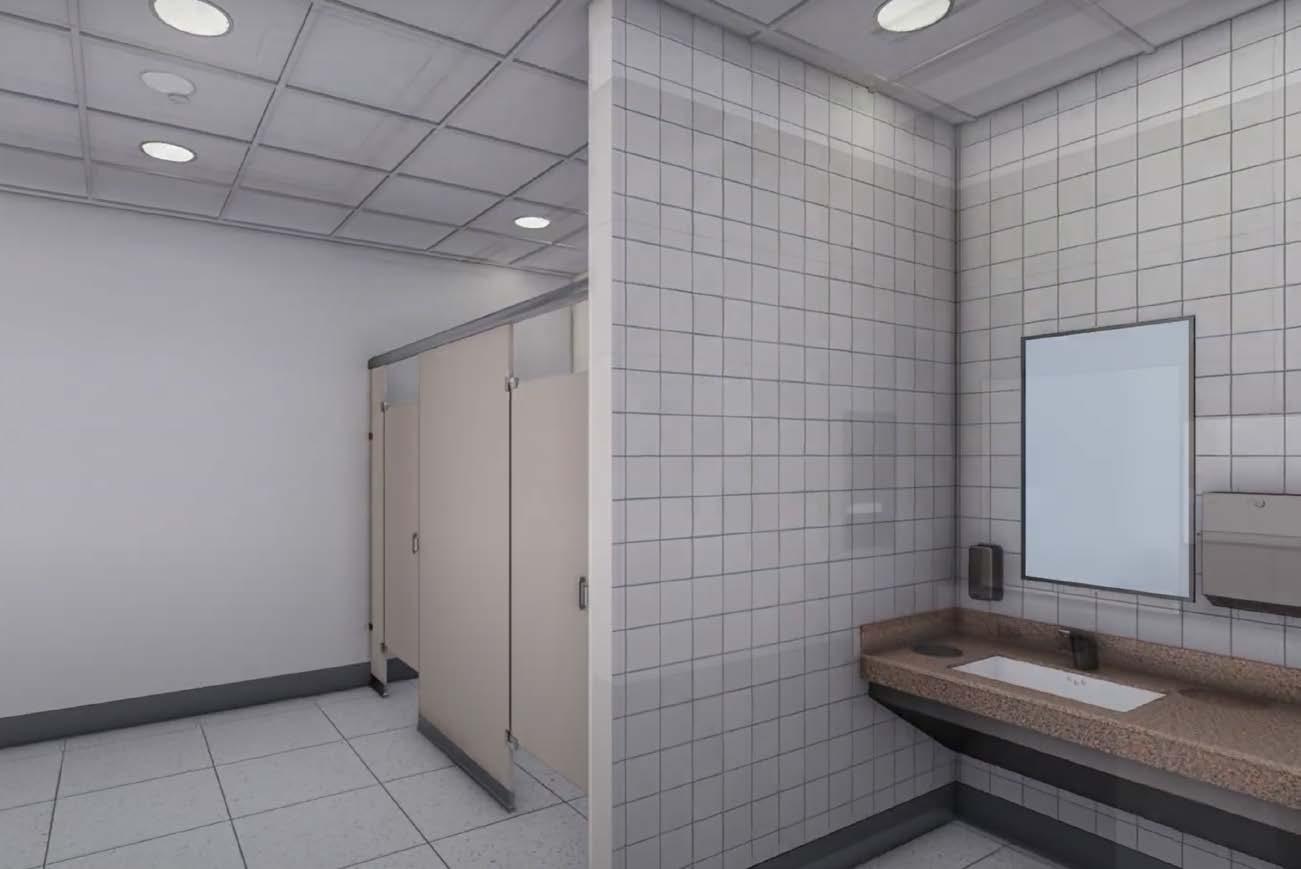
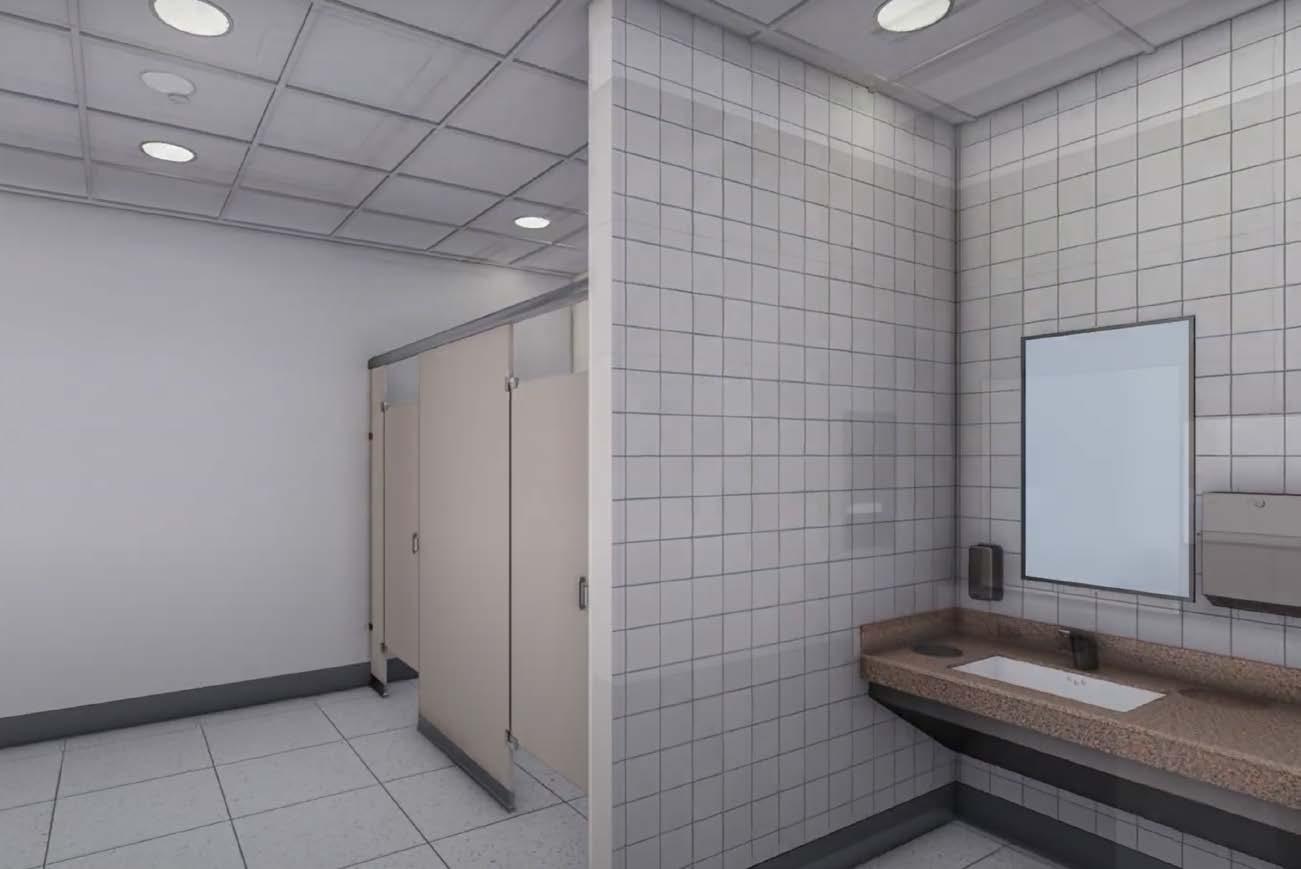
THE CHALLENGE
One of the major challenges airports encounter is the extended downtime for restrooms during renovations.
Prefabrication minimizes operational disruptions, alleviates labor constraints, and streamlines tight project schedules. Traditionally, Houston Airport System restroom renovations took eight months to complete. To accelerate this timeline, the design and construction team standardized essential restroom components, including ceilings and roughed-in wall modules. By fabricating these elements off-site in a controlled warehouse—complete with finishes— the team ensured a seamless, efficient installation process, reducing on-site work and minimizing downtime.

