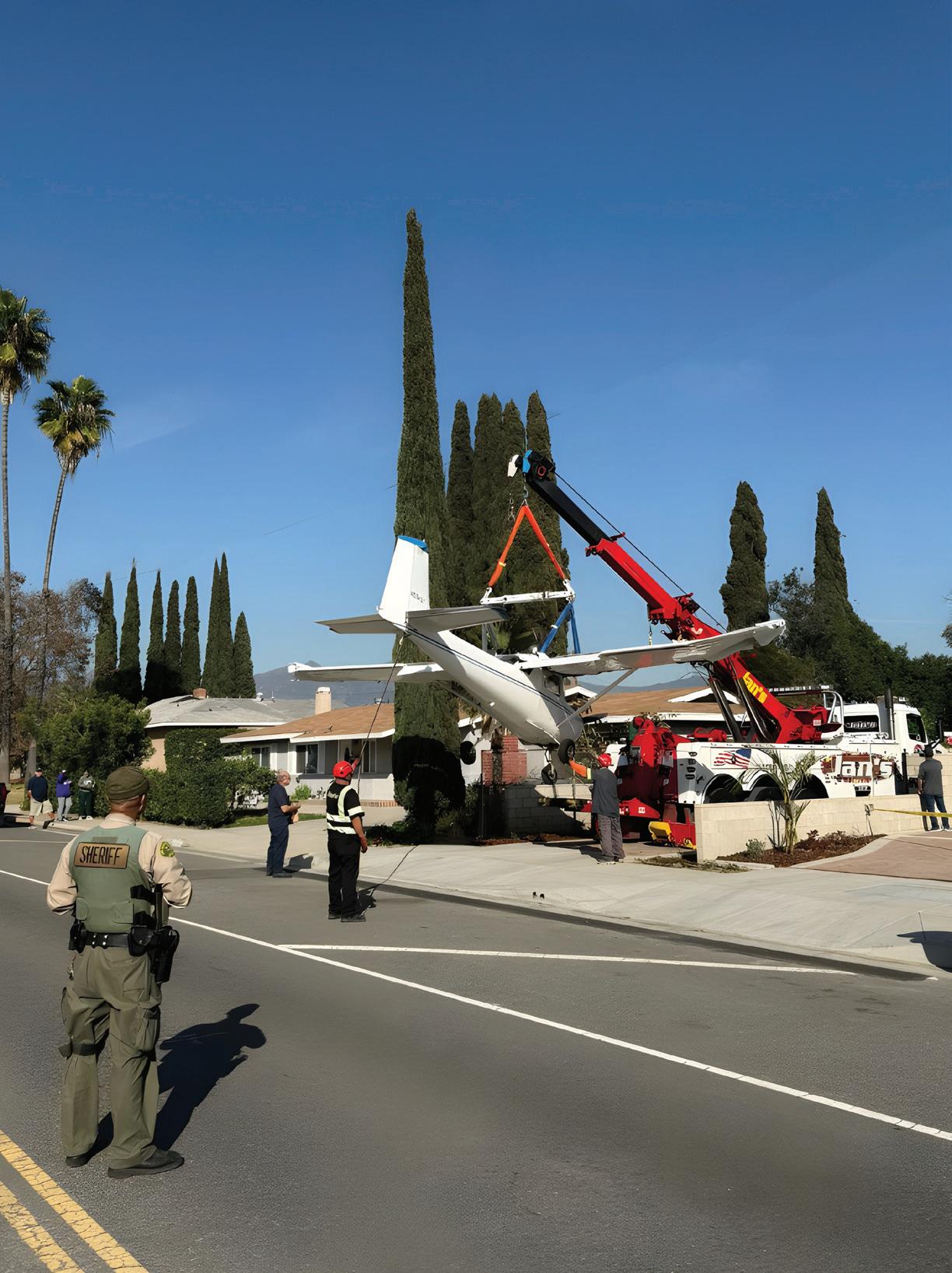
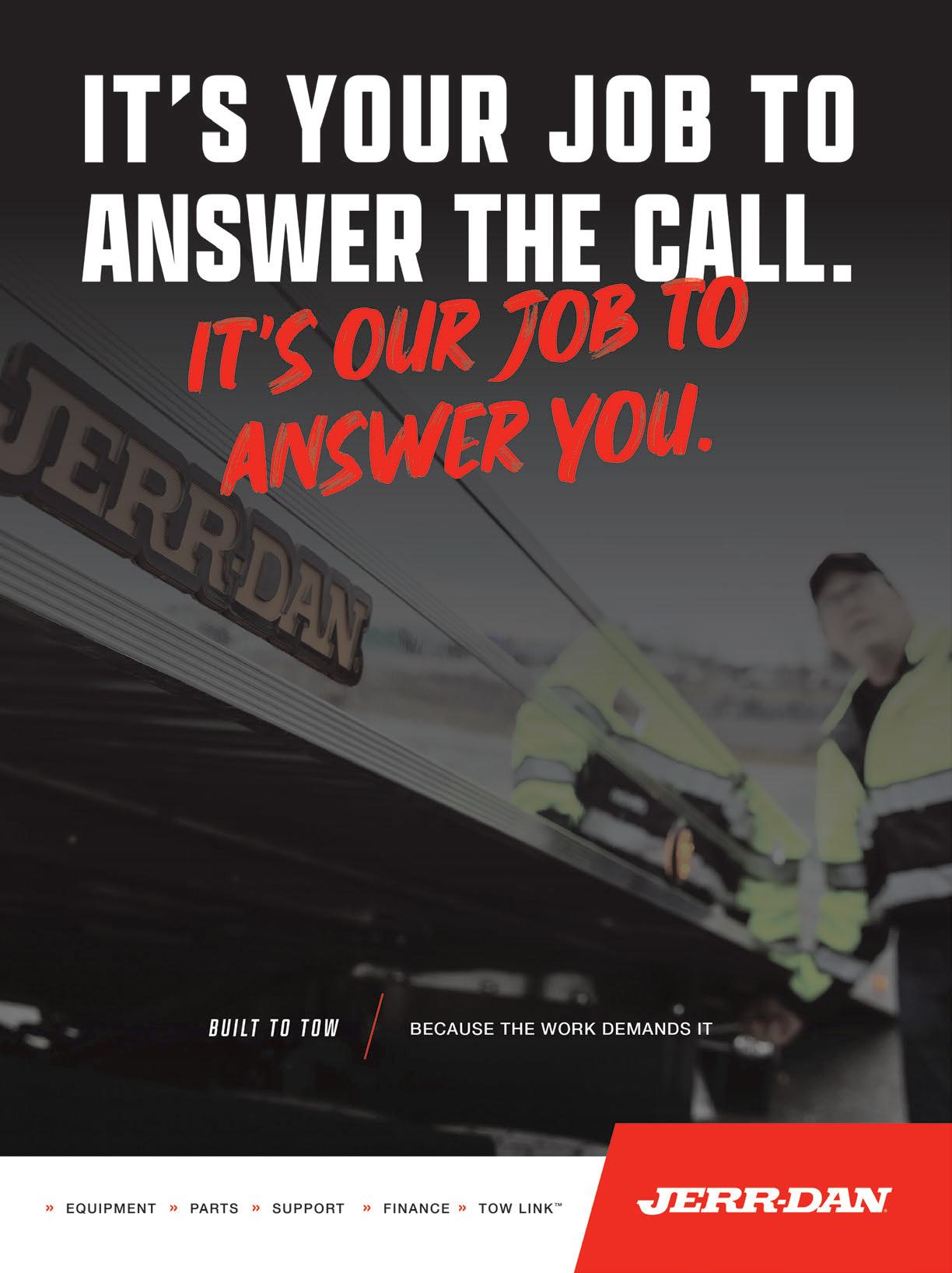
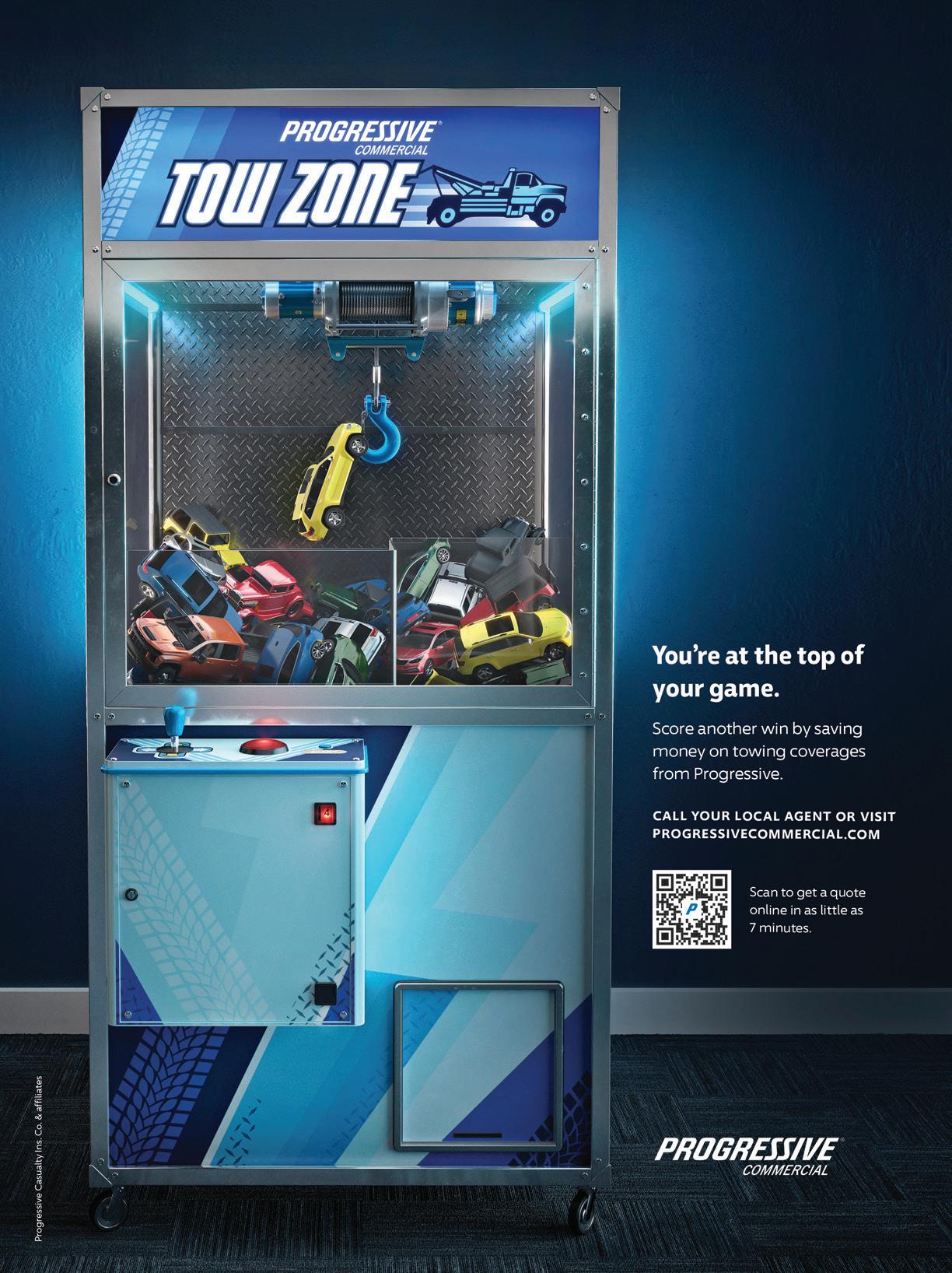
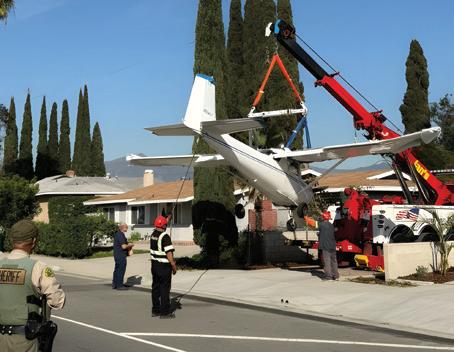
By George Nitti

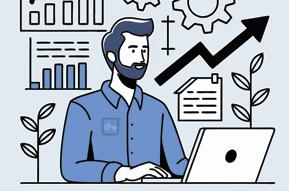

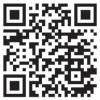
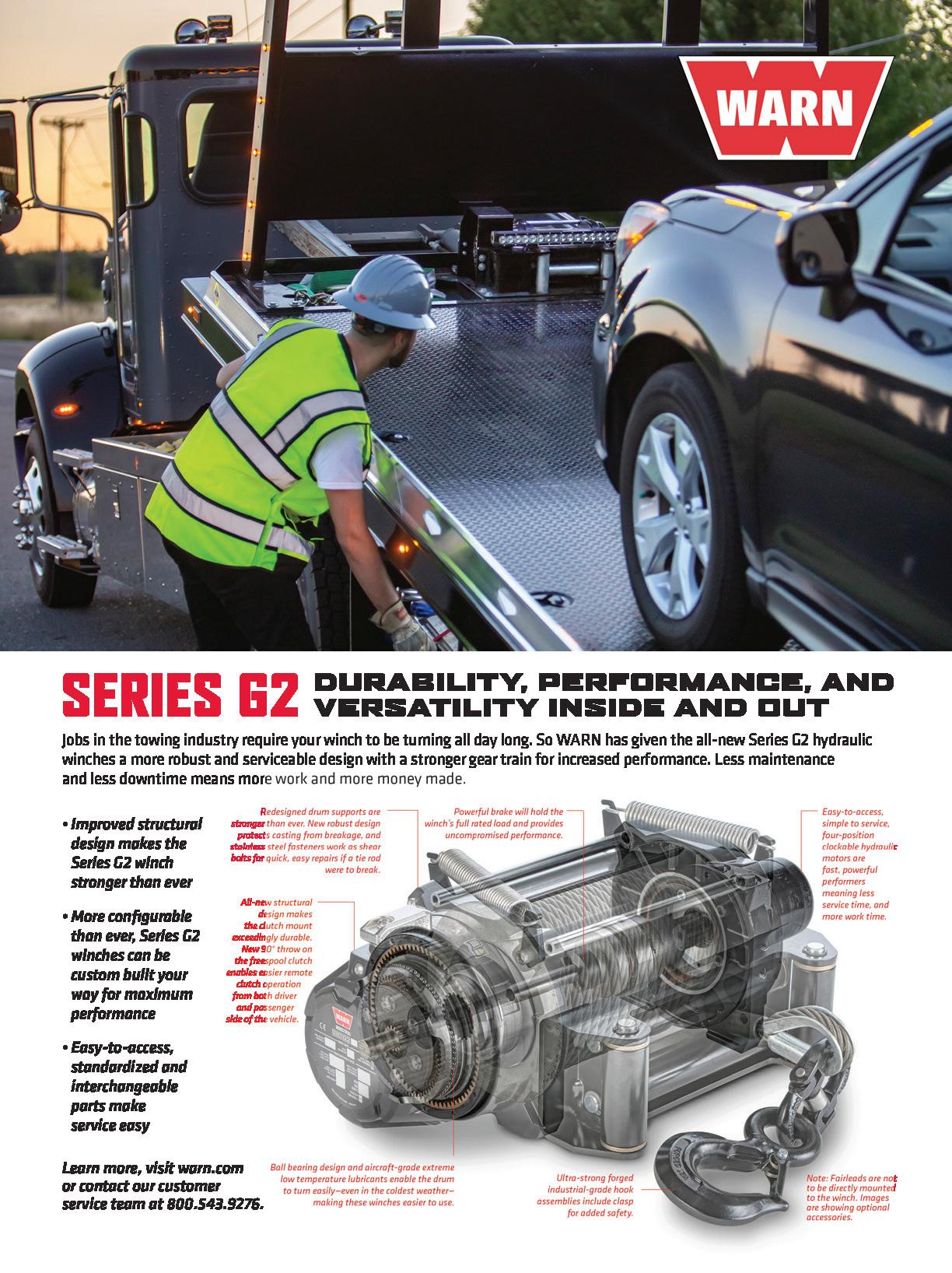
By George Nitti
Dennie Ortiz Publisher
As we celebrate the 249th anniversary of the signing of the Declaration of Independence, I would like to express my gratitude for the freedoms we hold dear. Being in an industry comprised mostly of independent businesses, we can relate to the desire to control our own destinies. Who doesn’t want to guide their business to success?
To achieve these ends, Brian Riker, draws a roadmap for our readers to follow. Brian, in his article, asserts that leadership is a key component to bringing prosperity to your company.
In fact, American Towman recently featured this topic of leadership at our online webinar series during which three industry movers and shakers shared their thoughts and experiences.
What’s more, during the AT Exposition in Baltimore this year, we are launching a new seminar track dedicated to this very same concept on the importance of leadership within your company and within the industry.
In this issue, we showcase the latest installment of our How It’s Made series, where our Editor, Steve Temple, takes you behind the scenes at prominent lighting manufacturer TowMate, to reveal how these products, used regularly by towers, are manufactured.
Not to be overlooked is the importance of formal training which is clearly emphasized in our Hands-On Tech department. Terry Abejeula shares his account of a recent in-person ERSCA course he conducted alongside tow business owner, Rodney Sellers of Bob and Dave’s Towing in Whittier, Calif. Rodney, a long-time advocate for training and education was a perfect host for this event. Having invited the city’s mayor, as well as officers from CHP and Freeway Service Patrol, Rodney said, “The best way to understand what we can do is by learning together and strengthening the relationships we have with other first responders that are on scene.”
All things considered, technology is great—when it works. However, there is no denying the efficiency and productivity that results from the use of digital dispatch within one’s operations. Dispatch being such a critical link in the chain to get a tow truck to where it’s needed, this technology can help propel your business to another level. Be sure to read the latest article to uncover the benefits of digital dispatch for your business.
Wishing everyone a great summer and as always, stay safe out there!
Steve Temple Editor
In every issue we strive to strike a balance, providing coverage on the latest in towing equipment, along with the human elements of running a tow business. For instance, the article on digital dispatch provides next-generation solutions to managing a fleet of tow trucks, improving efficiency and controlling costs. On the other hand, as highlighted in “Building a Winning Tow Company,” leadership and team development requires some social intelligence to inspire greatness in a towman. Having the latest gadgets is all well and good, but it can’t replace using good communication skills with tow operators and office staff.
The artfully executed airplane recovery in our cover feature is a good case in point. What’s the value of having a new rotator and car carrier, if the operators don’t carefully coordinate their efforts in handling a precarious casualty? This aspect is certainly brought home in the article on ERSCA training, and the company culture of “How It’s Made” at TowMate as well.
Running a towing business is certainly a formidable task, and we hope this issue’s articles can help to simplify and enhance complicated operations.
