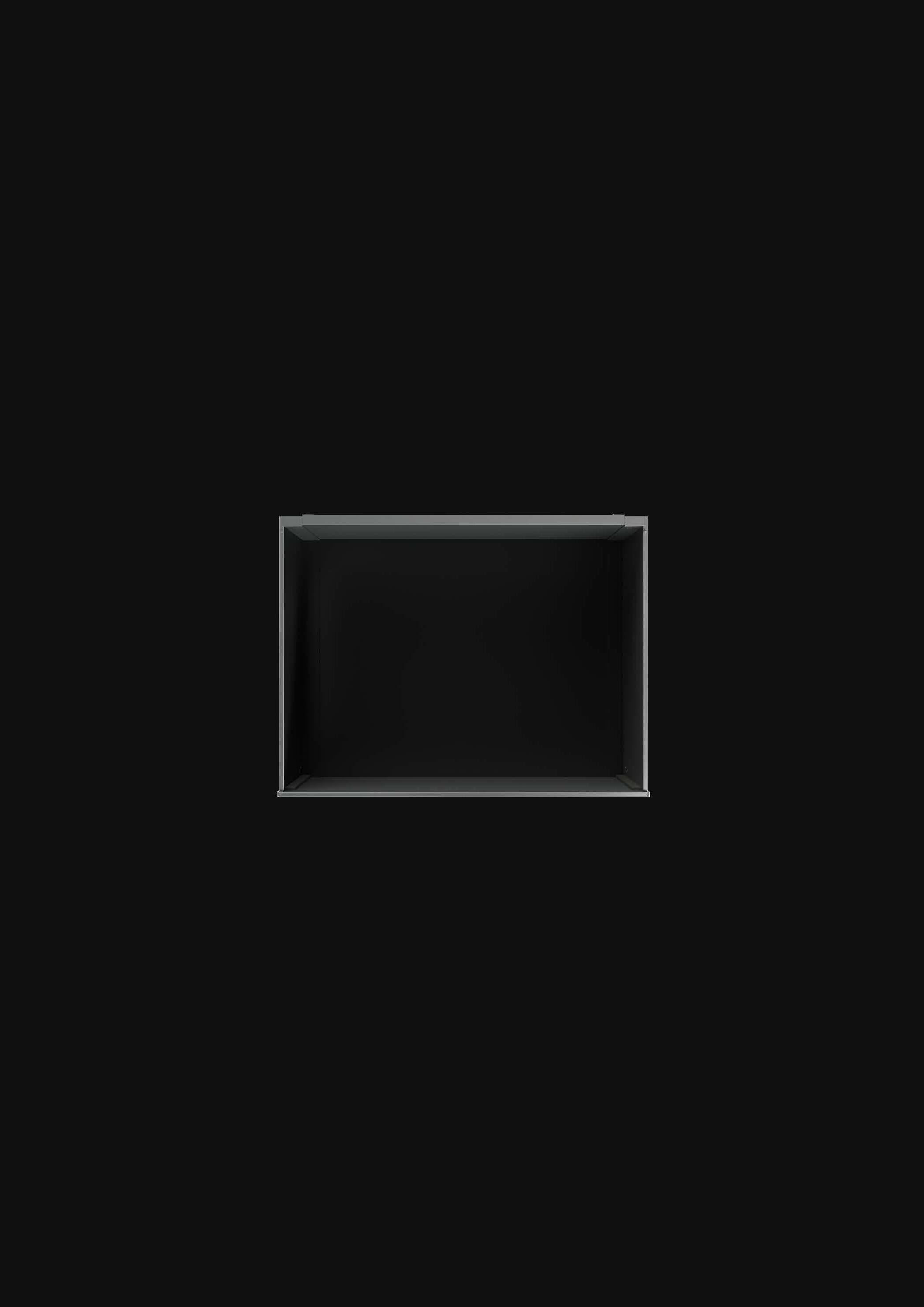
World’s first 7.2mm double-wall drawer profile
World’s first 7.2mm double-wall drawer profile
EXPERIENCE 5-AXIS CUTTING WITH THE THIBAUT TC425
Step into the future of stone processing with the Thibaut TC425. This next generation sawing and shaping centre combines precision and productivity with six integrated tools, including a saw blade, core drill, high-speed router, and Thibaut’s exclusive ACS jigsaw (optional). Designed for full autonomy, the TC425 simplifies complex jobs and transforms multistep processes into a single seamless workflow.
Welcome to the May / June 2025 issue of Supplier Magazine. Inside this issue you will find our annual Workplace Safety feature where we examine the link between a strong safety culture and positive business results such as decreased absenteeism, increased productivity, and better engagement. Good safety is good for business and despite manufacturing producing low incident numbers, manufacturers should not let their guard down.
Our Company Profile in this issue is on Wilson & Bradley. Family owned and operated since 1976, Wilson & Bradley is more than a hardware distributor, they are a trusted partner in shaping functional, inspiring spaces across Australia. Known for their hands-on service, premium products, and collaborative spirit, the company continues to lead with innovation and a customer-first approach.
Supplier Magazine is your industry voice so please feel free to contact me regarding any industry news, company events, training and or new product information you would like us to share at – michelle@elitepublishing.com.au
Until next time, enjoy your read.
Michelle Cammiade Editor
CDK Stone once again demonstrated its leadership in stone machinery innovation with a successful Machinery Showcase event held in Melbourne on March the 27th and 28th. The two-day showcase attracted a strong turnout from industry professionals across Australia, including interstate customers who travelled with CDK Stone team members to experience the latest in cutting-edge technology.
A major highlight of the event was the launch of the Thibaut TC425 Bridge Saw, now available in Australia through CDK Stone. Manufactured by Thibaut, an internationally recognised company with over 65 years of experience the TC425 is a next generation sawing and shaping centre built for precision and productivity. It features six integrated tools, including a saw blade, core drill, highspeed router, and Thibaut’s exclusive ACS jig saw (optional), offering complete autonomy in processing.
Joining the lineup was the Comandulli Coral, a compact edge polisher designed for versatility and ease of use. The new machine attracted interest for its space-saving design and solid construction, reflecting Comandulli’s ongoing focus on quality and performance in stone processing.
The event also marked the debut of the new Laser Hardware 5x LPI from Laser Products Industries, showcasing the latest advancements in digital templating for accurate, efficient stone processing.
A key highlight of the showcase was the strong presence of CDK Stone’s international machinery partners Thibaut, Burkhardt, Comandulli, Cobalm, Dal Prete, Taglio, Laser Products Industries, and Zoller. Their involvement provided valuable insight and support throughout the event, reinforcing the company’s close global partnerships and ongoing commitment to delivering expert advice.
While the machinery on display reflected the quality and innovation CDK Stone is known for, it was their team’s ability to guide customers through a range of options showing how each solution could support different business needs that left a lasting impression. The showcase reinforced CDK Stone’s commitment to helping fabricators move forward with confidence through practical advice and hands-on experience.
CDK Stone’s Machinery Showcase has become a must-attend event for those looking to evolve their operations and stay ahead of industry trends. With each event, the company reaffirms its position as a trusted partner in the evolving world of stone fabrication. z
The all-new GRASS Moved by Häfele mobile showroom is now on the road and making its way around Australia.
The mobile showroom is packed full of Grass products, including the TECMATOR drawer assembly machine that can assemble a drawer in under 25 seconds.
Also on display are the Nova Pro Scala product range of drawers, Tiomos hidden hinges, Kinvaro T-Slim Flap fittings and so much more.
Talk to your Häfele Account Manager today to ensure you don’t miss out on seeing the Grass Mobile showroom and TECMATOR assembly machine in action.
Ask us about the NEW, Nova Pro One range
In an increasingly multi-dimensional world, marked by continuous changes, Biesse has undertaken a deep evolutionary path to bring a new value proposition to the market: a renewed product offering to be explored in unique experience spaces.
The renewed Biesse Machinery portfolio guarantees significant improvements in the functionality and performance of machines for all materials, and expands the catalog, particularly for stone and glass. It also includes an innovative range of services and assistance, along with a new human-machine interaction. The new Human Machine Interface, clear and highly intuitive, has a unified design for all materials, improving the user experience and simplifying production processes.
In line with this evolution, the Biesse Material Hubs have been creating unique multi-material experience spaces where visitors can discover the company and its product portfolio. Through dedicated journeys, visitors can explore the offering through new methods of interaction and tools, both physical and digital.
The Biesse Material Hubs are part of a connected international Network that strengthens local expressions and the uniqueness of each market, activating synergies between physically distant hubs. This connected network not only enhances the experience and allows each hub to amplify its offering, but also reduces travel and emissions, promotes collaboration, and improves efficiency, in line with the company’s sustainability policy.
Biesse celebrates this important step forward in its evolutionary path with an event called ‘Embrace the Evolution,’ which took place simultaneously on March 26 at the first five Biesse Material Hubs of the network—in Sydney, Osaka, Lyon, Porto, and Toronto. The event featured a global format with a local flavor, embodying the full spirit of ‘International Natives.’
The renewed Biesse Machinery portfolio and the Biesse Material Hub Network are part of the long-term strategic plan called One Company, which has redefined the organisation, processes, corporate identity, product portfolio, and experience spaces. This
initiative represents a path toward leadership in multi-materiality in an increasingly uncertain and evolving scenario.
During the events, the Biesse International Design Award competition was announced, in collaboration with POLI.design, post-graduate educational center founded by Politecnico di Milano, one of the most prestigious Italian Universities with a strong international presence. The details of the competition, which will be revealed in the coming weeks, aim to involve students and designers worldwide in the creation of an iconic multi-material object designed to be exhibited in the material area of each Hub.
The concepts behind the Biesse Material Hubs were conceived in collaboration with Il Prisma, an international architecture firm with Italian roots, which, together with Biesse, has redefined the process of redesigning the experience. This transformation turns offices and industrial spaces into open places connected to international markets, offering a vision that goes beyond the limits of traditional fairs and production sites. z
Standards Australia's Universal Data Protocol Initiative
A Universal Data Protocol (UDP) for the built environment has the potential to drive sustainability and transparency across operations, meaning everyone from architects to suppliers can easily share and understand the same information. Patterning with the International Code Council to develop the UDP, Standards Australia is committed to supporting industry by reducing compliance burdens and positioning sustainability-minded players to remain competitive in the global market, while balancing the needs of people, the planet, and profit. In late 2024 at COP29, Standards Australia and the International Code Council announced their work to develop the new protocol to leverage transparent, trustworthy, and verifiable data across the built environment. This is set to impact suppliers and the wider industry in increasing ways given the built environment is a key sector in addressing the drivers and impacts of climate change.
In March 2024, 70 countries signed the Declaration de Chaillot, committing to net-zero emissions in the global building industry.
Despite significant investments in technology, much of the data produced remains fragmented and unusable across different disciplines or
stages of the building lifecycle. This creates challenges in compliance, reporting, sharing of data and efforts to improve reporting and meet sustainability targets.
