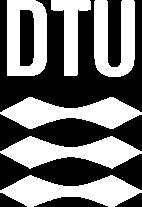
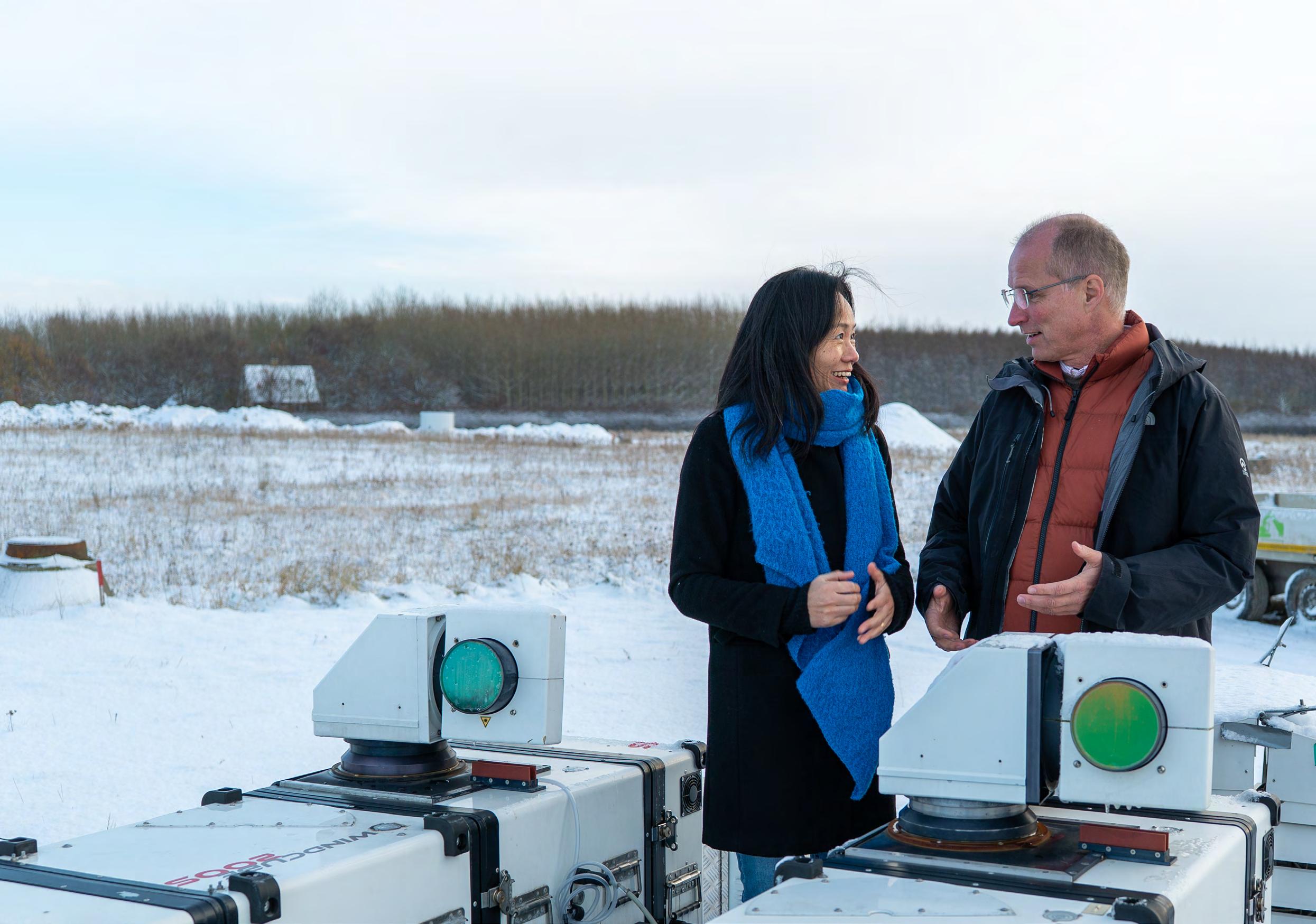
Research Infrastructure
Research Facilities
Østerild
Høvsøre
Poul La Cour Tunnel
Risø Research Turbine
Large Scale Facility
BladeLab
Risø Hybrid Power Plant
Rain Erosion Test Facility
Lidar Measurements
Material Lab
PowerLabDK
We operate some of the world’s most advanced research infrastructure and test facilities for wind energy. Researchers and companies can test everything from nano-scale materials, large-scale structures to fully powered demonstrations of turbines. All commercial test activities are supported by our dedicated researchers and engineers.