itowman.com americantowman.com
Copyright ©2025 American Towman Magazine is published 12 times a year by American Towman Media, Inc.
Subscription: Single Copy: $10 1 yr: $60 – 2 yrs: $110 International: $75 & $140
of a competitors product or service.
Vintage airplanes strapped to flatbeds rolled into Elkhart Municipal Airport, thanks to Tom’s Towing of Elkhart, Indiana. The towing company donated its time and equipment to transport three aircraft—two from Athens, Michigan, and a third from a hangar at Elkhart Municipal Airport—to the Mishawaka Pilots Club, home of STAY, Indiana’s youth aviation program.
“It wouldn’t have happened without them,” said Matt Branson, STAY Indiana CEO. “They stepped up big time.”
One of the planes is a rare pre-WWII model. Another, a 1948 Aircoupe, had sat untouched for over a decade. The aircraft will now be restored by high school students learning aviation mechanics, engineering, and piloting.
Board member Evan McCauley had originally contacted the seller looking for parts. Instead, he was offered everything— if he could move it. That’s where Tom’s Towing came in. Thanks to their help, students across Michiana (southwestern Michigan and northern Indiana ) now have access to hands-on training that could launch careers in aviation.
Source: wsbt.com
U.S. Senator Bill Hagerty visited Miller Industries’ headquarters in Ooltewah, TN to meet with company leaders and employees, discuss the future of manufacturing in Tennessee, and examine the regulatory challenges facing the towing and recovery industry.
Miller Industries, the world’s largest manufacturer of towing and recovery equipment, hosted a roundtable where Hagerty emphasized the importance of supporting domestic manufacturers and preserving Tennessee jobs. “Manufacturing is the backbone of our state’s economy,” he said, pledging to push back on burdensome regulations in Washington.
CEO William G. Miller raised concerns about California’s Advanced Clean Trucks (ACT) regulation, noting it fails to recognize the emergency role of towing vehicles, and could impose costly burdens on the industry. Despite challenges, Miller expressed optimism, hinting at potential expansion that could bring new jobs and investment to the region.
Hagerty’s visit concluded with a facility tour, where he met employees and observed Miller’s advanced production processes firsthand.
Source: Miller Press Release
Governor Jared Polis signed HB251117 into law on June 3, 2025, targeting predatory vehicle booting practices and increasing consumer protections across Colorado. Backed by Democratic lawmakers, including Representatives Junie Joseph and Andy Boesenecker, and Senators Julie Gonzales and Mike Weissman, the bill gives the Public Utilities Commission (PUC) new authority to oversee booting companies and enforce compliance.
The law requires companies to provide at least 24 hours’ written notice
before immobilizing a vehicle, unless it blocks emergency access or reserved spaces. It also bans indiscriminate patrolling, and mandates visible signage, documented justification, and clear contact information on company vehicles.
Booting firms are prohibited from charging multiple removal fees, and must release immobilization devices once $60 is paid. Additional restrictions apply if the vehicle was already booted, lacks proper notice, or is on private property without permission.
Supporters say the law ensures fairness and transparency. “This protects Coloradans from abusive booting,” said Weissman.
However, towing professionals warn the law could hinder enforcement, and embolden violators, limiting property owners’ ability to manage parking, and reducing compliance with posted rules.
