional expertise we have within the company, we are able to process high performance polymers, engineering thermoplastics, and bulk plastics, to make advanced injection moulded parts.”
In addition, Bäcker is able to supply hybrid solutions combining both plastic and metal; manufacture inexpensive products with internal and external thread; as well as products according to drawing. The company produces 24/7, with all the machines connected online via the ARBURG host computing system (ALS) – making it possible to monitor production anywhere within the business.
“By monitoring the machines we can see everything that we need, including which machines are running and how long
Fastening elements and caps from Bäcker.
We create connections
BÄCKER has been engaged as a high-performance manufacturer in the field of plastic processing for more than 35 years. With our focussing on a range of products for the trade in fastener technology, we offer to you the ideal supplement to typical steel fastening products – namely on a worldwide scale.
Screws, nuts and washers made of plastic material are part of our range as well as clamping levers, indexing bolts or protective caps. This combination makes us the perfect partner for the completition of your range of C-parts.
it is going to take to produce a particular batch,” mentions Alena Wied, marketing manager at Bäcker GmbH & Co KG and daughter of Gerhard. “We have made a huge investment in the machinery recently and are currently in the process of introducing new machines that are more energy efficient and faster. This will help us improve our productivity and efficiency, whilst continuing to produce high-quality products.”
to meet the company’s requirements and enable it to work efficiently on tool projects and meet deadlines. “Having the right tooling is very important and we make sure that we work with the very best injection mould manufacturers to guarantee the quality of our products for customers around the world,” states Alena.
Bäcker mainly supplies to the European market, but is able to provide products globally due to the reliability of its logistics. “We are always making improvements to our order processing system in order to speed up procedures, increase efficiency and meet deadlines,” points out Gerhard. “We use the latest information technology to guarantee flawless product distribution and data processing along the entire logistics chain.”
In its standard range Bäcker has over 5,000 products in a total of 23,000 different designs and dimensions, which can be delivered immediately or at short notice.
“Producing in Germany means that we can be very flexible and we can react immediately to any needs, which is very important,” says Alena.
Bäcker’s product range splits into four key lines: PlacoGrip® –a wide range of control elements that includes clamping levers, tension levers, index bolts and blocking handles; PlacoTec® –plastic standard elements such as screws, nuts, washers and spacer rolls; PlacoCap® – plastic protective elements such as hexagonal protecting caps, protecting plugs, ribbed plugs and caps; as well as PlacoEngineering – where Bäcker works closely with customers on design solutions.
“The PlacoEngineering line has become a key part of the business,” explains Gerhard. “First class products start with first class advice on the right design, construction, and choice of materials, in order to find what is most compatible with plastic and to develop the optimum part geometry for a product. The experienced and skilled specialists in our team mean that we are able to support customers at every stage of their project –from design and planning right through to series production.”
Alena adds: “We liaise closely with our customers to devise innovative solutions made of plastic. Functionality, ergonomics and design are all key factors in this process. We also take account of required plastic process tolerances in our manufacturing work and can produce 3D CAD designs.”
Through FEM calculations, injection moulding simulations, and distortion simulations, Bäcker is able to optimise the part geometry right at the beginning of the development phase and to factor in compatibility with plastics. “It is possible to run through a wide and diverse range of prototyping processes ahead of the actual tool manufacture and to produce samples made of original material in readiness for series production,” says Gerhard.
For its tooling, Bäcker collaborates with a pool of business partners from the tool making industry, which are equipped
“In addition to our headquarters in Germany, we have a warehouse in Poland – set up in 1998 – which is our distribution centre for eastern Europe. It is perfectly located to supply customers in eastern Europe and provide after sales support.”
“We focus on direct and regular contact with customers,” mentions Gerhard. “We look to create a partnership with our customers and ensure that our sales team have been trained to understand customers’ needs and to provide a first class service. It is only by creating a partnership that we can guarantee that we are supplying the products they need now and in the future.”
The company is currently working on the production of plastic screws with a six-spline drive, which is to be launched in January 2016 – enabling Bäcker to offer its customers an even more extensive product portfolio.
This commitment to provide customers with support and solutions has enabled Bäcker to establish itself as a leading supplier of control elements and plastics parts. Through its PlacoEngineering service the company is also able to work with customers on ideas and innovations – using its experience and knowledge, as well as modern and precise injection moulding machines, to create a variety of plastic solutions.
Gerhard concludes: “The plastics market is a growing market, and there is keen interest in our products and their capabilities. Plastic products offer multiple benefits to customers. They are lightweight, offer good insulation/non conductive, have a high heat resistance, and are available in a variety of different materials, colours and sizes – giving customers as much flexibility as possible. There are now high performance plastics, such as Grivory, which can partially replace metal fastenings with regard to the strength. Therefore fastenings made from plastic become a real alternative to metal in many areas.” www.baecker.eu
The new GESIPA®
The new GESIPA® CFRP blind rivet nut – The partner of choice for carbon fiber reinforced plastics (CFRP)
Main features
• Keeps away any possible corrosion
• Special geometry of the blind rivet nut
• Highly controlled deforming process and safe spread of the clamping force
• Large clamping range
• Can be used for various applications within a production process: Saves handling costs and keeps storage costs low
• Modifiable, depending on customer requirements
A market leader in CLT system engineering products, SWG Schraubenwerk Gaisbach GmbH –a daughter company of Würth Group – is best known for the manufacture of the ASSY® branded screw. Claire Edwards, deputy editor, visited Waldenburg, Germany, to fi nd out more about SWG’s Production division and the capabilities of its high-quality screw manufacturing facility.
In 1958 Prof Dr h.c. mult. Reinhold Würth established a production facility manufacturing brass screws at the Würth facility in Künzelsau, Germany. Due to the rapid development of the production unit, it was relocated to Gaisbach in 1962. Five years later, SWG Schraubenwerk Gaisbach GmbH began trading independently and its core business – chipboard screws –gradually replaced the production of brass screws, and the company continued to grow at the same rate as Würth Group. Today, thanks to decades of experience and cooperation with clients worldwide, SWG Production specialises in the development and production of top quality wood construction screws, including fully threaded screws for heavy timber applications (CLT). Its wide range also includes metal drilling screws and screws for joining plastics – for a multitude of different applications such as wood construction, frame carpentry, cabinet making, prefabricated house building, and façade building, as well as individualising of customised applications.
The main focus of the production unit is the ASSY® brand of screw – given its name because of the asymmetric, symmetric thread. SWG offers the full range of ASSY screws including the universal ASSY 3.0 screw; the ASSY 3.0 SK – designed for use specifically in timber construction and carpentry crafts; the ASSY P – suitable for the attachment of panel materials; and the ASSY plus VG – a fully threaded universal screw, which can be used in the wood glue sector, carpentry, and wood and modular construction industries.
SWG is constantly expanding and developing its product range, with innovation and development at the heart of the business. In January 2014 an engineering bureau was established in order to support the customers in the field of high performance timber engineering.
“An explanation is often required in order to grasp the actual performance potential of the screw in wood construction,” explains Tobias Schneider, head of sales at SWG Schraubenwerk Gaisbach GmbH, production division. “Therefore the engineering team supports the company and its customers in the planning and implementation of customer construction projects.”
Thanks to its modular technology building block system –which enables the combination of various head, thread and point geometries – SWG can cover a wide and comprehensive CE product range with a Würth ETA (ETA – 11/190). This applies to the smallest chipboard screws with a 3mm diameter up to screws for timber engineering with a diameter of 14mm and a length of up to 1,500mm.
74638
SWG ensures the high-quality and performance of its screws by obtaining approvals, not only in Europe but also for key target markets such as North America. In 2013, the CCMC 13677-R was obtained from the Canadian Construction Materials Centre (CCMC). In 2014 SWG also received ESR-3178 and ESR-3179 approval from the US – enabling SWG ASSY screws to be used for wood construction across the entire North American region. “SWG is the first production facility to have obtained all three of these technical approvals,” states Frank Föllinger, project manager sales at SWG Schraubenwerk Gaisbach GmbH, production division. “Thanks to more than 40 years’ experience, a future orientated management, and our modern equipment, we are able to offer bespoke solutions with uncompromising quality.”
SWG’s impressive 15,000m² production facility guarantees the quality of the products thanks to its vast number of machines including cold forming and thread rolling machines. “We produce such high volumes that efficiency is vital across all departments within SWG. Our production floor is run in a clear, concise manner where communication is a key factor,” states Frank Föllinger.
Every machine operator is responsible for several machines and is kept updated with sales figures and production targets –clearly displayed at the front of the production floor. In addition, SWG’s extensive thread rolling department enables it to offer a wide range of single, double, course, part and full threads.
After pressing, the screws are moved to SWG’s pinch pointing department, which currently runs at a very high capacity with millions of screws a day. Batches are then moved to SWG’s on-site heat treatment department comprising of five two-process heat treatment lines to facilitate hardening, annealing and tempering.
SWG also has a quality control department that encompasses tensile testing machines, hardness testing devices, torque testing equipment, and profile projectors.
SWG Production employs 191 staff members across all departments including manufacturing, development, quality assurance, sales and marketing, and IT. “SWG would not be what
it is today without such incredibly hardworking staff,” explains Tobias Schneider. “SWG Production stands for quality and high-end engineering. We create jobs and give people a future.”
The high qualification of its employees is achieved through constant training and further education within the company. SWG offers five types of apprenticeships within the business and currently has 15 trainees within the company. “It’s important for us to nurture our employees and encourage them to pursue their own ideas,” mentions Tobias.
The sheer scale of production at SWG is extremely impressive. Its commitment to quality and efficiency has enabled it to establish itself as a reliable partner for timber engineering. “Our goal is for SWG to be a technology leader together with our sales distribution network,” states Tobias. “Deep-rooted in Germany, we are a reliable partner in the field of timber engineering and look forward to creating new partnerships worldwide, and products, in the future.”
www.swg-produktion.de
Our products provide solutions for locking, sealing, assembly and disassembly. Especially designed with our unique microencapsulation technology for the pre-coating of threads our products offer many advantages compared to field applied adhesives. Constant product development due to extreme motorsport conditions guarantees the highest possible performance. Successfully tested on the race track our products show the same benefits in many other industries.
R+FK Schulte KG is a washer manufacturer that is taking on the challenge of becoming a ‘one stop shop’ for both standard and special washers – looking to utilise its ability to produce washers quickly and cost-effectively with ‘Made in Germany’ quality.
Originally known as Rudolf & Friedrich Karl Schulte oHG Press- und Stanzwerk –after brothers Friedrich Karl Schulte and Rudolf Schulte merged their companies into a general partnership –the washer manufacturer, now better known as R+FK Schulte, has been located on the same site in Plettenberg, Germany, for over 80 years.
“Being able to fulfil the quality demands for both standard and special parts puts us in a very strong position with customers,” adds Carl Philip. “Our customers can be confident in ordering all the washer products they need in any size –from one source – knowing that they will get a consistent high-quality product.”
says Peter. “It is only the ability to consistently and reliably produce to the highest standards that will enable you to win orders and build long-lasting relationships. At R+FK Schulte we can supply this quality.”
R+FK Schulte is still run by the Schulte family with F. Wolfgang Schulte, son of Friedrich Karl Schulte, the owner of the business and Wolfgang’s son Carl Philip Schulte the deputy chief executive officer. “We are very proud to be a family business and to still be producing everything in Plettenberg, including the tooling for the machines,” states Carl Philip.
Producing in Germany is a key part of the business and enables R+FK Schulte to underline the quality of its products. “Quality is a very important factor for us,” says Peter Schlütter, sales manager at R+FK Schulte KG. “We have one of the biggest and widest ranges of standard washers according to DIN/ISO standards and can also supply a great variety of special parts. It is vital that all our products meet the high standards we demand.”
R+FK Schulte’s ability to produce such a wide range of standard and special washers is down to three important elements – the machines, the tools and the employees. “If you have the know-how of these three areas then you have the ability to always produce a good quality product,” points out Peter. The company’s machining capabilities enable R+FK Schulte to produce washers with a thickness from 0.05mm up to 12mm – once again underlining the company’s competence. “Products with tight tolerances require machines and tooling with tight tolerances,” explains Carl Philip. “Our production is broken down according to product dimensions. It does not matter if it is a standard or special part, it is the dimension of the washer that determines which stamping machine is used. This means that we do not differentiate between the quality of our standard or special parts – they all have to be the highest quality.”
R+FK Schulte produces to the high standards of the automotive industry and has achieved ISO/TS 16949 accreditation, as well as ISO 9001. “We achieved these accreditations, but they can only get you through the door to speak to customers,”
A vital part of R+FK Schulte’s quality is its impressive tooling department and the vast depth of experience and knowledge of its tooling employees. “The tool shop is the beating heart of the company,” states Carl Philip. “Every tool that is used on the machines has been built in our tool shop. Thanks to the experience of our employees, we are able to create a wide range of new tooling – especially for special parts – which uses all of the knowledge and skill that has been passed down over the last 80 years.”
“We are immensely proud of our tool shop and its capabilities,” continues Peter. “We are regularly investing in new machinery to ensure that we are able to keep up with the latest technology and ensure that we are always able to offer the necessary tooling for customers’ solutions.”
Since its foundation, R+FK Schulte has always had the philosophy to reinvest profits into the business – focusing on growing organically whilst increasing productivity and efficiency. A prime example is the company’s recent decision to invest in a new 800 tonne stamping machine, but it wasn’t a simple case of just buying the machine.
“We wanted to increase our capacity and improve our production process, which is why we wanted the new 800 tonne machine, but our production area was already full of stamping machines,” explains Carl Philip with a smile. “Stamping machines aren’t the smallest machines, so we realised that if we were going to introduce the new machine we would also need to build a new production hall.”
So that is exactly what the company decided to do. Started at the beginning of 2015, the new 2,000m² extension is now complete with the 800 tonne stamping machine already set up and working on series production – giving R+FK Schulte the ability to be more productive and improve cost-efficiency for larger washers.
“When it comes to stamping, it is all about the parts you can produce,” explains Carl Philip. “The new machine is designed in a way that it works with special or standard parts that have a thickness of up to 12mm – in series production.”
“The new machine has definitely increased our capabilities,” adds Peter. “However, you can only create high-quality
products if you have the knowledge and experience that helps you to realise features that other companies cannot.”
The ability to realise features and work with customers on the development of special parts is something that the company wants to develop further. “The special parts business is about gaining knowledge and improving and improving again,” says Carl Philip. “We work closely with our customers on designing new parts to drawing, but also by looking at their application and whether we can substitute turned or hot forged parts into stamped parts. This is becuase stamped parts can offer significant cost savings, whilst still providing the customer with a quality product.”
Carl Philip continues: “Another key benefit we can offer is that we are also set up as a mass producer –all our processes, structures and organisation are streamlined to this –which has a great effect on our cost-efficiency. We can translate this into our special products, which means that we are not only attractive to customers for
the technicality of our special parts but also the cost-effectiveness of them.”
60% of R+FK Schulte’s customer base is distributors and wholesalers – mainly in Germany but also across Europe. Screw manufacturers – which require washers for screw and washer assemblies and HV sets – make up 30% of the customer base, with end users accounting for the final 10%. “We see wholesalers and distributors as partners that enable us to get to key markets and we work very closely with them,” mentions Peter. “By having a tight relationship we feel the pressures on the market and the prices, and try to pass cost savings onto the customer. The screw manufacturers are also essential partners as they challenge us with complex solutions for assemblies where our technical competence is giving us the edge over our competitors.”
R+FK Schulte is keen to continue to build its relationships with customers and ‘go the extra step’ where possible – as it did with its recent investment in its packaging department. The company has introduced three automatic packing machines – poly bags as well as carton – within the last two years. “Whilst it is not a core part of the business, we realised that we needed to be flexible to our customers’ requirements,” explains Carl Philip. “We therefore invested in the additional packing lines, which enable us to offer more capabilities and improve the overall process.”
This commitment to being flexible to customers needs – supported by a wide range of standard products – plus the ability to work with customers on special parts, means that R+FK Schulte has a commanding portfolio to offer customers. With Carl Philip in the company, the next generation has been established and solid foundations are being laid to take the next step in the company’s development.
“It is important that we prepare for the future and continue to provide both standard and special parts in the most effective manner possible,” states Carl Philip. “We will stick with organic growth and will keep our philosophy of reinvesting back into the business. In fact we already have two additional machines on order, which will be installed and running by the end of the year.”
Carl Philip finishes: “We are 100% committed to what we are doing and look forward to continuing to deliver a quality product with a first class service.”
Founded in 1999, Eurotec GmbH is predominately known as an established distributor of innovative fastening products. However, in 2013 the company introduced manufacturing capabilities for its most popular wood construction screws.
Here Fastener + Fixing Magazine interviews Markus Rensburg, managing director and founder of Eurotec GmbH, to find out more about the company’s manufacturing capabilities and German manufacturing in general.
What differentiates German manufacturing companies from their competitors?
“German companies with the ‘Made in Germany’ seal of quality profit mostly from all-encompassing high-quality standards, thanks to well-trained skilled workers and innovative engineering services. In addition, Germany is at the global vanguard of implementing a sustainable approach to protecting the environment. However, such high environmental standards are not inconsistent with highly successful companies. Also, extensive infrastructure –in tandem with high flexibility – enable fast response times, which is a key factor when supplying customers.”
What differentiates your company and its products specifically?
“We are still a very young company and we are continuing to grow and develop as a business. Currently, we distinguish ourselves with our comprehensive range of building construction products. Among our target groups are those involved in woodworking and roofing, as well as gardening and landscaping. We also serve joiners’ and carpenters’ workshops as well as those working in the area of general interior fittings, such as drywall construction and acoustic structures.
This means that we offer professional users innovative product solutions in areas such as wood construction screws, roofing screws, decking and gardening, and façade insulation systems. Alongside the complete range of fasteners for new builds, solutions for energy related renovation also form part of our portfolio. In this way we place a lot of value on a range of complete system solutions.
Our internal product development is distinguished by an above average proximity to the market. In this way our product managers and development engineers can take a targeted approach to finding the right solution for even complex job specifications. What’s more, our close relationship with customers is enhanced by detailed support for users in the planning phase, as well as during execution for implementing all types of projects. We also offer additional internal and external product training via our in-house application technicians.
As part of our own screw manufacturing, we focus a lot on efficiency. This is achieved thanks to the extraordinarily high-level of automation at our production facilities. For this we use complex machinery that takes on the roles of supplying adjusted wire segments; heading stations for shaping screw heads; pinching machinery for making drill points; thread rolling stations for thread shaping; milling stations for mounting locating grooves; and automated packaging for onward transporting. Thanks to this joining up of what would otherwise be individual process stages, we are able to bypass the need for in-house logistics during the production process and it also leads to shorter production times.”
What is the balance between your company’s domestic and overseas sales?
“Up until now Eurotec has focused mainly on the domestic market and exporting to the European market. In the past two years we have set-up an overseas sales department with the goal of achieving global sales of 10% – 15% of our overall turnover, within the next two years, and we are already seeing initial success. In order to increase our efforts, a marathon session of trade fairs is planned for all areas.”
What have been your successes during 2015?
What challenges has your business experienced?
“Eurotec already operates a fully developed programme for timber and decking structures. Alongside the further expansion of our existing strengths in timber structures, we will also focus on building up our product portfolio for concrete fastening, as well as our presence in all markets.
We are currently working intensively on the further development of an ETA for concrete screws. We are expecting our first breakthrough on this in the last quarter of 2015. In addition our range of bolt anchors was launched with an ETA Option 7 approval. We are working on Option 1 approval for this as well. Our production also took receipt of and put into operation second and third machines.
As we continue to grow our product portfolio and our business, it is important that we are conscious that one of the biggest challenges we face is recruiting appropriately qualified and motivated staff.”
www.e-u-r-o-tec.de
2016 promises to be an exciting year for Lueg-Stanztechnik e.K. Not only will the company celebrate its 50 th anniversary, but its recently purchased stamping machine will also be fully operational – enabling the company to increase its manufacturing capabilities.
Lueg-Stanztechnik manufactures stamped and bent parts and fasteners, such as washers, according to DIN/ISO standards, customer drawings, or samples, at its production plant in Herscheid, Germany. With its own tool shop Lueg-Stanztechnik is able to react quickly and flexibly to customer wishes, product changes or new enquiries.
The company recently invested in a refurbished machine, which will be fully operational by the beginning of 2016. The new machine means the company will be able to expand its capabilities to washers with a thickness up to 8mm, which will open up new opportunities and markets.