To address these issues, the UDP seeks to enable transparent, auditable, and verifiable data exchange for effective reporting and compliance across the building and construction industry.
The UDP will be an extension of the broader UN Transparency Protocol (UNTP). UNTP provides a secure, decentralised framework for data sharing, allowing cross-border, cross-sector data exchange without a central database. As more communities, organisations, and industries adopt UNTP, its impact grows, fostering a transparent global marketplace.
The UDP will serve as a Sustainability Vocabulary Catalogue (SVC) for the built environment, ensuring data is easily understood. Key benefits include:
• Decentralised verification: Data can be verified without relying on a single system, allowing each participant in the building lifecycle to prove their data’s authenticity.
• Interoperability: An adaptable framework links data from design, construction, and operations across borders, facilitating global compliance.
• Digital security: Using UNTP’s digital signatures and cryptography, UDP ensures data integrity and guards against tampering.
• Common language: Facilitates easy integration with existing systems, maximising current technological investments while adding a trusted datasharing framework.
• Open-Source access: Enables businesses of any size and in any market to adopt, collaborate, and advance sustainability together.
With implementation support from Pyx Global, Standards Australia and the International Code Council are focused on turning this vision into a reality. Both organisations will develop a proof-of-concept of the protocol to demonstrate its application with real world businesses.
Standards Australia said: "The launch of the report is a step towards unlocking the full potential of data and digital technologies. Potentially helping to create a safe, sustainable, and resilient future for Australia and the world."
"The launch of the report is a step towards unlocking the full potential of data and digital technologies. Potentially helping to create a safe, sustainable, and resilient future for Australia and the world."
Dominic Sims, CEO of the Code Council, added: “We are pleased to work with Standards Australia to develop a globally applicable solution that provides the certainty and reliability that actors from across the industry need to continue to progress on meeting their climate-related goals.
“The Universal Data Protocol, extending UNTP, will enhance data accessibility and transparency across the building sector. Pyx is excited to partner with Standards Australia and the International Code Council on this initiative, which will foster accountability and innovation in Australia and beyond,” said Zachary Zeus, CEO of UNTP implementation accelerator Pyx Global.
To learn more about the global challenges, solutions, and how UDP will work as an extension of the UNTP read this Standards Australia whitepaper: https://www.standards. org.au/documents/cop29-udp-whitepaper. z
Meet the Hideaway Compact Floor Mount Bins
Available from: Hafele, Carters, Impey’s and Industry HQ.
hideawaybins.co.nz
Article by Philip Ashley
Peter Mitchelhill believes that as an integral part of the building sector, the stone industry has a fantastic future. Having spent his entire working life in the stone industry, he ought to know. Serious, genuine, passionate, hard-working, determined and energetic, Peter is a real Terrier, an icon of the trade.
Here at Supplier Magazine, we sometimes have the pleasure of speaking with someone who has made a significant impact on the trades. You would pass them on the street and never know how they had changed the way you live and work. Icons like John Cover and Jake Martin; Bruce Evans, Barry Gabbett, and Richard small are some of the names who have shaped our future in the woodworking trades.
From the stone industry we recently had the pleasure of a chat with Peter Mitchelhill, a man who considers himself fortunate in every aspect of his life, from family to the industry he works in. He’s never officially done a trade but has worked in a trade all his life. Peter is an example of what learning by experience; on the job, is all about. Peter is one of the most knowledgeable people we know in the stone industry.
Peter was born in Melbourne and educated in Geelong, then university in Armadale in northern New South Wales. During his university years he would work at his uncle’s stone business during his holidays. He was about 20 at the time and recalls manufacturing abrasives to polish marble and granite. After university, his uncle asked him to work there full-time. Peter eventually took over the management and the business grew to sell diamond tools, machinery and stone working accessories.
When Peter started out he recalls, “There were a lot more stone quarries in Australia then, about 50 years ago now. A lot of the work was monumental and most of their material was sourced in Australia. Monumental masons were the trades that started manufacturing stone benchtops. With the introduction of engineered stone, the industry changed dramatically, the new material offered uniform colour and thickness, and you could process it almost the same as you would particleboard.”
Peter loves his work and the stone industry. He has a passion for small business he calls, ‘the salt of the Earth’ and considers them massively undervalued. Over the years
“With the introduction of engineered stone, the industry changed dramatically, the new material offered uniform colour and thickness, and you could process it almost the same as you would particleboard.”
Peter has involved himself in all aspects of the trade including the writing of technical articles and sitting in various positions on the Australian Stone Advisory Association. Peter considers his role is to mentor others wherever he can, to help others achieve their potential.
I asked Peter if he thought of himself as an expert and he said he didn’t consider that of himself. So, I looked up the definition in the Cambridge dictionary and found this: ‘An expert is a person with a high level of knowledge or skill relating to a particular subject or activity.’ And so, by definition, Peter is an expert. Peter currently works at CDK Stone in their machinery management team and is closely aligned to the service department. After recently celebrating 50
years in the industry and 15 years at CDK Stone he is looking forward to reducing his hours but has no plans to retire.
Growing up at the beach, Peter spent a lot of time surfing and still enjoys donning a wetsuit and riding a wave. He rides a motorcycle and takes his 90’s sports car out most weekends.
He and some of his friends have been working their way down the Murray in small tinnies, three to five days at a time, camping on the riverbank, enjoying the outdoors. Starting from the Hume Weir they are currently at Renmark and expect to complete the journey later this year. Peter is blessed with a wife and two adult children. z
pure pro spice/bottle drawer
The Spice/Bottle drawer boasts full-extension concealed runners with a 40kg load capacity and soft-close functionality for seamless, quiet operation. The Pure Pro Spice/Bottle Drawer comes in versatile 150mm and 200mm kits, designed to fit any kitchen space. Each kit includes low and high drawers with dividers sold separately, perfect for organizing a wide range of kitchen essentials with style and efficiency.
DTC Global leads the storage solutions industry with high-quality products focused on innovation, reliability, and sustainability. Their storage solutions use advanced technology and durable design for efficiency, scalability, and flexibility. DTC Global tailors its products to meet customer needs, improving storage systems and operations. The company also prioritizes eco-friendly practices to reduce its environmental impact. With a commitment to excellence and customer service, DTC Global is the trusted partner for businesses seeking top-notch storage solutions.
Tailored for upper cabinets that opens door up and away, this mechanism features a 107° opening angle and is engineered to suit door thicknesses ranging from 16mm to 28mm.
Designed for cabinets ranging from 200mm to 480mm in height, this mechanism accommodates door weights of up to 14kg, offering both horizontal and vertical mounting options.
Designed to increase access to multiple upper cabinets simultaneously, this mechanism offers comprehensive 3D adjustments, allowing for precise alignment of doors. With upper overall adjustments of +/-2mm and lower door adjustments of +2/-1 for height and +/-2mm for side and depth, it ensures a tailored fit.
In today’s rapidly evolving furniture market, the expectations placed on hardware solutions are higher than ever. Manufacturers, designers, and end-users demand systems that are not only durable and functional but also sustainable and adaptable to changing design needs. Rising to meet these demands is Harn’s latest innovation: the Alunan T7, the world’s first 7.2mm double-wall drawer profile. Which made its global debut at Interzum Cologne 2025. In recognition of its outstanding engineering and design, Harn’s Alunan T7 was honoured with the High Product Quality Award at Interzum 2025.
A new milestone in drawer system innovation
Harn, a Malaysian leader in highperformance drawer systems since 1994, has long been associated with engineering excellence, precision craftsmanship, and an unwavering commitment to sustainability. With Alunan T7, the company strengthens its ongoing commitment to innovation in furniture hardware.
Alunan T7 stands out with its 7.2mm ultra-slim profile. Traditionally, double-wall drawer systems have balanced strength with bulk, often sacrificing valuable storage space. Alunan T7 overcomes this limitation, delivering a sleeker, more spaceefficient profile without compromising structural integrity. It represents a leap forward, blending aesthetic minimalism with outstanding performance for today’s modern, space-conscious environments.
Harn’s commitment to responsible manufacturing is deeply embedded in Alunan T7’s DNA. Made from 99% recyclable steel, the system supports eco-friendly production and long-term environmental stewardship. Beyond material choice, Harn powers its operations with 5,400 m² of solar panels, generating 1.5 million kWh of renewable energy annually, and has transitioned to natural gas for powder coating line to further reduce its carbon footprint.
In an era where sustainability is no longer optional but essential, Alunan T7 offers furniture manufacturers a real opportunity to align with growing consumer demand for eco-conscious products without sacrificing performance or design flexibility.
One of the greatest strengths of Harn’s newest range of drawer profiles lie in its system: the RITMA T Platform. This advanced runner system is compatible with Harn drawer solutions Alunan T7, Alunan T, and RITMA Cube.
Featuring synchronised low-friction roller bearings, an I-Channel for enhanced stability, an anti-tilt mechanism, and SYLENT soft-close technology, the RITMA T Platform ensures silent, effortless drawer movement, even under heavy loads. With 35kg and 60kg load ratings, the platform easily supports a wide variety of applications, from residential kitchens to high-traffic commercial spaces.
Furthermore, the modularity of the RITMA T Platform allows furniture manufacturers to simplify inventory management. With shared runners across multiple drawer profiles, customisation becomes easier and production processes more efficient saving both time and resources.
Designed for modern manufacturing, supply chain, and living
Understanding the evolving needs of the market, Alunan T7 was developed with versatility and user-centric design at its core. Available in three heights—88mm, 120mm, and 192mm—and intuitive installation, the system ensures that adjustments and
upgrades can be performed effortlessly, even by end-users, allowing furniture to evolve with the needs of contemporary living spaces. Whether for minimalist kitchens, luxurious wardrobes, or flexible workspaces, Alunan T7 fits seamlessly into a broad range of interior styles and functional requirements.
An investment in sustainability
In today’s market, longevity is not just about how long a product lasts—it is about how well it adapts over time. Alunan T7 is engineered for enduring reliability. Its advanced motion technologies ensure that drawers perform flawlessly, day after day, year after year, enhancing user experience and reducing costly maintenance or replacement needs.
This focus on durability aligns with broader industry trends towards sustainable consumption and long-term value creation, making Alunan T7 a compelling choice for forward-thinking manufacturers and designers.
Preview the future at Kitchen + Bath Show 2025
Alunan T7 officially launched at Interzum Cologne 2025. Their following showcase will be at Kitchen + Bath 2025 at the MCEC Melbourne from the 12th to the 14th of June - Stand 838.
Visitors to the Harn booth will have the opportunity to experience Alunan T7 firsthand through live demonstrations,
showcasing its smooth, silent motion, modular flexibility, and cutting-edge design.
Bringing together sustainability, performance, and design versatility in a slim, precision-engineered solution, Alunan T7 aims to contribute meaningfully to the evolving standards of the global furniture hardware industry.
web www.harn.com z
Introducing Hafele’s new corner storage solution Ninka Trigon. Designed to maximise space in your corner cabinets, making organisation effortless and every inch of your kitchen more efficient.