Source: cohousedems.com
In North Dakota, the Grand Forks City Council is weighing a proposal to remove long-standing caps on towing fees, a change that could take effect as early as this summer. The proposed amendment would maintain licensing requirements and impound regulations set in 2011, but allow towing companies to set their own rates. The city’s current cap limits towing charges to $135, with added fees for flatbeds and heavy vehicles.
City officials implemented the fee structure over a decade ago to curb predatory towing practices. However, Interstate Towing manager Adam Berry says rising costs have made the capped rates unsustainable.
“Post-COVID, everything’s doubled,” Berry said. “Towing has become more of a burden than profitable.”
City Council member Rebecca
Grand Forks officials are reviewing a proposal to end regulated rates.
Osowski supports lifting the cap, citing trust in the free market. Others, like Council President Dana Sande, voiced caution but are open to the change if key protections remain. If approved, Grand Forks would join other North Dakota cities that do not regulate towing fees.
Source: grandforksherald.com
Connecticut’s Senate passed House Bill 7162 in a 33-3 vote, overhauling the state’s towing laws for the first time in decades. The bill aims to balance consumer protection with respect for the work towers do every day.
Prompted by a joint investigation from CT Mirror and ProPublica, lawmakers crafted a compromise with towing professionals. The bill clarifies private property towing rules, raises highway tow rates, and ensures due process before vehicles are sold.
A Michigan House bill to rename a stretch of M-6 as the Keagan Spencer Memorial Highway passed 104-3.
Keagan Spencer, a young tow truck driver, was killed on M-6 in November 2023 while trying to rescue a dog from the median. He had been towing two vehicles when a driver lost control and struck him. He later died from his injuries.
Rep. Angela Rigas of Caledonia, who sponsored the bill, emphasized the need for greater awareness. “This happens far too often with distracted driving,” she said. “Michigan’s Move Over Law includes tow truck drivers—they deserve our respect.”
Key changes effective October 1 include: requiring credit card acceptance, 72-hour grace periods for expired permits, photo documentation of violations, and mandatory certified mail notices before selling towed vehicles. Tow companies must also allow vehicle owners to retrieve personal property, even if fees remain unpaid.
Tim Vibert, president of the Towing and Recovery Professionals of Connecticut, initially opposed the bill, but later supported it after working with lawmakers. “We all need clear, easy-to-follow rules,” Vibert said.
The bill also creates a working group to study vehicle sale proceeds and a towing consumer bill of rights. Governor Lamont is expected to sign the tow bill into law.
Source: ctmirror.org
A bipartisan bill aimed at tightening oversight of North Carolina’s towing industry cleared a legislative committee. House Bill 199 would create a state-run Towing and Recovery Commission to issue, and potentially revoke, permits for tow companies based on their business practices.
Supporters say the bill addresses growing concerns about excessive charges and unclear signage. Complaints include extra fees for not paying in cash, daily storage fees on closed days, and sky-high recovery costs. Rep. Carson Smith (R), the bill’s lead sponsor, called the current situation “a mess.”
The bill would also cap certain charges, require clearer signage at tow zones, and create a statewide database where drivers can find their towed vehicles and see associated fees. Rep.
Laura Budd (D) said the database would protect both consumers and lawabiding towing operators by verifying signage and location details.
The proposed changes come amid rising tension between truckers, local drivers, and towing companies. The Towing and Recovery Professionals of North Carolina has yet to comment on the bill.
Source: wral.com
Spencer’s parents, Matt and Miko, have become advocates for roadside safety.
“We constantly hear from people who say they’re now slowing down and moving over,” Matt said.
If approved, the memorial would be the first in Michigan honoring a tow truck driver killed in the line of duty.
“It’s a legacy for the public, and especially for Keagan’s daughter, Leonora,” said Miko. “She’ll know her dad’s life meant something.”
The California Tow Truck Association (CTTA), along with the CTTA Foundation and the Emergency Road Service Coalition of America (ERSCA), has announced the appointment of Robert Craddock as its new Executive Director.
Craddock brings more than 40 years of experience in the towing and recovery industry, with a background spanning standard, medium, and heavy-duty towing operations. Throughout his career, he has managed towing operations in both rural and urban environments, and served as an Education Coordinator and Operations Manager for both CTTA and ERSCA.
In his new role, Craddock is committed to fostering collaboration among board members, industry partners, and towing professionals. He also plans to expand training excellence through ERSCA, and promote educational opportunities for tow operators.
“I am dedicated to promoting the objectives of CTTA and the CTTA Foundation,” Craddock said. “It is vital to maintain our training excellence and enhance the safety of our tow operators as they embody our future.”
Source: CTTA
Experience the power of illumination with Dynamic 7” and 9” LED driving lights. They feature a dynamic start-up position light in white and amber colors. An innovative successor to the original Dynamic light series, they offer a new prominent pattern for an impressive visual effect upon ignition. With a boost function, the TTZ Dynamic P7 & P9 emit 10,600 lumen, providing one lux (one lumen per square meter) at a distance of 680 meters. The driving beam pattern ensures optimal visibility with a wide and long-range reach. The lights have a color temperature of 5,000 K, offering pleasant illumination in all conditions.
Tow Ramps, manufactured by Race Ramps, is a U.S.-made product exclusively designed for towing and transport companies to load lowclearance cars. This lighter, safer, and stronger approach is made with Race Ramps’ patented 100% solid core design using heavy-duty foam technology that is finished with a durable exterior coating.
Tow Ramps are 74” long, 10” wide, and have a 5.2-degree approach angle. They are sold as a set and available in both a one-piece and twopiece design. The two-piece model provides convenience in storing during transport and maneuvering during a tow. Tow Ramps weigh only 19 pounds per ramp, yet support 2,500 pounds per wheel, equating to an overall 10,000-pound vehicle weight capacity.
Tow Ramps provide a professional image for towers, keep the vehicle safer during loading and unloading, and can instill confidence in customers.
Steck Manufacturing by Milton offers the LittleEasy Unlocking Tool Kit (STC32908-KIT). This compact and highly portable 30inch unit provides emergency access to vehicles, and is built for speed, efficiency, and convenience. Designed for professionals in roadside assistance, law enforcement, and fleet maintenance, the LittleEasy’s reduced size makes it ideal for use in smaller vehicles. Unlike other unlocking kits, the LittleEasy’s design allows users to quickly maneuver through tight spaces without sacrificing reach or risking damage to vehicle interiors. The slim form also ensures that it fits easily behind or under seats, in door pockets, or compact storage compartments—making it readily accessible whenever and wherever it is needed. The kit includes everything required for safe, damage-free unlocking: the 30-inch LittleEasy Tool, non-marring wedge, air wedge, paint protector, and Sure Grip knob lifter. The LittleEasy Kit’s compact size and full functionality make it a must-have for anyone needing fast, reliable access to locked vehicles.
The history of innovations in the technology of tow trucks is a fascinating subject, dating back to the early 1900s and inventor Ernest Holmes. This subject embodies the very fitting expression, “You’ve come a long way, baby” and certainly applies to Miller’s extensive range of wreckers.
Looking at one in particular, the 5130 is the Century model line’s largest single-axle, integrated towing and recovery unit with 128” of under-lift reach. This unit wrecker has the ability to tow most vehicles without sacrificing the maneuverability of a single-axle unit. The 5130 provides a 25-ton recovery boom and 25,000-lb winches for a variety of recovery and lifting applications.
Drawing from several years of experience with this model and feedback from users, Miller has recently enhanced several areas. This includes a 12.5% increase in capacity of the under-lift tilt cylinder. In addition, there are four-plate outer reinforcements to the under-lift, along with a better geometry that reduces stress on the pivot pin.
The 4-plate inner and outer jack legs feature Nylatron pads for strength and smooth operation, and cast D-rings on the inner boom replace the welded D-rings. Also, a lower 5x5-foot crossbar/pivot head increases the thrust area and has been reduced in height from seven to five-and-half inches, better for getting underneath causalities. Lastly, the 5130 has a new and improved pin-keeper design, and shackle lugs on the extendable outriggers.
All told, the Century 5130 reflects Miller’s ongoing commitment to engineering refinements that make a towman’s job safer and easier.
By Terry Abejuela
Photos by Allison
TField Editor Terry Abejuela has 40-plus years of light-duty towing and recovery experience. He is also a light-duty Level 1 instructor for the California Tow Truck Association.
he course on Essentials of Standard Duty Towing and Recovery offered by The Emergency Road Service Coalition of America (ERSCA) is designed for both new and experienced operators who operate tow and recovery vehicles with a gross vehicle weight rating of 26,000 pounds or less. This course can be completed either In-Person over the course of two (eight-hour) days, or in a Virtual On-Line format spanning three (five-hour) days. These courses meet all State requirements and is approved by the California Highway Patrol Tow Service Agreement Advisory Committee (TSAAC). They are also available nationwide and change to fit State-specific towing laws. The courses are heavily focused on safety, and reflect industry standards, manufacturers
guidelines, company policies, and federal, state, and local laws.
Many experienced tow operators feel that formal training is a waste of time and money for them. As a tow operator myself, I felt the same way until attending my first formal training class in 1982, having been operating a light-duty tow truck fulltime (usually 72 hours a week) for over five consecutive years. By the end of the first day I had learned so many things that I could have been doing differently that would have saved time, prevented damages, or been safer.
When attending a formal training class, students not only learn from the instructor’s experience, but also from the experience of others in the class, along with knowledge from previous students who share their experiences with the instructors. Many of the mistakes made by tow operators have already been made before, and everyone benefits by learning from others’ mistakes. While attending an ERSCA Essentials of Standard Duty Towing & Recovery course, students receive a comprehensive manual that supplements the training. In addition, this manual serves as a useful study guide for the certification test, as well as a reference guide. Students must pass a test to successfully complete the course and be issued a certificate.
ERSCA’s On-Line Essentials of Standard Duty Towing & Recovery course is a virtual class led by a live instructor over the course of three five-hour days. This is not a sit-down type of class in front of a computer to watch videos. It is a dynamic interaction with a live instructor where students can ask questions, provide input, and share experiences. The instructor guides the students through the certification-level curriculum as they follow along with the manual. Videos are used in place of hands-on demonstrations.
Alternatively, the ERSCA In-
Person Essentials of Standards
Duty Towing & Recovery course is presented over the course of two 8-hour days. The first day consists of classroom training utilizing a PowerPoint presentation and props such as chains, straps, hooks, and snatch blocks. All of the following subjects are discussed:
• Safety, Safety, and Safety
• Professionalism & Appearance
• Industry Standard Operating Procedures
• Cab & Chassis Ratings (GVWR, GAWR, GCWR)
• Equipment Working Load Limits
Intro To Towing—Online (Recorded)
Essentials of Standard
Duty Towing & Recovery
In-Person and Online Virtual with live instructor
Essentials of Heavy Duty Towing & Recovery
In-Person and Online Virtual with live instructor
Advanced Winch & Rigging Safety for Standard Duty—In-Person only
ERSCA Electric Vehicle
Operations Training
In-Person only
Website: www.ersca.org
(recovery boom, wheel lift, winch, wire rope, chain, synthetic straps, hooks etc.)
