
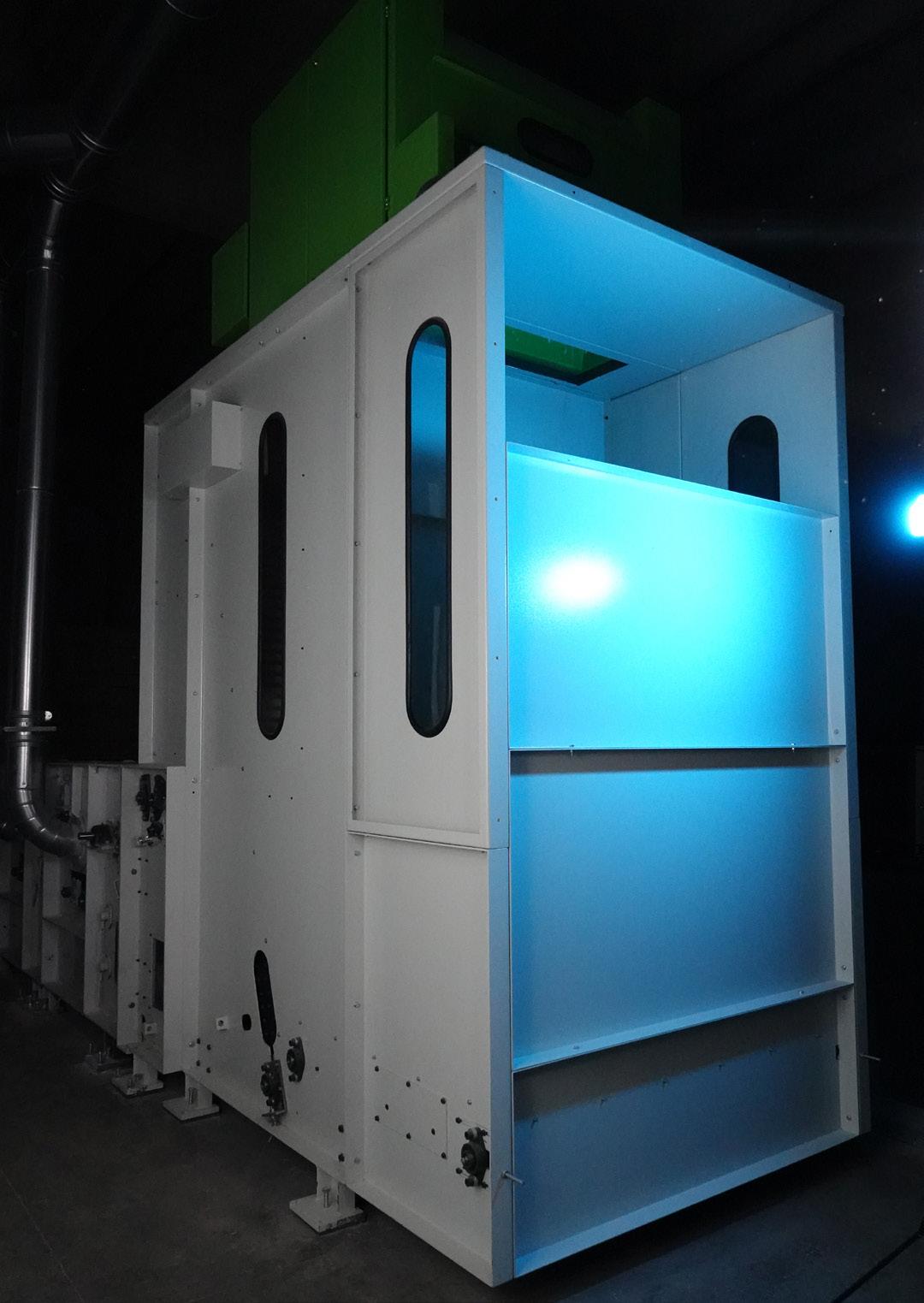
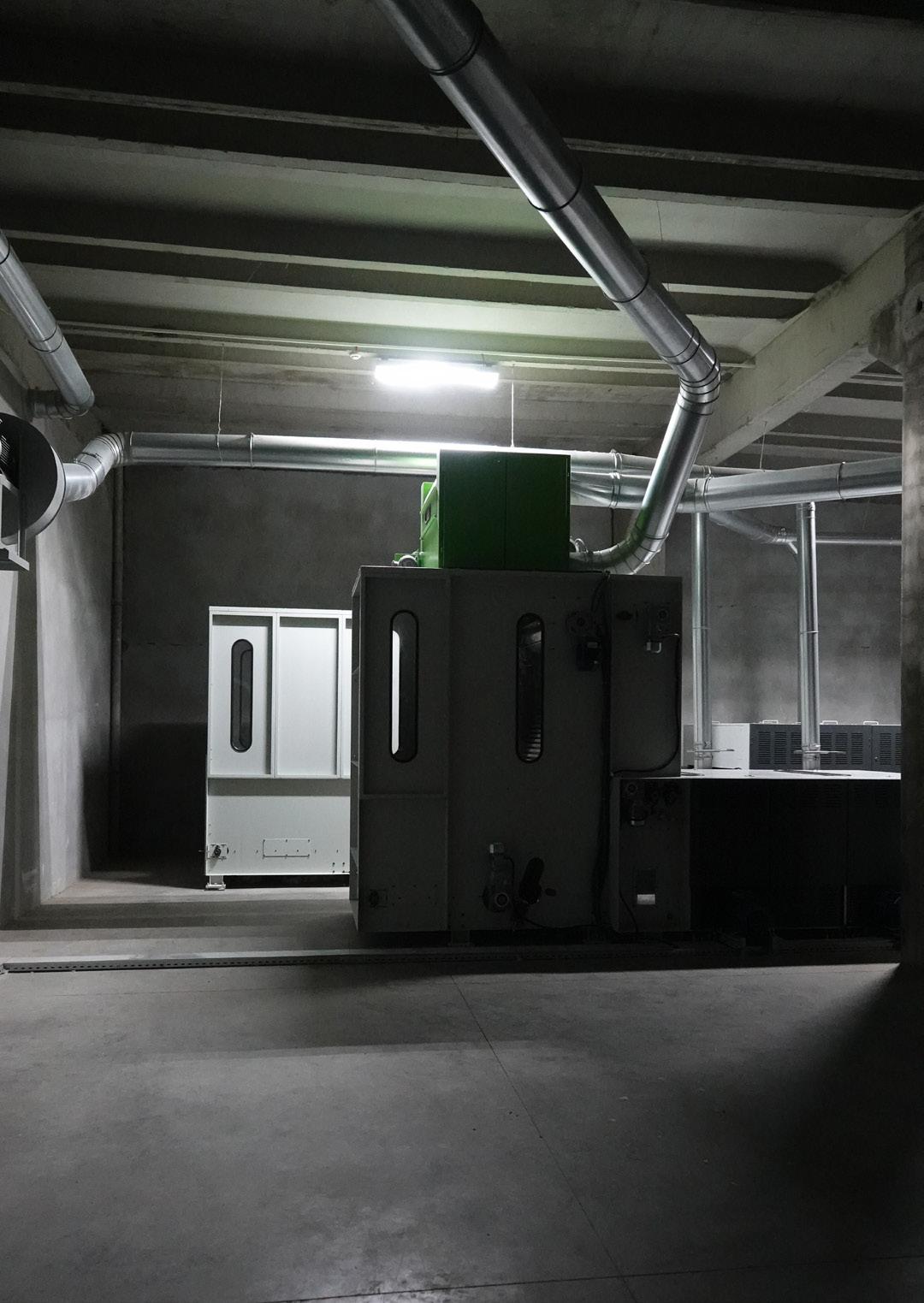

“ We are actively improving the circular economy, one metre at a time. ”
Säntis Textiles
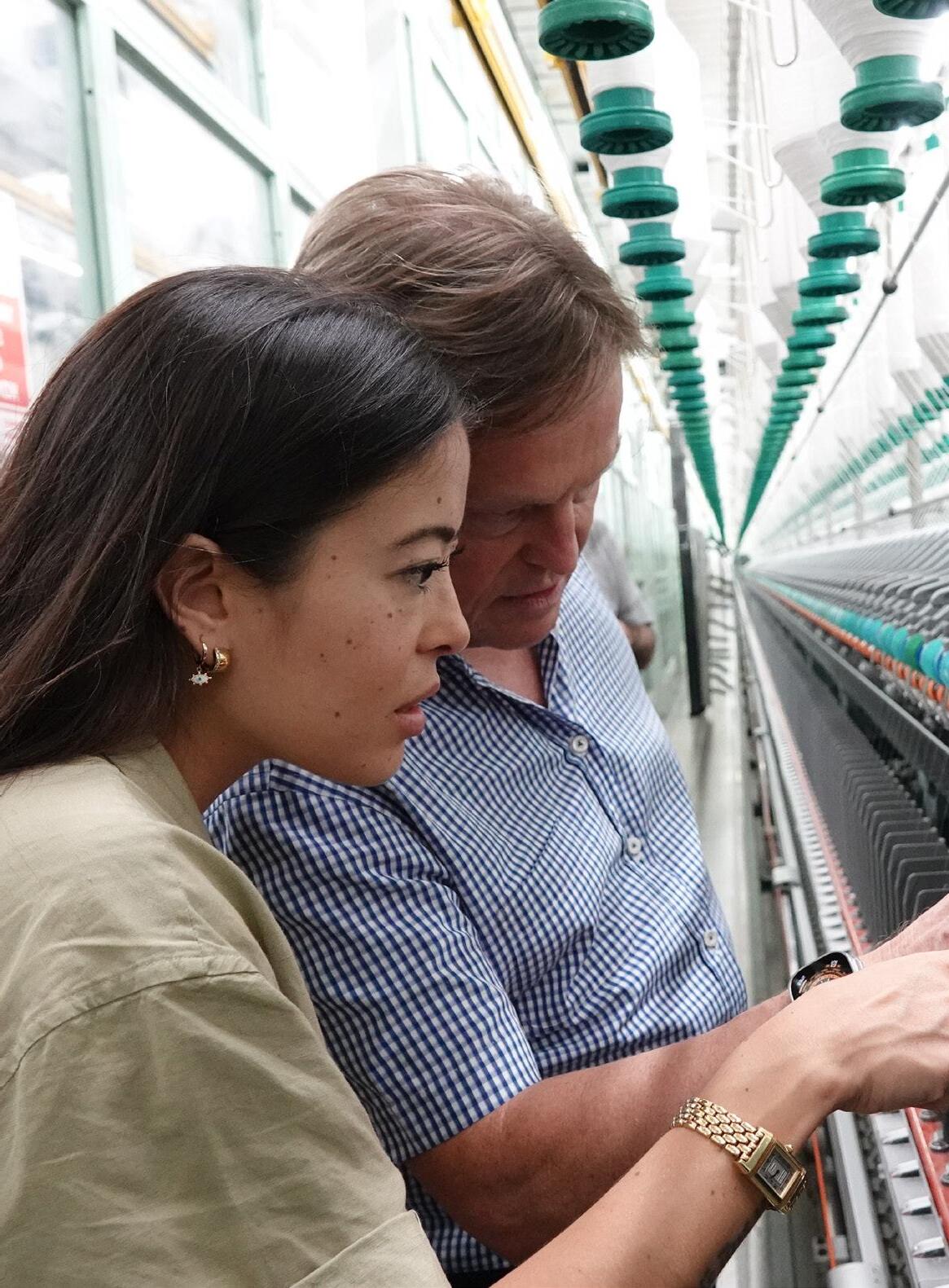
“ We are actively improving the circular economy, one metre at a time. ”
Säntis Textiles
We are a Swiss, family-owned and run textile sourcing and supply company headquartered in Singapore. Since 2005, we have specialise in material, fiber, yarn, fabric and technology development and sourcing for the global market in garment and technical textiles.
RCO100, our 100% recycled cotton technology, was launched in 2016, designed with the forward thinking customer in mind. With our RCO100 technology and product, we are actively improving the circular economy, one metre at a time. We are proud to be part of the <1% that recycles textile-textile directly.
Stefan embarks on his textile journey.
We are a Swiss, family-owned and run textile sourcing and supply company headquartered in Singapore.
We have specialised in material, fibre, yarn, fabric and technology development and sourcing for the global market in garment and technical textiles.
2016
RCO100, our 100% recycled cotton technology, was launched in 2016, we have been developing a mechanical recycling system for cotton.
Our first partner in this project was PVH Corp.
By the end of 2018, we successfully spun open-end yarns up to Ne20 using 100% pre-consumer industrial waste.
PVH Corp introduced 100% recycled denim at their Paris fashion show in early 2019. In addition, we established a partnership at Kipas in Kahramanmaras, Türkiye, where we installed our custombuilt recycling line.