RESULTS
BY THE NUMBERS
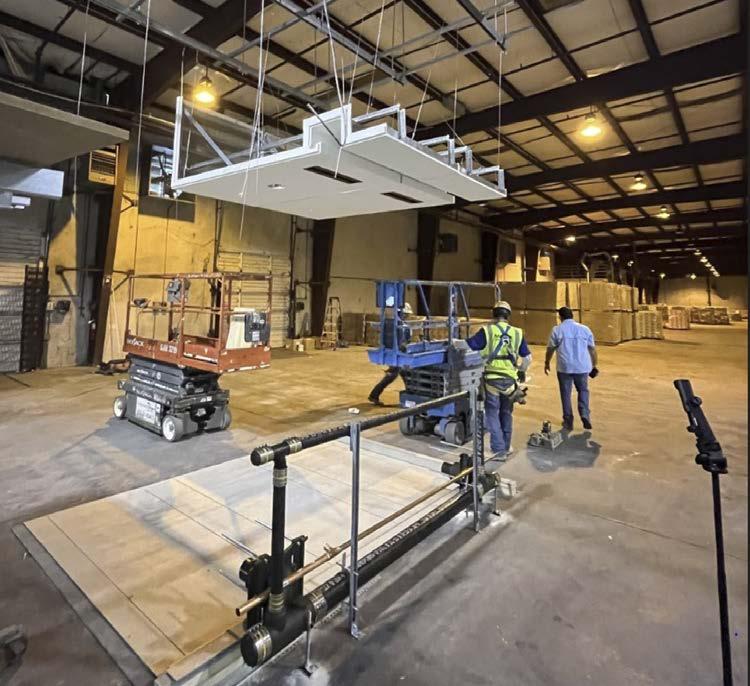
6 MONTHS
IN SCHEDULE SAVINGS
RESTROOM CLOSURES FOR MAINTENANCE OR SUBSEQUENT RENOVATIONS
REDUCTION IN ON-SITE LABOR COST PREMIUM
CLICK HERE TO VIEW THE TIMELAPSE
A VERSATILE SOLUTION
The team assessed feasibility through the creation of vignettes focused on intricate design elements, with particular attention to ADA compliance.
DIRTT Construction Systems’ prefabricated wall systems were implemented, featuring roughed-in modules equipped with integrated plumbing and fixtures. This approach illustrated the capability to isolate plumbing for completely removable units. By organizing fixtures on a universal frame, we established an adaptable framework that standardizes prefabricated components for any restroom layout.
REDUCED ONSITE LABOR
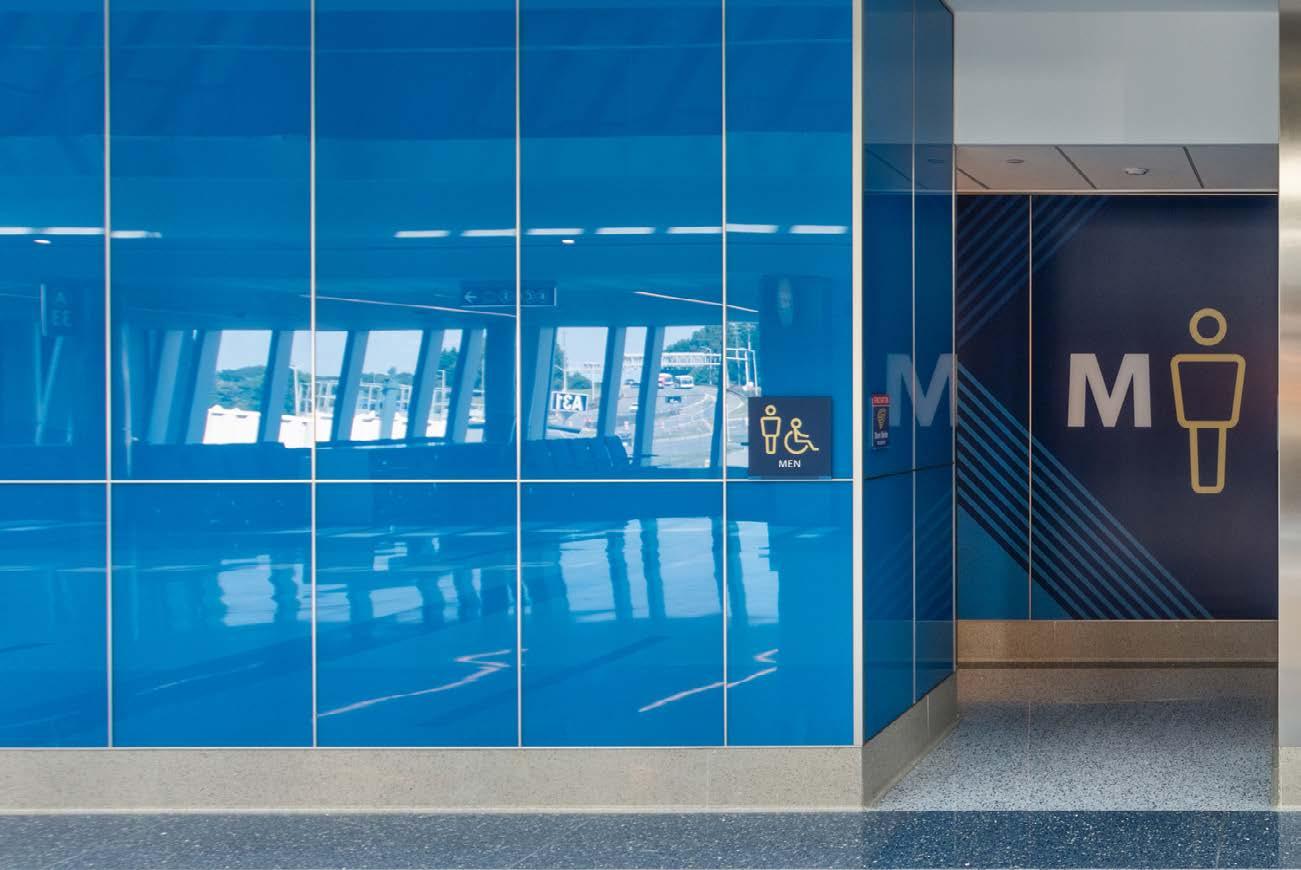
Offsite manufacturing significantly decreases the need for labor at the airport, mitigating labor shortages and minimizing security screenings. Fewer onsite workers also help accelerate the project schedule and reduce logistical challenges in a highly regulated environment.
MINIMAL AIRPORT DISRUPTION
By installing prefabricated components, a single stall can be closed for maintenance or repairs while maintaining water service to the rest of the restroom. This approach ensures continuous service, enhances safety, and limits disruptions for passengers and airport personnel.
BUDGET & COST CERTAINTY
Prefabrication secures labor and materials at predetermined costs, benefiting from economies of scale through mass production. Standardized designs allow competition among multiple vendors, ensuring competitive pricing and promoting cost control, quality, and long-term savings.