• Calculating Safe Steering Load
• Safe Driving Practices
• Safe Towing Equipment Operating Procedures (wheel lift, car carrier, tow dollies etc.)
• Tow Truck Inspections and Maintenance
• Service Call Procedures (battery, flat tire, out of fuel and lockout service)
• Basic Recovery and Rollovers
• Scene Management
• Hybrid and Electric Vehicles
The second day consists of handson demonstrations of a wheel lift hook-up, utilizing tow dollies, securing a steering wheel, attaching tow lights, installing safety chains, loading and unloading a car carrier, rollover techniques, and snatch block demonstrations.
Bob & Dave’s Towing in Whittier, California hosted an In-Person, ERSCA Essentials of Standard Duty Towing & Recovery course on May 6 and 7, 2025. I had the privilege of co-instructing this class with Rodney Sellers, owner of Bob &
Dave’s Towing.
The first day of classroom instruction was hosted by Sage Restaurant in Whittier, California. Sage prepared a great lunch for the students on both days and also displayed signage for Tow Industries (also a sponsor of the training) on the TV monitors in the restaurant. Tow
Industries also provided T-shirts for all of the students.
During our training event we had visits from a few special guests that included the Mayor of the City of Whittier, Joe Vinatieri, Bill Salazar, owner, of Royal Coaches Towing, Recovery & Transport, and California Highway Patrol officers David Nelson and Travis Iseri with the Los Angeles County Freeway Service Patrol (FSP). It was a nice moment when the Mayor addressed the students and thanked them for the work that they do. He shared his story of being rescued by a tow truck.
Bill Salazar, owner of Royal Coaches Towing, Recovery and Transport, is a big supporter of education. He has hosted many in-person classes at his facility and provided one of his newest car carriers for the hands-on demonstrations as well as stopping by the class to say hi.
It is always great to have law enforcement attend our tow operator training classes, especially if they work closely with the tow operators like the Freeway Service Patrol officers. It benefits the FSP officers to
see the type of training our operators receive, and also benefits the students to be able to interact with the officers away from the roadside incidents.
During our second day of handson demonstrations there was also the opportunity to utilize a Condor motorcycle dolly to load a motorcycle onto the car carrier. The equipment and/or a motorcycle is not always available, so it is an added training bonus when an actual demonstration is conducted.
A big “Thank You!” to the sponsors of this ERSCA Essentials of Standard Duty Towing & Recovery course:
TOWKING Network
Tow Industries
Sage Restaurant
Royal Coaches Towing, Recovery & Transport
Bob & Daves Towing
Last but not least, another big thank-you to Rodney Sellers, owner of Bob & Dave’s Towing, and TOWKING Network for organizing the training event, arranging guest visits, and securing all of the great sponsor support. Also, thanks to the sponsors, the students who had a great learning experience, and the great food—and even for the T-shirts!
Every year, several shaft-related incidents occur nationwide due to not following proper securement procedures.
By Randall C. Resch
SOperations Editor Randall C. Resch is a retired California police officer and veteran tow business owner, manager, consultant and trainer. He writes for TowIndustryWeek.com and American Towman, is a member of the International Towing & Recovery Hall of Fame and recipient of the Dave Jones Leadership Award. Email Randy at rreschran@gmail.com.
ome operators might view towing large trucks, buses and RVs as routine. They feel it’s just one of those everyday tasks that doesn’t involve advanced techniques and doesn’t require too much effort.
But imagine being in-tow and unexpectedly—“Wham!”— a five-foot long, heavy metal driveshaft drops below the towed vehicle, onto the roadway, and impales the windshield of a following vehicle. Suddenly, the risks and challenges are very real.
Every year, several shaft-related incidents occur nationwide. What if you were the operator who disconnected the towed vehicle’s shaft, but failed to properly secure it to prevent it from dropping? Every state has laws regulating secured loads, and a lost shaft is entirely preventable.
Even so, the dangers of driveshaft removal and securement are rarely discussed in safety meetings. When training isn’t conducted, operators are
forced to simply “wing it” and learn techniques on-the-job.
Proper driveshaft training identifies risks, techniques, and understanding applicable procedures relating to shaft removal. Fact: A driveshaft under load is a fatality or head injury waiting to happen. Consider these two operatorrelated fatalities:
Case One: A North Carolina tow assistant loosened a truck’s driveshaft by removing mounting bolts before determining the shaft was under load. When the third bolt loosened, it exploded from its mount striking the operator in the head. He died days later of trauma to the forehead.
Case Two: A California operator was killed removing a driveshaft that struck him in the head. OSHA reported the tow employee did not release existing torque load from the multi-section driveshaft. Both scenarios confirmed the dangers associated with removing driveshafts under binding forces. Removing an unbolted driveshaft requires specific training to identify the dangers that could arise if removal isn’t properly handled. A driveshaft under bind is a potentially deadly situation.
Another safety aspect is securing a loose driveshaft once it’s been loosened and not completely removed. Operators must work to ensure a disconnected driveshaft stays with the towed vehicle and doesn’t drop while they’re heading to repair destinations at freeways speeds. Dropping an unsecured driveshaft into the path of a following vehicle is capable of great bodily injury or death.
In yet another instance, a heavywrecker company responded to tow a broken-down RV with a blown radiator. With the driveline disconnected at the rear differential, the shaft dropped to the pavement, throwing sparks to the RV’s undersides. The RV caught on fire, and was totally destroyed.
A subsequent million-dollar lawsuit alleged the driver was clearly ◀
While working underneath a casualty vehicle is sometimes necessary, be sure to follow safety guidelines.
• Safety first: position chocks in front and behind tires to prevent unintentional rollaway.
• Be sure the towed vehicle is securely attached into the under-lift, with all safety chains and straps in place before the operator goes under the vehicle.
• Ensure wrecker’s emergency brake is fully applied.
• To lessen load bind, shift the transmission to neutral, jack one drive wheel off pavement, or move under-lift in or out to lessen bind.
• Spray WD-40 or similar lubricant to help reduce the breaking force of U-bolts, while being cautious not to snap nuts from U-bolts.
• Remove nuts and bolts to allow the shaft to loosen.
• Wrap electrical or duct tape around bearing caps to retain tiny bearing needles within bearing caps.
• If pulling shafts from transmission ends, models with automatic trannies may drip transmission fluid; position basin to capture escaping fluid.
• If left in-place, completely secure shaft up and away from the spinning differential during towing. Best practices recommend using a specially designed, shaft-capture device for safe retention.
• If the shaft is left in place, include a length of rope, motorcycle strap, or commercial-grade bungee cord that pulls the shaft toward the vehicle’s front-end to keep the shaft tightly retained within the transmissions tail piece.
unqualified to handle the tow and failed to bring and use proper tools and techniques to secure the shaft so it wouldn’t drag on the pavement. That’s a tough accusation to encounter, as it attacks the very core of a company’s competency. Many tow company owners are familiar with frivolous lawsuits, and statements like these are easy for plaintiff attorneys to claim and even more difficult for towers to defend.
Because driveshaft removal is a specialty niche, tow operators must be well-trained in all processes necessary to safely remove driveshafts and axles. Because drivesystems vary, towers should be well schooled in a range of how-to techniques for shaft removal. Once driveshafts are disconnected, they should be supported with specialty accessories designed for retaining and suspending loosened shafts from the undersides of towed vehicles.
This article isn’t about selling specialty products. It’s about being smart in selecting the right tools for the job in relation to the task being performed. The industry’s techniques and technologies have advanced well beyond using coat
hangers, bungee cords, and duct tape for securing loose driveshafts. In today’s market of advanced industry tools and safety accessories, wreckers should be well equipped with a bevy of wrenches, sockets, airtools, axle poppers, axle caps, U-joint pullers, and perhaps a commercially designed driveshaft retention device.
Especially true for heavy wrecker operations, tow trucks equipped with wireless controls are blessed with the ease and convenience these devices offer. When in the process of hooking up, dropping the shaft, or disconnecting, operators often lay under a lifted truck, and on-scene safety can be compromised if the controller device is carried in the operator’s jacket, vest, or pants pocket.
Case in point, in November 2022, a veteran, heavy-duty wrecker operator arrived to tow a disabled semi-tractor on a rainy day. When the operator
went under the tractor, it detached from the tow truck’s lift, trapping the operator under the rig. The tractor continued rearwards, dragging him some 50 feet before stopping. When paramedics and firefighters arrived, he was found gravely injured and unresponsive. The operator was transported to an area hospital where he died from his injuries.
It’s speculated that the operator may have placed the controller in one of his pockets. When positioning himself under the tractor’s frame, perhaps he rolled over a control button, causing the under-lift to lower. When working underneath the casualty being towed, operators are reminded to not “pocket” the controller to avoid an unintended mishap.
While towers are trained to never go under a lifted load, removing driveshafts requires working under a vehicle when they are being
readied to be towed. Obviously, some towers are bigger than the available space, so disconnecting a driveshaft often requires the vehicle is lifted first to allow the tower to gain access to the underside.
This can be a risky procedure, as already noted, and illustrated in this next example. In April 2025, a Virginia owner/operator was killed when a dump truck’s floating axle likely lost pressure and dropped from its raised position, falling atop the operator. While details aren’t exactly known, it was speculated that the axle wasn’t secured or lowered prior to the operator working to disconnect the truck’s driveshaft.
Towers are reminded that safety procedures must be carefully adhered to (see sidebar). Where necessary, OSHA requires positioning jack stands designed for supporting vehicle weight. Never rely on bottle jacks or floor jacks to safety support the weight of a heavy vehicle. ◀
Also, when going underneath, do so with a spotter present to monitor underside work, or, if alone, advise dispatch you’re going underneath a casualty vehicle. Raise the vehicle high enough to position large wooden blocks under both lifted tires, and then lower tires on top of the blocks to eliminate drop space and gain additional height for safety. Shift the casualty vehicle to neutral, or jack-raise the rearward wheel to remove bind at driveshaft.
For trucks with floating axles, never trust hydraulics or air systems to maintain height. Prior to removing a driveshaft, chain the axle to prevent a sudden drop.
Using proper tools and equipment to remove or secure a driveshaft is a modest expense compared to a possible lawsuit. Also, be smart about training operators to a level of competency to prevent unfortunate incidents.
In the event of a shaft-related lawsuit, the first thing that’s attacked is the driver’s training and ability to handle the task. When no training is provided, judge and jury may find tow companies responsible for a preventable injury or death. Consider how many tows it would take for a company to recover from a multimillion dollar, wrongful-death lawsuit resulting from operators not being properly equipped and trained.
By Steve Temple
Photos by Shiloh Janes
The comical character Mater, a wellknown cartoon tow truck, is a lighthearted fixture in all three of the Cars movies, as well as in the TV series Cars Toons and Cars on the Road. This lovable wrecker with big eyes and buck teeth has been widely imitated on a variety of classic trucks. The original Mater is a 1951 International Harvester L-170 boom truck with elements of a mid-1957 Chevrolet 3800. The one shown here is a 1956 Ford F600, running a 292 Y-block engine, 4-speed transmission, and 2-speed rear end.
and
The truck was initially owned and operated by Dick Jaeschke (Jeski) at the Square Deal Garage in Oneida, NY, back in the 1960s. Jeski was the main towing company in Oneida for over 30 years before his death in 1972.