2023
Säntis Textiles and partner Temsan is proud to bring to market the latest innovation in textile recycling RCO100.
Säntis Textiles, a multi-generational textile company, is proud to bring to market our latest innovation in textile recycling.
Our decades of knowledge have led us to develop a system that uses a mechanical fibre opening technology which treats the fibre gently and does not stress the material.
The aim was to develop a mechanical recycling system for 100% recycled cotton yarns and fabrics to maintain the best fibre length and strength possible.
Since 2016, we have been developing a mechanical recycling system for cotton. Our first partner in this project was PVH Corp.
By the end of 2018, we successfully spun open-end yarns up to Ne20 using 100% pre-consumer industrial waste.
These yarns have since been used to make the following yarns and fabrics: Denim, Chino, Canvas, Panama, Single Jersey, Pique and French-terry.
PVH Corp introduced 100% recycled denim at their Paris fashion show in early 2019. In addition, we established a partnership at Kipas in Kahramanmaras, Türkiye, where we installed our custom-built recycling line. Since then, we have continuously worked with leading
global brands such as Lacoste, Patagonia and Mara Hoffmann on development to further their circular initiatives.
This line produces approximately 300-350 tons of mainly preconsumer and post-consumer cotton bales per month.
With the help of our partners, Säntis Textiles launches our new RCO100 recycling system:
• Components engineered by Swiss engineering company Swinsol
• Machine built by Turkish textile air conditioning equipment supplier Temsan.
Santis Textiles is proud to give the license for the production, sales and service to Temsan, the global leading supplier in textile air conditioning equipment.
Additionally, together with Swinsol, we developed a mechanical compact ring spinning system, specially designed for RCO100 carded compact ring yarns. This system, which includes a unique compacting system for the roving frame is the most suitable for recycled cotton fibres.
Unique features of the RCO100 recycling system:
• Most gentle fibre treatment of all mechanical recycling systems in the market. Our task is protect the
fibers and to maintain maximum fiber lengths and strength.
• The standard line includes two conveyors and two strong built guillotine knives positioned in a 90º angle to achieve best possible cutting results.
• The initial buffer unit is also a mixing chamber for the cut material. It controls the feeding to the following pre-opener cylinders. The initial buffer unit also contains spark and metal detection.
• From the buffer, a feed table transports the material to the preopening cylinders. These are four modules which are configured with pin cylinders and / or saw tooth cylinders in order to optimize the pre-opening process.
• The feeding to these cylinders is through controlled feed rollers but without clamping points or counterrotating cylinders. Transport from one cylinder to the next is by perforated drums, which not only dedust the fiber fleece, but also forward it without stressing the material.
• The four pre-opener cylinders are equipped with covers on the bottom, which can be adjusted and equipped with carding elements, according to the in-feed materials.
• From the pre-openers, the material is sent to three parallel fine-opener lines, each equipped with 12 opening cylinder modules.
• The material is fed into chutes and then transported to the first opening cylinder which can be equipped again with pins or sawtooth / carding wires. The fibre fleece is again transported via perforated drums and no fibre clamping / squeezing is involved.
• Unopened yarn / fabric material drops below the cylinders to a suction and is returned to go around and start at the beginning of the opening process again. This feature allows the yarn/fabric cuttings to run through the system as many times needed or until the yarns are opened and the fibres flow free through the fine-opener arrangement. It is the most gentle way to treat the fibres and a crucial feature in our system to achieve best possible fibre lengths.
• Once the fibres are opened and de-dusted, they are sent to another buffer unit and then pressed to standard bales in a strong and efficient bale press.
• The dust is collected in a modern filter system.
• Future systems will include patented mechanical elastane extraction, patented direct can coiling and patented traceability technology.
• What is input and output of the machine? What kind of materials the machine can run?
The current machine is running at approx. 450 tons / month, i.e. this is approx. 10-12 tons / Day.
We can run any staple fibre fabrics. 100% cotton, polyester / cotton, polyester staple, viscose, cotton / nylon staple, linen, hemp (as long as it is cotton staple length).
What is the output fibre length?
Turkish cotton has a 80% staple length of approx. 31-32mm. When we recycle this we come out with a 80% staple length of approx. 2526mm.
In general the output depends on the input fiber length of course, but we can say that we have approx. 1520% loss. We can keep longer fibres also by reducing the production rate.
What kind of yarn can be produced with the output fibre?
