Precision Engineered for Success
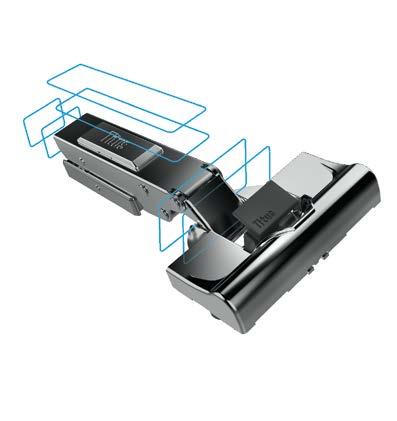
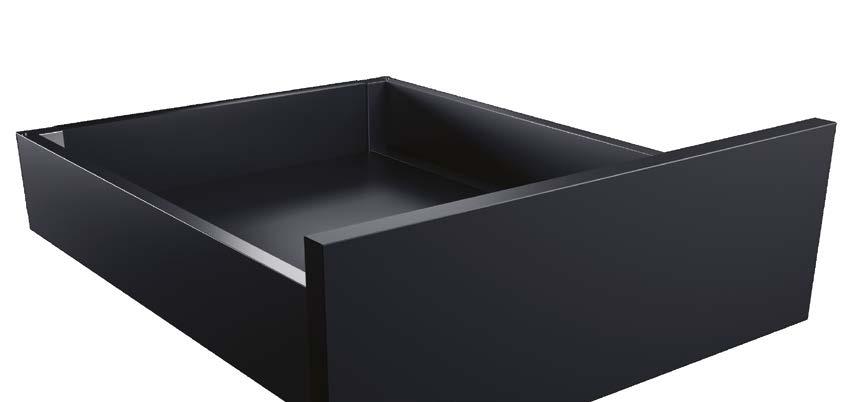
The all-new GRASS Moved by Häfele mobile showroom is now on the road and making its way around Australia.
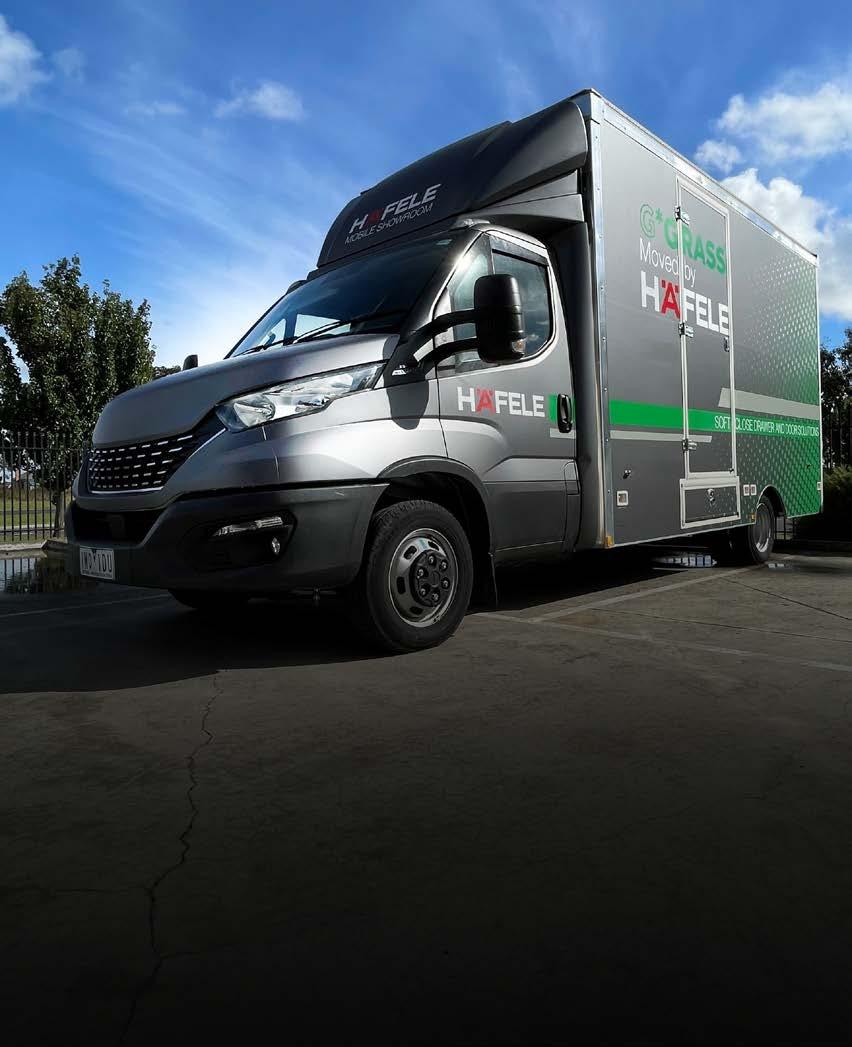
The mobile showroom is packed full of Grass products, including the TECMATOR drawer assembly machine that can assemble a drawer in under 25 seconds.
Also on display are the Nova Pro Scala product range of drawers, Tiomos hidden hinges, Kinvaro T-Slim Flap fittings and so much more.
Talk to your Häfele Account Manager today to ensure you don’t miss out on seeing the Grass Mobile showroom and TECMATOR assembly machine in action.

Ask us about the NEW, Nova Pro One range







Editor’s Note
Welcome to the February / March 2025 issue of Supplier Magazine. Inside the first edition for the year, you will find our Kitchen Fitouts and Trends feature. Philip Ashley writes that over the last decade the desire for good, innovative design and functionality has aligned with a strong preference for products that are environmentally sustainable. This year our feature focuses on the circular economy, a production and consumption model where manufacturers bring back materials into the economy instead of discarding them.
I recently sat down with Rebecca Hedley, Marketing Manager for Titus Australasia, to discuss all things business. And in our Q & A we unpack the Titus fit-for-purpose philosophy as well as their enhanced sustainability measures detailing how this company maintains its competitive edge.
Please feel free to contact me directly regarding any industry news, company events, training and or new product information you would like us to share at – michelle@elitepublishing.com.au
Until next time, enjoy your read.
Michelle Cammiade Editor

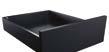

Ligna 50 Years
LIGNA celebrates its 50th anniversary this year. The fair was established in the German city of Hannover during the oil crisis of 1975 as the ‘International Trade Fair for Machinery and Equipment for the Woodworking Industry.’ The fair is now ‘The’ major trade show for the furniture, woodworking and forestry industries worldwide.
Ligna 50 Years
LIGNA’s origins date back to 1950, when it was the first ‘Woodworking Machinery Group Show’ at the German Industrial Trade Fair in Hanover, at that time covering 2,780 square metres. In 1975 LIGNA, a title derived from the German word for wood, had become so significant that it now stood as a major international event in its own right with exhibition space of 60,000 square metres.
The last Ligna fair held in 2023 was the first after the COVID enforced closures and despite both exhibitors and visitors being understandably cautious, 80,000 visitors attended to see 1,300 exhibitors. This year industry challenges include issues in construction, the shortage of skilled workers, and environmental issues like power supply, the circular economy and recycling, and
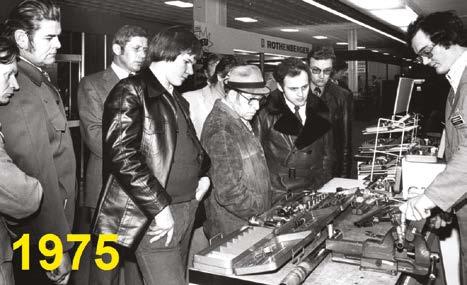
green manufacturing. Despite these current worldwide challenges, this year’s fair to be held from 26th to 30th May promises to be a significant event.
LIGNA 2025 will be one of the most important milestones for the woodworking and wood processing industry on the way to the hoped-for industry turnaround. Three months before the trade show opens its gates in its 50th anniversary year, more than 1,200 exhibitors from all over the world have booked 112,000 square metres of exhibition space, sending a strong signal in a challenging industry situation in politically tense times regarding tariffs and exchange rates.
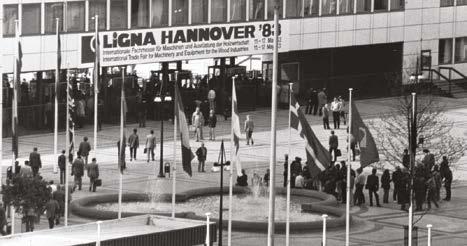
Truly Unique
LIGNA is a unique trade fair. Throughout its five decades, it has consistently succeeded in bringing together all industry topics under one roof while still providing each with its distinct space. The collective enthusiasm of industry participants for innovation and performance is unparalleled. The shared commitment to shaping technological progress and, in turn, ensuring business growth, stability, and prosperity motivates everyone involved.
“The success of German manufacturers of machines and tools for the wood industry would not have been possible without LIGNA. Becoming a world market leader requires being at the forefront of technology and showcasing this leadership on a global scale. I am not aware of any company in our industry that does not consider the next LIGNA date as the most crucial milestone in its innovation calendar. LIGNA is an inseparable part of our success story,” says Dr. Bernhard Dirr, Managing Director of VDMA.
Truly Historic
Some notable technologies and historic occurrences have happened over the last 6
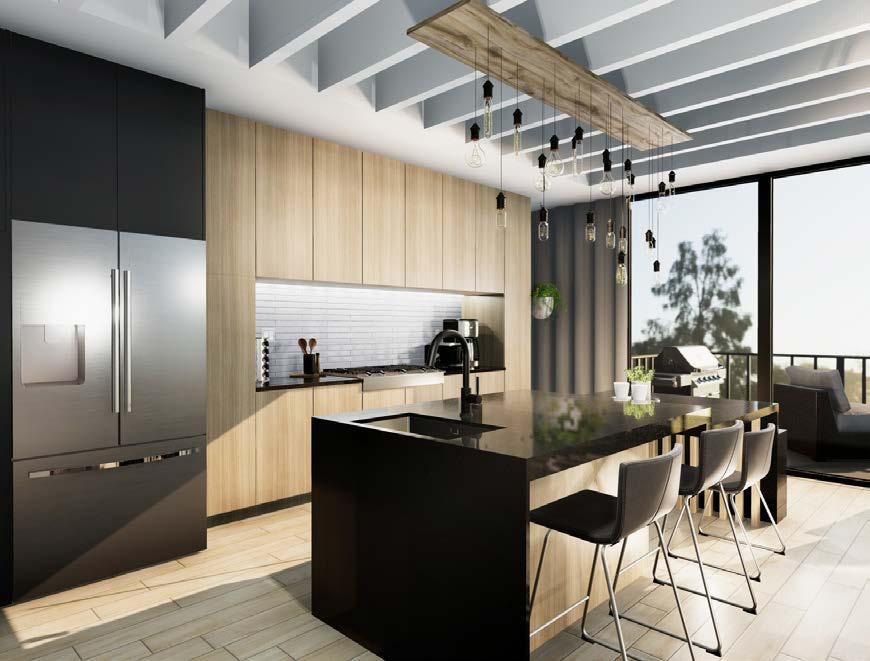
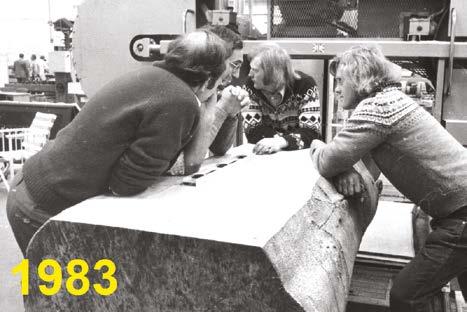
five decades. These include 1985 when microprocessor-controlled machines and equipment become more prevalent. 1987 and 1989 marked the era of the new electronic generation and the networking of entire operational processes. Individual CNC-controlled machines become interconnectable with each other. In 1991 the first LIGNA after the reunification of Germany (fall of the Berlin wall) was held.
In 1997 the fair was dominated by Batch size 1; the cost-efficient, adaptable serial production of furniture. In 2003 LIGNA faced a challenging situation with an economic downturn, terrorism, and SARS warnings, but by 2007 a construction boom and the global economic upswing started to turn things around but was dashed by the global financial crisis of 2008. 2011 saw the presentation of the first laser and plasma processing machines for edge banding.
In 2015, Industry 4.0 enters the wood processing industry. In 2021, due to the COVID-19 pandemic, everything changed. A physical LIGNA was not permitted, and any trade fairs that were organised were digital, so LIGNA launched the LIGNA.Innovation Network. At the last show in 2023 the demand for automation and processoptimizing solutions to offset the impacts of skilled labor shortages was high.
Truly Progressive
This year, LIGNA’s anniversary edition will focus on the circular transformation in woodworking and wood processing, digital networking, and the development of intelligent products.
Stephanie Wagner, Project Manager of LIGNA at Deutsche Messe AG said, “The primary goal is to initially build an active community where best practices, potentials, and challenges related to circular value creation can be shared. LIGNA.Circular aims to build
much-needed bridges between users, service providers, manufacturers, and craftspeople.”
May last year the world was at the low point of a severe economic downturn, yet 80% of the net stand space based on the total area of LIGNA 2023 had already been booked for LIGNA 2025. As of January 1st, 105,000 sqm of floor space has already been booked. Stephanie Wagner said, “That our customers are willing to make this investment despite the current economic situation underscores the high significance LIGNA enjoys.”
Dr. Bernhard Dirr, Managing Director of the German VDMA Woodworking Association believes automation solutions for all size classes, and solutions for resource-efficient production will help the industry to return to growth. If you plan on travelling to Germany for Ligna, and the Interzum fair in Cologne, held the week before, you may need to apply for an electronic visa. The new rules come into effect sometime this year, but the date has yet to be announced. The new rules are not likely to affect your Ligna visit this time, but to be sure, visit www.smartraveller. gov.au/before-you-go/the-basics/schengen website to find out more. z
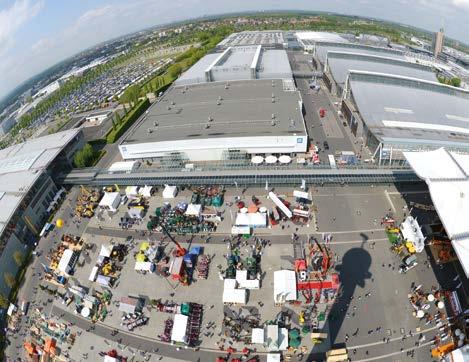
Important changes for your business in 2025
As 2025 begins, there are some changes that your business should be aware of.
Criminalising intentional wage underpayments
From the 1st of January 2025, intentional underpayment of wages by employers will become a criminal offence.
Employers will commit an offence if:
• They are required to pay an amount to an employee (such as wages), or on behalf of or for the benefit of an employee (such as superannuation) under the Fair Work Act, or an industrial instrument.
• They intentionally engage in conduct that results in their failure to pay those amounts to or for the employee on or before the day they are due to be paid.
The penalties for companies:
• If the court can determine the underpayment, the greater of three times the amount of the underpayment and $8.25 million, or
• If the court cannot determine the underpayment, $8.25 million.
The penalties for individuals:
• Maximum of 10 years in prison
• If the court can determine the underpayment, the greater of three times the amount of the underpayment and $1.65 million, or
• If the court cannot determine the underpayment, $1.65 million.
For small businesses, a Voluntary Small Business Wage Compliance Code (Code) has been established. The Australian Government has put together a Guide to paying employees correctly as well as help businesses to understand the Code. It offers practical advice and tools including a handy checklist, examples and best practice tips. Go to - www. fairwork.gov.au, for more information.
Changes to entry-level classifications in awards
In 2025 some awards will have new definitions and minimum pay rates for entry-level classifications.
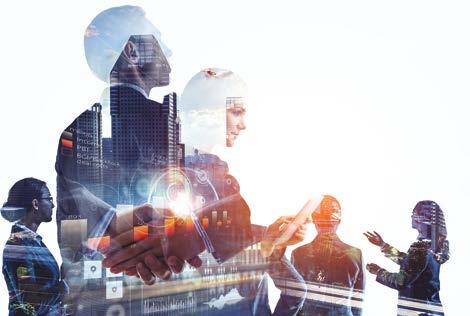
The key changes happening for some awards include:
• Introductory classifications can only apply for a limited time.
• New rules and minimum pay apply for introductory rates.
This is because employees who have been employed at their award introductory level for more than the maximum period may move to the next classification.
Any changes to an existing employee’s classification or expected progression to another classification should be discussed with the employee before the 1st of April 2025.
Mandatory climate reporting
From the 1st of January 2025, many large Australian businesses and financial institutions will need to prepare annual sustainability reports containing mandatory climate-related financial disclosures.
For more information on mandatory climate reporting go to – www.asic.gov.au/ regulatory-resorces/sustainability-reporting
Engineered stone importation ban
From the 1st of January 2025, a ban on the importation of engineered stone benchtops, panels and slabs will be implemented. The ban will provide an extra layer of deterrence at the border, as most engineered stone products are imported into Australia.
The ban on the manufacture, supply, processing and installation of engineered stone benchtops, panels and slabs came into effect in July 2024. z
Focus On
Titus Tekform markets innovative precision component solutions for the kitchen, bathroom, shopfitting and cabinet making industries. Providing their customers with functional, decorative hardware, technical knowledge, flexible service and efficient delivery at a competitive price. Supplier Magazine recently sat down with Rebecca Hedley, Marketing Manager for Titus Australasia, to discuss all things business.
1. What is the Titus Tekform story?
Titus Group develops, manufactures and markets innovative precision component solutions that improve the competitiveness of our customers. Comprising 23 companies globally, Titus Group is headquartered in London in the United Kingdom, where it was founded in 1973 by chairman Robert Appleby as a distributor of screws to the UK market. In 1980, Titus expanded to the US as a supplier of volume cabinet connectors, which would remain the focus of the business for the next two decades. This period included developments such as the CAF principle of Consumer Assembly Friendliness, a calculation applied to RTA furniture based on number of parts and ease of assembly, and the 1994 launch of the Quickfit Dowel.