Dick grew up in Hell's Kitchen, NY, towing for his father in NYC, using very short wreckers that could easily turn around in the Holland Tunnel. He purchased this particular truck from the Bell Telephone Company in Oneida and transformed it into a wrecker. He had two of these phone trucks, and the towing contract for cars and trucks from the New York State Thruway (I-90).
Back in the day, the going rate was $6 per car, plus mileage not to exceed $10 during the day, and
$15 at night. Dick at one point had up to six trucks. The wrecker body was either a Stringfellow out of Tennessee, or a Weldbuilt Wreckers out of Deer Park, NY. The current owner of this classic wrecker is Tim Janes, of C.T. Express, Inc. in Durhamville, NY. Before acquiring it a couple years ago, he watched this truck languish behind a tow business for probably 25 years. “I never drove by it that I didn't look at it,” Tim admitted.
Talking one day to Andy Parent of Andy's Towing, Tim mentioned that old truck to him, and was told it was for
sale. “Long story short, two months later the price came down and I bought it,” Tim related. After Andy delivered the old truck on his rollback, “It sat in my backyard for a couple years in really bad shape. A tire flat, engine seized up, a bad battery, absolutely nothing worked.”
But during the harsh winter of 2024 and 2025, he got busy, getting every mechanical component of the truck operational.
One day during lunch in a local diner, another friend (Chris) told Tim that he had a 292 Y-block engine that would go right into the wrecker.
Tim dragged the truck into his garage and started tinkering. The inner fenders were completely rusted out and gone. One of Tim's workers, Donnie Grogan, along with Tim’s son Shiloh, went to work on it in their spare time, replacing the engine, inner fenders, all wheel cylinders, brake lines, and 2-speed rear end.
Another friend of Tim’s, John Panos of Atlas Electric, found an original alternator in Ohio, rewired the whole truck, and got every original light working on it. Tim had a company sandblast and powder-coat the six original rims, and mounted on six new 8.25 x 20 Deestone tires. He also had the seat reupholstered and replaced a couple broken windows with all new window tracks. The bed now has a functional wrecker body (either a Stringfellow or Weldbuilt, but that’s to be determined). The bottom of both doors had panels replaced by Tim’s friend Rooster.
As for the celebrity treatment, “Back when it was in my backyard, Shiloh put the eyes in the windshield and it became Mater,” Tim noted.
Tim has been in the trucking business for over 50 years, with a small fleet of Peterbilts, and was always interested in wreckers, but never owned one.
“So now my wrecker bucket list is complete,” he laughs. “This has been a fun project and it has gotten a lot of local attention. I have had more fun with Mater in the last couple years than with my work trucks.”
As one example among many, when Tim first got it running, he would circle his garage driving it, and recalls a particularly memorable experience.
“One day I took two of my granddaughters for a ride, Addie and Lailynn,” he recalled. “After one lap, Addie said, ‘Grampa, I want to drive.’ I stopped immediately and switched seats. So, Addie is 13 years old and has already driven a wrecker LOL!”
Be sure to look for Tim’s Mater impersonator on the car show circuit this summer.
Tow4Tech, an innovative SaaS platform modernizing the commercial-fleet towing industry, is excited to announce the expansion of its business with Ryder System, Inc., with a real-time roadside dispatch solution across Florida.
Ryder is a leader in supply chain, dedicated transportation, and fleet management solutions. Based on encouraging results from a recent
pilot, the companies will now scale Tow4Tech’s real-time dispatch technology statewide.
By digitizing and automating the traditionally fragmented and manual towing process, Tow4Tech’s goal is to help Ryder improve fleet uptime, reduce roadside response times, and enhance visibility across vehicle service operations. With Ryder managing over 250,000 assets in North America, the expanded pilot is expected to deliver significant opera-
tional efficiencies in the region.
“The first phase of our relationship has shown encouraging results towards our goal of reducing downtime and improving the service experience for our customers when they have a roadside event,” said Jenn Dixon, Vice President of Maintenance Technology at Ryder. “Tow4Tech brings speed, transparency, and automation to the roadside process. Their innovative platform makes it easier for our teams to coordinate roadside assistance, and we’re excited to expand our pilot throughout Florida as they continue to build out their platform.”
Tow4Tech’s platform connects fleet managers and service centers with top-performing tow and roadside providers using real-time geolocation, automated dispatching, and digital job tracking.
"We are proud to expand our business with Ryder, an industry pioneer that continues to embrace tech-driven innovation," said Craig Schneider, CEO and Co-Founder of Tow4Tech. "This relationship reflects our shared commitment to transforming an outdated and often frustrating process into one that is intelligent, efficient, and accountable. Together, we are actively developing a technology roadmap, focusing on enhancing solution efficiency and defining a more streamlined, robust architecture to support future growth."
Tow4Tech and Ryder will continue to evaluate further expansion as performance data and operational outcomes are measured over the coming months.
www.tow4tech.com
The Ford Super Duty lineup is no stranger to Vincentric’s Best Fleet Value in America Awards. The Ford F-350 Super Duty wound up finishing first in the full-size one-ton pickup segment of the 2025 Vincentric Best Fleet Value in America Awards yet again, this time, in XL, Crew Cab, two-wheel drive, long wheel-base,
single rear-wheel guise—outperforming 178 competitor trims. The Ford F-350 won 15 of 28 lifecycle cost scenarios, and posted the lowest maintenance and operating costs in its class. Each year, Vincentric comes up with this list after performing a cost of ownership analysis based on how commercial fleets typically use their vehicles, using eight cost factors – depreciation, fees & taxes, financing, fuel, insurance, maintenance, opportunity cost, and repairs. For 2025, Vincentric performed that same analysis for more than 3,000 different vehicle configurations based on typical fleet use, and winners were identified by determining which vehicles had the lowest fleet lifecycle cost in the most scenarios within its segment.
By George L. Nitti
When a small, singleengine Cessna crash-landed this past January into a residential property in Temple City, California, near San Gabriel Valley Airport, the media swarmed, helicopters hovered overhead, and police cordoned off the neighborhood.
2022 Peterbilt with a Century 1140 rotator
2017 International Extended Cab with a Century 22-foot steel bed
That’s when Jan’s Towing of Pasadena was summoned to the scene by the Sheriff’s Department. Leading the operation were Jan’s seasoned tow operators: Steve Coffee, Ron Wallace, and Francisco Prado.
Commenting on the possible cause of the mishap, “From what we knew, they ran out of fuel,” said Wallace. “Fortunately, the pilot and passenger survived, walking away from the collision.”
Upon arrival, the crew encountered a tangled challenge: one wing was perched on a dividing wall, the other lay mangled and twisted in the backyard, and the nose of the plane rested against the house, narrowly avoiding further destruction.
“We had to figure out how to get it out without causing any more damage,” Wallace recalled.
The first step in the recovery was coming up with an effective game-plan. Coffee and his team joined FAA compliance officers and airport mechanics for a walkaround of the wreckage.
“We all got together and said, ‘OK, this is the plan,’” Coffee explained. “We figure it out between all of us. Then we set up the truck. Before we lift anything, we go through it again. Everyone talks. Anyone can say stop at any time.”
Coffee operated Jan’s 2022 Peterbilt with a Century 1140 rotator, which was carefully
Steve Coffee, rotator operator
Ron Wallace
positioned in a tight residential driveway. Working with precision, he used raptor controls to lift the fuselage and wings.
Francisco Prado, flatbed operator
“You have to be very gentle on the controls and very slow,” Coffee noted. “It looks like it’s not moving
After wrapping the wings and body, Jan’s crew lifted the aircraft up and over the
to go up, down, left, right—just a little—to make sure the plane doesn’t catch on anything.”
The crew wrapped the wings and
body before lifting the aircraft up and over the wall—carefully avoiding overhead wires—and lowered it onto the driveway.
“We rotated the plane in the driveway—grabbed each wing and spun it around so we could back it onto the flatbed,” Wallace said.
The bed was operated by Francisco Prado, who recalled: “It took coordination. I had to be in sync with the rotator so that when the plane came down, we were exactly where we needed to be. Everyone had to stay alert.”
The final leg of the recovery involved the plane’s two-mile transport back to the airport.
“Everyone was pulling out their phones. I felt like a movie star,” admitted Prado, who received a police escort along the slow drive.
“When we got to the airport, I backed it into place so they could re-lift the plane and rotate it over a fence onto FAA property,” added Prado.
“Once it touched down, the airport staff took over,” Coffee said. “As long as the wheels were intact— and they were—they could tow it with a golf cart to wherever it needed to be held.”
The entire operation spanned several hours.
“I’ve worked plane wrecks before—even jets,” Coffee said in hindsight. “This was a small one, but the setup was tight, and the potential for damage was high.”
For Wallace, the highlight was
seeing the crew function like a finetuned machine. “A professional makes things look easy,” he said. “It may not be easy, but we make a hard job look like anyone can do it—until they try.”
By Brian J. Riker
The American Dream for many consists of owning a successful company, controlling its destiny, and succeeding. While many towmen have thought about it from time to time, and others have tried their hand at it, only a few have succeeded. Why is that? Buying a job, or rather, a business, can be a great way to gain autonomy and flexibility, if having control over work life is a top priority. There are many successful one-truck owner/ operators in the towing community, truly professional operators that own a decent truck and do a fantastic job, but have no desire to expand beyond what they alone can provide.
But what about those towers who want more? How can they go from one truck and a dream, to owning a large fleet or a diverse group of companies offering a variety of
services? It all begins with a plan, the right mindset and clearly defined goals.
For towers already commanding their own company, it’s not too late to develop a detailed business plan. When crafting a company roadmap, focus on making it realistic and clear, and don’t stress too much about perfection—just be sure to cover the five “W’s”:
Who: The customers receiving services; that is, identify the business-to-business commercial work, law enforcement, motor clubs, specialty vehicles or other demographics in the community best to connect with.
What: Determine the unique strengths and services that will differentiate one tow company from other competitors in the local market. There is a lot of noise in the towing community, and prospective customers need to be able to hear a particular company above the roar. Offer better trained, more professional drivers, and specialized trucks, or perhaps get deeply involved in the local community. To ensure success, a growing tow company needs to be different, meaning better or more desirable, than anyone else in the area.
Where: Pinpoint the best location to expand. Whether in a satellite location in a neighboring town, a different state, or just expand service offerings into a different part of the local community, target a specific market segment and locale.
When: Nail down a timeframe for this expansion, or new operation. Identify how soon it could become profitable. It is unrealistic to expect a new venture to be self-sustaining from day one, so have sufficient capital reserves to support the operation, and personal lifestyle, for six months. On average, new ventures require at least this amount of time before any real income is seen.
Why: Figure out the reasons for wanting to grow, or even start a business. Is it simply for more personal control? Or, is the driving passion one of service before self? All of these are valid “why” answers, but they each will result in a different outcome over time.