This product is intended for use in basemounted blind corner cabinets. It features a scratch-resistant surface with a fine dimpled structure, making it durable and easy to clean. Installation is quick and straightforward, with tool-free assembly and removal of the pull-out shelves. The height of the shelves can be easily adjusted, and the design ensures that it does not block the adjacent cabinet in the blind corner. Additionally, it can be retrofitted into existing blind corner spaces. The product is made from 100% recyclable materials.
The shelves are made of plastic, and the spindle is constructed from steel. The finish is a dark grey colour, giving it a modern appearance.
This unit is suitable for cabinets with a width of 900 mm. It has a load-bearing capacity of up to 25 kg. It is compatible with cabinet door widths of 450 mm, 500 mm, and 600 mm.
The product is supplied with two pull-out shelves and one corner axle.
Note: If a soft-close mechanism is required, it must be ordered separately. The soft-close set for the right-hand side is item number 541.59.931, and for the left-hand side, it is item number 541.59.930.
For more information visit www.hafelehome.com.au z
Flexliner offers an extensive range of chair and table feet suitable for use on a variety of flooring types, including carpet, wood, tile, and polished concrete. Flexliner feet are manufactured from various materials to accommodate different flooring applications and are available in multiple sizes to suit both tubular and solid chair or table legs.
Types of feet
Tube inserts (push-in) for metal chair legs –These inserts are designed for use with modern chairs that typically feature hollow, round or square steel or aluminium legs, which may be straight or angled.
Angled feet for metal tube legs – Angled inserts are specifically designed to match the angle of slanted chair legs. These feet feature a base with an incline—commonly available in 9°, 10°, 12°, 15°, and 18°—and are suitable for both round and square legs.
Tilting angle feet – Flexliner offer a wide selection of tilting feet ideal for use on uneven flooring. These feet can tilt within a range of 0° to 10° or 0° to 20°, providing stability on irregular surfaces.
Saddle glides – These glides are intended for sled chair frames made from round tubing and are available in sizes ranging from 10 mm to 32 mm in outer diameter. They can also be supplied with either a felt or Teflon base to match specific flooring requirements.
Caps or chair tips – Designed to fit over the outside of the tube, these push-on caps typically feature a flat base and provide a simple yet effective solution for protecting floors and chair legs.
Feet for timber chair and table legs –(a) Nail-On Glides: These glides are attached using a single nail or pin that is bonded to a base made from materials such as nylon, felt, synthetic rubber, or Teflon.
(b) Screw-On Glides: These circular glides feature a central hole and are secured to the base of the chair or table leg using the wood screw provided.
Flexliner feet are made from a range of materials, each carefully selected to suit diverse types of flooring surfaces.
• Polypropylene (PP) is used as a general-purpose material and is suitable for a wide range of applications.
• Polyamide (PA), commonly known as Nylon, is a harder and more durable material, ideal for situations where extended service life is required.
• Bonded wool felt is intended exclusively for interior use on smooth, jointless floors.
• Felt made from woven polypropylene fibre is suitable for use on smooth, polished surfaces such as concrete, terrazzo, or epoxy-coated floors.
• PVC and soft PVC are materials typically used in applications where antislip properties are important.
• PTFE, also known as Teflon, or a super slide base, is designed for interior use on wooden, tiled, or carpeted floors to enable smooth movement.
• Rubber and synthetic rubber (SBR) are employed in situations where a strong anti-slip feature is required.
web www.chairfeet.com.au
web www.tablefeet.com.au
Article by Philip Ashley
So far this year, 26 workers have been killed in the workplace in Australia. Manufacturing fares pretty well with no fatalities so far, and only 7 last year, down from an average of 13 over the last 5 years. Despite manufacturing producing low incident numbers, manufacturers should not let their guard down.
According to Safe Work Australia, the proportion of people who experienced a work-related injury or illness in the previous 12 months is 3.5% roughly one-third the global rate of 12.1%. Of the 26 workers sadly killed this year so far in the workplace, 15 of those were in transport and warehousing (168 in total last year) and most of these by vehicle collision. Over the last 5 years the average was 191, meaning the numbers are falling; just slightly.
According to the latest Key Work Health and Safety Statistics 2024 Vehicle incidents continue to account for the largest proportion of worker fatalities (42%; 84 fatalities). This is followed by Falls from a height (15%; 29 fatalities), which have increased significantly since the previous year (from 17 fatalities; increasing 71%). 80% of all serious claims involve Body stressing, Falls, slips and trips, being hit by moving objects, or Mental stress.
Body Stressing (overexertion) is the leading cause of workplace injury in Australia. It includes repetitive strain injuries and injuries incurred from lifting heavy objects. Tripping, slipping and falling is a very common cause of workplace injury, encompassing everything from slipping on a wet floor, tripping over a cord to falling off a chair, ladder or down a flight of stairs. Being struck by objects. can result in serious injury or death from something as simple as a
hammer being dropped from an upper level of a construction site.
According to statistics from Safe Work Australia, and their report titled ‘Key Work Health and Safety Statistics Australia (2020)’ – the most common cause of work-related fatality is from vehicle collision. Furthermore, the industries where most of these fatalities occur are as follows: Agriculture, Forestry, Fishing, Transport, Postal and Warehousing. As a past manager of a large TAFE department my observation would be that all these industries employ people working remotely while manufacturers employ people working locally in a more controlled environment.
Australian Bureau of Statistics state that 96% of worker fatalities were male. There is also data to say that young workers are more likely to experience a workplace injury than older, and obviously more experienced
workers. I recall my early years tightening up a long cutting blade on a planing machine with a spanner that did not fit correctly… five stitches, my stupid fault. On another occasion I was cutting something with a box cutter, pulling it towards me…three stitches, again my fault through lack of awareness.
Australian Bureau of Statistics state that 96% of worker fatalities were male. There is also data to say that young workers are more likely to experience a workplace injury than older, and obviously more experienced workers.
My last early injury was setting the cutters on a multi-spindle planing machine with my supervisor setting another cutter head on the same machine. That old Jonsereds moulder had one motor, and all the cutter heads were driven off the on drive. When my supervisor turned his cutter, mine turned as well…seven stitches. All these incidents happened while I was in training, and I have never been bitten since. If my experience is anything to go by, a person’s most vulnerable time would be whilst still learning about safety. The fact that my supervisor 50 years ago had no clue as to the danger I was in is another story, but attitudes have changed, and we are in a far safer environment now.
Keeping your workplace safe and efficient is a challenge but the reality is that a safe work environment is also more productive. Workers feel better about what they do,
morale improves, and there is a positive impact on a company’s bottom line. Better safety reduces absenteeism and missed work. If workers are off on sick leave, your other people may need to do more work, and this could also result in injuries as people cut corners to get jobs done. It’s a vicious cycle.
A strong safety culture improves productivity. A study by Lockheed Martin found that when they developed a stronger safety culture, productivity went up 24%. Factory costs also went down. Employees focused on reducing errors that lead to accidents. Everyone stayed healthy, downtime was reduced and overall effectiveness improved. Lockheed found that extensive training, pre-shift preparation, and safety audits all improved employee confidence and improved their ability to do their job.
A study by Lockheed Martin found that when they developed a stronger safety culture, productivity went up 24%. Factory costs also went down.
Worker engagement comes from an emotional commitment to the company and its goals. Your employees will be more engaged in your safety objectives if they are focused on safety and are aware of the impact of their actions. When safety is the center of workplace culture, employees feel like they matter, and their work makes a difference. If you involve staff in setting up
and running your safety program, you’ll create an empowered workforce committed to doing things right.
One of the more recent safety issues is in the stone industry. As of 1 July 2024, the use, supply, and manufacture of engineered stone benchtops, panels and slabs is banned across Australia. Check the arrangements for your state or territory. The silica dust issue may be put to rest by legislation, but employers must still process wet, monitor air and water quality, and use personal protective equipment where specified. Crystalline silica-free materials are now available and while there are minor negative characteristics, these materials have been well received. Go to www.safeworkaustralia. gov.au/esban to find out the transition requirements in your State or Territory.
As CEO, manager or foreperson, you cannot be everywhere at once, it’s up to employees
to help each other stay safe. You need to promote responsibility and ownership, not just rule-following. Following a rule just because it’s there does nothing for a strong safety culture, cleaning up just before a safety inspection is just fooling yourself.
A strong safety culture is directly linked to positive business results such as decreased absenteeism, increased productivity, and better engagement. Good safety is good for business, it’s not just a rule. z
Whilst we highlight the importance to wearing PPE and correct safety equipment at work, Respiratory Protection Equipment (RPE) is one that is often overlooked.
Wearing respiratory protection is crucial to safeguard workers’ health by preventing the inhalation of harmful airborne wet and dry particles and/or gases such as chemicals when working in hazardous environments.
Employers and employees must understand the importance of using RPE to comply with occupational safety standards, as well as to ensure their health and well-being.
Key points about the importance of respiratory protection
Protection from irritants: Respirators can filter out contaminants like gases, smoke, and particles, which can cause discomfort, coughing, and eye irritation. RPE, as a control measure, is designed to protect workers from inhalable and respirable airborne particles which may pose significant health risks from exposure.
Prevents lung diseases: By filtering out harmful particles from the air you breathe, respirators can significantly reduce the risk of developing respiratory diseases like silicosis (from silica dust), asbestosis (from asbestos fibres), and occupational asthma.
Respiratory illnesses can lead to absenteeism and reduced productivity, which can be mitigated by effective respiratory protection.
Workplace Health and Safety regulations compliance: In industries with high levels of airborne contaminants,
wearing appropriate respiratory protection equipment is essential for workers’ safety. As such, it should conform to occupational health regulations and Australian Standards. Workplaces with potential respiratory hazards are required to implement a respiratory protection program, Australian Standard AS1715 section 2.1.
What are important considerations when using respiratory protection?
To select the correct respiratory protection, you need to first identify the type and concentration of airborne contaminants in the workplace, then choose a respirator with an appropriate assigned protection factor (APF) based on the hazard level, considering factors like the respirator type (air-purifying or air supply) and the workplace condition and environment.
Selecting the correct filter or filter combination is also essential and it should be based on the contaminants exposed during work, the work intensity and concentration of a pollutant.
Face fit testing is an important step in the process of selecting the right RPE mask for a worker. It helps to ensure that the mask fits properly and provides maximum protection against hazardous airborne particles and gases. RPE is also often used in combination with other forms of protective equipment such as safety goggles or hard hats, to provide additional layers of defence against workplace hazards.
web https://www.sea.com.au/wp-content/ uploads/2024/10/Sundstrom-Respiratoryprotection-factors-guide-Email.pdf z
A complete, simple and modular respiratory protection equipment range suitable for all construction industry types Select the respirator with increased protection factor to meet the new Australian workplace exposure standards
1. Choose your respirator
2. Choose your head-top for SR500 & SR700 PAPR
3. Choose the correct filters against contaminants
Protection
The discovery that microscopic crystalline silica particles, emitted during stone fabrication, causes severe respiratory illnesses has led to a crucial reassessment within the surface materials industry. Australia's prohibition of engineered stone with 1% or more crystalline silica not only represents a landmark legal change but also underscores a broader societal shift: safety and sustainability are now essential. However, the market demands more than just compliance; it seeks an integration of superior quality, sophistication, safety, and sustainability.