Q & A with Titus Tekform

The early 2000’s was a time of expansion for Titus Group, including the acquisition of manufacturing facilities in Europe and the US, and in 2005 Titus began manufacturing concealed hinges and combi dowels on Titusbuilt machinery. This investment in precision component solutions led to the conception of the Titus proprietary damping technology in 2009, an innovative multi-purpose hydraulic damping technology used in a wide range of applications across the furniture, consumer appliance, whitegoods and automotive industries. One of the main characteristics of hydraulic damping technology is a fully programmable and controllable damping curve that enables fine-tuned performance for specific applications and an extended temperature spectrum to provide operational efficiency even in extreme temperatures.
The acquisition of Australian distributor Tekform in 2014 and New Zealand distributor Stefano Orlati in 2015, helped Titus establish a more direct relationship with kitchen manufacturers. This association directly influenced the launch of the Tekform Drawer in 2015, a drawer platform tailored to suit the needs of the kitchen market. It was also with them in mind that in 2017 Titus launched the new generation of one of its flagship products, the soft-closing T-type hinge.
Today, Titus Group continues to prioritise innovation, with a fit-for-purpose design philosophy evident in all three key company divisions of Cabinet Hardware, Damping and Titus Technologies – a department dedicated to advancing automated assembly systems, custom tooling and die-casting technologies, and the Titusonic ultrasonic cabinet bonding technology. Titus Group enjoys a market presence in 70 countries worldwide and employs over 800 staff in its mission to identify customer needs and become the world’s best in engineering for precision components.
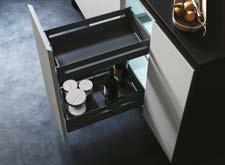
2.Titus Tekform is a proud member of the Titus Group of companies that sources, manufactures and markets innovative small component solutions in Australia and New Zealand. Explain the importance of the alliance with the Titus group of companies. Through our innovative product design, engineering expertise and effective service, we enable our business partners to improve their productivity and quality, as well as reduce costs of assembly, manufacturing and other processes. Our three key divisions –high volume cabinet hardware, innovative solutions for motion control and high volume precision parts manufacture – perfectly complement each other, allowing each division to provide a full service.
Focus On
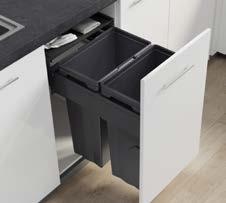
We pride ourselves on our totally integrated engineering program, and our expert engineering teams produce consistent and repeatable quality with unique product advantages. Titus is a trusted global precision component manufacturer, with Titus products used in whitegoods, furniture, automotives, and medical devices distributed be some of the world’s biggest brands.
The Titus Fit-for-Purpose philosophy is the backbone of our product design and as a manufacturer-distributor, our product engineering benefits from our direct market integration and decades of experience in cabinet hardware solutions.
Our global supply chain, along with the acquisition of the Stefano Orlati brand of decorative products in 2015, has allowed us to curate product ranges designed to maximise choice and flexibility without compromising on quality, with tailored product features and specification to maximise competitiveness in local markets.
3. Your online shop has an extensive product offering including everything from hinges, edgeband, lighting and door panels. Can you take us through your product offering with a look at some of the innovative new releases. Titus are committed to providing exceptional service and high quality products at a competitive price. Some of our most exciting product launches are now available, including
upgrades to our two most popular products –the T-type hinge and the Slimline drawer.
The newest addition to the T-type family is the T-type PressTo, featuring a tool-less hinge cup fixing system and the renowned T-type 3-way snap-on hinge-to-plate mounting, for our quickest and easiest installation yet. An audible click when pressed to lock ensures confident and reliable hinge cup attachment to the door, and the highly tolerant T-type design enables consistent door closing and reliable performance throughout the lifetime of the cabinet.
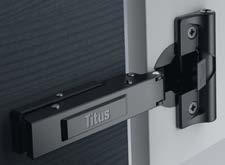
The perfect pairing to the T-type PressTo is our newest generation of Slimline drawer, the Slimline+ double wall drawer system. Slimline+ showcases the best in engineering expertise, with the new Titus Adaptive Response Technology damper, which adapts the damping force to any closing speed and ensure optimal closing performance. The
ART damper promises lifelong consistent damping, with always effortless pull-out opening force and smooth, efficient closing. Slimline+ is also our quickest assembly drawer. The colour-coded 3D adjustment grouping, controlling height, side and tilt adjustment, is located at the front of the drawer for easy access to create precise and uniform gap layouts of cabinets. The enhanced drawer front connection mechanism also creates a reliable and consistent engagement. The result is a streamlined installation process designed to save you time and money, even with large and heavy drawer fronts.
While we have devoted significant time to the design of our products, we have also launched our innovative new website and online shop, to make it easier than even to access our full range of products at any time of day or night. Our new online store works across all devices, so you can place your order from the comfort of your office desktop, or on-site from your mobile or tablet. With a Titus Tekform online account, you can access your custom trade pricing, save products to customised lists of favourites for easy re-ordering, and view or download product resources like installation manuals, technical specifications and CAD files.
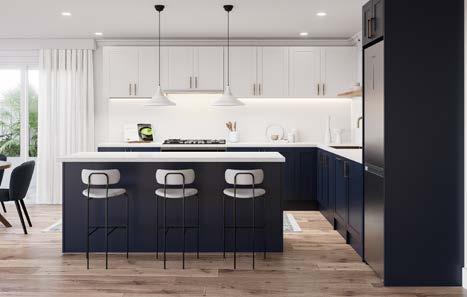
Focus On
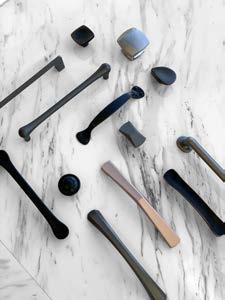
With our new online store, one of our favourite product ranges is now more accessible than ever before. Our redesigned Made to Measure door ordering app allows customers to order cut-to-size doors and panels in slab, sharknose or shaker profiles for fabrication in our Sydney factory. The MTM offering includes our full range of double-sided PET Matt, Gloss and Woodgrain OptiBoard finishes, including the newly launched Australiana décor colours. This cost-effective service can be custom specified with edging and hinge drilling to suit your requirements and is dispatched in just 5 business days. The online MTM ordering app is a quick and easy way to view live pricing adapted to your selections, and you can also save quotes to your Favourites list to finish later.
4. Discuss some of Titus Tekform’s milestone moments.
Tekform began in Australia in the 1970s under the leadership of John Tiddy, and quickly developed a name for itself as an innovative hardware distributor in New South Wales, often introducing new products to the Australian market. Over the ensuing decades, Tekform expanded to open branches in Melbourne, Wodonga, Hobart, Newcastle and Brisbane, before being acquired by Titus Group, at the time a current supplier, in 2014. The acquisition
married the knowledge and local expertise of the Tekform team with the global supply chain and engineering resources of Titus.
Together, Titus and Tekform transformed the Titus Tekform product range to incorporate a complete offering of high quality cabinet hardware and decorative products tailored towards the needs of the Australian market. Our customer promise is innovation, technical expertise and reliability as we endeavour to exceed our customer expectations by providing quality products at a competitive price.
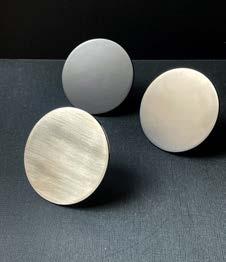
The onboarding of the Stefano Orlati brand in 2015 introduced a level of decorative expertise which has led to the creation of the Aura brand of European-inspired designer cabinet handles, and a market-leading Made to Measure LED Lighting program, as well as the 2017 launch of the OptiBoard PET decorative board range.
Our cabinet hardware portfolio has benefited from the Titus research and development team, with first the launch of the 2015 Tekform Drawer, the 2017 T-type Hinge, the second generation Tekform Slimline drawer in 2018, the Set 200 Sliding Door System in 2019, the Titus Push Latch S2 in 2022, and the more recent T-type PressTo hinge and Slimline+ drawer systems, as well as a complete range of industry-preferred
cabinet connectors. Other milestone products include the hugely popular Kosara undermount bin system in 2020 and the 2024 launch of the Vitek thin wall drawer.
Titus Tekform has a presence throughout Australia, servicing both metro and regional areas. In 2016 we expanded into Western Australia and the ACT, and we continue to focus on how best to service our customers, with our newest branch opening in Adelaide in 2023.
5. Looking ahead, what plans have you got for the future of Titus Tekform?
We’re very excited for the years ahead. Titus Group is focusing on strategic investments, innovation and sustainability to enhance our competitive edge and deliver value to our partners. Our enhanced sustainability efforts underscore our commitment to environmental responsibility, and this will continue to be an area of importance to us going forward. We have also increased our production capacity, which will allow us to continue to meet customer needs into the future.

As a company, we are continually expanding our product range to meet the needs of the Kitchen, Bathroom, Wardrobe and Bedroom industries, as well as the imminent launch of our new RV range of products tailored to the Leisure Vehicle market. Some of our most anticipated product launches this year include our vanity units, wardrobe storage, and updates to our range of handles and lighting. z
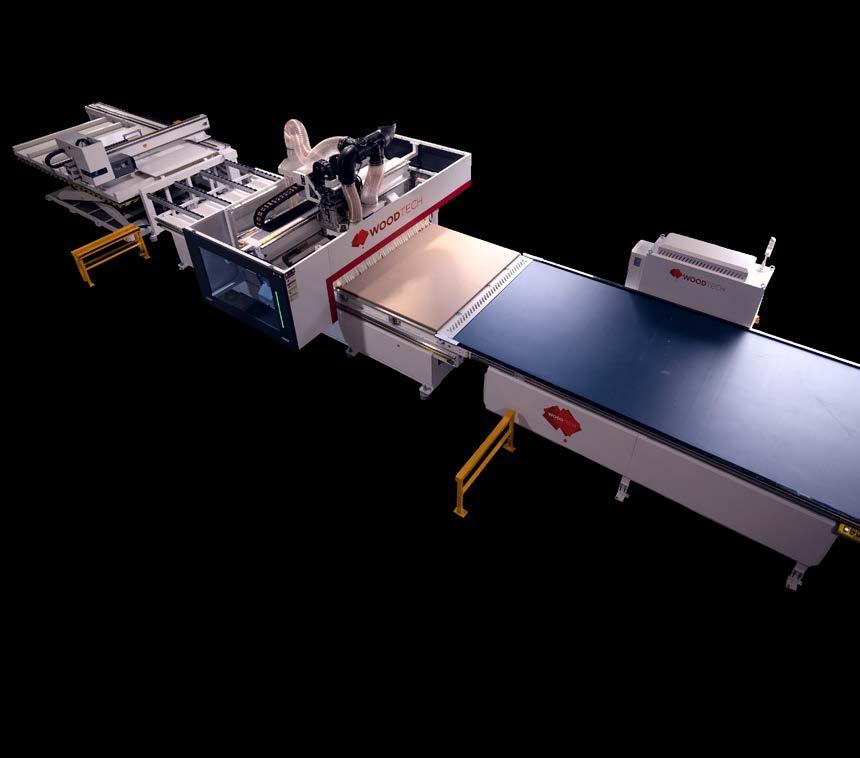


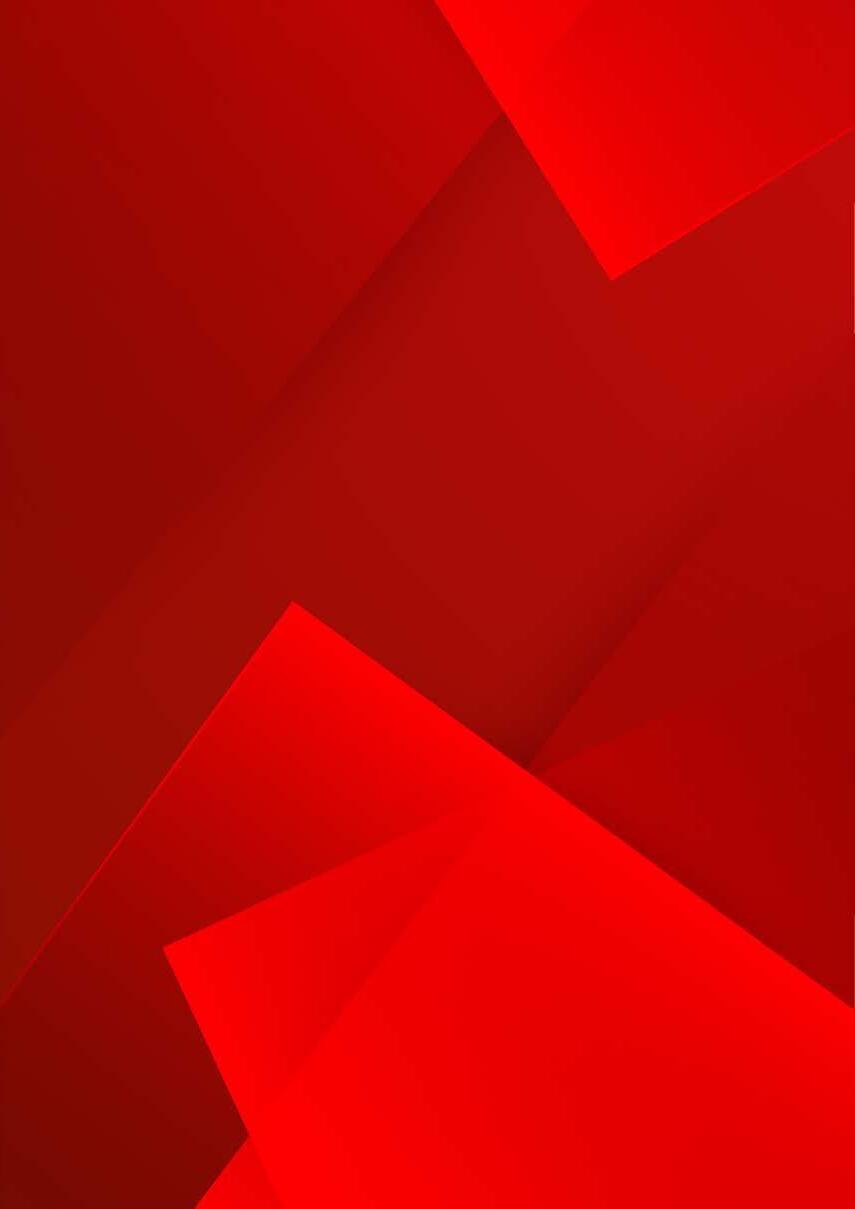
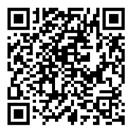
Kitchen Fitouts & Trends
Kitchen Trends and the Circular Economy
Article by Philip Ashley
Feature



Over the years, Australian kitchen and bathroom design has evolved to meet homeowners’ changing needs and preferences. Over the last decade the desire for good, innovative design and functionality has aligned with a strong preference for products that are environmentally sustainable.
In the past, Australian kitchens were mostly focused on simple designs and practical layouts. Over time, the focus shifted to aesthetics, combining elements of modern, trending design incorporating sleek, minimalist styles and clean, uncluttered lines. Today, Australian kitchen design is balanced, seamlessly merging form and function, creating visually appealing, highly functional spaces. Modern kitchens feature a wide range of materials, smart technologies, and lighting.
Consumer preference for environmentally sustainable products over recent years have shifted from ‘nice to have’ to ‘highly desirable’. Harvard Business Review reported, ‘Truly sustainable brands that make good on their promises to people and the planet will seize the advantage from brands that make flimsy claims or have not invested sufficiently in sustainability. We’re fast approaching this tipping point where sustainability is considered a baseline purchase requirement, and companies should prepare now’.
One recent aspect of the sustainability chain is circular manufacturing or circular economy, a production and consumption
Feature | Kitchen Fitouts & Trends
model where manufacturers bring back materials into the economy instead of discarding them. The ‘European Green Deal’ was introduced in 2019, aiming to establish a circular economy. Moving from resource drain ‘take, make and dispose’ to resource gain ‘reduce, recover and reuse’, circular manufacturing would strengthen supply chain predictability, resilience and control.
Kitchen and Bathroom Trends
SURTECO is on board with a commitment to ‘Permanently improve our environmental performance through appropriate measures in the entire life cycle of our business.’
Kylie Warren is Marketing Manager Asia Pacific. She tells us, “At the core of SURTECO Australia’s operations is our focus on circular manufacturing, which emphasises reducing waste, reusing materials, and recycling products to create a closed-loop system. This approach helps reduce environmental impact and aligns with the company’s commitment to sustainability”.
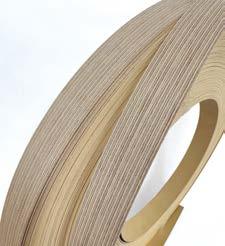
“We reuse approximately 70% of our product waste and supply the rest to a local plastic manufacturer who uses this as raw material for their products. Since its establishment in the mid-1980s, SURTECO Australia has been committed to local design, materials, and manufacturing. SURTECO Australia are the only manufacturer of ABS edge band in Australia and has been a staple in the
Australian manufacturing landscape, proudly employing local workers to create highquality products such as our new multiplex ply that is trending well,” Kylie adds.
Anastasia Parlamentas is decorative products Brand Manager at NIKPOL. She says, “At Nikpol, sustainability isn’t just a commitment; it’s the foundation of everything we do. From materials we select to processes we implement, our goal is to deliver high-quality, environmentally responsible surfaces that enhance interiors without compromising the planet. We believe true innovation lies in the balance between design excellence and environmental responsibility. We’re dedicated to bringing this vision to life by continuing to source sustainable surfaces that align with our commitment to both quality and environment.”
Anna explains, “NIKPOL embrace the principles of the circular economy, where materials are continuously reused, waste is minimised, and nature is regenerated. This philosophy is embodied in our PEFC and FSC-certified decorative range, which includes laminates, boards, and worktops designed to support responsible forestry and sustainable resource management. NIKPOL offer our new Linen range, crafted in Italy from 100% recycled materials, transforming old kitchens into stunning carcasses for modern spaces. It’s available in a variety of contemporary finishes, providing an ecofriendly solution for modern kitchens and interiors.”
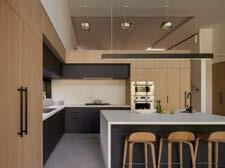
NIKPOL’s decorative boards are sourced from Europe, from a global leader in sustainability and innovation. Thanks to advancements in melamine technology, their surfaces feature deeper textures and more realistic timber finishes, including beautiful oaks, walnuts, and blacks, offering the perfect combination of style and sustainability. A standout in NIKPOL’s range is Master Oak, shown in our image Mars House Master Oak Limed Oak; a prime example of how premium design and sustainability can work in perfect harmony.
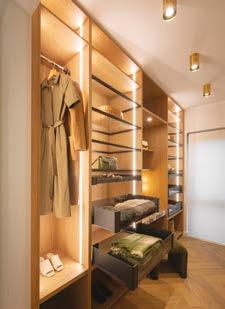
Gary Cahoon of Hafele Australia says, “Hafele ensures that where practicable, our activities prevent pollution of the environment, minimise the use of energy, conserve resources, reduce waste and encourage our customers, suppliers and contractors to follow our example. Though purchasing policies, we endeavour to identify goods and services which do the least harm to the environment in their production, delivery, packaging, re-use, recycling and disposal. We endeavour to purchase from local suppliers for our production activities to maximise our input into the local community and to minimise the impact of transportation.”
“Our Hafele Loox Lighting program is the first and only brand to combine the application areas of ‘Light in Furniture’ and ‘Light in the room’ to create an integrated, networked experience. Hafele lighting goes far beyond pure functionality, creating atmosphere, emphasising design and arousing emotions. Integrated lighting transforms furniture into dynamic elements that interact with their surroundings, enriching the overall ambience of a room. In 2025, 24V is the new 12V meaning longer cable distances without a drop in light intensity. Hafele will be introducing a whole new range of High Efficiency LED strips, requiring a reduced driver size and less power consumption.” says Gary.
“The most sustainable products are those that are used, reused, reconditioned and recycled as long as possible. GRASS MOVEMENT SYSTEMS are among the most climate-
neutral components because they last the life of the furniture. Movement systems shouldn’t need maintenance or repair if properly looked after. Integrating the entire cycle into a sustainability concept from the production and supply of our movement systems to their use and eventual disposal/recycling is a strategic goal of GRASS”, Gary adds.
Gary continues, “This means supplying materials that are replaceable, biologically degradable, or entirely recyclable in their natural life cycles. For example, we have developed the V8 sustainable drawer system which is produced and coated in an environmentally friendly manner and items can be recycled by material type. The concept of the world's first all-metal drawer side resulted from this. We have stopped using plastic elements, foams and adhesives in pursuit of robustness, sustainability and recyclability.”
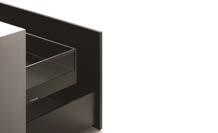
Wilson & Bradley are committed to continually upgrading their procedures and processes to ensure they leave as little waste and environmental footprint behind. Kate Fuller is marketing manager and said, “Sustainability is our commitment to responsible practices that benefit our environment, communities and business in the long run. Wilson & Bradley meet our commitments by improving our packaging, energy efficiency, sourcing materials more responsibly and increasing our supplier demands on the sustainability of their manufacturing processes”.
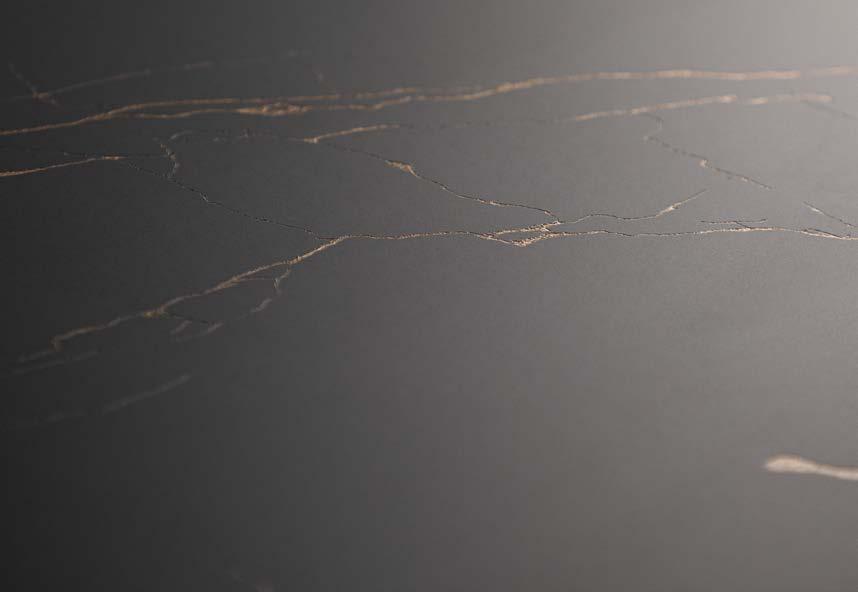
When the visual becomes tangible
For your exclusive designs, we have expanded the PerfectSense product family with elegant stone appearances: PerfectSense® Ambiance in F199 Black Marble impresses with refined golden vein inclusions, a super matte finish, and proven anti-fingerprint properties. The partial gloss effects of this new product are synchronised with the decor pattern. » EGGER products for furniture and interior design are available in Australia, from Nikpol and distributor ForestOne
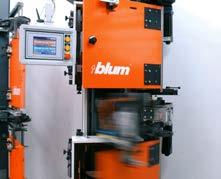
Alongside other sustainability-focused suppliers, Wilson & Bradley proudly offers BLUM products. According to Kate, “Austrian-made Blum products are innovative, high-quality, high-performance, and built to last.” This commitment to quality applies to BLUM products and their manufacturing processes, resource usage, and efforts to close ecological loops. BLUM considers the entire life cycle of their products, from procurement to recycling,
laying the foundation for efficient raw material use in new product development. They use resources effectively and strive to minimize environmental impact. The BLUM die casting process is highly efficient, with an impressive 85% of waste material being reintegrated into the process and the remaining 15% supplied to an external partner, creating a closed zinc loop.
Our Circular Future
According to the UN-aligned group International Resource Panel, the global use of resources has tripled since 1970 and could double again by 2050. Without more efficient use of resources, this surge in demand would exhaust the planet’s already stretched ecosystems, raw material availability and ability to absorb waste. Less than 10% of the 100 billion tonnes of resources that enter the global economy
every year are reused or recycled. Research by the Sustainable Design Institute underscores the emphasis on sustainable materials and eco-conscious design principles.
Approximately 80% of Australians prioritise sustainable choices when selecting kitchen materials, including the preference for recycled timber, energy-efficient lighting, and eco-friendly countertops and cabinetry to minimise environmental impact. There is no doubt that Australian suppliers of kitchen, bathroom and office furniture product and hardware are in tune with the need for the responsible use of resources, offering the Australian cabinet manufacturer products that are not only in line with current design and living trends, but also in unity with a long overdue respect for what the planet has to offer. z
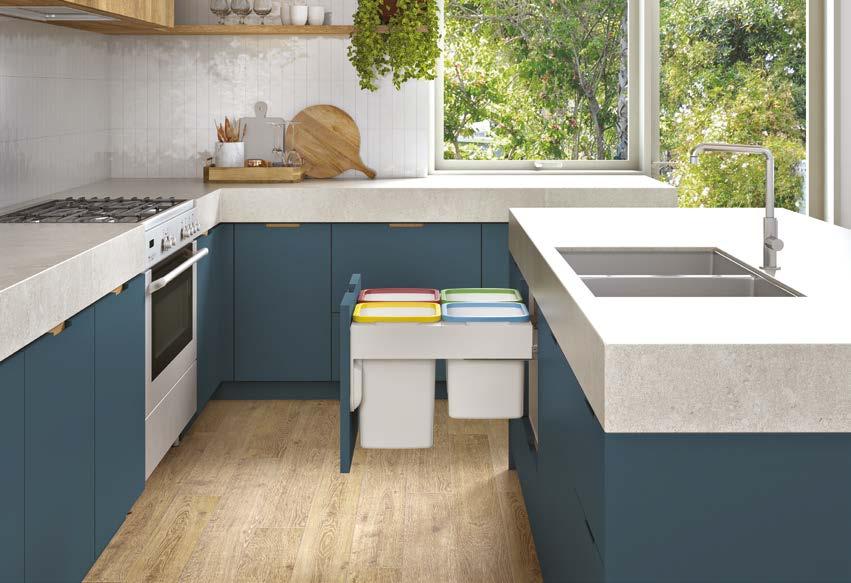