SCHEDULE CERTAINTY
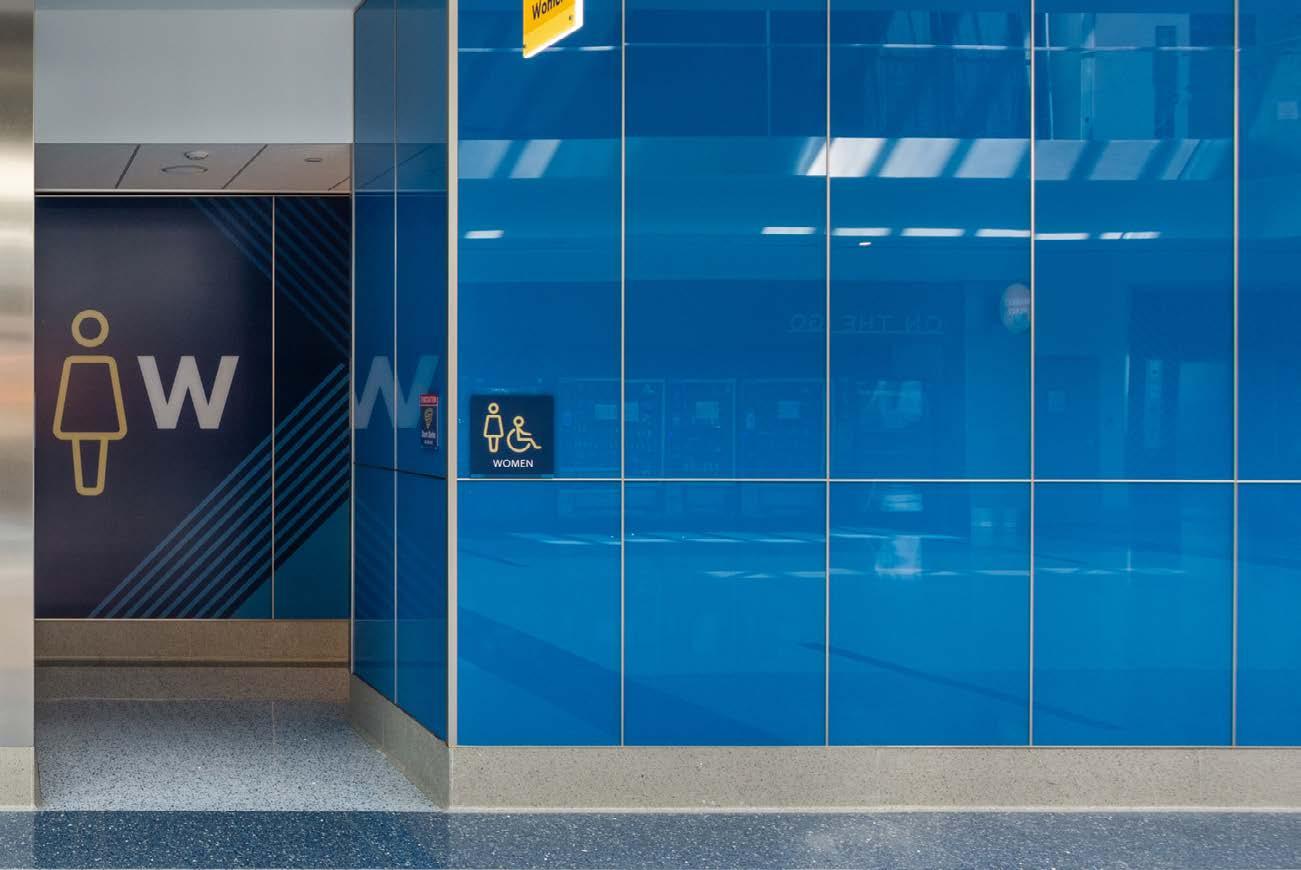
Offsite fabrication can begin before any onsite demolition, reducing procurement risks and compressing overall timelines. As a result, construction activities at the airport are more predictable and less prone to delays. This streamlined approach enhances efficiency and better coordination among all stakeholders involved in the project.
ENHANCED QUALITY CONTROL
Manufacturing in a controlled warehouse environment allows for thorough inspections of each prefabricated component prior to delivery, ensuring consistent quality and reducing rework. This streamlined approach helps shorten overall project duration and maintains high standards for finished installations.
PREFABRICATION PROCESS
DEFINE
We defined the vision and aligned with project needs, integrating prefab/modularization and off-site manufacturing (OSM) strategies in the early feasibility and concept phases.
ENGAGE US HERE
IDENTIFY
We developed a standardized grid layout to accommodate various restroom configurations. Additionally, we engaged prefabrication vendors with offsite manufacturing capabilities and the necessary capacity.

PLAN
During planning, we validated prefabricated designs, coordinated standardized frames and fixture integration, detailed wall and ceiling connections, and addressed logistics like weight, loading, and transportation.
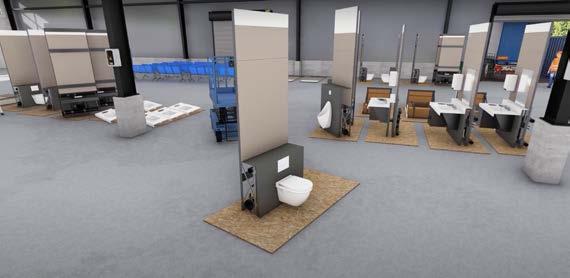
IMPLEMENT
During implementation, we developed rough-in plumbing, demonstrated the removal and replacement of components, and performed schedule and cost analysis.