We can spin Open End yarns from Ne5.9 - Ne20 and carded ring compact yarns from Ne8 – Ne30.
Additionally, we can spin carded ring compact core yarns up to Ne20 with 40 den and 70 den recycled elastane.
Cutters
Two guillotine cutters in a 90° angle arrangement conveyor belts/feeding funnels and buffer/mixing unit; spark and metal detection
Pre-Opener Section
Stage 1: 1 x Pre-opener module, cylinder diameter: 1000 mm; working width 1500mm
Stage 2: 3 x Pre-opener modules, cylinder diameter: 700 mm; working width 1500mm
Buffer / mixing unit feeding to fine openers
Fine Opener Section
Buffer / mixing unit / chute system for fine opener
Stage 1: 1 x Fine opener module, cylinder diameter: 400 mm; working width 1500mm
Stage 2: 11 x Fine opener modules, cylinder diameter: 250 mm; working width 1500mm
• Standard system consists of 3 fine opener lines with total 36 opening points.
• Material transport between modules by feed rollers and perforated drums
Buffer / mixing unit before bale press.
Production capacities*:
Pre-opener line capacity: 900 kg / h
Fine opener line capacity: 300 kg / h (3 x 300 kg / h = 900kg/h fine opener capacity)
Total system capacity 900kg/h
* The capacities are related to input material. Figures given based on yarn
waste
Equipment Specifications
Total installed power: 405 kW
System control Lenze
Inverter control for all reducers and motors
Reducers: Lenze
Electric Motors: Siemens IE3
Inverters: Lenze
Metal detection; spark/fire protection system for each module
Two guillotine cutters in 90° arrangement
Double head bale press for 6 bales / hour (190-200kg/bale) = 1200kg / hour
Filter package consisting of cabinet type pre-filter and rotary filter. Capacity up to 70’000m3/h
Stefan Hutter
Owner, Säntis Textiles
Annabelle Hutter
Managing Director, Säntis Textiles
Cem Erdoğrul
Managing Director, Temsan
Halit Gumuser
Managing Director, Member of the Board, Kipas Textiles
Dr. Laszlo Olah & Resul Istrefi Managing Director, Swinsol
My name is Stefan Hutter. I'm the owner of Säntis Textiles, headquartered in Singapore. I have a branch office now in Switzerland and branches in China, Vietnam, Indonesia, Pakistan, Turkey, the UK and the United States. The company has been in textiles since day one, 2005.
The main business of Säntis Textiles is still technical and home textiles. Since 2010, we have worked on recycling, initially on polyester, and in 2016 we started with cotton recycling.
I have been in textiles all my life. I did an apprenticeship in Switzerland, working as a technician with textile machines for several years in the United States and Mexico, and then went back to university, studied textile engineering in Germany, and then went for a Swiss company to Taiwan in the early 90s.
Recycling has become very important for us over the last 15 years. We initially started with polyester recycling, where we developed a technology to make spinnable polyester fibres for this big Swedish furniture house. And we ventured into cotton recycling in 2016. Recycling textiles will be a significant pillar at Säntis Textiles in the future.
We combine it with our standard products, our technical textiles, where we use more and more recycled fibres and in the future, recycling in the textile industry will become much more essential than it was in the past.
For me, it is like the closing of a cycle. I started in textile machinery after university. I worked for a prominent Swiss company in spinning, and they delegated me to Taiwan at the time. I was in textile machinery for a long time, went into textiles, and now I'm returning with a textile machine with a recycling system. So for me, it is a bit like closing a cycle or coming home.
It would not have been possible without partners, whether in China initially or currently in Turkey; it is essential to have partners to bring this project forward. We have a partner on the textile side, Kipas, and we have Temsan,
who has the license to produce the system, and without them it would not have been possible, especially not in this short time.
The inspiration came from a challenge I got from Daniel Grieder, the CEO of PVH Europe and Tommy Hilfiger Global in 2016, and today the CEO of Hugo Boss in Germany. He asked me whether it's possible to produce 100% recycled cotton, yarns and fabrics, and he insisted on 100%.
So that was the challenge, and with this task, I initially went to China, to an area in the southeast where a lot of recycling is happening. We did trials with different machine modules, and we moved them around and played with it until we had some encouraging first results. It took us about two years until we were able to produce denim fabrics and also some knits, and some chino fabrics out of 100% recycled cotton.