Once the five “W”s have been answered, it’s time to begin the real work. Paying for this new venture is very expensive, and most new businesses fail within the first year due to not having enough funding to make it through the startup process. Unlike working for someone providing a paycheck every week or two, there is no guarantee of collecting the money owed to a business owner.
In most of the U.S., more than 40% of all non-consent tows, such as police impounds and crashes, go unpaid. This leaves the tower to dispose of the abandoned vehicle at their expense instead of making a profit from their labor. Even in retail towing, credit card chargebacks and fraud are common, leaving the tow boss to wonder if they will be paid after spending time, money, and resources to provide a valid service.
While motor clubs and other commercial accounts can offer more reliable payment streams, they often come with their own set of challenges and limitations. Most commercial work is paid on terms, which means they want to pay between 15 to 45 days, and maybe even longer, after invoiced. That is a long time to wait for money to flow in, especially if you are a startup and the towing business is going to be your only source of income.
It is imperative to have at least six months of cash in reserve. There should be enough cash to cover fuel, insurance, truck payments, and other operating expenses, as well as additional funds for personal needs to carry for six months. Towers need to pay themselves a reasonable salary, one that supports a comfortable lifestyle, otherwise it’s merely an expensive hobby and not a business! A paycheck is not what is left over, it’s a business expense that fuels
the growth and keeps operations running smoothly.
As a company expands, accepting the transition from doer to leader is crucial, and learning to delegate effectively is the key to success. Many tow bosses began their company as the Chief Everything Officer, meaning they drove, took calls, did the books, fixed the truck and more. There is nothing wrong with that—for a while—but to really grow, step out of
the truck and let others do the daily tasks, ultimately allowing time to strategize the continued success and growth of the company instead.
It's important to maximize the following steps:
-Explore how to inspire and lead people, and not just be a boss. Only after becoming a good leader will a tow boss be able to find, and retain, the right people to grow a business. (Note, the most successful business owners are leaders, not bosses.)
-Recall qualities exhibited by ◀
a previous boss that were favorable. They likely included compassion and understanding, and also holding others accountable for their actions with a firm but fair demeanor. Good leadership is all about inspiring others to do their best, not from fear of punishment, but rather because they feel connected to the mission and truly want to be the best they can be.
Leadership is a selfless action, as historically, great leaders put people before themselves. Essentially, great leaders eat last, meaning they make sure all the needs of their team are taken care of before considering their own needs. This is the principle of Servant Leadership, where it is the job of the leader to remove obstacles and provide resources, as opposed to micromanaging the team’s every move.
As the owner of a company, there must be clear standard operating policies and rules the team must follow, however these must be designed with some flexibility to allow for individuals to perform to their best ability and perhaps even demonstrate innovation. Company policies should not only define operational guidelines, but also allow for each team member to complete tasks, within the legal and industry standard best practices, as they see fit.
Great leaders work with their team to teach them how to think— not what to think—so eventually the team will make the same or similar decisions as their leader might have. Once a team can anticipate a tow manager’s next sentence, the company is in a position for explosive growth.
After considering various leadership styles, and working towards becoming a better leader, how does a tow company owner hire the right people? A dear friend of mine once said, “I would rather soar with a couple eagles than a flock of turkeys.” Essentially, this means that setting clear expectations of the
tow team from the beginning, and then holding them accountable is of utmost importance.
As Dave Ramsey, founder of the Ramsey Group and author of Entreleadership, a book detailing how he built a $300 million empire from a card table in his living room says, “Keep crazy out of the building, otherwise you will end up running an asylum.”
A job description should be a living document, with new versions as job functions evolve. Provide a job description for every position in the company, from the highest to the most mundane, regardless of whether one person holds multiple positions. These descriptions should outline several key points, and be specific to the position, not to a person.
shall be performed are then defined by company policy, training, and from examples demonstrated by leadership. Effective leaders in any tow company have owners that hold themselves accountable to the same standards expected of their team members. If team members are expected to wear clean uniforms and proper PPE, then the manager must follow suit, at all times, without excuses.
Keep crazy out of the building, otherwise you will end up running an asylum.
The main purpose of a job description is to define the company’s vision of success. By all accounts, this includes a paragraph or two describing the daily responsibilities of the job, followed by the metrics on which performance will be judged. For example; a job description for a lightduty wrecker operator might include the following:
-Operate assigned tow equipment within compliance with all applicable laws, regulations, industry standard practices and consistent with training provided to provide safe, effective and efficient service to our customers as dispatched.
-Performance will be judged on not being involved in crashes, a lack of damage complaints, no citations or DOT violations, meeting ETAs, customer review cards, cleanliness of assigned equipment, attitude and appearance, among other criteria as revised from time to time.
These descriptions will set the guide rails for the job, while giving some leeway on how the job will be performed. The specifics of how it
Once the task of learning how to be a great leader is accomplished, and then providing clear guidance on what winning looks like at the company, can go a long way in the development of a great team. Building a team culture is perhaps the hardest part of growing any enterprise. As a leader and business owner, being a risk-taker, parent, and psychologist—all at the same time, is a job requirement!
One of the best ways to build a great team culture is to always model the behaviors the team should emulate. If a manager is moody, loses their temper, or takes shortcuts, then the team will do the same.
Tolerating toxic behavior until the pressure builds up, then snapping at the team, or ignoring poor behavior from a top-performer for fear of losing them, can lead to resentment and undermine team cohesion, ultimately costing more than the revenue they may generate.
Condoned behavior, good or bad, will quickly become the norm, so tardiness, chronic excuses, and substandard performance should not be allowed. Consistently demonstrating a good work ethic, along with humility and honesty when a mistake is ◀
made, will encourage the team to do the same.
Developing a team takes time and patience. Actively seek people that are more trained in a specific task, and put them in positions where they are the considered to be the expert. This will not only boost their confidence but will allow them to earn the respect of the team, fostering a culture of trust and expertise.
No single person can be an expert at every aspect of operating a company, so it’s best to create a team full of specialists. Growing a team requires CANI, an acronym for “Constant and Never-Ending Improvement,” meaning everyone on the team must always be learning something new.
Learn from team members and from peers. Join a networking group of other business leaders that meets regularly and discusses their own business models. This is a great way to discover alternative methods to tackling tasks. Team development is all about constant improvement and supporting each other, even through failure.
To allow for team growth, be comfortable enough with the integrity and intentions of the team that it will allow them to “fail forward.” Embracing failure as a learning opportunity empowers teams to grow, innovate, and ultimately make better decisions, which is a very important stepping-stone to success.
By Steve Temple
History is chock-full of inventions that were spawned by a pressing need. The wheel moves heavy objects, the telephone means faster communication, and the internet provides better access to information, among many other new technologies.
Tow truck engineering is yet another area benefiting from innovations over the last century or so. The shift to self-loading under-lifts, the creation of rotators, digital dispatch—the list is extensive. And consider improvements in tow truck lighting as well.
Specifically, TowMate is a leader in this field, making life easier and safer for tow operators with wireless lighting systems. What veteran towman doesn’t recall hassling with dangling wires on a casualty vehicle on a sling?
TowMate founder Bryan Anderson sure does,
In the drill room, James Eubank uses a hole saw to make openings in the plastic housing for heavy-duty wireless tow lights.
dating back to a frigid night in Kansas in the winter of 1985. He was personally handling a tow call for his staff, and struggled with connecting a stiff, unwieldy cord to tow lights on a casualty vehicle. Clearly there must be a better way, he figured, and a light went on his head: why not use a wireless system instead?
Easier imagined than done, as no product of this type was available, and implementing his idea took some time and persistence, but Bryan clearly prevailed. His company is now commemorating 40 years of production this year, which prompted a personal visit by us to his facilities in Rogers, Arkansas earlier this year. During our factory tour, we were impressed by the sophisticated level of engineering in its setup and production machinery, employing rotational molding, 3-D printing, and Vapor Phase Technology. ◀
Today, TowMate’s broad product line has expanded far beyond the original two wireless tow lights (a set for light-duty and a bar for heavy-
duty tow trucks). This firm now offers a comprehensive range of tow lights, along with emergency warning lights that include overhead light bars and
strobes for vehicle bodies and grilles. TowMate technology has broadened into some unexpected applications outside of the towing industry. These include safety solutions for the construction, utility, agricultural, and law enforcement industries as well.
The company’s roadside safety systems feature cone, post, and magnetic-mounted rechargeable warning lights. Additionally, TowMate has included state-of-theart technologies such as HINVII non-visible light that illuminates tow operators’ reflective vests.
All told, TowMate’s ongoing product development demonstrates a relentless commitment to ensuring the roadside safety and efficiency of towmen, who join in celebrating this company’s 40th anniversary.
towmate.com
By John Borowski
Atransforming how tow companies operate, offering a multitude of benefits.
Direct digital dispatch leverages modern technology, using GPS tracking, mobile applications, and cloud-based software to enhance and automate the entire dispatch process. Unlike traditional methods that are prone to human error, delays, and communication breakdowns, digital dispatch provides a real-time, transparent, and effective system for managing service requests and deploying tow trucks. As such, it’s no longer a luxury, but a necessity in today's competitive landscape.
One of the most significant advantages of direct digital dispatch is the dramatic enhancement of operational efficiency. By automating many of the manual tasks associated with traditional dispatch, digital systems free up dispatchers to focus on strategic decision-making and proactive problem-solving.
Digital dispatch software can automatically assign the nearest available and most suitable tow truck to a service request based on real-time location data, vehicle capabilities, and driver availability. This eliminates the time-consuming process of manually contacting drivers and determining the optimal assignment, significantly reducing response times.
cross the nation's highways and byways, tow operators navigate a demanding landscape where every minute counts. For years, their crucial services relied on traditional dispatch methods, often leading to delays and inefficiencies that frustrated both operators and motorists in need of roadside assistance. Today, though, a technological revolution is underway. Direct digital dispatch is not just streamlining operations—it’s fundamentally reshaping the towing industry by offering a pathway to unprecedented efficiency, customer satisfaction, and profitability in an increasingly interconnected world.
With real-time tracking and visibility, GPS integration provides dispatchers with a live view of their entire fleet, allowing them to monitor the location and status of each tow truck at all times. This graphic display facilitates management of resources, with quick identification of the closest truck for new calls, and accurate estimation of arrival times for customers.
In the fast-paced and demanding world of towing services, efficiency, speed, and accuracy are paramount. Stranded motorists, accident recoveries, and vehicle relocations require swift responses and seamless coordination. Enter direct digital dispatch. This technological innovation is ◀
In addition, digital dispatch systems can utilize real-time traffic data and intelligent algorithms to generate the most efficient routes for drivers. This minimizes travel time, reduces fuel consumption, and allows tow trucks to complete more jobs in a given period, thereby increasing overall productivity.
As a Towing Professional, be recognized by your Police or Fire Chief for serving your community in an exceptional way
Have your Police or Fire Chief nominate you for
Should you feel you qualify, take this nomination form to your chief.
• For the past 15 years over 2,000 police and fire chiefs across the U.S. have nominated towing professionals for The Order of Towman, presented by American Towman Magazine in recognition of their supreme dedication to their communities and to the professionalism in their trade.
