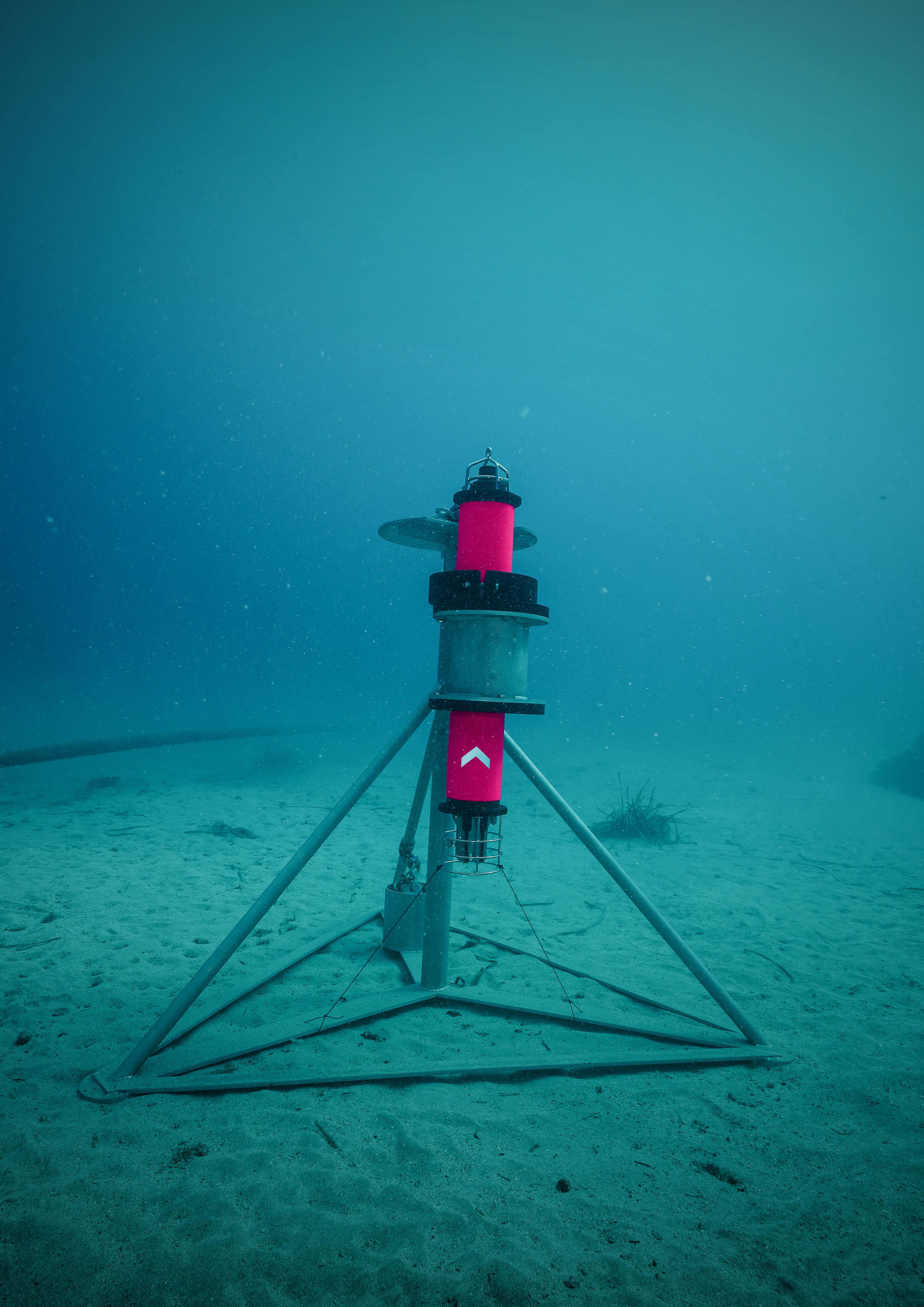

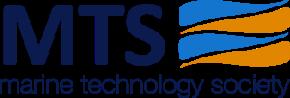
Full ocean depth capability
Cost-saving modular design
Available worldwide on short lead times
Interchangeable and reversible insert configurations
FCR and BCR rated to 600 bar back pressure
Designed and tested to IEC standards
Hybrid – singular connector with power, data and communication
SOCIETY FOR UNDERWATER TECHNOLOGY
Editor: John Howes John@ut-2.com +44 7859905550
Editorial Sally Mander
Research M Hamilton Perry
Advertising: Zinat Hassan UT3subsea@gmail.com
Tel: +44 (0) 845 6522 483 Mobile: +44 (0) 781 1200 483
Published by UT2 Publishing for and on behalf of the Society for UnderwaterTechnology. Reproduction of UT2 in whole or in part, without permission, is prohibited.The publisher and the SUTassumes no responsibility for unsolicited material, nor responsibility for content of any advertisement, particularly infringement of copyrights, trademarks, intellectual property rights and patents, nor liability for misrepresentations, false or misleading statements and illustrations.These are the sole responsibility of the advertiser. Opinions of the writers are not necessarily those of the SUTor the publishers
Exail Canopus LBL transponder, operating at depth down to 6,000 meters
MacArtney has opened a new office in Dubai as a regional hub to better serve a growing customer base in India, Middle East, and North Africa (MENA),
The expansion is part of MacArtney's strategy to be locally represented and close to customers. The company, headquartered in Denmark, currently operates 20 strategically located offices across the Asia-Pacific, Europe, and the Americas.
This ensures access to its comprehensive product portfolio of reliable underwater technology, both locally and globally, supported by a dedicated network of distributors.
The plan is to eventually cover the MENA area in cooperation with existing regional distributors. Over the coming months, the company will begin implementing a strategy in key markets, including countries such as Turkey, Saudi Arabia, Nigeria, South Africa, and Bangladesh, ensuring a robust and responsive presence across the region.
Saipem and Subsea7 have reached an agreement in principle for a possible merger. The proposed combination is expected to create a global leader in energy services.
The combination of Saipem and Subsea7, to be renamed Saipem7, will have a combined backlog of €43 billion, a revenue of approx. €20 billion and EBITDA in excess of €2 billion The global organisation of over 45 000 people, including more than 9000 engineers and project managers
The companies have highly complementary geographical footprints, competencies and capabilities, vessel fleets and technologies that will benefit the combined company’s global client base. The Saipem and Subsea7 shareholders will own 50% each of the share capital with Subsea7 shareholders will receive 6.688 Saipem shares for each Subsea7 share held.
Annual synergies of approximately €300 million are expected to be achieved in the third year after completion, with one-off costs to achieve such synergies of approximately €270 million.
The recent AGM of The Society for Underwater Technology (SUT) saw the announcement of newly appointed SUT Officers for the UK, Australia and the USA.
It was followed by a stimulating talk on The Crown Estate Marine Delivery Routemap by Alex Thompson Strategic Delivery Senior Manager at The Crown Estate.
SUT’S Chief Executive, Cheryl Burgess explained: “With Benj Sykes, Country Manager of Ørsted now in his second year as President, Mike Fearn of Bluefield Geoservices Limited becomes Chair; the Honorary Secretary is Dave Brookes of St
Jules and Gehrig Schulz of EPI is now the SUT’s Hon Treasurer.
Judith Patten and Ralph Rayner are now Hon Fellows”
• Professor Peter Girguis won the Captain Don Walsh Award for Exploration, a joint award with MTS
• Prof Deborah Greaves, University of Plymouth and SuperGen won the Lennard Senior Prize
• Dr Philippe Jeanjean, BP won the Mick Cook Award for Significant Contribution to Marine Site Investigation and Characterisation
• Jonas Wüst of Tethys Robotics was the winner of the Gwyn Griffiths Underwater Robotics Award:
JW Fishers Manufacturing are passionately dedicated to empowering divers of all backgrounds—whether a public safety dive team, police or fire department, commercial diving operation, military unit, or are a devoted recreational diver.
Their mission is to provide essential tools that enable you to carry out your important tasks efficiently and safely. Many police dive teams trust its advanced video equipment, reliable metal
detectors, and innovative sonar devices to locate crucial evidence, missing persons or valuable items lost underwater.
The Washtenaw County Sheriff's Office recently purchased a Fisher's MC-2HD Mini camera.
The Underwater Search and Recovery Team (USRT) is comprised of highly trained certified SCUBA divers from multiple divisions within the Sheriff's Office.
It is responsible for all water recovery operations within the County, including, but not limited to, the recovery of drowned persons. The USRT is also crucial in recovering criminal evidence and/or property within County waterways and is active in community water safety events.
WCSO Sergeant Joel Gebauer, Team Commander, states that the unit is working out great for their team. He states, “Our team utilises a variety of electronics to aid in the search of evidence ranging from side scan sonar, sector scan sonar, ROVs, metal detectors, and now the MC-2 HD camera system.
“Since the camera was delivered, we’ve deployed it in multiple training operations and evidence searches alike.
“It’s been beneficial not only for the topside support to monitor what the diver sees in real-time and to aid in searching for evidence but also for the diver to utilise the integrated dive light. The divers have reported that they like that the light is dimmable, so in areas of high silt or debris, it can be adjusted to prevent the search area from being over-saturated with light.
“Our team predominantly deploys surface supply diving equipment, and the camera cable is easily integrated into the diver’s umbilical and hasn’t had
problems getting tangled. Overall, we’re very pleased with the MC-2 HD camera.”
Fishers provides a range of video equipment tailored for diverse applications, ensuring you have the right tools for the job. A standout product in the lineup is the MC-2HD camera. This innovative, compact device easily mounts on Kirby Morgan helmets or can be utilised with an optional handle and added LED light.
This cutting-edge HD camera empowers divers to confidently navigate the depths while transmitting live video back to the surface team. Experience seamless, real-time communication between the diver and the topside crew, allowing for prompt guidance and support whenever needed.
NOR Offshore Rental (NOR) has ordered several units of Exail subsea Inertial Navigation Systems (INS) and Attitude and Heading Reference Systems (AHRS) as part of the company’s ongoing efforts to expand its rental equipment pool.