The team at Vicostone have always championed the belief that the allure and durability of materials should never compromise human health. For over two decades, across more than 50 countries, they have adhered to a core philosophy: crafting surfaces that are visually stunning, highly functional, and safe for both people and the environment. This commitment is embodied in their latest innovation, Vicostone Eco Surfaces—a groundbreaking advancement in surface material technology.
As a leader in premium building materials, Vicostone proudly introduces Crystalline Silica-Free products under the name Vicostone Eco Surfaces. Developed through rigorous research and innovation, these surfaces are completely free of crystalline silica, setting a new benchmark for safety and environmental stewardship. Their dedication to a sustainable future is reflected in the use of renewable energy, 100% recycled wastewater, and eco-friendly materials. This is their commitment to a cleaner, healthier world.
Drawing inspiration from nature, Vicostone Eco Surfaces heralds a new chapter in design with three collections featuring 36 distinctive colours. Each slab is a masterpiece, showcasing intricate patterns and textures
that blend elegance with originality, transforming any space into a work of art.
Renowned as a leading name among the world’s top surface manufacturers, Vicostone continues to innovate with unique designs and unparalleled quality. This standard of excellence has earned the trust of customers, architects, and interior designers in over 50 countries, including key markets like the United States, Canada, and Europe.
Recognising the uniqueness of each project, these Crystalline Silica-Free Surfaces are available in a wide array of sizes, including super jumbo sizes—the largest available on the market. Whether for boutique residential projects or expansive commercial developments, they provide the perfect dimensions to bring your design visions to life.
Vicostone Eco Surfaces are more than just a material choice; they embody a lifestyle. Each slab is a testament to a promise to prioritise human health and elevate industry standards. With Vicostone Eco Surfaces, experience not only breathtaking aesthetics but also the assurance of superior, sustainable materials.
web www.vicostone.au z
Versatility for Every Project - A Global Standard of Excellence - A New Era of Design Excellence
Scan the QR code to access more VICOSTONE® ECO inspiration and product information.
In the fast-paced world of cabinet manufacturing and joinery, staying competitive means not only producing efficiently, but also selling with impact. While software like Cabinet Vision manages production on the shop floor, Vortek Spaces enhances how manufacturers present their projects and attract new clients.
Designed specifically for joinery trade, Vortek Spaces is a real-time 3D visualisation tool that connects your productionready designs with high-impact sales presentations. Fully integrated with Cabinet Vision, it enables designers to quickly create immersive video walkthroughs and photorealistic 4K visuals based on manufacturable models, helping you present with confidence and close deals faster.
Vortek Spaces enables the transformation of technical drawings into high-quality visual presentations within minutes. It allows sales teams to present and adjust materials,
colors, and layout configurations in real time, whether during on-site meetings or remote sessions. This interactive approach helps build client confidence, accelerates decisions, and reduces the need for multiple revisions. No rendering expertise is required: a Cabinet Vision project can simply be imported, enhanced with finishes and accessories, and used to generate 4K images or a walkthrough video by setting customised viewpoints.
Because Vortek Spaces uses the original Cabinet Vision project file, the 3D visuals accurately reflect the final product. That
alignment eliminates disconnects between what is approved by the customer and what is built on the shop floor, cutting down on costly errors, change orders, and wasted materials.
This makes Vortek Spaces not just a sales enabler, but a safeguard, keeping production and presentation perfectly in sync.
Even small workshops can now pitch like premium design studios. Vortek Spaces gives your team the ability to present high-end visuals without the complexity of traditional rendering tools. Australian manufacturers using Vortek consistently report improved win rates and shorter sales cycles.
By linking your kitchen manufacturing projects with high-impact 3D presentations, it helps your team work smarter, sell faster, and stand out in an increasingly competitive market.
For forward-thinking factory owners seeking to optimise operations and drive growth, Vortek Spaces isn’t just another software, it is a strategic asset.
web www.planitaustralia.com.au z
idely known for their supply of premium cabinetry hardware, service and design guidance, Wilson & Bradley has built its reputation over nearly 50 years. As distributors of trusted international brands including Blum, Wesco L&S, SIGE, Cinetto and Furnipart, the company supports trade professionals and consumers through a national team of account managers who offer personalised support, product education and technical advice — backed by interactive showroom spaces in key locations. Arriving at the perfect fit every time is no accident; this energetic company drives innovation with a genuine focus on customer care.
Family owned and operated since 1976, Wilson & Bradley is an initiative of Graham and Lorna Wilson together with
John Bradley. The partners recognised an opportunity in the market for distributing Blum and other high-quality brands of hardware. With previous experience in an industry they knew well, Wilson & Bradley was formed. They held the shared vision for building a strong business to provide a future for their children and grandchildren. In 2019 Blum acquired the company, solidifying their time-tested relationship. Today, and as the original owners envisioned, Ashleigh Posterino, granddaughter of Graham and Lorna, continues the family tradition as General Manager of this nearly 50-years-young change maker in the industry.
Wilson & Bradley began with a clear mission: “Service and Civility — offering superior service.” It’s a principle and a
commitment that continues to define the company today.
Nearly five decades on, while the landscape of sales and marketing has changed, the face to face, get-to-know-each-other culture that differentiates Wilson & Bradley has only grown stronger and more meaningful over time. Acknowledging their heavy reliance on ecommerce, the company continues investing in building their network of Business Development Managers, highlighting the importance they place on face-to-face relationships with their customers.
Wilson & Bradley is guided by four key pillars that define who they are and how they work with their partners, customers, and the industry.
More than just hardware, Wilson & Bradley help bring ideas to life. From kitchens to commercial fitouts, their products are designed to be the foundation of functional, beautiful, and memorable spaces.
“Wilson & Bradley have been an incredible partner to our business. Their extensive product range means we always find the right solution for our projects, and their team consistently delivers exceptional service. They played a key role in helping us bring our new showroom in Richmond to life, supporting us with quality products and genuine advice every step of the way.” Derek De Betta of Mr. Cabinets / Casa Graziano.
Collaboration builds more than results, it builds trust. Wilson & Bradley believe in working side-by-side with their customers, manufacturers, designers, cabinetmakers, and retailers, to deliver the perfect fit, every time. Building relationships is at the core of everything they do.
Kitchen Craftsmen, with multiple showrooms and sales staff were looking for a top-quality product, and a simple way to purchase LED lighting for specific kits tailored to their business. Wilson & Bradley worked closely with the client creating individual kit codes for easy ordering. The Wilson & Bradley marketing team created
a handbook outlining all the kits, codes and requirements for a smooth, repeatable process that works.
"Working with Kieran Stirrup and the team at Wilson & Bradley has completely streamlined our LED lighting order process. With multiple showrooms and sales staff, we needed a simple, reliable solution and Wilson & Bradley delivered. “Kieran took the time to understand our needs, developed tailored kit codes with the help from the Wilson & Bradley team, and even provided a clear, easy-to-use handbook.
“The result? A quality product, ongoing support and a process that just works. Wilson & Bradley is now our leading supplier for LED lighting." Simon Avery, Kitchen Craftsmen.
From the early planning stages to final installation, the expert team and product support at Wilson & Bradley are embedded in the client’s workflow, on the ground, in real time, and whenever help is needed.
“Wilson & Bradley are our partners. We choose to work with them because we trust their recommendations. Their specification advice makes all the difference.” Steven Robinson, CEO of Brilliant SA.
Advancing Technology and Sustainable Practices
Smart solutions with better outcomes, for people and the planet. Building partnerships with brands that prioritise sustainability and innovation reflect the company’s investment in environmentally responsible alternatives.
Leading by example, Wilson and Bradley’s commitment to sustainable solutions is highlighted in the Woodleigh Futures Studio in Melbourne, a groundbreaking project that embodies the school’s commitment to innovation, future-focused learning, and regeneration. Pushing the boundaries of the traditional classroom, this designed space provides rich educational experiences while embracing sustainability at every level.
In partnership with Burmak Cabinets, Wilson & Bradley contributed to the project by supplying the Blum LEGRABOX box systems and Blum hinges, used throughout the project. The premium hardware solutions were integrated with 100% Australian-grown and made hemp joinery board, reinforcing the project’s dedication to using locally sourced, sustainable materials.
“We’re absolutely thrilled with how Wilson & Bradley partnered with us to bring the Woodleigh School project to life- now one of our most forward-thinking and sustainable initiatives. From the very beginning, the Wilson & Bradley team took the time to understand our goals and provided expert guidance on the best products to suit the school’s needs.
“We chose Blum LEGRABOX for the cabinetry, knowing Blum’s reputation as a leader in innovative and sustainable hardware solutions and it proved to be the perfect fit.
The Wilson & Bradley team supported us every step of the way, from technical advice to logistics, ensuring everything ran smoothly. Their attention to detail and exceptional service made a real difference, and we couldn’t be happier with the outcome.” Brad Kyle, Burmak Cabinets.
Above: Woodleigh School’s dedication to sustainability is showcased in every aspect of this innovative space — with Wilson & Bradley providing eco-conscious hardware solutions, including Blum Legrabox, to enhance both functionality and design.
Since 1976, Wilson & Bradley has been more than a hardware distributor, they are a trusted partner in shaping functional, inspiring spaces across Australia. Known for their hands-on service, premium products, and collaborative spirit, the company continues to lead with innovation and a customerfirst approach. Their national network of showrooms and expert support teams ensure clients always find the perfect fit. Backed by global brands and a legacy of family-led values, Wilson & Bradley is a driving force in the industry, setting the pace for what’s possible in premium cabinet hardware.
You will always feel welcomed in a visit to one of the Wilson & Bradley showrooms where you’ll find inspiration, learn about their range of products and enjoy exploring possibilities in an interactive space. Please come and visit. z
Established in 1989, SCF Interiors specialise in residential and commercial design, fabrication and installation of solid surface products. Flexible, high performance machinery is essential to their production. SCF rely on Farnese-Masterwood to supply and service cost-effective equipment matched specifically to their requirements.
Matt and Jason Biviano are secondgeneration operators of SCF Interiors, a business started when Dupont, the maker of Corian, approached their father to supply specialised solid surfaces for the industry. Jason has a shopfitting and detail joinery background and Matt’s background is in construction. Their skillsets are ideally suited to the business they now operate with 26 skilled professionals out of their premises in West Ryde (Sydney).
Matt said, “We believe we deliver a high quality product from high quality materials. Service and relationships are how we’ve developed our clientele. We still need to be competitive, and we do that by investing in good machinery and developing the right methods to do things to make the business
as efficient as we possibly can”. Jason adds, “We sell quality on the experience we have, and the projects we’ve worked on. We’ve been around for a long time and when people think about solid surfaces, they usually think about us.”