Lueg-Stanztechnik is currently an approved supplier for the aerospace industry and has established and maintains a quality management system according to EN 9100:2009, based on the ISO 9001:2008. The certificate is valid for the manufacturing and distribution of punching parts and fasteners of washers, securing plates, as well as drawing parts, for the aerospace industry and the general industry.
In addition to the processing of standard materials, Lueg-Stanztechnik is an expert in the processing of materials with special requirements, including Duplex/Super Duplex
(1.4462, 1.4410, AISI 324 SGB, AISI 329 SGB); corrosion resistant steels including 1.4529 (Alloy 926) and 1.4539-Uranus B6 (Alloy 904L); heat resistant alloys such as 1.4762 (AISI 446), and 1.4828 (AISI 309); offshore and corrosion resistant alloys 2.4630 – Monel 400; high nickel alloys including 2.4819 (HASTELLOY® C276), 2.4632 (Nimonic® 90), and 2.4602 (Alloy C-22); and super corrosion resistant alloys 2.4605 (Alloy 59) and 1.4562 (Alloy 31). Lueg-Stanztechnik is also able to manufacture standard stainless steels such as 1.4301 (AISI 304), 1.4310 (ASTM 301), 1.4404, (AISI 316L), 1.4512 (AISI 409), 1.4541 (AISI 321), 1.4571 (AISI 316Ti), and non-ferrous metals (aluminium, copper, brass, bronze) and titanium. Furthermore, different finishes and surface options according to customer requirements – such as nitrocarburising – are available on demand.
“With a vast experience using every type of stainless steel and alloy, coupled with dedicated and highly trained staff, we are focused on solving customers’ challenges. We are more than simply a supplier of products and look to develop long-term relationships with all our customers.”
www.lueg-stanztechnik.de
Washers and stamping parts according to DIN / ISO / NFE, customer drawings or samples.
Stainless steels, special alloys (e.g. Duplex, corrosion resistant steels, heat resistant alloys, offshore and corrosion resistant alloys, high nickel alloys), non ferrous metals, titanium.
Lueg-Stanztechnik e.K.
Osemundstraße 3
D-58849 Herscheid, Germany
Tel: +49 (0) 2357 172813-0
Fax: +49 (0) 2357 172813-99
email: info@lueg-stanztechnik.de
www.lueg-stanztechnik.de
Lightweight
Innovation:
▪ The Mubea Generation II Disc Springs
Advantages:
▪ Multiplied lifetime (by factor 10 possible, depending on application)
▪ Reduction of outer diameter up to 10 %
▪ Optimization of travel up to 40 %
▪ Reduction of spring stack installation length up to 20 %
Your benefit:
▪ Reduction of system size and weight
▪ Decrease of system costs
▪ Reduction of maintenance rate
www.mubea-disc-springs.com
Four months after its metamorphosis from an Anixter division to a standalone, independent business within the AIP portfolio, Optimas OE Solutions has acquired a UK-based manufacturer of bespoke critical fasteners and special cold forgings. Phil Matten, executive editor, explores the backstory to a strategic acquisition that substantiates Optimas’ determination to achieve excellence in its support for OEM partners.
Based in the historic spa town of Droitwich, south-west of Birmingham, Barton Cold Form Ltd demonstrates that advanced cold forming is very much alive in the UK. The name echoes the company’s inception as a manufacturer – 80 years ago – in the back room of a pub called the Barton Arms. Its modern incarnation, a 5,000m² production facility, into which Barton moved in 2006, was meticulously designed for efficiency and is equipped with a comprehensive array of forming, rolling and secondary operation machinery. Investment until now has been cautious and carefully targeted but has recently included a new pointing and drilling machine, a SEMS roller and a Tesa-Scan 52 laser measuring machine. Barton has now also introduced a 3D printing prototype service.
Long a trusted supplier to the automotive supply chain –including Jaguar Land Rover, Ford and several tier suppliers –Barton Cold Form holds ISO/TS 16949 accreditation. It has also demonstrated the ability to reshore manufacturing contracts that had previously migrated to Asia.
Remarkably, in 2008 Barton’s existence hung by a thread, its sales book in tatters from the collapse of automotive demand. Today’s GB£8 million business is not just testament to its manufacturing competence but also to a seventy strong team, whose resolve has been strengthened by the flames of near disaster.
All of which explains why Barton should, for more than a year, have been high on the Ian Clarke acquisition list. The Optimas leader is, of course, far from a stranger to manufacturing. The first two decades of his management development were with British Steel before moving on to managing directorship of a UK fastener manufacturer and then a global marketing role for Anixter Fasteners. In 2013 he was appointed executive vice-president, responsible for the Anixter OEM Supply –Fasteners business and is now president and CEO of Optimas.
Optimas already has an excellent manufacturing facility in Wood Dale, near Chicago’s international O’Hare airport. The acquisition dates to 2008 and, perhaps because of the downturn
in market conditions, it remained underutilised for several years. It was when Ian Clarke moved to the United States that the plant’s value began to be fully recognised. Since then Wood Dale has seen millions of dollars of investment, including the installation of additional National FORMAX machines – all aimed at optimising its operations, as well as increasing capabilities and efficiency. There has been equal emphasis on investing in the calibre of people at the plant.
For Ian Clarke the rationale is straightforward: “We’re investing in manufacturing because our customers increasingly demand we have these capabilities. Central to the strategy is a vertical integration that massively enhances our abilities to exercise control over the supply chain and deliver critical improvements in security to our customers.”
“Internally we’ve recognised the value of Wood Dale and the rapid returns delivered in response to investment in both machinery and talent. Even more importantly our customers have felt the benefit, in terms of the superior solutions we can provide, together with enhanced levels of flexibility and responsiveness.” For Clarke there is also a cultural, as well as practical benefit, as Wood Dale now plays a proactive role in the OEM interface, working tightly with engineers to develop the solutions they need.
The success of Wood Dale turned the spotlight on the critical need for similar manufacturing excellence in Europe, the lack of which signified vulnerabilities as well as representing a fundamental block to accessing business with certain supply and quality critical OEMs.
“The key for us was to find the right manufacturing partner, who could share a like vision of excellence,” explains Clarke. Barton is already a supplier to Optimas and its managing director, Andrew Nuttall, worked for one of the UK VMI distributors brought together to form Anixter’s OEM fastener business. “That means there is already a lot of like-mindedness, cultures that are in-line, and strong personal relationships,” says Clarke.
“ We see Barton as a centre of technical excellence, which already demonstrates expertise in engineering complex par ts to meet the needs of perfor mance critical applications.”
For Dan Jack, Optimas’ SVP for the EMEA region, the latest acquisition is integral to the company’s European growth strategy. “We see Barton as a centre of technical excellence, which already demonstrates expertise in engineering complex parts to meet the needs of performance critical applications.”
“Barton is ready to grow and we have both the current and potential customer demand that can deliver that growth. Equally important, as we have already demonstrated at Wood Dale, Optimas is strongly positioned to invest in the continued development of Barton’s manufacturing capabilities and people.”
Optimas also announced the appointment of Tim Taylor as its SVP global manufacturing. His presence at Barton Cold Form during the acquistion announcement was significant – and not just to those employees needing to know there was a real understanding of manufacturing amongst Optimas senior management. The appointment of someone of Taylor’s pedigree signals a far more strategic commitment to manufacturing: A recognition of its importance in enhancing supply chain security for OEM customers and to hone Optimas’ capability in developing specific engineered solutions for them. The learning curve at Wood Dale was an extended one. Listening to the presentations at Barton, there is little doubt the process will be more rapid and incisive this time –not least because the benefits are far more clearly identified.
While Tim Taylor and Dan Jack are understandably focused on the opportunities Barton brings, it was Mike Tuffy who placed the acquisition in the wider context of Optimas sourcing strategy. “Manufacturing will be an important part of our value proposition but it will not detract from the strategic supply partnerships we are now working hard to forge. Even with the investment Optimas will undoubtedly inject to develop Barton, it will remain a specialised plant with high added value capabilities, which we have to use selectively and to maximum effect.”
The message from all three Optimas senior managers to Barton was that this was an investment to protect key current business but above all to accelerate growth. Mike Tuffy is adamant that is how Optimas’ other suppliers will gain from the development. “This is one of a number of initiatives to drive Optimas’ growth. The ultimate benefit to the strategic supply partners that engage wholeheartedly with Optimas will be to win their share of that overall growth.”
The acquisition clearly validates Ian Clarke’s confidence in the investment partnership that launched Optimas as a standalone business. “There is now a seamless relationship with our business,” says Clarke, “and, in very short order AIP has demonstrated tangible, incisive support, evidenced by this acquisition.”
“Behind the scenes we have been able to make game changing investments in technology and systems that work specifically for Optimas, eradicating historic anomalies that had inhibited our ability to act as an integrated, global provider of OE solutions.”
“We have also benefited from crucial guidance in best practice –drawn from their experience of a wide range of previous investments mostly in manufacturing businesses.”
There is no doubt Optimas has now sharpened its pace and tightened its disciplines across all its spheres of activity. “The senior management team is now enabled to think and act far more strategically,” according to Ian Clarke, “and the focus on how we achieve operational excellence is rapidly permeating throughout our business.”
Where next for Optimas? Nobody is talking specifics but investment at Wood Dale has delivered a significant competitive advantage and been recognised as a real differentiator by Optimas’ customers. The Barton acquisition underscores the intention to replicate those advantages in every major continent that Optimas is active.
Developing manufacturing, though, is the proverbial tip of the iceberg. There have also been system, organisational and ongoing supply base improvements, aimed at enhancing the potency of the Optimas service delivery to existing customers and inspiring both internal and external confidence to fuel organic growth.
The appetite, and resource, to achieve greater, faster growth, is now manifest. In an increasingly challenging macroeconomic environment that is not going to come entirely from organic growth – which implies Optimas will not be long in turning its attention to increased market penetration through targeted acquisition of VMI distribution. The trick, as with manufacturing, will be to find the right – and available – targets. The intent and resource, though, are very evidently now there, so expect to hear more about Optimas’ developments in these pages.
“
…Optimas is strongly positioned to invest in the continued development of Barton’s manufacturing capabilities and people.”
In seven years GripIt ® Fixings has grown from a simple idea of a 13 year old boy to a manufacturing facility with the capability to produce GripIts in the millions. Claire Edwards, deputy editor, visited GripIt’s headquarters in Wiltshire to find out more about the UK fixing manufacturer and its meteoric rise.
In 2008 Jordan Daykin was a 13 year old boy who was helping his grandfather securing a blind to a window of a converted garage. The gap between the plasterboard and the steel lintel was too narrow and the drill bits kept snapping. The fixings available on the market at the time were not robust enough to secure the blind, so Jordan – along with his grandfather Stan –invented a new design of universal fixing that could be used with all types of plasterboard installation – the GripIt®
“When GripIt was launched on the market it provided an instantly popular and winning solution to an enduring problem. Large stores, tradespeople and DIYers welcomed this simple method of wall hanging on plasterboard because of its ease of use, high performance and convenience – and because it instantly trumped all other similar products on the market,” states Nicky Harding, sales and marketing manager at GripIt.
In 2012 a patent was registered and the GripIt was launched on the market. In the same year, the first order of 25,000 fixings was placed by ScrewFix Online, and GripIt also gained its first UK retail stockist, Gardner & Scardifield Ltd.
By 2014, the GripIt was available in 500 UK stockists, however manufacturing was still being outsourced to other UK manufacturers. Needing investment for his own manufacturing facility, Jordan – now 18 years old and managing director of GripIt – appeared on the UK television series Dragons’ Den. After pitching for two hours, Jordan’s passion and knowledge gained the respect of Dragon Deborah Meaden, and Jordan became the youngest entrepreneur in the show’s history to receive an investment of GB£80,000.
The investment enabled GripIt to expand into another unit at its Trowbridge headquarters and establish a manufacturing facility on-site.
“The GripIt is a British invention that is proud to be ‘Made in the UK’ for consistent quality and performance,” explains Nicky. “‘Made in the UK’ is a high accolade that customers can rely on, and more importantly – trust.”
Every part of the GripIt is now manufactured on-site, apart from its metal locking wings – which the company is planning to produce in-house in the near future. The company recently expanded its manufacturing capabilities with the introduction of three new machines. Now its manufacturing facility houses numerous plastic moulding machines, pin machines – invented by the GripIt team – and both a packing and sorting machine.
“Back when Jordan first started the company, his school friends used to sit around his grandparents kitchen table and assemble the GripIt fixing – our manufacturing facility is a far cry from those days,” says Nicky with a smile.
To further increase its efficiency, GripIt has zero plastic waste – with all plastic used in the manufacturing process recycled and reused. In September this year, GripIt’s manufacturing facility also obtained ISO 9001:2008 certification.
Even after all these developments, the company is still evolving and is now manufacturing – after feedback from customers – its ‘second generation’ fixing, which has been designed for use with all types of plasterboard installations. Like the original fixing, the second generation GripIt’s are available in four sizes: 15mm (yellow), 18mm (red), 20mm (brown) and 25mm (blue). Comprising of a circular plastic plug with a pair of uniquely designed slim gripping wings, the fixings are suitable for 9.5mm – 15mm plasterboard.
During installation the GripIt is inserted into a hole of the same diameter and tapped with a hammer to engage anti-rotation tabs. It is then screwed into place. “GripIt can be used on rendered or unrendered cavity walls, double thickness plasterboard, insulated plasterboard, or dot and dab walls,” points out Nicky. “It can be removed and reused indefinitely, adjusts to lining thicknesses and supports heavier loads. Our motto is simple: Just drill, tap and turn.”
To ensure that the second generation GripIt would meet the necessary shear and tensile strengths they were subjected to rigorous testing. A timber framework dimensionally representative of a domestic stud partition internal wall was erected and 15mm plasterboard was secured using drywall screws. Each type of GripIt fixing was separately secured into the plasterboard by following installation instructions. Using a specially designed test rig and digital weight monitor, each GripIt type was subjected to various shear and tensile tests. The results are displayed in the table below:
Recently, GripIt announced the appointment of a preferred global distributor partner – RS Components – for the second generation fixing. The partnership means the full range of GripIt fixings are now available in a total of 32 countries worldwide including Belgium, Denmark, France, Germany, Italy, Ireland, Spain, South Africa, the Netherlands and Turkey. “RS Components has a global reach with a large customer base. With this new business relationship we feel we are on our way to achieving our ambitious goals,” comments Nicky.
GripIt has come a long way since the design of the original GripIt in a garden shed, and the family business still has ambitious plans for the future. The company is planning to continue the expansion of its manufacturing facility and is looking to develop new worldwide markets for the second generation GripIt and other new products. “The capabilities of the GripIt and the numbers produced will grow every year,” states Nicky. “We’re proud to be a British manufacturer and will constantly strive to achieve the best. Watch this space.”
Coinciding with the World Trade Fair in Milan, FASTENERS MEETALY 2015 was heralded by its organisers as the fi rst world convention focused on fasteners. Phil Matten, executive editor, was at the Hotel ATA to listen to some thought-provoking presentations and discussions.
FASTENERS MEETALY was promoted by UPIVEB (Unione Produttori Italiani Viteria E Bulloneria), which deserves great credit for a polished and professionally organised day. The Italian fastener manufacturers’ association emphasised it was only possible through the support of key sponsors: Carlo Salvi SpA, Editoriale UPIVEB, NOF Metal Coatings Group, Ori Martin SpA, SACMA Group and Voestalpine AG – plus support from Banca Mediolanum SpA and the Italian Ministry of Economic Development.
The ambitious concept originated, UPIVEB President Sergio Pirovano told delegates, from a discussion eighteen months previously between himself and the late Giannantonio Brugola. The aim was to stage an event to analyse the global future for fasteners based on wide ranging presentations by speakers from the fastener industry, the banking sector, automotive and agricultural machinery OEMs, and academia. In that it certainly succeeded and amongst the delegates there was a significant proportion of international visitors, although at an estimate some 70% were from Italy or linked with Italian companies.
Sergio Pirovano’s opening comments highlighted the continued strength of the Italian fastener manufacturing industry, with some 230 large, medium and small participants, employing more than 7,500 personnel and generating annual sales of approximately 2.3 billion euros.
Enio Fontana, CEO of Grupo Fontana and EIFI vice-president, broadened horizons by presenting data from 2013 Freedonia research estimating global fastener demand at US$72 billion. By 2023, global demand for fasteners was expected to reach US$134 billion, reflecting an average 6% annual growth rate. In 2013 the Asia Pacific region represented 42% of global fastener demand, with the Americas accounting for 27.5% and EMEA around 31%. Future growth, Enio Fontana said, would be stronger in the Asian region and more limited in the Americas. He concluded: “We expect a rosy future for the fastener industry. The world market continues to grow, even if at a slightly slower pace than in the past.”
Optimism was unquestionably the by-word for Ennio Doris, president of Banca Mediolanum SpA, who invested absolute confidence in the self-correcting mechanisms innate in world economies. “If we consider the trend of the world GDP,” he said, “we can see that it is continuously growing over time, ranging from 4.5% to 5% in the most favourable cases, and from 3% to 3.9% in the less favourable ones. Negative years are now very rare.”
The destiny of the fastener industry is intimately entwined with that of the automotive sector and the morning programme featured presentations from vehicle companies and automotive analysts. Peter Weiss, Fiat Chrysler’s head of European supply chain management, detailed opportunities and challenges as automotive production increased across all global regions. He rehearsed the technology developments facing the automotive sector and its suppliers. These included ever tighter emissions regulations not just in Europe and America but also increasingly in other regions. Safety was a critical trend – epitomised by the introduction of self-stopping technologies. Consumers demanded higher connectivity in vehicles, which meant: “The level of electronics being introduced was unprecedented.” Platform reduction was the common approach to achieve cost reductions but, contradictorily, more responsive customisation to individual consumer demand proliferated the complexity of options.
One result was far greater cross-region dependency in the parts supply chain, increasing reliance on the supplier network, and creating greater vulnerability to geopolitical events. There was a direct call to action for the audience. “Look into real time
transparency, talk to your logisticians, use the modern tools of logistics engineering to optimise. Be flexible, make sure you know where the pinch points are in your supply chain and assess risks – make sure you are ready because it can hit at any time.”
Andrew Brumley, chief engineer for engine technology at Ford Motor Company, focused on engine downsizing in response to tighter emission requirements. He outlined the development of Ford’s Eco-Boost technology before exploring the future potential for smaller, lightweight gasoline engines – seeing opportunities for improvement through cost-effective electrification rather than replacement by electric power units.
Connectivity was central to the presentation of Andrea Marinoni of Roland Berger Strategy Consultants, who explored the opportunities for the automotive industry to benefit from Industry 4.0.
Bernhard Gerhlert of Bosch Group took the theme of ‘Connectivity and Convergence’, and painted a vivid and imminent scenario of pervasive personal and industrial interconnectivity.
Massimo Majowiecki, professor of structural architecture at the University of Bologna, illustrated how a combination of artistic vision and computer-aided design was leading to quite incredible structures in which fasteners were required to play a critical role.
Key to any event exploring future trends is establishing links with the now. MEETALY’s afternoon forum made a very credible attempt at doing so, with many participants applying thoughtful analysis to the issues.
Moderated by Professor Silvia Vianello the participants from Europe, Asia and the Americas were: Egidio Stefano Brugola (president of Brugola OEB SpA), Ramón Ceravalls (president of EIFI General Fasteners Group), Ming-Jou Chen (former president of TIFI), Dan Di Sebastian (vice-president of North America operations, Fontana Group), Anders Karlsson (president of EIFI), Fernando A. Gomes Martins (vice-president of SINPA, Brazilian Fastener Institute), and Paolo Pozzi (president of EIFI Automotive Group, and CEO of Agrati Group).
The influence of China at both macroeconomic and industry specific levels inevitably loomed large. For Ramón Ceravalls, experience taught the difficulties of predicting what will happen in China but he expected continued growth. Fernando Martins concurred, quoting Brazilian iron ore suppliers as expecting steadier growth and continued low raw material prices – moderated by some mines nearing end of capacity. Dan Di Sebastian saw “much opportunity for the fastener industry despite slower –not slow – Chinese growth”. He believed subdued global growth would suppress the potential for higher US interest rates and maintain capital availability.
For Ming-Jou Chen, overcapacity in Chinese steel production was not being addressed and ‘zombie’ mills were producing well below economic cost – depressing world steel prices and creating challenges for the Taiwan fastener industry. Taiwan, he said, must upgrade its fastener production to compete with China, noting there were now more than one hundred ISO/TS 16949 accredited fastener plants in Taiwan.
For Anders Karlsson the future for the fastener industry was more of the same – more consolidation, more globalisation. “We have seen the first Chinese people coming into Europe. We will see more of them,” he said.