UPDATE
As the scope evolved or was modified, the projectspecific prefabrication plan was updated with the most current information. CLICK HERE TO



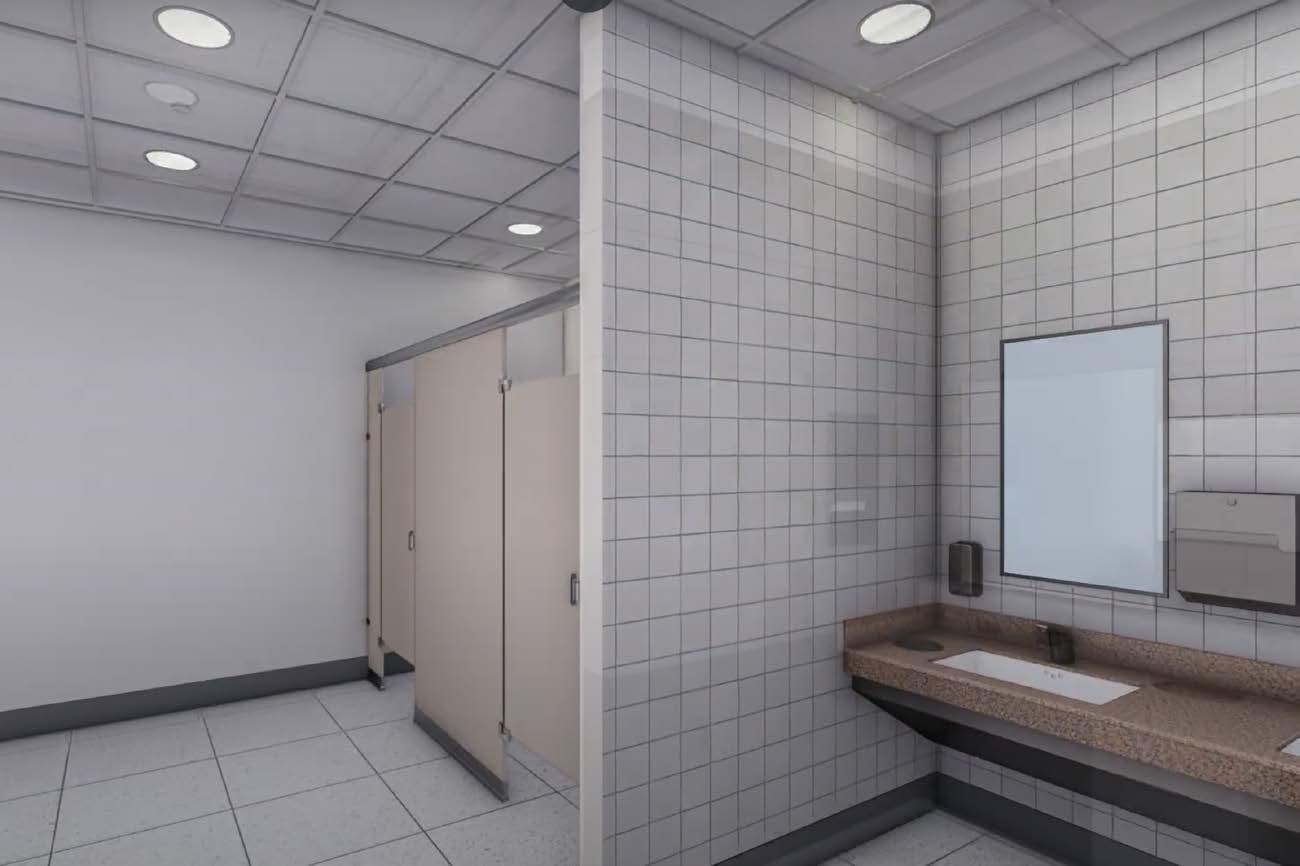