Jason and Matt have invested in Masterwood machines for over ten years. They operate two Masterwood 3-axis CNC flatbed machines and have recently installed a Masterwood ‘Titan’ 5-axis CNC machine from Farnese-Masterwood that enables them to process thermoformed surfaces, increasing their offering to their customers that includes Tier 1 builders and joinery companies producing designer projects in the commercial and high-end residential sectors.
Matt said, “The 5-axis Masterwood Titan is a relatively new machine for the joinery sector and Alex Farnese was here himself, making sure everything went to plan. Alex worked with us and our software provider to ensure it all worked as promised and we are very happy. Alex definitely gave it the time on the ground.” Jason adds, “The Titan cuts our materials consistently and the ability to process thermoformed designs has been a game-changer for us.”
“When we consider a CNC machine, Farnese is our first port-of-call. Our business is built on relationships, our customers are loyal to us so if Farnese is looking after us, we in turn are loyal to them. It comes down to what bells and whistles you really require, and Farnese was able to deliver the right product (machine) for our needs at a price point we were really happy with. Service is one of our highest factors when purchasing equipment critical to our operation and Farnese is only a phone call away. If there’s an issue, they come to the party quickly”, adds Matt.
Jason concludes, “I think what makes us stand out is our end-to-end offer. We employ a long-standing and talented team of professionals dedicated to providing quality service. We are committed to delivering new designs and applications of solid surface to the design community. We deal in superior products such as Corian, Hi-Macs, Staron, Marblo, & Meganite. We have the right equipment from Farnese-Masterwood, we have a wealth of technical experience, we offer a full showroom experience and like Farnese, our success hinges on the thorough and precise management of client requirements. z
ustralia’s cabinetry and joinery industries are changing fast - and the biggest winners will be those ready to adapt. With skills shortages growing and customer demands shifting toward customisation and faster turnaround times, investing in smarter machinery is no longer optional - it is essential.
Workshops across the country are realising that technology is not replacing craftsmanship - it is empowering it.
Smarter machinery, smarter businesses
Today’s machinery is designed to be intuitive, intelligent, and highly productiveeven with limited operator experience.
Modern CNC routers feature user-friendly touchscreen interfaces, automated setup processes, and smart software that guides users through job creation and execution with minimal manual intervention.
Advanced edgebanders now come equipped with pre-programmed settings for different
materials, glues, and profiles, meaning an operator no longer needs decades of experience to achieve perfect results.
Automation is not just about speed - it is about reducing risks and smoothing out operations. When a machine automates critical tasks like precision measurements, tool changes, and calibration, new team members can get up to speed faster and with less disruption to workflow.
The experts at Wood Tech, work closely with businesses to recommend the right machinery, provide comprehensive setup support, deliver operator training, and offer national after-sales service to ensure your workshop transition is seamless.
Shortening the learning curve
Traditionally, it could take months or even years for a new employee to confidently operate workshop machinery at full capacity. Today, with the right investment in smart equipment, that timeframe can shrink dramatically.
Features such as automated tool changers, camera-based registration systems for printed materials, intelligent label printing, and robotic material handling drastically reduce the training burden. Even staff with general trade skills - rather than specialised cabinetry experience - can become valuable contributors to a business in a matter of weeks.
This real-world productivity boost is critical in an environment where skilled labour is increasingly scarce and expensive.
Safety and staff retention benefits
Another major upside of smarter machinery is improved workshop safety.
Machines with intuitive controls, in-built diagnostics, and automatic error correction features significantly lower the risk of accidents.
A safer, more modern, and technologydriven environment also plays a crucial role in attracting and retaining younger talent - many of whom expect workplaces to be tech-savvy, efficient, and forward-thinking.
By upgrading machinery, workshops are not just improving output - they are building a more attractive, future-proofed place to work with less downtime and increased productivity with the added benefits of the latest technology.
Future proofing the workforce
Workshops that invest today in smart, user-friendly technology will be the ones best positioned to thrive tomorrow. Allowing for larger profit margins through higher productivity, reduced down time and labour costs.
When every edge counts, professionals turn to Wood Tech - the trusted name in high-performance edgebanding solutions across Australia. Our edgebanders are designed to deliver seamless results with speed, accuracy, and minimal operator input, whether you’re running a highvolume shop or a smaller production line.
When it comes to precision, performance, and productivity, the Wood Tech CNC exceeds all expectations. Whether you’re a cabinetmaker, furniture manufacturer, or custom joiner, our CNC machines are engineered to elevate your workflow.
When precision, reliability, and efficiency are paramount, Wood Tech’s panel saws stand out as the top choice for Australian woodworking professionals. Designed to meet the diverse needs of cabinetmakers, joiners, and shopfitters, our range combines robust engineering with user-friendly features to enhance your workflow.
Delivering precise, smooth, and consistent timber dimensions. Designed for both small workshops and large-scale operations, our machines combine robust engineering with user-friendly features to streamline your workflow.
Machinery can’t replace passion- but it can empower businesses to maintain highquality standards, grow production capacity, and operate profitably, even in challenging markets.
Wood Tech is leading the charge in smart workshop technology - offering a complete range of CNCs, edgebanders, material handling systems, and digital workflow solutions backed by expert support and service Australia-wide.
Trends cabinet makers cannot ignore
Several industry trends are accelerating the shift towards smarter, more adaptable workshops:
1. Digital Integration
Gone are the days when a tape measure and panel saw could sustain a workshop.
Today, digital workflows - from CAD/CAM software integration with CNC routers to barcode job tracking - are critical for improving speed, precision, and scalability.
Fully digitising planning, nesting, cutting, edging, and assembly processes dramatically reduces lead times and error rates, creating a clear competitive advantage.
The Wood Tech advanced range of CNCs and factory automation solutions help businesses seamlessly transition into the digital manufacturing era.
2. Batch Size One Production
Consumers increasingly expect bespoke kitchens, vanities, and furniture - not onesize-fits-all solutions.
This shift towards ‘batch size one’ production demands machinery that can mrapid
changeovers, varied materials, and short-run manufacturing without losing profitability. Smart CNC routers with automatic tool changers and dynamic nesting capabilities make this level of customisation not only possible but highly efficient.
3. Smart Material Handling and Workflow Optimisation
Efficiency isn’t just about cutting faster - it is about moving smarter.
Automated panel storage, intelligent labelling, and optimised material flow from cutting to assembly save valuable time, minimise material damage, and significantly boost daily output. By streamlining loading processes and reducing the need for forklift access on the factory floor, workshops can dramatically cut labour costs and reclaim valuable floor space - all without the need for physical expansion.
Wood Tech proudly supplies innovative solutions like Barbaric material handling systems, helping workshops eliminate bottlenecks and maximise overall productivity.
Preparing for tomorrow, today
The choice isn’t whether the cabinetry industry is changing - it is how quickly you choose to change with it.
Workshops that embrace smarter machinery, digital workflows, flexible production models, and smart material handling today will ensure they remain competitive, profitable, and ready for whatever tomorrow brings.
Ready to future-proof your workshop? Wood Tech’s innovative machinery, advanced automation solutions, and nationwide support team are here to help.
Visit www.woodtech.com.au to start your next chapter. z
Swift assembly and unmatched durability with enhanced front panel engagement
Precise alignment with convenient access to tilt, height and side adjustment
Exceptional drawer opening and closing with Titus next-generation adaptive ART damping
Push-to-open compatibility for simplified stockholding
Contact Titus Tekform www.titustekform.com.au
info@titustekform.com.au
Article by Cathy Brand, CEO, Brooks Australia
Which should your business choose?
Manufacturing is a critical decision for any business, especially in the built environment, where product quality, durability, and design play a central role in consumer satisfaction. Companies typically face two primary options: outsourcing production to third-party manufacturers or keeping production in-house. Each approach has its own set of advantages and challenges, making it essential for businesses to evaluate their specific needs, goals, and capabilities carefully before committing to a manufacturing model.
The case for third-party manufacturing
Outsourcing production to third-party manufacturers - especially in countries like China, India, or other regions with lower labour/production costs - can offer substantial cost savings, making it an attractive option for some businesses.
One of the primary advantages is lower labour costs, which contribute to reduced overall production expenses. Additionally, third-party manufacturers often have well-established supply chains and logistics networks, enabling businesses to scale production without investing heavily in infrastructure.
Beyond cost efficiency, outsourcing can provide access to specialised expertise and advanced production facilities that may not be feasible for companies to develop independently. Working with a third-party manufacturer can accelerate production timelines and ensure products are made using the latest technologies for businesses manufacturing kitchen appliances, high-end furniture, or lighting solutions. This allows smaller companies to launch new products faster and expand into new markets with minimal capital investment. Disruptors in
the market often use this approach, flood the market with cheap product to capitalise on an opportunity and then move onto something else.
However, outsourcing is not without its challenges. One major concern is the loss of direct control over the manufacturing process. Quality control is often more challenging to monitor when production is conducted overseas, as businesses must rely on external partners to maintain consistency and comply with both international and local regulatory standards. Any quality discrepancies can significantly impact brand reputation and customer trust for products in the built environment - where durability, safety, and aesthetics are crucial.
Another concern is intellectual property protection, particularly when dealing with overseas manufacturers. There exists
a risk of exposing designs or technological innovations to third parties, especially when the production process involves sensitive or proprietary information. Theft or misappropriation of intellectual property poses a significant threat, and enforcing intellectual property rights in foreign jurisdictions can be complex and costly. Additionally, navigating compliance with local laws, including safety and industry standards, can be more challenging when businesses are outsourcing production across borders. You often see the same product design by two different companies in the market both claiming to be different but essentially coming from the same thirdparty manufacturer overseas. We have seen this situation recently with the tariff increases from US to Chinese manufacturers, where in return they have removed labels from products and sold direct to the US consumer.
In-house manufacturing offers businesses with full control over the production process, a crucial element for industries where precision and consistency are essential. At Brooks Australia, we take the same approach with our manufacturing process – Smoke Alarms must meet rigorous safety requirements and Australian standards therefore quality cannot be compromised. By overseeing every step of production, from design to final assembly, we ensure our smoke alarms meet the highest quality standards, providing reliability for Australian homes and businesses.
One key advantage of in-house manufacturing is the ability to implement rigorous quality assurance measures. This particularly benefits businesses in the built environment, where customers expect long-lasting, well-crafted products. Whether it's ensuring the perfect finish on a kitchen countertop or the flawless integration of a smart lighting system, maintaining direct oversight helps businesses uphold their brand promise.
However, in-house manufacturing presents its own barriers. It requires significant upfront investment in equipment, facilities, and skilled labour. The costs involved in establishing and maintaining 40
a production plant can be prohibitive for smaller businesses, particularly due to ongoing operational expenses, including maintenance, utilities, and labour costs. These expenses require businesses to have confidence in their long-term demand projections, as sudden market fluctuations can result in overcapacity or underproduction.