We then took the whole project to Kipas in Kahramanmaras, Turkey, and worked on R&D, and a new machine. We installed a new machine at Kipas, from 2021 onward. And we have successfully run this plant since 2021, producing roughly 300-350 tons of cotton bales per month. From day one, we had to look at and keep the fibre length as our essential feature. Because only with good fibre length and when you keep the fibre strong can you achieve good results in spinning and weaving.
All the other players in the market come from the non-woven sector; it's about productivity, tons per hour, but a lot less about fibre quality. And this is the big difference between our system and what you see otherwise in the market.
I chose Kipas because they are the leading textile company in Turkey, fully vertical, with spinning, weaving, dying and finishing, and prominent in denim. In addition, Kipas introduced me to Temsan, and I partnered with them first because they are also a family-run business. Secondly, they are in the same area as Kipas, which helped us make the whole project very fast, with only half an hour away from Kipas to Temsan. If something was needed or something had to change on the machine, the guys from Kipas would go over to Temsan immediately. They can look at the issues, they can fix them, and they learn. And this makes us incredibly fast. It seems impossible to do this within 15 months; right from the day they got the first drawing to 15 months later, they produced a machine that can be sold.
As I mentioned earlier, I have been in this business for a long time, and I have never seen the determination and will elsewhere as I have seen here.
When the owners of Temsan decided to take up this project, the whole team was 100% behind it from day one and worked day and night under difficult circumstances, even after the earthquake. They have worked day and night to have this machine ready for ITMA; In the future, we have new developments, and we have new ideas on how we further develop this system also in combination with spinning technology to make sure that we can produce better quality 100% recycled cotton yarns. We also work on yarns and fabrics, and we also work on polyester-cotton blends, where we develop yarns and fabrics for the future.
The textile world is changing. It took a long, long time. There is regulation coming, first in the EU, and this will give the whole thing a big push.
I have been in recycling for a long time, in 2010 with polyesters and seven years in cotton, and nothing moved for the past few years. But now there are clear signs that the industry is changing, which motivates us again to develop new ideas based on the existing equipment.
I'm very happy to have Annabelle on board since 2020. She is in charge of the newly established company SÄNTIS TEXTILES in Switzerland, which focuses mainly on the marketing and promotion of recycled cotton technology. And for me, it is nice to have a family member to continue what we began. And it's nice to see how fast she learnt about the textile process and how she's willing to elaborate on her own ideas. Annabelle's also an inspiration for young women to work in this industry, and I couldn't be prouder.
“ Only with good fibre length and when you keep the fibre strong can you achieve good results in spinning and weaving. ”
Stefan Hutter Owner, Säntis TextilesAnnabelle Hutter Managing Director, Säntis Textiles
Hi, my name is Annabelle Hutter. I am the Managing Director of SÄNTIS TEXTILES Switzerland. I have been working at SÄNTIS TEXTILES for three, almost four years, alongside my father Stefan Hutter, and I'm really lucky to be working with my father on this recycling project.
So today we are in Kahramanmaras, which is where Kipas is located, and Kipas are one of our main partners in this recycling project. With Kipas we have developed RCO100 which is our 100% recycled cotton. Basically our 100% recycled cotton technology allows for us to recycle textile scraps into this amazing 100% recycled cotton in the world, but the best recycled cotton in general, is that our length of fibre is 26mm, and this is one of a kind, and no other company can do this. because the RCO100 technology, which we developed with Temsan and Kipas, basically allows for us to recycle any kind of textile waste, be it scraps, be it garments, yarn waste.
It can all be recycled to make this amazing fibre, which we achieve a 26mm length of fibre, which is unique in this industry, and nobody has ever achieved this before. I'm really excited because we will launch this machine at ITMA, which means that anyone from wool recyclers to garment manufacturers to yarn spinners can buy this machine and recycle their own cotton waste, or they can recycle wool, they can recycle silks as well. There's a whole abundance that can be recycled using our RCO100 recycling machine. So for me personally, as I have been on this journey with my father and the partners, I have learned so much about the industry and about where we're headed. And I definitely think that it is ingrained in me now. The word circularity, recycling, and sustainability really lies now in my subconscious, and I hope that in the future, generations to come can also have the same notion that I have when I approach my work. So I'm really excited to see what's going to happen.
I definitely believe that women play an incredibly important role in the textile industry, and I love to shine a light on this by just being present and making that known.