Our research spans the full spectrum of wind energy systems. From the investigation of nanoscale structures in turbine components up to the macro-scale of atmospheric flow; from designing the turbines of the future to more democratic renewable project planning.
The Danish national test centre Østerild is located at the west coast of Northern Jutland. It has some of the best wind conditions in the world and allows the manufacturers to test full-sized turbines before they enter the market.
• Nine test stands
• Turbines up to 330 metres
• Tallest turbine at Østerild is 280 metres
• Visitors centre with +50.000 visitors annually
The Danish national test centre Høvsøre is located on the West coast of Jutland, south of Østerild. At the seven testing stands, international companies test their wind turbine concepts and collect data from tests carried out on the turbines. It is possible to test and document safety, the turbine’s performance and noise emission.
• Seven test stands
• Turbines up to 200 metres
• Visitors centre inaugurated 2022
• Turbine heights to be increased to 275 metres while reducing number of stands to five
The largest university-owned wind tunnel in the world. It has been designed specifically for aerodynamic and aeroacoustic testing of airfoils and rotors. It is a closed-return tunnel with maximum flow speeds of up to 378km/h – comparable to triple the wind speed of a Category 3 hurricane.
• Maximum flow speed: 105 m/s (378 km/h)
• Turbulence intensity: < 0.1%
• Re number/m: 7 million
• Area: 2200 square metres
• Fan diameter: 4.7 metres
The research wind turbine is a 850 kW, 52 m diameter originally Vestas V52 turbine that is heavily instrumented for rotor and turbine loads measurements and also offers the opportunity for detailed (lidar) inflow and wake measurements. It is used for dedicated experiments and validation as part of our research.
The wind turbine is used for the researchers’ experiments at DTU. Especially for tests of meteorological equipment, structural and electric measurements and verifications of models of calculations. The work will bring better tools for optimizing current wind turbines and construction of the next generation of wind turbines.
V52 research turbine at Risø instrumented with several forwardmounted nacelle lidar systems for measuring winds approaching the turbine. The top-mounted system is the DTU SpinnerLidar which measures wind flows across the entire rotor area.
The Large Scale Facility at DTU Risø Campus provide research projects and companies with possibilities to perform tests at very large scale. In addition to the testing facilities, DTU Wind and Energy Systems offers cooperation with a dedicated team of leading scientists and techniques that can deliver state of the art analysis.
• 1560 square metre test hall
• 3 test stands capable of testing 45m, 25m and 15m blades
• Static servo-hydraulic actuators
• Point loading up to 300 kN and displacements up to 13m
• Hydraulic mass resonance excitation actuators
• Single or dual axis fatigue at broad band of resonance frequencies
A blade research and technology demonstration platform to put new concepts and research ideas into practice and validate simulation tools and prediction methods for future wind turbine blade generations.
• Composite structures of up to 15m length can be manufactured
• The BladeLab is equipped with modern resin mixing and injection machines to perform high quality infusion processes as well as with a glue mixing and dispensing machine to apply variable ratio meter mixing dosing systems for dispensing adhesive materials
• Wind turbine blade molds of the DTU 12.6m blade are equipped with integrated temperature sensors and heating/cooling systems
The Hybrid Power Plant (HPP) research facility combines two wind turbines, PV panels, electricity storage, and advanced test equipment to demonstrate the interaction with electrical power grids. The facility is prepared for extensions with electrolysers for hydrogen generation. The facility also includes a SCADA system, energy management system and plant controller.
• Grid connection capacity: 1000kVA
• Wind plant: 2x225kW wind turbines retrofitted to variable speed and grid compliance
• One of the wind turbines hybridised with a 60kW / 0.7kWh supercapacitor bank (high power storage) and a 79kWh / 30kW Li-ion battery
• Solar plant: 160kWp South oriented + 175kWp East-West oriented
• SAFT Battery: 1155kWh / 250kW
• Controllable grid interface: 1000kVA
• Controllable energy resources (load or generation): 250kW (TBC)
The facility will be researching in leading edge rain erosion - from understanding the atmospheric challenges to the aerodynamics to the material and composite side of the matter. Designed primarily for research projects, it is also open for commissioned work, ensuring both academic exploration and practical solutions in the wind energy sector.