In particular, in-house production can foster greater innovation in research and development (R&D). Companies can experiment with new materials, refine existing designs, and rapidly prototype new products. This is a crucial advantage for brands focusing on custom or highend home products, as the ability to innovate quickly enables companies to stay competitive and respond to market needs without the delays associated with thirdparty manufacturers.
Ultimately, the decision between thirdparty and in-house manufacturing depends on a company’s specific priorities, market position, and long-term goals. Businesses focused on cost efficiency, rapid scalability,
short term opportunity, disruptors may find outsourcing to third-party manufacturers the most suitable option. This approach offers the flexibility to get into the market and out meet demand without heavy investment.
On the other hand, companies that prioritise quality control, regulatory compliance, and brand reputation find that in-house manufacturing aligns better with their strategic goals. The ability to oversee every step of the production process provides a higher level of control, which can be critical for companies that require precision and consistency. Companies who are invested in the market and its outcomes.
By carefully weighing the pros and cons of each manufacturing model, businesses can determine the approach that best fits their needs, ensuring they can effectively manage production costs, quality, and scalability. Regardless of the path chosen, the right manufacturing strategy can provide a strong foundation for growth and success in today’s competitive business environment. This decision can define a brand's long-term success in the building materials industry-
where functionality, aesthetics, and safety intersect.
At Brooks Australia, we know that reliability is non-negotiable regarding home safety. By overseeing every step of production, we ensure our smoke alarms meet rigorous safety regulations and provide the reliability Australian homes and businesses depend on. We are also entrenched in the fire business, not a fly by night disruptor that will be here one week and gone the next – we have invested and understand the value of our and your reputation.
Brooks Australia has been a market leader in dry fire safety systems and solutions since its founding 50 years ago and was acquired in December 2022 by Irish company Ei Electronics. Recognised as a leader in the public housing sector, Brooks has developed and supplied an array of high-quality, reliable products based on its knowledge and expertise to help safeguard families with their residential and commercial fire panel systems. For more information, visit www. brooks.com.au. z
Two new machines were introduced to the Australian market in March, the Thibaut T512 Polishing and Texturing Centre and the Comandulli Coral Edge Polisher. The launches were supported by international suppliers Thibaut and Comandulli attending the CDK Stone Machinery Showcase on March 27–28, where the Coral was shown in operation and the T512 was introduced to the market.
These machines address key needs in fabrication, surface finishing and edge polishing. Offering solutions that are compact, adaptable, and suited to the diverse materials now used in workshops across Australia.
The Thibaut T512 brings a new level of control and versatility to surface finishing in stone fabrication. Designed for workshops handling a wide range of materials and textures, the T512 performs essential processes like including calibrating, smoothing, polishing, brushing, honing, and bush hammering, with the flexibility to add on milling, drilling, or engraving.
One of its standout features is Thibaut’s pneumatic pressure system, which automatically adjusts to the tool grit and compensates for uneven surfaces. This ensures consistent contact between the tool
and the material, helping achieve even, highquality finishes particularly important for decorative or restoration work.
The T512 is supplied in Australia with a suite of integrated technology to support precision and autonomy. A tilting worktable simplifies loading heavy slabs, while a slab thickness probe, tool wear sensor, and a 20MP digital camera work together to ensure the machine can adapt to each job. The machine also features a 10-position automatic tool changer for uninterrupted processing and a BT40 high-torque spindle for reliable performance across a range of tooling types.
“The T512 fills a real gap in the market. It’s compact but still offers a wide range of surface finishing functions, especially for decorative applications where precision and flexibility are essential,” said James Clark, Director at CDK Stone.
The Comandulli Coral is an edge polishing machine developed to balance performance with space efficiency. It features seven polishing heads and four chamfering units (two upper, two lower), enabling the machine to process a wide range of edge profiles such as straight edges, bevels, and partial polishes. This setup also allows for the processing of glued mitred workpieces and benchtops with sink cut-outs.
The Coral includes a calibration unit for thickness control and can perform additional operations such as blind cuts, upper grooves, and apron honing, making it adaptable to different fabrication needs. The machine’s software interface is designed for ease of use, allowing operators to set up repeatable programs and reduce changeover time between jobs.
“The Coral is ideal for Australian workshops. It offers full-scale edge processing in a more compact machine, something that’s becoming increasingly important as businesses look to maximise space and streamline operations,” said Jonathan Height, Joint Managing Director at CDK Stone.
The arrival of the T512 and Coral expands the range of machinery available through CDK Stone, providing solutions that help fabricators adapt to changing materials and customer expectations. Both machines offer compact footprints with the flexibility to handle multiple tasks, ideal for workshops focused on efficiency and quality.
For more information about the Thibaut T512 or Comandulli Coral, speak with a CDK Stone machinery specialist or visit cdkstone.com.au. z
Article by Philip Ashley
Humans are good at taking basic materials from nature and making them useful. Throughout history we’ve made things from materials starting with stone, moving to iron, bronze, and steel, building civilisation to what it is today. When science discovered the atom, everything changed, opening the door into advanced materials engineering.
Advanced materials manufacturing is a relatively new field of production. Advanced materials have properties that perform beyond everyday materials like steel, aluminium, and titanium, opening up the possibility of applications we are yet to discover. Advanced materials also provide a potential way of conserving resources, improving sustainability, and diminishing the impact of manufacturing on the environment.
Biesse, along with SCM are two equipment suppliers that produce machinery specifically for advanced materials manufacturing. Marco Sigismond is Biesse’s advanced materials product specialist and helped us out with some technical information. Marco explained, “Advanced materials are engineered materials that
have been studied and created with precise characteristics to be used in specific applications.”
Marco sites engineered plastics replacing steel and other metal parts as one significant advanced material. Engineered plastics don’t conduct electricity, they are heat resistant and do not expand to heat, and they need less maintenance. Advanced materials are used for specialist structural components. Marco tells us “Fibre based materials are becoming more common, and composite materials are able to achieve greater physical characteristics.” Marco advises there are very few advanced materials used in the cabinet making industry.
Advanced materials are used in laptop computers, digital cameras, smart cell phones, microwave ovens, computerised cars, thin film photovoltaics, and many other
intelligent devices and instruments used in many sectors that require special type of materials that have superior properties. Advanced composites combine two materials to create a material that is stronger than the original elements. Composite materials examples include carbon fibre composites, made by combining carbon fibre with resin. Carbon fibre features high strength, a good strength-to-weight ratio, high heat resistance, and low thermal expansion.
Engineered plastics are used in industry for gears, bearings, and seals because of their low friction and resistance to wear. They retain their shape at high temperatures, have good electrical insulation, and are light in weight. Engineered plastics are also used for precision surgical instruments in the healthcare sector. Advanced materials are used for 3D printed models and components.
Advanced materials are used extensively in the defence industry for reducing weight, increasing strength and corrosion resistance, and in protective equipment such as bullet proof vests. They are used in the marine and aerospace industries for similar reasons. An example is the long range Boeing 787 that is 80% composite material. Titanium is used for sporting goods and transparent aluminium is already commercially available for windows and domes. There are hundreds of machines already working in Australia working in the automotive, construction (acoustic and decorative panels) and refrigeration industries. Working advanced materials for these more common industries can be a lucrative business opportunity.
Smart materials are advanced materials that transform in response to an external stimulus. Smart materials include photovoltaic materials in solar cells, which convert solar radiation into electricity. They also include chromo-active materials that change colour in response to a change in light, temperature, or pressure, and magnetorheological materials, which change when exposed to a magnetic field.
Another example of a smart material is the shape memory alloy that can be bent but returns to its original form if heated up. This feature is known as the ‘shape memory
effect.’ One of the first shape memory alloys was nickel-titanium, which features a good level of corrosion resistance combined with outstanding electrical and mechanical properties. Shape memory alloys are widely used in medicine in stents inserted into patients to widen arteries because they can change shape in response to body temperature.
Current CNC machines for cutting wood and wood composites are able to produce components from advanced materials but may not provide optimum performance. A machine designed for advanced materials will have a higher level of accuracy,
dedicated cutting units such as knives, misting oil units and alternative holding of parts because vacuum holding does produce some slight movement and while for cabinet making this is not an issue, for advanced materials any slippage could matter. (Insert image 4 Biesse Rover)
Some exotic examples of advanced materials are titanium fluoride phosphate, self-healing polymer gel, platinum-gold alloy, composite metal foam, spider silk, carbon-reinforced concrete, aerogel, and rare-earth alloys. Advanced materials include everything from advanced metals, ceramics, plastics, and composites to smart materials such as shape memory alloys and materials manipulated at the nanoscale, a unit of length where one nanometre is equal to a billionth of a metre.
Thomas Edison perfected the incandescent light bulb through materials innovation, and today's smartphones would not exist without advanced materials. Marco says, “Advanced materials are the future, and we regularly test these at our facility in Sydney.” According to Madonna we are living in a material World, not the one she was singing about but nevertheless, it’s true. z
Precision and efficiency are essential in stone fabrication, especially when setting up and running Profile Tools on CNC Work Centres. With current pressures of premium materials, and tight project timelines this has never been more critical. While much of the focus is often on CNC Machinery and cutting tools, one of the most impactful ways to enhance productivity is by optimising the profile tool preparation process. A streamlined, repeatable workflow that includes efficient tool dressing, precise measurement, and consistent maintenance allows operators to run tools effectively without interrupting machine operation.
Q: How does accurate tool presetting impact machining outcomes in the stone industry?
A: Precise tool presetting directly influences surface quality, it significantly increases feed speeds, reduces tool and machine load, and overall enhances production efficiency. Whether processing natural stone, porcelain, or engineered materials, even minor tool misalignments can lead to reduced tool life, reduced feed speeds, chipped edges, inconsistent profiles, or rejected parts.
Regular recalibration and dressing of tools helps maintain optimal edge quality and prevent wear-related issues. When tools are properly measured and maintained, cutting speeds can increase, cycle times are reduced, and the risk of surface imperfections is minimised. This proactive approach not only improves product quality but also extends tool life, saving costs on replacements and manual touch-ups.
Q: What are some common challenges when working with complex profile tooling?
A: Setting up typical Profile Tools on a CNC Work Centre is often time-consuming, particularly when done manually. The more intricate the profile, the longer it takes to align and set the wheels. Configuring detailed edges like an F+V40, can consume significant production time, affecting workshop efficiency and project timelines.
A tool presetting machine such as the ZOLLER »smile« 420 simplifies this process. It allows even the most complex edges to be measured and preset with high precision, reducing setup time from hours to minutes all done offline while the CNC machine continues running. This approach eliminates spindle downtime, maximises productivity, and ensures consistent edge quality, regardless of the complexity of the profile.
Q: How can workshops identify and manage uneven tool wear before it affects production?
A: Managing tool wear effectively is crucial for maintaining high-quality edges and preventing costly rework. Regular
maintenance, including dressing tools with a dressing stick, keeps cutting edges sharp and free from imperfections. This not only improves the quality of the profile but also reduces the risk of visible lines and uneven finishes.