This latest order comes ahead of NOR’s new office opening in the Asia-Pacific (APAC) region, further strengthening its presence in the market and addressing the growing demand for highperformance navigation technology.
Exail INS and AHRS are engineered to operate at depths of down to 6000m, providing reliable and precise navigation data for both shallow and deepsea operations. Their robust design ensures consistent performance under extreme conditions, making them ideal for challenging subsea projects.
The addition of these systems to NOR’s rental pool of equipment will further enhance its capabilities in the APAC region, where demand for advanced navigation solutions is increasing.
Kraken Robotics has signed a definitive agreement to acquire3D at Depth for US$17 million. With a 15-year track record, 3D at Depth provides underwater LiDAR technology and services resulting in comprehensive, accurate data to enable informed decision making on underwater assets and infrastructure in a cost-effective, low risk manner.
Over the last three years, 3D at Depth has seen average project value increase by over 45% as demand for its subsea LiDAR technology. This is driven by needs for higher accuracy, enhanced data resolution, and need for the safe and costeffective management of underwater assets and infrastructure.
Teledyne Marine has integrated ClearSignal biofouling protection coating, into its SeaBat and BlueView sonar equipment. This enhancement is a welcome addition for customers who want durable, low-maintenance marine instrumentation.
ClearSignal is a nonstick, inert, and nontoxic coating specially developed to combat the biofouling of marine instruments. The coating reduces the amount of biofouling material that settles on the sonar systems, reducing maintenance costs while providing longterm operating reliability.
The ClearSignal coating is offered as an add-on to our products reducing maintenance downtime, and extended transducer life.
BREAKING WAVES ON THE WORLD’S COASTLINES CAN BE A MAGNET FOR SURFERS AND A HEADACHE FOR COASTAL DEFENCES
Leading UK and French scientists want to find out more about the impacts of coastal wave breaking on our climate system to plug a gap in current climate models.
Through an ambitious project led by scientists at University College London (UCL), the National Oceanography Centre (NOC) and the École Normale Supérieure (ENS) Paris-Saclay in France, scientists will use novel observations of coastal wave breaking with advanced modelling and machine learning to work out the importance of this notoriously complex and hard to measure phenomenon.
Specifically, the project, called WAVECLIM, will look to fill a gap in understanding about the role these often-dramatic coastal processes play in global climate modelling.
This innovative project is one of the first opportunity seeds in the UK's Advanced Research and Invention Agency's (ARIA)
Scoping Our Planet opportunity space, announced in October last year. ARIA’s seed funding supports ambitious research that can challenge assumptions, open up new research paths and provide steps towards new capabilities.
“It is well known that ocean wave breaking at the coast plays a big role in air-sea exchanges, sediment transport and coastal erosion”, explains Professor Christine Gommenginger, who leads the project at NOC. “But these complex coastal processes are largely absent from current climate models.”
“While waves in the open ocean are starting to be included in some climate models, coastal wave breaking is still disregarded”, adds Frederic Dias from ENS Paris-Saclay.
“This is a critical gap in our understanding of how coastal seas influence and impact the global climate system.”
The WAVECLIM project will change this using advanced sensor technology and machine learning to capture and integrate coastal wave-breaking dynamics into predictive models.
State-of-the-art monitoring equipment, including LIDAR, drones and stereoscopic cameras, will be deployed to provide unprecedented data on coastal wave breaking under diverse conditions.
Machine learning models trained on these observations will be integrated into climate models, addressing biases and enhancing the accuracy of future climate predictions.
“This pioneering approach builds on recent successes in embedding machine learning into climate modelling, promising more realistic projections at a fraction of the computational cost,” says Serge Guillas, principal investigator for WAVECLIM, from UCL.
Underwater positioning plays a crucial role in a wide range of subsea operations, from large-scale infrastructure projects to long-term monitoring of underwater assets. Exail Long Baseline (LBL) positioning system, featuring the Canopus acoustic transponder and Ramses acoustic transceiver, is renowned for its unmatched accuracy, robustness, and long-term reliability. This advanced technology has been deployed in numerous high-precision applications, including offshore oil and gas operations, deep-water pipeline monitoring, subsea infrastructure installation and scientific research.
LBL positioning is an established and highly effective technique for underwater navigation, particularly in water depths where USBL does not yield the expected accuracies. The system operates by deploying multiple seabed-mounted transponders as fixed reference points. A mobile transceiver, typically mounted on an ROV or AUV, interrogates these transponders, which then respond with
acoustic signals. By measuring the travel time of these signals and compensating for the sound velocity profile and ray bending, the system calculates the position of the mobile unit with high accuracy.
Exail LBL solutions feature Canopus transponders and Ramses transceivers, which provide exceptional stability and precise positioning. In addition, Exail inertial navigation systems (INS) offer reliable positioning even in challenging environments where acoustic signals may be temporarily blocked. This combination of technologies ensures continuous, reliable, and highly accurate subsea positioning across a range of operations.
MINIMISING OPERATIONAL DOWNTIME IN OFFSHORE OIL AND GAS
Exail LBL systems have proven essential for offshore oil and gas operations that require high precision and minimal operational downtime. In a West African project aimed at expanding an existing oil field, Canopus transponders were integrated into an already established LBL network to facilitate the accurate installation of new subsea flowlines.
After carefully calibrating the new Canopus beacons with the existing array, the system enabled the precise positioning of subsea vehicles during pipe deployment. This ensured the installation process proceeded smoothly, without delays or interruptions to ongoing operations. The system’s key benefits included high accuracy, robust performance in harsh subsea conditions, and efficiency with fewer transponders, making it an ideal solution for complex tasks.
AUTONOMOUS, REAL-TIME MONITORING FOR PIPELINE INTEGRITY
Exail LBL solutions were also deployed to monitor the position and integrity of gas
pipelines, which are essential for transporting gas across vast underwater distances. These pipelines, resting on concrete structures, are susceptible to shifts caused by environmental changes, seabed movement, and fluctuations in gas pressure. To monitor these critical subsea assets, Canopus transponders were strategically deployed on expansion loops.
These transponders provided continuous, real-time tracking of the pipeline's position, ensuring that any movements or displacements were detected early. The autonomous, long-term monitoring system offered engineers invaluable insights into the pipeline’s behavior, allowing them to make informed decisions about maintenance and ensuring the pipeline’s long-term safety and stability.
Exail LBL systems have proven indispensable for environmental and scientific monitoring, particularly in tracking earth plate movements. Canopus transponders were strategically deployed off the southern coast of France and Sicily, around fault lines, to monitor tectonic plate movements and earthquake faults, with a deployment period of four years. These transponders provided continuous, highly accurate ranging data, enabling researchers to detect even the smallest shifts in the plates.
With their long battery life and
reliable autonomy, Canopus transponders are ideal for longterm monitoring in remote and challenging environments. The collected data has yielded valuable insights into seismic behavior and the dynamics of fault movements, contributing to a deeper understanding of global geological processes.
IMPROVED EFFICIENCY IN ROCK PLACEMENT AND SUBSEA INFRASTRUCTURE INSTALLATION.
Exail LBL systems are extensively utilized in rock placement operations, where rocks are placed on the seabed to stabilize or protect subsea infrastructure such as pipelines. In a rock placement project in Turkey, Exail Ramses transceiver and INS were deployed to guide a fall pipe remotely operated vehicle (FPROV) in accurately positioning rocks on the seabed.
The system’s ability to operate with fewer transponders while maintaining decametric accuracy, despite the high noise environment, significantly
improved operational efficiency and reduced complexity. This high-precision navigation not only ensured the proper placement of rocks but also supported the installation of other subsea infrastructure, including offshore wind farm foundations and subsea cables, where accuracy and reliability are equally critical.
Exail is pushing the boundaries of subsea positioning technology with its innovative LBL systems. Combining Canopus transponders, Ramses transceivers, and inertial navigation systems, Exail delivers unparalleled accuracy and reliability across a wide range of complex underwater operations.
Whether monitoring pipelines, constructing underwater tunnels, or installing subsea infrastructure, Exail’s solutions ensure long-term, autonomous operation, seamless integration with existing systems, and exceptional performance in the most challenging environments.
The UK-based autonomous unmanned surface vessel (USV) developer ACUA Ocean has successfully completed the test launch of the USV Pioneer from its base at Turnchapel Wharf in Plymouth.
The launch of the USV Pioneer is a milestone achievement for ACUA Ocean as it sees its maiden vessel go to water for the first time.
The Pioneer-class programme began life in 2022 through funding from the UK Department of Transport’s Clean Maritime Demonstration Competition with initial concepts and designs developed by naval architect John Kecsmar of Ad Hoc Marine Design, a global leader in small waterplane area twin hull (SWATH) vessel design.
The launch is a major milestone for the Pioneer-class since completing its design phase in February 2024 before commencing build at Aluminium Marine Consultants (AMC) on the Isle of Wight in March.
USV Pioneer’s rapid design, development and launch meets two critical requirements for commercial and security end users.
It meets the increasing need to rapidly deploy the latest equipment and technology rather than multi-year procurement and build cycles of traditional vessels, while also bringing greater seakeeping stability and operational persistence not currently found in smaller monohull USVs capable of collecting data and deploying sensor and system payloads.
Digital simulations and scale wave tank testing undertaken by academics at the University of Southampton and the Wolfson Unit have shown the USV Pioneer, at 14.2m length and 25t gross weight, outperforms the stability and seakeeping capability of a monohull vessel over 10 times its displacement and 3 times its length.
Following the successful launch, the USV Pioneer now enters a three-month period of sea trials and crucial regulatory checks ahead of demonstrations in March 2025.
As part of the sea trials, ACUA Ocean will be working alongside Lloyd’s Register towards her Maritime and Coastguard Agency Workboat Code approvals.
Advanced 3D Imaging Beneath the Seabed
Discover the power of broadband, sedimentpenetrating Synthetic Aperture Sonar (SAS) for high-resolution imaging of buried objects.