So I definitely hope to see more girls and women get involved in the textile industry for the future and I hope that I can inspire them to do that.
So the word circularity for me, it varies every day and I feel like the more that I educate myself through, for example, learning about our RCO100 process, the more I realize that it is something that should be in our subconscious and not really emphasized in the way that it is through marketing or let's say greenwashing. I think that it should definitely just be something that we all strive towards and that is in our DNA rather than something that is a conversation topic at all times.
I'm really proud of the invention and development that my father made with our RCO100 technology because this machine is not exclusively designed to downcycle, it is designed to recycle. And this means textile to textile directly. That was the whole notion from the beginning. So definitely the unique factor of this machine is that it has a gentle opening system. It shreds very gently. It moves a lot slower and it's not as aggressive as the other machines in the industry. And we're really lucky to have been able to commercialize this since 2019. So that's a really great factor about our machine.
Working with my father has been definitely a very exciting journey. It hasn't been easy, although it is very rewarding. And I really believe that more daughters should hopefully strive to work with their fathers one day. I think it's a great synergy what we have. I am more of the creative thinker and he's definitely the technical brain in this family. So I really enjoy it so far. And together we have forged a really great path. We are both very innovative in our respective fields. So I can't wait to see where it goes.
But definitely the last few years have been great. It hasn't been easy to market this machine from scratch, of course, because my background is actually in art history. So I never studied textile engineering or machinery, but my father has taught me an immense amount. Also, our partners at Temsan and Kipas are always very happy to answer my questions and provide me with any information that I need. So I think that life is all about learning and evolving intellectually, and it's been really great for me to be able to learn along with my father, who also is learning as well while he's developing this project.
I really believe that I'm not going to ever be able to be the mastermind that he is, but it's great to be able to interpret this whole machinery process in my own language and I've been able to translate it to a wider audience who would have never been able to get interested in this kind of aspect of the textile industry, so I'm really happy for that.
My inspirations in life are definitely traveling. One of the biggest joys that I've had working on this project is being able to come to Turkey so many times and especially this area of Turkey. It's been amazing. Everyone feels like a family. And that brings me to my inspiration. I often feel like when I'm here in Kahramanmaras, it's as if I'm back with my grandparents who were my biggest role models, who they really taught me how to be creative and how to think outside of the box and always go with what my heart says and never try to be like everyone else. So that's really what we believe in here at SÄNTIS TEXTILES and also with RCO100.
“
I'm really proud of the invention and development that my father made with our RCO100 technology because this machine is not exclusively designed to downcycle, it is designed to recycle.”
Annabelle Hutter
Managing Director, Säntis Textiles
Tell us about your company and how you partnered with SÄNTIS TEXTILES
Temsan operates as a group company within the Kesim family. The company’s origins date back to the 1960s, and it has been active in the field of machinery manufacturing since that time. Additionally, it has specialized in textile air conditioning control systems for the past 35 years.
Thanks to its extensive process knowledge, experience in machine manufacturing, technological expertise, research and development efforts, and emphasis on human resources, Temsan has achieved an effective position in the global market over the past 10 years. During this process, the company has increased its brand value and reached a soughtafter position in engineering, quality, and service sectors. Temsan Makine has become a recognized and exemplary firm in the industry worldwide, earning the appreciation of all stakeholders.
By utilizing its knowledge and experience, especially in manufacturing and the market, Temsan Makine has strengthened its infrastructure in textile machine manufacturing. After a preparation period of five years, the company initiated this process effectively in 2017. As a result of these steps, the company has emerged with Temsan Dynamics, bringing a new perspective to the industry and attracting the attention of numerous firms and entrepreneurs on a global level.
Following this introduction, the first meeting took place at the Temsan factory. This meeting was held to discuss collaboration opportunities and business strategies between the involved parties. Later, in October 2021, the second meeting was held in Istanbul.
Kipaş Tekstil played an essential role in facilitating the initial meeting between Temsan and SÄNTIS TEXTILES.
In March 2022, Temsan officially started the project. The project, initiated by SÄNTIS TEXTILES, was developed in collaboration with Temsan, and it progressed to the production stage. In 2022, the Sustainability Talks Istanbul event served as a platform for showcasing the cooperation achieved.
Indeed, textile recycling is becoming increasingly significant in the future. Sustainability has become a critical factor in the textile industry. There is a growing recognition of the need for recycling, both pre and postconsumer, to reduce waste and promote a circular economy. While this may be an initial step, it shows that Temsan recognizes the importance of embracing recycling technologies to create high-quality, sustainable textile products.