A tool presetting machine enhances this process by allowing operators to measure tool wear with precision before it impacts
production. By presetting and inspecting tools offline, it ensures that only the minimal amount of material is removed by each position. This level of accuracy helps extend tool life, maintain faster cutting speeds, and reduce cycle times.
Q: How does digital measurement improve quality control and consistency in stone fabrication?
A: Consistency and accuracy are crucial in stone fabrication, especially when working with complex profiles or highvalue materials. Variability in manual measurements and operator setups can lead to imperfections, rework, and wasted materials. A tool presetting machine such as the ZOLLER »smile« 420 addresses this challenge through digital measurement and data integration.
The ZOLLER captures precise measurements and has the capability to automatically transfer this data to CNC machines, eliminating manual data entry. This ensures each process is executed to exact dimensions, maintaining edge quality and reducing the risk of rework. By standardising tool setup and integrating digital accuracy, stonemasons achieve greater consistency, improved quality control, and more reliable outcomes across every project. z
CDK Stone stocks a comprehensive range of high-quality tools and equipment designed to achieve precision in edge profiling for Porcelain, Ceramics, and Natural Stone.
Article by Sareen Stone
When specifying natural stone, the relationship between material and finish is critical. Your chosen finish defines aesthetics and determines suitability, performance, and longevity. Careful consideration ensures your design is both beautiful and fit for purpose.
Designers are gravitating towards finishes that enhance the natural texture of stone, adding depth and a tactile experience to spaces. This trend aligns with the broader design movement towards authenticity and natural materials.
Popular finishes include:
Honed Finishes: A smooth, matte finish achieved by grinding the stone surface to a consistent level. Honed finishes are favoured for their understated elegance and are commonly used in high-traffic areas for internal flooring.
Leathered Finishes: This finish provides a soft sheen and a textured feel, enhancing the stone's natural color and pattern. It is achieved by running diamond-tipped brushes over a honed surface, making it ideal for countertops and accent walls.
Split-Face Finishes: Created by mechanically splitting the stone to expose its natural, rugged texture. This finish is commonly used for feature walls and exterior facades, offering a rustic and organic aesthetic.
Natural stone finishes enhance both the beauty and functionality of a space. Here's a quick guide to their most common applications:
Honed and leathered finishes are popular choices for kitchen countertops and vanities.
Honed finishes are ideal for indoor flooring. These create a subtle surface that is durable and comfortable underfoot.
Flamed, sandblasted, and bush hammered finishes offer slip resistance, durability, and lasting natural beauty.
Textured and naturally split stone creates standout features with depth and visual interest.
1. Application Environment. The location determines the appropriate finishpolished or honed for interiors, and textured, slip-rated finishes for exteriors.
2. Traffic Considerations. High-traffic commercial spaces need durable finishes; honed surfaces often outperform polished ones for internal commercial settings.
3. Slip Resistance Ratings. P-ratings indicate slip resistance (P1-P5). Higher numbers provide greater safety: P1-P3 for interior applications with varying moisture levels; P4-P5 for exterior areas.
4. Maintenance Requirements. All natural stone needs sealing and care; the finish and environment affect how often and how intensively maintenance is required.
Honed
Produces a smooth, matte surface without reflection. This versatile finish works beautifully in contemporary interiors. Its low slip rating (P2-P3) makes it suitable for interior floors with moderate traffic. Popular for both residential and commercial applications.
Flamed/Exfoliated
Created by applying intense heat to the stone surface, this finish produces excellent slip resistance (P5) for exterior applications while maintaining a natural appearance. Particularly effective for granite and heat-resistant stones.
This heavily textured finish is ideal for exterior paving, cobblestones, walkways, and public spaces. The mechanical hammering creates uniform indentations that optimize slip resistance while maintaining the stone's colour intensity.
Offers a uniform textured surface with excellent slip resistance (P5). Creates a premium, elegant look for exterior applications while reducing colour intensity slightly.
Alfresco
This finish is a term specifically used by Sareen Stone to describe products that have undergone specific processes to make them suitable for outdoor use. These finishes achieve P4 or P5 slip ratings - the safest choice for exterior applications.
This means the stone hasn't received any surface treatment beyond cutting. The final appearance is determined entirely by the stone's inherent characteristics, making each piece unique. Suited for outdoor use on floors, however, is suitable for wall claddings.
Achieved by cutting stone with a guillotine that fractures the block, creating a textured, slightly undulating surface. This finish is particularly effective for wall cladding applications.
Created by directing high-pressure water across the stone’s surface, opening the pores and subtly texturing the stone. Varying the water pressure allows for different textures, depending on the desired look. Waterjet finishes are particularly well-suited for exterior applications.
Contrary to common client perception, all natural stone is porous to some extent. Regardless of the type, stone surfaces are vulnerable to staining, moisture absorption, and wear over time. All natural stone is porous and prone to staining and wear.
• Some sealers enhance (darken) stone
colour while others maintain their natural appearance
• Different stone types require specific sealer formulations based on porosity and application
• Always specify pH-neutral cleaners specifically designed for natural stone
• Never use vinegar, bleach, ammonia, or general-purpose cleaners
Resealing depends on the sealer, stone type, traffic, and environment. Clients should confirm maintenance requirements with their supplier to maintain warranty protection.
The natural stone finish you specify plays a crucial role in shaping not only the aesthetic outcome but also the functional performance and maintenance needs of the installation. By understanding the available finish options and aligning them with the specific demands of each project, you can ensure your specifications achieve both lasting beauty and durability.
For detailed technical information on specific stone finishes, slip ratings, or maintenance requirements, Sareen Stone's team of specialists can provide expert guidance tailored to your project needs.
web www.sareenstone.com.au
reasurer Jim Chalmers has handed down the fourth federal budget of his time in government. In a surprise move, the government announced a new round of tax cuts. The first marginal tax rate will be reduced from 16 to 14 per cent over two years, starting from 1 July 2026.
This means all taxpayers earning over $18,200 will get a $268 tax cut in 2026-27, which becomes $536 a year from 2027-28. Most of this tax cut will go to the almost nine million workers earning between $45,000 and $135,000 per year.
The budget notes signposted global uncertainty, however in Australia, growth has rebounded, inflation has moderated, unemployment is low, and real wages are growing.
A deficit of $42.1 billion is forecast for 202526, while gross debt is $177 billion lower in
2024-25 than forecast at the Pre-Election Fiscal Outlook (PEFO). Economic growth is expected to be 1.5% in 2024-25, 2.25% in 2025-26 and 2.5% in 2026-27.
Similar to the 2024 budget, energy bill relief again features prominently; the government will extend rebates on electricity bills by six months, providing a $150 cut to power bills for households and small businesses.
These rebates will be automatically applied to every household and around 1 million small businesses from July 1 and paid over two quarterly instalments.
Ahead of the budget, the MYOB research team found SMEs had hoped to see reduced cost pressures and support for cashflow prioritised. Some of the measures mid-sized businesses were focused on included access to finance, innovation and digitisation, as well as support for cybersecurity.
Small businesses didn’t see a lot in this budget, however, for certain businesses, some cost-of-living woes may be aided by support that includes:
• Prompt 20-day payment times for construction industry contractors/ subcontractors who complete work for Government Business Enterprises undertaking major construction activity (e.g., the NBN and Western Sydney Airport projects)
• A pause of indexation on draught beer excise and excise equivalent customs duty rates for alcohol producers and the hospitality sector
• An increase in support available under the current excise remissions scheme for alcoholic beverage manufacturers
• A Wine Equalisation Tax Producer rebate, that’s estimated to lower receipts by $165 million over five years
• The provision of $18 million for creditor assistance payments to support eligible businesses affected by the Whyalla Steelworks administration
• Energy bill relief, as listed below
• Government has committed to spending $20 million on a ‘Buy Australian’ campaign in 2025/26 to encourage Australians to buy locally-produced goods and services
• The Government is also going to help Australians have more scope to become entrepreneurs and earn more each year
by banning the use of non-compete clauses for low- and middle-income workers who earn less than the highincome threshold ($175,000 currently)
While there were few standout measures targeting mid-sized businesses, this year’s budget outlines national priorities and hints at where the federal government sees future growth.
• Return to Deficit: The government forecasts a $26.9 billion deficit for 202526, marking a shift from two consecutive budget surpluses. Rising structural expenses in areas like health, aged care and defence underpin this return to red ink.
• A $20 million Buy Australian advertising campaign that will encourage consumers to support local businesses amid the uncertainty of global trade wars and US tariffs.
• Clean Industry Focus: $2 billion in production credits for green aluminium manufacturing.
• Defence and Infrastructure Investment: More than $10.6 billion in additional defence spending and $7.2 billion for Queensland’s Bruce Highway demonstrate continued focus on national resilience and construction-led stimulus.
Households and small businesses will get an extra round of energy bill relief. There will be $150 wiped off power bills for the final six months of this year, which will help reduce consumer costs by 7.5 per cent, at a cost of $1.8 billion to the budget.
This energy bill relief includes the rebates that have already been paid to households and small businesses. When combined with last year’s budget, this is up to $800 for eligible small businesses.
“Small
businesses continue to face economic headwinds. With utility costs, fuel prices, and concerns about price margins and profitability topping their list of pressures, these targeted measures will alleviate some of the financial strain they’re experiencing.
• Medicare levy low-income thresholds will be increased (at a cost of $648m)
• $17.1b in new tax cuts for every taxpayer
There has been an increased, pre-election focus on healthcare announcements:
• Maximum price for a PBS prescription will be $25 ($7.70 for concession card holders)
• $8.5b for Medicare (improve bulk billing rates – 9/10 GP visits should be bulk billed by the end of the decade)
• Funding for more urgent care clinics, women’s health and public hospitals
Construction and apprenticeships will get $722.8m over four years (this is not new funding), including:
• Expansion of the New Energy Apprenticeships Program. It will be renamed and expanded to capture critical residential construction occupations
• Increase to the Living Away from Home Allowance
• Doubling the current maximum incentive payments for eligible housing construction apprentices from $5k to $10k
The 2025 federal budget measures encouraging consumers to Buy Australian, alongside cost-of-living assistance in tax cuts and energy supports, will flow through to the nation’s small businesses and midsized enterprises.
However, continued and consistent support will be necessary to energise the business communities that, combined, contribute half of the nation’s GDP.
MYOB CEO Paul Robson says while some of the latest budget measures will help the business community, additional measures, such as future certainty around the instant asset write off, would have been welcomed.
“As a homegrown Australian business ourselves, to see support for our local SMEs filter through in these cost-of-living measures is encouraging,” he says.
“Supporting local operators is an important agenda item for the government, the economy and Australian consumers.
“Small businesses continue to face economic headwinds. With utility costs, fuel prices, and concerns about price margins and profitability topping their list of pressures, these targeted measures will alleviate some of the financial strain they’re experiencing.