• Unmatched Clarity
See through the seabed with precision
• Compact & Efficient
High performance with reduced size & weight
• Seamless Integration
Pairs with EdgeTech 2205 for full-spectrum obstacle detection
eBOSS
Redefining subsea imaging for faster, more effective site clearance
Over the past few years, a record number of uncrewed boats have started appearing on the market, marking a considerable amount of investment in the sector.
Belgian company dotOcean has envisaged a modular, stepwise automation strategy – taking an existing hull and employing its Automate Your Boat (AYB) technology. Adding its advanced control systems can make it capable of autonomous and semi-autonomous operation.
“The AYB unit is designed to automate electrical propulsion systems, encompassing thrusters, outboards, pod drives, and hybrid drives,” said Walter Driesen, Business development Manager at dotOcean.”With compatibility across a range of market-provided motors and battery packs, the AYB unit delivers seamless integration for diverse maritime applications.”
At the core of dotOcean’s system is a sophisticated AI-powered control unit that processes realtime data from multiple sources, including GPS, LiDAR, radar, cameras, and inertial measurement units (IMUs). These components work together to create a continuously updated digital model of the vessel’s surroundings.
“In congested waterways, for example, the system can detect nearby vessels, calculate their trajectories, and adjust speed or heading to maintain a safe distance. Unlike traditional
autopilots that follow static waypoints, dotOcean’s AI dynamically recalculates routes based on real-time conditions, ensuring efficiency and safety.
“The first step in designing the system is selecting the appropriate electrical motors and batteries,” said Driesen.”The choice of motor depends on the specific application, with a preference for dual-motor configurations to facilitate effective steering without a rudder. The AYB unit currently supports all Torqeedo motors, Blue Robotics thrusters, ELCO,
Ripower and RIM drive thrusters and any ESC-controlled thrusters.
“Choosing the correct hull is equally important for optimal performance. A stable hull design, such as an NRS cataraft or another catamaran-style vessel, offers superior stability. A single-hull design features higher compactness and easier integration of survey equipment."
“Once the hardware components are selected, the AYB unit is connected. The standard AYB unit package includes a remote control (R/C), GPS capabilities, and a
tablet interface, all bundled with a dotOcean Cloud subscription. A SIM card is required to enable internet connectivity (4G/5G). After inserting the SIM card, the necessary motor connections can be made, completing the setup process.
The R/C has its own communication channel and can always be used to overrule the autonomous decisions of the AYB unit. When needed, the cellular connectivity is combined with WIFI connectivity and/or satellite connectivity in order to generate an additional level of connectivity redundancy.”
One of the most crucial features of dotOcean’s automation suite is its collision avoidance system. Using LiDAR and radar, the boat continuously scans for obstacles, from large cargo ships to smaller kayaks and floating debris. AIS is used to capture position, speed and heading of larger vessel in the surrounding.
The objects detected by all these sensors are being combined (sensor fusion), resulting in a comprehensive situational awareness. For every detected obstacle, the AI assesses speed, distance, and potential risk before executing an avoidance manoeuvre.
Situational awareness is also extracted from nautical maps, providing information about quay walls, buoys, etc. The AYB interface allows the operator to add custom objects and no-go regions on the map. When combined with high accuracy GPS positioning (eg RTK), the AYB unit is capable of auto-docking: the AI then calculates the optimal approach angle and applies precise throttle and rudder adjustments to dock smoothly, even in challenging crosswinds or strong currents.
Another key aspect of dotOcean’s technology is its ability to define and optimise routes based on weather, fuel efficiency, and sea state. In the AYB app, the user can manually define a custom path to be navigated. The user can also define a region to be surveyed and ask the AYB app to automatically generate a survey grid while avoiding quay walls, obstacles and user-defined no-go zones. Finally, the AI can also integrate realtime meteorological data, tidal predictions, and ocean current models to recommend the most efficient path.
The AI-driven route optimisation, combined with the fact that uncrewed vessels are always smaller than crewed vessels with equivalent capability
results in significant fuel savings and reduced emissions.
The adaptive control system also fine-tunes propulsion and stabilisation mechanisms.
Whether managing a twin-engine motor yacht or a single-prop fishing boat, the AI continuously adjusts throttle, trim, and rudder positions to maintain stability and optimise fuel burn.
OVER-THE-AIR
“Connectivity is a key feature of the AYB system,” said Driesen.
“Using 4G/5G, wifi and/or satellite technology, the AYB unit establishes a direct link to the dotOcean Cloud platform without
USVs of several sizes that can be acquired as a commercial product from our partner GEOxyz
requiring line-of-sight communication.
The AYB app in the dotOcean Cloud platform enhances operational efficiency by providing augmented maps, allowing the AYB module to make real-time navigational decisions. “These maps enable trajectory planning, area coverage optimisation, and object avoidance, ensuring smooth and reliable vessel operations.
“Through an onboard IoT (Internet of Things) module, boat owners can remotely monitor key metrics such as engine performance, fuel levels, battery status, and system diagnostics via a mobile app or web interface.
The AYB solution also provides bandwidth-adaptive video streaming to the dotOcean Cloud platform. In this way, even in case of bad internet connectivity, the remote operator will still see what is happening on and around the vessel while it is Beyond Visual Line of Sight (BVLoS).
Moreover, dotOcean provides overthe-air (OTA) software updates, ensuring that vessels stay equipped with the latest AI improvements and navigation algorithms. As machine learning models continuously improve from fleet-wide data collection, each vessel benefits from collective intelligence, learning from thousands of hours of real-world maritime conditions.
For deployment in very remote locations or in case connectivity to the internet is nonpreferred, the AYB solutions can be configured to operate in a stand-alone, local cloud mode without connection to the public internet.
dotOcean is collaborating with the Belgian Navy and the Royal Military Academy (RMA) on the groundbreaking Triple Helix research project MARSUR and its follow-up project MULTIMETER.
The MARSUR vessel created by dotOcean and RMA is an autonomous maritime vessel designed to enable operations with multiple heterogeneous unmanned maritime assets. Its capabilities include autonomous navigation, remote control, and coordination with other unmanned vehicles. The MARSUR is equipped
In the AYB app the user can manage autonomous tasks for several USVs at once
with advanced sensors (radar, AIS, 360° camera, PTZ camera and Lidar), communication systems, and onboard processing capabilities, allowing it to operate effectively in various maritime environments.
This collaboration enables coordinated missions, including surveillance, reconnaissance, environmental monitoring, and maritime security operations.
The GeoDrone 1800 and 3000 are autonomous surface vessels equipped with advanced sensors for survey applications. It can navigate shallow waters, collect data from both the seafloor and water column.
Its stable platform ensures high-quality data collection for various applications such as marine research, environmental monitoring, and hydrographic surveying. Overall, it autonomously conducts surveys, enhancing safety, affordability and data quality in marine operations. dotOcean has been collaborating with GEOxyz on this development
The USV Echodrone is an innovative unmanned surface vessel designed for survey operations in
shallow waters together with the Port of Antwerp Bruges. Its primary function is to conduct regular depth measurements in port areas that are typically challenging for manned vessels to access.
Equipped with advanced survey sensors and navigation systems, the Echodrone autonomously navigates and collects precise depth data, providing valuable information for port management and maintenance. Its low draft allows it to access areas that are inaccessible to larger vessels, expanding the scope of survey operations.
A marine contractor build their own vessel according to their requirements. dotOcean helped choosing motors and GPS. By adding the AYB unit, this marine contractor is now able to execute his own surveys and get real-time depth maps on his tablet. This greatly reduced their
operational costs per construction site.
MARINE LITTER HUNTER (MLH)
The MLH vessel was developed together with DEME Group in order to enable autonomous removal of marine litter that is floating on the river The Scheldt in Belgium.
The MLH is equipped with a large amount of sensors (radar, AIS, cameras and RTK GPS) and advanced health monitoring of the propulsion system.
The data from the sensors onboard the vessel are combined (fused) with data from vessels installed onshore (radar, tidal and current sensors) enabling the required situational awareness for autonomous navigation and auto-docking on the river in mixed traffic conditions (autonomous and crewed vessels operating in the same area).
Exail has announced the first sale of its DriX O-16, a transoceanic Uncrewed Surface Vessel (USV). Designed for long-range maritime operations, it has been acquired by an IndoPacific customer operating in the civil sector.
Equipped with advanced sensors, including a full-depth Multibeam Echosounder, the DriX O-16 enables operators to collect precise data for hydrographic, geophysical, and environmental missions. Its ability to deploy AUVs and ROVs enhances operational versatility and productivity as well as broadens the scope of its missions.
"The sale of our first DriX O16 so close to its debut is a testament to the trust our clients place in Exail’s forward-thinking approach to maritime autonomy," said Olivier Cervantes, Exail’s VP Maritime Autonomy Solutions. The vessel quickly set new benchmarks in efficiency, endurance, and flexibility, securing the customer's confidence just three months after its christening.
With its unparalleled combination of speed, endurance, and payload capacity, the DriX O-16 represents a groundbreaking step forward in Uncrewed Surface Vessel technology. It marks an exciting new
chapter in the evolution of USVs and their vital role in shaping the future of modern hydrographic, survey and inspection operations.”
As the maritime industry is undergoing a strategic shift toward adopting autonomous technologies and low-carbon impact solutions, the DriX O-16 supports this transition, offering operators a sustainable alternative to traditional crewed vessels.
Its hybrid propulsion and naval architecture minimise fuel consumption, while its optimised and innovative system architecture significantly reduces operational and maintenance costs, contributing to a lower environmental footprint.
British SME ZeroUSV is one step closer to offering the world’s first charter fleet of fully autonomous uncrewed surface vessels after its inaugural Oceanus12 touched the water for the first time at Manor Marine in Portland, Dorset.
The fully equipped vessel is now ready for commissioning and integration trials from ZeroUSV’s home port of Plymouth.
The launching of the first Oceanus12 represents the culmination of nearly 18 months of design, engineering and build effort from the team at ZeroUSV which has been built on the success of the Mayflower 400’s transatlantic autonomous voyage - a milestone achieved through the same inter-company collaborations between Zero USV’s parent company MSubs, their non-profit Promare and sister marine software company MarineAI.