Ramón Ceravalls saw the relevance of the morning topics depending on company scale. For smaller companies, he said: “The main challenge is to keep up with global/glocal market needs.” External challenges apart, the issue was to ensure continuity generation to generation. “A lot of the fastener industry is in the hands of family companies so this is very important.”
Paulo Pozzi believed the development of automotive powertrains presented a big opportunity – “a new paradigm driving the need to innovate new components”. Fernando Martins agreed but stressed: “The real challenge was for fastener makers to update their margins. No margin – no profit. No profit – no success.”
succeeded by deflation due to supply overcapacity. “Unless the capacity in steel production is radically reduced we will not see improvement,” he said. Egidio Brugola believed the commodity super cycle was almost over but said: “We won’t go back to previous levels.” He did not foresee significant changes in the steel market.
For Paulo Pozzi: “The most important thing is to understand we are experiencing a big technical discontinuity. The biggest difficulty concerns what we do not know”. He went on to add that while process optimisation was very important “we must not forget the challenge to create good organisations and to attract and develop good human talent”. Dan Di Sebastian reminded that the average age of skilled people operating fastener machinery continued to increase.
The fastener industry is traditional, said Ramón Ceravalls, making major innovations difficult. “At least in our company there will be no big steps forward – lots of little improvements.”
Dan Di Sebastian returned to the stringent cleanliness required of vehicle engines, believing this would demand new fastening concepts. “We will be challenged to come up with more innovative, lighter weight and stronger products,” he said.
The presentations on Industrial 4.0 and on connectivity impressed Dan Di Sebastian who reflected: “Fastener manufacturing technology has been around for a long time so how do we leverage connectivity technology to more efficiently manufacture products?” He also noted the difficulty of balancing the requirement for 100% accurate delivery with the cost of carrying inventory – heightened by the risk of geopolitical shocks that could make significant inventory obsolescent.
“I do not myself believe in the big technology revolution in our industry,” commented Anders Karlsson. “Our machines will look fairly similar in the coming years. This is old technology that has to be connected to new technology. The average age of fastener production machines in Europe or Taiwan is probably 20 years.”
The pressure to go global and set-up local production made short-term returns difficult, Karlsson also said. “This is a challenge not just for small companies but for bigger ones too.”
Asked about the commodity super cycle, Ramón Ceravalls noted deflation as a result of plunging demand had been
Anders Karlsson confirmed the automotive sector was most influential on the future of the fastener industry. He saw great political pressure in China for electrical vehicles, adding wryly, “even though they will be powered by electricity generated by burning coal”. These would need different fasteners than today and the switch to electric motors would mean a reduction in fastener demand in ten years time.
For Dan Di Sebastian the need to service customers in more locations combined with the requirement for continuous cost reduction would drive greater economies of scale. “We will continue to see a consolidation of the industry, as we all have to become glocal.” Anders Karlsson agreed: “The big will get bigger. Smaller entrepreneurial companies will be there but they will need to find an edge.”
Sergio Pirovano told FASTENERS MEETALY that he wished the concept of a forwarding looking conference for the whole fastener industry might be adopted and repeated in perhaps two years time. It is a worthy aspiration, echoing a comment made at another event by Anders Karlsson, which reminded that the fastener industry has far more in common than the differences on which it sometimes focuses.
I’ve never seen so many people being interested in fasteners. I am very pleased at that.”
Anders Karlsson, president of EIFI
Trade visitors to the EISENWARENMESSE – International Hardware Fair Köln, taking place from 6th – 8 th March 2016 – will also be able to visit the International Trade Fair for Retail Promotions and Imports (IAW), which is taking place from 7 th – 9 th March 2016.
For the first time ever, trade visitors will have the opportunity to visit both events due to a cooperation agreement between the organisers. “In Spring 2015, exhibitors of trade fair Asia-Pacific Sourcing benefited from increased attendance as a result of a strategic partnership with the IAW trade fair. We have entered this cooperation as we see similar synergy effects for the exhibitors of EISENWARENMESSE – International Hardware Fair Köln,” explained Katharina C. Hamma, chief operating officer of Koelnmesse GmbH.
In addition to related industries, the proximity of the two events also makes cooperation extremely favourable. EISENWARENMESSE is being staged in Halls 1-5 and in Hall 10 of the Köln fair grounds, which is directly adjacent to the exhibition space of IAW in Halls 6 and 9. The trade visitors can thus look forward to short routes.
At EISENWARENMESSE trade visitors from all over the globe gain a comprehensive overview of the products in the hardware industry from the tools, industrial supply, fixing and fastening technologies and fittings segments, as well as building and DIY supplies. The International Trade Fair for Retail Promotions and Imports specialises in promotional and trend-led products and high-volume orders.
Visiting IAW is free of charge after pre-registering. Tickets for EISENWARENMESSE are available from the online ticket shop.
www.eisenwarenmesse.com
Continuing strong demand for stands at next year’s Fastener Fair Italy in Milan, organisers Mack Brooks Exhibitions has opened an expansion area to meet further requests from companies wishing to take part in the event.
Many of the fastener and fixing industry’s top names, domestic and foreign, have already guaranteed their presence at the show, taking place at MiCo – Milano Congressi from 28th – 29th September 2016. The additional exhibition space will enable even more companies to join this key showcase for producers and distributors of fastener and fixing products and technologies in one of the sector’s major markets. Amongst prominent Italian companies will be cold and warm forming technologies specialist SACMA Limbiate SpA, rivets manufacturer BRALO S.A, and bolts and screws distributor – Ambrovit SpA. MARPOSS Italia SpA will also exhibit focusing on precision equipment for measurement and control in the production environment. Other notable Italian exhibitors include DFV Automazioni, Italbolt Inox Service Srl and Carlo Salvi SpA. Foreign companies, including European distributor Fastbolt GmbH and German-based supplier of stainless steel fasteners, Lederer GmbH, will also be exhibiting at the show. Other European exhibitors include NOF Metal Coatings Europe, Schwer + Kopka GmbH (Süd) and Lancaster Fastener Co Ltd.
“The level of demand that has led us to make more exhibition space available a year ahead of this event, reflects the industry’s view of the importance of Italy’s fastener and fixing market. It also confirms the reputation of the Fastener Fair brand as a highly effective showcase for the industry. The very strong support we are experiencing for Fastener Fair Italy sets the scene for what we believe will be a highly successful show.”
The professional brand for fixings and fasteners
Fastening technology for everyday use. High-quality, time-saving application in construction and installation. That is what the products of the Don Quichotte brand stand for.
The short-term delivery of our products and the direct, uncomplicated processing of orders make Don Quichotte a strong and reliable brand for users in the trade.
EISENWARENMESSE –International Hardware Fair Cologne
TOOLS, FASTENERS & FIXINGS, FITTINGS, INDUSTRIAL SUPPLY, HOME IMPROVEMENT. In 2014: 2,787 exhibitors, 43,879 visitors from 136 countries, 6 halls with 144,200 m2
Where: Istanbul, Turkey
Web: www.fastenerfair.com
Where: Basel, Switzerland
When: 12 Jan – 16 Jan 2016
Web: www.swissbau.ch
What: National construction fair.
When: 30 Mar – 31 Mar 2016
What: The fastener event for Turkey.
Where: St. Petersburg, Russia
When: 15 Mar – 17 Mar 2016
Web: www.ptfair.ru
What: Metallurgy, welding, metalworking, tools and instruments, materials and machinery exhibition.
Where: Poznań, Poland
When: 2 Feb – 5 Feb 2016
Web: www.budma.pl
What: Building technology, equipment and materials.
Where: Coventry, UK
When: 16 Feb – 17 Feb 2016
Web: www.totallydiy.co.uk
What: DIY, hardware, tools and security products.
bautec
Where: Berlin, Germany
When: 16 Feb – 19 Feb 2016
Web: www.bautec.com
What: Building and construction technology.
Where: Kiev, Ukraine
When: 2 Mar – 4 Mar 2016
Web: www.en.intertool.kiev.ua
What: International exhibition for hardware, tools + DIY.
Where: Köln, Germany
When: 6 Mar – 8 Mar 2016
Web: www.eisenwarenmesse.com
What: Hardware and DIY sector.
Where: Beijing, China
When: 29 Mar – 31 Mar 2016
Web: www.intersolarchina.com
What: Exhibition for the Chinese solar industry.
Where: Düsseldorf, Germany
When: 4 Apr – 8 Apr 2016
Web: www.wire.de
What: Wire and cable, including fastener manufacturing technology.
Where: Stockholm, Sweden
When: 5 Apr – 8 Apr 2016
Web: www.nordbygg.se
What: Nordic construction industry.
Where: Moscow, Russia
When: 5 Apr – 8 Apr 2016
Web: www.mosbuild.com
What: Exhibition of building and finishing materials.
Where: Hanoi, Vietnam
When: 6 Apr – 8 Apr 2016
Web: www.vietnammanufacturingexpo.com
What: Industrial parts manufacturing.
Following continuing strong demand for stand space, the first hall of Fastener Fair Turkey 2016 is already fully booked, meaning the third edition in Istanbul will be an even bigger and better showcase for the latest in fastener and fixing products and systems.
Taking place from 30th – 31st March 2016, exhibitors have now been assigned stands in a second hall at the IFM – Istanbul Expo Centre. This will be the first time that Fastener Fair Turkey has occupied two halls. Seven months ahead of opening, the show has already reached the size of the previous event in 2014. By August, more than 120 companies had confirmed their intention to take part in the show, which includes companies from China, Croatia, Denmark, France, Germany, the United Kingdom, India, Israel, Italy, Spain, Taiwan and Turkey.
Next year’s show will build on the success of Fastener Fair Turkey 2014, which was visited by approximately 1,700 managers, engineers and buyers. Half of those were either wholesalers or distributors. Fastener and fixing manufacturers accounted for a further 29%, while around 21% were end users. The majority of attendees were based in Turkey, but 25% were foreign, representing 47 countries.
Looking ahead to next year’s exhibition, Olivia Griscelli, exhibition director at organisers Mack Brooks Fuarcılık AŞ, commented: “The very positive response to our plans for Fastener Fair Turkey 2016 supports our strong commitment to this event. Turkey is an important market for the fastener and fixing industry. The high-level of international interest we are receiving also confirms Istanbul as the ideal exhibition location for companies targeting markets in the wider region beyond Turkey.”
Stand reservation for EuroBLECH – the 24th international sheet metal working technology exhibition taking place from 25th – 29 th October 2016 at the Exhibition Grounds in Hanover, Germany – has commenced.
EuroBLECH presents the entire sheet metal working technology chain including sheet metal, semi-finished and finished products, handling, separation, forming, flexible sheet metal working, joining, welding, tube/section processing, surface treatment, processing of hybrid structures, tools, machine elements, quality control, CAD/CAM/CIM systems, factory equipment and R&D.
The previous addition in 2014 saw 1,573 exhibitors from 38 countries on a net exhibition space of 86,500m2 and 59,618 trade visitors from 105 countries. “Similar to previous years, we are seeing a large number of returning exhibitors to EuroBLECH 2016. We recommend all companies interested in exhibiting to reserve their stand spaces as soon as possible, to ensure the company is placed within the relevant technology sector, as space may run out in particular halls,” says Nicola Hamann, managing director of the organisers – Mack Brooks Exhibitions.
“As the leading international trade exhibition for the sheet metal working industry, the upcoming show will be a platform for interlinked sheet metal working production. The ‘Internet of Things’, or ‘Industry 4.0’ as it is called when it refers to manufacturing production, poses big challenges for the sheet metal working industry and raises a multitude of questions. We are currently experiencing a revolutionary development in industry production and for manufacturers and suppliers of machines and systems, it is vital to be actively participating in this development. The exchange of expertise with users and the build-up of networks play a significant role for smart production, as the increased use of automation and software requires customised solutions that fit precisely into each individual networked fabrication plant,” explains Nicola.
An exhibitor brochure with detailed information about the exhibition and stand options is now available from the organisers and a revamped show website offers detailed information about the international event, such as an exhibition profile, facts and figures, details for stand bookings, an interactive floor plan, as well as video footage and photos from the previous event.
Nicola adds: “Manufacturers of machines, IT systems and tools for sheet metal working have to position themselves now, in order to rank first as a provider of expertise and innovation for this new era of industry production. EuroBLECH 2016 thus offers a unique opportunity to be involved in designing the future of sheet metal working.”
Show organisers of the 35th National Industrial Fastener & Mill Supply Expo, held from 21st October – 23 rd October at the Sands Expo Center in Las Vegas, USA, reported record exhibition space and a successful expo formula resulting in big crowds, busy booths, happy buyers and happy sellers.
National Industrial Fastener & Mill Supply Expo set a 35 year record for exhibit space, with approximately 7,701m2 occupied by 634 companies. Exhibiting companies came from the USA and from 19 other nations worldwide. There were also 110 new companies exhibiting this year.
“We had 2,040 fastener distributors, sales reps, and other buyers, specifiers and recommenders from all across America, plus 37 foreign countries, covering the globe, in attendance,” reported Susan Hurley, CEM, general manager. “Our exhibiting companies were pleased and the buyers were treated to a huge variety of the latest products and services.”
A full day conference programme kicked off the event, with many Expo visitors commenting favourably on the value of the educational meetings, programmes and workshops. This included presentations by the Fastener Training Institute, Manufacturers’ Agents National Association, National Fastener Industry Suppliers Financial Manager Network, Pacific-West Fastener Association, Women in the Fastener Industry and Young Fastener Professionals. The pre-show ‘Welcome Reception’ was a huge hit with everyone. “The meet and greet poolside at Treasure Island was the best one I’ve been to in 15 years. The weather was perfect, atmosphere was awesome, and the food was great,” commented Shawna Clark, president of Big Red Fasteners.
Looking ahead, Jim Bannister, general partner, predicts that the Expo will experience exponential future growth with the expansion of exhibit space beginning next year, as well as aggressive marketing to a broader audience of buyers, recommenders, and specifiers of industrial fasteners, fastener production machinery and tooling, inspection/testing/packaging equipment, hand and power tools, plant maintenance and safety supplies, software, and many other items of interest in today’s marketplace.
The 36th National Industrial Fastener & Mill Supply Expo will take place 25th – 27th October 2016 at the Sands Expo Center, Las Vegas.
Following extensive research, and after 21 years, the Totally DIY:Totally Tools show will move to a new two day format for 2016 – reflecting the shift in trading and buying patterns that are becoming increasingly evident in the UK home improvement market.
Totally DIY:Totally Tools will take place from 16th – 17th February 2016 at the Ricoh Arena, Coventry, UK. The show will also feature a packed seminar programme where leading industry figures and experts will present their ideas, giving visitors and exhibitors the opportunity to learn about future industry developments and stay up to date with the latest industry trends.
Backed by long-standing partners BHETA (British Home Enhancement Trade Association), which has greatly invested in up and coming innovators within the industry, the ‘New Product Showcase’ will once again be a central part of the exhibition –a place where visitors can see what the next generation of product designers are launching to the market and giving buyers the opportunity to source new and exciting offerings for their customers.
“Totally DIY:Totally Tools also enjoys support from the British Hardware Federation, the country’s top wholesalers, symbol marketing groups, and associations, all of whom will be part of the UK’s most important DIY trading event.”
www.totallydiy.com
The inaugural Torque-Expo event, held at Silverstone, UK, on 13 th – 14th October, demonstrated the vacuum left by the discontinuation of the UK Fastener Fair and the continued potential for a distributor-oriented event. It received a positive if not euphoric response from the majority of the 80 companies that exhibited at the two day event.
Despite headline intentions to represent nine industrial distribution product segments, Torque-Expo focused predominantly on the fastener and fixing sector, apparently failing to capture the commitment of major players in the UK tool, ironmongery, DIY security, PPE or general industrial consumable sectors.
Key exhibitors included Hexstone Group, with a dominant presence in the first hall; Fastbolt Ltd, Tite-Fix Ltd, Brighton Best International, Aptus Fastener Systems Ltd, Staytite Ltd, and TIMco.
bolts, and generated a lot of high-quality leads and enquiries. Overall we thoroughly enjoyed the show.”
Graham Joyce, managing director at Fastbolt Ltd, also reported a good show. “The main agenda for us was to promote our online facility FBonline. It offers so much more than online trading and provides huge administration savings and enhanced efficiency to our customer base – which we were keen to demonstrate to visitors. During the show we had a steady flow of customers with high-quality attendees. We met a couple of potential new customers but more importantly we saw a good number of existing customers in two days and it gave us the chance to get our message out in an efficient manner.”
Headline sponsor Hexstone Group presented all six of its businesses to visitors for the first time in the UK and committed a substantial budget to bring customers from across the British Isles into the event. An imposing and active stand dominated Hall 1, attracting and retaining a high proportion of visitor attention. Keith Harrison, chief executive of Hexstone, commented: “We were overwhelmed by the level of interest in our range. The event was a great success with the F1 simulator driving a lot of guests to our stand, enticed by the chance to drive a Ferrari around the world renowned Silverstone race track.”
Torque-Expo included industry seminars over the two days and an Innovation Zone for new products. On the first evening the Gala Dinner at Whittlebury Hall was a sell out giving attendees a great opportunity to relax and network, and proving a highlight of the event for many.
Whilst the majority of exhibitors reported a positive show –our editors heard more “it was ok” than “phenomenal” – there were consistent concerns over the level of visitor traffic and the poor flow between the two halls over both days of the show. Torque-Expo organiser, Jerry Ramsdale, refused to confirm exact visitor numbers, saying that they might be misinterpreted without meaningful comparison to other events but did tell us: “We’re happy with the quantity of visitors for the first event of its kind, and confident the numbers will build year by year.”
Jerry continued: “Overall we are thrilled by the reception the event received from exhibitors and visitors alike. Many exhibitors have already rebooked for next year’s event, where we plan to expand in many areas, particularly on the tools side. We’re grateful for the support of all this year’s exhibitors and visitors, and look forward to welcoming them again next year.”
Rebecca Fortescue, marketing manager at TIMco, commented: “It was great to have a fixing and fastener show back in the UK after so many years. We focused on our new C2 range of advanced screws, along with our Multi-Fix range of screws and
For Torque-Expo the main challenge appears to be to, at least, maintain the support of the fastener sector and radically increase the interest and commitment from the wider tools and industrial consumable supplier base.
There are literally hundreds of different screws but they are not all of the same quality. adverse conditions take their toll. a challenging climate, the huge forces experienced in buildings and special hygiene requirements – the products have to withstand all these extremes, and the selected material and quality must be just right. It’s a huge responsibility.
We are the specialist in high-quality fasteners made from stainless high-grade steel and special materials. We are used to extreme conditions and face the toughest challenges on a daily basis. We never lose sight of our aim to give the customer just what they want. and we always offer that little bit extra.
So, why not contact us?
Having just returned from Taiwan, Executive Editor Phil Matten assesses the prospects for next year’s Fastener Taiwan 2016 show at the modern Kaohsiung Exhibition Center.
In 2014 Fastener Taiwan was staged for the first time at the newly constructed Kaohsiung Exhibition Center in the southern Taiwan city’s harbour redevelopment area. The move transformed the event, providing sorely needed additional exhibition space and a massive improvement in the quality and attractiveness of the venue. 350 exhibiting companies, including this magazine, were there to welcome some 1,750 overseas buyers and more than 24,000 local visitors over the two day event.
The well designed and airy two halls, either side of a well provisioned central atrium, allowed Taiwanese fastener manufacturers – for the first time – to really demonstrate pride in their industry and its capabilities through the scale and presentation of their stands. Crucially the new exhibition centre in Kaohsiung meant the show could expand but continue to be located in the heart of Taiwan’s main fastener industry cluster. There are around 700 fastener companies within a half hour drive of the exhibition centre, and exhibitors took full advantage, inviting many buyers to their production facilities either side of the show days.
The co-location of the Five Region Fastener Association Conference brought high-level delegates from Japan, mainland China and Korea to mix with buyers from the USA, Europe and the rest of Asia.
In 2014 then, Fastener Taiwan came of age and justifiably joined the ranks of the most important fastener shows across the world. The key difference remains that this is a showcase for the Taiwanese industry, although 2016 will for the first time see a more significant content of non-Taiwanese exhibitors.
The 2016 show will once again be jointly organised by the Taiwan Bureau of Foreign Trade and Kaohsiung City Government, and delivered by the Taiwan Industrial Fastener Institute and the country’s export development agency, TAITRA. It will be longer, extending to three days at the request of exhibitors who wanted more time to engage with all the visitors. The next show will also be bigger, through more skilful use of the two halls it will accommodate 400 exhibitors occupying a net exhibition area of around 9,000m². All of that space is taken and TAITRA says it is already operating a waiting list. Exhibitors will again cover the full range of fastener and fixing products manufactured in
and better
Taiwan, together with wire rod product, fastener manufacturing equipment and tooling, inspection technologies and installation systems. TAITRA has released a key exhibitor list (see below), which underscores the calibre of participants.