• No one knows better than chiefs how towers rise to the occasion to face challenges at incident scenes or support their departments.
• While American Towman Magazine mails nomination forms to chiefs nationwide, it may take more than one notice.
Deadline: September 30, 2025 for nominations. The ceremony presentation of the Cross of The Order will take place at the American Towman Exposition in Baltimore. Nominee (Owner or
Direct communication between dispatchers and drivers is greatly enhanced through mobile applications and in-app messaging features. This eliminates the need for often unreliable radio communication, and provides a clear, documented record of instructions and updates. Drivers receive job details, navigation information, and any changes directly on their mobile devices, ensuring accuracy and reducing misunderstandings. Digital communication methods are more cost-effective than traditional radio systems as well, eliminating the need for expensive equipment and maintenance.
Digital dispatch systems also eliminate the need for manual paperwork associated with job assignments, service records, and invoicing. All relevant information is captured and stored electronically, reducing administrative overhead, minimizing errors, and facilitating faster billing processes. With improved accuracy and speed, digital recordkeeping and automated invoicing reduce the likelihood of billing errors and allow for faster generation and delivery of invoices, leading to quicker payments and improved cashflow.
Implementing direct digital dispatch can lead to substantial cost savings for tow companies in several key areas. These include reduced fuel costs by optimizing routing to minimize unnecessary mileage, a significant operational expense for towing businesses.
Not only that, automation of tasks reduces the workload on dispatchers and labor costs, potentially allowing for a more efficient allocation of administrative staff. Furthermore, improved communication and job management can minimize delays and errors, reducing the need for rework and overtime.
By optimizing routes and reducing idle times as well, digital dispatch can contribute to less wear and tear on tow trucks, leading to lower maintenance costs and extended vehicle lifespan.
The field of towing technology continues to evolve, with several exciting trends on the horizon.
In the service industry, customer satisfaction is paramount for building a strong reputation and fostering repeat business. Direct digital dispatch plays a crucial role in enhancing the customer experience by proving faster response times. Efficient dispatching and real-time tracking enable tow companies to respond to service requests more quickly, minimizing wait times for motorists needing a tow or other roadside services, a key factor in customer satisfaction.
In addition, real-time GPS data allows dispatchers to provide customers with accurate arrival times, keeping them informed and reducing anxiety associated with uncertainty. Many systems also offer the ability to send customers notifications with live tracking links, further enhancing transparency.
Digital communication channels facilitate clear and timely updates to customers regarding the status of their service request. Automated notifications can inform them when a truck has been dispatched, the estimated arrival time, and when the service is complete.
The overall efficiency and professionalism enabled by digital dispatch systems contribute to a positive customer perception of the
tow company. Streamlined processes and accurate information instill confidence and trust.
Digital dispatch also provides electronic documentation, such as service reports and invoices, which can be easily shared with customers. Furthermore, integration with mobile payment solutions offers customers convenient and secure payment options.
Effective communication is the backbone of any successful towing operation. Direct digital dispatch significantly improves communication and coordination among dispatchers, drivers, and even customers. The system’s software serves as a central repository for all relevant job information, vehicle status, and driver availability. This ensures that everyone has access to the same real-time data, minimizing miscommunication and errors.
The system can automatically send notifications to relevant parties, such as alerts to dispatchers about vehicle breakdowns or updates to customers about service progress. Some digital dispatch systems offer features that facilitate better collaboration among drivers as well, such as the ability to share location information or provide assistance to colleagues on nearby jobs.
Modern digital dispatch systems often include robust reporting and analytics capabilities, providing valuable insights into operational performance. Key measurements include response times, job completion rates, driver efficiency, and fuel consumption, allowing tow companies to identify areas for improvement. Access to detailed operational data enables informed decision-making regarding resource allocation, staffing levels, and service optimization. ◀
Towbook
Reports can be customized as well, tailored to specific business needs, providing practical insights for strategic planning and growth. Analyzing historical data can help identify trends, predict future demand, and optimize resource allocation accordingly.
The value of direct digital dispatch is further amplified when it is integrated with other essential software systems used by tow companies. These could include software for accounting and fleet maintenance. The
latter can track vehicle mileage and maintenance schedules, ensuring regular maintenance and minimizing downtime.
In addition, direct digital dispatch can often integrate with the platforms of motor clubs and insurance companies, allowing for seamless receipt of service requests and submission of billing information.
The field of towing technology continues to evolve, with several exciting trends on the horizon. Artificial Intelligence (AI) and Machine Learning (ML) can further optimize job assignments, predict demand patterns, and even assist with dynamic pricing.
systems will provide even richer real-time data on vehicle health and performance, enabling preventive maintenance and safer operations.
In conclusion, direct digital dispatch offers a significant transformation in how tow companies manage their operations. By moving away from outdated manual processes and embracing modern technology, tow businesses can unlock a wealth of benefits. In today's competitive environment, where speed, reliability, and customer experience are critical advantages, and an essential tool for tow companies looking to thrive and succeed. Embracing this transformative technology is an investment in the future, ensuring greater profitability, operational agility, and the ability to deliver superior service. Autura
Future systems will likely offer even more sophisticated data analytics capabilities, providing more insights into operational efficiency and customer behavior. Deeper integration with vehicle telematics
By George L. Nitti
When C&C Towing’s newest heavy-duty wrecker hits the road, it’s impossible to miss. With a blend of artistry, engineering, and tribute, this 2025 Peterbilt 567 fitted with a fully trickedout 30-ton wrecker from Custom Built LLC is a symbol of national pride and personal remembrance.
Since 1980, C&C Towing has been a family-owned and operated business in Dublin, Georgia, and specializes in heavy-duty towing and hauling. When it came time to create their latest wrecker, owner Casey Clark knew exactly where to turn: Custom Built LLC out of Kane, Pennsylvania.
This new Peterbilt marks the seventh truck C&C Towing has built with Nick and Derek D’Angelo’s team. “They just get it,” Casey noted.
“We sat down and went through what we needed— something updated, highly visible, with plenty of storage and versatility—and they delivered again.”
The truck is packed with thoughtful features to streamline operations and boost safety. It boasts a tunnel box and adjustable shelving in every compartment to accommodate a wide range of tools and equipment. High-body rear doors fold up to shield operators and tools from harsh weather, and an integrated handwashing station promotes cleanliness and safety on the job. Customized lighting, consisting of Boogey underglow LEDs and illuminated handles, ensures better visibility during night operations. Every element was designed with the operator’s comfort, safety, and efficiency in mind.
Rigging equipment is all neatly organized and colorcoded. Since it’s new, this wrecker has not seen much action yet, except for winch-outs, towing and the recovery of sunken trailers.
The goal: honor America, celebrate the company’s roots, and raise awareness for breast cancer, a cause near and dear to Casey.
Visually, Casey turned to Bombshell Customs in Hiram, Georgia, where Todd Powell led the creative process for the truck’s wrap.
The front of the truck unfurls a bold American flag, brought to life with deep highlights, shadows, and layered graphics that give it movement and emotion. A silvercolored tow chain, drawn with a
massive hand and arm, tears back the layers of wrap, symbolizing the strength beneath the surface. Hidden within the intricate design are 18 layers of deep blues, among which the original C&C Towing logo is boldly embedded.
The most touching details are reserved for Casey’s late mother, Kathie Clark,
one of C&C’s original founders. Her actual signature—preserved from a stamp she once used—is incorporated into the pink ribbon on the truck, a tribute to her battle with breast cancer. Butterflies, her favorite symbol, flutter across the hood, sleeper, and truck number. When the hood folds open, it reveals two hands gently holding a cross, surrounded by butterflies.
Engine: Cummins X15; 565hp, 2050 lb/ft torque
Transmission: 18-speed manual
Eaton Fuller
Chassis: 2025 Peterbilt 567
Body: Custom Built, LLC 30-ton wrecker
Custom Features: Boogey underglow lights and illuminated handles, tunnel box, and adjustable shelving in all compartments, hand-washing station, high-body rear doors fold up to protect from any weather
Graphics: Bombshell Customs (Hiram, GA) under Todd Powell’s direction
Building this wrecker was more than a business transaction—it was a collaboration between a family company, a trusted builder, and a skilled artist. C&C Towing’s newest truck reminds us: some things— like family, pride, and honor—are built to last.
By Steve Calitri
The American Towman Chopper was christened “Hero” when we built it 20 years ago. In this old picture that was put on this year’s T-shirt, Publisher Dennie Ortiz is riding Hero. I think it captures the spirit of tow-women, known for their independence and riding chops in a man’s industry. These women display the heroic spirit as much as any towman who operates a wrecker and a towing business, and many of these women do that, too.
We celebrate towing’s heroic character in this issue’s American Towman Exposition pages by making an implicit statement that the bronze Towman Monument represents the heroic nature of the full-blooded men and women who run this industry day to day—including those who make the American Towman Exposition the vibrant event that it is. We selected several of them and gave their images a bronze-effect to help make that statement.
Steve Calitri Editor-in-Chief scalitri@towman.com
Our readers and attendees make up this “Industria Heroica” (Latin for “Heroic Industry”, with a a strong focus on safety, diligence, and bonding). Collectively, they are the Towman Monument. This is the reason, I’m sure, the monument never fails to have those who see it up close for the first time get all choked up.
The American Towman Exposition is the largest in the world— in a class by itself in number of exhibits and attendees. But it has always been much more than that, driven by
the energy and spirit of those who participate.
From the very beginning in 1989, featuring the first American Towman Medal ceremony, our industry’s heroism has been reflected by the Exposition. The words, Industria Heroica, have always been inscribed in the show’s emblem ever since the unveiling of the Monument in 1998.
Our show portraying this unique industry is nothing new, but what is new is the day we greet upon waking each morning, and the daily acts of dedication and passion that continuously surface in moments calling for heroism. Moments that continue to call on our resolve to serve the motoring public, whether from the office or the wrecker. No matter the stress we endure, or the challenges we face, we continue to perform.
The heroism may be overt, like acts at the incident scene for which we award the Towman Medal, or the less obvious and more unsung, like the changing of a tire for a motorist as 18-wheelers blast by, inches away. It may be the process of clearing the highway of chaos in the aftermath of a multivehicle accident, as your mind wards off the stress of some personal strife that’s jolting the equilibrium of your life.
Many, if not most of our readers and attendees may think, “I’m no hero, this is just what I do.” And that is the epitome of how the brave feel.
American Towman has lain over 300 Medals around the necks of towmen. For years I would tell their amazing stories of heroism to the Festival Night crowd, thrilling to the suspense evoked by each line of the narration. Now Dennie stands to tells them, her softer voice a dramatic contrast to the action described by her words. Whether experiencing the Medal ceremony on Festival Night or walking into the hall with all the booms raised toward the ceiling, the presence of this Industria Heroica charges our bones, and inspires us all.
Longtime tower Allen “Jay” Bloodworth, known in the Kansas City metro area for running Private Party Towing, appeared in Jackson County court Thursday after being arrested earlier this week on eight felony charges—four for vehicle theft and four for forgery.