The launch of the first vessel in the Oceanus12 series, does not though mean any let up in the pace and the coming weeks will see a series of key milestones achieved, with vessel two due to be completed in late March and vessels three and four close by.
The Oceanus12, designed for long distance over-the-horizon operations, has also been designed to be mission agnostic, allowing a wide range of potential applications: from surveys and monitoring of critical assets to safety, geophysical surveys, border control, fisheries, defence
and more. Since the “charter” business model was first announced just under 12 months ago, significant interest has been generated which has led to exciting opportunities for these first two vessels, information on which will be announced in the coming weeks.
The Oceanus12 is groundbreaking in multiple areas of technology: from its hybridelectric drive system, with twin drives for redundancy and efficiency coupled with sufficient onboard fuel for a cruising range of more than 2500 nautical miles, to the use of the only truly fully autonomous software stack on the market – MarineAI’s Guardian software.
The Oceanus12’s represents a seismic shift in what is possible with an uncrewed 12m vessel. With ZeroUSV not only owning and operating the vessels, but also the ROC (remote observation centre), the Oceanus12 is a true “turnkey” package for charter customers.
Zero USV founder Matthew Ratsey, said: “Oceanus12 presents a quantum leap forward in autonomous maritime technology and this is a seminal moment for the team here at ZeroUSV.
“We’ve created the world’s first complete solution - not just a cutting-edge 12m over-thehorizon USV available for charter, but also full maintenance and support to ensure 24/7 operations
with minimal downtime.
“Designed with safety and efficiency in mind, Oceanus12 can take on a wide range of offshore over-the-horizon tasks that would typically require a crew, eliminating on-water risks and associated costs, including significant environmental benefits afforded by it being crewless.”
Working under high pressure DeRegt delivers
Feel free to reach out and connect
Working in oceanic depths under great pressure requires cables and connections you can rely on. At DeRegt Cables we provide outstanding technical solutions and custom-engineered cable solutions for the most challenging of circumstances. When you are raising the bar, we deliver the right solution.
• Top notch cable design
• Reliable cable manufacturing
• High end cable termination
• Thorough cable testing
• Outstanding field service
Call us for the best connection +31 180 66 88 00
Zaag 2-4, 2931 LD Krimpen aan de Lek, The Netherlands info@deregtcables.com | deregtcables.com
Later this year, the Brazilian company Tidewise will complete work on the remaining two Tupan class uncrewed surface vessels (USVs), joining the pair that are already operational.
The company recently announced plans to further expand its fleet and venture into the development of larger vessels to meet growing market demands. As a result, it will commence a 24m USVs called UMOVE in a project developed with Shell.
“We specialise in the development, integration, and operation of intelligent robotic systems to address challenges in the naval industry—be it in fluvial, port or maritime contexts,” said analyst Guilherme Cazé.
“Our mission is to accelerate the transition to a safer and more sustainable industry by aligning technology with enhanced safety, reliability, and significant reductions environmental impact and operational costs.”
In the defence market, Tidewise is better known for its Suppressor USV but sees its multipurpose Tupan range better able to performing a wide range of offshore operations.
Measuring approximately 5m in length, the vessel is constructed from marine-grade aluminium, ensuring durability in challenging offshore environments. It features a diesel-electric propulsion system that provides efficient energy consumption, allowing for continuous operation of up to seven days without refuelling. The
vessel can reach speeds up to 6.5 kts and has a payload capacity of 200 kg, making it able to accommodate various sensors and equipment for a diverse mission requirements.
“The Tupan USV is engineered to execute multiple maritime tasks, including:
MARINE SITE CHARACTERISATION
Equipped with advanced hydrographic sensors, the Tupan can conduct detailed bathymetric surveys, collecting high-resolution data essential for seabed mapping and underwater inspections.
The vessel can be integrated with an inspection-class Remotely Operated Vehicle
(ROV) capable of reaching depths up to 100 meters.
This configuration enables the inspection of subsea assets such as cables, pipelines, risers, and hulls, ensuring structural integrity and early detection of potential issues.
By deploying Unmanned Aerial Vehicles (UAVs) from its deck, the Tupan enhances its capacity to monitor large maritime areas. This capability is particularly useful for detecting oil spills, monitoring wind farms, and conducting surveillance operations.
The Tupan can be configured to transport small loads, carrying out transshipment activities involving cargo up to 200 kg.
This feature is beneficial for delivering supplies to offshore installations or conducting search and rescue missions.
The Tupan us equipped with advanced technology to enhance
its operational efficiency:
• Navigation and Control: The vessel uses WiseControl, a proprietary software system that enables autonomous navigation and mission planning. It also features an obstacle avoidance system comprising trajectory planning and situational awareness subsystems, ensuring safe operations in congested maritime environments.
• Sensor Suite: The Tupan can be outfitted with a variety of sensors including multibeam echo sounders for hydrographic surveys and LiDAR systems for precise environmental data collection. These integrations allow for comprehensive data acquisition across different mission profiles.
Since its launch, the Tupan USV has achieved several significant milestones:
• The vessel successfully completed a 43-hour
uninterrupted operation, covering approximately 230 km. This demonstration showcased its endurance and reliability for prolonged offshore missions.
• The Tupan conducted the firstever autonomous vessel operation in Brazil's Pre-Salt region, navigating over 120 km offshore while being remotely monitored by operators in Rio de Janeiro.
This operation reinforced the reliability of its control systems and redundant satellite communication links.
“The Tupan USV exemplifies the potential of autonomous surface vessels in revolutionising maritime operations. Its versatile design, advanced technological integrations, and successful operational deployments position it as a valuable asset for various offshore applications, from environmental monitoring to asset inspection and logistics,” said Guilherme Cazé
INFLATABLE Autonomous Surface
Vessels (ASVs) represent a novel category of marine robotics optimised for light weight construction, portability and adaptability.
These vessels are designed to address operational challenges across diverse aquatic environments, providing significant advantages over traditional rigidhulled ASVs. There are numerous technical benefits.
A standout feature is its portability and rapid deployment capability especially for time-critical missions. These vessels are also easy to handle and deploy without requiring heavy lifting equipment. It makes them a choice for operations where mobility and setup speed are essential.
In terms of durability, inflatable ASVs provide robust performance.
Their inflatable hulls are engineered to absorb impacts effectively, reducing the likelihood of structural damage from collisions with obstacles like rocks or piers. This impact resistance is particularly valuable in shallow, debris-laden, or high-risk environments where traditional rigid-hull vessels might sustain more significant damage.
Moreover, the soft, deformable structure minimises the risk of harm to surrounding vessels, infrastructure, or sensitive ecological zones, making them safe for deployment in congested or protected waterways.
Manufacturing costs are generally lower than those for rigid-hulled ASVs due to the use of flexible, lightweight materials.They tend to be fabricated from lightweight, high-strength materials such as Hypalon or PVC composites. Maintenance requirements are minimal, with repairs typically involving straightforward patching techniques that can be performed in the field.
The operational versatility of inflatable ASVs is further enhanced by their shallow draft which enables effective navigation in restricted or shallow waters where traditional ASVs might encounter difficulties. The lightweight hull design ensures good manoeuvrability in dynamic environments, extending their operational range to areas that might be challenging for heavier, rigid ASVs.
Deflated, these vessels occupy minimal space and can be packed into compact cases, reducing storage requirements and enabling standard shipping methods.
This logistical flexibility is particularly beneficial for field operations requiring frequent redeployment or for teams with limited transportation capacity.
By eliminating the need for specialised shipping and storage, inflatable ASVs offer a streamlined solution for geographically dispersed missions.
Environmentally, inflatable ASVs
demonstrate a lower ecological impact compared to traditional alternatives. Their lightweight construction and shallow draft minimise disruption to aquatic habitats, making them suitable for sensitive ecological surveys or water quality assessments.
Ease of handling reduces operational complexity, especially in scenarios requiring frequent launches and recoveries.
DotOcean’s Calypso was one of the very first inflatable autonomous survey platforms to reach the commercial market.
With a board length of 1800mm and a 210mm draft, it can carry payloads of up to 150g.
It is controlled by a R/C controller and/or a tablet with Internet connection to allow autonomous operation.
The Calypso uses its Cloud Link subscription to allow autonomous operation control, data visualisation and data storage.
The Calypso can be equipped with a Single Beam Echo Sounder (SBES), Multi Beam Echo Sounder (MBES), Sub-Bottom Profiler (SBP) or various other types of sensors like a camera, lights, gas sensors, temperature sensors,
ADCP or water sampler.
It is powered by a pair of 24V battery modules in individual waterproof cases
In its standard configuration, the Calypso is delivered with one black case that contains all electronics and has place for a 12V battery. However, this battery is not included in this standard configuration in order to allow for
Length board 1800mm
Width board 925mm
Draft 210mm
Weight 25kg
Payload 150kg
Endurance
Minimum 4 hours with a 12V/100Ah battery
Control Cloud control and R/C
Propulsion 2x 12V underwater thrusters (standard) 2x 24V underwater thrusters (optional upgrade)
Speed Max 3 knots (standard)
Max 5 knots (with 24V propulsion upgrade)
Steering
Differential control of the dual thrusters
Sensor mount 2x @100mm moon pools
Standard GPS accuracy 3000 mm (option for RTK GPS available)
easier and faster international shipping by air freight.
The user can choose to operate the Calypso with both 24V batteries
Inflatable ASV’s allow the operated to focus on the data and not the deployment. So says the Australian company Surfbee. It offers three main models of differing capacities.
The first is the Flow Seeker which Surfbee considers the daily driver and workhorse of its range. It is designed for a wide variety of gauging sections and sensor deployments.
modules at once (double energy autonomy) or with only one 24V battery module onboard (allowing to charge the other battery module at the same time).
pod which contains the control system and battery set. This module seamlessly integrates with the control system, providing a multiport plug for device connectivity. For some sensors, this connection hub can also provide power (12v 2 Ah)
It carries a Dual GNSS system with an onboard camera, an arrangement repeated across the range. Behind is an ADCP sensor which allows the vehicle to take autonomous transects and bathymetry readings.