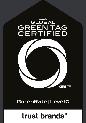
Sustainable kitchen trends with Surteco
Earth tones, muted colours, and natural stone finishes remain at the forefront of design trends, continuing to influence modern interiors. Soft browns, warm greys, muted pinks, and soothing sage greens are still prevalent in kitchen design, creating inviting and calming spaces. These hues not only evoke a sense of warmth but also allow for a natural flow between elements, making them ideal for both contemporary and traditional settings. At the same time, there is growing popularity of curved joinery, along with the revival of arched doorways, which are making their way back into the latest architectural designs. This return to softer, more organic shapes highlights the timeless appeal of these design elements—proving the adage, "everything old is new again."
In line with this shift toward organic and natural aesthetics, there's a clear increase in demand for materials that emphasise sustainability and authenticity. One such material seeing a strong uptake are the natural plywood edges. Surteco’s product range includes a wide variety of genuine timber plywood, which offers a rich and timeless look, as well as acrylic options. New to their collection is the highly realistic ABS plywood—an innovative solution that replicates the appearance and texture of real timber, making it one of the most convincing ABS edgebands on the market today. This material is perfect for creating both complementary and contrasting accents in kitchen joinery, providing warmth and depth to modern spaces.
While natural finishes continue to dominate, the team at Surteco are also witnessing a steady rise in interest for more industrial materials. Their Metals collection, which
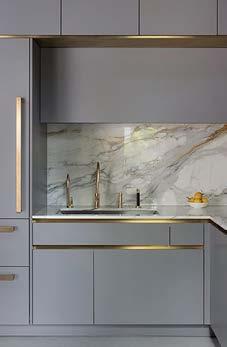
includes Deko Metal Laminates and Edgebands, is gaining significant traction. These high-quality laminates are made with real metals, offering exceptional durability and chemical resistance. They are perfect for vertical surfaces such as wall linings, ceilings, and commercial furniture. Additionally, they are well-suited for use in joinery displays in shopfitting, and even kickboards. Available in both brushed and mirror finishes, the six colours in this collection are thoughtfully curated to make a bold statement in any design project, providing both aesthetic appeal and functional versatility. Whether used as a striking focal point or an understated accent, the Deko Metal range is designed to elevate any space.
Sustainability continues to be a key focus within the design and manufacturing industries, with increasing attention on the environmental impact of materials and processes. This is especially evident in the
legislation surrounding silica content in manufactured stones and building materials, driving a shift toward more eco-conscious products. At Surteco, they have always prioritised sustainable, locally manufactured solutions. As an Australian manufacturer, Surteco takes pride in producing products that not only meet high standards of quality but also support local industries and minimise environmental impact. Surteco customers can have confidence in the integrity of their products, knowing they are made with care, precision, and respect for the environment.
Surteco Australia is the only ABS edge manufacturer in the country and is also a licensed user of the Australian Made campaign logo. This certification is a mark of quality and authenticity that they take great pride in. In addition, their ABS edge products continue to receive the prestigious Greenguard Gold Standard certification year after year. This certification is awarded to products that have been tested for low chemical emissions, contributing to healthier indoor air quality. It is an achievement that reflects an ongoing commitment to sustainability and the well-being of the environments in which Surteco products are used.
As the design landscape continues to evolve, Surteco remains at the forefront, offering innovative materials that are both functional and environmentally responsible. Whether you are designing a modern kitchen, a commercial space, or a retail environment, their diverse range of products ensures you can create spaces that are both beautiful and sustainable.
web www.surteco.com/au z

SURTECO Australia
We make rooms worth living in.
We’re leaders in Décor paper, technical foils & edgeband manufacturing. With over thirty years manufacturing edgebands in Sydney NSW, SURTECO Australia is the only Australian manufacturer of ABS edgebands. With ongoing investment, SURTECO Australia leads in design, quality and manufacturing & are committed to creating the highest quality product.
NSW/WA (02) 9421 0300 | QLD (07) 3245 1881
VIC/SA (03) 9798 6282 | Email info@au.surteco.com visit www.surteco.com/au for information
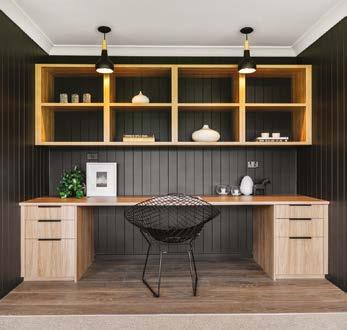
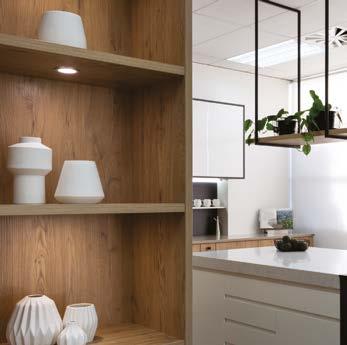
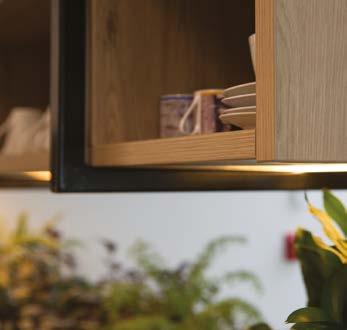



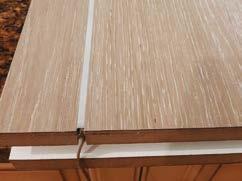

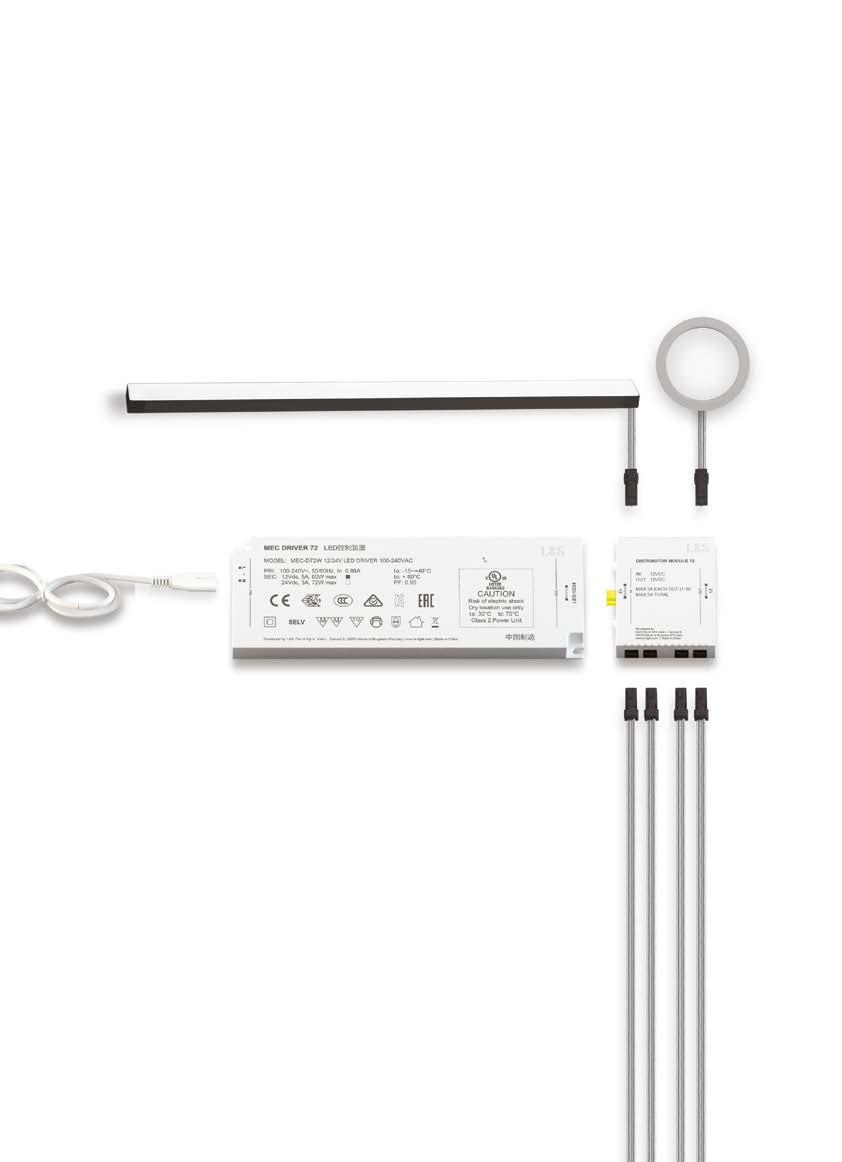
Navigating future kitchen trends with Wilson & Bradley
The growing demand for spaces in the home that support both efficient living and creative expression is now transforming the kitchen. Once considered purely functional, today’s kitchens have evolved into dynamic hubs where technology, sustainability and aesthetics converge.This transformation can be seen in the growing use of cleverly integrated, multifunctional storage solutions and adaptable layouts, advancing the design of the modern kitchen.
From pull-out pantry shelves to hidden drawer systems, today’s kitchens are being designed with efficiency and creativity at the forefront. These innovations maximise limited space while providing a visually cohesive environment. In addition, energy‐efficient lighting, digital interfaces and smart technology—such as automated lighting and voice-activated controls—further streamline daily tasks and provide a space experience that not only looks appealing but also functions seamlessly.
Wilson & Bradley have been at the forefront of this evolution, ensuring that cabinetmakers, designers, and homeowners have access to the latest advancements in kitchen functionality. As seen in Brilliant SA’s Adelaide showroom, modern kitchen spaces are being shaped by innovation—the seamless integration of technology and highquality hardware solutions that are defining future trends.
Future ready design: Balancing innovation and functionality
The future of kitchen design focusses on a seamless blend of innovation and practicality. Clean lines, adaptable layouts, and modular elements are redefining how kitchens function, making them more efficient and responsive to daily needs. Features like hidden storage, multifunctional islands, and flexible cabinetry allow homeowners to personalise their space while supporting our lifestyles that are continually evolving.
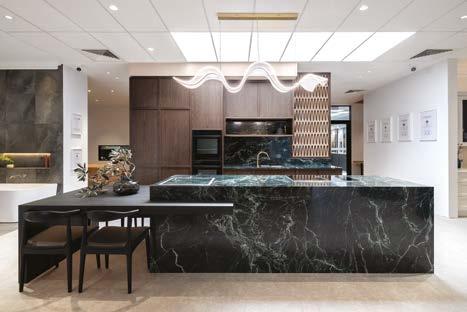
By prioritising smart storage and wellplanned workspaces, designers are creating kitchens that balance efficiency with a welcoming, interactive experience, ensuring they remain both functional and engaging for years to come.
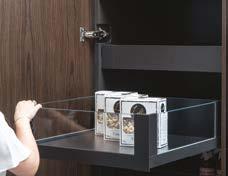
Blum’s Space Tower has full extension pull-outs that give you clear visibility and easy access to all three sides (left, right and even the front).
Eco-Innovation:
Sustainable Kitchens of Tomorrow
Sustainability is now a key focus in modern kitchen design, driving the use of responsible materials, energy-efficient appliances, and waste-reducing solutions. Designers are prioritising durable, long-lasting products that optimise resources while minimising environmental impact. As awareness grows, so does the demand for kitchens that balance sustainability with high performance. At Wilson & Bradley, this commitment is central to their approach. They collaborate with suppliers to develop responsible products that align with innovation and efficiency ensuring kitchens are designed for both today’s needs and long-term sustainability. This includes proudly partnering with Furnipart, whose handles have achieved Cradle to Cradle certification, underscoring their commitment to sustainable manufacturing practices.
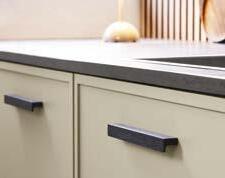
Above: Designed for the future of kitchen design, the Elan handle from Furnipart combines sustainability with a refined, high-quality finish. Its soft rounded edges and precise detailing enhance both function and style, aligning with the growing demand for innovative and responsible design.
Smart kitchens: The next wave of technological advancements Technology is reshaping every aspect of the modern kitchen, including cabinet hardware. Innovations like Blum motorised hinges for automated door movement, integrated LED lighting for seamless illumination and popup power outlets with charging capabilities are redefining how storage spaces function. These advancements go beyond convenience making cabinets more intuitive and efficient while enhancing the overall kitchen experience. As smart hardware continues to evolve, it plays a vital role in creating kitchens that are both highly functional and thoughtfully designed, setting a new benchmark for modern living.
More advanced lighting is becoming widely integrated into modern kitchens, improving both practicality and ambiance. With L&S lighting, spaces are designed to be smarter and more adaptable, supporting the way kitchens are used today and in the future.
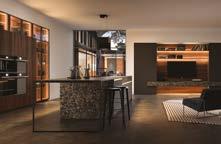
As kitchens evolve, functionality is becoming more seamless and efficient. Docking Drawer’s Pop-up Power Outlets provide a smart, space-saving solution keeping surfaces clutter-free while ensuring power is always within reach.
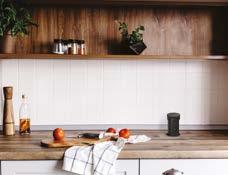
Customer showcase: A glimpse into tomorrow’s modern, traditional kitchens
In the ‘Brilliant SA’ showroom, two kitchen installations showcase the direction of modern kitchens. Both kitchens integrate cutting-edge innovation and smart technology with one featuring a modern design and the other a traditional style, both representing the future of kitchen trends. From advanced cabinet hardware to carefully selected lighting, every detail is designed to improve usability and enhance the overall experience. These kitchens demonstrate how thoughtful design can meet different needs while maintaining a balance of practicality and aesthetics.
“As a designer, we need products that look great but more importantly, function seamlessly —and that’s exactly why we use Wilson & Bradley and have it throughout our showroom. Blum’s hinges, drawers and lift systems make kitchens feel effortless to use, with that smooth, high-quality finish our clients love” Jo Niederer, Team Leader and Design Specialist at Brilliant SA.
Featuring in their showroom, Brilliant SA’s traditional kitchen blends classic design with modern innovation. Thoughtful details,

quality finishes, and smart functionality showcase how timeless style can evolve to meet the needs of future kitchen trends.
A commitment to
future ready kitchen design
Since 1976, Wilson & Bradley have built their reputation on providing cabinet hardware solutions that combine quality, durability, and innovation. As Peter Sveinsson, CEO of Brilliant SA shares, "When it came to fitting out our new showroom, Wilson & Bradley were an obvious partner. We’ve built our reputation on supplying only the best products, with impeccable durability and backup."
As kitchen design continues to evolve, the demand for smarter, more adaptable spaces is reshaping the way we think about functionality. For years, Wilson & Bradley have been a trusted supplier of choice, offering the full range of Blum products alongside leading brands such as Sige, Wesco, L&S Lighting, Cinetto and Furnipart all designed to meet the needs of modern kitchens.
Their commitment goes beyond products— it’s about the direct support they provide in the showroom, at the factory, and on the job. From design to production and after-sales service, the team work closely with customers to ensure they have the right solutions for today’s kitchens while anticipating the trends of tomorrow.
web www.wilbrad.com.au z
Flexibility and adaptability - The pillars of long-term success
The past few years have presented unprecedented challenges for our industry. While many businesses thrived during COVID, we are now witnessing a landscape where countless companies are being pushed to their limits. Economic pressures, supply chain disruptions, and evolving customer demands have created a volatile environment, requiring businesses to be more agile than ever before.
One critical lesson from COVID remains clear: stock is king. No matter how much capital a business had on hand, it was meaningless without access to inventory. Supply chain disruptions made stock acquisition nearly impossible, proving that preparedness and strategic investment are the ultimate safeguards against uncertainty.
With almost 100% of Nikpol’s products imported—primarily from Central Europe— supply chain stability is critical to their operations. During the pandemic, lead times skyrocketed from three months to nearly nine, creating major bottlenecks in production and delivery. Just as the situation began to stabilise, new disruptions emerged. The ongoing security crisis in the Suez Canal has once again thrown global shipping into turmoil, forcing vessels to reroute thousands of kilometres, adding up to four weeks to already strained transit times.
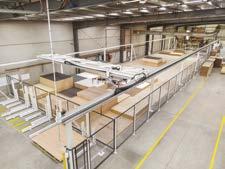

The only way to keep pace with market demand is by increasing stock levels, ensuring the right inventory mix, and delivering orders efficiently and quickly— sometimes within hours, not days. This is no easy feat, especially when customers require multi-colour pack lots rather than uniform batches, creating additional logistical challenges.
The team at Nikpol have embraced these challenges as opportunities for growth, continuing to invest in stock, supply chain resilience, and, most importantly, their people. By staying ahead of the curve, they can ensure that their customers get what they need, when they need it.
Fifteen years ago, the Melbourne head office installed a Homag panel-handling system—a move that revolutionised the way they safely, efficiently, and accurately manage 2800 x 2070 sheet sizes. Investing in automation and precision technology has not only increased efficiency but has also strengthened Nikpol’s commitment to safety and quality.
Today, they have taken that commitment to the next level with the installation of a sixth Homag Bargstedt, enabling stock to be delivered faster than ever before. This infrastructure investment allows Nikpol to meet growing customer demands while
maintaining the highest standards of accuracy and efficiency. With six Homag CNC machines, Nikpol has firmly established itself as a market leader in on-time, madeto-measure laminated bench tops and cutto-size boards, reinforcing their position as a one-stop supply chain solution for cabinet makers.