The case centers on cars towed during a high school prom event on April 14. Bloodworth says his team followed protocol, towing from a church lot with permission from venue staff. However, state investigators claim a required witness signature was missing and records were allegedly falsified.
“I’m innocent, and I’ll prove it,” Bloodworth said after court. “The venue made a mistake. We did everything right.”
His attorney argues outdated KCPD systems are fueling the case and warns towers could be unfairly targeted.
Source: fox4kc.com
A second lawsuit has been filed against Sheffield Towing Service and its driver, Alfredo Campos, following a deadly 12-vehicle crash on May 8 in Northwest El Paso.
Alfredo Sifuentes, 54, of New Mexico, is seeking over $1 million in damages, claiming severe, permanent injuries from the wreck. The lawsuit alleges Campos and the company were negligent, failing to hire, train, and supervise safe drivers.
The crash occurred around 6:20 a.m. in El Paso. Campos, 28, was towing a broken-down semi when, for unknown reasons, he failed to stop at a red light. The tow truck slammed into vehicles at the intersection, igniting a fiery chain-reaction crash.
One person, Aldo Jenkins, a passenger in the tow truck, died in the crash. His family has also filed a lawsuit, stating Jenkins was burned alive in the wreck. Campos has not been criminally charged. A jury trial has been requested, though no court date is set.
Source: yahoo.com
Known on TikTok as “Captain Repo,” 29-year-old Kirkland Smith built a following by sharing dramatic vehicle repossessions online. But on May 24th, his real-life tow run ended in tragedy when he struck and killed NC Fire Chief Pete Batton. According to the North Carolina Highway Patrol, Smith’s tow truck slammed into the back of Batton’s car. Troopers say Smith failed to slow down. Batton died at the scene.
Smith, who sustained minor injuries, was arrested and charged with second-degree murder and misdemeanor DWI. His bond was set at $5 million.
Source: curepossession.com
The U.S. Senate has voted to revoke California’s Advanced Clean Trucks and low-NOx Omnibus waivers, a move welcomed by the national Safe Roads Coalition, representing towing and recovery truck owners.
“California’s electric truck mandates were unworkable,” said Josh Lovelace, the coalition’s national director. “By preserving access to combustion engines, Congress has safeguarded affordable, reliable roadside services for the American public.”
President Donald J. Trump is expected to sign the legislation, following its passage in both chambers. Many states previously planning to adopt California’s rules in 2025–26
have now delayed or modified them. Maryland, Massachusetts, Vermont, and Oregon recently postponed implementation, joining others targeting 2027 for adoption.
The coalition argues that tow trucks play a crucial public safety role—clearing accidents, reducing traffic, and cutting emissions. In states like California, towing services partner with transportation agencies to offer free roadside help.
Source: Press Release Safe Roads Coalition
The Towing and Recovery Association of America (TRAA) and fellow members of the Professional Certification Coalition (PCC) are celebrating a key legislative win. Language from the Freedom to Invest in Tomorrow’s Workforce Act (H.R.1151) has been included in the House Ways and Means Committee’s new tax package. If enacted, the bill would expand the use of 529 savings accounts—traditionally reserved for college expenses—to cover costs associated with obtaining and maintaining professional certifications.
While not specific to the towing industry, TRAA says this change would benefit future tow operators by rebranding 529s as “career savings plans” and helping young people afford the credentials needed for trades and technical professions. TRAA and
the PCC have pushed for this shift since 2019, aiming to support pathways into skilled careers that don’t require traditional college degrees.
In other news, TRAA and fellow members of the Anti-Speed Limiter Coalition are proud to announce the reintroduction of the “Deregulating Restrictions on Interstate Vehicles and Eighteen-Wheelers (DRIVE) Act” in the 119th Congress.
If passed, the DRIVE Act would bar the Federal Motor Carrier Safety Administration (FMCSA) from mandating speed limiters on commercial motor vehicles weighing over 10,000 pounds engaged in interstate commerce.
The coalition argues that speed limiters pose safety concerns, especially in dynamic traffic conditions, and limit drivers' ability to respond effectively on the road. Although current political conditions— particularly a Republican-controlled White House and Congress—make additional speed limiter regulations unlikely, TRAA and its partners remain proactive in pushing legislation to protect industry interests.
Source: TRAA Newsletter
The U.S. Senate has voted to revoke California’s Advanced Clean Trucks and low-NOx Omnibus waivers, a move welcomed by the national Safe Roads Coalition, representing towing and recovery truck owners.
“California’s electric truck mandates were unworkable,” said Josh Lovelace, the coalition’s national director. “By preserving access to combustion engines, Congress has safeguarded affordable, reliable roadside services for the American public.”
President Donald J. Trump is expected to sign the legislation, following its passage in both chambers. Many states previously planning to adopt California’s rules in 2025–26 have now delayed or modified them. Maryland, Massachusetts, Vermont, and Oregon recently postponed implementation, joining others target -
ing 2027 for adoption.
The coalition argues that tow trucks play a crucial public safety role—clearing accidents, reducing traffic, and cutting emissions. In states like California, towing services partner with transportation agencies to offer free roadside help.
Source: Press Release Safe Roads Coalition
Longtime tower Allen “Jay” Bloodworth, known in the Kansas City metro area for running Private Party Towing, appeared in Jackson County court Thursday after being arrested earlier this week on eight felony charges—four for vehicle theft and four for forgery.
The case centers on cars towed during a high school prom event on April 14. Bloodworth says his team
followed protocol, towing from a church lot with permission from venue staff. However, state investigators claim a required witness signature was missing and records were allegedly falsified.
“I’m innocent, and I’ll prove it,” Bloodworth said after court. “The venue made a mistake. We did everything right.”
His attorney argues outdated KCPD systems are fueling the case and warns towers could be unfairly targeted.
Source: fox4kc.com
A second lawsuit has been filed against Sheffield Towing Service and its driver, Alfredo Campos, following a deadly 12-vehicle crash on May 8 in Northwest El Paso.
Alfredo Sifuentes, 54, of New Mexico, is seeking over $1 million in damages, claiming severe, per-
manent injuries from the wreck. The lawsuit alleges Campos and the company were negligent, failing to hire, train, and supervise safe drivers.
The crash occurred around 6:20 a.m. in El Paso. Campos, 28, was towing a broken-down semi when, for unknown reasons, he failed to stop at a red light. The tow truck slammed into vehicles at the intersection, igniting a fiery chain-reaction crash.
One person, Aldo Jenkins, a passenger in the tow truck, died in the crash. His family has also filed a lawsuit, stating Jenkins was burned alive in the wreck. Campos has not been criminally charged. A jury trial has been requested, though no court date is set.
Source: yahoo.com
Known on TikTok as “Captain Repo,” 29-year-old Kirkland Smith built a following by sharing dramatic vehicle repossessions online.
But on May 24th, his real-life tow run ended in tragedy when he struck and killed NC Fire Chief Pete Batton.
According to the North Carolina Highway Patrol, Smith’s tow truck slammed into the back of Batton’s car. Troopers say Smith failed to slow down. Batton died at the scene.
Smith, who sustained minor injuries, was arrested and charged with second-degree murder and misdemeanor DWI. His bond was set at $5 million.
Source: curepossession.com
The Towing and Recovery Association of America (TRAA) and fellow members of the Professional Certification Coalition (PCC) are celebrating a key legislative win. Language from the Freedom to Invest in Tomorrow’s Workforce Act (H.R.1151) has been included in the House Ways and Means Committee’s new tax package. If enacted, the bill would expand the use of 529 savings accounts—traditionally
reserved for college expenses—to cover costs associated with obtaining and maintaining professional certifications.
While not specific to the towing industry, TRAA says this change would benefit future tow operators by rebranding 529s as “career savings plans” and helping young people afford the credentials needed for trades and technical professions. TRAA and the PCC have pushed for this shift since 2019, aiming to support pathways into skilled careers that don’t require traditional college degrees.
In other news, TRAA and fellow members of the Anti-Speed Limiter Coalition are proud to announce the reintroduction of the “Deregulating Restrictions on Interstate Vehicles and Eighteen-Wheelers (DRIVE) Act” in the 119th Congress. If passed, the DRIVE Act would
bar the Federal Motor Carrier Safety Administration (FMCSA) from mandating speed limiters on commercial motor vehicles weighing over 10,000 pounds engaged in interstate commerce.
The coalition argues that speed limiters pose safety concerns, especially in dynamic traffic conditions, and limit drivers’ ability to respond effectively on the road. Although current political conditions—particularly a Republican-controlled White House and Congress—make additional speed limiter regulations unlikely, TRAA and its partners remain proactive in pushing legislation to protect industry interests.
Source: TRAA Newsletter
Read more towing news at towman.com Find us on Facebook
The U.S. Senate has voted to revoke California’s Advanced Clean Trucks and low-NOx Omnibus waivers, a move welcomed by the national Safe Roads Coalition, representing towing and recovery truck owners.
“California’s electric truck mandates were unworkable,” said Josh Lovelace, the coalition’s national director. “By preserving access to combustion engines, Congress has safeguarded affordable, reliable roadside services for the American public.”
President Donald J. Trump is expected to sign the legislation, following its passage in both chambers. Many states previously planning to adopt California’s rules in 2025–26 have now delayed or modified them. Maryland, Massachusetts, Vermont, and Oregon recently postponed implementation, joining others targeting 2027 for adoption.
The coalition argues that tow trucks play a crucial public safety role—clearing accidents, reducing traffic, and cutting emissions. In states like California, towing services partner with transportation agencies to offer free roadside help.
Source: Press Release Safe Roads Coalition
“It’s
Longtime tower Allen “Jay” Bloodworth, known in the Kansas City metro area for running Private Party Tow -
ing, appeared in Jackson County court Thursday after being arrested earlier this week on eight felony charges—four for vehicle theft and four for forgery.
The case centers on cars towed during a high school prom event on April 14. Bloodworth says his team followed protocol, towing from a church lot with permission from venue staff. However, state investigators claim a required witness signature was missing and records were allegedly falsified.
“I’m innocent, and I’ll prove it,” Bloodworth said after court. “The venue made a mistake. We did everything right.”
His attorney argues outdated KCPD systems are fueling the case and warns towers could be unfairly targeted.
Source: fox4kc.com
The U.S. Senate has voted to revoke California’s Advanced Clean Trucks and low-NOx Omnibus waivers, a move welcomed by the national Safe Roads Coalition, representing towing and recovery truck owners.
“California’s electric truck mandates were unworkable,” said Josh Lovelace, the coalition’s national director. “By preserving access to combustion engines, Congress has safeguarded affordable, reliable roadside services for the American public.”
President Donald J. Trump is expected to sign the legislation, following its passage in both chambers. Many states previously planning to adopt California’s rules in 2025–26 have now delayed or modified them. Maryland, Massachusetts, Vermont, and Oregon recently postponed
implementation, joining others targeting 2027 for adoption.
The coalition argues that tow trucks play a crucial public safety role—clearing accidents, reducing traffic, and cutting emissions. In states like California, towing services partner with transportation agencies to offer free roadside help.
Source: Press Release Safe Roads Coalition