Flowseeker is 1.65 m long and 0.7m wide. It contains two thrusters, a T 600 thruster on a keel and a T300 centre rear thruster which gives it a top speed of 4 m/s (3m/sec cruise speed). It weighs 13.5km excluding batteries and can carry a maximum payout of 10 kg yet it has a minimal draft of only 0.25 m.
Above the inflatable hull lies the
Flow Seeker
Dimensions: 1.65m x 0.75m x 0.1m
Weight: 13.5kg (without batteries) Max speed: 4m/s (3m/s cruise)
The the control body is designed to securely attach specific sensors or communication boards. Surfbee has designed these mounts to be highly adaptable, allowing for quick sensor swaps to meet various project needs in a single vessel. There are mounts for the Sontek M9, PCM, Sontek RS5 and RDI RiverPro.
The second vehicle is the Flow Scout, which Surfbee designed, to work in shallow waters. It is 1.35 m long and 0.7 m wide.
It is equipped with three underwater thrusters which gives it a top speed of 2 m/s. It weighs 11 kg without batteries and has a maximum payload of 8 kg.
It is designed to adapt to different sensors arrangements which the company says, ensures precise control through
SubCtechGmbH
Modular,easytouseandreliableauto-calibration monitoringsystemsforleakdetection(e.g.oilin water,Methan,pCO2),subsea/environmental monitoring&sampling.
Li-ionUnderwaterPowerSolutions
Highlyreliable,efficientandsafeLi-Ionbatteries Madeforharshoffshoreandsubseaconditions!
Flow Scout
Dimensions: 1.35m x 0.7m x 0.1m
Weight: 11kg (without batteries)
Max speed: 2 m/s
Minimum depth: 0.14m
autonomous movement, even in challenging conditions like windy and slow-moving channels.
The smallest of the three is the Flow Finder, which has a length of 1.2 m and is 0.7 m wide. It weighs 11 kg without batteries and has the maximum payload of 8 kg. This vessel is designed specifically for
Sontek RS5 deployment, taking advantage of the ADCP's new small form factor and depth range. Surfbee claims that it offers superior shallow water performance, and propelled by three underwater thrusters, it has a top speed of 2 m/s.
It features autonomous lateral movement for vessel control in difficult conditions such as windy, slowmoving irrigation channels.
Flow Finder
Dimensions: 1.2m x 0.7m x 0.1m
Weight: 10kg (without batteries)
Max speed: 2 m/s
Minimum depth: 0.14m
The AirCAT was developed by Subsea Tech in response to a challenge from a customer that required a complete USV and Multibeam Echo Sounder solution, able to operate at sea yet small enough to be easily transportable.
The designers came up with a novel inflatable catamaran design capable of operating in either teleoperated or fully autonomous modes. It can be packed into a bag and two cases that comply with the standards for checked luggage on airplanes.
The design is available in two versions.
The AirCAT 270 is 2.74m in length and 1.54m in width and weighs only 42 kg yet can can carry up to 180kg.
Subsea Tech also offers an AirCAT 400 version. It has a length of 4m and a width of 1.98m. Both stand 1.25 m high excluding antenna. The nominal draft is 10 cm with the motorised or 30 cm with the motor engaged.
The AirCat is manufactured from ultra-durable PVC structure with double inflatable tubes which ensure optimal buoyancy, even in the event of a puncture in one of the tubes.
The design offers good stability on both inland and coastal waters up to Beaufort 3 and can operate in 5kt currents.
single electric 24v DC 1100W outboard motor powered by a modular 100Ah LiFePO4 battery compartment providing an average endurance of 4hours. This can be doubled or even trebled (12 hours) with additional batteries, thanks to its high payload capacity.This all gives the vehicle a speed of 6 kt.
Communication is based on a 5GHz high speed Wi-Fi link with a range of 3 km backed up by a 4 GHz radio link. The navigation system is also assisted by HD colour camera mounted on a 360° turret and navigation lights.
Optional equipment includes an AIS system and an obstacle avoidance function. Its autonomous navigation software supports point-to-point routing,
The AirCAT is powered by a AirCAT
Vortex has just released their water / glycol powered 4 and 6 inch dredge build to run on the Schilling GEMINI WROV platform and any other water / glycol hydraulic system.
Using the same power motor and pump to maximise efficiency and suction performance this tool adds further capabilities to the GEMINI with day-to-day tooling such as dredging that give the ROV more work scope flexibility.
Suction capabilities 4 inch - 70 kpa using 162lpm (43 GPM) @ 206bar (3000psi)
Suction capabilites 6 inch - 40 kpa using 162lpm (43 GPM) @ 206bar (3000psi)
In recent years, uncrewed sensor platforms have gained significant popularity in the survey marketplace as people quickly recognised the cost advantages of autonomous data gathering.
Devices ranging from drifting data buoys to highly sophisticated but expensive autonomous surface vessels have been particularly active in providing services for the offshore wind sector.
One company, Plymouth-based Oshen, has identified a niche within this market: providing a much smaller autonomous platforms with a hull length of approximately one meter. These platforms can deliver large amounts of data while maintaining a price point well below many competitors in the market.
“Any small hullform has two major practical ramifications,” said cofounder Anahita Laverack. “They are considerably cheaper to manufacture and much easier to deploy.”
Some of the larger autonomous surface vessels need to be taken on-site and lowered into the water using a crane or towed by relatively large and expensive mother vessels. Smaller hullforms, however, require much simpler deployment systems.
Oshen is focusing on applications that require persistent data collection and wide spatial coverage—where deploying 10 or
even 50 devices in one location would be practically beneficial “This is particularly useful for weather forecasting,” Laverack added.
“Organisations such as the Met Office typically receive just one datapoint from an area, typically from a moored buoy. We're aiming to provide much higher spatial resolution of data from an adaptive network - picture a fleet of platforms automatically repositioning as needed. Not just to better predict the weather in general, but more importantly, to enable warnings of severe weather events.
“We are currently running a project to compare the data we collected from a recent mission in severe weather with up to 8m high waveswith the forecast from UKV, the high resolution weather model for the UK.
“Another application is marine mammal monitoring, potentially as part of the environmental assessments required before setting up an offshore wind farm. Presently, this is performed by ships or drones counting counting cetaceans, such as dolphins as they surface.
“Marine domain awareness not the same as the marine mammal monitoring side! Instead, we envision a fleet of fleet of five to ten of our devices operating for months in a proposed offshorewind side, providing a clearer baseline of cetacean activity though our high spatio-temporal coverage. We also envision marine domain awareness applications.
Oshen USV
For example, when addressing illegal fishing, having as many platforms as possible to detect audio signatures is ideal. A large, low-cost network of autonomous vessels with a small form factor, particularly windpowered for long durations, provides an excellent solution.”
“There is a lot of work being carried out around the general concept of numerous vessels working together in a swarm, constantly intercommunicating and aware of each other’s positions,” Laverack concluded.
Small, low-cost vehicles have a limited energy budget, so we need to find more efficient ways to coordinate vessel control information and receive the data. This can be done from a mothership or even from land We have 9 platforms, and have operated in three continentswe have one in the Pacific.
There are several wind-powered autonomous vehicles on the market, although few, if any, are as small as this. The company advised customers that its first generation platforms could operate in up to 2.5m wave heights, but recently pushed the operating envelope further, including a recent mission in a storm with 70mph forecast winds and 9m high waves.
While the rigid sail provides propulsion, power for the onboard electronics and sensors comes from solar panels mounted on the deck. Standard sensors on the vessel include those for wind speed and direction, air pressure, air
temperature, and humidity. It can measure significant wave height, maximum wave height, wave period, and sea temperature at depths of 0.1m and 0.7m.
Additionally, it features a passive acoustic and visual data collection system, though the exact payload is tailored to specific work requirements.
The hull is fabricated from fibreglass, though the structure can be constructed in various ways. The rigid wing sail is made from fibreglass or carbon fibre and is supported by internal struts.
Sail-powered USV
Ocean observation is critical to making informed decisions to protect and preserve the delicate balance of the planet for future generations. It plays an integral role in national security, determining how to defend offshore and onshore assets; creates a time series of ocean data necessary for understanding how climate change is impacting extreme weather events.
The US National Data Buoy Center (NDBC) says there are only about 100 weather buoys to cover almost 100 000 miles of United States coastline. The buoys are located in areas critical to forecasting and in areas that are highly difficult and dangerous to operate in, providing in situ
awareness for mariners, such as fishermen.
The NDBC Director Dr. William Burnett says there is an urgent need for what he calls a system of systems to resolve observation gaps.
“ We need a conglomerate of moored and uncrewed systems working together to resolve ocean observation gaps to protect our communities and grow our economy.”
Saildrone uncrewed surface vehicles (USVs)are very similar to weather buoys in the marine observations that they collect. Like buoys, they can stay in one place to provide a timeline of
data or be tasked with collecting targeted observations in a much larger area,which would otherwise require a whole network of buoys.
“Using Saildrone USVs could improve the larger picture of ocean observations” said Burnett.“Targeted observations could improve numerical weather prediction and provide broader spatial awareness in undersampled areas, where it might be cost-prohibitive to deploy a group of buoys. In some national marine sanctuaries, buoy moorings and anchors are harmful to the seafloor. In the event of buoy outages, uncrewed systems on standby can be deployed to maintain observations in key areas.”
Characteristic / Class
Last October, AUKUS partners cooperated in Exercise Autonomous Warrior, a large-scale demonstration of advanced autonomous vessel capabilities. An important feature of the exercise was Ocius’ uncrewed surface vessel Bluebottle. This has been gaining considerable interest in recent years.
Back in 2022 Ocius received a procurement contract for five vessels from Royal Australian Navy, followed by three more in 2023. In June 2024 it received an order another seven. This has caused Ocius to ramp up production capability and will soon meet a level of one vessel per month. By establishing a preproduction facility, the company is actually on track to reach a production rate of one vessel per week by mid-year. It is envisioning producing a fleet of 1000 autonomous vessels globally within the next 10 years
Ocius also recently announced a collaboration with BMT, to revolutionise maritime data collection and management, providing DaaS (data as a service). The companies will focus on co-developing a commercial model, initially targeting environmental monitoring for offshore wind development projects.