After 48 years in the industry, they have learned that survival isn’t just about reacting to change—it is about anticipating it. Flexibility, adaptability, and a deep understanding of customer needs are the pillars of long-term success.
The team at Nikpol don’t just aim to compete—they aim to lead. By continuing to invest in their people, technology, and supply chain, they are building a future where their customers can rely on efficiency, innovation, and an unwavering commitment to quality. Those who listen, evolve, and invest wisely won’t just compete—they will thrive.
web www.nikpol.com.au z
Flexliner Engineering has Australia’s largest range of levelling or adjustable feet and threaded tube inserts. Supplied Australia-wide by air bag or bulk road freight every working day. Using the highest-grade plastics of reinforced glass filled nylon, polyethylene, and polypropylene, with mild steel galvanised, stainless steel 304 grade and marine 316 grade threaded stems / studs they provide tilting and non-tilting (rigid) adjustable feet.
They also supply a large range of mild steel and stainless T nuts to suit all their levelling feet. Plus, round, square and rectangle threaded tube inserts, for attaching levelling feet, glides and castors.
Applications
Levelling feet are used on tables, benches, desks, workstations, shelving, cupboards, storage units, office and kitchen equipment housings to lift or raise a piece of furniture or object, by screwing/unscrewing the thread, to provide stability and reduce vibration by elevating the object above the floor.
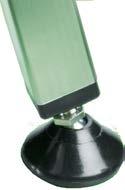
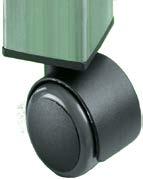
Level it with Flexliner

Capacity
The load capacity of the levelling foot depends on the thread size and type of base. As a guide refer to the list below.
• M6 thread: 50kgs to 150kgs - light duty
• M8 and M10 thread: 100kgs to 750kgsmedium duty
• M12 and M16 thread: 250kgs to 1000+kgs - heavy duty
How to choose a levelling foot?
Step 1. Determine the total load the foot must carry.
Step 2. Establish whether it is an indoor or outdoor application?
Step 3. Determine the condition of the floor, is it level. Do you need a tilting or non-tilt, foot?
Step 4. What is a suitable base diameter?
Flexliner Engineering supplies a broad range of customers in the metal fabrication, welding, shopfitting, interior building construction, park furniture, cabinet makers, carpenters, medical and hospital equipment suppliers, manual handling equipment, office furniture makers, kitchen builders, restaurants and the catering industry plus many specialty projects.
For more information email the team atparts@flexliner.com.au
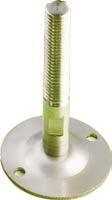
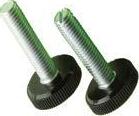
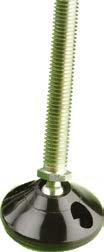






powering innovation
the future of hardware unveiled
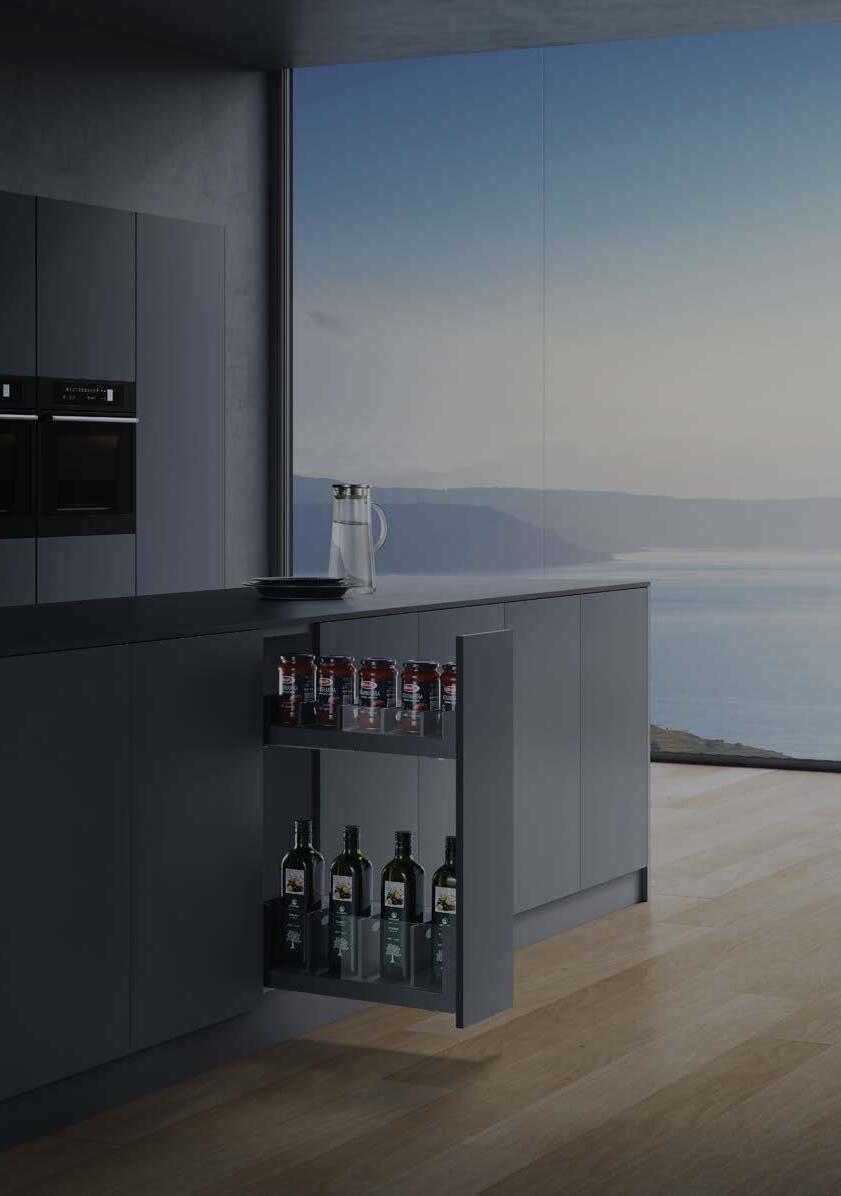

pure pro spice/bottle drawer
The Spice/Bottle drawer boasts full-extension concealed runners with a 40kg load capacity and soft-close functionality for seamless, quiet operation. The Pure Pro Spice/Bottle Drawer comes in versatile 150mm and 200mm kits, designed to fit any kitchen space. Each kit includes low and high drawers with dividers sold separately, perfect for organizing a wide range of kitchen essentials with style and efficiency.
why dtc
DTC Global leads the storage solutions industry with high-quality products focused on innovation, reliability, and sustainability. Their storage solutions use advanced technology and durable design for efficiency, scalability, and flexibility. DTC Global tailors its products to meet customer needs, improving storage systems and operations. The company also prioritizes eco-friendly practices to reduce its environmental impact. With a commitment to excellence and customer service, DTC Global is the trusted partner for businesses seeking top-notch storage solutions.
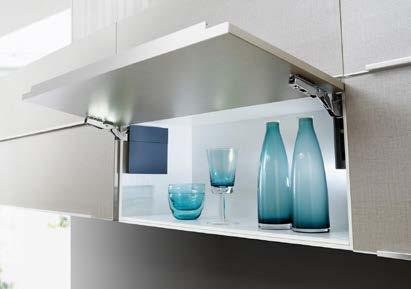
dtc top stays
Tailored for upper cabinets that opens door up and away, this mechanism features a 107° opening angle and is engineered to suit door thicknesses ranging from 16mm to 28mm.
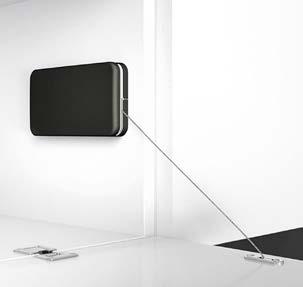

dtc down stays
Designed for cabinets ranging from 200mm to 480mm in height, this mechanism accommodates door weights of up to 14kg, offering both horizontal and vertical mounting options.
dtc bi-fold top stays
Designed to increase access to multiple upper cabinets simultaneously, this mechanism offers comprehensive 3D adjustments, allowing for precise alignment of doors. With upper overall adjustments of +/-2mm and lower door adjustments of +2/-1 for height and +/-2mm for side and depth, it ensures a tailored fit.
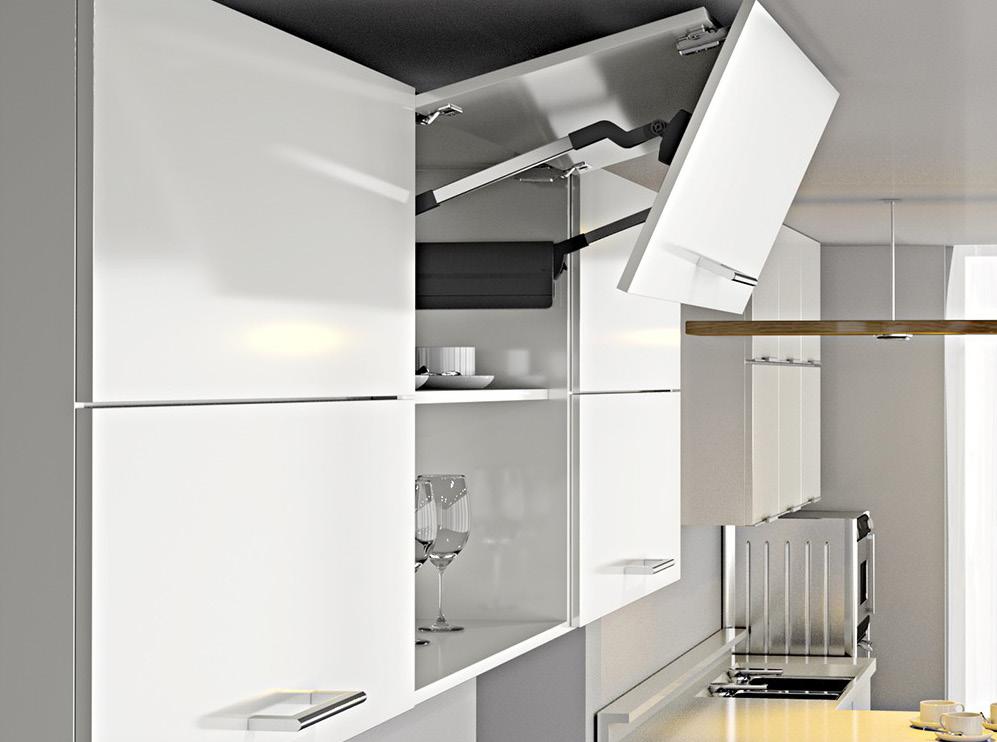

Hafele Ixconnect
The universal connector from Hafele
The UC 16/64, developed and patented by Häfele, is a true all-rounder. Whether as a one-piece corner connector, for angle applications, for panel mounting or as a classic connection bracket, it can be used multifunctionally, because depending on how you combine two or even more of the well-thought-out connectors with each other, you can create countless stable connections with it.
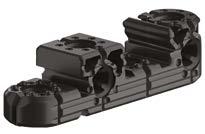
Depending on the installation situation, the universal connector can be slid open from the front, from the side or from above. It can also be used as an assembly aid for various applications in furniture and interior design.


Key Advantages
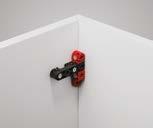
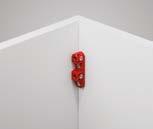
• One fitting for countless applications
• Compact dimensions (16x64x16mm), allowing use on the front side
• Screw connection with standard ø 4mm Hospa or Varianta screws
• Fastening options in 32mm grid
• Connector can be screwed on, hung, clipped on or pushed on
• Clip connection is removable
• The strength of the locking function can be varied by the number of connectors

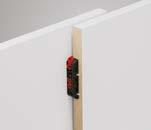
• The locking points allow the fitting to be fixed at different angles (90°, 135°, 180°, 225°, 270°).
• Can be used as a versatile assembly aid in furniture and interior design
For more information or to view the UC 16/64 fitting, please call and speak to your Hafele Account manager.
web www.hafele.com.au z
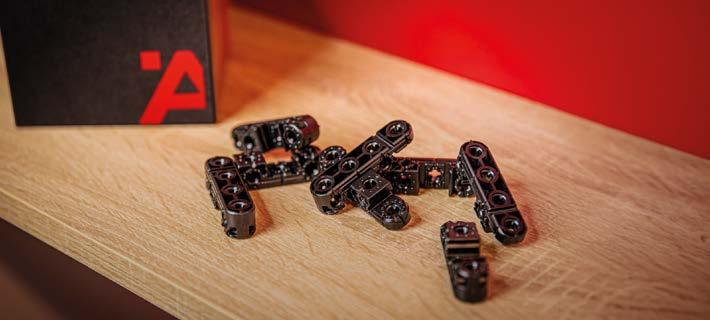
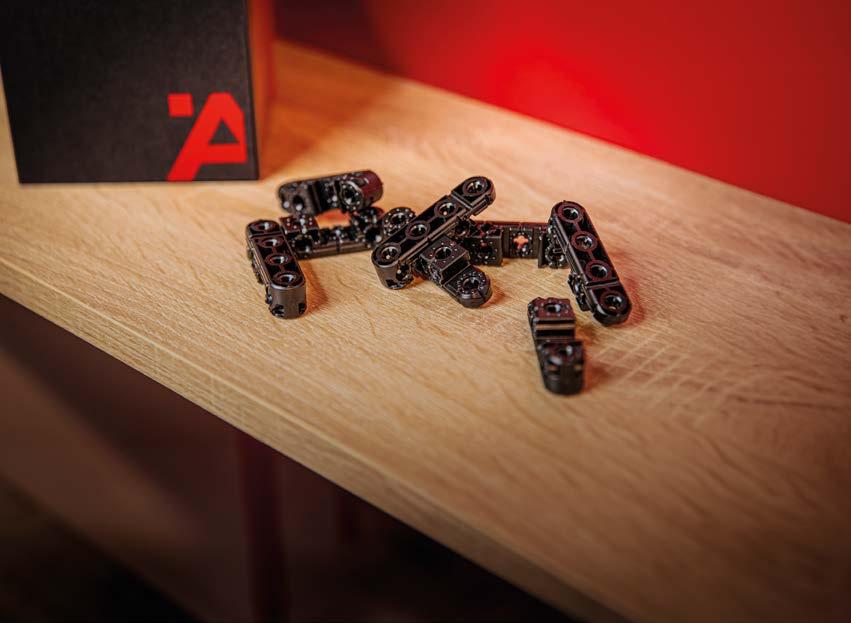


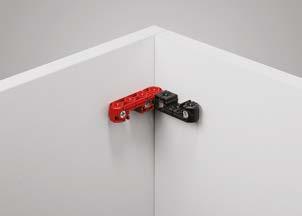

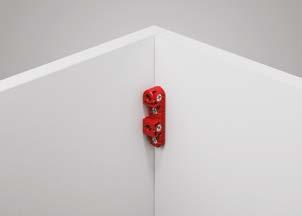
A fitting for countless interior design and furniture assembly applications.
> Extremely versatile range of applications.
> Easier to stock, as there is no distinction between frame and panel components.
> All conceivable installation tasks are covered by just one fitting.
> Can be screwed on, hooked in, clipped on or slid on.
> Can be used individually or in combination with several identical fitting parts.
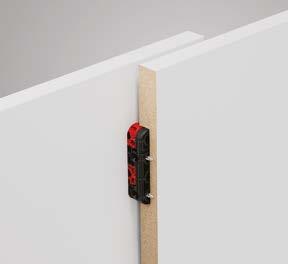
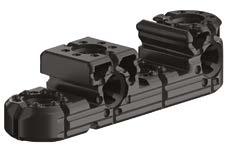
Celebrating 30 years of innovation, quality and sustainability
As Harn marks 30 years of excellence, they take pride in our journey— from a family-run business in Ipoh, Malaysia, to a trusted name in high-
key components—simplifying both customisation and inventory management. Designed with versatility in mind, its threedimensional adjustment options for height,
features the world's first 7.2mm doublewall drawer profile, perfectly pairing functionality with sustainability.
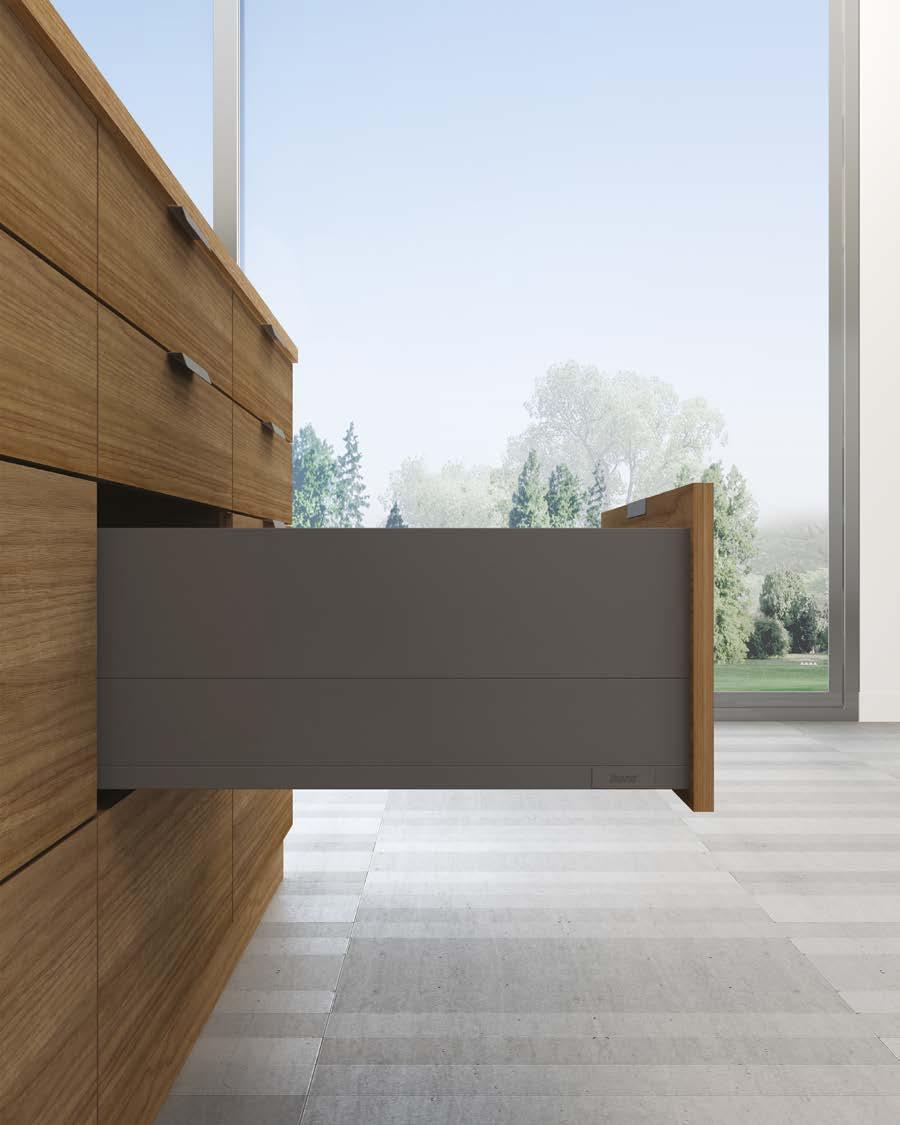
DISCOVER VERTICAL SCANNING WITH TAGLIO SLAB VISION
Elevate your stone fabrication using CDK Stone’s Taglio Slab Vision. Discover advanced vertical scanning capabilities tailored for marble, granite, other natural stones, and porcelain. Experience the forefront of automatic precision scanning technology.