ANCHOR FASTENERS INDUSTRIAL CO LTD
BOLTUN CORPORATION
CHINA STEEL CORPORATION
CHING CHAN OPTICAL TECHNOLOGY CO LTD
CHUN YU WORKS & CO LTD
CHUN ZU MACHINERY INDUSTRY CO LTD
FANG SHENG SCREW CO LTD
HOMN REEN ENTERPRISE CO LTD
HWA HSING SCREW INDUSTRY CO LTD
JAU YEOU INDUSTRY CO LTD
JERN YAO ENTERPRISES CO LTD
JINN HER ENTERPRISE CO LTD
JOHN CHEN SCREW IND CO LTD
LIH TA FASTENERS CO LTD
LU CHU SHIN YEE WORKS CO LTD
NATIONAL AEROSPACE FASTENERS CORP
PATTA INTERNATIONAL LIMITED
RAY FU ENTERPRISE CO LTD
RODEX FASTENERS CORP
SAN SHING FASTECH CORP
SHEH FUNG SCREWS CO LTD
SHEH KAI PRECISION CO LTD
SUMEEKO INDUSTRIES CO LTD
TAIKYU CO LTD
TAIWAN SELF-LOCKING FASTENERS IND CO LTD
TIAN CHERNG PACKING MACHINERY CORPORATION
TONG HWEI ENTERPRISE CO LTD
TYCOONS GROUP ENTERPRISE CO LTD
UNITECH PRODUCTS CORP
WEI CHIH STEEL INDUSTRIAL CO LTD
YESWIN MACHINERY CO LTD
YING MING INDUSTRY CO LTD
YOUR CHOICE FASTENERS & TOOLS CO LTD
ZYH YIN ENTERPRISE CO LTD
As before, Fastener Taiwan 2016 will arrange 1-to-1 procurement meetings between international buyers and Taiwanese producers. There will also be a Global Fastener Leader Summit and Gala Dinner, expected to attract around 800 international visitors and exhibitors, including representatives from the world’s fastener distribution and manufacturing associations.
TAITRA is emphatic about the role of the show. “Fastener Taiwan is the only international B2B fastener show in Taiwan. Serving as a trading platform for sourcing and procurement, Fastener Taiwan features a complete range of fastener products. It perfectly illustrates Taiwan’s status as ‘The Kingdom of Screws’ and provides an outstanding representation of the highly integrated supply chain of Taiwan’s fastener industry.”
The organisers also know they are building on a solid and improving track record. “98% of overseas buyers rated the 2014 show as ‘excellent’ and promised they would be back. 85% of exhibitors also vowed to return, a level of commitment that has already been thoroughly demonstrated.”
The world significance of Taiwan as an advanced fastener producer is no doubt. In 2014 Taiwan fasteners exports grew 10% to reach 1.55 million tonnes worth some US$4.3 billion –extraordinary for an island that actually has a smaller landmass than Denmark. Exports are critical to the fastener industry and indeed to Taiwan’s economy, accounting for 90% of total fastener production and explaining the extraordinary level of energy and professionalism being poured into the 2016 event.
Expect it to be a very busy but rewarding three days in Kaohsiung.
www.fastenertaiwan.com.tw
In October the Constuction Fixings Association (CFA) staged its 2015 conference at the National Motorcycle Museum, near Birmingham, UK. Phil Matten was among the fi fty delegates learning how the UK association is expanding on a number of important fronts. The packed agenda also provided briefi ngs on a wide range of technical topics.
In April the CFA full members – fischer fixings UK Ltd, Hilti (Gt. Britain) Ltd, Rawlplug Ltd and Spit Fixings – were joined by DeWalt, bringing ninety years of experience in manufacturing products for construction professionals. At the 2015 conference Mark Salmon, the CFA’s general manager, announced that EJOT UK would also become a full member of the CFA, quickly contributing to the extension of the product types for which it provides technical support to contractors, specifiers and suppliers.
Amongst its Associate Membership the CFA currently has twenty-six Approved Distributor members in the UK and some fifty Approved Testers, eleven of which are also distributor members. Criteria for membership of both categories are stringent, with clear expectations to live up to the CFA’s high standards in terms of customer service, technical support and commercial integrity.
supports using the best product possible at an economic price.” He concluded: “Experience is something we should all be very proud of and should use...”
The CFA also has three international members, attracted by the depth of expertise and guidance provided by the Association on its website to fulfil its commitment of ‘ensuring best fixings practice’. The value of the CFA online resource was reinforced by Mark Salmon’s report on website activity and particularly the substantial increase in hits on its Approved Distributor and Tester pages, as well as increasing downloads of its more than twenty Guidance Notes.
Delegates were told that the CFA was actively expanding the range of fixing products for which it provides guidance. New Guidance Notes are in the final stages of approval for powder actuated fasteners, gas nailing, and self-drilling screws. Mark Salmon said there is undoubtedly need for support for people using these product groups. He emphasised: “As with everything else the CFA supports, our objective is to give comprehensive technical support to these products.”
Reflecting a consistent commitment to ensure CFA training sessions are effective in instilling and requiring genuine levels of capability, Mark Salmon outlined a series of developments including changes to the CFA’s Competent Tester Scheme. These included new graduated tester qualifications, based on an evolution of the previous one day course, with additional opportunities to achieve advance testing status.
John Mallon, managing director at R J Fixings Ltd in Bathgate, near Edinburgh, epitomises the integrity of CFA Associate Members and made a characteristically direct presentation of the values he saw as being derived from CFA membership, both for the benefit of his own business and for that of his customers and the wider construction community. Reflecting on the continued use of what he called ‘rascal’ products in the fixings sector, he saw no place for the supply of products that did not carry ETAs. “R J Fixings,” he emphasised, “firmly believes and firmly
“ Amongst its Associate Membership the CFA currently has twenty-six Approved Distributor members in the UK and some fifty Approved Testers…”
Also at the conference, the team from Hydrajaws Ltd demonstrated the latest development of its Bluetooth digital testing system. Linked wirelessly to Hydrajaws’ widely renowned hydraulic tester this latest version of digital technology captures test results using a mobile phone or tablet device, providing immediate visual reports for on-site tests of anchors, eyebolts
and lifelines. The latest version now interfaces with both Android™ and Apple® operating systems, effectively making it a universal application and delivers important benefits in terms of productivity, accountability and safety.
Other presentations included Dr Tom Gunston, testing laboratory manager at VJ Technology, who impressed by proving it was possible to transform the distinctly dry topic of on-site dust control into an interesting and informative presentation.
Imad Mobayed, technical marketing manager – North Europe at Hilti GB, analysed the implications of a recent survey carried out by New Civil Engineer magazine regarding how engineers regard resin anchors. He noted the highly representative sample achieved in the research and results that highlighted a significant lack of confidence in the installation of chemical fixings. This, he said, demonstrated that the CFA still had a lot of work to do to promote BS 8539:2012, the UK code of practice for the selection and installation of post-installed anchors in concrete and masonry.
The day concluded with a series of further presentations focusing on new product developments from CFA full members. www.fixingscfa.co.uk
More often than not, fastener and fixing products are overlooked, from the design stages of a project through to the build itself. Given that they are the mechanisms that literally hold everything together, not enough emphasis is placed upon them.
We see this regularly at JCP, especially with anchoring products. Take, for example, the number of anchoring product variations in our portfolio alone – approximately 85 different product types –ranging from chemical anchors, throughbolts, drop-in anchors, heavy-duty anchors, and sleeve anchors, as well as others types of anchors. Each suits a different requirement and each can be tailored to meet a certain specification, dependent on the application, through our Anchor Calculation Programme.
Complex calculations are often required for fixings in the construction industry so we tend to find that engineers are over specifying as a precaution. However, when addressed correctly, with the required level of technical support, companies may find that cost savings can be achieved by selecting a more appropriate anchor. This needs to be addressed with caution but at JCP we believe we have the correct tools for the job.
Essentially, the properties of a base material are fundamental in the specification of anchor products. If the wrong anchors are specified for cracked concrete then the results could be catastrophic. However, where the concrete is not cracked, a saving can be made by using an anchor that has been tested for use in non-cracked concrete.
Another common assumption across the sector is that all products of a similar type perform in the same way. A key example here would be throughbolts that are typically used for fixing steel to concrete – not all of them perform the same. The engineer initially needs to look at the loads they will support in order to know which version they should be applying. We see many situations where we are asked to provide an alternative anchor product to one that has already been specified, to then see that it has previously been over specified for a stronger and more expensive option. Also we sometimes find we can be competing with a product that does not have the required technical support and is sold on price alone, which is potentially a dangerous practice and could result in failure of the connection.
So what classifies as non-cracked and cracked concrete? The BBA Guidance Note No. 39 is an industry document that is often overlooked. It states that ‘non-cracked concrete is concrete where the probability is acceptably low, that either cracks will form after installation of anchors or the width of any existing cracks will increase significantly during the life of the anchors.’1 It also gives
guidance on when cracked and non-cracked concrete may occur. One of the other main challenges that we face in the industry is comprehending changes in the Construction Product Regulations (CPR). We believe it is important that we communicate these with our customers to reassure them that the products they are specifying are absolutely right for the job. It is for this reason that I participate in the European Consortium of Anchor Products (ECAP), which provides a continent-wide platform for understanding the changes in regulations. We meet with other European manufacturers to discuss issues affecting the industry, which benefits our customers because we are always able to provide them with up to date accurate information.
Anchoring products quite regularly come under scrutiny with regards to European standards and assessments and, while a standard is compulsory and assessment only optional, our products will always adhere to assessment level regardless.
Part of the challenge for this industry is that a lot of it comes down to graduates coming out of university that have not been clearly versed in the important role of fixings. For example, I come across many structural engineering graduates who are highly proficient in the use of concrete and steel but not with fixings – they are just seen as an essential and reliable item that always does the job. However, there is so much more to the story.
For engineers, specifiers and architects who are unsure on the anchors that need to be specified on a particular project, there are a number of tools available, such as the JCP Anchor Calculation Programme (ACP). It simplifies specifying connections to surfaces such as floors, ceilings and walls, and takes into account loadings, spacings and edged distances. When configuring a solution for the project, it considers the thickness of the concrete, the temperature of the concrete for bonded anchors and whether the holes are dry or flooded. Other factors may be where lever arms are applied, and the facility to calculate resin loads with deeper embedments. This is one of the best calculation tools on the market, and we don’t charge a penny for it. We simply wish to offer the industry a fair and accurate tool that allows users to get the most out of their projects.
There is a huge advantage in using a credible supplier who can provide advice and guidance on which products are suitable for different applications, for both new builds and refurbishment projects. Not only will they be able to supply products with all of the necessary accreditations and proof, they will be well versed in all of the requirements of the new regulations.
1 www.bbacerts.co.uk/download/document-types/guidance/Anchor%20Bolts%20for%20use%20in%20Concrete%20-%20UK%20Guidance.pdf
Brian Deluce’s role as technical manager at JCP is to gain an understanding of European Technical Assessments and how they are applied to the construction industry and JCP’s products. Brian boasts 40 years’ experience in the industry and is a well known figure throughout. His roots as a toolmaker and electrician in the Royal Navy equipped him with all the necessary skills to combat technical issues and ultimately develop effective solutions.
HEXSTONE is the UK’s largest wholesale supplier of fasteners, fixings, hardware, ironmongery, and associate items to the engineering and merchant trade. The six faces of Hexstone combine to provide a total one stop solution for distributors.
hexstone.co.uk
pgb-Polska z.o.o – the Polish production plant of pgb-Europe NV – is able to supply a selection of high performance fi xing systems, providing solutions for every part of the construction industry.
In addition to its heavy-duty anchor and chemical anchor ranges, the company is also able to supply a wide variety of light-duty fixings, including:
This versatile plug with four expansion zones has optimal results in all building materials such as expansion in solid materials and knot-forming in hollow substrates. The collar prevents the plug from slipping into the drill hole. Suitable for wood and chipboard screws, the plug is available in all popular diameters.
This cost-effective standard wall plug is available in a full range, from diameter 4mm up to 16mm. This plug is available with or without collar and has a very good tensile strength in concrete and solid bricks. It is suitable for wood and chipboard screws.
Using push through installation, pgb’s universal frame anchor has an ETA and is easy to install. It is suitable for medium loads in many substrates such as concrete, solid brick and perforated bricks, and cellular concrete. The SMART frame anchors are also certified (ETA – 10/0392) for use in categories a, b, c and d. The full assortment on offer includes total fixing lengths ranging from 80mm to 230mm. The enclosed screw is available with countersunk head PZ3, T40, hexagonal head SW13, or hexagonal head SW13 with pressed-on washer and T40. The special screw is available in zinc plated carbon steel and stainless steel A4 for outdoor applications.
This strong plug is available from 5mm up to 14mm and comes with a small collar (type BP). The longer versions without collar (type LP) and with collar (type LBP) are available in 6mm to 10mm versions. pgb-Polska has received an ETA approval (ETA – 10/0392) for multifunctional plugs in combination with screws. The ETA covers diameters 8mm and 10mm for the long version, combined with different wood screws and hex lag screws.
pgb points out that the unique design of this hammer-in fixing combines appearance with efficiency. There are different collar types – countersunk, flat collar and mushroom collar. The nail plugs are preassembled, ready to install for hammer-in type through fixings. The nails are available in zinc plated steel and stainless steel A2 and have a POZIDRIV® recess for adjusting or removing the fixing.
SM0BP:
pgb’s drywall anchor type PCA is a plastic cavity anchor, which is the ideal solution for drywall fixings as the plug can be used in single and double boards.
Also available is pgb’s drywall anchor type GKP. The self-drilling gypsum board anchor is available in both nylon and steel. The anchor is easy to install as it requires no special tools.
These new screws have a countersunk head and T30 drive, ideal for use in aerated concrete blocks and other porous materials such as light expanded clay aggregate blocks.
Fast and easy to fix, this self-tapping screw with coarse thread assures a solid connection without pre-drilling or plugs, directly into the base material. The screws have a special zinc flake coating for high corrosion resistance.
www.pgb-europe.com
- Standard fasteners - DIN - EN - ISO
- Special parts
- Professional wood screws - CE/EN 14592
pgb-Europe has over 25.000 SKU of fasteners, fixings and tools in stock. With focus on high product quality and optimal product presentation we are one of the leading suppliers of fasteners in the Benelux.
Modern warehousing, uniform packaging, flexible order processing and many years of experience are just a few of our assets that makes this 100% family-owned company a trustful partner.
- Complete anchor program
- Calculation software
Tecfi SpA recently launched its new ZZE-Handyplug®, a HDPE multipurpose anchor for ETICS, which has achieved an ETA for a wide spread of base materials (a, b, c, d and e).
ZZE-Handyplug® provides many benefits to the user including simple and quick hammer set installation, anchorage without thermal bridge, reduced embedment depth, wide range in terms of thicknesses of fixture, and stiffness of the nail during the installation thanks to its ribbed neck and its thick head.
In addition to the ZZE-Handyplug, Tecfi’s research and development department has been studying seismic topics. As a result, in April this year, the company achieved the C2 Performance Category for the installation in high seismic hazard zones of its HXE-Concreto® concrete screws.
The C2 Performance Category is now available on diameter 16mm and Tecfi says will soon be extended to diameters 10mm and 12mm. It comes in addition to two other ranges of anchors that received the C2 Performance Category in 2014 – AJE wedge anchors and SWE dual component epoxy resin.
Tecfi points out its HVE-Rock® heavy-duty anchor currently has C1 Performance Category, and will soon have C2.
2015 also saw Tecfi open its new 7,000m² production facility, which has enabled the company to enhance its production capacity and invest in new high performing machinery to complement its already well equipped facility.
www.tecfi.it
HECO-Schrauben GmbH & Co KG has supplemented its range with the HECO-UFIX® MDF – a versatile MDF screw for use in cabinet making and interior fi nishing. Specially designed for MDF applications, the screw is also available with a newly developed drive: The HECO-Drive, with stick-fi t effect.
Due to the drilling point with its special shape, the HECO-UFIX® MDF screw has all the properties required for working with MDF such as predrilling effect and pinpoint accurate insertion, reduced splitting, and low driving torque. HECO explains the screw has user-friendly details including accurate-fit H-Drive with stick-fit effect, small countersunk head with milling grooves, serrated thread, cutting ribs on the point, and a spade like drilling point.
MDF is a popular material in furniture making and interior finishing on account of its homogenity and dimensional stability. It is easy to work with and has a wide variety of applications. However, because of the stability and high material density, the surface can bulge and the material is prone to splitting when screws are inserted. For this reason, the material is generally predrilled, to allow screws to be inserted quickly, and without force and splitting. The new HECO-UFIX MDF screw obviates this step.
The part threaded screw has a spade-like drilling point permitting easy central positioning. Cutting ribs below the point on the threaded part, and the specific geometry of the point, create a predrilling effect, which removes lots of drilling dust of the material during the insertion. This enables working close to the edge – including at the end faces of the board – without the material bulging or splitting.
These properties are an advantage when working on glossy finishes with a special coating or foil-coated components. In addition, the serrated HECO-plus thread saws one turn into the cylindrical hole, creating a simple, non-positive connection and reducing the driving torque, for effortless, fatigue-free installation.
The small countersunk head of the HECO-UFIX MDF screw has optimum cutting properties and allows a neat, flush finish between screw and material surface. At the same time, damage and cracks in the surface of the board are prevented. Exact positioning and assembling of fittings with the HECO-UFIX MDF screw is achieved due to the configuration of the screw head and the milling grooves letting the HECO-UFIX MDF screw fit neatly and perfect.
A special feature of the HECO-UFIX MDF screw is its newly developed system between bit and drive: The HECO-Drive (HD 20). Perfectly coordinated to the inner profile of the drive, the bit sits securely in the head of the screw and the optimum grip prevents the screw from falling out or wobbling. This makes it easier for the user to drive, and means the user can screw in with one hand with little effort. The new HECO-Drive takes the conventional T-Drive and enhances it with the stick-fit effect.
The HECO-UFIX MDF screw can still be driven in with standard bits for T-Drives, but this combination will not offer the convenient stick-fit effect for simple assembly.
“The HECO-UFIX MDF screw is available in the dimensions 3.5mm/4mm/4.5mm x 40mm/45mm/50mm/60mm in blue zinc-plated steel and is highly versatile. Its galvanised finish is suitable for applications in bathroom furniture making, shop fitting and in luxury interior design.”
www.heco-schrauben.com
HECO-UFIX ® MDF screw –The unrivalled screw for MDF and HDF
The new HECO-UFIX ® MDF screw with HECO-Drive: quality combined!
Possible to work close to the edge and axis
Screw connections possible at the end faces without predrilling
HECO-Schrauben GmbH & Co.KG
Exact, non-slip positioning on the surface of the material
Perfectly coordinated HECO-Drive and drive with stick-fit effect
Dr.-Kurt-Steim-Straße 28, D-78713 Schramberg
Tel.: +49 (0)7422 / 989-0, Fax: +49 (0)7422 / 989-200
E-Mail: info@heco-schrauben.de, Internet: www.heco-schrauben.com
FRÖWIS AG, based in Schaanwald, Liechtenstein, recently received a European Technical Assessment (ETA – 15/0305) for its Gecko U8 – a screw-in anchor combining an 8mm x 100mm dowel with a specially designed spiral.
FRÖWIS says that screwing the spiral into an insulation board and fixing it with the dowel makes the thickness of the insulation board irrelevant. Only one dowel length is necessary to cover the whole range of insulation thicknesses from 120mm up to 460mm. Gecko U8 is, therefore, a storage space saver and gives users the advantage of always having the right dowel on-site. The specially designed spiral is optimised to cut cleanly into the insulation and guarantees a strong hold of the insulation board on the façade.
The Gecko U8 is suitable for both new building and refurbishment projects and works with EPS, PUR and phenolic resin insulation boards. FRÖWIS says it is the first countersinking solution that requires no special tools.
FRÖWIS specialises in external thermal insulation composite systems (ETICS). “We cultivate lasting partnerships with suppliers of insulation systems, with whom we provide tailor-made, perfectly suited ETICS solutions. We enjoy a challenge and our love for technical innovation encourages the further development of our fastening systems.”