“The Bluebottle platform can operate in a variety of applications”, said CEO Robert Dane. “It can carry out Environmental Monitoring ( collecting data on sea life, water quality and other environmental parameters); Metocean Data Collection (providing accurate meteorological and oceanographic data to support maritime operations) and Security and Surveillance (providing real-time data on maritime activities).
“This innovative approach enhances the efficiency and effectiveness of maritime operations and offers significant cost savings compared to traditional monitoring methods. Bluebottle vessels have now completed
78 000 miles, equivalent to 3.5 times around the world at the equator and the current vessels average 1000 miles/week in a diverse range of maritime conditions from doldrums to storms.
Bluebottles USV come in two forms, the Bathy and Beth but both are characterised by high power, payload and performance. They have similar footprints and can operate under all conditions and remain at sea for months at a time.
The Beth is powered by solar, wind and has a rudder flipper that harnesses the wave energy, while the Bathy additionally has diesel hybrid propulsion. In both, the sail represents the main form of propulsion. This can fold down if the wind gets too strong and doing so may also provide a tactical advantage while allowing the vehicle to escape from strong currents.
The Bathy is 400 kg heavier and at 2000 W, has twice the allocated payload power. The payload includes MBS, side scan sonar and sub bottom profiler. There is a keel winch to lower sensors to variable depths.
Ocius also recently announced a collaboration with BMT which could revolutionise maritime data collection and management by providing DaaS (data as a service). The two will focus on codeveloping a commercial data collection and management model, initially targeting
environmental monitoring for offshore wind development projects. With the aim of deploying a fleet of 1000 autonomous vessels globally
within the next 10 years, BMT and Ocius will be able to provide a persistent and networked system of remote sensors to support a range of applications.
Introducing the Roto Climber Assessor Mini, our smallest and most lightweight device for cleaning and inspecting smaller sizes of pipe from 6” to 12” in diameter
• The Roto Climber Assessor Mini offers multiple inspection choices with four high quality cameras
• Cleaning: can be equipped with either Caviblaster or UHP water cleaning systems
• Inspection: can be equipped with Spot UT, Pulsed Eddy Current or Phased Array UT
• Visual: equipped with four DWE Explorer HD 2.0 (four units simultaneous stream) each with a resolution of 1920 x 1080 pixels
• Lightweight and compact
• Battery powered
• Small crew better HSE
• Minimal platform footprint
• No vessel needed
• Easy mobilisation
• 6 to 25 times cheaper than traditional methods
• Less carbon intensive
Last year Sailbotix was launched, offering a range of micro autonomous boats, engineered for extended data collection over months at sea. The company was founded by Colin Angus, a co-founder of Open Ocean Robotics.
“The inception of Sailbotix was driven by the ambition to overcome several pervasive challenges within the USV industry, including regulatory hurdles, prohibitive costs, and issues with reliability,” said Angus.
“Larger uncrewed surface vessels often face operational difficulties due to stringent government maritime regulations. Sailbotix vessels, in contrast, are designed to be compactenough to qualify as steerable buoys (legally categorised as “flotsam”), thereby avoiding regulatory challenges.”
The hull, decks and sails are made with vacuum infusion technologies and are comprised of S-Glass and vinylester resin. Vinylester has almost the same mechanical properties as epoxy but is better suited for vacuum infusion.
S-Glass is an exotic composite with similar strength to carbon fiber. Unlike carbon fibre, it is transparent to radio waves, so is more suitable for housing antennas within the hull and is invisible to radar.
The solar panel is 20 watts, and will generate about 40-100 Wh/ day.The vessels use under 2 Wh/day for basic electronics, sensors and communications. The vessels can carry up to 4 kg (properly balanced).
A 300 Wh battery can store power and provide increased power for short periods.
Sailbotix offers three different models
The lowest cost boat, it is a trackable free drifter guided solely by the prevailing winds and currents. Measuring under 4ft (105 cm) in length, it is powered by a cloth sail. Its progress can be followed in real-time via a satellite tracking
It can be can be equipped with additional sensors to collect environmental data, such as water and air temperatures, barometric pressure, wind speed and direction, and wave height.
Data collected by this boat is logged onboard, and can only be obtained when the boat is retrieved.
“Normally, the boat sails passively straight downwind but the sail can be configured to propel the vessel sideways.” said Angus. “This is useful for launching the vessel from areas where the wind blows parallel or towards shore.
“An alternative option, suitable for research purposes, is having the sail drop into the water, turning into a drogue. This slows the boat down, making it an ideal platform for gathering metocean data. This option is called
SailTimer and is available in our store as an option. It is ostensibly designed as an educational platform.
Silicon Sailor highlighting read solar panels
Claimed to be the world’s most affordable deep-ocean Uncrewed Surface Vessel (USV), this employs a a a rigid wing sail controllable through satellite. It can operate non-stop for up to six months, even in lowsolar conditions
A proprietary feature of the design is the elimination of a traditional rudder for steering.
“The number one point of failure in sailing USVs is the rudder.,”said Angus.”The rudder is vulnerable to getting jammed or tangled in seaweed or debris.Additionally, the rudder servo (motor) is heavily worked.
“We have completely eliminated the need for a by balancing the rigid wing sail relative to the keel.
“The rigid sail revolves around a stationary mast using a magnetic coupling. By having the mast stationary, rather than an integrated part of the wing sail, it provides a stable mount.
When the angle of the sail is changed, the boat will passively sail at a different angle relative to the wind. Since the vessel is balanced, no rudder or control system is required to hold course. When winds are steady, the sail servo may not need to be moved for days.
Communication and control is achieved through LTE and satellite communications. A cloud-based dashboard allows data visualisation and vessel control from anywhere in the world.
Silicon sailor is only 105cm long and weighs 14 kg.
This is the same as Silicon Sailor, but with an auxiliary thruster motor, allowing the USV to thread its way through congested waterways and then carry on to cross an ocean.
The sail is still the primary mode of propulsion but the thruster is available when the wind dies or precise navigation is required. The highly efficient pod can power the vessel for up to 10hrs/day at 2kts using exclusively harvested solar energy
OCEANDRONE is an independent spin-off from INNOVO to deal with submarine robotics and autonomously guided surface naval vehicles.It develops mechanical and control systems inhouse. In recent years, the company had been carrying out R&D work on a 4.5m prototype. This is now complete, heralding construction of a new 9m USV for blue water activities..
“In recent years, we have undertaken numerous endurance tests to verify and validate its capabilities and features" said Stefano Malagodi, CEO of OCEANDRONE, the engineering and construction house developing the system.
“A key feature is the use of Artificial Intelligence (AI) in decision-making to improve operations and enable fully autonomous navigation in order to maximise efficiency and safety. The AI will process data from multiple sensors, including cameras, LiDAR and sonar, to identify and classify vessels and foreign objects. It will also analyse weather data information, enabling the vehicle to adapt its route to optimise safety and efficiency.
“In case of unexpected events or emergency situations, the Al can be programmed to respond appropriately, such as altering the route or
notifying the control centre. Furthermore its Collision Avoidance technology allows safe sailing in crowded and restricted waters.”
At the centre of the vehicle is its large rigid sail which is balanced by an underwater keel.
A feature of traditional cloth sails is that they can be drawn in to reduce surface area when suddenly encountering severe environmental conditions.
The OCEANDRONE design incorporates an innovative telescopic sail system. This patented mechanism allows the sail to be retracted either partially or fully into the pocket keel when not in use, protecting and preventing damage to the sail even if the vessel capsizes.
While the sail provides the primary propulsion system, it is complemented by and electrical driven propeller powered from a Lithium battery within
KATFISH™delivershigh-speed,ultra-high-resolutionsurveyswitharea coverageratesexceeding3.5km²perhour,reducingsurveydurations andcosts.Capturingover3billionpixelsperhour,itprovides30times moredetailthanconventionalsidescansonar-enablingaccurate seabedinterpretationandsuperiorUXO discriminationforconfident decision-making.
Formoreinformation,visitourwebsiteor meetourteam atOceanBusiness–StandU33.
the hull. This is constantly charged by solar panels on the hull and sails. The battery also powers the bespoke sensor suite and optional payload.
The vehicle is equipped with a diverse array of sensors and positioning systems, including cameras electro/optical, LiDAR, and a weather station, etc.
Additionally, it supports a range of payloads such as Side Scan sonar, multibeam, USBL, hydrophones, among others. These systems can be seamlessly integrated beneath the keel within a dedicated gondola.
OCEANDRONE supports a variety of communication systems, enabling beyond-line-ofsight (BLOS) operation. These include Wi-Fi, 4G LTE, and satellite communication.
The designers envisage that it will operate across various domains.of applications including seabed infrastructure protection, maritime domain awareness and a communication hub between land and sea.
“Potential markets include offshore energy, renewables, ocean sciences, marine environmental protection and military,” said Malagodi. “We believe it could also be attractive for telecoms, subsea data storage, ocean research, fish farming, seabed mineral exploration, carbon capture, hydrogen generation and ocean science.
Offshore Sensing’s Sailbuoy design was one of the very first autonomous sail powered vessels on the market. The Sailbuoy MK 4 uses wind power for propulsion with solar panels providing power for the electronics and actuators. Data communication and control are established in real-time using the satellite system through a user-friendly web interface.
In 2018, it became the first USV to autonomously cross the Atlantic, proving its endurance and reliability. By 2024, over 30 Sailbuoy units were sold to energy companies, government agencies, and defence organisations, reflecting the growing demand for sustainable, cost-effective ocean data collection.
“The Sailbuoy technology makes the vessel use very little power,”
attractive platform for high latitudes with limited light.
To conserve energy, the sensor payload can revert to a low-power state until the Sailbuoy arrives at the area of interest or until the solar panels recharge the payload batteries. This is a unique feature not found on other autonomous vessels.”