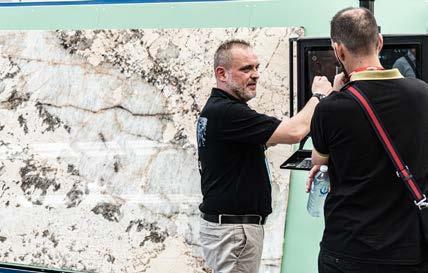
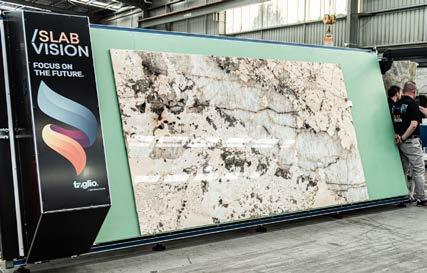
Design, Tools & Technology
The evolution of stone benchtop profiles
When it comes to stone benchtops, the edge profile plays a crucial role in both aesthetics and functionality. From classic bullnose edges to modern combination profiles, achieving precision and quality requires the right tools, techniques, and expertise. Edge profiles are moving beyond classic bevels and pencil rounds, with designers and stonemasons embracing more intricate, custom profiles.
As seen in Cassandra Walker’s Malvern House project that features a custom edge profile, seamlessly merging a bullnose and lamb’s tongue to enhance aesthetic appeal while highlighting the craftsmanship and creativity involved. Similarly, the MIM Design Horizon project showcases a striking double shark nose on the kitchen benchtop, demonstrating how layered profiles enhance visual impact.
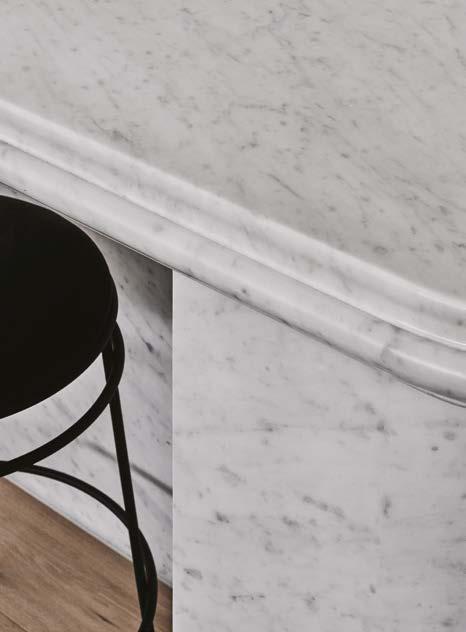
These styles build on classic profiles Waterfall, Ogee, Lamb’s Tongue, and Federation, while introducing modern twists to create bold, unique edges. As demand for custom detailing grows, so does the need for precision tools and craftsmanship.
Q: What tools are used to shape and polish stone benchtop edges?
A: Achieving a high-quality edge finish requires precision tools designed for shaping and polishing stone. CNC Milling Centres, profile wheels, and polishing systems all play a role in this process.
CNC Profile Wheels: These tools are mounted on CNC Milling Centres to shape stone edges with high precision. While they are designed for accuracy and consistency, selecting the correct wheel for the specific material is crucial to achieving the best results. Different stones, such as granite, marble, quartzite, and sintered stone, require specific bond types and cutting speeds to avoid chipping or premature wear.
Edge Polishing Machines: Machines such as Comandulli edge polishers refine the stone edge after shaping, delivering a smooth, polished finish. These machines can also handle additional processes such as thickness calibration and groove cutting, enhancing workflow efficiency.
Q: How do CNC profile wheels contribute to precision edge profiling?
A: CNC profile wheels are engineered for accuracy and efficiency. However, proper usage and setup play a major role in their effectiveness. Simply mounting a profile wheel does not guarantee a perfect edge,
Design, Tools & Technology
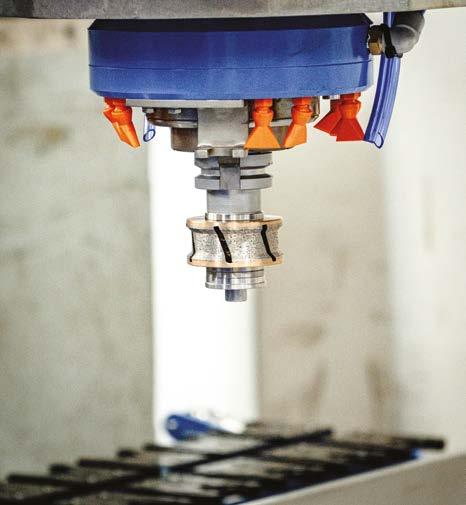
factors such as feed rate, cooling, and material compatibility influence the final result.
ADI Profile Wheels are designed for accuracy, efficiency, and durability. Their UHS (Ultra High Speed) technology enables feed rates up to four times faster than standard metal-bonded tools, boosting production speed without sacrificing precision or tool life. Precision-engineered water slots improve cooling and extend tool longevity by optimising water distribution, reducing thermal damage, and enhancing the final finish.
Each ADI Profile Wheel is individually measured to an accuracy of 0.001mm, ensuring precise setup and reducing downtime. These features make ADI Profile Wheels essential for achieving high-quality edge finishes in stone fabrication.
Q: What should fabricators consider when choosing edge profiling tools?
A: Choosing the right edge profiling tool depends on material compatibility, as different stone types require specific bond types to prevent wear and ensure a clean cut.
Complex profiles may need multiple tools, and proper feed rate and speed calibration are crucial for achieving the best finish and extending tool life.
ADI provides seven distinct lines of profile wheels, each tailored for specific materials and applications. From the TopLine series, ideal for processing larger profiles, to the Micron Line Series, designed for navigating tight corners in small-radius sinks, every line is carefully engineered and tested to maintain optimal feed and speed rates, ensuring both efficiency and durability.
The right tools make all the difference in achieving flawless stone benchtop profiles. ADI Profile Wheels and Comandulli Polishing Machines set the industry standard for precision and efficiency, helping fabricators produce high-quality results with ease. As designers and stonemasons continue to push the boundaries of edge profiling combining classic elements with modern craftsmanship investing in the right tools is essential to bringing these intricate, custom profiles to life
For more insights on professional stone fabrication tools, contact CDK Stone or visit our website..
web www.cdkstone.com.au z
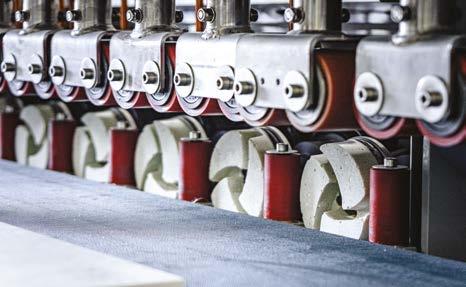
Case Study
For fifteen years, SALT Kitchens has maintained a reputation built on hard work, quality, honesty and accountability. For as long as they have been in business, SALT has relied on Brewer-Farnese Machinery as their reliable, trustworthy, and committed equipment supply partner.
SALT Kitchens is located in Forrestdale, Western Australia, half an hour from Perth CBD. With just under thirty employees, they’re not so big that customers are just another number, and not so small where corners are often cut.
“We want to be the provider people in Perth and the surrounding districts look to for their quality kitchen and bathroom renovations, cabinetry and joinery,” says SALT Kitchens director Heath Woollams.
Accessible and Accountable
“SALT Kitchens isn’t a business with a cookie cutter approach. Our focus on renovations tend to mean an emphasis on often unique, bespoke design so we need equipment that is reliable and flexible, supplied by someone who has taken the time to understand our business and the way we work. We’ve been with Brewer Machinery since the very beginning; they are hands-on, take ownership of their service and develop a level of trust that has continued through their recent sale to Farnese Masterwood,” Heath adds.
Todd is SALT Kitchens production manager. He said, “We operate two Masterwood CNC machines; our latest 3.6m by 1.8m capacity CNC machine was installed June last year when we moved to our new premises. While we need a level of flexibility, we decided that automation would also add value to our product and so, the Masterwood was
equipped with automatic labelling, infeed and outfeed and our Holz Her 1308 Auriga edge bander, a really good jobbing machine, was equipped with an automatic return.”
Todd continues, “Like most other cabinet makers we depend heavily on our CNC machines and our edge bander. Unreasonable downtime is unacceptable, and Brewer-Farnese has never let us down with prompt service. We can’t wait two days to get a return phone call; we need help immediately and we’ve never had a problem Brewer-Farnese was not able to solve within a very reasonable time. Brewer-Farnese are extremely accommodating and will stay on site until their work is complete. Nothing is an issue for them.”
SALT is a family business which holds itself to high standards, continually seeking out ways of doing things better. Heath says,
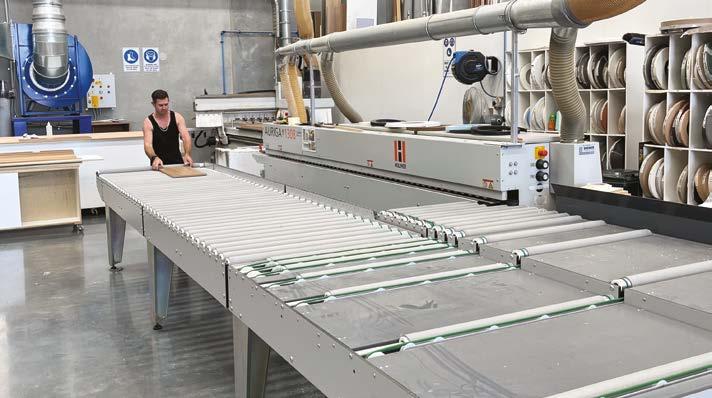
Case Study

“Every job we take on is different; with builders, designers, interior designers and owner-builders all seeking our unique skills. We build and install custom furniture, walk-in robes, TV/entertainment cabinets, alfresco or our famous kitchen and bathroom cabinets. We are accessible and accountable, and we expect no less from our supply and service partners.”
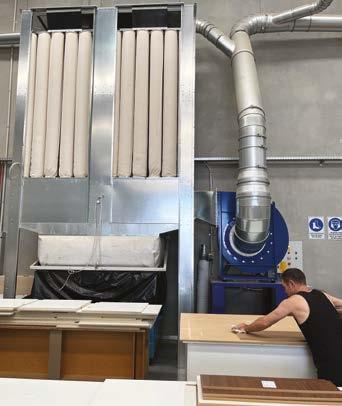
“When we first started to work with Malcolm Brewer, they were a small outfit as we were, it just suited our business. Over the years they’ve walked us through our challenges and have been very flexible to our needs. As we grew, they helped us to improve our efficiencies. We can’t fault their service and support and it’s a credit to them that they’ve continued that since Farnese Masterwood took over. Their professionalism, commitment and personalized service give us excellent value for money,” Heath adds. For further information contact Heath on (08) 9456 2700 or at SALTkb.com.au z
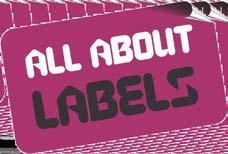



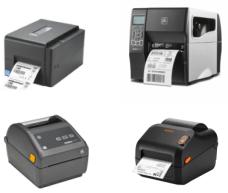


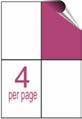
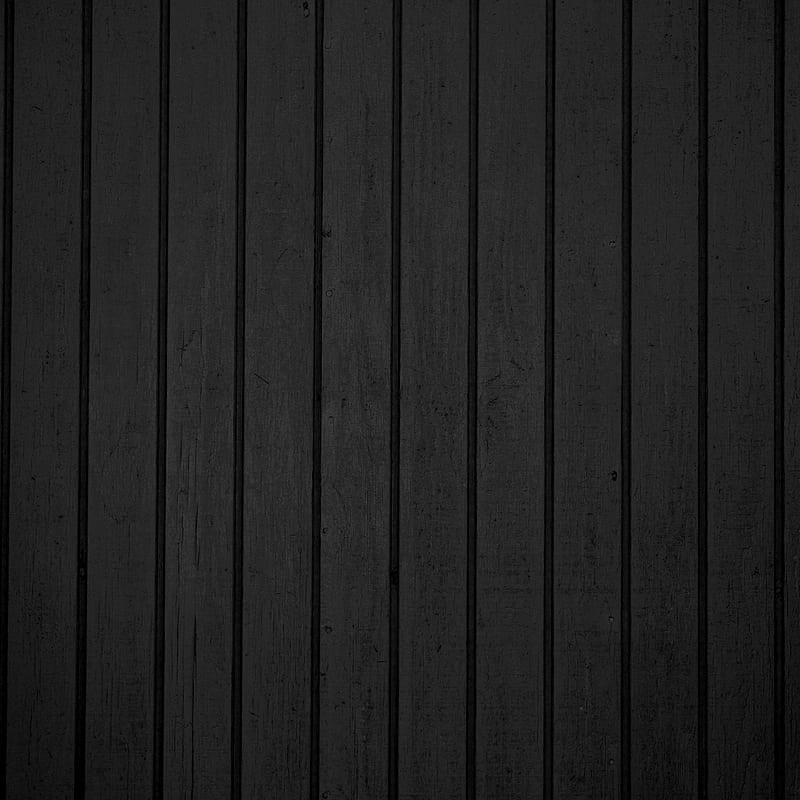


Company Profile
The Importance of Factory Workflow
Achieving efficiency and quality in cabinet making and joinery.
In today’s fast-paced industrial landscape, businesses must prioritise efficiency and quality to stay competitive. RJS Tech Group, an Australian-owned leader in the woodworking and manufacturing sectors, embodies this philosophy. Founded by Ron Smyth, a veteran with nearly 40 years of experience in the machine tool industry, RJS Tech Group oversees a network of companies, including Wood Tech, Prestige Precision Tools, Whitelaw Engineering Machinery, NanoTech, Metal Tech, Rogers Industries and PPE Tech. Each subsidiary is united by a commitment to delivering cutting-edge solutions that enhance productivity and profitability for their clients.
Among these, Wood Tech stands out as a trusted partner for the manufacturing industry of cabinet making and detailed joiners. Specialising in the full range of premium woodworking equipment, Wood Tech combines innovative technology with expert guidance to transform factory workflows, enabling businesses to do more with less.
The role of workflow in business success
The importance of factory workflow cannot be overstated. In the wood industry in general, where high volume demands meet precision and consistency, an optimised workflow is the difference between meeting client deadlines and falling behind. A streamlined operation not only boosts output but also ensures a higher standard of quality with fewer errors and reduced waste.
The financial impact is equally significant. Time saved in production translates to lower labour costs, fewer bottlenecks, and more orders fulfilled. Businesses that adopt modern workflow solutions find themselves in a stronger position to compete in an increasingly demanding market. As factory owners know, every saved minute and optimised square meter directly impacts the bottom line.
The ideal workflow setup
Efficiency starts with a well-designed workflow. A prime example is the integration of a panel storage system, Wood Tech have a very popular option for this, a CNC label line, and finishing equipment like edgebanders.
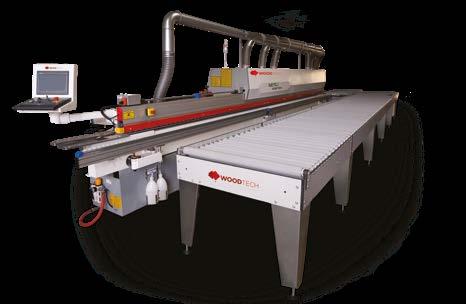
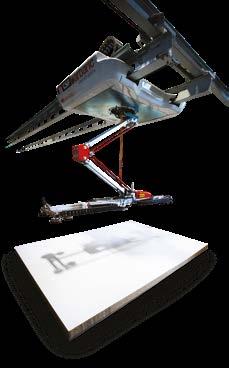
Here is how these elements work together:
1. Material management with a panel storage system
Sheets are stored in a designated zone on the factory floor (or optionally on a mezzanine above the CNC if you want to utilize available air-space and free up factory floor area) and retrieved by the fully automated storage system, which integrates with stock management systems. This setup increases productivity while reclaiming valuable floor space. With materials organised and easily accessible, factory owners can eliminate time wasted searching for inventory, significantly improving throughput. The storage system retrieves the sheet for the required job and sends it down onto the CNC for processing.
2. Streamlining with the CNC label line
The CNC label line begins by applying labels with board processing information and barcodes to sheets, enabling seamless
Company Profile
tracking and precision processing. This level of automation ensures that every sheet is accounted for, reducing errors and enhancing accuracy. Factory owners benefit from reduced material waste and improved consistency in production, key factors in maintaining a competitive edge.
3. Precision processing with the CNC nester
The CNC nester takes the labelled sheets and processes them with unparalleled precision. By ensuring every cut adheres to exact specifications, businesses can minimise waste and maximize material usage. This technology not only improves output quality but also reduces costs associated with remakes and errors.
4. Seamless transition to finishing
Once pieces are processed, they move onto a conveyor system leading directly to the operator. The operator transfers the components to an edgebander placed strategically within reach. This proximity reduces unnecessary movement, saving time and effort while maintaining a smooth workflow. The result is a finished product of exceptional quality, ready for assembly or delivery.
Why factory layout matters
An optimised factory layout is the backbone of efficiency. By placing key equipment in proximity to one another and ensuring a logical flow of materials, factories can significantly reduce downtime and labour inefficiencies. For example:
• Proximity of equipment: The conveyor’s direct connection to the edgebander eliminates the need for additional handling, saving valuable time.
• Strategic positioning: The panel storage system near the CNC label line minimises retrieval times and keeps operations running smoothly.
Every aspect of the layout—from material storage location to processing and finishing—is designed to reduce steps and streamline the production process. This holistic approach ensures that resources are used to their fullest potential, a crucial factor for profitability.
The Wood Tech difference
Wood Tech offers more than just machines; they provide comprehensive solutions tailored to the needs of each factory. Their team works closely with business owners to analyse existing workflows, identify bottlenecks, and design layouts that maximise space and efficiency. From implementing advanced storage systems to integrating state-of-the-art CNC technology, Wood Tech ensures that your factory operates at peak performance.
Beyond equipment, Wood Tech provides ongoing support and training, helping teams adapt to new systems and achieve sustainable improvements. Their goal is not just to sell machinery but to forge long-term partnerships with clients, empowering them to stay ahead in a competitive market.
Making the investment in efficiency
Investing in modern workflow solutions is an investment in the future of your business.
The initial cost of upgrading equipment or reconfiguring layouts is quickly offset by the savings in time, labour, and materials. Moreso, the introduction of a panel storage system could help reclaim valuable factory floor space, omitting the need to move to a larger factory and getting the most out of your space and ultimately saving you money.
With decades of experience and a proven track record, Wood Tech understands the challenges faced by factory owners today. Their expertise and commitment to innovation make them an ideal partner for businesses looking to optimise their operations and achieve measurable results.
Transform your factory with Wood Tech
Don’t let outdated workflows hold your business back. Discover how Wood Tech can help you reclaim valuable space, streamline production, and enhance profitability. Whether you are designing a new factory or optimising an existing one, the team is here to guide you every step of the way.
For more information on transforming your factory workflow, including case study videos and product information, visit rjstechgroup. com.au/woodtechfactoryworkflow/ z
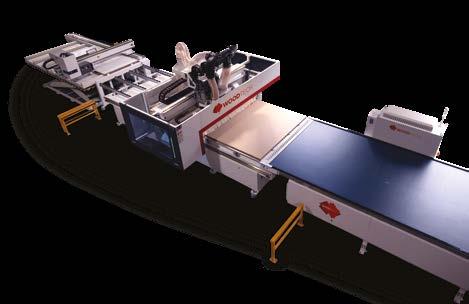
Bridging the gap between mega projects and small scale enterprise
In what might be an Australian—and possibly world—first, Carell has underpinned the full turnkey solution of design, manufacturing, and installation for the new Footscray Hospital—a flagship project in Melbourne’s rapidly growing western corridor. By uniting five major contractors, including Multiplex, Jacaranda, LL Installations, Sherwood, and overall coordinator Trendgosa, Carell has proven itself as the linchpin that keeps complex manufacturing processes on track.
A hospital project of unprecedented scale
The new Footscray Hospital represents one of the largest healthcare builds in Australia, designed to meet the evolving needs of a diverse and expanding population. Such a massive venture demands an equally robust technological backbone to handle intricate workflows, real-time collaboration, and extensive documentation. From high-level design management and manufacturing to assembly and on-site installations, every facet of this project relies on precise scheduling, accurate data, and seamless communication among all parties involved.