•
•
•
Multiple fixing solution for non-load-bearing systems in cracked and non-cracked concrete; metal sections; wire suspensions; wooden structures; ceiling cladding; square timbers; suspended ceilings; railing systems; wooden slats; ventilation and cable ducts
Following an agreement with the European Organisation of Technical Assessments, here is a list of recent ETAs published in the last two months on the EOTA website.
It is important to note that existing ETAs may be amended or withdrawn so this list should not be considered definitive.
Since 1st July 2013, as a result of the Construction Products Regulation, new ETAs are known as European Technical Assessments. European Technical Approvals published before 1st July 2013 will act as the new assessment until their expiry date. For further information and a full list of valid ETAs visit EOTA’s website:
www.eota.eu
ETAG 001 Metal Anchors for use in Concrete (all parts)
ETA – 14/0215Sympafix TB1- PLUS
ETA – 15/0055TOGE concrete screw TSM L 6
ETA – 15/0060UIP Injection System ubond PO-II
ETA – 15/0075Inoxmare IM93-72, IM9372-A4, IM9372-HCR
ETA – 15/0091Würth Concrete Screw W-BS Compact
ETA – 15/0122SM0IA, SMIAD, SMIAL and SMIAI
ETA – 15/0123Speer injection system Vinyl-Pro for rebar connection
ETA – 15/0124Speer injection system for Vinyl-Pro for concrete
ETA – 15/0130Injection system Chemfix 500 for concrete
ETA – 15/0157740 LANKOCELFIX bonded anchor
ETA – 15/0162Novatech Injection system Anchor 7 for concrete
ETA – 15/0163Novatech Injection system Novatio Q-Fix for concrete
ETA – 15/0164Knauf Ceiling anchor
ETA – 15/0165DX FAST ETA 7
ETA – 15/0166Ter Laare Drop-in Anchor IX FAST ETA 7 / IX-K FAST ETA 7
ETA – 15/0167Ter Laare Wedge Anchor DX FAST ETA 1 and DX-I FAST ETA 1
ETA – 15/0185weber.anc 405 BFX
ETA – 15/0226CHEMFIX 1-1
ETA – 15/0247 Injection system TCM385RE, TCM585RE, TCM1000RE,TCM1400RE for rebar connection
ETA – 15/0255 Chemfix PURE EPOXY bonded anchor for post-installed rebar connections
Sympafix B.V
TOGE Dübel GmbH & Co KG
UIP Gmbh & Co KG
Inox Mare Srl
Adolf Würth GmbH & Co KG
PGB – Polska sp. z o.o
Speer Fixings B.V
Chemfix Products Ltd
PAREXGROUP
Novatech NV
KNAUF Gesellschaft m.b.H
Ter Laare Verankeringstechnieken BV
Sodamco Holding SAL
Chemfix Products Ltd
TRUTEK Fasteners Polska Sp z o.o
Chemfix Products Ltd
ETA – 15/0256DESA-Chem VSF DESA
ETA – 15/0270Sikla Injection system VMU plus for Concrete
ETA – 15/0273Injection system Desa-Chem PEX 3:1 for rebar connection
ETA – 15/0275Injection system Desa-Chem PEX 3:1 for concrete
ETA – 15/0282Chemical Injection System EJOT Multifix VSF
ETA – 15/0288Injection System TCM Fix – Winter and Standard
ETA – 15/0313Vesta PRO-ONE
ETA – 15/0314Stud Anchor BOAX-FMC
ETA – 15/0323Q-MULTIFIX B15, Q-MULTIFIX B15 W and Q-MULTIFIX B15 T
ETA – 15/0324 Injection system Q-MULTIFIX B15, Q-MULTIFIX B15 W and Q-MULTIFIX B15 T for rebar connections
ETA – 15/0346Injection System Chemická kotva Polyester
ETA – 15/0361Apolo MEA Quick fix anchor BA and BA A4
ETA – 15/0394Q Wedge Anchor BZ Plus and BZ-IG
ETA – 15/0409 Mungo MIT-VE, MIT-VE PLUS, MIT-VE Tropical MIT-VE PLUS Tropical galvanized or stainless steel bonded anchor
ETA – 15/0454Desa-Chem VSF bonded anchor for rebar connections
ETA – 15/0479M-Power Kit steel bonded anchor
ETA – 15/0518AF.E 600
ETA – 15/0532Mägert 2KTec RED 500 for concrete (diamond drilling)
ETA – 15/0537Lindapter High Slip Resistance Clamps – Type AF and Type AAF
ETA – 15/0538Lindapter Floor Fixings – Grate-fast, Floorfast, GF3030, Type 1055
ETA – 15/0561MasterFlow 932 AN steel bonded anchor
ETA – 15/0562MasterFlow 932 AN for rebar connection
ETA – 15/0584Förch Injection System FIT-Z-MB 7
ETA – 15/0585J-Fix Polyester Styrene Free
ETA – 15/0586Förch Injection System FIT-Z-MB 7
ETA – 99/0011Würth Fixanchor W-FAZ and W-FAZ-IG
ETAG 014 Plastics Anchors for ETICS
ETA – 15/0214JANSA PTP SR 8/60-La
ETA – 15/0305Fröwis Schraubdübel Gecko U8
ETA – 15/0463TOP KRAFT PSK
ETA – 15/0464HTH
ETAG 020 Plastic Anchors (all parts)
N/A N/A
Sikla Holding GmbH
Desarrollos Especiales de Sistemas de Anclaje S.A
EJOT Baubefestigungen GmbH
Bouilding Fasteners Division
Tfix Polska Sp. z.o.o.
Fikstek Baglanti Teknolojileri San Ve Tic Ltd
SIMPSON STRONG-TIE
Qube Solutions Group S.à.r.l.
Den Braven Czech and Slovak AS
Apolo MEA Befestigungssysteme GmbH
Q-railing Europe GmbH & Co KG
MUNGO Befestigungstechnik AG
Desarrollos Especiales de Sistemas de Anclaje S.A
Pehu Tooling BV
AS SISTEM d.o.o
Mägert G&C Bautechnik AG
Lindapter
BASF Construction Solutions GmbH
Theo Förch GmbH & Co KG
Hexstone Ltd. JCP Construction Products
Theo Förch GmbH & Co KG
Adolf Würth GmbH & Co KG
Ing. Ján Skovajsa JANSA
Froewis AG
Top Kraft Handels GmbH
Hilti WDVS-Dübel HTH
N/A
Tillex says that its Stella plugs provide a quick and easy solution for fi xing heavy objects in plasterboards, chipboards, fi breboards and other boards used in cavity walls.
Tillex has been manufacturing in Denmark since 1954, and from the outset its aim has been to deliver the best products at the best price without compromising on quality.
Stella plugs can be used to fix shelves, radiators, cupboards, light fittings, lamps, and duct mouldings, in all types of boards used in cavity walls. Inside the tip of the Tillex Stella plug is a metal nut. When the screw engages the nut, the plug is contracted to form a star shaped knot behind the cavity. With a high load capacity, Stella plugs are easily fixed – with no special tools needed. The plugs are equally effective for insulated cavities and will not damage the plasterboard.
Available in red, 10mm x 49mm, and black, 10mm x 59mm, versions Tillex Stella plugs are made of nylon (PA6) halogen-free and can withstand temperatures from –40ºC to +80ºC. The screws are 4.8 steel and zinc-plated to a minimum 5 microns. Stella plugs are protected by EU Design N 778.345.
Made in Denmark since 1954.
Tillex is now searching for dealers & distributors.
For fixing of heavy objects in plasterboards, chipboards, fibre boards and other boards used in cavity walls.
High load capacity.
Easy fixing – needs NO special tools. Equally effective for insulated cavities. Will not damage the plasterboard.
Inside the tip of the Tillex Stella plug is a metal nut.
When the screw engages the nut, the plug is contracted to form a star-shaped knot behind the board inside the cavity.
Materials: Tillex Stella plugs are made of nylon (PA6) Halogen-free and withstand temperatures from –40 ºC to +80ºC. The screws are 4.8 steel, zinc-plated min. 5 my.
Double expanding. Quick and easy fixing. Universal.
Plugs expanding in both directions, which making it unique compaired to competing products on the market.
Plastmaterial: Polyethylen (HDPE) Halogen-free
Fastener + Fixing Magazine provides a unique reference guide that offers the industry a fast and easy way to source both current and upcoming product Catalogues. Use this convenient service to call, fax or email the companies to request a copy of their latest Catalogue and up to date product information.
email: info@achill-fasteners.com www.achill-fasteners.com
We’re the specialists for high-tensile 8.8, 10.9 and 12.9 bolts and screws. Socket- or hexagon-head bolts and screws, be they small, short, long, thin or simply “really big” – special formats and sizes are available alongside the standard bolts and screws in our classic-group We’re also able to provide a concept for supplying standard fasteners, developing special components and producing prototypes for customers in the field of industry. Literally a brilliant connection.
Apolo MEA Befestigungssysteme
Albert Pasvahl offers you its experience and expertise in special connection elements and accessories resulting from over 80 years in business. In the course of this time, we have become a leading stockist of special standard screws.
For example: Direct from stock
DIN 609/610/7968, ISO 7379
DIN 906/907/908/909/910/5586 B/7604 A/C
DIN 920/921/923; DIN 464/653/466/467
Tel: +49 40 532 852 0 www.pasvahl.de
DIN 561/564; DIN 478/479/480
DIN 912/931/933/7985
email: info @apolofixing.com www.apolofixing.com
GmbH offers technical know-how, innovative developments and design competence as a producer of fixing systems. Our state of the art products guarantee a maximum of application safety for your projects. Our customers benefit from an extensive assortment of light duty fixings, heavy duty fixings and chemical fastening systems as well as screws, electrical and sanitary fixings – One stop shop for quality.
BAER is your contact for all thread inserts, taps and dies and custom-made items. You benefi t from the huge product range and the fl exibility in production. BaerCoil ® and BaerFix ® thread inserts create and reinforce internal threads in metal and plastics. Highest precision and quality standards help to provide solutions for future construction possibilities.
email: info @baecker.eu www.baecker.eu
email: info @baercoil.com www.baercoil.com
Fax: +49 27 5359 5650 www.bum.de
For more than 35 years, BÄCKER has stood for solutions in plastics at the highest level. The comprehensive standard range of the plastics specialist comprises more than 5,000 different articles: PlacoGrip® control elements, including clamping levers, indexing bolts and star grips; PlacoTec® –standard elements such as screws, nuts and washers; PlacoCap® –protective elements such as cover caps and protective caps and PlacoEngineering project solutions to customers specifications.
30–31.03.2016
We are one of the leading manufacturers and exporters of connecting fi ttings for several industry branches. Our large warehouses located in Germany enable us to supply customers around the world with large quantities of various articles fl exibly and at short notice.
Ask for our free catalogue now.
email: bulte @ bulte.com www.bulte.com
BÜLTE is an ISO accredited supplier of plastic fasteners and protection products, with more than 25,000 articles.
In addition to a full standard range in natural NYLON (PA), BÜLTE also provides products in non standard materials – POM, PP, PVDF, PE…
Free on request our new leafl et which presents new products such as bushings, spacers, nuts, self locking grub screws…”
We are one of the leading European stockists of all types of industrial fasteners. 60,000 pallet locations of stock, along with over 900 employees make Dresselhaus your perfect partner for sourcing standard and specialised parts.
Tel: +49 52 21 9 32 0
www.dresselhaus.de
email: mks @ doerken.de www.doerken-mks.com
Dörken has been developing micro layer corrosion protection systems for 30 years and is European market leader for zinc flake systems free of chrome(VI). Under the brand name DELTA-MKS ®, Dörken produces and confi gures extremely effective surface protection mainly for fastening elements used in the automotive and wind industry. Our worldwide approved products like DELTA-PROTEKT ®, DELTA-eLACK ® and DELTA-PROZINC ® are specifi ed at many global OEMs.
We are a successful wholesaler of connecting parts with years of experience in supplying the industry and dealers throughout Europe.
email: info @ ernstreinhardt.de www.ernst-reinhardt.com
email: info @ e-u-r-o-tec.de www.e-u-r-o-tec.de
Tel: +49 751 407 0 www.schrauben-engel.de
The Ernst Reinhardt GmbH, established in 1937, is known for building exceptional industrial furnaces, in many different variations. More than 25 years ago, we added coating systems into our product portfolio. Since then we have been successful in constructing and manufacturing coating systems for bulk materials in many different variations. Customized solutions can be offered as well, we have solutions especially for small batch sizes. “Quality made in Germany” – this is what we stand for! Short delivery times along with a good price-performance ratio are a given.
E.u.r.o.Tec – The specialist for fastening technology – offers professional fasteners made of hardened steel, coated steel, stainless steel A2/A4, hardened stainless steel for timber constructions, real wood and composite deckings, glue wood, roofing, cladding, carpenter/framers accessories – all in german quality. All approved and with certified quality. The main goal is to create fasteners offering the professional end user the most possible benefits. For detailed information of the most recent developments, please refer to the EuroTec homepage.
1 03.11.15 10:10
email: info @ fastbolt.com www.fastbolt.com
Our high rack warehouse in Weingarten (Germany), which houses more than 8,000 pallets, accommodates everything our customers need for their day-to-day business.
Fastbolt is a leading wholesaler of industrial fasteners to European distributors only. Apart from a highly specialised product range ex stock Fastbolt offers individual supply solutions such as customised packing, direct container imports, pre-import quality inspections and a revolutionary online availability check and ordering system: FBonline.
Fastener 2000 GmbH is a stockist for long and large diameter screws, for example: DIN 912 – 931 – 933.
Offer screws from M 1,4 to M 64 and up to a length of 600mm direct from stock.
New on stock: ISO 14580 – 14581 – 14583
Tel: +49 (0) 4106 622 80 email: info @ fastener2000gmbh.de
Lederer is one of Europe’s most specialised suppliers for stainless steel fasteners. It has more than 20,000 different articles in stock, primarily normed and standardized parts (ref. DIN, ISO and others).
Industrial consumers, as well as retailers and wholesalers, all over the world rely on Lederer’s more than 40 years of experience.
Tel: +49 (0) 6105 9620 email: info @ gesipa.com
GESIPA ® Blindniettechnik GmbH operates on an international level. This means short delivery routes to all our customers around the world ensuring availability and service for all GESIPA ® products. With its innovative overall system comprising fastener, setting tool and setting technique, GESIPA ® offers one-source complete solutions for trade and industry.
New look Series 20 Lee Spring catalogue featuring almost 20,000 product types, including High Pressure Springs, Metric Bantam™ Mini-Compression Springs and the latest in Heavy Duty Die Springs.
To order visit leespring.com or call: DE: +49 (0) 2353 669933-0
UK: +44 (0) 118 978 1899
Fax: +49 2333 8309 18
www.lederer-online.com
Lindapter’s new German catalogue reveals the latest steelwork connections, which provide faster alternatives to drilling or welding, ultimately saving time and money for contractors. The catalogue also introduces new approvals including CE markings for Type A and Type B clamps and a full ICC-ES seismic approval for Hollo-Bolt.
Tel: +49 (0) 2353 669933-0 www.leespring.com
Tel: +49 0201 94668860
www.lindapter.de
OTTO ROTH is an innovative trading company for mechanical connecting elements and certifi ed manufacturer of turned and fi ne-machined parts with more then 100,000 products. We offer you rapid delivery from one source with individual logistics possibilities as well as comprehensive e-Business solutions, e.g. e-Shop with its opportunities for rapid data entry and online check of the current availability of products. Ask for our free catalogue now! Tel:
Nögel Montagetechnik is Europe's leading supplier in window (PVC, wood, Aluminium) and facade construction fasteners. Since 1981 we have provided the highest quality window screws, window self drilling screws, concrete screws, glazing blocks and bridges from our own production, plus much more. For more information contact us via our website, phone or email. email: info @ noegel.de www.noegel.de
Over 40 years experience in trading and supplying customers with inch sized fastening items.
• Inch sized screws available from stock.
• Availability of every current type of screw threads and materials.
• Special parts available as well.
• Large availability from stock of high quality as per ISO9001-2000 don’t hesitate to talk to us –we will be pleased to help you.
email: contact @ reyher.de www.reyher.de
REYHER is one of Europe‘s leading distributors of fastener and fixing technology supplying customers worldwide. High quality consciousness and strong technical competence characterizes us. With over 130,000 different items, REYHER offers a broad and deep range of products covering all needs. The webshop RIO – REYHER Internet Order ensures 24/7 ordering possibility.
Your specialist in stainless steel fasteners. An independent & reliable partner. We carry a stock of over 30,000 different products from the DIN/ISO standard parts sector that are available to you immediately. Our logistic partners guarantee shortest lead times worldwide. We combine quality and service. Take advantage of our excellent business connections.
Tel: +49 7941 6094-0
email: info @ schaefer-peters.com
Tel: +49 (0) 341 442 4610
www.sup-scs.de
We support European construction product enterprises in the development, implementation and sustained successful operation of individual and innovative design and calculation software. Products include: computer software and services, fully integrated software solutions, and internet solutions.
SPAX International stands for innovative and high-quality screws made in Germany. We offer an extensive product range for timber construction, interior fi xtures, furniture making and outdoor use, as well as for window construction and installation. We also produce tailor-made solutions and custom parts to meet customer requirements.
email: info @ spax.com www.spax.com
KG
Tel: +49 2359 7011
www.voehrs.de
One of the leading international manufacturers of nuts and stamping. Whether made out ordinary steel, high-grade steel, bright or standard fi nish surfaces –we offer the perfect solution for all your requirements. Our progressive and fl exible production allows us to manufacture to your exact specifi cation so you get the product you need – with no compromises!
email: info @ wasi.de www.wasi.de
WASI Product Catalogue NORM With about 26,000 listed products Wagener & Simon WASI GmbH & Co KG is a global player in the trading of stainless steel fasteners. On www.wasi.de you will fi nd further information about packaging, logistics and services, which simplify procurement management. The product catalogue WASI Norm shows the entire product range of standardized products.
For more than 10 years GEFRA GmbH has been able to offer a real 360° surround inspection using four cameras to inspect the surface of round parts to fi nd coating defects, head cracks and external thread damage.
One of the big advantages of the GEFRA system is that the parts run continuously with a speed of up to 600 parts per minute. This system can be used on a glass dial machine with standing parts, as well on the slot dial machine with parts hanging in the disc.
Since 1995, GEFRA has developed and manufactured optical inspection systems for fasteners, and other bulk products, for a variety of industries.
GEFRA states that its OPTISORT® systems ensure an efficient 100% automatic quality control where a cost-efficient and zero ppm error quote is needed. Complex geometric measurements, thread control, inspections for damages such as scratches, dents, points of impact, cracks, errors in colour and surface coatings, and more, can be realised.
GEFRA points out that over 280 of its systems are on the sites of many famous national and international fastener manufacturers and sorting companies.
OPTISORT the innovative optical inspection system for fasteners
OPTISORT the innovative optical inspection system for fasteners
· fast and reliable
· fast and reliable
· easy and safe handling
· easy and safe handling
· 360° inspection
· 360° inspection
· 5 min. set up
· 5 min. set up
· for stamping parts, nuts, screws, rivets, ...
· for stamping parts, nuts, screws, rivets, ...
fasteners
Speak with the experts at GEFRA if you value quality and safety.
Speak with the experts at GEFRA if you value quality and safety.
www.gefragmbh.de
info@gefragmbh.de
www.gefragmbh.de
info@gefragmbh.de
Our eyes for your success!
Over recent years the demands for thread inspection have become much more important for GEFRA’s wide variety of customers – including manufacturers of automotive and aircraft fasteners. That’s the reason why most of GEFRA’s inspection systems have the additional four cameras inside.
The 360° inspection system is very flexible and can be used for head cracks from the side, thread inspection on different length and also for bended parts. The position in the height of the cameras can be moved depending on the areas that are to be inspected.
The approved Windows®-based system software AUTOCONTROL, made by GEFRA, does the image processing and generates the IO/NIO decision with the help of an individual quality control
plane, which includes all important parameters of the part. While the program is running, it is possible to save the pictures of the checked threads. If the user wants to see the damages, they can recall the images from the computer storage. With these pictures the operator can compare the checked parts with the calibration part. The picture of the calibration part can be called up whilst the operator is adjusting, so the operator can make a direct comparison.
GEFRA’s product portfolio is complemented by a wide spectrum of accessories for packaging, service, maintenance and training. The GEFRA team guarantees a high availability of spare parts, and a short reaction time to enquiries.
“At GEFRA we are a reliable partner for all-in-one quality applications in the field of fastener manufacturing.”
www.gefragmbh.de
San Shing Fastech Corp has added new features to its SBM-35L First Article Inspection System, which was especially designed for fast inspection of bolt products during the manufacturing process – enabling quality control to be implemented on each manufacturing process.