• Enhanced Rain Flow: flow capabilities of up to 400l/h, surpassing the standard 120l/h, allowing for shorter testing times at tip speeds matching turbine conditions
• Dual Independent Droplet Manifolds: standard 600 and expanded 1200 needles droplet manifolds offering unmatched precision in simulating diverse weather conditions
• Expanded Heat-pump System: powerful 50kW thermal heating and cooling system allowing better testing stability and testing in different climate conditions. Expected +-15ºC Vs. ambient
DTU Wind is a pioneer in the development, testing, and certification of lidar instruments for remotely measuring the wind. We have introduced several new lidar concepts to support our research goals and benefit commercial applications.
Examples include:
• Short and Long-Range WindScanner systems: Versatile multi-lidar systems which operate together to measure 2D/3D wind flows
• SpinnerLidar: Fast scanning of 2D winds for turbine control and wake analysis
• Lidics: Short-range lidars with low uncertainty used as calibration references
DTU Wind also offers accredited lidar calibration services to the public, and can lead or support the execution of complex measurement campaigns.
State-of-the-art research and innovation are carried out within composite processing techniques, preparation of test specimens, accredited mechanical testing to meet industrial standards, X-ray computed tomography, electron microscopy, sensor instrumentation and signal analysis.
• Composite processing techniques
• Preparation of test specimens
• Accredited mechanical testing to meet industrial standards
• X-ray computed tomography
• Electron microscopy
• Plasma treatment and surface chemistry
• Sensor instrumentation
• Signal analysis
PowerLabDK includes a number of state-of-the-art facilities linked through communication systems, SCADA solutions etc. across four locations. The facilities are capable of testing and demonstration according to a variety of international standards, including IEC, CENELEC, IEE and others.
PowerLabDK is one entry to an umbrella of several advanced infrastructure facilities and PowerLabDK welcomes engineers and researchers from industry and academia as well as students.
• Control Center Lab
• Battery Lab
• Electric Lab
• EV Integration Lab
• High Voltage Lab
• Innovation Island Bornholm
• Power-to-X Lab
• Power Flex House
• Power Student Lab
• Short Circuit Lab
• Smart Converter Lab
• SYSLAB (Energy System Integration Lab)
For testing and simulating solutions in the transmission grid, the RTDS is available. The RTDS facility includes 8 NovaCor™ racks from RTDS Technologies, capable of real-time simulation of power systems with up to 5,500 buses. It supports energy management solutions like state estimation, dynamic security assessment, and protection schemes. Additionally, its communication network allows cyberattack simulations to evaluate their impact on system control and stability. It is possible to do both hardware-in-the-loop (HIL) and softwarein-the-loop (SIL) and combine the setups with other facilities in PowerLabDK.
A laboratory for investigating control and interactions in converter-based generators and transmissions.
Technology
• 10 kW 2-level VSC (2)
• 10 KW MMC (2)
• Speedgoat RT Machine
Control
• Detailed and flexible controllers
• Analyse control interactions and optimize controller performance Performance
• Flexible setup able to emulate multiple converter-based generators and plants:
• (offshore) wind and hybrid plants
• HVDC transmission
• PV & battery
For over 15 years, the Bornholm Energy & Utility company and DTU have collaborated on sustainable energy innovation, making Bornholm a hub for developing and testing green technologies.
Innovation Island Bornholm runs on 100% renewable electricity and heating across five district heating systems, providing valuable data to PowerLabDK for advanced grid research.
With a mission to drive the green transition, we strive to secure a greener future for Bornholm, and to demonstrate future green energy solutions for the rest of the world in a real society.
Demonstrated solutions are among others:
• Future green energy supply
• Sustainable energy systems
• Energy storage and grid balancing
• Sector coupling
DTU Wind and Energy Systems builds on a legacy of being a preferred partner to the energy sector and the academic community in developing green technologies.
150 Academic partners
280 Business partners
42 Different countries
Østerild and Høvsøre Test Centres
Poul la Cour Tunnel
Large Scale Facility
Material Lab
BladeLab
Risø Hybrid Power Plant
Rain Erosion Test Facility
LIDAR Measurements
PowerLabDK, RTDS and Bornholm
AC/DC Power Lab
Collaboration
Allan Vesth (alve@dtu.dk)
Christian Bak (chba@dtu.dk)
Kim Branner (kibr@dtu.dk)
Anthony Fraisse (antf@dtu.dk)
Philipp Ulrich Haselbach (phih@dtu.dk)
Poul Sørensen (posq@dtu.dk)
Nicolai Frost-Jensen Johansen (nijoh@dtu.dk)
Michael Courtney (mike@dtu.dk)
Frida Frost (ffrost@dtu.dk)
Oscar Saborío-Romano (osro@dtu.dk)
Mattias Andersson (matan@dtu.dk)