At the heart of this process is Carell’s cloud-based platform, which has been instrumental in co-ordinating the host of contractors and suppliers necessary for a project of this magnitude. The digital clarity provided by Carell ensured that tasks were assigned, deadlines met, and updates shared universally and instantly. This level of coordination not only minimised production issues and reworks but also enhanced contractor reporting and progress claims through real-time tracking and data-driven insights.
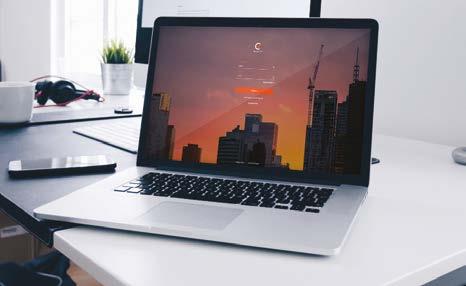
Streamlining design, manufacturing, and installation
Carell’s unified approach manages the entire lifecycle of fit-outs and joinery—from initial design to final installation. For the new Footscray Hospital, this meant that floor plans, shop drawings, and specifications were accessible to design teams, fabricators, and on-site crews simultaneously.
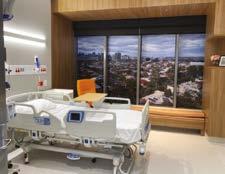
By facilitating immediate access to the most up-to-date digital information, Carell ensured that every stakeholder, whether working in an office or on location, operated with precision and accountability. This commitment to excellence has not only set a benchmark in healthcare construction but also demonstrated the power of digital collaboration in large-scale projects.
Software
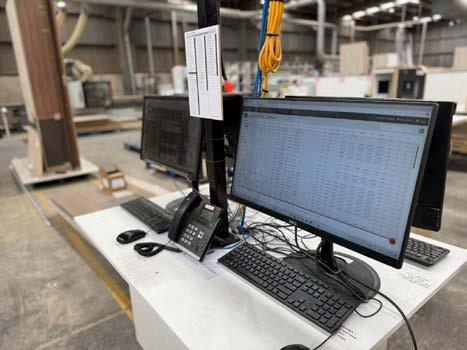
At the heart of this process is Carell’s cloud-based platform, which has been instrumental in co-ordinating the host of contractors and suppliers necessary for a project of this magnitude.
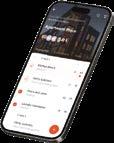
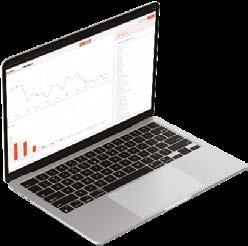
Elevating
custom craftsmanship in residential joinery
Equally impressive is Carell’s impact on smaller, bespoke projects. Consider the case of a specialist cabinet maker who delivers custom, high-quality residential joinery. In an industry where precision, craftsmanship, and personalised customer service are paramount, this cabinet maker faced challenges as critical as those in large commercial projects. They needed a reliable method to track production items, reduce reworks, and maintain a comprehensive digital record of every installation.
By adopting Carell, this smaller enterprise transformed its operations overnight. The platform provided an intuitive interface for logging every stage of the joinery process—from initial design sketches to final installation photographs—ensuring that each piece of joinery was meticulously documented for future reference.
This digital trail not only bolstered their quality assurance practices but also served as a powerful promotional tool, enabling the cabinet maker to showcase their detailed workmanship and build trust with highly valued clients.
One platform, endless possibilities
Whether it’s a sprawling hospital or a refined residential joinery project, Carell’s digital collaboration platform stands as a versatile solution that scales effortlessly. From co-ordinating multiple contractors on large commercial projects to providing bespoke tracking for custom home or custom fit-out installations, Carell delivers the precision, transparency, and accountability that every project demands. With Carell, no job is too big or too small—just a steadfast commitment to traceability, quality and data for every detail.
web www.carell.com.au z
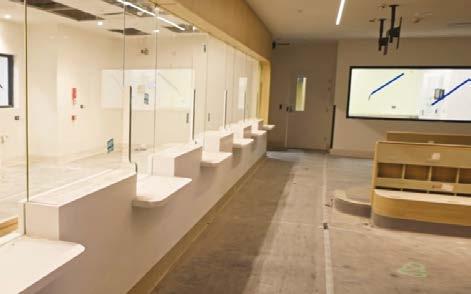
Software
Redefining the customer experience
By Gordon Guppy, National Service Manager, Planit Australia
In today’s fast-paced, technology-driven world, businesses are constantly seeking ways to streamline operations, enhance productivity, and deliver exceptional customer experiences. Planit Australia are proud to be at the forefront of this transformation, empowering businesses like Prominent Kitchens and Joinery and Urban Craft Joinery to thrive in the age of subscription software.
Recent interviews with Abdul El Masri, Director and Owner of Prominent Kitchens and Joinery, and Rory Hinksman, Owner of Urban Craft Joinery, provide compelling case studies of how cutting-edge software solutions like CABINET VISION, combined with a customer centric approach, can redefine the way businesses operate and grow.
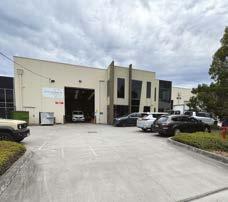
Embracing Technology: A family legacy meets modern innovation
Abdul El Masri’s journey into the woodworking industry is deeply rooted in family tradition. With over 30 years of family experience in joinery, Abdul has seamlessly blended this legacy with modern technology to build a thriving business.
“The industry is in our blood,” Abdul shared. “But to stay competitive, we knew we had to embrace the latest tools and software.”

“From the sales process to ongoing support, they are there for me every step of the way.”
Prominent Kitchens and Joinery is a shining example of how technology can transform a business. By integrating CABINET VISION into their operations, Abdul and his team have unlocked new levels of efficiency, accuracy, and customer satisfaction.
“CABINET VISION is not just a tool; it’s an asset, a necessity,” Abdul emphasised. “It’s like having an extra employee who never takes a day off.”
Similarly, Rory Hinksman of Urban Craft Joinery has embraced CABINET VISION to elevate his high-end architectural joinery business. “CABINET VISION is just so easy to use,” Rory said. “It’s transformed the way we work, from drawing walls to adding cupboards and making changes on the fly. It’s a game-changer for us.”
The Power of Subscription Software: Flexibility and growth
One of the key themes that emerged from conversations with both Abdul and Rory was the value of the subscription model. “The ability to pay-as-you-go is a game-changer,” Abdul explained. “It allows us to add features and capabilities as we grow, without the burden of large upfront costs. This flexibility is invaluable for a business like ours.”
Rory echoed this sentiment, highlighting how the subscription model has freed up cash flow for his business. “Instead of a massive upfront cost, we pay periodically, which allows us to invest in other areas like equipment, materials, and training,” he said. “It’s a one-stop package that gives us peace of mind.”
Software
A Seamless Customer Experience:
From sales to
support
At Planit Australia, they believe that the customer experience doesn’t end with the sale. Their commitment to providing exceptional service is something both Abdul and Rory highlighted during their interviews.
“Planit is totally unique,” Abdul said. “From the sales process to ongoing support, they are there for me every step of the way.” He praised Planit’s Concierge service and onboarding process, which helped him quickly integrate CABINET VISION into his operations. “The onboarding was comprehensive and unique. It took me from knowing nothing about Planit to understanding how to use the systems and best practices for getting help.”

Rory shared a similar experience, emphasising the ease of access to support and the regular check-ins from Planit’s team. “Laura, our Customer Partnership Manager, checks in with me every three months, if
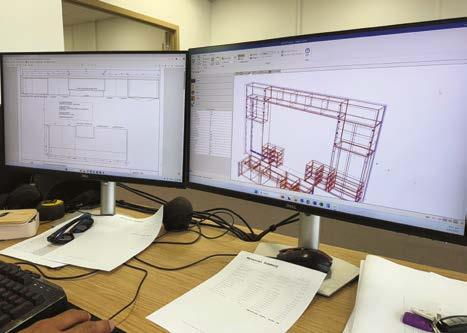
not more often,” Rory said. “It’s not about money or problems; it’s about making sure everything is running smoothly. That level of care is something I’ve never experienced before.”
Driving efficiency and innovation
Both Prominent Kitchens and Joinery and Urban Craft Joinery have seen significant improvements in efficiency and productivity since adopting CABINET VISION.
For Abdul, the software has streamlined communication between the drafting team and the factory floor, reducing errors and improving turnaround times. “Time is money,” Abdul said. “And CABINET VISION saves us both.”
Rory highlighted how CABINET VISION has simplified complex tasks, such as adding shelves or changing cabinet interiors. “It’s just a click away,” he said. “Compared to our previous software, which required multiple steps and workarounds, CABINET VISION is a breath of fresh air.”
Looking ahead, both Abdul and Rory have ambitious plans for their businesses, with
CABINET VISION playing a central role in their growth strategies.
Abdul envisions moving to a larger facility with more staff and additional CABINET VISION licenses. “We want to continue to evolve with the industry and the software,” he said. “It’s an exciting future.”
Rory, on the other hand, plans to focus on refining his operations and exploring new features of CABINET VISION. “We want to get even better at what we do,” he said. “With CABINET VISION, we can stay ahead of trends and set new standards in our industry.”
Planit Australia are proud to partner with businesses like Prominent Kitchens and Joinery and Urban Craft Joinery as they redefine what’s possible in their industries. By combining innovative software with a commitment to exceptional customer service, they are helping clients not only meet but exceed their goals.
As Abdul and Rory both emphasised, CABINET VISION and Planit Australia are more than just tools or vendors—they are partners in their success.
web www.planitaustralia.com.au z
Discovering Stone

Precision cutting for modern stone fabrication
Australian stonemasons are constantly seeking cutting-edge solutions that enhance accuracy, streamline production, and adapt to a variety of materials, including natural stone, porcelain, and engineered stone. The Thibaut TC425, an advanced 5-axis bridge saw delivers unmatched versatility and efficiency.
The TC425 saw is the only machine in its category with six integrated tools for total autonomy: a saw blade, separate core drill, a separate high speed router, Thibaut’s exclusive ACS jig saw (optional) or a second high speed router (optional) and vacuum manipulator to move the sawn pieces, as well as the possibility to produce textured finishes.
CDK Stone is bringing the Thibaut TC425 to the Australian market, introducing stonemasons to a state-of-the-art machine that redefines precision cutting. Manufactured by Thibaut, a global leader in stone machining solutions with over 65 years of expertise, the TC425 is built to handle complex cuts, mitres, and detailed profiling with ease.
Launching at CDK Stone’s Machinery Showcase Event on March 27–28, 2025, the TC425 represents the next evolution in fabrication technology. “The Thibaut TC425 delivers exceptional precision, versatility, and reliability, seamlessly integrating into modern fabrication workflows and setting a new standard for advanced performance.’” said James Clark, Director at CDK Stone.
Advanced technology for unmatched precision
One of the TC425’s standout features is its exclusive ACS jigsaw option; the only bridge saw in its class to offer this advanced capability. This system enables the saw to complete internal rectangular cut-outs and cut to the end of intersecting cuts, significantly reducing the need for manual repositioning. Additionally, the ACS jigsaw can be used to scribe irregular back edges, a task traditionally completed by hand or with a waterjet machine.
To further enhance accuracy, the TC425 is equipped with a crosshair laser, allowing operators to manually set the cutting length by pinpointing the start and end positions. The laser also enables precise measurement of wooden templates placed on the saw table, streamlining layout preparation.
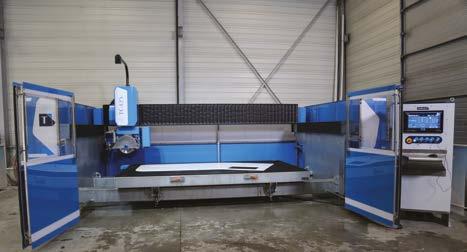

Equipped with both a primary saw spindle and a high-speed routing unit, the TC425 offers exceptional versatility in stone fabrication. The saw spindle delivers powerful and precise cutting performance, while the 10,000 RPM high-speed routing unit, now standard on all models sold by CDK Stone expands functionality beyond cutting. This dedicated routing system enables the use of drills, router cutters, milling cutters, and grooving fingers, while flange-mounted tools such as sizing cutters and texturing brushes enhance versatility.
Seamless integration with SeKON software
The Thibaut TC425 T’CUT software with PILOT interface includes all the options required for modern stone processing such as, fully automatic sawing including mitre cutting as well as manual processing, vein matching, a program for cutting UCS materials, multiple users and a post processor for integration with SeKON software. “SeKON software, provides fabricators with greater control over their entire cutting process, across multiple machines from different suppliers. From initial design to final execution, this system enhances precision, improves material utilisation, and streamlines production,” said James Clark, Director at CDK Stone.
Discovering Stone 41

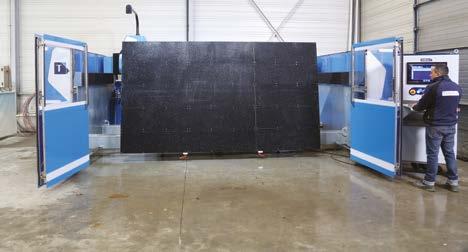
Compact design with versatile functionality
The Thibaut TC425 is designed with a compact footprint to fit seamlessly into a variety of workshop layouts. As well as a separate high-speed spindle (standard) and ACS jig saw (optional) the saw comes equipped with a tilting table to facilitate loading, blade measuring device and probe
for measuring the slab thickness, a remote pendant control and a blade sharpening station with software for cutting ultra compact materials.
Elevating the future of stone cutting
For Australian stonemasons looking to elevate their cutting capabilities, the
Thibaut TC425 offers the perfect blend of power, precision, and efficiency. With its seamless software integration, and versatile functionality, this bridge saw represents the future of modern stone fabrication.
To learn more about the Thibaut TC425 or to schedule a demonstration, contact CDK Stone today. If you are in Melbourne, see the TC425 and a range of other machines at CDK Stone’s Machinery Showcase Event on March 27–28, 2025. z
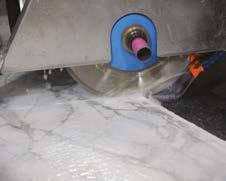
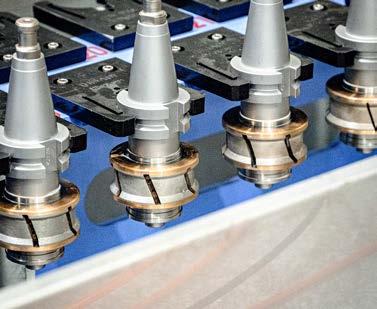
ENHANCED STONE PROCESSING TOOLS
TRIED TESTED TRUSTED
CDK Stone stocks a comprehensive range of high-quality tools and equipment designed to achieve precision in edge profiling for Porcelain, Ceramics, and Natural Stone.