The SBM-35L First Article Inspection System not only replaces the traditional measurement devices such as optical projectors, surface profiler, as well as hand measurement tools such as micrometer and internal gauges, it also integrates a database so that multiple measurement results can be stored for complete process capability analysis and failure tracking.
The SBM-35L manages to eliminate the erroneous measurement cause by negligence of operator, and new features further enhance the machine’s capabilities.
A long-awaited feature that is now available is geometric measurement, which had
previously always been a concern for fastener manufacturers. Now SBM-35L is able to inspect roundness, straightness, perpendicularity, eccentricity, concentricity, and parallelism. San Shing points out that these geometric features, together with previous measurable items, elevate the machine capability to a higher level.
Another new characteristic is the application of front light illumination in manual measurement. San Shing explains that whilst backlight illumination is undoubtedly the first choice for measuring, there are still blind spots that can be found during inspection, even with a rotation function. Therefore, San Shing has incorporated a front light illumination to SBM-35L. With the fine-tuned accuracy of ± 0.01mm, this alternative lighting produces a silhouette to measure various diameters, radius, and angles, which cannot be profiled from the backlight illumination.
www.sanshing.com.tw
SKAKO Vibration has introduced a new compact weighing and fi lling system to fi ll different kind of boxes, as well as plastic or steel returnable boxes (KLTs), which it says is especially designed for short and medium sized production.
SKAKO Vibration’s new machine offers quick changeover time, a compact design, and easy operation. In addition, it is easy to turn round, which has become more important for the fastener and automotive industry to ensure that there is no cross contamination of products before they reach the customer.
For many years SKAKO has manufactured vibrating equipment for the hardware industry, which has shown a significant growth especially in feeding, weighing and dosing equipment for heat treatment lines. Due to this, and with the experience of its employees, it was only a small step for SKAKO to develop a semi-automatic system for the packaging industry – where a lot of components can be used and have a similar function.
SKAKO’s system consists of a vibrating storage feeder, a vibrating feeder, a chute system with accumulation possibility, and a table with integrated load cells and integrated sample/check weigh platform. It can be configured in different sizes and can be supplied together with a lift and tip unit.
“We are proud to present the new system on the market. However, it is certainly not our intention to focus on further development for other packaging machines. SKAKO is mainly a producer of vibration equipment and a component supplier. Our customers are predominately OEM and end users. Within our OEM customers, however, there are also producers of packaging equipment with who we have a good cooperating and a long-term business relation.”
There is no second chance to achieve a good fi rst impression – which is why STRUBL GmbH & Co KG is convinced famous companies choose its Plug&Pack systems.
STRUBL has over 150 machines installed all over Europe, including in Würth, Dresselhaus, Electrolux, ITW, and fischer operations. As a result STRUBL has extensive experience and competence in realising customers’ requirements.
Customers can design their bags according to their individual requirements. Decoline bags have a special reinforced header with eurohole for a premium designed hanging presentation. Functionline bags are made for cost-efficient service packing and with Zipline bags customers receive resealable bags for more customer convience.
The STRUBL Plug&Pack technology can handle a bag size range from 50mm × 50mm up to 400mm × 800mm, with different materials or mono-composite films.
“With more than 60 years of experience in film and bag production we are a reliable, competent, and flexible partner for customers.”
We develop individual and flexible solutions for our customers.
We maintain a large inventory of over 2,000 different tools, ready for same day shipping. We provide fast turnaround on special made-to-order tools.
For calibrating wire from 2,0 to 35,0 m, in-line with cold headers and machines for chains.
For coil-to-coil wire drawing of cold heading wire from 5,0 to 32,0 mm. Our lines are supplied complete with uncoilers, wire pointers, take-up units, coil compactors.
With 25 years’ experience servicing industrial accounts, Schwer + Kopka GmbH has established itself as a leading provider of process monitoring and data acquisition systems for the metal forming industry.
Ahighly qualified team of 45 employees ensure that the solutions developed in the Swabian town of Weingarten, Germany, always represent the latest technology. Process monitors ‘observe’ a manufacturing process through a variety of sensors such as force, pressure, or strain, then ‘learn’ the correct sensor signal profile for a machine cycle, and check if each following sensor signal is identical or nearly identical to the ‘benchmark’ profile. Even small deviations from the learned profile, such as tool breakages, will be detected to ensure product quality. The machine will be stopped immediately to avoid the production of bad parts while also protecting the machine and the tooling against overloads.
Many users of the SK process monitoring systems are also networking the monitors to collect vital production data such
as up time, down time, number of parts produced, reasons for being down, and analysing their performance by means of the Schwer + Kopka SK-go!® system.
“Customers from around the world trust Schwer + Kopka when it comes to effective machine monitoring solutions, innovative sensor designs, and shop floor data collection solutions for entire factories.”
All of Schwer + Kopka’s products originate from its own R&D department, which enables it to react quickly and flexibly to special customer requests as well as to the general demands of the market. In addition, highly motivated and experienced service technicians stationed at four locations in Germany and in offices around the world provide superior technical support for the clients in multiple metal forming industries.
OSG USA Inc has announced the release of its latest thread milling NC code generator software – ThreadPro – which it says makes generating code for complex machining easier and eliminates the hassle of data entry.
OSG serves the fastener industry by offering a complete line of thread rolling, flat, cylindrical, planetary and trim dies. The company explains that the features of the ThreadPro software include simplifying the configuration of multiple paths, which was not adjustable before, to enable the easy creation of zero cut programs. In addition to multiple feed (machining at each cutting edge length) single feed (one pitch per cut) is
also available, which is ideal for machining high hardness materials. Last but not least, with the capability to review machining trajectory, trouble free tool movement can be confirmed to minimise tool damage.
The new ThreadPro is available in twelve different languages and supports eight NC programming languages. The software incorporates ‘RPRG’ value to reduce set-up, machining time and achieve stable tool life.
Brooks Forgings Ltd is always looking for new developments in technology that can help achieve and surpass the strict quality standards it requires, which is why the company has added a MARPOSS Merlin™ gauge computer to its QC department.
Brooks Forgings’ latest addition is primarily designed for the shop floor environment. The Merlin™ gauge computer is used for measuring applications and gathering statistical information.
The Merlin allows effective collection of data from up to 32 traditional or wireless measuring devices. This includes statistical process control that allows multiple measurements, data segregation and product batch tracking, all displayed in real time with on screen numeric and graphical layouts. Electronic bore and snap gauges are currently used in Brooks Forgings’ machining processes, allowing immediate and accurate inspection of machined internal and external diameters.
Prior to any measuring procedure, batch codes are allocated to maintain full batch traceability and a calibration routine is performed using fully traceable calibrated setting masters, ensuring accurate data is recorded. For ease of use by the operator, measurement values are recorded and displayed in a colour coded format, both graphically and numerically on the Merlin’s LCD screen. This allows the operator to adjust settings in the manufacturing process to prevent the manufacture of non-conforming parts and aid continual improvement of the overall process.
CAN-ENG Furnaces International has recently received four contracts for the design, manufacturing and commissioning of its 6,000lb/hour continuous mesh belt atmosphere furnace systems.
CAN-ENG focuses on the development of high volume continuous industrial furnaces for challenging applications and is the industry leader in the development of automated heat treatment systems for processing of fasteners. The company points out that its systems lead the industry in uptime reliability, energy efficiency and soft handling features – delivering superior part cosmetics. The four contracts are for systems that are designed to provide atmosphere hardening and tempering of high volume fasteners and include a computerised loading system, mesh belt controlled atmosphere hardening furnace, oil quench system, pre and post wash systems, and enhanced part tracking. The systems are also designed with an integrated state of the art
combustion system, which includes newly developed burner technology and provides significant benefits over conventional burner technology. They are also fitted with a modern radiant tube heating system that provides improved system efficiencies and reduced emissions.
“CAN-ENG’s continuous mesh belt heat treatment systems are recognised worldwide and have proven to meet and exceed the stringent demands of the global automotive industry through successful individual automaker audits and AIAG CQI – 9 assessments. The integration of CAN-ENG’s Level 2 automation systems, track product status and collect detailed process data that is used for continuous process improvement, equipment diagnostics, processing costs analysis and inventory management.”
The Nakashimada MST Series part formers elevate your production to a whole new level. Six forging stations, maximum cutoff length of 110mm, maximum kickout of 100mm, soft landing blank delivery, arc-action transfer and a standard NCS-III automated control system. Advanced features engineered to take your cold part forming in any direction
New & Improved transfer system
Increased speed, reliability and extreme precision.
NAKASHIMADA RONDERSON MACHINERY LIMITED
SHENZHEN, CHINA
Phone: +86 (0) 755-822-11008
Fax: +86 (0) 755-612-37382
Mobile: +86 1355-477-0032
Email: new@ronderson.com
Weighpack International (WPI Services B.V), a specialist in fastener inspection and packaging equipment, recently supplied a box handling system for short runs to OBO Bettermann in Switzerland.
Dutch-based Weighpack International points out that its flexible box handling system is able to erect, fill and close boxes from 50mm x 50mm x 40mm up to 200mm x 150mm x 150mm. Changeover from one size to another can be done quickly, with the capacity of the box handling system 12 – 15 boxes per minute. The machine can also be used for efficient short runs of 50 to 100 boxes.
The flat box system includes a magazine, which is available in different lengths and able to store up to 500 boxes. It also features a vibratory table in the box closing area that ensures the correct density in the box is achieved before the lid is closed. Labelling with barcoding can also be easily added on the filled box accumulation conveyor.
The box handling system can be connected to inspection machines, product counters or product weighing machines. www.weighpackinternational.com
Expansion
1. Glass Dial design, applicable for micro fasteners (M1.0~ M3), automotive and aerospace fasteners (M3~M12), and machining / turning parts.
2. Sorting Speed: 100~900 PPM (depended on size of parts)
3. Optical: Eddy current system for material mixup or heattreatment or not.
4. Optical: Prism system to inspect thread damage of bolts and screws.
5. Optical: External/internal 360 damage, feature or surface defects.
゜lens to inspect thread
360° external & internal inspection
6. Customized machine for bigger objects is also available.
100% inspection and quality control sorting of fasteners is a demand that is becoming more common in the market – requiring a company that is able to support customers with the latest technology.
Dimac Srl, with over 25 years’ experience, has established itself as a reliable partner to fastener manufacturers. Using its ability to establish a deep and mutual trust with its customers, Dimac says it is able to provide 100% inspection and quality control sorting of fasteners.
Dimac’s machines can inspect a wide variety of parts with microscopic thread defects – including bent parts such as brake booster bolts. The machines can also detect heads with very fine side cracks, as well as parts with heat treatment problems.
Another factor that is having an impact on inspection demands is the leaning of major car manufacturers to switch to lightweight materials. Dimac points out that with fasteners being made from new and different materials, it creates new and different defects that need to be detected using the latest technology.
Dimac uses advanced technology in its machines and can offer a complete range of equipment, which includes 3D 360° dimensional controls, eddy current inspection and sorting, as well as 100% traceability, according to the most important standards.
Networking features on Dimac’s machines also enable customers to monitor the machines all over the world, in real time, keeping the customers up to date with the sorting department situation.
Dimac is keen to point out that it has extensive knowledge of the entire manufacturing process of its machines, including all the hardware and software solutions, which enable it to provide high-quality inspection and sorting equipment, combined with packing lines – ensuring the 100% traceability of parts.
“With over 500 machines running 24 hours every day, 7 days a week – as well as a prompt, helpful service – we are a reliable partner that can help customers achieve ‘zero defects’.”
www.dimacsrl.com
Here Paul Black, CEO at sales-i, a global supplier of sales performance software, discusses how customer data – when analysed and presented correctly – can provide sales teams with actionable insights and greater visibility into their customers’ buying habits, enabling them to stay one step ahead of the competition.
Business and technology often have an uneasy relationship. Many fastener companies remain resistant to change even when all evidence indicates that it will only benefit them. In fact, a report from the Fortune Knowledge Group recently found that 62% of C-level managers ‘trust their gut’ as much – sometimes more – than real, measurable factors like data.
This is why big data is seen as a particularly intimidating subject – the larger the pool of information, the easier it is to become overwhelmed by the number of correlations and statistics. But if treated with proper care and the right tools, big data can redefine your business. You can base decisions on cold, hard statistics, not on your gut – helping to drive profits and cut inefficiencies.
So you’ve got customer data, what next? If you’ve ever poured through spreadsheet after spreadsheet in search of trends, you’ll know how great (and rare) those ‘Eureka’ moments are. But a single flash of insight can be enough to give you that edge, helping you to outflank the competition and boost your bottom line.
Well, what if you could automate the process of trendspotting? What if you could feed all your customer databases, sales records, and customer service call sheets into a neat A4 printout of trend analyses? That’s what big data enables. And the analytical tools that underpin tech
giants such as Google and Facebook are now being shrink-wrapped for us ordinary mortals under the friendly header ‘sales intelligence’. It’s a time saver and will give your sales team all the information they need to make a sale at the click of a button, which means no more spreadsheets.
At a ‘macro’ level, sales intelligence can make everyone on your sales team seem more switched-on and improve every aspect of your marketing function. It will identify wider trends such as seasonal changes in purchasing; shifts in popularity across your product ranges; and what’s hot and what’s not. This is the
kind of awareness that translates directly into increased sales. If, for example, you notice an uptick in screws and washers over the summer months, then why not offer a discount on bolts when purchased together or in bulk? But it can be even more effective at the ‘micro’ level.
Sales intelligence makes every salesperson look good. With full analyses of purchase histories just a click or two away, your sales team will know exactly when to pick up the phone to a customer. Better still, they’ll be able to anticipate their needs, helping you build stronger relationships and retain those all important customers. The technology has the potential to make every call and email a source of valuable data.
For example, if an executive wants to impress a potential or current customer before a meeting, they can – with the help of predictive analytics – access all of their critical information from a mobile phone. With modern technology, every customer can feel like your most important customer.
The biggest and most important advantage big data provides is efficiency –a prized quality in the fastener industry. ‘Best practice’ isn’t just a buzzword – with sales intelligence, you can hone your processes to their absolute peak and keep up with fast changing times. Sales intelligence software supplies real time updates and insights, enabling you to make large or small-scale changes as necessary.
…if treated with proper care and the right tools, big data can redefine your business.”
aPriori says its new product release featuring expanding regional data libraries provides customers with an estimated cost of purchased parts from around the globe – helping to improve product profitability.
As a provider of enterprise product cost management (EPCM) software solutions, aPriori says the newest version of its regional data libraries feature a significantly expanded portfolio of regional data including machine capabilities, material properties, and regional labour. It also includes overhead and material rate data for regions spanning the globe.
aPriori then researches, consolidates, and maintains these data libraries to provide a benchmark, reducing a manufacturer’s burden to collect the data on their own. When combined with aPriori
manufacturing process cost models and information about a company’s manufacturing practices and buying power, its EPCM solutions can be used to reasonably and reliably estimate product costs in specific regions.
The benchmark data included in the new regional data libraries enables customers to understand component cost drivers and use the benchmark estimates to help drive product profitability on current product cost reduction and new product introduction programmes. This includes global purchasing, sourcing, and cost reduction activities. Users will also
A space saving solution for the fast retrieval of inventory tools, developed by Kardex Remstar and its industry partner INTERTEX-Maschinenbau Ingeborg Deiss GmbH & Co KG, has recently been utilised by German manufacturer of components for the furniture industry – Paul Henke GmbH.
Paul Henke GmbH needed an efficient solution for its ever growing inventory of tools, which were previously stored on static shelving and resulted in employees travelling long distances to fetch the right tool from the warehouse during production changeover times. Paul Henke needed a storage system that could be installed on a small footprint whilst also allowing tools to be retrieved quickly.
The solution comprised of three INTERTEX TowerMat storage lifts, each 23.8m high, integrated into one storage tower on a footprint measuring just 55m², with a total capacity of 915 metric tonnes between them. Around 3,000 tools used in injection moulding are stored in these units. A centrally operated stacker crane in the TowerMat fetches the heavy parts from their storage space and automatically conveys them to the bottom in line with the goods-to-person principle. The tools are retrieved from there with the help of a crane and transported to the injection moulding production area.
Headquartered in Zurich, Switzerland, Kardex Remstar – part of the Kardex Group – supplies automated storage and retrieval solutions worldwide.
“With our tailor-made solutions, you can considerably reduce your company’s storage space. We have successfully installed more than 140,000 systems worldwide in sectors such as retail, warehouse and distribution since 1873.”
be able to evaluate a wider range of global sourcing alternatives and identify if they are overpaying for outsourced parts.
“Achieving a better understanding of cost drivers during both the early stages of product design, and when negotiating with suppliers, is a critical requirement across a variety of industry verticals. It has a direct impact on product profitability, and many of the world’s leading manufacturers are beginning to understand that EPCM solutions can help them address these types of challenges,” says Julie Driscoll, vice-president of strategic marketing and product management at aPriori.
FASTENERS, FIXING, HYDRAULICS
FOUNDED IN 1994
STOCK INVENTORY OVER 40 000 ITEMS EXPERIENCED STAFF
www.mekrs.com
Nuts and bolts are used everywhere. A bolting failure at home is usually only a minor nuisance. However, a similar failure at a nuclear power plant could be catastrophic, which is why bolt failure analysis of damaged bolted joints is so vital.
There are many reasons why bolting failures happen. In fact, they are often caused by a combination of factors. According to Laurent Dastas, a bolting analysis expert at Alstom Transport, there are four main root causes that can explain bolt failure:
1. The tightening operation was forgotten.
2. The tightening tool was not accurate enough regarding tightening tolerances.
3. An error in the fastener’s steel class.
4. A failure in the tightening sequence.
In technical terms, there are two main types of bolting failure: Static failures and fatigue – also called dynamic – failures. “The use of electronic keys, for the simultaneous recording of couples and angle values during the tightening operation, allows securing on every assembly according to these four parameters,” says Laurent Dastas.
Static failures are generally easy to identify. For instance, they occur during overloading, after overtightening of the assembly, through an accident of external loads, or due to a ‘non-conforming product’.
Superbolt® tensioners are used for their preload accuracy and because they allow the introduction of a high-level of preload with a small torque.
One customer tested a multi-jackbolt from another manufacturer in a structure. After some time, a failure of the structure occurred and the customer asked Nord-Lock to investigate.
“We used the 3D microscope to analyse the failure. We understood that the main cause of the failure was fatigue, and that preload had accelerated it,” says Zouhair Chaib.
The observed matting at the end of the jackbolts suggested that the preload was correctly introduced, but when the ‘course of jackbolts’ distance between the end of the jackbolt and the nut body was examined, there was a large difference in all the multi-jackbolts. One jackbolt had zero course. This was due to a self-loosening of the jackbolt.
“We also checked the capacity of the copy tensioner against the self-loosening, concluding that this factor was not considered by the copy tensioner. When we compared the copy with our tensioner, they both had the same thread diameter, the same material, and the same outside diameter, but some particularities of the multi-jackbolts were not respected,” explains Zouhair Chaib.
The tensioner had a good static capacity, but there was still the issue of self-loosening that caused the fatigue failure.
Fatigue failure is often more complex, because the fatigue develops during the service cycle. There can be cracks in the material, such as in the fasteners, the threads of the bolt, or any component of the assembly. These cracks will increase and propagate on the normal section (stress section) of the screw before the total failure of the assembly. “Crack related damage is the most dangerous failure in a bolted assembly,” says Zouhair Chaib, senior technical expert at Nord-Lock.
In fatigue failures, the assembly can be correctly tightened at first. However, after external loading, the bolted joint starts to lose the force of the preloads due, for instance, to relaxation or self-loosening.
“When the loss of preload starts, it is not so easy to stop. When losing preload, both the alternated stress and the sliding between parts increase. When the sliding is repeated, more and more preload is lost,” explains Zouhair Chaib.
The alternated stress also continues to grow, eventually resulting in a fatigue crack. Under the external and cyclic loads, the fatigue crack will propagate. After some propagation of the screw, and when there is enough capacity against the fatigue load, total failure occurs. A fatigue crack can be initiated by corrosion or an impurity in the screw material, by cutting quality of threads or by an accidental load (impact).
When multiple screws are involved, the failure of one screw can overload other screws nearby. Overloading will then create a chain reaction of failures that happens very quickly, and it does not have to occur many times before the screws start to propagate.
“In terms of fatigue failures, one never knows when the fatigue, the cracks, and the total failure of the assembly will appear. Generally, the fatigue failure appears suddenly and comes as a most unwelcome surprise,” says Zouhair Chaib.