“The sea surface is a harsh environment with many mechanical stresses, corrosion, and wear. An uncrewed surface vehicle has to withstand this environment for long periods of time. The Sailbuoy is designed and tested to withstand the environmental stresses of the North Sea, including cold, severe weather and little sunlight during the winter.
They currently operate across Europe, North America, South America, and Australia, supporting environmental monitoring, defence, offshore operations, and
The Sailbuoy has a length of 2m and displaces 60 kg. It can carry a 10 kg payload and move at speeds of 1-3 kts. It has passed tests in 30 m/s winds and has a mission duration of 6 months. The solar panels provide 30W of power.
Introducing Ally—VideoRay’s latest Mission Specialist underwater robot
Compact yet powerful, VideoRay’s new four-thruster Remotely Operated Vehicle (ROV) offers top-notch agility with speeds of 4 knots.
Compatible with our full line of Mission Specialist topsides and vehicles, Ally is the ideal tool for your day-to-day operations and/or fleet expansion.
Autonomous Marine Systems (AMS) has developed a patented twin-hulled uncrewed oceangoing robot powered by wind and solar.
The kickstarter campaign to develop a self righting sailing catamaran originally commenced in 2013. A year later, AMS moved to Massachusetts to become a part of the robotics community clustered around MIT, WHOI and other established maritime institutions. 2016 saw a seed round to fund the DATAMARAN Mark 7.
By 2019 the next generation DATAMARAN Mark 8 advanced multi-hulled autonomous sailing platform was launched.
Last year, AMS was acquired by JASCO Applied Sciences.
The Mk 7 was conceived for small, power frugal, sensor packages. With a length of 3.7 m (12ft), a beam of 2m (6.6 ft), a mast height of 3.1 m (10.2 ft) above water and a 0.3 m (1ft) draft, it has a displacement 192kg (425 lb) fully loaded.
It has a minimum speed of 3m/s and the maximum of 21 m/s. It has a typically end endurance of six months. The hosted payload is contained in a package 1m X 0.2 m X 0.2 m per hull It has through-hull access to water.
The Mk8 version is larger at 5m (16.4 ft) in length, with a beam of 3.3 m (10.8 ft), a mast height of 4.0 m (13.1 ft) above water and a draft of 0.8 m (2.7 ft). It displaces 360 kg (800 lb)
The catamaran cat travel at a minimum speed of 3 m/s up to a
maximum of 20 m/s and also has a typical endurance of months
It has a larger payload of 1.5 m X 0.3 m X 0.2 m per hull and can accommodate a payload weight 70kg (150lb). The available power is 95W continuous, 200 W peak with 24, 12, 5 and 3V available
Communications systems include Acoustic (1 Kbps), Satellite (2.4 Kb) GSM (12 Mb) and Wi-Fi (35 Mb) along with an AIS Class B transceiver.
It is designed for advanced metocean surveys including taking wind velocity profiles with altitude, water current, conductivity, temperature profiles with depth, hiresolution bathymetry, subbottom profiling, magnetometer measurements.
SubSeaSail (SSS) has received an award from the U.S. Department of Defense's (DoD) National Security Innovation Capital (NSIC) to help move its semisubmersible HORUS vehicle through manufacturing engineer design and long-duration testing into mass production (contract
Automatic mechanism that optimises sail position
manufacturing) as rapidly as possible. The multi-million dollar award from NSIC will help reduce the time to market for the SSS HORUS vehicle.
The HORUS USSV is an economical, long-duration sensor and payload platform. Wind is the primary source of propulsion with a thruster for station-keeping in low/no wind conditions and propulsion for near-shore navigation.
Solar panels charge the battery arrays to power sensor packages, payloads and thruster. The platform is capable of full autonomy, swarming, and manual modes.
The hull below the surface with wingsail above (patented): This reduces friction/drag with very little wake and a very low visual signature - or high visual signature if preferred.
The passive wingsail control mechanism does not include electronics, lines, or pulleys are required to optimally position the sail with respect to the wind direction, speed and desired path.
This feature significantly reduces cost and complexity, while increasing reliability. A single electro-mechanical servo for the rudder is the only moving part required for sailing control.
The user can select Solar power within the wingsail; a transparent wingsail and solar deck at the waterline for a lower visual signature, or a combination of panels on the deck and wingsail.
SSS is focused on design, prototype development, testing and sensor package and communication integration. It plans to outsource production to experienced contract manufacturing organisations that
can ramp up production rapidly as demand warrants.
NSIC is a component of the Defense Innovation Unit (DIU) that has a mission to accelerate commercial technology into the DoD. NSIC provides funding to early-stage companies to accelerate product development for innovations that can be used for both commercial and national security applications.
The HORUS sailing and in profile
Ocean Aero’s Triton is the world’s first and only Autonomous Underwater and Surface Vehicle (AUSV). It can sail and submerge autonomously to collect data both above and below the ocean’s surface and relay it to you from anywhere, at anytime.
The Triton was built to be versatile and to handle a range of missions across a number of industries. Our pre-packaged
payloads will cover 90% of the applications in the defence, research, and off-shore energy sectors, but the system is designed to support rapid NRE efforts for more specific usecases.
Optional state-of-the-art payloads include advanced modal communications for high bandwidth data transfer in remote areas as well as obstacle avoidance software/hardware to ensure autonomous reactions to unexpected mission complications.
The TRITON can sail autonomously for 3 months on solar and wind power at speeds of up to 5 knots. The TRITON acts a submarine and can submerge autonomously for 5 days at a time at speeds of 2 knots.
On-board communications packages include iridium, WiFi, 900Mhz, and some of the most advanced radio mesh networks in the world. Additional communication equipment can be outfitted to fit niche needs.
A lander deployment of the new camera system
Engineers in the National Oceanography Centre’s (NOC) Marine Autonomous Robotic Systems (MARS) team are leading the way in the advancement of marine technologies. They have developed a new standardised stills camera system to get a best of all worlds; crisp seabed imagery accessible across applications and disciplines, reducing barriers to entry and helping science join the dots. Dan Roper, MARS, explains
Subsea photography has been and remains an important tool in marine science. While a huge amount can be learned from broad swath acoustic techniques such as multi beam sonars, for very fine resolution measurements, nothing quite matches the resolution and information richness of optical images. Combined with high-speed strobe light sources, motion blur can be reduced in stills images, providing greater detail than freeze frames from rolling video, even with identical pixel resolution and focal length.
This type of camera system can be useful for a number of applications, including wide area ecological surveys and fixed location timelapse photography.
NOC has been operating both autonomous underwater vehicle (AUV_-mounted and timelapse lander cameras for some time. However, historically, these have used different camera systems to address needs specific to each application, each of which has its own challenges.
By taking tens of thousands of images of the seabed over a wide area, marine scientists can count species abundance in each image then average it out over a large area to statistically determine population densities.
This requires high resolution images to be able to accurately identify species – and the smaller the species, the smaller the pixel size required. Wide area coverage also typically involves mounting the camera on a moving platform, such as an autonomous underwater vehicle (AUV). This makes xposure time (the amount of time over which the light is measured) critical, to reduce any potential blur.
Timelapse images, where a camera is mounted to a lander frame, and images are taken periodically over the course of up to a year, also offer a wealth of information to marine scientists. This is a cost-effective way to understand long-term changes, such as how sedimentation changes though the seasons or the spawn cycles of coral.
Here, depth of field is an important requirement, to capture as much of the scene as possible. But this means operating with as narrow an aperture as possible, which means the sensitivity of the camera’s sensor is the limiting factor.
While, historically, different systems have been developed for both applications, MARS decided to develop a single system, harsh environment capable that could be used across both.
There are clear benefits to having a single system. A one-size fits all system would mean savings in terms of operator training and maintenance of systems and toolchains. It allows marine scientists to make a direct comparison of images taken in either application, which means
it’s easier to determine if a species identified by one system is the same as a species identified in the other – something that’s not a given when using different systems.
The new system builds on decades of work developing subsea systems, including underwater cameras and the highly successful previous generation of NOC Autonomous Ecological Survey of Abyss (AESA) stills camera system.
This system used a 5 mega pixel (MP) charge-coupled device (CCD) machine vision camera (formerly the default for laboratory grade digital photography), coupled with a Xenon high speed flash gun with a 1 millisecond exposure time.
Using a telescopic lens focusing on about 1 m sq of seabed at a time, it was able to resolve pixels down to 1mm in size, allowing identification of creatures down to a few centimetres in size.
Ready to be used in fixed locations or on mobile platforms
However, Sony, which manufactured the CCD sensor used in this system, has completely stopped making CCD sensors. This is because it now uses lower cost, lower power and now equally if not better performing, complementary metal oxide semiconductor (CMOS) sensors – the type more commonly found in consumer electronics such as smart phones and webcams.
So, for the next generation NOC AESA camera, a new sensor was selected from the Sony StarVis range of CMOS machine vision sensors, specifically designed for operation in low light applications and have become particularly popular amongst astronomy photographers.
The StarVis sensors also offer a higher pixel count, but they have a limitation around exposure time related motion blur, due to being on a moving sensor platform (the AUV). Instead, we decided to use the increased pixel count to increase the amount of the seabed that is captured with each photograph.
This was supported by retaining the AESA’s Xenon high-speed flash gun, providing exposure times that could not be matched by LED flash systems in such a compact form.
Finally, and critically, the system was built from the ground up with corrosion resistance in mind, so full ocean depth (6,000 m) titanium pressure housings were used, creating possibly the most corrosion resistant camera system at sea today.
The system has been deployed as a time lapse camera on a lander in both the Clarion Clipperton Zone (CCZ) in the Pacific Ocean and at the Porcupine Abyssal Plane Sustained Observatory (PAP-SO). Two-years’ worth of timelapse shots has been successfully collected, along with a number of shorter deployments focusing on higher frequency phenomena.
The AUV-based system was field trailed August 2023 from the RRS Discovery during engineering trials in UK waters. Following positive results, the system was deployed in January 2024 on the SMARTEX expedition in the CCZ, collecting around 18,000 seabed images in about 5,000 m water depth. These are being used to help understand this little explored deep seabed environment.