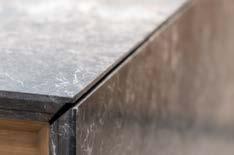
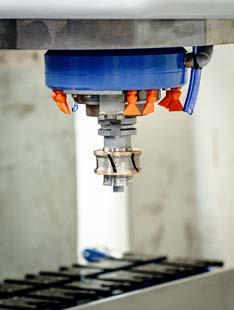
Discovering Stone

A design professional's guide to natural stone
Article by Sareen Stone
Recently the stone experts at Sareen Stone asked a team of architects and designers a range of frequently asked questions about natural stone. Here are their findings.
Natural stone has been the cornerstone of architectural brilliance for millennia - from the awe-inspiring pyramids of Egypt to the sleek, contemporary homes of today. In an era of endless material choices, what makes natural stone continue to captivate architects and designers? The answer lies in its unmatched ability to combine aesthetics with performance, and timeless appeal with modern design requirements.
Sustainability and environmental impact
Q: How sustainable is natural stone compared to other materials?
Natural stone stands as one of the more sustainable building materials in modern architecture. Its inherent longevity, spanning centuries, significantly reduces
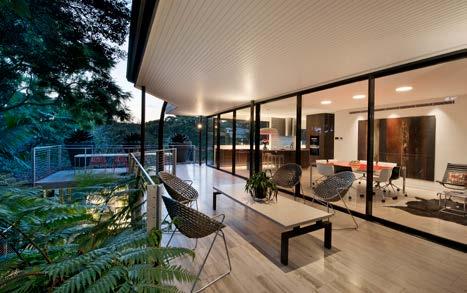
the need for replacements and minimizes long-term waste. Unlike manufactured materials, natural stone requires minimal maintenance over its lifetime, eliminating the need for harsh chemicals. While the extraction process involves environmental considerations, natural stone's resource efficiency compared to synthetic material manufacturing makes it an environmentally conscious choice.
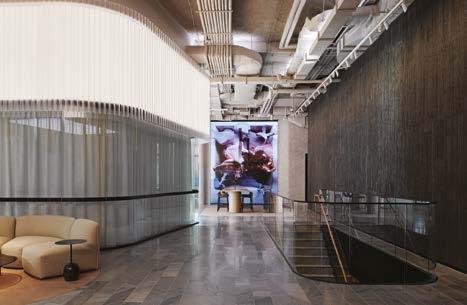
Understanding natural stone's evolution
Q: How does natural stone age over time?
Natural stone's aging process adds a unique dimension to architectural design, influenced by environmental and physical factors. As the stone weathers, it develops a natural patina that often enhances its aesthetic appeal. Different stones age uniquely: granite remains durable with minimal changes, while marble and limestone develop rich character and depth that can't be replicated artificially.
Practical considerations
Q: What should architects consider when specifying large custom stone tiles?
There are three key factors to consider when incorporating large-format stone tiles into a project’s design.
Size selection significantly influences both visual impact and technical execution. While standard formats, such as 600x400mm to
Discovering Stone

900x600mm, suit most projects, custom sizes, such as 1200x1200 or 1500x750mm, offer greater creative flexibility. The thickness of the material, typically 20mm to 30mm, must align with both structural requirements and application demands.
Custom sizes impact material costs and are a key factor in the specification process. Smaller tiles allow efficient use of stone and minimise waste during fabrication, largeformat tiles demand careful selection of slabs, potentially increasing material costs.
As the stone weathers, it develops a natural patina that often enhances its aesthetic appeal.
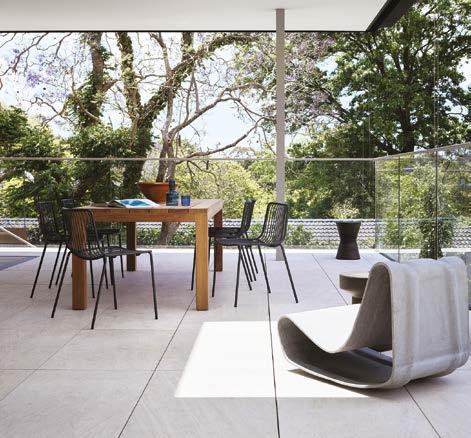
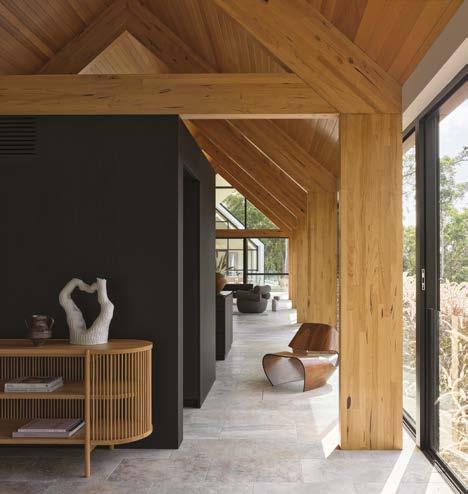
Installation also warrants consideration. Large-format tiles are significantly heavier, often requiring specialised equipment and multiple installers for safe handling. This added complexity can impact labour time and overall project costs. Understanding these parameters early in the design process helps achieve optimal results while effectively managing project expectations.
Design versatility
Q: How can different finishes transform natural stone?
Natural stone's versatility extends through various finishing techniques that dramatically affect aesthetics and performance. Split finishes preserve raw character for dramatic feature walls, while flamed surfaces create distinctive textures ideal for exterior applications. Sandblasted finishes offer subtle sophistication with superior slip resistance, and bush-hammered surfaces provide a practical grip without compromising design integrity. This range of options allows
Discovering Stone
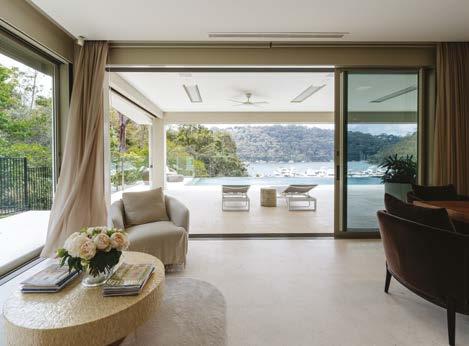
architects to precisely match material performance with design vision.
Creating seamless transitions
Q: What are the key considerations for indooroutdoor transitions?
Success lies in thoughtful material selection and precise execution. Using the same stone throughout, but with complementary finishes - typically honed for interiors and textured for exteriors - maintains visual continuity while
addressing practical requirements. Largeformat tiles minimize grout lines, creating uninterrupted flow, while careful attention to floor levels and threshold details ensures seamless transitions.
Material harmony
Q: How does natural stone work with other materials?
Natural stone's adaptability makes it an exceptional companion to contemporary
building materials. It creates compelling dialogues with timber, provides textural contrast to glass and steel, and either complements or contrasts with concrete's uniformity. This versatility extends to interior applications, where stone can make bold statements or serve as subtle foundation elements.
Understanding durability
Q: What determines stone performance?
Durability depends on inherent characteristics like hardness, porosity, and mineral composition. While granite and quartzite offer superior wear resistance, softer stones like limestone and marble require more careful consideration for specific applications. The chosen finish also impacts longevity - polished surfaces often resist staining better, while textured finishes might perform better in high-traffic areas.
Natural stone's enduring appeal lies not just in its beauty but also in its ability to tell a unique story over time. For detailed insights into material selection and technical specifications, visit www.sareenstone.com. au to connect with stone specialists who can guide you through the selection process. z
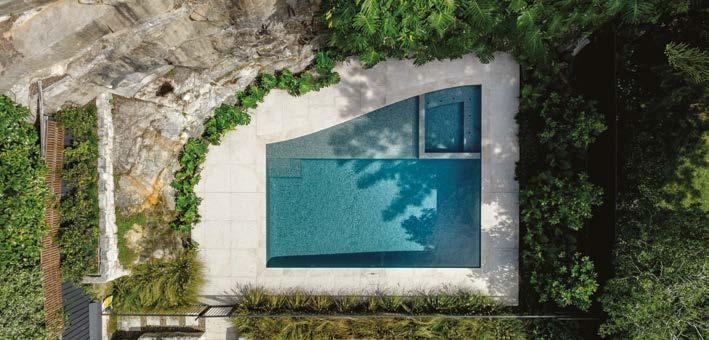
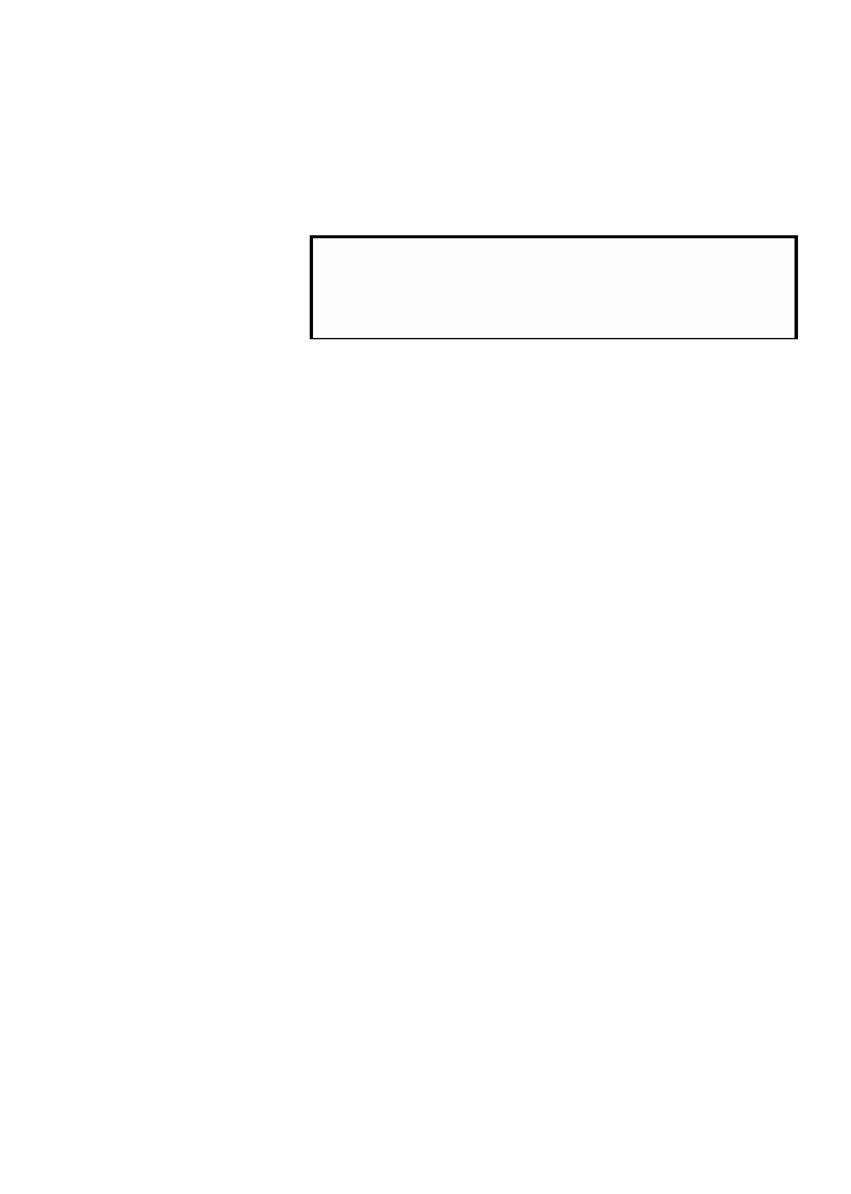

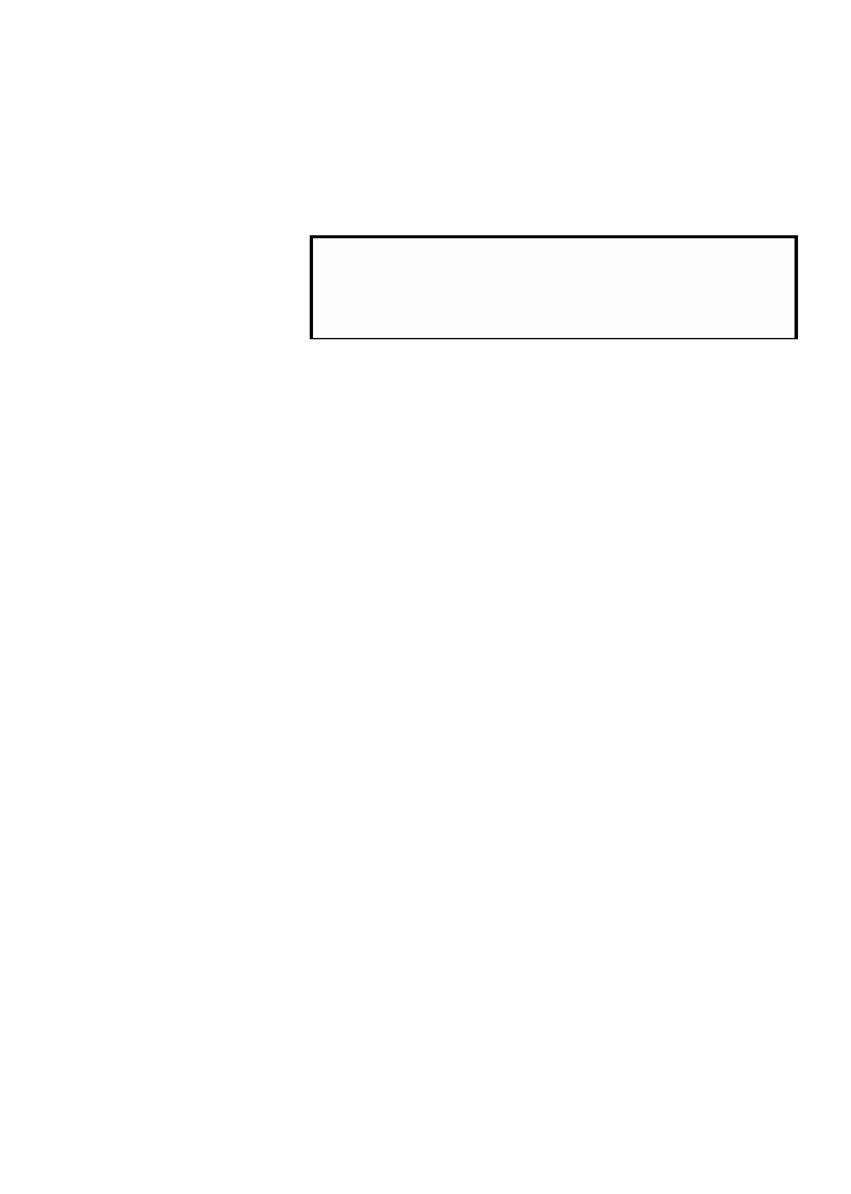
In My Opinion
Article by Philip Ashley
Industrial revolutions 1.0 (1765) through 4.0 were about technology. In the age of woke, the European Union sells industry 5.0 as the ‘Wellbeing of workers while respecting the production limits of the planet.’ Others say it’s ‘leveraging the unique creativity of human experts to collaborate with powerful and smart machinery.’
At the last Ligna trade fair in Germany in 2023 I asked senior sales representatives from Biesse, SCM, Homag, Felder and Weinig Group if AI (artificial intelligence) was industry 5.0 At that time, the concept of Industry 5.0 was a relatively new one. Not all said it was, but none disagreed it could be. Seems we got it wrong. According to recent media releases by the European Union, industry 5.0 is about ‘Being human-centric, sustainable and resilient, that promotes talents, diversity and empowerment.’
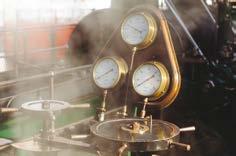

What Is Industry 5.0?
What the ‘Experts’ Say
The EU states, “Industry 5.0 provides a vision of industry that aims beyond efficiency and productivity as the sole goals and reinforces the role and the contribution of industry to society. It places the wellbeing of the worker at the centre of the production process and uses innovative technologies to provide prosperity beyond jobs and growth while respecting the production limits of the planet.”
Praveen Kumar Reddy Maddikunta et al. (2021) say the objective of industry 5.0 is to, “Leverage the creativity of human experts in collaboration with efficient, intelligent and accurate machines, in order to obtain resource-efficient and user-preferred manufacturing solutions compared to Industry 4.0. Industry 5.0 can enhance the quality of the production by assigning repetitive and monotonous tasks to the robots/machines and the tasks which need critical thinking to humans. In Industry 5.0,
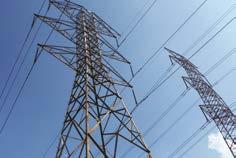
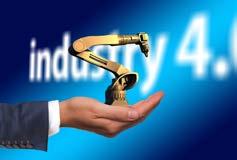
the majority of the production process will be automated.”
Forbes Councils Member Gisela Carere, MBA adds, “Industry 5.0 is focused on harnessing the synergy of human brainpower and AI to create a robotic workforce that is perceptive and responsive to human goals and desires, human value and potential. We as business leaders should look forward and collaborate with ‘robot colleagues’ to help humans focus on creativity and experimentation. Regardless of what industry you are in, adaptation and agility can keep you competitive while you capitalize on new opportunities brought on by technological advancements.”
Feelings or Technology?
There’s a lot to unpack here, and at the risk of criticism, I’ll take a critical approach to the subject. The ‘experts’ use terms like human-centric, diversity and empowerment, the wellbeing of the worker, and the production limits of the planet. Also in there are comments about technological advancements, automated production process; and the harnessing of artificial intelligence to create a robotic workforce. If you believe like I do that AI will be the most significant technological innovation in history so far, it’s difficult to believe that it has been watered down as a subset of current woke talking points.
Industry 4.0 was allegedly coined by Klaus Schwab, a German engineer, economist and founder of the World Economic Forum. Schwab described industry 4.0 as “rapid changes in industries, technologies and processes, fuelled by the integration of latest tech innovations.” Industry 4.0 removed
In My Opinion
workers from production and according to Schwab, industry 5.0 is putting them back in. Frost & Sullivan, a reputable American business consulting firm said, “Industry 5.0 will bring back empowered humans to the shop floor.” So, the question needs to be asked, “If the workplace is now full of automation and robotics, what will humans do when they are re-introduced to the new work environment?”
The Impact of Robotics
Industry 3.0 (computerisation, 1969) and 4.0 (digital and internet technologies, 2000) removed many humans from manufacturing. Some time ago the MINI car plant in Oxford in the United Kingdom replaced 2,640 workers (3.3 workers to each robot according to the Massachusetts Institute of Technology) in one production hall with eight hundred robots, now three maintenance people work there. If humans are to return to that facility, what will these ‘empowered’ people do?
And while you are thinking about that, take note that Time Magazine reported in 2020 that a paper by economists at MIT and Boston Universities said, “Robots could replace as many as 2 million U.S. workers (from 13 million as of January 2024 or around 15%) in manufacturing alone by 2025.” So, what is it? millions of jobs lost; or displaced workers returning to a workplace filled with automation and robots run by AI? In Australia, thewire.org.au states, “AI could replace over 1.3 million jobs in Australia by 2027 with up to 200,000 AI related jobs created.” A deficit of 1.1 million Australian jobs could hardly qualify as contributing to workers wellbeing.
Resources, Climate and Social Stability
The EU says industries can play an active role in providing solutions to challenges for society including the preservation of resources, climate change and social stability.
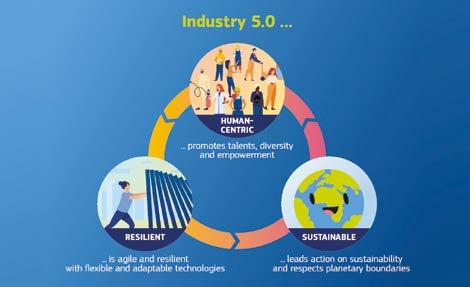
The preservation of resources is an easy decision and to that end, industry mostly pursues a circular economy where recycling and repurposing are key ingredients. Climate change is still a debatable topic if the recent overwhelming U.S. election result and the focus of the new administration are anything to go by. It will be interesting to see how the ‘European Green Deal’ fits into the next decade of international trade with America out of the Paris accord and China’s 20% emissions (Australia 1.46%).
Industry 5.0 is described by the EU as a Human-Centric Strategy where the primary focus will no longer be on growth, profit, and efficiency. It’s a strategy that many manufacturers may find difficult to process, since one of the main reasons an individual would start a business is to provide an income and a future for themselves, and in the process, for their employees. Also, in the EU infographic we see ‘sustainability’ as one of the three pillars of Industry 5.0 It’s an issue everyone is coming to terms with, from our suppliers, manufacturers and consumers. The third pillar is ‘resilience’ using flexible and adaptable technologies and Australia is well on track here.
Industry 5.0 Reality
So far, Industry 5.0 has not gained a lot of traction. Businesses are still heavily engaged
in understanding and implementing Industry 4.0 manufacturing strategies while tackling changing consumer demands and in some cases, the implementation of advanced materials. However, Artificial Intelligence is making its way into the timber and cabinet industries. One example is Weinig scanning technology using AI to identify a defect from tens of thousands of stored images within a split second. Preventative maintenance technologies exist on CNC machinery and coming soon, AI will be able to manage energy, vacuum and dust extraction requirements without human intervention.
So, what is Industry 5.0? One cannot argue that being human centric, sustainable and resilient are prominent issues but one that Australian manufacturers are already dealing with. Whether they constitute an industrial revolution is the question. Technology is acknowledged in the EU’s description of the revolution, but only as a means to support the three pillars. I still find it difficult to comprehend that workers feelings fall into the same category as the development of Steam, electricity, computerisation, and the internet. Just because Klaus Schwab says this, doesn’t make it true. For me at least, AI promises to revolutionise the way we live, and also the way we work and should have been designated Industry 5.0 z
Taking inspiration from the world around us
Rotpunkt, award winning designer and leading manufacturer of climate friendly German Kitchen furniture reveal the latest furniture trends to emerge in kitchen design this year.
As creativity and innovation continues to drive Rotpunkt forward, the company is able to pre-empt and keep pace with the latest consumer trends, which centre around personalisation, technology, and sustainability.
Matt Phillips, Head of UK Operations at Rotpunkt says, “Meeting individual needs and values, the UK home has evolved to the point where the kitchen has left behind the need for a separate dining room. Instead, multi-use spaces that are open to the main kitchen and social areas are now standard practice in the modern home, with a comfort-forward design style and sustainable living at their core.”
As such, Rotpunkt predicts the following trends will influence the modern kitchen in 2025.
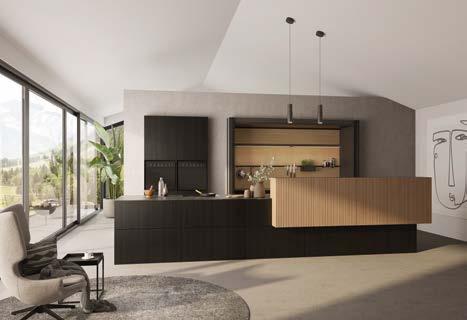
Style: Pure interior design is the freshest style trend to emerge in 2025, shaping quality home environments that promote relaxation and thoughtfulness in the home.
Combining minimalist cabinets, natural woods and a cosy approach to décor, purestyle interior schemes answer the growing desire for inviting home interiors, which are ultramodern and always ready to serve.
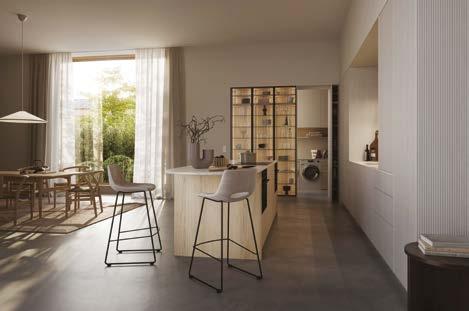
Colour: Taking inspiration from the world around us, this year’s colour palette for the modern kitchen will present a series of monochromatic and neutral shades that range from muted tones to bold pops of colour. Whether bright or soft, earthy shades of greenish-blue, terracotta reds, soft browns, and varying hues of deep purple are emerging as a popular choice in 2025. Likewise, shades of white, grey and black continue to stay the course, remaining a great foundation colour to either match, complement or contrast in style.
Material: 2025 will see a new focus on quality raw materials as a way to bring a cosy minimalist style and contemporary warmth to the UK home. Look out for a broad mix of dark and light hardwood timbers through to modern frame options, fluted designs in wood and glass, and metal décors, as these types of materials have become a staple in the modern kitchen for establishing a strong connection to nature.
Overseas News
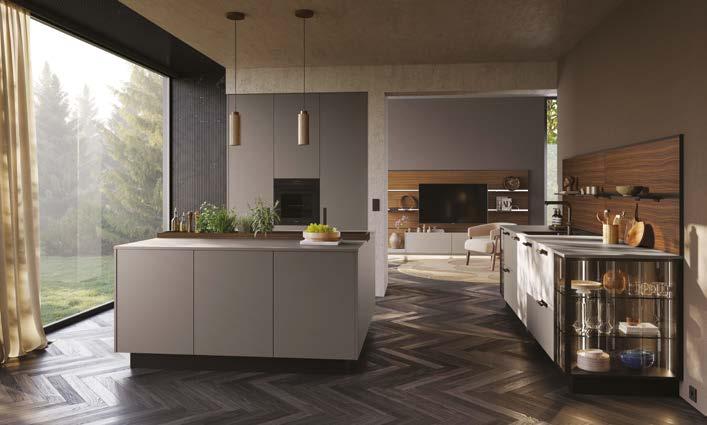
Natural walnut in shades of creamy white, light brown and dark chocolate are the wood of choice in 2025, with oak still considered the next best alternative for variety and texture.
Natural walnut in shades of creamy white, light brown and dark chocolate are the wood of choice in 2025...
Application: Consistency is key in 2025, and will provide a direct link between the furniture, surfaces, and lighting throughout the ground floor. From the kitchen furniture to your worktops, colour matched surfaces are the answer to a consistent look next year, as well as adding new form and function by extending the finish of both furniture and worktops to the walls to include complementary wall niches and panel systems. Size will also be a factor in
2025, with new dimensions being used to elevate standard furniture sizes and blend with special units which are multilevel and greater in width, depth, height.
From contemporary open-plan kitchens with custom table islands, café-style and
walk-in pantry solutions for today’s home chef, 2025 makes way for Rotpunkt’s most contemporary, diverse, and comprehensive product offer to date.
For further information visit www.rotpunkt. co.uk and www.rotpunktkuechen.de/en/ z