One way of finding out why a failure occurred is by using the Ishikawa (fishbone) diagram. This method is often used by the Nord-Lock Technical Center when helping its customers.
“ In technical terms, there are two main types of bolting failure: Static failures and fatigue –also called dynamic – failures.”
“Once there is a failure, before replacing the existing assembly and changing parts, the customer needs to secure the environment. Pictures of all parts need to be taken and all parts must be marked with a number. It is also important not to touch the failure surfaces, contact surfaces or threads. We also need a description of the accident and the failure conditions to quickly identify the problem,” points out Zouhair Chaib.
The customer also needs to protect all the parts against corrosion during transportation to the Technical Center for analysis – this is to avoid any erroneous assumption that crack failures were due to corrosion, when they were not.
“By doing all this, the customer helps us to analyse the situation quickly and accurately, which enables us to give a prompt answer and solution. After doing this, changing the assembly is no longer critical. The customer can change any endangered parts to continue production, for example,” explains Zouhair Chaib.
Customers often have constraints and need to restart production as soon as possible. For this reason, it is very important to check and verify the assembly during transit. In the meantime, the customer and the expert analysts can work together to find the best and most accurate solution to replace the existing assembly.
At the Nord-Lock Technical Center, all components are checked and photos are taken of all damaged parts. In some cases, a 3D microscope is used to compare and control some factors. External partner laboratories can also be asked to perform additional analyses. Finally, the results are analysed and the overall picture is defined.
“In our laboratory we can carry out vibration, torque and preload tests. We can also test the manner of the screw for instance – to be completely sure that the proposed solution will work correctly and safely. At the Technical Center we analyse several situations, identify the cause and propose a technical solution to the problem. We always take into account many other aspects, such as economical, practical and operational factors,” says Zouhair Chaib.
www.nord-lock.com
The customer had lost half of its assembly, but there was no visible damage to the threads.
“We asked the customer for additional information about the estimated load, and about the condition of the assembly. The customer said it was subjected to shock load, but no fatigue load. When we looked into the structure’s external profile, there was minor plastic deformation at the end of the threads. We also observed axial traces along the threads, and a non-constant outside diameter,” explains Zouhair Chaib.
The analysts identified a potential failure scenario – the outside diameter and the material properties were not resistant enough to support the hoop stress introduced by the thread angle and axial load. Under a full load part one expanded (radial elongation) and, due to the fine pitch, part two slipped and separated from part one.
“To validate this scenario we performed a FEM (finite element method) calculation and compared the measured diameter to the FEM diameter (after axial loading) and the thread form given by FEM and reality,” explains Zouhair Chaib.
FEM results were so similar to reality that this scenario was accepted and a practical solution was proposed:
• Increase the outside diameter of the threaded part.
• Use coarse pitch.
• Use a stiff material (high Young’s modulus).
• Optimised form of part one.
The customer used a standard bolted joint solution, while having a damaged assembly. The customer replaced the assembly with new bolts, nuts, flat washers and spacers, took pictures and sent in the damaged parts.
The customer also sent CAD, to provide information about the situation and the external load. The customer had used spacers to increase the clamp length, and believed that this would resolve the problem. After restarting the machine, the same failure occurred.
“After analysing the customer’s assembly, we understood that there was a fatigue failure. The assembly was highly preloaded. High preload is not dangerous and is a good solution generally. We had to look for another reason for the failure and investigate further. We concluded that, in this situation, there was a high shear loading – a transversal loading. The customer needed to use the same clamp length as before, but increase the preload level by increasing the torque and the grade of the screw to be able to use a securing solution. For transversal load, the
best solution was to increase the preload and maintain it using securing solutions,” says Zouhair Chaib.
“We suggested the customer used a Nord-Lock washer to protect its assembly against self-loosening. With our solution the customer required a few modifications to its assembly –two Nord-Lock washers with a high-grade bolt (10.9) and a suitable torque,” explains Zouhair Chaib.
During the inspection axial traces were observed along the threads, as well as a non-constant outside diameter
RotaBolt ® measurement fasteners have recently been fitted by BSP International Foundations Ltd to the largest hydraulic piling hammer that it manufactures. The hammer, which has a 40 tonne drop weight, has been operating on a site in Venezuela for the past year and has been trouble free.
BSP manufactures a range of hydraulic piling hammers from 1 tonne drop weight up to 40 tonnes. The CGL 590kNm hammers are 14m high and can accommodate a 2m diameter pile. The complete assembly weighs 84 tonnes and has two main sleeve flanges, which are now fitted with M24 and M36 RotaBolt® fasteners to assure overall integrity.
The RotaBolts have been used to connect the main flanged segments of the pile sleeve. “The hammers are subject to continuous high vibration and shock loads throughout their life,” commented Matthew Liddle, chief engineer at BSP. “We had tried all sorts of locking methods to prevent bolt loosening, but RotaBolts have helped to give us product integrity and have also made inspection and maintenance in the field much easier.”
Once the RotaBolts have been installed to the correct design tension, the RotaCaps on the top of each RotaBolt lock. Throughout the hammer’s operational life the RotaCaps can then be instantly finger checked to ensure that they are still maintaining the correct tension across the joint. If any tension should be lost, the RotaCap rotates freely and this can be quickly and easily detected.
90% of the hammers that BSP manufactures are exported for
use in a wide range of environments and climates. The use of RotaBolts is helping the company to ensure the hammers are not only assembled correctly, but they are also operated as efficiently as possible. BSP has subsequently fitted RotaBolts on another two smaller 20 tonne hammers and is now making RotaBolt fasteners standard fit.
RotaBolt technology is also being used to assure bolted joint integrity across a wide range of heavy engineering applications where vibration, fatigue and structural slippage can be problematic. The fasteners are being used on longwall mining shearers, large crane grab jaws, stacker reclaimers, military bridging systems, as well as on pedestal and tower cranes.
Dörken MKS-Systeme GmbH & Co KG has reported that it enjoyed great success on the press and trade visitor days of the recent IAA exhibition, in Hanover, Germany, which is the leading international trade fair for mobility, transportation and logistics.
Covering 230,000m² of exhibition space, IAA attracted around 931,000 visitors, 1,103 exhibitors and 219 world premieres, breaking all previous records. The Dörken stand attracted numerous interest from visitors, keen to find out more about Dörken’s theme of KTL 2.0.
Cathodic dip coatings (KTL) are the most frequently used surface protection systems in motor vehicle construction. With its Delta-eLack® KTL technology, Dörken MKS-Systeme presented
two new facets of this proven technology. In combination with the zinc flake technology the result is high performance cathodic protection, enabling corrosion durability of over 1,500 hours in the salt spray tests as per DIN EN ISO 9227 with a layer thickness of 10 + 10. The second aspect regarding KTL 2.0 was KTL coating in the bulk goods process – from small screws to more complex components. This involves the Delta-eLack system in combination with a specially developed engineering process, which enables coating in the drum with a throughput of up to two tonnes or 1,400 litres per hour.
One particular draw for Dörken at the IAA was the KTL unit, shown in action on the stand. There was much discussion regarding the comparison of different surfaces on a tracking rod, subjected to a 720 hour salt spray test (pictured left) after stone impact.
For over 30 years Dörken has produced micro layer corrosion protection systems in Herdecke, Germany, and is now the European market leader in chrome(VI)-free zinc lamella systems. Under the DELTA-MKS® brand name the company produces and configures extremely high performance surface protection, for use in the automotive and wind energy industries in particular. The globally specified products are free from heavy metals.
Berdan Civata was founded In 1980s in Tarsus/Turkey today has been manufacturing all types of 10.9 and 12.9 class of hydrogen embrittlement risks eliminated hot dip galvanized high strength bolts, nuts, studs and similar fasteners according to national and international standards.
Berdan Civata also has got one of the richest testing laboratory among fastener manufacturers in Turkey . This laboratory which is the first one among its sector in Turkey has been accredited according to the ISO 17025 and it has recently been audited for getting the authority marking of another international 11 0 11 quality certificate according to the standard DaSt-021 High Tensile Heavy Hexagonal Structure Bolts for Wind Power Generation
Being one of the most experienced CE certified fastening components manufacturer at Mersin Tarsus Organized Industrial Zone within 3 separated premises placed 33,000 m2 with its 220 employees, Berdan is serving to Refineries, petrochemical Flants, Machinery Construction & Steel Buildings, Structural Steel Industry Pressure Vesse I& Boiler and Valve Manufacturers as well as to the Wind Energy and other renewable energy sectors in land and abroad mostly 8.8,10.9 and 12.9 class of high quality products accordance with TSE ASTM,DIN/ISO and BS norms and deliver them to the customers with ISO EN 10204 3.1 Test Certificates.
The certificates which have been awarded to Berdan Ovata for the first time in fasteners sector in Turkey like CE Certificate for EN 14399-1 pre load products and EN 115048 non preload products, first accreditation according to ISO 17025 for the most equipped test laboratory in Turkey, as well as the patent for the trade mark of its eco friendly hot dip galvanizing process and similar certificates enable Berdan to receive strategical and big busines.
TFC Europe Ltd has announced that it has achieved AS9100C and AS9120 certifications for the aerospace industry.
Based on ISO 9001, BS EN9100 (AS9100C) includes additional aerospace specific requirements and provides the industry with a standardised set of requirements to help improve quality throughout the supply chain and reduce cost through continual improvement.
TFC states that quality runs through its entire business, not just its products, which is why it has continually invested in the right people to provide superior market knowledge and customer service.
TFC’s comprehensive product range means that the company is not restricted to specific ranges of parts in either standards or specials. All its products can be supported with either ISO, AS or individual OEM approvals with lot traceability certification as required. Its standard product range includes wave springs, Spirolox®, retaining rings, laminar sealing rings, circlips, O-rings, hose clamps, washers, rivets, sheet metal fasteners and stud bolts.
“As a result of these improvements to our business, we are looking forward to enhanced partnerships with our much valued existing customers and to forging links with new clients throughout the aerospace industry.”
NORMA Group has received a major order from a German car manufacturer to equip several million vehicles worldwide by the year 2027.
Beginning in 2017, the contract includes NORMAQUICK PS3 quick connectors and NORMAPLAST SV hose and pipe connectors in the nominal sizes 6mm – 32mm, which will be used in vehicle cooling systems.
NORMAQUICK PS3 quick connectors, made of recyclable materials, connect heating and cooling lines and charge-air systems. The compact design of the connector enables it to be used even where mounting conditions are tight and enables quick installation. Thanks to the integrated mounting bracket, PS3 quick connectors can be installed and removed without the use of tools. Assembly can also take place during fully automated processes. An integrated gasket ensures the proper tightness.
NORMAPLAST SV hose and pipe connectors connect plastic pipes such as PA6 and PA12 pipes. They are made of black polyamide 6 or polyamide 12 with 30% glass fibres and can be supplied with O-rings.
“We look forward to working with our customer on this large-scale global project,” says Werner Deggim, CEO of NORMA Group. “For us, this is also about our responsibility for a cleaner environment. After all, our weight-reduced products help lower emissions by reducing the total weight of vehicles and, in turn, reducing fuel consumption.”
www.normagroup.com
Bormann & Neupert GmbH & Co KG states that its Smart Band is a robust alternative to stainless steel fasteners and is ideal for demanding applications and extreme ambient conditions, such as in mining or onshore/offshore wind turbines.
The long-term maintenance free straps and clips of the Smart Band system bundle cables and pipelines or hold sensors and signs securely. The straps are available in various widths up to 32mm and can be cut to any length. Standard models can handle loads up to 440kg and even permanently withstand temperatures of up to 125°C, as well as highly corrosive conditions.
Bormann & Neupert points out that the Smart Band enables easy installation
even under difficult conditions, such as underwater use, and its flat patented closures enable quick and easy mounting. For faster and simplified installation, Bormann & Neupert also offers manual and pneumatic hand tools, which ensure a defined clamping force of up to 918kg. For even more demanding requirements, Bormann & Neupert provides the Smart Band Hybrid variant. These withstand extreme tensile loads up to 2,551kg and temperatures of up to 250°C. Depending on the version, the manufacturer
guarantees a service life of over 25 years.
“A special solution within the Smart Band system is the Smart Protector. It was originally developed for the protection of cables and hoses for deep ocean laying, but is also suitable for all other challenging environments,” says Andreas Kaulen, product manager at Bormann & Neupert.
The Smart Protector is compatible with all Smart Band variants and suitable for almost every cable diameter and for bundling several cables.
Invented in 1948 by SPIROL the coiled spring pin was specifi cally designed to address defi ciencies associated with conventional methods of fastening such as threaded fasteners, rivets and other types of pins subject to lateral forces.
Easily recognised by its unique 2¼ coil cross section, coiled pins are retained by radial tension when installed into the host component, and they are the only pins with uniform strength and flexibility after insertion.
Truly an ‘engineered fastener’, the coiled pin is available in three ‘duties’ to enable the designer to choose the optimum combination of strength, flexibility and diameter to suit different host materials and application requirements. The coiled pin distributes static and dynamic loads equally throughout its cross section without a specific point of stress concentration. Furthermore, its flexibility and shear strength are unaffected by the direction of the applied load, and therefore, the pin does not require orientation in the hole during assembly to maximise performance.
In dynamic assemblies, impact loading and wear often lead to failure. Coiled pins are designed to remain flexible after installation and are an active component within the assembly. The coiled pin’s ability to dampen shock/ impact loads and vibration prevents hole damage and ultimately prolongs the useful life of an assembly.
The coiled pin was designed with assembly in mind. Compared to other pins, their square ends, concentric chamfers and lower insertion forces make them ideal for automated assembly systems.
The features of the coiled spring pin make it the industry standard for applications where product quality and total manufacturing cost are critical considerations.
Flexibility, strength, and diameter must be in the proper relationship to each other and to the host material to maximise the unique features of the coiled pin. A pin too stiff for the applied load would not flex, causing damage to the hole. A pin too flexible would be subject to premature fatigue. Essentially, balanced strength and flexibility must be combined with a large enough pin diameter to withstand the applied loads without damaging the hole. That is why coiled pins are designed in three duties –to provide a variety of combinations of strength, flexibility and diameter to suit different host materials and applications.
It is important to start with the load to which the pin will be subjected. Then evaluate the material of the host to determine the duty of the coiled pin. The pin diameter to transmit this load in the proper duty can then be determined from the shear strength tables published in the product catalogue taking into consideration these further guidelines:
• Wherever space permits, use standard duty pins. These pins have the optimum combination of strength and flexibility for use in nonferrous and mild steel components. They are also recommended in hardened components because of their greater shock absorbing qualities.
• Heavy-duty pins should be used in hardened materials where space or design limitations rule out a larger diameter standard duty pin.
• Light-duty pins are recommended for soft, brittle or thin materials and where holes are close to an edge. In situations not subjected to significant loads, light-duty pins are often used because of easy installation resulting from lower insertion force.
Although this article offers general design guidelines, it is recommended that application engineers, who specialise in fastening and joining, be consulted to ensure the optimum coiled pin is specified for each application.
PREBENA Wilfried Bornemann GmbH & Co KG has launched a new pneumatic industrial stapler – BDI+ MODUL 11-Z64 – which is used for the laying of large-scale substructures out of wood, chipboard and much more.
BDI+ MODUL 11-Z64 offers many innovative features such as a laserpointer for easy tracking stability, empty shoot control and a stepless height adjustment. An application in single fire mode is also possible and an intelligent shunting mode enables the stapler to be used in inaccessible areas such as corners and edges.
The industrial stapler is supplied with a PREBENA module with changeable magazine for staples type Z up to 64mm, which is also applicable for stationary manufacturing plants. The tool has a staple distance from 50mm – 1,000mm.
By removing the handle, the BDI+ MODUL 11-Z64 is suitable for many construction site conditions and its practical control panels are effortlessly accessible in every application.
Poppers Senco UK Ltd has expanded its Duraspin collated screw fastening system family with a new range of attachment systems – the DS50 and the DS75 –which both feature patent pending corner fit technology.
The DS50 attachment system drives screws from 25mm – 55mm and is suitable for drywall and metal to metal applications. The DS75 attachment system drives screws from 25mm – 75mm and is supplied complete with an extension pole and adjustable handle for driving screws from a standing position. This makes it the ideal system for flooring including fixing timber to timber and timber to steel applications. Both the attachment systems are available for use with the Duraspin collated screw fastening tool, which is suitable for demanding steel framing and drywall applications. With a range of power and speed options in both traditional corded version and a cordless 18V lithium ion battery, the Duraspin can also be used by high productivity crews as well as one-man operations.
“Senco Duraspin technology continues to evolve to get the job done faster and more efficiently in a wider range of applications. We have the complete system to maximise customers’ productivity and quality while minimising downtime and waste.”
Bosch Power Tools has launched the GBM 13-2 RE Professional – a new high performance drill for faster drilling progress and precision results.
With its 750W motor, as well as a higher no load speed of 3,000rpm in the second speed setting, the GBM 13-2 RE Professional enables much faster drilling progress than the previous 550W model. Furthermore, the tool is more compact and provides better handling thanks to its soft grip. Users whose daily work involves pre-drilling and drilling lots of holes can therefore achieve even more precise results.
Thanks to its two speed gearbox and spindle speed preselector, the GBM 13-2 RE Professional is designed for a wide range of applications and for drilling in steel and wood. It is suitable for a variety of trades – for skilled workers in the metalworking and mechanical engineering sector, for carpenters and roofing contractors, as well as for installers working in the sanitary, heating and air conditioning sector.
For consistent levels of precision even in demanding applications, Bosch now also offers a precision chuck in addition to its quick action and keyed chucks. This chuck has an additional clamping ring, which reliably holds the drill in place even in demanding applications, such as drilling steel with the maximum diameter of 13mm. The tool also features a mechanical overload coupling for maximum control in any application. If the drill jams in metal or in a hard object, the motor cuts out. This minimises unwanted rotation of the drill and protects the user.
“GBM 13-2 RE Professional excels in daily use due to a rugged metal gear case, a spindle collar and a 4m long cable, and therefore has a long useful life and is comfortable to handle.”
POP ® Avdel® has introduced the ProSert™ XTN20 – a next generation high production blind rivet nut installation tool that helps increase manufacturing productivity.
ProSert™ XTN20 is a hydraulic-pneumatic blind rivet nut installation tool that has a thread size capacity from M3 to M10; a pull force of approximately 17kN at 5 bar; and provides up to 7mm stroke adjustment. Weighing just 1.59kg including the (M6) nosepiece assembly, Avdel® mentions the tool is lighter than most comparable tools and offers the highest pull force-to-weight ratio in its class. This enables assembly operators to be more productive with less effort and fatigue.
With a lightweight and ergonomic design, which includes ‘pull-to-force/pull-to-stroke’ dual operating technology, the ProSert XTN20 provides added flexibility, enabling operators to install a broad range of thread sizes and grip combinations – reducing the need for multiple tools at any given workstation. As a result, productivity is increased and lower total installed costs are realised.
“ProSert XTN20 provides high-speed installations, improved assembly productivity, clear and fast access to the workpiece, and setting adjustments easily made in a production environment. With the patented, quick installation mandrel exchange system and the tool-free stroke and force setting features, changeovers are easy and installations are consistent and reliable.”
Rivit Srl has added the RIV506 hydro pneumatic tool for blind rivets to its range of riveters – further expanding the Italian manufacturer’s comprehensive range of fasteners and tools it supplies.
RIV506 was developed with a 20mm stroke, enhanced version, and is designed for the installation of MAGNARIV, MONRIV and LOCKRIV structural rivets up to 6.4mm in diameter.
The riveting tool is equipped with a retaining system for the rivet, and recovery of the mandrel, and comes with a plastic handle and aluminium structure – making the tool light and handy and therefore easy for the operator to use.
“The RIV506 has competitive price that makes it unmissable for everyone looking for a professional tool supported by the quality of the Rivit brand.”
www.rivit.it
Supplying pressure:
Min/max air pressure:
Air consumption per cycle (6 bar):
Stroke:
Tensile strength (6 bar):
Weight:
Vibrations:
Noise level:
Direct Sales Ltd, a North American distributor of Cadex Tools, has introduced the V2/23.55 – a 23-gauge pin and brad nail gun, which it says is the fi rst tool to ever shoot nails in 23-gauge up to 2 3/8 inches (55mm).
Available across Europe through dealers of Cadex Tools, the V2/23.55 is the first of five tools in Cadex’s new V2 body platform. The tool is supplied with a built-in blowgun, anti-dry fire, and a premium systainer carry case.