Moving forward, there is always a desire to keep up with the latest technology. While this does provide the highest quality images possible, in many instances its more important that the scientists can compare images taken from one year to the next.
This is particularly important when using the latest artificial intelligence (AI) image recognition techniques, as changes to the capture methods can invalidate training.
For this reason, we don’t plan to iterate the AESA camera system as frequently as commercial product lineups and are committed to supporting this next generation of AESA camera system through until 2035.
In May 2023, The University of Western Australia (UWA), led by Dr. Todd Bond, embarked on a landmark project to explore and monitor Australia’s deepest Marine Parks. Central to this endeavour was the deployment of two custom-built, long-term observatories, each equipped with SubC Imaging’s Autonomous Timelapse System.
These observatories are enhancing scientific understanding of deep-sea biodiversity and ecosystem connectivity by enabling continuous, autonomous data collection over 18 months.
Australia’s Marine Parks, including the Perth Canyon Marine Park and Gascoyne Marine Park, represent one of the world’s most extensive networks of protected deep-sea ecosystems. Despite their ecological significance, these regions remain largely unexplored due to the technical challenges of operating in the deep sea and their sheer size.
To address this knowledge gap, Dr. Bond and his team designed a project with three key objectives:
1. Explore, describe, and understand what animals inhabit Australia’s deep sea beyond 1000m.
2. Analyse connectivity between deep-sea animals across different locations.
3. Continuously monitor two abyssal plains, located 1000km apart, for 18 months.
Achieving these objectives required overcoming several critical challenges:
● Extreme Depths: Operating at depths exceeding 5000m required technology capable of withstanding immense pressure and low temperatures.
● Long-term Timelapse Imaging: Continuous, autonomous, highresolution timelapse imaging over long periods was previously challenging.
● Operational Durability: The system needed to maintain functionality without intervention for months in challenging conditions.
● Integrated Data Collection: Integrating imaging, environmental sensor data, and physical samples into a unified solution was essential for success.
Addressing these challenges demanded an innovative, adaptable solution capable of reliable, long-term performance in one of the world’s most demanding research settings.
UWA selected SubC Imaging’s Autonomous Timelapse System as the core imaging solution for their observatories. The system integrates a high-performance Rayfin camera and subsea LED lights, along with intuitive software for seamless programming and operation.
Designed for long-term, batterypowered deployments, this system enabled UWA to achieve remote, continuous monitoring at depth greater than 5000m.
The SubC Autonomous Timelapse System offers key features tailored to deep-sea research:
● Extreme Depth Performance:
Reliable operation at depths up to 6000m.
● Customisable Timelapse Programming: Allows users to schedule image and video captures and adjust settings for lighting, focus, and exposure.
● Battery-Efficient Hibernation Mode: This optional feature can extend deployment durations by conserving power between imaging intervals.
● Comprehensive Integration: Supports additional tools such as sediment traps and oceanographic sensors, creating a multifunctional observatory system.
As Dr. Bond noted, “The SubC Autonomous Timelapse System was big part of the success of this project. Being able to capture high-quality data in the deep sea over long periods wouldn’t have been possible without this unique hardware and software.
It’s the only off-the-shelf system I’ve come across that combines very high quality timelapse imaging with a hibernation mode, which is exactly what we needed to monitor Australia’s deep sea. It’s made a huge difference in how we study these ecosystems through time and has given us insights we couldn’t get any other way.”
Deploying UWA’s custom-built observatories required meticulous planning. Each observatory
Autonomous Timelapse System
featured SubC’s Autonomous Timelapse System accompanied by a suite of oceanographic sensors to measure key environmental parameters like conductivity, temperature, and oxygen levels.
A sediment trap, positioned 300 meters above the main frame, captured falling organic material to provide insights into the seasonality and quantity of falling marine snow.
Components were carefully assembled and lowered into the sea, with the main frame and its steel ballast descending to depths of 4300 and 5100 meters.
Despite last-minute delivery delays for critical parts and challenging weather conditions, the team successfully installed the observatories, setting the stage for 18 months of continuous, autonomous data collection.
UWA’s observatories advanced
the understanding of deep-sea ecosystems in several key ways. Highresolution images captured every 12 hrs provided new insight into benthic activity linked to marine snow dynamics, revealing seasonal ecosystem changes and long-term environmental patterns. The optional hibernation mode played a pivotal role, conserving power and ensuring uninterrupted operation throughout the deployment.
In addition to the two observatories, baited landers deployed for 6 hours captured footage of rare and novel species, including snailfish, robust assfish, and deep-sea prawns, some of which were documented in Australian waters for the first time.
Data from sediment traps and oceanographic sensors further revealed connections between oceanographic conditions and benthic life, shedding light on how marine snow sustains these ecosystems.
Collectively, the observatories provided a robust dataset that not only enhances current knowledge but also serves as a foundation for future expeditions and long-term monitoring.
A perennial issue with photography is ‘camera shake’.
In stills photography, a blurred image can result from camera movement while the shutter is open, while in a video, watching the subject image gyrate across the screen makes uncomfortable viewing. Post- processing can sometimes correct unwanted movement, however, when video imaging using lenses with longer focal lengths, the shake may be enough to move the subject completely out of the frame.
One solution maybe to employ some sort of mechanical stabilisation in the form of a gimbal.
Some consumer electronics gimbals use accelerometers to measure movement from a point and feed a counter-movement back to the platform to cancel this, effectively keeping the camera stationary. The most advanced commercial camera gimbals, however, are Gyrostabilised.
These work by using a spinning gyroscope to set the base position. Motors are then employed to make continuous small adjustments if the movement deviates from this. The result is stable imagery, even from long-distance lenses mounted on fast moving helicopters and aeroplanes.
One company that has been active in supplying gyro- stabilised cameras is the New Zealand
company Immortal Camera Systems. Mostly mounted on helicopters, boats, planes, jetskis and cars, the company has recently explored the idea that there might be some value by adapting the technology to be used underwater.
“An underwater gimbal has to probably withstand even more severe shock loads, that in an aerial application, especially when passing through the air/water transition zone ” said Brad Hurndell, CEO of Immortal.
“Many film companies often get underwater footage by attaching cameras to poles and lowering them down from boats. The drawback to this is that the cameras have to remain at a fixed angle and move are subject to the up/down movement of the boat.
“The advantage using a gyro stabiliser is that it can once it is locked on to a moving target, it can track the subject automatically against a stabilised horizon. The camera can even pan up
and down, all without being subject to unpredictable shock loading of waves or sudden currents.
“It would be ideal, for example, when following a humpback whale that's moving at a reasonable speed but too fast for a diver to keep up.”
At the front of the unit is a custom-made dome with a diameter of around 250mm. Behind this, is the pressure isolated housing the camera into which, it is possible to fit a vast array of cameras and lenses. It weighs around 30kg excluding camera and lens, or nearer 50 kg with the camera equipment. It is neutrally buoyant in water.
Sensors allow the user to monitor and maintain a stable internal pressure. The controller can commuicate with the body via Ethernet Video and the images are transferred to surface via Fibre optic – Ultra high definition lossless video. It supports WIFI and Cellular access for configuration and live remote support. Cutting edge, modern electronics to remove obsolescence risks
“We see its greatest usage in the top of the photic zone – at least in the top 5m but probably mostly residing in the top couple of metres,” said Hurndell. “We probably
don’t want to go too much below this, as in practical terms, colours change if the camera is too deep. As such, we have taken a design depth of one atmosphere as a starting point, although its internal pressure compensation system gives it the potential for considerably deeper applications.
The body is designed to be securely attached to a vehicle –perhaps on bow of the boat or on water jets but has a track
record with helicopters, boats, planes, cranes and cars - basically any unstable platform - in applications moving at 500 knots and generating 5G of force. We believe that the maximum underwater speed will be around 12Kts.
It has a nodal roll axis with an unmatched 360˚ continuous range of motion.
“We see this as an untapped or unexplored market
segment. Fundamentally, our background is film and television, particularly in natural history programmes where filming in adverse conditions might be difficult for divers. It may be cold, dangerous or require filming for long periods of time such as filming chasing/ hunting or following pods of dolphins, but there may also be military applications.
“Our system is compatible with basically any modern camera and lens,” said Hurndell.” We manufacture a series of different brackets
“While the underlying technology is proven the submersible version is now at at the end of its testing phase. We are currently assembling systems to send to our first customers.”
The Advanced Capability (ADCAP) Manipulator camera kit from Australian-based company Se-Alt is designed to serve as a direct replacement for standard Schilling Robotics T4 wrist cameras. This next-generation camera system delivers good imaging capabilities, improving inspection and faultfinding tasks in subsea environments.
With enhanced zoom, focus, and lighting features, the camera provides full 1080p 60fps HD-SDI resolution, ensuring clear visuals even in challenging underwater conditions.
Equipped with a 10x optical zoom and a further 16x digital zoom, the camera allows for both manual and automatic focus adjustments, offering precision control over visual inspections. Exceptional low-light visibility and integrated image stabilisation reduce blurring caused by vibration, further enhancing the quality of captured footage.
One of the key advantages of Se-Alt’s camera is its high-performance LED lighting system. The camera features an increased lumen output, offering both high and low beam settings to suit varying operational needs. As an additional enhancement, UV fluorescence detection LEDs are currently under development, further expanding the system’s functionality for specialised inspections.
Seamless integration with existing Schilling Robotics OEM master controllers ensures that operators can control power, camera, and lighting functions without requiring additional training.
The familiarity of control mechanisms streamlines adoption and minimises downtime. An optional joystick controller is also available, providing operators with manual control over zoom and focus commands.
Engineered for extreme subsea conditions, it is depth-rated to 3000m, making it a reliable choice for deepwater inspections. It is based on the Tamron MP3010M-EV camera solution and incorporates a lightweight, compact 5-megapixel sensor. Featuring a high-sensitivity Sony IMX335 STARVIS CMOS sensor, the camera offers approximately 5,140,000 effective pixels and supports all HD modes up to 1080p/60.
• intelligent vehicles
• reliable communication
• accurate positioning
• modern sensor networks