Advertiser Index
All About Labels 33
Biesse Group Australia Back Cover
CDK Stone 29, 41
Egger 14
Farnese Australia Inside Back Cover
Flexliner 23
Hafele Australia Inside Front Cover, 27
Harn 28
Kitchen King 15
Laser Measure 45
Nikpol 24, 25
Planit 5
RJS Tech Group 11
Surteco Australia 17
Titus Tekform Front Cover
Wilson & Bradley 18, 19
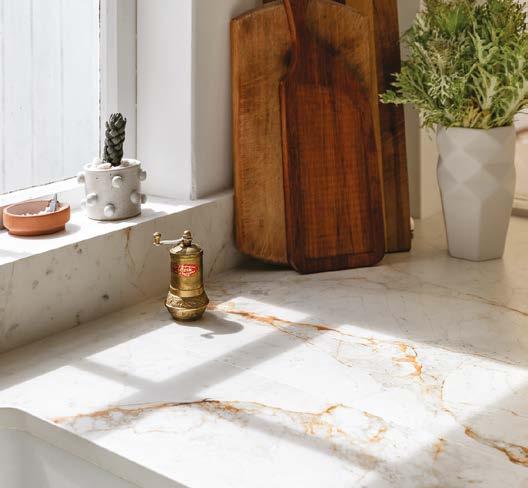
Contact Us
Proudly produced and printed in Australia
Published quarterly by:
ELITE PUBLISHING CO PTY LTD
ABN: 27 006 876 419
PO BOX 800, Templestowe, Victoria, Australia 3106
Ph: + 61 3 9890 0815
Email: info@elitepublishing.com.au
Web: www.suppliermagazine.com.au
PUBLISHERS
Georgia Gilmour
georgia@elitepublishing.com.au
Michelle Cammiade michelle@elitepublishing.com.au
ADVERTISING SALES MANAGER
Sandie Velkovska
sandie@elitepublishing.com.au
EDITORIAL
For editorial enquiries please email: info@elitepublishing.com.au
EDITOR
Michelle Cammiade michelle@elitepublishing.com.au
CONTRIBUTING EDITOR
Philip Ashley philipneilashley@yahoo.com.au
CIRCULATION
For circulation enquiries please email: info@elitepublishing.com.au
PRODUCTION
For artwork and production enquiries please email: production@elitepublishing.com.au
PRE-PRESS
Prominent Digital PRINTED BY
Prominent Press Pty Ltd
OVERSEAS REPRESENTATIVES
Representative Agent for Taiwan,China and Hong Kong, Robert Yu,Worldwide Services Co Ltd,11F-B, No. 540 Wen Hsin Road, Section 1,Taichung, 408, Taiwan Tel: +886 4 2325 1784 Fax: +886 4 2325 2967
Email: sales@wwstaiwan.com
ELITE PUBLISHING CO PTY LTD PUBLISHERS OF: Supplier Magazine, Flooring Magazine, and Tile Today
ELITE PUBLISHING CO PTY LTD. All rights reserved - No part of this publication maybe reproduced, transmitted or copied in any form or by any means, electronic or mechanical including photocopying, recording, or any information storage or retrieval system, without the express prior written consent of Elite Publishing Co Pty Ltd. Viewpoints, opinions, claims, etc expressed in articles appearing in this publication are those of the authors. The Publishers accept no responsibility for the information supplied or for claims made by companies or their representatives regarding product performance, etc or for any errors, omissions, misplacement, alterations, or any subsequent changes, or for any consequences of reliance on this information or this publication.

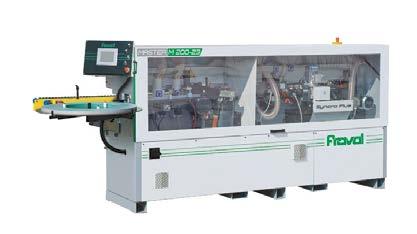

M200-23 EDGEBANDER
The modern, compact design of the Italian FRAVOL M200-23 EDGEBANDER saves space without compromising on performance or edge quality. A mix of solutions, applications and technologies in just 3 metres.
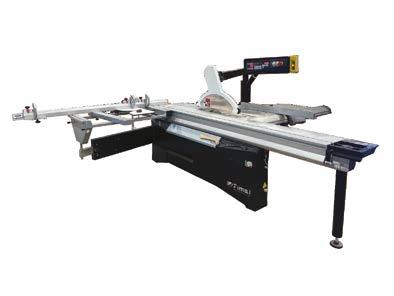
TABLE SAW FIMAL
A classic among machines for processing wood and wood products.F.I.MA.L. circular saws are the perfect woodworking solution for people who must perform frequent cuts with di erent angles.
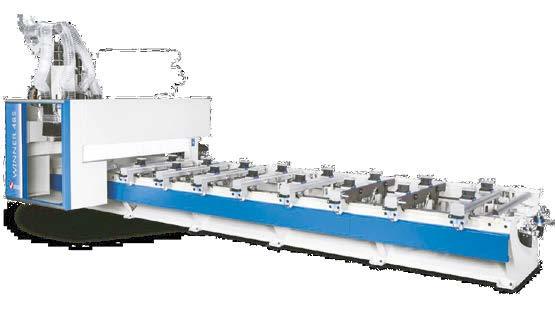
485 5 axis cnc WINNER SERIES
The Winner series from Masterwood has been designed to meet the needs of most companies, o ering the best technical solutions on the market. Winner machiningcentres o er flexibility of usage, reliability and high productivity
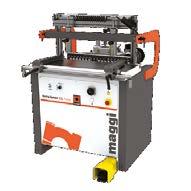

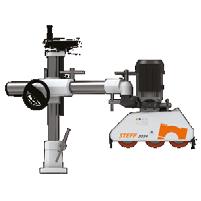
MAGGI MAGGI TECHNOLOGY
Founded in 1963 in Tuscany (Italy), designs and manufactures woodworking machines created to respond to the needs of artisans and small-scale kitchen and furniture manufacturers.
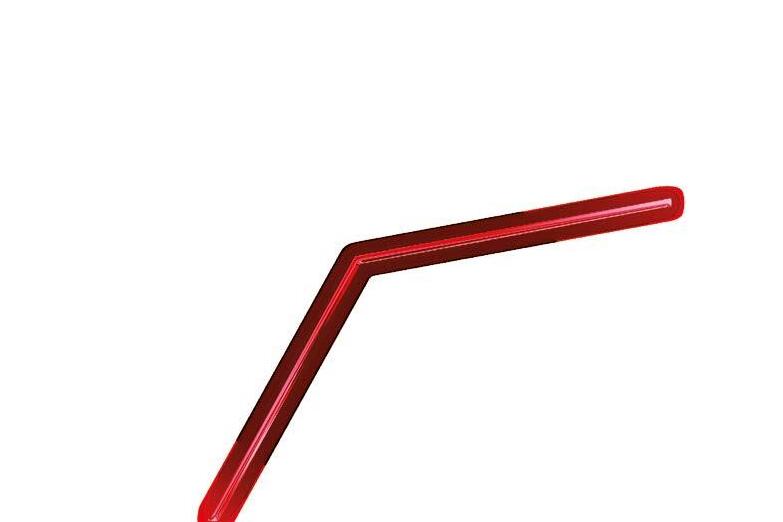
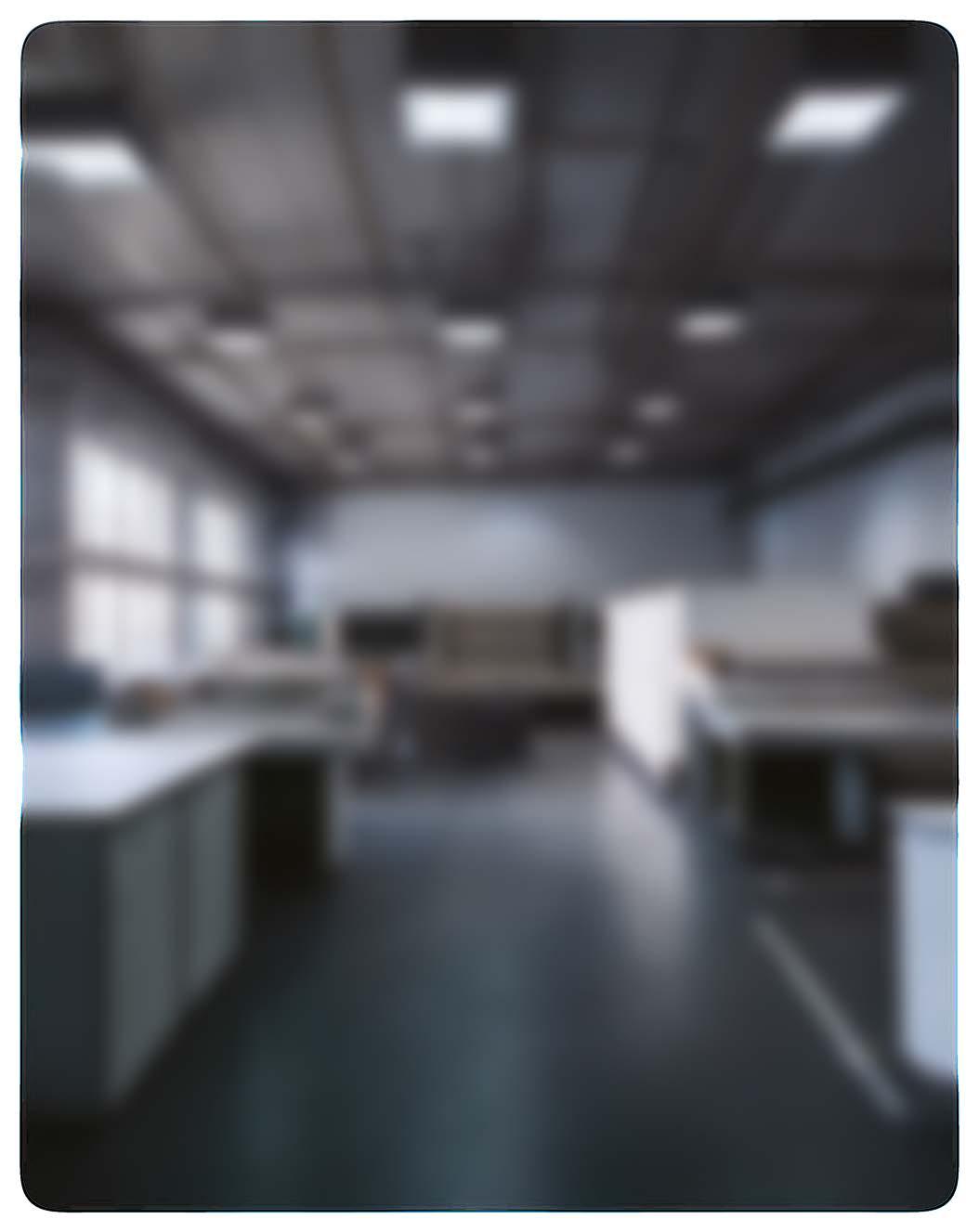
SANDING MADE EASY!
The Biesse Opera R is the only robotic sanding machine specifically designed for shaker doors. The automatic scanner works in conjunction with a robotic sanding arm to get a perfect and consistent finish on both shaker style and flat panels.
-Exceptional finish quality
- Can sand the component 'along the grain', regardless of orientation
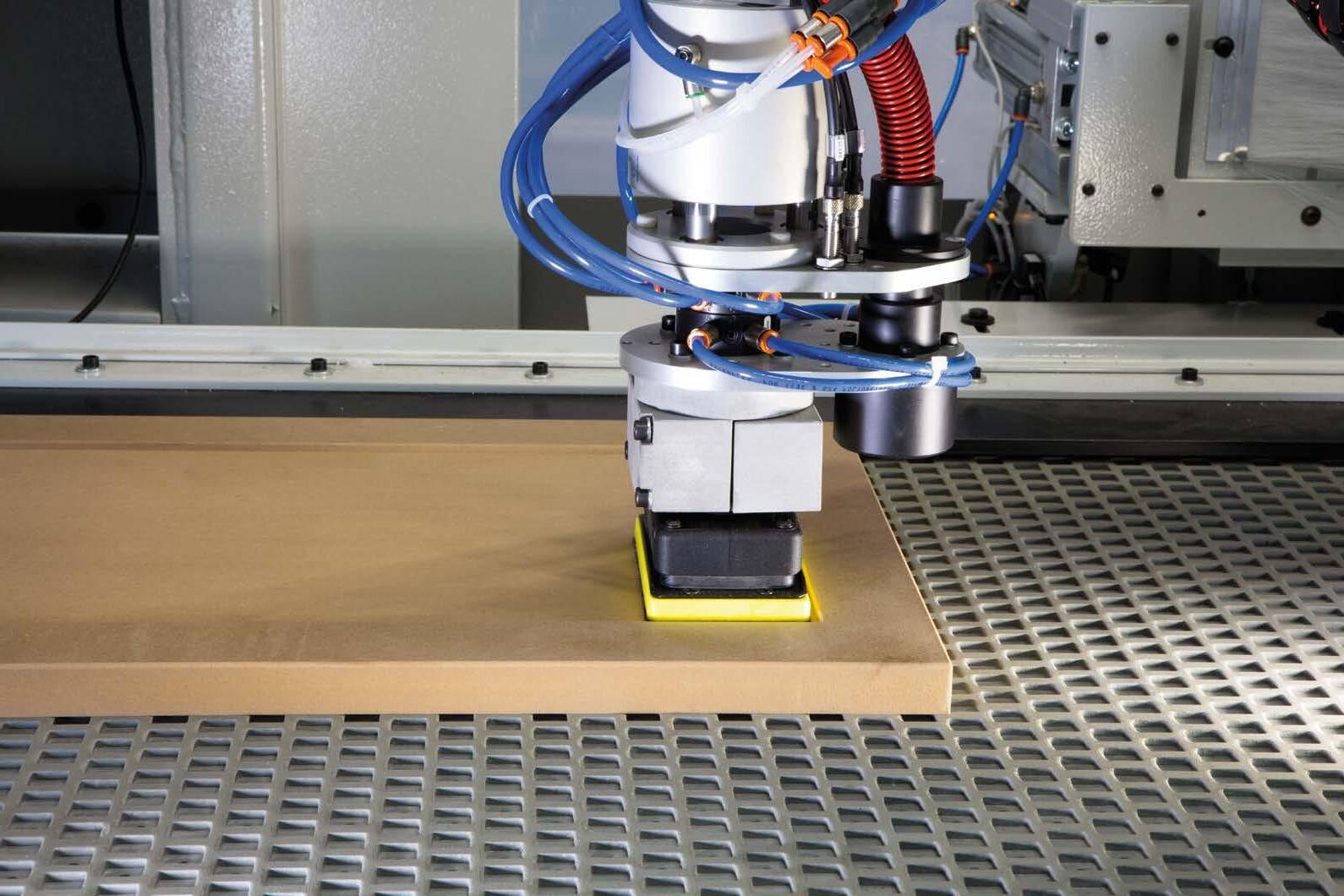