It also features a self-adjusting magazine and swivel coupler plug. Cadex has also pioneered a new silicone-based paint so its tool grips well in a user’s hand without slipping, which also helps to eliminate the need for bulky rubber grips. The tool’s new coating also enables the tool to stay cooler in the summer and warmer in the winter.
“Cadex has been in the market and distributed by Direct Sales Ltd since 1995, specialising in professional fine finishing tools. We believe the tool will be very well received by the professional fine finishing market and we will be completing the V2 body platform with the addition of the V2/21.55 and V2/18.50 in 2016,” explains Jamie Sikorski, president at Direct Sales Ltd.
JCS Hi-Torque Ltd, part of the JCS group of companies, has been developing and manufacturing worm drive hose clips for over 40 years – offering a wide range in design and material specification to meet the needs of an ever changing industry.
Located in Suffolk, UK, JCS Hi-Torque is known for the manufacture of its high-quality and high performance Hi-Grip®, Hi-Torque and Tamtorque® hose clips and clamps, which are exported throughout the world for use in a variety of industries such as industrial, automotive, marine, construction and petro chemical.
In addition to its broad range of hose clips and hose clamps, the company also manufactures and supplies sign fixing clamps, P-clips, stainless adjustable banding and mini clips.
JCS has its own design, tool making, testing and metal finishing departments, which enables the company to have complete control over quality and continuity of its products. This is reflected in the company’s approvals for BS EN ISO 9002, BSI Kitemark and Lloyd’s Register Type Approval.
“As a complete manufacturer we are also able to produce bespoke products for a number of specific applications. However, where there is potential to produce an original product with large volumes we are happy to work with customers to develop special clamps.”
Here the European Adhesive Tape Association AFERA – a not-for-profit trade association with over fifty years’ experience – explains the benefits of tapes for fixing and joining in product design.
Adhesive tapes are increasingly replacing rivets, screws, nuts, bolts, nails, staples, needle and thread, and welds. Often the use of tapes simply make fixing and joining possible, offering a unique and sophisticated attachment method that is revolutionising product design. This is especially true for challenging applications, which would have traditionally required rivets and welds, and for products designed with new composites, plastics, and a vast range of material combinations. There are multiple advantages of using tape in product design over other fastening methods, these include:
• Using lighter, thinner materials: Reducing the overall weight of the product, you can use lighter, thinner, and less expensive materials without worrying about distortion, splitting, or crazing at the mechanically fastened site.
• Uniform stress distribution: Bonding tapes distribute stress over the entire bonded area. By using tape, you can eliminate stress concentration caused by spot welds, rivets, screws, or other mechanical fasteners that decrease substrate integrity.
• Eliminate drilling time and holes: Save time and money and eliminate the tools required for drilling and tightening. In most cases, integrating bonding tapes into your manufacturing process requires minimal training and little or no investment in equipment.
• Improve appearance and reduce finishing: Bonding tapes, which are generally hidden between the bonded substrates, offer virtually invisible fastening to keep surfaces smooth and clean, with no screws or rivet heads, or protruding nuts and bolts.
Adhesive tapes are used in a wide variety of environmentally challenging areas, such as in extreme temperatures and weather, and exposure to UV and chemicals – resisting stress corrosion and cracking.
“With a track record of 60 years use in demanding applications, adhesive tapes and films continue to provide excellent solutions for innovative product design.”
Carbon fibre-reinforced plastics (CFRP) have fascinating advantages when it comes to saving weight. However, they are also particularly demanding and standard connectors are not good enough for this high-quality material. GESIPA® Blindniettechnik GmbH has now developed a blind rivet nut for composites, which meets these high demands.
GESIPA explains that its CFRP blind rivet nut now makes it possible to easily incorporate functional elements into fibre-plastic composites without material damage. This is achieved through a special geometry of the blind rivet nut. The deforming process is highly controlled so that damage to the component by setting forces is prevented. The closing head assumes a large diameter shape ensuring safe spread of the clamping force.
Due to its special form, the blind rivet nut can be used in a large clamping range, and can be used for various applications within a production process. This saves handling costs and keeps the storage costs low. The material used fits well with the CFRP and keeps away any possible corrosion. GESIPA points out that even after 1,008 hours in the standard salt spray test, the results showed zero or very little red rust could be detected. The CFRP blind rivet nut can be further modified, together with the thread size and length, depending on customer requirements. Other setting head geometries, seals or closed variations to name only a few, can be modified as well.
www.gesipa.com
F. REYHER Nchfg GmbH & Co KG is continually improving its webshop with new features to meet customers’ needs – with over 80,000 fastener and fixing products available to order at the click of a button.
REYHER says its RIO (REYHER Internet Order) webshop has proven very successful over the years and is well liked by its customers due to the number of different ways to place an order.
Its new layout focuses on ease of use with a multi-function menu and a new menu option – ‘my account’, which has all
Located near Milan, Italy, Viteria Fusani Srl has been manufacturing special and standard screws for 60 years – meeting increasingly demanding requirements and customisation requests for a wide variety of markets.
Celebrating its 60th anniversary in 2015, the family owned company is now in its 3rd generation. Originally the company manufactured threaded rods and standard screws, and it has continued to develop its capabilities to offer more sophisticated items.
Specialising in custom-made screws, Viteria Fusani says its knowledge, experience and technology enables it to meet the needs of an increasingly demanding and diversified market that requires special performances, sizes and materials. Its growing product range includes metric and self-tapping screws for all requirements, and custom-made screws from 1.6mm to 8mm diameter.
In 2012, the company laid the foundations for a brand new production unit, which became operational in 2014. The new factory consists of a roofed area of 2,400m² and an office building of 300m², located within a total area of 11,000m².
“This new unit, along with our commitment to grow, will enable us to build our international presence whilst offering products of a high-quality at a competitive price.”
customer specific information within a clearly arranged navigation path. This includes, for example, order history call up, feature searches on orders, and user data, all of which customers can change as they wish. These two new additions provide optimal transparency and efficiency in the ordering process.
In addition, the new flexible extra ‘label designer’ tool enables freely definable format sizes and content for creating labels. It is aimed at customers who place orders via barcode in the RIO | SCAN webshop extension. The new label designer tool provides an alternative to standard labels. There are options for single labels or sheets, freely definable formats, as well as freely positionable boxes.
The format selected is visible on the monitor after entering the label size. The boxes can include text on articles, product illustrations, free text and even photos that are already stored in the system. When the label is ready one click will produce a print ready PDF.
Another helpful feature of the webshop is the contact information for the relevant REYHER partner, which can be seen as soon as a customer logs on and calls up their account.
DEGOMETAL says its GOSTAR stainless steel peel rivet is specifically designed to fasten soft or thin materials, as it does not damage the support.
The French manufacturer of rivets explains that due to its material, the GOSTAR peel rivet is corrosion resistant and is suitable for use in plastic, wood, resin, and thin sheet applications. It can be used for a variety of applications including in the automotive industry for registration plates and airbags.
During setting, this stainless steel rivet body splits into 4 legs and the mandrel head is ejected. Compared to a standard rivet, the GOSTAR’s grip range and its shearing resistance are the most important features.
The peel rivet is available in a number of versions with different heads including domed head and large head. With the ‘T’ version, the mandrel head is retained after installation to obtain excellent shear strength. Leak-proof treatment can also be added upon request.
“With our commitment to quality, our reputation, and more than 45 years’ of experience – combined with a constant drive for research and innovation – DEGOMETAL is able to meet special requirements by changing standard features or by delivering adapted solutions.”
/ biingfeng@bestformer.com
Since 1976 we have been the leading Taiwanese manufacturer focused on Nut Formers & Part Formers. As well as standardised models we supply customised machines, which has seen our current range develop from 5 stations to 8 stations. In addition our new ‘Quick Change Tools’ enable users to change tooling easily and comfortably.
Biing Feng = BF = Best Formers = Best Friends
Thanks to its production facilities in Hellevoetsluis near Rotterdam, the Netherlands, GebuVolco B.V is able to produce a wide range of products based on customer drawings or samples – offering competitive prices and short delivery times.
Since 1947, GebuVolco has been manufacturing products such as hanger bolts, threaded studs, and U-bolts, on its fully automatic machines. Its products are available in many different sizes and materials including stainless steel, low carbon steel, and high-tensile steel.
Specialising in U-bolts, GebuVolco says its extensive manufacturing facilities can guarantee the efficient manufacturing of high-quality products. The company also has a ‘specials’ department, which is arranged to produce wire products in small series, specified to customers’ needs. Its manufacturing facility
also includes an in-house tool and die shop to make tools for special articles needed for manufacturing.
Besides its own production capabilities, GebuVolco also has a network of Asian producers, selected with the utmost of care, to meet its customers’ demands and to supply a reliable product.
“Doing business with GebuVolco offers you consistency and quality at a suitable price. Products of flat or round steel, brass, stainless steel, and synthetic materials, are all part of the possibilities. We invite you to get in touch for more information.”
www.gebuvolco.nl
GebuVolco and MERO-FIX are well known in the fastener industry as producers of high quality fastener products. Our European production facilities offer wire bending and thread rolling techniques to leading customers in the fastener industry. We have been focusing on the production of iron mongery and U-bolts according to DIN or based on your specification/drawing or sample. Our effective QA/QC system is implemented in all stages of our production. It is our goal to exceed your expectations, not only to meet them.
Quality, service and durable partnership is what we stand for. We are happy to offer custom made packaging and labeling solutions at best possible price and with the shortest delivery time possible.
Would you like to know more? Contact us today!
NORMA Group has developed a new plastic quick connector – NORMAQUICK SSL – for use on fuel and urea systems in passenger, commercial and agriculture vehicles, as well as in heavy equipment.
Responding to the customers’ growing needs for ease of assembly, the NORMAQUICK SSL quick connector features a secondary latch, which serves both as an installation aid and allows service personnel to disassemble the connection quickly.
NORMA Group’s quick connectors are characterised by a primary ‘click’ sound when installed correctly. The latch cannot be moved into the closed position until the quick connector is installed properly onto the mating spigot. The secondary latch of the NORMAQUICK SSL provides an additional level of security. During installation, the operator has to press the latch to hear another ‘click’, which verifies the connection. If the NORMAQUICK SSL needs to be disassembled for maintenance and service, the operator can easily access the connector and disengage
the connection by pressing the latch from the same side that the first one had been engaged.
The NORMAQUICK SSL can be used on both plastic and metal spigots designed per SAE J2044 specification. Made of recyclable materials it features extremely low permeation values. The NORMAQUICK SSL comes as standard in 0° and 90° versions – with special versions also available upon request. The connector will be produced in NORMA’s US manufacturing facility in St. Clair, Michigan.
“Our innovative solutions cater to our customers’ needs of enhancing their assembly processes and of making their products even more reliable. The new quick connector is yet another addition to our product portfolio that accommodates our customers’ demands,” says Werner Deggim, CEO of NORMA Group.
www.normagroup.com
HellermannTyton’s new single fix RFID cable tie enables users to easily integrate data within a cable tie and fix cables and equipment that need to carry a serial number for tracking and identification purposes. The single fix RFID cable tie provides larger capacity and productivity, working in sync with existing systems.
Although not a new concept, HellermannTyton points out that RFID is being used to work with existing coding and software and provides a fool proof way to ensure cable management is safe,
HellermannTyton has developed a range of nylon and stainless steel identification cable ties complete with an integrated RFID tag, which enable users to save time and implement secure cable management solutions.
secure and readable. Similar to a barcode the tag is a data carrier, which holds pre-programmed information in a small computer chip and operates on a wide range of frequencies.
Intelligent, ideal for use within all sectors, and compact, RFID data technology is being used within the industry to collate and register products that can talk to a network system. It acts as a tracker that can be read even when the labelling cannot. Benefits of the tags include taking away manual reading mistakes; the ability to pre-programme a serial number to provide a direct link
to a network without human contact; and compatibility with existing systems.
“This use of RFID within cable management means that not only can each cable or piece of equipment be identified, but the tags can potentially be changed, updated and locked, with risk of damage and marks being accidentally removed being greatly reduced,” says John Banks, UK national product manager in identification. “Although there is still a wider scope of opportunities for using RFID technology, it can provide the installer with a secure and reliable identification system.”
Earnest Machine has recently opened two dedicated engineering and manufacturing centres in the US and UK as part of a customer focused campaign to launch a new brand identity.
The new centres, one in the US and one in Wolverhampton, UK, will enable Earnest to further meet the needs of its customers. Customers will be able to design and engineer custom fasteners, made to print specials, and traditional secondary machining services. Along with the new centres, Earnest is also launching a new website and e-commerce centre, to enable its customers to understand the company’s new capabilities and products. The website will enable the company to better communicate with its customers and provide an easy to use platform to showcase its history. The new site has also been designed with the latest in e-commerce service technology.
“It’s a whole new Earnest,” states Kirk Zehnder, president at Earnest Machine. “The addition of our engineering and manufacturing centres allows us to provide a deeper level of service to our customers while promoting manufacturing and creating jobs both in the US and UK. We have always taken pride in our commitment to putting the needs of our customers first, and we’re stepping it up several notches this coming year.”
Kirk continues: “The ‘how can we help you today?’ campaign is more of a promise to our customers than a question, which reaffirms the vision my grandfather had for the company when he founded it 67 years ago.”
Headquartered in Bologna, Italy, ARSER Srl states that its wide range of socket set screws, hexagon keys, stud bolts, as well as cone point and flat point standard – all available in stock –means that it is able to satisfy any market request immediately.
ARSER has been manufacturing special socket set screws on bespoke machines and devices for over 50 years, with its high-quality products and service appreciated by customers all over the world.
The company’s facility meets quality requirements to guarantee its customers an excellent product and service. This includes staff training, process analysis, zero defects, maintenance management and planning for all machines and devices, as well as statistical analysis regarding process data. Meeting these requirements has enabled the company to meet the ever increasing demand for automotive parts. The company is also ISO/TS 16949 certified by TÜV.
“ARSER’s production flexibility means that thousands of variables can be offered, in order to meet every application. Our role is increasingly becoming one of a technical partner rather than just a simple supplier.”
PennEngineering® states that its PEM® self-clinching blind nuts permanently install into thin metal sheets – providing reliable and reusable metal threads for accepting mating screws and completing fi nal component attachment in an assembly.
PEM® self-clinching blind nuts feature a blind closed-end design, which effectively creates a barrier to protect the nut’s threads against foreign matter and to prevent potential damage to internal components from mating screws.
The carbon steel (Type B) and stainless steel (Type BS) nuts install quickly and permanently into aluminium or steel sheets as thin as 0.04 inches/1mm. The nut is inserted into a properly sized mounting hole in the metal sheet and then sufficient squeezing force is applied using a PEMSERTER® or any standard press until the nut’s flange contacts the mounting sheet. Upon installation, the nut becomes a permanent part of an assembly and throughout the process no secondary operations are required.
Standard thread sizes of PEM self-clinching blind nuts range from #4-40 through ¼-20/M3 – M6. Two different shank lengths for each thread size are available to accommodate minimum and thicker sheets.
Detailed specifications, animations, fastener drawings and models, and literature (Bulletin B) for these RoHS-compliant fasteners can be accessed online.
BUSHES AND STUDS FOR BONDING
• SHORT DELIVERY TIME
• 100% MADE IN ITALY
• DIFFERENT SIZES AND SHAPES AVAILABLE
• ZINC PLATED STEEL AND AISI 316 STAINLESS STEEL AVAILABLE
• EASY APPLICATION WITH ADHESIVE
BOOKMARK THE BRAND NEW FASTENER + FIXING WEBSITE FOR MORE… INDUSTRY NEWS, EXHIBITION NEWS, INSIGHT, CONSTRUCTION FIXINGS, MANUFACTURING TECHNOLOGY, MANAGEMENT + SYSTEMS, TECHNICAL, PRODUCT NEWS…
Following an amendment of BS 7671 in July 2015 – which requires cabling to be supported by fire-resistant fasteners and fixings –Partex Marking Systems UK Ltd launched a range of fire-resistant fixings.
Partex’s range of fire-resistant fixings included galvanised steel mini-trunking cable retaining clips, stainless steel cable tie mounts, and spacer-bar saddles. The galvanised steel mini-trunking clips have an M6 fixing hole and side tabs that can be easily bent over, without the aid of a tool, to retain the cables securely. Supplied in packs of 50, the MTCC-T2/6 version is designed for use with T2 mini-trunking. The MTCC-T3/6 version is suitable for use with both T3 and T4 mini-trunking.
The Partex SSTM cable tie mounts are supplied in packs of 50 and are available with either M4 or M6 fixing holes and provide a versatile and cost-effective fixing solution
when used in conjunction with Partex stainless cable ties. The cable tie mounts are manufactured from high-quality corrosion resistant 316 grade stainless steel.
Completing the family of fire-resistant fixings are white polyester powder coated, galvanised steel spacer-bar saddles. Supplied in packs of 10, the SBSW20 is designed for use with 20mm conduit, while the SBSW25 is for use with 25mm conduit. The durable white finish matches standard white PVC-U conduit, making them much more attractive in many installations. They are suitable for both indoor and outdoor applications.
Based in Birmingham, UK, Partex Marking Systems UK Ltd is the daughter company of Sweden-based Partex Marking Systems AB.
SD Products Limited has added several new lines of marine and fabric fasteners to its expanding catalogue, enabling it to offer easy to use products at low prices.
Products included in the new lines are spur teeth washers and grommets, as well as brass eyelets and rings – which are used extensively in the textile industry. In addition, there are tri snaps – which offer an economical snap fastener that is ideal for lightweight applications; as well as turnbuttons, which are positive locking fasteners assembled with a spring mechanism that holds the stud button in position until turned by hand.
SD Products also stocks a large range of DOT® fasteners, which are well known for quality and durability.
‘Durable Dot’ and ‘Pull the Dot’ ranges are manufactured from heavy gauge brass and 316 grade stainless steel – designed to withstand tremendous amounts of pressure without unlocking.
Heavy-duty components guarantee that these fasteners show improved performance and corrosive resistance in the most severe environments. The fasteners are self-piercing so they can be attached even to the roughest fabrics without the need for pre-punching.
“SD Products is committed to providing superior products, services and competitive prices for our customers. Thanks to our large quantities of stock we are able to offer speedy deliveries with next day dispatch to the UK.”
www.sdproducts.co.uk
Family owned Italian distributor, Berardi Bullonerie Srl, is proud to offer a consistently high-quality service to its customers with a wide range of standard products always available in stock.
Founded in 1919 in Bologna, Italy, the distributor has grown to offer a wide range of products including captive screws, security fasteners, and springs, and can also offer special fasteners as per customer request.
Berardi Bullonerie believes that quality and service is the key to success. All incoming goods undergo sophisticated controls to ensure the highest quality – all carried out by its skilled staff in its quality department. Goods are inspected using an altimeter, salt spray testing, XRF analyser for coating thickness, profile projector, Rockwell durometer, and Vickers micro durometer.
In order to satisfy its customers’ need of extreme accuracy Berardi has also added a Dimac MCV1 optoelectronic machine, which has three video cameras to enable 100% accuracy during quality checks.
www.gberardi.com
Techsil Ltd has launched the SnapSil™ TN8000 silicone adhesive –a versatile, high performance silicone adhesive manufactured by Japan-based Momentive™ Performance Materials Inc –into the UK market.
Techsil is Momentive™ Performance Materials’ RTV silicone distribution partner in the UK and Republic of Ireland. The company says the SnapSil™ TN8000 adhesive is a one component condensation-curing silicone rubber developed for sealing. It is easy to apply and versatile and can adhere to many materials such as metals, plastics, glass, and ceramics, without the use of primers. Providing insulation and waterproof, it can be considered for use in a wide array of industrial sealing and bonding applications such as electronics, solar and communications devices.
Key features and typical benefits of the SnapSil TN8000 adhesive include
high strength and elongation, excellent adhesion after extended aging, excellent properties after high temperature and humidity (85ºC/85%RH), and it is very stable in storage. Available in three colours – white, black and grey – the TN8000 is also flame retardant, UL94 HB classified, and has a fast room temperature cure and neutral alkoxy cure type.
“Techsil has a wealth of product knowledge and first-hand application experience gained by supplying materials that work in real production environments. Working closely with customers to overcome technical problems it can provide innovative ways to provide significant production benefits.”
do your clients ask how your work is checked? can you certify that each of your products is well made? stand out from your competitors! with the new Rivit’s Process Control System your work is always checked and certified.
CONTROLRIV allows to control the fastening according to predetermined settings made by the operator. Ergonomy, visual features and sound alarms make the CONTROLRIV easy to use. Furthermore it provides different intervention levels with password and data storage for later verification.