“ We can manufacture together. This is very important for Stefan, also for us, also for the world. ”
Cem Erdoğrul Managing Director, TemsanHalit Gümüşer Managing Director, Member of the Board, Kipas Textiles
Tell us about your company and how you partnered with SÄNTIS TEXTILES
Kipas Holding is serving with 25 companies in 6 main sectors with more than 10,000 employees with an annual return is more than 1 billion USD.
Kipas Textile is an advanced integrated company which has gained a place among the world’s prominent suppliers by exporting 60% of its own manufactured fabrics and yarns. Integrated textile plants owned by Kipas group companies are the preferred suppliers of the world’s leading brands, with an important annual production capacity including 400 thousand tonnes of yarn, 100 million meters of woven fabric (both denim and non-denim).
Today, we sell our advanced and high-quality products in over 60 countries worldwide. To achieve excellence, we have built close working relationships with the most innovative technology and fibre companies. And in this scope , we are able to produce almost all kind of staple yarns and woven fabrics in our own facilities.
As Kipas textile , to be able to widen our customer portfolio and company recognition in the market, thanks to talented and well educated sales team members, we have been participating in top leading tradefairs, using actively our web-site for high reachability and our long term customers’ and suppliers’ introduction and suggestion to the new customers.
By means of one of these methods , we established a valuable long-term partnership with SÄNTIS TEXTILES at the beginning of 2018.
How excited were you when SÄNTIS TEXTILES wanted to partner with KIPAS for the launch of this new recycling milestone ?
As one of the leading companies in the whole Europe in terms of production capacity, we have always paid serious attention to eco-friendly
approaches. We have always focused on reducing our carbon footprint and the reusability of our production waste. On the other hand , by the means of increasing consciousness of the ecological approach in both Türkiye and Europe of not only the public but also the governments via legislative regulations , we increased the level of our efforts in this area besides the number of our eco-friendly projects. During such a period, it was an excellent chance for us to meet and co-operate with SÄNTIS TEXTILES, who has the same point of view and a profound experience in the recycling industry. We have been maintaining and improving our collaboration day by day, and we have the same excitement even at the moment.
As you would appreciate, just due to the incredibely growing population of the world , naturally the consumption of textile products has been growing so fast as well. Moreover, we can not consider these products as only for the fashion industry but also for the whole life space as technical textiles, outdoor, home textiles etc.
For meeting such a high textile product usage necessity worldwide, a tremendous consumption of the raw material is needed. To be able to grow the naturel fibers and produce the men made fibers , there is a great water consumption and chemical usage requirement that harms enviroment. And also this new products have to be produced and released to the market in a really so short time period for the purpose of meeting the high demand. Just because of these reasons , recycling plays an essential role to eliminate the hazardous factors of re-producing the raw materials and contribute to fast service.
Tell us about your company and how you partnered with SÄNTIS TEXTILES
The company, based in Au (Switzerland), develops and manufactures a variety of components as well as technologies for mechanical compacting systems for ring spinning machines for processing natural and man-made fibers and their blends into yarns.
Swinsol is one of the most experienced providers of mechanical compact spinning processes worldwide and a leader in magnetic force technology.
We strongly believe that the success of our customers is our biggest mission and our greatest achievement. Therefore we passionately guide each of our customers in a concrete and practical way to build innovation into the fabric of their businesses.
Two years ago we had the great pleasure to welcome Mr. Stefan Hutter from SÄNTIS TEXTILES to our board of directors . We are very pleased to work with such a great Visionaire and experienced partner.
The combination rich on experience and a young and motivated team makes our collaboration unique and we were able to do great and innovative products which will shape and revolutionize the textile industry.
One of the products is the recycling line for pre & postconsumer textiles. We are very thankful that we got invited to participated on the recycling project initiated by SÄNTIS TEXTILES.
We strongly believe that recycling is necessary to reduce the CO-2 emissions and make the Textile industry more suitable and environment friendly.
Annabelle Hutter
Managing Director, Säntis Textiles
annabelle.hutter@saentis-textiles.com
Ökkeş Çiçek
Temsan Air Sales Engineer
okkes.cicek@temsanair.com
© Säntis Textiles 2023 | © Temsan 2023
All rights reserved.
Book design by ENDRIME®