“The success of our small and mid-sized business community is intrinsically linked to our nation’s economic prosperity. By addressing their key concerns around cost pressures, cashflow management, and investment support, the government would help to create an environment where these businesses can thrive in 2025 and beyond.” z
he objective of the Advanced Manufacturing Research Facility (AMRF) building was to provide the first-ever flexible and adaptable state-ofthe-art building that used unique modular disassembly components from concept to execution. Using this building as an example for leading change for more sustainable, innovative projects towards a viable future.
Built from prefabricated timber modules and inspired by the movement of water, the light filled design was led by architecture firm Hassell in collaboration with the Indigenous designer Danièle Hromek of Djinjama, a First Nations cultural research and design practice. With the goal of reaching high-end sustainability benchmarks, the project aimed for a NABERS Energy rating of 5.5 stars, a 6-Star Green Star certification, and the strict guidelines of the Living Project Challenge. These objectives highlight the building’s pioneering role in sustainable architecture inside the Aerotropolis, a forward-thinking new urban district located in Western Sydney.
AMRF is a collaborative space for government, industry and research to nurture and develop innovative manufacturing projects. It is the first building designed for the Aerotropolis, the new urban region in Western Sydney. The AMRF building is a workplace and will feature a visitor centre, public viewing spaces and is designed to showcase the real time building progress of Australia’s newest sustainable, connected city.
The building was conceived as a ‘kit of parts,’ featuring a timber structure and a bamboo façade made up of prefabricated modular components. These components were mechanically fixed together, allowing for disassembly, expansion, and even relocation. The proposal sought to create a material lifecycle that aligned with the natural rhythms of ecology, addressing the urgent need for sustainable materials within the future community’s ecological framework. This approach emphasised a regenerative cycle that gives back to the environment.
In collaboration with Hassell Studio, the House of Bamboo specifically focused on integrating engineered bamboo into the façade solutions. Bamboo is a highly sustainable alternative to traditional timber, as it grows rapidly (some species can reach maturity in just three to five years) making it a renewable resource that can be harvested without harming ecosystems. Its impressive strength to-weight ratio and flexibility enable innovative designs that fulfil performance and aesthetic goals.
The House of Bamboo’s collaboration with Hassell Studio involved extensive exploration of batten size, screen design, and manufacturing techniques to ensure ease of installation as prefabricated modular systems. The engineered bamboo batten screens not only provide façade articulation and shade to the high-performance glazed walls but also reflect a commitment to sustainability, reinforcing the project’s holistic approach to environmentally responsible design.
Externally screens were coated with a whitewash Woca oil plus two coats of Woca clear oil and a UV protective coating. All
panels, external and internal, include a standard mould treatment and coating. Samples were carefully prepared with subtle shade variations and presented to Hassell Studio. The aim was to blend with the Victorian Ash tones that were installed for the structural beams.
The Projects Architects originally wanted to specify Victorian Ash, but that selection became unfeasible and engineered bamboo was selected for its sustainability credentials, FSC and availability. The Bamboo engineered screens cover a total façade area of 1037m2 and are located externally and internally including cladding on chimneys and external lanterns.
The project delivery was manufactured in seven batches to align with the projects phased installation timescales:
• Batch 1 - Upper and Lower Manufacturing Hall
• Batch 2 - Internal Upper and Lower Screens
• Batch 3 - Plantroom Upper and Lower Screens
• Batch 4 - Roof Lanterns (with curved corners)
• Batch 5 - Rooftop Chimneys
• Batch 6 - Internal Screens in lower workplace
• Batch 7 - Manufacturing Hall internal doors
Packages were carefully grouped and labelled for easy identification on site to assist with the main contractors site organisation and installation sequence.
Flexible and adaptable programs were embedded into the fabric of the building. Reimagining the construct of a traditional building through providing modular panels that would work in conjunction with the site.
The use of sustainable materials like bamboo and rattan not only aligns with Western Parkland City Authorities environmental goals but also highlights the potential of these materials in complex, high-end commercial settings.
The engineered bamboo facade on the AMRF project exemplifies House of Bamboo’s expertise in merging sustainability with innovative design solutions. By overcoming significant engineering challenges, the team delivered a building facade that is both visually striking and environmentally responsible, setting a new standard for future projects in the Badgerys Creek, Western Sydney Aerotropolis. z
he finalists competing in the annual HIA 2025 Australian Kitchen of the Year awards have been announced. Congratulations to the below finalists competing to be the Australian winners at the 2025 HIA-CSR Australian Housing Awards.
ACT/Southern NSW - Harrison's Joinery and TG Homes
Hunter – Latham’s Kitchens
NSW – Studio Minosa and Panache
Kitchens
NT – 4 Kitchens
North QLD – Liam Gilligan Builders and Legacy Cabinets
QLD – Sarah Walter Building
Sa – Build Theory
TAS – Merlin Constructions and i.D Joinery
VIC – APC Build
WA – Calautti Homes and Cabinet Network
The HIA Awards identify, highlight and reward excellence throughout the housing industry, representing the finest tradespeople and their businesses throughout Australia.
The awards are split into regions throughout Australia. Participants enter at their relevant regional level, selecting their preferred category, and are judged by a highly experienced team of building experts.
Joint entrant for the ACT and Southern NSW - Harrison's Joinery and TG Homes -designed a remarkably bold kitchen that refuses to be ignored. The red and pink tones of the beautiful sedimentary
natural stone are the true feature of this kitchen. The craftmanship is undeniable with every meticulous detail poured over, multidirectional curves, an integrated stone sink and finishes that flow seamlessly throughout the space. The stone is complemented by neutral flat timber grain cabinetry, custom wrapped brass cylinder rangehoods suspended from the ceiling and gold handles.
A light filled butler's pantry is hidden away next to the arched bar, with joinery extending into the dining space this ensures a multiuse space perfect for entertaining. A unique, elegant and luxuriously designed space within the home and a standout from the moment you walk through the door.
web www.hia.com.au z
At Interzum Guangzhou 2025, DTC made headlines with an unforgettable event featuring its brand ambassador, Su Bingtian—the legendary Asian sprinter who holds the 100-meter Asian record of 9.83 seconds and is the first Asian athlete to qualify for the Olympic 100-meter finals. On March 28, Su partnered with DTC to unveil hardware solutions that operate five times faster than conventional systems.
One of the event’s highlights was the Blindfold Challenge, where Su, blindfolded, successfully installed DTC’s innovative anyway snap-on hinges, demonstrating a remarkable fivefold acceleration in assembly speed. The audience also witnessed the impressive loading capacity of DTC’s Dragon-pro drawer system as Su, who weighed 75kg, stepped inside the drawer himself.
Interzum Guangzhou 2025 provided a platform to spotlight DTC’s world-class manufacturing capabilities.
With six factories spanning over 650,000 m², DTC controls the entire production
process—from raw material sourcing to precision stamping, automated assembly, and rigorous quality testing. This vertical integration ensures consistent product quality and enables rapid innovation in response to market demands.
The company’s advanced R&D centre, backed by over 1,200 global patents and 258 technical staff, continues to drive breakthroughs in furniture hardware technology.
Currently, DTC's sales network extends to 130 countries and regions worldwide.
DTC and Nikpol have been working together to bring the DTC hardware to Australia for over 10 years.
Nikpol is a 100% Australian-owned and operated company that supplies hardware, decorative surfaces, and appliances. The company operates three facilities with over 140 employees and has become a leading supplier for the new home, renovation, and commercial joinery markets across Australia.
Some of their recommended innovations include:
1.Pivot-star hinges
An IF award-winning hinge, with excellent function of soft closing, lately have been added the feature of anyway snap-on, a quick and convenient mounting mechanism.
2.Stylish hinges
Elegant and slim design and the miniature damper technology brings a stylish new hinge. Assembly comfort is the new benchmark. The intuitive Anyway technique simplifies and speeds the process of mounting cabinet doors.
The DTC Dragon-pro drawer system combines sleek aesthetics with superior functionality.
The new improved version with tilt functionality and new Matt Grey colour takes the Dragon-pro drawer to a marketleading six heights with four inner drawer height options in three different finishes.
This slimline system is designed to complement any modern kitchen.
The double-wall profile and innovative dividing elements enhance both space efficiency and practicality, offering a perfect blend of style and utility. z
Interzum
20 - 23 May 2025 www.interzum.com
Ligna
26 - 30 May 2025 www.ligna.de
Design & Build Week (Melbourne) 12 – 14 June 2025
www.designandbuildweek.com.au
Irish Furniture & Homewares Show (IFHS)
24 - 26 August 2025
www.ifhs-tradeshow.ie
Woodtech 11 - 15 October 2025 woodtechistanbul.com
SICAM 2025 14 - 17 October 2025 www.exposicam.it
Young Furniture Makers' Exhibition 29 October 2025
www.furnituremakers.org.uk
Materials & Finishes Show 17 - 19 May 2026
www.materialsandfinishesshow.com
Proudly produced and printed in Australia
Published quarterly by:
ELITE PUBLISHING CO PTY LTD
ABN: 27 006 876 419
PO BOX 800, Templestowe, Victoria, Australia 3106
Ph: + 61 3 9890 0815
Email: info@elitepublishing.com.au
Web: www.suppliermagazine.com.au
PUBLISHERS
Georgia Gilmour
georgia@elitepublishing.com.au
Michelle Cammiade michelle@elitepublishing.com.au
ADVERTISING SALES MANAGER
Sandie Velkovska
sandie@elitepublishing.com.au
EDITORIAL
For editorial enquiries please email: info@elitepublishing.com.au
EDITOR
Michelle Cammiade michelle@elitepublishing.com.au
CONTRIBUTING EDITOR
Philip Ashley
philipneilashley@yahoo.com.au
CIRCULATION
For circulation enquiries please email: info@elitepublishing.com.au
PRODUCTION
For artwork and production enquiries please email: production@elitepublishing.com.au
PRE-PRESS
Prominent Digital
PRINTED BY
Prominent Press Pty Ltd
ELITE PUBLISHING CO PTY LTD
PUBLISHERS OF:
Supplier Magazine, Flooring Magazine, and
Equipped with a matrix table adapted to a variety of flexible working processes such as quick nesting, drilling, grooving and milling functions. The Titan 5 Axis CNC comes in multiple sizes to meet any work size requirements.
The APEX is a high-quality CNC machining centre with 3 controlled axes, equipped with a matrix table adapted to a variety of flexible working processes such as quick nesting, drilling, grooving and milling function. The APEX comes in multiple sizes for any work size requirements.
It features a quick-heating glue pot and is capable of applying PVC, ABS, melamine, veneer, and solid wood edges. The units are adjusted with a pressure bar equipped with a double row of wheels, ensuring precise and e cient operation.
Innovation. Automation. Satisfaction.
A fitting for countless interior design and furniture assembly applications.
> Extremely versatile range of applications.
> Easier to stock, as there is no distinction between frame and panel components.
> All conceivable installation tasks are covered by just one fitting.
> Can be screwed on, hooked in, clipped on or slid on.
> Can be used individually or in combination with several identical fitting parts.